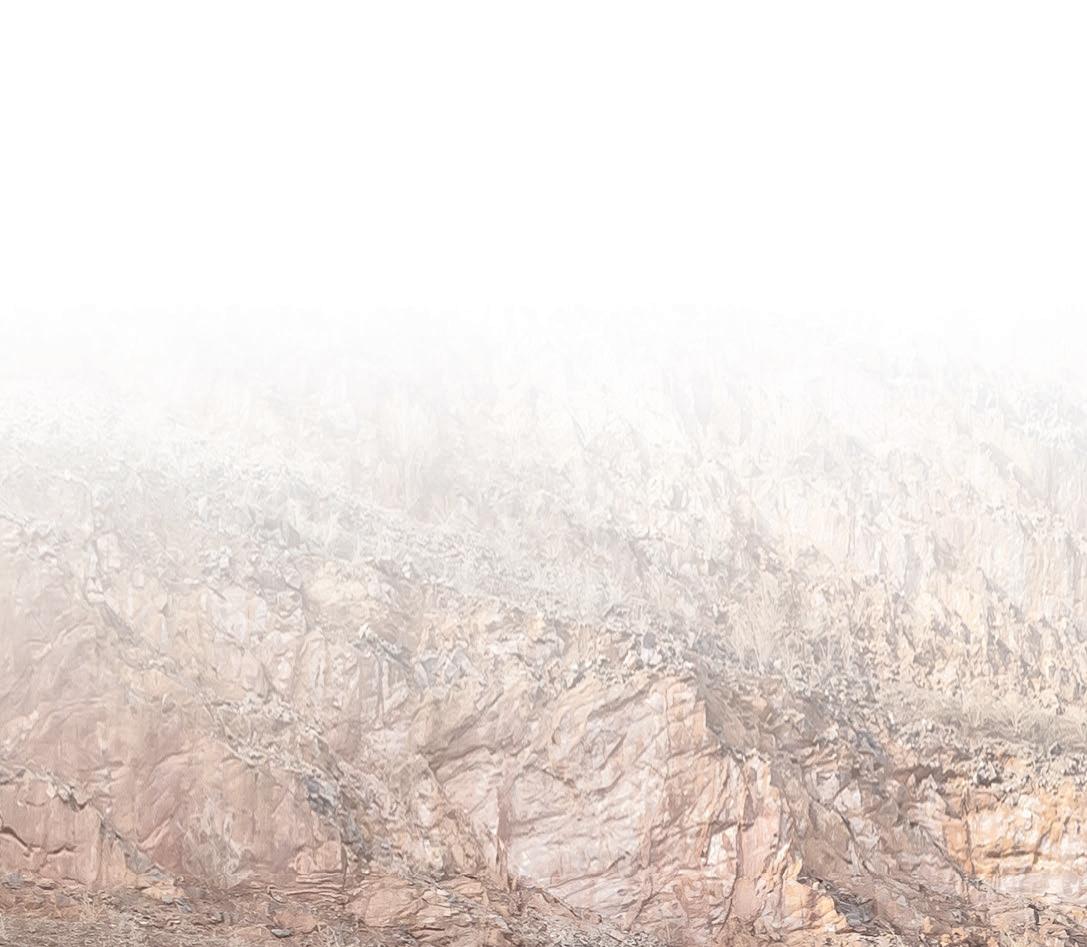

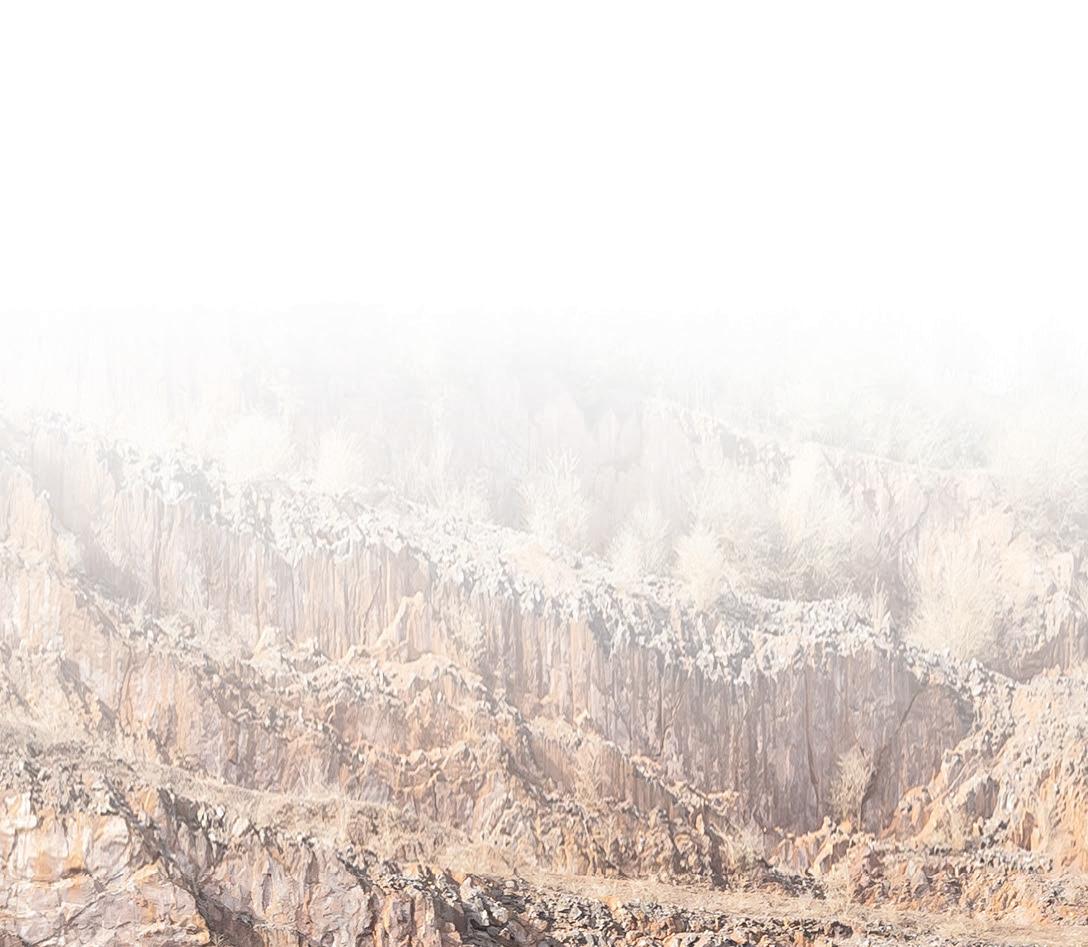
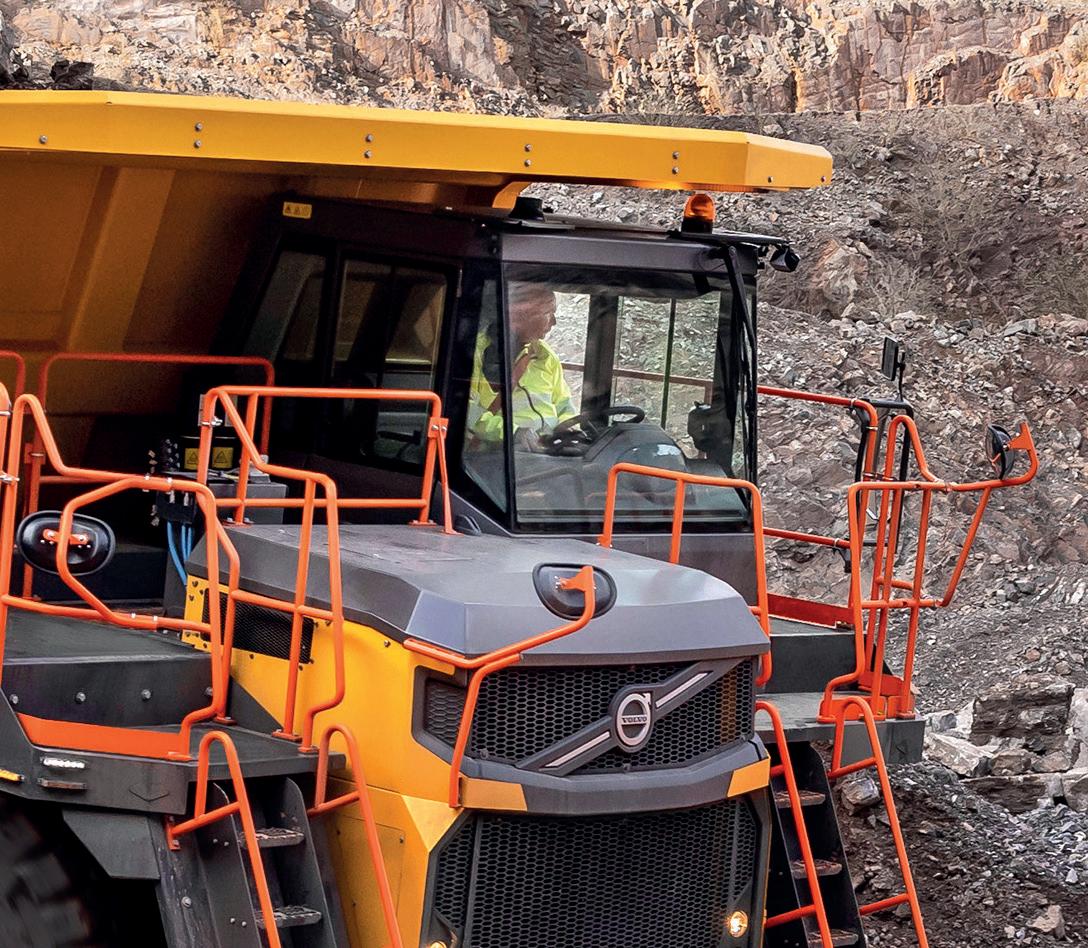

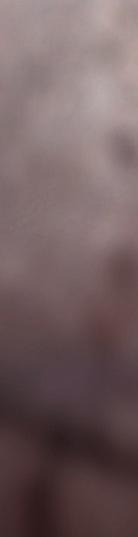

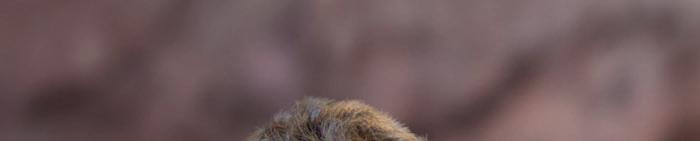
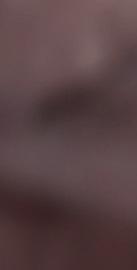
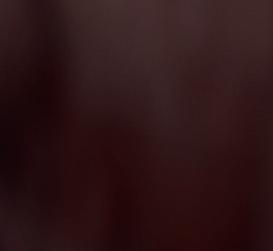
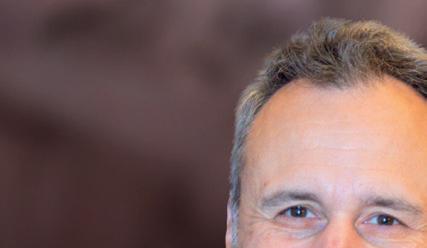
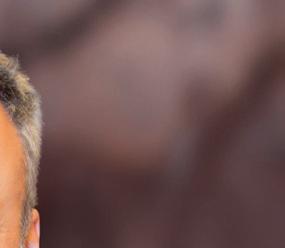

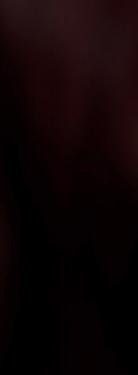
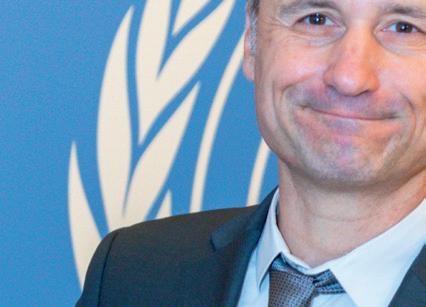
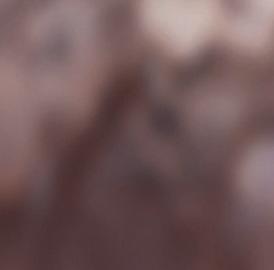
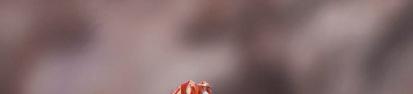
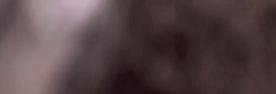
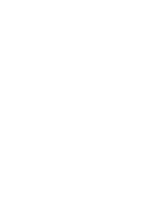

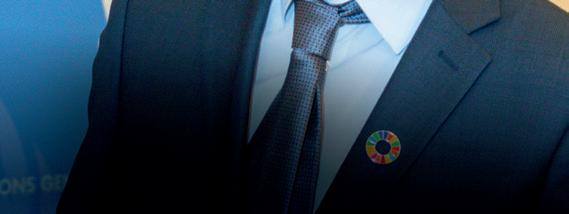
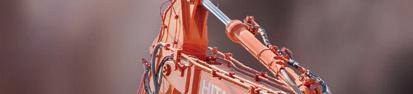
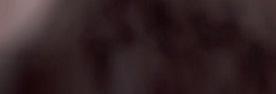
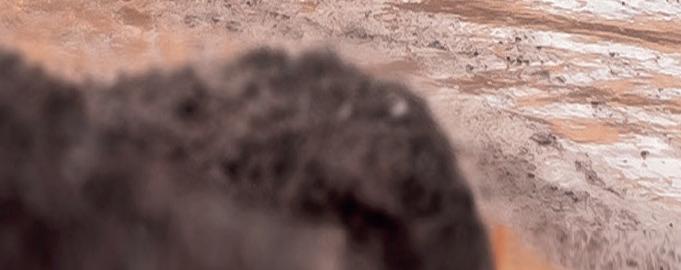
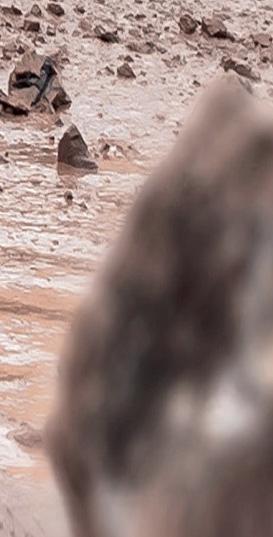
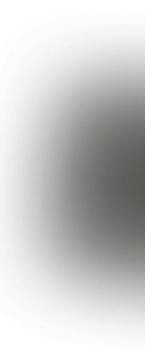

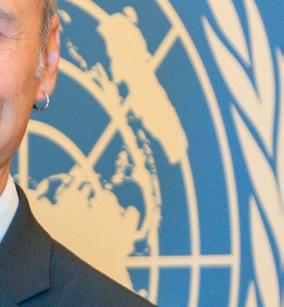
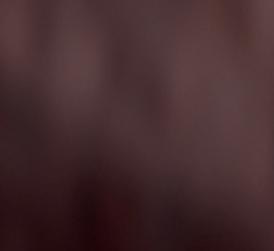
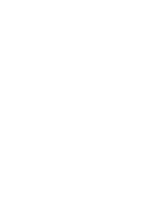
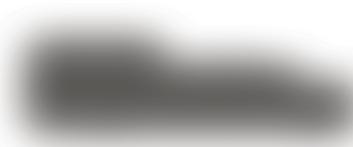
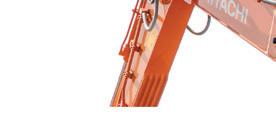
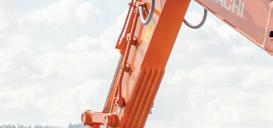
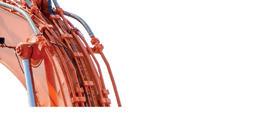
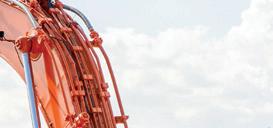
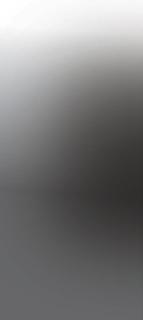



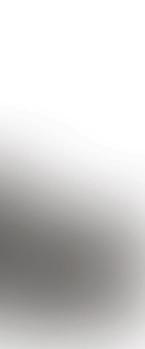
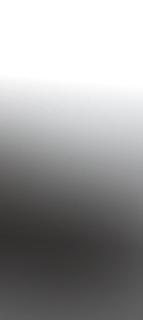
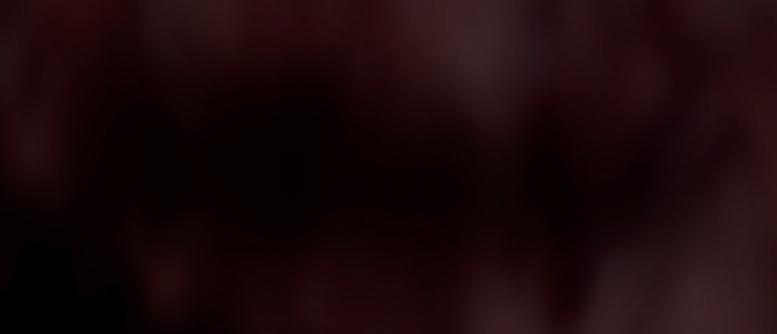
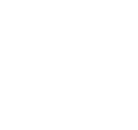
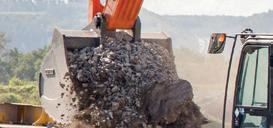
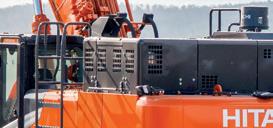
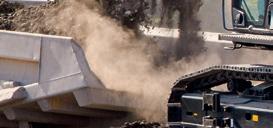
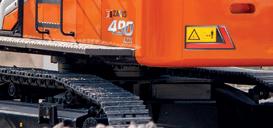
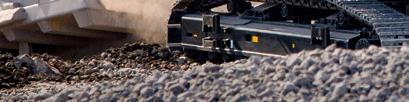
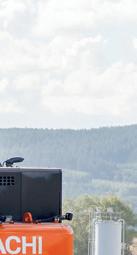
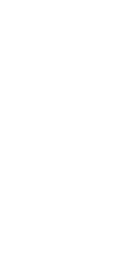
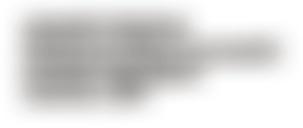
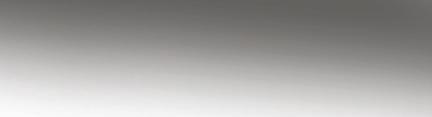
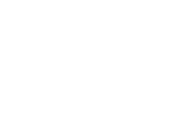


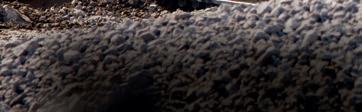
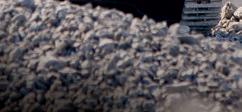
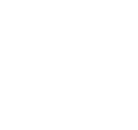
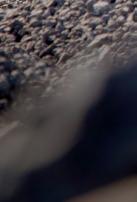

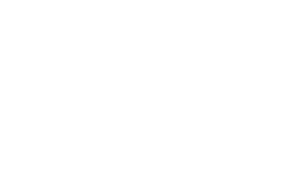
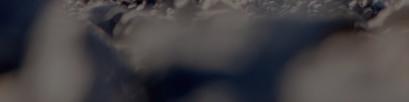
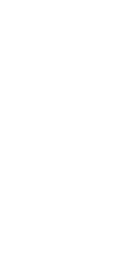
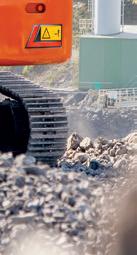
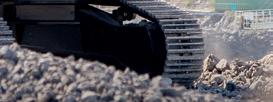
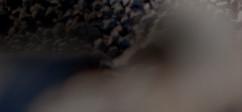
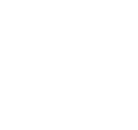
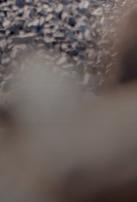
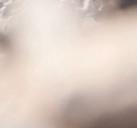
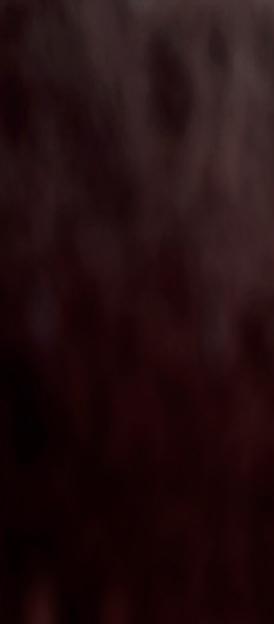
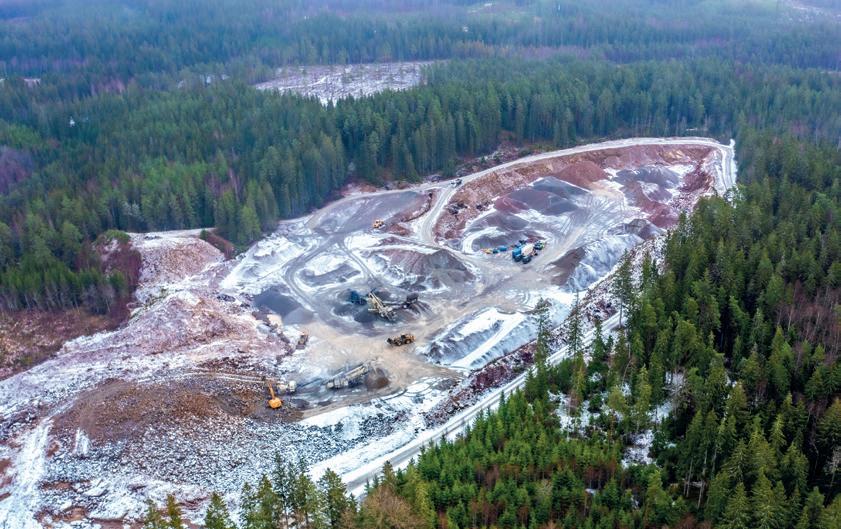

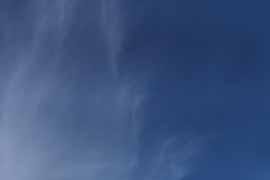
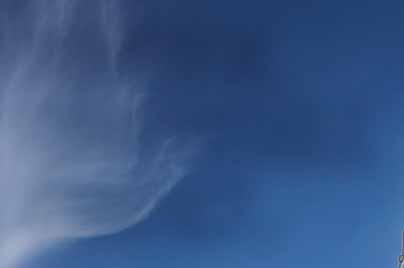
The Cat® M317 Wheeled Excavator offers more performance features and versatility than ever before. Its compact radius design lets you work in space restricted areas. With more digging force and increased swing torque, the M317 provides everything you need to get the job done quickly and efficiently. Low maintenance costs, longer service intervals, and reduced fuel consumption combine to provide low operating costs –keeping more money in your pocket.
“We have developed a technology using artificial intelligence (AI) to monitor sand extraction in the marine area worldwide” p11
05 COMMENT
It’s good to talk about world firsts
06 NEWS
Cemex UK R&D trials up to 100% recycled aggregates use; Holcim to deploy 1,000 Volvo electric trucks; Moviter marks 30 years as an HCME dealer
18 ASSOCIATION NEWS
Circular economy: the uncomfortable discussion we don’t (but should) have in Europe
50 EVENTS
All the key events in the quarrying & aggregates world
23 CRUSHING & SCREENING
The AI future of crushing & screening starts now
27 LOADING
Hydrogen-powered loading
29 HAULING
Rigid haulers delivering fluid production gains
32 ENGINES – 1
A revved-up engines & alternative-power sector
35 RECYCLING – 1
Recycled construction materials played a key role in a claimed world-first build
38 DUST SUPPRESSION
A new era of dust-suppression innovation
41 WEAR PARTS/SPARES
Not all parts are created equal
43 PORTABLE POWER – 1
Portable-sector power plays
11 INTERVIEW
COVER STORY: Volvo CE’s new R60 rigid hauler at work on a quarry site
Dr Pascal Peduzzi, director of UNEP/ GRID-Geneva, discusses a roadmap to a sand tomorrow
19 MARKET REPORT
Despite numerous challenges within the French aggregates, quarrying and construction equipment markets, good sales opportunities remain
45 QUARRY PROFILE
Metso is helping Kross & Maskin i Kisa future-proof its successful Swedish aggregates business
In a world where environmental standards are constantly changing, asphalt producers can survive – and even thrive – with the help of a plant retrofit.
A retrofit upgrades an old plant, so it meets new environmental standards – at a fraction of the cost of a new purchase. All projects are managed by the Ammann Retrofit Centre, which relies on proven processes and experienced technicians to troubleshoot any issues and ensure superior results.
What can you get with a retrofit from Ammann
• Increased RAP utilisation
• An electrically heated bitumen tank system that is so cost effective it pays for itself in a few years
• Noise levels that are reduced up to 20 dB without an impact on daily production
• An ability to use low-temperature mixes that reduce fuel usage and emissions
Contact us to arrange a free analysis to learn the best opportunities for cost-effective, environmental improvements at your plant.
HEAD OFFICE
EDITOR: Guy Woodford
ASSISTANT EDITOR: Liam McLoughlin
CONTRIBUTING
EDITORS: Munesu Shoko, V.l. Srinivasan, Shem Oirere, Partha Basistha, Eugene Gerden, Shadrack Kavilu
EQUIPMENT EDITOR: Mike Woof
DESIGNERS: Simon Ward, Andy Taylder
PRODUCTION MANAGER: Nick Bond
OFFICE MANAGER: Kelly Thompson
CIRCULATION & DATABASE MANAGER: Charmaine Douglas
INTERNET, IT & DATA SERVICES DIRECTOR: James Howard
WEB MANAGER: Sarah Biswell
SOCIAL MEDIA MANAGER: Tatyana Mechkarova
MANAGING DIRECTOR: Andrew Barriball
PUBLISHER: Geoff Hadwick
CHAIRMAN: Roger Adshead
ADDRESS
Route One Publishing Ltd, Second Floor, West Hill House, West Hill, Dartford, Kent, DA1 2EU, UK TEL: +44 (0) 1322 612055 FAX: +44 (0) 1322 788063
EMAIL: [initialsurname]@ropl.com (gwoodford@ropl.com)
ADVERTISEMENT SALES
SALES DIRECTOR:
Philip Woodgate TEL: +44 (0) 1322 612067
EMAIL: pwoodgate@ropl.com
Dan Emmerson TEL: +44 (0) 1322 612068
EMAIL: demmerson@ropl.com
Graeme McQueen TEL: +44 (0) 1322 612069
EMAIL: gmcqueen@ropl.com
SUBSCRIPTION / READER ENQUIRY SERVICE
Aggregates Business is available on subscription at the rate of: £85 / US$145 / €111 per annum. Single copies £20 / US$35 / €26 Email subs@ropl.com for further details. Subscription records are maintained at Route One Publishing Ltd.
SUBSCRIPTION / READER ENQUIRIES TO: Data, Route One Publishing Ltd, Waterbridge Court, 50 Spital Street, Dartford, Kent DA1 2DT, UK
TEL: +44 (0) 1322 612061 FAX: +44 (0) 1322 788063
EMAIL: data@ropl.com
No part of this publication may be reproduced in any form whatsoever without the express written permission of the publisher. Contributors are encouraged to express their personal and professional opinions in this publication, and accordingly views expressed herein are not necessarily the views of Route One Publishing Ltd. From time to time statements and claims are made by the manufacturers and their representatives in respect of their products and services. Whilst reasonable steps are taken to check their accuracy at the time of going to press, the publisher cannot be held liable for their validity and accuracy.
PUBLISHED BY © Route One Publishing Ltd 2023
AGGREGATES BUSINESS USPS: is published six times a year. Airfreight and mailing in the USA by agent named World Container Inc, 150-15, 183rd Street, Jamaica, NY 11413, USA.
PERIODICALS POSTAGE PAID AT BROOKLYN, NY 11256 US POSTMASTER: Send address changes to Aggregates Business, World Container Inc, 150-15, 183rd Street, Jamaica, NY 11413, USA. Air Business Ltd is acting as our mailing agent
PRINT: ISSN 2051-5766
ONLINE: ISSN 2057-3405
PRINTED BY: Warners (Midlands) PLC
IIt’s good to talk about world firsts
t’s good to talk, and there are no better places to start a conversation than La Madeleine. In the renowned Brussels citycentre hall attending the packed-out UEPG Sustainability Development Awards on 30 November last year, I began chatting with Dr Pascal Peduzzi.
Peduzzi proudly told me how he heads up a team of 22 data scientists at the Global Resource Information Database (GRID-Geneva), the UN Environment Programme centre for analytics, transforming data into information to suppor decision-making processes. He said he and his team were working tirelessly to secure funding to fully act on the headline findings of its landmark April 2022-published report on global sand sustainability, which includes a roadmap for future-proofing a more sustainable sand supply to meet the world’s building needs. I quickly realised he would be a great interviewee for Aggregates Business Europe
In this issue, Peduzzi explains that the world uses 50 billion tonnes of sand and gravel annually, enough to build a wall 27 metres wide and 27 metres high around the equator! “We have a lot, but we are using a huge amount. In some place, we are running out of these resources,” he stresses.
Peduzzi says the highly acclaimed GRIDGeneva report calls for sand to be recognised as a strategic resource, not only as a material for construction but also for its multiple roles in the environment.
The team emphasises that governments, industries and consumers should price in sand in a way that recognises its true social and environmental value.
You can read more about the GRID-Geneva team’s ten strategic recommendations to avert a sand sustainability crisis and more of Peduzzi’s wider thoughts on how people can preserve and best use the Earth’s mineral resources in our must-read four-page feature.
Who doesn’t like a world first? Heidelberg Materials and Linde recently announced plans to build the world’s first industrial-scale carbon capture and utilisation (CCU) facility in a cement plant.
Scheduled to start operations in 2025 at Heidelberg Materials’ Lengfurt plant in Germany, the project will be delivered under the newly
“Thanks to its purity, processed gas can be used in the food and chemical industries, such as carbonated mineral water”
established Heidelberg Materials-Linde joint venture (JV), titled ‘Capture-to-Use’ (CAP2U).
The facility will enable the captured CO2 from cement production to be reused as a valuable raw material in manufacturing applications. The planned volume of purified and liquefied CO2 is around 70,000 tonnes annually.
Linde will market most of the CO2 generated as part of the joint venture. Thanks to its purity, processed gas can be used in the food and chemical industries, such as carbonated mineral water.
Heidelberg Materials will use a smaller proportion to drive forward new CO2 recycling and recarbonation technologies.
For the implementation of this project, the substantial contributions of both partners will be supplemented by around €15 million from the Decarbonisation of Industry funding programme on behalf of the German Federal Ministry for Economic Affairs and Climate Action (BMWK).
Heidelberg Materials has already successfully tested CO2 capture based on amine scrubbing technology on an extended laboratory scale at its Norwegian cement plant in Brevik between 2012 and 2016.
Commenting on the landmark CCU cement plant JV, Dr Mathias Kranz, vice president of Linde On-Site & Bulk, said: “For our customers, a secure, high-quality supply of CO2 produced in a climate-friendly manner is of particularly high importance. With our partner Heidelberg Materials and the plant in Lengfurt, we will not only be able to expand our supply in the future but also provide CO2 in a sustainable and climate-friendly way with short transport routes.”
Seeing this pioneering industry project come to life will be fascinating. GW
Portugal’s authorised Hitachi Construction Machinery (Europe) dealer Moviter celebrated its 30th year of distribution for the brand on May 20th.
Moviter specialises in sales, rental and after-sales support of construction, mining/quarrying and agricultural equipment. Based in Leiria, the company was originally established by founder José Ribeiro Vieira in 1989 as part of the Movicortes group. The dealership has expanded since then and together with the headquarters in Leiria, centre of Portugal, the company has branches in Lisbon, Porto, Evora and Funchal (Madeira), as well as international locations in Angola (established 2008), Mozambique (established 2015), and most recently, Morocco and Guinea Conakry. By 2023, Moviter had grown to more than 100 employees. Moviter maintains that its close relationship with HCME is a key reason for its success.
The partnership with Hitachi has made it possible to complete the range while maintaining the quality of the products, supported by an efficient aftersales service close to the customers.
Cemex UK has been trialling the use of existing pre-cast material in its concrete products, including solutions made of up to 100% recycled aggregates.
These trials are the latest example of building materials supplier Cemex’s creative and dynamic efforts to reach its 2050 goal of operating globally as a net-zero company, in line with its Future in Action strategy.
The trials, conducted in partnership with UK-based Manufacturing Technology Centre (MTC) and First Graphene at Cemex’s National Technical Centre in the West Midlands, have utilised various unique production processes optimising incorporating recycled materials.
Following the success of initial testing, MTC and Cemex will now look to expand further into
larger-scale trials. Cemex understands that contributing to a circular economy is vital if netzero is to be achieved, which is why it has made circularity one of the key pillars of its climate-action strategy.
Mike Higgins, national technical manager for UK Research & Development, commented: “Reusing recycled products in our materials where possible reduces waste, helps replenish our aggregates reserves, and protects our business long-term.
“At our UK R&D facility, we are focused on pursuing innovation to increase the sustainability of our operations and are always keen to work with partners such as MTC and First Graphene. We believe there is a significant opportunity to incorporate recycled materials into our products and provide our customers with a solution for reducing the carbon footprint of their projects.”
Holcim will deploy up to 1,000 electric trucks from Volvo by 2030, with delivery for the first trucks starting in the fourth quarter of 2023.
The move represents the largest commercial order to date for Volvo electric trucks. The deal is part of a wider partnership between Holcim and Volvo Group to deploy electric trucks across Holcim’s operations in Europe between now and 2030.
Holcim and Volvo are founding members of the First Movers Coalition (FMC), a coalition of companies that use their purchasing power to create early markets for innovative clean technologies. Replacing diesel trucks with electric ones will reduce CO2 emissions from road transport by up to 50% per year.
Jan Jenisch, Holcim chairman and CEO, said: “The net-zero transition requires deep collaboration across value chains. We are excited to be partnering with Volvo to decarbonise our European operations’ logistics with electric fleets,
advancing our goal to reach 30% of zero-emission heavy-duty trucks by 2030.”
Martin Lundstedt, president & CEO of Volvo Group, said: “Longterm collaboration and a strong commitment to making a difference are essential for making big CO2 reductions a reality. I’m very proud of our partnership with Holcim and the results we are achieving together.”
The agreement will contribute to the sustainability targets Holcim and Volvo Group have set. In addi-
tion to being members of the FMC, both companies are committed to the Science Based Targets initiative (SBTi), which drives ambitious, science-based climate action in the private sector. In November 2022, Holcim launched its upgraded 2030 climate targets, validated by the Initiative, in line with its sector’s new 1.5°C science-based framework.
With these upgraded targets, Holcim confirms its commitment to decarbonise building in line with the most advanced science.
The Astec washing and classifying line provides tried-and-true solutions with cutting edge modern technology. With a complete offering of scrubbing, sand classifying, dewatering, water clarifying and fully-customized systems, we have what you need.
View our washing and classifying products.
Aggregate Industries has published the roadmap for its ambitious journey to net zero.
23/8to26/8
The strategy follows the launch of the business’s sustainability strategy, Building Progress for a Sustainable Future, which sets out Aggregate Industries’ vision to become the UK leader in innovative and sustainable building solutions and its ambition to embed sustainability in the future of construction.
Our Journey to Net Zero outlines what Aggregate Industries is doing today and its intention to decarbonise its operations across the business at pace and achieve net zero before 2050.
unblended gas oil usage by more than 90% by 2035; increasing the use of low-carbon fuels and hydrogen to more than 50% of the fuel mix by 2035; using more than 2,000 low-carbon trucks, such as electric or hydrogen, within the fleet network by 2040; producing more than 20GWh of clean energy per year from onsite renewable power generation by 2035; and beginning to capture and permanently store CO2 from the business’ Cauldon cement plant by 2030.
It identifies five workstreams that will accelerate the journey towards net zero and provide clear and deliverable actions and commitments for each of Aggregate Industries’ divisions to achieve by 2025. It then captures a series of long-term commitments beyond 2025 that will form an enduring change process. These include reducing
Aggregate Industries has published its roadmap of how it will achieve its ambitious journey to net zero
Metso Outotec is now Metso Corporation after the company’s Annual General Meeting (AGM) approved the Board of Directors’ proposal for the name change.
“After the successful integration of Metso and Outotec, we will focus on growing a strong, unified Metso company and brand,” said president and CEO of Metso, Pekka Vauramo.
“We have combined two valuable companies into one strong Metso. Our focus is clear: we continue enabling sustainable modern life and transforming the industry with
a clear strategy and strong culture, supported by a short yet established name and well-recognised among all our stakeholders. Services are an extremely important part of our business, requiring a strong name,” he continues.
Outotec continues as a product brand and carries significant value as the name of some key technologies and products.
The change of the parent company name to Metso Corporation is effective starting May 4, 2023, but globally the change will be implemented in a phased manner.
Pic: IQ
Mineral products professionals that choose to join the Institute of Quarrying (IQ) will do so at a reduced price for a limited time only, an initiative announced by the membership body to continue its support of the industry during the cost-ofliving crisis. New members get access to valuable continuing
professional development (CPD) resources, including brandnew e-learning health and safety modules and a series of Environmental Management books developed by industry experts, set to be released soon.
The half-price membership incentive follows the announcement earlier this year that IQ has frozen membership
Breedon Group has completed three bolt-on transactions with a combined enterprise value of up to £19mn. In Northern Ireland, the acquisition of Robinson Quarry Masters Limited, a family-run quarrying and concrete block business in Country Antrim, extends Breedon’s footprint north of Belfast. Robinson Quarry Masters boosts the group’s aggregates reserves on the island of Ireland and has a well-established customer base with exposure to housing, commercial and infrastructure end-markets.
Breedon has also acquired two downstream businesses. Broome Bros. Limited is a leading manufacturer of concrete blocks based in Doncaster, South Yorkshire, adjacent to one of Breedon’s existing ready-mixed concrete sites. Minster Surfacing Limited is an award-winning regional surfacing business based in Lincoln.
The firm has strong sustainability credentials delivering a diverse portfolio of works from the Midlands to London. Breedon chief executive officer Rob Wood said: “Many of our transactions come to us through our local knowledge and personal engagement with the owners. As a result, our active M&A pipeline has continued to yield high-quality, earnings-enhancing opportunities that will enable us to progress our sustainable growth strategy.
“Each of these independent family-run businesses is aligned with our vertically-integrated operating model, providing further opportunity to pull through upstream building materials while extending our downstream footprint to deliver profitable growth. We are delighted to welcome our new colleagues to Breedon and look forward to working with them.”
costs for 2023. Sarah Fry, IQ’s head of membership and marketing, says: “It’s been such a difficult and uncertain time for everyone but based on the number of people renewing their membership this year, it shows that being an IQ member is highly valued and worthwhile.
“Over the last year, IQ has enjoyed an exceptional 89 per
cent retention rate, despite the current health, social and economic uncertainties. We constantly review our processes to make sure that we are providing the highest levels of support for our members, and we are grateful that members value being part of the industry’s own professional membership body.
“The £91 it costs to join IQ today means that members can trial membership at half price for the rest of the year, with access to a suite of additional resources and networks that will help them to progress and develop their careers.”
The IQ promotes professionalism in the minerals products sector. Members benefit from career development opportunities with access to valuable CPD resources, internationally recognised qualifications and a network of professionals sharing accumulated knowledge and good practice.
Members are reminded that additional support is also available from the IQ Benevolent Fund.
Get ready to experience the ultimate working environment with Hitachi’s newly redesigned ZW-7 cab, ultra-spacious and equipped with top-of-the-line features! Say goodbye to noisy and uncomfortable workspaces, as the ZW160-7 offers some of the lowest noise and vibration levels in the market. With this machine, you’ll be able to work in style and comfort, making your job easier and more enjoyable than ever before.
Don’t settle for less - upgrade to the ZW160-7 and experience the best!
Dr Pascal Peduzzi is the director of UNEP/GRID-Geneva, a Switzerland-based centre of the UN Environment Programme (UNEP). Peduzzi heads up a team of 22 Global Resource Information Database (GRID-Geneva) data scientists transforming data into information to support decision-making processes. The team is working tirelessly to secure funding to fully act on the key findings of its landmark report on global sand sustainability, which includes a roadmap for future-proofing more sustainable sand supply to meet the world’s huge building needs. Guy Woodford reports
GRID-Geneva is the UNEP centre for analytics. Created in 1985 to help transform data into information to support environmental governance and policies, it uses statistics, satellite imagery, in-situ and GIS models and produces scientific information to assess current environmental status, identify past trends or predict future status based on modelling.
“Since 2014, GRID-Geneva has been working on the issue of sand and sustainability and was one of the pioneer institutions to alert governments regarding this looming sand crisis. It was an issue that had, until then, been totally overlooked,” explains Peduzzi, who was one of the selected authors for the 2012 Intergovernmental Panel on Climate Change (IPCC) Special Report on Extreme Events
“In 2019 and 2022, we issued reports with
The front and back cover of UNEP’s April 2022-published Sand and Sustainability report
recommendations to governments and other stakeholders. At the United Nations Environment Assembly (UNEA) in 2022, all 193 countries present gave GRID-Geneva the mandate to strengthen the scientific, technical and policy knowledge with regard to sand.
“We have developed a technology using artificial intelligence (AI) to monitor sand extraction in the marine area worldwide. Monitoring the extraction of terrestrial and riverine sand is not easy. We plan to create a Global Sand Observatory based on a wide network of partners and are currently raising funds for it. This network, and we already have 40 interested partners, will be monitoring sand use and sand-extractive impacts, issuing recommendations on
standards and policies, as well as gathering technical solutions.”
I ask Peduzzi, who holds an MSc and a PhD in Environmental Sciences, with a specialisation in GIS (geographic information systems), what impact the GRID-Geneva team’s April 2022-published report Sand and Sustainability: 10 strategic recommendations to avert a crisis has had on influencing key global decision-makers.
“It was circulated to UNEA-5 and led to the adoption of resolution 12 on environmental aspects of minerals and metals management. The media coverage was very high: more than 400 articles were in the main media in the week following the launch. It did shed light on this issue which was so far overlooked, yet a lot of things remain to be done to influence the global decision-makers. It will take more than a report.”
Peduzzi says the April 2022-released report made clear that sand must be recognised as a strategic resource, not only as a material for construction but also for its multiple roles in the environment. The GRIDGeneva team emphasises that governments, industries and consumers should price in sand in a way that recognises its true social and environmental value.
“Current practices do not include the real costs of sand. Sand is producing services which have a value, and this value has been dismissed,” Peduzzi explains. “If you extract sand from dynamic settings like the beach, rivers, lakes, and marine areas, you are affecting water supply, shoreline protection, biodiversity, fisheries and other livelihoods such as the collection of crabs. You are inducing land degradation, and erosion, affecting the river banks as well as coastal areas. All these impacts have a cost. So far, this is pushed on others, something economists call ‘externalities’. Now we can adopt new standards which will reduce such
Offering more power with less complexity and less weight. This engine delivers the productivity you need to keep your equipment running. Proven in a wide range of industrial applications, its power increases to 326 hp/243 kW enabling replacement of engines with higher displacement with no impact on productivity.
cummins.com/construction
environmental impacts and related costs.
“If higher standards are being accepted regarding sand extraction, this may be more costly to extract. Same if you need to provide funds for restoration after exploitation.
“The new price will need to integrate such additional costs. For the final users, this may only add a small percentage to the cost of the infrastructure.”
Peduzzi argues that while the price per tonne of sand will be higher, this doesn’t mean that this would be a loss for a business because if the standards are accepted internationally, it would level the playing field, and would benefit companies which are already well advanced in their extractive practices. “It is a matter of limiting the externalities of costs on social, environmental and other economic sectors,” he stresses.
UNEP’s April 2022 Sand and Sustainability report also recommends an ‘international standard’ on how sand is extracted from the marine environment – and the banning of beach-sand extraction. I ask Peduzzi who would set this international standard and introduce the beach-sand-extraction ban, how both would be policed, and whether penalties for breaches would be enforced through fines or court action leading to possible prison sentences.
“Extraction of sand in dynamic settings, especially with regard to beaches, is leading to significant impacts. Not only the obvious coastal erosion and the fact that this would prevent future touristic and recreational use of the beach, but the salinisation of coastal aquifers, the reduction of protection against storm surge, which will already be intensified with climate change and sea-level rise.
“This is why it is important for countries to ban beach-sand mining and to make this enforced via usual law enforcement ways for any law-breaking. This needs, however, to be done with support for the transition of the workers who shouldn’t lose their livelihood. This is why we need to invest in
There was huge global media interest in UNEP’s Sand and Sustainability report in the days after its publication, generating hundreds of print and broadcast reports
infrastructures and tools for extracting sand from quarries.”
Does Peduzzi believe a circular economy for sand is achievable? “Achieving circularity, given the dependency we have on sand and gravel, will not be easy. However, there are ways we can significantly improve the industry by adopting several practices. We can reduce the demand for sand and products derived from sand; replace naturally occurring sand with alternative materials; reuse sand and products made of sand at the highest value possible; and recycle sand and products made of sand that cannot be reused.
“We also need to rethink the way we are doing our development, transferring public mobility emphasis to metros and trains rather than individual cars. This would reduce the need for new roads and related sands. The new tunnels built for the metros can provide building materials, thus freeing up building materials to use elsewhere. This will also take up less of the earth’s surface area and transport people at a higher speed as metros and trains are not stuck in traffic jams like cars, which are, anyway, parked 98% of the time. It would also reduce the need for car batteries. Combined, these are
“Sand is the biggest solid material extracted by humans; this issue will not be resolved easily”
important steps in making the entire value chain more sustainable.”
I highlight to Peduzzi that across the world’s quarry and wider building materials supply businesses, there has been a big increase in recent years in the amount of manufactured sand being produced for use as a construction material.
Does he think this represents a longterm alternative in terms of quality and
sustainability to natural sand extraction?
“Despite the increase in energy, manufactured sand usually has less impact as compared with extracting sand in dynamic settings such as rivers, beaches or marine environments.
“There is a resource which is similar to manufactured sand, [which] is what we call ore-sand, i.e. the co-generation of sand from the mining of other ore, such as iron.”
I am curious to know what Peduzzi thinks would happen to the world’s sand resources if the work of UNEP/GRID-Geneva and other sustainable environmental campaigners ceased.
“This looming sand crisis is coming. UNEP is alerting on this issue; this needs to be addressed by countries and by the economic sectors involved. The issue will only become more acute. We are trying to
wake up various sectors on this. If we fail and no other institution succeeds in changing the practices, this sand crisis will get worse, and we will repeat what we have done for climate change, biodiversity loss and pollution, i.e. only reacting instead of preventing a crisis.”
Peduzzi outlines various reasons why he thinks very little attention has been historically given by politicians and the general public to sand sustainability.
“Governments have many issues to deal with - security, economy, development, climate and other environmental issues. Sand is only a new flashing red light on their
board. Secondly, we have the impression that sand is a common material and that we have plenty of it. However, our use has tripled in the last two decades. The amount we use is very large. And we are fully dependent on this material for all our infrastructures: roads, buildings, houses, schools, hospitals, dams as well as coastal protection, or industrial sand for glass or even computer chips. If our entire development depends on sand, it cannot be a common material but a strategic material. This requires a change of perception, but this takes time.”
Asked what he finds most satisfying about
his work, Peduzzi, a Swiss national who lives and works in his home city of Geneva, and who also works as a part-time teaching professor at the University of Geneva, says it means a great deal to him and his team that GRID-Geneva and UNEP at large are supporting global good by improving people’s relationship with the environment, while trying to facilitate the transition toward a more sustainable future. “I meet great people who are very keen to improve our sustainability practices,” he adds.
And what does he see as the biggest challenges he and his colleagues face?
“Humanity has never faced such large challenges. The triple planetary crisisclimate, biodiversity, and pollution - is posing many challenges. My team and I are working with many other actors, but the task is huge. We are struggling with the inertia of the system: the too little, too slow, too late decisions and actions toward sustainability. Most people are not aware of the urgency posed by the triple planetary crisis. We need more political will, more long-term vision for the economy and more resources allocated to dealing with these issues.”
I ask Peduzzi how he thinks UNEP/ GRID-Geneva’s work would be deemed a success. Are there specific targets he and his colleagues are working toward? “We need to work step by step, and UNEP cannot do this alone,” he stresses. “Sand is the biggest solid material extracted by humans; this issue will not be resolved easily. It will take more than a decade to improve the situation.
“We already had the success that in 2019, for the first time, sand was recognised as an issue by 193 governments. In 2022, we received an official mandate from those governments.
“If we succeed in creating the Global Sand Observatory, this will give us more weight to promote this issue and related solutions.
“Then, working through time, the adoption of new standards would be a great achievement.
“But clearly, the question is not about success for GRID-Geneva; it is about achieving sustainability.
“The question of sand is only one more issue. Climate, deforestation, biodiversity loss, overfishing, all these issues are telling us that we cannot continue to exploit the Earth in a linear way: extract - transform - use and dump material. Something that is sustainable is something that can last. Non-sustainable development will collapse. Sustainability is not a luxury for enlightened ecologists, it is the difference between living in harmony with nature or a collapse of our ecosystems. We are walking toward a cliff edge and about to make a great step forward. It is urgent to change the direction of our development and move toward sustainability. This will require completely changing the way we produce and consume goods and services. But it will greatly improve our quality of life.” AB
This exciting new development comprises six models for different feed sizes, all said by developer Moore Watson Mineral Processing to overcome the problems inherent with traditional crushers.
The time is now to discover how the revolutionary Hypro-Crush® can raise your materials processing to uncharted heights while boosting your all-important bottom line.
The remarkable Moore Watson HyproCrush® Model TJ12-18 Jaw Crusher
The new crusher, weighing 45 tonnes has a feed opening of 1200mm x 900mm and will use a 160Kw electric drive motor, whilst the crusher discharge outlet is a massive 1800mm wide and based on a 100mm closed side setting, (desired but seldomly achieved on large primary jaw crushers) is designed to
crush 350 mtph to minus 150mm material. Noteworthy is that this output is at 2.18 tons per Kw.
Compare this with a conventionally designed jaw crusher with a feed opening of 1200mm x 900mm, typically, these machines weigh from 26-30 tonnes and have an outlet discharge width of 1200mm, based on the same closed side setting of 100mm, it will produce 235 mtph of minus 150 mm material at 1.4 tonnes per Kw.
The improvement in crushing efficiency, which is attained by many innovative design features, such as the tapered frame, suspended jaw stock and no drawback rod, significantly reduces the cost per tonne crushed. The down-stream benefits of less crushing stages and greater efficiency are designed to simplify the crushing process.
On 15 June 1858, Eli Whitney Blake of New Haven was granted US patent No. 20,542 for a ‘machine for crushing stone’ – a magnificent design well ahead of its time. Since then, the same basic design principle has existed in all jaw crushers. But now it’s time for a new jaw-crushing era. Viva the Hypro-Crush® revolution!
crushed material, so will always need to be followed by a secondary machine.
If the mobile contracting machine applications are considered, the fuel consumption savings alone will make this new machine highly competitive.
The output of minus 150mm material from a 1200mm x 900mm jaw crusher, shows a capacity increase from 235 mtph to 350 mtph which is a “game changer”.
The Hypro-Crush® TJ 12-18 model Jaw Crusher, having a minimum 70mm and maximum 250mm closed side settings is only one example of a series of Moore Watson designs which cover the whole range of sizes and applications. “More than a hundred years of experience of hard rock crushing have gone into the new Hypro-Crush® series, for which patents are pending.”
Moreover, a conventionally designed 76 tonne machine (1600mm x 1200mm) cannot be set to achieve minus 150 mm
Duncan McGregor Nicky Watson
There is little doubt that European countries need to do more to rationalise their consumption of virgin resources. Concerns are not limited to protecting the environment from the detrimental impact of generating waste. The unstable and ever more entrenched geopolitical landscape forces Europe to reconsider its overdependence on other international actors to procure needed materials, products and processes. The European construction sector is not exempt from this.
The European Commission has set ambitious targets of circularity in our industrie: Minimisation of the overall amount of raw materials used in the proposed revision of the Construction Products Regulation; at least 30% of re-used or recycled concrete for the construction of new buildings; at least 15% for the renovation of existing buildings, at least 30% back into concrete in civil engineering, and at least 50% re-used or recycled material in structural road elements to become eligible for access to the much-needed sustainable finance. Given that the credibility of its targets determines the effectiveness of any plan, evaluating the feasibility of the aforementioned ambitions is crucial.
Aggregates Europe – UEPG and its 26 members across Europe, representing an annual production of 3 billion tonnes of primary and secondary aggregates, has been at the forefront of research and expertise concerning the treatment of waste from construction and demolition (CDW). Recent activities include publishing our Guidance on End-of-Waste Criteria for recycled aggregates
from CDW and providing advice to JRC, the European Commission’s science hub for waste streams. As such, we can form an authoritative opinion of the EU’s ambitions on the matter.
Our priority is and must remain, the production of safe and durable materials. No holding back may be allowed on this matter if we want to avoid the tragic images seen in other parts of the planet after an earthquake or a fire. Today, there is no study or previous experience about the durability of concrete produced with high values of recycled materials. On the contrary, technical experts across Europe raise the issue of compromising the future durability of some structures (e.g., buildings) in cases of high usage of recycled materials. A shorter lifespan of construction products or projects due to high usage of recycled materials could result in earlier renovation or demolition, leading to higher environmental, economic and societal costs. We believe this is not what the EU’s Action Plan was meant for.
In addition, even if we could magically circumvent the safety concerns, in Europe, there is not enough accessible CDW to reach all these different targets. On the contrary, even an incremental orientation of the construction sector towards the totality of these targets would create competition for access to recycled materials, increasing the costs and environmental footprint due to longer transportation distances. At the same time, the needs and ambitions of European countries and citizens (e.g., the Renovation Wave) require large amounts of construction materials from our industries in the coming decades. Thus, it should be clear
that, although our recycling efforts will be strengthened, most of these materials must come from primary extraction.
All the aforementioned elements highlight that we are having the wrong debate regarding the circular economy in Europe. Instead of focusing on substitution rates or minimum recycled content, we should focus on increasing the amounts of accessible CDW. Even more importantly, the discussion should be moved from recycling to prevention since there is no better way of treating waste than not generating it in the first place. The European aggregates industry is exemplary here, providing Europe with safe, durable, affordable and environmentally friendly materials. We have the potential to achieve the most vibrant circular economy if only we prioritise evidence over ideology and have this uncomfortable but critical discussion in Europe. AB
recently
There are numerous challenges to be faced within the French aggregates and quarrying and construction equipment markets, but good sales opportunities remain. Guy Woodford reports
The latest market overview from UNICEM, the trade association bringing together the French mineral-extraction industries and manufacturers of construction materials, highlights how the sluggishness in the French building-materials sector in 2023 follows on from a difficult trading landscape in 2021 and 2022. In just three years, the French building-materials sector, like many other sectors, has had to deal with great challenges linked to the COVID-19 pandemic and the Russia-Ukraine war. If the sector had shown itself to be resilient in its 2021 return to pre-COVID-19-crisis activity levels, 2022 saw it face the full aftermath of the pandemic, with high inflation and rising production costs linked to supply chain disruption affecting materials availability. This contributed to aggregates and readymixed concrete (RMC) production falling 4% in 2022.
According to early 2023 production estimates, UNICEM says building-materials production is set to be down again in 2022. Ready-mixed concrete production in March 2023 was down 8.2% compared to March 2022. Taking a 12-month rolling basis, the RMC trend was visible (-5.5% ) in March 2023.
On the aggregates side, activity again declined at the start of the year (-0.7%) between February 2023 and March 2023
(CVS-CJO data). Production in the year to 31 March 2023 was down 11.8% compared to the previous corresponding period.
Part of this is down to a particularly good aggregates-production start to 2022.
During the first quarter of 2023, aggregatesproduction decreased (-3.5%) compared to the previous months. Moreover, it was down in the same period of 2022 (-11.8%). At the end of March 2023, rolling year-on-year aggregates production volume was down 7.5%.
After observing a decline of 3.6% on a year in the fourth quarter and 3.1% in 2022, the French building-materials indicator contracted 9.8% in Q1 2023 (CJO data). This includes the impact of reduced concreteproduct production in early 2023.
According to the monthly French construction industry survey conducted by INSEE, the deterioration of the business climate, which began in January 2023, continued throughout the first quarter and April. While its level is still well above its long-term average, many signals confirm that the high point has passed and that the erosion of industry confidence will continue.
While legacy orders are still keeping material-producerbusinesses fairly busy, sector entrepreneurs are fearful about the future health of the marketplace. Tensions are evident around declining new building-
material orders, while supply chain and staff recruitment difficulties remain.
Moreover, the latest indicators of the French new housing market testify to a decline in housing demand. New-home sales on a 12-month rolling basis were down 32.4% at the end of March 2023, according to Markemétron (at 88,300 units, the worst number in 15 years).
Among promoters, with barely more than 102,000 reservations for apartments and houses in 2022, the dropout reached -14.6% over the year, the trend worsening in the second semester. Social housing demand does not look better, with 15% fewer 2022 block sales (9,107 units). These trends correlate with a downturn in issued housing permits that started a few months ago. Permits issued increased by 3.2% year-on-year in 2022 (to reach the ‘comfortable’ level of 483,400 units) but plunged 25.4% year-on-year in Q4 2022 and 30.9% year-on-year in Q1 2023 (to 441,400 units).
As for housing starts, they show a decrease of 5.2% in 2022 (at 371,000 units), still visible in the first quarter of 2023 (12.8% over a year). The non-residential segment is doing better with ‘authorised surfaces’, which, after an increase of +10.7% in 2022, remained positive Q1 2023 (+0.3% over one year). The economic climate to encourage new construction has taken a significant hit. The upgrading of the
usury rate drives this. Meanwhile, the rate of French ‘loans to habitat’ (mortgages) continues to grow rapidly, reaching 3.15% on average in April, a multiplication of 2.4 in just over a year.
At the same time, real estate inflation in new construction continued (+2.8% in one year and + 15.6% since 2020 for a house) under the effect of rising material prices and the introduction of RE2020, which, according to the FFB Housing division, increased construction costs by an average of 7.4%. With insolvency increasing, households face rapidly rising mortgage-refusal rates (+46.5% November 2022-January 2023 compared to the same months of the previous year).
Thanks to a new increase in activity in March 2023 compared to February 2022 (+1.5% in data CVS-CJO at constant prices), the volume of public works carried out rose compared to last year (+4.5%). However, over a rolling 12-month period, activity still showed a contraction of 5.1% as of 31 March 2023, according to the results of the investigation conducted by the FNTP (La Federation Nationale des Travaux Publics). Orders did, however, experience a strong rebound at the start of the year (+22.4% in Q1 2023), but this is exclusively attributable to the contract award for the third line of the Toulouse metro and does not reflect wider, stronger investment by public and private players.
Bergerat Monnoyeur (BM) is Caterpillar’s France dealer. Farida Selmani, BM’s marketing manager, says that as the aggregates and quarry business is a demanding sector where efficiency and productivity can make the difference between profit and loss, the company offers French customers a wide range of Cat products and services to support their goals.
“With fleets usually working long hours, a strong fleet management and maintenance programme are key to remaining productive and maximising uptime. We see a significant take-up for Customer Value Agreements (CVA). Those include preventive maintenance, remote diagnostics and fleet connectivity with VisionLink, the web-based
GlobalData’s March 2023-published report, France Construction Market Size, Trend Analysis by Sector (Commercial, Industrial, Infrastructure, Energy and Utilities, Institutional and Residential) and Forecast, 2023-2027, states that following marginal growth in 2022, the French construction industry in France is expected to shrink by 0.6% in real terms this year, owing primarily to subdued investor and consumer confidence, high consumer and construction-cost inflation, rising interest rates and supply chain disruptions which are
all expected to continue to weigh on the industry’s performance.
According to the National Institute of Statistics and Economic Studies (INSEE), the average construction-materials cost index registered a year-on-year (Y-o-Y) increase of 17.1% in the first nine months of 2022. A sharp decline in consumer confidence will also affect the industry’s output in 2023. According to the INSEE, the average consumer-confidence index fell by 13.3% last year, following a growth of 3.5% in 2021.
The industry is, however,
expected to rebound at an average annual growth rate of 2.6% from 2024 to 2027, supported by investments in transport and renewable-energy infrastructure projects. The government aims to reduce greenhouse gas emissions by 35%, compared to 2015, by 2030. To support this target, it is focusing on increasing renewableenergy capacity across the country.
In November 2022, the French Senate approved new legislation which requires all car parks – with at least 80 spaces – to be covered by solar panels by 2028. Previously
in February 2022, the French state railway utility SNCF also announced a plan to install approximately 190,000m² of solar panels in 156 stations across the country by 2025 and 1.1 million m² of solar panels in railway station areas by 2030. Moreover, in January 2023, the European Investment Bank (EIB) announced that it had provided €9.9bn in long-term financing to the private sector and regional authorities in France in 2022. Of the total, €5.9bn was allocated for renewable energy, green transport, and energy efficiency.
fleet management tool. CVAs allow customers to plan their future costs and limit uncertainty.”
Asked what type of quarrying equipment quarries in France are particularly looking for, Selmani says: “More than ever, quarry owners are looking for fuel-efficient equipment that delivers the lowest cost per tonne, as fuel costs remain a challenge. To reduce those costs and maximise efficiency, customers often opt for the Cat XE range, such as the 966 XE, 972 XE, 982 XE, 988K XE wheeled loaders and the D6 XE dozer as they provide increased fuel efficiency and premium performance.
BM Rent, allow customers to fill production gaps and expand their business without growing their balance sheet.
She says about large French construction projects influencing national aggregates and equipment demand: “Canal Seine Nord remains a huge opportunity over the next two years. Another large project is Tunnel Euralpin Lyon-Turin (TELT), creating the Tunnel de Base de Mont Cenis, which will run 57.5km from France to Italy. Early predictions call for the opening of many quarries to
forecasts. In addition, the demand for our core quarrying products – the large Zaxis-7 excavator range – remains strong due to their industry-leading reliability and durability, says Dimitrov. He continues: “The feedback from our customers is also positive, and we remain committed to serving their needs with our technical support, parts, fleet management systems and maintenance contracts. In addition, Hitachi Construction Machinery’s (HCM) Premium Used and Premium Rental products are gaining popularity in the French market.”
“Large excavators and rigid trucks remain among the most popular equipment combinations to transport aggregates to stockpiles or distribution centres. The range of Cat next-gen quarry excavators is expanding with the introduction of the Cat next-gen 350 that joins the 374 and 395 models. The 350 consumes up to 13% less fuel than the Cat 349 and is equipped with technology features such as Assist that help increase efficiency and Payload on-board weighing, which gives real-time weight estimates to achieve precise load targets.”
Selmani notes that another solution for customers is rebuilding equipment that allows a machine to have a second or, sometimes, a third life. “Through Cat Certified Rebuild, we rebuild Cat equipment in our workshops and return machines, components and systems that have reached the end of their life to a like-new condition. On average, we re-use 65% of the parts in a Certified Rebuild.”
Selmani also stresses that short- or longterm rentals through BM’s sister company,
“We believe that the building-materials market is continuing to grow in line with industry reports and forecasts”
Trayan Dimitrov, general manager of Hitachi Construction Machinery (Europe) France
support the project, one is expected to be the largest in France, and extraction is estimated to last for the next ten years.”
Like Caterpillar, Hitachi Construction Machinery (Europe) does good business in the French quarrying and large construction equipment market. Trayan Dimitrov, general manager of Hitachi Construction Machinery (Europe) France, and Patrick Top, director of sales and marketing, Hitachi Construction Machinery (Europe), see good market opportunities.
“At Hitachi Construction Machinery (Europe) (HCME), we believe that the building-materials market is continuing to grow in line with industry reports and
Dimitrov sees potential for HCME to further expand its quarrying sales and productsupport services in all regions of France, home to around 3,400 quarries. He sees further growth potential for HCME in other parts of the French construction industry.
“This is one of the reasons behind HCME’s recent decision to acquire its authorised dealer Cobemat (now rebranded as Hitachi Construction Machinery France – HCMF). HCME’s ambition is to expand its sales and rental network in France, in line with its strategy to expand the value chain, and there will soon be a new dedicated HCM rental company established in the Île-de-France region,” Dimitrov explains.
Top says HCME’s “market-leading” 50-90 tonne excavators – the ZX490LCH-7, ZX530LCH-7, ZX690LCH-7 and ZX890LCH-7 – remain the number one choice among its French quarrying customers. “These customers have a wide range of options at their disposal. These include the availability of heavy-duty and bulk excavation arm and boom types and strengthened arms, booms and undercarriages for harsh conditions,” he notes.
Top adds: “In particular, the ZX490LCR-7, ZX690LCR-7 and ZX890LCR-7 models are reinforced to work in the harshest conditions. And there is a wide range of high-quality attachments, such as buckets and breakers,
Hitachi Construction Machinery (Europe) continues to see strong quarry customer demand for its large Zaxis-7 excavator range, including the pictured ZX490LCH-7
and ground-engaging tools for HCM owners to choose from for their specific quarrying needs.”
Asked by Aggregates Business what role digitalisation, automation and machine telematics play in quarrying/buildingmaterials-processing-customers' application needs, Top responds: “The French market is one of the leading markets in this respect. For example, the first HCME Customised Solutions Zaxis-7 excavator with factoryfitted Leica Geosystems 3D machine control solution was delivered to the French contractor, Kerleroux. This is one of the optional extras available directly from HCME’s Amsterdam factory, empowering our customers to work more independently, productively and precisely.
“Further signs of growth are seen in the digital side of the industry. HCME is not only a manufacturer of equipment and machines but also a solution provider. Digital solutions have cut through in almost all areas, both on- and off-site, from telematics and datapowered machines to remote and fleet management solutions.”
Regarding the importance of sustainability issues to HCME’s French quarrying/ building-materials-processing customers,
Heidelberg Materials’ Bussac-Forêt cement plant
Top says: “As an indicator of the importance of sustainability within the industry itself, the annual UEPG [European Aggregates Association] sustainability awards receive an increasing number of entries every year. Traditionally, quarrying may have been perceived as a polluting and noisy industry, but it is fighting against that view by playing a bigger role in local communities across Europe. An example of this can be found in France, where one site was used for theatrical productions when the quarry was not in use.
“Developments in technology are key to helping the aggregates sector to face the challenges of sustainability and lowering the cost per tonne. Equipment manufacturers are taking an innovative approach with electrification and alternative powertrains, but adopting such innovations will take time”
Top notes that quarries find it difficult to go fully electric due to the infrastructure required. “There are more elements to be considered in a quarry than a mine, for example, and the associated costs. Quarrying is also a relatively conservative industry, and it is challenging to convert operators massively to a sustainable agenda.
“Nonetheless, they are interested in new
technology, particularly regarding potential fuel savings and reduced costs. While technology in mining is often considered too capital-intensive for quarrying, there is potential for both sectors to inspire each other, for example, concerning renewable energy and biodiversity.”
Dimitrov highlights major infrastructure projects using HCME machines: “The best example is the French government’s multibillion-euro investment between 2018 and 2037- the Grand Paris Express - the largest transport project in Europe and France’s biggest current infrastructure project.
“HCME’s acquisition of Cobemat and ongoing cooperation with its other dealers in France – will enable the company to take advantage of the new opportunities presented by key accounts. Existing customers will benefit from the availability of deals direct from the manufacturer and a nationwide service structure.
“Additionally, HCMF’s territory covers the Île de France province, the largest and most challenging region driven by OEMs. External trends influencing this acquisition include upcoming large projects, the high rentalpenetration ratio, and the needs of these key accounts.” AB
Heidelberg Materials is investing €65mn to accelerate the decarbonisation of its Bussac-Forêt cement plant in western France.
The plant will be expanded to include a facility to produce calcined clay, which can replace parts of the CO₂-intensive clinker in the cement. This will allow the launch of a new range of lowcarbon calcined clay cements containing less clinker.
"Our most recent investment in innovative technologies in France demonstrates Heidelberg Materials' strong commitment to decarbonise our products.
The launch of the transformative project in Bussac-Forêt will be supported by a favourable administrative and regulatory environment", said Dr Dominik von Achten, chairman of the managing board: "The project will reduce the site's CO₂ emissions by up to 20% and thus have a significant positive impact on Heidelberg Materials' carbon footprint in France."
Dr Nicola Kimm, chief sustainability officer and managing board member, added: "In Bussac-Forêt, we are investing in a technology with great potential. It will allow us to significantly expand the range
of low-carbon products. Using calcined clay as a clinker substitute is an important measure to reduce the carbon footprint of cement and concrete. In principle, a CO₂ reduction of up to 40% is possible when substituting cement clinker with calcined clay."
The company is currently piloting calcined clay technology in Ghana, where the world's largest flash calciner is being built with a capacity of more than 400,000 tonnes per year.
This latest investment is in addition to the €46mn already committed by Heidelberg
Materials to decarbonise the Bussac-Forêt cement plant by increasing the alternative-fuel rate from 30% to 80%. The Ecological Transition Agency financially supports the project as part of the France Recovery programme and benefits from support from the Nouvelle-Aquitaine region. It is fully in line with Heidelberg Materials' climate strategy, which has set targets to reduce specific net-CO₂ emissions per tonne of cement by 47% by 2030 compared to 1990. The Group aims to achieve net-zero carbon emissions by 2050 at the latest.
SBM Mineral Processing’s new AI-featuring REMAX 600 impact crusher during its official launch in Ramsau,
The incorporation of technologies such as artificial intelligence can revolutionise the crushing & screening equipment sector. Liam McLoughlin reports
More than 170 visitors to the Ramsau quarry in Lower Austria recently got an insight into the potential future of the crushing and screening equipment industry. The quarryoperated by Hans Zöchling GmbH - was the venue for the official launch of SBM Mineral Processing’s revolutionary new REMAX 600 track-mounted impact crusher, which features AI capability.
The machine was a major attraction at the 2022 edition of bauma, and the Ramsau event featured performance demos in natural stone and typical recycling materials that demonstrated the all-round qualities of the new 600 t/h crusher.
SBM cooperation partners from the University of Leoben (Montanuniversität of Leoben) gave insights into the ongoing development work around AI-based "autonomous crushing", which should soon be possible with the REMAX 600 and other SBM plants.
Helmut Haider, SBM sales director processing, says that more than three years of intensive development work by SBM and external experts have gone into the new machine.
"We have once again delivered on time," says Haider in view of the closely timed model premieres in recent years, with which the processing specialist has expanded its range of track-mounted JAWMAX jaw crushers and REMAX impact crushers into a highly up-to-date, well-rounded portfolio with six models each ranging from 23 to
160 tonnes transport weight. With the exception of the large jaw crusher JAWMAX 800, all models offer compact dimensions for economical one-piece transport, despite the diesel-electric hybrid drive with plug-in option and largely class-leading crushing and screening equipment.
SBM has been collaborating for several years with, among others, the Innovation Centre for Raw Materials (IZR) at the University of Leoben. The cooperation with the university has featured computeraided or experimental validation of new or further developed processing solutions and components from SBM’s own R&D department at its headquarters in Oberweis, Austria.
The aim is to develop "intelligent", selflearning mobile crushers that enable the decisive step from crushing, which is already largely monitored and optimised in terms of the interaction of all process steps, to autonomous, fully-automated production. The first milestone and ideal technology carrier for further development is the now market-ready "conventional" REMAX 600 with its extensive technical equipment, the further optimised electric drive and the latest generation of the CRUSH CONTROL machinecontrol system, which already processes a large part of the machine data generated today.
The teams are currently working on the development of the advanced sensor technology that will enable the machine to automatically detect the type and composition of the feed material and the particle-size distribution of the end
products. Together with the load conditions of the crusher and conveyors, which are also determined in real time, the CRUSH CONTROL system transmits all the values determined in the field via a cloud solution to the SBM headquarters. A ‘digital twin’ created there compares the actual machine performance with thousands of stored reference data from 1:1 quality tests, laboratory tests and computer simulations (rock properties, grading curves, particle shapes, etc.). The resulting optimisation potential is fed back into the machine's control system and, thanks to innovative machine-technology solutions, enables all process stages, right down to the air classifier and magnetic discharge, to be adjusted immediately and continuously on-site without interrupting operation.
According to SBM, autonomous crushing is designed to provide significant support and relief for operators and operating personnel: for example, the system can be configured precisely to requirements on a data-based basis, even before a change of location or material, through the correct selection of screening media. An interactive menu-control system allows even inexperienced operators to set up production precisely, depending on whether maximum output, minimum fuel consumption (‘eco-mode’) or optimised production of certain valuable aggregates is required. A new type of integrated tool monitoring in the impact crusher also helps to reduce quality losses due to wear during production and provides important support for predictive maintenance.
With the newly-developed REMAX 600,
SBM Mineral Processing relied on the highly mobile plant concept, which offers natural stone producers and recycling companies alike the full flexibility and high productivity of a large impact crusher.
SBM says the REMAX 600 defines a completely new performance segment in mobile primary and secondary crushing with the 600tph of its further developed 1400 impact crusher 13/14/4 with an intake of 1,380mm x 1,000mm (W x H) for feed sizes up to 900mm. Up to five high-quality fractions can be produced in one pass, thanks to efficient pre-screening, triple air classifying and high-efficiency magnetic separation, as well as the optional single/dual/triple-deck secondary screen.
Depending on the equipment, the REMAX 600 only weighs between 60 and 80 tonnes on the low bed – even when fully equipped, the machine measures a slender 22.0m x 3.49m x 3.80m (LxWxH).
The REMAX 600 is designed to offer a complete package of standard and optional equipment that ensures high added value through a variety of high-quality end products. In addition to the standard pre-screening via a double-deck circular vibratory screen (W: 1,300mm x L: 2,400mm), these include in particular the three optional circular vibratory post-screening units (1, 2, 3 deck; W: 1,800mm x L: 5,500mm) – each with oversize return and high-projecting discharge conveyors for large product stockpiles. According to SBM, a real innovation in this machine class is the highly efficient overbelt magnet with longitudinal discharge, which guarantees high purity of the end products, especially in recycling.
All equipment and the side walls of the 9m³ feed hopper can be hydraulically folded in and remain on the machine.
SBM says this means that, even in one-person operation, the column-free system can be set up quickly without the need for additional tools. The operator is supported by the start-up routines of the SBM CRUSH CONTROL system, with its central 25cm-display, multi-function radio remote -control and cloud-based remote access to all
operating states via smartphone or tablet.
As with all SBM mobile plants, the REMAX 600 features a fuel-efficient diesel-electric hybrid drive with optional mains operation: a compact unit consisting of a 15-litre Cummins turbo diesel (EU-V) and a 553kVa generator supplies all electric drives – from the 250kW electric motor of the crusher, to the complete conveying and screening technology, to the two electrically driven hydraulic units of the undercarriage and working hydraulics.
Thanks to this design, all plant functions remain available even in fully electric mains operation, which SBM says significantly reduces on-site emissions (exhaust gases, noise) compared to other hybrid concepts with short-term diesel intervention. The high-torque drive at permanently low speeds is also impressive in diesel-supported operation, which, in addition to the low
environmental impact, results above all in favourable fuel consumption, even when all the auxiliary units are working at high capacity.
According to SBM, the field tests , carried out since the beginning of this year by cooperation partner Hans Zöchling GmbH under construction-site conditions in the Ramsau quarry and adjacent recycling depots with several tens of thousands of tonnes of a wide variety of raw materials , have resulted in economic average values of 34–46 l/h diesel or an electricity consumption of 140–200kWh.
"This SBM-typical consumption advantage was undoubtedly one of the reasons why the enthusiasm felt at the BAUMA trade fair very quickly turned into real interest and concrete orders long before the market launch," Haider says. "In addition to our own dealers, the first end customers have already signed up – we assume that we may significantly adjust our production plans for the REMAX 600 upwards next year."
Belgium-based Keestrack is launching a new B7H heavy-duty hydraulic jaw crusher, specially designed for the US market and the toughest of rock conditions in quarrying and mining applications.
The 70-tonne B7H hydraulic jaw crusher has a 30-tonne jaw and is adapted from Keestrack’s existing B7 electric jaw crusher which was launched in 2018.
It has a vibrating feeder with 2-step grizzly of 2,200mm x 1,080mm (LxW) and a bottom deck in wire mesh of 1,450mm x 870mm (LxW) to optimise crushing results and to reduce wear.
The feed size of the material is up to 700mm, the feed opening is 1,200mm x 830mm and the outlet adjustment CSS is min.-max. 75mm–250mm.
The jaw crusher is equipped with the patented NSS (non-stop system ) which protects the crusher from uncrushable feed and resets the CSS automatic during operations.
Keestrack sales director Frederik
THE MOBICAT MC 110 EVO2 AND MOBICONE MCO 90 EVO2
TEAM PLAYERS THAT WORK TOGETHER INTELLIGENTLY AND STRENGTHEN EACH OTHER. In linked plant combinations, the MOBICAT MC 110 EVO2 jaw crusher and the MOBICONE MCO 90 EVO2 cone crusher really fl ex their muscles. SPECTIVE makes both plants easy and intuitive to operate. Also, an advanced drive concept ensures greater effi ciency with lower consumption. Maximum throughput is achieved thanks to the material flow concept coordinated via line coupling across both crushing stages. Go for the perfect team!
www.wirtgen-group.com/evo2-line-kleemann
Hoogendoorn says the mobile crushing and screening equipment company is a pioneer in electric quarrying and mining machinery, having launched its first electric machine in 2006.
He adds that 90% of Keestrack machines are available in three versions: hydraulic, electric, and zero-emissions plug-in.
“A focus on sustainability is at the core of our company as this is the origin of our business,” Hoogendoorn said.
“Producing and recycling valuable raw materials is what mobile crushing and screening is all about, and our efforts are definitely having a positive impact on the ecological footprint.
“As these heavy-duty industries need very powerful drive systems, Keestrack kept on searching for alternative drive systems,” Hoogendoorn explains.
“From load-sensing hydraulics to e-drives to Zero drives, (Keestrack offers) equipment with no combustion engines on board but only electric motors. This request is also a pull from mostly the North European market. This way we want to protect the planet and save money at the same time.”
He adds that 80% of US customers currently ask for hybrid machines and only 20% electric, but that this is changing with all-electric units becoming more common in the US market every year.
Astec unveiled its newest portable highfrequency screen plant at the ConExpo construction and quarrying equipment event in Las Vegas held on March 14-18.
The machine is equipped with 2.4m x 5.5m top deck and a 2.4m x 3.7m bottom deck, which the US-based manufacturer says makes it the widest high-frequency screen available.
The PTSC2818Vm features externallymounted vibrators at the ends of the tappets. Astec says this unique design creates a higher G-force and reduces heat load from material to motors as compared to single, centremounted vibrators. It also allows for easier maintenance and adjustments. The screen is equipped with hydraulic operating angle adjustment, a fines collection hopper, top-
and bottom-deck discharge chutes and an aggregate spreader.
Similar to other PTSC plants, the 2818VM features a nominal 137.16cm x 1,158.2cm delivery conveyor with hydraulic drive and full-length skirtboards. The chassis is fitted with manually-operating support legs, outriggers for additional support and folding walkways along the screen.
The new portable plant is available with a variety of options, including: steel screen cloth, vinyl dust cover, hydraulic levelling jacks, immersion heaters for hydraulic reservoirs, and starters for three off-plant conveyors.
Northern Ireland-based compact mobile crushing, screening and stockpiling equipment maker Screencore is broadening its scope to produce a range of dual-power crushers and mobile pugmills.
Screencore is located in Coalisland, and although a relatively new entrant into the global crushing and screening market, it has a management team with over 100 years of experience in the industry. The company says this has enabled it to develop a range of mobile – and now stationary – crushing, screening, stockpiling and pugmill solutions in a relatively short period of time.
All members of the range have been designed for users who require a powerful and transportable unit without sacrificing productivity. “Our focus on quality and performance means that our customers can rely on our units getting the job done, no matter where they are located, and virtually
whatever the applications,” says company director Ciarán Ryan.
“While our product line has expanded to encompass the formidable 237 trommel and the 30-ton Trident 165 scalper, our fundamental concept remains consistent: simplicity of use."
Ryan says this simplicity is evident in features like hassle-free transport, swift set-up time, intuitive control systems, and distinctive design elements such as full-sized bottom decks on scalpers or augers within the trommel hoppers.
The Screencore range consists of a selection of tracked and highly mobile scalping screens, trommels and compact, yet productive jaw crushers.
Collen Bros (Quarries) Ltd, a family-owned and-operated civil engineering company located in County Armagh, Northern Ireland, recently took delivery of a Powerscreen Premiertrak 600E (PT600E) jaw crusher, which is the first of its kind to be delivered in the UK and Ireland.
The Premiertrak 600E jaw crusher is part of the growing Powerscreen Hybrid range. It has been designed for large-scale operators who require high production in recycling, quarrying, construction and demolition, and mining applications. With significant operational savings, reduced fuel consumption, and ultimately reduced CO2 emissions, this machine is a popular choice for customers who want to maximise efficiency and minimise their carbon footprint. AB
new concept
An eye-catching alternative-fuel advance for quarrying-application-compatible excavators and how a leading global manufacturer’s wheeled loaders are a big fuel saver for a longstanding German building materials producer. Guy Woodford reports
Komatsu has developed a new concept medium-sized hydraulic excavator powered by a hydrogen fuel cell.
The Japanese quarrying and construction manufacturer says that by advancing the PoC (Proof of Concept) tests it started in May 2023, it has accelerated its efforts to embark on the commercial production of medium-sized and large construction equipment powered by hydrogen fuel cells in the near future.
In its mid-term management plan, Komatsu committed to minimising environmental impact throughout its business, targeting a 50% reduction in CO2 emissions from using its products and production of its equipment by 2030 (compared to 2010 levels) and a challenging target of achieving carbon neutrality by 2050. Komatsu says it has been providing customers various products, services, and solutions that reduce environmental impact,
such as hybrid hydraulic excavators and electric mini excavators. The company adds that it is also engaged in research and development to provide products equipped with new power sources.
For the new concept machine, Komatsu adopted a hydrogen fuel cell system and hydrogen tank produced by Toyota Motor Corporation on Komatsu's medium-sized hydraulic excavator. In addition to Komatsu's control technology, the combination of Toyota’s hydrogen fuel cell system and Komatsu key components, Komatsu says it is working towards zero-exhaust emissions and a significant reduction in noise and vibration while delivering the same powerful digging performance and high operability as enginedriven excavators.
Medium-sized and large construction equipment require a power source with higher energy density than small construction equipment, leading to electrification with batteries. Because hydrogen has a higher
energy density and can be refuelled in a shorter time than is required for recharging batteries, Komatsu has been advancing its R&D efforts as a promising electrification choice for medium-sized and large models.
The global off-highway equipment giant adds that it will continue its efforts towards commercialising medium-sized and large construction machinery equipped with hydrogen fuel cells by conducting PoC tests of this new concept machine.
August Lücking (Lücking) is a 123-yearold building-materials producer in northwest Germany. About two years ago, the company purchased a DL420CVT-5 wheeled loader from DEVELON (formerly Doosan Construction Equipment) to feed materials for the brick-production process. The purchase decision was based on trials that showed enormous fuel savings of more than 9 l/h, confirmed when the new machine began operation. As a result, when the time came for a new wheeled loader to be bought, the
Volvo Construction Equipment (Volvo CE) has launched a digital solution to simplify the load-out process - and help customers maximise their productivity.
Connected Load Out improves the efficiency and productivity of the load-out process by connecting the loader operator, site office and trucks. It is a digital solution for Volvo wheeled loaders with Load Assist and On-Board Weighing and Volvo excavators with Dig Assist On-Board Weighing.
It reduces administration and miscommunication by digitalising orders and load tickets, improves visibility and helps sites be more productive. A more efficient load-out process lowers fuel consumption, reducing costs and CO2 emissions. It is currently available on subscription in select markets in Europe and North America.
Cecilia Jonsson, product owner, Global Load Out Services at Volvo CE, says: “We continue to develop intelligent solutions that help our customers streamline operations and maximise efficiency.”
decision was made: the new machine should also be a DL420CVT, this time the nextgeneration DL420CVT-7 model.
When the purchase of the original wheeled loader was on the agenda about two years ago, a Doosan DL420CVT-5 was tested on-site in the company's brick factory. The requirements for the loading of clay for the bricks are particularly challenging. The clay has a high density and, therefore, a high weight. In addition, the material is extremely sticky and tough. A high degree of even force and heavy traction are required to penetrate the material with the shovel, especially on wet surfaces. The tyres also play a major role here. Lücking
Develon DL420CVT-5 and DL420CVT-7 wheeled loaders are big fuel savers for German building materials company August Lücking. Pic: Develon
relies on special tyres whose profile is more like that of a tractor than a wheeled loader. The grooves of the tread on 'standard tyres' clog up quickly due to the greasy consistency. These difficult conditions also drive up fuel consumption.
The previous machine, a competitor's wheeled loader with a conventional converter transmission, required an average of around 23 l/h of fuel under these conditions. When the authorised signatory at Lücking, Richard Lemke, asked the wheeled loader sales manager at Develon, Marc Glesius, about the consumption to be expected under these conditions during the handover for the test operation, he cited 14 l/h, a value that Lemke found difficult to believe.
Lemke offered Glesius the following bet: "If the DL420 with the CVT transmission only consumes 14 l/h, i.e. around 10 litres less, I will buy it immediately." The rest is history. The test consumption was the targeted 14 l/h, and the wheeled loader has been in service at the company for two years.
Lemke added: "In times of enormously high fuel and energy prices, 10 l/h naturally makes an enormous difference. In the last two years, the consumption of the DL420CVT-5 has levelled off at the 14 l/h already determined in the test operation. We also did not record any unscheduled machine failures during this period. Therefore, only a Develon wheeled loader with a CVT transmission was considered when purchasing a new vehicle. We are confident that the new wheel loader can confirm these positive experiences."
One of the main factors behind low fuel consumption is the variable transmission. Glesius said: "This transmission combines the advantages of a mechanical and hydrostatic transmission and excludes the disadvantages of both systems. The variable transmission switches continuously from the hydrostatic drive to the mechanical drive as the speed increases and depending on the application-related requirements. This system's advantages include, in particular, the excellent traction that a hydrostatic transmission offers and driving over longer distances with direct mechanical transmission. It owes the fuel savings to the lower engine speed than conventional transmissions, which is necessary to achieve maximum speed and traction." AB
Two major rigid haul truck launches offer much for quarrying customers looking for production gains from their hauling operations. Guy Woodford reports
olvo Construction Equipment (Volvo CE) says its new R60 rigid hauler offers customers a higher payload and uptime.
The new E-generation machine is suitable for heavyduty quarrying and mining.
Built for markets with Tier 2-compliant engines and based on the R100E model, the R60 has a higher payload than the D-generation model it replaces, along with a durable design and new comfort and safetyenhancing features – which Volvo CE says enables it to move more for less with every cycle.
Drew Watson, global product manager for the Volvo R60 at Volvo CE, says: “The Volvo R60 offers a 55-tonne payload and body volume of 36m³, enabled by a V-shaped body ensuring optimum load retention and minimal material carry-back.
“The rigid hauler is a perfect match for a 90-tonne excavator and meets the industry standard of 10/10/20 where it can take 10% overload for 10% of the time but should not exceed 20%. To help operators haul the optimum amount of material, an optional On-Board Weighing system provides realtime payload insight to the hauler operator via the on-board display and can predict the 10/10/20 payload.”
Contributing to speedy cycle times, the drivetrain combines high torque capability and high drive-axle multiplication to deliver the traction force needed to take on the steepest site gradients.
Volvo CE says the R60 is also fuel-
efficient. Thanks to Volvo Dynamic Shift Control, gear selection automatically adapts to varying conditions, whilst ECO mode enables the hauler to default to the most efficient gear-shifting schedule. In addition, auto engine-idle shut-down eliminates unnecessary fuel consumption and engine wear.
The rigid hauler is available with the Volvo CareTrack telematics system to enable remote machine monitoring and help further boost efficiency. Moreover, customers can gain recommendations on the optimum fleet configuration and site set-up from their Volvo dealer with the support of Volvo Site Simulation.
Designed to deliver high uptime and low
operating costs, the R60 is built to last with a 60,000-hour life frame and a list of features that contribute to long-lasting performance and component life, including a low centre of gravity and balanced weight distribution to provide rock-solid stability and spread the impact of loads and stresses across the machine; a high-strength, flexible chassis and responsive MacPherson strut with lower wishbone connection to absorb shocks and vibrations and improve the operator ride; a V-shaped body, manufactured from highimpact and high abrasion-resistant steel, with a minimal number of panels and welds; and neutral coast inhibitor and engine-overspeed protection to further minimise wear.
Servicing of the R60 is required every 500
hours and can be completed swiftly thanks to a straightforward machine design that includes grouped maintenance points located within easy reach either from the ground or the service platform, as well as commonsized bearings throughout.
On-board diagnostics provide insights into system pressures, temperatures, and fault reporting to facilitate and speed up troubleshooting.
Volvo CE says the R60 is built with operator comfort and safety top of mind. Operators can enter the cab from both sides using anti-slip steps and walkways. The cab is now pressurised, roll/fall overprotective structure-certified (ROPS/FOPS) and features a left-positioned operator station to aid safe passing. Volvo Smart View is an option to improve further visibility with a 360° birdseye view of the work zone.
Ergonomically positioned displays, responsive fingertip controls and low-effort steering combine to make operation effortless. The adjustable air-suspended seat and a Bluetooth-enabled audio system add to operator comfort.
The Volvo R60 has two retardation systems to keep a steady speed and facilitate machine navigation when going downhill, reducing the need for operator input. When manually selected, the transmission retarder slows the drivetrain to limit wheel lock-up, which is particularly useful on steep declines or wet conditions. The modulating braking retarder can be automatically activated when the operator’s foot is off the accelerator to maintain a gear-selected constant engine speed. Moreover, fail-safe braking and secondary steering systems add to job site safety.
Italian rigid haul truck manufacturer Perlini says its new DP265WD machine combines the company’s decadeslong experience of mining haul truck manufacturing with the latest technologies, such as new control electronics, modern GPS monitoring and electronic weighing systems, to produce a versatile, economical and reliable machine.
The Gambellara, Vicenza provincebased manufacturer states: “With its small dimensions, the new Perlini DP265WD is the ideal vehicle for quarries and public
works; the width of under three metres also allows road transport without special transit permissions or escorts.”
The company adds that the DP265WD has the usual prized Perlini features, including a brake/retarder system with oil-bath brakes, oil-pneumatic suspension, and typical Perlini stability and operator cabin comfort. The new RDT also has a sustainability-minded Stage V Scania DC09 engine and an Allison 4430ORS transmission with updated electronics.
First presented at bauma 2022 in Munich, Germany (24-30 October), the DP265WD was
also showcased by Perlini at the 31st edition of SaMoTer (3-7 May 2023).
Speaking at the exhibition, Paola Pugliani, Perlini’s sales marketing executive, says: “This is our first completely digital machine; the start of a new era. It allows our technicians to remotely control the haul truck and do preventative maintenance remotely. We can check the machine’s operation parameters hour by hour, not just fuel consumption and productivity but also whether something is wrong and needs attention. This system makes for easy maintenance working together with our customers.”
Pugliani says the DP265WD’s under-threemetre width is in response to many smaller quarry operators in Europe and North Africa requesting that kind of RDT over the past decade. “It is a very flexible machine that can work in a quarry and other work sites. We were recently contacted by an important customer in Ireland that was looking for a machine like ours. They have a narrow bridge to pass through in their quarry, and we are the only manufacturer currently offering an RDT of a suitable size.”
Perlini’s four-strong RDT range starts with the construction-and-quarrying-applicationsuited 26-tonne capacity DP265WD, followed by the also construction-and-quarryingapplication-suited 40-tonne DP405WD, the 65-tonne DP705WD, and the 100-tonne capacity DP905WD. “The last two models are aimed specifically at mining applications,” says Pugliani.
She adds: “Perlini is targeting many Central Asian countries full of iron and other material mines. Due to the war in Ukraine and sanctions against Russia, many BelAZ [Belarussian mining dump truck manufacturer] customers cannot get their trucks. So, they are now looking at other companies, like Perlini, to supply them with new machines.
“Many governments globally are also moving away from the gas and oil industry to the extraction of minerals in Central Asia and Africa. This means much finance is concentrated in this mining sector, which creates new opportunities for us. We are looking for good dealers in countries in these regions. They will need to do more than just selling trucks; they will need to offer customers quality after-service, including maintenance.”
At SaMoTer 2023, Perlini introduced its new Italian dealer, Rimini, Emilia-Romagnabased WR57. “The company is also a Hitachi Construction Machinery (Europe) dealer and provides our after-sales support, purchasing spare parts from us and selling them to Perlini customers. WR57 also offers Perlini dump trucks for rental. We are seeing more and more Italian customers wanting to rent our machines. Many of our customers see machine rental as the future. They are attracted by the ability to quickly change machines and always have the latest models, which is particularly important during busier periods.
“During the exhibition, we were visited by an important Italian company that runs cement plants nationwide and stressed the importance of rental machines. They like to test a new machine through a rental before purchasing it.”
Pugliani says Perlini is pleased to see Giorgia Meloni’s new Italian government continuing the infrastructure spending of the previous administration, creating good domestic business opportunities for off-highway machine manufacturers. “The previous government greatly supported
manufacturers and equipment end users. We have a specific Industry 4.0 offer that helps sell machines. Many customers near our factory are working on big high-speed train works, and there are many infrastructure works in southern Italy.”
Perlini plans to treble its production capacity after a sustained period of investment. “By 2025, we will be able to produce up to 120 units annually, up from 40 units,” says Pugliani. “We are hiring many engineers and spending time training them. Our products are complex from an engineering perspective and very attractive.”
Turning to Perlini’s sustainability credentials, Pugliani says they are partly reflected in the company’s choice of engine supplier: “In 2019, we switched from another engine supplier to Scania, as the Scania engines complied with new EU Stage V emission standard, and also offer lower fuel consumption. We cooperate well with them, and now they supply engines for our Stage II emission market customers. Unfortunately, Scania doesn’t offer an engine with the horsepower required for our 100-tonne RDT, so we have a Fiat engine in that machine for Stage V and Stage II emission market customers.
“We also focus on lowering the noise that can be heard inside our truck cabins. That’s important for our operators and the wider environment. Our customers are also interested in running hybrid diesel-electric versions of our trucks. It is a project we are working on, and I think we will be ready with our first hybrid-power models in a couple of years. The rigid hauler is in our DNA, and a sustainable product range is very important to us.” AB
A vibrancy in the global off-highway equipment engines and alternative power sector was evident at the recent CONEXPO-CON/AGG 2023 exhibition in Las Vegas, USA. Guy Woodford reports
At CONEXPO-CON/AGG 2023 (14-18 March), Cummins reaffirmed its commitment to reach net-zero emissions from its products and business by 2050 in line with its Destination Zero strategy. The US off-highway-equipment engines giant says this will be achieved by advancing internal combustion engine technology while reducing carbon emissions without impacting operations, weight, or uptime.
Cummins says its net-zero goal will also be secured by building the broadest combination of zero-emissions technologies dedicated to the commercial vehicle industry, including battery-electric and fuel-cell electric powertrain solutions and electrolysers for green hydrogen production.
This complementary approach, says Cummins, lowers emissions today by matching technology readiness with infrastructure readiness to drive wide-scale adoption using the right technology at the right time.
Eric Neal, executive director of Cummins Off-Highway business, said: “We aim to support our customers on their path to zerocarbon emissions. This means meeting them wherever they are on their journey. We are leading the energy transition by providing our customers with the right technology and utilising our deep understanding of their needs and applications.”
Cummins emphasises that it has the
knowledge, expertise, and scale across a range of solutions through growth and acquisitions to continue leading in the off-highway industry today and in the future.
“Cummins powers more types of machines and vehicles than anyone else. The breadth of our business across market segments and regions means we are the ideal partner to help our customers through this transition,” continued Neal.
Cummins showcased in Las Vegas its
new fuel-agnostic 15-litre engine platform with hydrogen, biogas and advanced diesel engines. It offers OEMs the opportunity to accelerate the decarbonisation of heavy-duty off-highway applications.
This new platform, designed for the next level of emissions, significantly increases power density with a more compact installation envelope, enabling OEMs to increase machine capability and productivity without impacting running costs.
The fuel-agnostic architecture of the 15-litre next-generation engine utilises a common base engine with cylinder heads and fuel systems specifically tailored for hydrogen, natural gas, diesel and biofuels, including HVO.
The 15-litre hydrogen engine will be available with ratings from 400-to-530hp and a peak torque of 2600Nm. For applications powered by renewable biogas, this engine will offer ratings from 400-to-510hp with a peak torque of 2500 Nm available. The advanced diesel version features a broad power range of 450-to-650HP, with an impressive 3200Nm peak torque.
Amy Davis, president of Accelera, the new brand for Cummins’ New Power business segment, said: “We understand that no single
solution or path to zero will work for all power needs, which is why we are developing the broadest combination of zero-emission technologies: fuel cells, battery systems and fuel-storage technologies.”
Cummins also highlighted at CONEXPO/ CON-AGG 2023 its next-generation fuel cell engine suiting heavy-duty off-highway applications' duty cycle, performance, and packaging requirements. Available in 150kW and 300kW fuel-cell engine configurations, it incorporates variable pressure technology, which provides improved power density, efficiency, and durability, all while delivering a lower total cost of ownership.
As a result of Cummins’ acquisition of Meritor last year, Accelera’s product portfolio was broadened to include complementary ePowertrain products and EV powertrain integration capabilities. As seen, the Electric Central Drive Unit (eCDU) is a remote-mount electric powertrain designed for space-limited off-highway applications. Its innovative architecture enables increased vehicle-design flexibility and the ability to be located as needed. It helps reduce investment in vehiclearchitecture changes such as hydraulic brakes and driveline parking brakes.
“Because of our global service, technical expertise, and ability to optimise the performance of applications, Accelera is in a unique position to help our end customers succeed during the energy transition. Working together with customer partners, we are rapidly evolving our zero-emissions technology to meet the diverse needs of our customers and further our shared goals of lessening our impact on the planet,” concluded Davis.
Volvo Penta demonstrated its own road to net zero at CONEXPO-CON/AGG 2023. The company showcased its electric driveline alongside its current portfolio of ultra-efficient EU Stage V and EPA Tier 4 final combustion engines – the D5, D8, D13 and D16. In addition to leveraging an array of proven technologies from across the Volvo Group, the innovative electric driveline solution would not have been possible without the firm foundation provided by Volvo Penta’s more mature
power solutions and the expertise of the company’s engineers. Volvo Penta also highlighted in Las Vegas how it’s delivering in its service offering, focusing on creating value with customers through connected solutions.
Fredrik Högberg, president of Volvo Penta North America, said: “To succeed on our transformation journey into new, sustainable technologies to meet the industry’s net-zero ambitions, as well as achieve the Science Based Targets initiative (SBTi) for net-zero value chain emissions by 2040, we believe that strong collaboration with customers and partners is crucial. We cannot deliver the changes that need to happen alone – that’s why we are working closely with our customers, supply chain partners, governments, societies and other stakeholders.”
A popular choice in a wide range of machinery from excavators and underground mining trucks to crushers and screeners, Volvo Penta’s industrial combustion engines have been proven and optimised to meet customer needs in terms of productivity, uptime and total cost of ownership (TCO). Passive regeneration of the aftertreatment system eliminates unplanned stops during operation, while fuel consumption has been reduced by up to 5% over the previous models.
Since 2016, Volvo Penta’s industrial engines can run on renewable diesel (HVO), enabling a more sustainable choice. Further supporting customers looking to transition to low-carbon solutions is Volvo Penta’s dual-fuel hydrogen engine – an evolution of the company’s proven D8 model. The engine mainly uses hydrogen as a renewable fuel source, reducing CO2 emissions by a claimed up to 80% without impacting power or performance. Volvo Penta will continue to evolve its engine range to run on compatible alternative fuels, enabling the transition towards lower emissions in those markets
that cannot yet support fully electric solutions.
Another aspect of Volvo Penta’s transformation journey is its growing foothold in electromobility as a system supplier. Volvo Penta’s electric-power solutions are backed by connectivity to help customers actively monitor the health of their drivelines in a predictive way throughout their lifespan.
“No matter where customers are on their transformation journey, Volvo Penta can offer solutions to meet their machine, application and business needs,” concludes Högberg. “We work closely with our customers and form long-term partnerships to create purpose-built power solutions based on their requirements. As part of the Volvo Group, we leverage proven technology, investments and competence from Volvo Trucks, Volvo Buses and Volvo Construction Equipment. We combine this with our customer, market and application knowledge, allowing us to optimise designs and technology for specific machines and applications, considering the duty cycles, climate and environment in which they will operate.”
The JD9 is the newest addition to the robust John Deere off-highway engine line-up. This powerful configuration is designed to deliver reliable power of up to 317kW while offering a lower complexity and installation cost. The JD9 is a new and improved iteration of the existing John Deere 9.0L engine and features Level 40 Engine Controls (ECU) and upgraded fuel economy.
The exceptional quality of the 9.0L has been improved by adding a low-pressure fuel system, which is common in 13.6L engines, and removing the venturi in the engine pipes. The crusher-suited JD9 also offers increased power with single and dual turbo configurations. Its simplified in-line aftertreatment solution contains a diesel particulate filter (DPF), diesel oxidation catalyst (DOC), and selective catalytic reduction (SCR) system, achieving Final Tier 4 and Stage V emission levels. (The current 9.0L in production will continue to be available.)
Caterpillar claims that its new C13D diesel offers the highest power density for its class, replacing the previous C13B engine. Because of its high power output, the new C13D unit can replace the firm’s 15-litre engine and even the 18-litre diesel for some installations. Development of the engine has utilised some of the latest digital technology, with the firm assessing assembly and servicing comprehensively to optimise these processes, even before the unit was in the metal. Designed to meet future requirements, the engine can use HVO and is being tested on B100 biofuels. It also has the potential to be modified to run on propane or even hydrogen, with Caterpillar having benefitted from its long experience developing gas engines.
There are eight power ratings ranging from 340-515kW for the six-cylinder engine, which meets the current Tier 4 Final and Stage V emissions requirements. However, the unit has also been designed with the capacity to be able to meet the Tier 5 and Stage VI requirements if and when these are introduced.
The new engine platform is 10% more efficient and offers an increase in power of up to 20% and up to 25% more low-speed torque than the previous generation Cat engines in its class. It is designed to perform at altitudes of up to 3,700m, which is twice as high as legacy Cat engines, and in extremes of ambient temperatures as high as 60°C and as low as -40°C with aids. Engine oil and service schedules have been extended due to the engine’s high efficiency and clean running. Engine life is likely to be long, with key components able to be reworked for reuse.
A spokesperson for the firm commented, “We’ve intentionally designed the cylinder head for a second and even a third life.”
The high power density means that OEMs selecting the unit can install it more readily in their machines, while the engine can offer reliability even in more extreme applications. So far, Caterpillar has carried out around 12,000 hours of engine testing, with the C13D now being used in the field to further prove the design. And Caterpillar is confident that the unit will meet customer demands when it is ready for market. Scheduled for production in 2026, the Cat C13D is targeted for a wide range of off-highway equipment, including rock crushers, screeners and grinders; trenchers; material-handling equipment; and large industrial pumps.
The new engine platform will be equipped with Cat Digital Services, an integrated suite of robust software and hardware solutions supplying the insight equipment owners need to make decisions on the fly, secure equipment health, and minimise downtime.
Hyundai Doosan Infracore (HDI) has announced its timetable to mass-produce hydrogen internal combustion engines (ICE). The new units will be installed on commercial vehicles such as trucks, large buses, and construction equipment for validation by 2024, and full-scale mass production is planned for 2025.
HDI's initial under-development hydrogen engine is an 11-litre-class engine that produces a power output of 300kW and a torque of 1700 Nm at 2000 RPM. It satisfies Tier 5 / Stage 5 / Euro 7 regulations which require the emission to be 90% reduced from the current level to meet Zero CO2 (below 1g/kwh) and Zero Impact Emission (Zero Emission in the EU). AB
Hyundai Doosan Infracore's initial under-development hydrogen engine is an 11-litre-class engine that produces a 300kW power output
Recycled construction materials played a key role in a claimed world-first build, while new and latest building materials processing machines are in demand for recycling applications Guy Woodford reports
erman company Büscher has used Keestrack crushing and screening equipment to convert demolition waste into sustainable construction material to build what it claims is the world’s first complete house comprised of 75% recycled construction and demolition waste. The load-bearing and non-load-bearing interior wall elements are made of 100% recycled aggregates.
In June 2021, Büscher became the only company in Germany to receive general building approval (abZ) from the German Institute for Building Technology (DIBt) for load-bearing and non-load-bearing interior wall elements made of recycled concrete
gravel and sand are completely replaced by mixed demolition material.
The company's choice to use Keestrack crushing and screening equipment is also driven by its commitment to sustainability. Oppermann & Fuss, the Keestrack dealer in Germany, advised Büscher which ZERO equipment was the best fit for its applications and capacity at its recylcing site.
The Büscher site has solar panels that deliver up to 323kW/h of renewable electricity to power the concrete factory, the Keestrack R3e ZERO impact crusher, and the K4e ZERO screen. Both Keestrack machines are fully electric, powered by renewable energy, and do not have a combustion engine onboard.
As the electric motors drive most of the
systems, both Keestrack machines run with ZERO CO2 emissions. Keestrack is known for being an innovator and early adopter of electric e-driven equipment, and most of the Keestrack product range is available in ZERO-drive.
When plugged into the grid, like at the Büscher recycling site, where they use renewable energy using photovoltaic solar panels, the R3 and K4 produce zerocarbon emissions. The energy cost will be approximately 152kWh. Operational and maintenance costs will decrease drastically as no engine is on board to maintain.
The innovative technology, its safety features and the design of the R3 impact crusher have won several European design prizes, one of them being the Red Dot award.
minimise wear, an inlet opening of 770mm x 960mm (HxW) and a rotor diameter of 1.100mm and a rotor width of 920mm. The crusher equipped in a closed circuit with a recirculation conveyor and a precession screen of 3.100mm x 1.400mm produces a defined aggregate product size. The installed wind sifter eliminates contamination of plastics, wood or paper, and the overband magnet separates the metals. The R3e ZERO weighs 32t, and its plug-out of 125A powers the connected K4e ZERO of 28t.
The K4e ZERO has a high production capacity of up to 350t/h. The double-deck screen box of 4.200mm x 1.500mm, standard heavy-duty plate apron feeder and hydraulic adjustable screen angle gives it very good screening capabilities. The numerous options and screen decks make the K4 suitable for each job. At the recycling site of Büscher, they choose to have the fine and middle
be used if the production is too dusty. Also, both are equipped with a Keestrack-er UMTS system. This telematics software system provides real-time data and analytics. The system enables you to check the location of the machines and if they are working correctly. All aspects of a machine can be checked, and remote updates to the software can be made if necessary. It is possible to run diagnostic tests for all components, including the feeder, screen, crusher and conveyors. The Keestrack-er also functions well for maintenance planning by Oppermann & Fuss, helping to keep machines in optimum shape.
Company co-owner Wolfgang Büscher says that getting 100% prefab concrete ed was difficult and took the company eight years of research and development to gain approval. “Concrete specialists, laboratories and certification specialists were very doubtful this could be done. They all said it is impossible and not legal”, says Büscher. Büscher asked researchers from laboratories and universities to scientifically prove what the material is capable of and what it’s not. They gave the parameters on what they wanted to achieve with the material and asked them to find out if it stood the test of time.
“By now, all scientific research has been done, and it shows exactly what is possible with 100% recycled prefab concrete and concrete elements. The new material functions perfectly, and the recipe has changed at Büscher,” says Hans-Jürgen Büscher, Wolfgang's brother and company
Hampshire, southern England-based waste management and aggregates company L&S Waste Management has taken delivery of seven new Cat machines thanks to business expansion and fleet replacement, citing a “reliable plant with a great backup service” from Finning UK & Ireland, the world’s largest dealer of Cat machines and equipment.
With waste-treatment and recycling facilities in Portsmouth, Fareham and Southampton, the company processes 275,000 tonnes of construction and industrial waste each year and supplies ready-mixed concrete and aggregates from its facilities. It has grown from 20 staff to 150 within the last 15 years. Having bought their first Cat machine 14 years ago, the relationship with Finning has gone from strength to strength as support from Finning’s expert team has minimised unplanned downtime.
The latest machines to join their fleet include five excavators and two wheeled loaders comprising two Cat 313s, two Cat 320s, a 325, and 962M and 938M wheeled loaders with additional fire suppression, guards, and belly plates due to the harsh environment they operate in. As all the machines come with a Finning premier warranty, each one is covered for all repairs
for up to five years or 8,000 hours, giving complete peace of mind.
Steve Harman, operations director at L&S Waste Management, said: “We’ve been working alongside Finning for many years as we get great service backup from their team, and the Cat product is high-quality and reliable, which is key for us, as we have such high volumes of material going through our sites.
“They stand the test of time, and they hold a good residual value, and with the warranty package and guaranteed buyback from Finning, you know what your costs are going to be, and there are no hidden extras.”
Jack Pilgrim, territory account manager for Finning UK & Ireland, said the team supported L&S with asset management as their fleet is connected with Cat VisionLink, which provides data on fuel burn, machine health and idle times. Finning also proactively provides a monthly fleet benchmarking report sent to each site manager and senior staff.
He said: “Keeping their machines running is a top priority for L&S together with running their fleet efficiently, especially since the switch from red diesel last year, so our report for L&S breaks down their data to cover average run time (hrs) and idle time (%), the average fuel burn for their fleet, and the amount of operator-induced fault codes.
“We’re proud to support L&S as they continue to grow and expand their fleet, and our extended warranty package gives them complete peace of mind that if anything goes wrong with their Cat machine and it needs to come back into the workshop, there are no hidden fees, while our UK coverage means we can get an engineer on site fast.”
At steinexpo in Homberg/NiederOfleiden, Germany, from 23 to 26 August 2023, Kleemann will showcase a range of its sustainable, recycling-suited crushing and screening plants and the SPECTIVE operating concept from its comprehensive product portfolio.
With the MOBIREX MR 130(i) PRO impact crusher, Kleemann presents the latest member of the PRO line. The machine combines output, precision and sustainability as a primary and secondary crusher.
Thanks to its all-electric drive concept with the option of an external power supply and, therefore, operation with zero local emissions, the plant guarantees low energy consumption per tonne of final product. The optional large double-deck post-screening unit permits the production of two classified final grain sizes. The MR 130(i) PRO covers a wide application range in natural stone and recycling. With its heavy rotor and powerful 250kW electric drive, the crushing unit guarantees a very high and stable throughput. The Continuous Feed System (CFS) guarantees a continuous crusher load.
Kleemann’s innovative digitalised operating concept SPECTIVE includes various components, such as an intuitive touch panel and different radio remote controls, that are ideally tuned to each other while accompanying the machine operator during
their working day. All relevant process information and reporting are displayed on your smartphone without having to leave the feeding device. New to the SPECTIVE world is the ‘Smart Job Configurator’. The tool supports the operator in selecting the correct machine settings, facilitates day-to-day work and ensures even greater cost-effectiveness.
The new MOBISCREEN MSS 802(i) EVO has been designed as a powerful mobile scalper for evolving application challenges. Its clever plant design and flexible conversion options guarantee an optimum material flow in natural stone and recycling applications.
Access to a large range of screen media and the simple setting of the screen parameters allow the MSS 802(i) EVO to adapt easily to new operating conditions. If a fine final product is to be screened from particularly coarse feed material, the machine can be quickly converted from three to two final grain sizes. Further advantages of the plant include its simple operability thanks to its intuitive control system, easy access to all relevant machine components and its drive concept with the option of an external power supply for operation with zero local emissions. AB
DustCat5000's ability to operate in challenging environments and reduce water usage will, says EmiControls, be an industry game-changer.
Pic: Boreas/EmiControls
A leading Italian manufacturer has produced a new machine that it says will be a game-changer for quarrying and mining operators looking for a comprehensive dust-suppression solution. Guy Woodford reports
EmiControls, a leading innovator in the field of dust abatement, offering tailor-made, watermist-based solutions for protection against dust, odour and fire, has recently launched a groundbreaking first all-electric dust-suppression vehicle, the DustCat5000.
Created in partnership with fellow Bolzano, northeast Italy-based companies E-Powertrac and Lanatec, the revolutionary machine is said by EmiControls to be designed to prevent and abate dust in difficult and inaccessible terrains, such as mines and quarries, minimising the impact of dust on the surrounding environment.
The idea was born at the request of one of Europe's largest mining and quarrying groups, which wanted to sustainably minimise one of its Swedish mine’s dust impact. In November 2022, the first vehicle was shipped and operated for test purposes.
The turbine-equipped vehicle is fully autonomous and flexible thanks to its six to eight hours of battery-powered operating time and a 5,000-litre water tank. Its crawler chassis allows it to navigate any ground condition and reach areas inaccessible by
traditional vehicles.
The turbine is said by EmiControls to boast impressive operational capabilities, including the ability to function at temperatures as low as -25C, and a water-mist-throwing distance of up to 90 metres, allowing it to cover a large area while minimising water consumption and costs. This is said to make it an incredibly sustainable solution for dust abatement, something EmiControls has always been committed to.
EmiControls says it is excited to bring this cutting-edge technology to its industry markets and looks forward to helping businesses in the mining and quarrying sectors improve their environmental impact. The DustCat5000’s ability to operate in challenging environments and reduce water usage will, says the company, be an industry game-changer.
Commenting on the prototype’s work at the Swedish customer’s mine, Alverman Soster, EmiControls Dust Division manager, says: “The mine extracts many different minerals. The problem is that an underground mine has this slag waste material generated by the extraction process. The mining group has to put that material somewhere, but it
is extremely fine and dry, so dust clouds can blow over many kilometres when the wind blows.
“The group had been looking for a solution for many years. They were using a helicopter to fly over the site and spray water – but you can imagine the cost of this approach. They were looking to buy rather than rent the helicopter, but then you also have the fuel cost, and a pilot is not a standard operator with a regular salary.
“I visited the Swedish mine in 2018, and we began thinking about a possible solution. Another company within our group started looking for an electric-vehicle solution offering a low carbon footprint that could run everywhere on site. We then put our dust-abatement system with this vehicle. The mining group did not use the DustCat5000 much in January, February and up to the middle of March, as there was some snow around. But in the last five to six weeks, they have been using it more and more every day, as it is getting hot and dry. The DustCat5000 has already done more than 450 working hours.”
Soster says the same large mining and quarrying group is considering investing in
another DustCat5000 machine to work at the same Swedish mine and further models to work at some of its other mine sites. “It is a very big group with other mines in Sweden, Norway and Finland,” he emphasises. “The group has one massive quarry in the north of Sweden and is looking at potentially investing in four DustCat5000s. The area they have to manage is like a huge lake.
“In the current test environment, dust can fly up to 30 kilometres! The main problem is the impact on neighbouring villages, which can occasionally be covered by white quarry dust. The slag in the fine dust contains metals, which creates a problem for agriculture, water ponds and local health. However, the DustCat5000 has been working well for the customer alongside our V22 Orca, which can also produce snow for dust abatement. Snow can be good for catching flying dust and is an effective alternative to spraying only water on a surface, especially in winter when water can easily turn to ice, creating another health and safety issue for site workers.”
Soster says he also has a copper mine in Poland whose operator is considering placing an order for four Dust Cat5000s. “They have the same issue as the Swedish mining customer in needing an effective dust-suppression solution that can cover a big area.”
Soster says DustCat5000 operators at the Swedish customer’s mine site have praised the vehicle’s cabin. “They say it is huge, very comfortable and offers a really good view. They also like the vehicle’s heating system. In many other machines in colder weather, they have to work wearing heavy jackets, hats and gloves. In the DustCat5000, they quickly remove
these items. The prototype also has a very good radio and music system that you can connect up to your smartphone.”
Commenting on the DustCat5000’s sixto eight-hour per electric-charge operating time, Soster says: “The operating time per charge depends on how much you drive the vehicle. The big advantage of its turbine is that you can park the machine in a certain position and leave it to do the [dust-suppression] job. Also, if you work in an area with wind, you greatly increase the spraying distance of the turbine. It can travel up to 150 metres. It takes a few hours to recharge the DustCat5000. Using our supercharger, you can reach 80% charge in a couple of hours.”
Soster says that EmiControls is creating more production capacity at its headquarters. Any customer placing an order for a DustCat5000 will have a lead time of around seven months. “We
eventually plan to offer the DustCat5000 as a fully remotely controllable autonomous vehicle, but at the moment, we are focused on taking it from being a prototype into full production.
“We see the DustCat5000 as initially being a vehicle for European customers. We also have seen interest from markets like North America, South America and Australia. However, there are different regulations and potentially high maintenance and servicing costs in making the vehicle more widely available. We will see how the product develops.
“We have a good partner in Australia, and business for all our solutions has grown there in the last year and a half. From what I’ve read, the Australian government is pushing more and more mining companies to use good dustsuppression solutions to protect their employees. Many employees suffer from silica and other dust-related illnesses after 20 years of work.”
Soster says EmiControls is also growing its US business. “We have two partners, one in Salt Lake City, Utah, taking care of customers in Utah and nearby states. The other partner is in Albany, New York state. It’s a small but very active company we teamed up with a few months ago. Many New York state officials are going around construction and other industrial work sites measuring dust levels and asking for fees if deemed too high. That is creating business opportunities for us. We are also looking for another partnership in Texas, a rich state with many commercial opportunities.”
Commenting on EmiControls’ European market footprint, Soster adds: “Scandinavia is investing a lot of money in our market areas, especially Sweden and Finland. Germany and Italy are always big markets for us. We have opened a subsidiary, EmiControls Europe, in Frankfurt. We are also seeing business in Spain and Portugal.”
While set to benefit commercially from the world’s increasing focus on greater sustainability and environmental protection, including via dust suppression, Soster emphasises that EmiControls’ dustsuppression solutions always look to deliver optimal performance while limiting water use. “We need to spray water when it’s needed to spray water. You can do that with a high level of automation. An automated solution means that when you don’t have so many people on-site when working,
for instance, on weekends, the work still generates dust that needs to be suppressed.
“Our new software management system allows many EmiControls’ machines to be automated, managed and operated remotely. We are working on it now and setting it up for remote use to control and monitor the system from anywhere in real time.”
Talking about the growth of EmiControls, Soster says: “I joined the company in 2015,
and there were just seven people, now there are 30 people. Our annual turnover in less than eight years has increased tenfold. We have invested a lot of money in development and research and are going forward. Of course, we are keen to sell the machines we manufacture, but we also want to sell more complete solutions. That means more aftermarket support on spare and replacement parts and product maintenance.” AB
Metso says using an incorrect wear part that does not perform can be very costly
The use of correct wear parts in applications such as crushing is vital, both in terms of plant efficiency and lifespan, and operator safety. Liam McLoughlin reports
When crushers and screens are tirelessly working far from your home base, everything can be going smoothly – until it isn’t. Applications can be demanding and when a component eventually fails, you need to be sure replacement parts perform as they should.
Maiju Niiranen, product manager, stationary equipment spares at Metso says that, although spare and wear parts may look the same from the outside, they may be very different in terms of quality and materials.
“The results of using an incorrect part that does not perform can be very costly – equipment can be damaged; the part’s lifetime may be considerably shortened, or the equipment could fail catastrophically putting the safety of workers at risk,” she adds.
Metso’s Nordberg C-series jaw crushers have been workhorses in quarries around the world for decades. When it comes to critical
components for the crusher such as the pitman assemblies or frame parts, using components designed for the machine is an important step to caring for your producing equipment.
Niiranen says factors that affect the performance and reliability of components can be difficult to see, such as the raw materials used, the casting technology, pouring plan, the exact tolerances, and contactsurface quality. There are also hours and hours of engineering, quality assurances and testing methodologies that take place before the manufacturing process of the units and spare and wear parts even starts.
“Fractions of a millimetre can make the difference between a correct and an incorrect fit, and between optimal machine performance and equipment failing”
She adds: “With Nordberg HP crushers, the case is similar. For instance, the thrustbearing design is very delicate and if not lapped correctly, may result in improper contact and having a different pressure profile than it was designed for.
“To the human eye, parts may look like the right fit but an important question to ask is whether it has been made to the right tolerances? Fractions of a millimetre can make the difference between a correct and an incorrect fit, and between optimal machine performance and equipment failing due to a wrongly-sized component. OEM parts are designed for fit and function and to bear the operating load at its design parameters, helping the crusher to avoid seizure or early failure.”
Unplanned issues can easily result in significant lost production and costly repairs so ensuring that replacement parts are made exactly to the specified dimensions, and fit, is a big part of maintaining the performance of your crushers and other machines.
Niiranen says that Metso premium spare parts are built to ensure crusher availability, uninterrupted work, and a long service life –in addition to safety and sustainability.
“An often-overlooked factor is an OEM’s ongoing R&D work that can take the engineering to the next level, bringing benefits to older Metso equipment,” she adds. “Besides keeping it in original working order, premium spare parts can also enable a full upgrade – adding crusher availability and capabilities.” AB
UK crushing parts manufacturer CMS Cepcor Group has reached an agreement with US-based Columbia Steel Casting to purchase key commercial and technical assets.
The agreement will see the CMS Cepcor Group incorporate a new company “Columbia Steel Cast Products LLC”, which will trade independently as “Columbia Steel” and retain the key engineering, sales, and commercial team of crusher wear parts provider Columbia.
CMS Cepcor says the move will expand its global footprint, as well as grow the respected reputation Columbia Steel has held in the aggregates and mining marketplace for decades.
Mike Moehnke, Columbia sales and marketing director, commented: “Columbia Steel customers will be able to get the same parts in the same alloys they have come to depend upon, and moving forwards they will be able to do so at a more competitive price point. In addition, key individuals in engineering and sales will be coming on-board to provide a smooth customer-service transition.”
Chris Sydenham, the CEO of CMS Cepcor Groups US operations, said: “As a long-proven market leader in crusher liner optimiSation, with strong technical capabilities and genuine customer focus, Columbia Steel is well aligned with CMS Cepcor.”
No matter how challenging your needs, BKT is with you offering a wide range of OTR tyres specifically designed for the toughest operating conditions: from mining to construction sites. Sturdy and resistant, reliable and safe, able to combine comfort and high performance.
BKT is with you, even when work gets tough.
For info: europe@bkt-tires.com
The portable power sector has seen some significant developments including a major player changing its global branding and a new product launch. Liam McLoughlin reports
oosan Group-owned Doosan Bobcat has announced its global branding strategy which will see Doosan Portable Power (DPP) - a global manufacturer of air compressors, mobile generators and light towersrebranded under the Bobcat brand.
Doosan Industrial Vehicle (DIV), a supplier of quality material-handling equipment, including forklifts, will also be moved to the Bobcat brand.
“Bobcat is an iconic brand that changed the world with the invention of the compact equipment industry, and we are excited to unleash the brand in bold, new ways,” said Scott Park, Doosan Bobcat CEO & vice chairman. “Doosan Portable Power and Doosan Industrial Vehicle have long legacies of developing high-quality products. Bringing these strong Doosan brands into the Bobcat portfolio allows us to further expand these business lines, while also growing our overall Doosan Bobcat business and providing even more solutions to help our customers accomplish more.”
to further strengthen overall brand equity, market recognition and consumer recall of all product offerings. The transition will create a cohesive customer experience and grow the organisation’s footprint, thus making the brand accessible to more customers and in more places.
Bobcat has broadened its product portfolio significantly within the past five years, launching more machines during this period than previously in its entire history. Doosan Bobcat says the Bobcat brand has successfully expanded its offerings with new technologies and innovations and expanded product lines, such as ground-maintenance equipment, which includes compact tractors, small articulated loaders, mowers and turf equipment.
The rebranding of the portable power and industrial vehicle equipment lines — two key business areas for Bobcat — is intended
design and aesthetic changes in alignment with current Bobcat branding.
The rebranded products were displayed at key global trade shows in March and April 2023: DPP displayed a portion of its product line-up rebranded in Bobcat trade livery at the CONEXPO 2023 fair in Las Vegas, 14-18 March. DIV also showcased rebranded Bobcat forklifts as part of the in-booth display at ProMat 2023 in Chicago, 20-23 March, as well as at LogiMAT in Germany, 25-27 April.
“The Bobcat brand empowers ambitious and passionate groundbreakers to accomplish more," said Laura Ness Owens, Doosan Bobcat vice president of global brand. "Across the globe, big challenges get smaller because of our equipment; from breaking down walls to building up communities, we’re proud to provide people with what they need to be successful in their endeavours.
"By expanding the Bobcat brand to the portable power and industrial vehicle industries, Bobcat can help even more customers, in more ways than ever.”
With this refreshed identity, the DPP and DIV product lines will, respectively, undergo
Bobcat-branded material-handling equipment and portable power products are expected to be available through Doosan Bobcat’s extensive, global dealer network at a later date. Bobcat and these rebranded product lines will proudly remain part of the broader Doosan Group portfolio.
Caterpillar has introduced the Cat XQ330 mobile diesel generator set, a new power solution for standby and prime power applications that meets U.S. EPA Tier 4 Final emission standards.
Powered by the efficient Cat C9.3B diesel engine, the XQ330 is rated for up to 288 kW in standby and 264 kW in prime operation at 60 Hz, and up to 341 kVA in standby and 310 kVA in prime power applications at 50 Hz. Engineered to operate at lower noise levels than competitive offerings, the XQ330 packages essential components in a weather-resistant enclosure that streamlines transport, deployment, and maintenance while offering exceptional sound attenuation. It is also equipped with numerous rentalready features, including a block heater, battery charger, permanent magnet generator (PMG), switchable voltage outputs, and
Caterpillar’s new XQ330 mobile diesel generator set
optional mounting on a trailer.
The XQ330 is equipped with the EMCP 4.4 digital control panel, which provides all generator-set controls and system indicators in a single, easy-to-access interface, as well as a programmable logic controller (PLC) functionality that improves reliability and flexibility for accommodating changes in processes or application requirements. Additionally, it includes fully featured power metering, protective relaying, engine, and generator parameter viewing.
It is equipped with Cat Connect technology to remotely track and manage the generator set and improve operational efficiency. The telematics send real-time information on fuel level, diesel exhaust fluid (DEF) level, battery voltage, and run status. Connected assets support peak operation with timely insights that help customers better control costs, improve performance, and reduce risks.
Cat diesel mobile generator sets meeting U.S. EPA Tier 4 Final standards can use up to 100% hydrotreated vegetable oil (HVO), a renewable diesel fuel meeting EN15940.
“Caterpillar has built a reputation for
offering customers mobile power solutions with exceptional versatility, and the Cat XQ330 is equipped with a wide range of easyto-operate features designed for numerous applications while meeting stringent emissions standards,” said Tom Caldwell, global general manager for electric-power rental solutions at Caterpillar.
Atlas Copco has unveiled its first battery-driven portable screw compressor. The manufacturer says the B-Air 185-12 represents a major milestone in the company's roadmap towards a sustainable future.
“We are committed to accelerating the transition away from carbon-dependency and towards renewable energy sources,” explains Maarten Vermeiren, product marketing manager of sustainability and digitalisation at Atlas Copco's Portable Air Division. “By introducing the first battery portable screw compressor, we want to play our part in enabling a sustainable transformation and help build a better tomorrow – for society and the planet alike.”
The B-Air 185-12 features 5-12 bar of pressure, a stable flow rate of 5.4-3.7 m3/
min and 55-kWh battery storage capacity. With power delivered from its onboard power pack, in operation a fully charged unit is independent of the need for fuel or a local power source to plug into, and has the capability to perform for up to a full typical work shift. In turn, it provides both portability and productivity for those working on sites where regular access to electricity is not practical.
Atlas Copco says that making the switch from an internal combustion engine (ICE) to electric motor brings with it a host of benefits, including less downtime and maintenance requirements. Due to having far fewer moving (and therefore wearing) parts compared to a diesel-powered unit, the electric B-Air 185-12 only needs to be serviced every 2,000 hours, as opposed to 500 hours for a typical ICE -powered unit. The machine’s state-of-the-art Variable Speed Drive (VSD) and permanent magnet motor drives down the total cost of ownership, automatically adjusting the motor speed to match air demand in real time and increasing energy efficiency by up to 70%.
The Atlas Copco B-Air 185-12 battery-driven portable screw compressor
Through Atlas Copco’s testing process, which includes rapid-ageing testing under harsh conditions and climatic-chamber testing, the B-Air 185-12 has been proven to perform optimally even in the most extreme of climatic conditions – ranging from +45°C (+113°F) to a glacial -25°C (-13°F); and 4,500 metres (14,764 ft) above sea level. The unit is also designed to excel in densely populated urban areas where emission and noise pollution are tightly restricted, thanks to it producing no local emissions and having low noise levels. The quiet nature of the compressor enables operators to work without noise distraction, enhancing both productivity and safety.
The B-Air 185-12 was first unveiled at the recent Atlas Copco’s ‘Journey to a Sustainable Future’ event in Antwerp, Belgium. Here, the company gathered senior business leaders from across the industry to discuss how best to tackle the transformation to a climate-friendly, low-carbon future. The company says its new battery-powered unit marks a vital step in the electrification of its product offering, and is just one of many developments it currently has in store to deliver sustainable solutions to its customers. AB
Metso is helping Swedish company Kross & Maskin i Kisa future-proof its successful aggregates business. Guy Woodford reports
Kross & Maskin i Kisa is based in Smaland County in central Sweden. Established in 2008 by Mikael Pettersson and Mattias Pettersson, the company mainly uses Metso’s Lokotrack mobile crushers and screens. It also utilises the OEM (original equipment manufacturer) wear parts and services from Metso for its Lokotracks. All its equipment is mobile, so it can move around to where the firm’s customers need materials for projects in central and southern Sweden.
Over the years, Kross & Maskin i Kisa has grown its reputation for producing high-quality aggregates and building good customer relationships. The company has varied customers for whom it produces housing, quarrying and construction aggregates. Its products, such as ballast and road base materials, vary from raw to finished aggregate.
The company has been busy crushing
granite at two job sites. The newest of its two Lokotrack LT120 jaw crushers with Nordberg C120 crushers, delivered in 2022, has been crushing 0-150mm aggregate fraction in Vimmerby for road base.
The other job site, in Sävsjö, has been operating two crushing lines. The first line consisted of a Lokotrack LT120 jaw crusher, a Lokotrack LT330D cone crusher with the Nordberg GP series cone crusher, and a triple-deck dual-slope screen. The second line had a Lokotrack LT300HPB with Nordberg HP300 crusher and screen and a third-party screen.
The two crushing lines in Sävsjö produce five different fractions. “We use the LT120 and the LT330D to produce 16-90mm fraction suitable for road base,” explains Mattias Pettersson. “Then we use the LT300HPB to crush smaller fractions out of the 16-90 mm for asphalt production.” The smaller fractions are 0-4, 4-8, 8-11 and 11-16mm. In addition to the Lokotrack units at these two sites, Kross & Maskin I Kisa also operates a
Lokotrack ST4.8 mobile screen elsewhere.
The company uses Metso wear parts in its crushers. Both the company’s LT120 jaw crushers are equipped with MX jaw plates. “We have used the MX jaws in our jaw crushers for many years already,” says Mikael Pettersson. “The operation is more secure, we get better material quality, and there are less operation breaks as we don’t have to do maintenance on the machines the same way.”
Mattias adds: “I think that the MX jaws last about 2.5 times longer than traditional plates.” With the MX jaw plates, Kross & Maskin I Kisa has had fewer maintenance breaks and, therefore, more time for crushing. The MX wears are a patented solution by Metso, combining manganese and hard metallic wear-resistant inserts for abrasion resistance; the result is longer wear life in demanding applications.
The second- and third-stage crushers use Metso manganese wear parts: medium or fine cavity and XT720 alloy. The company
takes advantage of Metso’s Full Container Load (FCL) deliveries and orders wear parts for stock to have the worn parts on hand when needed.
“We selected Metso [Outotec] because we think that [their solutions] give us a good operating economy and more secure operations. Their machines are also safer to work with,” Mikael comments.
The additional Metso’s Equipment Protection Service (EPS) covers some machines. “The warranty for these machines has been really good,” says Mattias. “Help has been available when needed – even during evenings and weekends.”
One of the challenges in the business is finding employees with the right skill sets. “Working in our line of business requires multiple skills – from maintenance to operating crushers, excavators and so on,” says Mikael. “We have solved the problem by training our employees ourselves.” Mikael and Mattias have a combined 30-plus years of experience in aggregate crushing.
A solid example of their skills is the LT300HP which is currently in the company’s workshop, having further work done on it. They built it by themselves from two different units. Now the crusher is getting an additional by-pass chute.
“I follow with excitement the future developments of the Metso crushers and the development of the whole industry,” says Mikael. “The future looks bright for our company. In the future, we hope to move more to electric machines eventually,” concludes Mattias. AB
“We hope to move more to electric machines eventually”
Mattias Pettersson
To drive efficiencies, the company invested in a new, state-of-the-art static plant in 2017
With no massive infrastructure projects on the horizon, the South African construction sector has endured a protracted downturn in the past decade.
To run profitable operations in such a low-margin business environment, Danoher Group is championing operational efficiencies at its Bloemspruit Quarry. Adopting new technologies is at the centre of improved product quality, increased productivity, reduced overheads and, more importantly, improved efficiencies. Munesu Shoko reports
By their very nature, quarries produce high-volume, low-cost material. To run profitable operations, quarry owners must find ways to drive operational efficiencies. Based on that understanding, Danoher Group, southern Africa’s leading quarry operator and mining contractor, has heeded the call for innovation to drive productivity and improve efficiencies.
Situated on the outskirts of Bloemfontein, Bloemspruit Quarry is endowed with a highquality, sought-after dolorite rock. Acquired by Danoher in January 2017, the operation produces all aggregate sizes, including crusher dust, washed super sand, 7mm, 10mm, 14mm and 20mm road and concrete stone, base and sub-base materials, as well as some specialised products.
During the initial days of Danoher’s ownership, the quarry operated mobile
crushing and screening equipment. By November 2017, the company had invested in a new, state-of-the-art static plant. “From the onset, we understood that for us to run a profitable business, we needed to invest in a new, efficient and flexible 250 tonnes per hour (tph) plant, capable of reacting to fluctuating market demand and supporting bespoke customer requirements,” explains Johann van Niekerk, business manager, Bloemspruit Quarry.
Bearing in mind the constant pounding these machines take, it is good to see how these new crushers and screens, being subjected to a stringent maintenance programme, have proven to be reliable and less prone to breakdowns, thus bringing about maximum plant availability and productivity. In addition, the new equipment, such as the two Metso HP300 cone crushers, contains the most advanced safety features, thus reducing workplace injuries.
“The investment in a contemporary plant was essential for us to drive productivity, plant uptime, efficiency and ultimately run a profitable business,” says Van Niekerk. “We have seen high levels of efficiency, which makes us competitive in such a cut-throat market.”
To meet the high demand for washed sand and washed super sand (high-end fine sand) used as input material by concrete product manufacturers, Danoher invested in a leading-edge 80tph EvoWash 102 wet processing plant from CDE, becoming the first and only company in the Bloemfontein area to run this type of technology.
Before investing in the CDE plant in 2020, Danoher previously utilised a bucketwheel system. Traditionally, bucket-wheel technology was deemed the mainstay for sand production in South Africa. It was cheap to buy. However, a major downside was that a substantial proportion of valuable fine sand
would be lost to waste dams.
In addition, high and variable moisture content and inaccurate material classification were some of the downsides of the bucket wheel that CDE’s cyclone technology has addressed. Unlike the bucket wheel, which relies on gravity as the means of separation, CDE’s cyclone technology uses centrifugal force to classify materials.
“We were aware of the quality variability and sand losses we incurred through the old-generation washing plant we had. We, therefore, had to seek ways to maximise our productivity and efficiency in difficult market conditions. With the investment in the CDE plant, we have seen massive benefits in terms of production, efficiency and reliable quality of the product,” says Van Niekerk.
The CDE cyclone technology has been an important technological advancement for the quarry. Firstly, Danoher is now producing two grades of sand – fine (0 - 1,5mm) and coarse (0 - 5mm) – compared to just the one grade of sand previously produced by the bucketwheel system.
More importantly, says Van Niekerk, production is up by 30%, while water usage has decreased by 15%. In addition, the quality of the product has improved significantly, thus setting Bloemspruit Quarry apart from competition.
“We have seen a high demand for our sand, particularly from brickmakers. They prefer it because of its high strength and quality. It is made from virgin blue rock, which is also good for the strength of the bricks,” he says.
Bloemspruit Quarry uses Loadrite beltscale technology from Loadtech Load Cells to further drive efficiencies. This has proved its worth in maximising equipment value by having it employed most efficiently.
The Loadrite belt scales give plant operators and the management team a range of powerful tools to measure the actual production from screens and crushers, analysing plant and machine downtime.
Besides these technologies, Van Niekerk and his team also pay special attention to their haul roads. Haul-road maintenance, he says, requires a dedicated focus and is addressed continually as part of the operational cycle since good roads improve production, extend tyre life and reduce overall operating costs.
“We haul around 500m one-way distances from the pit to the processing plant. To optimise our cycle times and trucks’ fuel efficiency and reduce tyre wear, we have tried to keep our haul roads as straight and free of inclines as possible,” he says.
Danoher has always preferred Volvo Construction Equipment for its load and haul equipment. Two Volvo A30 articulated dump trucks (ADTs) are deployed to haul material from the pit to the processing plant. These are loaded by a Volvo E480 excavator in the pit. Two Volvo wheeled loaders, L150 and L190 models, are deployed for stockpiling duties and loading customer trucks.
“As the Danoher Group, we have always
“We have seen a high demand for our sand, particularly from brickmakers. They prefer it because of its high strength and quality. It is made from virgin blue rock, which is also good for the strength of the bricks”
standardised our yellow metal equipment with Volvo. We get a good life out of the machines, while they have, over the years, proven to be fuel-efficient. Fuel is one of the biggest cost drivers in a load and haul operation, and it is therefore important to pick the best equipment to reduce your fuel bill. After standardising our equipment, spare parts, repair procedures, equipment and repair training have become much less onerous,” says Van Niekerk. “We also get good service from the local dealer, Babcock, which is key to maximising our equipment uptime, productivity and efficiency.”
A strong focus on keeping every part of the business in-house, from drill and blast to load and haul, helps improve efficiencies and reduces the cost of the material for customers. Additionally, this also helps with quality control.
Despite the generally depressed market conditions in the South African construction industry, Danoher has grown the Bloemspruit Quarry’s market share, which has enjoyed a good market run in the past few months, buoyed by its wide client base and a few road projects in the area. The company’s existing customer base includes aggregates resellers, brickmakers, asphalt plants, readymix plants, and property developers.
“The three months between July and September 2022 were our best ever. We broke our production record three times in a row. We have been fortunate to have the capacity to ramp up and supply a few road projects in the area without letting our base volume customers down. We are supplying three projects on the N1 South, the R30 and a new project on the R48,” concludes Van Niekerk. AB
AUGUST
3-4: 7th Future Heavy-Duty Powertrain Summit
Shanghai, China 2023
Fiveo Events
draymond@ma.fiveoit.com.cn
Tel: +86 21 5650 0750
23-26: steinexpo 2023
Homberg/Nieder-Ofleiden, Germany
Organiser: Geoplan GMBH
Tel: +49 7229 606 30
Email: info@geoplangmbh.de https://www.steinexpo.eu/
20-23: BICES 2023
Beijing, China
Organiser: AEM
Tel: +86 (10) 67870972
Email: bob.ban@e-bices.org http://www.e-bices.org/engdefault. aspx
OCTOBER
04-06 SIM 2023
Bordeaux, France
Organisers: Exosition SIM https://www.expositionsim.com/ en/index.htm
APRIL
24-27 INTERMAT Paris 2024
Paris, France
Organiser: Comexposium
Email: laura.sanchez@ comexposium.com https://paris-en. intermatconstruction.com/
15-17: Hillhead 2024
Hillhead Quarry Buxton UK
Organiser: QMJ Tel: +44 (0)115 945 4367 Email: hillhead@qmj.co.uk www.hillhead.com/
These dates were correct at the time of going to press, but please note that the COVID-19 pandemic means some events may be rescheduled with little advance notice
EUROPE: Ammann p4 www.ammann.com
Astec p7 www.astecindustries.com
BKT Tyres p42 www.bkt-tires.com
CAT IFC www.cat.com
Cummins p13 www.cummins.com
Develon p16 http://eu.develon-ce.com
Hitachi p11 www.hitachicm.eu
Komatsu OBC www.komatsu.eu
Martin Eng p28 www.martin-eng.com
ROKBAK IBC www.rokbak.com
Rubble Master p15 www.rubblemaster.com
Simex p37 www.simex.it
Steinexpo p8 www.steinexpo.eu
Tsurumi p9 www.tsurumi.eu
Wirtgen p25 www.wirtgen-group.com
INTERNATIONAL: Ammann IFC www.ammann.com
BKT Tyres p42 www.bkt-tires.com
Intermat OBC http://paris.intermatconstruction.com
Martin Eng p28 www.martin-eng.com
Powerscreen p11 www.powerscreen.com
Simex p37 www.simex.it
Wirtgen p25 www.wirtgen-group.com
Carved by a lifetime of hard work, Rokbak articulated haulers are built to perform. Day after day. Decade after decade. From the heat of the desert to the cold of the arctic, you can rely on Rokbak. Contact your local dealer
rokbak.com
The HD605-8 integrates the latest Komatsu engine technology, for increased power and reduced fuel consumption. Productivity is maximized and costs are reduced. The hydraulically-controlled wet multipledisc brakes and retarder give the operator great controllability, and a new spacious and ergonomic