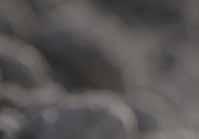
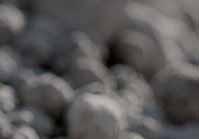
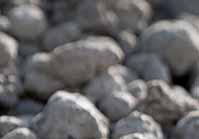
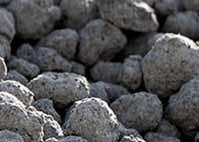
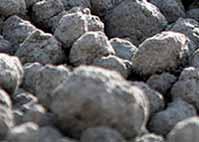
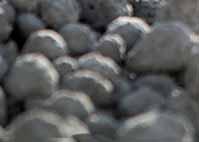

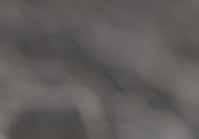
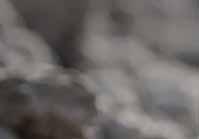
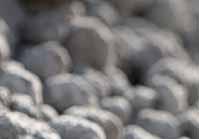
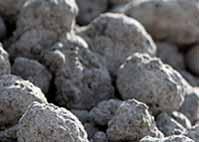
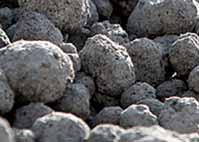
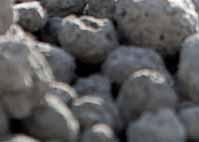
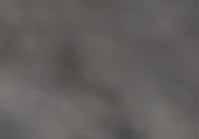
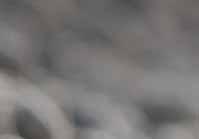
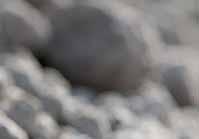
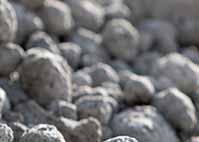
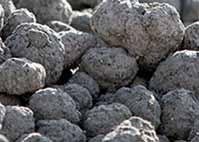
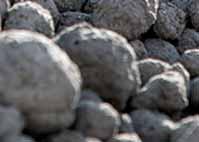

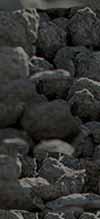
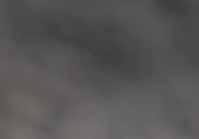
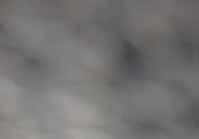
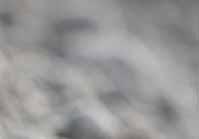
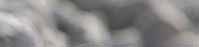
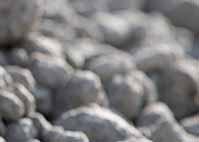
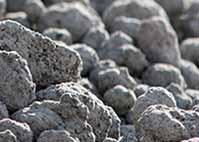
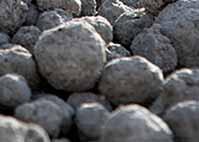


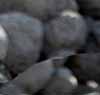

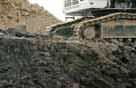
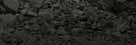
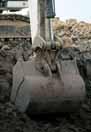
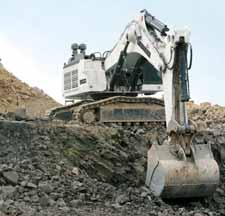
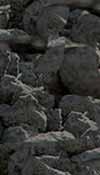
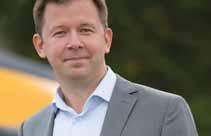
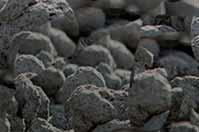
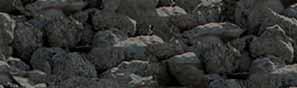
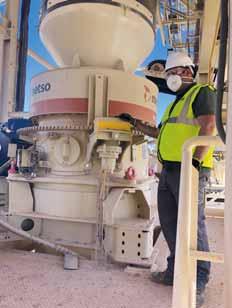
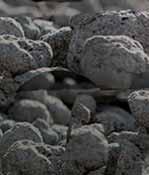
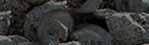
Rewrite the rules with our extended range.
THE NEW 336 & 336GC.
Our game-changing new machines will work even harder for you. Designed around you and your needs, these Next Generation excavators will totally transform your job sites - with the new 336GC providing lower cost of acquisition and fuel burn, and the new 336 achieving higher levels of productivity. So get ready to witness the revolution of an entire industry from the ground up, and rewrite the rules of operation. Contact your local dealer to find out more. #rewritetherules
“Recycled aggregates are increasingly in demand globally.” p39
A red wine-enhanced Spanish aggregates adventure
Harsco Environmental is first commercial pilot customer for Volvo CE’s new autonomous battery-electric hauler
A mining and minerals take on the legal implications of crowdfunding
How UK mineral products industry is ‘uniquely placed for net zero & net gain’
All the key events in the quarrying & aggregates
How a premium crushing and screening plant is helping OSF Group meet huge demand for ballast for the Basque Y highspeed rail project
Innovation is a key feature in the modern global quarry loading machine market. Aggregates Business assesses three major recent model launches
A leading articulated hauler maker discusses big machine development plans
Aggregates washing plant solutions are getting increasingly sophisticated and
– PART 2 New models and how best to future-proof the off-highway engines industry 37
The use of technology such as visualisation and drones is enhancing the efficiency and safety of blasting operations at quarry sites 39
OEMs aware of rising demand for recycled aggregates globally have been busy highlighting new and proven recycling-suited plant
O.C.O Technology’s M-LS carbon-negative aggregate is set to grow in popularity as the UK firm explores new export markets p12
O.C.O Technology managing director Steve Greig discusses the UK company’s exciting international growth plans for its innovative M-LS carbon-negative aggregate product
35 SMILEY MONROE – THE FIRST 40 YEARS AND WHAT’S NEXT?
The Northern Ireland-headquartered conveyor-belt solution specialist remains highly ambitious after an impressive first four decades
46 MARKET REPORT
Big infrastructure projects are the lifeblood of the Nordic aggregates sector
52 QUARRY PROFILE
One of the first Metso MX3 cone crushers installed in Europe is set to produce a big financial return for Emipesa
HEAD OFFICE
EDITOR: Guy Woodford
ASSISTANT EDITOR: Liam McLoughlin
CONTRIBUTING
EDITORS: Patrick Smith, Dan Gilkes
EQUIPMENT EDITOR: Mike Woof
DESIGNERS: Simon Ward, Andy Taylder, Stephen Poulton
PRODUCTION MANAGER: Nick Bond
OFFICE MANAGER: Kelly Thompson
CIRCULATION & DATABASE MANAGER: Charmaine Douglas
INTERNET, IT & DATA SERVICES DIRECTOR: James Howard
WEB ADMINISTRATORS: Sarah Biswell, Tatyana Mechkarova
MANAGING DIRECTOR: Andrew Barriball
PUBLISHER: Geoff Hadwick
CHAIRMAN: Roger Adshead
ADDRESS
Route One Publishing Ltd, Waterbridge Court, 50 Spital Street, Dartford, Kent DA1 2DT, UK
TEL: +44 (0) 1322 612055 FAX: +44 (0) 1322 788063
EMAIL: [initialsurname]@ropl.com (psmith@ropl.com)
ADVERTISEMENT SALES
SALES DIRECTOR:
Philip Woodgate TEL: +44 (0) 1322 612067
EMAIL: pwoodgate@ropl.com
Dan Emmerson TEL: +44 (0) 1322 612068
EMAIL: demmerson@ropl.com
Graeme McQueen TEL: +44 (0) 1322 612069
EMAIL: gmcqueen@ropl.com
SUBSCRIPTION / READER ENQUIRY SERVICE
Aggregates Business International is available on subscription. Email subs@ropl.com for further details. Subscription records are maintained at Route One Publishing Ltd.
SUBSCRIPTION / READER ENQUIRIES TO:
Data, Route One Publishing Ltd, Waterbridge Court, 50 Spital Street, Dartford, Kent DA1 2DT, UK
TEL: +44 (0) 1322 612079
FAX: +44 (0) 1322 788063
EMAIL: data@ropl.com
No part of this publication may be reproduced in any form whatsoever without the express written permission of the publisher. Contributors are encouraged to express their personal and professional opinions in this publication, and accordingly views expressed herein are not necessarily the views of Route One Publishing Ltd. From time to time statements and claims are made by the manufacturers and their representatives in respect of their products and services. Whilst reasonable steps are taken to check their accuracy at the time of going to press, the publisher cannot be held liable for their validity and accuracy.
PUBLISHED BY © Route One Publishing Ltd 2019
AGGREGATES BUSINESS INTERNATIONAL USPS: is published six times a year. Airfreight and mailing in the USA by Agent named Air Business, C/O WorldNet Shipping USA Inc., 156-15 146th Avenue, Jamaica, NY, NY11434. PERIODICALS POSTAGE PAID AT / US POSTMASTER
ADDRESS CHANGES TO: Aggregates Business Europe, Air Business Ltd, C/O WorldNet Shipping USA Inc., 156-15 146th Avenue, Jamaica, New York, NY11434
PRINT: ISSN 2051-5766
ONLINE: ISSN 2057-3405
PRINTED BY: Warners (Midlands) PLC
Ivery much enjoyed getting a close-up look at the Spanish aggregates industry during a recent three-day trip with Metso.
At Emipesa’s Cantera el Poyo Quarry near the fascinating and grand, historic architecture-rich city of Teruel in Aragón, Eastern Spain, I learned how a recently installed MX3 cone crusher – the first operating in Spain and one of the first deployed in Europe – is set to generate the company an additional €350,000 a year in aggregate product sales, thanks to increased productivity due to higher material throughput and reduced plant downtime. You can read my full take on Cantera el Poyo Quarry in this edition’s Quarry Profile feature.
Next, we visited two quarries near Haro, a town known for its fine red wine and the annual Haro Wine Festival, in the north-west of La Rioja province. Both belong to Ofitas de San Felices Group (OSF), a major family-owned national building materials supplier, which also operates a third quarry, producing limestone aggregates, in Granada, southern Spain. OSF’s huge Ofitas de San Felices quarry sits next to company boss Iñigo Ajuria’s own 34-hectare vineyard, which, being a keen red wine enthusiast, I found completely logical! Celebrating its 100th operating year in 2019 and one of the oldest sites of its kind in Spain, the quarry produces a wide variety of aggregates including some of the country’s highest quality ballast.
Nearby, Ajuria’s Ofitas de Santutis Quarry is currently busy using an all-Metso plant to produce ballast for the Basque Y high-speed rail project, linking the major Basque Country cities Vitoria-Gasteiz, Bilbao and Donostia-San Sebasitián. Originally due for completion in 2023 but now behind schedule, the 194km-route will transport passengers and cargo, significantly reducing journey times between the key destinations. You can read all about this site in the Aggregates Production feature inside this issue. Later, we were Ajuria’s guests at a specially laid-on lunch at an attractive villa he owns near
his two La Rioja quarries. After polishing off a lot of delicious food, washed down with a few glasses of Ajuria’s fine Tempranillo-grape red wine and a large glass of Chivas Scottish malt whisky, I had a warm and wide-ranging discussion with Ajuria about his company, the Spanish aggregates industry and exciting plans for OSF’s long-term future. You’ll be able to read all about it in the Interview feature in the January-February 2020 edition of Aggregates Business Europe
Another highlight of my autumn worktravel itinerary was a visit to Volvo Construction Equipment’s (Volvo CE) impressive Eskilstuna facility. After spending some time in an EX750E excavator, an L350H wheeled loader and A60H articulated hauler and hearing Volvo CE’s thoughts on current and likely future Nordic aggregates and quarrying machine demand, I had an interesting tour of the site’s axle and transmission factory. The two biggest sources of energy consumption at the plant are the ‘hardening centre’, where machine parts are heated to a high temperature and then cooled to ensure a tough surface and long life, and the ‘paint shop’, where components are heated so the paint dries. Given this, it was great to get a first-hand look at Volvo CE’s new €472,600 (5 SEK million) energy recovery system that conserves around 60% of the heat generated in the hardening centre and transfers it to the paint shop. As a result, the system is expected to cut the factory’s overall energy consumption by 4%. During my visit, I was told that Volvo CE is investigating new options for the painting process in order to further reduce energy consumption.
A packed schedule also saw me witness some autonomous hauler-testing as part of the Volvo CE and Skanska ongoing Electric Site project. As you’ll read in this edition’s News section, Harsco Environmental (HE) will be the first pilot customer for the project when a fleet of four updated HX2 concept haulers begins a year-long pilot program at an HE quarry in Sweden during Q1 2020. GW gwoodford@ropl.com
Harsco Corporation’s Environmental division (HE) will serve as the first commercial pilot customer for Volvo Construction Equipment’s (Volvo CE) new autonomous battery-electric hauler. While not yet on the market, the hauler is being heralded as the “next groundbreaking step in Volvo CE’s innovation journey.”
“We are delighted to partner with Volvo CE on this pilot,” said HE chief operating officer Russ Mitchell. “Our participation represents the fulfilment of the promise we make to every Harsco Environmental customer: that we will always seek solutions that are both innovative and environmentally responsible.”
Based on the HX2 concept model, a fleet of four updated machines will begin the yearlong pilot programme on a date to be decided in Q1 2020 at an HE site in Sweden, where it will be tested in a repetitive transport application. The machine is fully automated and uses shared and proven technologies from the Volvo group like batteries and driveline systems.
“We aim to raise the bar in what our machines can achieve for our customers, and this innovative commercial pilot represents the next phase of our journey into increased machine autonomy,” said Volvo CE president Melker Jernberg.
“By working alongside valued customers like Harsco Environmental, we are challenging our autonomous technology in demanding real-
world applications. Getting advanced prototypes into the hands of customers early also allows us to incorporate their feedback in the pre-production phase. This commercial pilot is an important next step in the process of industrialising this exciting future technology.”
Autonomous HX2 concept hauler testing has continued at Volvo CE’s Eskilstuna facility since the conclusion of the first phase of the Electric Site project in Q4 2018.
Aggregates Business reported at the start of 2019 that Volvo CE and its customer Skanska had recorded claimed ground-breaking results during the first project phase at Skanska’s Vikan Cross quarry, near Gothenburg, Sweden, from September to November 2018. Tests are said to have shown a 98% reduction in carbon emissions, a 70% cut in energy cost and a 40% drop in operator cost. The quarry is the second largest in Sweden.
The Electric Site project
aims to electrify each transport stage in a quarry –from excavation to primary crushing, and transport to secondary crushing. It incorporates electric and autonomous prototype Volvo CE machines, new work methods, and site management systems which together form a complete site solution.
In a linked big announcement, the Volvo Group says it will create a new business area for autonomous transport solutions from 1 January 2020.
The new business area, Volvo Autonomous Solutions, will accelerate the development, commercialisation and sales of autonomous transport solutions. This will enable the Volvo Group to meet a growing demand and to offer the best possible solutions to customers in such segments as quarrying, mining, ports and transport between logistics centres, as a complement to today’s
products and services.
With global developments that are characterised by higher demand for transportation, increasingly congested roads and major environmental challenges, Volvo says the industry needs to provide transport solutions that are safer, have a lower environmental impact and are more efficient.
Autonomous transport solutions, based on self-driving and connectivity technologies, are well-suited for applications where there is a need to move large volumes of goods and material on pre-defined routes, in repetitive flows. In such situations, autonomous transport solutions can create value for customers by contributing to improved flexibility, delivery precision and productivity.
“We have experienced a significant increase in inquiries from customers. With the Volvo Group’s wide range of offerings and broad experience of different applications, we have a unique opportunity to offer solutions that meet their specific needs. It is a logical next step for us to gather expertise and resources in a new business area with profit and loss responsibility to take autonomous transport solutions to the next level,” says Martin Lundstedt, Volvo Group president and CEO.
The head of the new Volvo Autonomous Solutions business area was still to be announced at the time Aggregates Business Europe went to press.
Extreme power
The new PC1250/SP-11 combines great performance and an impressive array of standard safety features with excellent comfort to ensure that your work can be performed safely and efficiently. The new “Power plus” (P+) mode allows full use of increased engine power to achieve up to 8% higher production with reduced fuel consumption.
Construction-materials
business Tarmac has partnered with the Port of Tilbury in London to create what is claimed to be the UK’s largest construction-materials aggregates terminal.
The terminal will be located at Tilbury2, the new port being constructed on the north bank of the River Thames which is due to open in 2020.
The work will see the creation of new aggregatesprocessing and manufacturing facilities, including an asphalt and ready-mixed concrete plant at the new port terminal, supported by the terminal’s deep-sea capacity for vessels up to 100,000 tonnes. The partners say that the riverside location will enable the easy import of raw materials and facilitate the use of the River Thames as a delivery route for processed construction
SUPPLIES BREST
‘HEAVY-WHARF’ PROJECT
LafargeHolcim has completed the delivery of 10,000 tonnes of cement for the ‘heavy-wharf’ expansion project at the French port of Brest. The €220m project in the Brittany region is designed to modernise existing infrastructure and increase capacity at the port. It includes the construction of a new wharf for handling heavy loads. LafargeHolcim also supplied nearly 0.165m tonnes of draining sand for the project, which is scheduled for completion in 2020.
The French buildingmaterials company says the scheme will expand port traffic by improving the nautical accessibility of some existing wharves as well as enabling the development of promising new sectors at the port, particularly those related to marine-renewable energies.
materials into Central London.
Martin Riley, senior VP of Tarmac, commented on the project: “It demonstrates our firm commitment to the development of industryleading infrastructure to support the delivery of the UK’s long-term built-environment ambitions.”
In February 2019, Forth Ports, owner of The Port of Tilbury, obtained approval
under a development consent order (DCO) from the Planning Inspectorate to build a new terminal adjacent to its current port in Thurrock.
The new, privately funded port is being built on a 152-acre site and it is envisaged that Tilbury2 will act as a satellite of the main port. Tilbury2 will feature a roll-on/roll-off ferry terminal for importing and exporting
containers and trailers.
There will also be a construction materials and aggregates terminal (CMAT) for importing, processing, manufacturing and distributing construction materials, in addition to a new nationally strategic rail and road connection into the site.
Mark Wood, Tarmac managing director – materials south, said: “This exclusive development will ensure the long-term security of aggregate supplies into London and the South East, allowing us to support vital construction projects while using alternative transportation methods for the movement of materials, taking vehicles off the congested roads around the capital and using the Thames as a means of importing aggregates and other bulk materials into London.”
Sandvik has posted better than expected earnings for the third quarter of 2019. The Swedish quarrying, mining and metalcutting equipment group said that adjusted operating profit remained largely stable yearon-year and amounted to SEK4.617bn (€430mn) in Q3 this year, compared with SEK4.587bn (€427mn) in Q3 2018.
The figures are said to have beaten the SEK4.48bn (€417mn) mean forecast from a Refinitiv
poll of analysts. Organic order intake in Sandvik’s Mining & Rock Technology business unit increased by 5% on Q3 as the underlying market activity remained stable at a high level. Revenues improved organically by 3% year-on-year. In total, orders for equipment remained at a high level and noted a mid-single-digit growth rate, positively impacted primarily by the underground load and haul, crushing and screening, and automation divisions.
Orders in the aftermarket business for the Mining & Rock Technology unit increased at a mid-single-digit rate, supported by positive development for both parts & service and for consumables.
The newly launched product line for surface drilling noted favourable development. The aftermarket business accounted for 63% of revenues, while the equipment business accounted for 37%.
FOR QUALITY SHAPED PRODUCTS, ESPECIALLY IN HARD ROCK. MOBICONE mobile cone crushers are used in medium-hard to hard applications as well in abrasive natural stone operations. They cover a wide range of applications: from small to medium-sized batches for short-term contractor operations, all the way through to large quantities in tough quarrying operations. The MOBICONE crushers are the perfect match for mobile KLEEMANN jaw crushers and/or screening plants. MOBICONE mobile cone crusher: efficient and strong.
www.kleemann.info
The resumption of public works in Italy is driving investment and growth in the country’s construction sector, according to the latest SaMoTer-Prometeia Outlook.
While the overall value of Italy’s construction industry in 2018 came to €139 billion, an increase of 3.5% is expected by the end of 2019 (+€4.8bn) followed in 2020 by a further 2.4% (+€3.3bn).
Terex Materials Processing (Terex MP) had another impressive quarter in Q3 2019 with sales of €305.42mn (US$339mn) - an increase of 8% on the same period of last year.
A Terex Corporation business segment that includes the brands Terex Finlay, Powerscreen, Terex MPS, EvoQuip, Terex Washing Systems, Terex Ecotec, Fuchs, CBI, Terex Bid-Well, Terex Advance and Franna Pick & Carry Cranes, Terex MP’s trading growth was said to be driven by global demand for its broad range of products and services. These include crushing and screening machines, material handlers, cement mixer trucks, and pick and carry equipment. Global Terex MP backlog in Q3 2019 totalled €237.84mn ($264mn) and bookings in the quarter were €212.62mn ($236mn).
Kieran Hegarty, president of Terex MP, said: “We had an excellent quarter in Materials Processing, thanks to strong operational execution across our businesses. Looking ahead, our bookings and backlog levels are
pointing to softening demand in our global end markets. Throughout the cycle, we will continue to invest in product and service innovation and geographic expansion that will enable us to serve more customers globally.”
Hegarty added that Terex MP’s manufacturing capacity investments in Northern Ireland and India “remain on track”. He continued: “These facilities will enable even more growth in the
expanding Environmental sector and position us to continue to grow in India and the broader Asian markets as customers adopt our mobile processing technology. I am encouraged by our consistently strong execution and long-term prospects for growth across our MP businesses.”
Terex Corporation, as a whole, posted sales of €900.94mn $1bn for the quarter, down 6.8% compared to the third quarter of 2018.
The SaMoTer-Prometeia Outlook survey analyses the performance of the Italian construction sector every quarter and is a tool that SaMoTer - the international construction equipment trade fair - provides companies to help them interpret market developments. The next edition of SaMoTer is being staged at Veronafiere in Verona 21-25 March 2020.
The October 2019 edition of the SaMoTerPrometeia Outlook survey suggests that investments in the Italian construction sector followed a variable trend in the first half of 2019. Strong growth in the first quarter was followed by a slight downturn in the following three months, although the trend for investments was still positive (+3.2% in the second quarter).
Buy-and-build construction aggregates provider SigmaRoc has announced plans to acquire aggregates company CDH
Développement for a total of €45mn. UK-based SigmaRoc said in a statement that CDH
Développement is the holding company of Carrières du Hainaut SCA and CDH International SCA, the Belgian blue limestone (“bluestone”) and aggregates business.
Founded in 1888, CDH is Europe’s largest bluestone quarry, with a 50% global market share. It is also a major aggregates quarry, producing 1.5mn - 2mn tonnes per year.
The site has 150 years of reserves remaining and 352ha of freehold land and minerals (subject to current consultation
regarding an extension).
SigmaRoc said that CDH is situated in a prime location and has infrastructure to deliver products into Brussels as well as into neighbouring countries. Currently 27% of revenue is generated internationally through more than 40 global partners. CDH has a diverse customer base, with less than 3% of revenue
being generated from its largest bluestone customer in 2018.
In a statement SigmaRoc commented: “Due to its high quality and distinctive characteristics, Bluestone is a Global Heritage Resource and a highly prized product that travels worldwide (unlike most aggregates). Bluestone can be used in residential, commercial and infrastructure projects, as well as for architectural and cosmetic applications.”
Max Vermorken, CEO of SigmaRoc, said: “This acquisition, which is consistent with our strategy of growth, provides us with an exciting opportunity to substantially strengthen our existing presence in Belgium, one of the highest infrastructure densities in the EU.”
Demand durability without compromising on performance. With robust and reinforced components, the ZW330-6 achieves excellent availability while effortlessly handling the rigours of heavy applications. ZW-6: designed and engineered for your needs.
O.C.O Technology is eyeing big growth for its highly innovative carbonnegative aggregate product utilising patented and state-of-the-art Accelerated Carbonation Technology (ACT). The company’s waste carbon dioxide capture solution is also attracting strong interest from firms looking for a more ecominded approach to landfill waste disposal. Guy Woodford spoke to Steve Greig, the company’s managing director, at O.C.O Technology’s Leeds, North-West England, facility to find out more
Landing a contract that will see air pollution control residues (APCr) arising from a new energy-from-waste station turned into 75,000 tonnes of high-quality carbon-negative aggregate every year for ten years is a pretty good way to advertise the renaming of a business.
The news of O.C.O Technology’s (O.C.O) agreement with Ferrybridge Multifuel 2 (FM2), a 50-50 joint venture between SSE and Wheelabrator Technologies, in Knottingley, West Yorkshire, came just a month after the carbon-negative aggregates specialist changed its name from Carbon8 Aggregates.
The move also led to a name change for the firm’s award-winning aggregate, previously known as C8Agg, to M-LS (short for Manufactured LimeStone).
O.C.O treats the APCr using its Accelerated Carbonation Technology (ACT), whereby carbon dioxide reacts with the residues and through the addition of various binders and fillers creates the firm’s M-LS carbon-negative aggregate product. A global first, M-LS manufactured limestone has many applications in construction, notably as an ingredient for use in the production of concrete building blocks. It can also be used in precast and readymixed concrete, screeds pipe bedding and various road applications.
Expected to be commissioned by the end of 2019, FM2 power station will export in excess of 80MW (gross) / 73.5MW (net) of electricity to the local power network. The contract with O.C.O will ensure that up to 30,000 tonnes per year of the APCr is recycled, permanently capturing around 3,000 tonnes of carbon dioxide. It means that FM2 will be a ‘zero to landfill’ site, fulfilling SSE and Wheelabrator sustainability goals for this station.
The 75,000 tonnes of manufactured limestone produced annually will also help preserve natural resources, with significant environmental benefits.
With the addition of the FM2 contract, O.C.O will be producing over 450,000 tonnes of M-LS aggregates a year at its three plants – Leeds; Avonmouth, near Bristol; and Brandon in Suffolk.
“What we will be able to do with the FM2 contract is continue to show energy from waste plant operators and local authorities that award contracts to them that we are helping the energy waste journey towards 100% recycling,” explains Steve Greig, managing director. “A tonne of APCr going through our process turns out, broadly, 2.5 to 3 tonnes of aggregate. And for every tonne of carbon-negative aggregate used, 1.4 tonnes of natural aggregates are saved. The latter figure is based on the lower density per cube [1100kg/m³] of our M-LS.”
Stressing the difference between M-LS and traditional aggregate products, Greig says: “When you excavate or mine
aggregate from a quarry, the product is what it is. Through our production process we rigorously test our aggregate for two aspects: is it chemically okay, and is it fit for purpose? We use our own laboratories and external accredited labs. We stress to our customers that because we manufacture an aggregate, we can make it different. We can make it harder, stronger, bigger or a different colour. We can almost make it whatever you want.
“We can be competitive on price. We also don’t have an Aggregates Levy to contend with. All our customers are large, sometimes national businesses. We never wanted to sell our aggregate by the tonne to the local market. It was all about having relationships with the large players. It is a recycled aggregate and we need to be conscious of the fact that like other recycled aggregates it can’t just go anywhere.”
O.C.O Technology’s spherical M-LS carbon aggregates are sold in sizes of 50mm down to 1mm, with the most popular sizes being 15mm downwards. “Our aggregates look like different-sized peas and customers generally want a grading to help create voids. This, together with the fact that we produce a lightweight aggregate helps in making the concrete product lighter, which has a number of structural and transportation benefits.”
Currently a £13 million-turnover business employing more than 90 staff, the company’s expanding customer portfolio means a fourth UK plant will be in construction soon. O.C.O Technology’s Leeds and Avonmouth facilities also have room to grow, and Greig expects company employee numbers to increase to 150-200 in the next three to five years.
“We currently recycle around 24% of the UK’s energy-from-waste sector’s APCr, and no-one else is doing what we do,” stresses
Greig. “That creates a big growth market. The energy-from-waste sector APCr market is growing and our ambition is to treat around 250,000 tonnes of APCr per annum, producing over 700,000 tonnes of aggregate per year in the next three to five years.
“We formed in 2010 as Carbon8 Aggregates specifically to look at APCr as a waste stream to see if we could take what was then a lab-based technology [ACT] and turn it into a commercial entity. We did a bunch of trials and tests to see if it would work. A significant achievement was when we achieved the UK Environment Agency ‘end of waste’ status at the end of 2011. We were the first company in Europe to achieve this status for an APCr waste stream. This demonstrated our credibility in the marketplace.”
Carbon8 Aggregates built its first plant in Brandon in 2012 due to its proximity to Lignacite, a concrete building blocks maker with whom the firm had formed a close working relationship during its initial ACT-testing programme.
“Brandon was the prototype to build Avonmouth in 2015,” explains Greig. “The reason we chose Avonmouth was because there were a lot of energy-fromwaste businesses in that area. There were also a lot of concrete building block makers in that part of the west of England. Strategically, it made sense.”
Carbon8 Aggregates then signed a framework agreement with Somersetheadquartered Viridor, one of the UK’s leading recycling, resource and waste management companies, to take all their APCr from their plants in Cardiff, Exeter, Ardley, Peterborough and Runcorn.
What was Carbon8 Aggregates’, now
O.C.O Technology’s in-house laboratory testing
O.C.O Technology’s, state-of-the-art Leeds site was opened in 2018.
Greig, who lives in Kent, South-East England, continues: “The ambition for our business was always to build it on the back of recycling APCr as a waste stream. We would then look to expand and incorporate recycling of various other waste streams, such as cement and lime kiln dust, steel slags and other thermal residues creating a UK business that was strong and stable which could give us the platform to look at opportunities overseas.
“Some of the things we are now looking at are not about aggregates, more around pre-treatment prior to landfill. This has led to our change of name to reflect what we are truly about - two oxygens and a carbon. We believe we are the pre-eminent company in using carbon dioxide for industrial waste recycling, and this is an opportunity before establishing ourselves on an international stage to create a brand that reflects our broader offer.”
In May 2020, O.C.O Technology and its new licensed Japanese distributor will open a demonstration plant in Japan to showcase its ACT technology to energy-from-waste companies keen to find a permanent APCr carbon dioxide capture solution prior to the waste’s disposal in landfill. Greig is excited about the massive growth potential for his company in the Japanese marketplace.
“In the UK there are about 50 energyfrom-waste plants. This will probably swell to mid-sixties to 70 plants by the time the market build-out has finished. Japan has north of 1,200 energy-from-waste plants, but a lot of them are principality- or local authority-led, so they tend to be a lot smaller. Each principality or local authority has to deal with their own energy waste stream, so our challenge is can we build a suitable in-line plant solution for them?
“There are other opportunities when it
comes to recycling Japanese waste streams. For example, the country is still building coal fire power stations. These bring with them lots of challenges in terms of waste stream disposal and how best to gain carbon credits, and huge opportunities for us.
“We are already in the top ten companies in the world for carbon capture. Our ACT technology not only permanently captures the carbon dioxide, it also removes the need for other more expensive
treatment layers that would be used to treat waste prior to it going into landfill.”
O.C.O Technology also has sights on the Australian market. “Australia is building its first energy from waste plant. It’s in Perth, Western Australia. There are many more plants planned as they start on their energy-from-waste journey. It’s a very interesting market for us,” explains Greig.
“We have entered into an agreement for our ACT Technology with Macquarie, a leading investment business with an ambition to be one of the leading energyfrom-waste operators in Australia.
Wheelabrator Technologies in the UK is part of the Macquarie portfolio. It’s a business that is investing in the energy-from-waste sector worldwide.”
Greig says O.C.O Technology’s research and development team is looking at how the firm can increase the value of M-LS, such as through its potential use in various foam- and traditional-based asphalts and whether it can be produced in different colours in a resin-based format, making it well-suited for use in residential and industrial driveways. “We are also testing M-LS in green [garden centre/nursery/ greenhouse] roofing as it retains water which can subsequently be used on plants. With M-LS being lighter, it also means the structure for making your roof does not have to be as heavy. All this could create different income streams and the ambition is to create different branded M-LS such as M-LS – Block Mix and M-LS – Coloured Aggregates.”
A former senior banking and corporate
“Some of the things we are now looking at are not about aggregates, more around pre-treatment prior to landfill. ”
O.C.O Technology’s growth plans are being ably supported by its primary investor Grundon Waste Management Ltd
finance executive, Greig was intrigued by the commercial potential for what was then a lab-based technology when helping a client sell his business in 2008. “Part of his business had planning permission for an energy-from-waste plant, and part of the process you go through when seeking planning permission is specifying what you plan to do with APCr residues. Some work had been done and it turned out that a spin-out company from the University of Greenwich, called Carbon8, had been looking to exploit this technology as an alternative to landfill.
“A few years later I was approached to
As O.C.O Technology manufactures an aggregate, it can make its M-LS product harder, stronger, bigger or a different colour
assist in funding this technology. Initially I assisted in arranging angel investment [affluent individual/s who provide capital for a business start-up, usually in exchange for convertible debt or ownership equity] and thought this was quite interesting technology. We did some trials but recognised that it needed more funding and commercial acumen if it was going to be successful. I went home and spoke to my wife and decided to give up my corporate salary and car and invest in Carbon8. I knew I wouldn’t be paid for several years, but I felt it was the right time. I was 40-years-old and had always wanted to run
my own business.”
Greig admits he and the rest of the O.C.O Technology management team have been on a “huge learning curve” over the last decade. “It’s been a fantastic journey, which is moving quicker and faster now than it’s ever done, supported by our primary investor Grundon Waste Management Ltd, who have been a fantastic partner. It’s good to be growing a business that is both sustainable and good for the planet. Without doubt, the drive towards a carbon-neutral footprint will have a huge impact on the construction industry in every shape and form.” AB
The UEPG Sustainable Development Awards 2019 emphasised just how strongly the European aggregates industry is committed to a sustainable Europe
In the Brussels Concert Hall ‘La Madeleine’ on the evening of Wednesday 20 November, UEPG - the European Aggregates Association - showcased and celebrated its European rock stars. A record 53 company entries were received from 13 countries for the 2019 staging of the UEPG Sustainable Development Awards. Nine of the 53 received a trophy while a further 21were specially mentioned for their achievements linked to the environment, social progress, economic contribution, communication and biodiversity.
The event welcomed around 200 participants from 20 countries including high-level representatives from the European Commission such as keynote speaker Peter Dröll, director Prosperity in DG Research & Innovation and William Neal, advisor to the director for Circular Economy and Green Growth in DG Environment. In response to the future policy trends laid out by the two keynote speakers, the companies E-MAK and INFORM presented their innovative products and solutions for the non-energy extractive industry.
UEPG president Thilo Juchem opened the ceremony by saying that aggregates producers too often are holding back their success stories in sustainable development. He said they need to show what they do, communicate it but also learn from each other and from external expertise.
The purpose of this major UEPG event is to reward and showcase the commitment of the European aggregates industry to
sustainable development. Moreover, it also creates opportunities to promote and disseminate good practice examples and encouraging projects that go well beyond what is required by regulators, setting new standards of excellence others could follow.
The five fully independent jury members had the difficult task of selecting the best of the best. UEPG is sincerely grateful to Ester Asin, director of the WWF European Policy Office; Jean-Pierre Damm, co-chair of the Sectoral Social Dialogue Committee Extractive Industry; Anna Ostrega, associate professor at the AGH University of Science and Technology; Slavko Šolar, secretary general of the European Geological Surveys; and Guy Woodford, editor of Aggregates Business Europe
Antonis Antoniou Latouros, 1st vice-president of UEPG, officially closed the ceremony and stressed that all 53 companies had made him proud of the industry.
UEPG represents the largest non-energy extractive industry in Europe with more than three billion tonnes of sand, gravel, crushed rock, recycled, manufactured and marine aggregates produced on 26,000 sites across Europe operated by 15,000 companies employing 200,000 people. AB
• UEPG would like to express its gratitude to the sponsors of this event: CTC Automotive Ltd – Caterpillar Dealer in Cyprus, E-MAK and INFORM (Gold sponsors) and Austin Powder
As a lithium-exploration company in the UK successfully completes a £1.4 million crowdfunding round, believed to be the first of its kind by a British mineral exploration company, Gavin Poole from the mining and minerals team at Stephens Scown LLP explores the legal implications of crowdfunding
In October 2019 Cornish Lithium welcomed more than 1,200 new investors following its £1.4m crowdfunding round via Crowdcube. The company, which plans to investigate the possibility of combining geothermal energy and lithium extraction in Cornwall, will drill its first exploration holes with the funds raised.
Equity-based crowdfunding involves members of the ‘crowd’ investing in shares in a company. In 2017 the value of equity-based crowdfunding in the EU (excluding UK) was 211 million Euros, a rapid growth from just 18.2 million Euros in 2012.
Legal issues to consider
Despite the various attractions of equity-based crowdfunding, including its flexibility and lower risk compared to debt finance, there are various legal issues that companies should be aware of.
Will you need to change your constitution?
Most crowdfunding platforms will have bespoke articles of association which participating companies are required to adopt. This is attractive in some ways because you don’t have to go through the extensive negotiation which often accompanies thirdparty investment, but equally there is the risk that you lose a measure of control over the company.
What about shareholders’ agreements?
If there is an existing shareholders’ agreement this will need to be disclosed to the crowdfunding platform. You will need to consider whether the shareholders’ agreement restricts the company’s ability to raise investment, and whether the investors will be required to sign up to the shareholders’ agreement (assuming it is in a suitable form for them to do so). It is also important to consider how the fundraising process generally – including any changes to the articles of association – will impact upon the terms of the shareholders’ agreement. It may be necessary to terminate or vary the shareholders’ agreement prior to raising funds from the crowd.
“Despite the various attractions of equitybased crowdfunding, there are various legal issues that companies should be aware of.”
Do you hope to attract further investment?
It is important to consider whether raising funds by equity-based crowdfunding now will make your company less attractive to potential investors further down the line.
Will there be different classes of shares?
The company will need to decide whether it wants to offer a different class of shares to investors to those held by the founders. Some crowdfunding platforms are very prescriptive about the class of shares that are to be offered to investors. Typically, a company may not want the crowd to have voting rights, for example, although bigger investors might expect to have voting shares and some platforms use a nominee structure which does confer voting rights on the crowd.
Are you ready for the additional strain of corporate governance?
Whilst crowdfunding platforms typically take some of the hard work out of post-raise administration (such as providing share certificates to investors and providing the company with the relevant information for its statutory registers) there may nevertheless be administrative and compliance implications for the company to consider. What happens if a member of the crowd chooses to sell their shares? Giving notice of general meetings, for example, is much more complex if you suddenly have hundreds or even thousands of members. You will also need to think about how you are going to communicate with the crowd, which will understandably expect to be kept regularly informed about the company’s progress.
Are there any potential reputational risks?
Equity-based crowdfunding is still an emergent, relatively new concept, and the first two successful UK exits only happened as recently as 2015. Difficulties may arise further down the line where members of the crowd start to become disillusioned at a lack of dividends or their inability to readily resell their shares. The crowdfunding platforms are likely to bear the brunt of such frustration, but nevertheless this is something that fundraising companies should consider prior to a raise. As with any form of third-party investment, it is important that companies carefully review the legal and commercial factors prior to engaging in crowdfunding. Taking legal and accountancy advice at the outset of any fundraising venture helps to confirm whether it is the right decision and avoid the risk of nasty shocks arising further down the line. AB
Gavin Poole is a corporate partner at Stephens Scown LLP. The firm has more than 70 years’ experience representing mining and minerals clients and its specialist team is recognised by independent guides to the law Legal 500 and Chambers.
Gavin can be contacted on 01872 265100 or email solicitors@stephens-scown.co.uk. For more information visit www.stephens-scown.co.uk
MORE POWER, MORE UPTIME, MORE PRODUCTIVITY. ALL WITH LESS COMPLEXITY, LESS WEIGHT AND LESS SERVICING.
AGE S TO
THE B6.7 PERFORMANCE SERIES STAGE V ENGINE FROM CUMMINS DELIVERS BENEFITS TO EQUIPMENT MANUFACTURERS AND OPERATORS ALIKE. THE HIGHER POWER OFFERS THE OPPORTUNITY TO INCREASE MACHINE CAPABILITY. ITS SIMPLER, EGR-FREE DESIGN IS EASIER AND CHEAPER TO INSTALL. FOR THE USER, IT IS MORE EFFICIENT, MORE RELIABLE AND CHEAPER TO RUN.
SEE HOW CUMMINS B6.7™ SETS THE BAR FOR PERFORMANCE AT CUMMINS.TECH/CONSTRUCTION.
Situated near Haro, a town in northern Spain’s stunning La Rioja province, Ofitas de Santutis (Santutis) quarry has been owned by Iñigo Ajuria’s family business, Ofitas de San Felices Group (OSF Group), since the 1960s. After a long period of closure due to reduced market demand, OSF reopened the ophite rock-rich site in 2016 as the company looked for extra mineral resources to produce ballast for the ambitious Basque Y highspeed rail project linking three major Basque Country cities – Vitoria-Gasteiz, Bilbao and Donostia-San Sebastián.
Originally due to be completed by 2023 but now behind schedule, the 194km(157km double track and 37km single track) route will transport passengers and cargo, the latter between the ports of Bilbao and Pasaia. Basque Y is set to reduce journey times between Vitoria-Gasteiz, Bilbao and Donostia-San Sebastián to less than one hour, compared to anything between one hour 40 minutes and two-and-a-half hours currently. The new line will also connect the Basque Country with the rest of Spain.
The impressive all-Metso plant set-up at Santutis quarry includes an LT125 Lokotrack jaw crusher, two HP4 cone crushers, two CVB 2060 screens, conveyors, feeders and a cutting-edge plant control system.
“At Santutis we are producing around 800,000 tonnes of material a year – 30% of which is ballast,” says Ajuria, during a September 2019 visit from Aggregates Business. “The Metso plant was very simple to install and is simple to run. The long experience we have of working with Metso
and the trust and personal relationships we have built up made the commissioning of the plant easy. For this site, we were extremely clear on what we needed.”
Ajuria says his HP4 cone crushers have proved ideal for ballast production. “They have proven over time to be the best kind of cone crusher for this kind of product. This is based on their capacity, the quality of the final product and the longevity of wear parts. HP cone crushers are also highly reliable machines. Given the hardstone in our quarry,
Guy Woodford sees first-hand how a premium crushing and screening plant is helping OSF Group meet huge demand for ballast for the Basque Y high-speed rail project. Meanwhile, a sector giant is expanding a major cone crusher range, while another ambitious plant manufacturer has staged a major demo-days event in Scandinavia
which has a Los Angeles abrasion value of 10, reliability is not always evident with every cone crusher. We also find that the Metso CVB screens are highly reliable and efficient. We’ve had our CVB 2060s for some time.”
Santutis’s Metso plant control system includes cameras on the jaw and cone crusher feed openings, for early detection of any oversized material blockages or other production issues. The quarry’s conveyors are not fixed to ground foundations to allow for production flexibility, easier engineering maintenance and cleaning. This is said to be a first conveyors set-up of its kind for Metso. Santutis operates 8am-5pm Monday to Friday for 10 months each year, closing in January and February due to the Basque Country’s severely cold winter weather.
As well as being renowned for its high-quality ballast, Santutis also offers customers high-quality 4-12mm, 12-20mm and 20-25mm aggregates products, plus a 0-4mm sand product for concrete production.
Santutis’s aggregates product customers, including general construction and highway contractors, are situated anywhere in a 150km-radius of the quarry. They either collect their purchased products from the quarry, or OSF delivers them by either one of the company’s own or a hired-in truck.
Santutis has 15 million tonnes of mineral reserves, allowing Ajuria and his OSF leadership team to plan for many more years of fruitful aggregates and ballast production at the site.
“In the future, we are looking at bringing
in another Lokotrack jaw crusher to meet demand on the Basque Y high-speed rail project. This will allow us to double our ballast output,” explains Ajuria, whose OSF business also operates the spectacular Ofitas de San Felices quarry, next to his own vineyard, near Haro, and a third quarry in Granada, southern Spain.
Swedish quarrying equipment giant Sandvik is expanding its 800i series of connected cone crushers to include three new crushers for aggregates and mining applications.
The three new models are the CH830i, CH840i and CS840i, and the manufacturer says that each crusher comes with its new Automation and Connectivity System (ACS) as standard.
Sandvik adds that the new 800i series of premium cone crushers features mechanical upgrades, connectivity, advanced automation and rebuild possibilities to predict performance, maximise uptime and offer sustainability at the lowest possible cost.
Connected to the My Sandvik customer portal, the 800i crushers are designed to enable managers and operators to make decisions based on facts and see areas for improvement directly, increasing uptime and availability. My Sandvik can be accessed using a smartphone, tablet or computer.
The 800i connected crusher series features the new generation ACS as standard. The system continuously monitors and optimises crusher performance and controls the complete lubrication system, increasing uptime and reliability.
The 800i series has been toughened and improved to offer greater reliability, higher availability and a low risk of critical failure.
Bolted rather than welded top and bottom shell liners are designed to make changing 90% faster.
“New, digital technologies will transform the way mines and quarries work,” said Mats Dahlberg, VP Lifecycle Service, Stationary Crushing and Screening, Sandvik. “My Sandvik is the first major step in gaining insights into productivity and predictive
forward. It’s great to offer our customers a service that will truly make a difference to their profitability.”
Keestrack’s dealer for Norway and Sweden, Fredheim Maskin, staged its 10th demo-days event at its Spydeberg, near Oslo, HQ on 17-19 October 2019.
A shuttle service to a nearby granite quarry was organised to showcase Keestrack’s solutions for modern aggregates production. Event attendees saw a fully electric-powered, 200tonnes per hour production plant line producing six end products. Machines on show comprised an electric feeding hopper on skids and a heavy-range Keestrack H6e cone crusher with infeed belt, single deck pre-screen and three-deck after screen with recirculation belt, which was supplying material to a K3e screen. To facilitate stockpiling, there were two S1e stackers with automatic swivelling function and one S5e track mobile stacker.
All plant line units, which also included a B7e primary jaw crusher and K7e scalper, were electrically powered by the H6e’s drop-off engine/generator unit. Keestrack says the key advantage of such a drop-off engine unit is it lowers the service costs due to less dust emissions in the filters, less vibrations, easier and safer maintenance due to working on ground level and lower machine noise levels.
had a combined fuel consumption of less than 90 litres per hour (l/h). The power needed by each plant is calculated at the following ratio: B7e 25 litres/hour (l/h), K7e 8 l/h, H6e 45 l/h, S1e both 1l/h, K3e 5l/h, S5e 5 l/h.
The granite-processing production line showed the huge saving potentials of the Keestrack ‘e’-version hybrid electric plug-in concept. Keestrack says gains would have been even higher if the complete production line was connected to the mains by plug-in. Compared to conventional diesel-hydraulic systems, Keestrack says plant production energy costs can be reduced by up to 80%, with plant noise levels during emission-free plug-in operation down by around 30%.
Keestrack says its modern ‘e’-version plant remain as flexible and highly mobile as conventional technology without having to add a lot of additional transport weight, compared to diesel-hydraulic plant.
The 700kVA genset supplying plug-in power to all the quarry-showcased
Even the larger hybrid plant can be transported in one piece, without dismantling. This, says Keestrack, also contributes to short set-up times. The full integration of all electrical system functions is controlled by intelligent Keestrack plant control. This includes numerous automated routines (sequential start/ stop) and comprehensive monitoring, with bi-directional transmission of machine and production data, via the satellite-based Keestrack-er system. AB
Ammann focuses on technologies that incorporate high percentages of RAP – and considerably reduce operating and materials costs in the process. These technologies aren’t baby steps – they’re significant advances that can greatly impact your business. And they’re PROVEN technologies that are in use at hundreds of plants around the world.
Ask us how a new Ammann asphalt-mixing plant or retrofit can help your business turn waste into profit.
Innovation is a key feature in the modern global quarry loading machine market. Mike Woof, Munesu Shoko and Guy Woodford assess three major recent model launches
It’s an exciting time when it comes to wheeled loaders and crawler excavators for quarrying customers, with many top global manufacturers having brought or preparing to bring new models onto the market this autumn.
Komatsu is introducing its highperforming WA475-10 wheeled loader, which replaces the previous generation WA475. Power comes from a 219kW diesel engine which meets the stringent Stage V emissions requirements for Europe, as well as the Tier 4 Final legislation.
First seen in prototype form at the bauma exhibition in Munich, Germany, in spring 2019, the machine’s key feature is its innovative, Komatsu-developed driveline. This K-HMT system utilises a combination of both hydrostatic and mechanical drive to deliver power smoothly and effectively. The combined powershift and hydrostatic transmission is integrated electronically with the engine to ensure effective moderation between the parallel drive systems. At low travel speeds the hydrostatic system allows precise control, while at high speeds the mechanical drive provides high torque. The system ensures that the engine runs in its optimum range and product manager Shayan Dadgar said: “We have a variable rate of output. The rpm is lower, but we drive in the efficiency zone.”
due to its sophisticated driveline. Of note is that Komatsu has the confidence in its sophisticated new technology to offer the WA475-10 with a five-year/10,000-hour warranty covering the driveline.
The engine itself benefits from performance gains in addition to its low emissions, providing a 15% increase in torque at lower rpm. The fuel filter system life is now 1,000 hours compared with 500 hours on the previous model while coolant does not need replacing until 6,000 hours, compared with 5,000 hours for the outgoing version. The diesel particulate filter (DPF) meanwhile achieves 98% passive regeneration and Dadgar claimed, “We have the best after-treatment system on the market.”
fleet management, allowing monitoring of operating parameters and providing alerts for service issues. Additionally, the system can track operator performance and highlight issues that may require amendments to working practices or additional training.
The cab is larger than on previous models giving plenty of space for the operator, while large glass windows give a clear view all round. Dadgar said, “It’s the biggest cab we’ve ever had on a wheeled loader.”
He said that because of the efficiency of the integrated mechanical and hydrostatic transmission matched to the engine, fuel savings of up to €32,000 can be achieved over a five year/10,000 working hour operating life (based on average fuel prices across Europe). At low speed the hydrostatic system allows precise movements and Dadgar added: “It’s also much smoother to operate.”
High efficiency is delivered through the power range due to the new transmission and Komatsu claims that the machine offers fuel savings of up to 30% over the outgoing model, predominantly
Novel control features include a function that raises the boom quickly without the operator needing to increase engine rpm. Another is the button that allows the operator to shake out any material retained in the bucket. And there is also a fast arm-lower function to return the bucket to carry height. The bucket configuration has been refined to optimise filling when entering the muckpile.
Liebherr Africa has launched the new Liebherr R 9150 B excavator with a specific design focus on increased productivity, efficiency and reliability – three key parameters that can provide African quarrying and mining sectors with some insulation against the cold whims of the market.
With an operating weight range of 128-148 tonnes, depending on the type of wear packages and attachment the customer requires, the new Liebherr R9150 B is a perfect loading tool for 50-tonne up to 135-tonne dump trucks.
Abie Kriel, technical manager Mining at Liebherr Africa, says the launch of the new B model is in line with the company’s strategy for the 100-150-tonne class excavators, which has been identified as one of the major growth drivers for Liebherr’s Mining Division. As part of that strategy, Liebherr Africa also introduced the 100-tonne T 236 rigid hauler late last year, which can be perfectly paired with the new R 9150 B.
As with other machines in the range, the loader is equipped with Komatsu’s remote monitoring package, KomTrax. This latest version allows more effective remote
Tom Munch, director Mining at Liebherr Africa, says the contract mining market is a major driver of the 100-tonne class. “We are working in a contract mining market. If you look at the type of equipment this group of customers requires currently, it’s mainly 100-tonne class excavators and 100-tonne dump trucks. This is due to the mobility they require, given that their contracts are limited to 3-5 years at most,” says Munch.
The R 9150 B’s productivity hinges on the machine’s fast cycle times, precise machine motions, high digging forces, power-oriented energy management and an exclusive EVO bucket solution.
With fast cycle times in mind, like all other Liebherr mining excavators, the R 9150 B uses a closed-loop swing circuit. The main hydraulic circuit comprises a combination of three main valves fed by three working pumps, providing flexibility of attachment control and force distribution, while allowing full oil flow integration for fast movement and fast cycle times.
“All Liebherr Mining excavators are equipped with a closed-loop swing circuit. Kinematic energy is recovered when the swing motion is used during deceleration, to drive the main and auxiliary pumps, reducing fuel consumption and allowing faster boom lift motion,” explains Kriel.
The R 9150 B integrates the Litronic Plus electronic control system, allowing for easy control even when simultaneous movements are required. The patented Liebherr electronic bucket cylinder damping system provides controlled end-cushioning for smooth attachment motions, thus increasing machine productivity. The integration of the electronic control system also enables maximum machine versatility and the use of various long-reach attachments and specific tools.
“The R 9150 B’s attachment is equipped with pressure-less, boom-down function to enable fast cylinder retraction without the need for pump energy. Intelligent energy management diverts the pump flow during boom lowering, allowing other cylinder motions to operate unimpeded,” explains Kriel.
Furthermore, the new R 9150 B comes with the exclusive EVO Bucket Solution with patented Liebherr design to maximise the loading capacity and ensure optimal penetration efficiency. Thanks to the contoured sidewalls and the augmented depth, the EVO Bucket backhoe bucket has a capacity of 8,8-9,6m³ for the R 9150 B. The bucket takes about four passes to load a 50-tonne off-highway truck.
Hyundai Construction Equipment Europe (HCEE) is launching its new HL900 A-series model range with three Stage V compliant wheeled loaders: the HL940A, HL955A and the HL960A.
All new series machines are fitted with new Cummins B6.7 engines with an all-inone exhaust after-treatment system. The engine is said to be easy to maintain, thanks to its connected diagnostics to Hi-Mate, the long service intervals and the DPF soot reset function for cleaning. As the exhaust after-treatment system does not need a manual DPF regeneration and is exhaust gas recirculation (EGR)-free, the platform is said to offer increased engine reliability.
HL900 A-series wheeled loaders’ IWM (Intelligent Work Mode) menu allows for three engine operation modes: Power, Power Smart and Economy, offering full engine power or reduced fuel consumption depending on the application. The Power Smart Mode is said to result in reduced energy losses and average 3% - 5% fuel savings. In addition, the engine performance is optimised to deliver higher torque at lower rpm. This provides another
means for improved fuel efficiency, while optimising engine power and improving engine response time.
Hyundai HL900 A-series wheeled loaders are equipped as standard with a rear-view camera developed in-house. Hyundai also offers an optional reverse-drive radar system, like a car’s, allowing the operator to quickly and reliably detect obstacles within 10 metres during day or night.
For increased safety on the job site, Hyundai’s AAVM (advanced around view monitoring) four-camera system is available as an option. The system informs you when people or dangerous objects are detected, giving the operator high-precision control over the machine and the surroundings. The camera system comprises two major features: AVM (around view monitoring) and IMOD (intelligent moving object detection). Four cameras film at each side of the machine which means the AAVM system offers a 360° overview of the machine’s surroundings. The IMOD indicates all movements around the machine. Movement is shown on the monitor by putting a rectangle around the moving object or by indicating the side at which there is movement by arrows.
The HL955A and HL960A come with an increased rear-axle capacity for better durability. Both machines can be ordered with an optional heavy-duty front axle for waste handler and specific industrial fields. The all-in-one main control valve – a combination of the ride control valve and the electronic proportional pressure reducing (EPPR) valve – leads to improved uptime as there are fewer hydraulic hoses –and subsequently a smaller risk of damage by leaks.
At Hyundai’s annual Construction Equipment dealer conference staged at the company’s European headquarters in Tessenderlo, Belgium, on 14 November, a brand-new look for A-series machines was revealed by the HCEE management team.
The new A-Series models, which include excavators as well as wheeled loaders, will now adopt a ‘fresh’ new colour combination - and the traditional yellow arm and boom, will be replaced by a modern grey-green tone, which is identical to the current colour of the undercarriage. AB
Extensive improvements have been made to Terex Trucks’ Motherwell HQ since the company was acquired by Volvo Construction Equipment in 2014
There is a hive of activity at one leading articulated hauler maker, while other prominent hauling machine and linked-technology solution manufacturers have been talking about eyecatching, forthcoming and current, cost-saving products. Guy Woodford reports
An expert team at Terex Trucks is hard at work across three key projects. During a recent visit by Aggregates Business magazine to the Volvo Construction Equipment company’s Motherwell, Scotland HQ, Paul Douglas, Terex Trucks managing director, explained how new Scania Stage V emissions-compliant engines for European customers would be introduced on the firm’s 28-tonne TA300 and 38-tonne TA400 articulated haulers in mid-2020, with a new state-of-the-art transmission on the TA400 also set to be introduced in the future. Longer term, work is also well underway on Terex Trucks’ next-generation articulated haulers.
“We’ve already installed a new highperformance transmission on the TA300, which offers 5% better fuel efficiency than its predecessor as well as improved performance, productivity and operator comfort. As far as the new transmission for our larger articulated hauler platform goes, our development work and tests show that we are on track to deliver similar efficiency savings as the TA300. We’ve been developing the concept layouts and key component specifics of the next-generation models. They
will continue to be robust machines with a strong emphasis on operator safety and comfort as well as total cost of ownership. Our customers like our machines because they are simple to operate and easy to maintain, so our future products will stick to this philosophy.”
Douglas says that Terex Trucks is lucky to be part of Volvo CE, where engineers are focusing on key areas for future development such as electromobility, connectivity and autonomous machines. But although he says the company will capitalise on the Volvo Group’s advances in these areas, there are no plans for this to happen in the immediate future. “Our next-generation ADTs will be connected machines, but they will have a diesel engine. We won’t be leading the way when it comes to testing future technology. It’s not what our customers are telling us they currently want, and their requirements always come first.”
Another big focus for Terex Trucks is expanding its dealer footprint. “We currently have 88 dealer partners across the world, and we’ve been working to expand this in key territories such as France, Germany and the US,” Douglas explains. “We are working
with strong partners who understand the local customers and can provide them with high-quality support and solutions, with the backing from us here at the factory.”
Five years on from Volvo CE’s acquisition of Terex Trucks, Douglas believes the integration of the brand into the Swedish construction and quarrying equipment giant’s portfolio was a turning point. Since then, there has been significant investment in the product, people, processes, equipment and the site itself.
During the trip to Motherwell, Aggregates Business had a first-hand look at the extensive improvements made to the site’s factory, as well as the strong emphasis Terex Trucks places on quality control and testing all the articulated haulers that come off the production line.
“Our facility here is nearly 70 years’ old. When Volvo acquired the site, there were investments they wanted to make around safety, quality, environment and efficiency.
“Under Volvo CE’s ownership, there has been a capital expenditure flat-rate spend on this site of about £2 million a year – so we’ve spent £10 million so far. On top of that, there’s been exceptional spend on one-off
Terex Trucks is working on a new state-of-the-art transmission for its popular TA400 articulated hauler
projects totalling £7 million, including a heat treatment plant. We’ve also ordered £2.5 million worth of welding robots. These are two huge welding robots that can weld hauler bodies and frames and will improve safety, quality and throughput from our fabrication facility. We are excited about seeing them in full production, which will be during the middle of next year. It takes a long time to install and commission these robots, each one is 15 metres wide, 10 metres tall and 30 metres long.”
Douglas says Terex Trucks has also been changing its Motherwell factory layout to make it more compartmentalised and, as a result, efficient.
“Five years ago, when you walked into the factory, you could see all four walls from any vantage point. It was completely open. Welding, metal cutting, machining, assembly and inspection was all under one roof.
“Now we’re sectioning off each part of the production process. We started two years ago and have just finished sectioning off articulated hauler production. Each sectioned-off area costs around £1 million. We’ve put in things like new heavy-duty industrial curtain walls and speed doors, plus installed new lighting, flooring and tooling. This has improved air quality,
energy efficiency, quality and safety, as well as instilling a sense of local ownership and creating a more pleasant working environment for employees.”
During our visit, Aggregates Business heard how Terex Trucks’ articulated hauler testing and inspections process at the Motherwell facility has also been comprehensively reviewed and updated.
Assembly line inspections start at the goods inwards point – when materials or parts from external suppliers are delivered to the site – with the thorough final inspections being the seventh and final assembly line stage. At this point, the ADT is thoroughly checked to see if it is built to the correct specifications. This includes a static inspection, speeds and pressures check, running check, running check rectification, four-hour test, four-hour test rectification, washing, unit paint touch-up, safety critical decals, a shipping inspection, unit waxing and after all this they are then ready to ship. During this process, checks are being made to ensure components are fitted as they should be, no parts are loose, there are no fuel or hydraulic fluid leaks, and that lights, indicators, windscreen wipers and other parts of the vehicle are functional. Each hauler is put through four hours of rigorous function
testing at the Motherwell site’s purpose-built test track. This may occasionally result in engineering tweaks being made to the model, which is then retested, and, if no further tweaks are necessary, signed off as ready for customer delivery.
Terex Trucks is also now benefiting from the use of a fault analysis tool. If a fault is found during final inspections, the fault is plugged into the analysis tool so the system can support the inspection team by helping them to identify what further checks to make. It also advises on potential solutions by looking at other logged instances of how the same fault was rectified previously. All of this helps to contribute to and drive a superior quality product from the manufacturer.
Rodney Aggregates Supplies (Rodney Aggregates) has been using a Loadscan load volume scanner (LVS) in its Whangaripo Quarry north-east of Warkworth, New Zealand, to minimise profit loss due to carry-back on their overburden stripping programmes.
Daniel Le Roux, business manager at Rodney Aggregates, says: “The scanner was measuring significant amounts of carry-back by the contractor, especially this season where the material was sticky and wet compared to previous years. This was often up to 5m2 per load, which on some trucks is 20-25% carry-back — obviously a huge saving for us.”
The Whangaripo Quarry is a regular supplier of high-quality greywacke products (asphalt and concrete aggregates through to base courses and bulk fill) to the North Auckland region.
They strip up to 2,500m2 of overburden material a day and if Rodney wasn’t using the Loadscan LVS the company wouldn’t be aware of the carry-back in the truck bins, which influences the final payments to the contractor. In the years that the firm used the surveyed volumes compared with truck load count, carry-back was never considered although it was present, therefore there was a discrepancy between survey and truck count volumes. In terms of financial cost, if 20% of a truck load is haul-back then the business suffers a $3,250 per day cost for material not hauled. Over their six-day working week that’s $19,500.
Terex Trucks managing director Paul Douglas has been highlighting the Motherwell-headquartered Volvo Construction Equipment company’s exciting, future articulated hauler range plans
Hypothetically, if the LVS unit has a conservative lifespan of five years (though being a touchless system with no wear parts it’s proven to last much longer!) that’s a saving of $4,875,000 in carry-back alone.
Loadscan’s LVS system utilises laser scanning combined with proprietary software that creates 3D model images of trucks to measure the exact volume of material loaded in a truck or trailer bin. Every system includes an RFID reader for the automatic identification of each vehicle, every load.
Not only does an LVS system enable proper management of loading and carryback, having highly accurate measurement of every load also gives users an auditable trail of transparent data.
For Rodney Aggregates that data has eased invoicing tensions. Le Roux says: “In the past we used to rely on an aerial survey to calculate volumes moved. This meant that during the season the payments/measures were based on load counts and the final payment was sorted at the end of the season after completing the final flyover. There were usually arguments over final amounts, so
final payment was often agreed up to three months after completion of the works.”
Loadscan’s LVS system is completed by a load-management reporting system called Overview. Overview provides Rodney Aggregates with the full picture of material movements on-the-fly. The firm is now equipped with the real-time actionable intelligence to monitor exactly how much product has been stripped by its earthworks’ contractor.
Le Roux says: “Another great benefit is having the data of loads/volumes real time in front of me. It makes monthly payments accurate and reliable — no arguing with the
contractor on volumes moved.”
efficient
The LVS model used by Rodney Aggregates is Loadscan’s mobile truckscanning solution (LVS-3TMM). The fully self-contained mobile truck-measurement unit is driven to site and fully set up and operational in as little as 45 minutes. There are a range of power options, plus the ability to transmit truck-measurement load reports via Wi-Fi, cellular modem or network cable.
Hauler carry-back identified by Loadscan’s innovative LVS system
Liebherr showcased its pre series TA 230 articulated hauler during the company’s recent International Construction Trade Press Information Tour
The scanner, with extended rigger, is set up to measure the 40-tonne articulated dumpers removing overburden from the quarry. Rodney Aggregates’ LVS is equipped with a built-in kiosk so that it’s fully selfcontained. Overview reporting software is used to process and sort scan data and to generate custom load reports. And the office is equipped with LVS remote control functionality via network cable/WiFi/cellular modem.
Liebherr has been carrying out rigorous semi-autonomous testing of a trio of pre series next-generation TA 230 articulated haulers on the state-of-the-art site test track at its facility in Kirchdorf an der Iller, Germany.
The German construction and quarrying equipment giant put its new 30-ton (27-tonne) model, due to come on to the global market in April 2020, through its paces during the company’s annual International Construction Trade Press Information Tour on 24-25 October 2019. The well-attended event was co-hosted at the Kirchdorf an der Iller site and Liebherr’s facility in Nenzing, Austria.
During a press conference, Liebherr revealed that the TA 230 would be one of a three-strong new articulated hauler series. The company plans to unveil its new 40-ton (36-tonne) and 45-ton (41-tonne) machines at the 2022 edition of the bauma exhibition in Munich.
Aggregates Business readers can read in more detail about the next-generation Liebherr TA 230 articulated hauler in the January-February 2020 editions of ABE and ABI. AB
New wet processing equipment is helping French aggregates producer Pélichet Albert to recycle an annual 200,000 tonnes of construction and demolition waste in a former quarry at Chauvilly. Liam McLoughlin reports
Pélichet Albert, a public works contractor and aggregates producer based in western France, is using a new washing plant at its Chauvilly site that will enable it to divert up to 200,000 tonnes per year of inert construction and demolition (C&D) waste from landfill.
Pélichet Albert says a recently commissioned, new 160 tonnes/hour plant from Northern Ireland-based wet processing equipment manufacturer CDE will provide additional revenue from the production of higher value products.
The company’s former quarry site at Chauvilly became the base of its recycling operations in 1998 and has processed C&D waste material sourced from Pélichet’s business activities ever since.
Le Pays de Gex region in the early 1990s, which halted the extraction of finite natural resources.
CEO Jérôme Pélichet commented on his company’s link-up with CDE: “More than a supplier, we wanted to find a partner to come on this journey with us; a company that would oversee the process, from design through to commissioning on site, and work in conjunction with us to fully understand our operation and our business objectives.”
Founded in 1921, Pélichet operates a circular economy business model with operations in demolition, groundworks, landfill and construction & demolition waste recycling. The company has adapted its business over the last two decades to pay greater attention to recycled materials for use in the construction industry. This follows the introduction of local legislation in the
and extracting high-value aggregates from,” he said. “We had access to similar grade material, but until that point didn’t have the technology to process it.”
The Pélichet plant mainly processes two types of feed material; firstly, excavated materials from its construction works and demolition operations, including 0-300mm clay-bound, silica-limestone material and, secondly, 0-40mm crushed C&D waste.
The presence of plastics and other organic contaminants retained after processing was resulting in second-rate products with lower value.
Water availability proved to be another significant challenge at the company’s Chauvilly site. Jérôme Pélichet said that it was imperative to have a plant which used water resources efficiently and reduced the demand on the limited on-site supply of natural water.
An abundant stockpile of heavily contaminated historic landfill material presented a challenge.
“We encountered the problem of quality,” Pélichet added, explaining the company’s old plant and process before it commissioned the new wet processing plant. “So, we took a different approach with the acquisition of this new installation. It allows us to manufacture quality materials that better meet the demands of our clients.”
He selected CDE as a partner after visiting a C&D waste recycling operation that utilised a CDE plant during a trip to the UK.
“We saw first-hand the challenging feed material CDE plant was capable of processing
CDE business development manager Marc Sopransi said that the commissioned plant is the result of a detailed site audit and clear understanding of the Pélichet operation’s aims and objectives.
“The technical approach around this project was based on the resolution of four objectives,” he added. “The main one being to maximise the incoming material, to be able to process more complicated materials than Jérôme was able to treat before. The second, improving the quality, so treating more dirty materials – ultimately to bring them to a better quality. The third, on the environmental side, to be self-sufficient in terms of consumption of water. And the fourth, to be able to implement according to the constraints of the site.”
Using CDE’s co-creation approach, a solution that married CDE’s technical expertise and Pélichet’s commercial and environmental objectives was developed.
CDE has designed and delivered almost 2,000 projects globally since 1992 to increase the efficiency of materials-washing operations. The solution is based on the
company’s latest patented innovations.
“Each customer has their own unique challenges, be they geographic – or site limitations – or related to feed material,” said Sopransi. “Every wet processing solution we commission is tailored to the customer.”
CDE presented the blueprint of a bespoke wet processing plant, including the R2500 primary scalping screen designed to handle heavy clay-bound gravel, rock and mineral ores and construction, demolition and excavation waste. The R2500 is designed to ensure the efficient delivery of difficult material to the wet processing plant.
It feeds the AggMax 251 modular scrubbing and classification system, engineered to maximise product yield from clay-bound feedstock.
CDE’s EvoWash technology – a compact, modular sand-washing system – integrates a high-frequency dewatering screen, sump and hydrocyclones to provide control of silt cut points and eliminate the loss of quality fines, producing a range of high-quality sands.
Addressing Pélichet’s desire to be completely self-sufficient in terms of water supply, the plant design incorporates a full water-management system which recovers and recirculates up to 95% of process water.
The system includes an AquaCycle thickener which uses a flocculant to separate clean water from the solid particles. The solid particles form a sludge which is dried further in the filter press, recovering more water for recirculation and creating a dry filter cake which can be used for pipe bedding and landfill capping.
Water supply to the system is fulfilled by a submerged rainwater storage tank located beneath the plant which can store up to 2,600m3.
“Highly efficient water management has resulted in considerable cost savings for our operation,” said Jérôme Pélichet. “The feedstock we process is challenging material and our old plant was returning recycled aggregates of a lower quality and value.”
He added that the new plant is maximising profitability by extracting more value from his company’s end product due to a more efficient process that returns higher quality recycled aggregates.
“We can step up the range of our materials, market them better and respond to the expectations of our customers,” he added.
The engineered-to-order wet processing system commissioned by CDE is supporting Pélichet to transform 160 tonnes per hour of raw feed into washed 0-4mm, 4-10mm, 10-20mm and 20-40mm aggregates for use in concrete mix and drainage systems.
An estimated 80% of the products produced are reused by Pélichet companies, and the company markets the remaining 20%.
Jérôme Pélichet said that there are both economic benefits and environmental benefits from the new plant and that, what was formerly an unsellable product destined for landfill, is being processed and recycled into valuable resources for the construction industry.
“My customers are increasingly concerned with making sustainable choices when it comes to their aggregates supply,” he said. He added that his company plans to continue to build upon its sustainability track record with the support of CDE.
“By adopting this sustainable business model with industry experts we’ve a
confident outlook for the future of the business, and specifically the lifespan of our Chauvilly site,” Pélichet added. “It is up to us to work with our customers to show them we can do things right and that recycling is important for everyone.”
All aggregate producers are affected by water and energy costs and should consider sustainable alternatives, according to Michael Honea, process engineer at Haver & Boecker Niagara’s Canada operation.
Honea highlights five issues that producers should consider when looking for a more sustainable washing system.
The first is power-saving designs that can lessen a plant’s energy intake by using a high-pressure aggregate washer.
“High-pressure washing equipment processes as much as 360 tonnes per hour while using 15% less energy than conventional washing systems,” said Honea. “It uses high-pressure nozzles to remove clay and additional impurities off of stones, which requires less energy than power-rotating paddles and screens.”
The second factor to take account of is water conservation, which Honea said can be decreased by upgrading your washing equipment. He adds that conventional washing systems can use as much as 800 gallons per minute (gpm) per washing cycle, while high-pressure washing equipment can range from just 27 to 211 gpm, depending on application and model size.
Thirdly, maintenance and upkeep should be considered. Generally, highpressure washing equipment requires less maintenance than a conventional system. Conventional washing systems have several parts that require frequent replacement, including bearings, belts and paddles, which can cause significant servicing downtime.
On the other hand, high-pressure washing equipment has two main wear parts: spray nozzles and valve seals. Its efficient design allows easy accessibility — through its drum lid to the wear parts — providing simple maintenance for a mechanic. The system also features sensors that stop operation when there is no longer material in the drum, resulting in less wear to the machine. Honea said that this all adds up to fewer wear parts
to dispose of, not to mention more uptime.
The fourth issue is the smaller footprint of high-pressure washing equipment. This type of equipment can be as light as 4,000 pounds - about 60% less than conventional washing systems - and takes up significantly less room. Due to its compact size — just under 4.6 metres tall and 3.7 metres wide — its operating and structural costs are considerably lower than conventional washing systems. Conventional systems also require a separate pump, which takes up even more space than the washer itself. That makes new, high-pressure washing equipment an easy fit into any operation.
Honea said the final factor that should be considered is the rapid processing times of a high-pressure washer which can process as much as 360 tonnes per hour by using its powerful spray nozzles. He added that other machines can’t achieve that without requiring operators using multiple machines.
“Best of all, this new, high-pressure washing equipment’s cleaning ability salvages value from what might have previously been deemed waste — reducing your waste stream and breathing new life into vital resources, while putting more money in the producer’s pocket,” said Honea.
“Overall, high-pressure washing equipment offers more benefits and advantages than a conventional washing system for aggregates and mining operations looking to cut costs from their energy and water bills.”
Reclaiming process water for reuse can help alleviate maintenance tasks or permitting issues in wet process systems, according to Scott O’Brien, director of
process engineering at washing plant manufacturer McLanahan.
“Not much good happens without water in your wet process systems,” said O’Brien. “When we look at how we can help you manage your water, we often consider a tiered approach, making use of technologies that fit both your budget and your needs.”
O’Brien said these tiers are based on three-unit operations to handle your tailings stream: ultra-fines recovery; sedimentation; and filtering.
These tiers may be implemented individually or in series depending on the level of water recovery and solids-handling the plant operator wishes to achieve.
While not necessarily a water-recovery operation per se, the McLanahan ultrafines recovery (UFR) system is typically used to offload pressure on a tailings pond by removing particles down through 30 microns (based on 2.7 specific gravity) while producing a very manageable (i.e., conveyable, stackable) fines product.
“For many years, producers struggled with these fines in their waste stream, mostly being focused on what sort of product could be made with these fines or how they might even be treated to a state where they were easily handled,” said O’Brien.
In 1993, McLanahan’s Linatex Process Technology Group combined cyclones with the company’s dewatering screen to provide a solution to this issue. The cyclones were set up to recover the solids, while the dewatering screen, with its attendant low open area and caking abilities, was used to trap ultra-fines in its oversize. O’Brien said that this solution has been used by producers
for a quarter of a century to extend their pond lifecycle and water quality.
“Were we to take the UFR on its own, it is obvious that while the UFR can help from a pond maintenance and extended water quality aspect, the water must travel to the pond and meander its way about through several ponds before it can be brought back to the plant for reuse,” O’Brien said. “The pond system, while seemingly benign in its day-to-day existence, does have its costs beyond the cleanout.”
He added that some issues include exposure of your resource (water) to losses through seepage from the pond and/or evaporation; safety hazards for employees while working near the ponds, and possibly overlying mineable reserves.
Sedimentation is the basis for the processes known as thickening and clarification. The devices normally used for these operations include high-rate thickeners, high-density thickeners, paste thickeners, and plate clarifiers.
Each of these units are different designs of buckets in which suspended solids are allowed the opportunity to settle by gravity through the water in which they are dispersed.
“You can imagine that these could be some large tanks if we wait for gravity alone to act on the fine particles,” said O’Brien. To assist this process, these suspensions of solids are destabilised by the use of two types of chemical reagents - coagulants and flocculants.
Coagulants typically carry a positive, or cationic, charge and attack the negative surface charge of the particles, reducing their ability to repel one another electrically.
Flocculants are often made of longchain polyacrylamide molecules that carry a negative, or anionic, charge. These reagents serve to attract positively-charged particles, which attach to the negative charge sites on the molecule. As small particles of solids accumulate on the chains, an aggregate is formed and gains sufficient mass to drop from suspension, therefore creating a clean water phase and a thickened, settled sludge zone in the bottom of the thickener.
Under this scenario, the accumulated mud has an appreciably higher solids concentration than the incoming feed. The water from which these particles settle rises up through the thickener, where it flows over a peripheral weir into a collection launder. This water is usually directed to a large water tank, where it awaits use as recycled water in the plant.
O’Brien said that thickeners come in a variety of designs: “The design that is right for your plant largely depends on your goals for handling the underflow slurry. The most common thickener style in the mining industry is the high-rate thickener.”
He added that high-density thickeners may be considered if you are planning on dry stacking your fine waste by processing the sludge through a recessed filter press or similar device. AB
The off-highway machine engines market is vibrant, with many leading players focused on the quarrying and construction worksite engines of tomorrow as well as of today. Guy Woodford reports
Cummins’ ultra-clean Stage V Performance Series-branded engines are proving popular with quarrying customers globally, partly thanks to their impressive power and torque gains compared to their Tier 4 Final predecessors. The 3.8-12-litre displacement, 75-382kW EGR- (exhaust gas recirculation) free units deliver strong solutions for material-handling applications with class-leading levels of power and torque. The F3.8, B4.5, B6.7 and L9 Performance Series range delivers up to 33%, 16%, 5% and 8% more power, respectively. Peak torque improvements are also eye-catching across the quartet – F3.8 (+27%), B4.5 (+11%), B6.7 (+33%) and L9 (+13%). Cummins Performance Series power units represent a simple drop-in solution for key applications such as crushers, screeners, drills, concrete pumps and air compressors.
During a recent visit by Aggregates Business to Cummins’ key Darlington engine plant in North-East England, Steve Nendick, Cummins marketing communications director, explained that the Performance Series has been designed to offer better performance through higher power density,
higher reliability and availability, a more compact and lighter engine package, average 10% higher power and 20% more torque, and the potential for engine downsizing.
When you add in lower installation costs, higher fuel efficiency, extended maintenance intervals, and Cummins Connectivity enabling faster response times, the Performance Series engines also offer, notes Nendick, reduced total cost of ownership (TCO).
Another advantage of Cummins Performance Series engines is their commonality as a global engine platform. They have the same base engine for all emission stages, offer common installation for domestic and export businesses, flexibility on export orders, and high sulphur tolerance of up to 5,000ppm (parts per million) without after-treatment.
B Series engines, including the B6.7,
make up two-thirds of all Cummins’ engine sales globally. Now in its fourth decade of continuous improvement, the B6.7 for 2019 features the previously mentioned EGR-free design. The EGR-free architecture reduces complexity, improves reliability and reduces the cooling system space claim. Multiple component options allow for easier installation and maintenance. These include a choice of front- or rear-sump oil pan locations, on-engine or remote-mounted options for ECM and maintenance filters, the option of Rear Engine or Front Engine Power Take-Offs, plus your choice of four turbocharger orientations; high-mount front and rear, or low-mount front and rear.
The Single Module after-treatment system combines DPF (diesel particulate filter), SCR (selective catalytic reduction) and urea dosing in one unit which takes up 40% less space and weighs 20% less than the prior system.
Moving forward, B6.7 owners will also be able to benefit from Cummins Connected Diagnostics, remote monitoring technology that wirelessly connects the user’s engine to Cummins experts for analysis and recommended action the moment a fault code is generated on machinery equipped with a telematics system.
In a presentation to Aggregates Business, Nendick highlighted how the NOx (nitrous oxide) and PM (particulate matter) content in EU Stage V off-highway engines had
been reduced by 96% and 97% respectively compared to their Stage I counterparts of 20 years ago. In fact, the actual PM reduction is even higher when factoring in count measurement. Each PM has a diameter ranging from 2.5μm (combustion particles, organic compounds or metals) to 10μm (dust, pollen or mould), considerably less than just one human hair (50-70μm) and fine beach sand (90μm). As Nendick points out, this has led to Cummins and other global market off-highway engine manufacturers needing to invest heavily in state-of-the-art PM- and NOx-measuring technology.
Given the huge progress in reducing off-highway engine emissions and Cummins ongoing dialogue with EU sources, Nendick thinks it unlikely that any Stage VI emissions regulations will be introduced for some time yet. He does, though, think there is the potential for off-road equipment to follow the on-road Euro 6 PEMS- (portable emissions measurement system) testing process. This ensures that the engines remain within the specified emission limits for their “useful life” of seven years. It would be used to test emissions of off-highway engines during job site applications.
Cummins off-highway engines sector sales were worth US$2bn in 2018 – with 145,000 engines sold to more than 1,000 original equipment manufacturers (OEMs), powering applications on every continent.
The U.S.-headquartered engine maker, celebrating its 100th birthday this year, has strong relationships with off-highway OEMs including Sandvik, Terex, Komatsu, Doosan, Hyundai, JCB, Wirtgen Group, Atlas Copco SANY and LiuGong.
In October 2019, Cummins signed a strategic cooperation agreement with XCMG, a major Chinese construction, quarrying and mining machinery manufacturer. The two companies will work closely on developing and integrating comprehensive product lines, while exploring new markets and sharing resources in the construction industry, ensuring continuous global R&D (research and development) improvement.
Cummins is investing heavily in developing future powertrains to help manufacturers define the best power source for their equipment, whether diesel, natural gas, hybrid electric, battery electric or fuel cell. This has led to five key acquisitions or partnerships being agreed since autumn 2017. In October 2017, Cummins acquired
North America-based Brammo, a primarily low-voltage battery designer. This was followed by Cummins’ January 2018 acquisition of Johnson Matthey Battery Systems, a UK-based mainly high-voltage battery designer, the July 2018 acquisition of Silicon Valley-U.S.-based Efficient Drivetrain Inc. (EDI), a fully-electric and hybrid powertrain provider, and the September 2019 acquisition of Hydrogenics, a Canadian hydrogen and fuel-cell technology supplier. Finally, in September this year Cummins signed a partnership deal with Hyundai Motor Company to collaborate on hydrogen fuel-cell technology, initially focusing on the on-highway engine sector.
At the world’s biggest construction, quarrying and mining equipment exhibition next year – CONEXPO-CON/AGG 2020 in Las Vegas, U.S. (10-14 March) – Cummins and EDI expect to showcase a diesel-electric hybrid service truck for the future worksite. The hybrid service truck will follow on from Cummins’ prototype-engine electric-mini excavator showcased at bauma 2019 in Munich, Germany. During the exhibition the 3.2-tonne prototype had eight BM4.4E modules connected in series, providing total energy of 35kWh. This is designed to suffice for a full work shift and to be capable of being recharged in three hours.
Mounted near the base of the excavator, the Cummins-designed and built battery modules use Li-ion technology to achieve a higher energy density, together with proprietary control technology to maintain the battery state-of-charge for a longer zeroemission operating time.
Nendick says no firm launch date has been scheduled for the mini excavator, with its zero emissions making it particularly suited to urban sites.
Cummins’ £20mn-plus (€23.4mn) Darlington hot-test replacement and facility
master-plan upgrade was nearing completion when Aggregates Business visited in mid-November, with all works due to be finished in Q1 2020. Cummins engines produced at Darlington range from 3.8-8-litres and 56kW-320kW. It includes the F3.8, B3.9, B4.5, F4.5, B5.9, B6.7, C8.3 and L8.9. The QSM11 Marine Up-fit and on- and off-highway aftertreatment solutions are also made on-site. The Darlington engine plant currently builds 300 engines a day – and is on course to produce more engines this year than the 67,000 made in 2018. The aftermath of the global financial crisis of 2007-2008 hit hard at the Darlington site with only 31,000 engines produced in 2009 compared to 78,000 in 2008. Last year’s production volume was the biggest at Darlington since 2008. Two-thirds (66%) of Cummins Darlington’s annual engine output is for construction customers.
Germany-headquartered DEUTZ, one of the world’s leading manufacturers of off-highway machine diesel engines and innovative drive systems, and joint venture partner SANY are busy building a new highperformance engine production facility in Changsha in Hunan province, south-central China. Following the establishment of the joint venture in June 2019, representatives of both companies signed an agreement with Hunan provincial government officials during a September 2019 foundation stone-laying ceremony for the new factory site. The Hunan government is contributing several tens of millions of US dollars towards the cost of the project.
The joint venture between DEUTZ and SANY, China’s biggest off-highway machine maker, is part of SANY’s intelligent heavytruck project, a big-ticket project within the framework of SANY’s digitalisation strategy. In addition to various off-road applications, DEUTZ is also taking over the manufacture of heavy-truck engines for SANY. Initially, the plan is to supply SANY with around 75,000 new engines for off- and on-road applications in 2022. These engines will comply with the China IV and China 6 emissions standards and will be built at the new plant, not far from SANY’s headquarters in Changsha.
DEUTZ recently announced that it had recorded further growth in revenue and earnings in the first nine months of 2019. Group revenue grew by 6.4% to €1.379.9 billion. The MaterialHandling application segment performed particularly strongly, delivering doubledigit revenue growth of 11.3%.
diesel-electric drive technology for wheeled loaders is now very well-proven. By early 2019, the firm had clocked over one million operating hours with its novel drive system as fitted to its 644K and 944K wheeled loaders. John Deere Power Systems (JDPS) now says it can leverage its expertise to help OEMs adopt electric drivetrain components.
While off-highway equipment manufacturers continue to research hybrid and electrification solutions, the demands of the end customer for reliability and productivity continue to increase. According to JDPS, it now has technologies to reduce emissions, improve fuel economy, and boost machine performance and reliability. The OEM electrification approach of JDPS can offer integrated solutions that address the interfaces between the electrical generator and/or motors, power electronics, and mechanical interfaces.
sales were close to the level of the prior-year period.
“Despite a general slowdown in market growth, we saw revenue advance in all regions and major application segments and also demonstrated our operational strength by delivering a high double-digit percentage increase in earnings,” said Dr. Frank Hiller, CEO of the Germany-headquartered DEUTZ Group.
As well as remarking on the importance of establishing the DEUTZ-SANY Changsha factory, Hiller also stressed the significance of DEUTZ’s recent addition of high-voltage battery technology as a key component of its E-DEUTZ strategy via the acquisition of battery specialist Futavis. “This is taking us another big step closer to a future of carbonneutral off-highway vehicles,” he emphasised.
DEUTZ sold a total of 155,780 engines in the first nine months of this year, meaning the group’s overall unit
John Deere says that its innovative
Meanwhile the firm also claims Stage V compliance for key models in its engine range. This includes its variable-speed engine families below 56kW and above 130kW as well as its constant-speed engine families. The Industrial Stage V line-up from John Deere now offers ratings from 36kW to more than 500 kW, with displacements of 2.9litres up to the new 13.6litre unit.
Key features are said to include increased uptime and low operating costs. The firm’s new Stage V after-treatment technologies are said to be optimised for flexible integration.
Andreas Viktorsson, Volvo Penta chief project manager for Stage V, has explained how the company has managed to increase uptime in its latest D5 to D13 off-road engines by minimising active regeneration.
“We know that downtime is a disadvantage for our end customers. The Stage V emissions legislation requires engines to have a diesel particulate filter (DPF), which captures and stores soot. This soot needs to be burned off periodically to regenerate the DPF and typically this is done while the machine is at a standstill (active
regeneration). But who wants to keep having to put their machine aside for this process, where it is not working and earning?
“In developing our new range of Stage V off-road engines, our vision has been ‘Regeneration Zero’. We have put this challenge at the forefront of our minds and sought to minimize the need for active regeneration as much as possible. This is to keep our end customers’ machines operational and profitable.
“From a strict technical point of view there will always be a need for at least some active regeneration if the engine is not loaded. However, we have really challenged ourselves to examine this and reduce it to an absolute minimum. We have seen really good results in the field tests of our new engines. When the engines stop for regeneration, it is often caused by running the engine for extensive periods of time in idle.”
cant improvements. Connected to this design philosophy, we have also achieved impressive fuel efficiency gures, helping customers to save costs and
Commenting on Volvo Penta’s success in avoiding stand-still regeneration, Viktorsson said: “Testing, testing and more testing. We initiated heavy testing to address the issue of regeneration and part of this involves deliberately installing unsuitable engines in some machines to stress the system and find problems for us to address. We have left no stones unturned in the process.”
Looking at how Volvo Penta approached ‘Regeneration Zero’ from a technical perspective, Viktorsson said that the off-highway engine maker’s aim was to
achieve synergies between the base engine and the after-treatment system so that all the features of the engine and software work together to minimise the need for active regeneration.
“For our Stage V off-road platform we have developed the engine and aftertreatment system hand in hand, and it has been an ongoing optimisation project for all engines in the range, which share a common architecture.
“For example, we have implemented new water pumps, new oil coolers, new piston rings and new thermostats – relatively minor changes all over the engine but combined
Emphasising why he thinks a quarrying or other customer should choose a Stage V Volvo Penta engine for their off-road application, Viktorsson said: “Since 2014, with the launch of the Stage IV ranges, Volvo Penta c off-road engine platform and it has been warmly welcomed by the market. Our off-road engines are tailor-made for applications in different segments, such as forestry, material-handling and construction applications, and we have managed to build a strong design solution with this bottom-up approach. We think about the customer and operator first and then create the best engine architecture with proven hardware – no new “off-the-shelf” solutions.
Finally, Viktorsson offered advice on how a customer can ensure they have as little active regeneration as possible from their engines.
“Having the right engine for the right application is important. We like to talk to both OEMs and operators to understand how their business works so that we can provide the right specification for minimal active regeneration, noise and fuel consumption. We want to be the strongest business partner possible for our customers, and that means letting us help them to drive profitability in their business.” AB
Outstanding cut and puncture resistance Extra mileage
Designed for hard and rocky surfaces
Conveyor belt company Smiley Monroe is celebrating its 40th year in business, but is not resting on its laurels. Its first US manufacturing plant opens early next year and it is aggressively targeting new opportunities in the road construction and environmental equipment sectors.
Liam McLoughlin reports
Since being set up in a garden shed in 1979 by Vaughan Monroe and his founding partner Mark Smiley, Northern Irish company Smiley Monroe has grown to become one of the giants in the conveyor belt sector.
The Lisburn-based business serves seven equipment segments: crushing & screening, recycling, washing, wood chipping, agricultural, bulk material handling and road construction. Its two main belt-product offerings are Endless conveyor belts and Zip Clip replacement belts.
The company is marking its fortieth anniversary with the opening of its first US manufacturing facility in early 2020, which Smiley Monroe Inc. will be showcasing on its outdoor booth at ConExpo in Las Vegas next March.
Smiley Monroe exports to over 60 countries and has a customer list that includes Terex, McCloskey International, Sandvik, Edge, Keestrack, Maximus, Aggregate Industries, Hanson UK, Astec Industries, CDE and Kleemann (part of the Wirtgen Group).
interest in conveyor belts. The initial business was as a distributor for rubber conveyor belting and providing a local vulcanising service.
The company has been owned by Vaughan & Mary Monroe since the early 1990s, and two of their sons, Tim and Chris, now work in the business. Tim joined at the end of 2006, following a career in film & tv art direction, and is marketing director. Chris
At the time they founded the company, Vaughan Monroe and Mark Smiley both worked for an engineering firm in Belfast that was involved in the production of forklift tyres. They decided to relocate to Lisburn to set up their new venture, and the first employee they took on, David Murphy, is still with the company today.
Vaughan Monroe’s original training had been with Goodyear, where he developed his
worked as a corporate solicitor in England prior to coming on board in January 2013 and serves as global sales director.
In terms of the biggest changes to the company over the last four decades, Tim says the major difference is in its core business. “Since around the turn of the millennium, Vaughan had realised the benefit that locally manufactured Endless belts could offer to customers,” he adds. “Acting quickly on that opportunity is what steered the company into what it is today in terms of Endless belts being our biggest core product.” Initially, the company’s main customers were end users and the core business was resale belts, selling rolls of conveyor belt and providing a tting service to quarries, mines and cement
“The value we added at that point was having a breakdown service and being able to supply high-quality heat-resistant belts for specialist applications such as cement clinker,” says Tim. “Now our core customers are equipment manufacturers - so from a service company we have essentially morphed into a manufacturing business. Looking back, our first experience of manufacturing was exporting rubber screen mats to Great Britain in the 1980s and conveyor impact bars and screen media to the US in the 1990s. Sustainability is another big change. Today our operations in Northern Ireland are powered by 100% clean, renewable energy.”
“In three years our sales have grown by approximately £10m to £25m at the end of 2019,” Chris says. This has been driven by the growth of domestic customers but also as a result of new export business. “Over the past 10 years our transformation has been from a local company with a good reputation to a global player.” Exports, from being a very small part of the business, now account for 45% of total sales.
Other major milestones in the company’s history include the £1.2m investment in its first purpose-built facility in Lisburn in 2002, the opening of its first Indian production plant in Hosur, India, in 2012, and a new £800,000 global distribution hub in Lisburn in 2014. To help it stand out from the crowd, the company has also put a strong emphasis on marketing over the years, with its ‘Giants of Belting’ campaign inspired by Northern Ireland’s Giant’s Causeway.
The new US production facility will be based in Franklin, Kentucky. The move has been driven by customer demand, strong industry forecasts and the need to protect the company’s export sales amid the uncertainty surrounding Brexit. Around US$2m is being invested in the plant, which will create 30 jobs.
Tim says the new plant will dramatically improve delivery times for US orders. “At the moment, from the receipt of order in Northern Ireland it can take seven to eight weeks to deliver to the furthest part of America,” he adds. “A lot of customers will have a four-week fixed window for their production schedule, so seven to eight weeks doesn’t crack it.
“By manufacturing in the US we can offer just-in- time (JIT) delivery to our American customers. We will be able to deliver goods to almost any part of America within two days, and all of the midwest and east coast within one day.”
Chris adds that the company has been working with US customers for six years, supplying them from Northern Ireland. “The plan with our plant in Kentucky is to move forward with production at the start of February, which is in good time for the official announcement at ConExpo in March,” says Chris.
The US currently accounts for around 5% of the company’s revenue and, with the opening of the new factory, the US business
is projected to increase annual sales in the US to US$10m within three years.
The Kentucky plant will have twelve employees in the first year and by the end of 2022 Smiley Monroe plans to have recruited somewhere between 30 to 40 staff. The site manager, Morgan Walker, will be relocating from Northern Ireland with his family to run the facility. “We were very keen to have the right expertise out there,” says Chris.
He adds that aside from new original equipment manufacturers (OEM) business, the company has great opportunities in the US within the aftermarket by working with OEM partners to promote the benefits of Smiley Monroe’s Zip Clip replacement belt.
“That is a big part of our business plan,” says Chris. “We have been listening to our customers about the cost of machine downtime in the field and in the importance of making sure machines can be up and running with a replacement belt as quickly as possible. We believe that Zip Clip is
the belt to maximise machine uptime by allowing operators to quickly fit Zip Clip belts themselves and ensure they aren’t waiting on service crews. The majority of sales of our Zip Clip product are into America and a big part of our growth in America is forecast to come from Zip Clip.”
In the US Smiley Monroe supplies the Astec Group, Terex and Wirtgen America. The company is also targeting areas where it currently does not have a big market share, with road construction being one such sector where it sees major opportunities. In April 2019, President Donald Trump and Democrat lawmakers agreed a US$2 trillion plan to overhaul ageing infrastructure in the US. As part of this, the proposed ‘Road Bill’ would authorise a 27% increase in expenditure over a five-year period to US$287bn.
“The Road Bill has released a lot of funding in the US and there is still a lot to draw from that,” Chris says. “We expect the US market to be buoyant for the next four to five years.”
The company is also targeting a potentially huge market for environmental equipment in America. “There is a lot of environmental business in the heavily forested areas in the north of the country, where wood is shredded and converted into renewable biomass fuel,” says Tim.
In terms of new product developments, Tim says customers are asking for an even more durable and puncture-resistant version of its ToughFlex conveyor belt, which is designed to handle tough conveying applications, such as mobile jaw and impact crushing.
“We are working on adding a new Premium Upgrade to our ToughFlex range at the moment,” he says. “It’s our response as problem solvers to new challenges within the ever-evolving recycling sector, where C&D materials such as concrete and steel rebar test conveyor belts to their limits.” AB
The use of technology such as visualisation and drones is improving the efficiency and safety of blasting operations at quarry sites. Liam McLoughlin reports
Digital and automated technologies are continuing to change the way the quarrying and mining industries operate.
To meet these requirements Orica, a manufacturer of commercial explosives and blasting systems for quarrying and mining, says it is advancing its digital expertise and solutions.
The company has added new features to its BlastIQ solution to bring additional capabilities and help customers reduce the overall cost of quarry and mine drill and blast operations, improve operational productivity and safety, and facilitate regulatory compliance.
Orica says that improvements to the BlastIQ user interface allow real-time access to the status of each blast through the centralised online BlastIQ Platform, enabling users to collate and collaborate on data from across the drill and blast process. Insights can be interpreted from data gathered with new visualisation features, accelerating planning, analysis and auditing of blast data to satisfy regulatory requirements.
Multilingual support has also been added across the technology suite, now supporting Spanish, French Canadian, Russian and Portuguese, facilitating broader access and adoption of BlastIQ for more customers around the world.
BlastIQ Mobile technology now provides a wider set of loading conditions through the seamless integration of loading rules, increasing on-bench quality-control management and productivity. Continuous loading rules can now be applied to blast holes in real time, even in areas without bench wireless connectivity, creating efficiency and quality gains on-bench.
Accuracy and efficiency of explosives delivery are significantly enhanced through real-time synchronisation of blast-hole data between Orica’s Mobile Manufacturing
Unit (MMU) and BlastIQ as changes occur in both design and actual loading data.
Using this data, Orica’s smart, connected delivery systems load the correct explosive type and quantity according to the original design, adjusted based on blast-hole condition measurements and the automated application of a defined set of loading rules managed by the drill and blast engineer.
The claimed industry-first, direct integration with the delivery control system automates process control thereby eliminating errors in manual product selection, process control and incorrect logging of loading actuals, as well as importantly reducing overall explosives loading times and increasing productivity on-bench.
Hole identification functionality available in both BlastIQ-enabled delivery systems and BlastIQ Mobile is said to improve in-field blast quality control and assurance.
The hole position identification feature helps operators to more easily identify holes on-bench, reducing errors from potential confusion over hole identification and ensuring accurate recording of which holes
have been dipped or loaded. This real-time data flow empowers rapid decision-making, such as accurately adding new holes and data as needed, improving operational efficiencies.
The new features are now available and applicable across mining and quarrying operations globally. As customers increasingly look to transform their operations with digitally connected technologies, Orica remains at the forefront of digital blasting to optimise blasting outcomes.
Orica global digital product manager Angelo Labriola describes how the company’s digital technologies are helping customers. “Every day around the world, engineers design blasts and those blast outcomes impact as much as 80% of the total mine or quarry processing costs.
The process of designing blasts, adjusting designs for real conditions encountered in the field, and understanding the outcomes of blasts is a manual, time-intensive task involving multiple inputs. Optimisation efforts suffer due to lack of time and tools to support that objective in the face of daily operational demands.
“BlastIQ saves time and improves quality by automating processes across the blasting workflow. Inspired by our customers’ feedback, the latest release of BlastIQ will enable our customers to make better decisions more rapidly and deliver improved blast outcomes across their operations.
“We’re aiming to develop the most robust, most user-friendly set of digital drill and blast tools available, with easy integration across the value chain and delivery of whole of mine and quarry insights required to drive material impact for our customers.”
Maptek, which supplies 3D modelling, spatial analysis and design technology to the global mining and quarrying industries, says that its BlastLogic solution enables
improved design compliance monitoring and downstream productivity optimisation across open-pit operations.
“BlastLogic is applicable to any opencut operation that conducts drill & blast and processes the output in plant or mill,” according to a spokesperson for Maptek.
The company says that, for mine and quarry operators, quantifying fundamental design parameters can highlight significant variability in the effectiveness of design execution. Once anomalies and non-compliance issues have been identified, operators can look to the cause and
focus on improved accountability around performance. It also helps operators better define the practical tolerances for execution of blast for their operation.
The drill and blast process typically equates to 20% of mining extraction cost per tonne and Maptek says there are significant opportunities for improvement and cost reduction. “In practice this could mean developing effective designs that align drill pattern, charge and tie-up plans to the specific mining conditions and measuring their successful execution,” the company comments.
Because blast performance is directly impacted by compliance to design, operators need tools to help them routinely and reliably measure the effectiveness of designs. The difficulty has occurred where insufficient information exists, or where the information exists but is not readily reconciled.
Measuring and tracking blast designs against defined tolerances during execution can therefore quantify the variability and facilitate objective assessments.
BlastLogic is designed to provide a platform where all an operation’s drill and blast data is stored in a single repository for analysis. Operators can then derive additional value from blasting practices, enabling opportunities through pattern expansion, steeper pit slopes, grade engineering and improved mine-to-mill practices such as fragmentation analysis.
Better fragmentation has been linked to a shovel improvement of more than 9%. Achieving optimal and consistent fragmentation improves ‘digability’ through easier handling and processing of excavated material. By looking at the broader picture of the entire comminution process, BlastLogic is designed to provide the means to measure and track drill and blast performance relative to crusher and milling throughput.
Maptek says that geo-referenced spatial data imported into the BlastLogic drill and blast management solution delivers greater understanding of blast execution and results, enabling future blasts to be refined and optimised to reduce costs and increase safety and productivity.
South African surface mining industry association Aspasa is extending its strategic service to members in the form of a new blasting audit.
According to director, Nico Pienaar, the association has decided to offer blasting audits to members due to its mining industry facing numerous practical-legal challenges since the Mine Health and Safety Act’s (MHSA) new explosives regulations came into effect on 14 December 2018. He adds that there have also been various demands made by affected communities and Department of Mineral Resources (DMR) officials. AB
Recycled aggregates are increasingly in demand globally, with original equipment manufacturers paying close attention to changing market trends keen to offer new and proven material recycling-suited plant. Liam McLoughlin reports
Northern Ireland-based Powerscreen is re-introducing its Phoenix mobile crushing and screening range.
Phoenix, one of the original machine ranges in Powerscreen’s product portfolio, is a collection of trommel machines that are predominantly used in recycling applications such as construction & demolition (C&D) waste, wood chippings, top soil, compost and green waste.
Through the processes of screening and separation, material is extracted to create recycled useable products, resulting in increased profits for the customer while being better for the environment.
Commenting on the decision to bring back this range to the Powerscreen portfolio, Powerscreen product manager Neil Robinson said: “The global waste management market is becoming more and more prevalent as government initiatives are geared toward better environmental practices, so it is an ideal time to bring back the Phoenix range with its proven track record in recycling applications.”
The re-introduced Phoenix range includes the Powerscreen Phoenix 1600, which comes in both tracked and wheeled versions, the mid-size Powerscreen Phoenix 2100 and the larger flagship Powerscreen Phoenix 3300.
The Powerscreen Phoenix 1600 trackedand wheeled-trommel screens have been designed to provide excellent fuel efficiency and low operating costs, whilst also reducing emissions and noise levels due to the machine running at a low engine RPM. With a 4.9m x 1.54m drum, unrivalled production throughput is guaranteed due to the screening area which is the largest in its class.
Powerscreen says the Phoenix 2100 trommel screen is designed to offer unrivalled production throughput and application flexibility. The robust design with optional features such as a heavyduty tipping grid or double-deck vibrating
grid makes the Phoenix 2100 the most versatile trommel on the market today. The machine performs equally well in heavy C&D applications as it does in high-volume compost production. The 180° swivel fines conveyor, with a 5.7m discharge, means the machine can generate massive stockpiles. This swivel feature can be controlled via a radio remote while the machine is in operation, minimising downtime.
The Powerscreen Phoenix 3300 trommel screen is also designed to offer unrivalled production throughput and application flexibility. Key features include having the largest screen area within the Phoenix range, a 180o swivel fines conveyor, with a 5.8m discharge and a powerful four-wheel drive system with high-performance friction grip wheels which is used to turn the trommel drum giving operators the ability to run bi-directionally. Options include a heavy-duty tipping grid or double-deck vibrating grid.
The Phoenix 3300 is claimed to be highly efficient in the separation and processing of wood chippings, top soil, compost, green waste and aggregates.
Powerscreen Pulse Intelligence is available on the Phoenix range of machines anywhere at any time, on a PC, tablet or smartphone. The system provides comprehensive
information on the GPS location, start and stop times, fuel consumption, tonnages, cone settings, wear ratings, operating hours, maintenance status, engine faults and much more.
The Phoenix range is now available to purchase from Powerscreen distributors worldwide.
At Mone Brothers’ Fireclay recycling centre to the west of Leeds in North-West England, a powerful Kleemann MOBIREX MR 110 Z EVO2 impact crusher is said to be proving its worth as it’s kept busy recycling brick and concrete rubble.
With several quarries and recycling centres around Leeds, Mone Brothers has a long tradition in mineral recycling. Since it was founded in 1965, the business quickly developed from a simple plant hire company into one of the principal providers of construction materials and recycling services in West Yorkshire.
In minute intervals, dumper trucks drive into the near 2.5-hectare Fireclay recycling centre site, bringing mixed rubble from demolition work and construction sites and
near Leeds
taking back crushed and cleaned material. On average, more than 300,000 tonnes of this material are processed here every year. While broken bricks are recycled into hardcore according to British Standard 6F2 and used primarily as a capping layer in road construction, the recycled concrete is used as a higher quality Type 1 layer for sub-base purposes.
Furthermore, Mone Brothers works a great deal with the local utility industry and supports the expansion of the electricity, water and gas network with its material. The companies deliver their mixed rubble and drive away again with recycled Type 1.
The different feed materials and required quality standards have an impact on the production process. Thanks to a higher permissible oversize grain content, it is possible to dispense with a closed circuit for 6F2 and, in doing so, increase the feed capacity. In this configuration, the MOBIREX MR 110 Z EVO2 of Mone Brothers has a capacity of 280 tonnes per hour.
For the recycled Type 1 material, the system changes its location in just a few minutes and the secondary screening unit is mounted in around 15 minutes. With the integrated oversize grain return conveyor, the capacity for this classified product is still 250 tonnes per hour while also meeting the highest standards in British road construction.
quarry applications. However, the decision to opt for an impact crusher for use at Fireclay recycling centre was made for a good reason.
Michael Coleman, managing director at Mone Brothers, says the final product quality has significantly increased. The impact crusher achieves a grain shape in one crushing stage that a jaw crusher could not come close to without a second crushing stage. The slightly higher fine content helps to bind the material during later use and therefore also equates to the required quantity.
In addition to product quality, the higher performance of the MOBIREX is also a highlight. While jaw crushers offer a recommended crushing ratio of 7:1 in recycling, impact crushers can achieve a ratio of 15:1 and thereby a greater feed size, which facilitates significantly higher performance.
“The output is truly mesmerising, and it has been a real benefit to the business,” said Coleman.
It is therefore easy to work out why Mone Brothers replaced two of its jaw crushers with just one impact crusher. Thanks to the diesel-direct-electric drive concept of the MR 110 Z EVO2 impact crusher, this is said to reduce what were already low operating costs by another 15%.
Despite many years of cooperation and positive experiences with the aftersales service, Coleman said the decision to invest in a Kleemann impact crusher was not a matter of course. “We did try other machines but actually they could not produce enough of the product at the right speed and they were much more expensive to operate.”
The 2,750-metre-long runway at Salzburg airport has been around for almost 60 years. Following a total shutdown of five weeks, Salzburg airport opened again on 28 May 2019. RUBBLE MASTER made a considerable contribution to the general renovation with a compact crusher from the Linz, Austria-based company, enabling 8,500 tonnes of material to be crushed on site and immediately reused.
“This job was a challenge due to its tight time schedule,” says Klaus Weickl, managing director of Weickl Erdbau. “We only had four
weeks to complete all the work.”
The rented compact RM 100GO! crusher only needed just under a week to crush all the material from the almost threekilometre-long Salzburg airport runway into a recyclable final aggregate. This value aggregate was used for the sub-structure of the new runway. Weickl is convinced of the sustainable use of resources: “The recycling of C&D waste creates a loop in which transport and material costs are saved and environmental impact is reduced.”
The core business of Weickl Erdbau, which is based in Hallein, a city less than 20kms south of Salzburg, is earthmoving and demolition. Due to the wide range of jobs they cover, it makes sense for the company to rent a compact crusher for certain contracts. Weickl has been using this rental concept for several years. “In our case, the volume we process is too small to justify the purchase of a crusher. The rental system is perfect for us for processing materials directly at construction sites,” he said.
Swedish recycling giant Swerock is using a Rockster R1000S compact mobile impact crusher to provide innovative solutions for the efficient reuse of construction waste.
It was Rockster’s Swedish sales partner Niklas Johansson of Biocare Svenska who first introduced the R1000S plant to Andreas Pettersson, the area manager of Swerock Recycling.
“High throughput of this compact machine, perfect transport dimensions and excellent access for maintenance have convinced my customers that the Rockster crusher is the right one for them,” said Johansson.
The machine’s hydraulically lowerable screen box, swivelling catwalk and swivel-up doors mean that service work, maintenance and the replacement of screen meshes can be carried out quickly and easily.
Due to the R100S impact crusher’s hydrostatic drive, which ensures a constant crushing power, the diesel consumption per tonne is claimed to be noticeably reduced.
Johannson added: “With Rockster’s hydrostatic system, the diesel engine always stays in the optimal RPM range, only the hydraulic pump adapts to the crusher’s power requirements, which results in lower
fuel consumption per tonne of final material.
“Additionally, the Volvo Tier 4f engine, with AdBlue, ensures very low NOx emissions.”
Swerock is one of Sweden’s largest suppliers of building materials and services for the construction and civil engineering industry. The company has approximately 950 employees and is part of the Peab Group construction company.
Mike Broad, who retired from the aggregates and quarrying business in September 2018, has been reflecting on a remarkable 48 years in the industry which he spent with just one company.
In October 1970, a 17-year-old Broad was fresh out of education at Wigan Grammar School in North-West England. He secured his first job with family-owned quarrying business Gaskell Bros, which is based in nearby Ashton-in-Makerfi
In his years as a director, Broad worked alongside Gaskell Bros. MD Mark Gaskell and the pair carved out a new path for the company. Venturing into the recycling sector in 1999, its primary focus was building and demolition waste from Manchester and the neighbouring counties.
Working alongside the Gaskell family, Broad forged a successful relationship during this period with wet processing equipment company CDE.
“First, we began operations in dry recycling, procuring a licence to process material that was destined for landfi Broad. “Though it did have its limitations. We weren’t the only player in the market at the time, and this was a challenge. We had to identify and produce a product that others weren’t yet producing, so we ventured into wet screening – or ‘wet recycling’ – adding water to clean the recycled aggregate. This also presented challenges for us as it was taking up to three days, in some cases, to fully remove moisture content from drying sand.
“It was a learning process and, evidently,
“When we thought we had it all figured out, other issues in our plant would start to surface. The log washer just wasn’t up to the job.
“CDE told us they had log washers, so Mark and I booked our flights to come over and see the plant. That was a formative trip for us. We visited and reviewed several installations. We were so impressed by what we encountered on the trip that we began preparations to invest in a complete plant to be fully installed by CDE.”
The turnkey solution CDE supplied Gaskell Bros. in 2004/05, a complete overhaul of the company’s recycled aggregate system, was the single biggest investment ever made by the company.
not without its challenges.”
This set the course for what was to become a long-running partnership between CDE and Gaskell Bros., leading to one of the first full-installation sand-washing and recycled aggregate systems in the UK.
“Enda Ivanoff, who is now CDE group business development director, was fresh out of university at the time we first made contact with CDE,” Broad explained. “He came over to see our operation and we explained the challenges we were facing; extracting moisture from the sand and excessive fines losses. Enda and the team at CDE implemented a sand plant that integrated seamlessly with our then current operation.”
Gaskell Bros. began processing reclaimed materials at a much faster rate. As little as 10% of materials was now destined for landfill. “We were processing materials we didn’t before, and the built-for-purpose plant resulted in a significant upturn in new business contracts. Efficiency meant we had a volume of product to fulfil almost any customer contract,” Broad said.
With an improved product base, Gaskell Bros. carved a reputation for producing some of the highest-rated recycled aggregate in the UK.
Ivanoff said Gaskell Bros. remains one of CDE’s pioneering customers: “From working with Mike and Gaskell Bros. to commission the first tailor-made C&D wash plant in the UK to commissioning the world’s largest C&D waste recycling wet processing plant in Norway, CDE is supporting companies around the world to extract value from C&D waste material destined for landfill.
“Every day, CDE wet processing solutions divert 63,000 tonnes from landfill, totalling gure
The mineral products industry has and will continue to play a vital role in delivering net zero carbon efficiency and biodiversity net gain. In his introductory address at Quarries & Nature 2019 held at The Royal Society in London, England, on 23rd October, Mineral Products Association (MPA) chief executive Nigel Jackson set out the industry’s action and showcased its achievements, while seeking recognition for the role mineral products commerce plays in protecting nature.
The full text of Jackson’s introductory address is reprinted below by Aggregates Business:
“These are serious times for far too many species, habitats and our planet.
I know that, MPA knows that, that is why we have not been wasting the last 30 years doing nothing. We have focused on delivering action rather than just adding to too much hot air.
Next year COP 26 is in Glasgow. This will be another important step towards confronting the harsh climate reality we all face. I think it will prove to be the most ‘can do’ yet. I hope so.
The MPA will be actively engaged as best we are able. Sticking to the science, staying practical and proportionate and guided by the evidence. Confronting our responsibilities, highlighting our practical solutions and responses and playing our part in the collective journey to net zero by 2050. I stress by 2050.
Determination and transparency will underpin our approach; not rhetoric, not exaggeration, not denial, not greenwash.
Some say ‘industry is doing nothing about climate change’ or more accurately global warming, or biodiversity loss, our twin and linked challenges, net zero & net gain.
We are. We have a long and proud legacy
when it comes to environmental action and as MPA represents over 90% of the mineral products industry, it means something.
Our Quarry Restoration Awards have been running for 49 years, showcasing hundreds of restored quarry sites all over the UK.
MPA continues to maintain the industry Restoration Guarantee Fund which has been running for over 40 years, an industry pledge that enables local authorities to claim for unfinished restoration of quarries if an MPA producer member goes bust. An unrivalled commitment recognised in planning guidance, a vote of confidence by the industry, in the industry, as no claims have ever needed to be made.
“These are serious times for far too many species, habitats and our planet.”
In 1998 we agreed our 4-point plan for National Parks with members yielding up old planning permissions, removing the possibility of quarrying in certain areas. That policy is being refreshed in light of prevailing government policy and once the government has responded to the Glover Review, we will publish it.
In 2005 we formed our partnership with English Nature, now Natural England, to showcase MPA members’ biodiversity achievements.
In 2006 we published our first annual Sustainable Development report; 13 years later we now produce five reports every year evidencing environmental performance in
marine aggregates, cement, concrete, industrial lime and all mineral products.
In 2007 we produced our first ‘carbon advice card’ setting out the measures members could take to reduce their carbon footprint. We are currently updating that.
In 2009 we were the first UK industry to launch a biodiversity strategy. I am not aware that any other industry even has such a strategy.
In 2011 we launched our carbon portal supported by the Carbon Trust giving further guidance on energy and carbon reduction to members.
In 2013 we launched our virtual National Nature Park which now hosts 80 sites restored for wildlife and with public access, field study or education centres, nature trails, many managed by or in liaison with the Wildlife Trusts and the RSPB.
In 2015 we launched the first Quarries & Nature event, a two-yearly celebration of the industry’s contribution to nature.
And in 2017 we launched the MPA Charter which sets out our seven Strategic Priorities of which Climate Change & Energy and the Natural Environment are but two. We also launched our Water Strategy.
And this year we are launching our new Good Neighbour Scheme, aimed at building more trust with local communities.
In the first 10 years of MPA’s life our members have planted 1.5 million trees and 100 km of hedgerows. Members have also built 40 km of dry stone walls. They have already created more than 8000 Ha of priority habitats with at least another 11000 Ha planned.
This year we have published papers
evidencing that we are recycling or reusing 82 million tonnes per annum of construction waste either as aggregate or to enable land restoration; the highest use per capita in Europe and therefore probably in the world. That’s 30% of total aggregate supply taking the pressure off the need to release primary resources.
So, like countless other scientists and practitioners, we too have been getting stuck in over recent decades, practitioners not preachers.
Unlike some other industries who have a far greater impact on the environment and many who fuel imports exporting their impacts, we pay over £1bn per annum in environmental taxes. Unlike certain harmful activities we are not subsidised. No public money for our public goods.
Unlike many industries we are not deforesting at scale to make way for damaging agriculture elsewhere in the world. Unlike many industries we have reduced our production carbon emissions from cement by 51% since 1990 - far better than the UK overall.
Real, measured improvements, not conjectural.
We are strengthening our carbon road map to ensure that, notwithstanding the inevitable footprint our production creates, our products in use will counterbalance it over their whole life. If we can get to net zero before 2050, we will.
But we will not join those who arbitrarily nominate unrealistic and opportunist target dates for short-term PR gain. This is not a time for empty gestures and virtue signalling. These issues are genuinely complex and not easy to resolve.
Quick, easy wins are fine and may make us feel good, but we need to realise that it will take time to transition to sustainable long-term changes at scale. Changing our historical and existing means of production is a massive challenge requiring both innovation and investment and crucially time, time we know is precious. Regulation alone will not be enough. Incentives to accelerate technological progress will be needed.
We are determined to contribute to achieving net zero whilst also creating net gain. Net zero, net gain.
All we ask for is parity of treatment across all business and industry activity using a balanced scorecard approach which links demand and need with supply. No more singling out, everyone subjected to equal
ABOVE: The MPA Biodiversity Strategy BELOW: Among many highlights of the Quarries & Nature 2019 event was the MPA Restoration & Biodiversity Awards. This year’s joint winners of the Cooper-Heyman Cup for outstanding restoration were Aggregate Industries for Ripon City Quarry in North Yorkshire (pictured left); and Tarmac for Broom Quarry in Bedfordshire
scrutiny.
The consumer must also ‘make the link’ between their quality of life and the resources they need to maintain it. Consumers and society drive demand for our products for good reasons. Our products are essential to our quality of life, they enable us to be civilised
by being safe, secure, healthy, protected and connected.
Above all, I would say this is not a time to exacerbate divisions. There should be no ‘them and us’. On our treasured planet there can only be ‘us’.
Our industry is as committed to the environment as anyone else. We will continue to work with valued friends and partners to share, listen and learn and rise to the challenges. This long-term industry has not only built a rich legacy of biodiversity assets over the last 50 years but is itself adapting and preparing for the next 25 years, the next generation, with vigour and resolve, and goading ourselves to go further and faster.” AB
New infrastructure projects are maintaining reasonably healthy aggregates demand across the Nordic region. But reduced residential construction and the fallout from a global economic slowdown are big concerns for the region’s major building material suppliers and quarrying and construction equipment manufacturers. Guy Woodford reports
The Nordic region has always been a hotbed for aggregates production, with a thirst for production innovation and environmentally friendly quarrying practices.
However, like any other world region, the Nordic countries of Sweden, Norway, Denmark, Finland and Iceland and their building material suppliers and quarrying and construction equipment manufacturers cannot be totally immune from the impact of a contracting global economy.
On a positive note, Jonas Staaf, business director Hub North, Volvo CE, says healthy investment by Nordic national governments in major new infrastructure projects has left the region well placed to withstand current and forecasted future volatility in the global economy.
“New infrastructure and housebuilding are always the drivers of aggregates demand. Housebuilding is not as strong as it was due to prices levelling out,” Staaf told Aggregates Business Europe during a recent visit to Volvo Construction Equipment’s (Volvo CE) key Eskilstuna facility.
Staaf says Volvo CE is among original equipment manufacturers (OEMs) that have been supplying machines for several major
new infrastructure works in the Nordics, including the Stockholm bypass project. Due to open in 2025, the new 21km-link, which includes just over 18kms of road tunnel, will connect the southern and northern parts of the Stockholm county, relieve the arterial roads and the inner city of traffic and reduce the vulnerability of the Stockholm traffic system. When the link opens for traffic it will be one of the longest road tunnels in the world. By 2035, the Swedish Transport Administration (Trafikverket) estimates that the Stockholm bypass will be used by around 140,000 vehicles every day.
Staaf continues: “Another big infrastructure project in Sweden that we are supplying equipment to is the West Link project, which is modernising the railroad connection in Gothenburg, making it double-track. There are also plans to build a high-speed rail connection between Stockholm and Gothenburg. These kinds of projects require a lot of ballast, concrete and asphalt, which is good business for quarries. We sell a lot of wheeled loaders, such as L180s, to quarry customers.
“Norway’s infrastructure project pipeline is also absolutely massive. They tend to divide their projects into SEK 3-5bn-
(€275mn-€460mn) sized works which can be handled by medium-sized construction companies. This kind of ongoing and pipeline projects is why we feel that there can be something of a soft landing in this region which can help it cope with any changes in the global economy.”
In November 2018, Volvo Construction Equipment and its customer Skanska revealed groundbreaking results at the end of the first stage of their Electric Quarry Site research project. The 10-week study at Skanska’s Vikan Kross quarry, near Gothenburg, which incorporated the use of electric and autonomous prototype Volvo CE loading and hauling units, showed a 98% reduction in carbon emissions, a 70% reduction in energy cost and a 40% reduction in operator cost. As reported elsewhere in this issue of A ggregates Business Europe , the second stage of the Electric Quarry Site research project is due to take place in 2020.
Staaf thinks that Nordic quarry operators are becoming more aware of the need to reduce their carbon footprint due to the volume of new regulations in other areas of the building materials supply and deployment chain, as well as high-profile projects such as the Electric Quarry Site.
The Sheehan Group, UK
•Producing 6 in spec products
•Over 1m tonnes diverted from landfill
•100% diversion from landfill
For over 25 years, our innovative solutions have enabled customers all over the world to reuse 80-100% of materials from construction, demolition and excavation waste.
Our advanced processing systems are tailor-made to maximise material recovery, and transform it into in-specification sand and aggregates for reuse in the construction industry. These are then used in high-value construction applications such as concrete and asphalt production.
At CDE, we know that one solution does not fit all. That’s why our expertise spans across C&D fines, earth and excavation waste, crushed concrete and railway ballast. Our solutions optimise material recovery by removing contaminants, converting waste into valuable resources and speeding up your return on investment. Want
82 million tonnes in 2013; Sweden’s producers produced 98 million tonnes (+22.4%); Finland’s 80 million tonnes (-6%); Denmark’s 52 million tonnes (+33%); and Iceland’s 3 million tonnes (same as 2013).
Headquartered in Gothenburg, Thomas Concrete Group is an SEK 6.5 billion (€635mn) annual turnover business with a footprint of 154 ready-mixed concrete plants in five trading countries – 79 across Sweden, Norway, Germany and Poland, and 75 in the USA.
“When you look at Sweden, the residential construction side of building materials demand has declined quite a lot in the last two years,” says Hans Karlander, CEO and president of Thomas Concrete Group, which operates the Thomas Betong AB subsidiary in Sweden. “The residential property market is down 30-50% in the Stockholm area, down an average of 20% in Sweden, but actually stable in
waiting for the economy to stabilise, before
Group is supplying ready-mixed concrete to the Marieholm Tunnel project. Due to be completed in 2020, the tunnel is located 5km north of Gothenburg city centre and will relieve the burden on the Tingstad tunnel, reduce the vulnerability of the road system and connect the Partihall junction, Marieholm junction and Tingstad junction to each other. Thomas Concrete Group is also supplying special low-carbon concrete to Gothenburg’s West Link project, which includes a new underground railway station.
Karlander says the Norwegian residential construction market is much more stable, with major national infrastructure projects in abundance. “The big infrastructure projects there are proceeding at a high pace, both along the coast and also in the metropolitan cities.”
Karlander says Thomas Concrete Group trading was “quite good” over the first eight months of 2019, mainly due to a significant increase in sales in the U.S. “This has been helped by much better weather there this year,” he explains.
Thomas Concrete Group has this year again introduced two new lower C0 2 footprint Thomas-branded concrete products. Karlander says the group will launch more in the next couple of years, given the demand among customers in Sweden, Norway and its other national trading markets.
“We’ve launched Thomacrystal in Poland and we’re just about to launch Thomagreen in Sweden. The Thomagreen product is more based on the use of alternative binder material to lower its C0 2 footprint.”
Looking at the mid- to long-term prospects for the Thomas Concrete Group and the wider building materials sector in the Nordic region, Karlander says: “The
Everybody knows that the data you receive from machine telematics can be incredibly useful – but do you really have the time to sift through it all? Insight Reports from Volvo take all of that data and tell you everything you need to know in a few short and simple statements. Insight Reports give you clear, concise signals that you can act on immediately without having to go through mountains of data – making sense of telematics. Talk to your local Volvo dealership today.
demand will shape up in 2020 and beyond. As a group, we have invested in more digital solutions and reshaped our internal business systems in order to become much more efficient going forward.”
Keestrack, the Belgium-headquartered global crushing and screening plant market manufacturer, notes that natural stone is Norway’s biggest export product in volume – with only oil a bigger export product in terms of value. As the global demand for aggregates is rising, Keestrack says the demand is also rising in the Nordic countries.
Fredheim Maskin sells and services Keestrack tracked-mobile crushing and screening equipment in Norway and Sweden and works closely with customers on their specific needs. The company recently staged a granite quarry demonstration of key Keestrack plant models during its 10th Demo-Days event in Spydeberg, near Oslo (see this issue’s Aggregates Production feature for more details).
“The Norwegian government and the general public are very concerned about their environment,” says Marcel Kerkhofs, Keestrack marketing manager. “Ensuring a zero-carbon footprint and environmental protection has high priority, especially when operating aggregates material processing plants in and near an urban environment. This is one of the reasons why our hybrid and electric plug-in plant solutions are popular in Norway. The additional higher investment for the electric-drive systems is earned back very quickly.”
Keestrack says replacing hydraulic drives on conveyors, screen shafts and crusher drives with electric motors negates the need for long oil piping with leakprone hose connections. Thermal problems during applications in extreme conditions are also eliminated.
lower oil quantities and extended change intervals, the smaller hydraulic systems of Keestrack’s ‘e’-versions not only save the environment but also real money. In full-electric operation, this also applies to lubricants, filters and other wear parts of the onboard diesel. Less engine hours mean less maintenance and downtime, which has a positive impact on total cost of ownership, as well as the higher value retention.”
Kerkhofs also stresses how engine problems on a diesel-hydraulic crusher can stop the whole production or job site. He concludes: “With a plug-in hybrid machine, a total breakdown can be avoided by providing an external gen-set to ensure the completion of a project without delay.”
Headquartered in Stockholm, Sweden, Epiroc produces innovative surface drill rigs, rock excavation and construction equipment for quarrying, mining, infrastructure and natural resources
countries.
Commenting on Nordic region aggregates and quarrying equipment demand, a company spokesperson says: “The last three years have seen demand at a steady high level. The housing market is uncertain but government-related infrastructure projects are being rolled out. We see the market continuing steadily but not increasing.”
The spokesperson says that the driving force behind equipment sales in Sweden and Finland has been surface mines investing in Epiroc’s SmartROC D65 surface drill rig. “We have seen an increasing interest in automation technology, such as our BenchREMOTE system,” adds the spokesperson. “Swedish and Finnish quarry operators are also looking to be climate smart, locating their sites close to the consumer so that transportation is kept to a minimum, reducing the environmental impact. This increases the need for surface drill rigs with noise reduction.” The spokesperson says this, for example, has led to almost eight out of 10 deliveries of FlexiROC T35R surface drill rigs to Swedish and Finnish quarry operator customers featuring a noise reduction kit.
Epiroc equipment is also being deployed in Greenland, where Munch Engineering is building two airports covering an area of 9 million m³. Meanwhile, 2017 and 2018 were record years for Epiroc heavy equipment sales in Norway. “The main driver for that was national infrastructure projects,” says the company spokesperson. “This trend is continuing in Norway in 2019. Our FlexiROC T35R and SmartROC T35/40 surface drill rigs are being used on some of the infrastructure projects.
“Environmental protection and health and safety are high focus areas in Norway. Noise, dust and other emissions controls are a top priority. Tools for planning and documentation of completed works are also required in more and more projects.” AB
The first Metso MX3 cone crusher installed in Spain, and one of the first installed in Europe, recently began processing aggregates for a major independent building materials company. Guy Woodford had a first-hand look at the landmark crusher and site
To be successful in the aggregates production industry, it’s important to keep your cost per tonne down, enabling you to start profiting from a return on your investment in new plant sooner rather than later. As such, Emipesa’s decision to acquire an MX3 cone crusher from Metso as part of an all-Metso state-of-the art production plant at its Cantera el Poyo Quarry near Teruel, in Aragón, Eastern Spain, looks like being a shrewd one. The quartzite aggregate and ballast products producer said the cuttingedge unit, which began crushing rock in August 2019, is set to generate the company an extra €350,000 a year in sales thanks to its greater production volumes, partly as a result of increased uptime compared to its predecessor.
“Before we installed and began operating the MX3 we were having to stop the crusher every hour and a half to adjust its production settings, given the abrasiveness of our quartzite aggregates. Each time we stopped we lost 15 minutes of production time. Over the course of a day, that equates to around 75 to 90 minutes of downtime,” said Pablo Perales, Emipesa aggregates manager, during Aggregates Business magazine’s September visit to Cantera el Poyo Quarry.
“With the MX3 we don’t have to stop production and can also process more material, over 215 tonnes a day more. It produces less sharp and good quality product. Our quartzite used to have a Los Angeles abrasiveness rating of 15-16, but that’s down to 13-14 after processing with the MX3. That’s a big difference and means our aggregates can be considered for use in a wider variety of construction works. I’m also very happy with the production capacity of the crusher.
“Most quarries in this region produce limestone. There is only one more quarry other than this that is producing hardstone aggregate. That gives us a commercial advantage.”
“Its design is based on our experience of working with the speciality rock we have and the latest Metso plant technology” Pablo Perales
Launched at the bauma 2019 exhibition in Munich, Germany, the Metso MX3 420 tonnes per hour capacity multi-action cone crusher is the ‘little brother’ of the up to 600tonnes and hour MX4, released in 2017.
MX multi-action technology enables cost-effective and safe operations with a high reduction ratio, great product shape and consistency, all of which are critical in aggregate applications. The patented technology enables higher uptime and savings in the operational costs of crushing operations. With the selective production features the MX solution offers, crusher production can be optimised to maximise the yield of desired fractions. Crusher operations are said to have been made easy and safe with advanced Metso IC series automation.
With a 420tonnes/hour material processing capacity, the Metso MX3 is suitable for secondary, tertiary and quaternary crushing stages. Designed for both hard and soft rock applications, the new Metso MX3 has been initially made available for stationary solutions.
Working alongside the MX3 cone crusher in the ultra-modern Metso plant set-up at Cantera el Poyo Quarry is a C125 jaw crusher, an HP300 cone crusher and a CVB2060 screen. Two thirds of the quartzite aggregate product produced at the site is subsequently used in concrete and asphalt for regional construction and highway infrastructure works, with the final third turned into ballast for national and regional railway projects.
Spain has the biggest high-speed rail network in Europe, and the second biggest globally. Among major high-speed rail links are the 600km Barcelona-Madrid route and the 600km Madrid-Seville rail link. Such scale creates huge demand for ballast and attractive commercial opportunities for ballast suppliers, including Emipesa.
As such, its unsurprising that ballast and 5mm-10mm grade aggregate are the quarry’s core products. However, there is also customer demand for 4mm-12mm, 6mm-12mm, 12mm-20mm, 20mm-32mm and 33mm-63mm aggregate products.
Emipesa’s aggregates sell for €9 a tonne, with the Cantera el Poyo site producing between 2,000 and 2,200 tonnes of aggregates a day.
A Barmac B8100 VSI (vertical shaft impactor) and HP200 cone crusher, currently situated a short distance away from the new plant set-up, used for 0mm-4mm manufactured sand production and aggregates fines processing are due to be integrated within the modern Metso plant set-up this winter.
Production at Cantera el Poyo runs Monday to Friday 7am to 6.30pm nine months of each year, with the site closed in
August and also in January and February, when temperatures in Aragón fall to as low as -15C.
During these months, the 20-plus workers at Cantera el Poyo work at Emipesa’s two other (limestone) quarries in Eastern Spain and carry out maintenance on the Cantera el Poyo Quarry fleet.
“The new Metso plant project was born in 2011. Its design is based on our experience of working with the speciality rock we have and the latest Metso plant technology,” said Perales. “It is a completely tailor-made plant, with all my thinking and wishes are covered in it, such as good plant access, the height of the conveyors and ease of transporting aggregate products around the site. Metso fully supported us as we were making our choices.”
The new Metso plant is managed by iPad or smartphone-controlled software co-designed by Emipesa and Talleres Rápidos, a software design firm based in Teruel. This allows Perales and his colleagues to monitor production very closely and easily adjust throughput speeds and levels to cater for changing demand. It also enables a swifter response to any production problems.
McLanahan UltraWASH Modular Washing Systems offer the same world-class washing technology we’ve been supplying since 1835, but in containerized modules for shorter lead times, quick setup and ease of transport if producing at multiple locations or one very large site. Produce up to five products – three clean aggregate and two washed sand products. Additional modules for crushing, screening scrubbing, thickening, and tailings management are also available.
SELF-LEVELLING PLANERS • CUTTER HEADS SCREENING BUCKETS • CRUSHING BUCKETS • WHEEL SAWS
VSE - Screening bucket with adjustable output size OVER 80 INNOVATIVE ATTACHMENTS TO FIND SOLUTIONS TO THE MOST CHALLENGING APPLICATIONS. FIND OUT MORE: simex.it
A few hours after visiting Cantera el Poyo Quarry, my Metso hosts and I met up with Carlos Pérez, managing director (MD) of Emipesa, in the stunning town of Teruel to learn more about the company’s investment in the MX3 and other Metso equipment.
“We have gained more production capacity than we expected from the MX3. It’s been trouble-free and produces a good quality final product,” said Pérez. “I had rung up Metso and requested a cone crusher that was easy to adjust without stopping production. After a couple of months of conversations, they said they had a prototype MX3 that they could give me to try. I liked its Multi-Action technology, with the automated piston and rotating bowl. We established a
mutual trust that the machine would work. It did, so I bought one.”
Emipesa’s MD said the MX3 purchase and new Cantera el Poyo Quarry plant set-up has evolved from an initial decision to take advantage of the slowdown in quarry equipment sales in Spain in 2011, due to the country’s economic crisis, to get good deals on buying a wide variety of Metso machinery.
Two years later, the company landed a big contract to produce aggregates to be used in asphalt by a contractor working on a Zaragoza-Soria highway project.
“At that point, we bought an HP200 cone crusher to work on the project. Then, in 2014, we bought an HP300 to work as a secondary crusher.”
Giving an example of the close working relationship between Emipesa and Metso over the past eight years, Pérez said: “We found that the liners on the HP200 needed replacing too often. Metso people in Mâcon (Metso France SAS) studied our rock and suggested we slowed down our production speed from 850rpm to 700rpm. This has helped increase material throughput and the life of the liners to around 180-190 hours.
“Overall, we have invested in our machines in a prudent way. When we integrate our Barmac VSI and HP 200cone crusher within our new Metso plant, we will also be able to recover a lot more waste material that we can turn into commercial products.” AB
New submersible pumps from Atlas Copco Atlas Copco Power Technique is introducing three new electric submersible pumps to the market.
Designed specifically for drainage and sludge-pumping applications are two sludge/trash pumps, the WEDA S30 and S60, in addition to the WEDA D80 drainage pump.
The WEDA pumps are designed to provide users with a fast and effective dewatering solution. They are compact, lightweight and easy to maintain, which Atlas Copco says makes them ideal for many industries, including construction and rental.
The company adds that the new pumps are built with the established characteristics of the WEDA lineup. This includes handling and transportability, with the new models being a claimed 15 to 30% lighter than comparable models and up to 15% more compact.
Atlas Copco adds that the new range offers rotation and phase failure protection, an efficient motor covering a wide range of voltages, high-quality chrome clog-free impeller, reinforced cable entry, adjustable wear-resistant rubber diffusors, built-in starter and motor protection system.
Other features include adjustable discharge connections, external plug for lubrication filling, while providing higher corrosion resistance is an improved aluminium alloy.
The new WEDA range is claimed to consume up to 20% less energy than comparable models.
Metso is expanding its mobile crushing and screening offering for the aggregates industry with a new 19-strong product portfolio.
The Nordtrack mobile range is designed to meet the requirements of general contractors in particular and includes jaw crushers, impact crushers, screens and conveyors.
Metso says the Nordtrack range is designed to make the contracting business more productive. It features standard designs for off-the-shelf availability, plug-and-play features and extensive Metso support network. The Finnish company says the solutions are suited for applications such as recycling, demolition, and the processing of sand and gravel.
The first deliveries are expected to take place during the first quarter of 2020.
The Nordtrack product range is available for global markets through Metso’s direct sales and distributor network. Nordtrack was launched during Metso’s global Distributor Days in October and will be introduced to wider audiences at the CONEXPOCON/AGG 2020 tradeshow in Las Vegas in March 2020.
“Our target is to create a comprehensive end-toend offering to serve diverse customer needs,” says Renaud Lapointe, Metso SVP, business and product management of aggregates equipment.
“Metso has traditionally been exceptionally strong in the most demanding aggregates applications, such as hard rock. Our new Metso Nordtrack range complements our offering to better address the needs of small and midsized companies and general contractors looking for the right combination of productivity, availability and dependability at an attractive price point.”
Engcon has introduced the ‘Engcon Approved’ service for purchasing second-hand machinery.
The service was introduced to the market at Plantworx 2019 and gives operators the opportunity to purchase approved used Engcon tiltrotators and attachments. The company says that all of the equipment has been inspected, serviced and certified by its expert engineers to the strictest and highest standards and comes with an extended 12-month warranty.
Engcon UK MD Robert Hunt said: “At Engcon, we are constantly looking at ways we can enhance the service we provide our customers and the launch of Engcon Approved is another way we are pushing the boundaries and innovating in the market to meet the needs of our customers.
“Engcon’s products have developed an enviable reputation amongst operators for being extremely reliable, durable and well engineered. It’s the strength of our build quality that gives our products longevity. This has given us the opportunity to launch this brand new service and target those operators looking at second-hand machinery.”
A range of approved used Engcon tiltrotators and attachments is now available, including ex-demonstration products as well as equipment that has been traded in for new. All the equipment has been fully serviced and worn parts replaced by Engcon’s trained engineers before being offered for sale as Engcon Approved products.
09-12 6th China International
Aggregates Conference 2019
Wuxi, China
Organiser: China Aggregates Association
Email: xubeibei@zgss.org.cn http://www.zgss.org.cn/
10-14 Excon 2019
Bengaluru, India
Organiser: Confederation of Indian Industry Tel: +91 44 42444564
Email: excon@cii.in https://excon.in/exconpub.php
04-07 World of Concrete 2020
Las Vegas Convention Center Organiser: Informa Tel: +1 972 536 6379
Email: registration@worldofconcrete.com https://www.worldofconcrete. com/
10-14 CONEXPO-CON/AGG 2020
Las Vegas, NV
Organiser: AEM Tel: +1 414 274 0644
Email: customerservice@ conexpoconagg.com www.conexpoconagg.com
21-25 SaMoTer 2020
Verona, Italy
Organiser: Veronafiere S.p.A. Tel: +39 045 8298561
Email: customercare@samoter.com http://www.samoter.it/en
23-25 Hillhead 2020
Hillhead Quarry, Buxton, Derbyshire, England
Organiser: The QMJ Group Tel: +44 (0) 115 945 4377
Email: Harvey.sugden@qmj.co.uk https://www.hillhead.com/ exhibitors/hillhead-2020#/
Throughout the year Aggregates Business travels the globe attending conferences, events and equipment shows, keeping you informed of the latest offerings. Why not come and join us for a chat at any of the events below?
MARCH 2020 10-14 CONEXPO-CON/ AGG 2020
MARCH 2020 21-25 SaMoTer 2020 Verona, Italy
JUNE 2020 23-25 Hillhead 2020 Hillhead Quarry, Buxton, Derbyshire, England
Advertisers in AGGREGATES BUSINESS can now be contacted via their websites - for instant links to all the websites listed below, by category, go to: www.AggBusiness.com
Ammann p21 www.ammann.com
BKT Tires p34 www.bkt-tires.com
CAT IFC www.cat.com
CDE Global p47 www.cdeglobal.com
CMS Cepcor p41 www.cmscepcor.com
ConExpo IBC www.conexpoconagg.com
Cummins p18 www.cummins.tech/construction
Hitachi p11 www.hitachicm.eu
Kleemann p9 www.kleemann.info
Komatsu p7 www.komatsu.eu
McLanahan p54 www.mclanahan.com
Metso OBC www.metso.com/agg-services
Rubblemaster p55 www.rubblemaster.com
Simex p38 www.simex.it
Smiley Monroe p4 www.smileymonroe.com
Superior Industries Inc. p43 www.superior-ind.com
Terex Washing p29 www.terex.com/washing
Verona Fiere p51 www.veronafiere.it
Volvo CE p49 www.volvoce.com
•Maintenance
•Upgrades
•Life