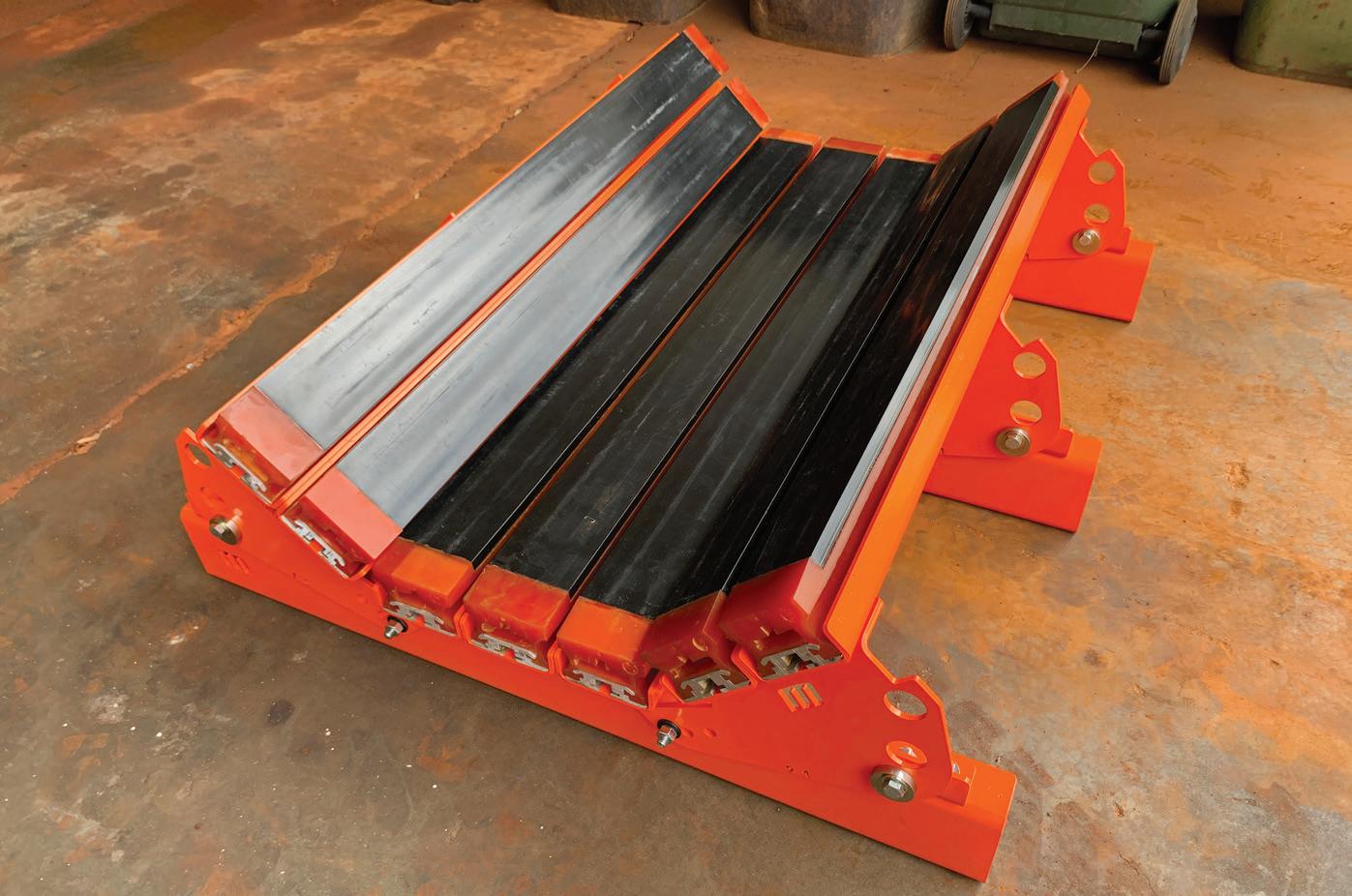
12 minute read
Going for gold in greenfield 36Go tougher, not thicker
Going for gold in greenfi eld
Transmin’s ConveyorPro range is targeting greenfi eld project supply in a new gold mine.
A NEW MINE IS BEING DEVELOPED
in Western Australia’s Eastern Goldfields. The estimated $226 million development is underpinned by the construction of a 4Mtpa processing plant, fed by the large open-pit and underground mine and complemented by a series of smaller satellite pits.
Bulk materials handling equipment supplier Transmin was contracted to support the development of the plant through its ConveyorPro team.
Amerander ‘Reddy’ Emmadi, Business Development Manager at ConveyorPro, said the company’s mission was to be a one-stop-shop for everything to do with conveyors.
“For greenfield projects like this one we previously might have only done the belting, or the idlers, or the pulleys,” he said.
“For this project, we could provide almost everything they needed – and that is something we have been aggressively focusing on.”
ConveyorPro began as a brand about five years ago, following significant requests from Transmin’s customers to provide additional accessories. The company would often go out to tender for its conveyor feeders or rockbreakers and be asked for equipment to supplement its offering.
The business had built up experience in the bulk handling equipment space and could see the benefits of providing a single package.
As part of its contract, ConveyorPro designed, manufactured and supplied all the rollers, idlers, pulleys, belting, impact beds and skirting modules for the goldfields project, which Emmadi said helped reduce overall costs and improves service.
“When it comes to greenfield projects like this one, we can combine packages together to provide a competitive price for the client,” he said. “Lead times are also reduced, along with overhead costs. It’s also a lot easier for project managers to handle.
“If you think about it, it’s a lot easier for one project manager to work with the one key account manager, instead of having to deal with four to five different suppliers for the same project.
“Our nature as a one-stop-shop also means we can reduce the number of contractors on site, as our teams are the subject matter experts for all of our products. That means less site inductions and faster service.”
Staff undergo monthly training with the different equipment in ConveyorPro’s range to help ensure they have the expertise required for field service work.
The ConveyorPro brand specialises in providing everything an
Transmin can supply ConveyorPro products beyond Australia’s borders.
Staff undergo monthly training with the diff erent equipment in ConveyorPro’s range.
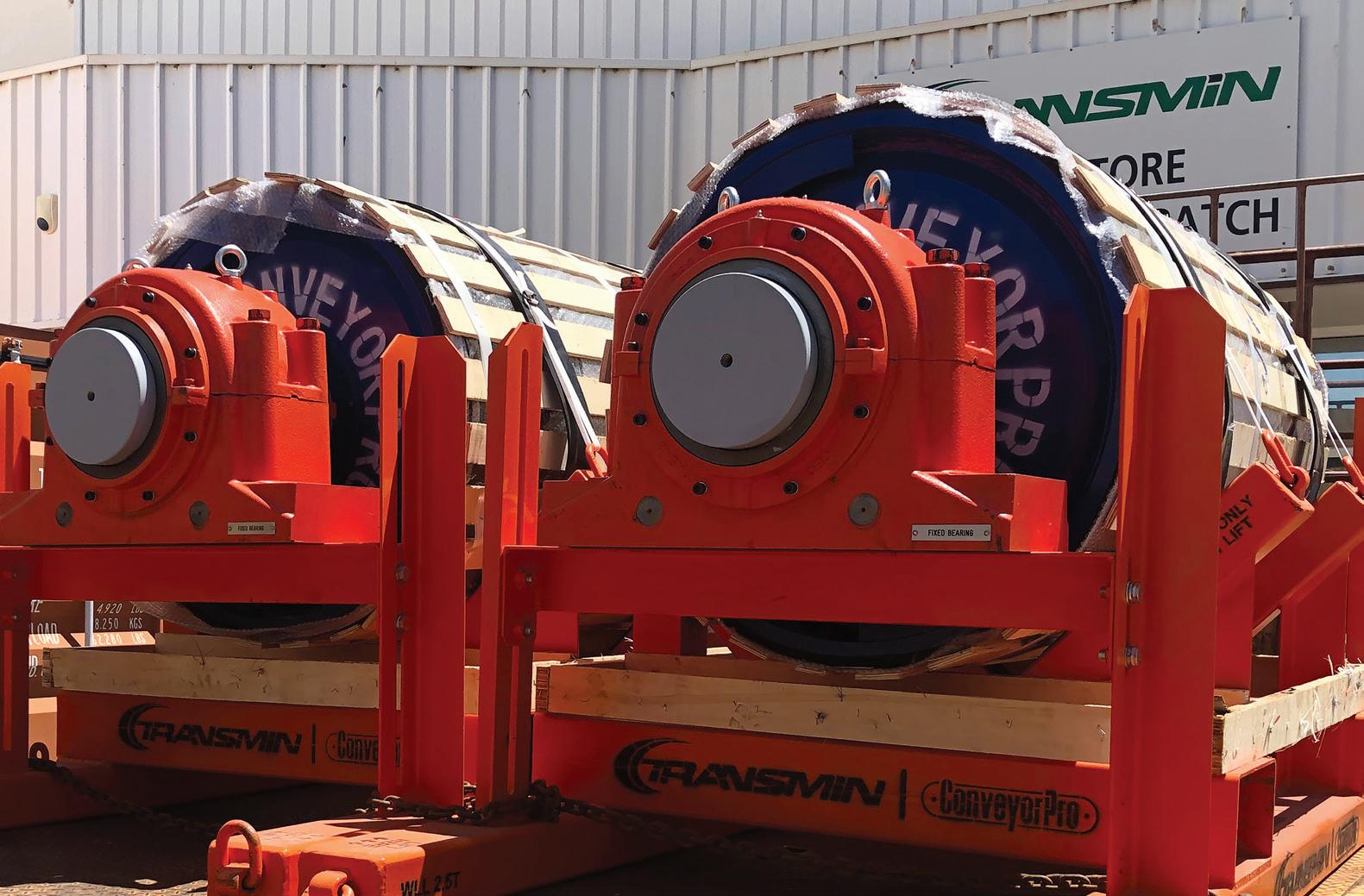
operator needs for a conveyor.
When it comes to belts, the brand offers steel cord, multiple fabric, bucket elevator, corrugated side wall, fire resistant, chevron, rip stop, heat-resistant and chemicalresistant varieties.
It can also offer other agency lines through partnerships with companies such as Martin Engineering or Thermo Fisher Scientific. Spare parts for all its equipment are kept well stocked, which helps to keep prices and lead times competitive.
Emmadi said ConveyorPro could also provide additional assistance when it comes to the design selection.
“As part of the service, we can select the right equipment for the application when clients are looking to upgrade or purchase new equipment,” he says.
“We can do all the calculations and design work for a specific application, then provide a quote.
“We’re based in Western Australia, which means we can provide fast, efficient turnarounds. We also carry a range of widely used, fast-moving items from our Perth and Brisbane warehouses to also reduce lead times.”
Transmin can supply ConveyorPro products beyond Australia’s borders. It has the capacity to send components to almost anywhere in the world, and has a presence in South Africa, India and Canada.
The company plans to continue growing its range of products, especially when it comes to rollers, composite rollers and conveyor guarding. The company’s latest high-density polyethylene guarding for low-profile feeders have been a major success, according to Emmadi, and it has also begun looking into providing similar products for conveyors.
“In the long term, we are looking at how we can provide full turnkey solutions for small-to-medium-sized conveyors,” he said.
“We hope to standardise the designs and use our fabrication expertise to deliver for medium-sized greenfield projects. Our teams are trying a lot of design aspects and will then move to feasibility studies.
“Constantly improving our products, in whatever form that needs to be, is key. Innovation is key to ConveyorPro’s success, so we are investing into our research and development.”
The ConveyorPro brand specialises in providing everything an operator needs for a conveyor.
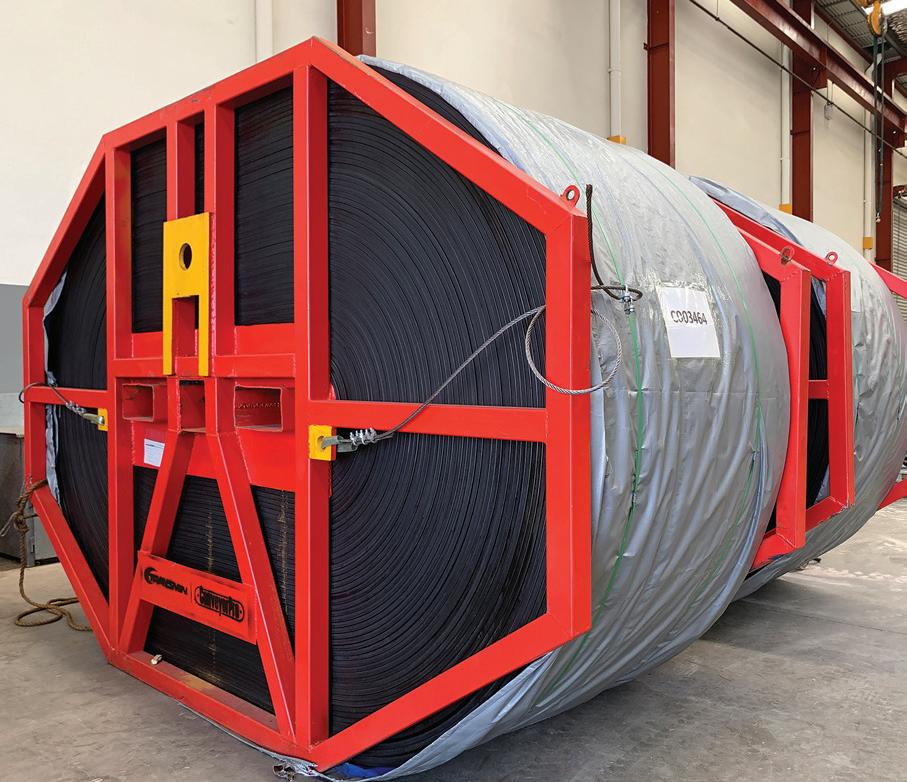
Job scheduling and dispatch software for growing businesses
vWork is fully flexible and can be configured to match your business requirements. Off the shelf integrations make tasks like invoicing and sharing proof of delivery data easier and vWork’s flexible API seamlessly integrates with other business tools. From defining job workflows to sending customer alerts, vWork is fully customisable and ready to be used within hours.
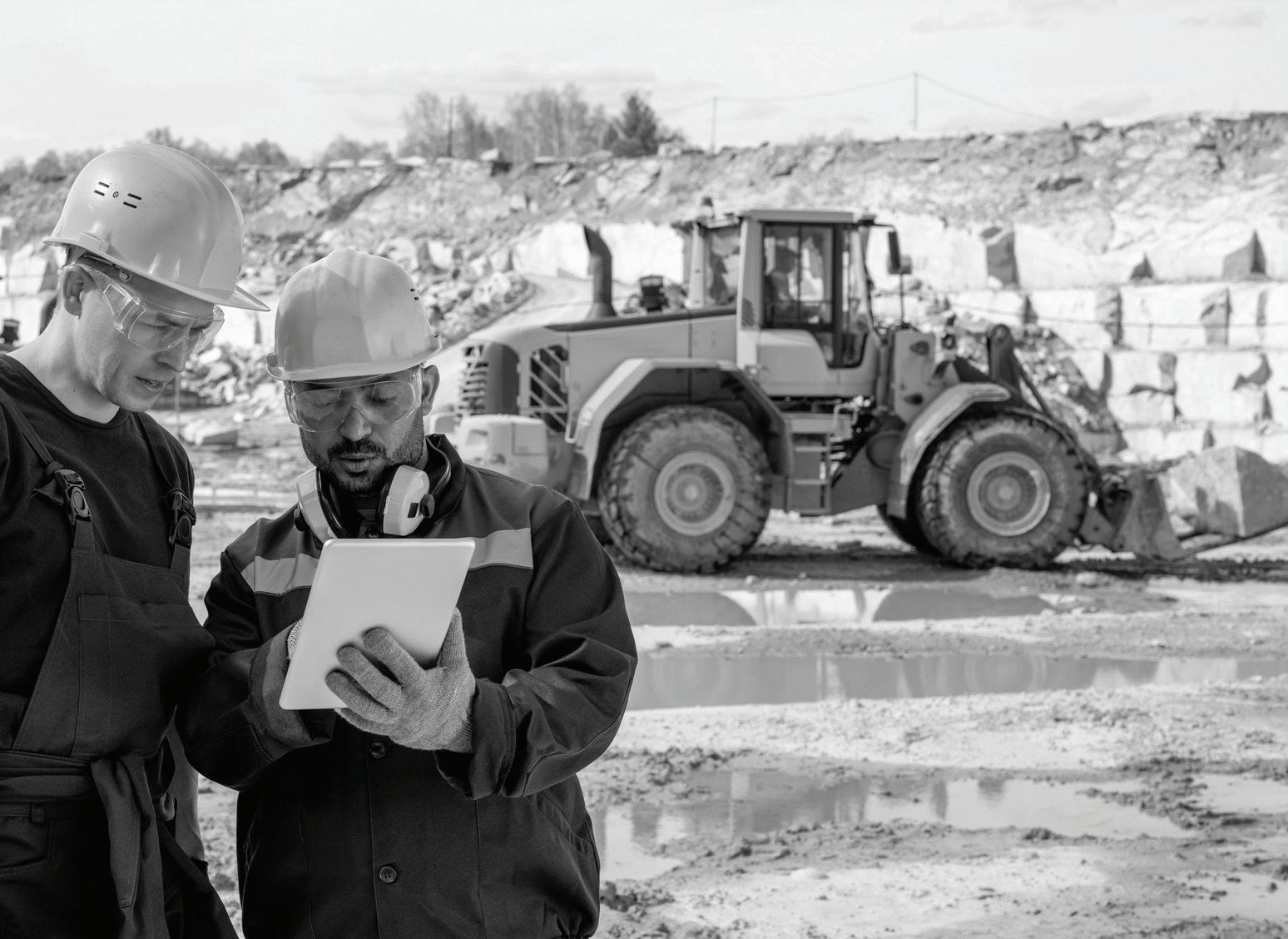
> Job Scheduling > Customer Communication > Route Optimization > Health & Safety > Flexible API > Advanced Reporting
Go tougher, not thicker
Fenner’s new Usfl ex super-heavy-duty belt can withstand some of the toughest environments the iron ore industry can throw at it.
WHEN IT COMES TO CONVEYING,
iron ore is notoriously rough on belts. Fines – the small sand-like material – are highly abrasive, while larger ore product can cut, gouge and rip through even heavy-duty belts due to the impact from ore loading.
The severe chute loading conditions were causing problems for a mine in the Pilbara region of WA. One of the mine’s feeder conveyors handling the large, heavy product was seeing consistent premature belt failure, causing issues with maintenance costs, delays and lost production.
To mitigate this issue, the mine reached out to Fenner Conveyors to find a solution.
Jayden Franklin, ECS Mechanical Engineer at Fenner, said the Team identified the main issue with the existing belt performance.
“Steel cord belts can be susceptible to impact damage in a large product environment, and this can cause significant damage to belt cords resulting in early belt failure,” he said. “The existing belt was consistently failing to meet the intended 24-week changeout lifecycle.”
The conveyor needed a tougher impact resistant belt, so Fenner began trialling its UsFlex D10 product.
The UsFlex Straight Warp construction has been engineered to provide high impact-resistance and protection against rips and tears. Usflex also has a longitudinal rip resistance three times greater than traditional plied belt. The straight laid yarns result in virtually no crimp, resulting in a belt carcass with very low stretch compared to other fabric belts. These characteristics make it highly favourable when replacing high-tension steel cord belts across several applications
Franklin explains, “Only Fenner has the manufacturing equipment and experience to manufacture UsFlex belting. The UsFlex product has been refined based on our experience in the Pilbara, providing the optimal balance of Impact Resistance and Low Stretch, which is specifically relevant to applications where it is replacing Steel Cord belting.”
“The UsFlex Straight Warp carcass, coupled with Fenner’s premium cut and gouge cover compound, Z-Tuff As, provides belt with superior rip resistance and impact absorption,” he said.
During the trial, the Usflex belt lasted 44 weeks in service, which roughly doubled the previous belts service life, reducing unplanned maintenance and lost production for the customer. This equates to operational cost savings of approximately $1 million annually.”
“In addition to the extended lifespan of the belt, the use of Usflex has the environmental benefit of reducing premature belt disposal allowing site operations to be more sustainable.”
Fenner plans to roll out Usflex belt in similar applications across the Pilbara. The company is available to assess customers applications where they are dealing with significant heavy-duty impact and ripprone environments.
“We’ve had similar success at other mines,” Franklin said. “Demand for Usflex is increasing as customers experience repeatedly successful trials.”
“Our Engineered Conveyor Solutions Team has the capacity to assess conveyor systems that are underperforming and collaborate with the mine, port and other materials handling operations to find an improved solution.”
Iron ore is abrasive and can seriously damage belts.
The UsFlex has been engineered to provide high impact-resistance and resistance to rips and tears.
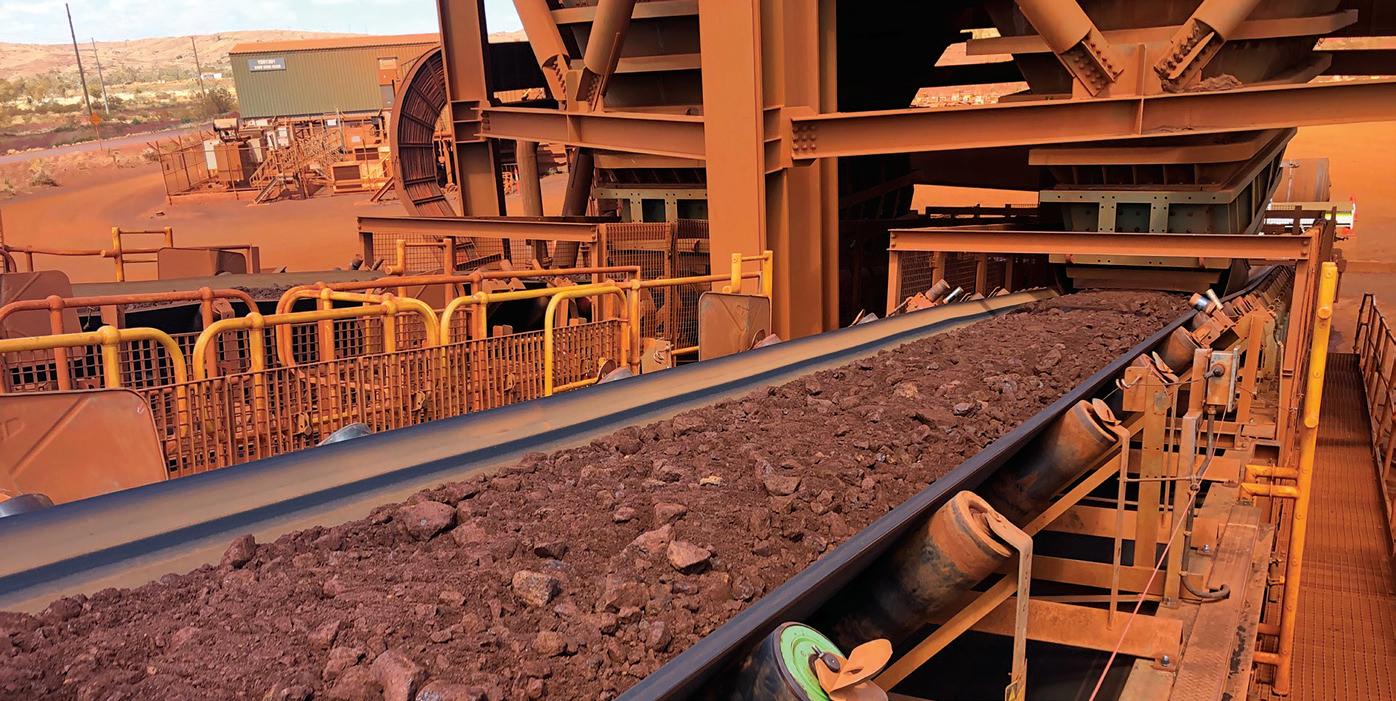

RKM rolls out HD Composite Roller
The RKM International Roller Company, in collaboration with composite fibre technology company Wagners, have developed a heavy-duty, lightweight composite tube suitable for handling some of the highest duty cycles.
THE COMPOSITE ROLLER USES
a unique pull-winding process, along with high-grade reinforcement and resins to bind the fibres together, providing flexural strength and stiffness comparable to steel.
Brett Maiden, RKM Director, said the composite roller has been developed specifically for the heavy mining industry, particularly iron ore, where rollers are subjected to harsh operating conditions and large tonnages.
“The challenge with previous heavyduty rollers made of PVC or HDPE was that they didn’t have the flexural strength and stiffness to handle the load required on the troughing side of the conveyor which meant they were mainly used on the return side of the conveyor. Steel shells were still required for the trough side,” he said.
“Our new light weight composite roller can handle the heavy weight that the trough roller encounters.”
The rollers weigh around half as much as conventional steel rollers and produce less noise without sacrificing durability, which helps make manual handling on hazardous sites safer.
The product is not classified as hazardous according to the criteria of the National Occupational Health and Safety Commission (NOHSC) Australia.
RKM has incorporated its RS seal package, along with a primary heavyduty nylon protective outer dual labyrinth shield into the roller. The shield provides additional protection against contaminant ingress and eliminates rock jamming.
The company also uses dynamic balancing machines to ensure the rollers meet AS3709 G16 and achieves the best possible TIR and MIS, reducing any noise generated from the belt running across the surface of the roller.
The materials used to build the rollers have already been tested across several mine structures including piping, casing, tubing, rebar, power pole cross arms, boardwalks, footbridges, road bridges, pontoons and jetties.
“Our new HD composite roller will be manufactured right here in Perth, enabling significantly shorter lead times for clients and quick deliveries for all non-standard and special orders,” Maiden said.
The roller, combined with the embedded Vayeron Smart Idler Technology, allows the user to predict the lifespan of each roller and receive alerts on upcoming maintenance and changeouts.
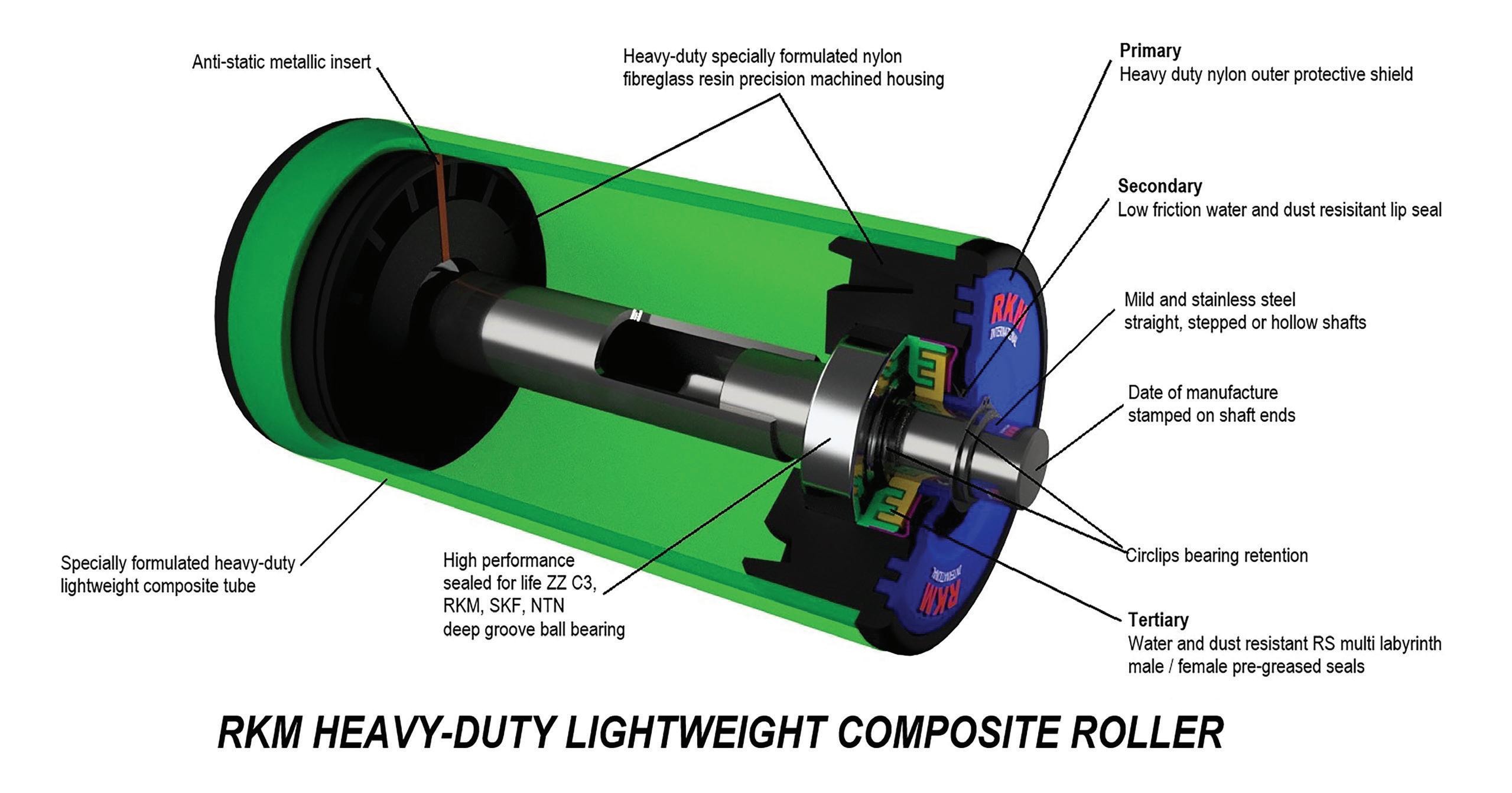
A breakdown of the composite roller.
Durable new roller cuts down on “pizza cutters”
Canada’s Enduride is bringing its new Ultim8 idler to the Australian market, which it claims is 25 times more abrasion-resistant than steel.
WHEN IDLERS BEGIN TO WEAR
out, there is a risk that the shell can create a sharp edge, colloquially known as a “pizza cutter”.
These sharp edges are in constant contact with the conveyor belt itself, one of the most expensive parts of many bulkhandling operations.
Jerome Guimont, Global Sales Manager at Canadian conveyor component manufacturer Enduride, has been involved in the mining industry for years, and one of the most common complaints he has heard is the need for idlers that can stand up to the rough conditions.
“Around the world, we are seeing issues with labour shortages,” he said. “Finding staff to manually replace worn idlers can be expensive and timeconsuming. Mining companies want to minimise interventions and downtime on conveyors, as it saves them a lot of money.
“We put our research and development team to work to create a new product that could reduce unscheduled downtime. What they created was a product that has 25 times more abrasion life than a standard steel roller.”
The Ultim8 roller’s durability comes from a mixture of engineered components. Enduride uses a proprietary ceramic called E20, which is embedded in a polyurethane base material. Following testing, the company found the roller had similar abrasion resistance to tungsten carbide.
It can be used in any configuration,
The Ultim8 roller’s durability comes from a mixture of engineered components. Development on the Ultim8 roller took around 18 months before the fi nal product.
including in a trough or as a return roller – which is often where abrasion does the most damage.
Development on the Ultim8 roller took around 18 months before the final product was created, when it was put to the test to find out what would and wouldn’t work. The final product has been field tested in mining environments, with customers already making use of it for iron, gold, copper and aluminium applications.
“Some of our customers used to change return rollers every six months. More than a year has passed since the roller was first installed on their site, and it is still going strong,” Guimont said.
Enduride is a Canadian manufacturer of industrial belt conveyor components such as idlers, innovative nets guarding solutions and impact solutions. Active since 2005, the company carries a portfolio of conveyor belt products to service a wide range of heavy-duty material handling applications.
Australia is a new market for the company and while Guimont said while Canada and the US are Enduride’s main market, abrasion is a problem that can affect you wherever you are in the world.
“Iron ore mines in Australia have similar problems to mines in Canada. There are some discrepancies, but the nature of the product is the same – highly abrasive,” he said.
“As a company, we have a lot of expertise in these markets, and we’ve been able to test our products in a wide range of temperatures.”
The company’s specialists are located around the world, and it plans to expand further into southeast Asia and Oceania.
“We like to have an innovative offering. We want to bring something to the market that stands out and provides real benefits to the customer,” Guimont said.
“We have heard feedback from the Australian market and hope to solve the problems they are facing.”
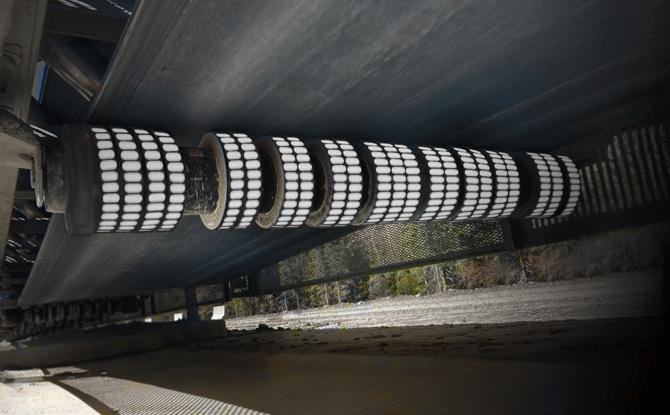
