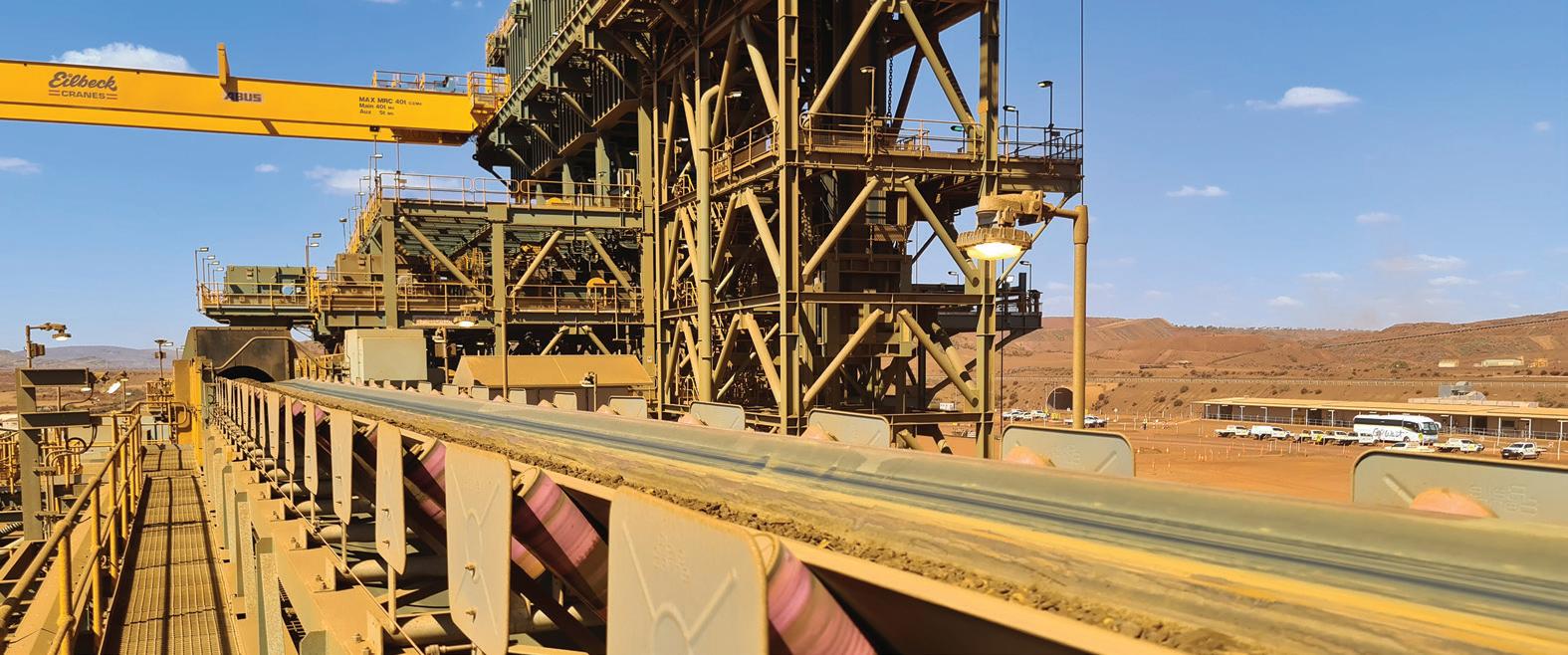
2 minute read
Rolling out idlers for BHP’s South Flank
One of Belle Banne Conveyor Products’ first customers serviced by its new WA facility is BHP’s South Flank project.
BELLE BANNE CONVEYOR
Products (BBCP), a developer and manufacturer of conveyor equipment, recently opened a new facility in Welshpool, Perth to better service its growing number of local clients.
BBCP was established in 2009, manufacturers products for the Australian, New Zealand, South American, and South Asian bulk handling industries. One of these customers is mining giant BHP, which contracted BBCP for conveyor frame and idler supply on the South Flank project.
To meet the needs of this large-scale project, BBCP’s in-house engineering, drafting and quality and logistics management teams have supplied over 13,800 conveyor idler frames, 41,000 rollers, 17,000 steel and composite wind guards, and belt handling frames.
Overall, the supply scope has included over 30 roller types and 90 frame types, all which were specifi cally designed to suit South Flank’s various conveyors– ranging in width from 750mm to 2400mm – and material capacities of up to 33,500 tonnes per hour.
Daniel Weekes, BBCP Managing
Operational bene ts from Ultraroll include its low noise certi cation and being “belt-friendly”. Director said, “The project has been a brilliant opportunity for BBCP to showcase its capabilities as both accomplished and competitive component designers and suppliers”.
“For instance, in an Australian fi rst, a full composite idler set was specifi ed using 219 mm composite rollers. This off ered the client a robust idler set, suited to the punishing Pilbara conditions”.
The majority of the idlers supplied to the project comprised BBCP’s proprietary Ultraroll rollers. A key feature of the composite UltraRoll is their friction welded housings, which ensure a fully supported bearing regardless of ambient temperature extremes.
All frame and roller design for the project were verifi ed by Finite Element Analysis, with our in-house engineering team using Ansys Mechanical to ensure the client’s technical specifi cations for the idlers – including infi nite life – were achieved.
Ultraroll features reinforced composite construction of both roller tube and bearing housings and is a key to reducing the weight in comparison with traditional idlers, helping to achieve weight reductions of up to 60 per cent, compared to standard steel rollers while not sacrifi cing roller longevity.
A positive fl ow-on eff ect of the
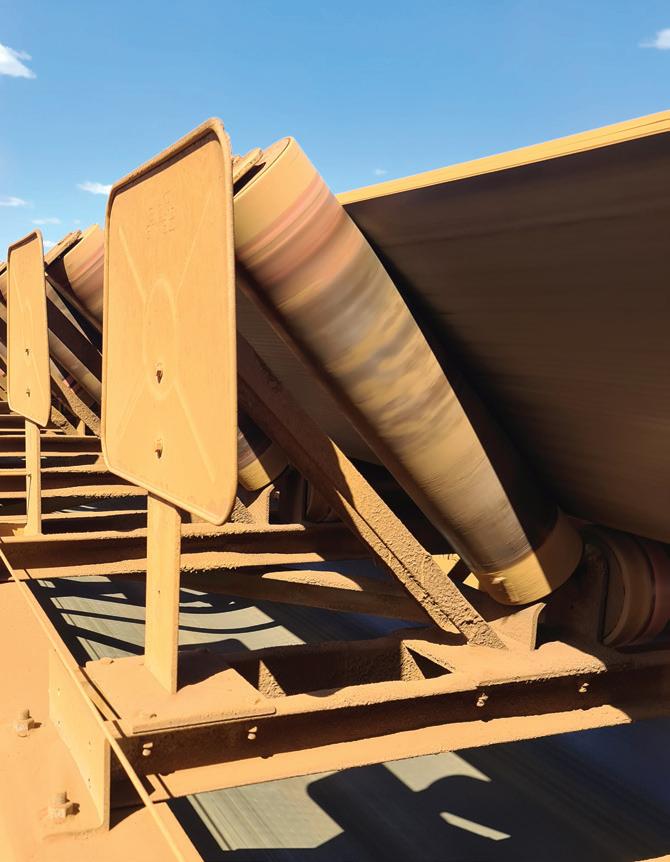
The supply scope has included over 30 roll types and 90 frame types.
lighter idler rollers is safer and easier manual handling. Operational benefi ts from Ultraroll include its low noise certifi cation and being “belt-friendly” (no sharp edges), as well as reducing whole-of-life asset cost. BBCP’s Ultraroll is manufactured in a distinctive pink colour making it instantly recognisable, while also drawing attention to several cancer charities that BBCP has aligned with. A percentage of proceeds from the supply of each idler delivered to South Flank will be donated to national breast, prostate, and melanoma cancer research foundations.
Weekes said the South Flank project had provided an excellent launch pad for BBCP’s growth in Western Australia.
“As a company, we’re delighted at being involved with BHP’s South Flank project,” Weekes said.
“With our new presence in Welshpool, BBCP can now off er a higher level of local engineering, design drafting and technical support on the ground in Western Australia.
“Our WA team is steadily growing with a number of recent local appointments, and we look forward to continue delivering a high level of service and support to South Flank along with other projects in the region.”