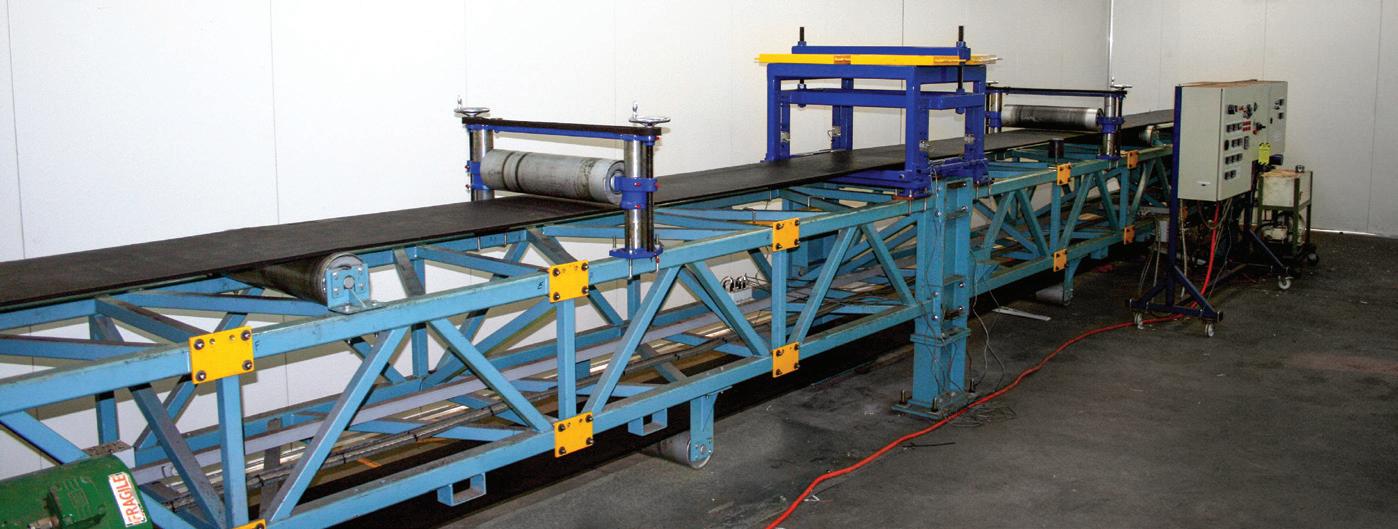
9 minute read
Evaluating the indentation rolling resistance performance of conveyor belt covers
As conveying distances and belt speeds continue to increase, greater emphasis is being placed on energy efficiency in belt conveyor design. As a result, TUNRA Bulk Solids has seen an increasing number of inquiries which focus on the testing and analysis of higher energy-efficiency conveyor belts and idlers.
RESEARCH BY HAGER AND
Hintz [1] has concluded that up to approximately 60 per cent of energy consumption in long distance conveying systems is due to the indentation of the belt cover passing over the idlers. Considerable research efforts have been placed in reducing such energy losses, including the development of low rolling resistance compounds by conveyor manufacturers [2].
Indentation rolling resistance is affected by several factors, including the idler roll diameter, belt loading, belt cover thickness and the viscoelastic properties of the bottom cover. Such properties are also dependent on operating conditions including temperature, belt speed and belt load, which imposes challenges when trying to predict the indentation losses of a conveying system.
Predicting indentation rollingresistance
There are two general approaches for determining the indentation rolling resistance losses of a conveying system, these are the large sample and small sample methods. The large sample method uses a full sample of belt in a closed loop, including the carcass, carry and pulley covers, whereas the small sample method uses a small sample of the pulley (bottom) cover of the belt only.
Large sample indentation loss method
There are different test setups associated with the large sample method, one such test method is described in German standard DIN 22123 [3] and another is included in Australian standard, AS 1334.13:2017 [4]. For these test methods, the indentation rolling resistance is measured directly by an instrumented idler roll, as a function of normal load, for a specific pulley cover compound, idler roller diameter, pulley cover thickness, temperature and belt speed [5]. The indentation rolling resistance is typically reported per unit belt width to enable comparison between compound types and to allow designers to scale results for the actual belt width to be installed on a system. The Conveyor Equipment Manufacturers Association (CEMA) [6] includes a method for utilising the large sample measurements to calculate the indentation losses when the required idler diameters and belt cover thicknesses of a system are different from what was tested.
The large sample testing facility located at TUNRA Bulk Solids, shown in Figure 1, can carry out indentation rolling resistance testing according to both DIN 22123 and AS 1334.13:2017, as well as having the ability to measure conveyor belt flexure resistance [5, 7]. It accommodates samples between 400 millimetres to 600 millimetres wide and 29,000 millimetres long (full spliced length).
Small Sample Indentation Loss Method
CEMA 7th Edition [6] has included a small sample indentation loss model with constants for several example rubber cover compounds that can be applied to the CEMA model for initial design feasibility studies. For the small sample method, the dynamic physical properties of a rubber sample piece, with a thickness of up to three millimetres, are measured over a range of temperatures, strain amplitudes and frequencies. The dynamic physical properties, being the viscoelastic properties of the belt conveyor cover rubber, are obtained by applying an oscillating mechanical deformation to a sample and measuring the resultant stress. The stress response of a viscoelastic
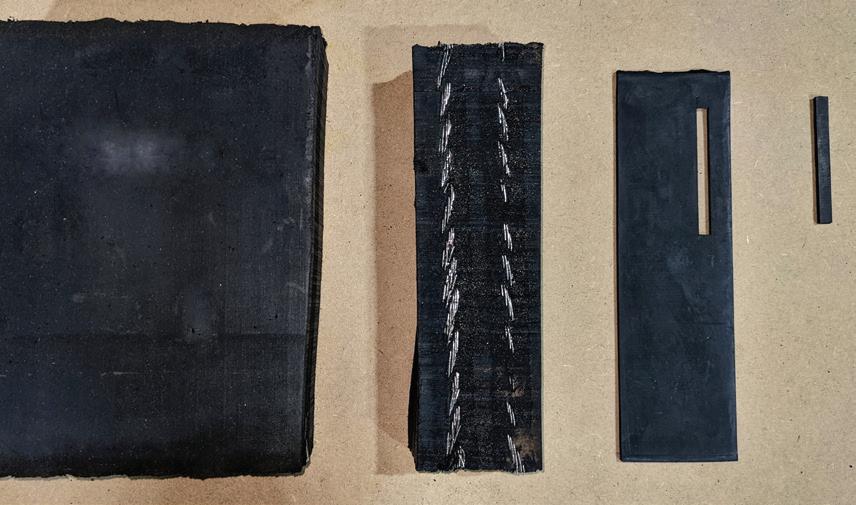
Figure 3: Small sample preparation from complete belt section. Figure 1: Large Sample Indentation Rolling Resistance rig at TUNRA Bulk Solids, the University of Newcastle
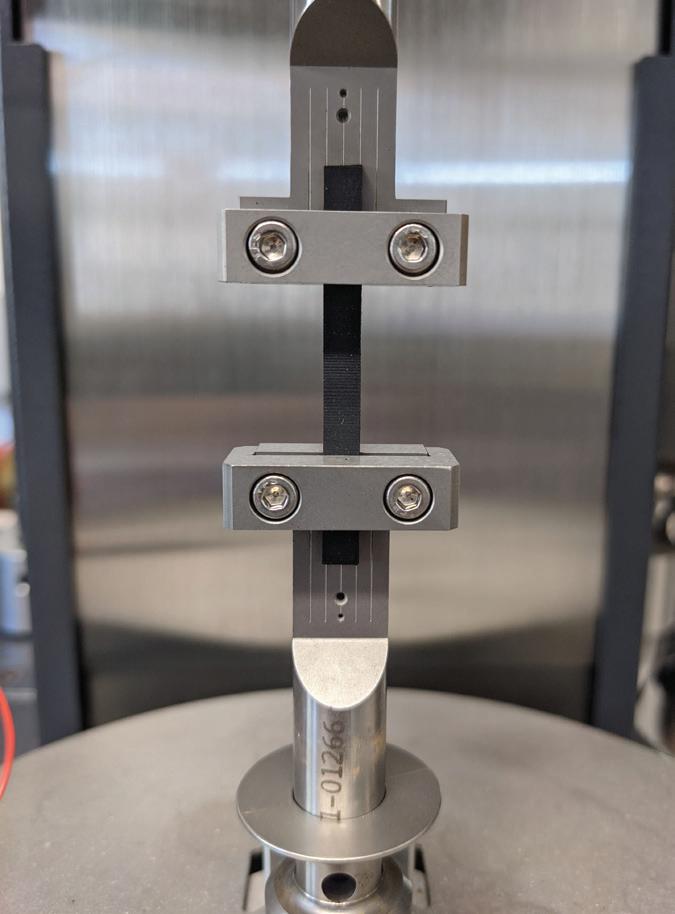
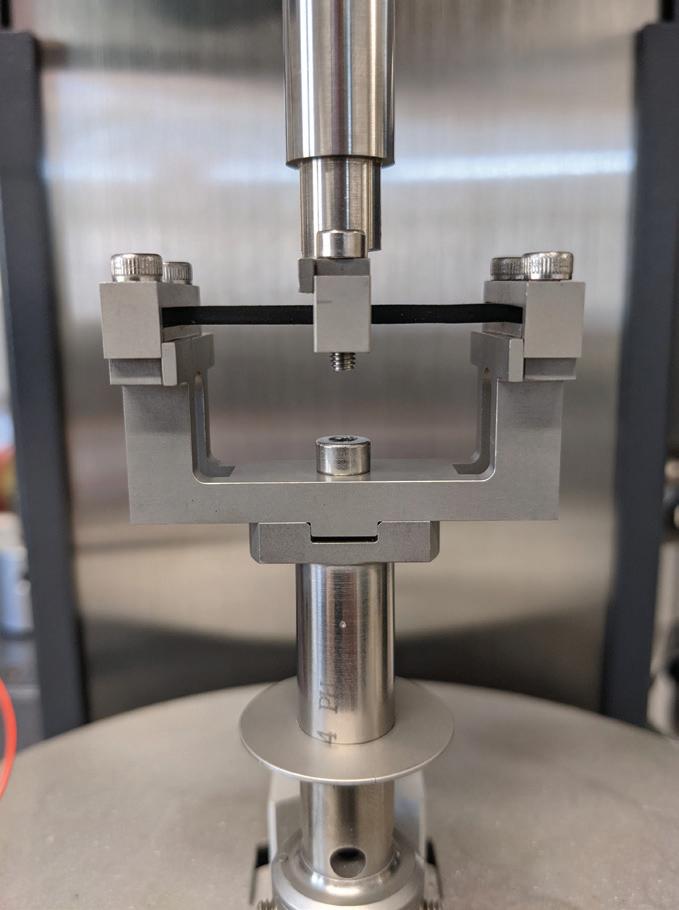
Figure 2: Small Samples mounted in (a) tension clamp and (b) dual cantilever clamp
material will be out-of-phase with the applied strain by an angle δ. From the results of these tests, the elastic modulus E’, loss modulus E” and phase angle δ can be calculated. Specialised Dynamic Mechanical Analysis (DMA) equipment is utilised to obtain these properties which are then applied to theoretical models to calculate the indentation rolling resistance per idler set as a function of loading, temperature, belt speed, cover thickness and belt width. The DMA testing equipment used by TUNRA Bulk Solids is a TA Instruments RSA-G2 Solids Analyser. Figure 2 shows sample test pieces set up in the RSA-G2 Solids Analyser using the tension and dual cantilever clamps. The deformation rate of the bottom cover of a conveyor belt due to the idler rolls normally ranges from 50 to 1000 Hz, which is outside the RSA-G2 testable range. To determine the viscoelastic properties at these equivalent frequencies, time–temperature superposition principles (TTS) are employed [2], which involves holding the temperature and strain amplitude constant while varying the frequency, from which E’, E” and tan δ master curves are derived. The temperature and frequency can be related through the Williams Landel Ferry (WLF) transfer equation [8]. The RSA-G2 has an axial force adjustment feature that senses volumetric changes in a sample from changes in temperature and adjusts the clamp position accordingly to ensure the actual force is kept constant throughout testing when using the tension clamp.
Samples to perform dynamic mechanical analysis can be purpose made, where a thin sheet of the rubber compound is cured in a mould. Alternatively, test samples can be prepared from the bottom cover of full sections of conveyor belt, where a segment of the bottom cover is passed through a belt splitter to obtain a sample with a near constant thickness. An example of the steps taken to prepare a sample from a full section (carcass, carry and pulley covers) is shown in Figure 3.
Case study:
Overview:
Table 1 Testing Specifications
Item
Test specifications
Clamp type Tension Frequency range 0.1 to 10 Hz Temperature range -40° to +50°C (in 5°C increments) Strain amplitude 2%
A recent project completed by TUNRA Bulk Solids involved an independent assessment of the indentation rolling resistance properties of a series of Fenner Dunlop belt samples.
Dynamic Mechanical Analysis (DMA) testing was conducted on conveyor belt bottom cover rubber samples to

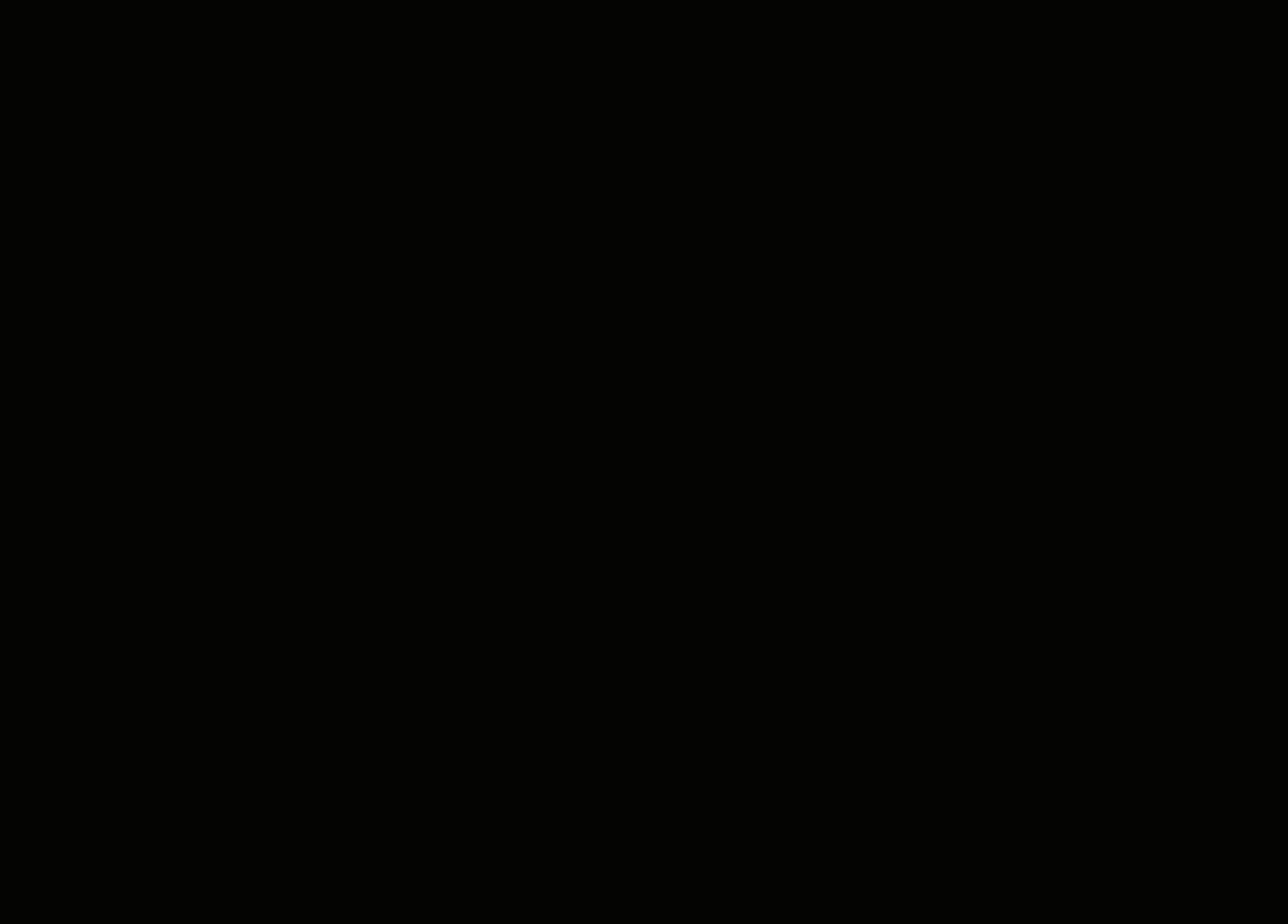
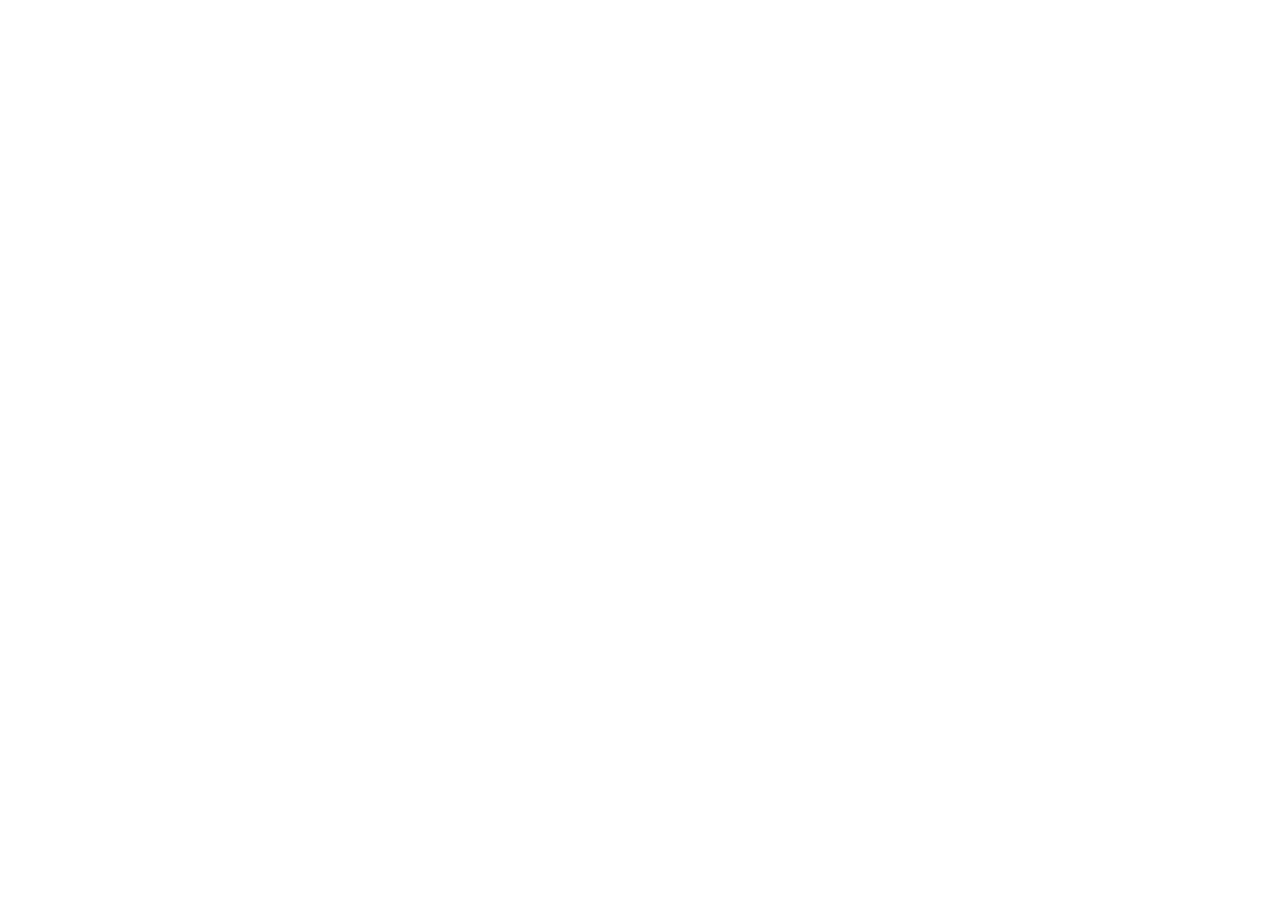

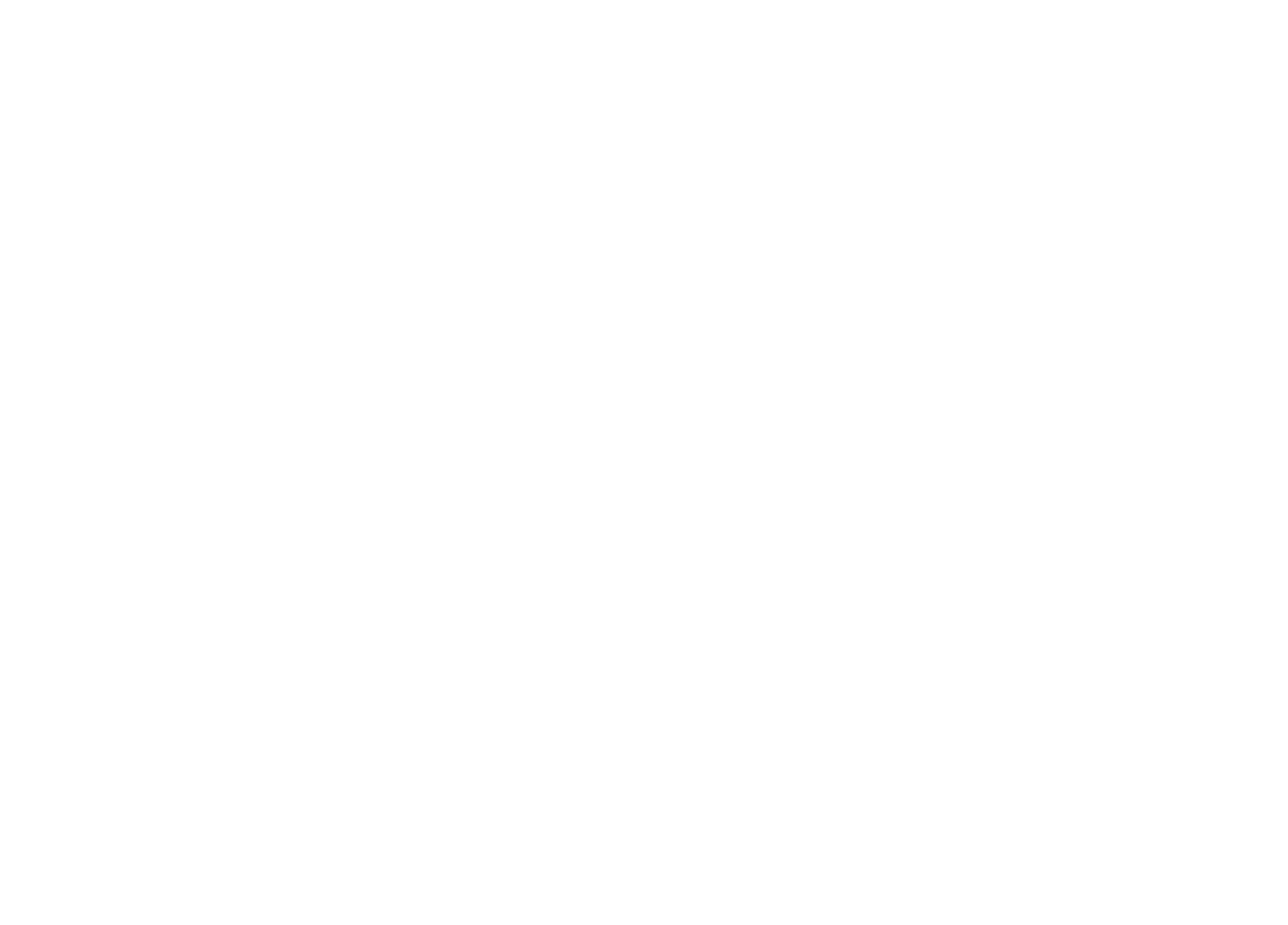
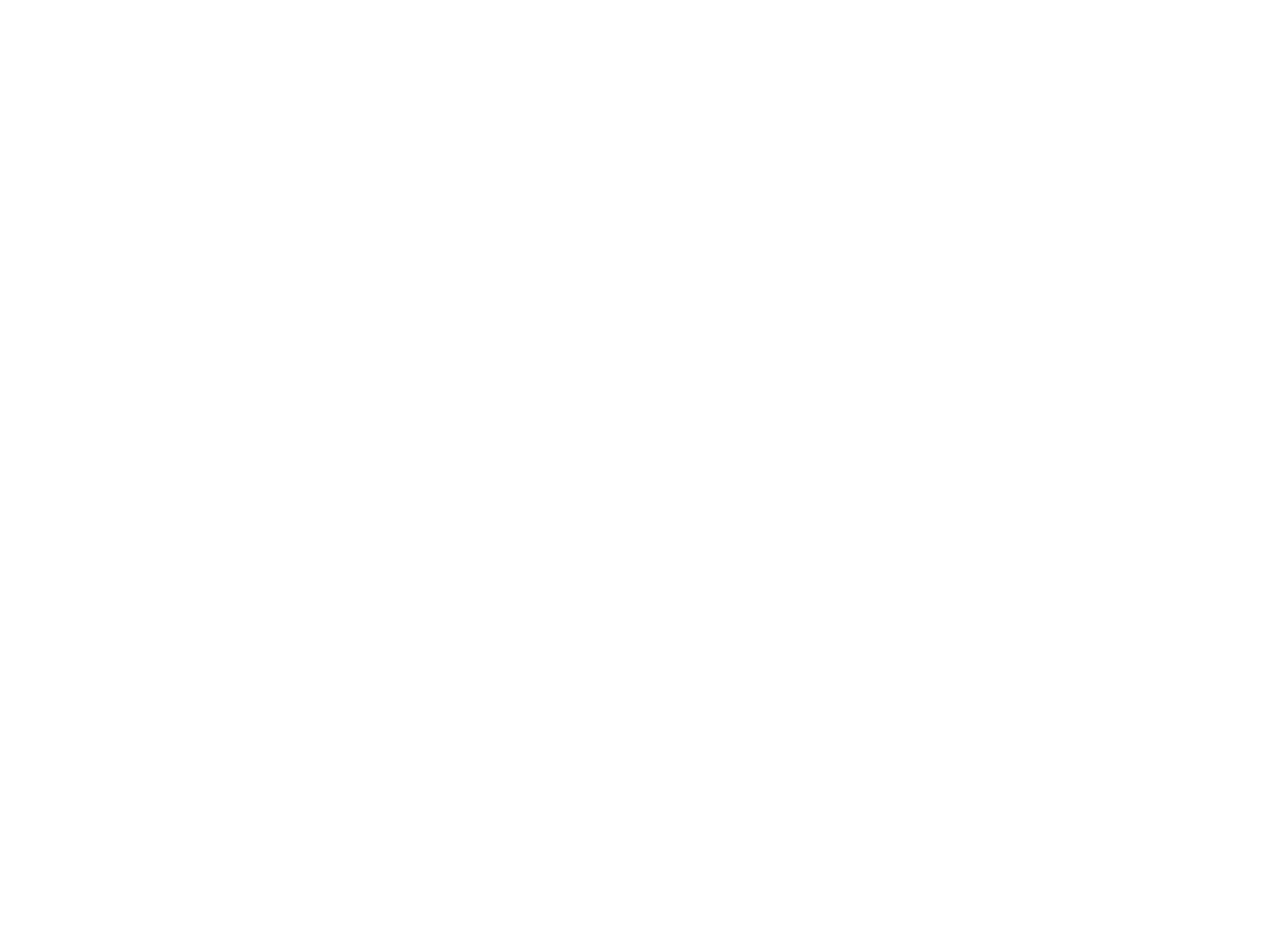
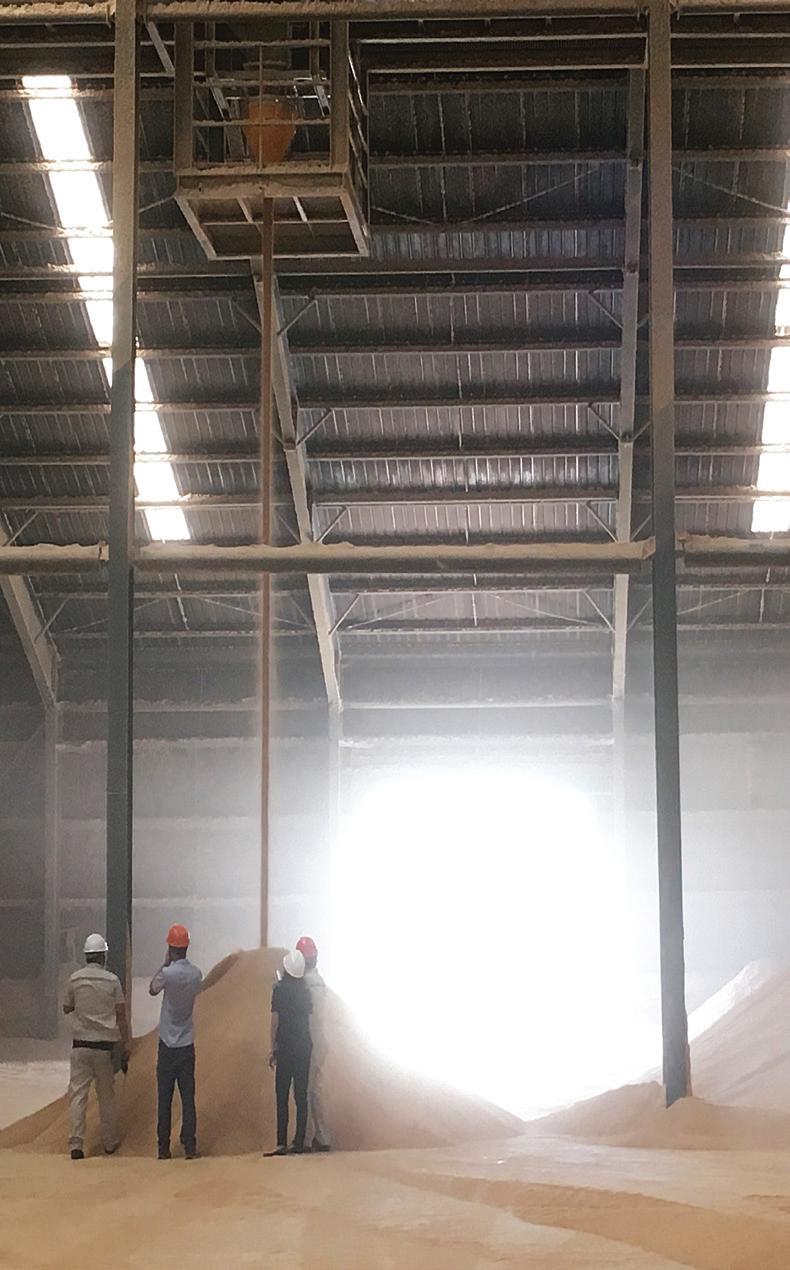
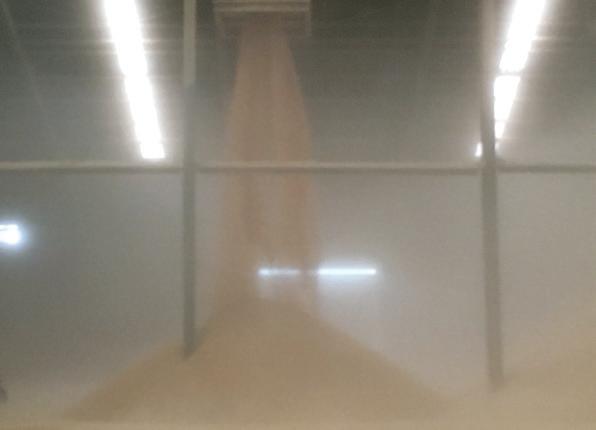
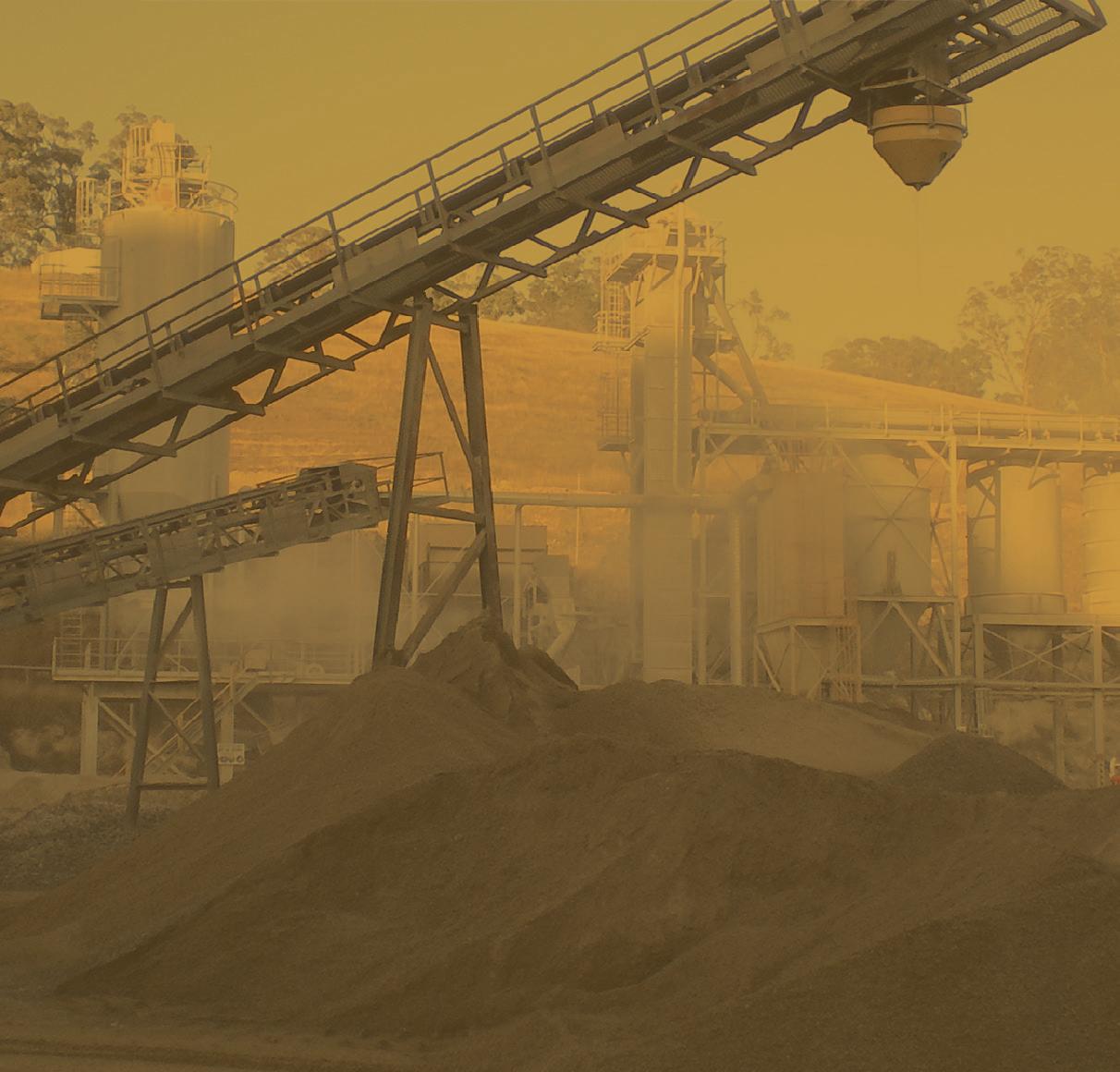
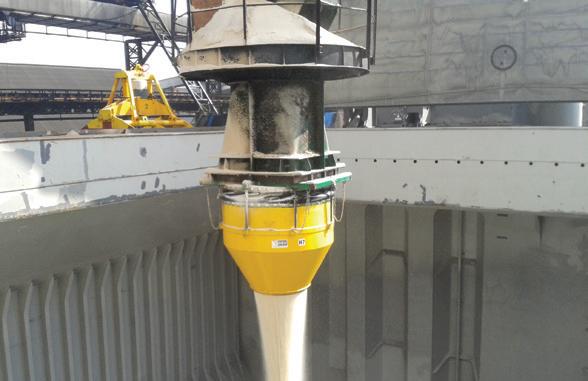
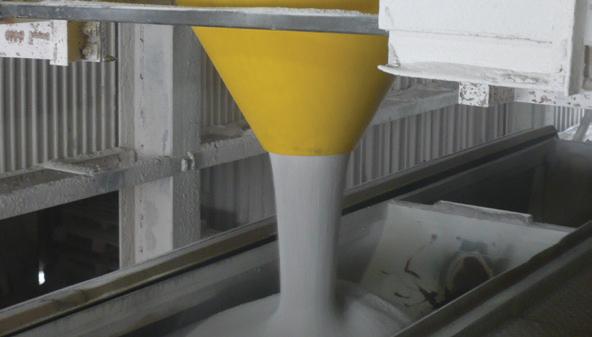
determine their viscoelastic properties. Specifications for the DMA testing are presented in Table 1.
The viscoelastic material properties were applied to the QC-N model from Qiu and Chai [9]. The QC-N model was selected to predict the indentation rolling resistance for this project due to previous research showing that this model performs favourably when compared to other commonly applied rolling resistance prediction models [10].
The predicted indentation losses of the pulley cover were then compared to measurements conducted on the large sample indentation rolling resistance test facility, shown in Figure 1, as a function of belt load for a belt speed of 4 m/s and belt temperatures of 20°C and 40°C. Details of the large sample belt conveying system are presented in Table 2. These are also the parameters used in the analytical model to calculate the indentation losses for the samples under the operating conditions described for a direct comparison of results between the small and large sample methods selected.
The apparent bottom cover thickness was used for calculations, which is equal to the bottom cover thickness plus half the cord diameter [11].
Results:
The indentation rolling resistance is presented for one of the small sample rubber compounds evaluated with the QC-N loss model against the large sample measurements, as a function of belt load. The pulley cover of the large belt sample tested was made with the same rubber compound tested as the small sample. The relative indentation rolling resistance is shown in Figure 4 for a belt operating temperature of 20°C and Figure 5 for a belt operating temperature of 40°C.
Furthermore, the indentation loss was calculated for the large sample conveying system in Figure 1 using the small sample method described in CEMA 7th edition, for the Default rubber and Type 1 (low rolling resistance) rubber for reference. The relative indentation losses have been in included in Figure 4 and Figure 5.
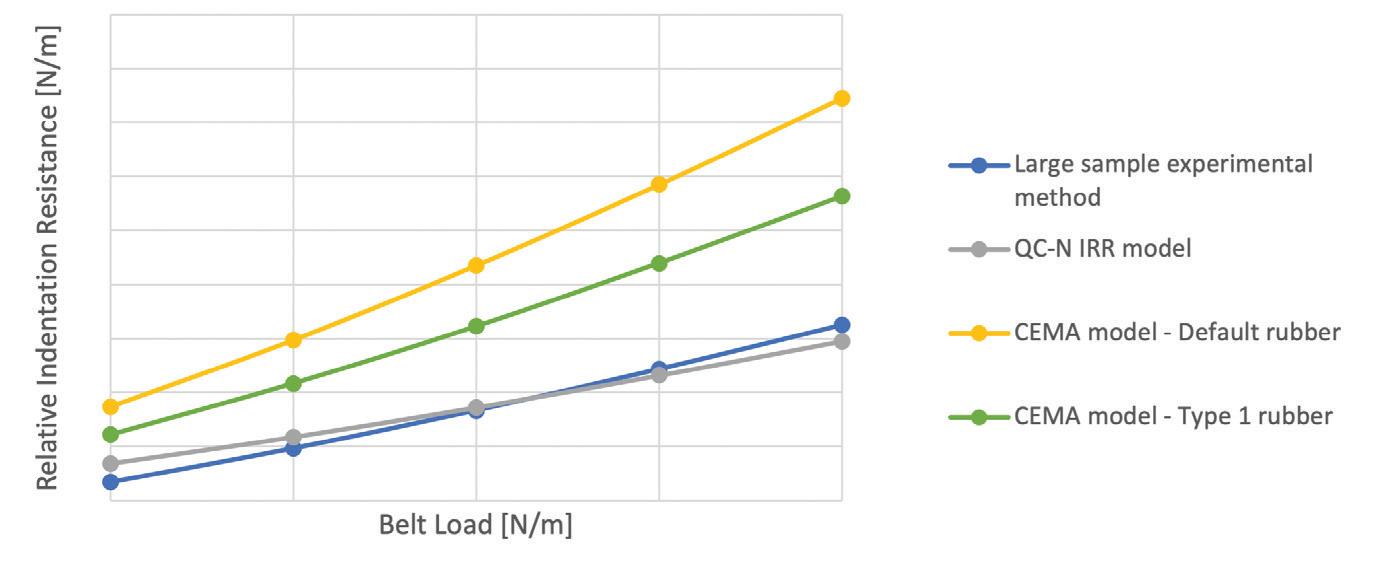
Discussion and Conclusion:
The results presented show a good comparison between the large sample
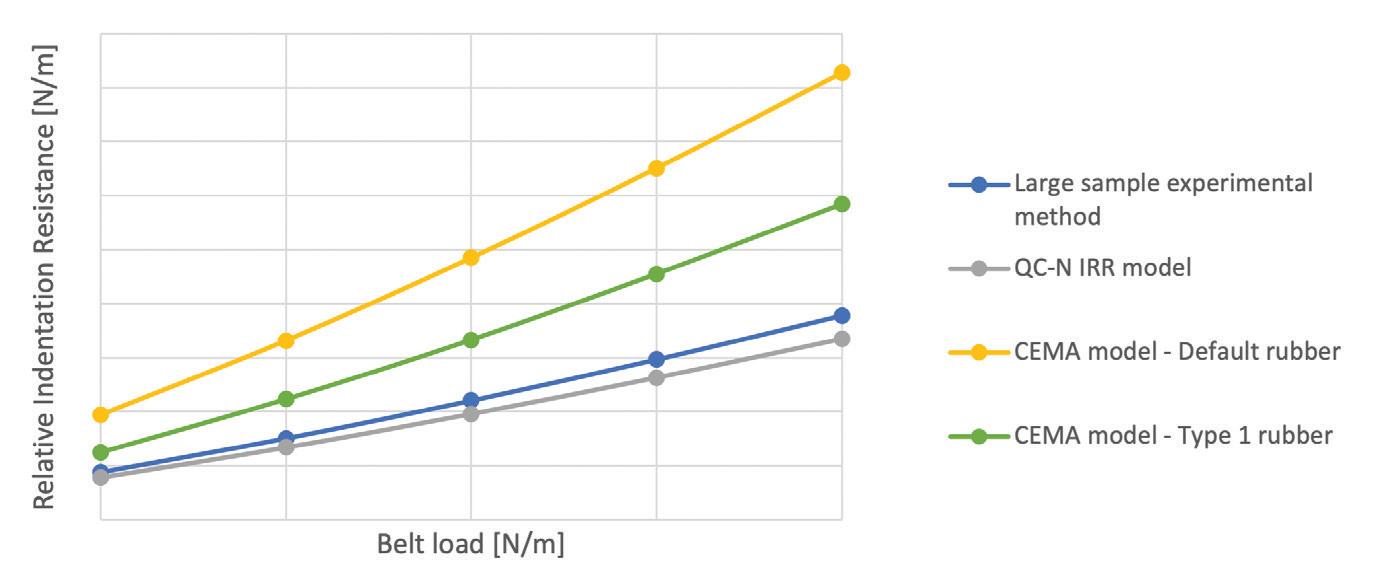
Figure 4: Relative indentation rolling resistance at 20°C.
Figure 5: Relative indentation rolling resistance at 40°C.
experimental measurements and the small sample prediction model for the same pulley cover compound. This indicates that the QC-N model performs relatively well at predicting indentation rolling resistance for the compound analysed.
The results also demonstrate that the indentation rolling resistance performance of the tested pulley cover compound is lower than that of the example rubbers presented in CEMA 7th edition. This shows that selecting a general rubber type, instead of evaluating the actual compound to be used for a conveying system, may result in inaccuracies when determining design values. This disparity may become particularly significant for long overland conveyor systems where indentation losses make up a large percentage of the total losses for a system. Since any calculation inaccuracies are compounded at each idler set, the cost of insufficient detail during design may result in costly over or under design of the system.
References: 1. Hager, M. and A. Hintz, The Energy-Saving Design of Belts for Long Conveyor Systems. Bulk Solids
Handling, 1993. 13(4): p. 749-758. 2. O’Shea, J.I., et al., The influence of viscoelastic property measurements on the predicted rolling resistance of belt conveyors. Journal of Applied
Polymer Science, 2014. 131(18). 3. DIN 22123: Conveyor belts - Indentation rolling resistances of conveyor belts related to beltwidth - Requirements, testing. 2012, German Institute for
Standardisation (Deutsches Institut für Normung) (DIN). 4. AS 1334.13:2017: Methods of testing conveyor and elevator belting Determination of indentation rolling resistance of conveyor belting. 2017,
Standards Australia. 5. Wheeler, C., et al., How to Design Energy Efficient
Belt Conveyors, in Bulk Solids Handling. 2020: bulk-online.com. 6. Conveyor Equipment Manufacturers Association (CEMA) 7th Edition. 2014, Belt Conveyors for Bulk
Materials. 7. Munzenberger, P. and C. Wheeler, Laboratory measurement of the indentation rolling resistance of conveyor belts. Measurement, 2016. 94: p. 909-918. 8. Williams, M.L., R.F. Landel, and J.D. Ferry,
The Temperature Dependence of Relaxation
Mechanisms in Amorphous Polymers and Other
Glass-forming Liquids. Journal of the American
Chemical Society, 1955. 77(14): p. 3701-3707. 9. Qiu, X. and C. Chai, Estimation of Energy Loss in Conveyor Systems due to Idler Indentation.
Journal of Energy Engineering-asce, 2011. 137: p. 36-43. 10. O’Shea, J.I., Mechanical and dielectric relaxation studies of conveyor belt compounds to determine indentation rolling resistance properties. 2015,
The University of Newcastle, Callaghan. 11. Wheeler, C.A. and P.J. Munzenberger, A pseudo 3D analysis of the indentation rolling resistance problem, in BELTCON 15 Conference. BELTCON 15. 2009, IMHC: Johannesburg, South Africa.