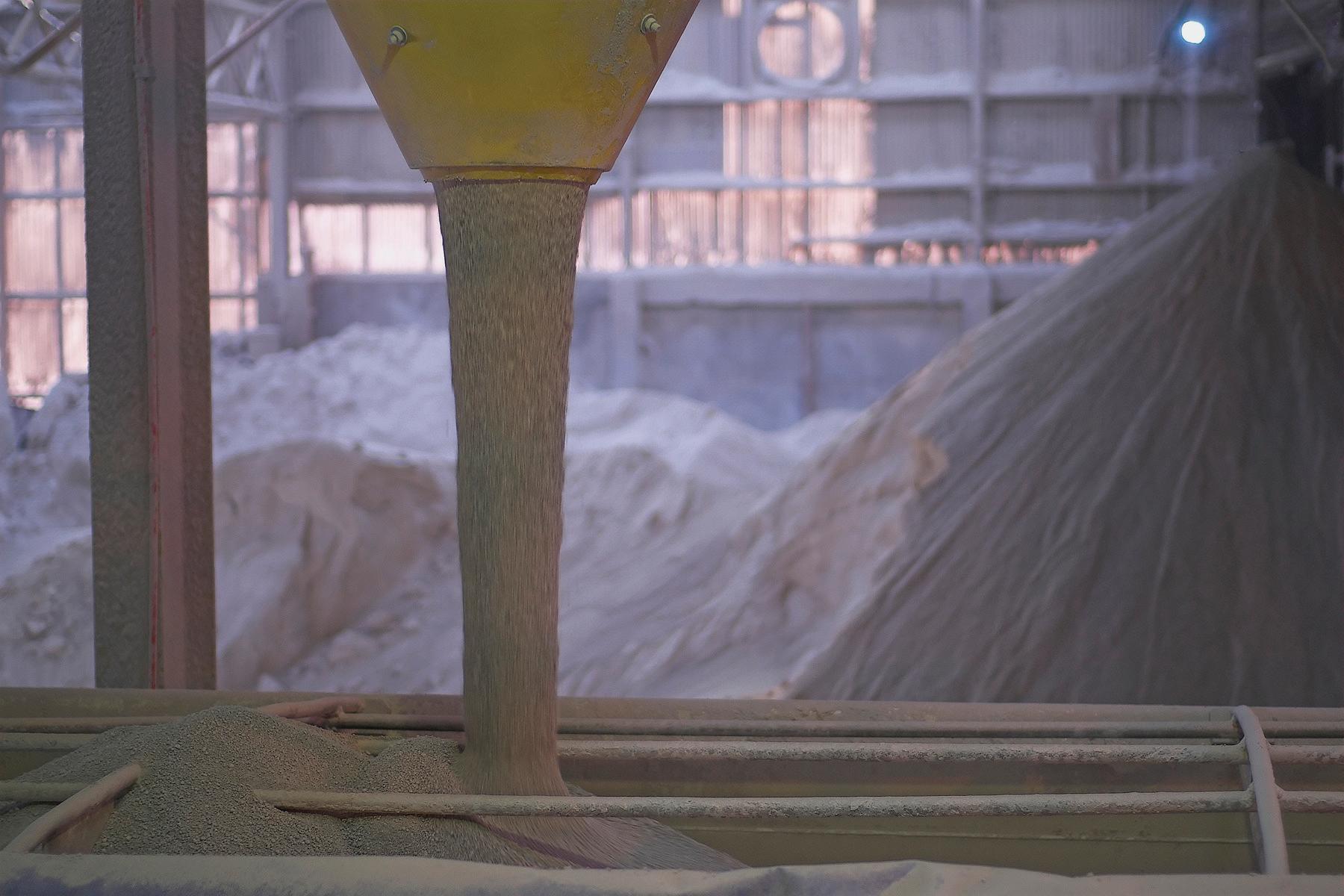
4 minute read
Defeating dust with simple physics
When they were first introduced, DSH Systems’ loading hoppers were called magic. ABHR speaks with Ian Walton, Chief Executive Officer at the company, to find out how they really work.
AS MATERIAL FALLS FROM A
loading hopper into a truck or vessel, it’s highly likely to create significant amounts of dust.
This dust poses several risks. In grain applications, the dust can be explosive. When working with sand and minerals it can lead to diseases like silicosis when inhaled, and when working near waterways, such as a port, it can be a potential source of pollution.
Ian Walton, Chief Executive Officer at DSH Systems says the business created an innovative solution when trying to solve a dust problem at a fertiliser plant.
“In 2004, Trevor Schwass – the company’s founder – was working as a contractor when he prototyped a technology that could solve the issue,” Walton says.
“After completing the contract, he cashed in his pension and started the business to share the technology with the world.”
The DSH hopper uses a central plug, fixed in position with a gap between itself and the hopper. When the hopper is loaded with material, springs extend and begin to control material flow so that a solid column of material exits.
Air is removed from the material and dust entrained in the column so that minimal dust is released and little to no segregation occurs.
Fine, moist, non-granular, and poor flowing materials, such as cement, milk powder, coal, or flour, don’t work with the system. The material feed rate also needs to be fairly consistent, as wild fluctuation cause instability in the material column.
Walton says in the early days, customers would call it the “magic bucket” or claim the evidence was photo trickery.
“The only wizardry is its innovative design, which combined experience in bulk handling with physics,” he says.
Global growth
The system has been used across the world to great success. Initially, Australia was one of the company’s starting markets, due to its proximity to New Zealand. However, the technology has spread far across the globe, to the point where Australia makes up less than 10 per cent of the business’s total turnover.
Walton says this growth has been largely driven by its customers, who have been impressed by the results.
In Vietnam, one of the country’s leading ports for bulk commodities was suffering from significant amounts of grain dust generated near active grain loading and transfer operations.
Incoming grain from ships and soybean meal produced at a nearby crushing facility was creating huge amounts of dust as they moved through the system, leading to low visibility and a potential explosive environment.
All the airborne dust was also considered waste, as it was not included in the final load. To solve the problem, the port invested in a DSH system installed at five key grain transfer locations, including inside a warehouse, at a barge loading dock and at three truck loading locations.
Each hopper is installed under a feed point where it can be suspended above the discharging target and kept at operating level. At the point of loading, the DSH system concentrated the discharge into a solid column, without the use of electric power or internal moving parts.
The installation of the hoppers resulted in a dramatic decrease in airborne dust during loading at these locations. In addition, loading processes were faster and cleaner, maintenance costs were reduced and the removal of air from the products increased storage capacity.
The port’s Environment, Health and Safety director, John Zhao, said investing in a healthier working environment was one of the ways the company showed care for the community and its employees.
When the hopper is loaded with material, springs control material flow so that a solid column of material exits.
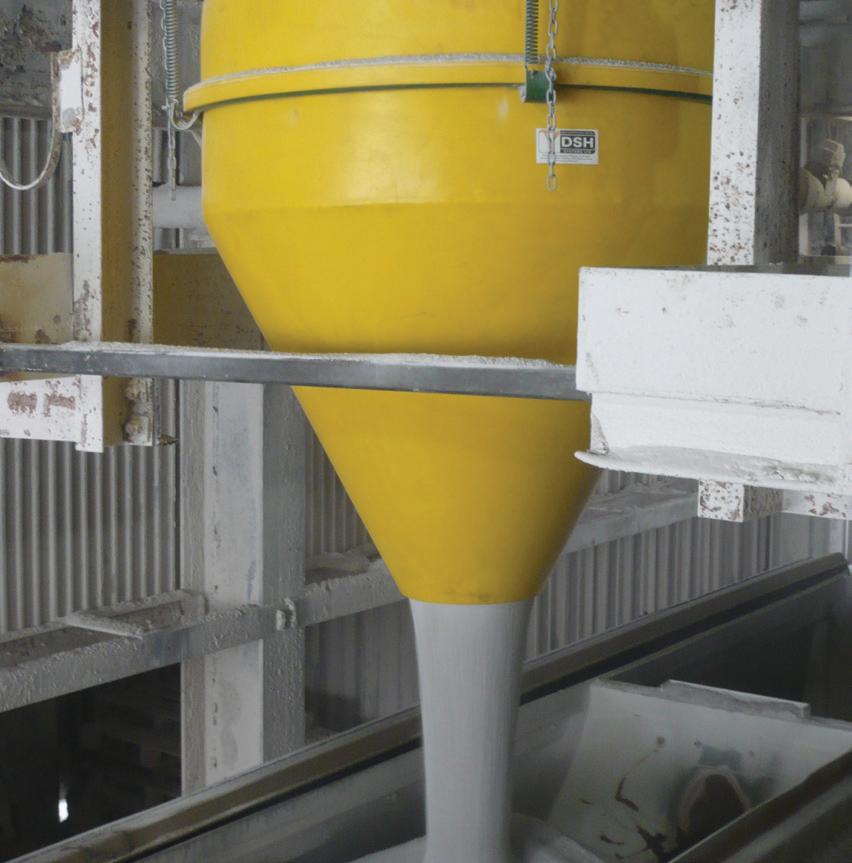
The system can drop material from significant heights with little dust emissions.
“Controlling dust risks isn’t just about ensuring that workers are wearing the right PPE for the job,” he says. “The best solution is always to eliminate or capture as much dust as possible at the source.”
The hoppers have also been used for non-standard applications and sizes. Walton says DSH works closely with its customers to find the right solution for specific operations.
“For example, in Brazil one of our customers approached us and asked if we could design a much larger version of the hopper for them,” he says.
“This is a common request. Often when people see how effective the regular hoppers are, they want to see them used for bigger, critical applications.
“Now, instead of loading 100 tonnes an hour, we have installed systems that are capable of loading 3000 tonnes an hour.”
The company is now working to further integrate the systems to be Industry 4.0 compatible. Following a request from a French customer, DSH has developed a hopper that interfaces with a programmable logic controller, allowing it to work alongside automated equipment.
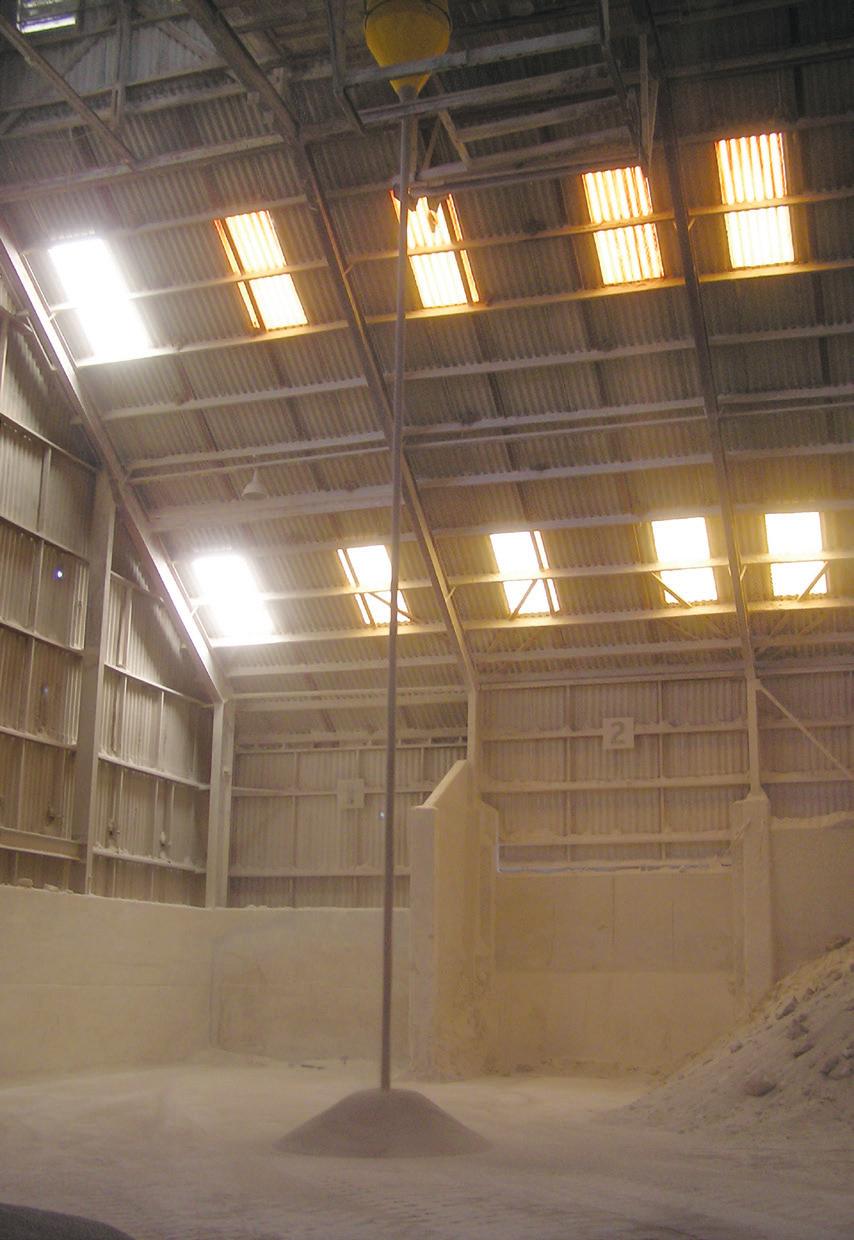

Loading trucks with dry material can create hazardous dusts, which the DSH system minimises.
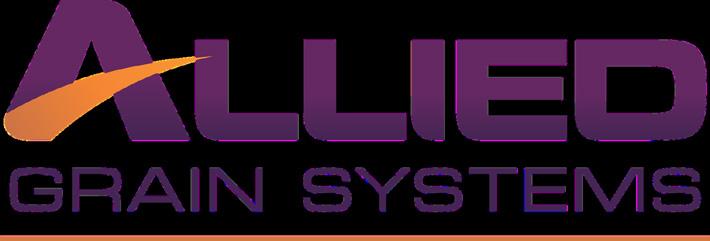
