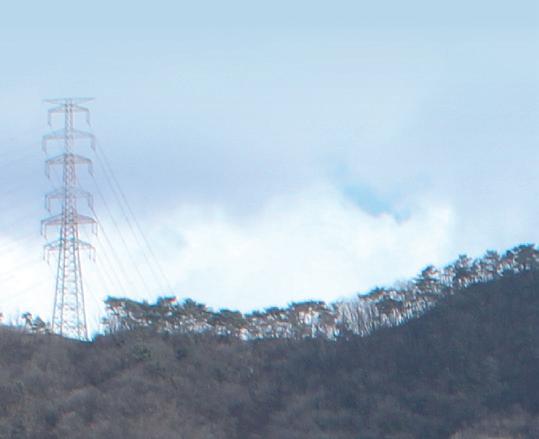
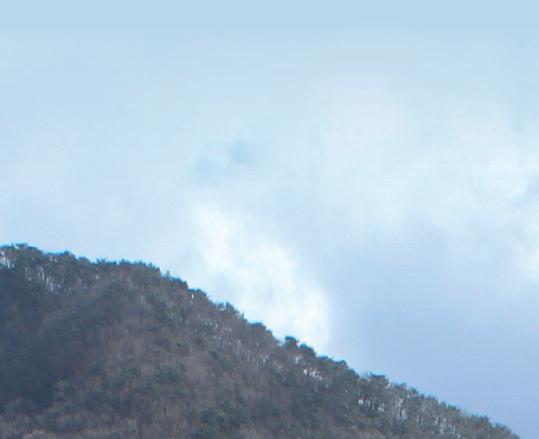
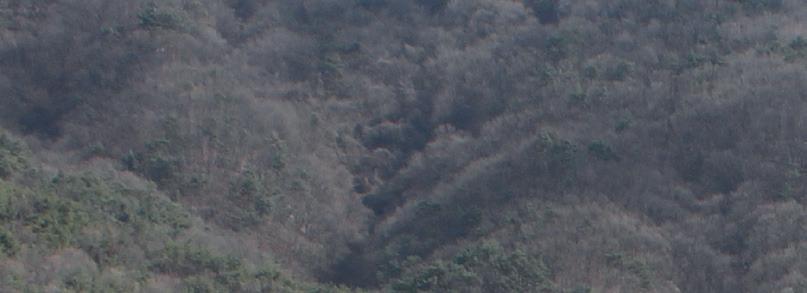
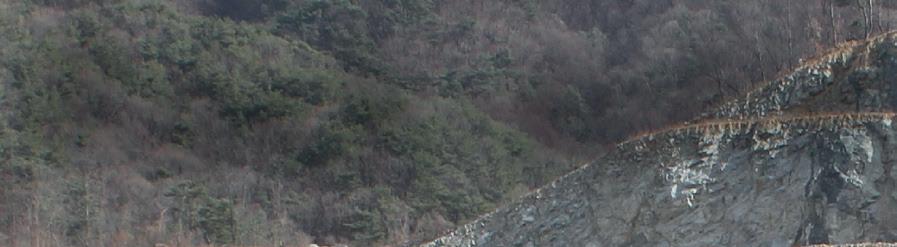


South Korea’s red-tape-busting aggregates advance p12
HEAD OFFICE
EDITOR: Guy Woodford
ASSISTANT EDITOR: Liam McLoughlin
CONTRIBUTING EDITORS: Patrick Smith, Dan Gilkes
EQUIPMENT EDITOR: Mike Woof
DESIGNERS: Simon Ward, Andy Taylder
PRODUCTION MANAGER: Nick Bond
OFFICE MANAGER: Kelly Thompson
CIRCULATION & DATABASE MANAGER: Charmaine Douglas
INTERNET, IT & DATA SERVICES DIRECTOR: James Howard
WEB ADMINISTRATORS: Sarah Biswell, Tatyana Mechkarova
MANAGING DIRECTOR: Andrew Barriball
PUBLISHER: Geoff Hadwick
CHAIRMAN: Roger Adshead
ADDRESS
Route One Publishing Ltd, Second Floor, West Hill House, West Hill, Dartford, Kent, DA1 2EU, UK
TEL: +44 (0) 1322 612055
FAX: +44 (0) 1322 788063
EMAIL: [initialsurname]@ropl.com (psmith@ropl.com)
ADVERTISEMENT SALES
SALES DIRECTOR:
Philip Woodgate TEL: +44 (0) 1322 612067
EMAIL: pwoodgate@ropl.com
Dan Emmerson TEL: +44 (0) 1322 612068
EMAIL: demmerson@ropl.com
Graeme McQueen TEL: +44 (0) 1322 612069
EMAIL: gmcqueen@ropl.com
SUBSCRIPTION / READER ENQUIRY SERVICE
Aggregates Business is available on subscription at the rate of: £85 / US$145 / €111 per annum. Single copies £20 / US$35 / €26 Email subs@ropl.com for further details.
Subscription records are maintained at Route One Publishing Ltd.
SUBSCRIPTION / READER ENQUIRIES TO:
Data, Route One Publishing Ltd, Second Floor, West Hill House, West Hill, Dartford, Kent, DA1 2EU, UK
TEL: +44 (0) 1322 612061 FAX: +44 (0) 1322 788063
EMAIL: data@ropl.com
No part of this publication may be reproduced in any form whatsoever without the express written permission of the publisher. Contributors are encouraged to express their personal and professional opinions in this publication, and accordingly views expressed herein are not necessarily the views of Route One Publishing Ltd. From time to time statements and claims are made by the manufacturers and their representatives in respect of their products and services. Whilst reasonable steps are taken to check their accuracy at the time of going to press, the publisher cannot be held liable for their validity and accuracy.
PUBLISHED BY © Route One Publishing Ltd 2022
AGGREGATES BUSINESS USPS: is published six times a year. Airfreight and mailing in the USA by agent named World Container Inc, 150-15, 183rd Street, Jamaica, NY 11413, USA.
PERIODICALS POSTAGE PAID AT BROOKLYN, NY 11256
US POSTMASTER: Send address changes to Aggregates Business, World Container Inc, 150-15, 183rd Street, Jamaica, NY 11413, USA. Air Business Ltd is acting as our mailing agent
PRINT: ISSN 2051-5766
ONLINE: ISSN 2057-3405
PRINTED BY: Warners (Midlands) PLC
India’s cement industry is expanding rapidly; our freelancer based in the country, Partha Pratim Basistha, reports in an in-depth feature inside this issue.
Cement demand is surging off the back of huge government infrastructure spending, with many major producers spending a significant amount of rupees on expanding their production capabilities and product ranges.
Partha’s excellent feature highlights how energy-efficient cement production, mainly through usage of fly ash from thermal power plants and other waste materials, is a growing trend among major and green-minded small- to medium-sized companies.
Another changing market trend is the grinding, processing, and consumption of breakbulk bagged cement. Furthermore, many producers are now looking to transport bulk cement in truck bulkers and specialised railway wagons for the ready-mix industry. Both modes of transport are also used to transport fly ash from coal-fired power plants. However, as Partha notes, some companies find that logistical issues can hinder their utilisation of fly ash.
Given the impressive expansion of India’s cement industry, it is no surprise that a recently published report from GlobalData, a major business market intelligence consultancy, paints an encouraging picture of the country’s construction sector. The current national building boom creates attractive commercial opportunities for leading global and Asiaregion quarrying and construction equipment manufacturers.
India Construction Market Size, Trends and Forecast by Sector – Commercial, Industrial, Infrastructure, Energy and Utilities, Institutional and Residential Construction, 2021-2025 tipped the Indian construction industry to register an annual growth of 17.5% in real terms in 2021, following a decline of 12.3% in 2020 – this compares to GlobalData’s previous estimate of a 15.9% growth in 2021. The upward revision in the December 2021-published report was driven by growth in the second and third quarters of that year, the continued relaxation of
restrictions, and the low base effect of 2020.
GlobalData expects the Indian construction industry to record growth of 5.8% in 2022, supported by a series of investments in transport, health, and housing infrastructure developments. The government unveiled its Pradhan Mantri Gati Shakti Master Plan in October 2021, an INR100 trillion (US$1.3 trillion) project to develop holistic infrastructure, aiming to boost economic growth through infrastructure investment and propel India’s development over the next 25 years. In June 2021, the government approved the INR500 billion (US$6.5 billion) Loan Guarantee Scheme for Coronavirus (COVID-19)Affected Sectors (LGSCAS) to provide financial guarantees for building new healthcare projects, as well as upgrading existing infrastructure.
A project can receive a maximum loan of up to INR1 billion (US$13 million), with the interest rate capped at 7.95%. Industry growth will also be supported by the government’s plan to significantly increase the stock of affordable housing units for low- and middle-income cohorts under the Housing for All programme by 2022.
Over the remainder of the forecast period, between 2023 and 2025, the Indian construction industry is expected by GlobalData to register an average annual growth of 6.2%, supported by investments under the INR111 trillion (US$1.5 trillion) National Infrastructure Pipeline (NIP), between the fiscal year (FY) 2020 and FY2025 (April 2019 to March 2025). To raise additional financing to implement infrastructure development, the government launched the National Monetisation Pipeline (NMP) in August 2021.
The plan focuses on raising funding from the private sector by leasing out stateowned infrastructure assets and investing the revenue generated through this transfer in new infrastructure projects. The government also aims to complete the construction of 23 new highway and expressway projects by FY2024/2025, with an estimated investment of INR3.3 trillion (US$46 billion) over the next five years. GW
Next-generation crushing meets superefficient screening plant
A new quarrying-suited premium crawler excavator range unveiled amid big demand for fuel-efficient and highly productive loaders 28
US & UK markets spearhead uptick in global ADT sales, driven by major infrastructure programmes
32
New launches offering operators increased performance and productivity
Why investing in high-quality screening media makes commercial sense
The latest global examples of moneymaking washing
08 INTERVIEW
Les Lothian unpacks South Africa-based Kemach’s transformation into a total solutions provider
12 MARKET REPORT
South Korea’s aggregates ascendancy despite the licensing red tape
16
A savvy Metso Outotec solution is helping Thai cement producer TPI Polene Cement lower its carbon footprint and production cost
43 INDIAN CEMENT
How strategic investments by major producers are creating a larger and smarter Indian cement sector
India-based Dalmia Cement has expanded the groundmounted solar-power capacity of its Cuttack plant.
Spread over 49 acres, the solar-power plant in the eastern Indian state of Odisha is set to generate 25.52 MU/ PA, which will be utilised for the energy requirements of Dalmia’s Kapilas Cement Manufacturing Works (KCMW).
Dalmia Cement says the expansion of solar capacity to 17.1MW (from the previous 2.4MW) furthers its sustainability goal of becoming carbon negative by 2040, and will enhance the plant’s energy efficiencies.
The 17.1 MW plant aims to reduce the KCMW Cuttack plant’s day-time power requirement dependency on fossil fuels by over 40% and replace it with a clean, emissions-free and renewable energy source.
“We see the solar-power plant expansion at our KCMW plant in Cuttack as providing the right impetus for our endeavours to continually adopt the cleanest and most economical fuel,” said Ganesh Jirkuntwar, national manufacturing head of Dalmia Cement.
Anew COVID-19 Response Report (CRR) maps out the wealth of opportunities that Egypt’s far-reaching urbanisation drive is producing for the construction sector and related industries against a backdrop of population growth and economic expansion.
The report - produced by Oxford Business Group (OBG) in partnership with The Arab Contractors (Osman Ahmed Osman) - highlights the North African country’s sustainable development strategy in an easyto-navigate and accessible format that includes key data and infographics.
It looks in detail at the new cities and megaprojects under construction or in the pipeline across the country, ranging from extensive utilities infrastructure to wide-ranging transport initiatives.
Initiatives explored include Egypt’s plans to increase its water desalination capacity fourfold, powered mostly by solar energy,
and make high-speed electrical rail a major focus of its transport infrastructure development.
The CRR examines how the construction sector responded to the pandemic and retained resilience throughout the health crisis while charting the rollout of key domestic developments and others launched elsewhere, such as the Julius Nyerere Hydropower Plant and Dam in Tanzania.
Sayed Farouk, chairman and CEO of The Arab Contractors, said Egypt’s construction project pipeline has changed the nature of operations in recent years.
“The series of megaprojects has helped us add value to our
operations in recent years, and we have worked to ensure projects are completed in a timely manner,” he added. “In order to achieve an accelerated timeline while ensuring projects were completed in line with international standards, we have invested in technology, human resources and high-quality inputs.”
Dana Carmen, OBG’s country director in Egypt, said that a decision to allow essential construction work in Egypt early on in the pandemic meant progress was made on key infrastructure projects, which, in turn, had a positive impact on the economy.
“Egypt was one of only a few countries to post positive GDP growth in 2020, with its strong economic performance driven in part by construction activity,” she said. “We expect further expansion across the sector and in related areas of business as the global recovery gathers pace and more of the megaprojects that characterise Egypt’s sustainable development strategy are rolled out.”
FLSmidth is delivering equipment to a new clay calcination project in Ghana that will replace cement clinker with environmen tally friendly clay.
The technology will cut up to 20% of CO2 emissions compared to current practices on site. The order given to Denmark-based FLSmidth includes what is said to be the world’s largest gas suspension calciner system and a complete grinding station, adding another 120% grinding capacity.
FLSmidth adds that the order is set to provide significant reductions in carbon emissions to CBI Ghana’s cement production outside of Accra in southern Ghana. Together with the new grinding station, Swissowned CBI expects both financial
The order will reduce CBI Ghana’s carbon emissions
and environmental return-oninvestment from lower specific CO2 emissions, energy and fuel savings, and reduced costs from clinker imports.
“Ghana is the perfect location for using clay as an environmentally friendly alternative to clinker,” says Frédéric Albrecht, CEO at
CBI Ghana. “West Africa is traditionally a clinker and cement importing region due to the lack of suitable limestone reserves.
“Developing countries with their young populations and a growing need for infrastructure and housing represent the future in cement consumption. Calcined clay cements are the most sustainable alternative to traditional clinker-based cement.”
FLSmidth says that using calcined clay to minimise the need for traditional, carbonintensive clinker is a key technology in eliminating the environmental footprint from cement production, which today accounts for 7-8% of the world’s CO2 emissions.
CNH Industrial has officially inaugurated its new India Technology Centre (ITC) in Gurugram, southwest of New Delhi in northern India.
This strategic hub is an integral part of the company’s global R&D footprint focusing on product development and digital solutions.
The ITC is the first of its kind in India for CNH Industrial, a global leader in construction and agriculture, whose Construction Equipment business includes the CASE Construction Equipment brand. It is equipped with the latest technology and capabilities, including an innovation centre, vehicle simulation and a state-ofthe-art extended reality/virtual reality laboratory to support global technology-led projects.
The centre has been operational since March 2021 and consider-
ing its early returns, the addition of further design development spaces for additive manufacturing, embedded software, data analytics, and user interface & user experience (UI/UX) with advanced simulation capabilities is foreseen. This site will play a strategic role in collaborative efforts with its sister R&D centres worldwide to innovate and leverage India’s leading-edge technology and digital ecosystem, with
increased efficiencies to benefit customers.
The centre will also focus on developing core competencies in customer-influenced software solutions and technologies, including cloud, embedded, electrification, autonomous, advanced analysis, simulation, automation and mechanical & electrical design.
Located in the Gurugram SEZ (Cyber City), the ITC employs over 100 people and is currently recruiting more through a rigorous and discerning talent search that prioritises diversity.
“India’s vast potential, thriving economic development and highly-skilled talent pool make it an attractive market for the expansion and growth of our business,” said Chun Woytera, president Asia Pacific, CNH Industrial.
Construction output in Northeast Asia is forecast to record a 4.2% growth and reach US$4.71 trillion in 2022 compared to $4.52 trillion in 2021. It will account for 39% of the projected $12.19 trillion of global output this year.
However, the growth of construction output in Northeast Asia in 2022 has been revised downwards by 0.8% this quarter due to the slowing construction activities across the region, says GlobalData, a leading data and analytics company.
GlobalData’s report, Construction Market Size, Trends and Growth Forecasts by Key Regions and Countries, 2022-2026, reveals that only China, Taiwan and Japan recorded real construction output growth in 2021. The remaining construction industries of the region recorded a second successive contraction last year, with the pandemic-induced scarring of potential construction output deepening as a result.
Out of the construction industries which contracted last
year, only South Korea is expected to recover to its pre-pandemic output this year.
A cause for further concern is the slowing of activity in the Chinese construction industry, the largest in Northeast Asia and globally, with growth slowing to just 2.1% in 2021 and headwinds mounting in the first quarter of this year.
Looking ahead, Willis Rooney, economist at GlobalData, said: “A tightening of restrictions in
Hong Kong and the lockdowns of Shenzhen and Shanghai in China following severe outbreaks of Omicron are likely to have weighed on construction activity in the first quarter of this year.
“However, with an ambitious economic growth target of 5.5% set at China’s National People’s Congress in March 2022, further fiscal stimulus and an easing of monetary policy are expected this year, which will underpin regional construction growth in 2022.”
Powerscreen has appointed MSM Group as its authorised distributor for Mongolia.
MSM Group will join Powerscreen’s global network of distributors to supply the full range of the Northern Irish company’s crushing, screening and conveying equipment, genuine spare parts, and machinery maintenance packages to Mongolian customers.
MSM Group has around 300 employees and offers a wealth of technical, electrical, and mechanical engineering expertise.
The firm’s main office is in Ulaanbaatar, with service points around Mongolia.
Matthew Metz, VP Industrial of MSM Group, said: “MSM has been working with the Terex organisation since 2014, and adding Powerscreen to our portfolio helps us meet the increasing needs of our customers in Mongolia. MSM will assume responsibility for sales, service, and parts sales for the entire range of Powerscreen products.”
James Vaughan, Powerscreen regional sales manager, commented: “We see fantastic growth potential for Powerscreen in Mongolia, proven by this recent signing of MSM Group.”
Having largely been a single-brand distributor for the past 18 years, Kemach Equipment, one of the leading equipment suppliers in Southern Africa, has over the past year transformed into a multi-brand equipment supplier. This follows the signing of strategic distributorship agreements with several leading original equipment manufacturers. CEO Les Lothian explains the thinking behind the new strategy. By Munesu
Shoko
Established in 2003, Kemach has over the years been the force behind the JCB name in South Africa and neighbouring countries such as Lesotho and Eswatini (previously Swaziland). However, following the end of the JCB dealership agreement in 2021, Kemach has adopted a multi-brand strategy that has seen the company entering into distributorship agreements with several premium equipment brands.
The business realignment strategy was put in motion in March 2020 when, in partnership with Anhui HELI, Kemach introduced its Kemach Forklift range, giving the company a footprint in the booming materials-handling market.
The distributorship agreement with McCloskey International in October 2020 was a further coup for Kemach in its quest to expand its products and services in the mining, aggregates, construction and demolition, recycling and infrastructure markets.
In July 2021, Kemach was appointed as the new supplier of the full range of BULL backhoe loaders in South Africa, Lesotho and Eswatini. This was followed by yet another strategic distributorship agreement with BOMAG GmbH in August 2021, allowing Kemach to market and support the full range of BOMAG’s heavy and light machines in South Africa, Lesotho and Eswatini.
During the same month, Kemach Equipment signed a distributorship agreement to sell and support the full range of Liebherr earthmoving equipment in South Africa. The range includes excavators (20 – 100t), wheeled loaders (10.4 – 25t), bulldozers (20 –73t) and a line of telehandlers.
The multi-brand strategy, explains Kemach Equipment CEO Les Lothian, is in line with the ever-changing needs of customers. With the evolution and transformation of project scopes, he says, the introduction of strong, high-performance products and cost-centric services is needed now more than ever.
“We felt that by being linked to a single brand we were limited to a certain extent.
There are several sectors of the South African economy which we couldn’t participate in. With a single brand, we were pretty much limited to the construction sector, and missed out on opportunities in the materialshandling, mining and quarrying sectors, among others” explains Lothian.
It is a common norm that businesses should never put all their eggs in one basket; this is the central thesis on which the concept of diversification lies. Given the importance of a well-diversified portfolio in any market condition, Lothian maintains that the multibrand approach places the business in a far more balanced position. In an event that one of the markets struggles, for example, when construction is down, the business can tap into other markets such as mining and materials handling to remain on a level footing.
“We are building our business around five different pillars – Kemach Forklifts (materials handling), McCloskey (crushing & screening), BULL backhoe loaders (construction), BOMAG (infrastructure development) and Liebherr, which gives us a footprint in not only construction, but also the logistical handling of mining materials. All of these segments leverage each other, giving our business the much-needed balance,” says Lothian.
Apart from diversification into different sectors of the economy, the multi-brand strategy also allows Kemach Equipment to offer a total solution to its customers. Since October 2020, Kemach Equipment has recorded remarkable success with the
With over 70 years of trusted machinery development and building across more than 10 industries, Liebherr products are a vital addition to the Kemach Equipment stable
As customers chase for the convenience that comes with dealing with a single provider for their different needs, the equipment industry has not only seen an accelerating trend towards consolidation within the supplier community, but also an expansion of the range of products and services offered under one roof. This has created true one-stop shops that are able to service a wide range of customers’ needs from one stable.
“In a crushing and screening application, for example, we are now able to offer a crusher and a matching excavator to load it. At the backend, the customer may need a wheeled loader to clean up whatever they are handling and to load material onto trucks. Previously, we were not able to offer that full value chain, but now we can,” he says. “We have also been very careful in selecting our OEM partners. All the products in our stable complement each other, are of the highest quality and offer true value for money”
The two brands that speak directly to the aggregates sector are McCloskey and Liebherr. Commenting on the McCloskey offering, Lothian says, “We chose McCloskey because of the brand’s stature in the South African and the global market at large. Being part of Metso Outotec, we felt that the brand was the right fit for our needs,” he says.
Since October 2020, Kemach has recorded remarkable success with the McCloskey offering, averaging a machine a month. The machine population is spread across quarrying, mining and recycling applications.
“Adding McCloskey to our range of leading brands enhances our ability to satisfy the growing needs of our customers, while also creating the opportunity to strengthen our position of being a total solutions provider to the markets we participate in,” he says. “With sustained and strong growth in the population and the required infrastructure, we anticipate
equally strong growth in the aggregates sector. Bringing McCloskey products to the market at this key time benefits our company and our customers.”
Having previously been a constructionfocused equipment supplier, the Liebherr earthmoving range gives Kemach Equipment a foothold into new sectors such as mining and quarrying.
Liebherr and Kemach are two household names in the South African earthmoving equipment industry. The two companies, says Lothian, will leverage each other’s
strengths to provide customers in South Africa with a high-end product that is backed by unparalleled aftersales support.
“With over 70 years of trusted machinery development and building across more than 10 industries, Liebherr products are a vital addition to the Kemach Equipment family and with this partnership, we can continue with our promise to be the best business decision for our customers,” says Lothian.
On the construction side of things, Lothian says Liebherr offers a strong offering in the 20 – 30 t excavator segment, which constitutes about 60% of the excavator market in South Africa.
The larger excavator range, together with the extensive wheeled loader offering, also allows the company to compete at the larger end of the scale, complementing the McCloskey offering in the crushing and screening space. Lothian is also excited about
The McCloskey S250 Screener is one of the world’s largest track mobile screeners
the prospect of having a dozer range in the Kemach stable for the first time.
“We have never had an experience with dozers. It’s a small segment of the market, but the value is substantial. The local market has a lot of confidence in the Liebherr product line and we are excited about the prospects of growth in that market segment,” he says.
“This is going to open new doors for us,” he adds. “Our experienced sales team is now equipped to provide current and future customers with a 360-degree solution across applications. If we can package this with extended warranties and service plans, we will be able to create absolute peace of mind for our customers.”
Commenting on the strategy, Lothian says one of the concerns around the Liebherr product in the local market has
always been the price. However, the two companies are working together to offer a price-competitive product to the market. Leveraging a strong support footprint at the back-end of the market, Lothian believes that the Liebherr venture will be a major success for the company.
“We have taken delivery of a few machines from Liebherr-Africa. We also have a large fleet on order, and when the product hits the ground, there will be substantial changes in the way we are going to market it.”
Key to success, adds Lothian, will be the company’s strong branch footprint across all key regions of South Africa and neighbouring countries. Sales, support and service are delivered through Kemach’s extensive southern African footprint, including its national office based in Gauteng, and branches situated in 11 locations throughout South Africa.
To ensure seamless operations throughout its territory, the company has a network of fully-fledged branches in Jet Park, Ethekwini (Durban), East London, Gqeberha (Port Elizabeth), George, Cape Town, Bloemfontein and Nelspruit. This is complemented by a network of sub-dealers strategically positioned in Schweizer Reneke and Polokwane in South Africa, as well as Windhoek (Namibia) and Swaziland. Kemach also owns and operates its own branch in Lesotho.
The company is also currently re-establishing branches in the mining towns of Rustenburg (North West Province), Middelburg (Mpumalanga Province) and Kathu (Northern Cape Province) in South Africa.
Looking ahead, Lothian is excited about the prospects of growth for the company across the infrastructure value chain. Given that South Africa’s economic recovery plans centre on infrastructure development, there is sentiment that many infrastructure projects will come to market in the next few years.
The South African government unveiled 62 projects at the Sustainable Infrastructure Development Symposium South Africa in 2020. While the pace of progress has been slow, approximately 33% of these projects are in construction and some have already been completed, with another 20% at various stages of preparation and feasibility.
“As a total solutions provider, we are in a better position to add value to our customers’ businesses. We are offering a product range that gives our customers value – lower cost per tonne, long life and high resale value. All of these parameters build value for the customer. Given the tough nature of doing business in the current environment, we believe we are geared to help customers make the best business decision,” concludes Lothian. AB
A vibrant South Korean aggregates, sand and gravel sector offers great commercial potential for suppliers of building materials and off-highway equipment manufacturers, but quarry licensing restrictions and a lack of sector workers are key issues that need to be addressed. Guy Woodford reports
South Korean aggregates, sand and gravel demand is rocketing. While high demand is not unusual given that 81% of its population of 51 million live in urban areas, creating a constant need for new infrastructure, such is the current building boom over 390 million tonnes were consumed nationally in 2021, according to figures published by the South Korea Ministry of Land, Infrastructure and Transport (MOLIT). That is a comparable consumption level to France. Furthermore, South Korean aggregates, sand and gravel consumption is tipped by the same source to rise to over 420 million in 2022. This represents a lot of orders for the country's 500-plus quarries.
The election of Yoon Suk-yeol, a conservative former prosecutor, as South Korea's new president in March 2022 is unlikely to impact the firm infrastructure spending commitments made by former president Moon Jae-in. Yoon and his People Power Party triumphed over Lee Jae-myung and his Democratic Party following a bitter battle in a politically divided nation. Under
the South Korean constitution, presidents are restricted to a single five-year term.
Washing plant giant CDE's PT CDE Southeast Asia business says the biggest aggregates, sand and gravel demand in South Korea is centred on the country's capital, Seoul, and Incheon, South Korea's thirdlargest city, in Gyeonggi province, in the north-west of the country (169.403 million tonnes in 2021)
Speaking about the key issues South Korean aggregates, sand and gravel producers face, a company spokesperson said: "Currently it seems to be very difficult to acquire permissions for new quarry or to extend permission period for existing quarry. This is due to restrictive environmental measures.
"We have heard complaints about decreased turnover due to the implementation of a government's 52-hour workweek policy. There are also challenges in finding personnel, and new legislation has been put in place regarding management and ownership accountability for severe accidents on sites."
Commenting on what kind of aggregate, sand and gravel washing plant South Korean quarrying customers are looking for, the spokesperson continued: "Because of high land prices, customers prefer compact facilities. Some are also looking at two-level washing plants solutions. All customers want high efficiency, low water content in their sand products and less water consumption."
Lee Yongjik, vice president of the Korea Aggregates Association (KAA), echoed CDE Asia's mostly upbeat appraisal of the South Korean aggregates market: "We're expecting aggregates demand to increase over the coming decade, as the [former Moon Jae-in] government announced a plan to provide 300,000 more houses in Seoul's satellite cities to stabilise real estate prices. The price of real estate has doubled in many parts of the country during the last couple of years, and it has become impossible for young people to purchase homes. Getting timely quarrying permits to meet increasing aggregates demand is a very important issue."
Lee said the government also committed to building a further 1.27 million homes in the metropolitan Seoul area through its New Town Development Plan. "It also secured land for another 830,000 homes, so we need to plan for the seamless supply of aggregates for those homes," he stressed.
Commenting on concerns over South Korea's aggregates extraction licensing rules, Lee continued: "The licence to extract aggregates is given by the Korea Forest Service. The main mission of the Korea Forest Service is to preserve the forest, not to ensure a timely supply of aggregates. There is not any institution that balances such conflict of interests. Thus, there is a problem with meeting demands for aggregates. About 40% of all aggregates supply comes from quarry extraction in the mountains.
"In order to make up for a decrease in other sources of primary aggregates, we need to increase quarry extraction, but getting a licence is very difficult. This can lead to unreliable aggregates supply. In 2017, 60% of the planned amount was met, whereas, in 2020, 94% of the planned amount was supplied. Taking an average over the past six years, 82% of the planned mountain aggregate amount was supplied."
Lee said that since 2021, incentive points are awarded in the Aggregates Extraction Competency Assessment to South Korean aggregates supply businesses operating 'environmentally friendly' facilities or equipment. Factors influencing an assessment score include deploying electric excavators, dust suppression systems, and operating closed stone crushing facilities.
"The Korea Aggregates Association and the aggregates industry are working hard to change laws so that local governments license businesses based on good production planning to ensure timely and quality supply
of aggregates," explains Lee.
"We are also pushing to find a good governance solution where the currently mandated need for resident/local fishermen approval for marine aggregates dredging can be negotiated to lead to a win-win situation.”
Lee said that the Korea Aggregates Association is also working to change the criteria of the Post-Environmental Impact Assessment (EIA) for closed quarries. "It is required for an aggregates supply business to conduct an EIA for three years after it has closed the quarry and has made restoration of the site. However, other development projects only go through an EIA at the closing of a site or project. It is unfair
that quarries are subjected to a different interpretation of the regulations."
Kyounghun 'KH' Lee, key account manager at Volvo Construction Equipment's South Korean business, said South Korean quarrying customers tend to opt for larger rather than medium-sized wheeled loaders and crawler excavators. "This improves productivity and reduces labour costs considering the expansion, strengthening and implementation of the 52-hour workweek (five days a week) policy and the Serious Accidents Punishment Act.
"For example, whereas the Volvo EC300E excavator and L150H and L180H wheeled loaders were the most popular in the past,
the most common models now are the Volvo EC380E and EC480E excavators and L220H and L260H wheeled loaders. Larger wheeled loaders with a bucket capacity of over 7m³ are generally preferred since these can load a 25-tonne tipper truck in three passes."
Lee said: major South Korean quarrying and aggregates customers are also greatly interested in Volvo Co-Pilot and Assist Services. "These customers are the most concerned about working efficiency and productivity. Load Assist with On-Board Weighing, for example, is becoming increasingly popular as it can calculate precise delivery amounts to eliminate conflicts between primary contractors and subcontractors due to inaccurate delivery amounts."
Asked about the growth potential for Volvo CE in South Korea's quarrying sector, Lee said: "We have strong opportunities to increase our sales of large excavators and wheeled loaders, which are highly preferred in quarries because of their superior operating performance, high productivity, high fuel efficiency, and strong durability. We also expect to increase our sales of articulated haulers, which work well in partnership with our larger excavators and wheeled loaders.
"We also have opportunities to support customers to decrease the carbon footprint of their operations. The recent strengthening of environmental regulations and volume restrictions for quarries
South Korea aggregates demand
Hyundai Construction Equipment (HCE) is investing US$170mn in its Ulsan production plant in South Korea, increasing capacity by 50%. The move will support the business's growing presence in the booming global construction equipment market while providing a manufacturing base for a new generation of electric- and hydrogen-powered equipment.
The investment, to be deliv-
ered over the next four years, will increase production at the giant plant by 4,800 units a year, bringing annual capacity to 15,000 excavators, wheeled loaders and other construction models.
HCE will merge the production and assembly functions currently in Factory 1 and Factory 2 into a single facility, simplifying processes and increasing savings by maximising efficiency. This will reduce the
working hours involved in machine production and cut logistics costs throughout the supply chain. The move will also reflect HCE's environmental, social and governance factors, using eco-friendly submaterials when conducting interior and exterior finish work.
The company is increasing its market share in every business region by responding to current market trends in the global construction equipment market and by looking ahead to the customer requirements of tomorrow's infrastructure and construction projects. The company is also planning to benefit from the recent US launch of the 'Build Back Better World (B3W) initiative for developing countries.
HCE announced in 2020 that it plans to bring to market a range of excavators powered by hydrogen fuel cells, produced in cooperation with Hyundai Motors, which has its largest automotive plant in Ulsan. The company has already unveiled a range of hydrogen-powered industrial forklifts that will launch in 2023. It continues to develop the
low- and zero-carbon emissions equipment that the customer will demand in the future.
"Strengthening the competitiveness of the Ulsan factory is the first challenge that needs to be addressed to reach the global top five, the goal of the construction equipment division of the Hyundai Heavy Industries group," said CEO Choi Cheol-gon. "With this investment, we will further raise our brand competitiveness by producing and delivering construction equipment with increased efficiency."
In November 2020, HCE completed the construction of a technology innovation centre, investing $65mn. The new centre includes 16 laboratories, employing more than 100 researchers. It is involved in research and development projects focusing on eco-friendly technologies, highefficiency and noise-reduction technologies and a virtual verification system. The site also performs quality research and verification of components and completed equipment.
have made aggregate supply unstable. Hence, aggregates producers are seriously concerned about environmental impact due to the growing possibility of a supply shortage of natural aggregates compared to demand."
Lee said that according to MOLIT, aggregates would be supplied this year based on the principle of regional selfsupply. If there is a shortage, the transport of sea sand from South Korea's EEZ and neighbouring areas will be adjusted to stabilise the aggregates supply for each region. An EEZ (exclusive economic zone), as prescribed by the 1982 United Nations Convention on the Law of the Sea, is an area of the sea in which a sovereign state has special rights regarding the exploration and use of marine resources, including energy production from water and wind.
"Given quarrying conditions and the trend to decrease natural aggregate sources, MOLIT plans to use forestal aggregates and crushed aggregates as much as possible, and to promote the use of alternative aggregates, such as recycled aggregates," continued Lee. "In addition, MOLIT plans to invigorate the production of crushed sand within regions lacking their own sand production and to meet the shortage by importing coastal sand from the West Sea EEZ and the Ongjin and Taean areas."
Lee said that as well as a major increase in housebuilding in 2022, as outlined by MOLIT, being good for aggregate demand, The Bank of Korea's economic outlook report also offers much encouragement for aggregates demand as construction investment in 2022 is expected to increase 2.9% compared to 2021. Major transport infrastructure projects, such as Seoul's GTX (Great Train Express) super-fast subway, will, believes Lee, also support increased aggregates demand. The first route of GTX railway is due to open in 2024. AB
Engineering researchers at three South Korean universities have developed cement-based composites with conductive fillers that generate and store electricity by contact electrification.
Smart cities that champion sustainable net-zero energy consumption are no longer a new-fangled concept. However, achieving this state seems plausible only in the distant future for the building sector.
Now, university researchers have developed a novel cement-based composite that can generate and store energy induced via contact between materials. This material could be used to build buildings that can harvest energy from human motion in their floors and wind and raindrops hitting them.
Everything around us is getting smarter, from devices to home appliances and eventually entire cities.
The concept of a smart city, which involves energyefficient ecosystems that can reduce carbon emissions, save energy, and provide better lives, is no longer a thing of the distant future. However, it's worth noting that since the building sector alone is single-handedly responsible for 40% of the entire modern world's power consumption, buildings need to be able to offset this energy consumption.
The solution to this prob-
lem may be closer than you might think. In a recent study published in Nano Energy, researchers from Incheon National University (INU), including Prof. Seung-Jung Lee, and researchers from Kyung Hee University and Korea University, addressed this issue by developing an all-new structural material that can make construction more eco-friendly.
The team developed a cement-based conductive composite (CBC) with carbon fibres that can also act as a triboelectric nanogenerator (TENG)— a type of mechanical energy harvester. This paper was available online on 3 August 2021 and was published in Volume 89, Part A of the journal Nano Energy in November 2021.
"We wanted to develop a structural energy material that could be used to build net-zero energy structures (NZES) that use and produce their own electricity. Since cement is an indispensable construction material, we decided to use it with conductive fillers as the core conductive element for our CBC-TENG system," explains Lee. The concrete exteriors of buildings are often exposed to external mechanical energy sources such as ocean waves, movement of objects, wind on the walls, and raindrops on the roofs. Cement-based TENGs can harvest energy from
these sources via contact electrification— a process where electricity is generated due to interactions between two materials.
The team designed a lab-scale NZES and a CBC-based capacitor using the developed material to test its energy harvesting and storage abilities. The results indicated that at a 1% volume of conductive carbon fibres in a cement mixture, the CBC mixture exhibits optimal electrical properties while retaining the superior mechanical properties of cement. The researchers' electrical measurements confirmed that CBC-TENG could be safely used as a building material as the current generated by it was much lower than the maximum allowable current for the human body.
Apart from energy storage and harvesting, the material could also be used to design self-sensing systems that monitor the structural health and predict the remaining service life of concrete structures without any external power. "Our ultimate goal was to develop materials that made the lives of people better and did not need any extra energy to save the planet. And we expect that the findings from this study can be used to expand the applicability of CBC as an all-in-one energy material for net-zero energy structures," concludes Lee.
Thai cement producer TPI Polene Cement Company Limited is lowering its carbon footprint and clinker production cost with a novel Metso Outotec solution. Guy Woodford reports
Following its successful usage of Metso Outotec’s in-pit crushing and conveying (IPCC) systems, it was no surprise that Thailand’s TPI Polene Public Company Limited (TPI Polene) turned again to the global premium building materials plant manufacturer to help reduce the carbon footprint and running cost of its cement plant, located 100 kilometres north of Bangkok, in Saraburi province.
Among the top three manufacturers and distributors of cement products in Thailand with an impressive history regarding plant sustainability, TPI Polene was the first cement manufacturer in Thailand to be awarded an ISO 9002 Certification for surpassing industrial and environmental protection standards. On top of that, they were also the first cement manufacturer to be awarded the Carbon Label for both Portland cement and mortar cement products. The Carbon Label demonstrates that the producer has proven data that shows it has significantly reduced CO2 emissions.
TPI Polene operates waste-heat-recovery
power plants that generate electricity from waste heat emitted from TPI Polene’s four cement production plants. They use refusederived fuel (RDF) to generate electricity in their RDF-fired power plants. As a result, TPI Polene has become a power plant operator in Thailand, with the largest waste-to-energy power plant operations and renewable energy to enhance environmental efficiency.
In 2008, Metso Outotec’s Thailand distributor, Uawithya, organised IPCC seminars for various Thai cement producers. After learning of Metso Outotec IPCC offerings, TPI Polene implemented IPCC systems into its operation. The move was mostly due to the personal involvement of company CEO Prachai Leophairatana, seen as a keen new-technology adopter within Thailand’s industrial sector.
“TPI Polene is a Public Company Limited with a very technical leadership, so it takes a different and more personal approach to decision making,” said Jorma Kempas, product manager, Lokotrack Solutions, Metso Outotec. “There is always a risk when you try something new, and many stakeholders in
big corporations choose to avoid that risk. It was such a smooth process working with him on this project, and he could see himself that we were making a difference.”
Operational costs, worker safety, and CO2 emissions are challenges most mines and quarries face today. While there certainly isn’t a magic remedy that would solve all problems overnight, Metso Outotec’s in-pit solutions, such as IPCC, are widely recognised as a good place to start.
In 2012, Metso Outotec delivered the first IPCC systems to the TPI Polene cement plant in Saraburi province, replacing its conventional truck haulage with mobile crusher and belt conveyers. This consisted of three Lokotrack LT1418E mobile impact crushers and Lokolink belt conveyors, each producing 600-700tph of 0/80mm limestone for cement production. Metso Outotec also delivered the in-pit conveyors, which convey the crushed rock from Lokolink conveyors to the overland belt conveyor. Since this successful implementation, TPI has reported a 50% haul cost saving compared to truck haulage.
Based on its positive experience from the earlier IPCC installation, TPI wanted to utilise the IPCC concept for an upcoming project. The objective was to initiate the specific IPCC benefits, such as lower haulage cost, less dust and exhaust gas emissions, and improved worker safety.
In 2017, TPI launched a project to open a new deposit at its Saraburi site to extract shale and andesite for clinker production. Initially, Metso Outotec planned to deliver a Lokotrack with a jaw crusher. However, since the deposit contains a lot of fine material, which appears highly sticky in the rainy season, it was decided to use a sizer type of crusher fed by the apron feeder instead of a jaw or impact crusher.
At this time, Uawithya Mining brought Komatsu Mining and its sizer technology into the loop. As a result of working together with Komatsu, the Metso Outotec LT1510RC was developed. Paired with the mobile Lokolink conveyors, this duo working in parallel gave TPI Polene the ability to maximise its operation while minimising its cost and environmental footprint.
The TPI Polene Saraburi cement plant is quite large in size and requires a lot of traffic and movement throughout the vast space. With multiple operating pits and the creation of a completely new pit to extract shale and andesite for clinker production, it was crucial to the site that they focus on optimal plant efficiency. With the robust and reliable mobile Lokotrack, the track-mounted construction allows machines to move around a
production site or between sites easily.
The LT1510RC (rated up to 1500tph) produces 900-1200tph (depending on the type of feed) of 0/300mm material. This is conveyed through the Lokolink conveyors and in-pit conveyors supplied by Komatsu Mining onto the overland conveyors that bring the material into the process plant.
A mobile Lokotrack with a sizer is directly loaded by a hydraulic excavator. Metso Outotec mobile Lokolink conveyors transfer the crushed material to a shiftable conveyor system. The secondary sizer (by Komatsu) is located at the first transfer point of the fixed conveyors, crushing the material down to less than 50mm. Overall, material hardness tends to vary between 20 to 200 MPa.
It is no secret that sticky feed is a rising global issue in mining and aggregates production and can cause various challenges within the operation. Whether it’s clogging the system, taking the time to clean, or starting the process again – sticky feed is a complete nuisance to any operating plant. However, the TPI Polene cement plant has begun to take action against this issue by implementing the Metso Outotec IPCC solution.
“The biggest benefit is that even with the sticky material, they are able to produce – this is the main thing,” says Jorma Kempas. “And they are using the IPCC system, which has lower cost and is environmentally better than if they were using a conventional truck haul. The site focuses on sustainability and lower operating cost, which we also strongly believe in.”
Fuel costs are also a major expense in plant operation. Therefore, low consumption is essential. In using the IPCC systems and the Lokotrack and Lokolink, the large site can further optimise their production and maximise their safety and sustainability - all whilst minimising cost at the same time.
“It’s important to note the safety aspect too – from a health and safety perspective, it reduces their mobile fleet, so they’ve got less traffic movement on the site, which is much safer,” Kempas explains. “From an environmental perspective, it reduces fuel consumption and the environmental impact of dust emissions. From an operational perspective, it does everything they need it to do and more.”
Following this success, TPI Polene has learned that Metso Outotec can deliver these systems and implement them responsibly and effectively. Metso Outotec says it takes great pride in creating and continuing its positive working relationship with the customer and distributor and looks forward to future opportunities that can arise on the back of this project.
“The reputable connection we have with our distributor Uawithya, and the site itself, is an excellent example of working together,” says Campbell Johnson, capital distribution manager - Asia Pacific, Metso Outotec. “The fact that they continue to choose us, and we are still the one, speaks volumes on our capabilities. From both a brand position and an operational point of view, the support we’ve provided constantly to our distributor has helped everything move as smoothly as possible.”
Metso Outotec says it is always exciting to find a company that exemplifies the same core values as itself. A company spokesperson said: “With our strong focus on sustainability and helping our customers optimise their operation, our collaboration with TPI Polene is understandably fitting. Through the choices we make together with our customers, we can influence the outcomes and take the industry towards more responsible use of the world’s precious natural resources. At Metso Outotec, our core expertise is to help our customers transform the industry. That’s why we are the partner for positive change.” AB
The latest launches in the crushing and screening sector include a range of trackmounted machines with electric drives that are claimed to lower both environmental impact and operating costs. Liam McLoughlin reports
Metso Outotec is developing a full range of electrically driven track-mounted crushers and screens in response to what it says is a growing demand for sustainable plant solutions.
The Finnish manufacturer adds that its new Lokotrack range will be built on an innovative platform that it has been developing since 2020 with a total R&D investment of €20m. The development work will primarily occur at Metso Outotec’s technology centre in Tampere.
The platform concept has now been developed, and Metso Outotec is currently entering the design phase of the first new products. The new Lokotrack range will be transformational for the whole aggregates industry of mobile crushing and screening. It will also significantly contribute to Metso Outotec’s Planet Positive strategy and commitment to reaching the 1.5OC climate target.
“The next generation Lokotrack range will address the needs of our crushing and screening customers by providing new easy-to-use diesel-electric equipment,” says Renaud Lapointe, senior vice president at Metso Outotec’s aggregates business area. “The possibility to run track-mounted machines from an integrated genset or connect to an external power source lowers operational costs and allows access to renewable energy for our customers,” he continues.
The new unique platform will enable a faster and more agile way to develop products and reduce the number of components. “Using one common architecture throughout the range allows scalable solutions that can be seamlessly combined and adapted for different applications and capacities,” says Jarmo Vuorenpää, director, new Lokotrack offering, aggregates business area at Metso Outotec.
“Harmonised design together with advanced digital solutions enables our global service network to support the customers throughout the entire equipment lifecycle.”
The concept of track-mounted crushers and screens was developed in Finland in
1985 to minimise the cost and energy use. The idea has grown significantly during the last 35 years, with thousands of units manufactured and sold globally every year. Lokotrack has made it possible to provide on-site mobility close to the processed raw materials, lowering transport and hauling costs and emissions.
In a separate move, Metso Outotec has added a new impact crusher to its Nordtrack mobile crushing and screening range, targeting especially smaller-sized applications and jobsites in the constructionand demolition-waste-recycling segment.
The Nordtrack I1011 mobile impactor has compact dimensions and a powerful, high-performance crusher, ideally suited for contractors and rental work. Equipped with a large hanging screen, it combines high crushing capacity with calibrated end-product accuracy.
The versatile Nordtrack I1011 crusher is suitable for working in different jobsites from rock crushing to concrete- and demolitionwaste-recycling. It is transported on a standard trailer, making it cost-effective and quick to move between sites. Metso says that, thanks to its agility, moving the equipment in tight places inside the jobsites is easy. The company adds that, with its service support and global inventory of parts such as different blow bar options, Nordtrack I1011 is a dependable choice for contractors and as a rental machine.
“We have listened to the feedback from our customers and are happy to offer this newest addition to our Nordtrack range. The launch of Nordtrack I908S was very successful, and consequently we have been asked for a bigger mobile impactor unit,” says Vesa Tuloisela, who heads the Nordtrack product offering at Metso Outotec. “The I1011 has a more powerful crusher and engine, resulting in a capacity as high as 300 tph. As a mobile crusher it also is well suited for the recycling of demolition and concrete waste, or reclaimed asphalt,” he continues.
In April, Metso Outotec signed an agreement to acquire Tesab Engineering, a Northern Ireland-based company offering mobile crushing equipment for aggregates applications, including quarrying, recycling, asphalt and concrete.
Tesab's turnover in 2021 was around €30m, and the company has more than 60 employees, primarily in Europe. The value of the deal has not been disclosed. Metso Outotec says that the deal, scheduled to close in the second quarter of 2022, will have no material impact on its financials.
Tesab's product portfolio includes mobile jaw, impact and cone crushers, mobile screens, scalpers and stackers. Metso Outotec says the acquisition will complement its current offering in the mobile crushing and screening markets. Tesab will continue as an
independent brand within Metso Outotec and manage its distribution network.
Cone crushers are an integral part of any comminution process – but how do you know if your process requires a live shaft or fixed shaft model? This question has been addressed by Mark Utecht, director of the comminution technology group at crushing and screening equipment manufacturer Weir Minerals.
Utecht says that cone crushers - such as Weir’s Trio TC live shaft and Trio TP fixed shaft models - offer robust reduction for medium- or above-hardness feed material and are suitable for secondary, tertiary or, if the application requires: quaternary crushing stages. “These compression crushers are highly effective in typical mining applications and when processing ballast,” Utecht adds.
Inside the crushing chamber, a moving cone (the head) compresses rocks against each other and the edge of the concave bowl. This reduces multiple-sized particles at once and minimises wear.
The concave shape of the bowl ensures rocks will be crushed several times before they exit the crusher, as the volumetric space between the head and bowl gradually narrows towards the bottom of the crushing chamber.
“The primary difference between our two ranges of Trio cone crushers, the TC and TP, is the rotating parts,” Utecht explains. “The Trio TC crusher’s classic live, or moving
shaft, design sees the entire shaft rotate eccentrically along with the head. While in a Trio TP crusher’s design, the shaft is fixed in the mainframe while the head rotates eccentrically. The TP’s design allows it to rotate faster and facilitates more interparticle crushing than the TC series.”
He states that Weir personnel are often asked: “Which cone crusher is better?”, adding that the answer is not as straightforward as it may seem, with factors such as the application and operating conditions determining the correct choice.
In the Trio TC cone crusher, both the shaft and head are moved in unison eccentrically during operation. Utecht says this proven design can be traced back to the original cone crushers invented in the 1920s, and a century of optimisation later, it’s one of the most reliable crushers in operation today.
“Although we always recommend all cone crushers are choke fed, the TC series’ straightforward design makes it ideal for use in applications where feed conditions are unreliable,” he says. “It has a slower rotation and a smaller throw (the space between the head and the bowl) compared to fixed shaft designs. It is also less susceptible to wear from intermittent feeds which leave the crushing chamber filled below capacity.”
Utecht says that Trio TC series cone crushers are based on a proven design and feature modern, easy-to-use control systems. He adds that their suitability for sub-standard
feed conditions doesn’t mean these are sub-standard cone crushers.
“Following months of operational and design upgrades, our Trio TC is a fully automated live shaft crusher, engineered to deliver maximum efficiency,” says Utecht. “It features state-of-the-art crushing technology with modern lubrication, power systems and optimised hydraulics. Every element has been considered in the design, from the gearing, to the motion of the shaft and eccentricity of the rotation.”
The Trio TP fixed shaft (or pedestal) cone crusher can utilise substantially more horsepower, with a bigger eccentric throw and a higher pivot point to deliver throughput as high as 1,000m/tph. The TP series is also said to benefit from higher percentages of interparticle crushing which enables it to produce a finer product curve compared to TC-style crushers.
The fixed shaft is more compact than live shaft designs, which Utecht says makes it ideal for mobile applications or plants with limited clearance.
“The easily adjustable closed side setting (CSS) makes it easier for operators to adapt to changing ore bodies, or for aggregate producers to achieve their preferred product,” he adds. “Our Trio TP series cone crusher naturally creates a cubical shaped end-product that can remove the need for further crushing and shaping.”
The flexible Trio TP series is available
in short-head and standard configurations offering 260-900hp, and is ideal for any project which facilitates choke-fed crushing.
Utecht concludes: “Using data from applications throughout mining and aggregates, Weir Minerals can support you throughout the entire process of cone crusher selection, installation, optimisation, and maintenance, from locations in more than 70 countries around the world.”
Wirtgen-owned Kleemann says two machines in its latest EVO2 generation of crushers are perfectly tuned to one another for line coupling in natural-stone-crushing applications.
The MOBICAT MC 110(i) EVO2 jaw crusher and the MOBICONE MCO 90(i) EVO2 cone crusher were developed with a focus on output, efficiency and flexibility. The mobile plants are frequently used together in the first and second crushing stage and pay off, in particular, due to the joint output level and simple line linking.
Kleemann adds that the two crushing plants in the latest EVO2 generation are harmonised with one another with regard to the transport points of the material, and the output also matches: the jaw crusher has the exact amount of power to perfectly utilise the cone crusher in the second crushing stage. The correct filling level of a cone crusher is particularly important to produce the highest grain quality with a minimum of wear. The MC 110 EVO2 can adjust its crushing gap
fully hydraulically by up to 180mm. The MCO 90 EVO2, on the other hand, can cover a gap range of 6-45mm with its new crushing tools. Depending on the feed material, a downstream screening plant can be used to produce concrete or asphalt grain sizes in a single operation.
The crushing plant of both plants is optimised automatically by the feed control CFS (continuous feed system) so that material is always conveyed with maximum efficiency through the machines. At the same time, the filling level of the crushing chambers is monitored. When the filling level reaches a height that can be defined in advance, the material feed of the machine is adjusted.
Kleemann says this system forms the perfect basis for the line coupling of an interlinked plant train. The optionally available probes at the crusher discharge conveyor and/or fine grain conveyor of the upstream machine monitor the filling level of the feeding unit of the respective upstream machine.
For safety reasons, the crushing and screening plants are connected to each other by a cable. If an emergency stop button is pressed on the plant train in the event of an emergency, all machines are safely stopped.
Finnish crusher and screener bucket maker ALLU has launched the new Transformer DC Series for the Chinese market. ALLU says it commenced its new Chinese manufacturing plan in 2021, after
No matter how challenging your needs, EARTHMAX SR 41 is your best ally when it comes to operations that require extraordinary traction. Thanks to its All Steel radial structure and the special block pattern, EARTHMAX SR 41 provides excellent resistance against punctures and an extended service life. In addition to long working hours without downtime, the tyre ensures extraordinary comfort.
EARTHMAX SR 41 is BKT’s response to withstand the toughest operating conditions in haulage, loading and dozing applications.
For info: europe@bkt-tires.com
listening to the needs of customers. The manufacturer adds that it was clear it needed a local facility to grow and support Chinese customers. The company says that investing in a local manufacturing facility has enabled it to make products tailored to the local market requirements.
ALLU operations director for China Pierre Bujes says: “Introducing the new DC Series, which ALLU has tailored just for the Chinese market will strengthen our support to our customers and operational presence, to help grow the region whilst being competitive in the local market.”
The ALLU Transformer DC Series parts are designed to be reliable screening attachments for a variety of screening, crushing, mixing, and aerating applications. All models are equipped with two hydraulic motors for maximum processing power. The attachments have reinforced sides, making the bucket robust and durable even in demanding environments and with demanding materials.
The main areas of application for the Transformer DC Series are: waste material handling & processing; compost mixing and aerating; pipeline backfilling/padding; stabilising clay; cable backfill; environmental remediation; and soil & gravel screening.
The Transformer DC Series offers two different blade options, TS blades and X-blades. The TS blades are suited for applications that require screening, separation, and aeration. They rotate between the screening combs, and the final fragment size is 25-50mm.
Swedish manufacturer Sandvik is introducing Endurance packages to help its
mobile crusher customers maximise their plant uptime.
The packages are configurable and can be tailored to meet specific customer needs and requirements. They provide all the necessary parts should the unexpected occur, allowing customers to replace these immediately, maximising plant uptime. They are said to be the perfect solution for sites working long hours (high utilisation) and/or remote locations, where availability and support are essential to customer operations.
The packages range from standard maintenance to major component ‘exchanges’, allowing customers to choose the package best suited to their operational needs. Sandvik’s maintenance, repair and overhaul package strategy can meet varying
customer demands and caters for all quarry, mining, and demolition and recycling applications.
SBM Mineral Processing plans to launch a redesigned version of its REMAX 600 impact crusher at this year’s bauma exhibition in Munich (October 24–30).
The Austria-based manufacturer says the new machine will set new standards in the up to 600 t/h power class, helped by compact transport dimensions and a machine weight of around 60 tonnes.
SBM adds that the REMAX 600 is an ‘intelligent crusher’ utilising the all-electric SBM drive system and process automation technology. High-grade sensors in the machine automatically monitor feed material and final products, record the load conditions of crusher and conveyors, and optimise all separation processes including overbelt magnetic separators and wind sifter.
US-based Astec’s new Ranger J20 tracked jaw crusher was on show at the co-located World of Asphalt/AGG1 exhibitions (29-31 March) in Nashville, Tennessee.
The compact unit is aimed at customers such as rental firms and is designed for versatility, mobility and ease of transport. It is suitable for customers wanting a crusher that can be used in comparatively small urban spaces. Designed to be mobile and easy to transport, the machine can be made ready for use within a short period of its arrival onsite. Power comes from a Cat C4.4 diesel rated at 129kW, which meets the Tier 4 Final/Stage V emissions requirements.
The machine is available in closed-circuit and open-circuit variants and can be used to feed into other plants if required. AB
A premium brand has unveiled a new quarrying-suited crawler excavator range. Meanwhile, a wide range of leading manufacturers are seeing big demand for their latest fuel-efficient and highly productive loaders. Guy Woodford reports
CASE Construction Equipment’s (CASE) new E-Series crawler excavator range features seven quarrying-suited models from 13 to 30 tonnes: the CX130E, CX160E, CX180E, CX210E, CX240E, CX250E, and CX300E.
Claimed market-leading features of the E-Series include new FPT Industrial Stage V engines, enhanced cab design and operator experience, improved hydraulics’ controls and settings, machine structure, undercarriage, and a new full range of CASE Service Solutions. As a result, customers are said to benefit from greater controllability, reliability, operator comfort, efficiency, productivity and total cost of ownership (TCO).
“Our customers are facing increasing challenges, which is intensifying competition. So, they look to CASE to develop machines that have the highest levels of uptime, efficiency and productivity,” explains Egidio Galano, director, construction equipment product management Europe, CNH Industrial. “In response, we developed the E-Series, delivering excellence, efficiency and economy.”
CASE’s Intelligent Hydraulic System (CIHS), a leading feature of the previous generation, is now integrated with four new work modes, with additional customisable hydraulic settings to adjust the flow priority for arm, boom or swing movements, all controllable by the operator. Efficiencyenhancing Super Power (SP) mode delivers
maximum productivity, Power (P) mode provides a surge of power when needed and Lifting (L) mode optimises object handling. When paired with the new FPT engines, the Eco (E) mode delivers remarkable fuel savings of up to 17% on some predecessor models.
For the new E-Series range, CASE reinforces the long-standing partnership with FPT, with its strengths in construction powertrain design. The new range incorporates more powerful and efficient Stage V engines in all new series models. The 13-18-tonne models feature N45, the 4.5-litre engines from the renowned NEF series, while the N67, from the same engine family, powers the 21-30-tonne models providing 6.7-litre displacement.
Describing the beating heart of the new E-Series, Galano highlights the FPT engines’ extensive new features: “CASE has introduced a solution free from exhaust gas recirculation (EGR), ensuring greater efficiency during the fuel combustion. When coupled with selective catalytic reduction (SCR) on filter, the E-Series delivers unprecedented total cost of ownership improvements.” The new E-Series is equipped with HI-eSCR2, the patented after-treatment solution by FPT that is completely maintenance free and built for life. There is no requirement for mechanical cleaning or replacement over the life cycle.
the maintenance intervals up to 1,000 hours for engine oil, fuel filters and oil filters.
Operators for leading UK construction materials group Breedon are highly impressed by the company’s two new Hitachi large excavators. The ZX890LCR-7s arrived at the Cloud Hill and Dowlow limestone quarries in Derbyshire, central England, in October 2021 and are utilised to load rigid and articulated dump trucks.
They are the first Hitachi excavators to be operated by Simon Ferguson and Stephen Tuft and have made a big impression. Simon, an operator for ten years, commented on the stability and performance of the Zaxis-7 machine: “It is very stable. The digging force is strong, and it is faster than the last machine that I used in this quarry.
“The ZX890-7 is very smooth, precise and responsive to operate – it does exactly what you want, and when you want it to. I opt for power mode with the heavy rock that we lift and load on this site, but this machine is more fuel efficient than its predecessor.”
The redesigned cab is another highlight for Ferguson. He said: “I’m six foot six inches (2m) tall and yet I find there is more than enough space in the cab. There is ample storage for my belongings, the Bluetooth functionality is great and overall it’s an impressive workspace. I also find that it is quiet – with so little noise from the outside – and the seat is comfortable.”
CASE has also improved the service experience with the new E-Series by doubling
Tuft, who has worked at Dowlow Quarry for 35 years,
is also enjoying sitting in the cab of the new ZX890LCR-7. “It’s really comfortable and nicely set out. The screen shows you everything you want to see. The radio is easier to reach than it was in the previous machine I used. The controls are really small and handy, and easy to manoeuvre. The slew is really quick and it’s got power too.”
Easy access to the cab and upper structure was commented on by both operators as a benefit of the new Zaxis-7 large excavators.
Hitachi Construction Machinery (UK) Limited (HCMUK) supplied both models with steps positioned to the side of the machine, rather than at rear, to meet Breedon’s requirements.
“There is easy access to carry out my daily checks around the machine – the engine and hydraulic oil, and the coolant,” says Ferguson. “There’s good all-round walkways where you’re not having to climb up or down anything. And there’s a firm grip on your feet so that there is no slipping on any plates.”
Safety is also a key aspect of the new
contract with Boliden, MD Lars-Göran ‘Lalla’ Rutqvist chose to invest in the new 90-tonne Volvo EC950F crawler excavator, despite it being completely new to the Swedish market and an entirely new experience for him and his machine operators.
machines for both operators and the excellent visibility of the Zaxis-7 machines is invaluable: “It feels safe to operate with the monitor in use for the camera views, which are especially useful to the rear and down the far side of the excavator,” adds Ferguson. To which Tuft agrees: “The camera system and all-round vision it provides are second-tonone.”
The first Volvo EC950F to arrive in Sweden, Volvo’s largest excavator, is a fitting match for Aitik – Sweden’s largest and the world’s most efficient open-pit copper mine.
The Aitik mine, run by Boliden mining company, never rests. Ore is mined here 24 hours a day, 365 days a year. This requires large, powerful and productive machines, and Rutqvists Schakt, which works under contract with Boliden, already has several Volvo EC700s and EC750s excavators and a Volvo A60 articulated hauler in its fleet of eight machines at the mine.
When Rutqvists Schakt signed the latest
“There was no time for a test drive,” Lalla laughs. “But I trust Volvo and Swecon. The decisions we make together always work. It also helped that I had read and heard from foreign colleagues that it was a good machine.”
From Volvo CE’s perspective, and that of dealership Swecon, it is a milestone to be able to deliver a machine of this size class in Sweden as well.
“There is trust in us that we need to live up to, and we are ready to deliver more machines of this class,” says Hans Olofsson, Swecon’s director of sales in Region North. By the end of September, some 900 working hours later – the massive excavator is working more than 10 hours a day, seven days a week. Lalla is now just one of its many fans. “We are very happy,” he says. “It’s surprisingly fast for its size. In this job, it’s important to combine capacity with speed. What’s more, fuel consumption is reasonable, and it’s a pleasure to drive.”
A lot has happened since 24-year-old Lalla, after five years as a machine operator, made an important decision one day back in 1992.
After simply telling his mother Ann-Christine that he was going to buy a tractor, he immediately went out and bought
a second-hand Volvo wheeled loader and set up the sole proprietorship under Lallas Traktorer.
Today, that company has been renamed Rutqvists Schakt and boasts about 35 employees and 27 production machines, the majority of which are Volvos tied to Swecon with customer-support agreements. This also includes the operation of Krossproduktion i Sverige AB, with three crushing plants in Norrbotten, which was purchased three years ago.
The Wron´ski Group, a family company based in northern Poland, has purchased the latest generation Doosan DL420-7 wheeled loader. The key purchase was strongly influenced by the performance of their existing Doosan DL420-5 wheeled loader which has completed over 18,000 hours of trouble-free service and is still going strong.
The new DL420-7 is working in the We˛siory quarry, one of several businesses run by the Wron´ski Group connected with the construction industry. Founded in 1992, the company’s operations cover all the territory of Pomeranian Voivodeship in Poland. The Wron´ski Group currently carries out general construction works and runs three building materials warehouses and a prefabricated products plant as well as the quarry, from which it obtains raw materials.
“We know the Doosan brand very well. The first machines in our fleet were two DL400s, which to this day are still used for smaller jobs,” recalls managing director, Mateusz Wron´ski.
The company has always been focused on developing the business with regular investments in new equipment and in 2015,
The DL420-7 wheeled loader at work in Węsiory quarry, loading a truck with quarried material
new-generation machine to test out, specifically the DL420-5 model. We were amazed by the speed and efficiency when working with the machine. The reduction in fuel consumption was so big compared to our old machine, that the money we saved allowed us to pay the leasing instalment,” Wron´ski explains.
After the successful test, the machine never left the quarry in We˛siory, where it continues to work without any problems to this day and has achieved an amazing 18,000 hours of problem-free work. “So, in 2020, when we wanted to buy a new wheel loader, we immediately knew it would be a Doosan,” adds Wron´ski.
The need to purchase a new machine coincided with the introduction of the new generation of Doosan DL-7 wheeled
Komatsu Europe has unveiled its redesigned PC170LC-11 excavator.
The latest addition to Komatsu’s EU Stage V emissions-compliant family, the 18.2-18.9-tonne operating weight PC170LC-11 excavator retains all the customer values of the previous model, and additionally benefits from EU Stage V emissions compliance thanks to Komatsu’s proven after-treatment system and a range of new customer-focused options. With growing demand for environmental solutions, and urban areas becoming increasingly sensitive to emissions, the PC170LC-11 EU Stage V crawler excavator provides customers with the opportunity to participate in any tender, demonstrate environmental credentials, and future-proof their investment.
with an operating weight of 23.4 tonne, is one of the larger models in the new Doosan DL-7 range.
The DL420-7 is powered by a Scania DC13 6-cylinder engine producing 257kW of engine output at 1800 RPM. The new engine meets Stage V emission regulations without the need for exhaust gas recirculation, through the use of selective catalyst reduction, diesel oxidation catalyst and diesel particulate filter (DPF) after-treatment technologies. The soot cleaning cycle on the DPF has been improved to over 6000 h and the operator is fully informed about the status of the DPF via a soot-level indicator on the new touchscreen display in the cab.
With no EGR valve and a choice of three power modes (SAT2, Standard or Power), fuel consumption is reduced by 5%. The machine
Komatsu Europe has unveiled its redesigned PC170LC-11 excavator
Paul Dickinson, product manager at Komatsu Europe, said: “The updated PC170LC-11 Stage V has many new features. The maximum efficiency and uptime.
The
performs very well in difficult terrain, thanks to another standard feature, the hydraulic differential lock (HDL), which is activated automatically at full torque without any additional action from the operator.
The five-speed PowerShift transmission gives the driver the option of three modes: manual, automatic or semi-automatic. A torque converter lock is also standard equipment, which significantly reduces fuel consumption during passes. The lift arm with Z-kinematics provides impressive breakout power and lifting capacity, while the large drop angle allows for efficient unloading.
The LIS (Load Isolation System) provides a smoother ride and higher comfort for the operator, as well as higher productivity due to improved stability when the wheeled loader is moving. Following the supplier’s recommendation, the bucket capacity has been increased from 4.3 to 4.5m³ and the blade has been fitted with rounded edges and a higher spill guard. This makes loading even more efficient and has a direct impact on reducing cycle times and increasing productivity.
“Our wheeled loaders are mainly used to pick up material from the quarry face and to load trucks. I can safely say that with the DL420-7 the work has become much faster, and the machine never lacks power. The loader is very stable, the hydraulics are smooth, which provides dynamic movements. The ability to control the direction of travel with the joystick is especially praiseworthy, especially when the work requires repetition of the same manoeuvres. For me, this hits the bull’s eye for loader operation. The operator comfort has certainly increased, the protection against shocks is clearly noticeable, especially when you are working a 10-hour day. Another important improvement for me is the easy access to filters and components, which means that daily maintenance requires a minimum of effort,” mentions operator, Rafał Pawłowski.
The operator’s cab is spacious, and the steering is electrically controlled. All settings and information can be accessed via an intuitive 8-inch touchscreen, which is easy to read in all conditions. Safety was one of the most important aspects when designing the DL-7 loaders. The operator’s field of vision is increased by enlarged windows, and LED work lights in a 4-front, 4-rear configuration
Group’s purchase
opportunity to test the capabilities of this excellent machine. When I choose Doosan, I get quality at a reasonable price. Without compromises,” sums up Wron´ski
Like all Doosan DL-7 wheeled loaders, another advantage offered by the DL420-7 is the factory-installed wireless fleet management system, DoosanCONNECT TMS 2.0, which provides extensive information about operating parameters, including work efficiency, via satellite and mobile networks.
The R 945 G8 crawler excavator is used at the Sablière du Beynon quarry, a 48-hectare site where SAB quarries 450,000 tonnes a year
The standard warranty on all Doosan DL-7 loaders is 36 months/5000 hours, whichever comes first.
French quarrying company SAB has expanded its machine fleet with seven new Liebherr loading models.
Since its foundation in 1985, SAB has invested in more than 50 Liebherr machines. Seven new Liebherr XPower wheeled loaders and an R 945 G8 crawler excavator are the most recent additions. The SAB machines are in operation for an average of 1,500 to 2,000 hours per year in three different quarries. Production covers a quarter of the demand in the French département of Hautes-Alpes.
“Choosing Liebherr is a decision for reliability and for the regular technical developments that meet our needs”, explains SAB director Lionel Para. “We have a very good personal relationship with both Liebherr and its sales partner ETS PIC.”
The origin of Liebherr machines is also a strong purchasing factor for SAB. “Buying machines made in Europe and even in France is an important signal at this time when we need to support our industries in an increasingly uncertain and globalised economic environment,” stresses Para.
SAB’s Liebherr fleet includes nine wheeled loaders, including the seven new XPower units. The XPower series is highly appreciated by Para for its ease of use and low fuel consumption. The XPower wheeled loaders are characterised by higher engine power and thus achieve better acceleration and speed values. The hydraulic system and working equipment have also been improved so that higher breakaway forces can be achieved.
The cab of the Liebherr XPower models offers full all-round visibility, is air-conditioned and features an adjustable 9-inch touchscreen and optional joystick steering to create a safe and comfortable working environment. Servicing the XPower wheeled loaders via the service access points is efficient, simple, quick and extremely safe thanks to non-slip areas and stable ramps in the access area. AB
MAXIMISING YOUR INVESTMENT ARE ABOUT POWER – PURE AND SIMPLE
What do the smallest Ammann plate compactor, the largest asphalt plant and every product in-between have in common?
• Innovation that boosts productivity and efficiency, ultimately improving your bottom line.
• Parts and components that ensure long life to maximise your investment.
• The commitment of a family business that has thrived in the construction industry for 150 years by keeping promises today – and knowing what customers will need tomorrow.
Rokbak says it is seeing huge demand for its RA30 and RA40 articulated haulers
The US and UK markets are spearheading an uptick in worldwide sales of articulated haulers, driven by major infrastructure programmes. Liam McLoughlin reports
The global articulated hauler market is continuing a general expansion with strong demand in all regions. The total global market was around 8,200 units in 2021 and this year could be as high as 9,000 according to Guy Wilson, global sales director at articulated hauler manufacturer Rokbak.
Wilson adds that the US is leading articulated hauler demand with huge infrastructure spend. A large amount of construction activity around house and road building means that North American customers currently account for about half of the total market.
The UK is the second-biggest market for articulated haulers, says Wilson: “Demand is increasing here thanks to the High Speed 2 (HS2) major infrastructure project that will connect towns and cities in the South, Midlands and North.
“It’s [been] one of the most important economic regeneration projects in Great Britain for decades and it’s already helped the UK articulated hauler market go from an average of around 400 machines a year to over 700 in 2021 – and it’s expected to increase further this year.”
Wilson adds that the Scotland-based, Volvo-owned Rokbak is seeing huge demand for its RA30 and RA40 articulated haulers, with both dealers and customers enthused by the new machines.
“On the HS2 project, the RA30 and RA40 are needed for preparatory work
and transporting materials,” he says. “This includes vegetation clearance and earthwork for tunnel portals and compound facilities. The project will also lead to an increase in the demand for UK aggregate production, which will again create a positive impact on articulated hauler sales.”
Rokbak’s Guy Wilson says the US is leading ADT demand
Rokbak has been celebrating winning the Marketing and the Young Person of the Year categories at the CeeD Industry Awards 2022. CeeD (Centre for Engineering, Education & Development) is a national body that supports a range of industry sectors in Scotland, bound together by a common aspiration to improve operational efficiency, effectiveness and profit through peer-to-peer
Rokbak’s entry for the Marketing category focused on the company’s successful global rebrand campaign. Judges were impressed with the passion shown by the marketing team, who worked in unison with other Rokbak teams, to help devise and drive the campaign – which also included direct feedback from both dealers and customers. This ensured Rokbak (formerly Terex Trucks) and its robust RA30 and RA40 haulers received extensive coverage in the national and international trade press, as well as
Rokbak’s evening of success continued as Rhys Dingwall was announced CeeD’s Young
The 19-year-old joined Rokbak through the company’s partnership with local authority, North Lanarkshire Council and their No Limits Scheme. The initiative is linked to the Supported Employment Scheme, which matches jobseekers who have additional support needs and/or disabilities
Sharing Rokbak’s plaudits was also Ross
Mitchell, who was shortlisted for the Young Person of the Year category. The 23-year-old joined the company in 2017 and has excelled working with the New Product Introduction teams, helping to implement quality processes and inspection documentation for Rokbak’s new haulers being distributed around the world.
Volvo Construction Equipment (CE) is continuing to evolve its range of articulated haulers, with enhancements designed to make them smarter, more efficient and easier to operate. The manufacturer says the improvements mean uptime is maximised, whilst maintenance costs are kept to a minimum, reducing total cost of ownership.
Volvo CE’s Haul Assist suite of tools is designed to get the most out of the company’s articulated haulers. Powered by a 10” Volvo Co-Pilot monitor – which is available on a variety of machines from haulers and excavators to pavers – it provides insight to help customers optimise the efficiency of their haul cycles and boost profitability.
A new addition to Haul Assist is the tyrepressure monitoring system, which enables monitoring of tyre pressure and temperature from the comfort of the cab. Volvo CE says that, with inflation pressure having a marked impact on tyre wear, proactive monitoring is invaluable to optimise tyre life as well as fuel efficiency, machine performance and operator comfort.
Map provides a real-time overview of the on-site traffic to help navigate more effectively. The whereabouts of every machine and vehicle – irrespective of the type or brand – as well as visitors on site are now
visible, so long as they are connected to the map application. Alongside haul roads, Map also shows load and dump zones, and flags single-lane sections, restricted zones and speed-restricted areas, helping to anticipate operating decisions and reduce unnecessary stops.
Volvo CE says that operator comfort has always been at the heart of its hauler design – from the centrally-positioned operator seat offering excellent visibility, through to user-friendly controls. It adds that a range of automated functions is now offering even more support to enhance ease of operation and performance.
Terrain Memory is a useful feature of the intelligent Volvo drivetrain that identifies and remembers slippery road segments to ensure optimised traction control and off-road mobility. OptiShift enables fast and smooth directional changes, whilst the downhill speed-control function automatically maintains a constant speed when operating on downward gradients; both these, and the cruise control function, have been fitted as standard since 2019 and are available for retrofit on older haulers.
Volvo’s articulated haulers are also designed to be easy to service. Instead of daily or weekly greasing, its haulers now
require the process every 250 hours, which the manufacturer claims is the longest time interval in the industry. In addition, there are long engine-service intervals – up to 1,000 hours on Stage V and Tier 4 Final models –and what Volvo claims is less than half the fluid volume of most of its counterparts when measured over the lifetime of the machine. It says the result is reduced maintenance requirements and consumables, helping to keep the machine at work while lowering maintenance costs and environmental impact.
One of Denmark’s largest construction companies, M.J. Eriksson, says it is reaping the benefits from deploying a Liebherr TA 230 Litronic articulated dump truck.
The company uses the new truck for large infrastructure projects in Denmark and southern Sweden. The articulated dump truck is the 300th Liebherr machine purchased by Eriksson over the years. For over 40 years Liebherr, the construction company and the sales and service partner Johs. Møllers Maskiner A/S say they have maintained a close working relationship based on trust.
M.J. Eriksson specialises in general civil engineering, special civil engineering and track construction work. The company claims to have the most advanced and largest machine fleet in the country. Over half of the machines are from Liebherr. It has been operating the TA 230 since 2021 and is using it successfully in various road construction projects. It is responsible for the movement of materials in remediation work of existing infrastructures or the creation of new infrastructures.
Eriksson says it is impressed by the overall concept of the TA 230, with the machine moving up to 28 tonnes of material per loading. A powerful drivetrain combined with the automatic traction control gives the machine excellent driving performance and combined traction. This increases the operating efficiency and ensures higher
handling capacity as well as greater cycle times on the construction sites.
The company uses the TA 230 at different locations with a radius of up to 500 kilometres. Another advantage of the Liebherr dump truck is that, thanks to the optimal transport width of under three metres, it can be transported quickly and without a costly special permit.
Arusha is Tanzania’s picturesque safari capital with Africa’s largest and fourth-largest mountains, Mount Kilimanjaro and Mount Meru, as its backdrop. The city is also the headquarters of Willy Enterprises, a multifaceted business involved in construction, drilling, mining/quarrying and plant hire, among other activities.
The company was founded in the late 1980s by Wilson Mgonja, a civil contractor and entrepreneur with over 30 years of experience, who says: “Growing our equipment fleet with premium machines has been critical to our growth and today we have a substantial fleet that includes graders, dozers, backhoe loaders, rollers, excavators, wheeled loaders and articulated dump trucks. We have 12 Bell machines in our fleet, having bought our first Bell ADT in 2012 through the previous Bell dealer in Tanzania.
“After a reference by a business partner we tried purchasing a B20E for a small project. Seeing how it outperformed other brands of ADTs we were happy to settle with it. After we landed a bigger project, we simply upgraded the size and will now never look back.”
Mgonja says his company was impressed by the quality, durability, efficiency and overall cost-effectiveness of the Bell machine.
Willy Enterprises’ newest Bell ADTs are two B30Es and two B40Es that were delivered in May 2021. They were bought from Bell Equipment’s dealer, Kanu Equipment Tanzania, with a standard warranty of 12 months/2,500 hours. They currently work at a major cement factory in the Tanga region of the country where Willy Enterprises has a production target of about 210,000-378,000 tonnes per annum. The ADTs haul limestone and red soil from the mine to feed the conveyor and crusher on a round trip that varies between 2,8km and 5km. “It’s steep terrain, which quickly turns muddy after a rain shower, but these vehicles have excellent traction control and work without any problem, no matter the underfoot conditions,” Mgonja says.
Each truck works two 12-hour shifts per day and averages about 423 hours of operation per month.
Bell’s Fleetm@tic telematics system ensures that Mgonja knows that production averages between 69.3 and 83.6 tonnes per hour and fuel burn is 12.9 to 16.1 litres per hour.
Bridgestone is launching a 3-star rigid dump truck tyre as an expansion of its 24.00R35 product portfolio, a line-up specially developed for mid-sized rigid dump trucks to carry hefty loads on flat terrain, often at quarries and mines. Featuring a
3-star rating, the new 24.00R35 delivers 8% greater payload capacity along with a deeper tread depth to provide excellent tyre wear and improved traction. Additionally, the tyre provides a high resistance to cuts and heat as trucks transfer larger hauls between long distances at high speeds.
"As demand continues to strengthen in the construction and quarry segments, we remain dedicated to helping maximise productivity for our customers by pairing intelligent products with best-in-class services and integrated technology solutions," said Rob Seibert, president, off-the-road tyres, Bridgestone Americas. "We are meeting growing industry demand with a superior product that features new technology and enhanced performance to optimise productivity."
Bridgestone is scheduled to begin production on the new 24.00R35 rigid dump truck tyre with an all-new traction pattern in late 2022, followed by a new hard-rock pattern.
US truck body design company PhilippiHagenbuch is now offering in-stock inventory of its most popular sizes of rear-eject bodies for trucks. The manufacturer says this reduces the rear-eject lead time for 35- to 45-tonne truck models to six weeks or less, in most cases.
Over the past 23 years, PhilippiHagenbuch (PHIL) says it has manufactured hundreds of rear-eject truck bodies to help customers increase their productivity, safety and stability for off-highway operations. Rear ejects are engineered and manufactured to fit the specific truck body chassis and are easy to operate in the cab, reducing dumping and spreading time by eliminating the need to stop and raise the truck body.
A variety of industries, including aggregates, general construction and mining, use rear-eject bodies and trailers to significantly improve their productivity
when dispensing material and overcoming situations where overhead barriers inhibit traditional dump bodies.
“We are dedicated to offering our clients the equipment they need, tailored to increase the productivity of their specific haul trucks,” said Josh Swank, Philippi-Hagenbuch vice president of sales and marketing. “We remain committed to offering customised solutions for our customers, including our rear-eject product line. However, we have found that the majority of our rear-eject bodies are for 35- to 45-ton trucks and we can now offer a faster turnaround time for those customers by maintaining an inventory of our most common models. This is especially beneficial with so many of our clients facing the current supply-chain and lead-time challenges.”
Philippi-Hagenbuch says it continues to custom engineer and build rear-eject bodies and trailers for a variety of makes and models of off-highway trucks to provide solutions for each customer’s unique needs. Beyond its in-stock sizes, the company manufactures rear ejects that can fit 25- to 60-tonne haul trucks. The rear-eject bodies are manufactured exclusively with high-strength, abrasion-resistant Hardox 450 steel for the greatest structural strength and durability. Due to their all-Hardox construction, which PHIL made as a commitment through SSAB’s ‘Hardox In My Body’ campaign, PHIL says its rear ejects are proven to last up to 20 years and are often put on a second truck after the first chassis has worn out.
“Over the last few years, we have made it a priority to evolve and update our rear ejects based on feedback to offer an even better product for our clients,” said Swank. “We had a vision to further develop not only the operation of both the ejector blade and the rear tailgate mechanism, but to reduce the number of parts, evolving the track design to strengthen the body sides and to decrease the need for maintenance or replacement.” AB
Caterpillar’s new performance series hammers are designed to deliver consistent breaking power
Caterpillar has launched the new H190 S and H215 S performance series hammers, built for high production on large excavators.
New launches from major players are offering operators increased performance and increased productivity from their hammer, breaker and drilling products. Liam McLoughlin reports
quarry, demolition and general construction applications.
Cat says the two new hammers –now available in Europe and the Americas – deliver consistent breaking power, and their extremely efficient operation cycle results in less waste from internal heat for more power delivered to the tool.
With piston and tool matched in diameter and mass, Cat says the two new hammers offer increased power transmission frequency. Operators can switch power mode from high frequency/low power to low frequency/high power, giving the ability to fine-tune power to the material being broken.
Cat adds that the new H190 S and H215 S hammers, in addition to being powerful, also enable operator comfort and machine protection with their proprietary buffering material that dampens vibration feedback to the carrier. Automatic shut-off that prevents blank firing and hammer damage can be temporarily turned off for horizontal and overhead operation in tunnelling and mining applications. The flexible hammers can be configured for joystick or pedal control to suit the operator’s preference when working in
Tuned to deliver the highest possible work rates with Cat next-gen excavators, the new H190 S hammer is sized for operation on Cat 349 through 374 models, while the larger H215 S is designed for the 374 and 395. Auto Stop instantly terminates hammering when the tool breaks through material, preventing damage to both the carrier and hammer.
Next-gen excavators automatically recognise the H190 S and H215 S hammers and prompt operators to select the correct tool programme.
Protecting the cab and keeping the attachment in predefined operating areas at the jobsite, the new hammer dimensions are included in Cat E-Fence technology. Cat says that through its Product Link excavator technology, users can quickly locate the hammer attachment using the Cat App. Hammer pressure and flow rates are viewed on the in-cab monitor and can be configured manually or automatically using the touchscreen display.
All daily checks and routine service can be performed without removing the new H190 S and H215 S hammers from the carrier, saving time. Steady internal gas pressure throughout
the duration of the annual service interval is designed to eliminate the need for frequent charge inspection. The lower bushing’s rotatable design optimises service life to minimise parts costs, while the bushing can be quickly serviced in the field using hand tools.
A standard on-board autolube system provides continual greasing during hammer operation to improve attachment longevity. For operating in extreme environments, an optional wear package protects the hammer housing from damage.
Japanese multinational Komatsu has expanded its range of hydraulic breakers with the new V-series, which is designed to be fully variable for helping to maximise productivity and lower cost per tonne. Used in a variety of rock and concrete demolition applications from scaling a tunnel, to running a pedestal-boom on a quarry, or tearing out reinforced concrete abutments, breakers are essential tools. Designed and tested for compatibility with Komatsu excavators from the PC210 up to the PC490, Komatsu says the new JMHB-V breaker series helps customers achieve excellent impact energy and performance in a variety of demolition applications.
With minimal wasted energy and subsequent higher operating efficiency, Komatsu adds that the 100% hydraulic-fired V-series breakers modulate their impact force and frequency with up to 16 working positions to match most applications’ requirements. Designed to help maximise productivity while helping lower cost per tonne, the breakers are also fitted with an innovative energy-saving recovery valve that recuperates energy to drive efficiency.
Depending on the application’s hardness, V-series breakers automatically select the best piston stroke length and speed. By adjusting to either hard material, with long and powerful strokes, or to softer material, with shorter, faster strokes, the breakers are designed to achieve high production output, with little wasted impact energy.
To help owners get more from their investment, Komatsu says the V-series breakers have several valuable standard features, including automatic greasing, advanced blank-firing protection, swivel hose couplings and heavy-duty housing. The shock-dampening systems in the form of upper and lower suspensions help reduce the risk of cracking excavator booms and breaker housings, while the mounted standard automatic lubrication feature helps guard against contamination caused by dust and debris.
For greater operator comfort, suspensions with rubber/poly components help absorb impact and reduce vibrations through the boom. The completely enclosed sounddampening housings reduce the amount of noise generated when compared to openstyle breakers, which Komatsu says offers customers a solution that addresses noise ordinances in urban applications.
To support regular maintenance of breakers, inspection kits are included with gauges to measure wear on all
critical components. Additionally, these breakers are backed by the Komatsu North America Attachment Division, a dedicated hydraulic attachments sales and service team that supports Komatsu distributors. These specialists are factory-trained and experienced with installation, operation, service and rebuilds.
Sweden-based Epiroc has partnered with ASI Mining to introduce Mobius for Drills, a new platform to convert drilling data into useful, actionable information in operations including surface mining.
Featuring embedded artificial intelligence, Epiroc says the user-friendly Mobius system enables multi-vehicle command, control and monitoring to maximise productivity and safety.
“We think of it as a tool to directly support
making quick and effective interrelated decisions,” says Tyler Berens, automation director, surface mining at Epiroc’s surface division. “Mines can get greater productivity and economies of scale as a single operator controls multiple remote and autonomous vehicles. Mobius for Drills is designed to tie the whole value chain together.”
Mobius for Drills displays data in an easyto-use layout to map drill usage, evaluate statistics, track consumables and compare planned outcomes against actual results.
“Mobius for Drills is an ideal management tool because of all the support it provides in decision making, but Mobius for Drills also helps with driller training, so it is useful for the whole workforce,” adds Christopher Blignaut, product owner - data solutions, Epiroc surface division.
By providing a single platform for all stakeholders within the drilling operation, Epiroc says users can quickly navigate the information, filter it to their needs and streamline the decision-making process, day-to-day or over time.
A claimed added value to Mobius for Drills is its ability to work across fleets with drills from multiple manufacturers, condensing all sources of information. It can be used as a fleet management system or integrate with a mine’s existing system.
Mahmood Hassan, engineering project manager – automation at Epiroc’s surface division, comments: “Mobius for Drills enhances engagement of all stakeholders with the drilling process. It provides valuable insight at each stage of the drilling process through a drill plan builder for planning, situational awareness for drill controllers and reporting for supervisors. It is a scalable product, which accommodates evolving needs of a mine.”
The platform imports drill plans, monitors drilling and creates the reports over a secure system on-site or remotely. It supports manned operations, teleoperation, semiand fully-autonomous modes and covers applications from drill and blast through to autonomous haulage systems.
In its aim to cultivate more environmentally friendly ways of operation, Sandvik says it has launched a new BIO Tool Grease that is designed to offer a greener alternative for the upkeep of hydraulic hammers.
The biodegradable grease is the first product in the Swedish company’s Green Range, and can be used with Sandvik hammers and those of its Finland-based brand, Rammer. It is specially formulated to be more environmentally friendly and safe for use in environmentally sensitive areas such as groundwater locations.
The lithium complex-thickened BIO Tool Grease is based on biodegradable esters and polyalphaolefin (PAO) and contains corrosion inhibitors, antioxidants, and bismuth technology-based extreme pressure/antiwear additives (EP/AW) additives. The special formulation makes the grease suitable for both high and low temperature applications and provides excellent wear protection and good load-carrying capacity. In addition, its complex soap structure ensures great mechanical stability, prolonging re-lubrication intervals and enhancing performance in vibrating housing.
BIO Tool Grease is supplied in three sizes: 400g, 500g and 18kg. The 500g cartridge is suitable for Ramlube II automatic tool greasing device, making it easy and quick to replace cartridges.
Jouni-Pekka Hiltunen, product line manager at Sandvik Rock Processing Solutions, comments: “When developing this new BIO Tool Grease, our two most important criteria were environmental friendliness and lubricity, and the new grease meets both of these excellently. Hammer applications place very high demands on
greases, and the new grease fits perfectly into our Ramlube II automatic tool greasing system.”
Arto Halonen has been appointed as CEO of Finland-based Robit Group. He takes over as head of the drilling products and technology company from Tommi Lehtonen who stepped down in March 2022.
Halonen, M.Sc. (Eng) and M.Sc (Econ.), has been employed as Robit's chief financial officer and chief operations officer since March 2020.
president global sales & marketing.
Harri Sjöholm, chairman of the Robit board of directors, commented on Lehtonen’s departure: “I would like to thank Tommi both on my own and on behalf of the board of directors for his input for Robit and the company’s growth, exceeding net sales of €100m. We wish Tommi all the best in his future duties.”
Robit has recently committed to new sustainability KPIs (key performance indicators) and is asking the company’s stakeholders to do the same.
The company says it has always had sustainable practices, such as sourcing materials from responsible partners, as well as setting a high priority on employees’ health and safety. Recently, however, it has been in the process of doubling down on its sustainability efforts and setting clear objectives for these practices, based on a common vision created through extensive cooperation between the management and the employees.
With the launch of the ESG (Environment, Social, Governance) roadmap in September 2021, the ESG practices of the company have been refined and further defined and Robit’s actions have been divided into four key areas: Sustainable partnerships; CO2 emission reduction in the value chain; healthy and happy workplace; efficiency throughout product lifecycle.
The company says the aim of these four pillars is to tackle sustainability issues from several directions at once.
Even though the concrete KPIs for these key areas were launched only last September, the company says there are already several actions taken and some significant results that have been reached.
Robit aims to have a minimum of 90% of its supplier spend coming from suppliers who have committed to Robit’s supply chain policy. The result at the end of 2021 was already at 79%.
A first step towards CO2 emission reduction was taken by building a calculation tool to recognise Scope 1 and 2 CO2 emissions caused by Robit’s own operations. The company says it will also increase the share of green energy in its factories, with the first changes having been implemented at its Australian factory in October 2021.
For a healthy and happy workplace, the KPI is to target zero lost-time incidents, based on LTIF (lost-time incident frequency). In 2021 the result was 2.1, which is already a significant improvement from 4.2 in 2020. In January 2022, Robit reached LTIF of 0.0.
To increase efficiency throughout product lifecycle, Robit has set a KPI of providing at least 1,000 hours of consultative sales training annually to the sales and technical personnel of the company and its distributors. Additionally, Robit has set the target to achieve over 90 percent wasterecovery ratio in its factory locations. The 2021 results for these were 921 hours and 87%, respectively, bringing the company very close to reaching these milestones. AB
Investing in high-quality screening media and diagnosing and eliminating early screening media issues can greatly improve your aggregate production operation. Guy Woodford reports
Resolve Aggregates discovered CDE technology and the benefits it could have for the company at ConExpo in 2014. Since partnering with CDE in 2015, the U.S. company has met production objectives at one site, relocated to grow and maximise opportunities, and now is expanding its CDE wet processing plant to explore additional new markets.
The sand and gravel company has been processing fine and coarse aggregates
Texas. The full sand washing plant was disassembled and containerised at Fort Worth, then relocated and installed by Resolve Aggregates employees in just 11 working days in May of 2017. It was recommissioned by CDE shortly after. The move, combined with CDE’s tailored wet processing solution, enabled Resolve Aggregates to expand its current wet processing system.
The partnership between Resolve
sand and gravel washing plant and the relationship with CDE by upgrading its plant for integration of a fine screen to diversify into golf sands to extend its product offering further.
CDE’s modular approach means its equipment can fit seamlessly into the existing process to minimise plant downtime while upgrades are commissioned.
The upgrade includes an Infinity F1-64 fine screen, integrated into the plant and
#30 cut - #140 golf sands. Through CDE’s guaranteed equipment performance, the final materials will meet the high-standard requirements of the golf industry and enable Resolve Aggregates to supply valuable products for new markets.
Commenting on the upgrade, Resolve’s spokesperson said: “Our relationship with CDE has been one of collaboration and trust, working with them to ensure the best for our company as we explore both new pastures and new markets. It is remarkable how a simple upgrade has built so easily into our existing plant while opening new possibilities for our company.”
James McShane, CDE business development, North America, said: “This upgrade is a prime example of and a great testament to the flexibility of CDE solutions. The extensive benefits of one straightforward addition highlight the ease of plant expansion with our modular approach and how it contributes to the future growth and success of a company that continues to develop and enhance its processes.
“We have been working with Resolve Aggregates for six years and have seen such marked differences in the company: from relocation to venturing into new avenues that help maximise return on investment. With full accountability for the service and direct support from our team, we look forward to continuing the journey as Resolve Aggregates grow further.”
Lars Bräunling, director of product technology at MAJOR, an innovative global manufacturer of wire screens for the aggregate, mining and recycling industries, has given his expert advice on how to diagnose and address screen media issues in aggregates and mining production.
“All operations have the same ultimate goal for their processing equipment: to improve the cost per ton. This is often accomplished by fixing or preventing
equipment issues and optimising performance. The screening process, in particular, is one of the most significant parts a producer should pay attention to,” he explains.
Bräunling says understanding what screening problems to look for and how to fix them can mean a positive ripple effect throughout the material separation process. He believes a proactive maintenance plan and the addition of high-performance screen media make remedying issues and improving efficiency even easier.
“Operations continuously look to improve their bottom line by decreasing the cost per ton. Plant managers must address how much can be produced with a given set of screens and reduce cost factors tied to poor performance, such as machine downtime or screen media change-outs.”
Bräunling advises producers to initially
work with an expert to conduct a screening performance assessment to see the complete picture of the operation. This should include an evaluation of the process and any direct screen media issues, the screen setup, the machine condition and how it affects performance. “Use a vibration analysis tool to look for abnormalities that need to be addressed and can’t be easily seen with the human eye. Also, listen to the deck while it is running to reveal loose media, clamp bars or broken wires. Listen for abnormalities or metallic sounds,” he continues.
Bräunling says producers should then examine the crusher feed belt coming off of the screen box to identify issues that could lead to a bottleneck. Improving screening efficiency directly in front of this point affects the entire operation in both directions.
He adds: “A visual check or a belt cut of the crusher feed belt is often enough to see if there is saleable rock that is being sent to the crusher as carryover because the deck capacity is exceeded. This is caused by blinding, pegging, poor open area, non-ideal vibration setup or the wrong screen media setup.”
Lastly, Bräunling recommends looking at used screen media’s scrap pile — also known as the boneyard. “Inspecting the underside of the spent screens is an effective way to diagnose installation challenges. Look for black markings on the underside of the screen media that show the panels have moved and rubbed against machine supports, meaning they weren’t fixed in place like they should have been. This primarily causes wear but can also lead to blinding, pegging and inefficiency. Signs of blinding, pegging or breakage in the used screen media pile are also a good way to quickly identify which machines and decks need attention.
“’Better screening is free crushing’ is a statement sometimes heard in the industry. There are many ways to interpret the saying, but it boils down to how an efficient screen box lessens the load on a crusher by sizing material correctly.”
Bräunling notes that many screening issues can be addressed with a change in screen media. “From traditional woven wire to polyurethane to high-performance screen media, there is no shortage of different styles of screens. The choices can seem daunting; frequently, one type works for specific situations or works best through a combination of different types. An exception is some styles that use advanced engineering to address screening issues with just variations of a single media type.
“High-vibration screen media is one such option. This advanced screen media is made up of independent wires bonded with polyurethane strips. The wires vibrate independently to add to a screen box’s existing vibration, speeding up material separation and passing.”
Bräunling states that screen media options that incorporate this design permit an increased screening action which helps to spread material over the entire screen’s surface area on all decks but, most importantly, accelerates the stratification process. He points out that this effect causes rocks of different sizes to separate, with fine material sinking down towards the screen surface and bigger rocks rising to the top of the material bed. Faster stratification increases the capacity of the deck and allows for a cleaner cut.
“The movement of wires helps to virtually eliminate near-size pegging on the top decks and fine material blinding and clogging on the bottom decks, resulting in higher-quality end product.
“In addition to considering a change of screen media, ensure tensioned screens are installed properly, and that surrounding equipment is operating correctly. Once the process is running productively and smoothly, operations should do what they can to maintain that performance. Develop a preventative maintenance plan that includes
vibration analysis tests at regular intervals to identify changes that may point to problems.”
Bräunling notes that it is important for aggregates processing and mining site operators to remember that screen media will wear out over time. Still, it should need replacing because it is “broken, pegged or blinded”. He advises operators to work with a dealer or screen media manufacturer to determine the best screen media options for your application and create a proactive maintenance plan to maintain optimum results.
Durex Products (Durex) showcased its screen media, liners, wear parts, and screen
accessories to more than 9,000 attendees at AGG1 in Nashville, Tennessee, 29-31 March 2022. Based in Luck, Wisconsin, the company offers numerous innovative urethane, rubber, and speciality wire screen media options, which allow customers to finetune production and increase tons per hour while keeping products in spec and lowering operating costs.
Durex has offered premium screen media technologies since 1965, including its well-known Livewire, Armor, Accuslot, and Vibraspan products. Wear liners and parts for aggregate equipment and screen accessories round out the company’s offerings. AB
Highly productive and efficient washing plant processing can boost your profit margin and ensure consistent high-quality final mineral product. Guy Woodford reports
Campbell Contracts’ CDE installation – including an M2500 washing plant, AggMax scrubbing and classification system and AquaCycle thickener – is proving a big money earner for the County Fermanagh, Northern Ireland-based company. The plant’s highly productive and efficient operation near Enniskillen has enabled Campbell Contracts to increase its annual sand product sales by an eye-catching 90%.
Before investing in its state-of-the-art CDE solution, Campbell Contracts had clay-bound sand and gravel, primary scalpings, and crushed rock fines that they could not process into saleable aggregates and sand. Now, all such material is turned into a high-quality final product. This is especially important in an area where good sand is not readily available, often needing to be trucked in from over 30 miles away.
Campbell Contracts’ previous washing plant was over 30 years old. While it worked reasonably well with cleaner sand and gravel deposits, processing up to 30 tonnes of product per hour, it struggled with more clay-bound material. Historically, such difficult material was backfilled into the pit and buried. The dirty primary scalpings, a by-product of Campbell Contracts’ quarrying operations, could also not be processed by the existing washing plant, leaving it stockpiled on site.
Speaking to Aggregates Business, Grainne Quinn, a Campbell Contracts’ director, said that the firm has been very impressed with its CDE washing plant. The tailored solution can process up to three aggregates and two sand products simultaneously. For Campbell Contracts, the plant is currently processing 60 tonnes of aggregate and 60 tonnes of sand product an hour 10 hours a day Monday to
Friday. The plant also runs for 6-7 hours on Saturdays. Campbell Contracts had put more than 350,000 tonnes of material through its premium CDE washing plant by the time of Aggregates Business’s site visit on 7 December 2021.
Quinn says that being able to monetise what had been previously unsellable material, coupled with general production quality and efficiency gains, had allowed Campbell Contracts to make a return on its CDE washing plant investment in just two years.
“We had initially looked at a payback of five to six years, so the plant has exceeded our expectations,” says Quinn. “We had been using our old washing plant since the early 1980s, but the customer demand for sand is huge; there was no way we could meet it with our existing setup.
“We spoke to a number of washing plant manufacturers but were very impressed with CDE from the start. They knew exactly what we needed and were good people to work with. We placed the order for the new washing plant in early 2019, and it was installed in October 2019. The AquaCycle was added this year [2021].
“The amount of quality sand we can produce with the CDE plant is great, as is our ability to process what was waste material.
Previously, some of our big concrete plant customers thought some of our sand product was a bit fine.”
Asked about any issues with the CDE washing plant, Quinn says: “As with any piece of equipment, we had some teething
Some of Campbell Contracts’ CDE washing plant processed aggregates
troubles getting the outputs exactly where we wanted them, but CDE worked with us until we and our customers were 100% happy.”
A longstanding family-run business, Campbell Contracts has traded since 2002 after initially being established by Quinn’s father, Jim Campbell, in 1968 as J.P Campbell Plant Hire. Campbell Contracts has a large and loyal customer base across the concrete supply and highways and infrastructure sector. Campbell Contracts also operates a highly successful civil engineering business and has a fleet of 30 tipper trucks.
“We look to buy a new tipper truck every year and this year also bought a new Volvo articulated hauler,” says Quinn. “We generate a lot of gravel stone, and I’d like to add to the current CDE plant setup – something like an oversized fines crusher. That would reduce waste even further along with the hauling requirement.”
As illustrated in the bespoke solution for Campbell Contracts’ aggregates and sand processing site near Enniskillen, CDE’s aggregates and sand washing plants tackle numerous customer issues, including the loss of quality fines to site settling ponds and clay contamination of feed material. Equipped with CDE’s patented Infinity screens technology, the plants efficiently remove -63 micron / 200 mesh material from sand and aggregate products while also recycling
up to 90% of production process water for recirculation, eliminating the requirement for settling ponds.
Terex Washing Systems has completed the installation of a wash recycling plant based in Geneva, Switzerland. The wash plant converts construction, demolition and excavation waste into two sands and three aggregate products that are stockpiled for use in the production of asphalt. All this is achieved while recycling up to 95% of the water used during the washing process.
The Terex Washing Systems engineers used over 60 years of industry experience and a product from their sister company Terex MPS to find solutions that would meet the customer’s needs. A complete crushing, screening and washing solution was provided to the customer on a compact footprint to meet their specific requirements. The aim was a throughput of 100 tonnes per hour with
the option of crushing oversized material.
The wash plant consists of an FM 120 2-G Sand Plant, an Aggrescrub 150 Log Washer complete with pre-screen and a Terex MPS Impact Crusher. This section of the wash plant washes, classifies and stockpiles aggregates while recovering two specifications of sand. Any oversized material fed into the system is directed towards the Terex MPS crusher, where it is crushed down to a manageable size before being fed back into the washing system. The customer can also feed oversized material directly into the crusher.
A fully integrated water treatment plant consisting of a deep cone thickener, flocculant dosing unit, and a filter press allows up to 95% of the water used in the washing process to be re-used. The dirty water is collected in a sump before being treated and allowed to settle in the deep
cone thickener. The thickened sludge is then compressed within the filter press so that the last remaining water is sent back into the system. The customer can then sell the filter cakes that are expelled from the filter press.
The Geneva-based customer can now divert thousands of tonnes of construction, demolition and excavation waste from landfill each year. It can achieve this while producing six different products to be sold or used during asphalt production and further reducing the environmental impact thanks to the water treatment plant.
Johnston Patterson, product and applications manager at Terex Washing Systems, said: “We have provided a complete
end-to-end wash recycling solution for the customer. Our ability to fully integrate washing, crushing and water treatment allows us to design and manufacture systems that perform to a higher standard. Everything is here, from feeder to filter press.
“This washing system provides the customer with a sustainable production line of sand and aggregate products from material that would otherwise be sent to landfill.”
The cost of a permanent plant is normally offset by higher throughput and a long-life span of the deposit. When higher throughput is not needed or possible, a modular wash plant can be put in place at a lower capital investment and deliver the required
The Italian waste management
firm Profeta has recently started a new washing and recycling plant at its waste recycling and processing facility in the Sicilian port of Palermo.
The new 10 tonnes/hour Baioni wet processing solution includes an integrated magnetic separator for separating non-ferrous metals from the waste stream.
Profeta will use the new Baioni plant with existing waste recycling and grading plants to recycle up to 90% of all incoming dry waste streams from its industrial and naval shipbuilding activities, producing recycled aggregates for the construction and recycling industry.
Profeta says the Baioni solution will help treat waste, like soils and sediments, using water with additives and reagents to ease the physical washing process of aggregates. Soils are subjected to multi-stage treatments while clarified water is reintroduced into a closed-circuit cycle.
The process helps the particlesize separation of the coarser fractions (such as sand and gravel) from silt and clay, concentrating the pollutants separately. After the process treatment and after accurate test analysis, the coarser particle-size fractions can be used again or relocated to the site of origin. The finer fractions, where all pollutants are concentrated, can now be sent for final disposal.
Before the new plant installation, Profeta hosted Baioni at the port of Palermo to allow the manufacturer to gain a better understanding of the firm’s needs and requirements. Profeta’s owner, Aldo Profeta, chose to partner with Baioni as he believed the company
had an in-depth knowledge of the project and was confident in its long-time expertise in aggregates washing processes.
Baioni has commissioned its ST 200 washing trommel, GRF hydrocyclone fines recovery plant and Baiwash water management system to run alongside Profeta’s existing waste recycling and grand plants setup.
Utilising Baioni technology, the new plant will enable Profeta to produce +2 mm gravel (36%), 0.063-2mm sand (30%), -0.063mm silt and clay (34%).
The Baioni plant offers flexibility in processing waste with varied granulometric characteristics of the waste to be treated. Larger particle sizes are separated utilising hydrocyclones and screens; both are highly productive.
Turnkey processing systems from Baioni come with a feeding process using a feed hopper
production level. The advantage of shipping a plant in containers does impact the size of the equipment, so throughput is lower than with permanent plants.
With a long history of designing, manufacturing and installing modular wash equipment, U.S. company McLanahan’s line of UltraWASH modular wash plants is said to supply the reliability, simplicity and efficiency that producers need from a modular plant.
All equipment that is part of the UltraWASH plants, including the vibratory screen, hydrocyclones, dewatering screen, sump and pump, is based on the company’s well-known, field-proven designs. UltraWASH plants are said to offer a quick, easy-to-install processing
equipped with protections and clod breakers and sensors for detecting and removing magnetic ferrous materials.
The second processing stage is washing and particle-size separation, leading to the transfer of contaminants from the solid waste matrix to the washing fluid (water or seawater) and separating the contaminated fractions from the recoverable ones.
Material washing is done in an ST 200 washing trommel followed by a wet screening of the coarse materials and a refining section of the sands using two Baibac Baioni attrition scrubbers. The third processing stage is the water treatment process using a highly efficient Baiwash water management system that significantly reduces water consumption by ensuring up to 90% of process water is recycled for immediate recirculation. The
Baioni water treatment unit, consisting of a thickener and polymer station, minimises the loss of valuable fines and reduces water and energy costs.
The final Baioni washing and recycling plant processing stage is fine fraction thickening, where sludge is concentrated in Baiwash thickener and a chemical plant. Sludge is further dehydrated through a solid/liquid separation process using a Baidec decanter. This process ensures a considerable reduction in waste going to landfill.
Profeta says its investment in a Baioni solution exemplifies the company’s commitment to environmental protection. The company has ordered a second Baioni washing and recycling plant for a different site, further demonstrating its environmentally conscious working practices and saving money by reducing waste and increasing efficiency.
system. These modular wash systems are ideal for producers facing criteria such as planning permits, multiple locations, shortterm deployment, or an unknown/variable feedstock (for example, C&D waste stream applications) that make implementing a customised, fixed processing solution difficult.
McLanahan says that one advantage of a modular wash plant is they tend to be fully designed and ready out of the box. They are manufactured on demand or are already in stock for faster deployment. Modular wash plants can be custom-designed for specific applications. But in the case of a timesensitive application, the standard unit will fit the situation better even if it is not an exact fit.
McLanahan currently offers nine different sizes and configurations for its UltraWASH, which can produce up to three aggregate products and up to two sand products. There is a single process water feed point and a single effluent discharge point. In addition to offering various configurations for helping producers meet their production goals, McLanahan designs and produces equipment for all stages of the wet process, from feed preparation to water treatment. These equipment offerings are available as add-on modules that can include log washers, blade mills and coarse material screws for feed prep, attritioning modules for specialty sand production, an organics removal module, an EcoCYCLE thickener for water treatment and an EcoPRESS filter press for complete wastewater treatment.
McLanahan UltraWASH also offers three different wash options, each with its benefits to the end-user.
The single wash model can create up to three aggregate products and one sand product. The feed is divided by the sizing screen, and the clean aggregate is separated and stockpiled with conveyors. The sand fraction is mixed with water in the sump and pumped to a pair of hydrocyclones, which remove the silts and clays before excess water is removed from the sand by the dewatering screen ahead of stockpiling.
The double wash model is ideal for extra dirty sand and requires additional contaminant removal. The difference between the double wash and single wash model is the addition of a divided sump and
secondary pump. Sand mixes with water in one side of the sump and is pumped to a large hydrocyclone, where the first pass removal of silts and clays is affected. The product of this process is a partially cleaned sand that is discharged back to the other side of the divided sand sump, from where it is picked up again and pumped to the smaller, secondary hydrocyclone for removal of the remaining silts and clays before being discharged onto a dewatering screen for excess water removal.
The twin sand variant allows the creation of separate coarse and fine sand products. This model also includes a divided sump and two hydrocyclone circuits and adds a splitdeck dewatering screen. In the twin sand model, the bottom deck of the sizing screen is divided, allowing the coarse sand fraction to fall into one side of the sump and the fine sand fraction to fall into the other side. The coarse and fine sands are then pumped separately to the hydrocyclones for single-pass removal of silts and clays. The sand is discharged onto separate sides of the dewatering screen for excess water removal, primary product blending and separate stockpiling.
McLanahan says that by selecting a plant that has been configured to address the specific needs of your application and provide long-term benefits to your site, you will see long-term advantages to the operation, capacity and most importantly, profit. The OEM (original equipment manufacturer) adds that expanding your plant means growing or changing your production capability and profits. When planned accordingly, an UltraWASH modular wash plant can include easily adjustable features that can improve your operation’s capacity and allow you to meet new demands. AB
Stuart Partners (Stuarts) operates a quarry located in Hill Barton Business Park near Exeter in Devon, southwest England. The company is licensed by the Environment Agency to handle the disposal or recycling of inert waste.
Since 1988, Stuarts have progressed from filling a hole in the ground to operating a successful recycling facility. Most of the material now brought into the firm’s quarry is recycled, with over 80,000 tonnes of inert waste processed each year.
A proportion of that is then resold as crushed hardcore
Matec Industries has supplied a complete, compact and mobile plant for UK-based
material sized 0-2mm, 2-5mm, 5-12mm, 12-24mm, 24-50mm, and +50mm.
To help Stuarts meet its quality and productivity targets, Italian washing plant experts Matec Industries recently supplied a complete, compact and mobile plant.
The installation includes an Aggretec 150 washing plant and a SCREENTEC two-deck, 1500mm x 5000mm mesh vibrating screen with free oscillation. The unit can process an initial feed size of up to 200mm.
The Matec plant setup also includes an up to 80
tonnes/hour SANDTEC sand recovery unit with hydrocyclones. The SANDTEC has a maximum wastewater capacity of 5000 litres/ minute.
Furthermore, Matec installed a SCRUBTEC log washer model with a 50m³/ hour and up to 70mm feed size capacity, a water treatment plant comprising a filter press with 170 1500mm x 1500mm plates, a stainless-steel vertical thickener (decanter), an automatic flocculant station, and a slurry homogeniser tank.
Indian cement producers are significantly increasing their production capacities while investing in advanced technologies to reduce production costs, increase profitability, and better meet forecasted higher future demand. Partha Pratim Basistha reports
India had a cement production capacity of 545 million tonnes in March 2020, accounting for 8% of global capacity, second only to China, according to the Indian Government agency IBEF (India Brand Equity Foundation). The country’s cement demand is expected to rise to 550 to 600 million tonnes by 2025, driven by an enormous upswing in infrastructure development, new residential housing and industrial construction.
It is estimated that power and fuel account for 50% of the Indian cement industry’s production cost, a percentage very apparent in the minds of leading national cement producers as they set about increasing manufacturing capacity to meet rising demand. Electricity conservation is a key goal in the Indian cement sector, achieved through using automatic Programme Logic Control (PLC)-based systems to run vital electric-powered units like fans and blowers.
On this subject, Vinay Saxena, senior vice president, operations and management at Shree Cement, said: “The advanced PLC-based systems also feature voltage variable frequency drives (VVFD), from ABB, Hitachi and others. VVFD has raised the initial investment costs. However, the newer technology has extensively contributed to energy conservation. The medium voltage drives on 11kva motors come with a much smaller footprint to run the plant’s electrical systems. The other most vital advantage is the easy flow of high levels of currents and minimal transmission losses.”
To have extended durability, it is essential that cement particles are uniform during the material’s production
Speaking about the impressive integrated and non-integrated reduction in cement-plant fuel use, Saxena says: “Most of the larger cement plants are migrating from fifth- to sixth-stage preheaters. This has made the plant suitable to use alternate fuels and raw materials (AFR). The sixthstage preheating systems have assisted fuel conservation in a bigger way.”
India’s cement producers, including Shree Cement, are also increasingly using waste recovery boilers in their fuel conservation efforts. The boilers capture and use steam to generate electricity to power cement plants. Most Indian cement plants are based on dry-cement producing technology, creating a near-zero wastewater industry.
UltraTech Cement (UltraTech), the flagship company of the KM Birla group, has been one of the Indian cement industry’s front runners in adopting advanced technologies and processes to curtail operational costs. Prasanta Paul, UltraTech’s
head of procurement- engineering and projects, said: “We use a heat recuperation system in the cooling mechanism of the plant. Some of the alternative fuels, like pet coke that we use, possess very high levels of calorific value. This allows for better heat recuperation and reduces the wear on some parts.”
With an installed production capacity of 115 million tonnes, up from 70.3 million tonnes about four years ago, UltraTech is the world’s third-largest cement business, excluding China-based companies. The company is engaged in greenfield and brownfield expansions, gaining 14.6 million tonnes of additional capacity by acquiring
Century Textiles’ cement business. The closure of some companies, including Reliance Cement, Binani Cement and Emami, has contributed to greater market consolidation.
Major integrated cement-producing entity Wonder Cement, part of the Rajasthan, North India-based R.K. Marble Group, has just completed the second-phase expansion of its Nimbaheda plant in Rajasthan’s Chittorgarh district. To curtail its production costs and create greater plant efficiencies, the company, like UltraTech, uses pet coke to power its cement plants rather than higher-sulphurcontaining bituminous coal. Pet coke is also cheaper than other fuels, requires less
gypsum, and, as previously noted, offers a higher calorific value (8000kl/kg) than bituminous coal (4000kl/kg).
Wonder Cement has invested in VRM technology from Pfeiffer to refine raw materials used in its cement production. The expanded Nimbaheda facility has also got new Thyssenkrupp equipment for processing and clinker grinding. Furthermore, the latest packaging technology has also been installed at the extended plant. Other auxiliary equipment has been sourced from the best of the industry, enabling the company to attain plant efficiencies and deliver quality cement at competitive prices.
To have extended durability, it is essential that cement particles are uniform during the material’s production. Furthermore, testing must be consistent across all production stages. Wonder Cement has invested in a cross belt analyser. The technology tests every quarried or mined piece of limestone to see if it meets the required quality or size. Later in the cement production process, the firm’s state-of-the-art Thyssenkrupp separator eliminates unwanted cement particles. Finally, Wonder Cement’s robotic laboratory with AQCnet software ensures that the right highly durable cement grade is produced.
Pankaj Agarwal, head of mines at Shree Cement, says that for better productionprocess-synchronisation and increased plant utilisation, cement producers value the increased digitisation of the production process via solutions from companies including ABB, Siemens, and Schneider.
“Shree Cement has been using GPS to streamline mining activities. This is from the movement of the raw materials like limestone to the crushers and for further movement. Plant optimisation is also achieved through high levels of automation based on fully PLC systems. There is an increased usage of computational flow dynamics model simulations to improve the performance of plant equipment such as kilns, boilers, heat recovery equipment, among others. Closed-circuit television monitors each area of plant operation for safety.”
Another big advancement by Indian cement companies, including Shree Cements,
on fuel conservation, while simultaneously improving their Puzzolana Portland Cement (PPC) mix, is their increased fly ash and steel slag usage. Fly ash is popular due to its high bonding properties. This prevents cracks in the PPC after its curing.
Shree Cement’s Vinay Saxena says: “Fly ash possesses higher calorific value, so when it is mixed during cement production, fewer clinkers require to be heated, curtailing carbon footprint.”
For environmental protection, cement plants in India are investing on a major scale in chimney and fugitive dust suppression.
For example, J.K. Lakshmi Cement’s Udaipur cement works in Rajasthan has installed an advanced dust-collection system from Thermax. The Thermax bag dust-collection system efficiently collects dust at every emission point through the suction points. The dust collector recirculates the dust in the plant while fine air is passed through the chimney. The new dust-collection system was installed to comply with the state government regulation for environmental protection due to Udaipur airport’s presence close to the processing facility.
The way cement production materials in India are transported is changing. An increasing number of companies are using specialist railway freight wagons, others are turning to more robust bulker trucks to convey certain materials via road. The changes are primarily due to new and evolving cement consumption patterns, both in loose or bulk form. Fly ash is one such raw material increasingly being used by cement producers in line with national and regional government policy.
Aurobindo Mishra, additional general manager of logistics at Mumbaiheadquartered JSW Cement, says the utilisation of fly ash in larger volumes by cement producers is due to directives issued to thermal power plant operators not to create environmentally damaging ash ponds. “Given the requirements, there is an evolution of newer variants of BCFCM [bogie cement fluidised – CM is the mechanical code of the Indian Railways] railway wagons to transport fly ash from power plants to the cement plants. These are being preferred
for transporting fly ash from power plants to cement companies, covering a lead distance between 100-500 kilometres. They are found to be viable compared to transport by bulker trucks, even with lead distances of 100-200 kilometres.”
A BCFCM railway wagon can be used primarily to transport fly ash and cement in loose condition with assisted gravity discharge through hoppers. The wagon has a 68.7-ton carrying capacity. It is covered with a roof with three hatch-covered inlets for loading.
The wagon features a unique fluidised system. A fluidised system for wagons is a hose work of a special textile design, exclusively for quick and complete discharge in the wagons. The arrangement includes air distribution chambers designed to ensure that fluidisation air is fed evenly across the
total cross-section of the wagon. This system provides quick, continuous and complete discharge of the cargo each time and avoids any funnel flow inside.
Fly-ash loading is being done from the captive power plants of the Singareni Collieries Company, a subsidiary of the Indian state-owned coal miner, Coal India Limited, for ACC’s cement plants. Fly ash is also being transported from NTPC’s power plants to cement production clusters in Madhya Pradesh and the Korba region of Central India.
For transporting fly ash, ACC and UltraTech Cement have got their own dedicated BCFCM railway wagons. These wagons are also being deployed to transport bulk cement. Bulk cement transported in BCFCM wagons is stored in silos at cement-plant bulk terminals from where
they are bagged and transported by road to distributors for end customers.
Venkatesh Ravula, CEO of DCL Bulk Technologies India (DCL), says integrated cement-plant operators in India also transport the bulk of their clinker via the Indian freight rail network. “We have set up, through turnkey support, 36 clinkerloading facilities for wagons spread across 14 integrated cement plants in India. Our systems can be designed to undertake loading of up to four wagons at a time.”
Ravula expects that with planned capacity expansion, cement plants and thermal power plants in India will install more wagon-loading systems to transport cement and fly ash, given the cost-saving benefits.
He adds: “DCL’s high-end 40-year engineering expertise in dust control and dry bulk loading, based on the wagon-loading model, provides complete pre-engineering support. This enables plant owners to decide on bulk silo capacity, outlet locations, and a minimum height of a silo bottom from ground level. This is crucial to designing cost-effective wagon-loading systems.”
DCL’s clinker-loading installations include one at UltraTech’s Rajashree production unit at Gulbarga, Karnataka, south India, another at JK Lakshmi’s Sirohi, Rajasthan site, one at JK Cement’s Mangrol works, an installation at Dalmia Rajgangpur’s site in Odisha, eastern India, and a loading installation for Ramco Cements in Jayanthipuram, near Vijayawada, south India.
In total, DCL has installed ‘hatch adapter’ clinker wagon-loading systems at 14 integrated cement plants in India.
DCL bulk-loading systems solutions are offered as a package. They comprise silo aeration, silo venting, flow-control gates, integral dust extraction systems, horizontal positioning systems, a PLC-based control system, and a telescopic chute with level indicators.
Ravula continues: “Our wagon-loading systems are suited for loading any dry bulk materials into open or enclosed wagons for use on India’s railways. Systems are designed in such a way to suit loading times stipulated by Indian Railways.”
This loading approach, according to Ravula, has revolutionised the clinker bulk loading in rakes as they are designed to load dust-free and are operation- and maintenance-friendly. This concept was first introduced in India by DCL in 2008 at M/S Rajashree Cement, replacing DCL’s earlier conventional bulk-loading system.
DCL is a 100% subsidiary of DCL USA. It has a global presence through its dust control and bulk-loading solutions for clinker, cement, fly ash, alumina, coal, and other dry bulk material-handling solutions, serving India, the Middle East, Africa and Southeast Asian markets. Headquartered in Michigan, DCL USA caters for North America, South America, and European market customers.
Buoyed by the rising need to transport fly ash and cement in bulk form, Braithwaite & Co, a production entity of India’s Ministry
of Railways, has developed its own BCFCM wagons.
According to Yatish Kumar, chairman and managing director of Braithwaite & Co: “The directives of India’s Union Government to thermal-powered plants to discard dumping its coal ash in ash ponds to prevent natural degradation and the ready availability of cement companies as buyers of fly ash for cement productions, augurs well for the demand of BCFCM wagons. The changing consumption pattern of cement away from the production centres, necessitating cement producers to move the cargo in bulk form for ready-mix concrete, also adds to the BCFCM wagons’ demand potential.”
UltraTech’s vice-president of logistics, Arun Salvi, warns of some challenges that need to be overcome to ensure greater use of wagons to transport fly ash used in cement production. “A great deal of coordination is needed between cement companies and power plants as many power plants are scattered in India. Another very important factor is the need to standardise a railway wagon model. This would enable its usage across all users of these rakes. This is important because storage-silo design depends on the wagon’s design. Differences in wagons could lead to loading issues with the end-user of these rakes. There will also be a need for proper coordination by the [Indian] railways. The greater use of these wagons is viable from an economy-of-scale perspective.”
Shree Cement’s Vinay Saxena shares similar views. “There is higher availability of waste materials, which can be used as alternative fuel for Indian cement production in India. However, concerted initiatives between the Government and consumers need to ensure the sustained availability of the waste materials. Further, there need to be scientific processes for segregating waste materials. Besides, there must be wastetreatment plants set up through public-private partnership to make it suitable for usage.” AB
JV AUTOBAHN has been the market leader in road and airfield construction in Russia for 25 years. A key reason for its success is its ability to prepare for future challenges – and opportunities.
The company handles various infrastructure-related work, including engineering surveys, new construction, reconstruction and repairs. In 2018, it introduced recycling to its business by purchasing an Ammann ABA 240 UniBatch Asphalt-Mixing Plant with a RAC25 cold recycling system.
The RAC25 enables mix production with up to 25% cold RAP (recycled asphalt pavement).
AUTOBAHN management saw this as a good start – but only a start. After discussions with Ammann engineers, company leaders decided to plan for the future. The purchase included a reinforced highcapacity AFA-3075 filter with 70,000Nm3/h exhaust gas volume that ensured the plant was properly configured so it could recycle hot materials at a later date.
The plant successfully operated for two seasons, producing various asphalt mixes, including those with 25% cold recycled materials and SMA (stone mastic asphalt) with 10% RAP.
Ammann engineers faced a significant task. In 2020,
AUTOBAHN added a second mixing tower and RAH60 parallel flow drying drum. The adjustment enabled 25% cold materials and up to 60% hot RAP utilisation. The RAH60 is designed to be part of a permanent plant. Yet AUTOBAHN needed to relocate the plant occasionally.
The Ammann engineering team rose to the challenge, designing and implementing a mobile steel foundation for a hot recycling plant.
The parallel flow dryer, support structure, conveyors and elevator were mounted on portable footings for easy assembly and transfer between locations. Ammann is the only plant manufacturer to offer this solution.
“We thought long and hard about which modern options our new flagship plant should be equipped with to support the entire range of innovations we were implementing,” said Nadezhda Savenkova, deputy managing director for innovation and quality at AUTOBAHN. “As a result, in addition to the cold and hot recycling, we ordered a foamed bitumen supply for use on its own and in combination with other technologies.”
AUTOBAHN can produce mixes with varying amounts of RAP because it has both hot and cold recycling systems. It can use the systems individually or
combine them while producing a single mix.
A cold feed group consisting of two 13m3 feeders supplies the RAP. The conveyor groups are designed so the operator can send material to the cold recycling system (RAC25), the hot recycling system (RAH60) – or to both systems simultaneously.
The principle of the RAH60 parallel flow dryer is as follows: recycled material and raw gas are fed in the same direction. To reduce emissions from the parallel flow dryer, the temperature of recycled material doesn’t exceed 130°C. The asphalt temperature increases when it mixes with the heated material from the mineral drum. This works in connection with the mineral drum, i.e., 60% of the material comes from RAH60 and 40% from the mineral drum.
“We do our best to make the most of the plant’s capabilities and produce mixes with higher amounts of RAP and foamed bitumen,” said Savenkova. “Of course, a lot depends on customers’ requirements. But for our part, we encourage the growing interest in recycling technology in Russia and are happy to be at the forefront. We hope to become the first company in Russia to successfully implement 60% RAP, ensuring the top quality of asphalt mixes. Recycling
technology has many economic and environmental benefits. It does require serious investment, but we are sure that the future belongs to recycling.”
To help control and optimise production, AUTOBAHN used the Ammann as1 Control System with an advanced Dynamic Recycling Addition (RAD) module. The company praised the features of the as1 – and the RAD module in particular.
“The as1 Control System is very user-friendly, allowing easy control of the entire production process,” said Sergei Kultygin, production manager. “This is especially important when producing complex mixes with RAP. We are now actively mastering the functionality of the RAD module, where RAP ratio can be easily changed during the ongoing production process with a click of the mouse without changing the recipe.”
Kultygin continued: “We are grateful to the Ammann engineering team for their hands-on help in implementing recycling technology at our plant.
As it turned out, there are many different nuances in preparing, selecting and feeding RAP into the system. The order in which material is entered into the mixer and the advanced technologies utilised also have a significant impact.”
ammann.com
An Indian construction contractor is using an MB Crusher crusher bucket to help build more than 100 kilometres of roads for the Border Roads Organisation (BRO), a government road construction agency providing support to the Indian armed forces in the Indian border areas and friendly neighbouring countries.
The MB Crusher customer’s roadbuilding project is in India’s northern mountainous region, 16,700 feet above sea level. Given the high altitude of the project site, installing a static crusher was very difficult. Additionally, due to the non-availability of electricity, the contractor had to rely on a diesel generator set (DGS) to run their static
crusher at the jobs site. Furthermore, the high-altitude working environment means that the oxygen level is very low, so the DGS cannot operate fully.
The contractor customer had deployed manual labourers at the road build to segregate small pieces of stones, but this could not generate sufficient productivity. Given the BRO-commissioned project’s route, the contractor’s team has to cope with severe snow for a large part of the works. While looking for a productive and efficient solution for preparing GSB (granular sub base) material for use in the project’s new roads and helipads, the contractor focused on MB Crusher’s BF90.3
ProStack has added the Ranger 4-15H and Ranger 4-15L to its Ranger series of tracked conveyors. These 50ft highlevel and low-level conveyors are said to be among the most cost-efficient and effective ways of stockpiling material on the market.
With a high level of portability and being suitable for almost any working environment, the new conveyors are ideal for operators who want to maintain a controlled flow of material when feeding secondary equipment, loading ships and rail wagons, or simply stockpiling material.
Operators can stockpile directly from crushers, screens or other material sources, removing the need for double handling of material.
This greatly reduces site traffic, labour and maintenance costs. Key applications include
quarrying, aggregates, mining and ports.
S4 crusher bucket. The firm had deployed the same model on a trial basis at its other recent project sites.
Despite the remote project location, the contractor has found the MB Crusher crusher bucket a very productive machine, saving time and transport costs. The contractor also found it easy to mobilise while generating lower operation and maintenance costs.
After being delighted with the BF90.3 S4’s crusher bucket’s performance, the contractor has bought three additional BF90.3 S4 units to use in its various ongoing projects.
mbcrusher.com
The Ranger 4-15H is a robust machine offering superior strength and can easily achieve an output of 450 tonnes per hour. Options include a choice of a 4-, 5- or 6-inch tipping grid, allowing for the removal of oversize materials, resulting in a betterquality product. There is also an option of a single-deck vibrating grid, and the machine can produce two separate products to
meet customer needs fully. There is a regulated flow of material from the feeder at the discharge point, ideal for operations where surging is a problem.
The Ranger 4-15L can be fed from three sides, allowing the operator to have greater versatility when loading the hopper. Hopper extensions can be deployed via hydraulics with support arms fitted. This removes the need for manual bolting of the hopper, which enables a faster set-up time. An optional feed hopper outlet door is fully adjustable, allowing the operator to control the amount of material passing from the feed conveyor to the discharge conveyor. Operators will have an unregulated flow of material from the feeder, resulting in improved handling of difficult material and elimination of feeder blockages.
terex.com/prostack
McCloskey International has introduced an exciting new way for customers to enhance business operations and boost productivity for their equipment in the field.
365SiteConnex, a complete connectivity solution for highly accurate monitoring of McCloskey products, is based on the latest communication technologies to collect, analyse and deliver information on the crushers, screeners and stackers customers relied on to produce the highest quality products with the least amount of downtime.
Monitoring a fleet is key to reducing this downtime and maintaining efficiency and profitability. With 365SiteConnex, key information for any machine can be obtained in just a few clicks, allowing users to review faults or status issues from a single notification feed, monitor fuel usage across all machines, and monitor service schedules and requirements.
Additionally, with GeoData, a machine’s current and previous locations can be tracked, from manoeuvres on a worksite to being transported halfway across a continent. Geo Fences can be programmed to be notified if a machine goes outside its designated area.
From onsite to the office, this key information is easily accessible across devices and grouped in easy to navigate pages, including engine and feeder data, diagnostics and
to have a full and comprehensive remote view of their operation.
In addition to standard functionality like machine status and location, 365SiteConnex will allow measurement of key production and cost efficiency indicators, including fuel consumption, production, and engine hours, to analyse idle vs productive time. As important, it will allow benchmarking between the plants to identify critical similarities and differences in operation and performance.
365SiteConnex serves as a valuable contributor to the machine’s lifecycle through
metal detector notifications to protect the equipment in tough applications. To extend the life of the machines, machine usage history information related to wear part history data and liner replacement information are programmed into the system to monitor machine performance on an ongoing basis.
“McCloskey’s success has been built on listening to our customers and working with them to design and develop the best features and functions for their equipment. Building on the latest technology platform based on this allows us to deliver an innovative
365SiteConnex telematics empowers operators keen to reduce crusher, screener and stacker fleet downtime and maintain efficiency and profitability
productivity for their operations,” vice-president, McCloskey International.
365SiteConnex will be available in the first quarter of 2022 through McCloskey dealerships as a subscribed service. The software will offer remote software updates to deliver the latest program upgrades and remote support from the 365SiteConnex service team. The information and analytics drawn from the ongoing evaluation of the program will allow for continuous improvement and development of additional features and benefits.
mccloskeyinternational.com
Command Alkon is now offering a new mobile app that helps optimise material hauling.
Called Ruckit, the tool can be used to manage a firm’s truck fleet and third-party haulers.
The tool can be used by asphalt paving firms, aggregate suppliers, contractors, haulage firms and truck drivers, all of which can collaborate digitally using a single platform.
The tool provides a seamless data flow according to the firm and helps to optimise scheduling and logistics. The system allows tracking of trucks’ hauling loads in real time and helps streamline invoicing, providing faster payments. commandalkon.com
05-07: RecyclingAKTIV & TiefbauLIVE
Karlsruhe Trade Fair Centre, Germany
Organiser: Messe Karlsruhe
Tel: +49 (0) 721 3720 2300
Email: verena.schneider@ messe-karlsruhe.de www.recycling-aktiv.com
17-21: Excon 2022
Bangalore, India
Organiser: Confederation of Indian Industry
Tel: +9144 42444555 Extn : 695
Email: excon@cii.in www.excon.in
JUNE
21-23: Hillhead
Hillhead Quarry, Buxton, Derbyshire, England
Organiser: The QMJ Group Tel: +44 (0) 115 945 4377
Email: Harvey.sugden@qmj.co.uk www.hillhead.com
JULY
06-09: EIG 2022
Exeter, UK
Organiser: EIG Conferences
Email: marcus.dorey@hanson.biz www.eigconferences.com /future-conferences
AUGUST
30-02: M&T Expo 2022
São Paulo, Brazil
Organiser: Messe Munchen
Tel: +55 11 3868 6340
Email: info@mtexpo.com.br www.mtexpo.com.br/en/
OCTOBER
24-30: bauma
Munich, Germany
Organiser: Messe München
Tel: +49 89 949 11348
Email: info@bauma.de www.bauma.de/en/
07-09: Trimble Dimensions
Las Vegas, NV
Organiser: Trimble https://dimensions.trimble.com /live
Advertisers in AGGREGATES BUSINESS can now be contacted via their websites - for instant links to all the websites listed below, by category, go to: www.AggBusiness.com
19-20: CECE Congress 2023
Chamonix, France
Organiser: CECE
Tel: +32 2 706 82 26
Email: info@cece.eu www.cece.eu/
31-03 Feb: bauma Conexpo India 2023
Greater Noida, India
Organisers: AEM and Messe München
Tel: +49 89 949 20251
Email: info@bcindia.com www.bcindia.com/
03-07: SaMoTer 2023 Verona, Italy
Organiser: Veronafiere S.p.A.
Tel: +39 045 8298561
Email: customercare@samoter.com www.samoter.it/en
14-18: CONEXPO-CON/AGG
Las Vegas, NV
Organiser: AEM
Tel: +1 (800) 867 6060 www.conexpoconagg.com
MEET THE TEAM
Aggregates Business travels the globe attending conferences, events and equipment shows, keeping you informed of the latest offerings. Come and join us for a chat at any of the events below.
JUNE 2022
21-23: Hillhead 2022
Hillhead Quarry, Buxton, Derbyshire, England
OCTOBER 2022
24-30: bauma Munich, Germany
These dates were correct at the time of going to press, but please note that the COVID-19 pandemic means some events may be rescheduled with little advance notice
Contact: Roger Adshead | radshead@ropl.com | +44 7768 178163
THE MOBICAT MC 110 EVO2 AND MOBICONE MCO 90 EVO2
TEAM PLAYERS THAT WORK TOGETHER INTELLIGENTLY AND STRENGTHEN EACH OTHER. In linked plant combinations, the MOBICAT MC 110 EVO2 jaw crusher and the MOBICONE MCO 90 EVO2 cone crusher really fl ex their muscles. SPECTIVE makes both plants easy and intuitive to operate. Also, an advanced drive concept ensures greater effi ciency with lower consumption. Maximum throughput is achieved thanks to the material flow concept coordinated via line coupling across both crushing stages. Go for the perfect team!
www.wirtgen-group.com/evo2-line-kleemann