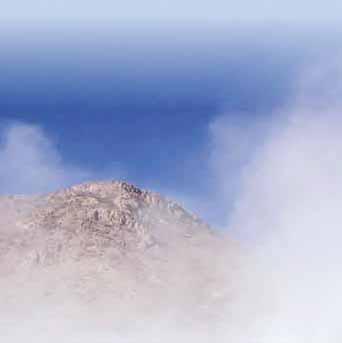
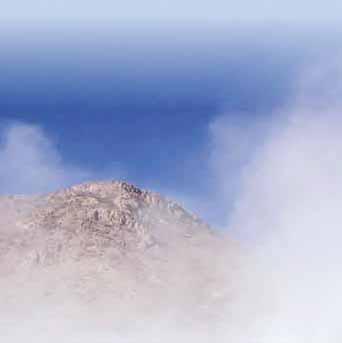
A crushing victory
A Namibian quarry triples production & sheds costs p13
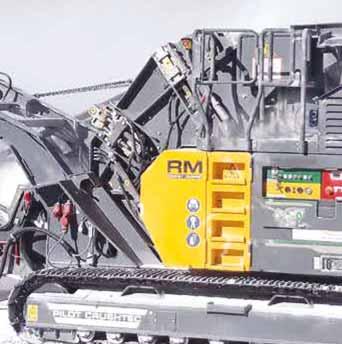
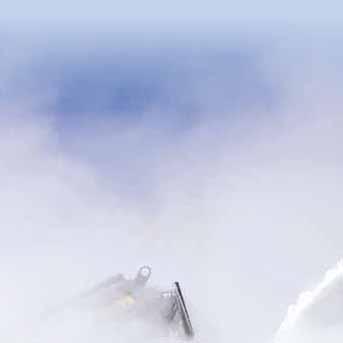
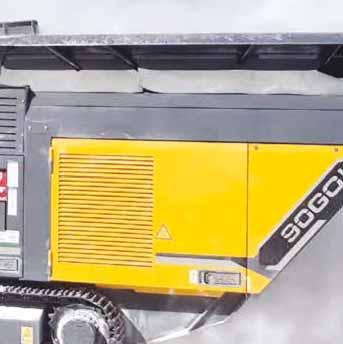

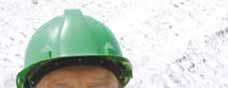

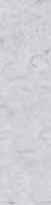
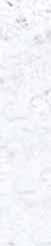
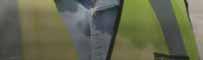
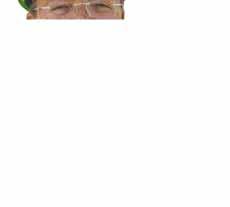
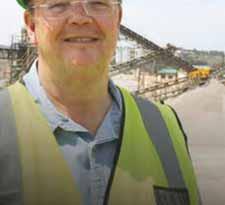
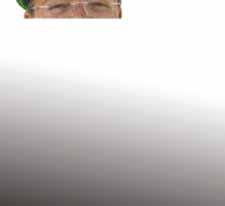
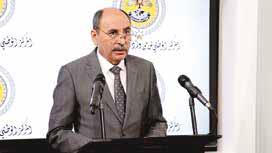
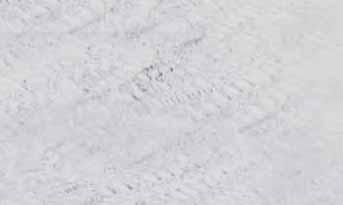
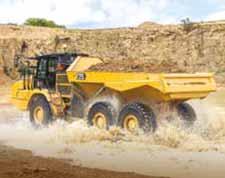
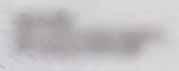
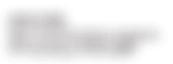
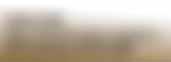
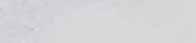
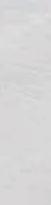
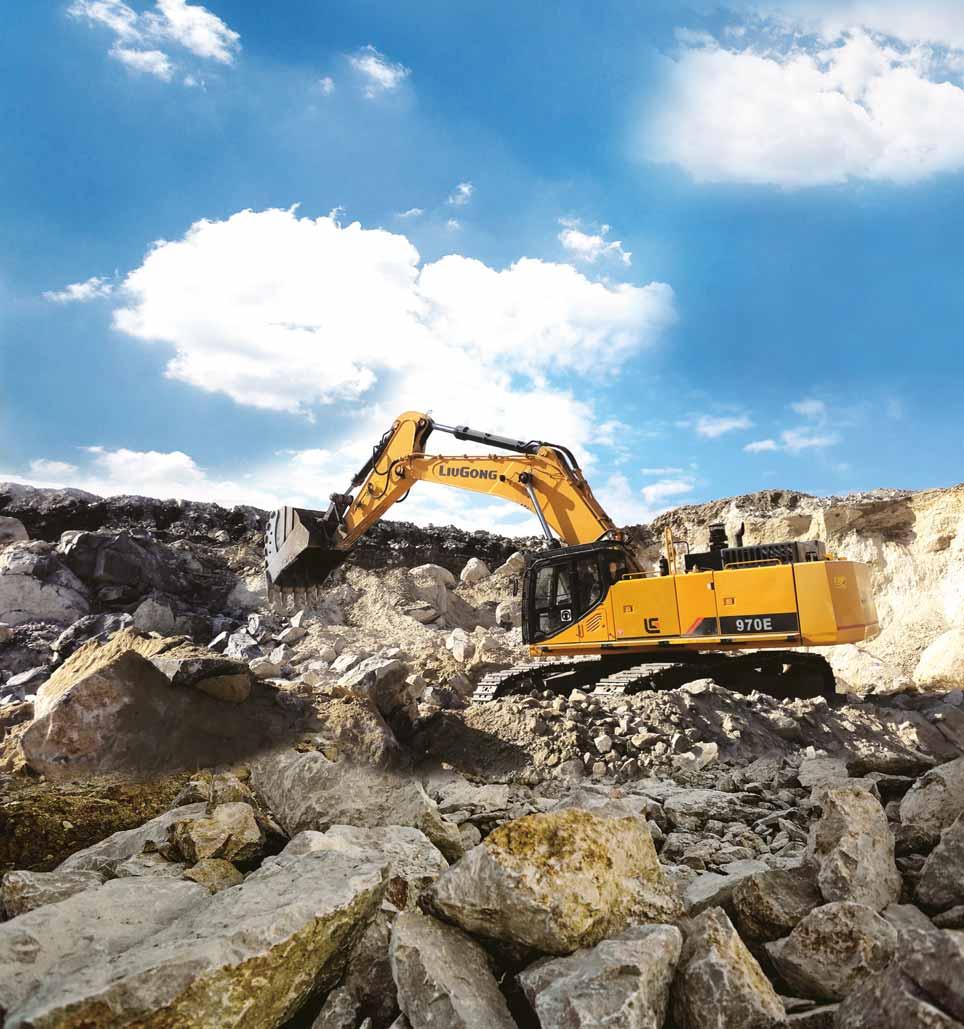
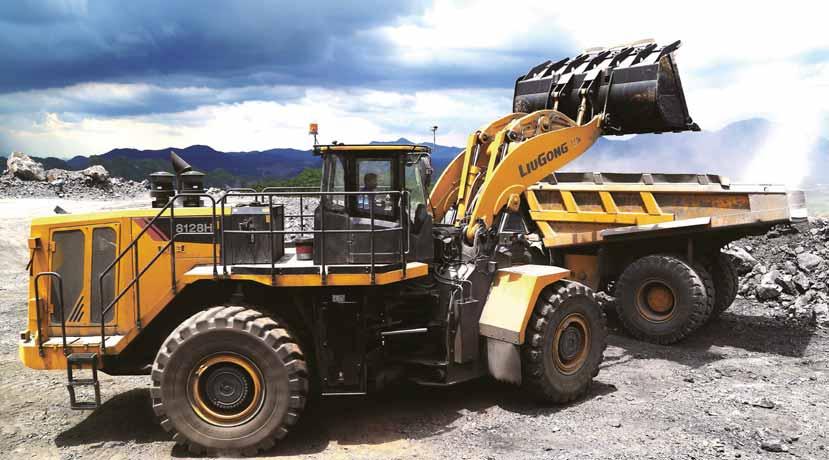
HEAD OFFICE
EDITOR: Guy Woodford
ASSISTANT EDITOR: Liam McLoughlin
CONTRIBUTING EDITORS: Patrick Smith, Dan Gilkes
EQUIPMENT EDITOR: Mike Woof
DESIGNERS: Simon Ward, Andy Taylder, Stephen Poulton
PRODUCTION MANAGER: Nick Bond
OFFICE MANAGER: Kelly Thompson
CIRCULATION & DATABASE MANAGER: Charmaine Douglas
INTERNET, IT & DATA SERVICES DIRECTOR: James Howard
WEB ADMINISTRATORS: Sarah Biswell, Tatyana Mechkarova
MANAGING DIRECTOR: Andrew Barriball
PUBLISHER: Geoff Hadwick
CHAIRMAN: Roger Adshead
ADDRESS
Route One Publishing Ltd, Waterbridge Court, 50 Spital Street, Dartford, Kent DA1 2DT, UK
TEL: +44 (0) 1322 612055
FAX: +44 (0) 1322 788063
EMAIL: [initialsurname]@ropl.com (psmith@ropl.com)
ADVERTISEMENT SALES
SALES DIRECTOR:
Philip Woodgate TEL: +44 (0) 1322 612067
EMAIL: pwoodgate@ropl.com
Dan Emmerson TEL: +44 (0) 1322 612068
EMAIL: demmerson@ropl.com
Graeme McQueen TEL: +44 (0) 1322 612069
EMAIL: gmcqueen@ropl.com
SUBSCRIPTION / READER ENQUIRY SERVICE
Aggregates Business International is available on subscription. Email subs@ropl.com for further details. Subscription records are maintained at Route One Publishing Ltd.
SUBSCRIPTION / READER ENQUIRIES TO: Data, Route One Publishing Ltd, Waterbridge Court, 50 Spital Street, Dartford, Kent DA1 2DT, UK
TEL: +44 (0) 1322 612079 FAX: +44 (0) 1322 788063
EMAIL: data@ropl.com

No part of this publication may be reproduced in any form whatsoever without the express written permission of the publisher. Contributors are encouraged to express their personal and professional opinions in this publication, and accordingly views expressed herein are not necessarily the views of Route One Publishing Ltd. From time to time statements and claims are made by the manufacturers and their representatives in respect of their products and services. Whilst reasonable steps are taken to check their accuracy at the time of going to press, the publisher cannot be held liable for their validity and accuracy.
PUBLISHED BY © Route One Publishing Ltd 2020
AGGREGATES BUSINESS INTERNATIONAL USPS:
is published six times a year. Airfreight and mailing in the USA by agent named
WN Shipping USA, 156-15, 146th Avenue, 2nd Floor, Jamaica, NY 11434, USA.
PERIODICALS POSTAGE PAID AT BROOKLYN, NY 11256
US POSTMASTER: Send address changes to Aggregates Business International, WN Shipping USA, 156-15, 146th Avenue, 2nd Floor, Jamaica, NY 11434, USA
Air Business Ltd is acting as our mailing agent
PRINT: ISSN 2051-5766
ONLINE: ISSN 2057-3405
PRINTED BY: Warners (Midlands) PLC
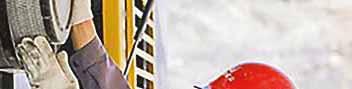
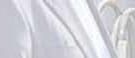

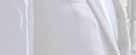
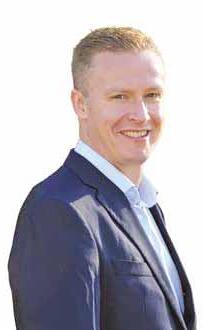
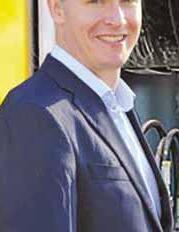
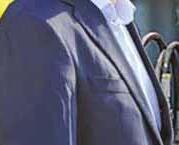
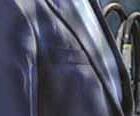
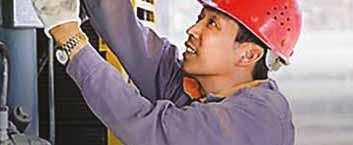
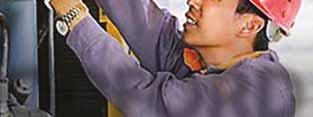

TChina’s key role in the post-COVID-19 recovery
he COVID-19 pandemic has caused massive disruption to the global aggregates and other building materials sectors, not least in this magazine’s core markets of Asia, Africa and the Middle East. To their credit, many national governments across the three regions took swift action to reduce the spread of coronavirus in their respective countries. Now, many nations are starting to emerge from lockdown, most notably China.
The world’s most populous country, home to 1.3 billion people, China is also the world’s biggest producer and consumer of aggregates. To put that in context, a study published last year by Persistence Market Research, a leading global business market intelligence consultancy, stated that 47 billion tons of construction aggregates were sold globally in 2018, at an estimated value of US$300bn. Given such figures, the fact that China is starting to get back up on its giant economic feet will be warmly welcomed by aggregates product producers and manufacturers of aggregates processing equipment.
Retaining a China focus, I read with great interest a new study by GlobalData, a leading global business market intelligence consultancy, looking at how China is continuing to increase its involvement in infrastructure developments in emerging Asian markets.
GlobalData estimates the total value of Asian infrastructure projects (including building materials) in which Chinese contractors are at least partially involved at around US$235bn. In South Asia alone, the project values total $191bn. China’s influence is expanding via its Belt & Road Initiative (BRI) – a more than US$1 trillion 21st century silk road, made up of a ‘belt’ of overland corridors and a maritime ‘road’ of shipping lanes. Under the BRI, China is improving infrastructure in emerging markets across the world, facilitating economic development through the companies that can transport goods more quickly and cheaply between countries along various routes.
Danny Richards, lead economist at GlobalData, notes that although wariness has been increasing among emerging-market
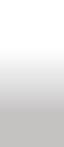
governments over the risks of relying heavily on China for funding and construction contracts, the wealth of opportunities provided under the BRI can be attractive for administrations with limited funding capacity and rising infrastructure needs.
Expanding on Richards’ comments, the BRI also offers highly attractive commercial opportunities to major and ambitious small- to medium-sized aggregates and other building materials producers and quarrying equipment makers.
From a broader perspective, GlobalData analysis shows that if all infrastructure projects in the pipeline across Asia’s emerging markets proceed as planned, spending on projects involving Chinese contractors could reach $64bn in 2020, up from $23bn in 2014.
China is also the most significant foreign player in infrastructure financing and construction in Africa, mainly through BRI. According to Deloitte’s Africa Construction Trends (ACT) 2019 report, China funds 92 projects, one in every five projects, across the continent (20.4% - up from 18.9% in 2018). It is the second-largest funding source after African governments.
The Deloitte report also highlights how China continues to dominate as the most prolific (and single country) builder of projects across Africa, constructing 140 projects (31%). Projects built by China fall primarily within the transport sector.
China has also become an increasingly significant economic player in the Middle East over the past decade, mainly via the energy markets of Gulf states and the BRI. Indeed, as the European Council on Foreign Relations (ECFR) notes, the region is a strategically vital crossroads for trade routes and sea lanes linking Asia to Europe and Africa, giving it a central role in the BRI’s future.
As the global COVID-19 pandemic crisis eases and with China’s strategic big-money investment in BRI and other less grand but still important building projects set to continue apace in the coming years, African, Asian and Middle Eastern aggregates demand in the short- to medium-term will remain strong. GW gwoodford@ropl.com

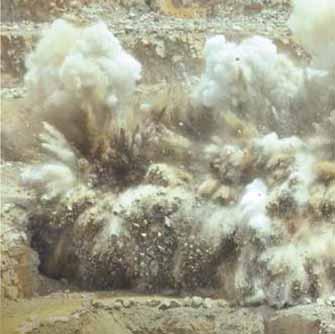
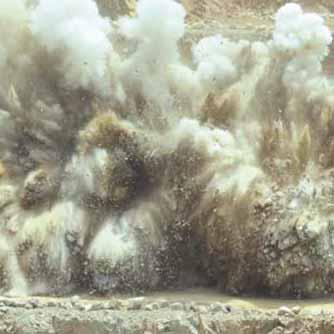
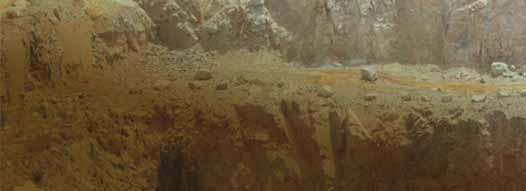
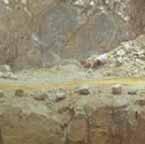
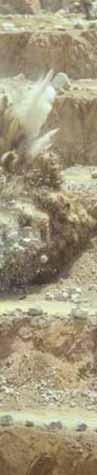
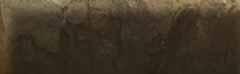
19 CRUSHING & SCREENING
New and proven premium crushing and screening plant have been very much to the fore in the first half of 2020
24 LOADING
Two new loading machine buys are helping a Scottish quarrying and construction company to maximise its recycling efficiency and reduce the amount of materials it sends to landfill
26 HAULING
Key construction projects give hauling

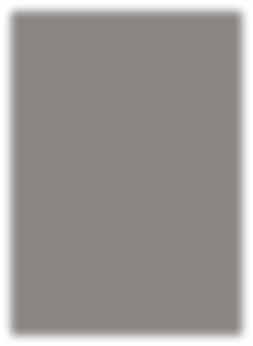

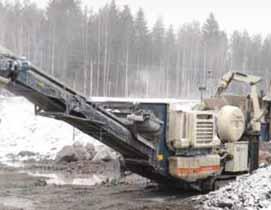
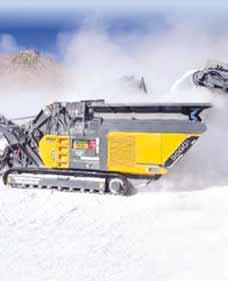



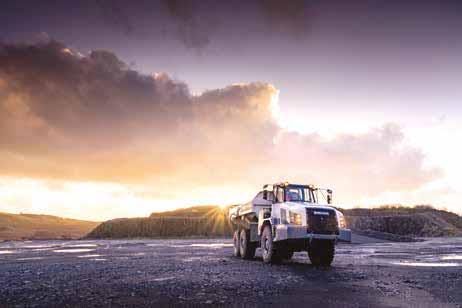
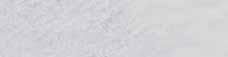


Mineral product producers keen to widen their income streams can find big commercial opportunities in recycled aggregate and concrete products PORTABLE POWER – PART 1
Portable power solutions for quarrying industry customers are getting greener and embracing new technology WEAR PARTS
Being able to quickly access and install high-performing replacement wear parts on quarrying plant reduces downtime leading to enhanced worksite efficiency.
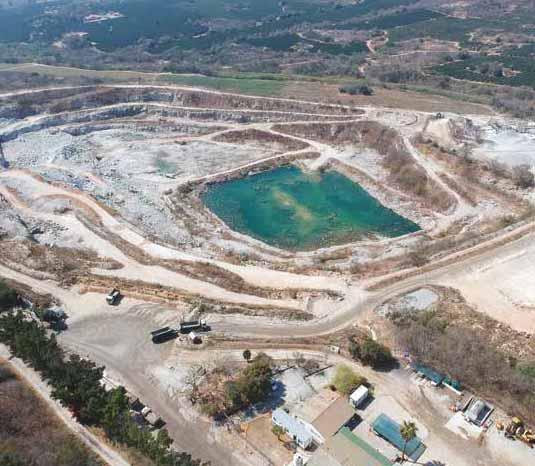

Specials
07 INTERVIEW
For more than two decades as director of southern Africa’s surface mining industry association, Aspasa, Nico Pienaar has
assocao,spasa,coeaaas directed his energy towards championing high levels of safer, healthier and more environmentally friendly mining practices
10 MARKET REPORT
Building activity loses momentum in the Middle East as the region faces twin challenges emanating from the coronavirus pandemic as well as plunging oil prices
13 QUARRY PROFILE
A recent installation of a Rubble African authorised distributor, Pilot Crushtec International, has helped triple production and reduce the cost of production significantly for a Namibian marble producer
15 ENHANCING QUARRY BLAST OUTCOMES
Having secured distribution rights for the Varistem, ERG Industrial is doing local trials
ase,Gdusasdogocaas to prove the potential productivity increase and downstream savings stemming plugs can provide to African quarries and mines
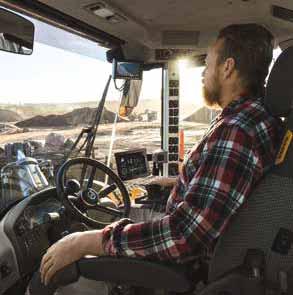

17
OPTIMISING EXCAVATOR UNDERCARRIAGES
Taking the time to inspect and maintain a crawler excavator’s undercarriage will help
caeecaaosudecaageep increase machine life
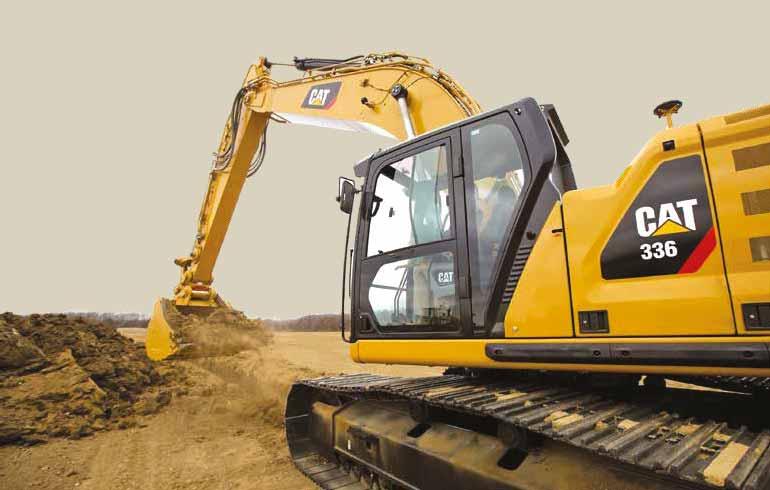
DOOSAN INFRACORE SEES BIGGER CHINESE PICTURE
Doosan Infracore is expanding its China market presence by selling large excavators, including its largest 80-ton excavator, the DX800LC, in various regions of the country.
The South Koreanheadquartered global market off-highway machine maker has won a series of new sales contracts for its lucrative large excavators in China, further strengthening its market base in the country.
As part of this, Doosan Infracore has announced that it has recently won orders for a total of 20 large excavators in various regions of China including Qinghai in northwestern China, Inner Mongolia, an autonomous region in northern China, and Shanxi in eastern China.
The industry anticipates that the annual sales volume of excavators in China will surpass the 2019 record of 200,000 units per year amid expectations about the government’s stimulus packages.
Doosan Infracore’s sales representative in China said: “Despite the increasingly intense competition in China, we will pursue sustainable growth by strengthening our line-up of large, highperformance excavators.”
Chinese excavator makers resume production
Chinese equipment manufacturers have pressed the “fast-forward button” to resume production in the wake of the coronavirus pandemic, according to the CCMA (China Construction Machinery Industry Association). Chinese excavator manufacturers sold a total of 49,408 products in March 2020, an increase of 11.6% year-on-year according to CCMA data. Domestic market sales accounted for 46,610 units in March, a year-on-year increase of 11.2%. Meanwhile, export sales were 2,798 units, a year-on-year increase of 17.7%.
Chinese manufacturers sold a total of 68,630 excavation machinery products from January to March (Q1) this year, a year-on-year decrease of 8.2% which was mainly attributable to the effects of the coronavirus pandemic.
The acquisition strengthens Ciments du Maroc’s position in the Moroccan cement sector
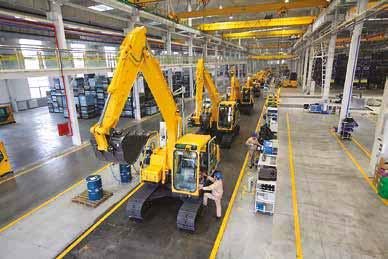
Domestic sales have been harder hit than exports. According to CCMA data, 61,277 units were sold in the domestic market in Q1, a year-on-year decrease of 11.6%. Export sales in Q1 increased to 7,353 units, a year-on-year rise of 34.9%.
China’s health authority, the National Health Commission,
claimed that coronavirus-related deaths on the Chinese mainland have fallen sharply in recent weeks.
The CCMA says that stateowned heavy-machinery manufacturer XCMG has returned to 100% production levels for the first time since the pandemic took hold in China in late 2019/early 2020.
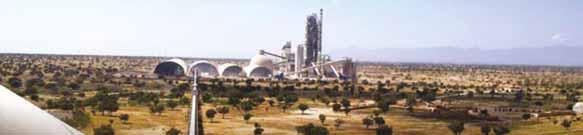
Ciments du Maroc completes Atlantic Cement and Cimsud acquisition
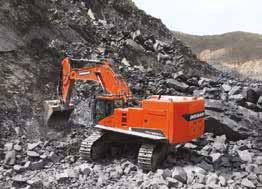


Ciments du Maroc has completed the acquisition of Moroccan building materials providers Atlantic Cement and Cimsud from the Anouar Invest Group following an agreement signed in July 2019. The agreement with the Anouar Invest Group means that Ciments du Maroc acquires 100% of the capital of Atlantic Cement and Cimsud. The value of the transaction was not
disclosed. Atlantic Cement is leading the project to build and operate an integrated cement production plant in the Settat province of Morocco. Cimsud operates a milling plant in Laâyoune with a capacity of 500,000 tonnes.
Ciments du Maroc, which is owned by HeidelbergCement, says the acquisition strengthens its position as a major player in the cement
Easing of SA lockdown allows materials to flow
The first steps in relaxing South Africa’s national coronavirus lockdown will allow critical supplies of cement and construction material to reach specified markets.
Local construction materials supplier AfriSam says that the lowering of the national
coronavirus level to Alert Level 4 will allow it to resume some of its production and to supply some customers.
“The company will now be supplying aggregates, ready-mix and cement products to permitted Alert Level 4 customers,” said
sector and marks a further step in the implementation of its strategy to develop its cement, aggregates and ready-to-use concrete businesses in Morocco. Ciments du Maroc operates three cement plants in Aït Baha, Safi, and Marrakech, in addition to two grinding centres in Laâyoune (Indusaha) and Jorf Lasfar, five quarries and 30 concrete-batching plants.
Richard Tomes, sales and marketing executive at AfriSam. The changes were recently signed into law by South Africa’s Minister of Cooperative Governance and Traditional Affairs Dr Nkosazana Dlamini-Zuma, in terms of provisions in the Disaster Management Act.
© Ciments du Maroc
The factory assembly line at SDLG’s Linyi, China HQ
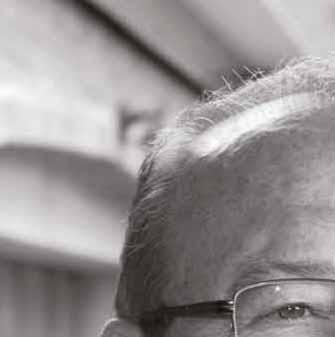
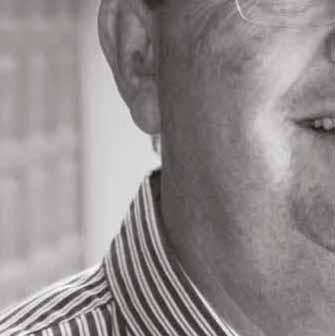
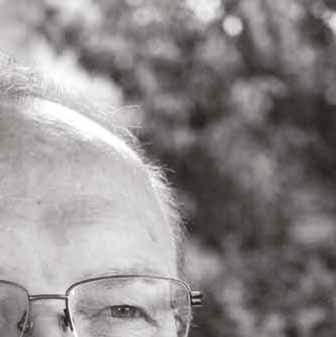
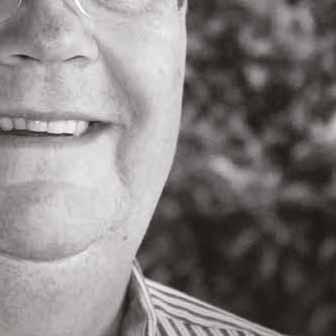
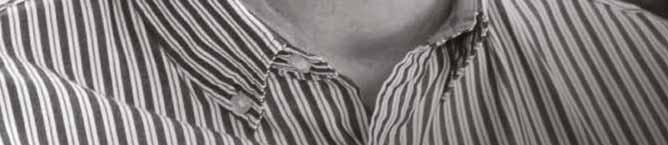
Southern Africa’s surface mining principal
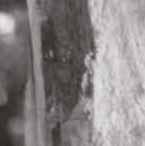


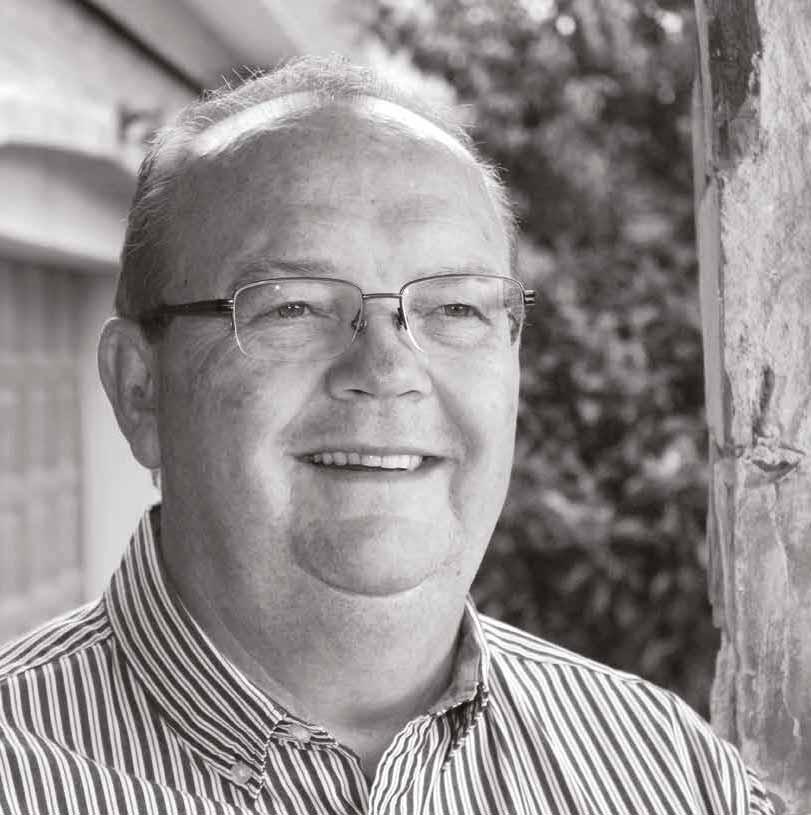
For more than two decades as director of southern Africa’s surface mining industry association, Aspasa, Nico Pienaar has directed his energy towards championing high levels of safer, healthier and more environmentally friendly mining practices. Munesu Shoko sat down with him to discuss his impressive track record and current Aspasa priorities
Armed with a Masters in Labour Law and Industrial Relations, Nico Pienaar spent most of the early years of his career in industrial relations. Notably, he was the first industrial relations advisor to the South African building industry through BIFSA (now Master Builders South Africa), a leading national representative body in the building and construction industry.
He eventually became a trade unionist, and worked for various institutions, including the then Building Industry Society, and eventually the United Building Society before it became a bank, which is today known as ABSA in South Africa.
Some of the biggest lessons he learnt during his industrial relations days were that “it’s always essential to stick to the rules, be fair and consistent”. These are some of the values he has lived by and championed for the past 21 years he has been at the helm of Aspasa, an industry association that initially looked after the interests of sand and aggregates producers in southern Africa, before it broadened its scope recently to become an all-inclusive surface mining association.
A few years after taking over the reins at Aspasa in 1999, Pienaar was also tasked with leading the Southern African Readymix Association (Sarma). He ran the two associations for some 12 years before Sarma was moved out of the Aspasa office to become part of the consolidated concrete industry bodies in 2017. Two years later, Sarma was closed at the end of 2019, “a very sad day” in Pienaar’s life, as he had, for over a decade, put a great deal of effort in building this readymix association. That Pienaar is passionate about what he does is very apparent – and many in the quarrying industry in southern Africa would agree. He has been the force behind Aspasa for two decades now, and has, over the years, revolutionised the association, which has since become a recognised voice of the industry.
For Pienaar, an association has to be of great value to its faithful members. This, he says, is a lesson he learnt during his trade union days. “You have to offer value and be of great help to members, who obviously look up to you as an association. An industry association has to be aware of the issues afflicting its members, something Aspasa has excelled in over the years.”
To meet the ever-changing needs of the industry, Aspasa has in recent years broadened its scope and also extended the range of services it offers to help members comply with the different legislations that apply to the industry.
In 2017, the association expanded its reach from its traditional sand and aggregates focus, to cover several other areas of the surface mining industry, including salt, dimension stone and clay brick. Affiliation now includes mobile crushing contractors, formal quarries, rubble crushing, ash, coal and borrow pit subsectors.
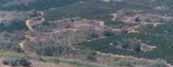
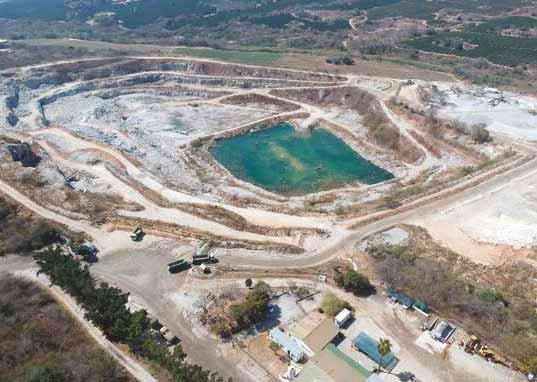
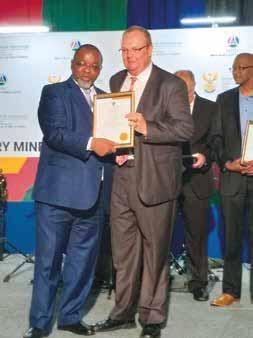
Also included are associate memberships for organisations such as the National Occupational Safety Association and heavy machinery manufacturers. These are all required to be legally compliant with legislation such as the Mine Health and Safety Act (MHSA), environmental legislation and the Water Act.
As the membership scope has been extended, so have been the services offered by the association. Aspasa’s service offering covers legal compliance; local, international and government liaison; health and safety audits and training; environmental audit and training; technical and transport support; as well as training and education.
In terms of legal compliance, the focus has traditionally been on health and safety and environmental practices. In recent months, the association has also added an array of compliance audits, including the Explosives/Blasting Compliance audit, the Quality/Technical Compliance Audit, Mining Charter Audit and a focus on Social Compliance and Community Affairs.
“Aspasa compliance audits assist operations, line managers, top management, boards and shareholders to ensure that operating standards are met in every aspect of the operation. The personal competencies of those operating the business are also addressed by a host of training topics that are covered by the association, while compliance audits point out issues that need attention,” he says.
Flagship audits within Aspasa have always been the health and safety audit, known as the ISHE Audit, and the environmental audit, named About Face.
The ISHE Audit has ushered in new health and safety standards in the industry. Aspasa members have reported no fatalities across their operations for the fifth year running –which is testimony to the level of health and safety excellence at member operations.
Explaining the key drivers behind the success of the ISHE Audit, Pienaar says the objective is two-fold. While it is a compliance audit protocol for legal requirements, own policies, standards, procedures and guidelines, as well as industry-leading practices, it is also an educational process where information is shared during audits on what is going on in the industry, how other operations are implementing required legislation and regulations to ensure high standards in health and safety performance.
ABOVE: Nico Pienaar receiving a special award from South Africa’s Minister of Mineral Resources in recognition of his valuable and ongoing contribution to the Mine Health and Safety Council
A view of Lafarge SA’s Karino Quarry in Nelspruit, South Africa, an Aspasa member operation
The ISHE audit generally covers MHSA regulations and Aspasa has recently received calls to expand it to cover the Occupational Health and Safety Act (OHSA). “We have, therefore, developed an additional audit protocol that will allow Aspasa to audit other functions that are associated with mining operations, such as readymix, bitumen, brick plants and workshops,” says Pienaar.
The environmental stewardship of Aspasa members has improved significantly since the inception of the About Face programme in 1994. This has guided and aided most members to elevate themselves from mediocre environmental performances to being among the best opencast operations in the world.
Pienaar says environmental compliance –from a community and regulator perspective – is also becoming a big issue in the industry. “The good housekeeping type of audits previously done have been changed, with specific focus now on being legally compliant by assisting mine managers to understand their roles and being not so dependent on consultants who often don’t grasp certain important issues themselves,” says Pienaar.
One of the newest service offerings from Aspasa is the Explosives/Blasting compliance audit. With blasting regulations changing, and communities being more aware of their rights, even when not often justified in their complaints, Aspasa has gone into an agreement with a blasting expert to conduct one-day audits to ensure compliance.
“We have decided to offer Blasting Audits to members because the mining industry faces numerous practical legal challenges since the MHSA’s new explosives regulations came into effect on 14 December 2018. There have been various demands made by affected communities and the regulator, the Department of Mineral Resources and Energy (DMRE) officials,” says Pienaar.
Increasing requirement for certified quality aggregates has also driven Aspasa to introduce its own guidelines and auditing systems to ensure testing of aggregates and crushed granular materials is done in accordance with South African National Standards (SANS) 3001 AG and GR series test methods.
In future, quarries belonging to Aspasa will have an option to participate in an annual audit designed to measure compliance of testing facilities, including their apparatus calibration and personnel competence against an abridged ISO 17025 format, to assist in ensuring the correct classification of products.
“Over time, as their systems improve, they can opt to obtain accreditation through South African National Accreditation System (SANAS) for ISO/IEC 17025 – general requirements for the competence of testing and calibration laboratories,” says Pienaar.
Following the publication of the Mining Charter’s Implementation Guidelines and Amendments in December 2018, Aspasa has now extended its service to members with a Mining Charter Audit.
South Africa’s new Mining Charter was developed to boost sustainable growth,
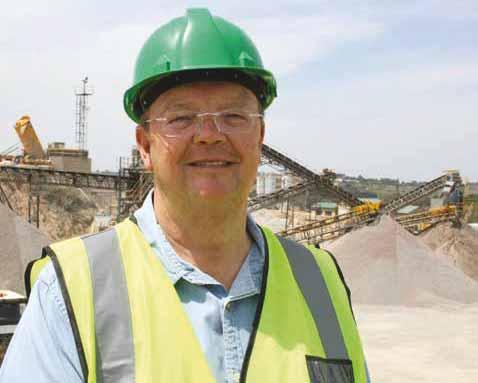
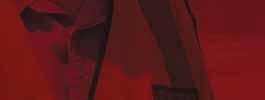
“The good housekeeping type of audits previously done have been changed”
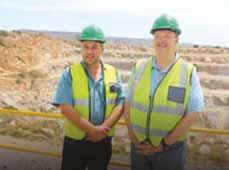
enforce procurement of local goods and to further support broad-based, meaningful Black Economic Empowerment of the South African mining and minerals industry. Pienaar cautions that it’s important for all South African mines to work strictly within the confines of the charter.
Pienaar says the biggest risk facing any operator is to be suspended because of non-compliance. “With the Mining Charter Audit, Aspasa members will be in a position to assess their compliance status and take
compliance inspections – the outcome of which can be punitive, costly and time-consuming.”
The business approach to running Aspasa is one of the reasons why the association has succeeded over the years. “I see Aspasa as a business, my own business,” he says. “I, therefore, have a great interest in all issues that affect the association’s members.”
For example, in the past two years, Aspasa has been tackling some new issues that have traditionally been beyond its jurisdiction. “We have also extended our scope to help members with security issues at mines, including attacks and theft. We have also started a community and social compliance group,” he says.
Pienaar’s efforts haven’t gone unnoticed. In 2018, he was honoured with two separate awards for his contributions to the industry. He was given a special award by South Africa’s Minister of Mineral Resources in recognition of his valuable and ongoing contribution to the Mine Health and Safety Council as director of Aspasa. Pienaar also received a CEO Global Titans Building Nations Award, which recognises unsung heroes of the African
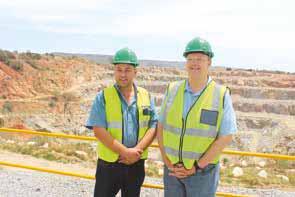
Aspasa has introduced its own guidelines and auditing systems to ensure testing of aggregates and crushed granular materials is done in accordance with South African National Standards
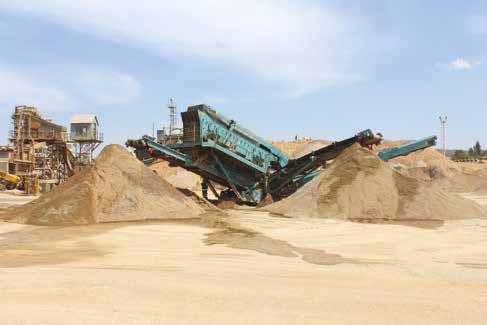
Nico Pienaar visiting one of the member operations in Gauteng, South Africa
Nico Pienaar with the mine manager of Drift Supa Sand, a member of Aspasa
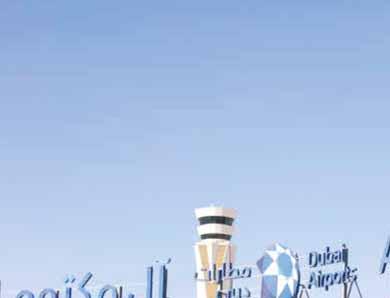
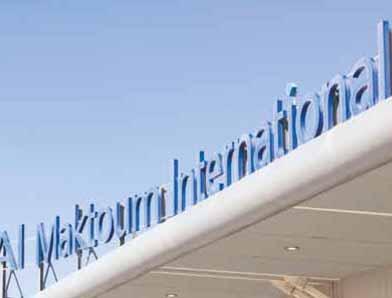

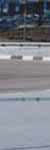
COVID-19 hits Middle East construction activity
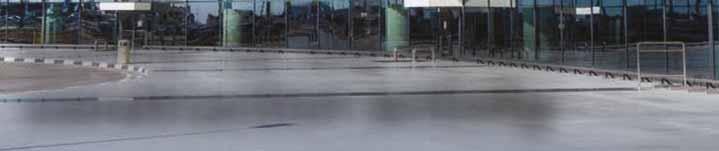
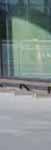
Building activity loses momentum in the Middle East as the region faces twin challenges emanating from the coronavirus pandemic as well as plunging oil prices. V L Srinivasan reports
In its regional economic outlook report for April 2020, the International Monetary Fund (IMF) has projected that the Middle East and North Africa (MENA) economies will contract by 3.3% in 2020, the biggest slump in four decades.
The report further said that the twin shocks of COVID-19 and low oil prices were likely to shave off US$323bn, or 12%, of the Arab world’s economy. Of this, $259bn is from the oil-exporting six-member GCC (Gulf Cooperation Council) countries alone.
Dubai, which was all set to inaugurate World Expo 2020 on October 21 this year, postponed the event by one year exactly. The UAE government has restricted air travel, announced a stimulus package of $34bn to support the economy, suspended issuance of new labour permits for the time being and has been allowing only essential personnel to visit the sites of projects under construction.
According to a report from Strategy& Middle East, part of the PwC network, the pandemic has hit the construction industry hard. Contractors have been facing budget overruns and delays, due to lockdown measures and strict hygiene and distancing restrictions resulting in low productivity.
Authored by Marwan Bejjani (partner), Alessandro Borgogna (senior executive adviser) and Elias Karam (manager), the
report states that construction materials were taking longer to source due to reduced manufacturing output and other supplychain issues. These are difficult challenges, but contractors in the GCC need to balance short-term measures to survive the crisis with medium-term measures to prepare for the eventual recovery.
“The ultimate impact on the GCC’s construction industry is still unclear, but we estimate that contractors in the region could lose approximately $30bn in revenue (20% of the GCC’s total construction market for 2020) if the current lockdown remains in place for three months,” the authors said.
If the lockdown extends through the end of 2020, the revenue impact would be about $65bn, a drop of around 45%, they added.
Crucial year
General manager of Emirates Building Systems (EBS) Joseph Chidiac said the UAE’s stimulus package aimed to cut the cost of doing business, support small businesses, and deliver significant government infrastructure projects.
companies in the UAE in the wake of COVID19 outbreak,” he said.
The UAE’s total construction contracts across all sectors were forecast to increase from $43.46bn in 2019 to $45.14bn in 2020. This includes the building sector ($25.2bn) followed by energy ($15.58bn) and infrastructure sectors ($4.3bn).
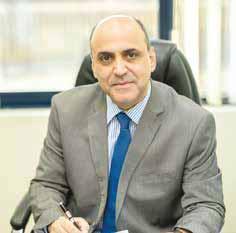
EBS is a wholly-owned subsidiary of Dubai Investments, and one of the leading manufacturers of steel structures in the Middle East with an annual production capacity of over 75,000 tons. “I feel 2020 is going to be a crucial year for construction
“I feel 2020 is going to be a crucial year for construction companies in the UAE in the wake of COVID-19 outbreak”
Joseph Chidiac
Al Maktoum International Airport- Dubai
“With the pandemic, oil price crash and the global economy in tatters, these figures are no longer realistic. The UAE, as well as other countries, are still fighting to keep the virus at bay and projecting a realistic forecast for the year is not possible at this stage,” he explained.
The contractors in the UAE may have to go through the price negotiation process again as project promoters are likely to insist on re-pricing contracts because of the changed circumstances. Even projects awarded as recently as weeks ago are undergoing re-pricing.
“The Abu Dhabi National Oil Company (ADNOC) has terminated engineering, procurement and construction (EPC) contracts it had awarded to the UK-based
Petrofac for its $1.65bn Dalma sour gas field development project. ADNOC has reportedly urged Petrofac for a discount on its contract value, which was turned down,” Chidiac said.
With regard to stock levels, he said that EBS was well stocked to take care of their immediate materials and consumable needs. It always keeps stock for at least six months and is not exposed to foreign suppliers. When required, the company sources from within the UAE or the GCC countries.
“Our policy is to purchase in bulk well in advance of projects’ schedules, and hence, for now, the virus is not having any material impact on us and our production is progressing as normal,” he added.
Downturn in GCC
The scenario is no different in the remaining five countries in the GCC region as the spread of the pandemic forced these governments to announce social lockdowns to contain its spread.
According to leading data and analytics company GlobalData, the region’s construction sector will face a downturn in 2020 over soaring COVID-19 cases and a slump in oil prices. The construction output growth forecast has been revised to -0.8%, down from the previous projection of 1.4% in mid-March (and 4.6% in its Q4 2019 update).
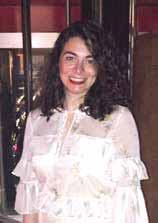
“Dubai’s Department of Finance has also ordered a 50% cut in capital spending and has called for a freeze on new public construction schemes”
Yasmine Ghozzi
*MENA coverage includes all the GCC Countries, north African countries of Egypt, Sudan, Algeria, Tunisia, Morocco and Levant countries such as Jordan, Lebanon, Iraq along with Iran
Source: BNC Intelligence
While Saudi Arabia has been maintaining its renewable-energy programme impetus and Aramco has been issuing tenders for offshore construction works, other parts of the GCC, including Qatar, Oman and Kuwait, are revising their spending and their construction pipelines.
“Dubai’s Department of Finance has also ordered a 50% cut in capital spending and has called for a freeze on new public construction schemes. Outside the GCC, Iraq announced that the COVID-19 pandemic constitutes a force majeure for all projects and contracts, creating uncertainty in Iraq’s construction sector,” GlobalData’s Economist Yasmine Ghozzi said.
Yasmine further pointed out that the outbreak was threatening to devastate Egypt’s $12.5bn-a-year tourism industry, which accounted for 12% of GDP.
In Jordan, the government has put in place a plan to jumpstart the construction sector, one of the most heavily affected by the COVID-19 economic fallout, to reboot the economy and provide jobs for day workers, according to the official Jordan News Agency.
Minister for Public Works and Housing Falah Omoush said the plan was aimed at stimulating the construction sector and addressing the economic ramifications of COVID-19. “Our plan seeks to support
and sustain the small and mediumsized businesses as they struggle amid governmental strict stay-at-home measures to stem the spread of the virus,” the minister said and added that strict safety measures would be followed.
Bahrain and Oman impacted Oman, too, has allocated $13.77bn for projects in its 2020 budget, and they include $7.01bn for industrial projects and services and $3.38bn each for infrastructure and for oil and gas projects.
The government, in tandem with the private sector, has been executing 2,410 construction projects whose combined value is put at around $188bn. They include 1840 ongoing projects valued at around $61bn on urban construction projects, 70 projects worth $39bn in the oil and gas sector, and 150 projects worth $32bn in transport. Additionally, 340 projects in utility and industrial sectors are being implemented, costing around $56bn.
But things changed after the COVID-19 outbreak and low oil prices and Oman’s federal bank – Central Bank of Oman – has announced a package to inject additional liquidity of over $20.8bn into the economy.
As part of the measures to mitigate the impact of COVID-19 crisis, Oman’s finance ministry has instructed all other ministries and civilian units to reduce liquidity for development budgets by 10%. Additionally, state companies will no longer be established for business activity to give way to the private sector.
Things are no different in Bahrain as it has announced that spending by ministries and government agencies will be slashed by 30% to help the country weather the coronavirus outbreak. Bahrain will also reschedule some construction and consulting projects to keep spending within the 2020 budget and make room for other expenditure needs emerging as a result of the disease’s spread, an official statement said.
M R Raghu, Kuwait Financial Centre executive vice president, said that although the GCC construction market continued to remain buoyant, with projects worth $17.5bn announced in February 2020 alone, the supply of materials was bound to face constraints.
Movement of construction materials and labour to construction sites remains a logistical issue due to lockdown and travel restrictions, he said.
Despite these hiccups, some of the GCC governments have allowed for critical construction works to take place provided guidelines issued by governments are followed. “The industry consensus is that, if we could overcome the COVID-19 pandemic in two months, the industry could recover faster,” he said.
“Projects envisioned as part of developmental programmes in Saudi Arabia and Kuwait would receive a renewed push in the post-COVID-19 scenario as the governments expect to accelerate their
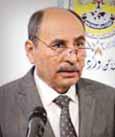
“Our plan is aimed at stimulating the construction sector and addressing the issues caused by the economic ramifications of COVID-19”
Falah Omoush
spending in various critical infrastructure projects. These include enhancing capacities of healthcare, education, roads, airports, power and housing projects,” he added.
Corporates join hands
Major companies such as Caterpillar and LafargeHolcim, which have been operating worldwide, including in the Middle East, have joined hands with the regional governments to fight the pandemic.
Caterpillar chairman & CEO Jim Umpleby said that his company remained committed to the safety, health and well-being of its employees around the world. The employees are delivering products and services that enable its customers to provide critical infrastructure essential to support society during the COVID-19 pandemic.
“In view of the pandemic, many governments have classified Caterpillar’s operations as an essential activity for the support of critical infrastructure. Working with our dealers, Caterpillar is delivering products and services that enable our customers to provide critical infrastructure that is essential to support society during the COVID-19 pandemic,” he said.
These products are being used by customers to provide prime and standby power for hospitals, grocery stores and data centres. They are also used to transport food and critical supplies in trucks, ships and locomotives, maintain clean water and sewer systems and mine commodities and extractive fuels essential to satisfy global energy demand.
“While employees who can work from home are doing so, in other facilities that remain open, Caterpillar is implementing safeguards to protect its team members in accordance with regulatory requirements and guidance from health authorities,” he added.
LafargeHolcim’s chief executive officer Jan Jenisch said that his company had also taken necessary measures to protect the health of its employees, customers, suppliers and other stakeholders since the beginning of the outbreak.
“While the construction sector and sites are generally more resilient than other sectors, the company has been experiencing disruptions in operations in various countries,” he said.
In China, the recovery of the construction sector has started, and all the company’s plants outside Hubei Province are operating.
“In most of the other key markets, the construction sector has been disrupted, and we forecast significant volume declines in April and May. While demand in Q1 was solid overall, LafargeHolcim expects a significant negative impact on its business in Q2,” he added. AB
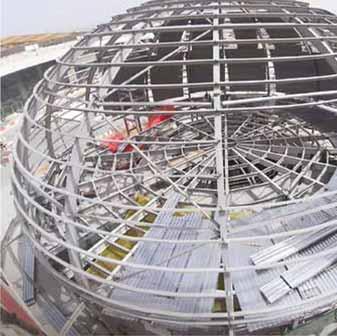
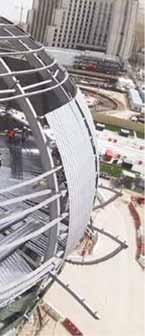
Russian Pavillion at Dubai World Expo 2020
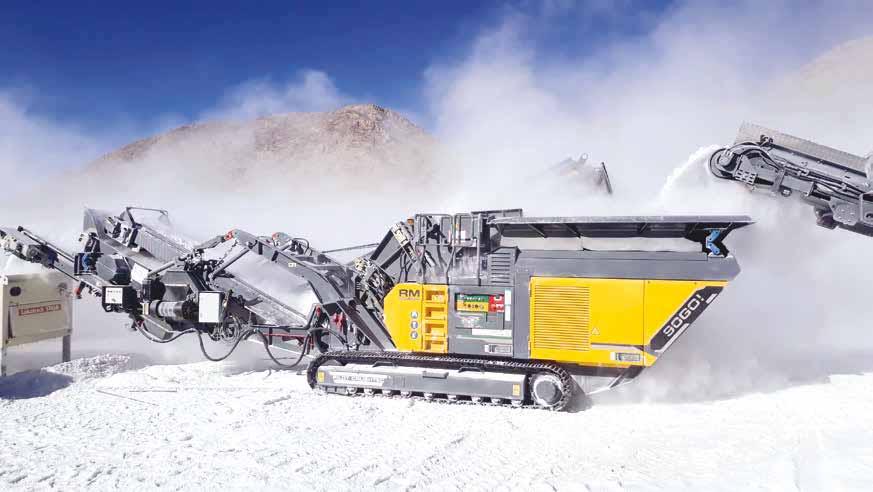
A Namibian quarry took delivery of a Rubble Master RM 90GO! in August 2019, which has helped triple production
RM 90GO! WINS THE DAY FOR NAMIBIAN QUARRY
A recent installation of a Rubble Master RM 90GO! by southern African authorised distributor, Pilot Crushtec International, has helped triple production and reduce the cost of production significantly for a Namibian marble producer. Munesu Shoko reports
To open up new alternative revenue streams, a Namibian marble operation decided to crush rejected marble slabs as a value-add to its business. Materials produced out of the waste comprise 0-1mm for various industrial uses, as well as 1-6mm, 6-15mm and 15-40mm for general aggregate.
“While well entrenched in the market, with a product ranked among the top qualitywise, there were two options to grow the business. They could either produce more marble, which was undesirable as that would compromise the lifespan of the quarry, or they could use waste material that continuously piles up on site. A decision was made to crush waste material into a valuable product,” explains Fernando Abelho, Africa sales manager at Pilot Crushtec. The newly crushed waste material has a number of uses in the
construction and industrial sectors, from tile grout to additives in commercial products –basically anywhere a fine powder is required.
Previously, the operation ran a Metso mobile jaw crusher and screen. However, with the old single-stage crushing set-up, it experienced high inefficiencies, which resulted in re-handling of material, translating into high cost of production per tonne.
“Initially, they were using a jaw crusher and screen to do single-stage crushing, but were achieving very low volumes,” explains Abelho. “The team from Pilot Crushtec spent about six months with the client in order to understand their business. The client did an exhaustive analysis in terms of what other industrial uses there could be for its waste and what specifications were required to compete in that market. Pilot Crushtec was then consulted on how to achieve the required product specifications.”
Pilot Crushtec’s initial idea was to just put in a screening plant to reduce double-handling of material, thus dropping operating costs. Essentially, this meant the material was fed into the jaw crusher, split into three usable products, and a fourth product that was still too large to be of any use had to be reprocessed.
The extra screen, however, would not solve the problem as the client’s production rates were just too low and the cost could not be justified. The only logical solution was to increase production, and the Rubble Master RM 90GO! impact crusher was deemed to be the perfect tool for the job at hand.
“The client needed a reliable crusher that could increase production significantly, provide flexibility in terms of product specifications and produce a high percentage of fines (due to the relatively small demand for aggregate products in the region),” says Abelho.
Capital costs of the equipment were a major concern as the concept was to beneficiate a waste product. While a secondary cone crusher could offer those benefits in the correct application, an impact crusher was considered a much superior solution for this project considering that the feed material is non-abrasive.
“Impact crushers offer much higher reduction ratios than cone crushers, and with variable speeds and crusher gaps, you have significant control over final product curves. From a maintenance point of view, impact crushers are also simpler to maintain and operate than cone crushers,” he says.
“The Rubble Master has been at the forefront of compact crushing and screening for a number of decades and offers premium models that punch above their weight without compromising quality. Combined with Pilot Crushtec’s commitment to parts holding and high calibre of support technicians, the final choice was an easy one for the client,” adds Abelho.
With the Rubble Master RM 90GO! in place, there now exists a thorough two-stage crushing process. The operation’s plant now produces at a much higher volume and with less re-handling. Abelho says during commissioning the plant achieved up to 280tonnes per hour (tph) peak production, which is not sustainable over a long period of time. However, the quarry is currently operating comfortably at between 180-200tph.
“Fixed operating costs have remained relatively the same, but production has increased considerably, while the cost per tonne has been lowered significantly, meaning higher profitability. Higher production and lower costs mean they are more competitive and are able to look for more clients,” says Abelho.
Explaining the mechanics of crushing, Abelho likens the process to driving a car. “One needs to go through all their gears to get to the top speed and it is the same when crushing. You have your first stage that will generally round off the material from 600mm to about 100mm,” he says.
“The second stage will then further reduce the size from 100mm down to
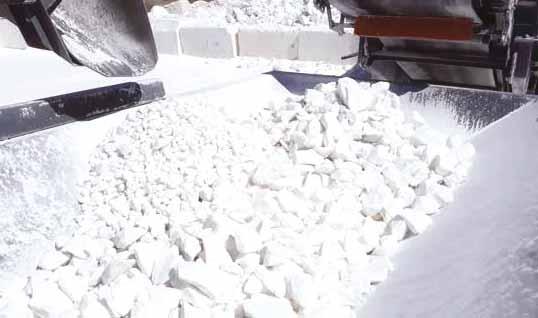
about 25mm. You can, of course, abuse the various stages but this does come at a cost. Your efficiency will suffer, wear and tear will increase and production levels will drop. The client has eliminated these negatives by installing a Rubble Master RM 90GO! and production has almost tripled. They are at a point where they have to find more clients for their industrial products,” adds Abelho.
The philosophy behind the design of the Rubble Master has always been simplicity in operation and maintenance without compromising on quality and performance. Pilot Crushtec often uses it to introduce clients with minimal experience to the crushing and screening industry.
“The Rubble Master is really easy to run. From a maintenance and operation perspective, there is nothing simpler. The control panel literally has four buttons that get the machine going; we call it the one, two, three, Go!. You push three buttons, and you are ready to start crushing. This is great as the learning curve for operators is very short, relative to cone crushers where countless set-up parameters are available via the PLC (Programmable Logic Control). All the intelligence is hidden within the machine,” says Abelho.
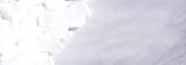
“Additionally, the size has intentionally been kept compact as it is often used in urban environments where space is at a premium. We have clients that use the Rubble Master to crush backfill when working on residential complex projects as the machine is incredibly mobile and has great sound insulation.”
The Rubble Master comes in three iterations that serve a wide variety of markets. Typically used in low-abrasion and construction and demolition (C&D) waste applications, the RM range can be used in some harder applications under correct circumstances. The starting point for any prospective client is most certainly the Rubble Master RM 70GO! 2.0 impact crusher.
The compact, track-mounted machine produces cubic-shaped grain in various product sizes and is designed to process a wide range of aggregates material. The diesel/ electric drive makes this unit economic and efficient and, due to its power and versatility, the compact crusher is a vital piece of equipment for companies specialising in recycling. “If you have wider application needs and more demanding power and handling expectations, the RM 90GO! is the answer,” says Abelho.
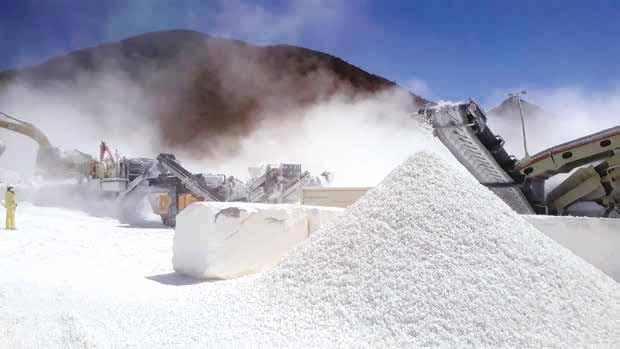
The RM 90GO! is a low-noise, highperformance crusher suitable for an array of applications. Set-up is simple and the machine is ready for action within a few minutes to rapidly and efficiently process any material, such as C&D waste, concrete, asphalt, glass, coal, natural rock and even reinforced concrete, to produce high-quality construction materials.
Rounding off the range is the Rubble Master RM 100GO! compact crusher. The track-mounted unit produces a high-quality, cubic-shaped grain in various product sizes. Due to its power and versatility, the compact crusher offers a flexible approach to highcapacity crushing. The Rubble Master RM 100GO! is a primary or secondary crusher with a refeeding belt that sends oversize material back into the vibro-feeder and returns it to the crusher.
“Diversification and identification of alternative revenue streams are the keys to success and sustainability in the 21st century. With a variety of applications that open up with the Rubble Master range, it has never been easier to retool or upgrade when the need arises,” concludes Abelho. AB
The newly crushed waste material has a number of uses in the construction and industrial sectors, from tile grout to additives in commercial products
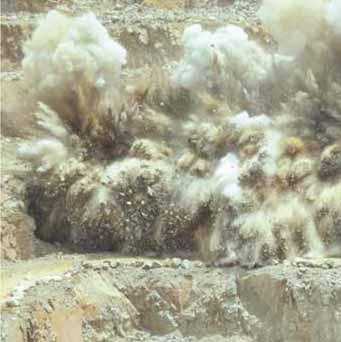
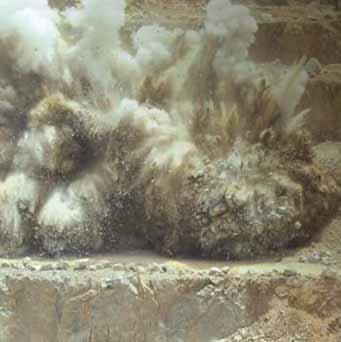
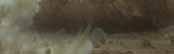
Independent studies also show that the Varistem can increase blast pattern spread by 10% or more, with the same fragmentation for major savings in drilling and explosive costs
Enhancing blast outcomes



Having secured distribution rights for the Varistem – a patented blast stemming plug for mining, quarrying and civil blasting applications – South Africa-based ERG Industrial is currently doing local trials to prove the potential productivity increase and downstream savings stemming plugs can provide to African quarries and mines. By
Of the various products that have come to market to improve blast performance, flyrock control and productivity, stemming plugs have probably been looked upon with some cynicism. At a time when South African quarries are contending with shrinking business due to a stressed construction sector, ERG Industrial, a young company that in 2019 acquired the distribution rights of the Varistem stemming plug range from United States company, MOCAP, believes stemming plugs are an opportunity to increase efficiency for quarries and mines, thus reducing costs.
Eugene Preis, MD of ERG Industrial, explains that stemming plugs are placed between the explosive column charge and stemming. Plugs work by creating an additional blocking effect within the drill hole when blast energy is released, directing more energy into the block and less energy upwards out of the drill hole. Upon detonation of the explosives, the plug is forced upward into the stemming material and “locks up”. The explosives gases and energy are prevented from travelling (venting) up through the drill hole.
Typically, the loss of explosive energy through stemming ejection reduces the performance of the blast. The fundamental theory promoting the use of blastimprovement and containment plugs is that they could enhance the effectiveness of stemming material in the blasthole. As a result, this would better contain the explosive energy within the rock mass and yield a more controlled and efficient blast.
Varistem is now available in Africa through ERG Industrial – excluding a few countries like Zimbabwe and Congo, due
to US trade restrictions in those countries. Varistem is a patented blast stemming plug designed for quarrying, mining and civil blasting applications. The plugs are said to contain blast energy for longer, resulting in a range of benefits depending on how it is incorporated into the blast design.
Preis says maximum blast containment means greater fragmentation and microfractures, with more tonnage processed at less cost. “Following ore body fractures created by the explosive shock waves, the Varistem improves expanding gas containment. The greater the gas containment time within the ore mass fractures, the better the fragmentation. Getting your fragmentation right is your fragmenta
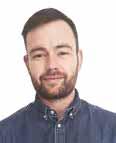
“The Varistem also enables consistent stemming heights when using gas emulsions”
Eugene Preis, MD of ERG Industrial
Munesu Shoko
substantially cheaper than having to do secondary blasting or mechanical breakage,” he says.
In some cases, the Varistem has achieved up to a 25% increase in fragmentation, which in turn reduces crushing costs and increases crusher throughput. Independent studies also show that the Varistem can increase blast pattern spread by 10% or more, with the same fragmentation for major savings in drilling and explosive costs. “Benefits abound – the Varistem provides blast confinement, resulting in better ore fragmentation, greater crusher throughput, reduced crushing costs and better blast control (less fly rock, vibration and noise),” says Preis.
There are several ways in which the Varistem can be used to improve blasting performance. One of them is air-decking. Historical studies show air-deck volumes of 10-15% can be realised without any major reduction in fragmentation. These studies used air bags for stemming support, which save explosives but do not improve fragmentation. Air-decking with Varistem achieves up to a 27% fragmentation improvement, while also saving on explosives.
“The Varistem also enables consistent stemming heights when using gas emulsions. Simply reduce the emulsion volume allowing for maximum expansion. Set the Varistem in an air-deck so that stemming heights are consistent in all drill holes. This will eliminate short stemming heights and blow-outs,” explains Preis.
Air-decking with the Varistem allows shorter stemming heights, while also reducing explosive column height to dramatically minimise over-sized cap rock from a common 10% oversized, down to a 2% oversized.
Flyrock and stemming ejection are also controlled.
When it comes to fragmentation, Varistem plugs increase blast-force retention times by two to four times. The blast force contained by the Varistem is conserved and directed into the rock, greatly increasing the level of fragmentation.
“In addition to the other benefits, quarries, contractors and blasters could potentially reduce the volume and expense of crushed stone stemming, allowing them to use less expensive drill cuttings for stemming as well,” says Preis.
There are several secondary cost savings which result from increased fragmentation –easier rock removal, less secondary breakage costs, increased truck capacity, less wear on crushing and grinding equipment – all of which contribute to the cost benefit of using the Varistem, and which will make the Varistem pay for itself many times over.
Varistem also improves blasting performance through increased pattern spread. The blast energy conserved by Varistem permits operations and blasting contractors to do a lot more with a lot less. Multiple studies have demonstrated that Varistem allows blasters to increase their pattern spread by 10-25%, without any reduction in fragmentation. The cost benefit of increased pattern spread is easy to see – 10-25% fewer holes drilled, 10-25% less explosives used – both of which can greatly help reduce the direct expense of drilling and blasting.
Varistem has been used in the United States for the past 16 years, and in Canada and Australia for the past 10 years. It has also been deployed at operations in Thailand, Ghana and multiple European quarries. In one of the flagship studies conducted by Holcim Cement at its St. Genevieve Quarry, data shows that the expanded pattern size of 14 x 19 inch with the implementation of
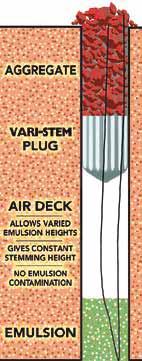
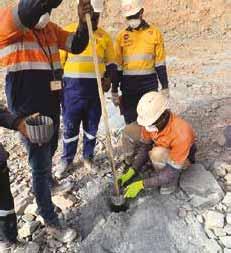
ABOVE: Plugs work by creating an additional blocking effect within the drill hole when blast energy is released, directing more energy into the block and less energy upwards out of the drill hole
the Varistem plug yielded improved overall fragmentation compared to the existing 14 x 18-inch pattern typically used by the operation.
The added fragmentation performance represented a reduction of 11.6% in the “mean” size of the rock. The increased fragmentation benefit permitted the usual 14 x 18-inch blast design to be increased to the 14 x 19-inch pattern, thus eliminating 6% of the blast holes necessary to produce the same volume of rock with improved fragmentation.
Studies and in-field tests from the very same operation also showed that the Varistem plugs could increase fragmentation significantly. Three test blasts were carried out at the quarry, with the initial test confirming a 27% fragmentation improvement using Varistem.
Elsewhere, Seven Pines Quarry in Ontario, Canada, recorded significant savings and environmental impact reduction from air blast. Using the Varistem, the operation saw double success though reduced noise/ vibration levels and a reduction in explosive costs of approximately 12%.
LEFT: Stemming plugs are placed between the explosive column charge and stemming BELOW: The Varistem is a patented blast stemming plug designed for quarrying, mining and civil blasting applications
Despite the proven successes of this technology, demonstrated by several successful case studies, ERG Industrial’s approach to local African sales is based on proving the capabilities at individual operations before commercially deploying the Varistem stemming plugs.
According to Preis, this approach is driven by the understanding that figures achieved at other locations may not necessarily be achieved elsewhere due to the varying nature of conditions and rock geology, among other factors. Therefore, each operation’s gains will vary depending on conditions on site.
ERG Industrial has already kicked off operational tests at some local quarries in South Africa. Between September and November 2019, the supplier conducted tests at four of Afrimat’s quarries. The main aim of these trials was to reduce flyrock and increase fragmentation.
“At two of the four quarries, we used the 102mm stemming plug to see if we could reduce flyrock and stemming ejection and increase fragmentation. The Varistem plugs were used on benches 10m in height, with stemming heights of 1.4m. Ideally, we would have wanted to increase the stemming height to at least 1.8m for the 102mm trials, but this was not possible at the time. Notwithstanding, we had zero flyrock, but still had some stemming ejection (albeit reduced). In terms of fragmentation, the results were the same as before,” he says.
ERG Industrial did two more tests with Afrimat, this time on 89mm blastholes. “Here, the stemming height was a bit higher, about 1.6m. This is roughly equivalent to having a 1.8m stemming height with 102mm holes. Previously there were problems with flyrock because blasting is very close to public roads. Using the 89mm stemming plug, the trials at the two operations achieved zero flyrock,” concludes Preis. AB
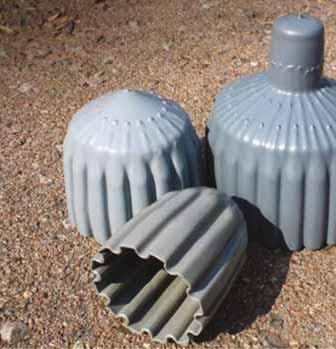
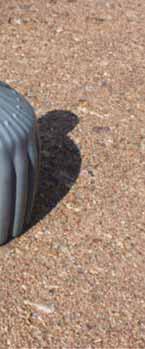
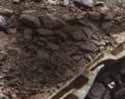
Optimising undercarriage life

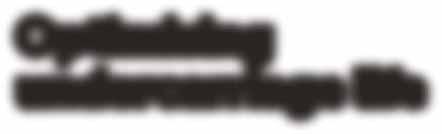
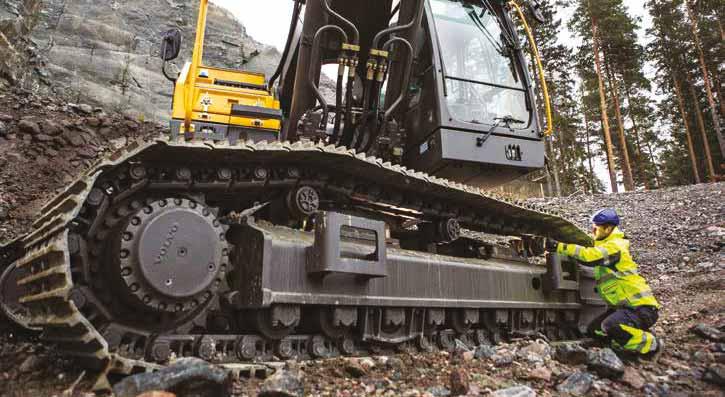
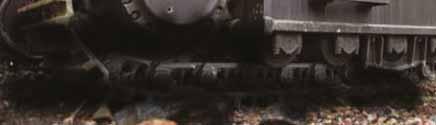
Taking the time to inspect and maintain a crawler excavator’s undercarriage will help increase machine life. If the undercarriage is not routinely inspected and maintained, it can easily cost owners valuable time, money and potentially decrease the track’s lifespan. By
Munesu Shoko
The undercarriage of a crawler excavator comprises many moving components that need to be maintained for it to function properly. Regular maintenance, coupled with correct machine operation, significantly reduces undercarriage wear, improves operating efficiency and reduces running costs. Håkan Karlsson, product manager for ground engaging tools, undercarriage and customer solutions at Volvo CE Sales Region EMEA, says a properly maintained undercarriage is important to the overall life of the machine. Wear parts in poor condition will shorten the machine’s service life and increase the risk of breakdowns and unplanned downtime.
Shumani Tshifularo, MD of HPE Africa, the Hyundai and McCloskey distributor in South Africa, says because crawler excavators have a strong, solid-steel construction, maintenance of the undercarriage is often neglected and that can be a costly mistake. “Research shows that repair costs for the undercarriage of a tracked excavator account for as much as half of all repair costs over the life of the machine. A worn undercarriage increases vibration levels of the excavator, which reduces service life of components like pumps, motors, electronics and the engine,” says Tshifularo.
The same view is shared by Garth Labuschagne, sales manager Africa for the Mining Mobile Plant division at Bradken, a Hitachi Construction Machinery company, who reasons that for many operations, the undercarriage is within the top 10 spend items during the life of an excavator. “A poorly maintained undercarriage will require a significant amount of time and money spent on it, which translates into reduced efficiency,” says Labuschagne.
There are several indicators that the undercarriage is not getting enough attention.
According to Labuschagne, typical indicators of a poorly maintained undercarriage include stretch in the track (which indicates pin wear), reduced component life, unusual wear patterns and increased failure rates such as roller surface delamination/compression.
Some of the indicators of a poorly maintained undercarriage, according to Lionel Hearne, national service manager at Wacker Neuson South Africa, include tracks slipping or sliding off, tracks screeching loudly and not moving due to damaged sprockets, tensioners or support rollers.
So, what does a proper maintenance regime of a crawler excavator undercarriage entail? There are several things that should be kept in check, given that the undercarriage comes with several moving components. Tim Nenne, senior undercarriage application specialist at Caterpillar, says one of the key parameters is to keep the tracks properly tensioned.
“A tight track is one of the top reasons for reduced life and failures in an undercarriage. This is especially true for the greased
lubricated tracks on excavators. Tight tracks increase the internal wear rate by pushing the grease from the joint more quickly,” says Nenne.
Karlsson advises that track tension should be checked at least once a week to prevent early wear. Track tension should always be a little slack; if the tension on the track is too tight, the pressure can cause unnecessary wear to the chain and sprockets. “This can happen if the distance from the bottom chain to the frame on the undercarriage has been measured incorrectly. It’s a different measurement depending on the type of material, so anyone carrying out the inspection should always check the operator’s manual,” says Karlsson.
Tshifularo believes that track tension should be inspected daily. “This takes no more than 10 minutes,” he says. “A track
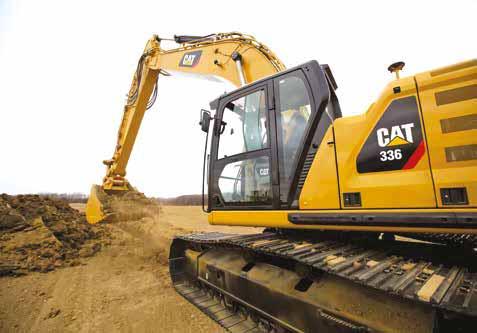
A properly maintained undercarriage is important to the overall life of a tracked excavator
The undercarriage of a crawler excavator comprises many moving components that need to be maintained for it to function properly
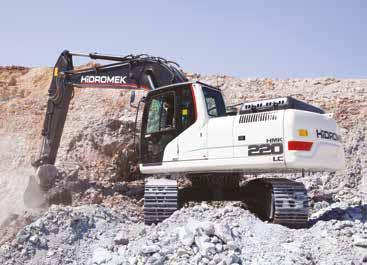
tension that is too tight puts extra load on the engine, which wastes fuel and can also cause premature undercarriage wear. A track that is too loose may come off and can also cause additional shock loads and side-to-side wear of components.”
When it comes to correct track tension, Vaughan Ellis, MD of Maximum Equipment, the South African distributor of Hidromek excavators and backhoe loaders, says the rule of thumb is to maintain the width of a hand between the bottom roller and the track, which is about a 12cm gap.
Apart from the track tension, Karlsson believes it’s also crucial to keep in mind that when one replaces any part in the track system, such as a chain, they also have to check the wear on other parts. For example, a worn sprocket may quickly wear down a new chain.
Ellis says leaving the undercarriage dirty for too long is a costly mistake. “Not washing the undercarriage is detrimental to its overall health. If you have been working in clay or muddy conditions, don’t leave the mud stuck to the undercarriage for too long. The mud sits in the pins, bushes and rollers and causes them to wear excessively,” says Ellis.
Nenne shares the same sentiment, saying that material build-up in the undercarriage system and on the roller frame can lead to tight track conditions. Such a build-up also increases wear rates as the links drag over it and it circulates through the link/roller system.
Tshifularo adds that packed debris and dry material should be removed from the undercarriage at the end of every shift, using a shovel, steel bar or water. Dry material increases track tension and prevents rollers from turning freely, which accelerates wear of components.
He also recommends that after every 1,000 hours of operation, a specialist undercarriage company should be commissioned to check the undercarriage. Excessive wear on one component causes accelerated wear on other components in the system.
Tshifularo says it’s also important to look at several other parameters, like total hours of travelling vs digging and total hours travelled in high-speed vs low-speed mode. “Torque setting on all the bolts on the undercarriage
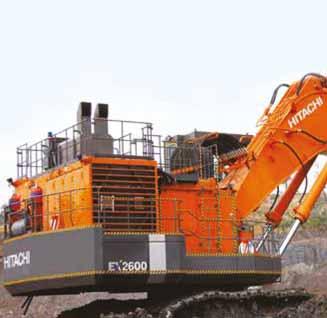

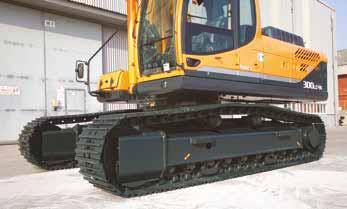
should also be checked – including roller and top idler brackets, track shoes, sprockets and final drives,” says Tshifularo.
Besides maintenance, operator technique is one of the most important factors in the health of an undercarriage. Ellis believes one can tell the difference between a good and bad operator by the undercarriage. “A bad operator thinks the undercarriage is designed to track over anything, including rocks and stockpiles. This is a common scenario in quarries,” says Ellis.
Commenting on the impact of machine operation to overall undercarriage health, Karlsson says operators should always travel and dig with the sprockets at the rear and the idlers at the front. “The idler has springs to protect it from pressure, but operating with it at the back will cause around 30% more wear on the sprocket and chain,” he says.
Tshifularo advises that operators should avoid travelling long distances in high-speed mode. The faster the travel speed, the greater the relative load between components, which increases wear. Over long distances, friction causes heat build-up within the rollers, idlers and drives and this can damage internal seals.
In fact, Nenne says there is a need to limit tramming (walking the machine). Any moving of the machine contributes to the wear on the undercarriage. “Keeping the amount of unproductive movement to a minimum will reduce the amount of wear per hour of machine operation. It is advisable that an excavator should not tram more than 15% of its total operating time,” he says.
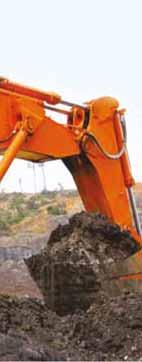
TOP LEFT: Sprockets on a Hidromek crawler excavator need to be replaced between 2,000 and 3,000 hours.
ABOVE: Operators should always prepare and make the ground flat under the machine before they start digging. This will avoid uneven pressure to the undercarriage
LEFT: To ensure long undercarriage life, operators should avoid travelling in high-speed mode on rough or hard terrain or inclines
Tshifularo adds that operators should also avoid digging or excavating with the boom over the sprocket. The overhead dig/dump cycle causes stress and wear at the point of sprocket/bushing contact over the sprocket. These forces should be over the idler, where minimal chain-rail wear occurs.
Tshifularo also advises that operators should work up and down a slope rather than along a gradient or slope. Working along a gradient tilts the machine to one side, which increases the load/stress on the lower track and this accelerates overall wear on this track.
“It is also important to balance slew direction under load. Because the dig-slewdump cycle puts pivot stress on the undercarriage on the dump side of the machine, the operator should balance the slew direction by turning the excavator around in the middle of the shift,” says Tshifularo.
Tshifularo adds that operators should try to reduce pivot/counter rotation turns on hard ground. Excavators are useful on restricted work areas because they are able to make pivot turns, but the operator should try to make wider turns to prevent grouser corner wear.
In conclusion, Karlsson says when using a hydraulic breaker, the idlers should always be at the rear. “Hydraulic breakers cause a different kind of pressure, so operators should always keep the sprocket at the front and the idler at the back to avoid unnecessary wear to the sprocket, chain and gear box,” concludes Karlsson. AB
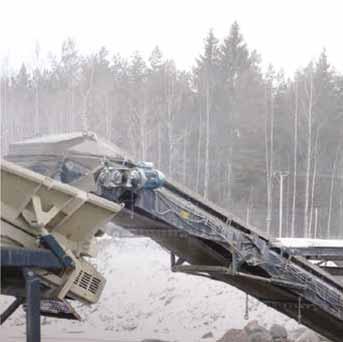

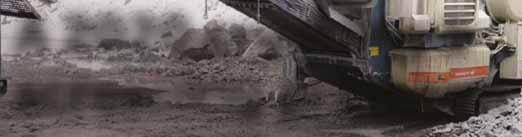
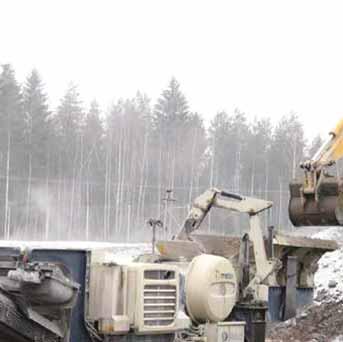
A 2020 crushing & screening premium
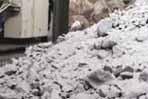
New and proven premium crushing and screening plant have been very much to the fore in the first half of 2020. Guy Woodford reports
Pärhä Oy, located in Orimattila, Finland, is famous for high-quality concrete gravel, delivered directly to production facilities. Metso’s diesel-powered/electrical Lokotrack double-stage plant ensures that different types of crushed rock are produced effectively and economically. As a bonus, the new Lokotrack ST4.10 screen operates carbon neutrally, using electricity generated by the tertiary crusher.
“Last year, we crushed more than 600,000 tonnes, of which some 250,000 tonnes were processed into different types of concrete gravel. The majority of the concrete gravel is delivered to five companies operating in the concrete industry in the Päijät-Häme region,” says Jari Pärhä, who is in charge of the crushing operations and production at Pärhä Oy.
“When such volumes are being produced by a single crushing plant, the machinery needs to be reliable. Metso is known as a dependable Finnish company that also provides well-functioning maintenance services.”
The family-owned company, established by Tuomo Pärhä in 1980, shifted from forestry to the gravel business at the beginning of the 2000s. Currently, the company specialises in crushing and transport services. Since the beginning of this year, the company has three partners: Petri Pärhä is managing director, Jari is in charge of the crushing operations, and Tommi Pärhä is taking care of the transport arrangements.
The company acquired its first Lokotrack LT106 jaw crusher in 2013, followed by a Lokotrack ST2.8 mobile screen. When the company decided to focus more on crushing operations, Pärhä Oy asked Metso for a new tertiary crushing plant. It turned out that the existing Lokotrack range did not have the right solution for the company.
“A few weeks later, Mikko Takaniemi from Metso came to demonstrate a raw version of the plant we were looking for. The cone crusher and screen plant included the pre-screen we had requested,” Jari says.
In 2017, a unique diesel-powered/ electrical plant, called Lokotrack LT330GPSE, started operating at Pärhä’s quarry in Nastola. The LT120E jaw crusher replaced the primary crusher, and last autumn, the screen was replaced by ST4.10, a new Metso model, equipped with a 1.5m × 6m three-
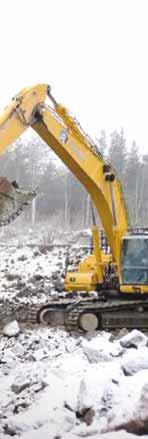
When different types of gravel for concrete and gritting are being produced, primary crusher feed enters first the LT330GPSE pre-screen, which removes the fine materials before going to the cone crusher.
“The pre-screen helps us to only feed pure rock material into the crusher, especially in wet conditions. This makes the production more effective and improves the quality of end products. Metso’s pre-screen works just as we planned,” Jari notes.
The double-stage plant and mobile screen produce gravel of 6–12 mm and 12–16 mm at an hourly rate of roughly 200 tonnes. At the same time, the process produces gritting gravel of 3–6 mm and fine rock dust of 0–3 mm. When coarser material is being produced, the capacity increases to 350–400 tonnes.
Pärhä Oy’s vehicles are used to deliver
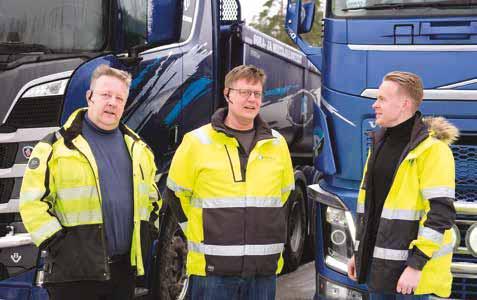
RIGHT: The three men behind Pärhä Oy: Petri Pärhä, managing director (left); Jari Pärhä, director of Crushing Operations; and Tommi Pärhä, director of Logistics
Pärhä Oy’s primary crushing is done by the diesel-powered/electrical Lokotrack LT120 jaw crusher
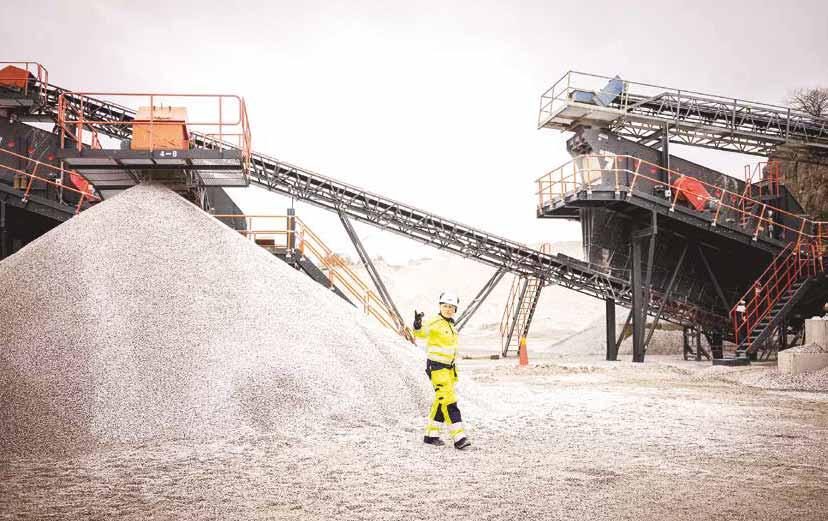
operating in the concrete industry, for infrastructure construction and to private customers.
“Quality and documentation are important to us. For example, we check the quality of concrete gravel after every 500 tonnes,” Petri says.
This year, Pärhä will expand its production to asphalt and railway ballast. The company has, therefore, acquired a quarry from Mäntsälä to produce high-quality aggregates.
Sandvik is introducing Peak Screening – said by the Swedish quarrying equipment giant to be an innovative screening solution that helps customers reach their full productivity potential.
A company spokesperson says: “Peak Screening is a complete package offer and performance concept designed to ensure every square metre of a customer’s screening is as productive as it can be for their unique operation.
“Most screening operations, even when they look fine, are capable of more. Often much more. Peak Screening is our term for a complete screening solution, including the right screen, screening media and warranty/ service program for any customer budget or need, all working together towards one goal – maximising the full potential of the customer’s screening operation.”
Sandvik says its screening equipment, screening media and services are designed to work optimally with each other and ensure the screening operation is as productive as it can possibly be. The company says that its customers will also benefit from having ongoing access to experienced Sandvik specialists who can help with the right configuration, optimisation, troubleshooting, and much more.
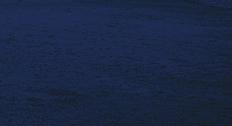
“Most screening operations, even when they look fine, are capable of more”
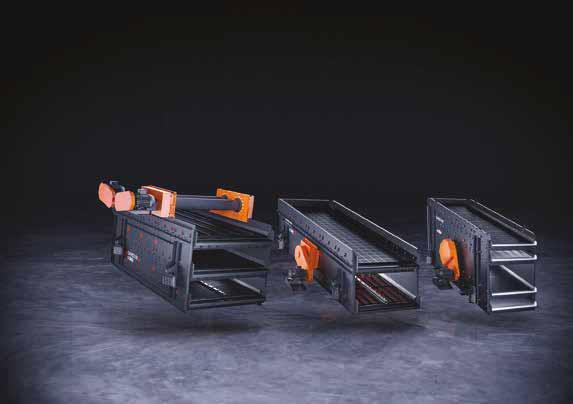
Sandvik now has three new ranges of maintenance-friendly, high-performing modular screens that are said to be more versatile, more reliable, faster to get on-site and safer to operate.
All Sandvik screens come with highquality Sandvik screening media as standard, unless otherwise specified. Sandvik says it works closely with customers to determine the right solution for their applications. This includes offering exclusive options such as Sandvik’s WX6500 tensioned rubber screening media with up to a claimed 15x
ABOVE: Sandvik Peak Screening is said to be an innovative screening solution that helps customers reach their full productivity potential
BELOW: As part of its new Peak Screening solution, Sandvik has three new ranges of maintenance-friendly, high-performing modular screens that are said to be more versatile, more reliable, faster to get on-site and safer to operate
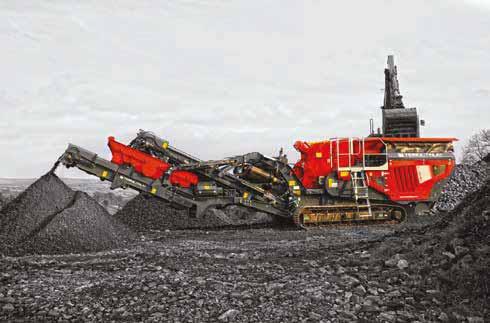
The Terex Finlay IC-100RS is one of a four-unit range of IC-compact impact crushers
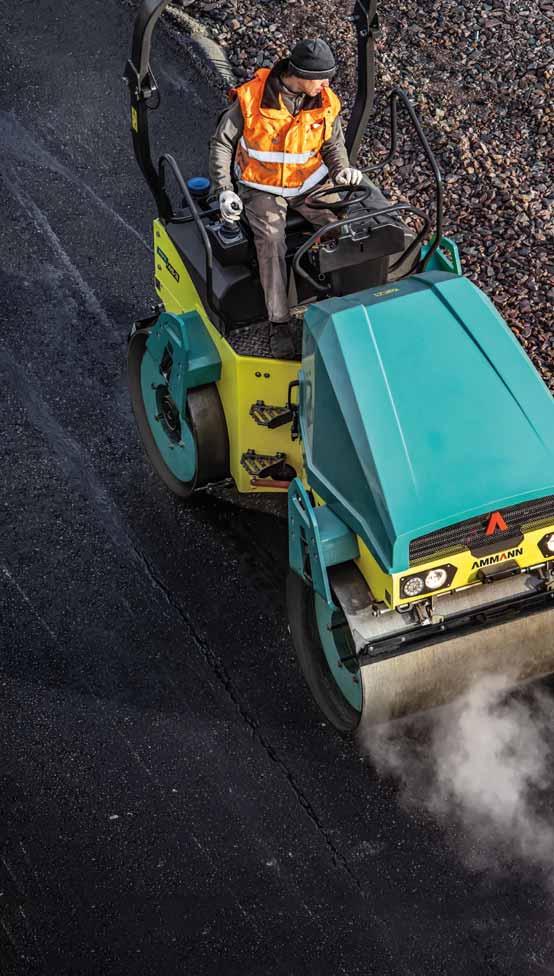
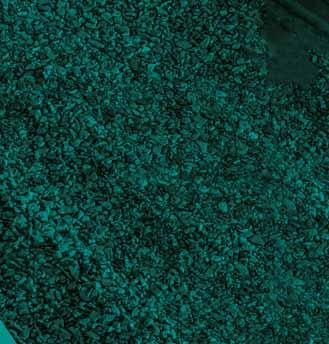
OBSTRUCTIONS? NO PROBLEM
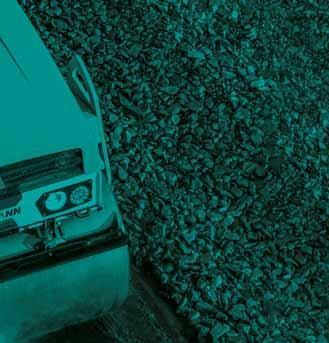
AMMANN ARX 4-2 LIGHT TANDEM ROLLERS
Ammann ARX Light Tandem Rollers excel in the open, where covering ground quickly is the goal. But other jobsites call for a compactor that can work tight against obstructions, such as curbs, without losing productivity.
Other key features
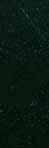
Ammann ARX series of light tandem rollers deliver in both worlds. They feature industry-leading compaction output to quickly reach targets when working in open spaces. When obstructions are a factor, the rollers can quickly switch from in-line to offset compaction, providing operators with improved vision and precision.
• Latest EU Stage V / U.S. EPA Tier 4f engine from Kubota


• Spacious operator platform with sliding seat
• Electronic drive lever for smooth starts and stops, especially important on asphalt jobs
• Optional ACEforce, the Intelligent Compaction tool for optimal efficiency
• Simple and reliable dashboard with intuitive machine control
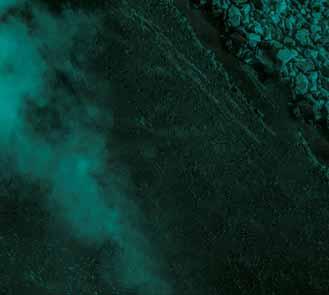
• Perfect all-around machine visibility and LED lights for safety on the jobsite
Looking for even more productivity? When the workday is done, maintenance points can be easily accessed from the ground to ensure quick completion of service work.
longer wear life than standard wire mesh, but with the same screening accuracy for better productivity and uptime.
Sandvik’s novel Reliability & Performance (R&P) package is said to protect customer investment. R&P includes two years extended equipment warranty, regular inspections, maintenance recommendations, troubleshooting and performance analyses that can help optimise service intervals and avoid costly breakdowns.
Screening solutions from Sandvik also come with a performance guarantee where Sandvik guarantees that the solution achieves the performance that has been agreed on together with the customer — or Sandvik will work with the solution until it does.
“Peak Screening shows our understanding of customers’ productivity needs, and commitment to solving their challenges in unconventional, industry-first ways. We want to help customers benefit from the competitive advantage Peak Screening can provide, while establishing it as the defining screening performance standard of our industry,” says Mats Dahlberg, vice president Lifecycle Service Stationary Crushing & Screening.
Terex Finlay is expanding its mobile crusher line with the introduction of its IC-Range of compact impactors. The IC-Range of small impact crushers has been designed explicitly for quarrying, construction and demolition debris, reinforced concrete
and asphalt recycling applications.
The new IC-range comprises four models: IC-100, IC-100RS, IC-110 and IC-110RS.
“The addition of these four new models complements our existing range of mobile impact crushers and opens up new opportunities at the smaller machine sector of the market. Each of these models has been rigorously tested and proven in a diverse range of applications. The compact size, ease of transport, quick set-up times and intuitive operation make each of these machines ideal for contract crushers, independent rental houses and small-scale operators,” says Alan Witherow, Terex Finlay lead technical support and product manager.
The IC-100 features an 860mm x 860mm direct-drive horizontal impact chamber with variable rotor speed. The advanced electronic control system monitors, controls and regulates the speed of the VGF (vibrating grizzly feeder) to maintain a consistent feed of material into the impact chamber to maintain optimal crushing capacity. The IC-100 provides operators with a compact and versatile machine that gives high material reduction ratios and produces a consistent product grading.
Based upon the IC-100, the IC-100RS features an onboard recirculating system and detachable sizing screen to provide the versatility of a compact crushing and screening plant on one mobile. If recirculating and sizing materials is not
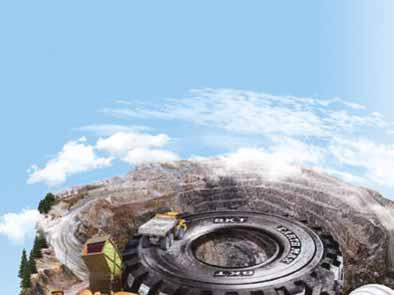
A LONG WAY TOGETHER
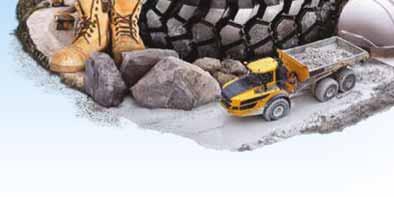
required, the sizing screen can be removed quickly from the machine without the need for secondary lifting equipment. The recirculating conveyor can also be utilised for stockpiling an oversize product.
The IC-110 features a 1034 x 1000mm direct-drive impact chamber with variable rotor speed and hydraulic apron-setting assist in providing convenient and efficient adjustment of the chamber aprons. The chamber is also fitted with a hydraulic overload protection system as standard. For operators in recycling and demolition applications, an underpan feeder is also available as an option.
The IC-110RS impact crusher provides the versatility of a compact crushing and screening plant on one mobile platform for quarrying, construction and demolition debris, reinforced concrete and asphalt recycling applications.
The machine features a direct-drive 1034mm x 1000mm horizontal impact crusher with variable speed control to give operators unprecedented levels of fuel efficiency and productivity. A vital feature of the machine is the onboard 2.74m x 1.5m single-deck screen. For applications not requiring recirculation of oversize material back to the crushing chamber or the stockpiling of an oversize product, the complete screening and recirculating system can be quickly detached from the machine.
In other Terex Finlay news, the company’s
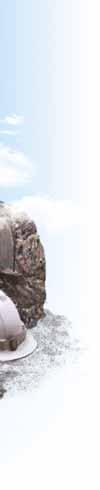
EARTHMAX SR 41
o matter how challenging your needs, EARTHMAX No 41 is your best ally when it comes to operations SR at require extraordinary traction. Thanks to its All th eel radial structure and the special block pattern, St ARTHMAX SR 41 provides excellent resistance EA ainst punctures and an extended service life. In aga dition to long working hours without downtime, add e tyre ensures extraordinary comfort. th ARTHMAX SR 41 is BKT’s response to withstand EA e toughest operating conditions in haulage, th ading and dozing applications. loa
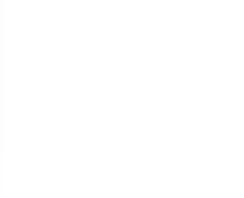
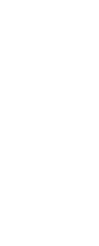
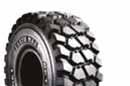
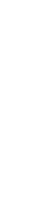
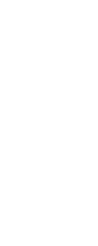
standard subscription for its T-Link plant monitoring and performance optimisation system is now available for seven years.
Introduced in January 2016 the T-Link hardware and software can be used on any Terex Finlay crusher or screener with an electric engine.
It allows operators at any given time to see the exact location and status of their Terex Finlay plant fleet.
Furthermore, T-Link shows what areas to improve upon to optimise profitability.
Now, all Terex Finlay machines that are already in the field and fitted with T-Link hardware and software will automatically roll over to the extended seven-year data subscription.
Alan Witherow says: “T-Link takes the guesswork out of machine monitoring and performance optimisation. Our sevenyear standard data subscription places us at the technological forefront of our industry.”
The Terex Finlay T-Link package provides operators with a userfriendly, unlimited portal to access all the firm’s machines in one place at one time. It also gives them key figures and performance metrics of their connected assets in the form of ‘Actionable Reports’ that they receive automatically weekly.
Superior Industries, a US-based manufacturer and global supplier of bulk material processing and handling systems, has unveiled a new series of modular plant for aggregates crushing, sorting, sizing and washing applications. Known as Fusion Modular Platforms, these pre-engineered, ready-to-build systems still allow customisation to achieve the best performance at each job site.
“Our plant designs are scalable and easily expand with a developing customer site,” says Mark Crooks, product manager at Superior Industries. “Producers can quickly expand capabilities as finances allow, the application needs change and as their market develops.”
Today, Superior has pre-engineered a series of plant packages and is working on designing more for its catalogue. Some examples include jaw, cone and impact crushing platforms, horizontal screening platforms with two-, three- and four-deck models, plus a group of traditional washing and modern low-water washing platforms.
“Overwhelmingly, our customers said they want scalability and flexibility in these modular offerings,” says Crooks. “Therefore, as we developed our strategy, we ensured flexibility from top to bottom, convenient installation or dismantling and seamless integration with Superior crushing, screening, washing and conveying machinery.”
Fusion Modular Platform systems are pre-engineered for earlier commissioning, are more cost-effective than a design-build plant, incorporate well into existing plants and utilise creative packaging to limit the number of flatbeds or shipping containers needed for transportation. AB
BELOW: Superior Industries has launched Fusion Modular Platforms, a new series of modular plant for aggregates crushing, sorting, sizing and washing applications
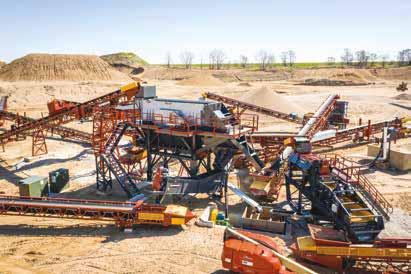
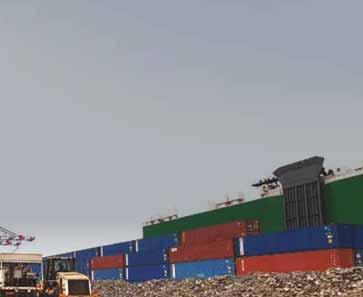

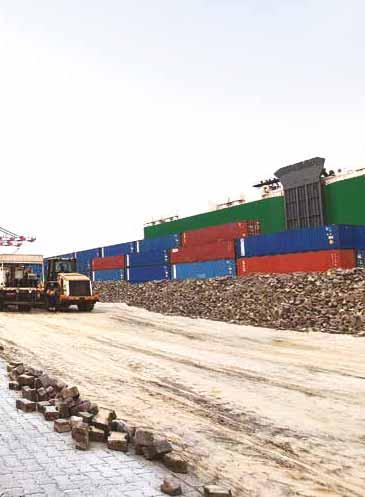
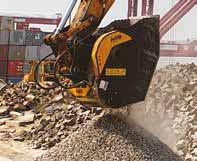
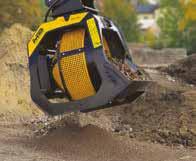
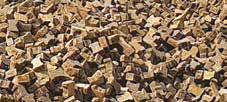
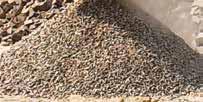

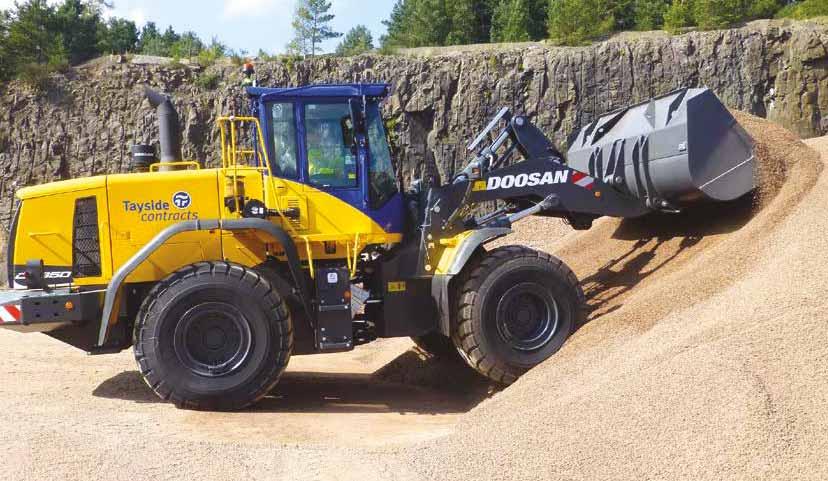
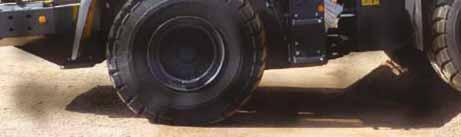
Loading boost to quarry recycling
Two new vehicle purchases are helping a Scottish quarrying and construction company to maximise the efficiency of recycling and reduce the amount of materials it sends to landfill
Tayside Contracts has purchased a new wheeled loader and excavator as part of a fleet of machines used in its quarrying, recycling and construction operations.
The Dundee, Scotland-based company bought a Doosan DL350-5 wheeled loader and DX255LC-5 crawler excavator from Balgownie, the local authorised Doosan dealer headquartered in Inverurie, Aberdeenshire.
The two machines can be moved around the various facilities run by Tayson Contracts, including both the quarries and the four recycling centres located in Arbroath, Forfar, Dundee and Collace.
The construction division of Tayside Contracts is a major civil engineering construction organisation in the Tayside area, employing over 400 people with a turnover of over £34mn. The new Doosan machines work mainly in its two quarries – Boysack Quarry near Friockheim in Angus and Collace Quarry in Perthshire.
A key objective of the construction division is to maximise the use of recycled material and minimise waste to landfill. As a result, all the recycling centres accept construction waste to produce a recycled sub-base and a recycled crusher run for further use.
Boysack Quarry produces Type 1 materials which are used internally and are also available for sale to external customers. Much of the product from Boysack Quarry goes to Collace Quarry, which manufactures a range of asphalt mixes including hot rolled asphalt, asphalt concretes, stone mastic asphalt, pre-coated chips and cold-mix for base/binders.
The Doosan DL350-5 wheeled loader has a bucket capacity of 3.5m³. It is made to meet a wide range of material-handling needs from loading and transporting
granular material (such as sand and gravel) to industrial and quarrying applications. Powering the DL350-5 wheeled loader is a Doosan DL08 diesel engine, with an output of 202kW at 1800rpm. The DL350-5 at Tayside Contracts has a five-speed ZF transmission with lock-up and a hydraulic differentiallock front axle for low fuel consumption and excellent productivity in all conditions.
The Doosan DX255LC5 excavator is said to offer comfort and controllability with a focus on increased power, robustness and agility. While overall dimensions are similar to the previous DX255LC3 model, Doosan says the DX255LC5 combines higher power with a 500kg increase in operating weight. This results in up to 17% more lifting capacity over both the front and side and a one dBA sound level reduction.
Volvo Construction Equipment (Volvo CE) has unveiled new enhancements to its H-Series wheeled loaders that it says will help reduce total cost of ownership.
The rimpull control system now comes as standard on all H-Series models. This function allows operators to minimise wheel spin and optimise the balance between rimpull and hydraulic functions. In turn, this helps reduce tyre wear and fuel consumption for more efficient bucket filling.
The L60H-L220H wheeled loaders were launched in 2014, with the larger L260H and L350H models following in 2017.
“Over the years we have built on experience and worked closely with customers to improve these machines,” said Volvo CE product manager Lars Eriksson. “Now, in 2020, we have introduced new features that take these machines to a new level of efficiency.”
The Volvo Co-Pilot monitor is now available on a broader range of machines from the L60H up to the L350H. The 25.4cm in-cab touchscreen provides access to several Load Assist applications (depending on machine model) aimed at optimising operator performance and site efficiency.
Firstly, there is a tyre pressure monitoring system that gives operators real-time information on the conditions of machine tyres.
A map application allows operators to get better visibility and understanding of the site layout and real-time site traffic situation, allowing them to adjust their driving behaviour accordingly. Weather, Calculator and Notes apps are also new, and these functions work similarly to those found on a smartphone and are pre-installed in the Volvo Co-Pilot.
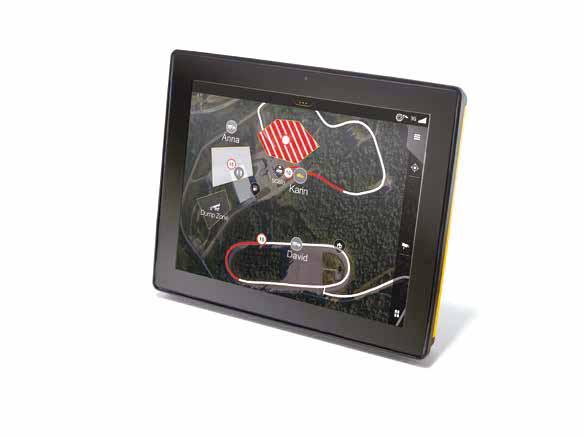
Tayside Contracts’ new DL350-5 wheeled loader in operation
The new map feature allows operators of Volvo CE’s H-series wheeled loader to monitor on-site traffic in real time
of machines, providing access to several Load Assist applications
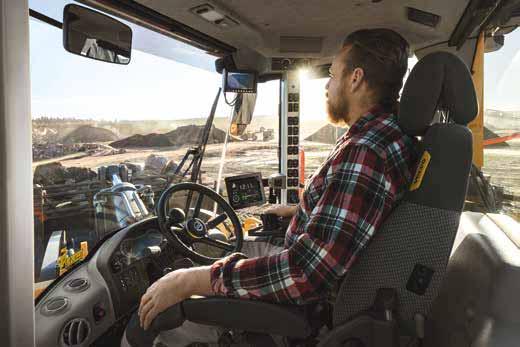
Designed to help load the optimum amount of material, the on-board weighing app is upgraded to include two new task modes – stockpiling and processing – adapting the on-screen layout and information displayed according to the task at hand.
For increased convenience and safety, both the rear-view camera and radar detector system feature on the Volvo Co-Pilot display. Volvo CE has also introduced an operator coaching application. This tool is designed to enhance operator performance, helping them get the most out of Volvo wheeled loaders and thereby reducing operating costs.
Additional new updates are designed to optimise maintenance procedures, thereby minimising downtime and service costs. Firstly, there is the extended engine oil change interval, which will be 1,000 hours as standard for H-Series models equipped with Stage V engines from April 2020. A quick-fit connector on the hydraulic tank is standard on all H-Series models. This feature is said to result in quicker and easier hydraulic oil filling.
On the L150H up to L260H models, a new quick-fit option enables cleaner and rapid engine oil changes – in as little as 15 minutes – helping eliminate oil spillage and contamination.
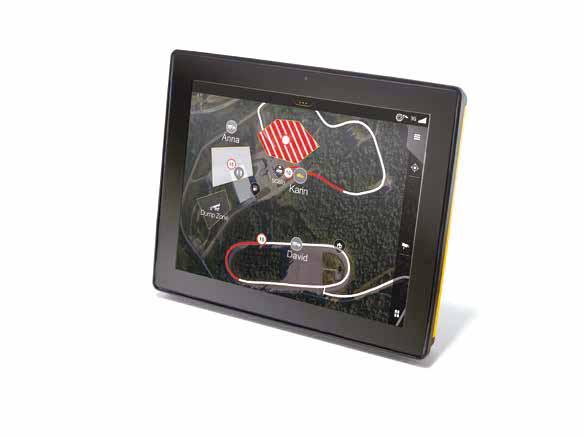
Volvo CE has also added five new applications to the Load Assist system for its H-series wheeled loaders.
The five new apps are aimed at enhancing the ease of operation, safety and overall site efficiency. Tasks that had to be done manually or required operators to step out of the cab can now be automated from the cab.
The tyre pressure monitoring system app enables the Volvo Co-Pilot touchscreen to display tyre pressure and temperature in real time. Each tyre is monitored independently, and pressure limits (low/high) are set per axle. If any of the individual tyres go outside of the set parameters, the operator will be alerted – alarm limits are displayed as nominal values and percentages.
The map app uses the loader’s built-in GPS for positioning and the telecom connection on the Volvo Co-Pilot to communicate between machines. The new map feature allows operators to monitor on-site traffic in real time and proactively adjust their driving according to traffic
conditions, especially in areas where multiple machines are operating close to each other.
The calculator app comes complete with basic calculation (addition, subtraction, multiplication and division) functions.
The calculator can also be used as a unit converter, quickly and easily converting six-unit types – length, mass, angle, time, temperature and speed.
The notes app is designed to remove the need for a pad and pen with a digital notepad, which can be used to write and save notes while in the cab.
The weather app informs the operator of current and upcoming climatic conditions so that they can adapt more efficiently and keep operations on track, whatever the weather conditions.
Several other existing features have also been upgraded. When the Radar Detect System is ordered, it is now integrated into the Volvo Co-Pilot, allowing operators to benefit from a rear-view camera and load information, which is all displayed on a single screen for increased convenience and safety when reversing.
The final update is the addition of two new task modes on the on-board weighing app. Operators can now choose from the trip meter, truck loading, stockpiling or processing mode. Each mode will adapt the Volvo Co-Pilot screen layout and provide relevant information for the operator to be efficient in the different applications.
Hyundai Construction Equipment Europe (HCEE) is continuing the rollout of the A-series with the HX300AL, a 30-tonne Stage V-compliant crawler excavator.
The HX300AL is suitable for infrastructure works and general construction. It features a new engine platform (Stage V), a new hydraulic flow regulation, improved operator controls with 2D/3D machine guidance and new safety features.
HCEE says the new machine offers improved uptime and productivity and incorporates some of its new technologies, including EPIC (Electric Pump Independent Control). By controlling the pump’s regulation independently, the machine is designed to offer improved fuel efficiency and controllability.
Other features include Auto Safety Lock, which prevents unintended operation/start of the excavator, which improves safety for the operator and on the job site.
Eco guidance indicates ‘inefficient operation’ status to prevent energy losses (fuel consumption, hydraulic power) by inadequate working habits which is displayed on the machine cluster.
MG/MC or Machine Guidance/Machine Control indicates the work status and automatically controls the attachment to assist the driver.
MG displays the position of the bucket tip and assists the operator with the use of positioning guidance. MC will automatically take over the grading with the bucket tip or face and has an automatic stop control: up, down, forward, and cabin protection.
“The new Electric Pump Independent Control is an energy-saving technology that reduces the pump flow rate during levelling and truck loading operation by controlling the pump’s displacement individually,” said Peter Sebold, product specialist at HCEE.
“Think next-level load sensing, a fuel saving of up to 8% daily average and general all-round operator and owner satisfaction, that’s just another win for this highly anticipated machine.” AB
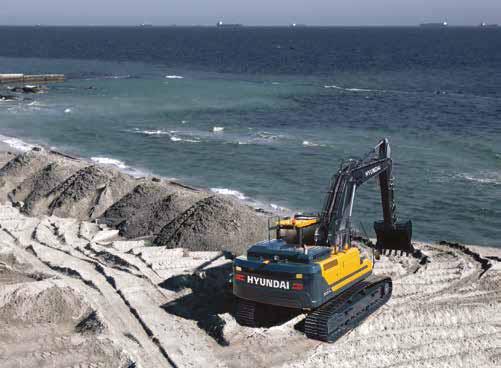
Volvo CE’s Co-Pilot in-cab monitor is now available on a broader range
Hyundai’s new HX300AL features a new Stage V engine

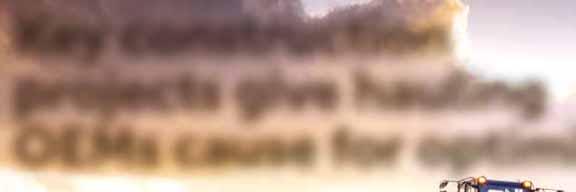

Key construction projects give hauling OEMs cause for optimism
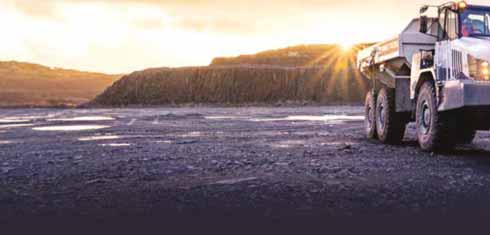
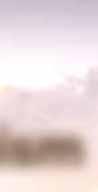
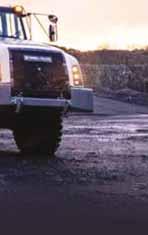
The COVID-19 pandemic has affected almost all markets and industries, with many countries going into lockdown. The MD of hauler manufacturer Terex Trucks predicts that the global construction industry – with help from government investment in key infrastructure projects – will be extremely important to economic recovery
The COVID-19 pandemic has forced most construction equipment manufacturers worldwide to reduce or suspend production at their factories over the last few months.
Around the end of March, in line with its parent company the Volvo Group, articulated hauler manufacturer Terex Trucks decided to temporarily suspend production at its facility in Motherwell, Scotland. The company says this was to ensure the health, safety and wellbeing of its employees, customers and the general public.
Speaking at the end of May 2020, Terex Trucks MD Paul Douglas said that the company is continuing to operate with a small team of dedicated employees who are working to support customers and maintain vital spare parts distribution.
Terex Trucks has recently started to see some OEMs (original equipment manufacturers) gradually bring teams back to work and begin a ‘new normality’ and Douglas adds that building sites are expected to gradually re-open over the next few months.
“Right now, it’s hard to predict exactly what’s going to happen in the global construction sector over the next few months, but we do see cause for optimism,” said Douglas. “The construction industry will be vital to global economic recovery. To kickstart economies, we expect that governments will invest in construction and infrastructure projects as an effective way to create jobs and boost their economies – and there are some key projects on the horizon.”
of Britain’s ten largest cities, this high-speed railway linking up London, the Midlands and the North is one of the most important economic regeneration projects in Britain for decades, which Douglas says is expected to kick-start not just the construction industry but the wider economy.
Douglas predicts that, due to this project alone, the UK could see demand for articulated dump trucks rise by an additional 1,000 machines over the next few years.
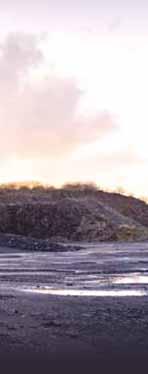
“In the first stages of the project, articulated haulers such as our Terex Trucks TA300 and TA400 will be used for preparatory tasks and transporting materials before the main construction work can begin,” he adds. “This includes jobs like vegetation clearance and earthwork for tunnel portals and compound facilities.”
In France, where Terex Trucks is expanding its distribution network and currently has four dealers – The Manu Lorraine Group, Framateq, Promatex and Griset Material – the population has slowly been returning to work during the last of weeks of May and Terex dealers have started up their sales activities again.
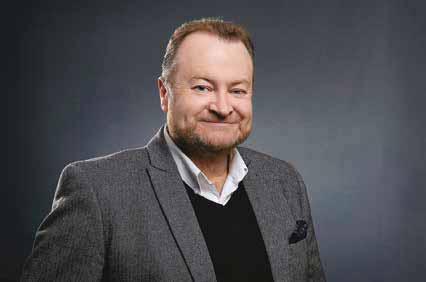
Looking ahead, Douglas highlights the Seine-Nord Europe Canal project, an important initiative that is expected to boost the French construction sector as well as the wider economy. This will involve the construction of a 107km inland waterway link extending from France to Belgium, connecting the Seine basin north of Paris to the Rhine basin and the northern European waterway network. For the construction, 55 of earth will have to be excavated and transported. Douglas says that robust and reliable dump trucks such as Terex Trucks’ own TA300 and TA400 models are a natural choice for this task.
In the UK OEMs are getting ready for the start of the major High Speed 2 (HS2) infrastructure project, which the government has approved work to start on. Serving eight
“The construction industry will be vital to global economic recovery” Paul Douglas
“While I do believe there is cause for optimism, the last few months have, of course, not been easy for OEMs,” he adds. “In the UK, which is the biggest market for articulated trucks in Europe followed by France and Germany, sales of construction and earthmoving equipment fell by 36% in the first four months of the year, compared with the same period in 2019.”
In April, the Construction Equipment
A Terex Trucks TA300 articulated hauler pictured at a Scottish quarry site at sunset
Association reported that sales fell by 74% compared to the same month last year.
As the lockdown in the UK came into effect at the end of March, Douglas says it is unfortunately the case that the industry’s sales will take a further dive in the second quarter of the year.
“As construction activity has slowed down throughout Europe during the last few months, the demand for machine rentals has also decreased,” he says. “This has had a significant impact on German rental companies – where renting accounts for 70% of the market activity – as well as the Italian market. In Italy, the rental trade association Assodimi-Assonolo reported that in March, 80% of rental companies experienced a downturn in orders.”
In Asia, which was amongst the places initially hit by the COVID-19 pandemic, the region has been one of the first to reopen its factories. In Korea and China, some construction equipment plants are already back up to full capacity and Douglas says there is a good level of demand. However, it still remains to be seen how this will develop over the next few months.
In Indonesia, for instance, the numbers of registrations for articulated haulers indicate a significant drop in demand. Last year, 177 machines were registered in the first quarter, whereas this year there were only four registrations in the same period. This is a completely different situation to Africa, where Douglas says that the number of registrations has been relatively stable so far.
“In other parts of the world, we are hearing that there won’t be any big projects starting over the next few months,” he adds. “In the Middle East, where many countries have oil-dependent economies, a lot of construction and infrastructure projects have been put on hold. This is due to low oil prices as the financing of construction and infrastructure projects in many Middle Eastern countries is often backed by oil revenues.”
The first two Komatsu HD605-8 dump trucks equipped with Metso Truck Bodies have been delivered to a porphyry quarry in Brabant Wallon, Belgium.
The deliveries by Metso distributor BIA Group are the first to be made in Central Europe and come exactly one year after the launch of the Metso Truck Body at the bauma 2019 fair.
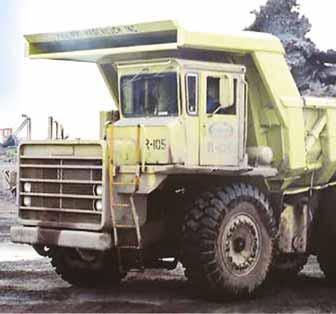
The tough and abrasive rock handled by the Brabant Wallon quarry had a significant impact on the previous conventional truck boxes. On a traditional box, the maximum payload is limited by the high weight of the lining and the box itself. Metso says its Truck Body differs from a standard box by its lighter, but resistant, rounded design in ultra-high-strength steel combined with the Trellex rubber lining. The Finnish quarrying equipment maker says this makes it possible to obtain a 20% to 30% lighter body without sacrificing rigidity.
The Metso Truck Body designed for the Komatsu HD605-8 truck weighs 6 tonnes less than a standard version fitted with a steel liner. According to Metso this weight reduction translates into a 10% additional payload and therefore offers greater efficiency from the first run. Likewise, during empty bucket journeys, the dumper will consume less fuel simply because it is lighter. Due to its rounded shape, less carry-back remains in the body, avoiding the transportation of unnecessary weight.
Off-highway truck customisation company Philippi-Hagenbuch has started using new SSAB Hardox HiTemp steel in its Hot Slag truck bodies.
The new steel is purposely designed to withstand extreme temperature environments and Philippi-Hagenbuch says
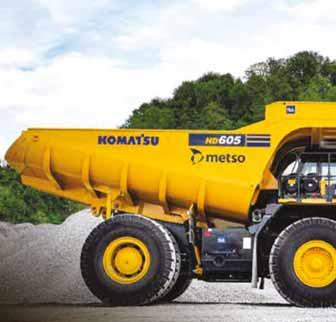
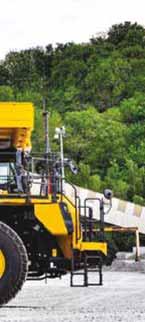
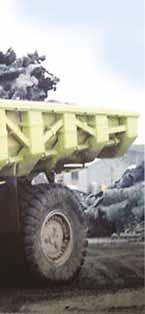
that it reduces necessary plate thickness while maintaining the product’s service life for increased productivity in processing applications.
“As a true custom manufacturer, every PHIL product is designed to excel in a specific application,” said Josh Swank, vice president of sales and marketing for PhilippiHagenbuch (PHIL). “In the past, steel mill clients requested a unique HiVol truck body to haul hot slag. Our engineers responded with the Hot Slag Body. Now, with the new HiTemp steel from SSAB, we can provide the same strength and durability with less steel, maximizing payload potential and providing our clients with a better product.”
The Hot Slag Body is comprised of two components — an exoskeleton superstructure, which does not come in contact with molten material, and loadcontaining pieces that do.
These pieces form an overlapping structure that is loosely strapped around the body of the exoskeleton to contain the hot slag during operation. This is designed to allow for differential expansion and contraction, where a traditional body would buckle under such extreme heat. When transporting molten material, the pieces expand and contract without breaking welds, binding up or warping. When a piece is damaged or worn out, it can simply be replaced without any structural welding requirements.
Following its acquisition of fellow Italian company Perlini in 2018, Cangialeoni Group has “rebirthed” the brand (now called Perlini Dumpers) from the start of 2020 with the expressed aim of returning it to the elite group of rigid dump truck (RDT) manufacturers.
This strategy has led to the company moving from the exclusively internal production of all components to a partnership with a group of twenty-three local suppliers and to the development of a new truck designed for the most advanced customer needs.
Perlini Dumpers will continue to produce dump trucks at the historic Perlini headquarters in Gambellara, Vicenza. The current range consists of three models, with 40, 65 and 95 tonnes of loading capacity and powered by two types of engines: for European Union users and for users in countries outside the EU.
Philippi-Hagenbuch has started using new SSAB Hardox HiTemp steel in its Hot Slag truck bodies
Metso claims its Truck Body is 20-30% lighter than a conventional steel-lined truck body
The just-launched Perlini RDT features a new Scania Stage V engine and a new Avtec transmission.
The 65-tonne model is due to be officially presented at the next SAMOTER exhibition, scheduled to take place in Verona from 21-25 October 2020.
The RDT hauler is designed to comply with recently introduced regulations on exhaust emissions; the new Scania Stage V engine is designed to meet the most severe requirements in this area, providing low fuel consumption and a high torque.
The haulers also feature an electronic weighing system, GPS locator, control of machine parameters and production monitoring in real time, allowing total control of the truck to provide a significant increase in production efficiency.
Cangialeoni Group says that the systems available on the new Perlini trucks mean it is possible to monitor the vehicle and its load at any time. The new electronic transmission control allows the operator to access data in a more comfortable and intuitive way. The selector display provides information on the transmission, allowing the operator to recognise any alarms and codes and integrates some diagnostic tools.
The GPS system collects a range of vehicle data. This information includes location, distance travelled, switchboard status (on or off), body activation (lifted or low), voltage in volts of the internal battery, primary power (on-off), GPS status (on-off), detection of CAN BUS data (non-invasive connection), environment temperature, detection of aggressive driving (acceleration, braking and sharp curves), remote commands (engine block), alert (alarm setting with notification via web and/or email), alarms (including area entry and exit, power failure, GPS/GPRS signal absence) and maintenance (checking of scheduled deadlines with reminder reception on a km/hour basis).
Komatsu Europe has launched its new HD785-8 Rigid Dump Truck. Built for mining and quarrying applications, the HD785-8 has
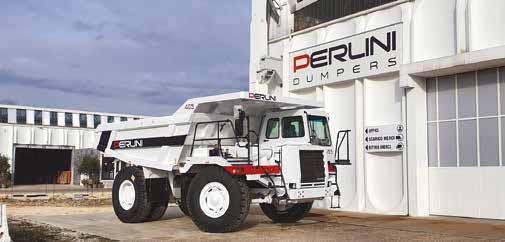
a Stage V Komatsu SAA12V140E-7 engine (849kW/1,140hp) and a payload capacity of 92.2 tonnes.
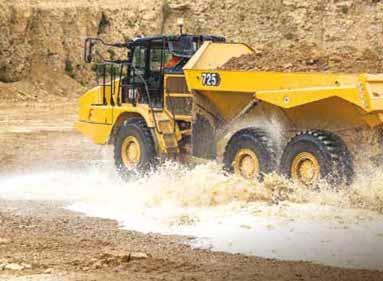
The EU Stage V after-treatment solutions use dual Komatsu diesel particulate filters (KDPF) – most regeneration is performed passively, with no action required from the operator and no interference to machine operation. There is no selective catalytic reduction (SCR), and diesel exhaust fluid (DEF), or AdBlue, is not required.
“The new HD785-8 proposes excellent operator comfort, great travel performance and the well-known Komatsu reliability of the previous model,” said Juuso Ahola, product manager at Komatsu Europe.
Key machine metrics for utilisation, production and machine health can be accessed remotely via the KOMTRAX telematics system or on the machine through the upgraded machine monitor.
The HD785-8 has a seven-speed, fully automatic transmission with two selectable reverse speeds. The Komatsu Advanced Transmission with Optimum Modulation Control System (K-ATOMiCS) is designed to ensure smooth clutch engagement for a comfortable ride and reduced material spillage.

The HD785-8 delivers fast acceleration out of the pit and has excellent travel performance on grade. Wet multiple disc brakes on all wheels provide great downhill brake-retarding performance. With a tight turning radius of 10.1 m the HD785-8 provides exceptional manoeuvrability when waiting to be loaded and positioning to dump. The Komatsu Traction Control System (KTCS) is standard on the HD785-
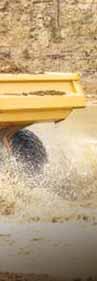
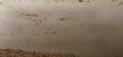
8. KTCS automatically applies pressure to independent brake assemblies for optimum traction in various ground conditions. Caterpillar has introduced the 725 articulated truck whose features include a ‘nextgeneration’ cab, a powerful engine meeting current emissions standards and automatic features to increase productivity.
The new 24-tonne payload truck is designed to build on the reliability and durability of the 725C2, offering increased performance for customers engaging in heavy and general construction, mining, quarry and aggregates, landfill, waste and industrial applications.
The articulated truck is the first to display the new Cat trade dress and offers improved lighting for easier night work with optional high-level LED, high-intensity lights, LED machine-width position marking lights and access lights on both machine sides.
The 20% larger cab features infrared blocking glass to reduce solar heating inside, while sliding windows increase ventilation and enable communication with the loading tool and workers on the ground. More vents positioned toward the operator with the new automatic climate control (HVAC) system deliver improved heating or cooling efficiency inside the cab.
The new 725 powertrain includes the Cat CX31 six-speed transmission with advanced features designed to deliver smoother shifting, up to 8% greater acceleration and increased speed on grade of as much as 9%. Advanced Automatic Traction Control removes all manual traction control decisions from the operator and automatically changes the differential lock engagement level on-the-go to continuously maintain traction, resulting in improved cycle times, increased productivity and reduced tyre wear. AB
Caterpillar’s new 725 articulated truck features a ‘next-generation’ cab
BELOW: Komatsu’s new HD785-8 RDT has a payload capacity of 92.2 tonnes
The new 65-tonne Perlini RDT
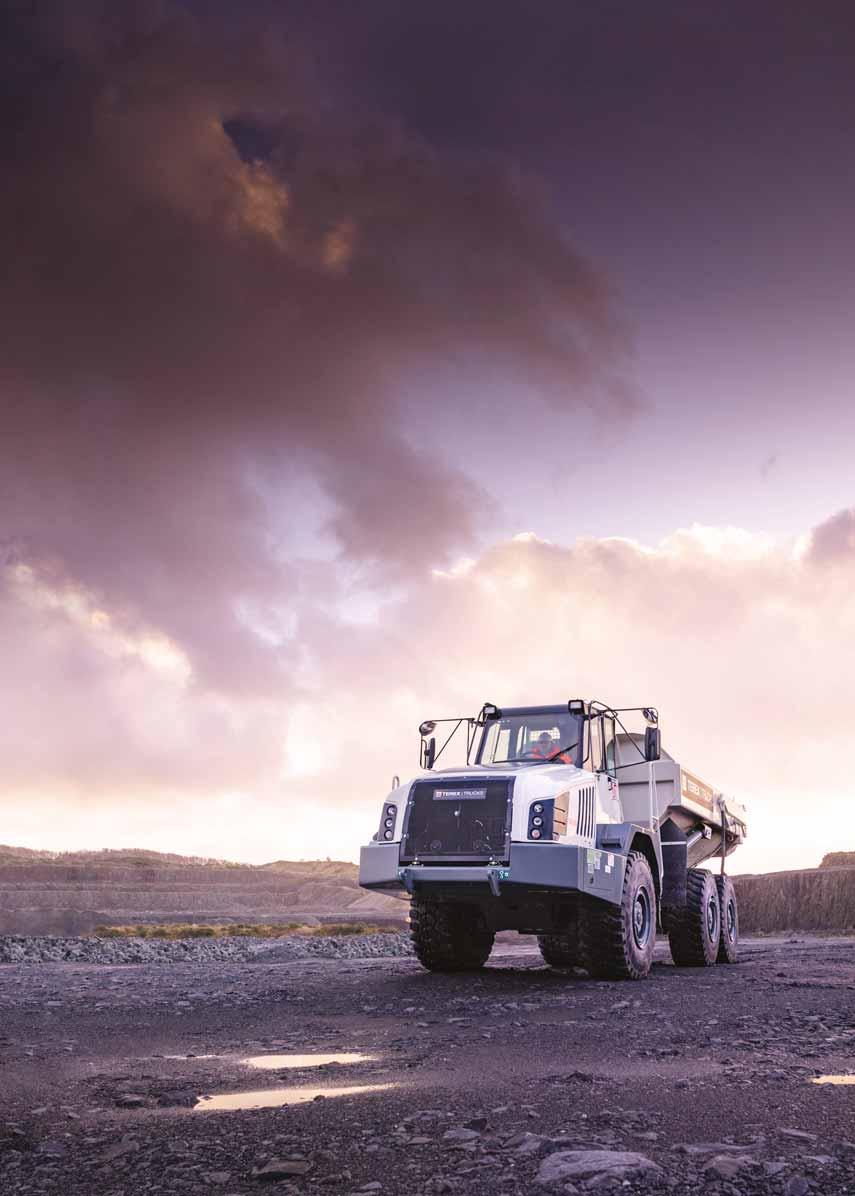
Start your engines for the return of COVID-19disrupted market demand
The off-highway machine engines industry is full of innovation, with manufacturers keen to get back to full production following the peak of the COVID-19 pandemic.
Guy Woodford
reports
Cummins is among major off-highway engine manufacturers looking for quarrying and heavy construction equipment demand to return to a healthy level as large parts of the world begin to emerge from COVID-19-triggered lockdown.
The US-headquartered company has continued to produce its wide engine range at a reduced capacity since the near total global introduction of lockdowns in the first quarter of 2020. It includes the production of its quarrying-suited 3.8-12-litre, 75-382kW, EGR- (exhaust gas recirculation) free EU Stage V Performance Series power units.
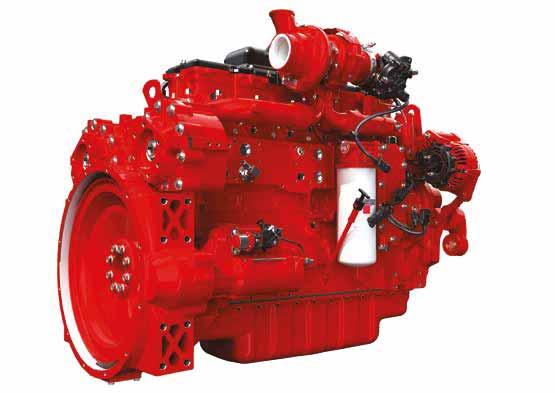
“In the UK, our Darlington and Daventry factories were producing at around 50% when social distancing and lockdown came in. The plant management teams have done a fantastic job in working out how we can keep employees safe, working at a 2m distance from each other, and keep engines moving through the production line. They also modified shift times, so we didn’t have lots of people entering and leaving site at the same time,” said Steve Nendick, Cummins marketing communications director. Certain customers like Komatsu, DAF Trucks and JCB closed down temporarily, so the number of engines needed was reduced, and we were able to keep other OEMs (original equipment manufacturers) up and running through this tough time.”
Speaking to Aggregates Business in late May 2020, Nendick says the Darlington and Daventry sites are now back up to at least 80% production capacity. “Things are going well in the UK, and our production in China is pretty much at 100%. The Dongfeng Cummins (Xiangyang City, Hubei Province) plant achieved record monthly production in April. In India, everything was shut down by the government, and is now restarting. In the US, most of our plants are back up and running now.
“Now that production is building back up, the next challenge for the industry is around
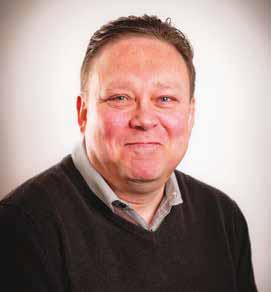
“They have the ability to efficiently drive more from the engine without the need for additional aftermarket systems”
Steve Nendick
supply chain. Suppliers are struggling or have shut down because of the crisis, and our team are working through the best ways to manage them.”
Cummins says its B6.7 and L9 Performance Series power units will now feature new engine power take-off (PTO) capabilities to support key applications such as crushers, screeners and cranes.
Launched at Hillhead 2018, Cummins’ power units are available from 75–503kW, delivered as a complete and ready-made package. This comprises an engine, exhaust after-treatment system, radiator and cooling system, plus auxiliaries such as mounting feet, hoses and an air cleaner. Crucially, Nendick notes that more than 60% of the content is pre-approved, making the machine integration process simpler and quicker.
“Our Performance Series power units offer a flexible drop-in solution for manufacturers. Because we were able to remove the EGR and push up the power, we’ve got excellent power density, particularly on the 3.8, 4.5 and 6.7-litre models.”
Such high machine capability, stresses Nendick, makes the Performance Series power units well suited to hard-working applications such as crushing, screening and pumping.
Examples of installations to date include the L9 power units powering Anaconda’s new J12 tracked jaw crusher, and I12 tracked
Cummins’ L9 Performance Series power unit with dual REPTO attachment
impact crusher. The B6.7 version is available with Bandit in their Intimidator 20XP tree chipper plus NLB Corp’s water-jetting systems.
“When we developed the Stage V Performance Series engines, we dualcertified them to Tier 4 Final for the US. That was one of the real benefits that Anaconda saw. It meant they could take the engine and package and build the same machine, whichever region it was destined for. From a production flexibility and capability perspective, they got a really good solution.”
Nendick explains that to increase the flexibility and capability of the Performance Series power units even further, Cummins is integrating new single and dual rear-engine power take-offs (REPTO). These complement its standard PTO capability used for items such as hydraulic pumps. Cummins is also making these available on the base engines without the pack.
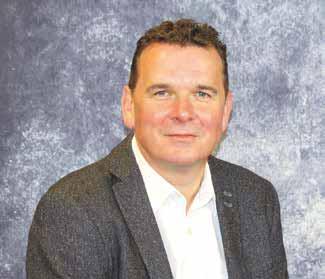
As an example, fitted with the dual REPTO, the L9 will have a total drive capability of 560Nm. This will make the engine capable of driving additional pumping capability through SAE B two and four bolt mounts. Integrated into the flywheel housing, the dual REPTO is compact and has a minimal impact on engine packaging. The added weight is approximately 100kg.
“For equipment manufacturers, they have the ability to efficiently drive more from the engine without the need for additional aftermarket systems. This would support the driving of hydraulic pumps for all sorts of machine functions from steering systems to fans, etc. It will reduce installation costs and complexity for a more integrated solution,” says Nendick. “I think the Performance Series power units plus the addition of REPTO, puts us in the driving seat to increase our business in the crushing and screening sector.”
John Deere Power Systems (JDPS) will begin full production later this year of its new CONEXPO/CON-AGG 2020 exhibitionshowcased JDPS 13.6-litre diesel engine (300kW to 510kW). The engine is said by Martin Ryley, JDPS worldwide business development manager, to be well suited to large crushers involved in quarrying applications.
Peak torque for the new 13.6-litre unit is 3050Nm with a series turbocharger, an 11% increase over previous models. With a single turbo, the peak torque rating is 2510Nm. The new diesel has up to a 6% fluid economy advantage, while heat rejection reduction is over 20%.
The JDPS 13.6-litre engine was built with a “clean-sheet” design, offering new levels of performance, serviceability and integration — all key characteristics for OEM customers. This design process — which now includes a DPF- (diesel particulate filter) free solution for Tier 4 Final variable and constant speed markets, in addition to the dual-certified solution for Tier 4 Final/EU Stage 5 markets — was driven specifically by customer requirements.
“We leveraged and optimised our proven
“If one piece of equipment goes down, the whole production chain goes down, and it becomes very expensive” Martin Ryley
technologies developed over the years to best address market and customer needs in heavy-duty applications. This ensured the final product would deliver increased performance and overall value to our OEM customers and end users,” says David Hoffman, director of worldwide marketing, sales and customer support at JDPS.
JDPS and its distributors are now accepting orders for the 13.6-litre engine.
Speaking to Aggregates Business, Ryley said JDPS is also developing an 18-litre, 500kW-plus engine for large quarry plant. The engine is earmarked to be available at some stage in 2022.
The new 18-litre model will move the top end of the JDPS power range to over 650kW. The engine, which will be JDPS’s biggest ever, will be built at the company’s Engine Works facility in Waterloo, Iowa, US. The launch of the unit will be timed, says Ryley, to coincide with construction and quarrying equipment makers’ product development plans.
Ryley says JDPS engines are ideal for quarrying applications due to their robustness and John Deere-proven high performance and reliability. The company has a wide range of engines for quarry plant, and Ryley stresses that this is an important part of the company’s business. JDPS engines are used in quarrying plant manufactured by a number of major global players such as Terex and Rubble Master. Both variable speed engines for industrial applications such as quarrying crushers and screeners, and constant speed engines for generator driven screeners, are available from JDPS.
Ryley notes that JDPS has consistently used high-quality diesel particulate filters (DPF) to meet off-highway engine emissions regulations as they’ve evolved over the years. The company, he says, is very proud of its record in this area. “We started with DPF in 2011. Not many of our competitors did. We have used that experience in hundreds of applications to make it work in even the most challenging of conditions. We’re very confident in our DPF solutions.
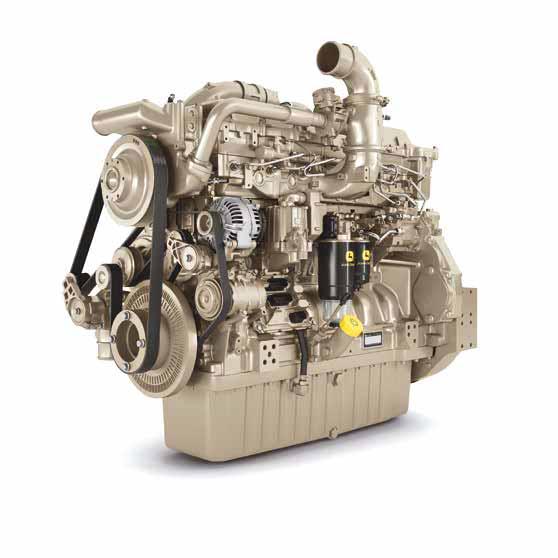
John Deere Power Systems’ (JDPS) new large quarry crusher-suited 13.6-litre engine will go into full production later this year
“We also have a strong focus on fluid consumption – optimising the mix of diesel exhaust fluid (DEF/AdBlue) and diesel to get the lowest machine running cost for operators.”
Ryley says that JDPS is looking to bring out an engine predictive maintenance solution/s in the next couple of years. “It’s what’s next – putting more engine data and control over maintenance into customers’ hands. John Deere is already developing predictive maintenance solutions for its machines, and we’ll apply that to our engines.
“Preventing machine breakdown is absolutely vital when it comes to quarrying. If one piece of equipment goes down, the whole production chain goes down, and it becomes very expensive.”
Ryley adds that the firm was also investing heavily in electrification - to meet the growing demand for fully electric and diesel electric drives for quarry and general construction plant and vehicles. “The benefits of electrification are enormous: it creates opportunities for much higher operation efficiency, much higher productivity, lower fuel consumption, and to downsize engines required on some machines.
“For a number of years now, John Deere has had a diesel-electric hybrid wheeled loader [the 944K] on the market. It’s an indication of where we see the market going.”
FPT Industrial, the global powertrain brand of CNH Industrial, has acquired Potenza Technology, a company specialising in the design and development of electric and hybrid powertrain systems.
The March 2020-announced acquisition represents another step in FPT Industrial’s path towards electrification, one of the pillars of its multi-power strategy.
“Sustainable powertrain technology is of increasing global focus and concern. Here at CNH Industrial we are committed to delivering solutions, which not only reduce emissions and enhance productivity but which deliver future-proof technology for the long term,” said Hubertus Mühlhäuser, chief executive officer, CNH Industrial. “This, our latest acquisition, is further testament to this.”
“FPT Industrial is acknowledged as a leader in alternative propulsion systems. The acquisition of Potenza Technology will further enhance our brand’s accelerating development of sustainable electric powertrains across a range of operating segments,” said Annalisa Stupenengo, president Powertrain, CNH Industrial.
Potenza Technology, based in Coventry, England, has been at the forefront of electric powertrain technology since 1999. The company has specific expertise in functional safety, battery management systems for traction battery packs, and electrical and electronic systems design and development.
Major global off-highway machine engines player Perkins has appointed Onnyx as its authorised distributor for Algeria.
A family-owned business, Onnyx has 18
years of experience with Perkins engines as a second-level dealer (DPA) since 2002.
Headquartered in the UK with an operations branch in Algiers, Onnyx has already established a strong 21-person team focused on engine and parts sales and the delivery of 24/7 technical service support to Perkins-powered customers.
“I’m excited to be working with Onnyx, which, through its former role as a secondlevel dealer, has a proven reputation for delivering customer service and quality,” said Jaz Gill, vice president of global sales, marketing, service and parts at Perkins. “I’m
confident this highly experienced team will provide the consistent service our customers in Algeria expect and deserve.”
“This is more than a collaboration,” noted Khaled Terai, country manager at Onnyx. “Becoming a Perkins distributor opens many more opportunities for us. With the best-inclass range of engines, the largest genuine spare parts stock in Algeria, premium product support and the best service team in territory provided by Perkins-certified engineers, we always target excellence to deliver the best customer experience. This is our commitment and promise.” AB
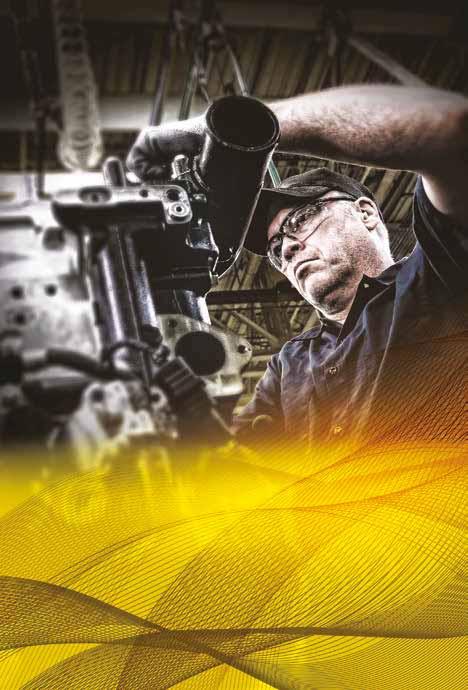
PROUD TO
POWER
We’re meticulous creators of power components that integrate easily and perform reliably. From inspiration to application, we celebrate the process of bringing your equipment to life. We truly understand the needs of the OEM because we are one. We’ll put our insight and expertise to work to provide a seamless solution for your machine — from the engine and electrification to the drivetrain.
We’re John Deere Power Systems. We’re proud to power you.
Campbell Contracts’ new 120 tonnes per hour CDE wet processing plant
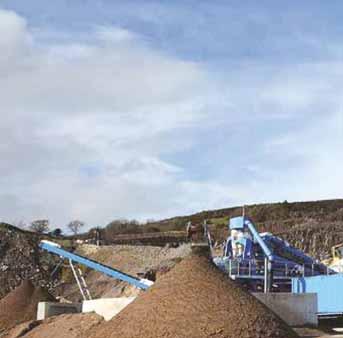
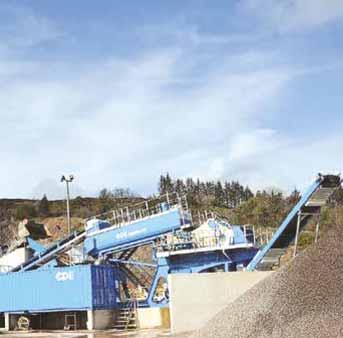


Rapid recycling gains
Mineral product producers keen to widen their income streams can find attractive commercial opportunities in recycled aggregate and concrete products. Guy Woodford reports
Campbell Contracts, a familyowned and managed business headquartered in Tempo, a small village on the outskirts of Enniskillen in County Fermanagh, Northern Ireland, claims to have doubled its materials processing ability since commissioning a new CDE wet processing plant. Operating from its Letterbailey Quarry, Campbell Contracts has been extracting sand and gravel for over three decades. In recent years it commenced controlled blasting activities and now counts sand, gravel, crushed rock, rock fill and screened topsoil among its growing product range.
In 2019, the Campbell family partnered with CDE, a leading global market manufacturer of wet processing technologies, to help it grow the business and diversify its portfolio of high-quality quarried aggregates.
For decades Campbell Contracts had utilised a traditional barrel washer, as company director Brendan Campbell explains.
“It was suitable for our business needs at the time it was installed, and it has served us well over its 30 years of service.
“Increasingly, we need to ensure we can recycle and reclaim as much primary aggregate as possible during the quarrying process and the barrel washer had its limitations.”
One of the earliest processes for washing aggregates, the Campbell Contracts barrel washer was efficient when processing cleaner virgin material. Its limitations became evident in its inability to wash heavier, claybound materials, rendering them as waste.
“This material was then backfilled into the pits and buried,” Campbell says. “Similarly, the unwashed primary scalpings we generated were inevitably stockpiled as we didn’t have the technology to efficiently process the material.”
Each stage of the quarrying process produces by-products in the form of overburden, scalpings and crushed rock fines. Often, quarry operators classify these as waste materials without commercial market value.
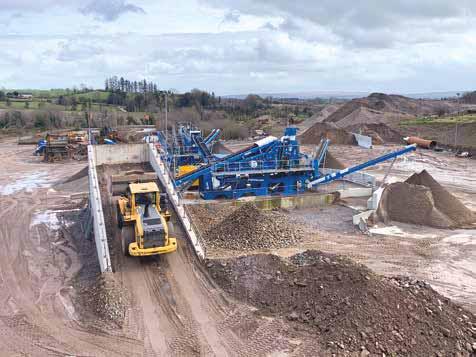

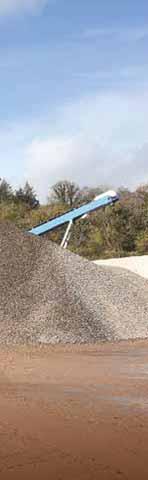
David Kinloch, regional manager for CDE in the UK & Ireland, says: “CDE engineers state-of-the-art wet processing technologies that offer quarry operators the solutions to enhance the quality of products they currently produce, while simultaneously supporting them to add huge commercial value to their enterprises by ensuring value is extracted from all available material, including those which are too often perceived as quarry waste by-products.”
CDE completed tests at Creagh Concrete on material extracted from the Letterbailey Quarry. Material was analysed, and results used to develop a bespoke wet processing system that responds to the needs of Campbell Contracts and would support the family business to stimulate growth.
“This was an important consideration for us,” emphasises Campbell. “CDE understood our operation and what we wanted to achieve with a new wet processing plant. It’s very much a journey and a partnership with CDE that extends beyond the commissioning phase, with first-class proactive and preventative measures to ensure the plant is operating at maximum efficiency.”
Campbell Contracts’ new 120 tonnes per hour (tph) wet processing plant includes the L35 Feed Hopper, M2500 incorporating the twin-deck P2-75 Infinity Screen and EvoWash, and CDE’s AggMax83, integrating the RotoMax RX80 logwasher and H2-60 Infinity Screen.
The fully integrated, modular plant combines feeding, screening, washing and stockpiling onto one compact and mobile chassis.
With the support of its new CDE plant, Campbell Contracts is successfully processing
LEFT: Campbell Contracts claims to have doubled its materials processing ability since commissioning a new CDE wet processing plant
three materials it previously categorised as waste from its quarrying operations: claybound sand and gravel, primary scalpings and crushed rock fines.
Campbell says it has had a transformative impact on the business.
“We’re recovering high-quality materials and value that we had effectively written off as waste. In retrospect, we should have partnered with CDE to commission the plant sooner.”
Virgin sand and gravel feed material is being processed at a rate of 120 tph producing 0-3mm and 0-6mm sand; 6-12mm, 12-25mm and 25-50mm aggregate; and +50mm oversize aggregate for a wide range of applications in the construction industry.
Kinloch adds: “Campbell Contracts is now processing three grades of material that it historically stockpiled or backfilled. CDE wet processing technology has demonstrated that all quarry by-products have the potential to be processed into marketable products that add significant value to a business.”
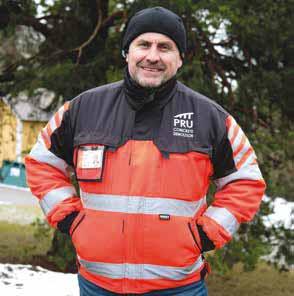
ABOVE: Marko Blinnikka, managing director of PR-Urakointi
Savonlinna is the home of one of Finland’s leading bridge demolition companies, Savonlinnan PR-Urakointi (PR-Urakointi). The firm’s processing of demolition concrete is said to be much more efficient thanks to a recently purchased noise- and dust-proof Metso Lokotrack Urban LT96 jaw crusher.
“The Lokotrack is at least five times more cost-effective than the crushing bucket we previously used. Depending on the feed, the LT96 can crush up to 150–250 tonnes per hour,” says Marko Blinnikka, managing director of PR-Urakointi.
“I must say that the Urban is truly quiet. The sound of crushing does not exceed the sound of the engine, and you can talk right next to the machine without raising your voice. Spraying water at high pressure into the crusher’s cavity and main conveyor prevents dust generation.
“As an additional benefit, the Lokotrack’s magnetic separator removes reinforcing bars from the crushed concrete, so that we can use the clean, crushed concrete for landfilling, often at the same site,” Blinnikka continues.
PR-Urakointi used its new Lokotrack Urban LT96 for the first time at Aholahti in Savonlinna. Approximately 20,000 tonnes of concrete from demolished buildings were piled up in an industrial area. The stockpile contained reinforcing steel bars, some of them only as thick as your little finger.
After a couple of days’ practice, crushing with the new tool was said to be effortless. Tomi Inkinen fed the concrete into the jaw crusher, Aulo Nemevalts immediately levelled out the crushed concrete artificial fill, and Jori Kettunen monitored the machine in operation.
Metso’s IC process control is said to have proven to be an excellent tool when getting to grips with the crushing process. The team was already well familiar with the different on-screen buttons after just a couple of days.
Consisting of pieces of concrete, bricks and fines, the feed was crushed in the jaws of the C96 jaw crusher at a setting of 90mm. The mountains of iron waiting to be recycled were an indication of the vast number of
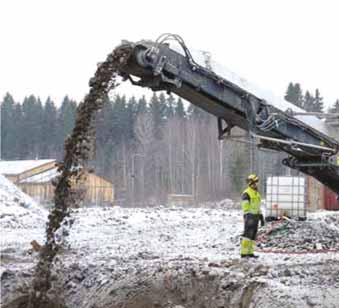
reinforcing bars contained in the concrete.
The processing of concrete does not require high crusher or diesel engine capacity. Consumption during crushing was around 13 litres of fuel per hour.
Every year, PR-Urakointi performs a large share of all the demolition contracts available in Finland. These also include demolishing buildings.
“It will be interesting to see how the Lokotrack can handle the concrete used in bridges, which is much harder than the concrete used in buildings. In addition to more reinforcing bars, bridge concrete can contain up to 50% natural stone,” says Inkinen from PR-Urakointi.
One bridge may easily contain up to 5,000 tonnes of concrete to be demolished. The Lokotrack enables crushing on-site, which results in savings in transport costs.
“When you’re demolishing a bridge, you must always know what you’re doing. Each bridge is a different story. Sometimes you have to perform the demolition work while cars are using one of the lanes, which is a whole new challenge,” Inkinen says.
PR-Urakointi has also been an industry pioneer in the development of demolition equipment. The company has developed an excavator attachment called the Power Dropper, which can easily crush even the most substantial concrete slabs in bridges without disturbing the environment.
Furthermore, the year before last PR-Urakointi expanded its operations to include the more demanding asbestos stripping.
Based in the northern Italian region of Trentino-Alto Adige, Martintoni has been a Rammit Spa (Rammit) customer for around 20 years. During this time the firm has bought breakers and other equipment from the Italian Rammer hydraulic hammer dealer. In recent years, however, Martintoni is said to have also transformed its material processing and handling operations with an Allu attachment for the screening and processing of soils and recycled materials.
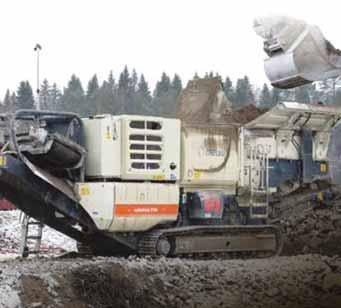

The noise- and dust-proof Lokotrack Urban LT96 crushes demolition concrete for PR-Urakointi at a speed of almost 200 tonnes per hour
A meeting at the Ecomondo exhibition in Rimini, Italy, in 2018 led directly to Rammit supplying a new Allu Transformer with the revolutionary TS blade structure, with the Allu attachment being fitted to Martintoni’s new Liebherr 556 Xpower wheeled loader. The proposed DS 4-23 TS16-32 model with screening blades was demonstrated working on topsoil and other materials that would usually be sent directly to landfill. However, to provide a more difficult proposition, a demonstration was arranged at Allu’s headquarters in Finland on particularly sticky and ‘difficult’ soil.
The demonstration in Finland went very well, with the representatives from Martintoni also taking the opportunity to visit the Allu factory, and inspect the production process, spare parts facility and inspect the quality of the components used in manufacture. Following a reappraisal of Martintoni’s requirements, it was decided to use an OilQuick hydraulic quick coupler (OQL 310) to hook/unhook the Allu attachment rapidly when the need arose.
Since its delivery and fitting to the loader, the Allu Transformer DS 4-23 TS16-32 is said to have performed well above expectations. It was commissioned for the customer by Allu-trained Rammit technicians and has been used regularly for screening soil from excavations carried out by Martintoni or by third parties.
Most of the excavated material contains a high percentage of roots and branches and other contaminants which the bucket, set with a spacing of 16mm, can screen very effectively. The Allu Transformer tends to work at its maximum capacity of 3.5m³. It is said to be able to achieve the desired daily production of over 1,000m³, processing the sticky material in 20-30 seconds.
Martintoni acquired 15,000m² of land, subsequently used to build a new fixed sand and gravel processing plant to enable the company to supply a broader range of aggregates for general structural construction. In addition to the processing
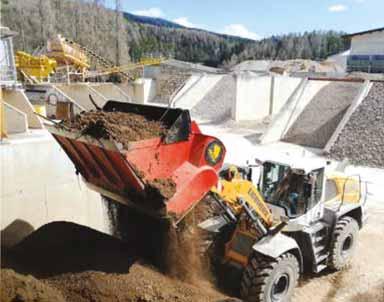

of aggregates, the company now receives and processes materials emanating from excavations, earthmoving, remediation, pipeline, roads, building construction and landscaping. To work with these materials, the company uses a fleet of trucks, excavators, rollers, wheeled loaders, as well as a new Allu TM Transformer DS 4-23 TS25 to help transform its operation.
Kiverco has bolstered its team with several key appointments to support business growth in the UK and increasing demand for its recycling solutions in Europe and around the world.
Combining more than a quarter of a century of engineering know-how with its popular technology brands, Kiverco designs, manufactures and delivers lasting recycling solutions for any waste stream anywhere - with more than 300 installations in the UK alone.
In recent years, the Northern Irelandheadquartered company has grown significantly as a result of increased demand for its recycling solutions in the UK, combined with considerable international expansion in Europe, the Middle East, North America and Australasia.
New staffers include Con Gallagher, who has become the company’s global head of sales, André Matula, the new key account manager/business development, and
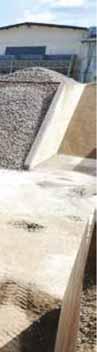
Angela Madden, who has taken up the newly created role of head of marketing & PR.
The company, renowned for its robust static recycling solutions, has also brought to market its modular plant range which is sold through its growing dealer network to meet demand. This range of products can run as single units or when combined, provide an alternative to traditional ways of processing waste. Product benefits include simple set-up within hours, reduced footprints and rapid relocation without the need for cranes, with all the benefits of a high-performance static plant.
Kiverco’s modular range can process municipal solid waste (MSW) as well as construction and demolition (C&D), commercial and industrial (C&I) or dry mixed recyclables (DMR) waste and includes material feed, screening, air, magnetic and manual sorting equipment. AB
BELOW LEFT: A materials recycling plant designed, manufactured and installed by Kiverco for Remondis BELOW RIGHT: Con Gallagher is Kiverco’s new global head of sales
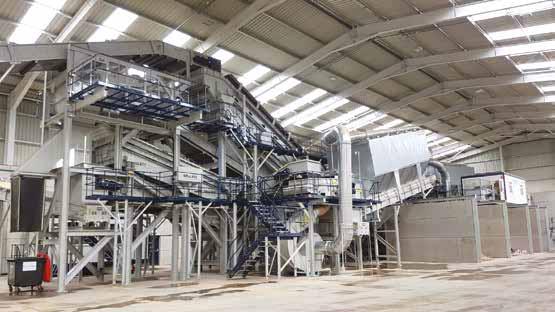
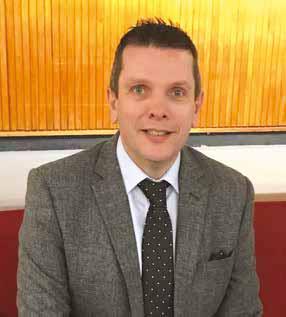
An Allu Transformer DS 4-23 TS16-32 attachment fitted to a Liebherr 556 Xpower wheeled loader is said to have performed well above Martinoni’s expectations
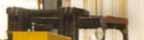
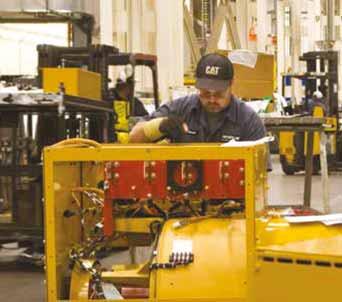
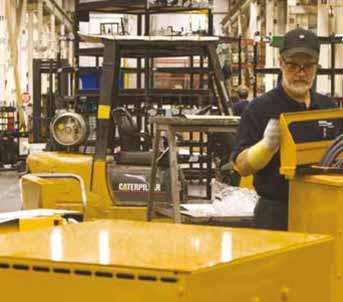
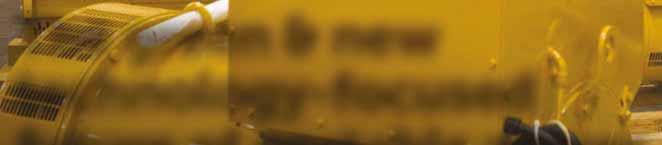
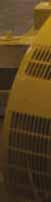
The green & new technology-focused future of portable power

Portable power solutions for quarrying industry customers are getting greener and embracing new technology. Guy Woodford reports
European legislatures began implementing emissions regulations for non-road mobile machinery in late 1997. These regulations apply to prime or standby power used in mobile applications such as drill rigs, wheeled loaders, bulldozers, highway excavators, forklift trucks, aerial lifts, mobile cranes and other non-road equipment including mobile generator sets.
Over time, the regulations have become progressively stricter to reduce further harmful engine exhaust substances, including carbon monoxide, hydrocarbons, particulate matter (PM) and nitrogen oxides. The standards have advanced from the initial Stage I to today’s Stage V, which is also known as EU Regulation 2016/1628.
As the mobile generator set market transitions from EU Stage IIIa to EU Stage V, customers will be challenged to adjust to the new product complexity and increased cost. The additional hardware needed to meet the updated Stage V requirements presents new challenges to the power rental market in Europe. Since the legislation for mobile generator sets skipped Stage IIIb and IV, a big jump in technology is required, including both engine modifications as well as off-engine aftertreatment.
For example, a diesel oxidisation catalyst (DOC) and diesel particulate filter (DPF) are required for all high-pressure fuel system units over 19kW, while selective catalytic reduction (SCR) will be required for all units above 56kW. SCR requires diesel emission fluid (DEF)/Ad-Blue to convert oxides of nitrogen (NOx) to harmless compounds. While AdBlue is a common fluid in
automotive and machine applications, it is an additional item to consider for a power rental operator who may be operating in a remote location.
EU Stage V also extends the scope to a broader range of engine types and sizes, regulating engine outputs higher than 560kW for the first time. This presents engine availability challenges for the large mobile power generation market. In addition to technical issues, commercial challenges exist as rental operators must work to increase rental rates to offset the significant increase in product acquisition costs, and maintain acceptable financial returns. As a result, in the years to come, rental rates will need to increase if rental companies are to maintain their return on investment.
The changes occurring because of EU Stage V, along with newly proposed particle number (PN) limits, effectively require the use of DPF to reduce emissions to compliance levels for engines within the scope of EU Stage V.
“The need for this additional hardware, combined with a significantly greater level of complexity in the engine design, requires a fully integrated solution tested for optimal performance and usability,” said Gareth Osborne, Caterpillar product definition manager for mobile generator sets. “Caterpillar is well-versed in the evolving European emission standards, and we have guided our mobile generator set customers through every phase of these regulations.”
At very high pressures, electric commonrail applications deliver fuel to electronically controlled fuel injectors. This process produces a very fine diesel spray resulting
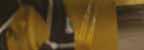

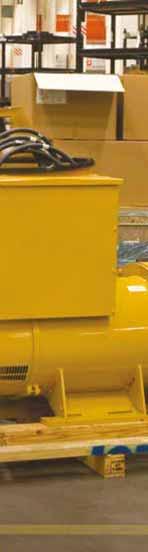
in minuscule soot particulates which pose potential health risks. While this type of system enables complete control over the combustion process and allows for thermal management of aftertreatment systems, the particulates must be managed to meet emissions regulations. A DPF filtration system is designed to reduce PM, including soot from the exhaust of a diesel engine. A series of alternately blocked channels forces the exhaust gas to flow through the channel walls, where the particulates are captured in the filter.
Many rental generator applications have low load factors or utilise oversized equipment because of limited information on the customer’s load profile, or large starting loads with relatively small running loads. During a low load operation, a DPF will accumulate PM due to low exhaust temperatures if the soot deposit rate is greater than the passive regeneration rate from the hot exhaust gas. The result is increased back pressure on the engine. As back pressure increases, eventually, the particulates must be removed from the DPF through a process known as regeneration.
By handling the regeneration processes internally with intelligent measurement of DPF soot level and on-package thermal management, Caterpillar’s high-speed system works without any interaction from the operator. This allows all rental generator sets fitted with DPF systems to have the flexibility to be used in any application and any environment.
“Caterpillar generator sets achieve this process transparently to the operator, without the need to take the generator
Caterpillar generator sets in production
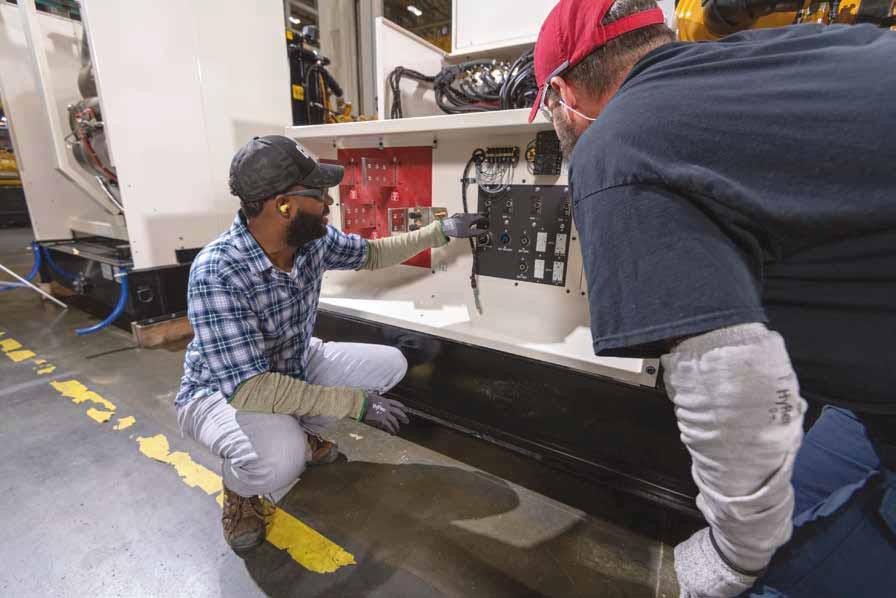
set offline or add load banks and other equipment that increases complexity, cost and weight,” said Osborne. “Through our unique position as both the engine supplier and generator set packager, we can ensure all EU Stage V packages our customers receive are fully integrated and tested for optimal performance and usability.”
To ease that change, however, Caterpillar is following the regulation’s built-in transition structure. This allows companies like Caterpillar to continue to manufacture equipment using the previous emission tier for 18 months after Stage V becomes effective. There is also a six-month allowance for generators to be sold after the 18th month of manufacture. Stage V became effective 1 January 2019 for all engines below 56kW and above 130kW.
For engines in the 56kW to 130kW range, the effective date is 1 January 2020. By increasing their EU Stage IIIA fleet before the legislation takes effect, fleets can maintain lower rental rates for their customers and reduce overheads. In contrast, early adopters of EU Stage V-compliant machines will benefit from a rental business in highly regulated spaces such as large cities. Whichever avenue a fleet chooses, Caterpillar says it can help navigate a strategy to reduce cost and complexities.
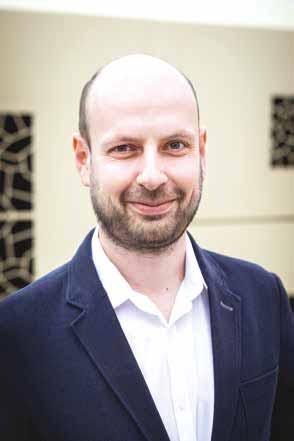
Cat Connect technology is available to remotely track and manage generator sets, integrating telematics information into business systems and improving operational efficiency. This technology collects data and reports on asset performance, run hours, fuel consumption, maintenance needs and other statistics. Timely information allows
“We see positive opportunities and growth in this segment”
Jan Moravec
customers to control costs better, improve performance and reduce risks.
Cat Connect technology can be used on generator sets and machines built by Caterpillar as well as equipment that is connected to the generator set, such as external fuel tanks for extended running, transformers or temperature control equipment.
Rental customers have access to remotemonitoring information that ensures generator sets are being utilised correctly and are ready to run when needed. Telematics can send real-time information on fuel level, DEF/ (Ad-Blue) level, battery voltage and status (Run/Stop/Auto). This information can be actioned quickly, before the generator set is called to start, ensuring no issues occur when power is needed. Connected assets are said to ensure peak operation of any emission tier of a generator set but are deemed especially valuable with EU Stage V product.
Speaking to Aggregates Business magazines, Jan Moravec, director of Product Management & Engineering for Doosan Portable Power EMEA (Europe, Middle East, Africa), spoke of where he saw growth opportunities in the global portable power market for quarrying customers. “Despite the existing, and we hope short-term, [COVID19] slowdown of the global economy, and shocks to the oil market, our customers in this segment still have to satisfy continuously increasing demand to support construction projects and higher consumption of minerals needed for new technologies such as battery power. So, we see positive opportunities and growth in this segment as the power provided by our products is required to produce these
Caterpillar engineers at work
materials. Though our machines are rather more ‘back-stage’ units than ‘frontliners’ - compressed air and generator power are still key. And the trend of several quarry and mining equipment OEMs (original equipment manufacturers) to move towards electrification for quarry and mining sites will further increase the demand for reliable sources of electric power.”
Commenting on Doosan Portable Power business priorities for 2020 and the first half of 2021, Moravec said: “We have two main strategic streams – the first is the Stage V transition for the EU market. We
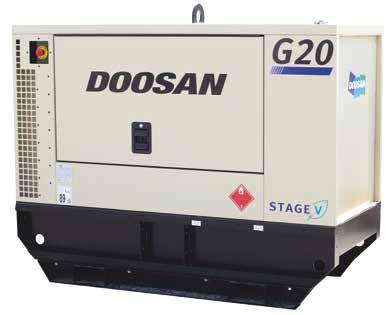
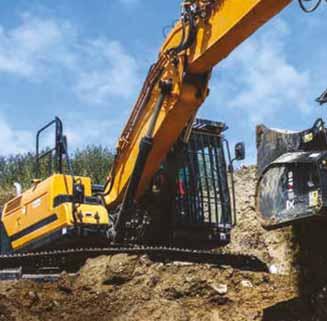




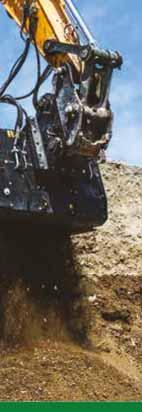
VSE SCREENING BUCKETS
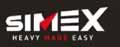

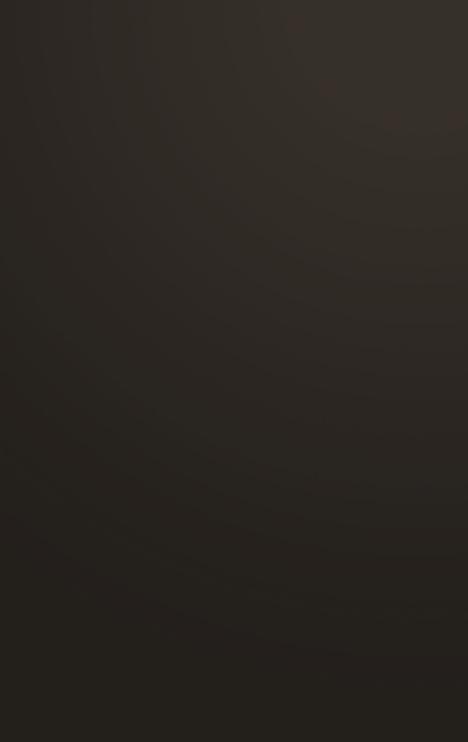
are using this as an opportunity to offer a completely new range of products with proven reliability and durability to serve any tough applications, with a focus on easy operation, serviceability and environmental protection. The second priority is to continuously increase our strong position in emerging markets, utilising the strength of our brand and the global organisation capability we have.”
“All our new products have sealed bunded frames to protect the environment from fluid leaks together with centralised, easily accessible fluid drains which together with easily accessible filters significantly reduce maintenance time and make it an easier task.
“Another of our features is ECOmizer, an automatic intelligent system, reducing fuel consumption by up to 70% during non-productive periods in applications.”
Moravec highlighted how in 2019 Doosan Portable Power introduced several new Stage V products including the company’s smallest 7/20 compressor, new medium- and large-size compressor platforms, the G20 generator and the LS9V lighting tower. He continued: “In the near future we plan to complete our Stage V compressor range, the first being the new 7/125-10/115 medium-size compressor platform which will be followed by a completely redesigned small compressor range. We are also working on new Stage V generators and new products for emerging markets.”
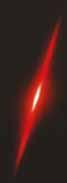
Asked by Aggregates Business how he saw the provision of portable power/ power generation solutions for quarrying customers evolving over the next five to 10 years, Moravec replied: “The business will grow as the development of infrastructure and new technology grows. The power sources need to complete work will still be required, especially the availability of electrical power when it is needed.
“As emissions will continue to be a very important topic, I believe there will be continued alignment between emission regulations in the different markets we deal with. This will drive more new technologies and new product development as the markets continue to grow, with the focus on lower emissions, new energy sources and digitalisation.” AB
Watch the video
simex.it
Doosan Portable Power G20 EU Stage V generator
Wearing well
Being able to quickly access and install high-performing replacement wear parts on quarrying plant minimises downtime leading to enhanced worksite efficiency.
Guy Woodford reports on some of the latest premium wear part options
Aproducer of high-quality crushers since 1896, Swedish quarrying plant manufacturer Sandvik says it has always taken great pride in its innovation and developing products which will improve its customers’ bottom line.
The company’s crushing chambers are based on quality products said to be built with superior finish and supported by in-depth knowledge of every aspect of the crushing process. “It is through this knowledge and expertise that we are able to understand the demands of our customers and develop high-performance wear parts, to ensure the reliable and smooth operation of Sandvik equipment throughout its entire lifecycle,” says Andrew Bolton, product line manager Tracked Mobiles, Sandvik Mobile Crushers and Screens.
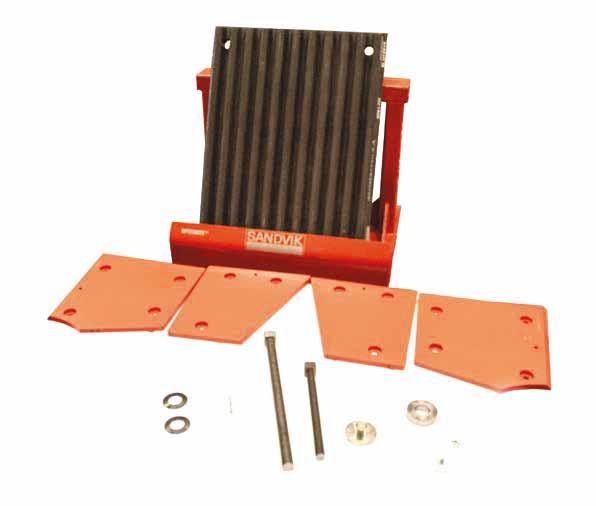
for Sandvik mobile jaw crushers. These have been designed to simplify customer service and increase maintenance efficiency. The tailor-made Optitooth kits are designed around the natural usage of the wear parts and offer all components a customer needs with just a single part number.
Following the successful launch of Sandvik Optitooth jaw plates, Sandvik Mobile Crushers and Screens has now created a number of ready-to-order maintenance kits
Key customer benefits are said to include easier and faster means of ordering replacement parts in one simple transaction; greater parts availability – so customers avoid delays or parts shortages with the delivery of all components in one shipment; less downtime - with wear parts replaced in just one service interval; and improved profitability - as enhanced maintenance
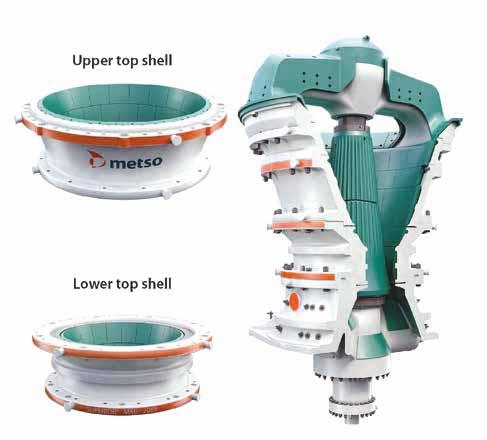
efficiency will, ultimately, boost customers’ bottom lines.
Sandvik Optitooth kits come in three different offerings. Optitooth Fixed Kit includes a fixed Optitooth jaw plate and lower cheek plates. Optitooth Swing Kit features a swing Optitooth jaw plate and lower cheek plates. And Optitooth Kit comprises one fixed and one swing Optitooth jaw plate along with upper and lower cheek plates.
All the necessary components are supplied with the kit to keep a customer’s crushing chamber operating at optimal performance.
“The new profile of jaw plate was designed for a higher percentage of the jaw to be utilised resulting in longer wear life and less manganese waste,” says Bolton. “The backing plate was redesigned to make it easier for removal, thereby reducing maintenance time and ultimately downtime, saving time as well as money.
“The improved profile also brings with it a number of additional benefits which all contribute to improved product shape. The unique profile was designed around the production of a more cubical material and reduction of elongated slab material which can cause blocking issues for secondary cone crushers.”
Sandvik says customer feedback on the Optitooth kits has been extremely positive. Average jaw crusher output is said to have increased from 200 to 250 tonnes per hour and wear rates increased upwards of 30% (the test results should not be treated as specifications and Sandvik does not guarantee, warrant or represent the outcome of test results in any or all circumstances).
LEFT: Metso’s Rotable Top Shells for Superior gyratory crushers are complete shell segments relined in advance (either on- or off-site) and ready to be installed
Sandvik Optitooth kits come in three different offerings
In addition to the increased wear performance, customers are also said to have seen benefits in relation to fuel economy — the improved transfer of material results in lower engine loading with faster material passage through the crushing chamber. Sandvik says results have proven savings of up to 15% less fuel (see above Sandvik comment on test results).
The improved design of the Optitooth jaw plate is said to allow for better breakage and improved material flow, resulting in a more cubical and higher quality product shape. The design is also said to make the plates easier to turn over or replace, saving customers time and money.
All of the above, says Sandvik, results in increased jaw crusher efficiency and higher productivity by up to 20% (see above Sandvik comment on test results).
Scottish quarrying customer G.F. Job is among those benefiting from the use of Sandvik Optitooth jaw plates. “They benefit us all round: we are crushing far more, getting better fuel economy, producing a better product and they last an awful lot longer,” says Graeme Watt, the company’s operations manager.
The Optitooth jaw plate has proved suitable for a wide range of applications, particularly abrasive quarry rock. It is fitted to all Sandvik Q-Range mobile jaw crushers as standard.
Sandvik always recommends using genuine spares and wear parts to ensure reliability and optimal performance of customers’ mobile equipment.
Metso’s Rotable Top Shell for all sizes of the company’s Superior primary gyratory crusher reduces crusher downtime thanks to speedier change-outs while, at the same time, increasing safety.
Most Rotable Top Shell-related work is completed out of the line of fire. There is a large reduction in risk as more tasks are done in a controlled environment, and the actual relining process can even take place off-site. During the time-sensitive changeout period, there are fewer parts to lift and manipulate. The solution includes hydraulic shell separators which also help to minimise human intervention.
By using the Rotable Top Shell’s additional shell segment(s), which are already inspected and lined prior to a shutdown, Metso claims a customer can save up to 45% in downtime for their primary gyratory crusher. This is exceptionally relevant to larger aggregates plant which are operating close to 24/7. However, this is also beneficial for plant which are not operating around the clock. As with this shorter window needed for shutdowns, most aggregates producers can fit the change-out in fewer shifts. Downtime can also be more easily scheduled either off-shift or during the off-season.
In addition to shorter shutdown, less manpower is needed for the complete Rotable Top Shell change-out process. This is said to provide added flexibility for operators who now have multiple options
for relining which won’t affect operations. Producers have the choice to do the reline work themselves, on- or off-site, or with a 3rd party, again on- or off-site.
With a streamlined process, being mostly implemented outside of the critical shutdown path, costs are more predictable, making it easier to plan and manage budgets. Additionally, some traditional cost elements can be minimised further, such as crane rentals, which are typically rented/brought in specifically for relines.
The Metso Rotable Top Shell is a new concept/solution which has been introduced slowly over the last few years as a “complete” customer solution. Four mine sites are currently operating with it now, and a handful is said to be in the final consideration steps.
“This has not yet been formally introduced to the aggregates industry; however, the benefits and process are nearly identical to mining” Terry Galvin
BELOW: A Metso Rotable Top Shell in action – ready to be installed during a planned shutdown at a Boral Australia gold and copper mine.
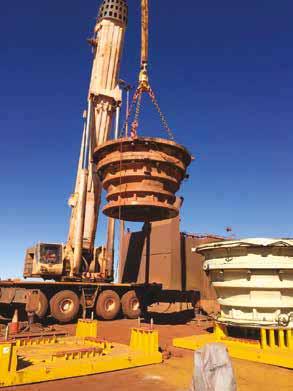
“This has not yet been formally introduced to the aggregates industry; however, the benefits and process are nearly identical to mining. With hundreds of Superior primary gyratory crushers currently in operation in aggregates industries around the world, this solution has great potential,” says Terry Galvin, Metso business development manager.
The Rotable Top Shell offers the most benefits to producers with a high wear rate on their primary gyratory crusher, where change-outs are happening regularly, i.e., hard and abrasive material, such as granite. Producers who operate a site close to an around-the-clock operation, have a lean maintenance staff, and have an older machine that they are currently considering for shell repairs will also, says Galvin, benefit greatly from using the Rotable Top Shell.
Additionally, given the smaller sized primary gyratory crushers present in the aggregates industry, the Rotable Top Shell can be a very affordable solution for sustaining capital.
“While there may be some suppliers offering additional shell segments in certain markets – as of today, we are the only OEM [original equipment manufacturer] with a complete solution for this – that we know of. We can offer end-to-end solutions (liners, installation, inspection programs, financing, online monitoring, etc.) – technical and commercial to fit individual producer’s operating budget,” Galvin added.
“We are currently evaluating and developing multiple complementary solutions. This includes applying our technology to other OEM primary gyratories, as part of our Metso Contender Series. This series of premium parts and solutions is specifically designed for non-Metso equipment in order to simplify the buying process for our customers.
“We are looking at supplying complementary products to make primary gyratory crusher shutdowns even safer and more efficient. This includes products such as fastening techniques, rigging techniques, and auxiliary components. We are also considering formalising similar concepts for our other crushing products, such as GP cone crushers.”
Inspired by key pain points Weir Minerals’ field staff observed across a range of mines and quarries, the company’s expert engineers have developed Linard modular anti-abrasion panels. The panels are said to provide a cost-effective and convenient solution for reducing downtime caused by high impact and abrasive wear in chutes and other applications in quarries and mines.
Available in 30mm and 50mm thickness, Linard modular anti-abrasion panels are ideally suited to minimising wear and maintenance in localised impact and wear points. The outstanding wear life is due to the wear material: Linard HD60 rubber in a rigid self-sealing construction with steel backing. The optional composite ceramic (92% alumina) or high-chromium white iron
inserts add to the claimed extraordinary wear life of the panels.
“Our new Linard panels have been designed from the ground up to last in some of the most arduous wear applications. Depending on the customer’s needs, we offer composite panels with either ceramic or high chromium white iron inserts. They combine with our Linard HD60 rubber compound to deliver world-class impact and abrasion resistance in chutes, hoppers and under-pans,” says Mark Doyle, global product manager – Rubber, Spool and Hose for Weir Minerals.
Linard modular anti-abrasion panels are said by Weir Minerals to have improved wear life by ten times after replacing a competitor’s teflon wear panels in chutes across two quarries run by Boral Australia. This is said to have saved more than AU$12,000 per annum (US$7,950) in direct costs and led to a significant uptime increase due to a 90% reduction in shutdowns.
The 300mm² panels interlock to facilitate quick and easy installation and replacement while reducing the potential for fine material to ingress between the panels. Linard modular anti-abrasion panels are supplied in a convenient kit including a range of holddown plugs. They can supply drawn arc studs which were needed to provide a convenient off-the-shelf but customisable solution to the application.
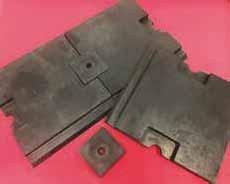
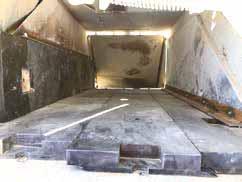
“Our engineers can replace these panels in minutes, reducing the amount of time they need to spend in chutes and other confined spaces. They are a bolt-in/bolt out solution and being modular they’re easy to fit onto any flat surface that requires extra protection. This also makes it easy to swap around composite and standard panels to ensure the highest wear areas are the best protected,” says Paul Duthy, Wear Solutions product manager, Weir Minerals.
Haver & Boecker Niagara is guaranteeing customers’ inventory through Make & Hold and Stocking Agreement programmes for screen media and wear parts. The programmes help mineral processing
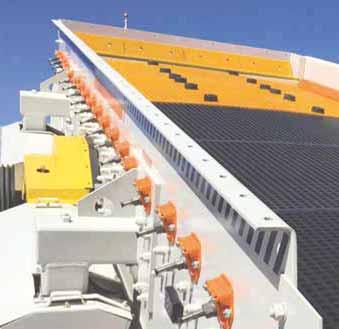
customers plan ahead and minimise downtime from long lead times while also providing options for pricing stability and simplified inventory management.
“We want to help ensure our customers have the screen media and parts they need to keep their equipment running and maximise production,” said Karen Thompson, president of Haver & Boecker Niagara’s North American and Australian operations. “That is why we provide Make & Hold and Stocking Agreements to help operations with inventory management and provide peace of mind.”
The Make & Hold programme guarantees customers the screen media and/or wear parts they require, and pricing is agreed upon at the beginning of the programme. Items are reviewed annually, and adjustments are made as needed. The manufacturer produces and packages the product in pre-determined quantities so it can be shipped the same day the order is placed. Stock is automatically replenished after shipment in preparation for the next time the customer requires it. The programme gives customers immediate access to items that would normally require longer lead times. Pricing is locked in, and the customer is only invoiced when the product ships.
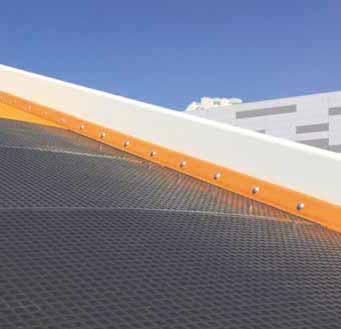
Haver & Boecker Niagara also offers Stocking Agreements — or blanket orders — for customers interested in a one-time annual agreement. The pricing is locked in for the calendar year upon agreement for a pre-determined quantity of product. Customers pay per shipment as they draw from their stock as needed throughout the year. The product is shipped the same day the order is placed.
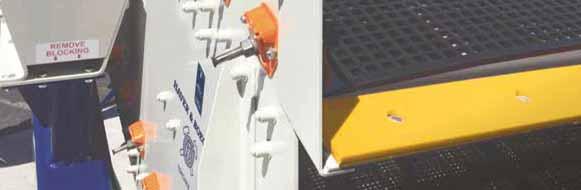
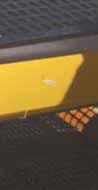
Both programmes are said to be an opportunity for operations to ensure product availability and price stability throughout the year and are particularly beneficial for products that may otherwise have extended lead times. AB
LEFT: Weir Minerals’ Linard modular anti-abrasion panels RIGHT: Boral Australia is among mining and quarrying companies currently using Weir Minerals’ Linard modular anti-abrasion panels
Haver & Boecker Niagara says it guarantees customers’ inventory through Make & Hold and Stocking Agreement programmes for screen media and wear parts

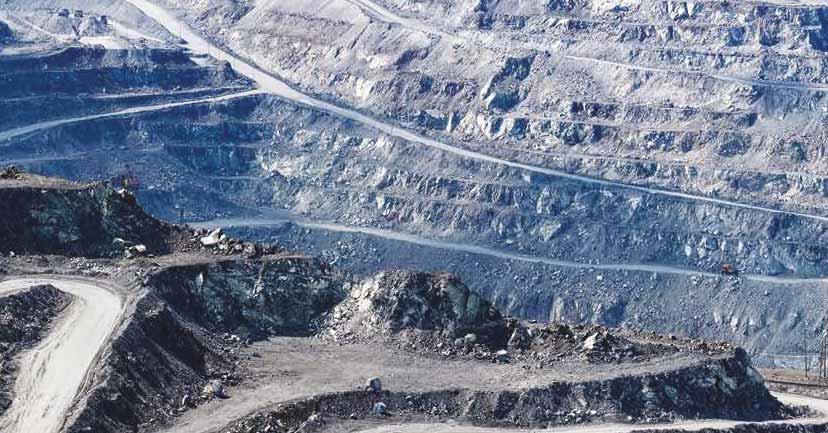
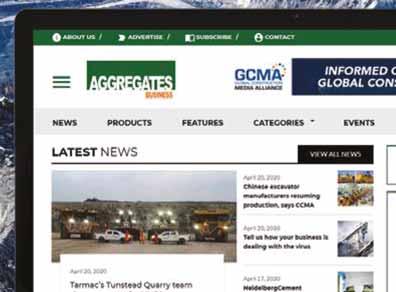

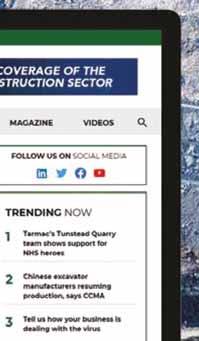
New Terex MPS jaw crusher for large quarries
Terex MPS (Minerals Processing Systems) has introduced the new MJ55 Modular Jaw Crusher, designed for large quarries or contractors that want a stationary-type design without the complexity of a standard stick-built plant.
The module is based on the existing Terex MPS JW55 jaw crusher. It combines the JW55 jaw crusher, sloped hopper, 52x20 feeder, and straight-line conveyor on a galvanised/painted steel structure. The standard structure can be transported in standard shipping containers plus a flat rack for the crusher and can be bolted together quickly onsite with basic tools. The three configurations offered for the feed hopper are said to allow for the optimum size to match up to the equipment that is being used to load the machine.
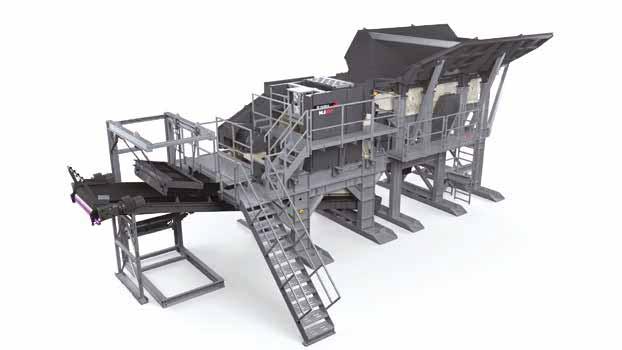
The structure includes oversize walkways, repositionable stairs and guard rails for safe access. Three plant emergency stops are placed conveniently around the platform for easy access during operation. Optional mounting feet allow for the basic unit to be installed on a compacted gravel base.
MB Crusher keeps coal costs down
In Indonesia, where more than 55% of electric power is generated from coal, MB Crusher’s MB-HDS323 shaft screener is said to be working to reduce all unnecessary coal quarry production costs, even during bad seasonal weather periods.
The unit’s operation is described as extremely smooth and simple: the padding bucket scoops up the damp coal, the rotating shafts reduce it down to smaller sizes while loading it to the truck—all in one step. The coal is then towed to the power plants, ready to be used.
Only one machine is used to load the truck and reduce the coal to a usable size; one excavator operator is needed, reducing labour costs. Middle loading and material moving and storing are eliminated with fewer phases meaning fewer costs. The entire operation is faster and safer, giving a boost to productivity.
The MB Crusher padding bucket is a hydraulic attachment for excavators, wheeled loaders or skid steers, transforming
The MJ55 comes with hydraulic CCS jaw adjustment controls. Additional options include a cross plant magnet, switchgear panel and off-plant conveyor starter kit. www.terex.com/mps
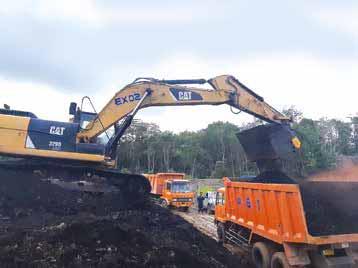
the machine it is mounted on in a high-performance mobile crusher or screener.
In one Indonesian quarry, the MB-HDS323 was working with damp coal, but the machine is designed to avoid blockage, even if the product is damp and sticky. The unit mouth opening is extensive, its work speed is said to enable the material to flow easily and the operator to reach high results, for a fraction of the operational costs.
By investing in an MB Crusher padding bucket, the Indonesian quarry is said to have been able to increase productivity, while reducing the overall coal price as they used the excavator they had at the quarry already.
With a loading capacity of 1.65m³, the MB-HDS323 is the widest of the range of MB Crusher shafts screeners, suitable for 18-35-tonne excavators and 10-15-tonne wheeled loaders.
www.mbcrusher.com
Bluetooth-enabled HH60 RFX Wireless Indicator
Intercomp has added Bluetooth technology to its HH60 RFX Wireless Indicator. Live axle weight data is now securely transmitted from the indicator to a user’s Bluetoothenabled iOS mobile device with the Intercomp iVehicleWeigh or iExactWeigh app installed. All indicators manufactured after 1 January 2020 have the chip installed as a standard feature, with current pricing remaining the same. Wireless communication from scale pads to the indicator will continue to utilise our secure, field-proven RFX Wireless Weighing technology. The new Bluetooth chip simply allows data sharing with one Apple mobile device. In this case, a mobile device can quickly become a second scale indicator, when needed. Like RFX communication, only those with the proper digital credentials can access weight data from an iPad or iPhone. During the connection process, radio and encryption settings are required to access the data stream. This ensures that only approved users can view axle weight information.
Part numbers used to identify and order the HH60 will not change following the Bluetooth addition. The ability to fully control up to six RFX scales within a 300-foot line-of-sight radius, peak hold function, and the ability to store and print weight records are some of the functions that will continue to be available with this indicator.
www.intercompcompany.com
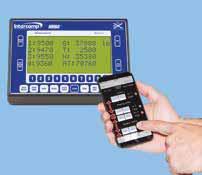
Terex MPS’ new MJ55 Modular Jaw Crusher
Weir Minerals’ Sand Wash Plant
The new Weir Minerals Sand Wash Plant is said to be a complete sand washing solution drawing on Weir Minerals’ long experience in the sand and aggregates industry.
The Linatex-lined plant produces more saleable product than conventional sand screw plants, with fewer moving parts and an optimised process that produces a drier, higher quality product with fewer fines.
their sales. This is why we’ve designed an integrated solution for washing their product, with a hydrocyclone which can deliver greater recovery than sand screws. In addition, every component has been selected by our expert engineers for its long service life, interoperability
and ease of maintenance.” says Bruce Cooke, Weir Minerals global product manager - Sand Wash Plants.
delivering more saleable product than a sand screw solution would.
Enduron dewatering screens reliably separate product with a high degree of efficiency, while robust Isogate knife gate valves contribute to the plant’s straightforward maintenance.
The solution is already said to have proven effective at sites like Coimbatore Minerals in Tamil Nadu, India. There, a custom-built Weir Minerals Sand Wash Plant reduced site management’s total cost of ownership by a claimed 51%, while also offering a 23% reduction in fines, helping their prod uct meet high industry standards.
“We know the most important thing for quarry operators in washing is recovering as much sand as possible to maximise
ewer parts ised that ier, fewer fines. on is said n effective at sites re ndia. a ant ment’s total ship a while also % reduction in prodnt ry
The compact solution features a range of Weir Minerals equipment designed for high efficiency in sand and aggregate applications, including Warman WGR pumps, Cavex hydrocyclones, Enduron dewatering screens, Linatex hoses and Isogate knife gate valves.
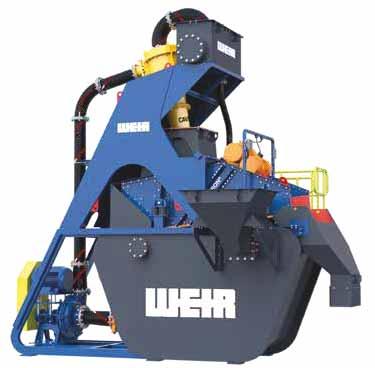
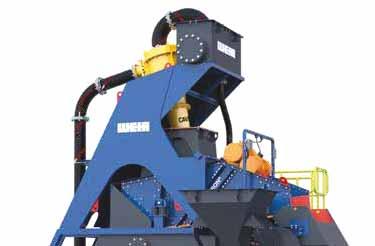
The Warman WGR is the pump of choice in the sand extraction industry, combining top-of-the-line hydraulic design with an adjustable impeller, long bearing life and a simplified wet end, making replacement predictable and cost effective. Precision-moulded and lined, Linatex premium rubber is used for wear zones throughout the plant due to its proven wear performance in wet sand applications in operations around the world.
Cavex hydrocyclones provide exceptional classification efficiency thanks to their unique 360° laminar spiral,
WGR pumps, C clones, Enduro screens, Linate g Warma pump of choic extraction indu with an adjust li maki Precis lined, Lin i zones t wea we ti a cy ex sification effi their 3
Direct X from WCCO Belting
WCCO Belting’s patentpending Direct X conveyor belt solution is said to be ideal for the crushing, grinding, sorting, screening, and piling operations in the aggregates and recycling industries.
The Direct X cleat profile is said to increase conveyor capacity by capturing more material across the belt width than standard industry patterns. Combined with the benefits of a specialised belt construction that is said to be thinner yet more durable and flexible in design, the product is, says WCCO Belting, a “high-value solution that reduces cover wear, increases energy savings and improves belt life”.
“As a company dedicated to value innovation, we have been looking for the right opportunity to expand our product offerings to meet the needs of the aggregates and construction industries,” said Jean Voorhees,
“For the new sand wash plant, we focused on making it quick and easy for quarry operators to get up and running. Its straightforward design means it can be assembled in just two days while its compact skids make it easy to drag into any operation. Efficient, reliable and easily integrated into flowsheets, we think the plant is a gamechanger for quarry owners,” says Surendra Menon, president, Weir Minerals India.
Like all Weir Minerals equipment, the sand wash plant is supported by Weir Minerals’ highly competitive global service network that includes more than 150 locations each with spare parts and expert maintenance support.
Weir Minerals sand wash plants are now available for customers in all regions. www.global.weir
vice president of Business Development at WCCO Belting.
“We are proud of the Direct X technology and its ability to redefine field performance and positively impact the bottom line for end users.”
The Direct X cleat profile is designed to improve product flow control directionally. The pocket-style pattern captures conveyed material immediately upon loading, reducing the amount of product movement
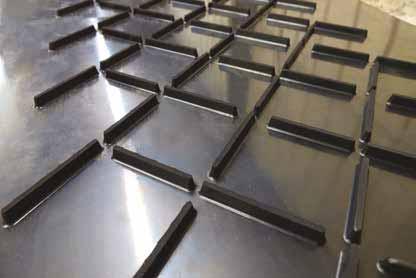
on the belt cover, which limits cover wear. The nested pattern is also said to promote a smooth, quiet transition on the return rollers, reducing noise and vibration in the field. Also, with WCCO Belting’s proprietary manufacturing process, the cleats are integrally moulded onto the base belt, meaning no cleat separation or delamination will occur.
The belt construction technology is made with a custom-engineered fabric that is claimed to be 206% higher in tear strength, 126% higher in tensile strength, with 64% better puncture resistance compared to the industry standard. It drives energy savings using a lighter, stronger, and more flexible belt carcass. Moreover, excess cover wear is reduced when used with the Direct X product flow control pattern. www.wccobelt.com
2020
SEPTEMBER
8-11 bauma CTT Russia
Moscow, Russia
Organiser: Messe Muenchen Rus
Tel: +49 (0)89 949 20251 info@bauma-ctt.ru https://bauma-ctt.ru/
16-18 Construction Indonesia
Jakarta, Indonesia
Organiser: PT. Pamerindo Indonesia
Tel: +49 3999905 0 contact@merebo.com https://ci.merebo.com/
16-18 Concrete Show South East Asia
Jakarta, Indonesia
Organiser: PT. Pamerindo Indonesia
Tel: +49 3999905 0 contact@merebo.com https://cssea.merebo.com/
OCTOBER
21-25 SaMoTer 2020
Verona, Italy
Organiser: Veronafiere S.p.A.
Tel: +39 045 8298561 customercare@samoter.com http://www.samoter.it/
NOVEMBER
03-06 bauma Conexpo
India 2020
Gurugram/ New Delhi, India
Organiser: AEM and Messe München
Tel: +49 89 949 20251 info@bcindia.com https://www.bcindia.com/en/
24-27 bauma China 2020
Shanghai, China
Organiser: Messe München
Tel: +49 89 949 20252 info@bauma-china.com https://www.bauma-china.com/
2021
APRIL
14-17 steinexpo 2021 Homberg/Nieder-Ofleiden, Germany
Organiser: GEOPLAN GMBH
Tel: +49 7229 606 30 info@geoplangmbh.de https://www.steinexpo.eu/
2021
JUNE
22-24 Hillhead Hillhead Quarry, Buxton, Derbyshire, England
Organiser: The QMJ Group Tel: +44 (0)115 945 4377 Email: Harvey.sugden@qmj.co.uk https://www.hillhead.com/
JULY
07-10 EIG 2021
Exeter, UK
Organiser: EIG Conferences marcus.dorey@hanson.biz https://www.eigconferences.com/ future-conference-2020
OCTOBER
13-16 bauma CONEXPO AFRICA 2021
Johannesburg, South Africa
Organiser: AEM and Messe München GmbH
Tel: +49 89 949 21480 johannes.manger@messemuenchen.de https://www.bcafrica.com/
MEET THE TEAM
Aggregates Business travels the globe attending conferences, events and equipment shows, keeping you informed of the latest offerings. Come and join us for a chat at any of the events below.
JUNE 2021
22-24 Hillhead 2020
Hillhead Quarry, Buxton, Derbyshire, England
JULY 2021 07-10 EIG 2021 Exeter, UK
These dates were correct at the time of going to press, but please note that the COVID-19 pandemic means some events may be rescheduled with little advance notice
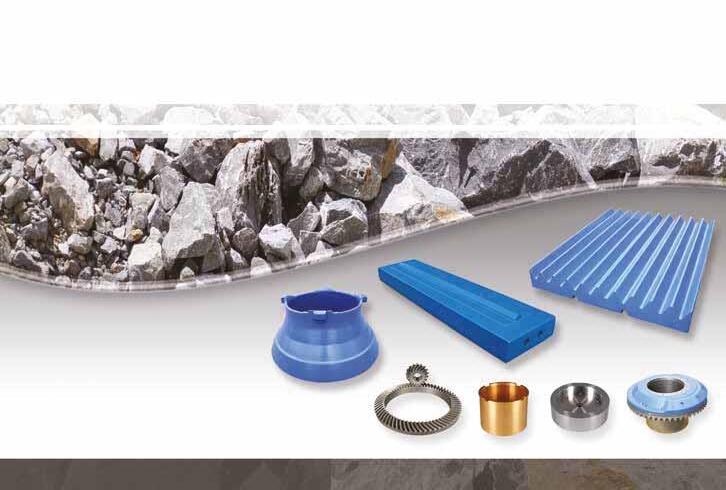


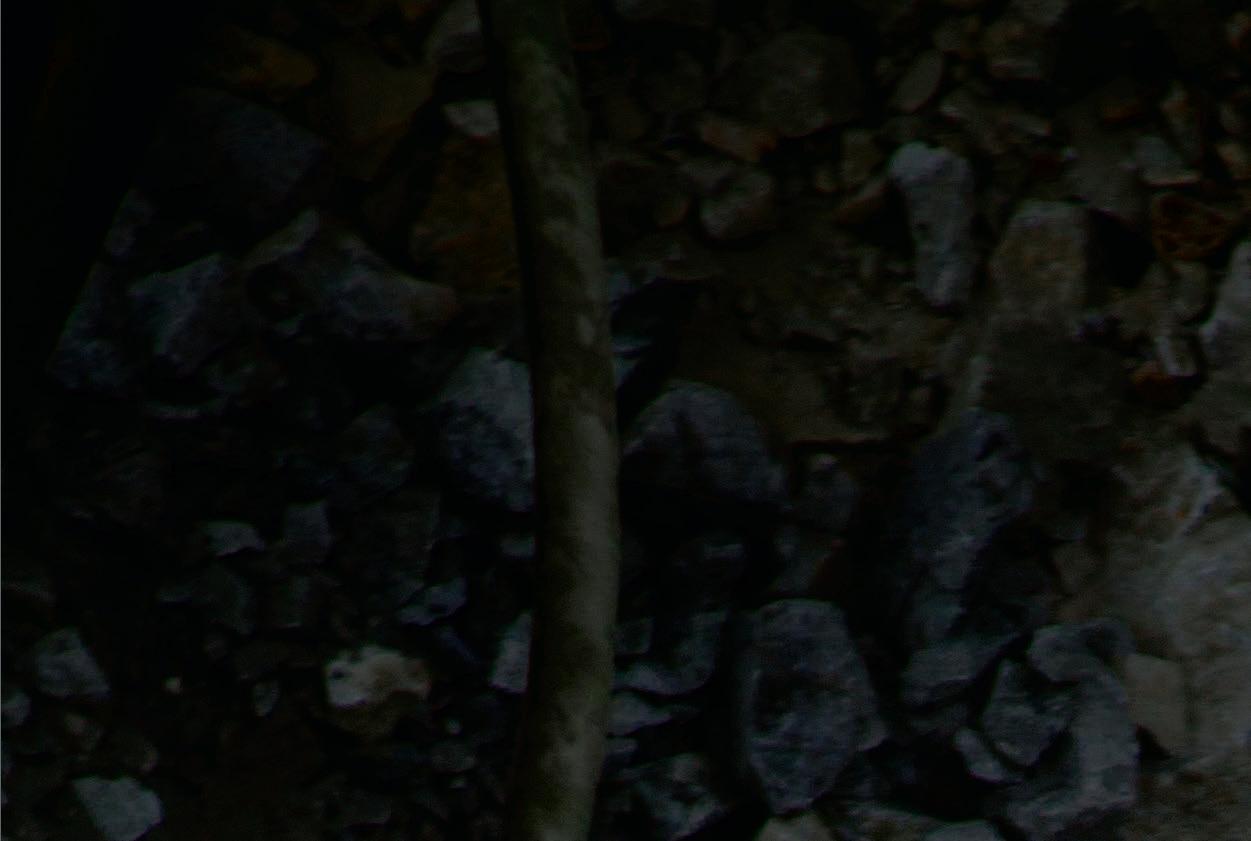
Metso Rotable Top Shell
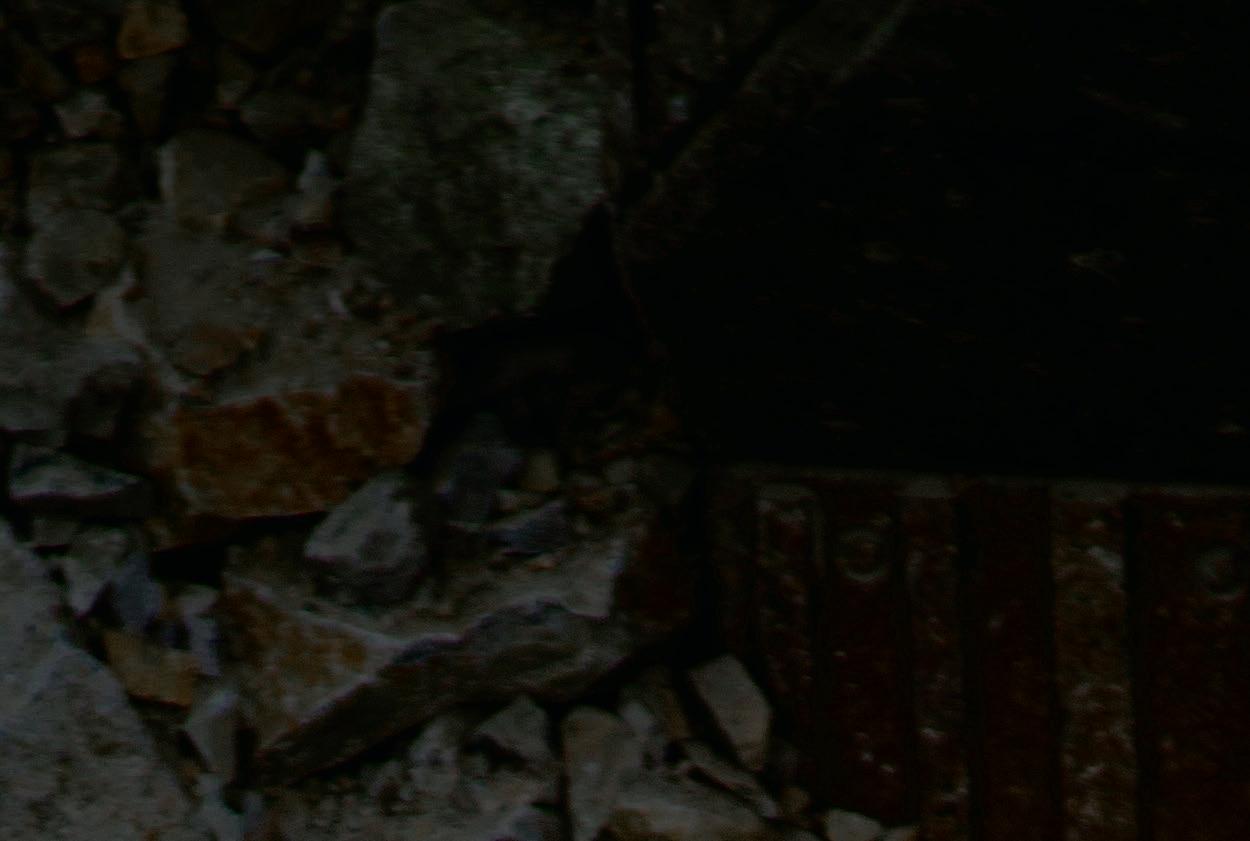
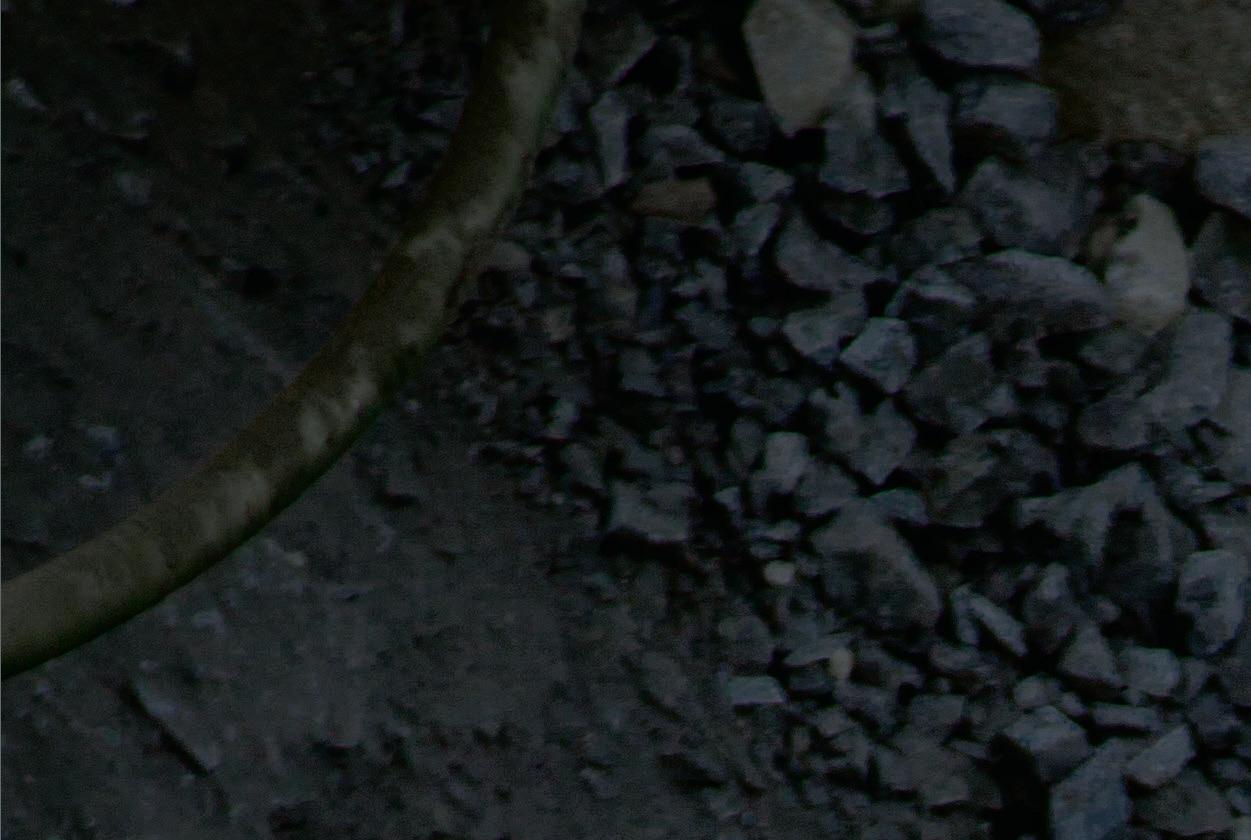
Every minute your primary gyratory is shut down, your bottom line is impacted. Relining a crusher can be a lengthy and complex process, which must be closely managed. Metso Rotable Top Shell enables you to save both time and money - when it matters most.
A simple solution with major impact - using additional shell segment(s), which are already inspected and lined prior to your shutdown, makes for faster, safer, and more economical wear parts replacement.
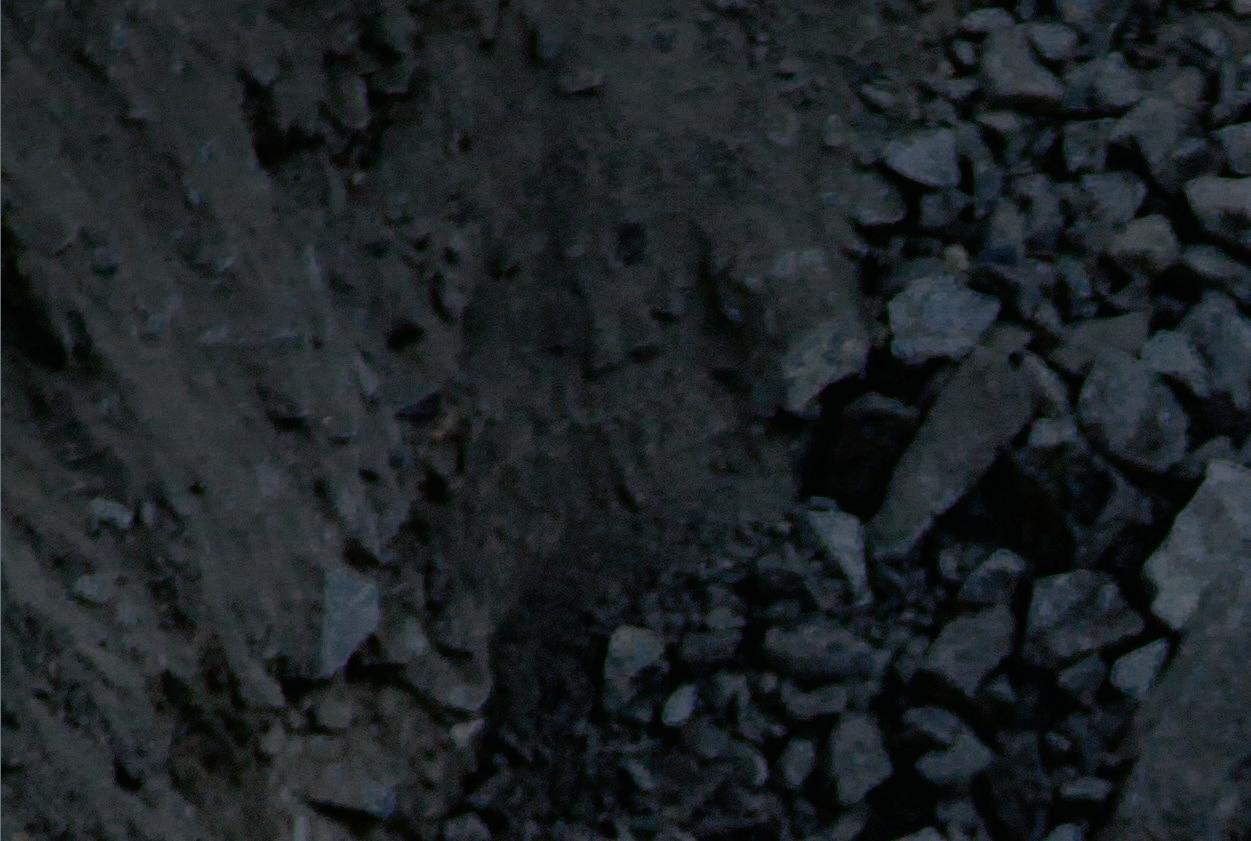
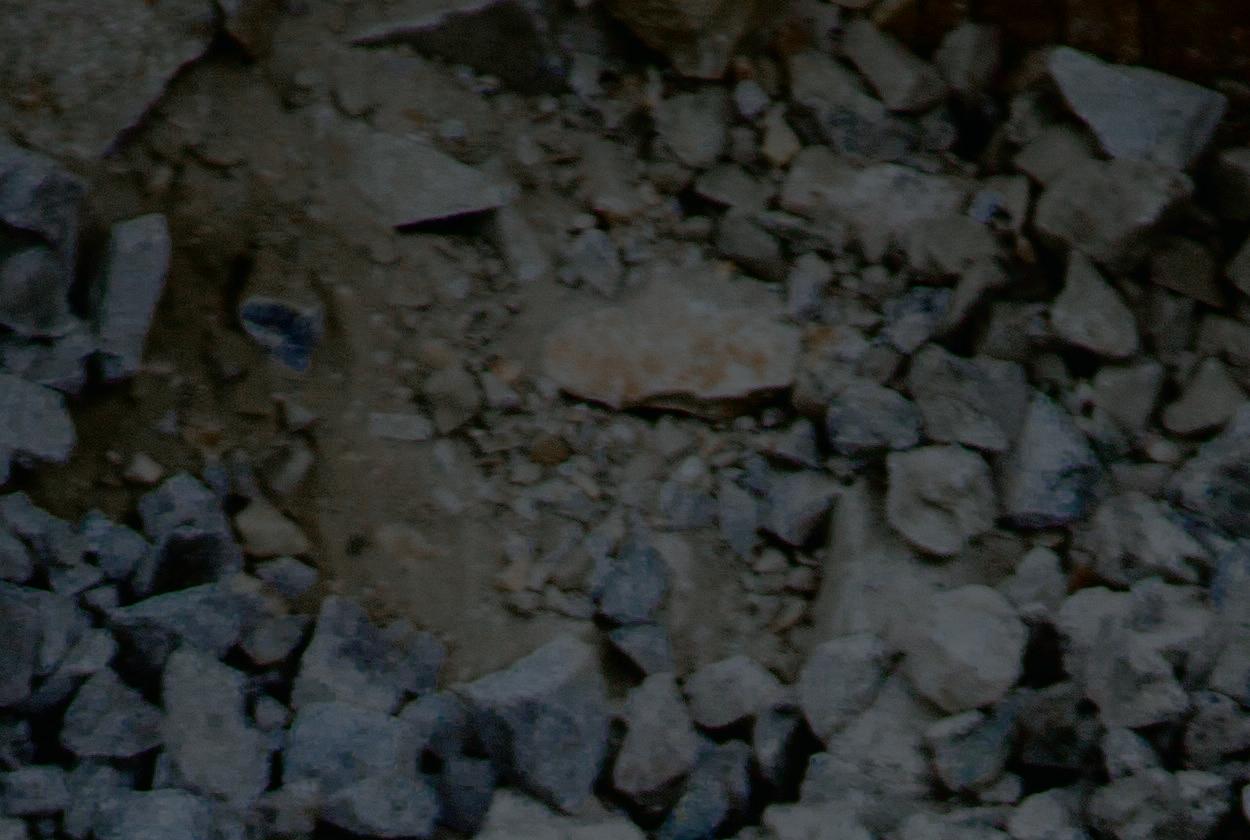
• Reduce downtime by up to 45%
• Minimize high risk maintenance work
• Optimize shutdown tasks
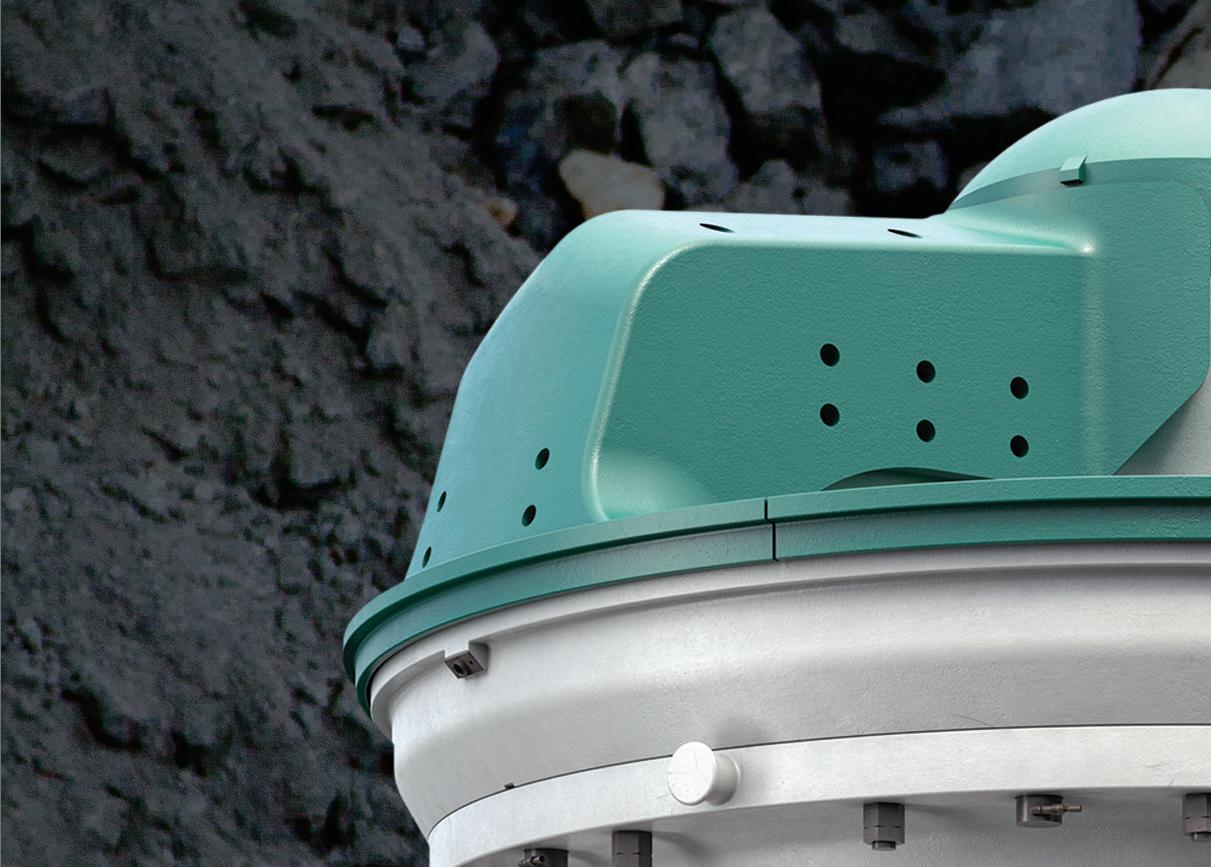
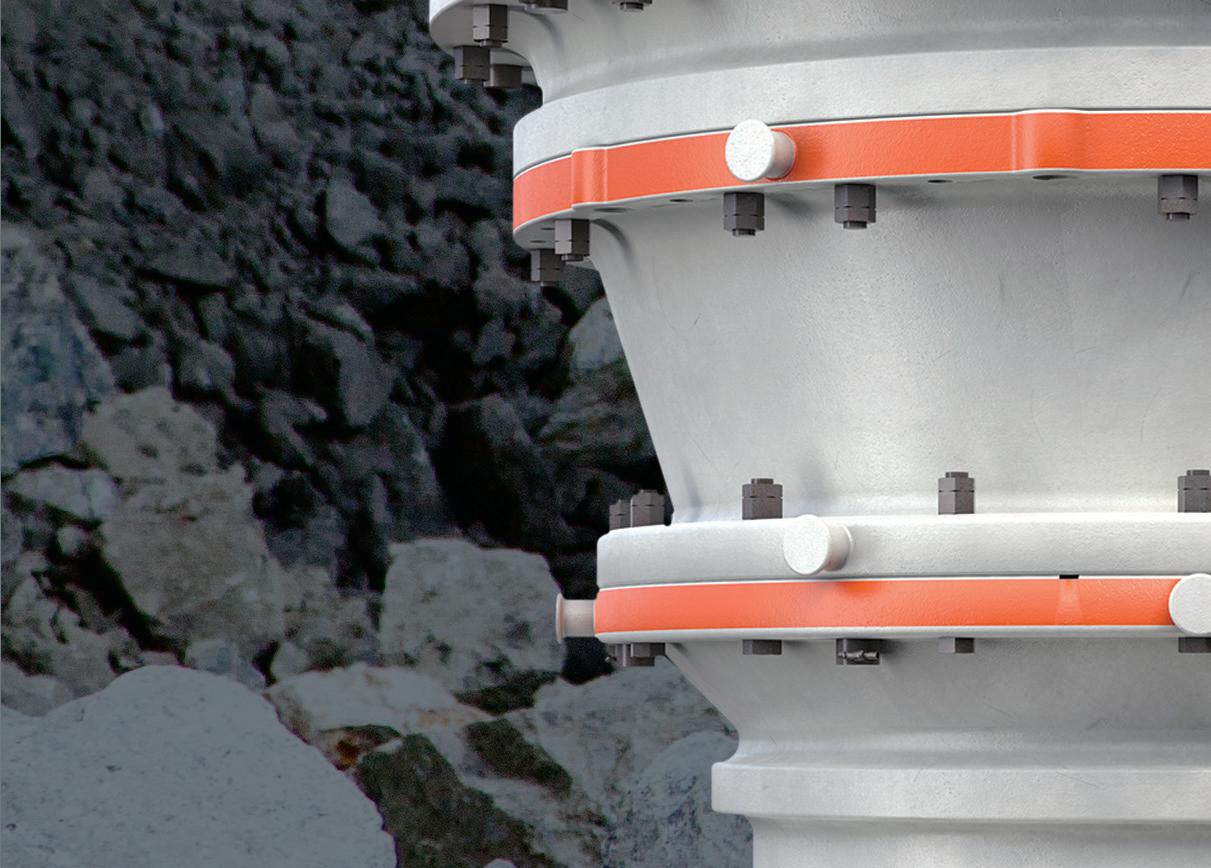
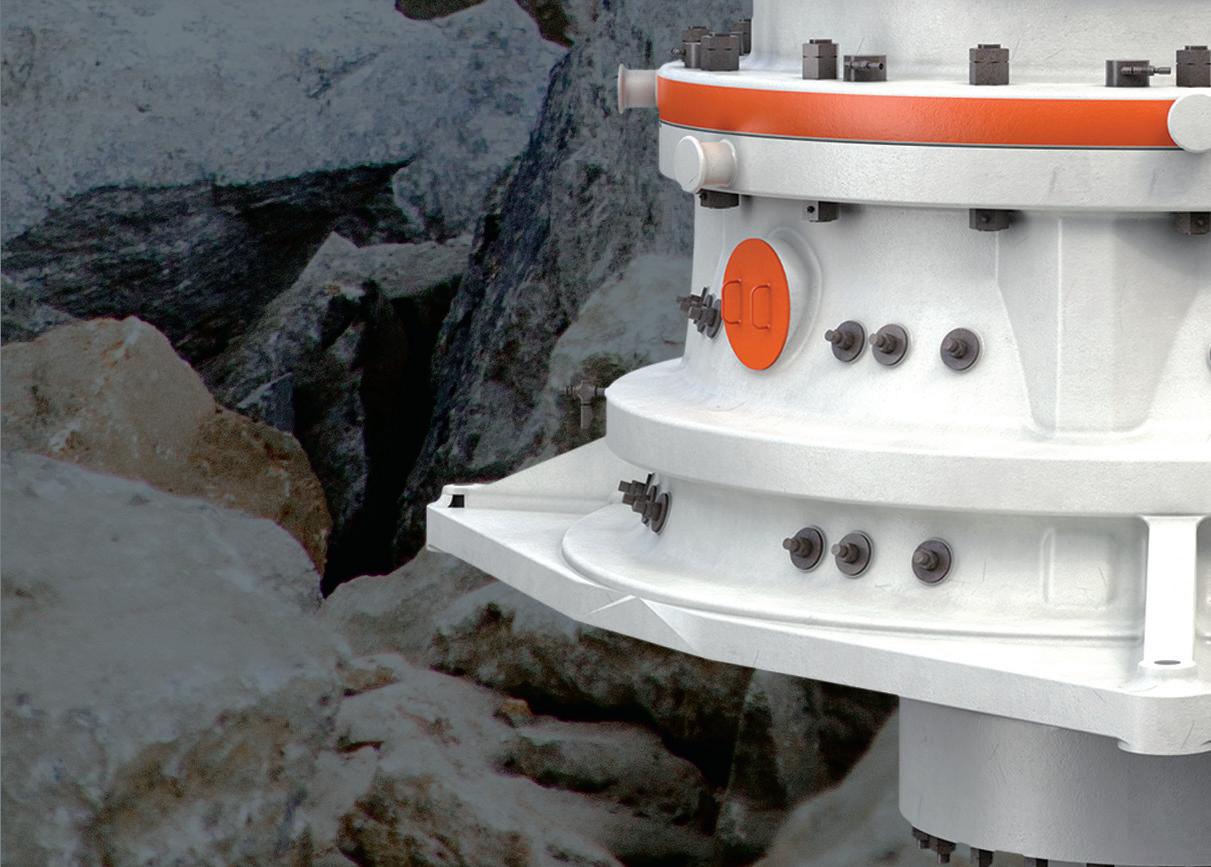
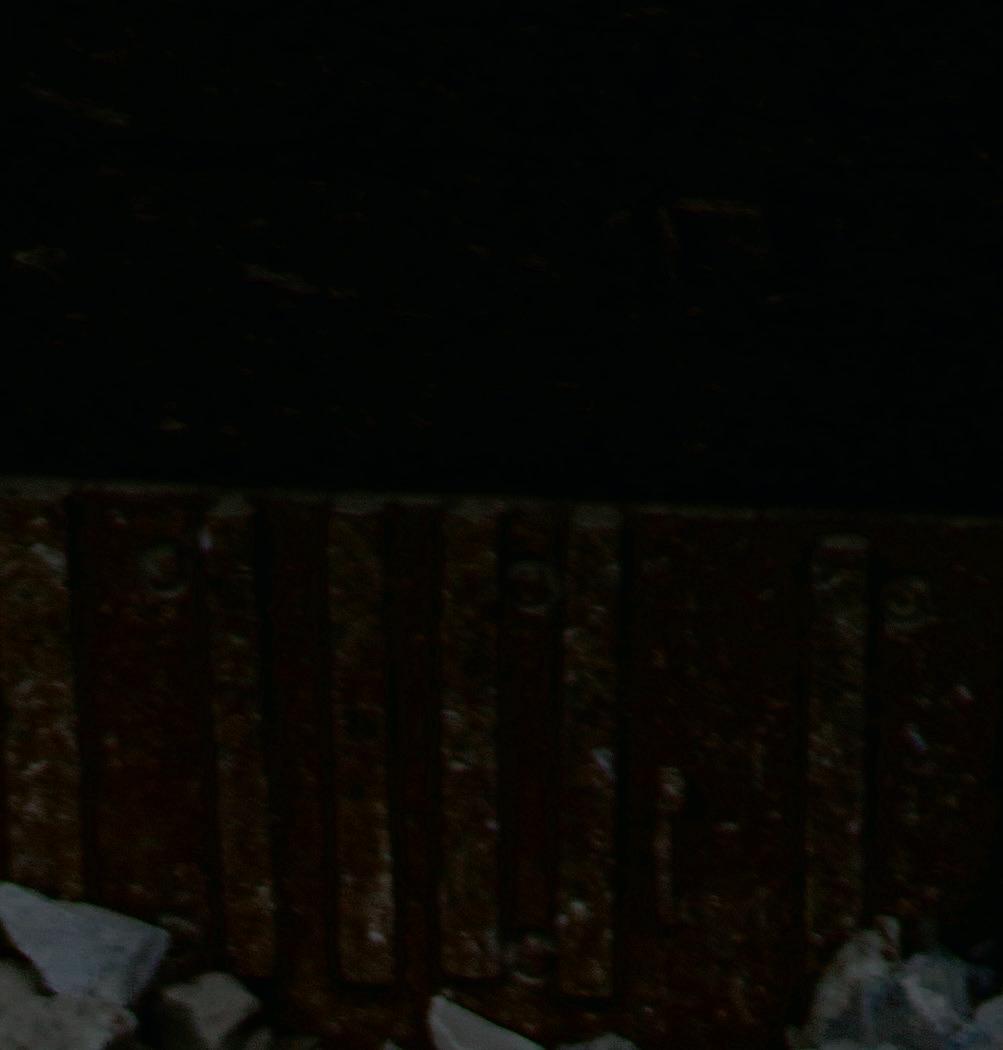
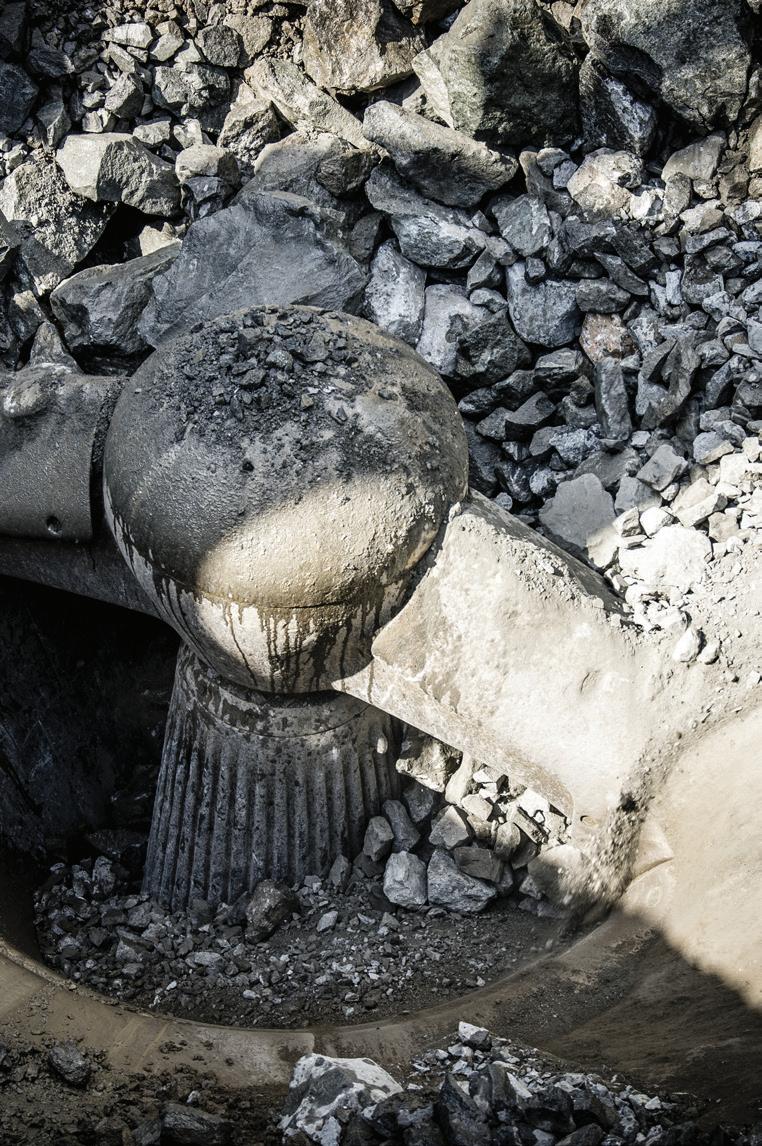
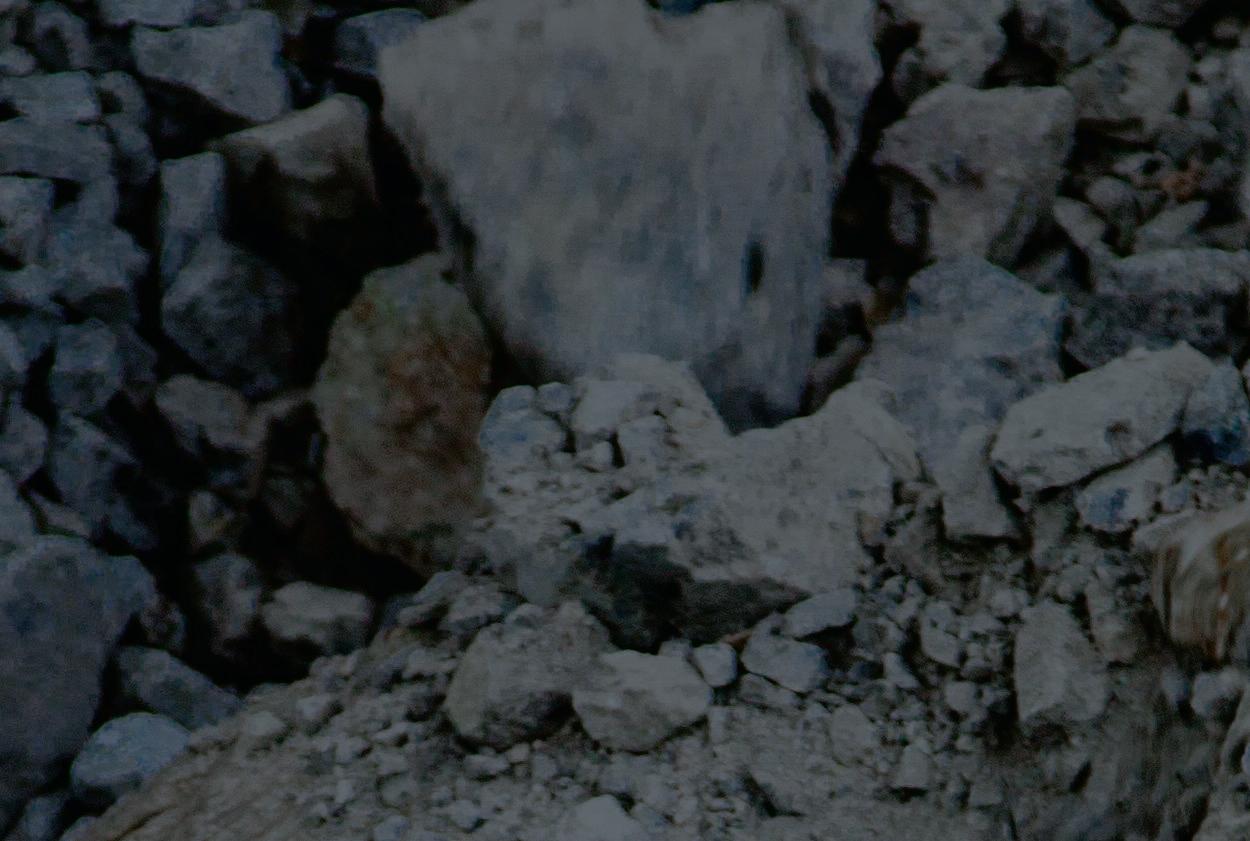
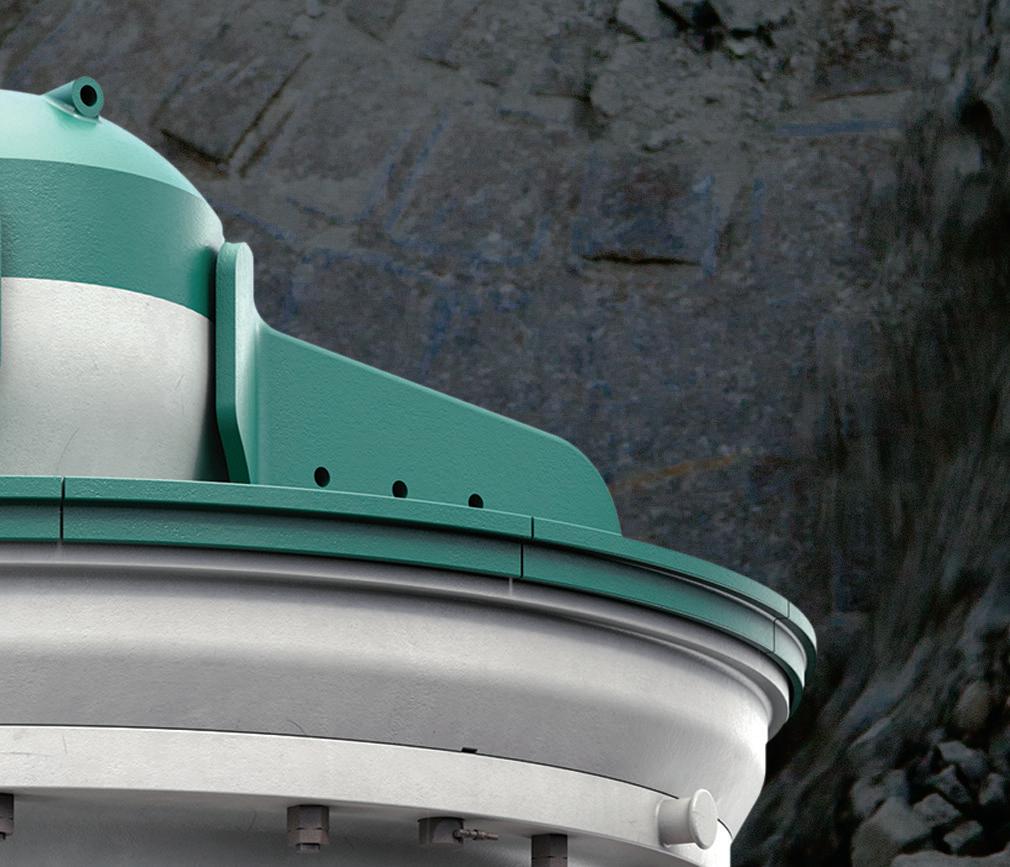
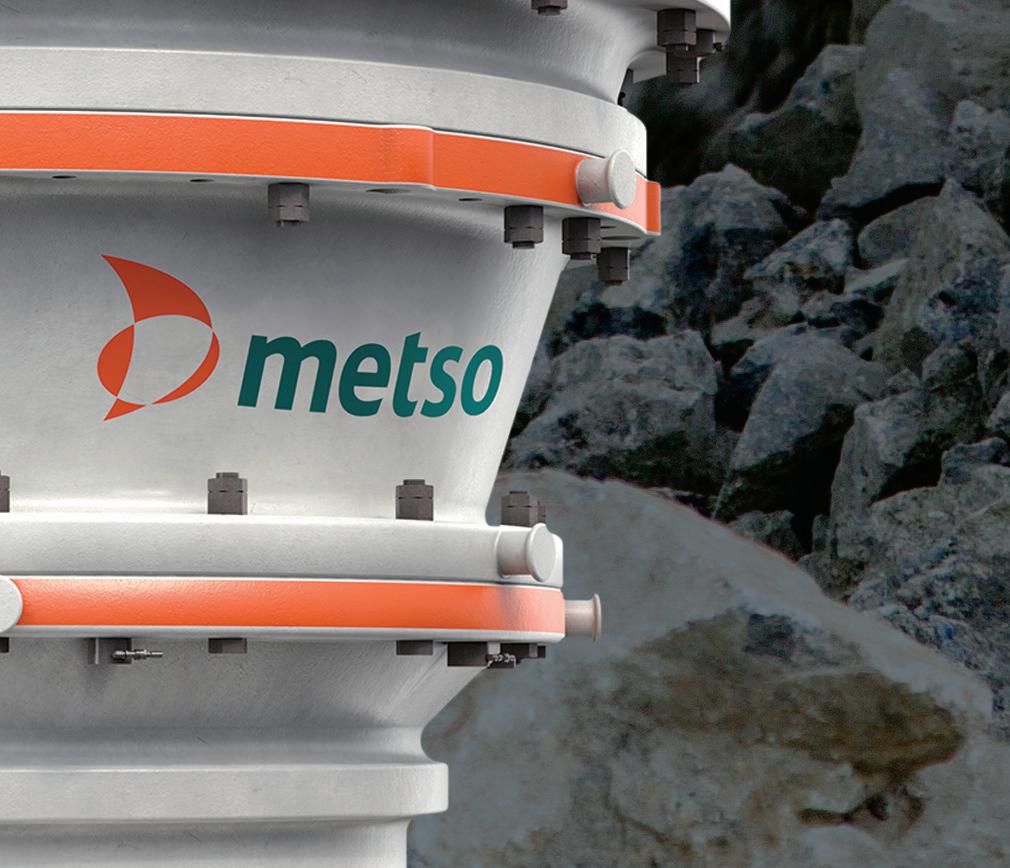
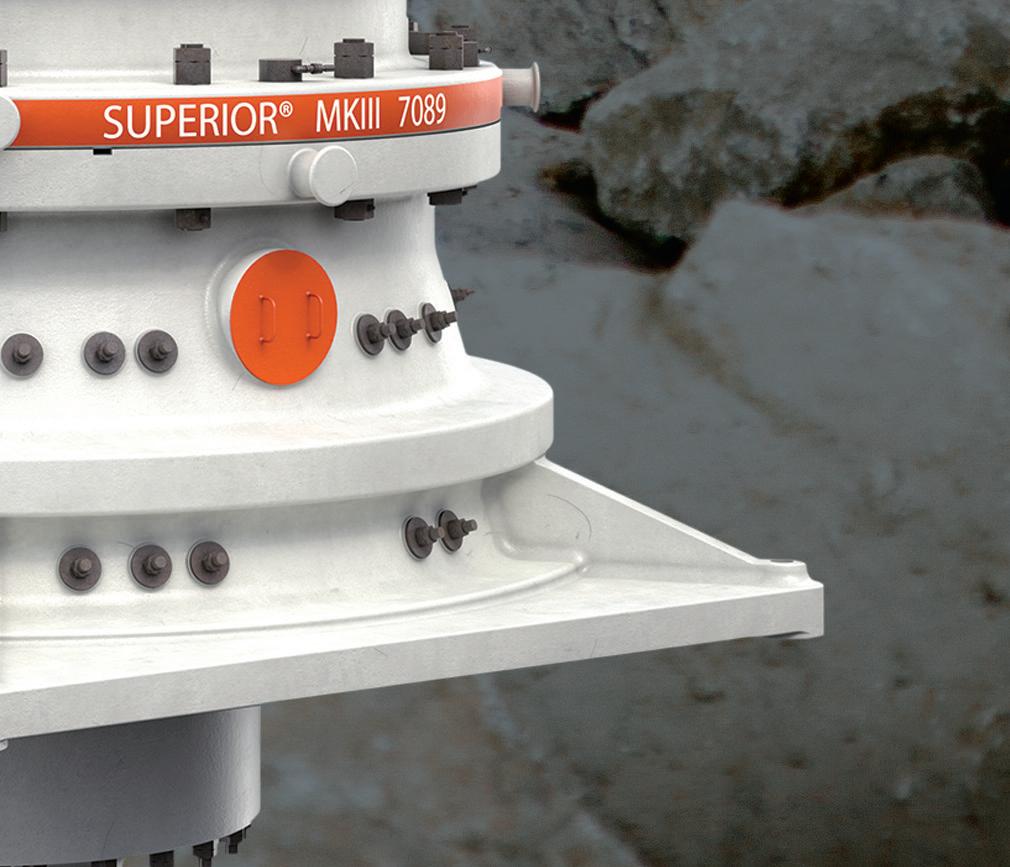

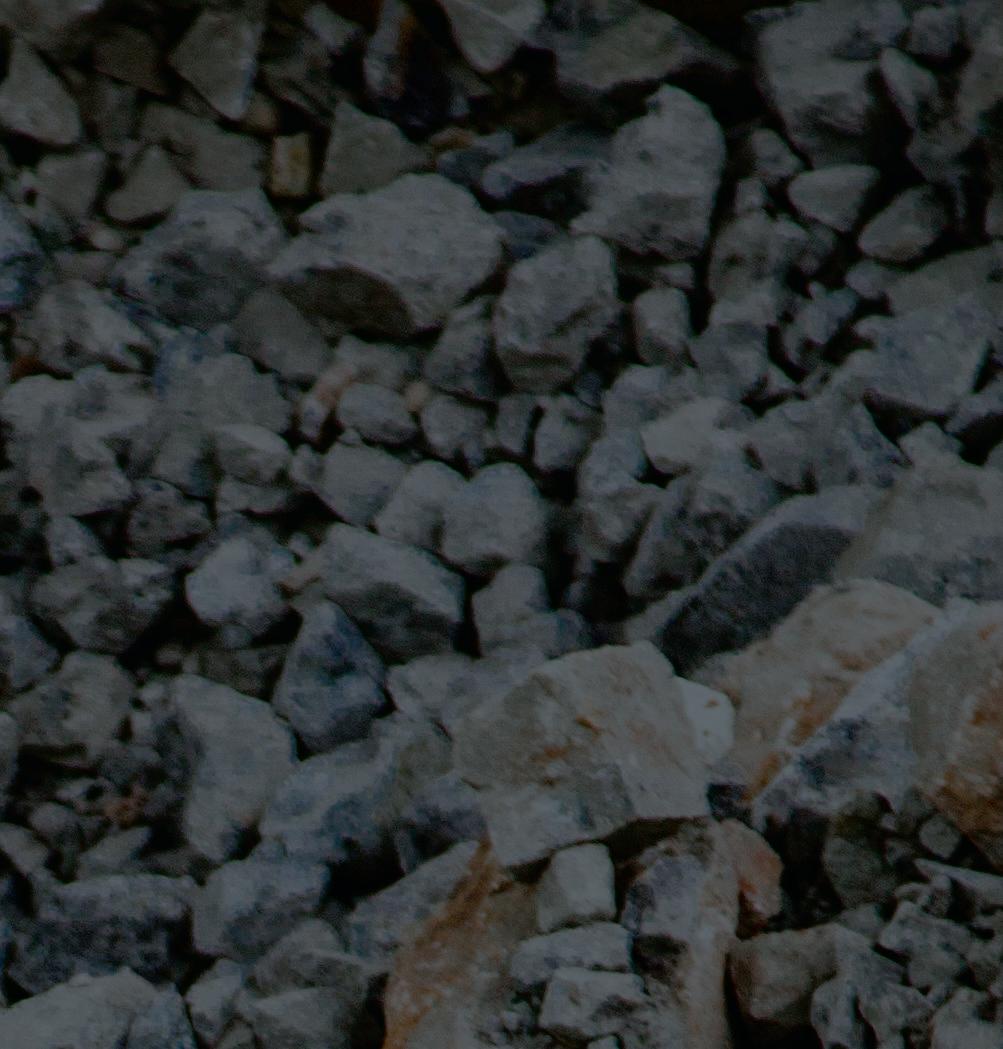
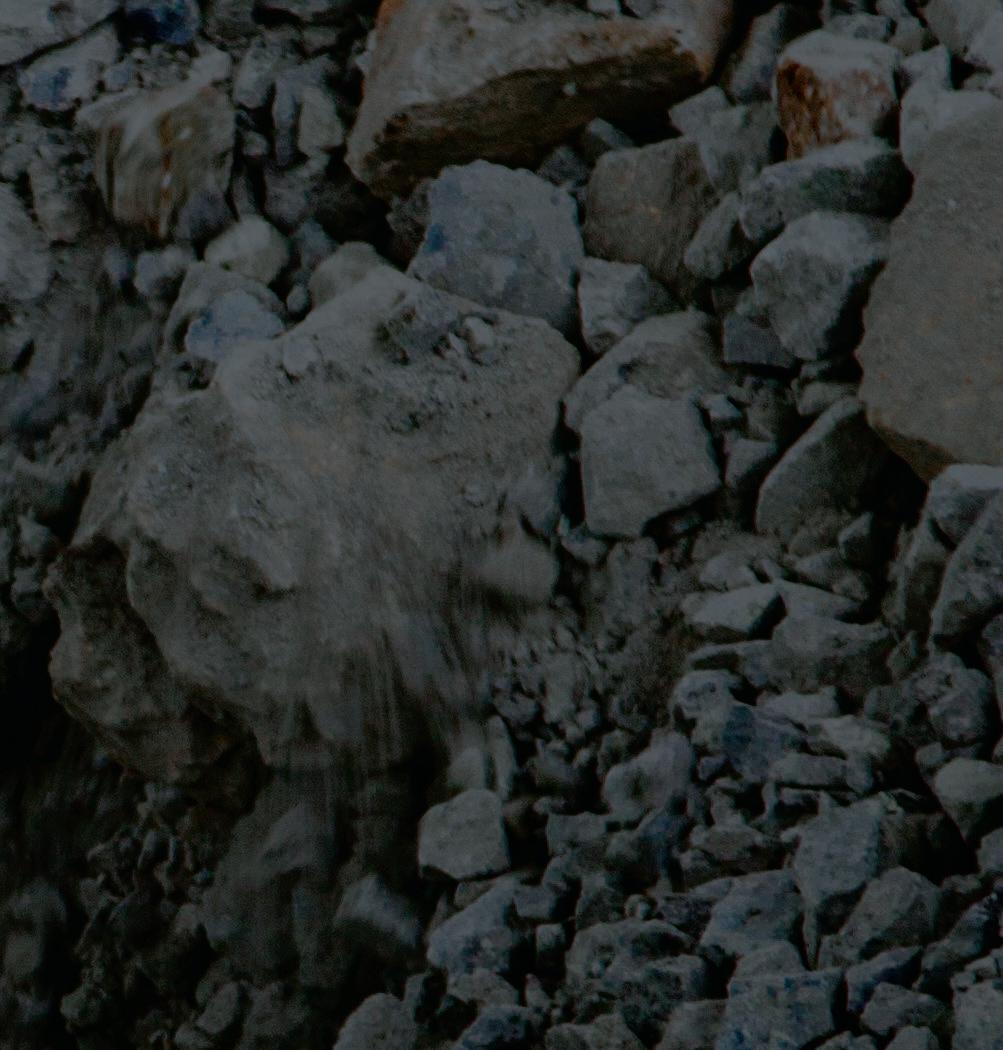


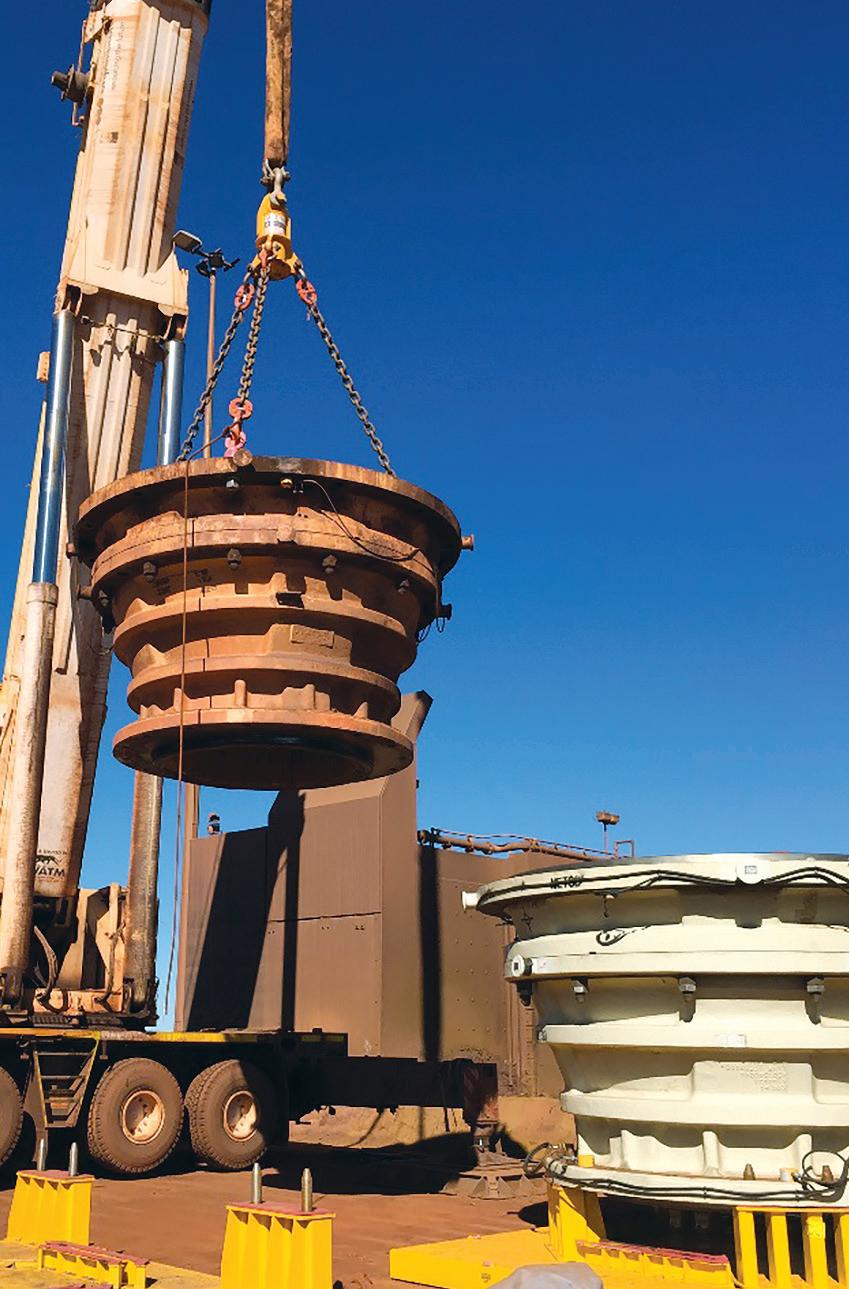

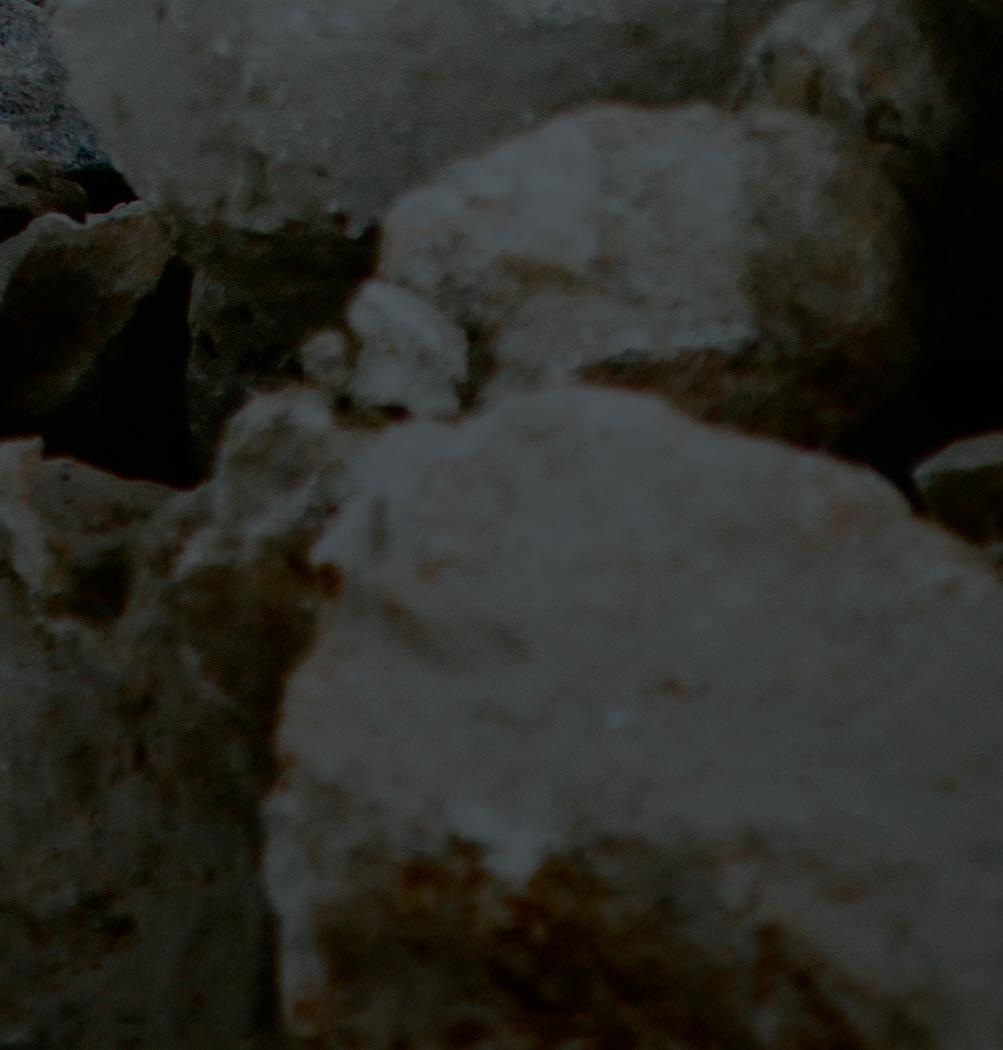
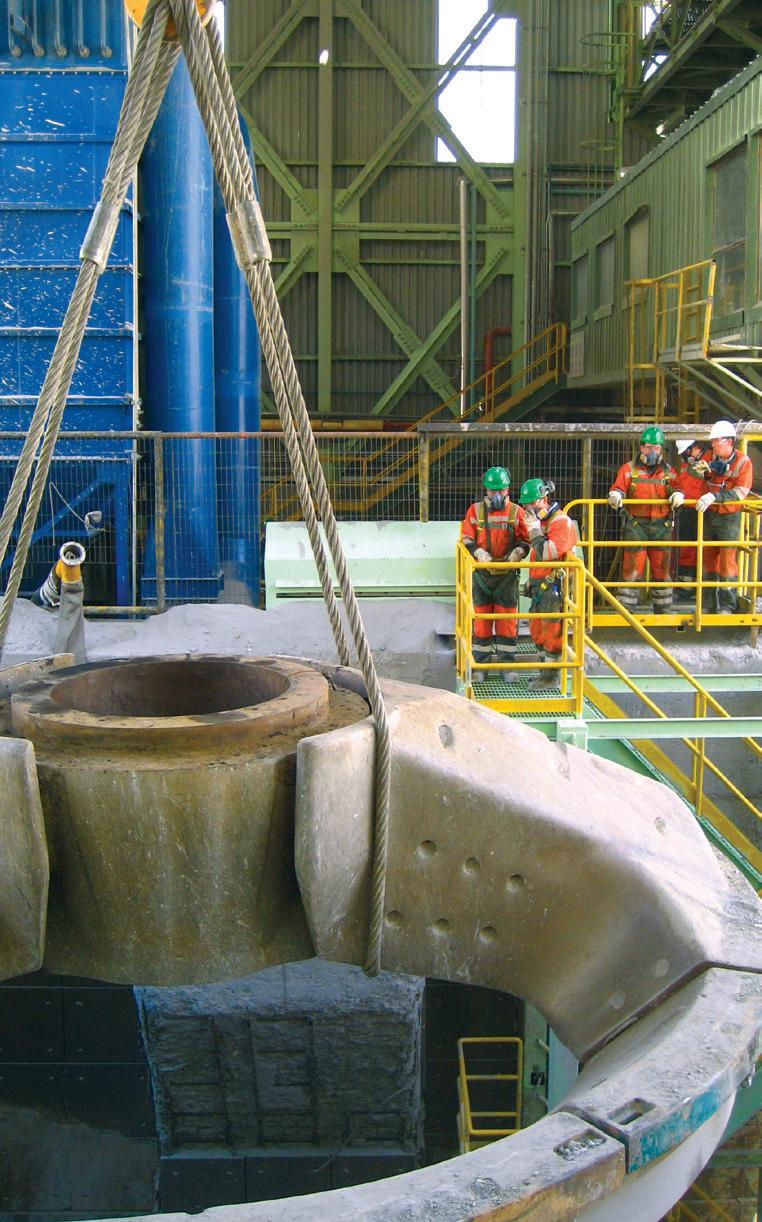
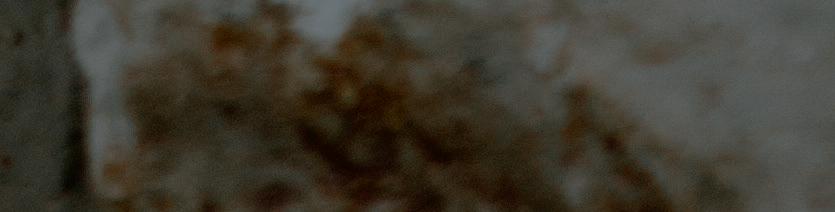
