
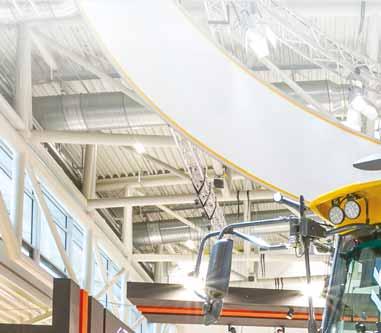
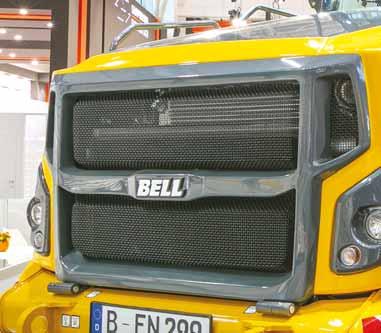
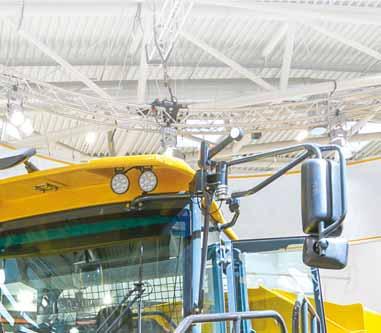
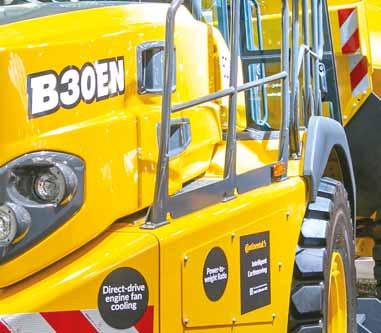

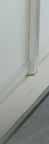
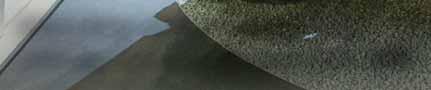

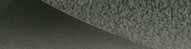
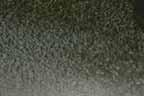
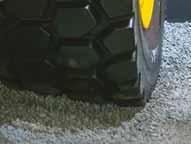
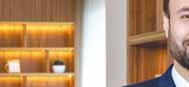
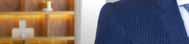


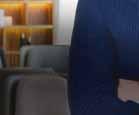
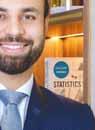
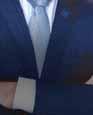
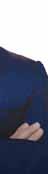
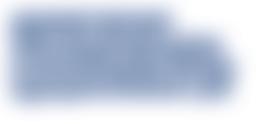
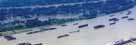
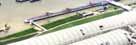
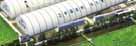




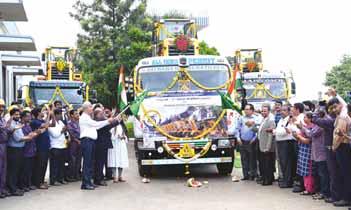

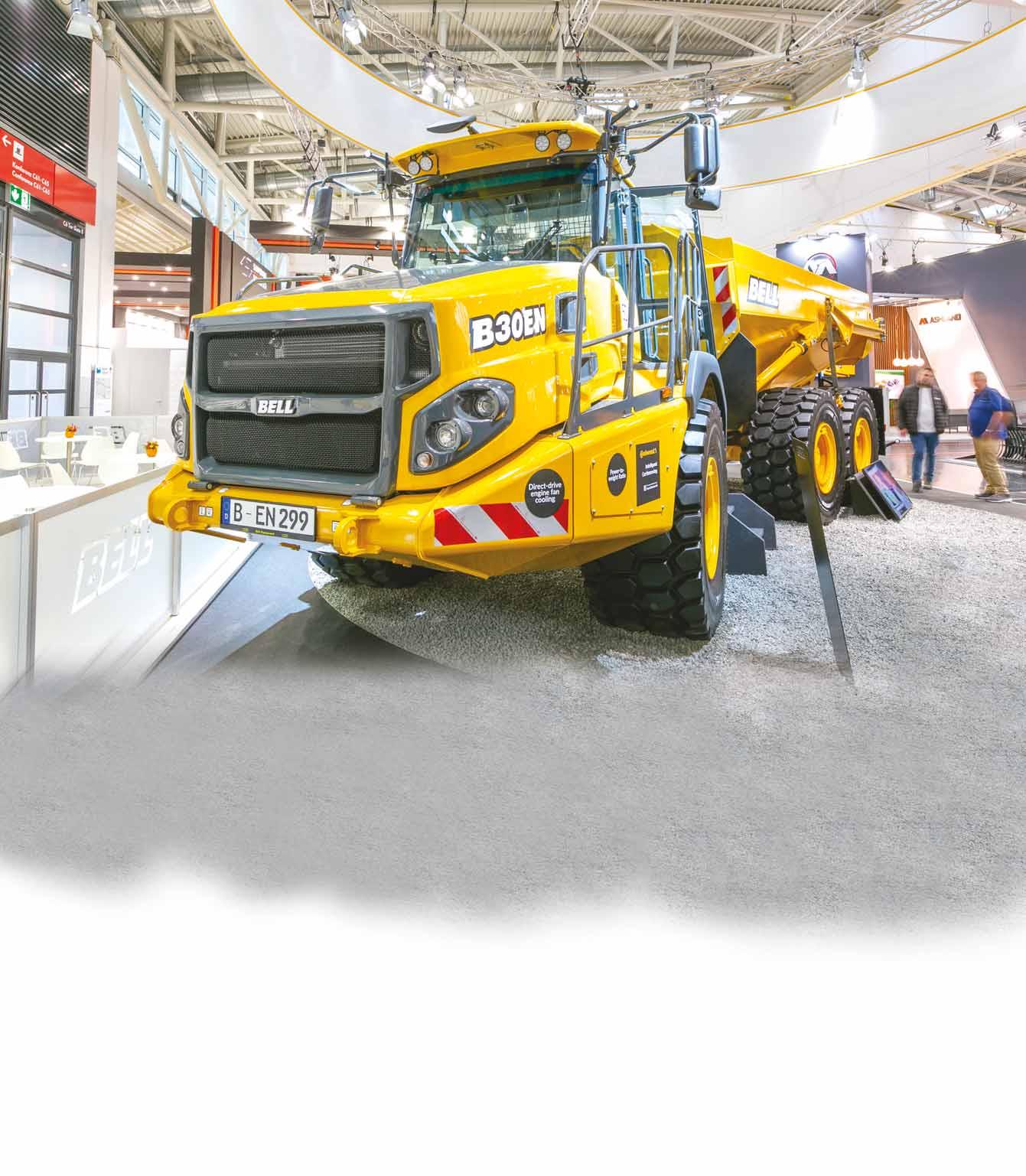
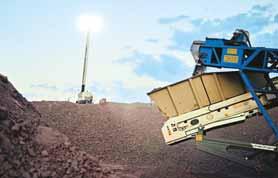

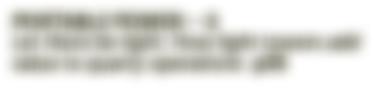
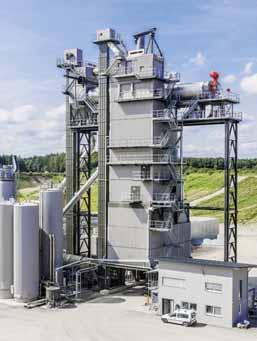
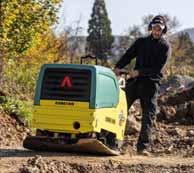
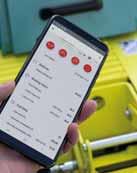
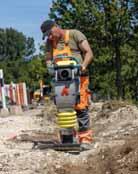
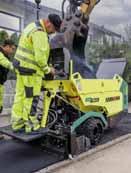
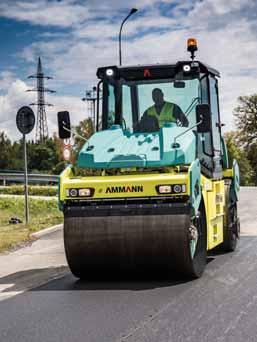
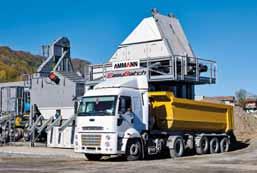
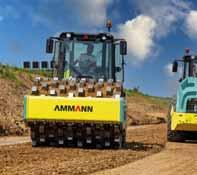

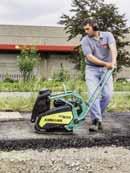
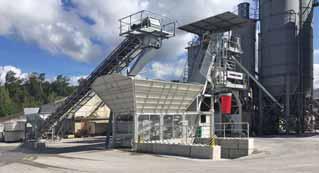
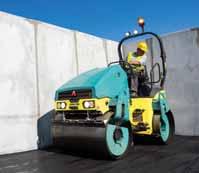
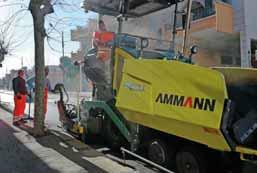
MAXIMISING YOUR INVESTMENT ARE ABOUT POWER – PURE AND SIMPLE
What do the smallest Ammann plate compactor, the largest asphalt plant and every product in-between have in common?
• Innovation that boosts productivity and efficiency, ultimately improving your bottom line.
• Parts and components that ensure long life to maximise your investment.
• The commitment of a family business that has thrived in the construction industry for 150 years by keeping promises today – and knowing what customers will need tomorrow.
HEAD OFFICE
EDITOR: Guy Woodford
ASSISTANT EDITOR: Liam McLoughlin
CONTRIBUTING
EDITORS: Patrick Smith, Dan Gilkes
EQUIPMENT EDITOR: Mike Woof
DESIGNERS: Simon Ward, Andy Taylder
PRODUCTION MANAGER: Nick Bond
OFFICE MANAGER: Kelly Thompson
CIRCULATION & DATABASE MANAGER: Charmaine Douglas
DIRECTOR: James Howard
INTERNET, IT & DATA SERVICES
WEB ADMINISTRATORS: Sarah Biswell, Tatyana Mechkarova
MANAGING DIRECTOR: Andrew Barriball
PUBLISHER: Geoff Hadwick
CHAIRMAN: Roger Adshead
ADDRESS
Route One Publishing Ltd, Second Floor, West Hill House, West Hill, Dartford, Kent, DA1 2EU, UK TEL: +44 (0) 1322 612055 FAX: +44 (0) 1322 788063
EMAIL: [initialsurname]@ropl.com (psmith@ropl.com)
ADVERTISEMENT SALES
SALES DIRECTOR:
Philip Woodgate TEL: +44 (0) 1322 612067
EMAIL: pwoodgate@ropl.com
Dan Emmerson TEL: +44 (0) 1322 612068
EMAIL: demmerson@ropl.com
Graeme McQueen TEL: +44 (0) 1322 612069
EMAIL: gmcqueen@ropl.com
SUBSCRIPTION / READER ENQUIRY SERVICE
Aggregates Business is available on subscription at the rate of: £85 / US$145 / €111 per annum. Single copies £20 / US$35 / €26 Email subs@ropl.com for further details. Subscription records are maintained at Route One Publishing Ltd.
SUBSCRIPTION / READER ENQUIRIES TO:
Data, Route One Publishing Ltd, Second Floor, West Hill House, West Hill, Dartford, Kent, DA1 2EU, UK
TEL: +44 (0) 1322 612061 FAX: +44 (0) 1322 788063
EMAIL: data@ropl.com
No part of this publication may be reproduced in any form whatsoever without the express written permission of the publisher. Contributors are encouraged to express their personal and professional opinions in this publication, and accordingly views expressed herein are not necessarily the views of Route One Publishing Ltd. From time to time statements and claims are made by the manufacturers and their representatives in respect of their products and services. Whilst reasonable steps are taken to check their accuracy at the time of going to press, the publisher cannot be held liable for their validity and accuracy.
PUBLISHED BY © Route One Publishing Ltd 2022
AGGREGATES BUSINESS USPS: is published six times a year. Airfreight and mailing in the USA by agent named World Container Inc, 150-15, 183rd Street, Jamaica, NY 11413, USA.
PERIODICALS POSTAGE PAID AT BROOKLYN, NY 11256
US POSTMASTER: Send address changes to Aggregates Business, World Container Inc, 150-15, 183rd Street, Jamaica, NY 11413, USA. Air Business Ltd is acting as our mailing agent
PRINT: ISSN 2051-5766 ONLINE: ISSN 2057-3405
PRINTED BY: Warners (Midlands) PLC
Facebook @AggBusiness
LinkedIn Aggregates Business Magazine
Twitter @Agg_Business
Instagram @aggbusiness_magazine
The global cement and construction industries are among the highest CO2 emissions generators in the world. The cement industry alone accounts for 8% of global emissions, not far behind the agriculture industry with 12%.
Given the above, we were delighted to recently report on how Holcim and CEMEX, two of the biggest names in the global cement industry, have both had their 2030 decarbonisation goals validated through the Science Based Targets initiative (SBTi) for alignment under its new 1.5°C scenario, the most ambitious pathway defined for the industry.
Indeed, this edition of Aggregates Business International includes an exclusive interview with Dr Edelio Bermejo, Holcim’s global head of research & development & intellectual property, in which he gives a detailed insight into the Switzerland-headquartered global industry major’s work on what was the world’s first 1.5°C science-based framework to decarbonise the cement industry, resulting from its partnership with the SBTi. This 2030-targeting framework was independently developed by the SBTi, in collaboration with an expert advisory group representing academia, civil society and industry to decarbonise cement in a rigorous and science-driven way. The Net-Zero Standard offers companies robust certification to demonstrate to consumers, investors and regulators that their net-zero targets are reducing emissions at the pace and scale required to keep global warming to 1.5°C.
The recent launch of Holcim’s SBTivalidated landmark framework could not have been better timed for Bermejo, a SpanishFrench dual national, given his key speaker engagement at CarbonZero: Alternative Fuels and Raw Materials 2022 on November 10 and 11. Featuring a conference and exhibition, the event was held at the Pestana Palace Hotel & National Monument in Lisbon, Portugal, focusing on sustainability and other big topics
that make the agenda of the world’s biggest cement and construction companies.
In its new 2030 targets, Holcim upgraded its target to reduce scope 1 and 2 emissions per ton of cementitious material by 25% by 2030 from a 2018 base year. Holcim commits to reduce gross scope 1 GHG emissions by 22.4% per ton of cementitious material and scope 2 GHG emissions by 65% per ton of cementitious material within the same timeframe. For other indirect emissions on scope 3, Holcim commits to reducing CO2 per ton of clinker and cement purchased from third parties by 25.1% from a 2020 base year.
The largest concrete producer in the western world and among global leaders in cement production, CEMEX has accelerated its decarbonisation efforts through its Future in Action programme, aiming to build a more sustainable, circular future, with the primary objective of becoming a net-zero CO2 company. The company has achieved record-breaking CO2 reductions, and its performance has given it the confidence to achieve a more accelerated pathway to 2030.
The comments made by CEMEX CEO Fernando A. González, after the Mexicoheadquartered global sector giant had its 2030 decarbonisation goals validated by the SBTi, emphasised why decarbonising the world’s building industry is a non-negotiable must.
“Climate change is the biggest challenge of our times, and the building materials industry must be at the forefront of decarbonising the built environment. We are committed to being leaders on the path to net zero through relentless innovation and aggressive targets that are backed up by meaningful and measurable progress. The SBTi’s validation is clear evidence of this. Through [our] Future in Action [programme], we are reducing carbon emissions in every part of our value chain and providing our customers with lower carbon products so they can also be part of the solution.” GW
“LSC Infratech’s new Manoharpura facility has a 50tph silica sand production plant, producing up to 15,000 tons/month of silica sand
COMMENT
Raising the bar on global cement industry sustainability 06 NEWS
CEMEX has strong presence at COP27; Lintec & Linnhoff go bigger in Malaysia; Marangoni extends footprint to North India
49 EQUIPMENT UPDATE
Global quarrying equipment manufacturers’ new model launches and applications
50 EVENTS
All the key events in the quarrying & aggregates world
October’s bauma show saw a host of new crushing and screening plant launches from the major manufacturers
22 LOADING
Electric prototypes, a new generation of large excavators, and a major equipment manufacturer making its debut in the European wheeled loader market
25 HAULING
Advanced testing of driverless articulated dump trucks (ADTs) and the growing presence of 4x4 ADTs are key talking points in the global off-highway hauler market
Washing plants are a crucial and evolving element of the production of high-quality aggregates and sands
With materials costs rising and resources depleting, regulations are calling for the adoption of sustainable solutions and recycling of construction waste
Atlas Copco’s Barbara Gregorio discusses how portable power solutions are part of a wider solutions portfolio helping to achieve more sustainable quarries
-highway engine manufacturers have made sustainability a priority alongside the renowned high performance and ciency of their solutions
Dr Edelio Bermejo, Holcim’s global head of R&D and IP, heads an extensive global and gifted team working daily on new, greener building materials that can drive down the global construction industry’s carbon footprint
12 INTERVIEW - 2
Farhad Azizi discusses how quality building materials sourcing has fuelled Azizi Developments’ Dubai rise
16 MARKET REPORT
Rapid urbanisation is helping fuel Chinese aggregates demand
LSC Infratech’s Manoharpura silica and manufactured sand production facility is benefitting from a big investment in advanced technologies, plant automation and new maintenance practices
Marangoni, a leading global tyre retreading specialist which started franchising operations in India in mid2018, has established its first exclusive franchisee in North India.
The business, Manoj Tyres, an existing retreader at Kanpur, one of the largest tyre markets in India in Uttar Pradesh (UP), was sourcing retreading material from two leading Indian retreading companies before switching exclusively to Marangoni India.
The Manoj Tyres and Marangoni India teams at the new facility
A new greenfield facility at a new site has been commissioned with new equipment, including Marangoni’s RingTreader RT920. Keeping with the culture of India, where any new venture has to receive blessings from family elders, the inauguration was graced by Shri Jagmohan Agarwal, the father of Manoj Agarwal, proprietor of the firm, accompanied by Hemant Kaul, CEO, Marangoni – India.
Kaul said at the occasion: “In Manoj Tyres, we have an experienced partner who understands the differentiation Marangoni brings to fleets compared to our competitors. Manoj Agarwal has a threedecade-long experience as a distributor of imported brands of new tyres, in tyre service through a CV wheel alignment centre and in tyre retreading. As new tyre technology advanced, he felt the need to ‘future-proof’ his business. After extensive due diligence, he zoomed in on Marangoni.”
CEMEX CEO Fernando A.
González was part of the First Movers Coalition panel at COP27 in Sharm-el-Sheikh, Morocco, alongside the World Economic Forum’s president, Borge Brende, Microsoft president Brad Smith, ReNew chairman and managing director Sumant Sinha, Volvo Group chief purchasing officer Andrea Fuder, and Special Climate Envoy John Kerry.
CEMEX is a founding member of the First Movers Coalition, a partnership between the World Economic Forum and the US Office of the Special Presidential Envoy for Climate, John Kerry. It is the only buyers’ club working to scale new technologies across the heavy industry and heavy-duty transport sectors. As a First Movers Coalition member, CEMEX committed to making 32% of its heavy-duty transport purchases zero emissions by 2030. This commitment aligns with the company’s ambitious goals of
reducing transport carbon emissions by 30% by 2030 and becoming Net Zero by 2050, part of its Future in Action programme to achieve sustainable excellence and become a net-zero CO2 company. This commitment is particularly challenging since zero-emission heavy-duty transport is unavailable at scale. At the panel on 8
Lintec & Linnhoff has started production of its asphalt and concrete batching plants at its newest facility, a manufacturing site in Johor, Malaysia.
New models for customers are already rolling off the production lines at the plant, which began limited-scale operations in 2021 before ramping up in 2022. The manufacturing facility covers 88,888 sq. ft., with two planned future expansions. Lintec & Linnhoff is manufacturing Linnhoff asphalt
mixing plants and Eurotec concrete batching plants at the factory, which replaces the previous manufacturing site in northeastern Johor. These plants are globally distributed, with most going to customers in South-East Asia, the Middle East and Africa.
Plans for the new Malaysia facility were unveiled in 2019, and work was completed in 2021. After unavoidable interruptions caused by the COVID pandemic, Lintec & Linnhoff is ready to showcase its
November 2022, González talked about how collaboration and innovation are at the core of its efforts. CEMEX is already piloting fully electric concrete mixer trucks with partners like Volvo. CEMEX is also investing in transition technologies such as natural gas, replacing 200 diesel trucks with this lower-emission alternative earlier this year.
newest facility and is extremely proud of its latest addition to its global manufacturing portfolio.
Daniel Chan, chairman at Lintec & Linnhoff Holdings, said the new factory demonstrates the group’s resilience and focus: “Over the past two years, the whole world faced the challenge of COVID, and many projects were put on hold. We faced our own roadblocks, but we were determined to bring our vision to life for this new Malaysian factory.”
The factory employs a team of 50, which is expected to grow in the coming months. Being strategically located in Johor, the plants can be shipped easily to customers across Asia, the Middle East and Africa via the three ports nearby. Some plants will be transported by land to Singapore before shipping via Jurong Port.
Others will go via two other nearby Malaysian ports in Johor. The new factory is just 36km from Singapore’s Lintec & Linnhoff global headquarters.
Dr Edelio Bermejo is Holcim’s global head of research and development (R&D) and intellectual property (IP). He oversees a large and highly gifted team based in different parts of the world which works daily on new, greener building materials that can drive down the global construction industry’s significant carbon footprint. Aggregates Business editor Guy Woodford spoke to him about his vital work
The cement and construction industries are among the highest CO2 emissions generators in the world. The cement industry alone accounts for 8% of global emissions, not far behind the agriculture industry with 12%. Given that context, it is not surprising on our Teams call that Dr Edelio Bermejo is keen to articulate the importance of discovering and utilising greener building materials if the cement and concrete industry is to achieve its ambitious goal of net-zero concrete by 2050.
“When you look at global population growth, there will be around 2.5 billion more people on our planet by 2050, 80% of which will be living in urban areas that will be built up vertically and horizontally. Two-thirds of the infrastructure required by 2050 is not yet built. Concrete will be in high demand, and as we emit CO2, we have no choice but to decarbonise it and go for net zero. We need to rethink how we design every building or other structure and reduce the amount of material going into it without reducing its final quality. It is also important not to lose sight of the present. Today, the equivalent of a New York City is built every month!”
Bermejo stresses that as the global cement and concrete industry gets nearer its 2050 net-zero goal, it will need a lot of financial assistance from governments and other bodies, such as the World Bank and the IMF (International Monetary Fund), to build and maintain the required infrastructure to store and utilise the captured CO2
“Guys, just trust us, and by 2050 you will get zero-emission cement”
When asked about the role of China, by far the biggest producer of concrete and cement, within the global industry’s efforts to decarbonise by 2050, Bermejo responds: “When China decides there is no other way to produce concrete and cement without decarbonising it, they will do it. In 2008, they decided there were too many cement players – around 2,000. They were emitting a lot of carbon. The Chinese government then said, ‘In four years, I only want 200 companies left operating. The rest will be closed’.
“What happened was that the very old plants were closed, and then the larger players bought the smaller ones and invested in new, greener production technologies. As a result, they have made a huge improvement in reducing their CO2 emissions.”
Aggregates Business recently reported on Holcim’s launch of the world’s first 1.5°C science-based framework to decarbonise the cement industry, resulting from its partnership with the Science Based Targets initiative (SBTi). This 2030 targeting framework was independently developed by the SBTi, in collaboration with an expert advisory group representing academia, civil society and industry to decarbonise cement in a rigorous and science-driven way. The Net-Zero Standard offers companies robust certification to demonstrate to consumers, investors and regulators that their net-zero targets are reducing emissions at the pace and scale required to keep global warming to 1.5°C.
The recent launch of Holcim’s SBTivalidated landmark framework could not have
been better timed for Bermejo, a SpanishFrench dual national, given his key speaker engagement at CarbonZero: Alternative Fuels and Raw Materials 2022 on November 10 and 11. Featuring a conference and exhibition, the event was held at the Pestana Palace Hotel & National Monument in Lisbon, Portugal, focusing on topics that make the agenda of the biggest cement and construction companies worldwide.
Highlighting the overall theme of the conference, Breaking old habits and patterns, Bermejo, who is based at Holcim’s stateof-the-art R&D headquarters in Lyon, France, talked about Holcim’s strategy for decarbonising the cement industry. Holcim dedicates more than 80% of its innovation resources to developing sustainable products and solutions. The group’s 2020-launched ECOPact range of green concrete is proving popular worldwide, and its recently launched ECOPlanet range of green cement is said to deliver at least a 30% lower carbon footprint with equal-to-superior performance. Holcim plans to produce 100 million tonnes of recycled materials by 2030 and utilise technologies like 3D printing that use 70% fewer materials without compromising performance. The group has further across value chain net zero by 2050 targets.
“I am very honoured to speak at this conference and to show that Holcim is the world leader in this area. It is a fantastic opportunity to focus on two key decarbonisation topics – alternative fuels and alternative raw materials. You need to
focus on them simultaneously and in the presence of senior representatives from large as well as smaller- to medium-sized industry companies,” says Bermejo. “The entire industry needs to move on this.”
Holding a PhD in Materials Science, Bermejo has 27 years of experience in product development, marketing, and operations in the cement industry. As Holcim’s global head of R&D & IP, a role he has been in for the past three-and-a-half years, his primary responsibility is accelerating the time to market of existing R&D projects and fostering a more visible innovation culture and external partnerships around new ideas and business models, such as the decarbonisation of the construction industry.
“The industry’s decarbonisation started decades ago and involved all key players. This has meant using alternative fuels, reducing the clinker factor, and leveraging the use of cementitious materials, including slag, pozzolana, and fly ash, across all geographies. What has not been developed enough is the use of alternative [building] materials. Our net 2021 CO2 emissions were 553kg of CO2 per tonne of cementitious material. We are on track to meet our 2030 target of 475kg of CO2 per tonne of cementitious material. We insisted on having interim targets. Otherwise, you are at risk of saying, ‘Guys, just trust us, and by 2050 you will get zero-emission cement’.
“As important as decarbonising our industry is making it circular, with very clear goals. From Holcim’s perspective, it means moving from 54 million tonnes of recycled materials used [in cement production] in 2021 to 100 million tonnes by 2030.”
Bermejo says Holcim’s 15,000m² Lyon R&D facility includes 210 fixed-post researchers, plus some internships, who are supported by a network of R&D colleagues based in Switzerland, Austria, China, and Mexico. “We have a centralised R&D operation, but when it comes to research ideas, it’s very decentralised,” he explains. “I cannot
invent the concrete needed in Manila to fight against flooding if I’m not in Manila. Local customisation is essential. We have more than 40 PhD holders working across continents on fundamental research.
“Eighty per cent of our R&D work is related to sustainability. We also work on product digitalisation and market differential. We have more than 1,800 product patents – and more than two-thirds are related to sustainability. I am very proud of our open Innovation platform through which we have strong partnerships with more than 120 start-ups, either through a financial or equity stake or via an MoU [Memorandum of Understanding].”
I am keen to discuss Holcim’s recent investment in COBOD International, a global leader in 3D construction printing, to advance world-class 3D printing materials, robotics
and automation. Building on its collaboration with COBOD since 2019, Holcim aims to grow its innovative range of proprietary ink, TectorPrint, tailored for 3D printing. Holcim and COBOD have collaborated on various novel building projects, from 3D-printed windmill tower bases with GE to the world’s rst 3D-printed school in Malawi and Africa’s largest 3D-printed affordable housing project in Kenya.
Holcim’s TectorPrint is an innovative 3D printing ink range that can be tailored for complex applications from residential buildings to infrastructure. Empowering smart design, 3D printing can reduce material use by up to 50% to build better with less, with no compromise in performance.
“The reason why we are moving into 3D printing is because automation is crucial to the future of the construction industry. If you look at productivity in construction for the last 70 years, it has been almost flat or very slow growth. We really need to increase automation in construction, and one of the mass-market solutions is 3D printing. With this technology, we are building houses in Africa and headquarters in Europe. In 2023, we are also going to be using 3D printing to build concrete windmills for General Electric in North America.
“There is also a sustainability benefit when we are building with 3D concrete printing, as we are just printing the amount of concrete needed. Last year at the Venice Biennale, we presented the Striatus arch bridge that we and partners built entirely with 3D concrete printing.”
COBOD International is also partnering with CEMEX and other major global building materials players, a development that Bermejo welcomes.
is among major materials suppliers that are partnering with COBOD International on
“I was more than happy to see CEMEX moving into this area. My view is, ‘Please, join us’. The more of us moving in this direction, the better chance we have of raising building standards by convincing politicians of the need for this approach.”
Another eye-catching area of research Holcim is involved in is the concrete inductive charging of electric vehicles. “This is using concrete roads and pavements to charge electric vehicles that are moving. The work in this area started with scooters. The IBIS hotel in Munich has scooters that charge when travelling over our concrete routes. We will then look at charging forklifts working in warehouses, buses and, finally, cars travelling on concrete roads. We don’t want to create over-expectation in this area. This is not widescale technology for tomorrow. It is research.”
In 2021, the GCCA launched its 2050 Cement and Concrete Industry Roadmap for Net Zero Concrete, setting out its member companies’ collective commitment to ensuring that the cement and concrete industry will play a major role in building the sustainable world of tomorrow.
Bermejo says the progressive approach to recycled building materials adopted by national and local government in Holcim’s native Switzerland enabled the group to develop, three years ago, the world’s first cement including 20% recycled construction and demolition (C&D) waste material. “That means 20% less primary resources drawn from nature. Since then, we have been looking to push building codes and create incentives to have more than 20% C&D waste in cement, not just in Switzerland but across Europe. Now, a new EU cement law being introduced in a few months will allow up to 35% of C&D waste to be used in cement for construction works. This is great circular construction progress made via the standardisation bodies.”
The ongoing development of low-carbon concrete solutions will need to answer a key question, as Bermejo explains: “Today, we have very much been producing lower carbon concrete with slag, but the lack of availability of slag, largely through steel production sites closing, is pushing its price through the roof. Fly ash is also disappearing globally. So, the key question is, ‘How can I develop a low-carbon concrete without slag and fly ash?’”
Bermejo says he and Holcim colleagues work very closely with other major and small- to medium-sized building materials companies via the London, Englandheadquartered Global Cement & Concrete Association (GCCA). Representing 80% of the world’s concrete industry outside China, the association’s mission is to position concrete to meet the world’s needs for a material that can build and support growing modern, sustainable and resilient communities.
“We are involved in the association’s common scientific network through which all company members can benefit from accessing the latest industry technologies, like CCUS (carbon capture, utilisation & storage). At the same time, I’m leading the GCCA Open Innovation Challenge involving the best startups whose ideas and solutions could benefit the entire industry by solving the issue of cement and concrete decarbonisation.”
Returning to the topic of rethinking the approach to the design of all new global infrastructure, Bermejo says: “We need to be thinking, ‘How can I make this fully recyclable and completely in line with the circular economy?’. For example, we ran a building project earlier this year where we created 100% recycled clinker to create 100% recycled cement. By the end of this year, we will start another building project involving 100% recycled concrete. We cannot do this every
day, but it can act as the lighthouse for the journey to show just what can be achieved by all of us.”
Asked how he sees the global building products industry in a decade, Bermejo responds: “It will be improving in its lower CO2 footprint, and very much about environmental transparency, with EPDs (environmental product declarations). There will be much more embracing of the circular economy and a lot more use of digital solutions, including the use of sensors in concrete to collect a lot of data that can be used effectively via artificial intelligence.” I end our conversation by asking what Bermejo enjoys most and least about his crucial work. “I like to find new ideas myself. When a new idea is coming, there is nothing better. I also like to encourage others to invent. My biggest frustration is the lack of speed in executing our plans. I know Holcim is a global leader in sustainable building product solutions, but for me, we are sometimes too shy and don’t want to be seen as arrogant. When I look at what Amazon and Google are doing, I would like us to be as arrogant as them! I always say to my teams, ‘Go, go, go and be part of the solution’.” AB
Fifteen years should be too short a timeframe for a company to become one of the top construction firms in a vibrant global business-minded metropolis like Dubai, but Azizi Developments has achieved this by building tens of thousands of homes for local and foreign buyers. As V.L. Srinivasan discovers while speaking to the company’s CEO Farhad Azizi, the business’s impressive rise has been built off the back of its highly reliable network of high-quality building-materials suppliers
Farhad Azizi is proud of his company’s strong track record and sizeable project pipeline through its extensive land bank and strategic partnerships with Dubai’s key master developers, and its instrumental role in developing world-class properties in Mohammed Bin Rashid City (MBR City), Palm Jumeirah, Dubai Healthcare City, Al Furjan, Studio City, Sports City and Downtown Jebel Ali.
Azizi Developments is currently working on close to 100 construction projects due for completion before or in early 2023, and a further 100-plus projects in planning, worth billions of US dollars, earmarked for completion between 2023 and 2025.
Azizi says Dubai’s real estate market has become a topic of major attention this year due to factors that were anticipated to impact the Emirate’s property industry’s trajectory, all pointing towards strong growth.
“In many respects, Dubai’s economic growth has been incredible. The UAE government has undertaken scores of measures and changes in recent years, mostly targeted at bringing more foreign direct investment into the city.
“The 10-year visa (also known as the golden visa) was created by the government to provide individuals with long-term residencies and attract and retain talented people in the country. Furthermore, legislation allowing for the ownership of businesses in the Emirate without the need for a local sponsor aided economic growth.”
Azizi states that Dubai’s exceptional success in the real estate market in 2021 piqued the interest of global property investors. The market, he says, outpaced other property markets worldwide, topping Paris, London, New York, and Hong Kong due to years of infrastructure and population expansion.
“Dubai is placed third in the world in terms of residential capital growth in 2021, with a
17% rate of transactions. Additionally, 2021 saw the biggest value in the sector’s history, totalling US$81.69 billion, a year-over-year increase of 72%.”
Looking ahead to 2022 and beyond, the Dubai real estate market is expected to maintain its upward trend, buoyed by a steady infusion of fresh money and a cautious release of new supply by government and part-government-run firms. With inflation on the rise and interest rate rises looming, Dubai real estate has proven to be an excellent hedge for investors.
Azizi highlights the huge interest in Project Riviera, part of Azizi Developments’ award-winning real estate portfolio. It is a stylish waterfront-lifestyle destination located in the heart of MBR City that comprises 71 mid-rise buildings which will have around 16,000 residents upon its completion, who will benefit from being conveniently located close to all Dubai’s business, leisure, and retail hubs.
Like many companies in Dubai, Azizi Developments made considerable gains due to Expo 2020. Originally scheduled for 20 October 2020 to 10 April 2021, the global event was postponed due to the COVID-19 pandemic, with the Expo 2020 name retained for marketing purposes. When it was staged from 1 October 2021 to 31 March 2022, the event recorded more than 24 million visitors.
Azizi says his company had a large concentration of projects in Expo 2020’s vicinity with direct connectivity to the site.
“We had two projects in Al Furjan-Plaza, a 448-unit development comprising 286 studios, 46 one-bedroom units, 86 two-bedroom residences, 16 luxurious penthouses as well as 14 retail units, and Star, a 499-unit development constituting 486 residential units and 13 highly sought-after retail spaces. The residential units comprise 334 studios, 48 one- and 94 two-bedroom apartments, as well as 10 spacious, luxurious sky villas.”
He continues: “Are you familiar with the term ‘the Expo effect’? It is used to describe the continuous positive impact the Expo has on its host country 10 years after the exhibition. Looking at previous host cities, real estate prices in Milan and Shanghai kept on soaring following the Expo. Dubai will be no exception to the Expo effect and considering how developed Dubai’s real estate market was even before the Expo, the gains will probably double.
“We have become a tech-savvy firm thanks to major digital transformation. We have become even more customer-centric and have built an experienced team of industry experts, responsible for reviewing and analysing our business model and offerings to provide corrective actions as and when required. Through our knowledgeable team and other market intelligence channels, we now have a solid understanding of our customers’ wants and needs.”
Azizi says that as oil prices continue to surge due to the Russia-Ukraine war, imports
“We have become even more customer-centric and have built an experienced team of industry experts”
of aggregates, steel and concrete were likely to increase proportionally in price. “Thankfully, we closed major lump sum deals months before the war began. These deals comprised fixed pricing, meaning that we are not absorbing increases in commodity prices, shipping rates and so forth.”
With Ukraine being one of the largest producers of structural steel globally, Azizi anticipates that the construction industry across the world will be affected in the short to medium term. UAE-based companies are impacted as shipping costs are on the rise again. To overcome the problem, all companies are working on one core principle – buying local wherever possible — because if they want anything that needs to be imported, they will have to pay much more. There are also inevitable delays in goods reaching the ports here because of container scarcity.
Anything shipped in from overseas is likely to have risen in price. This is purely due to the higher logistics costs. Timber prices too have affected joinery firms, with prices up by as much as 35% in some cases. Locally manufactured materials, such as concrete and aluminium, have remained the same or even decreased in price during this period.
Construction material, such as concrete and steel, are generally sourced from within the GCC (Gulf Cooperation Council) — the UAE, Saudi Arabia, and Oman — while products used for finishing, those that customers see and touch, are still mostly procured from well-known manufacturers overseas, especially those in Europe.
Azizi Developments buys the aggregates of different sizes such as 3/16” and 3/8” from various companies including Mohammed Al Nasseri, Sandstone Building Stones Est, Al Ebtikar, and Ahmd Sayed Saleh Al Hashmi on a regular basis. “We are relatively using the same materials for many years with quality remaining high,” Azizi emphasises.
Azizi requires 41,000m³ of aggregates and other construction material every year and there is no dearth of suppliers in the country. Dubai-based Sand Stone Building Material Trading supplies black wash sand, white
wash sand, road base, all types of aggregates, red dune sand, interlock sand, pebble stones, silica sand, silica gravel, and decorative stones.
Shamsaldin Khadempour, the company’s managing director, says Azizi Developments is among the few developers which source their own construction material. “Our premium washed black sand used in the developer’s masonry was deemed a perfect fit for many of the company’s projects, and we are confident of working with Azizi Developments for many years ahead.”
Another major Azizi Developments supplier is Fala Building Material Trading (Fala), known for its earthworks like
excavation and cart away, transport and backfilling material, laying temporary roadworks, interlock paving and supply and installation of all types of interlock and kerbstones. Fala also supplies building material (road base, sub-base, black sand, red sand, and all types of aggregates) and does fence works including fabrication, supply and installation of pre-painted galvanised iron (PPGI) temporary and continuous fencing.
Fala’s operations manager, Rammah H Kourbaj, says: “While we usually sell our products to contractors mostly, we welcome big orders from Azizi and appreciate working with them as it pays great attention to detail and a true customer-first mindset,
“Sustainability is very important, and we consider it in all our aggregate purchases”
evident in how it procures its aggregates and construction materials.”
Ahmd Sayed Saleh Al Hashimi Trading (ASSHT) supplies black washed sand, white double-washed sand, red dune sand, top-quality road base, crushed aggregate 3/4 (10mm-20mm), 3/8 (5mm-10mm) and singlesize aggregate 3/16 (2mm-5mm) to many of the Azizi’s projects.
ASSHT manager Ahmed Abdallah says that his company regularly supplies huge quantities of crushed sand for interlock paving laying within Azizi Developments’ construction projects. “Azizi’s procurement process is very comprehensive and stringent and meet the standards of the industry.”
Azizi Developments is aligned with the UAE’s commitment to reduce carbon emissions by 50% by 2050 and prioritises using eco-friendly building materials in all its projects. “Sustainability is very important, and we consider it in all our aggregate purchases. It is one of our core values, with our developments having carbon footprints as low as possible,” stresses Azizi. “Whether it is UAE-based steel or cement manufacturers or suppliers, such as RAK Ceramics, we are finding that being based close to our buyers is a winning strategy. We have signed over 35 major direct deals with suppliers of construction materials in the past six months alone.”
Azizi Developments has taken over procuring construction material from steel and concrete to tiling and doors, rather than letting contractors do it. Azizi adds: “These materials represent roughly 70-80% of the development costs. Now contracts signed with our contractors are roughly only 20%-30% of the value they used to be.
“We now hire contractors solely for their expertise and skill, manpower and mobilisation, rather than for their procurement capacity. This is a win-win for both sides – not only does it mean less risk for contractors who now don’t have to take on massive financing to purchase materials from their side, but more importantly, it gives
us as the developer much more control over the supply chain management, and ultimately, our quality.”
While the in-house construction-materialprocurement approach entails more burden, work and risk for Azizi Developments as a developer, Azizi emphasises that it ensures that the final build meets and exceeds customer expectations. “It is the key to customer happiness as it is quality which sells the properties. It also proves helpful when prices are volatile, as we can leverage economies of scale by making larger material purchases for several projects at the same time and can negotiate with suppliers directly, giving us more control.”
Azizi highlights that Azizi Developments has, to date, constructed nearly three million sq. ft of built-up area including 150 multistoried buildings, with over 150,000m³ of concrete poured in 2021 alone. “We are planning to hand over 42 projects comprising 8,895 units this year,” he says, proudly.
Dubai’s population is likely to double in the next 20 years, creating huge demand for new residential communities, and great commercial prospects for Azizi Developments. The company’s CEO is looking forward to what comes next, with the knowledge that his heavily localised building-materials supply chain can be relied on to help maintain the business’s eye-catching growth journey. AB
The fallout from the COVID-19 pandemic has affected demand for aggregates in China this year but CAA, the country’s aggregates association, says rapid development in urbanisation projects is supporting demand in the country’s quarrying sector. Liam McLoughlin reports
In recent years, China’s annual production/consumption of aggregates has remained at about 20 billion tonnes, with an annual output value of more than 200 billion yuan (€27.84bn), and transportation costs of more than 500 billion yuan (€69.58bn), accounting for about 1/40 of Chinese GDP.
This year, affected by the COVID-19 epidemic, the demand for aggregates has declined to some extent compared with previous years.
CAA, the Chinese national aggregates association, says that the main factors driving demand for aggregates in the country are real estate projects, large infrastructure projects such as roads, bridges, water conservancy and hydropower, the progress of the new urbanisation and rural revitalisation plan, and construction of functional areas for coordinated regional development.
In the first half of 2022, national aggregates production totalled 8.18 billion tonnes according to data from the CAA, a 14.4% decrease from the same period in 2021. In the first half of 2022, under the support of the government’s policy of “steady growth in infrastructure”, high investment in infrastructure provided strong support for aggregates demand, but the growth rate of real estate investment continued to
decline, which had an impact on demand for aggregates.
At the same time, affected by factors such as COVID-19 epidemic prevention and control and the high inventory of aggregates-producing enterprises, the CAA says production in the first half of the year declined to a certain extent year-on-year.
CAA chairman Hu Youyi says that, currently, Chinese quarry operators particularly are looking for quarrying equipment that is suitable for large-scale, automated, intelligent and environmentally friendly production.
“This is because China’s urbanisation progress is currently in a period of rapid development, and the demand for aggregates is large,” Hu states.
He adds that a large number of small quarries have been shut down, and the number of quarries in China has reduced from more than 50,000 in 2013 to little more than 10,000 in 2022. This reduction is due to regional governments promoting the integration and reorganisation of quarries, and the building of large-scale quarries.
Hu says: “In addition, China is vigorously developing the construction of [an] ecological civilisation, and environmental protection requirements are tightening. It is required that the quarrying equipment must meet the
environmental protection requirements.”
Due to the impact of the COVID-19 epidemic in Shanghai in mid-March of 2022, the CAA says the amount of aggregates consumed in the city in the first half of the year has decreased.
Shanghai is an area that consumes aggregates, but does not produce them. The aggregates are supplied by waterways and land routes along the Yangtze River Basin.
However, Hu says the lockdown’s impact on China’s wider aggregates industry is limited.
“As Shanghai lifted the lockdown in early June after the epidemic was under control, infrastructure construction projects in all aspects were launched in an orderly manner, enterprises resumed work and production, and the supply of aggregates returned to normal,” he adds.
In terms of major developments in the quarrying and aggregates sector over the next year to 18-months, Hu comments: “In China’s 14th Five-Year Plan, the government has proposed plans of new urbanisation construction, dual circulation (a new pattern of development that is focused on the domestic economy and features positive interplay between domestic and international economic flows), and infrastructure such as highway, railway and bridges.
“Therefore, China’s demand for aggregates will continue to increase in the future. Meanwhile, the CAA is working hard in the setting and revision of the standards for China’s aggregates industry, and quarry operators and equipment companies will continue to develop towards a large-scale, intensive, intelligent and environmentallyfriendly direction.”
Hu adds that some new types of quarry equipment have been launched in China this year, such as new hammer crushers and large-scale gyratory crushers. A range of testing equipment has also been introduced including rock-abrasion index-testing machines and rock-crushing work indextesting machines.
The most commonly used aggregates products in China are currently machinemade sand and crushed stone. The machine-made sand is mainly mediumcoarse sand, and the fineness modulus exceeds 2.3; the particle size of crushed stone is mainly between 5mm and 25mm.
In terms of the exporting of Chinese aggregates, Hu says that currently aggregates output in Taiwan, Hong Kong and Macau is insufficient, and they basically rely on the mainland’s aggregates to meet their levels of demand.
“About 100 million tonnes of aggregates (machine-made sand and crushed stone) are exported to Hong Kong, Macau and Taiwan every year,” he adds.
A number of recent Chinese government actions are currently impacting the quarrying and aggregates sector. In November 2019, 10 departments including the Ministry of Industry and Information Technology jointly issued the ‘Several Opinions on Promoting the High-quality Development of the Machine-made Aggregates Industry’, and in March 2020, 15 departments including the National Development and Reform Commission jointly issued the ‘Guiding Opinions on the Healthy and Orderly Development of the Aggregates Industry’, which the CAA says stabilised the supply of the aggregates market and maintained the overall stability of the aggregates price.
At the same time, the Chinese government is vigorously developing green mine and green factory construction, and has introduced strict environmental protection policies, which Hu says are all designed to promote the transformation, upgrading and high-quality development of the Chinese aggregates industry.
He adds that, to save primary quarry resources, reduce environmental pollution and waste of resources, China’s aggregates industry actively recycles waste including tailings, waste rock, stone powder, construction solid waste and cave slag. According to the CAA, there are more than ten enterprises in China engaged in the transformation of rundown urban areas, abandoned mines restoration, and comprehensive utilisation of tailings and waste rocks, with lots of successful cases.
“China vigorously promotes the comprehensive utilisation of C&D [construction & demolition] waste, tailings and waste rocks. Dozens of cities have carried out the construction of ‘waste-free cities’,” adds Hu. “The utilisation rate of construction solid waste in these cities has reached 55%. The relevant experience gathered from this will be used nationwide in the next few years.”
He says that dozens of enterprises across the country have been involved in the successful transformation of shanty towns, abandoned mines, and the comprehensive utilisation of tailings and waste rocks. He adds that there are many companies in
China that are able to provide the market with overall solutions for recycled building materials, such as recycled concrete, recycled blocks, permeable bricks and other recycled products. “These have been applied in many fields, forming a new model of material recycling,” Hu says.
The bauma China 2022 construction machinery exhibition planned to be held in Shanghai in November 2022 was a casualty of the country’s COVID situation. Organiser Messe Muenchen said the decision to cancel the event, which was taken at the end of September, was due to the Chinese Government’s current COVID-19 policy and its own concern for the health and safety of the exhibitors and visitors.
The bauma China 2022 show was to be held from 25th to 27th November 2022 at the Shanghai New International Exhibition Center.
“A successful bauma China with certainty for planning is our primary concern,” explained Xu Jia, CEO of Messe Muenchen Shanghai. “Due to the still unforeseeable circumstances, this objective is unfortunately no longer feasible. To avoid [a] last-minute decision which may bring financial loss to the
“ China’s urbanisation progress is currently in a period of rapid development, and the demand for aggregates is large ”
customers, we, therefore, cancel the show for 2022 with a heavy heart at this stage and hope that all exhibitors can now start their preparation and planning for a successful bauma China in 2024.”
bauma China will be back again in 2024, from 26 to 29 November 2024. It will be held once more at the Shanghai New International Exhibition Center.
China has published a roadmap for the country’s building materials industry, one of the biggest domestic emitters of greenhouse gases, to start reducing carbon emissions by 2030.
News site Caixin Global reported that the plan sets out requirements for the industry to adopt new materials and upgrade technologies to reduce energy consumption and carbon emissions in key sectors including cement, glass and ceramics during the 14th Five-Year Plan period between 2021 and 2025. The plan also encourages mergers and consolidation in the industry to better allocate resources and improve industry structure.
The World Cement Association says that cement production in China was down sharply in the first six months of the year, with a 15% fall to 977 million tonnes. WCA CEO Ian Riley told the Financial Times that a combination of the country’s real estate crisis and China’s zero-COVID policy has started to impact the country’s construction sector.
Despite this, a report from research company GlobalData predicts future growth in the Chinese construction market is likely to maintain demand for the country’s aggregates producers.
The construction market in the country was valued at US$4.5 trillion in 2021, according to GlobalData. It predicts the market will grow at an average annual growth rate (AAGR) of more than 4% during the period 2023-2026.
GlobalData says the key sectors in China’s construction market include commercial construction, industrial construction, infrastructure construction, energy and utilities construction, institutional construction and residential construction.
tourism and retail activity, coupled with investments as part of the 14th Five-Year Plan (FYP) (2021–25).
The industrial construction sector is expected to grow in full-year 2022, supported by an improvement in industrial, manufacturing and export activity, coupled with investments in automobile manufacturing to meet rising demand for new energy vehicles such as electric.
The infrastructure construction sector’s output is expected to grow in 2022, supported by investments in rail, highway, waterway, and civil aviation projects as part of the 14th FYP. The sector’s output will also be supported by the government’s plans to accelerate infrastructure spending to stimulate economic growth.
The energy and utilities sector’s growth over the forecast period will be supported by investments on renewable energy, liquefied natural gas (LNG) and telecommunication infrastructure projects.
The GlobalData report predicts that growth in the institutional sector between 2023 and 2026 will be driven by public - and private-sector investment on healthcare, scientific research, and educational buildings as part of the 14th FYP. The government expects the healthcare sector to grow by 2030, attracting further investment towards the sector.
In 2022, the sector’s output will be affected by the tightening of regulations on property lending and weak buyer confidence in the housing market. Over the forecast period, however, GlobalData says that
In the short term, the report states that the commercial construction sector is likely to be weakened by the imposing of strict lockdowns in several provinces. The sector’s output over the 2023-2026 period will be supported by a gradual recovery in domestic
output will be supported by rising household incomes, coupled with the government’s efforts to renovate ageing, urban residential areas across the country and increase the supply of affordable housing units in highdemand urban areas.
The Chinese government has been boosting infrastructure investment measures and says the country’s economy is still on track to a steady recovery with a gradual normalisation of activities and strong policy support. Profits at China's major industrial companies declined at a slower pace in August, government officials stated in late September.
Zhu Hong, a senior statistician at the National Bureau of Statistics, said that industrial profits improved in August, registering a narrowed year-on-year contraction compared with the previous month.
Zhou Maohua, an analyst at China Everbright Bank, highlighted the improvement in profits earned by midstream and downstream manufacturing enterprises amid the government's measures to ensure stable prices and supplies, ease enterprises' burdens, and increase financial support, saying that will help to stimulate market vitality, boost employment and expand consumption demand.
Charlie Zheng, chief economist at Samoyed Cloud Technology Group, estimated that China's GDP will grow by around 4% in the third quarter, as the government has rolled out a series of policies to bolster this expansion. AB
October’s bauma show saw a host of new crushing and screening plant launches from the major manufacturers. Liam McLoughlin looks at the latest offerings to hit the market
Visitors to the giant bauma show in Munich (October 24-30) were able to check out a range of interesting new offerings in the crushing and screening sector, including AI-based crushers and hybrid screens.
SBM Mineral Processing (SBM) has developed the REMAX 600 track-mobile impact crusher as a ‘technological platform’ for an AI (artificial intelligence)-based, fully automatic production monitoring and control system.
The technology is currently being developed by the company and researchers at Montanuniversität Leoben, Austria’s university for mining and metallurgy.
The REMAX 600 features a cutting-edge sensor system, video technology, powerful communication and IT networks. It will offer a set of technological innovations, such as an automatic gap adjustment facility.
It can offer up to five fractions in one cycle. With a feed capacity of 600t/h, the new machine can accommodate material feed sizes up to 900mm and a maximum total weight of 75 tonnes depending on the equipment.
Triple wind sifting and an ultra-efficient overbelt magnetic separator with longitudinal discharge as an option (a novel feature in highly mobile impact crushers) are said by SBM to ensure high purity of final products, even in recycling applications.
SBM stresses that the industry-first introduction of an 'autonomous crusher' will
help users and operators with all decisions, permanently support efficient operation, assure optimum product quality at all times, as well as make an important contribution to saving energy and costs during crushing.
The autonomous crushing R&D project has been running for two years and features interdisciplinary teams from the Montanuniversität Leoben chair of mineral processing and SBM research departments.
The project aims to make the decisive step from today’s already extensively monitored and optimised crushing operations to autonomous fully automated production by means of ‘intelligent self-learning’ mobile crushers.
The machine independently assesses feed material and final products via sensors and camera systems, registers better-than-beforethe-load conditions of crusher and conveyor equipment, and optimises all separation processes down to overbelt magnetic separators and wind sifters.
The SBM control system, Crush Control, validates all operating conditions and material properties in real time and sends the values to SBM’s headquarters via the cloud. A ‘digital twin’ compiled there matches the real machine data with thousands of stored reference data coming from 1:1 quality testing, laboratory tests and computer simulations (including rock properties, grainsize distribution curves, particle shapes, etc).
The optimisation potentials determined from this are sent back to the machine control system in real time. This allows immediate and permanent adaptation of all
process steps on site without any stoppages, says SBM.
By means of an interactive menu control, SBM says even inexperienced operators can precisely adjust the production process – depending on whether maximum output, minimum fuel consumption (eco mode) or quantity-optimised production of certain valuable grain sizes are required.
The newly integrated tool-monitoring system in the REMAX 600 is another benefit, one which counteracts shortfalls in quality due to wear during production and provides key support for preventive maintenance.
Large-scale test runs will take place in the coming year to make sure everything works as it should in practice.
Kleemann premiered its Mobirex MR 130(i) PRO mobile impact crusher. The latest member of the Wirtgen Group brand’s PRO line, the extremely powerful plant is used as a primary and secondary crusher in natural stone and recycling and meets high environmental standards, according to the company.
Local emission-free operation is said to be possible thanks to the model’s E-DRIVE diesel-electric drive with the option of external power supply.
Thanks to this external supply, the system can be operated without emissions. This ensures low energy consumption per tonne of end product. The electric drive also means that hydraulic oil is only required for setting and set-up functions. This minimises risk to the environment and further increases the system’s sustainability.
When the Mobirex MR 130(i) PRO is operated via the diesel unit, the performance and load-dependent fan is said to ensure efficient use of fuel and low noise emissions. The formation of dust is also said by Kleemann to be greatly reduced by water spraying at all relevant points, such as the crusher inlet, the discharge belts and the post-screening unit, as well as various belt covers.
The Kleemann PRO-Line system can process up to 600 t/h of material. The high output is made possible by the crushing unit with a heavy rotor and a 250kW drive in conjunction with efficient pre-screening. The Continuous Feed Systems’ (CFS) continuous feed control is said by Kleemann to ensure consistently high utilisation.
The company says it counters the increasing complexity of crushing plants with its intuitive operating concept, Spective.
In addition to a large touch panel and two Spective radio remote controls - one of them for operating all relevant functions of the automatic mode from the comfort of the excavator - Kleemann also offers Spective Connect.
The digital solution simplifies the construction site digitisation of the Mobirex MR 130(i) PRO. Spective Connect transmits all important system data to the user's smartphone and simplifies reporting.
With the Mobirex MR 130(i) PRO, the proven, robust crushing unit with its two impact rockers and versatile blow bar options, as well as the 8.4m² optional doubledecker post-screen, are said to ensure very good product quality.
Kleemann’s new impact crusher can produce and discharge two classified end sizes – without using an additional screening plan. The use of optional wind sifters is said by the German company to further increase end-product quality.
Austria-based RM has launched the new H50X hybrid screen, which can run in diesel or fully-electric modes.
As a hybrid variant, RM says the machine can be operated electrically to notch up zero emissions. It adds that the screen delivers impressive modularity and versatility.
“It’s a whole new conception of doing a scalper,” said Gerald Hanisch, founder and CEO of the RM Group. “It is not only electrified, it has all kinds of features – the mobility, the versatility, the simplicity and the energy.”
RM says that both the RM5H50X hybrid screen and the RM J110 jaw crusher – which will make its debut at Conexpo in March 2023 – have incorporated countless ideas and customer requests to redefine the application options of processing equipment.
RM says the use of a hybrid machine brings a 25% reduction in fuel costs compared to a diesel-direct crusher or a hydraulic screen, while combining them into one machine train increases the savings even further.
It adds that, when a diesel-direct crusher drives the new RM hybrid screen,
the customer saves up to 33% on fuel. In combination with an RM hybrid crusher, which drives the RM hybrid screen, the savings potential reaches up to 50%.
In addition, if only one engine is running because the crusher is driving the screen, the customer only has to refuel and service one engine, effectively saving fuel, time and money.
Hanisch added: “We have been electrifying our plants for decades, and consequently have the necessary knowhow. Now the time is ripe for us to fulfil the needs of customers with our productready solutions. The lowest possible fuel consumption and smallest carbon footprint are the order of the day for our customers to be successful.”
McCloskey International has unveiled the latest entry into its jaw crusher line in the European market, the heavy-duty J4. The crushers are particularly suited to aggregates, construction and demolition recycling, and site preparation. The Metso Outotec-owned, Canada-headquartered manufacturer says the J4 builds on the robust features of the existing product range, with a line-up of features aimed at boosting productivity and offering enhanced durability across applications.
Designed to withstand the toughest conditions worldwide, the J4 delivers high production due to its jaw chamber design and enhanced material flow. The large 1060mm x 700mm jaw opening accommodates large feed sizes, contributing to higher production in material processing.
The material path is enhanced with the 1064mm x 4247mm grizzly pan feeder under the hopper that allows for better sizing of material with a variety of mesh options. Options of either a short pan feeder to suit the pre-screen or a double-deck grizzly pre-screen are available, ensuring suitability and better sizing of material based on the application.
McCloskey says the J4 delivers effective stockpiling, with wide main and side conveyors for enhanced material flow. The angle-adjustable 1200mm-wide ToughFlex main conveyor features a 3.912m-high stockpile, and with quick release and groundlevel access, the belt is designed to be easy to maintain and service.
ToughFlex is constructed with a special weave of two fabric plies and an additional binder warp (without the need for steel wire) resulting in reduced belt weight. The plies are reinforced to resist puncturing and are protected with heavy-duty wear-resistant top and bottom covers.
the crusher and maximise the efficiency of a project site. The company adds that technology has been a key factor in the development of the J4, with a DSE control panel for the highest operational performance and reliability providing push-button control of the jaw, track and feeder functions. The crusher is fitted with a telematics modem for the new 365SiteConnex programme, a complete connectivity solution for highly accurate monitoring of McCloskey products.
365SiteConnex is based on the latest communication technologies to collect, analyse and deliver information on the crushers, screeners and stackers customers rely on to produce the high-quality products with the least amount of downtime.
responsible strategy will be the introduction of our electric crushers, scheduled to be available in 2023.”
Keestrack has premiered the completely redesigned I4e tracked mobile reversible impact crusher with an advanced dieselelectric drive.
Due to its RIC (reversible impact crusher) technology, this machine can be used in secondary and tertiary crushing of rock, oversized gravel and recycled building materials (for example asphalt).
Keestrack says the specific design of the reversible horizontal impact crusher with a large variable crushing chamber, powerful rotor and electronically monitored hydraulic gap adjustment (+80 to -220 mm with new tools) allows feed sizes up to 250 mm and ensures consistently high-quality end products of up to 0/2 mm in closed circuit.
Secondary and tertiary crushing can be combined in one highly mobile solution, which Keestrack says makes the I4e a real alternative to mobile cone crushers or vertical impact crushers, especially with regard to its outstanding production capacities from 100 to 250 t/h.
McCloskey says that portability has not been compromised with the J4, despite its powerful capabilities. Mobility on-site and between sites continues to be a feature with remote-control tracks to move and position
“The J4 continues the momentum for our jaw crushing product range, as we continue to develop new products that meet the evolving needs of our customers across industries,” said Toni Laaksonen, senior vice president, McCloskey International. “We have always designed our equipment to ensure it contributes to the productivity and business success of these operations. As a company that is involved in the handling and processing of the Earth’s resources, we also have our sights set on sustainability. Our next commitment to an environmentally
The manufacturer adds that the system also offers lower wear, better quality of the end products (grain shape) and significant energy savings in typical applications (for example sand production 0/4 mm: approx. -30% compared to cone crushers; -30 to -40% compared to VSI impact crushers) also due to the advanced electric ZERO drive concept, backed up by the drop-off engine/gen-set consisting of a 447kW diesel engine and 300kVa generator.
Electric drives for the crusher (160kW), feeders and conveyor belts as well as the system hydraulics enable particularly costefficient and emission-free plug-in network operation. Keestrack says that three specific patents illustrate the innovative potential of its new I4e concept.
The material enters the hopper of the I4e, the loading apron feeder, which grants no loss of fine material and ensures a long lifetime is then gradually feeding the reversable loading conveyor which has an integrated metal detector. When metal is detected the conveyor reverses and a drum magnet separates only the metal. The compact system (transport dimensions: 15,270mm x 3,000mm x 3,310mm), weighing 42-tonnes includes a single-deck after screen with return conveyor of oversized material.
“The closed circuit ensures a production of 100% final material with very high quality for any European norms,” Keestrack comments. AB
Electric prototypes, a new generation of large excavators, and a major equipment manufacturer making its debut in the European wheeled loader market are among the major recent loading-sector developments. Liam McLoughlin reports
Among the eye-catching new loader and excavator offerings at the bauma 2022 international fair in Munich, Germany (October 24-30) was the new next-generation model from Hitachi’s Stage V-compliant wheeled loader range.
The manufacturer says the ZW250-7 –which is suitable for quarrying applications - has been designed to put operators in complete control of their workspace – and master the toughest job-site conditions – with new safety features and improved comfort in the cab. It adds that the new machine puts owners in control of their profit with a high level of performance, low total cost of ownership and exceptional efficiency. Fleet and workload performance is improved due to remote-monitoring tools and services provided by Hitachi.
With the ‘aerial angle’ camera system, Hitachi says operators have an exceptional 270-degree bird’s-eye view of the job site, while the rear obstacle-detection and warning system alerts them immediately if anything is close to the rear of the machine.
Hitachi also showcased its nextgeneration of Zaxis-7 large excavators for quarrying and mining at bauma.
The cab of the new ZX890LCH-7 Stage V-compliant model offers reduced noise and vibration levels in the cab.
New features include the synchronised motion of the seat and console – to reduce operator fatigue – and the adjustable console height with three positions to choose from. Easy operation comes from the ergonomic design of the console and switches, and the hi-res anti-glare 8” screen is also easier to view.
Hitachi says that an impressive fuel saving of up to 20% (PWR mode) compared to previous models of the ZX890LCH-7 is achieved by its HIOS-V hydraulic system. It adds that this also enhances efficiency in the swing, boom lowering and arm bucket rollout. Productivity is further increased by the improved front speed for loading operations; and the increased engine output of the new Zaxis-7 machines contributes to a higher workload.
The fuel efficiency of the ZX890LCH-7 can also be controlled by using the new ECO gauge on the cab’s multifunctional monitor. Also on show at bauma was Komatsu’s
new 20-tonne class electric hydraulic excavator that is equipped with a lithium-ion battery system.
The battery system is supplied by US-based Proterra and, since January 2021, the two companies have been jointly developing electric medium-sized hydraulic excavators and conducting PoC (proof of concept) tests on advance research machines at customer sites. The machine is scheduled to be introduced to the Japanese and European markets in 2023.
Komatsu also showcased a prototype for its first fully electric compact wheeled loader at bauma. Recently designed and built together with Moog, the designer, manufacturer, and integrator of precision
control components and systems, this new connected and automation-ready construction machine is battery-powered with zero-emissions and is now ready for joint testing.
Moog’s intelligent electric system includes an electric traction motor, lift, tilt and steering electric cylinders, power electronics, system control computer, battery, and battery management system. The integrated control system connects and coordinates the actions across the machine, while the all-electric actuators and motors provide the force to the machine’s traction and loading system. The integrated nature of the system enables industry-leading system efficiency and controllability.
“To achieve our CO2 emission reduction targets from products in use of 50% by 2030 from 2010 levels, to achieve carbon neutrality by the end of 2050, we are looking for promising technologies from suppliers to accelerate our electric machine development,” said Seiichi Fuchita, chief technology officer and president of the development division at Komatsu. “The machine built together with Moog combines the strengths of both companies and was finalized within a short period of time and we expect the joint testing will show the advantages of a full electric machine and will prove collaboration is beneficial for both sides.”
The companies say they are jointly testing the fully electric loader after bauma to prove that it can achieve a new level of efficiency, operating time, and comfort. They add that the test will show that the machine’s operating cycle is extended, and, with innovative assist functions, that it provides a “fatigue-proof” and comfortable environment for the operator to manage the machine and his day.
The prototype’s intelligent machine electrification system is designed to be connected and automation-ready. The system has the sensing and control capabilities needed for automation while the integrated software framework comes with built-in tools to coordinate multiple axes of motion and precisely controlled torque, velocity, position, and force.
Michael Wadsack, senior product manager - product marketing, at Komatsu EU, says the machine is a very early concept and will be tested for use on construction sites.
“It’s a compact machine (0.95m3 bucket) and not a typical quarry or aggregate machine,” Wadsack added. “However, customers from these segments are using also compact wheeled loaders – more as a support machine for cleaning or other services.
“At a later stage the electric concept can also be transferred to larger machines, and this is something to be considered in the long run.”
Komatsu says that the machine design replaces the loading and powerline hydraulic completely with electrical actuators.
At bauma John Deere announced its first offering of wheeled loaders in the United
Kingdom and Germany. After making their debut in the United States in September 2022, the 744 P-tier and 824 P-tier models are the first performance tiered loaders available in select European countries. As part of the Deere & Company family of brands, the Wirtgen Group will manage distribution of the P-Tier line-up through their European dealer network.
"Our customers are an integral part of our product development process and incorporating their input guides our product decisions around the globe," said Luke Gribble, solutions marketing manager for loaders and aggregates at John Deere Construction & Forestry. "That’s why we are excited to introduce the versatile and performance-enhancing P-tier models to our customers in Europe."
The manufacturer says the 744 P-tier and 824 P-tier loaders offer exceptional results at high levels with reliable components such as extra-durable axles and enhanced transmission capabilities. The extra-durable axles feature larger capacity front-axle input bearings, axle-shaft diameter and bearing size increases, and pressure-lubed frontinput bearings designed to help reduce heat, increase component life, and boost overall machine reliability.
The P-tier transmission includes a standard lockup torque converter, which adds additional torque during operation and improves fuel economy while transporting materials. The improved lockup logic is designed to increase performance and shift quality, while the updated speed sensors improve low torque shifting and downshift, improving performance when going into piles. Both loaders come equipped with the John Deere 9.0-litre engine that increases horsepower while minimising fuel consumption.
Electric actuation has previously been utilised by Volvo CE on an electric mini excavator prototype in 2017, while RG
LeTourneau pioneered the technology in the 1960s.
The first Volvo EC550E excavators to be deployed in Great Britain are proving to be a highly productive and profitable addition to Ashcourt Group’s fleet of earthmoving equipment from SMT GB.
Yorkshire-based Ashcourt Group was the first customer to place an order with equipment dealer SMT GB following the launch of the new EC550E crawler excavator and has now received the first two units in the country.
The EC550E features a larger bucket and upgraded structural components to enable operators to achieve productivity comparable with a much larger machine, while the new electro-hydraulic technology is said to deliver significantly greater fuel efficiency.
“We were instantly impressed by the specification and the development of the machine with the new hydraulic system, the new electronics, and the new engine technology, so it was prime that we got the orders in,” said Paul Martin, plant director at Ashcourt Group.
The family-owned construction company will use one of the new Volvo EC550E excavators for civil engineering projects, where its strong lifting capacity will come into play. In mass excavation configuration, the second machine will work primarily
at Ashcourt Group’s Partridge Hall Quarry, helping on earthwork jobs as needed.
Ashcourt Group typically runs the chalk quarry near Burnby, which it has operated since 2014, with one excavator to rip out material from the face and one loading shovel to fill the mobile crusher and screeners, sort the piles, and load the Volvo FH trucks to transport the aggregates and lime away from the site.
“Because chalk has a low profit percentage, it is better to have fewer machines and staff but with greater productivity,” said Ashcourt Group’s quarry manager Damian Towse.
For the last few years, the company has paired a Volvo EC480E crawler excavator with a Volvo L260H wheeled loader. The new EC550E excavator, however, promises 20% greater production than the EC480E in typical dig and dump applications thanks to its larger bucket and faster cycle times.
The larger bucket is enabled through the increased undercarriage dimensions (for stability), as well as the upgraded structural component dimensions on the frames, boom, and arm. The faster cycle times result from the engine’s high torque at a relatively low rpm combined with large displacement pumps. The 2200Nm (340kW) engine is well in line with much larger competitor machines.
Martin commented: “Fuel efficiency is
A recently purchased Cat 374 crawler excavator has been showing its worth in loading and rock-breaking operations at the Arids Garcia granite quarry near Barcelona in Spain.
As well as primary loading, the excavator has already proved useful in a spectacular and productive speciality of dropping a 7-tonne iron ball to break up rocks instead of using a hammer for oversize management. The process is carried out by one specialist operator.
The quarry has a long history of using Cat loading equipment, having first purchased a Cat 950 wheeled loader in 1972. Since then, all the loading and transport operations at the quarry have been carried out with equipment from the same brand.
Currently, the quarry has four Cat 30- to 80-tonne tracked excavators for loading the material after blasting: a 330C, 340F, the newly-purchased 374 and a vintage 329E which has been on the site since 1987 and is used for operating a hammer. Four rigid dumper trucks (Cat 769 and Cat 771 models) transport the material from the quarry
key for us with red diesel no longer being available and the price of fuel going up. It's important for our cost per tonne in the quarry but also when we are pricing up external projects. We are now looking at fuel month on month across the whole fleet and are trying to drive down the cost of fuel as far as we can. We hope that buying these two EC550E excavators will help us keep on top of that."
The improved fuel efficiency on the EC550E comes from the new electrohydraulic system, which uses independent metering valve technology (IMVT) instead of a conventional spool-type main control valve (MCV) – an industry-first in this excavator -size class. Oil is pumped exactly according to demand to eliminate hydraulic losses, reduce fuel consumption, and give excellent controllability.
Ashcourt Group has been an SMT GB customer for around a decade. Currently, with 120 pieces of plant equipment, around 98% of which are Volvo brand, Ashcourt Group is incrementally increasing its fleet to meet market demand for both internal and external projects.
“Besides the two EC550E excavators, we are purchasing 45 other new Volvos this year. It’s a massive investment for the business, totalling over £5m, and we’re looking forward to seeing all the new equipment come through,” Martin said. AB
face to the reception hopper at the crushing plant. Four Cat wheeled loaders – a 966M XE 962K, 950H and 936E - handle the finished products and load external trucks, while a Cat 438 backhoe carries out small work and cleaning tasks.
The quarry produces about 500,000 tonnes per year, with a maximum production capacity of 6,000 tonnes per day.
The new 74.17 tonne Cat 374 produces 361kW of net power and is the largest excavator operating at Arids Garcia, replacing the previous version of the 374 it owned.
It started operating at the site on August 24 this year, and quarry managing director Jordi Garcia is already impressed: “It is a very good machine, it’s the second one we’ve bought of the same model. Its main characteristics are reliability, speed of movement and low fuel consumption.”
“We are satisfied with the quality and efficiency of the equipment. The new 374 consumes around 37 litres of fuel per hour, less than half that consumed by a larger excavator we were operating seven years ago for the same level
of production. We are very happy with the service we receive on our equipment from our Cat dealer Finanzauto.”
Finanzauto is the Cat dealer for Spain and Portugal. Its full line of quarry products includes wheeled loaders, tracked excavators, rigid dump trucks, articulated dump trucks, attachments, as well as generators and other auxiliary machines. It has around 4,400 quarry customers in Spain, mostly small, family-owned companies.
Finanzauto’s Barcelona branch manager and northeastregion director Luis Sánchez says that rental is important for the company, representing 20% of its business. “Usually we rent longterm – six months to one year,” Sánchez says. “In rental, excavators and wheeled loaders are the most popular machines. The Cat 950, 966 and 972 wheeled loaders are very popular.”
The Barcelona Finanzauto branch has a 1,700 sq m workshop which normally has around four machines being worked on by up to eight mechanics, which undergo Cat Certified Rebuilds including engine and powertrain rebuilds.
Advanced testing of driverless articulated dump trucks (ADTs) and the growing presence of 4x4 ADTs are key talking points in the global off-highway hauler market. Guy Woodford reports
At bauma Munich 2022 (24-30 October), Bell Equipment showcased its new generation, two-axle B45E 4x4 ADT and a Bell B30E with a vehicle width of less than three metres. The South African-headquartered articulated hauler giant also highlighted its eye-catching and extensive autonomous articulated hauler testing programme.
As reported by Aggregates Business earlier this year, as an addition to its range of seven ‘traditional’ 6x6 ADTs, with payloads from 18 to 45.4 tonnes, Bell Equipment is the only global ADT manufacturer to offer a parallel three-model (B60E 4x4, B45E 4x4 and B30 4x4) range of two-axle ADTs for the past six years. Each ADT is aimed at a different market segment and represents a strong operating offer thanks to the advantages of the 4x4 ADT concept. In the right applications, Bell Equipment says the models outperform conventional rigid dump trucks (RDTs) that need good haul roads and the three-axle ADTs are designed for extreme off-road mobility.
Speaking to Aggregates Business at the exhibition, Brad Castle, territory manager at Bell Equipment, said: “You don’t always need a 6x6 ADT in a quarrying environment. In a B30E, for example, the 4x4 version has a 13% smaller turning circle than its 6x6 equivalent. That makes a big difference when you need to turn around on-site. The 4x4 haulers also reduce tyre wear and road maintenance costs, as you don’t have middle tyres like a 6x6 dump truck, which causes scuffing.”
Castle says the fact that Bell Equipment
and Doosan Infracore are the only two ADT manufacturers offering 4x4 articulated haulers has facilitated adoption by quarrying customers. “It is a niche product line but one that is very much needed. The 4x4 models have been developed through our Specials [applications] department in [Richards Bay, KwaZulu-Natal], South Africa. The truck’s power head is the same as the 6x6 equivalent, with the rear end being the difference. Our 4x4s have become known in the US as a ‘quarry’ truck. It doesn’t replace our 6x6 ADTs; it competes against [40-tonneclass] rigid dump trucks.
“The fact that our 4x4s have drive on both axles, compared to RDTs with drive on one axle, gives it a capability edge. The B45E 4x4 now comes with full suspension as standard, rather than the previous rigid rear with no suspension on the back. This offers more operator cabin comfort. We also offer a narrow or standard bin option, with the narrow bin preferred when operating under a crusher feed hopper.”
Castle stresses that fuel consumption and tyre wear are the two biggest costs linked to running an ADT fleet, with Bell Equipment “known” to offer the lowest articulated hauler fuel burn globally. Now, with its 4x4 ADT range, Castle says Bell Equipment also has a great offer on reducing fleet tyre wear compared to 40-tonne class RDTs.
“We had a quarry customer in South Africa running B60E 4x4s. They calculated their tyre wear costs against their rigid trucks, and they narrowed it down to how much in rands and cents the B60E 4x4s’ tyres were saving them – and it was 2 rand 28 per tyre per hour. You add that up over many working hours across a fleet, and it’s a huge saving.”
In 2019, Bell Equipment completed a €17mn facility at its Eisenach-Kindel assembly plant in Germany. The new production complex makes ADT components for the Northern Hemisphere. With around 12,000m² of floor space, the facility tripled the available space at the Eisenach-Kindel site. The new site directly adjoins the main factory hall. It provides in-house manufacturing of truck components in Europe for all seven Bell ADT models (B20E to B50E) assembled in Germany. Emphasising the commercial
advantage this gives Bell Equipment, Castle says: “Like any heavy equipment, our ADTs are only as good as their support. You must keep the machines running, or customers lose money, so having a factory in Germany closer to our [Northern Hemisphere] customers is hugely important. We expanded the factory significantly two to three years ago, and it’s now three times larger.” Bell Equipment announced earlier this year that it would increase its ADT manufacturing at Eisenach-Kindel due to the strength of the company’s North America and Western Europe sales. Kiesel, Bell Equipment’s German dealer, reports that its strongest ADT demand comes from quarrying businesses, particularly keen on the 4x4 haulers.
Since 2020, Bell Equipment has been working closely with xtonomy and Voestalpine at a lime quarry site in the Alps, where xtonomy has fitted its iTruck autonomous haulage system (AHS) on two Bell B30E ADTs with great results.
A link-up with Pronto AI, an American safety and automation technology developer, followed, including the official launch of Pronto AI’s autonomous haulage solution at MINEXPO 2021 in Las Vegas last September. A full test site has since been established in Reno, California, where three autonomously operated Bell B45Es and a Bell B50E are working in a sand mine. A second US test site, at a Texas sand mine, has also been created in recent months.
“We now offer an autonomous-ready articulated hauler, with our partners’ technology talking to the machine,” says Castle. “We have customers talking to both xtonomy and Pronto AI about real-world applications.
“I visited Pronto AI’s Californian quarry test site last month [September], and it was quite something to see the ADTs driving around the site with nobody inside. We are actively talking to customers in America about this technology. It is very software intensive and hardware minimal, with the
“The challenge with hydrogen is how to store it on the articulated hauler, as it takes up a lot of space”
Tristan du Pisanie
head of product development
have videos playing here [at bauma 2022] of our test sites, and you see the driverless ADT stop when someone gets near it. Where site connectivity allows, the autonomous hauling solution in quarries will really take off over the next year.”
Joining Castle in conversation with Aggregates Business, Tristan du Pisanie, Bell Equipment’s head of product development, highlights the articulated hauler major’s development on making its machines compatible with alternative fuels.
“All our ADTs are fully compatible with HVO (hydrotreated vegetable oil). We believe HVO is a very good low-carbon solution,
The biggest controversy I have heard recently is people who get palm oil from countries where it is unsustainably grown. That can give HVO a bad name. If you use the right raw material, it is a great solution for our customers that are carbon-reduction minded.
“Longer term, the size of our machine range is probably not compatible with where batteries are today; they are too big, and the energy cost is too high, making them too expensive. So, we are looking at alternatives, and the only two things that look feasible are hydrogen fuel cells and hydrogen internal combustion engines. Both will need a lot of investment around production and supporting infrastructure. The challenge with hydrogen is how to store it on the articulated hauler, as it takes up a lot of space, considerably more than conventional fuel, like diesel. You need around twice the size of a diesel fuel tank to run on hydrogen for four hours at a time. It must be said, though, that we don’t know for sure the direction our low-carbon journey will end up taking us, and I believe that this is true for all OEMs. Technology is changing every day, and we don’t know which solution will advance faster than the rest.”
Volvo Construction Equipment (Volvo CE) has announced its intention to invest SEK 360mn (€33.05mn) into its production facility in Braås, Sweden, between now and 2027.
The facility in Braås, long recognised for its environmental credentials, specializes in the design and manufacture of articulated haulers for the global market. It produced a fossil-free construction machine that was the first in the world to be delivered to a customer - an A30G which is now in use on customer NCC's worksite.
The decision of AB Volvo's board of directors to invest in Braås means that the factory will be adapted over the coming years to enable it to produce a larger range of articulated haulers with different powertrain types, reflecting the shift in demand towards equipment with more sustainable power sources.
The investment will be used to extend production capacity at the 45,000 m² site in southern Sweden to broaden the product range going forwards, with the addition of new buildings and production equipment. Setting its sights firmly on the future and in line with its purpose to build the world we want to live in – and workplaces we want to work in - Volvo CE will also invest in
automation and ergonomics to both reduce the need for employees to engage in repetitive tasks and create a safer work environment.
Pioneering manufacturing techniques is nothing new for Braås. Since producing one of the world's first series manufactured articulated haulers, the ‘Gravel Charlie’, a 10-tonne hauler, in 1966, the facility has been at the forefront of innovation. The site is most famous for producing the largest articulated hauler in the world, the 60-tonne class A60H, a real feat of engineering.
As well as constructing the world's first articulated hauler made from fossil-free steel, the engineering talent based here has also been instrumental in the building of the world's first prototype articulated hauler powered by hydrogen fuel cells – the concept Volvo HX04 – which is currently the focus of testing to develop future hydrogen solutions.
Braås is also leading the way in environmental protection and was the first in the construction industry to achieve a carbon-neutral operation powered entirely by renewable energy. In 2018, the site also became a zero-landfill facility.
"The transport and construction industry is undergoing a transformation with, among other things, an increasing number of electrified vehicles," says Jonas Lakhall, site manager at Volvo CE in Braås. "This investment will enable us to adapt and extend our production facility so that we can offer a broader range of machines – with different powertrains – to our customers and help them meet their emission reduction ambitions.
"It is important for us to continue to be at the forefront and make clear decisions to meet our Science Based Target commitment to achieve net-zero value-chain emissions by 2040. By adapting our production for electric machines, we are progressing along our electrification roadmap.”
Hyundai is now offering two ADTs, the HA30 and HA45, with capacities of 28 tonnes and 41tonnes respectively. The machines may be new to the Hyundai brand but feature proven designs and technology.
The machines are the well-accepted Doosan models built in Norway and now being offered in Hyundai branding following the tie up between the firms.
The firm claims equal weight distribution due to the sloping rear chassis frame
design, which is said to deliver stability by distributing more load towards the centre of the machine and resulting in a low centre of gravity. The machines also have the proven tandem rear-axle bogie configuration, which is said to offer a higher degree of articulation than competing designs and optimises ground contact to maximise traction. The machines also feature the articulation joint-turning ring mounted close to the front axle, which further helps to equalise load distribution between the front to rear and across the front axle during steering.
The trucks are powered by Stage V-compliant Scania diesels. The HA30A uses a five-cylinder, 9.3-litre, DC9 turbocharged diesel, developing 276kW and 1,876Nm of torque. The larger HA45A employs a six-cylinder, 12.7-litre DC13 diesel engine, producing 368kW and 2,476Nm of torque.
Both engines drive through eight-speed ZF automatic transmissions, with integrated retarders. The torque converter has lock-up in all gears, reducing fuel consumption and increasing efficiency. Fuel, AdBlue diesel engine exhaust fluid and a standard auto-lube greasing system can all be easily accessed from ground level. The engine canopy tilts forward for access to filters and fill points, while the cab structure can be tilted to provide access for repair and maintenance.
Hyundai’s Himate telematic monitoring system is fitted standard, with satellite and GSM connectivity. This allows customers to monitor productivity, fuel consumption, system warning and maintenance status remotely, reducing downtime and improving fleet utilisation.
Italian company Perlini has launched the new DP265WD dump truck for the quarrying, mining and public works sectors.
Referred to by the manufacturer as “the little one” in its range, the 26.5-tonne truck features new control electronics, modern GPS monitoring and electronic weighing systems.
The width of less than 3m allows for road transport without the need for special transit permissions or escorts.
The vehicle’s features include a brake/ retarder system with oil-bath brakes, oil-pneumatic suspension, and a Stage V Scania DC09 engine and an Allison 4430ORS transmission with update electronics.
Showcased at bauma 2022, the DP265WD also features a new digital electronic system which enables real-time monitoring of all system parameters, including remotely.
The on-board GPS available in the new dump truck connects to the vehicle’s power supply and constantly collects the status of its main parameters including position, speed, direction, panel status check on/ off progressive mileage and on-hours of the panel. It then transmits them via GPRS to a web-monitoring platform.
Requiring a robust, reliable articulated hauler to remove overburden for ten hours a day, five days a week, Erdbau Schrader found the perfect solution with Rokbak and its RA30.
In a pit near to Calbe, a town in the district of Salzlandkreis, in Saxony-Anhalt, Germany, around 6,000 tons of gravel is removed daily by earthworks specialist Erdbau Schrader. Gravel extraction started at the site around 30 years ago and it’s expected to continue for another three decades. Now navigating this
tough terrain, up and down steep inclines to unload around two kilometres away, is the Rokbak RA30, the latest addition to Erdbau Schrader’s fleet.
"We chose Rokbak because of its reliability and the price-performance ratio, as well as the hauler’s ability to cope with our long, heavy off-road operations,” says Ines Schrader, managing director of Erdbau Schrader. “We also wanted to ensure that our experienced operators would be able to work with maximum comfort.”
Erdbau Schrader was founded in April 2011. The company specialises in removing overburden for gravel extraction and renaturation, utilising its machines at several locations near its bases of Staßfurt and Brumby. Erdbau Schrader already owned four Terex Trucks TA300s – which it bought before Terex Trucks rebranded to Rokbak in September last year. In July, the company added the RA30 to its fleet, purchasing the machine from Rokbak dealer KlarmannLembach. Three other articulated haulers are working alongside the RA30 at the pit near to Calbe.
“The Rokbak RA30 is a strong, reliable and high-performing machine – which is exactly what Erdbau Schrader needed,” explains Klarmann-Lembach salesman Thomas Keil, who recently visited the Calbe site with Rokbak to see the RA30 in action. “Our confidence in the Rokbak brand and the haulers is such that, when we were approached, we could assure our customer that the RA30 was the ideal addition to their fleet.”
Erdbau Schrader’s articulated haulers move at full power five days a week, for ten-hours from 6am until 4pm. Materials from the site are transported over sandy and spongy ground for two kilometres before being unloaded at a railway loading station. The RA30 has to navigate tough terrain, prove its durability over long shifts and be a machine that employees want to operate.
With the capability of transporting a
a maximum engine power of 276 kW (370 hp) with a heaped capacity of 17.5m3 (22.9yd3) and a maximum torque of 1880 Nm @ 1400 rpm. All Rokbak haulers can be relied upon to operate effectively and efficiently, with optimal traction in difficult terrain, combatting steep inclines with ease. Routine maintenance is as quick and efficient as possible, keeping service time and costs to a minimum.
Furthermore, the factory-approved parts are backed by a two-year/6,000-hour warranty – one of the most comprehensive guarantees in the industry. Operational comfort is also at the forefront of the RA30 design. A spacious, ROPS//FOPS-compliant, pressurised cab with excellent heating, ventilation and air conditioning (HVAC) keeps the operator comfortable and focused.
“Our operators have highlighted to us that
reliable and easily adapted to our heavy, difficult working conditions,” says Uwe Schrader, who oversees machine usage at Erdbau Schrader. “The notable construction of the front axle, with true independent front suspension, offers a very high level of operator comfort across a comprehensive ten-hour working day, which is further elevated by the fully automatic eight-speed transmission.”
The RA30’s EP320 transmission comes with eight forward gears as well as four reverse gears and features a top speed of up to 55 km/h (34 mph), high overall gearratiospread, equal ratio steps between gears and optimised gear shifting with partial load shifts. All of this means that the RA30 offers lower fuel consumption with smoother gear shifting and thereby higher levels of operator comfort as well as faster cycle times and reduced carbon emissions.
Overall, the entire drivetrain helps the hauler deliver class-leading rim pull for superior performance and productivity. It also ensures the machine offers excellent navigation and fast haul cycles. The RA30’s long-life transmission fluid increases the length of time between oil maintenance intervals to 4,000 hours. This helps customers achieve increased productivity and uptime, as well as lower cost per tonne.
“The RA30’s transmission strikes the perfect balance between efficient power, effective gearing and weight distribution, allowing the hauler to move more loads quicker,” concludes Thomas Schmitt, Rokbak’s customer support manager for Europe. “The RA30 is simple to operate and easy to maintain, it delivers low total cost of ownership with a fuel-efficient performance and high productivity – so it’s no wonder the Erdbau Schrader team are so happy with it.” AB
Doosan gave a world premiere at bauma Munich 2022 of itsfirstever 4x4 articulated dump truck (ADT). The new 4x4 version of the DA45-7 ADT complements the company’s standard, popular range of 6x6 ADT models, including the 28-tonne DA30-7 and 41-tonne payload DA45-7. The 4x4 DA45-7 aims to compete
with 40-tonne-class rigid dump trucks.
In Doosan’s new 4x4 ADT, the front truck and cab unit is the same as in the original 6x6 model, with modifications being made on the rear dumper unit only. Featuring a ZF EP8-420 transmission, the 4x4 DA45-7 is a two-axle ADT with twin wheels
at the rear, and with a dumper section like that on RDTs in the 40-tonne class.
Speaking to Aggregates Business at the showpiece event, Beka Nemstsveridze, Doosan’s ADT product manager, said: “This machine is an alternative to the traditional 40-tonne-class rigid dump truck applications. When
it starts raining and there is mud on a smoother surface, a rigid dump truck can stop working. The DA45-7 4x4 fills this gap and can increase the working season. You can also climb higher inclines with this ADT than a 40-tonne RDT, and there is a price difference between a rigid dump truck and an ADT 4x4.”
No matter how challenging your needs, EARTHMAX SR 41 is your best ally when it comes to operations that require extraordinary traction. Thanks to its All Steel radial structure and the special block pattern, EARTHMAX SR 41 provides excellent resistance against punctures and an extended service life. In addition to long working hours without downtime, the tyre ensures extraordinary comfort.
EARTHMAX SR 41 is BKT’s response to withstand the toughest operating conditions in haulage, loading and dozing applications.
For info: europe@bkt-tires.com
The comprehensive Matec Industries’ plant solution for AAL Recycling
Washing plants are a crucial and evolving element of the production of high-quality aggregates and sands. Guy Woodford reports on some of the latest in-demand solutions
UK-based AAL Recycling (AAL) began trading more than 30 years ago as a one-man, one-truck, one-excavator company. It is now one of the largest demolition, hauling, recycling and excavation companies in Jersey and the Channel Islands, employing more than 85 people and with a fleet of more than 70 vehicles.
Currently, AAL operates the island’s commercial and household construction waste-recycling centre in La Collette, supporting the island’s sustainability project in every way possible. The demolition and excavation area has had the company’s fastest growth, thanks to managing some of the most complex projects developed on the island in recent times. Given the great growth of AAL Recycling (AAL), its owner and CEO, Alan Langlois, approached Matec Industries (Matec) to find innovative and technological solutions that would allow processing up to 150t/h of recycled material, with water consumption of less than 25m³/h.
The plant would have to comply with all current regulations, ensuring low energy consumption, and maintaining a high washing and sorting performance of the processed material.
To ensure that more than 95% of water used during washing and sand sorting was recycled, a complete wastewater treatment and filtration plant was installed by Matec for AAL. From the collection tank, turbid water is pumped into the decanter through the stainless-steel piping via the
use of a centrifugal pump. The flocculating polyelectrolyte solution is injected into the feed line of the settler and reacts with the suspended solids in the liquid, speeding up the natural sedimentation of the mud particles.
The turbid waters arrive in the vertical decanter where the reaction of the polyelectrolyte takes place, aggregating the sludge particles and causing them to precipitate. The clarified waters, free of suspended solids, then rise to the top of the decanter and by weir and are collected in the perimeter channel located at the top of the decanter. They are then conveyed to a stainless-steel clean water tank. At this point they are ready to be reused in the production cycle again through the clean water relaunch pump.
The sludge, meanwhile, settles inside the cone and is discharged once it reaches the required consistency by the opening of the automatic valve. It is sent to the homogeniser tank below where it is kept in slow agitation. At this point it is ready to be fed into the filter press. The Matec filter press is an industrial machine designed to achieve the best results in dewatering industrial or civil fluids (often referred to as sludge).
Matec filter presses are designed for use with High Pressure Technology (HPT), capable of working at both operating pressures common to all filter presses and at higher pressures.
The wastewater treatment and filter press module consist of a 1500×1500 filter press with 170 TT plates; a BIFANG 100,000litre
sludge homogenisation tank; a 220,000litre static vertical decanter; a 6,000litre/minute clean water pump; two clean water tanks (10,000litre and 40,000litre capacities, respectively); a BIFLOC automatic flocculant management system; a 6,000litre/minute centrifugal pump for loading vertical decanter; and a 50,000litre dirty water tank.
An AGGRETEC 150 semi-mobile screening and washing unit, and a SCRUBTEC LW-080500 heavy scrubbing unit were chosen for washing, grading and drying AAL’s product range. AGGRETEC is Matec’s rapid
AAL Recycling’s Matec solution allows for the processing of up to 150t/h of recycled material, with water consumption of less than 25m³/h
including aggregates, recycling, reclamation and mining. Being a semi-mobile system, it is easily transportable making it ideal for working on construction and demolition sites. The solution for AAL consists of three conveyor belts (for 0-2mm, 2-4mm, 25-40mm product); a sand recovery unit with hydrocyclones; three-deck vibrating screens; a magnetic belt separator; a feeder screen; and a loading hopper.
The SCRUBTEC LW-080-500’s combination of an intense cleaning action and its removal of light contaminants are said to make it a key component in construction and demolition waste-recycling systems. It is also ideal for aggregates and mined materials with high clay content.
The material is rubbed through inclined paddles arranged in series inside the machine. These paddles slow down the material feed when it is very dirty but ease the feed when it is cleaner. The entire washer is coated with an interchangeable wearresistant steel armour.
The SCRUBTEC LW-080-500 comprises a log wash, impurity screen, a dryer/finishing screen, three conveyor belts (16-25mm, 10-16mm, 4-10mm product), and a pre-screening solution.
Skipway recently opened its doors
technology is supporting the Northern Ireland-based waste-management firm to divert over 95% of its trommel fines from landfill. The 16-17th November showcase began with a guided tour of CDE’s worldclass manufacturing facility in Monkstown, County Antrim, Northern Ireland.
Guests saw the 300,000 sq. ft. facility in operation, where CDE’s advanced wet processing solutions are commissioned for customers around the world, from Creagh Concrete in Toome, Northern Ireland, to Posillico Materials LLC on Long Island, New York; Repurpose It in Melbourne, Australia, to Feiring Bruk, Norway.
As part of a long-term investment strategy in its manufacturing capabilities, CDE recently commissioned two new Bystronic high-speed sheet-metal laster-cutting systems. The systems integrate with a new 400-tonne steel storage and management system incorporating fully automated loading and offloading of the laser cutters.
Following the tour of CDE’s facility, guests were invited to tour its latest trommel fines solution, designed and engineered for Skipway.
The new 50tph trommel fines plant, the first in Northern Ireland, has been commissioned at the waste-management
rm’s processing site in Dunmurry, near Lisburn, and is one of of three recycling facilities it operates (the other two are in Belfast and Portadown). The CDE solution for Skipway incorporates an AggMax modular logwasher, EvoWash sand wash plant with Counter Flow Classification Unit (CCFU), AquaCycle thickener and static screens.
The state-of-the-art plant diverts trommel nes from landfill and converts the material into a resource by producing recycled products with the same specification and quality as quarry-grade sand, therefore making it suitable for concrete and building products while also improving the quality of other recycled aggregates such as pipe bedding and recycled hardcore.
Skipway director Trevor Heatrick said: “By putting trommel fines through a wet processing plant, the clean sand and aggregates recovered can be resold and reused in the secondary aggregates market. This minimises disposal costs, as well as closing the loop on challenging waste streams to create a more circular economy and generating additional revenue for our business.”
Mansfield Sand Company Limited has been quarrying sand in Nottinghamshire, England, for more than 170 years. It is known countrywide as a supplier of materials for top-class sports and sporting venues across the UK and Ireland. It supplies sand material to 16 Premier League clubs, 16 Championship clubs and 120 other football league and non-league clubs for use in their stadia and training ground facilities.
Besides sand for football stadiums, Mansfield Sand also produces a wide range of products for landscaping and equestrian uses, including championship golf and world-class show-jumping arenas, as well as asphalt sand, foundry sand, and sand for concrete and brick products.
In 2014, Mansfield Sand wanted to upgrade its plant and control system to process a new deposit. It required a plant
that would process 300tph of -65mm sand to manufacture their various products, including golf sand that meets United States Golf Association standards, block pavior sand and asphalt sand.
In addition to this requirement, the local planning commission also set a noise restriction in place so the new plant would not disturb some rare birds nesting near the boundaries of the site. It was at this time that Neill Rowland, McLanahan applications engineer, knocked on their door. He explained that McLanahan could offer them a Hydrosizer sand plant that would produce five different products in one pass.
“One of the things that sold the plant was McLanahan’s technical ability to offer this,” said Rowland, noting that experience and confidence also played a role in Mansfield Sand’s decision to work with McLanahan.
Mansfield Sand was familiar with Hydrosizer systems from an existing plant they had been operating for several decades, so they had already realised the benefits of Hydrosizers for what they were trying to achieve.
“When you start getting down to really fine sizing, Hydrosizer classification is really more efficient and more cost-effective,” explained Rowland. “The Hydrosizer is the only piece of equipment suitable for the application to achieve the tight tolerances.”
McLanahan installed a Hydrosizer plant incorporating McLanahan Pumps, Sumps, Hydrocyclones, Separator, Dewatering Screens and Blending System with the ability of blending to 1% accuracy to help Mansfield Sand meet the strict specifications required of their final products. The final products are discharged at less than 15% moisture, which creates stockpiling efficiency and allows for further drying processes.
To meet the requirements set forth by the planning commission, the entire plant is housed within a galvanized structure, clad and insulated to reduce the noise level. The plant’s components are also lined with rubber to protect them from the abrasiveness of the sand. After some calculations from Mansfield Sand’s laboratory technicians, the company discovered the waste from the wash plant would fill their lagoon within 18 months, so it turned to McLanahan for help with its water management.
McLanahan provided an Ultra Fines Recovery System to recover fines down to 40 microns to extend the life of Mansfield Sand’s lagoon system.
“Anything bigger than 40 microns is recovered,” Rowland said. “Anything less is going to the lagoon.”
Since commissioning the Hydrosizer plant, Mansfield Sand Company has not received a single customer complaint due to the performance of the equipment. The plant’s modern control system gives Mansfield Sand the ability to adjust the product to meet consumer demands.
“The plant does have quite a bit of functionality for them to develop product and potentially react to market changes,” explained Rowland.
In four years of operation, the Hydrosizer plant has proven to be both stable and reliable. It produces a consistent 280tph, and to date, the plant has produced 2 million tons of sand for Mansfield Sand Company. Furthermore, the Ultra Fines Recovery system has doubled the life of its lagoon by allowing Mansfield Sand to capture the fine material.
“It’s a low-value product, but it’s a product they can sell, and it’s a product that isn’t filling their lagoon, which is the real benefit to them,” Rowland said.
Overall, Mansfield Sand is pleased with the Hydrosizer plant and Ultra Fines Recovery System.
“A good team effort by both parties and a professional working relationship providing a technologically advanced plant gives Mansfield Sand flexibility, controllability and future-proofing for the estimated 30-year life of the site,” said Richard Abraham, managing director of Mansfield Sand. “Now, four years
on, we continue to have a fantastic working relationship together. Our process plant continues to manufacture our premium quality sands to Mansfield Sand’s exacting standards.
The partnership between Mansfield Sand and McLanahan has rested on the McLanahan team’s awareness of the importance we place on the reputation of our products and our respect for their experience. The partnership had a lot to prove, and it proved to be a great success.”
Terex Washing Systems was at bauma 2022 in Munich, Germany, where it staged a live demonstration of its AggWash 60-1 washing and recycling plant, capable of producing up to four high-quality aggregate and up to two sand products at up to 70t/h.
An innovative plant that integrates heavy attrition with sizing, lightweight contaminants removal and hydrocyclonebased fines recovery in a single highly portable chassis, AggWash is a rapid-install solution for a wide range of applications within the aggregates, recycling, remediation and mining sectors.
The AggWash 60-1 has a modular design and comes pre-plumbed with a single connection point for quick set-up. The machine’s log-washer angle adjustment allows increased material retention and removal of trash, while the overband magnet on its feed conveyor removes ferrous metals. The AggWash 60-1’s rubber-lined pumps, cyclones and transfer points are also said to extend the plant’s life. AB
With materials costs rising and resources depleting, regulations are calling for the adoption of sustainable solutions and recycling of construction waste. Recyclingplant providers say the equipment is already there to produce the sustainable construction materials of tomorrow. Liam McLoughlin reports
As the construction industry continues to cope with issues around the availability and cost of raw materials, the potential of construction, demolition and excavation (CD&E) waste to address the challenges facing the sector has been highlighted.
CDE, the sand and aggregate wet -processing solutions provider for the natural -processing and waste-recycling sectors, set out the role of its technology in supporting the circular economy and zero-waste agenda at this year's bauma event in Germany (24-30 October).
The company was joined on its stand at the Munich exhibition by a number of its European customers for a series of round table discussions on the future of recycling. One of these was Norway-based sustainability pioneer Tom Wilhelmsen. The company’s waste-management division Massebalanse Norge is shortly set to commission its new CDE waste-recycling plant at Disenå in Norway’s second-largest county, Innlandet.
Tom Wilhelmsen’s CEO Gilberto Enkerlin says that, as part of the company’s sustainability drive, it has changed the way it manages its construction projects and this has not come without challenges .
“We have had to find synergies with our partners in order to find [new] ways of doing the same old thing,” he says. “We have done this by establishing one of our sister companies that has a temporary storage solution within the city lines.”
This means the company is able to deposit
material within 3-4km of the project that usually went directly to the landfill 30-40km away, and immediately load with aggregate ready for the project.
“The future is here today,” says Enkerlin. “We are implementing the technology daily which is way beyond the scope of what the normal construction companies are implementing. By looking at being a pioneer within the industry we are able to influence the whole construction industry in Norway one step further towards the right direction.”
The company has looked at all stages of its supply chain as part of its sustainability efforts, including quarries and landfills. Because of this , company founder Tom Wilhelmsen selected the CDE recycling plant, which is scheduled to be commissioned by the first quarter of 2023.
CDE's head of business development for North West Europe, Eunan Kelly, observes: "In the current economic and social climate, with materials costs rising, resources depleting, and regulations calling for the adoption of sustainable solutions, we should look to the technology of today to produce the sustainable construction materials of tomorrow; how CDE's waste-recycling solutions in their trademark blue can support the industry to transform CD&E waste into certified, in-spec sand and aggregates."
Earlier this year, a package of European Green Deal proposals was presented with a view to make sustainable products the norm within the EU internal market. The revised Construction Products Regulation (CPR) emphasises the value of construction to the EU as a key employer and economic
contributor. However, it also highlights the adverse impacts the sector has on the environment, as one generating some 30% of the EU's annual waste and contributing significantly to its domestic carbon footprint and emissions.
The construction industry is a major economic driver; in the EU alone, 25 million people are employed across five million companies, according to data from the revised CPR. So, when the COVID-19 crisis gripped economies and construction output fell to some of its lowest-ever levels, it was no surprise that robust recovery plans with a clear focus on investments in infrastructure were announced by nations around the world to rebound and stimulate economic growth.
However, the cost of raw materials and their availability remained a deepening challenge for the sector.
Materials shortages and their rising costs are not entirely symptoms of the pandemic, but they have been exacerbated by it and have become more acute, according to CDE's business development manager for the DACH region, Christoph Baier.
"Every day we continue to extract our fastdepleting natural resources to support rapid urbanisation and our modern, technological lifestyles,” says Baier. “Essential to this is sand, the second-most consumed natural resource after water and the most consumed solid material on earth."
In April, the UN Environment Programme (UNEP) published 10 recommendations to avert the impending sand crisis. It referenced how the use of sand, gravel, crushed stone and aggregates has tripled in the last two
decades, reaching an estimated 40-50 billion metric tons per year (UNEP 2019).
While COVID-19 economic-recovery packages may help to stimulate growth, Baier says they must be conditional on building back greener, more sustainably.
A circular approach is the only answer, Kelly corroborates.
"It can be the means to equip us with the resources needed to supply a sector charged with a key role in the economic recovery while addressing our collective environmental footprint by reducing waste-to-landfill volumes and extending the lifespan of precious natural materials,” he adds. “All the while continuing to supply a resource-intense sector with the materials it requires; materials often trucked out of our urban centres where they are needed most."
Kelly says the technology needed to extract recycled sand and aggregate resources from CD&E waste that are equivalent to their virgin quarried counterparts is already in operation throughout Europe.
CDE says it supports materials processors to realise the value locked in CD&E waste. Using innovative wet -processing technologies that scrub material, float off lightweights (demolition debris) and classify end products, this waste stream can be repurposed to produce washed materials free of contaminants and suitable for use in highvalue construction projects.
To date, CDE solutions have supported companies around the world to divert over 100 million tonnes from landfill.
"These are far from 'alternative' materials," Kelly explains. "Many material processors utilising CDE technology are successfully producing CE- and BSI-certified concrete products, including competitive concrete for non-structural – but still highvalue – construction projects, with some applications successfully achieving beyond C45 spec."
backdrop of the COVID-19 pandemic and continued rises in the cost of raw materials, these issues have been heightened and highlight the urgent need to radically adjust how we utilise the resources around us in a more circular fashion."
Finland-based aggregates equipment company Metso Outotec is in agreement that there is an imperative need to give new life to construction waste. It says legislations around the world are calling for more recycling of construction and demolition waste, and adds that re-using crushed concrete instead of natural rock and recycling metal saves both the environment and the constructor resources.
Pasi Tulonen, product manager of the Lokotrack contractor line at Metso Outotec, explains that the teardown of structures such as demolished buildings, old roads or bridges creates the opportunity of granting a new life to these materials through recycled aggregates.
essential that the units are designed to handle a variety of materials included in the recycled waste while separating the valuable metals with magnetic separator as well as lightweight materials from screened aggregates with a windshifter.
He adds that different products fit better for different types of waste. For instance, if you still have a great mix of materials after crushing, Metso Outotec mobile screens such as Lokotrack ST2.3, ST2.8, Nordtrack S2.5 and S2.11 are ideal for the job, as they are designed to process any type of concrete, asphalt, or slag.
“Our Lokotrack LT1213S mobile impact crusher offers a variety of features for recycling applications and has an integrated screen, which has made it a very popular solution for recycling applications as it provides great results,” says Tulonen.
Metso Outotec customer Joona Ahonen, of Ahosen Palvelut in Finland, comments on its deployment of an LT1213S impactor crusher: “The most important thing for generating profit will be that the machine continues to work with no sudden shutdowns. With the new Lokotrack, we can crush demolition concrete and asphalt, and produce good volumes of clean grades that meet the customers’ needs.”
Swiss-based global building materials and aggregates group Holcim has launched its upgraded 2030 climate targets, validated by the Science Based Targets initiative (SBTi), in line with its sector's new 1.5°C sciencebased framework. With these upgraded targets, Holcim confirms its commitment to decarbonise building in line with the most advanced science.
Luiz Amaral, CEO of the Science Based Targets initiative, commented on Holcim’s move: “This company is setting an example for the rest of its industry, and I urge others in its sector to set their own targets too."
DA Mattsson, based near Stockholm in Sweden, diverts almost 100% of its incoming CD&E waste from landfill through its CDE wet-processing operation. The company produces high-quality sand and aggregates that meet EN 12620 specification, and it supplies these concrete materials to the Stockholm construction market.
"We are faced with a myriad of challenges,” Kelly says. “Set against the
“After a selective demolition has taken place, instead of dumping the concrete into a landfill, it is possible to crush the waste material in order to give it a new life,” Tulonen says. “We in Metso Outotec have decades of experience in crushing and screening. We have machines that are designed to process construction waste into re-usable aggregates, these are mobile impact and jaw crushers, as well as mobile screens.”
Tulonen says that using the right crusher, depending on the materials that need to be processed, and sorting them accordingly afterwards are crucial exercises for a successful recycling operation. To succeed in the crushing operation, for instance, it is
Jan Jenisch, CEO Holcim, said: "At Holcim, we are committed to decarbonising building for a net-zero future. When I see the thorough decarbonisation plans we are deploying across our business, I am confident that we will decarbonise building at scale.”
In its new 2030 targets, Holcim upgraded its target to reduce scope 1 and 2 emissions per ton of cementitious by 25% by 2030 from a 2018 base year. AB
Barbara Gregorio, divisional product marketing manager Innovative Energies and Digital Solutions, Atlas Copco Power and Flow, discusses how portable power solutions are part of a wider solutions portfolio helping to achieve more sustainable quarries
Emission norms are changing operations in the entire construction industry, including quarries. On the journey towards stronger compliance with emission standards, the focus is now way beyond only health and safety regulations for operators. While productivity and efficiency remain the key priorities, the need for a balance with more sustainable solutions is now becoming more of a need than an option.
Quarries are evolving
Quarries are buzzing with round-the-clock extraction operations which feed granite and aggregates into the construction and infrastructure industries. When versatile giant equipment operates with high productivity targets and tight deadlines, emission control in mines and quarries becomes a critical focus.
The face of mining and quarrying is changing with a keen focus on contributing towards reduced energy consumption and higher energy efficiency. (Source: The integrated energy and climate change policy laid out in December 2008)
The changing role of construction equipment in quarries
From lighting to pumping to power generation, sustainable equipment profiles are becoming an integral part of the quarry portfolio. A few key ingredients in the sustainability strategy for quarries can include:
to meet their sustainability goals. Hence the push towards electrification in quarries is an important development which can be supported with standalone or hybrid options to cover unpredictable power loads.
The EU and international emission regulations aim to create a low-carbon and energy-efficient economy with goals to:
• Reduce greenhouse gases by 20%,
• Reduce energy consumption by 20%
• Meet 20% of the EU’s energy needs from renewable sources by 2020
Fuel efficiency: With Stage V and Euro 6 diesel engine regulations, advanced fuelefficient engines are the need of the hour. Forward-thinking construction equipment manufacturers are gearing up to get their machines equipped with the latest technology engines while demonstrating their commitment to a better environmental footprint.
Electric models: With stricter emission regulations, the transition from diesel to low-diesel-consumption equipment to electric models is gaining momentum. Not just electric cars, but also heavy-equipment manufacturers are rolling out electric versions of their earlier diesel-driven models
Hybrid: The new buzzword in the sustainability guide is hybrid. There is a whole new world emerging for hybrid solutions to bring in better energy efficiency with a substantial impact on emission levels. Hybrid power solutions are becoming a crucial asset in the quarry equipment profile so that energy consumption is managed with high efficiency while minimising costs, and quarries are more self-sufficient with clean energy sources.
Digitalisation in quarries: In the quest to achieve sustainability goals, safe operations in quarries remain a priority while bringing in energy-efficient operations.
Digitally connected intelligent machines dot the quarry landscape and reduce downtime while increasing efficiency in
quarry operations. Atlas Copco is launching new intelligent controllers which will optimise energy generation, distribution and consumption through advanced data management to improve machine performance and efficiency.
Pumping solutions: Quarries are prone to flooding, as is the case for abandoned quarries or underground quarries when they are dug below the water table. Managing the water that is accumulated from heavy rainfall and groundwater seepage in quarries is a crucial task which must be done effectively in order to protect construction equipment and allow for operations to continue.
The advanced pump portfolio from Atlas Copco offers electric submersible pumps under the WEDA pump umbrella, which has innovative features including a high performance-to-weight ratio, hardened high-chrome impellers and Wear Deflector Technology, which is designed to minimise wear, ensuring durability for a longer working life. By meticulously redesigning the pump range with the latest 3D modelling techniques, the pump’s efficiency can be increased while lowering unplanned downtime issues in tough working environments like quarries. Quarry owners will less often find themselves forced to replace pumps as service life and repairability are built in from the ground up. The future of pumps will be increasingly sustainable as electrical pumps will further reduce emissions when powered with fossil-free electricity.
technology for smart load management resulting in reduced emissions, better operational efficiency, lower total cost of ownership and higher ROI. When operating standalone in island mode, with zero emissions and zero noise, these modular energy storage systems operate as a primary source of power and accelerate the journey towards clean energy with practically no maintenance.
Energy storage systems: As the use of energy storage systems becomes more popular, new sustainable innovations will continue to bring more energy efficiency in quarries as well. Atlas Copco’s technologically superior Li-ion battery energy storage systems, when paired with its low fuel-consuming generators, redefine hybrid
Design innovation: With skilled design engineers and expertise in both generator and pump product development, a combined green solution engineered to dramatically reduce fuel consumption and CO2 emissions is an expected outcome. New emerging technologies like submersible pumps operating with medium-sized battery packs will transform the hybrid canvas and further reduce the total cost of ownership in quarry operations.
Renewable energy revolution: With renewable energy generation gaining
momentum, solar power has made its way into Atlas Copco light towers and battery pack development. The HiLight S2+ solarpowered light tower taps into solar energy to reduce CO2 emissions by up to 6 tonnes as compared with other technologies. This is a great asset in quarries for night extraction operations where bright and safe light enables operations to continue for 11 hours at a stretch. By reducing electricity costs in quarries with solar-energy options, compliance with CO2 emissions and noise regulations allows work in quarries to carry on autonomous operations all year round when the solar power is adequately tapped.
HVO – biodiesel hydrotreated vegetable oil is a next-generation fuel that further nurtures sustainability goals into construction equipment DNA, reducing the carbon footprint of the machines. This renewable fuel offers a 90% CO2 emission reduction compared to diesel and lasts longer in the tank, which in turn reduces the risk of water ingress, microbial growth, and overall risk of contamination to equipment, making power and pumping operations cleaner and greener.
For Atlas Copco, a quarry is not just a pit in the ground. It is a highly productive worksite which plays a crucial role in core infrastructure development such as roads, metros, expressways, airports, and highway expansion with its aggregate output. As quarries aim to complete the production cycle with as low as possible carbon footprint and with high productivity outcomes, Atlas Copco will focus on continuous innovations in engines, fuel, renewable energy, product design and other ways to calibrate a better balance between energy production and consumption.
With the ever-evolving new, clean energy technologies from Atlas Copco’s generators, pumps and light towers, the journey towards more sustainable quarries is better defined and more achievable.
Atlas Copco is committed to contributing to low-carbon emissions with state-of-theart advanced equipment serving various worksites, including quarries. AB
Tower lights and mobile charging systems can be valuable equipment for quarry operators, especially those working in more remote areas. Guy Woodford reports
Pilot Crushtec has enjoyed considerable success with its Generac mobile tower lights since introducing them to the South African market more than a decade ago. The tower lights have found favour with customers across a range of industries, including quarrying, mining and construction, and units are now operating throughout the southern African region, as far north as the Democratic Republic of the Congo (DRC).
“Pilot Crushtec, of course, is best known for its comprehensive range of crushing and screening solutions,” says Fernando Abelho, export manager at the company. “We introduced the tower lights as a diversification from our main product lines and we’ve never regretted the decision. We’ve notched up truly impressive sales, many of them repeat orders from very satisfied customers.”
When it decided to add tower lights to its product range, Pilot Crushtec concluded a partnering agreement with Tower Light, headquartered near Milan in Italy, one of Europe’s most successful tower light manufacturers. This company has since been acquired by US-based Generac, but Pilot Crushtec is still supplied from the Italian factory.
“The quality for which Tower Light was renowned has continued under Generac which has further developed what was already an outstanding product range,” says Abelho. “The Generac diesel-powered tower light is a truly premium product which is very compact, ultra-safe to use and extremely economic to operate. The attention to detail can be seen everywhere in the machine. The electrical wiring, for example, is all
all-in-one control panel has been developed by Generac specifically for use in light towers. In addition, all the units come with liquid containment tanks to prevent environmental contamination.”
While Generac has a very extensive range of tower lights, Pilot Crushtec focuses on a
single model, the VTevo, available in two variants, one equipped with a Kubota watercooled engine and the other with a Yanmar air-cooled engine. Standard features on both machines include an earth spike, a 4kg fire extinguisher, and the necessary switchgear to allow connection to a mains electrical supply when available. A low-speed, singleaxis towing trailer allows a high degree of mobility on site.
“The two variants both offer 4 x 320W energy-saving LED floodlights, able to illuminate an area of up to 4 500m²,” says Abelho. “The VTevo-Kubota, however, has some additional features that the VTevoYanmar lacks. These include a day/night sensor and a GTL-01 controller which provides a programmable stop/start, maintenance alarms and additional safety and protection features.
“We find that some customers prefer the lower spec VTevo-Yanmar as it is more competitively priced, and they feel they don’t need any high-tech features. Many others, though, opt for the VTevo-Kubota. They find the programmable stop/start to be indispensable and a great time-saver.”
Abelho also stresses the energy-saving aspects of the VTevo. “The G4 LEDs used are industry-leading and have a life expectancy
of 50,000 hours. They allow up to 220 hours of runtime on a single tank of fuel. Their efficiency is such that they can save up to 75 % of the fuel that traditional towers equipped with metal halide lights use, at the same time reducing carbon emissions by up to 10 tonnes per year.”
During Deutz’s recent Deutz Days showcase event in Germany (21-22 October 2022), the drive specialist presented its nextgeneration PowerTree mobile charging system, which can be used in the absence of any power infrastructure by customers including quarry operators.
The latest PowerTree version offers attractive features for Deutz customers, including an improved design that makes the 10ft container easier to transport. It is now also possible to scale the battery capacity, allowing for optimal adaptation to the customer’s technical and commercial requirements.
Doosan Portable Power (DPP) has launched its new quarryingcompatible G100 Stage V-compliant generator. Providing a prime power output of 100kVA, the new unit is powered by a Cummins F3.8 82kW diesel engine. Despite featuring an identical footprint to its predecessor, the Stage V G100 offers improved performance in most areas, including customer connections, autonomy, fuel consumption and noise levels. Thanks to its Cummins engine, service intervals have been extended to 1,000 hours and the risk of engine issues at low loads –a common issue in the rental market – is said to have been eliminated. The G100 is also compatible with hydrotreated vegetable oil (HVO), also known as renewable or green diesel, further reducing emissions. AB
Leading off-highway engine manufacturers have made sustainability a priority alongside the renowned high performance and efficiency of their solutions. Guy Woodford reports
Cummins has been at the cutting-edge of power solutions for over a century.
Moving forward, Steve Nendick, Cummins’ marketing communications director, notes that the US off-highway engine major has a two-pronged strategy: to continue to advance internal combustion engine technology with further advancements in performance, efficiency, and compatibility with cleaner fuels; and to innovate zeroemissions solutions like hydrogen fuel cell and battery technology.
“For construction and aggregates markets, the diesel engine will remain the go-to choice for the majority of machinery due to lack of infrastructure in electric charging and hydrogen supply,” explains Nendick. “While this alternate technology and infrastructure is being developed, Cummins can help operators now with solutions that reduce overall environmental impact of their operations. As well as reducing emissions, they will maximise the efficiency and performance of their machines and cut running costs. Operators can continue to use a tried and trusted power solution.”
Nendick says the latest generation of Cummins Performance Series Stage V engines can satisfy the duty cycles of a variety of construction demands, whilst generating near-zero NOx and particulate matter emissions.
Significantly, Nendick notes that Cummins Performance Series range has high power and torque for engines of their size. This means that they can replace Cummins and competitive engines of higher displacement without impacting productivity. It delivers a lower cost installation for the manufacturer
and a more efficient operation, with less fuel use and lower CO2 emissions for the end user. Nendick stresses that servicing costs are also reduced with less oil and filters needed.
“Each Performance Series engine can be matched to the OEM’s machine electronically. Cummins’ proprietary software calibration is tailored to the exact operational needs of the equipment to provide the ideal solution.
“The range is available from 3.8- to 15-litre displacement with power from 55 – 503kW. The engines’ up-to-nine-litre displacement are integrated with Cummins Single Module after-treatment systems
to meet the Stage V near-zero emissions levels without the need for cooled exhaust gas recirculation (EGR). This makes the engines lighter and more compact, and lower in weight, driving further efficiency and environmental benefits.”
Nendick highlights that ‘Stop-Start’ capabilities can be combined with the B6.7 Performance Series to lower fuel consumption by up to 10%, cutting CO2 emissions and overall operating costs, whilst also minimising on-site exhaust emissions and noise.
To integrate Stop-Start technology effectively, Cummins engineers work jointly with customers to tailor engine-control software to the OEM’s machine-controller software. The OEM controller observes the machine operations and relays them to the engine-control module when it is appropriate and safe for the machine to shut off. The engine controller monitors working parameters such as coolant temperature, intake manifold temperature, engine load, and fan operation to make sure it can shut down.
Due to this tailoring per application, with a limited number of stop-starts allowed per hour, this technology provides on-site emissions and sociability benefits without impacting durability.
Nendick continues: “Cummins has recently announced collaboration with a number of Telematic Service Providers (TSPs) to enable customers to remotely access their engines through Connected Diagnostics. These include Topcon, Trimble, TelliQ, Elevat and Saucon with more to come.
“Cummins Connected Diagnostics works by wirelessly connecting engines, allowing for constant monitoring and diagnosis of operating behaviour and potential causes of engine faults. Owners are then able to make informed decisions and take adequate actions as they can suggest adapting how equipment is being used or make pre-emptive repairs to prevent extended periods of downtime. This capability assists in improving operating performance, boosts asset utilisation and maximises uptime, increasing efficiency while also reducing overall costs.
“Working in tandem with Cummins technology, Elevat’s Machine Connect makes it simple for off-road equipment OEMs and fleet managers to gather and analyse data to
off-highway engine. This means that the full Performance Series from 3.8 litres up to 15 litres can utilise this low-carbon fuel.
Often described as a renewable diesel or green diesel, HVO is collected by processing lipids such as vegetable oil, tallow, or used cooking oil. It delivers up to a 90% reduction in greenhouse gas emissions compared to diesel ‘from well-to-wheel’. Sulphur-free and oxygen-free, it does not require any engine modifications for it to be utilised, with very little impact on service intervals.
“Using equipment installed with HVO-ready Cummins Performance Series engines is an easy, and economic step that allows customers to reduce their greenhouse gas emissions, with minimal impact to operations and processes,” explains Nendick.
Nendick emphasises that Cummins is a market-leading company progressing future energy solutions and developing innovative products to the market, spending over US$1bn each year on research and technology. This, he says, is evident in the additions of HVO and Stop-Start capabilities for the Performance Series, but also in the
Volvo Penta has taken another step on its journey towards creating a sustainable industrial future with the unveiling of its dualfuel hydrogen engine at bauma Munich. By using hydrogen as a renewable fuel source, the engine – which is an evolution of the company’s proven D8 model – will reduce CO2 emissions by up to 80%, without impacting power or performance.
The engine operates in a similar way to the conventional D8 model but uses mainly hydrogen instead of diesel. If hydrogen is not available, the engine can continue to run on traditional fuel, safeguarding productivity and uptime. This means that with dual-fuel technology, assets and business operations can be future-proofed – despite the fact there is not full coverage from a reliable hydrogen infrastructure in place today.
“The new Volvo Penta dual-fuel hydrogen engine offers customers a low-carbon interim solution before suitable zero-emissions alternatives become viable,” explains Anders Wernersson, product manager for the dualfuel hydrogen engine. “It delivers the same power and torque curve as a regular diesel engine but with significantly lower CO2 emissions. The technology is relatively simple and can be installed with minimal disruption, so we see this as being a cost-effective and robust solution for customers in a variety of applications – including construction, quarrying, and mining – who are looking to
The first engines will be working in end customers’ machines in Europe in 2023 as part of a market pilot project, which will be followed by small-scale production. It will be a stepwise introduction based on market and customer demand and there will be a focus on the fit between the technology and customer needs, ensuring it makes sense to choose a dualfuel powertrain.
“Collaboration and partnerships are essential to facilitate the transformation towards more sustainable power solutions,” says Wernersson. “This close partnership approach is a cornerstone of Volvo Penta’s long-term decarbonisation and business strategy. We work closely with our customers and partners to create tailored solutions based on their requirements. As part of the Volvo Group, we are in a unique position in that we can leverage proven technology and competence from Volvo Trucks, Volvo Buses and Volvo Construction Equipment. We combine this with our customer, market and application knowledge, allowing us to optimise and adapt our designs for a specific vehicle, considering the duty cycles, climate and environment it will operate in.”
The new, eight-litre model has been designed to reduce emissions by using a renewable, fossil-free fuel source, therefore it is recommended that customers will use green hydrogen to power their equipment. Green hydrogen is a renewable energy, created by the electrolysis of water using sources such as solar, wind and waterpower to create a fully-carbon-neutral, hydrogenproduction cycle.
The new, dual-fuel hydrogen-powered solution will help Volvo Penta on its way to reaching its ambitious commitment to the Science Based Targets initiative (SBTi), where the company aims to reach net-zero-valuechain emissions by 2040.
As part of the company’s enterprise strategy to support customers during the energy transition to a lower-carbon future, Caterpillar has highlighted its development of 48-volt, 300-volt, and 600-volt batteries for the off-highway industry.
Leveraging expertise across Caterpillar’s global network of technical centres in the US, UK, China and India, the programme focuses initially on battery solutions for equipment used predominantly in industrial applications.
The battery range uses lithiumion technology and features a modular design to optimize performance and packaging. Furthermore, it has been engineered with sustainability in mind throughout its lifecycle, with the potential to reuse and recycle at the end of life.
The development programme also encompasses inverters, motors, electronic
controls, digital services and other critical technologies to deliver the performance, reliability, durability, maintainability, and long-term value needed for equipment buyers working in harsh operating environments.
Caterpillar showcased prototypes of its battery technologies at bauma in Munich, Germany (24-30 October 2022).
“Caterpillar has demonstrated a longstanding commitment to sustainability through improvements in our operations and by helping our customers achieve their climate-related goals,” said Steve Ferguson, senior vice president Caterpillar Industrial Power Systems. “The announcement of our battery programme is our latest step in combining a wide-ranging inventory of innovations with extensive knowledge of the off-highway industry to offer solutions for a range of power needs, application types, duty cycles and operating environments.”
Perkins’ up to 430kW 12.5-litre
2406J-E13TA industrial diesel engine
Caterpillar has committed to 100% of its new products through to 2030 being more sustainable than the previous generation, which is reflected in Caterpillar’s line-up of industrial-power solutions and integrated services finely tuned for owners of third-party equipment powered by Cat engines.
“Improved sustainability is a journey, not a destination, and one size doesn’t t all in determining the appropriate power solution for equipment owners,” Ferguson said. “Our offerings can help customers and end users start improving the sustainability of their operations today through high-efficiency engines, fuels and digital solutions now available for the jobsite, by extending value and reducing waste over the lifecycle of equipment they already own, and by powering the next generation of equipment with innovations precisely gured for the jobsite.”
At bauma 2022, Caterpillar also showcased its 100kW Cat C3.6 industrial power unit and C7.1, C9.3B, C13B, and C18 industrial diesel engines. All meet EU Stage V and U.S. EPA Tier 4 Final emission standards while delivering claimed superior performance and low operating costs.
Perkins showcased at bauma 2022 Munich how it continues to invest in new engine technologies, including dual-label certification for EU Stage V and U.S. EPA Tier 4 Final. By what the company says is its optimising of the efficiency of the entire engine system from the air intake to the end of the exhaust pipe, Perkins has developed a full range of engines from 0.5 to 18 litres and 8.2 to 597kW with an integrated suite of advanced technologies. The units not only reduce GHG emissions, but also deliver significant improvements in power density, performance and operating efficiency.
The emissions of carbon dioxide and other greenhouse gases associated with these engines can, says Perkins, be reduced by up to 85% using renewable, lower-carbon intensity fuels derived from sources including planted crops (soy, palm, rapeseed, etc.), used cooking oil, animal fat, biomass, algae, and others. Every industrial Perkins engine from the 400 Series through the 2800 Series can use low-carbon-intensity fuels that meet the leading industry diesel fuel specifications.
Additionally, Perkins, which has a customer base of more than 800 original equipment manufacturers (OEMs), offers a powerful and growing portfolio of connectivity solutions that can help OEMs promote the optimal, sustainable performance of diesel engines. Available as a standalone service from Perkins or easily integrated with OEM fleet management offerings, connected engine capabilities deliver timely insights through a customisable dashboard of performance, fuel and oil consumption, and other vital engine data points that can maximise the
uptime of Perkins-powered machines and fleets.
These connectivity offerings are seamlessly integrated with expert maintenance and service capabilities from the Perkins global distributor network to prompt the proactive diagnosis and resolution of engine issues, helping technicians get the job right first time to minimise downtime and repair expenses.
For example, the free Perkins My Engine app has been downloaded more than 100,000 times since its introduction in 2017. It reduces paperwork and improves productivity by providing service reminders, electronic service logs, service publications, quick links to distributors, and simplified sharing of engine data for customers, which is especially useful for rental companies.
In an increasingly connected world, OEMs are looking for ways to leverage the large amounts of telematics data being collected every second.
Creating actionable opportunities to strategically use these thousands of data points is one of the pressing challenges facing the off-highway industry as more OEMs integrate telematics systems into their equipment with the goal of better serving end users. The off-highway vehicle telematics market is projected to have a compound annual growth rate of 15% from 2022 to 2032, according to a report by Future Market Insights.
John Deere has found a way to address this challenge with Connected Support.
Enabled through John Deere remotemonitoring and diagnostic services, Connected Support helps increase efficiency, profitability, and productivity by monitoring equipment health and triggering predictive alerts to dealers so they can proactively manage parts replacement and schedule maintenance to improve their customers’ uptime.
Connected Support leverages a suite of dealer and factory tools including the ability to remotely monitor fleet health, diagnose
machines, and program software. The Connected Support technology allows both dealers and end users to shift from a reactive maintenance mentality to a proactive approach.
John Deere is expanding its future telematic technology offerings to John Deerepowered OEM equipment through Connected Support with no subscription fees. Leveraging telematics will help ensure that OEM machines powered by John Deere engines are kept in peak operating condition, resulting in improved equipment uptime, and offering more insights into equipment performance.
Meanwhile, John Deere Power Systems (JDPS) is introducing two next-generation diesel engines, the JD14 and JD18, which have been designed from the ground up. These bauma 2022-showcased engines have capacities of 14 litres and 18 litres respectively and meet Stage V and Tier 4 Final emissions requirements for Europe and the US.
Nicholas Pfeiffer, an engine specialist from the company, said: “The 14 and 18 are the
next generation of engines from us. They’ve been developed with a focus on serviceability and have the latest diagnostics.” Pfeiffer explained that the diagnostics ensure that the engines offer predictive maintenance capabilities, catching potential faults before they develop and making significant reductions in maintenance costs while also preventing unplanned downtime. He said, “We have our telematics gateway and if you opt in, the dealer is able to call you even before you know there’s an issue.”
Meanwhile, the wiring harnesses are all external to the engines making them easier to maintain and less vulnerable to damage. Customers are also able to select different fuel and oil filter locations to best suit the installation. Pfeiffer added that the simplification of the after-treatment package for the JD18 engine offers significant benefits also, with fewer sensors required and a further reduction in maintenance costs. These engines are biofuel capable, and Pfeiffer added, “We are working on HVO.”
US off-road engine manufacturer Kohler has completed a recent 155,000m² expansion of its North American manufacturing facility in Mosel, Wisconsin, ahead of its 150th year in business in 2023.
The company has set out its new strategy toward a more sustainable future, revealing its long-term plan and next steps to transform the group from a power producer to an energy supplier. The company says the unveiling of this new strategy comes at a momentous time for the engine industry.
Kohler’s strategy incorporates alternative fuels, electrification and hybridisation to reduce engine size or achieve zero emissions during operation, and hydrogen as a potential green-source fuel.
The manufacturer recently acquired electric vehicle and hybrid applications company Curtis. Kohler says the acquisition expands and diversifies its product portfolio, leveraging Curtis’ expertise in electrification,
LSC Infratech’s May 2021-commissioned aggregates, silica and manufactured sand production facility at Manoharpura in the Karoli district of Rajasthan, North India, deploys a variety of advanced technologies, plant automation and new operating and maintenance practices, resulting in big economical, sustainability and health and safety gains for the company.
Partha Pratim Basistha went to get a close-up look at the state-of-the-art site
LSC Infratech (LSC) managing director Shiv Kumar says it has always been his company’s “quest” to incorporate the best plant technology and operating processes into its building materials production, with the cutting-edge set-up at Manoharpura the latest example of this.
“It enables us to run the plants with minimal levels of redundancies and the highest level of optimised operation, while allowing us to derive a wide variety of materials,” he explains. “We have been able to do this with our own critical engineering research in getting the exact desired technologies from OEMs [original equipment manufacturers]. This has been the case since 1991 when we set up our first plant at
Haldwani in Uttarakhand with toggle jaw, roller and impact crushers.”
Kumar says the advanced technology and automation-led plant set-up at Manoharpura has been realised through “sizeable” capital investment in a facility initially established to focus on silica sand production. He continues: “One of the key elements of the facility is systems installed to ensure there are minimal equipment break downs resulting towards very high levels of plant availability. We have also made sizeable capital investments in bringing newer operating and most importantly, maintenance process interventions. This is helping us to run the individual plants producing aggregates, manufactured and silica sand efficiently and generate profits in the highly competitive Indian crushing business.”
LSC has another two facilities in Rajasthan. One is at Ghatri at Bharatpur and Kotki near Ghatri. The Ghatri facility also produces crushed aggregates, silica sand and m-sand.
The company’s impressive new facility has a 50tph silica sand production plant, producing 13,000-15,000 tons/ month of silica sand. This volume caters for the rising demand of North Indian glass manufacturers. Manufactured sand production from the plant is 20,000 tons/ month.
The Manoharpura facility is also home to a 250tph crushing and screening plant. The set-up comprises a primary unit of a grizzly feeder, an AVJ 811 jaw crusher, a QM 250 cone and secondary crushers, and 2060 three-deck screeners. The entire
plant is from Propel Industries (Propel), the Coimbatore, southern India-based crushing, screening and manufactured-sand-equipment heavyweight. The crushing and screening plant produces between 35,000-40,000 tons/ month of aggregates. The first set of screens feeds to a stockpile off its conveyors. The cone crusher produces 10-20mm crushed aggregates and cone dust. The jaw produces 40-65mm of aggregates. 0-5 mm materials are sent from screens to an allmineral Asia (India) silica sand plant for producing both silica and manufactured sand.
To reduce operating costs, the new facility has two grizzly feeders, placed one after the other, followed by a jaw crusher. According to Sushil Chauhan, head of plant operations, maintenance & projects at LSC Infratech, Manoharpura’s Propel crushing and screening plant is a unique combination and at the forefront of Indian crushing and screening sites. “It has been successfully engineered by Propel, based on our own engineering inputs to cater our operational requirements. The objective to have two grizzly feeders is to rationalise the load on the single motor of jaw and cone crushers, for enabling the crushing units to do optimum levels of crushing. This is because the raw materials sourced by us for producing aggregates, silica and manufactured sand comprises both boulders, generally of 500mm, and ores.” He continues: “Using appropriately sized feed materials leads to much less wear and tear on the machine parts, reducing our maintenance costs.”
Rakesh Kumar, another senior figure at LSC Manoharpura’s facility, adds: “The uniqueness of the new Propel [QM 250] cone crusher is that the single cone crusher can be operated both for getting aggregates and fines involving cone dust. This can be done through simply altering the close-side setting. Getting the two products otherwise would have required two sets of individual cone crushers, leading to higher operating expenses.”
The compact design of LSC’s Manoharpura plant setup allows for operating flexibility while also cutting production costs. An example of the plant’s flexibility is its swivelling wheel-mounted conveyors. There are two swivelling conveyors, one connected to transport the manufactured sand throughput and the other, silica sand. The
“We are able to ration power use and save on its consumption.”
conveyors are driven by independent motors which stack the output in the stockyard. As compared to a static conveyor, the swivelling conveyor can be rotated across the entire stockyard. “The swivelling conveyors allow us to move wheeled loaders or excavators to either end of the yards, having the materials ready to completely load the Indian woodenbodied trucks or the rigid dump trucks. This also facilitates in turn quicker dispatch of the materials to our customers,” explains Kumar.
LSC’s Manoharpura facility also uses a Tata Hitachi wheeled loader, and a Liugong wheeled loader. The site also uses two L&T
Komatsu 2108 21-ton excavators and two Liugong 926E 26-ton excavators with 1.9m³ bucket. The excavators and wheeled loaders are used to load the crushed aggregates, manufactured sand and silica sand to the rigid dump and conventional wooden-bodied trucks.
High levels of plant availability, safety and attainment of the rated output are supported by Propel’s complete automated control system for running the entire crushing, screening, and conveying setup. The system shows the complete plant layout on a control panel, with digital electronic descriptions of
all the units, for running the crushing and screening plant.
Chauhan says: “Through the automated control system, the variable frequency drives can be pre-set and the RPM controlled. This can be set depending on the volume and size of the materials being processed by the plant. Through controlling the frequencies, in the jaw and cone, we are able to ration power use and save on its consumption.”
Among the vital safety attributes of Propel’s automated control system is its emergency shut off switch. The switch, once activated, can bring plant operations to a halt if any faults or safety lapses are detected. The panel also possesses relays that will trip automatically and suspend operations if there is overloading of materials in the processing operation. There are also circuit breakers that will trip automatically if they detect electrical cable faults, short circuits or earth faults, which may endanger operating personnel on the plant site. For additional safety, there are safety switches on the foot of each conveyor. The switches can immediately be activated if any lapses in safety are detected.
While advanced levels of technology are a big factor in keeping operation costs low at the LSC Manoharpura facility, newer plant operating practices are another cost-cutting facet. LSC plant officials are ensuring that crushing and screening plants are run with full material loads. Plants previously run with lesser loads had increased production costs.
The Manoharpura facility uses between 800-900 amperage a month. Power for running the plants is sourced from Rajasthan State Electricity Grid. The unit consumption of electricity is between 240,000-250,000 units. Power for operating the plant is through 33kva grid power. LSC has put in place 650kva stabilisers that can ensure consistency in voltage if there any fluctuations in the voltage from the grid source, which is not unnatural in Rajasthan.
Running the facility with multiple trains for mineral processing with electricity is cheaper for LSC compared to running the site off diesel generators. A 200kva generator would lead to diesel consumption between 100-110 litres/hour. The high cost of diesel fuel would have made this commercially unviable.
To ensure that there is a constant feed of raw materials for running the plants with a full load, adequate volumes of raw materials are kept at the facility’s stockyard. This negates any disruptions in supplies that may occur while transporting the raw materials from LSC’s mines at Kumar Harbals, five kilometres away from the Manoharpura plant.
LSC has taken on lease 23 hectares of mining area with estimated accessible reserves of 40 million tons. The plant’s current production output is 1.34mn tons per year (including silica sand, manufactured sand and crushed aggregates), with LSC planning to increase its production capacity by a further 100,000 tons/year in 2023. The company is awaiting environmental
clearance from the Rajasthan government. If approval is granted, LSC will have enough mineral reserves at Manoharpura for the next 20 years of production.
To get maximum output from the reserves, LSC follows higher levels of scientific and safety processes for extracting the rock materials. Controlled deep-hole blasting is done to get the materials with the right hole measurement so there is minimal rock wastage. Rocks won through blasting are then initially reduced in size by hydraulic rock breakers and jack hammers attached to excavators. The broken materials are then loaded by excavators with 2.4-2.6m³ bucket attachments on to LSC’s rigid dump trucks for transporting the materials to the crushing and screening plant.
Rohit Kumar, LSC’s senior geologist,
says: “The materials used for blasting at Kumar Herbals are fully certified by India’s Directorate General of Mines (DGMS). The personnel carrying out the blasting work are also DGMS-certified.”
To ensure the steady supply of raw materials from Kumar Harbals to the new plant, LSC has acquired four new Tata 40-ton 3525 rigid dump trucks (RDTs) with BS-VI-emission-norm-based electronic engines. It has also acquired one BS-VI variant Tata 2825 RDT with box body.
According to Anil Sharma, transport manager at the LSC Manoharpura facility, the Tata RDTs were purchased partly due to the very good on-site product support from the Rajasthan-based Tata dealership. Their perceived higher productivity against competitor trucks was another important purchase consideration. “The trucks can haul more volumes of materials across long distances with faster cycle times and higher levels of fuel efficiency with the BS-VI electronic engines. This makes the unit costs of the transportation cheaper for us,” explains Sharma.
He adds: “Another prominent attribute of the Tata trucks is that they can work on combined mode applications, while bringing up the mined materials to the surface before moving it on road. The trucks can also haul the materials on undulated sites with ease, with minimal breakdown. The additional axle between the front and rear wheels ensures easy turning of the trucks at shorter radius.”
“The only higher operating expenditure incurred in the trucks is through the separate exhaust gas treatment oil. For every 100 litres of diesel, the new BS-VIequipped trucks require seven litres of diesel exhaust gas treatment oil. This makes the trucks completely environment friendly. Environment friendliness is also achieved by a new nozzle pipe design, which releases the exhaust gas from the top. Overall, the
higher operating costs for the exhaust gas treatment are compensated by the high levels of productivity and fuel efficiency of the trucks.”
Vying in a competitive field to be the star attraction at LSC’s state-of-the-art Manoharpura facility is the allmineral Asia (India) silica and manufactured-sandprocessing plant. Chauhan says: “The plant delivers highest-purity silica sand that is strictly required by the glass industry. This is essentially achieved through the singlepressure mechanism of the plant, which delivers pressure from bottom to top in contrast from top to bottom with a dual-
pressure classifying system. While the bottom pressure ensures that the impurities and the other light particles are on top, it also reduces power consumption.”
The allmineral Asia (India) silica and manufactured-sand-production plant is highly automated via two HMI-operated electronic panels inside ‘shipping container’ control cabins. One HMI panel sets the working pressure required for segregating the impurities from the silica sand and manufactured sand from the all-flux systems. The chosen pressure setting takes into consideration the chemical analysis pinchvalue of the materials from LSC’s laboratory
“The trucks can haul more volumes of materials across long distances with faster cycle times”
at the Manoharpura plant. The other HMI panel with pinch-value controller assists in selecting the plant’s operating mode, including, among others, maintenance mode, automated mode, and without-speed mode.
To have uninterrupted HMI functioning, programme logic controls and variable
frequency drives, LSC has installed a battery backup to bypass power disruptions.
Furthermore, a protective, switch-mode power supply system (SMPS) from Siemens is also installed. The SMPS filters the negative voltage, that may come from the power-grid connection and harm the control
systems. All the electrical control systems of Manoharpura’s allmineral Asia (India) and Propel’s plants are SCADA (supervisory control and data acquisition)-based.
Another major attraction of LSC’s new plant is the Amar Plastics India filter press used to eliminate water wastage. The filter press is connected to the silica-sand-processing plant, separating the water from the slurry generated during production. Through separating the water from slurry, hardened ‘cake’ material is obtained. LSC Manoharpura is looking to sell the hardened materials to companies engaged in landfill works.
LSC’s Manoharpura facility also has its own dedicated workshop to do maintenance work on the site’s wheeled loaders, excavators, and rigid dump trucks. LSC also undertakes comprehensive preventive and predictive maintenance practices to optimise its plants’ uptime, including regular checks of the electrical systems and cable connections supporting the plant. It is vital to ensure that cable connections are not loose and do not overheat, especially when operating in the summer months. Regular maintenance is done by cleaning dust from the contactors of the PLC (programmable logic controller) systems and the variable frequency drive.
Given its advanced technology-enabled thoroughness and impressive cost-saving features, it is unsurprising that LSC Manoharpura facility is attracting great attention in the Indian aggregates, silica and manufactured sand sector. AB
24-30 OCTOBER, 2022
To see all our videos and to subscribe to our YouTube channel
Electric machines point to the future for Ammann at bauma 2022
CIFA launches new green K42E electric concrete pump
Komatsu plans to be completely carbon neutral by 2050
Produced in partnership with...
Benninghoven’s revolutionary REVOC technology slashes emissions
No compromises with Hamm’s new HD12e small electric tandem roller
It’s a RAP: state-of-the-ART road resurfacing from Simex
Gripping stuff - BKT Europe showcases EARTHMAX giants
Keestrack travels further along electric avenue
Vögele’s new Dash 5 paver is ready for the digital future
Screen grabs from the BMX Fragmenter post-blast analysis software
3GSM, a developer of software that optimises blasting and reduces inherent environmental issues, has launched BMX Fragmenter - new post-blast fragmentation analysis software that works as an independent module or seamlessly integrates into BlastMetriX UAV. BMX Fragmenter is described by 3GSM as a first-of-its-kind platform that automatically converts high-resolution drone images into a highly accurate 3D rendition of the muckpile with colour-coded delineation of gradation.
from other programs is its automatic combination of 2D and 3D analysis for a more accurate and comprehensive evaluation of the muckpile surface.
Outotec
Metso Outotec is expanding its innovative cloud-based Metrics monitoring system portfolio to customers’ stationary screening equipment. With its 24/7 online monitoring capabilities, Metrics offers improved safety, increased uptime and throughput, and reduced unplanned maintenance. It enables operators, controllers and service professionals to see real-time analysis of vibrating screen performance and bearing condition. Metrics is designed for intuitive operation. An easy-toread screen dashboard with OEM insights makes it possible to quickly detect potential issues and take corrective action in time.
The system accepts overlapping high-resolution images taken by the operation’s standard drone. Using an interactive or pre-programmed flight plan, the flexible system leverages the drone’s GPS coordinates, so no ground reference markers are required. To save time and improve efficiency, the images remain local to the computer and do not require time-consuming uploading to the cloud.
The new BMX Fragmenter generates millions of 3D data points, reviewing an average rate of 200 photos per hour, for more complete statistical particle analysis. 3GSM says that what sets it apart
A 3D post-blast model is automatically generated showing the width, throw and height of the muckpile. Particle sizes are colour-coded to give a quick gradation overview and for easy visualisation of oversized material. The system comes standard with editing tools for analysis refinement. Generated quantitative charts provide distribution of particle size and percent passing through the screen. Users can also assign fragmentation models like Rosin-Rammler, Swebrec and Swebrec extended to the analysis. Results can be exported and saved in PDF format. The BMX Fragmenter also generates comprehensive summary reports to be used for blast program optimisation. In addition to open-pit mining operations, the new system can be used in debris flow, dam and underground applications. www.3gsm.at
The S 56 SXF is the significantly lighter and modern replacement for the tried-and-tested S 55 SX.
The new model offers customers freedom in the choice of chassis and engine, as well as a large delivery line, small outrigger width through modern curved outriggers, no restriction in choice of pump battery and no complex conversion of the chassis. The new model is designed to pump large volumes over a long period of time and offers high pumping
capacity at low engine speed. The S 56 SXF has a reach height of 55.2 m, a delivery rate of 162 m3/h and a maximum delivery pressure of 85 bar over a five-section boom with roll-folding. The unit’s batteries guarantee an operating time of at least eight hours.
Meanwhile, the new S 51 SX sees Schwing introduce a new, large boom pump characterised by significantly reduced weight. Mounted on a 10x4 EURO 6 chassis, the unit has a typical
operating weight of less than 40tonnes due to modern lightweight construction, with sufficient reserve for additional equipment and payloads.
Operation and registration of the machine are significantly simplified, and fuel consumption is reduced. The combined RollZ-Fold boom with 235° and 230° rotation angles in the last two mast elements offers maximum mobility for construction sites. www.schwing-stetter.co.uk
In June, Metso Outotec announced a global cooperation agreement with Dynamox, which offers an innovative conditionmonitoring platform. Metrics for screens is the first solution utilising Dynamox’s easy-to-install instrumentation that can be complemented with comprehensive value-added services and remotemonitoring capabilities in the customer’s value chain.
“The customer feedback received has helped us to offer a solution focused on customer centricity and sustainability. Metrics for screens helps customers to optimise their process, as they can easily see how the changes implemented have impacted their screening operations. In addition, continuous monitoring helps in the avoidance of several potential breakdowns. It also has a positive impact on sustainability, as running the screen in an optimal way enables increased uptime and less consumption of media, spare parts, oil and energy. Our strong development roadmap will enable us to release more data-driven and value-added services soon,” says Jan Wirth, technology director with Metso Outotec’s Screening Solutions business. www.mogroup.com
JANUARY
19-20: CECE Congress 2023
Chamonix, France
Organiser: CECE
Tel: +32 2 706 82 26
Email: info@cece.eu https://www.cece.eu/
31 January-03 February: bauma Conexpo India 2023
Greater Noida, India
Organisers: AEM and Messe München
Tel: +49 89 949-20251
Email: info@bcindia.com https://www.bcindia.com/
10-12: B2W User Conference
Las Vegas, NV
Organisers: B2W Software
Email: vgarofalo@b2wsoftware.com https://www.b2wsoftware.com/
14-18: CONEXPO-CON/AGG
Las Vegas, NV
Organiser: AEM
Tel: +1 (800) 867 6060 https://www.conexpoconagg.com/
MAY
02-04: UK Construction Week
London
ExCeL, London
Organiser: Media 10 Ltd
Tel: +44 (0)20 3225 5200 https://www.ukconstructionweek. com/
03-07: SaMoTer 2023
Verona, Italy
Organiser: Veronafiere S.p.A. Tel: +39 045 8298561
Email: customercare@samoter.com www.samoter.it/en
06-08: APEX 2023
Maastricht MECC, The Netherlands
Organiser: Industrial Promotions
International Tel : +44 (0)7821 655 244
Email: max.hollick@khl.com https://apexshow.com/
AUGUST
23-26: steinexpo 2023
Homberg/Nieder-Ofleiden, Germany
Organiser: Geoplan GMBH Tel: +49 7229 606-30
Email: info@geoplangmbh.de https://www.steinexpo.eu/
MEET THE TEAM
Aggregates Business travels the globe attending conferences, events and equipment shows, keeping you informed of the latest offerings. Come and join us for a chat at any of the events below.
MARCH 2023
14-18: CONEXPO-CON/ AGG
These dates were correct at the time of going to press, but please note that the COVID-19 pandemic means some events may be rescheduled with little advance notice
IFC www.ammann.com
p29 www.bkt-tires.com
CONEXPO-CON/AGG IBC www.conexpoconagg.com
Sumitomo OBC www.sumitomokenki.com
Trimble Agg p11 www.goloadrite.com
Verona Fiere p38 www.samoter.com
MARCH 14-18 / 2023 / LAS VEGAS / NEVADA
250,000 sqm of Exhibits
130,000 Attendees
1,800 Exhibitors
150 Education Sessions
REGISTER at conexpoconagg.com
Save 20% with promo code SHOW20