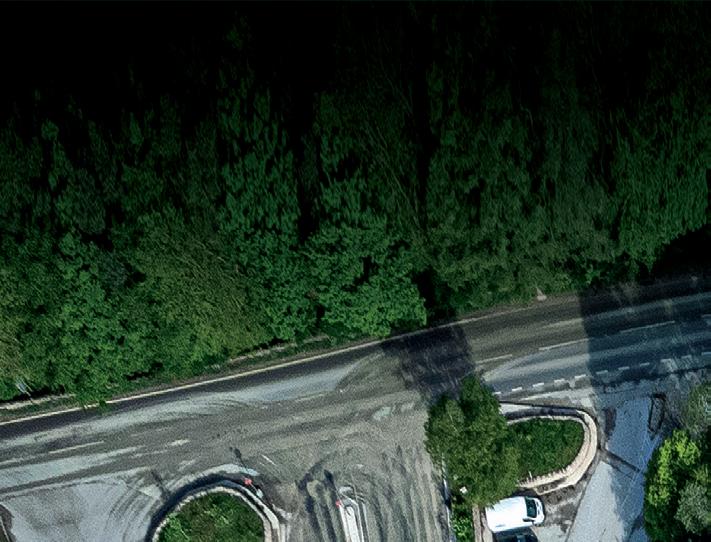
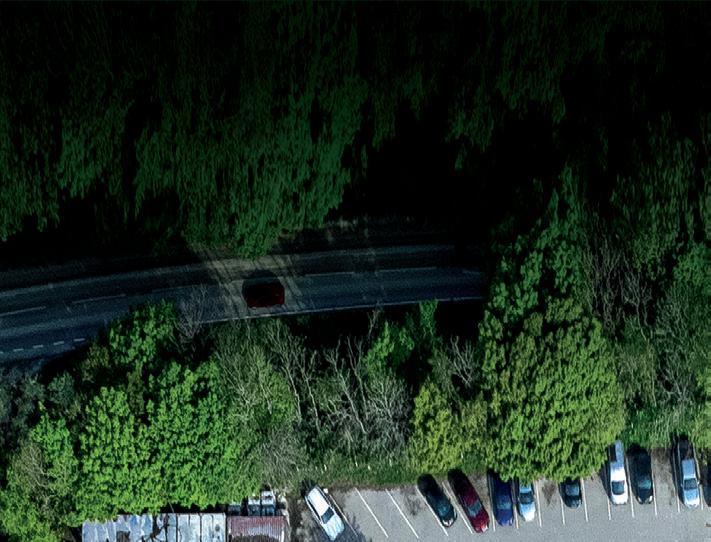
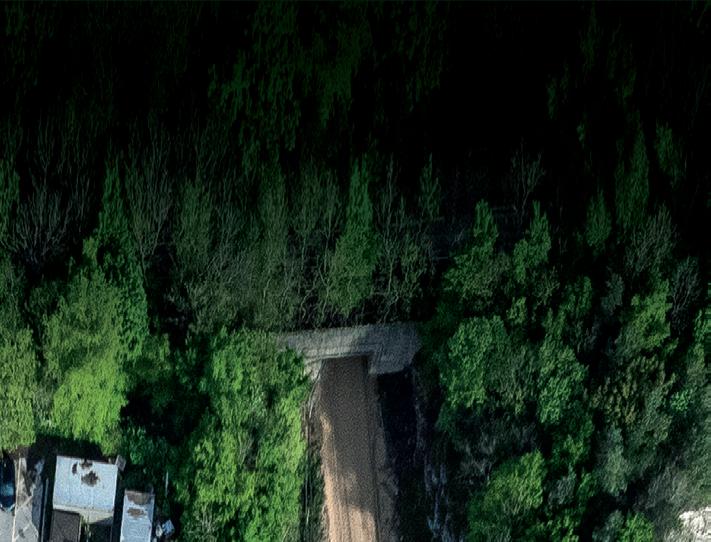
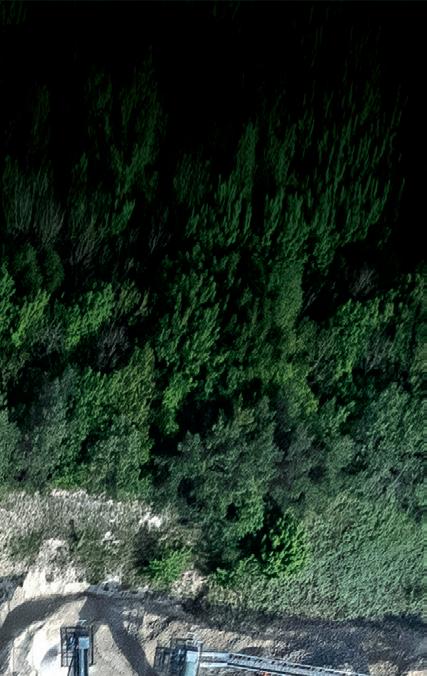

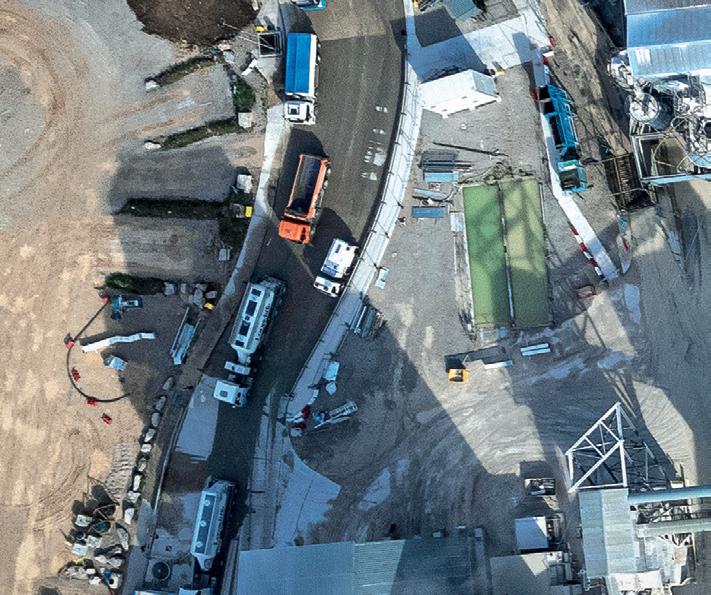
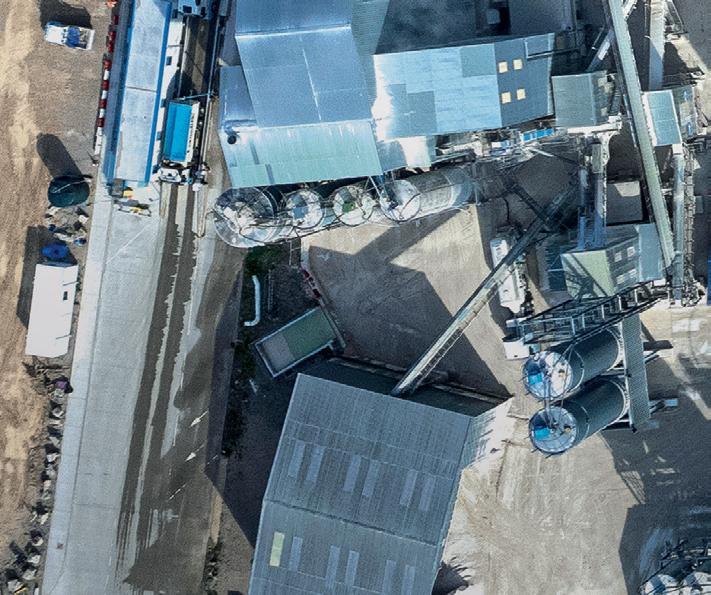
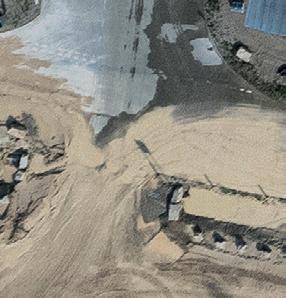
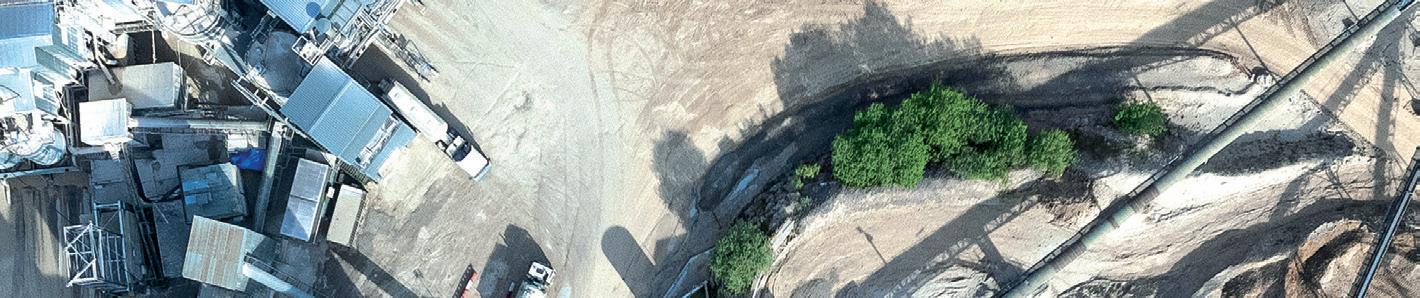


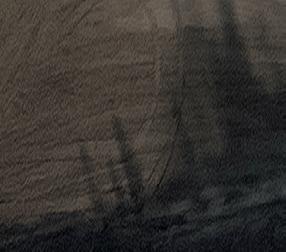

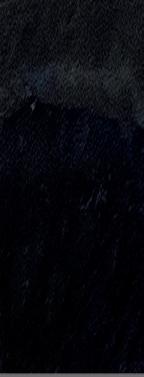

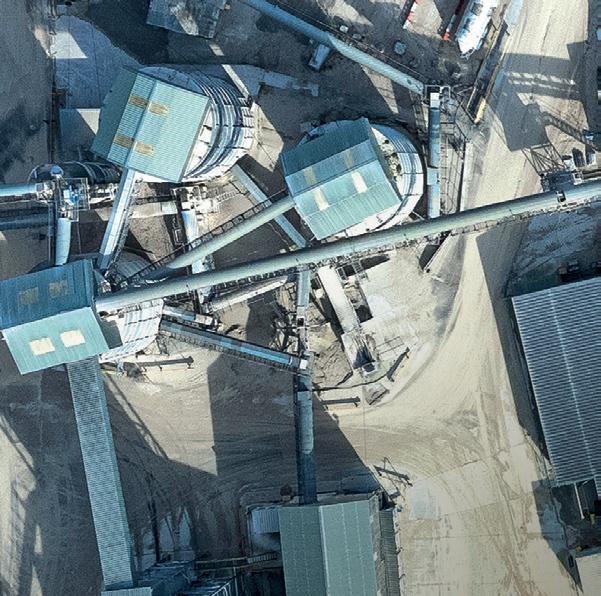
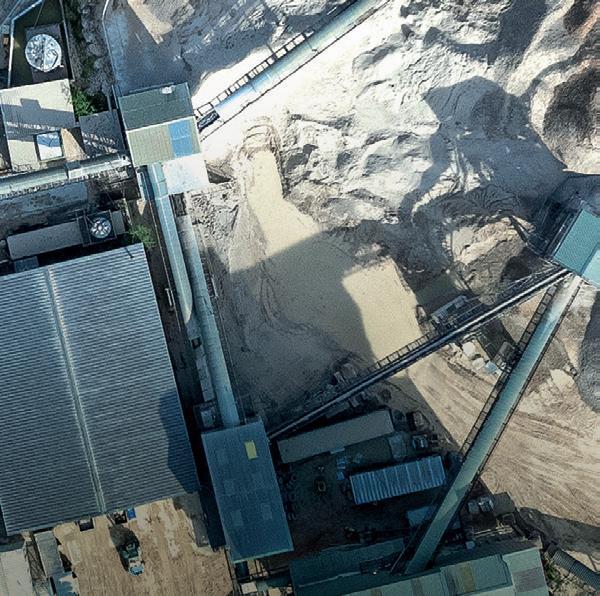

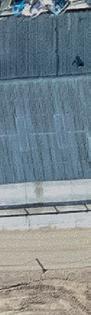
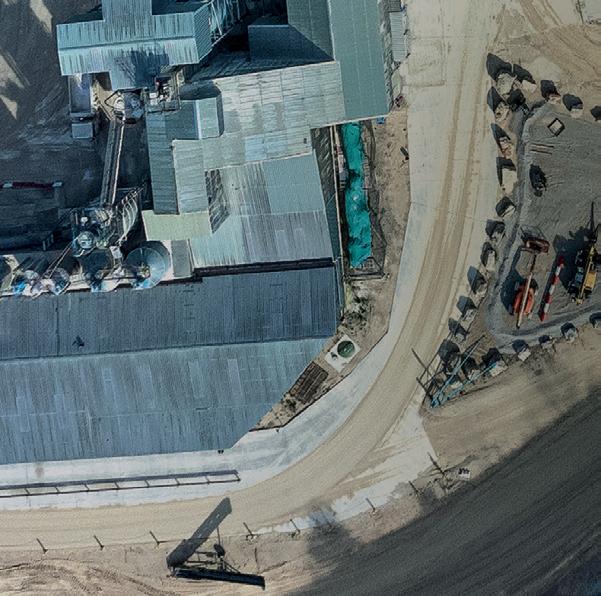
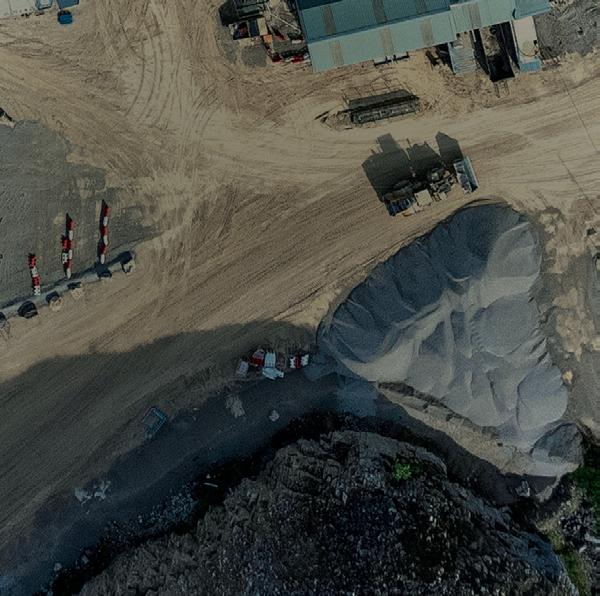
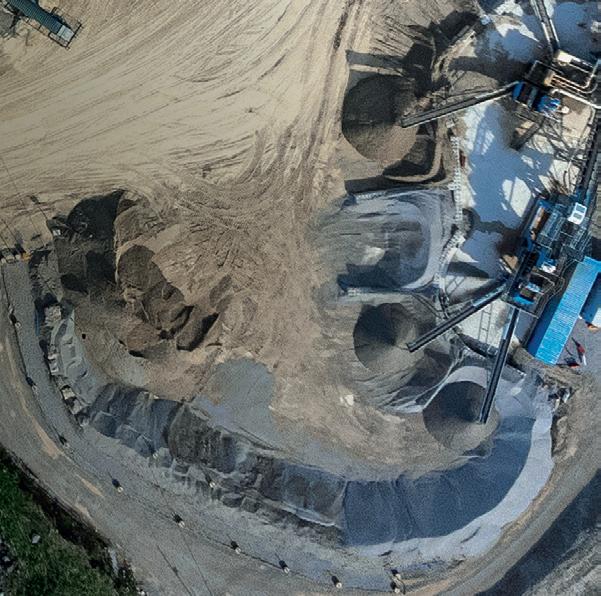






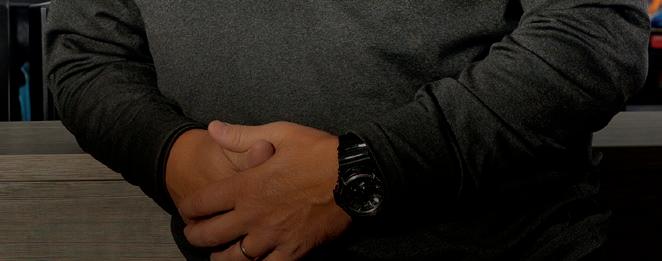

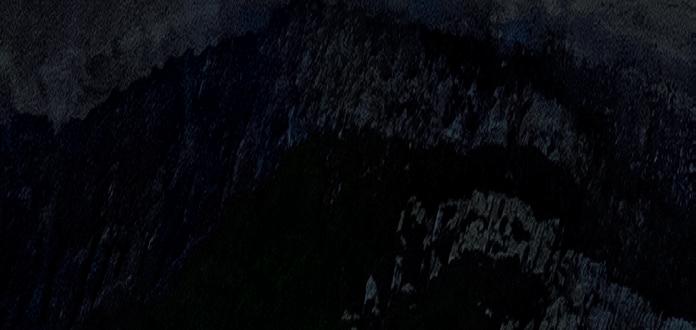


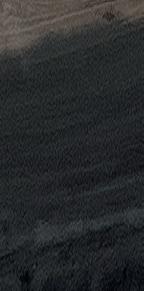
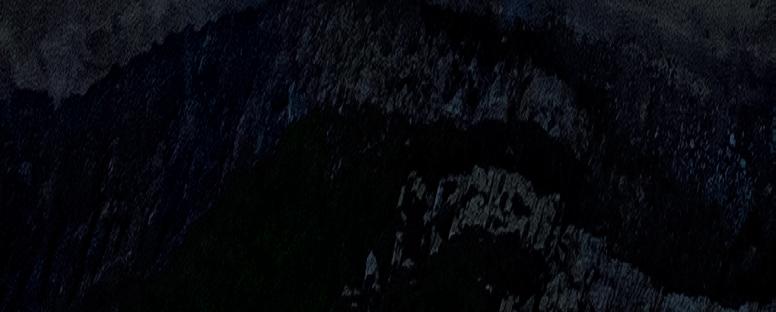
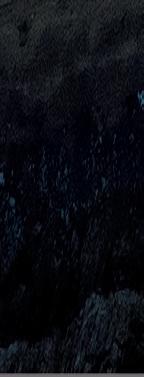


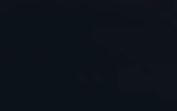

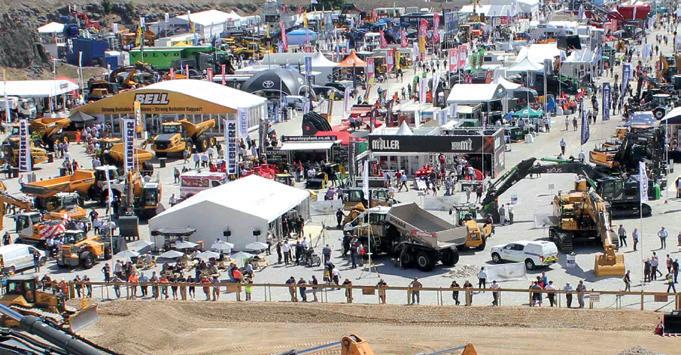
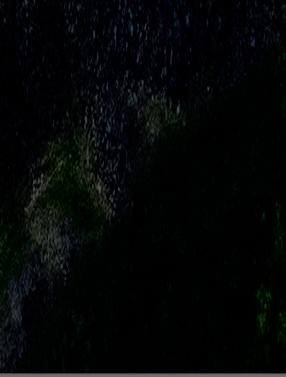


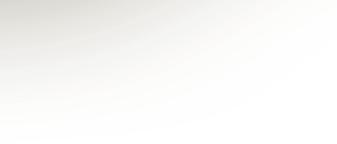
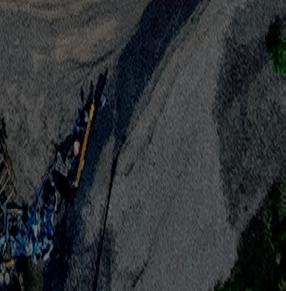
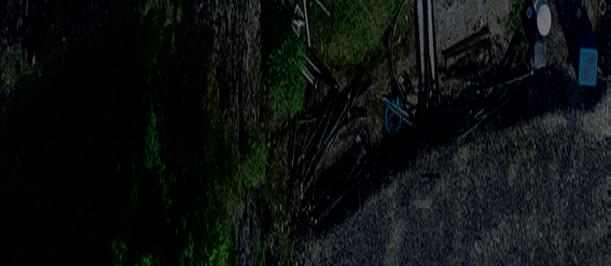

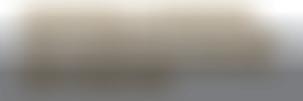
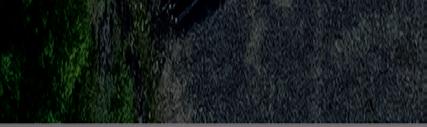
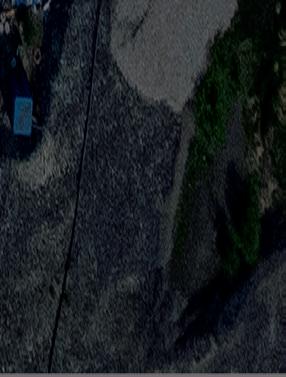
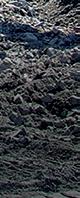
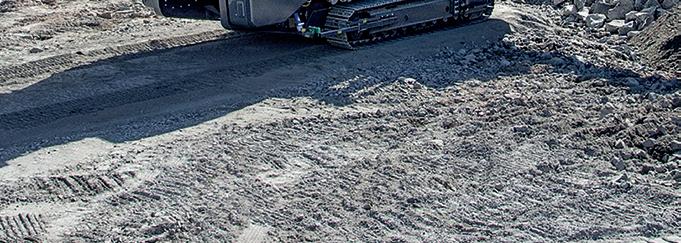
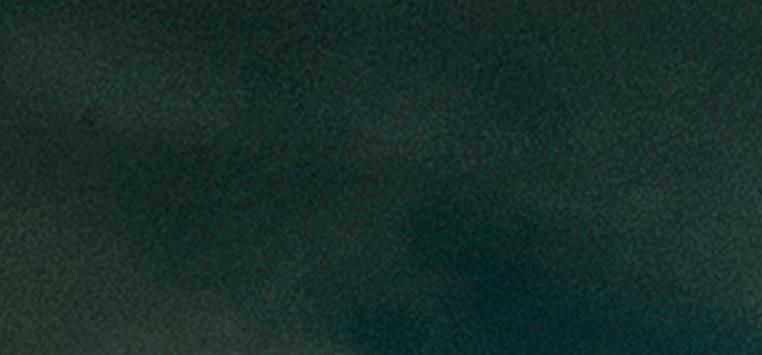
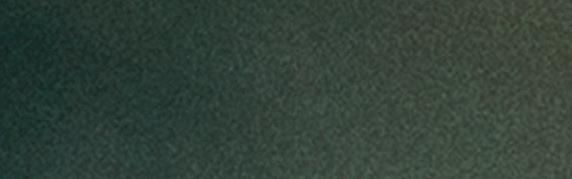

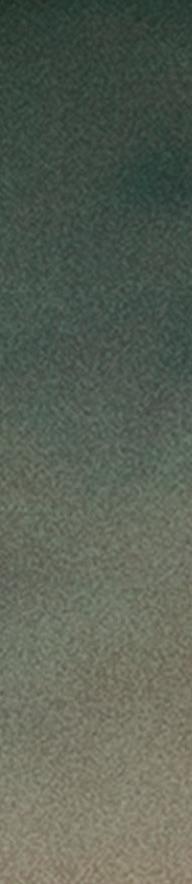
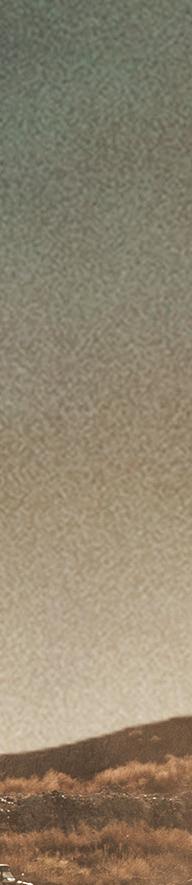
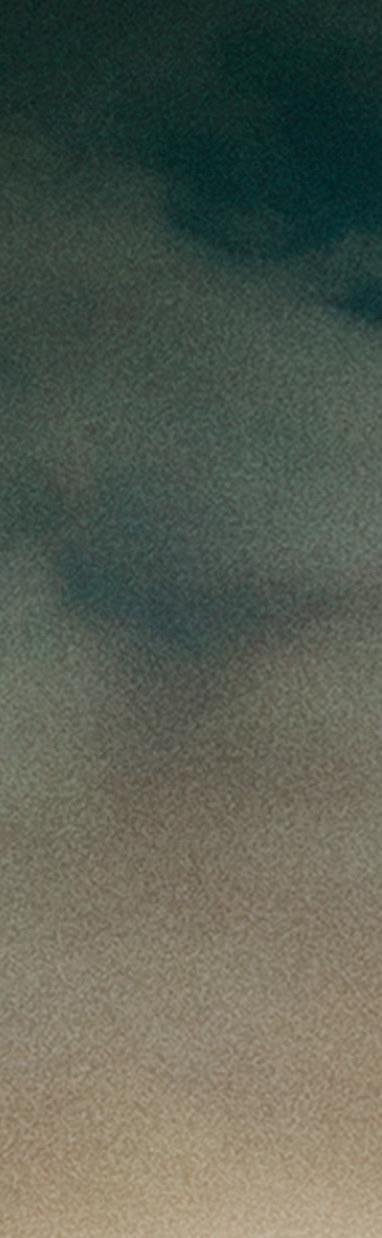
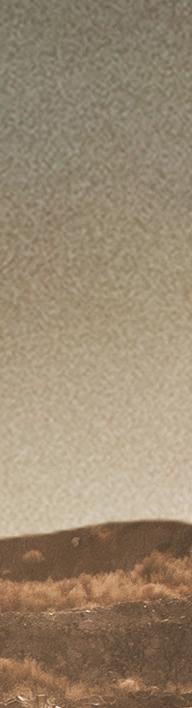
CAT® 980, 980 XE AND 982, 982 XE WHEEL LOADERS
These loaders give new meaning to high-production, low-cost-per-ton performance. Integrated Cat® Payload means accurate loads every time. Built-in Autodig delivers consistently high fill factors and reduces tire wear. Add low-effort steering, an all-new cab, a host of operator-first features and extended service intervals, and your operation is fully loaded for profitable performance.
“A shared urgent need to increase housebuilding & a growing sustainability agenda creates commercial opportunities for UK & Irish mineral product producers”
05 COMMENT
Fast-tracked electric dreams
06 NEWS
Recycled & secondary aggregates use reaches UK high; HMUK acquires Mick George; BIA Group keeps it in the family with new CEO
09 ASSOCIATION NEWS
Implementation of the Critical Raw Materials Act – side e ects for aggregates
51 EVENTS
All the key events in the quarrying & aggregates world
33 CRUSHING & SCREENING
New diesel-electric plants optimise independent operation time
36 LOADING
Develon says it can reflect on a successful debut year in Europe and worldwide
38 HAULING
Maturing battery technologies drive electric hauling potential
41 ENGINES – 1
Exciting new o -highway engine solutions o er flexible power options
44 RECYCLING – 1
Mobile materials recycling enhances the circular economy
46 PORTABLE-POWER – 1
Portable power solutions can be a highly e cient option for quarry operators
48 WEAR PARTS / SPARES – 1
Precise measurement is vital in the production of quality wear parts for quarrying equipment
50 SCALES & WEIGHING
On-board weighing technology enhancing outcomes on quarrying and construction sites
10 INTERVIEW 1
14 INTERVIEW 2
COVER STORY: Longcli e Quarries’ Brassington Moor Quarry is integral to the company’s sustainability-minded growth plans
Sean K. McLanahan is winning the aggregates-processing generation game
Dr Andrew Minson on life at the heart of the global cement & concrete industry’s ambitious journey to net-zero concrete
19 MARKET REPORT
Confronting myriad challenges in a bid to stimulate UK and Ireland mineral-product sales growth
Delivering Longcli e Quarries’ eyes bright, green future
28 HILLHEAD 2024 PREVIEW All the top quarrying OEMs at the 40th-anniversary Hillhead show
woodAmmann dust burners
OVER 15 MILLION TONS of asphalt worldwideproduced ... and counting
Pioneering sustainable combustion technology | Wood dust utilization
Limiting CO₂ through innovation | Years of use | Dozens of systems
The Ammann wood dust burner is growing in popularity. It’s easy to see why:
• Wood dust can be locally sourced, reducing transport costs.
• It’s a renewable energy source.
• The burner transforms a waste material into fuel.
• It’s a proven process, with millions of tonnes of mix produced by asphalt plants equipped with Ammann wood dust burners.
The Ammann wood dust burner can be retrofitted on plants provided by Ammann or competitive manufacturers.
HEAD OFFICE
EDITOR: Guy Woodford
ASSISTANT EDITOR: Liam McLoughlin
CONTRIBUTING
EDITORS: Munesu Shoko, V.l. Srinivasan, Shem Oirere, Partha Basistha, Eugene Gerden, Shadrack Kavilu
EQUIPMENT EDITOR: Mike Woof
DESIGNERS: Simon Ward, Andy Taylder
PRODUCTION MANAGER: Nick Bond
OFFICE MANAGER: Kelly Thompson
INTERNET, IT & DATA SERVICES DIRECTOR: James Howard
DATA & MARKETING MANAGER: Alan Cansick
WEB MANAGER: Sarah Biswell
SOCIAL MEDIA MANAGER: Tatyana Mechkarova
MANAGING DIRECTOR: Andrew Barriball
PUBLISHER: Geo Hadwick
CHAIRMAN: Roger Adshead
ADDRESS
Route One Publishing Ltd, Second Floor, West Hill House, West Hill, Dartford, Kent, DA1 2EU, UK TEL: +44 (0) 1322 612055 FAX: +44 (0) 1322 788063
EMAIL: [initialsurname]@ropl.com (gwoodford@ropl.com)
ADVERTISEMENT SALES
SALES DIRECTOR:
Philip Woodgate TEL: +44 (0) 1322 612067
EMAIL: pwoodgate@ropl.com
Dan Emmerson TEL: +44 (0) 1322 612068
EMAIL: demmerson@ropl.com
Graeme McQueen TEL: +44 (0) 1322 612069
EMAIL: gmcqueen@ropl.com
SUBSCRIPTION / READER ENQUIRY SERVICE
Aggregates Business is available on subscription at the rate of: £85 / US$145 / €111 per annum. Single copies £20 / US$35 / €26 Email subs@ropl.com for further details. Subscription records are maintained at Route One Publishing Ltd.
SUBSCRIPTION / READER ENQUIRIES TO: Data, Route One Publishing Ltd, Waterbridge Court, 50 Spital Street, Dartford, Kent DA1 2DT, UK
TEL: +44 (0) 1322 612061 FAX: +44 (0) 1322 788063
EMAIL: data@ropl.com
No part of this publication may be reproduced in any form whatsoever without the express written permission of the publisher. Contributors are encouraged to express their personal and professional opinions in this publication, and accordingly views expressed herein are not necessarily the views of Route One Publishing Ltd. From time to time statements and claims are made by the manufacturers and their representatives in respect of their products and services. Whilst reasonable steps are taken to check their accuracy at the time of going to press, the publisher cannot be held liable for their validity and accuracy.
PUBLISHED BY © Route One Publishing Ltd 2024
AGGREGATES BUSINESS USPS: is published six times a year. Airfreight and mailing in the USA by agent named World Container Inc, 150-15, 183rd Street, Jamaica, NY 11413, USA.
PERIODICALS POSTAGE PAID AT BROOKLYN, NY 11256
US POSTMASTER: Send address changes to Aggregates Business, World Container Inc, 150-15, 183rd Street, Jamaica, NY 11413, USA.
Air Business Ltd is acting as our mailing agent
PRINT: ISSN 2051-5766
ONLINE: ISSN 2057-3405
PRINTED BY: Warners (Midlands) PLC
iuGong has big BEV (battery-electric vehicle) dreams, and the many trade media at the Chinese off-highway machine maker’s Intermat Paris 2024 press conference were told that these dreams would not only be fully realised, but realised fast.
A demonstration of LiuGong’s ambition around BEV technology was present in an eye-catching Intermat exhibition line-up of four new electric machines, including the 856HE loading shovel. One of these wheeled loaders is being used by UK building materials giant Aggregate Industries at its Bow plant in East London. The 21-tonne unit is being used to load aggregates from the site’s Bow railhead, and on the London Concrete Readymix plant to keep the site clear.
With more than 40 new BEV machines in the pipeline, LiuGong aims to be the undisputed king of BEV-powered off-highway machinery in Europe by 2027. The company’s BEV pipeline encompasses excavators and wheeled loaders up to access platforms, reach stackers, skid steers and motor graders.
LiuGong aims to be a full BEV solution provider, further emphasised at the recent Vei og Anlegg show in Oslo, Norway. There, LiuGong launched two more battery-electric machines - the 870HE wheeled loader with a 4.7m³ bucket as standard, and the 45-tonnecapacity DR50CE rigid mining truck – said to be perfectly matched to support each other during quarrying, mining, and aggregates applications.
According to European product director Harry Mellor, LiuGong is “on a mission to create a more sustainable future in the construction equipment industry, and our continued investments in design, R&D and customer insight prove that we are leading the change.”
During the manufacturer’s Intermat press conference on 24 April, LiuGong senior management stressed that machine support would be paramount.
The rm’s European dealer network has either completed or is in the process of completing rigorous training to become ‘LiuGong BEV Certi ed’. Certi cation means that dealers will have passed the necessary high-voltage training, CATL technical training, and detailed service training. In addition,
“With more than 40 new BEV machines in the pipeline, LiuGong aims to be the undisputed king of BEV-powered off-highway machinery in Europe by 2027”
certi cation requires dealers to have mandatory spare parts and tooling before taking any machine into stock.
Alongside LiuGong’s investments in France, the manufacturer has also expanded its European operations with new regional of ces in Germany, Italy and Turkey. Major expansion plans are also in place for the UK with a new R&D Centre, proving ground, test area and customer solutions centre.
LiuGong Europe chairman Howard Dale, who I know well from a number of Aggregates Business editorial visits to LiuGong’s impressive Liuzhou, China HQ, and the company’s former Dressta dozer factory in Stalowa Wola, Poland, summed up the desire to rapidly build on what has already been a swift growth journey for the company, saying: “Now is an exciting time to be considering the LiuGong brand. Signi cant investments have been made, not just in product development, but in future-proo ng our business to be an even better partner for our customers. At Intermat we focused on our BEV products, but we will never forget that it’s relationships that really matter in our business.”
LiuGong is undoubtedly a big Asian off-highway machine manufacturing success story. In recent years, Aggregate Industries has been one of a number of notable European quarrying and building materials suppliers that have invested signi cant sums in LiuGong products for their highly productive equipment eets. Seeing the manufacturer’s electric dreams fully realised will add to our industry’s vibrant sustainability agenda. GW
The amount of construction aggregates from recycled and secondary sources in Britain has reached an all-time high as producers invest in more advanced ways to turn ‘waste’ into valuable materials.
That’s one of the key ndings of a new report from the Mineral Products Association (MPA) –which represents rms supplying over 90% of Britain’s aggregates – showing the total volume of
includes crushing, segregating (removing metals, plastics, etc), washing and screening, and blending to create materials that meet technical speci cations.
In the report, Construction Aggregates Supply in Great Britain: Primary, Recycled and Secondary Aggregates in 2022, the MPA demonstrates that non-primary materials accounted for over 30% of the country’s total demand for
solutions.
“That said, there are major investments taking place to improve the quality and availability of recycled and secondary materials, giving developers and contractors the con dence to specify them. Even the small amount of soft, inert waste that cannot be turned into aggregate is put to good use in quarry restoration and land remediation. Nothing is wasted!”
statistics. Recognising this, the MPA is leading industry efforts to address these data gaps to better inform evidence-based policymaking. Looking forward, the proposed introduction of a mandatory UK-wide digital waste-tracking system in 2025 should also help enhance the availability and quality of the data related to construction and demolition waste.
Despite the record recycling
Author of the report Aurelie Delannoy, director of economic affairs at MPA, emphasised the signi cance of recycled and secondary aggregates in meeting construction demands sustainably: “The substantial contribution of recycled and secondary aggregates to total supply is a huge but largely hidden success story for the industry. Aggregates producers have been recycling suitable construction and demolition waste for years to meet our construction needs as ef ciently and sustainably as possible, whilst meeting stringent technical standards.
“As we look ahead, further progress in recycling can be anticipated, supported by the major investments that have recently taken place in the extractive sector. However, it is important to recognise that
Heidelberg Materials UK has completed its acquisition of leading recycling company Mick George (MGL), following approval from the Competition and Markets Authority (CMA).
MGL has an annual turnover of around £220 million and
specialises in recycling and waste-management services. It operates around 40 recycling facilities, waste-transfer stations, aggregate quarries and ready-mixed concrete plants in East Anglia and the East Midlands.
To address the CMA’s
competition concerns, the company has divested eight Heidelberg Materials and MGL sites to PJ Thory and the Needingworth quarry to Brice Aggregates.
The acquisition strengthens Heidelberg Materials’ circular materials offering. It adds a
substantial recycling platform to the company’s portfolio, supporting the development of innovative technologies for processing waste and upgrading it as a valuable material for use in the construction cycle.
Simon Willis, CEO at Heidelberg Materials UK, said: “I am delighted to con rm the completion of the acquisition of MGL, which is an exciting milestone for us. It is a strong t and represents a major step as we embrace the opportunities the construction waste sector represents.
“It will allow us to drive the use of recycled aggregate in building materials and help us reach our target to offer circular alternatives for half of our concrete products by 2030.
“Promoting circularity and thereby reducing the use of primary raw materials is crucial to achieving net zero, and we are committed to playing our part.
“I am looking forward to working together to explore further opportunities and develop the combined business.”
BIA Group, a major distributor of equipment and services for industries including quarrying, mining, and construction, has unveiled its new CEO.
Vincent Bia, the current CEO, is handing over the reins of general management to Romain Bia, representing the fourth generation of the founder’s family. This transition, decided and validated by the board of directors and the family, reflects the solidity and continuity of the company, which has been in business since 1902.
Vincent Bia and Romain Bia will co-lead the company for a two-month period from 1 August 2024, ensuring a smooth and e cient handover. Romain Bia will take up his position as CEO on 1 October, and Vincent Bia will take the role of board chairman, continuing to contribute his expertise and strategic vision.
At the same time, the company has appointed Mariem Maiga as vice president of sales and marketing, replacing Romain Bia. With over 20 years of experience in the sector, notably with Epiroc and Atlas Copco, her mission will be to strengthen the BIA Group’s presence in its Benelux and African markets, where the company has developed its activities in the distribution of premium brands, including Komatsu, and associated maintenance services.
Vincent BIA expresses his confidence in this new step: “Passing the torch to the next generation is a moment of great pride and emotion for me. I’m convinced that Romain has the vision, dynamism and skills needed
to steer the company to new heights. This transition ensures continuity in our company’s values and ambitions while opening the door to new opportunities and innovations.”
Romain Bia, future CEO, shares his vision for the future: “I am deeply grateful for the trust placed in me by my father, the company and the Board of Directors. Taking on the leadership of the BIA Group is an honour and an important responsibility. With 1300 passionate employees and premium partners at my side, I am confident that we can continue to develop our market position. Digitization, sustainability and innovation will be important areas of development to continue bringing more value to our customers.”
After four years in consulting at Accenture, Romain Bia joined the company in 2011. Over the past 13 years, he has spent nine years in Africa and four years in Belgium. His career at BIA has been varied and comprehensive. He started out in finance (management controller, subsidiary, and regional financial director) before moving on to management roles, notably as country manager in Ivory Coast and regional general manager in Africa. He is currently vice president of sales and marketing, a position he has held since 2021.
In a record time, the EU Critical Raw Materials (CRM) Act has been adopted and entered into force on 23 May 2024, just 14 months after it was proposed by the European Commission. The focus is clearly on critical and strategic raw materials with some exibility for EU member states on allowing for other essential raw materials to be prioritised and taking appropriate measures at a national level.
While some Members of Aggregates Europe – UEPG might contact their relevant authorities to consider aggregates as part of a list of raw materials for priority treatment, the sustained focus on critical and strategic raw materials might have negative impacts on the length and costs of land use planning and permitting procedures if the current capacities of those authorities will have to prioritise their expertise and staff capacity for a few strategic projects.
The permanent attention of the European Commission and many national governments on critical raw materials and, recently, the events which were designed to improve access to raw materials in general might also take away the spotlight from the supply of essential raw materials.
Aggregates Europe – UEPG and its partners in ‘The Essential Raw Materials Coalition’, have discussed with Maive Rute, the Deputy Director General of GD Growth of the European Commission, about what
could be done to ensure sustainable access to essential raw materials because it is not addressed by the Critical Raw Materials Act. This could include relaunching the European Commission Raw Materials Supply Group, an expert group of industry and member states which stopped being active in 2021.
Aggregates Europe – UEPG will observe the implementation of the Critical Raw Materials Act because the green and digital
transition will require sustainable access to essential raw materials, often sourced from within Europe. By not addressing this crucial policy area, access to essential raw materials could become a critical issue. AB
McLanahan Corporation president and CEO Sean K. McLanahan represents the sixth generation of the multi-industry business’s family ownership and management. At the recent AGG-1 Academy & Expo 2024 exhibition at Music City Center in Nashville, Tennessee (25-27 March), he spoke to Aggregates Business about McLanahan’s growth strategy, current aggregates- and minerals-processing customer preferences and trends, and his approach to business leadership.
McLanahan’s large presence at AGG-1 be tted a company that has long been among the heavyweights on the global aggregates- and minerals-processing solutions scene.
Founded in 1835 by James Craig McLanahan and two investment partners known only by their last names, Evans and Devine, McLanahan is now led by Sean McLanahan, who oversees the executive management team and sets the corporation’s strategic direction and overall business development.
So, how does McLanahan’s president and CEO think the corporation is currently performing in the global aggregates-solutions marketplace? “We are performing very well. Over the last ve-plus years, we’ve seen substantial growth in our infrastructure and worldwide representative dealers’ ability to market our brand to customers.
“In some places, we go directly to the market as it serves us better. In other places, we rely on a representative company that introduces us to customers and acquires sales leads. We also have full dealers that stock machines and machine parts and have eld-service capabilities.
“We are seeing high demand [for equipment and solutions] in C&D [construction and demolition materials] markets. We have put great effort into developing products for those customers
and the accompanying ow sheets. Many C&D customers want us to work with them to deliver products they can sell ‘out the door’. We also see a lot of general quarrying crushing and screening activity.”
Sean says the 2022 acquisition of CMB International [CMB], a manufacturer of crushers, screens, feeders, and conveyors based in Leicestershire, England, has helped offer a wider range of solutions for quarrying customers. CMB is arguably most famous for its RubbleCrusher brand of compact crushers, which can be mounted on wheels, tracks, or skids and pulled behind a truck.
“The CMB acquisition particularly helped us on the customised screens side of our business,” Sean explains. “We can now really help a customer by installing a new screen that ts exactly into their stand without any changes to their operational structure. We may give them a more ef cient screen with a better drive arrangement.
“All our products come in a great standard range, but we can always customise if a customer needs something unique to their plant or a requirement they have due to a lack of water or the presence of too many material nes.”
Sean’s deep knowledge of the mineralsand aggregates-processing industries and McLanahan’s business operations are based on a wealth of experience. He began his career with the company in 1994 after earning a Bachelor of Science in Industrial Management and a Minor in Economics from Indiana University of Pennsylvania.
A popular and highly respected member of the National Stone, Sand, and Gravel Association (NSSGA), the King Coal Club, and the National Mining Association (NMA), Sean was elected to the NMA board of directors in 2018.
Asked about aggregates- and mineralsprocessing customer trends and challenges, Sean responds: “Power requirements and nes recovery are two big issues, as are tailing ponds in the United States. It is getting harder and harder for many American companies to have tailing ponds and get a permit to use them, especially in states where water is more scarce.
“We are close to doing a deal with one customer who has been buying over a million gallons of water monthly. They could use a McLanahan lter press and thickener [tank] to recapture 90% of the water, signi cantly reducing their expense.”
Sean says a lack of in-house personnel is also a big challenge for mining customers.
“As fewer people work at their mine sites, they rely more on equipment manufacturers for eld-service capabilities or plant operation. We do a lot of plant assessments and offer recommendations for more ef cient plant operation. In years past, they would have people within their company who would have gone around doing audits.”
Last year, McLanahan acquired Diefenbach, an Italian manufacturer of lter presses and thickeners. “Diefenbach and the earlier acquisition of CMB have helped us round out our product range and illustrate
what we are trying to do for our customers,” notes Sean. “We had developed a McLanahan filter press, but Diefenbach’s offer was fully developed and much broader, allowing us to get further into the marketplace while growing Diefenbach’s market share.
“With our [McLanahan and Diefenbach] filter presses, we now have many opportunities to help customers from the crushing side down to water management.
There are small product range gaps, but now we have the bulk of what we want. We’ve also taken a little side-step by acquiring the Anaconda [crushing and screening] brand and RubbleCrusher as part of the CMB deal.
“The CMB acquisition has helped us with our screening and cone crusher offerings and field-servicing capabilities in the European market. RubbleCrusher can piggyback on McLanahan dealers and Anaconda’s, being the baby within the latter’s machine range.
“We see great potential for the RubbleCrusher, particularly in cities and the C&D waste-recycling side. Given the permitting required for the demolition of buildings, you can’t get permits to take trucks on-site anymore. From what we’ve seen, it’s still an emerging market. It will be another ten years before it’s fully global, but there are places in Europe and the United States where compact crushers like RubbleCrusher are already in use.”
Sean believes the Diefenbach acquisition will help McLanahan further demonstrate its commitment to sustainability. “It does that through water conservation with filter presses and thickeners. We are trying to help our customers face their issues, which are increasingly related to water management and fine recovery. There are no hundred-year sites anymore where you can go in and put a plant. There are only sites giving you five years of production, and then you have to move your plant. This has made modular plants huge for us.”
Highlighting McLanahan’s investment in its manufacturing capabilities, Sean says: “We recently built new manufacturing facilities for Anaconda and McLanahan products in Northern Ireland. We are also looking at ways to grow Diefenbach’s manufacturing side. We’re also expanding our McLanahan manufacturing footprint in North America. Demand is so high for our products that we look everywhere at expansion possibilities.”
Sean says McLanahan’s strength and success start with its dealer network. “We have some of the best dealers in the world. We are always looking for more opportunities to grow. There are marketplaces we don’t yet have the resources to explore fully, but we will get there. It is often about finding the right dealer partner that can allow us and them to grow.”
Aggregates Business is curious about how Sean sees his leadership style. “I’m the sixth generation of our family. My dad is 85 and still doing well. I like to think I have a collaborative style. I like to hear lots of opinions and choices. I want everyone to have a say on what they think is a good
80% of the time, it’s been reached collectively. I don’t have to be the face of McLanahan. We have such great people. They are the face of the company, out there every day working with our customers. They are the ones helping to build our company and enabling us to grow.”
What about the up-and-coming seventh McLanahan family generation? Is there some interest among them in one day taking over the business’s leadership? “Our
pulled into the business. I didn’t know that growing up, I would come into it. I studied industrial management and economics and had opportunities to do some things, but I thought I had a great opportunity to get into McLanahan’s sales department. I worked there for ten years, travelling to see our customers and getting to know the pains they went through. Then McLanahan started doing some acquisitions that I helped integrate within the company. My management opportunities grew from that.
“The best part of my work is interacting with the hard-working, salt-of-the-earth people who run their businesses across the many industries we serve. You hardly ever meet a bad apple, which makes things fun. I am also extremely proud of the people who work within McLanahan and humbled by their expertise and dedication to the company and our customers.
“The flip side of my work is all the usual stresses of running a business. Every business has its ups and downs due to issues like changing markets, infrastructure or other limitations that need to be addressed, or geopolitical challenges. All that is constantly coming at you, and you need to figure out how to navigate it. It’s the least fun. As we’ve grown so much bigger, it’s become much more difficult to ensure we stay ahead of the game on all issues.”
So, what ambitions does Sean still have for McLanahan? “I want to continue to grow the company, and we have some further acquisitions in mind that will help us do that. We also need to grow our brand globally as best we can. We prefer a methodical growth that takes time. That’s okay, though, as I would rather things were done right.” AB
Settling for second best in crusher parts? Not on our watch. At CMS Cepcor, we combine our proactive service with reactive response times to reduce downtime and keep you crushing. From first call, to processing, packaging , and despatch, we’re dedicated to getting you what you need - faster!
Do you have a spare part strategy? We’d love to hear about it. Simply visit our site, fill out the form, and we’ll enter you into our free prize draw to win a Tag Heuer wristwatch. Now that IS worth waiting for.
Dr Andrew Minson is the Global Cement and Concrete Association (GCCA) director of Concrete and Sustainable Construction. He talks to Guy Woodford about his role at the heart of the global cement and concrete industry’s ambitious journey to net-zero concrete
The collective willingness of the world’s major concrete- and cement-sector players to deliver net-zero concrete by 2050 is a powerful driver of Dr Andrew Minson’s work.
“There are so many advantages when companies work together, which happens in all elds when competitors have common interests. The common interest for the cement and concrete sector is to decarbonise. Twenty years ago, we might have sat across a table from a government representative, architect, or engineer. Now we’re all on the same side of the table, and the discussions are about ‘how we’re going to do it’ rather than ‘whether we need to do it’.”
Based in Oxfordshire, England, Minson, an Australian national from Brisbane, joined the GCCA in September 2018 after many years as executive director of The Concrete Centre – part of the MPA (Mineral Products Association).
“I was a structural engineer based in London for ten years, working on real projects in different parts of the world. I arrived at the Concrete Centre in 2004, as it was beginning, and part of my role was building a team of engineers that could communicate back to [project] engineers how to use building materials most ef ciently and effectively.
“Then, in 2006, there was a bit of a watershed moment in sustainability, with politicians trying to ‘out green’ themselves by riding bicycles, which was an indicator that they were following public opinion. There was a big David Attenborough documentary, and Al Gore released his lm, An Inconvenient
Truth, so we pivoted more at The Concrete Centre to do far more on sustainability. I noticed some engineering design companies went from having specialist sustainable building groups to having sustainability as a key feature of all their work. While I missed being involved in real projects, I enjoyed even more playing a small part in trying to shape the environment in which the design and construction community worked.”
Headquartered in Paddington, central London, the GCCA is dedicated to developing and strengthening the sector’s contribution to sustainable construction. With its members accounting for 80% of cement-production capacity outside of China, the 2018-launched Association aims to foster innovation throughout the construction value chain in collaboration with industry associations, architects, engineers and innovators. In this way, the GCCA demonstrates how concrete solutions can meet global construction challenges and sustainable development goals while showcasing responsible industrial leadership in manufacturing and using cement and concrete. The GCCA complements and supports the work done by associations at the national and regional levels.
Around 4.2 billion tonnes of cement are produced worldwide annually, and the material is responsible for 7% of yearly global CO2 emissions. The world’s annual cement production is used to help make around 14 billion cubic metres of concrete a year. Minson stresses the vitality of understanding concrete’s “critical nature”.
“If it isn’t understood, the efforts of all the stakeholders to decarobinise production and
use the material more ef ciently won’t be made,” he says. “It will create an assumption that alternative materials or some magic solution might come over the horizon. The reality is that the scale and cost-effectiveness of concrete and its versatility to be used in such a broad range of applications means it’s here to stay. We have a pathway to decarbonise it, and we must get on with that.”
The pathway Minson is referring to is the GCCA 2050 Net Zero Roadmap. In 2020, association member companies came together as sector leaders to commit to producing carbon-neutral concrete by 2050, in line with global climate targets – accelerating the CO2 reductions already achieved. The GCCA 2050 Net Zero Roadmap describes how, collectively, in collaboration with built-environment stakeholders and policymakers, the global cement and concrete industry can be fully decarbonised, ensuring net-zero concrete for the world.
“Creating the Roadmap was an 18-month process involving over 100 experts from our membership and beyond, initially part of ve task groups and then a second phase of nine task groups. Ultimately, the [Roadmap] commitment was by CEOs. All the CEOs took the process very seriously. The last six months leading up to the agreed Roadmap were slow and quite hard going as they did look at every detail of it. It’s not a document that will sit on a shelf or another study of how net zero concrete could be done. It is a commitment to how it will be done.”
The GCCA also coordinates the Net Zero Accelerator Initiative. “This takes the global 2050 Net Zero Roadmap and uses it as a catalyst to support national cement and concrete industries and their associations in creating national roadmaps to help move towards the global net-zero concrete goal,” explains Minson. “One of the dynamics we see is leading GCCA member companies operating in countries driving national net-zero roadmaps as they want to have a level playing eld. This raises the bar for a country’s producers to make the changes required to deliver sustainable products
“The world’s annual cement production is used to help make around 14 billion cubic metres of concrete a year”
and for national governments to set policies allowing their domestic cement and concrete companies to deliver on decarbonisation. These national governments report to the IPCC (Intergovernmental Panel on Climate Change), so helping their cement and concrete industry decarbonise helps them meet their wider decarbonisation goals.”
A GCCA Green Cement Technology Tracker aims to support decision-makers and experts in policy, industry, academia, and civil society by tracking public announcements of investments in low-carbon cement technologies and presenting them transparently in one place.
The tracker currently includes carboncapture technologies and clay calcination kiln units. Carbon Capture and Storage (CCS) and Carbon Capture, Utilisation and Storage (CCUS) account for 36% of planned emissionreduction levers in the GCCA 2050 Net Zero Roadmap for concrete. Cement and binder savings, including calcined clays, account for 11% of planned emission-reduction levers in the same roadmap.
The GCCA 2050 Net Zero Roadmap includes 2030 interim targets. “By 2030, compared to 2020, the Roadmap aims for a 20% reduction in CO2 per tonne of cement and a 25% CO2 reduction per concrete unit,” explains Minson. Ten CCUS cement plants are also earmarked to operate at an industrial scale by 2030. Heidelberg Materials’ CCUS cement plant in Brevik, Norway, will become operational later this year, capturing up to 95% of the plant’s CO2 emissions. The same company’s CCUS cement plant in Edmonton, Alberta, Canada, is scheduled to be operational by late 2026 and to capture more than 1 million tonnes of CO2 annually.
“Whereas 15 years ago, there may have been suspicion about CCUS, in the last ve years, the process has taken great strides,” notes Minson. “We see recognition and support at the governmental level through European Commission funding and the United States’ IRA [In ation Reduction Act’s tax credit for carbon capture and sequestration] programme.
“In the CCUS story, there has been a separation of what hard-to-abate [emissions] industrial sectors, like cement and concrete, require from it, as opposed to the fossil fuels
industry. There was a suspicion in the past that any conversation about CCUS was really about a mechanism for the fossil fuels industry to keep pumping out fossil fuels, but this is no longer the case.
“There is a [ nancial] cost to carbon capture. In the developed world, that [ nancial] cost will be quite small at the scale of the nal project; per tonne of cement, there will be a bigger percentage increase. But cement goes into concrete; concrete construction is only a subset of a whole project. So, for a school or hospital, for example, built with net-zero cement, the incremental [ nancial] cost to that nal project will only be a single-digit percentage. It’s a good story for the school, hospital and builder to tell as part of the effort to combat climate change.”
Minson emphasises how the high-pro le annual COP (Conference of the Parties) summits allow the GCCA to interact with the global community addressing climate action while reinforcing GCCA members’ work towards delivering carbon-neutral concrete.
The Cement and Concrete Breakthrough Initiative launched at COP28 (30 Nov–13 Dec 2023) in Dubai, UAE, co-led by Canada and the UAE and supported by the GCCA,
is part of a broader industrial breakthrough initiative, including steel, launched at COP26 in Glasgow in 2021. It will enable countries to share best practices on various policies and other measures to help the cement and concrete industry decarbonise. The initiative also commits to working with countries, businesses and other organisations to accelerate investments in the technologies, tools and policies needed to help the industry achieve net zero by 2050.
“For cement to have its own breakthrough initiative is a huge recognition of the cement industry and the role governments can play in enabling it to decarbonise. It’s hugely positive,” says Minson. “In the last three years, we’ve raised the pro le of cement and concrete signi cantly. The scale of involvement we had in Dubai was far higher than in Egypt [Sharm El-Sheikh] when the buildings element of the breakthrough initiative was launched, and that GCCA involvement was far higher than the previous year in Glasgow.”
China is by far the world’s biggest national producer and user of cement, producing 2.1 billion tonnes a year, half the global total. India is a very distant second, producing around 410 million tonnes annually. Minson
reiterates that several big Chinese cement producers are part of the GCCA, and 80% of India’s cement companies are GCCA members signed up to the GCCA 2050 Net Zero Roadmap
In January 2024, the China Cement Association (CCA) and the GCCA signed a milestone MoU (memorandum of understanding) agreement to help accelerate the sector’s decarbonisation worldwide.
“We are delighted with this MoU and will work with the CCA to deliver a China cement industry roadmap similar to that used in India and the rest of the world to achieve decarbonisation. This means that the roadmaps are consistent and comprehensive across geographies.
“Getting China on board is also signi cant in a wider context, as the country is a
signi cant manufacturer of cement and concrete machinery and plants and a big contributor to the industry sustainability research agenda. China is also a major player in developing and commercialising carboncapture solutions.”
Minson says that in its communications about the GCCA 2050 Net Zero Roadmap, the association is careful not to appear to be “laying responsibility on someone else” in the supply chain, emphasising that the whole supply chain works within a “policy environment”.
“Producers worldwide are committed to doing what they can do in the production process to deliver net-zero concrete and are highlighting the role that others further down the supply chain can take.
“Policymakers have a role throughout
this: from helping to create infrastructure for CCUS to delivering more renewable electrical energy, which is particularly important as there will be more electrical consumption with CCUS. Governments must also play their role in promoting green public procurement. Governments and their agencies are responsible for purchasing 30, 40 or, in some countries, 50% of cement and concrete. Therefore, they have a role in how they procure it.
“One of our big messages is that using supplementary cementitious material from other industries’ waste, like y ash and GGBS (ground granulated blast-furnace slag), should be allowed in government procurement. Some governments still do not allow this in their cement and concrete speci cations and client briefs for projects. In time, as some of these supplementary cementitious materials become less available in some countries, calcined clay will be the large-scale supplementary cementitious material. It can deliver the cement content required and the nal concrete building at a lower CO2 footprint.”
Minson says that “assuming ef ciencies in design”, the GCCA forecasts that concrete demand volume through to 2050 will be pretty much the same as now.
“If those design ef ciencies are not implemented, there will probably be a 25% demand increase due to the sheer need for housing and other infrastructure. However, our 2050 Net Zero Roadmap forecasts that as building designers and the construction community recognise and implement ef cient design techniques that address the carbon challenge, they can use this versatile material and its inherent properties to get a 20-25% ef ciency saving.”
Asked about the biggest challenges he faces in his GCCA executive director role and his longstanding passion for improving all aspects of the built environment, Minson, an Oxford and Queensland University alumnus, responds: “The sheer scale of what we are working towards is a key challenge, and you overcome that through collaboration. We have to collaborate right down through the value chain.
“I wanted to get involved in engineering and doing things I could see that were tangible and made a difference. Ironically, while cement and concrete are visible, the key to achieving net-zero concrete is reducing the emissions of CO2, which are completely invisible.” AB
25-27.06.24, Buxton, UK
Built for reliability, safety, and top-of-the line operator comfort, the new Komatsu PC950/LC-11 empowers quarry operations to achieve new levels of efficiency. This advanced 95-tonne gentle giant features a new Power+ mode, an independent swing circuit, and large bucket capacities, allowing for enhanced productivity while achieving significant cost savings and reduced environmental impact.
The UK and Irish building materials markets face numerous challenges, but a shared, urgent need to increase housebuilding and a growing sustainability agenda o er attractive business opportunities. Guy Woodford reports
New gures from the Mineral Products Association (MPA) bring into focus the plight of a depressed British construction industry and the need for a robust growth plan.
The MPA has released the results of its quarterly members’ survey detailing Q1 2024 sales volumes for primary aggregates, asphalt, ready-mix concrete, and mortar, collectively seen as an important barometer for the construction industry as a whole.
The survey highlights continued challenges within the construction industry, which have resulted in persistent declines in demand across key markets for mineral products.
Despite a modest increase in primary aggregates sales of 1.1% over the last quarter, the overall trend across all monitored markets remains subdued. This, the MPA states, re ects the impact of UK economic stagnation, high interest rates, and a diminishing pipeline of new construction projects over the past 18 months.
The MPA notes that extreme weather conditions, including storms and record rainfall, further compounded the
situation at the start of 2024, impacting work on construction sites and demand for building materials. The Association says this is likely to result in extended project timelines, rather than any signi cant catch-up in demand during the spring.
The cumulative impact of these trends means that mortar sales – critical for bonding bricks, blocks and masonry – have dropped to their lowest volumes since 2014 (excluding covid-impacted Q2 2020), with a 27.5% decline in demand since the most recent peak in Q3 2022. This is attributed to falling housing demand and the knock-on implications for new housing construction since the Truss-Kwarteng budget debacle in October 2022, which precipitated signi cant increases in mortgage costs.
Similarly, ready-mix concrete sales have plummeted to historically low levels, hit by the contraction in housebuilding, which compounded longer-term weaknesses in demand from new commercial of ces and retail projects, which have been subdued since 2017.
The road sector has faced signi cant cost pressures
over the past two years, leading to project delays and cancellations on the National Highways roads programme and strained road funding for local authorities. As a result, asphalt sales fell to levels last recorded more than a decade ago in 2013.
The requirement for bulk ll materials on major infrastructure projects, particularly HS2, has supported demand for primary aggregates, but the lack of signi cant new infrastructure projects outside of the country’s only major rail scheme remains a concern.
Commenting on the ndings, Aurelie Delannoy, MPA director of Economic Affairs, said: "The latest survey results underscore the persistent challenges faced by the mineral products sector in Great Britain. Weak economic growth, high in ation and interest rates and construction project delays have collectively contributed to subdued demand across all major areas of construction. There are signs that construction activity may be beginning to stabilise, but lingering concerns over high costs, uncertainties surrounding future construction plans, and rising contractor failures are expected to impede any signi cant recovery in mineral products sales until at least 2025.
“As the General Election approaches, the MPA urges all parties to prioritise a robust return-to-growth plan, anchored by the timely delivery of the infrastructure pipeline. Streamlining planning processes for housing is important, but the Government must also tackle the signi cant cost pressures affecting infrastructure projects and local spending. Investing in local road repairs, upgrading transport networks, and delivering the housing, schools, hospitals, and energy infrastructure the UK economy needs are critical for both short-term and long-term growth, as well as advancing our goals to address climate change and sustainability. The mineral products industry stands ready to supply the essential materials needed.”
GlobalData, a leading business market research consultancy, estimates the UK construction market size as US$509.3 billion (£406.58bn) in 2023. The same source tips the market to achieve an AAGR (annual average growth rate) of more than 2% during 20252028 supported by investments in renewable energy, industrial, and infrastructure projects.
GlobalData says the British government’s focus on the construction of 180,000 affordable homes in the UK by 2026, with
Mineral products sales volumes in Great Britain, Q1 2014 -Q1 2024. Source: MPA
an investment of £11.5 billion, will support the residential sector output over the 20252028 period. The consultancy adds that investments in renewable energy projects, in line with the government’s aim to generate 95% of the country’s electricity from low-carbon sources by 2030, will also drive construction demand over the same period.
Irish Concrete Federation (ICF) chief executive Gerry Farrell tells Aggregates Business that after a sluggish rst quarter of 2024, mainly due to prolonged wet weather making it hard to get and keep construction
sites open, cement and concrete sales are improving in Ireland, particularly due to the critical need for more housing.
“Demand is improving in urban areas at the moment, possibly less so in rural areas”. There is a severe housing shortage in Ireland. The population is going up and housing is a hot political issue which should lead to increased demand for our members’ products.”
Farrell says that around 32,000 houses were built in Ireland last year, the highest amount in well over a decade. “There were a
further 12,000 housing unit commencements in the first quarter of 2024. I don’t think that level of housebuilding will continue for the full year, but it will be another significant year for new homes”. Farrell says Dublin and its surrounding four counties account for over 50% of Ireland’s homebuilding. “We have seen a notable increase in the construction of apartments in Irish urban areas. Apartment building went up 28% last year, and our members, particularly precast concrete manufacturers, are reaping the benefits.
“The Irish government is investing public money in the purchase and construction of houses currently. This represents almost 40% of Ireland’s national capital spending on infrastructure. Around €5 billion of public finances is going into the construction of houses each year. The Irish government has got involved because institutional investors are not there like they were in the past because of higher interest rates and the perceived lack of return. When interest rates come down, we will hopefully see more private finance coming into the housebuilding market”.
The Irish government is in the process of overhauling the Planning & Development Act in a bid to end the huge delays in the house planning system. “It is the biggest piece of legislation to come before the government in a long time,” says Farrell. “There are two years’ supply of new housing construction currently held up in the Irish planning system.”
Farrell says that around 4.5 million m³ of ready-mix concrete was sold in Ireland in 2023, approximately 7% down on 2022. He says the latest estimates indicate that slightly less concrete will be sold in 2024 compared to last year, given the uncertain first quarter.
In September 2023, the Irish government imposed a 5% levy on ready-mix concrete and concrete block sales to address a significant longstanding problem associated with concrete-block house construction, mostly in northwest Ireland.
“This problem has badly impacted on many people, particularly affected homeowners, and it has been a major political issue. The Irish government have allocated in excess of €2 billion to fix the mistakes of the past and it has decided that as Irish taxpayers are paying, the construction industry should also be making a contribution.”
Farrell says the ICF expressed its strong opposition to the levy and argued that the levy will have a negative impact on the entire construction sector, with the end customer having to pay more for concrete products.
The Irish cement and concrete industry has increased its focus on sustainability in recent years. As an example Kilsaran, a leading Irish manufacturer of concrete products, has recently invested in two electric-powered concrete mixer trucks.
“There is a major focus on climate change currently. From our own Federation’s perspective, we’ve recently recruited a head of sustainability who comes to us with great
experience in sustainability built up in his past employment with Arup Engineering Consulting. As an organisation, we can clearly see the challenge ahead, and we will resource our response to it in a big way in the coming years.”
Farrell says the Irish government is looking closely at the country’s cement and concrete sector and has drafted new criteria for the procurement of cement and concrete for public works.
“Initially, it will probably see the start of the phasing out of CEM1 cements in Ireland with a greater use of concrete with a minimum clinker replacement of 30%.
You’ll have CEMII cements being used with additions such as GGBS [ground granulated blast-furnace slag] and fly ash being mainly used to make Irish concrete products. In the longer term there will be leaner and smarter use of resources by designing better, specifying better and building better”.
Farrell says that May 2024 saw the ICF partner with Ireland’s Health & Safety Authority for a major safety campaign aimed at ensuring the safety of contractors working in Irish quarries.
A similar campaign focused on guarding and isolation is also due to take place in October this year. AB
Martin manufactures electric, hydraulic and pneumatic vibrators designed to efficiently sort bulk material by size. In fact, our electric vibrators are the industry’s go-to direct replacements for Derrick® shaker screen motors. And all vibrators come with an unsurpassed 3-Year warranty.
Martin Engineeering. Around the world, we deliver the cleanest, safest, most productive solutions to bulk material handling issues — now for more than 80 years
Longcli e Quarries is gearing up for sustainability-minded growth across its diverse product portfolio. Guy Woodford visited the Derbyshire, England-based company for a fascinating tour and wide-ranging conversation with the management team at the longstanding independent and still family-owned business
At a viewing point high above Longcliffe Quarries’ Brassington Moor Quarry (Brassington Moor) near Ashbourne, Jon Murgatroyd, the quarry manager, is talking to me about the site’s production process.
“We drill and blast to extract four different types of stone. A contract crusher takes the material from the upper benches and makes it into road stone for us. We have one [Epiroc FlexiROC
D55] drill rig here and another at our Ryder Point Quarry. Our in-house drill and blast team alternates via an access road between the quarries. Ryder Point is a [dolomitic limestone] aggregates quarry about a mile-and-a-half to two miles away. We use EPC-UK commercial explosives at both sites.”
Murgatroyd and I are joined by Paul Boustead, Longcliffe Group’s managing director, Ian McDonald, Longcliffe Quarries’ development director (process), and Chris Wainwright, the company’s
operations director.
“Having our own in-house drill and blast team gives us exibility when blending [extracted material] chemistry and enables us to react to customer needs,” explains Boustead.
McDonald adds: “We’re slightly unusual in that our blast sizes are not as big as they should be for economic reasons. Because we might leave the piles down longer than you would normally do, we can dry scalp and reclaim a lot more stone in the rst pass. If you move and re a
shot within two days, it’s not a problem, but Jon will have a high-quality shot down for a week, and you use the resulting material as you need it. What Jon crushes today is sold by tomorrow. We haven’t got the on-site storage capability to store a week’s worth of crushed material.”
“It’s little-and-often blasting,” says Murgatroyd. “We’re doing eight to ten holes, not the big 20-hole shots. We use Varistem stemming plugs. We were one of their rst customers in Europe. Using their plugs has reduced our blasting costs and given us better blasting fragmentation.
“At any one time, we can have up to ten shots down to mix and match the chemistry. As soon as they drill the shot, they take haul samples to our lab and run them through a spectrum analyser to give us an idea of what material we will get before we get it.”
Murgatroyd continues to explain Brassington Moor’s production process. “We have two excavators, a Liebherr 972 and a Cat 390, feeding three [Terex Trucks] TR70 dump trucks. This means I can blend stones from different parts of the quarry to try and mix their levels. This mixed stone is fed into a Metso Nordberg C160 jaw crusher. From there, it goes into an MMD [Group mineral] sizer. That leaves the sizer with 300mm down products. This is conveyed into the screen house and over a roll screen, and the feed is split into a large or small fraction. In the screen house are some reversible belts; depending on what chemistry we want in the nal product, half of it will go to the secondary crusher and the other half to the feeders. The feeders have a tunnel underneath them. We get enough stone on them to run production through the night. We work 11-hour weekday shifts plus Saturday mornings with the primary crusher. We ll the silos and the feeder throughout the daytime, and then the night shift can draw off the feeders and re ll the silos to keep them running throughout the night.
our [Brassington Moor] business growing and growing.”
He continues: “We’ve just agreed to buy another 15 Volvo HGV tractor units. The emission reductions and the attractive miles per gallon they give you have led to this new investment. We’ve demonstrated that in a fully laden 44-tonne articulated lorry, we can get 10.5 miles to the gallon. That’s classleading. Investing in the best technology exempli es Longcliffe’s commitment to its customers. Having mainly our own haulage eet, supplemented with local hauliers, gives us a business advantage. A sub-contractor haulier may say, ‘I’m not delivering those loads over that distance,’ but we will do so at the right price. Within 48 hours of placing an [industrial minerals product] order, we like to deliver it to the customer. Many of our aggregate customers collect their orders, with others delivered by us the next day.”
are lling out three big silos. One contains pure white, clean, clay-free stone that feeds the aggregate plant, and another feeds the Pyro plant for industrial and chemical mineral products. The third silo feeds an Ambuco plant that is producing products for glassmaking factories and animal feeds. We also have an attritor [mill] plant, which recycles excess material from the other two industrial mineral plants.”
Boustead, who became the Longcliffe Quarries group managing director in 2022, adds: “In the short time I’ve been here, we’ve built on the ‘customer rst’ approach and focused on how we can make their [working] lives easy.”
Has Longcliffe Quarries supplied materials for current or recently completed UK infrastructure projects? “At the start of the HS2, we supplied MOT Type 1 and 6F5. It was during COVID-19, and some major sites had shut down, but we could still meet orders. Due to the nature of our supply into critical industrial mineral processes, we could still supply as we had to remain operational,” says Boustead. “We also supply many industrial products for civil engineering contractors working on projects across the Midlands.”
“After the secondary crushing process, we
“We have 30 powder tankers and ten tipper trucks and supply the four corners of the UK from here,” notes Boustead. “With the recent changes to BS 8500 [UK concrete standards], with limestone llers replacing OPC [ordinary Portland cement], we can see
McDonald adds that the stone that built the visitor centre at The National Stone Centre in nearby Wirksworth came from Longcliffe Quarries.
Turning to the extensive ongoing work to create rollover slopes to improve the appearance of old quarried areas of Brassington Moor, Boustead says: “We use a wild ower mix on the rollover slopes, creating a meadow that encourages insects and other wildlife. With Longcliffe Quarries and some other local quarry operators’ success in creating rollover slopes, the landscape architect for Derbyshire [local authorities], who is also involved with the Peak District, has acknowledged that they meet its [restoration] standard and are great examples of this particular type of restoration. We are proud of that, and our restoration work is fundamental to our plans for extended quarry extraction at Brassington Moor. Indeed, the minimum now set down in new quarry planning applications is a 10% biodiversity net gain. Our calculations for the sympathetic restoration of the proposed new Aldwark South area result in just under 14% biodiversity improvement.
“We have two ex-worked quarries, Peak and Hoe Grange, and have partnered with Derbyshire Wildlife Trust and Butter y Conservation East Midlands to manage them sympathetically from a biodiversity
perspective. Hoe Grange hosts a ‘Butter y Day’ once a year, which attracts up to 450 people.” Volunteers from Butter y Conservation Trust have been walking a weekly transect at Hoe Grange for a few years, recording 29 different butter y species. Butter ies recorded include the Small Skipper, Large White, Small White, Green-Veined White, Orange Tip, and Small Copper. “More than 50% of the UK’s butter y species have been seen at Hoe Grange,” adds Wainwright.
McDonald notes that peregrine falcons have successfully bred at Brassington Moor and Ryder Point nearly every year over the last 30 years.
Murgratroyd drives us from our Brassington Moor viewing platform to the quarry’s state-of-the-art CDE plant for a close-up look.
In 2019, Longcliffe Quarries partnered with the major global market manufacturer of wet processing technologies to tackle the high volume of waste generated at Brassington Moor. The business had traditionally discarded its quarry by-product, a material with a higher clay content. However, feasibility studies and material testing to demonstrate market demand for products recovered from this stream showcased the potential for Longcliffe Quarries to realise its commercial targets without sacri cing its sustainability imperatives.
Installed in 2020 during the height of the COVID-19 pandemic, the only installation undertaken by CDE during the pandemic due to Longcliffe Quarries’ need to ful l its major customer product supply commitments, the £3.5 million, 220 tonnes-per-hour CDE stateof-the-art wet processing plant is the single largest investment Longcliffe Quarries has ever made.
Engineered to maximise product yield from heavy clay-bound feedstock, the bespoke plant features CDE’s signature AggMax modular logwasher setup for scrubbing and sizing.
It also incorporates CDE’s patented EvoWash classi cation and dewatering system, which offers greater ef ciency than traditional washing methods.
Central to the system and to address the availability of clean water on site is CDE’s AquaCycle thickener, which allows for up to
90% of the process water to be recycled and recirculated back into the system, offering near-total independence from freshwater supplies.
Exceptional water management means the CDE wash plant requires only a small top-up water supply, resulting in a highly ef cient system that extends signi cant operational savings to Longcliffe Quarries.
Previously discarded clay-bound material is now being processed through the wet processing plant, creating new, high-value revenue streams.
High-quality, single-sized aggregates and sand grades are among the key recovered products, maximising available reserves and supporting Longcliffe Quarries to realise its environmental targets.
The CDE plant features CDE CORE, a suite of smart technology tools that offers plant operators greater control over their plant and access to real-time data on how it operates to maximise plant uptime and throughput.
On arrival at the plant, I asked how it has performed since installation. “It is a very good wash plant that washes our harshest material. Waste-wise, it’s also made a big difference,” stresses McDonald. “It’s changed the whole structure of how the quarry works.
included areas to keep waste. Now you only design in lagoons. We’re down to only about 11% wastage from 25-30%.”
Murgatroyd adds: “We’re hoping that after I’ve put the next lagoon in, there can be a xed point for dewatering for a few years rather than weeks. We’ve been looking at how we will get power to that xed point.”
Brassington Moor, which includes two further extensive mineral extraction areas known as Pyro and Aldwark, produces 1.4 million tonnes of calcium carbonate powders and granules annually. As highlighted during my quarry tour, calcium carbonate forms the basis of many everyday products, such as animal feed, pet foods, drinking glasses, plastics, and pharmaceuticals. In addition to Brassington Moor’s output, Ryder Point produces up to 500,000 tonnes a year of highquality dolomitic limestone aggregate.
With a turnover of £50 million a year, Longcliffe Quarries produces 106 products for various industries. Two-thirds of production is dedicated to industrial minerals and a third to aggregates.
As we continue our Brassington Moor tour, I learn that 92% of Longcliffe Quarries’ 192 employees live within 20 miles of the business, with more than 80% living within 10 miles. Many employees take part in the company’s cycle-to-work scheme. Longcliffe Quarries is looking to take on another ve apprentices this year after what Boustead says had been the “great success” of its previous apprentice intakes.
I ask Boustead how dif cult it is to attract young apprentice talent to the business. “We are competing with the likes of Amazon and the general warehouse work environment. The beauty of our industry, and Longcliffe Quarries in particular, is that you may join us as an MPQC [Mineral Products Quali cations Council]- supported electrical engineer, but you aren’t wedded to that role for your career. However you enter the business, this can lead to a vast array of careers in our industry. We partner with a college in Stoke, are getting closer to Derby College, and do some work with the University of Derby.
“We are attracting more apprentice applicants now because of the breadth of
where the apprenticeship can lead you. I think we’ve got 12 who have their NVQ Level 6. We lost one of our apprentices when he nished his apprenticeship. He went to work at one of those warehouse jobs, and three weeks later, he rang up and asked if he could come back. He said the pay may have been a bit more, but he hated his working conditions and a work culture that made him feel like a number. He said he wanted to return to our ‘family’ culture.
“We have brilliant employee service, with some of our team having been here 30-years plus. Gerald Lees celebrated his 50th work anniversary here in 2018. He’s still one of my best excavator operators. However, in the next four to ve years, we will probably lose around 40% of the workforce to retirement,
Final-grade product stockpiled at Brassington Moor Quarry. Pic: Longcli e Quarries
so we are succession planning.”
On our return to Longcliffe Quarries’ head of ce, around a mile from the Brassington Moor Quarry Complex, via the impressive Curzon Lodge Transport Garage and Hoe Grange, Boustead highlights more of the company’s extensive sustainabilityenhancing projects. “We are targeting net zero to weighbridge by 2030, reducing electricity usage, and increasing renewable carbon-neutral energy sources, working with National Grid to direct more wind-farm power to Longcliffe operations. The head of ce is solar-powered, and we plan to install solar panels at our transport depot.”
An example of Longcliffe Quarries’ continuous investment in its business and part of a £3 million project to enhance its
Brassington Moor Pyro plant production, two new energy-ef cient TCM mills will be installed in the second half of 2024.
McDonald says: “The recycling of our materials has been quite inef cient. We bought the rst of our two existing attritor mills in the 1990s and the other in 2008. They have built up slowly to 100% capacity. The problem has been that they produce what are classi ed as two products when the market just wants one. This creates a big inef ciency. The new TCM mills will be more ef cient with a single-pass-through and classi er, making one product at a time. You cut out another big inef ciency because the classi er is in the milling process. The new mills will not be so maintenance-heavy and help avoid major failures that could stop
No matter how challenging your needs, EARTHMAX SR 41 is your best ally when it comes to operations that require extraordinary traction. Thanks to its All Steel radial structure and the special block pattern, EARTHMAX SR 41 provides excellent resistance against punctures and an extended service life. In addition to long working hours without downtime, the tyre ensures extraordinary comfort.
EARTHMAX SR 41 is BKT’s response to withstand the toughest operating conditions in haulage, loading and dozing applications.
production for up to a week.
“Over 20% of our calcium carbonate powder and granule sales are L150 cementitious replacement-type material. It is a growing market, but we only have 300 tonnes of storage for this particular product on-site. The two new mills will give us another 350 tonnes of storage to help schedule our delivery lorries.”
Established in 1927, Longcliffe Quarries is still owned by the Shields family. Current company chairman Robert Shields’ greatgrandfather started the business. Two of Robert’s sons, John and David, also have roles in the business. John is Longcliffe
Quarries’ energy director, leading the company’s sustainability agenda, and David sits on the management board.
Boustead says another example of Longcliffe Quarries’ family feel is the recent launch of Longcliffe Choices. “It’s a web portal where the team can get shopping vouchers and employee discounts. It also has their day-to-day work information, pension details, and wage slips. When the costof-living crisis hit, we helped staff not just with remuneration but also food shopping vouchers to support them during this difficult time. The team were appreciative.”
An exhibition held in March 2023 as part
of Longcliffe Quarries’ public consultation on its Aldwark South extension plans highlighted how the company contributes around £20 million yearly to the local economy through wages and using local contractors.
Furthermore, Longcliffe Community Fund allocates more than £70,000 yearly to local projects. These have included taking a team and a Longcliffe lorry to Anthony Gell School in Wirksworth to educate pupils about road safety as part of National Road Safety Week and a £3,000 donation to Cromford Church of England Primary School to help pay for a significant school playground makeover.
The exhibition noted that Aldwark South is already identified in the Draft Mineral Local Plan as a future source of high-purity limestone. If the planning application is successful, the quarry extension will secure Longcliffe Quarries’ future and protect many jobs.
“The main growth driver for our business is being able to offer our new innovative industrial mineral solutions and products,” emphasises Boustead. “From a high-purity resource point of view, which is our core business, we have identified medium- and long-term reserves, but this depends on a successful planning application. We have just submitted our formal planning application for Aldwark South. If successful, it will allow us to tap into another 27 years of high-purity industrial mineral reserves.” AB
Featuring over 600 exhibitors and set to attract more than 20,000 visitors, the next edition of the Hillhead exhibition will take place from 25 to 27 June 2024 at the Hillhead Quarry near Buxton, Derbyshire, England. Guy Woodford looks at some key highlights attendees can enjoy at the biennial industry showpiece, which celebrates its 40th anniversary this year.
Powerscreen is bringing a strong carbon-footprint-reduction focus to its Hillhead showcase. Sean Loughran, Powerscreen’s business line director & general manager, stresses: “As our mission towards net zero continues, we are excited to meet with like-minded companies to discuss how Powerscreen crushing, screening and conveying equipment can help crush their carbon footprint. Our latest partnership with CATAGEN, as part of the UK’s Red Diesel Replacement scheme (RDR) - is a prime example of our commitment to research and innovation in this eld.”
Based in Northern Ireland, CATAGEN is a catalyst testing expert that develops new technologies in green hydrogen and e-fuels. Powerscreen and CATAGEN are currently working on a joint project that will deliver a decarbonised end-to-end demonstration of a Powerscreen Premiertrak 450E crusher and Chieftain 1700XE screener, powered by green hydrogen and e-diesel, at a working quarry site in Northern Ireland later this year.
In addition to helping companies reduce carbon emissions in crushing and screening operations, Powerscreen will demonstrate the ability of its new 1300X cone crusher in the
demo area.
“At the Powerscreen World Dealer Conference in Italy last year, we launched our latest jaw-crushing technology with the Premiertrak 450 and our next-generation impact crushers with the Trakpactor 480 & 480SR. It’s now time to replicate these advances with cones and we are looking forward to showcasing these advancements in the demo area,” said Neil Robinson, Powerscreen product director.
The Wirtgen Group's exhibition lineup focuses on the themes of smarter, safer, and more sustainable.
Exciting premières for the British market include the world’s rst burner that can be fuelled exclusively with green hydrogen. Event visitors will also be able to take a closer look and discover more about the Wirtgen Group’s digital solutions.
On the road to making the future of road construction more sustainable, the greatest leverage potential lies in the eld of asphalt production. With the world’s rst burner that can be fuelled exclusively with green hydrogen, Benninghoven presents a groundbreaking solution for the
future that is already on the market today. Alongside the latest generation of burners for use with alternative fuels, the special presentation at the stand will also showcase further technologies for sustainable asphalt production.
The new Kleemann mobile impact crusher, the MOBIREX MR 100(i) NEO/NEOe, is making its rst UK appearance. The NEO line is Kleemann’s new, ef cient, compact class. Thanks to its compact dimensions and low transport weight, the MR 100(i) NEO/ NEOe can be used exibly, quickly and in a very wide variety of applications. All-electric operation is possible with the MOBIREX MR 100(i) NEOe variant.
Alongside machine ef ciency and alternative applications and methods, digitalisation and connected-system solutions are important drivers for more sustainability in the road construction process chain. “Digital-assistance systems, telematics solutions and the automation of processes will contribute to an increase in the ef ciency and cost-effectiveness throughout the road-construction-process chain and
Compact, powerful and versatile: Introducing the MOBISCREEN MSS 502i EVO mobile coarse screening plant. Its compact size, low transport weight and impressive feed capacity of up to 350 tonnes per hour ensure that this versatile machine can be used flexibly and quickly for even the most heavy-duty applications in natural stone and recycling. The compact MSS 502i EVO, with its advanced ergonomics, was designed for exceptional operability. It can also be operated electrically thanks to its optional dual-power drive. The MOBISCREEN MSS 502i EVO: the (small) multi-talented powerhouse.
www.wirtgen-group.com/mss-502-evo-kleemann
simultaneously further reduce CO2 emissions”, explains Paul Holmes, managing director of the British Wirtgen Group subsidiary Wirtgen Ltd. “The Wirtgen Group has a roadmap for this and will play a decisive role in the advancement of the digital transformation as a driver of innovation in the road construction industry.”
HD Hyundai Construction Equipment (HD Hyundai) will display its biggest Stage V crawler excavators so far, the 80-tonne HX800A L and the 100-tonne HX1000A L, at this year’s Hillhead. Both of these heavy-duty machines have been designed for quarry and bulk earthmoving duties. The HX800A L uses a 403kW Stage V diesel engine to power two 504lpm hydraulic pumps, while the HX1000A L uses a 469kW diesel engine to power three 523lpm pumps.
These heavyweight excavators take HD Hyundai into a new market sector in the UK and across Europe, providing a highly productive digging and loading solution for mines, quarries, bulk earthmoving contractors, and heavy civil engineering sites. The HX800A L is suitable for use with 4.255.24m³ buckets, and the larger 100-tonne machine can work with 5.4-6.8m³ buckets.
HD Hyundai will also unveil its biggest wheeled loader, the HL985A. This 35-tonne shovel can handle 7m³ buckets, making it ideal for digging and rehandling in the mining, quarrying, and heavy civil engineering sectors. Powered by a 321kW diesel engine, the HL985A boasts a bucket breakout force of up to 28,400kg and a full-turn tipping load of 22,950kg in standard con guration.
HD Hyundai recently added a range of HRB silenced hydraulic breakers to its line-up. The six breakers, which can be ordered in varying levels of speci cation, have been designed to work with carrier machines in the 1.2-26tonne sectors. The larger models are offered
Benninghoven will showcase the world’s first burner that can be fuelled exclusively with green hydrogen.
Pic: BenninghovenWirtgen Group
to a minimum and making the breakers ideal for use in urban areas.
HD Hyundai has moved to a new location directly in front of the demonstration area. At 1,220m², up from 750m² on the previous stand, the display will include two viewing areas, along with a range of hospitality. This will include HD Hyundai CE’s now famous pie machine, which will be making a welcome return to the show.
equipment we’ve ever had on show,” said Lee Appleby, head of marketing at HD Hyundai Construction Equipment.
Hillhead 2024 will provide the perfect platform to both display and demonstrate for the rst time at the show the latest products for the quarrying and construction industries from Develon, formerly known as Doosan Construction Equipment.
The static display on Develon‘s stand will include the DX530LC-7 53-tonne crawler excavator, the DL420-7 wheeled loader, and the DA45-7 articulated dump truck (ADT). In the demonstration area, further products for the quarry face will be showing their paces, including the DX420LC-7 43.5-tonne crawler excavator, the DL550-7 wheeled loader, and the DA30-7 articulated dump truck (ADT).
The new DX140RDM-7 22.5-tonne demolition excavator and the new DD130-7 dozer are among the new products being shown for the rst time at Hillhead on the Develon stand.
The DX420LC-7 and DX530LC-7 are part of Develon's range of large crawler excavators, which also include the DX800LC-7 80-tonne and DX1000LC-7 100-tonne machines. Overall, all the models in the DX-7 range of crawler and wheeled excavators from 14 to 100 tonnes combine enhanced comfort with the latest features to boost fuel ef ciency, uptime, and return on investment, with a focus on
increased power, robustness, and agility.
The DL420-7 and DL550-7 are two of the four biggest standard models in the DL-7 range of wheeled loaders from Develon, which also feature the DL480-7 and DL5807. With redesigned buckets offering up to 7% more capacity, these DL-7 wheeled loaders provide easier and faster loading with maximum bucket capacities from 4.5 to 6.4m³. Altogether, the 11 DL-7 wheeled loaders in the Develon range with bucket capacities starting at 2m³ provide increased productivity for a very wide range of materialhandling applications.
The market-leading DA30-7 and DA45-7 ADTs offer payloads of 28 tonnes and 41 tonnes, respectively. These models feature an articulation hinge behind the turning ring, providing equal weight distribution to the front axle even during maximum steer articulation. This, combined with a free-swinging rear tandem bogie, ensures equal distribution of weight to each wheel and guarantees permanent 6-wheel contact and drive for equal power distribution and excellent performance, particularly on dif cult terrains such as soft ground, uneven surfaces, very steep slopes, tight turns or a combination of all of these dif cult conditions.
The DA30-7 and DA45-7 6x6 ADTs are now complemented by a new 4x4 version of the DA45-7 ADT intended to compete with rigid dump trucks (RDTs) in the 40-tonne class. In the new 4x4 ADT, the front truck and cab unit are the same as in the original 6x6 model, with modi cations being made only to the rear dumper unit.
A host of new and improved CASE Construction Equipment (CASE) machinery will be on display at Hillhead 2024, both static on the stand and working at the quarry face. Standout machines include the recently unveiled 651G Evolution wheeled loader and CASE’s new CX210E-S crawler excavator. CASE will also have a glimpse of the future on show, with its latest fully electric compact wheeled loader, the 12EV.
The new 651G Evolution lls a gap between the 621G and the 721G machines. The larger 721G, 821G and 921G Evolution models have also been upgraded and now boast increased tipping loads and bucket dump heights, further improving customer productivity.
The 651G Evolution and the three larger wheeled loaders feature reinforced front and rear chassis sections to cope with the increased performance. Heavy-duty axles are now tted as standard, with a choice of differentials on each axle. Customers can choose between a 100% differential lock on the front axle and an open differential on the rear, a 100% differential lock on the front and a limited-slip differential at the rear, or a limited-slip differential in both axles.
waste and recycling area, in the secondary rock-handling area and in ‘Crusher Alley’, where blasted rock is initially processed.
At Hillhead 2024, keen operators will also be welcome to take a turn at the controls in CASE’s popular Operator Challenge, with a range of prizes available throughout the exhibition. There will also be live demonstrations of equipment in the quarry’s
Among Europe’s premier manufacturers of aftermarket crusher spares, Quarry Manufacturing & Supplies (QMS) is displaying a selection of jaw, cone and impact crushers, a number of screens, and a variety of wear parts and consumables.
Operating from an extensive purposebuilt facility in Coalville, Leicestershire, as well as other UK locations, QMS has
for supporting minerals extractive industries’ customers globally. The company possesses fully equipped manufacturing and repair workshops and prioritises investment in its people, technologies, processes, and supplier partnerships. QMS proudly continues to raise the bar in manufacturing excellence, delivering exceptional service and outstanding value.
At Hillhead, QMS specialists will offer advice on maximising investments, both in
equipment and processes.
Rapid International and its sister company, Rapid Power Generation, are gearing up to make a signi cant impact at Hillhead 2024.
Industry leaders in mixing technology and power generation, Rapid International and Rapid Power Generation will co-exhibit at the industry showpiece event, offering attendees a glimpse into their latest advancements and solutions. Rapid’s GB sales partner, Concrete Technology, will also share the stand, offering expert mixing-technology solutions to customers located in mainland UK.
Rapid International will exhibit its enhanced Trakmix 250 track-mounted, mobile, continuous-mixing plant. This groundbreaking plant revolutionises on-site material production with its unmatched ef ciency, exibility, and reliability for every mixing application.
Trakmix offers ultra-mobility via tracks, delivering fast, high-volume, mobile, continuous-mixing technology for a wide range of sites and applications. Producing up to 250 tonnes per hour, Trakmix is fully self-contained and can be set up and mixing in a matter of hours. Offering full weighing of all materials, Trakmix provides unrivalled accuracy and accountability.
In addition to showcasing the Trakmix 250, Rapid International will announce the rollout of new products in its continuous-mixing and concrete-batching ranges. Launching in Q3 of 2024 and extending into early 2025, these new offerings underscore the Northern Ireland-headquartered manufacturer’s commitment to innovation and meeting the industry's evolving needs.
"We are delighted to be exhibiting at Hillhead again. Our participation in Hillhead 2024 re ects our dedication to pushing the boundaries of innovation and delivering
collaboration."
Rapid Power Generation is showcasing a 160kVA Stage 5 Deutz genset equipped with a Mecc Alte alternator and Deep-Sea Electronics controller. This state-of-theart generator exempli es the company’s commitment to providing reliable, highperformance power solutions.
From its new location at the top of the quarry, MB Crusher will feature units from both its compact and heavy lines, presenting a diverse range of products tailored to meet the evolving needs of quarrying, recycling, and civil engineering customers. With solutions designed to seamlessly integrate with diggers, skids, and loaders, MB Crusher offers outstanding versatility.
MB Crusher's padding bucket is said to rede ne the process of handling materials on-site. The product’s versatility ensures that it can be seamlessly integrated into any eet, providing a customisable solution for different projects. From landscaping to pipeline construction, the padding bucket is a versatile asset that adds value across a spectrum of applications. MB Crusher's unique system allows the operator to purchase one unit and several interchangeable shafts, and having
grapple is a game-changer in ef cient material handling. Designed for precision, this grapple allows operators to pick, sort, and place materials with ease. Its robust construction ensures durability, making it a reliable tool for demanding job sites. Moreover, each unit can be accessorised to satisfy any type of job.
MB Crusher's team of experts will be available to discuss the features, bene ts, and applications of the manufacturer’s latest offerings. This interactive engagement aims to provide attendees with a comprehensive understanding of how MB Crusher can signi cantly improve their operations.
In response to the growing demand for its groundbreaking products, MB Crusher is excited to announce the nationwide availability of its innovative solutions for immediate delivery. This expansion ensures that customers throughout the UK can swiftly access MB Crusher's transformative machinery.
Hillhead has long been a calendar highlight for Smiley Monroe, but the 2024 edition is shaping up to be a special one for the Giants of Belting.
Sporting a refreshed brand identity that better re ects the group’s bold vision, the Lisburn, Northern Ireland-headquartered company will showcase its new, highperformance, ‘lightweight’ conveyor belts. These belts offer up to a 41% reduction in belt weight and a signi cantly lower carbon footprint compared to the alternative.
“Listening to our customers, it’s always been clear that they’re focused on reducing the overall weight of their machines without compromising on the performance of the belt conveyor components. We proved that our 2-ply ToughFlex belt, developed speci cally for mobile equipment’s smaller pulleys, outperforms a traditional 4 or 5-ply belt in the harshest applications. So, once again, we’ve collaborated closely with our key suppliers to bring to market a conveyor belt that is not only 30% thinner than the existing alternative, with the same impact resistance, but offers even better wear resistance. There’s already been a lot of interest from customers who are keen to trial our new reduced-weight belt for themselves,” said Chris Jones, Smiley Monroe’s head of product support.
Visitors can stop by Smiley Monroe’s stand to learn more about the manufacturer’s new ‘GoLite’ belts and range of problem-solving products and services. AB
The crushing and screening sector has seen some eye-catching, new machine launches, including a diesel-electric range of crushers from Metso and scalping screens from both Kleemann and EDGE Innovate. Liam McLoughlin reports
Metso has introduced a new diesel-electric power lineLokotrack EC - into its Lokotrack range of crushers for the aggregates market. All the process functions of the new Lokotrack EC range are electric, signi cantly reducing the use of hydraulic oil needed in the crushing operations. All Lokotrack EC range units can be powered with external electricity.
At its 'Lokolaunch' event in Tampere, Finland, Metso launched the rst two products of the new EC range. Lokotrack LT400J is a 68-ton mobile jaw crusher designed for the primary crushing of hard rock and recycled aggregates. Lokotrack LT350C is a 50-ton mobile cone crusher for secondary and tertiary crushing. To reach high capacity, LT350C is equipped with the new Nordberg HP350e cone crusher, while LT400J counts on the proven Nordberg C120 jaw crusher. Metso says both units can be seamlessly combined with each other as well as with the Lokotrack mobile screens to produce high-quality aggregates.
“When external electricity is available, the new electric-power transmission provides high capacity with minimised operational cost and CO2 emissions. When not available, the onboard diesel gensets allow maximum independent operation time. Also, auxiliary units, such as mobile screens and stackers, can be powered from the same gensets,
which will further reduce the needed power to run the complete plant,” says Jarmo Vuorenpää, director, new Lokotrack offering at Metso.
The Lokotrack EC range has been developed using new, modular architecture, which reduces the number of components and provides scalable solutions that can be adapted for different applications and capacities.
“The new way to do product development enables a faster and more agile way to meet the changing customer needs. Furthermore, it enables more ef cient support for the machines with fewer parts needed and easier upgrades of new features,” says Renaud Lapointe, senior VP of the Metso products business line in the aggregates business area.
The concept of track-mounted crushers and screens was developed in Finland in 1985 to minimise cost and energy use. Metso says its Lokotrack units are ideal for processing both natural aggregates and recycled materials.
Metso’s Lapointe has given an assessment of market conditions in the global crushing and screening market.
“Currently, demand for aggregates crushing and screening solutions is globally a bit softer than a year ago, but we see differences between the various regions,” he says. “We also see our dealers and equally the competitors’ dealers having a lot of machines in their backyard.”
2021 and 2022, when it was extremely high. In Europe, and especially in Northern Europe, the demand is soft currently . It was also very high in 2021 and 2022, but since 2023 it has decreased due to the high interest rates and high in ation.
“In Africa and Middle East area, the market for new equipment is active thanks to many ongoing infrastructure projects,” he states. “In Asia, the market is very robust especially in the quarry segment. In China, the main aggregates producers open new quarries of very high production capacity (up to 70 million tpa) and need big capacity crushers and screens for these new plants.”
Some global trends are in uencing the demand for new equipment. In the quarry segment, the existing crushing and screening plants need to produce more of higher quality products with less power consumption. In the contractor segment, aggregates producers need mobile and hybrid technologies to operate in sustainable conditions in compliance with governmental regulations.
He adds that in North America demand is improving but is still a bit weaker than in
He adds that two other notable trends are the fast development of the manufactured sand segment and the recycling segment. “As we all know, the construction industry is the biggest consumer of sand which is the most-consumed natural resource in the world after water,” says Lapointe. “Nowadays, dredging sand from rivers, lakes and other water bodies is more and more regulated and we ought to nd ways to produce sand with alternative techniques. Metso has developed a HRC crusher that can produce sand from crushed rock whilst consuming less power than a traditional crusher.”
Pilot Crushtec International is introducing a new line of Jonsson premium mobile crushers and screens in southern Africa.
The L 150 mobile jaw crusher from Metsoowned Jonsson is powered by a 400kVA generator set or via mains operation and is equipped with a Nordberg C150 jaw crusher .
The Jonsson range comprises tracked units, largely aimed at the premium hightonnage , heavy-duty segment of the crushing and screening market.
P.J. Jonsson och Söner is a Swedish mobile crushing and screening plant provider that has traditionally operated in the Nordic Region and was established in 1953. Following the 2018 acquisition by Metso, Jonsson is on a drive to expand its business internationally, and southern Africa is one of the strategic markets. The brand will leverage Metso’s existing eight-year partnership with Pilot Crushtec to grow its footprint in the region.
Adam Benn - director, capital sales, North EMEA, CEA and southern Africa at Metso – says that Pilot Crushtec is unique: “The primary focus on crushing and screening has over the years allowed the company to develop a profound understanding of the crushing and screening sector, which uniquely positions them to forge long-lasting connections with their customers in southern Africa.”
Jonsson’s range comprises tracked crushers and screens, unique double crushers and screens, feeders and conveyors.
Crushing and screening plant manufacturers are targeting emissions improvements from both a manufacturing production and equipment perspective .
At the recent Wirtgen Technology Days event in Germany, visitors gained some insights into the advanced manufacturing process chain at Wirtgen-owned crushing and screening plant manufacturer Kleemann. Since the opening of the new Kleemann plant in 2009, the highly-specialised facility has been successively extended and has been constantly upgraded for sustainable operation in line with the group’s sustainability strategy. The site features highly complex prefabrication centres in which the core components of the Kleemann plants are produced with exceptional precision.
“In past years, we concentrated our efforts on target-oriented expansion of our product portfolio and now offer suitable solutions for every application, no matter whether for recycling or natural stone processing,” said Kleemann CEO Alexander Knam, describing the development of the company’s headquarters site in Göppingen. “To achieve this, we invested in areas such as expanding our production capacities and improving our assembly or logistics processes.”
He believes that the materials-processingequipment specialist is ideally positioned for the future: “With these investments, we have laid the foundation for the ongoing production of our products and technologies under ideal conditions, namely sustainably and ef ciently.”
The 150,000m2 Kleemann facility at
new Kleemann
Göppingen has a workforce of more than 600 highly-skilled employees, and the crushing and screening manufacturer currently has 19 models in its portfolio.
“Sustainability is a very important pillar of our strategy,” said Knam. “The goal is to reduce 50% of our operational CO2 emissions by 2030 from the baseline year of 2021. At Kleemann we have already implemented some measures to improve our overall footprint. We have looked at our energy consumption and realised that electrical energy is really the key lever for us to pull, so as a rst step we invested heavily in all our lighting systems at Göppingen and have now fully converted them to LED lighting.”
He said this provides energy savings of about 1.5 million KWh per year.
“As a second step, for the remaining electricity we use on the site we decided to purchase clean electricity, and we have already more than achieved our target of 50% energy improvement,” he added.
Knam said that, despite exceeding its emissions-reduction target, Kleemann is looking at further options including photovoltaic roo ng on its factory.
Kleemann used the Wirtgen Technology
Days event to give the world premiere of its new MOBISCREEN MSS 502(i) EVO mobile scalping screen, designed for high exibility, simple operability and very good ergonomics.
The MOBISCREEN MSS 502(i) EVO extends Kleemann's portfolio of mobile screening machines below the established MOBISCREEN MSS 802(i) EVO.
Knam says the machine, which will be available to customers shortly, is very compact and easy to transport and he added that the ease of access to the engine for servicing will make it a benchmark for the industry. It can be operated all-electrically from the grid, scoring high with regard to sustainability.
He added that the noise level is signi cantly reduced by around 10 decibels compared to the previous MS 30 model. “The machine is an all-rounder for use with natural stone and recycling,” he added.
With its compactness, the MSS 502(i) EVO is optimised for the lower feed capacity range of up to 350 t/h. A generously dimensioned feed hopper, a screening surface of 5.4 m² and a wide main discharge conveyor guarantee excellent material guidance. For high exibility in the application, the speed of all conveyor belts is steplessly adjustable and a simple conversion from two to three nal grain sizes is possible.
Overall, the new machine offers comprehensive con guration diversity to
impress as a stand-alone or in conjunction with further Kleemann machines to precisely meet the customer’s needs.
Northern Ireland-based EDGE Innovate says its new SCREENPRO S18 heavy-duty, tracked scalping screen can transform the toughest feed material into pro t. EDGE Innovate – which designs and distributes a range of equipment used in the quarrying, port-handling and recycling industries –says the new scalping screen delivers high production rates and precision screening.
The dynamic 5.4x1.75m two-deck screen of the EDGE SCREENPRO S18 features interchangeable ip- ow and conventional scalper screens, providing unprecedented exibility. A highly versatile screening solution, the new SCREENPRO S18 is designed to process the most dif cult and demanding of applications, including aggregate, construction waste, sand and gravel, soils and organic materials. With numerous screen-media options and con gurations available, the EDGE S18 can be utilised as a stand-alone unit or if needed, placed before or after a primary crusher.
Impressive design features include a low-level feed hopper, 2- or 3-way split con guration, hydraulic folding discharge conveyors to facilitate the quick transition from operation to transport, and a fully integrated power unit with large service access. A user-friendly control system with sequential start/stop functionality provides exceptional operational performance and unit safety.
EDGE says the SCREENPRO S18 offers the largest hopper capacity in its class, encompassing a 1,400mm-wide, variable -speed feeder with forward/reverse functionality. A large feed opening ensures optimum ow of material to the scalping screen. EDGE’s intelligent load-management system constantly monitors conveyor
-load pressures and regulates feeder speed resulting in superior uptime by eliminating material overload and ensures optimum screening production at any given time. Hydraulic folding hopper extensions allow for side loading whilst a folding hopper rear door provides even further loading exibility.
At the heart of the SCREENPRO S18 is an EDGE-designed high-stroke scalping screen with a screening area of up to 18.3m² and a wide , variable working angle to suit an array of applications. The aggressive high-stroke action results in superior material separation and a generous screening area ensures precision nes separation. To ensure minimal downtime, the screenbox encompasses hydraulic lift-up functionality for a quick and ef cient mesh-exchange process, supported by full-access walkways on both sides of the screen.
Customers can choose from a wide range of screen-media options including woven mesh, punch plate, nger screens and bofor (grizzly) decks to achieve a variety of nal grain sizes and to process different feed material.
- ow screen. This exibility combined with numerous screen-media options and con gurations allows the EDGE SCREENPRO S18 to process a wide range of materials and to tackle screening applications that other conventional screens cannot, such as incinerator slag or wet, damp and sticky material.
For recycling applications, the SCREENPRO S18 can be equipped with both over-band magnets and magnetic head drums for the extraction and recovery of ferrous metals.
The oversize discharge conveyor features a heavy-duty 1,600mm, chevron belt as standard with a combination of impact bars and rollers absorbing the impact from loading material, thus prolonging the life of the conveyor belt. The oversize discharge conveyor can be lowered to 5° to provide superior access to the lower screen deck and aids in the screen-media exchange process.
Adding to the versatility of this new SCREENPRO range is its ability to interchange the highly aggressive scalping screen with EDGE Innovate’s award-winning ip
The EDGE SCREENPRO S18 also offers added remote functionality for improved operator ef ciency and safety. All major functions on the S18 including tracking, feed -conveyor speed adjustment, sequential start -up and hopper jacklegs can be remotely operated from a safe distance of up to 100m or in the operator’s cabin.
Powered by either a Caterpillar or Cummins Tier 4 Final/Stage V ACERT engine ensures the SCREENPRO S18 drive system provides the operator with a reliably durable and fuel-ef cient screening solution. An electric-hybrid option further enhances cost savings and environmental bene ts, combining the advantages of an electric -power unit with traditional diesel/hydraulic power. Utilising a small onboard diesel engine for tracking and set-up, operators can then connect to an external electricity supply once the machine is in position.
Tom Connolly, EDGE Innovate global sales manager, comments: “The EDGE SCREENPRO S18 is a highly functional, reliable, ef cient and easy-to-operate versatile machine that perfectly complements our other products and will serve to further raise and enhance the pro le of the EDGE Innovate brand in the years ahead.” AB
Develon says it can look back on a very successful debut year in Europe and worldwide. Guy Woodford reports
Develon was launched globally at the CONEXPO/CON-AGG exhibition in Las Vegas, USA, in March 2023 after Doosan Construction Equipment was renamed. Subsequently, local trade fairs across the globe have all been used to further debut the brand at a more regional level.
In Europe, Develon was introduced at Samoter in Italy, Plantworx in the UK, and steinexpo in Germany. In addition to the company’s facilities in the Czech Republic, Germany, the UK, and elsewhere, extensive rebranding has been conducted at the more than 80 Develon dealers within Europe, where all existing facilities and vehicles have been changed.
Jayden Lim, Develon Europe CEO, said: “I would like to thank all of our staff, dealers, suppliers, and customers for their support in the transition period. They have all embraced the new Develon brand. They are also happy with the fact that our core values, sales network, products, and technologies have virtually remained the same.”
Develon has continued to expand in the European market. Notable developments include the opening of a new European Training Centre at Nantes in the west of France and work commencing on a new company-owned store in Germany, targeted for opening in the second half of 2024. The store will offer direct sales, customer support and training, and a parts warehouse. The expansion and relocation of Develon’s Parts Distribution Centre from Germany to Belgium has also been announced, again aiming for completion in the second half of 2024.
In terms of the organisational structure
underpinning Develon, HD Hyundai is the holding company under which HD Hyundai Infracore (HDI) and its Develon brand and HD Hyundai Construction Equipment (HCE) with the brand Hyundai will continue to operate independently with their own brands in the market.
In addition, HDI and HCE will cooperate under HD Hyundai XiteSolution, an intermediary holding company that represents HD Hyundai's construction equipment business, to build more market presence.
Lim added: “In simple terms, Develon is the commercial brand used for our machinery, parts, promotions, communications, dealer facilities etc. and the HDI brand will be used more at the corporate level with of cial documents and titles."
Since launching the brand, Develon has expanded its product portfolio from mid-to-large-sized machines, adding a growing line of new in-house-designed mini-excavators. It has also strengthened its market position through strengthening the brand’s sales network.
From 2024 and beyond, Develon plans to enhance the balance among its sales regions and product portfolio to create a full line-up that will help the brand grow into a global top player. For regions with weaker presence, Develon plans to strengthen its dealer network while also expanding the product line-up: the new dozer line and the new mini-excavators including the company’s rst electric
model, together with special applications like demolition and waste handling to name just a few. The company also plans to enhance customer satisfaction by delivering products that match market requests, such as excavator and wheeled loader options/upgrades.
Develon demonstrated the latest update to the company's unique Concept-X automated construction equipment at the Intermat exhibition in Paris, France (24-27 April 2024).
Concept-X was unveiled in 2019 as the world's rst automated construction solution. At a demonstration of Concept-X in Korea, attendees witnessed autonomous construction equipment performing everyday jobsite tasks. The latest Concept-X 2.0 version showcased at Intermat included a new dozer added to the autonomous equipment line-up; autonomous driving and blade control based on the Global Navigation Satellite System (GNSS); automated 3D grading with tiltrotator accessory; enhanced machine-learning-based auto-digging and loading; an applied integrated workplanning algorithm; and advanced E-Stop safety technology.
The Concept-X 2.0 autonomous construction equipment involved in this latest iteration includes the DD100-CX dozer and DX225-CX crawler excavator. Both machines feature a new cabless design and a linear core-design language. A live demonstration of this autonomous construction equipment took place several times a day on the Develon stand.
Develon’s new Concept-X 2.0-based DX225-CX crawler excavator is cabless.
Pic: Develon
Concept-X integrates technologies related to ICT and AI to revolutionise the construction machinery industry and create sustainable customer value.
Concept-X includes automated construction site solutions, surveying tasks using drones, unmanned automation of equipment, and remote control based on 5G communication to increase productivity and reduce costs and risks based on accurate, fast work at the construction site.
The core of Concept-X is X-Center, which is a control system that enables the user to view equipment at the construction site and worksite at a glance. It surveys the terrain of the worksite through scanning using drones, and the data collected from various sites are analysed to instruct unmanned equipment and manage the equipment in an integrated manner.
UK building materials major Aggregate Industries, a division of Swiss giant Holcim, has added 21 HD Hyundai wheeled loading shovels to its equipment eet.
Delivered throughout 2023, with the nal machine arriving at the company’s readymixed concrete plant in Cambridge earlier this year, the loaders have been speci cally chosen to suit the needs of Aggregate Industries’ asphalt, cement and ready-mix plants across the UK.
Supplied by HD Hyundai dealer Willowbrook Plant, the deal includes one HL955A, two HL940A models and 18 HL930As. Of that number, two of the HL930A machines were delivered in a tool carrier layout, with parallel lift arms for more ef cient handling of bagged and palleted materials.
“The decision to go with Hyundai was partly driven by AI Holcim wanting to experience a wider range of equipment,” said area HME eet manager (South East) Steve McNamara.
“Willowbrook Plant, on behalf of HD Hyundai, won a tender between four manufacturers, and so far, the machines are doing well. The Hyundai loaders are high-speci cation machines, both in the cab and in terms of equipment. The All Around Viewing Monitoring (AAVM) camera system is standard, and the weigh loader is standard, both of which are extras with other suppliers.
“That’s a big uplift in cost, as our speci cation is already high, but the Hyundai
machines came with everything on.”
The wheeled loaders have a rolling service agreement with Willowbrook Plant and come with a two-year warranty. For machines further from Willowbrook's Midlands base, other HD Hyundai dealers can provide assistance if needed. The loaders are working as far a eld as Scotland and Cornwall.
“We are very proactive on preventative maintenance and we make sure that the machines are looked after,” said McNamara. “At Aggregates Industries we run a lean eet, so if a machine breaks down, it can have an effect on productivity on site. However, the Hyundai loaders have Cummins engines and ZF axles and transmissions, so we were con dent in the equipment.”
Willowbrook worked closely with Aggregate Industries to specify each machine to suit individual site requirements. That said, some of the production facilities work longer hours than others and machines of a similar size and speci cation can, in the future,
be moved between sites to keep overall operating hours similar.
“We specify the machine on the peakhour requirement,” said McNamara. “We have a massive campaign to ensure optimum fuel consumption and utilisation. We focus on productive working, and we measure performance to reduce idling. We save expenditure per hour on fuel.”
The company runs a pre-planned remould tyre cycle, so it insists on premium brands that can be remoulded for extended use. With that in mind, all of the HD Hyundai loaders have been supplied on Michelin rubber. They also feature all available safety equipment and, on dustier sites, secondary air lters. While Willowbrook will use Hyundai’s Hi-MATE telematic system to monitor the machines remotely and to plan maintenance, Aggregate Industries will also install IPlant.
“It’s there to protect the drivers and it’s good for us as a business to be able to analyse the data,” said McNamara.
At the Milton, Cambridge ready-mix operation, where working space is at a premium, Aggregate Industries developed a high-lift bucket from Haverhill-based supplier BA Caulkett for its previous machine. The HL940A that has been supplied to the site has been modi ed to work with that bucket, allowing a like-for-like replacement with no disruption to the operation.
“It’s a 2m³ high-tip bucket that we needed to get the volume of aggregate into the bins. The machine is handling it well,” said McNamara.
Willowbrook provided familiarisation training to Aggregate Industries’ operators and the rm’s engineers have adjusted some of the machines’ hydraulics to suit individual operator’s driving styles. With the last machine delivered, the HD Hyundai loaders are now proving their worth in everyday use.
“The drivers have all accepted the Hyundai loaders, they are very nice machines,” added McNamara. AB
Battery technology for use with the size of vehicles required in quarrying is now reaching maturity. Battery-electric and hydrogen machines will each have their role to play in achieving sustainable hauling in the coming years. Liam McLoughlin reports
Electric haul trucks are likely to play a key part in achieving meaningful emissions reduction in the quarrying and mining sectors and assisting equipment operators to meet their sustainability objectives. That is the view of Pranav Jaswani, technology analyst at emerging technologies research company IDTechEx.
Quarrying and material-extraction vehicles are some of the most polluting in the world, and Jaswani says that quarry operators looking to promote a more sustainable image might opt for an electric vehicle.
“We expect battery-electric to be the dominant powertrain solution,” adds Jaswani. “The technology and infrastructure required is at a more advanced stage of development than for hydrogen, and it’s also the more energyef cient choice for powering a vehicle.
“This holds true broadly for most quarrying haulers. It’s only when we get to the largest vehicles with load capacities of 200+ tonnes that we start to see hydrogen play a slightly bigger role. Batteries would still be the main power source, but the size and energy demands of these vehicles
means that hydrogen and even diesel will have a part to play in the total energy mix.”
Jaswani says that, in addition to the obvious bene t of reducing tailpipe emissions, powering a vehicle with electricity is up to 2-3 times cheaper than using diesel.
“For diesel-hungry haulers this represents an opportunity for operators to drastically improve their bottom line,” he adds. “These vehicles also typically need less maintenance, which is another nancial saving and reduces vehicle downtime.”
Electric machines are generally quieter and produce less heat or vibration, which is bene cial to worker health and safety.
Jaswani says that battery technology for use with the size of vehicles required for quarrying is just now entering maturity. He adds that multiple 60-80-tonne-capacity fully-electric haulers have already entered series production from some European and Chinese manufacturers, using 300-500 kWh batteries – 3-5 times the size of an average Tesla battery.
“Larger electric hauler prototypes (with a 200+ tonne payload) are also being
developed, with the largest batteries among those being 15 times the average Tesla battery and weighing up to 15 tonnes,” he adds.
“Present-day battery tech has shown that it can do the job for even the most intense applications, and battery manufacturers are now working on making technology for the industry that’s more affordable, energy-dense, and reliable.”
IDTechEx also expects that pre-2035, newer sodium-based and lithium-titaniumbased batteries will start coming into use for the heaviest-duty haulage applications. The rst uses of this have been seen in the mining industry at the start of 2024, and Jaswani says quarrying will likely make use of them in the future too.
He adds that deployment of electric vehicles is likely to be more rapid at quarries than mines, as the batteries required are not as large or expensive. “Fully-electric models are now commercially available which will be an appealing proposition to quarry operators,” he adds.
“That being said, smaller vehicles tend to burn through less fuel which means there’s less money to be saved upon
electri cation. It suggests that while early adoption will be more rapid in quarrying than mining, it may not always be so rapid moving forward – especially in times or regions where diesel fuel is comparatively cheaper.”
Jaswani says that retro tting is a viable option for electri cation, adding that was the model through which nearly all of the early electric models were developed, and it is still sometimes seen for repurposing haulers reaching end-of-life. However, retro tting comes at a very high additional cost which IDTechEx expects could be in the hundreds of thousands of dollars per vehicle.
“We are increasingly seeing companies involved in the space move towards an in-house electri cation model, wherein equipment manufacturers are forming their own links with battery suppliers to make electric versions of some of their existing machines,” he says. “Manufacturers are able to achieve lower costs for batteries and labour, which means the vehicles they produce are cheaper (and likely to perform better) than if a quarry operator undertook an independent electri cation process.”
In Europe, Volvo and Scania have come out with electric models – the Volvo FH Electric and Scania 25P XT. Jaswani says there has also been a big push from multiple Chinese manufacturers including XCMG, Zoomlion, and SANY (XCMG XDR80TE, Zoomlion ZT series and SANY SKT90E).
On the bigger end of the scale, Caterpillar and Komatsu are both developing electric versions of their agship machines, the 793 and 830E respectively. These are prototypes for now but both have stated they aim to be commercially available before 2030.
“Fully-electric models are now commercially available which will be an appealing proposition to quarry operators”
Pranav Jaswani of IDTechEx
Jaswani says that, with Chinese manufacturers being at the forefront of developing electric haulers, it’s no surprise that the country’s quarries have been some of the rst to embrace the change. “There’s also a number of electric machines now being used in South America, in certain regions of Brazil and Chile where it’s proven more economical to use electric power than having to transport diesel to remote sites,” he adds.
While sales of electric haulers in the quarrying sector were still at a low level in 2023 IDTechEx estimates that in 20 years’ time, nearly 50% of all new hauler sales will be electric. “However, in the shorter term over the next 5-10 years, growth will likely be consistent but slow,” says Jaswani. “This will then be followed by a much faster period of adoption in the industry in the proceeding years.”
At the April Intermat quarrying and construction equipment show in Paris, Volvo exhibited one of its machines, setting out a path towards a sustainable fuel future. The Volvo HX04 prototype, claimed to be the world's rst prototype fuel cell articulated hauler, is currently being tested in various customer applications to develop hydrogen technology.
The test-phase results provide important information about the possibilities offered by hydrogen and fuel cells as Volvo Construction
Equipment (Volvo CE) continues its research for future product-development programmes. It results from a research project between 2018 and 2022 funded by FFI, a national collaboration between the Swedish Innovation Agency VINNOVA, the Swedish Energy Agency and the Swedish Transport Administration to support strategic research, innovation and development of sustainable vehicles. Much of the development and construction of the six-wheeled prototype took place at Volvo CE's facilities in Braås, Sweden.
Engineers at the Eskilstuna Technology Centre in Sweden have contributed software development and knowledge from its fuel cell test laboratory. Although not yet available, the valuable information gained from this concept will inevitably inform future production.
Komatsu Europe has introduced the latest addition to its hauling lineup, the HD605-10 rigid dump truck. Drawing on more than
century of Komatsu expertise in quarry and mining operations, this large-class machine sets new benchmarks in safety, productivity, durability, and environmental responsibility.
Designed to maximise productivity while minimising operational costs, the HD60510 boasts enhanced engine power and torque, along with cutting-edge fuel-saving technologies. With a focus on meeting customer demands in quarry applications, the machine is said to offer unparalleled safety and comfort for operators, ensuring optimal performance at the lowest cost per tonne.
Juuso Ahola, product manager at Komatsu Europe, emphasised: "Our development teams have prioritised customer needs to deliver a machine that not only builds on the reliability of its predecessor but also introduces signi cant performance enhancements. These enhancements include increased power, weight reductions, expanded load capacity up to 64 tonnes with 43m3 body, improved durability, enhanced visibility systems, and reduced fuel consumption.”
Economic and environmental considerations are at the forefront of the HD605-10's design. Equipped with a powerful 610 kW Stage V engine, the machine delivers exceptional productivity while offering three selectable modes - Economy, Economy Light, and Power - to match various applications. Additionally, advanced fuel-saving measures, such as a new high-ef ciency cooling system and lightweight body option, ensure optimal fuel ef ciency, reducing operating costs.
In terms of reliability, the HD605-10 is engineered for durability and uptime in the most demanding conditions. Strengthened transmission, torque converter, main frame, differentials, and nal drive components ensure the machine's resilience and longevity. Combined with the additional bene ts of the Komatsu Care programme, the company says this provides users with complete peace of mind.
Safety features of the HD605-10 include a comprehensive LED lighting system for improved visibility, illuminated stair walkways for safe access to the operator cabin, and a brake-performance check system to verify brake functionality before operation. AB
Komatsu Europe’s new HD605-10 RDT draws on 50+ years of its expertise in quarry and mining operations
X TREMELY MODULAR – versatile solutions for all your crushing needs
X TREMELY POWERFUL & reliable – best throughput to weight ratio in its class
X TREMELY EFFICIENT – optimize your material flow & cut energy costs
X TREMELY USER FRIENDLY – increase your productive uptimes
A big showpiece event for a leading o -highway machine engine manufacturer to unveil its new sustainability-minded solutions. Guy Woodford reports
Cummins launched a new 15-litre diesel engine for the off-highway market at Intermat 2024 (24-27 April). The next-generation X15 diesel engine is said to maintain reliability and reduce operating costs while delivering reduced emissions and improved fuel-ef ciency bene ts. The engine is part of Cummins’ HELM (high-ef ciency, loweremissions, multiple-fuels) platform and offers customers the option to choose the fuel type that best suits their business needs by offering a common base engine design with cylinder heads and fuel systems speci cally tailored for a single fuel − advanced diesel, natural gas or hydrogen.
Well suited to powering over 30-tonne excavators and other critical quarrying machines, the X15 offers ratings up to 522kW and a peak torque of 3200Nm targeted for Stage V emissions and beyond. The new diesel engine is optimised with fuel consumption as low as 180g/kWh, reducing TCO and lifetime CO2 emissions. It has extended maintenance intervals up to 1000 hours, reducing service costs and downtime.
Beau Lintereur, executive director of Off-Highway at Cummins, stressed some of the key bene ts of the new X15, saying: “It is a state-of-the-art clean-sheet engine designed with more capability and less environmental
“What better than to offer them three different models of an engine with only one engine integration cost”
Jonathan Miller, Cummins O -Highway business development manager,
impact. The Cummins X15 offers fantastic power density for high-duty cycle applications, meaning it can displace larger comparative engines, reducing operating costs and overall emissions from equipment in the eld.”
Speaking to Aggregates Business at Intermat 2024, Jonathan Miller, Cummins Off-Highway business development manager, says the new X15 diesel engine is a prime example of the results of Cummins’ exciting ongoing research and development work, with the US company committing US$1 billion to R&D in 2024 alone.
“It’s a testament to how con dent we are in the longevity of ICE [internal combustion engine] products. We are here with a 15-litre product that is almost the size of a 13-litre product in some markets. The X15 comes in smaller packaging and offers around 8% more thermal ef ciency than the previous generation engine. It also offers a near 10% fuel-economy improvement to its predecessor. This reduces your initial investment and your TCO [total cost of ownership]. Service intervals are also 1,000 hours, which is a pretty large step forward. This provides bene ts to our customers’ sustainabilty as you are disposing of fewer oil lters and, ultimately, you have less downtime. Again, great bene ts for TCO.”
On the bene ts of Cummins’ HELM platform, Miller adds: “Customers are the beating heart of our organisation, and we want to help them with their investment criteria. What better than to offer them three different models of an engine with only one engine integration cost?”
Alongside the X15 diesel engine, Cummins exhibited at Intermat 2024 its new B6.7H engine, a hydrogen platform suited to various machines, including medium-sized excavators, involved in a wide range of off-highway applications. The B6.7H has a top rating of 216kW and a peak torque of 1200Nm
combustion engine is designed to use the same transmission, cooling systems and hydraulic systems as today’s diesel engines, reducing
complexity for equipment manufacturers and their customers wanting to switch to using a hydrogen-fuel-power solution.
In line with Cummins' Destination Zero strategy, a global initiative aimed at reducing greenhouse gas emissions and mitigating the environmental impact of products and operations, Accelera by Cummins, Cummins’ fth operating segment, showcased its 150kW fuel cell engine at Intermat 2024. This innovative engine is an ideal solution for mobile construction applications with heavy-
duty cycles and/or clean portable-power generation requirements.
Accelera is distinguished in the industry by its wide selection of zero-emissions offerings, empowering customers with choices as they transition to clean-power solutions. Among its offerings is the lithium-ion next-generation BP97E battery. On display at Intermat 2024, the BP97E battery has been designed for
electri ed vehicle applications, offering exceptional energy density, while catering to customers requiring weight-sensitive solutions and adaptable mounting options.
Furthermore, Accelera showcased its 1CS2016 NextGen motor, a single-winding permanent, synchronous magnet direct-drive
motor. Developed speci cally for highperformance traction motors, this NextGen motor delivers unmatched ef ciency of 97% across a broad spectrum of operational ranges.
NPROXX hydrogen tanks were also on display at Intermat. Cummins and NPROXX
The next-gen X15 diesel engine is part of Cummins’ HELM (high-e ciency, lower-emissions, multiple-fuels) platform
formed a joint venture in 2020. NPROXX is a world leader in high-pressure hydrogen storage for stationary and mobile applications. The storage tanks on the stand will have up to 700-bar pressure capability to maximize capacity and operating range. AB
More power with less complexity and less weight. The Cummins B6.7 engine delivers the productivity you need to keep your equipment running. The power increases up to 326 hp / 243 kW and peak torque up to 1014 lb-ft / 1375 Nm, enabling replacement of engines with higher displacement with no impact on productivity.
A major, new recycling hub is one of a series of eye-catching, recent moves advancing the reuse of construction waste, concrete, slag, road planings and reclaimed aggregates. Liam McLoughlin reports
Heidelberg Materials has opened a new recycling hub at its Appleford depot in Oxfordshire, UK.
It is the rst of several planned at the company’s sites this year as part of its strategy to conserve natural materials and promote the circular economy.
The Appleford hub will recycle construction waste, diverting it away from land ll and processing and reusing it to deliver sustainable products to its customers. It means the site is now a one-stop shop for customers, supplying primary aggregate, ready-mixed concrete and asphalt in addition to recycled material.
James Whitelaw, recycling managing director, Heidelberg Materials UK, said: “Recycling, reusing and reducing the use of primary raw materials is crucial to reaching net zero.
“Our network of recycling hubs will allow us to provide the most sustainable products to our customers through circularity and innovation to enable building more, with less.”
The recycling hubs form part of Heidelberg Material’s recycling business line, which includes rebranded Manchester-based A1 Services, acquired by the company in 2022.
In a separate announcement, Heidelberg Materials UK has invested in a Wirtgen mobile cold recycling mixing plant, demonstrating its commitment to conserving natural materials, promoting the circular economy, and decarbonising its products.
The batching plant can use reclaimed and primary aggregate to produce cold mix materials, providing a lower carbon solution
projects.
The Wirtgen KMA 240i mobile plant has a large mixing capacity (240 tonnes) and can process base materials, including recycled construction materials, asphalt planings and primary aggregate. It enables the company to use technologies such as foamed bitumen, emulsion, cementitious and biogenic binders to produce various cold mix materials.
Ian Price, Heidelberg Materials UK contracting managing director, said: “Our investment in this new mobile plant allows us to complement our existing range of sustainable solutions with the option of cold mix products, saving energy and associated CO2 emissions.
road construction and maintenance projects, allowing recycling of 100 per cent of wornout road surfaces, which can be recycled back into new materials, reducing the need for primary aggregate.”
In the UK, Heidelberg Materials (formerly Hanson UK) is split into ve business lines –aggregates (crushed rock, sand and gravel), concrete, asphalt and contracting, cement and recycling – which, together, operate around 280 manufacturing sites and employ more than 3,500 people.
An innovative Rubble Master crusher is generating 100% recycled slag and concrete for an Argentinian customer.
For the past four years, the customer of
Rubble Master (RM) dealer COVEMA has been crushing concrete and slag with the RM 100GO! crusher in a highly ef cient and environmentally friendly manner.
With a throughput capacity of 150 t/h, the RM 100GO! crushes concrete and steel slag from 0-500mm to 0-30mm directly on-site for eight hours daily. The customer, an expert in using and integrating recycled materials in road construction in Argentina, crushes concrete to reuse it to produce new concrete. In addition, slag is crushed for road construction and recycled to produce new steel. Thanks to the impact crusher, all the material can be recycled.
The RM crusher was ordered and put into operation over four years ago. It was particularly important for the customer to acquire a crusher suitable for various applications, a requirement that the RM 100GO! can ful l ef ciently. The impact crusher enables the crushing of concrete from demolishing old, rigid pavements and recycling other regionally available materials, such as slag. The outstanding quality of the machine and the favourable nancing conditions offered by COVEMA ultimately convinced the customer to purchase the crusher.
"Thanks to the extreme versatility of the RM 100GO! in recycling locally available materials, we can achieve the highest level of environmental commitment on the Argentinian road market," con rms the customer.
Slag is created during steel production and consists of mineral components and other elements removed from the metal ore during the melting process. Slag also usually contains iron, which can cause damage in the crushing chamber if the wrong crusher is selected.
The advantage with the RM 100GO! crusher is the RM Release System (impactor opening to remove blockages in the impactor), which opens if pieces of iron are present in the material being crushed, thus preventing damage in the crushing chamber. Nevertheless, large pieces should still be sorted out or pre-crushed before feeding, as iron parts that are too big can cause damage to the crusher despite the Release System.
In a UK recycling initiative, tens of thousands of tonnes a year of planings from
road maintenance schemes in London and the south east are being recycled and reused as part of Aggregate Industries’ commitment to the circular economy.
The major UK building materials supplier works with Day Aggregates to transport and process 40,000 tonnes of reclaimed asphalt pavement (RAP) a year.
Earlier this year, the company’s biggestever load of RAP was transported via train from Brentford in West London to Crawley, West Sussex. 1,500 tonnes, the equivalent of 79 lorry loads, were carried.
RAP is created by removing old roads and pavements. It is then crushed and processed for reuse in new asphalt products, reducing the use of virgin aggregate.
Once planings are removed from a site, they are transported by rail to Day Aggregates’ Brentford depot, where they are processed and transported back by rail to Aggregate Industries for use.
Thomas Edgcumbe, managing director of Aggregate Industries’ surfacing solutions division, said: “The use of rail to move RAP is an exciting development as it sees large volumes being able to be transported each time. This supports our drive for sustainability in the increased use of RAP whilst also reducing vehicle numbers on the roads. This is a huge change of concept that we are looking to grow further throughout 2024.
“Utilising what in the past has been a waste product and recycling it into new products is not only smart thinking but means we are preserving raw materials, reducing lorry movements by using rail and reducing emissions through less intensive production processes.
“But to make this a reality we need collaboration across the supply chain and we need the buy-in of our partners so it is fantastic to be working with Day Aggregates to transport and process the materials.
“Circularity in construction plays a huge part in our approach to sustainability and goes hand in hand with our drive towards net zero. By 2025 we are committed to increasing the use of RAP by 60 per cent.”
Adam Day, contracts director at Day Aggregates, said: “Day Aggregates look to use rail transport for moving heavy freight at all opportunities. Reducing lorry movements as much as possible brings massive environmental and social bene ts.
“This new ow makes a double win with the material carried being part of the recycled supply chain for our long-term partner in
Aggregate Industries. Collaboration and long term commitment from both companies has made this success possible.”
Aggregate Industries' asphalt products contain a percentage of RAP including its cold-mix Foamix product which contains up to 92% of recycled content.
Soil Link, a UK digital platform for aggregate recycling, says it has successfully completed its rst round of seed investment. The investment that will enable the continued development of the Soil Link Materials Exchange Platform (MEP) was underpinned by three angel investors, who have successfully built, grown and sold companies in the tech and sustainability space.
Will Rundle and Kobe Tonkin, Soil Links’ founders, conceptualised a national database to link major infrastructure projects all the way through to residential developments as well as service operators, including hauliers and recycling facilities, to enable the sustainable reuse of soils and aggregates.
Soil Link says its Materials Exchange Platform (MEP) is unique in its approach; harnessing technology to enable the construction industry to reuse and recycle soils and aggregates, therefore reducing reliance on land ll and depletion of natural resources. When compared to traditional methods Soil Link says its model saves on average 26% of costs and has proved to be up to 93.5% more carbon-ef cient, paving the way to net zero.
Stephen Kirk is the lead investor in this round of seed funding. He has grown and sold a successful technology test and certi cation business, followed by building a US$350m technology business for UL (Underwriters Laboratories). He has been critical to the growth and success of numerous businesses in the tech, ESG and sustainability sectors in his roles as business advisor, non-executive director and angel investor.
“The impact Soil Link’s model will have on the environment is enormously positive, it will enable companies to develop a circular economy and work towards a net-zero future,” commented Kirk, who is the founder of SK Consulting & Investment.
Soil Link co-founder Will Rundle said: “Soil Link stands out as the only Saas [Software as a Service] platform available in the UK, empowering users to view materials not just as waste, but as valuable resources. As we look ahead to 2024 and beyond, we are eager to witness the positive impact of Soil Link on the construction industry.” AB
Portable power solutions can be a highly e cient and cost-e ective option for quarry operators. Guy Woodford reports
Atlas Copco is offering quarry operators improved exibility with new power supply and lighting developments.
Tobias Schuster, divisional product marketing manager—Energy Storage Systems at Atlas Copco Power and Flow, and Eric Tomin, divisional product marketing manager—Light Towers & Portable Generators at Atlas Copco Power and Flow, give Aggregates Business an overview of how the leading OEM (original equipment manufacturer) sees this area of the quarrying machinery market and what it offers customers.
“A reliable power supply is critical to ef cient mining and quarrying operations. The major challenge historically has been the investment required to bring the necessary electrical infrastructure to large areas of exploration. Sites are often in places that are far from civilisation, where there is limited or no existing network infrastructure. Traditionally, in such remote locations, the only viable options for the mine or quarry operator have been to either invest in the necessary electrical infrastructure or rely on mobile generators to cover ef ciently the site’s energy demand.
for applications with high energy demand and variable load pro les, as they successfully cover both low loads and peaks.
“Atlas Copco ESS integrates the ECO Controller energy-management system (EMS), which enables mine and quarry operators to synchronise several models as the central piece of a microgrid to store and deliver energy from several energy sources – including the grid, power generators, and renewables. Based on lithium-ion batteries, these state-of-the-art ESS are designed with sustainability in mind, dramatically reducing fuel consumption and CO2 emissions.
“Even in locations with access to the power grid, there is still a signi cant cost associated with building the large internal infrastructure necessary to transfer the electricity around the site. In addition, the scale of this internal cable network leaves it vulnerable to theft, because cables and the copper in them have a high intrinsic value. That is why the most reliable alternative for mine and quarry operators has been to use diesel generators and lighting towers as their main or complementary source of power and light.”
Schuster and Tomin say the energy transition is driving the development of more energy-ef cient alternatives like lithium-ion batteries and photovoltaic panels. “These technological innovations are fostering the evolution of rugged and reliable mobile energy-storage systems (ESS) that give mining and quarrying operators greater exibility and increased operational ef ciency. Adopting alternative energy sources brings added bene ts of reduced fuel consumption, noise, and emissions, aiding regulatory compliance while improving worker safety and optimising energy usage.”
As Schuster and Tomin stress, Atlas Copco has been at the forefront of portable power technology for many years; rstly with low-consumption diesel generators and more recently as a pioneer of ESS technology. Its cutting-edge energy-storage systems are ideal
“The ESS range is further expanding to provide solar-powered options that offer even greater sustainability credentials while continuing to drive down costs, improve operational ef ciency, and ensure safer working conditions. These energy-storage systems optimise energy generation, distribution, and consumption onsite, ensuring ef cient operations in quarries and mines worldwide. Additionally, users can evolve from operating the smallest ESS systems to larger ones, with the same userfriendly plug-and-play experience across a whole range.”
Schuster and Tomin note that the evolution of alternative energy sources is also driving the development of a new generation of lighting towers. These models incorporate lithium-ion batteries and SMD (surface mount device) LED lighting technology to offer better performance while driving down operational costs and helping to reduce CO2 emissions.
“Atlas Copco’s range of lighting towers is ideal for mine and quarry applications due to their ability to operate reliably in harsh, dusty environments with extended autonomy. One example is the recently launched HiLight BI+ 4 hybrid light tower. Combining the use of lithium-ion batteries with a low-consumption Stage V diesel
Pilot Crushtec’s Mobi Lite range offers an ideal lighting solution for quarrying, mining, roadworks and construction sites.
Pic: Pilot Crushtec
engine, the new HiLight BI+ 4 light tower offers users maximum flexibility through four operating modes. It can be powered directly from mains electricity, from its lithium-ion batteries, from its diesel engine, or from a hybrid setting to make the most of the energy available.
“Using hybrid-energy lighting tower combinations means that mines and quarries can illuminate larger areas at a lower cost. These innovative lighting solutions not only provide greater visibility but also reduce the fuel cost per square metre illuminated. Savings of up to 40% are achievable, giving a big boost to profit margins and improving competitiveness while reducing overall energy consumption and CO2 emissions.”
In addition to the hybrid light tower, Schuster and Tomin highlight that the HiLight S2+ is a great match for quarries and mining sites with a great solar yield. This solar-powered LED light tower delivers 2,000m² light coverage for up to 11 hours. Its incorporated solar panels simply pull out and slide back in after use, making the HiLight S2+ easy to deploy. This model also features a dimming function to prevent light and energy from being wasted unnecessarily.
Schuster and Tomin say further developments in solar and hybrid lighting towers will likely be introduced during 2024.
Crushing and screening operations frequently run 24/7 to meet demand and optimise productivity. Given this, Pilot Crushtec, South Africa’s leading supplier of mobile and semi-mobile crushing, screening, recycling, sand washing, stockpiling, compacting, and material handling solutions, is introducing its own ‘Mobi Light’ brand of mobile lighting towers for these and other applications.
The company’s sales and marketing executive, Francois Marais, says that while Pilot Crushtec has supplied lighting products
before, it has never offered its own brand solutions.
“Our Mobi Light brand gives us the flexibility to source the right products internationally, and provide the high level of local support that customers have come to expect from us,” says Marais. “Owners of sites that operate after dark will benefit from this range, and we will also supply to plant hire companies who rent this equipment to mainly the construction and mining sectors.”
Marais says the Mobi Light range covers mobile lighting solutions from entry-level to premium applications. On the smaller end, a unit with four 320 LED floodlights will achieve a lighting area of up to 5,000m²; at the other end of the scale, a mining unit with six 320 WLED floodlights will light up to 7,800m².
Ben Armitage, sales engineer at Pilot Crushtec, explains that safety is a key consideration in the company's positioning of its offering.
“Not only do you need sufficient lighting for the stationary crushing and screening equipment on a site, but there are typically several pieces of yellow metal equipment such as excavators, trucks and loaders moving around,” says Armitage. “Good lighting is, therefore, a critical element of the industry’s quest for Zero Harm.”
Armitage notes that insufficient lighting also affects productivity. Where there is limited visual capacity, operators tend to reduce feed rates to plants – to avoid the
risk of blockages and spillage. This can have a substantial effect on production and the resultant cost of operating the site.
“Another factor that the Mobi Lite tower range considers is the height of our masts,” he continues. “With our high masts at 8.5 metres, this ensures an increased lighting area while reducing operator fatigue, as the light is high enough to never shine in the operators’ eyes.”
The range takes advantage of developments in lighting technology—moving away from metal halide and toward lightemitting diode (LED) technology. LED lights offer a much longer lifespan, operate at low voltages, and produce less heat.
“This has significant benefits for outdoor site operators,” he says. “LED lights light up the work area instantly and don’t require a cool-down period before the lighting plant can be relocated. These lights also consume less power, saving money especially when on-site power is diesel generated.”
Designed for demanding site conditions, the Mobi Lite lighting units have a robust steel canopy to house the generating unit and start-up panel. This strong structure prevents battery and diesel theft. Maintenance and inspection are also easier, as the steel doors on each side of the lighting plant can be opened for access to the large engine bay. AB
The Mobi Lite lighting towers are tow-behind, easy to transport and diesel-driven. Pic: Pilot Crushtec
Using alternative or substandard parts during maintenance can be a false economy that compromises the integrity of quarrying equipment. Liam McLoughlin reports
Articulated haulers excel at navigating challenging terrain while transporting heavy loads, making them indispensable in quarrying, construction, mining and infrastructure projects. However, the integrity of these machines can be compromised when tted with alternative or substandard parts during maintenance or repairs, according to Gary Bradburn, aftermarket commercial manager at Scotland-based articulated dump truck (ADT) manufacturer Rokbak.
“The importance of good quality, reliable parts when maintaining articulated haulers is paramount – especially with the increasing prevalence of lower-quality alternative components on the market,” says Bradburn. “While some ADT owners may view opting for non-factory-approved components as a cost-saving measure, it often leads to a false economy. The hidden costs of alternative parts include higher parts usage, higher operating costs through lower ef ciencies, greater risk of equipment failure and more frequent machine downtime.”
Bradburn says that Rokbak trucks are dependable and durable, built to perform on the toughest job sites and deliver maximum uptime with low total cost of ownership (TCO). “That’s why Rokbak factory-
approved parts provide unequalled levels of reassurance – they are built to the original design and material speci cations to deliver peak performance, reliability and durability in combination with your Rokbak truck,” he adds. The decision to use factory-approved parts extends beyond individual component integrity – it safeguards the integrity of the entire truck. “We know that the poor t and design of alternative parts can compromise overall safety and reliability, which can put both the equipment and operators at risk,” says Bradburn.
He adds that, when alternative parts' costs are particularly low, it’s suggestive of the low-quality materials that have been used to make them. This means components of incorrect speci cation and greater risk of consequential damage, jeopardising site and operator safety and leading to an eventual increase in TCO – with a higher frequency of replacement components needed.
“In contrast, genuine factory-approved parts ensure compatibility, durability and optimal performance,” Bradburn says. “Rigorously tested and meeting strict quality standards, of cial Rokbak components for the RA30 and RA40 articulated haulers offer peace of mind to customers and operators and prolong the equipment’s lifespan.”
As part of the Volvo Group, Rokbak says its commitment to quality ensures that every part meets exceptional standards. “At Rokbak, we stand by our products with one of the most comprehensive guarantees in the industry,” Bradburn states. “Our genuine replacement parts, designed and approved at our Motherwell factory in Scotland and supplied by an authorised Rokbak dealer, come with a 24-month or 6,000-hour warranty.”
He adds that, by using Rokbak factoryapproved parts for their Rokbak articulated hauler, operators will extend the truck’s service life, protect uptime and TCO, and optimise value for the long-term.
UK crusher parts specialist CMS Cepcor’s Technical Centre has recently acquired a stateof-the-art coordinate measuring machine (CMM), which the company says enhances its inspection capabilities signi cantly.
A CMM is an advanced device for precise measurement, autonomously guiding a probe to predetermined positions on objects based on instructions from inspectors via computer software.
CMS Cepcor states: “The primary advantage of a CMM lies in its unparalleled accuracy and repeatability, measuring down to 2 microns (0.002mm), signi cantly surpassing Portable CMM Arms’ accuracy of 40 microns (0.04mm). This heightened precision ensures that components supplied by CMS Cepcor [are] controlled as carefully as possible to the relevant speci cations, ensuring we consistently meet our rigorous quality standards.
“By strengthening our inspection capabilities, we foster greater con dence in our customers and suppliers, thereby improving our reputation and partnerships.”
Additionally, the CMM offers excellent repeatability. Like a CNC machine, the CMM executes semi-automated inspection programmes, allowing inspectors to allocate their focus to other tasks while the CMM ef ciently carries out its functions.
The company says: “At CMS Cepcor, we’re committed to excellence, and our investment in the CMM re ects our dedication to precision engineering.” AB
Deploying premium on-board weighing technology can be a game-changer for quarrying and construction works’ productivity and e ciency. Guy Woodford reports
T1 is Outset’s new concept of on-board weighing and productivity management for mining, quarrying, earthmoving machinery, and logistics.
The innovative T1 MMT Bluetooth weighing module allows direct and constant control of the loaded material and the job details, such as customer, material, vehicle ID, operator, etc., through an Android app for rugged smartphones or tablets. All weighing data and production databases can be transmitted via a serial or CAN bus line to the on-board computer, on external devices, or directly in the cloud, maintaining control and management of the productivity and safety of customers’ machinery.
Headquartered in Sandrigo, a town in the Vicenza province of northern Italy, Outset’s new generation of weighing systems uses the latest generation components that signi cantly improve and increase the calculation capacity and performance of the systems. The new T1 LOADER system for wheeled loaders is undergoing OILM R51 approval, con rming its superior precision and reliability of use.
The new T1 DIGGER system ENTRY
LEFT: Outset’s new T1 LOADER product for wheeled loaders is undergoing OILM R51 approval. MIDDLE: Data captured by Outset’s new T1 DIGGER system. Pics: Outset RIGHT: Luca Toneatti highlights Outset’s T1 DIGGER on-board weighing technology at Intermat 2024. Pic: Guy Woodford
LEVEL version for the excavator with two inclinometers has been implemented and upgraded to the ADVANCED LEVEL version, managing four inclinometers to make it even more precise and better performing, minimising the operator intervention.
The entire new T1 product range has been enhanced thanks to interconnection with the T1 CLOUD, permitting bi-directional communication in real time between the on-board weighing system and the ERP server, allowing you to send and receive, at any time, missions/jobs and load data updates (customer, vehicle, destination, material, etc.) directly to the vehicle’s weighing system in use by the operator.
Vice versa, the operator using the weighing system via the data SIM, the wi- connection, or via the satellite device can send the load data and the mission/job status directly on the T1 CLOUD, accessible via username and
password from any PC or mobile device. The interface has been designed to listen to the needs of operators in the sector with simple and intuitive menus that are easy to use, highlighting the most interesting data regarding on-board weighing, tyre pressure and temperature monitoring, vehicle geolocation, remote diagnosis, remote maintenance and automatic recognition of the out tting. Reports are available in various formats and are divided by eld (customer, vehicle, mission, weighing).
Speaking to Aggregates Business at Intermat 2024 in Paris, where Outset was showcasing its T1 on-board weighing solutions, Luca Toneatti, the company’s export and R&D manager, said France is a big potential market for the company, given its high demand for off-highway machines and linked technology. “Our existing customers say we have very advanced [on-board weighing] products. We can retro t our T1 solutions on any branded machine.”
Toneatti says Outset is busy looking for more distributors in North America, which the company sees as another attractive growth market. “We are doing well in Europe. We are in South America, doing business in the
mining and construction markets of Chile and Peru, and are also supplying customers in South Africa and Australia. We see Japan as another good market for us. There are a lot of Japanese OEMs [original equipment manufacturers] we can work with.”
Incorporating on-board weighing from Volvo Construction Equipment (Volvo CE) in load and haul operations is a game-changer for the construction industry, says the global off-highway equipment major. Volvo CE’s system displays real-time load data on the Volvo Co-Pilot screen in the cab to avoid under- or overloading. Furthermore, on articulated haulers, external lights provide a visual signal to the loading unit operator when the nominal load has been reached.
Volvo CE highlights six key benefits of its on-board weighing technology, which are equally applicable to quarrying customers.
1. Increased accuracy and precision
One of the key advantages of onboard weighing is its unparalleled accuracy and precision. Traditional methods of determining loads, such as weighing stations or scales, often involve interruptions in the workflow. In contrast, the real-time data from the Volvo system empowers operators to make informed decisions on the spot, optimising load capacities and reducing the risk of overloading. This improves operational efficiency and ensures compliance with legal weight regulations, reducing the possibility of fines and penalties.
2. Increased efficiency, lower fuel consumption and less wear
Efficiency is the backbone of any construction project. With on-board weighing, operators can load materials to the precise required weight, eliminating unnecessary back-and-
forth trips to load more materials or discard excess weight. This streamlined process significantly reduces fuel consumption, machinery wear and tear, and overall project time. By maximising efficiency, construction companies can enhance their bottom line and complete projects on schedule. The Operator Coaching app and on-board weighing through Volvo Co-Pilot with Load Assist further helps to improve efficiency.
3. Improved safety
Safety is a paramount concern in the construction industry, and overloading equipment can pose significant risks to operators, other workers, and the machinery itself. On-board weighing helps ensure that each truckload remains within safe operating limits, reducing the likelihood of accidents and minimising the potential for injury or damage.
4. Enhanced payload management
In load and haul operations, efficient payload management is essential for optimal performance. On-board weighing offers valuable insights into each hauler’s load, enabling operators to optimise payloads, balance loads evenly, and minimise idle time. Consequently, this efficient payload management leads to increased productivity, reduced cycle times, and better resource allocation.
5. Data-driven decision-making
In today's data-driven world, having access to real-time information is crucial for informed decision-making. On-board weighing collects and presents valuable data on material weights, load cycles, and operator performance. Construction managers can use this data to identify patterns, optimise workflow, and implement improvements where necessary. Additionally, this data can be used for accurate project costing, resource planning, and performance evaluations, fostering a culture of continuous improvement.
6. Reduced environmental impact
Besides the operational benefits, on-board weighing also contributes to environmental sustainability. By optimising load capacities and reducing fuel consumption, construction companies can minimise their carbon footprint. This aligns with the global shift towards eco-friendly practices, positively impacting companies’ reputations and attracting environmentally conscious clients. AB
25-27: Hillhead 2024
Hillhead Quarry, Buxton, UK
Organiser: QMJ
Tel: +44 (0)115 945 4367
Email: hillhead@qmj.co.uk www.hillhead.com/
MEET THE TEAM
Aggregates Business travels the globe attending conferences, events and equipment shows, keeping you informed of the latest o erings. Come and join us for a chat at any of the events below.
JUNE 2024
25-27: Hillhead 2024
OCTOBER
2-4: SIM 2024
Dijon, France
Organisers: Exposition SIM https://www.expositionsim.com/ en/index.htm
NOVEMBER
26-29: bauma China 2024
Shanghai, China
Organiser : Messe Munchen
Tel: +86 21 2020 5500 baumachina@mm-sh.com https://bauma-china.com/en/
Ammann 4 www.ammann.com
BKT Tires 25 www.bkt-tires.com
CAT IFC www.cat.com
CDE Global 42 www.cdegroup.com/quarry-waste
CMS Cepcor 13 www.cmscepcor.com
Cummins 43 www.cummins.com
Hitachi 27 www.hitachicm.com
Kleemann 29 www.wirtgen-group.com
Komatsu 18 www.komatsu.eu
Martin Eng 21 www.martin-eng.com
McLanahan 7 www.mclanahan.com
Outset 26 www.outset.it
Rokbak OBC www.rokbak.com
Rubble Master 40 www.rubblemaster.com
Smiley Monroe 40 www.smileymonroe.com
Tsurumi IBC www.tsurumi.eu