
15 minute read
ESG
EMBRACING THE ESG OPPORTUNITY
KAL TIRE TAKES PRIDE IN FOCUSING ON ALL ASPECTS OF ESG. AUSTRALIAN MINING SPOKE WITH MANAGING DIRECTOR MILES RIGNEY ABOUT THE COMPANY’S ONGOING EFFORTS TO BE A RESPONSIBLE EMPLOYER OF CHOICE.
It seems a simple proposition for a company: ask employees what they think you’re doing well and what could be done better to make them more comfortable in their job.
And, as Kal Tire managing director Miles Rigney told Australian Mining, that simple proposition can be an incredibly effective tool.
“If we have a workforce that feels we’re inclusive and they’re a part of things, then that helps us become an employer of choice,” he said.
“One of the initiatives we put in at the end of last year was, when we do our annual performance reviews with our team members we included a couple of questions around diversity and inclusion for the first time.
“That’s proved to be very enlightening, to hear the feedback from our team about what they think we’re doing well in the diversity and inclusion space, and to also hear their thoughts about what we could be doing that we’re not currently doing now.
“The process is not quite finished yet, but there’s no doubt in my mind that the feedback we’ve received from our team members will help steer the direction we move in over the next year and beyond.”
Environmental, social and governance (ESG) practices and the push towards a more sustainable industry have undoubtedly been recent drivers of the resources sector.
Australian mining long ago realised the importance of sustainability and the sector is a leader in the journey towards zero emissions. However, it’s important to remember that ESG is not limited to ‘environmental’.
Kal Tire is very aware of that reality, which is why the tyre services company continues to take major steps in developing its social and governance practices to create a safe and appealing workplace.
“There’s been a number of programs that we’ve run in the last 12 months which I think have really helped in that area,” Rigney said. “Particularly around the professional development of our team members and showing them a pathway that we’re
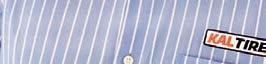

KALE TIRE MANAGING DIRECTOR MILES RIGNEY.
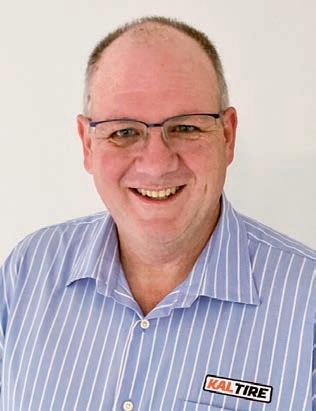
KAL TIRE’S NEW MAPLE PROGRAM IS A WAY OF CALCULATING CO2 AND OIL SAVINGS BY GETTING A DAMAGED TYRE BACK INTO SERVICE.
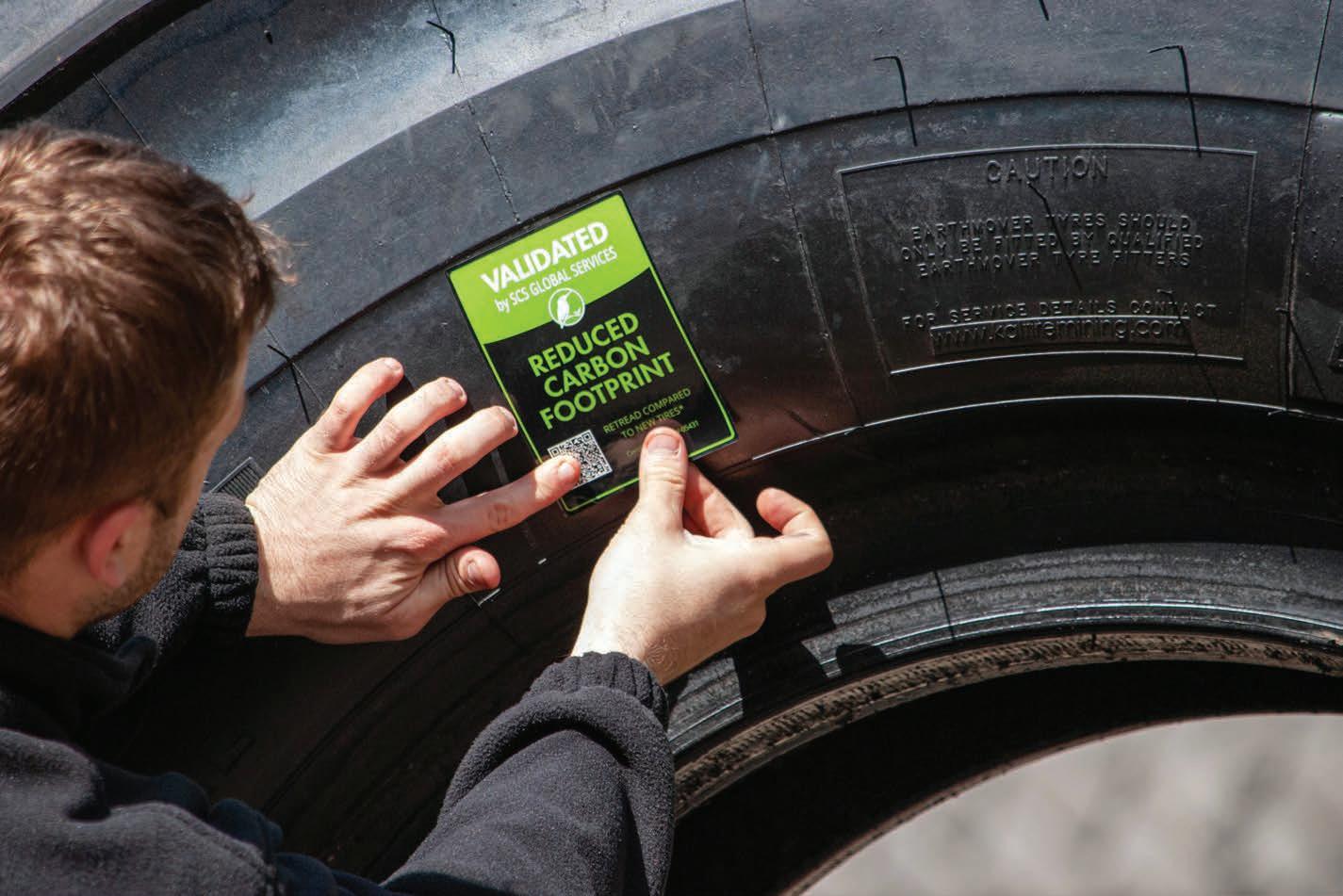
prepared to invest in their ongoing development to become future leaders in our business.”
That professional development has focused on two key areas.
The first is a trainee program that helps people new to the company learn how to complete maintenance activities safely and efficiently. The second is a focus on training more experienced team members to become future leaders.
“That means we’re fuelling our own growth,” Rigney said.
“In the competitive market we’re in at the moment, for us to be successful we must be the employer that our current team members choose to stay with because they appreciate that we appreciate them.
“I like to think we do well in that area, but we’re always going to continue to try and improve. We’re never going to get to the point where we say, ‘okay, tick, we’ve done that’.
“The foot never comes off the throttle. We’ve always got to listen.”
But Kal Tire’s social and governance practices are not solely directed inwards. The company is driven by its AIMS, a set of principles that “guide us to make the right decision”.
“These AIMS have been around for a very long time and it’s something that Kal Tire has continuously worked at,” Rigney said.
It was these principles that led the company to support the Small Steps 4 Hannah initiative, an Australian organisation – named for Hannah Clarke and her children – that works to halt the cycle of domestic violence. And it was through this support that Kal Tire ultimately became a sponsor of the Small Steps for Hannah Annual Lunch.
“The support of International Women’s Day correlates directly with the Small Steps 4 Hannah initiative,” Rigney said.
“We attended a charity launch
THE TYRE SERVICES COMPANY HAS BEEN PROACTIVE ABOUT SEEKING FEEDBACK ON ITS PERFORMANCE AS AN EMPLOYER.
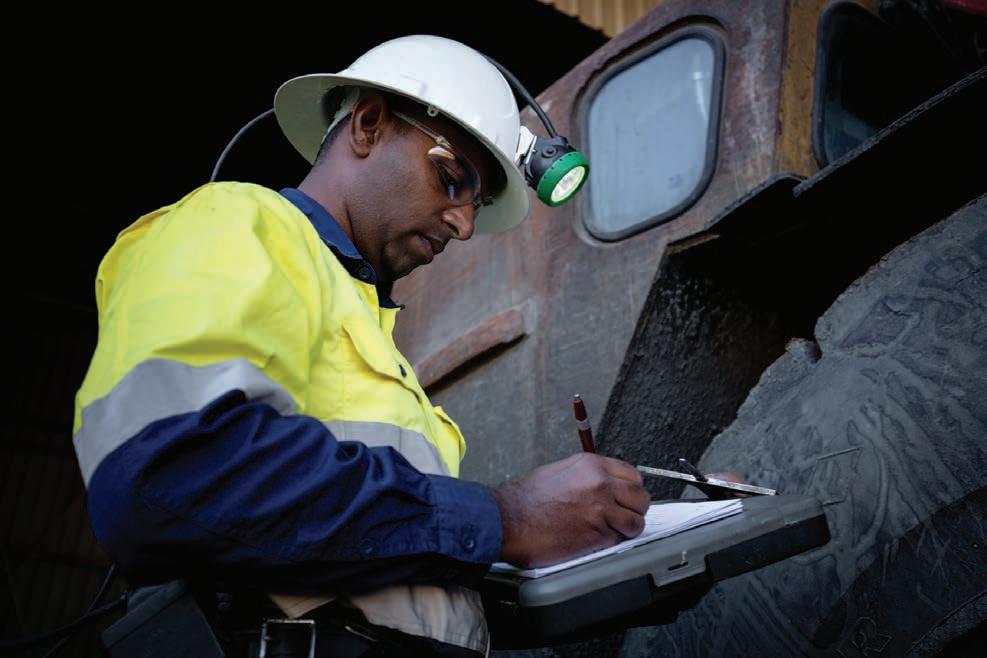
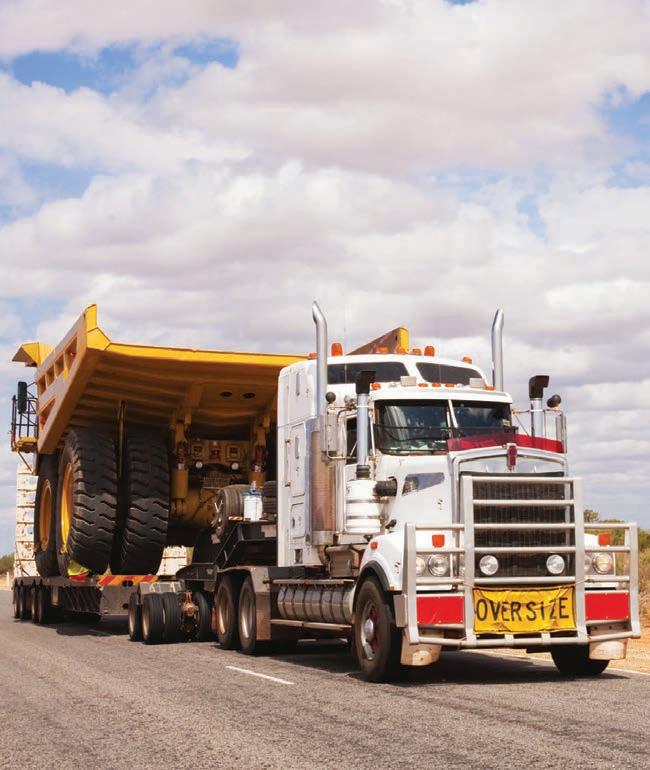
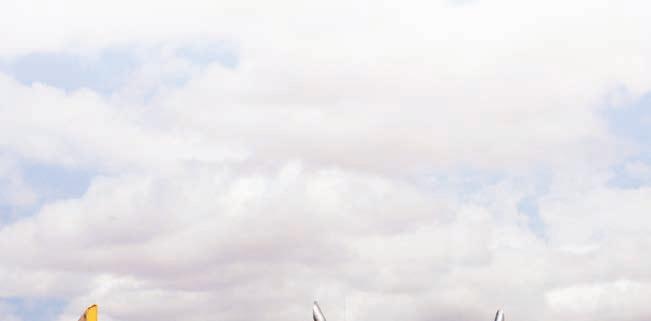

KAL TIRE’S PROFESSIONAL DEVELOPMENT INCLUDES A PROGRAM THAT HELPS PEOPLE LEARN HOW TO COMPLETE MAINTENANCE ACTIVITIES SAFELY AND EFFICIENTLY.

THE COMPANY’S PROPRIETARY ULTRA REPAIR PROCESS.

for the Small Steps for Hannah Foundation last year and we listened to the various speakers they had, the work they were trying to do, and it became very easy for us to say, ‘we think this is really, really important work’.
“So the decision to upgrade from being an attendee to becoming a sponsor was very simple.”
Looking outward, Kal Tire understands the need for continuous improvement and to be innovative for its customers, particularly in the area of sustainability. This thinking drove the company’s new Maple Program, which kicked off at the start of 2022.
“The Maple Program is based on a carbon calculator that we built and has been independently evaluated and accredited by SCS Global Services, a leader in sustainability standards and third-party accreditation. Essentially it’s a way of calculating CO2 and oil savings, in terms of kilograms, tonnes, barrels, litres,” Rigney explained.
Under the program, when Kal Tire is able to help a customer by repairing a tyre with its proprietary Ultra Repair process, they can then provide that customer with a certificate that outlines how much CO2 and oil was saved by getting that tyre back into service versus purchasing a new tyre.
Kal Tire is also very conscious that repairing and recycling tyres is not the start of the journey with its customers. The company’s expertise comes into play far earlier and is designed to maximise tyre life and minimise environmental impacts.
“The start for us is helping our customers firstly determine the most appropriate product or tyres for them to use: what tyres are most likely to deliver them the productivity that they’re ultimately looking for?” Rigney said.
“Once the tyre has been delivered to the operation, our area of expertise is understanding the capabilities of the tyre and putting management and maintenance practices around that tyre so the customer is able to get the most value from it, the most productivity.
“In a perfect world the tyre doesn’t get damaged, but it’s not a perfect world and tyres do get damaged … and that’s when the repair business kicks in.”
Once a repair is done, the tyre is returned to service and sees out the rest of its life. Only then does recycling come into play.
As a member of Tyre Stewardship Australia’s Tyre Product Stewardship Scheme, Kal Tire understands the importance and value of recycling tyres, rather than burying them in the ground.
That understanding is on display with the company’s tyre recycling plant in Chile, where the governmenthas mandated the recycling of off-the-road tyres. While Australia currently has no such legislation, Kal Tire is already looking at a similar local facility.
“We have to move at the right pace and make sure that when we do establish a facility that there’s an understanding that there’s no value in waste tyres,” Rigney said.
“At the moment when the tyres are being buried, they don’t represent a pile of gold. The reality is that the value of the offtake is less than the cost of the process, so customers have to pay.
“What will be the driver going forward for us is working with one, two, three, four customers who understand and are okay with that, and ready to enter into a longterm commitment to enable us to go off and build our first facility in Australia.
“Those discussions have started and I expect we may see some momentum build.” AM
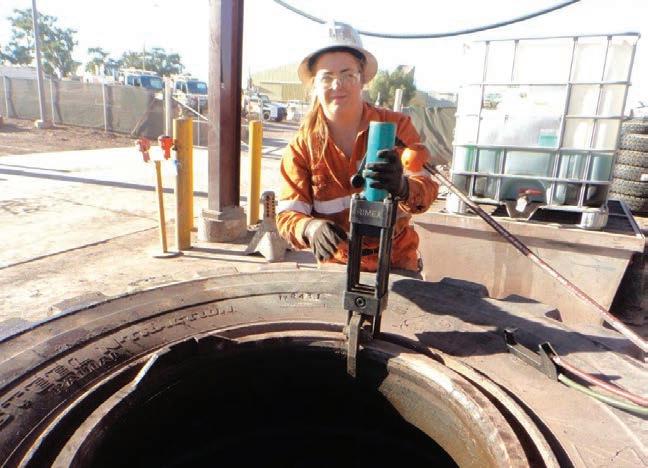
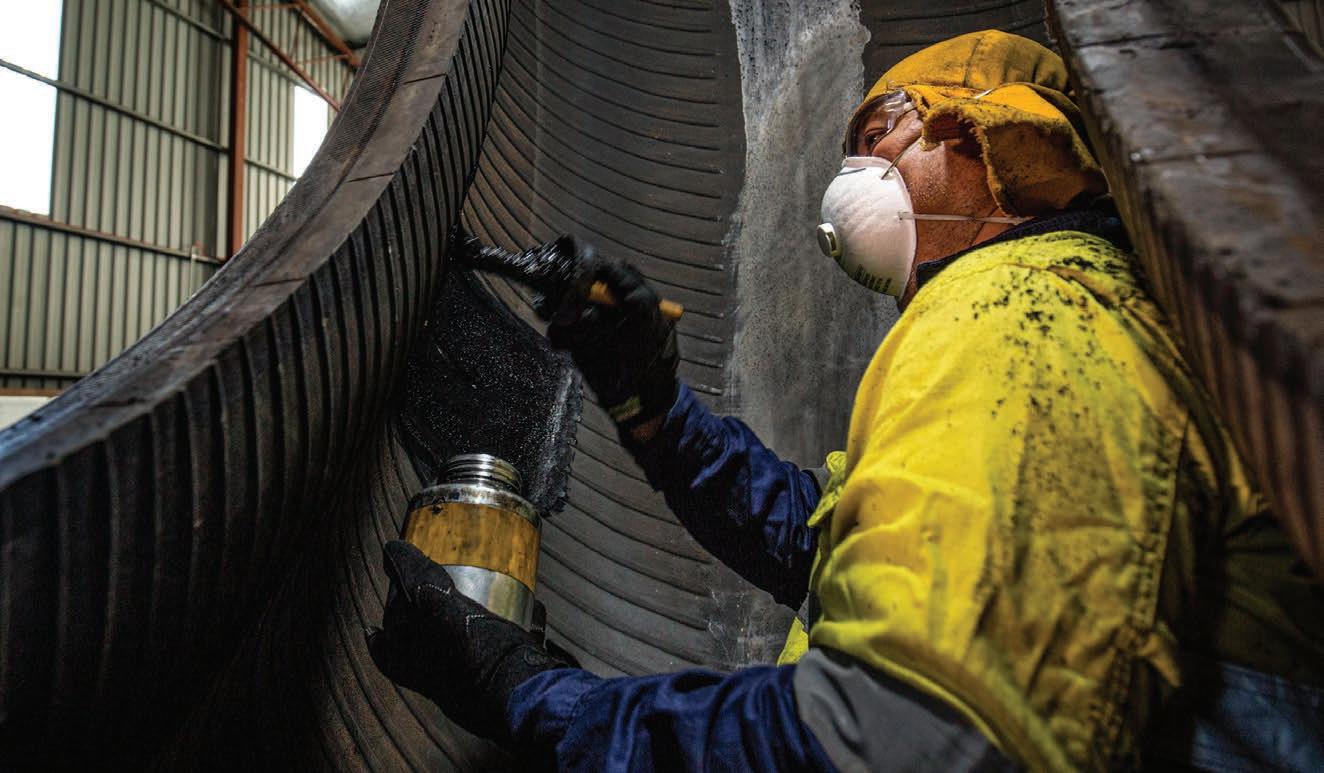
TOUGHER TO GO THE DISTANCE
STRENGTHENING THE METALS THAT QUITE LITERALLY KEEP A MINE RUNNING IS CRUCIAL. ARMORGALV CORROSION PROTECTION NOT ONLY IMPROVES DURABILITY, BUT CAN HELP MINES ACHIEVE THEIR SUSTAINABILITY GOALS.
THE PROCESS CREATES A MORE DURABLE MATERIAL THAT CAN WITHSTAND MINING CONDITIONS.



ArmorGalv corrosion protection is a galvanising process unique and exclusive to ArmorGalv Australia, the only plant of its kind in the country.
Rather than simply being a coating on ferrous and non-ferrous metals, ArmorGalv is a zinc-iron alloy, with the layers of thermal diffusion galvanising typically exhibiting hardness values greater than that of the parent material.
Surface hardness results typically exceed 35 Rockwell C, as referenced within ASTM A 1059/A 1059M – 08 (ASTM International, 2008).
Using a thermal diffusion galvanising process, multiple layers of zinc-iron alloy are formed, from a super corrosion-resistant gamma layer to a compact delta layer and then the zeta layer.
Each layer is harder, more corrosionresistant and more abrasion-resistant than the previous one, helping to increase the life of the part.
By strengthening the metal itself, the process creates a more durable material that can withstand harsh mining conditions by delivering better defence against deterioration.
ArmorGalv is an alternative to hotdip or electrolytic galvanising that was developed to replace cadmium and chrome in plating.
This cost-effective, environmentally-friendly and durable galvanising technique was designed in Israel in 1993. However, it did not find its way to our shores until ArmorGalv Australia was born in 2010.
ArmorGalv Australia general manager Clive Jones said the ArmorGalv diffusion process means the sacrificial layers are diffused deeper into the substrate to ensure it lasts longer.
“It’s embedded inside the material as well as on the top, so it’s harder, it’s flexible, and it’s a smart mixture of a zinc oxide which gives much more endurance to the finished product,” Jones told Australian Mining.
“It reduces internal stresses to the base material and removes any hydrogen embrittlement rather than inducing it like hot-dip galvanising does.”
Material fracturing as a result of hydrogen embrittlement is a safety issue on mine sites, a risk ArmorGalv eliminates. Mine sites are hotbeds of highambient temperatures, extremely high humidity, acid and dust, which results in high demands being placed on the need for corrosion-resistant machines and materials.
Corrosion resistance can be substantially increased through the application of a thicker coating or a top coating.
“With hardened and high-tensile steel, we don’t need to have it as thick as the softer zinc coatings because it’s a hard coating. So it’s not going to chip off so easily.”
When customers are looking for a longer lifespan, they’ll generally look for the thicker coating first, with the option to implement the ArmorPlex solution beyond that, where an epoxy coating will be placed over the top of the ArmorGalv corrosion protection without any further preparation.
“The thicker coating is sufficient for most mines, as it has quite a significant lifespan. It will be fairly extreme conditions, which may be heavily acidic ground, that sort of thing, where the customer might opt for the additional ArmorPlex,” Jones said.
ArmorGalv went through a series of salt spray tests that showed the lifespan of the corrosion protection can be from 1500 to 3000 hours, compared to approximately 500 hours with hotdip galvanising.
“Heavy equipment components used in mining environments such as cable trays, high-tensile fixings and anchors, rock bolts, small structural steels, springs for vibratory equipment, and conveyor components are all critical parts,” Jones said.
“When these parts are treated with ArmorGalv, they won’t be affected by hydrogen embrittlement, and instead will have the tensile strength customers can rely on to be serviceable for much longer.”
The machinery parts are also exempt from galling when galvanised with ArmorGalv.
Galling is defined as when two surfaces in contact seize up, and the materials gain their corrosion resistance from a passive oxide layer over their surface. Under high contact-force sliding this oxide can be deformed, broken and removed from parts of the component, exposing the bare reactive metal.
When the two surfaces are the same materials, these exposed surfaces can easily fuse together, causing seizure or galling.
Due to increased hardness and wear-resistant properties, the Thermal Zinc Diffusion process provides good anti-galling properties, predominantly facilitated by the absence of free zinc at the outer surface.
When it comes to sustainability, ArmorGalv Australia has worked hard to continuously improve its footprint both internally and for its customers.
The ArmorGalv thermal diffusion galvanising process provides important environmental benefits in comparison to other corrosion protection methods. It is a completely non-toxic and heavy metal free, environmentally responsible protection against corrosion and wear and tear.
“The mines that are looking into being more environmentallyfriendly and reaching net-zero carbon emissions, they need to be considering ArmorGalv,” Jones said. AM
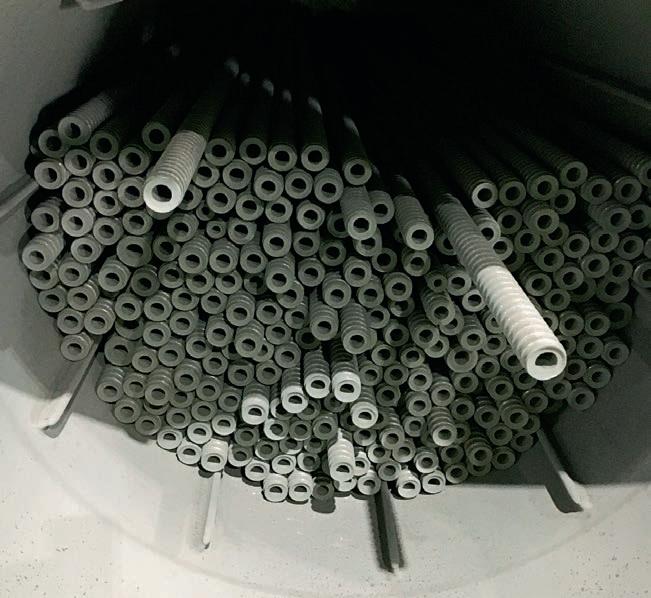
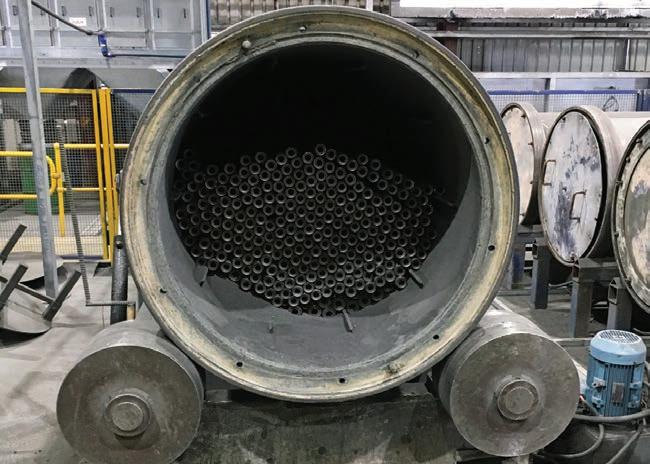
ADVANCING MINERAL PROCESSING THROUGH AUTOMATION
A FIRST-OF-ITS-KIND SOLUTION, THE ONLINE RHEOMETER HAS THE POTENTIAL TO REDEFINE MINERAL PROCESSING IN AUSTRALIA AND BEYOND.
Rheology Solutions has been servicing the mining and mineral processing industry for the past 25 years with specialist engineering supply and expertise, primarily in the measurement and characterisation of slurry properties.
Rheology Solutions developed the first OnLine Rheometer (OLR) – an instrument that can be fitted in a pipeline and can provide feedback on the flow properties of the materials that pass through it in real-time, without the need for manual sampling and laboratory testing.
Recently, the company has pioneered a more specialised version of the instrument, the OLR M2000, focused on the needs of the mining industry.
The ruggedised instrument can be fitted in a pipeline or thickener underflow and relays the measurement data to the process operator. The operator can input specific flow property data to establish optimal production specification parameters.
The OLR can then monitor proceedings and display the slurry conformance throughout the mining and production process.
The OLR M2000 is differentiated from all other instruments available in the market by its ability to index the yield stress. The yield stress is the minimum stress needed to make a concentrated slurry flow. It is often felt when rakes, mixers and pumps commence operation, and the machine requires more energy than normal to begin rotation.
The OLR provides a wealth of data and insight and the mining industry has shown particular interest in the product due to a specific valuable metric – the yield stress index (YSI).
The instrument not only accurately displays the YSI, but does so in an automated manner. This aids understanding of the presence of clays, for example, and accelerates rapid, informed process control by warning of adverse process conditions.
The OLR is evolved automation, because customers need to understand what the sensor is telling them and then act accordingly, whether it is through software-enabled process control or with operator control.
Rheology Solutions partnered with Rheological Consulting Services (RCS) to trial the OLR using slurry from Newcrest Mining’s Lihir gold operation in Papua New Guinea. Lihir had reported periodic “high viscosity events” in the pressure oxidation (POX) circuit with little warning, which reduced throughput, gold recovery rates and increased operating costs.
Following a thorough laboratory investigation, RCS found the yield stress of the slurries changed dramatically during these “high viscosity events”.
“If this number is really high then the material would become excessively thick and lumpy, flow will be affected, blockages may occur and the reactions and separations are not going to happen efficiently. All this means gold recovery decreases,” Rheology Solutions director of research Pradipto Bhattacharjee said.
“In some cases, you just dilute it. But you got to know ahead of time that this material coming in has got a yield stress of that level.
“If this figure is not good, then it may need to be diluted. Importantly, the level of dilution required can be determined and can be automated to reduce the downstream production effects caused by over dilution.”
The challenge was to find a way to constantly monitor the yield stress of the slurry such that a warning could be obtained for an imminent “high viscosity event”.
Manual sampling and laboratory testing could be done a finite amount of time during the day and was not an option.
This is where the OLR technology became relevant. Prior to the OLR, there was no suitable method for monitoring the yield stress of the slurry, in-line, continuously and in an automated manner.
Through the YSI, which correlates linearly with the yield stress, using the OLR to provide forewarning of a future “high viscosity event” became a viable option. First-of-its-kind laboratory and pilot work ensued and demonstrated that through the YSI metric the OLR detected small changes in material flow behaviour in response to very small changes in solids concentration.
These results showed for the first time that the yield stress of a concentrated particulate slurry could be measured in-line and in a flowing material, and were presented and published at a peer reviewed conference.
Rheology Solutions owner and managing director Patrick Griffin said while the OLR was a valuable mineral processing solution, it has the versatility to be used across various other applications. “There are many places in a mining operation where rheological information is needed,” Griffin said. “It is not just production but also waste management, other storage, and other operational needs.”
And when it comes to automation, the OLR has the potential to be a universal solution, uniting different applications under a single control.
“At Lihir, for example, the possibility is that OLR units could be placed at many various sites in the mining process,” Griffin said. “Then working again with RCS, OLR units could be the heart of automatic control and the data could be used to control the process automatically.” AM
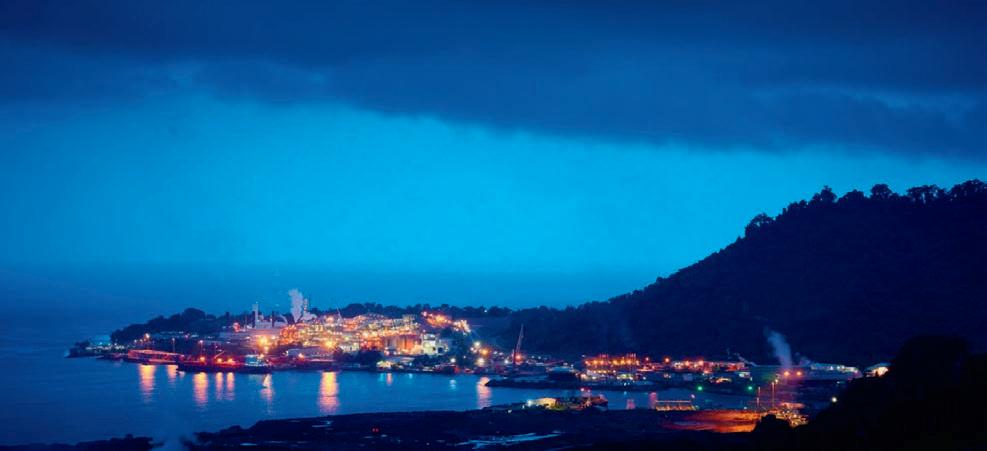
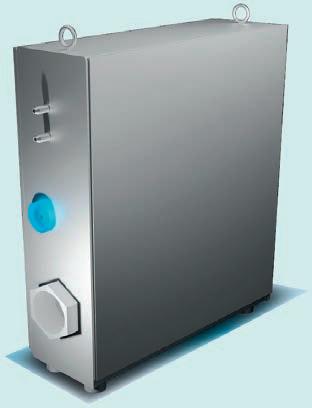
A MOCK-UP OF RHEOLOGY SOLUTIONS’ OLR M2000 UNIT. NEWCREST MINING’S LIHIR OPERATION IN PAPUA NEW GUINEA.