
20 minute read
MINERAL PROCESSING
THICKENER UPGRADE: WHERE FINANCIAL AND SUSTAINABILITY OVERLAP
UPGRADING THE THICKENERS AT ONE OF AUSTRALIA’S LARGEST GOLD PRODUCERS NOT ONLY BOOSTED THE MINE’S BOTTOM LINE, BUT IT ALSO REALISED IMPORTANT SUSTAINABILITY BENEFITS, AS THE FLSMIDTH TEAM BEHIND THE PROJECT EXPLAINS.
Thickeners are a ubiquitous feature at mineral processing facilities and have been for many decades. And in an industry where the lifetime of major equipment is often measured in decades, they are particularly long lived.
FLSmidth – whose association with thickeners goes back more than a century via the Dorr-Oliver and EIMCO brands that it acquired in 2007 – has many systems still operating at Australian mines that were installed in the 1960s, while a couple date back as far as the 1930s and 1940s.
In addition to its role in the production of target minerals, thickeners play an important part in mine water management and recycling: areas of focus in today’s mining industry where sustainability is becoming an ever more pressing dayto-day concern.
This is particularly true of mines in regions of high water stress, which is how the World Resources Institute categorises most of Australia.
With thickeners infrequently replaced, improving the performance of existing installations is key to meeting the industry’s changing sustainability and performance goals, according to FLSmidth Australia’s head of mining David Williams.
“Thickener technology is constantly evolving. Refurbishing and retrofitting therefore helps to ensure the ongoing integrity, reliability and productivity of existing machinery with the latest advances in thickener technology,” Williams said.
“At FLSmidth, we combine years of engineering expertise to offer a complete service package – from equipment and process evaluation to tailored upgrades, including complete new mechanisms, feed systems and new drives.”
FLSmidth’s experience and technology range is comprehensive, including the world’s largest and highest-capacity bridge and columnmounted thickeners.
Not keen to rest on its laurels, however, the company is always looking forward. Its research and development model integrates the evaluation of new technologies and concepts with continuous review and update of existing products.
“Our efforts focus on the development of solutions that combine high performance, reliability and availability with minimal environmental impact, in line with our MissionZero goal to reduce the water use and footprint of mining operations,” Williams said.
Among the latest developments in thickener technology offered by FLSmidth are its E-Volute feedwell and E-DUC and P-DUC feed dilution systems.
“The E-Volute feedwell is the result of many years of development work, including CFD modelling, at the laboratory and pilot scale,” FLSmidth global product line manager for thickening Fred Schoenbrunn said.
“The result is an involute design with sloped tapering shelf and sloped inner shelf, which promote superior energy dissipation in the feed stream, optimal mixing and improved shear profiles to ensure thickener performance and efficiency.”
According to Schoenbrunn, this provides a range of benefits including: • increased retention time in the feedwell • maximised solids throughput • reduced shear rates and minimised flocculant consumption • increased flocculation efficiency • even distribution of feed slurry/solids • enhanced settling rates and increased equipment capacity • optimised underflow solids • minimised short circuiting • reduced overflow solids.


Supporting the work of the E-Volute feedwell are the E-DUC and P-DUC feed dilution systems, both of which are designed to ensure even distribution of flocculated solids in the feed before it reaches the E-Volute feedwell.
“The E-DUC system is appropriate for applications that require consistently large volumes of feed dilution, whereas the P-DUC system incorporates a variable speed drive that allows for variable dilution flowrates in applications where large variations in feed flow or density are expected,” Schoenbrunn said.
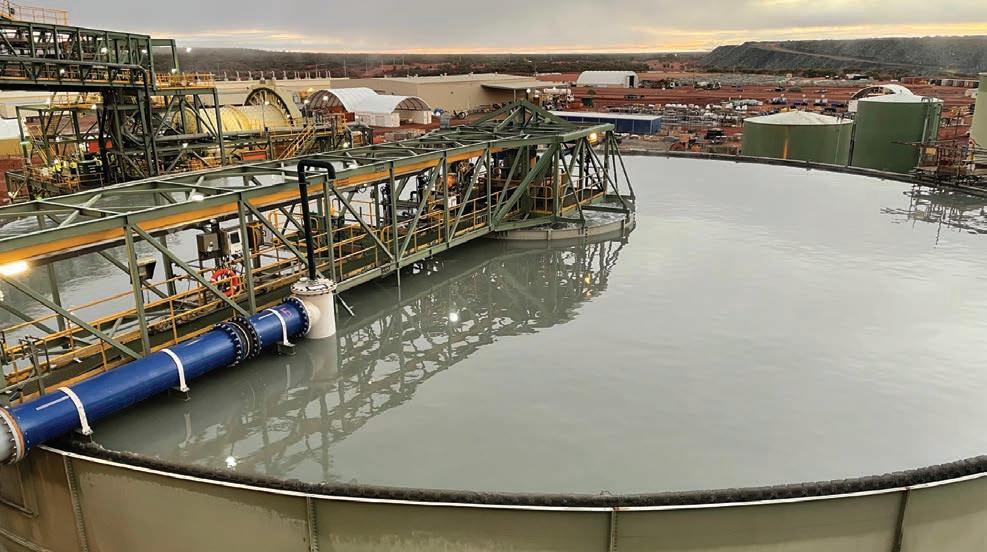
THE 44-METRE THICKENER WAS FITTED WITH A P-DUC MECHANISM AND E-VOLUTE FEEDWELL TO IMPROVE THROUGHPUT AND UNDERFLOW DENSITY ACROSS A RANGE OF FEED CONDITIONS.
Case study: Feed system retrofit at an Australian gold operation FLSmidth has supported thickener performance upgrade at one of Australia’s largest gold mines for several years.
When the mine first approached the engineering company, it was operating third-party 34m diameter leach feed and 44m diameter tailings thickeners, and nameplate capacity was 700 tonnes per hour (tph).
“We initially upgraded the leach feed thickener, installing an E-DUC dilution system and E-Volute feedwell,” FLSmidth regional product line manager for dewatering Anson Gilbert said.
“This increased leach feed thickener underflow density from 48 per cent to 54 per cent solids at 850tph of feed solids, resulting in significant savings in both lime and cyanide consumption, as well as increasing carbon in leach (CIL) residence times.

Flocculant consumption also fell by 34 per cent on a gram/tonne basis.
Return on investment was achieved in less than six months.”
The mine successfully operated with this upgraded set-up for several years. Over time, however, the thickener started to bottleneck the process and the mine again approached FLSmidth to help.
“The mine’s proposal was to swap the duties of the 34m leach feed thickener and 44m tailings thickener,” Gilbert said.
“When we were called in, we set about analysing the idea with a comprehensive program of onsite test work, process evaluation and structural analysis of both thickener bridges.”
Through this work, the FLSmidth team observed continuous pluming in the leach feed thickener in proximity to the overflow launders – with solid particles in the overflow visible at elevated throughputs – while faster settling rates and compaction times were seen in the tailings thickener.
“We were therefore able to prove the viability of swapping thickener duties to unlock additional thickener capacity,” Gilbert said.
“The faster settling tailings material could be treated in the smaller thickener, meaning the additional unit area required for the leach feed application could be obtained by using the larger thickener.”
FLSmidth recommended installing P-DUC mechanisms on both thickeners and an E-Volute feedwell on the 44m thickener.
The engineering team also recommended a larger feed box to allow for increased throughput and improved deaeration of the feed.
As a result of the upgrade, thickener throughput has increased from 1060tph to 1160 tph, without any increase in flocculant consumption on a gram/ tonne basis.
There is also now no visible pluming or particle carryover in either of the thickeners overflow.
“Thickeners are no longer the bottleneck to performance,” Gilbert said. “By increasing throughput and maintaining the same fixed costs, we also enhanced profitability, and payback has been achieved in under 12 months.”


The value of thickener upgrades “The retrofit demonstrates the potential improvements that a thickener upgrade can bring to an operation,” David Williams said.
“In both units, we achieved a large improvement in solid–liquid separation, which facilitated a further flowsheet change and removed a customer pain point.” Overall, the upgrade resulted in a 9 per cent increase in plant capacity allowing for reduced fixed cost per ounce.
This project also demonstrates the mutual benefits thickener upgrades can bring to a mine’s profitability and environmental performance.
There were multiple specific sustainability wins.
Increasing the underflow density from the leach feed thickener allowed for additional residence time in the CIL circuit, improving recovery at a given throughput.
This increased the production of gold without increasing the amount of ore mined.
The underflow water ratio in the tailings thickener dropped from 0.85 tonnes water to 0.75 tonnes water per tonne of solids processed – an 11 per cent reduction in water going to the tailings dam (even with the higher tonnage).
“These benefits align with our MissionZero sustainability program to drive sustainable productivity in mining – and demonstrate the complementary value this sort of project can bring to a mine’s productivity and environmental performance,” Williams said.
“As sustainability becomes an ever-important element in the performance of mineral processing operations, we believe the value of such projects will become increasingly important as mining companies seek to meet both financial and environmental goals.
“We are committed to supporting the industry on this journey.
“And, through our MissionZero program, we are working with our customers and other partners to build a truly sustainable mining industry.” AM
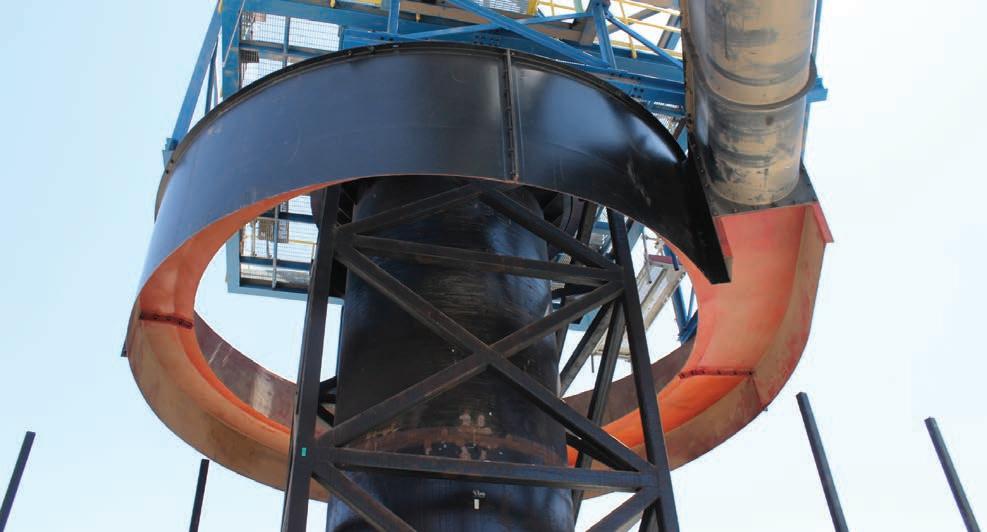
1988
THE E-VOLUTE FEEDWELL DESIGN ENSURES THICKENER PERFORMANCE AND EFFICIENCY.
Industrial Flotation Specialists
Custom designed and manufactured to suit your requirements

SINCE 1988
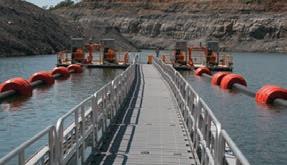
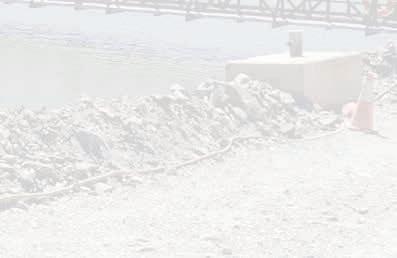
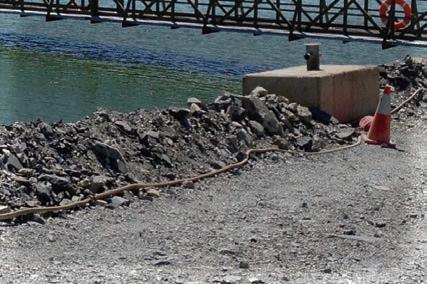

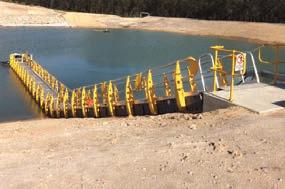
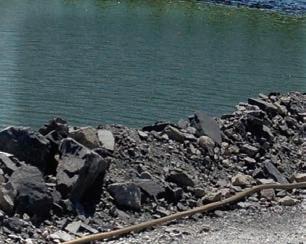
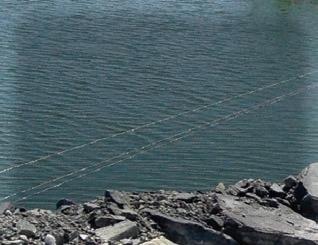
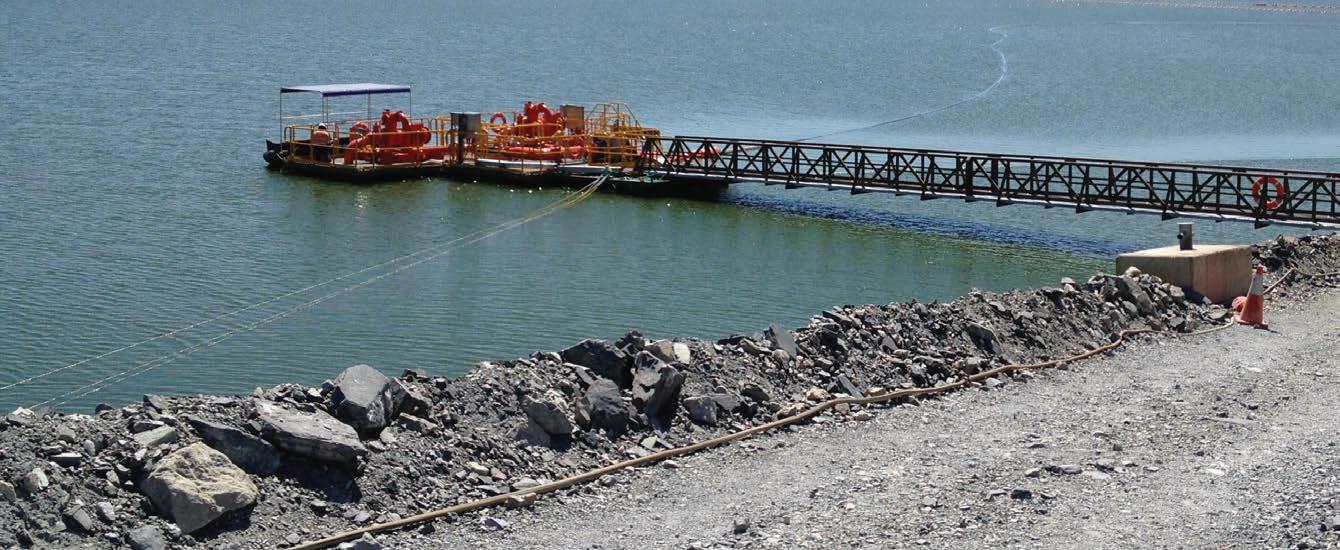
Pump Pontoons Pipe Floats Floating Walkways
All products manufactured in Australia Suppliers to the global major mining
companies & contractors
Aluminium gangway specialists Modular systems for easy installation 100% virgin PE materials used for
maximum UV protection and long life
Broad selection of products to suit all
mining applications
THE RESULT OF A WELL-OILED MACHINE
APRON FEEDERS ARE AN ESSENTIAL COMPONENT OF THE MINERALS PROCESSING CYCLE. AFTER DECADES OF MAINTAINING, FIXING AND INSTALLING THEM, MINPROVISE HAS ALSO BEGUN DESIGNING AND MANUFACTURING THEM.
Minprovise is a specialist engineering, products and services company providing expert support to the mining, oil and gas and construction industries throughout Australia, with key locations in Perth, Karratha and Port Hedland in Western Australia and Coopers Plains in Queensland.
The company offers everything from mineral processing equipment and fabrication to specialist industry products and site services.
Minprovise general manager of value-added services and engineering John Minnaar told Australian Mining that in the mining sector, Minprovise predominantly provides maintenance service, especially in the crushing and materials-handling environment.
“Part of that is also the supply of technical specialists, or subject-matter experts on equipment to maintain and optimise the equipment,” he said.
“We also provide parts and services as well as products to support the mining industry, and we assist clients to evaluate the condition of their assets to help plan and schedule maintenance.”
Minprovise was established in 2004 with a core business of reducing the risk associated with operation and maintenance of crushing equipment. Between that time and 2017, the company occasionally delved into refurbishing apron feeders; however, it wasn’t a main focus.
But in 2017 an opportunity presented itself for Minprovise to follow apron feeders down a more permanent path.
“That’s when Minprovise decided to set up an apron feeder division and an apron feeder specialist service that I headed in 2017,” Minprovise apron feeders and materials handling technical specialist Louw Scholtz told Australian Mining.
“From 2017 we’ve grown from refurbishing one apron feeder a year to eleven machines this last year across the board.”
When this apron feeder specialist service was implemented, the company’s technical experts provided maintenance on any apron feeder brand that its customers had installed on-site.
Minprovise gained experience and knowledge getting to know apron feeders inside and out – literally.
When Minnaar came on board with the company he managed to demonstrate the value of manufacturing Minprovise’s own brand of apron feeder based on the wealth of knowledge and experience accumulated through years of providing maintenance to other brands.
Minprovise has been able to take the best design elements from each model it encountered in the field, improve on them, and incorporate the results into its own well-oiled machine.
“An apron feeder is a fairly simple piece of equipment, but our team has done a lot of innovating, and research and development of safety items that we’ve designed and incorporated in our maintenance strategies,” Minnaar said.
“We were able to find out the good and bad points of all the machines out there are and put the best of it all together.”
Minprovise has considerable technical experience, with Scholtz’s team always working on, improving and maintaining apron feeders.
Adding to the team is Minprovise drawing office manager and apron feeder design and development leader Darren Brooke, with years of experience for various market competitors.
It’s the A-Team of apron feeder design, maintenance and optimisation.
“We believe we’ve got a very strong technical team who design the lifecycle of apron feeders, from the design through to operation and maintenance,” Minnaar said.
Apron feeders usually have a lifespan of four to five years before replacement.
Minprovise has now developed a unique process and methodology for this replacement that works in partnership with a client’s own standards and procedures, as well as their needs based on the data Minprovise has collected during the previous four to five years of maintenance.
Standards change and new ones are continually introduced; it’s a dynamic space.
“A lot of the plants these machines are in were designed before certain standards even existed,” Scholtz said.
“So we go out and assess the site for specific ways to improve that particular set-up and come up with ideas and designs to enable easier and more efficient maintenance.
“This can include building specialised platforms and devices that we can (use to) hook winches and access platforms onto the machine or build the platforms around the machine to carry out maintenance.”
This site-specific analysis, coupled with Minprovise’s more general database gleaned from years in the maintenance space of apron feeders and crusher circuits, results in a comprehensive approach with unique and often-subtle changes and adaptations that can have significant impact on overall efficiency and optimisation of the circuit and, more specifically, apron feeders.
Scholtz and Minnaar agree that a lot of the difficulties or challenges Minprovise has encountered have forced them to think outside the box and come up with unique ideas, designs and safety features that mitigate some of the risks generally present in this environment.
Minprovise is still consistent with its beginnings of “reducing the risks”, but as its entrance into the design and manufacture of apron feeders is showing, it takes its current positioning of “forward-thinking partners” seriously.
Part of this transition and growth has been an internal overhaul where Minprovise invested heavily in training so the revised teams can improve on their knowledge development of innovative solutions.
“We have very competent people that go into the field, assess and bring the information back to us in-house, where we combine it with our greater knowledge and experience and the client’s needs, and come up with innovative solutions” Minnaar said.
“The open field of development is a continuously ongoing process. We have our base designs, and we use our subject-matter experts to invest the knowledge back into our designs.”
Minprovise values collaboration and feedback and as a company it gets involved in community activities, supporting local in all aspects of the business – manufacturing, assembly, support for maintenance, and operation – as much as it can throughout its home state of Western Australia.
The experienced team at Minprovise will continue to improve safety and identify efficiencies in processes where possible, staying committed to reducing costs, risks and minimising downtime on-site. AM
MINPROVISE HAS THE A-TEAM OF APRON FEEDER DESIGN, MAINTENANCE AND OPTIMISATION.

DYNA ENGINEERING TAKES CONVEYOR GUARDS TO NEXT LEVEL
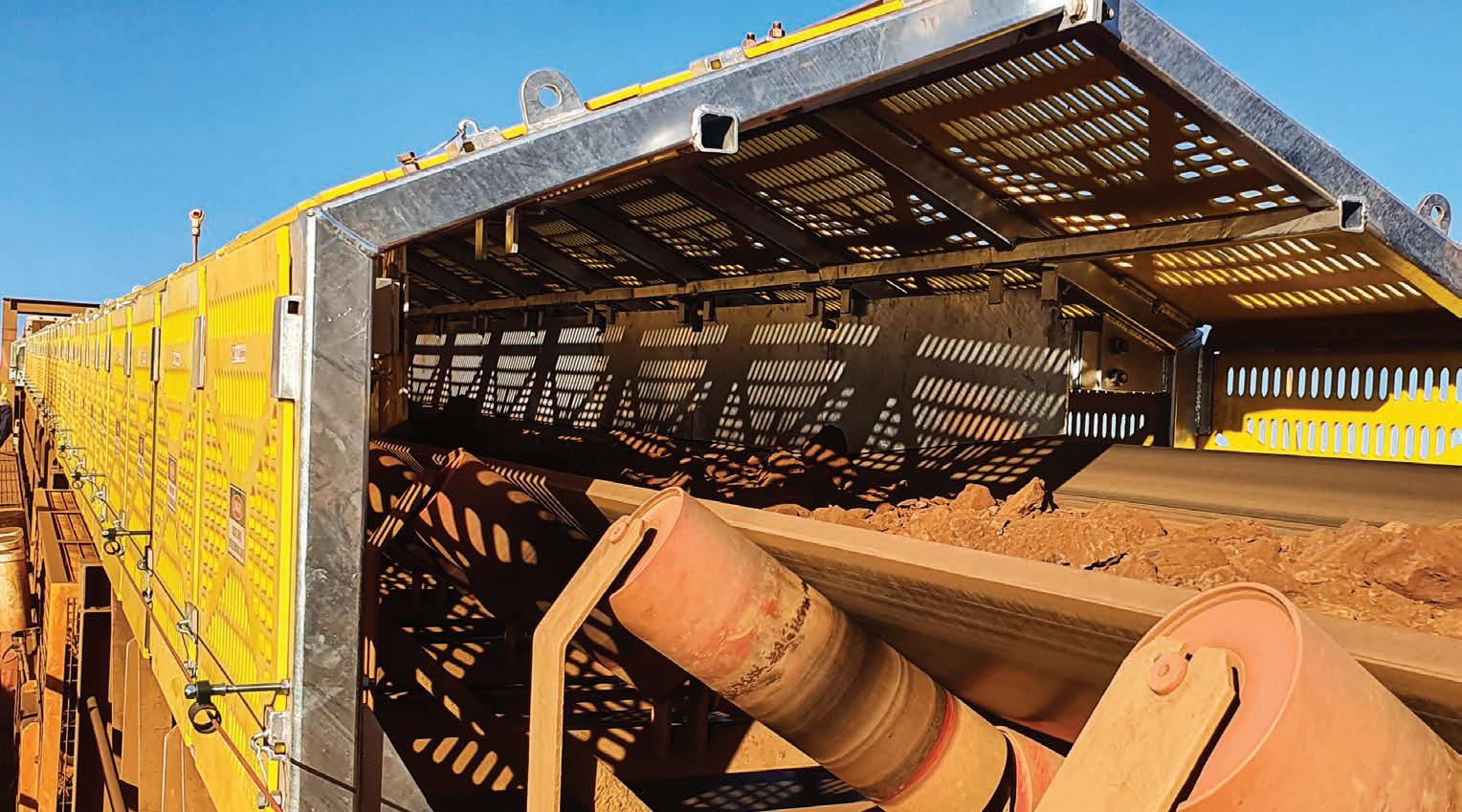
THIS REVOLUTIONARY TAKE ON THE HUMBLE CONVEYOR GUARD IS TAKING THE MINING INDUSTRY BY STORM, ONE PIECE OF RECYCLED PLASTIC WASTE AT A TIME.
Two years ago, DYNA Engineering recognised an issue with conveyor guards that had plagued the industry since the product was conceived decades earlier.
Traditionally, steel conveyor guards have capably contained conveyed material around a mine site, providing a relatively sturdy and costeffective option for the Australian mining industry.
However, traditional never meant problem-free, according to DYNA Engineering general manager Thomas Greaves.
“Steel guards have been used for 40 or 50 years and no one’s ever come up with something better. So customers have always had the same problems about corrosion and painting which they were looking to fix,” Greaves told Australian Mining.
“This presented a niche in the market and DYNA saw it as an opportunity to help. We started thinking about what sort of product could solve it and we came up with a material that’s lighter and that’s commonly used in mining processes. That was HDPE.”
HDPE – high-density polyethylene – has been recognised by DYNA as the best, most cost-effective, safest and longest-lasting material available for guarding bulk-handling systems.
DYNA’s take on the product is 40 per cent lighter than steel guarding, making it much easier and safer for maintenance teams to install and replace.
Compared to steel guards, HDPE is also very low maintenance due to its resistance to corrosion and abrasion.
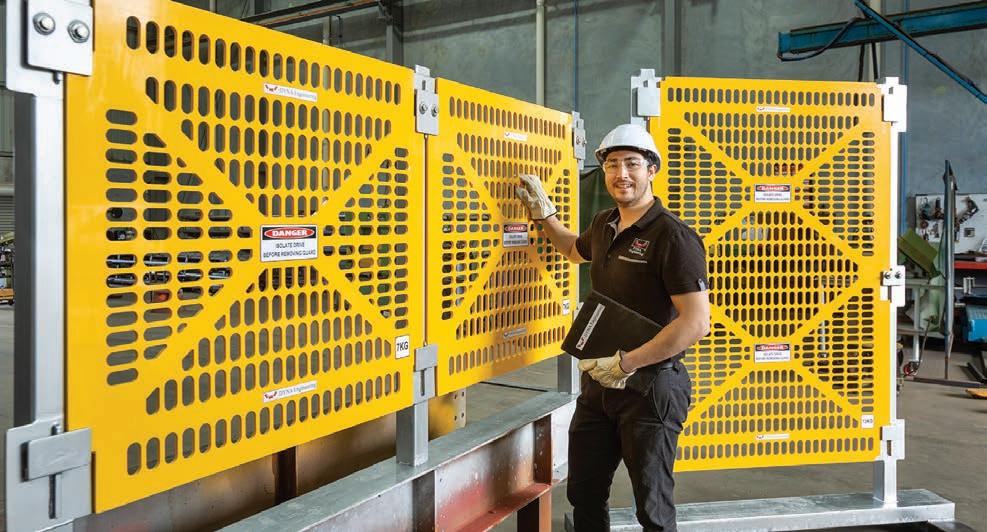
THE GUARDS’ X-DESIGN REDUCES MATERIALS AND IMPROVES STRENGTH.
DYNA ENGINEERING’S HDPE CONVEYOR GUARDS IN ACTION.
Greaves said all these benefits and more have made it a big success over the last two years.
“It’s quite new to the market and I think our version of the product is quite revolutionary. It doesn’t require any frame or stiffening to be added to meet Australian standards, which is one of our key benefits. This reduces the manufacturing costs and makes it competitive compared to its steel counterpart,” Greaves said.
“There have been competitors who have seen us achieve success, but we’ve got that first-mover advantage and we’re really starting to produce it at scale.”
This scale has included some of Australian major miners, mostly in Western Australia, but DYNA is aspiring to expand across the country and has also begun to see success in the eastern states.
In 2021, the company set up a dedicated workshop in Bayswater, outside Perth, which has allowed DYNA to cope with year-on-year growth in sales.
Greaves said the use of recycled plastics to create the guards was a big factor in their popularity.
“There’s always improvement to be made over time, but having a recycled and recyclable product is really in fashion these days,” he said.
“Everyone’s looking at their sustainability and ESG (environmental, social and governance) initiatives, and this product fits into that niche quite nicely.”
HDPE was chosen for the conveyor guards due to its easily recyclable nature. DYNA sources the materials from a local recycling partner and uses between 7–10kg of plastic waste per guard.
Greaves explained the inspiration behind the use of recycled plastic.
“We saw a lack of demand for recycled plastic even though Australia produces a lot of plastic waste and we don’t have a great use for it at scale,” he said.
“So something like the HDPE guards can take quite common plastics and make them into something that’s useful.
“Where a milk bottle has a two- or three-week life, the HDPE guards last for 10 to 15 years.”
Considering the higher cost per unit of HDPE, the team at DYNA Engineering had to ensure every piece of its conveyor guard was necessary.
They came up with their own X-design which was found to strengthen the panels substantially without requiring additional attachments or framing to strengthen it.
Greaves said without this key design feature, DYNA’s HDPE conveyor guards may never have gotten off the ground.
“To present a cost benefit for the customer, our X-design lowers the amount of components needed to make the guards and made our guards competitive against fabricated steel guards,” he explained.
“With our HDPE guards, you’re not paying extra but you’re getting all these other benefits with it, and that’s made the industry really sit up and listen.” AM
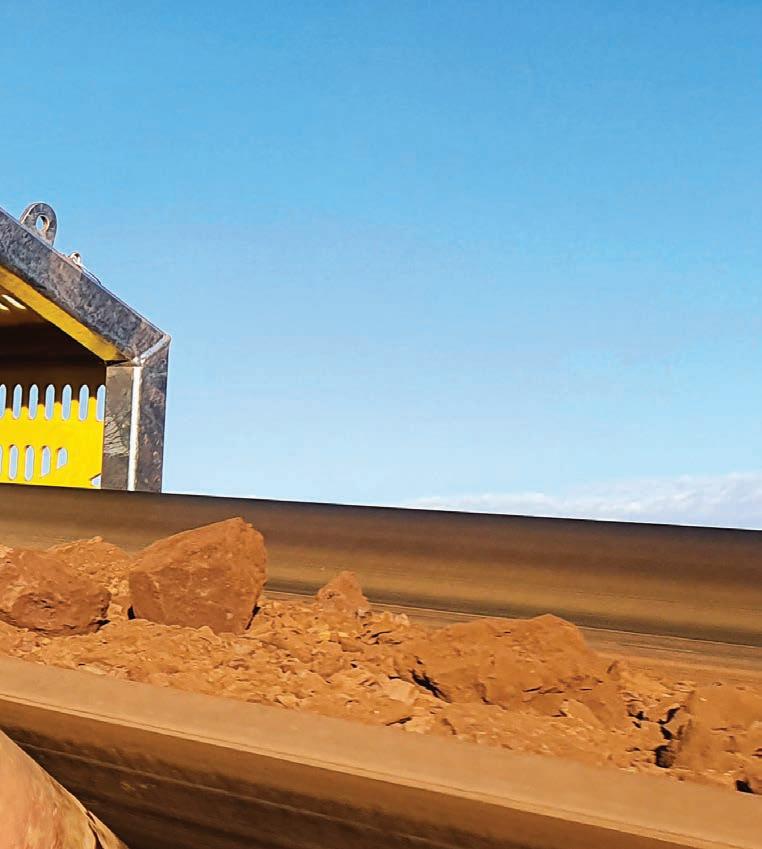

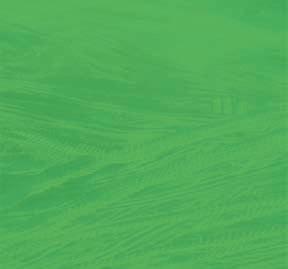
INNOVATIVE MINING SOLUTIONS

LASER MEASUREMENT SYSTEMS AND APPLICATION SOFTWARE FOR EFFICIENT MATERIAL HANDLING ¬ Stockpile Management ¬ Truck Load Measurement ¬ Conveyor Belt Monitoring
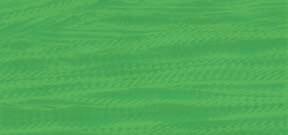
¬ Bunker Profile Detection ¬ Train Wagon Measurement ¬ Collision Prevention
MORE SOLUTIONS
REMOVING THE BUZZ ABOUT VIBRATING SCREENS
HAVER & BOECKER NIAGARA HAS SHOWN THAT GOOD THINGS DO COME IN THREES WITH ITS SUITE OF PULSE DIAGNOSTIC TOOLS TO IMPROVE SCREENING EFFICIENCY AND ENCOURAGE PREVENTIVE MAINTENANCE.
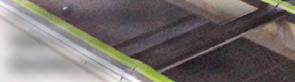
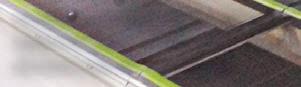

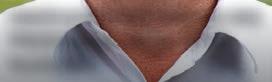
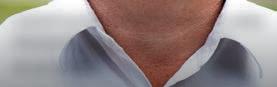
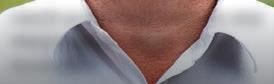
It goes without saying that digging up valuable ore is just one step of the mining process, and that without subsequent steps of processing and beneficiation such digging would be wasted time.
So the importance of keeping equipment like vibrating screens running cannot be overstated.
It is for this reason that Haver & Boecker Niagara has built a reputation with products and services like its Pulse Diagnostic suite, which includes the Pulse Impact Test, Pulse Vibration Analysis (Pulse VA) and Pulse Condition Monitoring (Pulse CM).
Peter Kilmurray, Haver & Boecker Niagara’s vice president of sales for North America and Australia, said the Pulse suite had customers’ best interests firmly in mind.
“Unexpected downtime is a huge source of lost revenue for producers, so we aim to create products and technology that prevent that,” Kilmurray told Australian Mining.
“We’ve engineered each system to optimise the health of vibrating screens – regardless of the brand – by detecting irregularities that could translate into diminished performance, decreased efficiency, increased operating costs and imminent breakdowns.”
The consequences of an undetected hairline crack or a twisted side plate can be severe for the longevity of a vibrating screen, so catching these issues before they turn into more significant failures can be a difference of thousands of tonnes or dollars.
Kilmurray explained each piece of the puzzle, starting with the Pulse Impact Test.
“Also known as the ‘hammer test’ or ‘bump test’, it’s part of our quality assurance program during factory testing as well as on-site,” he said.
“The advanced testing ensures each machine is properly calibrated to avoid operating in resonance for efficient operation.”
Next, Pulse VA is designed to capture a moment in time in a vibrating screen’s performance, so it can be compared to the machine’s past performance as well as original equipment manufacturer (OEM) specifications.
These moments are captured using eight wireless tri-axial sensors that fasten to key areas of the equipment. The information is then sent via WiFi to a remote device, allowing safe monitoring from a distance.
Kilmurray said the Pulse CM tool was the most comprehensive option.
“This system consists of permanently installed sensors to monitor the screening equipment 24–7,” he said.
“Pulse CM captures real-time information and provides alerts via e-mail when it detects the first sign of potential problems.
“By constantly monitoring the accelerations of the vibration screen, Pulse CM offers a forecast of the equipment’s dynamic condition in intervals of 48 hours, five days, and four weeks.”
And while these three tools don’t need to be used together, operations will benefit most from harnessing each of their individual purposes.
Kilmurray said the Haver & Boecker Niagara team would take the time to consult with customers to understand their needs and pair them with the best configuration for their application.
“By using the tools together, operations can get a holistic view of their equipment and help to ensure it operates at OEM standards,” he said.
“For some operations, it might be quarterly Pulse VA tests paired with a bi-annual Pulse Impact Test. Whereas for others, it might be a combination of the three.”
In any case, customers will only get the best out of these technologies when they’re paired with capable support from the Haver & Boecker Niagara team. That is something the manufacturer has developed in spades, according to Kilmurray.
“Customers benefit from site visits by certified technicians who not only know how to use the impact test, vibration analysis and condition monitoring, but are able to conduct thorough vibrating screen and screen media inspections to complement the analysis,” he said.
“Our Haver & Boecker Niagara certified service technicians perform each analysis, from placing the sensors in key locations and conducting the test to analysing the data and providing recommendations as needed.”
And if three isn’t the magic number for a given mining operation, Haver & Boecker Niagara will continue to fill gaps in the market with the next big thing in mining technology.
“Diagnostics are always evolving. We are constantly looking at what data can be captured and how it can help our customers run their operations’ more efficiently,” Kilmurray said. AM
HAVER & BOECKER NIAGARA VICE PRESIDENT OF SALES, PETER KILMURRAY.
PULSE DIAGNOSTIC TOOLS OPTIMISE VIBRATING SCREEN HEALTH, REGARDLESS OF THE BRAND.
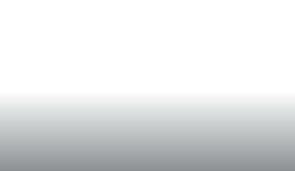

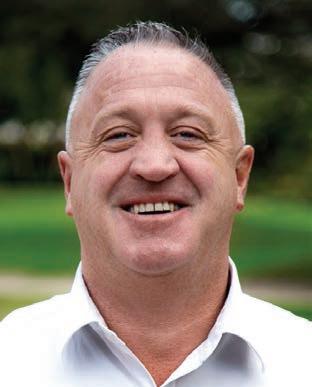