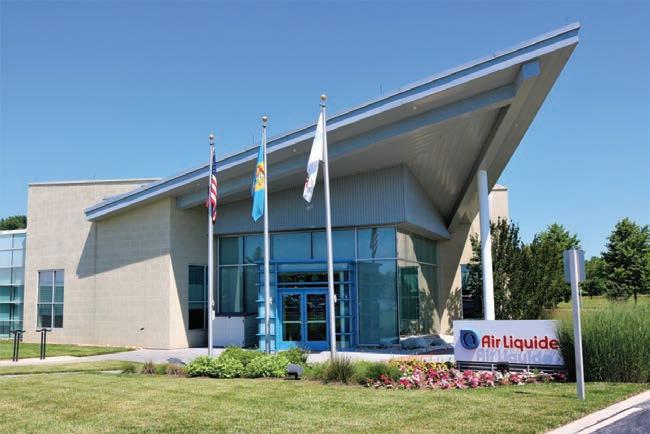
14 minute read
TECHNOLOGY
NEXT-LEVEL TECH INJECTS VALUE INTO MINING
AIR LIQUIDE HAS DEVELOPED A GAS INJECTION TECHNOLOGY CALLED NEXELIA TO IMPROVE SUSTAINABILITY AND QUALITY OF PROCESSES SUCH AS GOLD LEACHING AND LITHIUM CARBONATE PURIFICATION.
Air Liquide has grown out of France since 1902 to operate in 78 countries, employing around 64,500 people and serving more than 3.8 million customers.
With more than a century of experience in gas production technologies and applications, Air Liquide has served the Australian mining industry with mineral processing solutions for flotation and pH control, oxidative roasting, gold leaching and in-situ uranium leaching, process water treatment and nitrogen inerting systems for longwall underground mines.
The latest of these solutions is called Nexelia and it was designed in response to customers’ problems with chemical costs and sustainable processes.
Air Liquide regional operation centre market manager Eiichi Mizutani explained the motive behind Nexelia.
“Key objectives pursued by gold mine operators are to maximise productivity and gold recovery from increasingly complex ores, while doing
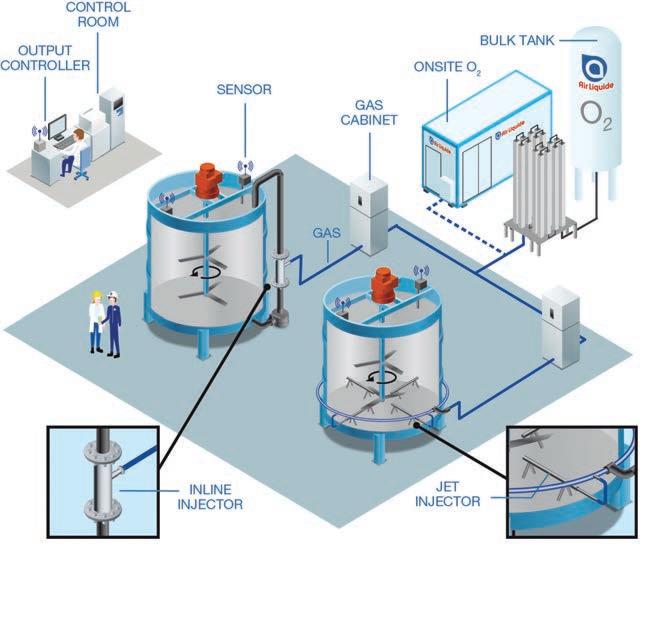
A FLOW CHART OF THE GOLD LEACHING PROCESS USING NEXELIA.
so in a competitive and sustainable manner,” he told Australian Mining.
“More than ever before, gold mine operators need reliable and costeffective solutions to meet their performance goals while respecting their commitment to corporate social responsibility.”
Nexelia for gold leaching is an all-inone gas solution that injects industrialquality oxygen into the pre-oxidation and cyanide leaching circuit in the most resource efficient volumes.
But no two ore samples are equal, and Air Liquide works with its customers to understand their material and design a system that will maximise productivity and minimise resource intensity.
“It all starts with process expertise, interacting with our experts either onsite or in the lab,” Mizutani said.
“By sending mineral samples to one of Air Liquide’s labs, we would design the experiment plan with different set-ups.
“Then for every set-up we measure changes in oxygen uptake ratios, cyanide consumption and gold increase yields with our commercial-level testing.”
By reducing resource intensity and minimising chemical consumption, mining companies can improve their sustainability and costs.
But the benefits of Nexelia stretch even further, according to Mizutani.
“In the gold mining field, the technology provides not only savings of cyanide consumption and sustainability, but it will also help to maintain or improve the gold recovery rate by verifying the mineral and adopting the oxygen transfer system for the specific application,” he said.
In keeping with current demands for technology-driven solutions, Air Liquide has rolled out a monitoring solution for dissolved oxygen and pH levels.
The Air Liquide wireless monitoring system is designed primarily for gold and copper leaching monitoring, Mizutani said.
“Using this system, the key data is uploaded almost real-time to the cloud, so we can check it anywhere from the smartphone or laptop,” he explained.
“By monitoring key parameters like dissolved oxygen, it ensures efficient oxygen usage and high performance of the process in terms of gold recovery and chemical consumption.
“The benefits of such tools are operational traceability, early detection of abnormal situations, alarms, getting real data and less travel to remote locations.”
But Air Liquide wasn’t happy with just serving the gold and copper sector, adding Nexelia for lithium carbonate purification to the fray. Another all-in-one gas solution, this applies to lithium carbonates produced by acid or basic routes from either brines or mined rocks.
Mizutani explained how carbon dioxide was used in a three-step process.
“It dissolves lithium carbonate from slurry, then solid impurities are filtered out. Finally, when heated up, dissolved lithium carbonate precipitates and releases carbon dioxide,” he said.
“The solution then captures the released carbon dioxide in this third precipitation phase and re-uses it in the initial dissolution phase.”
The result is battery-grade lithium carbonate and reduces the amount of carbon dioxide required per kilogram by three times – from 0.6kg of carbon dioxide per kilogram of lithium carbonate to 0.2kg of carbon dioxide.
Mizutani is excited to watch the results in Australia’s growing lithium sector after the technology showed its worth in North America.
“That was proven in Canada, but one of the strengths of our company is that Air Liquide’s efforts around the world can be replicated everywhere,” he said. “We feel that it is our mission to continue to contribute to the mining industry while grasping technological trends around the world.” AM
AIR LIQUIDE’S DELAWARE INNOVATION CAMPUS, HOME OF ITS GOLD LEACHING TESTING PLATFORM.
ATLAS CEA CONQUERS A POWER CONUNDRUM
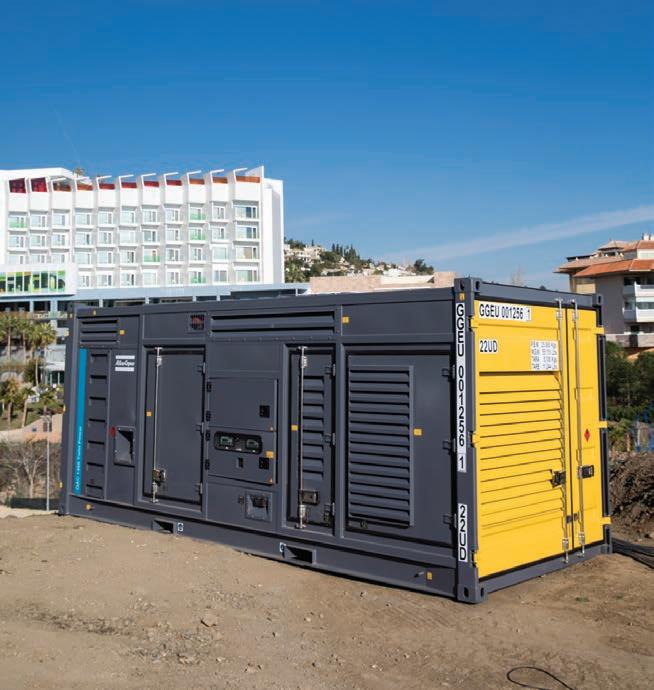
THE QAC 1450 TWINPOWER MEANS THE MINING INDUSTRY NOW HAS AN INSPIRED NEW POWER SOLUTION AT ITS DISPOSAL: TWO GENERATORS IN ONE.
Atrusted distributor of world-renowned manufacturer Atlas Copco, Atlas CEA has been supporting the Australian mining sector for decades.
Atlas CEA has overseen constant advancements in industrial productivity solutions over the years, but not many innovations compare to Atlas Copco’s new QAC 1450 TwinPower generator.
As Atlas CEA New South Wales branch manager Greg Conrad puts it, the QAC 1450 TwinPower is a beast.
“You get a powerhouse in a 20-foot container,” he told Australian Mining.
“You get two generators in one and it allows you to manage power delivery to your site better than you can from a single large generator.”
The dual generators give the customer more flexibility to provide optimal power at the right time, and more efficiently.
“Not everyone has a perfect load for a generator, so what we’ve done is design this unit to better benefit the customer and their site-specific needs,” Conrad said.
“In that, you can start the day with high loads and then as the day goes on, or as loads vary, the generator can transition from acting as one big generator operating at 1450 kilovoltampere (kVA) to a single generator operating at 725 kVA with reduced risk of damaging the engine due to low loading.”
In a mining setting, where operations often run 24–7 and maintaining uptime is critical, reliable power generation is imperative.
“Because you’re running two generators, you have less wear and tear and less fuel consumption,” Conrad said. “Maintenance costs are significantly reduced because you’re changing oil and coolant filters for two smaller generators instead of one big one.
“A customer that we recently sold the unit to starts the unit up in the morning with two engines handling the full load, but when the load drops, one engine automatically turns off and goes into standby until required.
“The cost savings from this are astronomical.
“As you can imagine, the equipment pays for itself pretty quickly if it’s used for that reason.”
If an operator wants to maximise their power even further, the QAC 1450 can also be connected to extra generators in parallel. Additionally, the unit can run as a single 1450 kVA generator connected to as single switchboard or run as two completely separate 725 kVA generators, each providing power to separate loads and operating independently.
The QAC 1450 is versatile in operation but also provides greater flexibility through its comprehensive but user-friendly control system.
“The control system is full of options that allow you to tailor the generator operation to your site needs,” Conrad said.
“The generator does what you want it to do; you’re not confined to the limitations of a single, big generator delivering full power all day long.
“So you can run it at full capacity or you can run it at half capacity. One of the nice features built for critical sites is that you can also program it for redundancy so one generator acts as the prime unit while the other one stays on standby.”
Conrad said the QAC 1450’s control system caters for many other powermanagement requests, including base loading or peak lopping, which is another example of its flexibility to meet various customer needs.
To support the QAC 1450, Atlas CEA has a comprehensive service team across its branches in Brisbane, Sydney, Melbourne and Perth, with technicians at the ready for servicing or if a customer runs into any difficulties. And the company’s service capability doesn’t stop there.
“We also have dealers throughout Australia to help support the extensive range of equipment operating across the country, and some of the maintenance can be done by your local or site mechanic if the requirement arises” Conrad said.
“We have local parts distribution as well as our National Distribution Centre in Sydney supplying parts throughout Australia.
“Then we also have Atlas Copco for support as well. They’ve been around for over 170 years specialising in construction and mining equipment.
“So we have a pretty high presence of service, parts, and technical support throughout Australia.”
Through the QAC 1450 TwinPower, Atlas CEA has innovated an inspired new way of combatting power concerns on mine sites.
Operators can do away with fears of low-loading, excessive servicing and high fuel consumption and now have the capacity to better manage their power usage across the working day.
It’s about flexibility, and the QAC 1450 TwinPower has that in spades. AM
RELIABLE POWER GENERATION IS IMPERATIVE TO MAINTAINING UPTIME. THE QAC 1450 TWINPOWER PACKS TWO GENERATORS IN ONE.
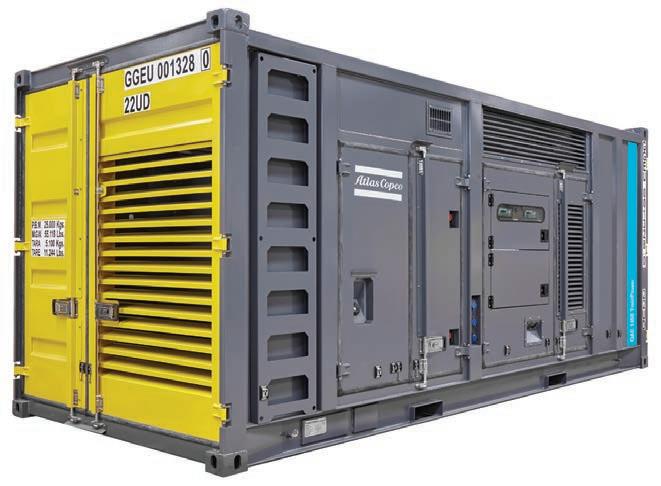
CONNECTED TECHNOLOGY WITH A PURPOSE
FARRUKH YAQUB, HEAD OF ROTATING EQUIPMENT PERFORMANCE AT SKF AUSTRALIA, CONSIDERS THE IMPORTANCE OF KEEPING PURPOSE IN MIND WHEN IMPLEMENTING DIGITAL MINING SOLUTIONS.
Digital tools for equipment monitoring are getting smarter, more powerful and more cost-effective. But as mine operators implement these new technologies, they should always keep their purpose in mind.
Predictive maintenance has traditionally been used by early adopters with an understanding of how strategic maintenance management can contribute to profitability.
High costs and complexity once limited predictive maintenance to the most critical, industrial assets. Today, exciting changes are afoot.
“New developments, including mobile computing, wireless communications, Internet of Things (IoT) and artificial intelligence (AI), make it feasible to add smart monitoring capabilities to a much wider range of machines,” Farrukh Yaqub, head of rotating equipment performance at SKF Australia, said.
“In such a fast-changing and dynamic environment, it is easy to get carried along by the hype.”
With technology companies and service providers offering to wire up anything and everything, the key question for mine operators is no longer whether they can monitor their assets, but how to manage the increasing volumes of data.
To find purpose, equipment operators need to begin with a clear vision of their end goals.
What are they trying to achieve with their overall maintenance and reliability program? How could digital technologies contribute to those aims?
In SKF’s conversations with miners, the company has heard several different answers to that latter question.
“Often they have strong financial goals, such as maximising the return on capital investments or minimising the total cost of ownership (TCO) of their assets,” Yaqub said. “Improved safety is another universal priority in demanding and hazardous mining environments.
“Resources companies are also prioritising actions that improve their operational sustainability, as part of the license to operate and to make it easier to attract and retain a skilled and motivated workforce.”
Setting out the goals of a potential machine-monitoring and predictive maintenance program provides a framework that helps owners prioritise their actions and implement the most appropriate solutions.
Mining equipment will always be exposed to wear and the risk of damage, but by identifying the assets and failure modes that have the largest impact on their reliability goals, operators can identify technologies that help them detect, predict and prevent those failures.
Once mining companies have defined the objectives of their monitoring and predictive maintenance project at the asset level, it is time to identify the right solution. That solution will typically comprise several connected hardware, software and human elements.
SKF finds it useful to break the solution down into four distinct parts: connect, detect, inform and improve.
Connect ‘Connect’ is about the equipment and infrastructure needed to measure and record reliability-related data. For bearings and rotating machines, that usually involves vibration sensors, since vibration is still the best way to spot early problem signs.
However, condition-monitoring systems are increasingly combining multiple data types, such as process data and production data from machine control systems or lubrication oil temperature and condition information from dedicated sensors.
Combined with handheld devices, sensors can be used to collect data periodically during walkarounds by maintenance staff. Or they can be permanently fixed to the machine, transmitting data via wired or wireless connections at an appropriate rate.
“The best approach depends on the type of asset being monitored and its role in the process,” Yaqub said. “Traditionally, permanent sensors and wired connections were expensive to
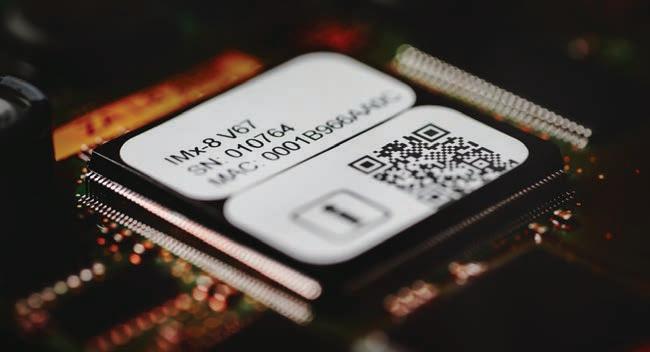
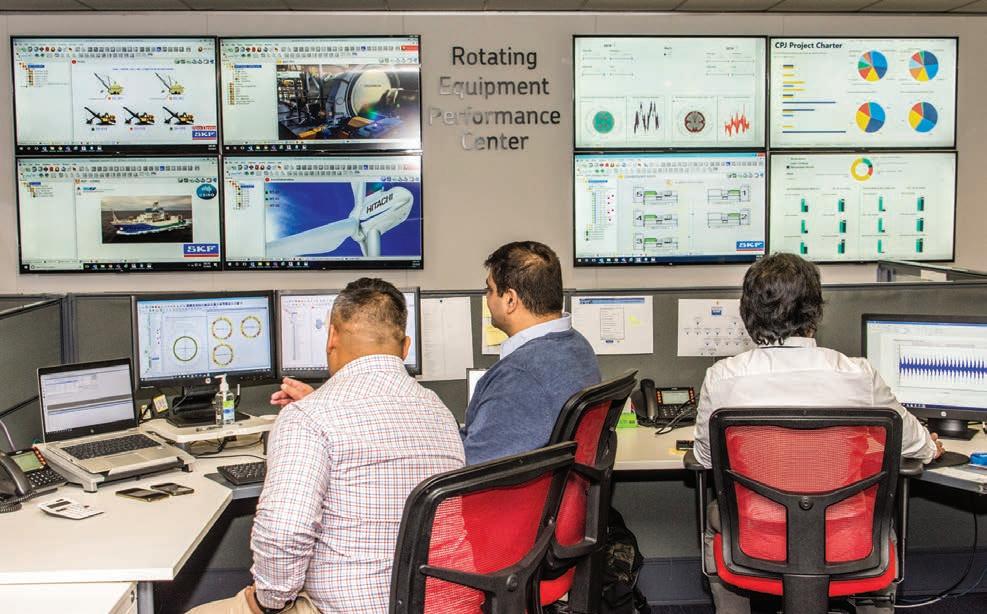
SKF’S ROTATING EQUIPMENT PERFORMANCE CENTRE.
install and were only used on the most critical assets.
“Balance of plan assets, such as pumps and fans, could be effectively monitored using handheld devices.
“Attitudes are beginning to change, however. This is being driven by the development of lower-cost wireless sensors that are quick and easy to install.”
Switching from handheld devices to wireless sensors frees up maintenance staff for more valueadding work and has come with safety benefits, reducing the need for personnel to approach running machinery for data collection.
Continuous monitoring can also allow for quicker problem identification than the traditional two- or three-week manual data-collection cycle, helping to reduce environmental concerns and save the planet’s resources.
Detect ‘Detect’ entails the analytical techniques used to identify anomalies in machine data and diagnose potential faults. This is a highly specialised task requiring a combination of sophisticated algorithms and human expertise.
Difficulty accessing specialist personnel can be a critical bottleneck for predictive maintenance programs, especially for miners operating in remote and inaccessible locations.
Today, the need for on-site expertise has been lessened by the development of centralised remote monitoring facilities, which use cloud technologies to share data from multiple sites and assets from a single hub. Specialist staff then analyse the data and diagnose problems.
“Some large organisations choose to staff and run such facilities themselves, but this can also be outsourced to specialist providers,” Yaqub said. “It is a service SKF provides for its customers worldwide through its network of remote diagnostics centres (RDC).
“There is also an ongoing drive to automate more anomaly detection and problem diagnosis using AI technologies.
“AI systems are already showing tremendous promise in machine monitoring applications, both by reducing the workload placed upon human experts and by spotting subtle signals people might miss.”
Inform ‘Inform’ is about translating the anomalies detected by the remote monitoring system into actionable information for the end user. For example, if a problem is detected in a bearing, the user knows they will need to inspect the machine.
What the user really wants to know is whether they should stop immediately or whether it will be safe to keep the machine running until the next scheduled maintenance intervention.
SKF’s experience suggests the ‘inform’ phase works best when it involves close collaboration between condition-monitoring and data analysis experts and the miner’s own operations and maintenance teams.
Improve The need for collaboration is even more pronounced in ‘improve’, which is often key to the most significant performance and value improvements.
It is about the robust application of traditional reliability improvement tools to prevent the reoccurrence of failures identified by the predictive maintenance system.
SKF harnesses ‘improve’ by working with its customers to identify changes in bearing selection or lubrication strategy that can prolong the life of equipment and extend the mean time between critical asset failures.
Case study A horizontal grinding mill was installed at an Australian mineral processing site, presenting some significant challenges.
The remote location of the site meant access to specialist personnel was not always available. In the past, the customer had experienced a situation where a critical failure was picked up too late, leading to a major unplanned shutdown.
A second challenge related to the nature of the mill operations. The asset rotated at low speeds of around 10 revolutions per minute (rpm).
This necessitated the use of highly sophisticated vibration analysis algorithms to extract valid data on the condition of bearings and gearbox elements in an extremely noisy environment.
SKF provided a mill-monitoring system that attended to the customer’s unique environment and situation.
“SKF monitored the mill on behalf of the customer, installing the necessary sensors and communication equipment and conducting analysis remotely from one of its RDCs,” Yaqub said.
“After only three months of continuous monitoring, the RDC identified an anomalous signal and was able to pinpoint the problem to a particular pinion gear within the machine.
“In this case, timely action to the problem saved the customer enough in avoided downtime to cover the cost of the remote monitoring system.”
New developments make it feasible to add smart monitoring capabilities in a much wider range of machines, but it is easy to be carried away in the hype. Break down the solution into four parts: connect, detect, inform and improve.
The key question that follows is: what is trying to be achieved with the overall maintenance and reliability program?
Once this is answered, the solution can be implemented. AM
HEAD OF ROTATING EQUIPMENT PERFORMANCE – SKF AUSTRALIA, FARRUKH YAQUB.
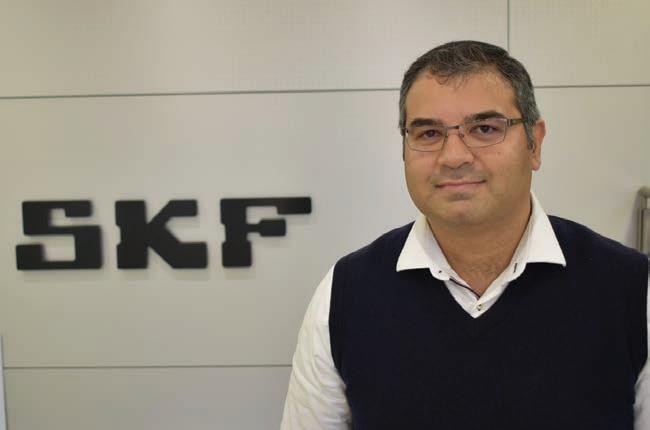

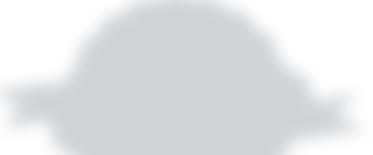
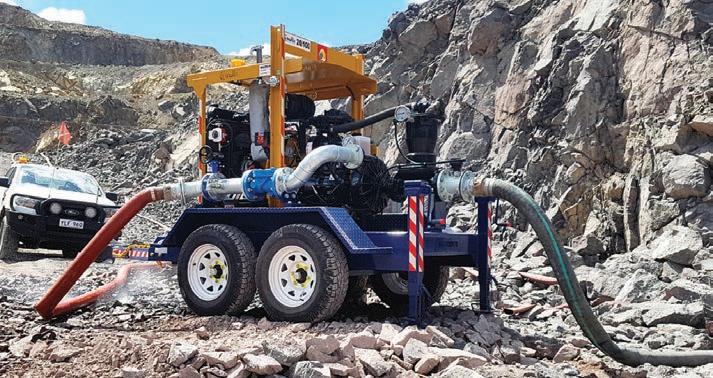
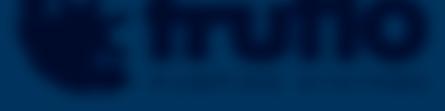
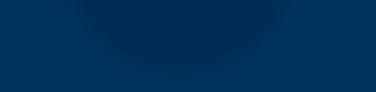
• TRUFLO• PUMPS • 2022
Excellencein 1992 DewateringSy s tem s
BUILT FOR EXTREMES
Our Pump Systems are Australian Made and Owned
30YEARS of ongoing success in the industry demonstrates that innovative design with outstanding and consistent performance in the field together with a 100% commitment to customer support, deserves the kudos of a legendary status.