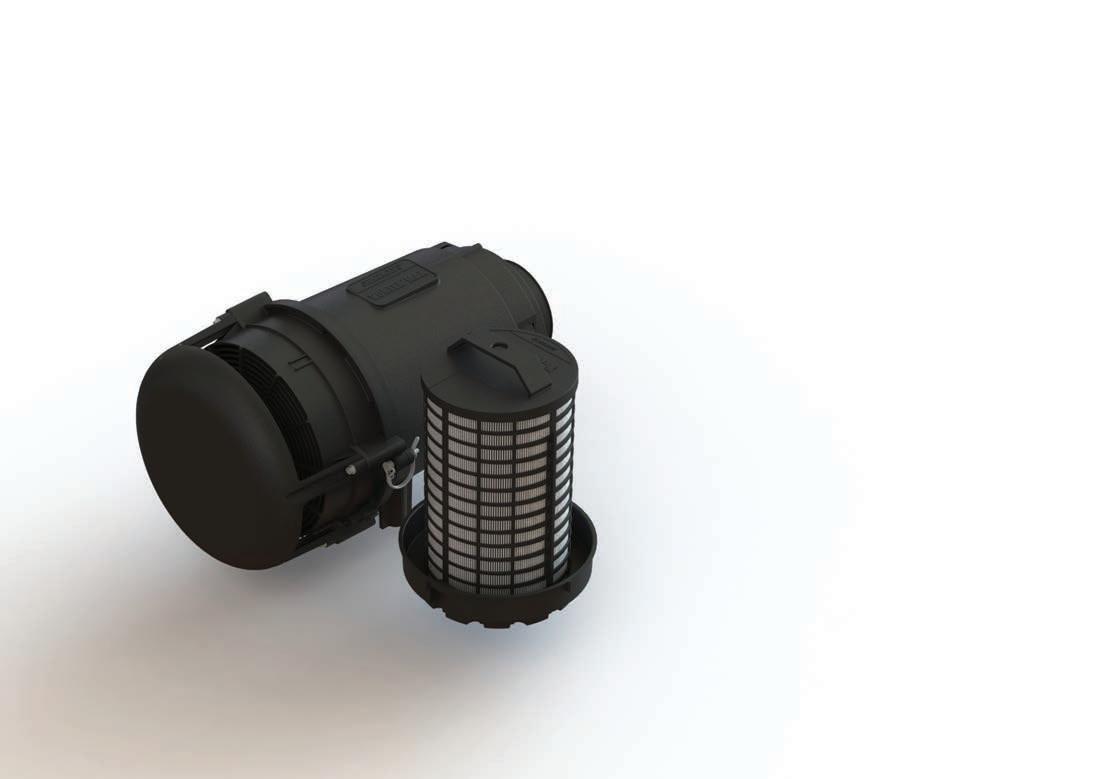
4 minute read
EFFICIENCY & OPTIMISATION
SY-KLONE’S NEW VORTEX MAX POWERED ENGINE PRECLEANER PROVIDES MINE SITES WITH THE BEST OPTION TO PROTECT EQUIPMENT ENGINES FROM THE EFFECTS OF DUST AND DEBRIS-LADEN AIR, LEADING TO MORE PRODUCTIVITY, MORE UPTIME AND A MORE PROFITABLE OPERATION.
Heavy mobile equipment and fixed plant machinery are critical assets to the day-to-day operations of a mine site and support the core business of mining and processing mineral resources.
A machine’s engine is one of the most expensive parts of heavy mobile equipment to maintain. In addition to repair costs, engines that are performing at sub-optimal levels reduce a machine’s operating capacity, jeopardising a mine site’s ability to meet operating metrics and performance goals.
A key contributor to engine failure and performance degradation is dust and debris-laden air, which can lead to contaminated engine oil and damaged exhaust and aftertreatment systems.
Australia Mining sits down with SyKlone to learn more about the key threats to an engine and how best to address those threats.
Dust and debris-laden air Dirty intake air enters the engine when small dust particles pass through the engine filter media or bypass engine filter seals.
Dust can quickly load an engine filter, resulting in more frequent filter changes and unplanned work stoppages.
Downstream dust is the beginning of big problems for the engine, as it only takes one teaspoon of fine dust to permanently damage an engine.
Contaminated engine oil Debris from the intake air makes its way into the engine cylinder, wearing down the liner and piston, and pushing down past the rings into the engine oil.
Engine lubricant, instead of allowing parts to glide smoothly, acts as an abrasive when mixed with debris, and can alter the viscosity and lower the film strength of the oil. This results in lower performance and ultimately engine failure.
Damaged exhaust and aftertreatment systems Airborne contaminants in the combustion chamber affect the efficient burning of fuel.
Unburned fuel and contaminants flow downstream, damaging the exhaust, and build up in the aftertreatment system.
Contaminant buildup in the exhaust and aftertreatment system impacts machine performance, including reduction in horsepower and eventual failure of the aftertreatment system and the diesel particulate filter.
Sy-Klone removes dust and debris from intake air By implementing the right controls at the air intake, mine equipment owners can reduce downstream dust, address the harmful issues described above, and prolong engine filter life.
Sy-Klone invented a new method of precleaning with the introduction of the XLR Powered Precleaner. The company is expanding the category with the introduction of Vortex Max, a 23-cubic-metre a minute (800plus CFM) precleaner, specifically engineered and designed for higher airflow machines operating in extreme dust environments.
Sy-Klone’s Vortex Max provides mine sites with a new option to protect heavy mobile equipment engines from fine particulate and microscopic debris.
The patent-pending product is designed to provide clean air downstream to engines on machines, including wheel loaders, excavators, dozers, crushers and more.
Sy-Klone sales and marketing vice president Austin Browne says the Vortex Max is based on the manufacturer’s proven, powered technology, combined with highefficiency filtration, ensuring only the cleanest air is supplied to the engine.
“The Vortex Max has a compact filter housing which features a durable motor to manage airflow, ejective filter ports to allow for precleaning of the largest dust and debris, and a high-efficiency filter to capture the smallest microscopic dust particles,” Browne tells Australian Mining.
The system, which is available in both 12- and 24-volt configurations, is easy to maintain and designed to facilitate quick filter changes.
It has a low profile and small footprint that provides installation flexibility, allowing it to be easily installed on a variety of machines. The system’s motor and fan provide continuous, clean air flow regardless of the machine’s operating state.
An always-on airflow in the Vortex Max results in lower restriction, high-efficiency precleaning throughout a machine’s operating activities, even at idle.
“The Vortex Max utilises the SyKlone Effect, a patented separation technology, that actively manages air, creating a rotating column of dirty air, ejecting the heaviest dirt and debris from the filter housing before ever reaching the filter,” Browne says.
“Only the finest dust remains, which is gently landed on the selfcleaning filter, where it eventually falls off and is ejected from the filter housing, extending engine filter life and providing low-restriction air flow.”
Clean air for engines improves performance Engine performance issues and engine failures due to dust downstream can bring a machine and a mine site operation down.
Fortunately, these problems can be prevented. Ensuring that the engine is protected from dust and debris can support a long, productive, and profitable operating life.
“Clean air to the engine leads to better-performing machines, and on a mine site, that equates to more productivity, more uptime and a more profitable operation,” Browne concludes. AM