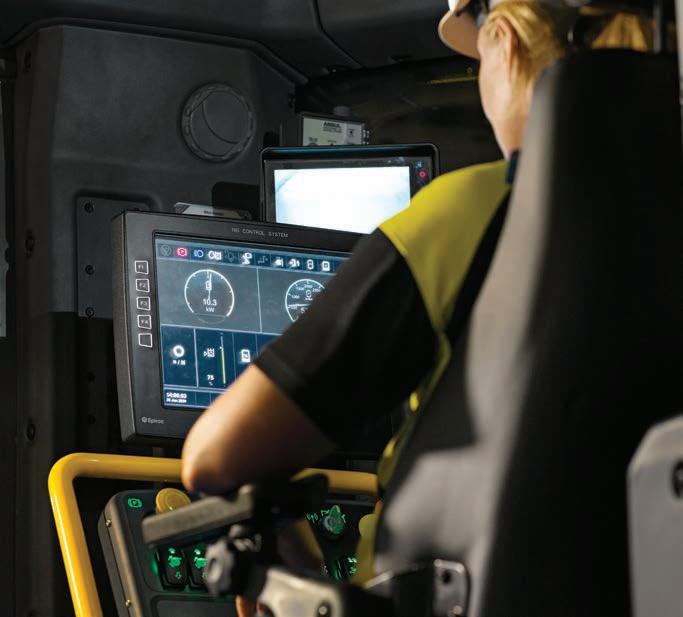
17 minute read
UNDERGROUND MINING
CHARGING FORWARD WITH THE BENEFITS OF BATTERIES
EPIROC AUSTRALIA UNDERGROUND BUSINESS MANAGER SHAIFUL ALI EXPLAINS WHY THE MOVE TO ELECTRIFICATION CAN HELP THE ENVIRONMENT AS WELL AS REDUCE OPERATIONAL COSTS.
THE M20 PROVIDES DIFFERENCE WITH THREE MAIN CRITERIA IN HEALTH AND SAFETY, PRECISION AND MAINTENANCE.
The environmental benefits of electrification are a major reason why the mining and resources industry has moved to embrace the technology.
Research shows that both industry customers and the general public are placing larger emphasis on companies with a greater social and environmental awareness.
However, environmental factors are not the only reasons companies are increasingly looking towards implementing battery-powered equipment in underground mining.
Swedish original equipment manufacturer (OEM) Epiroc recognises the importance of working together with industry and other manufacturers to give mine operators a range of options when it comes to choosing the right equipment for the right role.
In 2017, Epiroc began development of a battery platform and in 2018 unveiled its second-generation battery-electric equipment.
Epiroc Australia underground business manager Shaiful Ali says there are significant reasons behind the move to provide mine operators with a battery option.
“There is a lot of discussion around the health and safety aspect of using battery technology underground,” Ali tells Australian Mining.
“We see the benefits of batteries not only from a health perspective but also, long term, from a cost perspective. The cost benefits from using a battery are similar to the original costs of a mobile phone.
“When the mobile phone was first released it cost thousands of dollars, but as technology progressed and mass production starts, that is where you can see the cost benefit.
“There are also other cost reductions when using batterypowered machinery, for example, ventilation costs would be reduced, due to the the reduction in diesel fumes associated with battery equipment vehicles, subsequently providing a healthier environment for the operators underground.”
In 2020, the OEM unveiled its Batteries-as-a-service solution,
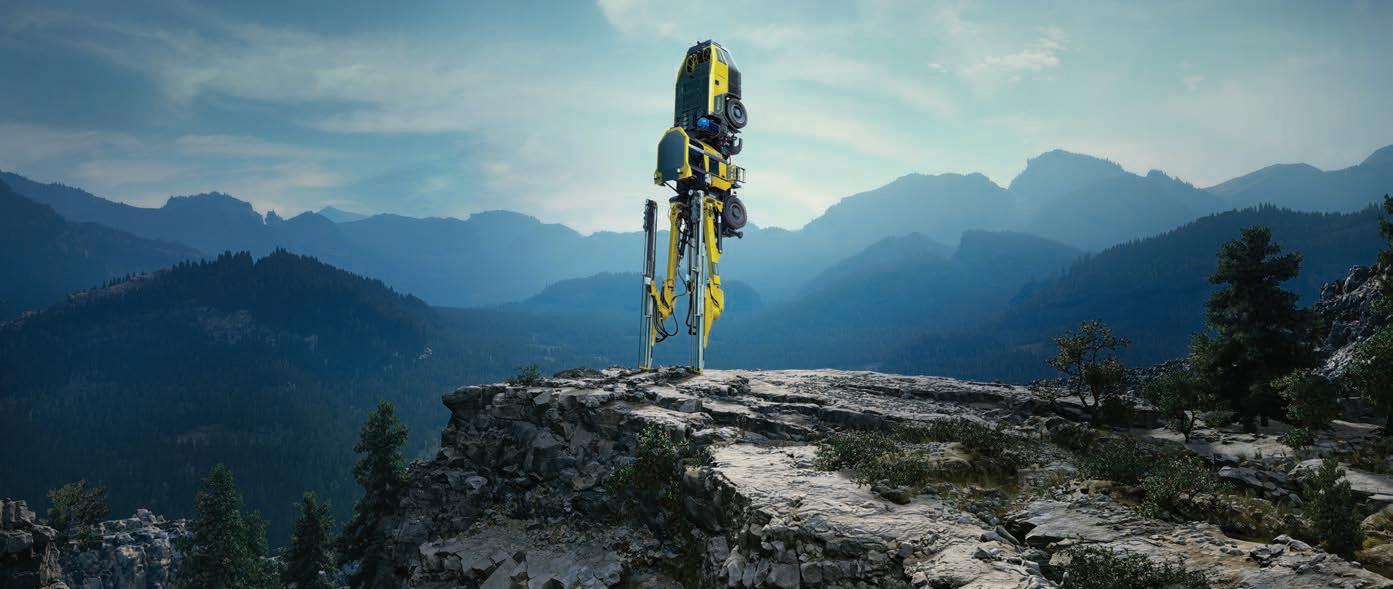
THE CABIN IS DESIGNED FOR THE COMFORT OF THE OPERATOR.
which is designed to provide a unique option for operators to costeffectively access its battery-electric machines.
“We sell the customer the machine but then the battery itself is an expensive commodity,” Ali says.
“What we did was propose an arrangement where the customer buys the machine, but we then lease them the battery. What that does is allow the customer to have more control over updates in technology.
“The service will provide the battery at a monthly nominal fee where Epiroc will be responsible for the management of the battery, the model advances of the batteries and the disposal of the battery.”
Epiroc’s development of its services and solutions has this year been complemented by new machinery releases, such as its next-generation development drill, the Boomer M20.
The Boomer M20 has a sturdy and robust design with an optional zeroemission battery driveline. This is the first rig of its kind to be able to drill partly on battery power.
Its new booms feature internal hydraulics and a hoseless design, meaning less unplanned downtime for hose repairs. The hoseless design gives the operator better visibility from the cabin, greatly improving operator safety.
Epiroc expects the M20’s features will increase productivity and machine utilisation, while facilitating planning of mining operations.
“The M20 provides difference with three main criteria in health and safety, precision and maintenance,” Ali says.
“The M20 will have the ability to be fitted with a battery driveline, it has internal hydraulics because we see the hydraulic hose as one of the real costs of failure underground when it comes to the operation.
“We also have the newly designed cabin on the Boomer M20 – the new cabin provides a reduction in noise to the existing cabin and is pretty much designed for the comfort of the operator.”
Another key feature of the Boomer M20 is Underground Manager, software designed for production planning and creating drill plans for the drill rig. The drill plans can be transferred to the rig via USB or RRA (Rig Remote Access).
Underground Manager logs position, angle and depth of each bolt installed. This gives quality control of the rock bolting to ensure proper bolt installation has been performed.
Epiroc has this year also launched its new Collision Avoidance System, which detects objects in the immediate area of machine operators.
“Previously we had a system that informs but did not react – it required the operators to react,” Ali says.
“This new system is able to react on behalf of the operator and works together with the proximity detection system, which will dictate what distance the machine will stop at.
“The Collision Avoidance System is primarily for our trucks and loaders. These recent products show how important safety is for our customers.”
Ali says Epiroc has been working with its mining industry partners to provide tailor-made solutions to increase safety in the workforce.
Automation continues to be a key aspect of the bespoke solutions that Epiroc is developing, with Ali saying the OEM plans to expand on what it offers in this area.
“Truck automation is something that we are working on as well, as we see that as the next step of our journey moving forward,” he says.
“I think that the concept of automation has now been accepted; I think what everyone is striving for right now is ensuring that the automated machines are able to duplicate manual operations.
“There is no real point in automating a machine if it only carries out 50 per cent of the productivity.”
Ali says Epiroc strives to anticipate industry needs and works with the industry to provide the best possible solutions.
The OEM has established a roadmap that looks at least five years into the industry’s future, taking trends in technology and evolving factors such as ESG (environmental, social and governance) into consideration.
“Technology has the ability to change so quickly and regulations are also changing around the world, so it is important to be able to move with the expectations of the customer,” Ali says.
“For example, diesel-free could be the future, but it is not yet, and at least we are working towards providing our customers with that option. The key is to have that option to move forwards and to try to understand exactly what the industry requires in its next step.” AM
EPIROC EXPECTS THE M20’S FEATURES WILL INCREASE PRODUCTIVITY.
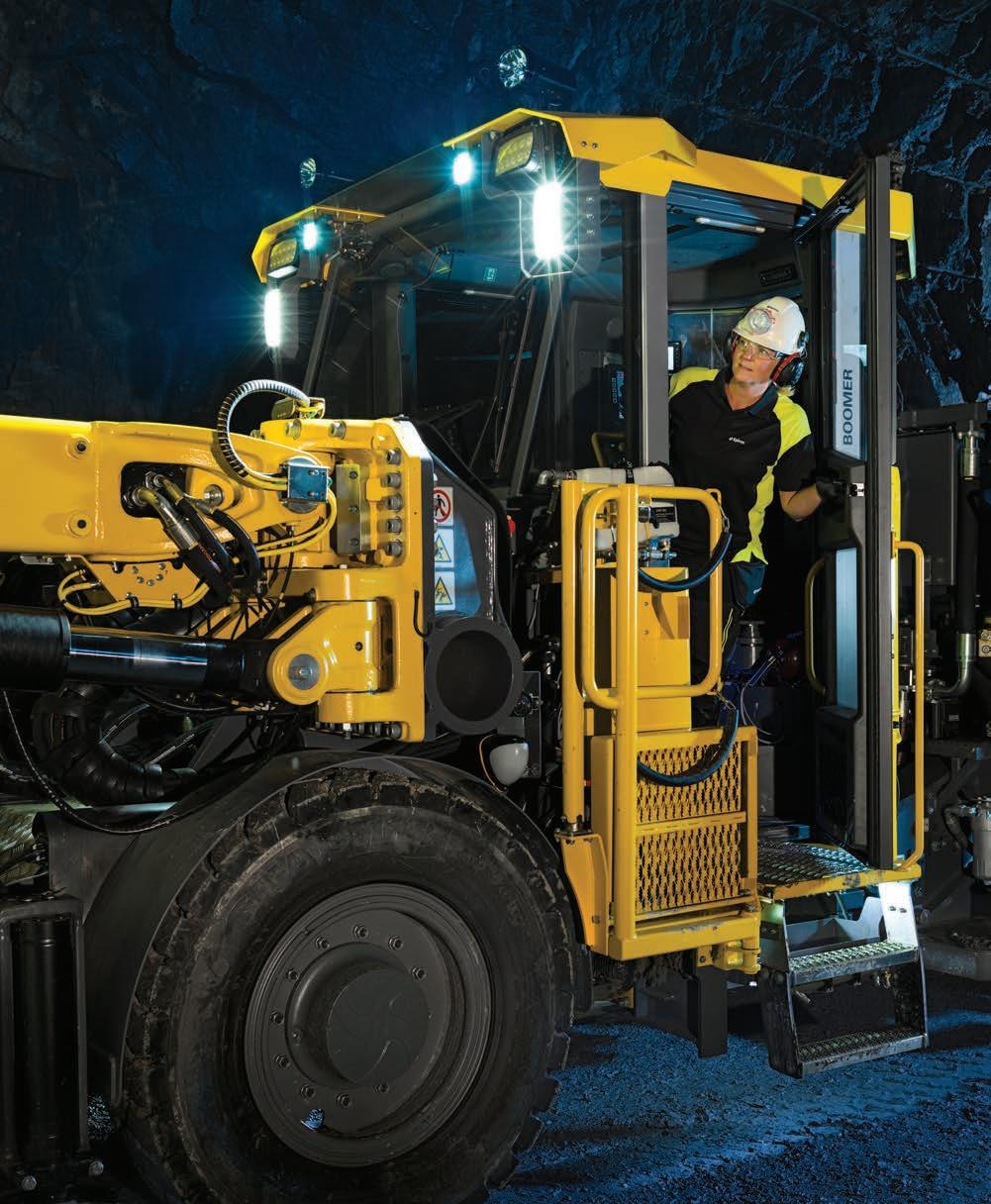
DELIVERING SPECIALIST LONGWALL SYSTEM COMPATIBILITY
WITH CONTRACTS WITH INDUSTRY LEADERS INCLUDING ANGLO AMERICAN, HASTINGS DEERING IS THE ONE-STOP SHOP FOR ALL LONGWALL EQUIPMENT COMMISSIONING AND REPAIRS.
Hastings Deering’s Mackay workshop will be home to a compatibility that will simulate an operating configuration, including equipment from seven suppliers to enable testing of an integrated system.
The mini-build allows for proof testing to be conducted in a safe environment, enabling a more efficient re-commissioning of the equipment once operational.
Hastings Deering was recently awarded a longwall contract for Anglo American’s Aquila coal project in Central Queensland.
Hastings Deering longwall projects manager Scott Barwick says once it is installed underground, the Aquila longwall will be 380 metres long.
“Our workshops are 100 metres long and 32 metres wide, so we are able to build an 80-metre longwall mini-build to conduct the compatibility in the workshop,” Barwick says.
“The logistics are incredible, with a steady stream of trucks being required to transport the equipment components to our facility and back to site.
“Over the course of the compatibility, various components will make their way through our gearbox overhaul centre, electrical and electronics workshops, electrohydraulic valve-shop, fabrication workshop and finally to the general fitting and assembly bay.”
In addition to the equipment assembly, there are approximately 1200 tests conducted – everything from initial function testing of individual components to major component and full system commissioning.
Barwick says at the end of the day, it is all about reducing and mitigating risk.
“If we can do all this testing above ground in a workshop before the unit goes back to work, we can more closely monitor and evaluate the equipment with our longwall technical resources and complete fine-tune adjustments as necessary,” he says.
“The benefit to our customer is confidence that their equipment is fully integrated into a single system and tested ahead of its return to site for production in an underground panel.”
Delivery of set one to the Aquila mine site is scheduled for early December 2021 ahead of production starting in the first quarter of 2022. Set two will complete its compatibility testing and be delivered to site in 2022.
The Hastings Deering underground facility is also home to Mackay’s only specialist shearer rebuild facility. The facility is equipped to perform 12-hour heat runs as part of the quality checks following an overhaul and regularly invites its customers
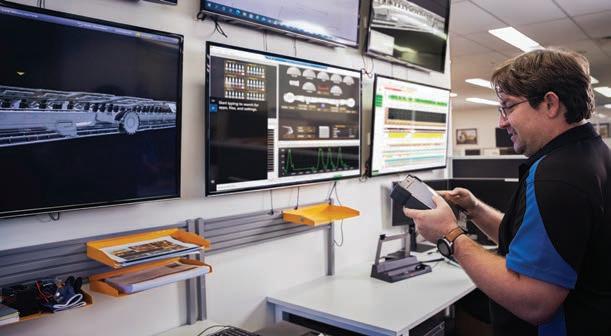
HASTINGS DEERING’S LONGWALL SERVICES HAVE A STRONG FOCUS ON CUSTOMER SAFETY. IN ADDITION TO THE EQUIPMENT ASSEMBLY, THERE ARE AROUND 1200 TESTS CONDUCTED.
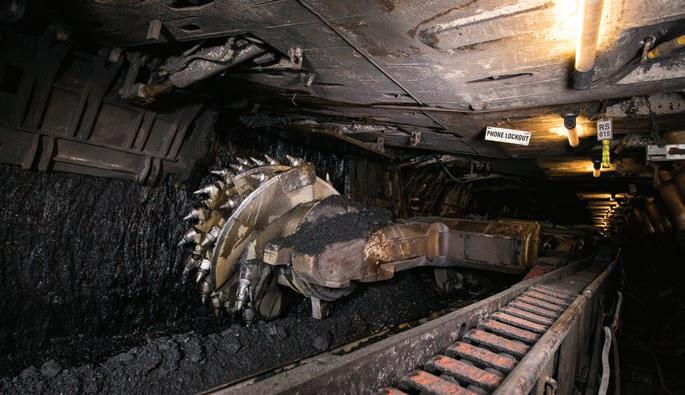
to be a part of the process.
Where AS3800 and flameproof repairs are required, the Hastings Deering underground workshops hold appropriate qualifications to achieve compliant rebuilds first time, every time.
All of the company’s electrical tradespeople hold EEHA Stage 1 and 2 accreditations. Its full electrical test facility is capable of testing and running up to 3.3kV, ensuring the rebuild quality of all electrical equipment.
A cable-making facility complements all underground overhauls with the ability to manufacture in-house. Full test facilities allow for high standards of quality assurance following component overhauls, with heat runs and vibration analysis providing confidence in overhaul quality.
Hastings Deering regularly partners with customers and reliability representatives where technical issues are encountered, and failure analysis is required.
A valve rebuild workshop also complements underground overhauls, with the ability to provide specialist rebuilds and in-house testing following an overhaul.
Barwick says Hastings Deering is a one-stop shop for all longwall equipment commissioning and repairs.
“Hastings Deering is the biggest and most experienced longwall workshop in Central Queensland and has completed many projects for large mining customers across the state,” Barwick says.
“Hastings Deering strives to be your first choice in supplying parts and service to the regions mining industry. We want our customers to choose us because we understand their needs and consistently deliver the best solutions.
“This is why we have invested to bring to our customers the expertise and capability to deliver just that.
“With our centres of excellence in draglines and longwalls, and our product performance centre, we have the operational and maintenance expertise to assist our customers to maximise fleet performance and optimise cost.”
Hastings Deering has more than 3500 employees incorporating 23 business service centres across Queensland, Northern Territory, Papua New Guinea, the Solomon Islands and New Caledonia, with its home base in Brisbane.
“We are stepping up our investment in technologies that will help our customers achieve the next level of productivity, cost and safety,” Barwick says.
“This, combined with more service operations, parts inventory, component rebuild centres, field service trucks and skilled advisors on customer sites across our region, we’re rising to the challenges our customers put to us every day to deliver.
“In aspiring to be our customers’ trusted partner, Hastings Deering is digging deeper than ever to assist them achieve sustainable success.” AM

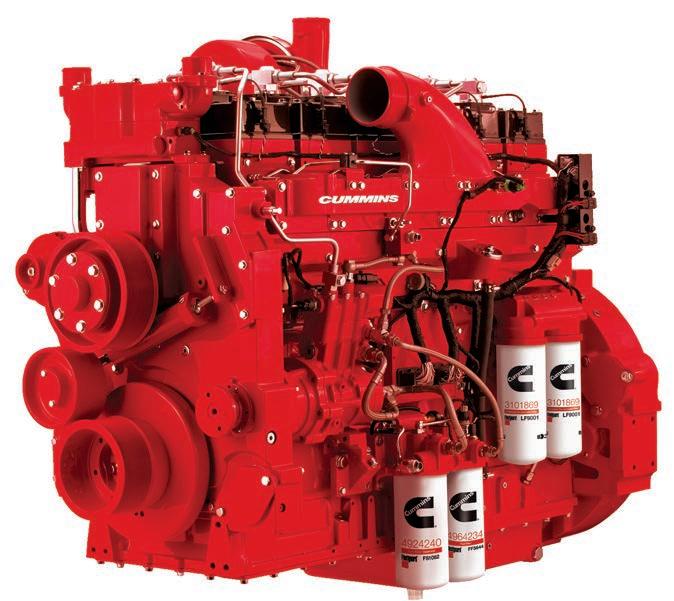
DRIVETRAIN WELCOMES KOVATERA’S BATTERY-ELECTRIC VEHICLE TO AUSTRALIA
FULLY ELECTRIC WITH TWICE THE PAYLOAD AND A LIFESPAN TO OUTLIVE SOME MINES, DRIVETRAIN IS NOW SUPPLYING AUSTRALIA WITH A TASTE OF WHAT THE FUTURE HOLDS.
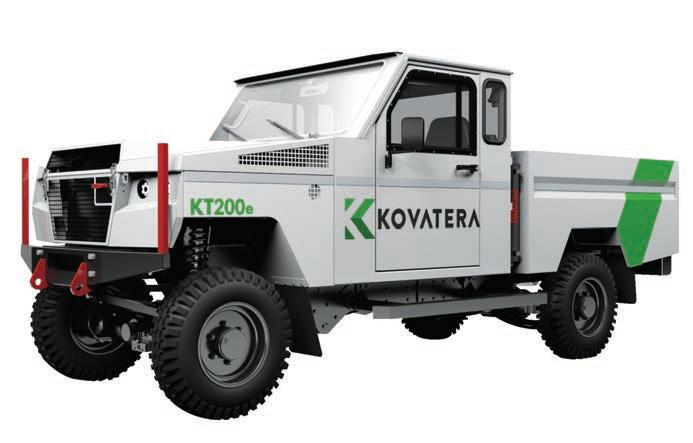
While traditional utility vehicles take on-highway models, electrify them and adapt them for the harsh conditions of underground mining, Kovatera has engineered the KT200e from the ground up.
Based on 13 years of development since the Kovatera UT99 diesel version was released, this electrified workhorse can be trusted to last for up to 10 years in mining conditions.
Such a bold promise can only be backed up by a comprehensive warranty, which is why Kovatera extended its chassis warranty out to five years – an unheard-of length considering most competing vehicles last around three years.
Kovatera general manager Will Gove explains how the vehicle manufacturer achieves such longevity in the KT200e.
“It’s in the design of the machine. One example would be our use of heavy-duty off-highway axels where the brakes are enclosed, whereas a traditional on-highway vehicle has them exposed,” Gove tells Australian Mining.
“Another example would be the chassis design. A traditional rolled chassis can allow water to get inside to rust the vehicle from the inside out. Our chassis is a fabricated steel chassis with a flat plate. So, the backbone of the machine is exceptionally strong.
“Thirdly, the standard thickness of automotive style vehicle body panels is about 0.9 millimetres. On our vehicle it’s about two millimetres, about twice the thickness.”
In a nutshell, it is components like these which enable the Kovatera to make a name for itself around the world.
Canada-based Kovatera has tested the KT200e in the North American country’s mines and has now found an opening into the Australian mining industry.
All Kovatera required to expand the vehicle’s global reach was a reliable Australian supplier such as Drivetrain with the right locations and people to support mining operations wherever they were needed.
Mark Griffith, general manager for sales and business development at Drivetrain, says Kovatera aligns well with where the Australian mining industry is moving.
As such, Drivetrain was more than happy to distribute the KT200e across the country’s major underground hard rock mines.
“Drivetrain is an established supplier to the mining industry, particularly to underground mining,” Griffith says.
“We provide maintenance solutions across most underground mines in Australia in some fashion. That allows us to assess their conditions and pick products from our international suppliers which meet their needs and drive better asset management for sustainability in their operations.”
While electric vehicles (EVs) are an emerging trend in the mining industry, Australian operators are known to take a tentative approach to technological developments, according to Griffith. But the KT200e is ready to work in Australian mines.
“They like to see it prove itself, and I think we’re at that point in our evolution in Australia where Australians don’t like to jump on a vehicle that’s just landed or hasn’t been fully commercialised and produced for a number of years,” Griffith says.
“The Kovatera EV has had nearly a decade of engineering design put into it, it’s had years of experience in Canadian mines and we’re confident it will prove itself here the way the diesel has.”
The KT200e comes in a standard 88-kilowatt-hour option, but for those concerned with forking out unnecessary funds, the 44-kilowatthour option caters to those with smaller mines and shorter-range requirements.
In either case, operators can be sure the charging capacity of the KT200e will be enough for whichever mine it’s thrown into.
“We also have two onboard chargers, so one can charge the vehicle on board and it doesn’t require any offboard infrastructure,” Gove says.
“You can bring the vehicle into the mine and leverage off the existing mining infrastructure, which is important for a lot of our customers.”
Naturally, some people may ask how much production is sacrificed for electrification in this future-proof utility vehicle.
Drivetrain business development manager of capital equipment sales, Joel Mathews, says the answer may surprise a few people.
“One additional item which makes the vehicle quite unique is the payload capacity, as traditional units in the market offer around half of what the KT200e does. It’s quite a workhorse for a small truck,” Mathews says.
Whether payload, range or lifespan are the deciding factor in a company’s next utility vehicle, Drivetrain is confident the Kovatera has their needs covered.
“We have seen an influx of opposition companies starting to enter this market, but the difference is these products are still in their research and development stages,” Mathews says.
“They haven’t put in the time or experience operating underground. Plus, Kovatera has the production capability. If a customer comes to us and says, ‘I love these machines, can I have 20 of them this year?’ We can say, ‘yes you can,’ and we can do it with confidence.” AM
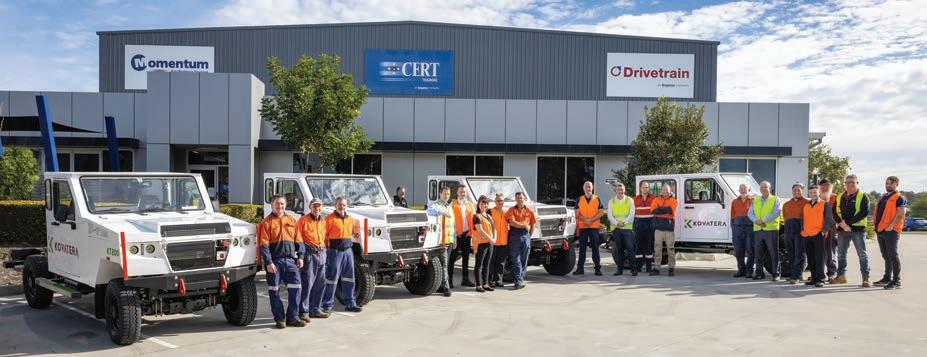
THE KT200E IS SPECIFICALLY DESIGNED AS A ROBUST OFF-HIGHWAY VEHICLE FOR THE MINING ENVIRONMENT.
The miner’s choice for fuel and lubricants
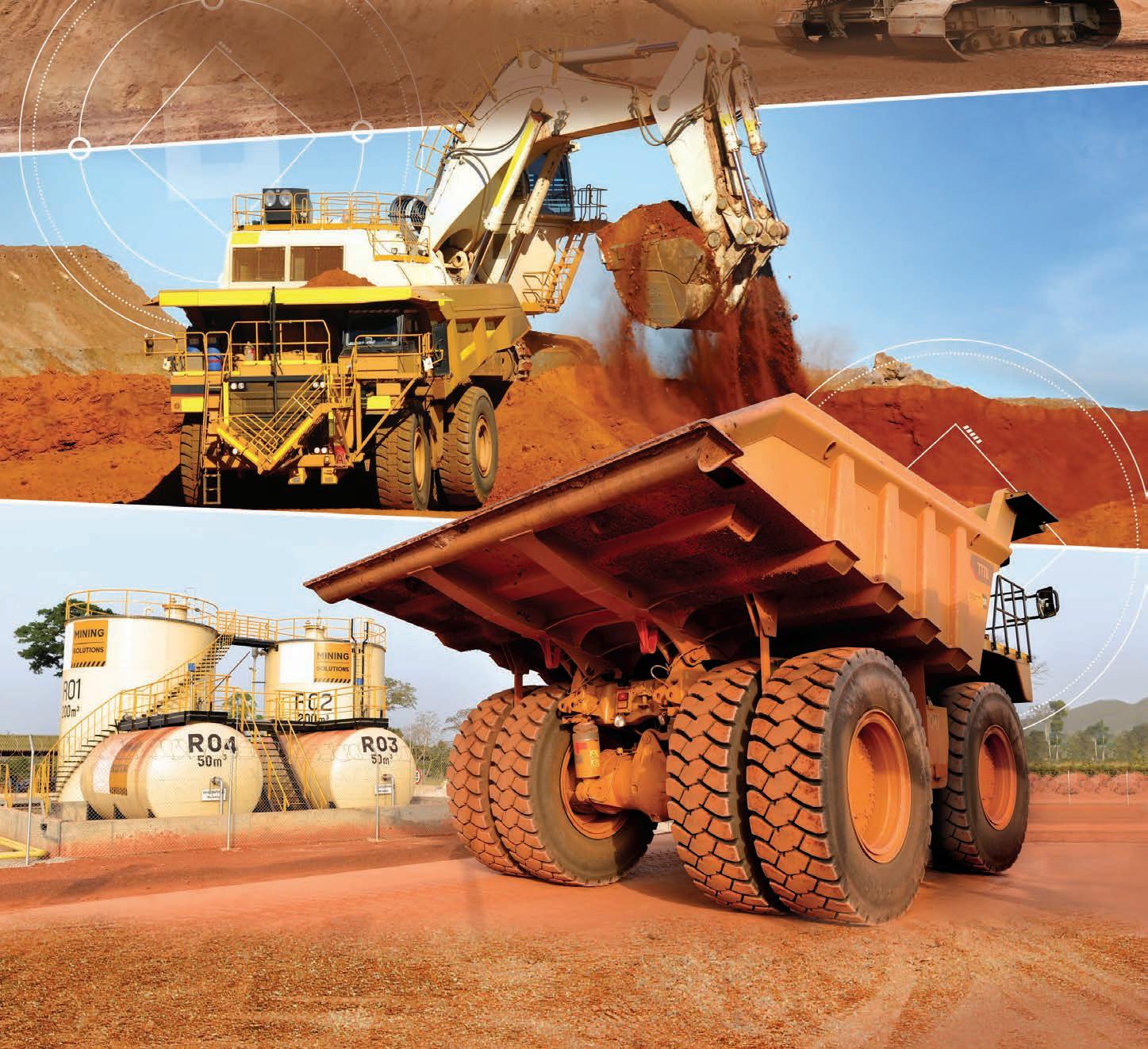
SPECIAL DELIVERY FOR ELPHINSTONE WR810 FLEET
THE ELPHINSTONE RANGE OF WR810 UNDERGROUND SUPPORT VEHICLES IS DESIGNED TO THRIVE IN THE HARSHEST UNDERGROUND HARD ROCK MINING ENVIRONMENTS. THE NEW WR810 DELIVERY WITH CRANE ADDS ANOTHER SUPPORT APPLICATION TO ELPHINSTONE’S EXPANDING UNDERGROUND SUPPORT FLEET.
Choosing the right support vehicle for an underground mining operation can significantly increase the productivity of the production fleet and reduce operational costs.
The WR810 is a highly configurable, 10-tonne nominal base platform, comprising a scissor lift, agitator (six cubic metres), fuel and lube truck, and water cannon.
According to Elphinstone’s regional sales & support manager for the Americas, Nick Furmage, the WR810 model range is growing.
“We aim to expand the range of applications to meet the underground support equipment requirements of our customers,” Furmage says.
With a payload of 9800 kilograms, the new WR810 Delivery with crane ensures parts, components, equipment and maintenance personnel are transported safely and securely throughout the mine. The fully integrated Hiab X-HiDuo 092 ‘optimal performance’ loader crane features a rated lifting capacity of 8.8 tonne metre and a 7.7-metre outreach, providing a reliable solution for day-to-day heavy lifting.
“Operated by manual lever control or via the wireless joystick remote, the operator can manoeuvre loads from a distance with built-in intelligence and automatic speed control (ASC) for safe and effective load handling,” Furmage says.
Safety features include emergency crane stops located on the manual control station and wireless joystick remote. Stabiliser legs with levelling sensors provide a safe foundation with easy pack up for safe transit. The checker plate deck features thoughtfully positioned tie-down points and three-point access with high visibility green handrails and ladders on both sides.
The C7.1 ACERT Tier 4 Final engine arrangement is optional, adhering to EU Stage V exhaust emission standards. The engine arrangement offers a dual horsepower configuration set at 151 kilowatts (202 horsepower) for a higher performance rating.
The lower reduced ventilation rating at 129 kilowatts (173 horsepower) is possible through a simple software change performed by a Caterpillar dealer.
The C7.1 ACERT Tier 3 engine arrangement rated at 168 kilowatts (225 horsepower) is the standard option for less stringent emission regulations.
Matched to the engine is a Cat five-speed (three-speed reverse) transmission fitted with a lock-up torque converter.
Downtime during service and maintenance is reduced through some clever engineering and design features.
Quick change air filters and 500-hour oil service intervals also reduce downtime and keep
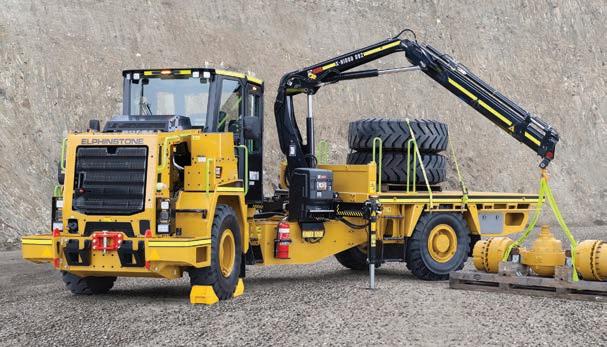
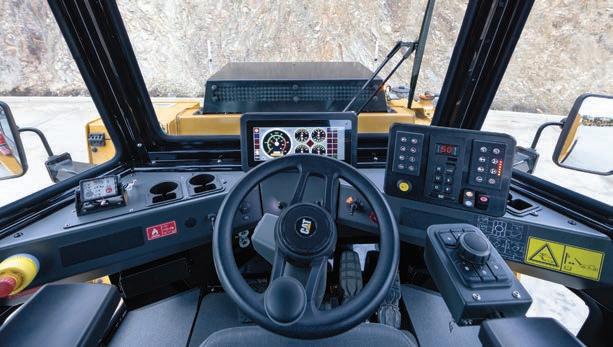
THE ELPHINSTONE WR810 DELIVERY WITH CRANE.
machines in operation for longer for greater productivity.
The on-board warning and protection system continuously checks all critical machine functions for early warning and fast fault finding, recorded for analysis.
Safety is one of the most important aspects of any piece of machinery employed in the mining world.
“The majority of key safety items on the WR810 are mandatory base machine options,” Furmage says.
Safety features include firewalls and heatshields, machine interlocks, centralised isolation points (engine disconnect switch, starter isolation switch, jump-start receptacle and fire system activation, if fitted).
Optional features include an integrated fire suppression system and metallic fuel water separators made from a non- flammable material.
Emergency stops are fitted as standard inside the cabin, at ground level on the front left-hand side of the machine and located near the access ladders on the left- and right-hand side of the deck.
Integrated into the WR810 operator station is a ROPS (roll-over protective structure) ISO 3471:2008 and FOPS (falling object protective structure) ISO 3449:2005 that offers protection to the operator.
The operator station is designed to seat three people in comfort with exceptional visibility. This is ideal for training purposes, and allows the complete crew to travel collectively rather than deploying an additional light vehicle for personnel transport.
The driver’s seat is a ‘T’ seat with air suspension, and the crew seats are a standard ‘T’ seat or optional ‘T’ seat with air suspension.
Ergonomically designed machine controls are located for the operator to control the machine functions with minimal effort. The result is greater concentration on vehicle operation, with reduced operator fatigue.
The oscillating hitch provides superior operator comfort, four-wheel ground contact and reduced wear on the hitch and steering components.
“The WR810’s oscillating platform stops the transfer of rough conditions from the rear frame into the front frame. The benefit is a far superior ride by allowing the rear frame to oscillate,” Furmage says.
Elphinstone has adapted well to Australia’s COVID-19 environment of challenging border closures by expanding its presence in Western Australia.
“Due to COVID-19 restrictions, we’re focusing on the Australian market by building local relationships to support our products,” Furmage says.
This move has progressed well, allowing Elphinstone to work much closer with underground mine operators.
All Elphinstone products, including the WR810, are sold through local Caterpillar dealerships. AM