
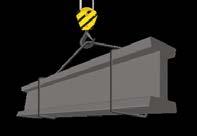
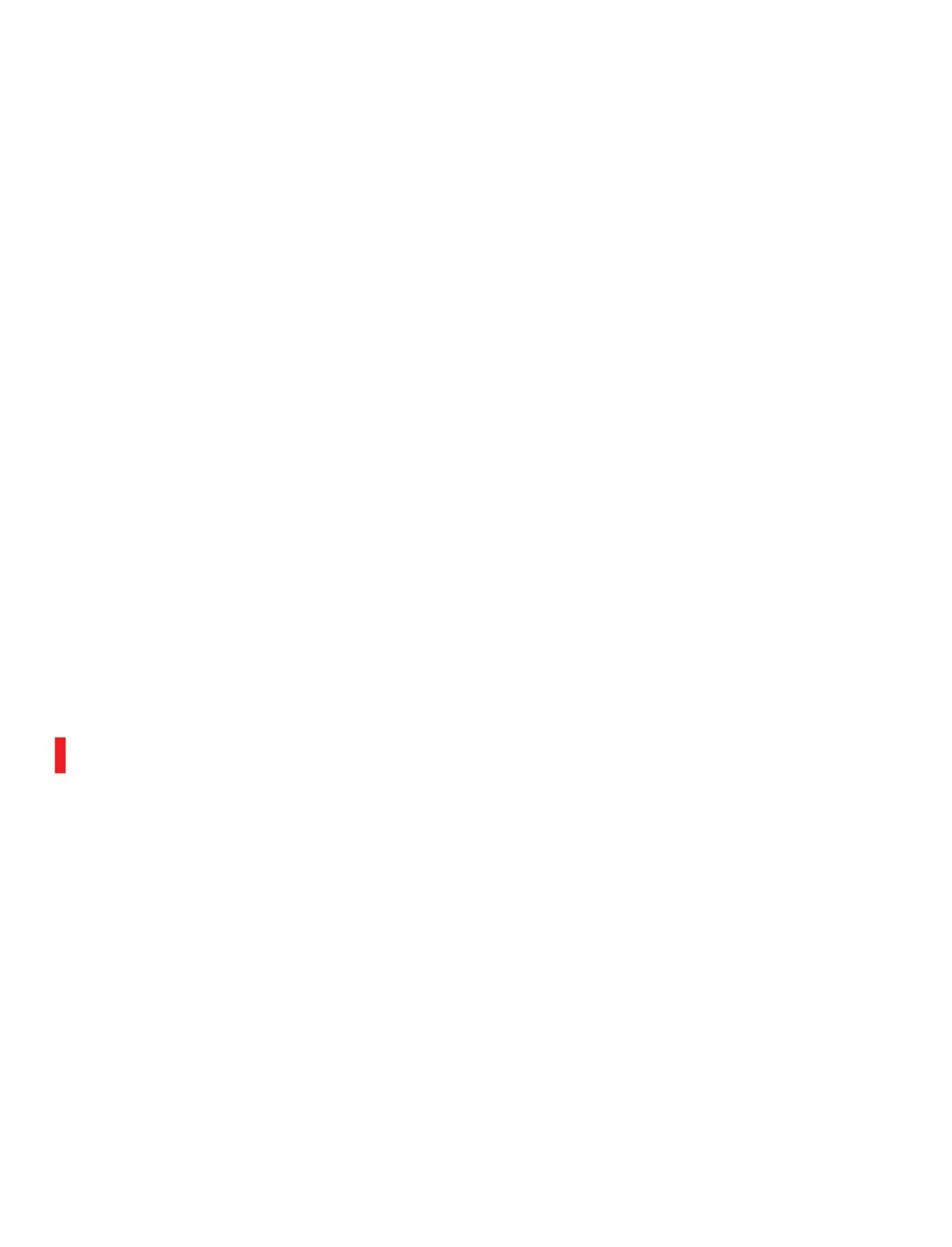
34 Andromeda
The team discusses the Superflex slings.
36 Bunzl
Bunzl Safety and Lifting explores the benefit of its Grade 100 lifting chain.
40 Precision Rigging Luke Williams discusses the growth of the company.
46 Vita Industries
Impressive lifting solution launched.
48 Reid Lifting
A brand new cutch released.
53 Manitowoc
Additional inserts expand MLC300 Wide Boom kit.
54 QUBE
The team completed an impressive tandem lif t recently.
58 TopGun Cranes
TopGun Cranes takes delivery of firsts Grove.
62 XCMG
Two new cranes launched at ConExpo.
64 Boom Logistics
Boom has a new Tadano delivered with the first E-Pack in Australia.
67 Crane Box
Purpose built organisational tool for operators.
68 Gleasons
A new Zoomlion rough terrain launched.
70 General Crane Hire
General Crane Hire take delivery of first HSC crawler.
74 ConExpo wrap up
Comprehensive wrap of the event.
76 Pace Cranes
Maeda going direct in the US.
80 TRT
New General Manager and first PC28-2 to be delivered.
NSW Labor will start building the chronically delayed second stage of Parramatta’s light rail in its first term of government; planning to spend an extra $200 million to finalise planning to fasttrack construction.
This funding commitment from Labor comes on top of the existing $602 million already set aside for constructing bridges and doing planning work to deliver the second stage of the multibillion-dollar light rail.
The state government expects it to take until 2031 before the line opens to passengers, about five years later than originally planned. When the proposed route of the second stage was unveiled in 2017, the previous government said it was hopeful construction would start before 2020.
Premier Chris Minns said western Sydney had waited long enough for the project.
“It’s time to get Parramatta light rail stage 2 built. Its time to stop talking about this project and start building. That’s what the people of western Sydney expect and need,” he said.
This massive infrastructure project along with others will keep our industry busy for years to come.
As always, this issue of Cranes and Lifting has something for everyone. We examine a number of high-profile lifts including the recent removal of the iconic Hard Rock Café guitar from the Gold Coast and our regular feature Between Hook and Load focuses on the critical nature of rigging.
The team at Cranes and Lifting has worked hard to bring you interesting content and as always, we hope you enjoy the read.
Published by:
Simon Gould Editor, Cranes and Lifting379 Docklands Drive, Docklands VIC 3008
T: 03 9690 8766 www.primecreativemedia.com.au
CEO John Murphy
E: john.murphy@primecreative.com.au
Chief Operating Officer Christine Clancy
E: christine.clancy@primecreative.com.au
Managing Editor Andrew Hobbs
E: andrew.hobbs@primecreative.com.au
Editor Simon Gould
E: simon.gould@primecreative.com.au
Journalist
Josh Farrell
E: Joshua.farrell@primecreative.com.au
T: 0420 298 087
Business Development Manager
Emily Schlegel
E: emily.schlegel@primecreative.com.au
T: 0466 317 555
Client Success Manager
Glenn Delaney
E: glenn.delaney@primecreative.com.au
Art Director Bea Barthelson
Advertisement Designer Lee Mawdsley
Imaging Assistant Paul Breen
Subscriptions
Frank Rapone
T: 03 9690 8766
E: frank.rapone@primecreative.com.au
The Publisher reserves the right to alter or omit any article or advertisement submitted and requires indemnity from the advertisers and contributors against damages or liabilities that may arise from material published.
© Copyright – No part of this publication may be reproduced, stored in a retrieval system or transmitted in any means electronic, mechanical, photocopying, recording or otherwise without the permission of the publisher.
FOCUSING ON THE IMPORTANCE OF ANDRIGGING LIFTING EQUIPMENT
Terex Materials Processing—global manufacturer of materials processing and lifting machinery—announces the division of Terex Cranes into two separate entities: Terex Tower Cranes and Terex Rough Terrain Cranes.
The reorganisation involves investment with independent leaders and brand identities as well as an expansion of manufacturing capacity, including a brand-new facility to manufacture self-erecting cranes. Terex Tower Cranes and Terex Rough Terrain Cranes will sit within the ‘Lifting’ category of Terex Materials Processing’s broadening equipment portfolio. Kieran Hegarty, President of Terex Materials Processing, explains more.
“We see a lot of potential for Terex Tower Cranes and Terex Rough Terrain Cranes,” says Kieran.
“Since they are two completely different sets of products, manufactured in two independent facilities, it makes sense to separate them to provide more focus and clarity. We have new brand identities for Terex Tower Cranes and Terex Rough Terrain Cranes and each business now has its own individual general manager who will execute independent growth strategies— broadening their specific product portfolio and expanding distribution partners for those products globally while enhancing support for their distribution network.”
Marco Gentilini – Vice President & General Manager, is heading up Terex Tower Cranes, to include Flat Top, Luffing Jib, Hammerhead and SelfErecting tower cranes manufactured at its Fontanafredda facility, in northeastern Italy. Terex Tower Cranes work on some of the most formidable jobsites around the world and provide strong performance due to its rugged set up and advanced technology. The company has also identified a particular room for expansion in Self-Erecting cranes, Gentilini says. “We have appointed Nicola Castenetto to lead the product
development, strategic planning, sales, and post-sales activities of Self-Erecting cranes. Nicola has been with us for 15 years and is ideally suited to strengthening the relationship with our existing partners while opening new markets - countries where in the past, Self-Erecting cranes have not been so present. Commercial expansion, in terms of new markets, channel development and expanding our distribution network is a key focus. Along with Nicola’s appointment we also have dedicated engineering team to lead product development, and a brand-new facility that will concentrate on the manufacture of self-erecting cranes. It’s an exciting time for this arm of our business and these investments show that we believe in the product and are committed to growing it.”
Giancarlo Montanari – General Manager, is leading Terex Rough Terrain Cranes, to include its RT range and more recently launched TRT range, which features the TEOS operating system that enhances information flow and operating efficiency, T-link features, a new ergonomic cab with wide visibility, new Stage V engines, and a new boom with three extension modes. Manufactured at Crespellano in Northern Italy, Terex Rough Terrain Cranes are compact, versatile, and easily manoeuvrable, with different steering modes to turn in very small spaces. “Being
physically based at Crespellano and having full responsibility for both the internal side of the Terex Rough Terrain Cranes business as well as the outside, customer-facing side ensures that there is focus, continuity of oversight, coordination and support across all departments,” he says.
Continuing on key priorities, Montanari says, “During my time so far with Terex, I have been able to meet distributors and customers; and the key thing they look for is performance. The crane must be easy to use and maintain, to maximise their productivity. And certainly, our TRT range with the new TEOS operating system and T-Link telematics ticks all those boxes. We know we have an excellent product, so our priority is on expanding our market presence into countries where rough terrain cranes are not so popular yet. Development of our distribution network is also a critical task, and finally, improving manufacturing capacity at Crespellano to meet growing demand.”
Hegarty concludes, “We are confident that this new structure will focus each business on strengthening their individual and unique brands. Both leaders have a wealth of experience, and our investments will support them in driving the long-term growth and success of Terex Tower Cranes and Terex Rough Terrain Cranes.”
The New GMK5150XL is the latest sibling of the GMK5150L-1, with longest boom (69m) and most versatile road weights in class
• Reach further with 69m boom and 30m hydraulic luffing fly
• 50t GVM with outriggers in situ for reduced cost legal travel in all Australian states and territories
• 10.2t counterweight in situ at 12t per axle
• Increased safety and flexibility with MAXbase variable outrigger positioning
• Faster, intuitive set-up with CCS (Crane Control System)
• Grove Connect Telematics
• Capacity: 150t
• Main boom: 68.7m pinned*
• Maximum Jib: 30.2m (40O hyd luff)
• Maximum tip height: 99m
Liebherr-International AG has made two new appointments to its administrative board.
On 1 April 2023, Jan Liebherr will take over as President, with Stéfanie Wohlfarth becoming the new Vice President. Dr. h.c. Willi Liebherr and Dr. h.c. Isolde Liebherr – the previous holders of these positions – will remain members of the administrative board. This transfer of further responsibility from the second to the third generation of the family shareholders is another step in the generational change in the company’s management.
All the representatives of the family shareholder’s third
generation, including Jan Liebherr and Stéfanie Wohlfarth, are long-standing members of the administrative board and have a great deal of experience in managing the Liebherr Group. Together, they stand for continuity, stability, and reliability. They ensure the Liebherr Group continues to be led as an independent family-run company based on values such as a long-term orientation, responsibility, solid management, pronounced customer proximity, and high technological competence.
The administrative board of Liebherr-International AG is the Group’s highest management body.
It is made up of family members and decides on all fundamental questions of corporate, development, and product policy as well as financial and investment policy. The active family shareholders in the administrative board are the siblings Dr. h.c. Willi Liebherr and Dr. h.c. Isolde Liebherr as representatives of the second generation, and Jan Liebherr, Stéfanie Wohlfarth, Sophie Albrecht, Patricia Rüf, Johanna Platt and Philipp Liebherr from the third generation.
Liebherr-International AG, located in Bulle (Switzerland), is the parent company of the Liebherr Group.
“The Liebherr Group continues to be led as an independent family-run company based on values such as a long-term orientation, responsibility, solid management, pronounced customer proximity and high technological competence.”
Our market proven CKS range is currently available with a 5 month ex-factory* lead time.
Limited production slots, talk to us today to secure your next CKS.
Plus we’ve got you covered with full backup sales, service, parts and support Australia wide with TRT.
TRT are your Asia-Pacific agents for Kobelco. Talk to us today about your next project!
Tutt Bryant Heavy Lift and Shift (TBHL & S) recently completed a series of heavy lifts on Brisbane’s Cross River Rail Project. Projects & Heavy Lifting Manager of East Coast TBHL & S Scott De La Rue discusses the project and the Sany cranes involved.
WITH AN ESTIMATED CAPITAL COST OF $6.3 billion, the Cross River Rail project is expected to be the largest transport project ever built in Queensland.
The new shared pedestrian and cycle bridge will link the Ecosciences Precinct of Brisbane’s Dutton Park, and the newly upgraded Park Road station over and across the rail corridor to the Princess Alexandra Hospital precinct and South-East Busway.
The bridge will provide much-needed connectivity and allow for easier movement on foot, by bike or scooter, or to connect with public transport.
The new pedestrian and cycling bridge is an architecturally designed cable stay bridge approximately 480m long with a cable stay spire approximately 45m high.
The main span of the bridge will consist of five steel girders weighing up to 133t each. They will be lifted into place by crane to form the main deck.
Construction of the bridge is expected to be complete in late 2023, weather and construction conditions permitting.
“The scope of our element of the project is the installation of a cycling and walking bridge which connects Boggo Road to the Princess Alexandra Hospital. It’s probably the most iconic part of the job that’s above ground and our scope is to install the bridge from end to end,” Scott said.
“There’s definitely some heavy lifting involved with the project, and we’ve mobilised our Sany SCC8000A 800t capacity lattice boom crawler crane for the major lifts - along with our Sany SCC2500TB 250t capacity telescopic crawler crane as an assist crane to the 800t and 2 SCC400TB 40t capacity crawler cranes for general site assistance during the project. One of the 250t’s first job was to build the SCC8000A.
“The cranes were set up on one side of the rail corridor where they carried out a series of lifts including the first two large girders and main pylon in February and March. We then demobilised the cranes to the other side of the rail for some larger capacity lifts. For these lifts we built the Sany SCC8000A with a fully dressed Superlift tray.
“For the superlifts the SCC8000A was lifting a total of 166t at a radius of 55m
which meant the crane was operating at high-capacity utilisation - that’s a big lift for the crane. The second lift is much heavier at 292t but with a much shorter radius of 28m. Crane is dressed with 78m of heavy main boom, 80t of body weights, 230t of rear counterweights and 390t of superlift, the total dead weight in this configuration is over 1200t.
“We are onsite for 10 weeks and the 800t will complete 25 significant lifts. There are four of the big girders that go up, but then there’s approach girders as well. So, I’d say 25 lifts for the 800,” said Scott.
The SCC8000A features 99 metres of main boom in standard crane, 111 metres of main boom with superlift attached, 123 metres of mixed (heavy and light) main boom in standard crane, 147 metres of mixed main boom and full superlift.
The SCC8000A also comes with 168 metres of power boom, including 3.5 metre sections fitted into the boom, and a super power boom. This is made up of two booms
the next generation of wind turbines. No other crane on the East Coast market has the capabilities for heavy lifting at a large radius or extreme heights,” he said.
The Sany SCC2500TB 250 was used to assemble the 800t SCC8000A and was the perfect crane for that job. TBHL&S then used the crawler to tail the pylons, which was the first lift in the scope. The 250 was then lifted out with the SCC8000A, and demobilised to the other side of the project, ready for when the larger crane is moved into position.
With the strongest lifting capacity and the longest boom in its class, the Sany SCC2500TB is an extremely versatile crane ideally suited for working in industry sectors such as construction and infrastructure, mining and resources, as well as energy and renewables.
side by side for a certain portion of the main boom. TBHL&S has also purchased the crane with a short fixed – wind jib which can be used to install wind turbines over 100t at a hook height of 175m. It has a full luffing fly of 96 metres as well which can lift up to 68t at 194m hook height.
“We bought every option for the crane. We have the Superlift and the power boom which provides an increase to the torsional strength of the boom at increased heights, it also features the wind turbine short fly and the large luffing fly. This crane has greater capacities than anything else on the East Coast market right now,” Scott said.
“The Sany SCC8000A is perfect for the heavy work and lifts in large infrastructure projects. It is ideal for large and heavy bridge builds or removals such as the one we completed recently. The Sany SCC8000A is also very suitable for work on
The Sany SCC2500TB’s 75.4m boom is made of high-strength steel structure with a U-shaped section area. It features seven sections with the basic boom at 14.4m and the maximum boom length at 75.4m. The boom has full power with a single cylinder and plug for telescoping. The fixed jib measures 43m in length and can be installed at angles including 0°, 15° and 30°.
Safe operation is at the heart of the control systems for the SCC2500TB and this includes the Smart Integrated Load Moment Indicator (LMI).
The Integrated LMI System is provided as standard, offering high safety, efficiency, and calibration of the crane’s control. Based on lifting mechanics mode, the LMI computing system enables precision loading and the protection of loading operations. If an overload situation occurs an alarm system alerts the operator.
The LMI system can automatically detect the suspended load weight, the working radius of the crane, and the
“We bought every option for the crane. We have the Superlift and the power boom which provides an increase to the torsional strength of the boom at increased heights, it also features the wind turbine short fly and the large luffing fly. ”
angle of boom, and compares rated load weight with the actual load. Under normal operating conditions, the system makes intelligent decisions and will automatically cut off the crane’s actions if they are over extending the crane’s capabilities. It also features a black box function to record overload information.
The load indicator light has three colours: green, yellow and red, and the real time load status is presented on the display. When the load is less than 90 per cent of the rated load, the green light will be on. When the load is greater than 90 per cent but less than 100 per cent, the yellow light will be on, the alarm light flashes, and the system emits intermittent sirens. If the load reaches 100 per cent of rated load, the red light will be on, the alarm light flashes and it sends out continuous sirens. When the load reaches 102 per cent the system will automatically cut off the crane’s operation.
The SYIC-II integrated control system has been independently researched and developed by Sany. The system features a high level of integration and controls the power system to the crane, the engine system, the main control system, LMI, auxiliary system and safety monitoring system. Data communication between the controller, display, and engine is conducted by CAN bus technology.
The SYIC-II integrated control system displays the engine rotating speed, fuel volume, engine oil pressure, servo pressure, wind speed, engine working time, load weight, boom angle and other working parameters and working conditions.
The ergonomically-designed Sany cab features the latest interfaces between the operator and the crane. The integrated
26.5cm touchscreen is programmable with ‘smart buttons’ to ensure the interaction between the operator and the machine are perfect.
The cab has been designed to offer as much full vision of the work site as possible. The finger-tip controls and buttons are designed to enable more comfortable operations. The cab is modelled with large areas of glass windows and additional features include the beam headlamp and rear-view mirror. It is also installed with air conditioning and a radio.
The armrest box features an operations handle and electrical switch. An emergency stop switch and ignition switch are installed on the left and right armrest boxes. The armrest box is designed to adjust with the operator’s seat.
The operator’s seat is a suspension type multi-mode, multi-level regulated seat that is fitted with an unloading switch. The air conditioning system manages the cooling and heating of the cab’s air.
Multiple cameras can be fixed to the crane and in various positions to monitor the performance of the wire rope on each winch in real time, for example, as well as the conditions behind the counterweight and those surrounding the machine.
The counterweights and trays ‘pile up’, which enables them to be easily selfassembled and self-disassembled. This facilitates greater ease of transport and quicker mobilsation and de-mobilisation. The rear counterweight weighs 60t and features self-assembly and self-disassembly functions. The carbody counterweight is fitted at the front and rear of the carbody and weighs 10t.
The crane’s super structure features high tensile steel and the layout of key components is designed to provide convenient access for technicians for maintenance and service purposes.
The traveling speed can be switched between high speed and low speed with a high speed of up to 2km/h.
The telescopic crawler’s reducer also features a concealed wet-brake and springloaded, fin engaged brake with spring force braking, which is oil pressure released. Pressure of 25MPa is generated by an auxiliary system that pushes the cylinder to
when they get to site and retracted for transportation purposes.
The jack pushes the guiding wheel and insert shims to adjust the tension in the crawler tracks. The track steering system manages single track turning and pivot turning and high-strength alloy milled steel prolongs the service life of track shoes, which are 1,100mm wide.
The crawler tracks feature a maintenance-free track roller, and an outrigger cylinder facilitates the track frame disassembly during jobsite transfer. Its main components include a monitor, controller, length and angle sensor, pressure sensor, etc.
When the crane gets to site, it can be put into assembly mode, which means certain safety devices are disabled to facilitate crane assembly. In work mode all safety limiting devices are activated to protect the operation of the crane.
In an emergency situation, the emergency stop button will cut the power supply of the whole machine and all actions stop.
A height limiter is equipped on the
is lifted to the limited height, the limit switch activates, and an alarm pops up on the monitor. If the lift continues, alarms are sent from the control panel, a failure indicator light starts to flash, and the hook hoisting action is cut off automatically.
A three-wrap protector is installed on the main and auxiliary load hoist to prevent over-release of wire rope. When the rope is paid out close to the last three wraps, the limit switch activates, and the system emits an alarm and displays the alarm on the monitor, automatically cutting off the winch action.
All of these features make the Sany SCC2500TB a highly competitive product in the telescopic crawler market. With the longest boom and highest lifting capacity in its class, the Sany crawler is a highly versatile and durable crane, ideally suited for applications in the construction and infrastructure sectors, mining and resources and the renewable energy sector. It is class-leading in any applications where a heavy lift telescopic crawler is required.
product in general.
“The Sany SCC250TBs are awesomeI have been really impressed with the Sany products. The new 250s, are stronger than any other telescopic crawler crane. My team and I love them. I jumped in and had a drive the other night and it’s as good as anything else and the operators like working with them.
“Another thing worth mentioning, is that TBHL&S took delivery of the first three SCC2500TBs produced by the factory anywhere in the world. There were a few minor issues we wanted to change, like the positioning of the screen, so I took a Sany engineer out to have a look. They had a solution designed within six hours, and the parts were immediately sent. Sany is quick and responsive to anything we want done with the cranes and I don’t think you will find that from the European OEMs,” said Scott.
“With this project we’ll be on site for about 10 weeks and there are some significant lifts. There are four of the big girders that go up and then there’s approach girders as well. There will be 25 lifts for the 800 tonner and we will be putting it through its paces, that is for sure,” he said.
IT’S HARD TO BELIEVE WE ARE ALREADY over a third of the way through the year. It was great to catch up with those who were able to head over to ConExpo-CON/AGG in Las Vegas in March, to see the latest in Construction technology.
This was the first time that CICA was invited to present at ConExpo, and Alice Edwards and Pat Cran did the Australian crane industry proud, educating over 150 construction professionals on crane basics.
It is very pleasing that the work done by CICA over the years is being recognised on the world stage with CICA leading the way on several projects with position papers.
ConExpo was well attended, with a strong Australian contingent as well, and we witnessed the evolution from the manufacturers regarding carbon emission reduction.
In speaking to others, it is worth noting that skills and labour shortages and inflationary issues are not unique to Australia and New Zealand. All continents represented, presented very similar views on the
Ben Pieyreconditions is often referred to as “buying work”.
labour market and the difficulties faced to attract and retain skilled labour, not only in the operator sector but also in the support functions
This combination of a shortage of skilled construction workers and increased material and labour costs has resulted in slower delivery times
and an increase in cost for home builds and major infrastructure projects.
Unfortunately, these factors have resulted in more building companies becoming insolvent. Reports of companies bidding for work at or below cost during tough economic
The aim of this high-risk strategy is to keep a business solvent and allow it to maintain its core workforce until the market turns and more profitable work can be found. This strategy can be high-risk, however, because it can leave a business with no buffer against financial shocks and, if a business does become insolvent before the market turns, its creditors’ losses may be higher than they otherwise would have been. “Cash is king” but cash flow strategies must be sustainable, of course each business must make its own decisions in an informed way.
“It is tempting during the current skills crunch to have the trainee working as much as possible, particularly once they achieve their high-risk work licence. But time for skills growth and completion of all the components of the traineeship will ensure the trainee is competent and operates as safely as possible.”
If you need help with contracts or understanding your legal position if a company you are doing work for becomes insolvent, CICAASSIST is available to CICA members. CICAASSIST is provided through Holding Redlich which gives members free access via email or phone to workplace relations and safety advice
CICAASSIST also gives members free access to a 7-day-a-week, 24hour hotline service to contact a lawyer in the event of a serious work health & safety accident/incident or a workplace regulator intervention or any unlawful union right of entry / industrial action.
The CICAASSIST Hotline is 1800 HR LAWYER (1800 475 299 31) or alternatively, CICA members can email: cica-assist@holdingredlich. com . CICA members will receive initial free legal advice on how to manage the incident. If members wish to engage a lawyer through the CICAASSIST Help Desk, then discounted rates for legal services will apply.
CICA continues to work hard to ensure that the traineeships in WA and NSW grow in awareness and uptake. The appointment of Kate Galloway as traineeship coordinator for CICA will support the industry’s efforts and drive to improve our skills shortage. It is imperative that employers give trainees exposure to a wide range of skills. It is tempting during the current skills crunch to have the trainee working as much as possible, particularly once they achieve their high-risk work licence. But time for skills growth and completion of all the components of the traineeship will ensure the trainee is competent and operates as safely as possible. This will pay dividends for the employer in the future.
Enjoy reading this issue of Cranes and Lifting magazine and stay safe.
Ben Pieyre CICA Board PresidentCICA BOARD
Ben Pieyre – President
Marcus Ferrari – Vice President
Tom Smith – Director
Danny Adair – Director
Danny Black – Director
Andrew Esquilant – Director
David Solomon – Director
Karli Sutherland– Director
CICA OFFICE
Brandon Hitch Chief Executive Officer 03 8320 0444 0428 228 048
ceo@cica.com.au
Paul Arztenhofer Membership Engagement/ Business Development Specialist 04 9093 9274 paul@cica.com.au
Alice Edwards Road Technical Engineer 03 8320 0440 alice@cica.com.au
Patrick Cran CraneSafe and CrewSafe Technical Advisor 0488 004 274 pat@cranesafe.com.au
Damien Hense CICA Road Policy Advisor 03 8320 0460 0488 007 575 damien@cica.com.au
Julie Turner CICA Executive Assistant / Office Manager/Vic Secretariat 03 8320 0411 julie@cica.com.au
Kate Galloway Traineeship Coordinator 0491 047 118 Kate@cica.com.au
Ashleigh Gould
Cranesafe and Crewsafe Administration Officer
Phone: 03 8320 0466
Email: ashleigh@cica.com.au
Michelle Verkerk Marketing Communications Officer 0404 938 714
michelle@cica.com.au
Justina Blackman
Member Events and Engagement 0403 717 626
justina@cica.com.au
Unit 10, 18–22 Lexia Place, Mulgrave Vic 3170
Phone: 03 9501 0078
Fax: 03 9501 0083
Email: admin@cica.com.au
Website: www.cica.com.au
For information, please visit our website or call the CICA office.
AN AUDIENCE OF OVER 150 CONSTRUCTION professionals filled the presentation room to better understand the many facets that need to be considered before and during crane lifts.
Alice unpacked why it is so important to;
1. Know the load – the weight, shape and centre of gravity.
2. Know the crane and rigging – to understand which crane is right for the task, what rigging is required and the implications of making the wrong choice.
3. Know the crew and their capabilities.
4. Understand the site condition, how to measure ground pressure, manage inclines and adjust accordingly.
5. Know how external environmental factors can impact crane works and how to mitigate the risks.
The presentation contained ‘meaty’ information but was also interspersed with some Aussie humour. This was the first time anyone from CICA had been asked to present at ConExpo and the feedback from attendees was overwhelmingly positive, many from the construction space affirming an appreciation for the simplified overview, which gave them a greater appreciation for the complexities of crane lifts.
Alice Edwards frequently presents at Monash University and is an advocate of cross-trade learning, believing that operating in silos does not benefit anyone. Alice believes that the crosspollination of learning and ideas in the construction sector will improve safety, employee engagement and is more likely to lead to solutions.
Winner of the 2019 Women in
“Winner of the 2019 Women in Industry Awards, Alice was recognised for her formulation of industry guidance papers, position papers, the Crane Industry Code of Practice, and industry standards – all of which contribute to a safe and efficient crane industry.”
Industry Awards, Alice was recognised for her formulation of industry guidance papers, position papers, the Crane Industry Code of Practice and industry standards – all of which contribute to a safe and efficient crane industry. Being asked to present at ConExpo-Con/ Agg was an honour, recognising both Alice and Pat’s experience and vast knowledge.
Held in March, ConExpo-Con/
Agg utilised more than 260 000m2 of exhibitor space and brought more than 1,800 exhibitors to Las Vegas.
It is the largest construction trade show in North America and the premier event that connects professionals from every major construction sector. Held every three years, planning for the next ConExpo-Con/Agg which will be held March 3-7, 2026, in Las Vegas, Nevada, is already underway.
In March at CONEXPO-CON/AGG 2023, the largest Construction Expo in North America, Alice Edwards, CICA Road Technical Engineer, and Patrick Cran, CICA CraneSafe and CrewSafe Technical Advisor, were invited to present on Crane Basics.CICA Road Technical Engineer Alice Edwards presented at ConExpo.
Camilleri Lifting Services (CLS Cranes) provides customised lifting services for a range of customers in numerous industries from its bases in Mackay, Nebo and the Bowen Basin. CLS is headed up by industry expert Charlie Camilleri.
CHARLIE FIRST GAINED HIS CRANE operator’s ticket at the age of 19 and worked on the construction of the Port Augusta Power Station, operating a 22RB.
“That crane had a V4 diesel engine rubbing up against your back as I was sitting on a bare steel tractor seat. There were 11 manually operated levers in front of
“From there I worked my way through construction projects throughout Australia.
“In 1985 I bought my first 20t Kato crane and became a sub-contractor for General Cranes in Sydney. After a few years I moved to Mackay working in the mining and constructions industries, working my way up the ranks to branch
Boom Logistics six years later the business consisted of five depots, 55 cranes, 140 forklifts and 75 employees,” he said.
Charlie and his wife Fiona started Camilleri Lifting Services in July 2020. Cranes have always been his passion and after selling his former crane company in 2006 he took a break from the industry but realised he missed it.
“When the opportunity came up to buy four crawler cranes from my mate Greg Lee, I thought the business would be a nice little hobby for me, 15 cranes later and here we are,” said Charlie.
“CLS is a proud family business. We are fortunate that each of us has our own skill set that complements the business. Fiona has a diverse wealth of business experience, having owned her own businesses and headed up the board of an international company.
“My son Jonathan started with me just after he left school when I had CIA cranes as a trainee crane operator/ dogger and has been in the crane industry since, having gained a wealth of experience in the last 17 years across various crane and construction companies,” he said.
CLS assists its customers in Mackay, all over the Bowen Basin and Queensland wide with its general hire and bare rental fleet.
“Being regionally based there is no typical customer profile, we look after anyone who needs a lift. We have customers in various industry sectors including Construction, Sugar Mills, Engineering, Industrial Services and Mining,” said Charlie.
“Customers keep coming back to our business because we always strive to provide an outstanding lifting experience and we aim to be their ‘one stop lifting
“Being regionally based there is no typical customer profile, we look after anyone who needs a lift. We have customers in various industry sectors including Construction, Sugar Mills, Engineering, Industrial Services and Mining.”
shop’. Our customers come to us with their problems, and we provide the solutions, whatever that may be, including lifting, logistics and storage. We have the best crew in the business and go the extra mile to assist our customers. We deliver on what we promise,” he said.
The Camilleri Lifting Services fleet includes Frannas, all terrains, rough terrains and crawlers.
“Our capacities go from 20t to 220t and we run various brands. We buy cranes
which best suit our fleet and our customer’s requirements at the time. The backbone of our business is our people. Our team is highly regarded by customers and they often tell us that our team are the best they have had,” said Charlie.
“Our team includes guys with over 30 years experience, as well as those just starting out in cranes as trainees. We have employees that worked with us over 20 years ago and have returned when we started up as CLS.
“We strive to create a family friendly environment; many companies talk a good game, but we live it. We love to see our guys take time to attend kids school concerts or sports training, any other important family events. Family is at the heart of our business,” said Charlie.
Customer service, support and safety are priorities for Camilleri Lifting Services.
“We are ‘laser focused’ on customer service and support, without customers there is no business. By ensuring we service our customers on their schedule, not ours, we demonstrate how important they are to us. Customers are more willing to be flexible when unexpected circumstances cause a disruption. Our business has grown organically based on our service to customers This leads to new business by word of mouth, which is the best form of advertising.
“Safety is where everything starts, we take it so seriously we are ISO certified. We believe it’s a great benefit to have a third party review our processes and procedures and highlight any gaps we may
have missed,” said Charlie.
CLS was a finalist in the 2023 Lift of the Year competition. Charlie explains more about the nominated project.
“We were approached by our customer V2R Projects at the tendering stage of the Berth 5 Approach Replacement. Being involved so early was the key to success for us and also V2R as it enabled both of us to identify potential issues early and work through the planning process together.
“This was important as there were several significant challenges including lifting over water and exposed fuel lines, limited access, crane positioning, ground bearing load restrictions, etc.
“We were so pleased to receive the Peoples’ Choice Award for this project at the CICA conference in Adelaide. There is nothing finer than being recognised by your peers for a job well done,” said Charlie.
The Crane Industry Council of Australia (CICA) plays a critical role in the industry and Charlie is a committed participant in various CICA initiatives.
“CICA is vital for our industry, and it is critical that we have a single and united voice. This ensures our industry is viewed by government, regulators and business in general as being professional, well organised and authoritative.
“I have been involved with CICA since the mid 90’s and today I am a member of QLD steering committee and sit on the National Reference Group. I believe the crane industry needs CICA to present a professional front and united voice for us.
“In an industry that is high risk and faces the continuous challenges of everchanging legislation, regulations, road regulations etc, CICA’s advocacy enables cranes businesses to focus on our core activities of getting our cranes out and servicing our customers.
“In my opinion, the CICA team are the unsung heroes of our industry, they work tirelessly in the background lobbying state and federal government agencies to help all of us cut through the red tape and bring innovation into our industry, saving us time and money,” said Charlie.
Capacity at Full Reach - 1.4t x 63.3m
Max Lift Capacity - 150t x 4.5m
Max Boom Length - 75.0m
In part two of his April article, Klaus Meissner looks at setting up supporting stacks for safe mobile crane outrigging.
MOST MOBILE CRANES NEED TO BE operated on firm support in a levelled position. If an uneven ground cannot be compensated by outrigger jacks or when the crane needs to be raised, stacks of timber or similar material are required. From time to time unique solutions are on display; but the fact that it worked does not automatically mean it was a sound set up. It is important to understand the forces acting on, and within, the stack to prevent mistakes.
IT’S FRICTION THAT PREVENTS CONTACT SURFACES FROM SLIDING BY HORIZONTAL FORCES.
The amount of friction force is proportional to the vertical force and the coefficient of friction between the two contact surfaces. Friction coefficients depend on the materials and texture of the surfaces and the state of the contact; there are huge differences from dry over greased to wet and special materials like PTFE (better known as Teflon). Steel to PTFE has a friction coefficient of 0.04, but steel to greased steel is about 0.12, steel on dry wood is the same as wood to dry wood - around 0.5. So a contact of steel on dry wood usually has friction forces exceeding the horizontal forces created by the crane. For metal outrigger pads resting on steel plates the horizontal force generated by the loaded crane may be quite the same as the maximum friction force which can be transferred.
If there is grease/oil at the contact surfaces the same wood-wood or steelwood combination has a friction factor dropping easily to 0.1! All of these
friction factors are the values observed before any movement (static friction or adhesion), they apply only up to the point when the horizontal force equals the friction force. Now the horizontal force may overcome the friction force and the two materials start moving relatively to each other. Usually, the friction coefficient then drops further (dynamic friction).
It is better not to rely too much on friction without extra friction material (e.g., rubber mats). We understand the need to secure heavy steel counterweight slabs on platforms of trucks or trailers to avoid them sliding off the platform by using rubber mats and adequate lashing.
With horizontal forces acting on the stack exceeding friction forces, the outrigger pad may slide off the stack and/or the stack may start moving and collapse. Some accessory manufacturers offer plates with recesses/cavities to capture the outrigger pad. Blocks with interlocking shapes or blocks with
special high friction surfaces to build up stacks are available in some sizes.
Considering the following will assist in building up solid and reliable support stacks (compare fig. 4, a setup which includes many, but not all considerations given below):
• C heck the ground beneath the stack for sufficient bearing capacity, including sufficient distance to trenches, pits, excavations, or underground facilities.
• E nsure the ground has been prepared and leveled to start with a horizontal base. Use wedges on inclined harder ground (e.g., road surfaces) to create a horizontal base, dig into an incline for a levelled base or use compacted, levelled gravel as a top layer on the soil.
• C onsider using a steel mat on softer ground.
• Us e graded hardwood timbers or synthetic blocks, which are
“Avoid mixing and matching different timber/block sizes in the same stack, at least all timbers or blocks in a layer are of same thickness.”
“All mobile cranes are designed with means for access in positions with outrigger jacks partially extended only, cranes on stacks may be positioned significantly higher.”
engineered as crane support, for building the stack.
• T imbers used should be approximately 2 by 1 times (width by height), timbers over time may lose their sharp edges and develop the tendency to roll.
• Avoid mixing and matching different timber/block sizes in the same stack, at least ensure all timbers or blocks in a layer are of same thickness.
• Avoid mixing different timber grades (i.e., types of wood) in the same layer to avoid an uneven settlement of timber under pressure.
• C reate friction between layers of timber by using dry wood; some engineered systems have special surfaces that increase friction or
use slotting mechanisms between layers.
• Ideally increase friction between the outrigger plate and upper layer of the stack by using a rubber mat.
• B e aware of friction between the lowest layer and the ground, take measures as necessary.
• Plan the direction of the crosswise laid timber or elements to ensure that the upper layer directly underneath the outrigger pad is placed parallel to the axis of each outrigger.
• E nsure that outrigger pads do not separate the upper layer, lay timber, or blocks of upper layer without gaps, and are wider than the outrigger pad. Consider using an additional plate.
• A rrange the other layers preferably with solid blocking to avoid gaps, if unavoidable, gaps should not exceed 2/3 of the width of the timbers/ blocks. As a minimum, do not reduce contact surface between layers in the direction from top down of stack.
• Th e stack should follow the simple 1-to-3-rule, always 3 times wider than high (the pyramid),
• E nsure that the outrigger pads are in the centre of the stacks with sufficient distance to the edges in case of moving.
• C reate stacks high enough to retract the outrigger jacks as much as possible (ideally the jacks are extended equally), more extension of the jacks always creates less horizontal stiffness. This will have you operating slower and may create more wear in the sealing of the jacks.
• Never use intermediate blocking under the outrigger beams.
All mobile cranes are designed with means for access in positions with outrigger jacks partially extended only, cranes on stacks may be positioned significantly higher.
DON’T FORGET MEANS FOR ACCESS. Check the setup again prior to commencing work and observe it regularly during working. The crane may “walk” due to changing horizontal forces, and remember, the ground may subside when working over a longer period, over a single outrigger or quadrant.
Last but not least – If it doesn’t look right, rethink.
Klaus Meissner has worked for more than 30 years in different R&D positions on mobile and tower crane design (Demag, Peiner) and provides consultancy on product safety and technical compliance matters. He is chairman of the workgroup for the European product safety standard for mobile cranes, EN13000 and is member of the supervisory board of the ECOL foundation (European Crane Operator License).
BORGER CRANES WAS ENGAGED BY Precision Rigging and Logistics to assist with the crane hire and planning for the removal of the iconic Les Paul guitar from its rooftop position at the Hard Rock Café, where it had sat proudly since 1996,attracting many thousands of fans to the restaurant.
According to Borger Cranes Supervisor Logan Alexander, the lift wasn’t without its challenges.
“Because of the many risks involved, we were using smaller cranes in our fleet with our Liebherr LTM1060-3.1 and Franna MAC25-4, but the lift still took plenty of planning. Risks included the proximity of major retailers, which meant there were plenty of hoops to jump through.
“On Cavill Avenue, there is a major supermarket just metres from the position of the cranes and the tram lines were a mere few metres in the opposite direction. This lift really took some planning - something that Luke Williams, Managing Director of Precision Rigging and Logistics and myself are used to, and as a result of the detailed planning, we once again nailed it,” said Logan.
With two blocks of Surfers Paradise shut down, the tram lines isolated, and the cranes positioned perfectly, the lift was completed without any issues.
“Our engineer estimated the weight of the guitar would be around 5t but it came in at 3.6t. This enabled us to configure the LTM 1060-3.1 with main boom and 12.8t of counterweight. We picked the guitar at a radius of 9m and landed it at 16m,” said Logan.
“There was no need for the SuperLift, so we configured the Franna with standard counterweight. The Franna was hooked on
Rigging & Logistics recently completed a lift which stopped the Gold Coast as the lights were finally switched off at the iconic Hard Rock Café on Cavill Avenue, Surfers Paradise.With the guitar weighing 3.6t, Borger Cranes was able to configure the Liebherr LTM 1060-3.1 with main boom and 12.8t of counterweight.
the lower end of the guitar to tail the load from vertical to horizontal, it then assisted the LTM 1060-3.1 with loading the guitar onto transport, as dual lift. From setup to pack up the job took five hours.
“From the start, there were a number of unknowns relating to the lift. We couldn’t get drawings for the guitar, so inspections were organised and we utilised John from Field Engineers for this process.
“Precision Rigging and Logistics removed the inspection hatches so a detailed report could be completed – outlining the makeup of the guitar and its structural integrity. Precision Rigging and Logistics and Borger Cranes offered a turnkey package, from start to finish, leaving nothing in our way, and never letting any obstructions hinder the project,” said Logan.
The 60t capacity Liebherr LTM 1060-3.1 has a 48 m telescopic boom and offers enormous load capacities. At a total weight of 36t and with a 12t axle load, it includes a 5.5t ballast, 445/95 R 25 (16.00 R 25) tyres, eddy current brake, 6 x 6 drive and a hook block. A special ballast plate configuration has been implemented in the design to offer the widest range of driving conditions under its 12t axle load.
“Our engineer estimated the weight of the guitar would be around 5t but it came in at 3.6t. This enabled us to configure the LTM 1060-3.1 with main boom and 12.8t of counterweight. We picked t he guitar at a radius of 9m and landed it at 16m.”
Depending on the crane equipment and the required vehicle payload, the ballast carried may be 3.7t, 4.3t, 4.9t or 5.5t.
To increase the load capacity, 7.3t of additional ballast is available so that the 60t machine can be used with a maximum ballast of 12.8t. Thanks to its compact dimensions, the three-axle machine can be manoeuvred easily, even if on-site space is tight. The 9.44m long chassis is just 2.55m wide, even with the 16.00 tyres.. The turning radius measured over the driver’s
cab is just 7.58m and the ballast radius is within 3.54m. A support width of 6.3m is achieved with single telescoping sliding beams. Where space is tight, however, a reduced support width of 4.5m or 2.3m can also be used. The crane can be completely levelled during the support process at the touch of a button.
The air activated disk brake first developed by Liebherr for a mobile crane gives the 60t crane increased safety and efficiency. They offer considerably greater
braking force than conventional drum brakes, which remains consistent even at high brake temperatures. Changing the brake linings is faster and easier, and they come equipped with wear indictors to signal when this should occur. The much longer service life durations also contribute to efficiency.
The active, speed-dependent rear axle steering system from Liebherr, tried and tested many times over, is used in the LTM 1060-3.1. This reduces tyre wear considerably. The driver has five different steering programs available that can be selected easily for a variety of driving situations.
The six-cylinder Liebherr in-line engine in the chassis achieves 367 horsepower (270 kW) and reaches a maximum torque of 1700 Nm. The force is transferred to the crane axles via the 12-speed ZF-AS-transmission.
A two-stage distributor gear permits minimal creeper speeds in manoeuvring mode. The ABS (anti-lock braking system) improves driving safety significantly.
The LTM 1060-3.1’s six part telescopic boom uses Libherr’s Telematik telescoping system to telescope in and out easily. Using a 9.5m-16.5m swing away jib, the unit can reach hoisting heights of 63m and boom radii up to 48m. The swing away job can be attached at an inclination of 0°, 20° or 40°. For work in two hook operation, a second hoist gear and a 2.5 m assembly jib and a rooster sheave is available.
The LTM 1060-3.1’s hydraulic lift system uses an electric “Load-Sensing” control that can actuate up to four movements simultaneously. Depending on the requirements for the lifting task and of the crane driver, the slewing gear can be easily switched from “open” to “hydraulic locked”.
It also uses the Liebherr LICCON2 crane control - a mobile, multifunctional control and display unit with a BTT Bluetooth terminal. The crane driver also has the option of attaching and removing the hook block on the crane bumper with visual contact via remote control of the hoist winch and the luffing cylinder of the telescopic boom.
The Liebherr LICCON2 mobile crane control can also be converted into a complete remote control system for the crane.
The MAC 25-4 is a mobile articulated crane with a maximum lifting capacity of 25t. It offers a design proven in a range of difficult lifting applications.
While it wasn’t necessary this time, the MAC 25-4’s optional superlift (SL) upgrade works in tandem with the existing MAC 25 counterweight, adding a low-slung additional counterweight piece to the rear of the machine that helps increase rated capacity of the machine by up to 30 per cent in some configurations.
First released in 2013, Franna’s patented Dynamic Load Moment Indication (LMI) system offers real-time calculation of rated capacity, taking into account boom configuration, as well as chassis articulation
and pitch and roll, enabling continual assessment of structural limitations, forward stability and side stability.
Increased resolution of rated capacity is made possible by finer measurement of articulation pitch and roll angles – which allows for improved machine capability compared to previous generation LMI systems. When operated over undulating terrain, the rated capacity will be updated continuously, providing instantaneous information on the percentage utilisation of the machine (0-100 per cent of available capacity). When operating on a side slope or undulating terrain, operators are no longer required to manually calculate a reduction of rated capacity; the Franna Dynamic LMI does that.
Reflecting on a job well done, Logan
“The Liebherr LTM1060-3.1 and Franna MAC25-4SL were the perfect cranes for the lift. They made the job quick and easy, and damn they look good doing it!”
“A massive thanks to the Borger Cranes’ crew for being able to adapt to the changing conditions quickly on their feet, going above and beyond as they normally do and for showing why we are the benchmark for mobile crane hire in South East Queensland.
“A special thank you to Luke and his team at Precision Rigging and Logistics for their ‘out of the box’ lifting solutions. Do not settle for less on your project, we have teams and partners dedicated to making your job easier, give us a call to streamline the process,” said Logan.
Size range 10mm - 96mm
Capacity 1t - 168t
Flat Woven Slings
Size range 50mm - 250mm
Capacity 1t - 48t
LIFTEX IS AN EVENT SYNONYMOUS AS THE Lifting Equipment Engineers Association’s (LEEA) global exhibition series. It brings together professionals from the lifting equipment industry in different regions of the world with the aim of promoting best practice, innovation and safety in our sector. LiftEx in Sydney will be the first outside the United Kingdom and is shaping up to be a hugely impactful event.
To be held on 24-25 May, LiftEx Regional in Sydney is an unmissable opportunity for industry professionals to connect with peers, gain insight into the latest trends and technologies and learn from speakers most wouldn’t consider involved with the Lifting Equipment Industry. With a packed schedule of speakers, Q&A sessions and exhibitors, the event promises to provide valuable information and networking opportunities to all those who attend.
The event features a diverse range of speakers who will share their knowledge and experiences to a range of members, industry participants and invited guests.
The brilliant speaker line-up will enlighten attendees with new ways of thinking about our industry, our people and our future.
Opening the event will be Charles Brass – Chairman of the Futurist Foundation. The thinking of a futurist isn’t simply in predicting what will happen in 2100, but to open participants minds to the thinking and process of how this will occur. As an example, in a non-related field - hospital emergency care - nurses see motor vehicle accident patients, but it’s expected that with the adoption of fully-autonomous vehicles these emergency presentations will eventually be zero. Adaption to new technology from collision avoidance systems will mean that nursing practice will change, teaching students processes and protocols in this field will then adapt
to this new technology and particular trauma response systems will be made redundant. I’m incredibly excited to hear Charles’ thoughts on how the Lifting Equipment Industry will change.
Another notable speaker will be Rose Read from the Product Stewardship Centre of Excellence. Rose and her colleagues are working with several major firms to better manage the impacts of their products and materials through their life cycle. The Lifting Equipment Industry has a good news story to tell from a metals recycling perspective, but we have other huge issues to get on top of and Rose will share some of her expertise on ways we can evolve in a sustainable way.
Additionally, we will have the phenomenal Alison Earl. She is going to show us ways to motivate and engage our people like never before. I always thought stress was a taboo issue and that it was as bad for us as smoking, but Alison changed my thinking. Learning from stress and changing mindset about how to use stress as a growth opportunity opened my eyes immensely. She has helped thousands of her major clients get more from their teams and her session is going to benefit our industry by passing on tips and strategies to get more from your team.
In addition to the speakers, we will also have a Q&A to embed the learning from these enlightening topics.
It’s also a great opportunity for members to meet experts and see the latest in product technology with the onsite exhibition and networking. The exhibition will feature lifting equipment manufacturers, distributors and service providers. The networking event is going to celebrate our members and their contribution to our industry.
The second day of LiftEx is the pièce de resistance, where we will be announcing an industry-changing education strategy.
With all the brilliance of day 1, day 2 will be even better. In addition to the education announcement, we will be updating the industry on our people attraction strategy, training provider solutions, new marketing direction and our latest sustainability objectives for 2023-24.
We’ve got some very long-term members who’ve supported LEEA and our objectives over a number of years. We are incredibly grateful for their ongoing support, dedication to our methodologies, commitment to safety and vision of a lifting and height safety industry which have eliminated accidents, injuries and fatalities.
Overall, LiftEx Regional - Sydney is going to be a great event, thanks to the hard work of the team, the highquality speakers, and the engaged and enthusiastic attendees. The event will highlight the importance of education, safety compliance and innovation in the lifting equipment industry and will provide a valuable opportunity for professionals in the sector to come together, learn from each other, and work towards a common goal of promoting best practices and improving safety standards.
If you are involved in the lifting industry, attending LiftEx Regional –Sydney is an absolute must.
The Lifting Equipment Industry focuses its eyes on Sydney for the upcoming LiftEx Regional event – Justin Boehm gives his take on what’s going to make this event stand out.
Justin Boehm, regional manager LEEA
ANDROMEDA INDUSTRIES IS BEST known for its Superflex steel cable, invented by Raymond McLaren in the 1970’s to service specific councils throughout Australia. By 1975 Raymond had created and commissioned the first of his orbital square plaiting machines which mechanically plaits the cables into their completed form, creating what we know today as Superflex.
As the name suggests, Superflex cable is a steel cable that his highly flexible, without losing its durability and toughness. The interplaiting of the steel cords creates a very tough and set resistant cable which consists of more wires than are available in a cable laid
wire rope. Superflex Cable incorporates 912 individual wires that are woven into the completed wire rope, in comparison, a standard 6x36 wire rope which is commonly used in the construction of wire rope slings has only have 216 individual wires.
Andromeda Industries produces Superflex cables ranging in size from 10mm right through to its extra-large range of cables coming in at a whopping 96mm. This covers an immense range of applications, with the smallest sling coming in with a WLL of one tonne, through to its unique Double Ended strop with a massive WLL of 168t in straight lift or 330t cradled.
Andromeda’s Twentyfour-0 Superflex Doubled ended strops were used on a project lifting concrete bridge beams weighing 200t. Coming in at an impressive 22m long, the stops were so large they had to be transported by a full semi-trailer.
Andromeda makes all of its slings to order and achieves short lead times as its Superflex cables are kept on hand, allowing the team to quickly respond to the needs of the industry.
Andromeda is an active member of the lifting industry and all of the gear is designed and built to the highest engineered standards. Every sling is proof loaded in either the vertical 40
tonne or the 300 tonne horizontal test machines. Andromeda’s test procedures are NATA accredited and conform to Australian Standards.
Andromeda continues to develop products that lead the way in the lifting and rigging sector. The latest development is the Dean-0 sling that is specifically designed to be made short and to provide a single lifting point under Ramshorn hooks on larger cranes.
The Dean-0 slings are offered several different capacities ranging from a WLL of 11.0t through to WLL of 165t. Suitable Master Links can also be fitted and removed from these slings as required.
Andromeda has seen continual
demand for the flat woven steel slings for nearly 50 years. These are regularly used for lifting applications where the objects need reduced pressure at the lifting point.
Flat Woven steel slings come in a variety of sizes ranging from 50mm nominal width through to 250mm nominal width and also a range of different applications such as Cradle Lift slings and Choker Lift slings and a WLL ranging from 1t through to 25t in single fall.
There are a variety of termination methods used throughout the Flat Woven Sling range, from steel u-terminations, soft eyes with
aluminium ferrules, trapezoidal and semi-trapezoidal links and low deformation steel ferrules. These allow for use within all lifting applications that require a flat and highly flexible sling.
Also available for the Flat Woven slings is a protective covering which not only allows for extra protection for the wires of the slings but protects the loads from being marked.
For all lifting and rigging solutions using Superflex Cables and Steel Flat Woven Slings contact Andromeda Industries’ helpful sales team on 02 6760 3773 or visit the website. www.andromedaindustries.com.au.
“Andromeda makes all of its slings to order and achieves short lead times as its Superflex materials are kept on hand, allowing the team to quickly respond when large slings are needed.”Typical application of a Flat Woven Sling
ASIDE FROM THE GROWING AVAILABILITY and affordability of Grade 100 lifting chain and fittings, Grade 100 chain slings offer multiple advantages over traditional Grade 80 product - and with innovations in manufacturing technology, some Grade 100 products are even more advanced.
One of the main benefits of using Grade 100 lifting chain is its higher strength-to-weight ratio compared to other chains of the same size and weight.
In fact, Grade 100 provides the user with a 25 per cent higher working load limit (WLL) than Grade 80 chains. This means that a worker can lift a load that is 25 per cent heavier before they need to select the next size of chain, thereby resulting in a 30 per cent reduction in the weight of the lifting gear.
These are significant factors to consider as industries seek to make operator handling easier by reducing the weight of their lifting equipment, without compromising on strength and durability.
Secondly, Grade 100 lifting chains are designed to better withstand wear and fatigue, which is particularly important in applications where the chain is subjected to repeated lifting and lowering. Because the chain and components are manufactured from hardened and tempered alloy steels it has a high resistance to impact and wear to meet critical requirements of AS2321.
Another advantage of some Grade 100 lifting products is their higher resistance to corrosion and rust, making them more suitable for use in harsher environments and industries.
“Bunzl Safety & Lifting manufacture Beaver BV100 Chain Slings, which offer a higher wear resistant finish and self-lubricating feature.”
Experts in the industry have also noted that since the release of the 2014 Standards for Grade 80 & 100 Chain Slings A3775.1:2014 and AS3775.2:2014, the guidelines and regulations on proof testing and clarity over working load limits for Grade 100 chain and fittings has also bought more confidence and validity to their use.
Bunzl Safety & Lifting is a leading manufacturer and supplier of chain slings in Australia. They use leading brands including Beaver BV100 chains and fittings which are manufactured to comply with and exceed Australian Standard 3775.
Beaver BV100 chain and components are stronger and more durable, making them ideally suited to heavy engineering industries. The chain is offered in preassembled or made-to-order slings for customers nationally. Beaver BV100
chain and components are highly reliable and cost-efficient and range in sizes from 8mm to 16mm in diameter.
The finish of BV100 chain has also recently been improved with a higherquality blue phosphate coated finish for even greater longevity and marked with full product traceability codes and information. It also has a self-lubricant feature which offers future oil-free maintenance.
All chain slings manufactured by Bunzl Safety & Lifting are proof tested as per AS3775 and supplied with NATA certificates. The company not only
manufactures and supplies chain slings, its fully trained and accredited team specialises in visual inspections, repairs and testing of lifting and rigging gear, including chain slings.
Australia wide on-site or workshopbased inspection services are available to ensure minimum disruption to daily operations. Their specialist team of LEEA-trained inspection technicians can carry out all on-site inspections and in-house proof load testing of lifting equipment.
For further information and advice, contact Bunzl Safety & Lifting.
From head to toe protection, lifting equipment or working at heights, we protect you. For Safe Working Lives.
“The finish of BV100 chain has also recently been improved with a higher-quality blue phosphate coated finish for even greater longevity and marked with full product traceability codes and information.”
From its humble beginnings out the back of a hatchback and then a 40-foot shipping container, Precision Rigging & Logistics has become a powerhouse in the rigging game, working with some of the largest crane companies in Australia.
MANAGING DIRECTOR LUKE WILLIAMS started Precision Rigging & Logistics in 2015. After joining the mechanical rigging/crane industry at the age of 19, he has brought his 14 years of industry experience to Precision Rigging to deliver a complete lifting solution.
“I started the company completing compressor changes with a chain block alongside Laurence Ratima and a lot of guys gave us the chance and wanted us to succeed but the feedback was always the same, ‘you need more gear and a larger presence to complete the larger projects’,” Luke said.
Luke and Laurence then purchased a shipping container and went about filling it with rigging equipment to
meet the needs of their clients.
Precision Rigging then welcomed Jennifer Campbell to the team as administration manager to ensure the company continued to meet its operational goals and responsibilities. A strong leadership team has ensured that Precision Rigging & Logistics is in a sound position for future growth.
Precision Rigging has grown to a team of 13, along with a large crane truck, in the eight years since it started. Luke explains how the company serves the lifting sector.
“What we do is extremely specialised, we are not a big rigging house that is completing hundreds of jobs in a day, we are doing bespoke
work on challenging projects.
“We have our team completing five to 10 jobs a day completing things that are not simply off the shelf, they need to use all of their skills and knowledge to complete them,” Luke said.
Precision Rigging has a close relationship with the Borger Cranes crew, as reported in the March edition of Cranes and Lifting ,and this means Precision can function slightly differently to other rigging companies.
“Someone can come to me for a lift and I can ring the team at Borgers for example and ask them to have a 55t crane at a location and the team can rig the crane themselves and complete the project,” Luke said.
“It is very accommodating that a company like Borgers lets you do that,” he said.
Luke explores why Precision Rigging has this type of relationship with companies such as Borgers.
“I think it is a relationship built on reputation and trust. We are proven to complete the works safely and efficiently and with an innovative solution for the overall project.
“I have built relationships with a lot of crane companies along the east coast of Australia as they assist us to complete our projects wherever the work may be, however being based in South East Queensland we have built a strong working relationship with Logan, Adam, Casey and Shawn at Borger Crane hire. They are our go to company for any size crane”
“Our other subcontractors are also the heart of our business, whether that would be TCI (traffic control), Simmons Logistics for additional transport, Field Engineers or Action Scaffolding for height safety, we require only the best when planning a large logistics project. We only want to work with the best to ensure the most professional outcome for our clients,” Luke said.
“We have been like a lot of other businesses in that we were growing up until Covid, and then since Covid it has gone absolutely berserk.
“We have worked hard to put the right people in place that helps our relationships with clients.
“Anyone can go out and get riggers and dogman tickets but we bring in people with great experience and who take ownership of the work they are doing to ensure they can deliver on their projects,” Luke said.
Precision Rigging has grown into a company that does so much more than simply rigging cranes. They are a one stop shop for any project, as Luke explains.
“We are able to link a whole heap of moving parts together, we can get the traffic control, transport,
“What we do is extremely specialised, we are not a big rigging house that is completing hundreds of jobs in a day, we are doing bespoke work on challenging projects.”
The PrecisionRigging
team can be found across a range of projects.Sometimes a lift does not require a crane but will utilise chain hoists and truck cranes to solve a problem.
scaffolding, builders works and equipment all organised, which means a project can be completed smoothly and efficiently.
The team at Precision Rigging takes pride in taking on the challenging jobs, they are firm believers that every project has a solution and that solution does not always rely on a crane.
“For a normal person who has no idea, to relocate a 900-kilogram compressor from level 46 of a building, we don’t use a crane for that. We have got gantries, we get it out, we relocate it, we lift it off, down through the building, put it on a crane truck, take it from site, take it back and then install it,” he said.
“We pride ourselves on a unique solution for each job, we get a lot of satisfaction from completing a
crane in for the project.
“Managing the project from start to finish ensures we can control all the activity along the way, minimising time wastage and giving the client the best possible outcome with one trusted contact point.
“My estimator Chris Finch has been in the industry for over 25 years. He knows the time we need to complete the works to give an accurate price when tendering large projects.
“Chris knows majority of the issues that may arise and is able to factor that into planning a project,” Luke said.
Precision Rigging maintains a vast array of rigging equipment in house to deliver on any project and to service its outside the box lifting.
“We now occupy a 520 square meter shed at Murarrie along with a vast range of rigging gear and it is always included in our costings, they are regularly inspected by our inhouse inspector Tony Williams. We have gone the extra mile with him, and he has completed all of his tickets for testing and tagging equipment.
“We will also pre-fabricate custom equipment for a project, which we
“We will also pre-fabricate custom equipment for a project, which we will then even sometimes leave with the client in case t hey need something similar for other work.”
challenging project that people say cannot be done,” Luke said.
Precision Rigging understands the importance of completing a job from start to finish, thus minimising delays and having full control over all works completed.
“We recently completed a project for the University of Queensland, we were brought in to complete the entire job ourselves. I had the engineer completely design the pad and then engineer the entire lift itself and then consulted with Borgers to bring a
will then even sometimes leave with the client in case they need something similar for other work.
“If we do not have the equipment we need, we have a good relationship with Ben from Queensland Rigging and he can supply any extra gear that we may need,” Luke said.
The team at Precision Rigging has completed some impressive projects recently, so be sure to pick up future editions of Cranes and Lifting to see what they complete as they continue their upwards trajectory.
Precision Rigging and Logistics provides an end to end solution for any lifting job in Queensland. Precision Rigging and Logistics can visit your site at any time to suit you, to conduct a comprehensive, cost free site evaluation and consult with you to provide you with a cost effective, efficient solution to all your logistical needs.
• On Site Mechanical Rigging
• Relocation and final positioning of sensitive and heavy equipment
• Removal of redundant equipment/debris from site
• Comprehensive crane, transport and traffic control logistics packages
• Demolition and removal of mechanical equipment
• Commercial and residential equipment removal & relocations
Precision Rigging and Logistics service a range of industries including:
• Mechanical Air-Conditioning
• Electrical
• Medical
• Heavy Industrial factory equipment
• Telecommunication and I.T Equipment
• Universities and Hospitals
• Heavy Art
Dynamic Rigging Hire has served Victoria for the last 12 years, providing a range of rigging gear hiring services, with the Melbourne-based company continually expanding its range.
RIGGING GEAR CAN OFTEN BE ONE OF those items that can upset even the best laid plans and Dynamic Rigging understands the challenges faced by riggers and operators. Ross Johnson explains how Dynamic Rigging Hire is supporting the region.
“Anyone working in and around the Melbourne construction industry would be only too aware of how busy the market is, and one major project seems to lead directly into another. Dynamic Rigging Hire continues to invest on not only more rigging gear but also in people to keep in step with the pace of the Melbourne crane and construction market,” Ross said.
“We now have two full time drivers busily moving around Melbourne every day, delivering gear direct to sites and yards. The very nature of the rental industry caters to all those on demand and instant equipment hire needs through to complex and heavy lifts planned well in advance,” he said.
The office team at Dynamic have many years of rigging gear knowledge and can work with the clients to fulfil any rigging gear needs.
“Dynamic Rigging Hire proudly choose to stock quality brands, one recent addition to our range is the RUD VLGB-Plus lifting points, widely known as ‘pinkies’ across the industry.
Dynamic Rigging Hire hold this product available for hire or purchase including the OEM longer bolt option,” Ross said.
“Also new to the range of rigging gear is the latest Reid 10t 3DX edge lifting clutches and we also hold the upgraded Ancon/Leviat 15t edge pro clutches for hire,” he said.
Whilst Dynamic mostly services the Victorian market, they have equipment on hire in most states daily for all those pieces of equipment not available locally. Recent jobs outside of Victoria include Loxton South Australia, Cobar New South Wales, Hobart and Sydney.
TENSION AND COMPRESSION LOAD CELLS, NATA CALIBRATED READY FOR HIRE
Dynamic Rigging Hire carry a range of quality load cells for hire Australia wide, we stock quality brands such as Crosby Straightpoint and MSL Safe T Weigh that are all individually calibrated and issued with NATA endorsed reports.
• Tension load cells in sizes, 6.5t, 12t, 25t, 35t, 55t, 100t and 120t
• Load cell shackles
• Single compression load cells in 10t, 25t and 100t
• Four x 150t compression load cell system
• CoG measurement calculations
SPREADER BEAMS
MATERIALS CAGES
CRANE WORK BOXES
GENERAL RIGGING GEAR
CHAIN BLOCKS
AIR HOISTS
WINCHES
Vita Industrial exhibited at ConExpo 2023 with an emphasis on how stabilisation technology can increase worker safety, project efficiency and profitability for lifting applications.
VITA INDUSTRIAL HELD LIVE demonstrations at ConExpo of its Vita Load Navigator (VLN) which uses a powerful system of sensors and air thrusters to automatically stabilise loads and prevent them from spinning.
Chairman and CEO of parent company Vita Inclinata Caleb Carr said the company was making the most of the opportunity to present the product to the industry.
“Vita Industrial was thrilled to be a part of the largest construction tradeshow in North America for the first time,” Caleb said.
“Construction companies and equipment suppliers in the U.S. and around the world are quickly learning how load stabilisation can dramatically improve their lifting operations. The VLN can speed up construction schedules and improve jobsite safety,” he said.
The Vita Load Navigator uses aviation sensors to detect load position, wind speed and hundreds of other data points per second.
High-powered air thrusters dynamically adjust loads within milliseconds with up to 1° accuracy. The unit can be controlled via remote for precise lifting applications.
At ConExpo, Vita Industrial also highlighted its work with DPR Construction, a leading U.S.-based general contractor with operations worldwide.
In recent months, DPR and Vita have partnered in a pilot program using Vita’s innovative hardware and software solutions at a Southern California DPR project site.
Robotics lead at DPR Construction Henning Roedel spoke about the exciting developments from Vita Industries and what it means for industry.
“Many of the tools of the construction industry trade haven’t evolved in decades. DPR looks for opportunities to adapt and use those tools in different ways to foster innovation,” he said.
“We like to work with companies that can think bigger — companies like Vita Industrial — and bring innovation that improves safety and efficiency
in construction sites everywhere,” Henning said.
DPR has more than 5,000 employees in the skilled trades and a dedicated innovation team that looks for solutions that can contribute to bringing their employees home safely every day.
“DPR is excited at the potential of adding Vita’s intelligent lifting system to our list of advanced solutions,” Henning said.
“Together we are taking an analog solution and making it a real-time, intelligent data system that significantly improves efficiency and profitability for crane companies,” he said.
“The Vita Load Navigator uses aviation sensors to detect load position, wind speed, and hundreds of other data points per second.”The VLN comes with a simple to use remote system. Vita Industries is working closely with DPR Construction.
With a history spanning over 100 years, Reid has positioned itself at the forefront of concrete reinforcement and lifting systems. More recently, Reid has been working closely with the crane sector to design its latest 3Dx 10t clutch and anchor system.
ALAN REID ESTABLISHED THE BUSINESS
that continues to bear his name in Sydney in 1921, selling wire rope to meet the growing needs of the Australian mining, construction and manufacturing sectors.
In 1973 Reid established the Reinforced Earth Company in Australia, which gave the business its first exposure to precast concrete retaining walls. This led to the introduction of the Swiftlift clutch and lifting anchor system in 1977, which has since expanded to the industry’s most trusted range of concrete lifting systems - providing a robust and safe solution for a wide range of concrete lifting and anchoring challenges.
Ian Ferrier is the Product Design Manager at Reid Construction Systems and is the driving force behind the development of the new 3Dx 10t Concrete Lifting System.
“Our clutches were originally developed with a flame cut handle which was soon enhanced with a forged handle design that is now widely used within the industry,” Ian explained.
“We took an in depth review of the existing lifting systems available and the recurring difficulties users were experiencing on a day-to-day basis. We approached CICA and a range of crane companies and learnt many were cutting the handles off clutches and placing hammer locks on instead. They did this to make using clutches quicker, simpler and better suited to the process of lifting and placing precast panels on site”.
“Looking at that process, we quickly understood the inherent risks and potential safety hazards this posed – not to mention voiding the warranty of their clutches. But why? What was the root cause? The modification of clutches to include hammer locks is intended to alleviate binding and
“The 3Dx has been designed in conjunction with the crane industry.”
spalling during panel rotation and erection. With that as the major pain-point to address, I began looking at an articulated clutch design that would deliver a tested and certified proprietary system – creating a far safer solution to meet the needs of the industry” he said.
Ian explains why Reid has developed the clutch to be articulated as opposed to previous models.
“When precast panels are lifted by a crane with a standard clutch, the position of the two anchors will cause the chain to rotate and come backwards over the panel’s edge. So, lifting from one point, the clutch would be pulled around the corner of the
panel which would see the handle bend, the new Reid 3Dx 10t Articulating Clutch can move in any direction, as well as self-right,” he said.
The new 3Dx 10t clutch also has the benefit of releasing quickly and remotely, meaning a user does not need to bring an EWP on site to quickly release the precast panel.
“Our intention was to hone in on designing “the” system that would satisfy the lifting requirements for over 95 per cent of precast panel configurations commonly cast throughout Australia. We know that most commonly, precast panels in Australia are transported by truck, in pairs. That
truck is limited to approximately 20 tonnes, hence the decision was made to develop a clutch that could safely lift 10t.”
Reid Construction Systems is proud of its long-standing partnership with Melbourne based manufacturer Townley Drop Forge, and was the obvious choice in both the manufacturing and testing validation of the 3Dx Articulating Clutch.
“As a design requirement, we wanted as much information as possible stamped on the clutch itself - such as a clearly stated WLL – that assures the riggers that they are using a genuine Reid, Australian Standards compliant, quality-assured product.” Ian said.
“The clutch is beautifully forged and includes the item part number, load limit and its batch code all clearly stamped on the physical product, for user peace of mind,” he said.
With the new design, Reid and Townley have included contingencies on the clutch to make it quick and simple for users to identify whether the clutch has been tampered with.
“The clutch has a rivet which holds it together, complete with the Reid logo. It cannot be tampered with, or easily knocked apart like a hammerlock clutch could be.” Ian said.
The information pertaining to the clutch is not only forged onto the metal but also appears on the stainless-steel tags supplied with each and every clutch. The tag includes a serial number, a barcode matching the serial number and a QR code.
“The QR code will take you to the Reid website and directly to the critical safety
the 3Dx clutch can be attributed to the close relationship with Rocky Galati and his team at Townley Drop Forge, as Ian explains.
“We are proud here at Reid to have a long and mutually successful association with Townley. From my very first interaction with Townley way back in 2001, we’ve known we can always trust the products manufactured here at Townley that brandish the Reid logo”, he said.
The Reid 3Dx 10t clutch was developed in partnership with Townley, which is NATA certified - allowing Townley to conduct compliance testing of all the clutches Reid delivers to the Australian market.
“All of our clutches whether they are manufactured here in Australia or imported, arrives through Townley and are tested and tagged. When you buy a Reid clutch, it has been proof tested, stamped and tagged. With surety you know that when you buy a Reid product it has been designed,
information for that clutch and any other associated Reid clutches. Our Reid website has a wealth of information for a range of stakeholders and users, including all safety and compliance statements, as well as Reid clutch and anchor compatibility and discard guides.”
“As with clutches from years ago, you’d be lucky if the tags would survive the journey from our warehouse to the precast yard or site. It was a worry back then to see tags in the bottom of an empty crate in the warehouse. Thankfully, the stainlesssteel tags we use now are robust enough to remain with the clutch.”
“The 3Dx Articulating clutch is traceable all the way back to the original raw material metal that arrived at Townley drop forge to ensure we have full traceability of material batch and heat-treatment certificates should these be required.”
A critical component of the success of
manufactured or assembled and tested in Australia – leveraging Reid’s 100 years of experience as a supply partner to the Australian concrete construction industry,” Ian said.
As a testament to their quality of output, Ian explains how Townley delivers a strong product for Reid.
“Townley manufacture the locking ring and the two forged parts of the 3Dx handles, each are magnetically particle inspected post heat treatment. The team will also inspect all of our products for any cracks or any surface problems which exceeds the requirements of the Australian standards.
“It gives us supreme confidence that everything we send to site is at the utmost level of safety and performance - delivering a robust, but more importantly, a safe and standards compliant concrete lifting system – The Reid 3Dx 10t,” Ian said.
“The 3Dx Articulating clutch is traceable all the way back to the original raw material metal that arrived at Townley drop forge to ensure we have full traceability of material batch and heattreatment certificates should these be required.”
The Foundation Awards recognise both individuals and businesses who excel in the industry and bring together different industry segments to one room on one night for a glamorous night of celebration.
MANITOWOC DEVELOPED THE SOLUTION based on the customer feedback it received, and it’s already proving successful.
Early feedback from leading players in the renewable energy industry highlights the huge operational and efficiency advantages gained by Manitowoc’s new Wide Boom Plus insert kit for its MLC300 VPC-MAX lattice-boom crawler crane.
The updated attachment offers a maximum boom length of 131m (429.8 ft), with a tip height of 137.8m (452.2ft) with the extended upper boom point. In addition to the longer boom lengths, the extra 30 per cent capacity allows contractors to respond to the trend for taller, heavier wind turbines while continuing to enjoy the benefits of operating smaller cranes.
Lomma Crane & Rigging is the first company to purchase the kit. Lomma partnered with JMS Crane & Rigging to install it on an MLC300 VPC-MAX for maintenance work on multiple wind tower sites across the upper Midwest in the United States. “We are excited to have been a part of the kit’s development and now see it at work in the field. It radically expands the use of the MLC300 for renewable energy jobs,” said Steve Burkholder, heavy lift manager at Lomma.
The added height and strong charts stretch the amount of work JMS can perform with their 386 ton (350 tonne) crawler crane. “We have one competitor with a 900-ton all-terrain crane that can’t do what our MLC300 VPC-MAX can,” added Rich Johnson, vice president of JMS.
“Now that 90- and 95-metre towers are
becoming more prevalent, we would have to rely on our larger Manitowoc Model 16000 or add a luffing jib to our MLC300 if Manitowoc hadn’t answered our prayers for the Wide Boom Plus kit. “It also enables a much friendlier crane build, with a smaller footprint, and saves us around 16-20 hours in assembly and disassembly time per job. Given that we might do that 300 times a year, it’s a major benefit to us,” Johnson said.
In addition to the reduced transport requirements of a nimbler crane, the contractor pointed to his operators’ familiarity with the MLC300, which allows for faster onsite commissioning.
“That extra boom gives a 138m (452 ft) tip height and is good for 124,400 lbs (56.5t)— that’s unheard of for a machine of this size!” Burkholder said. “Although wind farm installations can be tricky due to the weather conditions, there is still 100 per cent availability of the load chart in wind speeds up to 15 m/h (25 km/h).”
“Lomma and JMS were very vocal about their desire to have us develop this solution, so we’re delighted that it’s already proving highly successful,” added Brennan Seeliger, Manitowoc’s product manager for crawler cranes. “As wind turbines increase in size and weight, the need to be able to perform construction and maintenance above 90m without increasing crane footprint or setup time was a high priority for our customers — and that made it a high priority for us, too.”
Additional inserts expand the successful MLC300 Wide Boom kit to increase boom length and capacity. Using the VPC-MAX attachment, this new configuration offers the capacity of much larger cranes with the logistics and site benefits of the MLC300.Early feedback from leading players in the renewable energy industry highlights the huge operational and efficiency advantages gained by Manitowoc’s new Wide Boom Plus insert kit for its MLC300 VPC-MAX lattice-boom crawler crane
LCR, a QUBE company, executes precast girder installations utilising mid-air transfers on a purpose-built transfer triangle
LCR HAS CONTINUED ON ITS PATH OF impressive projects with the completion of a series of complex lifts on the $2.3 billion Bruce Highway upgrade project in Queensland. The lifts involved the LCR team completing the installation of 10 super T bridge girders over the electrified rail network connecting Brisbane to Cairns.
Among several challenges, the 10, 85t super T bridge girders were 33m long and required pre-delivery and stockpile outside of transport curfews to allow lifting operations to occur over the SCAS (shutdown) period.
Use of a crawler crane and single lift option were deemed not viable due to site conditions and positioning of the pads within the limited workspace. Methodology and lift plans were adjusted several times due to an unprecedented three major flood events in the region - with careful examination of the site and updated civil works required to make the installations possible.
After consultation with site engineers and governing bodies, with consideration to site conditions and restrictions around the SCAS, it was agreed a mid-air transfer
between a Tadano Demag AC1000/9 and Grove GMK7450 would be the best solution. The cranes worked with specialised transport equipment (LCR Jinker/Jinker combinations) for a lift and push placement.
The mid-air transfer was made possible by a girder specific triangle designed in-house. The triangle was purposefully designed in consultation with Edwards Heavy Lift to increase the distance between the tips of the cranes during transfer and to decrease the lifting radius of the secondary crane by a significant distance (2.5m).
The $2.3 billion Bruce Highway Cooroy to Curra upgrade is funded by the Federal and Queensland Governments.
It involves a 62km realignment and upgrade to four lanes between Cooroy and Curra and is among Queensland’s highest priority road projects. It aims to improve safety, flood resilience, and capacity along the highway between Brisbane and Cairns. It is designed to meet strategic transport, improve safety, flood immunity and capcity on the Bruce Highway.
LCR’s Tadano Demag 1000-9 was delivered July of 2021 and was the first to arrive in Australia. The crane was a momentous addition to the LCR (Qube) Lift fleet.
The AC 1000-9 is truly a superlative crane in the 1,200-tonne capacity class: With its 50m of main boom that comes as standard and the optional luffing jib, the crane reaches a maximum system length of 163.3 metres, which makes it unbeatable when it comes to large construction projects.
When it comes to the heaviest loads, the Tadano Demag AC 1000-9 is a true workhorse that refuses to give up even when handling large weights. The standard star-type outriggers, which reduce system deformation noticeably and accordingly provide for extraordinary stability at larger lifting capacities, play a crucial role in this.
The Grove GMK7450 is a 450t capacity crane on seven axles and a 60m twin-lock boom. The Grove comes with a graphic
display load moment and independent anti-two block system with audio-visual warning and control lever lock-out. These systems provide electronic display of boom angle, length, radius, tip height, relative load moment, maximum permissible load, load indication and warning of impending twoblock condition with lock-out hoist function.
The superstructure has a six-cylinder Mercedes-Benz engine producing 279 horsepower whilst the carrier has an eight cylinder Mercedes-Benz engine producing 571 horsepower with steering capable to all axles. It comes with an Allison automatic 4800 SP, 7 forward and one reverse speed, as well as transverse differential locks and a
transfer case with two speeds and inter-axle differential lock.
Prior to the commencement of operations, a mid-span launch ramp was constructed onsite to allow the girders to be pushed within radius. This meant updated methodology as the girders now required installation from the outside in. In addition, a temporary laydown was created along the alignment (400m from the bridge site) to store the 10 girders as lifting occurred outside of transport approved timeframes with nil exemptions available.
Constraints within the temporary works
“The mid-air transfer was made possible by an inhouse designed girder specific triangle so the Tadano Demag could pass to the Grove safely and then take up the rest of the weight via the back of a jinker trailer.”
With a number of challenges thrown at the team, they completed the project on time.
saw the crane pad construction occur an additional 6m away from the blade wall, increasing the SWL. Lift studies and approvals were updated to align with the changes.
The Tadano Demag was setup for the lift with 228t of counterweight, 45.6m boom and working at 91.2 per cent of its safe working limit (SWL). Rings, shackles and nylons in addition to the triangle were used for the rigging. The Grove had 120t counterweight, 30.5m boom, placing it at 88.5 per cent of its SWL.
On the day of operation, the rail network was isolated to maximise the safety for the teams involved. Due to the flooding events, the rail network isolation date was the only timeframe available to the project for the year and a maximum shutdown period of 18 hours was approved for the lifts due to the rail line being the main connection between Brisbane and Cairns. Due to the restrictions of the shutdown period and the multiple weather setbacks that had previously occurred, approvals were put in place to allow the project to be completed in severe weather conditions with the only weather event to stop the lifts being lightning. All weather appropriate PPE was issued to the crew in preparation.
On the day, the super T girders were loaded out from the alignment laydown to
jinker/jinker transport combinations using two 200t capacity cranes. On the launch ramp, the jinkers were positioned so the rear of beams were within radius of the 450t crane for the attachment of the rigging.
Once the 450t was rigged, the weight of the girder was transferred from the rear jinker to the crane. The 450t then slewed towards the 1200t whilst the prime mover simultaneously traversed the launch ramp - the girder weight split between the Grove 450t and the rear jinker trailer.
The 1200t hook block was then positioned
super T girder removing all of the weight from the trailer. The girder was then positioned on the head stock and the rigging removed. This process was completed another nine times within the 18-hour rail shutdown.
Whilst the project provided a number of challenges for the LCR team, they continued to work with the client to provide solutions to ensure that regardless of the continuous changes, the installation occurred within the project schedule. The project was completed within the time
at the rear of the girder in line with the 450t hook block. The transfer triangle rigging was then attached to both of the cranes utilising personnel in an EWP to allow the load transfer to begin.
Both cranes then began to simultaneously winch up and down to transfer the weight of the girder from the 450t to the 1200t. The Groves rigging was then disconnected from the transfer triangle with the weight then passed onto the Tadano.
The 450t then returned to the lead jinker trailer and rigged up to the front end of the
restrictions and with zero safety incidents, much to the credit of the LCR team on site.
National Key Account Manager Project Services Qube Heavy Lift Melira Lister discussed the importance of this project.
“Qube are extremely proud to be supporting the largest infrastructure project in Queensland. As a business, we recognise that we are only as good as our people, and we take pride in knowing that we have a great team onsite ensuring projects like this are executed to the benefit of our clients,” Melira said.
“The project was completed within the time restrictions and with zero safety incidents, much to the credit of the LCR (Qube) team on site.”
TopGun Cranes recently took delivery of a Grove GMK 3060L-1, the first Grove in the fleet. Business Owner Barry Ramm and Operations Manager Phill Martin provide some background to the purchase.
“THE PURCHASE REALLY CAME DOWN to a case of supply and demand. We had an urgent need for a 60t capacity all terrain and Grove was able to deliver it immediately. We had made investigations with other OEMs, but we were told it would be an 18 month wait for a new crane and six months for a used machine, we couldn’t wait that long,” said Barry.
The GMK3060L-1 combines compact dimensions with strong lifting capacities and long reach, thanks to the
48m, six-section MEGAFORM boom. With its additional 15m long hydraulic luffing fly jib, the Grove all-terrain crane can reach over obstacles easily.
The GMK3060L-1’s Hydraulic Luffing Jib load charts are impressive and start at a 0 degree boom angle and go out to 40 degrees, controlled from the cab, which is extremely useful in applications with tight tolerances. The large storage space with three storage boxes on the crane itself and the extensive storage compartment in the vehicle frame allows all sorts of crane accessories to be brought along without issue and these have also received positive feedback.
It is the most compact crane in the
60t class: In addition to having the shortest overall length and the lowest height it also scores top marks for the smallest tail swing.
Phill says the GMK 3060L-1 impressed TopGun Cranes from the beginning and was put straight to work on a range of projects.
“There are a number of features on the Grove GMK3060L-1 that have really impressed us. In particular, the 48m of main boom and the compact nature of the crane makes it ideal for sites with very tight tolerances. Its ease of operation is also a plus for us,” said Phill.
“All terrains can be complicated pieces of kit, but the Grove is very
“There are a number of features on the Grove GMK3060L-1 that have really impressed us. In particular, the 48m of main boom and t he compact nature of the crane makes it ideal for sites with very tight tolerances.”
straightforward, and it has been flat out since we took delivery. The telematics is a great feature for the product support going forward and we’ve been impressed by how quiet the QSL-9 Cummins is when working around the crane. The GMK3060-L also features the new style carrier cab which is great for the operator,” he said.
The new carrier cab has a modern design, which meets the latest crashtest requirements in Europe and is ECE R29-3 approved. Crane operators benefit from increased space within the cab, while the overall compact dimensions of the all-terrain cranes remain unchanged. Within a 2.55m width, Manitowoc accommodates
is further storage space between the driver and passenger seat.
The cab interior also incorporates cupholders and USB ports that allow mobile phones and other electronic devices to be charged. An ergonomic driver’s seat with air suspension, armrests and seat heating comes as standard.
User-friendliness and driver ergonomics were the priorities in the development of the new generation of Grove carrier cabs, so an understanding of operators’ day-to-day work conditions was essential to the process.
The CCS (Crane Control System) can be reached comfortably from a seated position and has been ergonomically integrated into the cab. The intuitive interface makes the operator’s job much easier as the most frequently used settings, such as chassis level and axle locking, can be selected via the CCS. Different drive modes can also be chosen via the CCS screen. As all CCS displays offer the same layout and navigation throughout the GMK model range, it is easy for operators to switch
from one Grove all-terrain crane to another.
Leon Brugman is operating the new Grove for TopGun Cranes. He’s been in the crane industry for close to eight years and working for the company for close to six.
“I started out dogging casually for a few companies and then landed a full-time job with TopGun and I’ve been here for close to six years. I started off on the smaller city cranes and the Maeda mini crawlers and slowly built up from the 20 tonner,
“The Cummins engine provides plenty of grunt upfront. Take-off from lights is no problem and when you get to site blowing out the boom is very straight forward, it’s a very powerful engine.”The new carrier cab has a modern design, which meets the latest crash-test requirements in Europe and is ECE R29-3 approved.
40 tonner, 50 and now on the new Grove GMK 3060L-1.
“The Grove brand is new to our yard. We had a couple of training days at Manitowoc’s yard where their technical team gave us a rundown on the operating platforms, how to set the crane up, swing the fly and more about the various features. Of course, it’s great to be in a brand-new crane and it drives nicely on the road and it’s a narrow little package for a 60t capacity crane,” said Leon.
He goes on to discuss how he finds the control mechanisms and the power of the crane.
“The overall operation of the crane is very smooth. You can dial in and adjust your settings if you want, with your speed and things like that, like you can with the other cranes. It is very smooth to operate and pretty quick on the jib
up too, it pulls up quite fast. It’s a long boom version, so it runs six sections of boom. It is nice and smooth on the slew and the foot brake’s really easy. With the Grove, you’ve got to remember to turn on your winch, your jib and your slew, whenever you’re getting it to operate.
Leon discusses the Cummins engine powering the Grove GMK 3060L-1.
“The Cummins engine provides plenty of grunt upfront. Take-off from lights is no problem and when you get to site, blowing out the boom is very straightforward, it’s a very powerful engine. It’s probably one of the toughest sounding cranes on the road. With the Telma braking and the big side exhaust, it sounds like a Mack truck coming down the road, which is alright,” said Leon.
Leon is more than comfortable with
Obtaining the credentials to safely drive an articulated steering mobile crane on-road
the layout of the newly designed cab with everything nice and close and easy to operate.
“I’m quite comfortable sitting in the cab, there’s plenty of room for me. It’s got the sports shift too, so you can go into sports manual mode if you want to shift up and shift down. The crane is very smooth in the gears.
“It’s a very compact crane for 60t capacity, and I haven’t had any dramas with access to the tighter sites where we operate. It has a very slim profile and I can drive straight in there, blow the legs out and start working very quickly. The air suspension is excellent. You can air up quite a way to get a couple of rows of timbers underneath the pads if you need to, and then jack it up from there. All round, it’s proving to be an excellent crane to operate,” said Leon.
THE LATEST ALL-TERRAIN FROM XCMG comes with a lifting capacity of 130 tonnes and a six section boom, with a length of 13.2 metres through to 62 metres and a maximum height of 92.5m.
Pat Carrigan from North West Cranes spoke about the latest crane from XCMG and what it will mean for the market.
“This is the 150 ton (136 tonne) all terrain crane, we’re particularly interested in it because it’s our crane and it’s coming home to Canada right after the show,” he said.
“It’s a five-axle machine with 200 feet (62m) of main boom, single engine machine, which most of the world’s manufacturers are going to now.
“We have had great interest for this machine in Canada, and most importantly, XCMG have paid particular attention to the carrier design so that we have proper weight capacities and allowances to get the crane on the road,” Pat said.
The new crane comes with a human
interaction system, intelligent crane boom technology and intelligent travelling control system offering intelligent operation planning and operation safety protection.
It also comes with a wireless remote control, providing additional convenience for users to operate outriggers, lifting, luffing and slewing on the crane.
“XCMG have been very attentive to our requirements and put a little more ergonomic design into it, a little more creature comfort and a little more room,” Pat said.
The new cab comes with a larger internal space helping make the driving operation more comfortable. The access system of the crane has been optimised making the climber far safer for the operator. In another safety improvement, cameras are installed at the boom head, winch and counterweight, with another backup camera in place.
The other crane released by XCMG at ConExpo is the XCR100, a rough terain which Pat says has a series of exciting additions in place.
“That’s the 100 ton (90 tonne) rough terrain crane which is really becoming the staple of the industry in our part of the world anyway,” he said.
“It has approximately 160 feet (50 metres) of main boom, but also four-wheel drive and four wheel steer and it is extremely manoeuvrable around refineries, plant sites and oil sands facilities.
“Again this crane has a new cab design, excellent ergonomic features throughout to optimise comfort for the operator,” Pat said.
“Really it’s become a staple of the industry, as we’ve moved along through the years, we’ve gone from 22 ton to 35 ton to 50 ton, and now pretty much that’s the predominant crane in the industry. We’ve got two of those on order this year and great interest in them on the way,” he said.
Pat goes on to explain the relationship with XCMG and how it is committing to the international market by listening to its local representatives.
“They’re extremely responsive every time
we reach out to them with a suggestion,” he said.
“Every time we’ve said to them, ‘we love this machine, but we’d like to see this a little bit different,’ or, ‘could you incorporate this into the design?’ The response comes very quickly, and more often than not, the next machine shows up with the equipment we’re looking for.
“They’re a great partner to work with, and we’re pretty excited about the prospects moving forward,” Pat said.
“They’re a great partner to work with, and we’re pretty excited about the prospects moving forward.”
With its 60m main boom, live capacity radar system and an Australian-first electric power option, Tadano’s new 80 tonne AC4.80-1 is the perfect partner for Boom Logistics.
BOOM LOGISTICS HAS A VARIETY OF TADANOS in an extensive fleet built over two decadesand its latest arrival, an 80 tonne AC4.80-1, will lead the company in a new direction.
More than just another crane joining an already massive fleet, the new AC4.80-1
With 60 metres of main boom the Tadano has an impressive reach for this class.
heralds an exciting move for Boom Logistics, being among the first to be paired with a new electric power option.
With over 260 cranes ranging from five to 750 tonnes, including mobile hydraulic models from 15-750 tonnes and crawler cranes from 50-750 tonnes, Boom Logistics has one of the largest crane fleets in Australia.
Some of Australia’s largest blue-chip companies rely on Boom as a service provider of choice for work across projects in high-growth industries, such as mining, wind, energy and infrastructure.
Incorporated in 2000 and listed on the Australian Securities Exchange in 2003, Boom Logistics today employs 750 people across 14 depots, servicing a range of clients across Australia.
The company also maintains a fleet of specialised access equipment, over 120 travel towers, boom lifts, scissor lifts and a fleet
of low loaders, with the aim of providing clients with an end-to-end solution.
It’s that commitment that led Boom Logistics to taking on Tadano’s E-pack mobile electric crane power system, Boom chief operating officer Ben Pieyre says, making the company the first in Australia to do so.
“In order to deliver meaningful change, we have to support new technologies. It is important to work with OEMs to drive improvements in the technological landscape in our industry,” he said.
“Carbon emission is a real issue, and we need to invest for better outcomes.
“Being the ‘first-mover’ with any technology poses various challenges but we know that we need to support change where possible with action – particularly in the area of sustainability and carbon emissions, Tadano’s support for its products assisted us in making the decision
to bring the E-Pack on board,” he said.
“The E-Pack offers great flexibility and can be shared between other models such as the AC2.40-1, AC3.45-1, AC3.50-1, AC3.60-2, AC4.70-2, which made it a smart investment for us” Ben said.
The E-Pack can power the superstructure of a Tadano crane without using its Mercedes Benz diesel engine. Instead, the E-Pack uses a 400 V / 63 A connection to connect to the power grid at a worksite.
Operators can also request the E-Pack be equipped to work with a 400 V / 32 A connection, albeit with reduced crane power.
The E-Pack creates opportunities for Boom Logistics to use its cranes inside buildings and other locations where it faces stricter emissions regulations – where working with diesel-powered cranes was previously impossible.
Whilst the E-Pack can be used across a
range of Tadano cranes, Boom will first use the system on its new AC4.80-1, Ben said.
“We brought the AC4.80-1 on board as it has 60m main boom with a max system length of 74.7m when fitted with the 16m fly, giving it an impressive reach” he said.
“It is the most compact four axle crane in the 80t to 90t class and comes with great technology – the IC-1 plus LMI system –which offers live capacity radar based on slew angle, main boom angle, counterweight and outrigger positioning.
“This crane also comes with automatic counterweight detection and flex base for stepless outrigger positioning,” he said.
Ben says these features will complement Boom’s continued efforts to improve safety on site for all its team members, with a lot of hard work done behind the scenes to ensure lifts are completed safely.
“Safety always comes first, and planning
is at the forefront of safety,” Ben said.
“Our whole team assists with lift planning and safety – from our sales professionals engaging with our clients to our front-line staff completing works.”
Ben adds that Boom carries out extensive training of and communication with its employees, helping make safety a centrepiece of the organisation.
“Lift planning is a collaborative process at Boom with the inclusion of engineering professionals (proficient with AutoCAD) who will develop formal lift plans; experienced and well-trained operational staff to undertake lifts and safety professionals who assist with the development of systems and processes to improve safety within the business,” he said.
“A lift or activity, when well-planned, removes a lot of potential hazards by having the right equipment with the right people and support at the right time.
“We have a mature Health, Safety, Environment and Quality (HSEQ) System certified to ISO 9001 and ISO 45001 which
provides a systematic approach to managing our risks that is applied across the country.
“Our experienced and well-trained supervisors and managers support our operations daily with assistance from our project specific, state and national HSEQ professionals,” Ben said.
With its first contract to be in Brisbane, the AC4.80-1 will benefit from its excellent on-road abilities.
“The crane has excellent roadability, with 20.5-inch (52cm) tyres, the AC4.80-1 achieves 12t per axle whilst carrying 9.3t of counterweight, (along with a) 6.5m fly and the 20t single sheave hook. Alternatively, 8t of counterweight, H2, 6.5m fly and the 20t single sheave hook can also keep the crane under the limit,” said Ben.
“We have a large range of Tadano cranes in our fleet, from smaller all terrains for refinery and project works, to rough terrains and telecrawlers on mine sites to large all terrains supporting our large client base.”
“It has a great integration of technology such as the IC-1 plus, the flex base and
Tadano surround view which allows the crane to be one of the safest on the market.
“Commonality of parts is a major benefit, which means they can be shared between other models such as AC4.70-2 (and the) AC3.60-1. The same operating system is used in the carrier deck and superstructure from the AC2.40-1 all the way through to the AC7.450-1, making operator familiarisation much easier,” he said.
Ben adds that the Boom Logistics crane operators have been enthusiastic about the new system, with many having a lot of experience with Tadano cranes.
“Our employees are very supportive of the product and the support through training and general assistance from Tadano means they appreciate the machines,” he said.
“The reliability for the operators is key as we often work in remote locations… and Tadano has developed a strong team around their product support with great facilities. We believe that service and support are as important as a quality product.
“Tadano has a strong quality range of products, the addition to the Demag range has really strengthened the product offering, not only in mobile cranes but also crawlers and tele-crawlers. The quality of the product and after sales service is essential to our relationship with Tadano,” he said.
“We brought the AC4.80-1 on board as it has 60m main boom with a max system length of 74.7m when fitted with the 16m fl y, giving it an impressive reach.”The E-Pack will be paired with the new crane.
AS IS OFTEN THE CASE, SOME OF THE best ideas don’t come from a boardroom but from those working on the ground who understand what users want.
Crane Box is a prime example of this and - developed by crane operators Delwyn Wright and Dallas Chenhall, who have 30 years’ experience as crane operators between them.
“Sick and tired of carrying multiple bags for lunch, paper work and ipads, we just had the epiphany that we should make one combined bag for everything an operator needs, and the Crane Box concept was born,” Delwyn said.
With its cooler compartment, you can keep your lunch and drinks cold all day long. The A4 docket book or iPad pocket is perfect for keeping your important documents and devices close at hand and the huge front double pocket is great for tickets, locks, keys, wallet, chargers, and the stretchy mesh side pocket is perfect for gloves or vitamins.
The material side pocket is great for taking crane radios, and the hard removable inside plastic bottom makes cleaning a breeze. The inside frame keeps food from squashing together, and the collapsable frame allows the Crane Box to fold flat into a suitcase for overnight jobs.
The D-ring is perfect for a hard hat and the adjustable strap can be used for over-the-shoulder or pick and carry. It can also fit in the back of a Franna, making it a great armrest for a rigger. It can fit a litre drink bottle and can hold up to 12 mining food containers.
The Crane Box is 390Wx292Hx199D in size and is the perfect solution for anyone in the crane or fieldwork industry looking for a convenient solution.
Dallas explains how the Crane Box can be customised to suit.
“We are able to print a company’s logo on the box and even customise it with an operator’s name to ensure it is truly personal,” he said.
The pair are using the opportunity they are given with the Crane Box to promote mental health discussions throughout the crane industry.
“Many of us in the industry have been touched by suicide and mental health struggles. We give anyone who
The team at DDX has designed a revolutionary organisational tool for crane operators across Australia.The Crane Box fits in the back seat of a Franna making it perfect for any operator. All PPE can fit perfectly on the Crane Box. purchases a Crane Box the opportunity to put a message on it promoting discussios around mental health with the crane indutry,” Dallas said.
The latest rough terrain from Zoomlion was launched at ConExpo 2023, boasting a 110-tonne capacity and a five-section boom.
THE FIRST ZRT1100 ARRIVED IN THE UNITED States in time to land at Zoomlion’s ConExpo stand - and for sales manager Josh Flowers and the team, it’s an exciting debut.
“This is our first ZRT1100 in the country, it has a 120 ton (110 tonne) capacity with a five section boom making it an impressive model for this class,” Josh said.
“We are just launching it at ConExpo, we expect it to be an extremely popular model in North America and I also expect in Australia as well.
“It comes standard with a Cummins engine, the DANA transmission, axle tech, 12 inch Hirschmann (WIKA) LMI screen and an integrated main valve, make it durable and reliable, and easy to maintain,” he said.
The Zoomlion has a 49m main boom of super large U-shape cross section allowing the ZRT1100 to have the best lifting capacity of its class.
It has 12.5t of counterweight and has four-wheel drive and a four wheel multimode steering system. The ZRT1100 is highly manoeuvrable and has a maximum speed of 35km/h and a gradeability of 96.7 per cent.
“The ZRT1100 come with a large 79-gallon fuel tank (300 litres) This large fuel tank allows users to increase their usage before their next fill and reduce the number of times the crane needs to refuel over a long project a crane will be on,” Josh said.
“This crane is built with the operator in
mind, it is supremely comfortable and comes with air conditioning, a tilt cab and excellent visibility,” he said.
The new ZRT1100 comes with an updated cab with a push front window and a panoramic sunroof. It also comes with a 12-inch display and a spatial arrangement within the cab to enhance the comfort of the operator.
Zoomlion has done extensive testing on these machines to ensure they can stand up to the rigours of the work they complete. Testing was conducted on plateaus, deserts mountains and hills to make sure the newest Zoomlion could stand up across the globe.
• MCH175A: 10t max lift & 55m Jib Length
• MCH125A: 8t max lift & 50m Jib Length
• Standard 1.6m masts
• 2m masts up to 58.5m height
• Fast erection < 4 hours
• Reduced Out of Service radius at 10m
Josh Flowers expects the model to be extremely popular.“The fuel tank is 79 gallons (300 litres) allowing users to get a full duty cycle of work out of it.”
General Crane Hire (GCH) recently took delivery of a new HSC CX2800A-3 from national distributor Tutt Bryant Equipment. GCH’s Nick Bucciarelli explains the background to the purchase and his past experience with HSC crawlers.
“OVER THE LAST SIX YEARS WE HAVE HAD numerous crawler cranes in our fleet with capacities varying between 160t to 750t, and they have been deployed to projects right across Australia,” Nick said. “The one constant model, and one which we believe every project we have undertaken has always required, is the HSC SCX2800A-3. This purchase was specifically designed to broaden our capabilities for our valued clients and to provide us with greater control of the capabilities we can internally provide as a business. Within two weeks of the crane arriving, we had secured our first project, and many more since,” said Nick.
After buying the SCX2800A-3, Nick says he won’t be waiting long to put it to work on the jobs it is best suited to.
“We have a pipeline of construction projects which will see this crane is scheduled out until Q4 2024,” he said.
The crane is currently positioned in the Pilbara Region of Western Australia, and it will then be moving out to the Goldfields Area for its next project.
“For General Crane Hire, the HSC SCX2800A-3 has been the most popular and versatile crane on the crawler market. To upskill our employees to operate these cranes has been relatively easy compared to other models, and in terms of
maintenance the HSC brand is very user friendly for our technicians and services teams.
“We have been hiring this model over the past six years and we have never had a breakdown with any of the machines. This makes us confident that we have made the right choice by selecting the HSC SCX2800A-3 as our first crawler to enter the market with,” said Nick.
The SCX2800A-3 crawler is part of the latest generation SCX-3 series from HSC Cranes.
HSC Cranes, formerly Hitachi Sumitomo Cranes, is renowned worldwide for class-leading products of exceptional quality. Drawing from many decades of Japanese crawler crane development, HSC Cranes has succesfully introduced to the market its new SCX-3 series.
Through the exclusive Australian distributor of HSC Cranes, Tutt Bryant Equipment, the SCX-3 range offered locally comprises the SCX1000A-3 (100t), the SCX1500A-3 (150t) and the SCX CX2800A-3 (275t).
Building on the highly popular SCX2800-2 crane, which is also a
mainstay on projects across Australia, the SCX2800A-3 comes in lift crane or luffing/tower configurations and it headlines a number of advanced features to further increase performance and efficiency.
With backward compatibility that allows interchangeability with components from the older model such as boom insert sections, owners have much greater flexibility and economical reasons to upgrade to the SCX2800A-3 while still utilising existing in-service crane components.
The SCX2800A-3 boasts a familiar yet elegant design that enables efficient transportation, assembly and disassembly, and much improved safety of the crane operator and those working in close proximity.
Along with extra-wide windows, ergonomic designs such as a new large sliding door, a wide platform, and a comfortable and highly functional operator seat are designed to reduce operator fatigue and increase functionality.
For better visibility when moving loads at height, a tilt mechanism allows the cab to be angled by up to 18 degrees optional handrails and walkways from the factory also ensure safety while working at height.
Productivity is further enhanced by the fine speed control dials for hoisting, lowering, swinging and boom hoisting operations - all of which are positioned beside the operator for ease of access.
A swing mode selector switch allows the choice between swing-free or swingbrake operation depending on work requirements and personal preferences.
The all-new Load Moment Indicator (LMI) with data-logging capabilities records duty cycle and winch hours, as well as load moment and line pull. This should, in theory, increase the safe operational age of the machine from current methods employed in complying with the new Australian regulations.
As a standard feature, remote sensing is installed in all machines to minimise downtime, ensure accurate maintenance
and improve machine marketability.
In addition to a powerful 13.5t rated line pull winch for steady operations, the SCX2800A-3 has an Eco-Winch mode which allows high line speeds under light loads without having to increase the engine speed (low rpm). Bringing lower fuel consumption and reduced noise, this is an eco-friendly feature that will save fuel costs and minimise environmental impacts.
Productivity gains are also achieved via a unique combined hydraulic circuit developed by HSC Cranes. By increasing and optimising the pump pressure through
the use of a mixed circuit to control the hydraulic oil from two hydraulic pumps, operability is enhanced when travelling, hoisting/lowering, swing and boom hoisting, all of which can be undertaken simultaneously.
The SCX2800A-3 is available with Stage IIIA / Tier three engines, and customers have the option to order the crane with a Cummins QSL9 engine that meets Stage IV / Tier four final emissions regulations. Along with major reduction in exhaust gas emissions, customers will benefit from reduced fuel consumption, saving cost and decreasing CO2 emissions.
A reduction counterweight specification is widely taken up by customers. By removing counterweights on the upper structure, this feature will allow the SCX2800A-3 to be utilised in four different capacity classes (275t, 260t, 250t and 240t).
This will enable the crane to come into its own in situations where a lower operating weight or reduced ground bearing pressure are required.
The SCX2800A-3 design enables efficient transportation assembly and disassembly. Reduction counterweight specification will further give owners the flexibility to use the SCX2800A-3 as a lower capacity crane, whereupon the
amount of counterweights needed to be transported to a job-site can be reduced.
The SCX2800A-3 also has optional 1260mm wide track shoes, some 140mm wider than the standard shoes. Reducing the ground bearing pressure by 12.5 per cent, this will make the crane more flexible and reduce the requirements for ground improvement tools.
Another option that will greatly improve safety around the crane is the swing restriction system.
Used to limit the range of slew to pre-set working zones, the system aims to allow smooth operations when working within tight constrained sites. There is an added slow-down function
prior to reaching the no-go zone, thereby minimising load swing.
Nick provides background to the relationship between General Crane Hire and Tutt Bryant Equipment, the National Distributor for HSC Cranes.
“GCH has a very strong relationship with Tutt Bryant Heavy Lift and Shift, and we expected there would be no difference with Tutt Bryant Equipment and it proved to be so, with the purchase and delivery experiences from Tutt Bryant being seamless.
“We worked with Tutt Bryant a few years ago when we purchased a Kato MR130 for our Perth operations which has been a great machine and served our business extremely well. Tutt Bryant’s history with the HSC models and the other brands it represent makes communication very easy, when we need to better understand something about the cranes, we have a good network of people we can call, ask questions and they are always there to support us. It’s the same with their parts holding, we know they have ample stock of critical parts if we ever encounter a problem,” said Nick.
He goes onto to explain how crawler cranes are becoming an important part of the General Crane Hire fleet.
“Crawler cranes have fast become a big part of the General Crane Hire fleet and business offering. The projects we now tender and get awarded are larger scale, with bigger lifts and longer durations. Our entry to the market with this crane will fit in nicely with our pipeline of work.
“We have been very happy with the performance of the HSC SCX2800A-3, and as we’ve seen with the machines we’ve hired in the past, it’s a well engineered crane and designed to handle Australian applications which can be tough on machinery especially cranes.
“The crane is popular with our operators and as I’ve said, we are more than happy with the support the team at Tutt Bryant Equipment provides. They have aways been there for us in terms of parts and product support which made the decision to make our first crawler purchase the HSC SCX2800A-3 an easy one,” said Nick.
Inside Construction Expo will deliver
Targeted messaging in over 19 industry-leading publications that reach more than 80,000 decision makers across multiple sectors
Digital communications to 28,000+ engaged readers
Premium networking opportunity with industry leaders at the Foundation Awards gala dinner
insideconstructionexpo.com.au
After five jam-packed days of innovative product launches and major company announcements, enlightening education sessions and countless networking opportunities, ConExpo-Con/Agg and IFPE 2023 have come to a close, but not before taking the construction industry to the next level.
THE SHOW EXCEEDED EXPECTED attendance numbers, drawing over 139,000 construction and fluid power professionals from 133 countries to Las Vegas from March 14-18 – making it the largest trade show in North America with more than 2,400 exhibitors from 36 countries spread out over 3 million square feet of exhibit space.
Caterpillar senior vice president and ConExpo show chair Phil Kelliher spoke about the event and its success.
“The innovations in the construction industry unveiled this week will play a role in helping construction professionals drive meaningful and sustainable economic growth,” said Phil
“Live events in the construction
industry are very important, because you can see, touch and experience the products. That value was reaffirmed this past week across the show floor,” he said.
This year’s show emphasised how the construction industry is evolving in many ways to adapt to sustainable technologies, products and practices. Show attendees were treated to sustainability
in action, from electric and hydrogen powered construction equipment, to more recyclable materials and waste reduction opportunities.
Across the show floor, sustainable technologies, products and practices included:
• Aerial work platform specialists Skyjack had its new SJ120 E on hand, a zero-emissions mast lift with a 30 per cent improvement in duty cycle.
• Construction pros wanting to maximise their energy efficiency explored Kubota’s V3307 MicroHybrid engine for installing in their existing equipment, saving
fuel with the attachments they use, like Rototilt’s Rototilt Control system.
• Contractors who work in disaster recovery will be saving up to 600 sand bags per barrier (and not worrying about disposal should it become contaminated), not to mention the fuel needed to haul it on and off site, with Rapid Barrier Systems’ waterinflatable barriers.
• Small engine specialists Briggs & Stratton brought its Vanguard brand’s swappable lithium-ion batteries for attendees to test out. And Redline Detection showcased its battery coolant and leak detector.
• B3C Fuel Solutions brought products to the show to help contractors eliminate waste by restoring emulsified/damaged oil, and make sure lubricant that does find its way to the environment is non-toxic and biodegradable.
• And AT&T’s Equipment and Machinery Solutions team brought a solution to help track its actual Scope 1 emissions versus their targets.
ConExpo also featured a wide range of educational opportunities, including 190 expert-led sessions on topics such as construction safety, equipment technology, and sustainable building practices.
Marcia Klein, Treasurer of CasappaCorp., and show chair of IFPE and spoke about the resilience of the industry.
“The success of ConExpo is a testament to the resilience and strength of the construction and fluid power industries, which has continued to adapt and innovate despite the challenges of the past three years,” Marcia said.
“We’re proud to have provided a platform for industry professionals from around the world to connect, learn, and discover new solutions for improving their businesses and the world we build,” she said.
• 3+ million net square feet (900,000 metres) of exhibits (10.5 per cent larger than 2020).
• 139,000+ registered attendees (6 per cent increase over 2020).
• 2400+ exhibitors, from 36 countries, including 603 new-to-the-show exhibitors.
• 24,000+ international registered attendees from 133 countries.
• 91,000+ scans of badges to access the 190 education sessions.
• 600+ global media from 33 countries
The next ConExpo-Con/Agg & IFPE will be held March 3-7, 2026, at the Las Vegas Convention Center in Las Vegas, Nevada, USA.
“ORIGINALLY, MAEDA HAD A DISTRIBUTOR which was called Maeda USA, and from what I understand, they were doing a good job. They were bringing units in, but the volume wasn’t where it needed to be for the goals that Maeda Seisakusho desired,” Duane said.
“My understanding is that Maeda Seisakusho spoke with our Chief Executive Officer, Tak Inoue, and asked him if he would be interested in setting up a wholly owned subsidiary distributorship as Maeda America. I originally met the Maeda America team in August of 2022 in my role as National Director of Crane Operations for Don Ahern at Ahern Rentals. Don Ahern was approached by the Maeda America team because they were interested in doing business in America with Ahern Rentals. Mr Ahern approached me and a President and Vice President of his other companies to evaluate Maeda America and if they are ready to do business with Ahern as a new startup company.
“My evaluation for Mr Ahern at the time was, “No. They’re not ready to do business in America with Ahern.” My evaluation of the equipment was very positive. I saw the product at the 2020 ConExpo, but they were missing a few things including not having battery operated units, lacking good distributorship and after-sales support, and not having a strong parts holdings. “Maeda Seisakusho truly listened to the feedback from its end users and customers here in the US and applied that to the equipment,” said Duane.
Maeda Japan took all that information from end users, mechanics, and people that would be using the equipment in America, and they engineered this information and fed it back into the machines to make them
more usable for the US market.
“The fact that Maeda Seisakusho really listened to the end users, is very important to me and that helped me decide to join them. Maeda listens to end users, listens to dealers, listens to distributors, takes that information in, and puts that into the machines. You don’t see that a lot with other manufacturers,” said Duane.
“Engineers have a plan; they have the design and they’re going to go with it no matter what. Maeda Japan does not do that. They really look at the big picture, and they put that into the machines which is very nice. They design and manufacture excellent products and I’m very happy to be on board.
“I’ve only been with the company for a little over a month, and they flew me to Japan to meet and congratulate me on joining the team and to see the factory firsthand. In terms of the US set up, my understanding is that we’ve absorbed the
Additionally, we had training last week here in Vegas, and we invited a number of dealers to attend. The dealers worked well together and expressed their excitement about the new models with Meada America supporting their dealer network. After the training concluded we took the dealers out to dinner to continue networking and building those relationships.” said Duane.
Currently, Duane is working on developing marketing and sales, service, and parts training as well as operational training.
“With Ahern Rentals, I was able to take an underutilised fleet and turn it into something that was profitable and my goal with Maeda America is to do the same thing. We’re going to do that through training, support for the dealers and after-product support. We are going to be there for our dealers.
“We’ll be developing training classes, including sales training, to help
dealers that Maeda USA originally set up, and we’re starting to grow by bringing more new dealers on board.
“Setting up a dealer network nationally in the United States I feel is the best route to take, to penetrate the market this will also give Meada the support for the Maeda Cranes throughout the country. One of our goals at Meada America is to support our dealers through after sales support, sales and marketing training, service training and assisting by identifying markets in their areas.
the dealers. Many of them are crane companies but it’s a different market with the mini cranes, it’s a different mindset. So, with my experience with mini cranes, I’m going to be able to help our dealers find the markets, find the customers that are going to be buying or renting these cranes which will help them grow. That’s going to be part of the sales training and the service training is going to be there to support them.
Duane goes on to explain where the Maeda product fits into the US market.
In a significant development for the US market, Maeda announced during ConExpo it would be changing the way it services the market. Duane Lloyd, Sales, and Service Engineer for Maeda America spoke exclusively to Cranes and Lifting about the development.
“Maeda listens to end users, listens to dealers, listens to distributors, takes that information in, and puts that into the machines. You don’t see that a lot with other manufacturers.”
“One of the things that made my decision to come to Maeda America and to help with growth for Maeda Seisakusho is the engineering that we talked about a little bit earlier. Maeda engineers really listen to the people that are going to be using those units and have implemented the feedback into the product. That’s going to be big for us in America.
“The end user friendliness of the Maeda machine is a major positive. You just turn that machine on and it’s ready to operate. Other brands have their own operating systems and they’re a little more complicated in some respects. Still a great product, just more complicated.
“The end user potential for Maeda is huge, especially in the rental market. With my role with other brands, I would spend four or five hours training guys and then go to job sites with them so they can learn more about the machines in a hands-on manner.
“There’s a lot of extra work that had to happen for that to be successful. With the Maeda brand, if we get the training right and get the dealers set up in the right manner, with full-service capabilities, and with the usability of the machines, it’s going to be a much smoother process. For me, what makes Maeda stand apart is obviously the support from Maeda Seisakusho, and what they’ve done with the products to improve the end user capabilities is outstanding.
Anthony Heeks and Michael Cawston from Pace Cranes were at ConExpo to share their knowledge and experience with the Maeda product.
“They’re great guys and it was a pleasure spending time with them. I believe having them here at ConExpo shows that globally Maeda has support for its equipment. Anthony and Michael have a lot of good ideas that I think will help grow things here in America with the Maeda product. And I think there’s a lot that we can learn from their experience with Maeda products, and we can bring some of their ideas to the US market.
“Americans have a different mindset, a different way of looking and doing things, but if it works and it’s profitable, then we are prepared to run with it. So,
I’m looking forward to working with the Pace guys and learning from them, and hopefully giving them some ideas that might help their approach to the Australian market.”
Anthony Heeks, Managing Director for Pace Cranes, says that he is also looking forward to developing the relationship with Meada America.
“We’ll be sharing a lot of information
on our success and the ways we’ve found that success, the different industries and different markets we’ve targeted, where the applications are, and some of the ‘outof-the-box ‘applications our customers have found for their Maedas.
“We’ll share our marketing strategies and what has worked for us in Australia. We’ll certainly be sharing all that information to Maeda America because at
the end of the day, as Duane says, it’s all about success for Maeda,” said Anthony.
During ConExpo Maeda America displayed a number of products including the latest additions to the MK Series. The MK3053C is the latest development in the knuckle boom range. Michael Cawston, National Sales Manager for Pace Cranes explains more.
“Maeda has been developing this knuckle boom style crane for some time, and there are a number of models in the range. Maeda has spent time developing the MK3053C to ensure the new model ticks all the boxes,” he said.
“It’s a cross between the MC305 and an MC285, which means it is a very compact crane with a small footprint and small ‘packed-up’ dimensions like the MC285. It can still fit through a doorway, but it has more reach than the MC305, being able to get up to that 17m mark. This is a game changer for Maeda in the small crawler crane market.”
In terms of powering the crane, the MK3053C is available in three versions including a standard diesel machine, a diesel electric option and a full lithium battery electric battery version. Michael explains the remote control is standard.
“The design of the set-up for the whole machine is managed by the remote control unit which comes as standard. This means the machine can be tracked and the outriggers controlled by the remote. The outriggers swivel by a hydraulic cylinder which means you don’t have to swing the outriggers out manually; it’s all handled by the remote,” he said.
“The MK3053C is a user-friendly machine and it is also a lot simpler for the operator, to the point where the operator doesn’t have to put pins in or pull them out. Another great feature with the outriggers is there’s no pinning required for the various angles.
“The machine can be set up on any angle, or the outriggers can be set up on any angle without the need to insert a pin. This is standard across the Maeda range. The winch is optional, but we’ll import units with the winch as standard unless there’s a special request for a crane without it,” he said.
LEADING FROM THE FRONT, TRT CONTINUES TO ENHANCE THE OVERALL OPERATOR EXPERIENCE AND PERFORMANCE WITH THE NEW TIDD PC28-2.
A more powerful front suspension improves lift capacity by up to 17%. New steps in the load chart improve lift control. Faster software processing gives even greater control response and the re-engineered ROPs cab has lower ambient road noise.*
Designed and manufactured by TRT, TIDD Crane offers a better experience and investment for the life of your crane.
GLEN HARNETT WAS APPOINTED AS General Manager of Capital Whole Goods on January 1, 13 years after he started with the company as a trailer sales engineer. In 2010, his aim was to increase trailer sales and provide support for TRT’s growing customer base. In his new role as GM of Capital Whole Goods, Glen will have responsibility for the frontline focus on capital wholegoods sales in New Zealand and Australia. This includes TRT’s full range of cranes and other OEM-manufactured products including Heavy Haulage Trailers, ESS Platform Trailers, Crane Trailers, and the TIDD Pick and Carry Crane.
TRT’s Director of Innovation and Sales, Bruce Carden, says “I am pleased that Glen has accepted the role of GM of Capital Whole Goods. This is a critical role
TRT confirmed its commitment to innovations and future development when announcing the launch of the Tidd PC28-2 pick and carry crane.
for TRT, and we need the right person to lead this. We needed someone that shared our vision for the future while acknowledging the rich history and legacy of TRT that was created by the innovative thinking and intuition of its founders. Glen is that person”.
Bruce continues, “Glen has demonstrated commitment and notable success in executing new strategies that have delivered significant results for TRT. His considerable experience in business management, heavy steel fabrication and engineering, positions the company to provide better support for our growing customer base and a greater level of focus to out-serve our customers.”
Glen’s knowledge of the industry derive from when he started his own company building car transporters. Following this, he joined BPW Transport Efficiency NZ Ltd as a Sales Manager for eight years. This is when the relationship with TRT started, as TRT was one of BPW’s largest parts and service customers.
Glen says, “product knowledge is very important when providing customers with transport solutions. Knowing what the customer wants to achieve and being able to provide this is very rewarding. We have many customers that continue to buy TRT products because they trust the product, the people, and the complete ongoing company support.”
“We strive to provide high-quality products that provide the ultimate
solution for our customers. Being an ISO 9001:2015 manufacturer, TRT must meet stringent auditing standards. All processes are managed in-house at our head office and manufacturing facility in Hamilton, New Zealand, from engineering design right through to customer delivery so we can be confident we are providing the end product the customer expects.”
“TRT was created by the innovative ingenuity and relentless hard work of its founders, the Carden family, and has grown into what it is today. I love what I do, and I am looking forward to trying new things both internally and externally and influencing decisions that benefit the future development of TRT,” said Glen.
Towards the end of 2022, TRT confirmed its commitment to innovations
and future development when announcing the launch of the Tidd PC28-2 pick and carry crane.
Leading from the front, TRT continues to enhance the overall Tidd crane operator experience and performance. The upgrades to the newly named Tidd PC28-2 are driven through TRT’s focus on continuous improvement, with consideration of industry and operator feedback.
“The Tidd PC28-2 is the better pick and carry crane experience. The new upgrades to the Tidd PC28-2 stem from our continuous focus on innovation and actively exceeding expectations for our customers,” said Robert Carden, TRT’s technical director.
“These new upgrades deliver a better all-round experience for the life of your crane, and we are looking forward to delivering the first orders to our customers next year.”
There are four key areas of improvement in the upgraded Tidd PC28-2. It features more powerful front suspension cylinders. This new
“We thrive to provide high-quality products that provide the ultimate solution for our customers. Being an ISO 9001:2015 manufacturer, TRT must meet stringent auditing standards.”
GlenHarnett, General Manager (GM) of Capital Whole Goods,
TRT.
system offers a greater lift capacity when articulated and working on a side slope, boosting lift capacity by up to 17 per cent.
New steps have been added to improve lift control. An additional three steps on the Tidd PC28-2 load chart deliver significant improvement when the crane is articulating. So, for the operator, this means that, as the crane articulates, it reduces the rate of the load chart decrease.
The Robway Tidd crane operating software has been upgraded with improved functionality. This enables faster processing and greater control responsiveness for the Tidd PC28-2 operator.
“TRT has always focused on the people when considering advancements in technology for the Tidd crane,” said Robert.
“With operator and dogman comfort central to the design of the Tidd crane, this new model also features a re-engineered ROPS cabin.
“This has been tested with a measured reduction in cabin noise levels by 8dBa at 80km/h when on the road.”
As well as these considerable upgrades, TRT has been focused on ensuring that Tidd customers and operators are fully supported for the life of the crane, from onboarding of operators to parts and service support Australia and New Zealand-wide. TRT also launched its new Tidd Crane Operator Familiarisation Program.
“From the start, the development of the Tidd crane was intended to set new standards in articulated crane performance, and we continue to focus on how we can advance this to provide the
best possible solution for our customers,” said Bruce Carden.
“The Tidd crane has come a very long way in terms of design, capacity, and functionality. The new Tidd Crane Operator Familiarisation Program is another example demonstrating our commitment and focus towards providing a better overall experience for Tidd crane operators.”
The new program includes a new Tidd Crane Operators Familiarisation Video, designed for experienced pick and carry crane operators to quickly and easily understand the Tidd crane operation, its functions, and the features of the crane, with access 24/7.
“This exclusive program is designed to suit our customers’ operations,” said Bruce.
“We also offer in-person training from one of our factory-trained experts, online manual access 24/7, remote video with one of our experts, and a dealer and service support network Australia-wide. We truly believe that this journey has created an overall better experience that pick and carry crane operators have been demanding.”
TRT’s dealer support and service network includes Baden Davis Crane Connection, based in New South Wales and the Australian Capital Territory, RMB Service Group in South Australia, Ronco Construction Equipment and Engineering in Western Australia, JDM Diesel Services in Victoria and Complete Crane Solutions in Western Australia, Karratha, Pilbara Region.
TRT’s dealers and service agents are selected based on their experience and knowledge of cranes and pick and carry cranes, and as importantly, on their commitment to providing a continued high standard of ongoing customer service and parts support locally.
“The new Tidd Crane Operator Familiarisation Program is another example demonstrating our commitment and focus towards providing a better overall experience for Tidd crane operators.”TRT Recently launched its new TIDD Crane Operator Familiarisation Program.
CraneSafe complies with Australian Standard recommendations
CraneSafe is supported by major crane manufacturers
CraneSafe is accepted by all State OH & S departments
CraneSafe is nationally recognised by the CFMEU
CraneSafe assessors are independently audited
CraneSafe is the only NATA accredited crane inspection program www.cranesafe.com.au