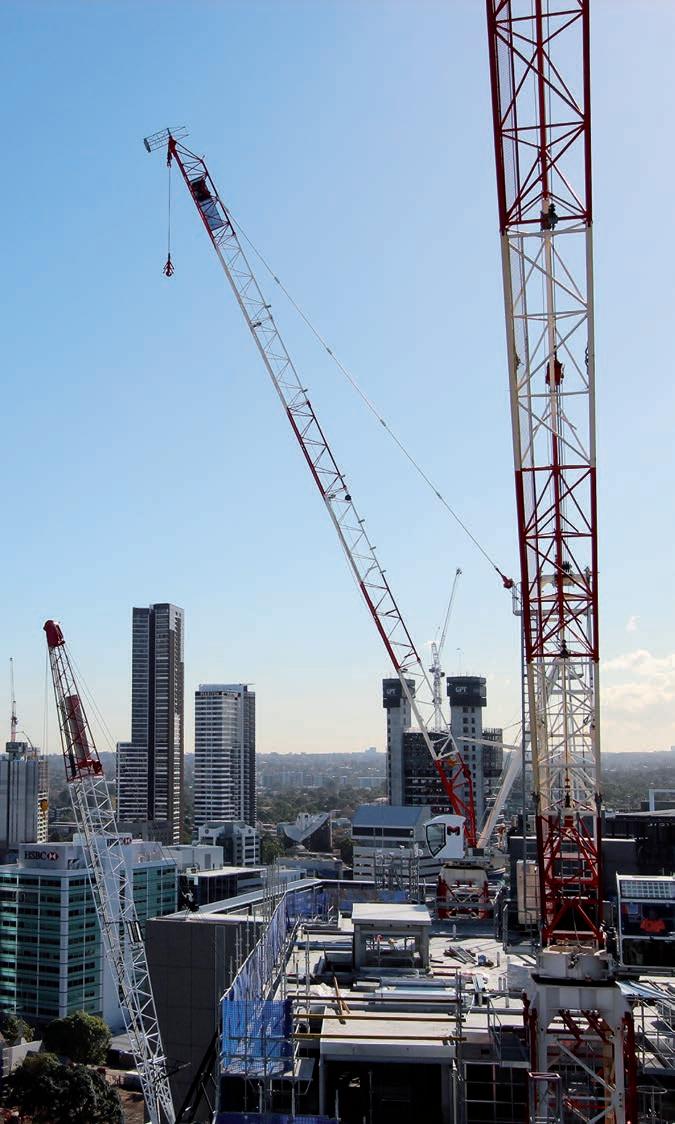
7 minute read
A new name in tower cranes Jarlway brand has been steadily building its reputation with help from national distributor Hardiquip
BUILDING THE BRAND The Jarlway name will be new to some, but to many it is a brand that has been steadily building its reputation throughout the tower crane sector for the past few years. Cranes and Lifting reports.
A Jarlway JTL180G14 and JTL160G10 at work in Sydney.
WHILE CERTAINLY NOT NEW TO THE
Australian market, changes in how the local construction industry must approach the issue of air rights over the past few years has certainly fostered the growth of the Jarlway tower crane brand in Australia.
With its focus on the luffing tower crane segment, Jarlway continues to produce cranes that keep pace with the market needs, and they don’t shy away from customising their product to give customers what they require for specific projects.
With a product range that covers everything from a 6t recovery crane to an 80m jib 32t flat top and a 60m jib 24t luffer, Jarlway certainly has a machine for most needs, however it’s been their luffers that have found them a niche in Australia.
“Since 2015, our cranes have been working in the Australian market, with customers like VTS Cranes in Brisbane adding the JTL120E8 luffing model with its 8t capacity and 45m jib to their rental fleet”, said Paul Gao, sales manager of Jarlway from his office in Guangzhou where the Jarlway factory has been located, since they started manufacturing cranes in 2004.
“We have learnt from our Australian dealer and customers, what is needed on our cranes to make them suitable for the market and what we need to offer as a manufacturer to support our product.
“Features like a secondary brake on the hoist winches are a standard item, not an option, and we use larger cabins and seats to suit the preferences of the Australian operators and our electrical cabinets are all stainless steel for durability. We know that one of the most important needs of any customer is the speed of the response from the manufacturer and with our factory team being almost on the same time zone as
the east coast of Australia and on the same time zone as the west coast, we are able to handle issues in normal business hours for our customers and mostly on the same day,” he said.
Making sure Jarlway cranes meet the Australian market requirements is another important step and the team at ADG Engineers play an essential role in this. Starting with a gap analysis to the Australian Standards, ADG Engineers perform a detailed design verification of every model of Jarlway tower crane imported by the Australian dealer. Reviews of the technical literature and design calculations are done as well as a visual inspection of the model on arrival in Australia to verify the crane has been manufactured according to the information given to ADG Engineers.
Principal of ADG Engineers Construction Services division, Graham Mapri, said.
“Dealing with the people at the Jarlway factory and with their dealer here in Australia is straightforward and quick. Being on roughly the same time zone means we can address any matters quickly and most are done on the same day. The factory is also open to our feedback on areas we think can be improved, and they have implemented many of these suggestions, so we’re pleased to show that our experience with tower cranes adds value.”
When it comes to getting the Jarlway tower cranes to fit the jobsites in Australia, the application engineering and customisation ability of the product is essential. This includes designing the tower crane to fit existing accessories for the rental company. Designing tower sections that can work within the available space yet are strong enough to reach the freestanding height needed with the jib length required, through to designing the crane to park in tight positions. The team at Jarlway works closely with Australian consulting engineers to get this done.
One such challenge was a tight parking requirement in Parramatta for a JTL160G10 luffer with a 50m jib on the 10t capacity model. Working with the
Steve Hardiman, managing director, Hardiquip.
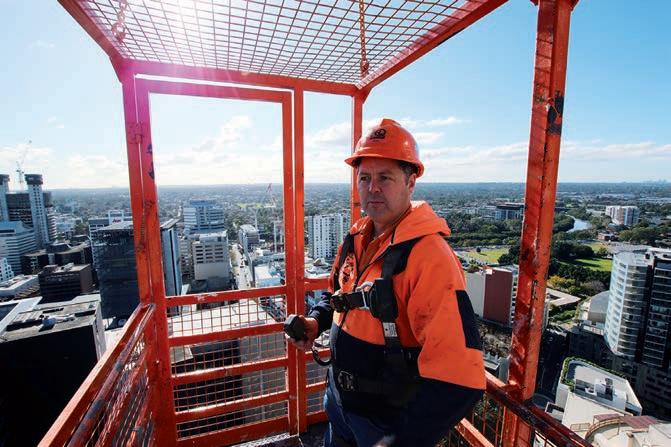
team at O’Hearn Consulting in Sydney, a simple and effective mechanism was designed and installed at the factory to allow the jib to park at a radius of 9.5m.
“Once we identified the need for the tower crane to have a non-typical, out of service configuration, we started working with Jarlway and the dealer on a solution”, said Matthew O’Hearn, principal of O’Hearn Consulting.
“Making sure that the result addresses all aspects of the installation design is critical and this involves looking at everything from the foundation, the tower sections, the jib and how the parking mechanism will be used by the operator each day. We were able to come up with something that not only worked well but was very cost effective for the customer,” he said.
Keeping the tower crane within the project boundary often involves installing it within the building footprint and that’s where the size and strength of the tower sections comes into play. For the people at Cosmo Cranes in Sydney, they needed their JTL160G10 to have a tall free stand with a 50m jib but fit within an elevator shaft that was too small for the typical tower sections used by this size of crane.
“Jarlway designed and made a customised tower type to suit this site that solved the project need, but Jarlway did it in a way that makes that customised tower something we can use in our standard project needs as well. They also kept the standard foundation accessories in the design, so we didn’t have the cost of a bespoke item,” said John Handley, business owner at Cosmo Cranes.
Sometimes, having the crane ready to go quickly is just as important as choosing the right crane for the job.
“We found ourselves in this position a few years back”, said Nuno Ribeiro, managing director of Access Cranes in Melbourne.
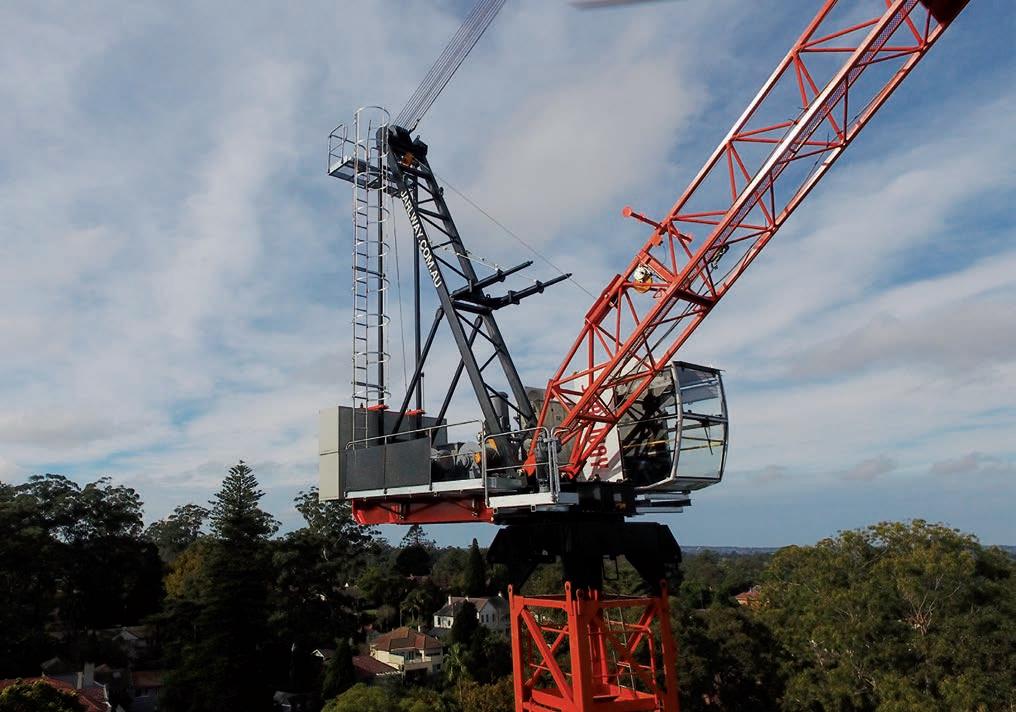
A Jarlway JTL110D6 operating in the suburbs.
“One of our customers was told they could not install the tower crane they planned to due to issues with the jib of the crane going outside the project boundary. Through our business relationship with a company in Hong Kong, we knew that Jarlway had designed a compact luffer to suit the narrow sites in Hong Kong, some of which are only 12m wide and 30m deep but have tall buildings on three sides. So, we contacted them and saw that the compact luffer would solve the problem for our customer here in Melbourne,” he said.
“Working with Jarlway on the production and shipping time of the crane and towers, we were able to come up with a solution that allowed our customer to continue with some of the construction of the project and we installed the tower crane into the partially built structure. Because Jarlway’s lead time is very short and shipping to Australia is only a few weeks from factory to our yard, we had the 40m jib, 16t capacity JTD4020D16 installed in a little over two months from the time of the call, including the Plant Registration with WorkSafe Victoria,” said Riberio.
What’s next for Jarlway in Australia will be something their newly appointed dealer, Hardiquip, is busy working on.
“Right now, we are seeing an increased demand for luffers to fit on job sites that previously would have used a small hammerhead or even a self-erector”, said Steve Hardiman, managing director of Hardiquip.
“Just making the crane fit the site space isn’t all that’s needed as quite often there are power supply limits we have to work within, and the cost of a generator is outside the budget for some projects. We’ve come up with a Low Power option on some models, which allows us to have the crane work from the grid without reducing too much of the crane’s performance.
“We’ve added quite a few of the small capacity luffers to our fleet in the past two years and we plan to continue investing to meet the market demand. Our technicians and riggers have been to the factory and are trained in the product there, including the erection work which we do on all new models we bring to Australia,” he said.
“Our parts stock is good, and we continue to add to it so we can support all the Jarlway owners in the market no matter where they are. With the factory team being so accessible during business hours and having the ability to get something from the factory to us overnight when needed, we feel confident that we can meet the needs of the market. It’s nice to have a good warranty and a factory that’s nearby, but it’s better to have a crane that’s built well and just works.
Reliability is what people remember,” said Hardiman.