
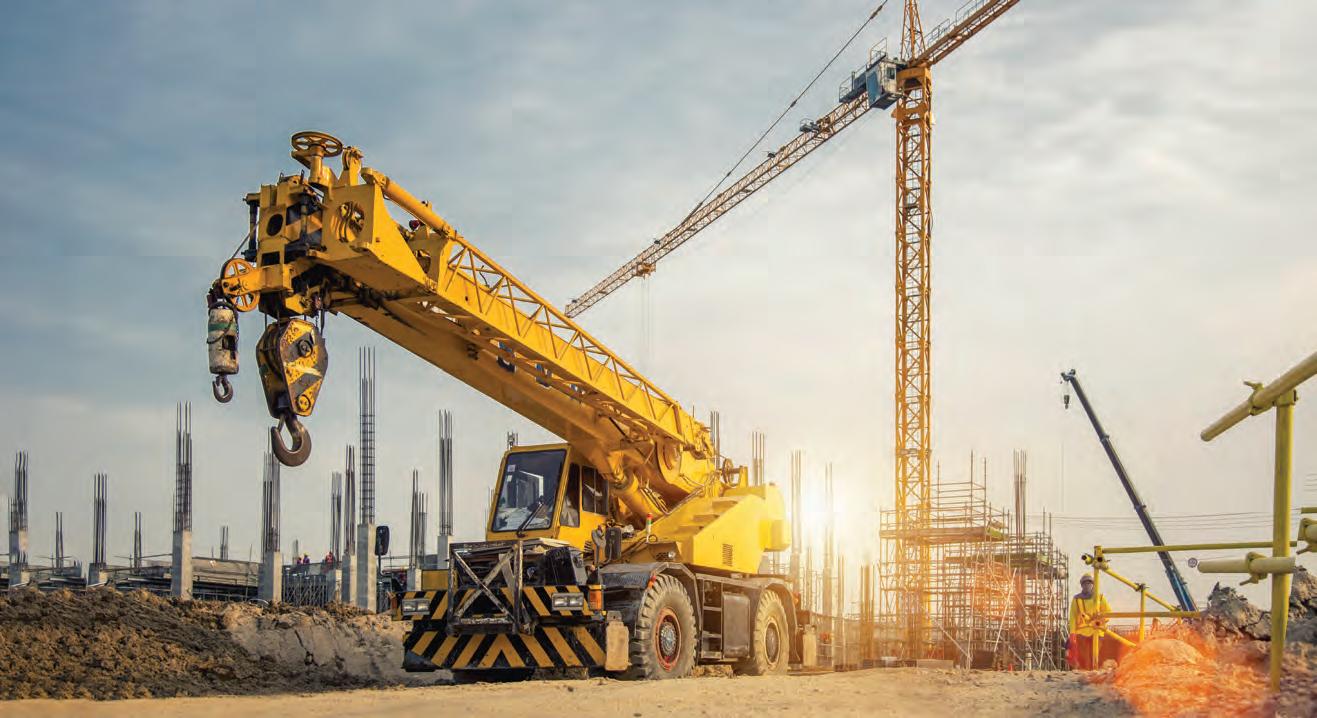
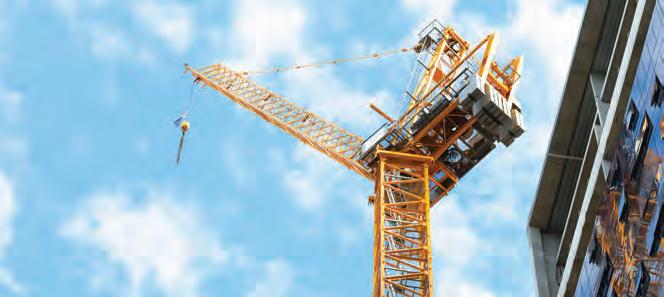
Cranes and Lifting Magazine cranes_and_lifting Cranes and Lifting
Between Hook & Load
38 Ranger Lifting
Importance of a successful LiftEx for the lifting sector.
41 Andromeda
The “climax design” that brings innovation and imagination to the industry.
44 Titan Lifting Technologies
An indepth look at Titan Lifting’s extensive range of lifting products.
47 Certex
20 XCMG
New 60t all terrain which won’t break the bank.
23 Boom Logistics
Taking a look at Boom Logistics Heavy Lif t capabilities. 28
A brief look at Libeherr’s recent Customer Days.
33
Delivers new TIDDs to Qube Heavy Lift.
Ganz International Ganz International to deliver Zoomlion
adano and Tenacity Cranes
Tenacity Cranes takes new 80t Tadano.
Safety first at JYC.
ampson Australia
John Lee discusses the art of safety and eparation when carrying out all tasks,
New Maeda tele crawlers delivered to
Equipment Planning and Organisation
Freo Group’s strategic decision to bolster ersatility and performance.
88 Potain Potains tackle viaduct project.
90 Manitowoc
New Potain delivered to RAR Group in Canberra.
93 Crane Engineering Service Marcus MA outlines the crane major inspection process.
Three women tell their story of breaking down barriers in the industry with the help of Certex Lifting.
50 LEEA and SpanSet
LEEA supports local manufacturing and testing.
53 Reid Reid’s 3Dx Lifting System provides high lif ting capacities.
57 Dynamic Rigging
Dynamic Rigging takes stock of a new crane in a push to be more sustainable and efficient.
60 LEEA Official LiftEx Gold Coast Showguide.
THE RECENT NEW SOUTH WALES BUDGET delivered good news for the construction sector, with regional communities benefiting from safer and more reliable road and transport infrastructure.
The Minns Government’s second budget invests in regional roads and bridges that will improve travel times for communities and support safer, more productive movement of freight in the regions.
The 2024-25 NSW Budget delivers $3.3 billion to rebuild road and transport infrastructure damaged during natural disasters which hit regional NSW the hardest.
To save lives and protect communities, the road safety budget will be increased to $2.8 billion. Additionally, an extra $28.6 million will be put towards building and upgrading 13 heavy vehicle rest stops.
Roads and infrastructure to better enable transport of Renewable Energy Zone components will receive $128.5 million for upgrades, including along the Golden Highway.
An additional $70 million will be invested to remove railway level crossings along the Inland Rail route at Tichborne
on the Newell Highway, between Parkes and Forbes, and on the Olympic Highway at Harris Gates near Illabo.
The 2024-25 NSW Budget contains $44.5 billion for regional transport and roads, as part of various NSW and Australian Government funded projects.
In this issue of the magazine, you will see a comprehensive guide to the LiftEx Gold Coast Exhibition and Conference. This is an important event for the lifting sector of our industry so please put the dates in your diary.
Other highlights are Borger Crane Hire constructing five bridges in five weeks, a look at Boom Logistics’ heavy lift capabilities and TRT delivering two brand new TIDDs to Qube Heavy Lift.
As always, the team at Cranes and Lifting has worked hard to bring to you the latest news and information from our industry and we hope you enjoy the read.
Simon Gould Editor, Cranes and Lifting
Published by:
379 Docklands Drive, Docklands VIC 3008
T: 03 9690 8766
www.primecreativemedia.com.au
CEO
John Murphy E: john.murphy@primecreative.com.au
Chief Operating Officer
Christine Clancy E: christine.clancy@primecreative.com.au
Managing Editor
Andrew Hobbs
E: andrew.hobbs@primecreative.com.au
Editor
Simon Gould
E: simon.gould@primecreative.com.au
T: 0404 865 109
Journalist
Jacob Lynch
E: jacob.lynch@primecreative.com.au
Business Development Manager
Emily Schlegel
E: emily.schlegel@primecreative.com.au
T: 0466 317 555
Client Success Manager
Glenn Delaney
E: glenn.delaney@primecreative.com.au
Art Director
Bea Barthelson
Imaging Assistant
Paul Breen
Subscriptions
Frank Rapone
T: 03 9690 8766
E: frank.rapone@primecreative.com.au
The Publisher reserves the right to alter or omit any article or advertisement submitted and requires indemnity from the advertisers and contributors against damages or liabilities that may arise from material published.
© Copyright – No part of this publication may be reproduced, stored in a retrieval system or transmitted in any means electronic, mechanical, photocopying, recording or otherwise without the permission of the publisher.
It’s our competitive ethos of solving the unsolvable, finding a way, and just getting on with it, that helps us make things possible for ourselves, our partners, and our customers.
It’s this drive that has led to our new generation TIDD Pick and Carry Crane. See for yourself and talk to us today about the TIDD PC28-3G.
Diab Engineering’s recent experience with the SANY SCC2500TB highlighted that telescopic crawlers are ideal for
Major engineering and fabrication business DIAB Engineering recently ordered a number of SANY hydraulic telescopic crawlers from Tutt Bryant Equipment, including a 250t SANY SCC2500TB, a 100t capacity SANY SCC1000TB and two 60t capacity SANY SCC600TBs. Ben Smit, Diab Engineering’s Manager of Engineering and Manufacturing, explains more.
FOR 50 YEARS, DIAB ENGINEERING HAS provided industrial maintenance and fabrication services to the mining and resources sector. In addition to two fabrication workshops, DIAB Engineering maintains staff and permanent mining maintenance services operations at remote mining sites, working at multiple sites acoss Australia.
DIAB Engineering’s projects require significant cranage and the engineering business owns a fleet of all terrains. Over the years it has also dry hired various cranes from Tutt Bryant Heavy Lift and Shift.
“We operate our own cranes and crews and ever since I’ve been with the organisation, we have been dry hiring
various capacity cranes from Tutt Bryant Heavy Lift & Shift. More recently, we dry hired a 250 tonne capacity hydraulic telescopic crawler, a SANY SCC2500TB, for the Kathleen Valley Lithium Project.
“With this project we built what we call a ‘dry plant’, which is a crushing and screening plant. We had five or six cranes on the project at any one time,
and the SANY was the largest capacity crane. Typically, when we get to site for a project like this, we are going to be there for anywhere between six months and two years, so we are deploying the cranes for a significant amount of time,” he said.
“Our first significant investment in the fleet was some 15 or so years ago and most of our cranes have been through their major 10 year inspections. Back then, telescopic crawlers were not that common, so we invested in various models and capacities of all terrains. But our recent experience with the SANY SCC2500TB highlighted that telescopic crawlers are ideal for our kind of work,” said Ben.
With the strongest lifting capacity and the longest boom in its class, the SANY SCC2500TB is an extremely versatile crane ideally suited for working in industry sectors such as
construction and infrastructure, mining and resources, as well as energy and renewables.
The SANY SCC2500TB’s 75.4m boom is made of a high-strength steel structure with a U-shaped section area. It features seven sections with the basic boom at 14.4m and the maximum boom length at 75.4m. The boom has full power with a single cylinder and plug for telescoping. The fixed jib measures 43m in length and can be installed at angles including 0°, 15° and 30°. Safe operation is at the heart of the control systems for the SCC2500TB and this includes the Smart Integrated Load Moment Indicator (LMI).
The SYIC-II integrated control system has been independently researched and developed by SANY. The system features a high level of integration and controls the power system to the
crane, the engine system, the main control system, LMI, auxiliary system, and safety monitoring system. Data communication between the controller, display, and engine is conducted by CAN bus technology.
The ergonomically designed SANY cab features the latest interfaces between the operator and the crane. The integrated 26.5cm touchscreen is programmable with ‘smart buttons’ to ensure the interaction between the operator and the machine are perfect. The cab has been designed to offer as much full vision of the work site as possible. The finger-tip controls and buttons are designed to enable more comfortable operations.
“DIAB Engineering has been providing solutions to the mining sector for 50 years. I’ve been with the business for 20 years and I am focused
on the construction and maintenance of infrastructure such as processing plants for large mining operations. I am responsible for approximately 200 guys spread across two or three construction projects at any one time, and we have up to 20 cranes across these sites,” said Ben.
“Most of our work is processing plant-related, and it involves Structural, Mechanical and Piping (SMP) construction. Typically, we fabricate a processing plant in one of our ‘state of the art’ workshops, take it to site, put it all together, stand the building up, install mechanicals and the pipework, put the cladding on and install electrical packages as well. We offer the full gamut of services,” said Ben.
According to Ben there are significant advantages with operating hydraulic telescopic crawlers.
“The SANY telescopic crawler proved ideal for our type of work and that’s why we decided to order four of them. With our work, we move the cranes around the site as elements of the project are completed. With the all terrains, we are packing up the counterweights, de-
slabbing and re-slabbing every two or three days and this can take a lot of time even if you are only moving the crane 20 meters. With the telecrawlers, we don’t have to pack up the counterweights, we simply drive the cranes to where they are required next. Another advantage is the setup of the telecrawler is not necessarily driven by ground conditions,” said Ben.
Ben and his team have been impressed with the performance of the SANY and with the service and support they have received from Tutt Bryant.
“The performance of the SANY was beautiful, and we had no issues with reliability. It was a brand-new machine, so you expect the performance to be pretty good, but we not quite sure what to expect. But it worked out beautifully and we had issues with the crane for the best part of 12 months we had it out on that job. Our operators had no issues, it was straightforward and simple to use,” said Ben.
The new SANYs are additions to the existing fleet and Tutt Bryant have been very supportive throughout the hiring and sales process, said Ben.
“As I mentioned before, most of cranes date back to 2010 plus or minus a year or two when we bought a lot of cranes. They’ve all been through their ten year inspections and they’re still all working really well. The SANYs are all additions to the fleet.
“The support from the team at Tutt Bryant has been consistently excellent. Thanes is one of their operations and service guys working out of the Karratha branch. He is really easy to deal with, very helpful and always spot on with the advice he provides. In terms of other general matters, there are another couple of guys we deal with down in Perth, who are also really easy to deal with and very responsive to any issues we might have.
“When you call, you know they’ll pick up straight away and if they can’t, they’ll call you back shortly after. We are finding this kind of response and commitment to service and support increasingly rare in the crane industry, so full credit to the team at Tutt Bryant for setting the bar high and continuing to maintain their high standards,” said Ben.
WE HAD OUR FIRST CICA WA GOLF Day on May 15 and were blessed with gorgeous weather. About 50 enthusiastic members came out to show their skills on the golf course. While some swings were impressive and others not so much, the event was a resounding success. If you missed this round, don’t worry – it’s been added as an annual event to the CICAWA Calendar, and you’ll have another shot next year.
We continue to engage with key government bodies, ensuring that our members’ issues are heard and addressed. WorkSafe has been working with industry to complete the major
inspection program, and though the state is still a couple of years away from catching up, the governing body has been proactive in collaboration and we’re grateful for it.
Training development is a key directive of CICAWA, and we continue to develop the training program with key stakeholders and events.
As we look forward to the future, we are excited to announce the return of the CICAWA Annual Family Fun Day for its fifth consecutive year. Scheduled for the third Sunday in November, it’s a day for families to come down to the foreshore and enjoy some rides, food and engagement with industry. This
event has always been a great one on the calendar, and we hope to see our members and their families join us again.
Finally, after 10 years I am resigning from my position. It’s time to hand over the reins and look to other projects, but before I do so I’d like to reflect on some of the fantastic successes I’ve seen in my tenure here and emphasise how much I’ve enjoyed the position and pushing for better outcomes for our industry.
Number one being the Certificate 3 in Mobile Cranes, which I hope industry embraces – it’ll improve us for the better.
I’d like to thank all who have helped me over the years. Brandon Hitch has always been a phone call away and has been patient with some very grumpy conversations. Ben Pieyere has been with me through a lot of this journey, and his support has been fantastic. To my executive teams over the period for all that they’ve done, and last but not least Allan Macpherson. This has always been his association, and many of the systems in place in Western Australia are because of Allan – I have always tried to represent the industry on his behalf to the best of my ability, and I feel honoured to have been a part of his legacy.
Anthony Grosser Chair, CICA Western Australia
“WorkSafe
has been working with industry to complete the major inspection program, and though the state is still a couple of years away from catching up, the governing body has been proactive in collaboration and we’re grateful for it.”
CICA Board
Ben Pieyre – President
Marcus Ferrari – Vice President
Danny Adair – Director
Danny Black – Director
Andrew Esquilant – Director
David Solomon – Director
Karli Sutherland– Director
CICA Office
Brandon Hitch
Chief Executive Officer 03 8320 0444 0428 228 048 ceo@cica.com.au
Paul Arztenhofer Membership Engagement/ Business Development Specialist 04 9093 9274 paul@cica.com.au
Alice Edwards Road Technical Engineer 03 8320 0440 alice@cica.com.au
Patrick Cran CraneSafe and CrewSafe Technical Advisor 0488 004 274 pat@cranesafe.com.au
Damien Hense CICA Road Policy Advisor 03 8320 0460 0488 007 575 damien@cica.com.au
Julie Turner CICA Executive Assistant/ Board Secretariat 03 8320 0411 julie@cica.com.au
Kate Galloway Traineeship & Industry Engagement Coordinator 0491 047 118 Kate@cica.com.au
Shane Coupe CraneSafe & CrewSafe Administrative Assistant Officer shane@cica.com.au 0491 047 134
Madeleine Flynn Senior Marketing Communications Officer madeleine@cica.com.au
Justina Blackman Member Events and Engagement 0403 717 626 justina@cica.com.au
For information, please visit our website or call the CICA office.
We have the capability to heavy lift and shift loads from 30 tonnes through to 3,000 tonnes, enabling us to efficiently support our clients.
• Heavy Lift
• Project Hire
• Quality Endorsed
• Specialised Engineering
• Heavy & Oversized Transport
Lampson Australia
21 Toronto St, Toronto NSW 2283 (02) 4941 0400 info@lampson.com.au lampson.com.au
Ashleigh Gould Office Operations Coordinator, ashleigh@cica.com.au
03 8320 0466
Unit 10, 18–22 Lexia Place, Mulgrave Vic 3170
Phone: 03 9501 0078
Fax: 03 9501 0083
Email: admin@cica.com.au Website: www.cica.com.au
The Crane Industry Council of Australia (CICA) took a deep dive into the Verification of Competency (VOC) licenses at the recent New South Wales CICA Industry Day.
BEGINNING WITH A WELCOME AND acknowledgement of country by Preston Hire’s Stephan Becherand, the topic of competency and experience demonstrated by an official VOC endured a sustained and thorough examination through a contractor panel moderated by Tadano’s Jay Gower.
Answering the questions and leading the discussion were David Solomon from the Master Builders Association, Warwick Johnson of Multiplex, Grant Gjessing from Strait Up Cranes & Rigging, Conan Jenkins of John Holland and Ryan March of Borger Cranes Hire.
The panel was first asked to discuss how it felt about the current VOC system and the requirements by most Tier One contractors to only accept VOCs by suppliers of their choice, before moving on to examining if the current VOC system genuinely measures a worker’s competency or if it is now just a box-ticking exercise.
Next, the panel delved into how it felt about rigging, dogging and crane operator high-risk work licenses being obtainable through a four-to-five-day course, with the legitimacy of VOCs versus traineeship program-acquired
skills also being cross-examined. Furthermore, the panel discussed the best way to properly ascertain the level of competence a worker possesses to complete certain tasks.
Following this, the panel talked advancements in crane technology and whether or not it is driving complacency as well as a lack of fundamental basic crane knowledge, the management of industrial relations, the future of the construction and infrastructure sectors, and how best industry practices are being relayed to workers.
Also on the agenda for the CICA Industry Day was a speech from Endeavour Energy’s Riley Bryn, discussing working safely around electricity. Discussing the Look Up and Live app, Riley said the app was a free powerline planning tool that utilises geospatial data over satellite imagery to
“The panel talked advancements in crane technology and whether or not it is driving complacency as well as a lack of fundamental basic crane knowledge, the management of industrial relations, the future of the construction and infrastructure sectors, and how best industry practices are being relayed to workers.”
provide accurate locations of powerlines that may be in the vicinity of worksites. According to Riley, the tool is free and easy to use, possesses a range of features and identifies the voltages and relevant asset owners.
Furthermore, Riley also said it can be viewed on a standard web browser or downloaded via an app to use on a mobile device.
Speeches from CICA CEO Brandon Hitch and SafeWork NSW’s Joshua Kent
immediately ensued after the lunch break, before Transport for NSW’s Brian Sheedy provided a thorough demonstration of the new dogging and rigging handbook.
The day was then rounded out by CICA’s Paul Arztenhofer expanding on CICA’s training initiatives and concluded with a speech from Preston Hire’s Stephan Becherand. The next CICA industry day will be held in Queensland on August 8.
⊲ Mercedes-Benz OM936
⊲ Stage V and Tier 4 Final compliant engine
⊲ Surpasses the latest Australian Design Rules (ADR) for cleaner emissions
⊲ Exceptional reliability and has been meticulously integrated for optimal performance and efficiency.
Not only compliant with current ADRs but also anticipates future regulations. ety as Standard Safety remains paramount. All machines incorporate the Franna Safety Radar as a standard feature, adding an extra layer of protection and awareness for operators.
Redesigned to improve user experience. Each model has recieved upgrades to streamline your operations, from simplifying maintenance tasks to providing safer and more streamlined access.
The right for an employee to disconnect from their workplace is a recent change to employment laws that has employers in the crane industry scratching their heads. Along with new rights given to union representatives when exercising their right of entry, employers need to be across the detail of the recent workplace law changes which have shifted the dial on employee rights.
IN THIS ARTICLE, WE DISCUSS THE NEW ‘right to disconnect’ and its interaction with modern awards as well as provide an overview of recent changes to WHS legislation in Queensland and South Australia that deals with rights of entry and the rights of unions to represent workers and health and safety representatives (HSRs).
Australian workplaces have a new ‘right to disconnect’ which allows employees to refuse contact from their employer (or a related third party) outside their working hours as long as the refusal is reasonable.
Whether or not a refusal will be reasonable will depend on a number of factors including:
• t he reason for the contact.
• whether the employee is compensated for:
- b eing available in the period when contact is made or attempted, or
- working additional hours outside their ordinary hours of work.
• t he nature of the employee’s role and level of responsibility.
• t he employee’s personal circumstances, including family or caring responsibilities.
While many operators in the crane industry may say that contact after-hours is an essential part of the business, particularly with last minute arrangements for crane hire, the new
right poses a risk to employers who do not manage those communications reasonably.
This is because the new right will be recognised as a protected right under the general protection regime under the Fair Work Act 2009 (Cth) (FW Act). In other words, if an employee chooses to refuse to respond to an employer’s contact after hours, and the employer takes disciplinary action against the employee because of that refusal, it might be the employer who now will be disciplined with a penalty for breaching the new law.
The new law will apply to large
business employers (more than 15 employees) from 26 August 2024 and to small business employers (15 or less employees) from 26 August 2025.
The new laws also require the Fair Work Commission (FWC) to:
• i nclude a ‘right to disconnect term’ in all modern awards by 26 August 2024; and
• prepare guidelines on how this term will operate (there is no legislative deadline for the guidelines).
The content of the model award term has not yet been determined. However, the FWC recognised that terms in modern awards will interact
with the new right and so it prepared an audit of all modern awards to identify which award provisions will impact the development of the model ‘right to disconnect’ term, including the Mobile Crane Hiring Award.
As a result of this audit, the FWC identified that, broadly, the following award provisions are likely to be impacted by a ‘right to disconnect’ term: spans of hours, employer notice requirements, requirements for employees to be on call/recall to duty/ remain on standby, and classifications that include manager or supervisory responsibilities. In the Mobile Crane Hiring Award the ‘right to disconnect’ term is likely to impact:
• Shift work (clause 23)
• E mployer notice requirements (clause 12.3, clause 13.7, clause 15.1, clause 23.10)
• O n call, recall and standby (clause 22.9 and clause 22.9(b))
It is expected that these clauses will be amended to take into account the new right. The new draft award terms are expected to be published for comments on 15 July 2024.
CHANGES TO WHS LAWS- QUEENSLAND
New rights for HSRs and clarification of the rights of WHS Entry Permit Holders (EPH) are also coming into force in Queensland under the Work Health and Safety Act 2011 (Qld) (QLD WHS Act) . In particular, there are changes to who can assist or represent an HSR or worker.
There have been many disputes about who can come onto site to help an HSR or a worker, either in a dispute or to give advice to the HSR or worker. To address this confusion, from 20 May 2024, the law now provides that a ‘relevant union’ is able to represent or assist a worker or the HSR. This covers any union which the worker is a member of, or is eligible to be a member, and whose rules entitle the union to represent the worker’s industrial interests. The union must be an employee organisation registered under the Fair Work (Registered Organisations) Act 2009 (Cth) or
Industrial Relations Act 2016 (Qld).
CHANGES TO RIGHTS OF WHS EPHS
There is often confusion and debate about whether an EPH can enter a workplace or not. To make it easier for right of entry, the law now that, as of 20 May 2024, an EPH can enter the workplace for the purpose of giving notice of entry and they do not have to first wait outside the workplace. Also notice will not be invalid simply because it contains a minor administrative error (e.g. spelling error or incorrect name of a person or relevant union which is otherwise sufficiently identified in the notice).
An EPH may also enter a workplace to inquire into suspected contraventions of the WHS Act or Electrical Safety Act 2002 and remain at the workplace, during its normal working hours, for the time necessary to achieve the purpose of entry. There is now no separate
Act) regarding civil dispute resolution processes for WHS matters, right of entry and improvements for victims and families affected by serious workplace incidents. The new law is due to become operational in the second half of 2024.
Going forward, while EPHs must still notify SafeWork SA before entering a worksite, they are now no longer required to issue a report to SafeWork SA about the visit. If they do issue a report, then SafeWork SA must now advise the WHS permit holder about what the regulator’s response is to the report.
In balancing issues regarding misuse of the right of entry powers, the South Australian Employment Tribunal (SAET) now has the power to issue a ‘probationary declaration’ against a union if the union has a significant record of refusing or failing to comply
“A number of recent changes to WHS and workplace laws will impact operators in the crane industry.”
requirement to give additional notice to view relevant employee records or other documents held or accessible at the workplace, or to consult workers about the suspected contravention, if the EPH has already entered and remained at the workplace. This removes the confusion around whether an additional notice of 24 hours is required or not.
And to further protect the EPH, the new law removes one of the methods in which a PCBU could look to delay the EPH, by now providing that a PCBU is not allowed to request the EPH to comply with a WHS requirement if it would unduly delay, unreasonably prevent or hinder the EPH exercising a right of entry.
A number of important changes have also been made to the Work Health and Safety Act 2012 (SA) (SA WHS
with obligations applying to WHS right of entry. A declaration will remain operational for two years, during which time the union:
• c annot seek civil penalty orders from SAET; and
• officials of the union who hold a WHS entry permit must notify SafeWork SA before exercising a right of entry and must provide a written report to SafeWork SA within 14 days setting out the details of their investigation.
A number of recent changes to WHS and workplace laws will impact operators in the crane industry. In particular, employers will need to implement processes to manage the new ‘right to disconnect’ laws as well as the modified WHS right of entry rules. Being wellprepared will reduce the risk of exposure to a claim or a penalty.
P.A. Construction Equipment Pty Ltd (Pace Cranes) was established in 1987 to provide the construction industry with an independent Australian owned and operated crane sales, crane service and crane spare parts organisation.
For over 30 years Pace Cranes have offered premium quality equipment to the Australasian market with a dedicated and unrivalled service, supported by specialist technical advise across the full range of equipment sold.
Advanced control features
Smooth, precise operating system using advanced technology. Equipped with a remote control that features a large-screen and power-saving color LCD display.
Reliability you can trust
Engineered meticulously to easily handle loads in versatile environments and has been tried and tested by the industry. Known for its quality and performance.
Best-in-class service & support
Our technicians are fully equipped with the tools and experience; and are trained specialists in loader crane servicing. So invest with peace of mind.
Giant to enable offshore wind construction methodologies as components grow.
MAMMOET HAS RECEIVED ITS FIRST Liebherr LR12500 crane. With a capacity of 2,500t and a 200m hook height, it will help to ensure the constructability of future energy and infrastructure developments.
Seeking greater build efficiencies, projects across a range of sectors are increasing the size and scope of prefabricated construction methodologies. As a result, assurance is needed that today’s project planning will match tomorrow’s equipment.
Energy projects in both the nuclear and oil and gas sectors will rely heavily on high capacity lifting equipment to bring forward the date of first power, while increasing the cost-effectiveness of the build phase in the case of new construction, and reducing downtime in the case of turnaround projects.
Offshore wind turbine components are growing at a fast rate, with nacelles of 1,000t, tower sections of 2,000t and jackets and monopiles of 3,000t in production. Companies across the sector need peace of mind that components currently planned can be transported and assembled by future equipment – as lead times increase, doubly so.
“Despite its large size, it folds into dimensions small enough to remain in-gauge.”
Similarly, civil megaprojects will depend on high-capacity lifting equipment that allow more construction to take place away from the project site, with both cost and environmental benefits.
In all cases, Mammoet says the new LR12500 unit will support these construction methodologies, building in larger pieces to cut down integration and transport schedules.
The LR12500 features a wide high-performance boom, which offers
increased stability at reduced (self) weight. Despite its large size, it folds into dimensions small enough to remain in-gauge. Both features increase the cost-effectiveness and sustainability of its mobilisation.
A 100 metre main boom and 108 metre luffing jib help the LR12500 to reach 200m maximum hook height. Dual engines with redundancy ensure high levels of reliability, as the crane can continue operation using just one power unit.
XCMG has released a new Australia-ready all-terrain crane, the XCA60_AU. XCMG’s ANZ Crane Manager, Stephen Broomfield, discusses how the model promises to thrive in Australian conditions and the competitive advantages it offers to prospective buyers.
THE 60-TONNE ALL-TERRAIN MARKET IS one of the most competitive in Australia.
As one of the most competitive markets, manufacturers are looking for any point of difference they can acquire over each other.
For XCMG and Stephen Broomfield, the message is simple: the delivery of reliable, high-quality machinery to crane yards at prices that won’t make business owners’ eyes water for the next 10 years.
“At the end of the day, a crane is a crane,” he says. “They’re large investments that require financial borrowing and, in today’s markets with soaring interest rates, coupled with lengthy lead times, buyers are waiting longer for cranes that are taking 150 per cent of previous times to pay off.”
And, in a positive turn of events for crane hire companies looking for
a roadable, reliable, robust taxi crane, XCMG has developed a new crane to counteract current market trends: the XCA60_AU. As part of a series of cranes released from the manufacturer specifically designed to thrive in Australia’s climatewhich recently has seen machines operate comfortably in the Pilbara, Stephen says the crane is set to soar Down Under.
“XCMG’s never made a crane in this kind of area: it’s the first 60-tonne all-terrain crane we’ve manufactured, and we’re confident in the crane’s capabilities,” he said. “We know that anyone who drives and operates this machine will see the quality that we know the XCA60_AU possesses.”
The three-axle, 60-tonne all-terrain crane possesses a maximum hook height of 64.1m and a maximum operating radius of 40m. As a taxi crane, accessibility is at the forefront of the crane’s design with the machine measuring in at 12m long, 2.8m wide and 3.9m tall. The six-section, U-shaped boom possesses a single-cylinder
The XCA60_AU is compliant with ADR/04, competitively priced and high performing.
pinning telescoping system and, on its own, can reach heights of 10.7m through to 50m. With the fixed lattice jib fitted on, the crane receives an extra 9.2m-to-16m in height that can be offset at angles of 0, 15, or 30 degrees. The crane can be optionally fitted with a 2.5m independent jib head and a 46-tonne hook block.
On the counterweight front, the XCA60_AU can hold a maximum of 13 tonnes of counterweight that is available in six different combinations: 2.4 tonnes, 3 tonnes, 7.5 tonnes, 7.9 tonnes and 13 tonnes. When it comes to roading the crane under the 12 tonne per axle load limit, the crane can be configured in two different modes. The first configuration includes the auxiliary sheave, jib bracket, 2.4 tonnes of counterweight and the 30.5 tonne hook block. The second reflects the first, however can carry the auxiliary winch in tandem with a lighter hook block measuring in at 13.5 tonnes in capacity.
As mentioned before, the XCA60_AU possesses a lifting capacity of 60 tonnes, which the crane can lift at 2.1m in radius; at the crane’s maximum telescopic extension of 50m. At an operating radius of 36m, the crane can lift 900kg with the full complement of counterweight attached.
On the technology front, XCMG has installed a Load Moment Indicator that audibly and visually warns the operator when they are close to overloading the machine. Operations are automatically stopped before overloading occurs, while overload memory function and fault
diagnosis are available as standard.
XCMG has taken further steps to enhance the safety of its machines, installing hydraulic balance, two way and relief valves, a lowering limiter for preventing the wire rope from over releasing, and an anti-two block at the boom head to prevent the wire rope from over-winding.
What’s more, XCMG has installed a new steel cab on the XCA60_AU that is capable of being tilted by 20 degrees. Featuring a spacious interior, operator comfort has been kept forefront in the cabin’s ergonomic design, with the seats being made of leather and breathable mesh as well as a human machine interactive
The XCA60_AU can hold 12 tonnes of counterweight and is roadable under the 12-tonne per axle limit with 2.4 tonnes of counterweight plus its 30.5-tonne hook block.
control panel and a 12-inch display.
Powered by a Mercedes Benz engine, the crane is not only ADR/03 compliant; XCMG has taken steps to ensure the crane presents a long-term asset that operates at a high level for a sustained period of time by manufacturing the crane to be ADR/04 compliant, meeting EUROMOT 5 regulations in the process.
“We’re injecting high performing machinery into the Australian crane market that is environmentally sustainable,” Stephen said.
“Furthermore, the lead times are significantly shorter due to the rapid automated manufacturing capabilities in Xuzhou, while prices offer the chance to have the crane paid off within a much shorter time frame than the 5-7 years currently being seen with our competitors.”
Ably supported in the west of Australia by Ronco and in the east by D&D Diesel, XCMG has invested in both its support networks as well as the quality of its machinery in the Australian market which, for Stephen, is typified by the arrival of the XCA60_AU.
“The crane represents exactly what XCMG is striving to do globally,” he says. “We are committed to selling Europeanstandard cranes at cost-effective prices with immediate delivery.”
The New GMK5150XL is the latest sibling of the GMK5150L-1, with longest boom (69m) and most versatile road weights in class
• Reach further with 69m boom and 30m hydraulic luffing fly
• 50t GVM with outriggers in situ for reduced cost legal travel in all Australian states and territories
• 10.2t counterweight in situ at 12t per axle
• Increased safety and flexibility with MAXbase variable outrigger positioning
• Faster, intuitive set-up with CCS (Crane Control System)
• Grove Connect Telematics
• Capacity: 150t
• Main boom: 68.7m pinned*
• Maximum Jib: 30.2m (40O hyd luff)
• Maximum tip height: 99m
Boom Logistics has recently showcased its capabilities by completing a major project within Perth’s Metronet construction program. This involved the installation of over 530 precast L-beams and 180 piers for the Victoria ParkCanning Level Crossing Removal Project. Dave Barfield, Boom Logistics’ Regional Manager since 2017, shares insights into the company’s journey and achievements in heavy lifting.
STRATEGIC INVESTMENTS AND GROWTH
When Dave joined Boom Logistics, the company’s heavy lift division had a 450t crane, with its 500t crane having been relocated to East Coast projects in 2016.
“The decision to acquire a 750t capacity crane in 2017, instead of another 500t all-terrain, was a game-changer,” says Dave. This led to the addition of the Liebherr LTM 1750-9.1 and the Grove GMK7450, marking the inception of Boom Logistics Heavy Lift WA.
Boom Logistics’ first significant project was the $417 million Great Northern Connect (GNC) contract for work on Perth’s Tonkin Highway. “GNC was the first project to kick off Boom Logistics Heavy Lift in its current form. Since then, our team has grown exponentially, supported by a first-class engineering department known for its precise and reliable drawings,” explains Dave.
Other successful infrastructure projects in Western Australia include:
• Roelands rail bridge replacement project
• A lbany Ring Road
• K arel Ave upgrade Armadale Road Project
• Th omas Rd Upgrade
• M itchell Fwy Extension
• Melconnx project
• Q uindanning Rd upgrade
Boom Logistics recently completed its heavy lifts for the Armadale Line Upgrade Alliance (ALUA) which is delivering part of the Victoria Park Canning Level Crossing Removal project, lifting over 270 beams, 145 piers and 60 headstocks. “This is the largest infrastructure project in Perth and likely the biggest we will see for some time,” says Dave. Despite the heavy-lift scope being completed, Boom Logistics’ cranes will continue to
support the construction of the rail line, stations, and associated infrastructure.
Dave elaborates on the meticulous planning required for such large-scale projects. “We were involved early in the tender process, which started approximately two years ago, with heavy involvement in planning for about 18 months. This involved our heavy-lift team, superintendents, and engineers working closely with the client’s teams,” he explains. Mobilising the Liebherr LTM 1750-9.1, for instance, requires up to 16 truckloads of gear, highlighting the logistical complexity involved.
Dave further highlighted a challenge of the project: limited space for both operations and construction.
“The success of our lifts and overall project execution relies heavily on the expertise of our operations and heavylift teams,” he said.
Dave explained the strategic
approach taken with the Liebherr LTM 1750-9.1 and Grove GMK7450 during the heavy lifts: “We approach each project with efficiency as a priority. This often involves using less counterweight on the 750 and 450 cranes, allowing us to relocate them more easily without the need to strip and rebuild. In some cases, the most efficient method is to fully counterweight both machines and install as many beams as possible from a single location.”
Boom Logistics’ crane division plays a crucial role in supporting the heavy lift division, working synergistically to ensure seamless project execution. The crane division complements the heavy lift operations by providing the necessary equipment and expertise required for complex lifts. This collaboration is meticulously coordinated through Boom Logistics’
dedicated logistics team, ensuring every aspect of mobilisation, operation and demobilisation is handled efficiently.
Dave Barfield elaborates, “Our crane division and heavy lift division operate in perfect harmony. The logistics team coordinates the deployment of cranes, ensuring they are in the right place at the right time. This synergy allows us to tackle even the most challenging projects with precision and efficiency.”
This integrated approach ensures that Boom Logistics can consistently deliver high-quality service, maintaining its reputation for safety, reliability and excellence in the heavy lift industry.
Managing assets effectively is crucial for Boom Logistics to ensure the availability of the right capacity cranes for any project. Dave mentions the recent relocation of a second Liebherr LTM 1750-9.1 from the East Coast to WA due to increasing market demands
and the company’s growing footprint. “Sometimes it feels challenging, but with a strong team it always works out. Our team’s dedication and expertise ensure we meet our commitments,” he adds.
Boom Logistics prides itself on transparent communication and exceptional service and support. This commitment is exemplified by the successful, incident-free completion of the heavy lift element of the Victoria
Park-Canning Level Crossing Removal Project, which finished ahead of schedule.
“In a competitive market like WA, success comes from commitment to the client and delivering on promises. Our team remains grounded, humble and focused on providing the best service possible. That’s what sets us apart,” Dave concludes.
Boom Logistics continues to build its reputation for efficiency and safety, reinforcing its position as a leader in the heavy lift industry.
PROJECT OF THE YEAR
WINNER 2023 - John Holland for the Batemans Bay Bridge replacement project.
The Crane Industry Council of Australia (CICA) recognises excellence and innovation in the Australian crane industry with the CICA Lift Of The Year Awards.
PROJECT OF THE YEAR
INNOVATION OF THE YEAR
LIFT OF THE YEAR –UNDER 20T
LIFT OF THE YEAR –OVER 20T
THE INNOVATION AWARD went to Bullivants for the ADAPTA Adjustable
LIFT OF THE YEAR
LESS THAN 20 TONNE WINNER –
McMahon Services won for removal of the Heritage Listed Copper Kettle during demolition of the West End Brewery.
LIFT OF THE YEAR MORE THAN 20 TONNE WINNER -
Walz Group won for several Triple Crane Lifts completed to extract the 60m-long DN500 Jacketed Pipe Units at an alumina refinery.
RITCHIE BROS., A GLOBAL LEADER IN asset management and disposition, has announced its Australian National Unreserved Auction, scheduled to take place on August 21 and 22, 2024. This highly anticipated event will feature a diverse selection of machinery, including assets from a significant fleet realignment from LCR, located at the Ritchie Bros.’ Brisbane yard at 1-57 Burnside Rd, Brisbane, Australia, 4207.
HIGHLIGHTS OF THE AUCTION
• 2010 Terex Demag AC80-2
• 2015 Tadano GT-600EX
• 2 x 2014 Franna MAC25
• 2008 Franna MAC25
• 2005 Franna MAC25
• 2 x 2013 Franna AT-20
Cody Irvine, Regional Sales Manager at Ritchie Bros. Auctioneer, said: “We are excited to host Australia’s National Unreserved Auction on August 21 and 22. This auction presents an exceptional opportunity for buyers to acquire high-quality machinery from a fleet realignment. The lineup includes reputable brands such as Terex, Tadano, and Franna, all well-maintained and ready for immediate use. Interested parties are encouraged to inspect the items at our Brisbane yard. Feel free to contact me directly for any enquiries or to arrange an inspection.”
Anthony Donegan, National Asset Manager from LCR Customer, said: “As a part of our strategic fleet realignment, we have consigned a selection of our machinery to the upcoming Ritchie Bros. auction.
Our 2010 Terex Demag AC80-2, 2015 Tadano GT-600EX, and various Franna models have been meticulously maintained to ensure they meet the highest standards of performance and reliability. We trust that these assets will serve their new owners well and
continue to deliver excellent results.”
Ritchie Bros. invites all interested buyers to attend the auction and take advantage of this unique opportunity. The auction is unreserved, meaning every item will be sold to the highest bidder, regardless of price.
Potential buyers are encouraged to inspect the items prior to the auction and register at rbauction.com.au.
To arrange an inspection or for any enquiries, please contact Cody Irvine at +61 474 418 818.
Liebherr unveiled the world’s most powerful 6 axle crane on the market, the new LTM 1400-6.1.
1,500 customers were flown in from all over the world to witness the best of Liebherr’s innovation and 80 Australian and New Zealand Liebherr customers were very impressed with the Consistently Innovative themed event.
VARIOUS TECHNOLOGIES WERE demonstrated live and in person to guests in the Innovation Park. There was also an opportunity for visitors to get hands-on with various cranes: crane operators had the opportunity to test the superstructure operation of machines equipped with the latest LICCON3 control system and drive mobile cranes via wireless remote control. An LTC 1050-3.1E with electric drive was also available for test drives.
The Customer Days at the Liebherr plant in Ehingen, Germany, have established themselves as a globally
recognised industry event for mobile and crawler cranes. They took place for the seventh time in mid June this year.
A special highlight was the unveiling the world’s most powerful 6-axle crane on the market: the new LTM 1400-6.1. The 400-tonner has a 70-metre telescopic boom and is characterised by clever yet simple set-up processes. The new crane is the successor to the proven and successful LTM 1350-6.1. Like its predecessor, the LTM 1400-6.1 is now the smallest crane with Y-guying, making it the perfect introduction to this boom technology with
its enormous increase in lifting capacity. The new all-rounder is extremely flexible and economical, thanks to a wide range of equipment, a highly functional modular boom kit and the familiar Liebherr technologies.
Australian and New Zealand Liebherr customers were very impressed with the Consistently Innovative themed event.
In accordance with EU Regulation 2019/2144, driver assistance systems will ensure greater road safety in future. Accordingly, multiple information systems will also help drivers of Liebherr mobile cranes to navigate areas that are difficult to see, for example on the passenger side of the crane, as well as behind or directly in front of the vehicle. These systems are designed to significantly increase safety, especially for vulnerable road users such as pedestrians and cyclists. The new LTM 1300-6.4 and LTM 1400-6.1 cranes come equipped with these assistance systems as standard. These technologies will gradually be made available for all other mobile crane models in the Liebherr portfolio by mid-2026.
One of the most important new features is the Blind Spot Information System, whereby a camera monitors the entire side area of the crane.
When the crane is turning, the Blind Spot Information System warns the crane driver both visually and audibly if there is a person or an obstacle in the lateral danger zone. The moving off information system also provides a visual and audible warning
as soon as someone is in front of the crane. Due to the crane’s design, the driver’s view is somewhat restricted by the hook block and boom. Children are at particular risk since they are even less visible from the driver’s seat due to their height. The moving off information system monitors the area in front of the crane to prevent accidents.
Shawn Borger, General Manager Borger Crane Hire and Rigging Services, has this to say about the Liebherr Customer Days.
“Firstly, let how say how impressed I have been with the whole week with Liebherr. It’s been a week full of highlights, including the accommodation, the food and the people on the trip but the Customer Day was very exciting for me.
“There were so many new cranes on display featuring the very latest technology and the crane demonstration really stole the show for me. During the crane demonstration we watched Liebherr demonstrate its commitment to the day’s theme ‘Consistently Innovative’ and to see a crane remotely driven onto a jib section and then lifted into the air was super impressive. Then big surprise came during
the night with the drone show which was just next level. I think it was a great, great achievement by Liebherr and all the people that put in for the big day,” said Shawn.
The launch of the new 6-axle LTM 1400-6.1 crane, a powerful 400-tonner with a 70-metre telescopic boom which is designed with a clever yet simple set-up processes, was also a highlight for Shawn and his team.
“We had a group of 13 here because we view the Liebherr Customer Day as being very important in the global crane calendar. We fly some of our senior staff over so they can see how our fleet is going to look in the future.
“We were all impressed with the 400 tonner and we’ve already put an order in for four units already on the strength of what we saw during the day. They won’t be delivered until 2027 but they will be an important addition to our fleet.
“The continued renewal of our fleet is an important strategy for Borger Crane Hire. It is important that customers see we are continually investing in the very latest technology which will help deliver their projects, safely, in full, on budget and on time,” said Shawn.
Second-generation owner of Lindores Mobile Cranes, Chantelle Lindores, discusses the history of the company, her key lessons learned in owning a business, and the “things that parents throw at you”.
IN 1985, PETER LINDORES BEGAN TOTAL Rigging, a crane hire company dedicated to providing rigging and crane services to the South East Queensland construction market.
However, go back to the late 80s and early 90s and ask Chantelle Lindores what she would be doing in her career, and her answer would resolutely be anything but what her parents did. And yet…
“Here I am,” she says, “currently living in my parents’ house, running a crane hire company after buying into the industry whilst my Dad still ran a large crane company and my mother had started her own EWP company doing exactly what they had done for years.
The journey from 1985 to 2024 in the crane industry has not been a smooth
one for Chantelle Lindores. By her own admission, she frequently ponders what keeps her in the crane industry and, to find the source of that passion, she takes us back to her foundational years.
“Cranes have always been in my DNA,” she says. “Right from a young age, I was always around the office and crane yard, I was giving up my school holidays to help with administration, and even today, as an owner, I’m still working around some people who worked with my Dad,” said Chantelle.
From writing her own Franna licenses with her girlfriend, to helping her Mum, Colleen, in accounts, to travelling into the office on school holidays to answer phones, Chantelle holds a unique insight into the foundation of the company that is today
named Lindores Mobile Cranes – and the story of how it got there is an emotional one.
Following the initial introduction of Total Rigging that was started by Peter and co-investor, Boyce Narung, in 1985, Peter made the decision to buy out his co-owner and go solo in 1987. For the next two decades, the company evolved to become a staple in general the general construction industry – a time that Chantelle reflects on with fond memories.
“I grew up around these people as a baby, and I always had fun and felt like they were a good bunch of people,” she says. “I’ve got distinct memories of being hosed down by one of the team just for a laugh, and I’ve always felt the fun nature of the industry has suited me.”
After two decades under Peter and Colleen, however, the business had run its course and, following the handover of Mini Cranes Queensland from Chris Austin to the Lindores family in 2007, the company focussed a lot more on the mobile crane hire side of operations. Now under the joint ownership of Chantelle and her partner at the time, she says the days between 2007 and 2015 when she took sole ownership of the company were some of the hardest that she’s faced, both professionally and personally.
“I raised three kids while he ran the
business, and he didn’t do a very good job of it,” she says. “When I found out what he was doing, I thought ‘we need to turn it around’. Step one in that process was taking control of the business myself, getting divorced and step two was streamlining the business,” said Chantelle.
And streamline it she did. Rebranding as Lindores Mobile Cranes in 2015, Chantelle leaned on the niche market of smaller crane hire and mini crawler cranes to get the business back on its feet. Today, the company owns a range of mini crawler cranes spanning from 2.8 tonnes in
capacity through to 4.8 tonnes, a 13-tonne Kato City Crane, a range of Franna pick and carry cranes, one 35-tonne Humma pick and carry crane, and a whole range of slew cranes spanning up to 55 tonnes in capacity. With more to come.
For Chantelle, the journey to take the company from where it was to where it is today represents a story of peaks, troughs, and perseverance.
“The hardest time for me was right when I took sole ownership; I was feeling like I didn’t know anything and there was one time I said to my parents that I was
done, and I just couldn’t do it anymore,” she says. “They reassured me that it would all be okay, and I persisted through the hard times to get to where we are today.”
And, through that perseverance, Chantelle, by her own admission, enjoyed her time – especially with the unwavering support of her team by her side.
“I had three guys working for me that I relied on greatly at the time; one of them Tez, is still here, as he came to the business back in 2007,” she says. “He’s a crane driver and without his support, I would not be here today.”
Despite getting business back on track, however, the world still held more curveballs to throw at Chantelle and the fortunes of Lindores Mobile Cranes; fortunately for her and the team though, the COVID-19 pandemic didn’t just not break the Southeastern Queensland crane hire company, but instead made it what it is today.
“Before COVID we weren’t doing as well as we’d have liked; then, as soon as the pandemic hit, conversely to a range of other small businesses, our workload tripled,” she says. “We came out the other side of the pandemic still going strong and today we’re still doing just as much if not more.”
With a laugh, she says the uptake in business has forced her to develop her financial and business acumen; looking to the future, with a proper accounting structure in place and plans to purchase more machines in the next decade or two, she says Lindores Mobile Cranes is in a strong position to continue as its tracking – as long as that falls within its modus operandi.
“Our outlook over the next 10 to 15 years would be to buy at least another 10 cranes and continue revitalising our fleet,” she says. “I’ve always said I wouldn’t go over 100 tonnes, because I just don’t want to deal with all the big boys and their toys; I want to be general hire and looking after the customers that we’ve already got.”
Because, for Chantelle being good at her niche is what’s taken Lindores Mobile Cranes to the heights she’s hitting today. Labelling her father’s desire for her to purchase 10 350-tonne crawler cranes to go and service the telecommunications aspect of crane hire as ‘the random things parents throw at you’, Chantelle says the company is perfectly happy to keep things simple and straightforward ahead of getting too adventurous.
“We’ve got some really good customers in building houses and general hire,” she continues, “and I’d just like to look after them so we can continue to specialise in our niche. We’re not here to take over the world, we just want to be good at what we do.”
As Chantelle mentioned, from an asset point of view, Lindores Mobile Cranes
is more than covered when it comes to its future plans; in its second generation of Lindores family ownership, however, Chantelle has one eye on the future and the prospect of her kids taking the business into a third generation of family ownership. Saying that she’d love for her three children to either take over the business or play some integral role in its future, she’s also keen to stress that, as long as they’re happy, then so is she.
“My parents are 71 years old and still working, because they love what they’re doing; I want to be enjoying my retirement at that age,” she says. “My children are in a mixture of travelling, schooling, and apprenticeships, and whatever choices they make, I’ll support them entirely.”
“My parents never pushed the business onto me; it just happened through being in the right place at the right time and taking an opportunity that presented itself, and that’s how I want to be with my kids” she continues. “Some of them have said they want to work elsewhere which I’m all for because we can’t just work for our parents for our entire lives. I would never push this onto my kids but, on the other hand, if they want to come back into the business, they’ll be welcomed with open arms because I’d love it if they took it over.”
Because, despite the trials and tribulations that she’s faced in the industry over the past 40 years, according to Chantelle, the people that she’s met, the projects that she’s worked on, and her own personal successes have brought a lot of fulfillment and self-development to her life and taught her what it means to persevere through adversity.
“My time working around cranes has shown me that I can survive anything, and that level of belief is irreplaceable,” she says. “There were days where I just didn’t feel like it, but we’ve rebounded to the point where I know that it’s going to be okay with the right level of application.”
And as for her key lesson learned?
“Finding the right people to support you is the thing,” she says. “Knowing other people in the industry who can sympathise with you is a godsend, and sharing in each other’s successes is what makes the job enjoyable at the end of the day.”
Servicing the Major Infrastructure, Construction, & Renewable Energy sectors, Johnson & Young Cranes (JYC) provide mobile crane hire solutions Australia wide.
With a state of the art mobile and crawler crane fleet with capacities ranging from 3t to 800t, an expert team and a wide variety of truck & trailer combinations, JYC ensure safety, reliability and exceptional performance for all lifting requirements.
Partner with Johnson & Young Cranes to lift your next project to a higher standard.
SEPTEMBER 12TH & 13TH
Ranger Lifting’s Managing Director Ashley Thacker is urging the lifting industry to back a brand-new event that will showcase just how far the sector has come.
THE LIFTING SECTOR SUPPORTS A significant number of Australia’s key industries, including construction, mining and energy. In recognition of this, the Lifting Equipment Engineering Association (LEEA), the global body representing the industry, is organising its first trade show and conference in Australia later this year.
LiftEx Gold Coast will combine a conference and exhibition, offering lifting industry professionals the opportunity to share best practice and showcase the latest safety equipment.
Ashley Thacker, who is on LEEA’s regional council for Australia, said: “LiftEx is well established in the UK as a place where a lot of business gets done. LEEA is bringing this successful format to Australia, and it’s now down to our industry to make the most of this opportunity.
“Technology moves at such a rapid pace that it’s not always easy to keep up with the latest safety innovations. Bringing them all under one roof is a great way to help accelerate their adoption.”
LiftEx Gold Coast is aimed at everyone from riggers and WHS officers to purchasing professionals. Along with cutting-edge technologies from leading industry suppliers, there will be a conference offering free training sessions and a platform for debate.
In the UK, LiftEx is a popular annual event. However, Ashley is warning his peers that if they don’t support LiftEx Gold Coast, this might be the one and only time it takes place.
“This is the first show and it’s on all of us to make it a success,” he said. “If this one doesn’t succeed, there will be no more events like it. It’s therefore in the industry’s interests to ensure there are plenty of exhibitors and visitors alike.”
Ashley is excited about the prospects for LiftEx Gold Coast and what it can bring, but says it is going to require the collective support of the industry if it is going to be successful. In some cases, this means a change of mindset, to start thinking of what’s best for the industry rather than an individual company.
“On a day-to-day basis, lifting companies are of course competing with each other,” he said. “But we need to set aside that mentality for LiftEx Gold Coast and adopt a more collaborative approach. LEEA is a leading industry body but everyone on the council is part of a lifting business.
“As individuals, when we sit as a council, we take our commercial hats off
“Proactive industry participation in this event will help underline the great strides the industry has taken in recent years and help accelerate adoption of the latest safety equipment.”
and we put our collaborative, industry hats on. We want the best for the overall industry and a successful LiftEx Gold Coast is a key strand in that strategy,”
The lifting sector is rapidly evolving, whether this is adopting new technology, improving training, or expanding to support new industries like wind power.
“Proactive industry participation in this event will help underline the great
strides the industry has taken in recent years and help accelerate adoption of the latest safety equipment,” said Ashley.
“This is our showcase to the sectors we serve and support. Along with deals to be done, this is a great chance to network and to celebrate the lifting industry’s recent successes, such as improved training and accreditation.”
He firmly believes that making the most of end-user engagement is pivotal
to the overall prosperity of the industry.
“The end-users are the demographic that really supports equipment advances,” he said. “We are a massive island continent in a remote part of the globe, we have a population that is approximately one quarter of the UK’s. This means suppliers and major manufacturers don’t promote their products here unless they are in the oil and gas and mining and resources sectors, renewable energy sector and major infrastructure projects. As an industry, we need to do the same.”
Formerly LEEA’s regional director for Australia, Ashley is a well-known and passionate advocate for the lifting industry. He has supported drives to professionalise the sector including the Safe Use of Lifting Equipment – the first LEEA-accredited training course to be fully aligned with the Australian Standard. Ashley’s company, Ranger Lifting, was the first in Australia to join LEEA and the first to offer the new training course.
“At Ranger we’ve always taken the approach that what is good for the industry is good for us,” said Ashley. “We’re not afraid to take chances and that’s why Ranger was the first company to book exhibition space at LiftEx.
“In a normal business environment, the last thing we’d do is encourage our competitors to get in front of the same customers as us. But LiftEx Gold Coast is one of those examples where we’re stronger together, so we’d welcome and encourage more of our peers to book space alongside us.
“We need the industry to get behind LiftEx Gold Coast and we want people from our industry to come to and experience the event. This is then only way we can establish LiftEx as a regular, must-attend event. A successful first event gives us the foundation to build and grow. In future years we can move it around the country so everybody in our industry gets to benefit,” he said.
The LiftEx Conference and Exhibition, run by LEEA, will be held on the Gold Coast on the 12th to the 13th of September.
To take a product from the lawns of Newcastle Technical College in 1957 to the yards and warehouses of some of Australia and New Zealand’s biggest crane companies and rigging equipment distributors respectively in 2024 takes imagination, innovation and engineering know-how. Raymond McLaren, founder of Andromeda Industries has done this with his “climax design” that is The Superflex Cable.
Andromeda’s Superflex is a specialised wire rope that possesses 912 individual wires, ultimately forming the
WITH HIS EARLY INTEREST IN WIRE ROPE manufacturing and splicing beginning with the steel tube manufacturer Stewart and Lloyds, Raymond’s interest quickly became a passion that saw him put his mechanical engineering nous to further use, inventing a machine that - 50 years later - still has no equivalent in the wire rope industry the orbital square plaiter. Commissioned in 1975, the orbital square plaiter is the machine responsible for the unique and
exclusive design patented by Andromeda: Superflex cable.
Andromeda’s Superflex is a specialised wire rope that possesses 912 individual wires, ultimately forming the complete wire rope. By point of comparison, a standard 6 x 36 wire rope contains 216 individual wires. The idiosyncratic feature of these wire ropes is that, unlike conventional laid or twisted deigns of wire rope, Andromeda’s are plaited, ultimately giving the ropes
extra flexibility. - akin to that seen with a synthetic sling.
According to the manufacturer, the plaiting of the steel cords creates a very tough and set resistant cable composed of many more wires than is possible with laid wire rope. Using a durable material such as steel provides extra assurance as well, giving the product extra durability and performance when it comes to hotter environments.
Since being brought to the market in 1975, Andromeda’s products have developed expansively through innovation and research. Today, the company’s inventory includes Flat Woven Slings through to Staytight Cattle Cable.
Through Superflex-exclusive lens, the company manufactures and distributes cables, slings and strops to holistically service the between hook and load market in the crane industry.
The unique and innovative creation of Andromeda’s Dean-0 Sling is designed to be made very short and provide a single lifting point under a Ramshorn Hook on large cranes.
This enables a singlepoint of load to be attached and still maintain centreline loading on the cranes lower hoisting block assembly. With sizes ranging from 11 tonnes to 165 tonnes, this sling provides a plethora of lifting needs.
As mentioned above, the Dean-0 Sling is only one of many different slings that Andromeda Industries produces.
Other products produced by the Moonbi manufacturers include the Superflex Sling, Superflex Strop, Superflex Double-Ended Strop, Steel Flat Woven Slings in both cradle lift and choker lift configuration and cover all bases of slings ranging in size from 10mm ND through to 96mm ND.
Depending on the sling or strop required, the Superflex slings range has lifting capacity from 1 tonne in a straight pull through to 168 tonnes when assembled into the Superflex Double-Ended Strop.
Additionally, the sling can increase to 330 tonnes in cradle configuration and everything in between, allowing for vast coverage of various lifting applications.
Its expansive inventory has come in for high praise from high-profile crane and lifting equipment companies.
According to Pilequip, Andromeda’s Superflex range represents the “pinnacle of lifting solutions” with the range thriving in heat-intensive environments such as pilling, while Borger Cranes endorsed this product as providing “structural integrity, versatility and capacity” that other brands “can’t match”.
The company possesses NATA accreditation and full membership with LEEA, indicative of the company’s attitude that safety and quality are paramount in the high-risk work industry of heavy lifting.
Before a product is distributed to a client, Andromeda tests all its products to Australian Standards, utilising its 300-tonne capacity horizontal test bed, its 40-tonne capacity vertical test bench and a 4200tonne Talurit press.
Thus, founded on the back of passion and innovation, Andromeda’s journey from a student’s interest in 1957 to a national lifting and rigging equipment staple in 2024, may be a long winding 67-year-road, but its been a road where innovation, quality and safety have been emphasised at every corner - notions that still permeate through the company’s operations to this day.
Founder Raymond McLaren, now in his late 80s, expressed his desire for his lifelong commitment to thrive for many years to come.
In line with this, Annette Williams, a dedicated employee of Raymond’s, has acquired the company.
Annette, who has been with Andromeda for nearly 19 years and served as general manager for over 6 years, is devoted to maintaining Andromeda’s reputation as a prominent supplier in the crane and lifting industry, while also preserving “Raymond’s legacy.”
Managing Director and founder of Titan Lifting Technologies, Ian Allan, expands on the company’s extensive lifting products and its point of difference when it comes to quality control.
LOOP BACK TO THE 1970S AND IAN ALLAN was doing his time working as a national sales manager for Robert Bosch power tools.
With a penchant for equipment and a commitment to quality, Ian was steadily building his way into a career in power tools until a lifting equipment company came knocking on the door to poach him to be marketing manager of its operations.
From that point, by his own admission, he just fell in love with the industry of lifting equipment.
“At the end of the day, nearly everything that you think about and use requires some piece of lifting equipment,” he says. “It’s multi-faceted, it’s dynamic, and high quality equipment that is integral to people’s lives.”
Founded in 1998 as Allan Marketing Group but known colloquially as Titan Lifting, Titan’s journey began back in 1974 when founder and current Managing Director, Ian Allan, moved from tools manufacturing with Bosch to working with an international lifting equipment company, Columbus McKinnon (CM) USA. From there, his investment in passion for high quality, safe, reliable lifting equipment organically grew, resulting in the development of Titan Lifting Technologies. From his time at CM then PWB Anchor (now Kito PWB), Ian became well acquainted with the international lifting equipment market and set his sights on expanding the company beyond the Australian market; today, headed up by himself and Chief Operating Officer, John Di Michele, the company sees its products distributed worldwide, prevalent throughout Asia and reaching as far as South Africa and the USA – such is the quality of the products Titan distributes. For Ian, the differentiation between Titan’s products when compared to some of its competitors is apparent.
“The differentiation, in our opinion, is
that lifting equipment is nothing to play with; it’s very serious gear that has fatal consequences if it’s not used correctly,” says Ian. “At Titan, all the products that we supply to the lifting industry are all fully compliant and meet International as well as Australian standards.”
“Lifting is a dangerous game – you’re not playing with toys, you’re talking about heavy loads being lifted by heavy pieces of equipment, and we take that very seriously,” he continues. “We comprehensively test our products to the point of destruction because we view it as our responsibility to ensure any manufacturing, design, or labelling defects are caught by us so that, at the end of the day, every one can go home safely after work to their lives.”
At the forefront of Titan’s lifting equipment is the extensive range of precision hoisting and lifting equipment that it designs and develops using its 50 years of expertise in the industry. Marketed under the Titan Lifting &
AMG brand names, the products include hoists, girder trolleys, lifting clamps, wire rope winches, G80 and G100 chains and fittings, wire rope, synthetic slings, lashings and tie downs, shackles, rigging hardware, stainless steel rigging and weighing systems. Furthermore, on top of its own designing and manufacturing of lifting technologies, Titan has also made moves to ensure it stays at the top of the market when it comes to supplying lifting equipment through a range of international brands that it partners with, including: Van Beest - Green Pin (Netherlands) and its shackles, globally renowned height equipment specialist Tractel (France) and its original Tirfor winch, civil construction lifting gear company Probst (Germany), automated hydraulic testers, wire rope swaging machines and wire rope ferrules from Wirop (Taiwan) and Caldwell –Renfroe (USA) lifting equipment and plate clamps.
Titan’s diverse range of Australian and International Standards-compliant
designed and imported lifting gear seeks to cover any industry that may require lifting equipment to support its operations; and, through its extensive customer base, it demonstrates that it does exactly that.
Today, the lifting equipment specialist sees its products distributed to a range of different industries from mining through to everyday construction, with colossal companies such as McConnell Dowell, Rio Tinto, Essential Energy, BHP and BlueScope representing just some of the repeat customers calling for Titan’s specialised lifting equipment.
“At the centre of our product range is a commitment to providing more than just consumables; the lifting gear that we provide is all very high-end, technical gear that is designed to last for a long time, rather than being discarded after one or two uses,” says Ian. “Our products are thriving across all sectors and have been used in events such as Cirque-du-Soleil, to lifting two-tonne road barriers, to providing the heavy-duty shackles needed for major lifting in construction across the renewables, mining and infrastructure sectors.”
As mentioned, Titan ensures its products are compliant with both Australian and International Standards;
compliance, however, is only the tip of the iceberg for the international lifting equipment specialist. At its base in Melbourne’s northern suburbs, Titan Lifting operates two warehouses: one for incoming stock, and one for outgoing stock. When a product initially arrives at its facilities, Titan quarantines the shipment in the first warehouse until it is comprehensively tested and inspected, ensuring that any product entering the lifting equipment market will do exactly what it says it will do. For Titan, this is enhanced by its partnership with Wirop, another international relationship the company has leant on to deliver an automated hydraulic tester. Titan also has a vertical tester designed specifically for electric and manual hoists. All lifting and lashing products undergo the required load testing relative to their respective Standard. Once a shipment has passed Titan’s rigid QC, relevant test documentation is filed according to batch numbers. This not only proves the products’ compliance but permanently files records for future reference amd traceability. After QC, products are then moved to Titan’s second warehouse, where they are ready to be shipped out to its extensive range of customers.
“The products arrive here with test certificates from our manufacturers, along with material and heat treatment certification, all the things we require to make us comfortable that they’ve done it right,” says Ian. “But to be even more certain, we conduct our own extensive testing. Nothing goes out the door until it’s tested by us.”
Further compounding Titan’s commitment to the stringent compliance in the lifting industry is its LEEA membership status. Highlighting Titan’s involvement as “one of the earliest members” of the organisation in Australia, Ian says LEEA’s specialised training on lifting equipment reflects Titan Lifting’s attitude to safety in the industry.
“LEEA has always been in and around the end-users and government departments to get them all on board in acknowledging the severity and highstakes nature of lifting equipment,” says Ian. “LEEA is completing a lot of important work around certification of skills because misuse can happen across the industry; LEEA is about stamping it out to ensure lifting equipment is adequately manufactured, certified and used, and that’s something that Titan Lifting Technologies supports 100 per cent.
In addition to the off-set lifting beams, we have recently attain even more telescopic spreader bars. These are custom made and unique to their nature.
We are now able to supply spreader beams ranging from 1.5t – 80t. Some of them extending from 1.5m to 12m in length. With modular beams on offer, we are well covered to suit any challenge coming our way.
Dynamic Rigging Hire has acquired 30 off-set lifting beams. Adding these to its diverse range of equipment for old and new customers. Each beam comes with a designated counterweight. The beams are commonly used for façade panels, glass installation or pre-cast panels. In accordance with the engineering design, we can modify the beams to suit the right application. Like everything in our fleet, off-set lifting beams will be supplied with current certification.
Certex celebrates the tales of three women, as their curiosity and commitment to safety helped them prosper.
CERTEX LIFTING IS DEEPLY COMMITTED TO fostering an inclusive and diverse working environment where every individual is valued and given the opportunity to thrive. The company recognises the importance of embracing employees from all backgrounds and experiences and is dedicated to nurturing a workplace culture that celebrates diversity.
Certex Lifting is challenging stereotypes, by working towards a more diverse workforce, encompassing gender equality international backgrounds and age groups.
At Certex Lifting, diversity is not just a buzzword, but a core value that is lifting the organisation to new heights. The company understands that embracing individuals with different perspectives, skills and experiences can cultivate a dynamic and innovative workforce that contributes to the overall success of the business.
Certex Lifting not only values diversity, but also actively works to develop and empower employees from all walks of life. By investing in training, mentorship and professional leadership programs, the company ensures that every employee can reach their full potential and contribute meaningfully to the organisation.
By creating an inclusive and diverse workplace, Certex Lifting sets a powerful example for other companies in the industry. Dedication to diversity and inclusion not only enhances employee satisfaction and performance, but also fosters a culture of respect, understanding, and mutual support.
Baylea Mussen, Jessica Bellamy, and Courtney Constable have entered the
industry with different stories. What attracted these three women to the lifting industry?
Baylea, a Testing Technician in training, found a sense of belonging at Certex Lifting through curiosity and an encouraging work environment.
Baylea started at Certex Lifting doing casual work while still in school and found herself down in the testing department asking questions. The support from her colleagues played a pivotal role in her career choice. Saying Certex Lifting has a cooperative, cohesive and supportive culture, Baylea highlights the importance of clear and effective communication and states, “It’s
“Management are easy to approach, providing support and workplace flexibility. It is an encouraging and suppor tive organisation.”
really nice to see people so supportive of each other... it makes all the difference.”
A sentiment echoed by Jessica and Courtney, who also both speak to the respectful and open team dynamics at their branches. Fostering a culture of acceptance, personal development and general support are key. Jessica underlines the importance of leadership and states: “Management are easy to approach, providing support and workplace flexibility. It is an encouraging and supportive organisation.”
Courtney feels the full support of colleagues, as well as her manager, is pivotal in workplace satisfaction: “At my branch, I feel supported and respected, and our manager discourages biased culture. I’m sure
our team’s friendly and welcoming nature contributes to our successes,” Courtney said.
The message encourages other women and empowers them to take the leap and pursue a career in traditionally maledominated fields. Baylea’s advice is short but strong: “Give it a crack. Experience is everything, and your role may encourage others to join too.”
“With the right support everyone can thrive and contribute to changing the industry landscape,” Courtney adds.
THE EVOLUTION OF CERTEX LIFTING: EMBRACING CHANGE FOR SUCCESS
Certex Lifting is now one of the country’s largest lifting service and equipment
“Certex Lifting has also remained committed to safety, with a strong emphasis on “Lifting KnowHow” as a company commitment to improve operations and services.”
companies and has been at the forefront of the lifting sector since entering the Australian market in November 2022.
Certex Lifting has stayed ahead of the curve by providing innovative solutions and high-quality products while focusing on safety and reliability. The company keeps up with technology advances and industry developments.
One of the most significant aspects of Certex Lifting’s evolution has been its embrace of new technologies and methodologies to improve its product offerings and services. The company has consistently invested in staying at the forefront of the industry, from introducing a more sustainable range of products to providing Magnetic Rope Services and niche products tailored to the Renewables sector. This dedication to advancement has solidified Certex Lifting’s position as a leader in the
lifting sector and has allowed the company to better serve its customers with safe, efficient, and reliable solutions.
Certex Lifting has also remained committed to safety, with a strong emphasis on “Lifting KnowHow” as a company commitment to improve operations and services. By prioritising safety in every aspect of its operations, Certex Lifting has built enduring partnerships and delivered peace of mind to its clients.
In summary, Certex Lifting’s evolution demonstrates its ability to adapt, innovate and lead. The company champions diversity and inclusivity, embraces technological advancements, and prioritises safety. As the industry progresses, Certex Lifting stands ready to meet new challenges and pioneer new solutions, remaining a steadfast partner for businesses in need of top-tier lifting and rigging expertise.
With an extensive range of precision hoisting and lifting equipment, we have what you need to get the job done.
• GIRDER TROLLEYS
• HOISTS & LIFTING CLAMPS
• WIRE ROPE WINCHES
• G80 AND G100 CHAINS & FITTINGS
• RIGGING HARDWARE & WEIGHING SYSTEMS
• SYNTHETIC SLINGS
Lifting Equipment Engineers Association (LEEA) Regional Manager-Australia and New Zealand Justin Boehm recently visited SpanSet Australia’s Emu Plains manufacturing facility in the foothills of New South Wales’ Blue Mountains. Managing Director, Kristian Pritchett, gave him a tour.
“I WAS VERY IMPRESSED WITH SPANSET Australia’s manufacturing facility, it is fantastic. I was impressed with the work they do, how they hand craft their range of products on wildly impressive automated sewing machines. It’s actually a great Australian manufacturing story. For someone seeing for the first time how these synthetic slings and height safety equipment are actually manufactured is a genuine eyeopener,” said Justin.
“The research and development that goes into every product is excellent and seeing the quality of and how carefully the products are put together and then tested and certified needs to be told more broadly to the Australian crane and lifting sectors. In terms of the testing and understanding how much SpanSet Australia has invested and can categorically prove their products conform to Australian Standards, is very impressive,” he said.
Justin goes on to discuss the industrywide issue of how synthetic slings are treated. In many instances cheap synthetic slings are used as ‘one-offs’ for a lift or they are not cared for carefully enough and they end up in landfill.
“In my opinion, we’ve got a massive
problem with synthetic slings and synthetic products in general, it’s a race to the bottom on price, which ends up being so bad for the environment. When you look at the lifting industry and see that thousands and thousands of slings are being imported used once or twice and then discarded, it’s having a massive environmental impact. As an
industry we have to look what we’re doing and instead of companies saving $2 per sling, they should be examining the long-term cost of these cheap disposable products. It’s an industry wide issue we want everyone to be talking about,” said Justin.
Justin goes on to observe how Tier One builders, Tier One Offshore Oil and
Gas providers, and Tier One resources companies are examining ways of reducing carbon footprints and understanding environmental impact requirements.
“Increasingly, these major Tier One projects are looking for sustainable construction methodology in everything they do, and they are driving that back down to their suppliers to understand what contributions they are making towards reducing carbon footprints. One off usage of synthetic slings and lifting equipment is not going to ‘cut it’ into the future,” said Justin.
“For me it’s pretty basic, the industry needs to consider how it is sourcing these synthetic products and examine their quality and the longevity. It might be a simple task of maintaining the products, cleaning them after each project and storing them properly between jobs,” he said.
Justin goes on to highlight the significant impact Scope 3 Emissions Mandatory Reporting is going to have on the industry. Scope 3 emissions represent the indirect greenhouse gas emissions generated throughout a company’s entire value chain.
“Scope 3 Emission Mandatory Reporting will have a major impact on the lifting industry. Companies will have to report on the amount of their emissions particularly when it comes to Tier One Government projects. So where are we going to be in the next five years as an industry? We will have to be smarter and stop buying products on price that are sent to landfill after one use. We need to invest in quality products and service them carefully between projects,” he said.
“This is a topic we touched on at LiftEx last year and 12 months on we haven’t confronted the issue, we haven’t examined what we are actually doing as an industry. But seeing what SpanSet Australia is doing and seeing that they already have some projects on the go to try to address the issue to correct wastage and to address and educate the industry on how to reuse or clean these slings has doubled down on my thinking. As an industry we’ve got to do something and it’s time to get the ball rolling,” said Justin.
Justin was impressed with SpanSet Australia’s latest investment, the 600-tonne 45m long tensile test bed.
The size of the test bed gives SpanSet unparalleled scope to proof test high-tonnage lifting slings at exceptionally long lengths.
“The other thing that strikes me with that test bed and the certification of products, safety is obviously paramount. I think a big topic is around how we ensure the safety of slings. The certification and documentation for a lot of these products may be dubious,” he said.
“I put this in my last article. If you go to ‘Hammerbarn’ (that’s a Bluey reference,) the slings have been certified by the exact same person every single time. Are they actually doing the tests required under Australian Standards? I mean really is a $6 sling that’s lifting a $100,000 piece of equipment or $10,000 piece of equipment, who cares how much it costs if you need the job done safely. If you are trusting your lift to the cheapest product, you’re asking for trouble in my opinion.”
Justin is also concerned about the safety element surrounding non-conforming, cheap products and the potential for any
incident to be catastrophic.
“There have been a number of incidents recently as an industry we are lucky no one is dead. The Chain of Responsibility (COR) is going to be a significant issue. If you are a Director of the business and they know they are buying second rate equipment just to get a job done and that equipment fails and there is a fatality, that Director is going to jail.
“It’s the same for the Dogman and Rigger, if they know the product is second rate and it fails, COR means they will be in serious trouble also, as they are legally and financially liable for the fatality. So I applaud Kristian and his team at SpanSet Australia for sticking to their guns and doubling down on the need for our industry to purchase quality, tested and certified product and to look after it, for the wellbeing of those lifting with the product as well as the environment,” said Justin.
We have extensive experience in providing lifting equipment and connected services to customers across Australia. Certex Lifting has branches in New South Wales, Victoria, South Australia and Western Australia. Our nationwide presence allows us to support our customers wherever and whenever they need us.
Our products include customised and standard lifting equipment, steel wire rope, hoists, cranes and fall protection equipment. We source products from the world’s leading manufacturers, including our own brands.
With a stock of over 12,000 items, we are able to provide quick delivery to meet urgent requirements.
• Design, engineering and manufacturing of customised lifting tools
• Statutory offsite and onsite inspection
• Proof load testing
• Crane and davit inspection and repair
• LEEA certified and GWO trained technicians
• Fall arrest equipment and P(F)PE inspections
• Wire Rope assemblies with custom end fittings
• Onsite Wire Rope services
• NDT and Magnetic Rope Testing services
• Installation of Height Access and Fall Protection Systems
• Maintenance and repair services
• Technical support
Certex Lifting is part of the Lifting Solutions business group within Axel Johnson International, which comprises over 24 companies across 19 countries.
The latest released 3Dx™ Edge Lifting System from Reid has been well received by the precast, crane and lifting industries.
DEVELOPED, MANUFACTURED, AND TESTED in Australia by Reid™, the 3Dx Lifting System provides high lifting capacities and increased levels of efficiency and productivity. The unique and patented anchor design distributes loads in the concrete in three dimensions, maximising capacity while reducing outward bursting loads and potential panel damage.
The 3Dx lifting system provides precasters with one lifting solution to cover over 90 per cent of types of panels. The patented forged design, made from tough Alloy Steel, allows for faster installation for Precasters. The compact design of the 3Dx
is easier to manoeuvre around the mesh and fittings, yet delivers 10t WLL capacity.
Compliant to AS3850.1:2015 (+A1 2019) 3Dx has been designed to meet the needs of the Australian precast market.
Reid clutches were originally developed with a flame cut handle which was soon enhanced with a forged handle design that is now widely used within the industry.
An in depth review of the existing lifting systems available and the recurring difficulties users were experiencing on a day-to-day basis led to Reid approaching the Crane Industry Council of Australia (CICA) and as well as range of crane
companies and learning that many were cutting the handles off clutches and placing hammer locks on instead. They did this to make using clutches quicker, simpler and better suited to the process of lifting and placing precast panels on site
Reid examined that process and quickly understood the inherent risks and potential safety hazards this posed – not to mention voiding the warranty of their clutches. The modification of clutches to include hammer locks is intended to alleviate binding and spalling during panel rotation and erection. With that as the major painpoint to address, Reid began looking at an articulated clutch design that would deliver a tested and certified proprietary system – creating a far safer solution to meet the needs of the industry.
Reid has developed the clutch to be articulated as opposed to previous models. When precast panels are lifted by a crane with a standard clutch, the position of the two anchors will cause the chain to rotate and come backwards over the panel’s edge. So, lifting from a single point, the clutch would be pulled around the corner of the panel which would see the handle bend, the new Reid 3Dx 10t Articulating Clutch can move in any direction, as well as self-right; mitigating any damage to the panel or clutch.
The 3Dx 10t clutch also has the benefit of releasing quickly and remotely, meaning a user does not need to bring an EWP on site to quickly release the precast panel.
Reid’s intention was to hone in on designing the system that would satisfy the lifting requirements for over 95 per cent of precast panel configurations commonly cast throughout Australia. Most commonly, precast panels in Australia are transported by truck, in pairs. That truck is limited to approximately 20 tonnes, hence Reid made
the decision to develop a clutch that could safely lift 10t.
Reid Construction Systems is proud of its long-standing partnership with Melbourne based manufacturer Townley Drop Forge. With Townley being an independent ISO accredited, NATA certified business, it was the obvious choice in both the manufacturing and testing validation of the 3Dx Articulating Clutch.
As a design requirement, Reid wanted as much information as possible stamped on the clutch itself– such as a clearly stated WLL – that assures the riggers that they are using a genuine Reid, Australian Standards-compliant, quality-assured product. The clutch is beautifully forged and includes the item part number, load limit and its batch code all clearly stamped on the physical product, for user peace of mind.
With the new design, Reid and Townley have included contingencies on the clutch to make it quick and simple for users to identify whether the clutch has been tampered with.
The clutch has a rivet which holds it together, complete with the Reid logo. It cannot be tampered with, or easily knocked apart like a hammerlock clutch could be.
The information pertaining to the clutch is not only forged onto the metal but also appears on the stainless-steel tags supplied with each and every clutch. The tag includes a serial number, a barcode matching the serial number and a QR code.
The QR code will take users to the Reid website and directly to the critical safety information for that clutch and any other associated Reid clutches. The Reid website has a wealth of information for a range of stakeholders and users, including all safety and compliance statements, as well as Reid clutch and anchor compatibility and discard guides. The 3Dx Articulating clutch is traceable all the way back to the original raw material metal that arrived at Townley drop forge to ensure Reid has full traceability of material batch and heattreatment certificates, should these be required.
3Dx has been designed to meet the needs of the Australian precast market.
The Reid 3Dx 10t clutch was developed in partnership with Townley, which is NATA certified – allowing Townley to market.
WHAT CUSTOMERS ARE SAYING
Graham Polley is the Production Manager at Advanced Precast. “We know Reid 3Dx 10t clutch is safe, we have never had a panel with Reid lifters fail. What’s cemented Reid as a standout lifting supplier is that their system gives us confidence. Confidence that not only is the system safe but also increases cycle time of precast panel production. We also have the confidence to lift at early concrete strength which allows us to produce more panels in a safe and efficient manner,” he said.
to say.
“The hole in the lever can be used to insert ground release ropes and the articulating clutch avoids human error and the compactness of the clutch allows more movement beneath protruding bars now that it has a shorter handle.
“They are the safest clutches I’ve ever used & I would never want to use anybody else’s. I’ve been using Reid for 28 years and the way they’ve designed this system is beautiful. Old clutches sometimes jam up or bend, with the new ones, the clutches self-right. There are no issues with them whatsoever,” he said.
Leading Victorian rigging equipment supplier continues to plan for a sustainable future with a significant investment in new products and a battery electric crane to manage the lifting and shifting of product around the Truganina facility. Dynamic Rigging’s Ross Johnson explains more.
DYNAMIC RIGGING IS BASED OUT OF Truganina, in Melbourne’s outer west, and is a leading name in lifting and rigging
“We provide premium lifting equipment and rigging solutions for the crane sector. Anything that goes between the hook of a crane and the load the crane is lifting is our space, we provide all sorts of specialised rigging equipment and send it around the country to projects our mobile crane customers are working on,” Ross says.
Dynamic Rigging started in 2010. Ross was the first employee and a self-confessed ‘Jack of all Trades’. Ross knew early on that he loved this type of work and has now grown his staff to seven in 2024.
In 2022, Dynamic Rigging was acquired by a privately owned Swedish company –Axel Johnson International.
Its Truganina facility is an 1,800 square metre factory that provides plenty of storage space and room to load trucks inside the factory with a clean modern environment for staff.
As Dynamic Rigging continues to invest in equipment and lifting solutions Ross recognises the industry is tasked with managing much heavier lifts and the rigging equipment he is offering needs to reflect this.
Emblematic to that of a duck on water, Ross has been moving quickly throughout his entire time at Dynamic Rigging, especially of late, as he initiated the acquisition of a fleet of offset lifting beams from GTC Engineering in late 2023.
The lifting beams added to their wide range of lifting equipment have proved to be a very successful move into a new
product range. Like many things, the offset beams have purpose across many applications but are generally used to position a load beyond the crane hook position, so for example, a small offset beam might be used in conjunction with a glass handler to install glazing, whereas, a larger offset beam might be installing 12t pre-cast panels with a tower crane.
Another shrewd feature introduced by the team at Dynamic Rigging is its new online system.
“We’re on track to provide all the certification and safety documentation for the bulk of our equipment by QR code, something like a crane work box, for example,will have the manufacturer’s certification, Vic Workcover design registration, certificate of inspection and NDT report all accessible via the QR code
to anyone with no special login required,” he says.
In a first for the business, Dynamic Rigging has made the acquisition of a 13-tonne electric Valla V130RX crane, a state-of-the-art battery electric crane Dynamic Rigging hopes will make monotonous mechanical beeping and oil droplets a thing of the past.
A positive impact on the environment and a more sustainable future for the business was one of the attractions for Ross with the new battery electric powered Valla, he said.
“I simply couldn’t have a crane with a big noisy diesel engine either sitting idle, or generating exhaust emissions all day when it is operating dropping oil all over my factory floor,” said Ross
“The Valla is a great product and electric cranes really tick the boxes in terms of a healthier work environment and increasing sustainability in our business. They are so much cleaner in comparison to a diesel engine machine,” he said.
Despite there being no current plans to head further into the crane market,
General Manager of Dynamic Rigging, Ross Johnson believes the purchase from Pace Cranes will improve efficiency and operations within his factory.
“Historically, we’ve just used forklifts and attachments on forklifts to sort of turn them into something that is not quite a crane,” he says. “Some time ago, even under our former ownership, we identified that we simply had to be smarter in the way we handled our equipment in the facility,” says Ross.
“The Valla is quite unique for us. With its 13t lifting capacity it’ll help us in our normal operations and it will pick up a five tonne block, position it anywhere that driver wants it on his truck, no problem at all.”
The Valla V130RX crane will undertake plenty of lifting work.
“It will be used to lift big pieces of equipment like sections of pipe and larger spreader beams as well. It’s not going to drop oil all over the floor and it’s reasonably compact in size. It’s not much bigger than our larger five-tonne forklift,” said Ross.
“I had plenty of guys in the crane industry saying, just go and buy a secondhand crane and there are plenty that could sell a crane, but I’ve got a factory environment I need to consider,” he says.
Another exciting feature of the new crane is the way the battery is charged, with solar power. In 2025 the roof of Dynamic Lifting’s factory will be fitted with a system of solar panels which provide the energy to charge the crane’s battery.
Ross says it was a positive factor when considering the purchase of the battery powered crane.
“In the grand scheme of things, we could see the opportunity charging a battery electric crane indirectly through the solar energy we capture from the solar panel system on the roof. Like all environmentally focused businesses, we are focused on reducing our emissions and our carbon footprint wherever possible, and so the Valla fits nicely into this strategy,” he says.
The new crane is also very user friendly.
“The operator can control the crane completely remotely. With the remote controls, he can walk at 90 degrees to the crane, to behind the trailer where he has a clear view of where he wants to place the load and he can bring the crane in and place it exactly where it needs to go,” Ross says.
Ross says the control system looks as easy as playing a console game, “It looks like a PlayStation controller and provides the operator will full control without needing to be at the crane.”
The crane left the factory in Italy earlier this year to come to Australia via Singapore. In Sydney the crane will be put through a gamut of pre-delivery checks, conducted by Pace Cranes. It will then get loaded onto a truck and the final destination will be Dynamic Rigging in Melbourne, where Ross and his team will be eagerly waiting for their new crane.
The brand-new crane is expected to be in the trusted hands of Ross and his team at Dynamic Rigging by August this year.
Despite the initial plans to not offer it up for hire and operate it solely at Dynamic Rigging, Ross says in due time, the right dry hire offer may turn his head.
12-13 September 2024
The Star Gold Coast Australia
Join the only dedicated event for the lifting and height safety industry in Australia
Key Features:
• Exhibition: See the latest in lifting equipment and innovations in action
• Conference: Hear end-user presentations on new technologies and advancements in lifting safety
• Free Training Sessions: Opportuntity to earn CPD points
• Networking: Forge connections during breaks and the drinks reception
If you are a user of lifting equipment, you should attend this event
It is with great pleasure and enthusiasm that I extend a warm welcome to LiftEx Gold Coast, the premier event for the lifting and height safety industry in Australia. Our event brings together leading lifting and height safety equipment suppliers with end-users who are engaged in operating, inspecting and testing lifting equipment across diverse sectors such as Mining, Oil & Gas, Infrastructure, Construction, Ports & Marine and Renewable Energy.
LiftEx Gold Coast promises an unparalleled opportunity to connect, collaborate, and engage with LEEA members, stakeholders, decision-makers and end-users in the lifting industry.
On the show floor you’ll see cutting-edge technologies showcased by leading industry suppliers - from a variety of hoists, rigging equipment including slings, shackles, hooks and lifting chains, lifting accessories to safety harness systems, there will be an array of products and technologies designed to elevate industry standards and drive excellence in lifting practices.
Our two-day conference program also includes complimentary professional development training workshops on the pre-use inspection of lifting equipment, valued at $600. These workshops offer a unique opportunity to enhance your skills and knowledge.
I would like to extend our thanks to our sponsors: Austlift, Pacific Hoists, and TNC Cranes, for their generous support.
LiftEx Gold Coast will showcase new thinking, technologies, equipment and best practices that are transforming the way we help lift and move heavy loads, ensuring safety, efficiency and sustainability. On behalf of LEEA, we sincerely hope that you forge lasting connections, take away key actionable learnings - as well as have an enjoyable stay on the beautiful Gold Coast. #liftexgoldcoast
Best wishes,
Justin Boehm, Regional Manager Australia and New Zealand LEEA
Contact: Annette Williams annette@andromedaindustries.com.au https://www.andromedaindustries.com.au
Andromeda Industries is a proudly Australian owned and operated manufacturing company producing Superflex Steel cable and is renowned throughout the lifting and rigging industry for our unique products that complement a vast and varied industry.
Andromeda Industries manufacture Superflex steel cable, slings and steel flat woven slings to meet a wide range of industrial applications, such as mining, military, manufacturing, construction, off-shore oil and gas. Ensuring the highest standards of workmanship are met, all of Andromeda Industries Steel Slings and cables are stringently tested to meet and exceed Australian standards, giving customers peace of mind for any lifting application.
Contact: Jason Myburgh jasonm@austlift.com.au https://www.austlift.com.au
Austlift is a well recognised wholesaler in the Lifting Industry. The Australian owned company has been running for over 20 years in Lifting and Rigging and has been dealing in Material Handling for almost 10 years. We offer Lifting and Rigging, Load Restraint and Height Safety products as well as the installation and service of Tailgates, Docks, Cranes and other Material Handling equipment. Our network reaches across Australia and we have branches in Sydney, Melbourne, Brisbane and Perth reaching out to our chain of national distributers making Austlift one of the leaders in the lifting Industry.
Contact: Angela Wälder angela@ketten-waelder.de https://www.ketten-waelder.de/en
cromox® is proud to be represented in Australia by Gold Coast based Bridco. At LiftEx Gold Coast the team from cromox® would like to meet existing customers from Australia and show our products to the wider regional lifting industry.
We will be exhibiting our wide range of high-quality Grade 60 stainless steel products for industrial lifting. Visit our stand to see the most advanced engineered range of fully stainless hoists and trolleys. Our in-house engineering facility specialises in bespoke lifting solutions in the most demanding harsh environments. cromox® products are manufactured to the highest standards of strength, corrosion resistance and safety. At the Ketten Wälder GmbH headquarters in Bavaria, Germany, our facilities are a certified test facility for Lloyds Register and we have recently achieved full member status with LEEA.
Contact: Justin Boehm justin.boehm@leeaint.com https://leea.com.au/
LEEA is the globally recognised trade association for all involved in the design, manufacture, hire, repair, maintenance and use of lifting equipment. We promote enhanced safety standards, competence beyond compare and sustainable development for the worldwide lifting and safety industry.
LEEA plays a key leadership role in this specialised field. For 80 years we have been the industry’s go-to body for training and standards setting, through to health and safety, the provision of technical advice and the development of examination and licensing systems. LEEA insists our Full Members are using best practice for the inspection, testing and certification of lifting equipment, to ensure end users across our sectors minimise their risk.
Contact: Hadley Price hadley.price@rentlgh.com https://rentlgh.au
LGH, a global leader in lifting and rigging equipment hire, is excited to announce our expansion into Australia. With over 50 years of industry expertise and a legacy of lifting excellence, LGH provides a massive and comprehensive inventory of high-quality gear, including hoisting, rigging, jacking, pulling, material handling and safety equipment. Founded in Manchester, England, by Bill Parkinson in 1970, LGH has grown to become the largest lifting and rigging hire company across both North America and Europe. Through dynamic leadership and investment in innovation, we continue to elevate rigging and lifting standards globally. This entry into the Australian market continues our life-long commitment to safety, security, quality and excellence in the crane industry. What elevates us above the competition is our relentless focus on customer service, expert technical support and industry-leading testing and certification processes. Every hire from LGH guarantees that clients like you dominate jobsite projects. As we establish our presence in Australia, we look forward to supporting your lifting and rigging needs with the same dedication and expertise that have made us a trusted name worldwide.
Contact: Sam Maranzano sam@lincer.com.au https://lincer.com.au/
Lincer is a new distributor of the renowned Smart Group brand of Glass Vacuum Robots. We are excited to exhibit at LiftEx Gold Coast, showcasing the revolutionary SG 350, SG 450, and SG 650 models. These advanced glass vacuum robots are transforming the industry with their exceptional reach and unparalleled safety features. In addition to our cutting-edge product offerings, Lincer is dedicated to providing comprehensive services including inspection and testing, parts and repairs for lifting equipment. Our commitment to quality and innovation ensures that our customers receive the highest level of support and performance. Join us at LiftEx Gold Coast to experience the future of glass vacuum technology and discover how Lincer can enhance your lifting operations with our state-of-the-art solutions and expert services.
Contact: James Moule james.moule@pipanz.com https://au.linqhs.com
LINQ Height Safety, Lifting and Rigging products are created for safety without compromise, by using the highest-quality materials engineered for comfort, performance and durability. LINQ’s premium products are certified beyond AS/NZS safety standards for your peace of mind. We pride ourselves on providing comprehensive product support and training, with four distribution centres within Australia and one in New Zealand.
Our unique ability to manufacture and test products in our NATA accredited and BSI recognised Australian headquarters, means LINQ is always at the forefront of new technology, standards and industry requirements. When you see LINQ, you are seeing a better product.
Contact: Holly Moran hmoran@pacifichoists.com.au https://www.pacifichoists.com.au
Pacific Hoists, established in 1976, is a Australian owned family business dedicated to delivering lifting and material handling solutions across Australia and New Zealand. We pride ourselves on our LEEA-accredited expertise, offering comprehensive services including customisation, repairs, inspections, testing, and after-sales support.
At LiftEx this September, we are excited to showcase a wide array of hoisting equipment from renowned brands such as Hitachi, Vital, J.D. Neuhaus, Yale, CM Lodestar and more. Attendees will have the opportunity to view our updated product lines and view our extensive range of wireless radio remote controls. Our technical team will be on hand to provide insights and answer any questions. Don’t miss our live demonstrations, where you can witness the precision and reliability of our solutions firsthand.
Contact: Laura Bugg jnl@pewag.com.au https://www.pewag.com.au
Pewag was established in Brückl, Austria -1479, a place where we still manufacture today.
In 2012 pewag Australia was opened, being the first subsidiary to open in the Southern Hemisphere. Pewag Australia provides the highest level of service, sales, and support to our valued partners across Australia and New Zealand.
All our products we offer are sourced from 100% European Factories based in:
• Austria • Netherlands • Czech Republic • and France
Our steel is predominantly sourced from Voestalpine steel in Austria and all pewag products can be traced back upstream to have the most transparent and highest of integrity made today.
Contact: Will Freeman Will.Freeman@probst-handling.au https://www.probst.com.au
Around the world, Probst is the solution provider for handling systems of construction and landscaping materials. Its products are designed to help people work safely and more productively. The foundation of its success is continual innovation which has established its position as market leader.
Having grown into the leading global developer and manufacturer of grab and installation technology, the last 50 years of the company’s history have seen Probst create trend-setting standards and guarantee a constantly high level of quality. Probst is the driving force behind a number of innovative technological advances, which we are proud to be offering to the Australian market.
Contact: Mel Ireland
Mel.Ireland@rdmw.qld.gov.au https://www.rdmw.qld.gov.au/manufacturing
The manufacturing industry is experiencing substantial growth in what is arguably one of the tightest labour markets in our history. As such we’re seeing manufacturers across Queensland diversify their workforce.
The Queensland Government is committed to arming local manufacturers with the tools, skills and funding to ensure that they can diversify their workforce to remain competitive and become market leaders.
To enhance these opportunities, the Department of Regional Development, Manufacturing and Water will be available on stand 4 at LiftEx to support manufacturers to do things differently by helping them to:
- reimagine the workforce
- rethink recruitment practices and programs
- give greater value to diversity and inclusivity in the workplace.
Contact: Ashley Thacker ashley@ranger.com.au https://www.ranger.com.au
We are an Australian owned business providing specialist lifting, rigging and safety solutions to clients in the Mining, Civil, Construction and Rail Industries as well as Government sectors. We have a proven track record of supplying equipment that improves safety and productivity in the most demanding applications and environments in Australia. For many years, professionals have consulted our team to source the safest, most durable and efficient lifting and working at height equipment, selected from the world’s leading innovators and suppliers.
Contact: Andrea Luna aluna@reidanz.com https://reid.com.au
Reid Construction Systems is a diversified manufacturing company, which brings together the combined skills and expertise of market leading brands - Reid™ and Danley™. Specialising in engineering solutions for wet concrete construction, we work with developers, builders, specifiers, precasters, subcontractors, distributors and the wider industry to support and advance concrete construction. With manufacturing hubs located in Melbourne and Brisbane, Reid Construction Systems services the Australian and New Zealand concrete construction industry across the residential, industrial, commercial and civil construction sectors.
Contact: Ian Allan ian@titanlifting.com https://www.titanlifting.com
Allan Marketing Group is an Australian Company that has been using its 45 years of expertise to design and develop its own brand of precision hoisting and lifting equipment for Australia and the world. These products are marketed under the Titan Lifting Technologies brand name. Our product range covers most of the related products used in the Lifting, Rigging, Mining, Shipping, Construction and Transport Industries. We specialise in Chain and Lever hoists as well as the Titan Single and Variable speed Electric Chain Hoist and Motorised Trolleys. We also produce lashing and loading equipment, load and lifting chain, shackles and ratchet straps, hooks and wire cable products. Our objective will be to illustrate Titan Lifting’s broad involvement in the Lifting Industry. We are an Australian owned company based in Australia servicing the Australian market, but also supplying a considerable number of lifting countries overseas. We not only manufacture lifting products in the TITAN brand but also partner with a number of international lifting companies whereby we hold exclusive and shared agencies with Australia. We are proud to have a good number of employees from within the lifting industry. Our Exhibit will demonstrate the broad range of quality lifting products available to the Australian market and our ability to service our customers Australia wide.
Contact: Tony Radford tony.radford@tnccranes.com.au https://www.tnccranes.com.au
At TNC Cranes, we are dedicated to providing dependable and robust lifting solutions. We are excited to announce the launch of Tragen Cranes at LiftEx, showcasing our latest advancements in electric hoist technology. The Tragen Cranes brand stands for reliability and strength, offering a range of hoists built to withstand the most demanding conditions. Our hoists, featured under the Tragen Cranes brand, are engineered for durability and superior performance. Join us at LiftEx to experience firsthand the exceptional reliability of Tragen Cranes and learn how our comprehensive service and technology platforms, including Turn Key for major projects, can enhance your operations. Discover why TNC Cranes is the trusted partner for mining, construction and process manufacturing industries.
Contact: Christian Trikolas christian@townleydropforge.com.au https://www.townleydropforge.com.au/
Established in 1911, Townley manufactures a premium range of high quality lifting and rigging components. Trusted by the industry for more than 100 years, our products are routinely used in many of the country’s largest mining and infrastructure projects, where performance and reliability is paramount. In addition to our core range, Townley can also custom design and manufacture steel forged products to your exacting specifications. Our Melbourne facility has the latest technology and machinery which enables us to produce one-offs through to large scale production runs. So when quality and performance matter, choose Townley, you can depend on us.
Contact: Martin Tognola Martin@vectorlifting.com.au https://www.vectorlifting.com.au/
Vector Lifting is a 100% Australian Owned and Operated Company specialising in materials handling and height safety equipment located in Perth, Western Australia. Since our inception in 1989 we have developed an extensive range of products and undertaken a variety of engineering projects both locally and abroad. Our locally engineered product coupled with our range of aluminium Reid Lifting dual use portable gantries and portable davits allow us to offer solutions to most lifting, materials handling, height safety and confined space access needs as well as offer specialised engineered solutions for major project needs. At LiftEx, we will be promoting the following products: Porta Gantry Rapide
The Porta gantry Rapide is a dual use portable gantry suitable for lifting, fall arrest and confined space access and recovery applications. Manufactured by Reid Lifting UK out of anodised marine grade aluminium. Available in capacities up to 1T with in multiple heights and spans, its light weight, ease of assembly and dual use capabilities make it the perfect solution for many on site challenges that would usually require the installation of overhead frames and or mobile crane hire.
Portable Davits
Portable Davits are a light weight dual use portable davit system suitable for lifting fall arrest and confined space access and recovery applications. Manufactured by Reid Lifting UK out of anodised marine grade aluminium. With a variety of models for different applications lifting capacities up to 600KG and a reach up to 1500mm, Portable Davits can be used in multiple locations with the use of an installed socket or portable bases. With its unique patented king pin that allows the davit to rotate around the king as opposed to rotating in the socket, the Porta Davit is a superior light weight high quality davit that can be used in multiple applications and industries.
Contact: Andrew Sutherland andrew.sutherland@wireco.com.au https://wireco.com.au
WireCo Australia are pleased to be attending LiftEx 2024 to exhibit our extensive array of products and services including our wire ropes from Casar and Oliveira, Lankhorst Synthetic ropes, lifting and rigging gear and testing services.
Our point of difference is we just don’t supply full reels of rope, we can cut rope to specific lengths, splice, swage, socket, test, and more. We will have industry experts with many years industry experience on hand to answer all your questions regarding wire and synthetic ropes, with staff from our Lifting and Rigging and Crane Rope Divisions attending.
We will have synthetic rope splicing demonstrations occurring at regular intervals over the course of the event conducted by our factory trained and internationally renowned master splicer Rick Daly, and samples of our lifting products will be on show ranging from G100 chain assemblies, green pin shackles, synthetic lifting slings, to our Big Tow recovery strops.
Contact: Demi Wang demi_wang@mail.yoke.net https://www.yoke.net/english
YOKE is Taiwan based manufacturer of lifting fittings for chain, wire rope and webbing slings for more than 35 years. Certified by ISO 9001 as well as DNV, API, ABS and DGUV. YOKE supply digital product line (Supra Digital Chips) and qualified products tested in accordance with EN1677, i.e. Lifting Point(YP), DA shackle(DNV 2.7-1 approved), and G100 lifting components. “Safety” is the core element for all safety hook products. As a proponent of “safety” as a value, we have embraced “pursuit of quality perfection, constant innovation and development, sustained management improvement and creation of customer satisfaction” as our management philosophy.
THURSDAY 12TH SEPTEMBER
10:00 - 10:10 Welcome Session
Justin Boehm, Regional Manager Australia & New Zealand, Lifting Equipment Engineers Association.
10:10 - 11:30 Women in Industry
Teagan Dowler, Department of Regional Development and Manufacturing, Qld Government
Teagan will demonstrate how the Qld Government is committed to arming local manufacturers with the tools, skills, and funding to ensure they can diversify their workforce to remain competitive. In this session, delegates will understand how to:
• R eimagine the workforce
• R ethink recruitment practices and programs
• G ive greater value to diversity and inclusivity in the workplace
11:45 - 13:15 Pre-Use Inspections for Riggers and Dogman
Warwick Bright, Tower Crane Training
Pre-use inspections are a critical, but often overlooked part of lifting operations. From this session, delegates will learn:
• H ow to conduct thorough pre-use inspections, identifying potential hazards and ensuring that all lifting equipment is in optimal working condition before use
• T he relevant safety regulations and standards, along with best practices for documenting inspection results to ensure compliance and accountability
• E ffective strategies for reporting inspection findings and communicating with team members to ensure a coordinated and safe lifting operation
14:15 - 14:45 Queensland Government Code of Practice
Stuart Davies, Qld Government – Office of Industrial Relations
The Qld Government is investigating ways to better protect workers by implementing a possible change to the way concrete panels are lifted. Delegates will hear about these changes and what implications it has for the lifting industry.
14:45 - 16:00 Panel Session - Standards Development and Industry Issues
• Stuart Edwards, Principal Engineer, Edwards Heavy Lift
• Ashlea Johnson, Branch Manager, Bunzl Safety
• Justin Boehm, Regional Manager, LEEA
Industry standards and best practice in safety go hand in hand. Development of AS4991 – Lifting Devices, has been a topic of contention for a number of years. This panel session will discuss the development and options to better develop this “catch-all” standard. Additionally, we’ll hear from LEEA about AS1353 development, edge protection and host a forum for new and better practices for safety around development.
16:00 Round up of Day 1
Justin Boehm, Regional Manager, LEEA
16:00 - 18:00 Networking Drinks Reception sponsored by TNC Cranes
FRIDAY 13TH SEPTEMBER
09:30- 09:40 Welcome to Day 2
Justin Boehm, Regional Manager Australia & New Zealand, Lifting Equipment Engineers Association. Review of Day 1 and introduction to Day 2.
09:40 – 10:15 Panel Session - Military Transition Scheme Launch
In this panel discussion, delegates will discover how the MTS program will connect skilled and experienced individuals transitioning from the armed forces into civilian life and potential employment in the lifting industry.
10:15 – 11:00 LEEA – Shaping the industry
Matt Barber, Director of Membership, Lifting Equipment Engineers Association
Matt discusses LEEA program updates and developments that will change the face of service delivery in the region.
11:30 – 12:15 Offshore Energy
Offshore Energy is a significant industry for our current energy requirements in Oil and Gas or future Hydrogen and wind resources.
12:15 – 13:00 Exhibitor Round Up
13:00 – 14:00 Beaconsfield Mining Disaster. Decades on, what have we learnt?
Brant Webb, Beaconsfield Mining Disaster Survivor
Brant will tell his extraordinary story of survival and resilience after the Beaconsfield gold mine in 2006.
His story serves as a stark reminder to delegates of the importance of safety protocols and procedures in high-risk environments.
14:00 - 15:00 LEEA Membership Awards and Prize Draws
The Crane Industry Council of Australia’s (CICA’s) National Conference and Exhibition will attract over 600 dedicated crane and construction leaders from across Australia, New Zealand, Europe, Japan the US and China. Themed Building a Sustainable Tomorrow this exciting event ensures that delegates will be immersed in the latest thinking and exposed to the best information, resources and networking opportunities enabling them to plan for a sustainable future.
Adelaide will host this unique Conference and Exhibition experience from
The October issue of Cranes and Lifting magazine will be in the hands and satchels of every attendee, with hundreds of extra copies to be printed and distributed during the event.
For the first time, the team at Cranes and Lifting will be presenting a ‘South Australia Feature’ in this issue. The feature will include insights from leading South Australian crane hire businesses and crane distributors.
The October issue presents a great opportunity for your organisation or business to feature in the magazine, and to have your products, services and brand connected to the crane sector.
Cranes and Lifting magazine proudly sponsors the CICA Lift of the Year Awards and also the CICA Photo of the Year and the winners of each category will feature prominently in magazine.
“Increasingly, I hear people in our industry referring to an article or advertisement they have seen in Cranes and Lifting magazine. The quality and popularity of the magazine continues to grow, and I believe it is now a world leading publication for the crane sector. The October ‘CICA Conference and Exhibition edition’ will be extremely well read and widely distributed.
“Cranes and Lifting magazine also sponsors the CICA Lift of the Year Awards and the CICA Photo of the Year demonstrating their commitment to celebrating innovation and achievement in our industry,” Brandon Hitch, CICA CEO.
The purchase of the new TIDD PC28-3G and the TRT 12 Row ESS Trailer are part of Qube’s ongoing commitment to renew its crane fleet in a sustainable manner.
Qube Heavy Lift, part of Australia’s largest logistics provider Qube Holdings, recently took delivery of two TIDD PC28-3Gs and a 12 Row ESS Modular Platform Trailer designed, engineered and manufactured by TRT. Matt Arkinstall, Qube Heavy Lift’s General Manager, explains how the purchases are a key element of Qube’s plans for a more sustainable future.
prioritising safety and performance throughout its design and class-leading features including the Euro 6 Cummins engine, the highest emission control diesel engine available with significantly more horsepower.
Neil Webb, General Manager at TRT Australia, speaks about the features and benefits of the new TIDD PC28-3G.
“The new TIDD PC28-3G features the new Cummins ISB6.7 Euro 6 on road engine. This is a deliberate step us by us, because Euro 6 will be the new Australian Design Rule (ADR) in November 2025. The shift to Cummins was due to after-sales service and support throughout Australia.
“The crane has moved from our previous standard Mercedes package to the new Cummins engine which generates an extra 34 kilowatts more horsepower, which is a considerable amount of difference in terms of operation.
“Obviously Slew Safe is a key safety feature and has featured in our cranes from the beginning. The feature, developed and patented by TRT, serves as a significant standard for safety. It is specifically designed to assist operators in preventing rollovers. This preventative tool functions by alerting the operator when they are slewing in an unsafe direction, prompting them to slew back towards safety. This ensures a clear understanding of the operator’s role in maintaining safety standards. The feedback from our customers on the PC28-3G, especially from Tier One builders, has been fantastic,” said Neil.
The new TIDD PC28-3G features the TRT patented Traction Air System.
“The Traction Air System is currently operating in approximately 10 countries around the world as a CTI system. It was initially designed for logging equipment, and we moved it into our TIDD pick and
carry crane. It’s an option but we see more and more safety requirements from sites, and from customers which means it is almost a standard option that’s ticked by our customers.
“The Traction Air System provides a management system for tyre pressure. It allows the tyre pressure to increase or deflate to ensure optimal pressure of 130 PSI is maintained. It’s a great safety feature for the crane. Because the tyres are always at the correct pressure you also get better usage and less wear and tear. During lifting the tyres are at an optimal lifting pressure, ensuring you are performing every lift safely,” said Neil.
“TRT has always been big on our braking systems and when we first designed the PC25, we had ABS brakes under our machines. Obviously, ABS has just come in as a requirement for ADR.
“When we began redesigning to comply with the new ADR emission standards, we assessed areas for improvement. We focused intensely on the exhaust brake system and decided to switch to a retarder. It is very similar to the technology used in a lot of heavy equipment, like large all terrains, and this Allison Transmission with Retarder really puts us ahead of our competition,” said Neil.
There are three key benefits; it allows for less wear and tear on the brakes, noise is greatly reduced and overall stopping
performance is significantly improved.
“It’s essentially an additional safety feature for our crane. Our customers recognise that TRT doesn’t just aim to meet standards; we consistently exceed them and continue to innovate. We are highly customer-focused, incorporating their feedback into our product designs,” said Neil.
With improved engine performance, increased horsepower and better braking, the TIDD PC28-3G has been accepted into the marketplace really well. Another added safety feature involves neutralising the gearbox when the holding brake is on.
“This ensures the operator can’t take off
down the road with the brake on, causing damage to the braking system. Also, during operation, it can be unsafe if the operator’s left the crane in drive and engaged the holding brake. The load can lurch when he applies the throttle. It’s just another complimentary feature, along with our EN13000 approved system, which allows us to have a 75 per cent static chart. We’re not just a pick and carry crane. We also have a static chart, which gives it a greater performance to 75 per cent instead of 66 per cent, which is a huge feature when you’re talking loads,” said Neil.
Tier One Builders are particularly focused on safety on construction sites, and sustainability within the construction processes. Neil explains how the TIDD PC28-3G and TRT fit into this scenario.
“Obviously we always want everyone who drives our cranes to go home safe every day, and that’s why we continually innovate around the whole machine, but especially around safety. From a sustainability point of view, we have been carrying out a huge solar panel project on our facilities in Hamilton and we now generate approximately 80 per cent of our power through this solar panel system. We are definitely aligned with Tier Ones and also our smaller customers providing a package that suits all requirements,” said Neil.
Neil explains the rationale behind Qube’s decision to purchase TRT’s Electronic Steering System (ESS) trailers.
“Qube conducted an extensive case
study, which included several factory visits to our Hamilton facility where they observed our trailers in action during product demonstrations. They were highly impressed with the overall quality, performance and innovation of our products.”
“We are one of the only trailer manufacturers in the world that can have a trailer that’s in a 12 line configuration, which Qube has purchased, and it can be reduced down to an eight line configuration in 40 minutes. Our ESS technology is a game changer as is our Quick Connect system for our platform trailers. Qube’s second trailer is really exciting for the renewable/wind industry, and we look forward to delivering that in the next couple of months, with more to come.
“At TRT, we take great pride in our in-house design and manufacturing capabilities. Our high-quality and innovative solutions likely contribute to
our multiple ongoing contracts with the Australian Defence Force,” said Neil.
Matt goes on to discuss the reasons for purchasing the TIDDs and also the TRT Lead up to the purchase of the TIDDs and TRT 12 Row ESS Trailer.
“These are the first TIDDs in Qube’s Heavy Lift fleet. We were really impressed with the low emission Cummins engine and also the safety features including the Dynamic LMI with a deadlock switch inside the cabin and an LMI bridging switch outside the cabin.
“The TIDD PC28-3G features the latest emission controls which help work towards Qube’s Sustainability Roadmap. We already have a number of EV Vehicles in the fleet and our facilities and offices around the country are already off grid or on the way to being so, following our ongoing investment in solar energy. As a corporation, Qube Holdings is dedicated to ensuring we continue our path to limit emissions
and reduce our carbon footprint wherever possible,” said Matt.
Matt discusses the relationship with TRT.
“The sales process around the TIDDs and the trailer was fantastic. The team at TRT are focused on our needs for this first trailer, their approach was very personal and they were very attentive throughout the whole process to ensure they delivered the right equipment for our purposes. The 12 Row ESS Trailer was our first TRT Platform with a second due in August 2024,” said Matt.
“We use the TRT ESS 12 Row Platform with the Quick Connect system for transporting wind turbine components and moving our own fleet of equipment to better service our clients. TRT manufactures a range of quality products that can be tailored to suit our specific needs. We appreciate TRT’s dedication to deliver on our requirements and we certainly impressed with the support we receive from the entire TRT Group,” said Matt.
Managing Director of crane, foundation and piling equipment supplier Ganz International, David James, shares insights on the manufacturing quality coming from China and his unwavering confidence in the Zoomlion brand.
IN AN ERA OF RISING INTEREST RATES and lengthy wait times for heavy-duty construction machinery, businesses are increasingly drawn to the allure of Zoomlion’s Machinery. When seeking a brand of cranes to introduce to the New South Wales market, David James, Managing Director of Ganz International, was no different. Offering speed of supply, a sizeable cost benefit and a machine that performs just as well as its competitors, Zoomlion cranes ticked every box.
Based just outside of Newcastle in
New South Wales, Ganz International distributes a range of machinery across Australia and New Zealand. As the exclusive agent for Zoomlion crane equipment in NSW and Zoomlion foundation equipment across Australia and New Zealand, Ganz is establishing itself in the lifting market and continuing to grow its foundations and drilling business.
Beginning his business during the early stages of the COVID-19 pandemic in June 2020, David has grown Ganz International into a reliable and reputable
dealer of foundation and piling equipment. David holds extensive experience in heavy-duty construction machinery; he is a fully qualified electro-mechanical technician. He first ventured to Australia in 2013 to work in sales with some large construction equipment companies across Australia and New Zealand, before starting with Ganz International.
“I have an extensive background in heavy duty equipment,” he says. “I’ve always had a passion for providing good service with quality equipment, which
led me to start Ganz. The opportunity to work for other companies in Australia enabled me to build contacts throughout the Asia Pacific region and develop a deep understanding of the Australian market, which now complements my European knowledge.”
According to David, the quality of Zoomlion’s crane equipment stems from substantial investments in manufacturing facilities and a shift towards automation on their smart production lines. This, he says, ensures high product quality at a lower production cost, translating into significant savings for end-users who receive high-performance cranes akin to European machines, but without the hefty price tag or long wait times.
Ganz International has simplified the process of working with Chinese manufacturers to deliver unparalleled service and support to customers
“Zoomlion equipment performs as well as anything on the market, and at a fraction of the cost compared to its more established competitors, making it a compelling value proposition,” David says. “Zoomlion’s heavy investment in the Australian market, including a new
PDC opening in June, reflects their confidence in us as their NSW market representative.”
“We’re privileged to promote and support Zoomlion crane products in NSW and Piling Rig products across Australia & New Zealand,” he continues. “We’ve scaled up our operations significantly to accommodate their expanding range and to ensure we are able to support the needs of an increasing customer demand.”
Streamlining operations with Zoomlion has made customer support seamless. Ganz International now stocks a wide range of Zoomlion cranes, from 30-tonne telescopic crawlers to large lattice boom crawler cranes, the allterrain range and truck crane range. David notes that Ganz has already sold multiple machines to Tier One construction companies – a testament to both the quality of Zoomlion’s products and the customer experience provided by Ganz International.
“All cranes in our yard undergo
CraneSafe inspections upon arrival,” says David, “ensuring they meet stringent safety standards prior to sale.”
With Zoomlion’s reliable equipment and streamlined processes, choosing their cranes is an easy decision for customers seeking compliant, high-quality products with shorter lead times and significantly lower costs. The robust post-sale service and support further enhance customer confidence. Recently, when a crane needed calibration, a Zoomlion technician arrived onsite within three hours, resolving the issue within 30 mins – a testament to the efficiency and support provided by Zoomlion.
“At the end of the day, a piece of machinery is a piece of machinery; what sets businesses apart is their ability to provide exceptional service and support,” says David. “Through our partnership with Zoomlion, we’ve simplified the process of working with Chinese manufacturers to deliver unparalleled service and support to our customers.”
Tenacity Cranes recently took delivery of the first Tadano AC 4.080-1 in Queenslandonly the fifth unit in the country. Company Director Santino Silvestro explains more.
“When I had finance approved, I couldn’t find the right piece of equipment and then the finance period ran out. I wasn’t getting anywhere, and starting to get frustrated, I said to my wife, “I make good money working for other people, I’m not going to bother.” she said, “You’ve got the tenacity, you’ll get it done. I know you will,” and that’s where the name Tenacity Cranes came from,” he said.
Santino found a market for City Cranes on the Gold Coast. He knew a guy who had been chasing one to dry hire for some time, so Santino bought a 10t City Crane.
“I didn’t borrow, I bought the crane with cash. I just spent a big chunk of the money that I’d saved, and I dry hired that out whilst I continued working for another company. It was 2016 when I decided to work for myself, and Tenacity Cranes was really born.
“In 2017, I started quoting small structural steel projects for that little crane and I started winning work. I then moved on by adding a small Maeda mini crawler, a truck, then a truck mounted, 25t capacity City Crane.
“With the older gear, I was mainly working in structural steel, however the goal was to build the bank, I bought more City cranes over the years including a 12t and 16t Tadano City Crane, and eventually replaced our older cranes with newer models and that’s when the business really started to kick goals. I’ve replaced all the machines to brand new and I still have every capacity I started with, but they are now brand new.
The 80 tonne all terrain was Tenacity Cranes fifth, brand new Tadano. The AC 4.080-1 blends outstanding reach with exceptional versatility. Its compact size on four axles gives this all terrain crane bestin-class jobsite accessibility. It can transport up to 9.3 tonnes of counterweight itself while remaining under a 12 tonne axle-load limit, and all while also carrying the swingaway 16 metre jib. The AC 4.080-1 will set standards in its class. With its 60m main boom length, it can lift up to 5.4 tonnes. With this, an operator can take on jobs for which they would normally need a 90t or a 100t crane.
The AC 4.080-1 comes with the IC-1 Plus control system. In combination with
Flex Base, you can extend the outriggers to any point within their range. That means that it can determine the max available lifting capacity in real time with any outrigger configuration.
Whether used as a main crane or a powerful assist crane, the lifting capacity in steep boom positions makes the AC 4.080-1 unbeatable in its class.
Tenacity Cranes has always been well positioned in structural steel but after COVID-19, Santino started targeting government work. He knew that was where the money was getting spent and he started quoting on the installation of gantry signs and winning more Tier One work.
“We have been working on the inbound and outbound Brisbane Metro Bus terminals. We installed all the gantry and road signs for the Burpengary by-pass and we are working on the gantries for the Tugun and Currumbin upgrade. We are working on the Victoria Street bridge crash rail, and it looks like we are in the hot seat for work on a couple of the bridges on the Coomera Connector as well,” said Santino
With the new cranes, Santino also moved the business into more general industrial applications, including the structural steel element of distribution centres for major supermarkets.
“With all new cranes in the fleet, targeting general hire was the next step. Where we are quoting for the structural steel install, the builder will generally give us a general crane hire package as well. Now we manage the crane hire prior to the structural steel, and then come back with our new cranes and install the structural
steel and assist other trades after the structure is complete like roofing and air con contractors.’
“We also operate an access division which is under the same banner. We’ve got our own small scissor lifts and boom lifts, so when installing the structural steel, our tilt tray brings our scissor lifts, or our boom lifts to site. We’ve got our own boiler makers, site supervisors, riggers as well as our own new cranes, so we have the capabilities of bringing the complete package to site,” he said.
Santino’s relationship with Tadano started when he first started operating cranes 20 plus years ago.
“I have always been drawn to the Tadano brand, their cranes are easy to operate, they are great lifters, and the models feature really good charts. Over the years I’ve operated every brand including Liebherr,
friction driven cranes and that’s real oldschool, but for me, Tadano’s have always been a good crane to operate and I have always been drawn to that.
“I bought my first brand-new Tadano in early 2021 and that was a ATF-50, 50t all terrain. After that, I bought the GT-300EL, which is a 30t truck mount. I then bought a GR-200EX 20t City Crane and then the GR-130EX, 13t City Crane and now the Tadano AC 4.080-1. There’s a strong market for this size crane on the Gold Coast and in Brisbane, especially with the way it travels with counterweight,” said Santino.
Santino goes on to discuss the ease of buying Tadano cranes.
“We aren’t just buying the Tadano brand and the user-friendly operator system, the key factor in my continued purchase of Tadano is the product support I receive, and this has been second to none.”
“We have built our business on relationships, valuing trust, reliability, and mutual support above all else. This philosophy aligns perfectly with Tadano. Just as we prioritise long-term connections and consistent support, Tadano’s teamfrom sales to product support to the branch manager - embodies these same principles. Their readiness to assist, resolve issues promptly, and ensure customer satisfaction mirrors our own dedication to building strong, enduring relationships. This shared ethos of putting people first is a cornerstone of both our success and Tadano’s, making them an ideal partner for Tenacity Cranes.
Building the Foundations of Tomorrow: We are engineering the future, one project at a time.
Scan the QR code to find out more!
Empowering Industries. Building Futures. One lift at a time.
HSEQ Manager at Johnson & Young Cranes, Amanda Hermoso, provides a detailed overview of the stringent safety procedures at the East Coast crane hire company.
AT JOHNSON & YOUNG CRANES (JYC), safety is not just a priority—it is the cornerstone of the company’s operational philosophy. JYC’s commitment to safety permeates through every aspect of the business, from its rigorous training programs to the state-of-the-art equipment and comprehensive safety protocols. This dedication to safety ensures that JYC not only protects the crane hire company’s employees, clients and the public, but also enhances the overall efficiency and reliability of the services the company offers.
The foundation of safety culture at Johnson & Young Cranes lies in its comprehensive training programs, says Amanda Hermoso, JYC’s HSEQ Manager.
“We believe that well-trained employees are the key to a safe work environment. Every new team member undergoes an intensive training regimen that covers both theoretical knowledge and practical skills. This training includes detailed instructions on the proper use of our cranes and other heavy machinery, as well as in-depth education on industry safety standards and regulations,” she says.
“Our training programs are continually updated to reflect the latest advancements in technology and changes in safety regulations. This ensures that our employees are always equipped with the most current knowledge and best practices. Moreover, we provide ongoing education opportunities, including regular safety drills and refresher courses, to keep our team members sharp and prepared for any situation.”
At Johnson & Young Cranes, the company understands that the safety and reliability of its equipment are paramount – hence why the company has invested heavily in state-ofthe-art cranes and machinery, ensuring that all of its equipment meets the highest safety
standards. JYC’s fleet includes a variety of cranes equipped with the latest safety features, something that is typified by JYC’s most recent acquisition of two Liebherr LTM 1110-5.2 cranes.
Regular maintenance and rigorous inspections are critical components of JYC’s equipment safety strategy. The crane hire company employs a dedicated team of experienced technicians who perform routine checks and maintenance on all of the equipment. This proactive approach helps the team identify and address potential issues before they become hazards, thereby minimising the risk of accidents and ensuring optimal performance.
JYC’s commitment to safety is further reinforced by the company’s strict safety protocols that are designed to protect everyone on the job site. These protocols are meticulously developed in accordance with industry best practices and regulatory requirements. They cover a wide range of safety measures, including site assessments, hazard identification, risk mitigation and emergency response procedures.
“Before any project begins, our team
JYC invests in stateof-the-art equipment to deliver a diverse range of projects with fully compliant machinery, as seen by this unique lift involving two LTM 1750-9.1s on a Victorian wind farm.
conducts a thorough site assessment to identify potential hazards and develop a customised safety plan,” says Amanda. “This plan outlines specific measures to control risks, such as proper crane positioning, load handling procedures and the use of personal protective equipment (PPE).”
Fostering a strong safety culture is a continuous effort that starts at the top. At JYC, the leadership team is deeply committed to promoting and maintaining a culture of safety. They lead by example, according to Amanda, demonstrating their commitment through visible actions and decisions that prioritise safety over productivity or cost-cutting.
“We encourage open communication and feedback from all employees regarding safety concerns. This inclusive approach ensures that everyone feels responsible for maintaining a safe work environment,” says Amanda. “Our leadership regularly engages with employees through safety meetings, training sessions and site visits, reinforcing the importance of safety and recognising individuals and teams that demonstrate exceptional safety practices.”
Behind every big lift at Johnson & Young Cranes is an even bigger commitment to delivering each project as safely as possible.
Innovation plays a crucial role in enhancing safety at JYC, exemplified by the crane hire company’s continuous pursuit of new technologies and methodologies to improve safety outcomes. For instance, JYC utilises advanced software for load planning and risk assessment, helping the company identify potential hazards and optimise crane operations.
Additionally, JYC is at the forefront of integrating usable technology into its safety protocols, digitising safety documentation and equipment compliance packs using QR codes and the use of data logging technology throughout its Franna pick and carry crane fleet. These technologies allow JYC to monitor real-time data on the health and safety conditions of its workers and equipment; and, by leveraging these innovations, JYC can respond quickly to any emerging risks and ensure a safer working environment.
Despite the company’s best efforts to prevent accidents, JYC recognises the importance of being prepared for emergencies; therefore, JYC puts robust emergency response procedures in place, designed to protect lives and minimise damage in the event of an incident. JYC’s emergency plans include clear protocols for evacuation, medical response and
communication with emergency services. Regular emergency drills are conducted to ensure that all employees are familiar with these procedures and can respond effectively under pressure.
Furthermore, JYC actively collaborates with industry associations, regulatory bodies, and safety organisations to stay abreast of the latest developments in crane safety. The company participates in industry forums, workshops and conferences to exchange knowledge and learn from the experiences of others. This collaborative approach helps JYC continuously improve its safety practices and align with the highest industry standards, as Amanda says.
“Compliance with all relevant safety regulations is non-negotiable at Johnson & Young Cranes,” she says. “We strictly adhere to national and international safety standards, including OSHA (Occupational Safety and Health Administration) regulations and ISO (International Organization for Standardization) certifications. Our compliance efforts are regularly audited to ensure that we meet or exceed all regulatory requirements.”
The company’s commitment to safety extends beyond its immediate work sites to
the communities and environments in which JYC operates. Taking proactive measures to minimise the impact of its operations on surrounding areas, JYC ensures that public safety and environmental protection are integral parts of its project planning and execution.
“We implement noise and dust control measures, secure work zones to prevent unauthorised access, and carefully manage waste and emissions,” says Amanda. “By doing so, we demonstrate our responsibility not only to our employees and clients but also to the broader community and the environment.”
At Johnson & Young Cranes, safety is more than just a priority—it is the bedrock of the company’s operations, according to Amanda. Through comprehensive training, state-of-the-art equipment, strict safety protocols, and a strong safety culture, the East Coast crane hire company strives to create a work environment where safety is paramount. Its continuous pursuit of safety innovations, emergency preparedness, industry collaboration and community responsibility underscores the company’s commitment to protecting lives and ensuring the highest standards of safety in every project it undertakes.
“At the end of the day,” says Amanda, “we just want to make sure that everyone goes home safely– irrespective of the task at hand.”
Lampson Australia is no stranger to complex projects, but there is always one constant before all jobs, big or small, and that’s the importance of safety above all else, says Managing Director John Lee.
IT’S THE EARLY HOURS OF A COLD AND dark Friday morning, wind swirling, and the streets are empty. Suddenly, two blue hauling trucks cover the road and slowly move towards the intersection.
Orange flashing hazard lights bounce off all reflective objects with the beeping of the trucks ringing on the airwaves, as the team at Lampson Australia calmly move an ultra heavy piece of equipment.
Lampson Australia has been a leader in the heavy lift and transportation industry for over 75 years, with a strong haulage history in Australia for over 33 years.
The company was originally founded in the United States, Kennewick, Washington and founded Lampson Australia in Toronto, Australia during 1990.
Managing a group of people and heavy integrated technology excites John and he lives for the challenge.
“As a young person, I always looked toward the role of managing a company; it was an inbuilt ambition, which was not a bad thing to have, and you think one day you’re going to be in charge of, whatever business you come into,” he says. It does not always work out that way and is certainly something I am thankful for.
Originally an engineer with Lampson Australia it was a dream of his to step into a role and lead one of the strongest hauling and lifting companies in Australia; John, however, believes luck is always some part of success.
Now 12 years into this role, “you can always do your best to prepare” he says, but there will always be the unexpected, and that keeps things interesting.
In John’s line of work, as the unpredictability of moving extremely large
items can always put someone on edge. All scenarious are possible and we do our best to plan for the worst and aim for the best.
Most recently, Lampson Australia hauled an 8m wide, 156-tonne spiral case, part of Snowy Hydro 2.0 Project. The spiral case ensures even water flows at speed into a turbine to generate clean hydro-power.
Even though we done our CAD work, prepared the calculations, engineering drawings and lift plans and had it all checked by someone else there is always an element of risk. “When you go to site and you watch the load being moved or
lifted, you’re still nervous, because you’re rethinking all that you’ve done to make this go right. It’s only because you care that you’re nervous,” John says.
“I think that when you put that much effort into something, you want it to go right, and you hope you haven’t missed anything, and you hope that the person that checked it hasn’t missed anything, and the guys that are doing the job haven’t missed anything.
“The the relief that follows does makes it worthwhile, in what makes yet again another successful Lampson project: there are high-fives all around,” he said.
Lampson Australia has been a leader in the heavy lift and transportation industry for over 75 years, with a strong haulage history in Australia for over 33 years.
John gets a thrill out of the fast-paced nature of the business.
“The change is good, and because we can’t predict the future it keeps it interesting.
John also described the large-scale hauling projects as “live action drama”.
“It really is, and if you’re not checking what you’ve just done or checking what you’re about to do, things can go pretty crazy pretty quick.”
But it’s not just the big jobs John enjoys.
“I don’t mind the little jobs either. It is amazing how you can help someone else by just giving them the right piece of equipment, the right tool. And if they don’t have that tool, they might still be able to do the job, but they won’t do it as well or as quickly or as efficiently,” he says.
Complexity in the workplace is an everyday item, but it doesn’t discourage John from doing what he enjoys.
“I really get enjoyment of supplying the right tool to the right application – big or small. The bigger and more complex jobs, they’re also very rewarding, because it takes more thought and you feel like all the study that you’ve done and the experience that you’ve obtained is better utilised.”
Camaraderie is key to what John says is a strong culture at Lampson.
“That is also really rewarding too: the friendships within the company is like an
unspoken understanding, as we all share the same experiences with the heavy equipment, cranes, trucks and trailers.”
John also says safety comes first and the knowledge of machines is paramount to this.
“When we look at a crane, a trailer or piece of equipment, before you start working it you’ve got to know the history of that piece of equipment, you’ve got to know where it was made, how it’s been maintained, how it’s been used, abused, repaired, he said. “Then you need to know what you’re going to do with it,” he says.
John also said the connection is not too dissimilar to driving your personal car.
“So that’s the next stage. And then you need to do a condition report to see what the machine is like right now – something that we conduct with every piece of equipment,” he says. “You don’t just walk up to it and start using it. You don’t just go, here it is, go ahead and send it out on rent it as is; it’s like your own vehicle, your own car; you know what it’s done, what it’s capable of, and how it’s been treated.”
The preparation for longer heavy haulage involves plenty of planning and vehicular preparation, according to John.
The connection between staff and trucks is the key to safety and a smooth journey. The team at Lampson lean on their experts to ensure everyone and everything is safe.
“You’re very thorough with each piece
of equipment, I think that’s where you need to start, at least for best utilisation.”
When it comes to risks, John says it is unconditional. “It is all based on safety first”.
The company’s relationship with the United States parent organisation helps John feel supported and energized about the overall mission Lampson is embarking on.
John says he leans on the American counterparts to ensure machinery and production is running smoothly here in Australia, as he travels to the States when needed.
I’m certainly supported by those guys, technically and physically,” he says.
“If we need equipment or backup for spare parts, just about anything, those guys send us what they have, and that keeps our equipment running here,” he says.
John has fostered a strong relationship with his fellow leaders in Kennewick.
“It’s a family-owned business and we know each of them personally. It’s a healthy situation, and it’s a really good company,” he says.
At the end of the day, safety is king; John’s priority is that everyone comes to work and goes home at the end of the day in one piece.
“If it’s ever going to be unsafe we will change that task and manage that risk. There is always another way.”
AM Cranes and Rigging has been providing clients lifting solutions in the Northern Territory since 2007. Today, the business offers the largest and most diverse fleet of mobile cranes in Darwin and Katherine in the NT and Kingaroy in Queensland. Adam Murrihy explains why he recently added two Maeda telescopic crawlers, a CC985S-2 and a CC1485S-2, to the already extensive fleet.
“WE OPERATE AN EXTENSIVE FLEET OF 13 Liebherr all terrains which include capacities ranging from 230t down to 30t. We also operate Tadano truck mount cranes and an 80t rough terrain. Our fleet includes a range of pick and carry cranes, including 16 Frannas with capacities ranging from 15t to 25t, and six TIDD PC28s. We also operate a couple of the smaller Maeda mini crawler cranes with capacities of 4.9t and 6t, as well as eight road trains supplying transport options for our clients across the Northern Territory,” said Adam.
“I have known David ‘Chalky’ White for many years and on one of his visits to Darwin, he informed me he was going to be selling Maeda and other brands represented by Pace Cranes. We had
researched the market regarding small crawler cranes, and I found the Maeda brand kept coming back as the premium product in its class.
“I spoke to Chalky and he recommended we look at the CC98SS-2 and the CC1485S-2. These mini crawlers are a first for our business though I had been toying with the idea for some time. Now, we just need to get them out into the market and see how they perform. Every crane has its pros and cons and I believe having the smaller cranes in the fleet will increase options for our clients moving forward, which includes giving the developers savings on their projects,” said Adam.
Chalky had this to say.
“When I first met Adam back in
2007/8, he had a truck crane and an old Rough Terrain crane, he was in a small yard with a donga for an office. Adam also had an enormous amount of confidence, and a deliberate plan to grow his business.
“It has been fantastic to watch how he has grown the business over the years, including moving from the small yard to a larger yard, to eventually his own, purpose-built depot that he now has in Darwin. I believe that the Maeda Cranes he has purchased will fit into the whole growth pattern of this very professional company, perfectly,” he said.
There are four models in the Maeda CC range, with capacities starting at three tonne capacity moving through to five and six, finishing at eight tonne.
Adam confirms his crews and operators have been impressed with the new Maeda mini tele crawlers.
“The majority of our work is in general crane hire on major construction sites. Since we took delivery of them, the Maedas have proved to be a well utilised asset and our operators have been impressed with how they handle and their lifting capabilities. We can see them being a valued addition to our fleet,” said Adam.
Matusch provides a holistic overview of its E.P.O.S system that reduces administrative paper flow within an organisation and drastically enhances resource scheduling as well as project invoicing.
MATUSCH GMBH, BASED IN COBURG, Germany, is one of the leading companies specialising in the development of the software E.P.O.S. (Equipment Planning and Organisation Software).
The company was founded more than 30 years ago by owner Christian Matusch and today employs more than 15 dedicated staff members.
With a customer base of over 300 companies worldwide and a presence in Australia for over 15 years, Matusch
works closely with its customers to develop customised solutions for their individual requirements.
The German company’s software is aimed at companies that rent, plan and/ or sell equipment, including mobile cranes, tower cranes, construction equipment rental, work platform rental, heavy haulage, construction companies, traffic control and more.
Matusch says E.P.O.S. suits every type of company, from small companies with just two users to major customers
Above: What a schedule looks like in Matusch’s E.P.O.S. Image: Matusch.
with more than 100 people using the software.
Matusch’s customer base includes crane rental companies with a fleet of five to 500 cranes, work platform rental companies with 50 to 3000 work platforms, companies with hundreds of tower cranes as well as wind power manufacturers, trailer manufacturers and mobile roadway providers.
E.P.O.S. offers a variety of functions to support companies in the area of equipment rental, planning and sales.
The main functions include:
• Inquiry management
• Onsite Inspections
• Quotation management with customised prices and project prices
• Scheduling
• Project management
• Permits
• Various interfaces to tracking systems such as Navman, TomTom
• Tablet solutions for iPad and Android devices
• Invoicing, Automatic Invoices
• Late reminders
• Export to all common accounting systems such as MYOB, Quickbooks, Odoo, etc.
• Various statistics such as utilisation, average prices, etc.
• Other functions such as workshop management, scheduling for personnel and equipment
• Personnel qualification
• 24-hour hotline for support
information is brought together.
Matusch works closely with its customers to continuously improve the software and adapt it to current and future requirements. Currently, Matusch is working on refining the app
E.P.O.S. can map the entire operational process of a company, but has a modular structure so that customers only need to purchase the modules that are relevant to their specific requirements.
E.P.O.S. can map the entire operational process of a company, but has a modular structure so that customers only need to purchase the modules that are relevant to their specific requirements.
The core area of E.P.O.S. is the scheduling plan, in which all relevant
StartSafe is comprehensive tool designed to streamline your crane operations, enhance safety, and ensure accountability.
Machine specific checklists are in line with the CraneSafe program.
StartSafe streamlines the process for collecting pre-start information, with instant data retention to a central location for the crane owner to access.
Photos tell the story.
When a faulty item is recorded by the operator, the maintenance team is notified of the issue by email, which includes photo evidence of the fault. This also assists with gathering major inspection data.
to better meet the needs and wishes of Australian customers. At the same time, another team is working on the optical redesign of the program.
E.P.O.S. will again be present at this year’s CICA National Confereence in Adelaide, where visitors can get more information at the company’s booth.
Freo Group, one of Australia’s leaders in crane hire and logistics, boasts an impressive fleet of over 500 cranes; this includes a significant number of Franna pick and carry cranes. This strategic decision by Freo Group speaks volumes about the versatility and performance of Franna’s offerings.
FREO GROUP CATERS TO A VAST ARRAY of industries across Australia, including mining and resources, civil construction, and renewable energy, with each sector presenting unique lifting challenges –environments where Franna pick and carry cranes excel.
The ability to drive right up to load, all terrain capability, and various configurations translates to unmatched manoeuvrability on terrains and industries, a crucial factor for Freo Group’s diverse clientele.
Construction sites are often congested with equipment and uneven surfaces that Franna’s pick and carry cranes are designed to thrive in.
Their compact size and four-wheel drive enable them to navigate tight spaces with “ease”, according to the manufacturer. Franna’s unique central pivot steering, provides a high level of agility, allowing for precise positioning around obstacles.
This translates to efficient lifting
operations, minimising downtime and maximising productivity – a critical aspect for Freo Group’s time-sensitive projects.
Versatility extends beyond just movement; within its inventory, Franna offers a range of pick and carry cranes with lifting capacities of up to 40 tonnes. This allows Freo Group to assign the right crane for the job, ensuring efficient lifting of materials across various weight categories.
Furthermore, Franna cranes boast impressive telescopic boom lengths for a crane with no outriggers, enabling them to reach over obstacles and access hard-toreach locations.
This versatility is particularly valuable in the renewable energy sector, where Freo Group frequently deals with wind turbine installations and solar panel placements.
Innovation is paramount, Franna understands this well and continuously strives to maintain its edge. Franna employs key strategies to remain the undisputed market leader.
Franna consistently implements cuttingedge technologies in its cranes. Features such as overload protection systems, improved operator visibility and enhanced stability enhance safety and efficiency, qualities highly valued by Freo Group.
Franna recognises the importance of operator comfort for peak performance. Ergonomic cabins with climate control and user-friendly controls minimise fatigue and allow operators to focus on the task at hand, ensuring smoother and safer operations – a priority for Freo Group, which emphasises safety on all its projects.
Franna understands that reliable support is crucial for its customers. Therefore, the manufacturer has established a comprehensive service network readily available parts and expert maintenance services, including 24/7 phone support.
This ensures Freo Group’s Franna cranes remain operational and minimise downtime – something that is crucial for maintaining their service excellence.
Franna actively seeks customer feedback and utilises it to refine its products and services. This ensures its cranes remain tailored to the evolving needs of the industry, making them the preferred choice for leading companies like Freo Group.
Freo Group’s heavy reliance on Franna pick and carry cranes speaks volumes about the latter’s performance and adaptability. Franna cranes’ high level of manoeuvrability, diverse lifting capacities,
Freo Group caters to a vast array of industries, with each sector presenting unique lifting challenges and environments that Franna pick and carry cranes excel in.
across Australia. Furthermore, the strong relationship between the two companies fosters a collaborative environment that emphasises continuous improvement. This ensures both Freo Group and Franna remain industry leaders, delivering exceptional service and innovative solutions to their respective clientele. Freo Group’s significant investment in Franna cranes signifies a strong and mutually beneficial relationship. Freo Group leverages Franna’s versatility and performance to deliver exceptional service to its clients across Australia. In turn, Freo Group’s vast industry presence and established reputation undoubtedly contribute to increased brand recognition for Franna cranes, creating a win-win
Freo Group’s significant investment in Franna cranes signifies a strong and mutually beneficial relationship.
Europe’s largest-ever Potain top slewing cranes tacklemassive-Gravagna viaduct refurbishment in Italy.
Europe’s largest ever Potain top-slewing cranes tackle massive Gravagna viaduct refurbishment in Italy.
MANITOWOC MARKS A SIGNIFICANT achievement with the successful assembly of the world’s first four Potain MDLT 1109 cranes for a complex project – the refurbishment of the Gravagna viaduct near Genoa, in Italy. The MDLT 1109 is a powerhouse in Potain’s top-slewing crane range, boasting an impressive 40 t maximum load capacity and an 80 m jib with an 11.1 t capacity at its tip. It is the largest top-slewing crane ever produced from Potain in Europe.
The MDLT 1109 replaces the hugely popular MD 1100 with two main upgrades – a modular K mast design and the Manitowoc Crane Control System (CCS). K masts feature individual sections that can be easily assembled and disassembled, offering the ultimate flexibility in configuration for diverse needs and efficient transportation. The design also enables the option of the innovative Potain Cab-IN internal mast operator lift, which improves access to the
crane cab while retaining the traditional ladder.
The CCS, meanwhile, is a game-changer for precise and efficient operation. The user-friendly system streamlines set-up, optimises lifting performance for accuracy and speed and provides real-time crane data and diagnostics that empower operators with crucial insights.
The MDLT 1109 cranes are also equipped with the new Potain CONNECT™ telematics system. This remote technology platform ensures high uptime for cranes through faster identification and resolution of issues, preventing escalation through earlier insight. It offers remote access to crane data for troubleshooting and fleet management, enabling Potain customers to get more from their machines.
Manitowoc deployed the first four of these giant cranes for construction company ITINERA, a long-standing Potain partner. Their mission is to meticulously
dismantle and rebuild the 1,067 m Gravagna viaduct on the Cisa highway, a vital artery connecting Parma and La Spezia. The project demands a segment-bysegment approach mirroring the original construction sequence for structural integrity.
Reflecting on the assembly, Manitowoc technician Cyrille Giamello commented: “We have assembled many Potain tower cranes over the years and were expecting a complicated job with these four MDLT 1109 units because of the impressive dimensions of the components. The work was certainly demanding but the final assembly turned out to be much simpler than anticipated, which enabled us to respect the deadline for the work.”
His fellow technician Massimo Rizzo added: “The ease of assembly is testament to the exceptional quality and reliability of our products, and we are so proud to have been part of this milestone for Manitowoc.”
RAR Group recently took delivery of the new Potain MCT 565. It is the latest addition to the largest fleet of tower cranes and mobile cranes in the Canberra region. RAR Group Director Andrew Bodman explains more.
RAR GROUP WAS ORIGINALLY FORMED in 1993 as Rumbles Cranes and has grown to provide the Australian Capital Territory with the largest range of mobile and tower cranes. In recent years RAR has expanded its business to be able to service Sydney and country NSW with mobile cranes, tower cranes and rigging crews. RAR’s team now totals 80 plus, and the rigging crews specialise in the erection of precast concrete and structural steel, tower crane erection and machinery movements.
The Potains have proved to great performers for the business, over a long period of time.
“We operate a large fleet of mobile cranes ranging from a Maeda mini crawler through to our 400t capacity Grove GMK 6400. We run a number of Frannas, including the 100th AT40 manufactured by Terex and we also have an extensive fleet of tower cranes with the majority of these being Potains,” said Andrew.
Potain tower cranes have proved to be ultra reliable, says Andrew.
“The Potains have proved to great performers for the business and over a long period of time. We bought the first MCT 385 in the country and now the first MCT 565. Potain have been a really
“With a compact design and innovative, space-saving features such as a folding cab on the slewing unit and a folding counter jib, each crane’s upper section can be shipped in just nine containers.”
good brand for us; they are great cranes to put up and pull down,” he said.
The MCT 565 offers a maximum potential jib length of 80m, also giving users a flexible choice of jib options, with contractors able to configure it in 5 m increments from 25 m up to the maximum 80 m. The Potain MCT 565 is also available in 20 t and 32 t maximum capacities, the crane has several advantages beyond its recognised ease of transport and assembly, with better load charts than competitors in its range.
With a compact design and innovative, space-saving features such as a folding cab on the slewing unit and a folding counter jib, each crane’s upper section can be shipped in just nine containers – four fewer than competing tower cranes of a similar size. There are also three counter jib options of 17 m, 21 m and 24 m to match the chosen jib length – a design feature that not only aids transportation and erection, but also optimises the crane’s overall footprint on tight job sites.
“We have a strong relationship with the team at Manitowoc and we are delighted with the performance of the Potains in our fleet. The Groves - the GMK 6400, and the GMK 5250XL-1 - have been great, all the Grove products we’ve had have been terrific. But the Grove GMK 6400, it’s been a great crane since we purchased it and we have been particularly impressed with its performance,” said Andrew.
The Grove GMK6400 400t capacity all terrain has the best lifting capacity of any six-axle all terrain. It features a 60m main boom and up to 79m of luffing jib, giving it a maximum possible tip height of 136m. It can handle loads out to a maximum radius of 96m and comes with the optional self-rigging Mega Wing Lift attachment for additional capacity.
TBHL&S operates an extensive fleet of cranes. The all-terrain element of the fleet is dominated by Groves.
The Grove GMK6400 is an allrounder well suited for a number of industry sectors, including wind farm construction and maintenance, erecting and dismantling tower cranes, installing precast concrete panels, infrastructure projects and data centre construction.
Operators like to work with the Grove GMK6400 because of the ease of rigging and smoothness of operation.
The Grove GMK5250XL-1 is one of the most powerful and versatile five-axle cranes on the market. The 250-tonne capacity all terrain features 78.5m of main boom and boasts the quickest setup time in its class.
The cab is tiltable to approximately 20 degrees and offers a commanding view of the jobsite.
The Grove GMK5250XL-1 is supported by Grove Connect, the digital platform which enables remote monitoring through an app-based system providing owners and operators with the ability to view real-time crane information. The versatile platform advances fleet management, boosts sustainability, streamlines service and maintenance for users, and improves connectivity to cranes with the easy-to-use platform working across smartphones, tablets, and laptops.
The GMK5250XL-1 all-terrain crane is quick and simple to set up, thanks to the self-rigging auxiliary hoist and CCS (Crane Control System) with jog-dial, boom configurator mode and MAXbase variable outrigger positioning. Additionally, the unique Grove MegaTrak independent suspension with all-wheel steering making it easy and comfortable to manoeuvre.
“Our mobile cranes and tower cranes suit the work we have which is mainly multi residential projects in and around the Canberra region, but we are also involved in wind farm maintenance particularly with the Grove GMK6400,” said Andrew.
CES carries out routine maintenance and inspections daily
Routine maintenance is at the forefront of Crane Engineering Service, a major player in the field to keep our machines running smoothly.
ROUTINE MAINTENANCE IS AT THE forefront of Crane Engineering Service, a major player in the field to keep our machines running smoothly.
Crane Engineering Service (CES) is a leading Australian crane and heavy lift inspection company that prides itself on ensuring Australian cranes are operational and safe for use.
CES works with many major crane brands and is known to be reliable in the crane and heavy lifting certification and inspection space, having built a strong reputation.
Inspections are carried out by fully
qualified engineers and crane technicians who dedicate their jobs to dotting all I’s and crossing every T when inspections are undertaken; Inspections are in accordance with Australian Standards, Crane Code of Practice, and Work Safe requirements.
CES also offers different inspections for various categories of cranes and machines, from all terrain cranes to vehicle loading cranes and mobile elevating work platforms. Major and annual inspections, design approval and plant registration, are a part of the versatile array of CES services.
Marcus Ma, Senior Mechanical Engineer at Crane Engineering Service, also says that CES services are very affordable compared to some market competitors, which is a drawcard for many industry brands.
CES’s competitive pricing is designed to ensure customers get the best value for money, however ensuring the process is followed diligently to meet compliance and be cost-effective at the time same.
“We do have cost effective methods – where some manufacturers – they ask you to do the whole lot to replace everything. But we inspect it (the crane),
Inspection devices are used diligently to identify health of cranes and machinery
ensure we identify what is working well and what needs changing,” Marcus said. “You don’t necessarily have to change everything, helping customers to save money, and at the same time meeting compliance.”
CES is an established business, with up-to-date technologies and systems that allow many inspections, such as major crane inspections, to occur.
Major crane inspections, which occur every ten years, is a big strength of Crane Engineering Services.
“Australian Standards cover safe use, which consists of; maintenance, records, and major inspections, so that’s where we come in,” says Marcus.
“For older cranes, say, over ten years old, we do major crane inspections, we do structural assessments, and also we check on different components, encompassing mechanical, electrical, hydraulic,” says Marcus.
CES also undertakes a NonDestructive Test, or NDT – for short;
the NDT involves performing inspection on the crane’s weldments to verify the structural integrity.
Marcus outlined the major inspection process.
“We inspect and verify that there are no formation of cracks, defects or deviations from the proper conditions that affect the safe operation of the crane. We also review components to the standard, like for instance, the computer, once you go into overload, it must have cut off motions over 100 per cent,” says Marcus. “The computer should also prompt you with a warning of approach to the rated lifting capacity starting from 90 percent,” he added.
Major crane inspections can be completed by CES in a week and the team at CES treats each case with diligence, by adhering to Australian standards and manufacturer’s specifications.
Crane Engineering Services General Manager Natalie Francis says the
relationship between customers and crane certification and maintenance companies is imperative.
CES is dedicated to providing a quality and seamless experience for you to obtain your certification.
“Crane Engineering Services have recently invested in a new Client Relationship Management System to improve customer service,” says Natalie. “Reminders can be sent to ensure customers are ahead of their certification requirements and reduce any risk to their compliance and most importantly the safety of their team.”
CES aims to continue the push towards industry safety and machine safety compliance. It encourages existing and emerging customers to continue to seek the meticulous, timely and costeffective services CES provides its valued customers with.
To view their range of services, head to craneengineeringservices.com.au or contact the team on 1300 008 838.
Longest powered boom to 20.9m with 5.5m telescopic fly extends to 26m
All Models (25T, 35T, 55T) rated @ 1.4m boom position, highest boom strength available, fully fabricated
Air-spring suspension with shock absorbers eliminating cabin noise and vibration
High Stability at all positions to 42 degrees
Low centre of gravity with rigid chassis design, safest crane available
Dynamic Load Chart and Digital Rope Compensation
Safe road speed 90-100kph with 180 degree unobstructed front vision with four cameras to sides and rear
Humma Heavy Lift Crane design, specification with proven componentry has set the new Industry standard for performance. ONE FOOTPRINT FOR ALL MODELS.
Crane owners require low operating and maintenance costs, highest level of safety in both driving and crane mode, achievable on all Humma Models.
Patented Auto-leveller on Humma 55, the largest and safest Pick and Carry available.
Highest level of safety at all articulation positions to 42 degrees using Humma low twist chassis design.
Cabin rated the safest and quietest available at 65 decibels.
Remove the removeable counterweight from 35T and 55T and you have a heavy duty 25T and 35T.