

EXPERTS IN MOBILE PLANT INSURANCE
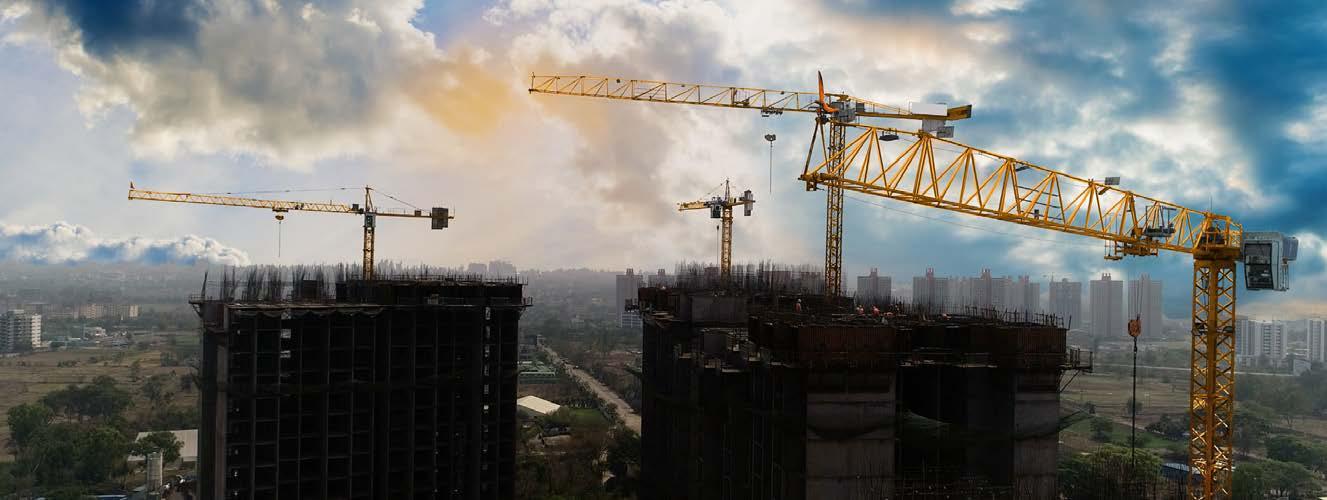
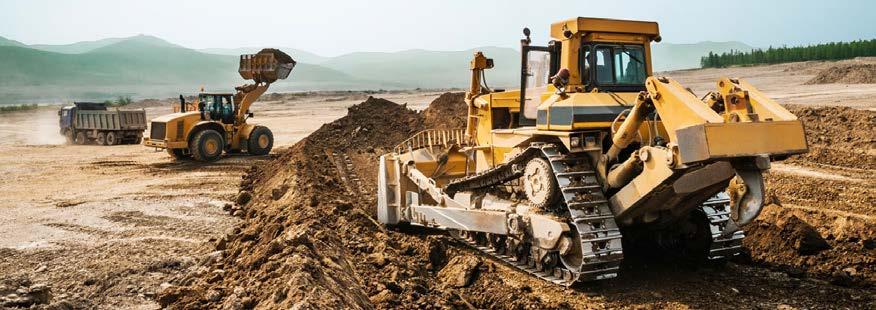

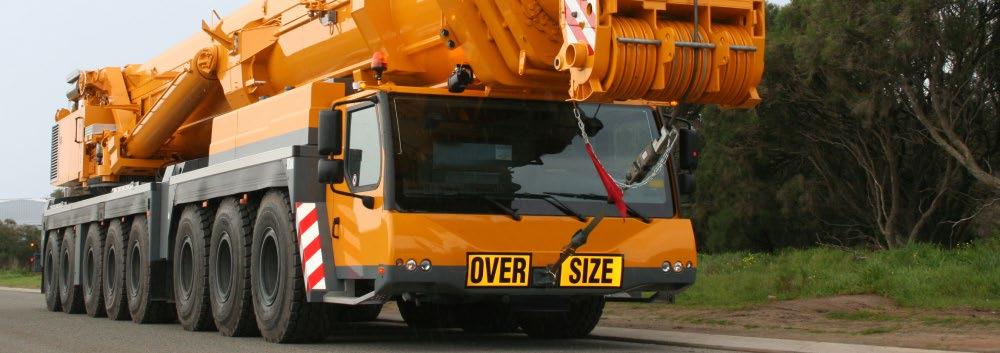

WELCOME TO THE OCTOBER 2022 ISSUE OF CRANES AND LIFTING
THE TEAM AT CRANES AND LIFTING has been busy preparing this issue of the magazine which will coincide with The Crane Industry Councils’ (CICA) National Conference and Exhibition. There is great anticipation for this years’ event which will be hosted by Adelaide, the City of Churches. The Adelaide Convention Centre has been chosen as the venue as it is a central location for the major states including Western Australia.
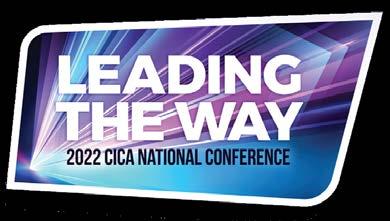

At the end of July, a strong contingent of Australians attended the Crane Association of New Zealand Conference and Exhibition which was staged in Hamilton. The conference was extremely well attended, and delegates enjoyed a series of interesting papers. Like the Australian construction sector, New Zealand governments are investing unprecedented amounts on infrastructure. In turn this sees NZ crane hire businesses investing in new cranes, making for a very buoyant mood during the conference.
As always, there is something for everyone in the October issue. Almac Pacific make a major announcement
regarding the representation of the range of AlmaCrawler Multi Loaders. UAA celebrates 50 years in business by becoming the Platinum Sponsor of the CICA National Conference and Exhibition, and battery powered cranes continue to be topical with SANY being the latest OEM to launch new models.
A reminder about the CICA Lift of the Year Awards. We are encouraging all crane hire companies to consider entering this years’ awards. Categories include Lift of the Year over 20t, Lift of the Year under 20t and Project of the Year. The lifts can date back to 2020. The competition is FREE to enter with application forms available on the CICA website or you can contact the team at Cranes and Lifting. The magazine will be promoting the winners of each category throughout the year.
As always, the team at Cranes and Lifting hope you enjoy the read.
Published by: Simon Gould Editor, Cranes and Lifting11-15 Buckhurst St
South Melbourne VIC 3205
T: 03 9690 8766
www.primecreativemedia.com.au
CEO
John Murphy
E: john.murphy@primecreative.com.au
Chief Operating Officer
Christine Clancy
E: christine.clancy@primecreative.com.au
Group Managing Editor (Northern)
Syed Shah
E: syed.shah@primecreative.com.au
Editor
Simon Gould
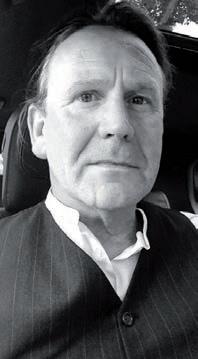
E: simon.gould@primecreative.com.au
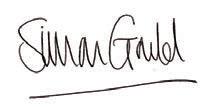
Journalist
Joshua Farrell
E: Joshua.farrell@primecreative.com.au T: 0420 298 087
Business Development Manager
Emily Schlegel
E: emily.schlegel@primecreative.com.au T: 0466 317 555
Client Success Manager
Justine Nardone
E: justine.nardone@primecreative.com.au
Production Co-Ordinator
Cat Fitzpatrick
Art Director
Bea Barthelson
Advertisement Designer
Lee Mawdsley
Imaging Assistant Paul Breen
Subscriptions
Frank Rapone
T: 03 9690 8766
E: frank.rapone@primecreative.com.au
The Publisher reserves the right to alter or omit any article or advertisement submitted and requires indemnity from the advertisers and contributors against damages or liabilities that may arise from material published.
© Copyright – No part of this publication may be reproduced, stored in a retrieval system or transmitted in any means electronic, mechanical, photocopying, recording or otherwise without the permission of the publisher.
Up front
Tadano delivers two new AC 7.450-1s.
CICA President’s R eport
A look at the CICA National Conference and Exhibition.
legal advice
Holding Redlich examines dry and wet hire contracts.
Tech Corner
Importance of the CICA Lift Supervisor Course.
Liebherr WA
Meet the team behind the success of Liebherr WA.
Cranes
value of major inspections.
to Kings Cranes
Kings Cranes thinks Tidd is a game changer
Groves to Elliott Crane Hire
Crane Hire buys new Groves for the first time.
Rigging Hire
A new premises, new equipment and transpor t: QRH is on the move.
46 Fullers Mobile Cranes New Tadano Tadano AC 7.450-1 to Fullers.
50
Ben Baden Ser vices Melrose turn to Ben Baden for new livery.
54 Almac Pacific Almac Pacific appoints Pace Cranes as distributor for the Multi Loader.
58
Melrose Crane & Rigging
lifts with varying boom configurations.
Rigging
lift approach to rigging.
66 Borger Crane Hire and Rigging Ser vices
lifts on bridge project.
UAA UAA continues to expand operations.
80 Crane R opes
World class wire ropes supported by industry leading experience and service.
84
Cranecorp Cranecorp continues investment in Tadano products.
88 Hevway
The new ‘gamechanging’ mapping service for crane hire businesses.
92 Pilequip Pilequip launch new rubber shock absorbers for cranes.
96 Terex Franna
Franna launches a new 25t capacity spreader bar.
98
Membrey’s Cranes and Transport
Membrey’s continues 60th birthday celebrations with the arrival of its third Franna AT40.
102 Ronco
Ronco continues growth with the WA dealership responsibilities for XCMG.
106 Tutt Bryant and Big Rhino
Big Rhino Crane Hire take delivery of new Sany all terrain.
110 Global Machiner y Sales
A new spider crane range enters the market in Australia.
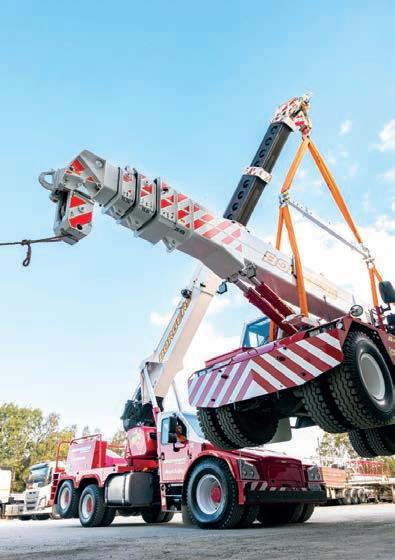
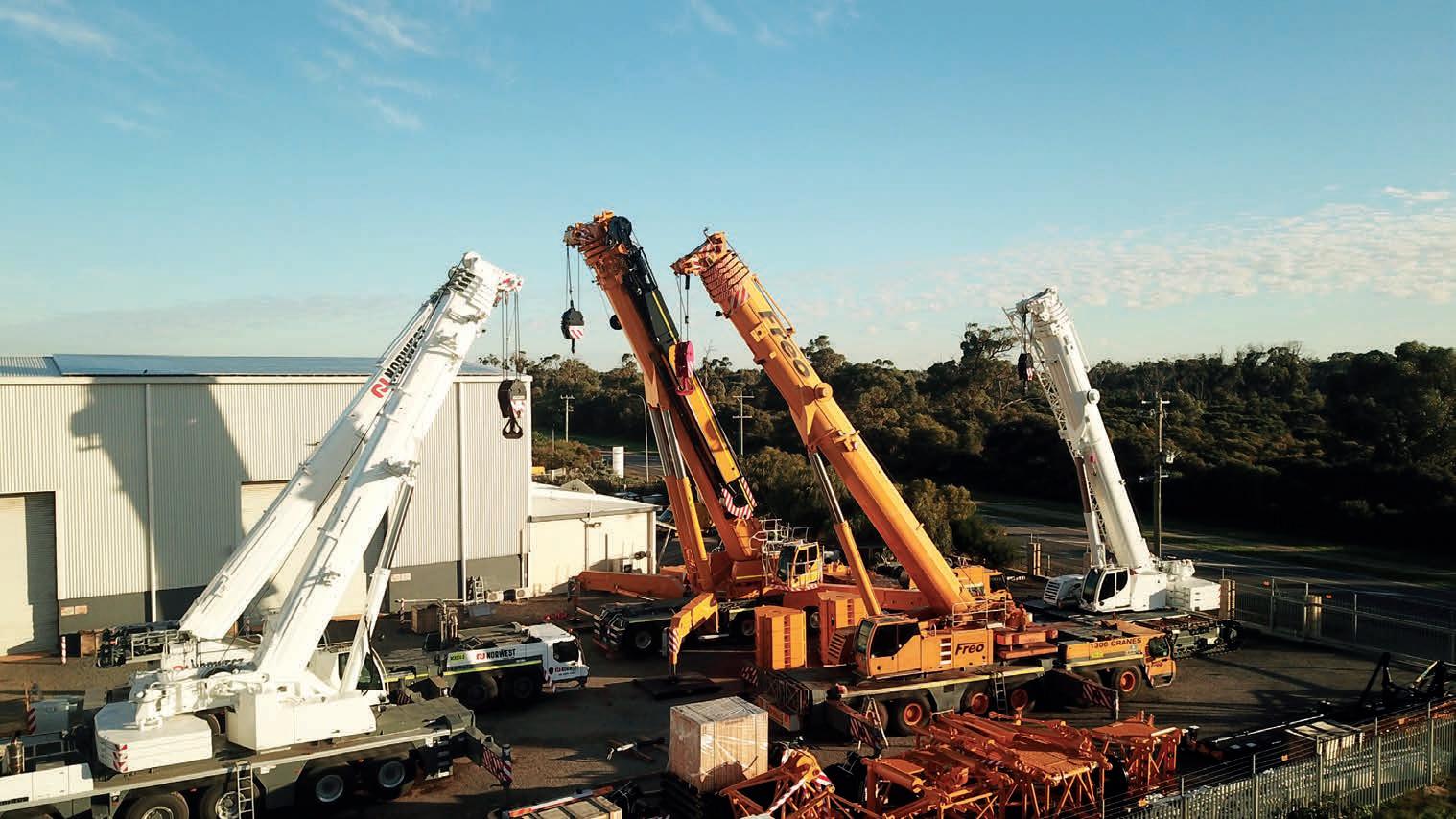
114 Sany’s new batter y electric range Sany announces a new model in the battery electric powered telescopic crawler range.
74
Sandersons Insurance Sanderson Insurance celebrates 50 years.
76 Preston Hire’s SuperCrane SuperCrane continues to add new models to the fleet.
117 Ledge Finance
How ready is the crane sector for renewable energy?
120 Tidd upgraded
TRT announces upgrade detail for the Tidd.
123 Liebherr used cranes
Hawkesbury Cranes receives two used Liebherrs.
126 Finlease
A good, bad and ugly look at the 2021/2022 financial year.
128 Comansa LCH300 hydraulic luffing jib crane.
131 Universal Cranes
Universal Cranes’ Project & Heavy Lift division has been busy working in a variety of industry sectors.
134 BuildAI
BuildAI improving crane safety and efficiency one site at a time.
137 MCT Equipment
Magni open days a big success for MCT.
141 Comansa Tower cranes
Bespoke tower crane for Norwegian port.
144 Imperial Oil Oils to suit any challenge and good for the planet.
147 Bridon Beaker t Cradle to grave approach to high performance ropes.
150 Pervidi Pervidi’s paperless solutions to asset management.
154 DRA Engineering and Humma Hedland Harbour Industries turn to Humma.
156 Marr Contracting Marr Contracting provides a flexible craneage solution for Sydney Metro.
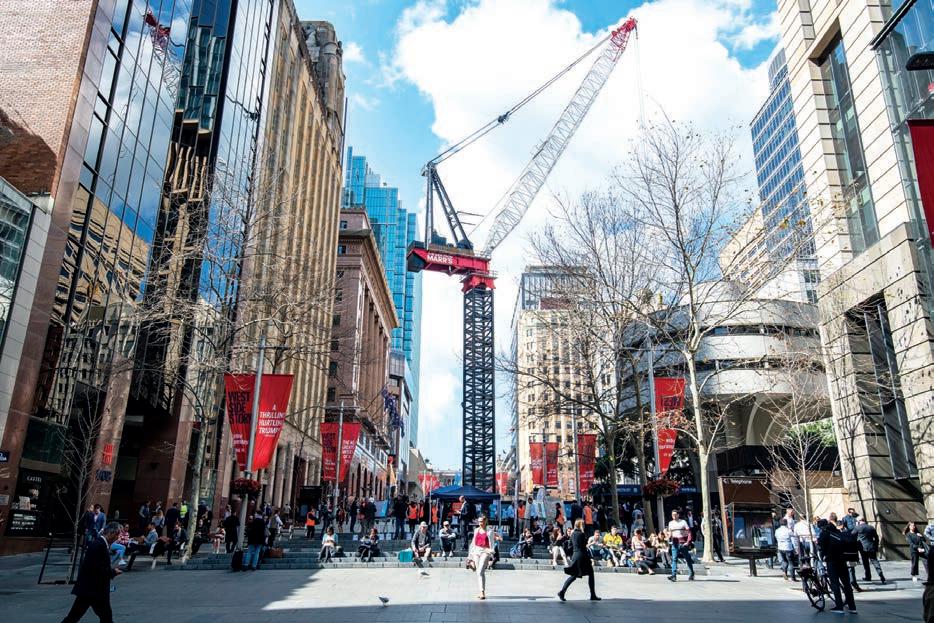
159 vWork vWork designed to streamline asset management.
162 Grove rough terrain upgrade Grove’s new heavy-duty jib equips rough-terrain crane for precast work.
164 Protective Pty Ltd
A different approach to overhead protection.
167 XCMG
Matt Mollross has joined the team at XCMG.
171 Action Crane Hire
Action Cranes recently purchased its first set of engineered outrigger pads from DICA.
173 Liebherr Transform
The new upgrade, modification and overhaul service from Liebherr.
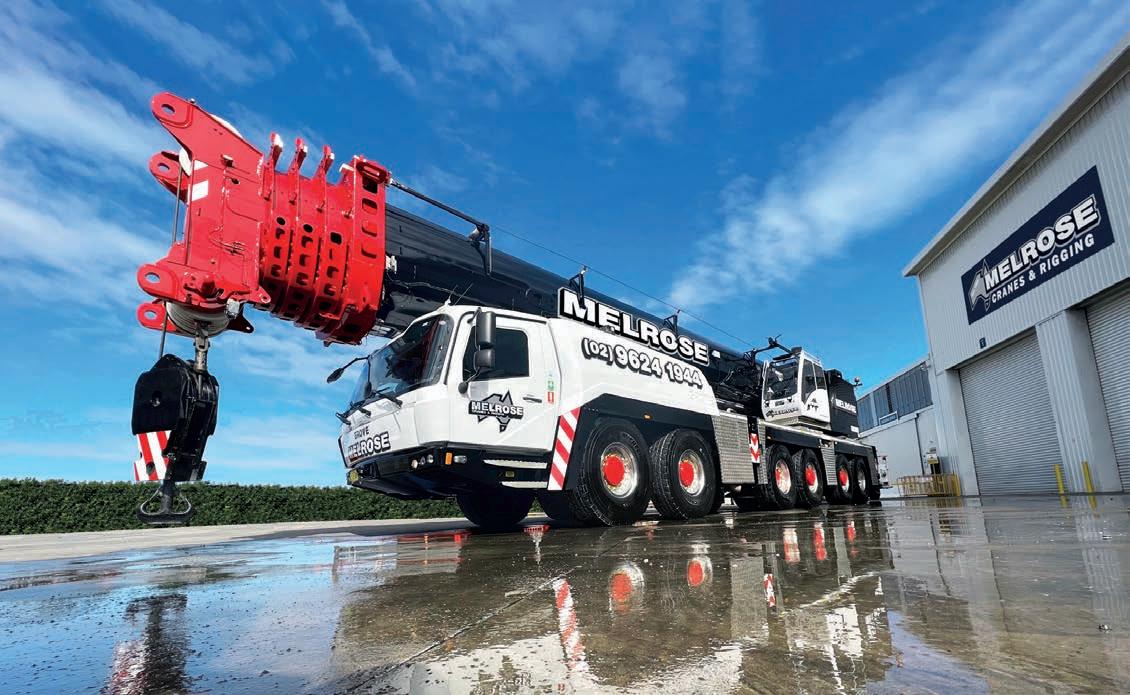
NEW BOOM INSERTS EXPAND MLC300 REACH FOR WIND TURBINE WORK
As wind turbines grow taller, Manitowoc has expanded its MLC300 boom insert options to increase boom lengths for greater reach.
The new Wide Boom Plus inserts boost the MLC300’s flexibility to complete more jobs with the crane.
Manitowoc is expanding its boom insert offering with the new Wide Boom Plus kit for its MLC300 latticeboom crawler crane. The new inserts will give crane operators extra reach by lengthening their booms up to 429.8ft (131m) when used in combination with the VPC-MAX and extended upper boom points. They will be particularly useful for assembling wind turbines.
The height of utility-scale, landbased wind turbines has increased nearly 60 per cent in the last two decades, reaching an average of 295 ft (90m) in 2020 in the US. Wind turbines are expected to keep growing in size in the coming years, as building the turbines to higher elevations enable the wind towers to harness stronger winds. The new Manitowoc boom inserts will enable the 386 USt (350t) MLC300 to construct these increasingly tall wind towers.
Brennan Seelinger, Manitowoc’s product manager for crawler cranes, said wind turbine work above 295ft (90m) currently requires a 450 USt (400t) or larger crane, which can result
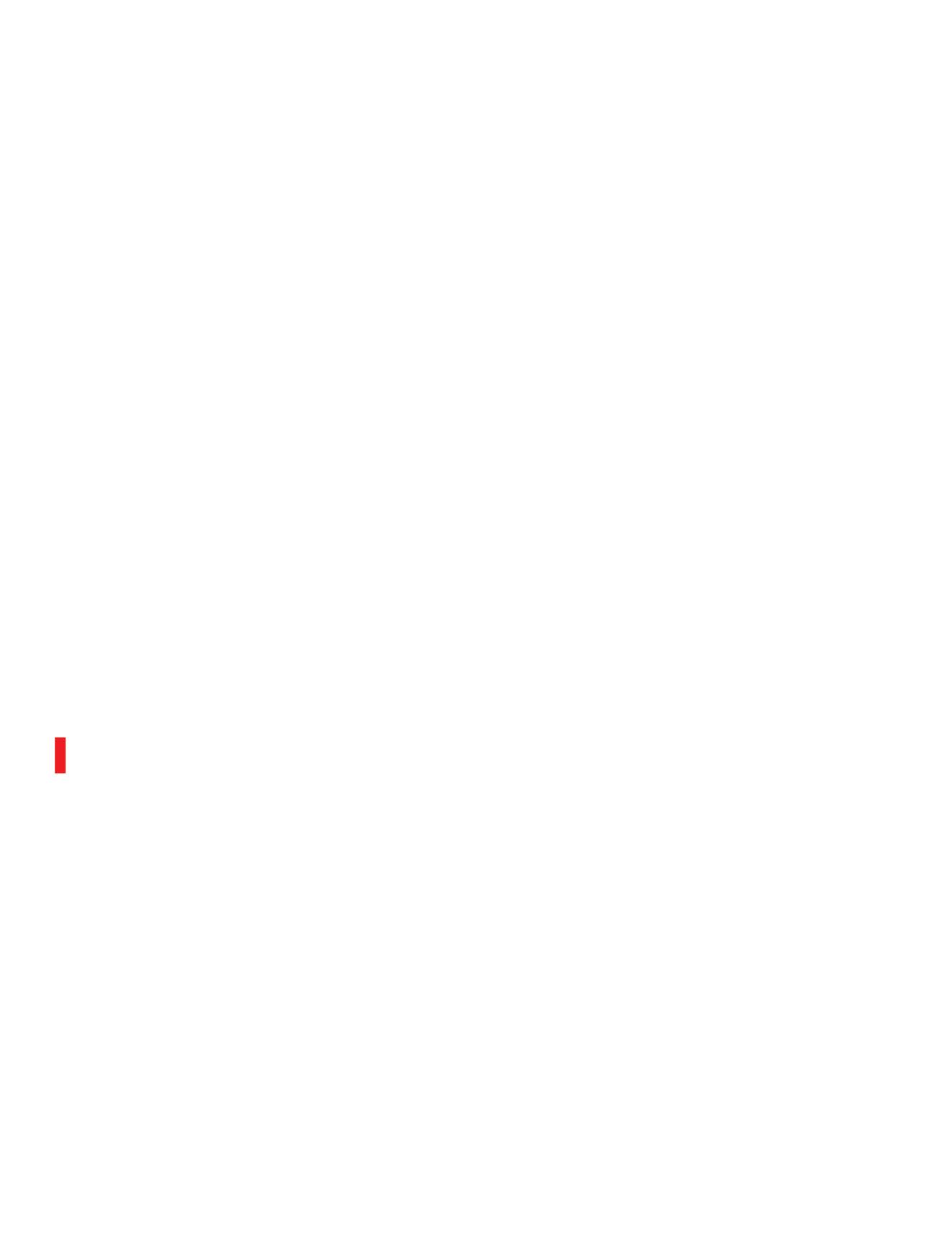
in higher costs for operation and transportation.
“Our new boom inserts will open up more jobs for our crawler crane owners,” he said.
“They will increase utilisation of our MLC300 crane with added flexibility. Where before crane operators would need to bring in a larger crane to reach heights above 295ft [90 m], now they’re able to employ their MLC300 with boom inserts and take advantage of increased reach from its smaller footprint.”

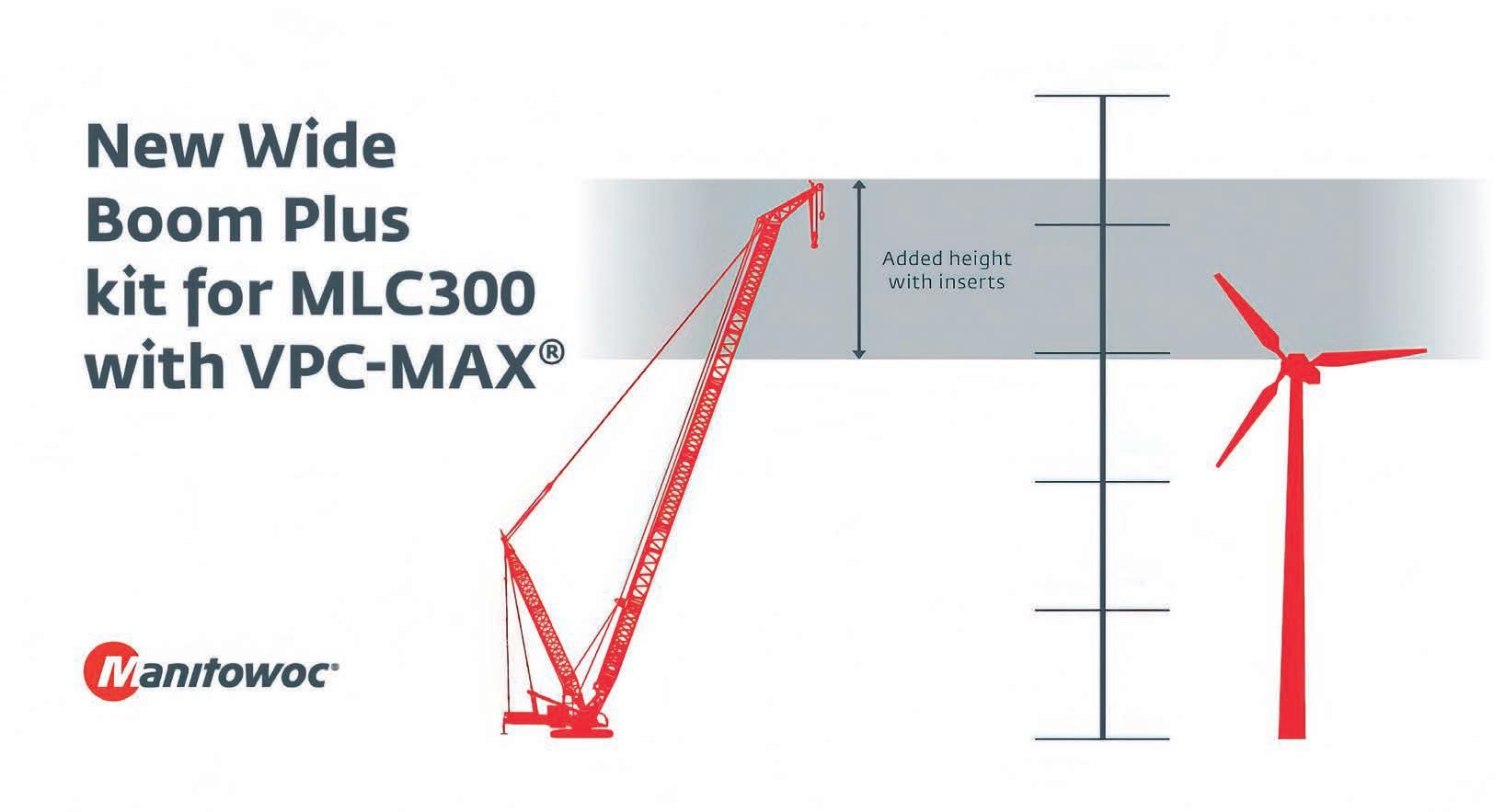
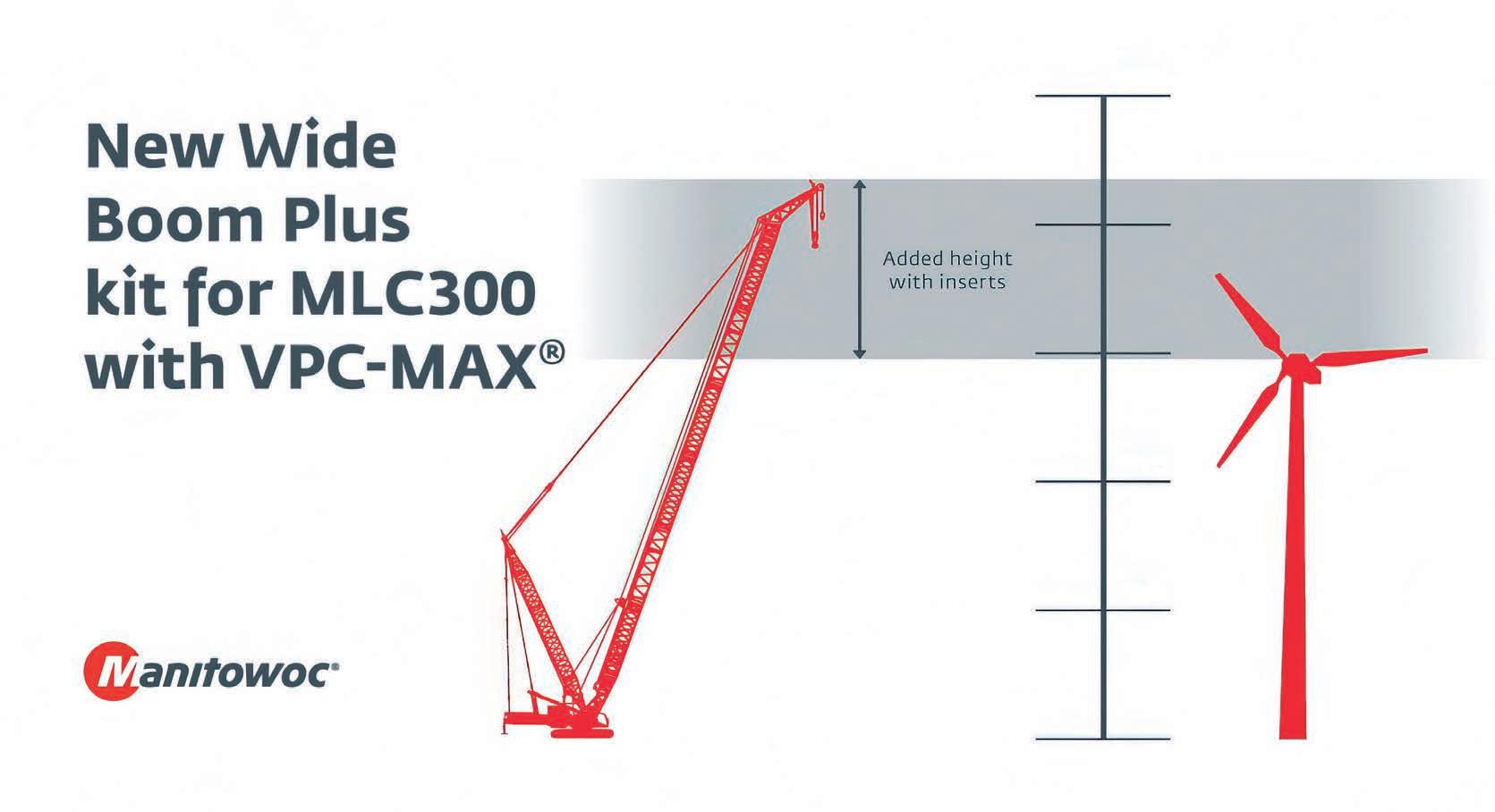
The new Wide Boom Plus inserts kit is now available for purchase everywhere Manitowoc cranes are sold.
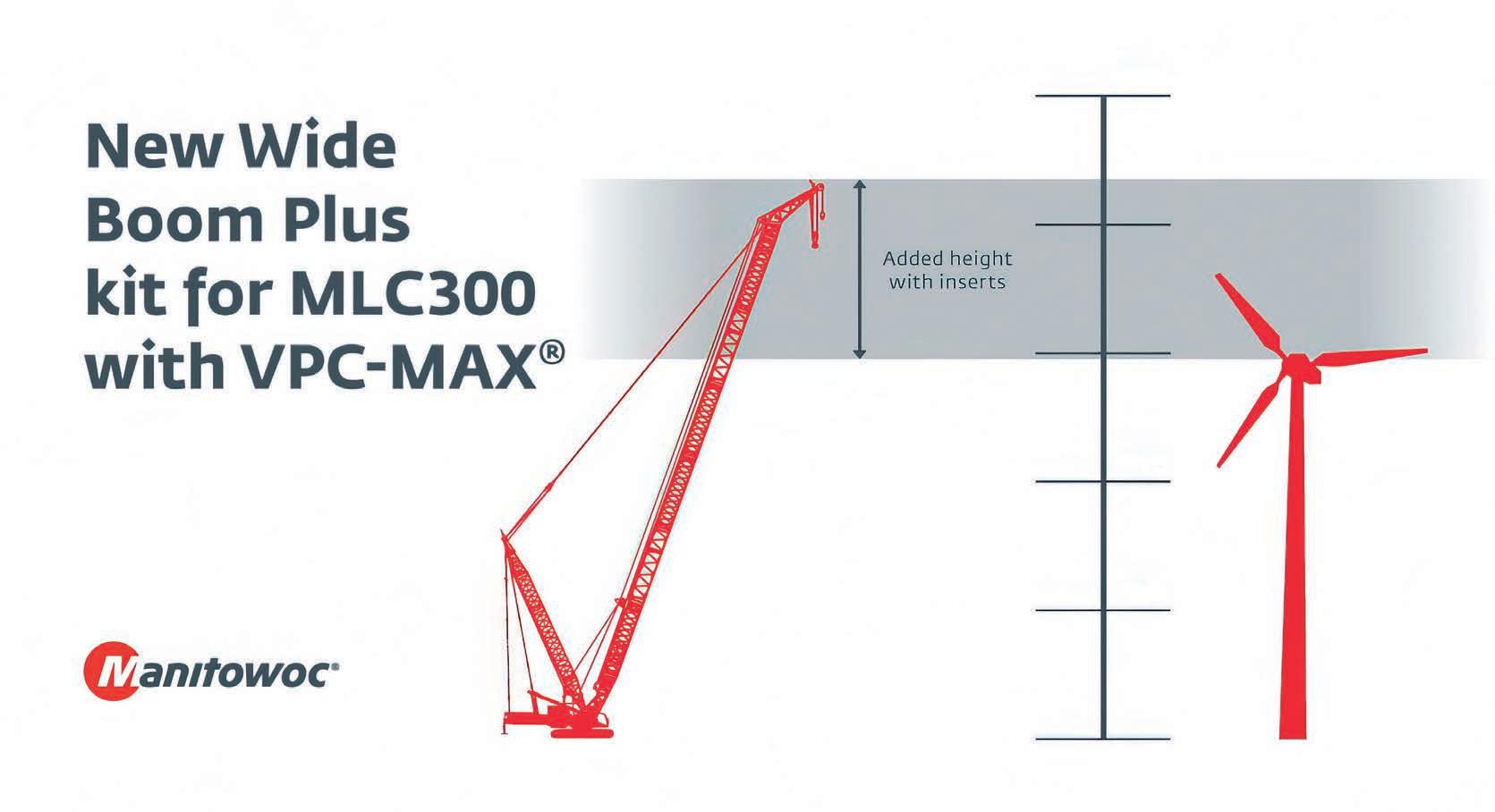
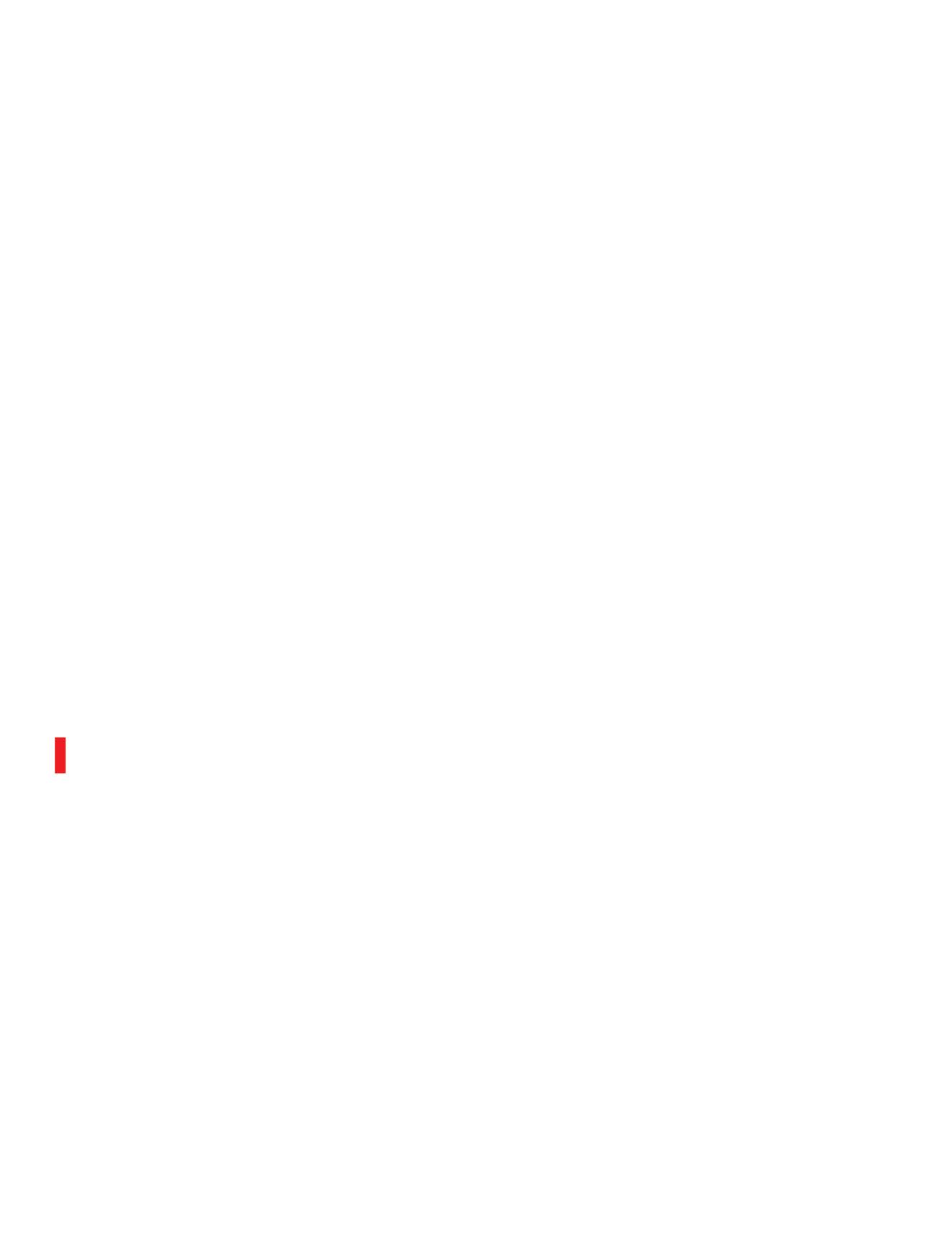
NEW TADANO 450T ALL TERRAINS FOR THE EAST AND WEST COAST
Tadano recently delivered two new AC 7.450-1 to General Crane Services WA (GCSWA) and Fuller Mobile Cranes in Sydney. The cranes are a big step up in capacity for both businesses.
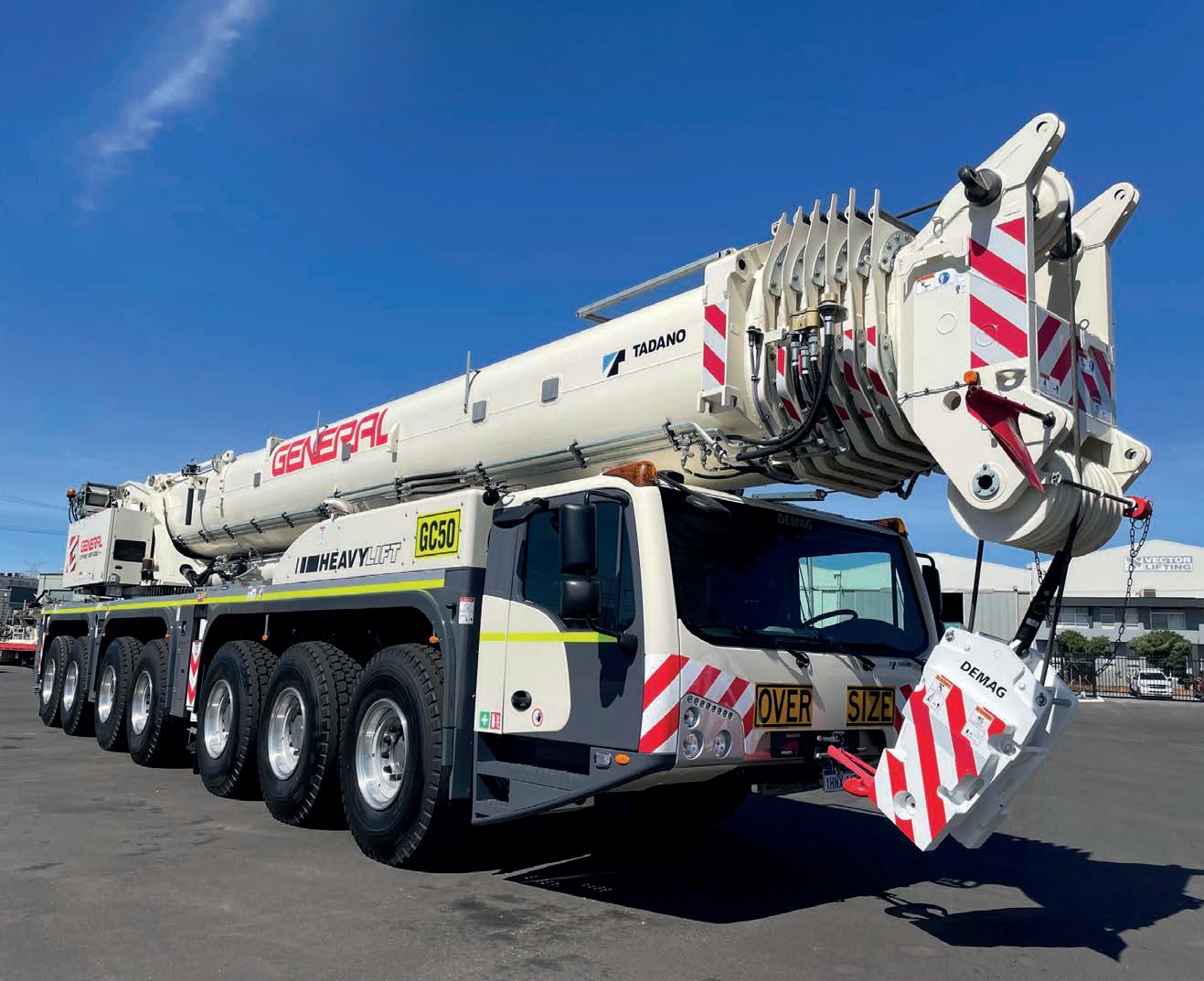
BOTH GCSWA AND FULLER MOBILE CRANES have seen significant change and growth within their businesses, which led to the purchase of a Tadano AC 7 450-1. Nick Bucciarelli, managing director of GCSWA, explains more.
“We recently moved our operation into our new purpose-built head office in Cockburn Central,” he said.
“The new facility covers 13,000 square metres and includes a 1,500 square metre bay workshop for all maintenance and repairs, a two-storey office with shared space, and private and common areas. We are in a prime location, central to all works in the Perth Metropolitan area, with access to all main highways. The new facility is five times the size of our previous facility and
provides us with plenty of growing room as GCSWA is just getting started.
A key to the success of our business is the commitment from our staff. They have have supported our family business and the General Crane Services brand and we wanted to provide them with a dedicated crane yard and facility they would be proud to work in every day.”
GCSWA runs a fleet of all terrains with various capacities up to the new AC 7.450-1, a fleet of crawler cranes up to a capacity of 280t, and a fleet of Frannas, including five AT40s.
GCSWA has been a long-term partner of Terex Demag and now Tadano. Bucciarelli discusses the background to the relationship with these brands.

The Tadano AC 7.450-1 maximum boom system length is 132m. The luffing jib can be divided into 3m segments from 24 to 81m. In addition to the luffing jib, Tadano also offers configuration options for a fixed extension, and even a runner.
“Our business is built on loyalty; we focus on and stick to the Tadano product and the team associated with it. In turn they provide us with great product support and spare parts availability.Selecting the Tadano brand means we have commonality across all of the fleet, which provides an obvious advantage for our staff and for the image of the business,” said Bucciarelli.
“For any crane hire business, the support you receive from the crane OEM is critical and because we have continued to purchase the Tadano brand, we expect spare parts support and afterhours support in return.”
He goes on to discuss the relationship GCSWA has with James Greenwood and the Tadano team and what he likes about the support they provide.
“GCSWA bought its first crane through James Greenwood in 2011, and we are proud to continue the relationship today. It allows us to have a central point of contact for any issues or information we might require,” said Bucciarelli.
“The parts and service support from Tadano has been great. They certainly listen to the customer and want to understand what we would like to see more of and actively work to provide that level of service for us.
“In terms of product support, we have watched the transition from the Terex Demag brand to the Tadano/Demag brand and there has been no change in the high levels of service and parts support we receive.

“This provides us with the confidence that we have selected the right brand. The team behind Tadano support us 24/7 and we could not be happier with the relationship we have and the support we receive when there are breakdowns issues or any maintenance advice we might need.”
The new Tadano AC 7.450-1. is the largest capacity crane in the GCSWA fleet. Bucciarelli explains why he chose this model and the type of work it will be best suited to.
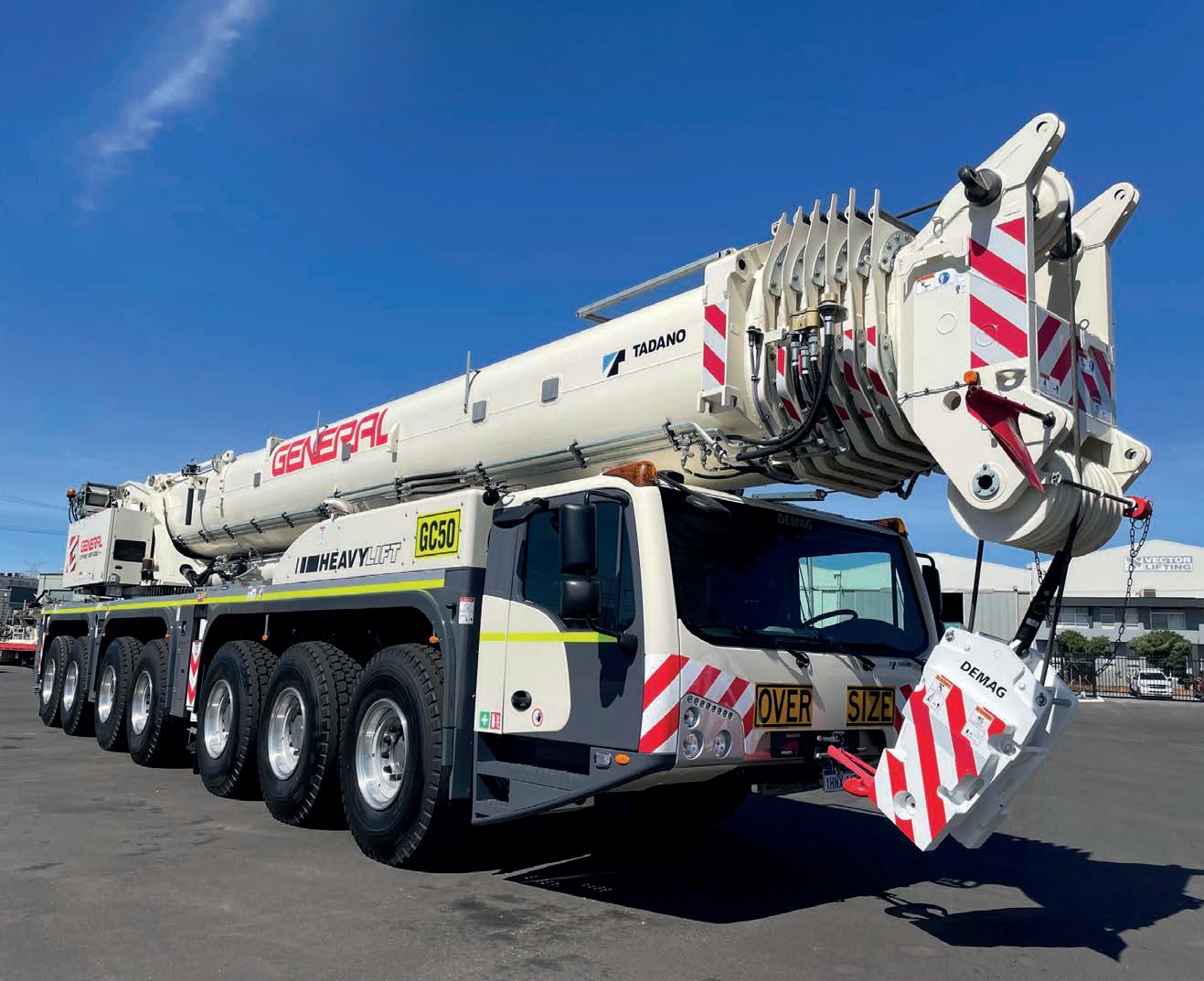
“We selected the AC 7.450-1 for a few reasons, with staff retention and development first and foremost. We have a very experienced work force whuich we want to retain. Providing pathways for their futures is important, and this includes new technologyy ongoing training,” he said.
“This machine provides the team with brand new technology to learn, and it will open up new types of work and projects for them to be a part of. All of this will continue to make working at GCSWA interesting.
“Staff retention is a high priority to us. We have amazing people in our team, something we are proud to say no other crane company can match us on, and we want to repay the support our staff show the business.
“We want to be the leaders in lifting solutions in WA. Being a purchaser of Tadano product, we wanted to be the first company to bring this new machine into the country.
“We knew it would also open doors for
us and attract to new types of businesses.
“Getting an asset of this size internally will also give our customers the General Cranes service delivery they are used to in a greater capacity. We have always provided cranes of this size in our service offering, but bringing it internally allows us to do it our way, with our people, which is why our clients choose us,” said Bucciarelli.
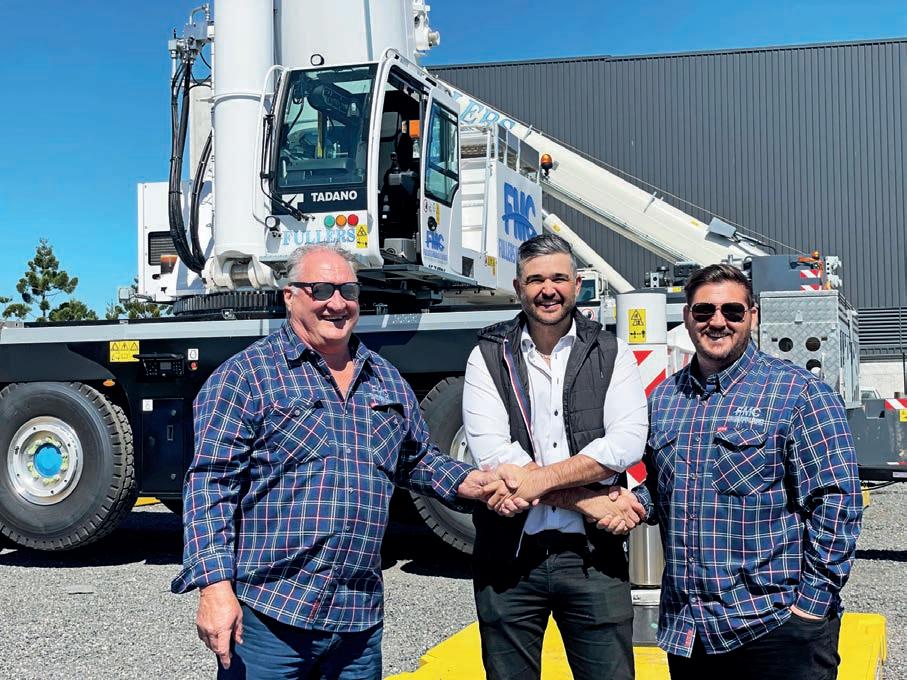
COMPACT AND MANOEUVRABLE –LIKE A SIX-AXLE CRANE
With a carrier length of 15.99m, a total length of 17.62m, and an outrigger base of 8.45m, the AC 7.450-1 does not take up more space than a six-axle crane at the job site. However, it offers significantly larger lifting capacities and a longer main boom that comes in at 80m. All seven axles on the AC 7.450-1 are steered, and four of them are driven. This makes the crane so manoeuvrable that it can handle tight work sites at least as well as a six-axle model.
SPOILED FOR CHOICE – POWERFUL, VERSATILE BOOM OPTIONS
With its fully telescoped 80m main boom, the AC 7.450-1 reaches lifting capacities of up to 25t. If the main boom’s length is not sufficient, it can, for example, be extended with a luffing jib with a maximum length of 81m. The crane’s maximum system
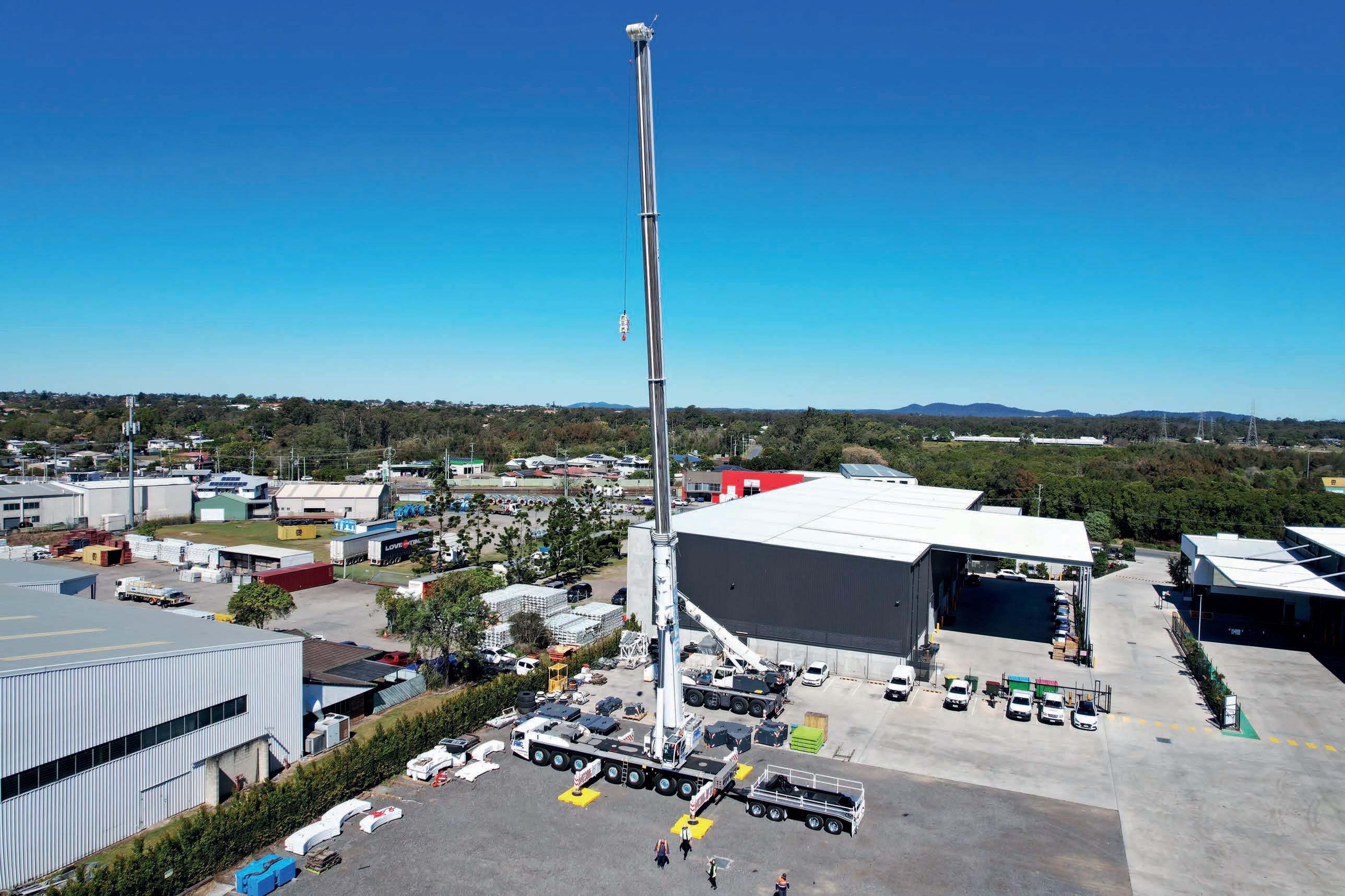
length is 132m. The luffing jib can be divided into 3m segments from 24 to 81m. But that is not all: in addition to the luffing jib, Tadano also offers configuration options for a fixed extension, and even a runner.
FUNCTIONAL AND POWERFUL –THE NEW SUPERLIFT DESIGN Tadano is using its new engineering design for the Sideways Superlift system for the first time ever on the AC 7.450-1. This new design is a decisive enhancement to the well-known Tadano SSL solution. The Superlift arms are now mounted all the way in the front, on the head of the base section, meaning that they are ultimately longer and accordingly well-suited to larger lifting capacities. This means that the AC 7.450-1 is considerably superior to other seven-axle cranes – in fact, it even leaves some eight-axle units behind in a number of boom positions, said Tadano.
The functionality and handling have been improved as well. The new design only requires one single wire rope line for the connection between the main boom head and the SSL arm. In addition, the SSL arms are pinned hydraulically on the main boom, which reduces manual work for securing the arms and the associated work at height.
EVERYTHING IN VIEW –360° SURROUND VIEW
The AC 7.450-1 features six cameras that keep everything in view. With the help of a computer-assisted diagram, this makes it possible to graphically show the possible extension lengths for the outriggers and the counterweight tail swing radius on the display in the carrier cab. This makes it significantly easier to position the crane at job sites. Surround View also helps on the way to the site by making it easier.
LONG-TERM RELATIONSHIPS
Bucciarelli goes on to discuss how GCSWA services its customer base.
“We have a very solid customer base, and many have been with us since the inception of the business. As our customers have grown, we have grown our business alongside them and we have always invested in new technology and bigger equipment.
“We service a number of industry sectors including mining where we work on maintenance and construction. We are also strong in the telecommunications and renewable energy sectors. We service our customers here in the Perth metropolitan area and all the way out to the Pilbara region and the Goldfields of WA,” he said.
He highlights how experienced the team at GCSWA is.
“In terms of our operational staff, we are proud to say we have a 100 per cent staff retention record since the business started. Our operations team can job share across the fleet. We don’t pigeon-hole staff to a certain type or size of crane, we want them to learn new disciplines, which will help keep their job interesting and challenging and we want them to keep working at General Cranes.
“We have employees who have been in the industry for their working life, and we have employees who are just starting in the industry. We take our time to recruit the right person, and our decisions are not based on experience but on personal attributes. We offer them all the training they may require and as they learn the General Crane’s way, we trust them to be leaders out in the field and to represent the General Crane’s brand well.
“Our team also includes an internal
draftsman and an engineer, which enables us to provide our customers with the confidence they have made the right choice in aligning with General Crane Services. Our CAD planning has recently moved to 3D.
“Safety is at the heart of everything we do at GCSWA, and this is a major reason we continue to invest in the latest technology like the Tadano AC 7.450-1. Not only does it provide us with extra capacity to conduct the bigger lifts safely, it features the very latest safety technology built into the crane to ensure the operator, the riggers and dogmen are working in the safest possible environment.”
Kane Fuller, general manager at Fullers Mobile Cranes, went through a different justification process when it came to the purchase of the new Tadano AC 7.450-1.
“When you compare the 450t to a 500t capacity crane, we might not have the same lifting grunt, but you need a second crane to build the 500, which comes at a cost to the customer. It also requires significant set-up space. With the 450 featuring 80m of main boom and the mega wing system, the crane is lifting 37t, so it is perfect for tower crane work for example.
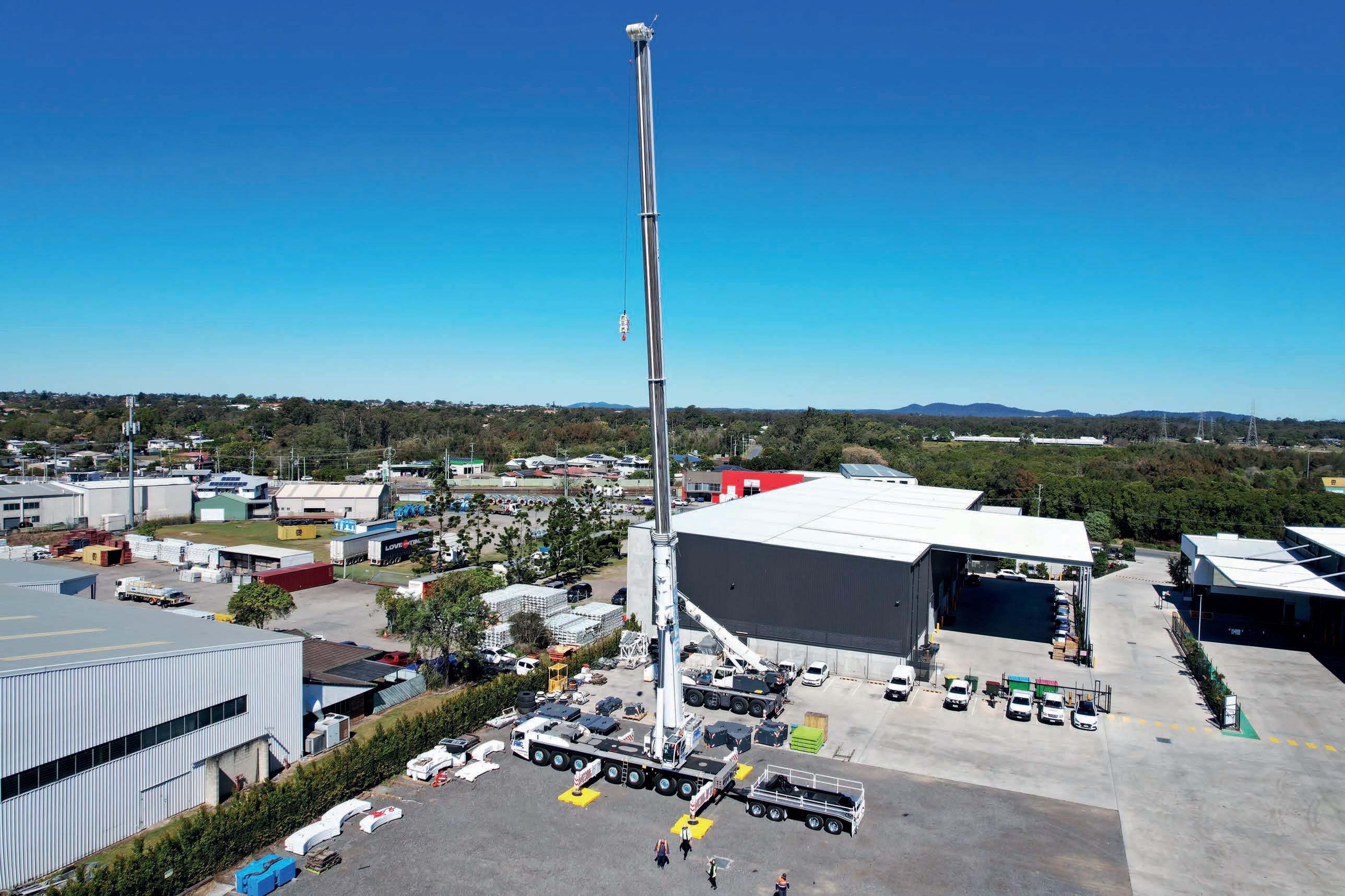
“For our Tier One customers, we can now complete the bridge beam lifts on the massive infrastructure projects. We are not out to challenge the larger crane hire businesses. We will stick to what we know best and that is servicing our customers with the best range of compact cranes we can offer.”
He goes onto explains how lifting capacities are changing the industry and how larger capacity cranes will help Fullers Mobile Cranes stay ahead of the general crane hire market.
“We are seeing a rapid evolution as crane capacities increase. 10 years ago, a 130t capacity crane was a rare site, now they are everywhere. We are seeing the same with 250t capacity cranes, they are becoming increasingly popular. We are seeing subcontractors running one or two cranes and they will include a 220 or a 250 in their fleet. We could see we needed to take the next step to stay ahead of the general pack and the Tadano AC 7 450-1 is that step,” he said.


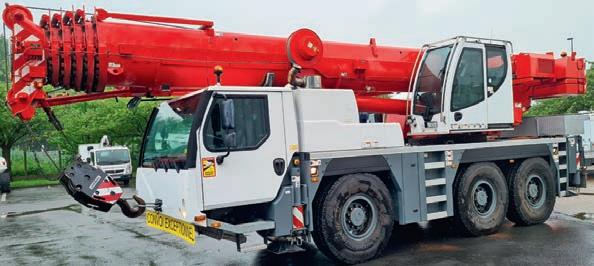
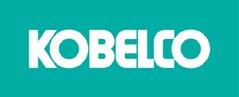

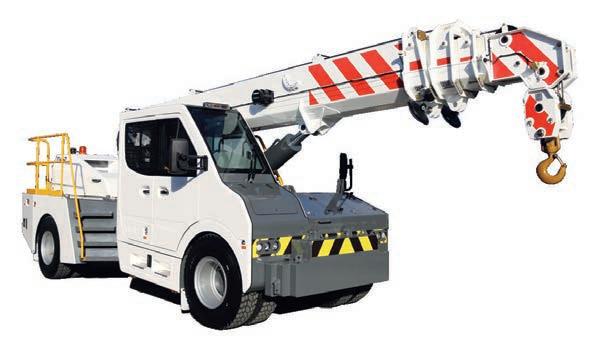
The Crosby Group, a global leader in lifting, rigging, and load securement hardware, has launched upgrades to its popular range of Crosby BlokCam crane camera systems, including battery improvements.
The updates extend the legacy of the original X2 and M3 systems, which have delivered clear enhancement of load handling in several sectors, most notably construction and renewable energy.
The X2 is renowned as the industry’s first fully modular system compatible with tower cranes, while the M3 is the first fully modular camera for telescopic and mobile cranes, mainly because it can be installed in just five minutes.
The Crosby Group has unveiled a series of additions and enhancements, including a new version of the X2 and M3. Most of the benefits are shared between the two systems, such as a new transmitter that can connect to up to two sensors upon request; a repeater that comes with ball joint mount (reducing


the ports required); new sensor with integrated audio and video plug; and assembly with an improved Wi-Fi signal.
X3L and M3L versions are also available with a state-of-the-art lithium-ion battery and charger, compared to the NiCAD (nickel-cadmium) battery with the standard product. Key comparisons between the lighter lithium-ion and NiCAD are a longer battery life, four-and-a-half hour’s recharge versus eight, and a charger versus a docking station. The lithium-ion battery also boasts a light-emitting diode (LED) to indicate charging status.
Thomas Dietvorst, director of Crosby’s Technology Solutions division, said: “The upgraded system is better, faster, and smarter – improving safety and reliability. The game-changing BlokCam product range has been an excellent addition to the Crosby family and is a standout innovator in the portfolio, as recognised by LEEA [Lifting Equipment Engineers Association] giving us its Best Innovation Award last year. We are proud to bring these ongoing

generational improvements to our growing customer base.”
Following 2021 acquisition, The Crosby Group has leveraged its global outreach to position Crosby BlokCam close to the point of use through its network of channel partners.
He added: “We are thrilled to see more and more of our end users and distributors experience first-hand the benefits of the quality, ease of use, and modularity of the Crosby BlokCam systems. In addition to construction and renewables, which are widely regarded as the technology’s pioneering markets, we see continued adoption in transportation, offshore construction, nuclear, rail, mooring, and others. These products have delivered clear enhancement of load handling everywhere they’ve been used, and the user benefits are highly improved.
X3L, M3L, and an upgrade package, are currently available to order from The Crosby Group’s global distributor network.
Port of Newcastle has taken a critical step forward in its important diversification agenda to unlock trade opportunities within regional and rural NSW, support local industry and create jobs, with the arrival of two Liebherr mobile harbour cranes.
The LHM 550 cranes sailed into Newcastle Harbour on August 2 onboard general cargo ship UHL Fighter, after leaving the Port of Rostock in late June.
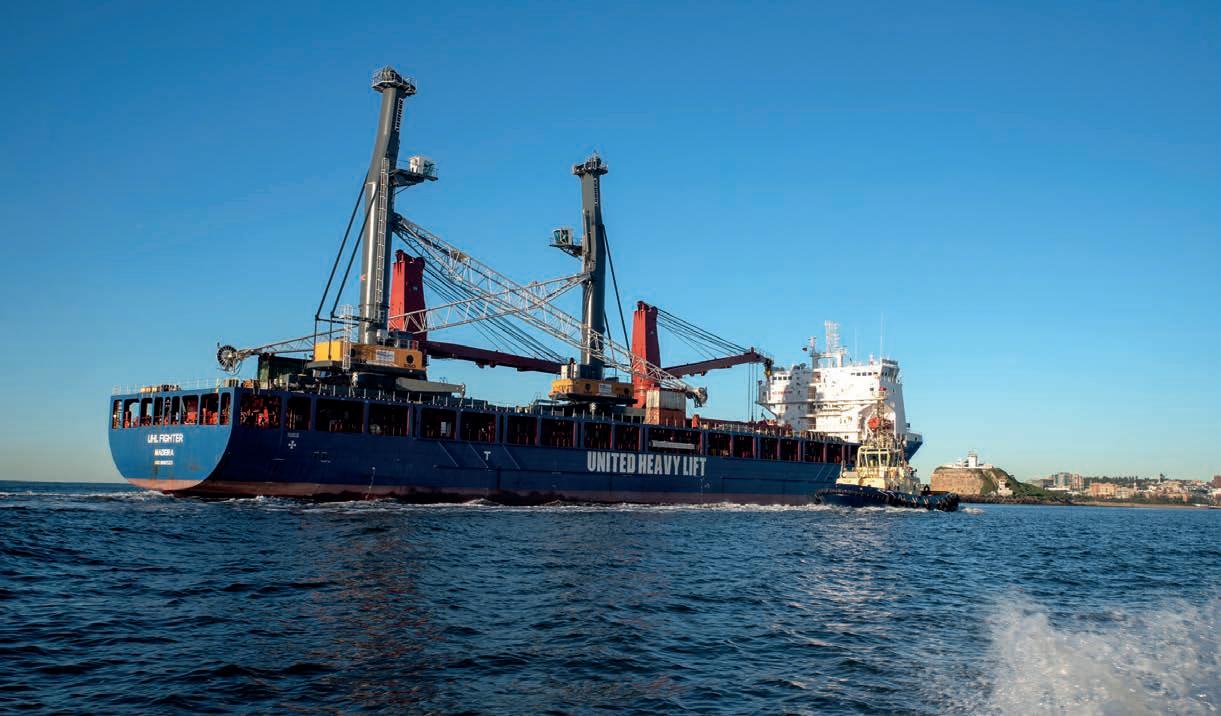
Port of Newcastle CEO Craig Carmody said the $28.4 million investment marks a significantly
They have been swiftly put to work in the hub.
increase in container handling capabilities at the Port’s versatile Mayfield 4 berth.
“Industry has been very clear –they don’t want to have to pay more to send their container exports to Port Botany or Port of Brisbane when they could be taking advantage of Port of Newcastle’s enviable road and rail network and potentially save millions of dollars a year,” said Carmody.
“These two new mobile harbour cranes will allow us to move cargo and containers within the limits that the Port Commitment Deeds [PCD] bind us, so that we can give our customers a viable alternative.
“As a global trade gateway and the world’s largest coal export port, diversification isn’t an option, it’s a must, so we are taking what action we can while continuing to advocate for the removal of the PCD.
“The future of the Hunter region, of local industry and of local jobs is far too important for us to sit idly by.
“As the saying goes, ‘if you build it,
they will come’, which is essentially what we are doing.
“By proving that there is demand for containers out of Newcastle, we hope the NSW Government will finally see the irrefutable benefits and remove the PCD.
“Independent analysis has shown a Newcastle deep water container terminal would contribute $2.5 billion to the national economy and generate more than 19,000 direct and indirect jobs, while reducing road and rail congestion and providing cheaper freight costs for regional importers and exporters, which in the end means more money back into the pockets of local farmers and businesses.”
The 550-tonne Liebherr mobile harbour cranes feature the latest lift assistance systems for safer lifts and can handle a diverse mix of project cargo, including wind turbines, timber, steel coils, transformers and mining equipment.
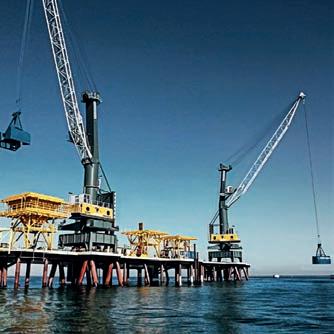
They also have the capability to work in tandem for heavy lifts and lift two 20ft or one 40ft container in a single move.
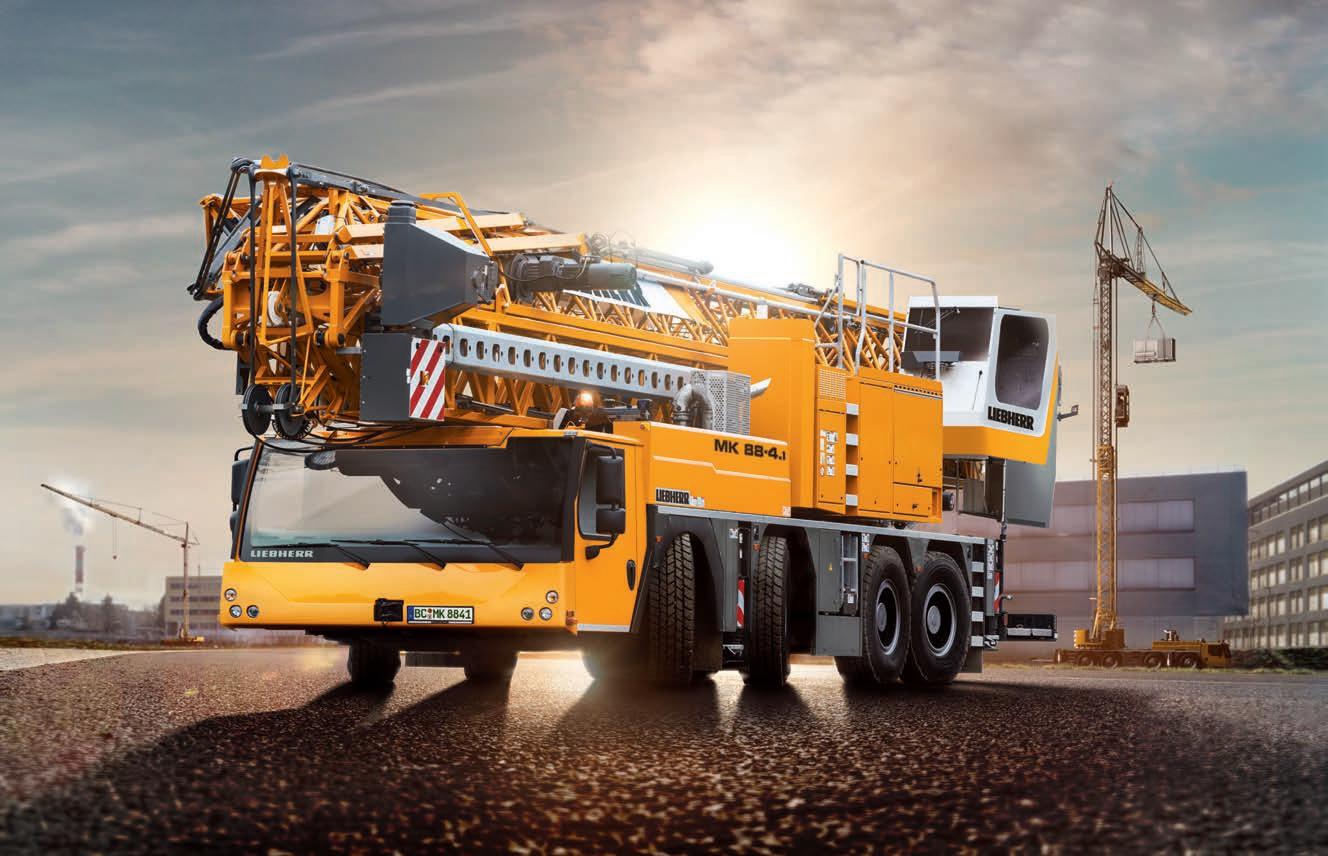
Experience the Progress.
The MK 88-4.1 mobile construction crane is a consistent further development of its popular predecessor. In addition to the compact transport dimensions and the outstanding tip load capacity of 2,200 kg at a 45-metre reach, it is above all the intelligent energy management that makes the four-axle crane stand out: It allows emission-free and silent operation also while using weaker power supplies. Liebherr MK mobile construction cranes – We are building the future.
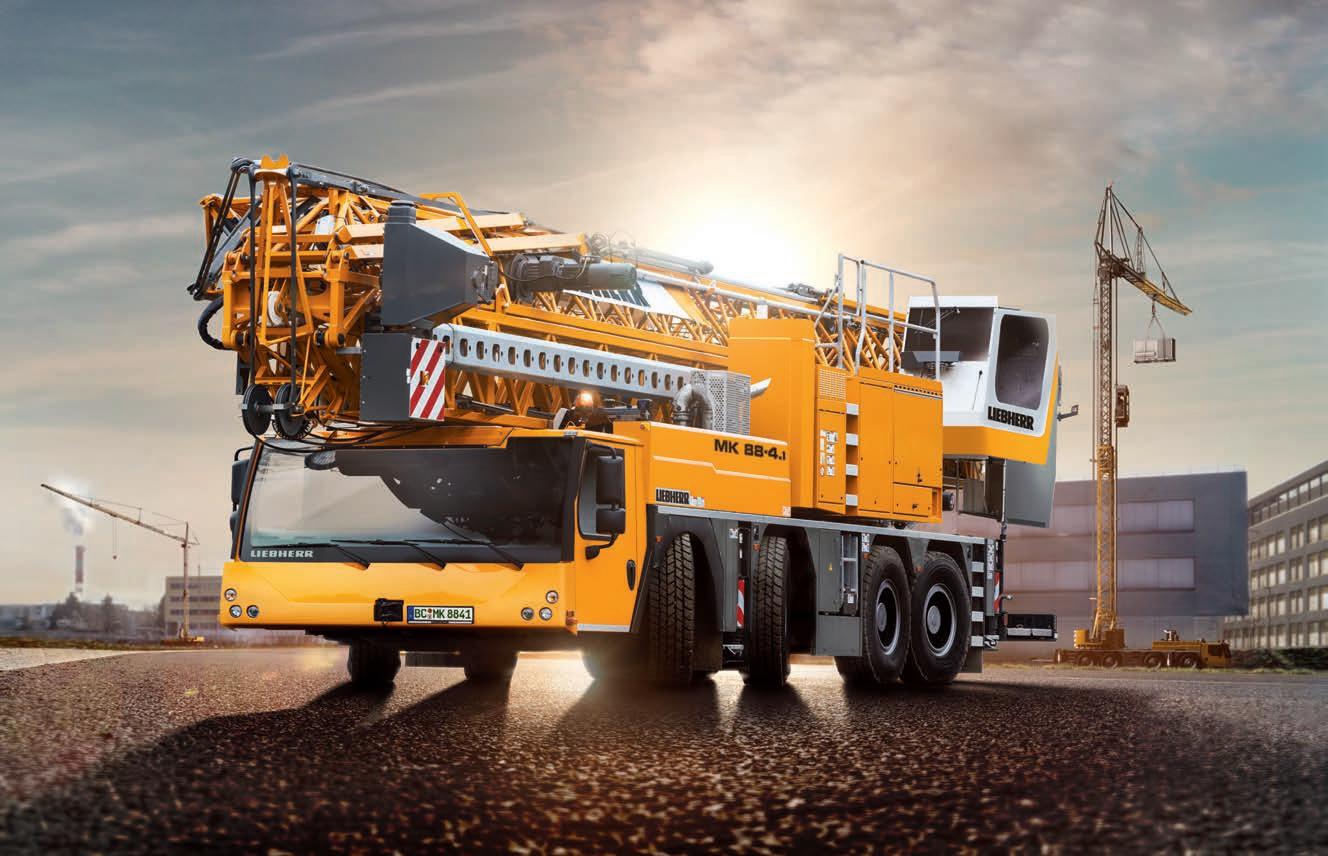
Plus package: Powerful lung, Load-Plus and additional ballast
Hybrid power concept: Emission-free or self-sucient – the right drive unit at the right time
Adjustable axle loads: Less than 10 t thanks to the divisible and removable basic ballast
New control system: Half-sided support and set-up status detection system possible
Optimised working environment: Better view and more comfort in both cabins
WELCOME TO THE OCTOBER ISSUE OF CRANES AND LIFTING MAGAZINE (CONFERENCE EDITION)
It is a privilege to be reporting in this bumper 2022 CICA National Conference issue of Cranes and Lif ting magazine. During the Covid years our plans were stalled and stifled, so we’ve been keenly anticipating this conference – a time to get together once again.
IF YOU ARE READING THIS AT THE conference, welcome to this inspiring event where you and the other anticipated 500 delegates will be immersed in the latest thinking and exposed to the best information and resources. Sharing the latest in theory, policy and practice, our hope is that this conference is an event that challenges your thinking and fosters innovation and ways to make the crane industry safer and more efficient.
The 2022 CICA Conference will also host the prestigious CICA ‘Lift of the Year’ Awards. CICA thanks
the winners will be publicised nationally and internationally.
CICA STATE BRANCH ANNUAL BUSINESS MEETINGS
CICA relies on the contributions of an active branch executive in every state, these committees strive to work positively to promote CICA community connection locally. These committees put in a significant amount of time and energy, and I want to take this opportunity to thank the outgoing members and welcome the new branch executive. This process keeps the committees fresh and CICA
Cranes and Lifting magazine for its sponsorship of these awards, as it acknowledges and celebrates the contributions of exceptional crane and site teams who perform challenging lifts, and those who develop innovations to solve complex challenges.
These are the pinnacle awards for lifting professionals in Australia and thanks to the vast distribution of Cranes and Lifting ,
is fortunate to have such a skilled experienced group of individuals willing to step up to the plate. I thank all committee members most sincerely for their support and efforts.
CICA BOARD
At writing, the CICA Annual General Meeting is yet to happen, so the CICA Board will most likely have changed by the time this issue
is distributed. CICA is a broad peak body, and our organisation has historically had the right board members and skillset at the right time, to navigate the challenges of the day. Again, I would like to thank the departing board members for their invaluable contribution and time and welcome new and returning board members. CICA relies heavily on your vision and strategic direction.
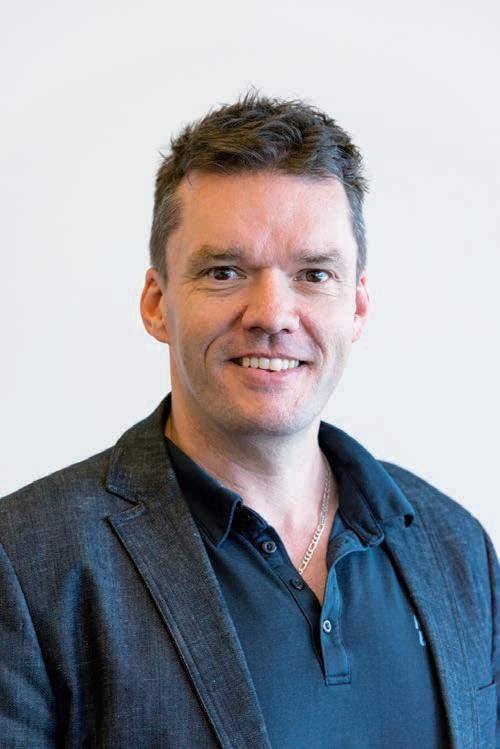
“Sharing the latest in theory, policy and practice, our hope is that this conference is an event that challenges your thinking and fosters innovation and ways to make the crane industry safer and more efficient.”
CICA STAFF
Interaction between staff and volunteers is an important information network for CICA.
from CICA staff is also an important element in the management of our branches, businesses and relationships with enabling stakeholders. The CICA staff assist with road and network access, crane weighing, lobbying,
management, and provide a myriad of resources and networking opportunities. All of this is much appreciated, and I hope you’ll get the opportunity to meet some of the newer CICA Staff members at this conference too.
I look forward to seeing you at the 2022 CICA National Conference in Adelaide. The Adelaide Convention Centre is a world class facility, and Adelaide’s central location brings the country together with ease. I encourage you to make the most of the local sights and experiences on offer.
I would like to take this opportunity to reflect on the sad passing of Gilbert (Gibby) McKay, the founder of McKay United Crane Hire. He was the most amazing and unique character and I am forever privileged to have worked alongside him for many years. Most of us at the conference have fond memories of Gibby, and I’m thankful to the hundreds of you who have contacted me with your condolences. Gibby loved the crane conference. He was a professional “networker” at all of these events, attending every social event possible. It is a fact that Gibby never attended a single conference session for the many years he attended, other than a social event! Please take a moment while you’re socialising during this event and raise your glass for Gibby.
Tom Smith CICA president managing director – McKay UnitedCICA
Tom
Damien
Julie
Unit 10,
Patrick
UNDERSTANDING WET AND DRY HIRE
Both wet hire and dry hire agreements are common place in the hire industry. In this article, Holding Redlich lawyers Jacqui Doyle (partner) and Sam Billingsley-Dadd (associate) explain some of the key clauses that builders and suppliers need to be aware of when entering into these types of arrangements.

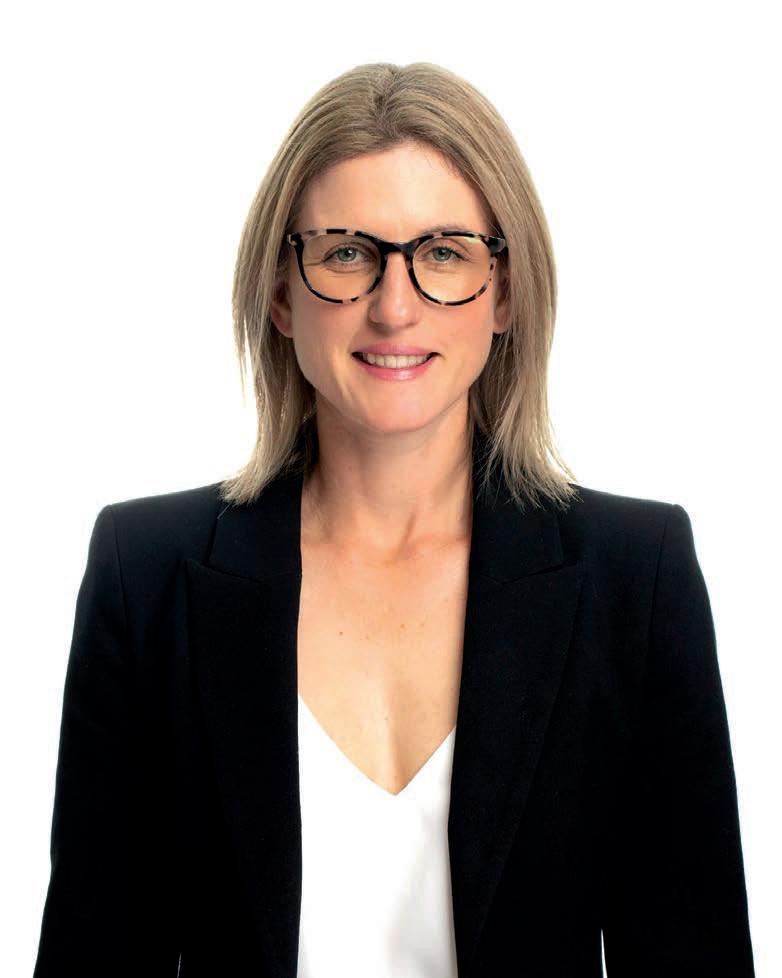
DRY HIRE VS WET HIRE – WHAT’S THE DIFFERENCE AND DOES IT MATTER?
In a dry hire agreement, the equipment is supplied by the supplier and the hirer is responsible for sourcing an operator.
Conversely, in a wet hire agreement both the equipment and the operator are sourced by the supplier.
While a dry hire will typically be cheaper if a hirer already has an appropriately qualified staff member on-site, a wet hire will often provide significant risk and liability benefits.
LIABILITY UNDER A WET HIRE AGREEMENT
One of the most important things to understand in any hire arrangement is who bears responsibility should something go wrong.
Typically, wet-hire agreements will assign liability for damages caused by:
1. t he actions of the operator to the supplier; and
2. t he actions of the hirer’s staff to the hirer.
However, parties need to be careful when drafting liability clauses, as overzealous drafting can lead to clauses that unduly burden one of the parties. This issue was discussed by the court in Westina Corporation Pty Ltd v BGC Contracting Pty Ltd (2009) 41 WAR 263 (Westina v BGC) .
BACKGROUND FACTS: BGC Corporation Pty Ltd (BGC)
form wet hire agreement with Westina Corporation Pty Ltd (Westina). Under the agreement, Westina would supply a truck (the Westina Truck) and operator (Mr Ingold) to BGC, so that BGC could transport iron ore from the mine to a nearby railway siding.
The contract contained an indemnity clause that:
“Where the plant [the Westina truck] is hired on a wet hire basis, the supplier [Westina] shall… bear the risk of loss in the hiring of the plant
death, claim or other loss arising from the hiring of the plant.”
During one of the trips between the mine and the siding, the Westina truck collided with the trailer of an oncoming truck owned by BGC. The driver of the BGC truck had lost control and its trailer had flipped over onto the wrong side of the road. The collision killed Mr Ingold and caused irreparable damage to the Westina truck.
Westina sued BGC for the loss of the truck, alleging that the driver of
the BGC truck had been negligent and that BGC was vicariously liable for their actions.
BGC sought to rely on the indemnity in the contract and argued that the indemnity clause covered all losses associated with the hiring of the truck, including where the loss was caused by BGC’s own negligence.
THE ORIGINAL DECISION
The trial judge found that:
1. t he BGC truck driver had been negligent and caused the accident; however
2. t he contract drafting meant Westina could not recover damages from BGC even where the accident was caused by BGC.
WESTINA APPEALED
The Court of Appeal allowed the appeal, and found that the indemnity:
1. w as intended to protect BGC from any loss caused by the negligence of Westina or its employee while operating the truck;
Pre
General Responsibilities
condition
Insurance
public
workers
– plant & equipment
Post Hire Machine inspection and condition
Mobilisation
Demobilisation
Minor
Major repairs (parts & labour)
Supply major components (e.g. engine, radiator)
Daily servicing (fuels, oils, air cleaners,
Hirer
Accident damage/missing parts while on hireSupplierHirer
1. It is important to note that while a PCBU may rely on a specialist contractor it will not completely absolve them of their duty of care.
CICAASSIST is a service available to CICA Members and offers free access to a seven day a week, 24-hour hotline service to contact a lawyer in the event of a serious work health & safety accident / incident or a workplace regulator intervention or any unlawful union right of entry / industrial action.
CICA members receive initial free legal advice on how to manage the incident. If members wish to engage a lawyer through the CICAASSIST Help Desk, then discounted rates for legal services will apply.
2. s hould be read against the interest of BGC as the party receiving the benefit of the indemnity; and
3. d id not release BGC from any loss caused by their own negligence.
Although ultimately the court found in favour of Westina, the above case demonstrates why it is important to review the risk allocation clauses in your contract carefully. A well drafted liability clause should eliminate the risk of these misunderstandings and operate to ensure that all parties to the agreement have the same expectations should an accident occur.

KEY CONSIDERATIONS IN A WET-HIRE CONTRACT
The sbove table provides a summary of some items you will need to consider when entering into a wethire agreement.
As discussed above, who actually bears the risk and responsibility for an item will come down to the specific terms of the contract, so it is important you review your contract carefully.
Obtaining legal advice can be useful in avoiding risks. This extends to having your hire arrangements reviewed regularly to ensure they remain consistent with any changes to relevant laws.
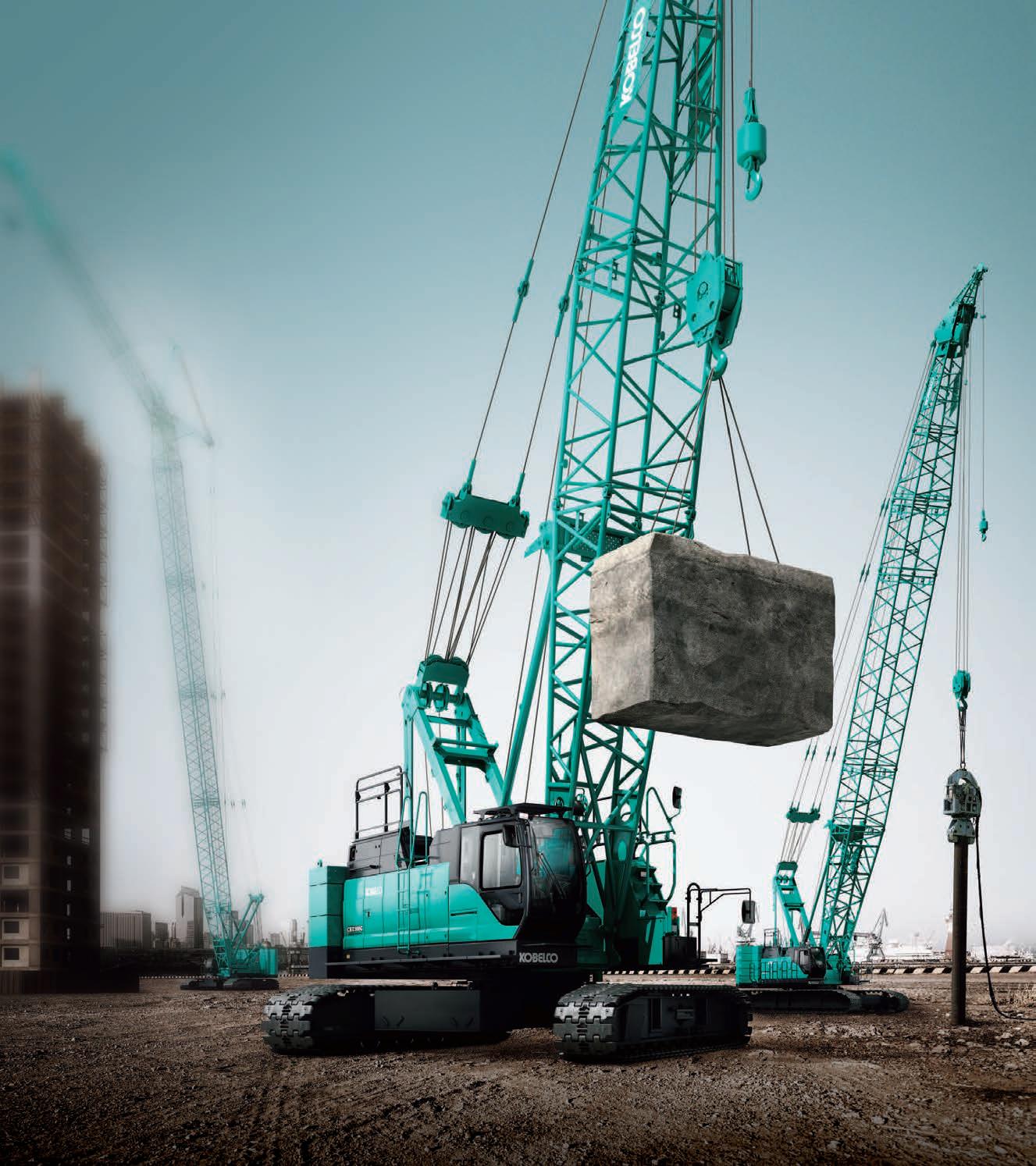
CICA LIFT SUPERVISOR PROGRAM
DELIVERED IN A NEW FORMAT
In the February Tech Corner article, the CICA technical committee examined the causes of accidents and introduced the CICA Lift Supervisor program. A great number of responses were received from industry indicating support or interest in the program.
TO DELIVER THE PROGRAM EFFICIENTLY and effectively, the Level 1 – Lift and Transport portion of the program will be split into two parts: an online selflearning program and a face-to-face classroom teaching program.
The online learning modules focus on reviewing the knowledge and skills learnt from the high-risk work (HRW) licence training, plus some basic crane related knowledge that is useful and practical for providing guidance as a lift supervisor for crane operations.
Although HRW training organisations follow the content set out in the regulations, they may focus on some aspects and overlook others, or some of the knowledge learnt from HRW training may not be used frequently enough for the crew member to have consolidated the skills to be competent a few years after the training. It is imperative that the lift supervisor be very familiar with all aspects and provide guidance if required.
The online self-learning part includes five modules:
• Engineering principal basics
• Sling and rigging basics
• Dif ferent types of cranes and crane charts
• Specific lifting operations (powerline, workbox, marine lift)
• Transport safety
The face-to-face classroom teaching aspect incorporates three modules and a final assessment:
• Engineering calculations and rigging stability
• Crane loads and lift planning
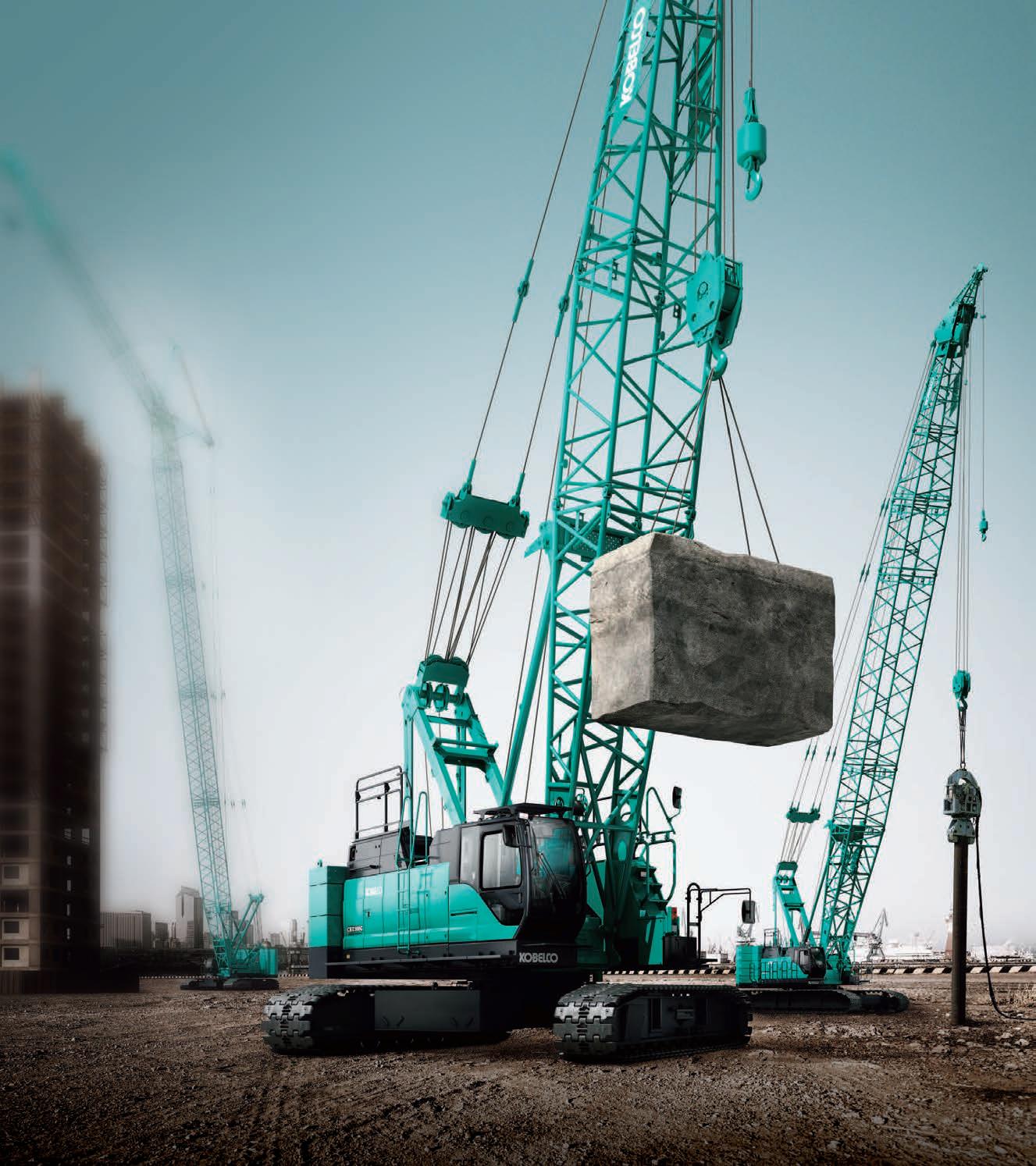
• Complex lift (multi-crane/multi-hook lift, precast lift)
Program participants will be required to complete the online self-learning modules prior to attending face-to-face classroom teaching.
An adaptive learning platform was selected over other formats, to deliver the online learning modules.
WHAT IS ADAPTIVE LEARNING?
Adaptive learning delivers a personalised learning experience that address the unique needs of an individual participant through just-in-time feedback, pathways, and resources (rather than providing a one-size-fits-all learning experience). Adaptive learning uses an AI algorithm to shape content to the needs of an individual student, just as an instructor does with students in oneto-one conversations.
Adaptive learning is conducted on a web-based platform, that contains all
the important information related to the class and guides the participants on their learning journey. When the participant attends the class online, the platform software can make calculated decisions for the best course of action for the student. Each journey is personalised to the participant, based on their unique needs.
WHY USE ADAPTIVE LEARNING?
The ideal candidate for Level 1 of the program is someone with C6 or above, HRWL crane licence and Intermediate Rigging Licence with at least two years of crane industry related experience.
As mentioned earlier, HRW licence training can vary, and attendees will bring along different experiences obtained/learnt from companies or projects they have worked for/on before. For example, participant A may work for a crane company that mainly uses crawler cranes for civil construction projects, and participant B may work for a small crane

company that uses articulated steering cranes for small lifts in the residential market. These two participants will have different levels of practical experience in many aspects including operating cranes, lift planning, rigging, knowledge, etc.
Adaptive learning will accommodate these by allowing the participant to work at their own pace, checking competency on concepts already mastered, while reviewing and practicing less familiar concepts at a slower pace. This style of learning also improves student engagement by providing lessons and activities that closely match their needs and readiness.
Adaptive learning is a new concept for the crane industry. The training received for most crane crew (HRW training) assumed that the starting point for participants was zero knowledge, and all participants are trained at the same speed. Adaptive learning gives participants a greater sense of autonomy as the learning plan is catered specifically for them.
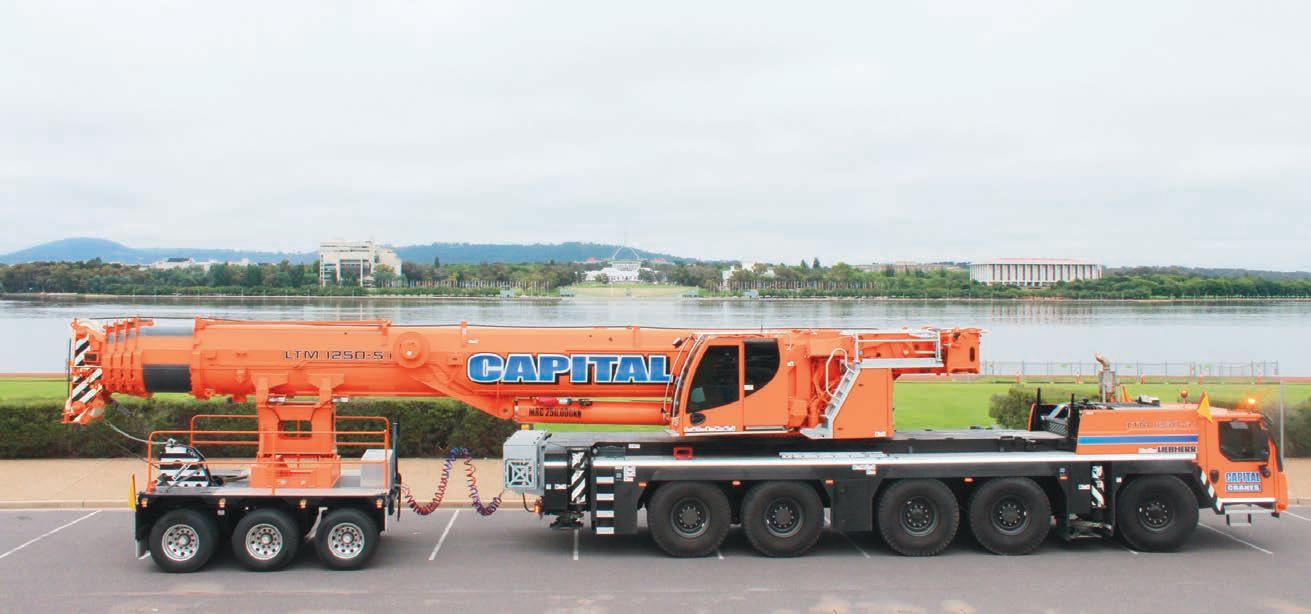
HOW DOES ADAPTIVE LEARNING WORK?
The four stages of competence, also known as the four stages of learning, as shown above right, relate to the psychological states involved in the process of progressing from incompetence to competence in acquiring a skill. For example, a participant in ‘unconscious incompetence’ will respond differently to training than a participant in ‘conscious incompetence’. If the participant doesn’t know there’s a problem or a knowledge gap, they are less likely to engage in the solution. On the other hand, if someone is in conscious competence, they may just need additional practice rather than training.
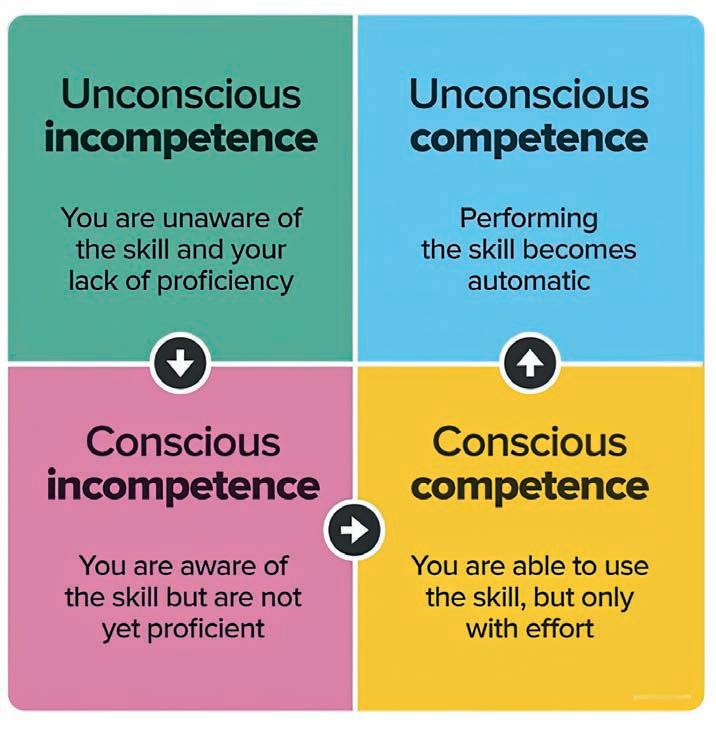
The four stages of competence are core to the algorithms used in adaptive learning technologies. By knowing which stage a participant is in for a particular topic, an adaptive learning platform can select content on that topic that will help the
participant uncover and recognise ‘unconscious incompetence’.
Using the previous example of participant A and participant B - before they start the training, participant A may not be aware that even though they have a licence to operate articulated steering cranes, the operating feature of such a crane is totally different from operating other types of mobile cranes (i.e., side slope derations). Participant A is at the ‘unconscious incompetence’ stage.
Through the training and by answering questions asked by the software, the participant becomes aware of a skill or knowledge gap and understands the importance of acquiring the new skill, which motivates the participant to learn more in the relevant area. As training progresses and the software learns more about the participant through using AI algorithms, it will create more relevant content (i.e., demonstrate ‘step-by-step’ how to read a
deration chart) to assist the participant to complete the learning stages. For participant B, on the job training may have put him or her at the ‘unconscious competence’ stage of the learning process for articulated steering crane operations, once the software identifies this, it will place more focus on other areas.
WHAT TO EXPECT NEXT?
CICA is currently working with a world leader in the technology that hosts the adaptive learning platform and provides content production services, to develop the online part of the Lift Supervisor Level 1 Lift and Transport modules. The online portion of the program will be available by the 2022 CICA National Conference, where more information will be made available.
If you are interested in this program, please contact Alice Edwards (alice@cica.com.au).
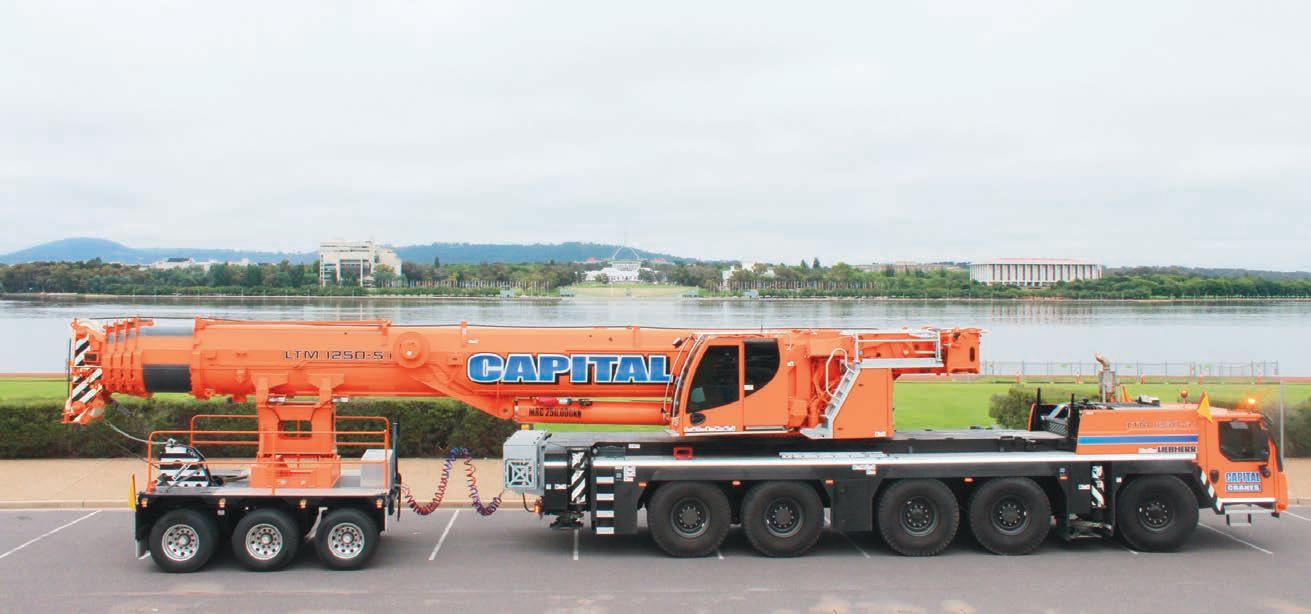
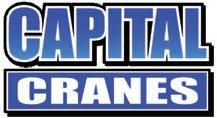





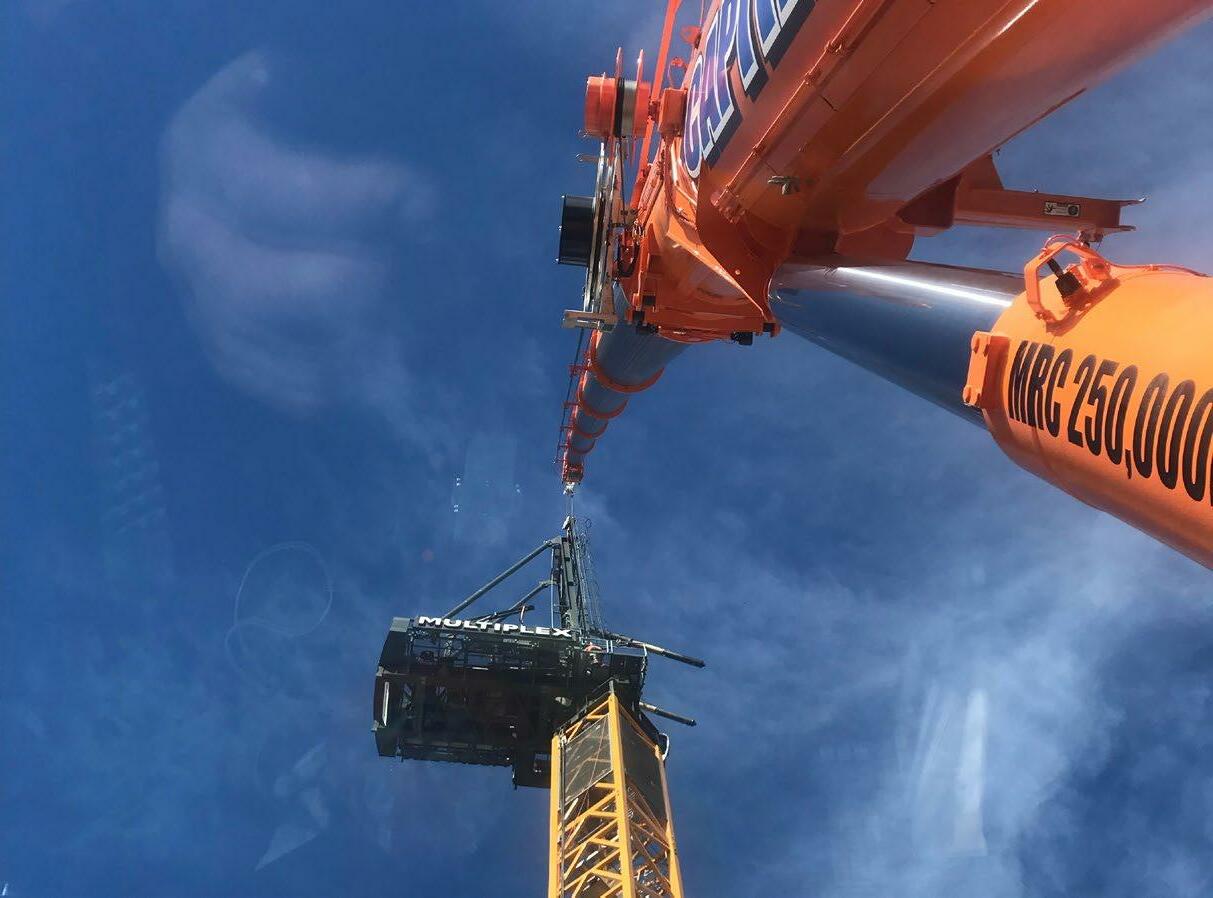
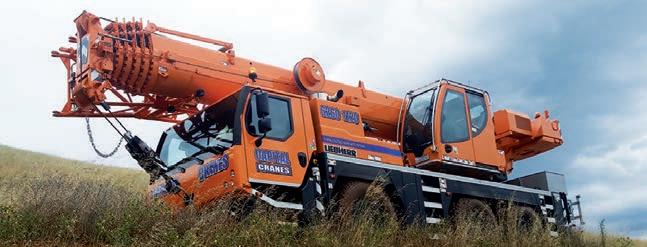

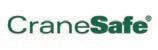
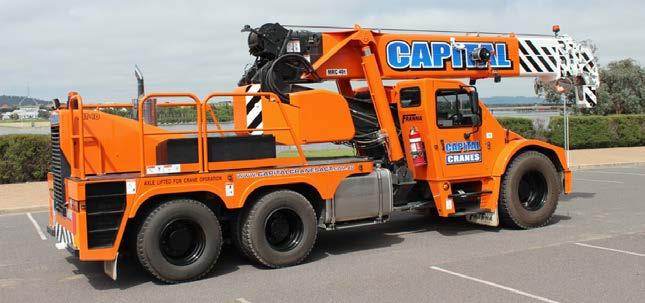
SERVICE AND SUPPORT KEY TO LIEBHERR WA GROWTH
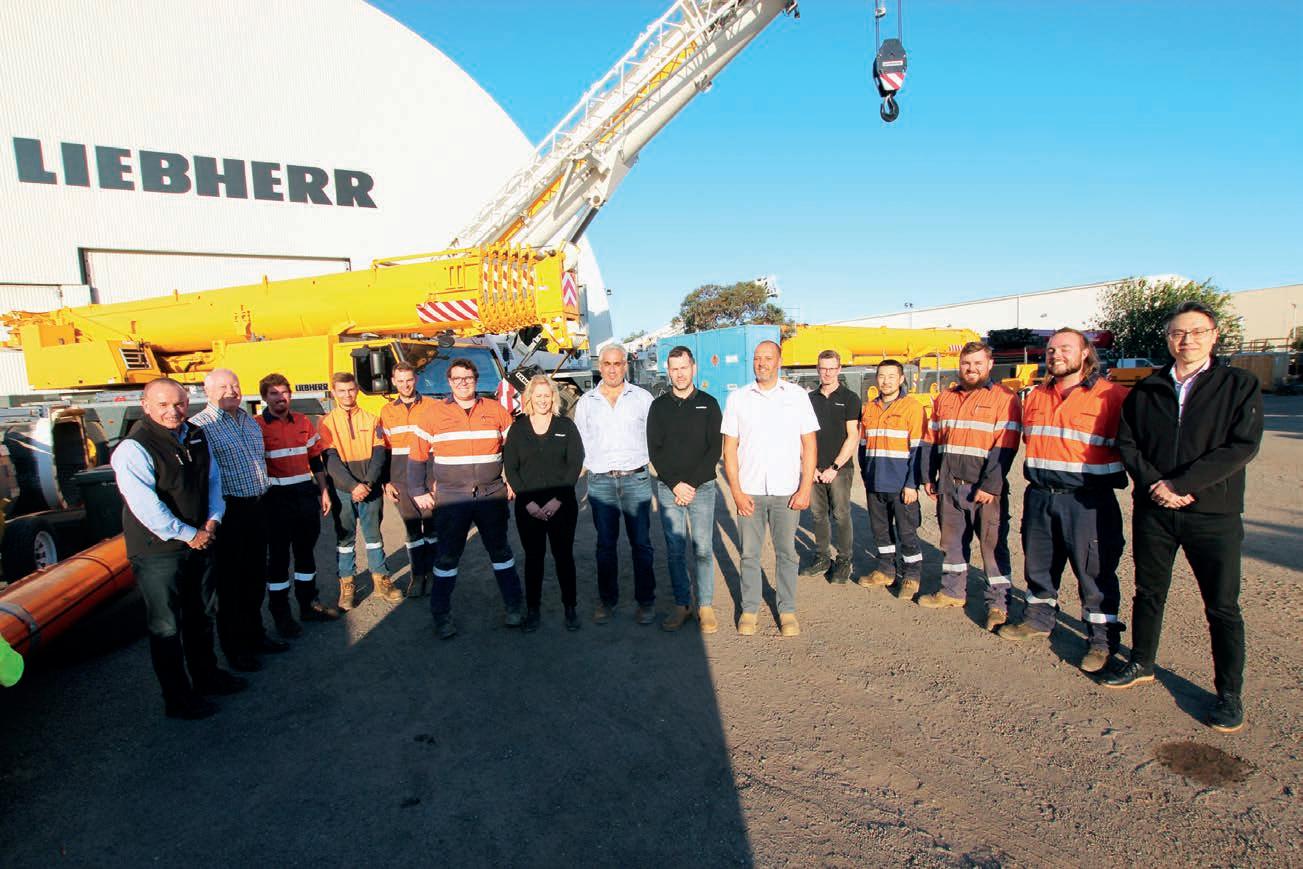
Partnering customers with high levels of service, support, and spare parts availability have been key to the growth of the Liebherr Western Australia operation. Richard Gulbis, regional service coordinator, has been with organisation for 14 years. He explains how the business has needed to change during his tenure.
GULBIS STARTED HIS CAREER IN THE UK.
On leaving school, he started working with Ainscough Crane Hire in its Manchester branch. He was an apprentice at the college that had opened next to it. The leading hand at Ainscough knocked on the door and said: “We need someone”. Gulbis was the lucky guy. Ainscough Crane Hire is now a major crane hire business in the north of England.
“I was working in the UK until 2008, when a colleague who had left and migrated to Australia said to me: ‘Give this opportunity a go,’ and sent my CV. I flew over, I was interviewed, I was offered the job and we decided Perth was for us,” he said.
Gulbis moved straight into a field service role, but the early days were difficult. He had moved from a professional and organised outfit to one that wasn’t so organised. He could see what needed to be done but was a field service technician and not in a position to effect any change at that time.
“Two years later the opportunities began to present themselves when a few people moved on. We had lots of international field technicians, which made stability an issue. They were being flown in from all over the world.
“Working in crane hire in the UK, we had the same Liebherr guy visit the yard to service the cranes, so you had a relationship with him and a continuity with the Liebherr brand.
“When I joined the team here, we had nothing like this. When the leading hand role became available, I didn’t think I was qualified, I was a technician, but I applied and got the job.
“So, we went about making some changes. As a leading hand, there is a limit to what you can do initially, and you can only fix what is around you. But as new team members were introduced we stuck to the philosophy ‘if we look after the team, the team will look after the customers’.”
From getting the basics right, the Western Australian branch began to grow and sold more cranes. And with more cranes sold the more the business had to strive for improvements in service and support.
“We recruited more technicians, many of them with plenty of experience from the UK. They arrived and worked with our local recruits, and they helped to train them up,” said Gulbis.
He goes on to explain how the business realised the critical importance of the team of service technicians running around in service vans, and how the right parts needed to be in the right vans.
“We developed a common understanding of which parts were required more frequently, so we kitted the vans out with the components that would get a crane back up and running.
“Obviously, we can’t carry an engine or a gear box, but we can carry LSB sensors and slip ring contact sets. So, the vehicles had the emergency parts, and the technicians were in a position to get a crane up and working if there was an issue,” said Gulbis.
The next focus for Gulbis and his team was the spare parts department. At the time, the parts department was not big and it probably wasn’t being run by the right people.
“If a business is going to succeed, you need the right people running the departments in the business,” said Gulbis.
“It took us a while to get the spare parts of the business working well. When the right people were in place, the parts holding developed and it now occupies a full bay of the workshop which now accommodates the spare parts we need to support the massive population of cranes we have in WA,” he said.
Matthew Clark runs the spare parts department in WA and he works closely with the national parts manager Manson Tong.
“Matthew works closely with the service team. He’ll come to us with a new model crane and ask what we know about it and what parts we will need to keep in stock. Matt talks to the service technicians to ensure we have the right mix and levels of stock on site,” said Gulbis.
“The connection between spare parts and service is absolutely critical. We can have parts in stock, but we still have to get them to the client and the crane. And this is where the relationship with the customer is so important. They will tell us how urgently the part is needed. If the crane isn’t working, we’ll get the part on the next available flight.
“For me it doesn’t matter if it’s a small LTM 1030 or an LTM 11200, I’ve got to work out the priorities. Obviously the 11200 earns a lot of money for the customer but it might be sat in the yard whilst the LTM 1030 could have a man box 30m in the air. Given these instances, it is clear which job will be the priority.”
Liebherr has a technical department
that includes Gulbis and Derek, who is also the trainer for the branch.
“Our technicians have as much experience as we do. They work closely with us, but they also work closely with the customer, who doesn’t care how we do it, he just wants the crane up and running again and earning money,” said Gulbis.
“My background is in cranes and for 50 per cent of our technicians it is the same. We know what can go wrong with the machines. When I first moved to Australia, 14 years ago, I didn’t know what the conditions were for the cranes.
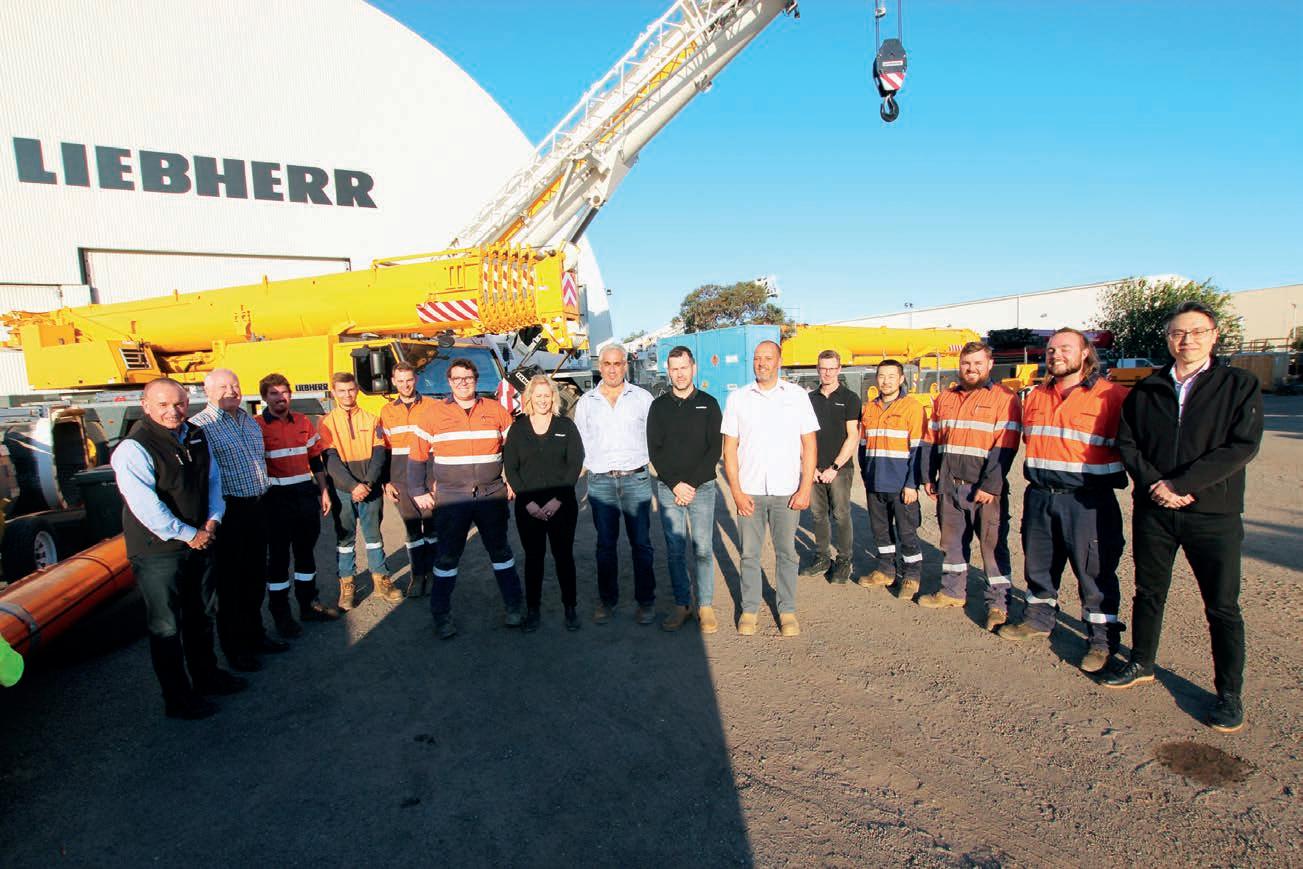
“In the UK everything is on the road and the roads are salty, so corrosion was a major issue in terms of preventative maintenance. We don’t have salty roads here; we have corrugation and a hot climate. Corrugation majorly impacts the crane, and we know with every major inspection the running gear will have been pushed to the maximum.
“At any one time, we know we have a number of major inspections coming into the workshop and we work with the parts department to ensure we have enough brakes, brake expanders, brake drums, brake discs and brake shoes.
“We know we are going to need axle
parts torsion rods, ball joints, steering parts, we know which parts are going to be worn and will need replacing. The parts team is prepared, and they do their best to ensure the parts are here and ready for when the crane arrives.
“We only have a certain amount of space for parts but, percentage-wise, based on a five-axle machine, if we were to send a list of parts for the carrier I would estimate 90 per cent of the items would be in stock. The remaining 10 per cent are usually the bigger items, which may sell infrequently or never sold before. These parts might have to come from the factory, which will delay things,” he said.
From a major inspection point of view it is very much based on the experience of the team, said Gulbis.
“As far as the superstructure is concerned we don’t find anything wrong. We don’t find any cracks or structural damage. Luffing cylinders and tele cylinders leak but that is the environment we are operating in. Our challenge is understanding the environment the cranes are working in and catering for that well in advance of the crane arriving in the workshop,” he said.
Gulbis explains what will simplify
Liebherr’s processes in terms of service and support based on customer feedback and information. Cranes are more intelligent, and they are monitoring themselves as well as being diagnostically accessed remotely, but the customer still has an integral role to play.
“It starts with training. We provide a familiarisation package with every crane, and we encourage every customer to take full advantage of this package. We take the familiarisation back to the basics and, although everyone is busy, it does pay huge dividends if the customer has as many staff on hand for the familiarisation,” said Gulbis.
“We use the familiarisation as an opportunity to explain how Liebherr approaches its machines. We explain how we understand our cranes will be operating in remote areas, where phone signal is not always available and, if the crane has a fault, the customer needs to know what to do to get it back up and operating.
“We focus on the basics of how to retrieve an error because a lot of operators don’t know how to do this. You might have to drive several kilometres to receive a phone signal and the first question we ask is ‘what’s the error code?’ They then have to
drive back to site and back again to answer the question. It can be that basic. We can do our job remotely over the phone, but without the basics of understanding the error code and the serial number, this is going to be impossible,” said Gulbis.
He talks about Liebherr’s mobile service technician fleet and the support they provide to customers.
“When I was in the leading hand role, we asked the question: ‘What do we need to service our customers?’ The high percentage of our cranes were in the Pilbara region, but we didn’t have anybody there.
“We did have a roster system, but it was quickly obvious we were going to need somebody based there permanently. We looked internally to see if anyone from our organisation would be interested and Lee Sutherland immediately put his hand up.
“Lee served his apprenticeship with Liebherr – he is factory trained and he understands the ‘Liebherr Way’. Liebherr rented a house, and he was underway. He made contact with all of the major customers in the region and basically ran his own diary.
“He now has a family and bought his own house, and he a permanent resident in Karratha. The business has been growing
exponentially in the region and could support a second field service engineer.
“Including Lee there are seven in the technical and service team, plus Derek, who is our trainer and also technical support, and he also has a vehicle. Derek is the highlevel guy for the large cranes and the more technical issues. We cover the entire state from the branch, which is ideally situated in Rockingham, an hour south of Perth. The work is inland towards Kalgoorlie –there’s a lot of activity in Geraldton,” he said.
Matthew Clark is the spare parts supervisor/facility manager and he has been with Liebherr for eight years. He discusses Liebherr’s approach to spare parts support from the WA branch.

“I didn’t have much experience with cranes as I had been working on conveyor belting for the 10 years before joining Liebherr,” said Clark.
“When I joined, we had a small team and although it wasn’t a bad set up, there was room for improvement. We have since improved our ability to manage the parts business out of sight. We have changed the structure and when Manson Tong took over as the national parts manager, he created the role of parts supervisor for me.
“I report back to him, and we are in constant contact about how things are going, what the issues are, etc. Manson also appointed an inventory stock controller who continually goes over our systems, and forwards spreadsheets determining what he is going to be ordering out of the factory, what we are selling a lot of and what isn’t selling to determine what parts we going to need.”
Clark explains how it is his role to ensure he has the right parts in the right place at the right time and how he manages the parts required by the mobile technicians and the benefits customers receive from the focus on spare parts.
“We have a good idea of what parts need to be in stock, but you can never be 100 per cent accurate. Obviously, our systems show which parts are being ordered, which parts are fast moving, like filters and pressure sensors, and which parts are slow moving.
“I stay very close to our technicians, both the team out in the field, as well as the team here in the workshop, because they are working on the cranes all day every day. They see which parts wear and why and so we also use their knowledge to ensure we have the right parts in stock,” said Clark.
“Often the demand for spare parts will
come down to the manner in which the customer maintains their cranes and how the operators treat them in the field. We can provide advice about generally maintaining the crane, like regularly greasing the boom. That sort of maintenance is so simple, and it can put more life on the crane.
“We have a lot of cranes operating up in the Pilbara region, which is a harsh environment. It gets very dry and, being so close to the ocean, corrosion is an issue. So, we have to factor in these different issues when we are maintaining stock levels.”
Major inspections can put significant pressure on the parts team. Customers don’t want their cranes in the workshop any longer than they need to be and so the parts need to be available.
“When it comes to major inspections, the team in the works shop strip the crane down and we will be confident we will have 85 per cent to 95 per cent of the required parts in stock,” said Clark.
“There might be some instances where we have to order parts from the factory and the turnaround on these parts can be anything between 14 to 18 days, which is a quick turnaround given the challenges we have been facing over the last two years.”
From a spare parts perspective, he
believes ensuring the Liebherr service technicians have the right stock when they get to site is a priority.

“We try to ensure our service technicians have the right parts when they get to site. They are then in a position to look after our customers. Their vans are stocked with emergency spare parts and if we are smart in the way we supply that stock, there should be no delays in the technician dealing with the issue and getting the crane back to work as quickly as possible,” he said.
Recently there was a change for Clark and Gulbis. When a colleague left the organisation, general manager Andrew Esquilant and the senior management team decided to create roles for them to help oversee the WA business and to support the team in any way they can.
“This was as a result of the travel restrictions associated due to Covid, which meant the senior management team
demand for cranes in Western Australia has gone through the roof. No one could have predicted this and we’ve doubled the size of our team to manage the growth.”
Part of this growth saw Jacqui Stewart appointed to the role of service administrator.
Stewart started with Liebherr at the end of 2018 and she has played a major role in the business ever since. Stewart organises all travel, accommodation, and site requirements for the field service technicians.
“Jacqui Stewart started her crane journey with one of our customers, Joyce Krane,” said Clark.
“With Joyce she gained a lot of knowledge and was in a similar role for a period of five years with them. Jacqui brings to the team a bubbly personality and is the first person you are greeted by when you walk through the doors at our Rockingham yard. Currently, Jacqui and Lara are in the
couldn’t be here in person. We are the eyes and ears on the ground here and we report back directly to the management team,” said Clark.
“We help make the day-to-day decisions for the business and seek input from the senior management team when high level decisions need to be made. But, locally, we work as a team, we support Stef wherever we can in terms of sales. We also support Morgan, the workshop leading hand who joined us recently, and he has been a breath of fresh air to the business.
“He was with Max Cranes and so he brings a lot of experience as a Liebherr customer, which is always insightful. Lara is our service administrator and planner. She’s been with the business for almost a year. She hit the ground running and is a great asset to the business.
“All of this has been necessary because
progress of training Tahlia Reen, who is in her first year of administrative traineeship.
“The senior management team are incredibly supportive of what we are doing here, and it is a pleasure to play my part in supporting our customers in the best possible way I can.”
Morgan Henderson, Liebherr WA’s workshop leading hand, and Lara Chaisty, service administrator and planner, are also part of the team.
Henderson was with Max Cranes for eight years and was the senior crane technician before moving to Western Australia with his partner who wanted to move home.
Henderson talks about his experience with Liebherr and how he goes about the servicing of cranes that arrive in the workshop.
“My previous employer runs a lot of
“We have a lot of cranes operating up in the Pilbara Region, which is a harsh environment. It gets very dry and, being so close to the ocean, corrosion is an issue. So, we have to factor in these different issues when we are maintaining stock levels.”Often the demand for spare parts will come down to the manner in which the customer maintains their cranes and how the operators treat them in the field.
Liebherrs, so I already had significant experience on the cranes,” he said.
“So, I have experience as a service technician in a crane hire business and now as the workshop supervisor with Liebherr, and I can see how different the approaches are. When it comes to service maintenance and support, Liebherr are prepared to go above and beyond industry standards to deliver the right solution for the customer.
“Take major inspections. Liebherr is prepared to strip back every element of the crane, service and replace parts as required, and the crane will leave the workshop as if it were new.”
Henderson supports Clark’s approach to an open conversation about parts and how his team can provide details regarding the wear and tear on parts.
“If we are seeing a repeat failure or repeated parts that we are using more frequently, we let Matt and the team know that we are going to need more of these parts on the shelf and ready to go. Having the right parts means we don’t have to ship parts from other states or the factory which ultimately saves the customer time and money,” he said.
He goes on to explain how the workshop handles 10-year major inspections.
“With 10-year inspections, we’ll visit the site and conduct a pre-inspection on the crane,” he said.
“We know the disassembly and the reassembly of the crane generally takes between six and eight weeks. And then it depends on what we find during the major inspection. A crane might need the steering completely overhauled or some welding completed on the boom, or maybe the telescopic cylinder resealed. This will add time,” he said.
Henderson goes on to discuss the benefits of an OEM like Liebherr managing a comprehensive 10-year major inspection compared to a third party workshop, which might be offering a ‘middle of the road’ option or a ‘cheap and cheerful’ one.
“With 10-year major inspections, all of our directives come direct from the factory. In the operators’ manual, to properly inspect the boom welds you have to have the boom stripped. This is because the areas for the pinning and supports, basically all
the important stuff, are all internal – you can’t actually see them without stripping the boom apart.
“It’s the same with the outriggers. All of the important elements of the outriggers are the parts that you can’t see, and they have to be stripped back also. That’s why our major inspections will always be better than the Australian Standards because we see and work on more elements of the crane than we actually need to,” he said.
“The other point is our technicians are Liebherr factory trained and when the crane goes back together, it does so as if it were being fitted by the factory. All of our team have the High-Risk Licences which they need for the relevant activities they are conducting. That’s where the factory training is important, they all know how things come apart and go back together again, there’s no guess work.”
Chaisty is responsible for the service and administration support for the team in the workshop. She manages the paperwork for the team, and she also works closely with Henderson in terms of scheduling the cranes through the workshop.
“With his mechanical knowledge, Morgan estimates how long a job is likely to be in the workshop and how many man hours the job is going to take. I then provide the customer with a quote and if they are happy to proceed, we schedule the crane into our program,” she said.
“When it comes to major inspections, we advise the customers of the weekly progress we are making on the crane. We advise them of what needs to be done and why, and they approve the work. In some cases, we might need to order parts from the factory. In this instance we get the customers’ approval because they will take time to arrive, and we don’t want to delay the delivery of the crane any longer than we have to.
“With this open and transparent
communication, the customer knows how the major inspection is progressing and, if we find other issues, we will call them and let them know. The communication is transparent and there are no surprises when the major inspection is completed.
“We also have new cranes arriving all of the time. When a new crane arrives, everything required for a new crane build is completed by our team. External suppliers come in and provide their services and we then hand the customer the ‘ready to go’ crane.
“We thrive on a positive work environment, and everybody works together as a team. The Liebherr business in WA is growing exponentially and many of us are new to the crane industry, but we do have mechanical and administrative backgrounds.
“Understanding the service side of the Liebherr business is critical and makes our roles exciting. Our team is focused on ensuring a crane gets through our workshop expediently and with the best possible result for the customer.”
Stefan de Silva is Liebherr’s mobile cranes sales manager for Western Australia and South Australia.
De Silva has been around cranes for most of his life. His family has a background in civil engineering, operating an engineering workshop in New Zealand, which his father and uncles worked in. This morphed in a new business called Hydraulic Machinery Company and this business assembled the Palfinger knuckle boom range of products.
“I used work there in the holidays and in the stores, unload containers and set up stuff to run the cranes. My father then moved into his own business selling knuckle boom cranes,” said de Silva.
He went on to study at university, and then headed overseas. He returned and decided to join the family business.
“The lack of problems we are seeing with the gear is a result of the increase of aids and technology built into the equipment and there is a lot more sophistication in the cranes.”
“We had the business going for a few years, but the New Zealand market is made up of lots of small to medium sized businesses, so there is only so far you can go,” he said.
Post-global financial crisis it was tough going in NZ and he was looking to move. De Silva was considering all options and he was always aware of the Liebherr brand. At the end of 2012 he met with Andrew Esquilant and was offered the WA role.
“I met Andrew in Sydney and the first time I stepped into WA was to start my role with Liebherr, without knowing a single person. I started my network from scratch,” he said.
“When I arrived, we were based in Guilford and part of the mining business, and it was growing beyond the capabilities of the facility. It was undergoing a refit and refurbishment to accommodate this growth. Our current Rockingham facility had already been secured and as soon as this was available, we moved the mobile crane division.
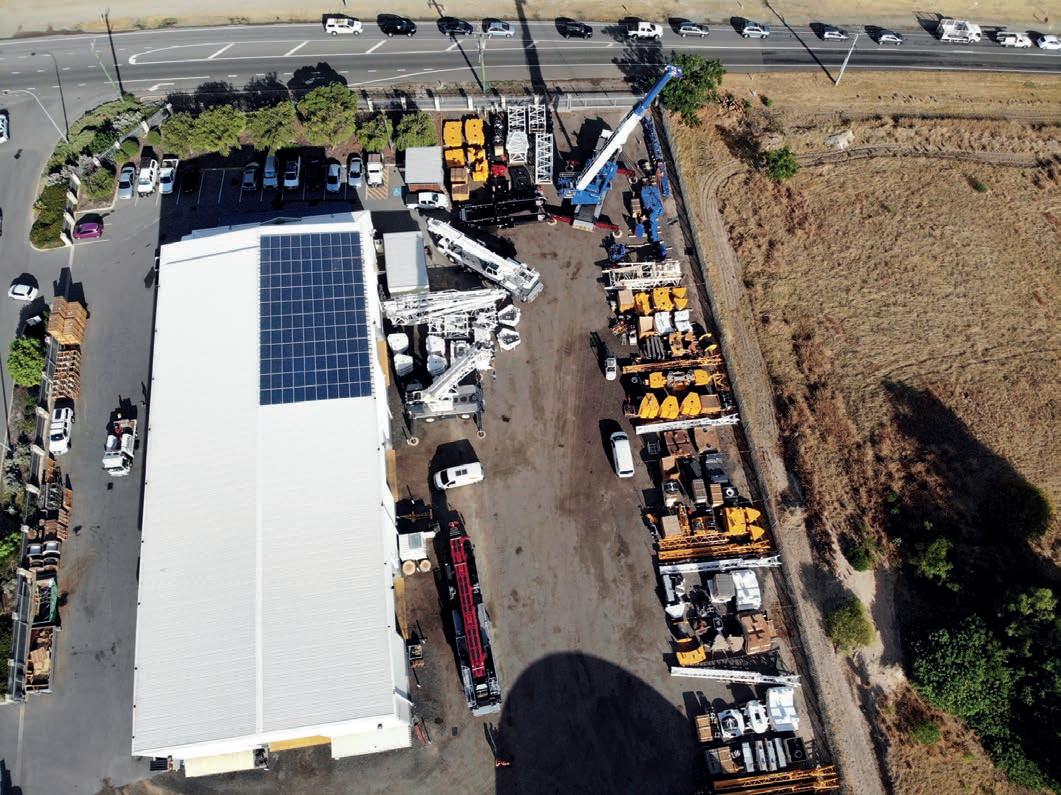
“Service and support are critical to Liebherr. I work with the customer to ensure we are providing the right cranes but repeat business is not possible without the dedicated support of our service tech and spare parts teams.
“Our team has years of experience with Liebherr product and we have individuals who have spent the bulk of their careers working on Liebherr cranes.
“Richard has spent his career working on Liebherr cranes. He’s worked on the cranes in crane hire businesses and now he is working directly with Liebherr. He is the best service technician I’ve ever worked with and he is passionate about what he does. He is also cool calm and connected when it comes to dealing with the customers.”
Service is sometimes a thankless part of the business, said de Silva.
“When a machine is down, all the customer wants to hear is how quickly we can get it up and operational again and Richard and his team tell the customer what we can and can’t do and what needs to happen to get the crane operational again. The experience we have in our service team is a major reason why the business continues to grow,” he said.
“Training is also a key focus for the team, and we have a couple of trainers who are also passionate about what they do. Their experience is great in terms of raising the skill sets of the operators and the service engineers of our customers. This makes a huge difference as to how our products are received by our customers and how well the products are operated.
“The lack of problems we are seeing with the gear is a result of the increase of aids and technology built into the equipment and there is a lot more sophistication in the cranes,” he said.
He discusses how the right crane ultimately reaches the right application for a customer.
“Customers often know what they want so it really is trying to fill in the technical gaps. A lot of the time I will be the intermediary between the customer and the factory, ensuring everyone is on the same page. Whether that be from a commercial point of view or from technical perspective.
“We have worked hard on building solid relationships with our customer base. Customers understand what the Liebherr brand stands for, they understand the quality of the equipment. We work closely
Major inspections can put significant pressure on the parts team. Customers don’t want their cranes in the workshop any longer than they need to be and so the parts need to be available.
with our customers, to understand the projects they are working on and what their requirements are likely to be in the future. It is very much a partnership approach to doing business.
De Silva explains more about the Western Australian market and why it has been so buoyant for the crane sector.
“The resources and commodities sector has been driving a terrific amount of the crane activity,” he said.
“We’ve also seen the state government invest in large infrastructure projects, including a record $6 billion investment across Metronet, $9 billion on major road projects and upgrades, $1.7 billion on major port projects and $347 million on pedestrian and cycle infrastructure.
“The demand for cranes from the renewable sector is increasing sharply and there are massive oil and gas projects planned. All of these projects will lead to increased demands for cranes right across the capacities. But we wouldn’t be growing at the rate we are if we didn’t have such a strong focus on the basics of supporting our customers with an unparalleled approach to service and parts support,” he said. w
Once in the yard, Pace conducted more tests, including the hydraulic system. When the crane was fully washed, it was moved into the workshop and completely stripped down.
SERVICE AND SUPPORT AT PACE
Patrick Mardaymootoo is the service manager at Pace Cranes. After initially gaining his Cranesafe accreditation at Pace and after 25 years, Patrick left to be a full time CraneSafe inspector. Seven years later, he moved back to Pace Cranes. Mardaymootoo explains how focused the business is on service and support.
“SINCE I’VE BEEN BACK, WE’VE rearranged the workshop to make it self-sufficient. This includes supporting the new cranes including delivery and ongoing servicing, and also the provision of major inspections for our customers’ cranes and other equipment,” said Mardaymootoo.

“This doesn’t mean we are only conducting major inspections on
our brands, including Maeda and Sennebogen. We have worked on most brands of equipment and recently completed a major inspection on a Kobelco. We also have a Ranger pick and carry in the workshop for a complete rebuild. We have also refurbished telehandlers and elevated work platforms. All of this has kept the workshop very busy,” he said.
Pat goes on to discuss the process he and his team go through when assessing equipment prior to a major inspection.
“We have good relationships with our customers, and we are building a strong reputation as a trusted maintenance and service provider. We have a customer, Saunders International, who asked us to
conduct a major inspection on one of their cranes. They were really impressed with the mechanical and the cosmetic finish of the crane, so when it came to a second crane and a major inspection, they called me.
“After I received the call the first step was to drive to their yard and visually assess the crane. The crane was a Kobelco lattice boom crawler, and we tested the crane on site. We then dismantled the crane, loaded it onto trucks and brought it to our yard,” said Mardaymootoo.
“Once in the yard, we conducted more testing, including testing the hydraulic system. When the crane was fully washed, we moved the crane i nto the workshop and completely stripped it down, including all the winches and the drive systems for the tracks, and everything was brought right up to date.
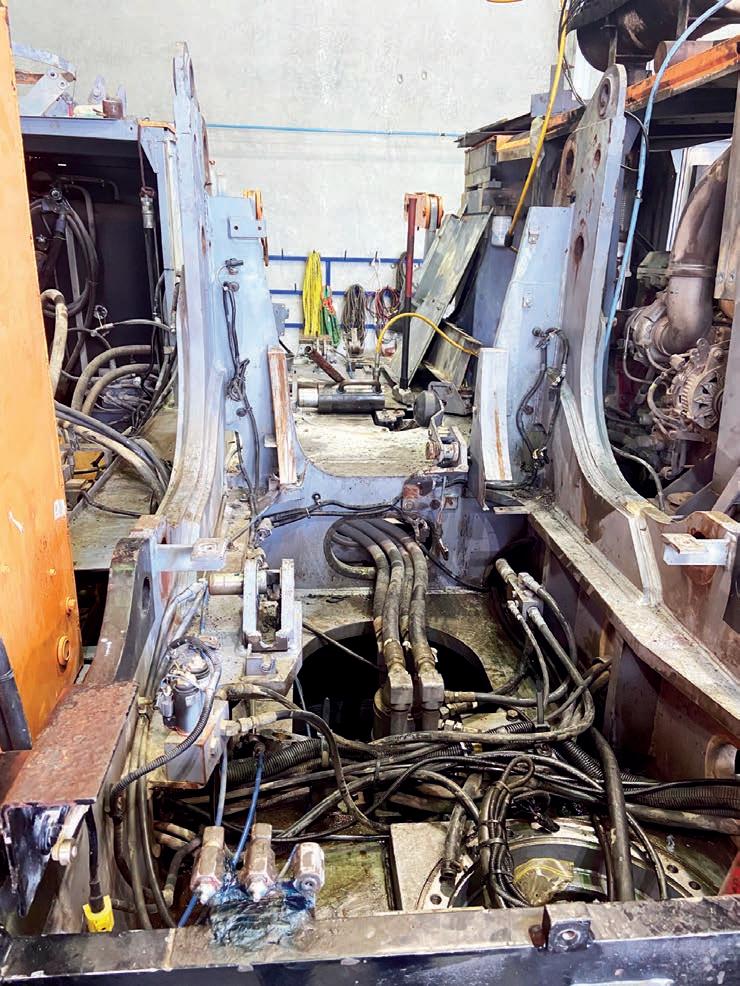
The internal features of the cabin were worn and basically unserviceable, so we replaced everything and took the interior back to its original finish as if it were brand new. When we had finished our work, we sent the crane back to our painters where they sand blasted the crane, completed panel and rust repairs, and then painted the crane,” he said.
“Whilst the crane was stripped down all the lattice boom sections were sand blasted and all the lacings which required replacing were replaced. The crane was NDT [nondestructive testing] crack tested. The various ropes, including the winch and luffing ropes, were replaced. When we completed the overload test was undertaken at 25 per cent over, as per the Australian standard, and all winches were tested at 10 per cent over.
“When this was completed, we returned the crane to the customer’s yard. I took two mechanics with me, and we spent two days putting the crane back together and then went about testing the crane. The overload test was witnessed by our third party engineer, who has been following the progress since the crane arrived in our
Some customers are not aware of what’s involved in a major inspection and the costs involved, but Pace Cranes has not seen a customer who is disappointed with the end result.

workshop. So, during each stage of the inspection, we sign off on the work we have completed, and the engineer certifies this work. The crane’s major inspection was completed five months ago and it has been operating every day and there has been no need for any follow up work, it is as good as new.”
This major inspection involved approximately 200 man hours. As the crane is being stripped down
the mechanics are able to access the components of the crane and the required original parts are ordered from the original equipment manufacturer or from the distributor.
Some customers are not aware of what’s involved in a major inspection and the costs involved, but Mardaymootoo has not seen a customer who is disappointed with the end result.
“We have good relationships with our customers, and we are building a strong reputation as a trusted maintenance and service provider.”
“During major inspections, we have found issues which could have caused major issues in the crane. For example, with the recent Kobelco, we found the main brake spring for the luffing function, which is the most important part, was broken and although the crane was still working it could have failed at any time,” he said.
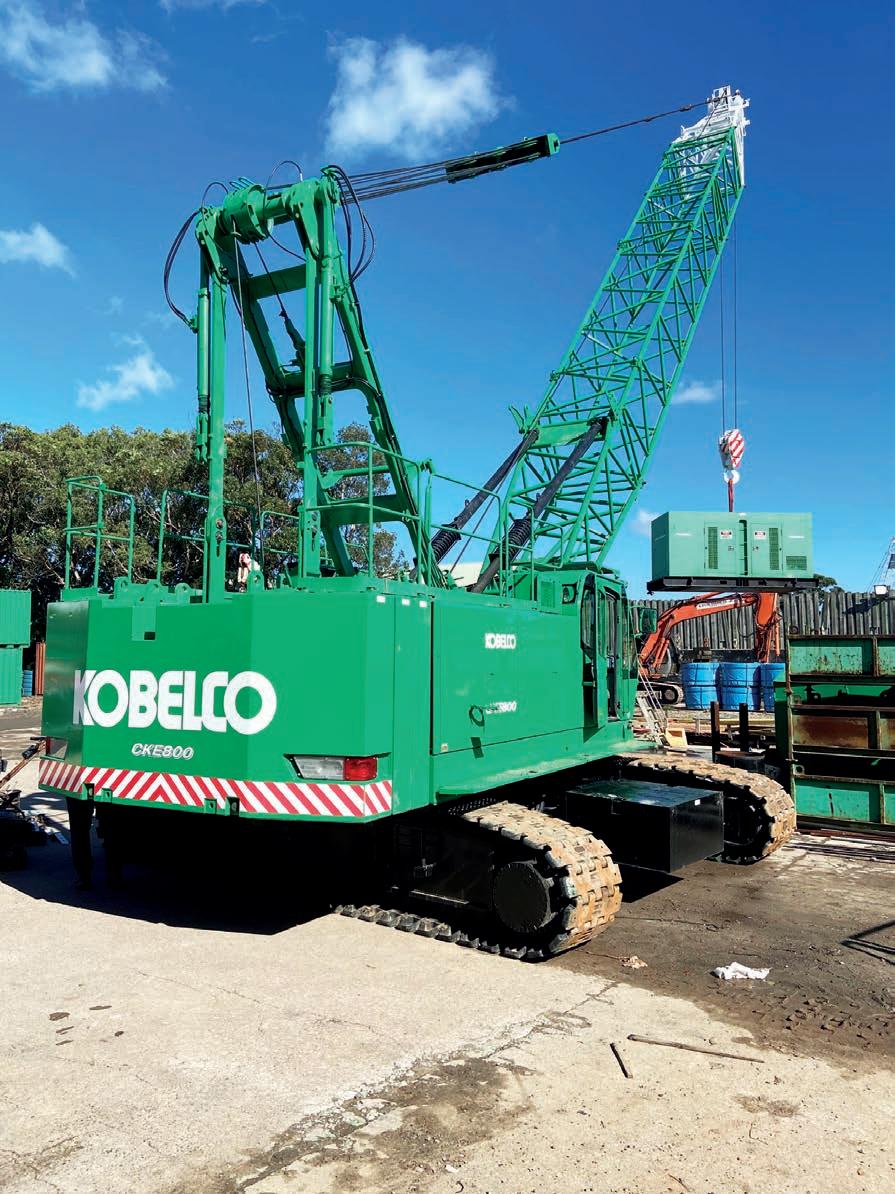
Obviously, the major inspection is a major investment for any customer. But when you factor in the cost of a new crane, the lead time for a new crane and the general lack of availability of cranes, the cost justification process of inspections becomes simpler to justify.
“If you have been operating a crane, from new, for 10 years, you know the machine and your
operators know the machine and they are very comfortable with the crane. Investing in some cases a large amount of money on a major inspection is a major investment, but it is worthwhile,” he said.
Mardaymootoo goes on to discuss the service and support Pace Cranes provides to Maeda mini crawler crane customers.
“A high percentage of Maeda customers are not crane hire
businesses. They are niche operators in the commercial glass handling sector, they are small and large builders, air conditioning installing businesses, but they are not ‘Cranies’,” he said.
“We understand that when these businesses buy a crane from Pace Cranes, they are also buying our service and support, and spare parts capabilities. Our technicians are ready to help our customers who might have an issue of changing from four falls to two falls, which can be confusing for a customer, and we’ll send a technician to help with the reconfigurations.
“Pace Cranes is focused on partnering our customers for the life of the crane and I think this is the reason why customers continue to return and purchase new cranes from us. A good example is SVSR Mini Cranes, who have just purchased another three 4t capacity Maedas, and we have been servicing their entire fleet for years. They started out using the cranes in their sewer vent services businesses and now they have moved into mini crane hire. We have also completed 10 year major inspections on two of their Maedas,” he said.
He goes on to discuss the experience within the workshop.
“The technology in the cranes is always changing and we receive ongoing factory training with engineers regularly travelling from Japan and Germany to Australia, keeping our staff up-to-date with new models and technology. Our national service agent network also participates in these programs. The product support we receive from the manufacturers we represent is great,” said Mardaymootoo.
“The technology in the cranes is always changing and we receive ongoing factory training with engineers regularly travelling from Japan and Germany to Australia keeping our staff up to date with new models and technology.”Investing in major inspections can be significant, but it is worthwhile when customers see the end result.
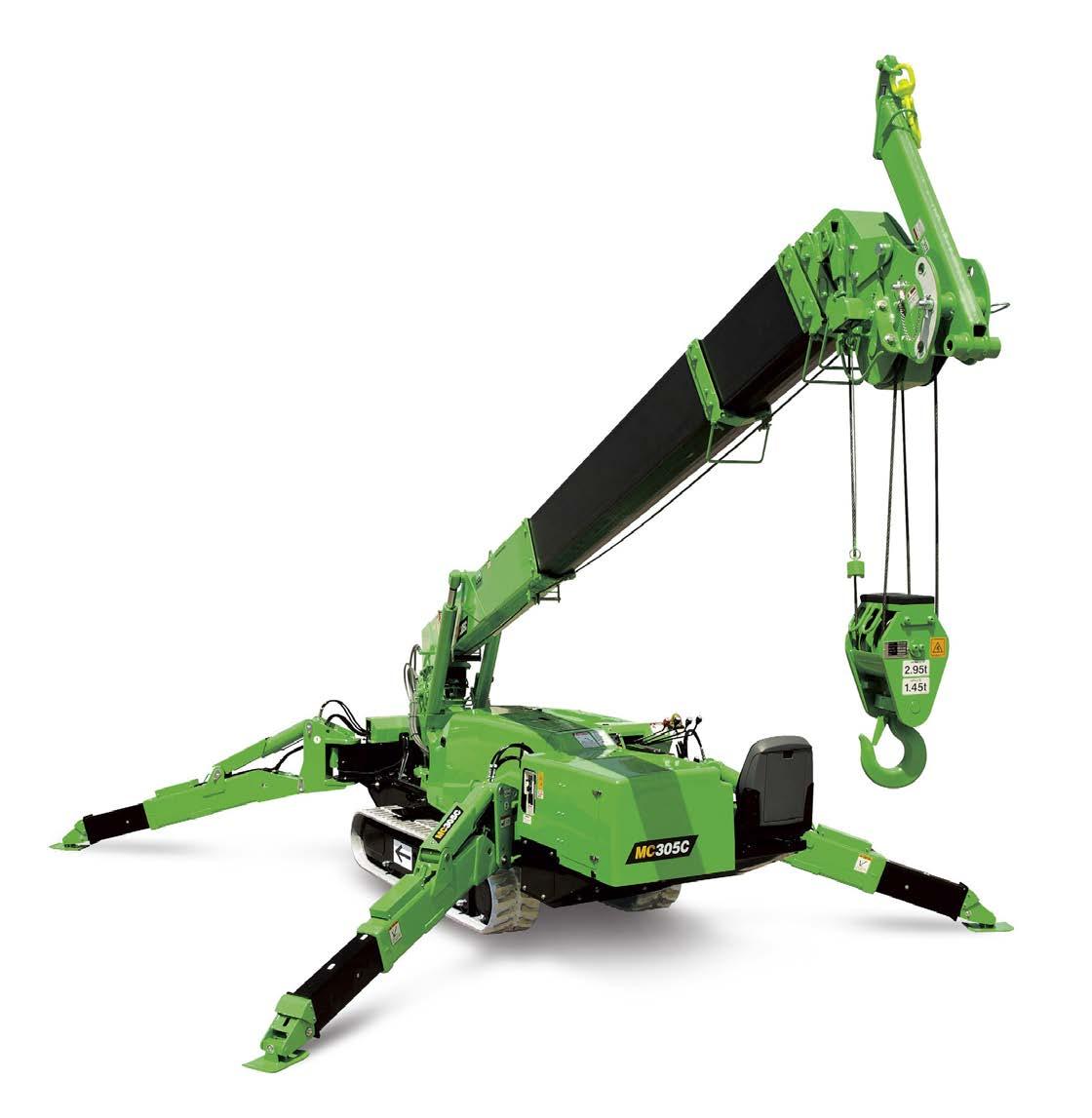
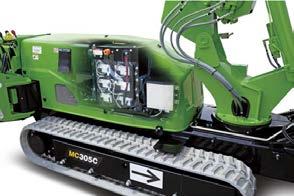
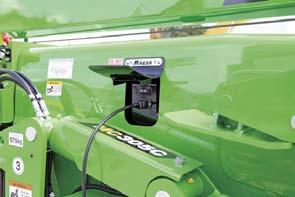

TIDD PICK AND CARRY A GAME CHANGER FOR KINGS CRANES
Although Jamie King has only been operating the TIDD for a couple of months it already has 550 hours on the clock.
Jamie King has been in the crane sector for 20-plus years and has been operating his own crane hire business, Kings Cranes, for 10 years. He recently took delivery of a new TIDD PC28 articulated pick and carry crane from TRT Australia. He describes the crane as a ‘game changer’ for his business.
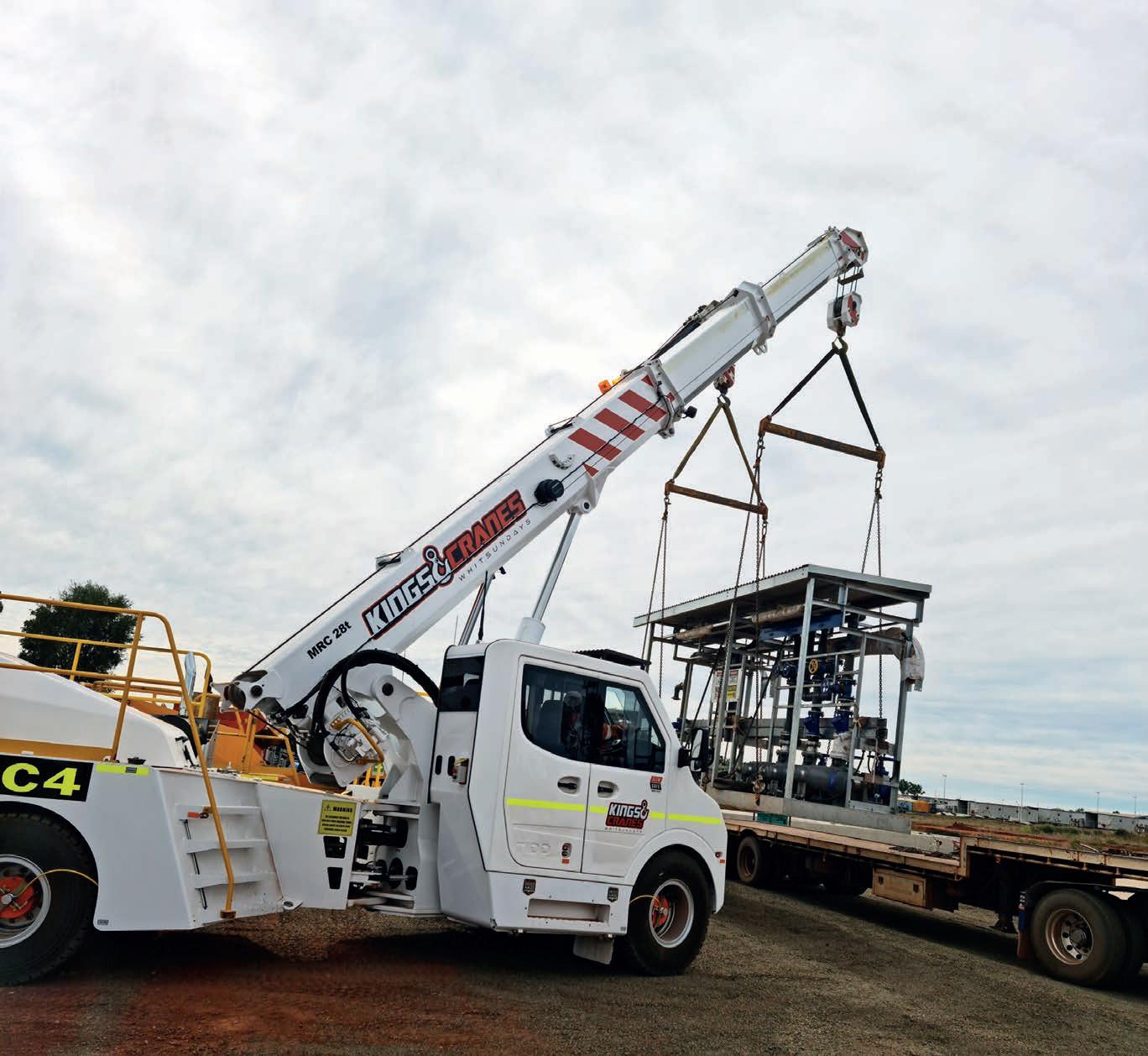
KING STARTED IN CRANES AS A JUNIOR, learning all aspects of the rigging side of lifting, and progressed to becoming a crane operator. He was originally based in Mackay but then followed the crane work all over Queensland.
Today, Kings Cranes services an area covering the Bowen Basin to the Whitsundays.
“Shutdown work in the coal mines is a major focus for the business, but we are also servicing work in the rail sector, main roads, as well as general hire, where we manage general taxi work and conduct lifts around town as well,” he said.
“Customers that know me understand how I operate, and they know I have access to any size of crane, which I will hire in for a particular job and operate the crane if required. I am just starting to build my fleet
now. I’ve got a 20t capacity Franna that I’ve had for nearly 10 years, and recently brought a brand-new TIDD PC28 from TRT Australia.
“Although I’ve only been operating the TIDD for a couple of months it already has 550 hours on the clock. It pretty much hasn’t stopped working since I got it. I’ve been so impressed with its performance and the reception my customers have given it, I’ve ordered a second TIDD, and this is due to arrive at the end of the year or early in the new year,” said King.
He goes on to discuss the reasons for purchasing the TIDD, especially when he’s been driving a Franna pick and carry for such a long time.
“The good thing about the TIDD is how far it has advanced in a short period of time, it has come a very long way in terms
of design, capacity and functionality. In my opinion, it’s a more advanced machine for the type of shutdown work I’m managing on the mines. It’s a pick and carry crane that has a high utilisation rate, which is what you need as crane hire business.
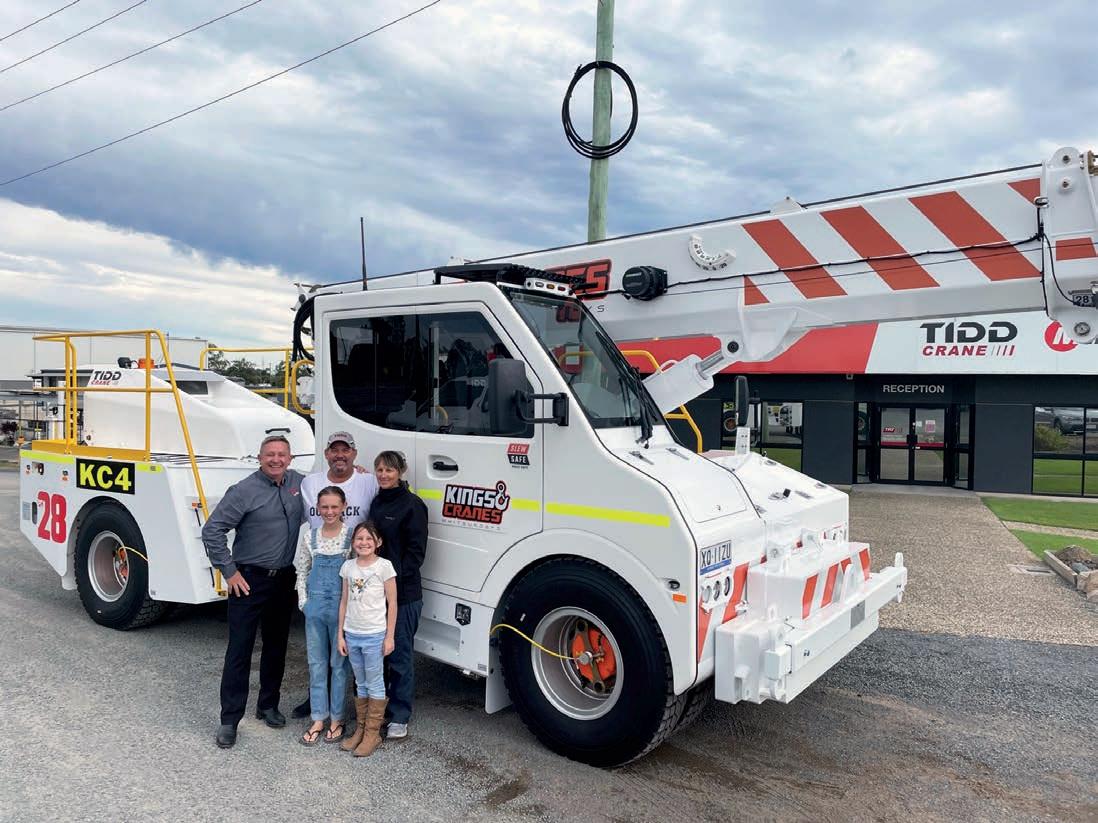
“As I said, I’ve got 550 hours on the TIDD and there have been no issues with it at all, and it’s done everything that I thought it would do, and more,” said King.
The TIDD PC28 features improved operational features designed to help operators work more efficiently and comfortably on construction sites and as well as on the road. Increased lift capacity and greater manoeuvrability, in smaller work areas are key benefits of the new crane. The TIDD PC28 is constructed using the highest quality components with safety a major focus with every element of its design.
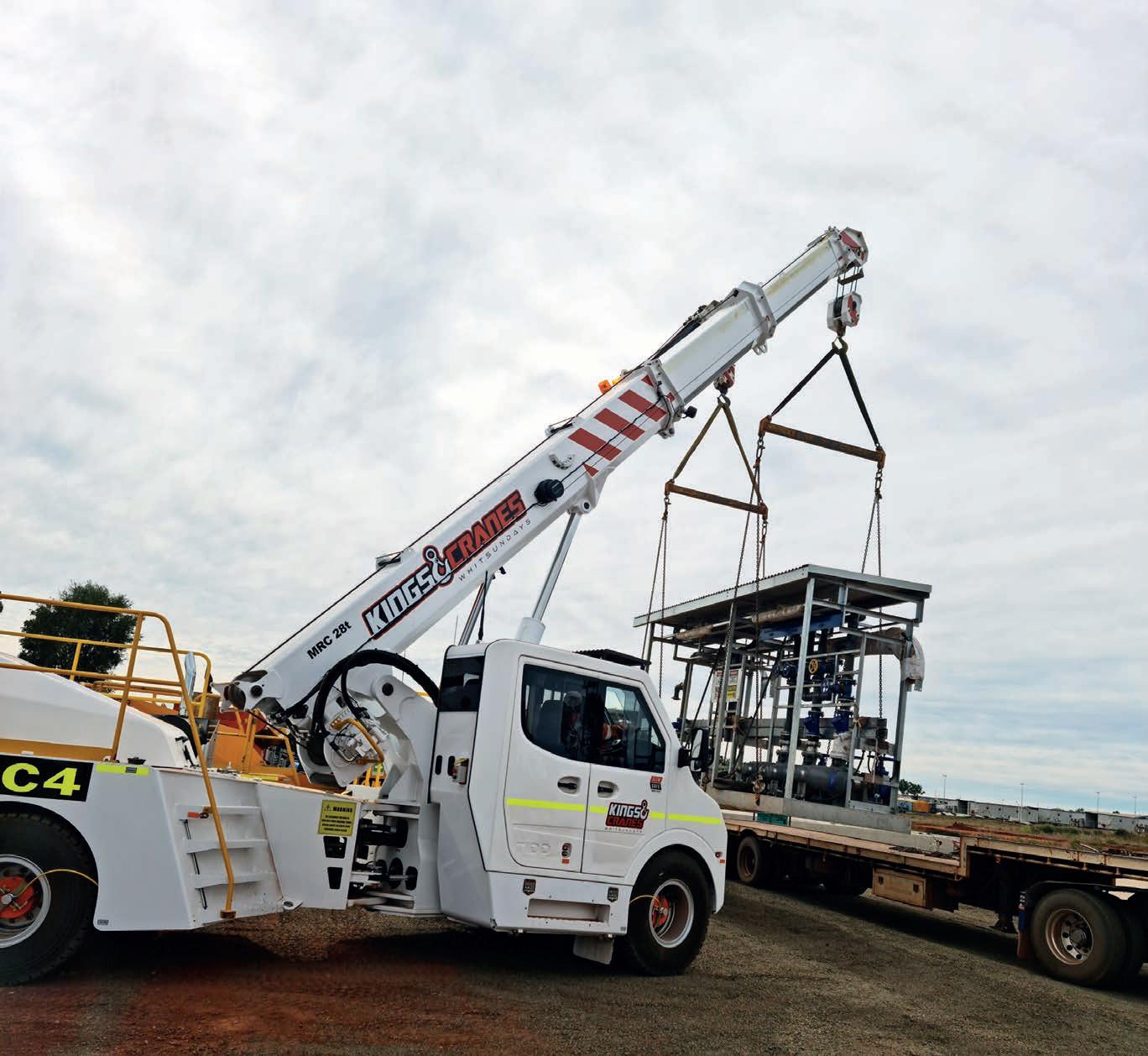
Safety features include Dynamic LMI with a deadlock switch inside the cabin and the LMI bridging switch outside the cabin. Slew Safe is a key safety feature on the Tidd PC28.
TRT has developed a significant new safety feature called Slew Safe. It is designed to prevent rollovers and works with a number of features including audible alarms, LMI warnings and power steering is restricted to 15 per cent to prevent further slewing.
The TIDD PC28 is the only pick and carry crane with this level of safety and Slew Safe can be retrofitted to all existing TIDD PC25s.
Slew Safe is an effective system to restrict the driver from operating off the chart. With audible and visual alarms along with steering restriction in the unsafe direction when overloaded. Slew Safe cannot be over-ridden but will operate normally in the safe direction.
• an outstanding turning radius, articulating 44° either side
• 2.3t roadable, front and rear counterweight
• Mercedes Benz DM906 six-cylinder, turbo charged intercooled 205kW diesel engine
• 6.12–18.64m high tensile steel boom with four telescopic sections
• 28t capacity on fixed tug (stationary) 27.6t capacity on running rope
The Tidd PC28 has also been designed with operator comfort in mind.
The ergonomically designed forward mounted rollover protection system cabin, with two-door configuration, ducted air conditioning, 150kg-rated air suspension seats and three-point safety belts, means comfort over long hours, helping to reduce operator fatigue.
Many of the key features are designed on industry feedback and include:
• European standard automotive finish
• shortest forward projection in its class
• Allison 3000 series automatic transmission, six speeds forward
• Kessler high-speed planetary axles with diff lock on front axle
• Meritor transfer case
• two-stage engine and exhaust brake
• 410L tank with locking cap
• automatically activated emergency hydraulic steering
• duel line airbrakes on all wheels with ABS
• pneumatically released spring applied emergency/park brake on all wheels.
I’ve been so impressed with its performance and the reception my customers have given it, I’ve ordered a second TIDD, and this is due to arrive at the end of the year or early in the new year.”
For Jamie the TIDD is a game changer. It is a step up and, moving forward, it’s changing a lot of ideas.
is listening to customers, listening to operators in terms of what they would like to see changed, and you’re seeing these changes built into the TIDD. It’s a completely different machine compared to the earlier models. You can see the inbuilt quality in everything relating to the engineering of crane. It’s built to last,” he said.
King has spent plenty of time behind the wheel of the TIDD, starting with the day he took delivery of the crane.
“I picked the TIDD up from TRT in Brisbane and drove it the 12 hours back to Prosperine. I wanted to really get a feel for it on the road and to see if it could handle the roads up here in Queensland as they can be pretty bad.
The new 18.64m high tensile full power boom features a 75 per cent stationary chart for the heavy lifts and 66 per cent pick and carry chart. The boom’s telescope Sections 1 and 2 are fully synchronised and provide hook compensation. Telescope Section 3 is independently operated with its own hydraulic cylinder.
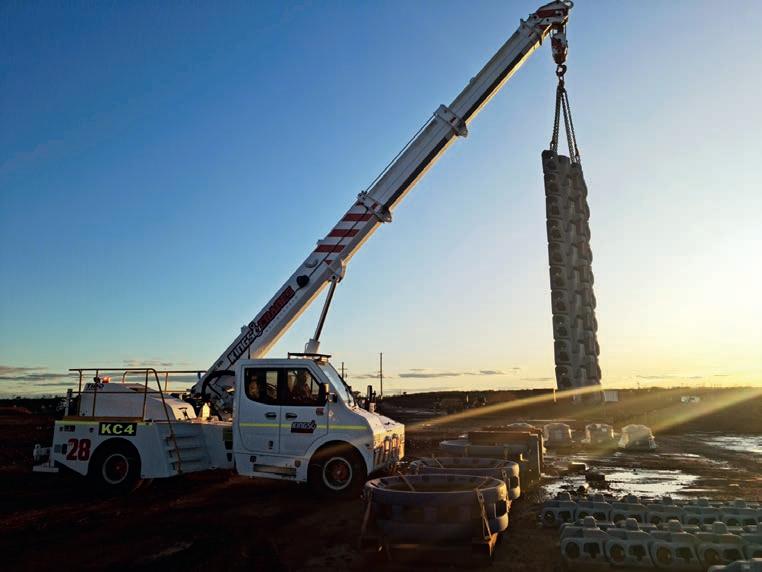
The TIDD PC28 features a 28t maximum lift on the lug and 27.6t on the hook block, delivering lifting capacities for improved efficiency and greater lift options, setting a new benchmark in the industry.
Moving from the stationary chart to the pick and carry chart is as simple as turning off the hold brake.
King explains what happens when he turns up to a mine site or construction site that hasn’t seen a TIDD pick and carry before.
“In the areas that I’m working, they don’t really know a lot about the TIDD. As I’ve been driving around and working on the sites, customers are becoming increasingly comfortable with the crane,” he said.
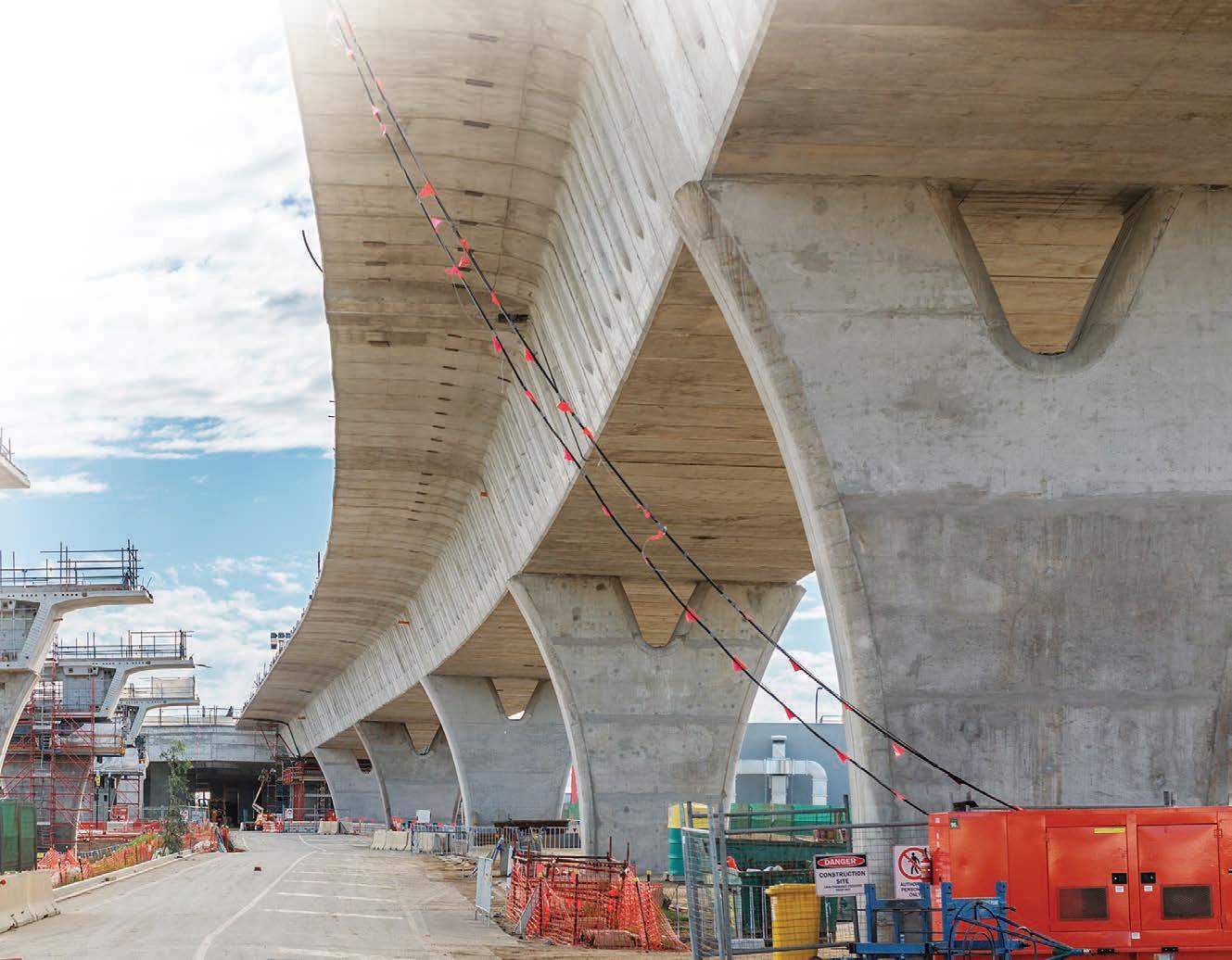
“No one else in this region is operating a TIDD so it is new to a lot of customers, but since I have taken it to site, there have been a significant number of inspections from all of the mines and it’s passed with flying colours. To be honest, it hasn’t stopped working since I got it back here. Initially, it got some funny looks and it’s taken a while for everyone to get used to it. But the TIDD
is now readily accepted by my customer base, including the mines,” said King.
King believes the TIDD brings a different level of sophistication to the design of articulated pick and carry cranes.
“It’s a machine that TRT has approached with a completely different attitude in terms of design, and I believe it will eventually be a game changer in the pick and carry market. I also know TRT are slowly working through the TIDD, modernising aspects of its operability and generally fine tuning everything. As TRT goes through this process, I believe you’ll being a see a lot more of them,” he said.
King thinks the market is gradually changing and understanding there are now viable options when it comes to articulated pick and carry cranes.
“The Franna brand has had a long history and it’s proved its reliability over many years. Every crane hire business has owned a Franna. But now TRT has stepped up with the TIDD PC28.
“For me this is a game changer again. The TIDD PC28 is a step up and, moving forward, it’s changing a lot of ideas. TRT
“I have always thought if you’re going to get a machine, you might as well drive it straight up to get the feel for it. And because most of our work is on the road and running around you need to understand how it will cope.
“The TIDD is a good drive and it’s a completely different setup on the road. It’s not like the spring packs, the suspension takes the bounce out of the drive. The Tidd is a lot smoother than you realise once you are in the cab,” said King.
With the 28t lifting capacity, King has found the TIDD to be a good lifter.
“No regrets there,” he said.
“People ask me why did you buy the TIDD? I say, I’ve been watching the development of the TIDD for a long time. I know a lot about the various brands in the pick and carry crane game and I just see the advantages in the Tidd.
“At the moment it’s out operating in a very harsh environment and it’s still going good. There are no regrets from my perspective, the TIDD has delivered above and beyond my expectations, hence the second TIDD will be arriving in a few months,” said King.
“It’s a machine that TRT has approached with a completely different attitude in terms of design, and I believe it will eventually be a game changer in the pick and carry market.”
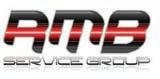
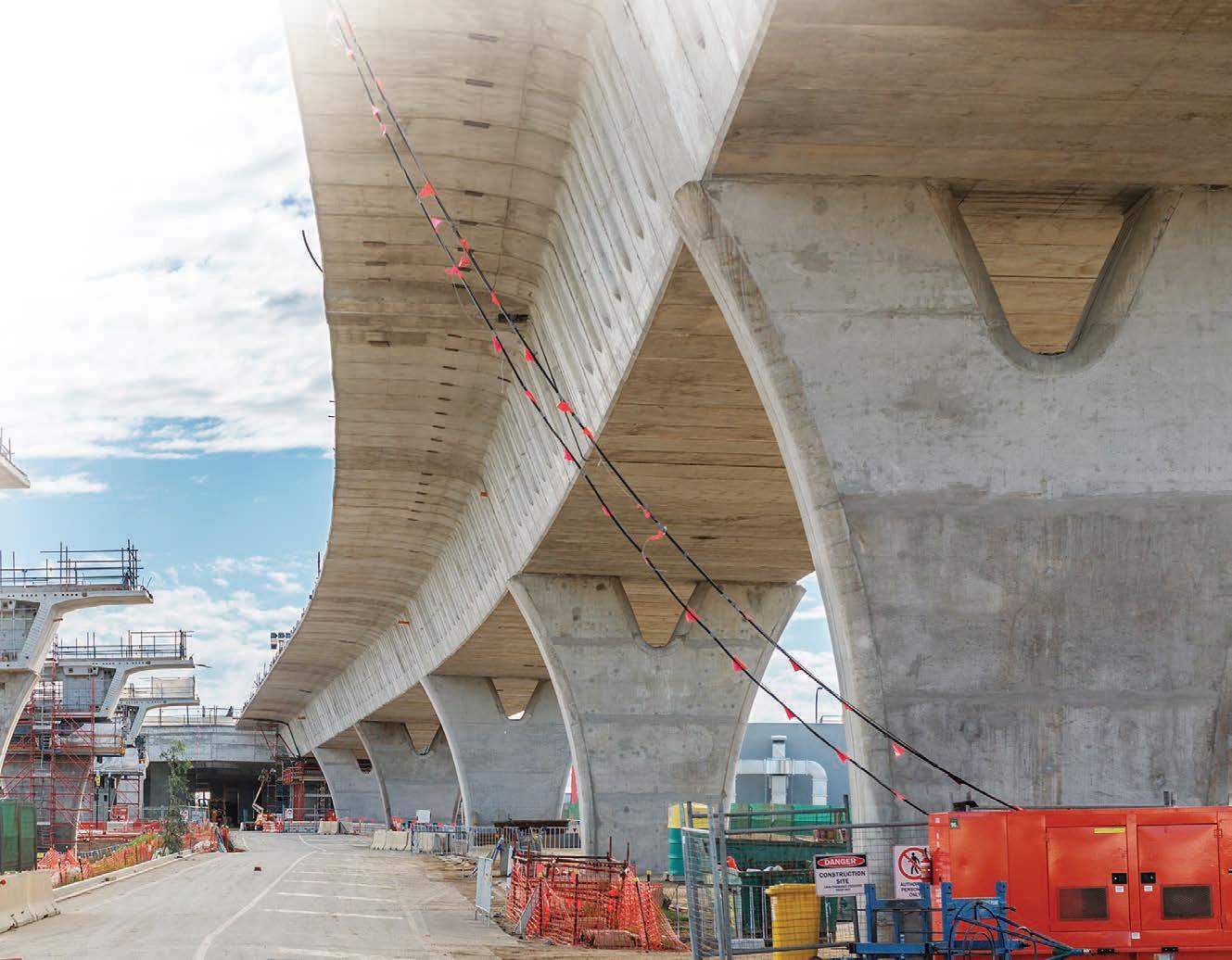

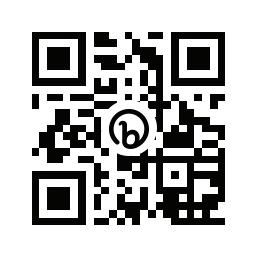
NEW GROVES TO THE APPLE ISLE
The Tasmanian construction sector is currently strong as a result of private and government investment in infrastructure. To help with the increased demand for cranes, Elliott’s Crane Hire has invested in two brand new Grove all terrains. This is the first time the business has purchased new cranes. Elliott’s Crane Hire managing director Greg Smith explains more.
“THERE HAS BEEN A SIGNIFICANT INCREASE in general construction and infrastructure projects across Tasmania, but particularly in Southern Tasmania,” said Smith.
“In November of last year, we bought a brand-new Grove GMK4100L-1 fouraxle 100t. It features 60m of full boom. Over the last few years, the business has developed significantly, and we have progressed to a point where we can justify the investment of these new cranes.
“We are extremely pleased with the GMK4100L-1, it has not missed a beat since we took delivery. It has been well received by the operators and riggers. Equally important is the fact that our customers have been really impressed with the performance of the crane.”
Today, Elliott’s Crane Hire runs a fleet of Grove all terrain cranes with capacities including 220t, 200t, a five-axle 100t, an earlier four-axle 100L, the new fouraxle 100L-1, 80t and two 60t three-axle all terrains, including the GMK3060L
The GMK4100L-1 not only offers the best load charts in this class in its maximum counterweight configuration, but also in its most common taxi configuration with a weight of less than 12t per axle.
which has just been purchased new. To complement the fleet of Grove all terrains are two 65t truck cranes, a 40t Tadano, a 30t Kato, a city crane, and four Frannas. Elliott’s also has a range of HIAB trucks and specialised semi-trailers & floats.
The new generation Grove GMK4100L-1 is a super compact machine ideal for the Hobart construction sector, said Smith.
“Hobart features tight streets and construction sites with very limited access, so the Grove is ideal for getting in and out of tight positions. And, with 60m of boom, it’s a great lifter in these tight situations.”
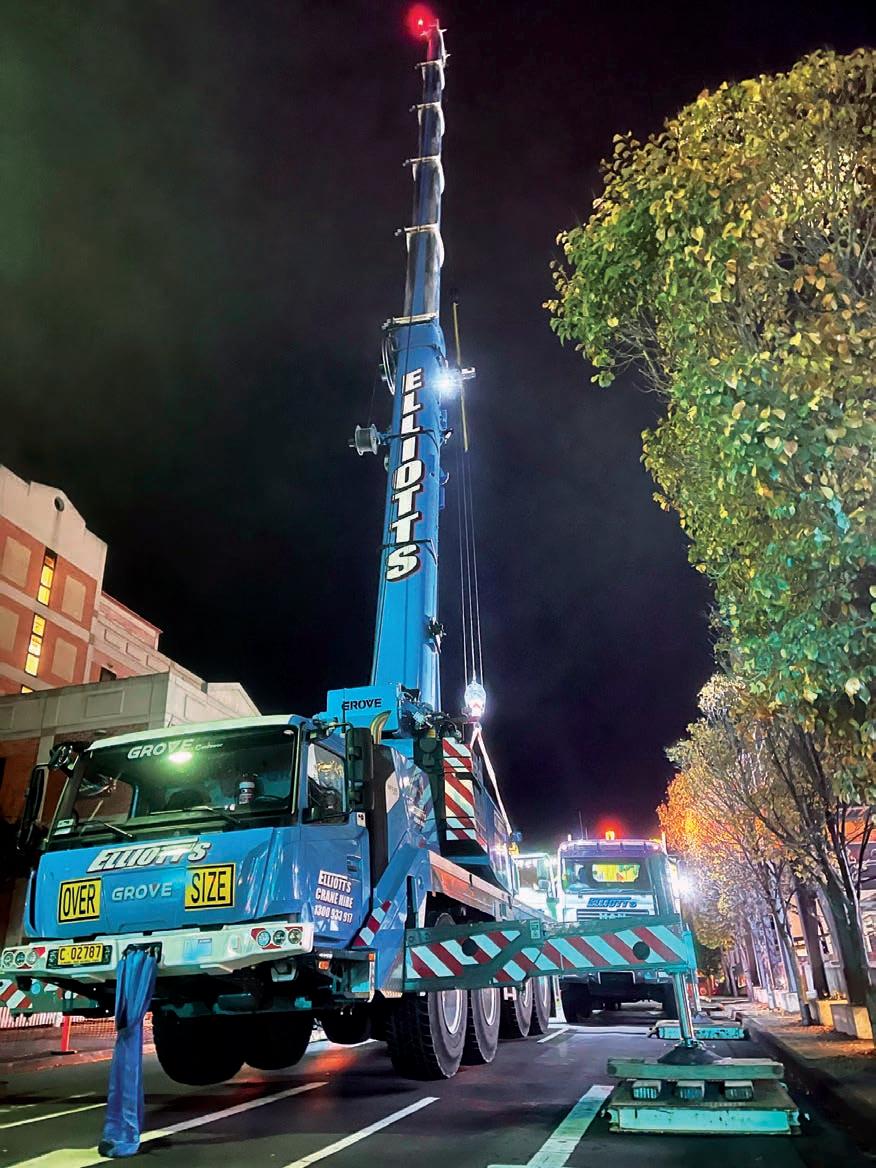
The Grove GMK4100L-1 offers unique innovations and class-leading capabilities in the taxi (road travelling) category. The
four-axle all terrain boasts the best load charts in its class and its compact design makes it easy to access and manoeuvre on the narrowest of job sites. The 100t capacity crane replaces the GMK4100L and is part of a new generation of Grove taxi cranes.
Grove was the first manufacturer to produce a 100t capacity crane on four axles when it introduced the GMK4100L. Now, the new GMK4100L-1 has raised the bar even higher with some notable improvements.
The GMK4100L-1 not only offers the best load charts in this class in its maximum counterweight configuration, but also in its most common taxi configuration with a weight of less than 12t per axle (a common
axle load limit in many countries).
Compared with the older GMK4100L, the new GMK4100L-1 delivers 20%+ better structural capacities and equally strong improvements at longer radii with the max 26.2t counterweight configuration.
In the taxi configuration with 6.7t of counterweight on board, the GMK4100L-1 really shines with significant gains throughout the chart and 15% increases with the full 60m.
Boosting the crane’s overall reach is an 18m hydraulic luffing fly, which can be extended with an 8m boom extension for a total jib length of 26m. The telescopic swing-away jib offers an improved offset of 0–45°.
The GMK4100L -1 is more compact than its predecessor, making it even easier to access narrow job sites.
The GMK4100L-1 is powered by a single engine, which reduces the weight of the crane, allowing it to carry more counterweight and delivering superior lifting capacities by putting the steel where its needed.
The Tier IV Final/EUROMOT 4 Mercedes-Benz OM470LA is a six-cylinder diesel engine with a 320kW rating at 1,700 rpm and a maximum torque of 2,100Nm at 1,300 rpm.
The crane is also available with an equivalent Tier III engine. Better profitability for users is available through the inclusion of the Fuel Saver function on the Tier IV Final/EUROMOT 4 engine.
Life is also made easier for the operator with Manitowoc’s new Crane Control System (CCS) and the new Boom Configurator Mode. The standardised CCS is a user-friendly interface that Manitowoc is featuring on all new crane models.
The CCS components and operating software have been specifically designed, developed and tested by Manitowoc engineering and innovation teams worldwide to ensure the highest reliability standards.
The highly intuitive Boom Configurator Mode makes it quick and easy to select the optimum boom position for a specific lift.
The operator inputs the lift parameters such as radius, load, or boom length to be moved and the system
Boosting the crane’s overall reach is an 18m hydraulic luffing fly, which can be extended with an 8m boom extension for a total jib length of 26m. The telescopic swing-away jib offers an improved offset of 0–45°.
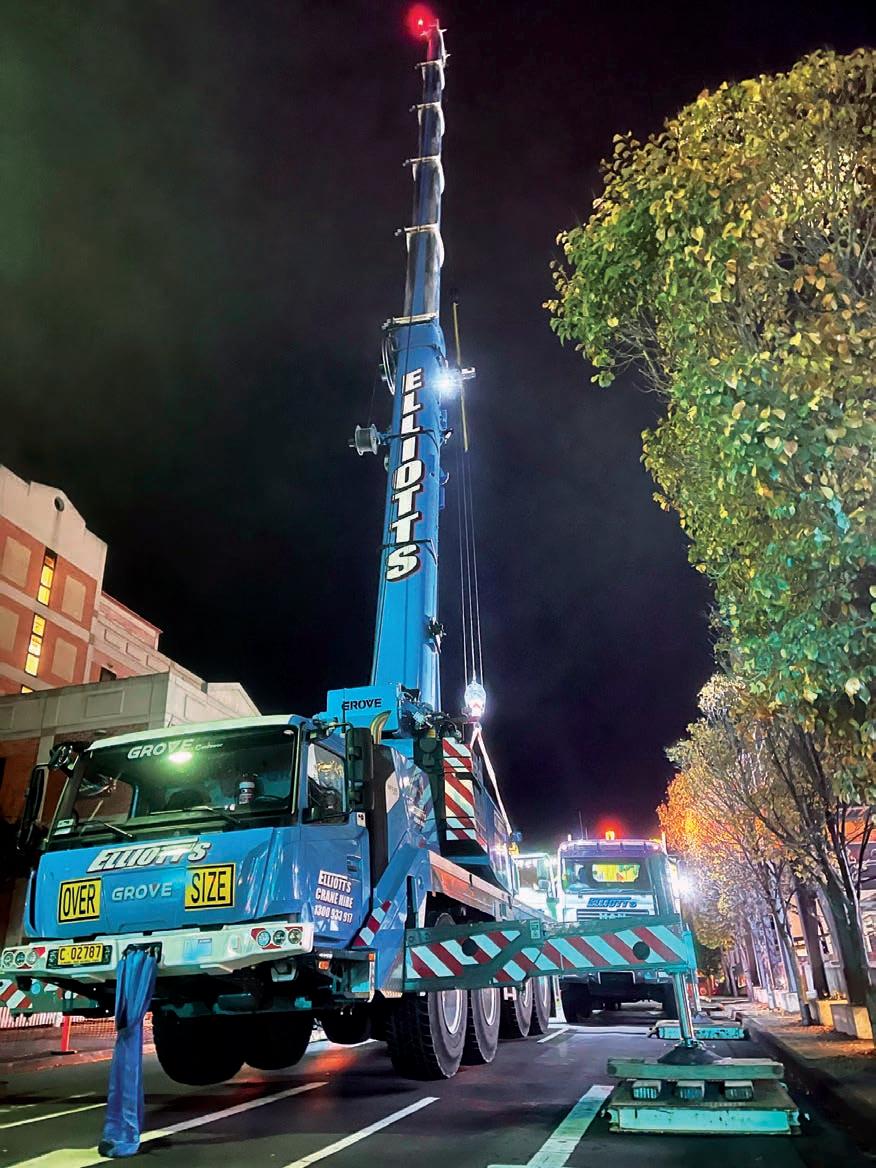
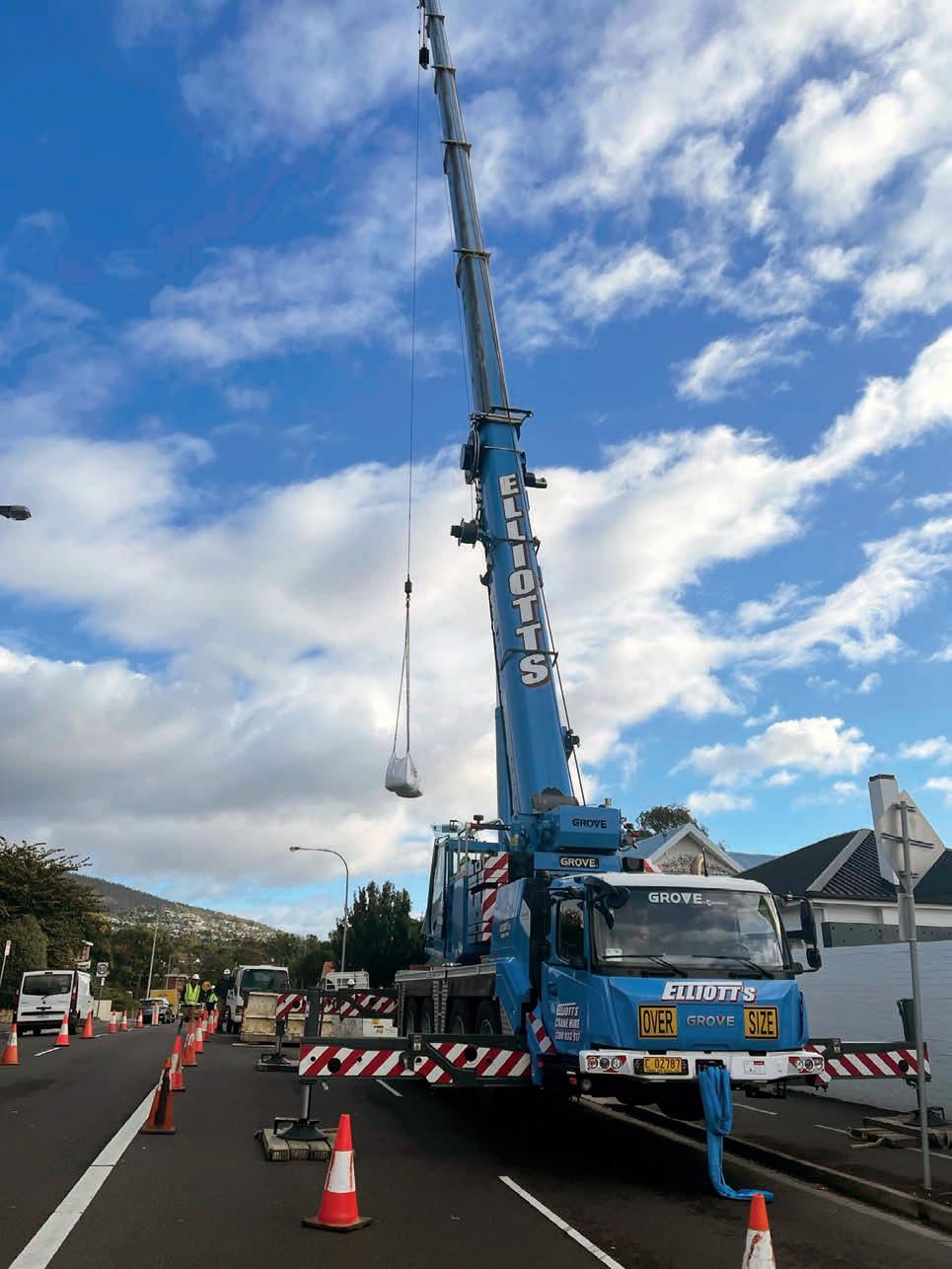
“Hobart features tight streets and construction sites with very limited access, so the Grove is ideal for getting in and out of tight positions and, with 60m of boom, it’s a great lifter in these tight situations.”
calculates the best boom configuration.
Once the operator selects the preferred option, the boom automatically extends to the required length.
The look of the new generation has also changed with the Grove Cab2020 that includes new ergonomic features in the carrier cabin.
As one would expect, trademark features such as the Twin-Lock boom pinning system, Megaform boom shaping and Megatrak independent active suspension are all included in the new GMK4100L-1.
Elliott’s Crane Hire is also taking delivery of a brand new three-axle 60t capacity Grove GMK3060L.
“The new 60t Grove will replace our old 55t Grove. The GMK3060L is ideal for taxi work. We’ll be using it for steel erection and installing air conditioners. You can send it out and it will basically do anything you want it to do. It’s a great all-rounder,” said Smith.
The Grove GMK3060L all terrain
crane is the successor to the popular threeaxle GMK3060L.
It is based on its predecessor’s design but has a longer boom (48m instead of 43m). It features compact dimensions that allows it to access tight jobsites, manoeuvre easily around city centres, and even work indoors.
The chassis of the GMK3060L is almost as compact as a two-axle model and up to 1m shorter than competitive three-axle cranes, with a carrier length of only 8.68m and a minimum overall height of 3.48m with the suspension fully lowered.
The GMK4100L-1 is powered by a single engine. This reduces the weight of the crane, allowing it to carry more counterweight, which delivers superior lifting ability.
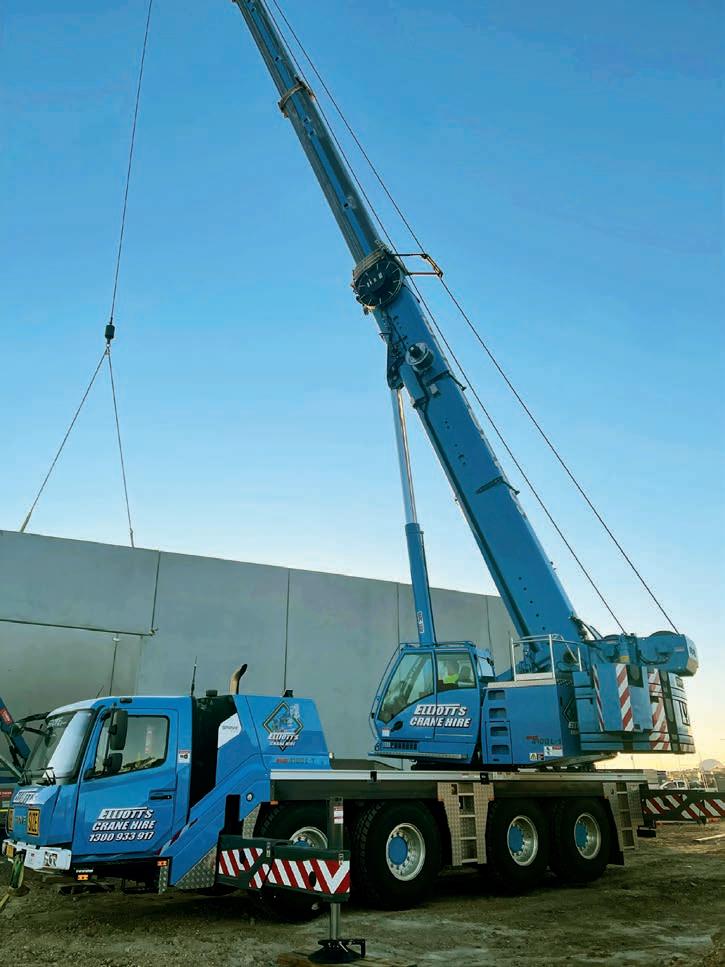
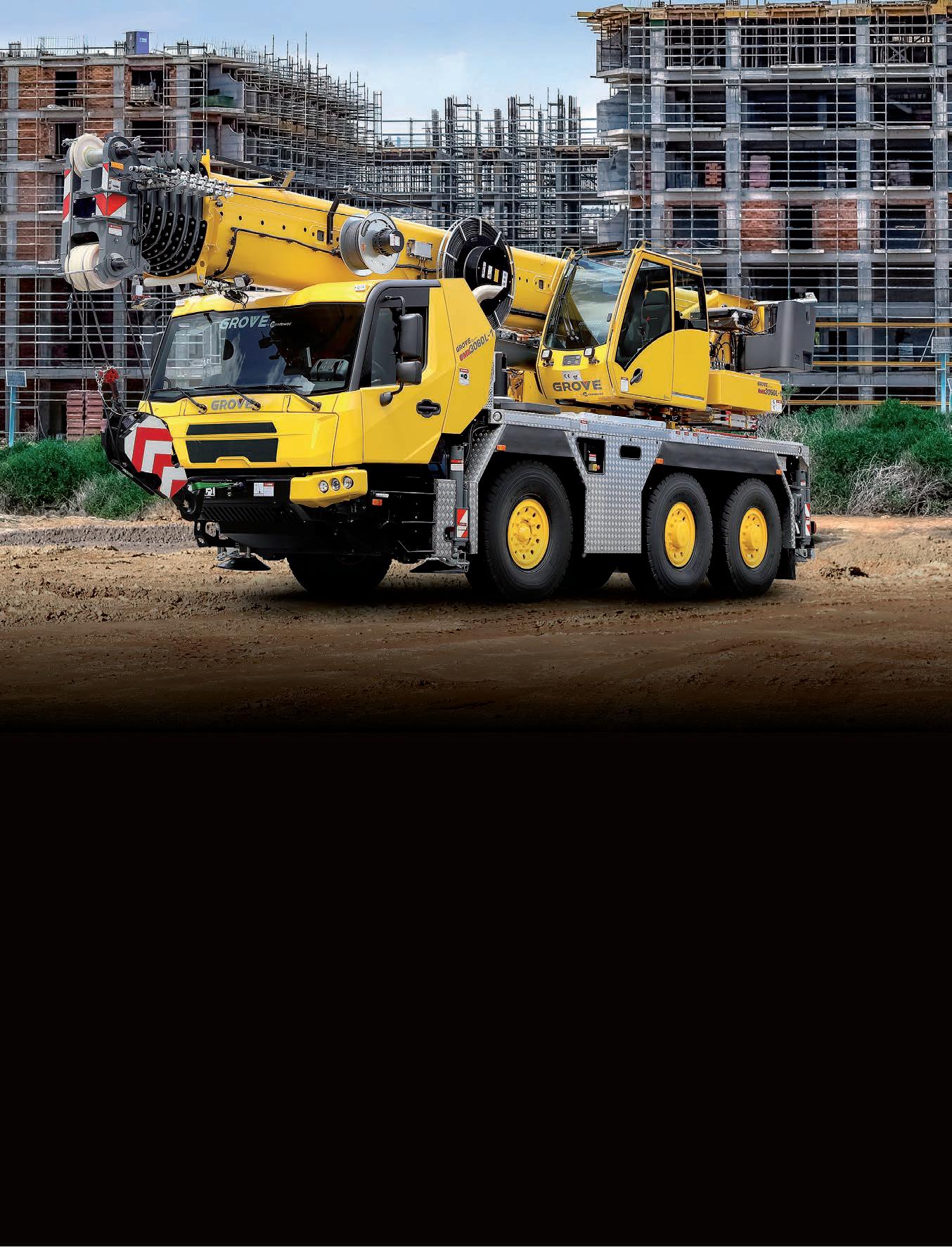
The GMK3060L offers a longer, 48m seven-section Twin-Lock hydraulic pinned main boom and boasts significantly stronger load charts.
The GMK3060L is also equipped with Manitowoc’s CCS, as well as a boom configurator feature. As a result, operators can input basic lift parameters such as load, radius and load height, and the system automatically provides optimal boom options for performing the lift.
This saves time at the jobsite and makes the setup process much easier. The crane features the MAXbase option for
variable outrigger settings and increase load charts in certain working ranges.
The Cummins QSL9, a 254kW sixcylinder in-line diesel engine, powers the new GMK3060L.
It is available in both Euromot III/Tier 3 and Euromot V/Tier 4 Final variants to cater for all markets. The crane includes a ZF TraXon automatic transmission, giving it 12 forward speed options and two reverse.
“We have plans to expand our fleet with further new cranes, and we are excited about the opportunities that future may hold,” said Smith.
“The GMK3060L is ideal for taxi work. We’ll be using it for steel erection and installing air conditioners. You can send it out and it will basically do anything you want it to do. It’s a great all-rounder.”
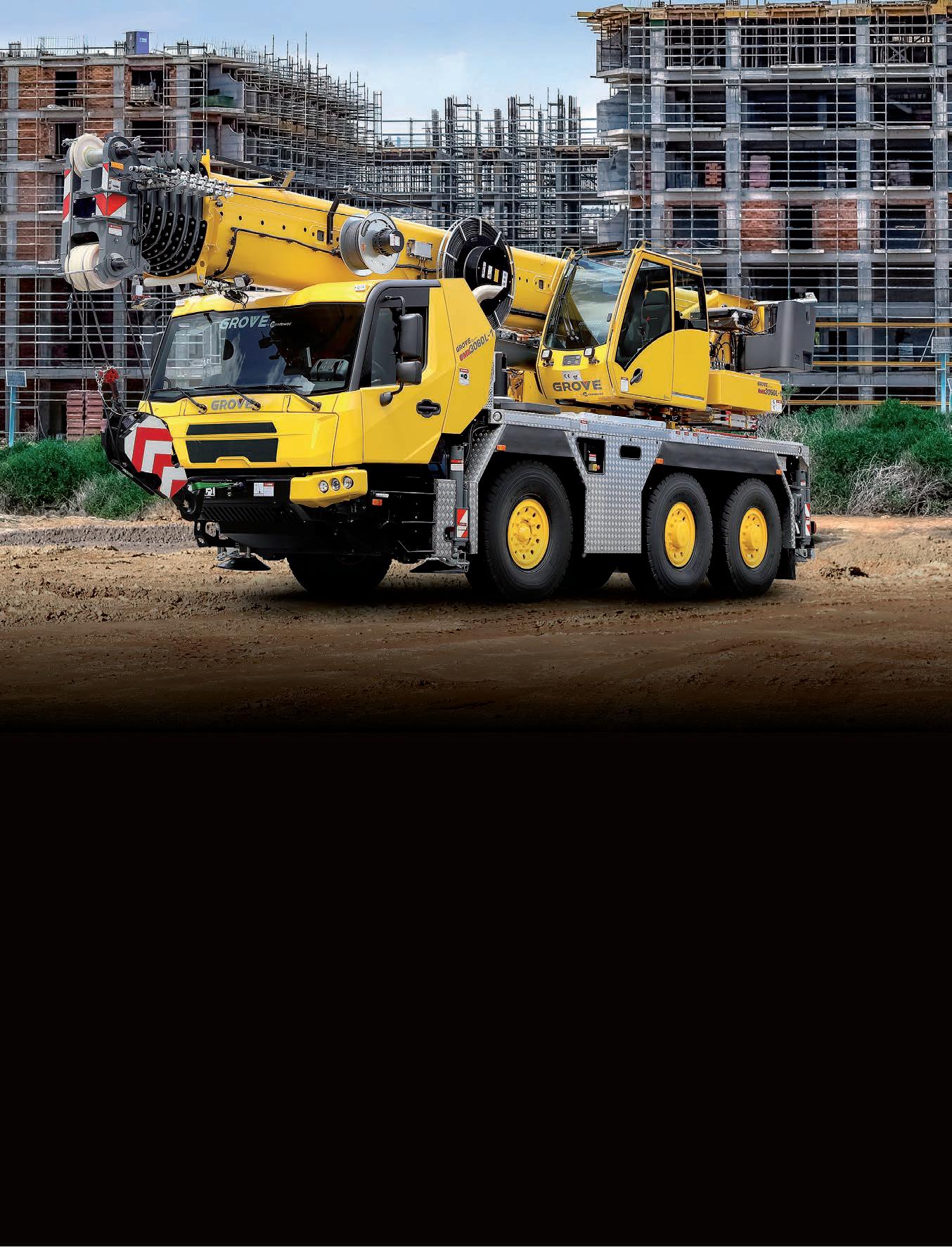
FRESH SITE HIGHLIGHTS THE GROWTH OF QUEENSLAND RIGGING HIRE
The fresh new premises for Queensland Rigging Hire (QRH) herald an important moment in the company’s history. A site three times larger than its previous will allow it to keep up with the growth that has seen it succeed thus far.
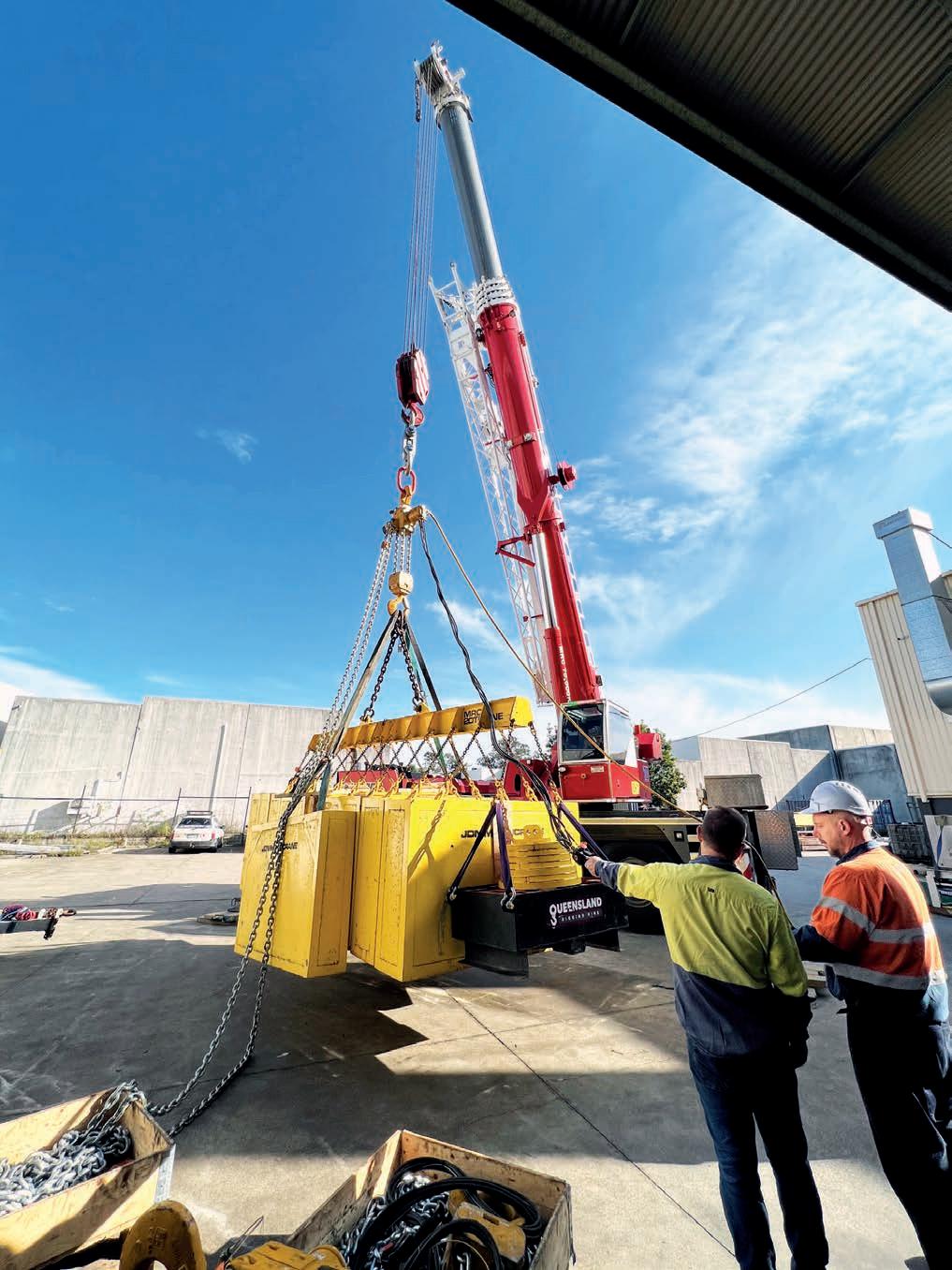
The new site will allow QRH to stock an even more diverse range of equipment.
PRIOR TO LAUNCHING THE BUSINESS
2017, Ben Fitzgerald was the national sales manager for a lifting equipment wholesale company, and he had been in that role for three years.
“My wife Jess and I started the business in March 2017 and we went all e knew the industry and what we were doing had a place within it and this new site is the culmination of that hard work,”
“We have a very extensive range of specialist rigging and lifting equipment that we know is the gear crane operators
“We are both extremely proud of how far we we have come. We have millions uality rigging equipment and there are not many jobs we say no to,” he said. ved from its original premises on the Gold Coast to the new facility based in Archerfield, only 10 minutes from the Brisbane CBD, with the facility undergoing a full renovation of its offices, bathrooms,
“We have put a lot of effort into making this new site a one stop shop, and making it a much easier experience to find exactly what you are looking for. A client can walk in, and we have a room set up with shackles, a room with clutches and rooms for load cells,” said Fitzgerald.
QRH has put plans in place to build a mezzanine within the warehouse that will allow them to install sandblasting facilities, painting stations, test benches, and mechanical maintenance equipment.
“We have been able to significantly increase our turnover in the new premises, as not only can we fit more equipment in, but we can pick multiple jobs at the same
time and have them ready to go much quicker, said Fitzgerald.
“Cranes continue to grow in size, so it is important we keep up with the rigging that goes with them. We now have more space for much larger equipment, we can invest in bigger and better equipment,” he said.
QRH has been growing its offering to the industry, recently purchasing a Maxibar 300 modular spreader bar. This spreader bar gives it much greater options for girder installations with a 300 tonne working load limit (WLL) out to 13m, and tapering down to 150t WLL at its maximum span of 26m. It was only in the warehouse for a couple of weeks and it is straight out on its first job, assisting with some large precast structures for the Cross River Rail.
Maxirig and Modulift spreader bars in modular, telescopic, and combination variations are also kept on site, with all rigging gear associated with these present.
Delphi load cells are an important part of the QRH fleet, ranging in size from 2t through to 300t capacities in tension, and compression load cells with the capacity to weight equipment up to 600 tonnes.
“We have been dealing with Delphi Measurement since day one and it’s been one of the best decisions that we have made. They are local, their aftersales service and repairs is fast and efficient and they are really great people to work with,” said Fitzgerald.
“All of the Delphi Measurement equipment runs Mantracourt T24 software and we have the capabilities to data log, join multiple cells together when used at the same time, and work our centre of gravity measurements.
“The newer cells we have added to the fleet also have peak hold function. The simplicity of the load cell systems makes them user friendly and uncomplicated,
which also makes them robust and long lasting.”
An exciting addition has been the 5t counterweight lifting beam that Fitzgerald believes will be an asset for the industry.
“We have teamed up with local engineering and fabrication companies to make this happen and feel like the product we have invested in is a good one size fits most approach. Based on years of research discussing our customers’ requirements, the industry has been desperate for a product like this.
“This lifting beam is a significant investment for us at QRH and unlike anything else in the hire market in Queensland, so we expect it to be extremely popular. The benefit of this lifting beam
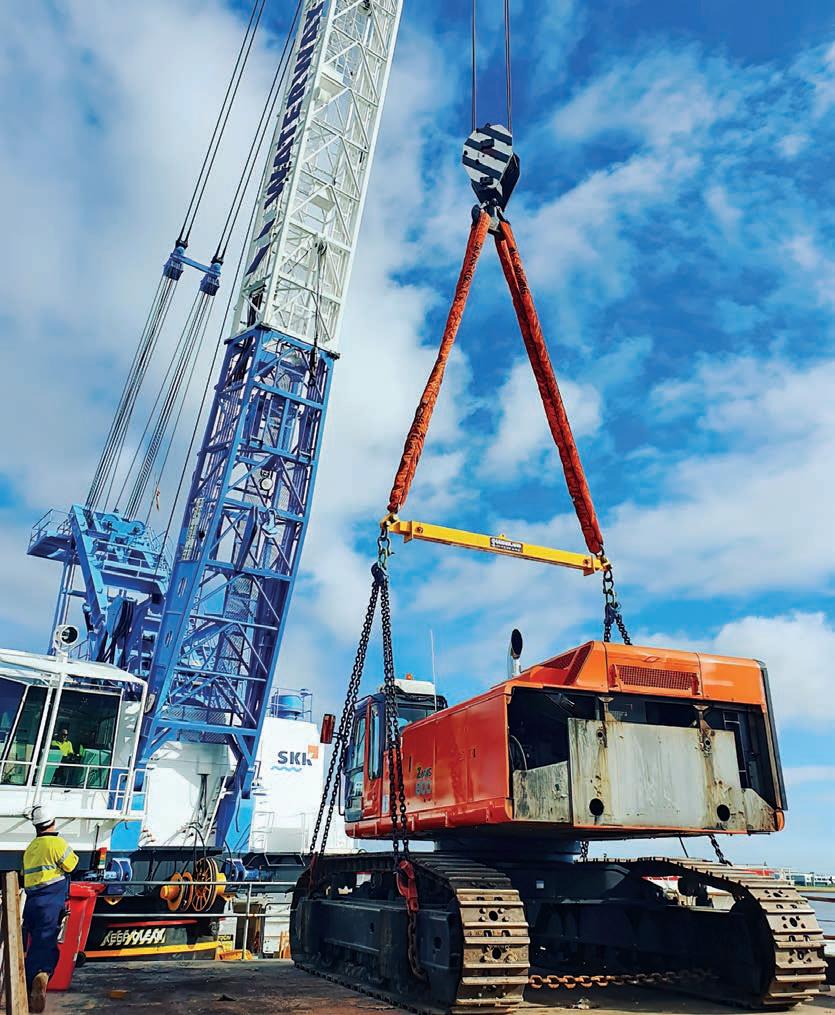
is to be able to position equipment underneath structures with a crane. This bar has offset positions of 2m, 2.5m and 3m offsets,” he said.
Crane outrigger pads are a vital part of any lift and often forgotten by rigging houses, QRH has invested in new pads due to the greater space at its current site.
“These have a capacity of 210t each and a ground coverage of 3.6 square metres, our customers have been asking for these for a long time,” said Fitzgerald.
With the rapid growth of the company, it is easy to forget what made the company a success, but QRH knows it must remain customer-focused.
“We like to operate under the motto that our job is to make your job easy. We make sure the customer gets what they want and we do the hard work,” said Fitzgerald.
“Just recently we were working with a crane hire company up in Gladstone and they needed a sling and its size was far greater than anything they had, so within
“The benefit of this lifting beam is to be able to position equipment underneath structures with a crane, this bar has offset positions of 2m, 2.5m & 3m offsets.”The gear from Queensland Rigging hire can tackle some of the most challenging lifts.
10 minutes we had it packed up and on the truck and within 24 hours they were able to complete that lift.
“We can have gear on a crane in Perth in 48 hours, gear in Gladstone in eight hours. We have a hot shot company just down the road that will pick up gear within the hour and get it to site.
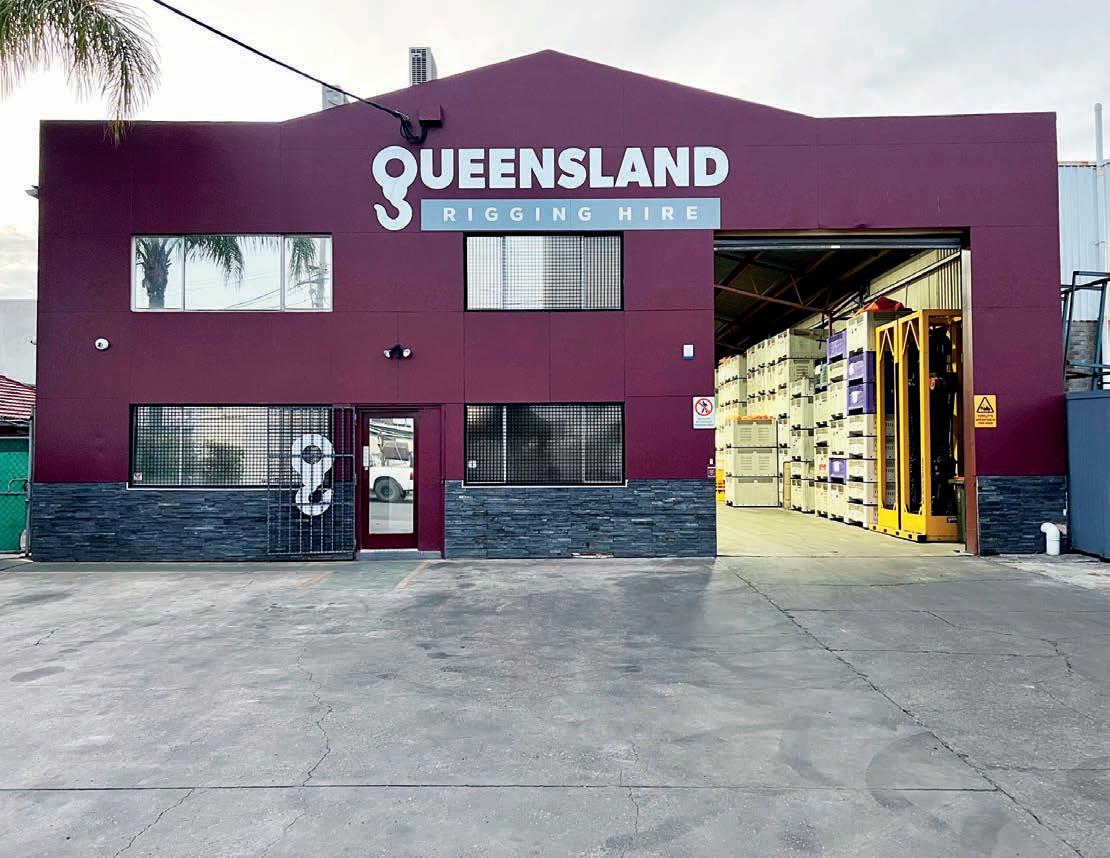
“We love being to help those small to medium size crane and lifting companies compete against the bigger ones. They can take on bigger projects without having to outlay so much money to service the job.
“We understand the industry. We are open 24 hours, seven days a week. Sunday
night at midnight we were working – the operators working night shift know they can call us if they need to.”
The company recently made the decision to invest in its second, much larger truck and, after 15 months of intense work, it has recently hired a second driver to keep up with demand.
“We also have a fleet of smaller utes as well as a Ram 1500, which we have a custom 6m flat deck trailer for that it tows on long drives when the truck isn’t available and we have to deliver equipment quickly to job sites,” Fitzgerald said.
The team at QRH continue to grow. With the recent arrival of new employees it has brought the team up to six people.
“We have recently made some staffing changes promoting our longest standing employee Trey Yee to operations manager. Trey started with us in 2019 as our first employee and he has done a wonderful job for us to fly the flag for QRH over the years and is proud to be a part of our organisation,” said Fitzgerald.
“Jeremy has been with us for 18 months in a warehouse and driver position and has recently been promoted
to warehouse manager and we have just had a new driver come on board to assist with local deliveries.
“The newest addition to our team is Nigel Houslip. Nigel has been behind the scenes for us since the beginning, being a great long-time friend of ours.
“Nigel is at the top of his game in the HVAC industry and wanted a change to come on board for us our maintenance manager, specialising in the repairs and maintenance on our hoists and winches,” Fitzgerald said.
Houslip’s first job has been the commissioning of a pair of new JDN 20t air hoists with Juuko wireless 2.4Ghz remote controlled hoists. These hoists are the largest in the company’s growing air hoist fleet and, with the wireless controllers, they enable the operator to stand in a safe place away from the lift.
“It is our ambition to switch all of our hoists and winches to this wireless control system, which takes the safe operation of hoists and winches to a new level of safety not seen in the lifting equipment hire industry before in Australia,” said Fitzgerald.
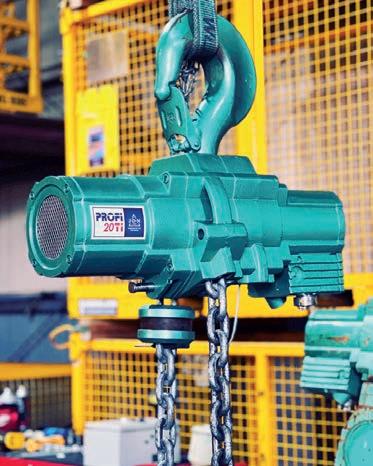
“These hoists are the largest in QRH’s growing air hoist fleet and with the wireless controllers they enable the operator to stand in a safe place away from the lift.”The new JDN 20t wireless air hoists offered by QRH. QRH moved from its original premises on the Gold Coast to the new facility based in Archerfield, only 10 minutes from the Brisbane CBD.
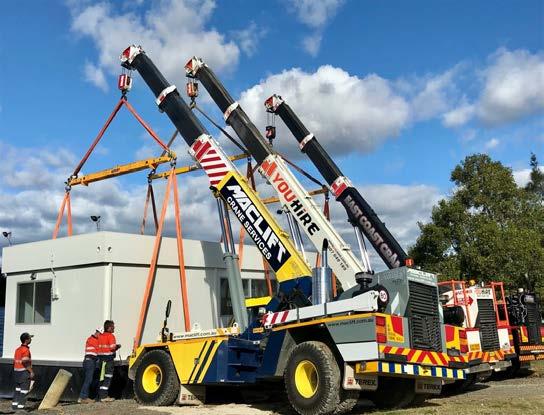

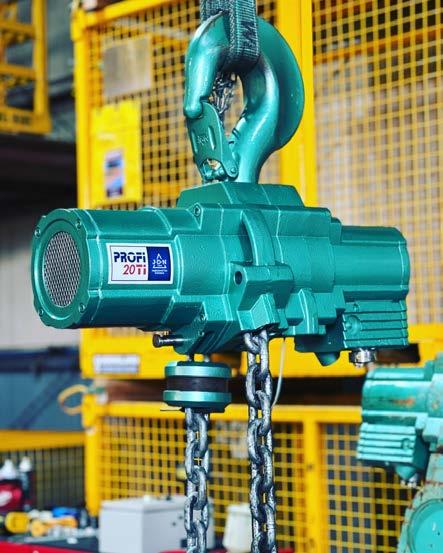
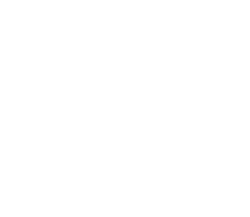


The AC 7.450-1 does not take up more space than a six-axle crane at the job site. However, it offers significantly larger lifting capacities and a longer main boom that comes in at 80m.
PROGRESSIVE THINKING BEHIND NEW TADANO PURCHASE
A new yard, a new Tadano AC 7.450-1 and Supply Nation accreditation, Fullers Mobile Cranes is on the move. Father and sons team, Larry, Kane and Locky Fuller, provide a number of updates on the business and the reasoning behind the latest addition to the fleet.

“WE HAD BOUGHT DEMAGS IN THE past, which included an 80t and 55t all terrain as well. But when Grove launched the GMK5130 we grabbed one and decided we didn’t want a fleet which included various brands. Operators don’t cope well with changing cranes and different operating systems, so we have stuck with Grove for a few years now,” said Larry.
The compact nature of the Tadano AC 7 450-1 was a major attraction for Fullers Mobile Cranes.
“We really like the compact size of the 450. It’s about the same size as a 400t, which has six axles, whilst our 450t is on seven. Our fleet has always revolved around being compact, and with sites getting tighter and going right to the boundaries, we’ve won a lot of jobs with the 55 because it has been able to get in and lift where larger cranes couldn’t,” said Kane.
“The 80m of main boom was also a
very attractive feature for us. When we get to site, our customers want the boom in the air ASAP and the lifts happening. ‘You’re taking too long’, is an often-used observation. We can have 80m of main boom out with 12.5 minutes. With the other models in this category featuring 60 plus metres of boom, they can be up to 1.5 hours and they are still setting up the fly and jib,” he said.
Compact like a six-axle crane, powerful like many eight-axle units –the AC 7.450-1 is in a class of its own. It is the first machine from a new highefficiency crane family and makes a compelling case with a series of forwardlooking solutions and impressive technical specifications.
COMPACT AND MANOEUVRABLE –LIKE A SIX-AXLE CRANE
W ith a carrier length of 15.99m, a total length of 17.62m, and an outrigger base of 8.45m, the AC 7.450-1 does not take up more space than a six-axle crane at the job site. However, it offers significantly larger lifting capacities and a longer main boom that comes in at 80m. All seven axles on the AC 7.450-1 are steered, and four of them are driven. This makes the crane so manoeuvrable that it can handle tight work sites at least as well as a six-axle model.
SPOILED FOR CHOICE – POWERFUL, VERSATILE BOOM OPTIONS
With its fully telescoped 80-m main boom, the AC 7.450-1 reaches lifting capacities of up to 25 t. If the main boom’s length is not sufficient, it can, for example, be extended with a luffing jib with a maximum length of 81 meters. The crane’s maximum system length is 132 meters. The luffing jib can be “divided up” in three-meter segments from 24 to 81 meters. But that is not all: In addition to the luffing jib, Tadano also offers configuration options for a fixed extension, and even a runner.
FUNCTIONAL AND POWERFUL – THE NEW SUPERLIFT DESIGN
Tadano is using its new engineering design for the Sideways Superlift
system for the first time ever on the AC 7.450-1. This new design is a decisive enhancement to the well-known Tadano SSL solution. The Superlift arms are now mounted all the way in the front, on the head of the base section, meaning that they are ultimately longer and accordingly well-suited to larger lifting capacities. And while on the subject of lifting capacities, this means that the AC 7.450-1 is considerably superior to other seven-axle cranes – in fact, it even leaves some eight-axle units behind in a number of boom positions.
The functionality and handling have been improved as well. In fact, the new design only requires one single wire rope line for the connection between the main boom head and the SSL arm.
In addition, the SSL arms are pinned hydraulically on the main boom, which reduces manual work for securing the arms and the associated work at height.
EVERYTHING IN VIEW –360° SURROUND VIEW T he AC 7.450-1 features six cameras that keep everything in view. With the help of a computer-assisted diagram, this makes it possible to graphically show the possible extension lengths for
the 450 featuring 80m of main boom out and the mega wing system, the crane is lifting 37t, it is perfect for tower crane work for example.
“The crane fills a gap in our fleet nicely. We can now cater to our customer requirements rather having to outsource the work. For our Tier One customers, we can now complete the bridge beam lifts on the massive infrastructure projects. We are not out to challenge the larger crane hire businesses. We will stick to what we know best and that is servicing our customers with the best range of compact cranes we can offer,” said Kane.
He goes onto explains how lifting capacities are changing the industry and how larger capacity cranes will help Fullers Mobile Cranes stay ahead of the general crane hire market.
“We are seeing a rapid evolution as crane capacities increase. 10 years ago, a 130t capacity crane was a rare sight, now they are everywhere. We are seeing the same with 250t capacity cranes, they are becoming increasingly popular. We are seeing subcontractors running one or two cranes and they will include a 220 or a 250 in their fleet. We could see we needed to take the next step to
“Compact like a six-axle crane, powerful like many eight-axle units – the AC 7.450-1 is in a class of its own. It is the first machine from a new high-efficiency crane family and makes a compelling case with a series of forward-looking solutions and impressive technical specifications.”
the outriggers and the counterweight tail swing radius on the display in the carrier cab. This makes it significantly easier to position the crane at job sites. Surround View also helps on the way to the site by making it easier. Kane explains a bit more.
“When you compare the 450 to a 500t capacity crane, we might not have the same lifting grunt, but you need a second crane to build the 500, which comes at a cost to the customer. It also requires significant set up space. With
stay ahead of the general pack and the Tadano AC 7 450-1 is that step,” he said.
A significant and recent development for Fuller Mobile Cranes involves the business being recognised as Supply Nation registered. Larry explains more.
“Supply Nation Certification will be a massive step forward for our business. For the Tier One builders working on major government infrastructure projects being built throughout Sydney, the Indigenous element to each project is becoming increasingly important.
We are more than happy to play our role and make our contribution to this important issue for our nation,” he said.
Kane and Larry go on to discuss the challenges relating to the last couple of years.
“The business had been operating out of Parramatta for 20-plus years. We purchased the Grove GMK5250L-1, which brought with it more trailers and support vehicles and we also invested in middle-class cranes with capacities of 60t and 90t. Both of these were Groves. We wanted to consolidate the entire fleet under the one roof, and so we moved to our new premises in Woodpark Road, Smithfield,” said Kane.

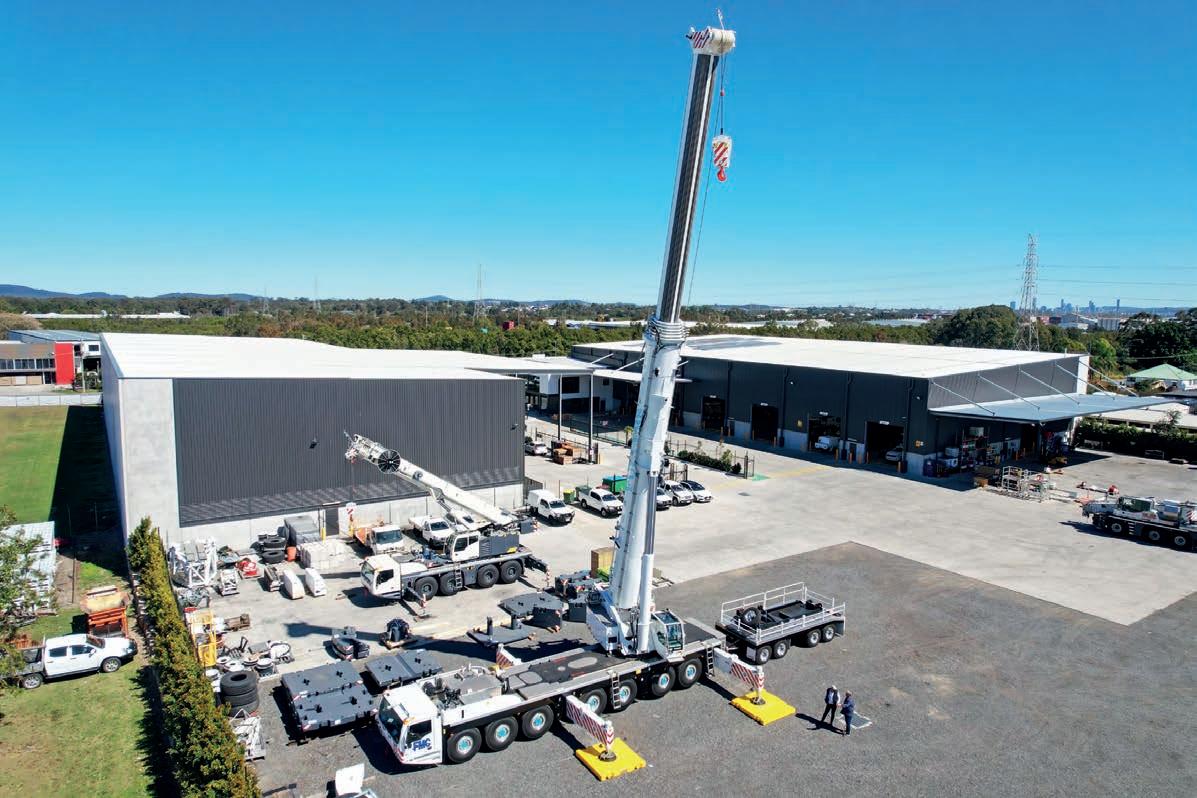
“Shortly after signing the lease on the new premises, Covid hit and we went from owning our own yard to seeing our business world turn upside down, as it did for so many other businesses.
“We went from staffing levels upwards of 40 down to 18. Crane hire businesses were panicking and sending cranes out for a quarter of the value of the job, which we refused to do. We decided to stick to our guns and not compromise on price whilst not going backwards by having the cranes sat idle in the yard,” said Kane.
“It was a difficult and stressful time to navigate because the challenges were new and complex. It was the same for everyone. The vaccination program roll out was confusing and caused us endless grief. Initially it was about getting the guys vaccinated and then we found the expectations of sites were not feasible. As did the rest of the industry, we
“The record amounts of rainfall have not been helpful, but our third quarter of 2022 is looking solid. We have secured significant contracts, we are bringing new people on board, and we are about to take delivery of the Tadano AC 7.450-1, which is designed to take our business to a completely new level,” said Kane.
Like all crane hire businesses, Fullers Mobile Cranes is focused on the future and attracting the younger generations to the business and industry in general. Two years ago, Chris Hull was the CICA NSW trainee of the year. Larry provides an update on Hull’s progress.
“Attracting youngsters to our business is a passion for both Kane and I. They provide us with the opportunity to train them the way we want them trained, so they have the right outlook and approach to the work.
“Chris is now fully qualified and dogging the cranes and driving trucks. He has been so happy with the business, the nature of the work and how we have trained him, he introduced his younger brother Shane to the business. Shane has the same, if not more potential compared to his big brother.
muddled by and we have been extremely grateful to the past federal government for the schemes it put in place, especially Job Keeper, without which we would have been in a world of grief,” he said.
Just as the industry seemed to get on top of Covid and there was a return to a normal way of doing business, the La Nina weather event occurred, which has been incredibly destructive for some regions and disruptive for the Sydney crane hire market.
“The CICA traineeship program has been a great initiative for our yard. Our more experienced team members have embraced the concept and have been prepared to share their knowledge and help the youngsters along.
“I think all crane hire businesses will have the same story to tell; it is hard to find good people, and when you do, they are coming from another business that has a different outlook and culture. This can make the integration process long and sometimes painful,” said Larry.
“Supply Nation Certification will be a massive step forward for our business. For the Tier One builders working on major government infrastructure projects being built throughout Sydney, the Indigenous element to each project is becoming increasingly important.”

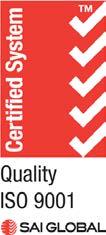
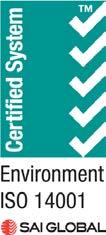
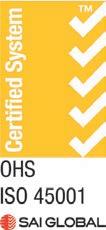
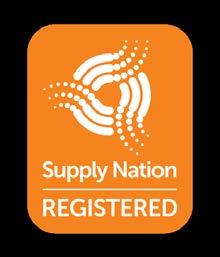
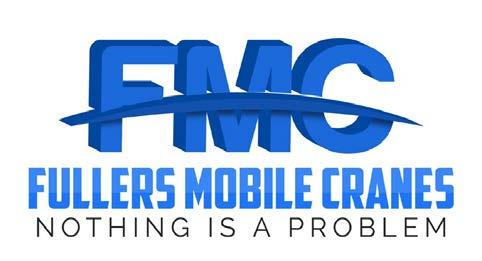
MELROSE CRANES TURN TO BEN BADEN SERVICES FOR NEW LIVERY
Melrose Cranes & Rigging is currently upgrading its crane fleet to a new black and white livery, and they turned to Ben Baden Services for the recent paint upgrade on its Grove GMK 6400, 400t capacity all terrain. Melrose Cranes & Rigging general manager Ryan Melrose takes up the story.
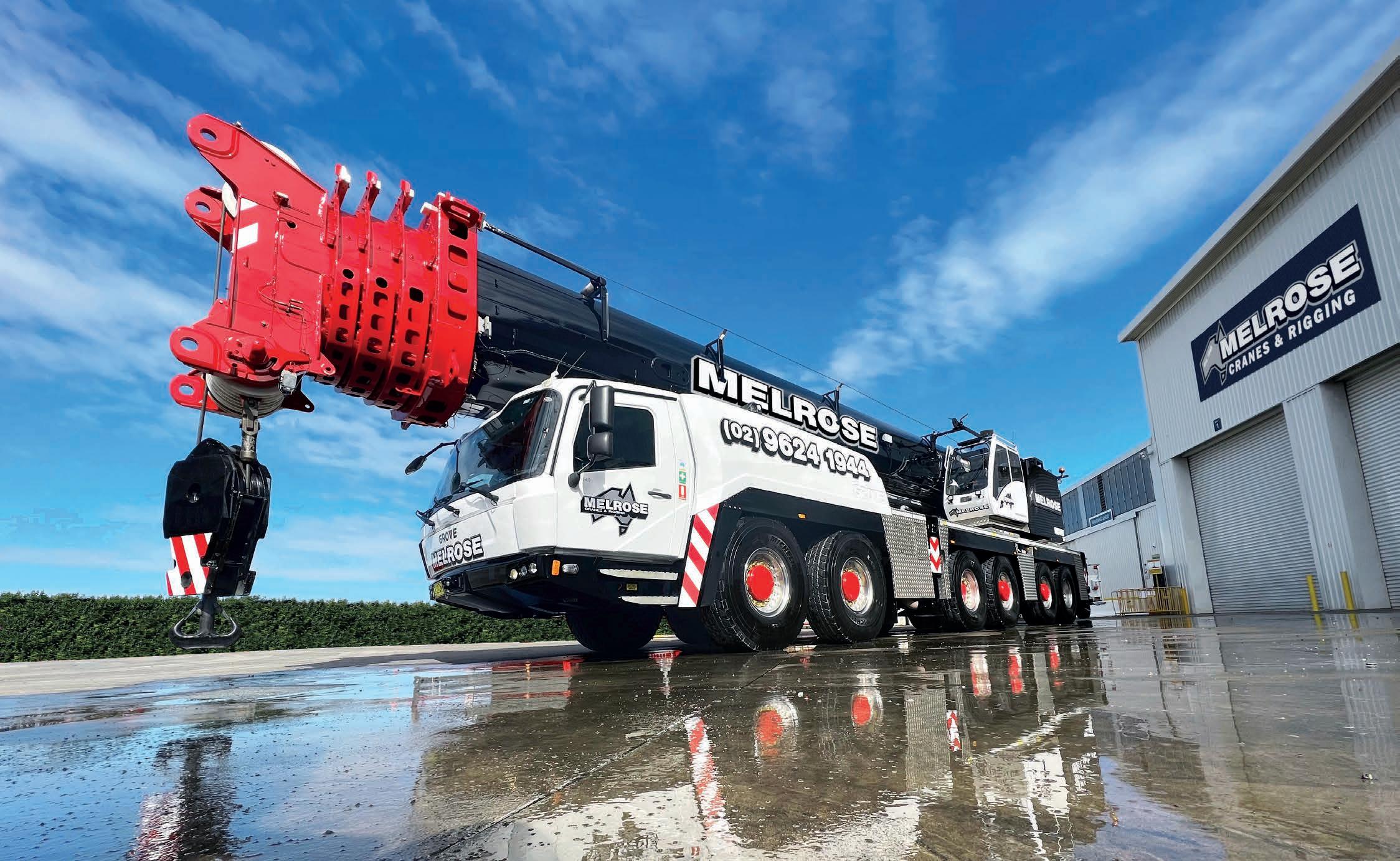
“WELL, I’D LIKE TO SAY I COULD JUST get every existing crane painted in the new livery straightaway, but this is not always possible,” said Ryan.
“Obviously, everything takes time, and we must consider continually adapting to the workload, which has
been intense lately. We have needed our larger capacity cranes to be available.
Simply having a crane off the road for the required amount of time to paint it, can be hard to justify,” he said.
Melrose Cranes has a new 25t capacity Kato on the way. And that was
a good reason to update the 13t Kato already in the fleet.
“The 13t Kato is a 2017 model and the paint was still in good condition, but we want to be able to put the two city cranes side by side and have them matching with the same livery and
“The 400t crane is the last of the heavy crane fleet to be painted or ordered in the new livery. It will be great to see it work alongside our 500t, 450, & 250t cranes.”
branding. We want them to look like a big brother and little brother,” said Ryan.
“So, we are gradually moving through the fleet. The 400t crane is the last of the heavy crane fleet to be painted or ordered in the new livery. It will be great to see it work alongside our 500t, 450, and 250t cranes. Our latest Tidd PC28 was ordered in the black and white colors. Baden’s also repainted a PC25 that was damaged by a customer.
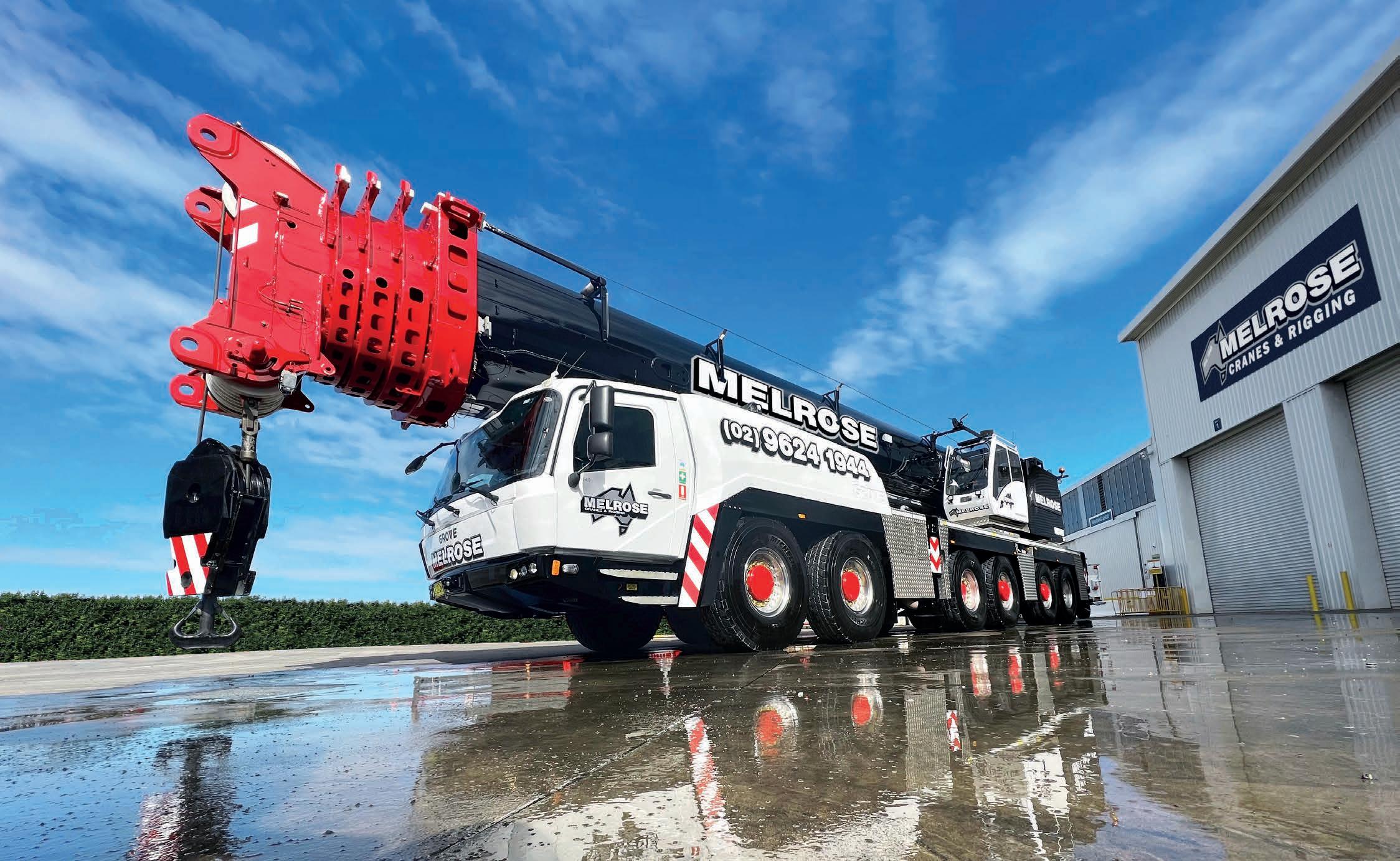
“ We’ve just completed another MAC25 in the new livery and it was done by Ben Baden Services. When the cranes arrive back, they look brandnew. Baden’s does an extremely good job with an almost ‘mirror’ finish on the black.
“The intent is to keep moving through the fleet but to spread the cost over whatever time it takes and not to impact on the client’s needs and our ability to service their requirements. So often we’ll pick Christmas and quieter times for this kind of work,” said Ryan.
The relationship between the Melrose and Baden families dates back to 1988 (Ben was eight years old!). Gregg Melrose and Gerhardt Baden knew each other well from working in different businesses opposite each other in a little cul-de-sac in Wetherill Park.
In 1995, Gerhardt became Liebherr’s national crane distributor and, in 1998, Gregg started MCR. The relationship grew.
“Ben has an impressive paint shop but he generally only paints equipment that comes to him via insurance
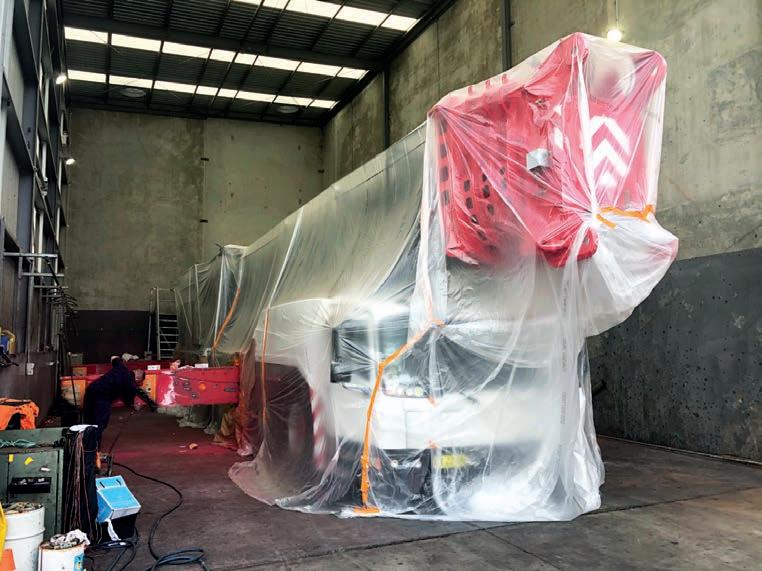
The paint crew paper wrap and tape every little component. Their masking ability and attention to detail is pure quality.
his schedule that he needed to fill and asked if we were interested. A mutually beneficial favour, if you like,” said Ryan.
“Gregg asked me straight away: ‘Which cranes do you want to paint?’ If I’m choosing, the number one priority was the Grove GMK 6400.”
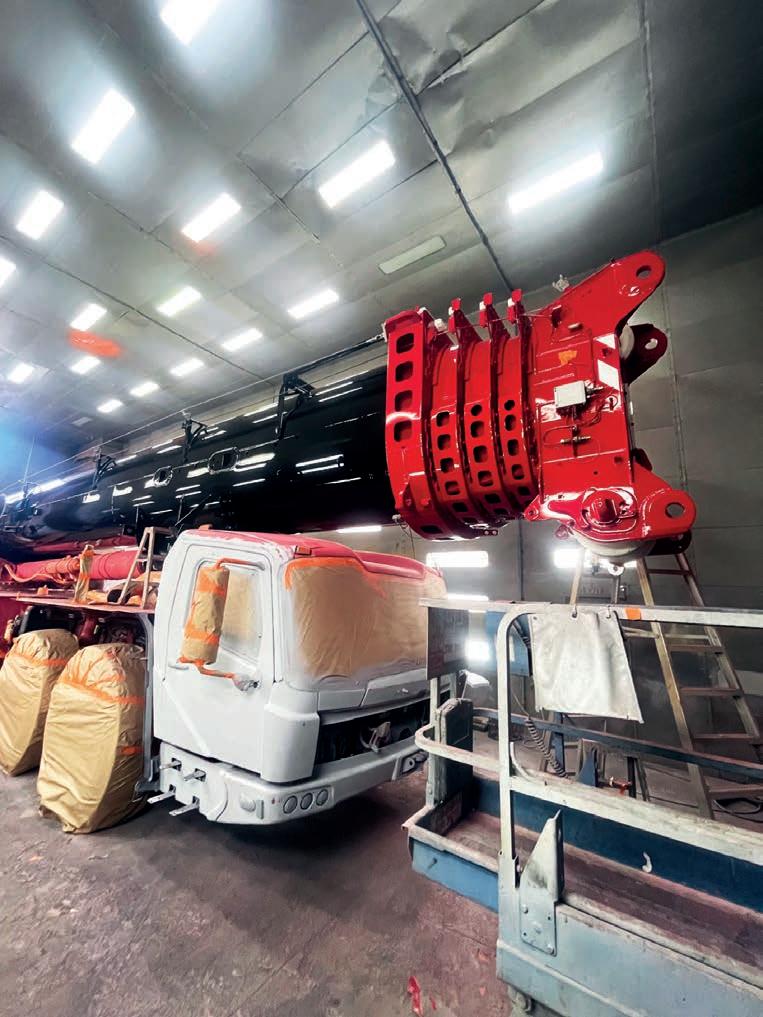
When Melrose Cranes purchased the GMK 6400 it was already red, which was close to the Melrose livery at the time, and the decision was made to get it into work to back up the Grove GMK 7450.
“So, it st ayed red, and the logos went wherever they could to cover where the old logos had been. It has remained that way ever since. The 400 was our first choice, but Ben originally declined and said: ‘I won’t have enough time for a 400, can you give me something smaller?’
“We made the choice to do the 13t Kato to match up to the 25, and then a MAC25 because they commonly
get some scars as a constantly moving crane in an ever-changing work environment. During this time, Ben made contact and noted some further delays. As much as he didn’t want to tackle the 400t a deal was done and it was in his yard before he could deny us,” Ryan said with a smile.
“It’s nice to bring them back to looking shiny and new. The operators appreciate the facelift as well. They are always happier and tend to look after them and keep them clean once they are repainted.”
Ryan goes on to highlight Ben Baden Service’s approach to the painting of the Grove GMK 6400, the detail that goes into the painting and the benefits of the final look.
“The quality of the finish is something that Ben and his team have always excelled in. To my knowledge
and in my experience, they are the best in the business. They have a quality process to make sure it is all perfect before the crane comes back to you.
“They’ve got those quality checks and measures in place to make sure it’s coming out looking brand new. Paint a surface with black paint and it will look shiny, but when Ben and his team paint a black surface, it almost becomes a mirror. It’s a great job when you look at metal that’s painted black and then realise that you can almost see your face in it,” said Ryan.
Communication is the key when a crane is in for painting, servicing, or repairs.
“I’ve got a very open line of communication with Ben. We could talk multiple times a week, even if we don’t have a job taking place with them at the time. We have a great relationship, and it is the same with Anthony Davis. Anthony’s
obviously more involved in The Crane Connection and Ben’s more focused on the repair and maintenance side, both of whom are MCR’s first choice in what they specialise in.
“Their painters are also really nice blokes. When you visit the paint shop, it’s all very welcoming. When you see them paper wrap and tape every little component – their masking ability and attention to detail – it’s just pure quality. Our depots are also very close to each other, which is beneficial.
“Even though there are obviously stages to painting, someone like Ben has a process of blending it all properly, not just chucking a bit more black in there or brushing a bit. You wouldn’t know it was completed in stages; it is like it was all done at once. Experience counts for everything and Baden’s has it in spades! said Ryan.
“It’s nice to bring them back to looking shiny and new. The operators appreciate the facelift as well. They are always happier and tend to look after them and keep them clean once they are repainted.”
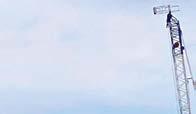
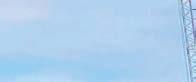



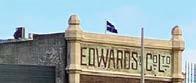
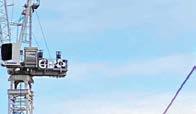
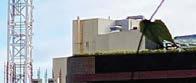













KEEPING PACE WITH ALMACRAWLERS
Almac Pacific recently announced that Pace Cranes had been appointed the national distributor for the AlmaCrawler range of MultiLoaders. Almac Pacific general manager Bob Mules, Pace Cranes managing director Anthony Heeks, and Pace Cranes national sales manager Michael Cawston provide the background to the development.
“WE’VE BEEN LOOKING FOR A DEALER FOR the Multi-Loader product for the last 9–10 months,” said Bob Mules.
“I’d approached and had several conversations with a couple of different crane companies that were maybe looking at diversifying their offering, and then I was looking through a copy of Cranes and Lifting magazine and I saw Pace Cranes. I knew of the business from my previous life with Gillespie Cranes back in the early 2000s when I was helping run their EWP fleet.
“Looking at the range and what they offer I saw they had the track carrier and I wondered if our AlmaCrawler range would be competing with their offering or was it going to align with, and maybe compliment, what they had.
“I rang Anthony, and we decided it was worth at least a conversation. Anthony
confirmed they’d been getting calls from their customers about the carriers, but they wanted larger capacities or something a little bit different.
“As we chatted, we thought the AlmaCrawler range would probably compliment what they already have. And, from my perspective, the relationship really fits into that crane and lifting environment and also infrastructure and construction sectors we are looking to target with the range.”
Anthony Heeks explains how he sees the range fitting into the Pace Cranes suite of products.
“The tracked carriers work very well with spider cranes, which do have limited pick and carry capabilities,” he said.
“Our Madea range is ideal when you are working on sites with narrow access, or working behind houses, whether
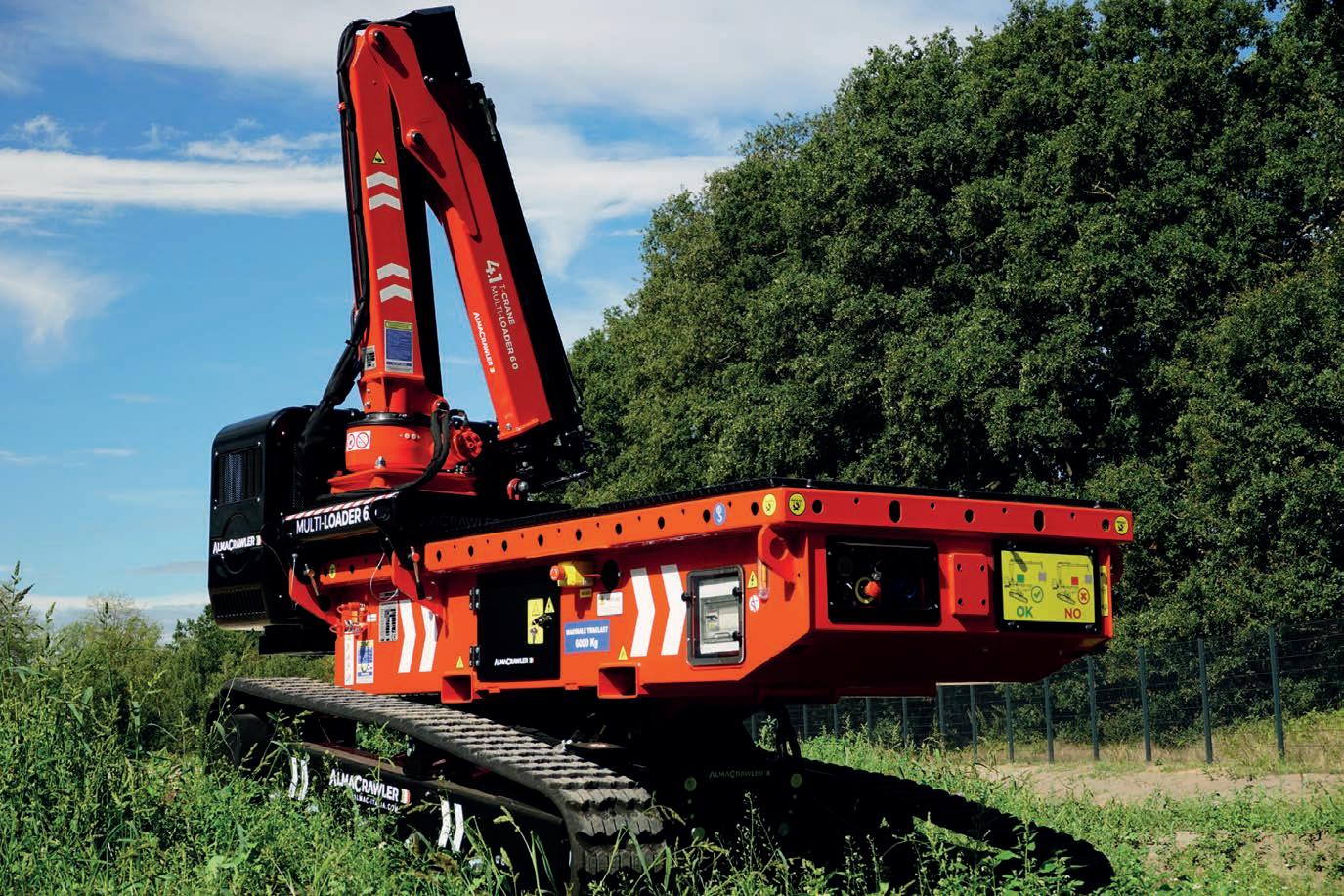
three-tonners arriving early November. So it’s about keeping that pipeline coming and understanding what we think the stock levels need to be,” he said.
“The new three-tonner will appeal to a different market compared to 2.5t and 6t capacity Multi-Loaders, which feature the bi-leveling system. The new 3t ML 3.0FX Multi-Loader doesn’t have the bi-levelling and so it is a little cheaper. It is ideal for the tighter applications.
“The ML 3.0 FX is smaller overall and weighs less than 800kg. They are ideal for production-type facilities, warehousing and industrial environments, where people have them online, and I know there are a couple of rental companies operating them and they see opportunities in lift and shift-type applications.”
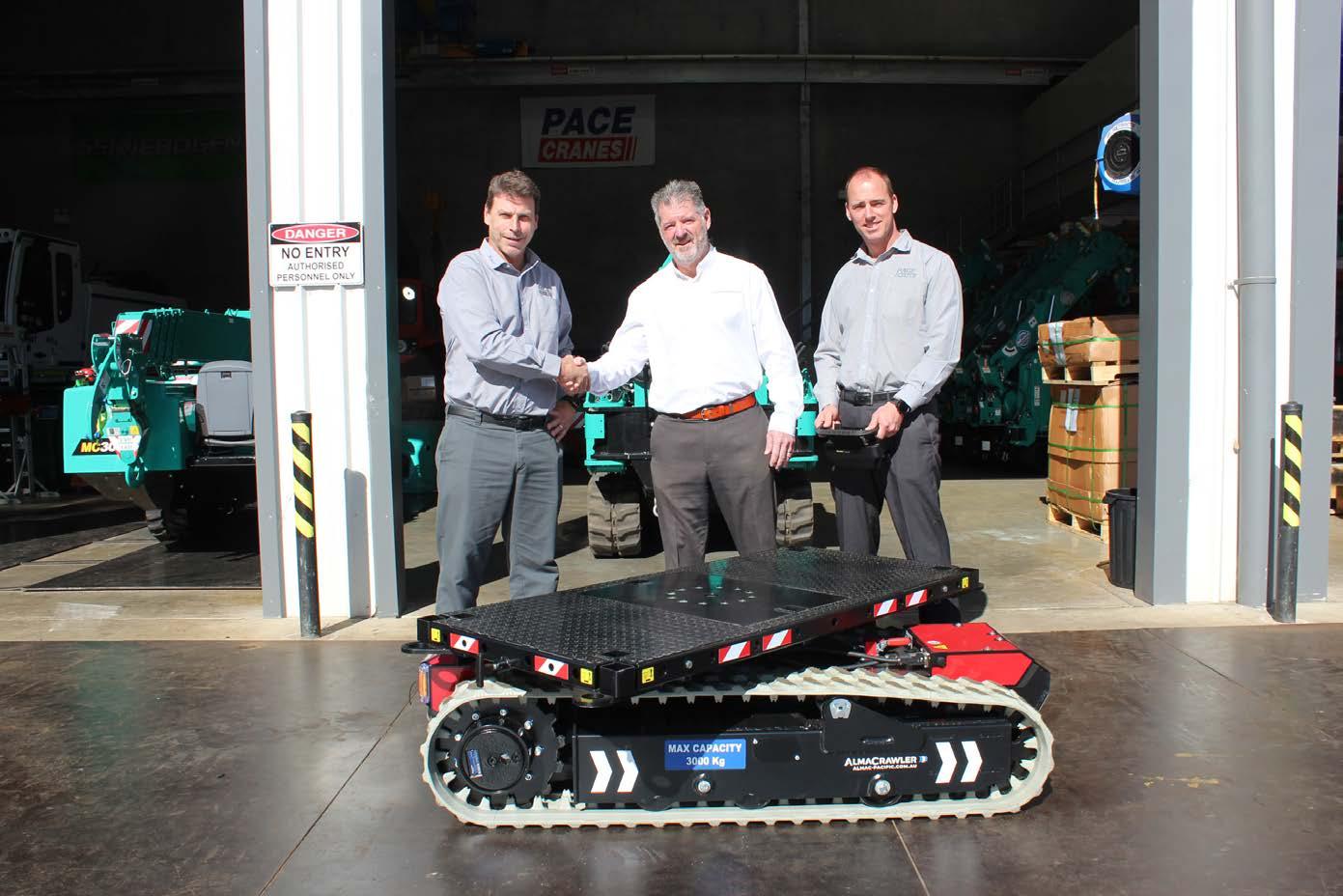
Mules discusses the application for
a crane hire business should be looking at this capacity and at tracked carriers in general.
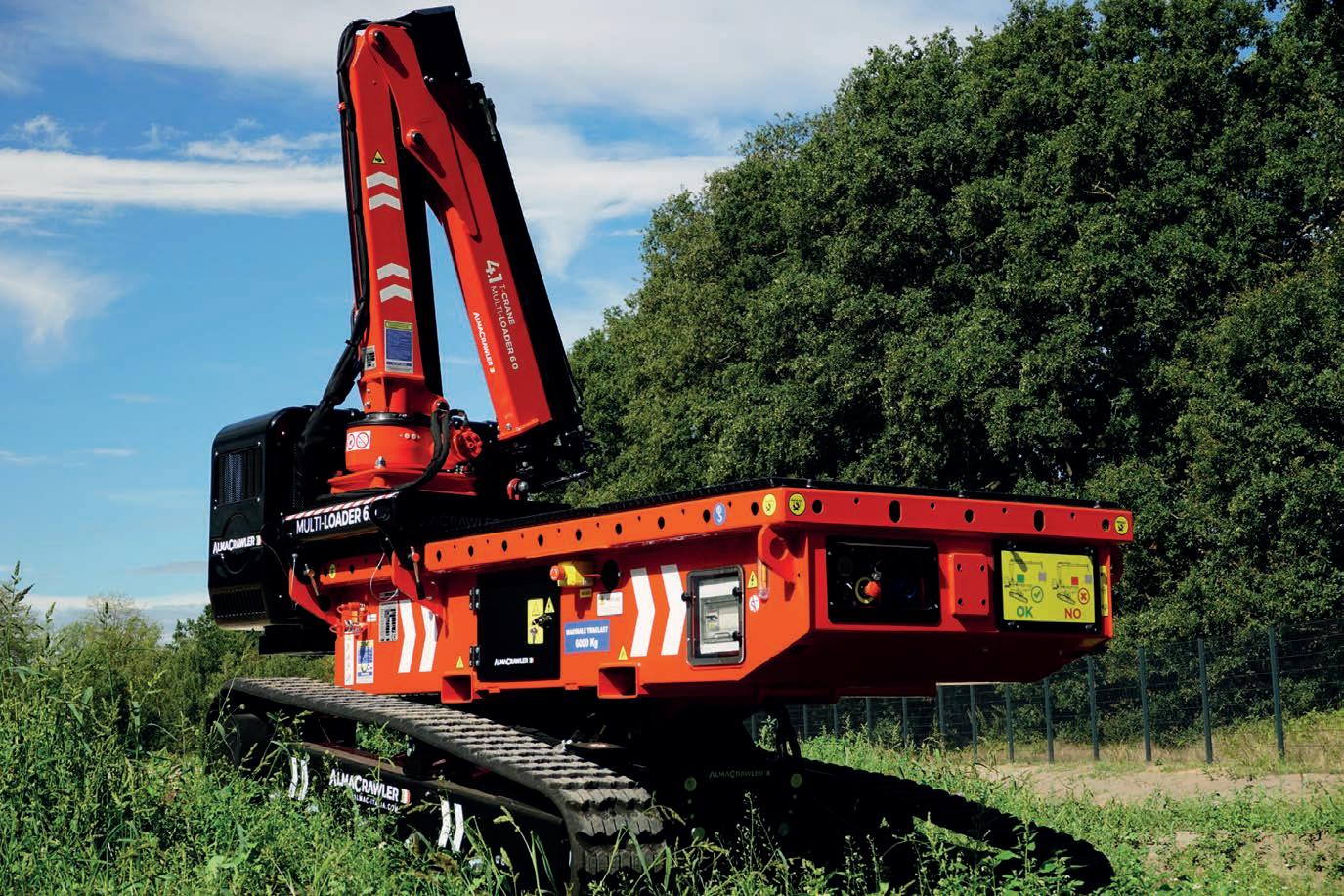
“With a 6t capacity and a mini crane with a 1t lifting capacity, we see the Multi-Loader 6.0 working well in large infrastructure projects, like the tunnelling we are seeing up and down the east coast. It would be ideal for transporting equipment and materials into areas where cranes or other pieces of large equipment cannot access,” he said.
“They are designed to transport equipment and materials from point A to point B and then allow the cranes to lift them into place. Both the 2.5 and 6.0 Multi-Loaders self-level up to 20 degrees, meaning the carrying platform remains level whilst traversing up and down inclines. These are the opportunities we
team at Pace Cranes have that connection and long-term relationships with those customers. That’s the exciting opportunity for all of us,” he said.
Heeks is confident the Multi-Loader range will prove to be popular, even though it still a new concept for much of the market.
“In the past, we’ve been successful with niche products that have been new to the market. Some have been new concepts too and we know it is important to have the machine available to not just demonstrate, but to have stock units here, which we can hire out and get them in the market,” he said.
“That way they are seen and recognised. Customers can see them operating and they can ‘try before they buy’. Or, if we have machines available, we can offer them
as loan machines, we have that flexibility. This strategy has worked with a lot of our products, and it gives the customer the option to see the product in action. With any new product, you really need to get it out there, there’s no sense it sitting here in the showroom,” he said.
Mules goes on to explain how customers are utilising the Multi-Loader and what they think of the concept.
“We have a customer in New Zealand and they have both the Multi Loader 2.5 and 6.0. They have shared videos with me showing different applications they have used these units in: from moving long beams down steep, narrow driveways, through roller doors of a small warehouse, with the ML2.5, to relocating large statues down grassy inclines with the ML6.0 with the crane attachment.
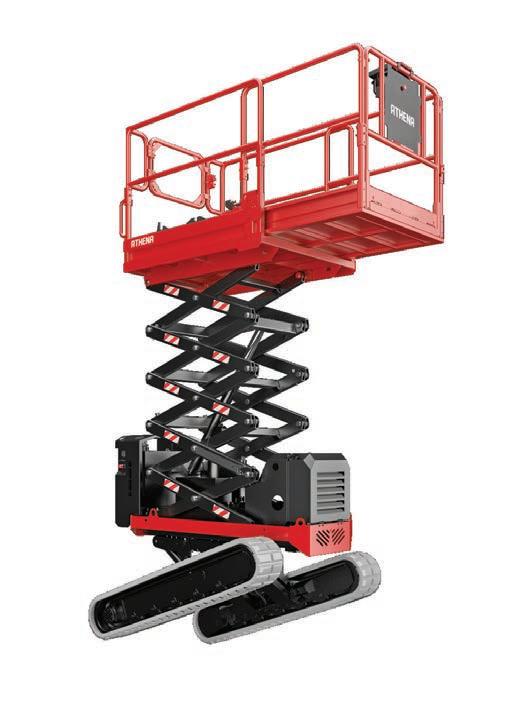
“They have also used the ML2.5 in the film industry – when they were shooting a commercial down on a creek, they had to get the equipment down a steep incline into this wet, rocky creek area below. They were able to strap the camera and boom onto the ML2.5 and drive it down the incline. They said they’d normally have three or four people up and down the incline, carrying the equipment,” he said.
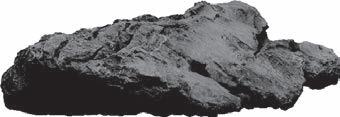
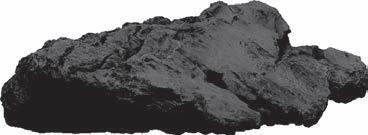

Almac Pacific and Pace Cranes will work together in terms of product support and the service side of the business explains Mules.
“Our technical manager, Josh Coulson, works out of Melbourne and will support the Pace Crane team. He will provide the team all the relevant training on the products, so customers can feel confident they will receive the right levels of support. We also have a full range of spare parts on the shelf in Melbourne, so from that perspective, we are fully supported by the factory,” he said.
Michael Cawston discusses the MultiLoaders potential in the crane sector.
“From a couple of conversations we’ve had I think there’s potential for us to sell multiple units to our existing customer base,” he said.
as far as it can, but it just keeps going even further with something,” he said.
Mules recently received a call from one of the head ergonomic engineers from Work Cover who had seen an article on the Multi-Loader 6.0 with the crane.
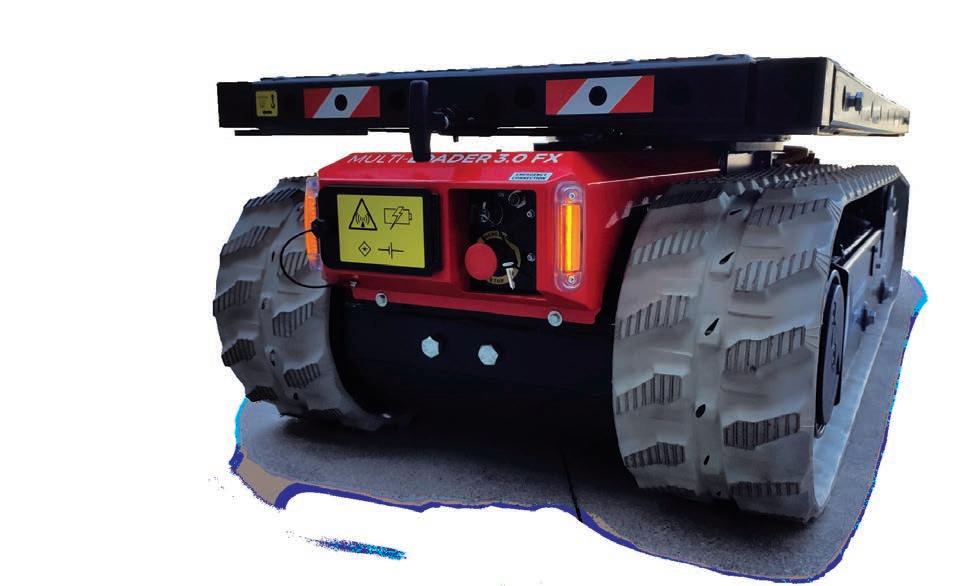
“He rang for a bit of a chat. He’d been talking to a kitchen fit-out business and they had a job which involved big, heavy stone bench tops. Apparently one of the guys tried to lift it and hurt his back.
“He wanted information to see what was available, how much they were, and discuss the capabilities of the MultiLoader range. I said for a little builder they may seem a little expensive. He said,
“When you are talking to crane hire companies who are purchasing cranes, when they look a Multi-Loader it isn’t that expensive. We are trying to get a handle on exactly how many we sell. But I think the potential is certainly there.
“We think a major driver will be the focus on safety on sites. The days are over when people are breaking their backs carrying materials, it’s just not allowed. We keep thinking the safety industry has gone
if it helps to reduce injuries and claims, then it’s not expensive at all. Their policies and premiums won’t increase and if they can cost it over two or three jobs, it isn’t that expensive for them.
“It’s not a bad point. We are talking about picking up safely and completely avoiding Occupational Health and Safety issues. There will no doubt be numerous applications that we aren’t even thinking of. Tier One construction sites, infrastructure sites, and mines are focused on safety of their crews on sites.
“Customers that are using the MultiLoaders understand how to utilise the gear and when it becomes a well utilised asset, the price becomes less of an issue. It’s about getting the concept out there and once people see what it can do, they understand just how valuable an asset they can be, and then it snowballs from there,” he said.
“If you’ve got injuries and Work Cover is involved, and you are looking at workers comp and your staff is off work, that gets to be very expensive. We are very confident that when the market fully understands the benefits of the Multi-Loader concept, and the role they can play in and around work sites, the acceptance levels will increase,” he said.
“We are talking about picking up safely and completely avoiding Occupational Health and Safety issues.”


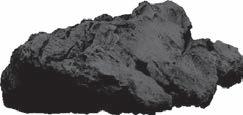
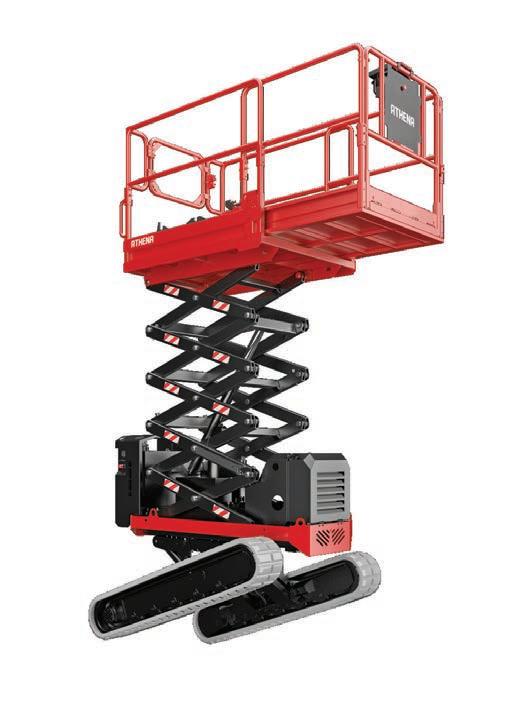

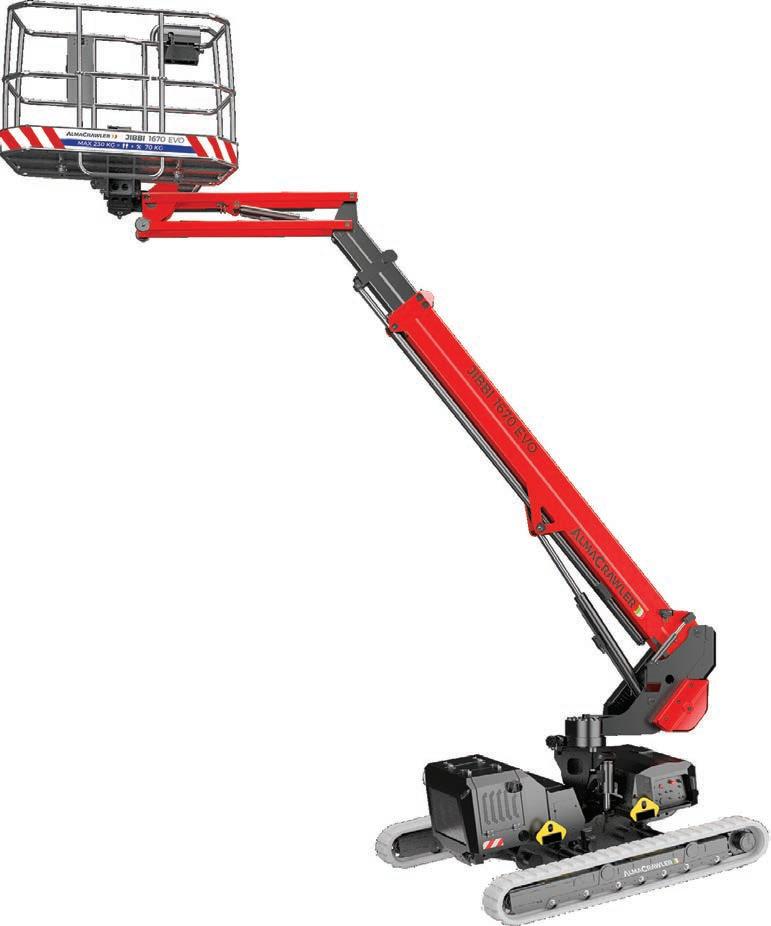
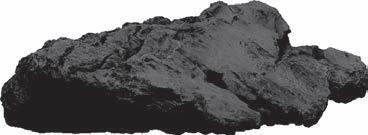
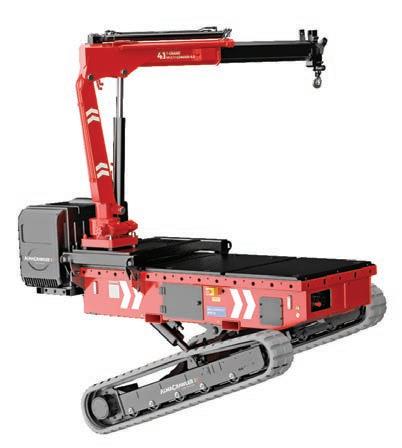
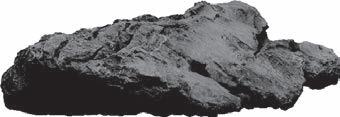

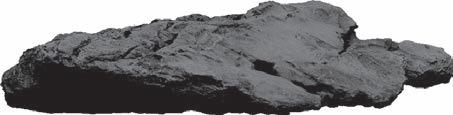
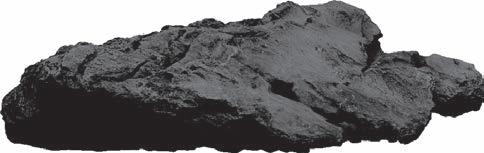
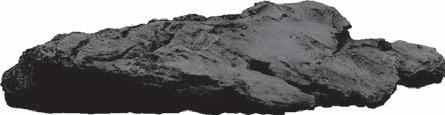
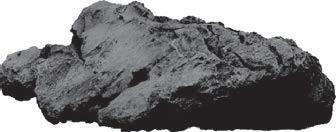
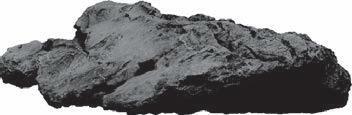
EVOLUTION’S BOOM FLEXIBILITY KEY TO MELROSE LIFTS
Melrose Cranes and Rigging recently completed a series of lifts on Sydney Metro’s Barangaroo Station site in Sydney. ‘Evolution’, Melrose Cranes’ Liebherr LTM 1500-8.1, was deployed for the project. Once on site the crane’s boom had to be reconfigured to manage a range of lifts. Melrose Cranes’ project manager Andrew Baly explains more.
“THE LIFTS WERE AT THE BARANGAROO Station site which is being built by principal contractor BESIX Watpac. MCR has primarily worked for onsite subcontractors, most notably the removal of the steel beams and girders from under Hickson Road for Delta Group,” said Baly.
Interestingly, Melrose Cranes had helped install the steel beams and girders over two years ago, which enabled the station box to be built and the tunnelling to start under Hickson Road. There were 140 plus lifts during this part of the project.
“The heaviest beams were about 11t, and we were lifting at a radius of 68 meters in luffing fly configuration. For other lifts the Liebherr LTM 1500-8.1 required 84 meters of main boom fitted. This meant we had to reconfigure the 50m to 84m boom and put Liebherr’s Y Guying system on, further increasing capacity,” said Baly.
“Switching out boom sections is quite a complicated process, and we normally take the crane back to the yard, but in this instance it was managed on site with a 130t assist crane. It was a matter of having enough space on site to blow the boom out slightly, lay it flat, take out one section from the 50m configured boom length, and then replace it with four sections which gives the boom length a total of 84 meters,” he said.
Predominantly, ‘Evolution’ is configured with a 50m of main boom.
“We needed the extra distance to get the steel beams out. Once we had the beams in the air, they were temporarily stored on timber dunnage for load out onto transport.
“We had the Liebherr LTM 1500-8.1 there for a total of three weeks for Delta Group and during this time we completed three separate setups. It didn’t work every night, but it worked probably about 11 or 12 nights in total.
“From our perspective, the project wasn’t too complicated, we just had to work with all parties in planning where we were going to be able to set up the crane. We found there was a better location for this particular scenario of 84 metres of
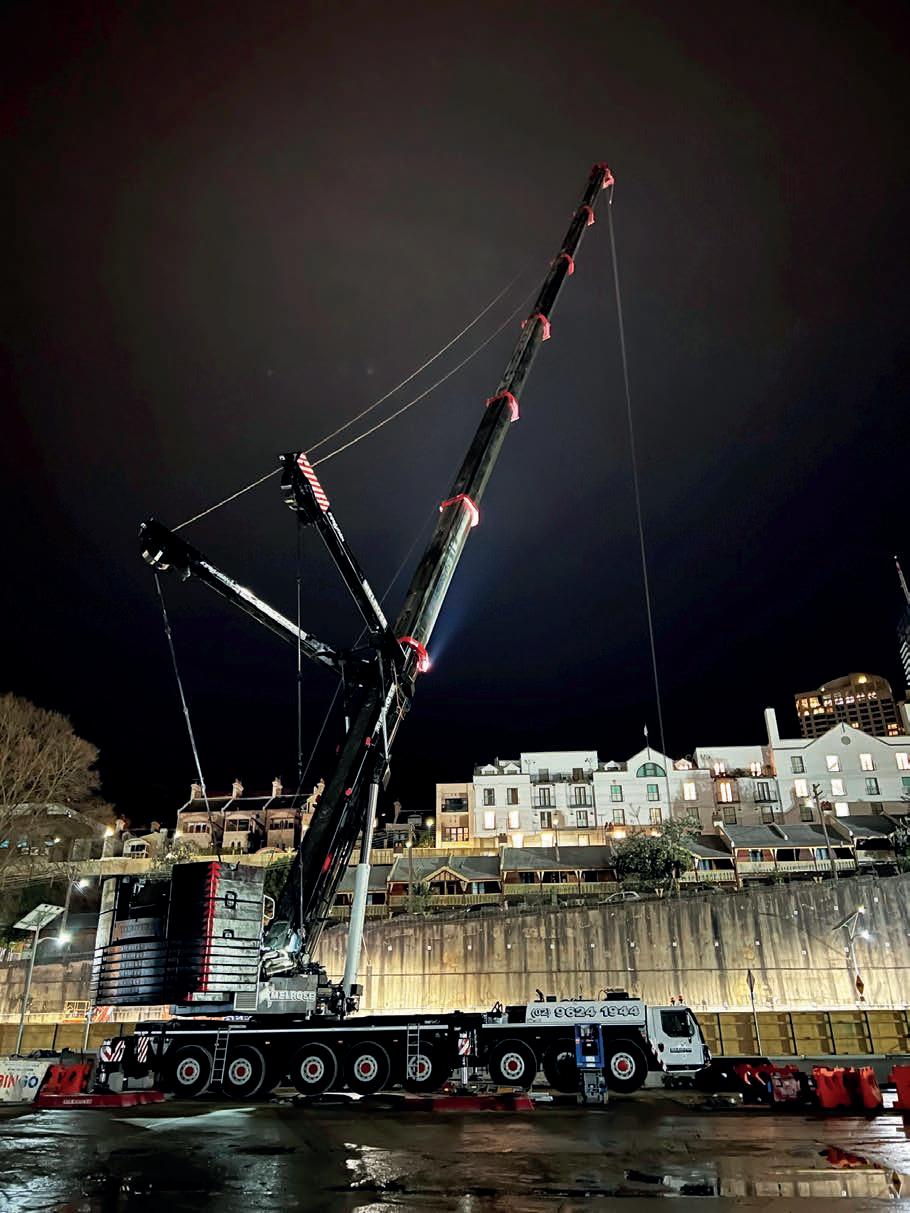
main boom and the Y Guying system, and it worked across all three setups,” said Baly.
“The initial set up location was tight as we had to tuck the crane in between the newly built temporary Hickson Rd and an excavation for a stormwater pit being constructed.
“We had to build up our pads to match the height because it was inconsistent ground. It was really a case of intricate planning to ensure the jobsite remained accessible and productive.
“Dual lifting using our 450T and 500T cranes was considered but the configuration changes to the 500T saved space and expense. It worked our really well,” said Baly.
When approaching the end of the program for Delta Group, BESIX Watpac asked Melrose Cranes if they could conduct some further lifts for them to install the main entry escalators for the new underground station.

This was done at a radius of 66m and they weighed 10.5t. We also lifted two 20t transformer rectifiers at 52m radius and lifted in a 22t crawler crane into the underground station at 38m radius. This took place from one of the exact locations we had been in for Delta Group. We had to change the configuration back to the 50m main boom, remove the Y Guying system and install 63m of luffing fly to complete the lifts.
“Everything went perfectly to plan, apart from high winds on the first night, however programs were adapted to meet safety requirements and the rest of the job was smooth sailing.
“The 500T crew, Terry, Blake and Muz, managed the lifts onsite effortlessly and without incident whilst completing all movements and reconfigurations successfully,” said Baly.
Terry Rust is Evolution’s operator. He has been operating cranes for 22 years and has been with Melrose for five years. This is Terry’s third year of operating The Liebherr LTM 1500-8.1.
Rust explains what is involved in reconfiguring the boom from his perspective as the operator.
“There are a lot of technical steps in
the process that need to be monitored on complex cranes and even something simple like boom grease is very important.
“The crew wears different gloves and get suited up to do it properly, because it’s quite a dirty job. And it’s a lot of slow going to ensure that everything is completed per the Liebherr instructions,” said Rust.
“When the crew has greased
everything, we use a 130t support crane to take one tip section out, which weighs 7t. We then replace it with a further four sections that are pre-assembled. They weigh 21t and when you pick them up, you’ve got to make sure they’re completely level so it fits perfectly into the 50m base boom.
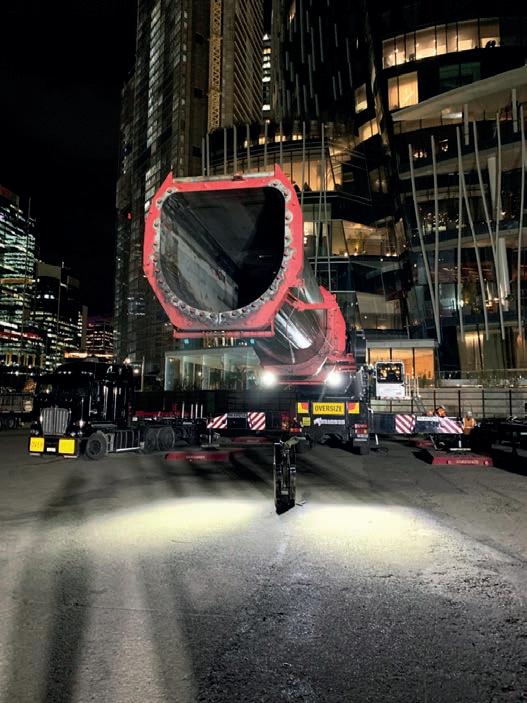
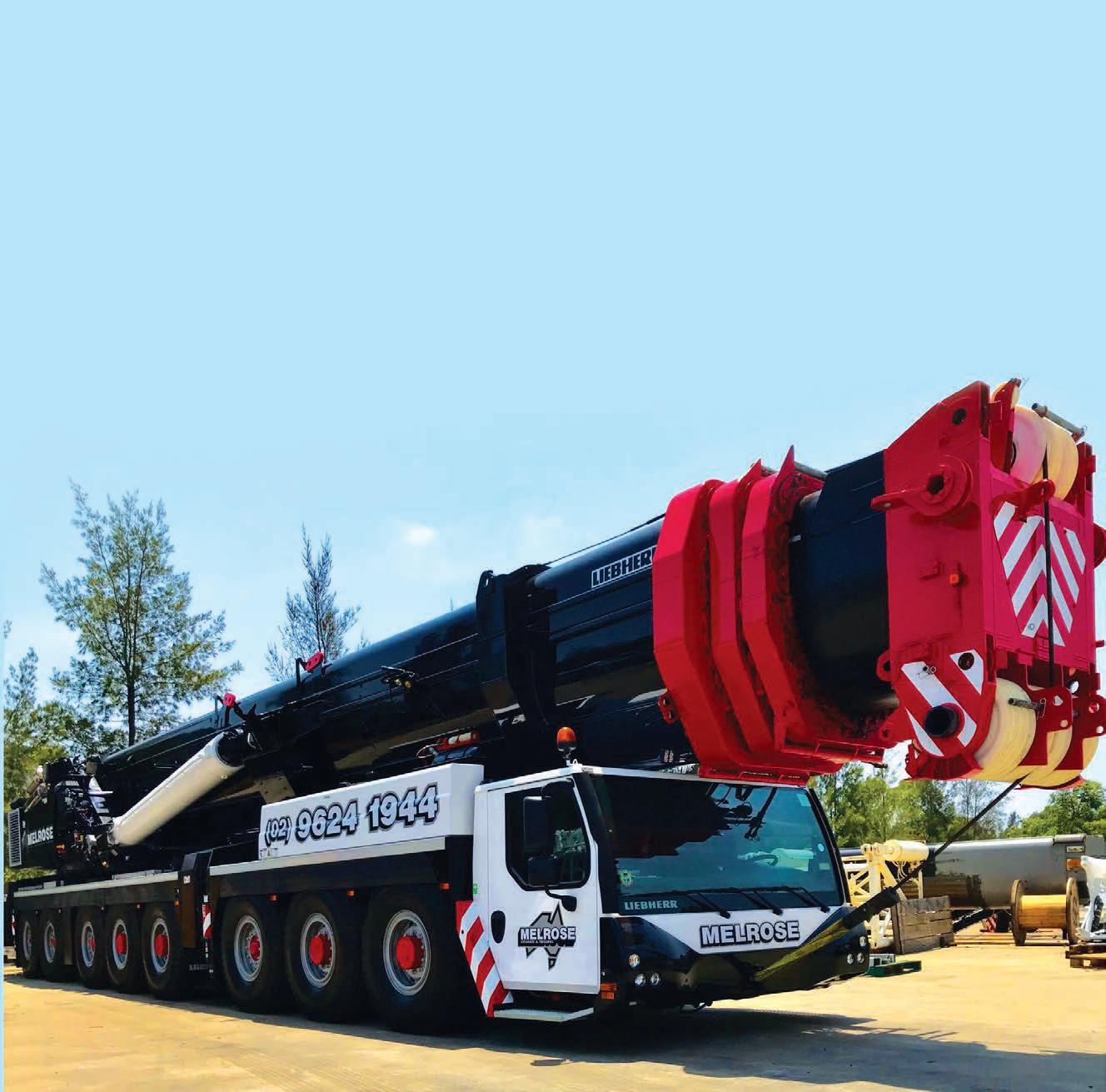
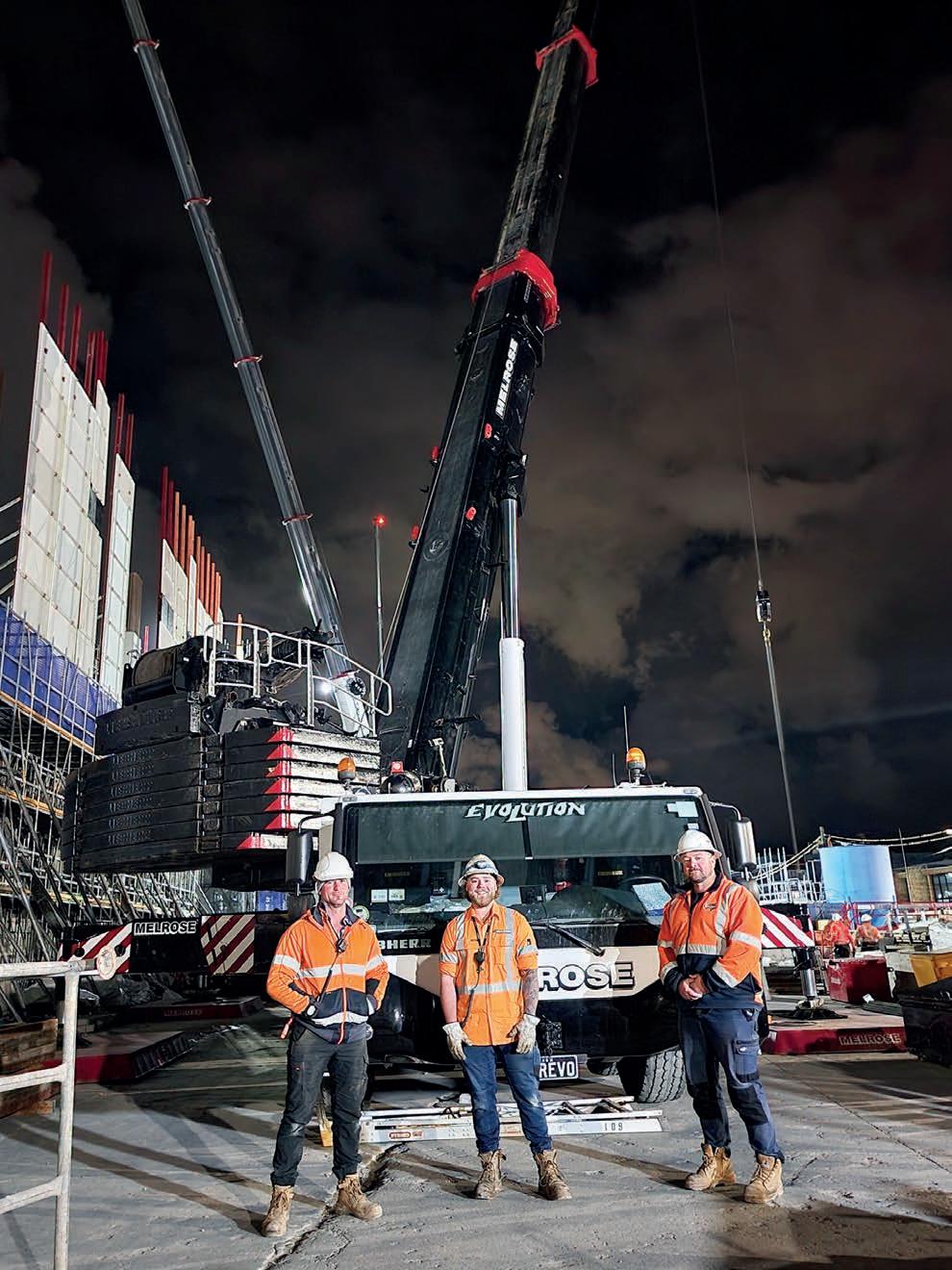
“We were working at full capacity in all of the various configurations used onsite. I love this type of work and the
reconfiguration of the boom.
“There’s a lot of communication that goes on between the riggers/dogmen and the operator to line the locking pins up. It can take some time, but we’ve got it down pat now and it gets done pretty quickly,” said Rust.
“Evolution has six or seven different configurations all built into the computer, so once the sections are in place, it recognises that it’s done and you can program it.
“The functionality of the crane doesn’t change. It’s one of the better built cranes from Liebherr, it’s probably the best one in my opinion. It’s a beast of a crane and loves every minute of the work,” said Rust.
“Evolution has six or seven different configurations all built into the computer, so once the sections are in place, it recognises that it’s done and you can program it.”Muz Basanovic, with Blake and Terry Rust. (Photo staged elsewhere.) The boom mid changeover with sections removed.
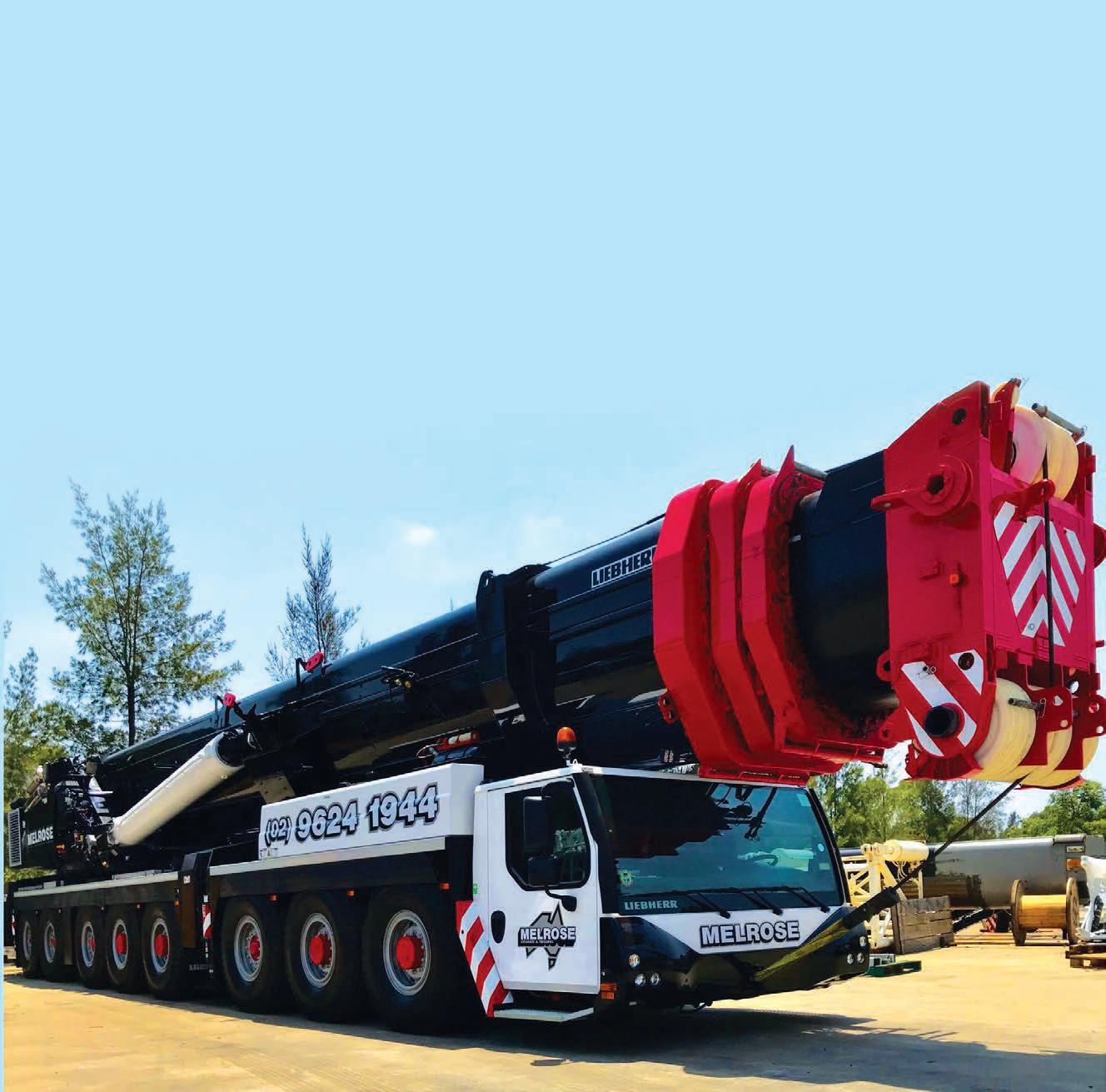
A ONE-STOP SHOP FOR HEAVY LIFT GEAR
System Rigging envisions being a one-stop shop through all aspects of the heavy lift, crane hire, construction, renewable energy, and mining & minerals sectors with their top-quality product lines. The family-run business, founded by Garry and Declan Kearney, brings a deep understanding of the industry through its global background and experience.
DECLAN AND GARRY STARTED THEIR working relationship through an engineering consultancy business, where they absorbed significant industry experience across the globe.
The consultancy group specialised in heavy lift, constructability, modularisation, and logistics. Although the father-son duo enjoyed this aspect of the industry, they decided to shift their focus closer to home and the idea of System Rigging was born.
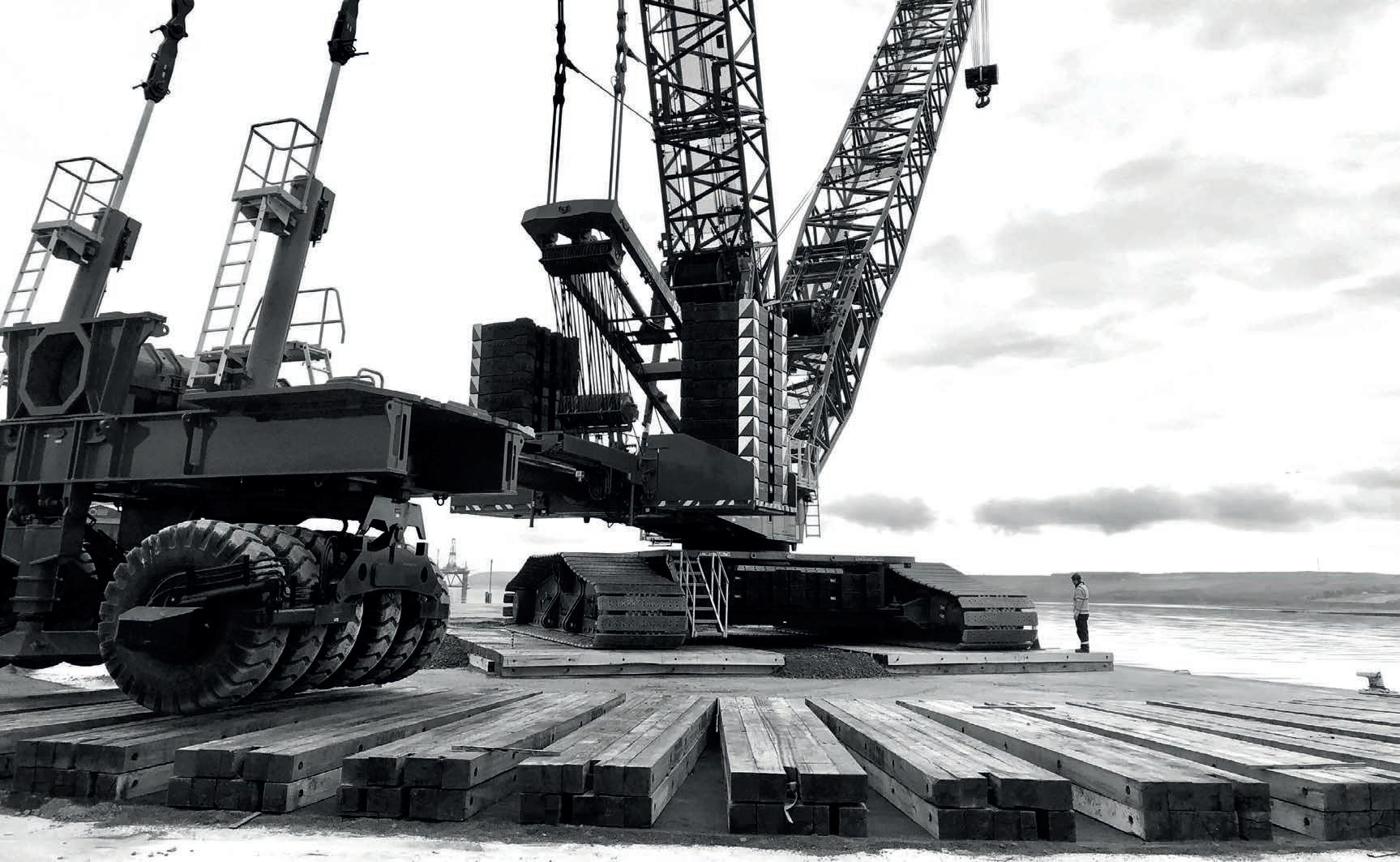
Garry explains how they reached this point of their journey, and what they hope to accomplish.
“Our firm belief was that by combining practical and innovative thinking with our deep industry knowledge, we could offer our clients truly independent solutions to their
challenges. We can help ‘shape’ our client’s strategies, by providing the right equipment to get the job done,” he said.
After years of recommending and designing equipment for others across the globe, it was the perfect catalyst for System Rigging to find its place in the market.
“Before setting up the business, we did a large amount of market research to find gaps in the market, and where we could position ourselves. We found the lifting equipment sector was rather crowded, but it was something we always wanted to be involved in. This is where our business model came to life, where we would offer a one-stop-shop solution for crane and ancillary equipment, a niche,” Declan stated.
What does this unique selling point
of System Rigging offer to the industry? The Kearneys describe their business model as any equipment “below the crane” or “under the hook”.
“It was clear that finding suitable ground support equipment away from the OEMs was a difficult task for crane owners, so we started off with designing our own range of steel outrigger pads.” said Declan.
The Australian Made certified range of steel outrigger pads proved to be a great kickstart for the business, they both knew if they could bring the Australian made quality to the product, it would become a welcome addition to the industry.
“We strive to achieve higher capacities than other pad designs out there, and the feedback we have received on their
robustness has been great,” explained Garry. Although the steel pricing has been so volatile over the last year, clients are still acknowledging what high-quality Australian Steel can offer.
System Rigging recognised that ground protection could be a very
important part of their business and didn’t stop their innovation and development at steel solutions. Australia hardwood timber cribbing was also introduced into their capabilities, however, with the rising timber shortage and supply chain issues, System Rigging needed to adapt and think of a different solution.
“Hardwood outrigger cribbing will always have a use in the industry. However, it is an organic material and brings with it plenty of exposure. The properties and performance of hardwood outrigger pads change as it becomes exposed to the environment, moisture, chemicals, and excessive usage. The hardwood begins to deteriorate and decay, and with continued use under load distribution pressure, it heightens the risk of both operators and equipment. Sometimes it’s hard to tell when the
timber is even damaged,” said Declan.
From months of investigation and development, they found themselves offering a new product line, ultrahigh-molecular-weight polyethylene (UHMWPE) cribbing blocks. UHMWPE is a very tough material, with the highest impact strength of any thermoplastic presently made. It embodies all the characteristics of high-density polyethylene (HDPE) with the added traits of being resistant to concentrated acids and alkalis.
“When evaluating outrigger pads, crane mats, and cribbing blocks, it is important to understand how strength and stiffness attributes of different materials and design affect the safety performance of the products in this application. Selecting the right combination of strength and stiffness to support your equipment safely and properly is a critical decision. We have found the UHMWPE material is the best suited for this cribbing application, and with our in-house designed test bed, we can truly put it to the test.” Declan stated.
Although these composite and steel outrigger pad solutions offer ground protection for mobile cranes, the largest aspect of System Rigging’s capabilities is its fleet of hardwood bog mats.
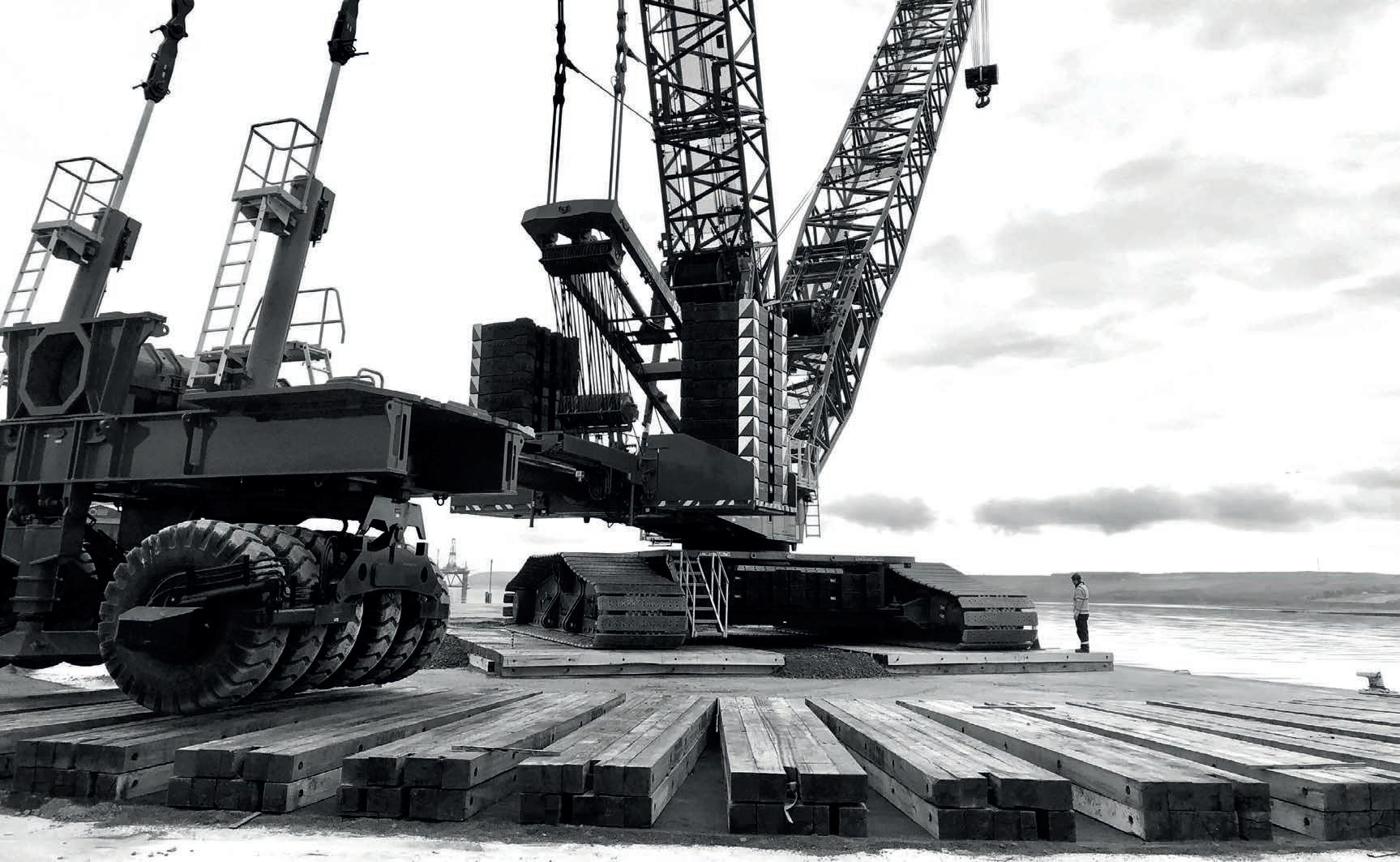
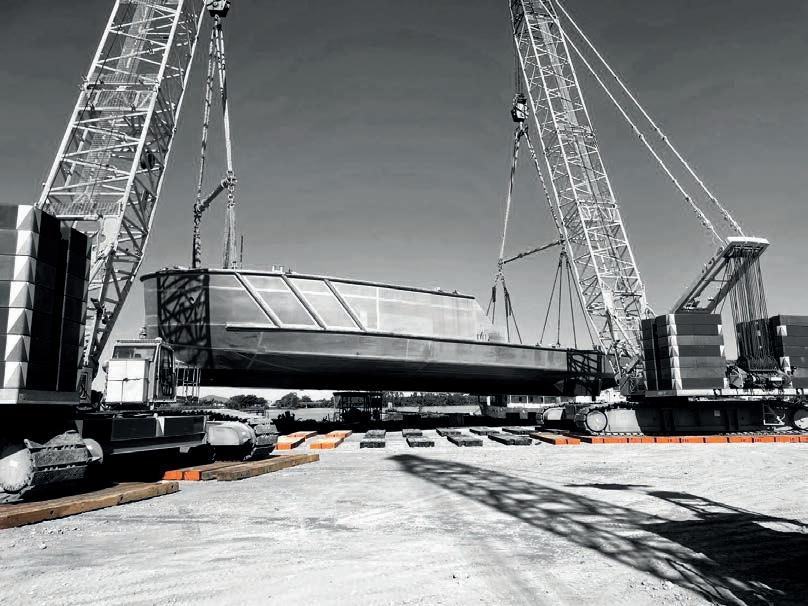
“We have conducted extensive research to best understand hardwood timber characteristics from around the globe and listened to what our clients need to reduce their ground bearing pressures [GBPs] on site. Our hardwood mats range from African Tropical Hardwood such as Azobe/EKKI, European Hardwoods, and Australian Hardwoods such as Karri,” said Declan.
Hardwood bog mats offer good flexibility and elasticity, allowing them to absorb and dissipate the forces of heavy vehicles, machinery, and materials.
“With both hire and sales opportunities available for these hardwood bog mats we have seen these are not just limited to the crane industry. They have become very popular for other applications, such as renewable energy, barging, temporary
“It was clear that finding suitable ground support equipment away from the OEMs was a difficult task for crane owners, so we started off with designing our own range of steel outrigger pads.”
The hardwood matting sourced by System Rigging is designed to support cranes and be far more durable.System Rigging takes the under the crane products as seriously as the rigging it supplies.
roadways, and pipelines. We have had the luck of providing some of the biggest companies in Australia with these products,” Declan explained.
Although a natural product, System Rigging still provide an engineered solution with these bog mats, offering the ability to provide crawler crane track GBP calculations if required.
Recently being awarded with Full Membership of the Lifting Equipment Engineers Association (LEEA), it also provides an extensive range of highquality lifting and rigging equipment from the world’s leading manufacturers. The full range offers products just like any other lifting house, with lifting chains, slings, rigging hardware, fabricated items, and transport restraints.
“We try and push Australian Made products as much as we can through our business, but its difficult to ignore the high-quality European imports for rigging equipment. One of our first ever orders was for some Grade 120 Pewag chain slings for a wind farm project. It matched our core values of providing good quality gear, at a fair value,” Garry said.
System Rigging has also recognised an opportunity to offer an alternative in the lifting device space, by developing its own Australian Made modular spreader beams. Locally sourced and manufactured, this reduces timeframes and lead-times for clients and projects needing this specialised equipment.

“Just like our steel outrigger pads, we strive on achieving high capacities than the competition. Although our beams are slightly heavier in tare weight, we are very
happy with how the Australian highgrade steel performs for these products,” said Declan.
“Technical people want to talk to people with technical knowledge. We are not just a family-run business, we are associated with a team of experts of heavy lift engineers, naval architects, and marine surveyors. We have brought over our own intellectual property from the consultancy business to provide a full engineered solution. When a job
gives you a problem, we’ll find you a solution,” said Garry.
System Rigging has been in operation since the start of 2021. With 18 months of trading under the belt, it is continuing to grow across Australia, providing products and solutions to clients across every state and to even exporting to PNG. With its motto of a one-stop shop, look no further than System Rigging for all your crane and rigging equipment needs.
“Technical people want to talk to people with technical knowledge. We are not just a family-run business, we are associated with a team of experts of heavy lift engineers, naval architects, and marine surveyors.”System Rigging manufactures a range of spreader beams.
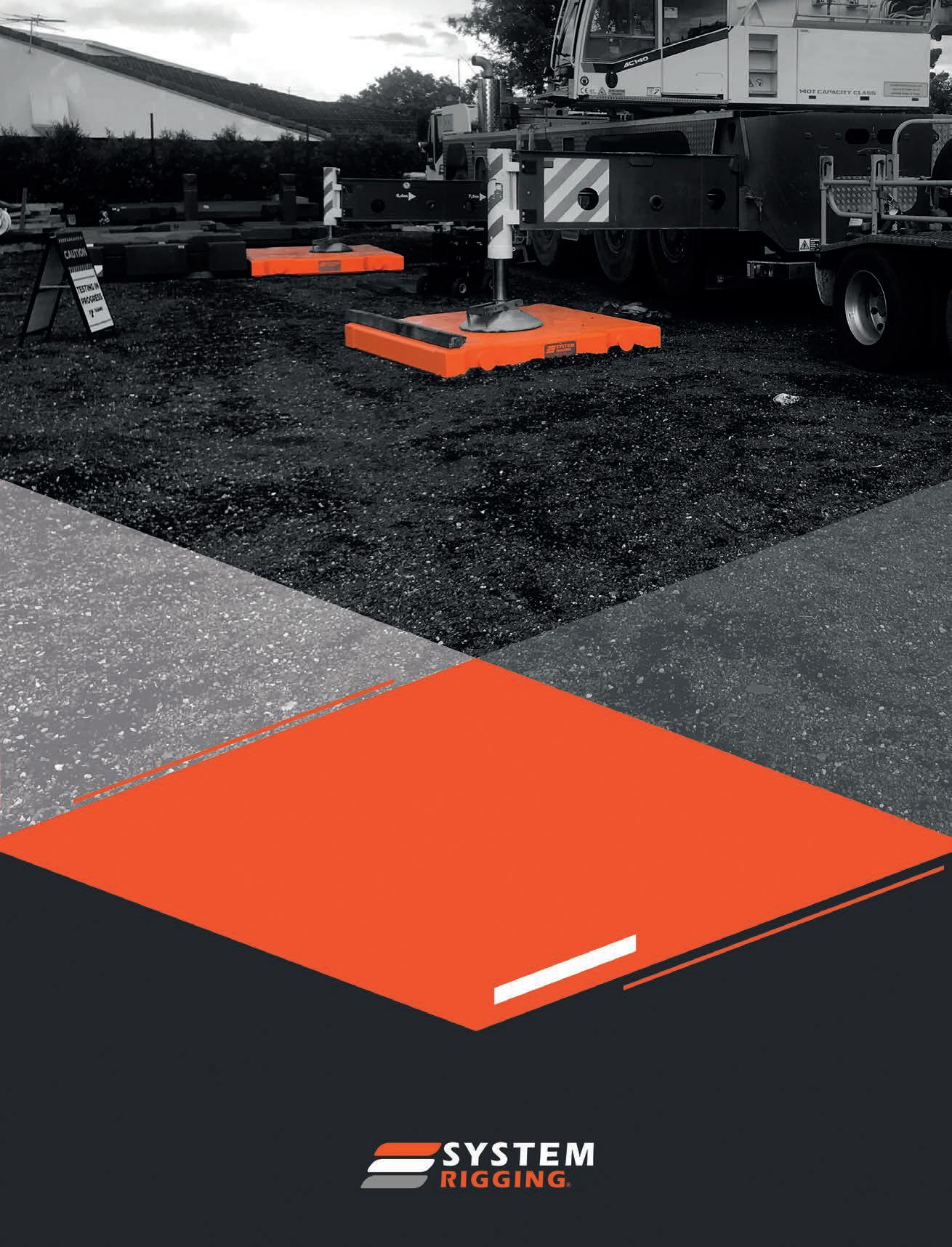

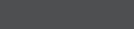
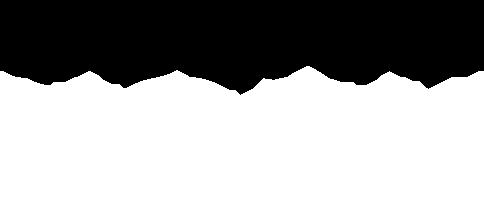
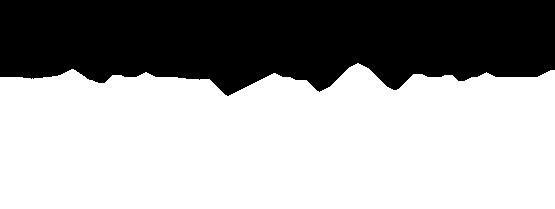
BORGER CRANES HEAVY LIFTS IN BRIDGE CONSTRUCTION PROJECT
Borger Crane Hire and Rigging Services recently completely a series of heavy lifts on the upgrade $178 million upgrade of the Pacific Highway in Lisarow. Borger Cranes’ technical supervisor and heavy lift specialist Jon Gibbin explains that a key feature of the upgrade is the new rail bridge across the main Sydney to Newcastle rail line and how Borger Cranes deployed its 600-tonne capacity Liebherr LR1600 to complete the lifts.
GIBBIN HAS BEEN IN CRANES AND RIGGING for over 30 years and has a wealth of experience in heavy lifting, both offshore, onshore, in the oil and gas sector, and mining – basically anywhere heavy lifting is required. He’s been with Borger Crane Hire and Rigging Services for three years.
“I look after the wind division, so I tender and quote for all the wind farm projects around Australia,” he said.
“I go to the site and project manage, and then finalise everything for the customer handover. I have the same role with major projects like the Pacific Highway upgrade at Lisarow and anything involving the Liebherr LR1600 or the CC2800 or other large capacity cranes.”
The project is the second phase of the upgrade at that section of the Pacific Highway. Borger Crane Hire and Rigging Services completed the first section last year, deploying its CC2800. The recent lifts were completed with the LR1600 narrow track crane, and the last section of the project included the placement six beams. These were managed with a dual lift with a 400t capacity all terrain. Borger Crane Hire and Rigging Services was working for the principle civil contractor, Daracon.
“Daracon were the civil construction company for the project. They are an excellent company to work alongside. I’ve worked with them a couple of times
previously. They’re very much like Borger Crane Hire and Rigging Services: a familyowned business with the same sort of values about planning the job properly, trying to complete the project on time and under budget,” said Gibbin.
“As a result of the meticulous planning, we finished that project a shift and a half early, so it went together very well. There were a lot of site meetings on the job site itself, not only in the boardroom.
Nathan Borger and myself attended three or four meetings on site to meet up with the site crew and go through everything to make sure the measurements were totally accurate, the lift studies were right, all the weights of the beams were correct. When we got to the job site, we built the crane and executed the project very efficiently.
“The LR1600 had 190t of counterweight on the back for the first beam that went in, which was the heaviest at 83t. The crane didn’t need the super lift tray for that lift because the first beam was the closest to the crane itself.
“From then, we had to use the super lift tray. We went to the opposite end of the bridge to the first girder. There were 21 beams in total along that section. We put the first beam in with the walkway across, so we could actually access both sides of the rail corridor. We then came across and
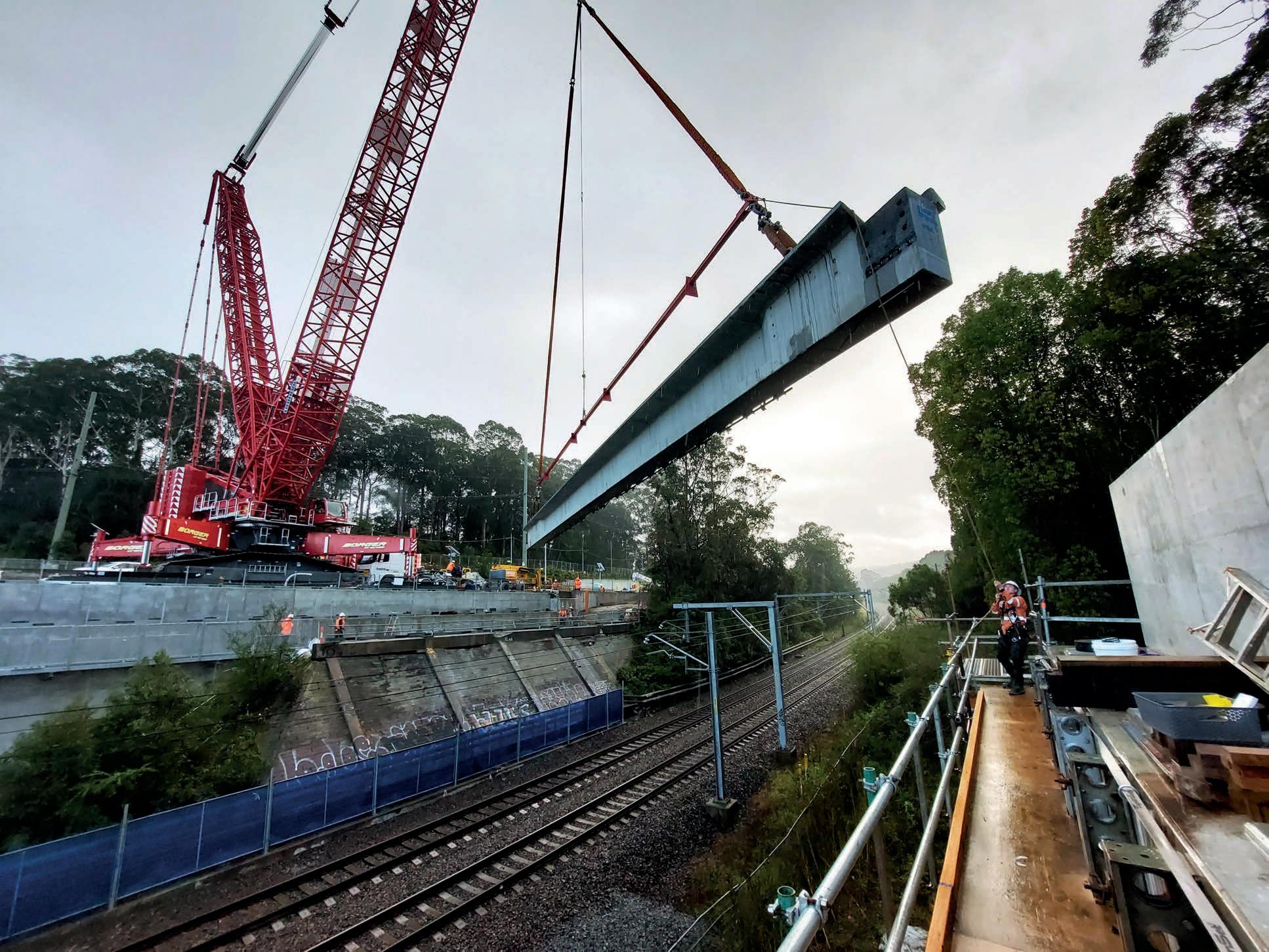
started at the opposite end. With the first of seven beams we had 200t on the super lift tray,” said Gibbin.
“For the next four beams, we had 150t on the tray. This happened in three shifts, which was the Saturday morning, Saturday night and Sunday morning shift, and that opened up the rail corridor because it had protection over the top.
“We then completed the lifts of the final six beams with dual lifts involving the Grove GMK 6400 400t capacity all terrain. The LR 1600 needed 200t on the super lift tray for the first two beams and then dropped down to 160t for the last four beams.”
The LR 1600/2 was originally designed as a crane for wind power. In addition to the standard version, a version with narrow crawler track, known as the LR 1600/2-W includes a main feature that enables it to travel along narrow crawlers roads in wind farms considerably more easily than the standard version.
Initially, the LR 1600/2 was delivered in its SL4DFB configuration, designed for wind turbines with a hub height of 130 to 135m. In this configuration, the crane had a main boom of 138m and a fixed jib of 12m. This was the benchmark for turbines with a hub height of 135m.
Over the next few years, however, the
size of wind turbines increased dramatically up to hub heights of 150m or more. This altered the requirements for the crane, which the designers at Liebherr followed closely.
The lifting capacities and hoisting heights of the boom systems were continuously modified with the SL10, SL14, and SL13 versions, which became established on the market. These booms enabled the crane to handle wind turbines with hub heights of 150m.
However, the LR 1600/2 was not just used for wind power, it was also used in industry and for infrastructure projects shortly after the first one was delivered to
its customer. Often equipped with a ballast wagon or suspended ballast, the 600t crane impressed users with its lifting capacity.
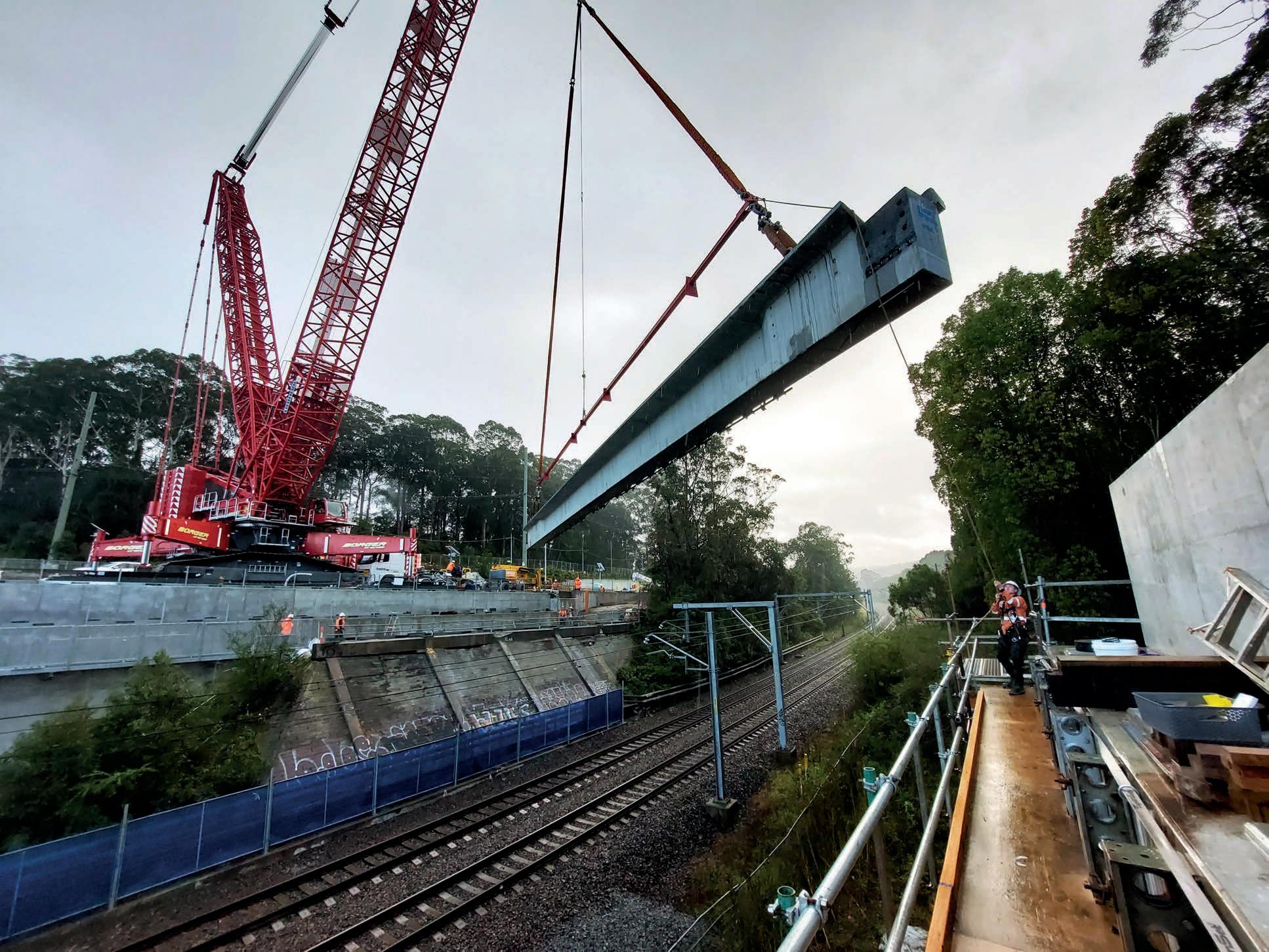
Over the years, Liebherr unveiled more innovations for its crawler crane portfolio, such as the B2 guide and VarioTray for suspended ballast, which eliminates the complicated stacking and unstacking of ballast slabs by simply disconnecting a whole ballast pallet.
Gibbin explains how the LR1600 was lifting in terms of radius.
“The first beam that we picked up, we actually picked it off the back of the truck and had a radius of 30m, and installed it at 26m,” he said.
“We did the same with the next four beams, which we picked up off the truck and at 30m. We then slew around with the beam itself and picked up the super lift tray. We then installed those beams at 47m. Then, obviously, as we went along that row of beams, the radius got shorter to around about 43.5m to 43m install radius,” he said.
The LR1600 was ideally suited for this type of work, said Gibbin, and the Borger Crane Hire and Rigging Services crew are dedicated to the heavy lift side of the business.

“The lifts were similar to the year before when we deployed the CC2800, which is also a 600t crawler. With the radiuses as they were, that was the choice of crane. It had the reach, the capacity, and everything else to go with it. Erika Huang, our draughtsperson at Borger Crane Hire and Rigging Services, worked tirelessly generating and changing the lift studies for the project.
“The crew for the LR1600 has a lot of heavy lift experience and it is the same for
the riggers with that crane as well; they’ve got a lot of a heavy lift background.
The crew included dayshift operator Rob Cooney, dayshift rigger Tierney Muller, nightshift operator Glenn Ryan, nightshift riggers Troy Gallagher and Steve Bozic, and nightshift supervisor Adam Little.
“One of the riggers on the job, Shaun
The project was the second phase of the $178 million upgrade of the Pacific Highway at Lisarow.
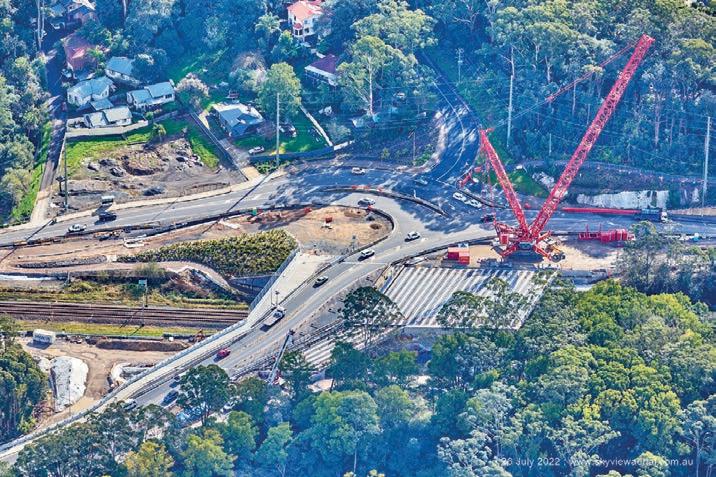
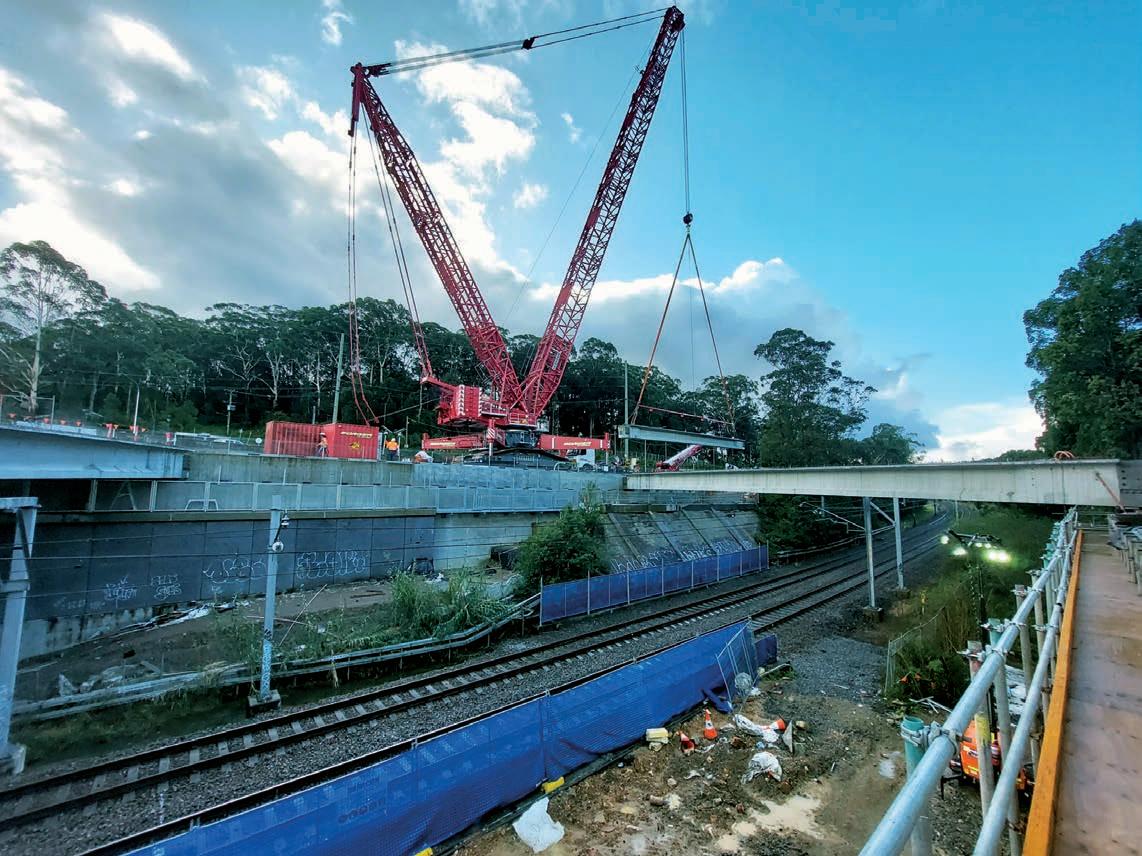
Tweedie, is only young, he’s in his early 20s, but he’s been right through the Borger apprenticeship program, and he’s worked on that crane as well ever since we bought it. I received an email from the project manager saying how great his attitude and skill set were and how he’s an asset to Borger Crane Hire and Rigging Services.
“That’s the good thing about our approach to the next generation coming through. We are not frightened to give them responsibility and the older team members are happy to mentor guys like Shaun and share their knowledge and experience,” said Gibbin.
“The crew for the LR1600 has a lot of heavy lift experience and it is the same for the riggers with that crane as well, they’ve got a lot of a heavy lift background.”The LR1600 was ideally suited for this type of work and the Borger Crane Hire and Rigging Services crew are dedicated to the heavy lift side of the business.

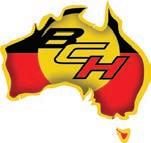
UAA CELEBRATES 50 YEARS IN BUSINESS
2022 sees Underwriting Agencies of Australia (UAA) celebrate 50 years of being the number one provider of insurance for the crane and mobile plant and machinery sectors. A key element of the 50th bir thday celebration sees UAA as the Platinum Sponsor of this years’ Crane Industry Council of Australia (CICA) National Conference and Exhibition.
FROM NOTHING TO $450 MILLION per annum in 50 years, the growth of UAA has been exceptional. With a growing global footprint, and celebrating 50 years in business, UAA recently made another major announcement that it had agreed to merge with MECON Insurance, a construction and plant and equipment specialist in the Australian market.
The history of UAA starts with humble beginnings in 1972 as Sanderson Insurance Brokers based in Newcastle, founded by Phillip Duncan. As an insurance brokerage, it was identified that sourcing specialised crane insurance for customers was difficult and further investigation identified a need to develop a product for our Australian crane industry.
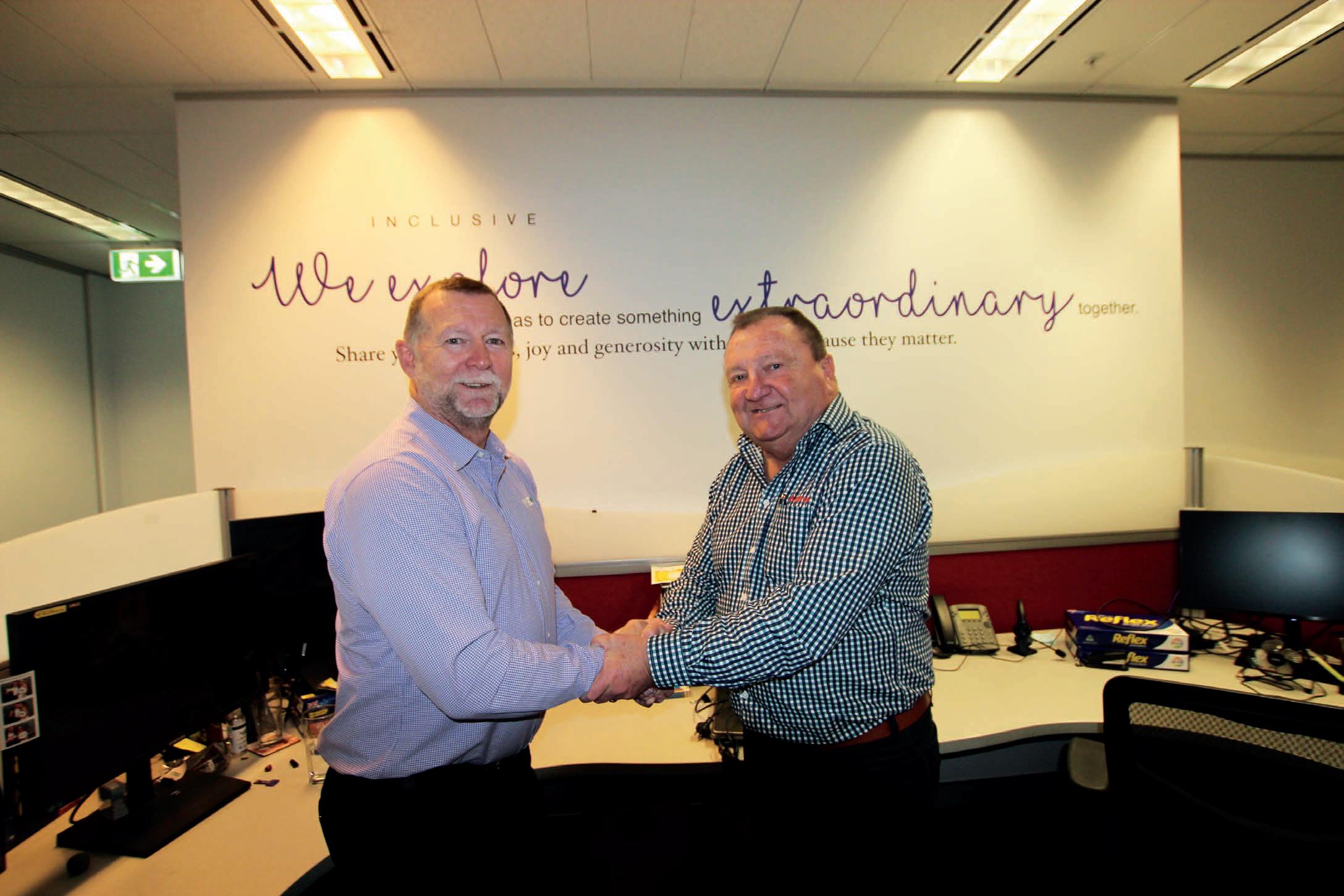
Phillip Duncan packed his suit and flew to England to visit the global insurance market Lloyds of London, to see if he could source a product for crane insurance. He found a syndicate with a very basic product that developed into Contractors Plant Insurance (CPI) in Australia and went on to build an incredible relationship with Lloyds of London.
There was an aspiration to further develop this product and further service the needs of the entire insurance Australian industry through a broader distribution and a specialised underwriting approach that assessed and correctly priced the risk. To do this it was identified that the next step was to become a recognised niche underwriting agency that specialised in crane
and machinery insurance and to utilise the national insurance brokers network to distribute the product to their clients.
In 1988, UAA was born, maintaining a strong relationship with the Lloyds of London syndicate who provided the security that backed UAA. This meant that UAA was able to autonomously underwrite their own crane and machinery risks, and importantly also allowed to manage claims and service their customers. UAA became the first niche underwriter in its class to pioneer such a specific product in the Australian market.
The product continued to develop and grow over the years into the industrial special plant (ISP) cover customers are accustomed to today that expanded to seven sections in order to adequately cover the exposures associated with mobile plant and equipment across a wide variety of industries. These sections now include:
1. M aterial damage (accidental damage), to
2. H ired in plant
3. A dditional benefits such as auto multi lift covers, damage to lifted goods, recovery costs (damage or no damage), etc
4. Fi nancial Protection such as; loss of revenue, increase cost of workings, lease protection and lease gap protection
5. B reakdown cover
6. R oad risk liability to third-party property – for road registered machines
7. B roadform liability – covering personal injury, property damage
and products liability associated with declared activities of a client’s business, not just when in operation with a machine as a tool of trade.
UAA’S HEAD OFFICE IS IN NEWCASTLE, THE BIRTHPLACE OF THE UAA BUSINESS
In 1988, UAA followed the mining industry and opened its second office in Perth, followed by Brisbane, Melbourne and Adelaide.
Each of these offices services brokers within the state with local underwriters and business development managers servicing customers ‘tailored needs’. Our expert claims team is centralised in Newcastle but broken into state teams to encourage relationship building and enhanced customer and local supplier knowledge.
UAA has seen many competitors come and go over the years. Most have attempted to ‘copy and paste’ the UAA ISP product, but UAA has stood the test of time and most importantly maintained its enormous autonomy and reputation in the insurance industry as the experts in mobile plant and machinery insurance – globally.
UAA works closely with the industries they insure to understand the ever-changing landscape and exposures to not only provide adequate coverage but to also assist in mitigating some of these risks through improved industry behaviour and increased safety standards.
In 2002, UAA formed a relationship with QBE Insurance, which assisted UAA as a security and lead
underwriter for a portion of its Broadform Liability insurance.
In 2008, this relationship then led to the sale of UAA to the QBE Group. QBE became the owner, security, and lead underwriter across all of UAA’s covers in the ISP product.
QBE recognised and valued UAA’s expertise, ensuring that the UAA business maintained its entrepreneurial flair, nimbleness, and autonomy to remain the leading niche
underwriter it had worked hard to establish over the years.
During this period, UAA took advantage of QBE’s global footprint and the intellectual property embedded within the business to expand globally, particularly as it was identified that no other insurer in the global market offered the niche product and services of UAA.
In 2012, UAA moved to Chile in South America as the first offshore business and, within 18 months,
wrote over US$6 million of premiums on local QBE paper. From there many of the other major Latin American countries came knocking on UAA’s door and the business expanded into other Latin American emerging markets like Colombia, Mexico, Ecuador, and Brazil.
In 2014, UAA entered New Zealand and formed Underwriting Agencies of New Zealand (UANZ). UANZ is now UAA’s largest business outside of Australia and the leading specialist
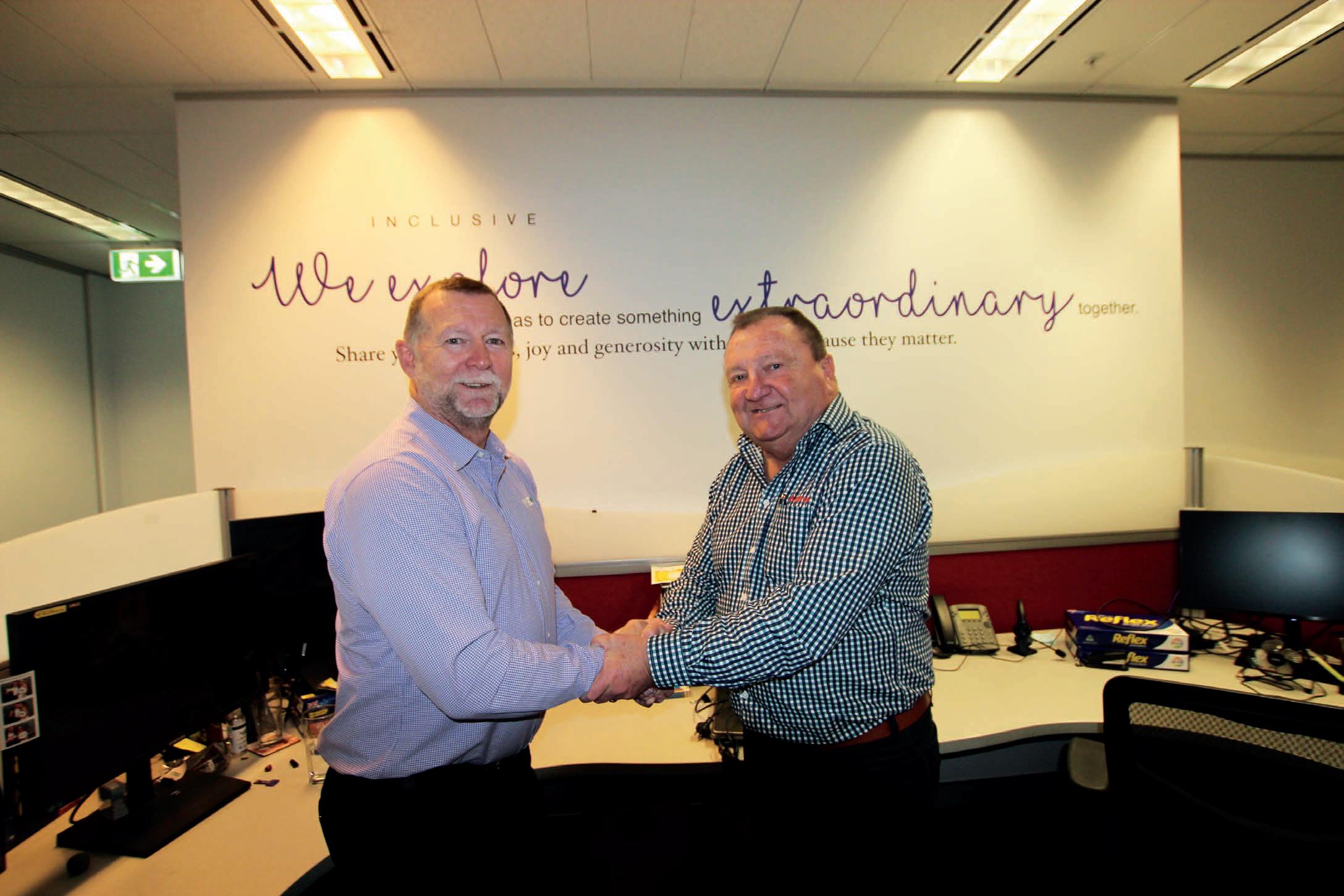
“UAA has seen many competitors come and go over the years. Most have attempted to ‘copy and paste’ the UAA ISP product, but UAA has stood the test of time and most importantly maintained its enormous autonomy and reputation in the insurance industry as the experts in mobile plant and machinery insurance – globally.”
mobile plant and machinery insurer in New Zealand. Soon after, UAA entered the Pacific Islands, based in Fiji, forming Underwriting Agencies of Fiji (UAF) in order to support its New Zealand and Pacific customers.
Between Australian and New Zealand, UAA now underwrites over 80per cent of the crane industry insurance.
In the same year UAA took the business to Singapore to attract the South East Asian market including Hong Kong, and formed Underwriting Agencies of Singapore (UAS). Yes, you guessed it, UAA is not very creative when it comes to naming its business offshore, as CEO Michael Murphy says, but one thing for certain is that it knows how to support the industry – globally.
The ownership with QBE lasted seven years. In 2015 QBE sold UAA to the Steadfast Group, which is the largest general insurance broker network and the largest group of insurance underwriting agencies in Australasia, with over $11.5 billion of premium per annum across its network. The Steadfast Group is a publicly listed ASX 100 company.
Through this acquisition Steadfast hold 88 per cent share of UAA, while the remaining 12 per cent is owned by the UAA executive team, Michael Murphy (CEO), Stan Alexandropoulos (COO), George Grasso (CCSO) and Jane King (CUO).
UAA’s relationship with Steadfast has further strengthened its capabilities in working with all insurance brokers and their combined mutual customers from the plant and machinery industries.
The role of a broker is to dig deep with its customers to understand their exposures and help mitigate these risks by finding solutions to reduce these exposures. Where needed it will go to the market to find the most appropriate insurance coverage for its clients. When it comes to mobile machinery insurance, UAA is front of mind for most brokers.
At UAA there is the saying that all of its policies are hand crafted because no two businesses are the same. UAA tailors coverage to suit individual customer needs in the crane, mobile plant and construction equipment sectors.
UAA is respected and trusted by the insurance industry across the globe, which has enabled it to build an extensive network of industry repairers and professionals that assist its customers at their time of greatest need: during a claim.
To coincide with the UAA’s 50th birthday celebrations, UAA and MECON Insurance recently announced the two businesses have agreed to merge.
MECON is short for Mechanical and Construction and, as an insurance business, has been operating in the construction
and we like to think UAA is the best underwriter of plant and equipment. The power of bringing the two together is insurmountable.”
The merger means UAA and MECON will have a large market share in the construction insurance space at large. The combination of UAA’s strength in plant and machinery combined with MECON’s strength in construction means there is a high chance UAA will be managing the insurance for machinery and plant and MECON the insurance of the contract works.
UAA conducts a Net Promoter Score survey through the network of insurance brokers it works with and the most recent results have come back at plus 56. MECON also enjoys a high NPS, gauged through annual surveys with brokers.
insurance and plant and equipment space for 18 years. Both businesses are under the Steadfast Group umbrella. MECON is considered a leading construction insurer in the Australian market and will continue to operate under their own established brand.
Michael Murphy discusses the benefits that clients of UAA and MECON will see following the merger.
“The message to our clients, the insurance brokers and also to our end users, is ‘Two brands one family’. Clients can now come to one family for the best two products and receive the unparalleled service we are now capable of offering. In our opinion, the delivery mechanism is compelling,” he said.
“MECON is the best contract works specialist underwriter in Australia
“Most insurance and finance companies are happy to register a positive result. UAA’s results increased by 12 points compared to the previous survey. This is as a result of how the claims team performed during the recent flooding disasters. We challenged our team to be superstars during what was an extremely challenging period and they delivered,” said Murphy.
One thing the UAA Group has never done is rest on its laurels and 2023 will be another big year in UAA’s history as it continues its global expansion into the Canadian market and beyond.
It looks forward to continuing its journey as a driving force behind mobile plant and equipment protection globally for at least another 50 years.
“We have a saying at UAA that all our policies are hand crafted because no two businesses are the same. UAA tailor coverage to suit individual customer needs in the crane, mobile plant, and construction equipment sectors.”
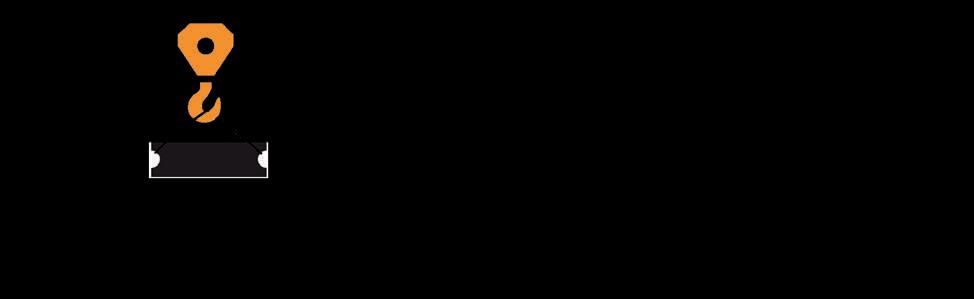
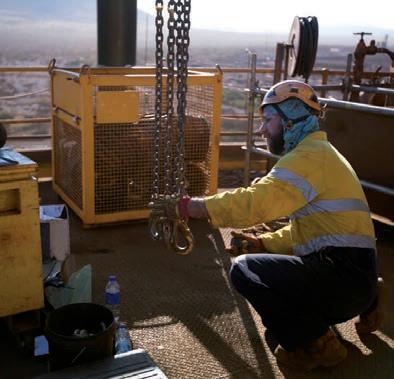

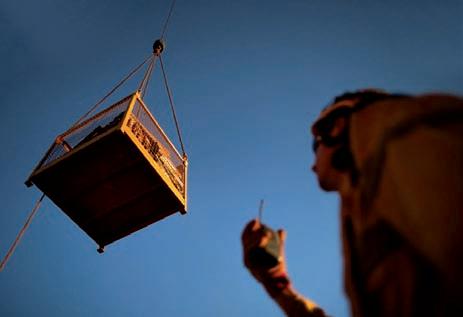
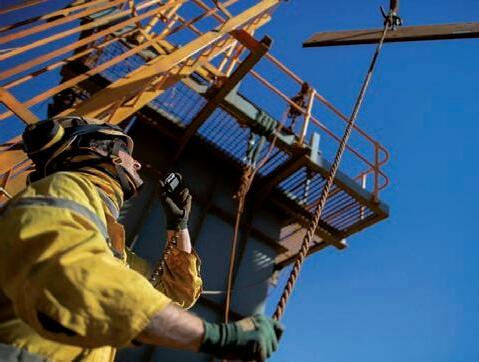
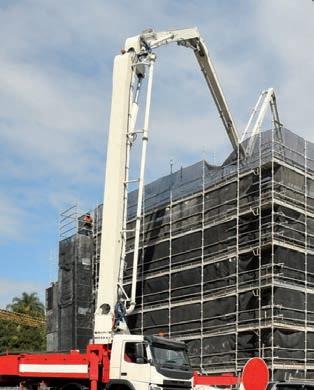
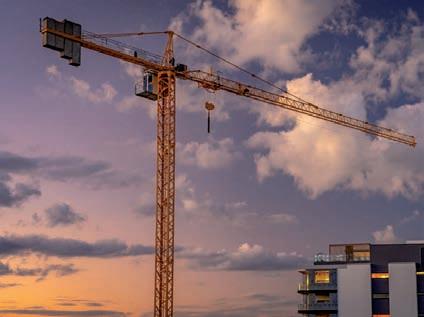
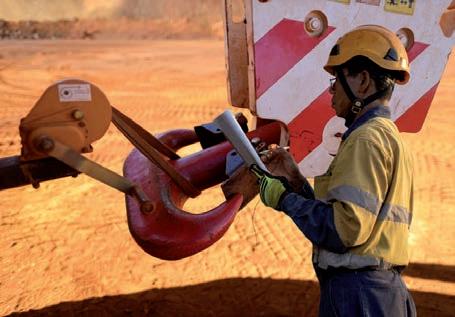
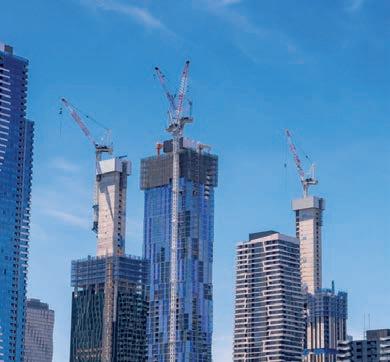
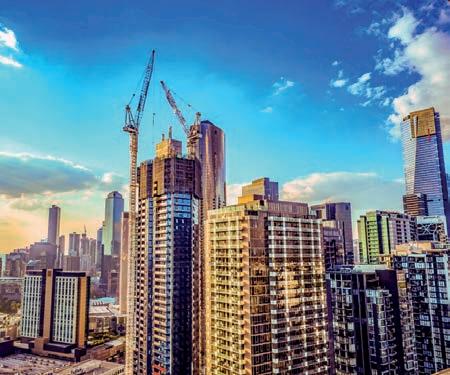
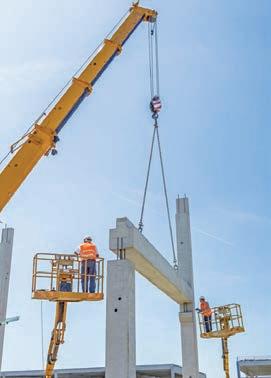
SANDERSON INSURANCE CELEBRATES 50 YEARS
This October, Sanderson celebrates 50 years of being in business. Begun in 1972 as an insurance brokerage Sanderson have had a history closely tied to the crane industry.
SANDERSON SENIOR BROKERS
include Andrew Bramble –whose father was involved in the development of UAA and who was also a senior broker with Sanderson for over 40 years – and Gina Brasher, daughter of Lach McKeough, Austbrokers Holdings founder and former CEO. There is little doubt that both Bramble and Brasher have lived and breathed insurance for
majority of their lives and, with their combined experience within the brokerage industry of over 40 years, they make the perfect partnership to head up Sanderson Insurance.
Bramble joined Sanderson in 2005, and Brasher in 2009, with both having managed and developed the business since.
“We both bring different strengths to the table, but one thing we have always had in common is that we both really enjoy helping people. We have never focused on chasing dollars, but instead on what is best for each and every one of our clients,” said Bramble.
“Whether they are our largest crane account or an individual domestic property owner, we always take the time to provide advice and offer solutions where we can and this in turn has built the trust and embedded the strong relationships that we have maintained with our clients for many years,” he said.
Sanderson’s portfolio is heavily weighted within the mobile plant and equipment space. With its vast experience in this industry, it has become a specialist broker in this field.
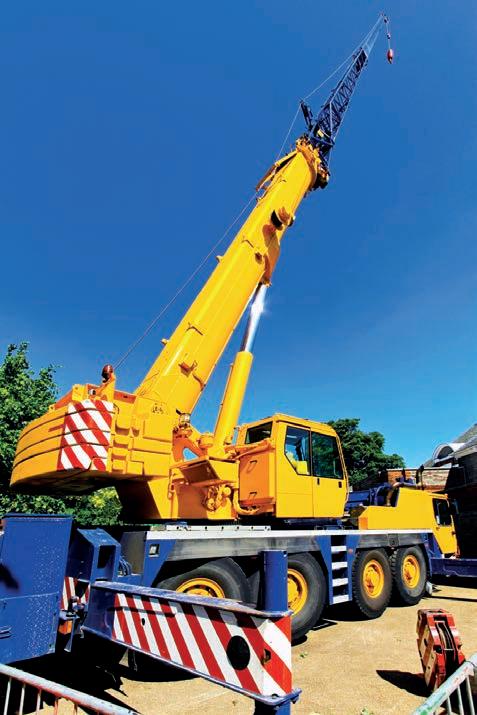
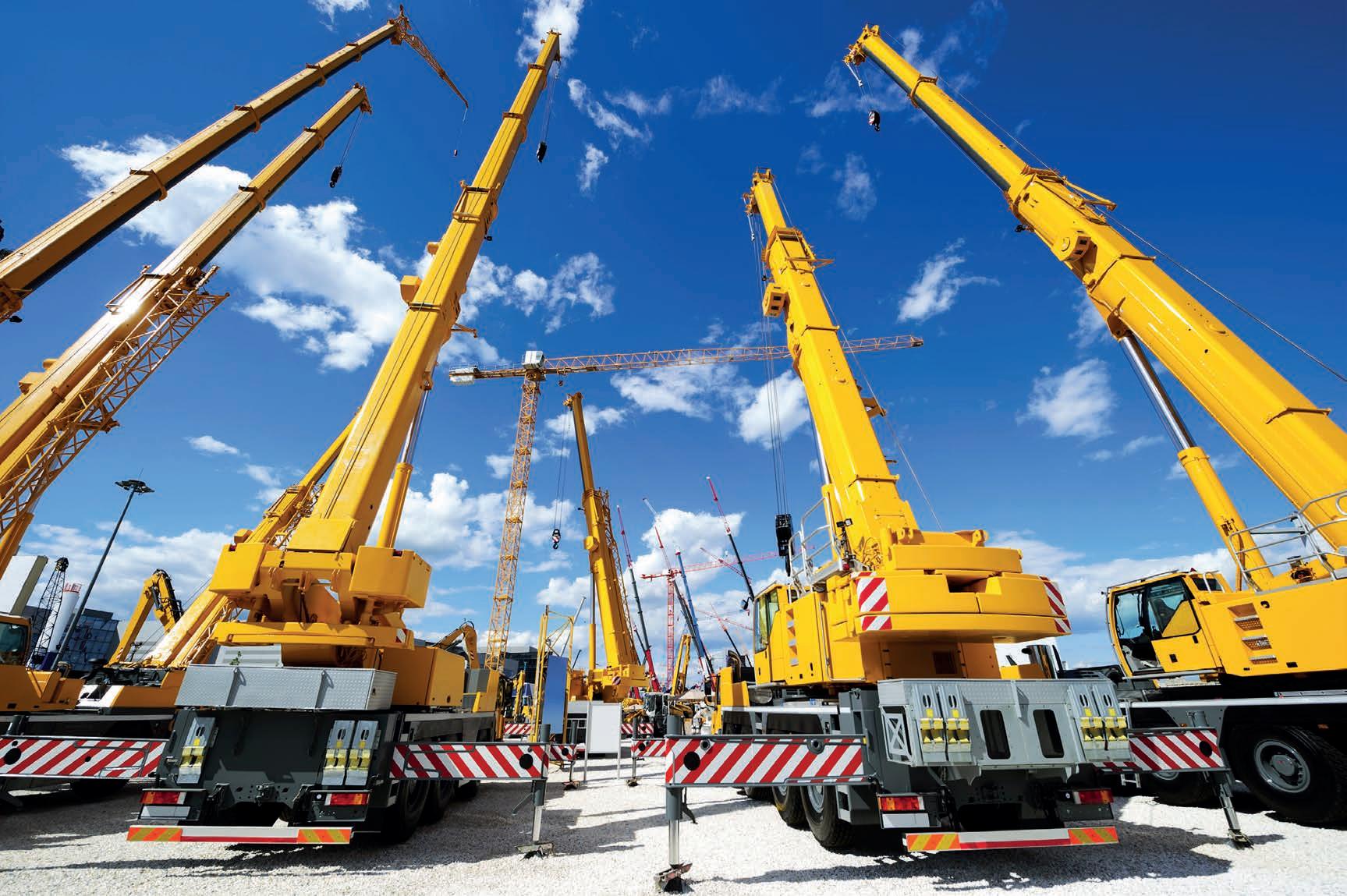
Within the current climate, with many businesses facing staff shortages and financial pressures, now more than ever clients need to be able to rely on the expertise of their broker, especially within the niche mobile plant and machinery sector.
Knowing what products and insurers may suit your business now and throughout the policy period is crucial when structuring a client’s insurance program.
The relationships Sanderson has developed over the years with insurers, claims teams, and repairers plays a huge role in ensuring that claims run smoothly and Sanderson can get its clients back on site as quickly as possible.
When establishing or reviewing your current insurance program with your broker, Sanderson recommends paying particular attention to the following key elements:
• E nsuring that the goods you are lifting are adequately covered by your accidental damage goods on hook limits and continually ask questions of your customer, including the value of items.
• H aving conversations with your broker and insurer to keep them in the loop with future business plans. Often some insurers may not be able to accommodate higher
value items or certain industries. Having these discussions at renewal will help your broker ensure your cover is placed with the most appropriate insurer and changes can be made in a timely manner if and when required.
• I n the current climate replacement costs for plant, some machinery, and vehicles have seen increases in excess of 30 per cent. With this in
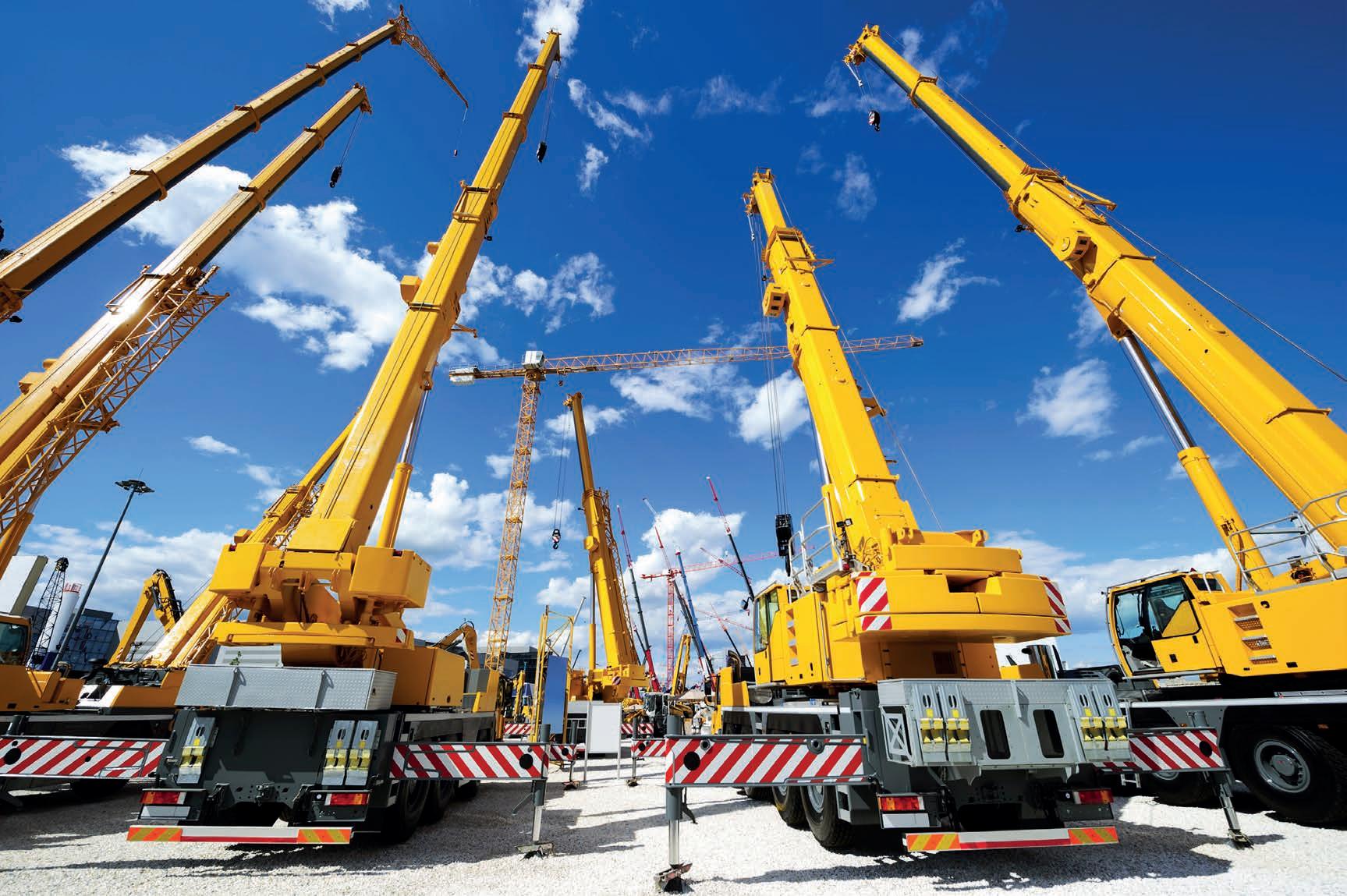
mind you need to review all fleet sums insured to ensure they reflect the current market value. If this practice isn’t adopted you may be grossly underinsured.
Having a close relationship with your broker and actively keeping them involved will assist with them ensuring your coverage is placed with the correct market for your business.
“Whether they are our largest crane account or an individual domestic property owner we always take the time to provide advice and offer solutions where we can and this, in turn, has built the trust and embedded the strong relationships that we have maintained with our clients for many years.”Sanderson wants to grow with businesses and future proof insurance policies.
PRESTON HIRE’S SUPERCRANES PILING ON THE SERVICE
With the unprecedented investment in infrastructure projects continuing, the piling sector is increasingly turning to crane hire companies for support cranes and lifting solutions.
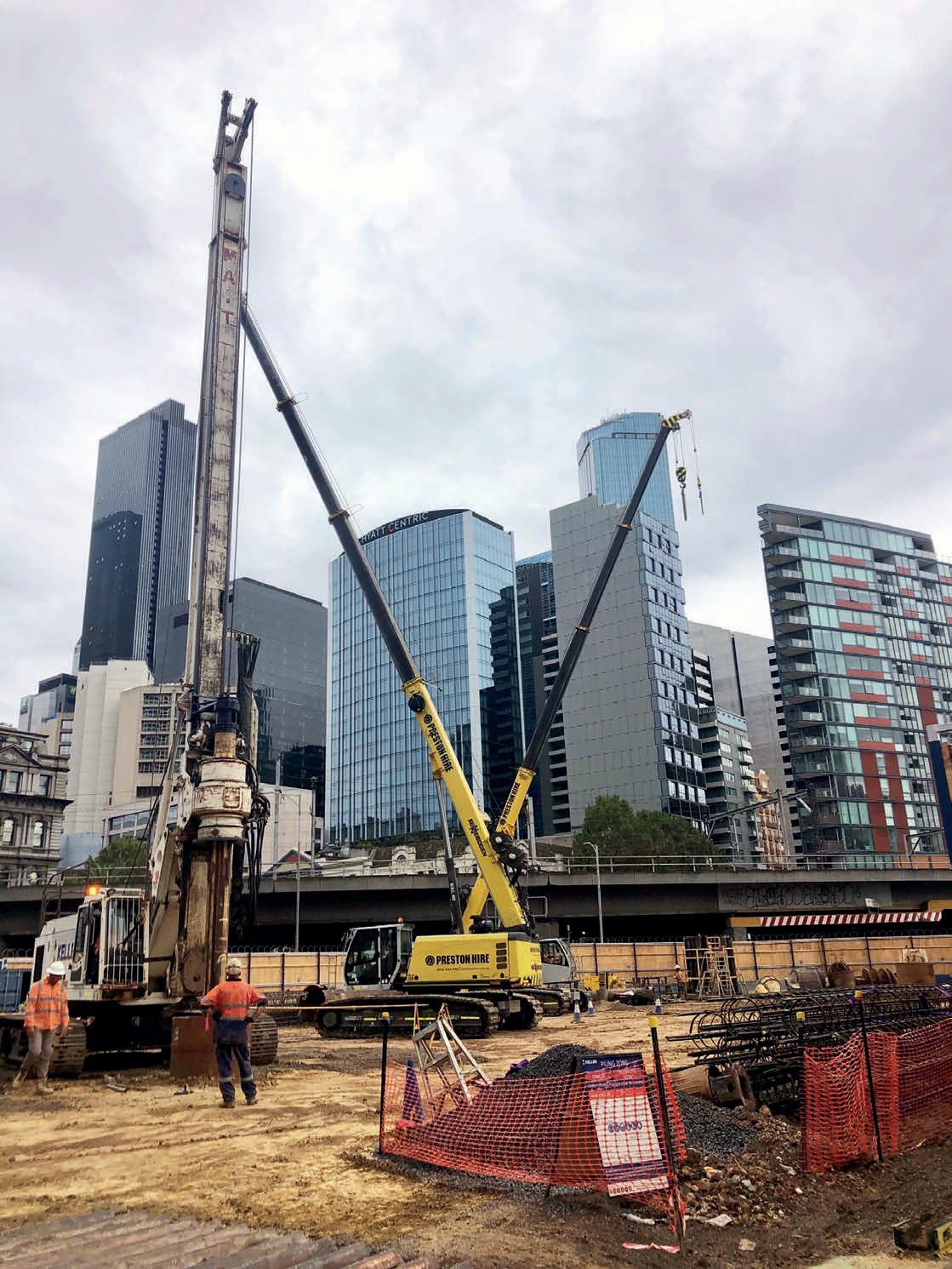
PRESTON HIRE’S SUPERCRANE FLEET IS leading the way by providing a range of cranes to various leading piling companies and projects. Stephan Becherand, Preston Hire Head of Cranes, explains more.
The infrastructure and piling sector is currently booming resulting in a significant demand on the products and machines that Preston Hire provides to the market. Becherand has proactively chased these opportunities with the support of his team resulting in the Preston Hire SuperCrane fleet being busier than ever.
“Piling companies are a growing part of our clientele. Their requirements are detailed with very specific needs per job. The complex nature of these briefs requires experienced crane professionals to review and provide recommendations. Crane capacities and capabilities vary per job and dictate what machine, or combination of machines, is required. We are very fortunate that our fleet caters for such a vast range of applications that we haven’t had a scenario we can’t handle. The majority of work is completed by our Tele Crawlers, however on occasion other models have been utilised for specific tasks,” he said.
Becherand goes into more detail regarding the Preston Hire SuperCrane tele crawler fleet.
“The crane hire market, and more specifically the piling industry, continues to demand specialised cranes. Projects are becoming increasingly involved which increases the number of challenges customers face and the need for specialised equipment to provide solutions. Our SuperCrane fleet has always focused on providing the industry with unique equipment that delivers power, performance and precision,” he said. “Our Tele Crawler fleet has been carefully
selected based on the machine’s ability to perform varying tasks and deliver on crucial elements such as a compact footprint, precision, manoeuvrability and lifting abilities. We have expanded on the machine brands we now supply to our customers in addition to now offering up to 100T lifting capacities,” he said.
This market approach and resulting supply of machines is clearly working with the Preston Hire team involved in a number of major projects for key customers across the country including:
• Wagstaff Piling - Western Sydney Airport NSW
• Avo Piling - Sydney Gateway Project NSW
• Geotech – Northeast Link VIC
• Geotech - Bunbury Project WA
• Keller - Power Museum Parramatta NSW
• GFWA – Yanchep Project WA
productively complete the piling works.”
“It is incredibly rewarding to be involved in such large projects that will provide genuine advantages, new facilities and improvements to each city and state,” said Becherand. “It appears to be a new era of work with today’s projects requiring cranes with smaller footprints yet with the expectation for the same loads to be lifted. Customers are looking for larger capacities from smaller cranes to manage their lifting plans. Preston Hire has embraced these challenges and invested in machines that compliment and meet market demands, providing genuine solutions for customers,” says Becherand.
“Our fleet has been built with a blend of machines unlike any other business in Australia. With both tele handlers and Mini Crawlers, we truly have something for everyone. Our Mini-Crawler range is one of the largest in Australia and has been a point of difference for us in the market
One of the projects the Preston Hire team has been involved with is the new Western Sydney Airport terminal, working closely with Wagstaff Piling. Thadu Khin from Wagstaff Piling said “This was a landmark project for Wagstaff Piling with the construction of over 1200 No. Bored Piles up to 28m in depth. Due to the stringent lifting requirements of our principal contractor we relied heavily on Preston Hire’s cranes, operators, workshop and management to provide the necessary expertise to safely and
delivering impressive lifting capacities, easy operation and lightweight solutions for lifts in challenging conditions.
“Mini Cranes were originally our main focus, however as more and more clients enjoyed the experience of working with Preston Hire and the service proposition we offer, growing demand became evident for our hydraulic crawler range to also grow. Pending the specific tasks of our Piling customers, the majority of our crawler fleet have been utilised to complete works for this sector,” he said.
“The major advantage to customers who hire their equipment with Preston Hire is the flexibility to secure machines that cater to their site requirements and deliver the correct capacity needed.”
Projects are becoming increasingly challenging and the need for specialised equipment is growing.
The full Preston Hire SuperCrane fleet ranges from 1t through to 100t capacities which is across the mini cranes, hydraulic crawler cranes and mobile cranes. The fleet includes models that feature the latest ecofriendly, electric and battery technologies.
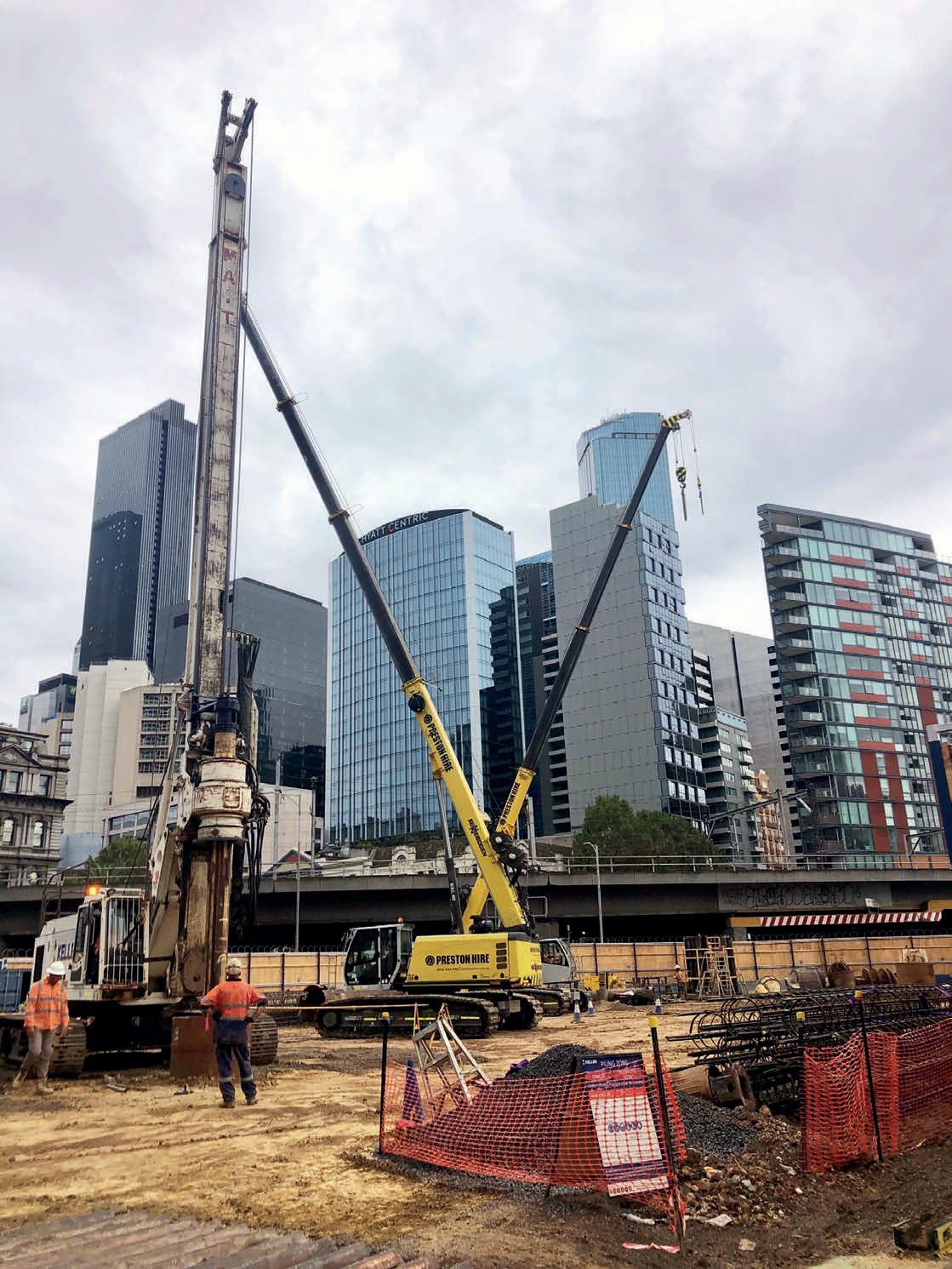
The SuperCrane fleet is made up of Kato, Maeda, Liebherr, UNIC, SANY and Sennebogen machines in various models and capacities. Each machine has been carefully selected based on its unique abilities, quality craftsmanship and the benefits it can provide to a broad range of disciplines. All cranes are available for both wet and dry hire depending on the needs of the customer.
Preston Hire has branches nationally servicing all regions of each state. Pending the needs of our customers, we can transport machines from one state to another to ensure the correct capacity and capabilities is available where needed. With a fleet of over 100 cranes, most states have a broad range of machines ready to go.
Becherand goes on to discuss the advantages of hiring cranes from Preston Hire’s SuperCrane fleet, compared to a business purchasing and operating cranes themselves.
“The continual change of requirements per job requires the right machinery for the task at hand. A cookie-cutter approach to equipment selection can be limiting, and in some instances dangerous if the wrong machine is used for the job. The major advantage to customers who hire their equipment with Preston Hire is the flexibility to secure machines that cater to their site requirements and deliver the correct capacity needed. When a customer moves to their next job, we can once again assess their needs and change the machinery selected if required,” he said.
There are also significant costs associated with purchasing heavy equipment. Maintenance, servicing, the initial purchase price, interest payments, storage, insurance, licencing and transport should all be considered. All of these responsibilities and costs sit with Preston Hire to manage on behalf of its customers. This is yet another major benefit for hiring product.
and innovation. Working alongside an equipment hire specialist is an ideal way of keeping abreast of industry developments, as they occur.
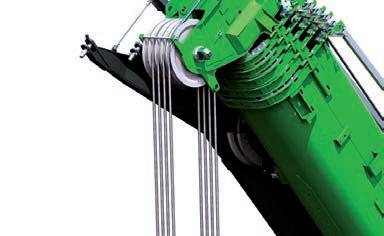
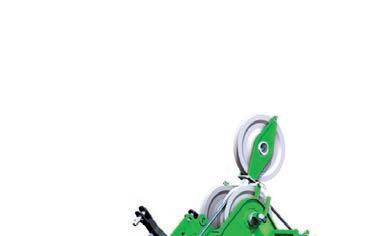
Becherand explains how Preston Hire ensures it has the right equipment available for its customers.
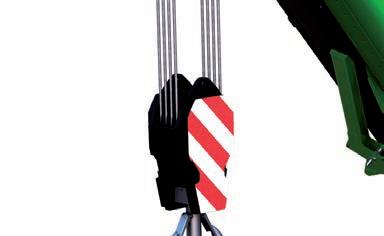
“Conversations with our customers is key. We pride ourselves on having honest, transparent conversations to learn what they need. Across the country, we are continually assessing the amount of works in the pipeline and based on market feedback and the requests we are receiving from our customers, we will
Becherand takes a look into the not too distant future where crawler cranes are being viewed as multi-functional tools with large capacities and pick and carry capabilities. He explains how Preston Hire sees this developing over the next few years and how this will impact the expansion of the SuperCrane fleet.
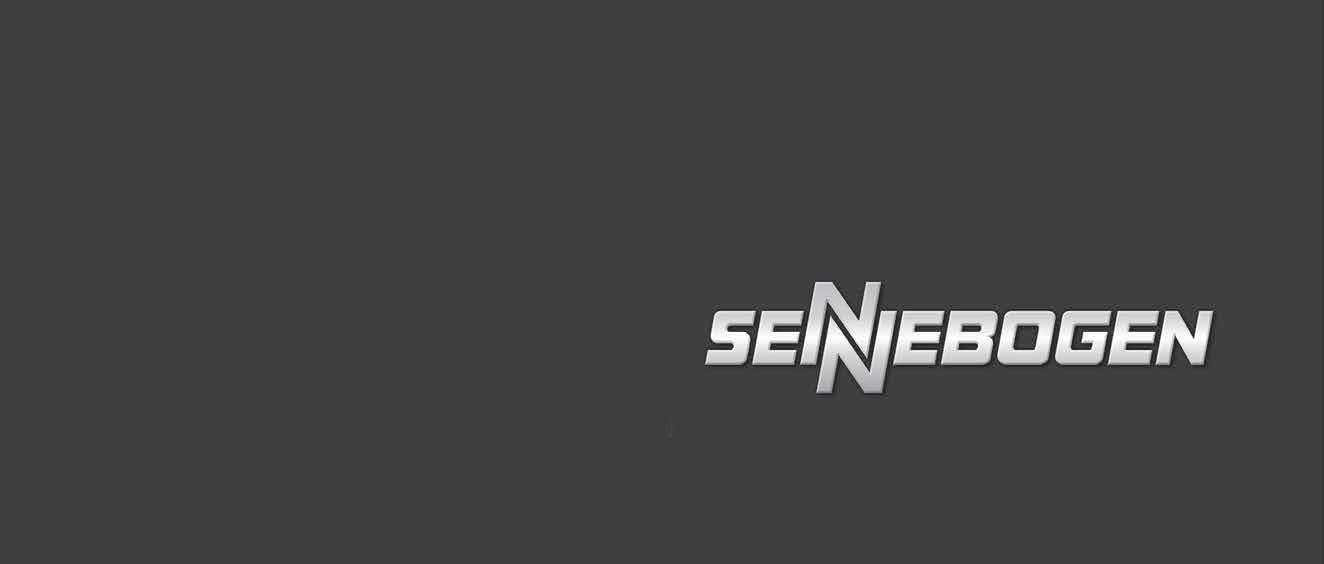
“Preston Hire has been investing in the latest cranes which feature Ecofriendly technology, and we will continue to do so. We are seeing increasing demands for fully electric options from various industry sectors including construction, mining as well as retail and other types of indoor applications where emissions are unacceptable. The Preston Hire SuperCrane fleet will continue to remain focused on providing environmentally friendly options as they become available,” he said.
Becherand is not alone in his thinking. Masis Tevanian, National Operations Manager of Avopiling commented; “We have developed a great relationship over the years with the Preston Hire team. The cranes that we have used in the past have not only been suitable but have increased our efficiency in our projects. We need companies like Preston Hire to develop new products coming into the market and we believe the new cranes that are being supplied
be increasing our fleet in both size, and capacity,” he said.
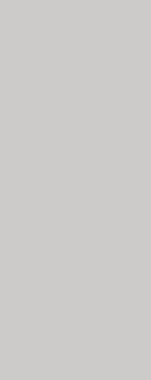


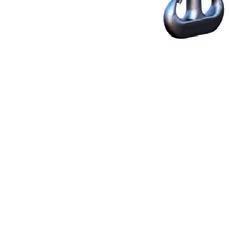
This approach to customer service has not gone unnoticed. Andrew Grenenger from Geotech commented; “We’ve been using Preston exclusively for the last few years now for all of our crane requirements. Their fleet is constantly updated and large enough to meet our scope locally without the need for interstate floats. The price is always competitive and the personal touch in regards to service ensures we only ever make one call when looking for a crane.”
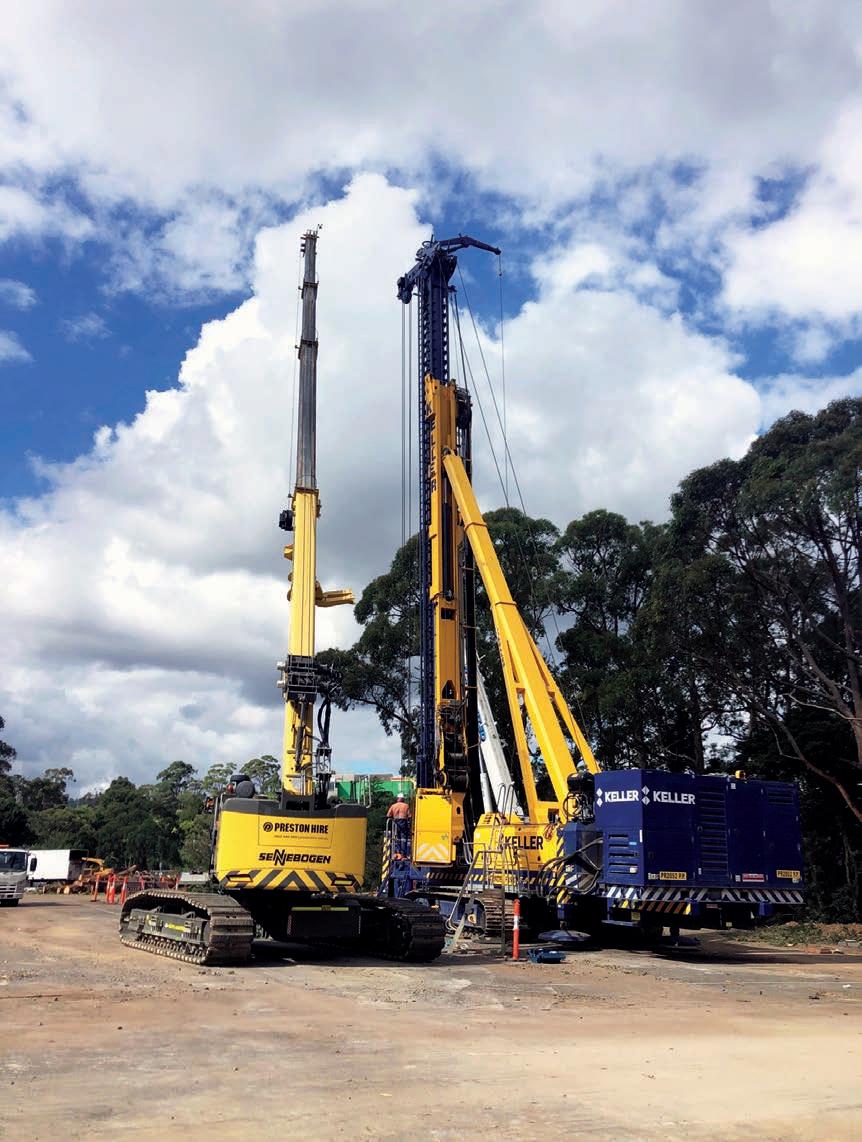
are a growing trend in what is to come in the industry.”
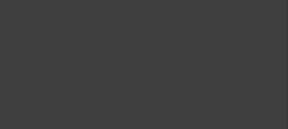
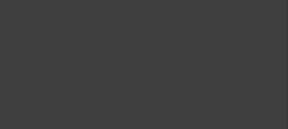
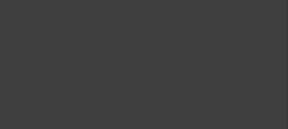
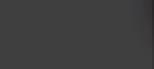
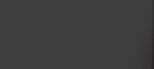
“It is an exciting time for the crane hire industry with so many opportunities available if you are willing and able to adapt, service and deliver,” said Becherand. “Preston Hire has worked hard to demonstrate to customers across multiple sectors our commitment to quality and our exceptional experience and knowledge around our crane capabilities. As always, you can COUNT ON US for an outstanding hire experience.”
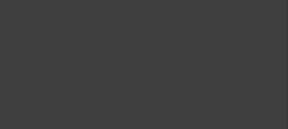
“Preston Hire has been investing in the latest cranes which feature Eco-friendly technology, and we will continue to do so.”Preston Hire’s SuperCrane telecrawler fleet has been carefully selected based on the machine’s ability to perform varying tasks and deliver on crucial elements. These include a compact footprint, precision, manoeuvrability, and lifting abilities.
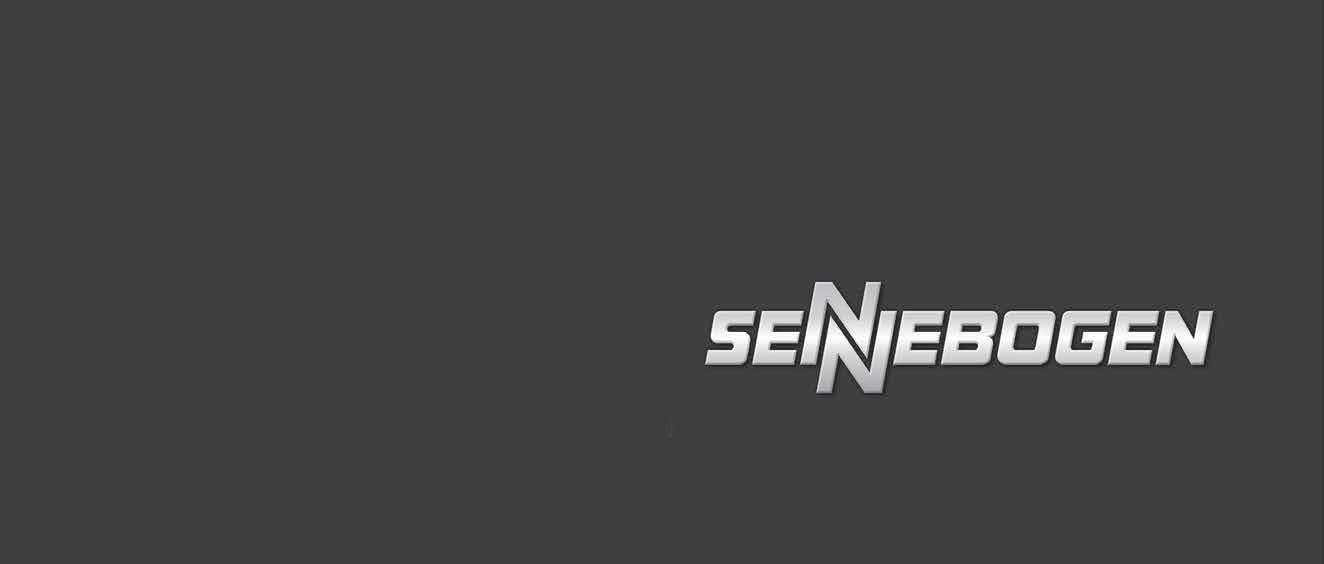
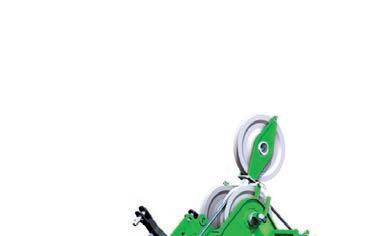
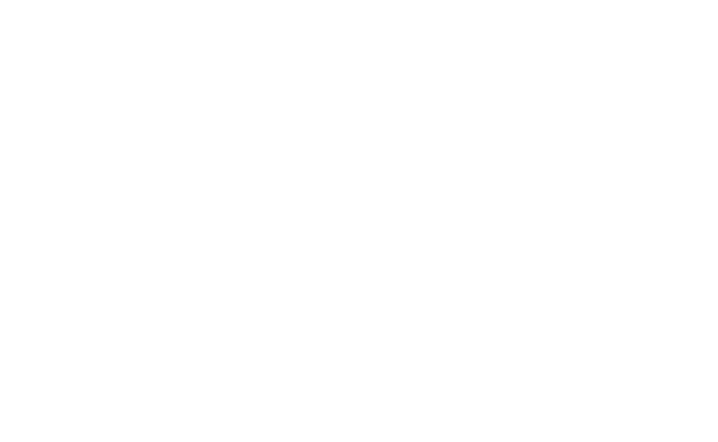

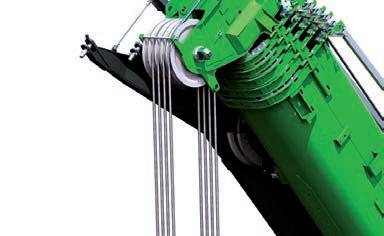
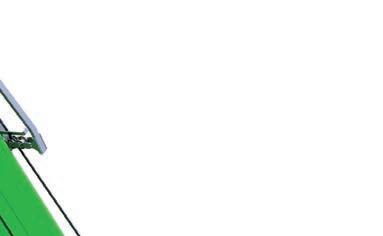
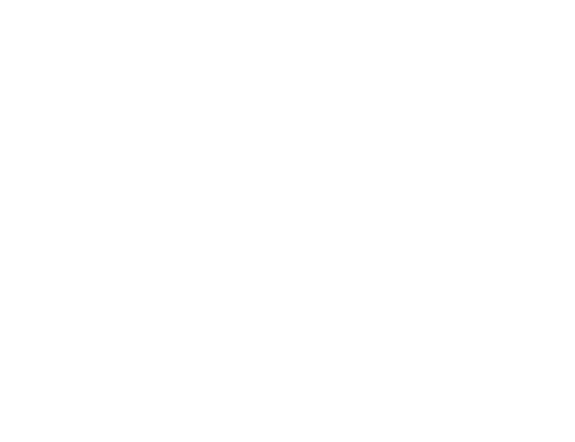
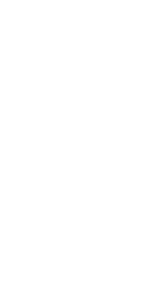
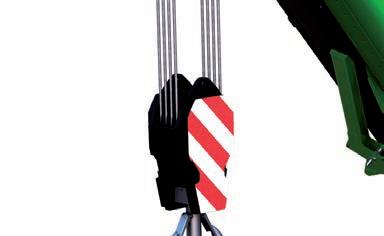
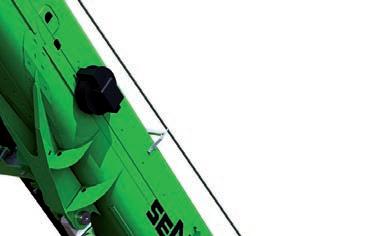

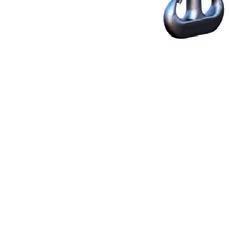
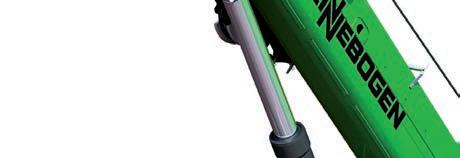
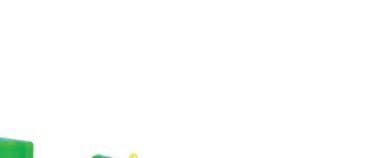
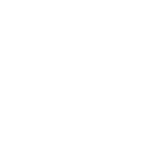

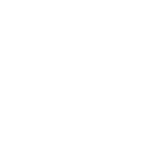
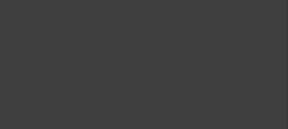

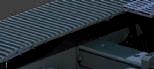
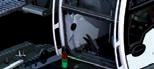
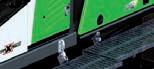
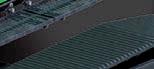
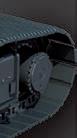
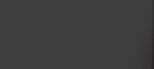
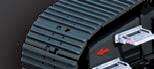

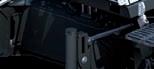

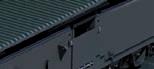
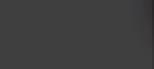
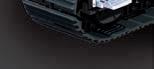
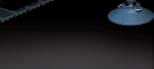

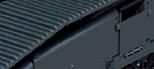
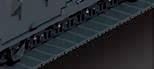
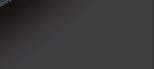
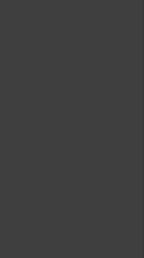
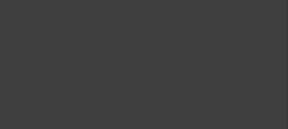
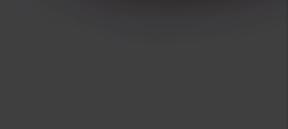
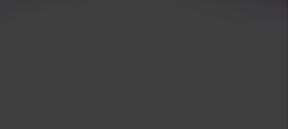
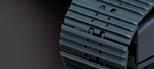
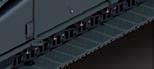
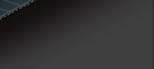
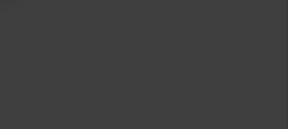
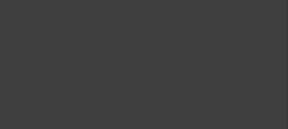
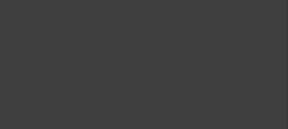
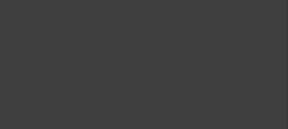
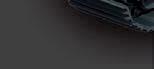
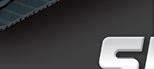
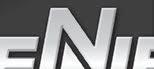
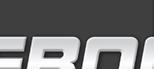
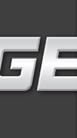
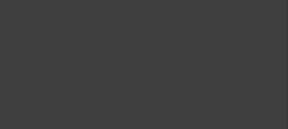
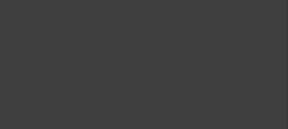
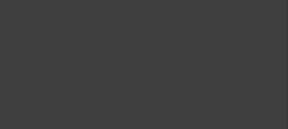

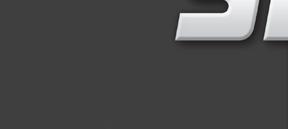
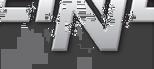

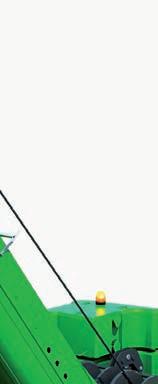
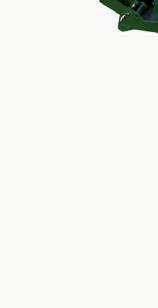

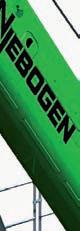
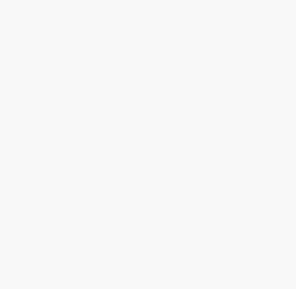
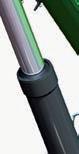
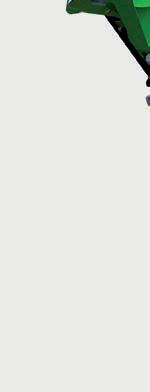
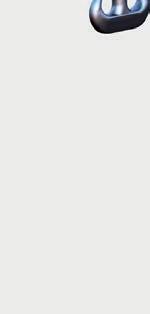


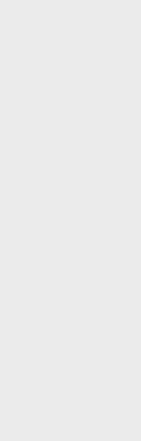
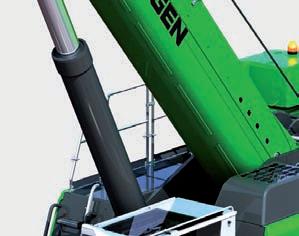
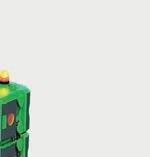
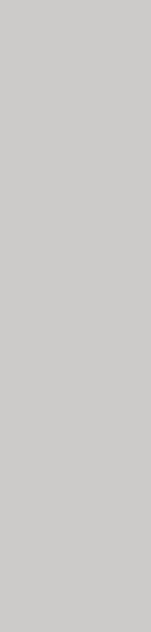


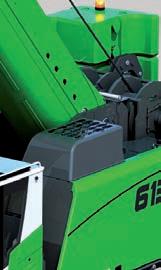
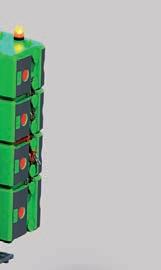
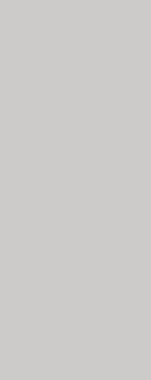
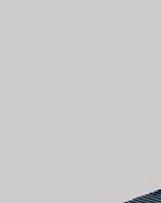

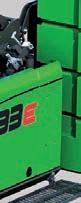
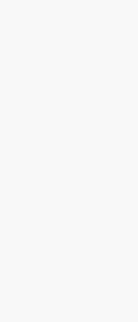
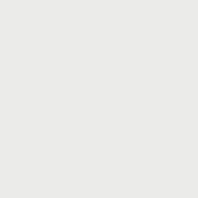






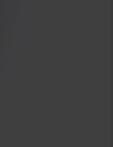






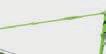
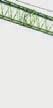



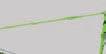
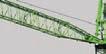

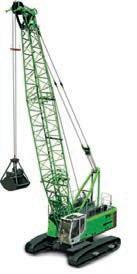
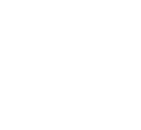








WIRE ROPES FOR ALL TYPES OF APPLICATIONS
Having been in the industry for 25 years, Mark Eberhard has a strong insight into wire rope and lifting equipment, where the industry has come from and where it is headed. Having been recently appointed as the chair for the South Australian branch of CICA he is eager to bring his experience to the role.
“I AM EXCITED TO TAKE ON THIS NEW role. I have been on the committee for a long time and this position will have its challenges, but I am excited for the opportunity,” said Eberhard.
Eberhard has a slightly different background in the industry to other members, but his experience will add value. Owner of both Crane Ropes Australia and LiftQuip, he has the opportunity to communicate to crane hire companies as well as a wide cross section of industry.
With many years of experience
in the wire rope industry, including inspection, testing, and manufacturing through to supply, Crane Ropes Australia aims to use its valuable experience to provide crane owners with a partner that not only understands the technical aspects of this valuable product but aims to provide the highest levels of customer service. Eberhard explains more.
“We are effectively a one-stop shop for companies. We have all of their wire rope needs covered. This enables our customers to come to us with their

requirements for all of their cranes rather than have to individually contact each OEM,” he said.
“When we are sourcing our ropes, we are working closely with world leading manufacturers. Often they are the same suppliers providing ropes for the leading OEMs.
“There is a group of manufacturers that we use to ensure we are offering the highest quality ropes available in Australia,” Eberhard said.
For Crane Ropes Australia and the team, some of the standout products
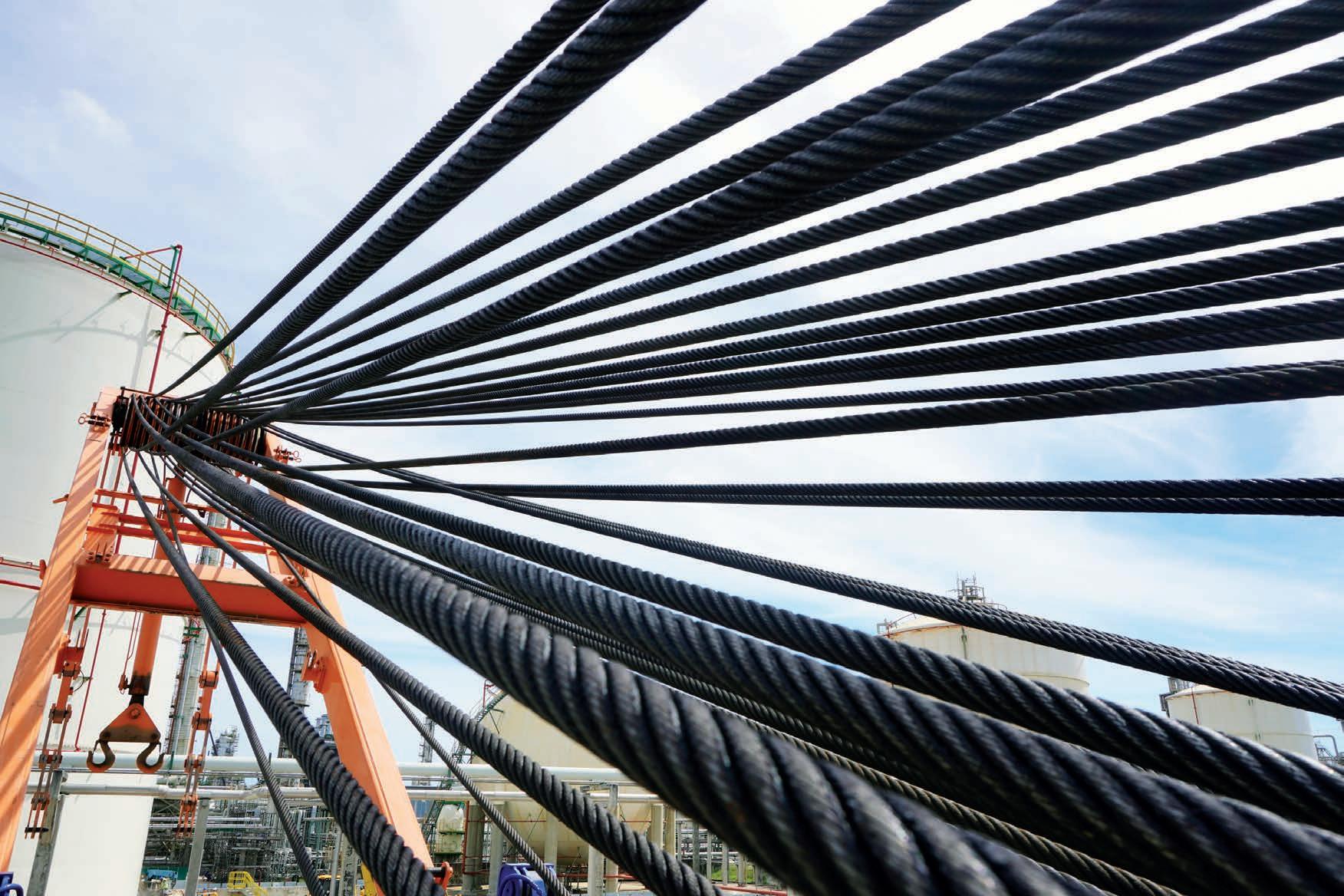
have been from manufacturers Bridon and Casar.
“Both products are excellent, they really impress with their performance, and the ropes are designed to withstand the rigours and demands of our industry,” Eberhard said.
B oth wire rope products have a high breaking point and great wear characteristics that make them stand out in the market.
High performance ropes are designed for the highest breaking loads by a combination of various technologies. This includes: a large number of strands, which increases the metallic area of the rope; parallel lay, which leads to a more compact rope construction; a plastic layer, which reduces internal stresses; compacting of the strands, which
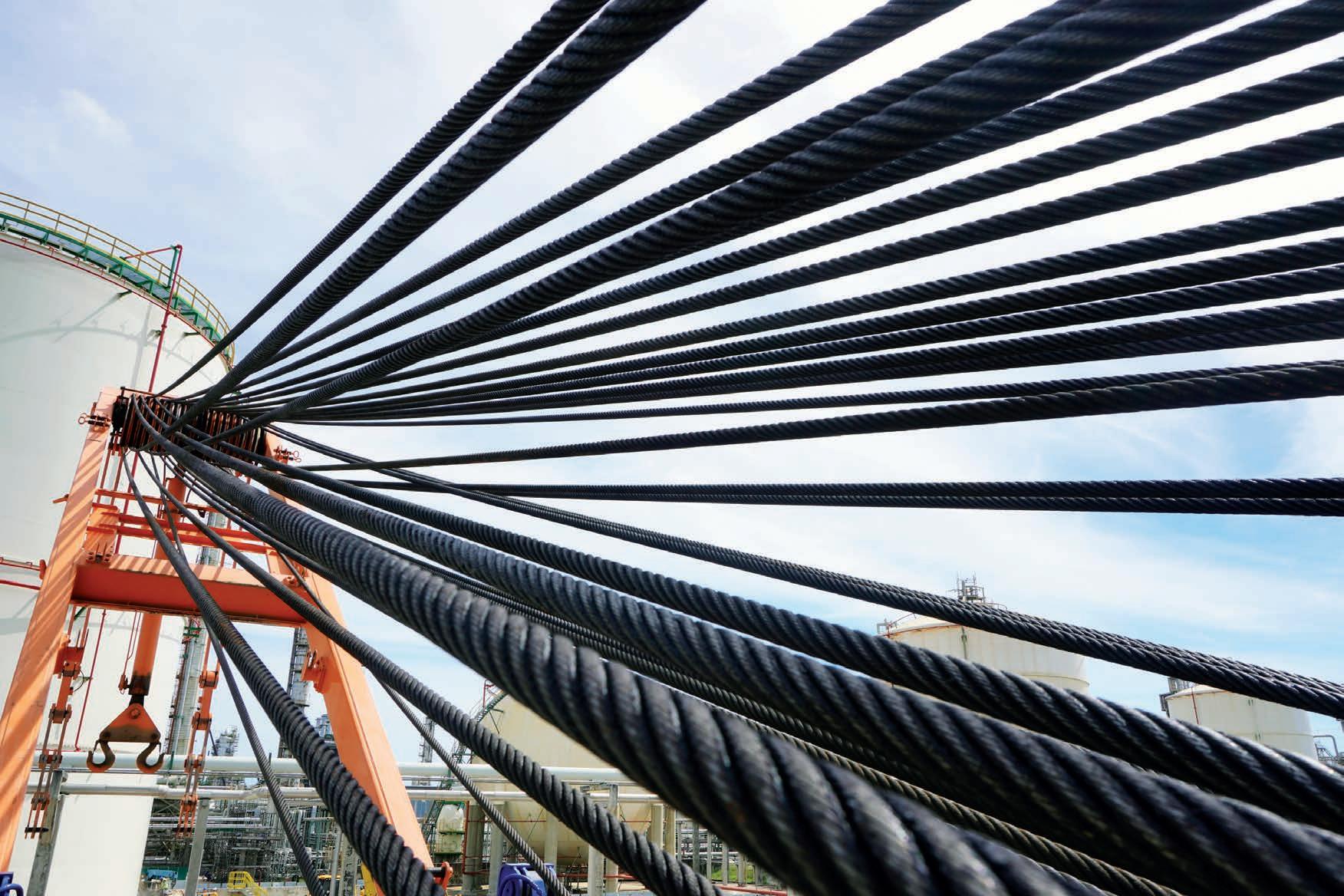
increases the fill factor of the rope; and the tensile strength of the wires is chosen according to the requirements.
Wire ropes are designed using a computer aided rope design program to ensure the rope itself can stand up to the wide spectrum of mechanical stresses it faces. This is backed up by many hours of lab testing simulating operating conditions.
Eberhard speaks of stock during a challenging Covid period and how the team problem solves for clients.
“Stock levels are beginning to improve, and we are getting more consistency from overseas supply lines, but it is not quite back to the pre-pandemic levels,” he said.
“We obviously have stock in our own workshop but we also have good working relationships
with the manufacturers, which allows us to be flexible. We are not t ethered to one brand; we can provide options to ensure down time is kept to a minimum.”
S olving problems is a big advantage that Crane Ropes Australia offers.
“ I think being in the industry for so long, we have seen a wide range of problems arise before. The thing to remember is that not all problems are straightforward, sometimes you have to work through what has happened to get the right solution.
“Now, when clients contact us, most people have the ability to t ake videos on their phone so we can work through situations and find a solution without always having to go out to site.”
Being in the industry for such a
“We have begun to expand into drilling, winches, and marine applications as well as being absolutely focused on the crane industry. We can find solutions for any application.”
long time has advantages that benefit crane owners.
“We have a large database of different types of cranes and what the requirements are of that rope – breaking strength, diameter, and length, etc,” he said.
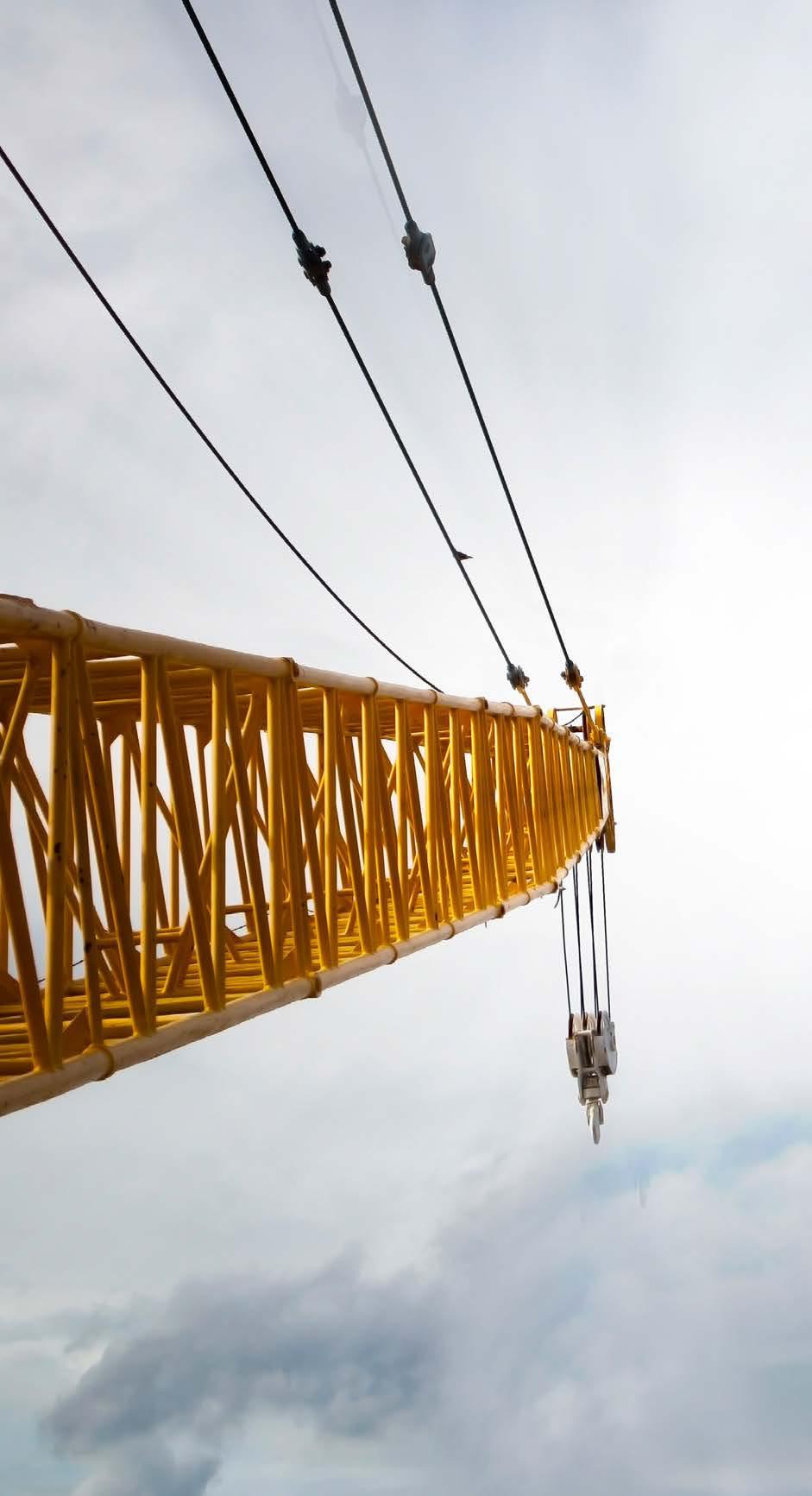
“Our team is trained by the rope manufacturers to install end terminations to specification and ensure they stand up to the rigours of the industry.
“ Let’s say a crane owner did not want to replace the rope, they just wanted a new end fitting, we can go to site and replace that socket,
test, and have the crane up and running quickly.
“It is about minimising downtime for our customers. For example, we keep replacement ropes for some crane models on the shelf, and we might get a customer calling saying they have damaged a rope and we can freight it out that night. When someone calls up and says ‘look we are in trouble here’, we can be super responsive and get a rope transported quickly.
“It is not just a part number to us –I have been in the wire rope industry for over 25 years – we understand what the problems are, and we can talk to
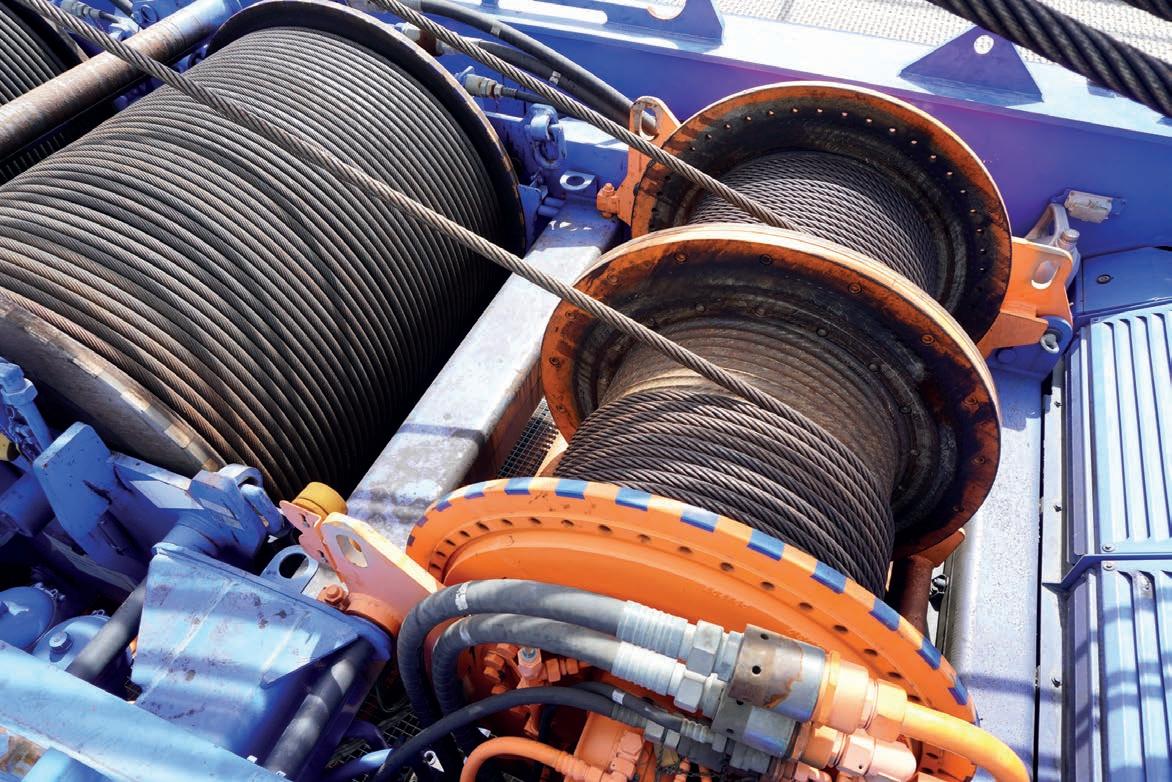
the customers about their problems and attempt to provide them with a solution, quickly.”
Eberhard explains how Crane Ropes Australia’s location is a benefit for its Australia wide servicing.

“For us, being in South Australia means we are incredibly central, we can quickly get products across to all parts of Australia and we are overnight to Melbourne.
“We have begun to expand into drilling, winches, and marine applications as well as being absolutely focused on the crane industry. We can find solutions for any application.
“ We can provide advice and solutions on all aspects of wire rope and its maintenance, ensuring it stands up to the rigours of any environment our products are working in,” he said.
a huge range of ropes from world leading manufacturers, Crane Ropes Australia is a one stop shop for all your mobile, truck mounted, overhead, and fixed crane requirements.

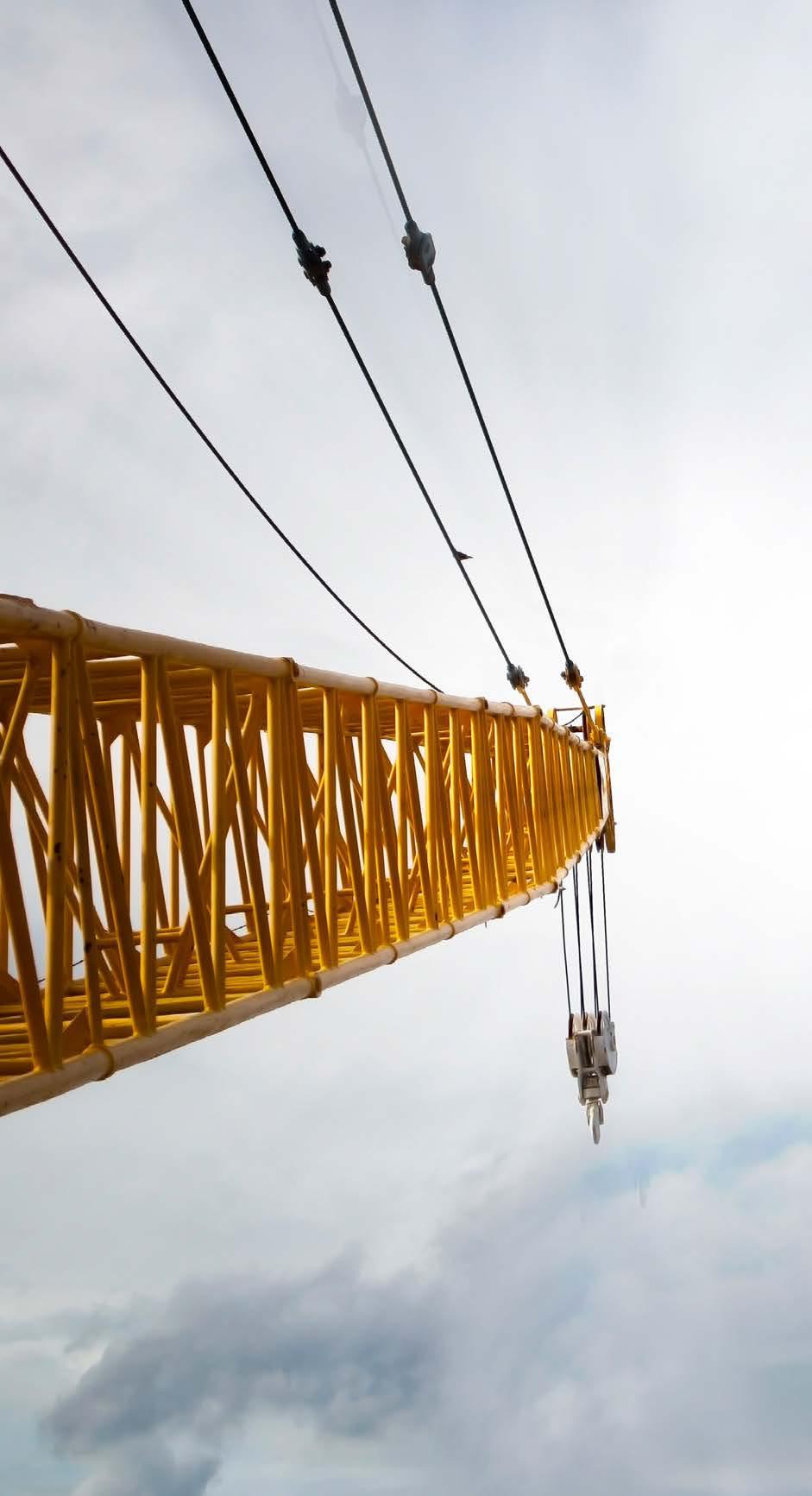
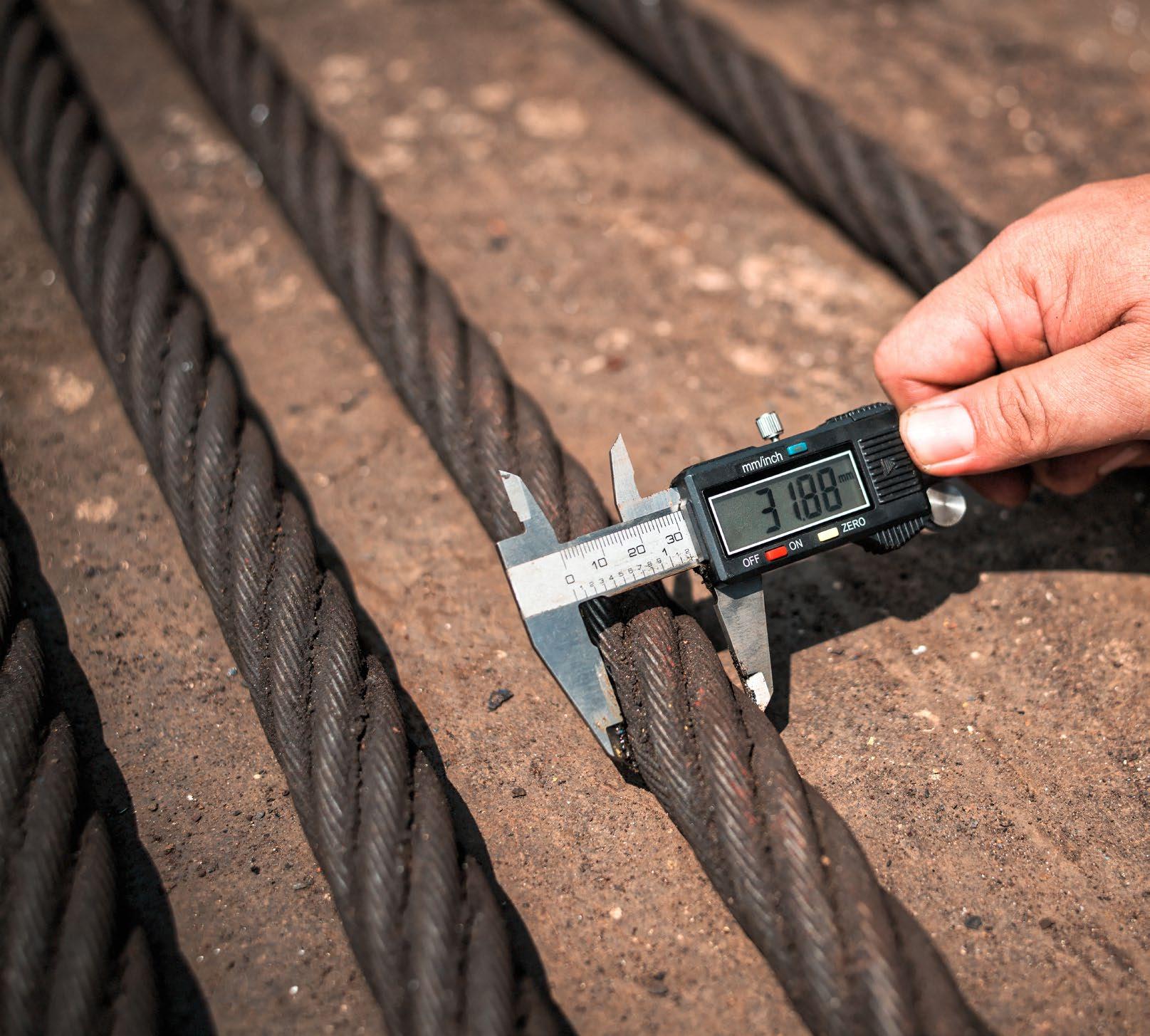
expert team work with clients Australia wide to find solutions for every make and model.
Huge Range of Ropes
Fast Delivery Australia Wide
Every Make and Model
Expert and Experienced Team
out to our team on 08 7089 8335.
CRANECORP’S ASSET MANAGEMENT PLAN WITH TADANO
Brett Hartman is the executive general manager, strategy & commercial for Cranecorp. He is responsible for planning the asset requirements for the business over the long-term. A key element of this planning has been the relationship with key supplier Tadano. Hartman explains more.
Cranecorp has a five-year asset management plan to predict well ahead of time what assets will be needed, what will be acquired for the fleet and what assets will need to be refurbished.
“I WORK WITH THE BUSINESS ON THE longer-term asset planning. We have a five-year asset management plan and plan well ahead of time in terms of what assets we’ll need, what we’ll be acquiring for the fleet and what assets to refurbish,” said Hartman.
“We are very data-driven when looking at the composition of our fleet. We look at a lot of information about what our customers have been lifting
in load sizes. We examine whether we have had to hire additional assets during periods of peak demand to cover customer needs and look to replace that into the future with our own assets.
We regularly look at the historical customer information, have a look at potential contracts we have in our sights, and then try and work out what might be the best cranes to include in the fleet and the most economical crane to use.”
Cranecorp has grown significantly since starting in the West Australian Goldfields as Goldfields Crane Hire just under 30 years ago. Cranecorp continues to operate as Goldfields Crane Hire throughout the Goldfields Region but now operates Cranecorp Australia throughout the rest of Western Australia with depots across the Pilbara, Geraldton, Perth, and South West, as well as the original depots in
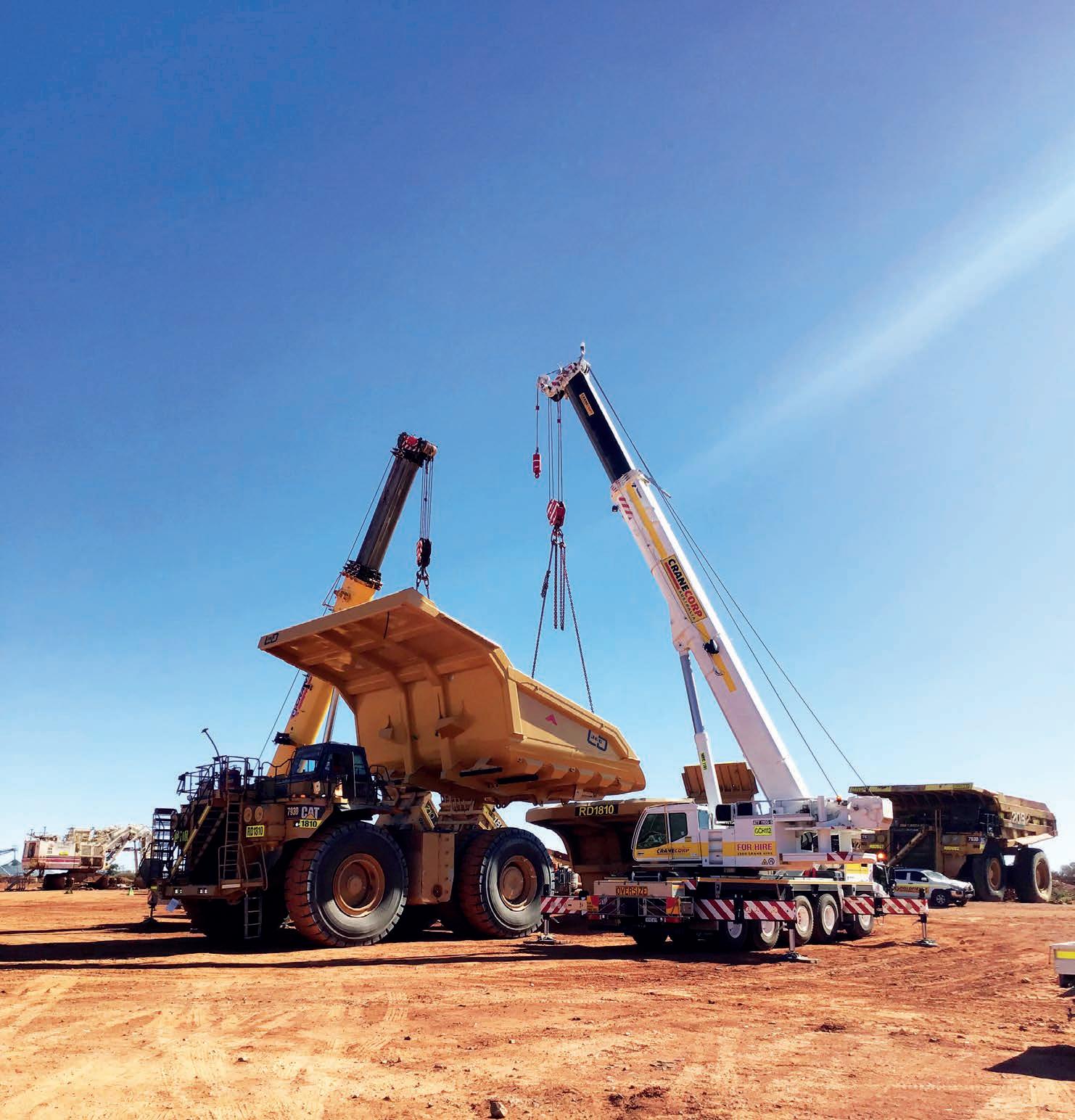
Kalgoorlie and Northern Goldfields.
During that time Cranecorp continued to grow and this included acquiring a number of cranes from other smaller companies that the business took over. This left the company with a bit of mixed slewing crane fleet, but predominately Tadanos.
“The very first slewing crane Cranecorp ever bought back in the early days was a Tadano crane. Over the last few years, we’ve tried to tidy this this up and get more commonality to the fleet and Tadano has been the preferred supplier in this process,” said Hartman.
“Recently a major corporate change occurred at Cranecorp. In 2020, one of the founding partners sold out and private equity partner Viburnum moved in. Viburnum are now a major shareholder, along with the original owner, Rick Musarra, and senior management also hold a share. Cranecorp is now well positioned with Viburnum onboard to take the business to the next level. With Viburnum’s support Cranecorp has undertaken a fair
amount of fleet renewal and expansion over the last two years.
“Over the last two years we’ve taken delivery of 16 new cranes from Tadano. This has provided our workforce with one of the best fleets available in Western Australia, with improved operational, comfort, and safety features over the older cranes that some of our competition run. The cranes we have brought range from 90t rough terrains to a fleet of three new AC300 Demags. We didn’t make this significant investment lightly because we wanted nice, shiny, new cranes. We made the investment to ensure the cranes are up and running for our customers whenever needed, safe for the operators to use, and as comfortable as possible out in some very remote locations that we operate in.
“As part of our streamlining process we now are now trying to concentrate on reducing the variety of cranes across the fleet, which is why we now have for example five AC160 Demags in the fleet. This reduces the need to VOC staff on a wide range of cranes and improves
operational efficiencies, which makes Cranecorp more competitive.”
The interchangeability of key components across the Demag range was also an attraction in the purchasing decision for the new fleet. Many of the components such as flys and winches can be shared across different sized Demags and this reduced the overall cost of the acquisition program.
“At the end of the day, we are constantly trying to find ways to compete against business that are bigger than ourselves and believe we punch above our weight. Our staff are our key to that success but they are supported well by the growing Tadano fleet. It means that we’ve now got one of the youngest fleets in WA. With the changes in the fleet, our average fleet age is now below five years old,” said Hartman.
“The recent changes to the laws in Western Australia has reinforced the need for tighter compliance requirements. This is proving to be a challenge for the crane industry in WA but Cranecorp has been working on a
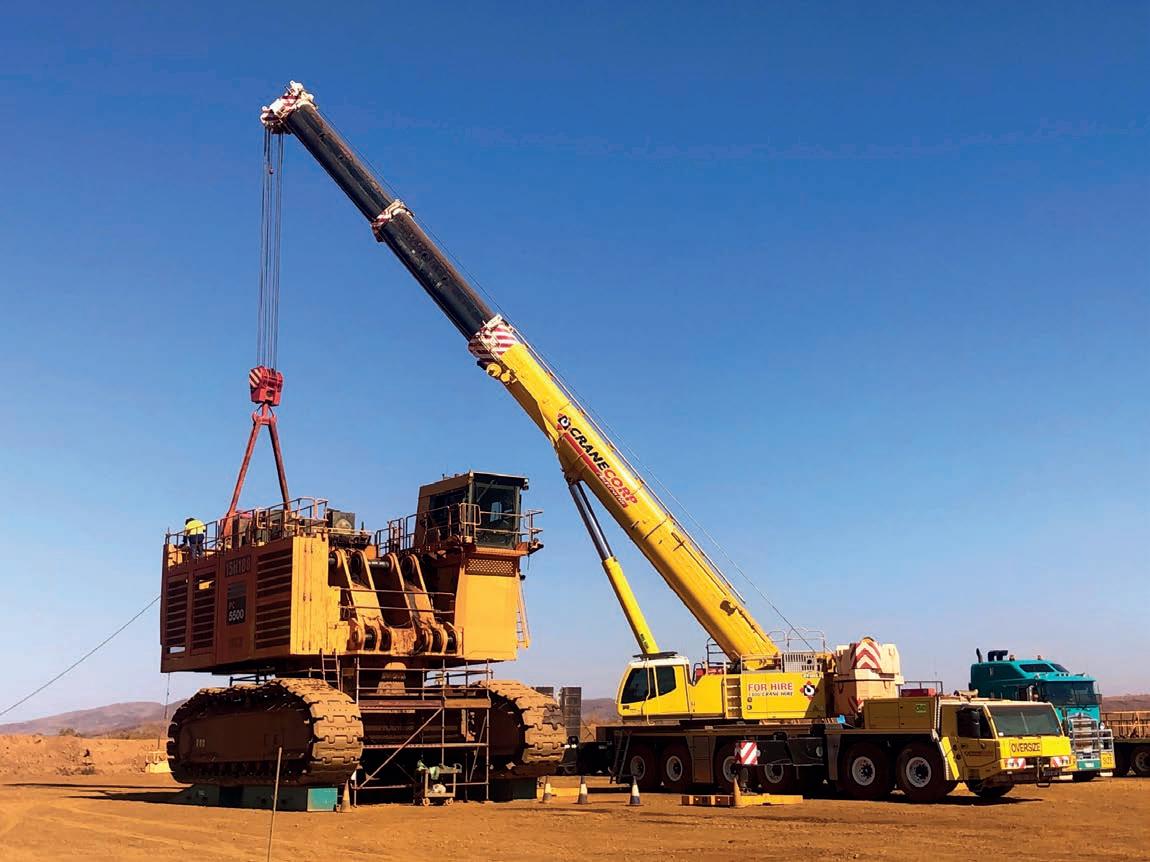
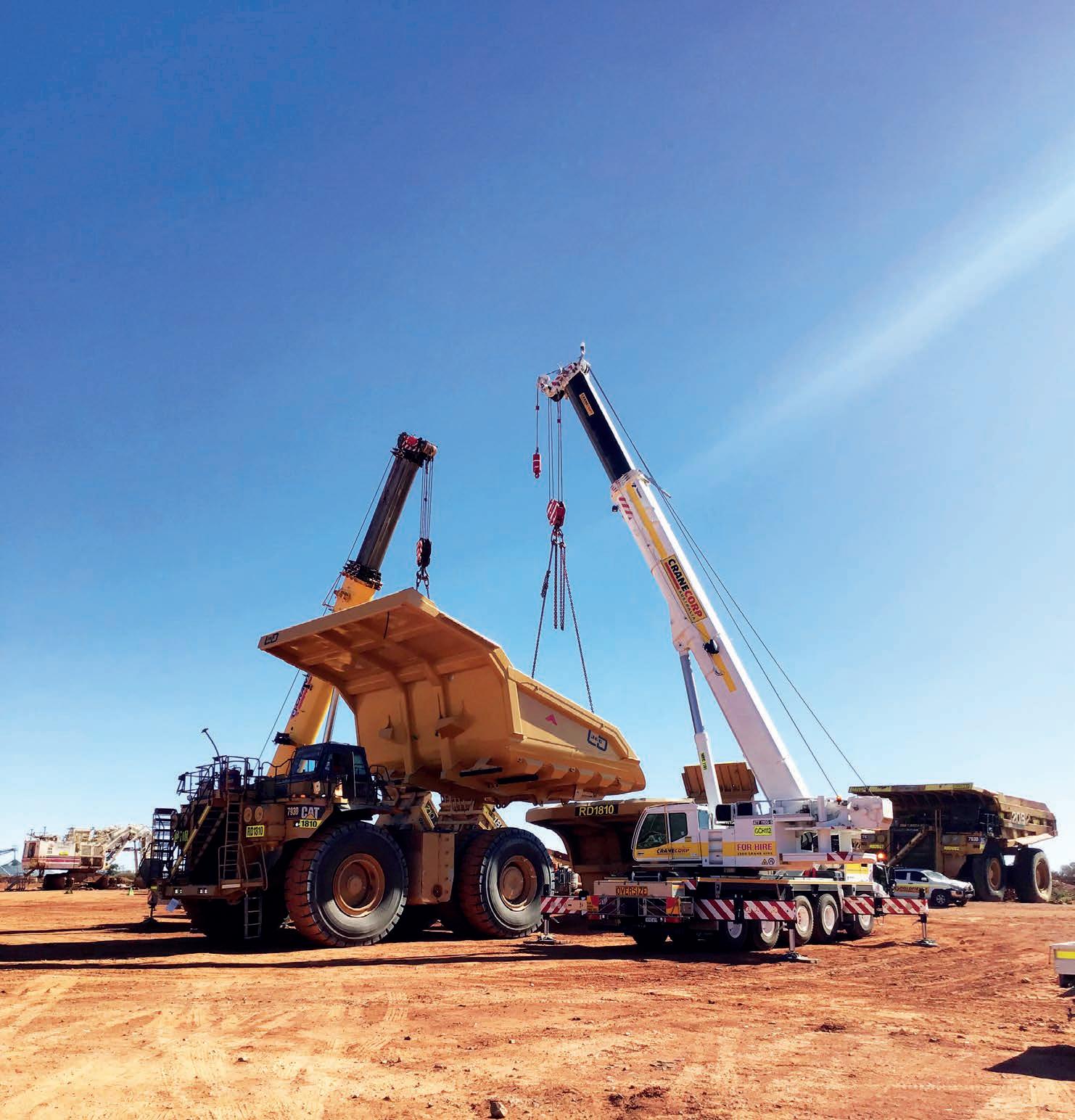
compliance program for the last few years along with the support of key suppliers including Tadano to have us well placed. From my understanding a number of other companies are just starting that journey and are finding it difficult due to the lack of resources currently available in WA.
“Cranecorp has its own team of highly skilled technicians and service depots across the regions it operates in, but this is supplemented by support from the team at Tadano.
“Tadano is currently refurbishing a number of cranes for us as part of our 10-year compliance program. It is pleasing to see the investment that Tadano has made both in its Brisbane and Perth facilities. This has improved the ability of Tadano to support customers like us well into the future.
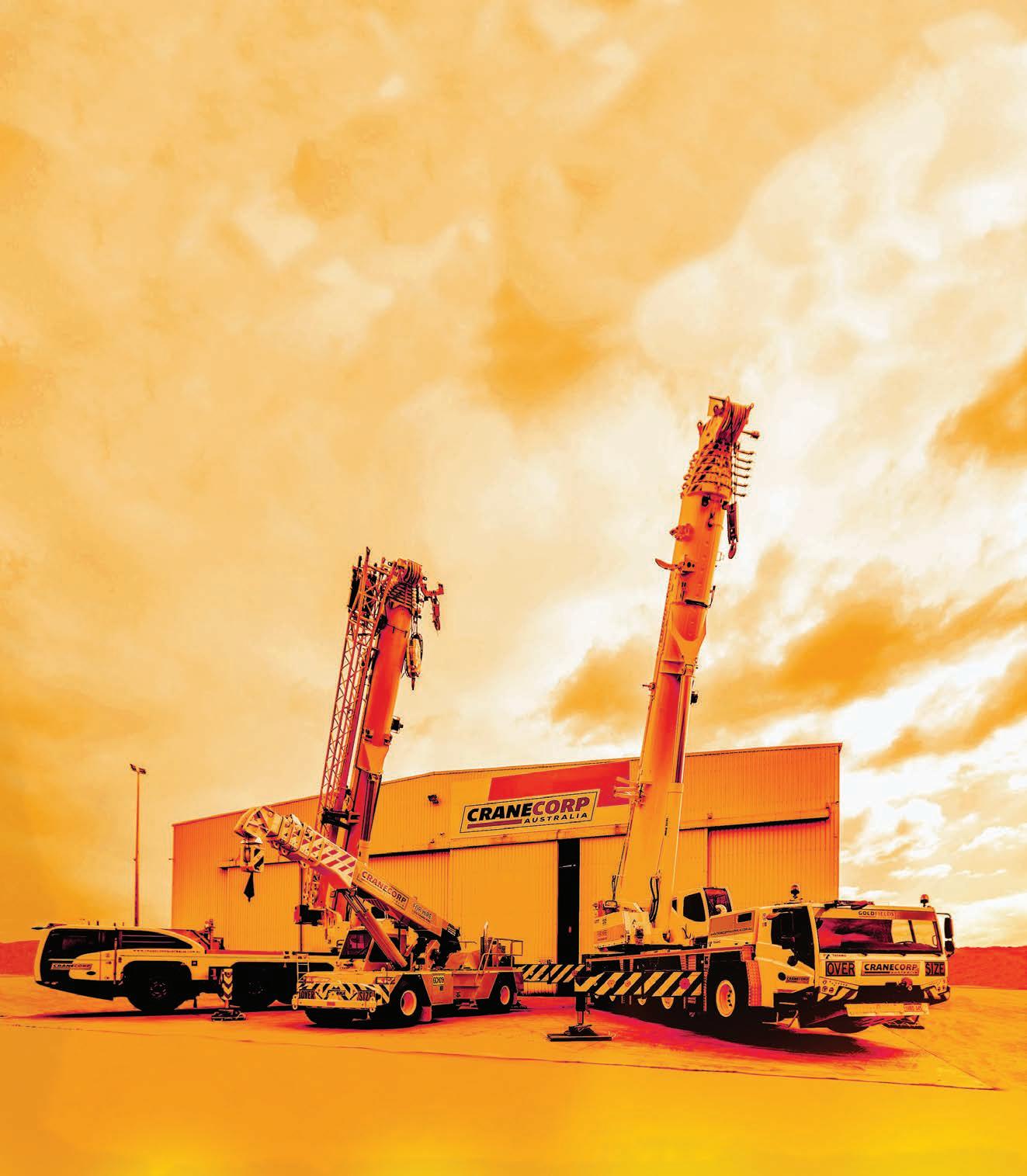
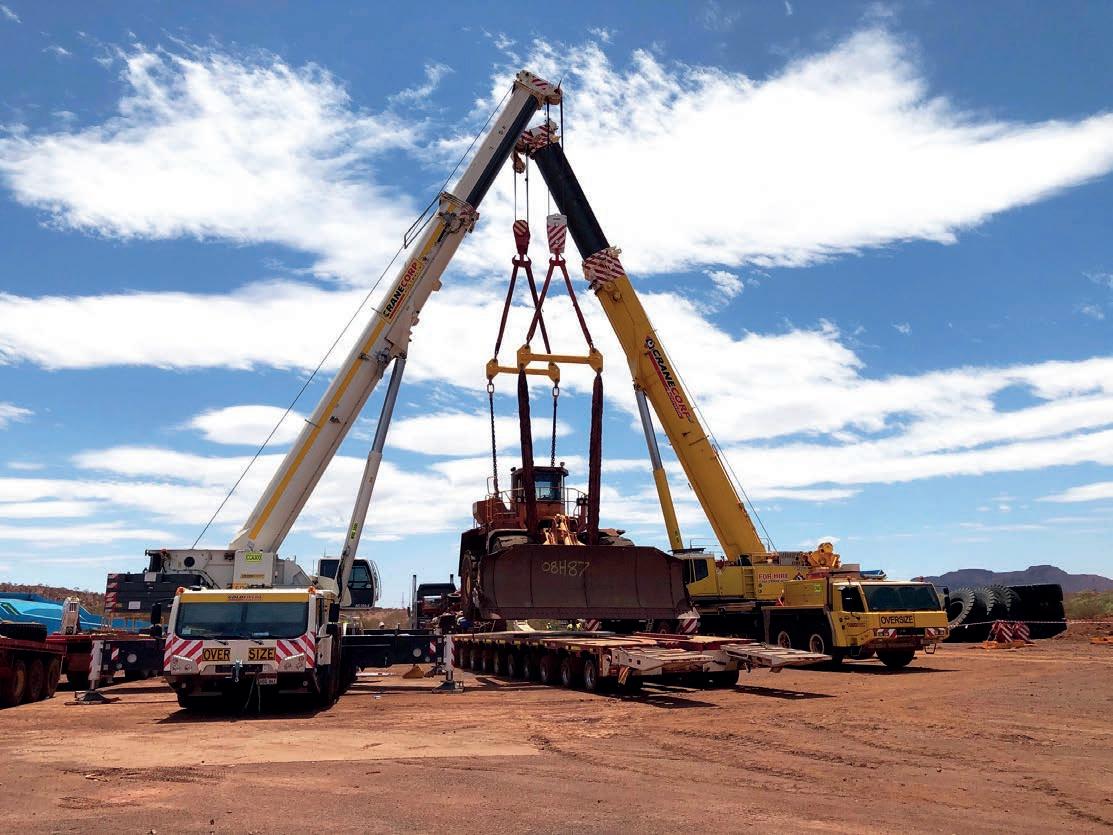
“We see the information age as key to our continued growth in providing customer solutions. Cranecorp invested
heavily several years ago to provide customers with a paperless system. This system utilises iPads in all cranes for all workorders and customer signoff and provides a lot of useful information to ourselves and ultimately our customers.
“The next level is to start using onboard crane data. The technology now featured on Tadano cranes, provides the ability to remotely access onboard data and diagnostically assess the crane. Customers are constantly pushing for continuous improvement and real time data is key to understanding areas for improvement. Access to this data will allow our lift engineering team to review the lifts carried out and better plan shutdown lifts for our key mining customers and look for ways to reduce costs further,” says Hartman.
“The relationship with Tadano and Cranecorp has been developing over many years and there are a number of
touch points between our organisations. A good working relationship between our organisations is important. My regular contact is with the state sales manager Darryl Reeves but I can equally call the Tadano CEO Takehiro Kusumoto or speak to national sales manager James Greenwood if Darryl is not available for whatever reason,” said Hartman.
“Darryl and the team in WA are a big part of the success relating to my dealings and those of our asset manager Joe Pito with Tadano. He’s been with Tadano for a few years and he has been around the industry for a long time.
“The fact that he has spent some of his time on the customer side of the industry is also an advantage as he understands what is important to companies like Cranecorp. Darryl is a genuine guy and he knows his stuff.
“We look forward to growing into the future with the ongoing support and relationship with Tadano.”
“The next level is to start using onboard crane data. The technology now featured on Tadano cranes, provides the ability to remotely access onboard data and diagnostically assess the crane.”
The technology now featuring on Tadano cranes, provides the ability to remotely access and diagnostically assess the crane is beginning to help with the service, support and maintenance of the cranes.
right crane right location right team
Precision engineering, advanced technology and people with the knowhow to save you time, money and risk – it’s just what a smart crane company does.
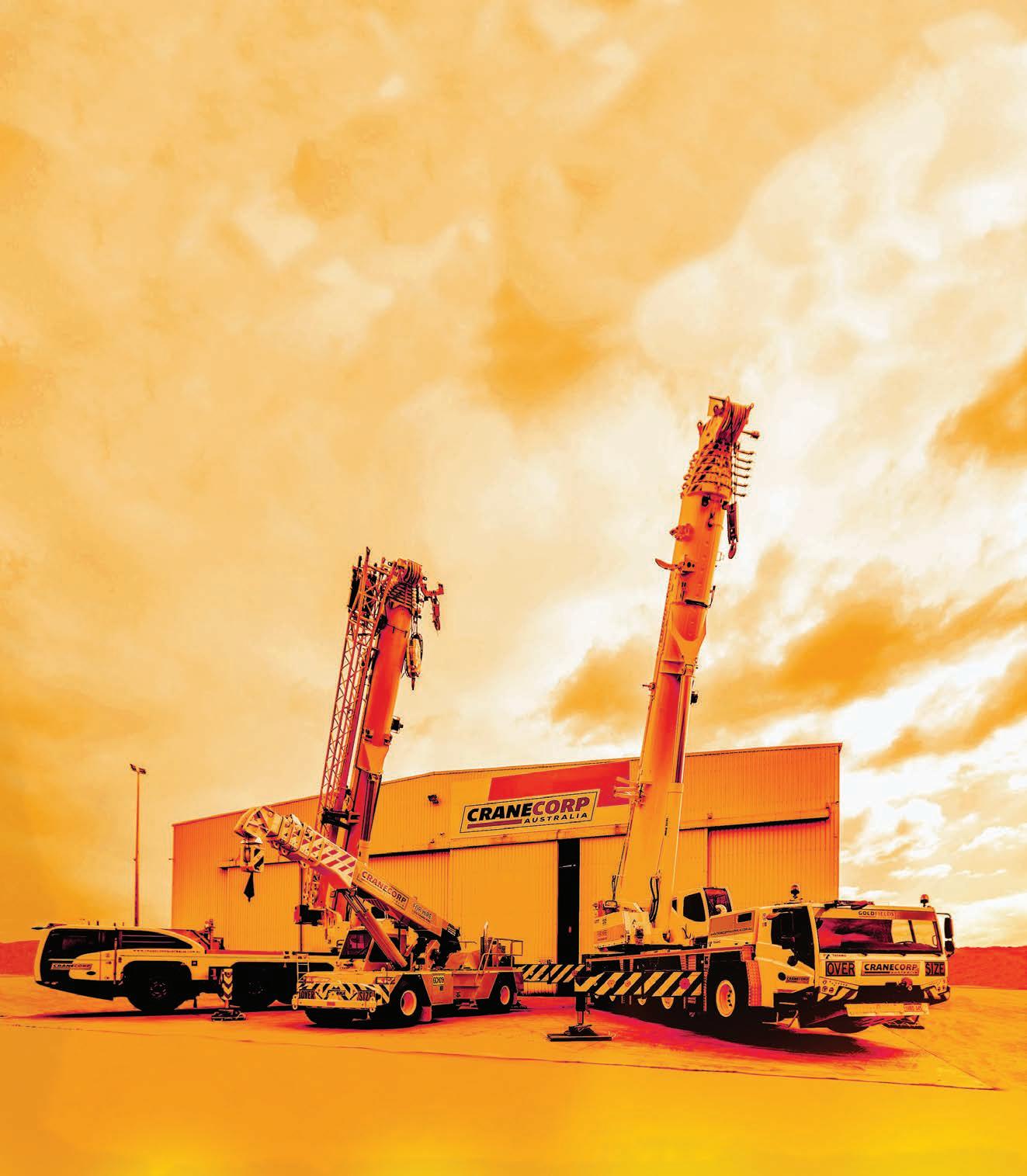
The Hevway app clearly shows an operator the route and the roads close by that can be taken.
YOU CANNOT RUSH SOFTWARE THAT WILL CHANGE THE CRANE GAME
If you asked who the perfect two people would be to develop an app that was designed specifically as a map service for the crane industry, the ‘Peoples Brothers’ would be pretty close.
TOM AND BERNIE PEOPLES BEGAN THEIR journey with Hevway back in 2017 after Bernie – a crane operator – came to brother Tom – a software engineer – with an idea for an app that would make the life of operators easier.
Hevway is a revolutionary app in the crane sector – a navigation service that understands the roads cranes cannot access due to Vicroads restrictions and creates an optimal route for a driver based on the crane they are using.
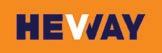
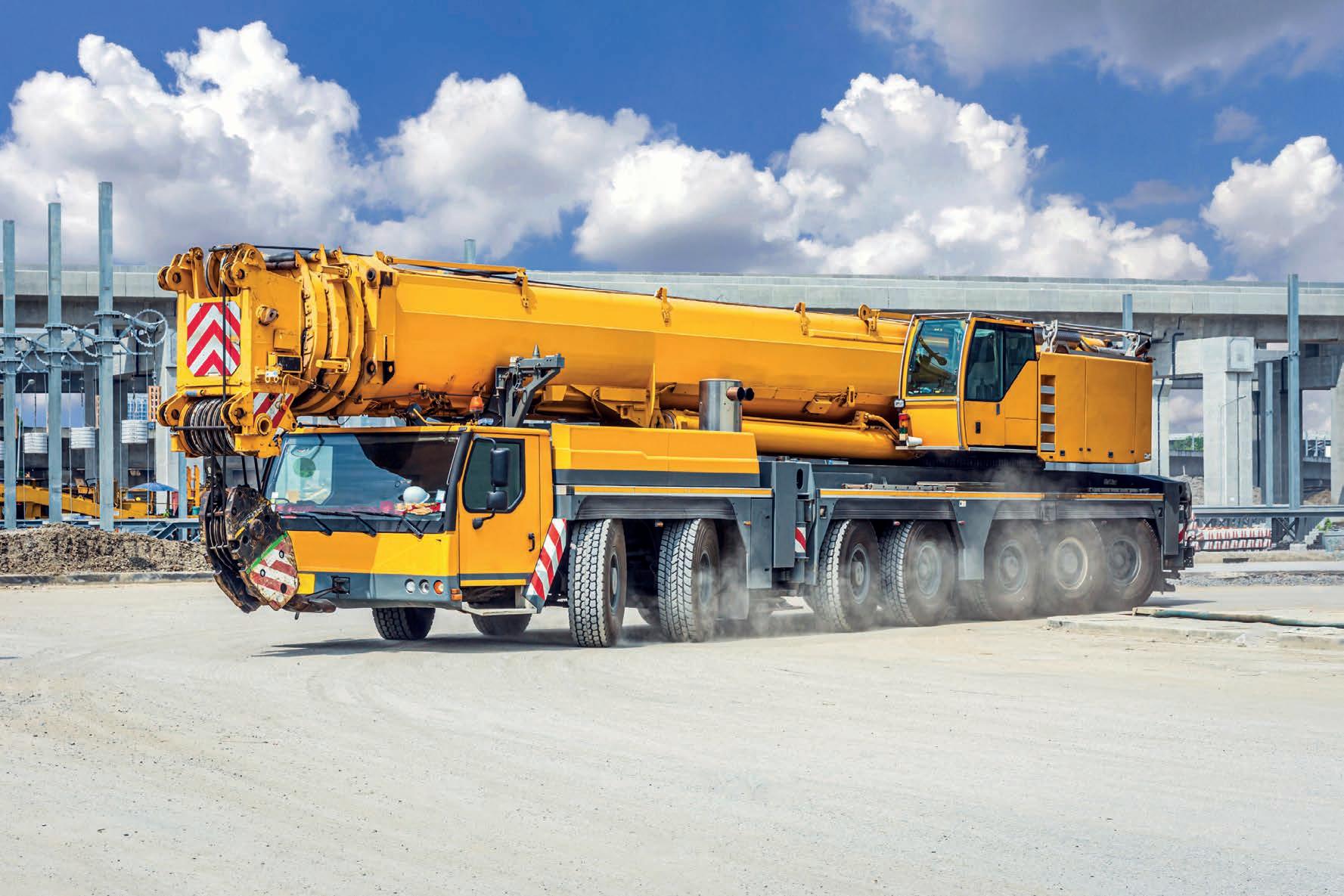

Tom has spent time at numerous software companies, including telecommunications providers, trailer manufacturers, air traffic control software developers, and many others, honing his craft.
Bernie has over 10 years of experience working for a range of crane companies including Boom logistics and Advanced Crane Hire in Ballarat. He recently took a position with Metcalf based in Melbourne. He explains where the idea came from for Hevway.
“I was driving cranes for Advanced Cranes, out of Ballarat. Getting around, obviously you’re in a big machine, so they give you the permit you’ve got to follow and they’re difficult to keep up with if you don’t know the area,” he said.
“I said to Tom at Christmas one year: ‘I have this idea for an app that would make life so much easier for crane drivers, do you think you could do it?’ and he turned me down a couple
of times. There should be something better than the system that’s there. Whether we can make that into some sort of business is another thing, but there’s definitely a problem to be solved within what we’re doing.”
The program is currently being trialled across a number of companies utilising current and previous colleagues of Bernie’s.
Getting the Hevway program off the ground was always going to have a number of challenges for Tom.
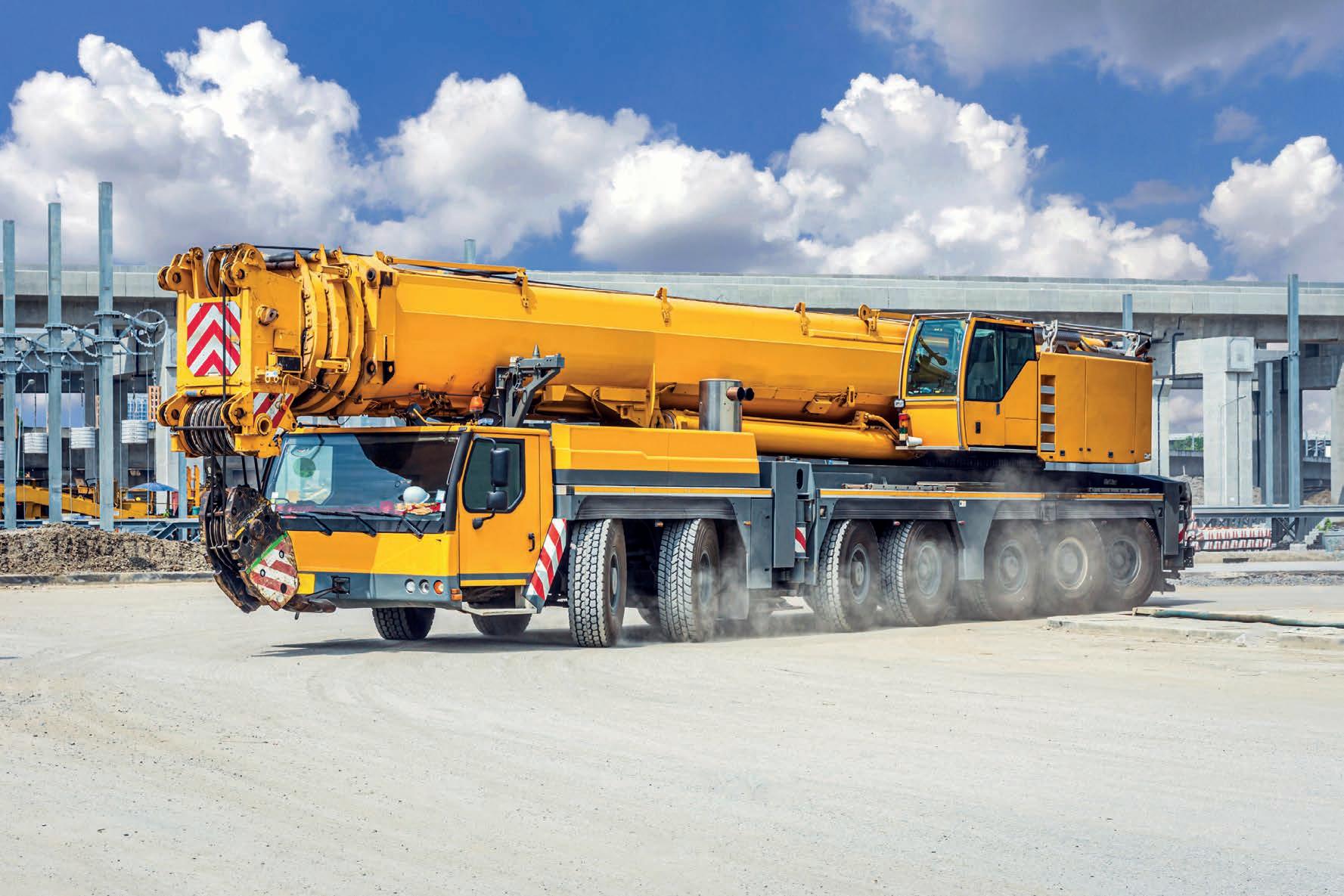
“When I agreed to have a look, I could see all of the government maps were open source and the routing options were there and, to be honest, we thought someone must have already done this,” Tom said.
“It’s not as simple as just putting the
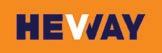
running, but I’m not a designer, so to be honest it was very ugly.
“We brought a design company onboard and they just sent me designs and a flow chart showing us what it should look like and how to transition from what we had to the better design and that is how we got to the app as it is today,” Tom said.
As soon as the pair got the correct routes and we were confident in the process, it was another year part time for Tom honing Hevway to ensure it was meeting their standards and then at Christmas 2021 he quit his job and went full-time on it.
Bernie explains how he utilised his contacts within the industry to ensure the product was the highest quality for when it eventually hit the market.
getting a broad understanding of what is needed,” Bernie said.
“They gave us great feedback, initially it was just the bare map like you see on Google or Apple maps. They gave us the feedback that we should have the red roads on the map as operators travel in case they quickly need to deviate off course. This led to us putting the Vicroads data in the app so it was clear to users which roads were the ones that could be travelled on,” he said.
Bernie goes on to explain how he believes the app will be used by operators.
“I can see this app being used the night before by operators. Instead of going home and using your two screens to plot out a route and spending an hour or so working out where you can
Being a crane operator is challenging enough without having to labour over maps to find an acceptable route.it as is. I think, for me, we all love what we do but we work long hours so when we go home we want to spend time with our families. This gives us the chance to go home and clock off from work and be prepared for the next day.”
The 24-hour nature of the crane industry posed extra challenges for Tom and Bernie. This included anticipating night works and noise restrictions on a journey. The app will show nightworks so you can ensure you are not taking a route that is inaccessible at specific times.
When an operator is travelling towards a road with specific conditions, the Hevway app will count down the distance to these conditions starting, to ensure the driver is prepared. This is just one of the ways the app is designed by a driver for drivers.
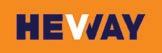
“If a driver takes a wrong turn the app will not automatically re-route them, this is to ensure they stop and check the new route conditions so for example they do not travel down a road that they need a pilot for when they don’t have one,” Bernie said.
The pairing of Tom and Bernie and their individual experience became an
“Soon we will look to incorporate permits into the routes where someone working in the office can add these permits when they arrive and the app will route over them. The whole system will be continually improved.”
asset when planning the app. This was centred around not simply being an app that worked but one that understood the challenges of getting a crane from point A to point B.
“I had to make sure that the app understood it may be simpler for a crane driver to take a left turn, to go around a roundabout and come back instead of making a difficult right turn. Building this into the app was a challenge but important,” Tom said.
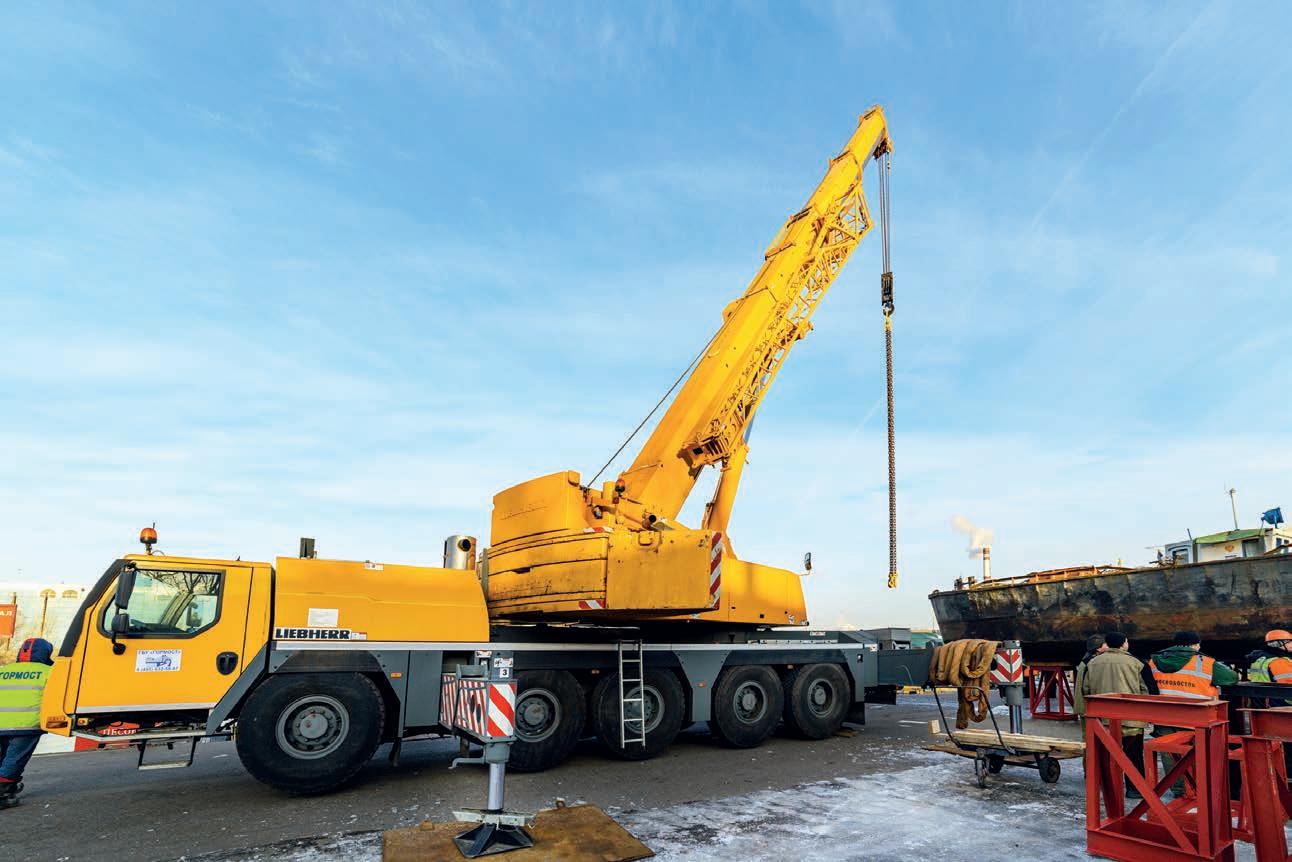
Whilst Tom and Bernie are prepared for the launch of the app, they believe it will only improve from its first iteration.
“Soon we will look to incorporate permits into the routes, where someone working in the office can add these permits when they arrive and the app will route over them. The whole system will be continually improved,” Tom said.
The duo is taking the launch of the app very seriously, ensuring it will get off the ground without any issues.
“These guys are working with beautiful pieces of technology. They do not want an app that is subpar, we knew we had to be 100 per cent confident when we launched it,” Tom said.
“We have had over a dozen different guys, from different companies and in varying machines, testing it. Of course, it had issues but we asked them to be brutal with the feedback but it has never taken a driver down a road they cannot use.
“After the first month or so the issues stopped and, now, we are extremely confident in the product. We will be continually working on it and listening to feedback to make sure this is the perfect app for the industry,” Tom said.



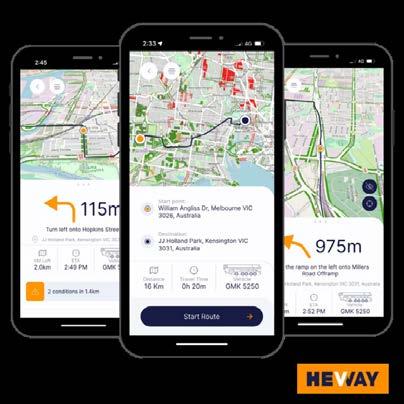

PILEQUIP LAUNCH NEW RANGE OF SHOCK ABSORBERS
Piling and vibratory equipment specialist Pilequip recently announced it will be representing the Tünkers range of shock absorbers. David Hopkins, Pilequip’s national sales manager, provides some background to the Tünkers product and explains why the crane sector should embrace the product.
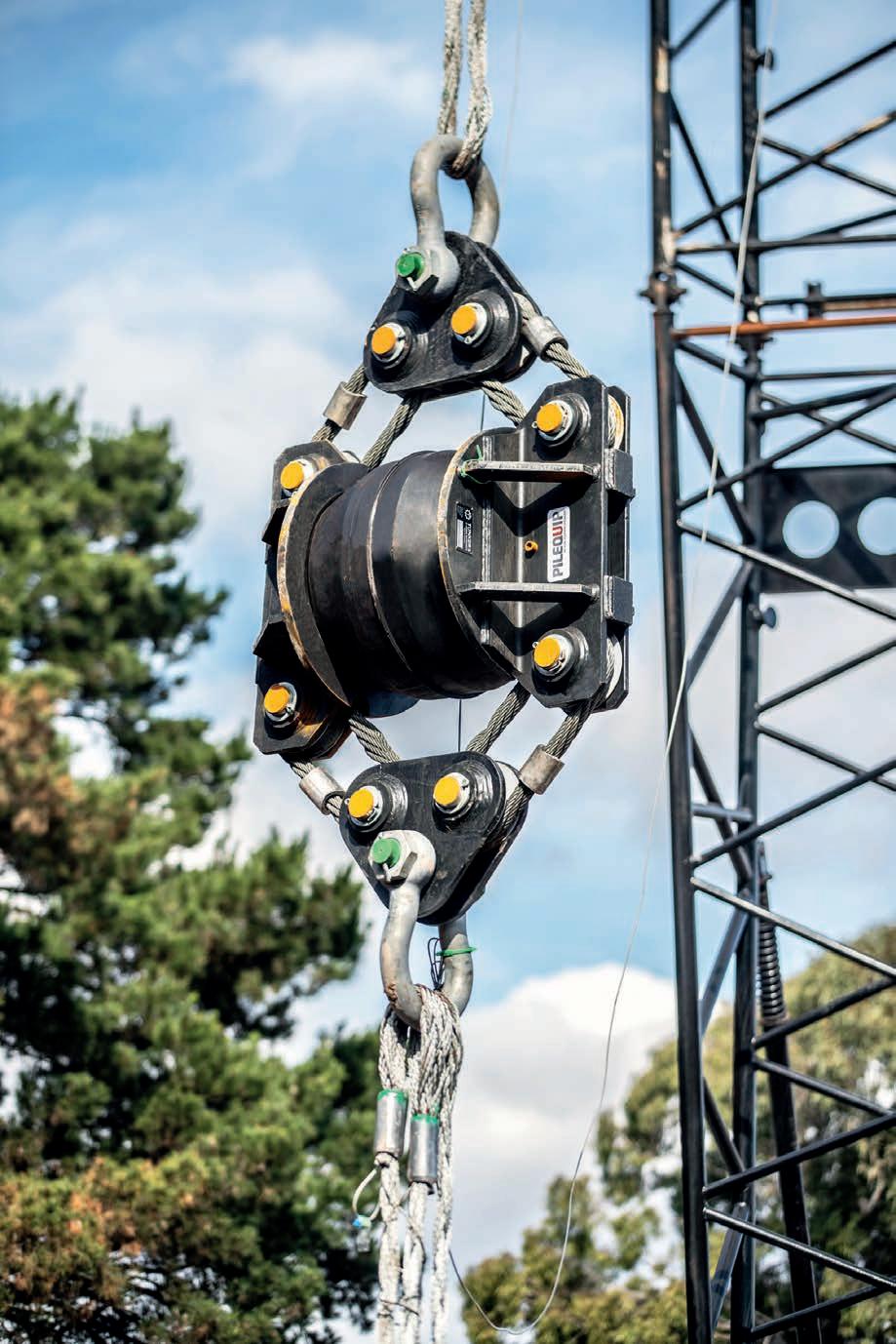
TÜNKERS IS A GERMAN MANUFACTURER of specialised industrial equipment. Its range includes piling equipment and vibratory hammers for sheet piling.
“Unlike the products we sell, which have a series of rubber absorbers above the vibrating unit, Tünkers’ own piling equipment doesn’t have any, so they developed a range of auxiliary rubber shock absorbers for their own vibratory equipment, which, when used in combination with the latest vibratory technology, from manufacturers such as Dieseko, create a very effective damping mechanism,” said Hopkins.
“There are, typically, two types of vibratory hammers. There’s a staticmoment vibratory hammer and a variable moment hammer. The biggest issue with the static-moment hammers is, when you turn them on, they spin through the low frequency until they get to their peak frequency. When it’s moving through the low frequency, it starts to shake. It’s a bit like an offbalanced front-load washing machine. When it’s a little bit off balance and starts to spin slow, it starts to jump around, but once it gets up quite fast, it quietens down.
“When it starts and stops, we get those really big shock load vibrations going up into the crane. It’s not good for the computers. It’s not good for any componentry on the crane itself, and some of the crane OEMs state in their literature that they need to have a shock absorber when using vibratory equipment.
“It’s not just the starting and stopping of the equipment. There are heavy vibrations even at the peak frequency, particularly if you’re pulling up on the vibratory hammer. You’re still getting quite a lot of vibration going up through the crane line and into the crane. We found the Tünkers shock absorbers eliminate up to 75 per cent of that shock load vibration and up to 93 per cent of peak frequency vibration.
Pilequip tested the shock absorbers in its yard on a 75t capacity crawler. It engaged VMS Australia, a specialist vibration monitoring company, to measure the vibration. VMS put up four different measuring points on the crane: above the hook, at the top of the jib, midway on the boom, and in the cab.
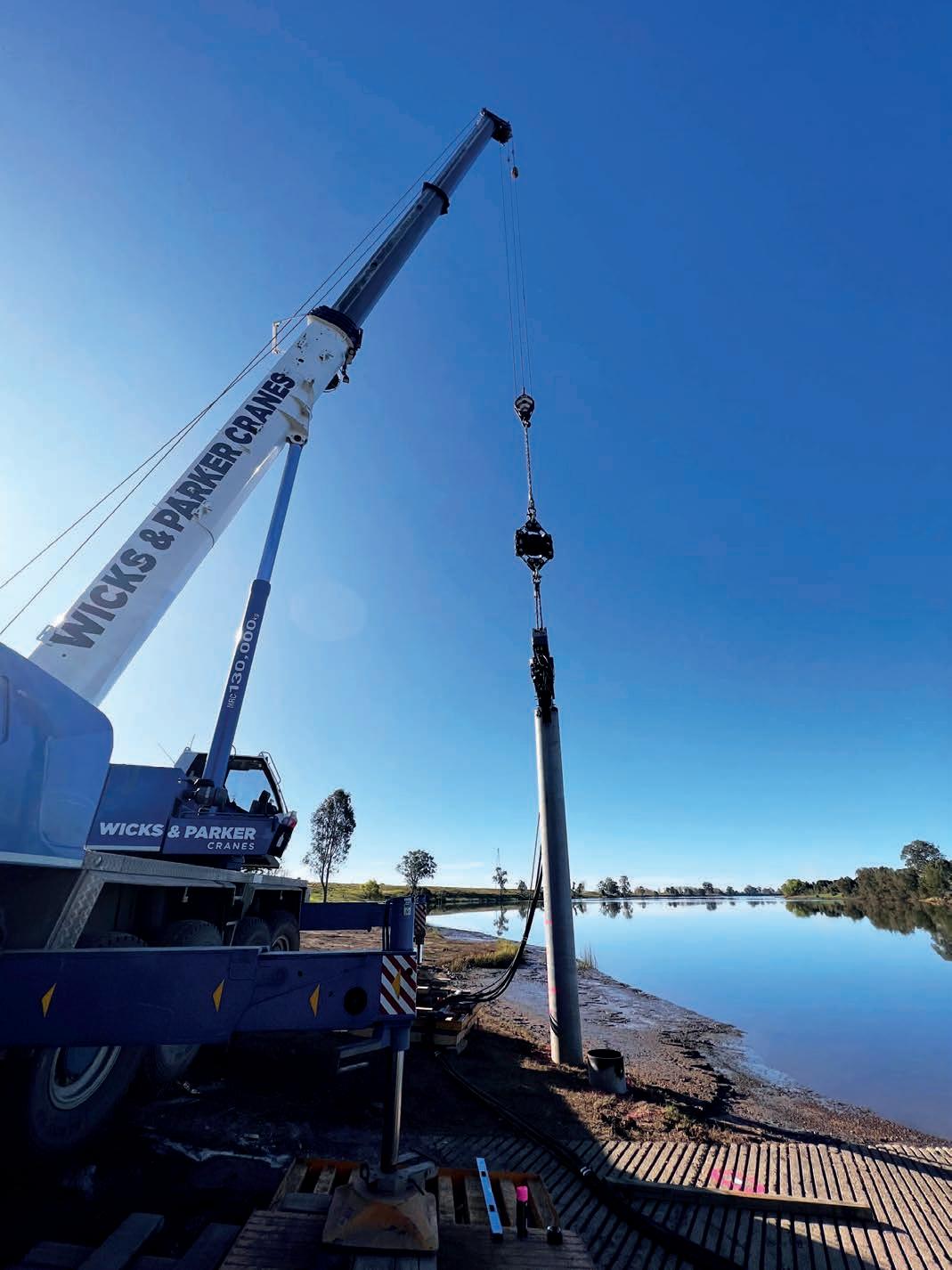
“We tested the shock absorbers on a static movement hammer, an ICE 32NF, and we also tested a variable moment hammer, a PVE 28VM. A variable moment hammer doesn’t have that start and stop shock as I mentioned earlier. So, essentially, it doesn’t start vibrating until the frequency is high. But, as soon as you start pulling on that vibrator, you get that same peak frequency vibration going up through the crane. That doesn’t change whether it’s variable moment or a normal frequency hammer.
“As I have said, the Tünkers rubber shock absorbers reduced the vibration by up to 93 per cent. Obviously, there are huge benefits for crane companies considering this product. I’ve spoken to customers operating cranes and computer systems can’t handle the vibrations. It keeps resetting or it keeps getting errors.
“Obviously, the absorbers will help prevent general wear and tear on the crane. I’ve spoken to customers who have got a crane down because
they started a big static-moment hammer, the ropes were jumping around all over the place, and this caused damage to a point where they couldn’t operate it anymore, they had to fix it,” said Hopkins.
Anyone that owns a crane and is planning to put a vibratory hammer on it, utilising the Tünkers rubber shock
“We found the Tünkers shock absorbers eliminate up to 75 per cent of that shock load vibration and up to 93 per cent of peak frequency vibration.”
absorbers seems to be a fairly straight forward business decision to make says Hopkins.
“They’re relatively inexpensive to either rent or buy, when compared to the cost of a crane or fixing the damage vibration has caused your crane. It’s the unknown damage that needs to be considered.
“I don’t know if there’s any studies on the impact of long-term use of a vibratory hammer on your crane, but you can only assume that it would be significantly less when we’re talking about the vibration reduction that these shock absorbers can achieve,” he said.
The Tünkers rubber shock absorbers are also relatively low maintenance. The wire links in between the shock absorber seldom do they need replacing if they are well looked after and and inspected regularly.
“You can expect years of service life from a Tünkers rubber shock absorber, with minimal maintenance, they are virtually maintenance free,” said Hopkins.
The Tünkers rubber shock absorber range includes five different types of shock absorber ranging from 12t of line pull up to 80t of line pull. Pilequip is stocking three types,
Anyone that owns a crane and is planning to put a vibratory hammer on it, utilising the Tünkers rubber shock absorbers seems to be a fairly straight forward business decision.
from 25t to 80t, these being the SD70 with 25t line pull, the SD-130 with 50t of line pull and the SD-185, which has 80t.
Pilequip has been providing products to the piling industry, in Australia for over 30 years. Over this period there have been a number of owners. Two years ago, Pilequip was bought by Dieseko, a Dutch company that manufactures vibratory hammers, piling rigs, and impact hammers.
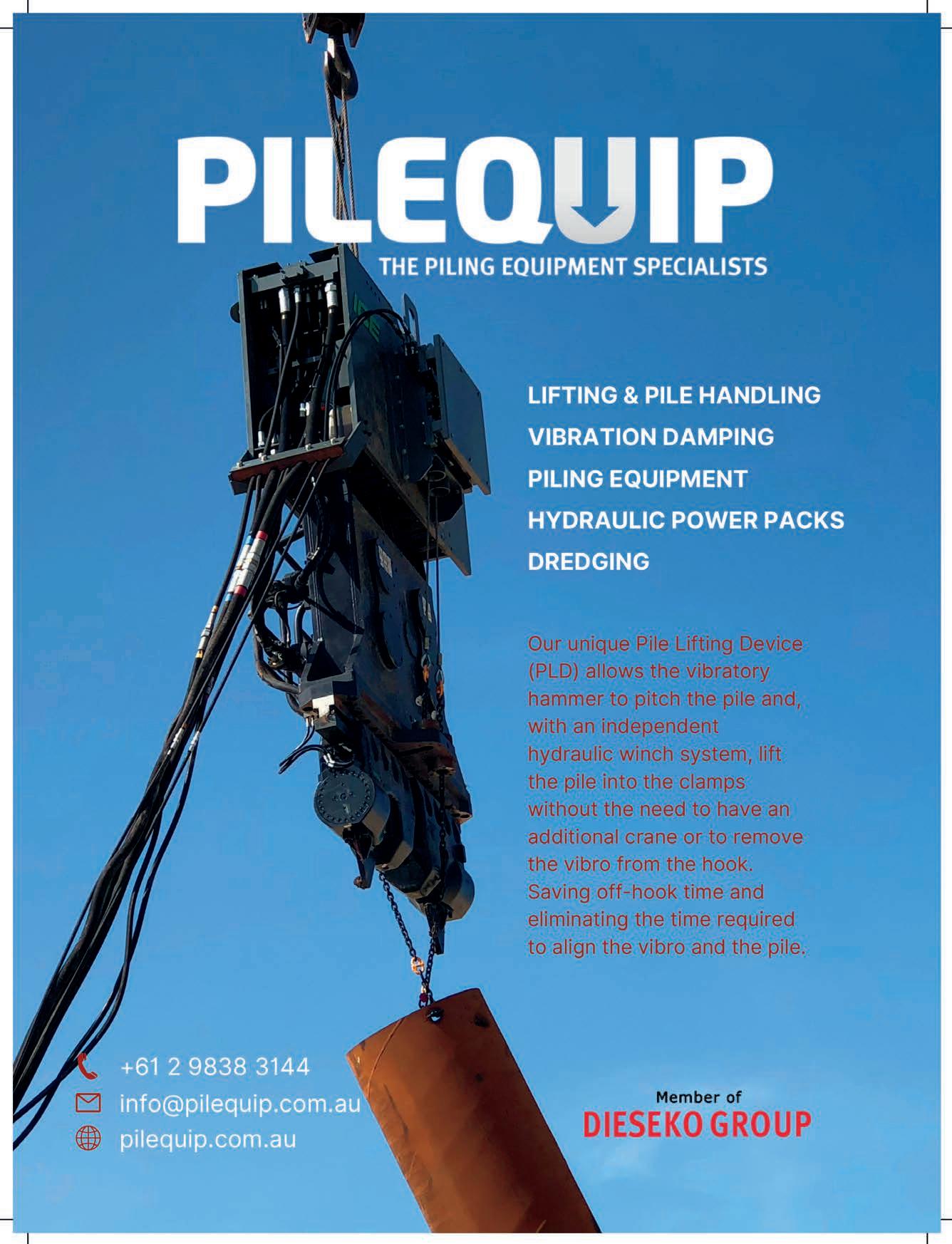
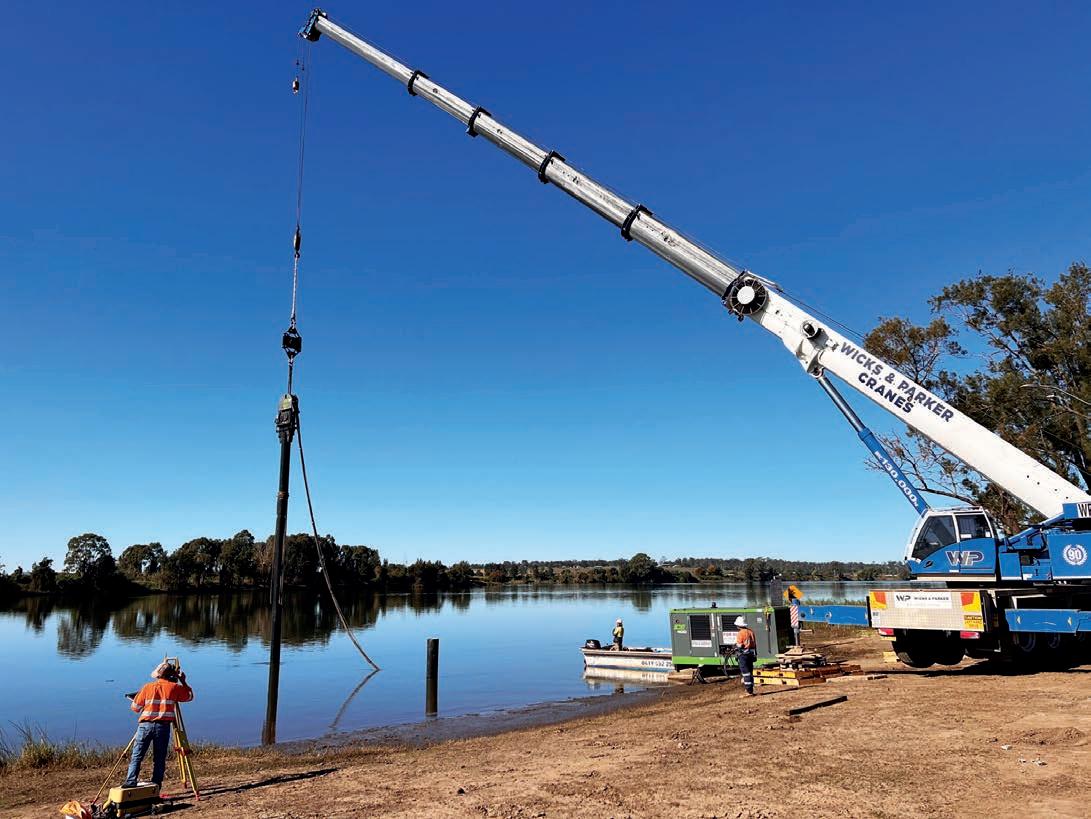
“Being a member of the Dieseko family is the next stage for our business. There is a vast amount of product in the piling industry that has been sold and serviced by Pilequip Australia, and that’s not just vibratory hammers and impact hammers.
“There are very few piling companies out there that have had no interactions or purchases from us and we hope it the be the same with the crane industry with the Tünkers range of rubber shock absorbers,” said Hopkins.
“I don’t know if there’s any studies on the impact of long-term use of a vibratory hammer on your crane, but you can only assume that it would be significantly less when we’re talking about the vibration reduction that these shock absorbers can achieve.”
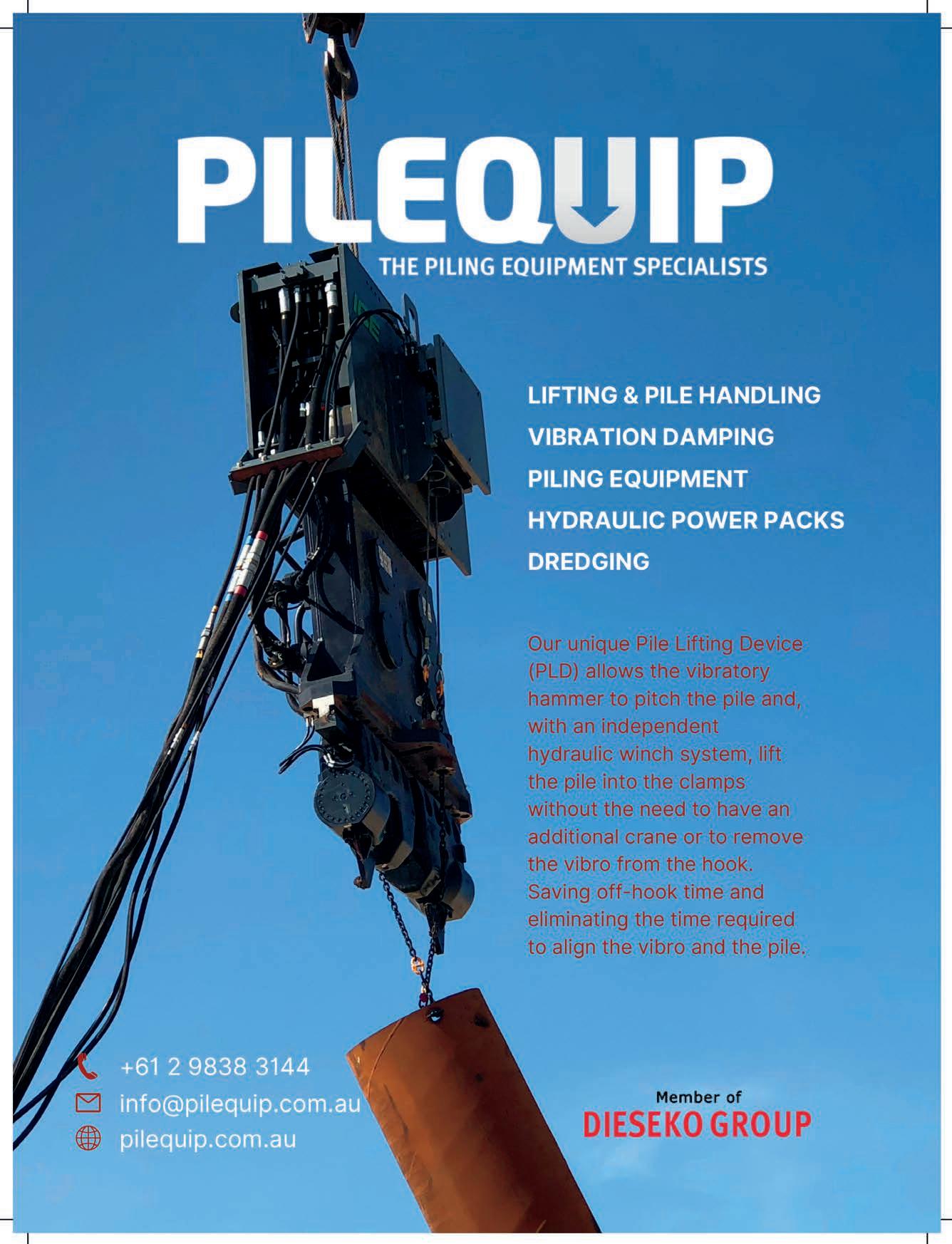
FRANNA LAUNCH
CAPACITY SPREADER BAR
A critical parameter for the design was to keep the spreader the same size so it would fit onto the existing Franna models.
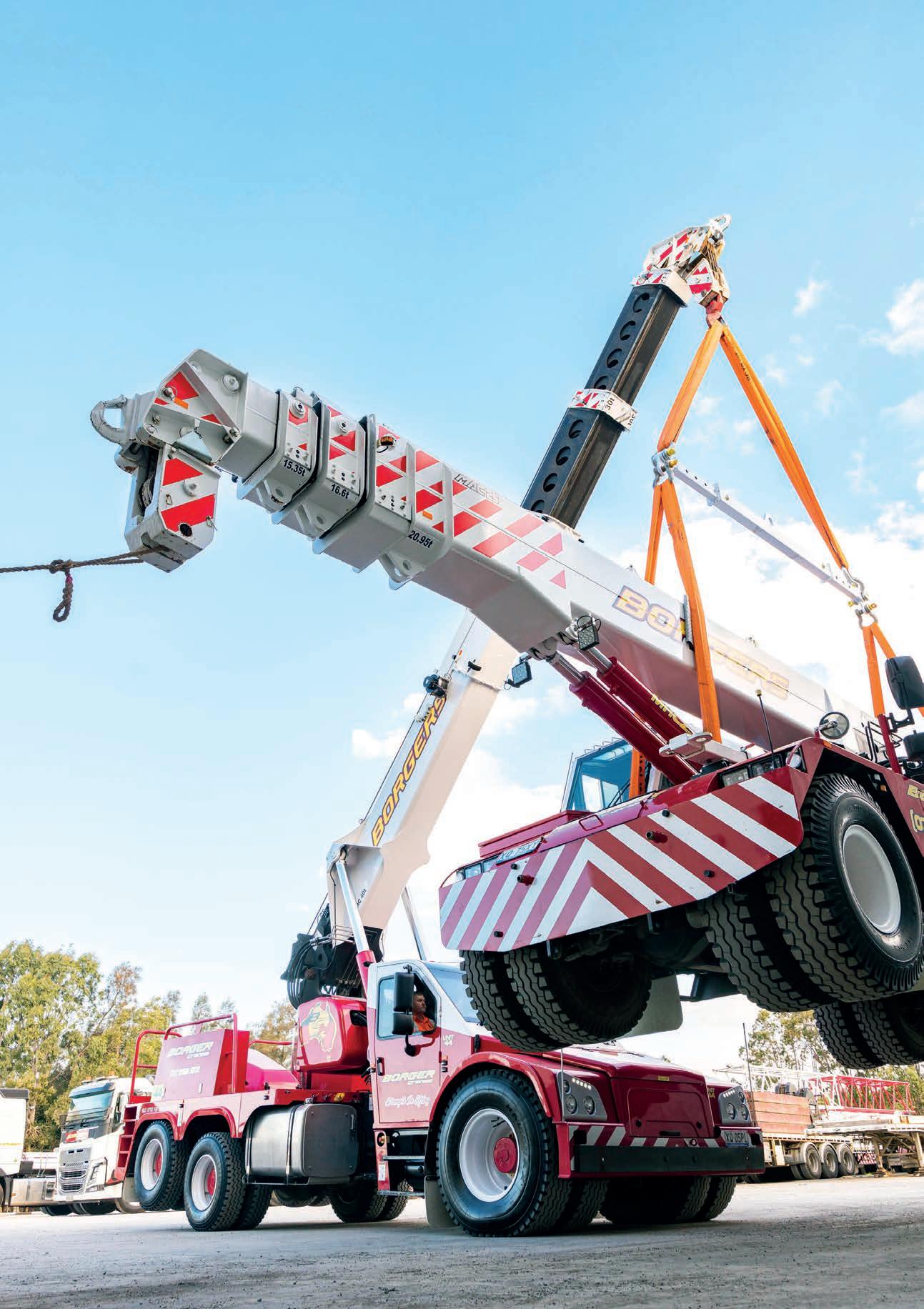
Terex Franna recently announced it has designed, engineered and manufactured a new 25-tonne capacity spreader bar. Matthew Edwards is a design engineer at Terex Australia and led the development. He provides the background to the launch of the new product.
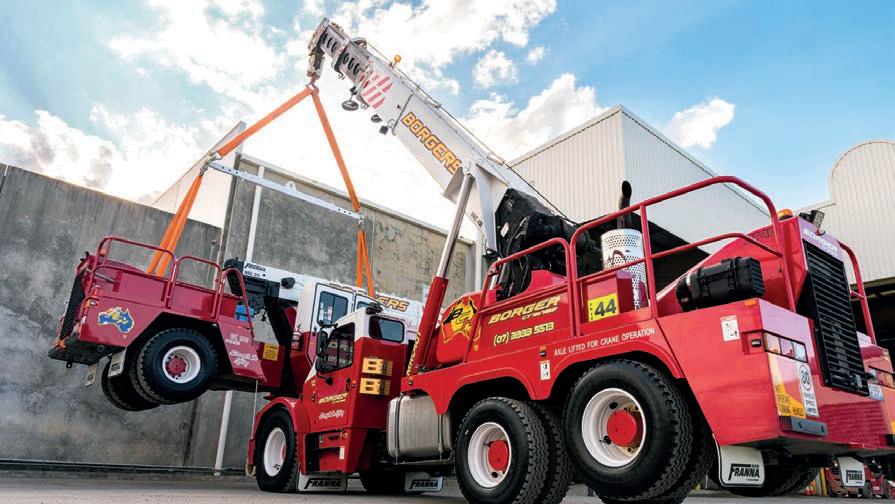
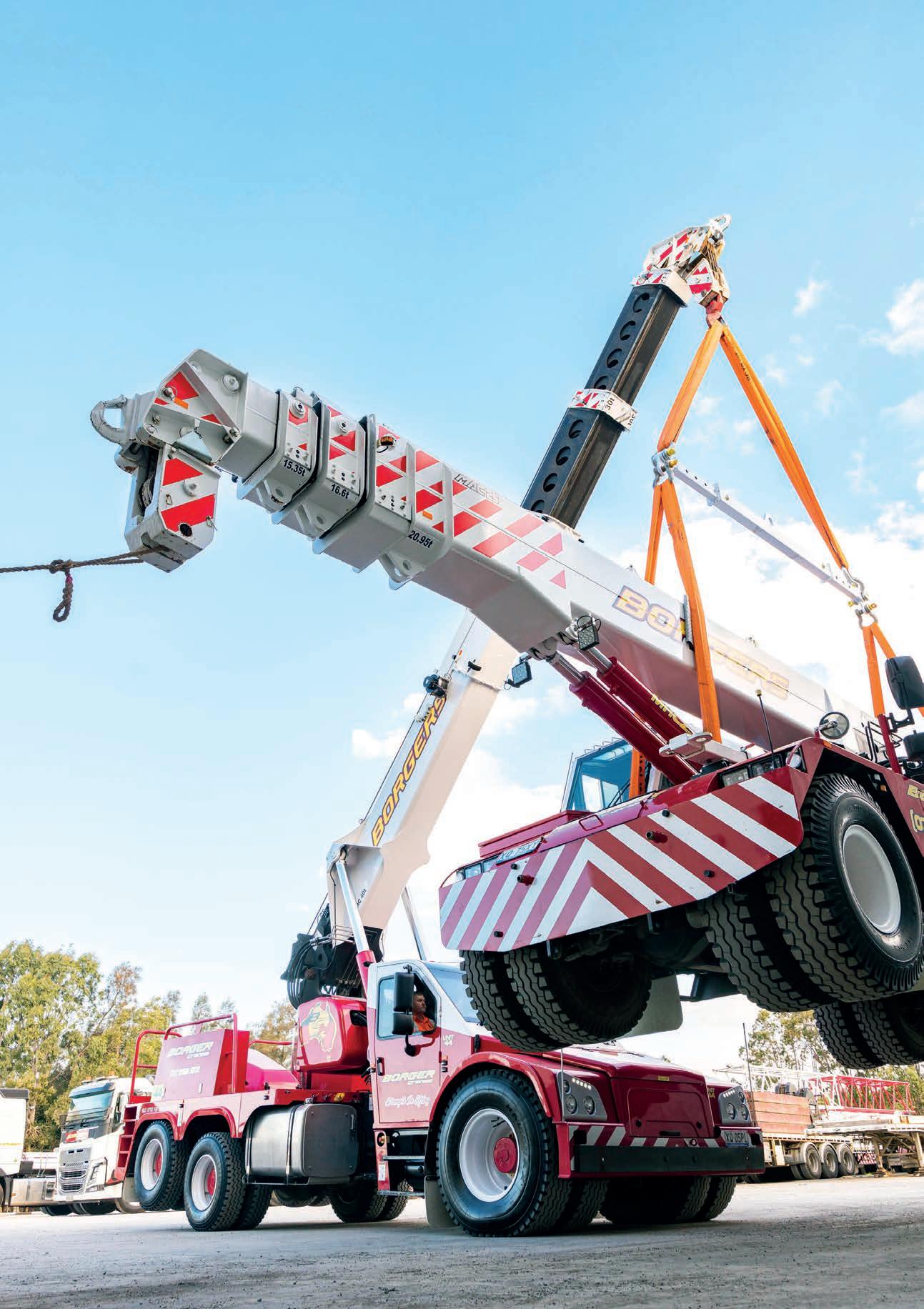
THE DEVELOPMENT STARTED AROUND THE
end of 2020 when a customer asked for clarification around the setup requirements of Franna’s existing 15-tonne spreader bar that has been offered for many years.
“I was looking into the enquiry when I noticed in the formulas that form part of the design calculations, it looked like we could make a much more efficient design. We realised there was an opportunity to improve on the design of the existing spreader bar and some quick calculations said it might be possible, so we went ahead and started the detailed design process for a larger capacity spreader bar,” said Edwards.
A critical parameter for the design was to keep the spreader the same size so it would fit onto the existing Franna models.
“The starting point was the existing Franna spreader bar mounts and then optimise the design to make a higher capacity bar that could still use these mounts. Then we just went back and said: ‘How efficient can we make that size spreader bar.’ Through a range of design improvements and calculations, it turned out we could take the existing approximate size and increase the capacity to 25 tonnes through clever engineering principles.
“The engineered part of the design comes from the fact that we’ve shifted all of the load onto the neutral axis of the bar or the centerline of the bar. The 15 tonne bar that we’ve offered for a long time has two lifting points, one above and one below the neutral axis which introduce bending into the spreader bar itself. For the 25 tonne bar we have shifted the connection point directly onto the neutral axis, i.e. straight
onto the centerline of the bar, which takes out the introduced bending, and makes it purely a compressive load, which significantly increases the capacity.
“The lack of introduced bending allows riggers and lift planners a greater variety of rigging options. This 25t bar is capable of multiple sling angles to work with, each with a unique working load limit based on the configuration of the rigging setup. This variety of sling angles allows lift to be completed within external conditions, such as limited head height, without compromising on the lifts safety.”
The new bar fits in the same mounts as the 15t bar it’s approximately the
the AT40 went to market, customers were asking for a larger capacity bar.
The new spreader bar is going to be offered as an option for existing customers and new customers on the MAC25 and AT40 models. If existing customers have a crane already in the field, they can order it through Terex’s spare parts department, or if a customer is ordering a new crane, they can order it as an option.
same length, and it is only 10kg heavier than the existing Franna 15t bar. The initial feedback Franna received when it was presented to customers has been very positive.
“They were concerned about manual handling, and the weight of a larger capacity spreader bar. But it’s still easy enough to rig with one person. It’s very similar to how you’d use the standard 15t bar, but obviously you are getting a much larger capacity,” said Edwards.
The target market for the new bar will the MAC25 models up to the AT40. When
“To our knowledge, this is the first time there’s been a ‘small-scale’ pick and carry spreader bar, in the market with a 25t capacity range. Plus is it is designed by Franna for Frannas. It is a completely Australian designed, engineered, and manufactured product, made with Australian steel,” said Edwards.
He goes on to explain the testing process of the spreader bar.
“We manufactured a prototype which we designed and tested to AS4991 to learn as much as we could. We found a few small things in the design that we could improve on and so we went back and tweaked a few things. We then built a second prototype, which exceeded the requirements, and when we destructively tested it, let’s just say it damaged the rigging gear before it damaged the bar,” said Edwards.
“This 25t tonne bar is capable of multiple sling angles to work with, each with a unique working load limit based on the configuration of the rigging setup.”
MEMBREY’S CONTINUES TO CELEBRATE 60TH BIRTHDAY
MEMBREY’S TRANSPORT AND CRANE HIRE celebrated its 60th birthday with the arrival of a new Franna AT40 in Melbourne and the opening of a new branch facility at Crestmead in Logan, west of Brisbane.
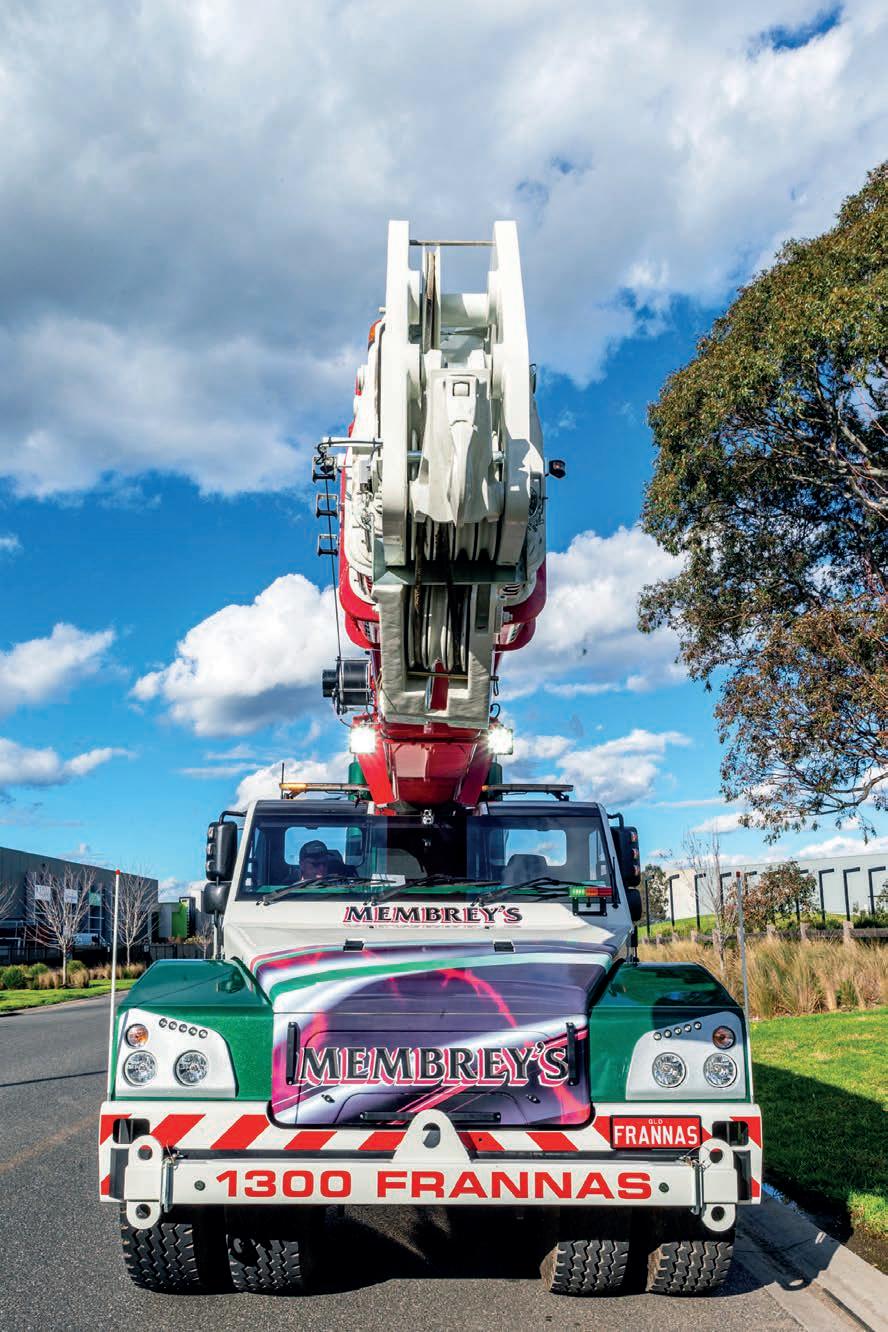
The new Terex Franna AT40 articulated pick and carry crane is a true workhorse for any construction site, featuring a huge maximum lift capacity of 40t, and boasting 44 per cent more load moment than the MAC 25.
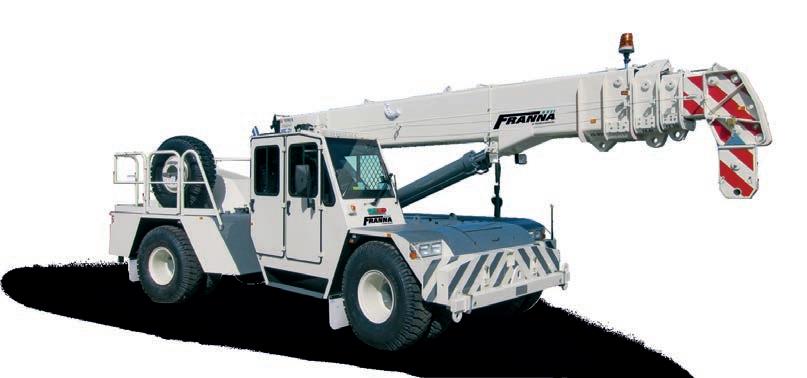
The AT 40 features a three-axle design that eliminates the need for a removable counterweight. The third axle control system also raises axle three when operating on a work site, providing a similar turning circle as the MAC 25. Maximum road speeds of up to 75km/h allows the operator to move swiftly and safely from job to job.
Additional features include a full width isolated cabin, articulating counterweight, and increased cabin storage.
The AT40 also comes with Franna’s Dynamic Load Moment Indication (LMI) system. First released in 2013, Dynamic LMI remains a pillar of safety, underpinning the electronic control and user experience offered today. The system is designed to offer ‘real-time’ calculation of rated capacity, taking into account boom configuration as well as chassis articulation, pitch, and roll, enabling continual assessment of structural limitations, forward stability, and side stability.
Not only that, the increased resolution of rated capacity the crane enjoys is made possible by finer measurement of articulation pitch and roll angles, allowing for improved machine capability compared to previous generation LMI systems. When operated on a jobsite over undulating terrain, the rated capacity will be updated continually, providing instantaneous information on the percentage utilisation of the machine (0–100 per cent of available capacity).
When the crane is operating on a side slope or undulating terrain, operators are no longer required to manually calculate a reduction of rated capacity; the Franna Dynamic LMI does that.
The crane also comes with operatorsettable maximum working height, a maximum working radius, and a

Membrey’s Transport and Crane Hire celebrates its 60th birthday with the arrival of a new Franna AT40, the third in the fleet.The new Franna AT 40 is the third in the Membrey’s fleet.

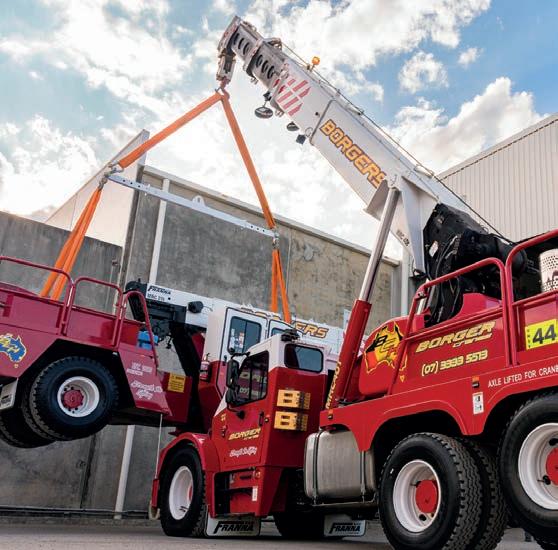
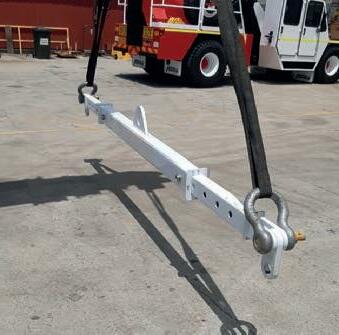
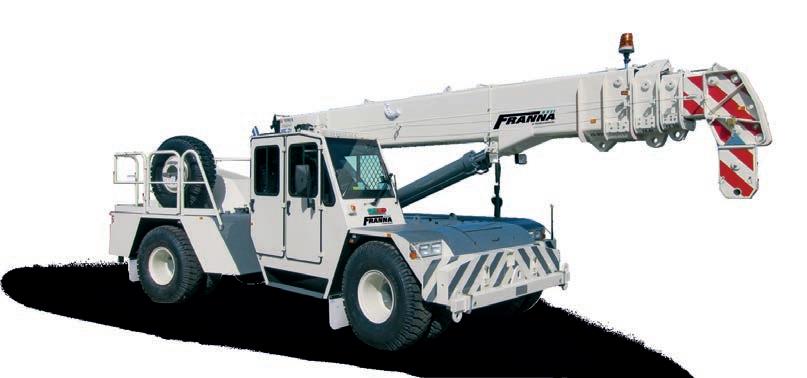
percentage of rated capacity. These features further enhance the safe operation of the machine when site conditions get tough and are available in retrofit form for all Mercedes-powered Franna cranes.
Membrey’s transport and crane fleet is impressive by any standards and the AT40 will no doubt be an excellent addition. Membrey’s managing director Craig Membrey provides more detail.
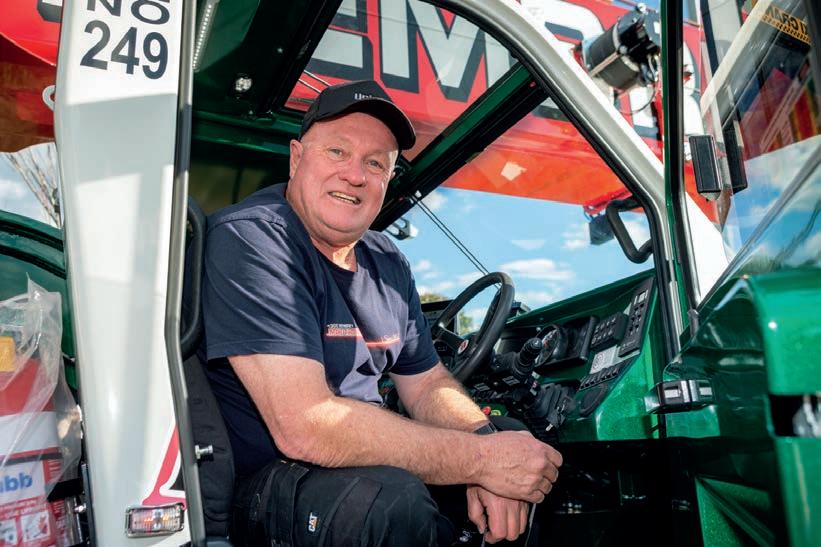
“We continue to invest heavily in our fleet and the last 18 months has seen the business invest in four new Frannas, two additional Maeda mini crawlers, several new trucks including trays and heavy rated vehicles, along with several new JLG boom lifts, light towers, scissors lifts, telehandlers, and forklifts,” he said.
“Membrey’s approach to the equipment we operate has always been about ‘Best of Breed’ and ‘Brand Loyalty’. To that end, our fleet of articulated pick and carry cranes are Terex Frannas and our all terrains are Liebherr and, of course, our heavy haulage fleet is Kenworth,” he said.
Membrey’s operates eight all terrains with capacities ranging from 40t up to the Liebherr LTM 1350 -6.1 with a 350t capacity. There are 12 Frannas in the fleet ranging from 12t to 40t capacities, including three AT 40s. The fleet also includes a Kato MR 13t capacity city crane. ‘The Beast’, the recently arrived Liebherr LTR 1220, adds a completely new dynamic to the fleet. The move into Brisbane has been some time in the planning and Membrey is excited about the possibilities.
“We have a lot happening within the
business and we’ve been looking to diversify and expand our operations for some time. We are experts in end-to-end transport and logistics solutions, including craneage, and many of our customers in Victoria operate up and down the east coast.
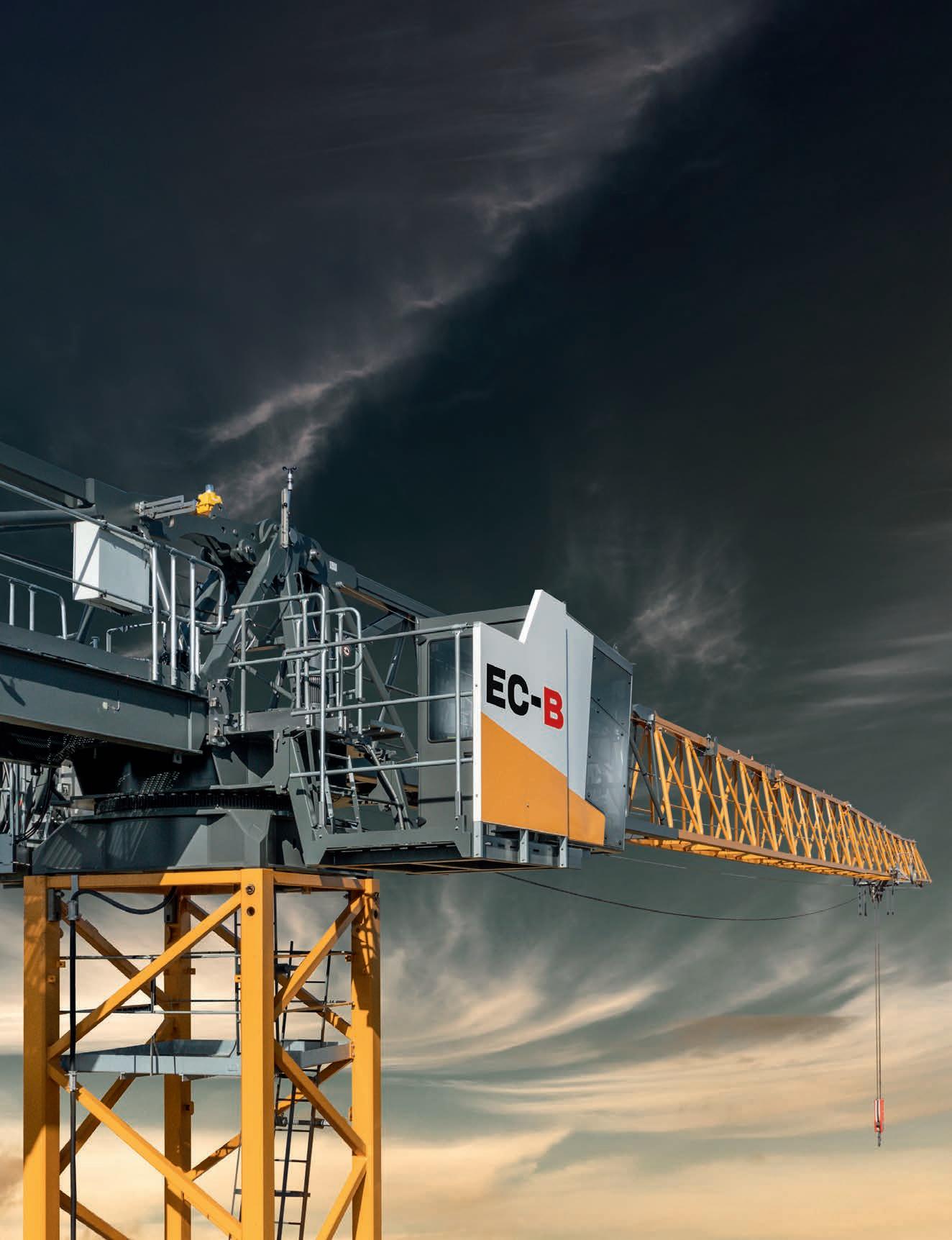
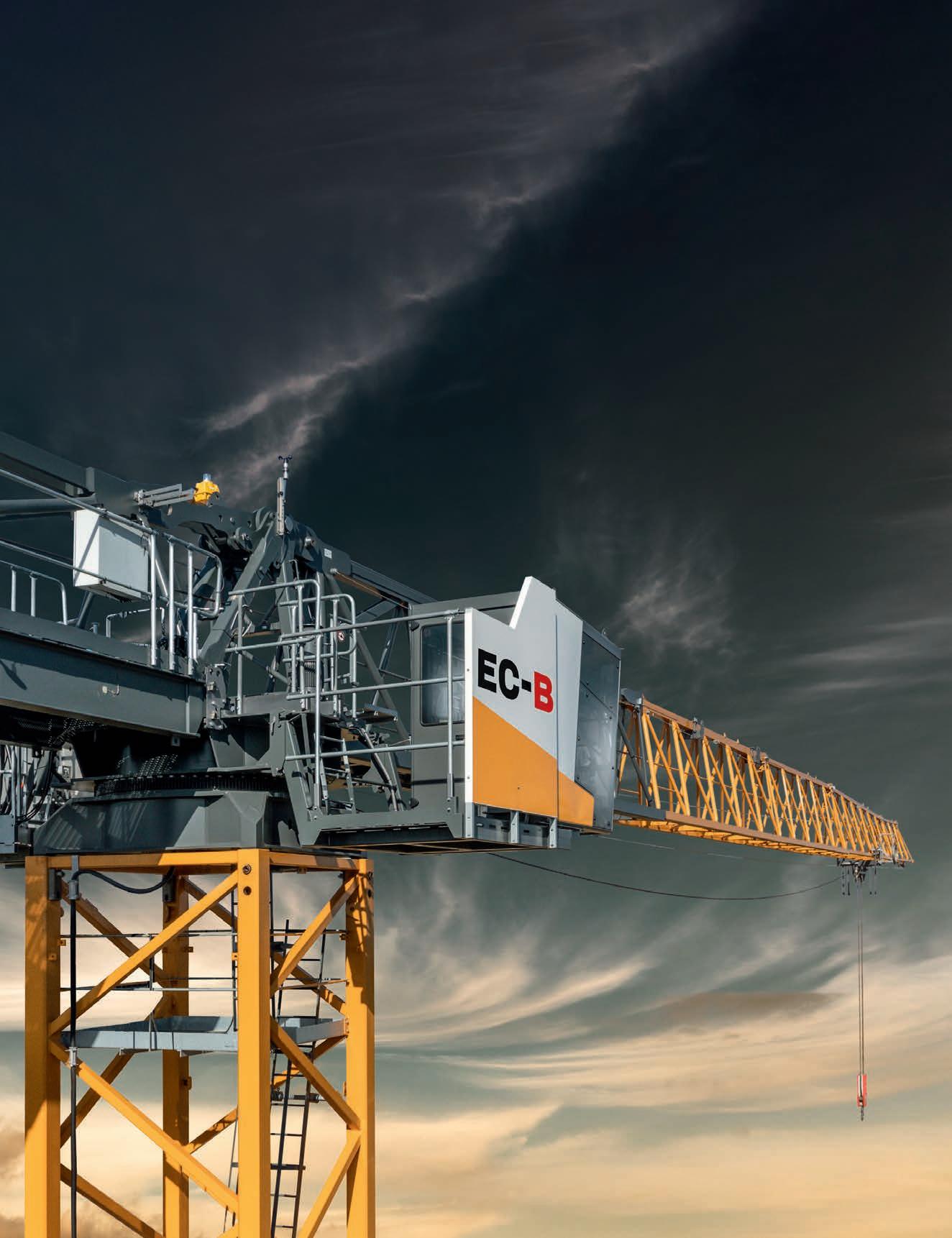
“The move to Brisbane reflects the changing needs of our clients and the projects they are managing. As borders become less relevant and with renewed focus on experience and professionalism, Membrey’s capabilities set the standard our clients expect,” he said.
“Initially we’ll have a focus on some of our specialty trailers to support current opportunities and this will be quickly expanded to respond to customer and
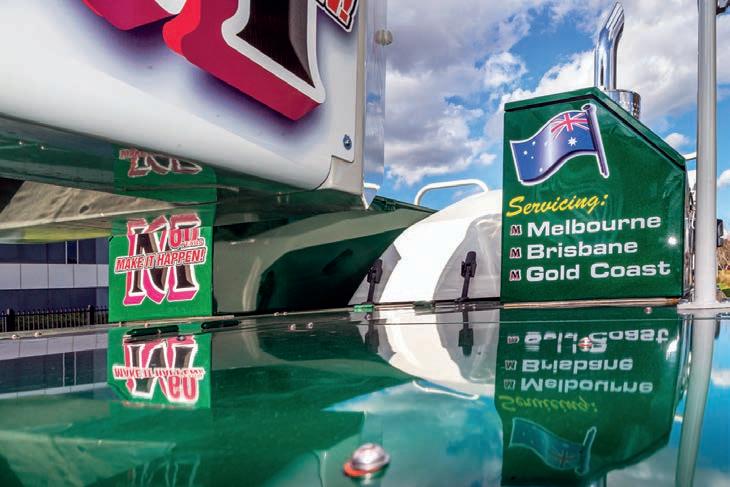
project needs. To start with, we will base a couple of Frannas there to support current activities, and on the transport front it will be what Membrey’s is best known for. Bigger is better and this will include support vehicles.
“We recently signed a lease on a yard in Crestmead in the west of Brisbane and there’s a lot of development happening in the region. The move gives us a solid foot hold in south east Queensland and we are very excited at the prospect of servicing existing and new clients with our ‘make it happen’ approach throughout the region,” said Membrey.
Membrey’s general manager, Leigh Canet speaks about the importance of the Terex Franna relationship and the benefits Membrey’s enjoy well beyond the standard supplier/customer model which he largely attributes to Terex’s customer-centric approach they instil within the business and customers.
“The industry leading benefits of Terex are underpinned by strong relationships with their customers and industry. At a time when we all face challenges with parts, supply chains, staffing and the broader costs associated with today’s markets having strong & reliable trusted relationships to support our business is absolutely invaluable,” he said.
“Membrey’s transport and crane fleet is impressive by any standards and the AT40 will no doubt be an excellent addition.”Membrey’s managing director Craig Membrey. Membrey’s now services Melbourne, Brisbane and the Gold Coast.
EC-B
When the going gets tough, the tough get going.
The EC-B series has what it takes for the rough and tough world of construction sites: Unrivalled performance and ingenious assembly solutions – all with a smart operating system and impressive design. www.liebherr.com

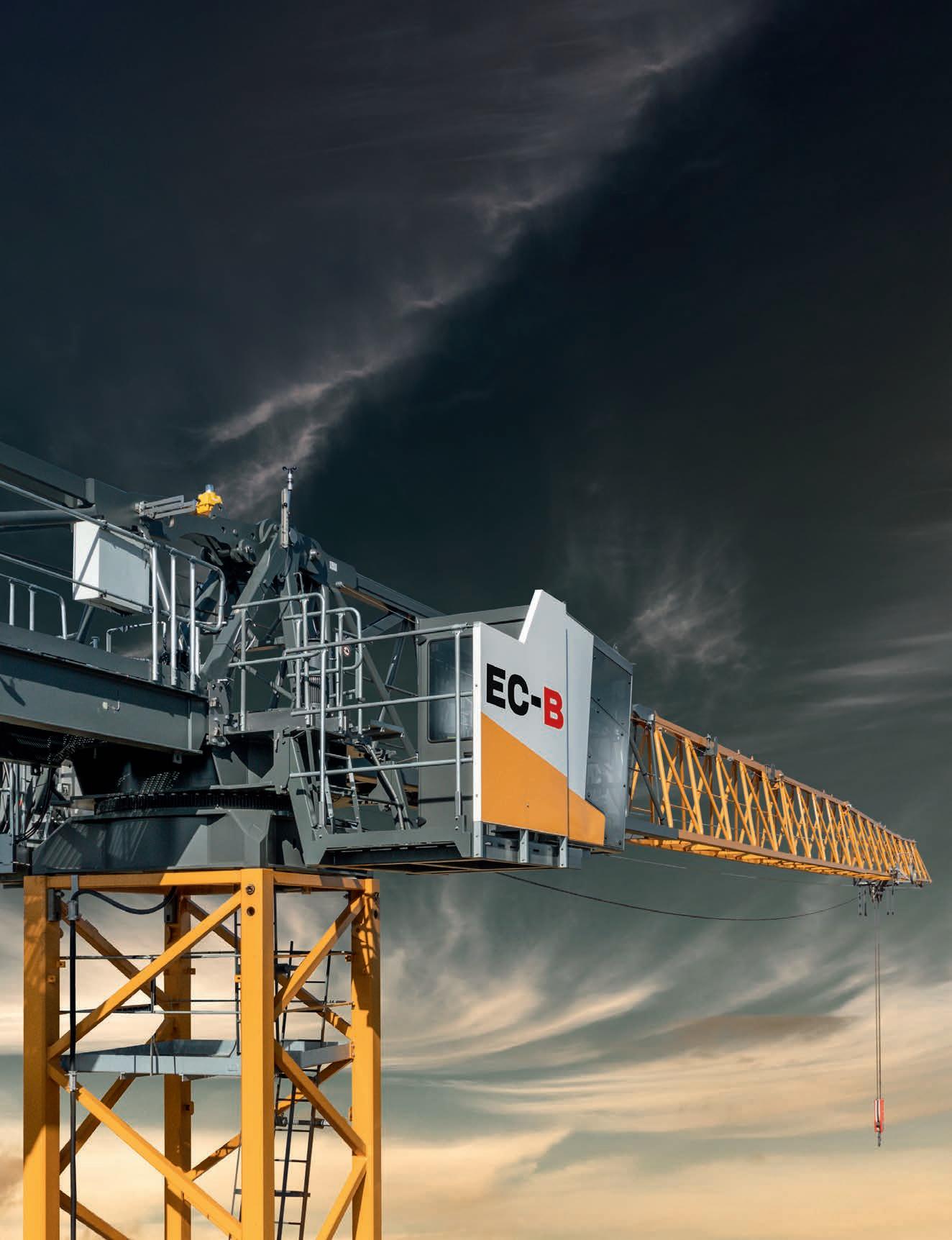
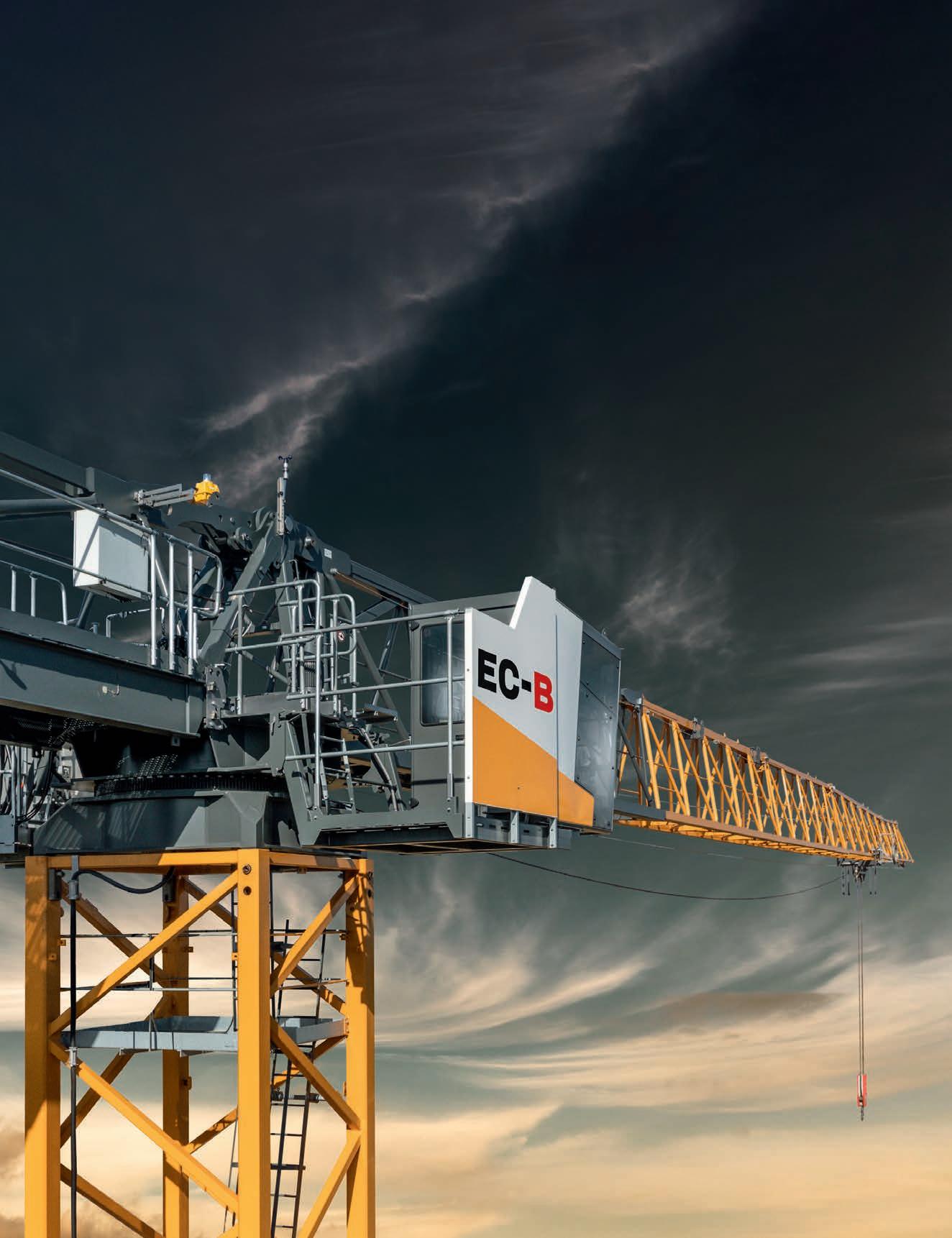
RONCO CONTINUES THE GROWTH OF THE BRAND
Ronco has been in the crane industry for over 27 years. Started by the Downie family and today still employing a member of the Downie family, the company was purchased by Robert Smith in 2010 and he continued on with the passion for cranes.

RONCO MADE THE MOVE IN 2012 to incorporate quality major inspections of varying types of cranes into its operation. Its premises today covers 16,000 square metres in Maddington, Western Australia, with a 1,400m 2 workshop with access from the Tonkin Highway.
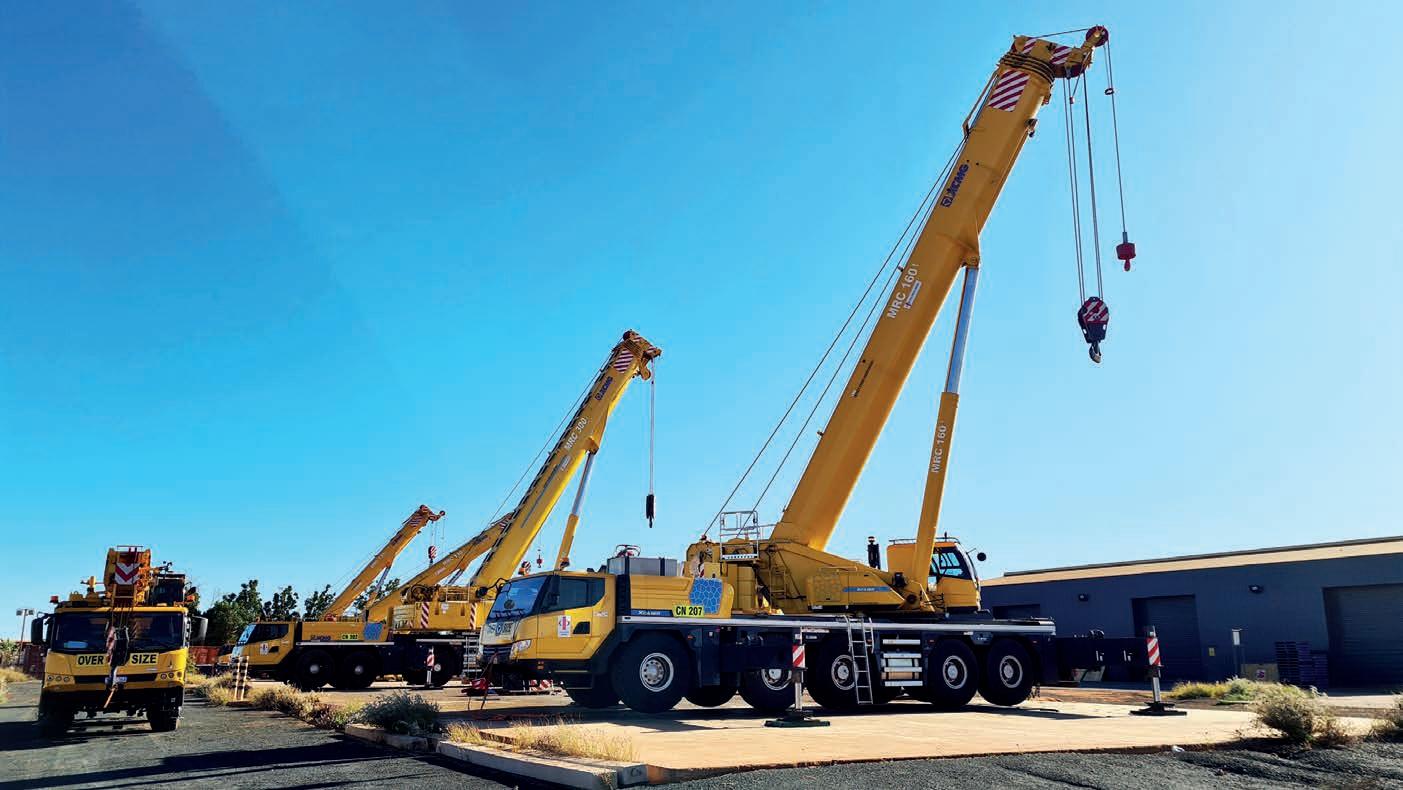
The workshops are not hindered by power lines, allowing Ronco to accept and erect crawlers and larger all terrains at its facility.
“We are very proud to display our CICA awards in our reception. These plates were awarded against customer assets after vigorous scrutiny of the MI process and final reports by CICA and CraneSafe, as requested by the client and encouraged by Ronco management,” Smith said.
Ronco’s service and parts team
Ronco has stocked the Tidd range for a number of years.
have a range of service vehicles for both metro and country runs. Its tooling level runs on a philosophy of ‘if we have to rent it more than twice, we buy it’.
“As such, we have presses, mobile diesel welders, compressors, steam cleaning and sandblasting,” Smith said.
Ronco’s boiler maker paired with its design engineer will often repair boom sections rather than force operators down for lengthy periods of time waiting for new telescopic boom sections when they are dented, or when lacings need to be replaced on lattice boom sections.
Its boiler shop can easily accept 12m sections that are easily handled and rotated by its twin overhead cranes. It has the ability to preheat large sections and slow cool when required. All boom repairs have written procedures and physical visits from its in-house design engineer.
DESIGN AND FABRICATION AT RONCO
Ronco was approached by Superior Energy, which was building a mobile fracking head control centre. It explained that it was searching for a corner-mounted VLC but fabricators could only supply a standard out of the box straddle ‘T’ boom crane.
“We looked carefully at the requirements for the lifts. We purchased a new stock standard HIAB T270 ‘T’ boom and redesigned it to the needs of the customer – getting to work cutting the crane into pieces. The main requirements were rear corner-mounted with outriggers that deployed beneath the trailer deck,” Smith said.
Ronco completed the project and delivered to the customer, which put it to use immediately.
After a brief phone call two years ago between Smith and TRT executive director Bruce Carden, Ronco began to supply and service the Tidd range across Western Australia, demonstrating the growth of the company.
“We had delivered TRT pole borers before to Rio Tinto and maintained those TRT units since delivery, so TRT knew we were flexible and had an understanding of the machine. We were honoured that TRT saw us in a position to sell and support the Tidd PC28 product.
“The workshops are not hindered by power lines, allowing Ronco to accept and erect crawlers and larger all terrains at its facility.”
They have been fantastic loyal manufacturers and suppliers of the Tidd product,” Smith said.
“Recently we embarked on a new three-year dealership contract for WA with XCMG, who are the world’s fourth largest manufacturer of cranes, whilst in China they are the number one construction machinery manufacturer.
“They had a number of machines in stock – truck cranes and all terrain cranes. Speaking at length with David Kapahnke [managing director of D&D], he has put the cranes through their paces and initially had some issues with weights.
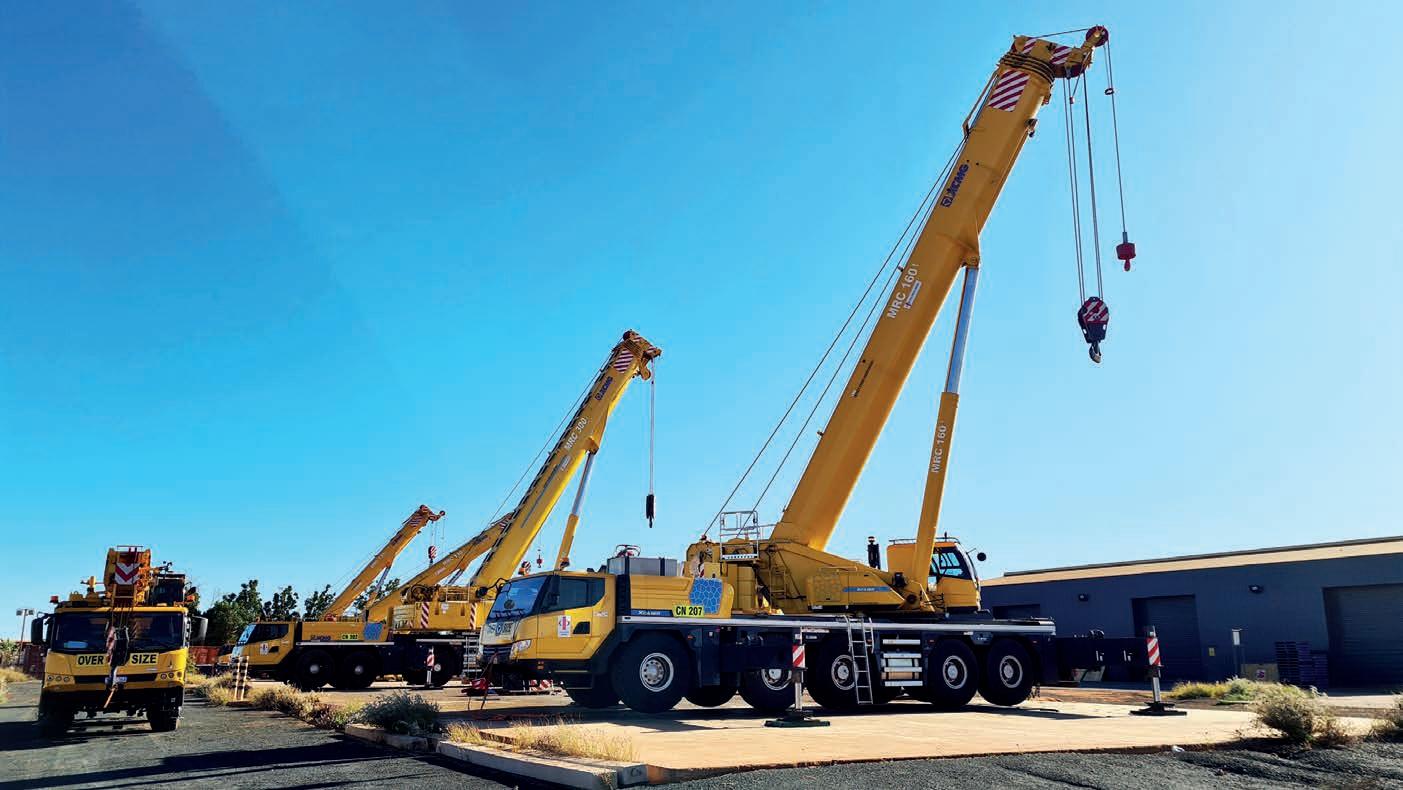
“Today, with the modifications for Australia that the team from XCMG have made, the three-axle 60t all terrain weights are for all states in Australia,” Smith said.
“The next research mission before deciding to stock the XCMG range was to the north west of WA to see a number of all terrains, some crawlers, and the XCMG office and workshop in Karratha.
“I was impressed that the northwest Western Australia XCMG had two mine spec service vehicles, over 10,000 line items to support the north west cranes, and five technicians, all specialising in different disciplines being hydraulic, electrical, mechanical, and R&D.
“The cranes up north are all design registered in Australia, passed CraneSafe, passed inspection by asset management engineers, and are all road registerable at 12t per axle,” Smith said.
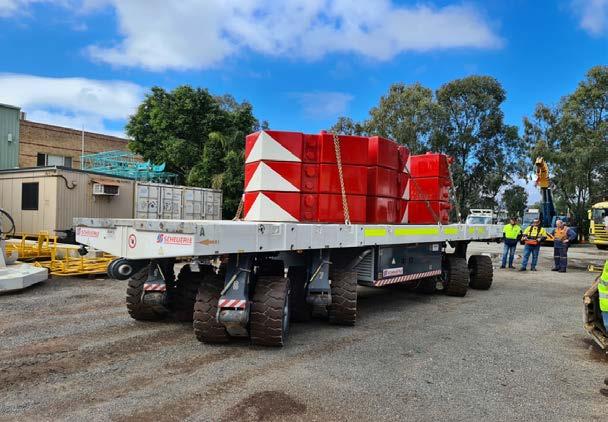
“In 2023, we look forward to showing the market that a reasonably priced crane can do the same work as the more expensive brands, with lower repayments and the same returns.”
Ronco is the dealer for Australia for Scheuerle SPMTs. It has trained technicians who provide backup and operator familiarisation with the product. This, coupled with the 24/7 support by the factory, means
reduced downtime. Ronco even has a SPMT 170.8.4 174t capacity crane in its hire fleet.
“We also we have plans to install a paint booth and embark on painting inhouse rather than using an external provider. This will allow us to not have wait in queues at paint shops for plant and equipment,” Smith said.
Within Ronco Group lies Empire Equipment Hire, which was founded from the purchase of two Ronco R6000 cranes that were taken out of operation by Alcoa Alumina. They were quickly refurbished and major inspections (MIs) were completed
to CICA Gold Plate Standards. They went out to Alcoa while its fleet of R6000s came through the Ronco workshop for their MIs.
“From there we were asked mainly for pick and carry cranes, while smaller business brought theirs in for MI. This meant that they could continue to service their customers and retain their crane operator in employment while the crane was out of service,” Smith said.
Today Empire Equipment Hire has a fleet size of 14 pick and carry cranes, from 28t Tidds to R6000s and a Scheuerle SPMT, all available to hire by crane owners.
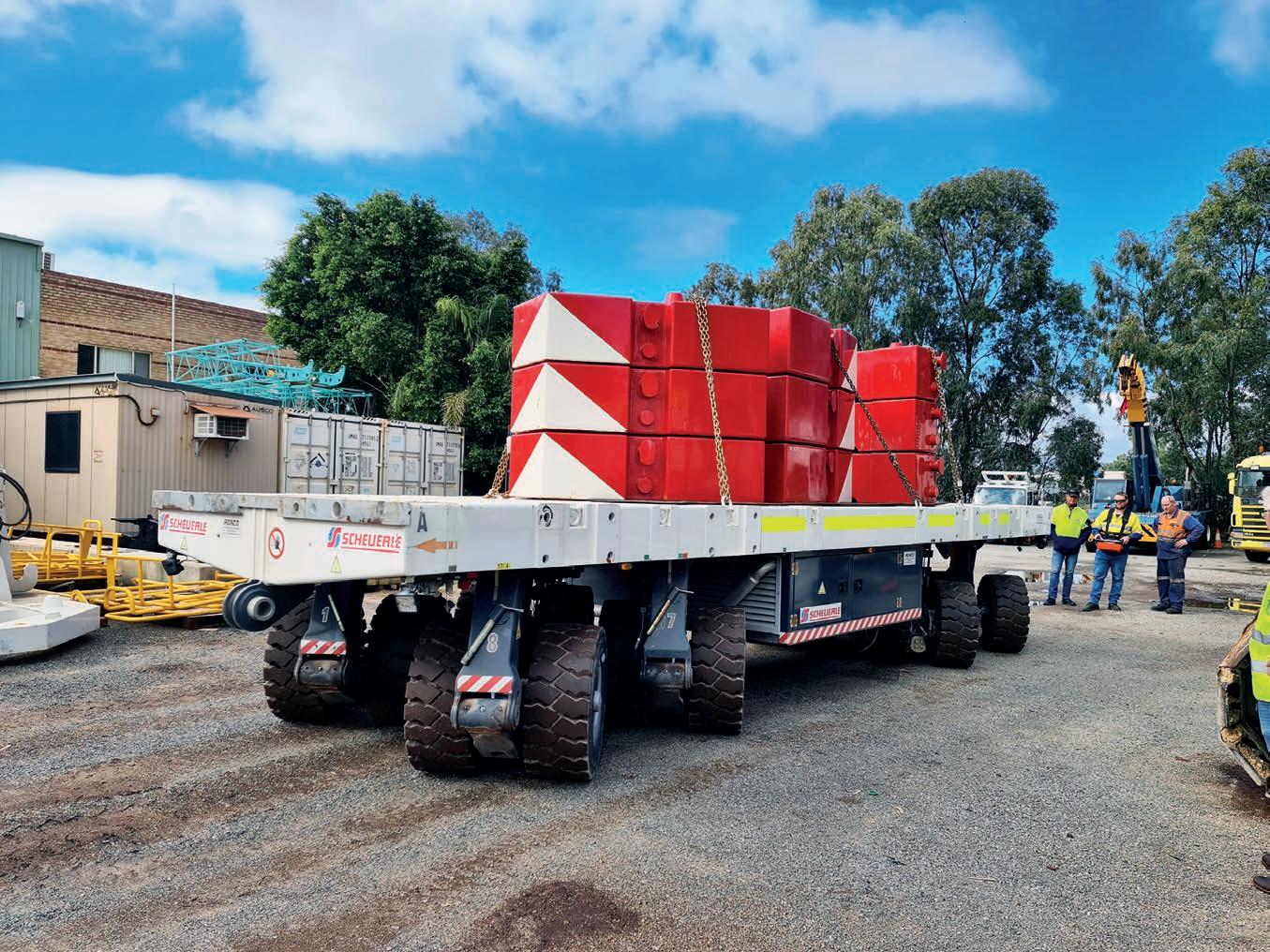
“We also we have plans to install a paint booth and embark on painting inhouse rather than using an external provider, this will allow us to not have wait in queues at paint shops for plant and equipment.”
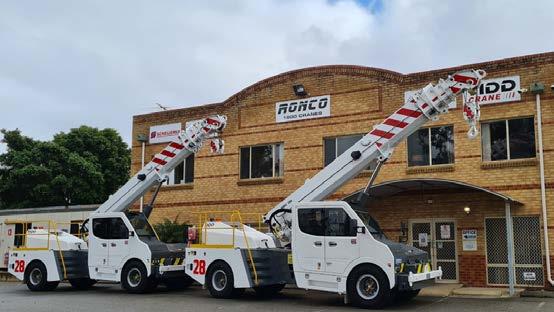
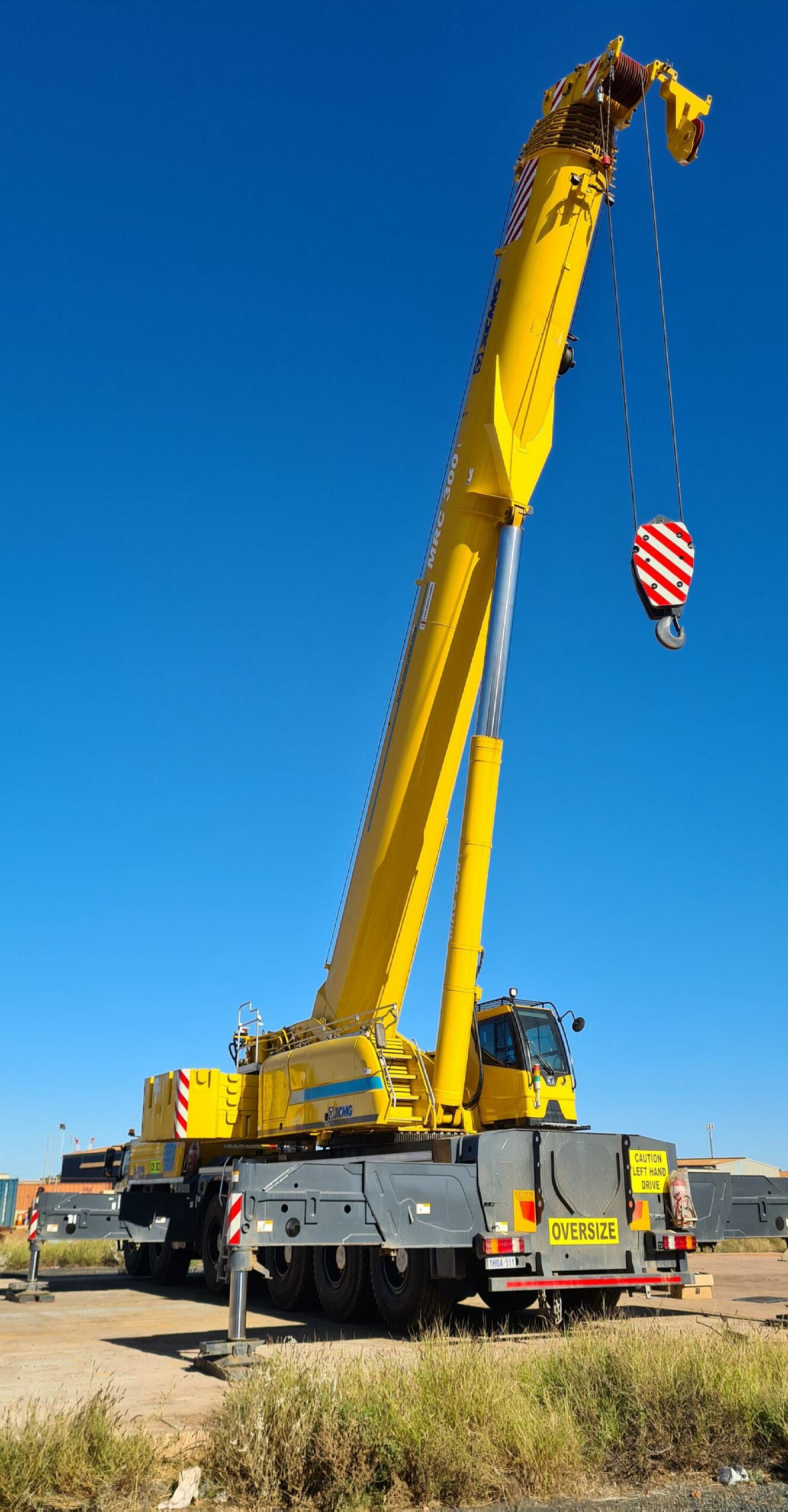
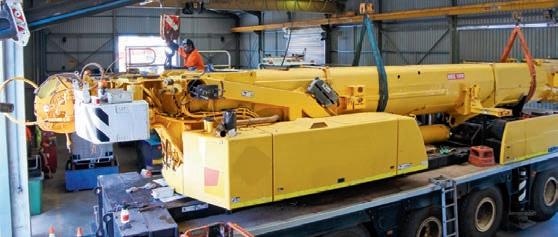
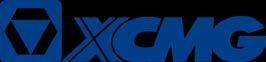
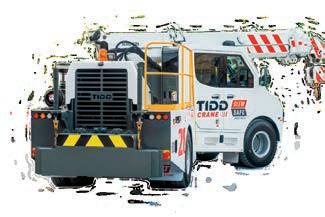
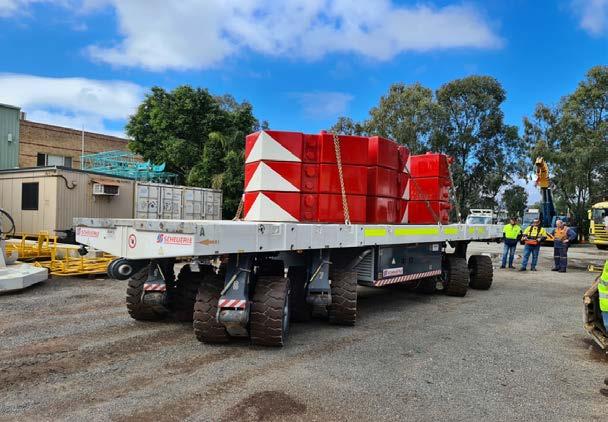

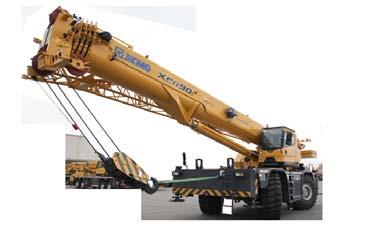
BIG RHINO HOOKED ON SANY
Brisbane-based Big Rhino Crane Hire recently took delivery of a Sany SAC600E, 60t capacity all terrain. The Sany features 50 metres of main boom and is one of the first to be delivered in the country.
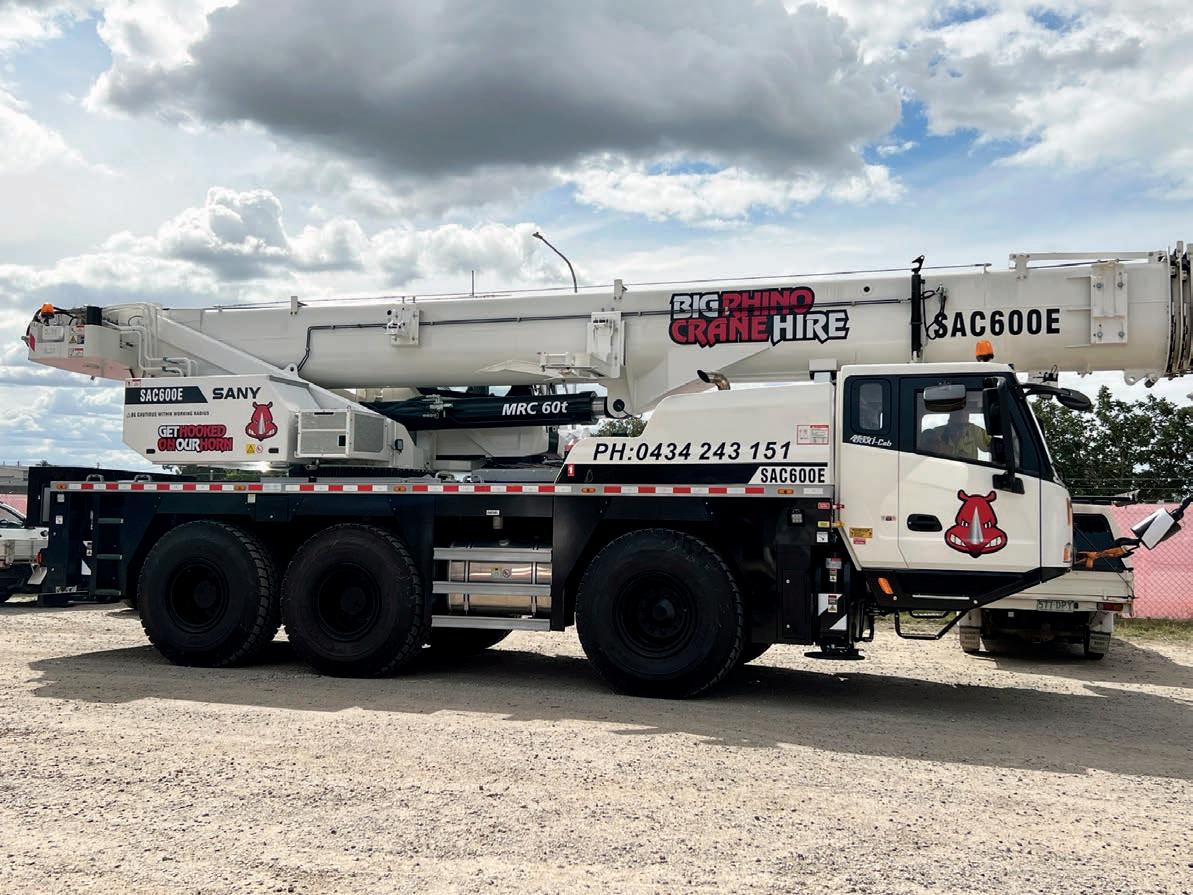
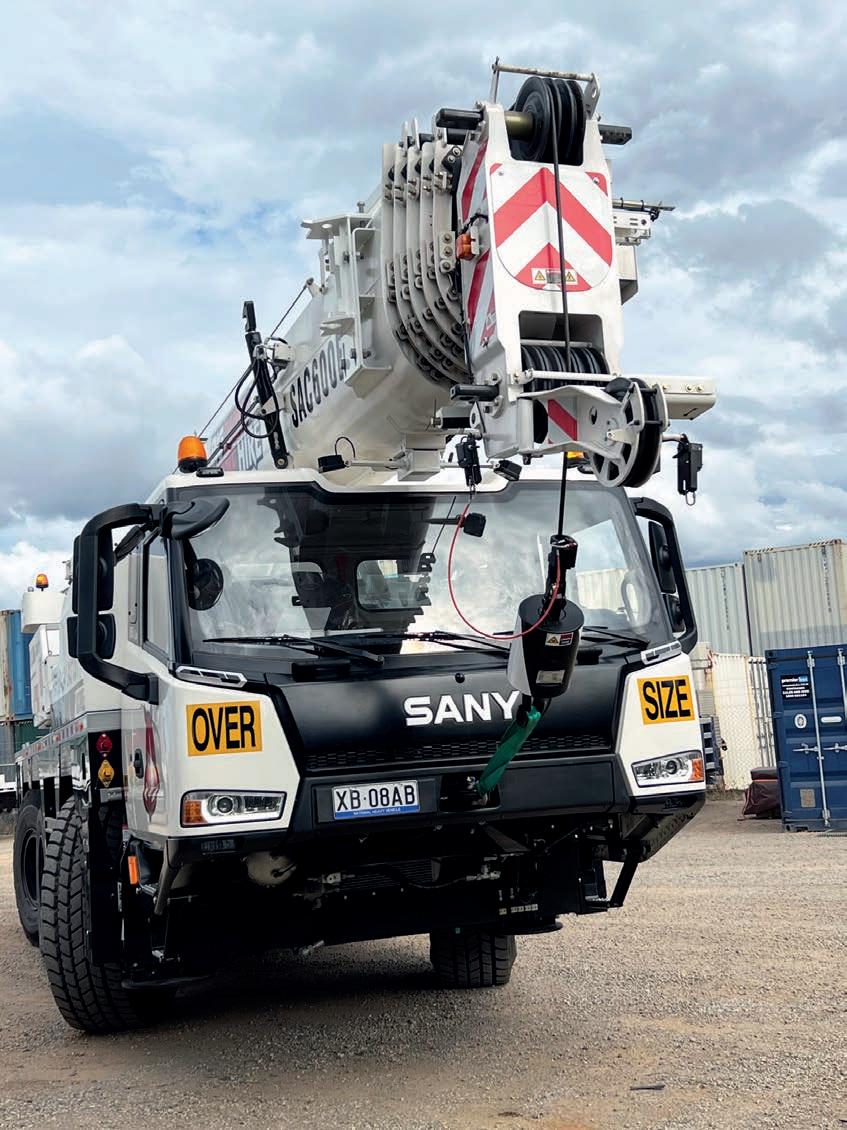
The Sany SAC600E 60t capacity all terrain crane, is a high-quality crane with a 50m boom.
BIG RHINO CRANE HIRE IS A PRIVATELY owned family business that has been operating for almost 14 years. Like so many crane hire businesses, it was started by frustrated individuals who could see there was a better way to work in the crane hire sector.
Marg Gravener, managing director of Big Rhino Crane Hire, provides some background to the business and the purchase of the Sany.
“My husband and two sons were all working in the industry, and they were frustrated with the lack of honest communication between customers and the crane hire businesses. They could see this was leading to general levels of dissatisfaction within the industry,” she said.
“It was a random comment around the dinner table when I asked: ‘Why don’t you get your own crane then?’ 14 years later, we are operating four Frannas, four city cranes and our brand new Sany SAC600E 60t all terrain.”
Big Rhino Crane Hire is a great name for a crane hire business and Marg provides some insight into it.
“My husband Paul’s nickname is ‘Biggen’ and our eldest son Ryan, who started the business with us, has the nickname Rhino, hence Big Rhino. The tag line for the business ‘Get hooked on our horn’ is a bit of fun and one we couldn’t resist,” she said.
“We started the business in November 2008, just as the big storm hit the Gap and South East Queensland. Our only crane was available, and we started work.”
Today, Big Rhino Crane Hire operates all over Brisbane as far North as North lakes, out to Springfield and Redlands and South to Yatala. The typical profile of a client is anyone who needs a crane, including construction companies and pool installers through to an individual who needs a massive bird’s nest moved.
Marg confirms how Big Rhino Crane Hire has recently expanded its business.
“By our standards, we have just had a massive expansion. We moved into a larger yard, and we currently operate four Frannas, four City Cranes and our brand new Sany SAC600E 60t all terrain.
“With the pick and carry Frannas, we have two 15t capacity and two 20t capacity machines available and these are currently in very high demand. The city cranes range from a small 10t capacity up to the Kato 20t capacity machine. These are a very versatile crane that can fit into small spaces with great lifting capabilities. In our opinion, they are still relatively unknown for their lifting capacity in the construction industry. We then have our new Sany 60t, which is a great asset to us for those bigger, heavier lifts,” she said.
The Sany SAC600E 60t capacity all terrain crane is a high-quality crane with a 50m boom. Whilst remaining lightweight in concept, it has remotely adjustable boom work lights, wind speed anemometer, boom tip camera, fall arrest cables on both sides of the boom, access ladders to each side of the cranes’ deck, with stairs and safety rail allowing entrance to the rear of the crane.
The crane comes with a 16m folding fly jib with off sets of 0°, 20° and 40°. Around the deck, the Sany SAC600E features a 9kg fire extinguisher, hi vis side stripes, a battery isolator, starter isolator, at the rear of the cranes’ deck there is a ring feeder mounting with air brake supply and amber
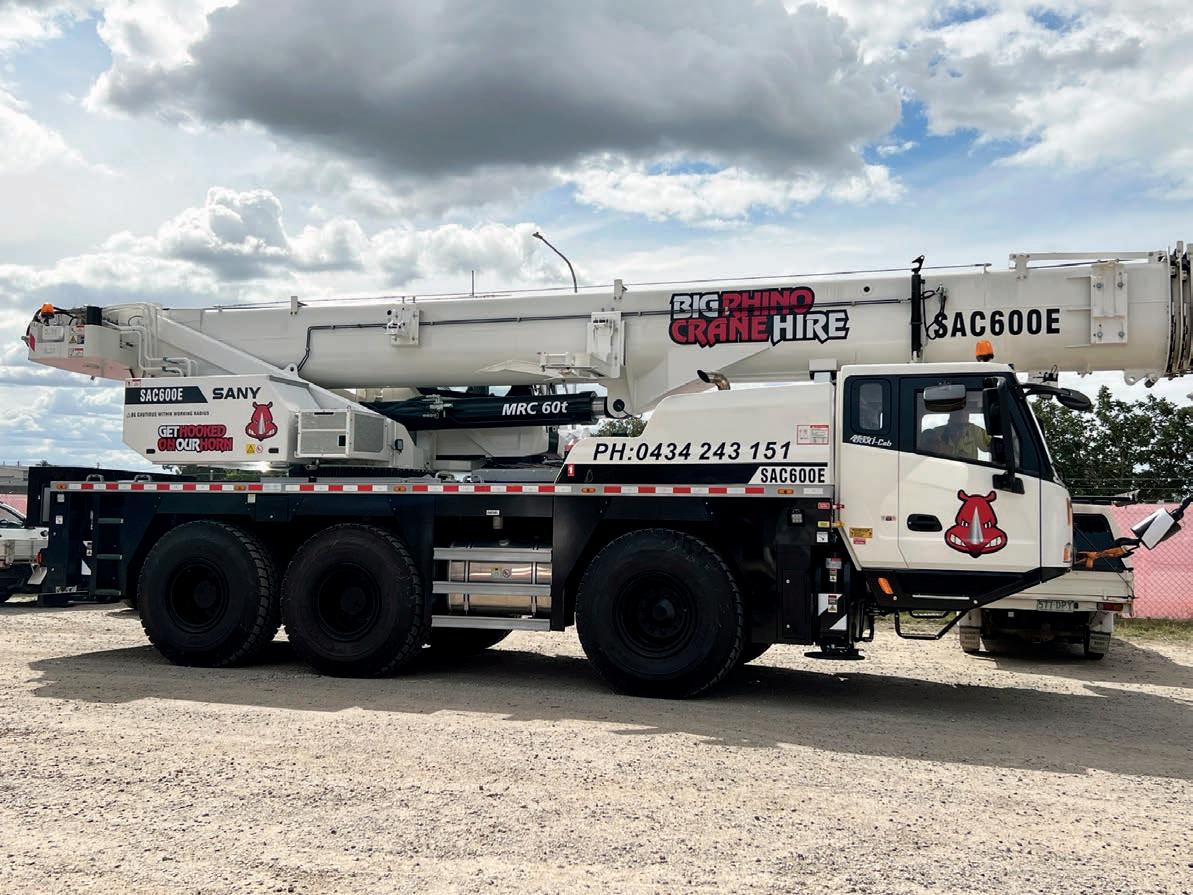
flashing beacons on the cranes’ structure.
The Sany SAC600E is powered by a Mercedes Benz inline six-cylinder diesel engine that generates 280kW at 1,600 rpm and it complies to Euro 3 emission standards. This allows the crane to use a miserly 60L per 100km, and also features an Allison auto transmission with 12 forward and two reverse gears, split between high and low range ratios.
Danfoss hydraulic valves ensure reliable and constant hydraulic pressure and adds to the cranes’ control and smooth operation. It also features six steering modes on the three axles with diff locks to promote great manoeuvrability. The weight of the crane is less than 36t, which enables it to be road ready with an Aux winch, headache ball, single sheave main hook, timber box, 3.3t of counterweight and still be under 12t per axle limit. Site works lifts the cranes axle capabilities to 16t per axle, which means mobilisation can take place with more counterweight.
The Sany SAC600E has a comprehensive remote-control, which means the operator can set up the crane, extend the outriggers, levelling the crane, slewing and positioning boom in place ready for loading of counterweight. The operator can then enter
the cabin to commence their lifting duties.
Sany is in a continual process of upgrading models and this crane now includes an operator’s cab that can tilt to up to 20° allowing the operator a better and more relaxed operating and viewing position, relieving aching neck & back muscles to observe the rope, from the top of the boom down. The newly designed cab maximises safety, comfort, and ease of operation. All operations in the cab are joystick controlled; the crane features a large viewing touch screen that is ergonomically fitted for ease of operation and shuffling through the various programs of the crane.
Cameras for downward vision and at the winch drum provide the operator with a view of the site they are operating, and keeping an eye on the winches to ensure correct laying of the wire rope.
The operator’s cabin is air conditioned, with premium comfort seating and fitted with AM FM radio, hands free phone, USB point and an operator’s manual in English.
Marg explains how the work conducted by the business influences the make-up of the Big Rhino fleet.
“The industry has trends, so you need to be aware of what type of crane is in demand
before buying. You don’t want the machine sitting in the yard looking pretty, it needs to earn its keep. Our approach to ensuring the fleet is contemporary with assets fully utilised revolves around great relationships with our customers,” she said.
“Our guys are always out in the field working with our existing customers, understanding what projects they have in the pipeline and ensuring we have the right solutions for their businesses. We have built a reputation for managing difficult jobs, the type of work other crane hire businesses won’t touch. We also work for such a diverse range of industry sectors, there is no typical profile for our customers.
“We are strong in the construction sector, lifting trusses, and that sort of work, but we have also been used in the movies, and we have completed unusual work, such as shifting a massive bird’s nest so a council could replace the rotting post it was on,” she said.
Big Rhino Crane Hire has long-term relationships with customers, explains Marg.
“Some of our customers have been with us from day one. We are proud of the loyalty they have shown us, which is hard to find in today’s competitive market. I come from a retail background and as a team we are focused on delivering a highly personalised service to our customers and
we see this approach as one of the greatest assets for the company,” she said.
This approach also translates to the approach Big Rhino has towards its suppliers, and in particular Tutt Bryant Equipment (TBE).
“TBE has been distributing and supporting cranes and various brands of construction equipment for some time. Our relationship with TBE began a few years ago, with the purchase of our 20t capacity Kato city crane,” said Gravener.
“The Kato has been a great crane for us, and the team is more than happy with its capabilities.
“Peter Lawgall, Business Development Manager (Cranes) at TBE has always been very easy to deal with; they are happy to discuss any issues we might have and to jump onto any problems that need solving. They are very responsive and are happy to answer any questions we might have,” she said.
“The new Sany has a much larger capacity to the other cranes in the fleet and addresses a void we have seen for some time. Our customers are faced with heavier lifts and the 60t capacity is designed to address these demands.
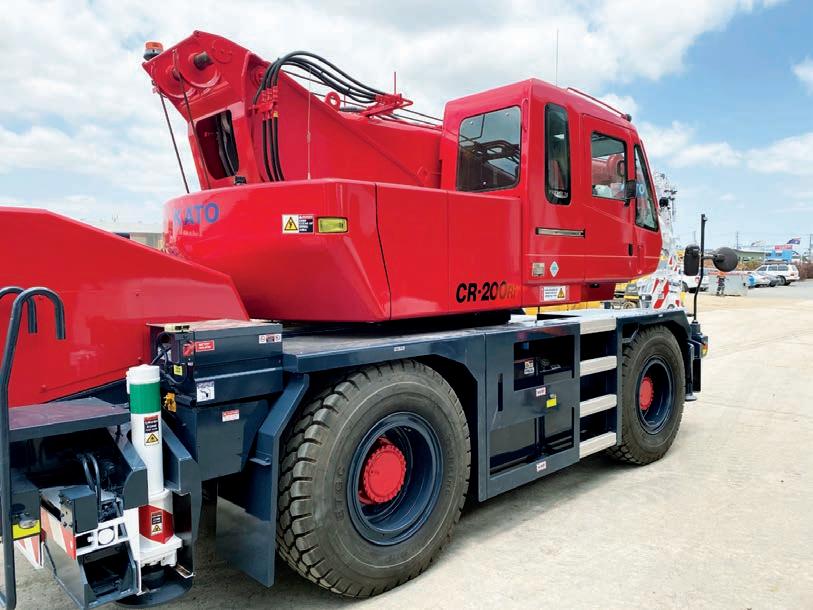
“This particular crane was recommended by Peter and, when we examined its specifications and capabilities, we could see it met all of our requirements, and the fact that there will be specific

‘factory trained’ technicians available to support the crane is a wonderful bonus for us,” said Marg.
SAFETY IS A KEY FOCUS FOR BIG RHINO CRANE HIRE
“Our very experienced crew will discuss the job with the customer and with team internally, to ascertain the best approach. If it is a difficult job, we will have a supervisor on site as well. Safety drives everything we do at Big Rhino,” said Marg.
“Our site inspections are a free service, and we strongly advise a new customer to take advantage of this service. It is always better to get the best crane for the job first time.
“Lift planning is conducted after a site inspection and following discussions with the customer. The lift planning is the responsibility of our business manager who has vast experience in this field,” she said.
THE EXPERIENCE WITHIN THE BIG RHINO TEAM IS A KEY REASON FOR THE SUCCESS OF THE BUSINESS
“Between our operators, riggers, and dogmen, back room and office staff, we have well over 90 years of experience, with some having a wide variety of different work experiences.
This enables us to cover a varied area of lifting. We have a positive culture within the team and that makes a huge difference to having smooth operations.
“Our manager and allocator have very friendly and easy to approach personalities, which works well with the crew and our customers.
“Our office has an open-door policy, and it is a happy environment to work in. All of this translates to a positive approach to the service we deliver to our customers.
“Where do you we see the business in five years? With our growth over the last 12 months and the recent expansion into the new yard, I believe we will be a ‘better known brand’ that will continue to grow, by providing an honest and reliable service to our customers.
“This will be achieved by a fantastic team backed up by great equipment,” said Gravener.
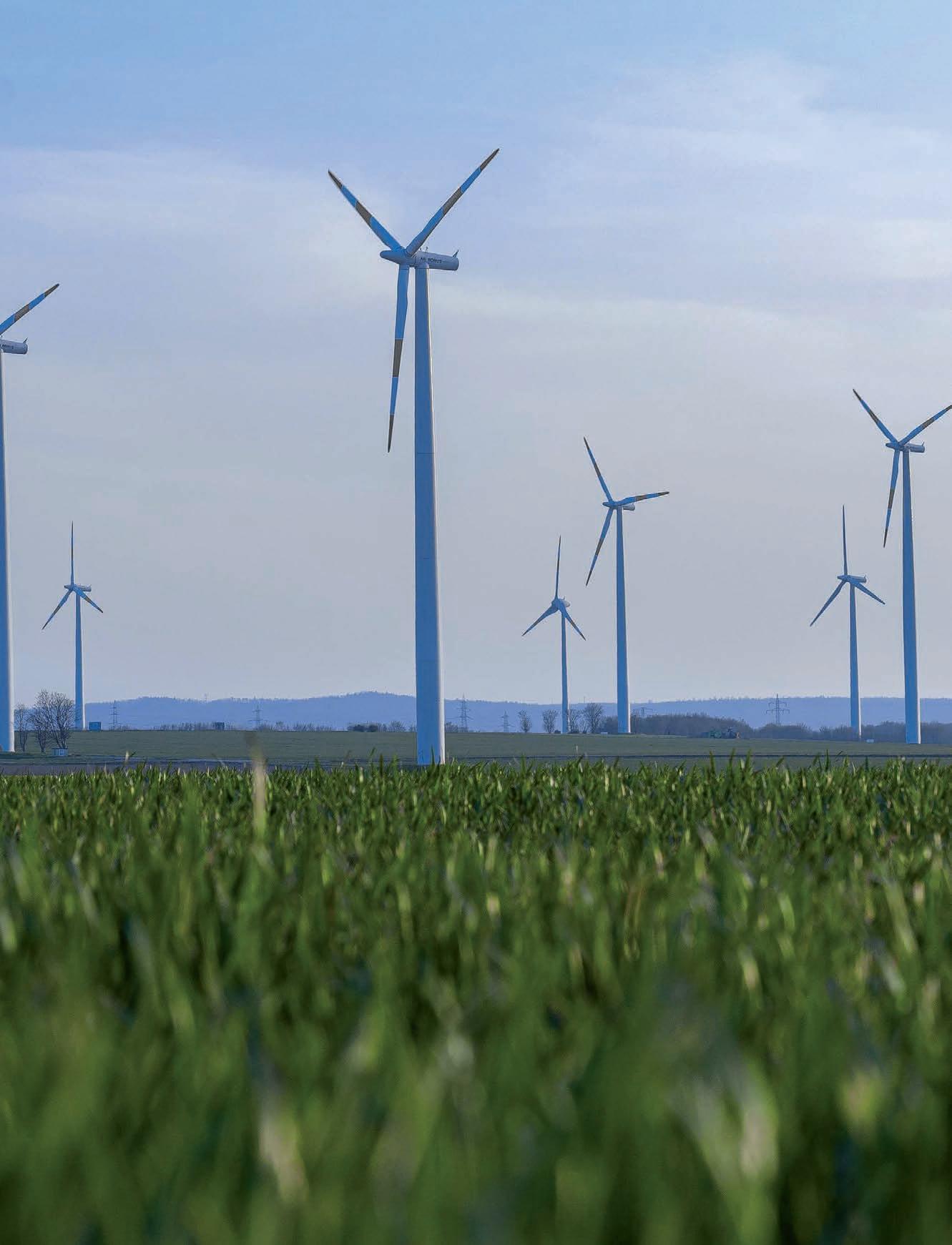
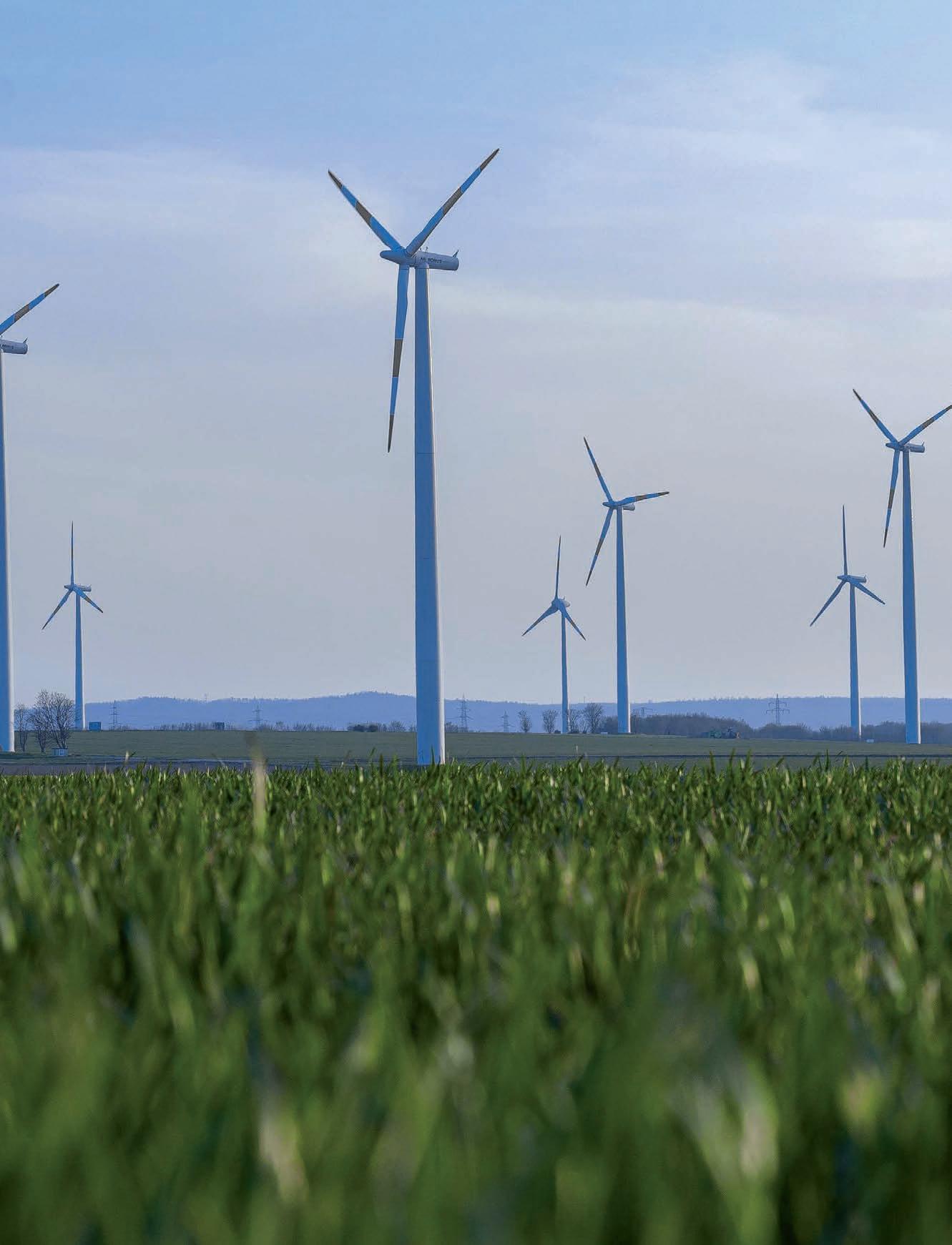

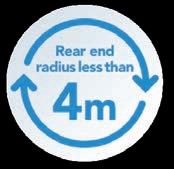
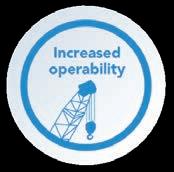
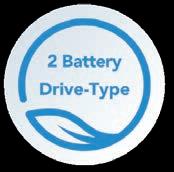





INTRODUCING A NEW MINI CRAWLER RANGE TO SHAKE UP THE MARKET
The BG Lift spider crane has the capability to squeeze into even the most confinded spaces.
Brian and Sam Evans from Global Machinery Sales (GMS) have always been impressed with the flair of Italian designed and manufactured industrial equipment. GMS has represented the Italian-made CMC spider lift range since 2012 and recently announced it will be representing the BG Lift range of compact crawler cranes.
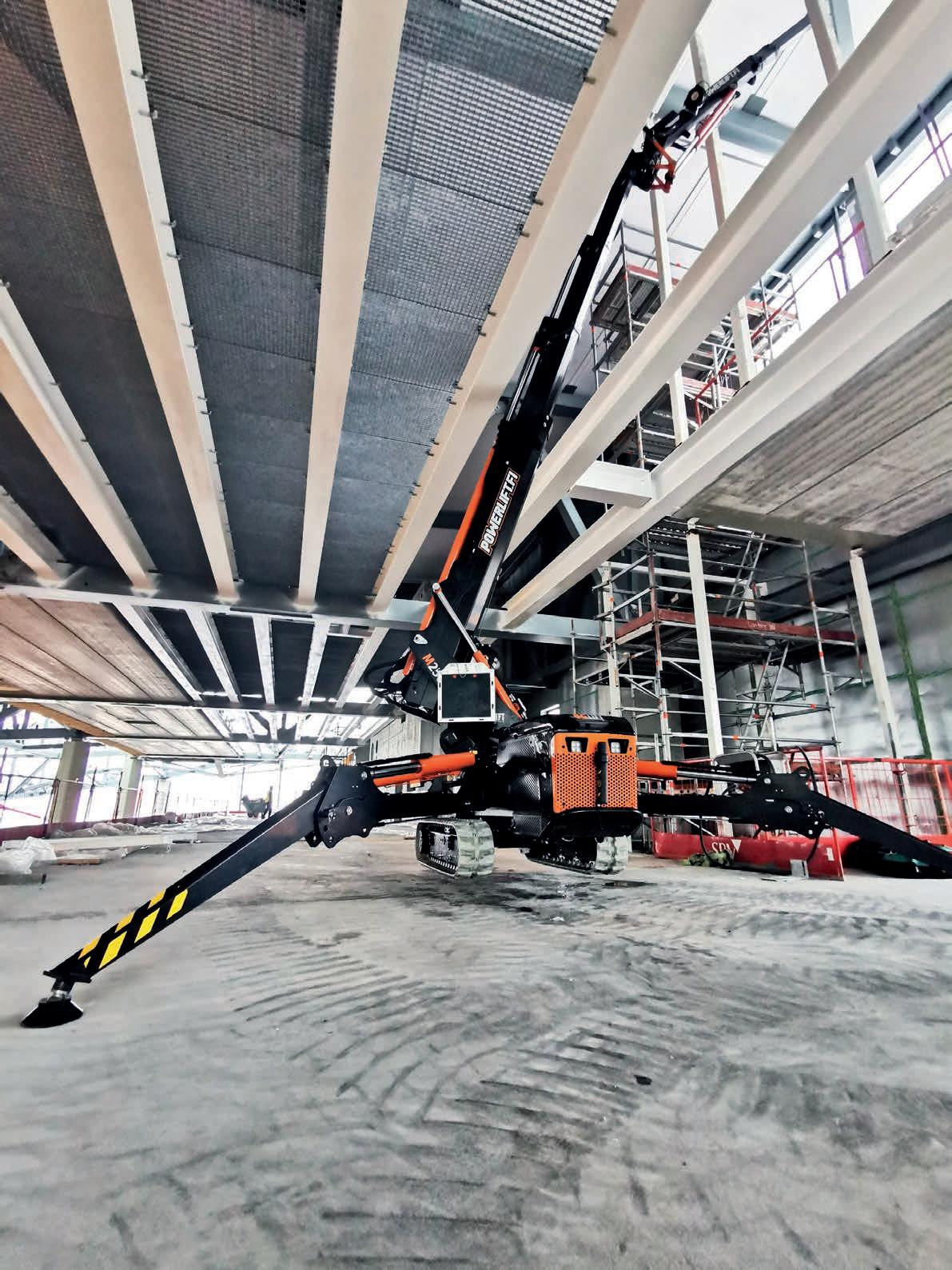
with great success as reported in the September edition of Cranes and Lifting magazine.
The decision to bring the BG Lift range to Australia signals a shift in focus for the GMS team, but they will be bringing their experience and passion to the new venture.
“We have been looking at moving into the construction space for two to three years and, last year, we decided this was the next logical step for the business so we proceeded with our relationship and negotiations with BG Lift,” Brian said.
GMS started out small with the CMC range of spider lifts focusing on the arbor sector, but the business quickly recognised the capabilities of the products and how well suited they would be to the construction industry.
With their industry experience, Sam and Brian were confident about bringing
due diligence.
“For us, it was similar to the process we went down with CMC spider lifts. We researched the brand and the products, and we could see they had an excellent name and reputation throughout Europe. It was obvious BG Lift design, engineer, and manufacture a quality range of mini crawlers.
“We have had good success with CMC being an Italian brand, and so bringing the BG Lift range to Australia made a lot of sense. We then utilised the services of an Italian business consultant to conduct additional research because we wanted to ensure we would be representing a quality product we are proud to sell and also support.
“With the winter months, our arborist side of the business slows, which has provided us with the opportunity to focus on the BG Lift range. We want to
in the product when we are talking to interested customers,” Sam said.
“The BG Lift range slots into the market really well. It will be simple for operators to learn the controls of the cranes and customers will quickly understand the quality that comes with the machines. Much like the CMCs, we believe customers won’t be able to wait to get their hands on one,” Brian said.
Lifting on construction sites is getting more complex and the importance of mini crawler cranes and the role they play is only going to increase, said Sam.
“Every lift is getting more challenging. Access on construction sites is getting increasingly tight and, despite these restrictions, there is an expectation that lifts will get heavier. The role of mini crawler cranes is only ever going to increase on construction sites,” Sam said.
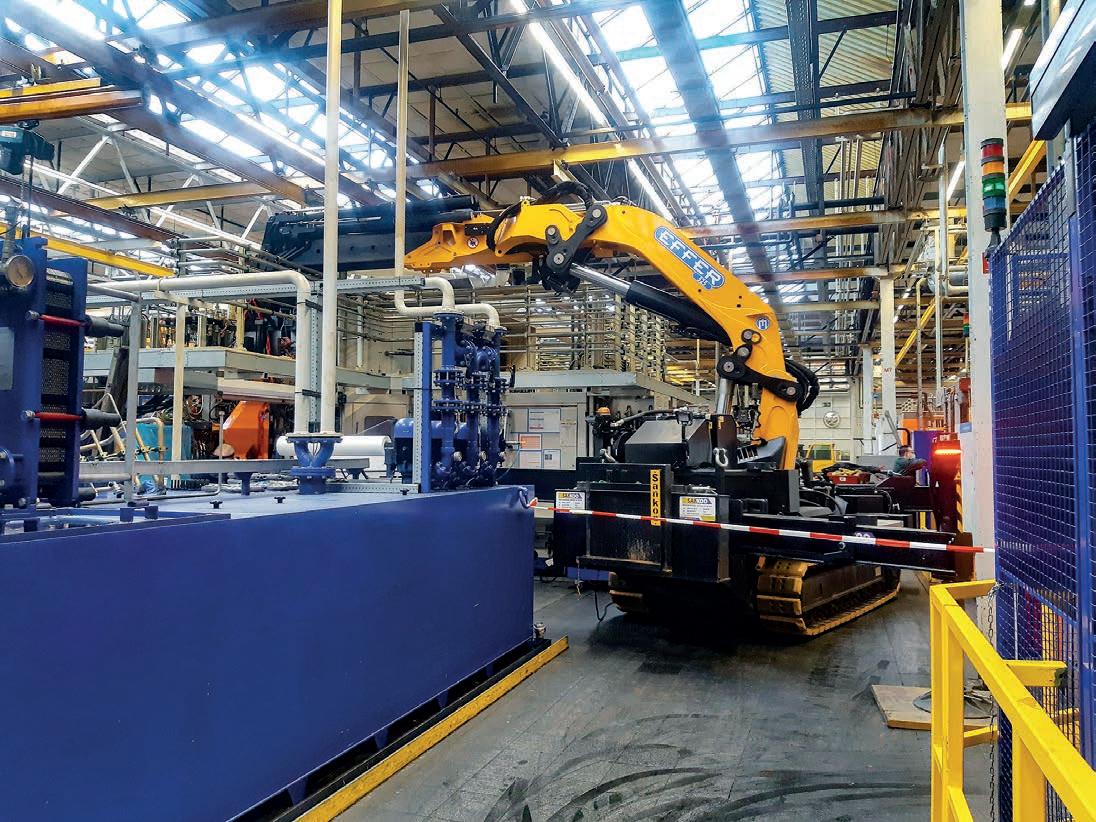
The BG Lift product will enter
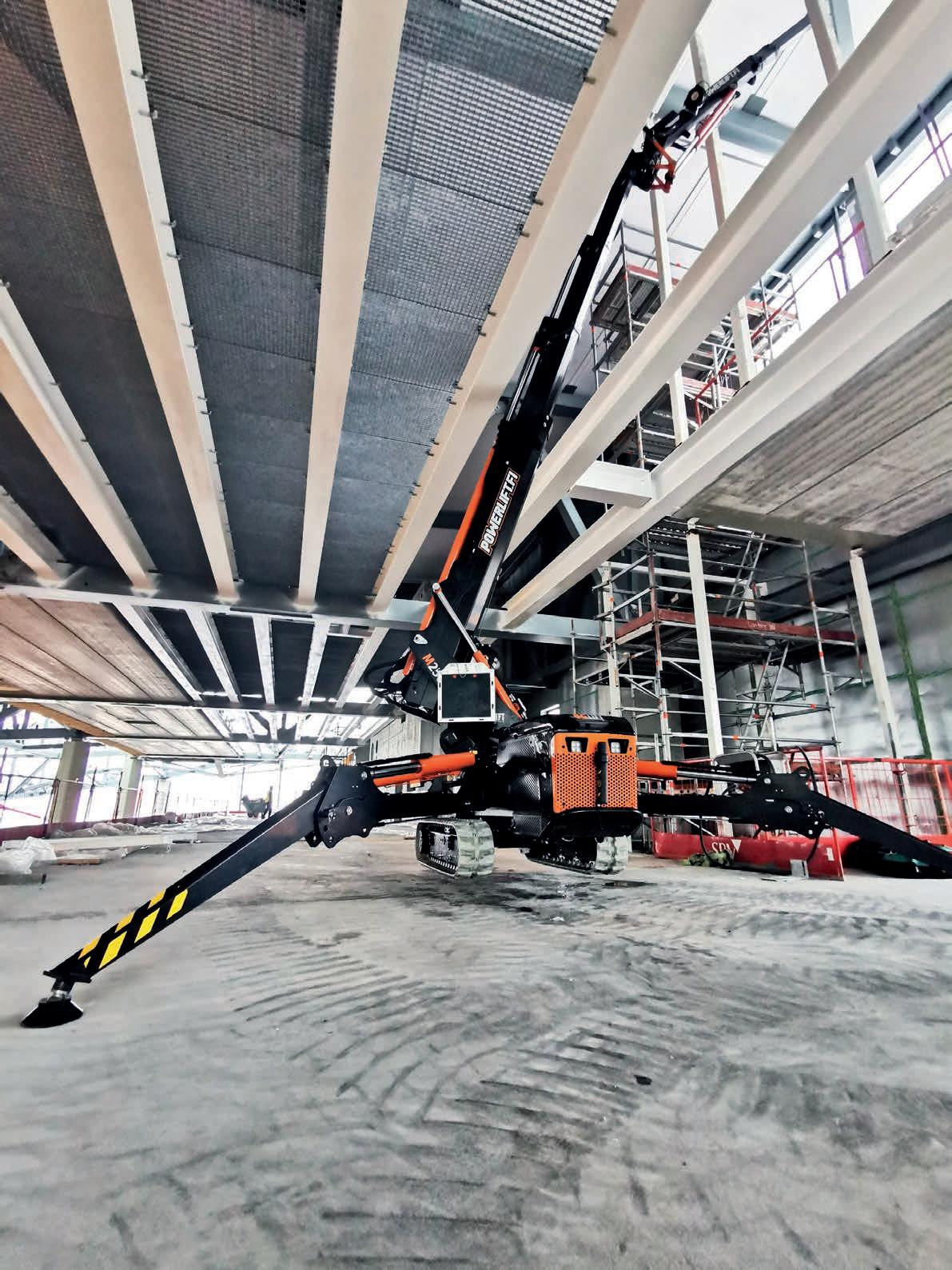
Australia with a broad range of lifting capacities ranging from 580kg all the way up to 14.5t.
The CWE 525 has a 14.5t capacity with a max outreach with a jib of 29.5m giving it an impressive reach for any application.
The multifunction proportional radio remote control provided with an integrated control display, allows the operator to verify in real time all the parameters of the machine to maximise its safety.
“We have a lot of experience with this type of controls on the CMC machines and the feedback has been nothing but positive. The remote controls are all standardised so, if you know one, you tend to be able to use any of them. They are incredibly simple to move. You have great accessibility and vision by not being tethered to the machine,” Sam explained.
The CWE 525 has a removable ballast mounted on the chassis to allow the continuous ‘in shape’ rotation. The ‘X’ configuration of the outriggers allows it to be operated with narrow outriggers and minimum obstruction.
“They have a small footprint as well which means they only need a small area once inside, so they are perfect to work in established buildings,” Brian said.
The rough terrain version (RT) gives the machine even greater versatility. The higher power of the diesel engine (55kW) and the major crawler torque improves the performance during heavy
conditions on mud and rough terrain. The generous ground clearance assists getting to challenging sites and allow loading of the CWE 525 to be completed with ease.
The integrated control system gives the crane infinite stabilisation possibilities, automatically upgrading the load limiting device to the situation determined by the position of each outrigger. This allows the machine to be operated at its optimal level of safety.
The M 060 is the smallest in the range with a lifting capacity of 580kg but a width of only 0.780m, making it perfect for compact spaces coming in with a max outreach of 4.25m.
The ‘pick and carry’ mini crane provides 50° of rotation. Extremely
the client needs, so they can come diesel powered, hybrid or with battery systems, depending on the type of work they are completing,” Brian said.
“The hydraulic jibs are a big plus, that coupled with the remote control, sets these machines apart from the others in the industry,” Sam said.
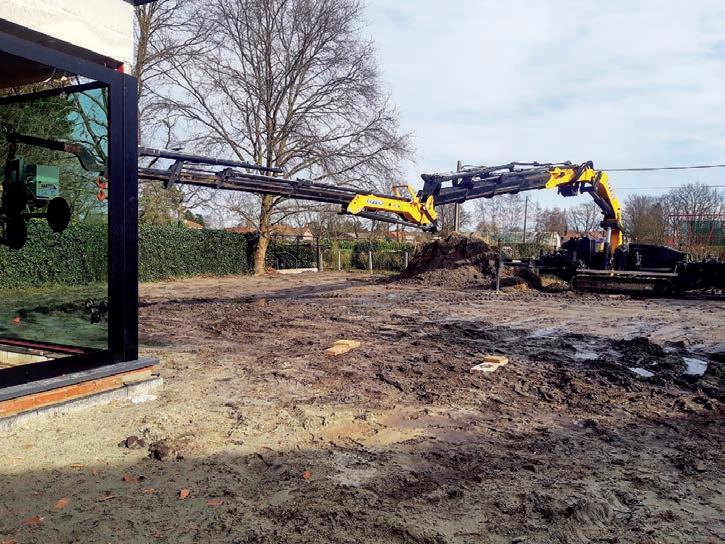

“The first machines arriving in Australia will be fully optioned. This provides us with the opportunity to fully understand the product and its capabilities. The first machines will be out on hire providing us with the ability to put them through their paces, to send feedback to Italy and ensure the machines we are offering suit the market perfectly,” he said.
compact and ergonomic, it can fit into the tightest of spaces. Designed by BG Lift to be agile and robust for use in narrow and limited access spaces, it is perfect for indoor and outdoor use.
“We are seeing them going in tunnels and into buildings across Europe that were built in the 1300s and 1400s. They are light and nimble which is perfect.
“They come optioned with whatever
The machines come with an impressive reach.
“We will work closely with clients to understand the specifics of what they need from their crane, and we understand every client will be different.
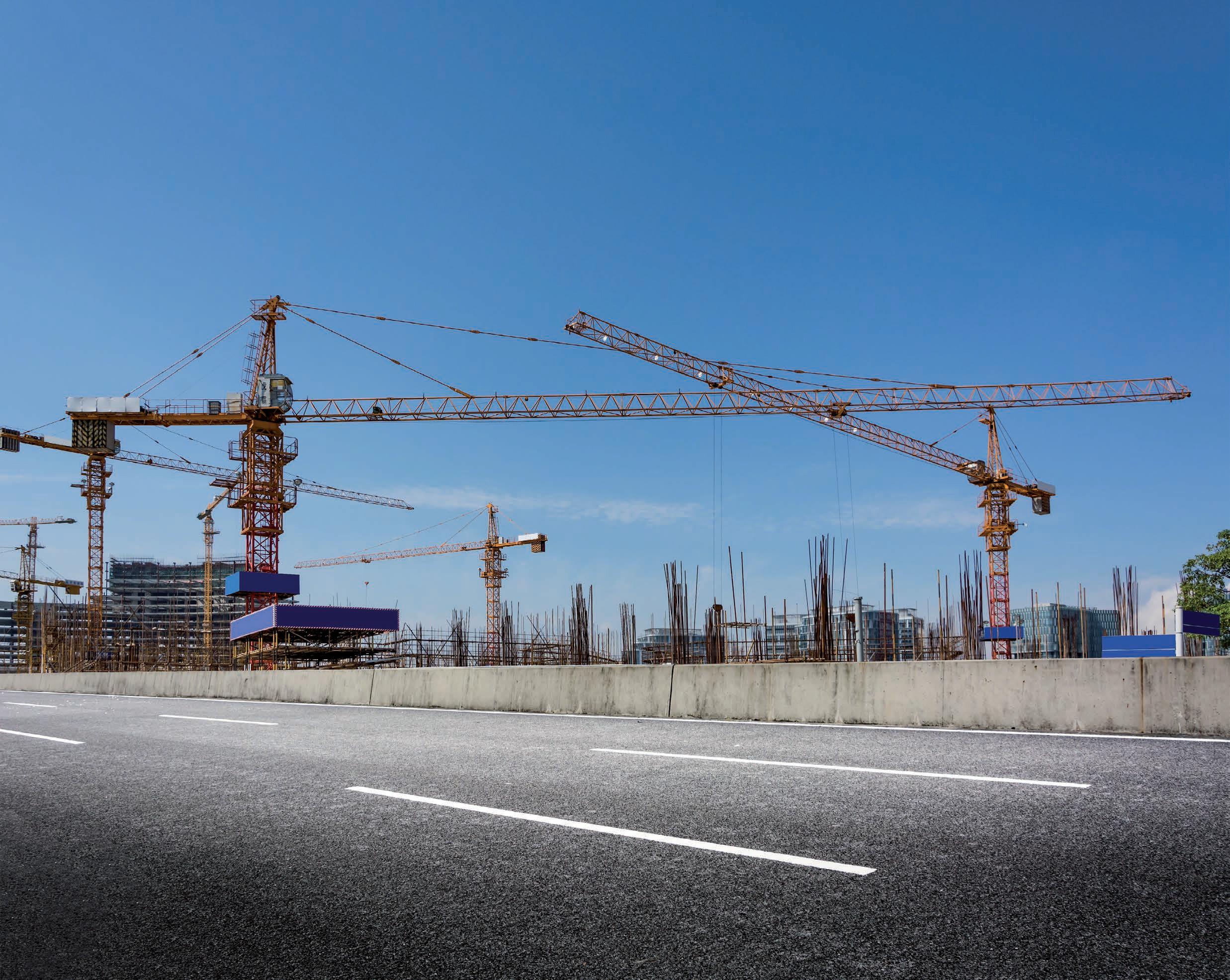
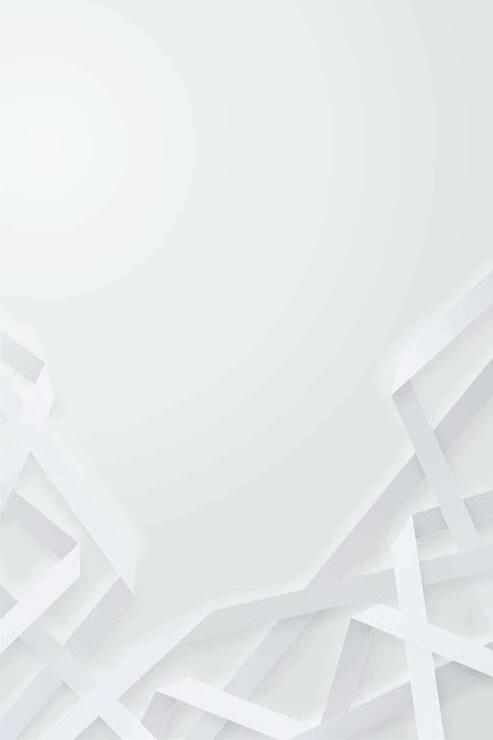
“Having represented the CMC range for some time, we understand the challenges that come with having parts coming from Europe. When it comes to the BG Lift range, we will stock the important fastmoving parts and then provide quick turnarounds for the delivery of parts if they need to come from Europe,” Brian said.
The team at Global Machinery Sales will take a similar approach to the BG Lift range as they did the CMC range of spider lifts, and that’s providing regular feedback to the factory in Italy.
“We enjoy working with the Italians, they listen to our feedback and are always looking to improve their products. Like the CMC product line, we are confident the BG Lift range can be ‘Australianised’, to suit the very varied conditions our continent provides,” Brian said.
“When it comes to the BG LIFT range, we will stock the important fast-moving parts and then provide quick turnarounds for the delivery of parts if they need to come from Europe.”
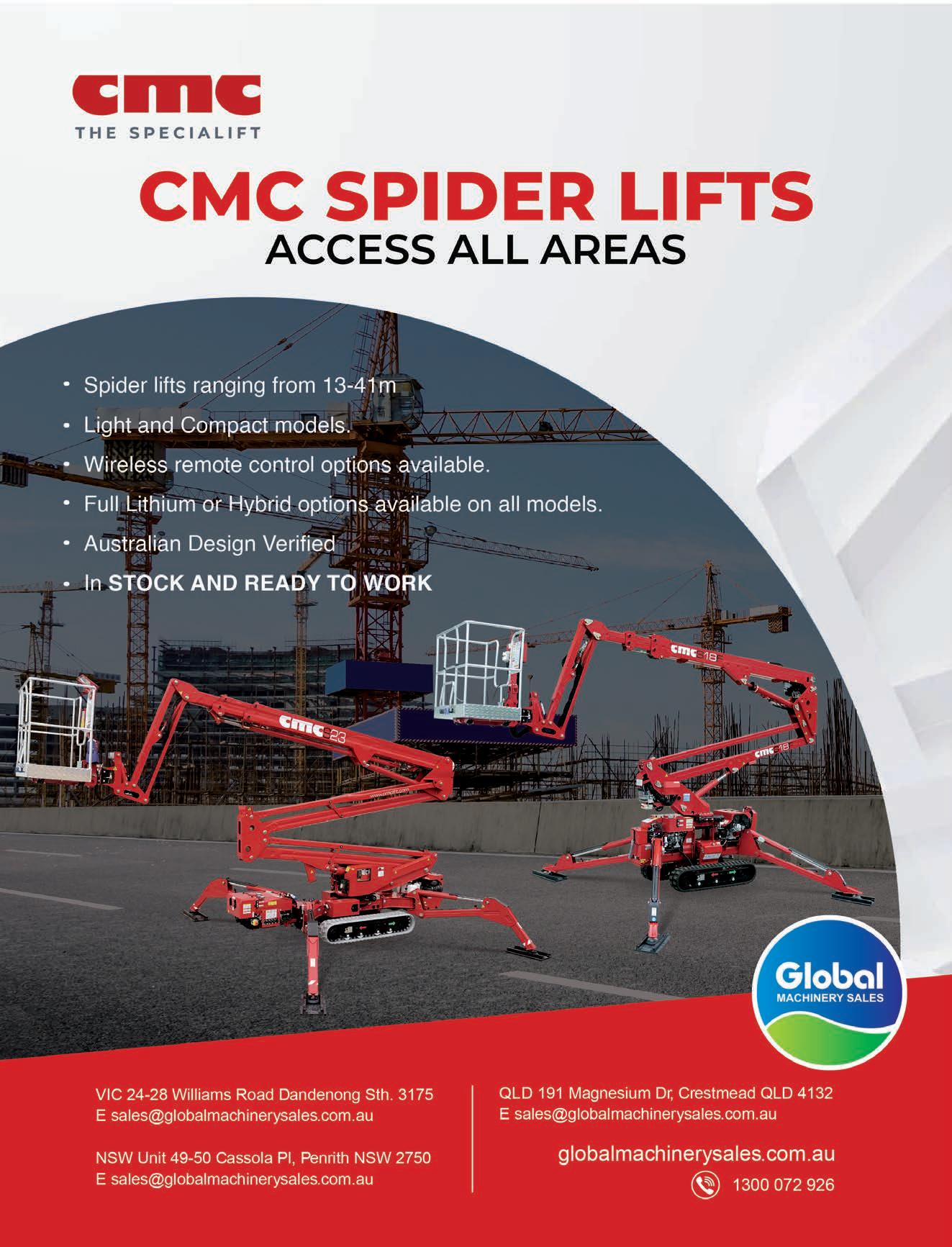
SANY LAUNCHES NEW BATTERY ELECTRIC TELESCOPIC CRAWLER
Sany recently announced the launch of a range of battery electric powered telescopic crawler cranes. The first model to be released will be the SCE800TB-EV.
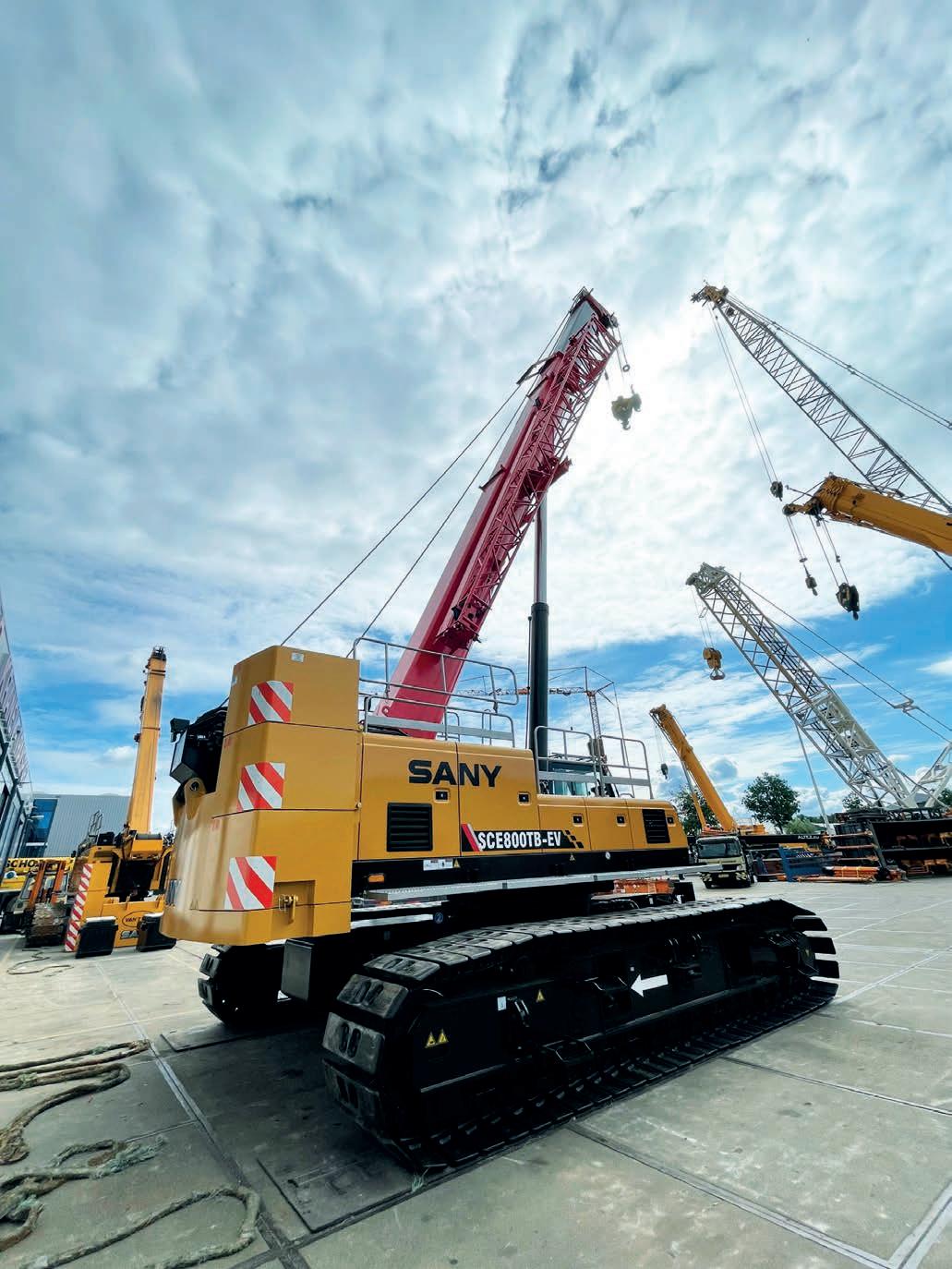
THE SCE800TB-EV IS A BATTERY electric powered telescopic crawler w ith a lifting capacity of 80t. The new battery electric crane is based on the highly popular SCE800TB, with the engine replaced by an electric operating system capable of retaining the high level performance of the diesel powered version.
The SCE800TB-EV has a maximum boom length of 47m with an optional jib length 17.5m. The boom is made of high-strength steel structure with a U-shape section area. It features five sections, of which the basic boom is 12.2m. It also features dual cylinder, full power rope row for telescoping.
The SCE800TB-EV includes a number of features designed to provide safe and reliable operation whilst reducing maintenance costs. The battery electric telescopic crawler is equipped with the Danfoss EMPM1375-T1100-1500 motor with peak power up to 336kW and dual motor controller, which can provide torque of up to 2,500Nm.
The SCE800TB-EV is also equipped with a 282kWh lithium iron phosphate battery (LFP battery), which is capable of managing eight hours of operation depending on the work required on site. The BMS intelligent piping system monitors the battery voltage and temperature in real time, and the battery interior is made from VO-grade fire-proof material.
For the launch of the SCE800TBEV, Sany has developed the SYIC-III Integrated Control System that is designed to deliver high levels of integration, precise operation, and reliable levels of crane operability.
The battery power system includes a
main control and a slave control in each battery pack and these adopt a ‘daisychain communication’ to achieve the required levels of power in real time and efficient battery system data acquisition and control.
The vector control drive motor system achieves high precision control of motor output and prevents overload, over heating, short circuiting, overvoltage protection as well as other safety functions.
The SCE800TB-EV Control System manages the battery system, the drive motor and power supply systems, main control, torque limiter, auxiliary and safety monitoring systems. The controller features CAN bus technology which is applied between the display monitor, the battery power system and the drive motor system providing line data communication.
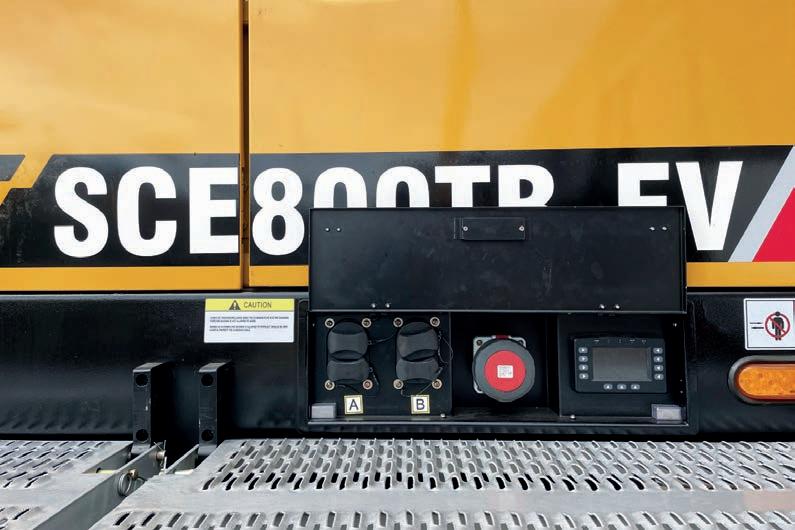
The display screen in the cab can then display the battery’s state of charge (SOC), power battery voltage, power battery charge and discharge. It can also display the instantaneous power of the driving motor, charging mark, lifting weight and boom angle, as well as other working parameters and numbers relating to the working status of the crane.
Sany has designed a number of key safety features into the SCE800TB-EV telescopic crawler.
These include a high voltage safety design system that protect against electrical leakage. The high voltage systems on the crane have real-time insulation monitoring functions that are able to cut off circuits should a sudden electric leakage occur.
The boom hoist mechanism on SCE800TB-EV features a dual-acting single piston hydraulic cylinder, with safety balance valve, and a luffing angle of -1.5°–80°. The cylinder allows luffing down through self-weight to reduce energy consumption and increase the stability of luffing down operation.
The swing mechanism adopts a wet swing brake that is a spring loaded. It is normally a closed brake with braking provided through a spring force. The
swing system is equipped with an integrated swing buffer valve that has a free slipping function. This assists with a steady start and control of an excellent inching function.
The unique swing buffer design and steady brake provide an external gear swing drive with a 360° swing range, a maximum swing speed of two revolutions per minute and maximum drive pressure reaching 20MPa. The
framework, with no torsion or deformation. The parts are set out in a manner that makes maintenance and service easier.
The SCE800TB-EV features an intelligent work environment for the operator.
“The battery electric telescopic crawler is equipped with the Danfoss EM-PM1375-T1100-1500 motor with peak power up to 336kw and dual motor controller which can provide torque of up to 2500N.M.”
swing lock cylinder device ensures the upperworks are locked in four directions after the work is done or during transport.
The counterweights are designed into blocks for self-assembly and easier transport. The rear counterweight totals 26t and is capable of selfassembly. The car body counterweight includes two 3t counterweights at the front and rear.
The upper works of the crane features a high-strength steel weld
The integrated Load Moment Indication (LMI) Control System is standard, and it is calibration-free. It ensures the safe operation of the crane and improves the crane’s productivity and efficiency.
The LMI system can automatically detect the weight of the load, the working radius and boom angle and compares this with rated load weight and actual load, work radius and boom angle. In normal operation, the LMI control system will make judgments and cut off operations if the crane is headed beyond it’s designed capacities. It also acts as black box to record overload information.
Over-release protection device of the main/auxiliary winch features a three-wrap protector installed on the main and auxiliary load hoist winches to prevent an over-release of wire rope.
When the rope is paid out close to the last three wraps, the limit switch is actioned, and the system sends an audible alarm as well as a displayed alarm on the instrument panel, automatically cutting off the winch action.
If the function lock level is not in the work position, all other handles won’t work, which prevents any mis-operation caused by accidental collision. The electrical swing lock will only allow swing action when the lock is released, so as to prevent any operational error and
“When the actual load is between 90 and 100 per cent of the rated load, the yellow light switches on, the alarm light flashes and sends out intermittent sirens.”
ensure the safety of the operator and those working close to the crane.
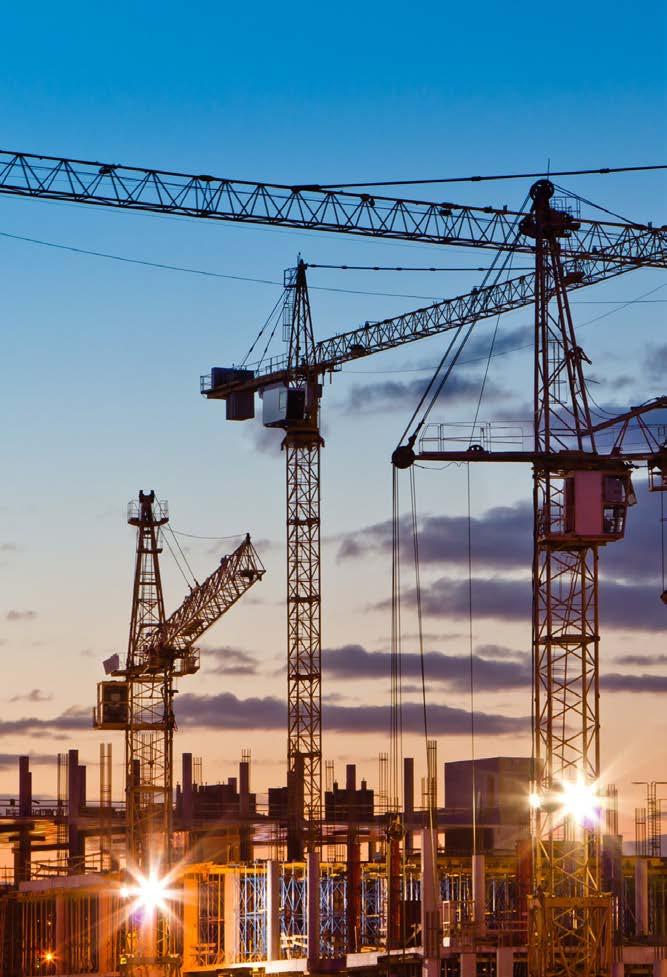
The remote monitoring system is a standardised providing functions like GPS locating, GPRS data transfer, machine status inquiry and statistics, monitoring of operational data and remote analysis and remote diagnosis of failures.
The load indication panel features three colours, green, yellow, and red, and these indicate the position of the load in real-time. When the actual load
is less than 90 per cent of the rated load, the green light remains on.
When the actual load is between 90 and 100 per cent of the rated load, the yellow light switches on, the alarm light flashes and sends out intermittent sirens. If the actual load reaches 100 per cent of rated load, the red light switches on, the alarm light flashes and the emits continuous sirens. Should the actual load reach 102 per cent of rated load, the system will automatically cut off the crane’s operation.
PLANNING FOR FUTURE DECARBONISATION IN THE LIFTING SECTOR
The arrival of the Anthony Albanese Labor government heralds a push towards renewables with a target of net-zero emissions by 2050.
Ledge Finance is encouraging crane hire operations to consider utilising the Environmental, Social and Governance (ESG) framework when planning for the future.
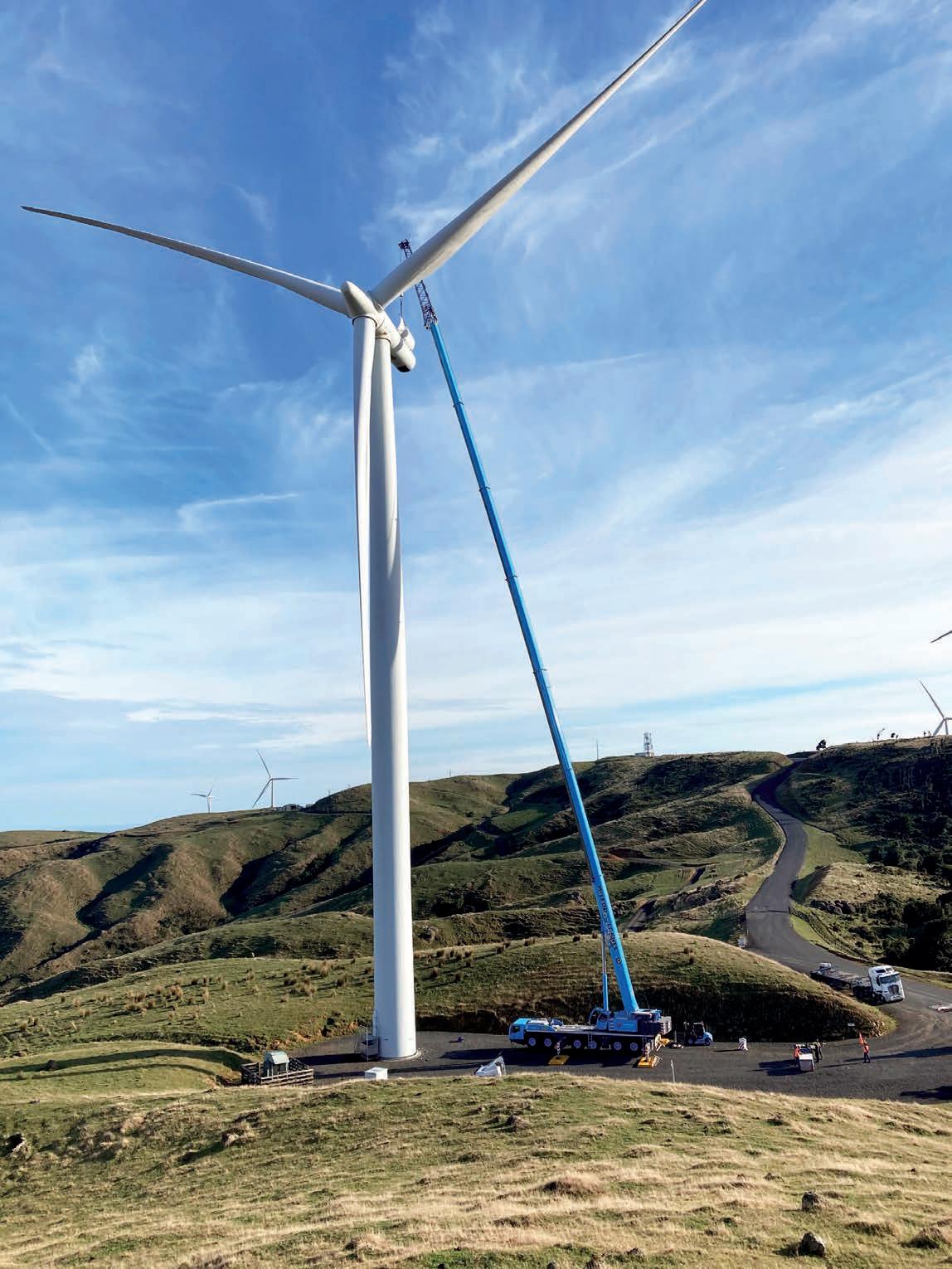
ACCORDING TO LEDGE FINANCE, CRANE
hire businesses need to position themselves to scale-up with a mix of fleet assets to ensure they can service the expected unprecedented demand from the renewables sector. They also need to understand how to onboard debt to support their growth aspirations and not miss out on these significant opportunities.
The direction in which Australia’s energy providers are heading is apparent. New wind farms are being constructed across the country and the construction process is only made possible by the crane industry.
Ledge Finance has recognised that crane companies need to consider positioning themselves to scale-up with the move towards the renewable sector. This includes a transition plan across the fleet to ensure they are future proofed and renewable.
Ledge Finance is encouraging crane hire operations to consider utilising the Environmental, Social and Governance (ESG) framework when planning for the future, with ESG being positioned at the core of a crane organisation’s planning, strategy, and approach to operations.
ENVIRONMENTAL
Environmental factors relate to a business’ commitment to the natural world both in current projects but also how they evaluate environmental risks for future projects. These include deforestation, carbon emissions, energy efficiency, waste management, and air and water pollution.
SOCIAL
This looks at the business’ relationships with customers, suppliers, local community, employees and other stakeholders. Social factors can include data protection and privacy, gender and diversity, community engagement, employee health, and safety and human rights.
GOVERNANCE
Governance in ESG is the internal
systems of practices, controls, and procedures. These can include tax strategy, stockholder involvement, accurate accounting and reporting, corruption and bribery, board diversity, and structure.
According to a study by PWC on family businesses, sustainability is a low priority for many Australian businesses, with only a third putting sustainability at the centre of what they do compared to 49 per cent globally. However, consumer expectations around ESG factors are rising, with 43 per cent expecting businesses to be accountable for their environmental impact. Consumers, investors, and lenders are prioritising investment in businesses with ESG credentials.
In the last 20 years approximately 2,725 wind turbines have been built. But there are plans for 1,083 new turbines offshore and 4,355 onshore.
At circa $4 million per turbine, this equates to a $17.5 billion project pipeline in just onshore wind farms alone. Many of these projects will be seeking to lower emissions during the construction phase, thus demonstrating the importance of the ESG framework. Energy efficient fleets with lower emissions will be pivotal for the awarding of contracts in the near future in Australia.
Under its plan to modernise transmission networks, the Albanese government’s $20 billion Rewiring the Nation election policy will consider
“For crane companies to remain competitive they need to look towards the ESG framework and understand what is involved to help them future-proof their fleets and organisation more broadly, to comply with the requirements that are unavoidable and just around the corner.”
Many businesses view a focus on ESG as a cost, however Ledge Finance says this should not be the case. Having a strong ESG proposition can save your business money and lead to value creation.
As an example, if a business becomes more conscious about reducing its carbon emissions, it is not only more energy efficient and saving money, which it can reinvest, it is also more appealing to a large company looking for a supplier with a commitment to net-zero emissions.
Businesses that adopt a robust ESG strategy may not only save money and secure contracts but may also experience several other benefits.
A focus on the environment is going to be a pivotal cornerstone for the crane industry. Ledge Finance says there is significant opportunity from a project pipeline, skills, and resourcing perspective.
priority investments in projects including expanding the NSWVictoria interconnector, the Hume Link in NSW and Marinus Link, which will pump renewable power from Tasmania into the national electricity market.
For crane companies to remain competitive they need to look towards the ESG framework and understand what is involved to help them futureproof their fleets and organisation more broadly, to comply with the requirements that are unavoidable and just around the corner.
Ledge Finance recommends businesses plan for a mix of fleet assets, ensuring they are fit for purpose to onboard debt to support their growth aspiration with these opportunities on the horizon.
Ledge Finance is happy to discuss any of the issues raised in this article. Visit Ledge.com.au today
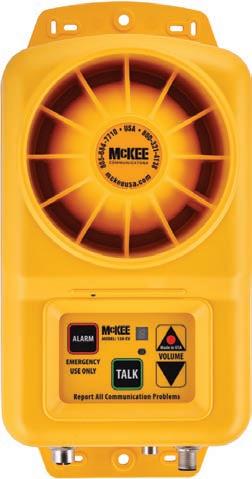
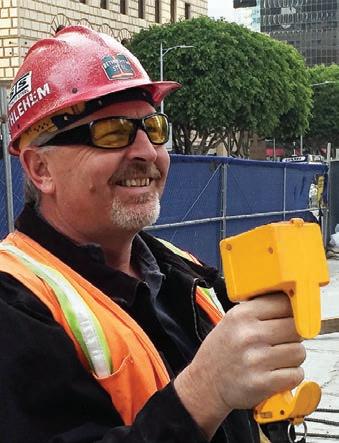
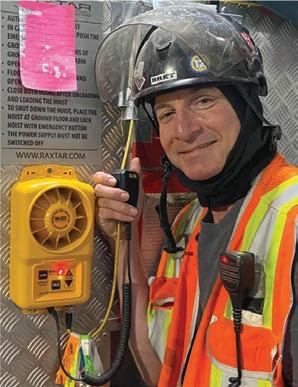


TRT has recently launched their new TIDD Crane Operator Familiarisation Programme.
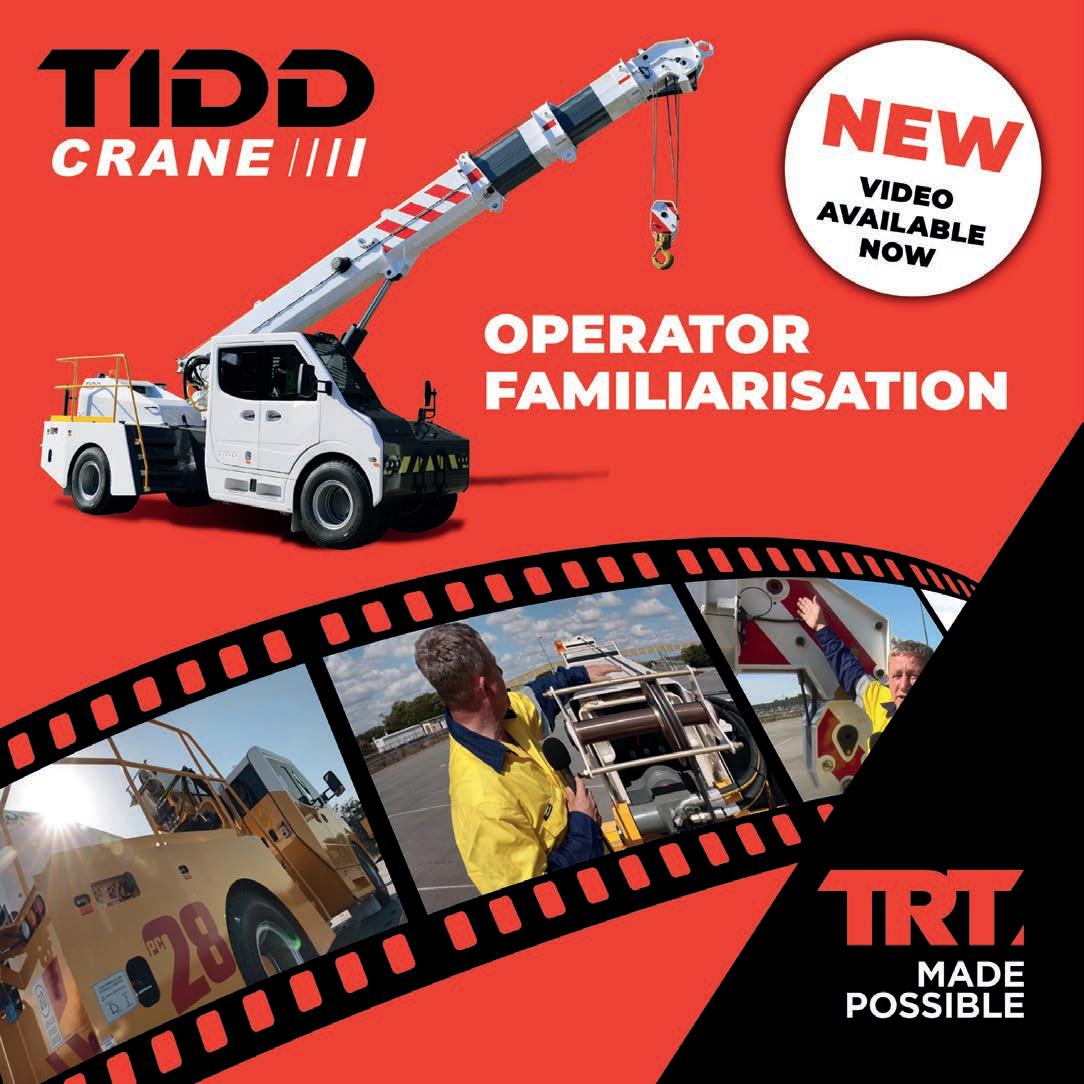
TIDD PC28-2; THE BETTER EXPERIENCE
TRT announces the launch of the Tidd PC28-2 pick and carry crane, which will be available from March 2023.
LEADING FROM THE FRONT, TRT CONTINUES to enhance the overall Tidd crane operator experience and performance. The upgrades to the newly named Tidd PC28-2 are driven through TRT’s focus on continuous improvement, with consideration of industry and operator feedback.
“The Tidd PC28-2 is the better pick and carry crane experience. The new
upgrades to the Tidd PC28-2 stem from our continuous focus on innovation and actively exceeding expectations for our customers,” said Robert Carden, TRT’s technical director.
“These new upgrades deliver a better allround experience for the life of your crane, and we are looking forward to delivering the first orders to our customers next year.”
There are four key areas of improvement in the upgraded Tidd PC28-2. It features more powerful front suspension cylinders. This new system offers a greater lift capacity when articulated and working on a side slope, improving lift capacity by up to 17 per cent.
New steps have been added to improve lift control. An additional three steps on the Tidd PC28-2 load chart deliver significant improvement when the crane is articulating. So, for the operator, this means that, as the crane articulates, it
The Robway® TIDD Crane operating software has been upgraded with improved function, enabling faster processing and greater control responsiveness for the TIDD PC28-2 operator
The Robway Tidd crane operating software has been upgraded with improved functionality. This enables faster processing and greater control responsiveness for the Tidd PC28-2 operator.
“TRT has always focused on the people when considering advancements in technology for the Tidd crane,” said Robert.
“With operator and dogman comfort central to the design of the Tidd crane, this new model also features a re-engineered ROPS cabin.
“This has been tested with a measured reduction in cabin noise levels by 8dBa at 80km/h when on the road.”

As well as these considerable upgrades, TRT has been focused on ensuring that Tidd customers and operators are fully supported for the life of the crane, from onboarding of operators to parts and service support Australia and New Zealand-wide.
TRT has recently launched its new Tidd Crane Operator Familiarisation Programme.
“From the start, the development of the Tidd crane was intended to set new standards in articulated crane performance, and we continue to focus on how we can advance this to provide the best
said Bruce Carden, TRT’s director of innovation and sales.
“The Tidd crane has come a very long way in terms of design, capacity, and functionality. The new Tidd Crane Operator Familiarisation Programme is another example demonstrating our commitment and focus towards
providing a better overall experience for Tidd crane operators.”
The new programme includes a new Tidd Crane Operators Familiarisation Video, designed for experienced pick and carry crane operators to quickly and easily understand the Tidd crane operation, its functions, and the features of the crane, with access 24/7.
“This exclusive programme is designed to suit our customers operations,” said Bruce.
“We also offer in-person training from one of our factory-trained experts, online manual access 24/7, remote video with one of our experts, and a dealer and service support network Australia-wide. We truly believe that this journey has created an overall better experience that pick and carry crane operators have been demanding.”
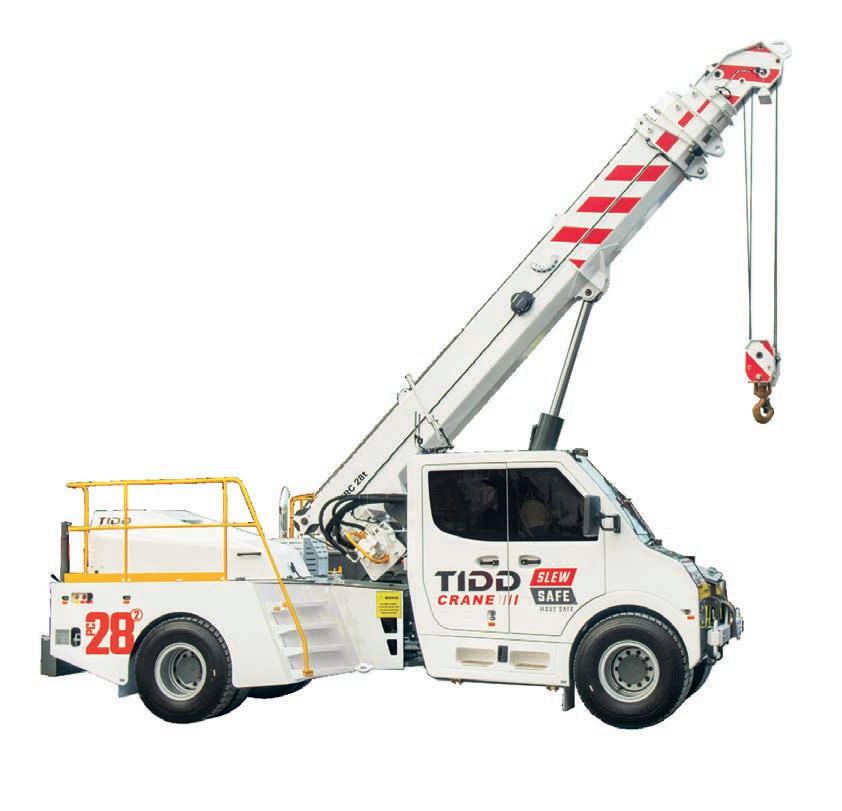
TRT’s dealer support and service network includes Baden Davis Crane Connection, based in New South Wales and the Australian Capital Territory, RMB Service Group in South Australia, Ronco Construction Equipment and Engineering in Western Australia, and JDM Diesel Services in Victoria.
TRT’s sealers and service agents are selected based on their experience and knowledge of cranes and pick and carry cranes, and as importantly, on their commitment to providing a continued high standard of ongoing customer service and parts support locally.
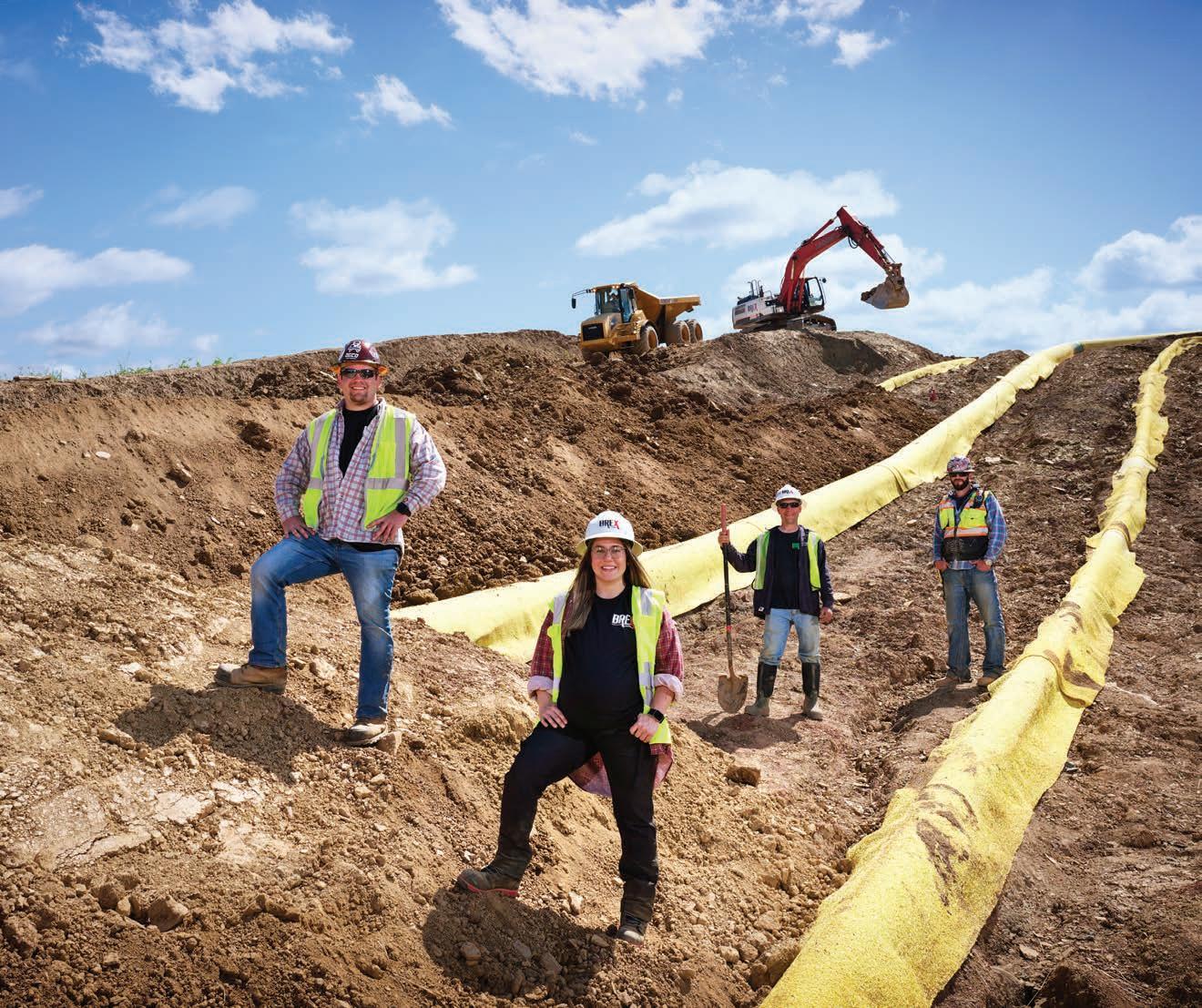
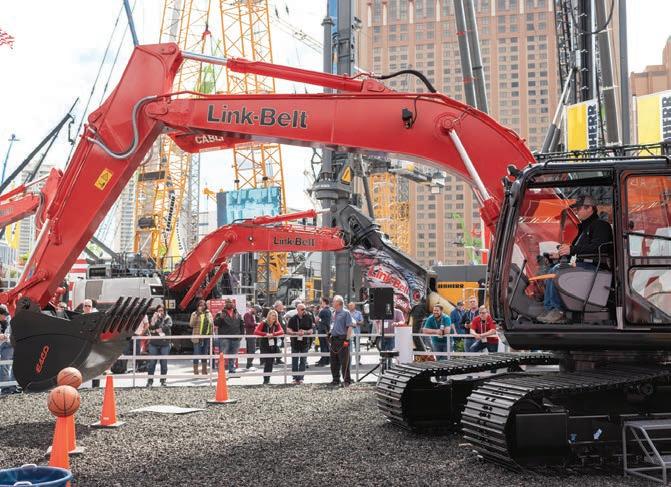
LOYALTY A HALLMARK OF HAWKESBURY CRANES
HAWKESBURY CRANES HAS BEEN AWARDED a number of utlities contracts recently, which has seen the need for it to grow its fleet. It has done so with the addition of a Liebherr LTC 1050-3.1 and a LTM 10904.2. Jungherr explains what has made the company a success.
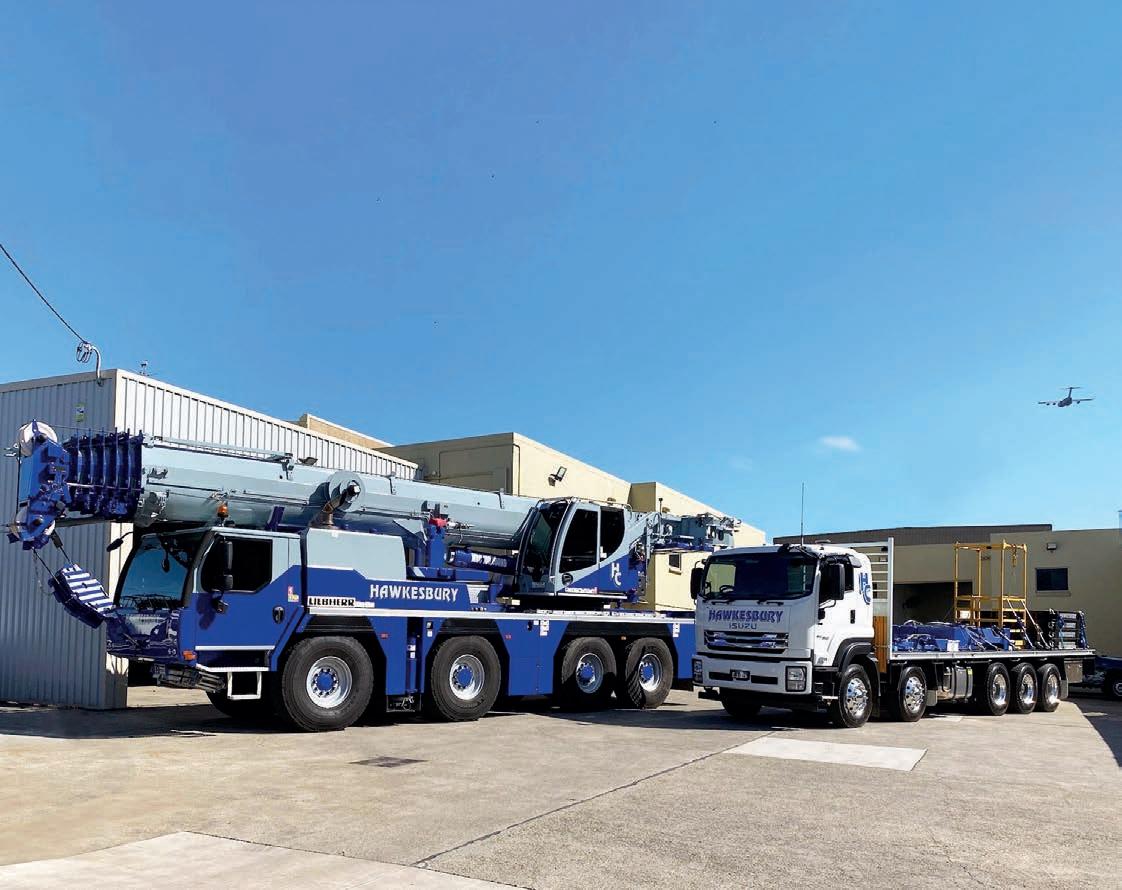
“We live by the old adage of going above and beyond for clients. I am on the tools every day and working with them. We pride ourselves on the work and having a good crew. With these projects you could have a breakdown at 12 o’clock at night and you need to dispatch somebody to keep it on time,” he said.
Tom Grady is the national used crane manager for Liebherr and worked closely with Ernie for the purchase of the two Liebherrs.
“Ernie came to me in March 2021, looking for an LTC1050-3.1. I discussed with my colleagues in Liebherr Werk Ehingen and we came up with a fully specced factory test crane,” he said.
“This was the first LTC1050-3.1 fitted
with a Cummins Stage 5 engine. I knew that this crane in particular would suit Ernie well. We delivered it with our factory warranty and in the Hawkesbury livery. The crane was a 2021 model and had only 3,000km and 100 upper hours on it, which was from our in-house testing. This also meant Hawkesbury Cranes were the first owner.”
“In May 2021, Ernie and I had another chat around the possibility of adding a larger crane into Hawkesbury Cranes fleet. After a meeting or two with Ernie and Cam Greedy, who is Hawkesbury Cranes’ operations manager, we knew that a 2018 LTM1090-4.2 with only 14,000km and 2,000 upper hours that I had already ordered for Sydney as a stock unit would be very well suited. Knowing the work Hawkesbury Cranes do, and working in such tight spots, a LTM1090-4.2 with VarioBase and VarioBallast would be absolutely ideal,” Tom said.
The Liebherr LTM 1090-4.2 is the biggest to enter the Hawkesbury Cranes
fleet with a capacity of 90 tonnes, a boom length of 60 metres, hoisting height of 76m and a radius of 62m. The crane’s superstructure is powered by the engine in the undercarriage, which lowers costs as there is one less engine to maintain.
The LTC 1050-3.1 is a compact crane with an impressive capacity and reach for its size, making it an asset for sites with tough access. Its width is only 2.55m with a low weight rating of 12t per axle.
Its VarioBase support system with outriggers extended to different lengths mean that constricted conditions are not a problem for this compact crane. It carries all its own equipment and ballast, thus significantly reducing the time required for jobs. The elevated cab delivers maximum safety by providing improved all-round visibility from the cab.
Jungherr explains why he has decided to purchase these two Liebherrs and what has been the standout with them.
“I have chosen to go with Liebherr for all of my cranes now. That is simply because
Ernie Jungherr has spent much of his life in the crane industry, since the mid 1980s he had been honing his skills towards his eventual opening of Hawkesbury Cranes in 1999 and going alone in 2003.Ernie and the team at Hawkesbury take great care in the cranes they run.
you cannot get a better product than the Liebherr in the crane industry. It is like comparing a Kingswood and a Mercedes, there is no comparison,” he said.
Once the local roadability and safety items were fitted, which included a threecamera monitoring system, Grady and Liebherr then carried out the CraneSafe, plant registration and NSW road registration, and the last of the detailing, with a final quality assessment by Grady.
“The LTC looked fantastic in Hawkesbury Cranes’ colour scheme. With Ernie’s and my own high attention to detail it was a great feeling knowing that Ernie was extremely happy with the final delivered product,” said Grady.
“When Ernie and I began discussing the LTM 1090-4.2, the crane was still with Liebherr-Werk Ehingen getting put through its paces for the factory six-month warranty process as well as being fitted out with a new self-assembly second winch, rooster sheave, hydraulic luffing for the existing swing away jib, single sheave
hook, anemometer, and flight light.
“Ernie and Cam also got us to supply a new H/D 2m erection jib and a set of our Liebherr 2m x 1.8m crane mats. Before leaving our factory the whole package was then sprayed in the Hawkesbury livery.
“Upon arrival into our facility in Erskine Park, like with the LTC1050-3.1, we installed the local roadability and safety items package.
“As the crane timbers are installed internally on our LTM1090-4.2s we also installed a timber box to the rear of the crane. As with all our used cranes final detailing and QA then took place.”
Jungherr added: “We bought our
Liebherrs with plenty of options on it. This means we are maximising the resale ability of these cranes. We have extra winches and a luffing fly jib as well; we keep them parked undercover unless they’re out on site to ensure they are in pristine condition.”
For Jungherr and the team at Hawkesbury Cranes the affiliation with Liebherr goes so much further than just the crane itself, it’s the care that Grady and the team put into the success of the company.
“If you have a breakdown and that is the only version of that crane, you need it repaired ASAP. They do that at Liebherr, they always go above and beyond,” said Jungherr.

“We bought our Liebherrs with plenty of options on it. This means we are maximising the resale ability of these cranes. We have extra winches and a luffing fly jib as well; we keep them parked undercover unless they’re out on site to ensure they are in pristine condition.”Tom and Ernie at the handover of his Liebherr LTC 1050-3.1.
“I have now started to get all of my Liebherrs serviced and repaired by Liebherr. They come to the yard and I know that the OEM is the only person servicing my machines and the highest quality work is being done with a deep understanding of that machine.
“We can only compete with these big companies if our downtime is kept to a minimum. These bigger guys can just bring out an equivalent crane, whereas if my biggest goes down I need it to be fixed quickly.
“I cannot speak more highly of Tom Grady, he is fantastic. He has that mechanical background as well, so he knows a bit more than your regular salesman. Mark from spare parts and George and Nathan in the servicing team all work closely with us and they have been sensational.

“With Liebherr it is the attention to
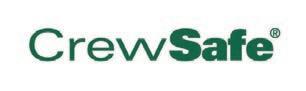
detail as well. Every time they work on it, they get it detailed. Once, when we picked it up, it had just rained and he got it detailed again to make sure it looked perfect,” Ernie said.
Loyalty is a cornerstone of Jungherr and Hawkesbury Cranes, whether it is the Liebherrs, his fuel provider, or his broker, he stands by the people who work hard for him.
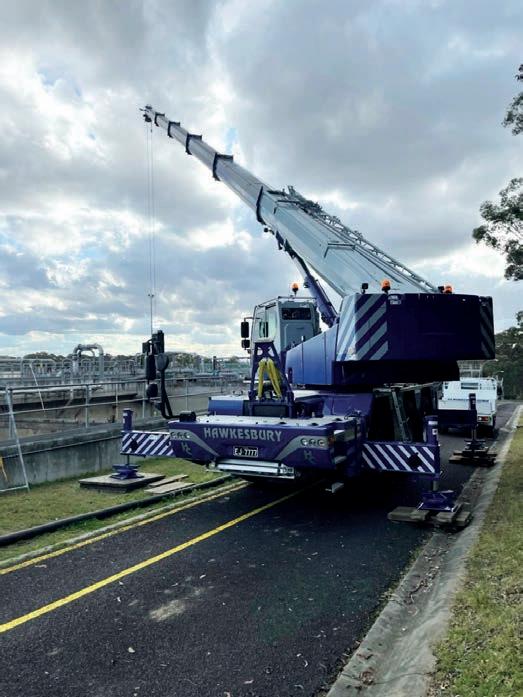
“I have been with Jeff Wilson since 1999 for all of my brokering – I will only use Jeff,” said Jungherr.
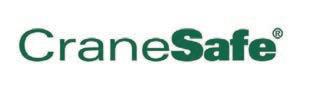
“I showed him that the money he was brokering to me was going to be spent well and we have built that trust and he is someone whose opinion I value greatly.
“He has given me great advice over the years, he works closely with the crane industry. I stick with good people, Liebherr, Franna and Jeff.”
Insurance doc.s Registration doc.s

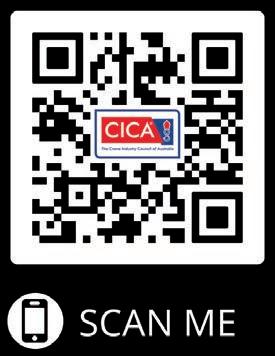

FINLEASE END OF FINANCIAL YEAR WRAP UP
The GOOD, the BAD and the UGLY. Jeff Wilson, senior partner at Finlease, takes a look at the 2021/2022 financial year.
• fixed-rate five-year home loans are now pushing high five to low six per cents
• vehicle and equipment finance hovering around mid to high six per cent
• raw material, component, and labour costs escalating due to demand exceeding supply and/or an inability to ship is driving the costs of all three areas significantly higher and, in the process, adding to the existing inflationary pressure.

It’d be fair to say that this is a short-term issue that will be rectified when supply equals or exceeds demand. However, one can’t help but take the view that most of these areas will come back to some extent but not to those historically lower levels.
IT WOULD BE AN UNDERSTATEMENT TO SAY that this past year has been far from sailing on smooth waters.
As we conclude the 2022 financial year and move into the 2023 financial year, this forward landscape will again test us at many levels.
It will very much be a case of the good, the bad, and the ugly.

THE UGLY
The Covid legacy, China, and the Ukraine have seen us quickly move from international economies working desperately to maintain economic momentum to now applying the brakes to slow down the risk of rampant inflation.
As we write this article in August of 2022… interest rates are back to 2015 levels (3 per cent above the very low interest rates we saw less than 12 months ago)
THE BAD
On the local front, no doubt many who’ve committed to, or are in the middle of, fixed-price supply contracts are in a world of pain. This is a particularly concerning area, not only for those organisations but for any suppliers to them.
SO WHAT DOES THIS ALL MEAN MOVING FORWARD?
We may see a spate of companies going into voluntary administration as a defence mechanism.
This may set the platform for renegotiation of supply or protect those owners from being liable for knowingly trading their companies whilst insolvent.
If this does occur there is a high likelihood that suppliers to those organisations will be caught with bad debt. They may also be subject to the clawback of prior monies paid under the
powers of an administrator where they may deem those suppliers had received a preferential payment prior to the company going into administration.
What steps can be taken by suppliers to minimise this potential damage?
Several service providers can assist in reducing these risks. It real is a matter of understanding what it is you are wanting to protect/insure.
The use of a personal property security register to position you the supplier as a secured creditor could afford protection from a preferential payment clawback, plus improve your chances of any residual
debt recovery. You could also use a debtor monitoring type platform or insurance to insure your creditors.
We are still a little upstream from potential issues, and time spent now may substantially reduce downstream stress.
THE GOOD
On a positive note we can see that a number of businesses do have a lot of work in their pipelines. Their biggest challenge is simply managing the level of work or potential work they have ahead of them.
For clients acquiring additional or replacement capital equipment over
the next year, they have the luxury of the existing government tax incentive, allowing them to 100 per cent write off for equipment purchased and installed before June 30, 2023.

We’re seeing the early shoots of clients bringing in offshore labour under the 482 Visa arrangements. At this stage it’s a slow burn but we expect it to gather momentum.
The component and raw material aspects are largely governed by the present international issues, and we expect to see improvement in this space, if both the China and Ukraine issues are resolved.
Whilst the mainstream media would have you believe that the world is coming to an end, it does need to be said that in these unusual times we are seeing several businesses taking the opportunity of adjusting the way they operate and interact with their customers, which in turn is also creating further opportunity.
The current environment is certainly one filled with obstacles but a calm approach and really understanding your business and your customers will certainly see you navigate through these times.
COMANSA PRESENTS THE NEW LCH300 HYDRAULIC LUFFING JIB CRANE
The Spanish tower crane manufacturer will present its innovative model at the end of October at Bauma Munich 2022.
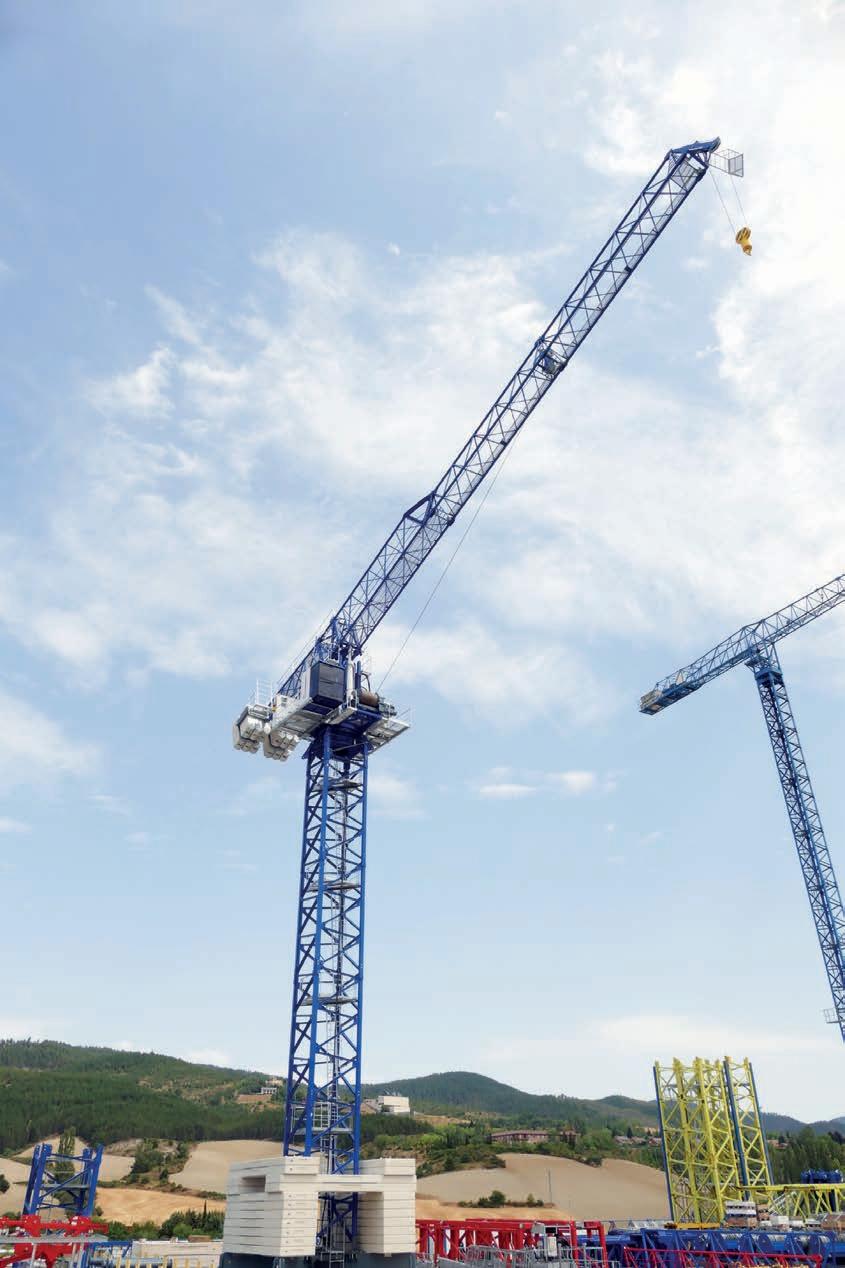
COMANSA EXPANDS ITS RANGE OF LUFFING JIB cranes with the launch of the LCH300, its first hydraulic model, with a maximum load capacity of 16 tonnes and reach of 60 metres. The tower crane manufacturer will officially showcase this innovative model at the Bauma 2022 trade fair, which will be held from the 24th to 30th of October in Munich.
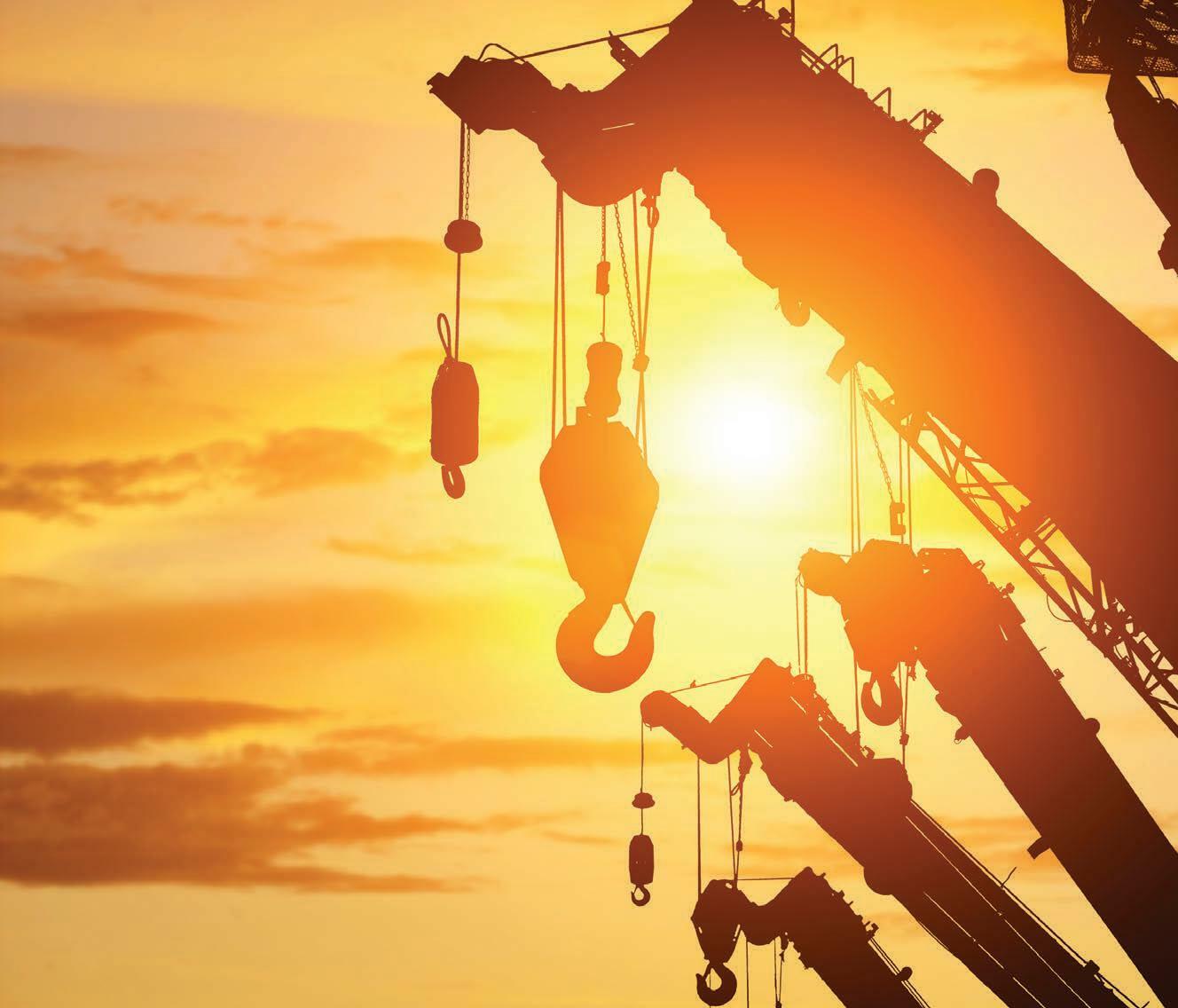
The LCH300/16t is available in various versions: embedded, supported on bases of 6 or 8m, or movable. The crane can be assembled with 2.5 x 2.5m tower sections. Its modular jib has a reach of 25 to 60m, with configurations every 5m. It has a minimum working radius of 4m and a minimum radius of 9m when out of service.
It has manual transmission combinations of 1t (direct pulling) and 2t. The maximum load capacity is 8t with the 1t configuration and 16t with the 2t configuration. The maximum load at the jib end is 3,400 and 3,150kg, respectively.
The luffing moves the jib and counter jib jointly by a hydraulic cylinder at the cathead and jib hinge assembly. The hydraulic pump unit is located on a movable platform in one piece.
From the cabin there is direct visibility of the lifting mechanism of between 50kW(standard) and 65kW (optional). Thanks to the Effi-Plus technology, it is possible to increase the speed of the lifting mechanism without affecting consumption, which allows loading cycles to be considerably reduced, thereby improving the productivity of the crane.
The design of this new rotating part – jib, cathead, and counter jib – as well as the mechanism, cabin, and hydraulic unit platforms, optimises the transport of this model, which may be supplied by eight trucks or containers.
This new luffing jib crane from Comansa incorporates the award-winning Cube Cab (L or XL) with split type air conditioning. The cabin platform, like the lifting and hydraulic unit platforms, can be transported in a single piece.
Comansa luffing jib tower cranes offer optimal performance where horizontal jib cranes cannot move loads freely due to space limitations. Now, with the incorporation of the LCH300 hydraulic model, the luffing mechanism is optimised to offer even greater performance and an efficient assembly, as well as reduction of the radius when out of service.
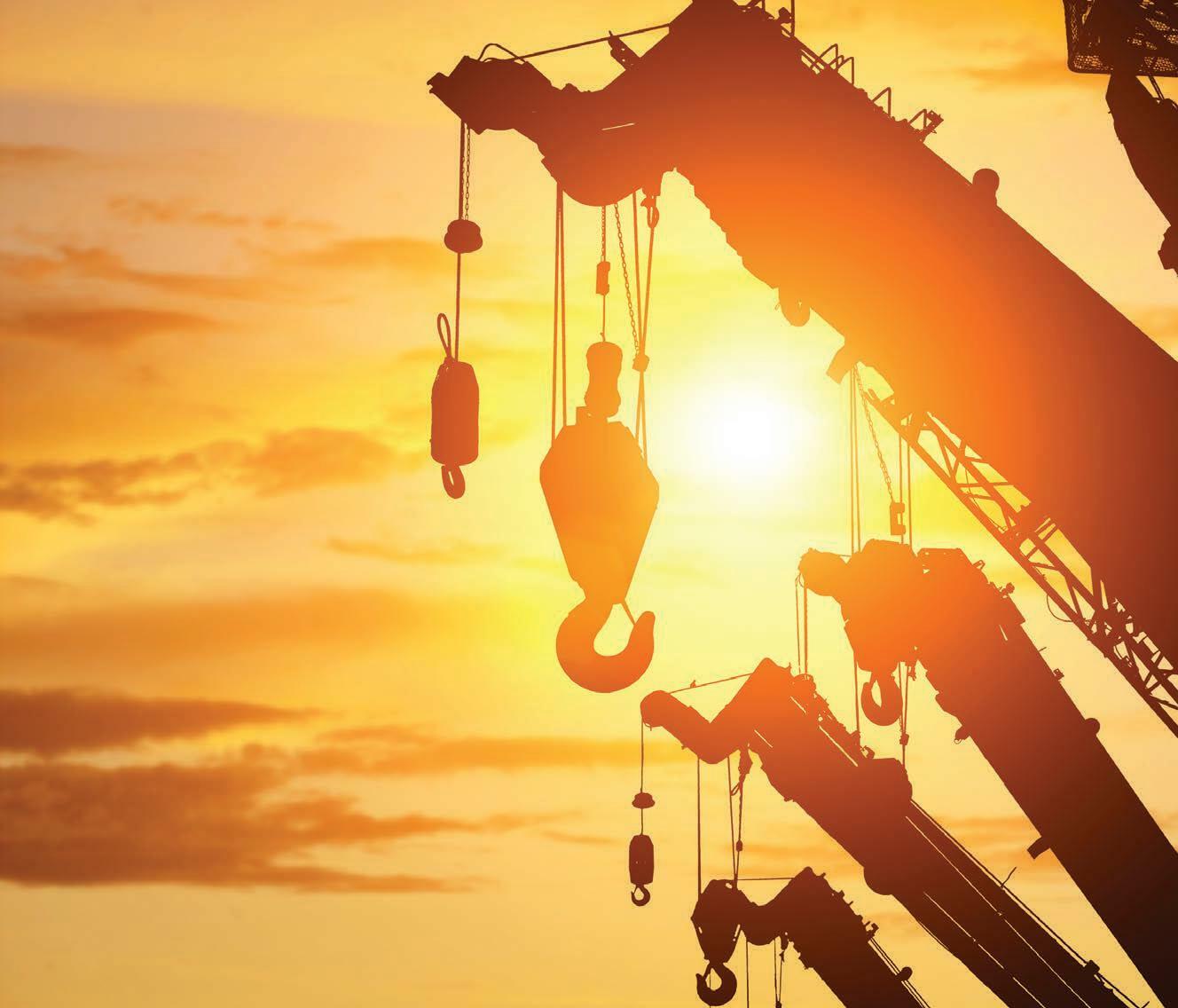
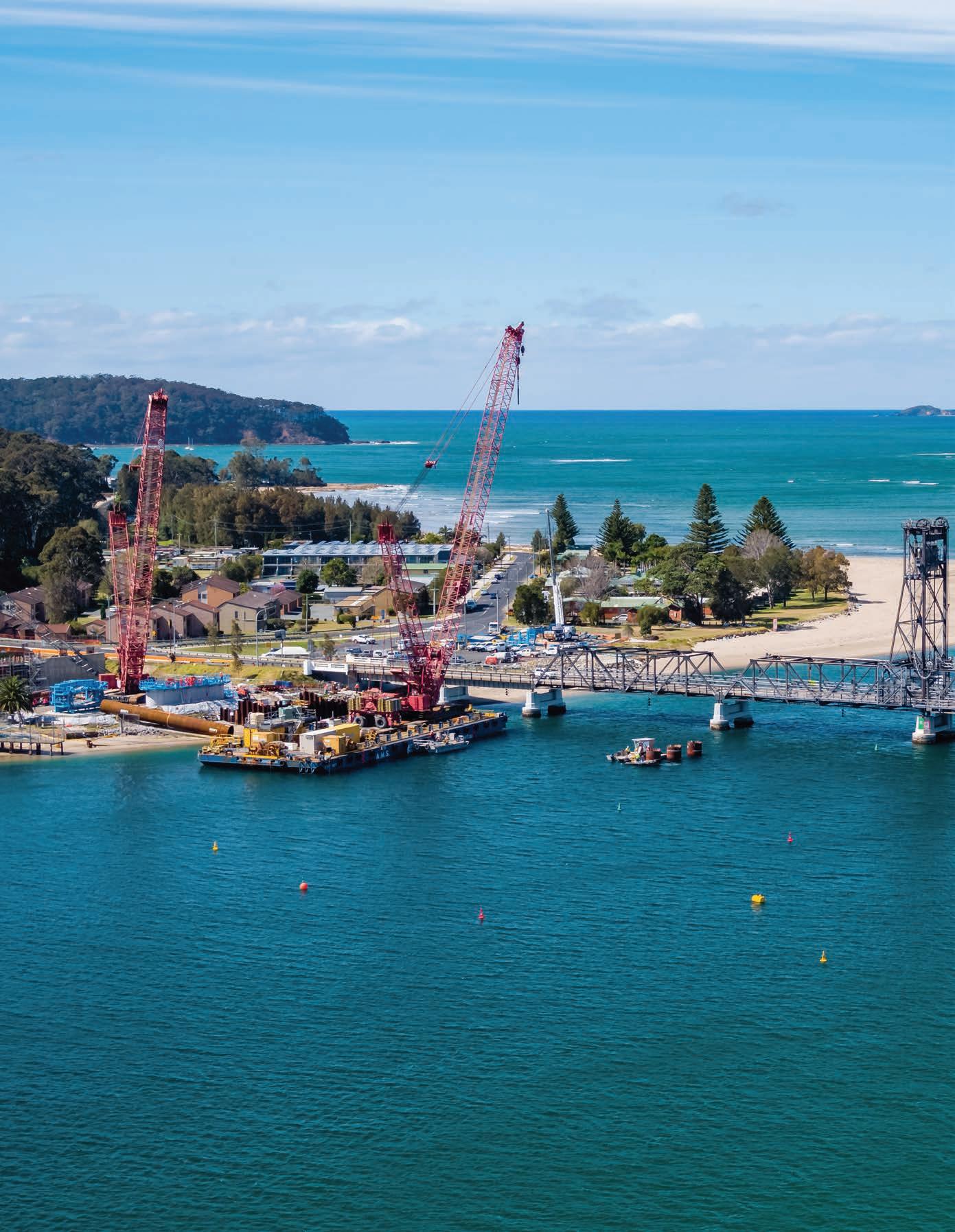

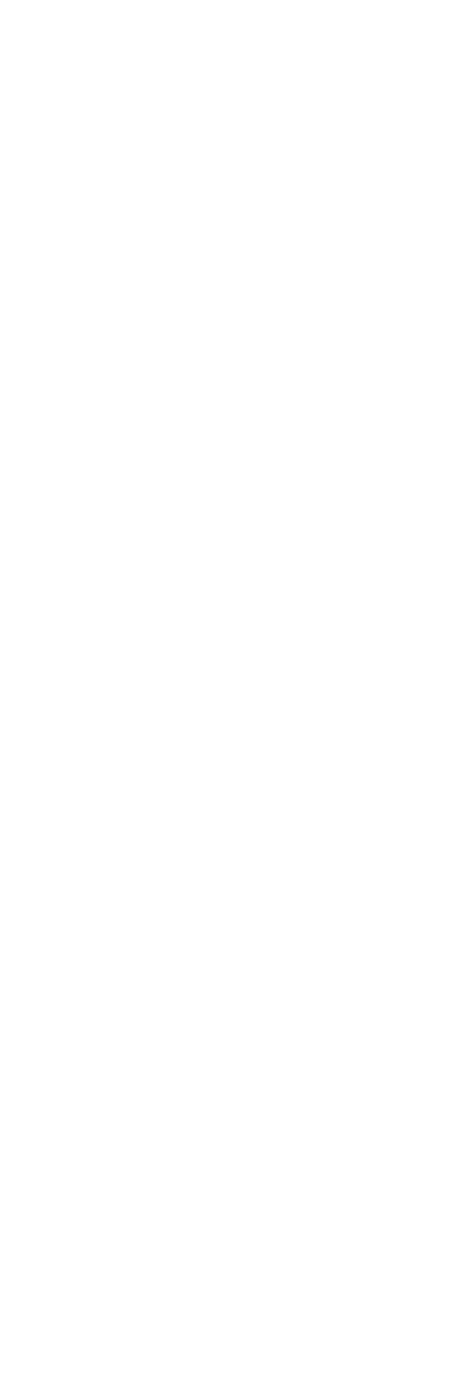
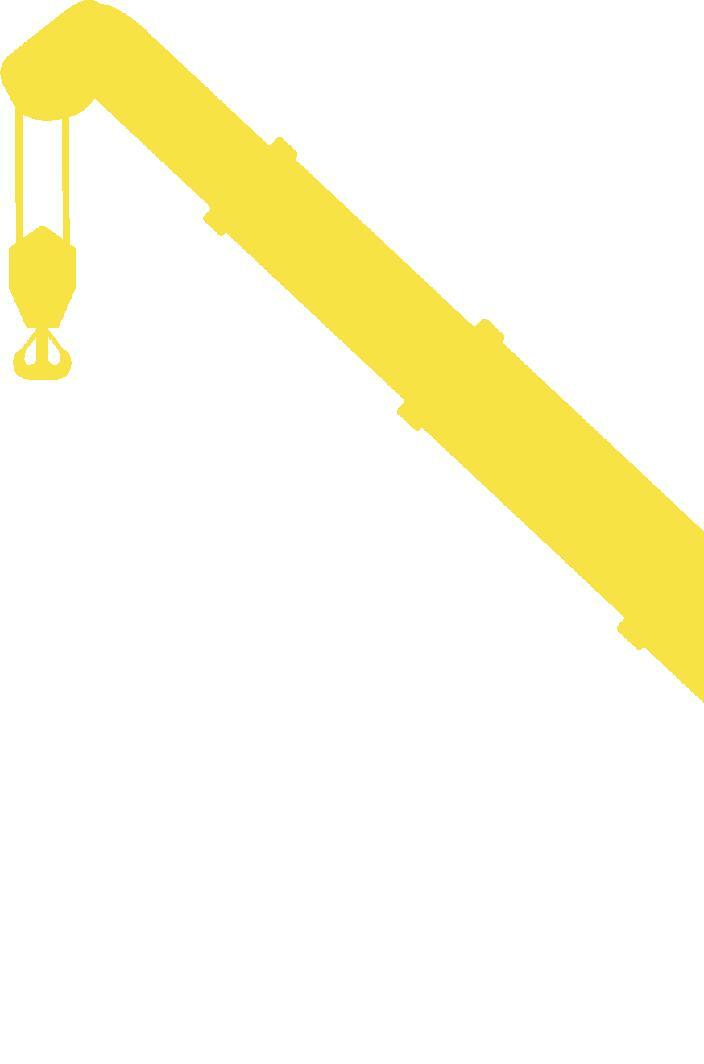
UNIVERSALS LIEBHERR LR1300 BEING KEPT BUSY
Universal Cranes’ Project & Heavy Lift division has been busy working throughout Australia in a variety of markets, including industry, resources, renewables, oil and gas, mining, construction, civil, marine, petrochemical plants and wind farms.
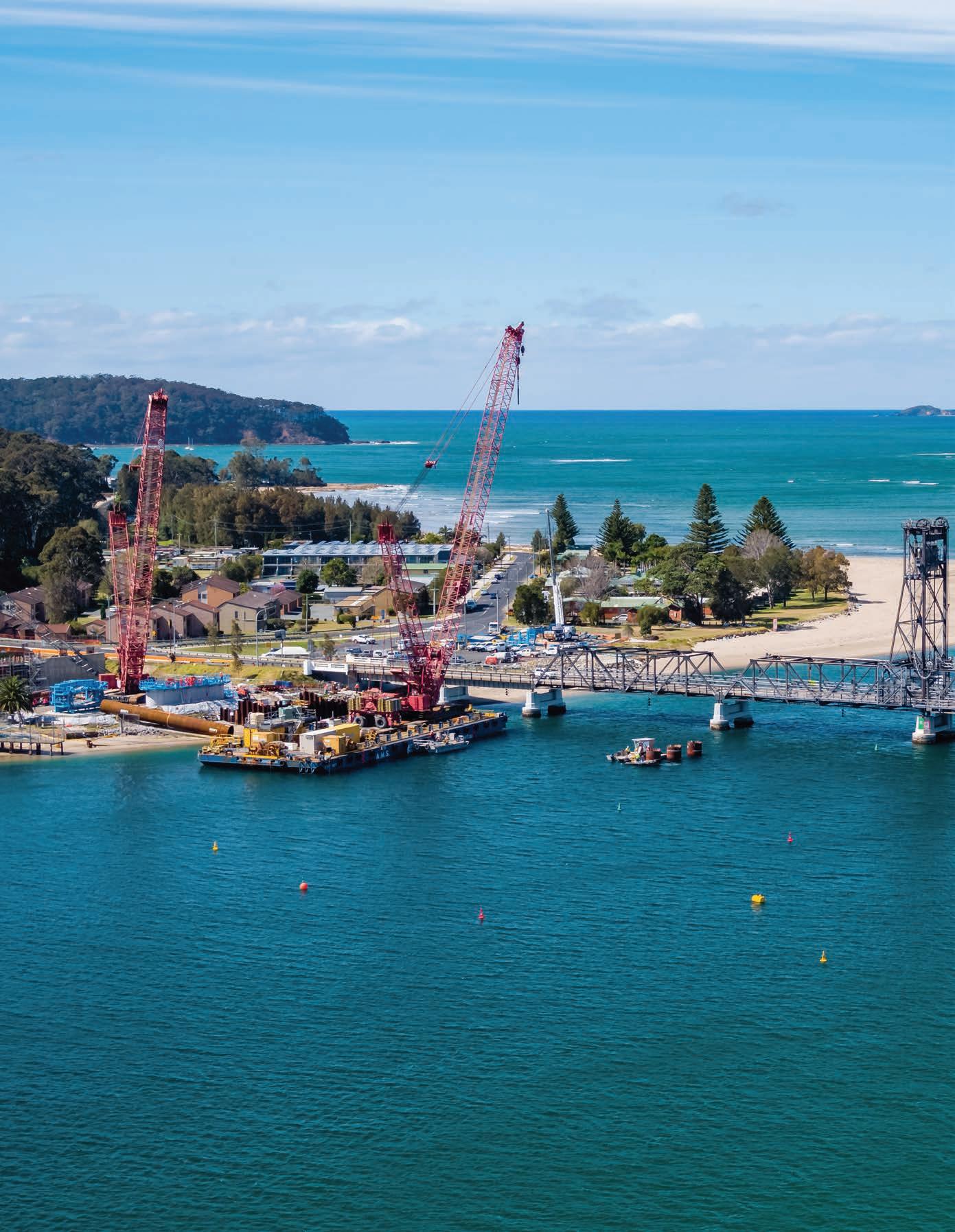
WITH ACCESS TO A CRAWLER CRANE
fleet of 34, Universal Cranes can deliver the most cost-effective options within tight timeframes for any large, heavy and/or complex lift and project requirements.
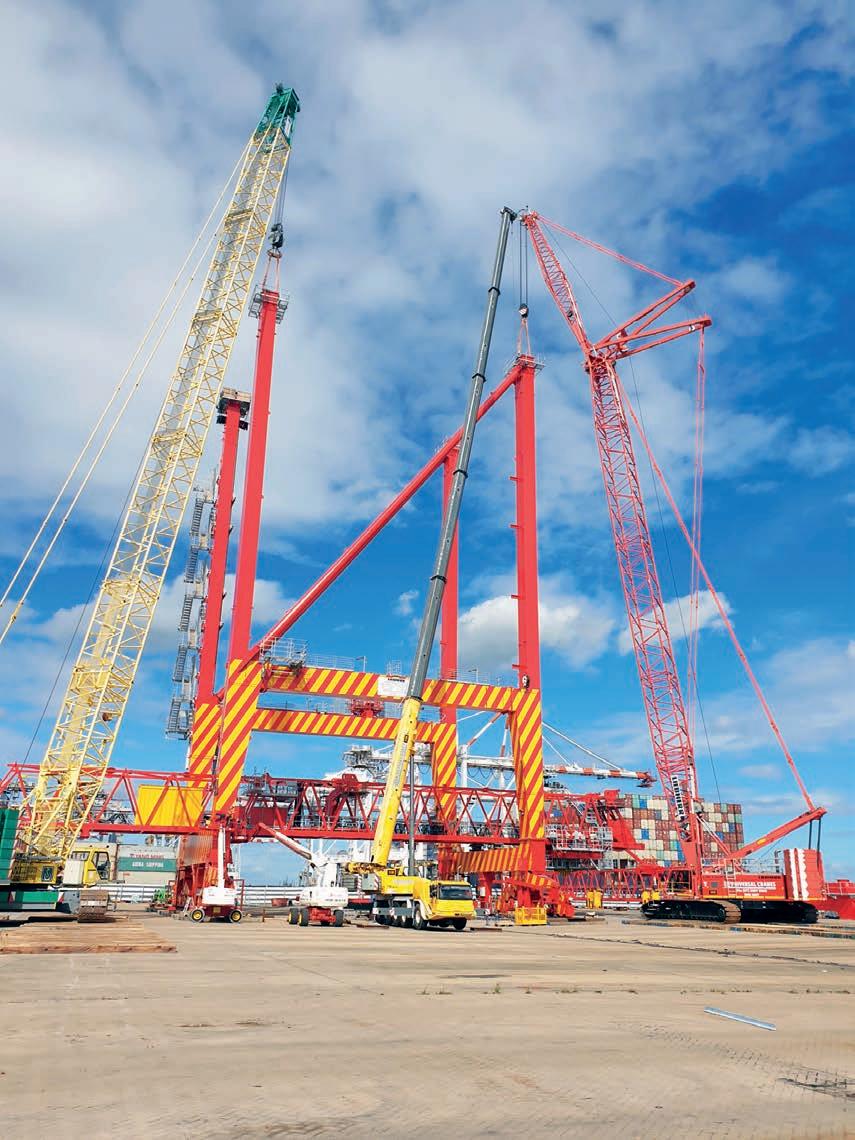
Universal Cranes has two LR1300s and one with a wind kit with additions to the set-up including a derrick, luffing fly, fixed fly, narrow track and wind jib.
SO WHAT HAS THE LR1300 BEEN UP TO?
December 2020 – January 2021
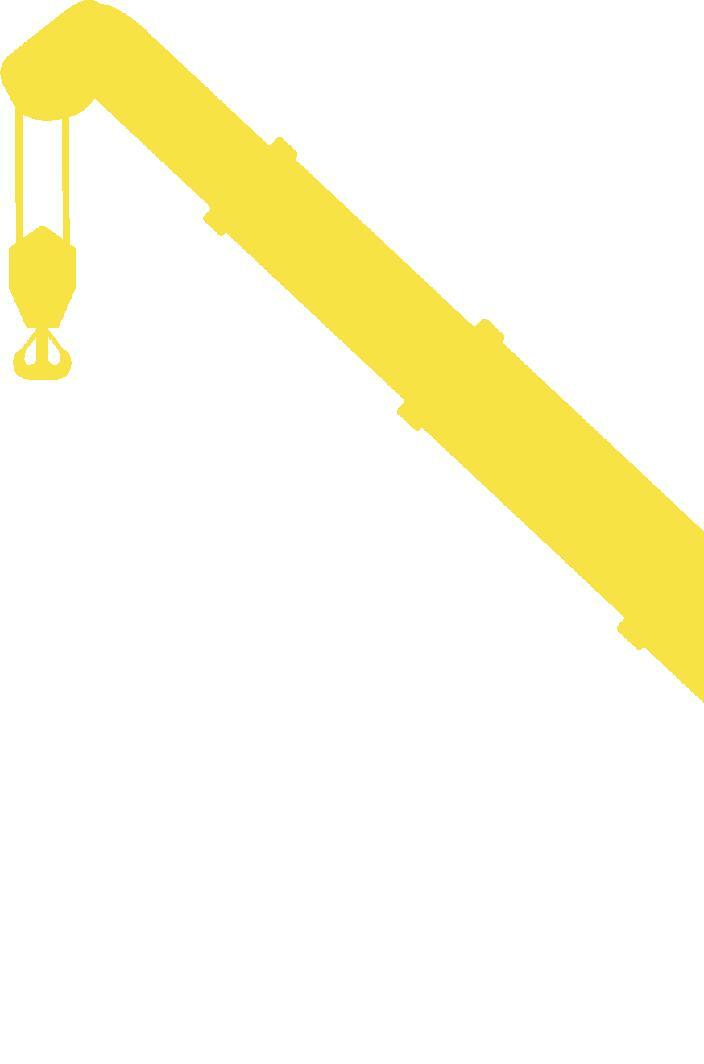
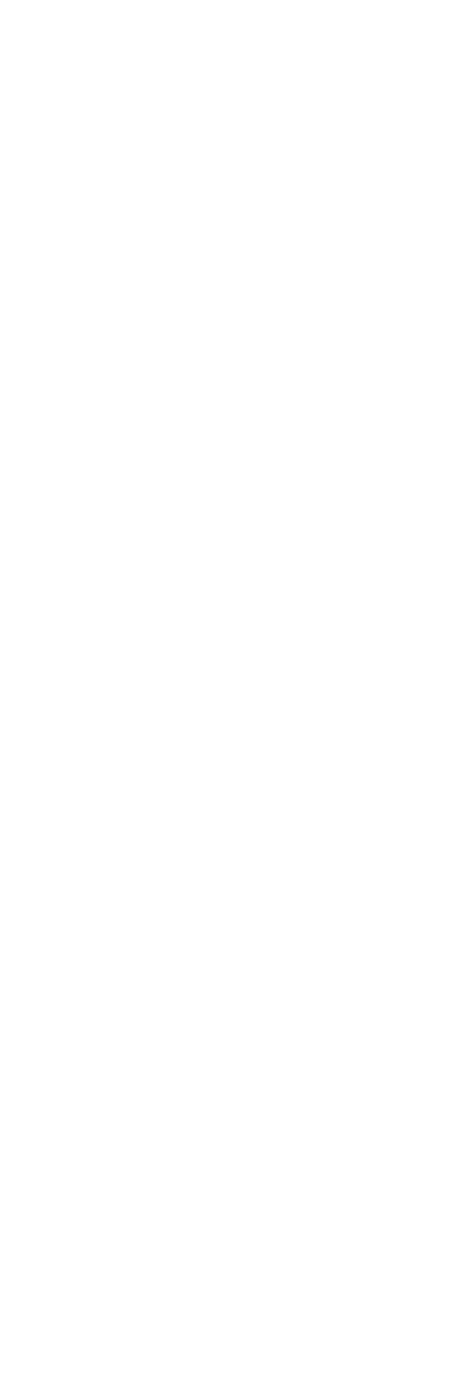
Universal used its two LR1300s with luffing fly and main boom configurations to construct the Ship to Shore crane in Townsville. I n addition to crane hire it provided operators and supervision, transport equipment, wet hire, and supply of miscellaneous equipment.
April, 2021
For this renewable energy project, the LR1300W equipped with 110m main boom derrick and suspended ballast tray was on site at the Mt Emerald Wind Farm, located approximately 50km outside of Cairns in Queensland, doing various maintenance works.
June, 2021
In Central Queensland, supporting the oil and gas sector, Universal dry hired its LR1300 to construct a wash plant using its derrick and suspended super lift tray.
June, 2021
On the Palm Beach to Tugun Highway Upgrade, its LR1300 with main boom configuration was used to safely operate a fy drill.
KEY FACTS TABLE
2022
Universal swung its two LR1300s on the Hay Point upgrade, assisting with the berth replacement.
The LR1300 is a versatile machine and, with the additions of extra components, it can work on a range of projects across a variety of sectors. It can reduce mobilisation and rental costs due to the crane’s increased capabilities with the derrick attachment, which allows the crane to operate in the 400t crawler crane class.

FAST FACTS FOR 2022
Universal Cranes Brisbane acquired a 350t all terrain Demag AC350/6, a 120t all terrain Liebherr LTM1120-4.1, a 25t Terex Franna MAC25 and a 90t all terrain Liebherr LTM1090-4.2.

North Queensland welcomed a new 150t all terrain Liebherr LTM1150-5.3 and Terex 40t Franna AT-40 while Gold Coast Cranes added a 250t all terrain Liebherr LTM1230-5.1 to their fleet. Universals Project and Heavy Lift team secured ownership of a Demag CC2800 600t crawler and Liebherr LTR1100 100t teleboom crawler. On the horizon, Smithbridge Group has ordered two Liebherr LTM1150-5.3s (150t all terrain) and a Liebherr LTM1350 (350 all terrain).
With so many jobs on the horizon, the company grew its team by 25 to accommodate its increased workload.
Universal is celebrating 53 staff members’ work anniversaries this year, ranging from five to 30 years.
Thirty-four per cent of its staff have been with Smithbridge Group for over five years. Universal says it is proud of the signifcant years of service milestones achieved across its team.
“Universal is celebrating 53 staff members’ work anniversaries this year ranging from five to 30.”
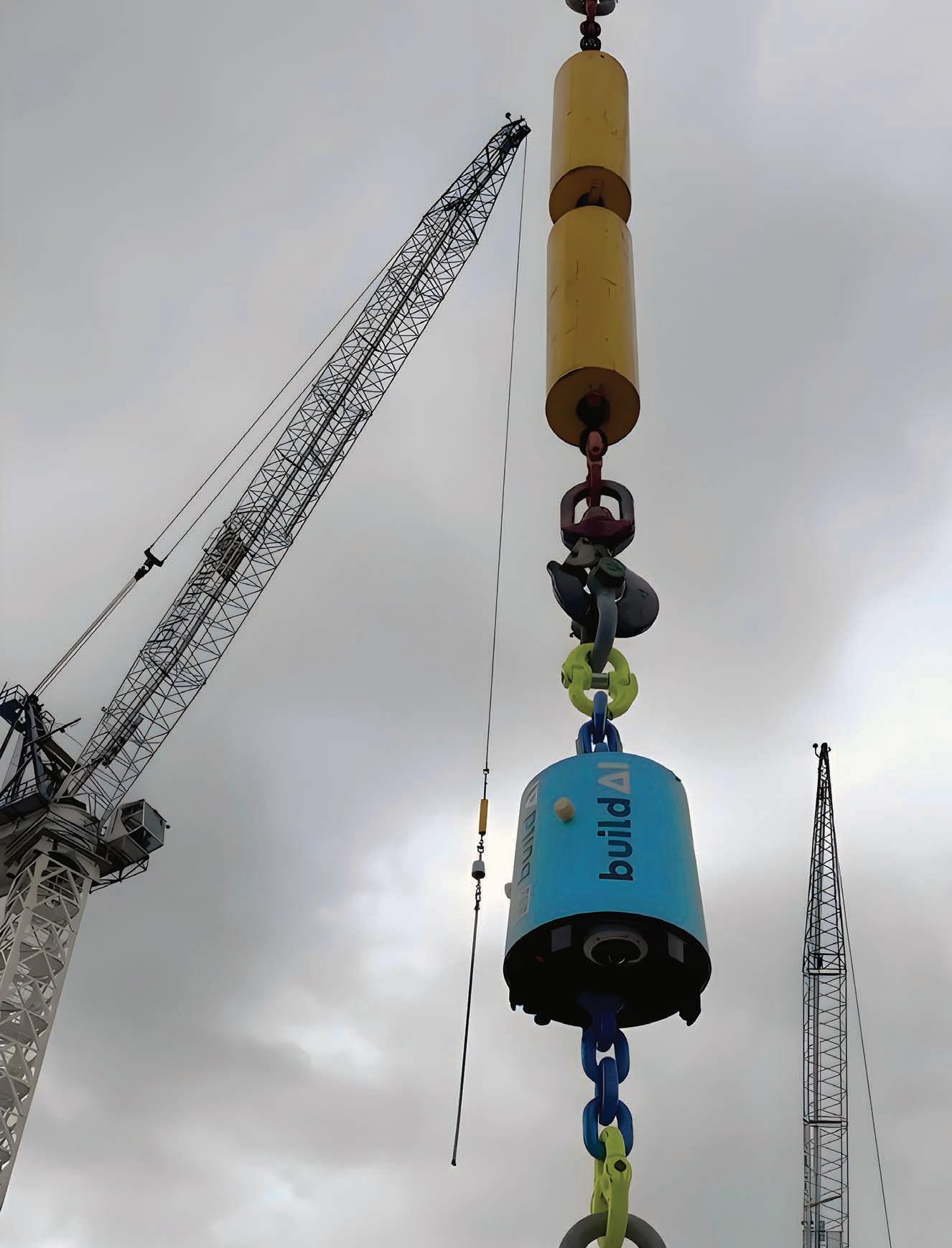
A FRESH PERSPECTIVE FOR CRANE SAFETY
MARR CONTRACTING IS AMONG THE FIRST to experience the benefits of CraneCast and are utilising it across multiple sites as managing director Simon Marr explains.
“CraneCast’s technology is a gamechanger for our industry. Although there are lots of crane cameras out there, CraneCast’s unique ability to provide a 360-degree view and capture data is the missing link for us in delivering even safer, faster, and more cost-effective
solutions for our clients,” Marr said.
CraneCast is currently deployed on Tier 1 projects in Sydney, including on the four tower cranes at Multiplex Western Sydney Airport terminal building, providing superior vision to the crane operators.
CraneCast is the crane driver’s extra set of eyes to look out for those working in the vicinity of loading, lifting, and rigging. Every lift is monitored, with unprecedented vision streamed live to the


BuildAI has developed Cranecast with industry experts to improve safety on work sites and create more efficient crane operations, with a different approach to the crane camera from others.The BuildAI Cranecast system is an extra set of eyes for the driver.
driver’s cabin. CraneCast is fitted with the latest camera technology, providing high-resolution vision ‘at the hook’ including sideways to see what’s nearby during slewing. This vision maximises the driver’s situational awareness at the hook to reduce risk to people, plant, and structures in the vicinity of the lift.
In addition to the vision, the system is capable of capturing data of every movement and relaying this in real-time to a Cloud-based software platform that automatically produces lift, load, rated capacity, and overall utilisation and efficiency statistics.

This provides crane and site management with automated hook analysis and reporting on planned versus actual lifts, understanding of how the cranes are performing in real-time, and ultimately improves crane management with data-driven decision-making. As the system can automatically generate lifting logs with crane time categorised, it can integrate with other existing crane booking or delivery scheduling software packages such as Voyage Control –helping you get the most out of your
resources. With this ultimate transparency of what the crane is doing, project delivery teams have their finger on the pulse of all critical path activities.
The physical dimensions of the device have been intentionally designed to mimic ponder weights used on tower cranes. The unit, including rigging assembly, is less
Cranecast provides accurate reporting functions for operators and owners.
the boom. This means it can be fitted to luffing, hammerhead, crawler, and all terrain cranes. The system also comes with a device stand that remains on site, to enable safe and efficient servicing.
BuildAI CEO and founder Kristian Butcher explains some of the challenges
“CraneCast’s technology is a gamechanger for our industry.
Although there are lots of crane cameras out there, CraneCast’s unique ability to provide a 360-degree view and capture data is the missing link for us in delivering even safer, faster and more costeffective solutions for our clients.”
than 200kg and housed in a polymer shell, engineered to withstand impact of regular crane operations. Supplied with its own certified rigging assembly proof tested to 32T SWL as standard, it can be easily attached to an existing chain setup.
CraneCast is fully independent, using battery power and wifi connectivity; there’s no need for cabling runs across
the construction sector faces when adapting to new technology.
“Construction is a fragmented field requiring a lot of labour-intensive hours. There is poor communication and a lack of data transparency, leading to the inefficiencies which currently characterise the industry,” Butcher said.
“This current model places incredible
The system attaches subtly to the machine and is simple to use for riggers.
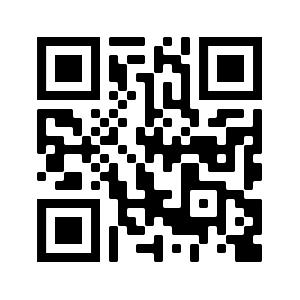
stress on the individuals that work in our industry, which is why we wanted to be part of the solution.
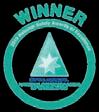
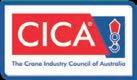
BuildAI is not about replacing jobs. Instead, AI is used to provide more connected productive work environments and to give employees flexibility they never had, which means more time with their families.”
Leveraging artificial intelligence technology including computer vision and deep experience in construction and commercial environments, BuildAI supports project delivery teams to optimise the critical path.
Integral to the critical path of any project is the safe and efficient operation of the crane, since it’s the timely movement of materials from the delivery zone to the work face that drives the progression of critical activities.
Coordinating material deliveries and lift plans is a daily occurrence and requires
constant rescheduling to meet overall project program milestones. Often this is done manually and lacks transparency for all relevant participants such as sub-contractors, material suppliers, and project management.
This dynamic environment places crane operation teams under pressure, while requiring the highest safety standards are maintained. BuildAI’s capabilities are dedicated to relieve these challenges.
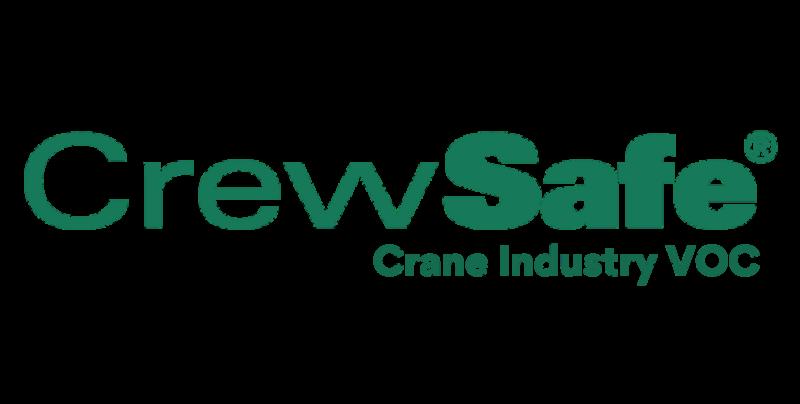
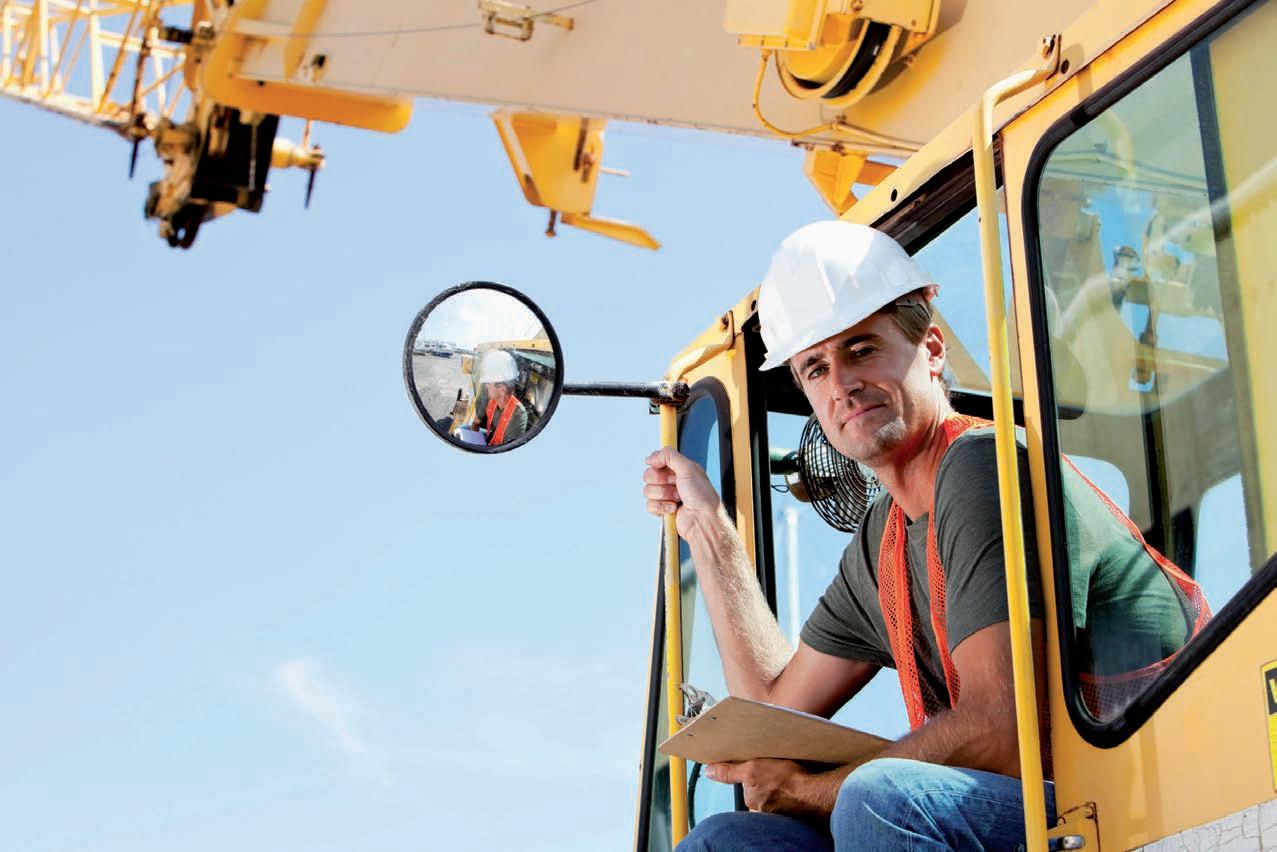

CrewSafe is the standardised VOC assessment tool for the Australian crane industry.
CrewSafe provides machinespecific, impartial, peer assessment with documented evidence of competency.
BUSINESS IS BOOMING AT MCT EQUIPMENT
WITH OVER 30 YEARS OF COMBINED experience across a multitude of industries, including mining, construction, infrastructure and more, and now with another year of experience under its belt, MCT continues to lead the way in providing unique and innovative lifting solutions for its valued clients.
The last 12 months have seen spectacular growth across all three of MCT’s core divisions – new equipment, used equipment and workshop. The rapid expansion and intense market demand for major inspections, quality used equipment, and alternative lifting solutions, plus a sizeable workshop and parts storeroom, has seen the need to relocate to a bigger and better facility in Henderson, which will open this month.
MCT prides itself on offering an extensive range of world-class lifting equipment and accessories from tried and trusted brands, including Italian market leader Magni Telescopic Handlers, and Danish glass robot revolutionary Smart Group. Continuously adding to its new equipment product range, MCT searches worldwide to source and deliver the best in safety, innovation, efficiency, craftsmanship, and performance.
Separating itself from the competition with its promise to ‘think different, lift different’, Grosser saw potential in the market to bring Magni telehandlers Down Under, and, in October 2021, secured exclusive distribution rights within Western Australia and the Northern Territory. While Magni
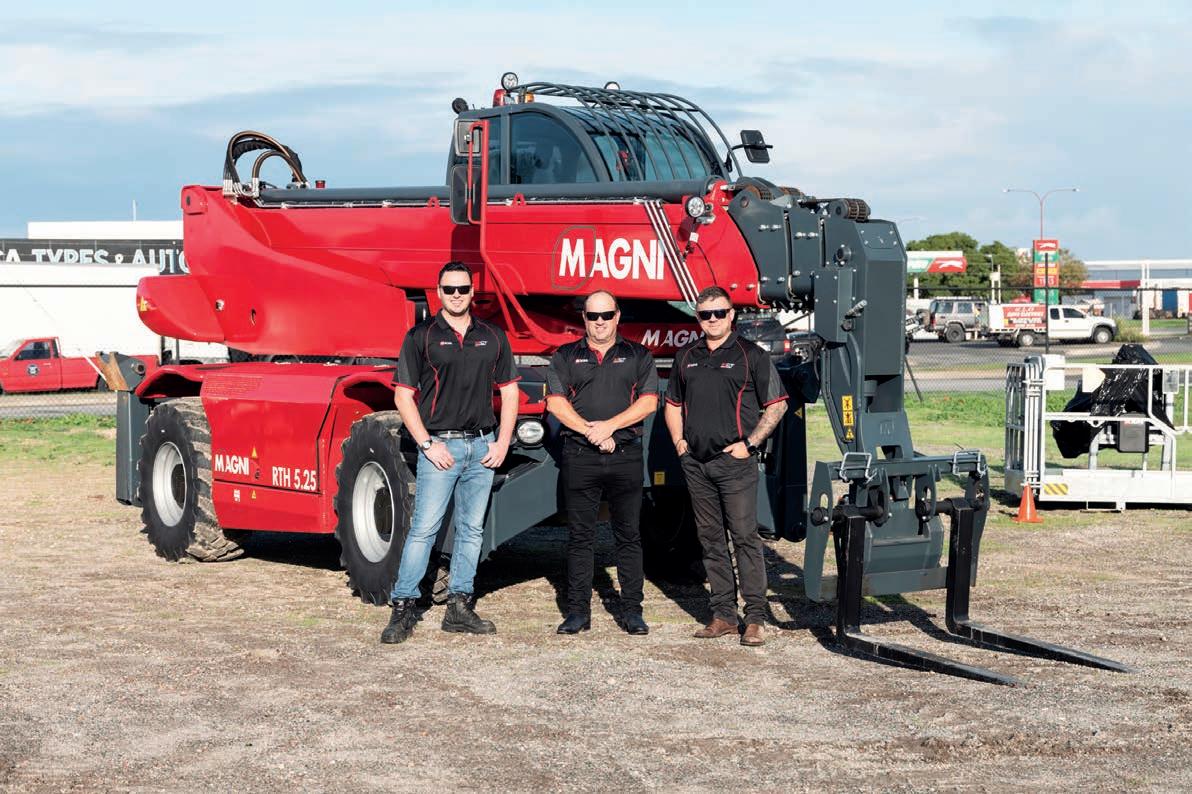
telehandlers haven’t always been the traditional choice, thanks to MCT they are rapidly becoming a preferred brand within Western Australian and Northern Territory clientele due to their innovative features, reliability, and versatility.
To celebrate this partnership, and to bring awareness to their customer base, MCT hosted Magni Days – a two-weeklong event that showcased what Magni has to offer. The demo days gave existing and potential clients the opportunity to push a Magni telehandler to its limits and experience its full capabilities. The event also allowed the team at MCT to engage face-to-face with its customers; a hugely important aspect of Grosser’s business model, as he aims to build genuine relationships with clients and suppliers.
As MCT Equipment approaches the end of its first year in business, founder and managing director Anthony Grosser takes some time to reflect on its achievements and the immense growth of the team, their capability and overall operations.The
Through a deep network of industry contacts and suppliers, both locally and internationally, MCT is able to source, sell, or dispose of existing machinery and equipment.
Before selling second-hand machinery to a new owner, the team in the used equipment division can complete a comprehensive inspection, and full refurbishment if required, always to the highest standard of quality and safety compliance. A structured sales methodology, combined with years of industry experience, ensures that the customers’ used equipment experience is handled professionally and efficiently.
The team at MCT are just as committed to the aftersales support of their customers. From servicing support and training to diagnosing critical failures, to offering general advice, the efforts of the workshop division have increased 10-fold
over the past 12 months as the number of equipment sales increased. With an understanding that minimising downtime and disruption is key to achieving profitability, it is no mean feat to offer around-the-clock support to customers.
Highlighting their “think different, lift different” mantra, is MCT’s pledge to constantly strive for unique and innovative solutions for their clients. This year has seen the team design and manufacture tailored storage solutions, heavy lifting outrigger pads, and safe access and handrail systems. MCT knows how to meet the demand of a machine’s application as well as the needs of its customers.
MCT does not just value the financial success and growth of the business, but also places a huge emphasis on family. Evidence of this can be seen with the addition of Grosser’s son, James, to the
MCT team, ensuring the longevity of the business and the legacy of the Grosser name in the crane industry.
Despite a phenomenal first year in operation, at its core, MCT is a family business. Grosser is understandably grateful to have assembled a growing team of employees who share the same values and dedication to exceptional service and performance.
With equal importance placed on working hard and enjoying life, the team is encouraged to ‘build a career, build a lifestyle’. With the number of employees expanding in unison with their operations and capability, MCT was thrilled to introduce two heavy vehicle apprentices into the business.
As any business owner will tell you, the past year hasn’t been without its challenges, but with such remarkable growth and achievement in so little time, it can only be a sign of good things to come for Grosser and the team at MCT Equipment.

To learn more about MCT Equipment’s range of lifting machinery and accessories, call 08 6500 3460 or visit https://mctequip.com.au.
MCT has recognised the importance of after sales servicing for its equipment.
“Highlighting its ‘think different, lift different’ mantra, is MCT’s pledge to constantly strive for unique and innovative solutions for its clients.”
ACHIEVE
Unlock
with
City Class Crane
The winch attachment is compact and sturdy. Designed for effortless
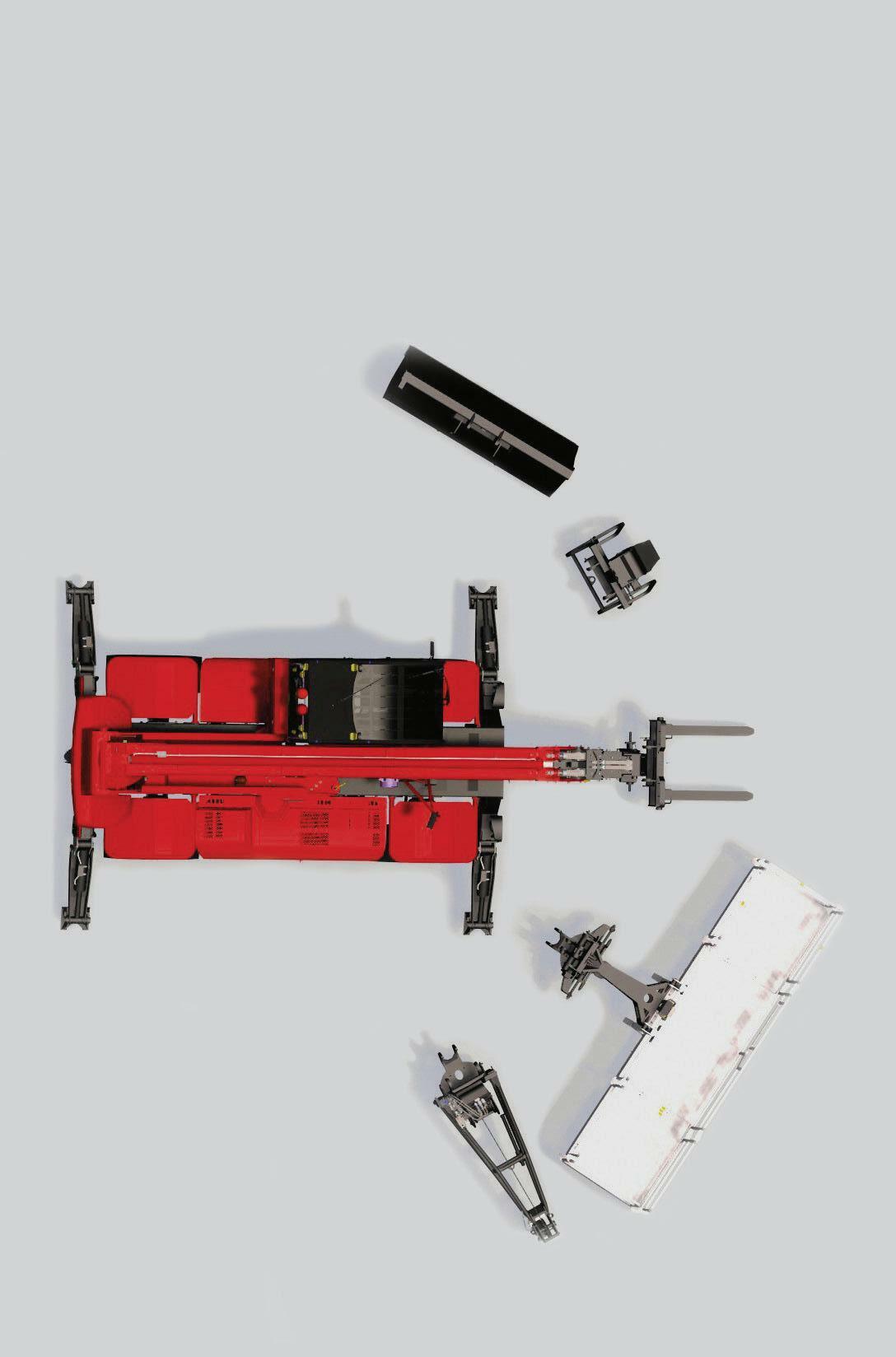
moving
even in tight
Elevated Work Platform
Wide range of platforms available for working at heights in total safety or where accessibility is an issue.
Pick & Carry Crane
Magni approved hooks offer a wide solution for use in the construction world, including 360° rotation and load control system that detects the risks of overload during use.
Site Clean Up
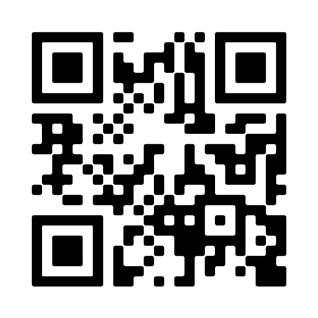
The bucket is perfect for transporting sand, gravel and rubble and maintaining a safe worksite, available with up to 3000L load capacity.
Telehandler
With a large range to meet market needs and to assist our operators directly in the workplace. From the simplest fork carriers to those with heavy-duty capacities and larger fork sizes able to perform aggravating work in the most extreme conditions.
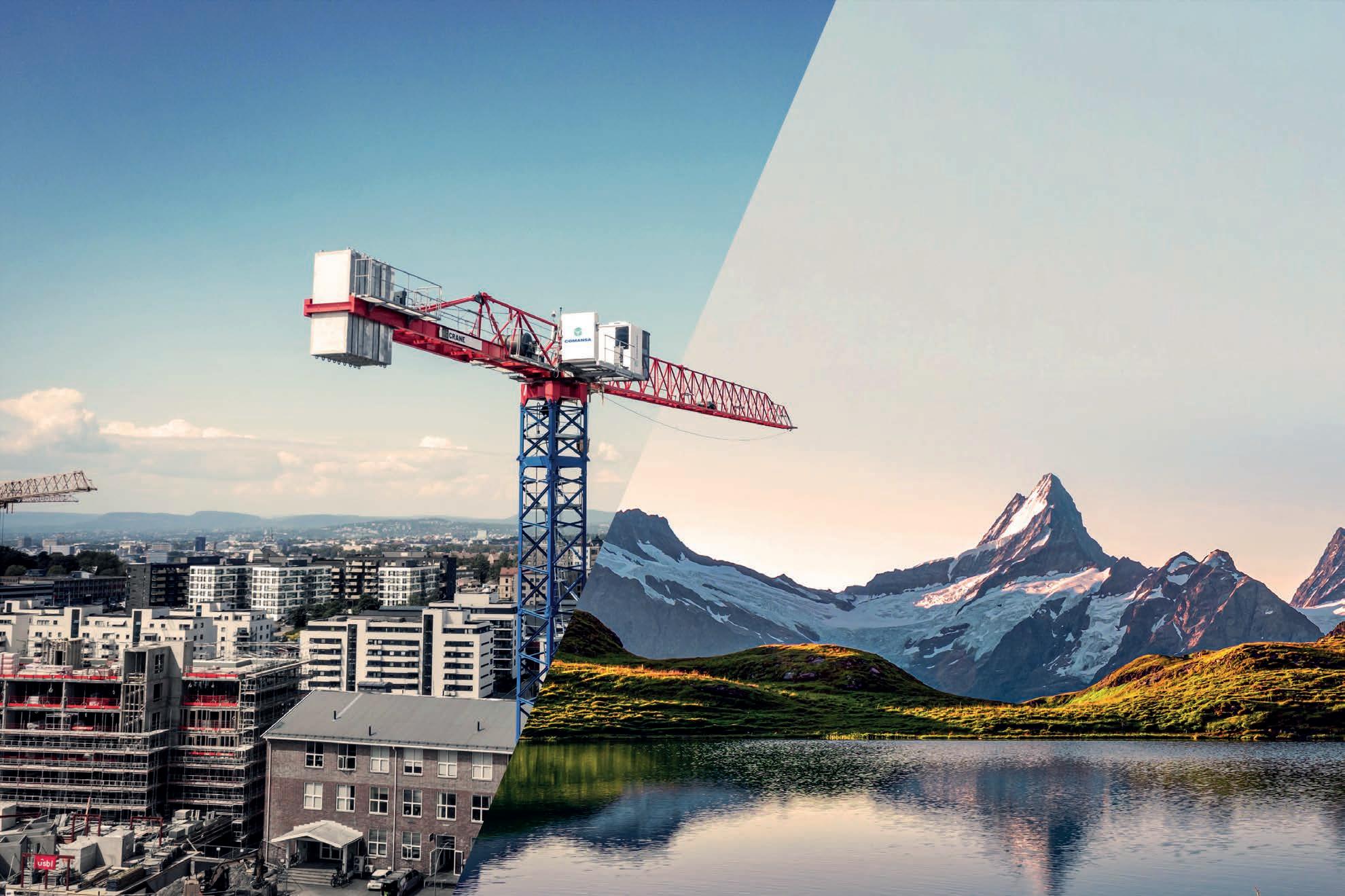
COMANSA BUILDS A BESPOKE TOWER CRANE FOR A NORWEGIAN YARD
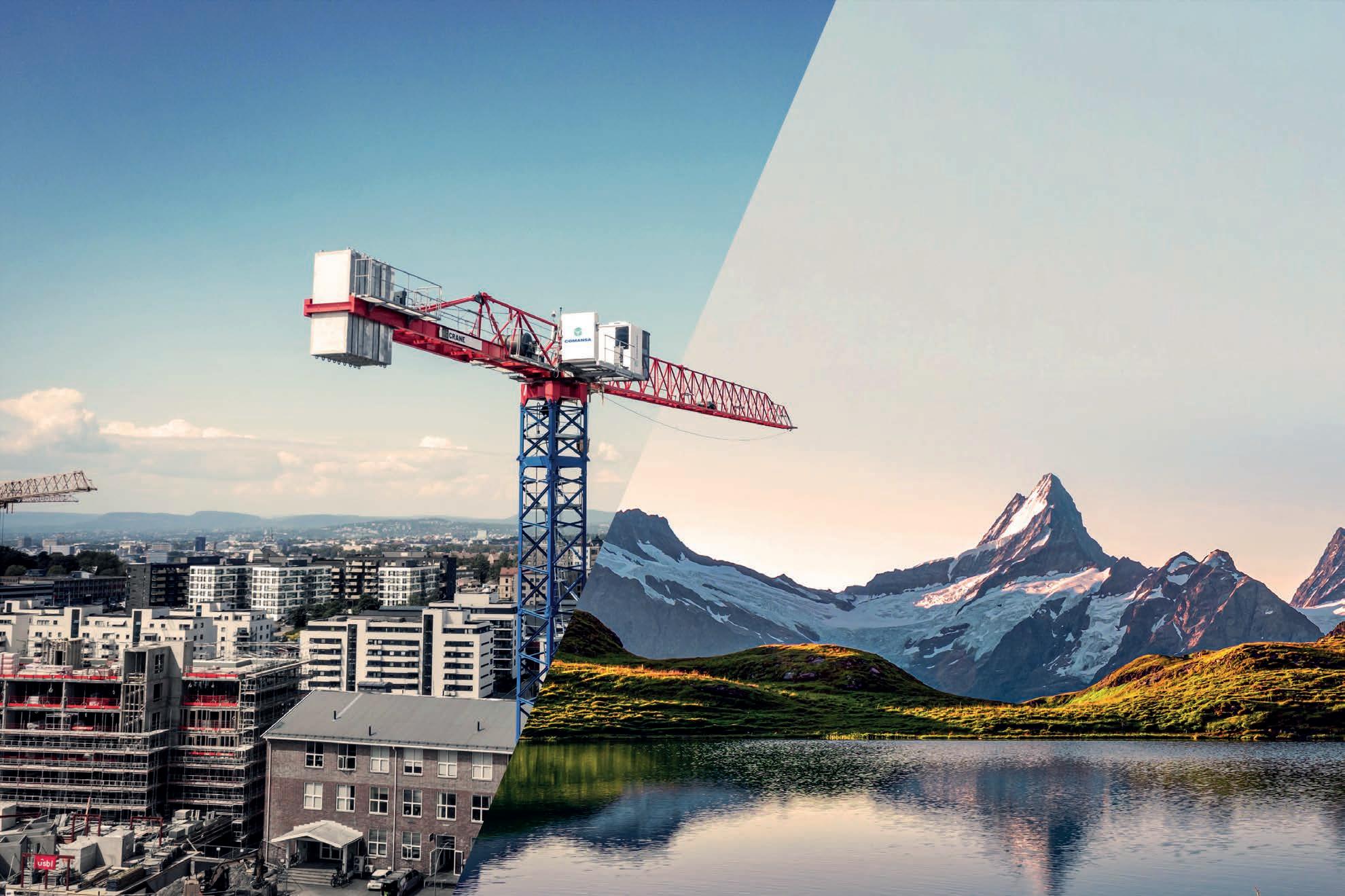
date, and it has been used to lift very different loads 24 hours a day, seven days a week.
Its 80m boom length has made it possible to reach the entire platform with a single tower crane.
REINFORCED PORTAL
To meet the demands of the project (withstand the 400t per corner that originate from a crane of more than 90m, in a D25 wind zone, and facilitate worker and
vehicle transit) Comansa built a reinforced portal of 10m, which was assembled by its Norwegian distributor in the yard.
Furthermore, the portal means it can be used in two ways: with movement on rails so it can be transported from one side to another and supported with levelling screws.
Due to the yard’s geographical location, close to the North Sea, the tower crane is designed to with stand wind pressure pursuant to European D25 standards.
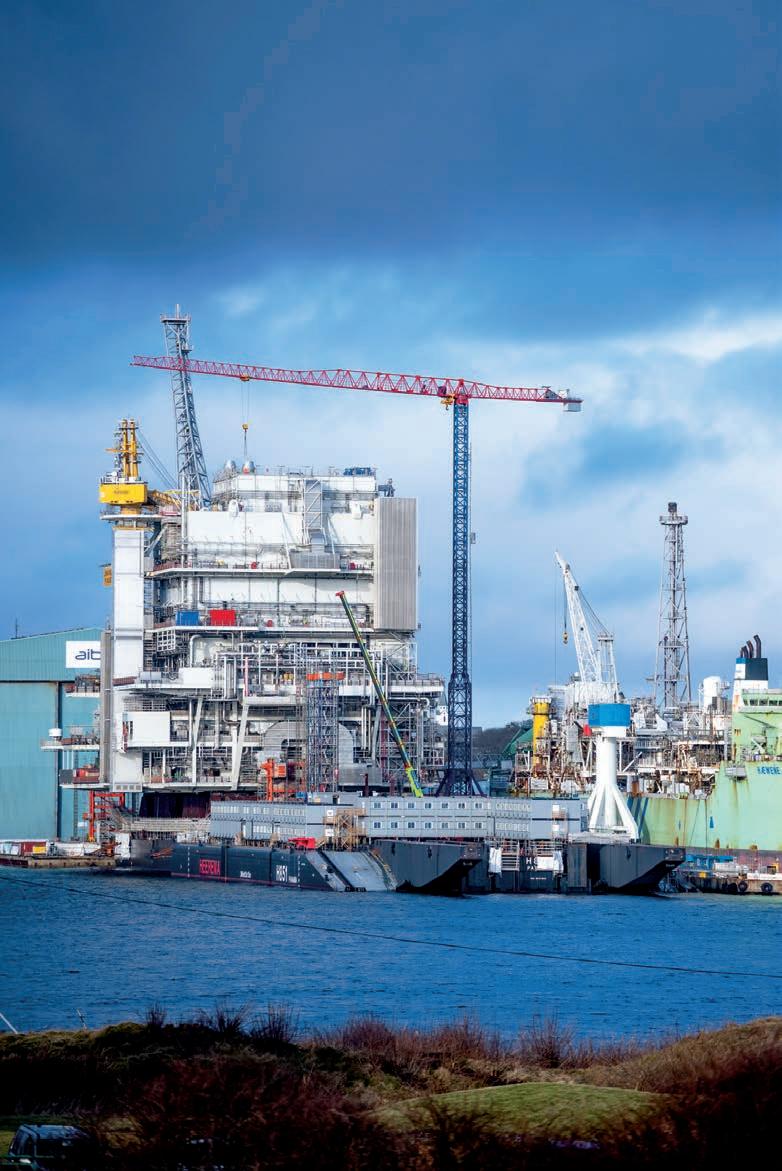
DESIGNED TO WITHSTAND INCLEMENT WEATHER
D ue to the yard’s geographical location, close to the North Sea, the tower crane is designed to with stand wind pressure pursuant to European D25 standards.
Furthermore, to protect it against inclement weather, Comansa has
Comansa and the Rental Group Crane AS technical team have responded with success and agility to the specific needs of Aibel’s yard.
To meet the demands of the project
Comansa built a reinforced portal of 10m, which was assembled by its Norwegian distributor in the yard.
used special protection elements and materials, as well as 250-micron paint to prevent corrosion.
SAFETY EQUIPMENT
The tower crane is equipped with numerous options to guarantee safety at all times: vision camera on the trolleys to view the loads and the environment more safely, alarm signals, high-luminosity LED lights on the boom for the area workstations with on/off from the ground, signalling lights, counterweights protected with galvanised steel frames, stainless steel electrical cabinet, and activation of the windrelease system from the base of the crane, among others.
FLAT-TOP DESIGN
Thanks to its ease of assembly and smaller space requirement, Comansa’s flat-top design has made it possible
“Thanks to its ease of assembly and less space requirement, Comansa’s flat-top design has made it possible to overcome the logistical challenges arising from installation in a small (600–700 square metre) and windy space like the Norwegian yard.”
to overcome the logistical challenges arising from installation in a small (600–700 square metre) and windy space like the Norwegian yard.
The Aibel yard lent its facilities and helped to pre-assemble the necessary parts (which arrived on 32 trucks). For the assembly, a 500t mobile crane with a height of 115m was used. The heaviest piece to assemble was 23t.
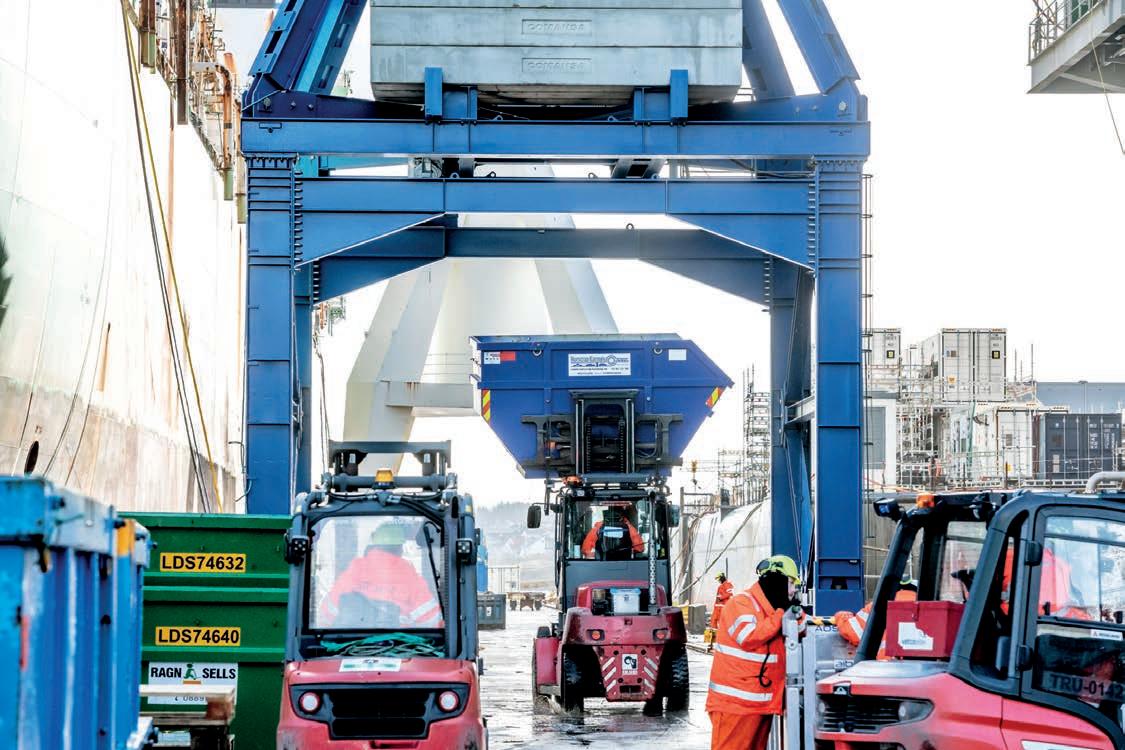
Once the foundation was laid and the portal installed, the crane was assembled in just two days.
TECHNICAL SERVICE
The speed when it comes to having spare parts and being able to move the crane to another point in the yard to undertake new projects is essential.
R ental Group Crane AS’s technical service is only two hours from Aibel and can provide parts such as moving or electrical elements, in addition to support. Comansa can also provide other types of special parts within just one day.
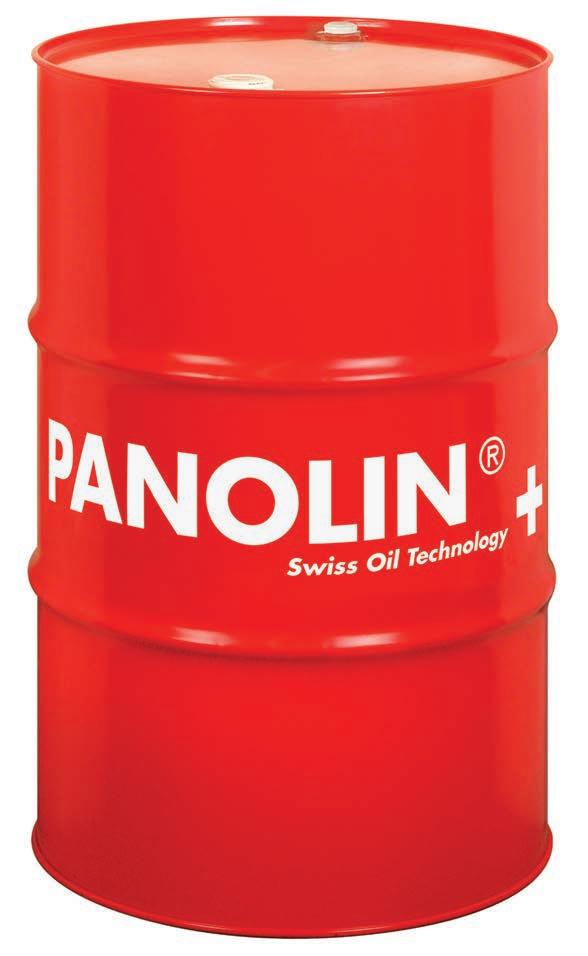
AN OIL TO SUIT ANY CHALLENGE AND GOOD FOR THE PLANET
It is no secret that the crane industry is tough, equipment is required to lift extreme amounts of material and machines have so many parameters needing to be considered, including ensuring they are operating in an environmentally friendly way.
FOR THE LONGEST TIME, MAKING USE of equipment or products that were environmentally friendly would often mean reduced perfomence or greater challenges. Panolin’s biodegradable lubricants have eliminated these challenges and have surpassed the performance of mineral oil-based lubricants.
Panolin has been operating in Switzerland since 1949 and has been creating environmentally considerate lubricants since 1983. The company has grown an impressive amount since its first iteration and now exports its products to over 56 countries.
Panolin services industries such
as construction, marine, dredging, offshore wind farm construction and railways, among others.
Panolin’s HLP Synth is one of the world’s leading fully synthetic, long life, readily biodegradable hydraulic fluids. Having been available since 1985 and used in equipment for in excess of 1 billion hours the credibility and experience of HLP Synth is unparalleled and supported by over 200 original equipment manufacturer (OEM) approvals.
Panolin’s biodegradable lubricants, including HLP Synth, are the products of choice for improved environmental and technological
performance and cost effectiveness in major construction, dredging, piling, bridge building, offshore construction and subsea projects. HLP Synth is also used extensively in railway maintenance and, very importantly, the crane industry.
Imperial Oil & Chemical, Panolin’s Australian distributor, has been bringing the Panolin products to Australia for many years. For some time now Imperial Oil has been supplying shuttle boom grease two and HLP Synth, to the mobile crane industry.
More recently, HLP Synth has been adopted as the bio-hydraulic fluid of

choice by a major Australian crane company and, for the first time in Australia, HLP Synth will be used in a fleet of hydraulic tower cranes.

It’s great to see an iconic Australian company taking such a responsible position in protecting the environment, said Imperial Oil’s MD, Brad Langford.
The company selected Panolin’s HLP Synth, based on biodegradability, high performance, and overall cost savings, due to its exceptionally long fluid life, and plan to use it in its entire fleet of tower cranes.
Panolin’s HLP Synth was originally chosen for a project located near the coast. It has since decided to convert all of its cranes to HLP Synth.
HLP Synth is the only biodegradable hydraulic fluid approved by Bosch Rexroth and qualifies for the very stringent RDE 90245 standard.
“Panolin’s products are world renowned, with HLP Synth being used in the Eiffel Tower, the Panama Canal, the London Eye, Niagra Falls, and the Sihwa Tidal power plant in Korea,
among many others, standing up to the challenges of all.
ORIGINALLY CHOSE Panolin has, for many years, supplied HLP Synth to a number of OEMs in the Asia Pacific region. HLP Synth was originally approved and used in machines that were being exported to the European market.
More recently, some of these OEMs have been using HLP Synth in equipment that is being used in Asian domestic markets.
In Europe most construction sites require equipment, including cranes, to use biodegradable lubricants, due to restrictions implemented by governments across the European Union. Australian operators are now also moving towards the use of environmentally friendly biodegradable lubricants.
The benefit for the Australian crane industry is that it allows operators to look toward the European market and understand where Australia may be moving to in the next five to 10 years. This insight allows crane companies, to prepare for more stringent regulations in the future.
“When considering the conversion to biodegradable lubricants, crane operators have to consider the performance and life expectancy of the lubricants. HLP Synth is higher performing than many competitor products.
Under the right conditions, HLP Synth can offer crane operators a product capable of ‘fill for life’ performance.
The point of concern for many users of lubricants in Australia is whether they can stand up to the rigours of the often harsh environment and extreme temperatures. Some operators may have machines operating in temperatures up to 50 degrees Celsius. HLP Synth can easily handle extended operating hours in high ambient temperatures.
Another very important factor in
supplying biodegradable lubricants is being able to provide aftersales service, including product sample analysis.
Panolin recommends that customers sample their oil every 500 hours and provides a free oil testing and evaluation service from its laboratory in Switzerland.
Imperial Oil can also arrange for local sample analysis for a very quick turnround.
Panolin has been consistently developing environmentally friendly products for the crane industry for many years, including the very successful Shuttle Boomgrease 2 and the wire rope lubricant Biotrack E 700, which is more than capable of standing up to the tough challenges of lifting heavy loads.
“Panolin’s biodegradable lubricants, including HLP Synth, are the products of choice for improved environmental and technological performance and cost effectiveness in major construction, dredging, piling, bridge building, offshore construction and subsea projects.”
The London Eye has undertaken 100,000 operational hours without an oil change
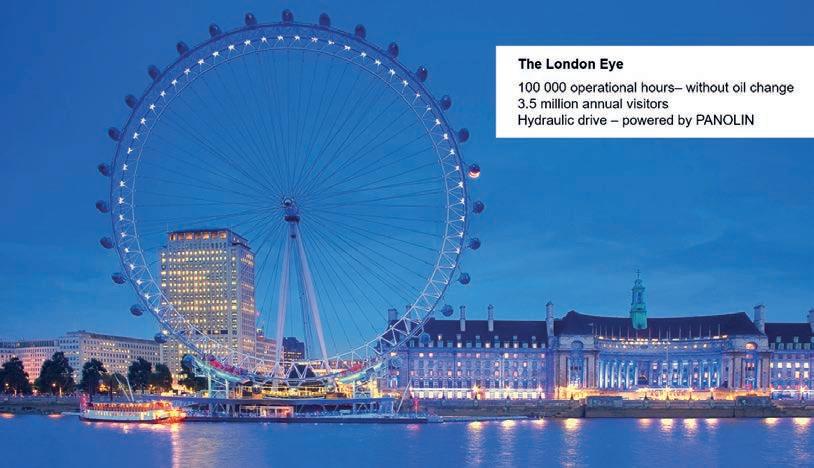
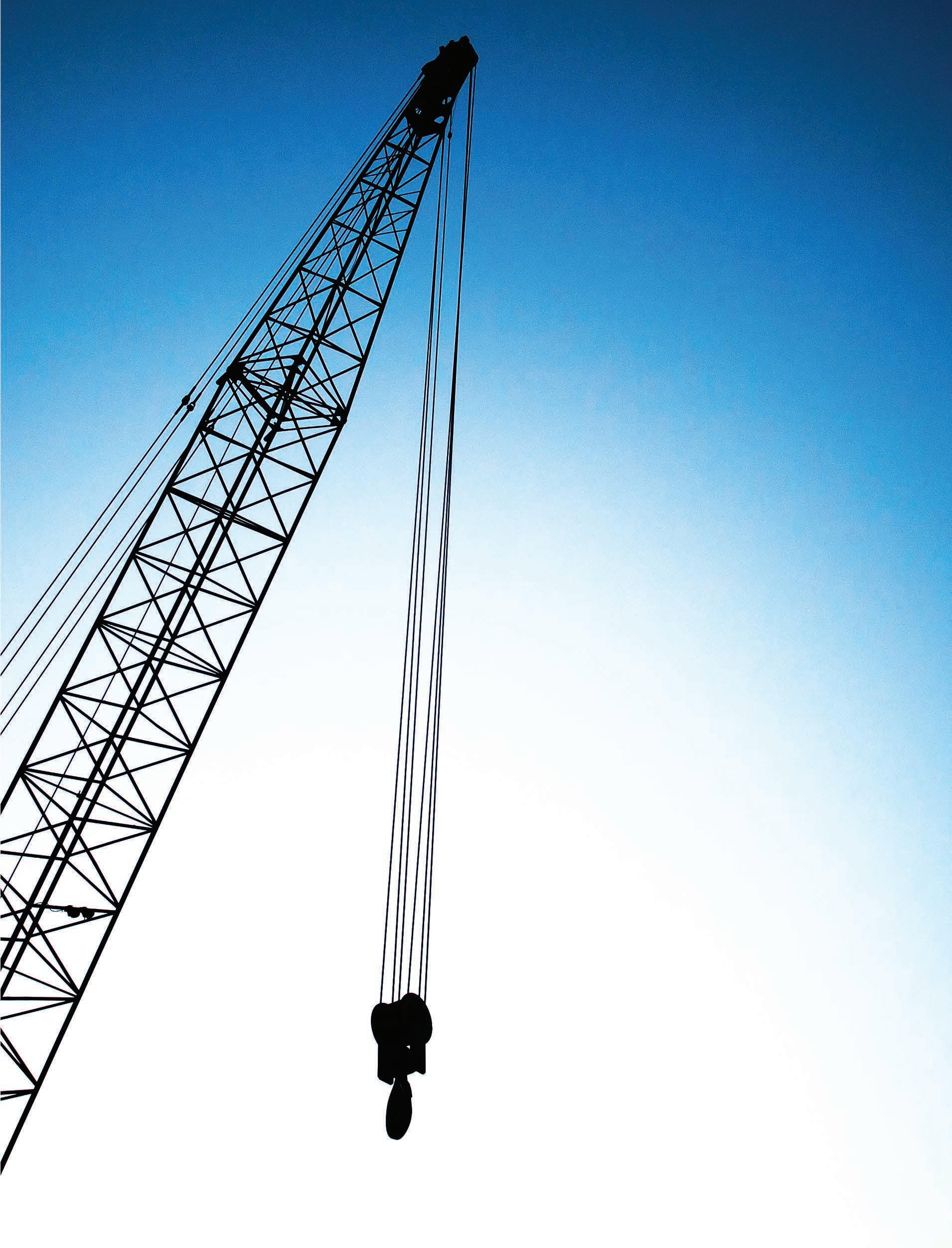
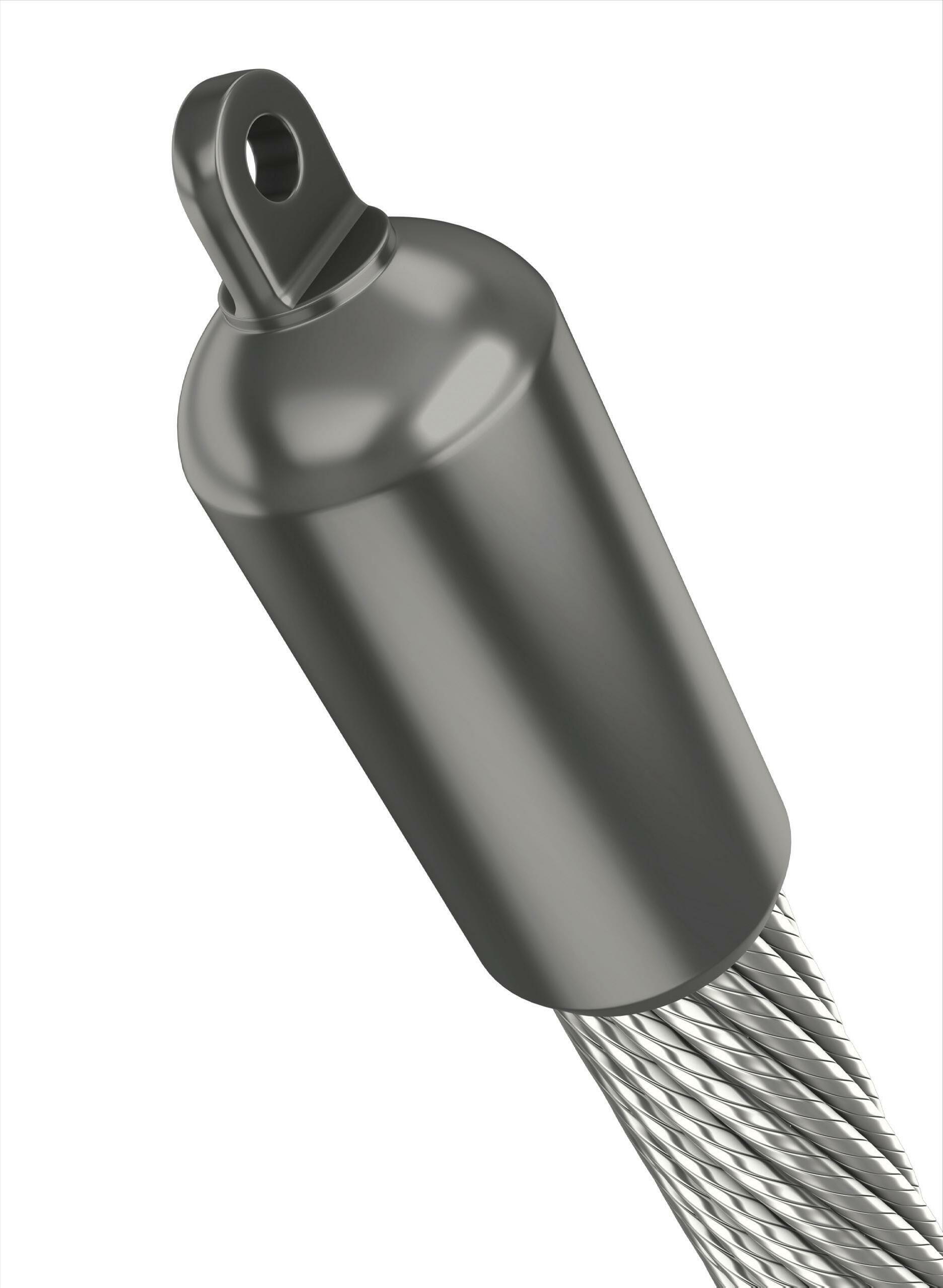
ADOPTING A CRADLE TO GRAVE APPROACH TO HIGH PERFORMANCE WIRE ROPES
Bridon Bekaert Ropes Group (BBRG) Australia has just completed a highly successful year of engagement with the
BBRG HAS EXPERIENCED SIGNIFICANT growth in key industry sectors, including mining and resource, oil and gas, onshore and offshore, and also in the heavy lift sector of the crane sector, which is focused on major infrastructure and construction projects.
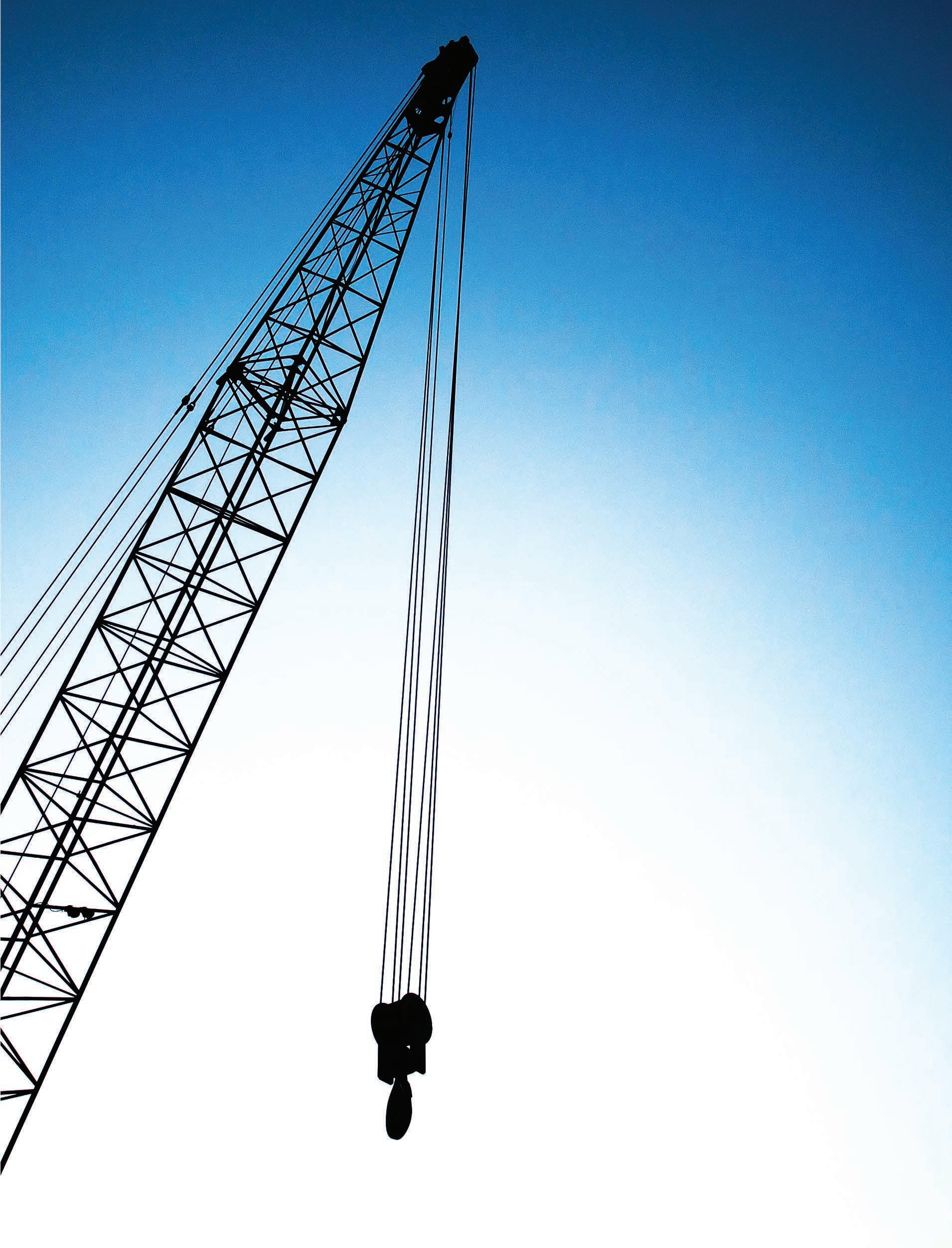
will continue to see BBRG being recognised as an Australian leader in the manufacturing, supply, and support of high-performance wire rope products.
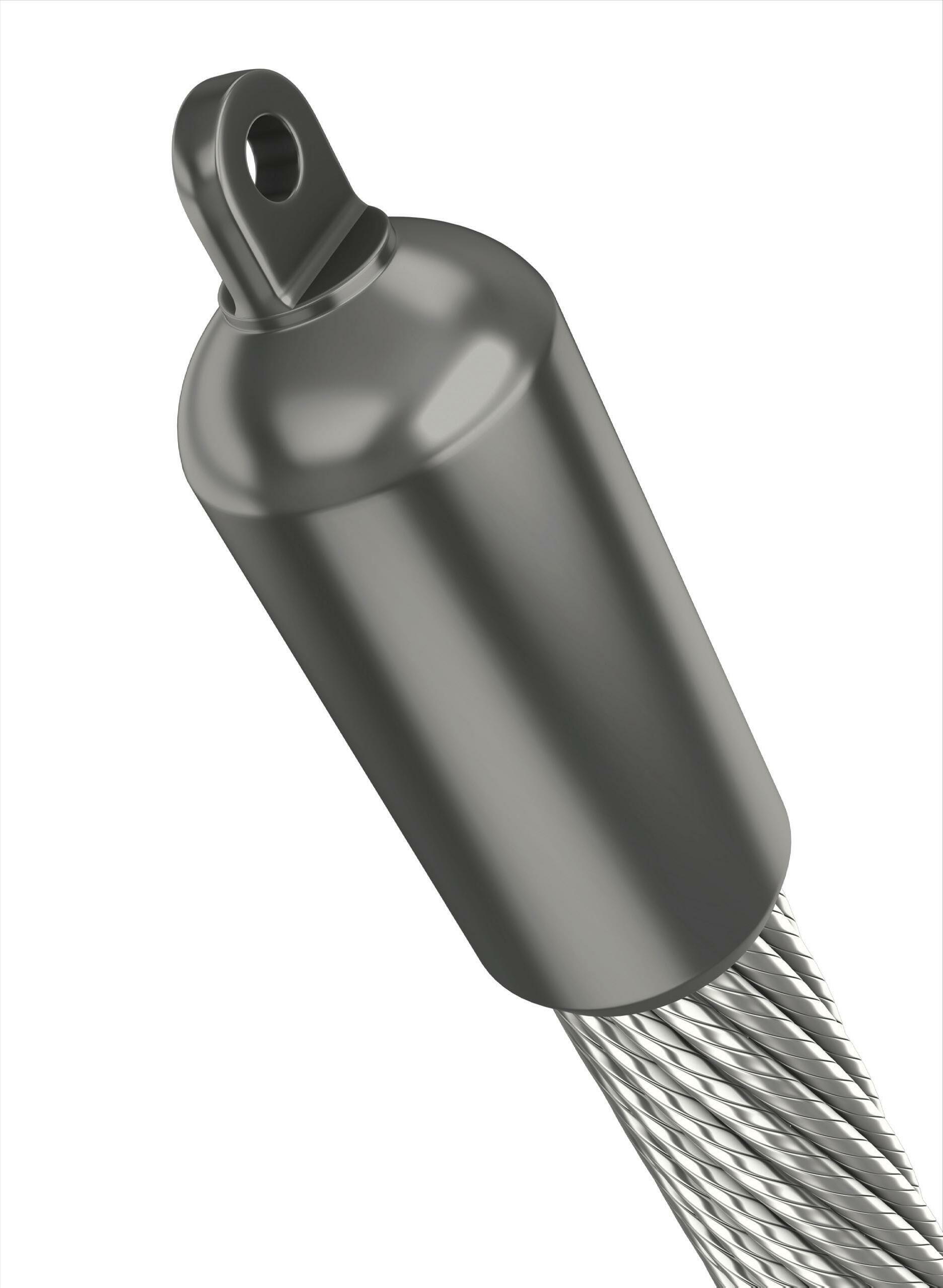
The BBRG vision is simple: provide the market with a trusted high performing product, superior service, technical backing, and the aftersales support to go with it.
BBRG recently installed a state-ofthe-art service centre – a first for the wire rope industry in Australia – and with the support of its 14 manufacturing plants
BBRG has invested heavily in its plant, manufacturing, and testing equipment, stock holdings and people over the past 18 months.
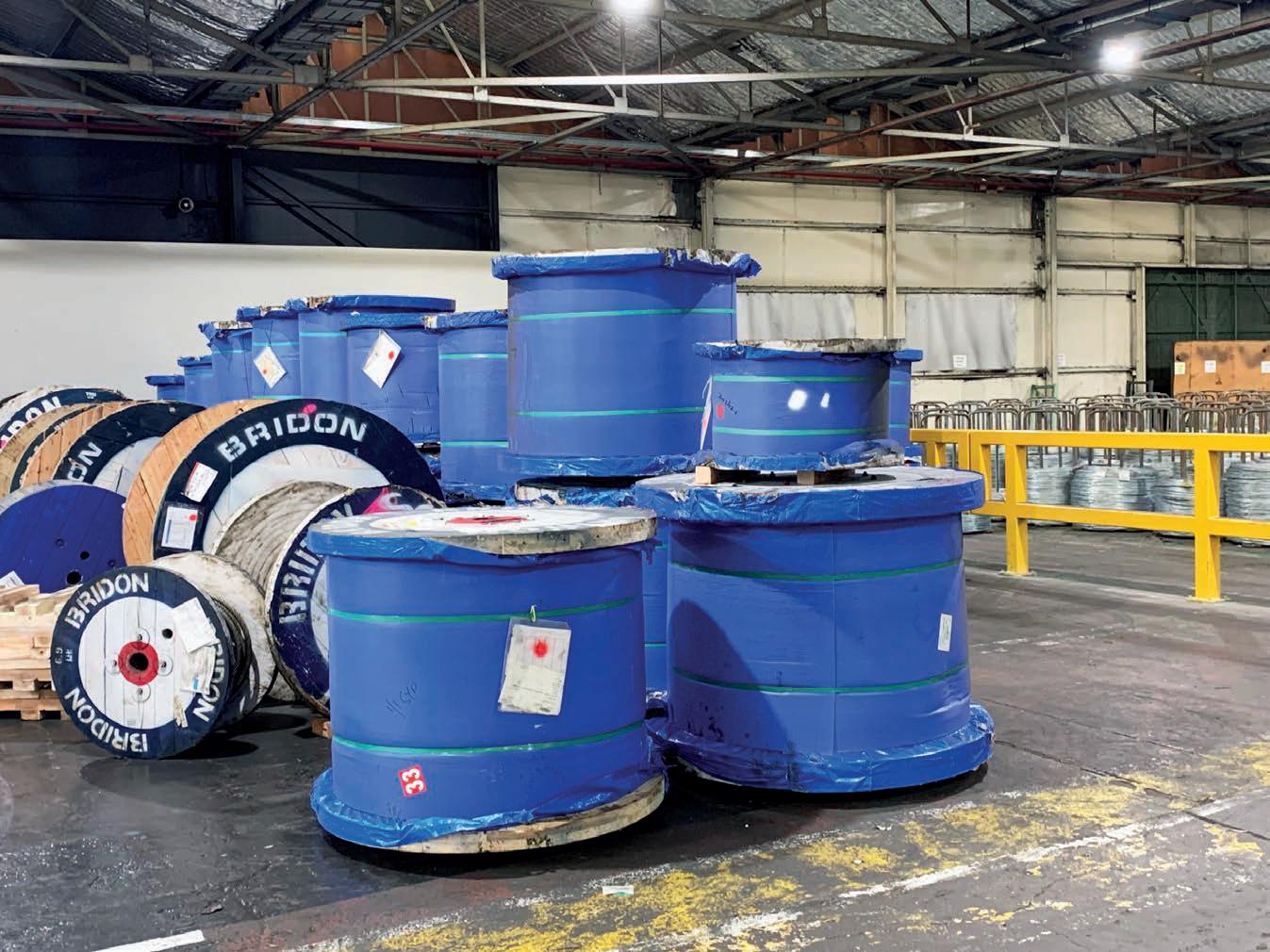
globally, the company is well positioned provide a vast array of wire rope products and services across the country, well into the future.
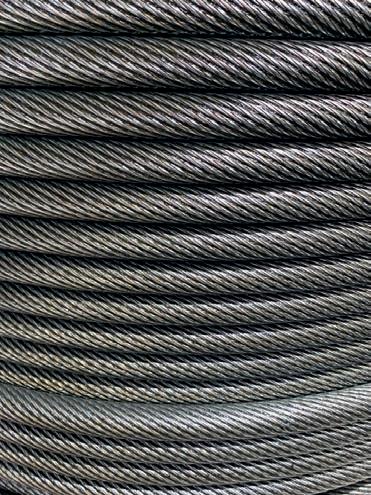
BBRG support and service capabilities range from a cut piece of rope, and standard run-of-the-mill termination, to specialist crane rope fittings, visual inspection, rope cleaning, re-lubrication, advanced lubricants and non-destructive examination (NDE).
Advice and services can also include application recommendations, custom rope design, VisionTek 3D optical rope analysis, post life examination, the Maximum Operating Rope Efficiency (MORE) program and NATA testing and forensic services.
According to Stuart Coxon, BBRG’s technical accounts manager, BBRG is at the forefront of the wire rope industry here in Australia and worldwide. The

continued investment in the business is designed to streamline sevices BBRG is able to offer customers.
“We have heavily invested in our stock holdings locally and this is designed to service the numerous customers we have in critically important industry sectors across Australia,” he said.
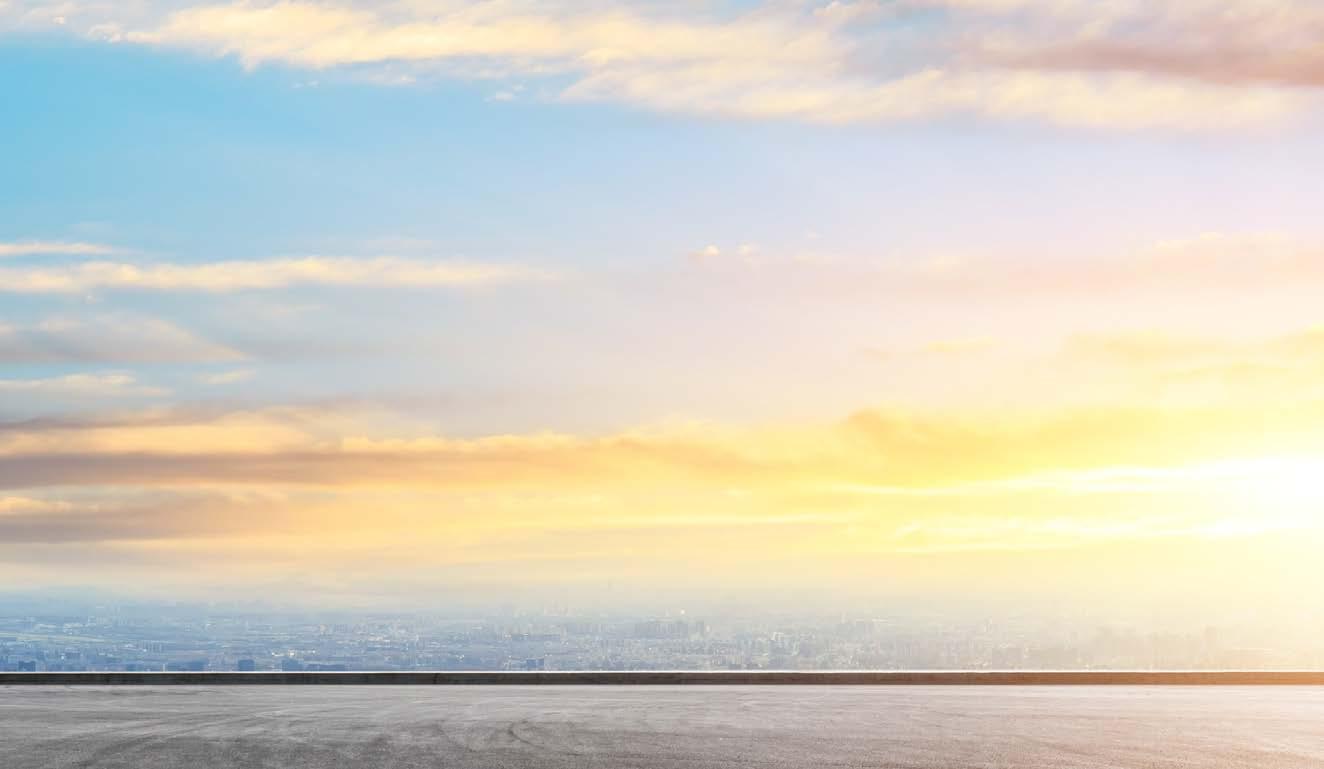
“The cradle to grave approach taken by our team at BBRG Australia stems from users wanting the optimum performance from their asset. For a customer to receive the full benefit of the resource behind the BBRG team, there needs to be an initial discussion with the technical team which, where possible, will start with a machine audit.
“This will involve our team understanding the type equipment involved, the conditions our ropes
will be operating in, and any issues the customer may be experiencing etc. This will provide our team with the data required to select the best possible rope for these specific applications.
“Many factors will come into play in terms of a rope’s selection, and these will include breaking force requirements, flexibility, rotational resistance, high corrosion protection, crushing, and
“The technical team will perform several specific in-house tests on the rope to work through its failure mechanisms, residual break force, retention of lubrication, and so on.”
elasticity, to name a few” said Coxon.
During the life of a BBRG high performance wire rope, if a customer requires any assistance or has technical queries around the ropes performance, BBRG has a local technical team that can be contacted to work through their requirements.

“From a more critical asset management perspective, where rope life can play a part in dictating the production. We like to take advantage of our post-life rope analysis.
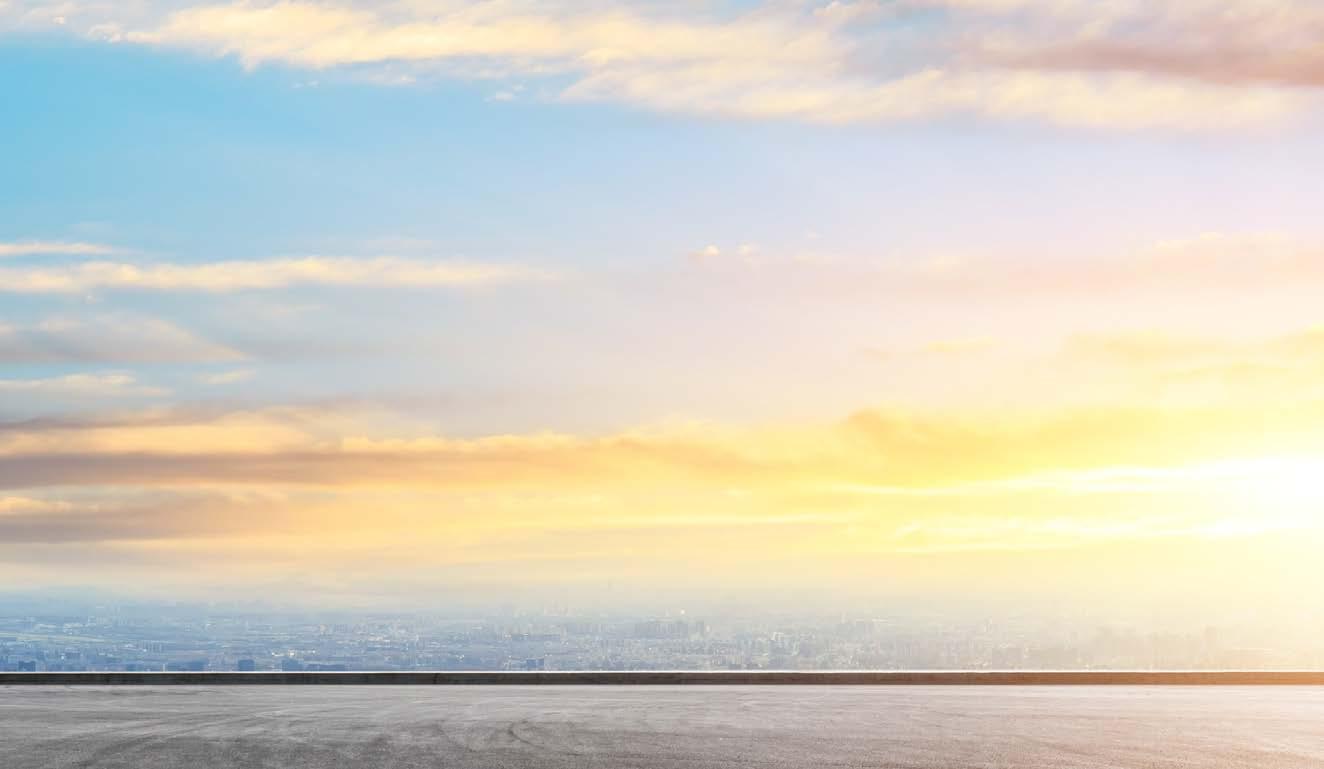
“The technical team will perform several specific in-house tests on the rope to work through its failure mechanisms, residual break force, retention of lubrication, and so on. This provides our technical team with an insight into how we can look to change or even redesign the rope differently to enhance performance and keep the customer’s asset operating for greater periods
between downtime and change outs,” said Coxon.
BBRG Australia also understands that this holistic approach is not always for everyone. At times, a customer may just want a fast and urgent turnaround on a common rope, or cons truction, wants to get its crane or asset back to work.

“In these instances, our experienced team at BBRG is well equipped with a state-of-the-art facility, the stock and expertise to get our customers back to work,” said Coxon.
“So, whether it’s a rope for your a pick and carry, the workhorse of your fleet, your all terrain, crawler, foundation/ piling rig, tower crane or ship to shore critical asset, BBRG Australia has a high performance rope to suit your application, and the service and support capabilities to manage the rope from cradle to grave.”
The BBRG vision is simple, provide the market with a trusted high performing product, superior service, technical backing and the aftersales support to go with it.Pervidi Paperless
to
is
current systems.
ASSET MANAGEMENT MADE EASY –PERVIDI’S PAPERLESS SOLUTIONS
The uptake of technology in industry is causing the construction sector to quickly pivot towards widespread use of paperless inspection and digital management solutions.
THE CONSTRUCTION INDUSTRY HAS BEEN wary of integrating digital technology in recent times, but as it improves and becomes more reliable, it’s evident that this represents the future for the industry.
Statistics collated by the Office of the Chief Economist show: 3.3 per cent of construction businesses have introduced or changed their digital business strategy; 5.1 per cent approved investment in new digital tech or infrastructure; and 4.7 per cent introduced new training programs.
Pervidi’s paperless solution tool recognises this shift towards digital technologies, and has a range of uses and applications, including maintenance and periodic inspections, pre-start checks, logbooks, pre and post-hire inspections,
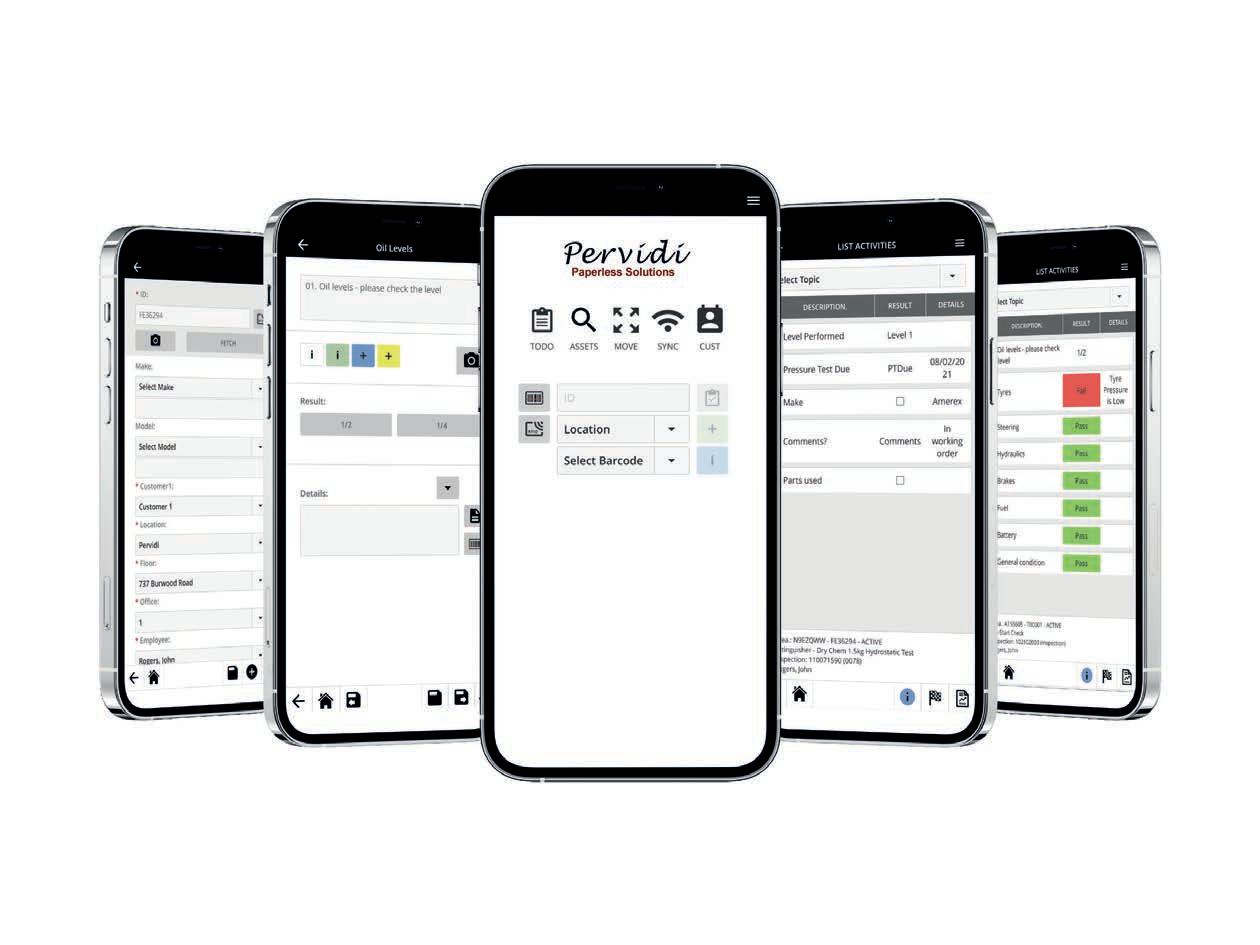
job safety analyses, safe work method statements, repairs and service, safety inspections, site inspections, data collection, and incident reporting.
The use of mobiles across a vast array of industries is currently revolutionising workspaces, and this will also likely be evident in the construction sector.
Former executive chairman of Google, Eric Schmidt, noted in 2010 that: “Mobile will ultimately be the way you provision most of your services. The way I like to put it is, the answer should always be mobile first.”
The construction industry has held onto much of its paper operations far longer than many other sectors, and this continues to often create chaos at work sites.
With most inspections and pre-
start checks completed on paper, the current method can create issues. Details are handwritten, images used to demonstrate issues must be attached manually, corrective actions are then manually completed without confirmation, and paper inspection reports are then stored in folders, which can then become challenging to retrieve. The list of issues is both lengthy and argues for change.
By transitioning to a paperless solution many of these challenges are removed. Inspection management is streamlined into a simple process in which all stakeholders are actively involved, and engaged machinery can be taken out of use, until any issues are rectified.
By successfully implementing
the use of mobile technology such as smartphones and tablets, the stereotypical image of the construction sector can be changed, and be made more appealing to younger employees.
Seeing cutting-edge tech like robots, drones, artificial intelligence, and augmented and virtual reality in action, can make a real difference in recruiting a younger workforce.
Features such as barcode scanning, speech-to-text capabilities, picturetaking and annotation are ensuring every pre-start check, service, or periodic inspection can record the very best information – invaluable for later inspections and use of a piece of equipment. Similarly beneficial to an inspector, operator or technician is the attachment of machinery manuals, previous inspection reports, or any other reference material; for example, Australian Standards 2550, AS 1418 etc., deemed necessary to a specific checklist.
No more large manuals or logbooks to carry around for every crane or hoist check just in case it’s needed; each checklist item can be linked to a specific manual/reference material section.
The paperless checklist can also be broken down into subsections with standardised responses, recommendations, or larger regular textbox sections. Each digital checklist can be updated remotely, in real time, allowing new regulations or important information to be transmitted to inspectors and machinery users instantaneously. This means that the newest regulation on safety for any piece of lifting equipment can be passed onto inspectors in the field as soon as it’s issued. Operators can truly make use of the very best mobile device technology to speed up their inspection, service, and pre-start procedures.
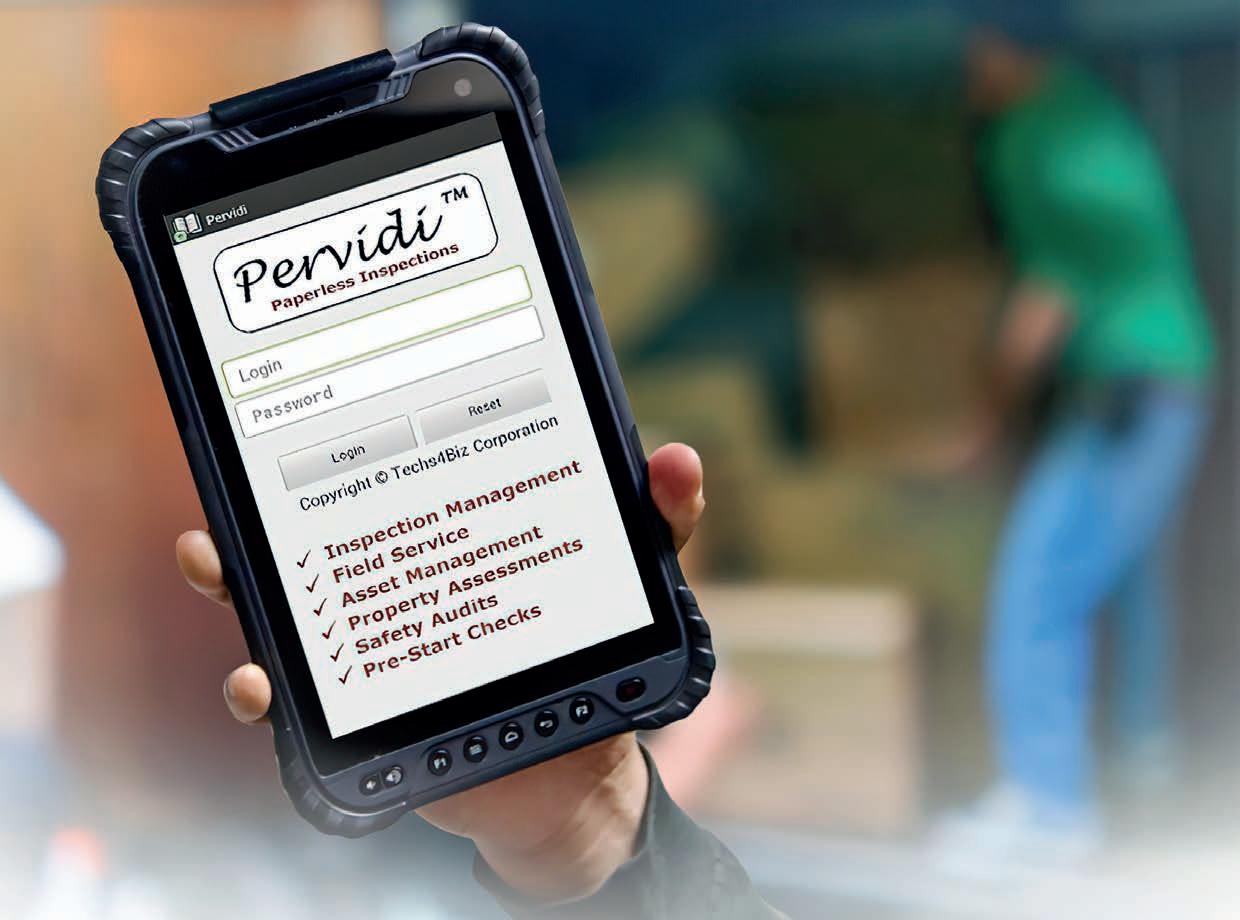
Another important part of the Pervidi paperless solutions is the integrated web portal management system.
The application on a smartphone or tablet is paired with a highly adaptable
management system, accessible from any device via a web-portal 24/7. This is available to end users and customers. The system can integrate with any existing enterprise resource planning, business intelligence or accounting software, giving automatic scheduling and real-time reports to technicians and customers, providing in-depth analysis of data.
Data can be split across different checklists for different types of equipment, depending on what your business uses. Results and detailed reports can be automatically sent to management teams via customised triggers, saved to an electronic logbook, or downloaded to any computer. Whilst keeping your data secure, the powerful
problem trends, and correct deficiencies before they become a large issue, through notifications.
Management can easier calculate the return on investment of their lifting equipment via analytics, which is provided after every lifting inspection report. They can also configure preapproved corrective actions that are triggered via the inspection interface by certain data inputs. This can give quick and appropriate solutions to lifting inspection queries, that may occur in the field. Instead of having to be on call for approval of actions during an inspection for incidents that are discovered, management can pre-authorise certain corrective actions ahead of the inspection.
The benefits of utilising mobile devices are truly widespread across the organisation, but most often tend to include a decrease of costs, providing greater flexibility, helping organisations sustain a competitive advantage, and leveraging existing infrastructure to maximise potential.
By utilising Pervidi’s suite of paperless inspection tools, administration times to complete tasks can be lowered by between 33 and 55 per cent. Administration tasks can include: locating and identifying equipment, determining the status and
history of machines, data entry, paper filling, scheduling, collecting run sheets, creating and managing reports, and dealing with deficiencies.
The Pervidi paperless solution minimises costs for end users, enables a safer environment for operators, and creates a streamlined system to improve workflow across a business.
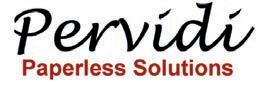
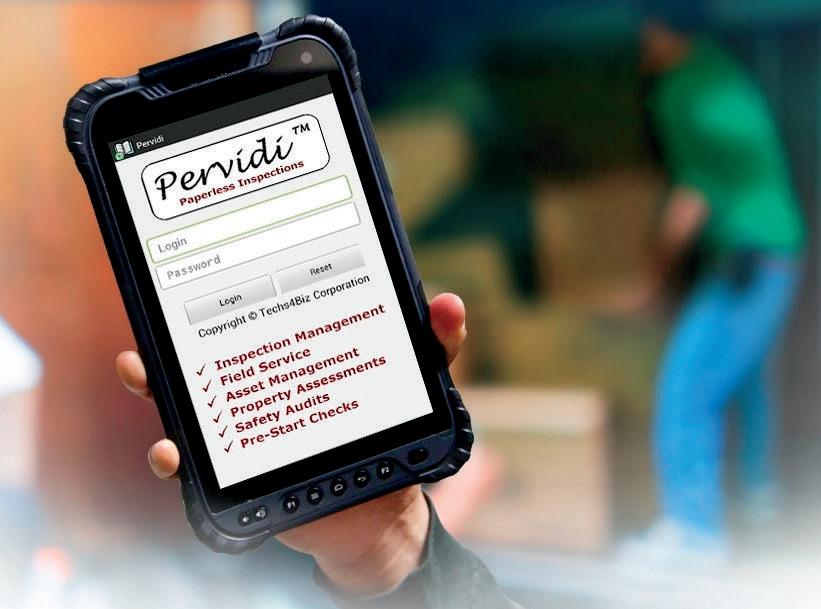
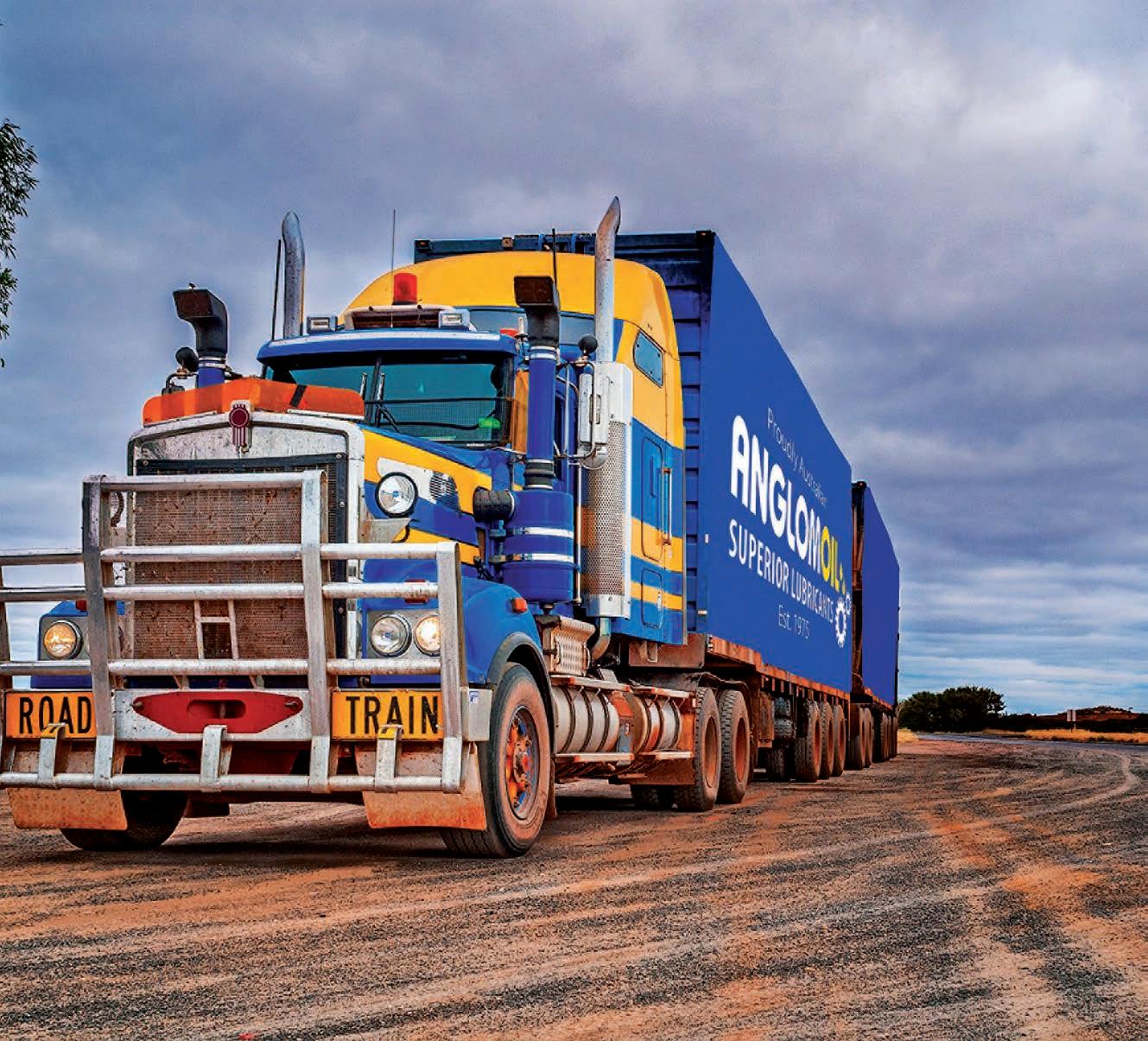
In an era of rapid technological advancement and a highly competitive construction industry sector, what reasons are there to stay with paper checklists? Go paperless with your lifting inspections now.
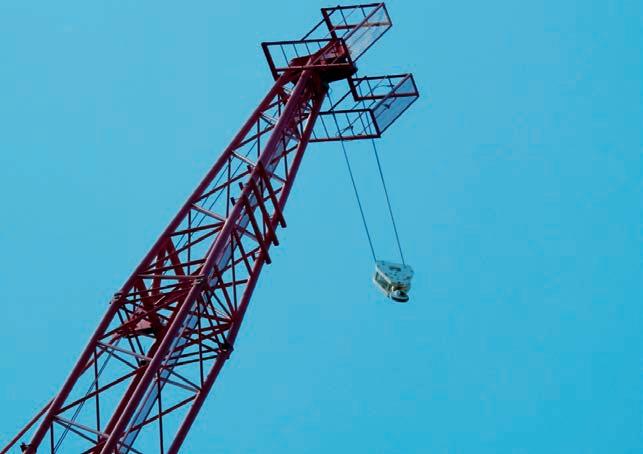
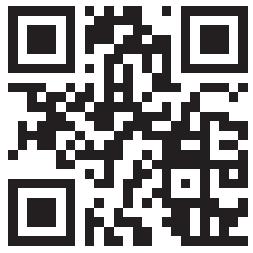
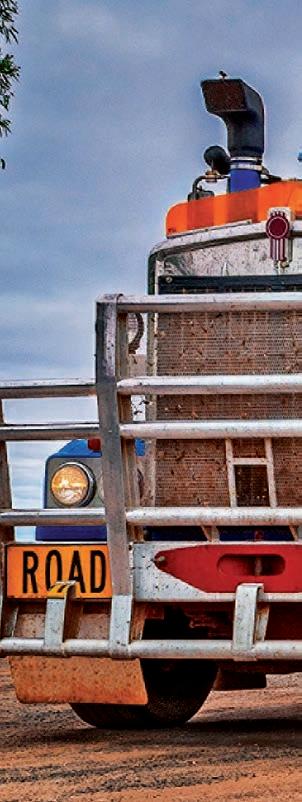
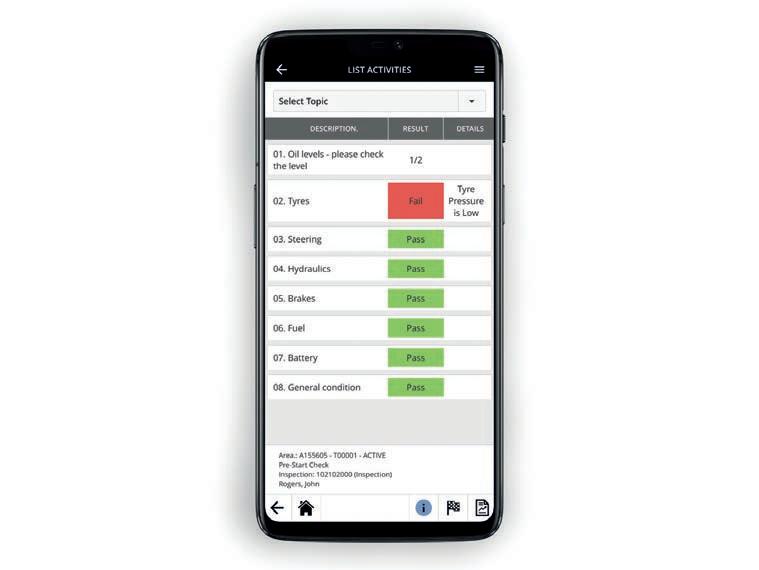
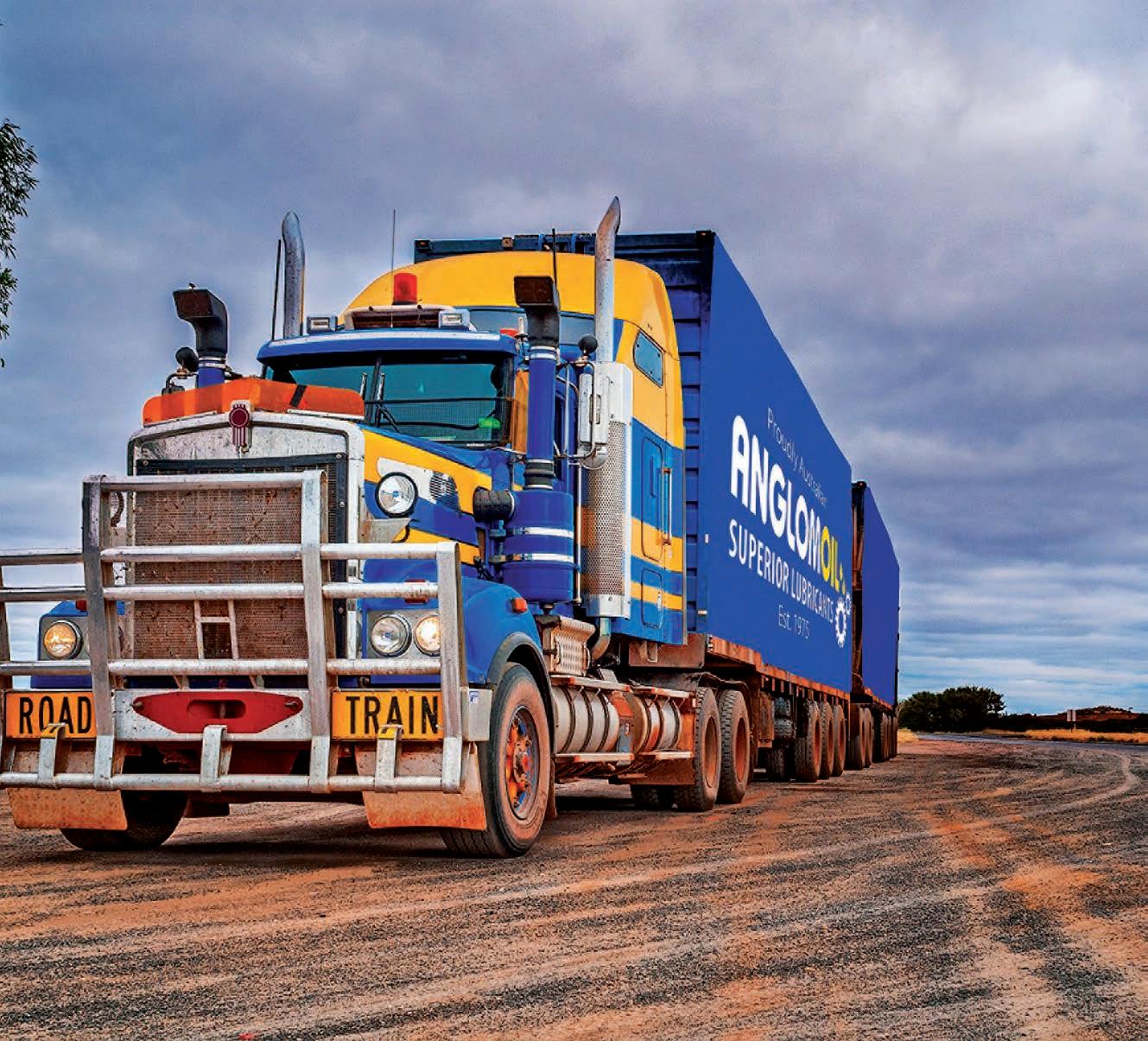
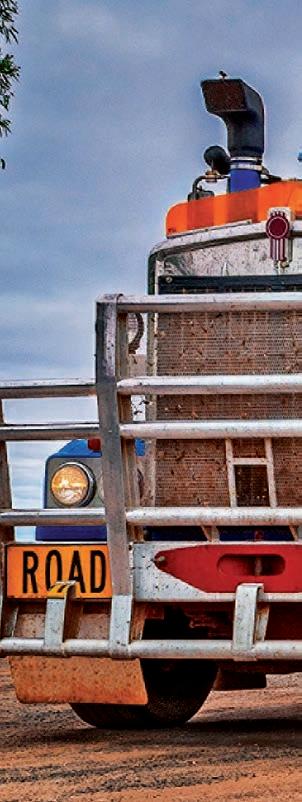
HEDLAND HARBOUR INDUSTRIES TURN TO HUMMA
Hedland Harbour Industries Pty Ltd (HHI) has been operating in the Pilbara iron ore region of Western Australia for over 10 years as a crane hire and mine services company. The founder and director Shannon O’Brien and co-director Michael Hynes discuss why they changed from their Franna pick and carry fleet to Humma in 2021.
HHI OPERATED A NUMBER OF CRANES ranging in capacity from 13 to 220 tonnes and, when necessary, would dry hire various capacity cranes to supplement their fleet. The working environment in the iron ore industry is severe on all mobile plant working 24/7 in hot, dusty conditions. Mobile cranes must be safe to operate, tough, and reliable, with minimal downtime.
HHI operated a number of Frannas that had been working under these conditions for some time. They had become unreliable,
with high maintenance and repair costs impacting on the profitability of the business. Clients were also expressing dissatisfaction with the performance and reliability of the cranes.
For some time, O’Brien had been looking for a more reliable pick and carry crane. He had heard about Humma and Tidd so, when discussing a way forward with fellow HHI director Hynes, it was decided they would buy a Humma 35 MK3 and a Tidd PC 28 for evaluation. They wanted to see if the performance,
reliability, operating costs, and safe operation were better or similar to the Frannas they were operating.
At the time, HHI were operating a fleet of seven units including AT20s and MAC25s. The decision to move away from Franna and test other pick and carry cranes on the market was designed to see what else was available. There were also long lead times for Franna compared to the Humma and TIDD products. Shannon requested a price and details on a Humma 35, he received a quote that was accepted and an
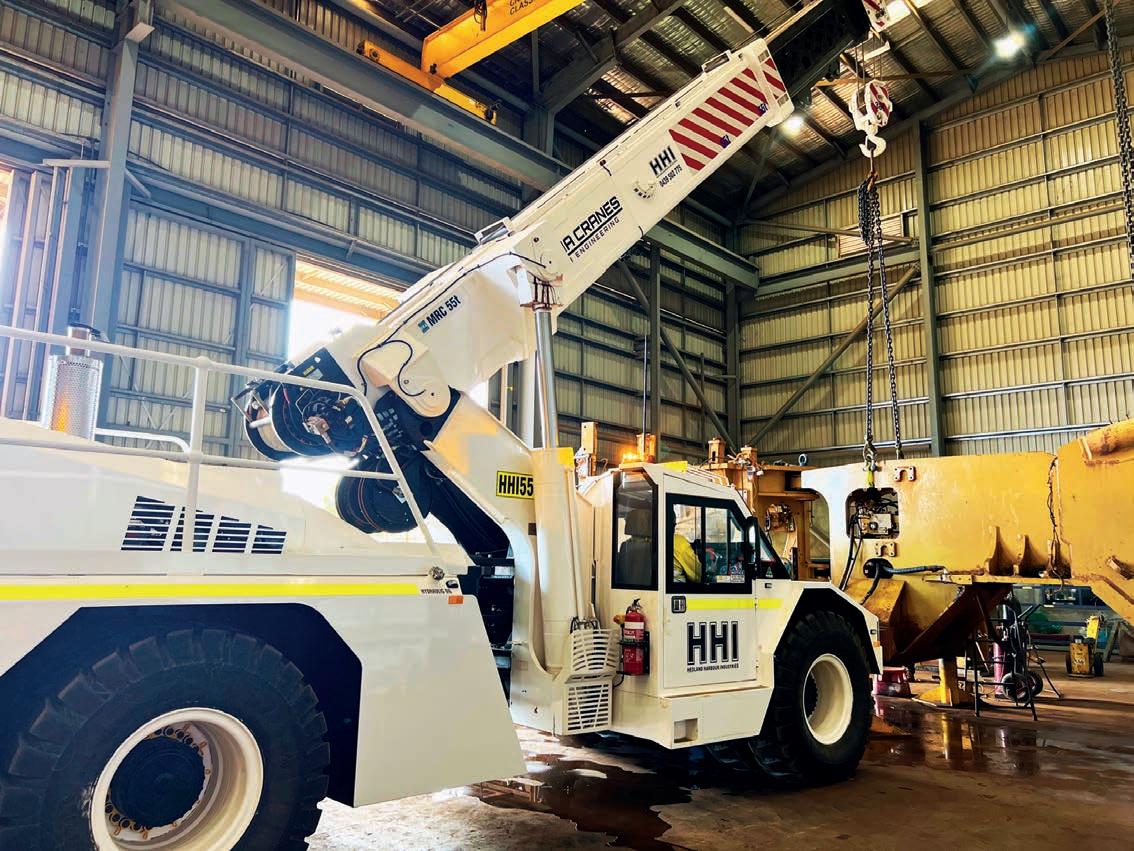
order was placed with DRA Engineering.
On seeing the order, Peter Dalla Riva, operations director for DRA Engineering, telephoned O’Brien and enquired what type of work the Humma was going to be conducting and had he ever driven one. O’Brien confirmed he knew about Humma and had seen them in the region.
In his usual direct manner Dalla Riva said: “You need to come and visit us and test drive the crane. You need to see how they are built as it is a big investment for your business. If you find it does not meet your specification then don’t buy it.”
O’Brien was surprised to hear these comments as it appeared Dalla Riva was not interested in selling a Humma to HHI. After they had met, he had a clearer understanding of the passion that exists within DRA for the Humma product.
During his visit to the impressive Humma facility he met both Peter and his son, Peter, the engineering manager who runs the R&D and production department. He has been at DRA for 20 years and is a mechatronic engineer responsible for introducing electronics to the industry, dynamic load chart, digital rope compensation and auto-leveller, to name some of the innovations he has been responsible for.
The Humma manufacturing process is impressive. Watching a Humma start its life as bare steel, then move through the fabrication process and on to the largest robotic weld station in West Australia, is as a result of significant investment by DRA Engineering.
The robotic welding unit is producing perfect welds before the components move into the grit blasting chamber for blast cleaning followed by epoxy priming and urethane finish. You can see the quality and see why Humma is so robust and tough, and capable of handling minesite conditions.
The assembly area with the various modules, cabin, engine, suspension, preassembly ready for fitting into the chassis, impressed O’Brien providing him with the confidence to buy a Humma 35.
During the same tour O’Brien saw a Humma 55 on the factory floor and said: “I am sold, I want one of these also.”
After the tour of the factory, Peter sat down with O’Brien for a decision on Humma 35. He ordered two and enquired about the delivery times on the Humma 55.
Humma 55 prototype produced in 2017 had been undergoing performance testing through the company’s dry hire operation with the first production units progressively released from 2020.
After placing the order for two Humma 35 and after surveying the local mining market, O’Brien contacted Peter about a month later and ordered two Humma 55s.
The first Humma 55 was collected by O’Brien in March on a Saturday, and it was scheduled to be onsite at Tom Price some 1,500km from Perth for a project start on the Tuesday. The Humma 55, being 3.1m wide, could not be transported at night and the only way to get the crane to site was to drive it.
Peter objected strongly to driving a new crane 1,500km non-stop. O’Brien pleaded, so he accepted provided it was not driven at the top speed of 95km/h.
HHI has been operating in the Pilbara iron ore region for over 10 years as a crane hire and mine services company.
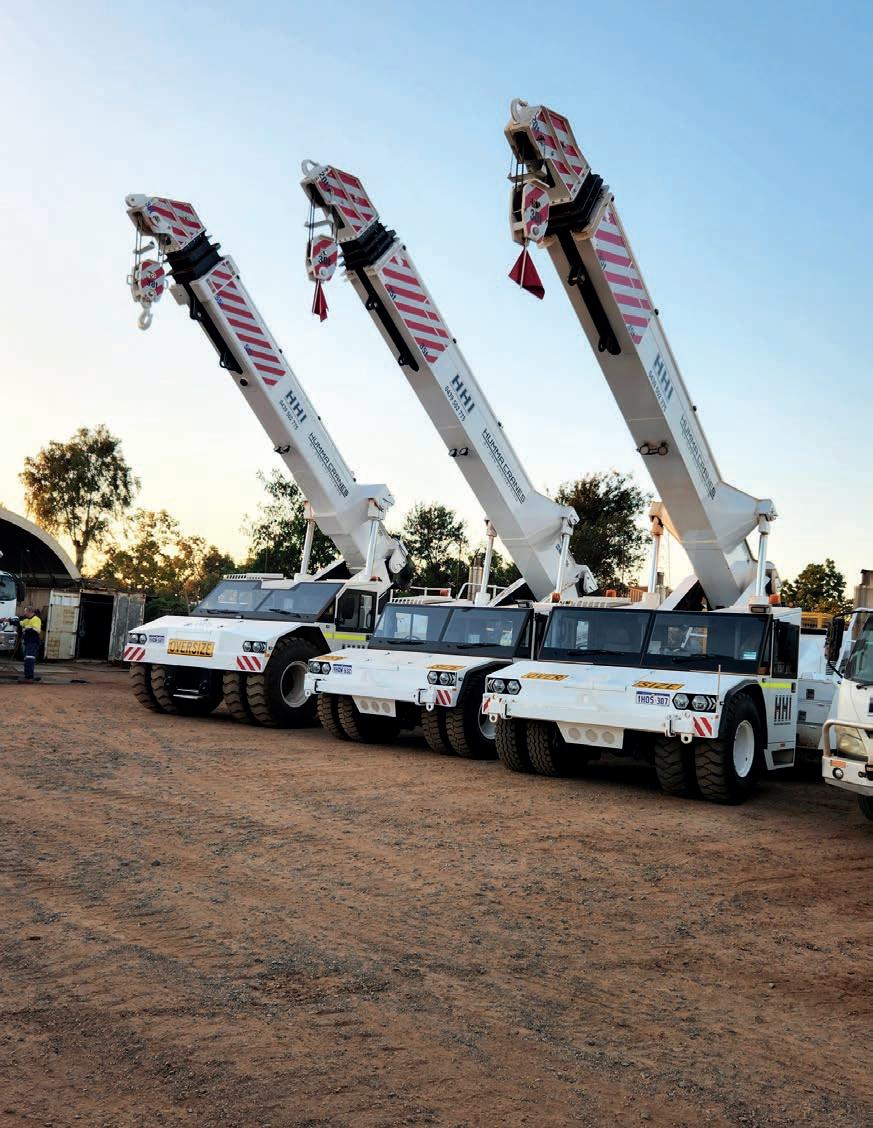
Monday morning, O’Brien rang Peter and said: “You worry too much. The crane went to work on the Tuesday and has been working 24/7 for about a month.”
O’Brien goes on to say that wherever the Humma 55 was operating the comments were: “IT’S BIG”. And so, the number plates were changed to ‘ITS BIG01’ and ‘ITS BIG-02’.
The second Humma 55 was collected in July with the second Humma 35 Mk3, with both going to waiting projects.
During a recent Humma meeting, O’Brien and Hynes confirmed that both Humma 35 and Humma 55 are performing well, with crane drivers finding the robustness and stability exceptional when lifting and great when driving.
O’Brien closed the meeting saying: “I personally look forward to a great ongoing working relationship with a great family company.” Peter’s response was: “We have been trying for the past 50 years, welcome on board.”
O’Brien then ordered ‘ITS BIG-03’ and two Humma 25s and the meeting closed.
FLEXIBLE CRANEAGE SOLUTION FOR A MAJOR INFRASTRUCTURE PROJECT IN THE HEART OF SYDNEY’S
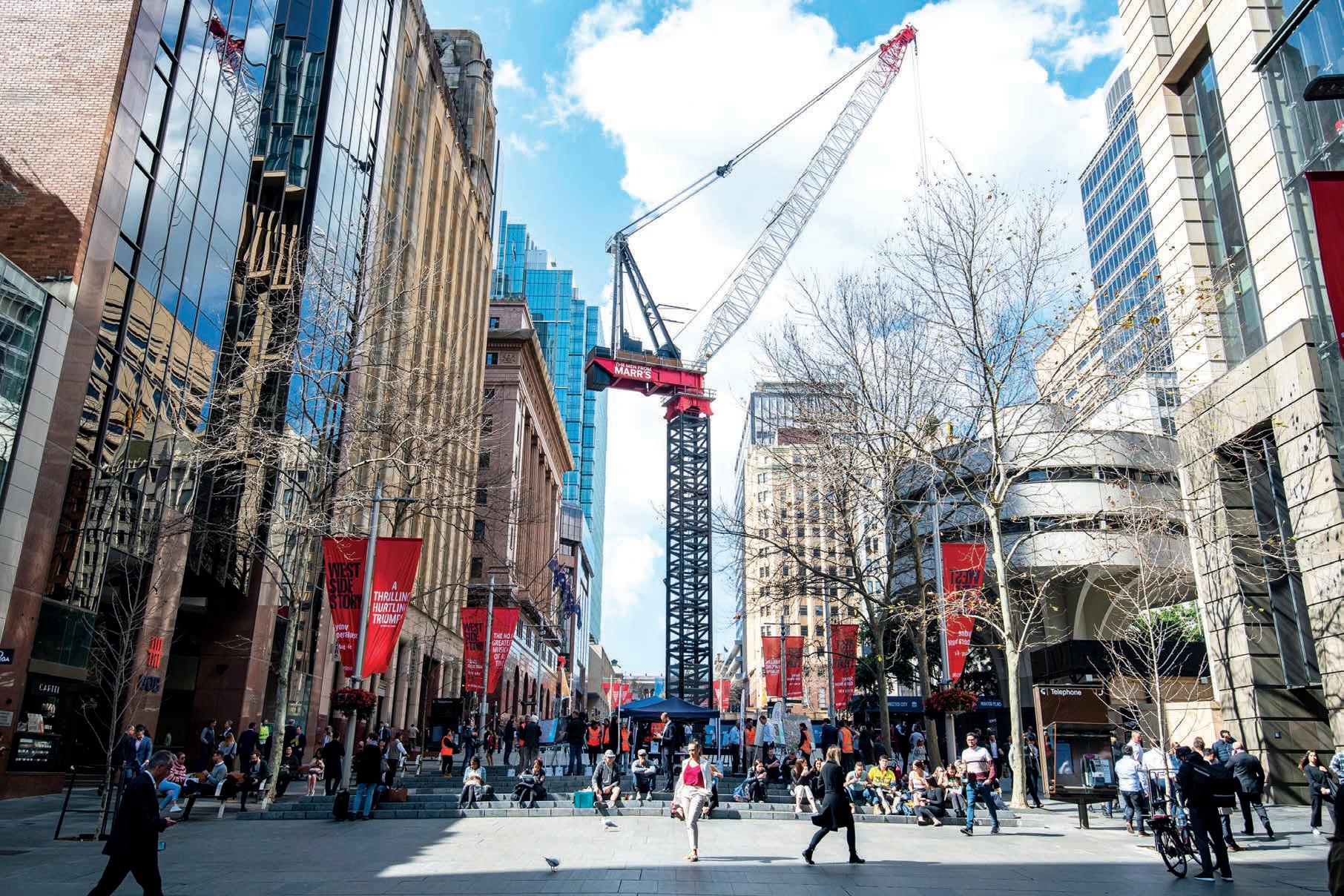
A
FROM
Station,
The benefits of using Marr’s technology –using fewer cranes with greater capacity and reach to deliver less complex, more efficient, and safer ways of constructing
solutions across another four stations on the Sydney Metro City and Southwest line, including Barangaroo, Central, Martin Place, and Crows Nest.
Key to the successes Marr has achieved for its clients across these projects has been the willingness of client project teams to engage their craneage partner early in the planning stages – and to think differently about how craneage solutions can be procured and delivered.
Similar projects around the world have adopted the cut-and-cover box method, where crawler cranes are nearly always the immediate consideration, but Marr’s approach has consistently
demonstrated that installing the right cranes can change the way an entire project is constructed, principally because of the ability to lift bigger pieces and remove the requirement for costly, challenging, and time-consuming groundworks.
The benefits of using Marr’s technology – using fewer cranes with greater capacity and reach to deliver less complex, more efficient, and safer ways of constructing – is a gamechanger for future projects of this scale.
THE PROJECT
Located in the heart of Sydney’s CBD, the new Sydney Metro Martin Place integrated station development will include the new Martin Place metro station, two new commercial buildings above the station, a retail space, new underground pedestrian connections, and improvements to the public domain.

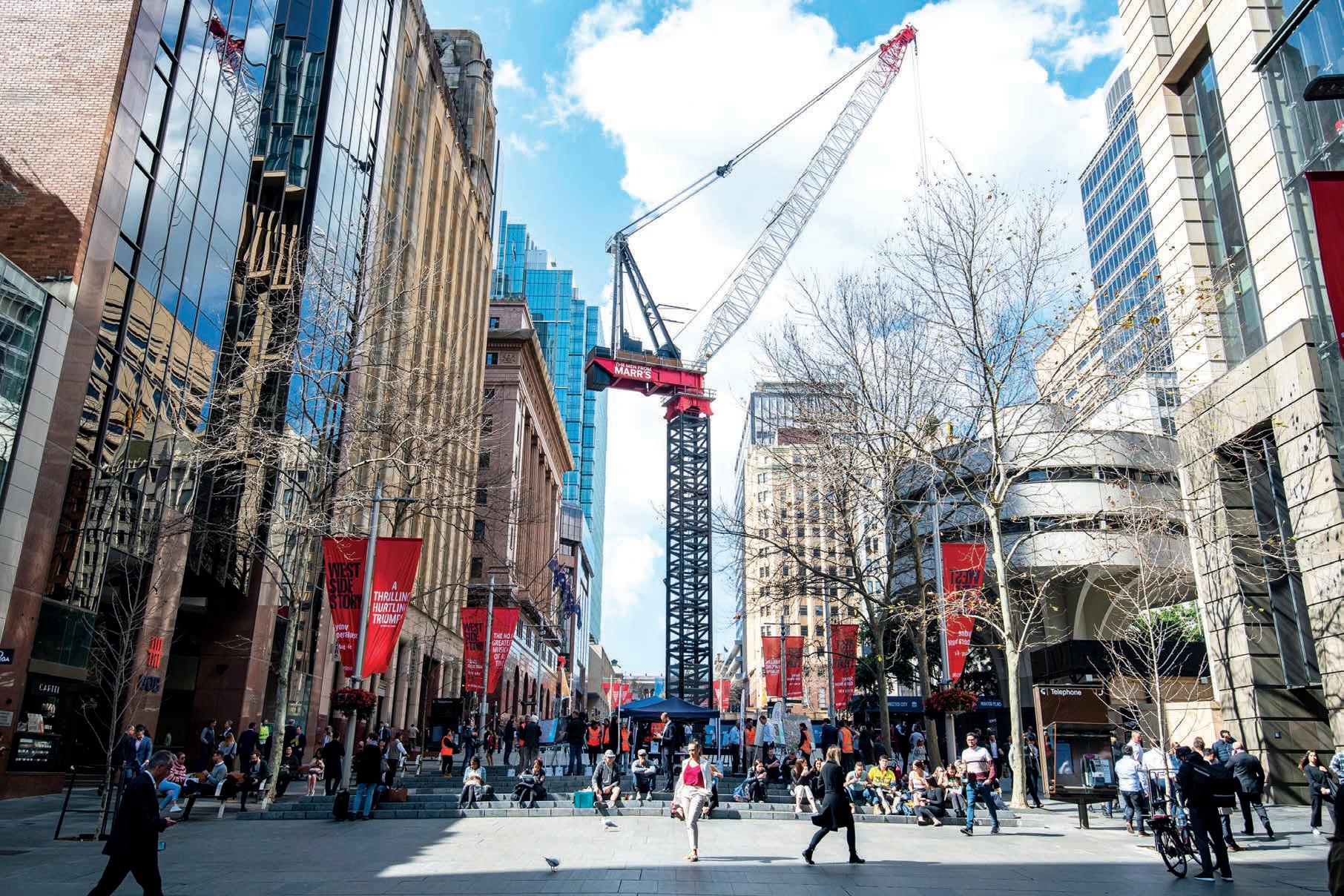
John Holland CPB Ghella (JHCPBG) Joint Venture was contracted to complete excavation and civil works for
the station redevelopment as part of the contract to design and construct the tunnel and station excavation works for the Sydney Metro City and Southwest project.
Construction included building an underground platform-to-platform connection between the existing heritage-listed Martin Place Station and the new Sydney Metro Martin Place Station – built mainly by excavating new pedestrian tunnels from the Sydney Metro construction site.
Faced with a number of project constraints and a challenging schedule of works, JHCPBG turned to Marr for a solution.
THE CHALLENGE
Excavation and construction works on a congested CBD site in the middle of a busy pedestrian thoroughfare and high vehicular traffic area presented a number of challenges in terms of access, and the heavy equipment required onsite at different stages of the works to meet the demanding program.
“The benefits of using Marr’s technology – using fewer cranes with greater capacity and reach to deliver less complex, more efficient, and safer ways of constructing – is a game changer for future projects of this scale.”
Added to these constraints, JHCPBG’s scope of works included lifting 14 plunge columns that were 30-metres long and weighing 80 tonnes each as well as the associated 90t drilling rigs, excavators, and spoil removal.
The original craneage scheme proposed using two crawler cranes and a small tower crane installed on a steel platform to complete general and medium lifting requirements.
For the heavy lifting requirements, a mobile crane operating on the street was proposed, but this would have required costly road closures and associated risks to the construction program. This solution could also only deliver the plunge columns in 20t sections, which then had to be assembled and welded onsite prior to installation.
MARR’S SOLUTION
Marr’s solution was to eliminate the need for road occupancies by installing one of its M1280D heavy lift luffers to do all the lifting from a single point within the site. This solution also allowed for the 80t, 30m plunge columns to be prefabricated offsite and lowered into their final position.
The M1280D heavy lift solution gave JHCPBG the flexibility to meet the demands of lifting a range of different equipment as requirements changed on the project – which meant delays to the construction schedule were avoided.
“As tunnellers, tower cranes are not necessarily something we have a lot of experience in, and certainly as we discussed at the start of the project there were some fears of that unknown quantity that the tower crane and its operation introduced,” said CPB Contractors director Will Freelander (a member of the joint venture).
“ These fears were unfounded. Proposing the idea of the 400t set-up on our steel platform was a massive win for us.”
THE RESULT
The Martin Place South site was delivered ahead of schedule and Marr Contracting has now been engaged by the construction partners appointed to construct the follow on aboveground works on Sydney Metro Martin Place Station.
“The reduction on mobile cranes and lift and shift equipment improved the site productivity by more than 100 per cent – i.e. we would have taken more than the same time again if we had used crawler cranes onsite,” said Freelander.
“The risk of traffic and external factors affecting delivery was also eliminated by freeing up space on site,” he said.
JOB SCHEDULING SOFTWARE DESIGNED FOR CRANE AND LIFTING BUSINESSES

can
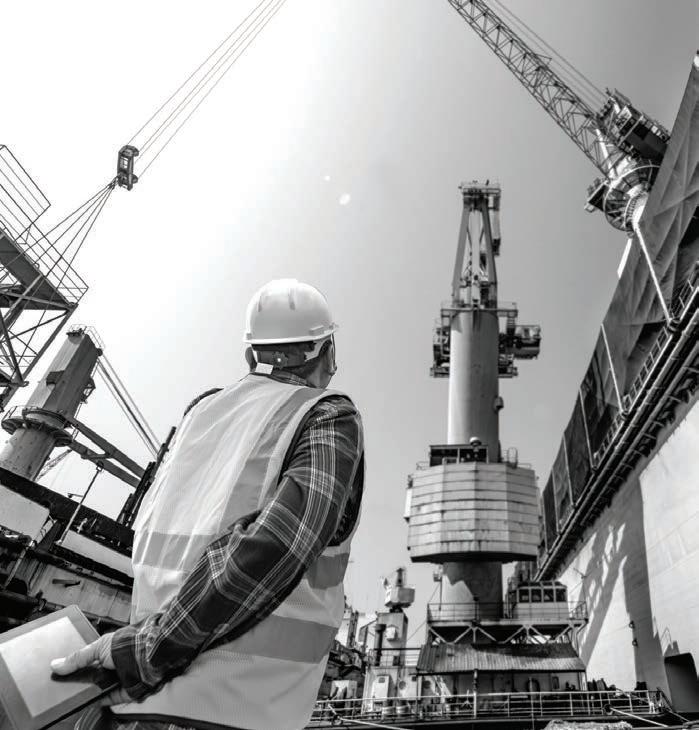
SCOTT MCLEOD, Managing Director, McLeod Cranes
vWORK’S VERSATILITY AN ASSET
THE VWORK JOB MANAGEMENT SOFTWARE
streamlines the scheduling systems for crane hire companies, allowing teams to clearly and efficiently plan a day’s scheduling across a number of assets.
Sam Edmond and Dean Oswald have helped a range of companies roll out the product and have an in depth understanding of the features and benefits of vWork.
“For many businesses, planning a day can be extremely challenging,” said Edmond.
“Crane companies have a range of assets and crews deployed to a vast array of sites on any given day. vWork is designed to simplify the planning processes for these businesses.”
“There are obviously numerous moving parts around the operation of a fleet of cranes, and vWork helps the business to centralise the management of disciplines such as allocation and scheduling, as well as managing paperwork relating to site compliance and induction,” he said.
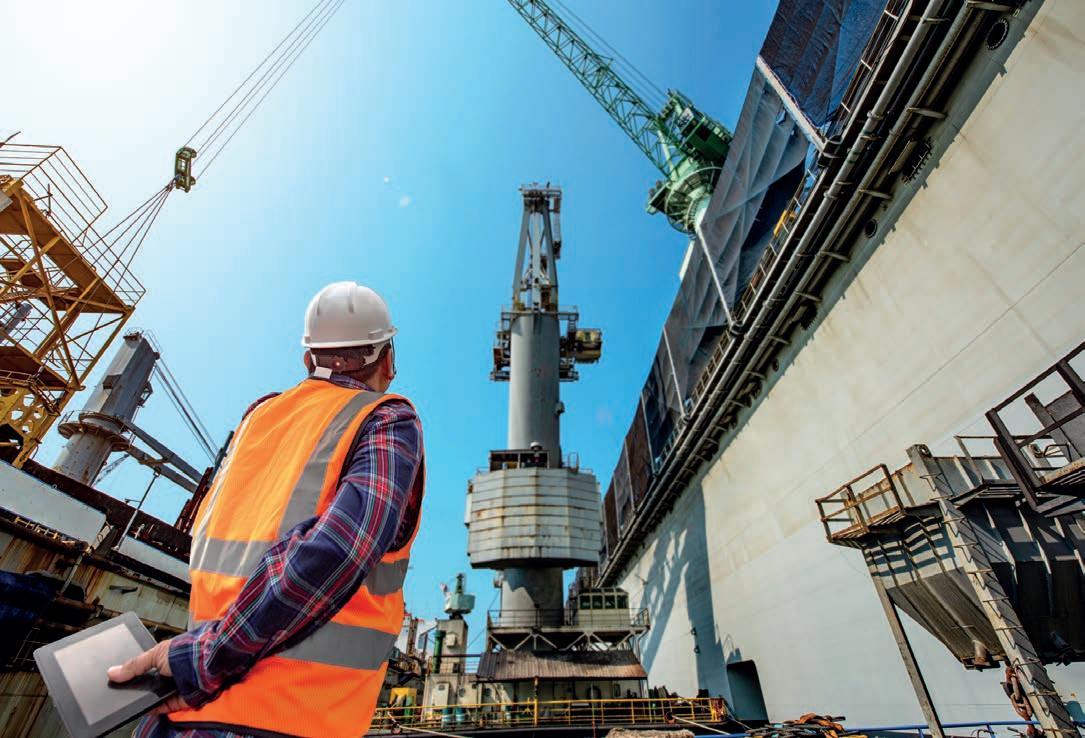
vWork features a drag and drop scheduling process. This feature enables the user to move jobs around easily with visual aids, helping to simplify the process. The drag and drop feature can help the allocation of different types of equipment in the fleet, including cranes, but it can also manage the allocation of the work force, moving individuals from job site to job site.
vWork features templates that help to manage the required checks on a crane before it is mobilised to site. The templates include pre-start checks, rigging equipment inspections, and counterweight inspections, ensuring all the required equipment is packed and ready for action when the crane and support vehicles get to site.
vWork assists in all facets of preparing the crane and crew for the lift.
“One of the unique features of vWork is the customer communication and alerting system. If a step is missed in the process for whatever reason, an alert is immediately sounded for the dispatcher or line manager,” said Oswald.
vWork assists in all facets of preparing the crane and crew for the lift. When a crane arrives on site, vWork asks the team if the lift plan has been completed for the job and only when a crew member acknowledges that there is a lift plan in place does vWork sign it off so the lift can commence.
“In terms of health and safety, vWork
ensures that critical documents are prepared and included or acknowledged before a lift can proceed.” “vWork helps identify issues. These are flagged and alerted straight away, and teams can jump on to and manage any issues immediately. Dispatchers and site crew collaborate seamlessly, rather than relying on site workers to report back to head office at the end of the working day. There are no delays in reporting and actions can be managed in real time,” said Oswald.
vWork also allows the placement of ‘tags’ on a particular item or piece of
Having already made waves within the transportation sector, vWork is not a business to rest on its laurels. It has identified the potential for crane companies to benefit from using its cloud-based software.
a robust API [application programming interface] which can integrate the platforms,” said Oswald.
“A key example is invoicing. vWork integrates with Xero and MYOB AccountRight so, when a job is completed, the invoicing process is automated. If it’s time-based billing, it’s down to the minute and, once the job is completed, it generates an invoice in their relevant accounting platform and prints the invoice.”
The challenge in an established industry such as the lifting sector is making changes in technology as simple as possible. vWork endeavours to work closely with operators to make this transition seamless.
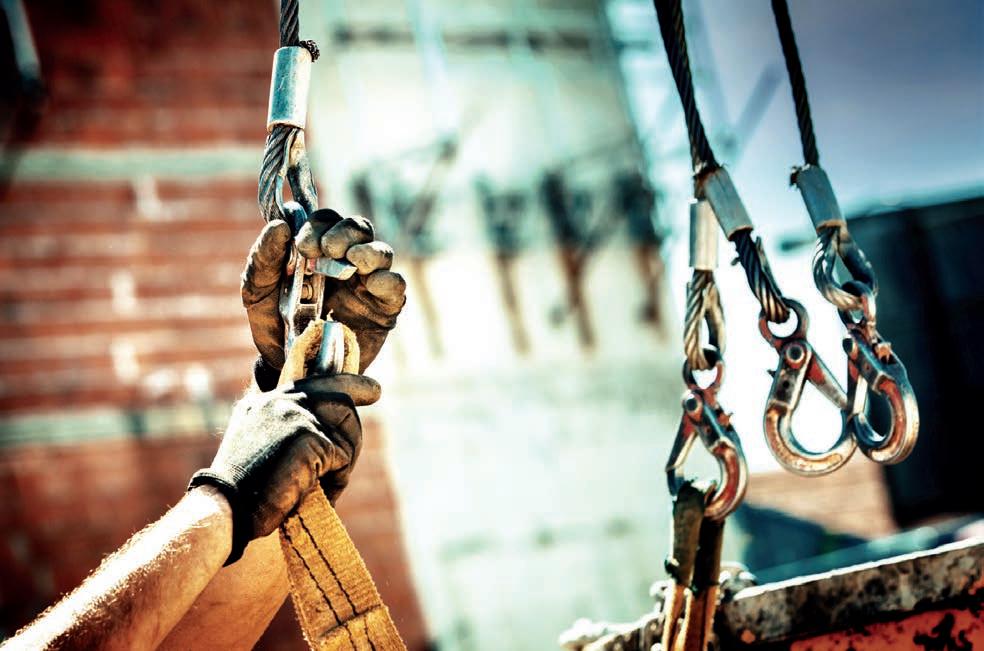
“Whilst vWork is simple to use it is not a plug in and play. Our onboarding team work closely with customers to
equipment. The tags enable the user to view the certificates and compliance information relating to the equipment.
vWork also provides flexibility. A hire company, for example, can schedule future jobs to a specific piece of equipment or specific workers. The vWork dashboard is an asset for users – it simply lays out schedules and gives quick access to equipment its working and service history.
“When we are setting up vWork for a customer, we can list all of their equipment or cranes, and its utilisation for the day, week, or month. Depending on how they want to receive the reports, customers are able allocate revenue against a specific piece of equipment or user,” said Oswald.
“The reporting function also enables the customer to understand what the piece of equipment is generating in realtime and it also ensures that equipment is not being overworked helping to reduce downtime and the need for servicing and repairs.”
A challenge faced by planners and allocators is understanding where each equipment piece is required at any given time. vWork eliminates this problem.
For the planning stages, vWork provides different job statuses, including
draft, assigned, unpublished or published. This will be an assigned or unpublished job, depending on the stage of booking.
The planner can record a job with a start date and start time and put it in the workbench. This, this acts as a timeline and shows every customer that has requested a job. A dispatcher can then go into the program and confirm jobs and move them around to ensure there is no crossover of the same asset.
In the customer portal, vWork provides three options that show a dispatcher the ‘resource level’. Green indicates there are a number of availabilities in terms of equipment and staff. Grey indicates nothing is available and yellow indicates equipment and staff are moderately available.
vWork has the ability to integrate across other platforms to ensure users are minimising errors and enhancing business processes.
“Whether it’s a CMS, another tool or another piece of software, vWork provides
customise templates the features to meet a company’s specific needs. Once onboarding is finished, we continue to work closely with our customers to ensure the vWork runs as smoothly as possible,” said Oswald.
“vWork is very flexible and we’ll work with the customer on their specific requirements and there is often the potential for us to build features to suit specific needs. What a customer’s business needs today, isn’t necessarily what it will need tomorrow or next month, let alone next year.
“vWork is designed to move and grow with the customer’s business. If changes are required to templates, there is no need to engage a software developer, we will manage this in-house.
“We understand a customer’s business will change and evolve and so will the demands on its assets including its work force. We see this as a great opportunity for vWork and we are more than prepared to move with them,” said Oswald.
“vWork has the ability to integrate across other platforms to ensure users are minimising errors and enhancing business processes.”
vWork templates include pre-start checks, rigging equipment inspections, and counterweight inspections, ensuring all the required equipment is packed and ready for action when the crane and support vehicles get to site.
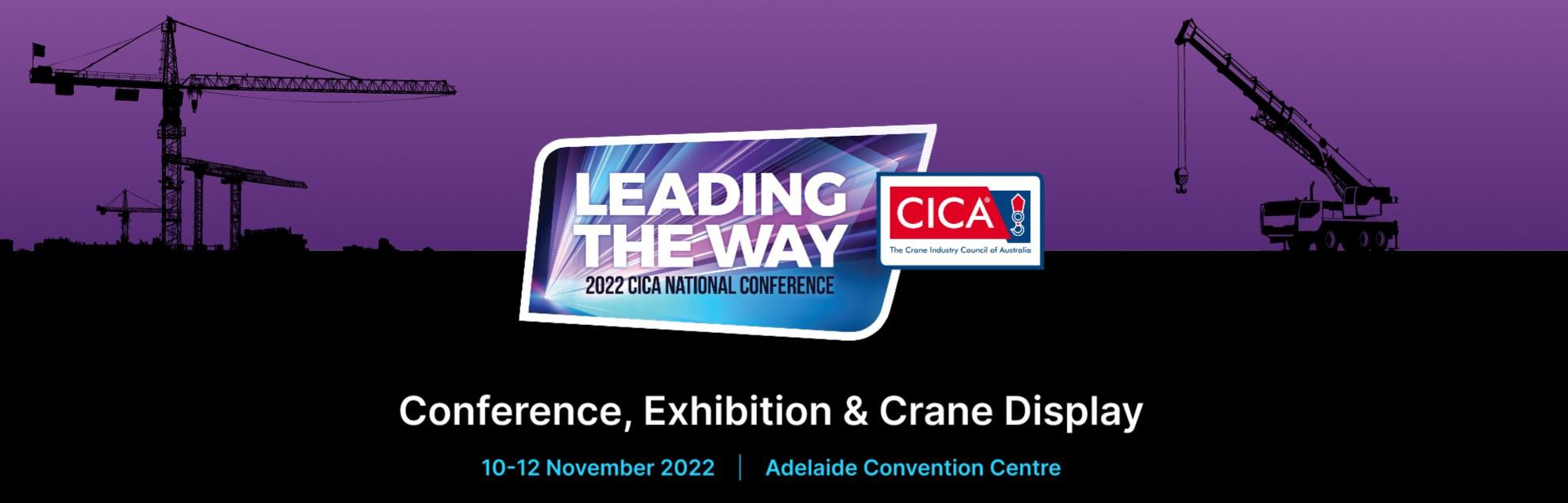

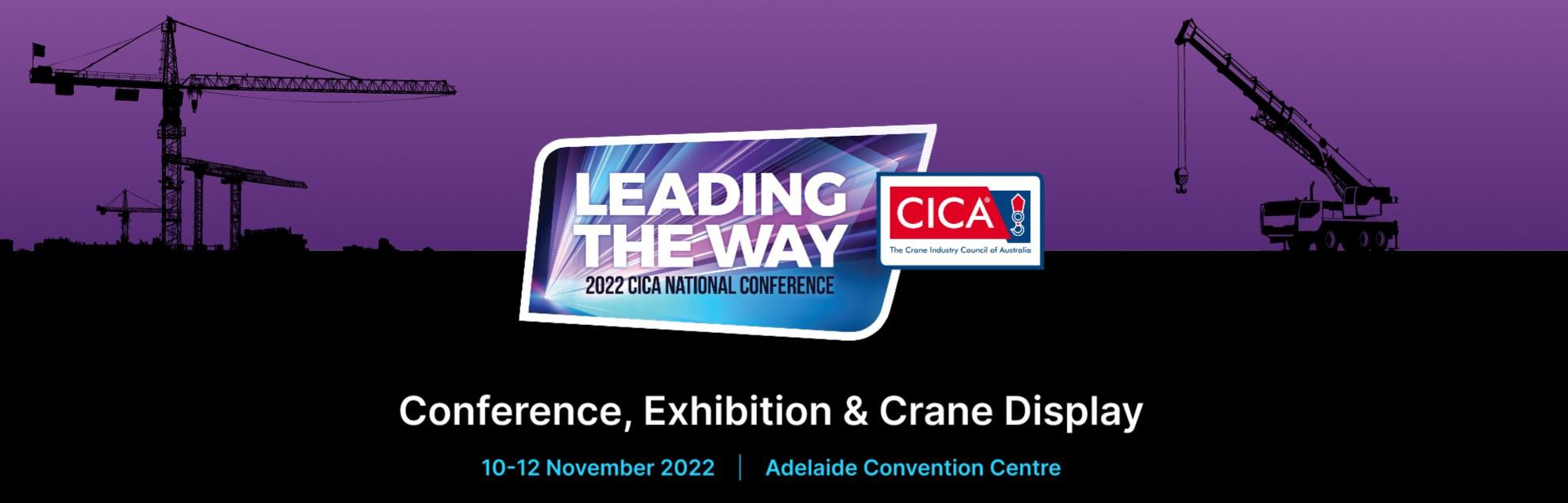
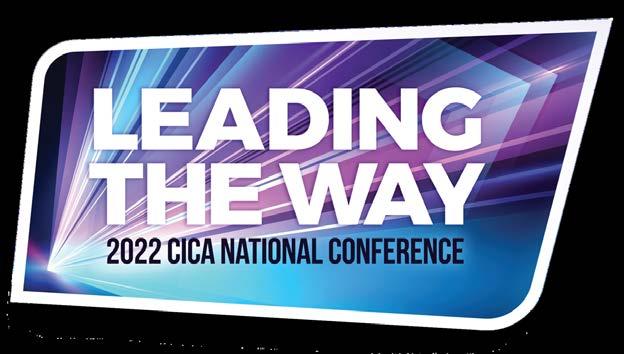
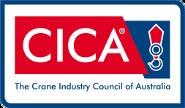
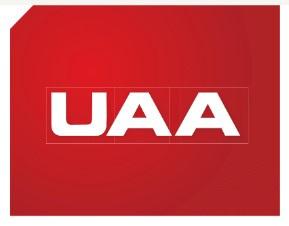
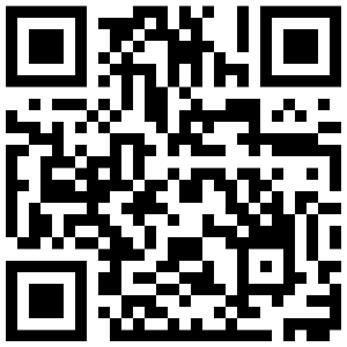
GROVE’S NEW HEAVY-DUTY JIB EQUIPS GRT9165 ROUGH TERRAIN CRANE FOR PRECAST WORK
Grove introduces a new heavy-duty jib option for its GRT9165 rough terrain crane. The GRT9165 with jib provides a competitive edge for setting precast concrete panels, due to its fast setup and economical transport.
GROVE IS OFFERING A NEW HEAVY-DUTY jib extension for the Grove GRT9165 rough terrain crane that increases the 150t crane’s utilisation abilities. It provides a competitive edge for setting precast concrete panels, as it’s easier to transport and faster to set up than competitive cranes for tilt-up work.
The jib is 3.8m long and designed with two sheaves, for up to four parts of line, and can be hydraulically offset from 0° to 50°. The compact but stout jib has a max lifting capacity of 31t. The new jib has up to 20 per cent greater capacities on average than its closest competition. The two-hook design gives operators tight precision when positioning panels, with the hydraulic jib controlled via an in-cab switch for faster operation and convenience.
The heavy-duty jib was designed to meet the fast-changing precast concrete panel market, one of the most common off-site techniques used during construction. This type of work is expected to grow 5.6 per cent annually over the next five years alone. Its benefits include efficiency, cost reduction, speed, and more consistent quality. Precast concrete yields added environmental benefits, too, as the hollow core uses half the amount of concrete without
The heavy-duty jib was designed to meet the fast-changing precast concrete panel market, one of the most common off-site techniques used during construction.
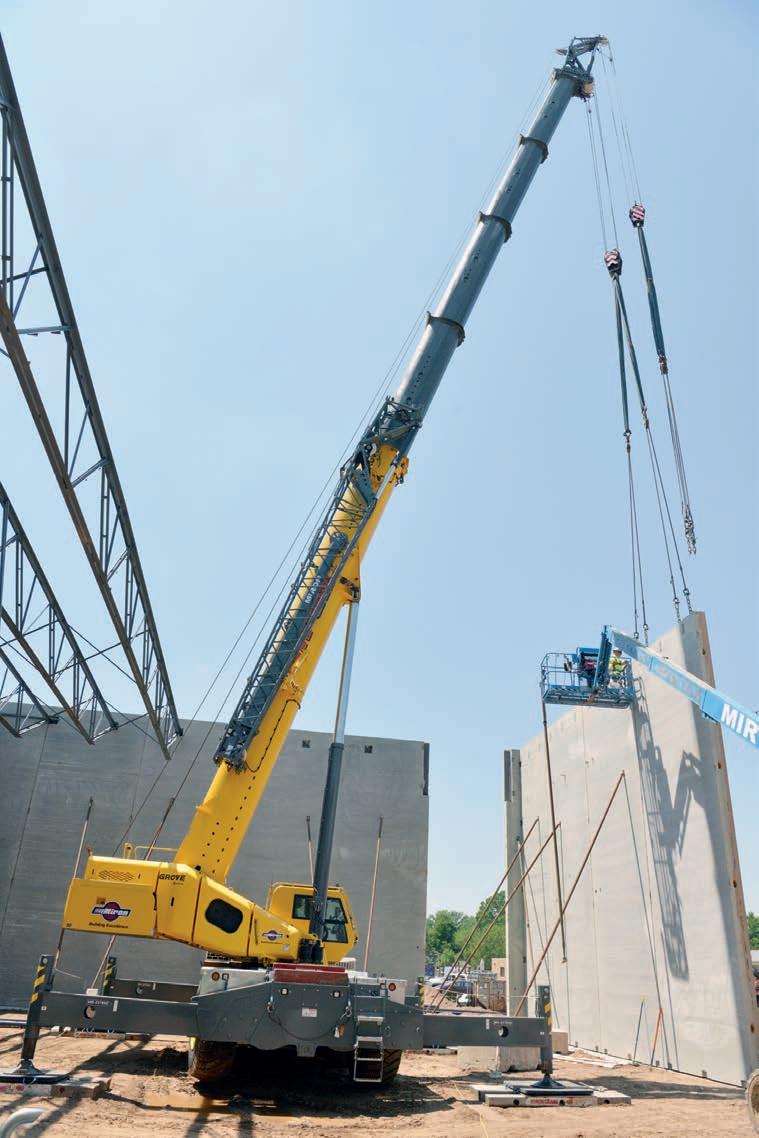
The jib is 3.8m long and designed with two sheaves, for up to four parts of line, and can be hydraulically offset from 0° to 50°.
development of the jib extension to make it purpose-built for precast.
“We took feedback from Miron to develop preliminary charts and stayed in close contact through the testing phase, making real-time modifications to deliver a final product that meets the market need from day one,” said John Bair, Grove rough-terrain product manager.
In June, Miron used the jib to set panels for a new high school in western Wisconsin. The GRT9165 was configured with its full 26t of counterweight and working at a max tip height of 38m with a 15m radius and zero-degree offset.
“It’s great to have the ability to luff the jib up and down for increased or decreased separation as needed, and it’s quick and easy to install and uninstall the jib,” said Luke Rathke, project superintendent with Miron.
The crane’s long boom, paired with the heavy-duty jib, is a bonus when working under height limitations. It has already allowed Miron to win more industrial work, including at large paper mills where overhead piping and ductwork limit access by other types of mobile cranes.
“The GRT9165 with the heavy-duty jib is the perfect package for what we need. It has strong capacities and precision for precast and is a solid all-around crane for the wider range of work we do,” Klosterman said.

compromising on strength. This results in up to a 25 per cent reduction in a building’s CO2 construction footprint.
Wisconsin-based design-build contractor Miron Construction Co. (Miron) is the first customer to use the new jib on its GRT9165. Miron’s clients are rapidly shifting to precast concrete for healthcare, warehouse, manufacturing, and higher education builds across the country. The size of concrete panels is growing in tandem with demand, averaging 3.7m wide and over 7.3m in height, and weighing upwards of 27t.
“It takes a larger crane to lift and
rotate the concrete panels and vertically set them in place. Our precast jobs have a short duration and we wanted to minimise transport and setup costs,” said Pete Klosterman, executive vice president, field resources for Miron.
Miron, Grove dealer American State Equipment and Grove’s product development team collaborated on the
“We must be more efficient and versatile in how we approach our jobs. You’ve got to stay ahead of the game, and it helps when the equipment we’re using can make that happen.”
The heavy-duty jib extension is available for order on all new Grove GRT9165 rough-terrain cranes and as a retrofit for cranes in the field.
“The two-hook design gives operators tight precision when positioning panels, with the hydraulic jib controlled via an in-cab switch for faster operation and convenience.”
A DIFFERENT APPROACH TO OVERHEAD PROTECTION
Safety around powerlines is serious business, it can mean the difference between getting a job completed and dealing with a serious catastrophe. Remaining vigilant and following procedure can only take you so far, simple human errors on a worksite can spell disaster.
THAT’S WHY AUSTRALIAN COMPANY
Protective have created a suite of reliable devices to help operators of construction equipment avoid contact with powerlines and other overhead hazards.
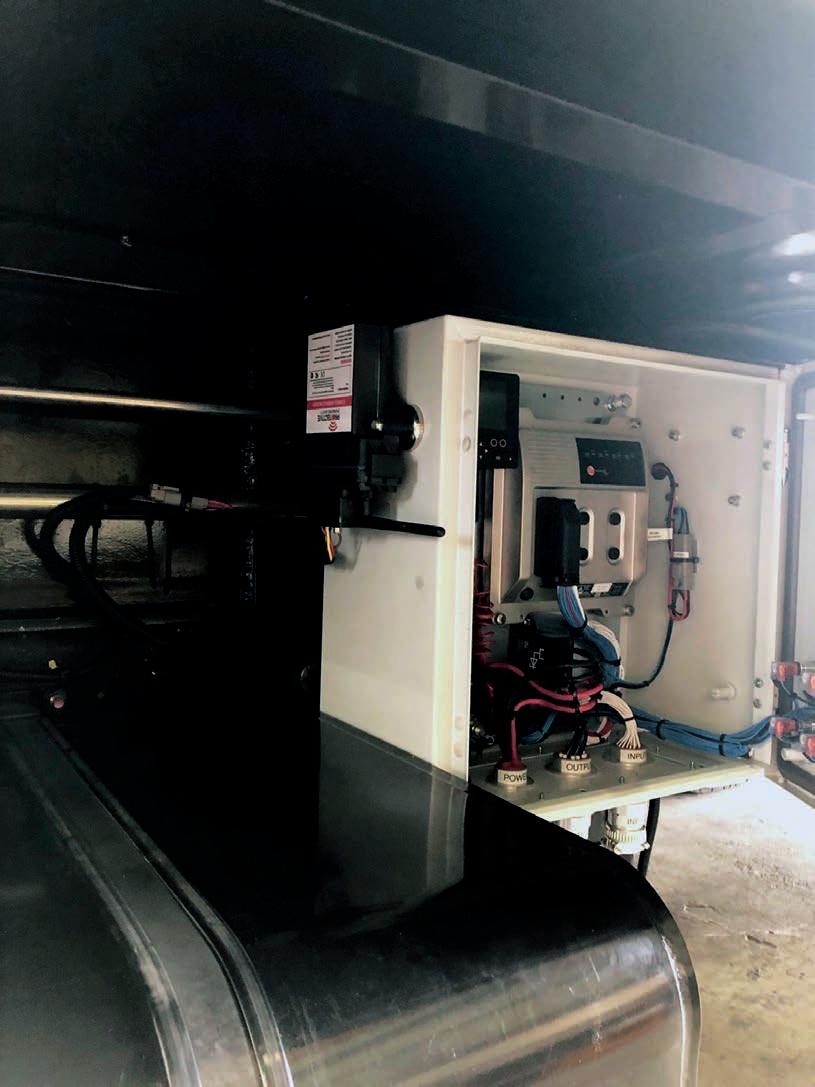

Protective’s story started when the company’s chief technology officer, Karl Rosewarne, was working as a safety inspector and saw too many incidents with powerlines. From then on, he realised that a gap in the market existed; to provide high quality engineered safety devices that help keep workers safe around electricity.
He then teamed up with Protective’s
current CEO, Shane Ballingall, and the pair decided to utilise their skills to bring this product to the industry.
The first product Protective launched, and which remains its cornerstone is GoUpSafely (GUS). GUS, is a small safety device that can detect high voltage power sources. GUS is designed to be attached to construction equipment, such as a crane, that is at risk of encountering powerlines.
GUS is then able to detect when the operator and their equipment is at risk of making contact with a power line and can provide feedback to them when they get
too close. Protective’s device also comes with the option to be integrated into the vehicle’s control system so in the event of a safety risk GUS can stop the vehicle moving towards the hazard, but still allow for movement away from the HV source
Protective’s business development manager Jason Jordan explains how the system works.
“When a high voltage source is detected, it will start measuring the strength of e-field signal as you’re moving towards it. We have a graduated alerting system, so you’ll get an initial
override, so you don’t lose productivity,” says Jordan.
The GUS system is different to other examples of HV detection products; it has software that specifically filters out anything that’s not in the proper range, which is between 50 to 60 hertz. The current of a powerline is within these parameters so GUS minimises the possibility of nuisance alerts.
GUS is a must have for worksites dealing with cranes and large construction equipment due to how simply it can be retrofitted to vehicles. The device itself is wireless so all that’s

doesn’t mean it will interfere with other radio channels that might be in use at a construction site. This is because It’s on a closed MIL-SPEC wireless network. The sensor device gets its power supply from the sun thanks to solar panels fitted to the outside with the base control unit using 12v or 24v power. It’s also incredibly durable and weather resistant (IP67 rated).
“We’ve passed pretty much every environmental test down to about negative 55 degrees up to 90. So, we’re confident the typical Australian operational environment is not going to be a problem for us. “
The main point of difference for Protective’s product is how easy it is to use out of the box and generally simple for operators. Protective has also prided itself on the way GUS is able to filter out false negatives
“We have software that specifically filters out anything that’s not in the proper range, which is in the 50 to 60 hertz range. And the reason that’s unique is because that’s where the power line frequencies sit,” says Jordan.
In addition to cranes, tipper trucks, excavators and other equipment likely to contact powerlines, Protective also makes a product to ensure the safety of workers on elevated work platforms (EWP), such as scissor lifts.
This is what Protective calls MEWP shield, a crush protection system using ultrasonic sensor technology for proximity detection and control. Their patented MEWP Shield system engages the worker protection function to identify potential hazards before an EWP incident occurs.
MEWP Shield can provide many of the same features as GUS, that is providing feedback to operators as
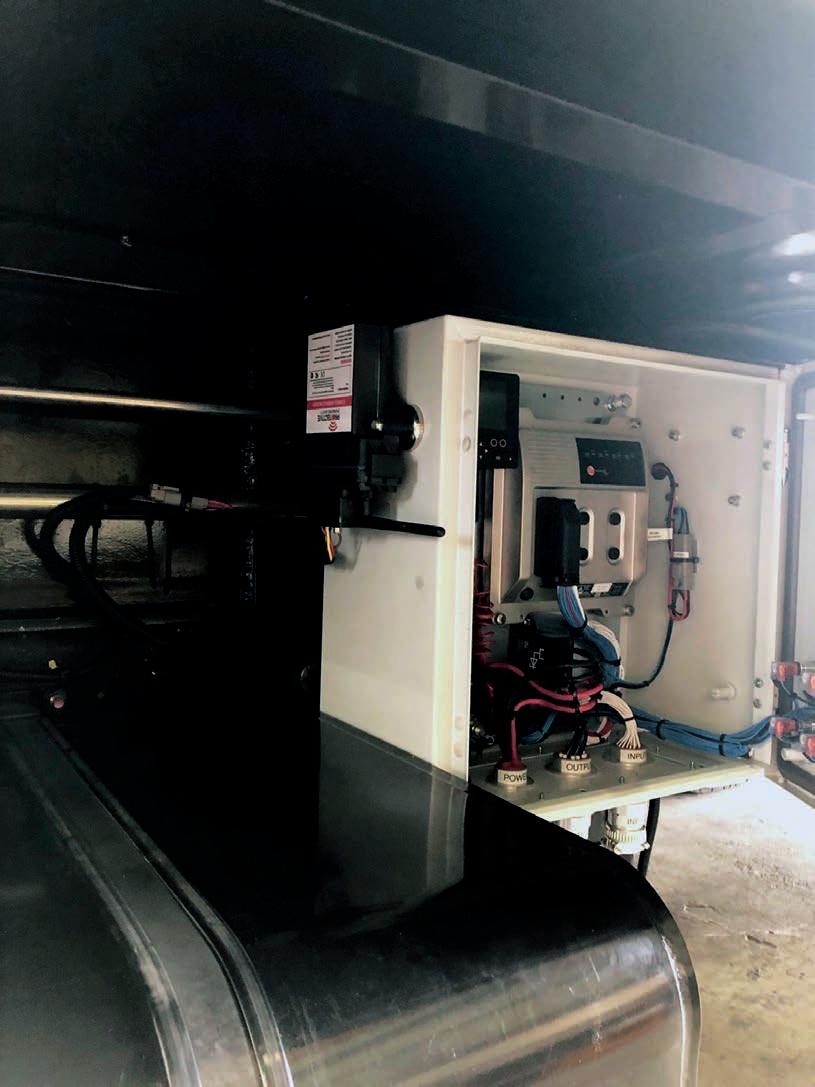
“When a high voltage source is detected, it will start measuring the strength of e-field signal as you’re moving towards it.”An auto electrician can easily install the product
they come in proximity to a hazard and even overriding the vehicle and stopping it if needed. MEWP Shield has been designed to accommodate EWP applications.
Protective is confident in the products they create and sell to their clients; they offer full after sale support to clients if they need it. Jordan says they rarely need much support, however.
“We haven’t had many calls to our support team, but when somebody has called us and said, “Is this thing doing what it’s supposed to?” we go through everything with them. We have a special support line set up and we have a brilliant team of mechatronic engineers who methodically work through any issues with our clients.”
Jordan says though they have a team of talented engineers ready to help, because of the design of their products
often they can fix issues clients are having completely remotely.
“We had one scenario, and it was right after the sale, whereby the client wanted to increase the sensitivity of the detection as they were working around a lower KV line. We were able to log into the system remotely and make the required changes getting them up and running in minimal time.”
Protective stresses the fact that their products are not a replacement for following procedure and taking responsibility for worksite safety. Instead, products such as GUS and MEWP Shield act as important engineered safety devices designed to reduce the impact of human error: stepping in when all else fails. That’s not to say their products aren’t incredibly important. Jordan gives an example of their product working in
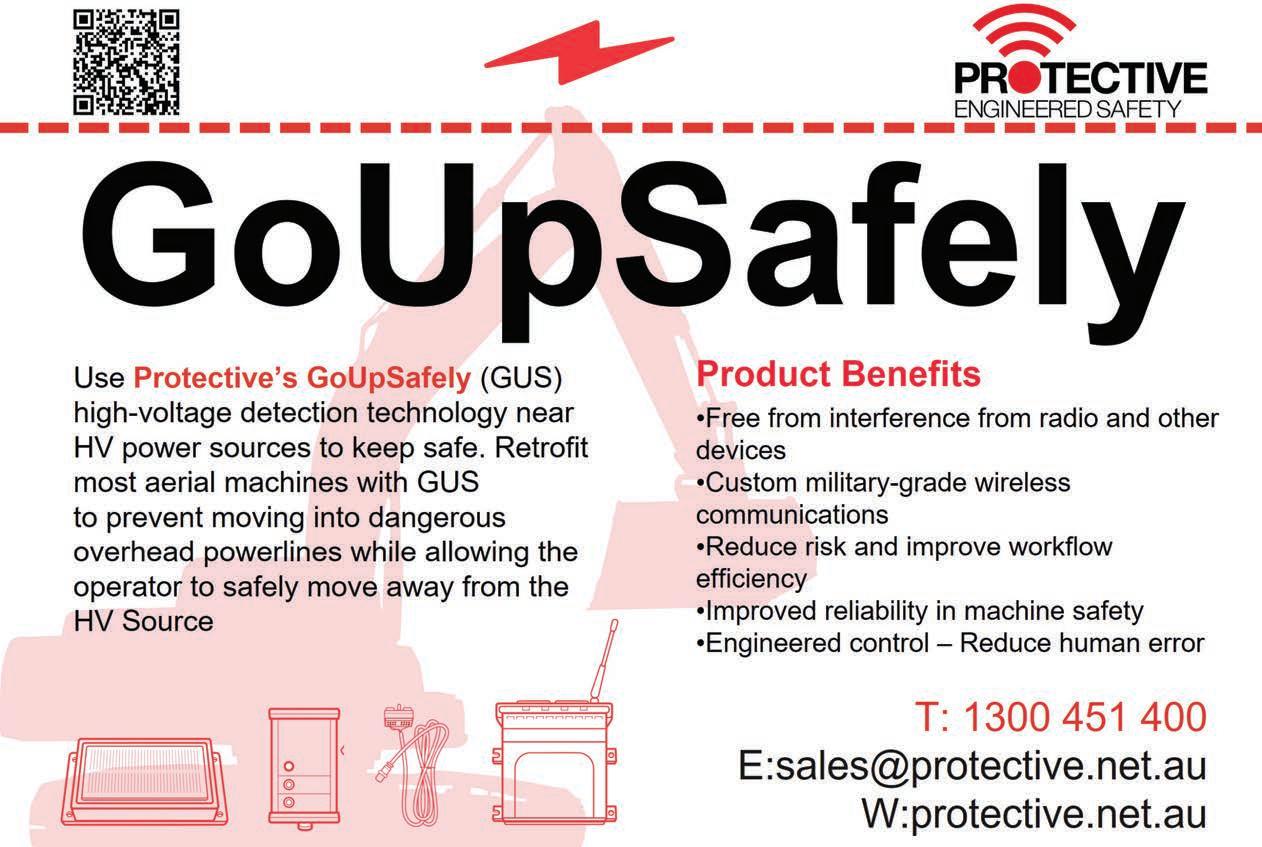
a situation that most workers would overlook.
One of their clients in Melbourne were working on a site with an excavator next to a metal fence on a particularly humid day. Jordan tells what happened next.
“They got in the excavator. As soon as they got in, turned it on, the system started alerting. What had happened was they hadn’t grounded the metal fence which was directly beneath a power line. The overhead power line through the humidity was charging the fence. The system was doing exactly what it was supposed to do. We told them to get out of there until somebody could help them get the fence safely grounded. So, they sent out one of their safety team members, they had a look at the scenario, and they said absolutely that was the problem and your system probably saved a life that day.”
THE MOLLROSS NAME RETURNS TO THE INDUSTRY WITH XCMG
“I AM SO PASSIONATE ABOUT THE lifting sector, from my time at Liebherr, and in rigging I am just excited to be back in the industry that has been such a constant in my life from my Dad through to me,” said Mollross.
“We alw ays find our way back to
the sector because it is so good to be a part of.”
Mollross experience in the industry can trace its way back to his father who worked for the likes of the Men from Marr’s and Heavy Haulage expert Rex Andrews.
“I am very excited about leading
the XCMG crane division into the future with a strong focus on winning the trust of the Australian market with a strong range of cranes at my disposal,” he said.
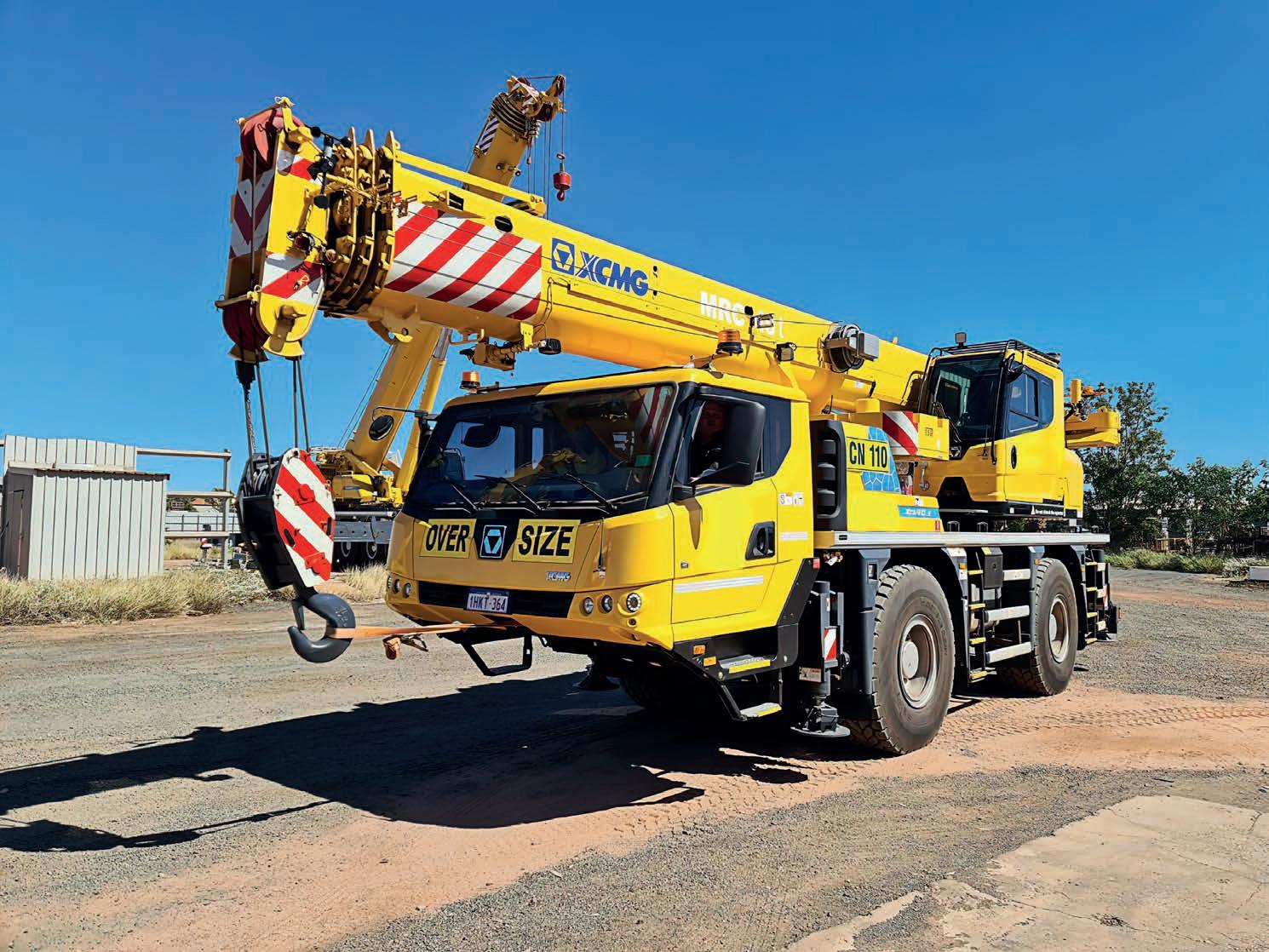
“I will be focusing on customers’ wants and needs along with XCMG support and willingness to react
The XCMG canes have been adjusted to suit the Australian market.
Matt Mollross has joined the team at XCMG as national crane manager, marking a return to the industry after nine years working in his own lifting and rigging business.
quickly to the needs of operators. We have a good product and I know the industry well and will draw on this knowledge to lead XCMG to new goals, increased market presence, and continued improvement to better the customer experience and create the perfect cranes for Australia.”
XCMG is currently ranked number one in wheeled-based crane sales in the world according to the authoritative release from British KHL group, it has been producing cranes for more than 70 years. XCMG also has risen to be the third largest machinery manufacturer in the world only surpassed by Caterpillar and Komatsu, and the desire to be number one is strong in the vision of XCMG.
The XCMG mobile crane factory located in Xuzhou Jiangsu has a land size of 73 square kilometres with six production units and 33 production lines pumping out 5,500 cranes per year.
In production XCMG concentrates on best practice and employing
the best technologies for example in the field of welding. XCMG has recently purchased 32 robotic welding machines to ensure quality control and uncompromised skill on a continuous level, along with state-of-the-art laser hybrid welding machines and Swedish built Ursvken 4,000-tonne bending machine to manufacture the special curved boom sections.
XCMG globally has grown to 110 dealers worldwide with over 2,000 service centres 6,000 technicians and 5,000 salesmen and women working in 176 different countries.
XCMG offers an extensive range of cranes with an impressive capacity across the fleet, this includes:
• a ll terrain cranes from 40t two-axle to 4,000t 10-axle
• r ough terrain cranes 25t up to 130t
• t elescopic crawler cranes 25t to 220t
• pin jib crawler cranes 55t to 4,000t
• h igh duty cycle crawler cranes 35t to 100t
• t ruck cranes 8t to 220t including a new hybrid electric truck crane the XCT25EV.
“In the Australian market interest has been shown for a large mobile crane to tackle the new challenges facing the increase in weight of wind turbines and XCMG is up to the task,” Mollross explained.
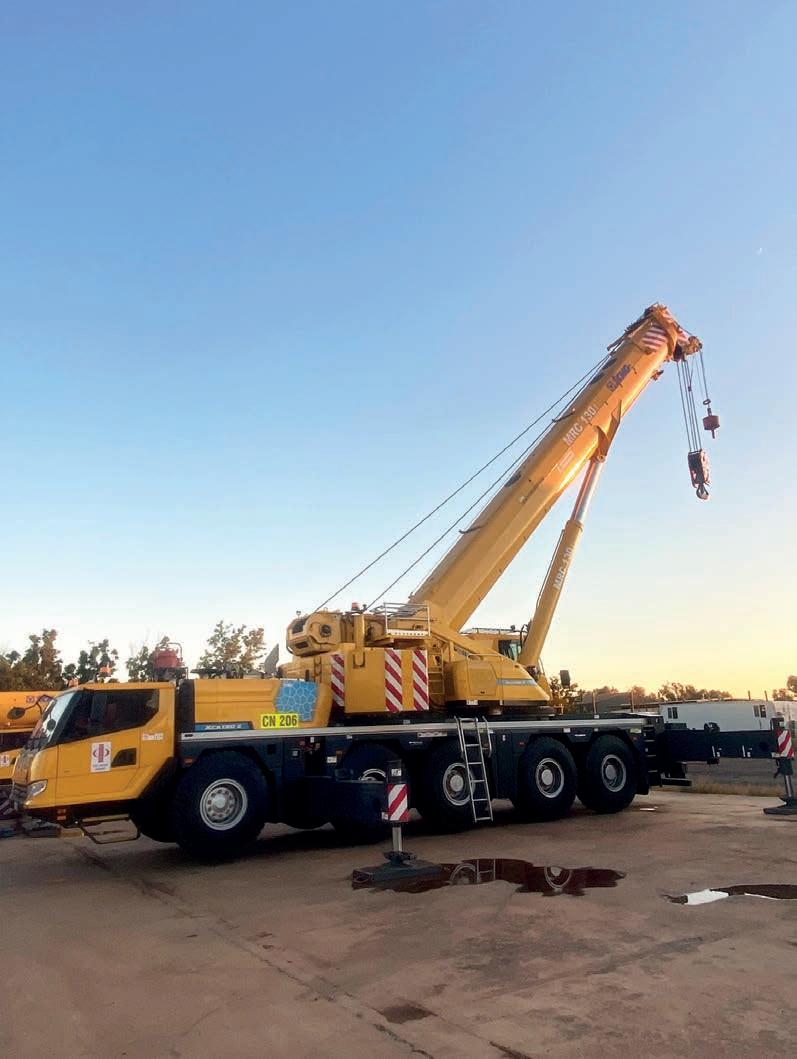
“The XCMG XCA2600 has all the answers, with an impressive capacity of 160t load to a hook height of 160m at a radius of 26m, or alternate 240t load to 120m at a radius of 20m.
The XCA2600 has an in-principal road approval on 10 axles at a reduced travel weight of 75t, slightly less than its ability to travel on site at 317t complete with main boom, super lift, all out riggers, and part of the fixed fly.
“XCMG, since becoming number one in crane manufacture, has expressed its desire to keep growing around the world. Australia was a key market to start a new drive to demonstrate to the crane owners that XCMG has a commitment to starting a long relationship with the Australian market by providing excellence in service, parts, and technical support, partnered with our dealer network alongside the likes of D & D Diesel Melbourne and newly appointed dealer Ronco in Perth,” he said.
XCMG will also be investing in growth, having already secured warehouses in Melbourne and Karratha, with more servicing centres to be finalised in the next 18 months on the east coast to offer customers ease and accessibility to service.
XCMG realises its goal is to support the customer not only at the point of sale but beyond throughout the machine’s lifespan. This will be the cornerstone of Mollross’s time at XCMG.
XCMG has already grown to more than 25 people around Australia (excluding dealer personnel), led by the GM of XCMG Oceania Eric
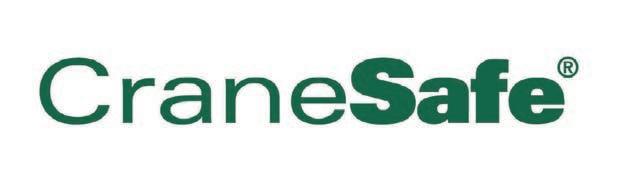
Renhua and Country GM Roy Rossini, with a team of dedicated people leading the other divisions in excavators, road building and mining machinery.
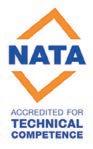

“XCMG staff come with great depths of experience that will, in turn, strengthen the desire to demonstrate high levels of customer focus in every task we accept,” said Mollross.
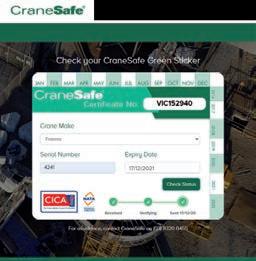
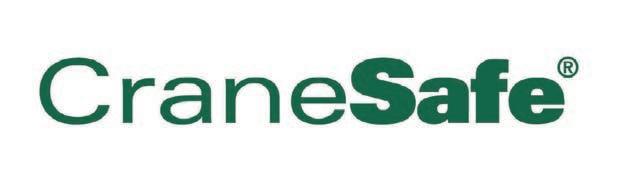
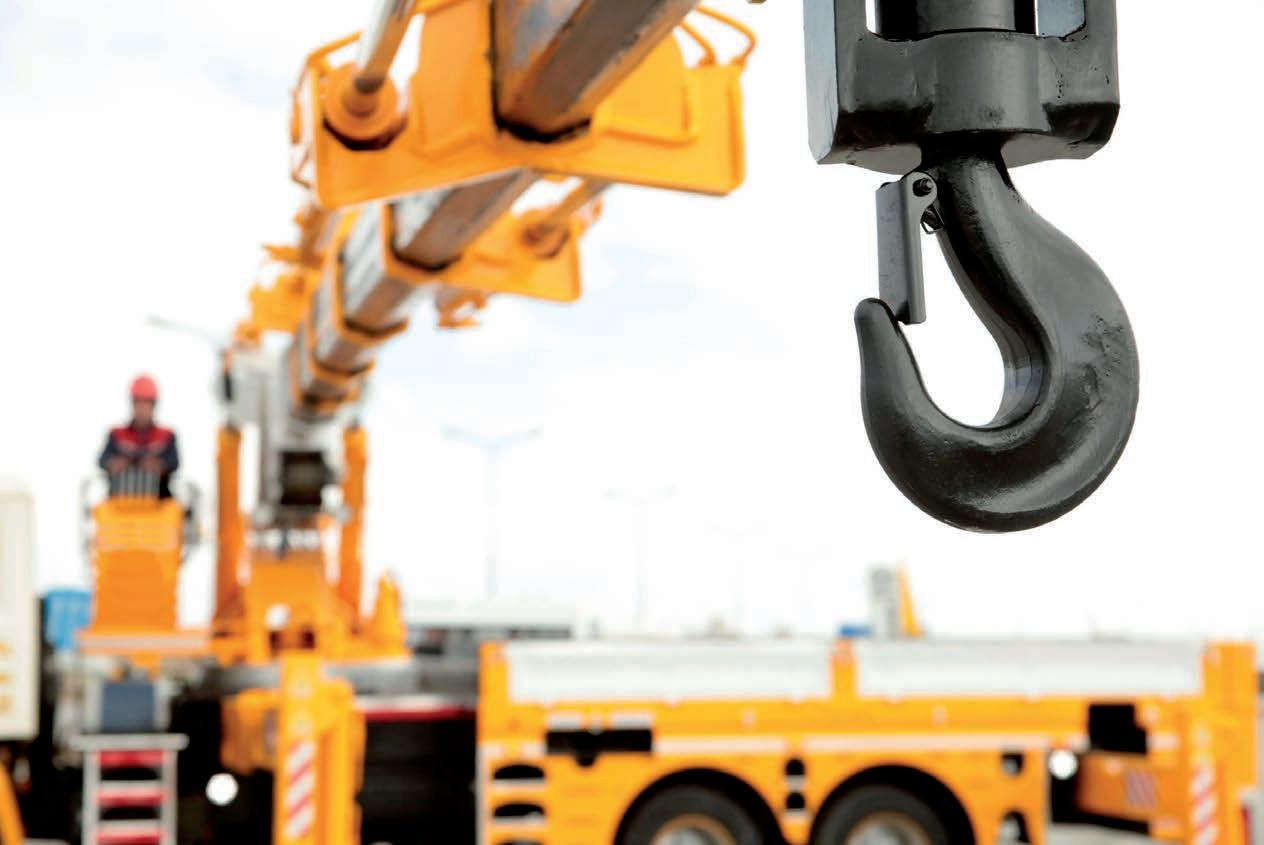
“Our logo states XCMG ‘For your Success’ and that is how we approach every operator we work with and how we will work in Australia.”
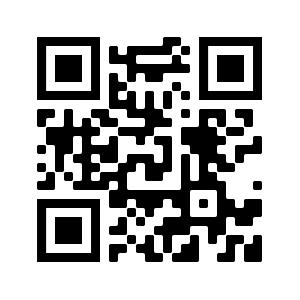


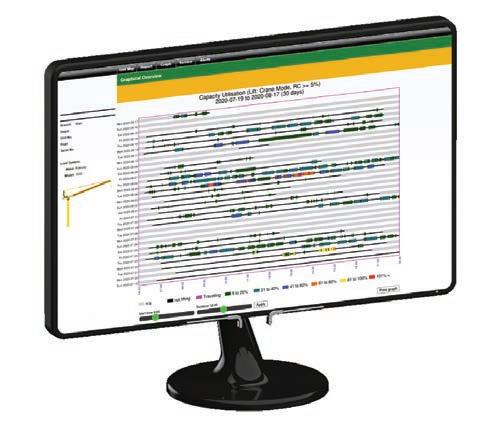

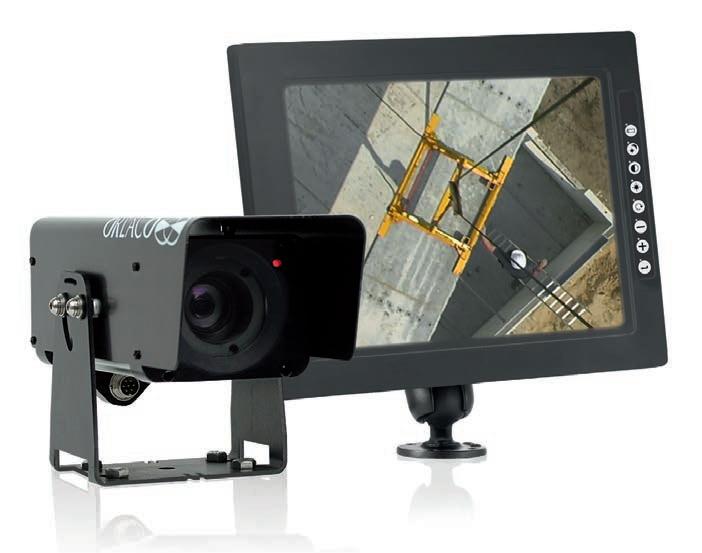

AN INVESTMENT IN PEOPLE
“ATTENTION TO GROUND CONDITIONS AND crane setup is becoming highly scrutinised, especially on Tier 1 and Tier 2 projects. Our company policy is to always exceed regulatory requirements,” said Clinton Forner, general manager of Action Cranes.
Action Cranes previously used hardwood timbers under outriggers, but when Forner saw other crane rental companies chatting about a new engineered crane pad on an industry Facebook page, he became interested in learning about a better solution.
Action Cranes purchased a set of four FiberTech FTR48-1s (48”x1”), which is the largest standard size fibre reinforced polymer (FRP) pads that DICA manufactures. Each four foot round FiberTech pad weighs 65kg, which is considerably less than the 204kg weight of the hardwood timbers Action Crane used before.
“I wanted to make setup safer and easier for our crane crews,” said Forner.
“These engineered pads can be rolled
into place by one person. One pad is the equivalent of placing down 10 hardwood timbers – 40 timbers total,” he explained.
The result is much less physical handling by personnel, which reduces strain and makes setup more efficient.
FiberTech outrigger pads are made of 13 layers of quad axial continuous glass fibres and polyester resin, which gives them exceptional strength and stiffness to distribute loads. They do not absorb water, chemicals, or contaminants, and are easy to clean.
“Action Cranes has a high commitment to safety. The company was looking for the lightest weight solution available that would also reduce risk and provide them with the peace of mind they need when it came to setting up cranes in a variety of ground conditions,” said Kris Koberg, CEO of DICA.
PERFORMANCE PROJECTIONS
“The selection process was really easy, I just gave DICA the crane models I was
planning to use the pads with and they gave me several options, with reports showing performance projections. I then compared that to typical ground loading limits that I knew I wanted to stay under,” explained Forner.
Action Cranes sought recommendations for three crane models – Liebherr LTC 1050-3.1 50t city crane, Liebherr LTM 10603.1 60t all terrain crane, and a Grove GMK 4100 100t all terrain crane.

DICA presented Forner with 11 different models of SafetyTech, FiberTech, and FiberMax outrigger pads that would target the average allowable ground bearing objectives.
“We work with customers to identify options that have the appropriate strength and stiffness needed for their applications. When determining outrigger pad types and sizes many crane companies embrace DICA’s strategy of selecting a set of outrigger pads that meet the needs of most everyday lifting scenarios,” said Koberg.
He explains that most crane companies
Action Cranes has been serving Sydney and the surrounding market since 1971.
The company recently purchased its first set of engineered outrigger pads.The FiberTech pads are a lighter weight alternative to hardwood pads.
have critical lift thresholds, such as a maximum allowable percentage of the chart.
“Based on this information and the outrigger reaction forces, we calculate the minimum pad area needed. When operating in the 70–80 per cent range it is unlikely the crane will generate outrigger reaction forces that would exceed the threshold,” said Koberg.
This approach allows owners to choose a pad type and size that aligns with the planned use of the crane, which is often smaller than if sized for the maximum outrigger reaction forces.
“The benefit is that everyday pads will weigh less and cost less,” said Koberg.
“Of course, any time the lift exceeds the chart thresholds set by the owner then the crane company should create a specific lift plan that may require a different outrigger pad type, size, and thickness than the assigned everyday pad.”
To narrow down the final selection, DICA assisted Forner in evaluating the performance characteristics of different products and surface conditions. Based on the pad stiffness and pad to ground interaction, charts were provided demonstrating load displacement based on soft, hard, and concrete ground conditions.
“Forner wanted to understand the data so that he could put that info to use to solve his unique setup scenarios,” said Koberg.
“He was looking for the lightest weight solution based on his ground bearing
pressure requirements. Of the three products he evaluated – two SafetyTech and one FiberTech pad – the FiberTech FTR481 was the option that met his needs.
“FiberTech was more expensive, but the stiffness to weight ratio was the best for a variety of soil types,” said Forner. Weight savings was an important factor in Forner’s decision. A 1-inch thick FiberTech pad is equivalent in stiffness and performance to a 3-inch thick SafetyTech pad, but weighs about 25 per cent less.
“They are much lighter weight, easier to store, and easier to handle, which makes it less likely that crane crews will take short cuts by using small timber pads.”
The response from crews?
“We absolutely love these DICA FiberTech outrigger pads,” said Forner.
PUTTING FIBERTECH TO WORK
Shortly after receiving the FiberTech outrigger pads, Action Cranes put them to use on two projects.
The first project involved lifting materials in a skip bin from 50m below the Warragamba dam. The company’s LTC 1050-3.1 was set up on concrete on the top
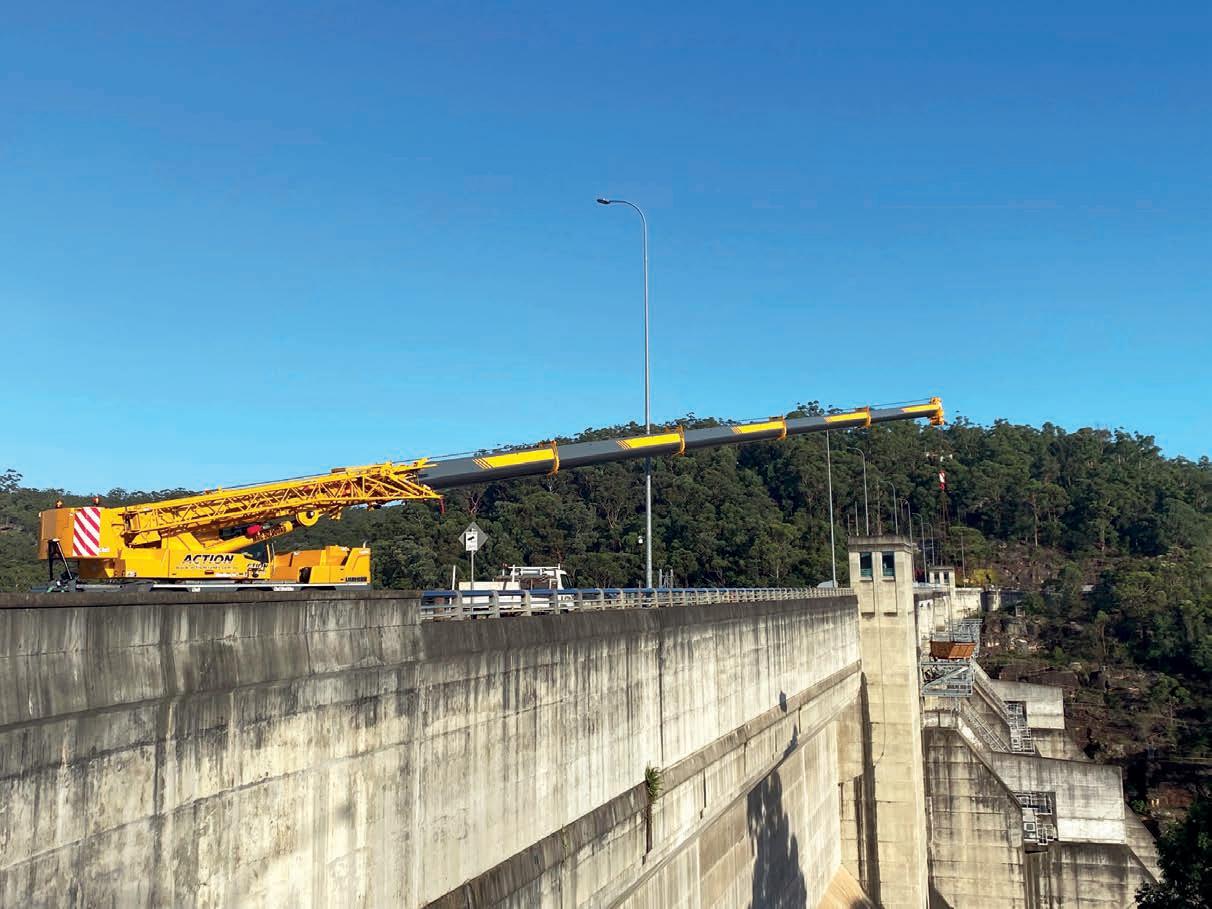
of the dam. The second project, using the same crane, involved lifting steel beams on a residential construction project in Balmain, Sydney.
In one position, the crane was set up on hard packed dirt, and in the other, it was set up on asphalt.
“I was worried about small, hard blue metal rocks damaging the pads, but the pads are really hard and the rocks were just crushed with no damage to the pad,” said Forner.
Since then, Action Cranes has had a chance to use its new FiberTech outrigger pads in softer ground conditions with equal success.
Although Forner considers the purchase of the FiberTech outrigger pads to be an investment, he is already predicting that their life expectancy will at least double that of the hardwood timbers he used to use. Even more important was choosing an outrigger pad that made life easier for his crews.
“It was refreshing to work with a company that cares so much about their people, their equipment, and their reputation,” said Koberg.
“Of course, any time the lift exceeds the chart thresholds set by the owner then the crane company should create a specific lift plan that may require a different outrigger pad type, size, and thickness than the assigned everyday pad.”Liebherr LTC 1050-3.1 50t city crane at work.
LIEBHERR TRANSFORM: UNLEASH THE
POTENTIAL
Liebherr Transform, the new upgrade, modification, and overhaul service, has a tailormade solution for all customer needs. It is available for crawler cranes up to 400t, deep foundation equipment, and duty cycle crawler cranes.
THE NEW LIEBHERR TRANSFORM provides tailored solutions that respond to the continuously growing demands on today’s businesses. A range of ingenious upgrades, clever retrofits, machine overhauls, and service modifications breathe new life into customers’ existing machines. Using the latest technology and years of experience, Liebherr brings you a combination of sustainability, smart technologies, maximum productivity and cost-effectiveness in one complete solution. This allows existing equipment to reach its full potential.
OVERHAULS, UPGRADES, RETROFITS, AND MUCH MORE
It is inevitable that equipment becomes outdated over time but that does not mean it has to be replaced. As the name suggests, existing m achines are transformed using affordable complete or partial machine overhauls, retrofits, and upgrades. This not only saves the increased capital expenditure of investing in new machines, but also reduces the carbon footprint by avoiding the need for new equipment through the extension of the service

life. A number of retrofits and upgrades are available that increase versatility and performance, or ensure compliance with more stringent regulations, and so open up a wider spectrum of opportunities. At the same time, operators do not have to get used to new machines and can
continue to benefit from their vast experience with existing equipment.
The Liebherr team of expert engineers takes care of the entire planning and implementation of Transform projects – from consultation, through to installation, technical support, and service.
Liebherr Transform helps to lighten the load through a comprehensive range of structural, electrical, mechanical, ergonomic or digital modifications.

STRONGER, FASTER, SMARTER, GREENER
Companies are under pressure to increase volume and performance, widen scopes, or reduce emissions and costs, the list is endless.
Liebherr Transform helps to lighten the load through a comprehensive range of structural, electrical, mechanical, ergonomic, or digital modifications. Through the application of new technologies and expertise, Liebherr machines are transformed for the workplace of the future. They are stronger, faster, smarter, greener, and ultimately... better.
“The Liebherr team of expert engineers takes care of the entire planning and implementation of Transform projects –from consultation, through to installation and technical support and service.”
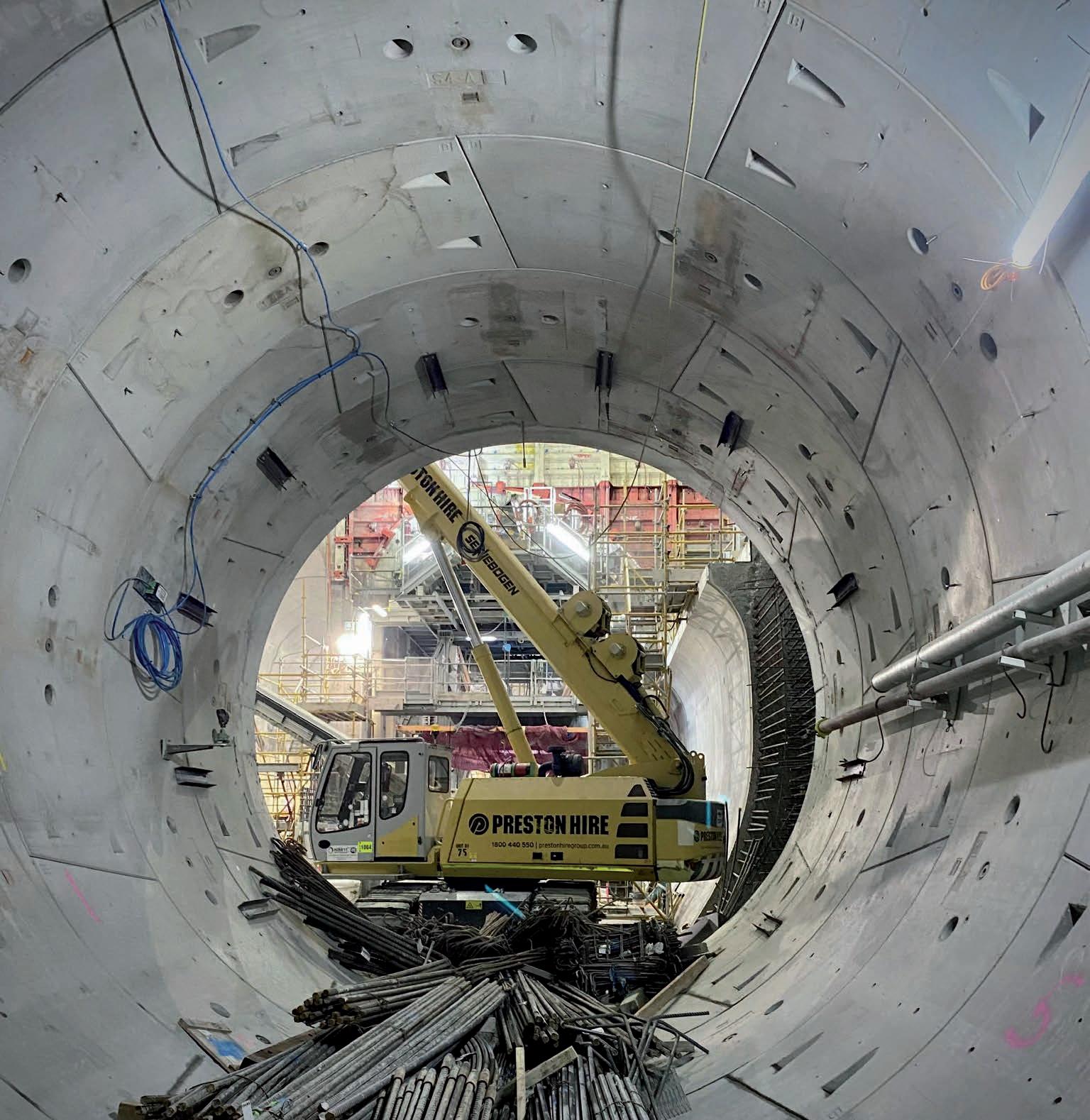
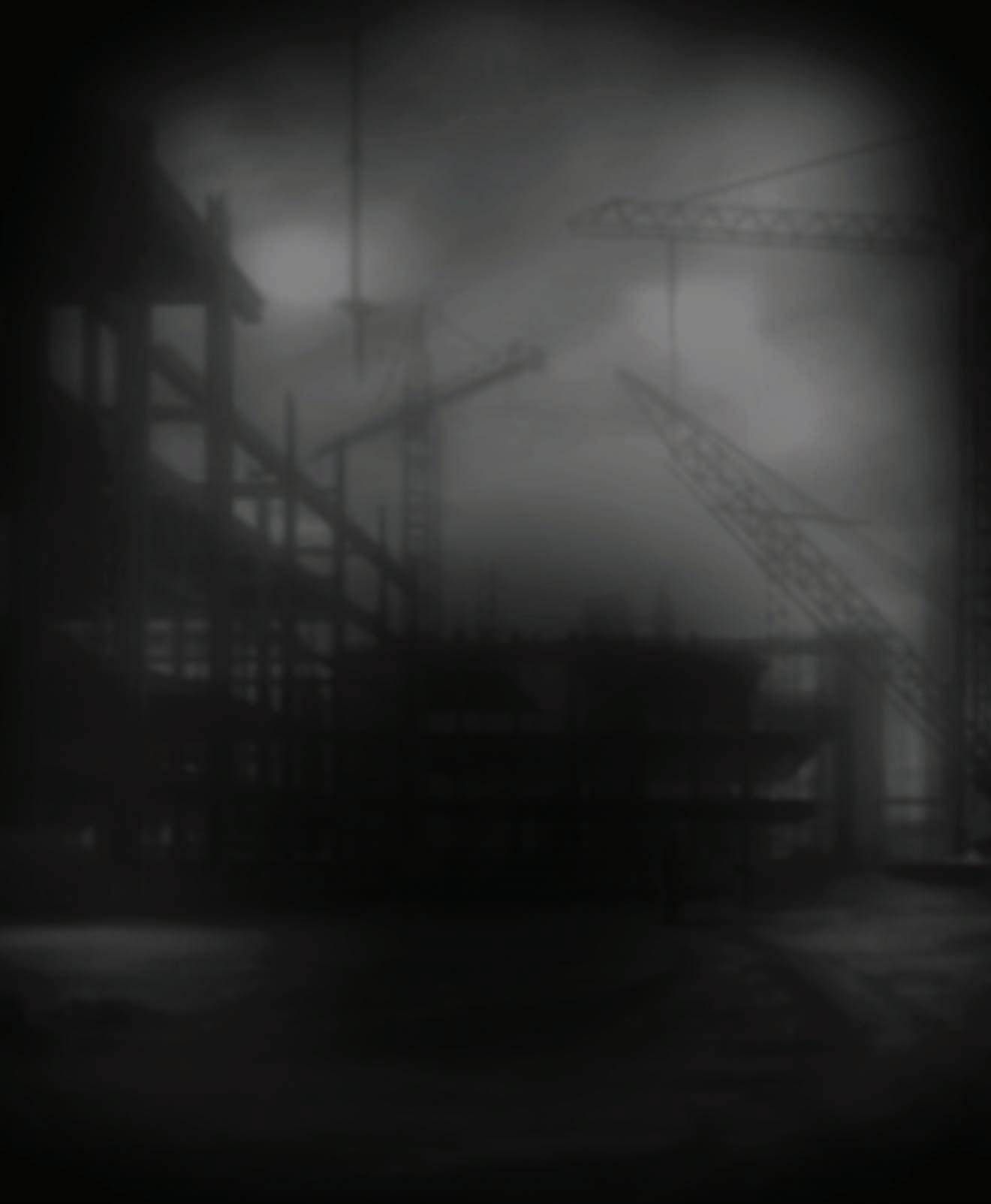
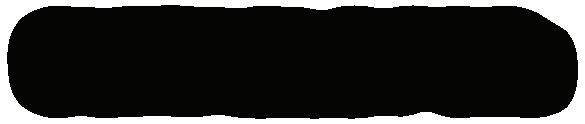
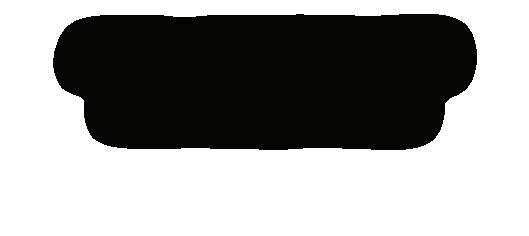


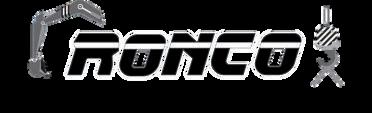
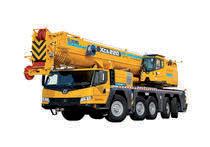




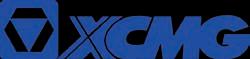
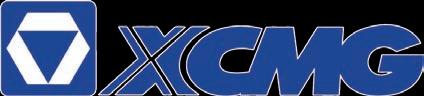