
20 minute read
BECOMING MORE CONNECTED
by Prime Group
The trucking world is waking up to the powerful opportunities available to the industry in terms of safety, productivity, planning and transparency, which can be gained by the interconnectivity possible from systems communicating, in real time, across the truck, the operating base, the customer and with the surrounding infrastructure.
As business systems, truck telematics and smart software generate more and more useable data for every aspect of the trucking industry. There is now a trend where the need for in-cabin convergence is coming to the fore. There is often a range of electronic devices all working independently in a truck and the next stage in development will see these technologies converging to a greater extent.
It is not a matter of ‘if’ these systems will converge, but a matter of ‘when’ they will converge. The fragmented nature of the electronics fitted in different trucks, fleets and industry sectors means the process of integration and convergence could take a number of twists and turns on the way to the ‘nirvana’ of a single integrated data flow from the truck, to the operator and from there into the various business systems involved.
Simply put, we are looking at a future where there will not be five black boxes with five SIMs in a truck, all talking to a different system online. Instead, what is now a black box will be a series of apps on a single interface, where smarts can feed data to other control systems as well as online to other management systems. Data will be available wherever it is needed, in real time, all the time.
The concept of convergence will also go way beyond the reduction in the number of black boxes in the cabin. There is also the convergence of the data that all of these different pieces of equipment pump out constantly. Yes, vehicle data may be going to the maintenance department back at base and the driver behaviour data to those in charge of safety and compliance, but contained in that flow is a massive amount of data which the business can use elsewhere.
This will be another stage of convergence in which the data from the truck converges with the data travelling around within the business system of the operation. This is where artificial intelligence should create another major step forward in its effectiveness.
Utilising all of the data flows around a trucking operation, business intelligence will be able to identify behaviours and trends way before they would become obvious to the casual observer. In this way, the data convergence becomes a teaching tool for an overall system which can pursue the targets set by the management.
In this first part of an ongoing series
of articles, Diesel looks at the front end of this data flow, the truck and trailer themselves. This is where a lot of the raw data is generated which affects a large part of the parameters on which the business model is based.
The costs are examined as the data flows from the truck itself, the fuel use and maintenance requirements. There is also the drivers and their behaviour, which can affect other areas of the business.
The simple location of the truck is also a valuable tool in the business as the operation knows exactly where its assets and the freight are at any point in time. Adding in other simple functions like geofencing enables automatic processes to take the place of a lot of paper shuffling.
Combining the location data with load sensing systems fitted on the truck and trailer can also give road authorities the peace of mind to allow higher masses to be carried in some cases. This process is very piecemeal at the moment, but developments in the Heavy Vehicle National Law could make load and location assurance a useful productivity tool.
COMPUTING POWER The amount of computing power fitted into a truck as a matter of course has multiplied considerably in recent years. the amount of data flying around in a CANbus on a Euro6 truck is many times greater than that used in its Euro5 predecessor.
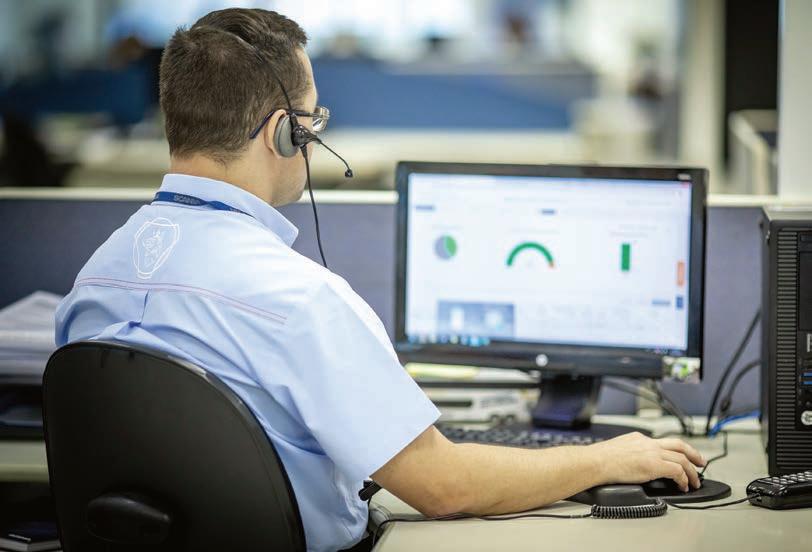
The truck system is no longer a central ECU with a multiplexed wiring harness. It is a series of computing modes around the truck working together to run all of the control systems. Running the vehicle is only a small part of the system’s capability. The modern truck has a lot more going on under the hood than that.
The modern European prime mover, and now, the latest US truck models, have enough capacity to fulfil many more functions than simply running the truck and telling us where the truck is and how fast it is going.
This level of sophistication is used
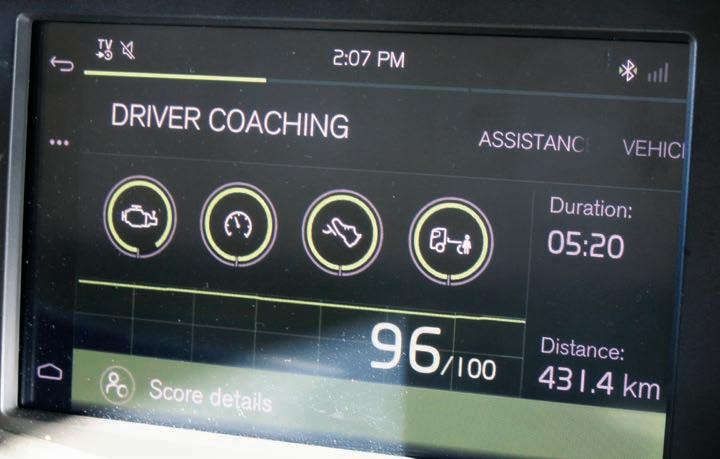
in Europe and more recently in North America to run a full business system out of the truck. For a subscription, the truck’s computing power will run a complete business system, compatible with operation control systems back at base and able to provide a data flow for areas like maintenance, compliance and other parts of the business.
One example of this kind of system is the one fitted in trucks sold by the Volvo Group. The system may have a different name in different brands, but it is essentially the same one customised to reflect the Volvo, Mack and UD Trucks brand identity.
The basic Dynafleet system has been a part of the Volvo offering for quite some time and each new model release sees a major jump in the telematics’ capabilities. The telematics provided can vary in price depending on the amount of data being processed and sent from the truck to the operator’s computer systems.
Basic data about how the truck and driver have performed is communicated back to base. Adding in positioning increases the cost, enabling options like ring fencing and notifications about exactly where the truck is and when.
There is an option known as RFMS, which is less detailed and suitable for less sophisticated business systems. This level can often be used by an operator to demonstrate compliance with the rules, but it concentrates less on driver behaviour, while not costing as much as the more complex options, which also use considerably more data.
The next cab off the rank for Volvo and its electronic offering will be Volvo Connect. This is not a system which introduces even more data, but is a portal through which the operator, driver or scheduler can see what’s going on in all of the Volvo Group trucks in its fleet. This will be arriving next year in Australia, offering what amounts to an improved and customisable interface between the operators and their trucks.
This kind of system is currently available in all of the European truck brands to some degree. The functionality is certainly built into the trucks because European customers demand it. Some brands here is Australia choose to offer the full suite to their customers while others have chosen not to use that capacity at this time, supposedly having decided that the Australian market does not have sufficient demand for this kind of product at this time.
There is likely to be more consolidation of data in the truck as time goes by but for some operators, the inbuilt truck system has a couple of disadvantages: It does not work in mixed fleets with different brands and it cannot be integrated with some other systems in the truck or back at base.
In fact, in the past, Scania had developed a system known as Interactor, which was designed to be open for the use of third-party applications related
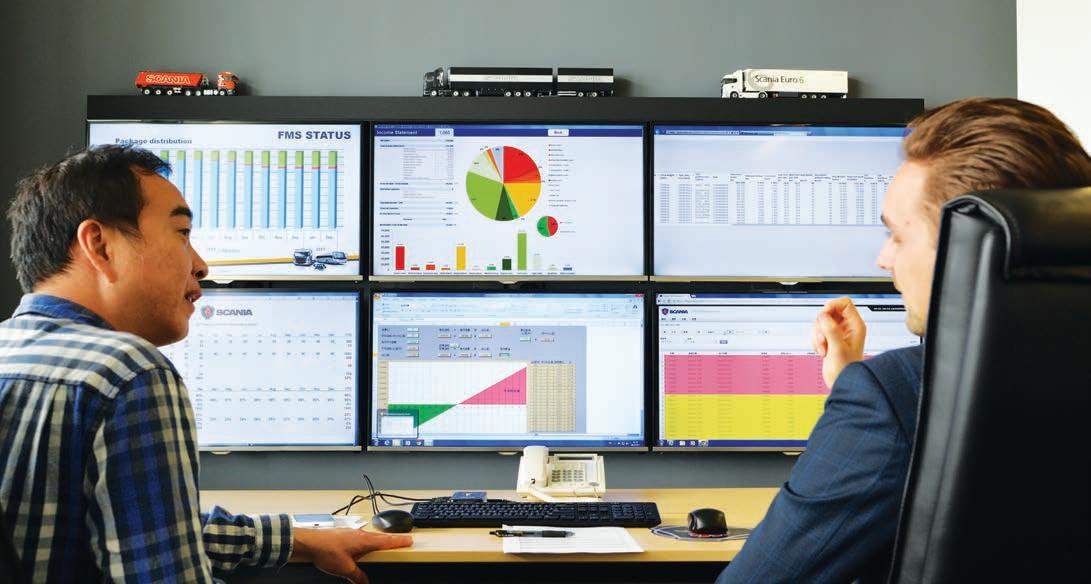
to the truck. However, the design was dropped after Scania found that the kind of things operators wanted to do with the system were so task and operator specific it would be impossible to include options in one system that the broader trucking industry would need.
BLACK BOXES IN THE CABIN Many fleets have specific needs to be met by whatever telematics or monitoring solution they are using and often each one of these equates to more black boxes in the cabin. However, convergence is also happening in this part of the industry.
Systems like the one produced by CombineIT are currently a standalone product, with a driver tablet or phone app as the interface in the truck, but the strength of the system is in the back office applications which pull data down from the tablet and push data back to it. It is simply a web-based freight management system creating consignment notes, taking customer orders as well informing dispatch and job pricing.
This system can also be integrated into other parts of the business, interfacing with accounting software like Xero and customer relationship management applications. The operator’s customer can also access the data on their own business systems, if required.
CombineIT have also gone one stage further and been able to integrate the system with the larger MTData telematics platform, where the functionality of the CombineIT system can piggyback on the MTData equipment. This is where some real convergence can begin, where, what is currently a piece of har dware with its own SIM card and communication channel becomes an app on the main platform and is still able to fulfil the same function for which it is designed and useful for the operator.
This kind of convergence may have been available to the larger fleets for some time, because they are big enough to be designing their own systems and building in the functionality their large fleet requires.
For the smaller fleets, which make up the vast majority of trucks plying their trade on our roads, the solution has to be different. This is where solution providers like CombineIT, and others, can come in. Apps specifically suited to the task or safety concerns the operator is involved with, can be added to some basic recording and tracking devices in order to create the quality of data flow into the operation to improve productivity and safety.
Similar integration is taking place between the various safety systems that can be fitted in the truck cabin. Each system may be able to be fitted with its own functionality in the cabin, but from the
point of view of the operator, it is preferable to package them in a way where they use common platforms for communication.
Currently, DriveRisk are also working in the mining industry and can work together with other safety system suppliers to cover all the bases.
“We have a number of partnerships with companies supplying to the mining sector,” says Craig Forbes of DriveRisk. “We have an agreement with one of our customers where we are putting in a full advanced driver assistance system with breathalysers, seat belt sensors, driver alerts, fatigue management, vibrating seat pads all talking to each other. We are also a partner with the Mobileye organisation.
“All of that information needs to go somewhere, so we have developed a system which takes all of the information from all of the safety systems, from everybody, and throws it into one dashboard, so the customer can see all of it in one place.
“We are even going deeper than that. Having different systems in the cab is
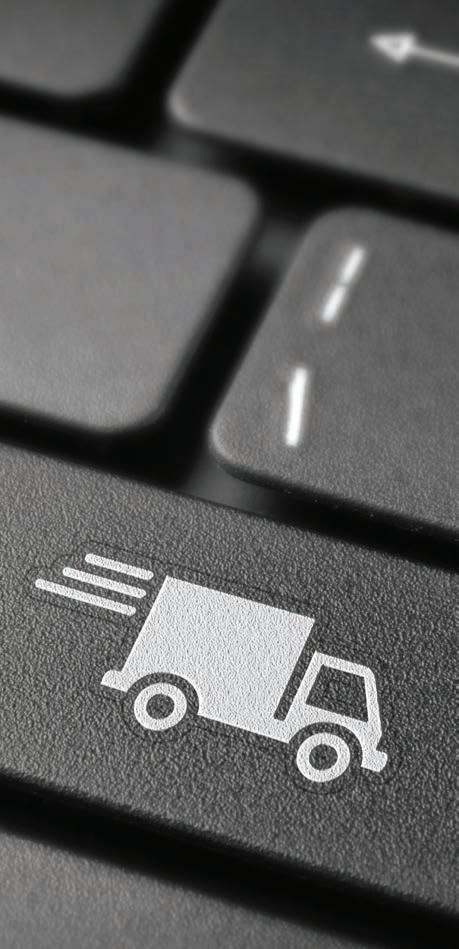
one thing, having them talk to each other is another, and extracting the data is a further opportunity. The question we are starting to ask is what are you doing with that data? It needs to be ranked and stacked, based on a critical occurrence. What are the priorities for addressing all of the information you are getting from all of these devices?
“We should be able to go deeper into the data and work out what are the ongoing issues and what are you doing about them. Is there a process so that these issues do not reoccur? In terms of in-cab convergence, nirvana’s a wonderful thing, but with them all talking to each other, what is the customer doing with the data?”
Data in the truck, becomes data in the operations system and in the client’s systems. Just having the data isn’t enough, the operation needs to analyse it in order to get some value from it.
“You could almost ask yourself, what is our industry,” says Patrik Tharna, Scania National Aftersales Manager. “Are we in the trucking industry? Or are we in some
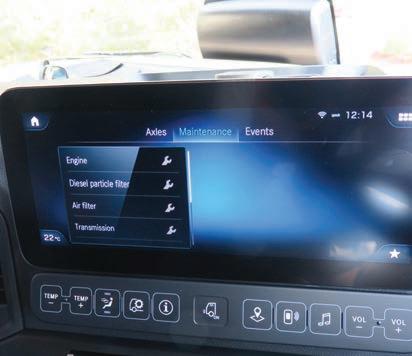
new space where logistics and trucking are all coming together? We have to look for convergence within this eco-system.
“In this space, there’s some very specific trends that we can identify. Everything is going to be connected, there will be electrification and things will be autonomous. T here will be new business opportunities for new players who weren’t active in this space in the past.”
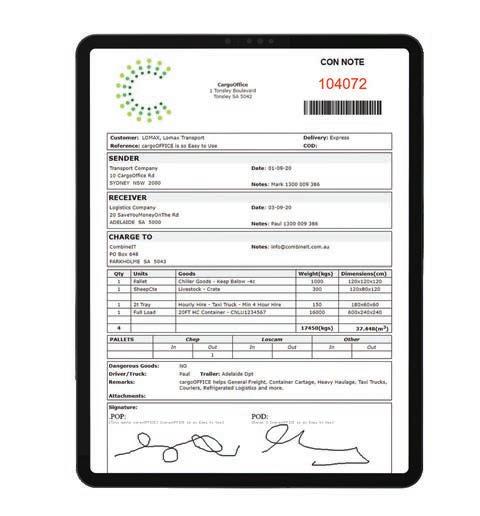
Trailer Telematics:
Information Integration
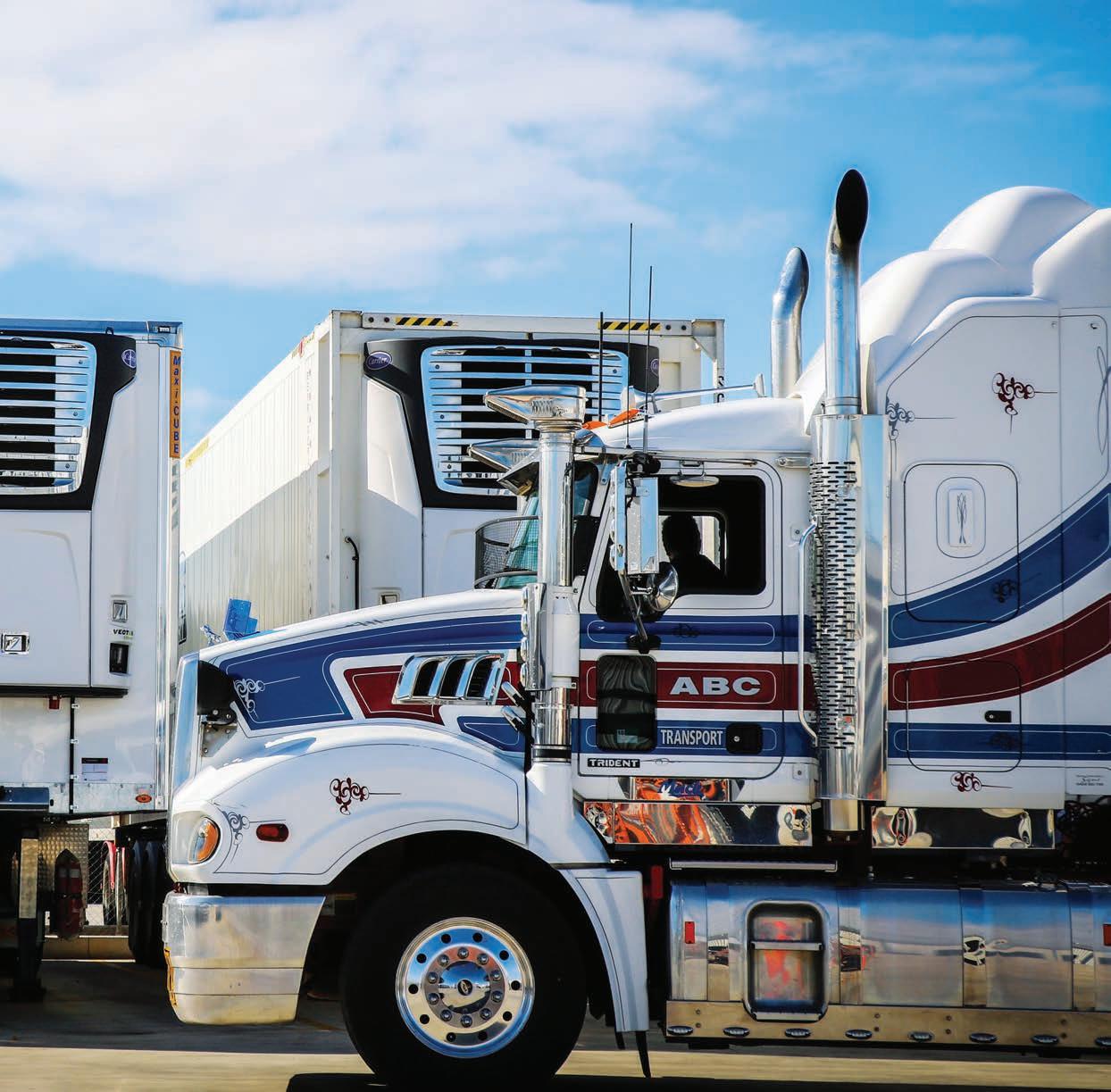
The ongoing advancement of information technology for trucking applications is providing an increasingly integrated solution where a large number of parameters relating to trailer operation and load integrity can be monitored remotely using a device or screen. Paul Matthei looks at some examples of where this new data is being used.
Gone are the days when every individual aspect of truck operation that requires close observation needed to be monitored using an individual system for each element.
The modern CANbus system of communication enables all facets of truck operation including but not limited to GPS tracking, axle weights and temperature control of refrigerated trailers to be monitored via a device or computer screen.
A great example is the new Loadman App-based onboard weighing system which is compatible with Android devices. The system Loadman offers is a Garmin Fleet 790 Tablet which, in addition to being the seven-inch capacitive touch display for the Loadman scale system, incorporates reverse camera input, truck-specific GPS navigation, dash cam and Bluetooth connectivity for mobile phones. It is also possible to use the system for GPS tracking, subject to compatibility with “IN REGARD TO REFRIGERATED TRANSPORT EQUIPMENT, THERMO KING HAS A LONG AND SUCCESSFUL HISTORY IN THIS COUNTRY AND TK’S BLUEBOX TELEMATICS SYSTEM IS DESIGNED TO IMPROVE THE LEVEL OF REAL-TIME INTELLIGENCE AVAILABLE TO DRIVERS AND FLEET MANAGERS IN RESPECT OF TEMPERATURE CONTROL AND THE CONDITION OF REFRIGERATION EQUIPMENT.”
the tracking company.
According to Loadman Managing Director, F rank Parker, the system has graphics applicable for all rigid trucks with up to and including five axles, with the font colour automatically changing to red when the truck is overloaded.
“With the App-based system, we no longer need to install the typical screen we have always used as a display,” says Frank. “With rigid trucks there is a direct connection from the applicable sensors into a two-channel – one for the steer and one for the drive axle group – CAN Coder which connects directly to the tablet display.”
Frank goes on to explain that removing the meter and replacing it with the Garmin tablet does not significantly change the cost of the system in rigid truck applications, although he stresses that multi-combination vehicles require an additional interface component.
“The App enables calibration and other setup and troubleshooting functions to be completed using the tablet screen,
Makes Trucks Safer
Mobileye’s retro-fit solution upgrades any vehicle:
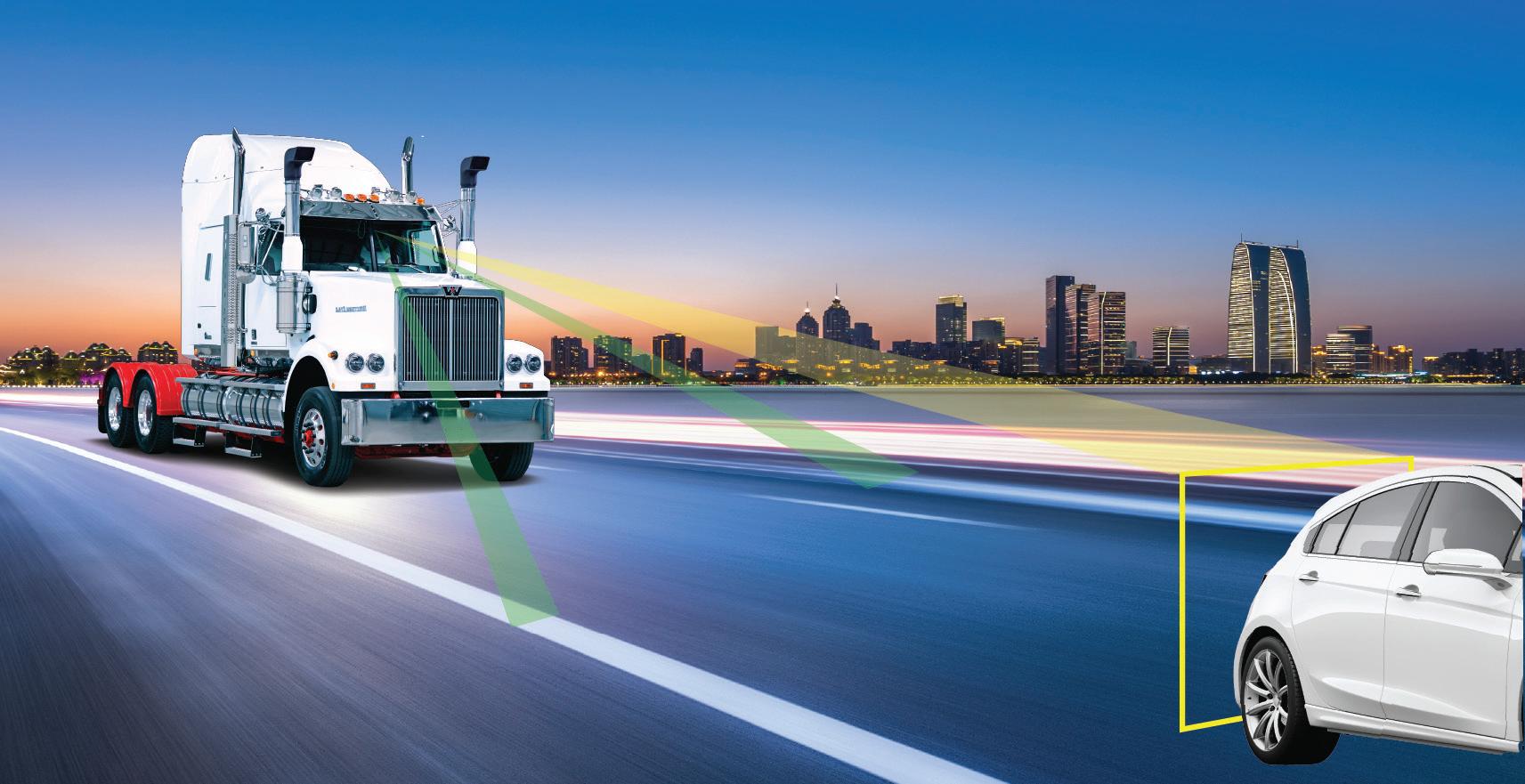
• Lane Departure Warning • Forward Collision Warning • Pedestrian Collision Warning • Speed Sign Recognition • Tailgating Reminder
With no ongoing subscriptions, data costs, maintenance or servicing requirements, Mobileye is a cost-effective one-off investment. With a 3 year warranty.
Finance now available.
It’s never been easier, or more affordable, to enhance the safety of your truck.
with access to the system controlled by password protection,” says Frank.
THERMO DYNAMIC In regard to refrigerated transport equipment, Thermo King (TK) has a long and suc-cessful history in this country and TK’s BlueBox telematics system is designed to im-prove the level of realtime intelligence available to drivers and fleet managers in respect of temperature control and the condition of refrigeration equipment.
The system comes standard on the TK SLXi platform of trailer refrigeration units, offer-ing access to the raw data needed to help improve both fleet efficiency and the quality of delivered cargo. To access the data, operators only need theTK Reefer app, which is a free of charge app that enables remote Bluetooth connectivity to TK SLXi units.
ON THE PULSE Braking Specialist WABCO offers a trailer telematic solution called TX-TrailerPulse.
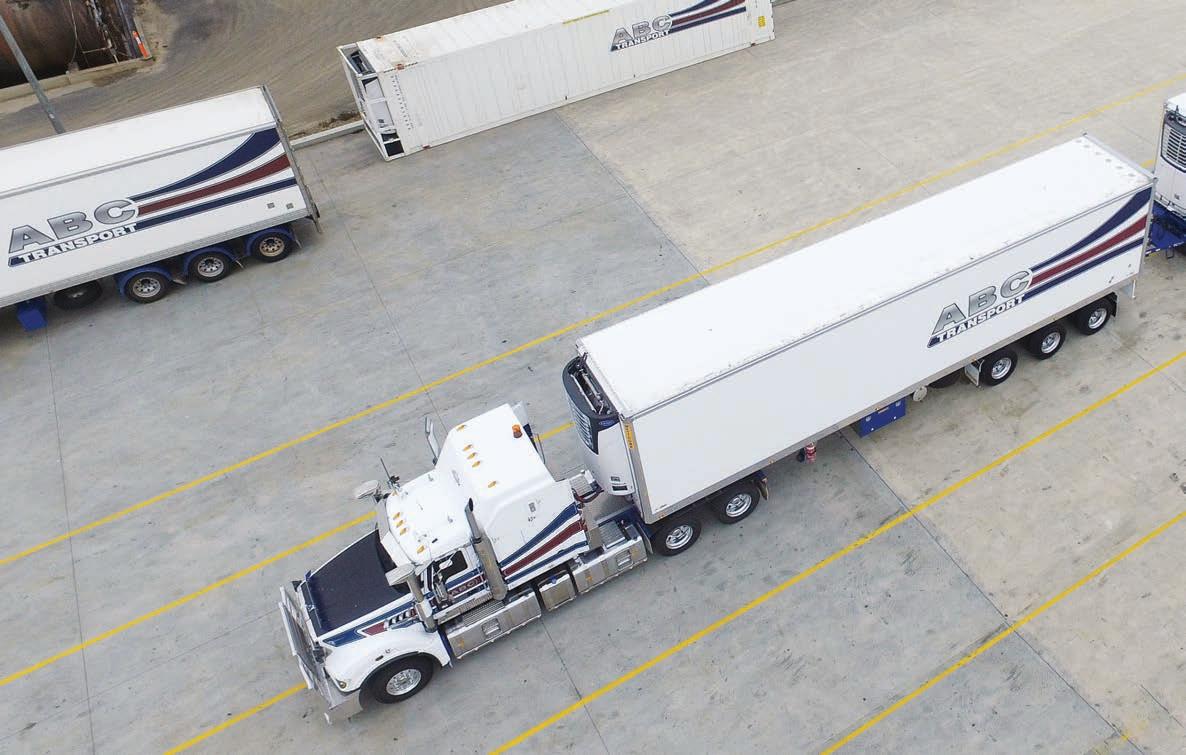
This is a system that links up with the Trailer Electronic Braking System (TEBS) elec-tronic control unit (ECU) and reads braking information and then feeds the information to the Cloud for companies to access it.
Directly connected to the TEBS, the solution captures and processes TEBS and trailer diagnostics data via the webbased TX-TRAILERFIT portal, which assesses the tech-nical health of the trailer and can provide, for example, root cause indication and repair hints.
Additionally, operators can monitor the TEBS use over a trailer’s lifetime and check critical TEBS events. Health and diagnostics insights can be shared easily and securely with workshops and service partners, building a digitally connected repair and mainte-nance chain which can create a direct positive impact on the total uptime of fleet vehicles.
Besides providing the same information in the back office as a technician would access with a physical readout in the workshop, TX-TRAILERPULSE makes the data available remotely and in real time.
Specifically, the solution can zoom in on trailer details, providing, amongst others, the trailer brand, model, EBS type and axle configuration. As for diagnostics data, TX-TRAILERPULSE processes the diagnostics code history as recorded by the Operating Data Recorder (ODR) that addresses topics related to maintenance and uptime management, specifically highlighting events such as tilt alerts, insufficient tyre pressures, roll stability (RSS) events, warning lamps, supply pressure warnings, wheel-speed sensor, demand pressure sensor and axle load sensor data.
The occurrence of any new Diagnostic Trouble Code (DTC) or EBS warning lamp forces a new read-out of ODR data and results in a constantly updated trailer health score for each vehicle.
A historical overview of these error codes and warning alerts in the TX-TRAILERFIT portal allows for determining patterns or reoccurrences
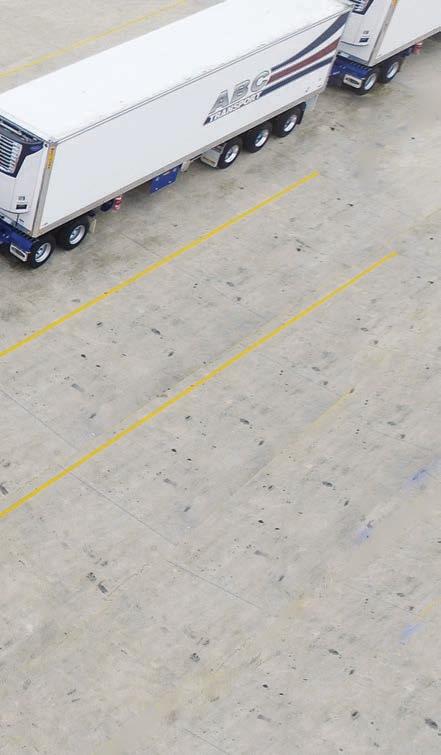
of technical issues.
Taking DTCs and contextual data into consideration, a health score is generated for each individual asset of a fleet, allowing the fleet operator to better prioritise maintenance activities, and to act preventively on any degradation of a trailer health score.
Fleets can securely share these overviews with workshops, allowing accelerated repair and maintenance by improving the communication flow throughout the service chain regarding trailer health, its generated error codes and diagnostics data.
Therefore, workshops can be better prepared to perform analysis, to determine the best course of action and make prompt decisions, and to be practically prepared by the time the trailer arrives.
CARRIER CONTROL Drilling further into the refrigerated transport sphere reveals a similar level of sophistication exemplified by Carrier Transicold’s eSolutions platform, which also enables op-erators to intelligently monitor connected refrigeration systems from anywhere in the world.
The system provides vital information for producers, drivers, transport managers and retailers on the products being transported and the vehicles transporting them. Accessible via desktop, smartphone or tablet, the eSolutions software offers operators 24/7 ac-cess to valuable data on their refrigeration systems, including: • Remote temperature monitoring • Two-way operational management and control • Capability in-depth service and utilisation reports • Geo-fencing • Operational alarms
There are two eSolutions service packages options, Access and Premium. The Access package supplies fleet managers with the relevant features for their business, including temperature monitoring, geo-localisation, service and utilisation reports. The Premium package additionally provides the possibility to control the unit at a distance and gives additional access to functions relating to service and regulation.
Each package is fully accessible through a standard web browser
“With the App-based system, we no longer need to install the typical screen we have always used as a display.”
and includes the installation of the box embedded into the refrigeration unit to collect, share and analyse all cold chain data.
According to Carrier Transicold, reefer telematics can help food processors, trucking operations and grocery retail operations maintain endto-end cold chain integrity. The company says more fleets are taking advantage of telematics systems to control transport refrigeration equipment from a central location, including changing cargo temperature profiles and set points, and making adjustments as needed whilst the cargo is in transit.
These systems also enable customers to apply telematics capabilities to provide records for tracking and traceability purposes. Fleets can remotely and intelligently monitor and download temperature data reports from anywhere in the world via a desktop, smartphone or tablet, and share information with key cold chain stakeholders without having to collect data onsite at the point of delivery. This provides vital information for producers, drivers, transport managers and retailers on the products being transported and the vehicles transporting them.
According to Carrier Transicold, the additional demands COVID-19 has
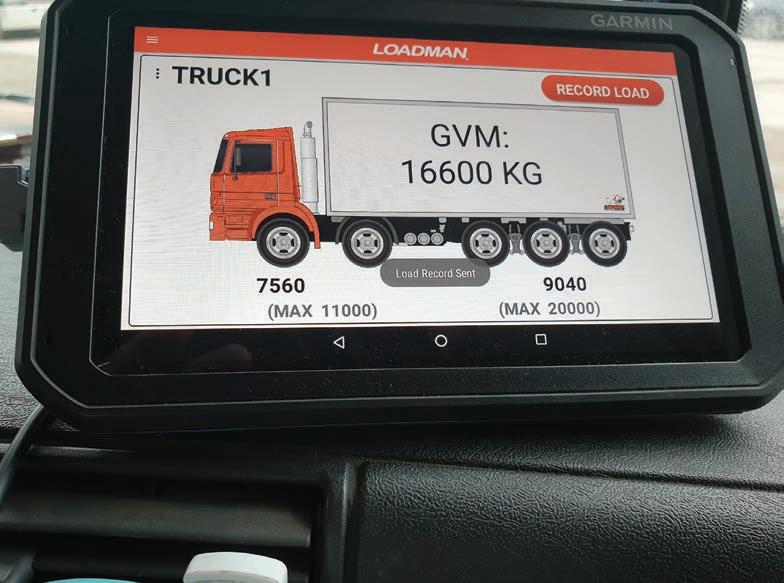
placed on cold-chain networks have been met by these systems in assuring consistent supply availability for the likes of supermarkets and other retail food outlets during the pandemic.
Greater connectivity can improve efficiency and reduce waste for the entire cold chain, helping food and pharmaceuticals safely reach the consumers who need them. It can also help transport operators better manage shifts in demand, like those recently seen between food service and food retail.
THE CRUCIAL LINK An operator who appreciates the value of Carrier Transicold’s eSolutions technology in ensuring cold chain integrity is Simon Fraser, owner of Link Cold Storage and Transport based at Wangaratta in country Victoria.
The company runs a fleet of refrigerated semi-trailers and delivery vans servicing clients in Victoria and New South Wales, transporting the likes of hanging meat as well as chilled and frozen palletised products.
Having certification for food transportation standards including HACCP, Australian Government Department of Agriculture and Water Resources and PrimeSafe, Simon says the ability to constantly monitor the temperature in each trailer and van is crucial to the operation of the business.
“It certainly gives you more power and control within the business because you’re eliminating the mistakes that people can make,” says Simon. “It enables you to have more than one set of eyes watching one truck, one fridge and one temperature, in our game temperature is everything.”
Simon explains that in addition to temperature monitoring he uses Carrier Transicold’s eSolutions to glean information such as geographical location and as an early warning system for potential problems that could pop up.
“It also gives us peace of mind in that we can prove to customers that while their product was in our care the correct temperature was consistently maintained,” he says. “We can send that information to the client in PDF form and it puts their mind at ease.”
Conversely, Simon says, it provides a record of accountability along the cold chain, particularly in the case of a product not being within its correct temperature range when picked up.
“In that case we can prove to the customer that the product was hot when it was loaded, and we have done this with a customer who subsequently accepted that this wasn’t our fault. This can be proven on the spot, before the truck even gets home, which instantly takes the doubt out of the situation.”
According to Simon, the information also enables the company to help its customers with their product handling procedures, given the temperature information at the point of loading is readily available.
“For our peace of mind, we quite often download the information and have a look at what’s happening with our loads and if we see a discrepancy we can talk with the customer and help
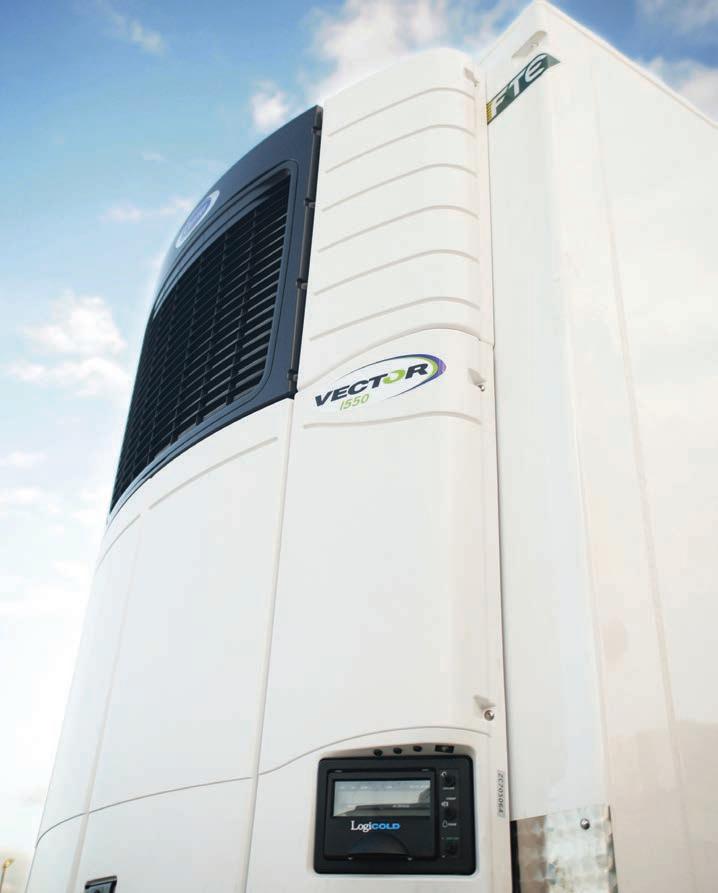
them improve their practices. It helps us work with our customers to get the best results for everyone.”
The company’s Volvo prime movers are equipped with Dynafleet monitoring systems which track the vehicles and also provide operational data on how the vehicle is being driven.
CONVERGENCE The data captured on trailer health is intended to also enable fleet operators to more easily comply with regional or national regulations related to road safety. Whether it be monitoring axle weights, trailer refrigeration temperatures or tyre pressures, the latest technology in trailer telematics enables these and many more data sets to be monitored by operators via a com puter screen or device from any location in the world.