
18 minute read
KEEPING FREIGHT COOL IN BRISBANE
by Prime Group
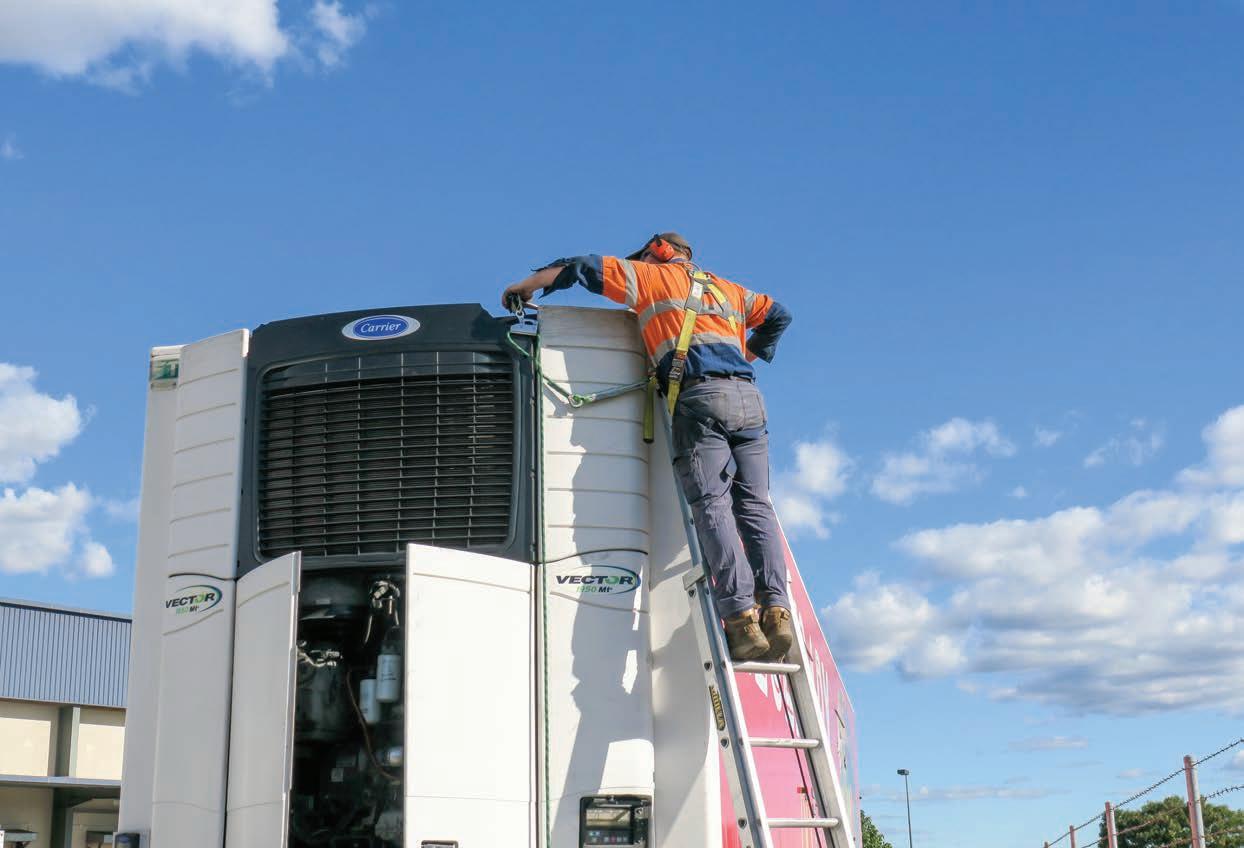
COOL KEEPING FREIGHT IN BRISBANE
Tech Know visits the Carrier facility to see how the job of keeping freight cool in Brisbane is handled on a day-to-day basis.
Here in Australia, though we may not realise it, refrigerated units have to work in the harshest conditions they experience anywhere in the world. This means keeping the wheels of refrigerated distribution turning is one of those tasks that has to be done, and done well.
Carrier Transicold is a part of the global Carrier organisation, which supplies HVAC, refrigeration, fire, security and building automation technologies all over the world. The company’s integrated network of support begins at the factory and ends with the end customer.
Altogether, Carrier employs around 50 people around Australia, with many fulfilling maintenance roles in the company’s facilities. Tech Know visited the Carrier facility in Brisbane to see how the system works.
Carrier’s customers in different states look for different kinds of services. Most Queensland customers prefer all maintenance work to be done on their own site, while Victorian customers prefer to drop a trailer of rigid into the Carrier workshop for repair. The Sydney operation has an even spread of customers across both preferences.
The Melbourne operation is one of the largest, as this is also where brand new units destined for the Victoria-based trailer manufacturers are stored. The Sydney operation is the main location for parts warehousing, with the city only an overnight delivery away from most of the Carrier locations around the country.
Carrier’s technicians need to know how to handle all of the latest technology, while also at times working on units as old as 20 years or more. As we know, all levels of technology have moved forward dramatically over this period, but the technicians need to be ready for any kind of problem.
The skilled Carrier technicians have access to the global Carrier network with the latest diagnostic tools, software updates and factory service bulletins, with the Field Service system giving them instant access to unit history and fleet data as well as manuals and any technical resources required. Using iPhones as their interface, they can also supply the data specific to the fridge on which they are working, including service history and any faults which have been detected. The system also handles job allocation and keeps the managers and customers up to date on job progress.
Some refrigeration units may only get any attention when there is a problem, while, at the other end of the scale, some may well get serviced more than necessary to enable the maintenance intervals to tie into the maintenance needs of the trailer to which they are fitted. From Carrier’s point of view, normal maintenance is needed every 3000 hours or 24 months, whichever comes around first.
Preventative maintenance is the name of the game with these refrigerated units. In
the latest generation of units, they include machine learning able to flag potential problems by monitoring the unit all of the time. This gives Carrier the ability to swap components out early any avoid unforeseen breakdowns.
The latest fridges have changed over from the conventional set up, where the small diesel engine on a fridge unit would run the fridge and generate electricity to run the fans. Now, with the Vector design, a diesel generator supplies electric power to run a fully electrified cooling and fan system. With this simplified system, the costs of maintaining fridge units has dropped dramatically.
Carrier Transicold workshopsintegrated service network covers a large part of Australia with service centres strategically located close to main roads, industrial centres and transportation hubs. Customers access help through Carrier Transicold’s OneCALL 24-hour nationwide emergency service.
Carrier Field Service systems gives customs easy access to their fleet data with a customised portal. When combined with Carrier eSolutions telematics, along with temperature monitoring and GPS tracking, it also provides important maintenance information such as unit engine hours and other important data.
The connectivity available in a modern
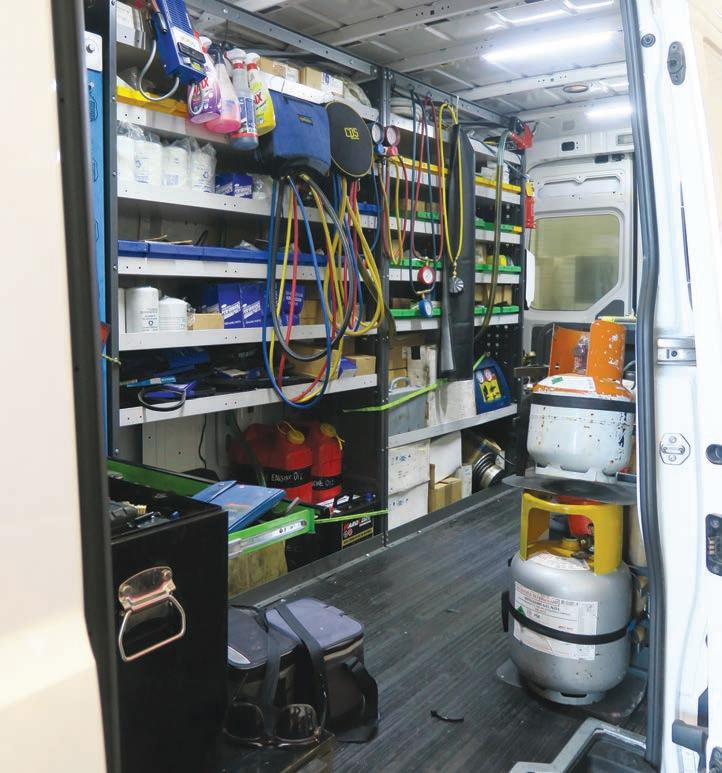
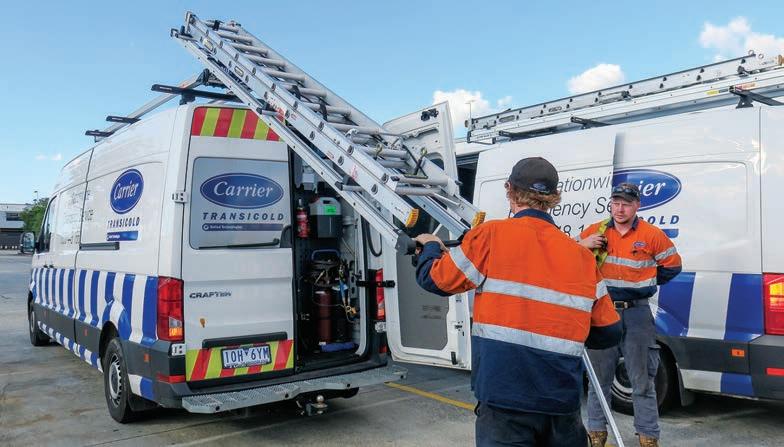
fridge unit means that the Carrier operatives can contact any of the latest generation units and pull down any of the required data about the service history and condition of the unit. The data flow can be used to give the operator and the Carrier technicians a heads up about any potential problems.
In terms of maintenance agreements, Carrier has developed a tiered service model offering customers a range of options to meet the particular needs of their business.
The basic Core tier is a maintenance scheme developed for customers who have a warranty, but in the long term will probably carry out most of the maintenance on the fridges themselves.
Stepping up to the Enhance level of contract maintenance is more akin to the kind of contract maintenance system used by many operators for their trucks. There is a monthly fee based on the type of work the fridge units are required do and what their maintenance requirements are.
The Elite maintenance plan offers the most comprehensive service available to Carrier customers and it is said to have one purpose, which is to provide customers with complete peace of mind. Carrier will manage the customer’s maintenance program for them. In fact, what is happening at this level of support, is that Carrier is actually managing the fridge unit for the customer. It is monitored and that data is analysed to look for early signs of any possible issues with the aim of making preventative interventions to keep the fridge unit running most efficiently and reliably.
GETTING TO KNOW YOUR BRAKES
Trucks, trailers and buses demand a lot from their brake components as they have to perform in the toughest of applications. Meritor is one of the few foundation brake manufacturers that can offer a complete portfolio of air disc, hydraulic disc and air drum brakes.
One of the most popular brake set-ups in Australia is the Meritor Q-Plus brake. Here are some tips on how to get the best out of this braking system.
The Q-Plus shoe is designed to contact the centre of the shoe at the new lining condition. This designed “crown” is necessary to control brake torque. Due to tolerance stack ups, the crown is designed to contact the drum first.
This condition will exist until the linings wear to the drum’s inside diameter over several brake applications.
This is often called “bedding”, “burnishing” or “green lining condition”. Once the bedding is complete, a full contact will exist between the lining and the drum.
A “bedding-In” process in accordance with the Australian Air Brake Code Of Practice is required whenever new linings, brake shoes and or brake drums are replace to achieve good brake performance.
BRAKE MAINTENANCE AND DIAGNOSTICS The point at which the brakes need to be relined is when the lining thickness reaches 0.25 inch (6.3mm) at the thinnest point. To avoid damage to the components, rivets must not touch the drum.
Meritor recommends that you replace the springs, rollers, camshaft and anchor pins at each reline. Check the drum and perform major inspection when you reline the brakes.
Check the up-and-down and sideto-side end play of the camshaft to determine if you must replace the camshaft bushings. If the total movement is more than 0.03 inch (0.76 mm), replace the bushings.
If axial end play exceeds 0.06 inch (1.52mm), remove the snap ring and add an appropriate number of spacing washers between the slack adjuster and the snap ring. Correct specification is 0.005 – 0.06 inch (0.127 – 1.52mm).
Brake force imbalance will result in premature lining and drum wear from the brakes being over-worked. Brake imbalance can be defined as each brake in a vehicle or a combination vehicle not doing its equal share of the braking.
Brake imbalance can be caused by pneumatic imbalance, well-adjusted and poorly-adjusted brakes, incorrect lining mix for the application, using the trailer brakes to stop the combination vehicle, worn foundation components, etc.
A defective brake, (out-of-service) is defined as brake with one or more of the following conditions: - Lining cracks or voids over 1/16 inch (2mm) in width observable
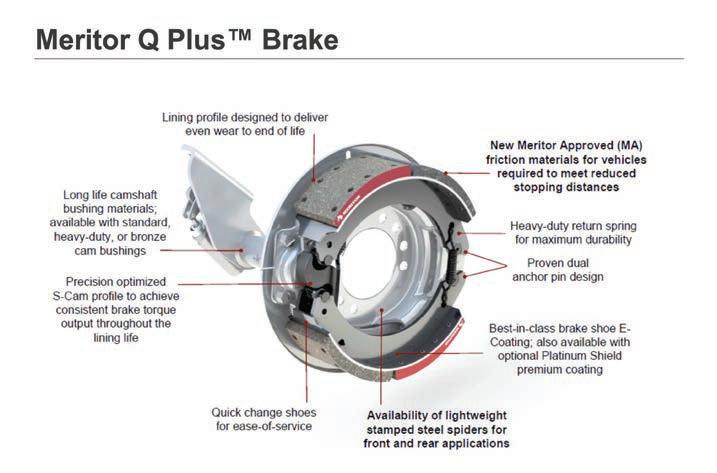
at the lining edge. - Cracks that exceed 1.5 inch (38mm) in length. - Missing portions of a lining segment such that a fastener is exposed when viewed from the lining edge. - Cracks extending across the lining face through the lining edges. - Loose lining segments. - Complete lining segment missing.
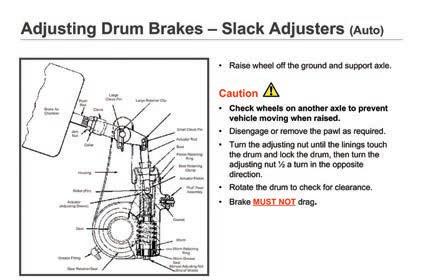
TRW: The True Experts in Braking
Available through ZF Services Australia, the TRW brake pad line up sets a new standard for commercial vehicle braking, with an expert range transforming the premium end of the replacement aftermarket.
With a reputation earned through 100 years of OE quality components across the automotive spectrum, ZF’s current TRW offering, features a selection of commercial vehicle brake pads, suitable for most popular makes of truck, bus and trailer.
“ZF Aftermarket with its TRW product brand has developed a worldwide topflight reputation for their superior braking products, recently we have expanded our offering within passenger car with all applications finding favour with local workshops,” said Steve Borg, Business Development Manager for TRW.
“TRW’s intimate knowledge of the field results in braking components that not only show the way in terms of safety, but also for ease of installation by technicians.
“With the input of 6,000 experts, engineers and designers worldwide, TRW brake pads are formulated with advanced friction materials for improved efficiency, which results in a product that has been verified in independent tests to outperform comparable OE parts.
“For workshops, TRW brake pads from ZF Aftermarket come complete with all necessary accessories and instructions in the one kit for quick and simple installation.
“What’s more, the disc pads are fully compatible with the latest anti-lock braking systems, where applicable.”
Since brake discs started to supersede drum brakes in the commercial vehicle market during the 1980s, TRW has been at the forefront of developing specialist products that lead the replacement parts aftermarket.
For instance, the patented backing plates specific to the heavy vehicle market produced in-house by TRW, resulting in significant improvements in the shear and material contraction properties of the pads.
Years of expert input has seen friction materials developed that have a high resistance to brake fade, while also featuring the ability to recover quickly when wet, at the same time providing the driver braking force that is consistently proportional to the pressure applied on the pedal.
Much of the research and development comes off the back of extensive product testing, with three key areas focussed on, including high performance testing of bedding-in behaviour and brake fade, alpine simulations on long downhill sections, and dynamometer testing in conjunction with benchmarking to the ECE R90 homologation standard.
Via independent analysis carried out by leading German applied research organisation, the Fraunhofer-Gesellschaft, ZF’s TRW products proved to outlast the competition in extreme conditions, including OE products.
TRW brake pads produced using Powder Adhesive Technology, which bonds the pad to the carrier plate without the use of solvent-based adhesives.
By using powder, a total of 150 tonnes of solvents are eliminated from the manufacturing process each year, a process which earned ZF the Partslife environmental award for 2019.
To find the TRW brake pad kit from ZF Aftermarket that is ideal for your application, check out the TRW website at www.aftermarket.zf.com/au/trw with the range complimented by all necessary consumables, including fluids, greases and brake cleaning products. services, and a worldwide service network has made ZF a sought-after partner and number two in the global automotive aftermarket.
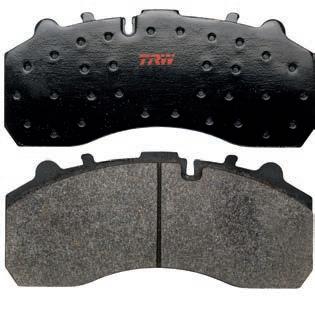
GREASE FREE 5TH WHEELS



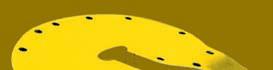
• 30 + years in the market place • Clean, grease-free fi fth wheel • More cost effective • Easy to fi t • Consistent steering characteristics • Environmentally friendly • Australian designed & manufactured • Used by some of the most highly respected companies since 1990
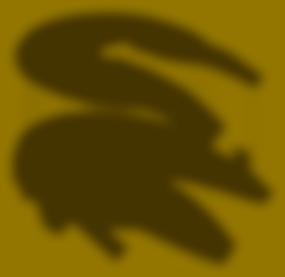
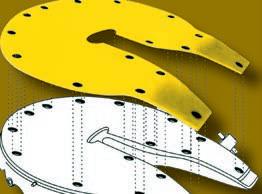
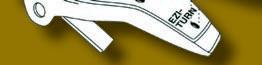
EZI EURO 16B
EZI JGL
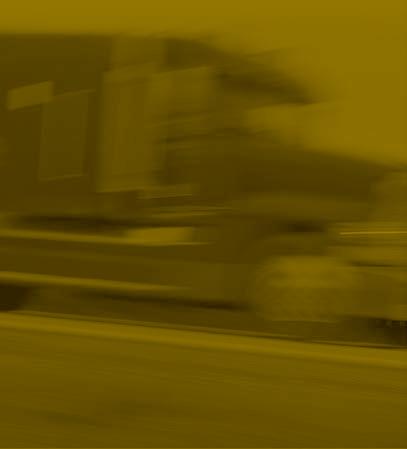
WE STOCK AFTER-MARKET REPLACEMENT KITS TO SUIT MOST GREASELESS OR LOW LUBE FIFTH WHEELS
IS MANUFACTURED IN AUSTRALIA BY: EZI PRODUCTS PTY LTD
Let’s Talk About Air Supply
No, we’re not talking about the Australian 80s pop band. Let’s talk about air supply, as the crucial link between the driver’s brake pedal and the trailer braking system.
With extended truck service schedules and greater vehicle reliability, it becomes easy to overlook what used to be a daily chore for drivers, that is, checking the air supply is dry and without leaks.
The demands on the truck air supply has increased over the years with more axles and longer trailers. When you add additional functionality, such as a tyre pressure inflation system, lift axles, steer axles and supplementary equipment, that load gets even greater. It becomes a challenge to provide clean, dry air at sufficient pressure through these extended circuits to enable correct operation of these various systems.
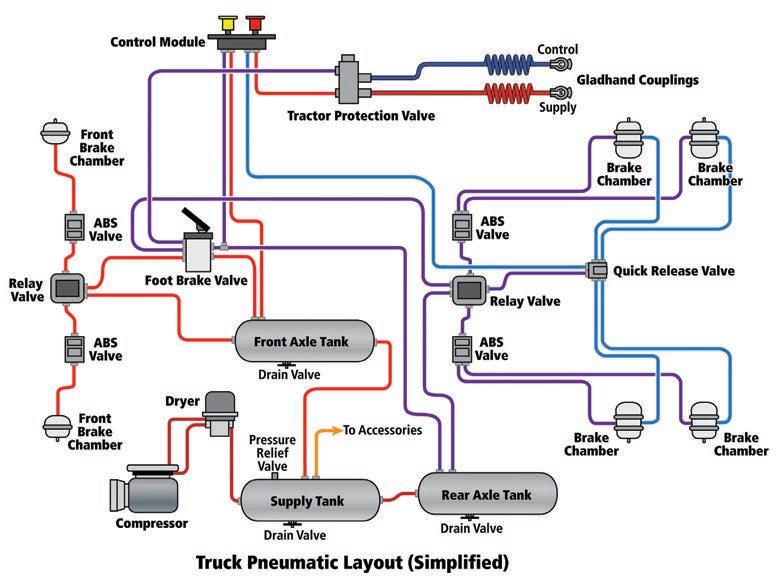
COMPRESSOR The compressor is the starting point for the air supply system. It needs to be able to supply enough air pressure and flow to ensure all systems can operate correctly. The drive belt, air filter, lubrication and air dryer cartridge all need regular checking and replacement where necessary.
Trailers having difficulties with air springs, or associated systems, should have the pressure checked at the rearmost point on the trailer system when it is connected to the truck and in operation. That is when the system is raising the suspension.
Often, the pressure at the truck’s compressor is nowhere near the pressure reaching the last axle on the trailer. The system must be checked for air leaks, kinked or damaged air lines. If everything is in serviceable condition, a simple solution to a low available air pressure may be to raise the pressure setting of the compressor. However, that is not always possible, especially on an older truck, and even then, it may not overcome insufficient air volume capacity from older air pumps. In these cases, a new air compressor with higher flow rate and/or higher pressure setting would be advisable.
CONTAMINATION The air system should be checked regularly for contamination by oil or moisture. Traces of oil coming from the compressor are normal, but it must not be any greater than that. Moisture in the system is difficult to eliminate entirely. However, most moisture should be removed by the dryer and regular (daily) drainage of the air supply tank. Most trucks now use automatic drain valves but the operation of these needs to be checked regularly. The system air dryer should be inspected or replaced at regular intervals.
It is important to rectify any problems quickly or it will result in corrosion in brake valves, brake chambers and other pneumatic systems. Lift axle control valves and advanced automatic tyre pressure control systems, such as Hendrickson TIREMAAX PRO, are particularly susceptible to dust and moisture contamination.
Regular checking, cleaning and examination is a vital part of regular air supply maintenance. It is important to remember that the driver also plays a vital part in these precautions.
THE SWEET SPOT: A HOT TIP FOR OPERATIONAL EFFICIENCY
With economic recovery a key focus for the latter months of 2020, many businesses will be looking outward for opportunities to maximise operational potential, while getting back to business.
In an ever-competitive truck market, selecting equipment that is specifically designed for the application at hand, and which can be put to work without hesitation, is critically important for buyers.
THE CHALLENGE At this point in time, a large portion of those buyers are plying their wares in the trade and construction industry. The effects of the pandemic have placed renewed demand on this sector, with many participants taking advantage of government stimulus measures and choosing to ‘pull the trigger’ on upgraded equipment.
Challenges in this rugged application are common across the country. Payload, manoeuvrability, and access key amongst them.
The lion’s share of construction and trade work takes place in our densely populated cities and built areas. Margins are shrinking, sites are getting tighter and tighter, and the call for efficiencies on all these fronts is ever-growing.
Purchasing a truck is a significant investment in time and money for business owners, so ticking the box on the aforementioned items is a ground level requirement. Above all, the equipment must be fit-for-purpose.
THE SOLUTION To this end, Isuzu Trucks has long recognised the need for a light-duty, factory backed tipper with increased payload capacity and improved manoeuvrability.
The recent introduction of the NMR 60/45-150 Tipper and NMR 60/45-150 TriTipper to the market is a timely response this growing market demand. Both variants are available with a Torque Converter Automated Manual Transmission (TC-AMT) or a manual transmission, offering complete flexibility and driver access.
Critically, the NMR 60-150 Tipper and Tri-Tipper models offer operators additional payload, whilst preserving an efficient, compact footprint.
Purposefully designed with compact dimensions, the NMR Tipper and TriTipper models allow for the navigation of cramped construction sites and material yards, with operators also gaining the benefits of increased payload and the resultant operational efficiency.
Isuzu’s ECE-R29 compliant narrow-cab design delivers attentive ergonomics, including class-leading frontal and peripheral visibility and a complete safety suite, including driver/ passenger airbags with seatbelt pretensioners. The models also include Isuzu’s Electronic Stability Control (IESC), Anti-lock Braking System (ABS), Anti-Skid Regulator (ASR) and HillStart Assist (HSA) for manual models.
The NMR Tipper and Tri-Tipper models feature a high-quality, Shinmaywa-built steel tipping body with cubic capacity of 2.0 m3, while the innovative Tri-Tipper variant has the capacity to tip the load to the rear, left or right.
Isuzu Tippers and Tri-Tipper bodies also come standard with an array of features, including rope rails, non-slip side steps and an auto-release body lockdown hook and two-way tailgate. The truck and tipper body, along with all genuine OEM and Isuzu parts and componentry, are covered by the brand’s 3-year warranty*.
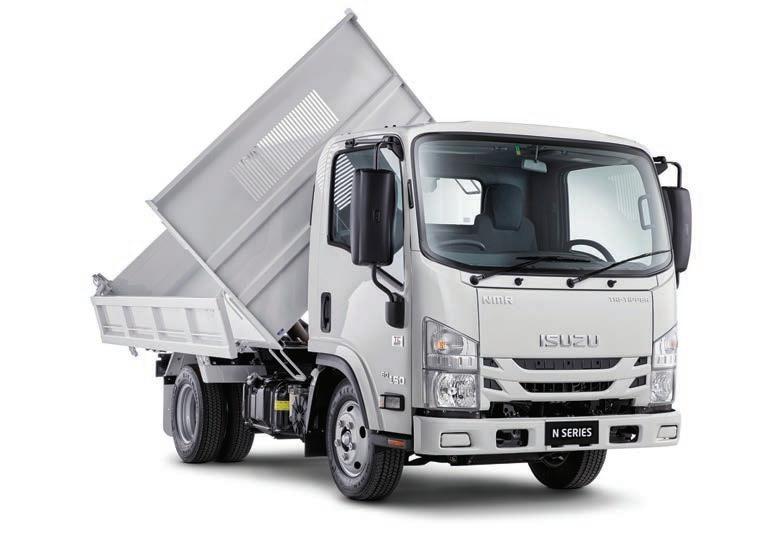
OPERATIONAL ADVANTAGES The NMR Tipper and Tri-Tipper models are available in two GVM ratings—6,000 kg and a 4,500 kg option for car license drivers.
Powered by the 4JJ1-TCS Isuzu engine, rated at 150 PS (110 kW) @ 2,800 rpm and 375 Nm @ 1,600 – 2,800 rpm, both the NMR Tipper and Tri-Tipper offer a combination of performance and economy.
NMR Tipper and Tri-Tipper models are available with Isuzu’s Torque-Converter Automated Manual Transmission (TC-AMT), further enhancing durability and parts longevity. *For warranty terms and conditions please visit: https://isuzu.com.au/caresupport/warranty/
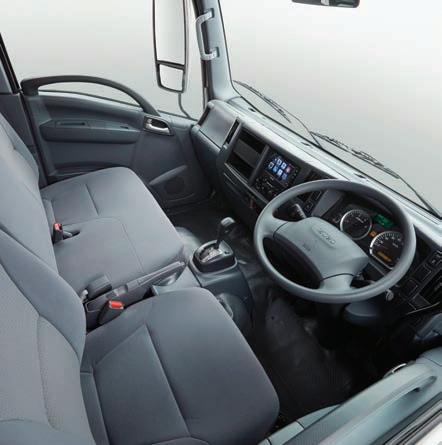
Isuzu’s ECE-R29 compliant narrow-cab design delivers attentive ergonomics.
UNDERSTANDING FIFTH WHEEL COUPLINGS
There are several critical safety aspects to heavy vehicle combinations, one of which is couplings and understanding fifth wheel couplings is vital to the safety and efficiency of a trucking fleet. Bob Woodward, Chief Engineer, Australian Trucking Association, explains.
Too often fifth wheel couplings are taken for granted because of familiarity. However, if those critical safety items are functioning normally, and in accordance with requirements, regardless of what else may happen, the vehicle can be brought to a safe stop.
Mechanical couplings that connect vehicle units, prime mover to trailer, or trailer to trailer have been developed to facilitate interchangeability and accordingly, standards have been developed to ensure connectivity compatibility of the various coupling types.
The most common mechanical coupling used in multi-vehicle combinations is the fifth wheel and kingpin. But these are available in several sizes two inch, three inch and 3.5 inch, check the fifth wheel and the kingpin.
Coupling and uncoupling also varies from operation to operation, from once a month or once a week, to as much as eight times in a single day. The more often coupling and uncoupling occurs, the greater possibility of a critical aspect being overlooked.
To combat this and assist operators with their procedures, the ATA’s Industry Technical Council has developed the Fifth Wheel Coupling and Uncoupling Guidelines Technical Advisory Procedure (TAP).
The TAP is a set of guidelines that provides a consistent, clear and safe procedure for coupling and uncoupling prime movers and semitrailers using fifth wheel couplings, and addresses several key factors including technical and safety considerations, visual inspections, and coupling and uncoupling procedure.
The TAP was created by an expert Industry Technical Council working group, before review by the ITC and approval from the ATA General Council. Developed by the industry, for the industry, the TAP was created to meet the needs of operators and fill the gaps in the vehicle standards.
Fifth wheels allow quick coupling and uncoupling of semi-trailers, provide articulation for the combination, and provide additional stability and support to the semi-trailer. Where a fifth wheel is specially designed to have a turntable base as an integral part, the term ‘fifth wheel assembly’ includes that turntable base, and does not include the skid plate and kingpin, which are parts of the semi-trailer.
All procedures demand consistency, following an uninterrupted routine with an understanding of the importance and relevance of each step, and it is recommended that only one person undertakes the coupling or uncoupling procedure to prevent missing critical steps.
The Fifth Wheel Coupling and Uncoupling Guidelines TAP is now freely accessible on the ATA website, and designed to help those who unsure of technical interpretations, how to best meet their compliance requirements, or work as efficiently as possible.
Not only does the suite of ATA ITC Technical Advisory Procedures provide informative guidance and advice to industry members, companies also use the material to improve their current practices and for training purposes.
To view the Fifth Wheel Coupling and Uncoupling Guidelines TAP, go to www.truck.net.au/resource-library/ fifth-wheel-coupling-and-uncouplingguidelines , or to find out more about the Industry Technical Council at www.truck.net.au.