
11 minute read
A NEW STAR RISING
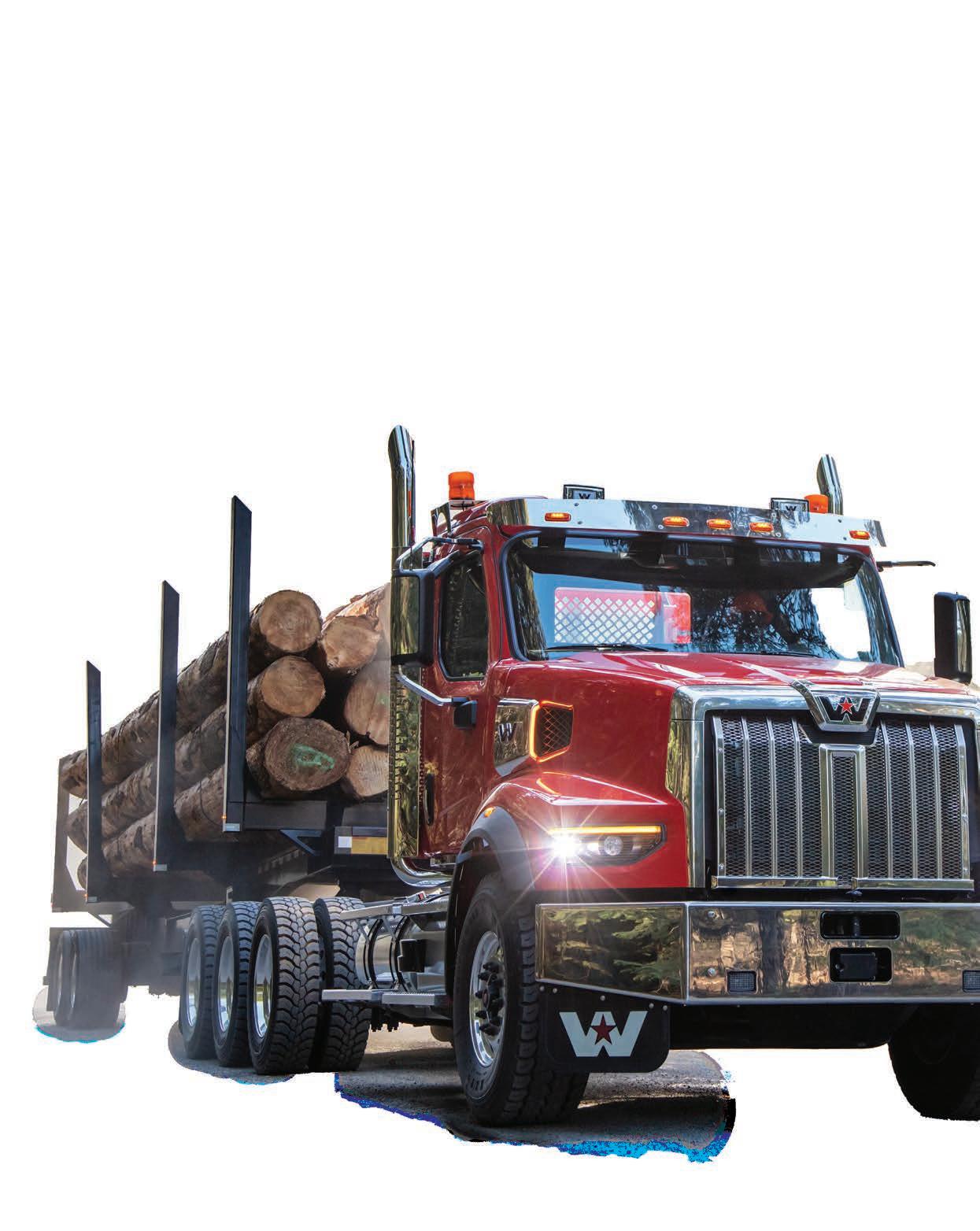

With the announcement of a new set of models from Western Star, Diesel looks at the X-factor which is now part of a new Star rising.
The release of the Western Star 49X sees the brand in the US bring all of the latest technology from the Daimler group into the design of this one truck.
The announcement took place, virtually, launching the truck onto the US market, with a new look and a new model classification. Immediately after this global launch, Diesel got an exclusive interview with David Carson, Senior Vice President Vocational Segment Western Star to get the latest on this new model and when it’s likely to arrive here in Australia.
The 49X is a radical overhaul of the Western Star platform and sees all of the major components either replaced or upgraded significantly throughout the truck. The 49X has a new, stronger, but lighter, chassis design and also includes a new modular cabin design, which is likely to be included in the upgrades of other Western Star models down the track.
Another radical change is the inclusion in the new models of the Detroit DT 12 automatic manual transmission. This is the US development based on the Daimler group’s AMT, which is also used in the Mercedes-Benz Actros and the Freightliner Cascadia. This means that the Western Star will be coming into line with the Daimler policy elsewhere in the group of having a driveline available, which is sourced from within the group itself.
The DT12 Vocational series of transmissions include side PTO capabilities that allow for added flexibility, and application modes and shift map strategies for all types of terrain. There is a Rock-Free Mode allowing the 49X to free itself from wheel stuck situations, an Off-Road Mode enables smooth driving on extreme terrain, Power Launch provides powerful takeoffs while protecting the clutch and driveline, and a Paver Mode which allows the truck to shift from Neutral to Drive without depressing the brake pedal when pulling away.
The new model also includes the latest iteration of what is known as Detroit Assurance, the complete electronic safety package, which has been developed by Daimler to be offered in all of its trucks. This system included features new to the brand like Side Guard Assist (SGA), Active Brake Assist 5 (ABA5), Tailgate Warning, Adaptive Cruise Control (ACC) to zero km/h, Lane Departure Warning, Video Capture, Intelligent High-Beam and Automatic Wipers and Headlamps.
The main engines on offer are the DD16 and DD15, which have had a successful run in both the Freightliner Cascadia, and also, in a European guise, in the OM473, which is fitted in the high power Actros models. This engine is renowned for its fuel economy and smooth application of power, especially when coupled with the group’s AMT.
“We’ll offer multiple options in transmissions, where we have invested $100 million in development of our DT12 vocational transmission,” says David Carson. “We will also offer other engine options which come from outside of the Daimler family. There will be other engine
and transmission options like Cummins, Allison and also different features which the market in Australia is accustomed to using.”
However, the test trucks which are going to be brought to Australia to test out the functionality of the new models in our conditions, will all have Detroit engines and the Detroit transmission, although some may use the Allison auto box. Currently, there is quite a large proportion of Western Stars being sold with Cummins engines on board, but the Penske organisation in Australia expects the DD16’s performance to sway a number of those Cummins loyalists across to the engine.
ASSURANCE “The way we sell the Detroit Assurance 5.0 in the US and in Canada is as an optional extra,” says David.” All of the new trucks which we are building for our dealers in North America as part of training and demonstration processes, will all have the full Detroit Assurance suite fitted as standard. We believe we are going to be successful in having customers who see the system as a value proposition when purchasing the truck.
“With the current models, we built them both in Portland, Oregon and in Cleveland. We will start production of the trucks in Cleveland and then we will industrialise our facility in Portland, but not start building them there immediately. We want to be sure, as we introduce a new product that we have our processes and our supply chain solidified.
“We have an extremely flexible production system here in the US, but we believe that both Cleveland and Portland will continue to be production locations for our trucks. With our flexible production system we are able to build current Western Star, new Western Star and new Freightliner in the Cleveland plant. In Portland, not
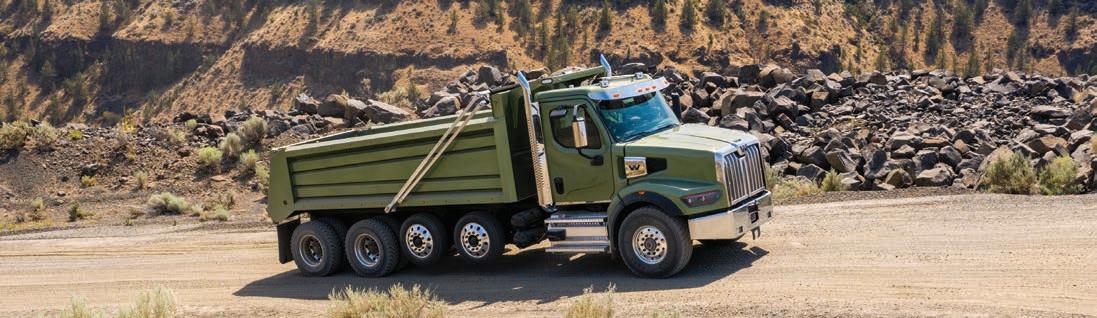
only will we be building the Western Star product, but also electric trucks. It’s a flexible production network with multiple product and multiple brands.”
One of the things which differentiates the Australian market from the US market is the level of customisation to meet individual customer needs that Australian operators are looking for. The plan is for the new production processes to be able to handle a larger amount of the kind of customisation Australians are looking for, actually on the production line in the US, with the rest of any customisation required to be done on its arrival in Australia.
With the introduction of the Detroit Assurance suite of safety systems in the new models, Western Star are picking up on the trend to increase the level of on-board safety electronic systems to safeguard and improve the comfort of the driver.
There is a balance to be had for Western Star, one of the important aspects of these new models is that the brand has to persuade potential customers that the unique appeal of the Western Star brand, which has served them well in the Australian market, is not diluted by its association with all of the componentry being introduced from elsewhere in the Daimler group.
“We are not unlike other global transportation companies,” says David. “It doesn’t make sense to have mutually exclusive capital investment on features and components which are more modular types. For safety technology, you don’t create safety technology for one brand that’s completely different from the same type of technology for another brand, it doesn’t make sense, or value for us as a company.
“What’s really great about the new 49X is that we get to utilise components and technology from the Daimler capability that exists for our trucks. We utilise all of this in such a way to create value for our dealers and our customers. Everything else is really brand specific. In developing this new truck our ‘true north’ heading was all about Western Star, but using best in class technology.
“When you look at the new dual stage LED headlights that we are introducing on these trucks. First, they look fantastic, but secondly they have this incredible functionality which is unique to this truck. It does not exist anywhere else in the Daimler suite of products and it is very specific to the 49X.”
David Carson was unwilling to go into detail about the timeline for the introduction of other models within the Western Star range, which will be developed in a similar way to the 49X. The future development of any other models, which are likely to make their way to Australia will have to go through the same process as has happened for the 49X, while, at the same time, keeping that balance between the traditional ruggedness of the Western Star brand with the realities of modern technology and the requirements of customers into the future.
“We’ll have trucks here next year for testing,” says Craig Lee, General Manager On-Highway Penske Australia. “We will begin testing trucks, suited well to Australian conditions. Then we will have trucks in Australia for delivery, either late 2022 or very early in 2023. We are very confident that this truck will be ideal for tasks like B-double prime mover as well as in rugged heavy duty and vocational work.
“The new truck, with its safety and all of the new technology, is going to allow us to be far more competitive in the general on highway long haul segment of the market, than what we are today.”
IT’S A DIRTY JOB,
BUT SOMEONE’S GOT TO DO IT
Livestock transport has been a part of Australian farming since 1788. Livestock must be moved throughout their lifecycle for breeding, fattening, sale and slaughter. While moving herds through country towns with drovers is largely a thing of the past, more animals than ever before are travelling around Australia on the back of a truck.
There is one thing that hasn’t changed and never will, food and water goes in one end and effluent comes out the other. This happens whether the animal is standing in a paddock, being walked through town or being carried on wheels.
Livestock can lose up to 5 per cent of their weight as effluent during transit. And because livestock trailers must be designed to provide ventilation, it is simply not possible to contain 100 per cent of the effluent that is produced. Modern trailers do however include internal drainage systems which may include an effluent capture tank.
So, you’ve hit the road with a full B-double load of cattle. You are heading out of a regional feedlot towards a processor in the big smoke 400km away. Just like people on a ride at the fairground, those tummies are not taking it well and within the first 100km you’ve got yourself a full effluent tank, with plenty more still to come.
Up ahead, there is a steep hill where uncontained effluent may escape onto the roadway. You also need to take two 90 degree turns through a major regional centre before you arrive at your final destination. The copper there is pretty tough and you’ve already worn a couple of $350 blisters for breaching load restraint laws in the last six months. Every time that happens you’ve lost your wages for the trip.
In Australia, livestock processing facilities are not required to provide disposal areas for captured effluent and primary producers will not accept it onto their property due to biosecurity concerns. Nervously, you decide to pull into an unofficial rest area outside of town to check your load and empty your tank. Today you were lucky. Last month, a mate of yours was busted by the EPA for illegal dumping and fined $3,000.
Every year there are more feedlots opening in the area, more livestock trucks on the road and more residential and business development along this important stock route. It’s an unsustainable situation that is not going to magically resolve itself.
Good preparation of the livestock before they are loaded onto the truck can help reduce the problem. But you don’t have control over that, and many livestock producers do not support the application of pre-transit feed and water restrictions due to concerns about negative impacts on weight and meat quality.
In New Zealand, national and regional governments are jointly funding, building and operating a network of purpose-built livestock effluent disposal facilities on public roads. Road transport laws have also been changed so you cannot be booked for effluent loss while you are loaded.
This common-sense approach is exactly what is needed for the Australian livestock supply chain to co-exist and grow alongside expanding urban populations where livestock sale and processing facilities (and the hundreds of thousands of jobs they support) are typically concentrated.
So why is it so hard to fix in Australia?
Well, unlike NZ we have a third layer of government, the states. The states own most of the important livestock roads and make the laws applicable to heavy vehicles, environment, animal welfare and domestic biosecurity. But they are not at the coalface like regional councils who depend on livestock industries and manage local effluent complaints. States are also apparently not attuned to the bigger picture ‘national interest’ either.
The states exist in a ‘no man’s land’ regulatory zone, not willing to accept responsibility or fund solutions. They just do not understand that simply fining drivers will never ever make the problem go away.
To their credit, the Australian Government has committed $400,000 to establish a pilot roadside effluent disposal facility, provided $50,000 to develop an effluent code of practice and, via the NTC, proposed to change the Heavy Vehicle National Law to encourage improved livestock preparation. Several regional councils have identified preferred locations for disposal facilities to be established and written to their state government demanding action on the issue.
ALRTA is continuing to work with all levels of government to proactively find solutions. We have travelled to NZ to inspect their effluent management system. We have funded the construction of free disposal facility in Horsham Victoria. We have worked with the supply chain to develop a code of practice. We are seeking regulatory solutions via the HVNL review. And we are continuing to invite state governments to the table, because, whether they recognise it or not, they are a necessary part of a longterm holistic solution.