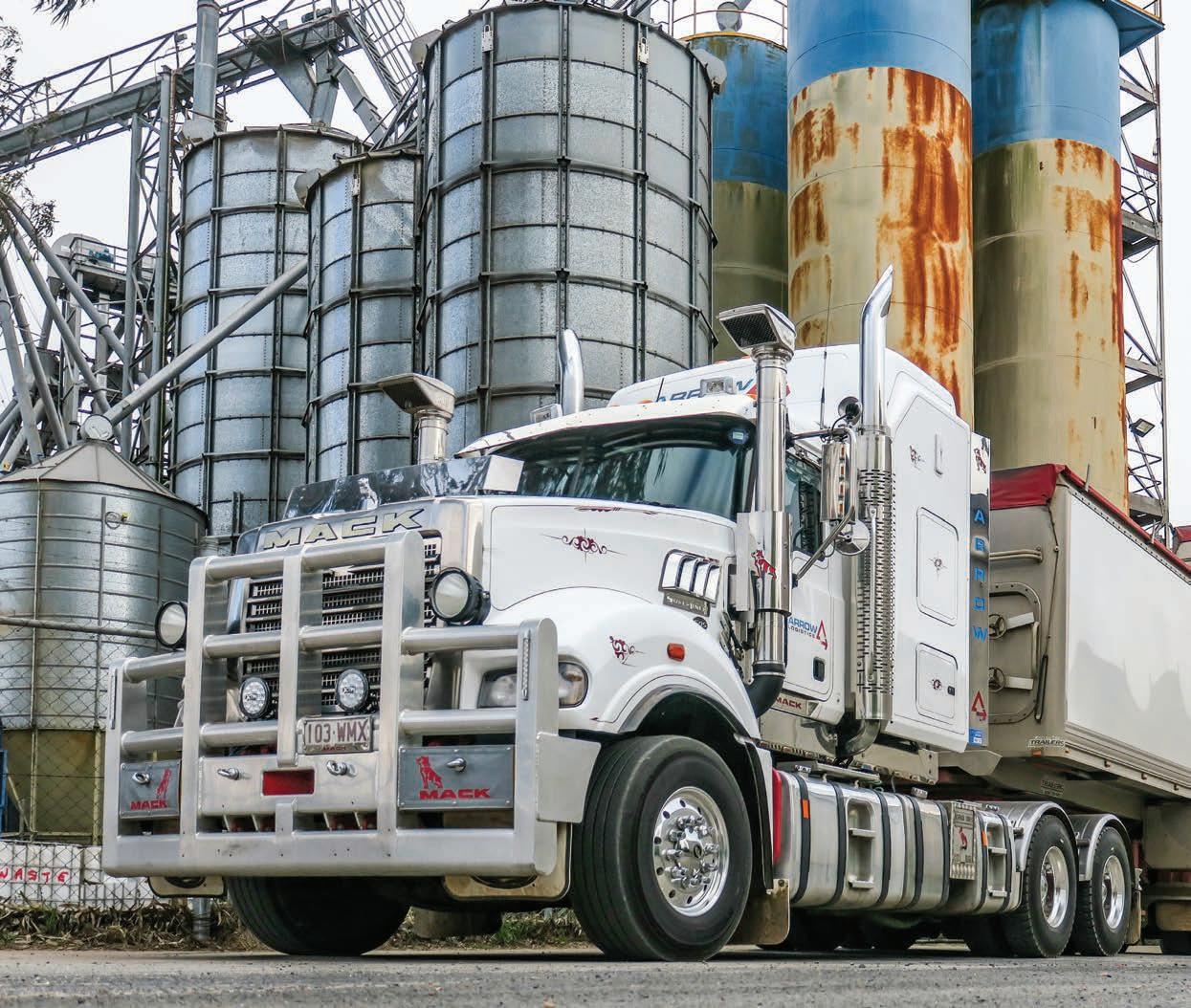
35 minute read
STRAIGHT AND SIMPLE AS AN ARROW
from Diesel November 2020
by Prime Group
The increasing complexity of road transport and the systems around it does not have to be so complicated. Especially when you have a small footprint solution, which is as straight and simple as an Arrow Logistics application, on your phone. Tim Giles meets Arrow’s founder, Ian Forster.
Computerisation and its development over the last 30 years has made it seem that the world is growing ever more complex and sophisticated. However, now we seem to have reached a point where the smart use of complex technology can help those in the trucking industry return to a more simple life.
This is certainly the case with a phone app that Diesel came across recently. The whole idea sounded too good to be true, but Diesel followed it through and found development of, what can be, very complex systems, which are making life a lot easier for small trucking operators and owner drivers.
The small to medium sector of the trucking industry is probably the one which finds the increasing complexity of compliance and business systems most onerous. It is okay for the larger trucking operators to have a department in the business which deals purely with the technology involved in running the business.
For the small operator, there is not enough activity in the business to justify a specialist in this area. This is where some smart thinkers in the trucking game in Australia are starting to come to the fore, with smart ideas which are designed to make the small operator’s life just a little easier.
Arrow Logistics uses a simple platform able to be accessed on a mobile phone which keeps all of the people involved in the bulk grain supply chain informed about what loads are available to be transported, what trucks are available to do that load and where the product has to be delivered.
It also enables everybody involved to keep track on exactly what is happening with their product, or their trucks, or their deliveries. One of the most important aspects of the system is its transparency, but also the way it is tailored so that the person accessing it is getting the information they need to have on hand.
The genesis of the Arrow Logistics operation begins with Ian Forster working as a barman in a pub in Toowoomba. A friend of his from Clifton asked him to help out with his transport business.
“I ended up learning the trade of how
Arrow Logistics’s founder, Ian Forster.

to organise trucks,” says Ian. “He always said to me, don’t ever get your truck license. He wanted me to just focus on organising and to do what I was good at. If you start driving, you will start going on trips and then you will get distracted.
“Over the years we have bought two AB-triples and a couple of sets of road train trailers, I just don’t know how to use them that’s all. When I was 18, I was advised that I should always look for someone who is better than me at something. I always knew that I would be in my own business eventually.”
The operation for which Ian was working in Clifton began getting into

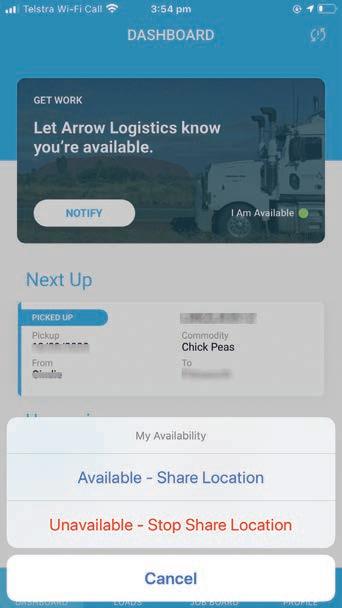
financial difficulties and Ian moved on to a transport operation in Millmerran, doing the same job and organising the transport. This was his first experience with building up a sub contractor base for a transport operation. Unfortunately, the drought in 2010 hit them hard and Ian was made redundant.
“I was left with the decision as to whether I would go and work for someone else or have a crack at this, “ says Ian. “I had got to know a few owner drivers by this time and I had spent a good deal of time in the field by then. So, I approached a few of them and asked them, if I found them some work would they come and work for me, they said yes.
“I just focused on helping four trucks to begin with and they sort of became my trucks, without me owning them. I just worked in my backyard, with a phone, a printer and a computer, and worked seven days a week for about two years.”
The business concentrated solely on just moving grain and fertiliser. He worked with fertiliser companies, grain traders and larger transport companies. After two years without a break, Ian decided to expand and bring a few people on board to help run the business. He took on a coordinator, who still works for him in the same role.
The next step was to start a separate equipment division of the business. This is

the entity that owns a couple of trucks. At the same time, a driver with whom Ian had worked at the original company in Clifton, approached him and said that he would be willing to drive for him.
“He said, that if I bought a truck, he would treat it like his own,” says Ian. “I had known him for seven years and thought he was one of the best in the trade. We bought a truck for him, and he’s still with us as well.”
For the next two years the team buckled down and continued to grow the business. However, in 2014, the business had a bit of a hiccup, with a truck going to the wrong delivery address because the text which have been sent with the information had been misinterpreted.
“It was the truck driver’s fault, but our system was not robust enough to have picked up on it,” says Ian. “Our system was excellent, but it was cumbersome, everything was a five step process. We were making notes on a bit of paper, then we would put it on the spreadsheet, then we would text message the driver. After this, we made notes on the spreadsheet, and then, when the notes came in, we would type up the invoice and then the corresponding supplier invoice.
“It was a cumbersome process, it was methodical, and it took ages to do. It was open to human error and I was constantly
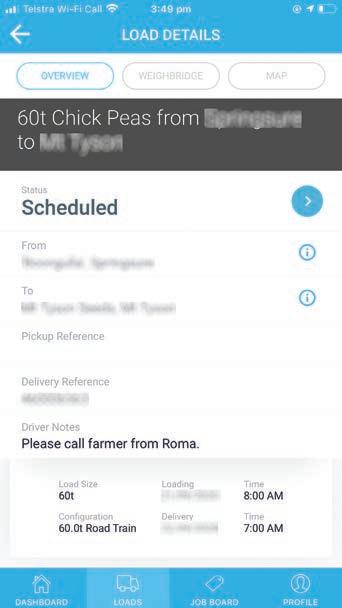
having to keep checking things to make sure everything was right. An error with the client lost us a trader who was giving us significant business at that time.
“It was enough for me to go, right, now I’m going to fix this. So I began to become aware of some software programs that were out there. I then spent the next two years trialling a number of off-the-shelf products for use in the business. They were job management programs, but they were either for tradies or something like that. There were a couple of transport related ones, but they seemed to be developed for companies which used mostly their own trucks.”
The applications Ian tried had been developed by software experts with little expertise in the transport industry. Not only were they not ideal, they were also relatively expensive for a small operation like Arrow Logistics. Ian was not willing to spend a lot of money for something which would not solve his problems, just create new ones.
By 2016, Ian has decided he was going to build a system himself. He didn’t have any expertise in developing the systems, but he has spent the previous two years investigating software and discovering the problems. He was taking little bits from everything he had tried and eventually shortlisted three developers, before
deciding on one supplier.
“It ended up costing four times what I was originally quoted, but I think it was worth it,” says Ian. “We ended up with a web-based platform, which also synchronises with a mobile app. Mainly, the carriers download the app at this point in time, it’s free on Google Play and the Apple App Store. I asked the developer, on a scale of 1 to 10, how hard was it to build, and he said it was about an eight or a nine, not because it was super complicated, but because it was important to make it simple to use.
“The whole premise, when I was building this was to have one program which would replace that five step process, with a single entry. We only enter the information once, the platform sends the messages to the trucks. The driver gets the information on the app. When the platform gets confirmation about a load it automatically sends the correct data through to the Xero accounting software.”
The old system took 30 minutes to set a load up for transport. Now, that process has dropped to less than one minute for the team. Time is being saved in booking loads, but also, instead of making twenty or so phone calls to find an operator and a truck for a load, the job board on the platform means the operators come to them.
At the moment, Arrow still get phone calls from grain traders – many still rely on the traditional method of phoning up and telling Arrow about their particular job. Often, people working in the rural community tend to prefer that social “WE ONLY ENTER THE INFORMATION ONCE, THE PLATFORM SENDS THE MESSAGES TO THE TRUCKS. THE DRIVER GETS THE INFORMATION ON THE APP. WHEN THE PLATFORM GETS CONFIRMATION ABOUT A LOAD IT AUTOMATICALLY SENDS THE CORRECT DATA THROUGH TO THE XERO ACCOUNTING SOFTWARE.”
contact, However, the platform does have the functionality for them to enter any work they have on offer, into the system.
The details of a particular load are entered into the system with the date and the time included. At the same time, the trucks which have the app are able to share their location with the platform.
If the truck driver has enabled the location sharing on their app, when a load is entered into the system and if they are within 500km of the location, they will get a notification about the fact that a new load has just appeared on the system.
“We have an Uber-type scenario with a map showing all the truck locations,” says Ian. “If a job comes in, say in Moree, we can look and see all of the trucks in a 100km radius and we can phone those trucks first.”
At the moment, there are about 20 trucks which are working for Arrow Logistics all of the time and then there are much larger number of operators, between 100 and 200, which do work for other operators, but will regularly take up work
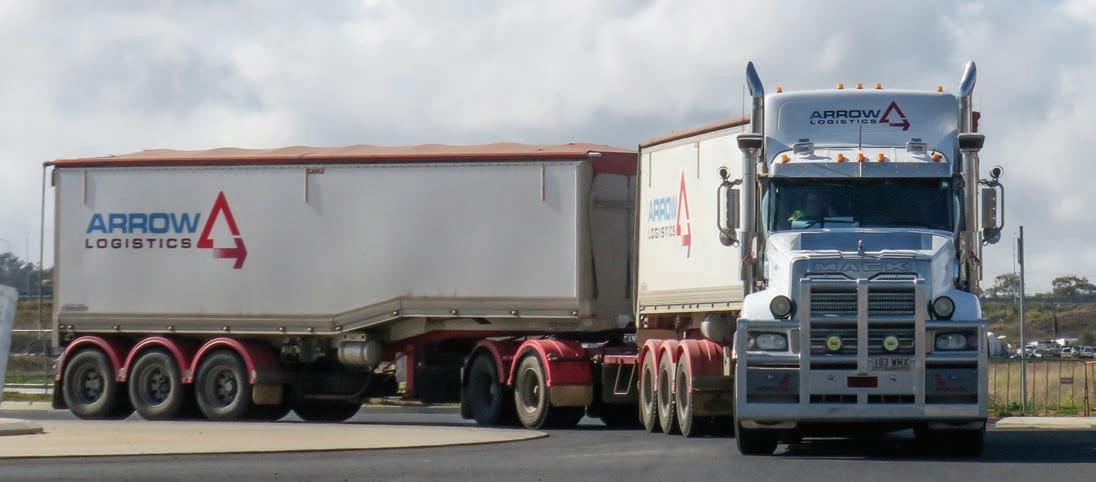
from Arrow. Between 80 and 90 per cent of all those trucks involved have the app on their phones in the truck.
Once the load is allocated, the driver of the truck receives all of the details about the load through the app on their phone. It is then up to them to make the appropriate phone calls from within the app, pick up and deliver the load and take a photograph of the weigh-bridge dockets, using the app.
The allocation data is loaded directly up onto the Arrow website, then Ian’s team look at the details and approve it. Once the job is approved, the client and the transport company can also see the load on the website. Then both the sender and the carrier are sent the appropriate paperwork.
“There are three of us, full-time, sitting in our office in Toowoomba,” says Ian Forster. “There are also five trucks out on the road with Arrow Logistic’s paintwork on them. When I am talking to people and tell them that we are Arrow, they are surprised when I say that we only own two
trucks. They swear we have 20, from the amount they have seen.”
What this operation actually is, is a very modern version of a transport company. The actual entity which is doing most of the business is, in fact, three people, plus a part-time bookkeeper, some computers, some phones and some quite expensive software. The vehicles actually handling all of the freight task are outside of this business.
“It’s good having the two entities separate, because you can manage your cash flow better,” says Ian. “If you run the two together, I think it can get confused. Sub-contractor money can be spent accidentally.”
When a transport operator registers on the Arrow website, Ian will contact the operator and run through exactly what they have in terms of equipment, insurance, compliance and processes within their business. If the operator gets approved, they get onto the system. During the period when they handle the first few loads, Ian will monitor their performance, to ensure consistent behaviour.
“I would say that 99 per cent of the people who come on board have been pretty good,” says Ian. “I’ve been around

in the business long enough to be able to pick up stories if there is anything wrong.”
LOOKING TO THE FUTURE The growth in the business has been largely organic and the operation has developed as the work has come along. There was a long period where they were handling around 12 loads a day and now the average is around 20 loads a day.
Although most of the work is based out of Queensland and New South Wales, there is regular work in an out of Melbourne and occasional work into South Australia and Western Australia. The system itself has no limits to its geographical coverage in Australia.
“We are just about to have a very big harvest in NSW, so expect some big numbers in the next few months,” says Ian. “All of our growth has been fairly organic so far, we haven’t done any real marketing, other than a few Facebook posts. We are still setting carriers up onto the system and probably getting about 10 new operators every month.
“This means we are starting to cover more and more ground and make things better for more and more companies. A big selling point is that we have a mobile job board, so that they can see at a glance where the nearest load is. The driver can simply click on their iPhone and see what work we have available.
“It’s helping drivers to link up with loads, when they have loads of their own, they can look what we are doing and try and tie it in with their own work.”
As with many areas of the trucking business in Australia, there are always new operators coming into a particular region and competitive rates are offered in an attempt to win some work. Ian has seen a number of competitors come and go over the years, but points to the consistency in the way that the Arrow platform works.
“Grain traders love this system because they can log into our website and reconcile dockets and registrations as the work is happening,” says Ian. “Whereas with other systems and other operators they may have to wait a week or two. We just try and make it as easy as possible for each end user.
“The system is quite expensive to run and there is one thing I have discovered and that is that software is not cheap and there are quite often little bugs. Overall, I have had excellent feedback, because it was created within the industry, so I knew exactly what was needed.”


Take Two Trucks
Here are two trucks from the same stable: Daimler. Tim Giles test drives the Mercedes Benz Actros and the Freightliner Cascadia to see how the European vision compares with the US one when they both have access to the same technology.
It has been a protracted process for the major truck manufacturers around the world, but the fruits of a long labour have appeared in the past few years. The process was born back at the beginning of the century when a number of truck manufacturers around the world became part of large global groups.
At that time, Volvo acquired Renault Trucks, which had just bought Mack Trucks and followed this with the acquisition of UD Trucks from Japan. Around the same time Freightliner trucks, which had been bought by Mercedes-Benz sometime before, acquired Ford’s truck operations in the US and soon after the company known as Mitsubishi Fuso, which is now known as Fuso trucks. Then we saw the Paccar group expand from its ownership of Kenworth and Peterbilt in the US to acquire DAF Trucks, which had recently acquired the Leyland trucks organisation.
Financial issues with trucking manufacturers, combined with the ever-increasing costs of research and development in creating new, much more sophisticated designs, had put some truck makers into trouble, enabling the cashed up manufacturers to build global empires.
The watchword at the time was that the formation of these three global truck makers would make it ossible to develop global platforms for future trucks. The plan was to spend billions of dollars developing a single engine, for example, which could be adapted for all of the different truck markets across the world. The same could be done for chassis systems, axles, transmissions, vehicle
electronics and telematics.
These kinds of development projects have a long gestation period, so it wasn’t until after 2010 that we saw the first signs of the new global technologies emerging. Daimler developed a ‘global’ engine in the DD15, DD13 and later DD11, initially fitted in North American trucks and later adapted in a 16 litre guise for Mercedes Benz and at a lower capacity for Fuso trucks.
There were a few false dawns where a truly global technology platform looked to be arriving, only to develop problems in adaptation. However, in the last ten years the whole globalisation project has begun to bear fruit. Volvo Group run the same set of engines and transmissions around the world, as does Paccar product, to a lesser degree.
The group which bought into the package most enthusiastically was Daimler. The DD family of engines are now used right across the range, as is the Mercedes Benz AMT, even though it is branded as a Detroit in the US and Benz in Europe.
Now, here in Australia we are able to compare and contrast trucks branded differently, but fitted with the same basic technology in the most important components, like engine, transmission, electronics, safety systems and so on.
In the last issue of Diesel, it was the Fuso Shogun which was tested. This issue sees the two big boys, the Mercedes Benz Actros tested alongside the Freightliner Cascadia. Both pulling B-doubles and running the same route from Toowoomba to Warwick, before descending over Cunningham’s Gap into Brisbane, and then heading back up the mountain to Toowoomba.
The object here is not to compare like with like. They are different trucks built to handle different tasks. Diesel is looking at how the North American trucking philosophy uses the basic technology as opposed to how it is handled by the Europeans. In essence, this is not a truck comparison – it is a trucking culture comparison. Examining how different
truckies perceive their trucks.

TAKE ONE European Truck
The new Actros from Mercedes Benz has been with us for a while, but this year it gets an upgrade with the addition of some new technologies and the mirrorcam system.
After a number of ups and downs and a long period when the truck was not particularly fashionable, this latest version of the Actros has had considerable success since its Australian arrival in 2016. There are a number of reasons for this success, not least it’s frugal fuel use and also a long-term change in the attitudes of the trucking industry in Australia, which is seeing European cabovers increasing in market share.
From the driver’s point of view, test driving a truck like the Actros, is simply a matter of making sure they know what all the buttons on the dashboard do and then working out how to set it up correctly before setting off down the road. It is possible to drive this model in a semiautonomous way. Much of the time on long runs all the driver has to do is steer the truck and keep an eye out. The automated systems do the rest.
The truck on test is probably the ideal B-double prime mover in this model range. It is an Actros 2663 with the StreamSpace cabin, which includes a flat floor. In fact, this particular cabin is laid out in the SoloStar configuration, which Mercedes-Benz have introduced as an option, but not many truck buyers have shown a lot of interest.
The SoloStar seems well worked out. The bunk folds up to the rear wall of the cabin. On the passenger’s side there is a seat underneath bunk which fold up so that the seat-back is resting against the folded up bunk. The side wall of the cabin is cushioned so that there is a, sort of armchair in the corner of the cabin. This leaves the space where the passenger seat normally lives as clear open space.
This means there is a comfortable seat for the driver when resting, but a passenger has to do without a passenger door window. The space created is
Climbing up into the cab is literally that, climbing up four steps and then up again onto the flat cabin floor.

welcome in a European cabin, where it is always at a premium, but it will probably not spark much interest among Aussie drivers.
The engine in this truck is the OM473, rated at 625hp (460kW) and this puts out 3000 Nm (2230 ft lb) of torque. This engine is based on the same engine block and many other engine components as the Detroit DD 16 used in the Freightliner range.
Approaching the truck, the driver will see the familiar tall Actros shape, but
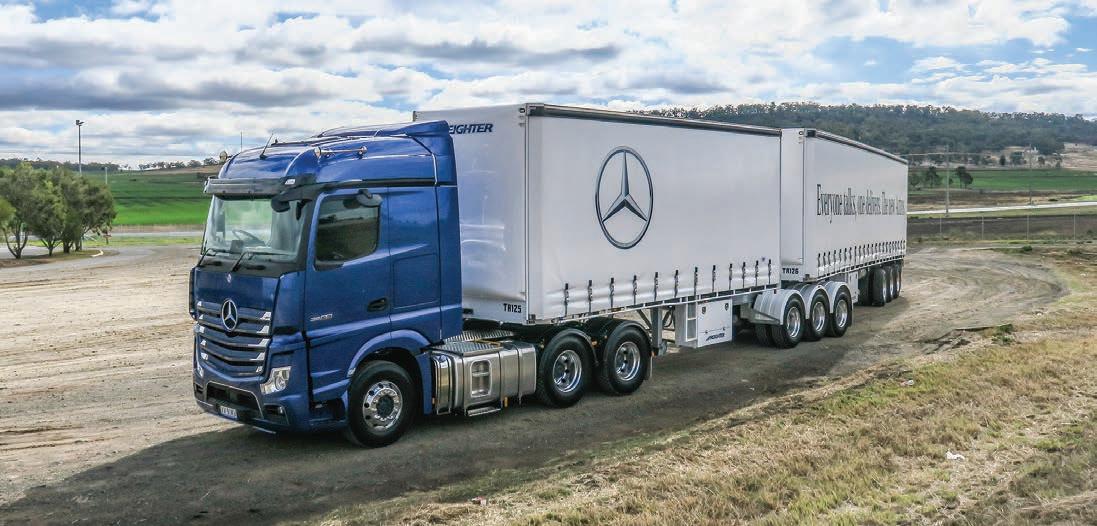
The 2663 with the StreamSpace cabin, which includes a flat floor.
also notice that there is something a little different about this truck. The introduction of the mirrorcam option is an Australian first. As to whether the Australian trucking industry will be willing to accept this new concept? The jury is still out. There is no doubt about the improvement in the aerodynamics and also in visibility for the driver by fitting this new system.
In fact, the introduction of the mirrorcam has been on the cards for some time, as European hauliers seek fuel economy and as safety systems becomes more important. Add in the fact that video cameras and video processing computers become smaller, lighter and cheaper, and they become inevitable. Over the next 10 years they are likely to become an option on every heavy duty truck, before becoming standard when we finally get used to them. By that time cameras, instead of mirrors, are likely to be ubiquitous on all vehicles.
CLIMB ON UP Climbing up into the cab is literally that, climbing up four steps and then up again onto the flat cabin floor. It is quite a way up there, but all of the handles are well designed and the steps themselves are easy to negotiate.
While settling into the driver’s seat the full array of electronics available in this truck becomes obvious with two large screens, one directly in front of the driver and one to the left, on firing up the truck they light up in all their glory.
This is clearly the way that the truck interior design is going to be in the future, even the new Kenworth has an LCD screen on the dashboard with an option to show analog instruments. In this brave new world, most drivers will still choose conservatively and configure the screen directly in front of them with the usual tachometer and speedometer left and right, plus fuel gauge, with indicators of gear selected, trip and odometer in the middle.
The screen also shows which automated systems the driver has activated and how they have been set. This will show whether the active cruise control is activated and what distance the driver has set as the closest it can get to the vehicle in front.
There is a lot to learn about all of these systems which are available in the Actros. A certain amount of training on handover is vital for any driver taking over this truck. Although many of the controls are relatively intuitive, for many drivers, the sheer volume of different systems which can be turned on and off may be confusing. Clear and concise training and instructions will solve any problems.
The screen in front of the driver can be adjusted and controlled via the buttons on the steering wheel. The screen to the drivers left is more about items like entertainment systems and other information for the driver.
After starting the truck, the parking brake release is simply a large switch. The transmission is controlled by a stalk on the right hand side of the steering
column. Most of the time the driver will need simply to leave it in the drive position and let the computer technology do most of the work.
This G330 12 speed PowerShift transmission is well proven and this basic technology is now used throughout the Daimler heavy truck range. At the beginning, the early Actros models struggled with automated manual transmissions, but when the Mercedes-Benz engineers finally got the transmission right, they really did get it right.
Surprisingly, the safety pack, which includes all of the safety systems, is an optional extra. This pack includes Lane Keep Assist, Attention Assist, Active Brake Assist 5, Proximity Control Assist and Automatic Main/Dipped Beam and Cornering Light. In these very safety conscious times including this set of equipment in your options list would seem to be a no brainer, as long as the operator can be certain that their drivers will not simply switch all of the automated systems off as soon as they sit down in the driver’s seat.
The side wall of the cabin is cushioned so that there is a, sort of armchair in the corner of the cabin.
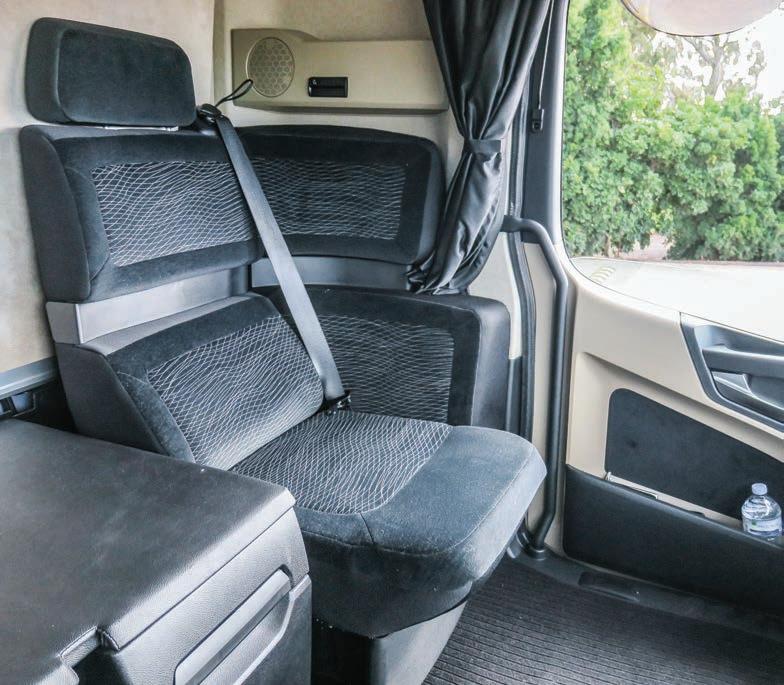
DRIVING EXPERIENCE What we are examining in this test is the driving experience in the Actros using as much of the automated, automatic and other safety systems as possible. This may not be the choice of all of the drivers who end up in this driving seat, but all of these systems are on offer. We are trying to examine exactly how all of them can work together, they’re all turned on and this driver will note how the systems react to
The introduction of the mirrorcam option is an Australian first.

different driving conditions.
The basic active cruise control which Mercedes-Benz call proximity control has been with us for some time. In fact, this driver drove an early version of the system in Mercedes-Benz Actros on the autobahns of Germany over 16 years ago. This system is much smoother now than it was at that time and the mix of camera and radar produces great results.
In urban conditions the driver simply pushes the accelerator to go and hits the brake to slow. Once out on the open highway it’s a simple matter of setting the maximum speed, for the section of road and ensuring that the following distance is set at a reasonable number of seconds and any over run is limited to two or three km/h.
This model is fitted with the optional Predictive Powertrain Control, which means that the system is loaded with topographic maps of the main highways of Australia and this will inform the cruise control about the road ahead. This means that the AMT may select a lower gear just at the foot of a climb, or cruise control will cut torque just before the crest of the hill to allow the forward momentum of the truck to take the combination over the top of the rise and use the downward grade to pick up speed again.
Also available is the eco-roll system, which will disengage the clutch when the system recognises that the current speed can be maintained without any input from the power train. Recent examples of these types of systems have begun to be more effective than they were when they first came out. Now, you can expect the system to take advantage of any situation where there is a slight incline and disengage the clutch allowing the rpm levels to drop to around 600.
VIRTUALLY SEAMLESS The way all of these systems work together is virtually seamless in the Actros. This is the trick to getting a state-of-the-art truck right. A lot of these automatic driving systems are generic and they come from different suppliers, but it is in the way that they are integrated into one system, which makes them more effective and also more useful to the driver, ensuring they are more likely to use most of these automatic systems in their normal daily driving.
This appears to be the essence of what we are looking for in a modern topend highway prime mover. Many of the systems are very similar across different brands, but the brand which can make all of these different components work together holisticly is the one which will be more attractive to drivers and operators.
In terms of integration, Mercedes-Benz have got a lot of things right. Some of the electronic safety or driving systems may not be perfect, and we may see them disappear in the next few years. However, altogether and over time Benz seem to have got quite a lot of this integration correct.
Drivers can configure the screen directly in front of them with the usual tachometer and speedometer.
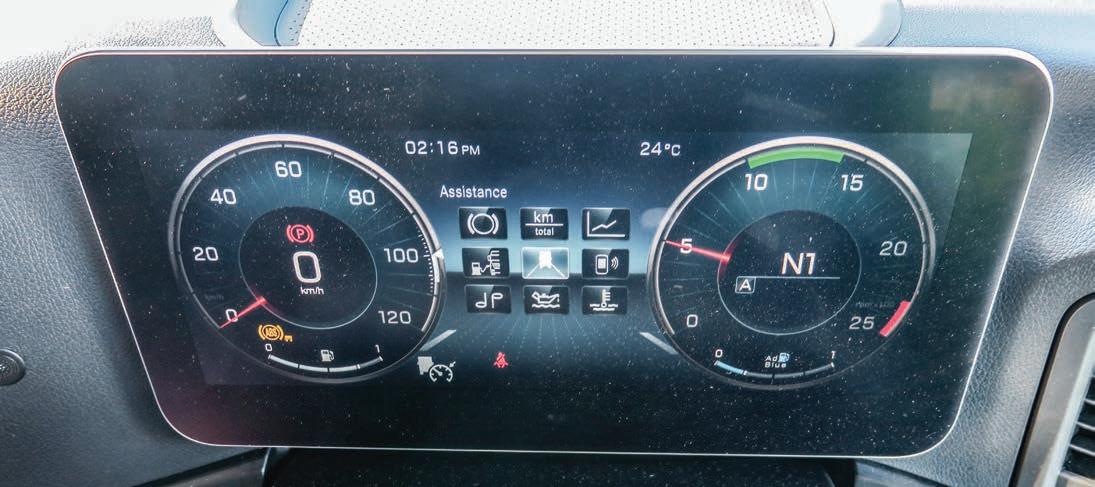

Take One North American Truck
The Freightliner Cascadia is a totally new truck on the Australian market and sees the first appearance of the full Daimler suite of systems, and their utilisation, from a US point of view. The core components are the same as they are in Europe and Japan, but this is how Freightliner take an ultra-modern North American truck to market.
The Freightliner Cascadia has status in the US heavy duty market, and adapt to the various market into which it been an enigma for some time. bring the brand to the point where it sold around the world. The Cascadia would In the past, Freightliner would completely dominates heavy duty truck have the DD series of Detroit engines fitted, develop a truck for the US truck sales Stateside. with the AMT which had been so successful market and then make some adaptations It is clearly something different. It for Mercedes Benz in Europe behind it. to suit Australia, meaning it would end up was said to be too wide and too difficult Drive and steer axles also came out of being launched here a couple of years to change to right hand drive in the the Detroit plant, although they were also later. early years. At the same time as it was similar to those in the Benz.
On the other hand, the first Cascadia cleaning up in the US, with consistent low Daimler was also developing a came out in the US in 2007, but didn’t make fuel consumption results, from excellent sophisticated electronic platform with it to Australia until late 2019. This is clearly aerodynamic styling, driving sales. all of the latest safety bells and whistles, a very different truck both for Freightliner The concept had been simple, Daimler alongside diagnostics and other and for Australia. This is the model which had decided to design all of its major functions connected back to base at all helped Freightliner regain number one components at a global level and then times. The concept saw Daimler develop
global solutions to be packaged and sold regionally.
The truck we now have on sale in Australia is the third iteration of the Cascadia, released in the US a couple of years ago, but the first to be developed with right hand drive in mind. This aspect of the design is obvious when climbing up into the truck – the expected lack of space in the foot well for the driver’s left foot is not an issue here.
It is good to see a truck coming out of North America which is had some genuine design input. The sophistication of design is obvious on the production line where these trucks are made in North Carolina. The complex panels are placed together by a set of robots and automatically welded into place to form a strong and complete whole. This is very different to the way cabins were built on US production lines in the past, with teams of workers riveting sheets of aluminium into place on a frame over a much longer period of time.
Walking up to the new Cascadia, the eye is drawn to the clean lines of the aerodynamic design. Within the typical US prime mover silhouette there is a smoothness to the shape, indicating how much work has gone into this design in the wind tunnel at the Freightliner headquarters in Portland, Oregon.
The level of sophistication and complexity of design which goes into this truck is not particularly obvious from the driver’s seat after you climb in. The layout looks similar to what one would expect from any North American prime mover.
There is a clue in the LCD screen on the dashboard which provides all the driver information required. The driver also has the steering wheel with plenty of buttons on either side, which is now used across the Daimler truck range.
The information screen directly in front of the driver, between the tachometer and speedometer is relatively small, but has been very well designed. Using the buttons on the steering wheel, the driver can scroll through a number of different pages and get the kind of information they require, and also adjust the settings for more automated driving.
In fact, behind this dashboard this is a fully multiplexed computer controlled electronic system, but it does not show off its sophistication. Instead, it looks like it has been designed for the more conservative US truck driver, there are no surprises in layout or feel.
The appearance of this interior does suggest that this is a truck which can be driven completely conventionally, but at the same time, there is a high level of automation and automated systems available to the driver if they wish to use them. On this test Diesel decided to turn all of them on.
ROAD TRANSPORT WORKHORSE The example of the Cascadia driven in this test is the truck which will be used by many fleets as the road transport workhorse, as it plies its trade on Australia’s highways. This is the day cab Cascadia 116, fitted with the Detroit DD13 engine rated at 505 hp (377 kW) and putting out 2508Nm (1850 ft lb) of torque. The transmission is the Detroit DT12 AMT, although traditionalists can opt for a manual RoadRanger gearbox if they so desire.
Unlike their counterparts in North America, Freightliner here in Australia have decided to retain the front and rear axle options with which Australians are more familiar, supplied by Meritor. The suspension is the familiar Freightliner Airliner.
These specification choices demonstrate the North American philosophy of truck design. This truck is highly sophisticated and state-of-the-art in certain places, but, at the same time, enables truck buyers to make choices which they are more comfortable about.
Where the Daimler trucks in Europe leave the driver in no doubt that this is a highly sophisticated modern 21st-century truck, the output from the same company in the US is designed to make the driver comfortable with plenty of familiar aspects to the design and specification. This is essentially where the difference between the two ways of looking at truck design can be seen at their most obvious.
It is almost possible to forget that this truck has all of these highly sophisticated systems, as it looks so similar to its predecessors and one small screen on the dashboard does not suggest a state-of-theart 21st-century truck.
The fact of the matter is, however, that the systems do work really well and are effective doing what they’re supposed to. It is possible to drive his truck, pretty much, semi autonomously all of the time. Click it into drive on the transmission controller, release the 20th century maxi brakes and you are off on a smooth and effective drive.
The combination of a fully loaded B-double and a 13L engine means that the transmission really has to do the hard yards to keep progress going out on the road. This is a very responsive transmission, which is receiving enough data for it to make intelligent decisions at the right time and in the right way.
On the Cascadia, the system using topographical maps to inform the engine and transmission about the road ahead is called Intelligent Powertrain Management. This system relies upon the correct mapping being available for the highway on which the truck is driving and for the truck to know exactly where it is. Sometimes, this relatively new concept
Side Guard Assist watches back towards the rear of the truck to see if there is any object which the driver should be made aware of.
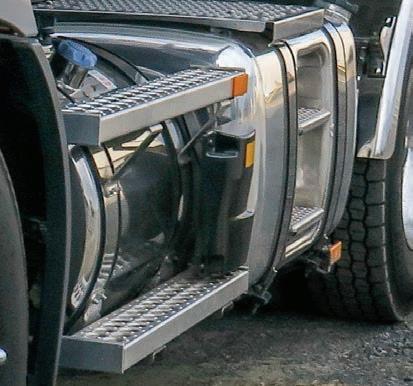
does not get all of its data, but when it does it does make the correct decision at the foot of an incline, ready for climbing or just before a down grade.
SAFETY SYSTEMS The safety systems in the Freightliner come grouped together under the appellation of Detroit Assurance 5.0. This includes all of the usual fruit we have come to expect out of the top of the range Daimler trucks, there is Active Brake Assist, Adaptive Cruise Control, Lane Departure Warning, Intelligent high beam et al.
There is one system which is available
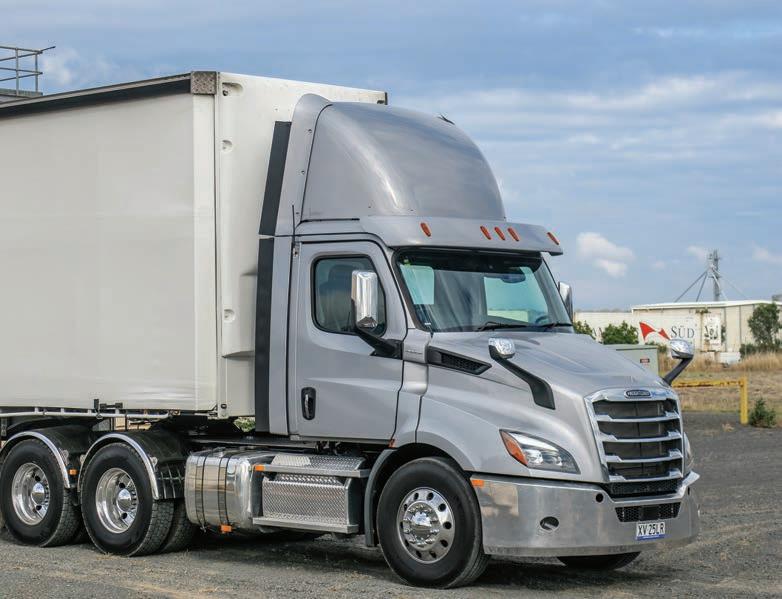
on the Freightliner trucks, which you will not find in Mercedes-Benz or Fuso. This is the Side Guard Assist, which uses a radar which is fitted to the passenger side fuel tank on the prime mover and watches back towards the rear of the truck to see if there is any object there which the driver should be made aware of.
The area covered by the system is quite substantial, from five metres behind the rear of the trailer to a few metres in front of the prime mover. If there is a vehicle or any object in that area, and the system calculates that it may be an issue for the truck, it will issue a warning.
This warning consists of a buzzer, coupled with a triangle on the passenger side B pillar which illuminates if something is detected in the danger zone. This system works well, the initial buzzer alerts the driver, making them look towards the passenger side of the vehicle and the illuminated triangle will confirm there is an issue. The driver can then look slightly to the left to check in the mirror if there is anything wrong.
On this test drive the alarm did go off a couple of times with cars sneaking up on the inside at road junctions. On another occasion it warned the driver when the rear trailer got close to a signpost.
Even though the mirrorcam system is
The warning consists of a buzzer, coupled with a triangle on the passenger side B pillar.
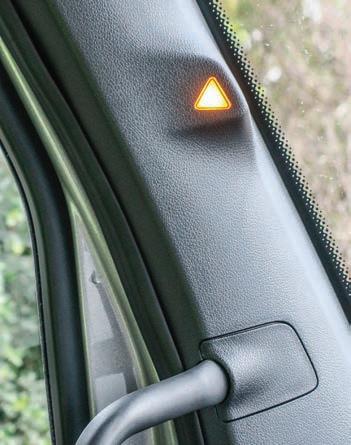
available in other Daimler trucks, it has not arrived in the Freightliner product just yet. The original design of the screens were for them to be mounted on the upright A-pillar on the Actros. However, the angled A-pillar on the Cascadia is proving a little more difficult for the engineers to get just right. Perhaps the next iteration of the Cascadia will arrive with this system, if the technology proves to be useful in a North American truck.
OVERALL IMPRESSION There is no doubt that the Cascadia is a truck which has created a lot of interest. The reasons for this interest become even more obvious after some time behind the wheel of the new truck. There are so many things that Freightliner (or should that be Daimler) have got right. The integration of the various systems is nearly as seamless as it is in the truck’s sister, the Actros.
The distinction between how modern truck systems work, and the actual design of the truck, is very different in a North American truck. In terms of climbing into the cabin and getting a look and feel of what’s going on, the Cascadia is similar to any other US truck of the last twenty years.
The modern sophisticated, state-ofthe-art stuff is all under the skin. The only giveaway is a modern steering wheel with a wide array of buttons and a modest LCD screen in front of the driver. Where the European truck designers seem to prefer to flaunt the modernity of their trucks, for the Americans it seems that modernity is screened off behind a very traditional interior design.