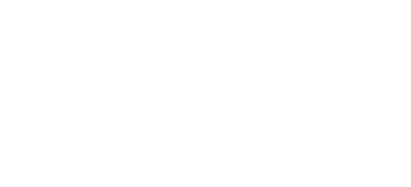
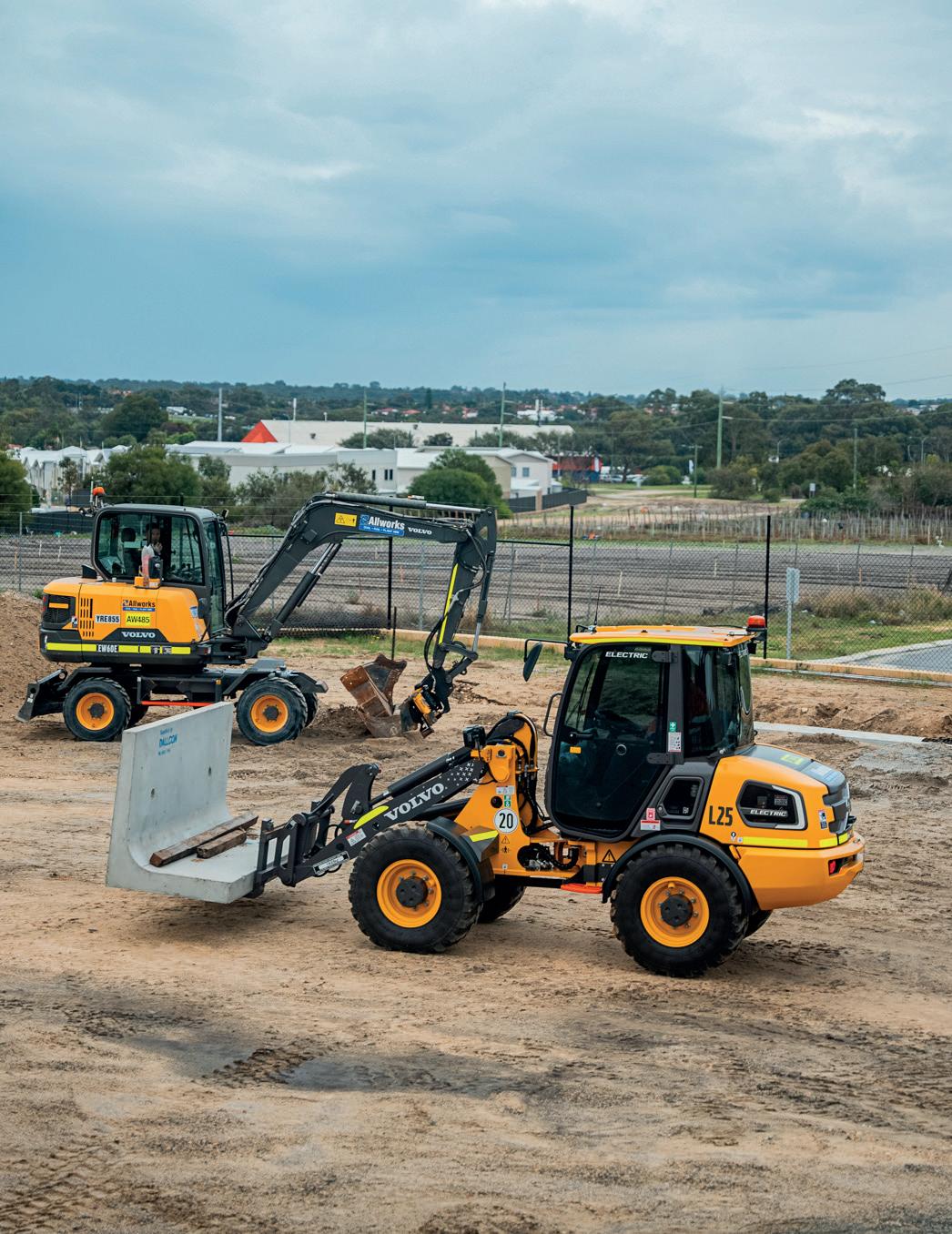
VOLVO’S FIRST ELECTRIC LOADER HAS LANDED IN AUSTRALIA AND IS ALREADY HARD AT WORK ON VARIOUS WA PROJECTS
VOLVO’S FIRST ELECTRIC LOADER HAS LANDED IN AUSTRALIA AND IS ALREADY HARD AT WORK ON VARIOUS WA PROJECTS
Elevate your worksite efficiency with Komatsu Excavators.
Engineered for strength and precision, these machines redefine durability in every dig, conquering any terrain effortlessly.
Ray Chan Editor
This month, the spotlight shines on the humble machinery attachment: buckets, grapples, rippers, blades, hammers, couplers, and even a rock saw that would be the envy of any James bond villain.
No matter how powerful, fuel-eff icient or comfortable a piece of earthmoving equipment is, it’s really only as good as its range of specialised tools.
That gleaming new machine you might have acquired would have limited functionality and eff iciency without these value-adding gadgets. When looking over a potential purchase or rental in the showroom or in the used saleyards, consideration should of course be also directed towards the type and quality of accessories that come with it.
The importance of these implements in the industry is often underestimated, yet they are critical for maximising the eff iciency, versatility, and cost-eff ectiveness of heavy machinery.
The main benefit of attachments is the enhanced versatility they bring, enabling a single piece of equipment to perform multiple functions, such as digging, lifting, grading, and compacting, thereby reducing the need for multiple machines.
Diff erent devices are designed for specific tasks, ensuring that each job is performed with the most suitable equipment, enhancing precision and quality.
Productivity and eff iciency are also optimised, with quick and simple attachment changes allowing operators to switch between tasks without significant downtime, speeding up project timelines.
Needless to say, investing in a variety of attachments is more economical than purchasing multiple dedicated machines, leading to significant cost savings and consequently lower maintenance expenses, reducing the overall cost of ownership. Neglecting their role can in fact lead to missed opportunities for improving eff iciency, reducing costs, and enhancing safety, with some companies
often focusing more on the initial cost of equipment rather than the long-term savings and eff iciencies gained through the use of the tools.
There are many other benefits as well: too many for us to dwell on here, but you can read more about them in this edition, as we focus on businesses which specialise in producing some of the best attachments and accessories available on the market today.
Meanwhile, as in every issue, our expansive case studies take us all round the country as we focus on some of the industry’s leading earthmoving operators and the equipment they use to maximise their profitability.
In WA, we look at three separate equipment rental companies and their operations: find out about how an electric loader from Volvo is making an impact; read about Komatsu's Intelligent Machine Control technology which integrates advanced automation and precision control directly into the equipment; and discover how Caterpillar equipment is helping service the diverse needs of WA’s massive Goldfields region.
Then we travel to Queensland, where we chat to an earthmoving enterprise which swears by its Kobelco machines to ensure the tasks are carried out to perfection; we move northwards to Townsville to interview local MotoGP identity Jack Miller as he put the new Cat® 255 Compact Track Loader through its paces; and in the same locality, we visit the Smart Iron field day, an innovative event designed to freshen up the skills of operators using Cat equipment.
Then a quick trip over to NSW, where we focus on a regional construction business’ love aff air with LiuGong machinery, and how the brand is helping Chinese equipment become highly competitive on the global stage.
All this is in your hands, plus a feature on excavators, several articles from our industry experts, showcases on innovative products, dealer profiles, latest news and developments, and incisive opinions from our regular partners and commentators.
Happy digging!
Earthmoving Equipment Magazine is published bimonthly by Prime Creative Media Pty Ltd.
ray.chan@primecreative.com.au
Brand Manager KahChi Liew kahchi.liew@primecreative.com.au 0421 474 407
Production Editor
Michelle Alder michelle.alder@primecreative.com.au
Design Cat Zappia
Subscriptions
P. +61 3 9690 8766 subscriptions@primecreative.com.au
Website www.earthmovers-magazine.com.au
Copyright Earthmoving Equipment Magazine is owned by Prime Creative Media and published by John Murphy. All material in Earthmoving Equipment Magazine is copyright and no part may be reproduced or copied in any form or by any means (graphic, electronic or mechanical, including information and retrieval systems) without written permission of the publisher. The editor welcomes contributions but reserves the right to accept or reject any material. While every e ort has been made to ensure the accuracy of information, Prime Creative Media will not accept responsibility for errors or omissions, or for any consequences arising from reliance on information published.
The opinions expressed in Earthmoving Equipment Magazine are not necessarily the opinions of, or endorsed by, the publisher unless otherwise stated. © Copyright Prime Creative Media, 2024.
Articles
All articles submitted for publication become the property of the publisher. The editor reserves the right to adjust any article to conform with the magazine format.
Head O ice 379 Docklands Dr, Docklands VIC 3008 P: +61 3 9690
JETLAND is a leading supplier of high strength & heavy duty Aluminium loading ramps in Australia. High quality raw material and safety testing systems ensure a safe and reliable product.
No manufacturing delays, all ramps listed online are in stock at our warehouse in Mordialloc, Victoria.
We can also supply Custom built ramps - made to your specifications for your particular needs.
60 MONTHS/10,000 HOURS POWERTRAIN WARRANTY ON NEW -7 EXCAVATORS
Allworks WA has become the first Australian customer to use Volvo’s new emissions-free workhorse, the L25 electric loader.
Throw a dart on a map of Western Australia, and chances are it will land on an area that bears the footprint of Allworks WA.
The ubiquitous provider of dry and wet hire equipment and personnel for the civil, mining and rail industries has long demonstrated its ability to produce eff icient, consistent quality results, with operational locations strategically located to support major projects across Australia.
It has supplied machinery for tasks of all sizes, from smaller civil works to the likes of the Metronet rail projects in Perth, Inland Rail in NSW, and a number of large rail projects for Roy Hill, Rio Tinto, Fortescue and BHP.
The family-owned business, with Angelo Sarich and wife Robin at the helm, has been operating since 1999, with its key staff each having many years of experience in rail and civil works.
One of them is Allworks general manager Nick McLoughney, who spoke with Earthmoving Equipment Magazine about the company’s move into electric vehicles.
“The pillar of our success to date can be
attributed to our industry alliances and connections which we have developed over the past 25 years,” Nick said.
And among those is the close partnership with CJD Equipment, which began in the early
2000s and has continued to grow in strength, particularly over the past 15 years.
“The relationship has really developed. They are one of our trusted suppliers for our equipment across the entire fleet,” Nick said.
“We own about 300 key assets. The majority of those are loaders and excavators and almost 100 of them are Volvo machines obtained from CJD.
“We've got in excess of 70 Volvo loaders, as well as their trucks, excavators, some graders, some rollers. It’s quite an extensive Volvo fleet and they’re always in demand.
“All of them have been powered by diesel fuel. But this year we decided to bring in the first electric loader from Volvo.”
The nudge into action occurred when Allworks had been contracted to help build a tramway extension at Whiteman Park, a unique recreation and conservation reserve and a major tourist destination located 28km from the Perth CBD.
With a need to work quietly and safely in an environment habited by fauna and frequently surrounded by visitors, the company wanted a loader that reduced worksite emissions and noise pollution.
“We'd been talking to CJD for a number of years about electric options because it is something that our customers are interested in,”
Nick said.
“We were always keen on equipment that let us work more quietly in metro areas, for
example, so when we have night shift work in and around residential areas, there’s less noise. And obviously the lack of emissions are a benefit.
“When we heard of the new Volvo L25, we wanted to use it for the Whiteman Park project.
“Volvo is a trusted brand. We were confident of getting one of the first machines, knowing that it was backed by CJD as well.”
The Volvo L25 Electric is the first such loader sold by the company in Australia. It combines the proven Volvo compact wheel loader platform with outstanding lifting and breakout forces, zero-tailpipe emissions and an extremely low noise level.
The five-tonne wheel loader features a lithiumIon 48V battery with a capacity of 40kWh.
The quietness means the machine, with its distinctive rounded contours, can operate anytime, anywhere, even in populated areas. Zero emissions also mean there is no need for costly fume extraction systems when working indoors.
“The loader has already been out on a couple of jobs already. Of course, the first was at Whiteman Park, a very sensitive area, operating around local wildlife and the public” Nick said.
“Also we've used it in a couple of metropolitan jobs where its lack of emissions was great; it's a very quiet machine and
being Volvo, it's extremely reliable.”
Nick said one of the best attributes of the model was the world-class cab for which Volvo is renowned, including wide entry, the superior visibility and comfort levels, further enhanced thanks to a dramatic reduction in noise, vibration and heat, and no exhaust fumes. This all contributes towards a quieter and cleaner jobsite, improving communication and working conditions for all personnel.
“Our operators are pretty happy with the comfort and ease of use,” he said.
Featuring a 1.2m3 standard bucket, forklift, grapple, or material handling arm, the L25 is a solution for a wide range of projects.
“It's an all-terrain unit, and it's very nimble, so enabled us to get into some of the tight spaces in and around our metro projects,” Nick said.
“It’s got the bucket and the forks. So we can move things around the side, as well as loading and shifting.”
Nick said charging the loader was also carried out with a minimum of fuss.
“It's very versatile in terms of charging. It's got many different charging options right down to a normal 240 Volt, 10 amp plug. You can literally charge it from anywhere there is power.” he said.
“In fact, we haven't actually exhausted it during operations. You can do a fast charge
mid-shift if required, but we we're generally getting a full eight to 10 hour shift.”
Being a compact wheel loader, Nick acknowledged that the L25 was the smallest model in the fleet.
“But that’s all you need for some of the metro projects that we're working on, and they’re so versatile,” he said.
“I am sure CJD or Volvo will be coming up with bigger electrical models soon. They’re already talking about the electric options for the L120 size, which is the majority of our Volvo loader fleet. And that's something that we're looking very closely at … the options to be able to utilise those machines.”
CJD Equipment state sales manager for
construction equipment in WA, James Daniels, was equally thrilled at the success of the electric loader in Allwork’s projects.
“I’ve been involved with getting Allworks into our newer products, such as the EW 60 excavator, and now this L25 loader,” he said.
“We had started the conversation on electrics about 12 months ago. Some of Allworks’ end users said they were going green and the company always wanted to sort of match that and follow that pathway,” he said.
“So we started talking about loaders and we moved on to electrics and what's happening in the future, and said this is where Volvo was heading.
“We've had the electrics for in Europe for about three years, and in the initial stages, Volvo was selective in where they were selling them to.
“We then got two electric machines, the L25 and the ECR25 excavator, brought down to Australia and we had them on show for a little bit and tested the market.
“Allworks showed a definite interest in trialling such models. When this machine became available, we did a demo at Allworks’ site in Wangara, and the rest is history.”
James echoed Nick’s enthusiasm about the L25’s features.
“The best feature undoubtedly is the fact that it's electric. And it’s quiet, but has a lot of ground torque,” he said.
“Its lack of emissions while maintaining its versatility is a winning combination.
“And it's not like a conventional engine where it's constantly on idle and using fuel. If you're not using it, there's no power being drawn from the battery. So it's about seven hours of work time rather than any idle time mixed in with that.
“So this is the first Volvo L25 that's been sold in the whole of Australia. It’s a small order, of course, but with its success, we're looking to make even bigger electric models.”
James said among these were the L90 and L120 electric loaders, and a 23-tonne electric excavator, the EC230, all of which were revealed at Volvo’s showcase Volvo Days event in Sweden in late May.
“We’re hoping that these will be available in Australia in the not-too-distant future, maybe even by the end of the year,” he said.
Electrifying specifications
Operator comfort
• Low vibration, low noise levels, no exhaust fumes
• Wide three-point cab access
• Best all-round visibility
• Intuitive interface, electro-hydraulic controls
• Electric parking brake with hill hold functionality
• Programmable cab heater (option)
New opportunities
• Perfect fit for noise sensitive areas
• Ability to work out of standard hours
• Zero-tailpipe emissions: work indoors and in emission-restricted zones
Uptime you can count on
• Work a full day – operating time calculator available
• Make the most of every charge: fully electric driveline with energy recovery function and auto-shut off function
• Choice of charging solutions: 0-100 per cent in up to two hours
The best battery technology
• Lithium-Ion 48V battery – 40kWh
• On-board charging done via Type 1 automotive standard inlet
• Comes with 6kW on-board charger, charging cable, plug and adapters
• Fast charging possibilities
• Can be charged at any State Of Charge (SOC)
• Theft protected fixed battery D
• designed to deliver up to 2500 full charge cycles
Less maintenance
• Maintenance-free electric motors, featuring auto shut off to save wear
• Fully electric driveline reduces hydraulic oil need by half
• Easy ground level access to lubrication and maintenance points
Work anything, anywhere
• Perfect fit for confined and narrow spaces
• Wide range of Volvo Attachments
• Attachment bracket with integrated third hydraulic function
• Customisable work modes including traction force, joystick and accelerator pedal sensitivity
• Maximum speed of 20km/h (12mph)
Proven performance
• High lifting and breakout forces, superior rollback and dump angles for bucket applications
• 100 per cent parallel movements, outstanding lifting height and forward visibility for fork applications
• Rigid planetary axles, with 100 per cent mechanical differential locks on the front and rear axles, offer maximum traction and minimal tire wear
• Articulating-oscillating centre joint provides the best off-road capability and stability
The CJD connection
For many years, CJD Equipment and Volvo CE have been supplying premium construction equipment tailored to the specific needs of Australia’s diverse industries.
Their collaboration over 30 years has ensured the delivery of high productivity, fuel eff iciency, and safety solutions, enabling machines to operate at peak performance.
CJD Equipment boasts an extensive national support network, guaranteeing comprehensive assistance regardless of location or time.
For further details, please reach out to your local CJD branch at 1300 139 804 or visit cjd.com.au
Battery run time of up to 65 minutes SINGLE QUICK COUPLING MOTOR CAN BE USED WITH MULTIPLE QUICK PUMPTUBES
Flow rates up to 4.3L/min
Streamline your workshop operations with the Alemlube 11028 Battery Operated 20L Oil, ATF & Coolant Drum Pump. This portable and easy-to-use pump, powered by a 21.6V 2.5Ah Li-ion battery, delivers up to 280 litres per charge, making fluid transfers efficient and effortless. Designed with a sealed system to prevent contamination, it also features a drainback nozzle holster to keep your workspace clean, and a height-adjustable pickup tube for compatibility with various 20L drums. Whether handling oils up to SAE140, ATF, or coolant, the Alemlube 11028 ensures reliability and productivity, helping you get more done with ease. 2 * A
*Figures as above based on 5W-30 engine oil
Embarking on the 180-kilometre journey north from Adelaide to the Goyder South Windfarm unveils a landscape defined by its vastness and remoteness. Here, an e icient operation has been carved out by John Buttrose and his team amidst this challenging terrain.
At this expansive site, the team relies on a temporary workshop and Starlink Wi-Fi, to seamlessly order genuine Cat® parts through the parts.cat.com platform.
The platform has helped streamline the Buttrose Earthmovers workflow by providing instant access to availability, pricing, and delivery times, eliminating the need for cumbersome phone calls.
Reflecting on the transformative impact of parts.cat.com on his business, John said his operations now extend across civil, mining, and quarrying sectors, with a significant emphasis on bulk earthworks, land development, roadworks, and underground pipe works.
“There's simply no going back to the old ways of relying on a parts interpreter or a single person to manage orders,” he said.
“Every mechanic must have the ability to use parts.cat.com, which is not only reliable but also remarkably user-friendly.
“This way, the mechanics working directly on the machines can easily locate and order the necessary parts, with precise knowledge of delivery times.
“After the growth we've experienced over the past decade, reverting to the old system is simply unthinkable."
As a mid-sized civil contractor frequently operating in remote locations like Goyder South Windfarm, Buttrose Earthmovers previously faced the frustrating task of making phone calls from the rare hilltop that offered a sliver of reception.
However, with the integration of parts.cat.com and the cutting-edge capabilities of the stateof-the-art Parts Centre at Cavpower — the off icial Caterpillar dealer for South Australia — the business has achieved unparalleled control, reliability, and accuracy.
This streamlined process has not only accelerated its fleet management but also ensured that machines return to operation swiftly.
Parts.cat.com has not only accelerated Buttrose Earthmovers’ fleet management but also ensured that machines return to operation swiftly. Images: Cavpower
This newfound eff iciency directly contributes to the team's profitability across all projects.
"Having the same mechanic working on a specific machine, with the ability to open his laptop and see exactly when a part will arrive and to order it directly, has been a gamechanger,” John said.
“If a part is urgently needed, we can arrange same-day pickup or delivery, even utilising services like Uber.
“Additionally, our team can assemble parts lists on SIS, dragging over excel spreadsheets or lists to expedite the process and minimise human error."
Cavpower also boasts a dedicated technical support team to ensure a smooth and userfriendly experience across the parts.cat.com platform.
As Buttrose Earthmovers prepares for a similar rate of growth over the next decade, it has full confidence that the parts.cat.com platform, supported by Cavpower's advanced Parts Centre and expert team, will be pivotal in propelling its business forward exactly when it needs it most.
Visit parts.cat.com/cavpower to order genuine Cat parts today.
Komatsu Australia has launched a program which will help develop young talent and showcase the diverse range of opportunities available in the mining and construction sectors around the country.
Launched as part of the recent National Skills Week, the program targets school and university students along with recent school leavers.
It will include initiatives like promoting STEM directly through schools, technical workshops and seminars tailored to students and educators, work experience and placements throughout Komatsu, and partnering with educational organisations to help develop curriculums and hands-on learning experiences to raise awareness of the roles and opportunities available.
Komatsu Australia’s General Manager for People Experience, Zara Carey, said the program would help prepare the next generation of industry leaders with the skills they needed for a future in heavy equipment or mining.
“Often people think the only jobs available in heavy industries are for mechanics or service technicians, but as our sector embraces more technology and innovative solutions, our workforce is shifting, too,” she said.
“We’re seeing a stronger focus on STEM opportunities, and we want to demonstrate this variety of career options available to the youth of today.
“Komatsu is a unique workplace as we offer multiple pathways for employment.
“You might start in a hands-on role, but often can shift sideways or upwards to a
more managerial or technical role, such as analytics engineering, data science or software development.
“This is what we want our youth program to promote: that there are different opportunities out there that school leavers might not know of, and Komatsu could just be the place for you.”
As part of National Skills Week, which ran in August, Komatsu partnered with educational organisation STEM Punks to deliver a workshop for students in years 7-9, where they got to learn about autonomous vehicles and the data and technology that drives them, testing it in real time with simulations and challenges.
“We started and ended National Skills Week with these two workshops at our Innovation Hub in Brisbane,” Zara said.
“The students learned about sensor systems, wireless communication, cloud data, and Komatsu’s intelligent Machine Control (iMC), and how to code and apply these new skills to control a robot platform.
“We’ were excited to offer this program in partnership with STEM Punks, and to get our wider youth program underway throughout National Skills Week, as we look to support a future workforce equipped with the technology and skills they need to progress in their careers.”
About Komatsu
Komatsu develops and supplies technologies, equipment and services for the construction, mining, forklift, industrial and forestry markets.
For a century, the company has been creating value for its customers through manufacturing and technology innovation, partnering with others to empower a sustainable future where people, business and the planet thrive together.
Front-line industries worldwide use Komatsu solutions to develop modern infrastructure, extract fundamental minerals, maintain forests and create consumer products.
The company's global service and distributor networks support customer operations to enhance safety and productivity while optimising performance.
Need to offload your used trucks and machinery? DIYinspect is a self-inspection app powered by Pickles. Asset owners can simply download the app, complete an in-app inspection and receive an offer to purchase equipment. Start the process anywhere, at any time.
DIYinspect helps customers sell their assets with ease and in their own time and space. By conducting remote inspections, sellers can maximise their time and return on their assets.
Customers receive data-led offers to purchase, eliminating the expense and hassle of conducting in-person asset inspections.
Sellers can offload a range of equipment including trucks, buses, excavators, and loaders.
Head to DIYinspect.com.au for more information, or simply download and get started!
Auction house Pickles talks about the importance of volunteer auctioneering, charitable giving and community fundraising.
As an Australian business with a rich history dating back more than 60 years, Pickles has long known the value of charitable giving.
More than knowing the merit of giving back, Pickles understands the immense responsibility that large businesses have to positively contribute to communities.
That’s why Pickles invests each year in a range of organisations, both big and grassroots, with funds, sponsorships and plenty of free auctioning services.
In a year like 2024, where the average giver has reduced charitable giving, it is up to leaders like Pickles to spread plentifully to those who need it most.
In recent months, charities are noting up to 80 per cent of givers cutting their donations compared to previous years, leaving those fighting the good fight to do so underresourced.
As cost-of-living pressures have steadily increased in 2024, it is often non-necessity spending that is stopped first, like that of charity donation.
Unfortunate as this may be, therein lies an opportunity for Australian businesses to play a pivotal role in the economy and community. Beyond commercial activities, big businesses have a social responsibility to uplift the communities around them with philanthropic efforts.
This responsibility cannot be overstated and it is something Pickles actively encourages from other companies through networking and joint endeavours.
Charity is a cornerstone of Pickles and a theme that is present in the everyday operations and planning of the business.
It’s an undercurrent that is felt through every department and by Pickles huge national staff of more than 850 people, many of whom participate in workplace giving or their own fundraising which is supported by colleagues.
Fostering a community of givers is a source of Pickles pride and is something the business encourages by leading by example.
This is done in a range of ways including giving funds, donating valuables, sponsorships, hosting fundraisers, offering free auctioneering to charity auctions and many other ways.
These initiatives are spread far and wide across Australian organisations, with Pickles supporting well-known initiatives like the Westpac Rescue Helicopter Service, Variety Adventure Ride, School for Life and Healthy
Heads in Trucks & Sheds, and with grassroots giving for local sporting teams.
Pickles National Sales Manager, Trucks and Machinery, James Chauncy said doing this work was part of Pickles’ social responsibility.
“Giving back is extremely important to us, we feel that supporting charitable initiatives is not just an opportunity we have, but a responsibility,” he said.
“Pickles has been operating for 60 years and we’re proud of our country and want to support the communities in it in every possible way.”
James has worked at Pickles for 18 years and during this time, he’s used his hard-earned auctioneering skills to lend a practical hand to charities during fundraisers.
One such event is held each year by School for Life, a not-for-profit organisation that provides rural Ugandan communities with quality education, employment and healthcare.
During School for Life’s annual fundraising event, James volunteers to take centre stage to auction off millions of dollars worth of items.
It’s not uncommon for James to spend his time volunteering his auction services at events,
which has become an excellent opportunity for him to network and meet like-minded people from other industry bodies.
It is when industry organisations come together with the common goal of doing good, that true progress takes place.
Such is the case with VE Group, a Queensland-based earthmoving, quarry supplies and logistics company run by equally enthusiastic philanthropists.
Nathan and Bronwen Howell from VE Group realised the value of working together with other industrial businesses herself, after her close friends needed the help of an Australian charity in 2021.
The organisation that answered their call for help, Childhood Cancer Support (CCS), is one of Australia’s longest running charities, providing short and long-term accommodation to rural families whose lives have been impacted by their children undergoing cancer treatment.
When Bronwen saw first-hand the value of the charity, she decided to put the call out using a personal letter to her wide network of
transport and civil insiders to fundraise.
Bronwen says putting the call out put things in motion that had a huge roll-on effect on the funds raised for CCS.
“‘I kept thinking, there’s got to be something we can do and so I reached out to everyone I knew in the industry,” she said.
“Australia’s transport and civil industries are really such giving sectors, so we were able to attract lots of people to lunch to support a great initiative.
“Our first year saw 110 people. The next year we more than doubled our numbers. For our 2024 event, we sold out in under a month with 320 tickets sold. To date, we’ve managed to raise over half a million dollars for CCS using fundraisers and other events.”
VE Group’s Charity Long Lunch has become a very successful annual event, attended by hundreds of industrial insiders.
It’s one that Pickles is proud to have a presence at, by way of James’ services that auction off goods to raise funds for CCS.
The lunch is an event that has had a roll on effect throughout the industry, with Bronwen seeing other business operators become inspired to lead fundraising events.
Childhood Cancer Support Specialist, Pat Hopper, said that the rallying of help from big businesses cannot be overstated.
“Having businesses get involved created growing awareness in the sector. Now that businesses know who we are, we’re seeing lots of organisations host fundraisers and designate CCS as the charity recipient of the funds. It’s had a huge knock-on effect,” Pat said.
For more information on Pickles initiatives, head to pickles.com.au/about/ community-service.
To donate to Childhood Cancer Support, go to www.ccs.org.au.
Since its release over a year ago, Leica Geosystems’ iCON site excavator system has proven to be popular among businesses aiming to optimise the earthmoving jobs of compact excavators.
The innovative iCON solution expands the machine control of trenching and excavating tasks, and provides higher accuracy work with less over-digging, rework and fewer errors.
The one common software and hardware platform offers similar menus and workflow across application, while key hardware components can be moved on different machine applications.
The simple, easy-to-use application integrates easily to existing iCON site applications, so users can benefit from new workflows that combine measuring, stakeout, excavating, and reporting in one easy package.
The iCON site excavator system builds upon the powerful iCON Site platform, allowing compact excavator operators to dig to designs easily and precisely, and is available for use both as a standalone option or can be combined with an ICON Site GNSS rover.
The solution introduced three new components to the existing iCON suite: the iCON Excavator application itself, a dual
GNSS receiver (the Leica iCON gps 100) and an optional communication device for GNSS corrections (the Leica iCON CR50), encompassing a set-up that delivers versatility in tackling a range of applications.
Designed for simple ease of use, the system provides greater flexibility and underpins eff icient and effective equipment and personnel deployment by enabling operators to optimise earthmoving tasks, with the versatility of on-machine and off-machine options in one software.
The Leica iCON site excavator also provides the unique capability to first measure an area, create a design, and then directly dig according to that design, by simply using the same field controller in the excavator cab.
The machine control solution guides the operator using reference models and GNSS in 3D.
Design information and real-time cut/fill indications are displayed in the cab on the control panel, allowing users to rapidly excavate
to the reference design.
This ensures more uptime and operator satisfaction while increasing safety and productivity.
In effect, with this solution in place, compact excavators working on big projects, together with larger earthmoving machines equipped with other machine-control solutions, can now join the digital workspace.
The Leica iCON site software enables compact excavators to use the same digital designs as the big machines in the project ecosystem, meaning the same digital plans can be shared among all machines working on the same project.
And in case of design updates, the same updates can be communicated to the entire 'connected' fleet via Leica ConX, if installed. Indeed, the Leica iCON portfolio is developed with its users' pain points in mind.
The software offers construction-tailored workflows, which make the solutions easier for everyone to deploy within a few hours.
The GNSS receiver and communication device are designed specifically for compact machines, allowing greater flexibility to adjust to di erent sites and project requirements.
The iCON site excavator application follows the portfolio-wide philosophy of 'dirt simple solutions', with its map driven selection and navigation, traff ic-light indication of work results and split-screen functionality that allows different viewing perspectives.
It combines all of the powerful features of these Leica iCON products:
• Leica iCON CC70, CC80 or CC200 field controllers
• Leica iCON site excavator application
• Leica iCON gps 100 GNSS receiver
• Leica iCON CR50 communication device (optional)
• Leica iCON CGA100 antennas
• SJB21 Smart Junction Box
• Leica iCON site software for more heavy construction applications (optional)
• Leica ConX cloud platform (optional)
The GNSS receiver and communication device are designed specifically for compact machines, allowing greater flexibility to adjust to different sites and project requirements.
All iCON products are available through C.R. Kennedy, the sole and exclusive distributor for Leica Geosystems in Australia.
The company is focused on providing high-quality products and tailored solutions for industry, supported by its comprehensive national after-sales network, including training,
service and repairs, technical support, hire equipment, and customer care agreements.
Based out of Port Melbourne, C.R. Kennedy’s national network spans major state off ices in Brisbane, Adelaide, Sydney, Hobart, Perth, and Cairns, with its workforce comprising over 260 staff, including product specialists, qualified surveyors, support staff, and factory-trained service technicians.
C.R. Kennedy is o ering purchasers of an iCon site excavator system a chance to win a trip to attend next year’s edition of bauma, the world's leading construction machinery trade fair. All buyers will go in the draw for a ticket.
Images: Alexander/stock.adobe.com
Insuring assets and knowing what levels of protection to take out can be confusing: but NTI is there to help customers every step of the way.
Business owners who depend on machinery for their livelihoods should consider appropriate insurance for their needs, as underinsurance or having no insurance can be quite risky.
But sometimes the process can be overwhelming, with adequate values of protection diff icult to ascertain.
One insurance company strives to make it all easy: with more than five decades of experience in the insurance industry, NTI is a leader in mobile plant and machinery insurance.
NTI’s Yellow Cover package (subject to eligibility) can insure the smallest mobile plant item through to the largest and most complex infrastructure projects.
Its Mobile Plant and Equipment Insurance is a comprehensive cover option delivered by a team of mobile plant and equipment insurance experts, combined with NTI's outstanding service, unparalleled expertise, and essential local knowledge that provides industrial strength protection across a complicated and specialised range of exposures.
The general Equipment and Machinery Insurance component is designed to provide protection and comprehensive cover tailored around small to medium business operations, equipment and machinery.
An important feature of the policy is that it does not exclude coverage for natural disasters such as cyclones, floods and bushfires.
And that’s a big comfort as the country approaches the months and seasons where the risk of catastrophe is higher.
Policy holders can feel assured that they have cover if they are affected by any of these exposures.
As NTI national product manager for mobile plant David Kidd explains, the company’s main priority is protecting customers’ property and plant, and getting them back into production quickly whether by repair, replacement or cash settlement.
“We know Australian weather can be unpredictable, and a higher probability of severe weather events adds an increased risk to transport, shipping and logistics, and machinery and equipment business owners and operators,” he said.
“Severe weather can escalate quickly, so equipping yourself with an action plan ahead of time, communicating that plan across the business, and checking weather warning systems is essential for preparing for severe weather and keeping your business running.
“We’ve taken our wealth of experience, an innovative approach and local expertise across the country to deliver an industry-leading policy for your mobile plant and equipment.
“If you’re an owner-operator, earthmover or civil contractor, work in quarry and mining applications or farming and agricultural operations, then have a look at our Yellow
Cover offering. We also offer cover for the plant and equipment hire industry as well.
“Plus you can tailor your cover to match your specific needs.
“Add to this our award-winning Accident Assist service, the Premium Repairer network — with in-house mobile plant and heavy machinery specialists to streamline the repair process — our Repair Guarantee, essential local knowledge from capital cities to regional centres across Australia, and value for money premiums.”
Yellow Cover provides customers with industry-leading products, access to NTI’s award-winning claims solution, a lifetime guarantee on authorised repairs and a team of experts and recovery operators all over Australia.
There is also a range of specialist covers, including:
• Substitute Hire Costs for Mobile Plant
• Ongoing Hire Costs
• Finance Payment Protection
• Mobile Plant Damage Waiver
• Overseas Air Freight
• Market Value Plus for Mobile Plant
If you’d like to learn more about risk management and how to protect your business, contact your insurance broker or NTI today. Visit: https://www.nti.com.au/ yellow-cover
Understanding the needs of clients is just one reason why leasing specialist Finlease’s services continue to be popular among businesses seeking equipment finance.
For new businesses starting up in the earthmoving sector, finding the funds to finance equipment purchases is one of the first obstacles.
NSW-based Bryant Civil was one such company, formed in 2020 to service regions in and around Shoalhaven on the state’s south coast.
The versatile operation is involved in a whole gamut of tasks, including house and driveway cuts, pool excavation, rural driveways, subdivisions, car parks and various small building projects.
Director Chris Bryant boasts about 20 years’ experience in the industry, starting off as a labourer with another civil construction company straight after leaving school.
After completing the necessary certificates and moving on up to run some civil projects, he attained enough skills, acumen, and more importantly, the desire, to start up his own business.
Like any fledgling enterprise, initial progress was slow and steady, but as word of mouth of its proficiency spread, so too did the number of contracts, with notable projects so far including the Warden Head Lighthouse Upgrade, the Berry to Bomaderry Bypass, and some smaller tasks within the HMAS Albatross naval station.
“We currently have a fleet of two trucks, five excavators and one Posi-Track,” Chris said.
“I started off with a 5-tonne excavator which I used just doing weekend jobs for mates, then eventually picked up more work, which led to purchasing a truck. Our fleet has expanded due to the amount of work we have.
“The business currently consists of two directors — myself and my wife Melissa — along with six employees.”
Through it all, Chris said the assistance from equipment and machinery finance and leasing specialists Finlease has proved invaluable when it came to stocking up the fleet.
“We approached another broker for finance as well as a finance company, but they weren’t very accessible,” he said.
“Then we heard from Luke Carroll from Finlease, who reached out to us after coming across our Instagram page.
“Luke was a breath of fresh air. He has been so helpful since the first contact was made.
“Luke went above and beyond to get our loans approved and settled in a timely manner, and he continues to do so.
“He will drive down to site for us to sign loan documents, he will always liaise with who we are purchasing from, our accountant and whoever he needs to make all our purchases and leases a seamless and stress-free experience for us.
“There is a great relationship with Luke; he takes a genuine interest in our business and goes out of his way to make our life easier.
“Applying for finance through Finlease is always an easy simple process, the team is flexible and works with us and our needs.”
As for Luke, going above and beyond for clients like Chris was all in a day’s work.
“We keep hearing from our customers that the banks can be hard to approach, especially for newer businesses in a growth phase,” he said.
“In addition, when they do engage with a bank, they quickly realise equipment finance isn’t really the bank’s speciality … whilst we deal with it every day.
“The other one we hear is that their bank manager has left so they have to start all over again with a replacement!
“So when we come along with the ability to help grow their fleet, make securing good finance outcomes easy and be on the journey with them for the long term, we’re
like a breath of fresh air.”
Luke said businesses could also lean on Finlease for advice.
“It’s pretty common for us to have seen a similar scenario for another customer previously, so we can pass on some words of wisdom or provide the right contact for them to talk to,” he said.
“And yes, I’ll regularly go meet clients at their job site or outside normal business hours because it’s about making it easy and allowing them to get on with their business. We really do look to put ourselves in their shoes.
“There’s obviously competition around, but I think my customers like that I’m from the local area with a genuine interest in supporting local business owners on their journey. I don’t believe many other brokers enjoy the same level of connection to the area.”
Cat Grade with Assist for Cat Excavators can help make jobs MORE EFFICIENT by getting to GRADE FASTER, with MORE ACCURACY.
Available as part of Cat Grade, it automates bucket and boom movements for more precise cuts with less effort.
BENEFITS INCLUDE:
DIGGINGGRADINGLOADINGTRENCHINGSLOPING ✔ SIMPLIFIES OPERATION ✔ HELPS IMPROVE EFFICIENCY ✔ HELPS IMPROVE ACCURACY ✔ HELPS REDUCE REWORK
BUCKET ASSIST
Maintains bucket angle and keeps the cut accurate in sloping, leveling, fine grading and trenching applications.
0103 0204
BOOM ASSIST
Automatically raises the boom to keep the excavator from lifting off the ground when digging, lifting or rotating under load.
SWING ASSIST
Automatically stops excavator swing at defined points when truck loading and trenching, helping to reduce fuel usage and improve cycle times.
TILT ASSIST
Takes over bucket angle movements to automatically maintain the desired slope.
Max Capacity: 7,000 kg
Max Lifting Height: 9.65 m
Max Power: 125 hp (93 kW)
Max Speed: 40km/h
With exceptional power and agility, the Samson 70.10 telehandler is designed for demanding tasks in construction and industrial environments.
Boasting superior handling, precision movement control and advanced soundproofing for unmatched comfort, this telehandler offers three steering modes and an intuitive control layout, making it incredibly user-friendly and efficient.
Perfect for environments requiring the handling of large volumes, the Samson 70.10 stands out for its versatility. It can be equipped with a wide range of accessories, adapting effortlessly to your needs. Maintenance is a breeze, thanks to its durable, long-lasting components and materials.
To find out more, contact the Dieci Australia sales team today.
Contact Dieci on 1300 888 479 or visit www.dieciaustralia.com.au
Enhance profit and productivity with Caterpillar's new and improved VisionLink® application.
Whether your fleet is big or small, VisionLink® gives your business the insights to take decisive action.
With an updated interface and industryleading features, VisionLink gives you the edge in fuel and time eff iciency, uptime, and machine health – meaning greater profitability across the board.
Keeping customer needs central
Business is advancing rapidly and Caterpillar customers are embracing technology more than ever – with growing expertise.
They understand that to improve operation management, they need insights informed by data. Experts in the industry are already extremely good at managing their logistics to improve profitability. But as the industry progresses, technology will be the key to success.
This is where VisionLink proves its value. It helps contractors view their fleet holistically, schedule maintenance and assign tasks. Caterpillar developed these processes with input from customers to optimise fleet eff iciency.
The standout customer request was to make the interface easier to use. New VisionLink delivers in spades. It’s simpler and much more intuitive, helping you ensure that work is done safely, on time and on budget.
Caterpillar understands the importance of accuracy when bidding for jobs. Overquoting can lose you a job while underquoting causes financial strain. That’s why data accuracy is paramount with the new VisionLink.
VisionLink is an integrated full- and mixed-fleet management solution.
It tracks assets and gives you the information you need to optimise uptime and utilisation.
Plus, it integrates fully with Caterpillar’s digital ecosystem. The new interface enables you to manage your entire fleet eff iciently.
Whether you own, lease or rent your machines, you’ll have access to the data and insights you need to make informed decisions.
VisionLink is cloud-based and accessible via desktop, tablet and mobile. That means metrics such as asset location, fuel level and idle time are available in real time. With a simple dashboard, you can manage assets by group and geofences.
You can easily generate tailored reports to simplify activities and pinpoint underutilised machinery.
To simplify fleet management, VisionLink integrates my.cat.com, the Cat® app and past VisionLink applications in one. It also offers subscription options, so regardless of your fleet size or nature of your work, there’ll be a setup for you.
“Before we used VisionLink, we were very manual-driven. Now it’s immediate. We can look at problems almost in real-time, and attend to them immediately.
“WBHO is one of the biggest construction companies in Africa, with sites all across the continent. Before we used VisionLink we would have guys onsite who would inspect on a daily and weekly basis. But now it’s immediate. If there’s an alert, we can action it immediately. We can look at problems in real time and fix them.”
Zane Baily WBHO Construction Johannesburg,
South Africa
“Before VisionLink, our equipment management was very reactive. VisionLink has really improved our maintenance program, reduced planned downtime and maximised efficiency.
“We’re using the VisionLink platform and data to help us achieve the absolute highest level of success that we can. Now we can instantly see the hours on each piece of equipment, when the last maintenance was done and get when the next one is due.
Anthony Guho Guho Corp, Idaho, USA
Ready to have the power of knowing in your hands? Find out more at cat.com/visionlink or contact your local Cat dealer.
So you’ve taken out insurance cover for your mobile plant and equipment. But when it comes to making a claim, have you considered how di icult or slow the process could be?
UAA aims to get customers back on their feet again as quickly as possible. Backed by more than 50 years’ experience in the sector, the company prides itself on innovative insurance solutions in Australia, New Zealand and in various international locations.
The UAA Group Claims Department comprises of staff with extensive expertise in exclusively managing machinery claims.
UAA Group Executive General Manager –Claims and Procurement, George Grasso, said the team’s ethos was ultimately to expedite claims after incidents with machine(s), material damage and legal liabilities.
“We provide confidence to our clients that their future, assets and liabilities are protected by delivering on our promise,” he said.
“Our claims team consists of over 35 claims experts and professionals across Australia and New Zealand who specialise only in mobile machinery and contracts works claims. This includes material damage to machines, hired-in or hired-out machines, business interruption, third party liability matters that may occur whilst a machine is operating as a road registered vehicle, and or other third party broadform legal liabilities.
“We also handle contracts works that include single or annual projects involving construction material damage and public liabilities, and third-party personal injury.”
George said UAA had been managing niche machinery claims for more than 51 years, with the combined experience exceeding more than 250 years of claims relating specifically to mobile machines and contracts works.
“Our intel specifically to this industry, along with our niche repairer network, loss adjustors and supplier expertise across Australia, New Zealand, Singapore, and our global networks of suppliers, endorses our ability to support and help our customers get back on their feet again as quickly as possible,” he said.
“We manage in excess of 10,000 claims per annum totalling close to $200 million worth of claims across our group portfolio.
“All of our claims experts are based here in Australia and some in New Zealand that manage our NZ customers.
“We are heavily focused on local expertise helping local customers, taking a real handson personal approach. This includes all industries and hazards that involve all type of machinery and brands, for example managing a claim involving lifting equipment such as a crane; earthmoving such as dozers, excavators, dump trucks; concreting industry such as pumps and agitators, drilling equipment,
hiring equipment; and construction projects that include construction material and legal liabilities.”
The assessment process
George said the first thing UAA assessors does in processing any incident is to immerse itself into the client’s shoes.
“We don’t act like faceless insurance claims staff awaiting for claim forms first,” he said. “Once we have learnt of an incident, we immediately work with the client’s insurance brokers and our mutual clients in assisting with recovery of machines in precarious situations, and/or exposure to legal liabilities that the clients may be facing,” he said.
“We immediately appoint loss adjusters/experts specific to the machine/industry affected and that can quickly advise UAA severity of damage, and how to expedite the reverse of damage and or quickly obtain facts to mitigate legal liabilities a client may face.
“In terms of machinery claims, UAA works closely with the loss adjustors in determining if a damaged machine is a repairable proposition or an economic total loss.
“If it is a repair, we work closely with the client and loss adjustor in establishing the best repairer that can expedite the repairs.
“UAA then provides an authority to the repairer and continues to monitor the progress and quality of repairs along with expected and agreed time frames.
“If any change occurs, we ensure communication is at is optimum with the customers. On completion of repairs UAA pays the repairer directly once the customer is also satisfied with the repairs.
“The same goes for our contracts works claims services in working with supplier networks to reinstate the loss incurred.”
George said UAA acted instantaneously in appointing experts once incidents occur.
“We know that these types of claims are not like domestic insurance products, for example when alternate transportation can be arranged,” he said.
“In our industry, claims are treated with the highest priority as it impacts the business and the livelihoods of not just the clients, but also their staff, their families, the contractual agreements with their customers and most importantly their reputation and goodwill.”
Each claim/machine is assessed on its own merit and its economic damage condition.
If we refer to a damaged machine and it is deemed an economic total loss, a market valuation is conducted by one of UAA’s independent valuation experts and reported to the claims department,” George said.
“If the market value is less than 85 per cent of the sum insured, then UAA pays the market value
plus 15 per cent of the market value,” he said.
“If the market value is within the 85 per cent percentile, then UAA pays the sum insured.
“As an example, if the machine is insured for $100,000 at the time of a total loss, and the market value is deemed at $90,000, UAA will pay the full $100,000 as the figure is within the 85 per cent percentile.
“But if the market value is deemed at $70,000, UAA will pay $70,000 plus the additional benefit of 15 per cent ($10,500), making the total indemnity paid at $80,500.
“There is an immediate benefit to a customer knowing that they will be paid at least 15 per cent more of the market value. This is an automatic added-free benefit provided.
“Therefore, it is important for customers to annually review their sum-insured amounts on each machine and ensure that the nominated amounts are as accurate as possible to the actual market value.”
George advises that nominated suminsured amounts play a significant factor in the calculations for premiums.
“You don’t want to overstate greatly as you are technically paying extra premium for no benefit, and again not too low neither, otherwise you will negatively impact the true market value of a machine, let alone impact the value of indemnity that would/could have been provided.”
George said the major claims made in the earthmoving sector are:
• General impact damage: machines hitting property and other objects in general, which includes at-fault and not-at-fault, accidental and reversing incidents
• Theft • Rollovers
• Fire
• Liability claims relating to damaging underground services
In summary, George said that to obtain the best cover, businesses should speak to their insurance brokers to clearly define their activities and ensure they can assist in providing the appropriate specific protection.
“The more detail you provide your brokers, the more they can ensure to help protect you. Don’t ever take for granted the little things you might think should be common knowledge, as it might not be so common,” he said.
“Ensure your sum insured amounts reflect the value of your assets and the true value of the projects for contracts works. Ensure appropriate risk mitigation strategies are in place, monitored and tested.
“Have a safety first focus, which includes competence training, daily log books, strict maintenance, strict safety and daily checks as per industry and Australian standards, along with OEM guidelines.”
A new durable cover for hoses has been developed that o ers sturdy protection against the impacts of harsh environments.
Hoses are critical components in hydraulic systems used in various types of equipment, from industrial machinery to construction vehicles.
So it’s important that they are protected from impact damage from external factors, particularly in harsh working environments.
For a long time, the best alternative for rugged applications has been to use expensive hose guarding or complicated routings to protect the hose, both of which are less than ideal and incur extra handling and additional labour costs.
Reducing maintenance time and expense is important. If a hydraulic hose can last longer, productivity increases, leading to savings across the board.
But there’s a better way of damage control than using clumsy guards, or complex bend radius and clamping configurations which add to the weight.
The Hose Products Division of Parker Hannifin Corporation, the global leader in motion and control technologies, has developed a hose cover that offers sturdy protection against the roughest of elements.
Parker has long led the way when it comes to providing durable, long-lasting hydraulic hoses, with its product line renowned for its sturdiness, radius flexibility, resistance to temperature, bursting and impulse pressures, and chemical compatibility.
With more than 100 years of engineering excellence in a wide range of diversified industrial and aerospace markets, Parker has acquired the engineering expertise and a broad
range of core technologies that helped uniquely position the company to help solve the world’s most significant engineering challenges.
Parker designed the Global Core range, consisting of six hydraulic hoses and two fittings series, which provided the first comprehensive hose and fitting system that encompasses the most common constant working pressure classes.
The Critical Protection Hose Cover is the latest addition to this range, which is fast establishing a new standard for hose failure prevention.
What makes this cover unique is the combination of impact and abrasion resistance, making it the ideal choice in any application where the hose is exposed and could be subject to external damage.
Imagine, for example, if rocks fell onto hoses out in open terrain; without adequate protection, they would split the covering and break reinforcement layers, leading to hose failure.
Parker’s CP cover, developed from bullet-proof body armour and using shear-thickening fluids (nano technology), offers protection against such impacts, without the need for operators to use spiral guards and other similar forms of wraps and sleeves.
The weather-resistant, black synthetic cover is embedded with an orange nylon leno fabric, a weave in which two warp yarns are woven around the weft to provide a strong yet sheer product.
The covers have been extensively tested in the field, where they have demonstrated reduced
maintenance time and expenses and allowed for increased productivity.
In some applications, hoses with the CP cover had double the life of other abrasion-resistant hoses.
In short, the CP Hose Covers serve customers facing demanding applications without sacrificing hose performance or flexibility. They are available in sizes 8, 12 and 16 on GlobalCore 487, 777, 787 and 797 hoses.
The hose covers are available through Parker’s national distribution channel of ENZED Service Centres and Hose Doctors, the supplier of choice across a wider range of Australia’s largest industries.
ENZED boasts extensive experience and a strong record of delivering high quality products and services including flexible hose, fittings and adaptors for all hydraulic, pneumatic and industrial machinery.
ENZED’s capability is more than technical know-how and product solutions: it encompasses accreditation, scale, experience, distribution and the dedication of the ENZED network of brick and mortar franchised Service Centres and mobile 24/7 Hose Doctors.
Hose Doctors provide services akin to mechanical house calls, providing onsite maintenance as well as emergency callout services, helping to maintain plant and equipment eff iciently and always at the ready to service and replace all types of industrial and hydraulic hose and fittings.
If you’re in the earthmoving game, you’ve probably heard a fair bit about soil testing.
But what’s it all about, really? Think of soil testing as the foundation of your project – quite literally. Before you start shifting dirt or laying down concrete, you need to know what you’re dealing with beneath the surface.
I caught up with Matt Neville, acting GM and Lab Manager at Benchmark Geotechnical, to learn more about the “Dirt Doctor” game!
Why bother with soil testing?
You might be thinking “Why do I need to test the soil? It’s just dirt, right?”
Well, not exactly. The soil on your site can make or break your project. Whether you’re building a road, setting up a structure, or digging out a trench, the type of soil underfoot matters.
Imagine laying a foundation on soil that’s prone to sinking or cracking.
Not good, is it? Soil testing helps you suss out any potential issues before they become fullblown disasters.
It tells you things like how much load the soil can handle, how well it drains, and whether it’s likely to shift around when wet.
It’s about being prepared, so you’re not caught off guard halfway through the job.
Soil testing conducted during the project also provides quality assurance of the works you’re performing allowing the completed project to be signed off and moved onto the next step leaving you with peace of mind.
The key tests you’ll need
Now, let’s get into the nitty-gritty of what soil tests you might come across. First up, primarily before any works are conducted or even designs are finalised, soil classifications are performed.
This is done via site investigations engineers using drill rigs to drill numerous bore holes throughout the site to visually inspect the soil at various depths.
During this process, samples are taken back to the laboratory for testing to determine the characteristics of the soil.
Tests such as PSDs (particle sieve distribution for gravels), Atterbergs (plasticity for clays) and CBRs (bearing strength of the soil) are commonly performed. This provides data to confirm whether the soil is a gravel, sand, clay or silt based which is necessary as all these soils behave very differently, so this is crucial info.
Next, there’s the moisture content test.
This one’s pretty self-explanatory – it measures how much water is in the soil. Too much moisture can turn the soil into a sloppy mess, while too little can make it dusty and tricky to work with.
Moisture content tests are generally performed on all most other tests as this is considered a critical factor.
Design specifications will often state an “Optimum Moisture Content” on all soils on the project. Hitting that sweet spot often gives you the best outcomes in using the soil saving time in the long run.
Then there’s the field density/compaction test: the most commonly performed test on projects and no doubt you would have seen a soil tester using a bright yellow gauge on soils just recently compacted.
This test is about determining the current density of the compacted soil onsite and comparing this with the maximum density compaction that soil can achieve.
A soil tester will collect density readings from the gauge of that soil on site, retrieve a sample where the gauge was and take this back to the laboratory.
A compaction test is done to determine the max density this soil can achieve, comparing this data with the density readings on site allows a density compaction ratio result to be given.
In short, if the field density readings are too low then often further compaction on the soil on site is required.
Ultimately this is to avoid uncontrolled settlement of this soil after the project’s completion and prevent damage to the new structure built over that area.
Every time you see a pothole on the road, think poor compaction. This one’s all about finding the sweet spot for compacting the soil.
You want it packed just right, so it’s solid and stable under whatever you’re building.
Now, let’s talk about the gear you’ll need to get the job done.
With such a wide range of soil tests that can be performed, specialised equipment is required.
Each laboratory would house sieve shakers, drying ovens, load bearing machines, compaction machines and numerous others. Each apparatus is calibrated regularly to NATA requirements for quality assurance to provide accurate results.
In most cases, you’ll only ever see the nuclear density gauge (yellow machine) which is used on sites for compaction which all soil testers are required to be trained and accredited to use.
So, there you have it – the basics of soil testing in a nutshell, plus the tools you’ll need to get the job done.
It might seem like an extra step, but trust me, it’s worth the effort. By knowing what’s going on beneath the surface, you can tackle your earthmoving projects with confidence, avoiding those costly and time-consuming headaches down the track.
Whether you’re a seasoned pro or just starting out, getting a handle on soil testing is a smart move. So, give it a go, and keep your projects rock-solid from the ground up! Soil testers are there to assist and help provide input on how to best achieve high quality standards. Think of them as a guide to getting the job done right and not a hindrance.
Ultimately completing a project on time, within budget and to a high-quality standard is everyone’s objective. We all drive on these roads or use structures where this process has been performed prior.
Australian Earth Training scott@australianearthtraining.com.au www.australianearthtraining.com.au
Bundanoon Sandstone Quarry in NSW has acquired the vital machine it needs, thanks to Yellowgate Group’s popular Rent Now, Buy Later solution.
If you’ve always believed that renting machinery instead of buying it outright is poor economics, then Yellowgate Group would have you think again.
The equipment rental specialist says that one of the biggest misconceptions throughout the equipment industry is asset hire equates to dead money.
National Sales Manager, Noel Rosario, says the notion is simply untrue.
“There are a variety of reasons that make renting machinery a better option compared to buying or using traditional financial instruments,” he said.
“For example, a business could be experiencing high growth today, but deep down they have a burning desire to eventually own the equipment outright tomorrow.
“They could be seeking a manageable operational expense that isn’t cash intensive up front; and is unlikely to affect their future borrowing capacity.
“Or they could be still setting up following a recent acquisition of a pre-existing business – and the primary focus is to preserve working capital, reap the benefits of the asset immediately and capitalise on it later.
“They understand that access to the right equipment – through a flexible solution like our Rent Now Buy Later (RNBL) product - shouldn’t be a barrier to growth."
The innovative solution provides a flexible option that sets clients on the path to future asset ownership.
Accumulated rental payments may contribute towards the overall cost, making it an appealing choice for those looking to eventually own the equipment.
“In addition to the flexibility of our product, it helps that we have built a reputation for deploying assets anywhere in Australia, fast,” Noel said.
“But most importantly, we’ve got the ability to grow with our customers businesses as they adjust their fleet requirements.”
The Bundanoon experience
One happy beneficiary of Yellowgate’s RNBL solution is Bundanoon Sandstone Quarry in the heart of the Southern Highlands in NSW.
Travel out to the site and you can’t help but notice a big yellow machine in action, using a buzz saw attachment to carve rocks like a hot knife through butter.
The appliance is a Liebherr R 945 Excavator, which plays the primary role in extracting stone for all of the quarry’s products.
As Bundanoon Chief Executive Off icer Troy Stratti explains, the three-metre Stratti rock saw is used to cut sandstone in-situ in a grid pattern.
“Bundanoon has some of the densest sandstone in Australia, but the power of the Liebherr allows us to cut with ease,” he said.
“Retrofitting the excavator to the rock saw has revolutionised our extraction process at Bundanoon.
“The implement is engineered for high torque at low speed, and the dedicated hydraulic pump of the Liebherr R 945 delivers consistent oil flow and pressure, free from interference by other control movements in the excavator's hydraulic circuit.
“With one of the three hydraulic pumps solely committed to the attachment circuit, we have been able to fully exploit this capability.
“By maximising the torque output of the saw — traditionally adjusted to suit various brands of excavators with lower torque output — we have significantly enhanced our cutting eff iciency.”
Bundanoon boasts a storied history deeply intertwined with the fabric of Australia's architectural heritage.
Established in 1850, it stands as one of the nation's earliest sandstone enterprises, pioneering the extraction and refinement of the natural resource.
“Looking ahead, we plan to capitalise on the excavator’s versatility by retrofitting our dual and multi-blade saws as the quarry continues to develop,” Troy said.
“The unique benefits provided by the Liebherr R 945 have shaved months off our extraction process, underscoring its pivotal role in our operation's success.”
Troy said it was also easy to teach new, youthful operators how to use the Liebherr technology.
“Developing a youthful team for the succession of the quarry is paramount to Bundanoon’s vision,” he said.
Partnering with the best Bundanoon General Manager Brendan Matthews said that the procurement of the Liebherr R 945 has been critical in setting up Bundanoon Sandstone Quarry for growth.
"We thoroughly researched the entire market and considered a range of approaches to acquire our new equipment," he said.
“One company stood out: Yellowgate. Their vision is to be the partner of choice for Australian businesses who are looking for equipment to grow their business.
“Yellowgate caught the eye with their appetite to do business, willingness to support growing companies, and their detailed knowledge of mining equipment.
“The structure of the RNBL solution is financially attractive. Rental payments are considered an OPEX (Operational Expense) – making them tax-deductible; but those payments could become equity if we choose to purchase at the end of the 12-month rental agreement using our CAPEX (Capital Expense)."
Liebherr Australia National Major Account Manager, Earthmoving and Material Handling Division, Scott McClement, said the Generation 8 Liebherr crawler excavators such as the R 945 were “a look into the future”.
“Liebherr completely revised the basic concept of the machines in order to offer
customers even higher-performance and more comfortable products,” he said.
“The highlights of the new crawler excavator generation include the higher engine power, the heavier counterweight for higher bucket capacities and minimal fuel consumption.
“Other innovations are the boom concept with modified head for better boom forces and the optimised load curve, which leads to fuel savings. All engines comply with the requirements of EU emission stage V.”
Scott said the new crawler excavators have higher digging forces and greater traction of the undercarriage, while the swing torque of the upper carriage was also optimised.
These improvements to the excavator result in higher performance and improve fuel eff iciency.
“Low fuel consumption and enormously highperformance guarantee outstanding economic eff iciency,” Scott said.
“In addition, these machines stand for high reliability and maximum comfort. These features make Liebherr crawler excavators powerful, productive and eff icient in mass earthmoving, material processing and particularly quarrying.”
There are four machine control systems available for the Liebherr G8 crawler excavators:
• 2D iCON IXE3 “3D Ready” passive Leica designed for Liebherr
• 2D iCON IXE3 “3D Ready” semi-automatic Leica designed for Liebherr
• 3D iCON IXE3 passive Leica designed for Liebherr
• 3D iCON IXE3 semi-automatic Leica designed for Liebherr
“The R 945 has great reliability and
productivity for working up to 12 hours per day on sandstone quarrying, which Bundanoon valued,” Scott said.
“Liebherr is committed to supporting our customers throughout the purchasing process to ensure they receive our machines at the optimal time for their business.
“This support may come directly from Liebherr or through facilitating processes with third parties such as Yellowgate.”
For Troy and Brendan, they know that the Yellowgate plan definitely helps set up the quarry for future growth and consolidation.
“While Bundanoon Sandstone Quarry is not a new mining site, the resource that sits beneath our 160-acre property is expansive and will see the business through another 175 years,” Troy said.
“The vision of Bundanoon Sandstone is to preserve the stone industry for generations to come.
“What that means is supplying world class sandstone to market, and being a leader in defining quality, as well as developing Australia’s masons of the future by transferring knowledge and techniques to the next generation.”
Brendan said because Yellowgate truly understood business and equipment, Bundanoon sees huge potential to continue the partnership for many years.
“In fact, we believe that we will grow faster and be able to take on more opportunities with Yellowgate as our partner,” he said.
“Big projects require big equipment. Yellowgate has the vision to assess project feasibility.
“They are willing to support us by acquiring equipment using their RNBL product."
Meet the Lovol Alfa WL918K: a compact wheel loader known for its e iciency and versatility in various construction and agricultural tasks, and making inroads in the European and Australian markets.
Lovol’s new Alfa series of hydrostatic transmission (HST) machines, with its advanced features and high quality and reliability, continue to gain traction in Australian construction and earthmoving industries.
The latest addition to the Lovol arsenal — brought in by Equipment Specialists Australia (ESA) — is the WL918K, a 6-tonne operating weight, 2-tonne rated wheel loader.
According to ESA Operations Manager Lawrence Perkins, while the model is the smallest wheel loader in Lovol’s range, it packs a punch well above its size, able to navigate smaller job spaces with ease, yet maximising production with HST drive for fast and smooth operation.
“With an ISO quick hitch for attachment options, this machine can handle all the garden centres and smaller sites with ease,” he said.
“Ideal for moving materials across longer distances, the WL918K features a full Linde HST drive system, and full hydraulic wet brake axles, pumps and valves from Linde.”
The high quality and renowned main componentry of the Kubota V3307 engine means reduced long-term maintenance costs, giving buyers piece of mind along with known trusted local support and parts. Untainted by the addition of Adblue, the workhorse generates an impressive 55.4 kW (75hp).
A double steering cylinder ensures synchronised left-to-right, right-to-left turning of the hardy L5 radial tyres, while articulated steering means less instances of skidding motion, which causes abrasion and diminishing tread life.
“This is just one of the ways that a compact wheel loader like the WL918K series is superior to a skid steer,” Lawrence said.
With the HST, things in the cab are a lot more operator-friendly, allowing for a smoother ride, which benefits operators for longer hours of operation.
Indeed, operator comfort is at the forefront of the new Lovol Alfa series models. A better cab experience means better operator productivity for longer, and in-turn, more eff icient productivity as compared to older machines.
Lovol Australia and ESA double down on this focus with an air conditioner and heater, a fully sealed rollover protection and falling object protection certified cab, air-suspension seat, adjustable steering column, and a 360-degree camera for unrestrained operation visibility.
All in all, the WL918K offers better manoeuvrability, better turning, unmatched operator comfort, and reversible hydraulic cooling.
“Economically friendly with reduced fuel usage
and less emissions due to HST technology, the machine is energy eff icient, saving up to 25 per cent on fuel and tyre life, and over 80 per cent brake life savings with the hydrostatic driveline and wet brake axles,” Lawrence said.
“The standard features of the WL918K are also commonly optional add-ons for competitor loaders in the high class range.”
Lawrence said Lovol was now entering the highly competitive European market, taking on the bigger established brands in the region.
“The Lovol machines have the same specifications as the big names, but are almost half the price,” he said.
ESA has spent the past few years as the authorised distributor for Lovol excavators and wheel loaders in Australia, but offers many more brands and makes.
The range includes heavy machinery to suit smaller operations right through to large quarries and smaller mining, with the wheel loader range spanning 6t to 35t.
And all sizes of excavators are available, whether it be for personal landscaping use with the 1.8t mini digger, right through to mining operations with 200t machines at the ready.
The best part is that, apart from outstanding service and reliability, the equipment all comes at affordable prices, much less than competing brands.
“Dare to compare,” Lawrence said.
Key features of the WL918k include a robust engine, high maneuverability, and a durable build suitable for heavy-duty operations.
For more information about the ESA range, get in touch with Equipment Specialists today at 1300 EquipU (378 478) or www. equipmentspecialists.com.au
The WL918K is equipped with a counterweight that enhances its stability and balance during heavy lifting and material handling tasks, ensuring that the loader maintains proper weight distribution, especially when carrying heavy loads in the front bucket.
When an excavator attachment rental specialist decided to move into hiring out the actual machines themselves, not only did it know that it had to get Kobelcos, but also where to get them from.
Australian Hammer Supplies Hire — or Hammer Hire, as it’s often referred to — is proud to claim it’s Sydney’s leading supplier of excavator attachment hire solutions.
Based in Ingleburn, NSW, the company stocks a wide range of excavating and earthmoving equipment, as well as the largest fleet of earthmoving attachment dry hire solutions across the eastern seaboard (NSW, Victoria and Queensland).
Hammer Hire sales manager Blake Wilson said the extensive range of attachments included hydraulic hammers, diamond blade rock saws, auger drills, bucket crushers, hydraulic compaction plates, bulk pulverisers, hydraulic rock-grabs, twin head rock grinders, combi-cutters, bucket screeners and much more, all available for long and short term hire.
“We pride ourselves on providing the latest models of top brand equipment, and along with our industry knowledge, this means we can supply you with quality products and advice to get the job done right,” he said.
“We have all leading industry brands under one roof, and all equipment is well maintained and serviced regularly with in-house technicians.”
But while Hammer Hire has been an attachment hire specialist since its inception 12 years ago, it is now moving into hiring out the actual machines as well.
“With a vision to better support our customers, it was only natural to transition into owning equipment such as excavators as the next level of offering,” he said.
The Hammer Hire offering now includes excavators ranging from 1.7 tonnes right up to 70t, site dump trucks and skid steer loaders.
In total, the fleet consists of more than 130 machines, comprising the excavators, Positracks/skid steer loaders, rollers and site dumpers, as well as over 400 attachments suited to the above machines, and more.
Blake said that when choosing equipment for the business, it was important to look not just at the capabilities, but other factors.
“We want a low total cost of ownership coupled with overall reliability, a cornerstone of our machine requirements,” he said.
“For us, Kobelco ticked the boxes.”
“The result of Kobelco’s advanced technologies beautifully balances all the demands of today’s construction industry.
“Backed by greater digging capacity and improved fuel eff iciency, these hydraulic excavator machines offer a more economical and environmentally friendly earthmoving equipment solution.
“With machine sizes ranging from 13t to 35t in both zero and conventional tail swing options, and up to 50t in conventional tail swing, we are confident we have the right machine to meet a wide range of requirements.”
Hammer Hire had already been using Kobelcos for the past five years, so when the time came to expand the excavator range, it looked towards the brand again.
“We wanted to add more Kobelcos to the 34 we already had,” Blake said.
And for these purchases, there was only one dealer at front of mind.
“We get our Kobelcos from STM Trucks and Machinery at Smeaton Grange,” Blake said.
“This is mainly due to their wide stock availability, family business values and an ability to drop anything to make things happen.”
The latest Hammer Hire STM acquisitions comprised:
• SK135SR-7 medium excavator
“This was to update the fleet as we had recently sold some older units,” Blake said.
“This machine is an extremely versatile machine which is in demand across all industries and projects.”
• SK135SR-7 O set Boom
The SK135SR-7 Off set Boom is designed with an integrated off set boom that allows the boom to swing left or right independently of the cab, making it ideal for working in tight or confined spaces.
“This was our first off set boom into our fleet as we were seeing increased demand for this type of 14t model,” Blake said.
“This version is often requested on utility projects and earthmoving jobs that need work to get close to perimeters.”
• SK380 SRLC excavator
The robust, large excavator is designed for heavy-duty tasks.
“We were impressed with the SK380 zero swing we purchased last year and it was a good fit to get this into the fleet at this time,” Blake said.
“This machine is a workhorse in civil and earthmoving applications with a larger lift
capacity than a lot of the competition.
“This allows for larger attachments with the ability to undertake a more diverse range of on-site duties.”
Of equal importance to the business is the level of service provided by STM.
“We have always been to STM for the Kobelcos, and the service we get from the STM team is second to none,” Blake said.
“Regardless of the issue, there is always a solution.
“We have great trust with STM’s aftersales. All of our Kobelco machines are under service contracts, ensuring the professionalism of
dealer maintenance.
“The STM service and parts team are a great helping hand to our operation.
“Downtime is the worst thing that can happen to a hire company operationally. It costs our clients time and money as well as ours.
“Equipment maintenance is the highest priority to us and STM understands this.”
Blake said Hammer Hire was committed to offering the latest fleet of excavators and plant and equipment available for hire.
“And that means Kobelcos will continue to feature in future purchases for Hammer Hire,” he said.
For almost half a century, STM has made it possible for businesses across NSW to power up – supplying and servicing quality trucks and machinery to meet the demands of any job.
Starting out in a single shed in the 1970s, we know what it takes to build a business – and are passionate about helping you grow yours. Today, our family owned and operated enterprise is proud to offer a multi-site, modern service, with a team of more than 120. We care about giving every customer the best experience possible – with a wide range of trusted brands, flexible finance, spare parts, repairs and personal service.
We may have come a long way from that shed, but our family commitment to quality remains. Whatever your size, whatever your budget, STM is your one stop shop – with everything to keep your business moving.
2017 CATERPILAR 990K
11,000Hrs, A/C ROPS Cabin, Rock Bucket, Supp Steer, GP Radio & Ride Control 2022 CATERPILLAR 980NG
2,375Hrs, TIER 4, New GP Bucket 5.7m3, Auto Lube, E-Stops, Isolators & New Tyres 2014 CATERPILLAR 980H
10,600Hrs, GP Bucket, Isolators, E-Stops, Loadrite with Printer, Reverse Camera & UHF 2017 CATERPILLAR 972M
8,350Hrs, 5M3
6,945Hrs, Grapple Bucket, Rear Guard, Auto Lube, 3rd Valve, Supp Steer & New Tyres
KOMATSU WA380-8
1,605Hrs, A/C ROPS Cabin, GP Bucket, Beacon, Reverse Camera, & Road Fenders
CATERPILLAR D8T
7,342Hrs, SU Blade, Single Tilt, MS Ripper, ARO Ready, Diff Steer, Isolators & U/C > 50%
SANY’s powerful mini excavators have quickly become a digger of choice in the construction industry.
With the global market value of mini excavators projected to reach $10.23 billion by 2028, the demand for these versatile and powerful machines continues to rise.
In Victoria alone, the State Government has committed $19.2 billion over the next ten years to major infrastructure projects.
One of the most significant projects is the North East Link, a $10 billion investment that will create 6.5 km of tunnels linking Melbourne’s freeway network.
This project, along with other major infrastructure developments, underscores the critical need for reliable and eff icient construction equipment.
Mini excavators account for a significant share of this market. SANY is ensuring the supply of quality machines that offer superior maneuverability, better site access, and low operating costs.
SANY excavators are designed with the operator in mind.
The premium cabins offer exceptional comfort and visibility, ensuring that operators can work eff iciently and safely.
The clever design of SANY excavators allows them to fit seamlessly into busy construction sites, providing superior access and manoeuvrability.
Built for Australian standards, SANY excavators can handle the unique challenges of the local construction industry.
This commitment to quality and durability makes SANY Oceania a trusted choice for Australian contractors.
Introducing the all-electric
SANY leads the way in innovation with its new all-electric range of excavators.
The SANY SY19E 1.9 mini electric excavator, for instance, features a high-power capacity and a short charging time. Its innovative battery pack enables the mini excavator to operate continuously for up to six hours on a full charge, making it perfect for a full working day.
Eff icient operators deserve excavators they can trust. SANY is a global leader in the development of high-quality, innovative, and efficient equipment, including excavators and other construction equipment.
Renowned for their eff iciency, durability, and power, SANY’s mini excavators have quickly
become a digger of choice in the construction industry.
The great power of these compact earthmovers ensures optimal performance in even the most challenging of environments, with their superior fuel eff iciency also helping lower operating costs.
Greater manoeuvrability and a lighter tread
make these excavators ideal for reducing the risk of damage to pathways, gardens, or driveways.
The ability to pair your SANY mini excavator with a variety of attachments unlocks the impressive versatility of these machines, with operators able to easily switch between tasks without the need for multiple machines. Long
service life, comfort and ease of operation, and superb reliability are other standout features of SANY mini excavators.
Another way that SANY is meeting the need for quality earthmovers is through its commitment to providing excellent customer service, from the point of purchase through to after-sales support.
Recognising that routine equipment servicing plays a critical role in minimising downtime, SANY has placed focus on ensuring parts support through improving maintenance services for their clients.
A robust network of dealers and service centres across Australia has been specifically chosen so that timely servicing and parts availability can be offered to customers. Josh Holz, Head of Parts at NSW, ACT, and Qld dealer Yello Equipment, commends this initiative by SANY.
“By providing dealers with consignment stock, we can better cater to the parts, repairs, or maintenance needs of customers, from supplying a new service kit right
through to being able to undertake major componentry replacements like cylinders, booms, and motors,” he said.
“This also allows one party to look after a customer’s needs throughout the life of their machine. From purchasing OEM parts to routine maintenance, customers can continue liaising with the dealer they purchased the machine from.”
As Australia embarks on ambitious housing and infrastructure projects, the need for eff icient and high-quality machinery becomes critical.
With its proven track record of reliability, superior performance, and unwavering customer support, a SANY mini excavator is the earthmoving tool of choice, helping get the job done effectively and eff iciently.
To learn more about SANY’s impressive fleet of mini excavators or to discuss your earthmoving requirements, contact your local SANY dealer.
Alemlube has introduced its newest product for workshop e iciency — the Alemlube 11028 battery-operated 20L oil, transmission fluid and coolant drum pump.
This advanced pump tool is designed to make fluid handling in busy workshops quicker, easier and more eff icient.
Whether you’re dealing with gear oils up to SAE140, engine oil, hydraulic oil, transmission fluid or coolant, the Alemlube 11028 20L drum pump delivers a fully mobile, effortless and fast solution for all your fluid transfer needs.
The pump is engineered to handle a variety of vehicle fluids with ease.
Its high delivery rate — of up to 4.3 litres per minute with 5W-30 oil and 4.6 litres per minute with coolant — ensures that you can complete oil and vehicle fluid transfers quickly, significantly reducing downtime in the workshop.
With a fully charged battery, the pump offers a run time of up to 65 minutes, allowing users to transfer up to 280 litres of 5W-30 engine oil before needing a recharge.
This extended run time makes the Alemlube 11028 ideal for intensive workshop
environments where eff iciency is paramount.
One of the standout features of the Alemlube 11028 is its portability.
Powered by a rechargeable 21.6V 2.5Ah Li-ion battery, the 11028 drum pump eliminates the need for cumbersome power cords and expensive compressed air lines, allowing technicians to move freely around the workshop and access hard-to-reach areas with ease.
The battery recharges in just 45 minutes, minimising downtime and keeping your operations running smoothly.
The Alemlube 11028 is not only powerful but also practical. It comes equipped with an integrated carry handle that makes drum changeovers a breeze, even when you’re in the middle of a busy workday.
The pump’s single quick coupling motor can be used across multiple quick coupling pump tubes, adding to its versatility and convenience.
This modular design ensures that you can adapt the pump to a variety of tasks, further enhancing a workshop’s productivity and profitability.
The pump’s swivelling head is another feature that enhances usability.
By eliminating the risk of hose kinks, the swivelling head ensures smooth, uninterrupted fluid transfer and addresses operator frustrations.
Additionally, the pump is designed with an extendible plastic sleeve on the pump tube assembly, allowing it to be used with the vast majority of oil company drums of differing diameters and lengths.
This adaptability means you can use the Alemlube 11028 across different containers without needing to invest in multiple pumps. In a busy workshop, maintaining a clean and safe working environment is important.
The Alemlube 11028 is designed with this in mind, featuring a drainback nozzle holster that
The pump is designed with an extendible plastic sleeve on the pump tube assembly, allowing it to be used with the vast majority of oil company drums of di ering diameters and lengths.
prevents annoying oil leaks and drips.
This thoughtful design feature not only helps keep the workshop clean but also reduces the risk of spills that could lead to accidents and WH&S incidents.
The Alemlube 11028 comes as a complete package, ensuring you have everything you need to get started right out of the box.
The package includes a modular motor assembly (IK10 rated) for impact resistance, ensuring durability even in the toughest workshop conditions.
The 21.6V Li-ion battery (IK9 rated) for drop protection, provides reliable power for all your fluid transfer tasks.
The package also includes a 240V battery charger, allowing you to quickly recharge the battery between uses.
If workshop productivity and profitably is a front-of-mind matter for you, the new Alemlube 11028 battery operated oil drum pump ought to be on your radar.
With a delivery rate of up to 4.3L/min, a battery run time of up to 65 minutes, a battery recharge time of 45 minutes and a from full-to-empty battery delivery of up to 280 litres, effortless, fast and eff icient oil transfer is available now.
Whether the priority is saving energy for other more important tasks and functions in the workshop during business hours, or for your hobbies and pastimes after hours, the Alemlube 11028 can deliver workshop eff iciencies and an improved work/lifestyle balance for you and your team.
Many brands aspire to be thought leaders in their field, but often don’t know where to start, or what to say. The team from Hardman Communications o ers some suggestions.
Thought leadership has to be engaging. And it has to be leading.
You must add something of value to the conversation.
If you’re saying what everyone else is saying, that’s not thought leadership.
According to FT Longitude, executives spend five hours per week consuming intelligent content. But you may only have 30 seconds to make an impact.
These are the three questions decision makers ask when deciding whether to read or engage with your thought leadership content:
1. Is it strategic enough?
2. Do you understand the sector?
3. Can you give me actionable recommendations?
So, with that in mind, how can you create effective thought leadership?
Along with the above, there are things that differentiate thought leadership from your usual media relations campaign.
Getting thought leadership right Yes, thought leadership content should say something new and add to the conversation or debate.
You also need to share a genuine, fresh insight, that isn’t simply pushing your brand’s agenda or products.
Qualitative or quantitative data often gives your thought leadership content the edge it needs by helping you dial into a perspective that is current and is credible as it’s from an outside source.
Thought leadership content should say something new and add to the conversation or debate. Image: Billy/stock.adobe.com
It gives you a hook that will pique not only your audience’s, but a journalist’s attention.
Another option is external sources, such as case studies or key opinion leaders (KOLs). These help back up your thought leadership with insights and advice from those who are either experts in their field, or are real-life examples of the idea you are trying to convey.
If you’re looking to create a compelling thought leadership campaign or want to turn your research into compelling content, we’ve worked on plenty of projects, large and small (including some award-winners) that have seen great results.
So drop Hardman Commumications a line if you want to chat – hello@hc.net.au
A new slew of technology package upgrades for the Cat® D4-D8 dozers has been recently introduced to further cement their positions as state-of-the-art industry-leading dozers.
Customers can now look forward to Cat Assist with ARO (attachment ready option) features (previously known as ARO with Assist), embedded as a standardised feature on newer Cat D4, D5, D6, D6 XE, D7 and D8 models.
Cat Product Specialist Sean Ho said that in introducing Cat Assist with ARO as a core proponent across the fleet of medium dozers, operators can enjoy greater productivity and eff iciency while utilising them in their day-today work.
As part of the Cat Assist with ARO package, medium dozers will now sport the Steer Assist feature that helps operators doze straight.
“A seasoned dozing operator knows that dozing straight is a task that is far from simple,” Sean said.
“The ability to doze properly comes with years of experience that an operator would need to rack up.
“With our Steer Assist feature, we aim to reduce the skill level that an operator needs to
utilise the machine properly.
“The Steer Assist feature helps the operator in the box maintain precise steering to doze as per their requirements on both flat ground and side slopes.
“For an operator, the volume and type of material pushed will vary on a case-by-case basis.
“As the blade tilt steering is automated to help push heavy loads with less effort, operators can be assured that our medium dozers will be up for the task.”
The Steer Assist feature is also complemented by the Slope Assist™ feature to maintain a consistent blade across slopes when the dozer is in operation.
This ensures consistent results across the different skill levels of operators. Automating such a function would reduce operator fatigue.
Aside from the Steer/Slope Assist, newer D4–D8 models will also come with the Traction Control feature.
“With the Traction Control Feature, operators will be able to navigate many different terrains,” Sean said.
“Reducing track slippage is important for operators who are operating the dozers in less-than-ideal soil conditions, and that is what the team here at Caterpillar is trying to achieve with the introduction of this feature.
“Reduced track slippage directly translates to reduced maintenance cost and greater fuel eff iciency.”
Traction Control comes in two modes –Normal and Low Slip. Normal mode will be the recommended option for most applications whereas the Low Slip mode is recommended for applications where any amount of track slip may be undesirable.
Sean said the Traction Control feature brings about benefits beyond track slippage.
“In preventing track slippage that can cause greater track wear, changing gears frequently can cause operator fatigue,” he said.
“With the newer medium dozers equipped with Traction Control, operators get to maintain their top form even with prolonged operating hours.”
Additionally, Cat medium dozers will be equipped with the Stable Blade function that provides a precision-based finishing touch to the ground that the operator is working on.
“Stable Blade gives the operator better blade control to create their desired surface with minimal passes,” Sean said.
“Operators with varied skill levels will be able to produce their desired results easily.”
Stable Blade comes with three blade functions – Lift, Tilt or both Lift and Tilt – to suit a variety of different applications.
To better help operators create their desired surface, Stable Blade also has three different response settings – Low, Medium and High.
“Low response setting is primarily for creating smooth surfaces,” Sean said.
“Operators can also explore utilising the medium setting to create contoured surfaces. The high setting can be used for creating flat or sloped surfaces.
“In rolling out these features as standard across our line of medium dozers, the core intent is to make it easier to help operators become more productive while reducing operator fatigue.
“We believe the right way to assist operators is through automating skill-based work.
“AutoCarry™ is also another key feature that would be able to give operators greater control over the work they do with minimal effort.
“AutoCarry automates the adjustment of blade lift and this allows operators to scoop up a consistent, fully loaded blade with every pass.
“This means being able to move more with less fuel. But of course, no two sites are the same.
“Operators will be relieved to hear that AutoCarry is capable of adjusting the blade load for working in different ground conditions and on slopes.”
Operators can look forward to managing these settings on the Blade Load Monitor located within the cabin.
The Blade Load Monitor will be able to reflect the load capacity in three levels – Partial Load, Target Machine Load and Excessive Load.
The newer D4–D8 models will also come with another package upgrade – Cat Grade 3D. Cat Grade 3D gives operators the ability to operate the dozers with minimal effort and maximum precision by leveraging GPS signals.
“Cat Grade 3D lets operators extract the most value out of their Cat dozers. With greater precision, operators can now get their job done in a fast and accurate manner, reducing the cost needed for unnecessary reworks,” Sean said.
These models will have the required sensors and systems built into them right from the
point of purchase. This would include a 10-inch touchscreen display in the cabin.
With a 3D-ready dozer, operators who would like to opt for this optional upgrade can speedily upgrade their systems through the purchase of necessary licenses through their Cat dealers.
For more information about the new technology package upgrades for Cat Medium Dozers, contact a Cat dealer or visit www.cat.com.
NSW/ACT WesTrac 1300 881 064
VIC/TAS William Adams 1300 923 267
Western Australia WesTrac 1300 881 064
QLD/NT Hastings Deering 131 228
South Australia Cavpower 08 8343 1600
NZ TERRA 0800 93 39 39
Followers of Australian Grand Prix motorcycle racing are familiar with Jack Miller, a highly popular and unique character in the sport.
Winning a maiden MotoGP event in 2016 at the age of just 20, Jack has made a name for himself on the global circuit, with several podium and top 10 finishes.
With such an illustrious pedigree, no-one can blame Jack for building his own dream motocross dirt track on his property in Townsville, Queensland, where he can practice and perform as he pleases.
And to help him move the dirt around and upgrade the existing bike tracks on the property, there was really only one brand on his mind.
From a farming background, Jack’s been around Cat® equipment since he was three years old.
Indeed, he’s as passionate about Cat machines as he is about motorcycle racing. Having grown up around his grandfather's D3 dozer from the 1940s, Jack always dreamed of having one of his own.
In 2021, that day finally came, when he took delivery of a new Cat D3 dozer followed by a 259D3 compact track loader, primarily for jobs on the home farm.
Last year, Jack needed more machinery to build his very own motocross track. A quick call to Cat dealer Hastings Deering and the Cat Rental Store in Townsville led to a procession of latest technology equipment making its way to the Miller homestead, including a Cat D6 dozer, a 330 excavator, a 730 articulated dump truck, and a 970F wheel loader, adding to Jack’s existing machines.
Cat compact track loaders are renowned for their strength and versatility, featuring a steel embedded track and steel undercarriage components for maximum life in applications where maintenance, operator technique and underfoot conditions may not be ideally suited for a skid steer loader.
When Cat equipment specialist Rohan Mills learnt of Jack’s bike track project, he wanted to get the rider to have a test drive of the new Cat 255 loader, released earlier this year and already receiving widespread favourable reviews.
“We’ve made some significant improvements on the 259D3, the predecessor machine that Jack's got,” Rohan said.
“That model was the number one selling machine in the whole Cat range in Australia … and the new model has a range of feature and performance improvements.
“We've really upped the ante with the 255, the key platforms being improved power and more performance. There’s a lot more torque giving more ability to push through piles or climb slopes.
“The 255 has a Cat C2.8 turbo charged engine. In this machine, we’ve increased the engine torque. Operators are loving that these new loaders will give them more pushing power and more ability to move dirt faster.
“We’ve got more hydraulic capability, more performance. We’ve increased bucket breakout force by 36 per cent. That’s massive and something operators moving from the 259 are really going to notice.
“We’ve increased the rated operating capacity from 910 kilograms up to over 1100 kilograms, so that’s a 24 per cent increase.
“So better dump height, more bucket breakout and lift force, greater lift capacity and tipping loads.
“Comfort is next level too, with advanced controls and an 8-inch touchscreen monitor,
everything is at the operator’s fingertips, which is really nice and comfortable.”
For his part, Jack was as keen as mustard to try it out.
“From the start, I wanted to get into this thing. It looked awesome,” Jack said.
“There's been a lot of hype around the 255, and I'd been hearing last year about the new tech that was coming in and the capabilities of the unit.”
Jack especially liked the higher lifting capabilities, essential to not just shift earth, but also help mound the various hills, slopes and berms of a sound motocross layout.
He was also keen to see how the 255 functioned with a grader blade attached.
“It gave me the perfect opportunity to do a little bit of track maintenance,” he said.
“Some of the tracks needed a bit of TLC, they’re a bit bumpy. I’m keen to try out one of these attachments on parts of the track which have never been levelled up quite properly.”
Twenty minutes of playing with his new toy was all it took to convince Jack of its merits.
“The machine exceeded expectations in pretty much every area, from the fantastic build to the pallet lifting capabilities,” he said.
“To be able to lift the bucket up that high is a game-changer. I was lifting it so high but not feeling like the load was too heavy.
“From the first time I hopped in it, I had that same old Cat feeling, but also that it had all the new creature comforts.
“With the advanced joysticks, I was able to get up to speed with how the machine worked very quickly, it’s so easy to use.”
Rohan said coming from a very experienced operator like Jack, the comments were high praise.
“It was great to see him working the machine, really picking up big loads of material in that bucket and just seeing that he had a nice degree of stability with that machine,” Rohan said.
Jack’s final word?
“I was really struggling to get the 255 to slow down on me anywhere, you can definitely feel the increase in power and torque. All in all, I love it. I definitely need to look into upgrading my 259 and getting a grader blade as well,” he said.
Cat is running demo opportunities for the Cat 255 throughout the country. If you want to try one out, contact your local Cat dealer.
Cat 255 features
With its vertical lift design, the Cat 255 delivers extended reach and lift height for quick and easy truck loading. Its standard torsion suspension undercarriage system provides superior traction, flotation, stability, and speed to work in a wide range of applications and underfoot conditions.
It offers 13 per cent more torque than the previous model and more lift height together with greater lift and tilt breakout forces.
The larger cab features a redesigned layout with more cab space and easier entry and exit, delivering a significantly larger operating environment, and combined with additional seat travel, provides more space for operators of any size.
• The optional one-piece, sealed, and pressurized cab offers a clean and quiet workspace with excellent air distribution through optimally placed vents throughout the cab.
• The high-performance power train provides selectable settings for drive power priority and maximum travel speed (overdrive) to customise the machine performance to match the task.
• Three levels of auxiliary hydraulic performance are available. Standard flow is used for attachments that require a base level of auxiliary flow and horsepower, High Flow boosts the auxiliary flow for applications that demand additional hydraulic flow for increased attachment performance, and the High Flow XPS hydraulic system provides maximum auxiliary hydraulic performance by delivering additional flow and additional pressure for the most demanding attachments and applications.
• The standard torsion suspension undercarriage and standard two-speed travel, combined with the optional speed-sensitive ride control system, improves operation on rough terrain, enabling better load retention, increased productivity, and greater operator comfort.
• The 20.3 cm (8-inch) advanced touchscreen monitor offers cutting-edge functionality and control that includes an integrated radio, Bluetooth connectivity, and multi-camera (side-view) option, and supports 32 different language choices.
• In the cab, the advanced joysticks provide unmatched control of machine functions and adjustments within the display without the operator having to remove his hands from the controls. This includes on-joystick navigation of the advanced touchscreen monitor, radio volume up/down/mute, creep activation, creep on/off, creep speed increment/decrement, one-button smart attachment control activation, and additional auxiliary control buttons that deliver single-button control of complex attachment functions.
• For easy maintenance, ground-level access to all daily service and routine maintenance points help reduce machine downtime for greater productivity.
From the smallest jobs to the biggest projects, Queensland business D&K Earthworks relies on the blue beasts to ensure the tasks are carried out to perfection.
Like all good success stories, it started with an ambition and a dare to dream.
David Stalling grew up operating machines with his uncle since he could walk and has been working in the earthmoving industry since he was 16.
In 2010, with the itch to run his own earthmoving business needing to be scratched, Dave persuaded now-wife Karlee to team up in the venture, and they secured finance for a dozer.
Although still working as a plant operator, Dave carried out his side jobs during his free time and over weekends, gradually growing his clientele and reputation.
With enough support garnered, the day finally came when he could ditch the hardhat and was able to work for himself full-time. And thus D&K Earthworks was born, based in the rural Queensland township of Stanthorpe, and which provides both civil and agricultural services.
“Anything from car parks and sub-divisions to large scale levelling and water storage construction for large growers,” Dave said.
Dave serves as the director of the company, responsible for job scheduling, crew organisation and machinery timetabling as well as quality management and plant operating. Karlee is the business manager and oversees HR, OHS, administration and finance as well as helping out in the workshop and on-site when needed.
“Our local area is where our typical clients are; they are mainly local growers,” Dave said. Indeed, when Earthmoving Equipment
Magazine visited the Stallings, they were flat out building drains and tunnels for strawberries as part of a hydroponics project.
“We have also had contracts north of Brisbane, as far up as Bundaberg. We are interested in increasing our clientele to include local government and private civil works,” Dave said.
To grow the business and carry out major projects eff iciently, Dave realises full well the importance of running a well-maintained fleet of eff icient machinery.
“Our fleet has grown steadily over the last 14 years,” he said.
“It had always been a dream of mine to have my own machinery. I have extensive knowledge of all things related to earthmoving, and being my own boss has allowed me to sharpen my skills, fine tune my processes and pass the knowledge on to our employees.
“We now have about 30 items of plant, some of which are GPS-enabled, allowing us to complete almost any contract without having to organise sub-contractors or hire in machinery.
“I am pedantic about taking exceptional care of my machines, and often sell them on for a good price. This has allowed us to slowly build up our finances to be able to purchase newer machinery.”
The highlight in this regard for the Stallings was when they were able to buy their first brand new Kobelco in 2019.
“We now have four Kobelco excavators, the latest being the SK235SR-7 medium excavator,” he said.
“We found that the Kobelco excavators provided excellent value for money, parts are easy to source, and the cab provides exceptional comfort.
“It's pretty important that it's comfortable for operators when they have to sit in it all day, you know, 10 hours a day. We've got some other
brands in the fleet but the boys all prefer the Kobelcos.
“They're just smooth and quiet. They're fuel eff icient as far as we're concerned: a powerful Tier 3 engine with minimal emissions, no AdBlue problems. This is our fourth Kobelco and we've had no issues with any of them.
“Our Kobelcos are utilised in all of our contracts, whether it’s excavating core trenches and building batters in dam construction, plumbing and electrical trenching, loading fill or debris, stump removal or rock wall construction. The right attachments allow our Kobelcos the versatility to excel.
“And let’s be honest, we love the colour. We have even redesigned the D&K logo to incorporate Kobelco blue!”
The love affair with Kobelcos began after
the Stallings were introduced to local Kobelco dealer and BrisVegas Machinery sales representative Marco Marabini.
“Our relationship with Brisvegas began with our first Kobelco purchase - an SK260–8,” Dave said.
“We found it to be such an easy transaction that we’ve since purchased three more excavators off Marco.
“Marco is always just a phone call away to provide assistance for any of our issues, parts are sourced and sent out quickly and BrisVegas service is outstanding. We will continue to work with Marco and his team for many years to come.”
Marco said the Stallings’ first Kobelco purchase opened the door for more acquisitions after they saw how well the machine performed.
“They traded that machine back in for a new one. He's then bought an array of different machines over the years,” he said.
“Dave's just one of your typical country boys, pretty easy going and super easy to deal with. Dave is one of those customers you like having on board and enjoy the friendship as well as the customer experience that we exchange with each other.”
Marco said D&K Earthworks ran bigger gear and the Kobelcos suited the business perfectly.
“Dave's got a couple of 26-tonners as well as a short radius 235. The 235 he bought from me about four years ago was the ‘dash-2’ model. Dave has recently taken delivery of the brand new 235 ‘dash-7’,” he said.
“The ‘dash-7’ will replace or supersede our ‘dash-2’ model, which we've been selling since
The optional heavy counterweights and balanced chassis layout deliver exceptional lifting capacity.
its inception about 10-12 years ago. The ‘dash-2’ is just a super reliable machine. People just know what it is and know what it does.”
“The new SK235SR-7’s delivers greater eff iciency and productivity with increased power and speed, along with uncompromising operator comfort and machine operability, with several updates and new features.”
“We have been fortunate to retain a Tier 3 diesel engine without any AdBlue or DPF.
“We have the new cutting-edge Series 7 cabin for unrivalled ergonomics and operator comfort; it has a 10-inch colour screen that includes an eagle eye camera, phone holder charging ports, Bluetooth radio, all the bells and whistles.
“It also incorporates a new independent travel for the undercarriage. So when you're multifunctioning, it's not going to steal oil from a different circuit. It's all working independently to make a smoother transition and operation.”
The ‘dash-7’ offers extremely precise operation through excellent controllability and smooth hydraulics. The optional heavy counterweights and balanced chassis layout delivers exceptional lifting capacity, which is ideal for heavier tools and attachments.
The new arm and bucket cylinders have been reinforced, providing more digging power and durability. The plate thickness of the arm has been increased by 25 per cent (1.25 times stronger than the previous generation model).
The bucket cylinder has been reinforced by enlarging the flange and increasing the rod side pin diameter from 80 to 85 mm.
Introducing Kobelco’s powerful new ultra-compact 23-tonne range, featuring the cutting-edge Series 7 cabin for unrivalled ergonomics and operator comfort.
Equipped with a high-performance Tier 3 engine, these machines deliver an impressive 127kW output with 22% higher torque than previous models and eliminate the need for DPF or AdBlue.
These state-of-the-art Short Radius machines are built to excel in the tightest working conditions, boasting reinforced durability and exceptional stability for improved productivity.
Elevate your excavation game with Kobelco’s SK225SR-7, SK235SR-7, and SK270SRLC-7 today!
Three of the machines that Versatile depends on for its road projects: a Cat CW34 pneumatic roller, a Cat 150 all-wheel drive motor grader, and a Cat 434 backhoe loader.
Versatile by name, and versatile by nature: this equipment rental company is servicing the diverse needs of WA’s Goldfields region thanks to the e iciency of Caterpillar equipment.
Spanning 771,276 square kilometres, the Western Australian Goldfields-Esperance region is bigger than states such as NSW, Victoria and South Australia.
So if you’re an equipment business hoping to service the area, having reliable, eff icient machinery with solid backup is an absolute must.
It’s a lesson Phil Yates has learnt well, since landing in the Goldfields hub of Kalgoorlie in 2006 with the objectives of driving roadtrains and operating mining gear.
“The gold mining industry here was founded in the late 1800s,” he said. “That is what attracts people to the area, as tourists, investors, families looking to get ahead, or professionals looking to gain experience and build a career in the largest gold-producing region in Australia.
“After 12 years or so doing retail excavations in Sydney I was ready for a change, and Kalgoorlie offered opportunities to do earthmoving work that you just don’t get in a major city.
“Quad roadtrains, mining excavators, dump trucks, bulldozers. They don’t exist in Sydney, and the money on offer was mind-blowing at the time.”
So he spent six years spent working with roadtrains and in open pit mining in the goldbearing dirt around the Goldfields, which eventually gave him the opportunity to start up his own earthmoving business, Versatile Plant Hire & Contracting.
“I started with a Bobcat on hire to a mill just out of town and added a second one for mine site jobs on my week off,” he said.
“Before too long I found myself with five Bobcats, a 3.5 tonne excavator and a fivetonne tipper. No employees, just me and the machines working a 7-days-on roster.”
It was a far cry to where the business is at now. Thirteen years after buying his first machine, Versatile Plant Hire & Contracting has a fleet of more than 50 machines and trucks and around 40 staff, and Phil is back to using the skills he learned working on building sites and in backyards in Sydney.
“The mining industry is massive, and a lot of the contracting companies that serve it are focussed on production contracts and the bigger gear that minesites use to move bulk earth,” he said.
“We specialise in doing the human-scale earthmoving our customers need to establish or expand a mine site. We’re a service provider working in the gaps that mining fleets can’t fit into.
“The gold mining industry is relatively small compared to things like coal and iron ore, and that suits us fine. We’re comfortable being the size that we are – it allows us to stay focussed
on the type of work we do, maintain our standards of quality and customer service, and to build a small team of the best civil operators in the region.”
Like any earthmoving business, mechanical support is critical to the daily operation and long-term viability of Versatile Plant Hire & Contracting.
“I love operating machines and driving trucks, it’s what I was born to do and I learned from a very young age that if you look after your machines, they will look after you,” he said.
“But when we started buying dozers, rollers, graders and a fleet of light vehicles and trucks, I started to struggle with the maintenance task. It was costing a fortune and we were at the mercy of our mechanical service providers’ availability.”
Luckily, one of those mechanical service providers saw an opportunity and seized it.
“Lee Boath had his own mechanical contracting business, with field service trucks and some highly skilled guys working for him. They’d done a lot of work for us over the previous years and when he came to me with a proposition it didn’t take me long to see that this was the way forward for us,” Phil said.
Lee said he had worked hard to grow his own business and was doing well.
“But there’s economies of scale in business and Boath Mechanical was ready to take the next step up. Versatile had the admin staff , the workshop and the business systems that I knew I was going to need if Boath
Mechanical was to grow.
“And Versatile had a need for in-house mechanical support. I felt that Phil and I would be able to work well together.”
The merger was sealed over a couple of beers, and Lee is now a director at Versatile, where he looks after the maintenance and logistics within the business.
“We have a great workshop in West Kalgoorlie that enables us to service, repair and rebuild earthmoving gear for ourselves and our customers, and field service vehicles equipped for anything the remote areas of the Goldfields have to offer,” Lee said.
Phil said the fleet is maintained to the standard he “always wanted”.
“I used to include contingencies for breakdowns when planning jobs, but now I send the gear out with complete confidence,” he said.
Phil says that like any business, people are the key to Versatile’s success.
“As FIFO has become more common, Kalgoorlie’s population has fallen by around 4000 people. So finding people has become a tough challenge for any business based here,” he said.
“A small business like ours can’t afford to be flying people in and out on rosters, we need people who live here.
“We have a couple of long-termers who we fly in and they stay in a unit that the business rents, but the majority of our workforce is residential and we’re proud of that. The money
we make, the wages we pay mostly stays in the town.
“We aren’t a fluff y feel-good modern company; we do a tough job and we’re all hard workers. But we are a tight team where skills and experience are highly valued and I believe in reward for effort. It’s our motto.”
“Plenty of people have come and gone, but we have a core group of long-term team members now and we’re picky about who gets to wear a Versatile shirt these days.
“I believe in treating our people with respect, understanding that sometimes home has to take priority over work, paying them enough to remove money as a motivation and giving serious earthmoving operators the best tools available to do their job.
“That said, we’re always on the lookout for new talent. If you're looking for work in the WA Goldfields, come and call us.
“We’ve worked closely with various labour hire businesses in town in the past, and we always weigh up alternative methods for getting work done with fewer people. But
nothing beats having our own guys in the seats of our own machines.”
One of the avenues Phil and Lee have headed down is dry hire.
“We have a lot more machines than we have operators,” Lee said. “Utilisation of people might be at 100 per cent, but that still leaves half the fleet under-utilised. So we’ve invested in machines that are always in demand for short and long term hire in the area.”
Dry hire now accounts for about 20 per cent of Versatile’s revenue, and Phil and Lee plan to grow that figure.
“We have more machines on order, and we’re planning to stick to the meat and potatoes side of the dry hire game – rollers, dumptrucks, loaders, watercarts. Our point of difference will be that if it’s in our yard, it’s ready for hire,” Phil said.
“The jobs get bigger, the fleet keeps growing and new business opportunities present themselves almost daily. We’re well positioned to make the most of the local mining industry, as a medium-sized fish in a small pond.”
The CAT connection
Phil and Lee make no secret of which brand takes pride of place in their fleet.
Lee said that when he first joined Versatile, there were eight different machinery makes in the fleet.
“Now we only buy new Caterpillar machinery, not just for their performance and eff iciency, but importantly the service and availability of parts,” he said.
“Of the 30 or so machines in the fleet, about 20 of them are now Cats. As we make additions to the fleet, we are only buying Cat.
“There are some other brands still in there but they are either machines that are not available from Cat, or older machines which will be replaced by Cat versions as they age out.
“We recently started a new contract for the Shire of Coolgardie doing road maintenance. We were awarded the project because we are local and have been providing a high quality, cost effective earthmoving service to them for some time now.
“The Shire has 1200 plus kilometres of dirt roads and now we are solely responsible for maintaining all those roads. It's a big contract, so we've ordered Cat machinery that can do the jobs: a Cat 150 all-wheel drive motor grader, Cat 434 backhoe loader, and a Cat CW34 pneumatic roller.
“It’s the second 150 grader that we've bought. The first one's been a great performer, it’s out working on civil projects at the moment.”
The Cat 150 has long been an industry leader when it comes to road maintenance and construction tasks.
The motor graders have been designed specifically for activities such as road grading, shaping shoulders, slopes, and ditches.
Motor grader frame and drawbar components have been built for performance and durability, with a one-piece forged steel circle standing up to high stress loads.
The drawbar, circle and moldboard make it easy for operators to keep the components tight from the comfort of their cabs, while shims and patented top-adjust wear strips are easy to add or replace, reducing downtime.
“When we signed the road maintenance contract, we had to add another grader and the Caterpillar was the automatic choice,” Lee said.
“With a lot of the roads that we work on, we cut drains that run out into the bush, and the ground around here is pretty soft when it's wet; so really an all-wheel drive is the only option we had and this is going to be a great machine for our operation.
“As far as I'm aware, this is the first all-wheel drive 150 Cat grader that's been sold in the Goldfields region. We're proud to be trailblazers in this industry in our local area and we're really excited to see what this machine can do for us.
“In fact, all the Cats are ideal machines for what we do. We know the quality of the equipment, but equally vital for a region as big as the Goldfields is the backup that's available in the regional area.
“Our machines are often working hundreds of kilometres out of town. If we need service or parts, we just get onto Cat dealer WesTrac and they send someone out.
“Or we can log onto parts.cat.com to find the genuine Cat parts we need. It makes it easy for me to order the right parts before I drive 200 kilometres to the machine.
“We don't need to keep the stock of parts because we know that WesTrac has them on the shelf and the genuine parts will fit the first time, every time.
“We have peace of mind using the genuine parts and also knowing that if we do have any dramas, they're always backed up by the support they give us.
“So it’s great in knowing that with our machines working so far away and over such great distances, the support from Cat is always right there.”
One of the points of contact at WesTrac for Versatile has been the dealer’s Territory Manager Sales, Fintan Kearns.
“With so many different manufacturer brands in the fleet in the past, I've come across a lot of sales reps in my time,” Phil said.
“The change to Caterpillar brought not only better backup service, but the sales relationship is excellent. We've known Fintan for 10 years now, and if I need a machine, I can call him and he'll bend over backwards to deliver what we need when we need it.”
Fintan said he was delighted to see how much Versatile has grown over that time.
“They had five to 10 machines with a mixed fleet of different manufacturers at the start,” he said.
“I sat down with Phil, had a conversation in regards to swapping the fleet completely to the Caterpillar product and we proved that we
could support him in his growth.
“Phil likes to keep up with technology. Caterpillar product has all that to offer.
“So we've seen this fleet grow substantially. We have the 150 all-wheel drive going to be put into the road project. We also have a new 434 backhoe loader. Phil is very excited to get both products in the field and working.”
WesTrac customer support manager for the Goldfields, James Robertson, reiterated the strong level of reliable backup in terms of service and parts.
“If they've got a problem, they give me a call. We’ll sort it out for them straight away, whether it’s parts availability, service needs, warranty issues with machinery.
“I help them make it easy to own the product.
“I’ve showed them how various Cat tools can help them get their jobs done on time and keep them ahead of their projects.
“We also recently spent a bit of time on the Caterpillar Vision Link app, which leverages real-time data and analytics, helping users optimise their operations, reduce costs, and improve eff iciency.
“We have 14 assets connected to the machines where Versatile can look at a number of different things, such as fuel burn of the machine, idle time of the machine location hours, and other relevant information that is
very valuable and can actually enable the customer to better utilise his productivity within his fleet.”
Lee was definitely impressed, saying the fleet management tool enhanced the monitoring, maintenance, and overall performance of heavy equipment.
“We do most of our maintenance inhouse. VisionLink makes it easy for me to keep track of what's due for a service,” he said.
“Most of our fleet has GPS tracking and cameras on board, but we use VisionLink to keep track of engine hours, locations, working times.
“Our machinery is spread all over a 500 kilometre radius from Kalgoorlie and the app makes it easy for me in the off ice to make sure that everyone's doing what they should, it lets me know where the machines are and how close they are for a service.”
Fintan said that ultimately, WesTrac aimed to be a partner with Versatile rather than just a supplier.
“James and I work closely with Phil and Lee. We partner together, we come up with a solution,” he said.
“We put it in the field and we support it from there, which works really well for both companies.”
From Filters and Fluids to Planned Maintenance Kits and Self-Service Options to do your own repairs, you can rely on genuine Cat® parts for every job.
• Instantly access parts that fit when you shop with your Cat equipment information.
• Enjoy fleet management made easy with access to free operation and maintenance manuals, parts diagrams and more.
• Fast and easy checkout. Get parts shipped to you or pick them up in-store.
• Use your existing parts.cat.com account details to seamlessly use the Cat Central app. Shop the largest selection of genuine Cat parts on parts.cat.com, and download the Cat Central app from your preferred app store.
Find the right fit on parts.cat.com and the Cat ® Central app
Komatsu's Intelligent Machine Control (iMC) technology provides significant benefits to earthmoving machines by integrating advanced automation and precision control directly into the equipment.
Imagine if the blades of your dozers and excavators could be automatically adjusted to utmost precision, without having to rely on manual surveying or cumbersome calculations in the cab.
The technology that enables this is already here. Komatsu's iMC technology transforms traditional earthmoving operations by enabling fully automated blade control.
The system integrates 3D GPS technology with sensors and controllers, allowing the machine to perform tasks with unparalleled accuracy. For example, when grading a site, the iMC system automatically adjusts the blade position in real-time based on the preloaded design plans, ensuring the earth is moved exactly as needed without over-excavating or under-filling.
This level of precision significantly reduces the need for manual staking, streamlines operations, and minimises material waste. Operators, regardless of experience level, can achieve consistently high-quality results, leading to faster project completion times and reduced operational costs.
One company making the most of this leap in automotive innovation is dry hire company Mayday Rental, which is upgrading its fleet to complement its impressive new headquarters located in the bustling industrial precinct at Neerabup, north of Perth.
Freshly completed in 2023, the huge 7000m2 premises is designed for eff iciency and safety, with the workshop including a nine-bay facility for servicing light and heavy vehicles, two gantries for supplying oils, coolants, water, and
air, and a waste evacuation setup.
Earthmoving Equipment Magazine caught up with some of the company’s staff at the site recently, to discuss its operations and how the Komatsu initiative is helping improve machine productivity for its clients.
Director Bryce Abbott said the family-owned and operated business specialised in highquality rental machinery. Previously known as Mayday Earthmoving, the company has supported local shires, civil and earthmoving companies for over three decades.
“My father Ken founded Mayday in 1992, and we've now been servicing the rental market for 32 years,” he said.
“Mayday Rental specialises in supplying premium heavy equipment across WA. We've supplied sites with machinery from Wyndham
to Albany and everywhere in between.
“Focused on our customer’s success, our team strives to provide high-quality and reliable equipment to reduce downtime and promote eff iciency.
“Combining industry experience with reliability and professionalism, our team consistently delivers fantastic customer service, follow-up support, and rapid response times.
“When we started up, we supplied everything from Bobcats to excavators to tippers. We have grown into a much larger fleet now of predominantly rental equipment, such as excavators, dozers, loaders, dump trucks and graders.
“Mayday Rental currently runs a fleet of over 100 Komatsus across the state.
“At the moment we have a team of about 12 dedicated field experts, and that means that everyone's roles are dedicated to looking after that plant for our clients.”
Bryce said that since becoming the company's sole director in 2020, it had been incredibly rewarding to see the company continue to grow, overcome challenges, and achieve some significant milestones.
“A highlight is coming to work each day and being surrounded by a team of like-minded people, working hard towards the same goal, and having a laugh at the same time,” he said.
But the journey hasn’t been without obstacles.
“Like most other companies, COVID presented some of our biggest times of uncertainty,” he said.
“The biggest challenge was building our
new headquarters in Neerabup. Constructing a purpose-built industrial workshop and off ice of this calibre requires a lot of planning, collaboration, and patience.
“The build had to not only accommodate our current requirements but also grow with the company as it evolves.
“Building our new headquarters was a long and demanding process (made easier by the Armada Construction and the Mayday team), and our biggest challenge became our biggest accomplishment.’
Bryce said the leading criteria for equipment is reliability and innovation, features that the company’s client wanted and expected.
“We experience a high demand for all our Komatsu machinery, particularly our iMC dozers and excavators. Our clients prioritise the increased eff iciency and accuracy offered by these machines,” he said.
Working in tandem with Bryce is Mayday Rental General Manager Kye Keenan, who oversees the general operations of the business.
“This means looking after sales support, backup for our customers and the maintenance of our fleet of predominantly Komatsu equipment,” he said.
“We choose the Komatsu line of products in our day-to-day operations for the fact that
they're local. We use their support network for maintenance and field service parts. Their customer support is second to none.
“In our opinion, the support that we need in running an operation this size, with this amount of equipment, has really led us down the path of aligning with one OEM. And Komatsu is our machine of choice.”
Kye said Mayday Rental started a journey three years ago to build a state-of-the-art purpose-built facility for machine maintenance and its service team.
“Our service team is now operating out of this facility with dedicated approved wash pads. The setup has been custom-designed and built for our operation, where our service crew run our maintenance vehicles and breakdown departments to the minute,” he said.
“We needed to set something up that basically streamlined our operation for maintenance and breakdowns in the metro and in regional areas.
“This new facility is equipped with everything: every oil, every coolant, everything that the boys need on a moment-to-moment basis, to service machines and our service trailers, including evacuation points and bits and pieces.”
Kye said the off ice space at the new location was a testament to Mayday Rental’s commitment to a healthy work-life balance, filled with natural light, greenery, and timber and marble-sequel finishes.
“The meeting rooms are equipped with modern amenities and luxuries, including a boardroom with an adjoining undercover
alfresco area. Bryce is also in the process of building a gym and wellness space at the facility, further enhancing the team’s wellbeing and productivity,” he said.
Mayday Rental’s new workshop and off ice have been designed with an innovative layout and meticulous planning, highlighting the commitment to safety and eff iciency, and providing a secure and comfortable workplace.
The expansion followed the 2021 acquisition of an in-house transportation fleet to meet the growing demand for equipment transport options.
“Our trucks comprise of triaxle drop decks and quad/dolly combinations to move a selection of client-owned equipment in addition to our rental machinery state-wide,” Kye said.
“From the Kimberley to the Great Southern, our experienced truck drivers quickly and safely deliver your rental machinery to site, meeting pickup and delivery times.”
Supporting the Mayday Rental team on the Komatsu front have been the manufacturer’s Construction Sales Business Development Manager Lindsay Nelligan, and WA/NT Sales Manager Chris Hovelle.
Both were quick to point out the benefits of the groundbreaking iMC application.
“One of the strategic advantages Mayday Rental utilised with the commercial equipment is our iMC product, which serves not only as a point of difference to their customer base, but also provides an eff iciency gain that they can offer to their customers over and above any other brand,” Chris said.
In short, with iMC, equipment operators — even those with less experience — can work with utmost efficiency, guided by sophisticated automation.
According to Mayday Rental Operations
Manager Lucas Sartori, the 3D design data basically gets put directly into the machines and from there, through using the sensors, the GNSS antennas and the automated controls, the dozers and excavators are able to give the operators autonomous control, which allows them to focus less on cutting to grade and more about pushing the material.
“They don't have to worry about damaging the design surface or the material they're moving. They just focus on operating," he said.
Komatsu has already released a significant update to the iMC technology, known as iMC 2.0, that delivers major productivity, eff iciency and cost saving advantages to its latest model “intelligent” dozers and excavators.
Businesses using iMC can be confident that they’re getting the most from their machines, crew and carefully designed plans.
Incorporating a host of advanced, proprietary machine technology, iMC presents the opportunity to take advantage of sophisticated, productivity-enhancing automation and cutting-edge job site design.
With the tool, users can:
• Get new operators up to speed quickly
• Go from mass excavations to finished grading faster than ever
• Fully integrate 3D design data into machines
• Empower operators to work eff iciently, pass after pass
iMC excavators give operators the power to work more eff iciently than they ever could with conventional aftermarket machine guidance or manual operation.
With semi-automatic control, they offer the capability to work smartly, from rough digging to finish grading, and help minimize overexcavation to make every pass count.
iMC dozers enable operators to work to plans with utmost eff iciency and accuracy.
Through automatic dozing, rough cut to finish grade, iMC-equipped machines help make every pass count to achieve superior production compared to traditional aftermarket systems.
Features include a factory-installed, integrated system; no coiled cables between machine and blade; GNSS antenna and mast removed from blade; and no daily connections required between machine and blade.
Lucas said Mayday Rental had recognised the problems the construction industry faced with a lack of skilled operators, an issue made more prominent during the height of COVID.
“Komatsu’s iMC technology was developed to help less skilled operators come up to speed,” he said.
Lucas said operator feedback had been extremely positive, with users welcoming not just the iMC features, but also the operator cab visibility and comfort.
He welcomed the solid support from the Komatsu smart construction team, with iMC training easily organised either on-site, in-house or at Komatsu’s head off ice in Welshpool.
Also giving the thumbs up for the backup service was Mayday Rental’s Marketing and Brand Coordinator Maddison Genovese.
“I often speak to the operators, see what their experience is with the machines, and it’s always very positive, they find them really easy to use,” she said.
“Komatsu's follow-up support really aligns with ours because what we really aim to do is provide our clients with a very seamless experience when renting heavy equipment, because a lot of things can go wrong.
“Mayday Rental, along with Komatsu, are very good at allowing our customers to have a very easy experience in renting equipment.”
Lindsay said the relationship between Komatsu and Mayday Rental was more than “just transactional”.
“It is a true relationship. If something's needed, Kye gives me a call, and we work it out. We introduce new technologies, and we try and assist that with the changed management or trying to get it into the marketplace,” he said.
“The relationship with Komatsu is more than 20 years old. Mayday Rental and I have been going way back, originally dealing with Bryce and his father, and now dealing with Bryce and with Kye.”
Bryce said Mayday Rental has been purchasing Komatsu plant from the Welshpool branch over that period, with the partnership growing strongly purely on sales support.
“The backup with Komatsu along with our own team has been second to none. The support from Komatsu alone has been
phenomenal,” he said.
“One of the main reasons Mayday Rental gravitates towards Komatsu equipment is the exceptional after-sale service, parts, and support. We promise our clients premium follow-up support, so having a reliable and responsive OEM enables us to reduce machine downtime for them.
“By aligning with Komatsu, Mayday Rental is known for offering clients premium, highquality machinery with exceptional follow-up support. Our access to Komatsu's expertise
also helps us keep our clients updated with innovative new features, making Mayday Rental an industry leader in providing iMC rental solutions across WA.
“The company’s fleet of iMC equipment is expanding to meet a growing demand for precision earthmoving, enhanced eff iciency, and accuracy. We aim to remain WA's most trusted supplier for exceptional plant and service, and we will continue to provide innovative and reliable rental solutions to our clients.”
LiuGong earthmoving equipment has advanced significantly in recent years, so much so that it has now become highly competitive on the global stage.
Out Temora way in NSW’s Riverina, the New family has long been part and parcel of the local community, and pretty much the same can be said of their business, New Earthmoving.
Currently run by Ian (Herbie) and his son Ryan, the company has been around for more than 60 years, playing a considerable part in shaping the town and surrounding areas by building roads, contour banks, dams and the like, including various farm works.
Indeed, the flood of projects continues unabated, a good problem to have. When Earthmoving Equipment Magazine caught up with the News, they were busy installing bunkers for grain handlers Altora Ag.
“My father was from a property in the district, a family farm,” Herbie said.
“He had bulldozers and made his own dams. After a while, he sold the farm, moved to Temora and set up the company.
“He started doing road works, house sites, shed sites, all sorts of earthworks and constructions.
“Then I took over probably about eight years ago. Sadly, dad passed away last year, but we’re carrying on the business and tradition.”
An interesting part of the New Earthmoving
legacy has been its association with heavy equipment suppliers LiuGong.
Herbie’s father was impressed by LiuGong’s rollers, which feature an advanced vibration system that delivers superior compaction and smoother operation, backed by low fuel consumption.
“My dad’s first LiuGong was a 614H roller. It’s now just over 20 years old, and still performing well without any issues,” Herbie said.
Over the years, the LiuGong stable grew with the addition of an 848H loader, another roller — the 6615E — and the latest acquisition, a 4230D grader.
“I’ve had no problems with any of them,” he said.
“LiuGong is an upper market Chinese brand and does exactly the same job as many other bigger brands, but much more affordable.
“The power of the machines has been fantastic. They’ve done everything I've asked them to do and wanted to do.
“And for consistency and simplicity, we like to keep the same brand. At least you know where you're up to. You know where every part is, you have the same service people.”
Herbie said there was a stigma associated with Chinese-made machinery that was unfair.
“A lot of people don't like them because it's Chinese. But end of the day, you can end up buying two or three of these for the price of just one big name brand, and they perform just as well and have the same types of high end components,” he said.
“I’ve now got these four LiuGong pieces. I really love the quality. What you get for the price is just fantastic. And that's why we’ll stick with them.”
Herbie was also rapt with the six-year warranty offered with his purchase of the grader.
The machine, which includes a 4270mm blade width, 18,000kg operating weight and 270l fuel tank, comes with a standard twoyear/2000 hour warranty that can be extended by four years or 6000 hours if desired.
For the News, service is also not far away.
“They’ve got a branch nearby in Wagga, so they come out and carry out the service,” Herbie said.
“You can’t do any better than that.”
Herbie was effusive about the relationship between the business and Liam McCormick
“We met Liam at the start of the year at a field day down in Sydney,” Herbie said.
“We spotted the grader and chatted with Liam. He called me later and asked what I
thought of it, and we ended up going to Sydney for another look at the machine.
“At the end of the day, I told Ryan it looks like we're buying a grader.
“I’ve known Liam for only a short time but he’s a great bloke.”
Returning the compliment, Liam said he had been familiar with Herbie and his business for many years.
“So they've had the loader and roller, and bought the second roller. And then I had this opportunity to bring the grader here for a demonstration,” he said.
“Herbie and Ryan saw the value in the LiuGong product, and saw it as a real option, not only because it's very well priced, but because it works really well.
“The big thing about LiuGong is not only the reliability, but the extra warranty that we sell with them — the four-year/6000 hours.
“We have 32 dealers in the regional areas throughout the East Coast of Australia, so can provide that local support in servicing, making sure to minimise any downtime and get them up and running again if needed.
“We make the relationship very personable too; customers are not just a number, they're valued customers.
"And we want to make sure that everyone with a LiuGong has a great experience.”
Liam reiterated the value for money in LiuGong equipment.
“Obviously the cost of capital and everything else now is very expensive,” he said.
“And I think what we present is a really good quality product.
"LiuGongs are very high quality machines with very good warranty and backup service behind them.
“Big earthmoving companies like New Earthmoving have realised that they're not trapped into your traditional brands.
“The LiuGoing name is very strong worldwide, and the company has invested a lot into R&D as well as facilities, factories and everything else in automation.
“The range of products is diverse, from civil construction, to electrical plumbing, through to mining and now electric machines.”
Liam used the company’s venerable 614H as an example of LiuGong’s quality and robustness.
“It’s a great testament. Products have come a long way since this model. It’s more than 20 years old, still operating and it's still going very well,” he said.
“We've got a long association with LiuGong and we're seeing a lot of repeat buyers who have been getting many hours out of them and the common componentry.
“They know that they can source a lot of the parts and everything else locally and don't have to actually get a branded part. So the machines are very easy to service and parts are very easy to find.
“And having that local dealership close by is a big plus. We've also got our own national technicians that can be called on for hands-on help through training.”
LiuGongs are very high quality machines with excellent warranty and backup service behind them.
As Herbie says, LiuGong is an upper market Chinese brand and does exactly the same job as many other bigger brands, but they’re much more a ordable.
Hastings Deering’s Smart Iron Training Event has helped Cat operators to hone their skills at operating the machines and understand the new technologies available.
Cat® machines are renowned for their innovation and eff iciency which constantly keep them ahead of competitors. But with technological improvements advancing at a furious rate, sometimes keeping up with the latest developments can be diff icult.
A recent training event was designed to help operators of Cat machines to enhance their skills and make the most of the advanced features available on the equipment, ensuring that operators are well-equipped to utilise the full potential of Cat machinery, leading to improved eff iciency, productivity, and safety on job sites.
The three-day Smart Iron Training Program, organised by Hastings Deering and hosted by Diamond Excavators at its property in Townsville, drew participants and visitors from both Queensland and the Northern Territory.
Hastings Deering is one of the leading Cat dealers globally, with exclusive distribution rights for the sale of Cat equipment, technology solutions, parts and service in Queensland, the Northern Territory, Papua New Guinea, and the Solomon Islands. In 2022, Hastings Deering celebrated 90 years since it was founded by Harold Hastings Deering, a pioneer in the mechanisation of Australia.
The sessions focused on educating customers on the most advanced equipment in the
industry, and tailoring education around theory, demonstration-based training, and machinebased training.
It also included sessions in which participants could demo the machines, test their skills and compete in an operator challenge.
• Day 1: Attendees were allocated to a group
where they were rotated across six areas each with information surrounding a different machine group. They were trained by Hastings Deering product specialists, accompanied by a Caterpillar subject matter expert.
• Day 2: Attendees rotated in groups again and were required to complete tasks with the
machines using the technology they were shown in Day 1.
• Day 3: This optional day consisted of an operator challenge, where attendees tested their skills on the course.
The product categories and machine models in the training and demonstrations included:
• Hydraulic excavators: Cat 315 and Cat 340
• Dozers: Cat D5
• Motor graders: Cat 140 and Cat 150
• Wheel loaders: Cat 980
• Articulated trucks: Cat 745
• Rollers: Cat CS19 and Cat CS79
• Compact Track Loader: Cat 255
At the completion of the training, participants received copies of all training materials, as well as exclusive access to Caterpillar and Hastings Deering product experts.
Smart Iron in action
Earthmoving Equipment Magazine caught up with several of the key personnel involved with the event.
Seb Banks, Executive General Manager, Construction Industries, Hastings Deering, was delighted with the success of the Smart Iron Training Program.
“This three-day event was conceived when I was talking with Shane Poole from Diamond Excavators and his wife Kylie last year,” he said.
“Shane lives and breathes Caterpillar, and knows we have some of the best technology on the Cat machines.
“And he said it was important to understand and learn about the technology as soon as customers bought the machines.
“But he also said that after a while, operators can lose some of that knowledge, so it would be really useful if we could run a sort of regular training seminar: get all the operators from the local regions coming in, learn how to use the machines, learn the technology again.”
Diamond Excavators operates in Far North
Queensland and is involved with plenty of mining and civil projects.
“We're predominantly an excavator company, but we have excavators, dozers, Moxys, water carts, a bit of every sort of plant we can to carry out the different contracts going on,” Shane said.
“What we've been trying to do here in the last 18 months is bring the technology that Caterpillar has available to all our operators, and train them up a bit more.
“So I’d been travelling around a little bit and having a look at what Caterpillar can provide, I talked to Hastings Deering, offered my premises, and finally here we are in Townsville: it’s an opportunity to bring everybody around the whole of Queensland to come and have a look at a lot of different plant and equipment.
“The technology coming forward is something we've got to catch up with. We're paying a lot
of money for the technology and we're only probably using 20 to 30 per cent of what's available out there at the moment.
“To update and keep above the progress, the main focus on everything is a lot more training, so hopefully this event can showcase what is available in each one of these machines.
“In that way of moving forward with Caterpillar technology and our companies, we can start training our operators to be a lot more adaptable in different environments and in the construction industry.”
From the conversations with Seb, the concept grew quickly. Shane lent Hastings Deering his huge facility and property in Townsville to host the event.
“We brought the crew in. We brought all of our machines in, each one operating on the latest technology that we have with Caterpillar and
Hastings Deering,” Seb said.
“And then we invited all our customers. We flew customers in from Brisbane, from Cairns, and locals from Townsville, giving them an opportunity to try each one of our machines and learn how to use them properly.
“In the end, although the technology is fantastic, without the people operating machines correctly, running them and making sure they are at full operational capability, the technology is not worth it, right?
“It’s not just about the onboard technology, it’s about making sure that our customers understand what goes behind this and the support that goes with this technology.
“These machines always need to be looked after. It's making sure that customers understand it end to end.
“It's the people at Hastings that train them. It's how our customers and our people work together in partnership to make them the most productive that they can be.”
Shane said the event owed much to both Hastings Deering and the Caterpillar team.
“Ryan and Alana from Hastings Deering really went above and beyond with helping to get this developed and put it all together. It takes a lot of work to get this up, especially in the regional areas of Townsville, so it’s much appreciated.
“And of course, thanks to Caterpillar. We love the machines, the way they're bringing the technology out and everything, and we look forward to the future.”
Ryan Canal, Construction Industries Product Manager, Hastings Deering, was busy taking Smart Iron Training Program attendees through the updated/latest technology.
“There has been a lot of interest in the latest technology included in excavators, dozers, compactors and graders,” he said.
“In particular, we went through the Infield design capabilities of the Next Gen excavators. We're using the latest Cat grade firmware, showing our customers how to build the Infield design, attaching it to an existing design and where they can use it in their everyday process.”
The Next Gen latest generation of excavators have been designed to offer improved performance, eff iciency and ease of operation,
equipped with cutting-edge technology and enhanced features to cater to the evolving needs of the construction and earthmoving industries.
Ryan was impressed with the turnout at the event.
“It’s such a community effort from everyone here in Townsville. it's awesome to see the way we've managed to pull this together in collaboration with customers,” he said.
“We should all be pretty proud of what we've done here.”
Also delighted with the day was Steed Sheppard, Geospatial Solutions Manager, Trimble.
Trimble and Hastings Deering have a 25year partnership, and Steed was on hand to view some of the Cat grade technology on the machines.
“We're looking at the Infield designs and how people can get the best out of these machines. We can now create designs in the cab, which enables jobs to get done quicker,” he said.
“The enthusiasm from everyone at the event has been awesome, but the amount of machines that we've got here and the participation from everyone in the local area is just really spectacular.
“It’s a great event to be involved in.”
Greg Vaughan, General Construction Industries Business Manager, Hastings Deering, handles large equipment: excavators and larger machines
from 13 tonnes to around 95 tonnes and everything in between.
And he was excited at the opportunity to show visitors the many features that come installed with the equipment right from the factory.
“I have a Cat Next Gen excavator on site and most of the features I talk about extend from the 313 all the way to the 395,” he said.
“When we go through the ease-of-use features, we generally talk about those technology and productivity programs such as Payload, E-Fence, Lift Assist, Grade with Assist, etc.
“All of these are designed and they're factory options. They're installed. They're available as the machine arrives here in country and they just allow us to work in a way more productive, way safer environment.
“So with things like E-Fence, where you set up a virtual wall in front of above or below the machine, you can set up slew restrictions. All of this is done from inside the cab.
“Lift Assist can allow you to pick up objects such as pipes, concrete barriers, and the like, and the machine will provide a lifting style chart ... much like you would see inside of a crane, it not only shows you how much the machine is lifting, but it also shows you how much the machine can still lift in that position.
“The load chart is dynamic, so as you move around with the machine, it will show you that you're working either in or outside a safer operating space.
“Payload is another great feature that's factory installed. When operators load material, they need to know three things: what got loaded where, how much went on each truck or in the hopper, and where it went from there.
“Payload technology not only delivers that information and keeps track of it over time, it also helps loader operators get the right load on board, the first time, every time.
“With the click of a button, the target payload is set and then you can work to that. So what we're doing with that is stopping overloading, and protecting the owner and operator from overloading trucks as they hit the road, avoiding fines and liability issues. “
Greg said the best thing about the event was the opportunity not only to have Hastings Deering staff meet customers, but also for clients to come through and see the equipment working in action.
“They’re taking on all of the technology that
we have available to us and really going to the in-depth parts of it.
“We're giving the opportunity for customers to get on machines to actually try this technology out. And a lot of our customers actually already own this equipment, but this serves as a great refresher for them, who may not always get an opportunity to come out to see these things in action.
“It really was smart iron in action.”
Dick Mars, Product Application Specialist, Caterpillar, said the day allowed him to show off the myriad of features that will be part of Cat’s newly released Next Gen 980 medium wheel loader, a versatile and powerful machine designed for heavy-duty lifting and loading tasks.
“For example, one of the new features is a new tyre pressure monitoring system option. We put a sensor on the valve and then we build into the monitor the actual display showing the individual pressures between the two front tyres and the two back,” he said.
“Tyres are a huge cost item and we don't always give it consideration we should. If we monitor tight pressures and as long as we have the appropriate pressures, we can extend the life of those tyres.
“And you don't have to sit there and watch these things.
“We have a low pressure alert and we have a high pressure alert. So even if they haven't got the tyre pressure monitor on physically enabled in the display, it'll throw up an alert and then they'll know if the wheels are low or high in pressure, and then do something about that.”
Dick was also keen to highlight the new pedal set-up for the machine.
“We’ve long had the integrated braking system, but customers had been telling us that it's a little bit too aggressive,” he said.
“So what we've done is we've changed the disengagement strategy. In simple terms, that means as you depress the pedal when we are changing gears, it's less aggressive.
“We've changed nothing in the software between level moderate and aggressive modes in the integrated braking system, and it just gives a better feeling.”
On the safety side, the loader uses a new collision warning system.
“With the current platform, we've got a camera and we've got the 360° motion detect and so forth. But literally it can't differentiate between a person and an object,” Dick said.
“With the new system that's going to be available later this year, that system will include a smart camera.
“It won't have active braking to stop the machine, but it uses motion-inhibit. It means basically that if the operator is in the cab and he puts it in reverse and the smart camera detects a person approaching at the rear, the machine will not go into reverse: hence inhibiting motion.
“The way to override that is the driver has to go back to neutral and then he can re-engage. In short, it provides enhanced safety.”
Dick said that all in all, there were probably about 18 to 20 new features for the Next Gen 980, which has just landed in Australia.
“It's going to be a cracker of a platform. Most of those features are focused on improving the
operator’s performance and productivity,” he said.
Dean Alley, Territory Manager for Paving Products, Caterpillar, spent the Smart Iron Training Program days showcasing Cat’s technology offering in the compaction field.
Cat’s Compact technologies provide advanced measurement options and reliable reporting capabilities to help operators consistently meet compaction targets with more speed and less rework.
“We've got what we call intelligent compaction as an offering here in Australia, and essentially what that does is it allows us three things,” Dean said.
“First of all, it gives us capacity to measure our level of soil stiffness. Secondly, it enables us to have a mapping system to show exactly where we've been and how stiff the soil is.
“And lastly we have the Cat Connect offering which enables the machines to communicate to each other so they know who's done what area and what area still needs to be done.”
The system connect six types of technologies that can be mixed and matched to suit the unique needs of businesses.
“Through the use of Wi-Fi, we can also send the signal up into the cloud into someone's off ice so that they can see for themselves just how the soil lift has been compacted,” Dean said.
Chris Barrett, Technology Specialist, Caterpillar, was on hand to explain more about Cat’s new D5 Next Gen dozer, with one of the first 3D-ready units on display at the site.
The 3D grade system uses machine integrated sensors, enabling the blade to move automatically to help keep your grade at the required level. Infield designs can be applied to the machine while working on a country road, without the need for surveyors coming out.
“At the factory, we fit all the 3D ready hardware on. The dealership sets it up ready to go, and if the customer wants to take the machine and maybe try or demo 3D, they can, or if they want to activate it in the future, they have all the hardware on the machine set to go,” he said.
“We've also introduced a feature called Steer Assist. You can either have this from a design that comes in the off ice, or create a design, select
that and the machines automatically control the blade and also the steering. It’s a really nice feature for operators.
“Also if you're doing more production dozing, we've got tilt steer. So what that will do is, if you're on the slot pushing out material rather than sort of fighting the dozer, trying to keep it straight in the slot, it's going to automate the tilt to basically keep you in a straight nice line as you go through
“Another feature we've got on the Next Gen dozers is an option to get a grade radio and grade cellular modem. They come with Cat components covered under the Cat warranty.
“You can use the Product Link modem for sending design files through our Vision Link productivity platform, getting production data back, checking on performance and how much volume you've moved for the day.”
Chris said the Next Gen models were the culmination of a building block of technology, which had been based on a simple function called Stable Blade, designed to work seamlessly with operator inputs to help produce a smoother surface when operating manually.
“Stable Blade complements the operator’s blade control inputs to help reduce small imperfections and control blade aggressiveness. It helps the operator take out jolts and bumps that might sort of come in during dozing,” he said.
“Then we sort of moved on to Slope Assist, which allows the operator to basically put in slope and mainfall data, hit the auto button, and the machine will maintain that information for the slots.
“All these features work in with Cat’s AutoCarry, which provides automatic blade height control, making sure operators carry and keep as much material as needed.
“So if you're doing that heavier dozing and a full blade load, AutoCarry will kick in, automatically managing that blade load, keeping having nice full loads, and this can be monitored.
“And now we have 3D, where we get auto steer going. All those sorts of innovations help the operators stay productive and do really good quality work regardless of the skill level.”
(For more on these new features, see page 68.)
From its humble beginnings in 2010, Kenter has swiftly evolved into a global logistics powerhouse.
With a collective experience of more than 50 years in handling heavy lift cargo and container shipping, Kenter has cemented its reputation for delivering exceptional results and unparalleled customer service.
Initially focusing on air and sea freight, Kenter has expanded its offerings to encompass a comprehensive suite of logistics services, including warehousing, distribution, and customs clearance. Today, it boasts a vast network of partners and agents worldwide, enabling it to reach even the most remote corners of the globe with reliability.
Kenter’s unwavering commitment to integrity, respect, and excellence ensures that every client receives the highest level of care and support.
Founder and Managing Director Emily Jackman said the business was a logistics company that’s all about getting the job done right.
“We keep things simple, communicate clearly, and always go the extra mile for our clients. That’s how we are still in the business for 15 years,” she said.
Kenter’s mission is to streamline and optimise clients’ supply chain operations by providing tailored logistics solutions.
“We strive to exceed expectations, offering superior customer service and innovative approaches to meet the unique needs of each client,” Emily said.
“Through our extensive network and expertise, we aim to simplify complex logistics challenges and deliver tangible value to our customers.”
The Kenter services
• Freight forwarding: The Kenter team of logistics experts ensures that shipments reach their destinations safely, eff iciently, and on time. It handles all aspects of the logistics process, from planning and documentation to customs clearance and tracking.
• Heavy haulage services: Need to transport heavy and oversized cargo? Kenter has the knowledge and experience to handle the unique challenges associated with heavy haulage, ensuring the safe and secure delivery of clients’ valuable assets.
• Customs clearance: Navigating customs procedures can be complex and timeconsuming. Kenter customs clearance experts possess in-depth knowledge of international trade regulations and work closely with customs authorities to ensure smooth and eff icient clearance of goods.
• Warehousing and distribution: Warehousing and distribution solutions can be tailored to specific needs. The company’s strategically located warehouses provide secure storage and eff icient inventory management, while the distribution services ensure timely delivery to desired destinations.
• Value-added services: In addition to the core
logistics services, Kenter provides valueadded services such as packaging, labelling, and order fulfillment. These services help streamline operations and enhance customer satisfaction by ensuring accurate and eff icient order processing.
Emily said Kenter has established strong partnerships with carriers, suppliers, and customs authorities worldwide.
“This extensive network enables us to provide eff icient and cost-effective transportation solutions, regardless of your shipment’s destination,” she said.
“As well, we leverage the latest technology and tools to optimise our logistics processes and enhance supply chain visibility.
“Our advanced tracking systems allow you to monitor your shipments in real-time, providing peace of mind and control over your logistics operations.
“At Kenter, we prioritise building strong relationships with our clients. We understand that every business has unique logistics needs, and we work closely with our clients to develop customised solutions that align with their objectives and requirements.”
The company also recognises the importance of environmental responsibility and strive to minimise its carbon footprint.
“We prioritise sustainable practices in our operations and collaborate with carriers who share our commitment to environmental stewardship,” Emily said.
The Kenter team
• Emily Jackman, Founder and CEO: With an extensive career in the logistics industry and an absolute drive for achieving exceptional client satisfaction, Emily is the powerhouse within Kenter, operating on three key values: passion, service and experience.
• Toni Pearce, Accounts: The proficient bookkeeper of Kenter, Toni is a master of
numbers and organisation. From ensuring seamless payroll processing to maintaining debtors’ and creditors’ ledgers, Toni has mastered the art of financial management.
• Lee Holmes, Customs Manager: A seasoned professional with a strong background in logistics, customs, and operations management, Lee’s focus is on process improvement, customer satisfaction, and cost reduction. Lee is well-equipped to handle various aspects of freight forwarding and customs activities.
• Renae Grant, Operations Manager: Renae brings more than three decades of experience in the freight forwarding industry to the table. With a strong reputation for problemsolving, enhancing customer satisfaction, and improving operational eff iciency, she has consistently proven her ability to drive positive results. She is proficient in various areas, including dangerous goods handling, air freight security, and warehouse management.
• Terry Riches, General Manager for Kenter New Zealand: Over the Tasman, Terry brings more than 40 years of industry experience in shipping, airfreight, and trade management to Kenter’s New Zealand branch. His career highlights include pioneering sales at Auckland Airport for Brambles Australia, founding Strategy Exports, and holding key positions with Jebsen Line and Tasman Jebsen Line. A notable achievement was his leadership in building Kiwi Car Carriers, which was later acquired by Hoegh Autoliners.
• Stef Caballes, Team Leader Operations: Kenter’s Operations Lead, backed by six years of experience, excels in import/export across multiple commodities, and is a rare gem in both container and RoRo freight. She ensures seamless visibility throughout the supply chain, swiftly eliminating roadblocks, working closely with new clients and providing tailored logistics solution.
In
the construction, quarry and mining industries, the e iciency and safety of heavy machinery are paramount; and in this regard, the Volvo EC950E Excavator stands out as a beacon of engineering brilliance.
The Volvo EC950E Excavator is not just about raw power; it embodies a perfect blend of strength and cutting-edge technology designed to easily tackle the most demanding projects, thereby providing the "Volvo Advantage".
The Volvo EC950E is a testament to engineering excellence and innovative design in heavy machinery.
Boasting a formidable 450kW Volvo engine, this excavator delivers unparalleled digging force, making it exceptionally effective against hard and heavy materials.
Its stability is unmatched, thanks to a wide track gauge, long track length, retractable undercarriage, and optimised counterweight, ensuring solid balance even in the most challenging environments.
With advanced technology rooted in decades of engineering expertise, the EC950E is not just a machine; it's a powerhouse of productivity and precision.
Performance and productivity
One of the biggest challenges in construction is maintaining high productivity while minimising downtime.
The Volvo EC950E is engineered to excel in both areas. Its robust design ensures it can handle the toughest environments, significantly boosting project eff iciency, leading to fewer delays and more consistent progress, directly translating to cost savings and timely project completion.
• Power and e iciency
The Volvo EC950E Excavator is powered by a robust 450kW Volvo engine built on decades of engineering experience, ensuring high productivity and superior performance.
This model also features Volvo's unique ECO Mode and an advanced electro-hydraulic system, which achieve outstanding fuel eff iciency by optimising hydraulic flow and reducing losses in the hydraulic circuit.
The integration of these technologies allows the EC950E to perform various tasks with greater speed and eff iciency, whether in quarrying, mass excavation, or other demanding.
• Digging force and capacity
The EC950E stands out with its superior digging force, making it highly eff ective in tough applications involving hard and heavy materials.
This capability is supported by constant high hydraulic pressure that delivers the necessary power precisely when needed.
The Volvo EC950E is engineered to handle the toughest environments.
As Volvo's largest crawler excavator, the EC950E boasts a high bucket capacity that significantly enhances on-site production, allowing for more tons per hour and increasing overall profitability and productivity.
• Work modes and attachments
Volvo's EC950E excavator offers unmatched flexibility and versatility through its range of attachments and work modes tailored to meet various job demands.
The attachment management system allows operators to pre-set hydraulic flow and pressure from the comfort of the cab, ensuring optimal use of various attachments.
Furthermore, the integrated work mode feature permits operators to select the best mode for the task at hand, ranging from Idle to Power max, which enhances the machine's eff iciency and adaptability to different working conditions.
Fuel e iciency and eco-friendly features
The demand for sustainable machinery is higher than ever.
The EC950E addresses this need with its exceptional fuel eff iciency and eco-friendly features.
• ECO mode and fuel consumption
The Volvo EC950E Excavator achieves outstanding fuel eff iciency by integrating Volvo's unique ECO Mode and an advanced electro-hydraulic system.
ECO Mode is specifically designed to optimise the hydraulic system by minimising the loss of flow and pressure, which significantly reduces fuel consumption.
This model is complemented by intelligent technology that controls on-demand flow and reduces internal losses in the hydraulic circuit, ensuring that the excavator operates eff iciently without compromising on performance.
• Operator safety and comfort
The EC950E prioritises operator comfort and safety with its ergonomic design and advanced safety features.
This focus ensures that operators can work longer hours without fatigue, maintaining high productivity levels while staying safe.
• Industry-leading cabin design
Maximising operator productivity, the Volvo EC950E features a cab designed for comfort, spaciousness, and a low-noise environment.
The cab's ergonomic design includes
large windows for greater visibility and large entrance doors, complemented by well-placed handrails ensuring safe 3-point contact.
Additionally, the cab is supported on hydraulic dampening mounts to reduce shock and vibration levels, coupled with soundabsorbing lining to keep noise levels low, enhancing the overall operator experience.
• Visibility and safety enhancements
Rear vision and optional side vision cameras minimise the risk of damaging the machine during manoeuvres on the job site.
Furthermore, the upper house area is easily accessible and features well-positioned handrails and footsteps for secure three-point contact, increasing safety and accessibility.
The upper house also boasts punched steel tread plates that provide reliable footing when inspecting the engine from above.
• Ergonomic controls and accessibility
All machine interfaces, including the joysticks, keypad, and LCD monitor, are ergonomically positioned for optimum control and eff iciency.
The operator's seat is a testament to ergonomic design, offering 12 different adjustments and can be moved independently along with the joystick console to accommodate the operator.
Maintenance and durability
Its durable construction and easy maintenance mean fewer breakdowns and longer service intervals.
This reliability reduces the total cost of ownership and ensures that the machine remains a valuable asset for years to come.
• Easy access for servicing
The Volvo EC950E Excavator's maintenance is streamlined, with wide-opening compartment doors that provide easy access to essential maintenance points.
These points are conveniently located and accessible via central and surrounding walkways, ensuring that service tasks can be performed quickly and safely.
• Durable construction and wear-resistance
The Volvo EC950E features a heavy-duty boom and arm and a strong frame structure.
Additional protection is provided by a builtin, heavy-duty plate shielding the machine's underside.
A wide range of wear parts, including teeth, adapters, segments, side cutters, and shrouds, are available to protect the complete bucket, further enhancing its durability.
The Volvo EC950E has state-of-the-art technology, including sophisticated machine monitoring systems.
These systems provide real-time data and insights, allowing for smarter decision-making and proactive maintenance.
This technological edge ensures that the EC950E can adapt to evolving project demands, making it a versatile and intelligent choice for any construction site.
• CareTrack telematics system
Volvo's CareTrack system is a state-of-theart telematics solution designed to enhance the eff iciency and productivity of the Volvo EC950E Excavator.
This advanced system allows operators to monitor various machine parameters, including location, fuel levels, and total machine hours, providing crucial data to optimise operations.
CareTrack also seamlessly integrates with old and new machines, ensuring operators can achieve maximum eff iciency regardless of the fleet's age or composition.
Furthermore, CareTrack offers different subscription levels: CareTrack Start, which is included with new machines, provides basic machine status information, while CareTrack Advance, available via subscription, includes detailed support for optimising production with data on load eff iciency, performance, fuel consumption, and utilisation rates.
• Machine monitoring
The GPS monitoring program within the CareTrack system works in conjunction with the machine's diagnostic system, enabling remote tracking of usage, productivity, fuel consumption, and more.
Real-time tracking ensures that operators are fully aware of the machine's operational status and geographic location and even helps prevent unauthorised use.
Additionally, the system provides the following:
• Important service reminders
• Significantly reducing downtime by scheduling maintenance around operational needs
• Thus maintaining continuous productivity
Volvo's commitment to sustainability
Volvo's dedication to sustainability is evident in its rigorous testing and development process, which ensures the production of wellengineered components that are purpose-built for the job and proven reliable in the toughest applications.
This commitment extends to the company's core values, emphasising safety,
The Volvo EC950E is built to withstand the rigours of demanding applications, featuring a heavy-duty boom and arm and a strong frame structure.
The excavator’s superior digging force makes it highly e ective in tough applications involving hard and heavy materials.
environment, and operator comfort.
Volvo aims to lead the industry in fuel economy with its D16 engine, noted for its high kW rating and high torque at low RPMs.
This engine design contributes significantly to the EC950E's outstanding fuel eff iciency, enabling it to offer the best m³ per litre production in its class.
Conclusion
The Volvo EC950E Excavator stands as a pinnacle of engineering excellence, combining raw power with cutting-edge technology to meet the rigorous demands of modern construction and quarry operations.
If you're ready to elevate your operations with a machine that delivers unmatched productivity, reliability, and eco-friendly performance, now is the time to act.
Contact CJD Equipment today to learn how the Volvo EC950E can transform your construction, mining, or quarrying projects.
Embrace the future of heavy machinery and ensure your projects are completed on time, within budget, and with the highest eff iciency and safety standards.
A business whose name is synonymous with quality construction work in Brisbane, D & M Plant Hire, relies on Develon equipment for most of its earthworks projects.
When it comes to plant and machinery hire in Brisbane, one name stands out from the crowd: D & M Plant Hire.
Indeed, it’s fair to say that the business’ services and equipment have helped shape the Queensland capital into the bustling metropolis it is today.
The large earthmoving family business was literally built from the ground up with one truck and a lot of determination after it was first established by Doug and Margaret Phillips in 1972. Over the decades D & M Plant Hire grew substantially, evolving into a robust plant hire business.
After Doug passed away, his son Ray took over the reins as Managing Director, having inherited his father’s prowess, hardworking attitude, remarkable business acumen and strong proactive focus on providing excellent customer service.
Ray said that D & M Plant Hire was a leader in wet and dry hire of late model civil construction equipment and trucks for bulk and detailed earthworks on oil, gas and mining sites, road and rail work.
“We are based at Cleveland in the bayside of Brisbane, providing excavation services to major construction groups, throughout the greater Brisbane metro areas including Ipswich, Logan, and Gold Coast areas,” Ray said.
Just a partial list of clients read like a Who’s Who of the earthmoving industry: for example Golding, Pensar, Boral, Brisbane City Council, BMD, CCA Winslow, Gold Coast City Council, HEH Civil and Shadforth Civil, Opalyn Constructions, Nulla Contracting, Redland Council, Seymour Whyte, and Sawtells Earthmoving.
“All our equipment is fitted with the latest safety and operating eff iciency features, as standard items, including low emission motors and reversing cameras,” he said.
“Today we have over 40 pieces of equipment, with the latest GPS systems and hydraulic hitches and array of buckets and attachments from rock breakers to augers to compaction wheels.”
With such an impeccable pedigree, it is vital for Ray that the company only brings in the best equipment available.
“We look for value for money, and also look for good back-up service and a strong relationship with the salesperson involved,” Ray said.
One brand that definitely fits the bill is Develon, which Ray has been incorporating into his fleet since the turn of the century, when it was still named Doosan.
“We currently have 16 excavators, Doosans and Develons, ranging from 14 tonne to 34-tonners,” Ray said.
Ray finds that their capabilities and power are perfect for the various earthworks, major projects and domestic jobs that D & M Plant Hire are involved with.
“We get all our Develons from Clark Equipment. That’s where we got the first machines from and we have an ongoing and strong working relationship with them, built on trust and respect,” he said.
“In terms of maintenance, repairs, parts and the like, we have good service from Clark Equipment, and Sales Account Manager
Andrew McLeod is easy to talk to on a daily basis if needed.
“There’s no doubt that we will be buying more machines from Clark Equipment, as the Develon product is good and reliable, and the pricing is great.”
• The DX140LCR
This excavator delivers excellent durability and trusted reliability. When it comes to performance and productivity, the engine and hydraulic system of the DX140LC are unbeatable. Improved ergonomics increases comfort and excellent all round visibility ensuring a safe and pleasant working environment. Increased reliability is achieved through the use of high performance materials combined with new methods of structural stress analysis.
• The DX235LCR-7
This crawler excavator offers a reduced tail swing counterweight design and a tighter front minimum swing radius for working confidently in congested or confined roadway or transfer station jobsites.
This standard arm configuration machine is easy to manoeuvre and offers superior hydraulics for enhanced performance when digging, loading trucks and more. The onetouch power boost momentarily amplifies hydraulic power for diff icult digging conditions that slow other machines down.
• The DX300LC-7
The hydraulic crawler excavator is available in standard arm, long arm or super-long reach configurations to help users take control of today’s complex work.
Count on exceptional productivity thanks to superior hydraulics that provide ample power to the arm and bucket.
Push the one-touch power boost button and get a momentary increase in hydraulic power for breaking into hard materials
A pair of JCB mini-excavators has helped a plant hire and landscaping business establish itself in the industry.
If it ain’t broke, don’t fix it.
That could be the philosophy of Greenstar Hire’s Managing Director Sam Kirkby, who says he only stocks his fleet with industry-leading brands.
“I don't reinvent the wheel when it comes to choosing new products, and cannot afford to let my customers down with inferior items,” he said.
Greenstar Hire — based in Alstonville near Ballina, NSW — evolved from Greenstar Earthmoving, a business started more than 10 years ago that specialised in all aspects of land clearing and property development, including civil works such as property subdivisions, school car parks and council works.
“Greenstar Hire came about because I could see about five years ago that labour, and in particular, experienced people, were becoming short in supply,” Sam said.
“Therefore I transitioned my business, retaining administration, mechanical workshop facilities and much of my equipment, to an exclusively dry hire model.
“We’re now one of only two independent hire companies in the Ballina area.
“I also have a landscape supplies yard business, Plateau Landscape Supplies, which has become an agent for Greenstar Hire, and offers the shopfront for processing transactions, displaying machines and arranging deliveries and pick-up of machines and products.”
This unique connection enables customers the luxury of purchasing any of the products that Plateau Landscape Supplies offers — including bulk sands, gravels, decorative pebbles, bricks, blocks and pavers — and not only be able to have these delivered, but also have dry hire machines moved to the same destination and have the convenience of having it all on the same transaction.
“Being a small business, we can provide excellent service by way of our off ice staff and also through our full time mechanic and call-out service, where necessary,” Sam said.
“We have in excess of 100 pieces of hire plant and equipment and have around 15 staff within the hire and landscape businesses.
“The items for hire range from small pieces of equipment such as compaction plates, cement mixers, log splitters, small track dumpers, stump grinders, scissor lifts large and small, mini excavators, loaders and rollers, up to 5-tonne excavators and Posi-tracks.”
And so back to Sam’s creed of buying only the best, and listening to his customer requirements.
“It’s not just about performance. Critical features that I require when selecting products include great backup service, availability of spare parts, and access to advice over the phone (when we are in the field),” he said.
“I look for resale value and ruggedness.
Reliability is the most critical, therefore some machines with too many "bells and whistles" won't work for our clients.”
And as a testament to this, Greenstar Hire has just taken ownership of two brand new JCB 18-Z mini-excavators.
“JCB had a fantastic deal, price-wise. They are a well-established and reputable brand,” Sam said.
The "Z" refers to a zero-tail-swing design, which means the rear of the machine doesn't extend beyond the tracks when it is rotating, making it especially useful for working in confined spaces or near obstacles.
Due to its maneuverability, durability, and ease of use in various small to medium-scale operations, the excavator is particularly useful for the landscaping jobs that Sam’s business deals with, such as digging and material handling in gardens or parks.
“The 18-Zs are not a complicated or 'fussy' machine, comprising the right balance of technology and operating features with reliability and necessary functions for our clients,” Sam said.
“Maintenance-wise, the machines provide very good access to the engine bays via large swinging rear covers.”
Sam bought the machines from CEA in Brisbane through territory manager Chris Kane, and particularly values the after-sales service, which “has been excellent”.
“We have been very excited about the introduction of the two new units to our fleet,” he said.
“JCB have such a great range of machines and products that we are definitely considering introducing more to our fleet in future.”
• Cost of ownership
Spending less throughout the life of the 18Z has been a key design criteria.
Boom, dipper and blade pins have 500-hour greasing intervals for reduced downtime and extended pin and bush life, which means that greasing only needs to be completed as part of a 500 hour machine service.
This is achieved by using sealed bronze graphite impregnated bushes. The seals on the outside of the bushes keep the grease in and dirt out.
The standard heavy-duty kingpost optimizes service life and lowers the cost of ownership due to the durable re-bushable pivots. This eliminates the cost of complete kingpost replacement when the pins wear into the cast.
The expanding undercarriage uses sacrificial wear pads so that metal to metal contact is eliminated as the track legs extend and retract.
Replaceable wear pads is a much lower cost compared to building up or replacing worn metal slide components.
O-ring faced seals throughout the hydraulic system increase the durability of the hydraulic system with higher reliability for eliminating leak paths.
The 18Z is supported with a three-year/3000 hour Premier Warranty package. Australian dealers offer full service benefits to owners through their experienced aftersales operations.
This combination of support attributes, have proven to provide low whole of life costs and exceptional machine residual values delivering the most cost effective solution for mini excavator users worldwide.
• Durability
A strong and durable design underlines the mini excavator’s DNA.
It starts with the 100 per cent steel bodywork for maximum impact protection and ease of repair.
Designed specifically with the rental and contractor segments in mind, all owners secure the advantage of JCB’s vision to improve the products durability in the toughest industry segments.
Robust steel panels can be quickly and easily repaired if required which is vitally important in a hire fleet with optimum usage rates.
Toughness is personified by the full width solid cast 173kg counterweight that provides maximum protection for the rear of the machine.
The heavy duty strong H frame undercarriage
provides rigid support and an open design allowing spoil to fall readily through to the ground preventing excessive componentry wear and minimal cleaning time.
For ultimate rigidity, the extending (from 980-1330mm) undercarriage beams are constructed from 25mm solid steel plate.
The high tensile four-plate boom and dipper design provide maximum strength and durability.
The 1800mm main boom with top mounted lift ram provides maximum protection for the hydraulic cylinder components.
Tough “power-matched” engine and hydraulic configurations give this machine the dig-strong performance others find hard to match.
• Performance
Working faster is a standout characteristic of the 18Z.
The hydraulics give operators the capability to simultaneously multi-task any combination of excavator functions smoothly and with full power for unrivalled output that means less time to complete the job.
Straight-line tracking when using any other hydraulic functions contributes to increased productivity and safety.
Redesigned track levers now come with T-bar controls that allow the operator to manipulate the machine position quickly and smoothly using just one hand.
Sloping track legs make it easier and quicker to clean the excavator undercarriage between jobs.
New dozer geometry allows the blade
to become free of material build up easier increasing productivity.
The dozer blade extensions can be swung out without using tools. They pivot past the respective tracks with plenty of clearance regardless of the blades above ground position.
Ten sturdy tie-down points have been built into the frames make the tie down process quicker and easier being easily adaptable to different truck and trailer tie down configurations. Safe and easy access to the tie down points means quicker turnaround times between sites.
• Safety
The model is the safest to operate in the zero tail swing segment.
JCB’s unique “2Go” risk mitigation hydraulic isolation system prevents excavator operation through unintended control lever movements. The operator must make 2 deliberate and separate inputs before the controls are functional.
Quick, safe and easy access on and off the operators platform is aided with hand rails that provide the operator with the all-important 3 points of contact and once seated, the seat belt is available to strap in and complete the safety loop.
The 2-Post canopy structure is ROPS, TOPS and FOGS certified. Increased all-round visibility to work site from the operator’s seat is a standout feature on the 18Z with the 2-Post canopy.
Ten integral easily accessible tie-down points make the transportation tie down process safer and quicker whether on a trailer or truck.
The collision avoidance system enables full intervention control of a machine if required. Image: Aptella
Aptella introduces intelligent anti-collision technology designed to increase safety for heavy machinery operation without reliance on tags or identifiers.
Automation and positioning specialist, Aptella, have entered a distribution agreement with Torsa to supply and support advanced collision avoidance solutions for the mining and quarrying industries throughout Australia, New Zealand and Southeast Asia.
With a proven track-record in mine and quarry sites around the world, Torsa’s safety solutions are designed to perform at the highest standards to reduce risk and safeguard heavy machine operations.
Aptella CEO Martin Nix said prioritising safety was the lead value at Aptella and of equal importance to any customer that works with heavy machinery.
“As we continue to seek the best innovation from around the world, we are excited to bring this advanced solution from Torsa to our local customers,” he said.
Torsa collaborates with peak industry bodies to remain at the forefront of regulation and safety standards, including the International Council on Mining and Metals (ICMM) and the Innovation for Cleaner Safer Vehicles (ICSV) program.
The ICSV program brings together 27 of the world’s leading mining companies, machine and technology manufacturers, to accelerate heavy machinery development in a noncompetitive forum.
The collision avoidance system is certified to levels seven, eight and nine, enabling full intervention control of a machine if required.
Torsa’s solution is configurable to each site and customer’s requirements, and suitable for
all asset types including draglines, dozers, haul trucks, and light vehicles.
Torsa CEO Juan Raúl Santana said the company believed in creating systems that can be used for all assets, on all sites.
“That is why we engaged at the Earth Moving Equipment Safety Round Table (EMESRT) and with the ICSV,” he said.
“With the ability to work across all makes, models and types of machinery, Aptella was a natural choice as our distribution partner in the region.
“Our team looks forward to working together to enable advanced safety for Aptella’s customers.”
With locations throughout all States and Territories of Australia, in Southeast Asia and New Zealand, Aptella supports the civil construction, building, mining and geospatial industries with world-leading technology solutions.
Under the agreement, the company will offer full sales, deployment, training and technical support to customers.
Aptella Executive Manager of Mining Andrew Granger said Torsa’s collision avoidance system complemented its safety portfolio and range of machine guidance and fleet management solutions for the mining sector.
“With a large network of technical and application specialists, we offer customers full support from a local team,” he said.
For more information, contact the Aptella team on 1300 867 266 or visit www.aptella.com
As a team of diverse specialists, Aptella works to provide advanced solutions that enable real eff iciencies for business. It is solutions-led and customer-focused, understanding customers’ business first, ready to solve their needs with the right innovative positioning technology.
Aptella advises customers on the best solution for their project, enable them with the right technology products and systems, and support them as their long-term partner. The team of more than 400 employees is tapped into the latest innovations from around the world, which the company sources, tailors and deploys to meet the local needs of customers throughout Australia, New Zealand and Southeast Asia.
Torsa, based in Málaga Tech Park (Andalucia, Spain), focuses on the design, manufacturing and implementation of innovative systems to improve productivity and safety in critical sectors such as mining.
With a strong commitment to excellence and innovation in all their solutions, it works closely with leading industry institutions to ensure their products are of the highest quality and safety standards around the world.
Agreements with top-level companies, such as Aptella, and with international presence through their headquarters in Peru and South Africa, allows it to offer solutions and technical support to clients in different regions, with complex industrial environments.
Hard rocks need not mean hard work. A Hitachi ZX490LCH goes through its paces easily with an impressive e iciency and fuel economy to match.
NSW-based Mulgoa Quarries (MQ) is celebrating its 60th anniversary this year, a sure sign of its longevity and strength in the industry.
The family business, headquartered in the Sydney suburb of Erskine Park, is a civil, excavation and transport contractor, with services including contract quarrying, bulk earthworks, landfill infrastructure, contamination remediation, bulk material supply and transport, bulk waste disposal, and various civil and road contracting works.
Company director Matt Wearn said he and his brother Tom were carrying on the legacy of their grandfather John, who started MQ as a quarrying operation in Mulgoa in 1964.
“Originally, we had a quarry which supplied shale to the Sydney brick yards as well as road base to the market,” he said.
“The quarry has since been remediated and the land was sold to developers. The Mulgoa Quarry allowed us to build a relationship with the brickyards that is still strong today, with a lot of our work being for Brickworks & PGH Bricks.”
Matt and Tom’s father Rob, along with uncles Adrian, Bill and Bruce, took over the business when John passed away in the early 80s.
Bill and Bruce left the business by the early 2000s, leaving Rob and Adrian to grow MQ into a multi-faceted business which now serves many industries in Western Sydney.
“These include housing and industrial estates, landfill construction, large land contamination
remediation and road and civil works,” Matt said.
“MQ now employs more than 140 people and over 50 per cent of those have worked at MQ for more than five years, and 30 per cent over 10.
“Some of our clients are Brickworks, PGH Bricks, CSR Property, Sydney Business Park, Cleanaway, BINGO, Veolia and more recently Goodman Property Group.”
Such success of course depends on the ability to run a fleet of eff icient machinery.
The current line-up consists of about 110 pieces of heavy plant, including a number of
dozers, compactors, excavators, loaders, dump trucks, graders, mobile crushers and screens. Additionally, MQ has a fleet of 22 trucks and dogs of varying payloads.
“When choosing our machinery, we look for equipment that is consistently reliable, environmentally effective, productive, comfortable for our operators and is competitive in price,” Matt said.
For the business, one brand that ticks all those boxes is Hitachi.
“We recently purchased a Hitachi ZX490LCH excavator to work with our MDS trommel as part of one of our rock processing crews. This
machine has been the standout of our recent plant purchases and we are stoked with how it has been performing,” Matt said.
Capable of a higher workload than the previous model, this version boasts 11 per cent reduced fuel consumption, enhanced eff iciency due to Hitachi’s industry-leading hydraulic system HIOS V, higher productivity from improved front speed and increased engine output, and an industry-leading cab with firstclass comfort and safety features.
“We’ve been very impressed with the fuel eff iciency of the new excavator. We had one in our fleet of excavators previously and were happy with the productivity and worklife we got out of it,” Matt said.
“They are also a favourable machine from our operators, who have mentioned that the breakout force was excellent as well as the comfort that the machine provides.”
MQ also currently runs nine Bell B45E Articulated Dump Trucks in its fleet of 23 ADTs.
The South African Bell ADTs, distributed by Hitachi, are another operator favourite among the MQ team.
“The comfort is excellent and again fuel eff iciency is a standout, while the auto greasing is also a great feature” Matt said.
Indeed, it was the purchase of ADTs that kicked off the relationship with Hitachi.
“We bought three Hitachi AH400 dump trucks back in 2006, mainly because of their fuel eff iciency without reducing productivity,” Matt said.
“With environmental consciousness becoming a front-of-mind item and fuel being
one of our biggest costs for the business, fuel eff iciency plays a big part in our decision when we are looking to purchase new plant.”
Matt could not be happier with the connection between Hitachi and MQ.
“We have loved working with them over the last 18 years and intend to continue the relationship into the future,” he said.
“Our plant workshop manager had a strong relationship with Steve Gibson from Hitachi in its technical services department for a long time, up until Steve retired earlier this year.
“Steve was always able to diagnose any issues that were had with the machinery quickly and get the machines back working.
“While Steve has retired there is still a good relationship with the team at Hitachi and our workshop guys.”
Today Matt and Tom continue to work
strongly with Steve’s son Bryce, who has taken up the sales mantle at Hitachi.
“We have a team of 10 in-house fitters who maintain, repair and rebuild our fleet of equipment and road trucks,” Matt said.
“We have always been very impressed with the serviceability of the Hitachi and Bell machinery.
“With the fleet the size it is, the ability to do services quickly is always important. Our fitters always have a full list of work orders to complete, therefore it’s important to keep the machinery downtime to a minimum.
“The ability to get parts quickly is one of the reasons that we have Hitachi machinery in our fleet today.”
Matt said Hitachi equipment is always a “great addition” to the fleet.
“We intend to purchase more in the future,” he said.
This excavator is built with highstrength steel and reinforced components, making it capable of withstanding the rigours of heavyduty operations. Images: XCMG
When it comes to excavators, the XE1350 from XCMG stands out as a testament to engineering excellence and innovative design.
The XE1350 is not just a tool but a critical partner for any construction or mining operation that demands power, precision, and reliability.
The machine is built to handle the toughest jobs, offering a blend of advanced technology, durability, and versatility, making it a superior choice in the heavy machinery market.
At the heart of the XE1350 lies a robust and eff icient engine that drives its impressive performance.
Equipped with a high-powered diesel engine, the XE1350 is capable of delivering substantial horsepower, making it suitable for the most demanding excavation tasks.
The engine meets the latest emission standards, ensuring that the machine is not only powerful but also environmentally friendly. Its high torque output allows the XE1350 to handle heavy loads with ease, maintaining optimal performance even under the most challenging conditions.
The XE1350 features an advanced hydraulic system that is designed to maximise eff iciency and control. This system is pivotal to the excavator's performance, allowing for precise
and smooth operation of the boom, arm, and bucket.
It is engineered to provide optimal flow and pressure, ensuring that the machine can handle various materials, from loose soil to dense rock, with precision.
The XE1350’s hydraulic components are also designed for durability, reducing the risk of breakdowns and minimising maintenance needs.
Durability is a hallmark of XCMG’s machinery, and the XE1350 is no exception.
This excavator is built with high-strength steel and reinforced components, making it capable of withstanding the rigours of heavy-duty operations.
The undercarriage, a critical component in the overall stability and lifespan of an excavator, is particularly robust, offering enhanced protection against wear and tear.
The XE1350’s design incorporates features that reduce the impact of harsh working environments, ensuring that it remains operational and eff icient for longer periods.
One of the most significant advantages of the XE1350 is its versatility.
Whether it’s digging trenches, bulk handling, or performing demolition work, the XE1350 can be adapted to meet the specific needs in any application.
The quick coupler system makes it easy to switch between different attachments, reducing downtime and increasing productivity on the job site.
This adaptability makes the XE1350 an excellent investment for companies looking to maximise the utility of their machinery in any production environments.
XCMG places a strong emphasis on operator comfort and safety, and the XE1350 is designed with both in mind.
The operator’s cab is spacious, ergonomically designed, and equipped with advanced features that enhance comfort during long hours of operation.
The seat is fully adjustable, allowing operators to find their ideal working position, which reduces fatigue and improves overall eff iciency.
The cab is also fitted with a state-of-the-art air conditioning system, ensuring a comfortable working environment in all weather conditions.
Safety is another critical aspect of the XE1350’s design. The excavator is equipped with a range of safety features, including a
rearview camera, proximity sensors, and a reinforced cabin structure that offers protection in case of an accident.
The machine also has an advanced monitoring system that provides real-time data on the excavator’s performance, alerting operators to potential issues before they become serious problems.
This proactive approach to safety helps reduce the risk of accidents and ensures that the XE1350 operates smoothly and eff iciently.
In today’s construction industry, fuel eff iciency is more important than ever, both from an economic and environmental standpoint.
The XE1350 excels in this area, offering impressive fuel economy without compromising on performance.
Its engine is designed to operate eff iciently at varying loads, reducing fuel consumption during both idle and active phases.
This eff iciency is further enhanced by the machine’s intelligent hydraulic system, which optimises power usage based on the task at hand.
Over time, the fuel savings provided by the XE1350 can significantly reduce operating costs, making it a cost-effective choice for contractors and fleet managers.
Maintenance is a critical consideration for any heavy machinery, and the XE1350 is designed to be as maintenance-friendly as possible.
The excavator features easy access to all major components, allowing for quick inspections and routine maintenance tasks.
The hydraulic system is equipped with filters and diagnostics that help identify issues before they lead to costly repairs.
Additionally, XCMG offers comprehensive support and service packages, ensuring that XE1350 owners have access to the parts and expertise they need to keep their machines running at peak performance.
The XE1350 is not just a brute force machine; it is also a smart excavator, thanks to the integration of advanced technology.
The machine is equipped with a sophisticated control system that allows for precise operation and real-time monitoring.
This system includes features like automated digging functions, load sensing, and GPSbased positioning, which enhance accuracy and eff iciency on the job site.
The intelligent control system also allows operators to customise settings based on the specific requirements of the task, ensuring optimal performance in every situation.
In an industry that is increasingly focused on sustainability, the XE1350 stands out for its environmental credentials.
The excavator’s engine meets stringent emissions standards, significantly reducing its environmental impact.
Moreover, the machine’s eff icient fuel consumption contributes to lower carbon emissions, making it a more sustainable choice for construction and mining operations.
XCMG has also designed the XE1350 with a focus on reducing noise pollution, incorporating sound-dampening materials and technology to minimise the machine’s acoustic footprint.
These features make the XE1350 an ideal choice for projects in urban areas or environments where noise levels are a concern.
XCMG has established itself as a global leader in the construction machinery industry, and the XE1350 is a key part of its product lineup.
This excavator is used in a variety of applications around the world, from largescale mining operations in Australia to infrastructure projects in Asia and beyond.
Its reputation for reliability and performance has made it a popular choice among contractors and fleet managers looking for a machine that can handle the demands of modern construction.
A significant part of what makes the XE1350 a compelling choice is the support network that comes with it.
XCMG is known for its robust customer support and after-sales service, ensuring that owners of the XE1350 have access to the resources they need to keep their machines operational.
This includes everything from readily available spare parts to expert technicians who can provide on-site support. The company’s commitment to customer satisfaction extends beyond the sale, with ongoing training and support that helps operators get the most out of their equipment.
In summary, the XCMG XE1350 excavator represents the pinnacle of modern construction and mining machinery. Its combination of power, precision, and durability makes it an invaluable asset for any operation.
Whether it’s the advanced hydraulic system, the intelligent technology integration, or the focus on operator comfort and safety, every aspect of the XE1350 is designed to deliver superior performance in the field.
For companies looking to invest in a machine that will not only meet but exceed their operational needs, the XE1350 is a choice that offers long-term value and reliability.
As the construction industry continues to evolve, the XE1350 is well-positioned to meet the challenges of the future, making it a future-proof investment for any forwardthinking enterprise.
The XE1350’s combination of power, precision, and durability makes it an invaluable asset for any operation.
In the competitive landscape of demolition, having the right tools can make all the di erence; and in this field, Epiroc continues to set the standard with its innovative equipment.
Epiroc is a global leader in sustainable productivity solutions.
Among its impressive range of products, the Epiroc MG800 grapple stands out as a versatile and powerful tool that is transforming demolition projects for businesses like All Cleared Demolition.
The Epiroc MG800 is designed to meet the demanding needs of modern demolition work, offering unmatched versatility and precision.
Engineered for carriers weighing between 10 to 16 tonnes, the MG800 is ideal for loading, sorting, and demolishing various materials, including wooden and masonry structures. Its robust design ensures it can handle the toughest jobs while maintaining superior performance.
A standout feature of the MG800 is its 360° endless hydraulic rotation, which allows for optimal positioning and precise handling of materials.
In demolition, accuracy significantly impacts the eff iciency and safety of operations.
The MG800’s ability to rotate endlessly gives operators the flexibility needed to tackle complex tasks with ease, making it indispensable on any demolition site.
Epiroc has integrated advanced features into the MG800 to meet the highest performance and durability standards. The grapple includes an integrated mechanical stop, reducing the load on cylinders, extending the equipment's lifespan, and lowering maintenance costs. This thoughtful design enhances the MG800's durability and contributes to reduced operational costs over time.
The MG800's solid perforated shells provide excellent visibility during operations, a critical factor in maintaining safety and eff iciency on the job site.
Operators can easily monitor the material being handled, reducing the risk of errors and ensuring the job is completed to the highest standards.
This attention to detail reflects Epiroc’s commitment to delivering equipment that performs well and supports the safety and wellbeing of its users.
For tasks requiring additional precision, the MG800 offers optional tooth blades for block and stone handling, along with replaceable and reversible cutting blades.
This customisation allows the MG800 to be tailored to specific job requirements, further enhancing its versatility.
Additionally, the grapple’s ability to switch between rotation and non-rotation modes adds flexibility, ensuring it can adapt to various demolition scenarios.
After integrating the MG800 into its operations, All Cleared Demolition has seen significant improvements in project e iciency and capability. Image: Epiroc
Epiroc’s dedication to innovation and customer satisfaction is exemplified through its Epiroc partner BA Equipment Group, which takes pride in having a talented team of product selection specialists in all its locations.
The factory-trained trade qualified service technicians specialise in installation, commissioning and operation/maintenance/ service support backed by a large inventory of hydraulic attachments and spare parts.
After integrating the MG800 into its operations, All Cleared Demolition has seen significant improvements in project eff iciency and capability.
The enhanced capabilities provided by the MG800 have enabled the company to take on more complex and challenging projects with confidence.
As a result, it decided to order a second MG800, reflecting its growth and trust in Epiroc's equipment to support its expanding operations.
All Cleared Demolition Managing Director Hunter Lawrence said the MG800 grapple had been a game-changer for his business.
“Its precision and versatility have allowed us to take on more complex projects
with confidence. We're excited to continue expanding our operations with Epiroc's reliable equipment,” he said.
The Epiroc MG800 grapple is more than just a tool; it's a testament to Epiroc’s unwavering commitment to driving progress in the demolition industry.
By providing innovative, reliable equipment, Epiroc empowers businesses like All Cleared Demolition to not only meet but exceed the demands of modern construction and demolition projects.
This partnership between BA Equipment and All Cleared Demolition highlights the synergy between cutting-edge technology and practical application in the field.
For All Cleared Demolition, the MG800 has been a pivotal addition, enabling the company to tackle increasingly complex projects with heightened precision and eff iciency.
This collaboration underscores Epiroc’s role in not just supplying equipment, but in actively contributing to the growth and success of its clients.
As All Cleared Demolition expands its operations, it does so with the confidence that comes from knowing it is supported by a leader in the industry.
All Drott Services and Norm Engineering have fostered a partnership built on mutual respect and collaboration, helping create the most e ective, e icient tools to suit the needs of any task.
Sometimes factory-made attachments, as good as they are, just can’t cut the mustard … or in the case of earthmoving tasks, maybe “cut the soil” is a more appropriate term.
So when bespoke tools are need, it’s good to know that there is a company which specialises in making them for client needs.
Scott White, a veteran of the domestic building sector, says it’s not uncommon for him to seek modifications to various attachments to enable him to better carry out his construction and land clearing jobs.
Scott manages All Drott Services, a Loganholme-based provider of earthmoving services to the residential market in South East Queensland.
For his projects, the business utilises a fleet of about 15 machines, comprising excavators, drotts, dozers and Posi-tracks.
“Attachments that come with the major brands do not suit all surfaces,” Scott said.
“On many occasions, I realised that the implements could be more productive on particular jobs with minor tweaks, but of course the manufacturers do not redesign them just for one or two clients.”
That’s when Scott looked to Norm Engineering, conveniently based 20 minutes away in the suburb of Darra.
The company has earned a reputation for designing and building highest quality earthmoving attachments for mini loaders, skid steers, track loaders, excavators, backhoes, telehandlers and tractors.
It excels in builds aimed at enhancing the functionality and eff iciency of the machines,
making them indispensable tools on any construction site.
Its extensive range of attachments include buckets, hydraulic rear rippers, dozer blade stick rakes, hydraulic rock grabs and much more.
It was this expertise that led Scott to head towards Norm Engineering over a decade ago, armed with ideas for improvements and enhancements to help maximise his building operations, and most recently when it came to house pads.
The Norm Engineering team has worked closely with Scott and his team to provide custom solutions tailored to their specific needs.
“Traditionally, house pad cutting involved the use of heavy machinery like big excavators or drott machines, which, while effective, come with significant operating costs,” Scott said.
“With house pads shrinking in size, the use of these large machines has become less costeffective. I needed a more versatile solution to keep up with the shifting market demands.
“I wanted the shape changed on some of the buckets, and tines and angles configured for a rear ripper, which Norm Engineering duly delivered.
“I asked for buckets designed with large capacity and specific geometry, allowing them to tackle jobs with greater eff iciency.
“Norm Engineering's rippers enable businesses to convert their skid steers into powerful earthmoving tools, giving smaller, more versatile machines the ability to handle the tough jobs once reserved for bulkier equipment.
"The attachments help us complete jobs with
the same eff iciency as larger machines but at a fraction of the cost."
Scott welcomed the level of communication he had with the manufacturer, and its willingness to listen.
“Norm Engineering makes any improvements asked for by clients to create the most effective, efficient attachment that is fit for purpose,” he said.
“It’s not just about selling a product — it’s about developing attachments that work perfectly with specific machines.”
Norm Engineering’s reputation has been achieved through simply listening to customers and producing tough, quality-built products. The high level of work is a direct result of the feedback Norm Engineering receives from customers like Scott.
By attending closely to their needs and incorporating that input into the design process, Norm Engineering has refined its research and development process to ensure its attachments meet the precise demands of the job.
The company doesn't take a cookie-cutter approach, instead priding itself on its ability to adapt and customise attachments based on the unique requirements of its clients.
One of the standout aspects of Norm Engineering's offerings is the build quality of its products.
Known for their strength and durability, Norm Engineering's attachments are crafted from the highest quality materials and designed to withstand the rigours of demanding work environments like those found in Southeast Queensland, a feature valued by Scott.
“Their attachments are tough and ideal for the conditions we work in,” he said.
But it’s not just the product quality that has kept All Drott loyal to Norm Engineering for more than a decade. The company’s commitment to customer service is unparalleled.
“Norm Engineering’s willingness to collaborate and make any necessary alterations or customisations really sets them apart. They understand what our industry requires and always provide the best fit-for-purpose solutions,” Scott said.
As All Drott continues to grow and adapt to the evolving needs of the construction industry, Scott is confident that Norm Engineering will remain a key partner.
“In the future, I see Norm Engineering continuing to help my business by providing the highest level of customer service and maintaining the exceptional build quality they’re known for,” he said.
“I would not hesitate to recommend Norm Engineering’s products to others in the industry. Norm Engineering understands our industry inside and out, and they always deliver attachments that are built to last.”
Engineered for e ciency and convenience, this bucket seamlessly transitions between digging, dozing, loading, and grappling tasks with unmatched ease. Its intuitive design ensures straightforward operation, allowing operators of all skill levels to maximize productivity on the job site.
Customizable with optional teeth, choose between chisel or tiger teeth to suit your speci c needs and terrain conditions. Whether you're breaking through compacted soil or gripping uneven surfaces, these optional teeth enhance the bucket's performance.
The Standard 4-in-1 Bucket features a load guard engineered for enhanced visibility. Designed to optimize safety and e ciency, the load guard provides clear sightlines, ensuring operators can work with con dence even in challenging environments.
Digga has released the new MM14K, a state-of-the-art screw anchor drive.
In the ever-evolving world of construction and engineering, the demand for eff icient, durable, and high-performance equipment is paramount.
Leading the charge in innovation, Digga has developed an industry-leading screw anchor drive for mini machines, designed in collaboration with top installers globally.
This system is designed and manufactured in-house, embodying Digga's commitment to quality and performance.
One of the standout features of this new drive is its compact high-torque gearbox.
Manufactured by Digga, the gearbox is engineered to withstand the rigorous demands of screw anchor applications.
This durability ensures that host machines operate within the most eff icient power range, minimising wear and tear while optimising performance.
The result is not just enhanced operational eff iciency but also maximised returns on investment.
Navigating confined spaces is a common challenge in many installation scenarios.
Digga addresses this with a gimbal design that is both lightweight and compact, allowing for ease of movement even in the most restricted environments.
This user-friendly model does not compromise on power or performance, making it a versatile choice for a wide range of applications.
A notable addition to the MM14K is Digga’s HALO alignment system.
This feature enhances precision and accuracy during installation, reducing errors and improving the quality of the final result.
The HALO alignment system exemplifies Digga's commitment to incorporating advanced technology into their products, setting a new standard in the industry.
The integration of a high-eff iciency Danfoss/ Digga geroler hydraulic motor further elevates the system's capabilities.
Known for its reliability and eff iciency, this motor ensures smooth and powerful operation, contributing to the overall robustness of the equipment.
With more than 40 years of design and manufacturing experience, Digga brings a wealth of knowledge and expertise to every product they create.
This extensive experience is evident in the meticulous craftsmanship and thoughtful design of their screw anchor systems.
In conclusion, Digga's screw anchor drive for mini loaders, and machines up to 3.5 tonnes represents a significant leap forward in construction and engineering equipment.
With its combination of durability, eff iciency, and advanced technology, it is poised to revolutionise the small pile industry.
As demands continue to grow and evolve, Digga remains at the forefront, delivering solutions that meet and exceed the highest standards.
Manufactured by Digga, the compact high-torque gearbox is engineered to withstand the rigorous demands of screw anchor applications.
The high-e iciency
Danfoss/Digga geroler hydraulic motor ensures smooth and powerful operation, contributing to the overall robustness of the equipment.
Aus Final Drives, renowned for its specialised expertise in providing aftermarket final drive solutions to the Australian earthmoving and construction industry, has been acquired by industry leader ITR Pacific.
The acquisition marks a significant milestone in ITR Pacific’s expansion strategy, positioning it to deliver an even broader array of services and enhanced expertise in the critical area of final drives.
Aus Final Drives, founded by experienced engineer Shaun Morton-Jones, saw accelerated growth over the years due to its innovative approach to providing cost-effective, highquality aftermarket final drive solutions.
Shaun's initiative began when he faced the challenge of high costs and limited availability of final drives in Australia, prompting him to seek more affordable alternatives.
Through collaborative efforts with likeminded engineers, he spent two years exploring international manufacturers and testing their final drives to ensure reliability and performance.
This thorough approach, which included accelerated lifetime testing to identify the highest Mean Time Between Failure (MTBF), laid the foundation for Aus Final Drives' reputation for quality and reliability.
By 2018, the company's reputation for delivering high-quality, affordable final drive solutions had spread widely through wordof-mouth, resulting in a significant uptick in demand.
Off icially rebranded in January 2021, Aus Final Drives quickly became a leading supplier of aftermarket final drive solutions across Australia.
Known for its engineering prowess, problemsolving skills, and unwavering commitment to customer satisfaction, Aus Final Drives filled a crucial gap in the market, often being the go-to option when other suppliers were unable to meet customer needs.
Over the past nine years, Aus Final Drives has built a strong reputation for its extensive range of complete final drive assemblies for most makes and models up to 50 tonnes and being able to provide a cost-effective solution when no one else can.
Additionally, Aus Final Drives has gained recognition for its expert advice and timely support, assisting customers in selecting the right parts and resolving issues with eff iciency.
The acquisition by ITR Pacific not only complements but also amplifies this successful business model.
By integrating Aus Final Drives into its operations, ITR Pacific enhances its market presence and service capabilities.
Customers will now benefit from the expanded reach of ITR Pacific’s network, which includes branches and warehouses in Brisbane, Mackay, Sydney, Melbourne, Adelaide, Perth, and Kalgoorlie.
This expanded geographical footprint allows for same-day pickup options across major hubs, greatly increasing convenience for customers.
ITR Pacific’s acquisition of Aus Final Drives represents a strategic alignment of strengths, with the combined resources and expertise poised to meet the growing demands of the Australian earthmoving sector.
This integration not only broadens the product offerings but also provides a onestop solution for all earthmoving machinery up to 190 tonnes.
The enhanced capabilities will deliver increased value to customers, streamlining their access to quality cost-effective final drive solutions and comprehensive support.
For more information, visit www.ausfinaldrives.com.au or www.itrpacific.com.au.
What sets Coast 2 Coast Attachments apart is its focus on products that are supplied exclusively from European manufacturers and designed for highly specialised applications and solutions.
Australian-owned Coast 2 Coast Attachments (C2CA) is well-known for supplying machine attachments to the Australian mining, civil construction, scrap metal processing, waste, recycling and demolition industries.
The company is headed by Managing Director Luke Preston, who had previously worked in a national Australian and New Zealand role for a large construction company.
With almost 25 years’ experience in the mining, civil and construction industries, his industry experience has given him practical insights to every application challenge, enabling him to develop a keen appreciation for tools and attachments that deliver safety, eff iciency and productivity.
“My comprehensive industry experience and the advice and value I can bring to customers has been widely appreciated,” he said.
“In addition, they understand the high level of integrity and support they receive from dealing with global brands that have a reputation in the marketplace for performance, reliability and eff iciency.”
Exclusive European manufacturers
Luke said the company’s products were not sold to a price point.
“C2CA only sells and supports well known European manufacturers that are regarded as industry leaders,” he said.
“The benefits of attachments such as Oilquick, Kemroc and Rotar, used in the mining, civil construction, recycling and demolition industries, are demonstrably superior and stand out in this competitive market.
“Many of these brands are not yet well-known in Australia, therefore our strategy is to focus on their high quality European manufacture and how they deliver results when deployed for specific applications.
“While they are established brands in Europe and around the world, they have only been in the Australian market for a short while, which provides challenges in terms of establishing brand reputation.
“We are seeing sales growth as a result of their growing reputation and positive feedback commentary within the industrial community.
“We know it’s only a matter of time and having satisfied customers who share their experience that will give confidence to others to invest in these attachments.”
C2CA services all of Australia except for Western Australia and Northern Territory, which has different arrangements.
It also manages the New Zealand market for the Rotar product only from its Melbourne head off ice.
Customers are supported by a network of service agents in Queensland, New South Wales and South Australia who attend to installation, parts and service and provide a full backup for all the company’s brands.
“Right now, it's about making sure the products are positioned well in the marketplace and we fully support our customers with service and spare parts and whatever they need to get the job done eff iciently,” Luke said.
“We may consider adding to the range however any additions will be compatible and complementary with our existing products.”
Luke said that Oilquick was an automatic quick coupler system that lets operators change attachments from inside the machine's cabin.
“The system offers safe and eff icient operation by allowing machine operators to change between various work tools within a few seconds,” he said.
“The fully automatic coupling system is a fast and precise attachment fit, preventing unnecessary exposure to risks and eliminates the need for manual handling of couplings covered in oil.”
The Kemroc chain cutters, drum cutters and
The Oilquick automatic quick coupler system lets operators change attachments from inside the machine's cabin. Images: Coast 2 Coast Attachments
cutting wheels are backed by more than 20 years of experience and built to deliver maximum cutting performance.
“They are engineered for high durability to ensure they perform eff iciently for longer, resulting in a reduction in costs due to wear,” Luke said.
The Rotar attachments are used in the demolition, waste and recycling industries and are regarded by many as state-of-the-art attachments for hydraulic excavators and wheel loaders.
“Rotar has a comprehensive range of attachments that include sorting and demolition grabs, concrete cutters, demolition pulverisers, scrap shears, rail cutters and combi shears,” Luke said.
“As the exclusive distributor for Rotar in Australia and New Zealand, this partnership means we deliver premium attachments and tools that meet the highest standards of performance and reliability.
“Contractors also have the comfort and support of Rotar’s guarantee of operational continuity, reduced operational costs and optimal availability. These factors make them the favourite work tool supplier across a wide range of industries.
With years of industry experience, Luke said the company’s team possesses the knowledge and skills to assist customers in selecting the right equipment for your needs.
“Our commitment to excellent customer service means we are always available to answer questions and provide support,” Luke said.
For further information, visit www.c2ca.com.au/
Servicing Australia and NZ with sub dealers in all major cities.
Meet RaptorTech: a pioneering technology company specialising in delivering innovative solutions, and is setting new standards for machine control.
It goes without saying that businesses in the earthmoving, construction and mining industries will want as much leading technology as possible for their machines.
But with so many innovations and automation apps around, finding products for optimal machine control can be diff icult and confusing.
One business was created specifically to make this task easier. RaptorTech was founded in 2018 with the vision of providing all levels of industry with access to leading technology, from the Tier 1 multinational companies to single machine owner operators.
As RaptorTech General Manager (Construction) Ryan Finn explains, the company believes that technology should work on any brand machine, while empowering owners and operators to achieve their business goals.
“We understand that the technology you add to your machines is a vital cog in your business, and we treat it with the utmost importance,” he said.
“We are trusted by thousands of machine owners, both nationally and internationally,
to provide them with business-critical technology.”
RaptorTech provides world class hardware at the best value prices, along with software that is easy to use and quick to learn.
“But paying less doesn’t mean compromising on quality - we stand by our products and offer a two-year hardware warranty and field support for any issues,” Ryan said.
“Our software has best-in-class features and is easy to use, learn and support.”
• Excavator Machine Control
Ryan said RaptorTech had products which seamlessly integrated with every excavator type – from nimble mini-excavators to mighty longreaches, crawlers, and wheeled excavators.
“Experience unmatched precision and responsiveness in 3D guidance, regardless of the attachment or size,” he said.
“We support multiple excavator configurations including swing boom, dual boom, tilt rotator, wheeled and dual swing boom, while also
catering for a range of different scenario applications including grading, trenching, dredging, and excavation.”
• Wheel Loader Machine Control
This is a simple way to hit the right grading level every time to avoid unnecessary re-work and downtime.
“The virtual guidance of the 3D machine control enables operators of all levels to view the real-time working processes and provide as-built data for quality control,” Ryan said.
“In various tasks, direct feedback on grading level, slope angle, and excavation in various tasks, according to design, improves operator independence and fleet effectiveness.”
• Dozer Machine Control
These products are designed to ensure accurate leveling with centimetre accuracy, whilst providing exceptional effectiveness and intelligent, automated blade control that makes the work smarter, regardless of the experience level.
“Integrating state-of-the-art GPS grading
control, digital terrain models, and real-time data processing, enables machinery to achieve precise grading and site preparation with minimal human intervention,” Ryan said.
“This ensures that projects adhere closely to design specifications and reduces material wastage and operational costs. Additionally, the immediate feedback these systems provide allows for quick adjustments on-site, reducing errors and rework.”
• Skid Steer Machine Control
With this in place, the operator’s job is simplified, avoiding unnecessary re-work and downtime.
“We have developed a user-friendly system at a competitive price regardless of operator skill level: automatic grade control for grading attachments that supports a six-way blade, and automatic side shift control,” Ryan said.
The Unicontrol partnership
RaptorTech has recently partnered with Unicontrol, to distribute the Unicontrol3D Machine Control, Unicontrol Rover and Unicontrol-Cloud platforms.
Ryan said that Unicontrol was a dynamic company that was created with the vision to make work easier and faster for the machine operator.
“Their systems are user-friendly, customisable, and designed to support all earthmoving machinery,” he said.
RaptorTech and Unicontrol teamed up after identifying a need in the market for a product that was user-friendly for both the operator and support staff, had a quick customer support resolution timeframe and appealed to the price-conscious consumer.
Today, Unicontrol products are sold in more than 27 countries including the United States, Canada, the United Kingdom, Germany, France, Denmark, Australia and New Zealand.
RaptorTech has the Unicontrol distribution rights for NSW, WA and the NT, and handles all local sales, service and support.
• Unicontrol3D
Unicontrol 3D was developed with direct input and testing from the people who use it— contractors and machine operators.
“Their invaluable feedback has allowed us to refine a product that truly enhances their work, eliminating the need for complex technical knowledge,” Ryan said.
The system can be customised to specific tasks, projects, or operator preferences, allowing designs to be created in 3D.
The simple interface caters to advanced features and intuitive machine guidance, regardless of the size or type of machine, while the intuitive tablet design ensures that essential features are easily accessible, with straightforward navigation and no superfluous interactions.
“The key advantage of adopting machine control like Unicontrol3D is the ability to get the job done correctly on the first attempt,” Ryan said.
“Operators can accurately gauge the amount of material to remove and precisely place it,
ensuring the right location is achieved, and the work is documented.
“This significantly reduces the risk of errors and the need for costly do-overs, conserving valuable resources.”
Supported machines include excavators (full swing boom support), skid steer and grading attachments (automatic blade control and side shift), dozers (automatic six-way blade control) and wheel loaders (full articulated body support).
Key features include:
• Real time 3D visual guidance
• Advanced in-field Designs
• Automatic in-field designs
• Automatic as-built documentation
• Customisable interface
• 2D operation without GPS
• Triple-band satellite tracking: (GPS, GLONASS, BeiDou, Galileo)
Ryan said the majority of operators could grasp the essentials of operating Unicontrol3D within 30 minutes or less, and if necessary, RaptorTech can carry out remote training.
“Do not worry if you are unfamiliar with the technology — we are here to assist with navigating surveys, file types, and system setups, wherever you are,” he said.
• Unicontrol Rover
Experience surveying at its best with Unicontrol GNSS Rover, a highly accurate GPS surveying equipment.
“With built-in tilt functionality, it's designed for user-friendliness, requiring no prior technical knowledge – the Unicontrol Rover makes surveying accessible for everyone on the construction site,” Ryan said.
“Streamline your workflow with instant file synchronisation between the UnicontrolRover and your operating machines via Unicontrol Cloud.
“Share files directly with the off ice, operating machines and workstations - a perfect synergy to save time and improve collaboration.”
Engineered for precision, the rover receives signals from satellites across GPS, GLONASS, BeiDou, and Galileo, features built-in tilt compensation, and connects via cellular networks and built-in radio, ensuring accurate measurements everywhere.
• Unicontrol Cloud
UnicontrolCloud revolutionises project management and collaboration, making communication between machines and workstations seamless and paper-free.
This cloud-based solution enhances onsite eff iciency and teamwork by providing a centralised project management platform.
Ryan said that with UnicontrolCloud, uploading project data, design files, and as-built information is quick and effortless, allowing for real-time management of all machinery directly from the off ice — eliminating the need for timeconsuming data transfers between machines and the off ice.
UnicontrolCloud delivers comprehensive diagnostics for every machine in your fleet, streamlining the process of identifying and addressing operational issues.
Operators can also back up their calibration settings and quickly restore them if any functional problems arise.
With every machine purchase, RaptorTech includes 10 hours of support.
“We can also solve most issues remotely and quickly with our phone and remote access support service,” Ryan said.
“Our support team will help you set up and work directly with your site surveyor and operators to on-board you and avoid issues when starting a new job.
“We have locations in both Perth, WA and Newcastle, NSW, and have a dedicated team of technicians, engineers and support staff in each location to assist with after-sales enquiries and support.
“We also run complimentary monthly training sessions, designed to empower our customers with the skills, knowledge, and confidence needed to fully utilise the product.
“However, due to our unique remote login feature that is included standard in every sale, we have the ability to rectify over 95 per cent of customer concerns remotely, minimising downtime and operational disruptions for our customers.”
Customers can request a quote online through the website www.raptortech.com. au and following the links, emailing enquiry@ raptortech.com.au or calling one of the branches directly: (08) 6383 9088 (WA) or (02) 8069 6455 (NSW.
TerraTyre was born out of a necessity in the Australian mining industry for a hard-wearing and hardworking tyre to meet the rigorous needs for performance, durability and economy.
With increasing cost pressures on mining and trucking operations throughout Australia's toughest regions, it's no wonder that mine owners, transport operators and contractors are always looking for tyres that perform well but don’t break the bank.
As OTR General Manager – Sales, Travis Parsons, explains, there are many challenging conditions on and around mine sites, and Australia's tough outback conditions punish tyres “like almost nowhere else on earth”.
“Faced with this challenge, TerraTyre was developed primarily for mining equipment; and the high success in meeting customer expectations in that market was the catalyst to extend the design concept to additional configurations for other vehicle applications,” he said.
“Mine sites in Western Australia needed tyres that did the job for a certain cost and this was where the first design came from. The design immediately proved to be successful.
“The design of the TerraTyre range was targeted at the heavy machinery market to operate at an attractive value point.
“Having achieved this, the product range grew into the more standardised range that offers good value.
“These products deliver excellent usage hours and don’t cost an arm and a leg, striking a great balance between functionality and cost investment.”
Travis said that since the introduction of the brand, OTR had sold tens of thousands of units throughout Australia.
“Much of the success is demonstrated by the very low warranty claim level which outperforms that of many of the major brands,” he said.
“Customers love these tyres and the tyre fitters report a great experience with them. Overall, it's been a great success story.”
Australian ingenuity
OTR says what sets TerraTyre apart is its unique combination of Australian design innovation with world-class manufacturing.
This synergy results in a product that not only meets the rigorous demands of the industry but also delivers exceptional cost per hour value.
This formula has earned a loyal customer base, with many operators consistently returning to the brand.
OTR has been in the global tyre industry for more than 30 years and is 100 per cent Australian-owned, ensuring the TerraTyre brand has been engineered in Australia.
Despite its competitive price, the range uses the industry’s best quality materials such as steel cords manufactured by Bekaert in Belgium, while the natural rubber is sourced
only from Malaysia and Thailand, used in compounds to suit tyres for specific applications and usage.
Other components such as butyl polymers come from Exxon Mobil Chemical in the USA.
TerraTyre is manufactured in a highly reputable factory that produces more than three million units annually.
Tyres meet or exceed ISO TS16949, ISO 9001 & DOT specifications and carry the S-Mark in product performance and safety.
Quality and value
“TerraTyres have become synonymous with quality and value across Australia's earthmoving industry,” Travis said.
“With a strong reputation built over years of reliable performance, TerraTyre offers a range of tyres that cater to the diverse needs of heavy machinery operators.
“We have a commitment to performance, value, and reliability that you can count on.
“Whether you're navigating challenging terrains or requiring enhanced durability, Terra's selection of tread patterns, compounds, and designs ensures you have the right tyre for the job.”
The Australian-designed TerraTyre has become synonymous with quality and value across the earthmoving industry.
TerraTyre is fully supported by OTR’s national warranty and service and have service locations Australia Wide.
To learn more about OTR’s quality products and the many benefits they can bring you, contact OTR – Tyres, Wheels and Axles on 1300 CALL OTR, or visit www.otraustralia.com
TerraTyres have been designed to cope with Australia’s harsh environments. Images: OTR
OTR Australia supply earthmover, agricultural, truck, bus and light vehicle tyres and rims from 6” through to 63” in diameter, to blue chip mining, civil contracting, road transport companies, agricultural dealerships and end users.
We maintain a healthy inventory of new and used earthmover tyres of critical sizes and have the ability to custom manufacture Australian Made wheels in 1 of our 10 locations Australia wide.
ASV takes safety seriously. That’s why it’s fitted its popular Posi-Track loaders with a detection system that alerts operators to pedestrians operating in the job vicinity.
ASV Posi-Track Compact Track Loaders (CTLs) are considered by many to be the industry’s most comfortable, operator-friendly and high performing of such machines on the market.
Following a customer-focused constant improvement methodology with all machine designs, ASV continues to deliver premium machinery and maximum operator satisfaction with the CTLs – including unmatched quality features on its renowned line-up.
Every ASV Posi-Track machine is built to lead the industry in hydraulic performance, tractive effort, undercarriage technology, reliability and serviceability – ensuring you can take on your next job like never before.
Add to this the finest engines, hydraulic systems, counter-balancing configurations and overall performance delivered by the entire range of ASV Posi-Tracks, the result is a range of CTLs that owners and operators can trust for the long haul.
But apart from these features, there’s another important aspect that ASV takes seriously: and that’s safety.
The company prides itself on delivering complete customer service, support and satisfaction. With client demand growing for added safety technology, especially in public works and projects where risks of accidents are higher, ASV was determined to invest in the best machinery setups available to ensure safe working environments.
Recently, as part of a contract to supply a major Government agency with a number of machines, ASV chose the Proxicam AI Pedestrian Detection and Proximity Warning System as an optional add-on to the equipment.
Proxicam’s AI-powered smart cameras identify and track humans, alerting machine operators to their proximity, while enhancing visibility up to 360° around the machine, with
up to four cameras in use.
Unlike human users, the system doesn’t get distracted or tired and operates in all weather conditions, day and night, in effect providing an extra eye on the task and offering management total peace-of-mind, ensuring everyone gets home safe.
Proxicam is the perfect complement to the MAX-Series cabs in the Posi-Tracks, named for providing the absolute maximum in operator comfort, control, performance and productivity to deliver enhanced overall return on investment.
The MAX-Series loaders are already
designed with safety in mind. They feature the industry’s best all-round visibility, a more spacious operator area, a fully adjustable deluxe seat, a state-of- the-art seven-inch touchscreen display including machine operational statistics, diagnostics and controls, and increased space to jump in and out of the cab.
In addition to better visibility and comfort, the models include the industry’s first compact loader roof escape hatch, allowing operators to exit the cab rapidly in emergency situations.
MAX-Series Posi-Tracks also include ROPS and reinforced windows for impact resistance.
Of course, despite these safeguards, human factors remain a variable and can be unpredictable. Operators can’t see everything all at once, particularly if they are often intently focused on running an attachment in front of the machine, and therefore have limited awareness of people and other hazards moving around it.
That’s where an AI warning system like Proxicam is so valuable.
Operators benefit from not only enhanced site safety, but also the peace of mind that comes with using technology that serves as extra ‘eyes’ for the machine.
Proxicam can be fitted to any ASV Posi-Track loader by technical specialists around Australia, either at point of initial sale, or retrofitted to already working machines, ensuring customers have the setup and support they need from their local supplier.
ASV’s intelligent software systems and functional engineering mean that add-ons like
Proxicam are eff icient to install and easy to run.
The results are already speaking for themselves, with users, operators, site supervisors and safety representatives all appreciating and valuing the extra safety afforded.
So what happens when a pedestrian steps in front of an ASV Posi-Track machine fitted with Proxicam?
Firstly, the system will confirm that the pedestrian is indeed a human, and not an inanimate object. This takes just milliseconds.
Proxicam is able to achieve this detection through world-leading computing vision. Deep learning of neural networks and simulated training to mimic our eyes and brains, allowing Proxicam Smart Cameras to quickly and accurately distinguish humans in all types of complex environments.
When there are blind spots, the risk in complex work environments intensifies. Any ASV track loaders or skid steers fitted with Proxicam can have up to 360º visibility for the operator.
Proximity alerts are delivered 24/7 in real-time via an LED buzzer or full high-definition, 7” LCD monitor.
Unlike other systems, Proxicam doesn’t require RFID tags, specific safety vests or other hardware to ‘see’ personnel, eliminating the risk of human error.
This is even more valuable for worksites located near high pedestrian traff ic that can encroach on exclusion zones.
The Proxicam system is also easy to configure and quick to deploy.
Indeed, Proxicam can be installed onto any type of machine. From landscaping to
construction, materials handling to mining, the pedestrian detection system is suited to all types of equipment and can be installed by any auto electrician.
The Proxicam calibration app allows complete customisation of detection zones and alerts for your exclusion zones. Set-up takes just minutes using any smartphone.
Installation of the system is truly plug n’ play. The screw-lock waterproof aviation connectors make fitting Proxicam like any regular camera system.
Protecting your people is Proxicam’s number one priority.
However, every potentially life-saving proximity alert can be recorded and viewed on-demand.
Proxicam’s DV Hub will record critical event video and data which can be used to monitor incidents or breaches into an exclusion zone for any machine or plant equipment.
Safety managers can now reform engineering controls, evaluate the effectiveness of training, and prevent near-misses from escalating into incidents.
The DV Hub is a MIL-SPEC water and dustproof DVR with up to 2TB of hot-swap SSD storage. Lockable and tamper-proof, DV Hub will ensure data security and integrity in any environment.
Safety managers can also receive immediate back-to-base notifications via SMS or email when subscribing to the Proxicam’s asset intelligence platform, FleetHQ.
For more information on Proxicam visit: www.proxicam.ai, email hello@fleetsafe. com.au or call 1800 227 548.
For precision and control in road maintenance applications, Simex’s range of attachments is designed for accuracy and reliability.
Simex self-levelling road planers and stabilisers are designed for removing an entire layer of asphalt or cement in preparation for trenching, or for milling deteriorated road sections for later resurfacing.
With Simex planers, users can maintain constant milling depth in any condition regardless of the ground contour, as lateral slides on the planer automatically align to the milling surface.
Both slides move independently, providing greater stability and more precise planing movements as well as reducing material overflows. Dust is also controlled through a built-in water tank and spray system.
The PL range of planers can be used on skid steer loaders, hydrostatic drive loaders and backhoe loaders.
With the option of using multi tooth special drums the operator can remove horizontal road markings, perform road scarifying or take off the top few millimetres of a concrete or asphalt surface.
Maintenance costs are kept to a minimum, since the only requirement is the replacement of worn teeth.
PL planers are available in a range of models that run from the PL 25.10 with a 250mm width and 70mm maximum depth, the PL 75.20 with a 750mm width and 170mm maximum depth, through to the PL 2000 with a width of 2000mm and depth of 130mm.
Covering a range of standard, high flow, milling and high depth planers, this range is suitable for small to medium-sized roadworks and is particularly useful for precision work around potholes and kerbs.
Various drums and teeth layouts are available for asphalt or concrete, as well as a multi-tooth drum for finer surface milling.
Qld Rock Breakers area sales specialist
Craig Einam said the planers were used for patch repairs on roads and “that kind of thing”.
“The big selling point of our units is that they’re compact compared to what else is on the market, so they can get into tighter areas and work closer to obstructions,” he said.
“There’s also a built-in water tank and spray system, which means you don’t have to put a water tank on the roof and run hoses.
“Another key point is that we have independent left and right depth control for greater precision.”
Craig said that feedback from the industry on the Simex planer range had been “awesome”.
“They’re balanced, they’re smooth, they’re compact, they work well – we have very few issues with them,” he said.
“We get people coming to us and asking us for Simex planers because their friends have got them – we gain a lot of our business through word of mouth. We also sell to a lot of OEMs who put them on brand new machines in a package deal.
“People tell me that these are the best planers they’ve ever used.”
Alongside the planer range, Simex also manufactures a variety of attachments for what Craig says are more niche markets.
For example, the Simex T/TA range of trenching wheels is designed for small "fixedsection trenching, cutting and microtrenching, with the Simex trenching wheel saws able to cut concrete, asphalt or rock up to a maximum depth of 800mm and a width of 250mm.
The range runs from the T200, with a maximum 200mm cutting depth, through to the T800, which has a 800mm cutting depth and can work in reverse.
The T450, T600 and T800 models come with hydraulic depth adjustment, while the T450 and T600 also come with an optional trench clearing device.
The wheel saws feature wheel protection at any working depth, ensuring maximum safety of operators and property.
Other options for various models include a water spray for dust control, a conveyor belt
PL planers are suitable for small to medium-sized roadworks and is particularly useful for precision work around potholes and kerbs. Images: Simex
for loading of material into a bucket and the ability to aspirate excavated material for a vacuum truck.
For compacting trench bottoms, Simex also offers vibrating compaction wheels for skid steers, front end loaders and five to 12-tonne (4.5 to 10.9-tonne) excavators.
These wheels can be quickly changed on site, with widths extending from 150mm to 400mm and a maximum depth of 700mm.
The rotation device can be mounted to allow for compaction in any position to reach diff icult spots.
With the reverse-rotation vibrating twin shaft positioned at the centre of the wheel, this increases operator comfort.
In addition to the above, Simex also offers the ST200 asphalt float for skid steers, backhoe loaders and front end loaders.
The ST200 has been designed for applications such as laying asphalt on footpaths and utility trenches, sealing road shoulders or widening existing roadways.
For more information, contact your SIMEX dealer:
VIC/SA/TAS: Walkers Hammers
NSW: Groundtec
QLD/ NT: QLD Rock Breakers
WA: Total Rockbreaking Solutions
Discover the power of SIMEX ST Asphalt Floats — your key to faster, flawless results. Engineered for efficiency, these floats excel in:
• Streamlining asphalt or waste material application in set-section trenches,
• Crafting smooth and durable footpaths,
• Expanding and perfecting existing roadways.
Experience precision and performance with every project. Choose SIMEX ST for superior quality and quicker processing times.
Scan for Simex dealer locations in Australia: QLD | NSW | VIC | SA | WA | TAS | NT or visit attachmentspecialists.com.au/simex
For over 35 years, Peely’s Earthmoving in Yannergee, Spring Ridge, has been a name synonymous with quality, dedication, and reliability in the earthmoving industry.
Founded by Warwick Peel, Peely’s Earthmoving has become a cornerstone of the community, delivering top-notch services that have stood the test of time.
Today, the business is in the capable hands of Warwick’s son Grant, who took over eight years ago, ensuring the continuation of a proud family legacy.
Grant's leadership has maintained the high standards set by his father while introducing new eff iciencies and innovations.
A key factor behind Peely’s success is its strategic partnership with Tilly's Crawler Parts, a company known for its high-quality machinery parts and excellent customer service.
In the earthmoving industry, the brand of parts used can be crucial.
Traditionally, the OEM badge has been a symbol of trust and reliability, something that customers often insist on.
However, Grant’s experience has shown that while some businesses avoid non-genuine parts, there are alternatives that offer the same, if not better, performance at nearly half the price.
For example, the cutting edges used in Peely’s machinery have over 3000 hours of service life, matching the performance of genuine parts at a fraction of the cost. Grant has thoroughly compared and tested products, and the results speak for themselves.
Tilly’s Crawler Parts has provided Peely’s Earthmoving with top-tier alternatives that deliver exceptional value.
The Bedrock rippers, for instance, have clocked over 10,000 hours and are still going strong.
Grant also favours the Bedrock stick rake, which outperforms more expensive competitors while being half the price.
It’s not just about cost savings; it’s about selecting the right parts for the job. Peely’s sources a wide range of components from Tilly’s, including wear parts, track blades, ripper boots, rollers, idlers, and buckets for excavators.
Each of these parts is chosen for its reliability and performance, ensuring Peely’s Earthmoving continues to operate at peak eff iciency.
The Tilly's sales team plays a crucial role in this successful partnership.
Their expertise and dedication ensure that Peely’s always has the best parts and support.
Grant often refers others to the team at Tilly's, confident in the excellent service they will receive.
Grant is also mindful of warranties. While OEMs offer strong warranty coverage, Grant
is aware of the potential trade-off s when using non-genuine parts, especially for critical components like tracks for dozers.
Balancing cost-eff iciency with warranty considerations is key, and with Tilly’s, Grant knows he’s in good hands.
Peely’s Earthmoving continues to thrive, not just because of its history, but because of smart decisions, trusted partnerships, and a commitment to quality.
Under Grant’s leadership, and with the support of Tilly’s Crawler Parts, this secondgeneration business is set to continue serving Yannergee, Spring Ridge, and beyond for many years to come.
Bedrock has a reputation as one of the world’s largest construction machinery attachment manufacturers, providing costeffective alternatives driven by quality and built to last.
With a rapidly increasing level of demand for Tilly’s range of genuine, low-hour OE machines has come matching demand for quality, compatible attachments.
Attachments currently in stock at Tilly’s Toowoomba HQ for dozers include rippers, stick-rakes, scrub canopies, sweeps and cutter bars.
Grader attachments include front blades, moldboards, push blocks and belly guards.
Rounding out the range are wheel loader quick hitches that can carry buckets, forks, stick-rakes, lifting jibs and rippers, and excavator attachments including buckets, thumbs, grabs, tynes, cab guards and longreach booms kits.
Customers purchasing machines from Tilly’s inventory can make their selection of complementary attachments and have them fitted by the experienced team in their onsite workshop prior to delivery.
Add to this the extensive range of over 40,000 new alternative part-lines in stock and Tilly’s customers are guaranteed quality, long-term solutions for their machinery maintenance and repairs.
Contact the team at Tilly’s who are always happy to assist or check them out at www.tillys.com.au
Thumbs up for Remu PD2160 padding buckets: the extra strong frames are designed to stand up to the hardest use when a screening bucket is the only available tool. Images: Remu
In the competitive world of pipeline construction, maximising e iciency and profitability is crucial for success. One of the most e ective ways to achieve this is by using Remu screening and padding buckets.
Remu manufactures innovative soil and material handling equipment, screening and crushing buckets, as well as pontoon platforms for excavators to enable dredging and excavation work even in the most challenging environments.
These buckets work seamlessly with wheel loaders, excavators, and skid steers, allowing you to screen, crush, mix, and load materials—all in one stage.
This integrated process not only speeds up operations but also significantly enhances the profitability and eff iciency of your projects. By streamlining multiple tasks into a single, cohesive operation, Remu buckets help reduce downtime, minimise the need for additional machinery, and ultimately lower operational costs.
Unmatched performance in challenging environments
Remu Padding Buckets are made of Hardox, a durable and wear-resistant material, and designed to fulfill the requirements of challenging pipeline and trench backfilling projects as well as padding cable and utility line excavations in the most demanding environments.
The models comprise the EX140 for 200-class excavators, the PD2160 for 250-class excavators, and the PD3160 for 300-class machines.
The PD3160 is specifically designed for pipeline padding to preparing padding material used to protect pipelines from damage by any sharp particles.
Mountable on a 30- to 40-ton excavator, this bucket offers customizable blade spacing
— 20mm or 24mm — to achieve the perfect padding material size, typically 0-12mm or 0-16mm.
This flexibility allows users to tailor the padding material to meet the specific requirements of their projects, ensuring that the pipelines are adequately protected.
Moreover, the PD3160 is available with other blade spacing options, providing even more customisation to suit diverse project needs.
Remu padding buckets' compact and eff icient design allows them to be easily moved to any location on-site where they are needed. This mobility ensures that you can respond quickly to changing project demands, reducing downtime and keeping the project on track. Furthermore, it is an effective tool for pipeline padding and backfilling, because it allows material to be screened on site and then backfilled directly into a trench, eliminating the need for a dedicated stationary screening machine.
The result? Significant time and cost savings, enhancing the overall eff iciency of your pipeline padding and backfilling operations.
The PD3160 padding bucket is available now directly from Remu ANZ and its distributors: BA Equipment Group in QLD, VIC, WA and Onis Equipment Group in NSW.
> www.remu.fi
> baeg.com.au
> onisequipmentgroup.com.au
Remu screening buckets have a long history dating back to the late 80s and recent models have gone through rigorous development.
Having made a name for itself in its home country of Finland and across Europe over more than 30 years, the company is now taking steps to expand its global footprint by increasing its
presence in Australia.
Remu’s expansion plans were also recently boosted by a distribution collaboration with the BA Equipment Group, a leading Australian supplier of excavator hydraulic attachments, with off ices in Queensland, Victoria, and Western Australia, and Onis Equipment Group based in NSW.
For more information on Remu products, email australia@remu.fi or call 0488 877 785.
Remu screening buckets can be used for tasks such as:
• Topsoil screening
• Sorting and separating aggregates
• Composting
• Pipeline and trench backfilling
• Waste recycling
• Landscaping works
• Construction site cleanup
Why leave your machinery out to rust in the rain? Now you can protect them with a range of weatherproof covers and tarpaulins produced by an enterprising couple of brothers.
It seemed like such a simple idea. But as the saying goes, that’s how the best discoveries are made.
Luke and Joel Pfitzner had been running their own outdoor construction business back in 2018 when the lightbulb moment occurred.
As qualified carpenters, the pair focused on complete backyard renovations, including decks, pergolas, landscaping, retaining walls, concreting, and the like.
But they had been getting frustrated at the damage caused to their mini-excavator because it was at the mercy of the elements.
“It was constantly getting wet and dirty out in the weather overnight and when it was parked up,” Luke said.
“We were sick of seeing it deteriorate and mum was sick of us using her towels to dry the seat down every morning.
“With nothing available, we used a king-size mattress bag to slip over our machine each night; however this was more of a pain.
“We needed something custom-fit which was easy to slip on and slip off. We went through a couple of designs before a few more people noticed them and also wanted one.”
And thus was born the first DiggerLid product: a cover specially made for a 1.7 tonne machine.
By April 2020, the brothers decided to finish up in construction, sell the truck and machines, and put more time, money and focus into the new company.
Based in Chirnside Park, Melbourne, the Pfiztners launched a very basic online store in November 2019; and today it has grown to servicing “anywhere our couriers will ship”, Luke said.
“Our main areas are Australia, New Zealand, USA/ Canada and the UK.”
DiggerLid currently provides a wide range of weatherproof covers and tarpaulins, working enclosures and polycarbonate weather shields
for mini-excavators, a range of universal covers to suit all other sorts of construction machinery, and a handy range of accessories and merchandise.
“DiggerLid, put simply, exists to make your day as an earthmover better. We’re here to provide trusted and reliable products which contribute to the success of our customers and also protect their valuable investments,” Luke said.
“Our motto is ‘Keep working, keep earning’. Our flagship PRO Enclosure helps operators work more while keeping them comfortable and protecting their machine.
“This helps bring more cash in and keep jobs running on schedule, all while protecting the machine and operator.”
Engineered to protect equipment and operators from the harshest elements, the PRO enclosure ensures that projects stay on track.
Equipped with windows on the left, right, and rear panels, as well as an open front section, operators can get more work done in comfort. Additionally, machines will maintain a pristine and professional appearance.
Luke said that crafted with durability in mind, the PRO Enclosure is rugged and lightweight, making it ready for any jobsite.
“It uses super tough rip-stop PVC fabric (490 GSM) and trusted YKK hardware, solidifying DiggerLid as the industry leader in weatherbeating excavator accessories,” he said.
“Choose from our six universal and adjustable sizes, available for over 100 models of miniexcavators.
“We are continuously expanding our range of sizes to accommodate even more machines. If you can't find the right fit, get in touch with us and we will provide you with an update.”
Luke is proud to claim that the DiggerShields are the “pinnacle of weather protection for mini-excavators”.
“Tailor-made with precision-cut 6mm polycarbonate panels, the DiggerShield fits your machine like a glove, providing crystalclear or tinted protection against rain, wind, and sun,” he said.
“This premium, Australian-made solution requires no drilling, making it a durable and versatile investment.
“Enhance your brand visibility, maintain machine access, and ensure top-notch protection with DiggerShield. Invest in the best and weather any storm with confidence.
“The fact that an operator has invested in a Digger Shield sends a message that they have got what it takes.
"They work smarter and harder, driven by sheer grit and determination to go over and above.
“They will out-perform, and out-earn the competition, every single day.”
Grease is the word DiggerLid has also added a range of grease and maintenance products to its arsenal.
“These products are just levels above what’s currently available,” Luke said.
“We’ve recently added the Kajo industrial and biodegradable grease range, which is an absolute game changer for maintenance.
“They come from Germany, while our grease adapters are from Australia.
“We’re a fully Australian-owned and designed business.”
More information: www.diggerlid.com/
In a world where speed, re-use and recycling are more important than ever,
Flip Screen’s
screening bucket attachment stands out as a beacon of Australian ingenuity.
Designed and built in Wagga Wagga, NSW, this game-changing invention is transforming industries far and wide with its innovative approach to portable material screening.
Flip Screen’s standout feature is its hydraulic flip-over action.
This clever design allows for continuous screening, which means you can process more material with less manual effort.
The result? A major boost in productivity and a significant cut in operational costs. Whether you’re running a small operation or a large-scale enterprise, Flip Screen’s attachment promises impressive benefits across the board.
One of the best things about a Flip Screen is its versatility.
With models available to fit any size of machine, it’s easy to incorporate a Flip Screen into your existing business.
No need for expensive new machinery or major modifications – just attach and go. Its adaptability and portability make it a valuable addition to any operation requiring quick and eff icient material processing.
Traditional sorting methods can be a real drag – labour intensive and time-consuming.
Flip Screen changes the game by allowing eff icient separation of a wide range of material.
A Flip Screen improves recovery rates, and supports more sustainable practices.
It’s a win-win for both your bottom line and the environment. You name it, you can screen it.
Flip Screen’s commitment to innovation and
Flip Screen’s hydraulic flip-over action allows for continuous screening. Images: Flip Screen
durability has set new standards in recycling, mining, and local government sectors just to name a few.
Over the years, Flip Screen has shown that blending cutting-edge technology with practical solutions can drive success and redefine material screening processes across many industries, all over the planet.
As Flip Screen continues to push boundaries and refine portable material screening, it proves that Australian innovation can compete on the global stage.
For businesses looking to enhance sustainability and increase eff iciency, adopting a Flip Screen attachment isn’t just a smart choice – it’s essential.
The future of material handling is here, and it’s embodied in the revolutionary Flip Screen attachment – a true game changer for the modern industrial world.
For more information, visit Flip Screen’s website at www.flipscreen.net or call (02) 6931 8002.
Flip Screen’s portability makes it a valuable addition to any operation requiring quick and e icient material processing.
The versatility and performance of LiuGong wheel loaders is rapidly expanding their workplace experience across Australia, including into the yards of scrap metal recyclers.
Immix Integrated Metal Management has built a strong history in this sector in Melbourne and regional Victoria, as well as into New South Wales.
In addition to Melbourne, the family-owned business has sites at Shepparton, Wangaratta, Hallam, Wodonga and Wagga Wagga.
The company has contracts with regional councils, helping to reduce scrap metal loads in landfill, it has bins placed with numerous building and mining industry organisations, and it also collects scrap metal from the farming sector.
Most typical scrap metal is processed and exported, while recycled, non-ferrous material is generally sold locally.
At its Wodonga site, Immix recently upgraded from using a JCB loader and decided to invest in a LiuGong wheel loader for the first time.
A high-spec 835H model was selected by the company to join the working rigs at the site, which includes Kobelco excavators and Sennebogen material handlers.
The LiuGong loader works with a mesh screen to sieve dirt out of scrap metal collections before processing, while a large bucket with grab also assists to push up and tidy the scrap metal piles.
LiuGong wheel loaders are renowned for their build quality, featuring Cummins engines and German transmissions, simple operation, particularly in relation to their electrical systems, as well as their performance and comfort.
The turbocharged and air-to-air intercooled, six-cylinder, Stage III Cummins engines offer speeds up to 40 kilometres per hour, while
the countershaft, power shift transmissions provide four forward speeds and three reverse speeds.
The 160-horsepower 835H model at the Immix site at Wodonga offers a 7.9-tonne tipping load and has chalked-up about 600 hours.
Comfort, visibility and safety have been other major focus areas for LiuGong with its wheel loaders and this has been recognised by the Immix team.
The 835H model has 360-degree surround handrails and anti-slip steps, leading into an ergonomic, fully-pressurised cab with multi-
adjustable arm rest, joystick and air-suspension seat. Cabs are similar on all loaders, also featuring curved, panoramic glass windows.
Branch Manager Tim Karpeles, who joined the business about 18 months ago after working in the defence industry, said there was some initial hesitation from some of the company’s operators over jumping in a LiuGong loader, but this was short-lived.
“They are certainly happy to get behind the wheel,” Tim said.
The LiuGong wheel loaders also incorporate easy-to-access service points that allow for fast maintenance checks. Wide-opening engine hoods reveal the easy service points, while hydraulic hoses and air, diesel and oil filters can all be easily reached and quickly changed.
“We had to look into a few things with the setting up of the mesh screen and we rerouted some of the hydraulics to keep them out of the way, but otherwise we have had no issues and no complaints,” Tim said.
Immix purchased the wheel loader through Pacific Machinery Group and Tim said the dealer completed the 500-hour service and had provided good support with the machine. All other services are completed by the Immix team.
LiuGong’s high-spec wheel loaders offer a range of extra features in addition to the standard models, including reversing fans, variable hydraulic transmissions, radial tyres, ride control, rear view cameras, larger buckets on some models, air suspension seats and auto lubrication.
Tim said Immix was now considering further LiuGong machines to support a system for farm clean-ups it was hoping to progress into 2025.
The all-new CASE Minotaur DL550 is a groundbreaking addition to the construction equipment industry, establishing an entirely new category: the compact dozer loader.
This exceptional machine merges the robust performance of a dozer with the agility of a loader, creating a versatile and powerful tool designed to transform the job site.
The Minotaur DL550 stands out with its fully integrated C-frame, delivering genuine dozer capabilities along with the finesse and precision of a loader.
This unique combination ensures that the Minotaur can handle everything from heavyduty dozing to delicate fine grading with ease.
The addition of an industry-exclusive integrated ripper and compatibility with hundreds of attachments make this machine unrivalled in versatility and functionality.
At CASE Construction Equipment, innovation is driven by customer needs.
The Minotaur DL550 is a testament to this commitment, backed by 29 patents and over 10,000 hours of rigorous field testing.
The CASE team conducted multiple customer clinics and countless operator evaluations, continuously refining the product based on real-world feedback.
This exhaustive process ensures that the
Minotaur DL550 meets the highest standards of quality and performance.
The Minotaur DL550 is engineered to dominate the job site with its massive power and unrelenting hydraulics.
Whether ripping, dozing, or loading, this machine delivers unmatched productivity.
The intuitive controls and comfortable cab provide a seamless operating experience, whether you are in dozer or loader mode.
The Minotaur's fully chassis-integrated C-frame, equipped with the same blade featured on the CASE 650M dozer, boasts 25,826 pounds of drawbar pull.
This ensures smooth and eff icient dozing, while its impressive vertical lift path and 5500-pound rated operating capacity make it the ultimate site loader.
The CASE Minotaur DL550 represents a significant leap forward in construction equipment, embodying innovation, power, and a customer-centric design.
Transform your operations and elevate your productivity with this revolutionary compact dozer loader from CASE Construction Equipment.
Whether dozing or loading,
productivity.
MEET THE INDUSTRY FIRST MINOTAUR DL550.
GET IN TOUCH WITH YOUR LOCAL DEALER TO LEARN MORE ABOUT THE INNOVATIVE HYBRID DOZER LOADER AND ADD ANOTHER CASE TO THE FAMILY.
LEARN MORE
In Canada, FT Aggregates aims to produce highest quality aggregates on time, all the time. Helping the company achieve its ambitions are its trusty Rokbak RA30 and RA40 articulated haulers.
Sand and gravel producer FT Aggregates is a premium aggregates supplier to the Greater Edmonton area of Canada with a reputation for reliability and relatability.
To maintain this reputation, the Albertabased earthworks specialist relies on using the very best equipment, including articulated haulers from Scottish articulated hauler manufacturer Rokbak.
FT Aggregates produces over one million tonnes of sand and gravel every year.
A symbiotic relationship with Rokbak and local construction equipment dealership Headwater Equipment has formed a powerful team in this part of North America and aided FT Aggregates’ consistent service quality.
FT Aggregates has employed four RA40 articulated haulers since 2023 and added an RA30 to its fleet less than a year later.
FT Aggregates runs a highly eff icient operation and its Rokbak trucks must handle large volumes of material, essential for productivity and consistency of performance, with the trucks on maintenance plans to ensure minimal downtime.
Every RA40 moves between 100 and 120 loads and 5000 tonnes of material every day, five or six days a week, and the RA30 is an operator’s favourite for its comfort and surface handling.
FT Aggregates President Shane Smith said if the company’s operators had to pick a truck amongst the fleet to run on site, it would be a Rokbak truck.
“We’ve been very impressed by the fuel economy, the look and the comfort,” he said.
At FT Aggregates’ ‘Pit 23’, located south of central-Albertan city Camrose, excavators load overburden into the RA40’s all-welded body, which has a capacity of 38 tonnes (41.9 US tons).
Each RA40 at Pit 23 transports the overburden, sand and gravel material for production.
The truck's body is fabricated from highhardness steel with a 1000 MPa (145,000 lb/ in²) yield strength and features a dual-slope tail chute that facilitates material ejection.
FT Aggregates continues to test its Rokbak trucks, showcasing the ADTs’ reliability and performance under the extreme conditions of Western Canada. The company operates in harsh climates, from -40°C in winter to +35°C in summer, requiring robust equipment and flexible operations.
“The seasons are not kind,” Shane said. “And that means we’re probably one of the best places in the world to put trucks through their paces. We’ve found that the Rokbak trucks can be relied upon to operate effectively and efficiently, regardless of conditions.”
Fully automatic transmission ensures smooth gear shifting, reducing fuel consumption and
increasing operator comfort, even in tough environments.
The pressurised cab with HVAC offers enhanced control and comfort. Key features include excellent traction and a strong power-toweight ratio, ensuring fast material movement, maximising productivity while minimising costs.
FT Aggregates was formed when the Camrose area was identified as a major source of aggregates for Edmonton, the capital city of Alberta.
Beginning in the mid-2000s with just one crusher, one screener and one wheel loader, and a workforce made up of Shane and ‘just a couple of guys’, FT Aggregates has experienced substantial growth in recent times, doubling its staff in the last year from 25 to 50, employing 75 to 100 subcontractors and operating six pits across Alberta.
FT Aggregates plans sustained growth by adding new crushing and wash plants, aiming to strengthen its market position while maintaining the quality of personal customer interactions. The introduction of new plants has created employment opportunities in the local area, contributing to the community's economic development.
Rokbak Regional Sales Manager Greg Gerbus said being part of FT Aggregates’ success had been a privilege.
“Working with them and seeing their growth has significantly bolstered our own reputation and presence in the Canadian market,” he said. There have, of course, been challenges. The ‘Great Recession’ of 2008 to 2009 halved gravel prices and the effects and restrictions of the COVID pandemic caused the loss of almost half the sand and gravel producers in the province.
FT Aggregates, however, prevailed and are predicted to ship over one million tonnes of aggregate into the Greater Edmonton market in 2024.
“Our success has been down to establishing
teams to empower each other,” Shane said.
“Personal connection is vital to us. We’re always at the end of the telephone and it’s why Rokbak and Headwater Equipment are such a perfect fit. We’re not just a number to them. We drive one another, and the relationship always comes first.”
Close relationships are fundamental to FT Aggregates’ framework. It’s a real family affair.
Shane’s son Josh runs the operational side of the business, and his nephew Reuben is the production supervisor. Shane’s wife handles the HR, and his two daughters own the coffee shop at the landscape yard.
Differentiating itself from larger, more faceless competitors, this personal approach is a key aspect of FT Aggregates’ success and operational model.
FT Aggregates’ rapid growth is both a positive development and a challenge, as maintaining personal connections and being approachable despite size and market share increase is crucial.
“We pride ourselves on being able to turn on a dime and build whatever a customer is needing,” Shane said. “Each endeavour is with the intent of helping people. We’re able to respond very quickly to our customers’ needs.
“Our choice of partner has to fit in our operating system. We have an affinity for Rokbak in its similar position as a growing player in a big market.
“The support we have gained from both them and Headwater is incomparable. When I see how they can take care of us, it provides me with a sense of how our customers feel about our ability to take care of them. It’s synchronous.
“We’ve worked hard to establish a reputation of quality and dependability, and we identify these standards with Rokbak and Headwater also. The challenge for all of us is to maintain that individual relationship with our customers. But our greatest strength is the relationship we have with each other.”
ASV Posi-Track loaders have long set the standard in the construction industry, renowned for their comfort, versatility, and top-tier performance.
Expanding upon this legacy, ASV recently introduced the groundbreaking MAX–series VT-100 compact track loader into Australia, which has quickly turned heads with its range of tools that enable improved productivity and provides unmatched operator comfort.
The vertical-lift machines excel in loading and grading applications in landscaping and construction. While ASV MAX-Series models are purpose-built with the same technology as the brand’s full line-up of compact loaders, they also feature a brand-new, next-generation cab and same unique Posi-Track undercarriage technology for a premium operator experience like never before.
• Power A 103.5 horsepower Tier 4 Final Yanmar diesel engine and standard 151.4lpm high flow delivers maximum power.
Large line sizes, hydraulic coolers and directdrive pumps transfer more flow and pressure directly to the attachment and reduce power loss.
The VT-100 features a 1588kg rated operating capacity and 4536kg tipping load.
• Performance
Improve jobsite productivity with intuitive features that make the VT-100 easier – and more enjoyable – to use.
Pair that with ASV’s patented Posi-Track rubber-track suspension and suspended
wheels and axles, and faster speeds can be achieved.
It adds up to high travel speeds of up to 14.9km/h and a low 4.0 psi ground pressure for improved performance.
• Comfort
Premium 360-degree visibility and a stateof-the-art 7-inch colour display improve convenience on the jobsite.
The display provides vital monitoring tools, shows the view from the backup camera, and integrates with service schedules and history for added convenience.
The fully adjustable suspended seat and smooth ride allowed by ASV’s Posi-Track undercarriage contributes to more comfort on bumpy terrain. Additionally, the VT-100 includes optional ride control.
• Serviceability
ASV stands behind the reliability of its PosiTrack loaders with an industry-leading twoyear, 2000-hour warranty.
The warranty includes the industry’s first and only no-derailment guarantee and covers the tracks for the entire warranty period.
The new compact track loader also incorporates Yanmar’s optional SmartAssist telematics system with features ranging from error detection and notification to real-time operational status updates, daily work reports and integrated theft protection.
One delighted VT-100 user has been Donal Ryan, director of WA-based construction firm Ryano Civil and Plant.
“We run a few ASV Posi-Tracks,” he said.
“We were the first in WA to purchase a VT100, about three months ago, and have been
running it day and night and there have been no issues so far.
“It has great power and reach and is a very versatile machine. I don’t think anyone rivals the comfort of it on the market.
“We geared them up with GPS as well for our clients’ needs.
“We like the ASV brand, and the backup from the Perth branch is great. “
Good news for landclearing businesses is that ASV has also recently released a Forestry model in Australia which offers dedicated addons for heavy-duty forestry applications.
The machine is built to deliver forestrygrade performance in a 100hp compact track loader, including guarding that meets forestry safety standards to hydraulic flow rates and cooling capacities to keep up with demanding attachments.
The VT-100 Forestry model is engineered with extra durability to tackle demanding applications like mulching and site preparation.
Like the general VT-100, it prioritises enhanced comfort, visibility, and performance, solidifying ASV’s status as leaders in the compact track loader category.
The two new loaders are the perfect option for those looking for a little more size and power than the RT-75 but without needing the massive frame and capacity of ASV’s (and Australia’s) largest CTL, the RT-135.
Find out more about ASV’s all-new VT-100 and VT-100 Forestry Posi-Track loaders, plus the full range of 25 to 132 horsepower ASV machines, at www.asvaus.com.
Not only is the C12R a real step up for Anaconda, but it looks just as good as it performs. Image: Anaconda
Anaconda’s new flexible crusher provides solutions for mobile crushing applications that others don’t.
Anaconda Equipment specialises in designing, manufacturing, and providing a diverse range of products for the material handling sector.
The range includes crushers, screeners, scalpers, feeding conveyors, and mobile conveyors.
The business collaborates closely with customers and distributors to create cuttingedge, solution-oriented machinery.
Anaconda’s philosophy from the outset has always been to make life as easy for the end user as possible.
It released the new Anaconda C12R Recirc Cone recently at Hillhead 2024, the UK’s largest quarrying, construction and recycling exhibition.
It was a perfect venue to demonstrate the capabilities of this cone crusher, which is ideal for secondary and tertiary crushing applications.
This innovative machine is an extremely flexible crusher and provides solutions for mobile crushing applications that others don’t.
Anaconda National Sales Manager for Material Handling, Sam Powell, and our Product Support Manager for Crushing and Screening, Jason MacDonald, attended the event.
Cone Crushers are typically used as secondary and tertiary crushers. They are capable of handling a variety of materials, from tough and abrasive rocks to softer materials such as limestone and dolomite.
“The secret to maximising production with a cone crusher is ensuring the cone chamber is continuously kept choked, reduction ratios are kept as low as possible to ensure good shape and reducing bottle necks in the screening process, which is what the C12R is designed to do,” Jason said.
What sets the Anaconda C12R apart • Capabilities
The C12R Cone Crusher is an aggressive and powerful mobile cone crusher, boasting the proven ability of the FLSmidth Raptor 250 cone chamber within an innovative Anaconda Tracked Solution.
With an industry-leading 89mm throw within the crushing chamber, faster, more effective crushing can be made. A higher eccentric throw reduces crushing zones, leading to a quicker passage through the crusher. The faster the material passes through, the higher the capacity of the crusher.
To optimise this, the advanced control system offers users intuitive operation and precise adjustments, making it easy to optimise performance for different materials and output requirements.
The C12R utilises an extremely fuel eff icient and powerful hydraulic system which allows the machine to provide excellent levels of productivity but also the ability to create a fine, well-shaped product.
The feeder is fitted with an ultrasonic level sensor which dictates the speed of the feeder to continuously keep the chamber choke fed achieving optimum crushing productivity.
A cone crusher benefits from choke feeding as it ensures that the crushing chamber is consistently full, leading to more eff icient and effective crushing.
This practice helps to maintain a uniform particle size distribution, which can improve the quality of the final product.
Additionally, choke feeding minimises wear on the crusher components by reducing the amount
of stress and strain they endure, ultimately extending the lifespan of the machine. Properly managing the feed can also enhance the crusher's throughput, ensuring that operations run smoothly and eff iciently.
The C12R stands out from competitors with its unique dual 12x5 screen box.
Unlike many competitors that feature a single, often smaller screen box, the 12x5 is true to size on both decks. The screen box can often be the bottle neck in the cone crushing capabilities, however with the dual screen box you are doubling the screening capabilities.
With the dual screen box, the top deck can act as a relief deck, improving the screening of fines in the remaining material. This innovative design ensures a more eff icient separation process, reducing the load on the primary screen and extending its lifespan. Additionally, the dual screen box allows for a higher throughput, increasing overall productivity and minimising downtime.
The physical size of the C12R is substantial and with a quick set up time it is very impressive how quickly and easily the Cone can transition from transport, to operating, to optimising, to ultimately packing back up for transport. Moreover, the mobility of the C12 allows for seamless transitions between job sites, significantly reducing downtime and increasing overall productivity.
With safety and environmental considerations in mind, the C12 also incorporates dust suppression systems, ensuring that it not only performs exceptionally but also minimises its impact on employees and the surrounding environment.
• Versatility
The Anaconda C12R Cone Crusher offers a wide selection of liner options, including short and standard head configurations, with a range of CSS (Closed Side Settings) from 6mm to 45mm, catering to fine, medium, and coarse feed sizes. The standard head and short head configurations provide different crushing capabilities, with a minimum of 6 liner options available.
The crusher offers further versatility to suit the end user, with the quick release screen box which can be removed in around 15 minutes. Should the specifications dictate a bigger screen for more production this allows the crusher to work alone for higher or finer production with the use of a larger mobile screen like the Anaconda SR520.
The Anaconda C12R also features a Radial Recirculating Conveyor designed for both closed and open circuit operations. This allows the operator to either return the material to the crusher for further processing or to stockpile as a separate finished product. Enabling operators to meet a variety of specifications and create a high-quality final product using a single machine.
• Accessibility and serviceability
Unrivalled access from ground level for daily maintenance requirements ensures that all necessary tasks can be performed quickly and eff iciently.
This ease of access minimises downtime and boosts productivity by allowing maintenance teams to address issues promptly.
Additionally, the design prioritises safety,
reducing the risk of accidents and injuries during routine checks and repairs. Overall, this thoughtful approach to accessibility not only enhances operational eff iciency but also contributes to a safer and more sustainable working environment.
Key features of the Anaconda C12R
• It can be direct fed with a primary crusher, conveyor, wheel loader or excavator to suit almost any plant configuration
• Fitted with a Cat C9.3B diesel engine rated at 415hp
• Unrivalled access from ground level for daily maintenance requirements
• 6.3m³ feeder fitted with twin drive motors, hydraulic wing extensions, twin coil metal detector and feeder bridge, Hardox wear liners
• Ultrasonic level sensor with feeder start/stop
• Radio remote control for tracks and feeder operation
• Proven FLSmidth Raptor 250 Cone – Direct Drive system, industry leading 89mm throw for increased production
• Large variety of liner options including short and standard head configurations with range of CSS (Closed Side Settings from 6mm-45mm)
• Available with or without Dual 12x5 screen box
• 12x5 (2-deck) screen box allows for increased tonnages
• 3 way split with optional mids conveyor fitted
• Radial Recirc Conveyor for closed or open circuit operation
• Main conveyor discharge height 3.8m
• Work lights
• Dust suppression “The C12R is a real step up for Anaconda,
they’ve taken their usual engineering philosophies of 'Make it easy to run, make it easy to maintain' and added more than a pinch of design flair,” Sam said.
“The maintenance and engine access is ample and all at ground level; the Raptor 250 is a very hungry cone that will kick production goals, and not only is the 12x5 side tensioned screen box super productive, it’s extremely versatile.
“With just an Anaconda J12 Jaw and C12R Cone Crusher we can make up to fur products, simultaneously, in one pass – it’s a contractor’s dream.”
Anaconda Equipment is distributed by Onetrak in Australia. Onetrak’s national dealer network of service, sales and spare parts ensures all Anaconda customers are well supported nationally.
Onetrak partners with its customers and ensures the support extends past the initial purchase. From initial enquiry, Onetrak’s dedicated crushing and screening specialists can offer guidance and advice around what machinery will best suit the intended application.
At the time of delivery, Onetrak’s product specialists together with the service department will come to site to do a full commission of the new machine and ensure it’s all running at optimal levels so you can get the most out of your new investment.
Onetrak also offers flexible purchase solutions including Rent-To-Buy.
To learn more about Anaconda Equipment or to enquire visit www.onetrak.com.au.
Australian worksites will shine brighter than ever, thanks to Atlas Copco’s new BI+4 Lighting Towers, which have recently been released in the country.
The all-new HiLight BI+4 is an innovative and easy-to-use light tower that delivers energy-eff icient light coverage to help boost operational productivity, minimise environmental impact and meet stringent safety standards.
It’s the latest model in the HiLight range, which offers a wide variety of choices, so users can choose the right lighting tower for their application.
Atlas Copco supplies to a multiple range of industries with a flexible and dynamic approach
Each light tower has four floodlights providing 150W power per light head to reliably cover 4000m2 at 20 luxes, ensuring a brighter, safer and more productive sit. Image: CEA
to operations, addressing eff iciency and safety on site.
Operators can also be assured of the robust build quality and compact size for which Atlas Copco is globally recognised, as well as the company’s innovation stamp on LED technology.
The HiLight BI+4 incorporates state-of-theart surface mount device (SMD) LED lighting technology and lithium-ion batteries to provide excellent performance and eff iciency.
The lenses in the LED light towers have a
very special optic designed specifically for the toughest and most demanding conditions. This fully directional lens design means light coverage is maximised and “lighting waste” reduced.
Combining the use of batteries with a lowconsumption Stage V diesel engine, the new HiLight BI+ 4 offers users maximum flexibility as it has four operating modes: it can be powered directly from mains electricity, from its lithium-ion batteries, from its diesel engine, or from a hybrid setting to make the most of the energy available.
These hybrid light towers have a battery autonomy of six hours when operating at their full potential. And, when using their dimming function, they can provide up to 20 hours of silent and emission-free operation with a single charge.
With a battery recharging time of just four hours, the HiLight BI+ 4 can also feature an external power plug as an option.
Introducing the ability to use batteries reduces the use of the engine, which extends the unit’s lifetime and results in a temporary lighting solution with a low Total Cost of Ownership (TCO).
With a 60 per cent reduction in engine runtime, service intervals are three times longer than light towers that run solely on diesel.
The HiLight BI+ 4 requires minimal maintenance every 1500 hours of lighting, so users can save on costs associated with servicing.
The flexible temporary lighting solution features highly eff icient SMD LED floodlights.
Each light tower has four floodlights each providing 150W power to reliably cover 4000m2 with an average of 20 luxes of brightness, ensuring a brighter, safer and more productive site, extending the working days and contributing towards a safe working environment.
Operators at construction sites, events, mines, emergency applications and rental companies will be able to reduce their carbon footprint and operating costs while improving sustainability levels – both environmentally and in business. Thanks to the incorporation of a battery, operators can reduce up to seven tonnes of CO2 per unit, per year, compared to traditional diesel-powered light towers.
By optimising their energy consumption, users can reduce their environmental impact and improve their profitability considerably.
For more information, visit www.atlascea.com.au.
Businesses needing a powerhouse of a telehandler suited for intensive work should look no further than Dieci’s Samson 70.10.
When it comes to telehandlers, the Dieci name stands as tall as the heights attained by its renowned range of hydraulic lifting units.
The machines, with lift heights from 5.8 to 25 metres and in a range of sizes from 2.5 to 23 tonnes, are a common sight on many building worksites around the world.
The Italian company’s dedicated construction telehandlers have been made specifically for the sector: machines which are designed to handle, transport and lift both loads and people.
Available with or without rotating turrets, Dieci’s versatile telehandlers can easily replace forklift trucks and cranes in the workplace. Indeed, they have the ability to reach higher and further due to the telescopic booms, with their lateral positioning enabling greater visibility.
The telehandlers are robust and easily manoeuvrable in confined spaces, thanks to the use of two steering axles, making them suitable for performing multiple jobs. Whether it’s for the smallest yard or biggest construction site, there is a Dieci telehandler that can do the job.
One particular model that has been proving
popular for heavy-duty applications has been Dieci’s mighty Samson 70.10 fixed telehandler.
Inspired by the legendary warrior of prodigious strength, the extremely robust and strong model delivers outstanding power and lifting capacity, making it particularly suitable for intensive work, both in the construction and industrial sectors.
The Samson 70.10 is so named because it has a maximum lifting capacity of 7000 kg, making it suitable for handling large and heavy loads, and a maximum lifting height of 9.65 metres, enabling operators to reach significant elevations with ease.
It comes with many other features that make the machine a joy to operate, including excellent handling, precision movement control, sound proofing for absolute comfort, three steering modes including 2WS, 4WS and crab steering, along with an intelligently designed control layout, making it simple, intuitive and comfortable to use.
As well, maintenance is straightforward, with durable components and materials designed to last.
The agile and versatile machine is designed for projects where strength and speed are
essential features to achieve maximum productivity, and there’s a need to handle large volumes and reduce work cycles.
In the field of construction, whether the job involves new buildings, roofs, coverings or renovations and restorations, the Samson is at home with its strength and ease of use in different environments and situations.
Thanks to the available accessories to Dieci products — such as forks, buckets, lifting hooks, baskets, winches, and jib cranes with hooks — the telehandler can act as an elevating work platform, and when fitted with a bucket it can easily handle aggregates such as gravel, earth and bricks.
Of course, the telehandler is versatile enough to be employed in various construction projects beyond traditional building tasks, for example setting up large temporary structures like event stands, concert stages, and amusement park stands.
The Samson has also demonstrated its usefulness in renovation, maintenance, restoration and conservative refurbishment projects, where unforeseen challenges frequently arise and diff icult to anticipate during the design phase.
The machine’s adaptability, coupled with the versatility offered by the various accessories, equips construction firms with the necessary tools to address industrial and construction requirements effectively.
You’ll also find the Samson and other Dieci telehandlers employed in ports and airports for tasks such as handling airplanes during routine maintenance, or transporting materials from depots to the docks for embarkation.
Features in focus
The Samson 70.10 reflects the characteristics of Dieci products and their hallmarks of technology, reliability and durability. Let’s take a closer look at some of the features.
• Advanced telescopic boom
The reinforced boom is made of high resistance steel with load sensing and flow sharing distributors that offer simultaneous movements for more eff icient work.
• 4-in-1 joystick
The boom can be fully operated by the hydraulic control distributor-single joystick with proportional and simultaneous controls, which also incorporates Forward-NeutralReverse functionality for easier and more practical direction control.
• Perfect climate
Equipped with an integrated electric driver’s window, standard heater and a semiautomatic air conditioning system with six outlet vents, this set-up allows perfect air circulation inside the cabin for maximum operator comfort.
• Powerful and stable
Whether the boom is retracted or extended, the Samson remains an extremely rugged machine with exceptional loading capacities in all operating conditions: a transversal levelling device keeps the chassis in a horizontal position, even on uneven ground.
The 70.10 boasts a maximum lifting height of 9.65 metres, enabling operators to reach significant elevations with ease.
• Maximum safety
The ROPS-FOPS approved cab is designed with a safety cell to provide maximum safety to the operator at all times. All Dieci telehandlers comply with AS1418.19 / 10896.1.
A deadman sensor, combined with operator presence sensor in the seat, prevents accidental operation.
As well, the load limiter device analyses vehicle stability in real time and inhibits any aggravating movements when the pre-set safety limits are reached.
• Side shift carriage
The machine is equipped with a side shift carriage, making it an effortless task to reposition and stack loads tightly.
• Single compensation cylinder
Patented by Dieci, this component, located
With a maximum lifting capacity of 7000 kg, the machine for handles large and heavy loads with ease.
inside the lifting ram, ensures that the load on the boom is balanced at all times, thereby improving durability.
• Inching pedal Speeding up, slowing down or stopping momentarily is carried out by this essential control, which still offers maximum power to boom functions to increase precision and productivity for delicate operations.
• Hydrostatic transmission
The servo-controlled two-speed gear box and constantly varying hydrostatic drive guarantees top end speed and low end torque. The 130 l/min hydraulic flow maximises manoeuvrability in all applications.
• Panoramic views
Inside the cab, large, curved windows offer a complete 360° outside view with uninterrupted visibility.
• Angle rotation
The 134° fork swivelling capability is specially designed to increase the operating arc, particularly useful when unloading with the boom raised.
• Reversible fan
Operators can work in a dust-free environment, with the engine cooling system utilising a reversible fan that blows any dust and fibres away from the radiator.
• Comfort and ease of access
The Samson’s spacious cab has been designed for operator comfort and ergonomics, adjustable steering wheel (height and depth), air suspension seat and storage compartments.
To have a closer look at the Samson 70.10, call 1300 888 479, or visit www.dieciaustralia.com.au
Toolkwip manufactures Flo-Kwip
The name of Toolkwip Pumps has become synonymous with providing pumping solutions that are … simply better!
Since 1993, Toolkwip Pumps has emerged as a leading force in pump, water treatment, and related fluid control equipment, with a diverse clientele spanning the Australian industrial, civil construction, quarry, and mining sectors.
With a wide range of high-quality industrial pumps and equipment and a strong emphasis on customer service, it has established itself as a reliable source for all pumping needs.
Its comprehensive services include everything from initial consultations and advice regarding the most suitable equipment for site requirements, through to installation, ongoing technical support, and the provision of service technicians for regular pump maintenance.
As well, the family-owned and operated company is renowned for its ability to customise solutions to better meet clients' needs.
With off ices in Melbourne and throughout NSW, Toolkwip expanded to Queensland in 2023, a branch that celebrated its first anniversary in September.
Toolkwip’s dedicated team of industry experts boasts more than 30 years of collective industry knowledge and is committed to delivering superior service and support.
• Suction hoses
Suction hoses are an essential component in the management of water.
Toolkwip stocks a range of suction hoses available in different materials in standard sizes and lengths which can be cut for specific requirements.
Selecting the right suction hose is crucial to ensure optimal performance and longevity of the pumping system.
• Pipe floats
The stock of pipe floats are designed and engineered for a wide range of applications, including quarry, mining, dredging and marine and come in various sizes to fit pipes from 10mm-650mm.
• Pumps
When water or sludge needs to be removed from trenches, footings or other site preparation works, Toolkwip provides environmentallyfriendly, eff icient and reliable equipment that is essential to complete the task.
Whether it’s a basic trench or footings that need pumping out with a small electric submersible pump or a flex-drive submersible pump, through to large wellpoint dewatering projects and river diversions, the company provides it all.
A large range of dewatering, submersible, bypass pumps is available, with popular brands including:
• Selwood auto-prime pump sets
• Flo-Kwip trash pumps and submersible pumps
• Hydra-Tech Hydraulic submersible pumps
• Sulzer submersible dewatering pumps
• Tsurumi submersible pumps
• Flextool flex-drive pumps and drive units
Toolkwip Pumps is the authorised distributor of the complete range of Selwood Pumps across Vic, NSW, Qld, SA and Tasmania, and maintains a full inventory of pumps and parts for the leading UK brand.
The Selwood range of Super Silent Pump units are ranked the quietest pumps on the market, based on the EU directive 2000/14/EC.
Selwood super silent canopies significantly reduce noise for the comfort and safety of workers and the public in projects near urban and residential areas. They are engineered to a high technical standard, complete with
silencers and protective enclosures, and incorporate world-leading sound attenuation on both diesel and electric motors.
Toolkwip Pumps also manufactures Flo-Kwip Pumping Solutions, the preferred pumps of construction, rental, drainage and electroplating companies.
The range of pumps are built for Australia’s toughest sectors: construction, mining and quarry.
• Layflat
Toolkwip stocks a range of Layflat hoses in several different grades, each with a different pressure rating and wear life.
Lengths of 20 metres are standard or can be supplied up to 200 metres and fitted with a range of couplings, including camlocks, Bauers, and flanges. They range in size from 25mm through to 900mm.
• Road ramps
Flo-Kwip road ramps are designed to provide safe transfer of pumped water across roadways and footpaths, safely and with minimal disruption to traff ic flow.
Designed for minimal water friction losses, they boast dedicated load-rated lifting points and hold-down/retention points.
With customisable flange sizes, they are easy and fast to install, are transportable and stackable, and are available with 4”, 6” or 8” connections.
• Standpipes
Custom-designed and engineered to meet the harsh demands of the Australian environment, the high quality standpipes are designed for reliability and eff iciency in water transfer and are an essential piece of equipment for water supply.
Available with engineer certification, these
standpipes are available in 4”, 6” and 8” pipe sizes and are in a range of heights to suit different water carts.
The standpipes are also collapsible for ease of relocation and transport and available with forklift lifting channels.
The range has painted/hot dip galvanised or poly options and comes standard with layflat hose on discharge.
Toolkwip Pumps prides itself on after-sales service, providing on-site and in-workshop repairs, and service for customers – ensuring minimal downtime and higher productivity.
But many customers are unaware of Toolkwip's breadth of services, which extend beyond supply. The company’s repertoire also includes comprehensive services for pump repair, servicing, and rebuilding, highlighting its versatility and dedication to customer satisfaction.
Toolkwip fully understands the multitude of challenges posed by pump downtime. It's not merely a temporary pause in operations – it’s a disruption that resonates throughout a project, leading to missed deadlines, distracted staff, unhappy customers, and potentially severe financial implications. More crucially, it can sometimes cause flooding issues on the site, leading to costly and time-consuming clean-up operations.
With in-depth industry knowledge and extensive experience, Toolkwip is placed in a prime position to offer services to eff iciently counter these downtime challenges. The
company is committed to helping customers maintain uninterrupted operations by providing rapid and reliable services that keep the pumps working at their optimal capacity.
Toolkwip is not just about fixing pumps; it's about providing comprehensive solutions that cover every aspect of pump operation. These services include design and fabrication of pumprelated equipment, troubleshooting of pump systems and pipework, noise and vibration analysis, servicing and rebuilding of diesel engines, and providing electrical services.
By offering a wide range of services, Toolkwip positions itself as a one-stop-shop for all pump-
related needs, ensuring customers need not engage multiple businesses for different tasks. This holistic approach streamlines operations, cuts down on administrative hassles, and ultimately, saves time and money for the customer.
What’s more, Toolkwip champions a proactive approach to equipment management.
It promotes the routine maintenance of pumps to prevent breakdowns and ensure reliable and eff icient operations. By identifying potential issues before they escalate into major problems, Toolkwip helps to reduce downtime and associated costs.
JMP Excavations values the fuel e iciency of machines like the PR 716 G8 dozer. Images: JMP Excavations
A range of Liebherr machines has helped Sydney-based JMP Excavations establish itself as a sought-after business in the plant hire sector.
For the past few years, Sydney-based JMP Excavations has built up a reputation for providing a wide range of quality wet and dry hire equipment for earthworks projects of all types.
The range of equipment is comprehensive, including dozers, drotts, excavators, tipper trucks, and dump trucks, enough to meet all earthmoving and commercial excavation needs.
And of the machinery in JMP’s arsenal, the majority comes from the Liebherr factory: a testament indeed to the quality of the products made by the German company.
Earthmoving Equipment Magazine caught up with JMP director Jerry Phillips to chat about the appeal of the Liebherr products and why they hold a special place in the fleet.
“We specialise in plant hire and cover pretty much the whole of NSW,” Jerry said.
“We try to stay local as much as possible, but we'll go where the work is, we don't discriminate on who we service.
“So we do jobs for local mums and dads who maybe want a motocross track built for their son or daughter, for example, to a lot of the
bigger guys doing the big subdivisions in the area.
“We do a lot of Tier 1 work, a lot of rail projects. We have supplied equipment for the Western Sydney airport project, and we’ve been there for about 18 months now.
“We're doing all the finished work along the runway, landscape preparation and stuff like that. At the busiest stage, we had five machines on that job and now there are two remaining there as it starts to wind up.”
To provide quality service and continued support from clients, Jerry said it was crucial to use equipment that performed to highest expectations and that didn’t malfunction.
“It's imperative as the business continues to grow,” he said.
“In the beginning, we had a lot of small, older equipment which broke down a lot, causing us stress and costing us a lot of money.
“As well, we were letting down our clients, who need eff icient machines to be able to meet their deadlines.”
Then the fateful day came when Jerry was introduced to a Liebherr track loader: the LR 614.
“This was a purely opportunity-based purchase, as at the time there were no other drotts for sale. I had been operating one for a friend on weekends and I really liked it,”
Jerry said.
“He off ered it to me and I quickly snapped it up.”
The LR 614 is part of Liebherr G4 crawler loaders, and quickly proved itself at JMP for its power, agility and innovation.
But what also swayed Jerry to Liebherr was the quality of service that he received.
“Liebherr really looked after us. The service was unreal,” he said.
“As it was an old machine, it was out of warranty. And we didn't have an account with them or anything, but they chatted with us and helped service the equipment when it was needed.
“And then so when it came time to buy another machine, we didn't even look anywhere else.”
JMP moved on next to an LR 624. “That was a great machine. At that time, we needed a bigger machine,” Jerry said.
“Again, it was a used machine and out of
warranty, but Liebherr looked after us.
“So then, as the business grew and started looking at dozers and newer equipment, there was only one brand we wanted.”
Currently, JMP boasts seven Liebherrs for hire, a mix of loaders, dozers, diggers and trucks.
“We've still got the LR 614, which is currently undergoing a complete rebuild. That's got 16,000 hours and still going strong,” he said. “We have a Generation 8 LR 626 loader to complement it.
“The three dozers are the PR 716, 726 and 736 models, and they’re just absolutely fantastic performers. We're currently considering pulling the trigger for a PR 756, which is like a D8 equivalent.
“On the excavator front, we have the 14-tonne R 914, which features a powerful diesel engine and particularly high break-out forces. It is a very, very good machine and very reliable.
“Then we've got the TA 230 30-tonne dump truck, known as the Rolls Royce of dump trucks.”
Jerry said apart from the service, there were several other factors which attracted him to Liebherr machines.
“Their price is always pretty good. Obviously they look after us fairly well on the price at the minute, as we spent a lot of money with them,” he said.
“They obviously know that they've got that commitment from me for their brand. The relationship that we have is very good. “But the standout thing for me is the fuel
efficiency of the machines.
“In the PR 736 dozer for example, at full tilt it's usually using like 18 litres an hour, which is 180 litres in a 10-hour day. That’s like running on air.
“Many other brands don't even come close to the fuel efficiency, which in turn obviously helps our bottom line, as much as it does the environment.
“It also lets us tender competitively for jobs because with better fuel efficiency, our rates can be lower.”
Then of course there are the basic operations of the machines themselves.
“The operability and hydrostatic operations: they’re very smooth to operate. Very powerful,” he said.
“And the comfort is unmatched. You put anyone in a Liebherr cabin and they're all going to say the same thing about the operator comfort.
“It's just on point there. Liebherr definitely nailed it with the comfort.”
Jerry said he communicated regularly with Liebherr’s Earthmoving and Material Handling division.
“I chat with them pretty much daily, even if it's just to chinwag,” he said.
“The Liebherr sales manager Tommy Matijasko is great and very approachable,” he said
“If we have a problem, we'll bring it to his attention. He’s always got our backs. There's always that support there.
“He makes sure they always do the right thing. If we experience a breakdown or require replacement parts, we simply contact Tommy,
and the Liebherr team will address the issue immediately.
“If a machine fails during lunchtime, it is almost certain that it will be repaired by the following morning.
“Liebherr is highly proactive in evaluating available parts and ensuring that machinery is quickly restored to optimal function.
“The best thing with me there is that they completely understand that when it comes to my business, if we're not working, we are not making money.
“Liebherr is very proactive with getting things sorted.
“I’m very happy with them and we’ll continue to be back for more machines in the future.”
For more information: visit www.liebherr.com.au
LR 626 G8 Litronic crawler loader
Operating weight: 16,460-19,360 kg
Bucket capacity: 1.50-1.80 m³
Emission stage: Tier 4f
Engine output (ISO 9249): 110 kW/150 hp
Engine output (SAE J1349): 110 kW/147 hp
Travel speed: 0.00-10.00 km/h
PR 716 G8 crawler tractor
Operating weight: 13,300-15,800 kg
Blade capacity: 2.92-3.30 m³
Emission stage: Tier 4f
Engine output (ISO 9249): 97 kW/132 hp
Engine output (SAE J1349): 97 kW/130 hp
Travel speed: 10.00 km/h
PR 726 G8 crawler tractor
Operating weight: 17,500-20,800 kg
Blade capacity: 3.33-3.87 m³
Emission stage: Tier 4f
Engine output (ISO 9249): 125 kW/170 hp
Engine output (SAE J1349): 125 kW/168 hp
Travel speed: 11.00 km/h
PR 736 G8 crawler tractor
Operating weight: 21,200-25,500 kg
Blade capacity: 4.10-5.56 m³
Emission stage: Tier 4f
Engine output (ISO 9249): 160 kW/217 hp
Engine output (SAE J1349): 160 kW/214 hp
Travel speed: 11.00 km/h
TA 230 Litronic G8 dump truck
Empty vehicle weight: 24,600 kg
Payload: 28,000 kg
Max. dump body capacity: 18.10 m³
Emission stage: Tier 4f
Engine output (ISO 9249): 265 kW/360 hp
Travel speed forward: 57.00 km/h
Travel speed backward: 16.00 km/h
R 914 G6 Compact Litronic
Operating weight: 14,750-16,750 kg
Backhoe bucket capacity: 0.32-0.80 m³
Tail radius: 1550 mm
Emission stage: Tier 4f
Engine output (ISO 9249): 90 kW/122 hp
Standing out among the impressive range of machinery on display at McIntosh & Son’s Perth branch are the glistening green giants of Merlo: not just for their colour, but also for their performance.
Anyone driving along Great Eastern Highway in the Perth suburb of Redcliffe can’t miss it: a veritable smorgasbord of the latest releases from various leading brands, on full display in the yards of McIntosh & Son.
One of WA’s biggest machinery dealers, the company was established in the agricultural town of Wongan Hills in 1955, growing to be a leading Australian dealership group specialising in agricultural, construction and grounds care machinery, incorporating sales, finance, service and parts.
With 11 dealerships strategically located across WA and one in Dalby, Queensland, McIntosh & Son provides a complete solution for the market – comprising new and used machinery sales, precision farming, finance solutions, spare parts, and qualified mobile field and workshop service.
General Manager Mike Foskett said McIntosh & Son’s aim was to build a continuously improving stable of products and services to help customers achieve their productivity and financial objectives.
“In turn, this will drive our business and create opportunities for employee growth, resulting in
recognition both as an industry employer and an equipment supplier of choice,” he said.
The Perth branch has an enviable rolling stock of machinery to cater for customer needs, and currently focuses on construction and grounds care equipment, supporting a portfolio of 11 machinery brands, including Merlo, New Holland, CASE Construction Equipment, LiuGong, Jacobsen and Redexim.
These are in addition to a long line of consumables that the branch supplies via its parts department that include STEDI, GME radios, Omicron and SafeStyle.
Mike said the Merlos were definitely a standout, and not just for the iconic bright green colours.
The Italian company is of course renowned for its innovative and high-quality machinery and equipment, particularly in the construction, agriculture, and industrial sectors, notably establishing itself as a leader in the design and manufacture of telescopic handlers, concrete mixers, and other heavy machinery.
“We look for equipment that is proven and performs well in Australian conditions, and in this regard, Merlo ticks all the boxes,” he said.
“Also the relationship with Merlo is fantastic. It’s always good in a dealer-supplier relationship for it to be positive and collaborative. It makes everyone’s job a lot easier.
“What’s important for us is being able to sell the product with confidence knowing that the dealer-supplier relationship is healthy.
“We get good support from Merlo Australia. The relationship is positive and we’ve got a really collaborative approach with them.
“We are able to support our customers and they’ve got confidence that we can back them up. It has really made a difference in McIntosh & Son being able to grow Merlo market share in our area.”
Mike said that the beauty of the Merlo offering was that there were plenty of options to suit what people wanted in terms of different needs.
“They definitely have some features and benefits that add value for customers, but also the support we offer makes a difference,” he said.
Mike said one of the best sellers was Merlo’s most unique product, the Multifarmer, which combines the dual benefits of a telehandler and tractor.
“Two Multifarmer models are imported to Australia – the MF44.7 and MF44.9,” he said.
“Both models offer a 4400kg maximum load capacity and maximum reach of 1.7m while at capacity.
“The MF44.9 has an increased lift height of 8.8m, compared to 6.8m on the MF44.7, plus has a greater overall maximum reach of 5.8m, compared to 3.6m on the MF44.7.”
To service the large number of Merlo customers, McIntosh & Son provides an experienced product specialist is dedicated to Merlo products, while also maintaining a workshop exclusively devoted to the brand.
“Our product specialist has been working
with Merlo products for over 30 years, and while our all of our sales team have access to supply the Merlo range, we believe it is important to have a dedicated product specialist, as his depth and breadth of knowledge is invaluable both internally and to our customers.”
The Multifarmer in focus
The versatile and innovative hybrid Multifarmer was developed by Merlo to meet the diverse needs of operators who required a machine capable of performing multiple roles. It is commonly used for:
• Material handling: Lifting, transporting, and stacking various materials
• Earthmoving and farming work: Performing tasks such as ploughing, harrowing, and seeding using traditional tractor implements
• Livestock management: Feeding livestock, cleaning out pens, and other tasks that involve heavy lifting
• General maintenance: Towing trailers, clearing paths, and performing maintenance tasks
By merging the lifting and loading capabilities of a telehandler with the power and versatility of a tractor, the Multifarmer offers several advantages, including:
• Cost eff iciency: Combining the functions of multiple machines into one means the Multifarmer reduces the need for additional equipment, leading to lower overall costs
• Space-saving: Where there is limited space, the Multifarmer’s ability to perform multiple tasks helps reduce clutter and the need for storing multiple machines
• Increased productivity: With the Multifarmer, users can switch between tasks quickly and easily, increasing overall productivity.
Like other Merlo telehandlers, the Multifarmer is equipped with a telescopic boom that can extend to lift and place loads at height.
This boom is highly manoeuvrable, providing the reach and flexibility needed for a myriad of tasks.
For farmers, the Multifarmer features a standard rear three-point linkage and PTO (Power Take-Off ) system, which allows it to operate a wide variety of agricultural implements, such as mowers, tillers, and seeders. This makes it suitable for fieldwork and other tractor-based operations, adding to its versatility on the farm.
The machine is built to handle heavy loads, with impressive payload and lifting capacities. This makes it ideal for tasks that require moving large quantities of materials, such
as loading silage, transporting hay bales, or handling bulk feed.
And because Merlo places a strong emphasis on operator comfort and safety, the Multifarmer is equipped with a spacious, ergonomic cab featuring climate control, excellent visibility, and intuitive controls.
Importantly, the model is powered by fueleff icient engines that comply with the latest emission standards, offering a balance of power and economy.
This ensures that the machine can perform demanding tasks while minimising fuel consumption and environmental impact.
For more information on the Merlo Multifarmers, visit: https://www.merlo. com/aus/en/p/telehandlers/multifarmer/
UHI bulldozers and graders are versatile heavy construction machines made for precise grading tasks.
Bulldozers and motor graders usually lead the effort when the job is moving mountains of material, preparing sites and performing final trimming on roads, sports fields, car parks and infrastructure.
UHI bulldozers are engineered for tasks such as grading surfaces to prepare building sites, roads, or repair landscapes.
Designed to push large volumes of material and remove obstacles such as trees, rocks, and brush, they are equipped with powerful tracks and a robust blade.
Manufactured in a world-class manufacturing facility, UHI special edition bulldozers are custom-designed and tailored specifically for the Australian working environment.
The latest models feature a “SHIG Golden Powertrain” for more power, enhanced reliability and better fuel economy.
Power for the UHI bulldozer range comes from their turbocharged direct injection Weichai WP4 engines.
A new and eff icient Linde electronic controlled hydrostatic transmission system (HST) consists of dual-path closed circuits with variable displacement piston pumps and travel motors.
This allows for quick shift or variable speed selection.
UHI bulldozers are made from a thick box section material and other components provide increased rigidity and strength.
Improved durability comes from a highrigidity simple main frame structure combined with thick plates and steel castings.
A palm command control system (PCCS) provides fully automatic shifting and enables smooth machine control.
The UHI bulldozers have long track-onground contact with six track rollers that improve machine stability, grading and dozing performance.
The productivity of these bulldozers is enhanced by their constantly variable speed and 360-degree counter-rotation turn.
The bulldozers feature a “SHIG Golden Powertrain” for more power, enhanced reliability and better fuel economy.
The rugged and well-engineered graders are suited to the most demanding construction tasks. Images: UHI
Hydrostatic steering removes the need for steering clutches and brakes, providing smooth and powerful turns.
A multi-function monitor provides status of the machine as well as self-diagnostic information and a maintenance reminder. Operators will appreciate the comfortable airconditioned cab that’s equipped with the added convenience of front and side sunshades, a USB charging port, radio and fan.
All UHI bulldozers have a draw bar as standard and optional attachments are available, such as a multi shank ripper used for breaking ground.
Daily maintenance access is convenient, with ground level access to the engine and the centralized hydraulic pressure testing location.
All models are fitted with a tilt blade and a rear ripper. UHI bulldozers have a three year or 5000-hour full warranty and a 10,000-hour warranty on engine parts.
Models available are:
• UHI-DH13: 141hp rated power 13.4-tonne
• UHI-DH17: 188hp rated power 18-tonne
• UHI-DH24: 248hp rated power 23.8-tonne
UHI motor graders
UHI special edition motor graders will satisfy the scrutiny of the most critical and experienced operators.
These rugged and well-engineered machines are a great solution for contractors who work on demanding road construction and maintenance, shaping ditches, helping to manage drainage and erosion.
They are manufactured in a world-class facility and are custom-designed and tailored specifically for the Australian working environment.
The range of UHI motor graders is designed with external ground-level accessible lubrication points and a centralized pressure testing system.
Additionally, all oil filters are externally accessible.
Operators will welcome the cabin’s comfortable mechanical suspension seat, as well as the cab design that cuts the A-pillar and presents an expansive 320-degree wide field of vision.
An electronic control handle contributes to a more comfortable and convenient operating experience.
The UHI special edition motor grader range offers the flexibility to be fitted with a selection of attachments, including the standard front mouldboard and rear ripper which enables the machines to meet construction requirements across diverse working conditions such as leveling, trenching, scraping and stripping. UHI motor grader models are available in popular capacities: All UHI motor graders have a full three-year or 5,000- hour full warranty.
• SG15: 150hp Cummins Engine 13-tonne
• SG17: 170hp Cummins Engine 14.8-tonne
• SG19: 190hp Cummins Engine 16-tonne
• G21: 215hp Cummins Engine 17-tonne
For further information on the range of heavy duty UHI bulldozers and motor graders, visit https://www. unitedheavyindustries.com.au/
Putting in place a water management strategy for a big mining project is no easy task; so the call went out to Pinnacle Hire.
Pinnacle Hire has made a name for itself as an agile hire business focused on providing advanced dewatering, pumping and water treatment solutions to the infrastructure, civil construction, mining and quarry sectors.
Among its most recent successes has been a major expansion assignment in the Pilbara region of Western Australia.
A mine site in the area had embarked on a significant project to establish a new run-ofmine pad and primary crushing facility, which required extensive water management solutions to sustain high-grade iron ore processing.
Pinnacle Hire, renowned for its water treatment expertise, was selected to tackle this challenge.
Pinnacle Senior Dewatering Engineer Myles Martin explained that the customer processed 25 million tonnes per annum (Mtpa) of highgrade iron ore.
“The site includes various critical infrastructure elements like an Overland Conveyor (OLC),
Heavy Vehicle (HV) and Light Vehicle (LV) roads, and a construction village,” he said.
“To sustain and enhance its operations, our customer required a reliable and eff icient water management system to support its bulk earthworks and other construction activities.”
The primary challenge for the Pilbara project was ensuring a consistent and adequate water supply for construction purposes, particularly for bulk earthworks.
The project required about 1.9 million kilolitres of water over its duration, with peak daily demands reaching 7-8m litres.
The site also needed robust infrastructure to manage water quality and distribution, critical for pavement construction and dust suppression.
Myles said that Pinnacle Hire provided a comprehensive water management solution, including state-of-the-art equipment and expertise.
Key components of the solution included:
• Bore pumps: Supply, install and maintenance of three bore pump packages (2xSP46-10 and SP30-13) and mine spec generators.
• Diesel centrifugal pump: Supply, install and maintenance of the 80/180 diesel centrifugal pump.
• HDPE pipeline: Supply and installation of approximately 12km of HDPE pipeline.
• Automated pump control: All pumps were set to start/stop automatically based on turkey’s nest (dam) water levels.
“Upon mobilisation, Pinnacle Hire swiftly established temporary water infrastructure and integration into already existing overhead tanks and turkey’s nests for water storage,” he said.
“The Pinnacle team installed bore pumps and tied them into existing water bore infrastructure, ensuring seamless water extraction and distribution.
“The setup included multiple turkey’s nests
with capacities ranging from 3-4m litres, supported by an intricate network of HDPE piping and booster pumps.”
The implementation of Pinnacle Hire’s solutions led to significant improvements:
• Reliable water supply meeting peak demand rates of up to 110 litres per second.
• Enhanced water quality suitable for various construction purposes, ensuring compliance with environmental standards.
• Eff icient distribution and usage tracking through installed flow meters, ensuring optimal resource management.
• Automated pump operations based on turkey’s nest water levels, ensuring eff icient and responsive water management.
Myles said the company’s knowledgeable staff were passionate about providing rapid responses coupled with ‘higher levels of expertise’, ensuring customers can get access to the most fit-for-purpose equipment, when and where they need it.
Pinnacle brings to the market a selection of brand-new state-of-the-art equipment, including nationally and internationally
recognised brands such as Selwood from the UK, BBA Pumps from the Netherlands, Tsurumi from Japan, Sulzer from Switzerland, Grindex and Atlas-Copco from Sweden, as well as Fortress Tanks and Elementz Treatment Plants from Australia.
“We also bring the advanced range of EnviroHub Water Treatment products and system from the UK for the first time,” Myles said.
Pinnacle Hire took flight in early 2021, with the goal of building a highly professional, nationwide hire business, supporting responsible management of water when it needs to be treated, stored or relocated.
Integral to that plan was the need to draw together the skills and resources of team of industry specialist who shared a passion for the journey ahead.
“Pinnacle has built a structure to remain nimble and flexible in our ability to deliver,” Myles said.
“We’ve also invested in a formidable new fleet of pumps and treatment equipment that is the envy of the industry.
“This has enabled us to grow from just a single location based in Victoria, to 13 locations in six states.
“We’ve also successfully delivered thousands
of projects to our core customers as well as providing substantial pumping power during flood events in Victoria and NSW.
“We also fully understand the dynamic nature of your Industry, the daily pressures and the high standards required to get the job done safety, securely and effectively.
“So, we leave no stone unturned to provide you the most ‘fit-for-purpose’ solution for each and every project, no matter how large or small.
“We’ve also build strong relationships with our nationally and internationally recognised equipment suppliers, allowing us to offer you the very cream of crop.
“And when your equipment arrives on site we are there every step of the way, with full support and backup to help you meet your project goals.”
Contact Pinnacle Hire today to discuss your specific requirements and discover how its innovative solutions can optimise your operations.
Phone 1300 447 392 or email hire@pinnaclehire.com.au
Tigercat’s new 6900 Grinder is a robust upswing model grinder, designed for e icient material reduction and mulch production with high throughput capacity.
Equipped with a powerful Cat C32 engine and aggressive teeth on the top roller, Tigercat's new 6900 Grinder can handle a wide variety of materials, from logs, tree limbs and brush, to waste material and more.
The grinder's durable construction ensures longevity and reliable performance even in the most demanding conditions.
Operators will appreciate the intuitive control panel, which offers straightforward operation and easy adjustments to optimise processing eff iciency.
The machine features remote control capabilities and a user-friendly 25cm (10 in) display screen for monitoring the machine and adjusting its functions, for easy operation and on-site mobility.
Tigercat’s 6900 Grinder has a built-in service mode that allows all machine functions required for service to be actuated without the need to start the engine, so the engine is always off for any service functions.
During this service/maintenance mode, an auxiliary electric pump powers the top feed roll, both the feed and discharge conveyors, grate frame extend and retract, and virtually every other function except for the track drives for safer, quieter maintenance routines, fuel savings and reduced engine hours.
Maintenance becomes effortless with convenient service access provided: The split hog box opens over the centre for complete access to the rotor and screens.
The anvil and screens can be hydraulically retracted.
The single discharge conveyor is open at the bottom for seamless operation and easy maintenance.
All lubrication points area remotely located for access via ground or maintenance platform locations.
A tool storage area is positioned on the machine's side, which can be hydraulically raised and lowered for added convenience. This removes the need for anybody doing maintenance, to carry items up a ladder.
Each machine is supplied with a Milwaukee three quarter impact wrench, blower and charger
It’s a very well-thought-out machine regarding safety, convenience and accessibility for maintenance and servicing.
This carries through to the operation and design of the machine when in action.
Adequate belt and ground clearance offer benefits in muddy terrain and on uneven surfaces.
The 6900 model features a distinctive tilting frame that pivots on the undercarriage, enabling operators to stack materials higher and adjust the infeed angle as needed.
This flexibility also allows operators to navigate rough terrain and modify the pivot for increased ground clearance or to reach heights necessary for loading products into trucks.
Whether used in forestry, landscaping, or waste management, the 6900 grinder is a versatile and indispensable tool that helps professionals get the job done with precision and speed. Images: Onetrak
An optional large diameter magnetic head pulley is available to effectively remove metal from the end product and protect the machine.
An additional protection and safety measure is the impact detection system that has a series of actions that mitigate damage.
It is operated by an accelerometer that triggers the retracting of the grate frame and reversing of the infeed when it detects a particular impact.
This action creates an opening for the trapped material to be released. In the case when the object is too large to be released and causes another impact, shear bolts enable the grate frame to retract even more.
Finally, there are two shear pins that will disengage on the two sections of the grate frame as a result of another impact.
Whether used in forestry, landscaping, or waste management, the 6900 grinder is a versatile and indispensable tool that helps professionals get the job done with precision and speed.
The Tigercat 6900 Grinder’s carefully planned design, safeguards both the users and the machine, ultimately ensuring the protection of your bottom line.
Onetrak is the o icial dealer for Tigercat in Australia. Please contact Onetrak on www.onetrak.com.au or call 1300 727 520 to speak with the Tigercat experts.
Tigercat durable design
Timed knife arms and triangulated feed
Wireless head communication
Best suited to trees in 40-60 cm diameter range
Dasa D7 fully optimized system (StanForD compatible)
305 cm colour touchscreen (Windows 10)
Back or lower knife option
Introducing the Tigercat 573. A powerful, triangulated three-wheel drive harvesting head with positive control and precise measuring. Versatile for roadside processing and in-stand harvesting. Excellent performance and productivity in medium to large sized timber.
Contact Onetrak today.
www.onetrak.com.au
One of the most e ective strategies in fire prevention and management is the creation of defensible spaces—bu er zones around properties designed to reduce the risk of fire spreading.
As fire season becomes increasingly severe, homeowners and land managers must take proactive steps to safeguard their properties.
Central to a defensible space approach is forestry mulching, a method that not only helps to clear flammable vegetation but also offers numerous environmental benefits.
Forestry mulching involves the use of specialised machinery to grind vegetation into mulch, which is then spread across the ground.
This mulch layer serves a dual purpose: it reduces the amount of dry, combustible material that could fuel a fire, and it retains moisture in the soil, making it less likely to ignite.
The practice of forestry mulching is gaining recognition as an essential tool in the fight against wildfires.
Lance Mikisch, a farmer from the Hunter Valley, highlights the immediate and long-term benefits of forestry mulching with a Fecon machine.
“The beauty of the Fecon mulching any tree at all is what you get left behind. As a farmer, you look at improving your soil,” he said.
“I mulched this area three weeks ago, and you can already see it starting to break down. You can see new grass and little roots coming through. It actually starts up the organic matter and just builds from there.
“In just a short time, the benefits are clear. This hill never held moisture before. Now, you can dig down, and it’s moist. It’s absolutely amazing.”
Lance’s experience underscores the effectiveness of forestry mulching not only in reducing fire risks but also in enhancing soil health and promoting new plant growth.
Fecon, a leader in land management equipment, offers a range of tools specifically designed for forestry mulching.
The company’s equipment, which includes forestry mulching tractors, hydraulic mulching heads, and excavator-mounted mulching attachments, is instrumental in creating firebreaks and defensible zones around populated areas.
With Fecon's robust machinery, you can swiftly clear underbrush that may contribute to the spread of fires, helping to protect your property and enhance safety.
Edan Brennan, a forestry and fire mitigation specialist in Victoria, shares the impact of using Fecon machinery.
“Our work in stump grinding has seen us grind in excess of 2000 stumps along forestry roads, providing a clear path for future maintenance of the roadside vegetation,” he said.
“And the ability to mulch fine fuels in environmentally sensitive areas means we’re able to reduce the risk of bushfires to local communities.”
Edan’s work exemplifies how forestry mulching can play a pivotal role in protecting local communities from the devastating effects of wildfires.
Beyond wildfire prevention, forestry mulching offers several additional benefits:
• Less smoke: Reduced fuel results in less intense fires and smoke, leading to improved air quality and lower health risks.
• Better wildlife habitat: Mulching fosters new growth and biodiversity, creating healthier habitats for wildlife.
• Erosion control: The mulch layer stabilises soil, reducing erosion and runoff, particularly in sloped areas.
Matt Gregory from Beaver Mulching in New South Wales recognised the brand as the pinnacle of mulching technology:
“I choose not to compromise on quality, a decision that has proven invaluable time and again,” he said.
“The eff iciency gained by utilising Fecon
equipment is unmatched, allowing for remarkable time savings on every project.
“Whether tackling lantana, privet, long grasses, or navigating steep slopes, the Fecon mulcher seamlessly integrates with Beaver Mulching’s excavator, fulfilling a much-needed service in our niche market.
“The productivity achieved with Fecon equipment far surpasses traditional methods, highlighting its superiority in both performance and eff iciency.”
For those interested in enhancing their fire preparedness, Fecon Australia provides a range of 100-300 horsepower mulching tractors, excavator mulchers, and skid steer mulchers, including the all-new and highly eff icient Disc Hawk mulcher just released in Australia.
These tools are essential for anyone looking to create and maintain defendable spaces, ensuring that properties are better protected during fire season.
For more information contact your local dealer or to schedule a product inspection, visit www.fecon.net.au or call 1300 FECON1 (1300 332 661)
A Western Victorian plant hire company has celebrated 30 years in operation by buying a brand-new Toyota Huski skid-steer loader.
Graham Koschman’s G.K. Auto and Hire, a highly valued small plant supplier in Horsham, 300km northwest of Melbourne, has become the proud owner of the latest evolution of Toyota’s Huski 5SDK5 loader.
It was delivered personally by Toyota Material Handling Australia’s (TMHA’s) area sales manager Mick Holohan, who responded to Mr Koschman’s call to buy a new one, only the third in the life of his company.
Indeed, Huskis have been the business’ anchor since it started in 1995.
“I bought my first, a second-hand blue 2SKD, when I was running a mechanical repair business and was looking for additional income,” Graham said.
“It already had 8000 hours on it, and I added at least 2000 more.”
Confidence in the quality of his Toyota Huski skid-steer soon convinced Graham to dry hire it, which in turn led to the formation of his now thriving rental business with an inventory of more than 30 machines and implements.
“The Huski is bulletproof, even in the hands of multiple hirers,” he said. “It’s not something you can say for a lot of machines.
“You can buy some cheaper, but there’s a reason they’re cheap.”
Graham’s machine maintenance regime is meticulous, ensuring that his fleet of rental vehicles are always performing to a high standard despite their tough usage requirements.
“Specified service schedules are usually in excess of 200 hours, but we’ve halved that to 100, even with the Huski,” he said.
“Hire machines get used really hard, and yet people tend to push out their maintenance to the extremes. We go the other way.
“Oil is the best insurance policy you can buy”.
Graham said the Huski’s reliability has been a standout feature despite the punishing use that it gets when being hired out, calling his TMHA machines “bulletproof”.
His uncompromising work ethic requires a machine that will go the distance with him, often working around the clock to get a job finished which has earned him a strong reputation in the Horsham area.
G.K Hire has taken a unique position, complementing larger hire companies by offering service and individual solutions and seizing on customer-driven opportunities.
It specifically ordered the Huski 5SDK5 to meet demand for short-term hire in tight
access situations like domestic back gardens.
The Huski’s large seat, with ten length adjustments, made it ideal for hire to a multitude of users, while its simple and easy-tooperate cabin layout is well suited for shortterm hire purposes.
Featuring an operating load of 430kg, the Huski 5SDK5 provides powerful and rugged performance expected of a larger machine, while being compact enough to fit into tight spaces – perfect for residential use.
The ability for contractors to legally tow the 1865kg Huski behind their cars or utilities was a further market driver.
“I leave it to the larger hire companies to have larger machines,” Graham said. “Local contractors know where to come when they need something purpose-built for their needs.”
The arrival of G.K. Hire’s new Huski 5SDK5 was a cause for celebration.
“I’m 62 years old and I’m finally making money,” Graham said. “We bought the new Huski outright.”
Like his first Toyota Huski, it will be the cornerstone of his business.
For more information visit www. huskiconstructionequipment.com.au
Bred Toyota tough, Huski skid steer loaders are the perfect mix of performance, reliability and durability. Developed and tested in Australia, Huski features best in show strength, manoeuvrability and driver comfort, and can handle operating loads from 320kg to a whopping 900kg.
Best of all Huski skid steer loaders are backed by Toyota’s trusted reputation for delivering quality equipment and loyal after sales support.
So if you’re looking to put your business at the head of the pack, you can’t go past a Huski. Australia’s Top Dog in the Dirt.
To ensure maximum safety, concreting contractors must ensure they use the right loading ramps.
In the concreting industry, eff iciency and safety are paramount.
For concrete contractors who often deal with heavy machinery and materials, the use of equipment loading ramps can significantly impact the workflow.
These ramps are not merely accessories but essential tools that enhance the functionality and safety of operations.
For Brad Armitt from Allpro Concrete, safety is a primary concern in any work environment.
“As a concreter, we work with an excavator and its associated tools. I have always been aware that manoeuvring equipment without proper loading and unloading mechanisms can lead to accidents and injuries,” he said.
Brad had been working as a concreter for around 15 years.
He decided to set up his own business around 12 months ago, performing specialist concrete work for building companies.
Brad carries out most of the site preparation and formwork himself but also uses sub-contractors on tasks such as concrete pouring.
“We have a Kubota U55 5-tonne excavator which is used for material removal for concrete slab work,” Brad said.
“Most of our work is for residential foundations, footings and slabs. We also have a tray truck which is used to transporting our concrete working and finishing equipment.
“Our projects are not only in the southeastern part of Melbourne where we are located, but work is also done throughout the greater Melbourne metropolitan area.
“Safety and time are major considerations for our business.
Brad Armitt says Jetland ramps provide a stable and controlled means for machinery to move on and o his transport vehicle. Images: Brad Armitt
“We spent some time investigating the available options for loading ramps to safely load and unload the excavator off the truck.”
Brad said the search ended when he found the range of ramps offered by Jetland.
“They were the best choice for our business,” he said.
“The excavator and all attachments are loaded on the one truck so it's important to have ramps
that allow them to be stored neatly and easily accessible for removal, use and storage every day.
“When I started the business, the ramps we were initially using showed signs of bending and deforming with the constant use of moving the excavator.
“It became obvious after some time that they were not going to be safe and could not be guaranteed to do the job properly for us.
“We needed loading ramps that were safer and more robust. We are very happy with the performance of the Jetland ramps which are perfect for our application and are up to task despite constant tough use in the most challenging circumstances.
“Our Jetland ramps provide a stable and controlled means for machinery to move on and off our transport vehicle.
“They provide a gradual incline, reducing the risk of tipping over or losing control of heavy machinery and minimising the likelihood of accidents. They are designed with non-slip surfaces and side rails, which provide additional safety measure.
“The safe surfaces ensure that machinery can move without slipping, even in wet or muddy conditions. The side rails guide the excavator and prevent it from veering off the ramp, further enhancing safety.”
“Time is money in the concreting business and eff icient loading and unloading of equipment translates directly to increased productivity,” Brad said.
“Jetland ramps enable us to quickly and safely load and unload the machine and tools onto our
trucks, reducing the downtime between jobs.”
Jetland ramps are versatile and adaptable.
Concrete contractors often work in diverse environments, ranging from urban construction sites to remote areas.
Jetland loading ramps can be adapted to various terrains and conditions, providing a consistent loading solution regardless of the site.
It says the adaptability of its ramps lets contractors use them for a wide range of equipment sizes and weights.
This versatility is particularly beneficial for when it comes to transport of different types of machinery for various tasks.
Whether it's a small concrete mixer or an excavator, well-designed Jetland ramps can handle the load.
“I have always believed that Investing in the right equipment is cost-effective in the long run,” Brad said.
“By improving safety and eff iciency, our Jetland ramps help reduce the potential costs associated with workplace accidents and equipment damage.
“I firmly believe the investment in high-quality ramps is off set by the savings from reduced downtime, reduced risk of injury, and less wear and tear on machinery.”
Used correctly, ramps can extend the lifespan of vehicles and equipment.
Proper loading and unloading reduce the strain on machinery, which can otherwise be damaged by improper handling. This preservation of equipment integrity means fewer repairs and replacements, contributing to overall cost savings.
Another aspect of using Jutland’s ramps is the demonstration of contracting professionalism, which adds to an enhanced reputation that is built on reliability and care on site.
Using Jetland loading ramps is a visible demonstration of a contractor's commitment
to safety and eff iciency. Clients are more likely to trust and engage contractors who invest in proper equipment and adhere to best practices.
A professional image can lead to more business opportunities and client referrals.
In a competitive market, standing out as a contractor who prioritises safety and eff iciency can be a significant advantage.
According to Jetland, many concrete construction sites may be subject to safety regulations and standards.
Using equipment loading ramps can help concrete contractors comply with these regulations.
Occupational Safety and Health Administration (OSHA) guidelines, for instance, emphasise the importance of safe equipment handling and transportation.
Jetland ramps meet industry standards to ensure adherence to these guidelines, avoiding potential fines and legal issues.
Compliance with safety regulations is not only a legal obligation but also a moral one.
Ensuring the safety of workers and the general public is a critical responsibility for any contractor. Jetland loading ramps play a vital role in fulfilling this responsibility.
The environmental impact of construction activities is an increasingly important consideration.
Well-engineered loading ramps can contribute to environmentally friendly practices by minimising the need for heavy machinery to traverse uneven or unstable ground.
This reduction in ground disturbance can help preserve the natural landscape and reduce soil erosion.
The design and functionality of Jetland equipment loading ramps have evolved with advancements in technology.
Ramps are made with lightweight but durable aluminium, which provides strength without adding excessive weight.
These technological advancements mean that contractors have access to state-of-theart equipment that enhances their operational capabilities.
Staying updated with the latest ramp technologies can give contractors a competitive edge and improve their overall project execution.
In short, Jetland equipment loading ramps are indispensable tools for concrete contractors. They enhance safety, improve eff iciency, and offer versatility and adaptability across different work environments.
As technological advancements continue to improve ramp designs, their value to concrete contractors will only increase, cementing their role as essential components of modern construction practices.
“In the demanding field of concrete construction, Jetland equipment loading ramps provide us with the support needed to achieve safe, eff icient, and successful project outcomes. Their importance cannot be overstated, making them a critical consideration for any concrete contractor,” Brad said.
Jetland loading ramps offer a range of features designed to enhance safety, eff iciency, and versatility in the loading and unloading process. Their high-quality materials, non-slip surfaces, and additional safety features make them a reliable choice for various industries.
The benefits of using Jetland ramps include cost savings, increased productivity, and improved worker morale, all of which contribute to a more eff icient and successful operation.
Whether you’re in construction, mining, agriculture, or logistics, Jetland loading ramps provide a practical and effective solution for your equipment handling needs.
For further information on Jetland Ramps visit jetlandramps.com.au/
Construction equipment managers are beginning to adopt better preventative maintenance and lubrication practices to optimise machine longevity.
Images: Viva Energy
Improvements in the delivery, storage, and handling of lubricants are just as important as advancements in lubricant formulations.
The effectiveness of lubrication can be significantly impacted by contamination.
Particulate contamination is the number one issue causing premature wear and component failures in the construction industry.(1)
Construction equipment managers are beginning to adopt better preventative maintenance and lubrication practices to optimise machine longevity.
Correct storage and handling of products are critical to reducing the risk of contamination, premature damage, misapplication, crosscontamination, and safety incidents.
For Shell Lubricants, the quality leaving the refinery or blending plant is closely monitored and controlled.
Technical Specialist at Viva Energy Australia (Shell Lubricant Macro Distributor), Silvana Farrugia, explains that stringent care is always taken in manufacture, packing, and transportation to ensure products are free from contaminants and meet or exceed specifications.
“However, once lubricants leave Shell or its agents, their continuing quality for use depends on subsequent storage and handling procedures,” she said.
“When it comes to delivery, the old school practice of unloading lubricants off the delivery truck with an old tyre should be avoided. This practice is unsafe and can contaminate the environment if spillage occurs.
“Many construction businesses are investing in hydraulic lifts to help move drums of oil from one place to another.
“The standard 209-litre drum weighs about 185kg when filled with oil. It’s important drums must never be dropped when being unloaded or moved. Hydraulic lifts or forklifts are recommended instead.”(2)
With bulk lubricants, Silvana said it was essential that the correct grade is stored in the right tank, so supervision and tank labelling are essential.
A responsible person should supervise all deliveries, to ensure that the correct quantity and grade of lubricant is off-loaded or discharged.
Head of Lubricants Sales and Marketing at Viva Energy, Renee Reilly, said the processes for storage of lubricants had upgraded significantly in recent decades, with colourcoded options and associated tags to minimise confusion.
She also recommended construction sites install satellite storage rooms and contamination control tools like desiccant breathers on machines, such as hydraulic fluid tanks. This can help provide cleaner storage facilities and prevent moisture and particles from entering and contaminating lubricants. While such improvements require additional financial outlay, they protect your investment in high-quality lubricant products.
“It starts with getting the basics right: having a clean lube room and dispensing area,” Renee said.
“If these are not clean, then any advancements or innovations to the lubricants may not deliver their full value.”
For assistance with how best to store and handle lubricants, Viva Energy Australia’s technical team can provide expert knowledge. Call 1300 134 205 or email technicalhelpdesk@vivaenergy.com.au.
Sources: ShellContentServices – Whitepaper 2024 Shell Lubricants Storage Handling HSE Guidelines
In a one-man operation, choosing the right equipment is crucial. And for Brisbane business Gingex, Kobelco was the choice of machinery.
Tony Kelly's passion for the industry ignited while working for a previous employer on civil construction projects.
He was particularly intrigued by the streetscape works, such as landscaping, fencing, and retaining walls.
“One day, I saw the work that was going on and decided to put my hand up and give it a go,” he said.
This decision set him on a path that eventually led to the creation of his own business, Gingex, formerly known as Ginger Landscaping.
Venturing boldly into the trade, Tony immersed himself in both civil construction and landscaping, steadily building his practical knowledge and experience.
After years of navigating between the two fields, Tony relocated from Canberra to Brisbane, where Gingex was born.
When Tony started Gingex, he had no experience running a business.
The first five years were challenging as he navigated the commercial landscape and sought out the right equipment for his growing company.
Tony went through a variety of machinery in search of the perfect fit. He began with a Vermeer stand-on loader, then after a year he added a car-licence tipper, which worked well for his residential landscaping jobs and as a tow vehicle.
Eventually, this was upgraded to a larger capacity tipper as he shifted focus to excavation works, which he still uses today.
His first machine, was a great asset for landscaping, helping him move material quickly across job sites.
However, as Gingex shifted focus to earthworks, the loader became less eff icient for his needs.
Today, Tony's main piece of machinery is a Kobelco SK17SR-6 mini excavator, a machine he decided to purchase after a series of positive
experiences with his local Kobelco dealer, BrisVegas Machinery.
Initially, Tony had another brand excavator but his bad experiences with the local dealership led him to look at alternative brands.
A special promotion on the Kobelco SK17 caught his eye, and his interactions with Marco Marabini, his local sales rep from BrisVegas, solidified his decision.
Marco, who has himself amassed an industry following on Instagram (@kobelco_marco), connected with Tony through social media, eventually meeting in person at the Toowoomba Field Days.
After a thorough inspection of the machine and a prompt quote from Marco, Tony decided to make the purchase.
“The SK17SR has been an excellent choice for my line of work. Despite being relatively new, it has already proven its worth. The comfort level of the 1.7 tonner is exceptional, especially for a mini excavator,” Tony said.
He is particularly impressed with the tilt hitch operated by joysticks—a feature not commonly
found in other brands.
“The build quality is another highlight, with tight pins and rams, unlike previous machines I’ve used that have been sloppy at zero hours,” he said.
“The excavator's ability to retract its tracks to a narrower width has also been beneficial for our tight access works.”
Moreover, the SK17’s stability has surprised Tony—unlike his previous machine, he doesn't have to lower the blade every time he moves the arm.
While Gingex is currently a one-man operation, Tony is gradually building up his workflow and hopes to bring someone else on board soon.
Looking ahead, he has his eye on the newly released Kobelco SK26SR-7, an excavator that offers slightly larger dimensions while still fitting into tight spaces.
“It looks awesome compared to other machines in that class, still offering tight access but great for work where I have a bit more room to move about and need that extra power and lift, whereas the SK17 can be used on the smaller spots,” Tony said.
Tony is confident in the support he will receive for his new purchase from BrisVegas.
"The SK17 is still fairly new, so I haven't encountered any problems yet. However, I bought a mini dumper from them a year ago, and they've been excellent with servicing it. I have no complaints,” he said.
Tony’s dedication to his work and his willingness to travel wherever the job takes him has led to some unique opportunities.
Recently, he spent a week in Ballina working on a project for Foxtel’s Selling Houses Australia—just one of many exciting jobs in his growing portfolio.
Through persistence, smart equipment choices, and a commitment to quality, Tony Kelly has built Gingex into a thriving business, and he continues to look ahead, ready to take on new challenges.
The Melbourne Convention and Exhibition Centre is set to debut Converge, an innovative new event focusing on the municipal works, commercial and civil construction industries.
construction
Construction industry leaders and representatives will converge for Converge on September 17-18 next year, bringing together top decision-makers from the sector, creating a space to share cutting-edge tools, ideas and technologies that will shape these sectors.
As Australia’s only one-stop-shop for sub-contractors, project engineers, council fleet managers and large-scale construction contractors, the event promises an immersive experience that takes visitors on a journey from the small scale to the large.
It will bring together leading decisionmakers from these sectors to see the latest developments that is helping them build Australia’s future infrastructure.
Attendees can anticipate live demonstrations, equipment showcases, and engaging conference spaces offering invaluable solutions for the future development and maintenance of Australia’s infrastructure.
The event will bring delegates to major utility centres, public lands and civil and commercial construction sites.
Co-located with No-Dig Down Under, Converge will attract engineers involved in infrastructure construction and management, attending as part of their continuing professional development through Engineers Australia.
No-Dig Down Under — the southern hemisphere’s only large scale conference and exhibition dedicated to trenchless technology
— draws managers from utility companies and councils keen on the latest trenchless technology.
A significant segment of the show will be dedicated to civil construction and road maintenance.
Tier 1 to Tier 3 contractors will gain exclusive insights into the latest equipment and technology reshaping the industry.
Leaders from major civil works projects will share their knowledge on Victoria’s Big Build and the state’s 10-year, $120 billion infrastructure pipeline.
From construction sites to boardrooms, Converge will provide leaders with solutions for managing large-scale projects.
A dedicated construction technology space will showcase live demonstrations of the latest software transforming commercial construction.
For smaller projects, Converge will cater to councils and asset managers with a niche area showcasing the latest tools available in municipal works.
From horticulture equipment to road maintenance and large-scale trade tools, this section will serve as a one-stop-shop for council fleet managers and sub-contractors, with a special focus on zero-emission technology.
Drawing from extensive media partner databases, Converge anticipates a significant turnout of engaged decision makers.
With a total media exposure exceeding 1,007,070 across print and digital platforms, the event leverages leading industry publications to ensure a high-quality attendee base.
Connect and converge
Don’t miss your chance to be part of this groundbreaking event for the Australian construction industry.
Early bird stand enquiries, conference speaking positions and sponsorship opportunities are available now.
Converge at Converge 2025 and be at the forefront of Australia’s construction evolution.
Date: 17-18 September 2025
Venue: Melbourne Convention and Exhibition Centre
Registrations: Tickets to attend the exhibition are free. For more information, visit convergeexpo.com.au
Enquiries: converge@primecreative.com.au
Komatsu Australia is providing jobs for people with disability through the renewal of its partnership with disability service leader Endeavour Foundation.
Endeavour Foundation is an independent, forpurpose organisation that supports people with disabilities through independent living or other forms of accommodation, community initiatives and employment opportunities.
The partnership between Komatsu and Endeavour Foundation focuses on providing employment opportunities within Komatsu’s Oil Wear Analysis (KOWA) division.
Supported employees in the program clean the 100 per cent recycled plastic canisters so they can be reused up to six times.
Komatsu Australia’s Executive General Manager - Supply Chain, Russell Hodson, says the compoany has been working with Endeavour Foundation since 2021, and was excited to continue the partnership for another three years.
“We’ve been able to not only offer meaningful employment to a number of people, but with more than 30 per cent of Komatsu’s plastic packaging waste generated through our KOWA bottles, this program and partnership also
means we can significantly reduce the volume of plastic packaging waste that we are sending to landfill,” he said.
“As a large, global company, we are always looking at ways we can use our presence to bring about some good in the world.
“This partnership is just one of the ways we are focusing on our ESG principles – it helps Komatsu reduce their environmental footprint, while also providing some meaningful employment to people with disabilities – and has proved to be such an important part of our overall supply chain in the KOWA division.
“Since we began our relationship in 2021, together we have recycled more than 450,000 KOWA bottles that has prevented 12,000kg of waste going to landfill.”
Endeavour Foundation’s Executive General Manager – Work, Shannon Foley, said access to employment opportunities was an important goal for many people with disabilities.
“Meaningful employment is valuable to everyone, and we’re proud to play our part by
helping to create roles for people with disability. We’re looking forward to continuing to work together with Komatsu on this valuable initiative and seeing what other future opportunities we can create,” she said.
Komatsu develops and supplies technologies, equipment and services for the construction, mining, forklift, industrial and forestry markets.
For a century, the company has been creating value for its customers through manufacturing and technology innovation, partnering with others to empower a sustainable future where people, business and the planet thrive together.
Front-line industries worldwide use Komatsu solutions to develop modern infrastructure, extract fundamental minerals, maintain forests and create consumer products.
The company's global service and distributor networks support customer operations to enhance safety and productivity while optimising performance.
Three of the best technicians from Caterpillar’s Asia-Pacific dealers are a step closer to the finals of an event designed to find the best Caterpillar support sta in the world.
The Asia-Pacific leg of the inaugural Caterpillar Global Dealer Technician Challenge was held in Melbourne recently, aiming to find the most proficient specialists in the region.
This event, for independent Cat dealers that choose to participate, is designed to showcase how skilled technicians are part of a high-tech, high-impact, high-demand career.
Caterpillar Global Service Vice President Henry Venneman said the hands-on, skillsbased competition tested the technicians’ agility, resilience and versatility.
“These trained experts are on the front line of support, working to keep machines and engines up and running to help ensure our customers’ critical projects are completed,” he said.
The Challenge continues to take place over a series of regional and semifinal competitions around the world. The top 10 finalists will have the opportunity to compete in the finals in March 2026 at CONEXPO/CON-AGG in Las Vegas.
The four-day Asia-Pacific round involved seven Cat dealers, with Australian representatives from Victoria, WA and Qld-NT all vying to win.
The full list of participants for this first regional qualifier were:
• William Adams (Vic) – Ben Peters
• Hastings Deering (Qld/NT) – Rhys Bishop
• WesTrac (WA) – Leon Archibald
• Terra Cat (NZ) – Brenton Page
• Tractors Singapore – Seng Kin Wai
• Tractors Malaysia – Umar Zakir Bin Lamiron
• Trakindo (Indonesia) – Aditya Pandu Winata
The winners were Leon Archibald (1st); Rhys Bishop (2nd); and Brenton Page (3rd), who have all booked their tickets for the semi-final in Malaga, Spain.
Cat dealers globally are experiencing a growing opportunity for technicians. By the end of 2026, it is estimated that Cat dealers may need to hire more than 44,000 technicians. This competition is also designed to help raise awareness of the opportunities in this career field.
“There are thousands of opportunities available globally for those who are interested in a hands-on career,” Venneman said. “Cat dealers are often looking for individuals who are problem solvers, mechanically inclined and tech savvy.”
Stephanie Daemon
National Communications Coordinator National Association of Women in Construction
The Male Allies Program is a five-digital module online course aimed for men in the construction industry to build awareness, and knowledge – exploring key concepts, engaging in interactive learning experiences, and developing actionable plans to drive cultural change within their teams and organisations. While our program is targeted towards men, it is available for all NAWIC members for free,
to understand and champion diversity and inclusion in the workplace.
Male allies play a crucial role in advancing gender equality and dismantling stereotypes. By actively supporting and advocating for women, they help to create a more inclusive society.
Their collective voices call for equal opportunity, respect, and recognition for all genders, contributing to a more balanced industry and increasing the rates of attraction, development, and retention of women.
Program participants will develop a comprehensive understanding of gender disparities, biases and challenges faced by women in male-dominated industries, recognise the importance of male allyship in creating inclusive workplace culture and fostering diversity, acquire practical skills and
strategies to support and advocate for female colleagues, challenge biases, and promote gender inclusivity.
By exploring individual and collective roles in fostering gender inclusion, including person, social, societal, and organisational levels, participants will commit to implementing action to promote gender inclusivity, being advocates for change and shifting the culture.
With program structures for both individual and corporate pathways, there is an option for everyone.
The Male Allies Program is exclusive to NAWIC members – you can join us today via our membership page.
With options for students and apprentices, individual and corporate with added membership benefits for both men and women, we welcome you to the NAWIC family.
The winners of the 2024 Civil Contractors Federation Queensland (CCF Qld) Earth Awards, People’s Awards, and Industry Training Awards have been announced.
The awards were handed out at the Excellence in Civil Construction Awards held at the Brisbane Convention and Exhibition Centre, with special guest Transport Minister Bart Mellish in attendance.
CCF Qld President Mark Goodwin highlighted the importance of the prestigious event as the organisation celebrated 31 years of the CCF Queensland Earth Awards.
They recognise outstanding quality in civil construction – including roads, bridges, railways, marine structures and utilities.
The awards are designed to recognise the impressive engineering techniques and achievements by the Queensland civil construction industry over the past 12 months, and are held in high distinction by industry.
These awards were presented in six groups according to project value, listed below with respective winners.
• Projects valued up to $2 million Albino Rock Helipad & Access: CivilPlus Constructions
• Projects valued $2 to $5 million
Mount Nebo Road Safety Upgrades: Durack Civil
• Projects valued $5 to $10 million DriveIT NQ Pty Ltd: BMD Constructions
• Projects valued $10 to $30 million
QR Tablelands Bridge Replacement: Doval Constructions
• Projects valued $30 to $75 million
Smith’s Gap Fauna Crossing: RMS Engineering & Construction Pty Ltd
• Projects valued greater than $150 million
Bruce Highway Upgrade/Caboolture-Bribie Island Road to Steve Irwin Way – Contract 2: Fulton Hogan Construction
The People’s Awards are highly coveted by industry after being introduced in 2018 and
celebrate excellence in people working in civil construction across the state.
There were a record-breaking number of nominations this year. Below are the winners of the 2024 CCF QLD People’s Awards.
• Site supervisor of the year
Craig Irvine, McIlwain Civil Engineering
• Work health and safety champion of the year
Kate Pollock, Haslin Constructions
• Plant operator of the year
Ken Duff, Civil Mining & Construction
• Project manager of the year
Keegan Neal, BMD Group
• Environmental and sustainability champion of the year
Dallas Frazier, Fulton Hogan Construction
• Engineer of the year
Kurt Lembo, Seymour Whyte Constructions
• Support champion of the year
Peta Hughes, Fulton Hogan Construction
The CCF QLD Industry Training Awards recognise talented up-comers in the Queensland civil construction industry who are currently studying, or recently completed their studies with Civil Train (RTO #5708).
The 2024 Training Awards Winners are:
• Certificate II in civil construction student of the year
Aaron Young, WorkCon
• Certificate III in civil construction student of the year
Baxter McCort, CC P & C Pty Ltd
• Certificate IV student of the year
Dimitrios Sofatzis, McIlwain Civil Engineering
• Encouragement award
Rogan Rodgers-Falk, McIlwain Civil Engineering
• Diploma student of the year
Tomasz Walczak, KPI Services
• Outstanding commitment to training and skill development (individual)
John Fonua, Bielby Holdings
• Outstanding commitment to training and skill development (employer)
Albem Operations Pty Ltd
• Overall student of the year
Baxter McCort, CC P & C
CCF Qld congratulates every finalist and winner of this year’s Excellence in Civil Construction Awards.
Nominations for the 2025 awards series will open in February 2025 via www.ccfqld.com and those interested can express interest via email to qldevents@ccfqld.com.
The Allied Earthmovers Association has helped support a Men’s Shed event as part of its commitment to give back to the community by way of involvement in charitable activities and functions.
Ann Callaghan Manager Allied Earthmovers Association
As mentioned here in the last issue of Earthmoving Equipment Magazine, the objects of our Association state that we will promote friendship, co-operation and support, work quality by sharing trade skills and information and helping each other out.
On a larger stage, we also promote a fair code of ethics in the earthmoving industry, present our views to Government and relevant bodies and promote equitable trade within the earthmoving industry.
All members sign a Code of Ethics and are expected to abide by these objectives.
The last object in our Constitution is to contribute back to the community by way of involvement in charitable activities and functions.
Opportunities to fulfill this object don’t come by very often, but recently we were able to help out a good bunch of guys who have built a “Men’s Shed” at Grasmere near Camden, NSW.
This movement is very important, because “men don’t talk face to face, they talk shoulder to shoulder”.
With just some levelling off and spreading material around, it was expected to be a small job, so with five willing volunteers we thought we’d be done by lunch time.
However, the job grew as the day went on and
the last machine wasn’t turned off until about 5pm and of course the site looked great.
Committee member Grahame can be congratulated for a well-ordinated, successful Charity Day. Thanks also to Wayne, Lou, David, Alex and Ismail.
Our last meeting of members was our Annual General Meeting and the existing volunteer Board members were very willing to step up again.
With a minor change, our Chairman Matt (who is also our Patron) declared all positions filled and congratulated the incoming Committee.
We look forward to a busy, full new year, with Trade Nights planned at Semco and CJD Equipment to kick it off.
The next meeting will be held at the premises of Semco at St Marys.
Steve and the team have been supporters of our Association for many years and it was due to their financial support that we were able to produce our first Year Book back in 2001.
Our Association thrives on the support of sponsors like Semco and we encourage all our members to use Semco, and all other sponsors, whenever they can in the course of their business.
It is also that time of year when our members’ insurances are due and insurance is often the reason many of our members join our Association in the first place.
We are pleased to have AEI Transport Insurance Brokers looking after us and we encourage any owner operator to give us a call when your insurance is due.
image and below: Members
You will save well in excess of your membership but also get to enjoy the other perks of membership. Why should you be missing out?
If you are an owner operator and would like to see what we are about (and no, you don’t have to volunteer to sit on the Board – unless you want to of course) why not give us a call?
We’re an easy-going, informal bunch and you might just find you’ll fit right in.
A municipal works, civil and commercial construction event.
17-18 September 2025,
In September 2025, a new event will be landing at the Melbourne Convention and Exhibition Centre. Converge will bring together leading decision makers in the Municipal Works, Civil and Commercial Construction space, to share the tools, ideas and technologies that are shaping these sectors.