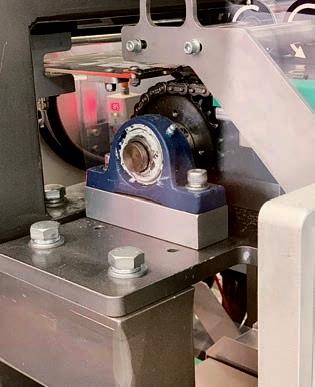
4 minute read
LUBRICATION
Cut carbon output by up to 30 per cent with automated lubrication
SKF’s automated lubrication technology has helped customers increase uptime while saving money and creating a more sustainable production line. Food & Beverage Industry News explains.
According to experts from SKF, a Swedish company that specialises in bearing and lubrication technology, switching to an automated lubrication system in the food and beverage industry can slash CO2 output by as much as 30 per cent.
“At the moment, companies and the industry are very focused on sustainability going forward,” said Cenk Ozbilgen, business development and technical support manager at SKF.
“What we achieve with our customers is to install an intelligent connectivity between all products with a uniform and energy efficient lubrication system.”
Ozbilgen said there are many advantages in using automatic lubrication systems. Including reducing waste and bearing failure, cleanliness, less labour and improved health and safety.
“The overall cost of manual lubrication is often overseen by the industry” he said.
“They need to consider downtime and loss of production cost per hour, average parts cost and associated man hours per repair, time required lubricating equipment, lubrication frequency, number of accidents caused by manual lubrication tasks, and costs of lubricants & lubricant management.”
It is anticipated that poor manual lubrication causes up to 50 per cent of all bearing failures.
“From a sustainability point of view, you are increasing the carbon output by a lot,” said Ozbilgen.
“From manual to automatic you can reduce that grease consumption by 30 per cent and by extension emit less carbon dioxide.”
Ozbilgen said the advantages of switching to an automated lubrication system, was an obvious choice for the food and beverage industry as sustainability be-comes a hot button issue moving forward.
“Put some reasonable connectivity behind it, sensors, lubrication systems, things of that nature, and the benefits are almost immediate,” he said. Ozbilgen used large bakeries as an example for moving away from manual lubrication and onto an automated system.
He said when done manually, a worker will wait at the end of the conveyor and lubricate the chains as it continues into the oven to bake the food product. However, this creates the conditions for possible over lubrication, and in turn, potential contamination of the food.
Also keeping in mind that deploying automatic lubrication systems can free your skilled maintenance technicians from time consuming basic activities to provide extra value.
Another example is SKF’s work is with a meat processing factory’s overhead conveyor.
SKF implemented a centralised automatic lubrication system in place of the existing manual system, and this increased uptime and reduced maintenance costs.
In terms of cost savings, prior to switching to an SKF automated lubrication system the meat processing factory was losing $3,000 for every hour of downtime, and in total 35 hours per month, which equated to $105,000 in lost capital due to down-time.
Overall, the installation was calculated to have saved the meat processing factory at least $100,000 in downtime costs per month.
Ozbilgen also highlighted the importance of connectivity for clients so that they can get real-time data from the factory and act accordingly.
“We have sensors for vibration so you can see if any machine is going to fail, but you can also see whatever is happening on the lubrication side as well. This then leads to smart lubrication systems, which can adjust themselves according to the problems identified,” he said.
SKF is currently working on a project where if the system recognises vibration is-sues it can identify if the problem is lubrication starvation.
“You still might have some problems on the bearings and other machines so the system can act accordingly and make necessary extra lubrication cycles when required,” said Ozbilgen.
Meanwhile, Graham Thomas, business development manager at SKF, said the company complemented its automated lubrication system offerings with a focus on safety regulations and food recalls.
“We constantly develop new market offers for the food and beverage industry specifically. Food and beverage products are a very big focus for SKF with bearings and bearing units along with lubrication technologies,” said Thomas.
“Even seals and power transmission products, it is a constant line of development for SKF.”
Another case study from SKF detailed how the company optimised lubrication of beverage filling machines using SKF Lincoln progressive lubrication.
The beverage industry is becoming more competitive and growing consumption now demands 24-hour production that leaves little time for maintenance stops, so maintenance tasks must be done while equipment is operating and SKF were able to achieve that in this case.
For example, targeted at more than 80 per cent, Overall Equipment Effectiveness (OEE) often is around 60 per cent, and machinery breakdowns affect availability. However, automating essential tasks like lubrication eliminates human mistakes, simplifies lubrication management, reduces lubricant consumption, and enhances line efficiency.
The analysis results shows that the actual lubrication system was not working at all, as it was completely corroded.
SKF Lincoln Automatic Progressive lubrication system provided the means for an optimum lubrication to the various components of the filling machine, with stain-less-steel components.
“The industry is under constant pressure to reduce maintenance costs and increase uptime and lubrication systems and other technologies and SKF is helping facilities achieve that goal,” said Thomas. F
Producers must consider downtime and loss of production from manual lubrication.
