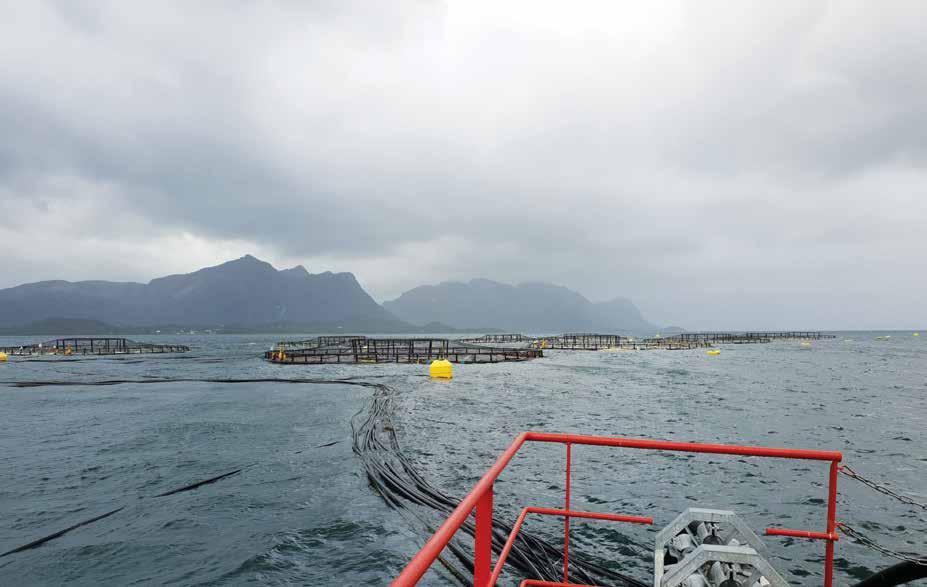
6 minute read
INSTRUMENTATION
Aeration in fish farming
AMS is a company that specialises in mass-flow controllers. Food and Beverage Industry News explains why this type of instrumentation is important in the aeration in salmon fish farms.
Fish consumption is rising. With the increase of the world population and the need for nutritious food, health-conscious consumers are looking for alternatives to “a nice slice of meat”. And they end up eating more fish or vegetarian food.
Specific species of wild fish are getting scarce in open water due to the impact of industrialised fishing fleets and overfishing. In a trend towards sustainable food production, fish farming is gaining increasingly interest.
Fish farming is the aquatic version of farming cows, sheep or chicken. For many years, humans have been farming food by having it grown in greenhouses, stables, or fields. Fish farming is heading in the same direction.
When people hear about fish farms, they might think of an aquarium, a little pond or a floating net. But in Norway, a major player in fish farming, people think on a larger scale. A typical fish cage near the Norwegian coast has a diameter of tens of metres containing 200,000 to 300,000 salmon. In the near future, these designs will upscale to one or two million salmon. In Norway, at the beginning of 2018, more than 3,500 cages for fish farming were floating in the sea.
The country is expanding its knowledge and technology across the world, where people are interested in large-scale harvesting of fish in the sea – and maybe on land.
Salmon is a typical example of a fish that can be fish farmed. They need cold water – 7˚C-9˚C is what they like most, which is why this aquaculture is happening in the Northern Hemisphere, off-shore in the fjords. Salmon is a popular fish so there is a high demand.
Aeration In fish farming, aeration is of vital importance. In addition to food, the fish need oxygen that is supplied in the form of tiny air bubbles – aerated – to the water. But aeration has other advantages, too.
In the early days, the salmon suffered from infestations of lice. Since salmon lice had an impact on harvest, the fish farmers had to look for solutions. For some reason – maybe it was an experiment or it happened by accident – the farmers started to purge air from the bottom of the cage.
And they observed that the movement of the fish started to change. Instead of circling day in and day out – as salmon normally do – they started to move around the cage and became more agile. If the salmon are more agile, their muscles have to work more. This results in their meat being of better quality. At the same time, the fish farmers detected that aeration helped them to create a more thermal friendly water environment. With an advantageous temperature, conditions and amount of oxygen, this resulted in a decrease in lice numbers. So aeration had two advantages: improving the salmon quality, and reducing the unwanted lice.
Aeration of fish farms using mass flow controllers The process of aeration is simple. The air bubbles can be generated by natural
water currents (off-shore, down-hill), pumps, impellers, variable area flow meters or by mass flow controllers and compressors.
A compressor generates compressed air from the surrounding atmosphere, and feeds this to the mass flow controller for controlled aeration of the water in the fish cages.
To run fish farms that are remotely controlled and without much manpower, automation is needed. This includes automated feeding. When the fish are fed, the air purging needs to be interrupted to give the fish the opportunity to hunt for the food before it floats out of the cage. In between the feeding periods, the aeration improves the condition of the water and the salmon.
It helps that mass flow controllers are remotely controlled from the control room at land. The aeration is stopped when the feeding starts, and when the feeding is over, the previous set point will automatically return and the water condition is as stable as it was before.
Mass flow controllers provide a potential for saving energy due to better conditions in the cage. The accuracy of the devices is important. Every cubic metre of air saved by the device being accurate – faster control or opening of valves – is of direct influence to the costs for running a compressor. In stormy weather, fish farmers can reduce the aeration, but during a long dry period without water movement, more air bubbles are needed. So essentially, this accuracy and flexibility leads to a better controlled environment.
With Mass-Stream mass flow controllers, farmers have a robust instrument, which is performing well in the harsh surroundings. By the manufacturer’s Bronkhorst’s standards, this kind of aeration is high flow. Typical air flows for a fish cage are in the range between 600 and 1,400 litres per minute.
Mass flow controllers for other types of aeration Mass flow controllers are suitable for other types of aeration in aquaculture and agriculture. If users farm salmon, they need to breed the fish, which normally occurs on land. Fish eggs and young fish are even more vulnerable to changes, so the environment has to be more stable than for grown fish. Depending on the type of fish, the balance of oxygen in the water is delicate and has to be controlled accurately.
In algae farming, CO 2 gas is one of the food components for these species to grow, which needs to be supplied under defined conditions.
A well-known application of aeration is in food and beverage industry. Every soda or carbonised drink is a liquid purged with carbon dioxide gas. Related to that, when packaging food, the packaging is purged with nitrogen to remove the oxygen before the food enters the packaging, as one of the steps to prolong the shelf life of the food. F
In early 2017, following a change in ownership and management, MAdE Establishment conducted a review of its records and identified circumstances where it had failed to correctly pay many of its employees. MAdE Establishment self-reported this to the Fair Work Ombudsman (FWO) which subsequently commenced an investigation into Jimmy Grants and the MAdE Establishment group of companies, being the Hellenic Republic, Press Club and Gazi restaurants.
Since first identifying the underpayment issues, the MAdE Establishment group has back-paid 515 current or former employees $7.83m. This amount comprised underpayments for the admitted contraventions listed below. In some cases, workers were incorrectly classified. Record-keeping laws relating to time records for some annualised salary employees were not adhered to, contributing to underpayments.
The FWO also found underpayments of about $16,000 for 9 employees at two Jimmy Grants stores. Jimmy Grants (Emporium) and Jimmy Grants (Fitzroy) incorrectly classified some workers and for some employees the wrong award was applied, resulting in underpayments of base rates for ordinary hours and a range of penalty rates.
MAdE Establishment has formally admitted to the FWO that contraventions relating to the following failures occurred and has entered into an Enforceable Undertaking (EU) with the FWO (available at www.fairwork.gov.au) committing to a number of measures to remedy the contraventions, rectify workplace practices and ensure future compliance: • failing to pay: minimum rates of pay, casual loadings, Saturday, Sunday, Public Holiday, early morning and evening penalty rates,
loadings; failing to conduct annual reconciliations for those employees paid through an annual salary arrangement to ensure those employees had been properly remunerated for all accrued overtime and penalty rates; failing to make and keep part time work agreements; and failing to keep a record of start and finish times for employees on annualised salaries.
The commitments made by MAdE Establishment in the EU include: • a contrition payment of $200,000 to the Commonwealth; • committing to workplace relations training for all staff with responsibility for human resources, recruitment, on-site management or payroll functions; • completing audits for a period of three years; • implementing systems and processes to monitor compliance at all times; • registering with the FWO ‘My account’ portal; and • leaders about the importance of complying with the Fair Work Act.
MAdE Establishment expresses its sincere regret and apologises for the conduct that resulted in the contraventions. MAdE Establishment is committed to ensuring compliance with Commonwealth workplace laws and becoming a force for change in the industry.