
3 minute read
BELTS
Solid and perforated steel bake oven belts
IPCO bake oven belts have a long history in the food industry, and can help save time and money for its clients. Food & Beverage Industry News explains.
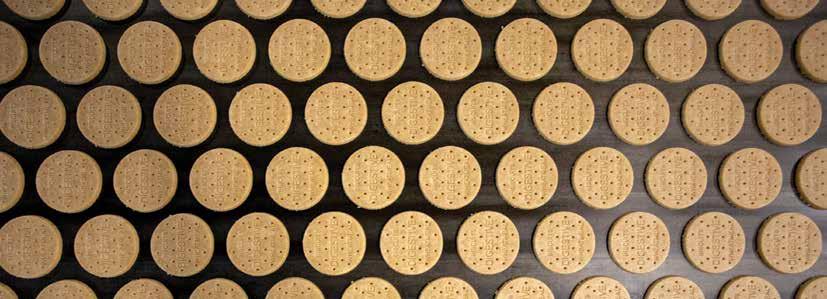
Up to 25 per cent of energy consumption can be used heating the conveyor belt in a bake oven.
IPCO offers a range of steel-grade belts to suit different needs and environments. IPCO 1100C grade is a carbon-steel product that is used by the bakery industry, while IPCO 1200SA is a stainless-steel grade suitable for applications such as food conveying, cooling, freezing and drying. Both are available either in solid form or perforated. IPCO also offers belt grades suitable for special needs, such as resistance to corrosion or abrasive materials.
However, it is important to note that the material, or grade, is only the start of the story. Production of a belt requires the necessary mechanical properties of flatness and straightness to be engineered into the belt. The belt must also be able to transfer the heat from the heating media to the product in an even way. This means the colour of the belt surface is important. Consistent belt colour will maximise heat transfer and ensure an even bake. Specific heat treatments are therefore applied during the production process.
In terms of supply, IPCO can provide as much, or as little input, as an oven builder requires. This can be as straightforward as belt supply through to various levels of technical advice, or consultancy to ensure that the belt delivers maximum return on investment, as well as key conveyor components such as tracking systems and graphite stations ensure smooth operation. For instance, in cases of complete belt upgrades, moving from mesh to solid or perforated steel, IPCO will often supply all conveyor components – sheaves, bearings, framework and all other required accessories.
Wide belts for enhanced productivity One area of increasing interest to many oven builders is IPCO’s ability to produce bake oven belts up to 3,500mm wide. This makes it possible to build wider ovens, increasing productivity without having to invest in factory extensions or new facilities. An oven with a 1,500mm-wide belt offers almost twice the productivity of one with an 800mm belt without any increase in the line length. An upgrade to an oven with a 3,200mm belt or larger, will increase throughput by a factor of four. The use of a steel belt of any size also has the potential to reduce baking times. The combination of a steel belt’s heat transfer qualities and comparatively low weight often means that belt speed can be increased, cutting baking time by as much as 25-30 per cent.
Reducing carbon footprint through energy efficiency Bake ovens can account for as much as 45 per cent of a bakery’s overall energy consumption and as much of 25 per cent of this is used heating the conveyor belt. The bake oven belt can, therefore, have a major impact on overall energy costs so ensuring maximum efficiency here is important.
A solid-steel bake oven belt weighs 30 per cent less than a comparable mesh belt and therefore costs up to 30 per cent less to heat. And perforated belts weigh as much as 35 per cent less again.
As well as cutting heating costs, this weight advantage also means less energy is needed to drive the belt through the oven.
Apart from these energy savings, steel belts are also easier to clean being flat and smooth. This not only delivers savings in water and detergent but also means greater overall productivity, with time spent baking instead of cleaning.
And there’s an additional point worth making: these benefits don’t just apply to baking. IPCO belts are used across the food industry for cooling, freezing, cooking, forming and drying.
IPCO Australia enhanced technical and service support throughout Oceania IPCO held the grand opening of its new Melbourne (Burwood Industrial Park) headquarters on July 9th. The company is owned by FAM AB, which is part of the Swedish Wallenberg group, and has production facilities in the Americas, Asia and Europe and a worldwide technical service for quick response wherever and whenever it’s needed.
As a partner to the bakery industry since 1925, the company has built long-term partnerships with both OEMs and end customers. IPCO engineers have a wealth of experience in supporting the bakery industry and can deliver the most appropriate solution for any requirement whether it is a new installation, an upgrade to an existing facility (from wire mesh to a solid or perforated belt), or simply supplying a replacement belt. F
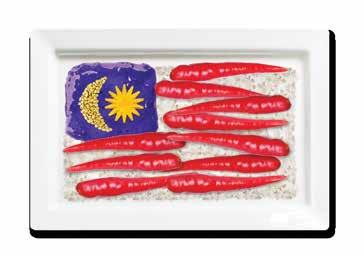
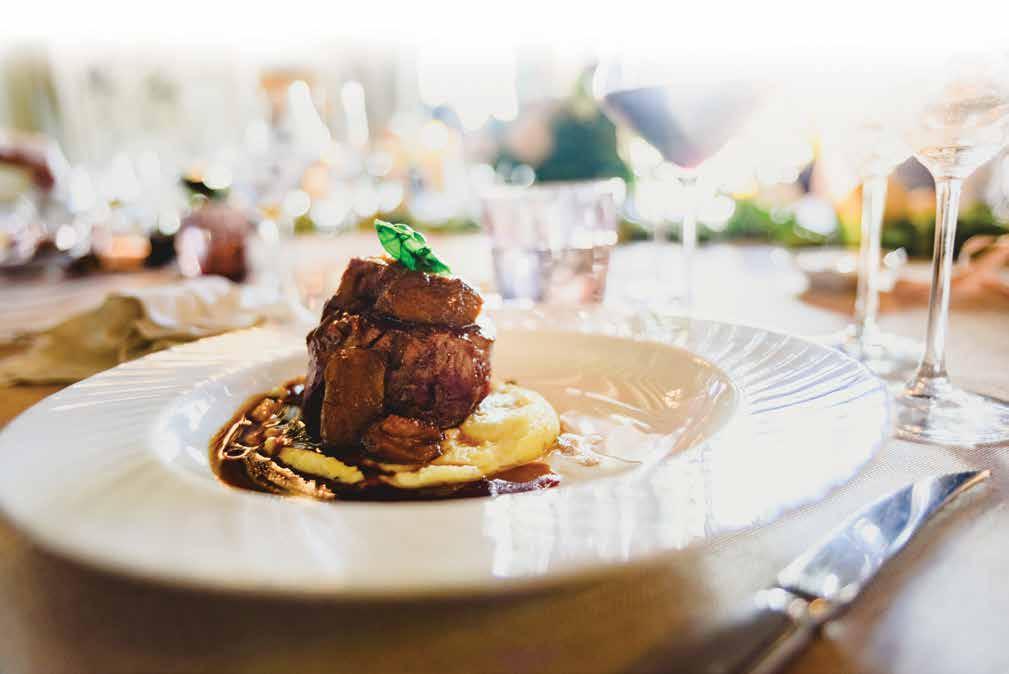