

Quality air is CRITICAL TO COMPRESSION
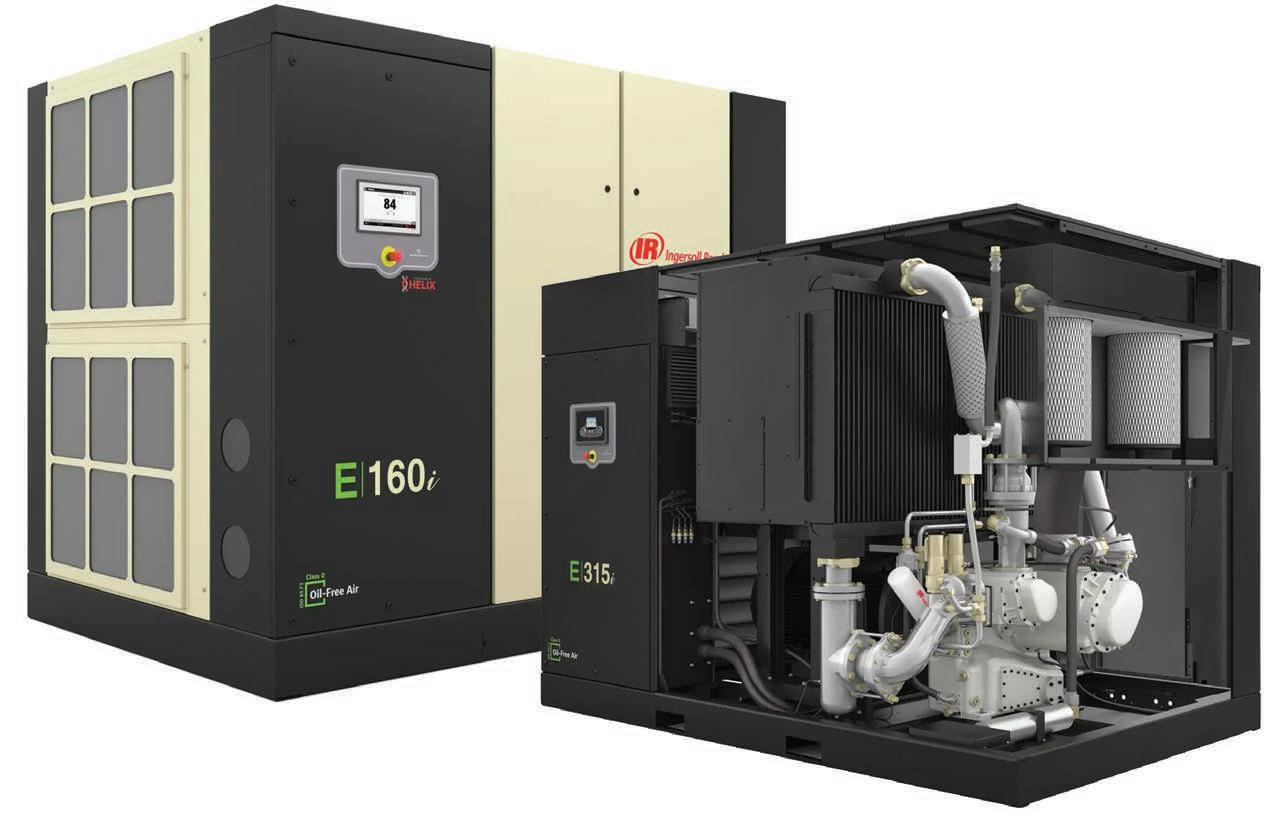
CEO: John Murphy
COO: Christine Clancy
Managing Editor: Mike Wheeler
Editor: Adam McCleery
Ph: (03) 9690 8766
adam.mccleery@primecreative.com.au
Art Director: Michelle Weston
michelle.weston@primecreative.com.au
Sales/Advertising: Joanne Davies
Ph: 0434 785 611
joanne.davies@primecreative.com.au
Production Coordinator:
Salma Kennedy
Ph: (03) 9690 8766
salma.kennedy@primecreative.com.au
Subscriptions AUS NZ O/S
1 year subscription 99 109 119
2 year subscription 189 199 209
For subscriptions enquiries please email subscriptions@primecreative.com.au
The backbone of F&B manufacturing

TCopyright
Food & Beverage Industry News is owned by Prime Creative Media and published by John Murphy. All material in Food & Beverage Industry News is copyright and no part may be reproduced or copied in any form or by any means (graphic, electronic or mechanical including information and retrieval systems) without written permission of the publisher. The Editor welcomes contributions but reserves the right to accept or reject any material. While every effort has been made to ensure the accuracy of information, Prime Creative Media will not accept responsibility for errors or omissions or for any consequences arising from reliance on information published.
The opinions expressed in Food & Beverage Industry News are not necessarily the opinions of, or endorsed by the publisher unless otherwise stated.
© Copyright Prime Creative Media, 2023
Articles
All articles submitted for publication become the property of the publisher. The Editor reserves the right to adjust any article to conform with the magazine format.
Cover
Image: CAPS
Head Office
379 Docklands Drive
Docklands VIC 3008
Ph: +61 3 9690 8766
enquiries@primecreative.com.au
http://www.primecreative.com.au
Sydney Office
Suite 11.01, 201 Miller St, North Sydney, NSW 2060

Printed by: Manark Printing
28 Dingley Ave Dandenong VIC 3175
Ph: (03) 9794 8337
Editor: Adam McCleery
he journey for any food or beverage manufacturer begins with the right facility design and layout.
By successfully achieving this, a manufacturer can optimise flow and dramatically improve productivity by strategically arranging production lines, storage areas, and packaging stations.
Equally important are machinery solutions that facilitate improved food processing. From mixers and fryers to automated filling and packaging lines, the right equipment ensures food products are prepared and packaged correctly, minimising human error and upholding product integrity.
Labelling machines also play a vital role, ensuring accurate representation of ingredients and compliance with nutritional guidelines, which has become increasingly important as consumer demands around these points continues to evolve.
Meanwhile, automation is transforming production processes several industries, including food and beverage.
By integrating automated systems, manufacturers can achieve improved consistency and output while quality control systems equipped with sensors can detect deviations in real-time, allowing for timely adjustments and minimising waste, an essential feature in today’s efficiency and sustainability focused world.
With all of this in mind, it is easy to recognise that the reliability of machinery and facility solutions cannot be overstated.
But it’s not just about production output. Implementing preventive maintenance schedules is another crucial aspect when it comes to reducing downtime and extending the lifespan of equipment.
Meanwhile, in an industry increasingly reliant on technology, predictive analytics powered by IoT and machine learning have demonstrated the ability to forecast equipment failures, allowing manufacturers to address issues before they impact production.
Then there’s solutions centred on improved sustainability.
Modern machinery often includes energyefficient features that lower operational costs while
simultaneously reducing environmental impact. Furthermore, equipment designed for effective waste management is essential for complying with increasingly stringent environmental regulations.
Safety and compliance with regulatory standards are paramount in food manufacturing. Facilities and machinery must align with guidelines set by organisations like the FDA and USDA, ensuring rigorous sanitation and hygiene protocols.
Additionally, worker safety remains a priority; features like emergency stops and safety guards on machinery protect employees in a demanding manufacturing environment.
Technology continues to revolutionise the sector with Enterprise Resource Planning (ERP) systems becoming increasingly popular, from inventory management to production scheduling, all designed to enhance overall operational efficiency.
Traceability solutions, such as 2D Barcodes, are another innovation that has helped strengthen the supply chain, which has proven crucial for quality assurance and effective recall procedures moving forward.
Finally, the human element cannot be overlooked. Ongoing training and skill development for operators ensure that the workforce is equipped to handle the latest machinery and maintain high quality standards.
This investment in people is what ultimately drives innovation and competitiveness.
This interplay between facility design and machinery solutions is vital for the food and beverage manufacturing sector.
As technology evolves and regulatory landscapes shift, manufacturers must adapt to maintain their edge. The commitment to efficiency, quality, safety, and sustainability will determine who thrives in this competitive industry.
And as we delve into those themes in this issue, we invite you to explore the innovations and strategies that are helping shape the future of food and beverage manufacturing.
Until next month, happy reading.
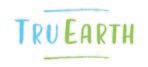

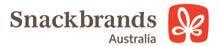
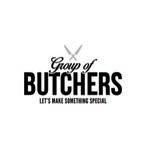
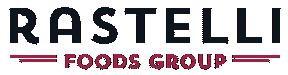
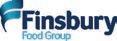
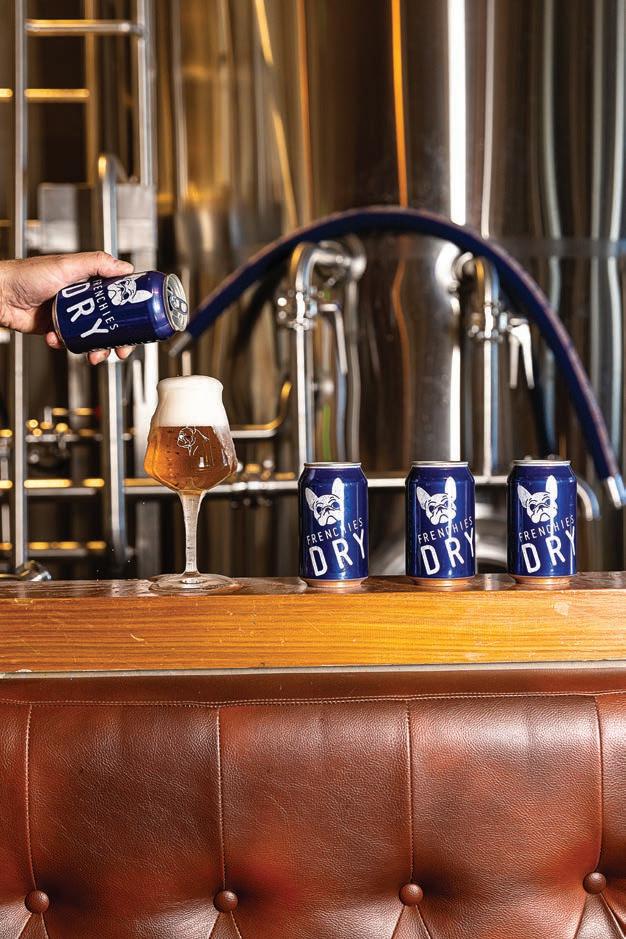
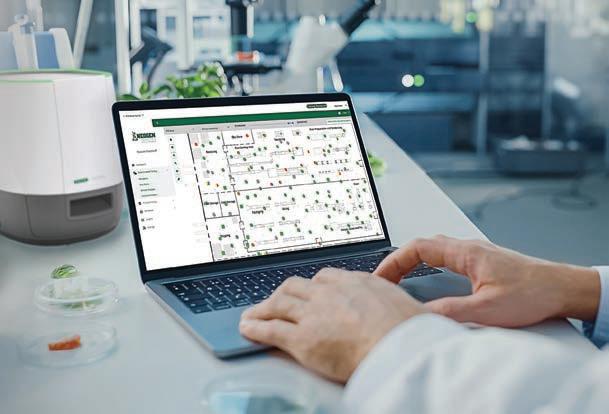
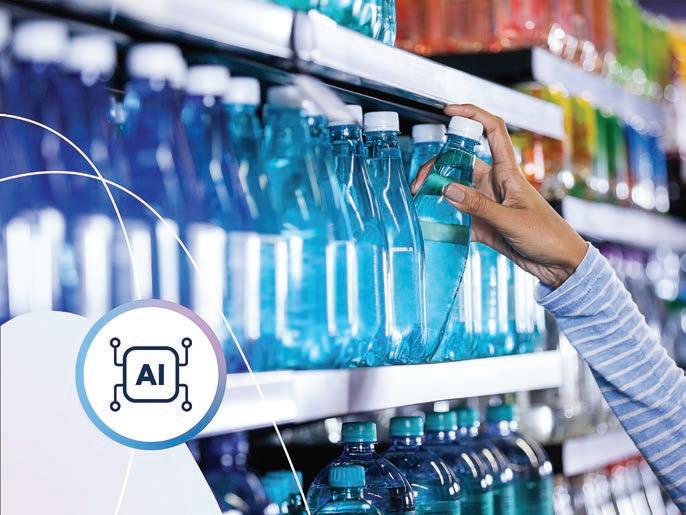
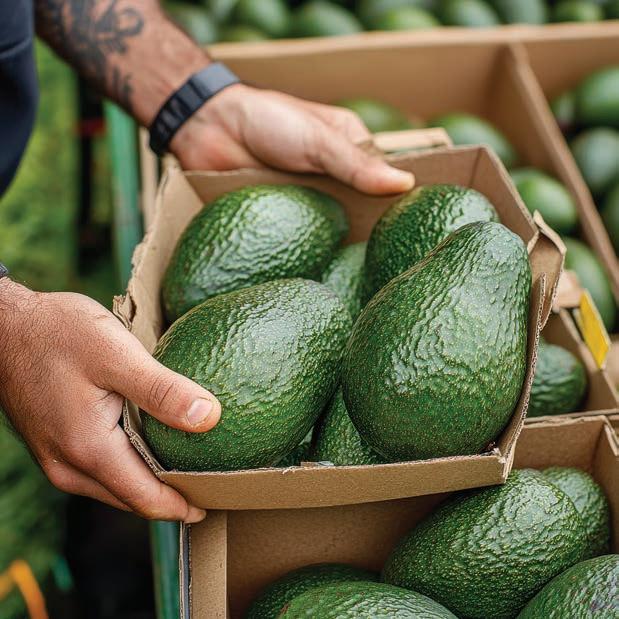
16 MEET THE MANUFACTURER
Frenchies Brewery has adapted to the Australian market, creating a unique blend of two esteemed brewing cultures.
20 AIR COMPRESSION
Optimised air compression systems, like those from CAPS, play a vital role in the success of food and beverage manufacturers.
22 PACKAGING
Krones and PureCycle Technologies are working together to transform polypropylene recycling.
24 AUTOMATION
Automation in manufacturing offers many benefits, as demonstrated by Lumix’s solutions.
26 DIGITAL SOLUTIONS
Neogen Analytics is helping transform how food and beverage manufacturers manage and interpret data.
28 TRACEABILITY
GS1 helps manufacturers adopt 2D barcode technology to improve transparency and enhance consumer engagement.
30 COLD CHAIN
WestCool Transport offers reliable, high-quality refrigerated transport services with the support of Scully RSV.
32 INGREDIENTS
Biospringer by Lesaffre was the first company to manufacture yeast extract for commercial purposes back in 1958.
34 DIGITALISATION
RELEX Solutions is helping the industry capitalise on the rise of Artificial Intelligence and Machine Learning technology.
38 MEGATRANS
A wrap up and review of this year’s MEGATRANS expo from the heart of Melbourne.
40 GOVERNMENT INVESTMENT
Government investment continues to help enhance the Australian food manufacturing sector’s global competitiveness.
42 CIRCULAR ECONOMY
Chemists at the University of New South Wales have developed a new battery component that utilises food-based acids.
44 SOFT PLASTICS SCHEME
The Queensland Government has committed to launching a new pilot program for soft plastics recycling inside the state.
46 FOOD SCIENCE
The University of Queensland has created new tissue-culture technology specifically for the improved production of avocados.
48 CROP OUTLOOK
The Australian agriculture sector’s gross value of agricultural production is expected to rise over the coming year.
50 PRODUCTS
Celebrating four decades of OrgraN
As OrgraN celebrates its 40th anniversary, the business reflects on a journey marked by innovation, resilience, and a steadfast commitment to health and wellness.
As one of the first companies to innovate and produce gluten free products, the OrgraN brand has continued to be recognised by consumers across the world.
Since its inception, OrgraN has grown from a small retail store in Victoria, into a globally recognised allergen-free food producer, with its products now reaching over 70 countries.
This milestone is not just a celebration of years but a testament to OrgraN’s enduring impact on families and individuals around the world who rely on safe, nutritious, and delicious food options.
OrgraN was founded with a clear mission: to create food products that cater to the growing need for allergenfree options. In the early years, from
1985 to 1990, OrgraN’s rapid growth saw the company relocate five times in just five years as they revolutionised the market with their allergen free products.
Each move represented a step closer to fulfilling its mission, driven by a passion to ensure that those with dietary restrictions could still enjoy delicious and wholesome meals.
Today, OrgraN’s product range includes over 100 products, from breakfast cereals to crispbreads, pasta, and flour. Max Buontempo, the managing director of the business, adds that OrgraN offers safe and healthy solutions for every meal.
“This mission is more than just a statement, it’s a guiding principle that influences every aspect of the company’s operations. Roma’s values-led approach is evident in its commitment to its people, the health and wellness of the community, and a deep pride in its heritage, which spans more than seven decades,” said Buontempo. innovate, introducing new product lines its consumers,” F
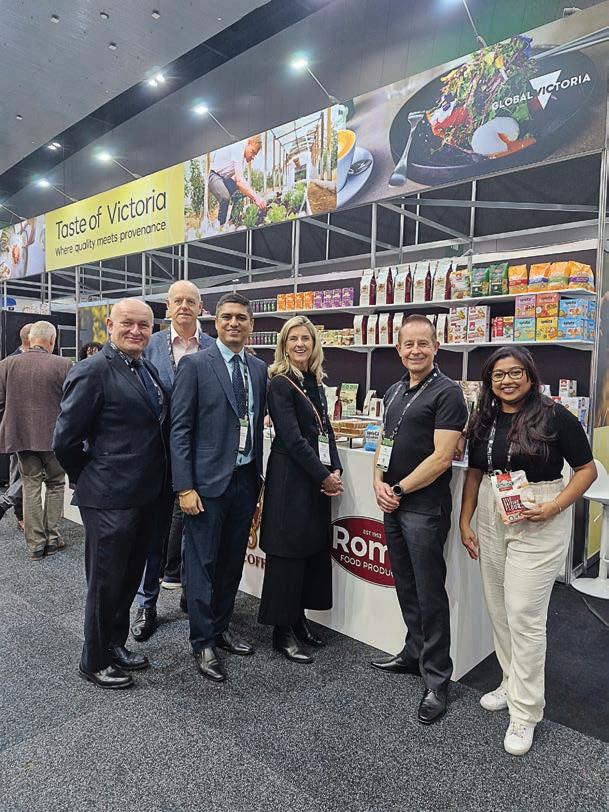
Nissin Foods acquires Australian frozen food manufacturer
Nissin Foods has signed a Share Sale and Purchase Agreement to acquire the Australian frozen food manufacturer.
The company, ABC Pastry, is based in Sydney and manufacturers frozen dumplings, offering both its own and third-party branded products.
The acquisition is valued at AU$33.7 million, and upon completion ABC Pastry will become a wholly owned subsidiary of Nissin Foods, focusing on the frozen food market and serving retailers across Australia.
Nissin Foods anticipates that its expertise as a publicly listed company will enhance ABC Pastry’s operational and financial management, supporting its long-term growth and diversifying Nissin Foods’ business portfolio.
This acquisition is seen as a strategic move for Nissin Foods to enter the expanding Australian frozen food market.
Demand for frozen dumplings is increasing, driven by rising Asian migration to Australia and a growing
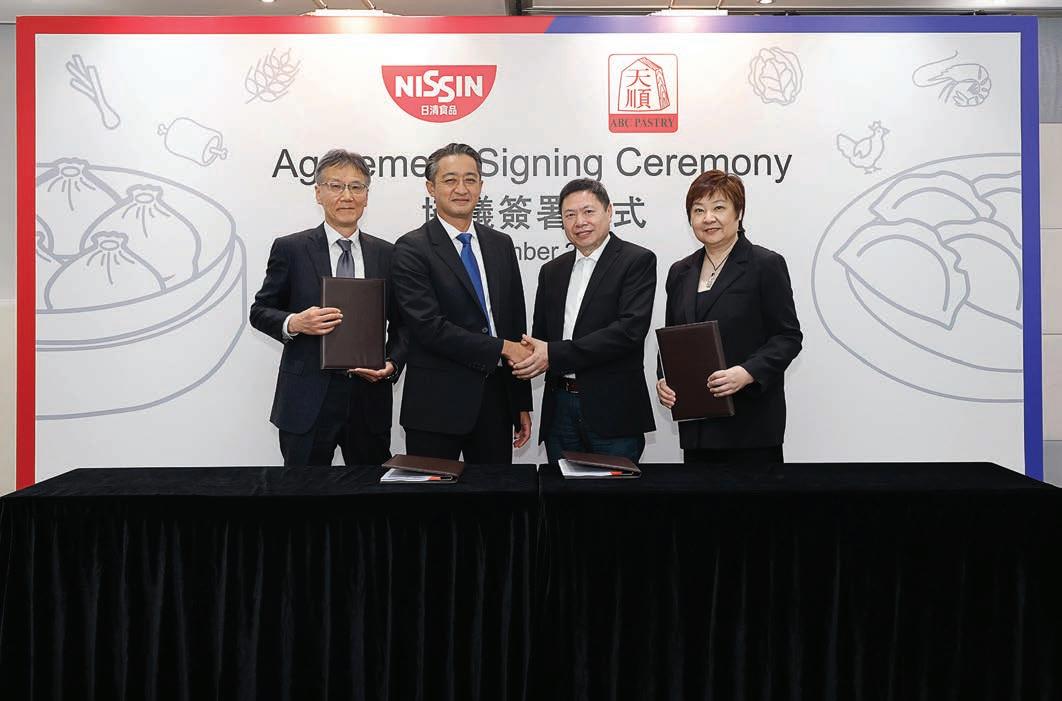
Food Group
OrgraN has grown from a small retail store in Victoria into a globally recognised allergen-free food producer.
The Nissin
expects opportunities for growth in the premium frozen food sector in Australia.
Reduce salt while improving taste of your formulations thanks to Biospringer’s fermentation-based ingredients
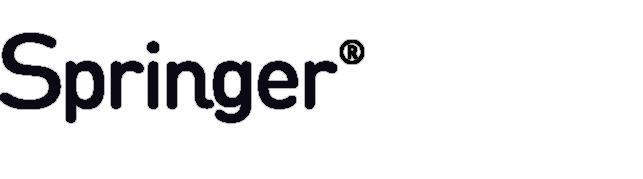
Your main challenges:
Reducing salt
Improving taste naturally
Selecting clean label ingredients
Our ingredients benefits:
Springer® Umami is a range of fermentation-based ingredients labeled as “yeast extract” in Australia. Yeast extract is a versatile ingredient that enables food formulators to reduce salt and sodium levels by up to 30%, while improving the taste of the final product, thanks to its naturally occurring umami.
Biospringer by Lesaffre’s guarantees
Multipe sourcing
We have 10 manufacturing sites worldwide*
Sustainable ingredient
Our ingredient is coming from fermentation, a natural process used for centuries Visit our website to learn more www.apac.biospringer.com
Lead time
Be delivered quickly and on time, thanks to our multiple factories
Product quality
French product quality and consistency
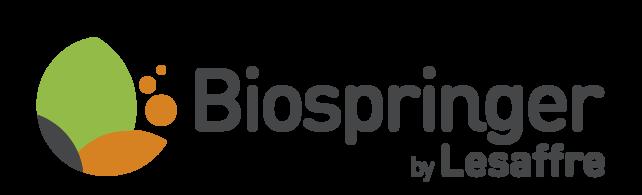
Global brewer continues to invest in Australian market
The name and design for the $1.8 million upgrade of the James Boag’s Brewery visitor centre has been revealed, with the iconic visitor attraction to be relaunched as the Boags Brewhouse.
The Boags Brewhouse will serve as the new home for Tasmania’s beloved James Boag’s Brewery brand and its products, becoming a key tourism destination for both locals and visitors.
The development will honour the heritage of the existing building while introducing a new brewhouse hall, tasting area, and a redesigned beer garden. A relocated Boag’s museum will also be featured, highlighting the iconic brand’s 143-year history.
Inside, the Boags Brewhouse will incorporate Tasmanian timber throughout, from the bar to the ceiling. The walls will display approximately 1,000 limited-edition beer cans and bottles, alongside memorabilia spanning
Local distiller takes home highest honour at IWSC awards
Naught Gin has made history by winning the IWSC Classic Gin Trophy at the renowned International Wine & Spirit Competition (IWSC), the oldest spirits competition worldwide.
Earlier this year, Naught’s Overproof Gin earned a gold medal at the IWSC and since progressed to trump other classic gins from around the globe to secure the IWSC Classic Gin Trophy.
This achievement follows a series of gold medals for Naught in 2024 at major international spirits competitions, spanning the San Francisco Spirits Competition, Global Gin Masters, Singapore World Spirits Competition, and the Australian Distilled Spirits Awards.
With this latest win, Naught Gin has cemented its reputation as one of Australia’s, and the world’s,
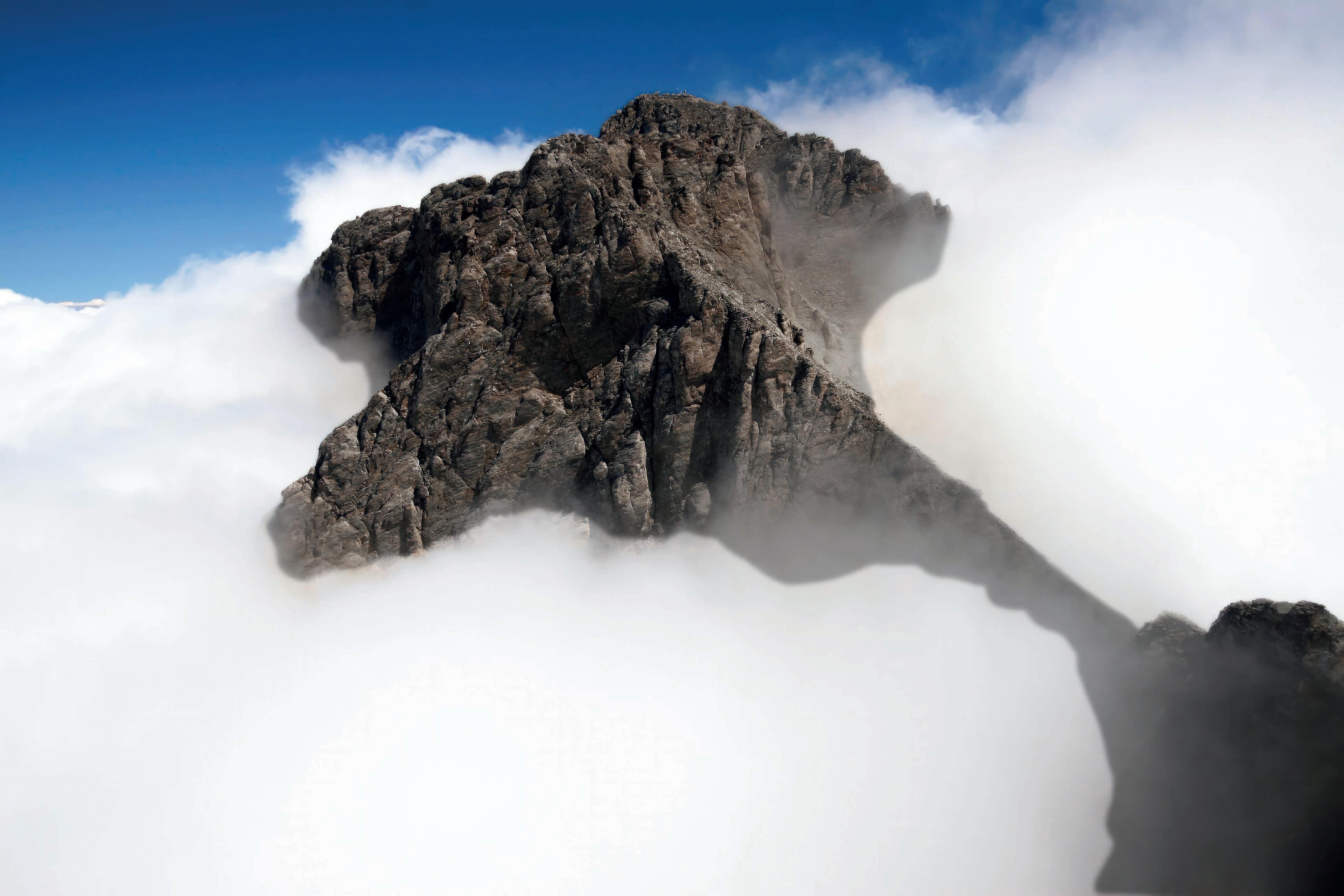
Your Confidence in the Future
Mixer grinder
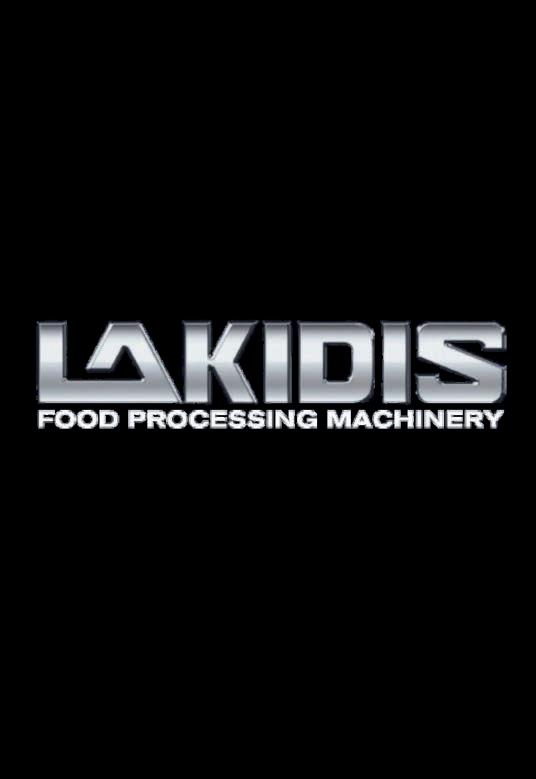

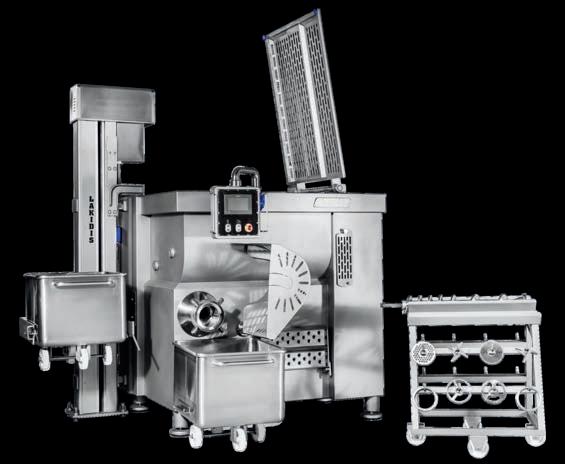
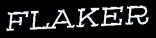

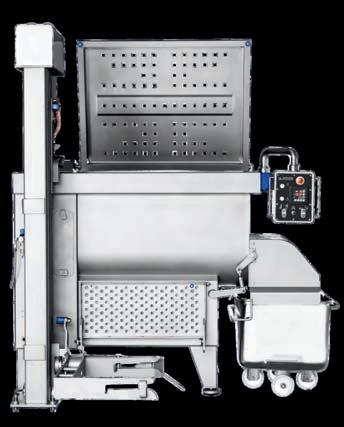
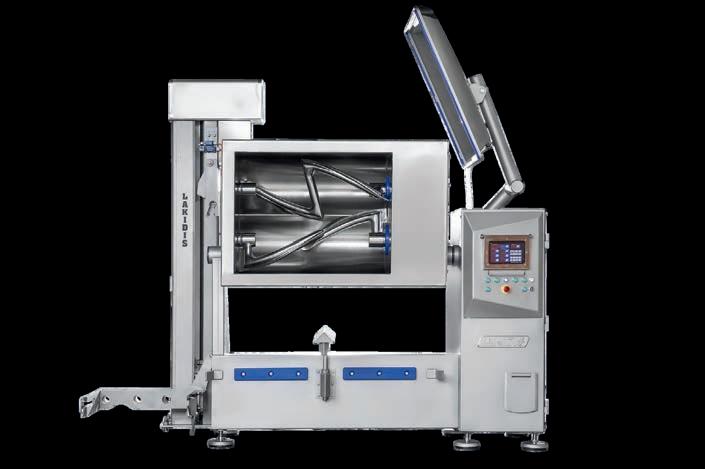

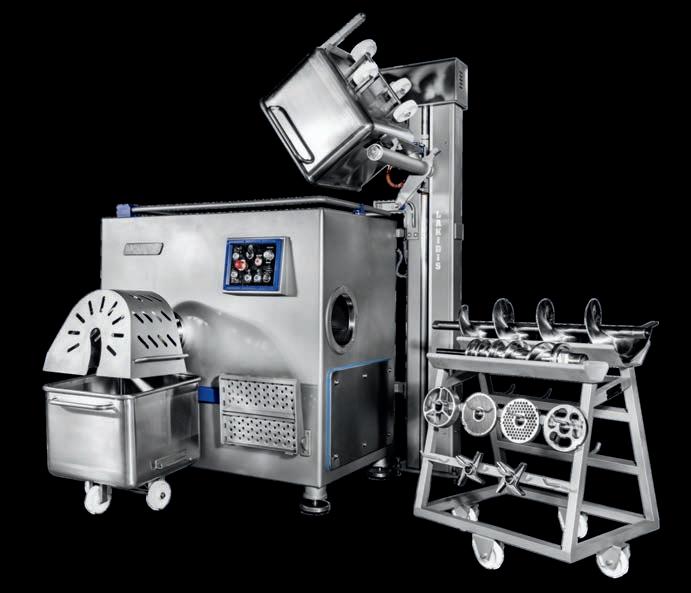
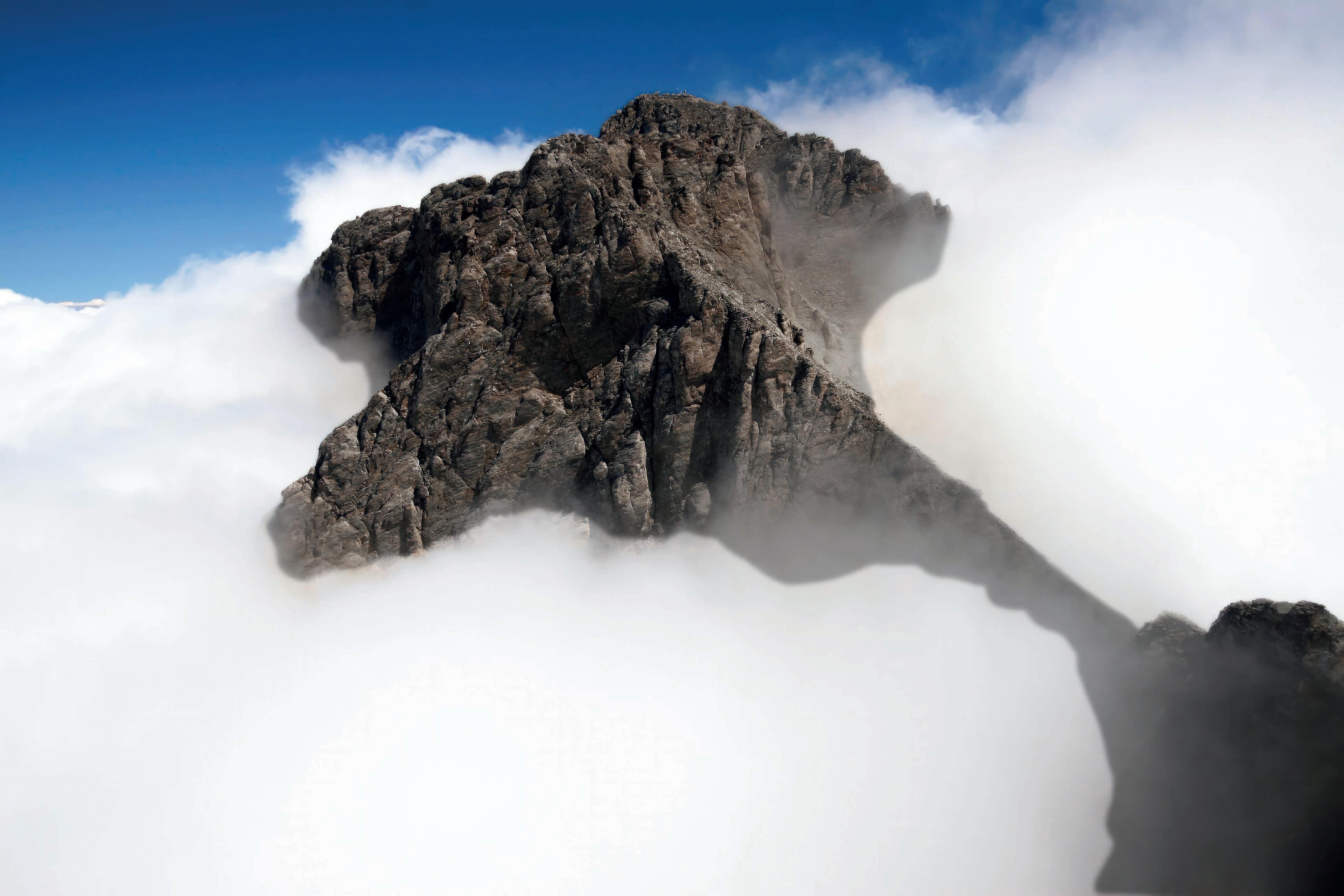
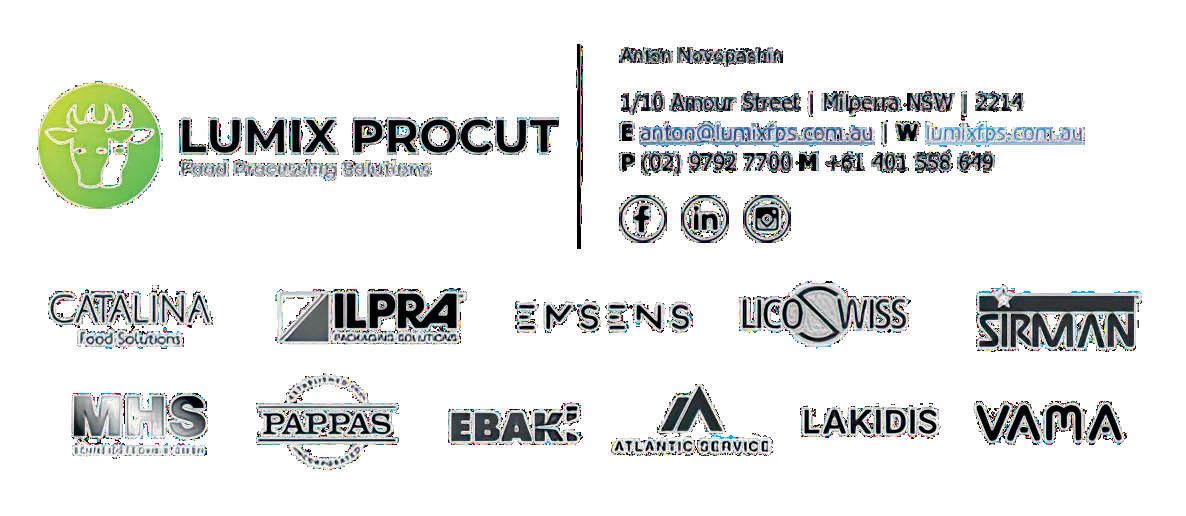

Coca-Cola Europacific Partners (CCEP) Australia has announced its founding membership of the Empowered Women in Trades (EWIT) Alliance.
EWIT is a not-for-profit organisation focused on increasing women’s participation in the Australian manufacturing, construction, and renewable energy sectors.
Its goal is to raise the percentage of women in skilled trades from 3 per cent to 30 per cent by 2030. The alliance was created to enable organisations of all sizes to support EWIT’s objectives.
Alliance members will participate in initiatives aimed at promoting skilled trades to women and girls, including tool skills days, talent attraction programs, school outreach, and participation in expos, conferences, and advocacy efforts.
CCEP Quality Assurance team
CCEP becomes founding member of women in industry alliance SPC and The Original Juice Company merge
Two iconic Australian businesses are merging, together with the powdered milk business of a third Australian founded business, Nature One Dairy.
The Original Juice Company will acquire SPC Global, and the powdered milk business owned by Nature One Dairy via a binding Merger Implementation Deed and Share Sale Agreements subject to several conditions including approval by the Original Juice Co. shareholders in November 2024.
The Original Juice Company intends to issue 133 million shares to the shareholders of SPC as consideration for the Transaction. Concurrently with the acquisition of SPC, OJC intends to issue up to 29 million shares and pay cash of up to $6 million to the shareholders of Nature One Dairy.
On completion of the Transaction, OJC, SPC and NOD shareholders are expected to hold 15.5 per cent, 69.2 per cent and 15.3 per cent of the Combined Business respectively. The Combined Business is expected to deliver more than
member, Bolor Erdenekhuu, is an example of the successful work being undertaken by EWIT to promote the benefits of a skilled trade to women.
“I am a tangible example of how programs like EWIT can effectively support women entering skilled trades,” she said.
“EWIT not only provide technical skills but also build confidence and open pathways for women in industries where they are traditionally underrepresented.
“Programs like EWIT not only benefit individual participants but help businesses address skills shortages and improve workforce diversity.”
A key pillar of CCEP’s ‘This is Forward’ global sustainability action plan is to champion inclusion, challenge inequality and support economic mobility.
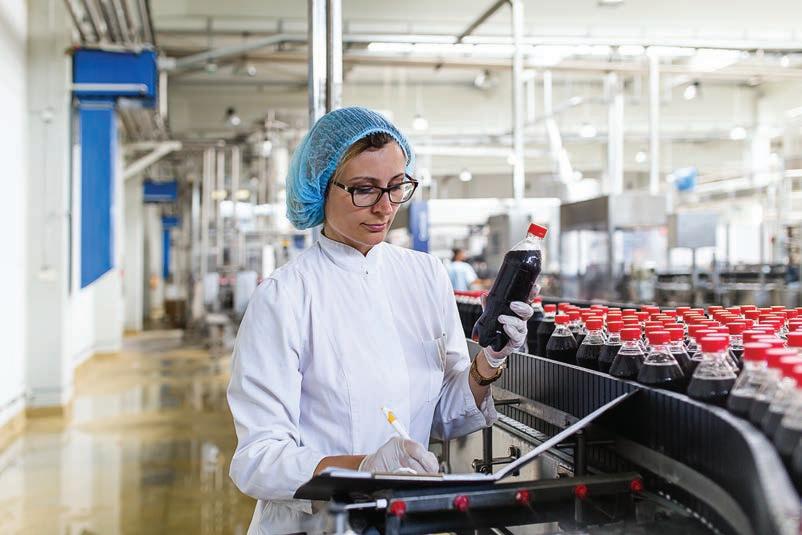
Focus areas include enhancing the company’s gender diversity and fostering the growth of emerging female talent.
Focus areas include enhancing the
company’s gender diversity and fostering the growth of emerging female talent as it strives to meet its 2030 goals of having
one-third of its workforce be women and 45 per cent of management positions held by women. F

$400 million of revenues and more than
$29 million of EBITDA in FY25.
Former Asahi Beverages Group CEO and current SPC director, Robert Iervasi has been appointed the managing
director of the merged business, which will own and operate three business divisions, namely SPC, The Original Juice Co. and Nature One Dairy. Together the businesses create a
substantial Australian based and owned global food and beverage companies that will continue to support Australian producers and execute on a global growth strategy. F
Concrete consisting of coffee grounds makes its debut
Major Road Projects Victoria (MRPV) and BildGroup are using concrete mixed with biochar from spent coffee grounds as a partial substitute for river sand in the Pakenham Roads Upgrade.
Organic waste like spent coffee grounds contributes 3 per cent of greenhouse gas emissions and can’t be directly added to concrete due to decomposition risks.
Instead, the grounds are converted into biochar.
Australia generates 75 million kilograms of coffee waste annually, which could replace 655 million kilograms of sand, while globally, 10 billion kilograms could replace 90 billion kilograms.
For this project, five tonnes of coffee grounds (about 140,000 coffees) were converted into two ton of biochar, laid in a 30-cubic-metre footpath.
This initiative is part of broader
circular economy efforts, including reusing soil and using foam bitumen and rubber tyre road barriers. MRPV’s Brendan Pauwels highlighted the ecological benefits and cost-cutting potential of coffee concrete.
RMIT’s Dr. Rajeev Roychand emphasised the importance of diverting organic waste from landfills.
BildGroup’s CEO, Stephen Hill, noted that this project diverted 140,000 coffees from landfill and saved over three ton of sand. RMIT previously conducted a trial in Gisborne, Victoria, showing coffee concrete’s potential to be 30 per cent stronger by using low-energy biochar production.
RMIT is now seeking commercialisation partners in construction and agriculture to further develop biochar products, with support from various organisations and local Indigenous coffee suppliers. F

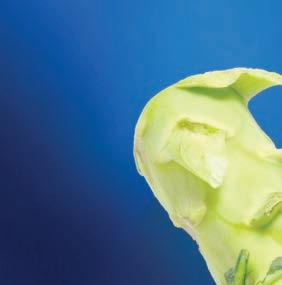
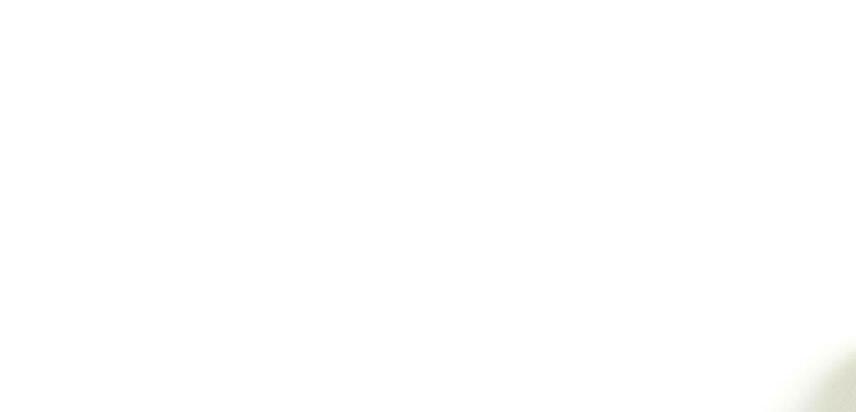


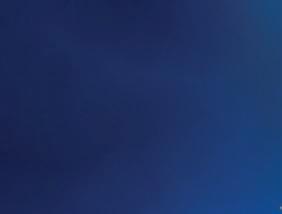



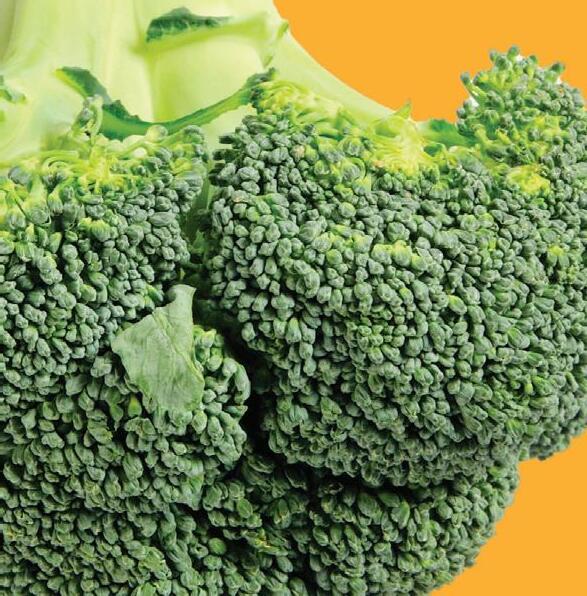

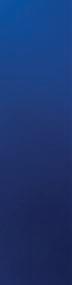
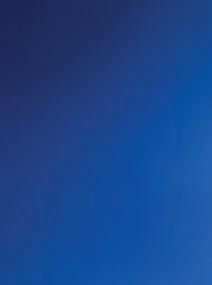
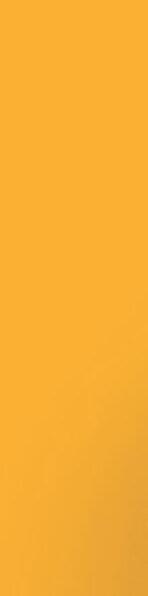


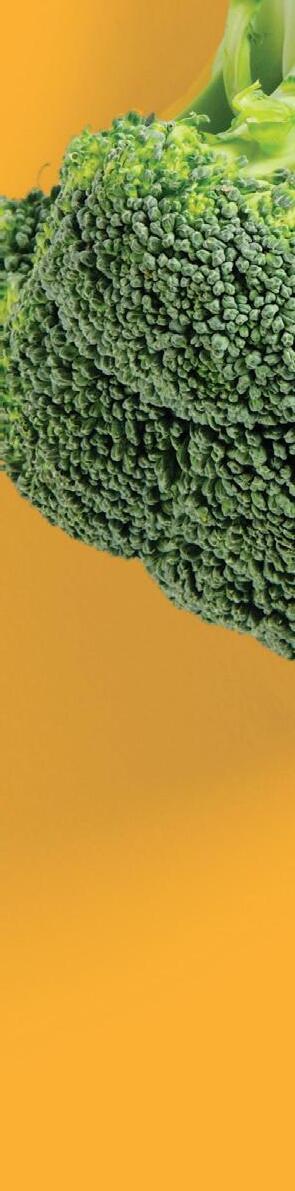
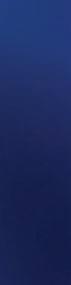
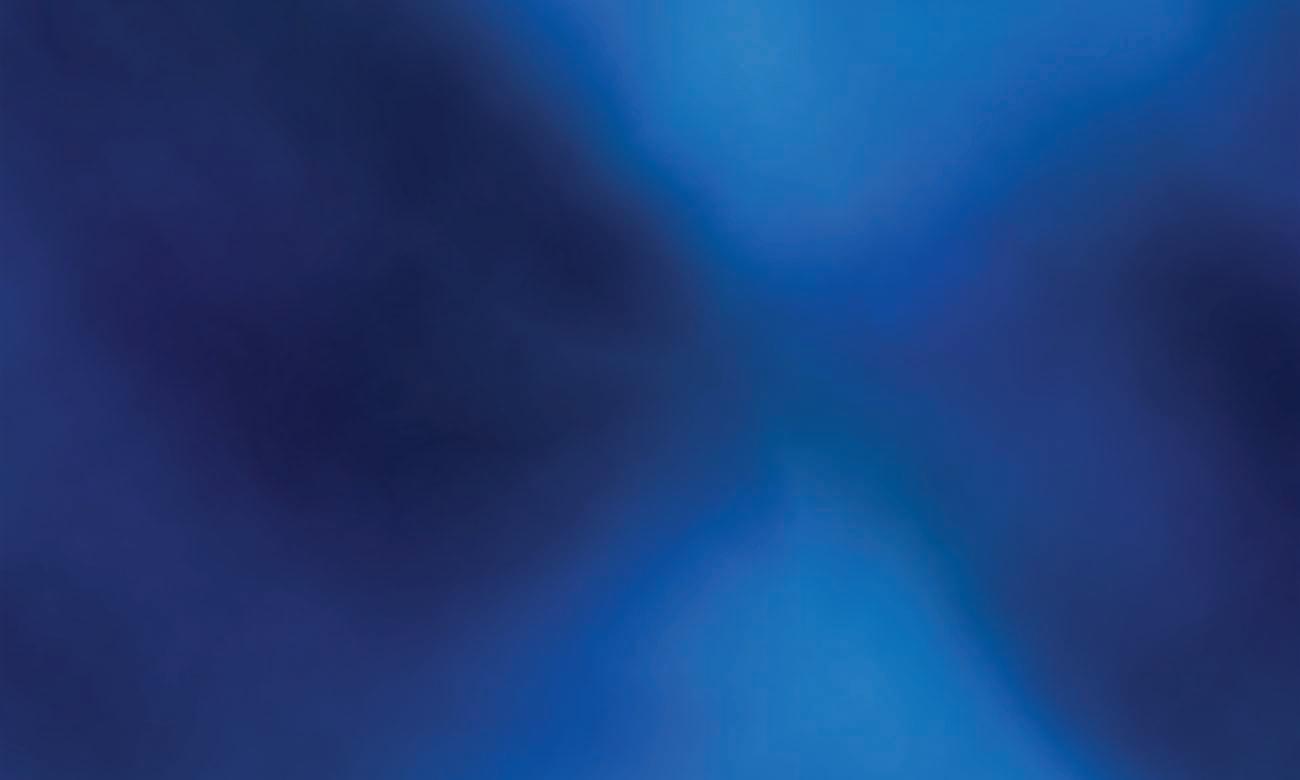

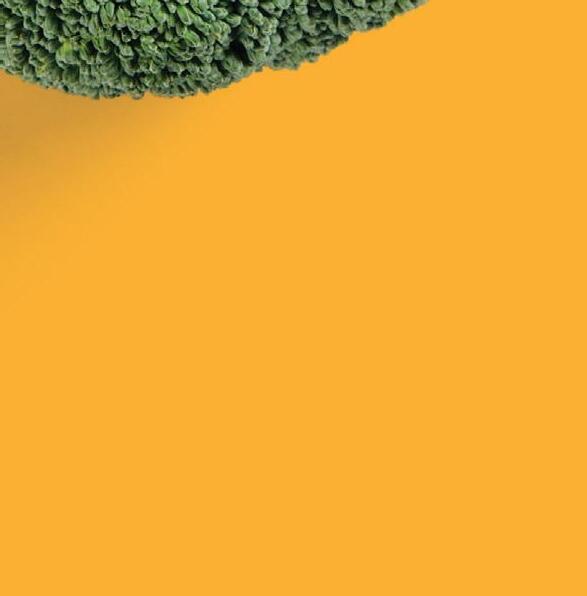
RMIT’s Dr. Rajeev Roychand emphasised the importance of diverting organic waste from landfills.
Image:
Carelle
Mulawa-Richards, RMIT University
ACCC receives boost in funding
The ACCC has welcomed the announcement of $30 million in additional funding over three and a half years for investigations and enforcement relating to the supermarket and retail sector.
ACCC Chair Cass-Gottlieb said the added resources would greatly strengthen the ACCC’s enforcement and compliance efforts in a crucial sector that millions of Australian consumers depend on.
“Active, evidence-based enforcement of the Competition and Consumer Act is core to the ACCC’s work, and is essential for deterring conduct that harms consumers, competition and fair trading, and by extension productivity and the wider economy,” said Cass-Gottlieb.
“The ACCC’s work has always reflected the current issues impacting the Australian economy, consumers and businesses – informed by evidence, information and intelligence from a range of sources.
“This includes reports to our Infocentre and social media, engagement with consumer stakeholders and other government departments and regulators, as well as pro-active surveillance.
“This funding will enable us to escalate a range of investigations in this sector, including in relation to potential
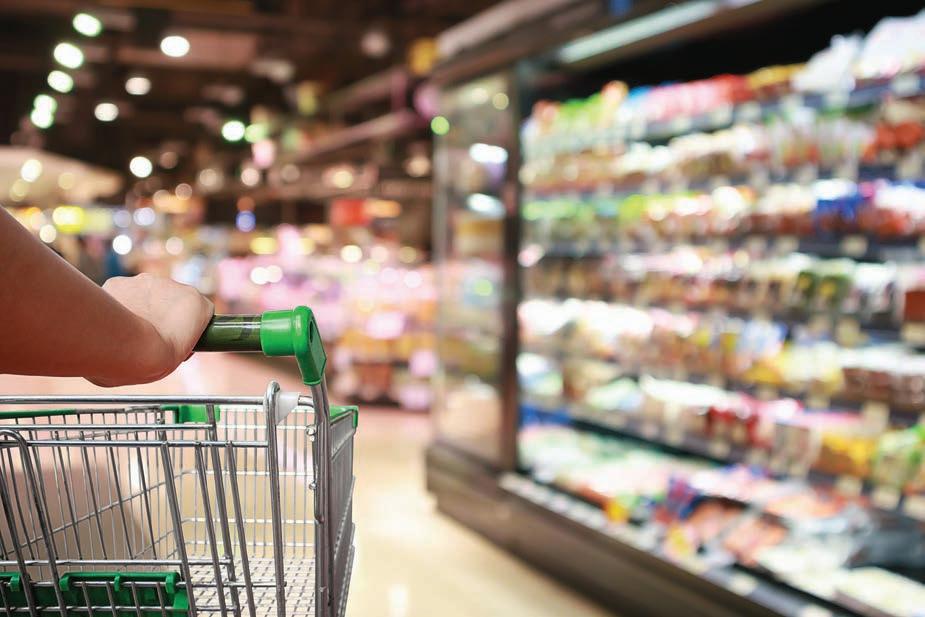
misleading pricing claims or practices, claims about delivery timeframes and costs including for regional and remote Australians, and businesses misrepresenting consumers’ rights under the Australian Consumer Law.”
Each year in February and March,
the ACCC outlines its compliance and enforcement priorities.
This year, those priorities include addressing competition, consumer issues, fair trading, and pricing concerns in the supermarket sector, particularly focusing on food and groceries. While
New appointments to Coopers Foundation Board
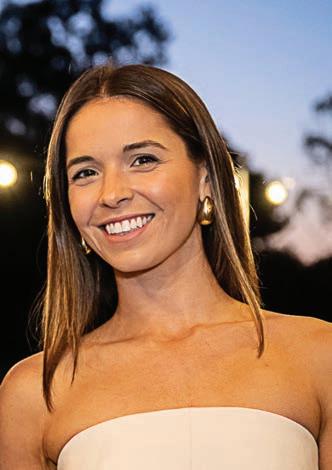
Aformer South Australian Premier and a sixth-generation family member have been appointed to the Board of the Coopers Foundation.
Steven Marshall and Bec Cooper have joined the Board of Governors of the charitable foundation established in 2006 by Coopers Brewery and the Cooper family.
Marshall served as the 46th Premier of South Australia from 2018 to 2022.
After 14 years of dedicated service, he left Parliament in February 2024. A recipient of the Centenary of Federation Medal in 2001 for his services to the disability sector, Marshall is also Chair
of the Australian Advisory Council for MITRE.
Bec Cooper has worked in the advertising and fashion industries, and currently operates a veterinary practice for racehorses which she co-founded.
The daughter of Coopers Foundation chair Mel Cooper, Cooper has worked at the Brewery in various casual roles and supported the Foundation over the past 10 years.
“Steven and Bec both have a strong commitment to community service in line with the Foundation’s aim to improve the quality of lives of Australians in need,” said Mel.
“Throughout his whole career, and
The ACCC has welcomed the Federal Government’s additional funding which is designed to support investigations and enforcement in the supermarket sector.
the ACCC is already actively pursuing these issues, the additional funding will enable it to identify, advance, and expedite further matters.
The funding will add approximately $8.5m each year for the next 3 and a half years from January 1, 2025. F
most notably during his time as Premier and a member of Parliament, Steven has given tireless service to the community. Steven also comes from a family business background and shares the high value our family places on philanthropy.
“Bec is the first of the sixth generation of the Cooper family to join the Foundation Board. Bec has been actively involved with the Foundation’s fundraising work for over a decade and I’m delighted to see the next generation continuing the family’s charitable work.”
The total amount of funds it has donated is now more than $7.8 million, with 260 charities having received financial support since its inception. F
Image: Coopers Foundation
Bec Cooper is the first of the sixth generation of the Cooper family to join the Foundation Board.
Fonterra release revised strategy to grow value
Fonterra Co-operative Group Ltd has released its revised strategy, which will see the Co-op deepen its focus on its high-performing Ingredients and Foodservice businesses to grow value for farmer shareholders and unit holders.
This follows a strategic review that confirmed the Co-op’s strengths as a B2B dairy nutrition provider, resulting in Fonterra’s decision to explore divestment options for its global Consumer businesses.
Chairman Peter McBride says the revised strategy creates a pathway to greater value creation, allowing the Co-op to announce enhanced financial targets and policy settings.
“Through implementation of our strategy, we can grow returns to our owners while continuing to invest in the Co-op, maintaining the financial discipline and strong balance sheet we’ve worked hard to build over recent years,” said McBride.
“We have increased our target average return on capital to 10-12 per cent, up from 9-10 per cent, and announced a new dividend policy of 60-80 per cent of earnings, up from 40-60 per cent. At all times, we remain committed to maintaining the maximum sustainable Farmgate Milk Price.”
Looking out to the next decade and beyond, Fonterra has made six strategic choices.
The first is to deliver the strongest farmer offering by working alongside farmers to enable on-farm profitability and productivity and support the strongest payout.
Fonterra are also aiming to deepen Fonterra’s position as a world-leading provider of sophisticated dairy ingredients and build trading capability to grow both the Farmgate Milk Price and earnings.
The company wishes to keen up its momentum in Foodservice by expanding its successful Foodservice business in China and other key markets to grow earnings.
Investing in operations for the future is also massive for Fonterra.
The co-op will invest in an efficient manufacturing and supply chain network that allows flexibility to allocate milk to the highest returning product and sales channel.
Fonterra is also prioritising sustainability by further improving the Co-op’s sustainability credentials and strengthen partnerships with customers who value this position.
The co-op will also prioritise using science and technology to solve the Co-op’s challenges and build on competitive advantages. F
Fonterra has made six strategic choices including working alongside farmers to enable on-farm profitability.
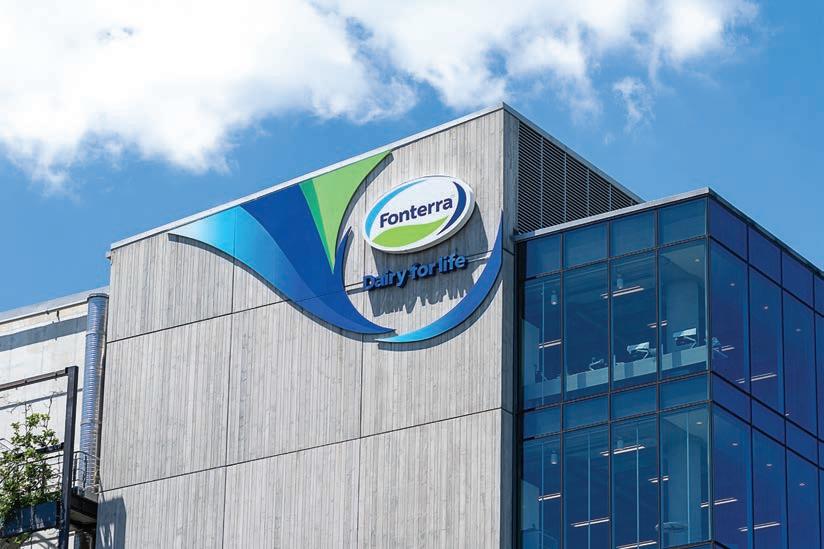
& Beverage Industry News, 150 x 195 mm, Packaging,
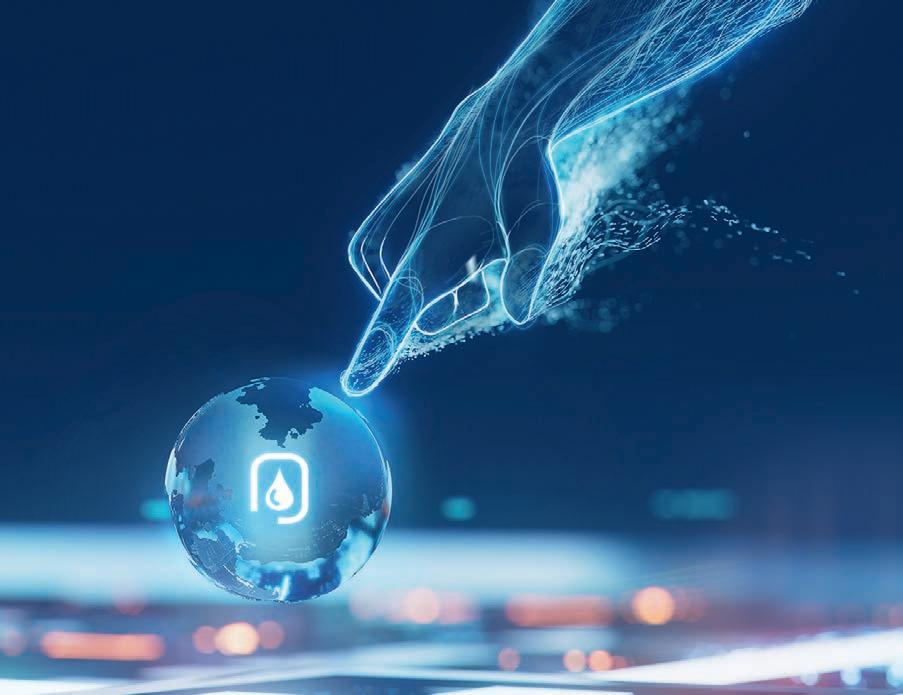

Perfectly integrated packaging solutions
Reliability, efficiency and optimised resource consumption: Krones’ innovative filling and packaging concepts are perfectly tailored to your particular needs – for glass bottles, PET containers or cans.
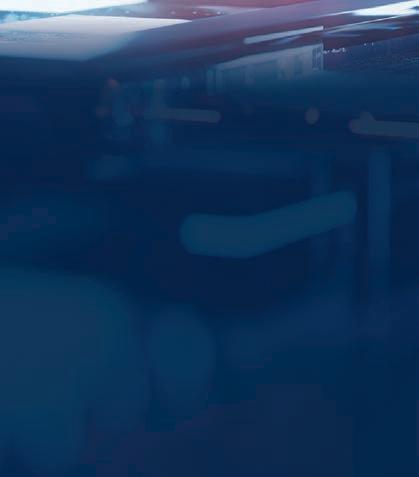
The Federal Government has appointed five new directors to help Wine Australia in research, development, and extension, covering issues of national importance for the local wine industry.
These new director appointments work to ensure compliance with Wine Australia’s regulatory functions by investing in research and development, building markets, and disseminating market information and knowledge.
Minister for Agriculture, Fisheries and Forestry, Julie Collins, announced the directors who she said were qualified and possess a wealth of skills, expertise, and board experience.
“They will help foster and encourage profitable, resilient and sustainable Australian winegrape and wine businesses,” said Collins.
“Wine Australia is well positioned
New directors appointed to Wine Australia board Report reveals how AUS red meat stacks up globally
MLA has released the 2024 State of the Industry Report on the economic importance of the Australian red meat sector and how it stacks up against our global counterparts.
Entering 2023, the red meat sector was on the tail end of three years of rebuilding.
The sector shifted during the year, driven by worsening conditions and poor seasonal outlooks, which impacted confidence.
Peak production and slaughter numbers started moving through the supply chain, driving prices down to long-term lows. Despite the ease in prices, industry remained resilient in the face of this instability due to strong demand across a diversifying export market and strength in the processing sector. Industry turnover remained above levels from five years ago, totalling $81.7 billion, though it was 2 per cent below the previous year.
to continue supporting a competitive wine sector, growing domestic and international markets and protecting the reputation of Australian wine, thanks in great measure to the contributions of the outgoing board members.”
All newly appointed, the following directors will serve a three-year term from 1 October 2024.
• A ngeline Achariya, Victoria
• Roslyn Baker, Queensland
• A ndrew Kay, South Australia
• E lizabeth Riley, New South Wales
• Peta Slack-Smith, Victoria.
The appointments join Wine Australia’s incumbent chair, Dr Michele Allan AO.
They replace the outgoing board of Catherine Oates, Catherine Cooper, Frances-Anne Keeler, Mitchell Taylor, Justine Brown and John Lloyd.
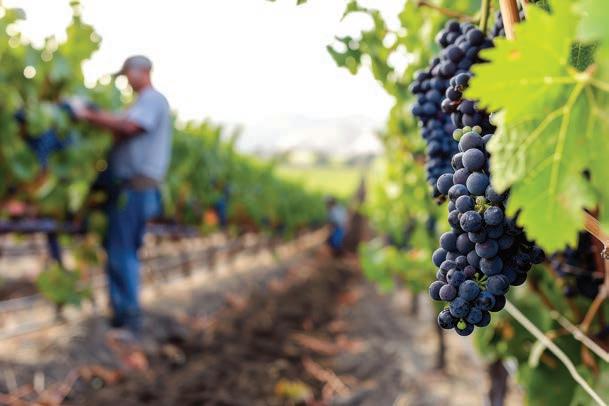
The Government’s $3.5 million Grape and Wine Sector LongTerm Viability Package includes an independent impact analysis led by Dr Craig Emerson.
This package concerns fair trading, competitive relationships, contracting practices and risk allocation in the sector. Public consultation for the analysis is now open. F
Most of this turnover came from three states: NSW (28 per cent), Victoria (24 per cent) and Queensland (22 per cent), with WA (14 per cent), SA (8 per cent), Tasmania (3 per cent), and the NT (1 per cent) rounding out the remaining.
Over 400,000 people were employed through the sector, lifting last year alongside 76,999 red meat businesses, also up 3.2 per cent on the previous year, indicating strength in the industry.
The value of red meat and livestock exports rose 3 per cent to $18.2 billion in 2022–23.
In 2023, Australia was the secondlargest beef exporter and the world’s largest sheep meat and goat meat exporter.
Volumes of Australian beef and veal exports lifted 27 per cent on 2022 totals.
Sheep meat exports were up 15 per cent, creating the highest export figure on record, while goat meat exports lifted an impressive 55 per cent.
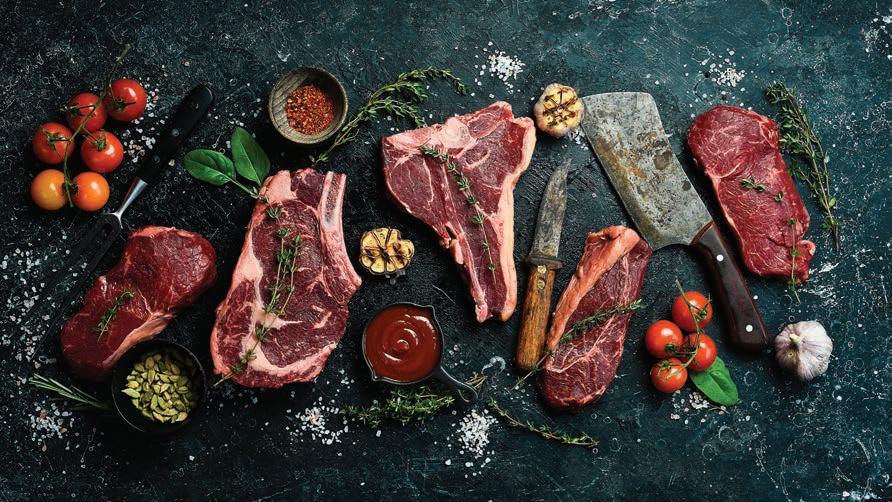
The United States and China were
Industry turnover remained above levels from five years ago, totalling $81.7 billion.
markets that supported exports during this period of high supply.
Goat meat exports totalled 33,904 tonnes shipped weight in 2023, up
55 per cent on the year prior. The US remains the largest destination for goat meat, accounting for 42 per cent of exports or 14,477 tonnes in 2023. F
The new appointments join Wine Australia’s incumbent chair, Dr Michele Allan AO.
Ken Whittingham and Mark Robinson of Fort Restructuring have secured the sale of pioneering plant-based food producer Fenn Foods’ major assets, days after the Sunshine Coast company entered liquidation.
Gold Coast-based Smart Foods have entered an agreement to purchase plant and equipment, stock, vEEF and LOVE BUDS brand names, registered IPs, and other intellectual property related to the producer of meat-free alternatives.
“As one of the largest suppliers of plant-based and meat free products to major supermarkets in Australia, there was a very real risk that consumers could have faced product shortages,” said Whittingham.
“This combined with the fact we are dealing with stocks of perishable goods
Queensland food producer’s assets saved from liquidation Coles opens second automated customer fulfilment centre
Coles has opened its second Customer Fulfilment Centre (CFC) in New South Wales.
It’s the second of two CFCs to launch this year as part of a $400 million partnership with global leader in online grocery transformation, Ocado, with the first CFC opening in Truganina, Victoria last month.
The CFC will house a range of specialty brands and local foods from smaller suppliers like the Byron Bay Peanut Butter Company, who first started selling their product at local Byron Bay markets.
The extended product ranges also span the health and dietary, vitamin and baby categories.
meant that we needed to move quickly to ensure the best possible outcome –with this transaction being completed within seven days of our appointment as liquidators, after discussions with several potential buyers.”
The asset sale, for an undisclosed amount, is also expected to see up to half of Fenn’s 32 employees offered new roles with Smart Foods and continued production at a state-of-the-art Sunshine Coast facility.
Liquidators are also working towards secured creditors and employee entitlements being paid out of remaining company assets with Fenn Foods Pty Ltd, ceasing to operate as an entity.
Fenn Foods was founded in 2015 and merged with a competitor in 2023, with its vEEF and LOVE BUDS brands stocked by Woolworths and Coles.
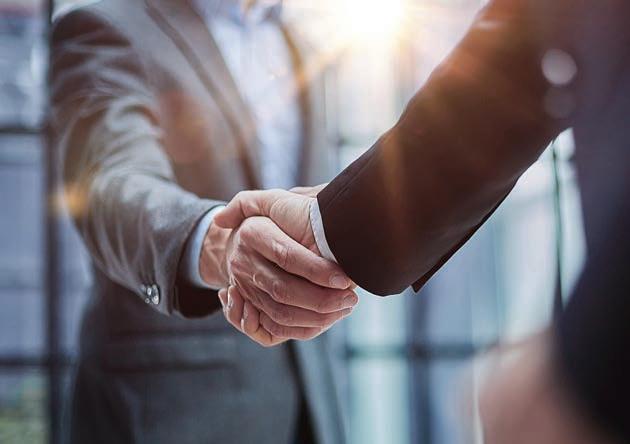
The asset sale will see up to half of Fenn’s employees offers new roles within Smart Foods.
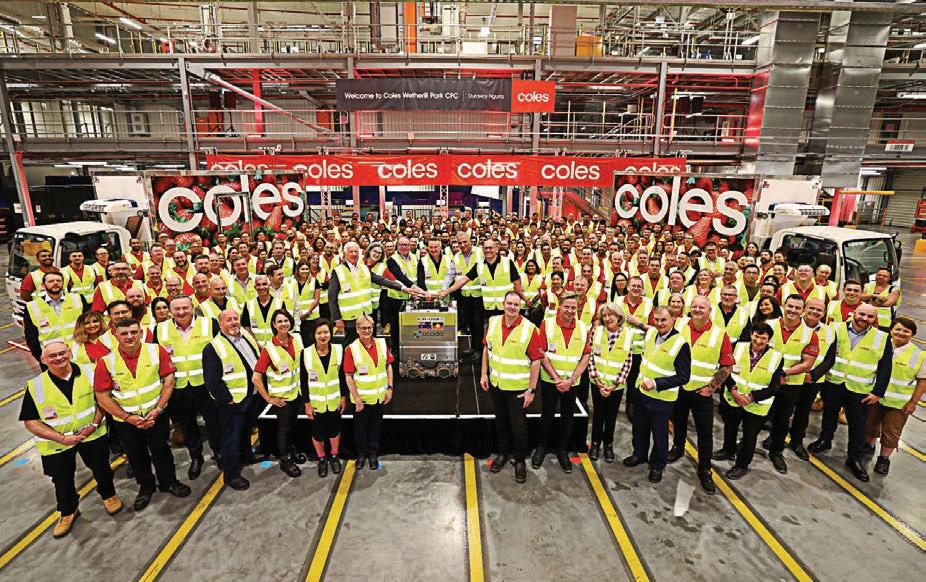
The new Coles automated fulfilment centre will also employ more than 1,000 team members.
Customers will also have the choice of extended delivery windows from 5am to 10pm, with later cut-offs for both next day deliveries in the morning and evening. The Ocado technology utilises artificial intelligence (AI), robotics and automation to transform the way Coles Online orders are picked, packed and delivered.
The Wetherill Park site has a footprint of more than 87,000 square metres – four times the size of the Sydney Cricket Ground – and can hold three million units of stock while having
the ability to process more than 10,000 customer orders per day when running at full capacity.
The site features a centralised hub, known as ‘The Hive’, where a fleet of more than 700 bots will fulfil a
customer order containing 50 items in just five minutes, while an AI ‘air traffic’ control system will oversee the bots as they move around 3D grids, transporting containers of grocery items to be packed and delivered. F
Founded by Michelin star chef Alejandro Cancino, the company had invested
heavily in research, product development and manufacturing facilities. F
Where Australian beer meets European craftsmanship
In its seventh year, Frenchies Brewery has adapted to the Australian market to thrive as an establishment that unites the best of two renowned brewing cultures. Jack Lloyd Writes.
Frenchies Brewery co-founders, Vincent De Soyres and Thomas Cauquil, were destined to take French flavours abroad from the moment they met at catering school in 2005.
“I was honing my skills as a brewer and Thomas was training to be a chef. We quickly became good friends,” said De Soyres.
When they two weren’t studying, they were soaking in culture, inspiration and knowledge from travels around Europe.
One of their more outlandish expeditions took them to the volcanoes of far east Siberia, where the duo’s mission to launch an authentically French brewery first began.
“It’s this very spot where we came up with the concept of launching our own brewery, where I would oversee the beers, and Thomas the food,” said De Soyres.
A s plans progressed and ideas turned into possibilities, the pair moved to Australia where they would search for an ideal gap in Sydney’s brewing market.
After much deliberation, De Soyres and Cauquil noticed that most breweries were heavily reliant on food trucks for food options. This would motivate the pair to focus on providing the finest French beer and food styles in one venue.
“ We wanted to differentiate ourselves by being the brewery who offers the best food in Australia.
Thomas comes from a Michelin star background, so it is extremely good quality food,” said De Soyres.
After struggling to find a space that
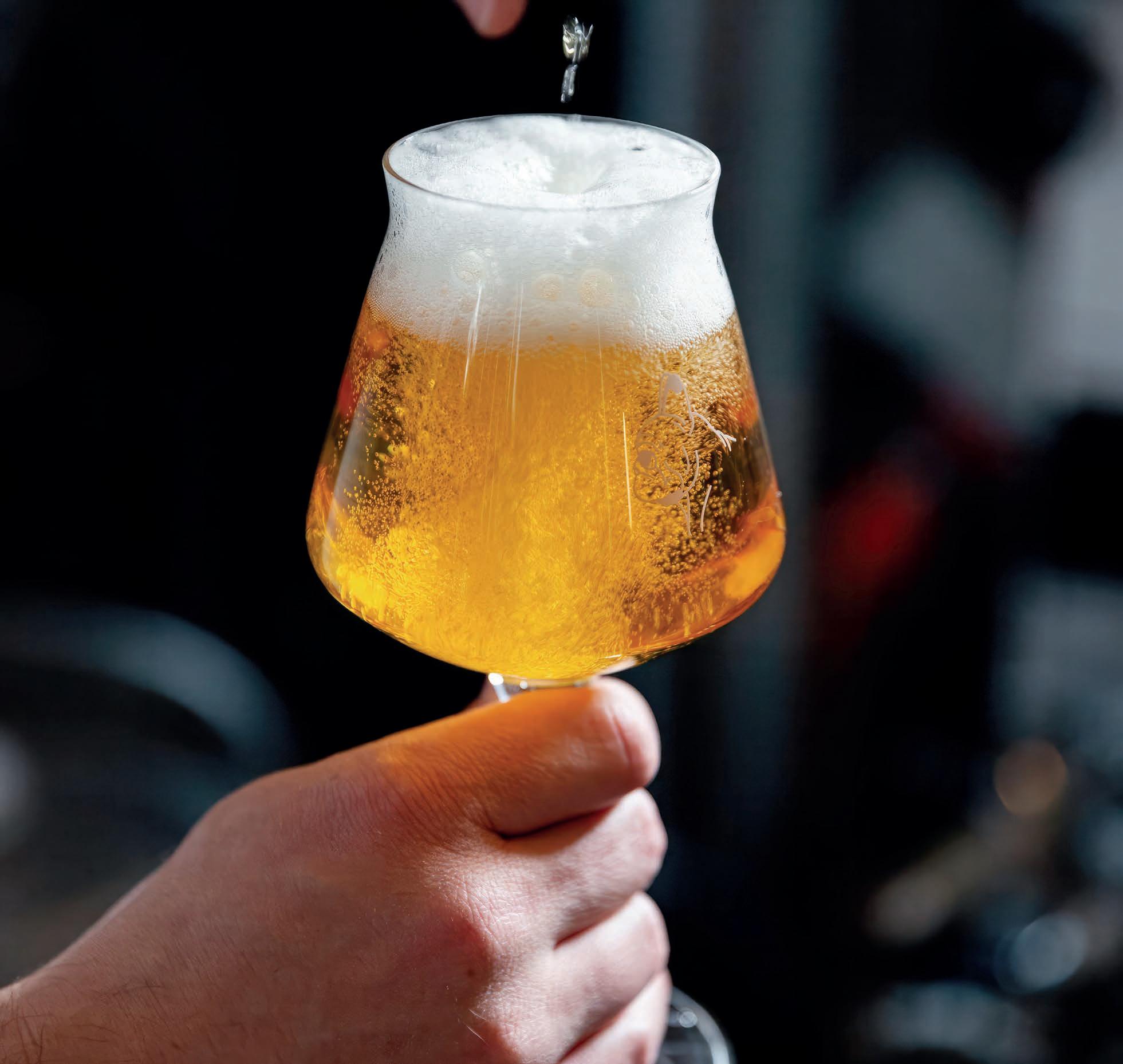
could accommodate their ambitious ideas, they eventually found The Cannery.
De Soyres said the Rosebery industrial complex turned shopping centre was too perfect to turn down. It had the correct zoning, great foot traffic and a sizeable loading dock.
“I remember saying, it’s got everything, let’s give it a crack,” said De Soyres.
T he Cannery has been home to Frenchies Brewery since it launched in 2017. Now in its seventh year, the brewery experienced growth to the point where Frenchies now has its own bakery.
Ushering in a new generation of brewing
After more than half a decade entrenched in brewing production and processes, De Soyres now finds himself with different responsibilities.
“A lot of my days consist of managing brewing contracts and maintaining relationships with hop and malt partners and canning companies,” he said.
While still involved with the recipes, ingredients, and delivery timelines, De Soyres has handed the reins to now Head Brewer, Sam McDonough.
“He’s got heaps of experience and different techniques. He looks after the day-to-day process in the brewery,” said De Soyres.
Having avoided any transitional pains, Frenchies Brewery’s production system is operating at full capacity.
McDonough and his team stand to benefit from numerous systems that help the brewery excel in quantity and quality.
Frenchies Brewery was founded to provide the finest French beer and food styles all in one venue.
Images: Frenchies Brewery
Among the systems is a massive three vessel brewhouse, which ensures that product supply meets demand.
“It allows us to make 6000 litres of beer a day. It’s a super vessel,” said De Soyres.
A longside capacity, Frenchies’ European flair shines through. Instead of jacketed steam-based systems typical of Australian breweries, Frenchies use tanks that are heated using direct fire.
“The direct flame heats up the bottom and the sides of the tank. That creates a bit of caramelisation. It’s very typical of French brew houses,” said De Soyres.
“ We don’t need as much caramel to get a sweet note in the beer.”
Frenchies’ European heritage is further represented in its Horizontal Bright Beer Tanks that offer gentle and efficient clarification.
“Horizontal Tanks are typically European. In France, Belgium, and Germany, maturation tanks are quite shallow but very long,” said De Soyres.
“They allow us to clarify the beer a bit faster, without having to go through the centrifuge.
“For typical tanks, it takes days for a little particle of protein or yeast to go from the top of the tank to the bottom. Whereas our particles have to just fall from one metre.”
Frenchies utilises lenticular filters for the safety and efficiency benefits they offer.
“ These are very specific to us, because it’s not a centrifuge, it’s not a platen frame filter,” said De Soyres.
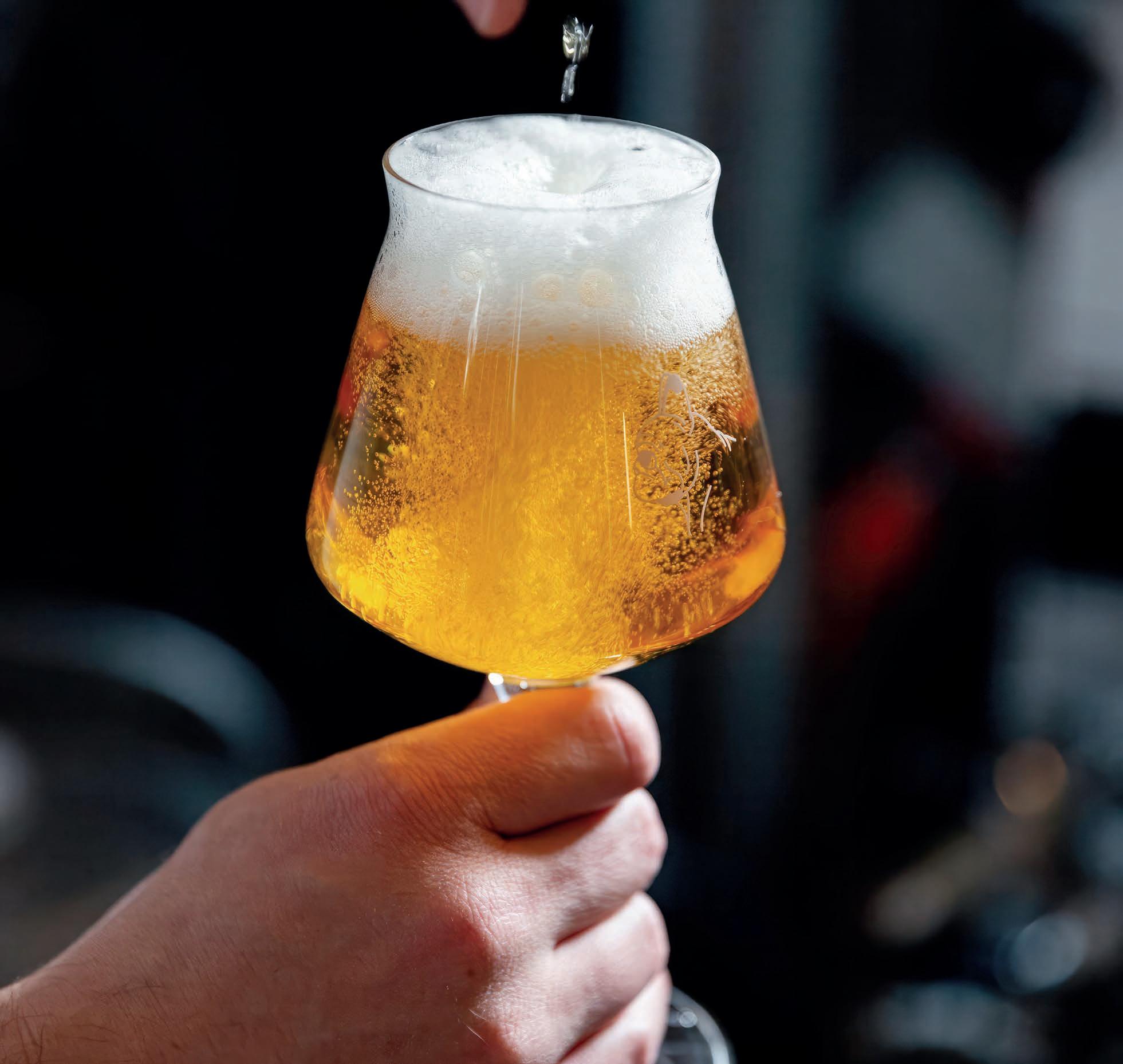
“It’s completely enclosed under pressure. You have a gentle filtration so you can be very precise on what you want to remove and what you want to keep in the beer.
“That is how we managed to get our lagers crystal clear.”
Unlike other breweries who outsource yeast, Frenchies owns a yeast propagator that allows it to grow yeast, which helps cut costs.
“They’re small tanks where we can grow our own yeast and use specific yeast strains that you can’t find easily on the market. They are very high quality and very expensive,” said De Soyres.
“Belgium and France are quite yeast driven. When transforming the sugar into alcohol, the yeast produces those very particular flavours.”
Adapting to market dynamics and overcoming financial pressures
De Soyres said equally important to these processes is identifying and staying ahead of market trends and financial dynamics. Since Frenchies’ inception in 2017, the industry has been unstable due to factors such as the pandemic and the cost-of-living going up.
Despite Frenchies’ evident European influence, this uncertainty meant the brewery had no choice but to experiment and adapt to a market that is looking to avoid expense.
“With the cost of living, what people and pubs are after is cheaper beer,” said De Soyres.
To cut these expenses, Frenchies

To hit market successfully, Frenchies began to develop affordable Australian lagers with Frenchies Mid and Frenchies Dry.
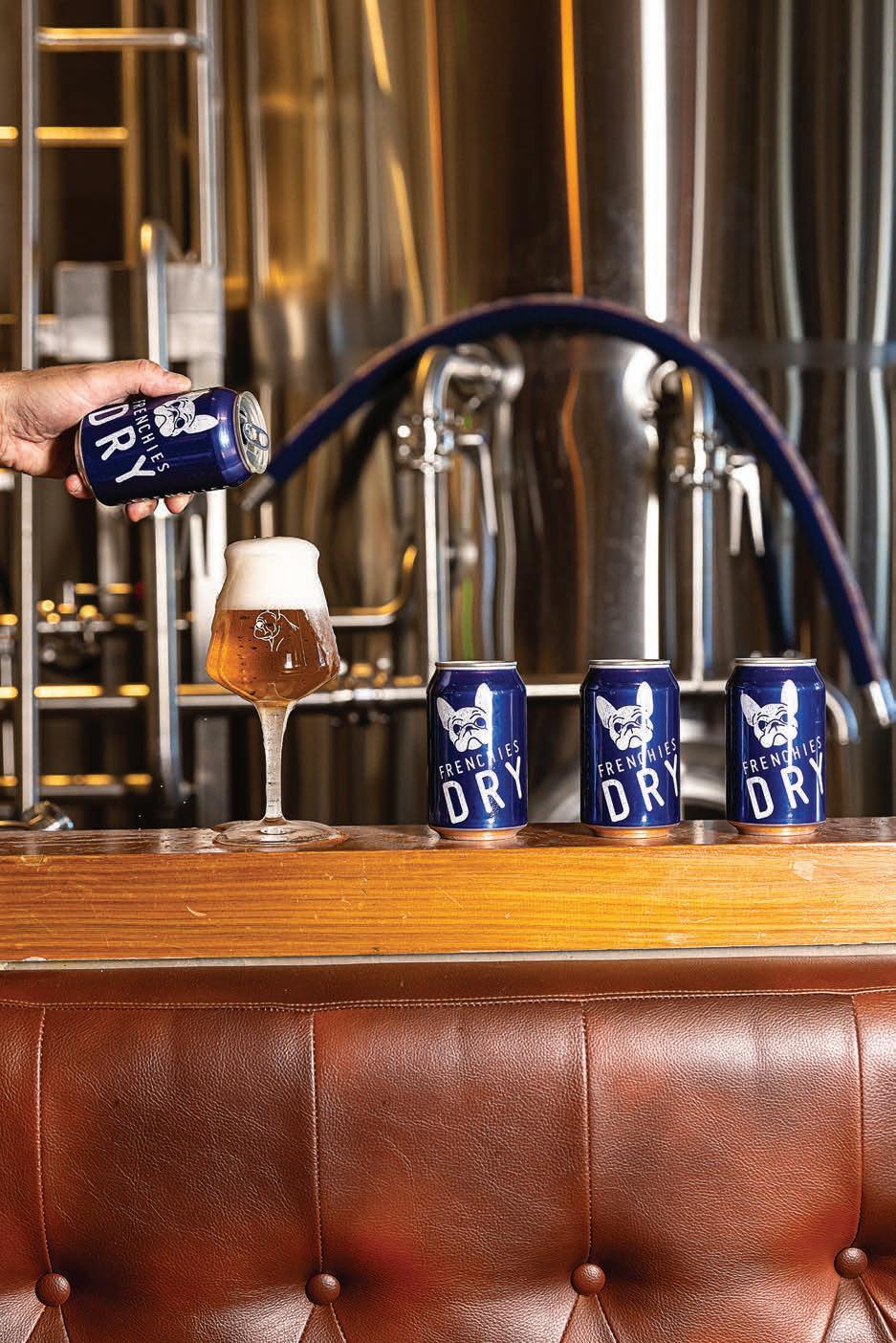
All vessels have automated temperature control
• 3000L x 3 vessel Brewhouse
• Direct Fire Kettle
• 5 x 2600L CCV fermenters
• 3 x 2800L CCV fermenters
• 3 x 6000L CCV fermenters
• 3 x 2800L Horizontal BBT (Bright Beer Tanks)
• 2 x 750L Horizontal BBT / serving tank
• 2 x 6000L Horizontal BBT
• 2 x 200L automated yeast propagators
• Pilot batch system: 200L
• Triple Lenticular Filtration Plant
• ECC Codi counter pressure canning line
• 3 Head Keg Cleaner
• 2 x 4 head keg racking bench
• 2 x CIP cart
• 1.5 inch and 2-inch hoses
Co-founder Vincent De Soyres is now focused on managing brewing contracts and maintaining relationships with clients and customers.
Frenchies Equipment Snapshot
began to develop affordable Australian lagers.
“We have done two new beers. Frenchies Dry, and Frenchies Mid. These taste like the typical Australian beer,” said De Soyres.
“You’re getting all that Australian lager flavour, yet it’s much cheaper to produce and sell. Pubs buy their kegs from big brewers for $300 to $400. We can sell all kegs for way cheaper than this to them.
“There’s not much that goes into these beers, and that’s what the market wants.”
Despite its growth beyond an exclusively European offering, Frenchies still maintains a distinctive French touch.
“Being a French restaurant that makes French food with French beers, we were trying to be unique to ourselves. It took us a while to realise that people want cheaper beers,” said De Soyres.
“However, we still have our products still have the French touch from our equipment and brewing processes.”
After beginning to experiment with other styles of beer, De Soyres was led down an entirely different path of revenue. This is where Frenchies would introduce contract brewing.
Upon researching the concept, De Soyres realised contract brewing was a major source of income for most large breweries.
“All the established breweries do contract brewing. If you go to Heineken, they have many different brands, and they also brew for other brands,” said De Soyres.
“Obviously you can’t have breweries everywhere. That’s why there’s an actual demand for this. We have the expertise in brewing, so we thought, this can pay the bills.”
Flash forward to 2024, and Frenchies finds itself producing kegs and cans of beers, cocktails, sparkling waters, seltzers and functional drinks for startups, brands and large companies.
“We can help people go from the very start of the idea all the way to commercialisation. This helps us with the daunting economy,” said De Soyres.
Utilising software to streamline operations
Behind the production process is the reliance on various softwares that ensure consistency. De Soyres said that a huge help in maintaining process structure is a brewery management software.
“You can follow who’s doing what in the brewery. You can see who added
what hops at what time, at what year, at what temperature, at what gravity,” he said.
To ensure recipes remain correct, De Soyres utilises another software system that is aimed at the brewing sector specifically.
“That’s where we do all our recipes and measure our efficiencies. There are heaps more relevant metrics that we manage and follow,” said De Soyres.
Pioneering a circular economy
As well as ensuring equipment, processes and quality control systems are in check, Frenchies has started doing its part in an industry-wide sustainability shift.
De Soyres said that every week Frenchies donates a few tonnes of spent excess grain to a local farmer to feed cattle and pigs.
“Every time we do a batch, you’ve got about half a ton of spent grain. We take all the sugar out of the grain, and we give them the grains with all the proteins,” he said.
Beyond this, the brewery ensures that leftover bread from Frenchies Bakery does not go to waste. The team extracts all complex sugar from the bread to incorporate into their brewing process.
“ We use the leftover bread that hasn’t been sold at the bakery and cut it, dry it, and then put it into a mash to extract all the complex sugars out of it,” said De Soyres.
“Bread is pretty much solid beer. It’s made from the same ingredients, so it’s easy for us to reuse those.”
Frenchies has a three vessel brewhouse, which ensures that product supply meets demand.
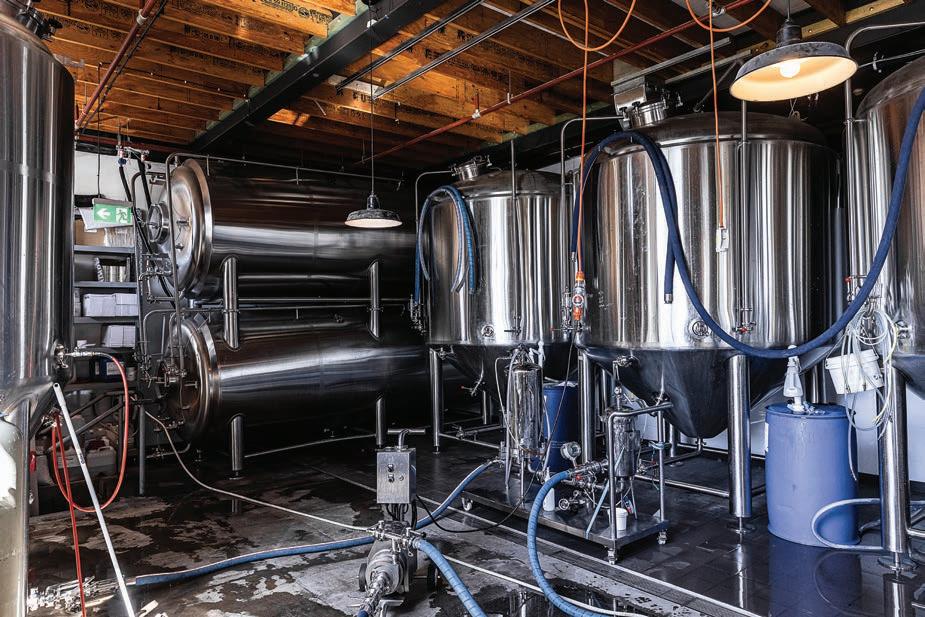
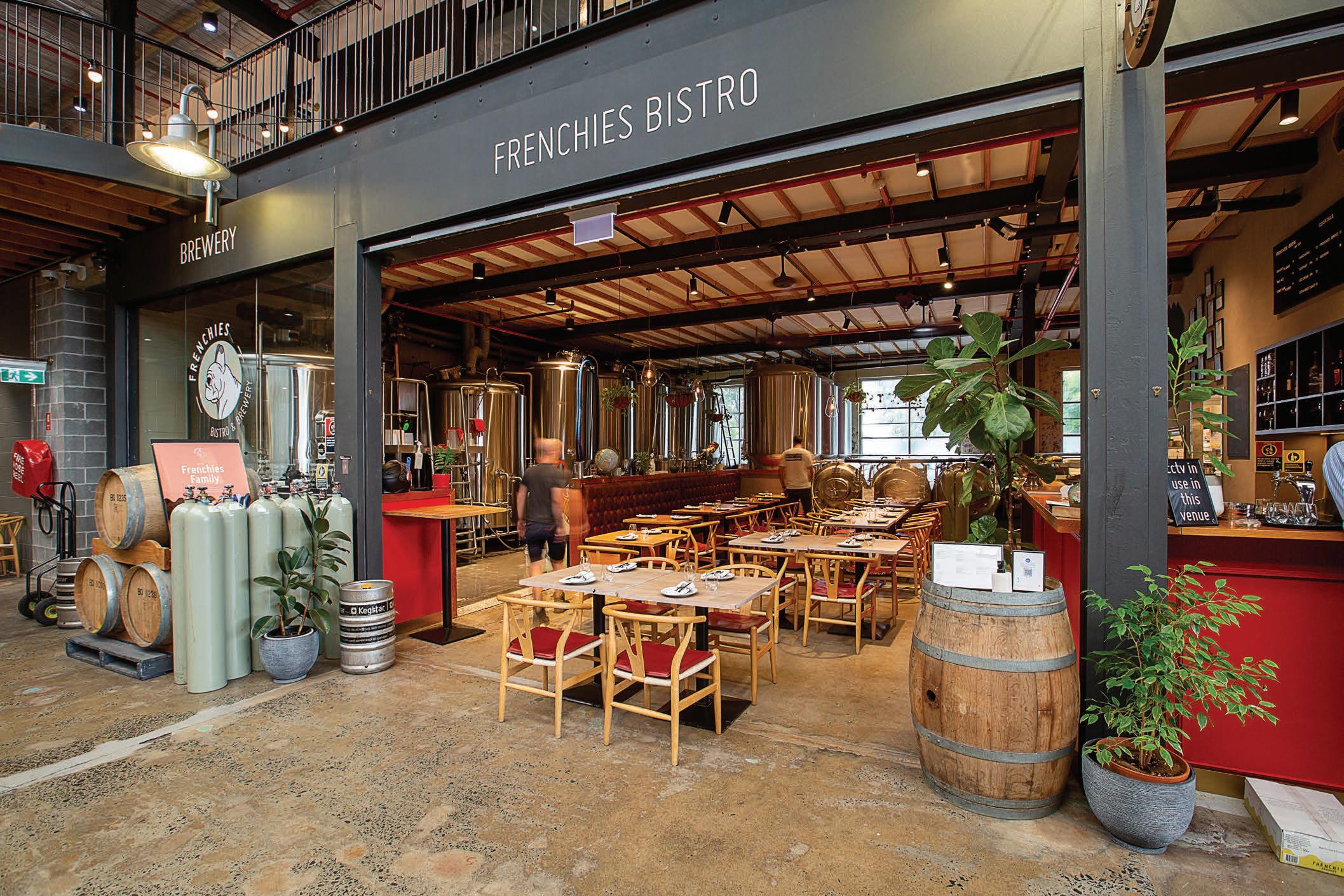
‘The Cannery’ has been home to Frenchies Brewery since it launched in 2017.
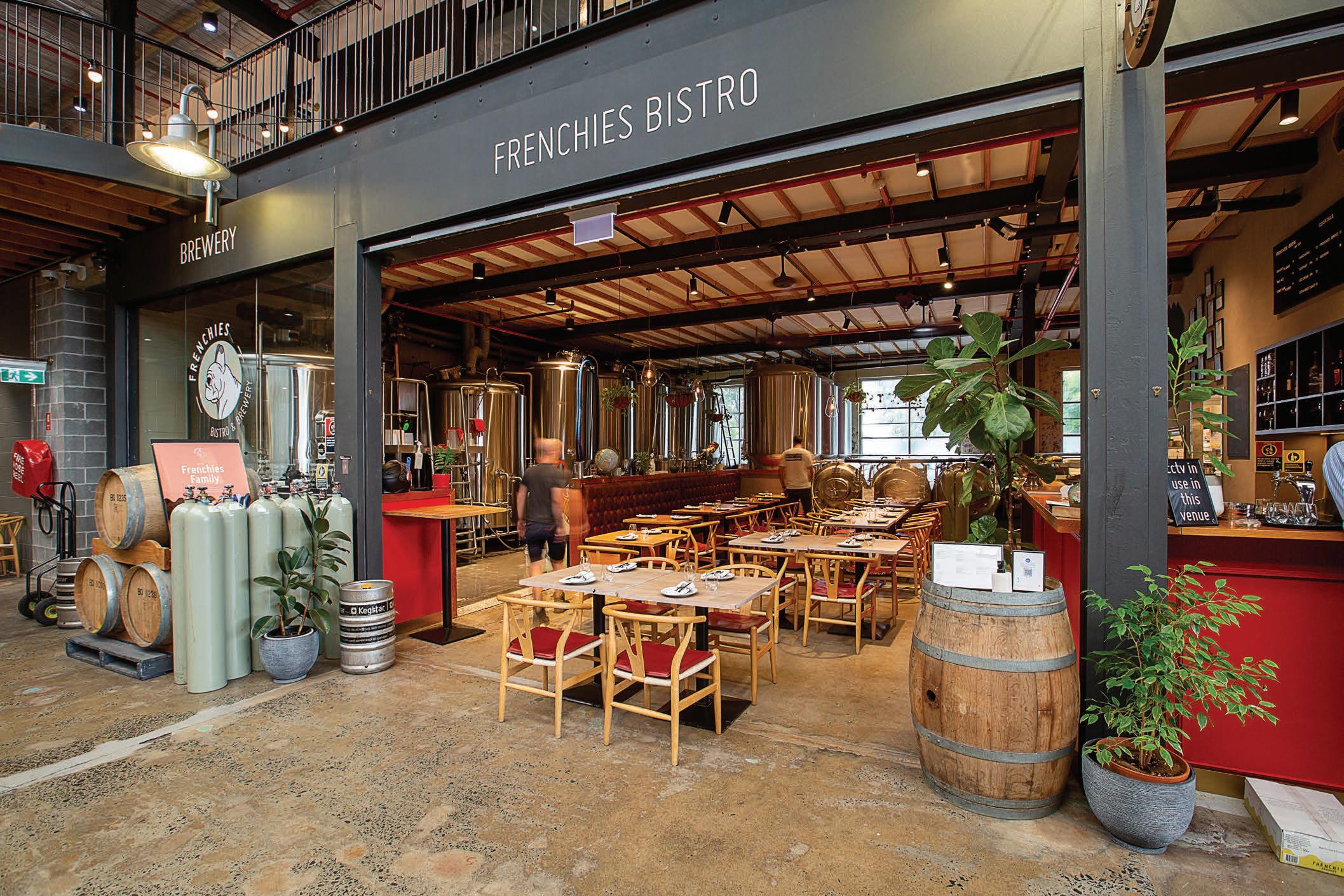
Building community and fostering feedback
Another fundamental process to the core of Frenchies’ identity is its free bi-monthly tasting nights. De Soyres said these are run to provide insights for both the brewers and customers.
“From these sessions we get feedback on what people like, don’t like, and what they’re looking for in beer. It keeps us really in touch with the core market,” he said.
“We present all the new beers that we’ve released and talk through how we made them, what makes them special and what sort of flavour to look for.”
De Soyres said the nights are also a chance to give back to the community.
“The free tasting is our way of giving back to our customers and to thank them for following us,” he said.
Celebrating Seven Years
A recent tasting night celebrated the
seventh birthday of Frenchies. De Soyres recalled becoming emotional when he reflected on how much the brewery has grown.
“ We’ve grown steadily and continuously, through lots of hard work, stress and reward. Last year, we doubled in capacity,” he said.
“Celebrating this with our friendship family of around 60 people was great. It was emotional.”
De Soyres admitted that the anniversary is even more special when you consider for a long time, the brewery wasn’t on stable footing because of the pandemic.
“We almost didn’t make it the first year, or in the third year, and now it’s the seventh year and we’re still here. We’ve managed to keep our head above the water and to be there celebrating us was great,” he said.
“We are now striving as much as we can in this economy, compared to other
heartbreaking scenarios of some who went into administration or liquidation.”
In classic brewing fashion, Frenchies marked the milestone with a new Belgian Golden Ale. ‘The Devil’ pays homage to a classic ale, which is often cracked open in celebration.
“It is our seventh anniversary beer. We really want to pay tribute to historically, one of the best beers in the world,” said De Soyres.
“When you open a bottle of Duvel, it’s an occasion, especially in Australia. We thought for a seventh birthday that it was quite fitting.”
Expanding Operations / Future of Frenchies
Moving forward, De Soyres said Frenchies is targeting more restaurants and small bars as outlets for Frenchies’ products.
“We haven’t found any space but we’re looking at it. We have a few
customers of ours who run bars, restaurants or pubs, who also were looking at growing with us hand in hand,” he said.
With a keen eye on the market, De Soyres is focused on tapping into the carbonated drink market and further enticing Sydney bottle shops.
“From an innovation perspective I think we’re trying to keep an eye on soft drinks and carbonated drinks in general,” he said.
“We also want to keep increasing our presence in Sydney… We really want to refocus on our local customers.”
Not only is Frenchies targeting the expansion of its brewing operations, but more bakery outlets are also in the works.
“ We’re thinking perhaps opening more bakery outlets or shop fronts, because we can produce a bit more than we do at the moment,” said De Soyres. F
Delivering solutions to maintain air quality
The need for optimised air compression systems to prevent contamination on the production line is crucial for the success of food and beverage manufacturers.
Air purity is critical in food and beverage manufacturing. Optimising the operation of your air compression while maintaining protections against contamination from particles, water, and oil, across multiple facets of production is vital to quality and output.
Choosing the right solution is not only about delivering the required performance outcomes but ensuring you have the service and support available, especially when any downtime has a costly impact.
As an industry leader, CAPS Australia offers multiple ways to successfully achieve your performance outcomes. Providing compressed air and power generation solutions across Australia, CAPS has an extensive range of products and brands to provide complete air and power solutions that are suitable for local operating requirements.
Oil-free compressors
The food and beverage industry requires clean, dry compressed air to comply with safety and hygiene standards. The ideal approach to achieving and maintaining this critical air purity is to minimise the risk of contamination in the first place by using oil-free compressors.
Though they can come with a higher initial capital cost, oil-free compressors offer long-term benefits associated with less ancillary equipment and servicing, as well as a significant reduction of risk, often making them a more valuable investment.
CAPS Australia meets this requirement with its range of ISO Class 0 oil-free compressors, guaranteeing 100 per cent oil free air for industrial applications.
For larger scale applications, CAPS has a full range of oil-free centrifugal compressors as well as rotary screw compressors from 37kW to 355kW in either fixed or variable speed.
These machines are versatile
and tailor-made, so there are many factors to weigh up when choosing the right compressor. Elements such as size, speed control, continuous or intermittent usage, portability, and site operating conditions including altitude and ambient temperature, can all impact which system will suit your needs.
T he experts at CAPS can help you assess your requirements to find you the perfect match.
On a smaller scale, CAPS can offer scroll compressors in an all-in-one solution with a dryer, storage tank and compressor in a single unit, keeping the real estate of the system as compact as possible.
T his smaller footprint translates to higher efficiency, a key component when choosing the right compressed air system, particularly as energy prices continue to climb across the country.
Offered as single phase from 1.5kW – 2.2 kW or three phase from 3.7kW to 7.5kW, CAPS suggests this integrated solution as ideal for small food and beverage applications requiring oil-free air. Setups can be configured to support the industry’s vast array of end process needs.
Cost-effective solutions
Due to their lower initial costs, many manufacturers opt instead to use oil-lubricated compressors with air treatment processes downstream.
From 5kW through to a 315kW, there are many technologies and brands to choose from, meaning it can be quite challenging to evaluate different compressors and select the best technology for your system.
CAPS offers a full suite of compressed air solutions and have the expertise to help you choose the right
equipment to suit your needs.
CAPS understands that every application is unique, which is why it offers customised solutions and provides ongoing support to ensure optimal performance.
Air treatment
Air dryers are an essential to meeting the quality of air critical to food and beverage manufacturing.
Air dryers help to remove moisture from compressed air systems, decreasing the humidity and preventing bacteria from growing, as well as warding off rust and extending the life of the machine.
Desiccant air dryers are popular for industrial applications and processes that require extremely dry air, where a desiccant material such as silica gel, molecular sieve or activated alumina is housed in a container through which
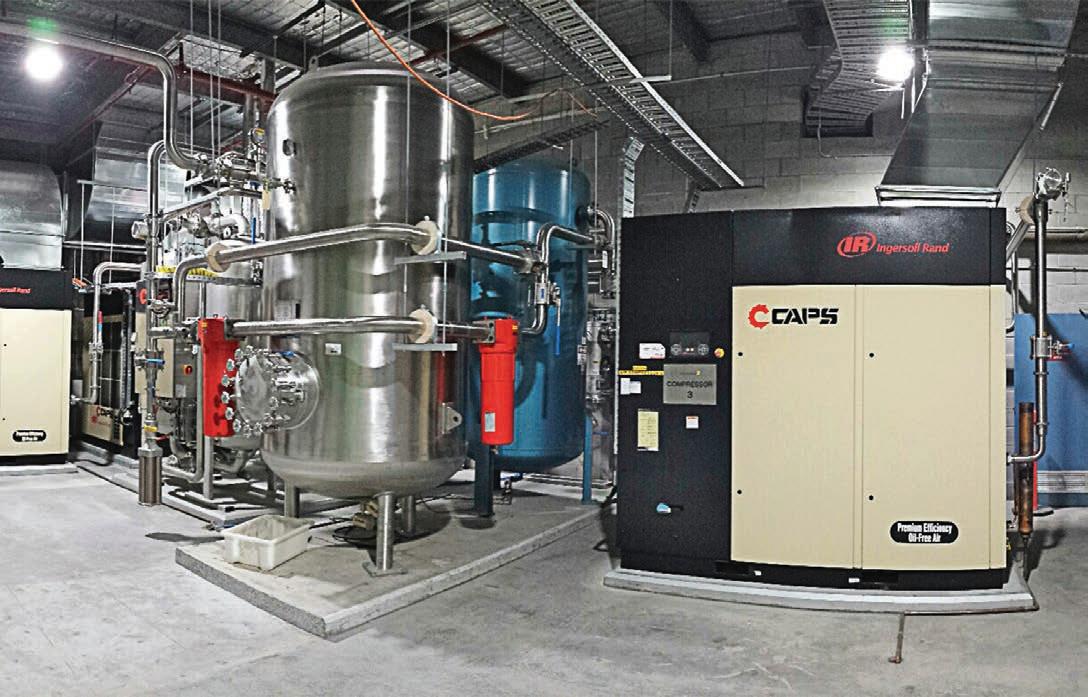
Images:
CAPS Australia
CAPS Australia offers multiple ways to successfully achieve your desired air compression outcomes.
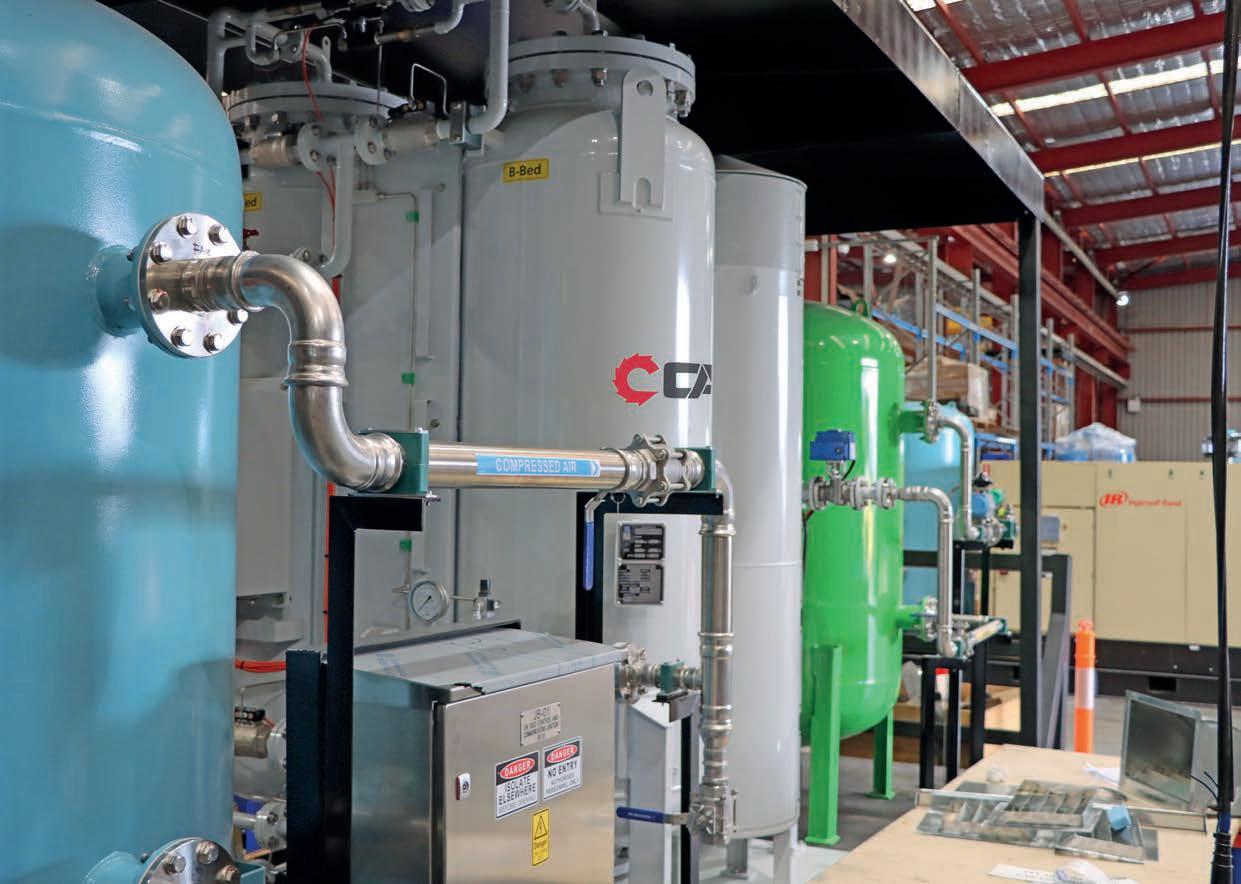
cleaned before it can be compliant with relevant standards. Filters use a variety of technologies, including coalescing and adsorption, to remove dust, oil, and other contaminants from compressed air systems. Reliable and customisable, they are available in various sizes and configurations to meet your specific needs.
T he at-scale generation of nitrogen to support operational needs is a challenge that CAPS Australia has efficient solutions for with engineered nitrogen (N2) generation systems to support on-site demands. Producing dependable and economical supplies of nitrogen, the systems allow you to generate the quantity and purity of nitrogen necessary for any application on site.
Systems designed to suit the application
CAPS delivers complete solutions, designed, developed by its in-house engineering team, and supported through its Australian ISO9001 accredited manufacturing facility. The custom-built systems are perfectly matched to clients’ requirements.
This expertise also enables CAPS,
performance and life of equipment and infrastructure.
Local knowledge and support
Founded in Western Australia in 1980, CAPS joined the Ingersoll Rand family earlier this year expanding its access to the Ingersoll Rand’s global offering of innovative and mission-critical air, fluid, energy, and medical technologies that enhance industrial productivity and efficiency.
With 10 branches nationwide, the dedicated CAPS team delivers exceptional service, expert advice, support and spare parts.
Their 24/7 maintenance and breakdown service ensures customers’ operations run smoothly.
The national footprint means CAPS has skilled teams working in the same time zones as its clients, enhancing their support to customers through the entire process - from understanding their requirements, offering suggestions, and providing advice, to ultimately delivering the solutions they need.
The support continues throughout the equipment’s operational life, with CAPS providing Ingersoll Rand
Ingersoll Rand.
Scheduled air compressor maintenance, as well as using predictive analytics, helps prevent unexpected interruptions in your production.
With more flexibility than an extended warranty, PackageCARE maximises your equipment uptime.
Rental equipment to keep you operating
CAPS can also get clients operational without big capital costs by delivering its competitively priced, turnkey rental solutions.
Keeping your operations running smoothly all year round, CAPS offers short and long-term rental of compressors and generators across Australia.
Ideal for special projects, seasonal peak demand requirements and covering any operational breakdowns, renting provides the flexibility to suit your needs.
With vast experience in renting equipment, CAPS has a large fleet of units ready for immediate dispatch from our local hubs satisfying a wide range of applications, including mining, agriculture, and industry, all while
Global technology, suited to local conditions
Utilising quality products with proven reliability, CAPS’ range of industrial equipment features worldrenowned partner brands such as Ingersoll Rand, AIRMAN, Mitsubishi Generator Series, Sauer, Next Turbo Technologies, Bollfilter and more.
This enables CAPS to provide customers with access to the best technologies in:
• rotary screw and centrifugal air compressors
• portable diesel air compressors
• power generators
• i ndustrial filtration
• a ir blowers
• g as generators (oxygen and nitrogen)
• a ir treatment equipment including custom built heavily engineered vessels
• engineered packages to suit customer’s needs and location
• parts and accessories
CAPS delivers global technology, suited to Australian conditions, backed by local service. F
To learn more, get in touch with the CAPS team on 1800 800 878 or visit www. caps.com.au.
The team at CAPS Australia understand that every application is unique, which is why the company offers customised air compression solutions.
Closing the loop on polypropylene
Krones and PureCycle Technologies aim to overhaul polypropylene recycling through advanced technologies to enhance production efficiency and sustainability.
Originally a mechanical engineering firm, Krones has expanded its solution offerings to include bottling lines, packaging machines, and digital solutions. However, the company’s diversification doesn’t stop there.
K rones also offers a range of innovative technologies that are designed to enhance production efficiency and sustainability, especially for food and beverage manufacturers.
As the industry evolves, Krones continues to focus on meeting the changing demands of consumers and manufacturers alike, positioning itself at the forefront of modern beverage production.
That’s why Krones partnered with PureCycle Technologies, known for its patented process of purifying polypropylene waste into high-quality recycled resin, to advance the recycling of polypropylene and ‘close the loop’.
PureCycle Technologies’ innovative approach utilises a unique solvent-based method that separates and purifies polypropylene from contaminants and other plastics.
This process not only enhances the quality of the recycled material but also ensures that it meets the rigorous standards required for various applications, from automotive components to consumer goods.
Polypropylene is a plastic that poses environmental challenges due to its low recycling rates.
These challenges include:
• non-biodegradability;
• m icroplastics;
• resource-intensive production;
• chemical pollution;
• end-of-life challenges; and
• ecosystem disruption.
Addressing these challenges requires improved recycling infrastructure, development of biodegradable alternatives, and greater public awareness of responsible plastic use.
This collaboration aims to develop innovative solutions for the recycling and repurposing of polypropylene waste.
Using the proprietary process to create ‘ultra-pure’ recycled resin from used polypropylene plastics, PureCycle is




Automation in the face of labour shortages
The benefits of automation in food and beverage manufacturing are numerous, including the ability to mitigate risks associated with labour shortages.
Post COVID, industries have had to face and deal with the issue of staff shortages, none greater than the meat and food manufacturing industry
This had led to industry looking to automation solutions to combine the lack of skilled labour and staff shortages to keep up with domestic consumer demand.
A key player in this field, LUMIX Procut, specialises in providing automation systems designed to meet the needs of food and beverage manufacturers, and to en-sure products move smoothly down the line without delays.
The company offers a range of solutions through its various distribution partnerships, which enhance production process, including automatic skewering and filleting machines, and process automation in cutting, mixing and packaging steps.
This focus on automation not only provides solutions in staff shortages but also boosts efficiency and product quality improvement in the process.
The industry is grappling with labour shortages – with some manufacturers finding it difficult to acquire enough skilled and qualified workers – which has promoted many companies to seek out automation solutions.
And as the need for efficiency grows, so does the demand for smarter technology to streamline operations.
The team at LUMIX Procut are actively provide feedback to their manufacturing partners, such as EBAKI, MHS, EMSENS, and LAKIDIS, on these pressing issues.
As a result, the team at LUMIX Procut are well placed to provide the right solutions for the issue at hand.
One standout example of the solutions offered by LUMIX is EBAKI’s horizontal filleting machine, which has already been successfully
implemented for several medium-sized food manufacturing customers across the country.
This machine, which cuts boneless meat horizontally, has transformed the workflow of these customers, being able to put out a week’s worth of cuts in a matter of hours.
Previously, one customer relied on two skilled butchers who worked 38 hours a week to fillet chicken breasts for skin sales.
Now, with the EBAKI solution, the process has been revolutionised. The compact machine, capable of producing up to 400 kilograms of product per hour, allowed the customer overhaul and streamline its production tasks.
“Our solutions allow qualified butchers to spend more time honing their craft,” said Anton Novopashin, partner, and director at LUMIX Procut.
“They can focus on making sausages or preparing special cuts of steak, as that’s their expertise.”
By doing so, the customer could also expect a quick return on investment through efficiency and output than prior to the solution’s application.
The implementing of automation also means businesses can shift their skilled workforce from manual jobs to more specialised tasks, ultimately enhancing product quality.
Another meat producer invested millions in a new chicken schnitzel line, but it struggled with the portion sizes required.
In response, and in collaboration with LAKIDIS, LUMIX Procut provided the meat producer with an ideal solution.
However, the transition to automation isn’t without its challenges.
Many companies find that using unskilled labour in a highly automated environment is not effective.
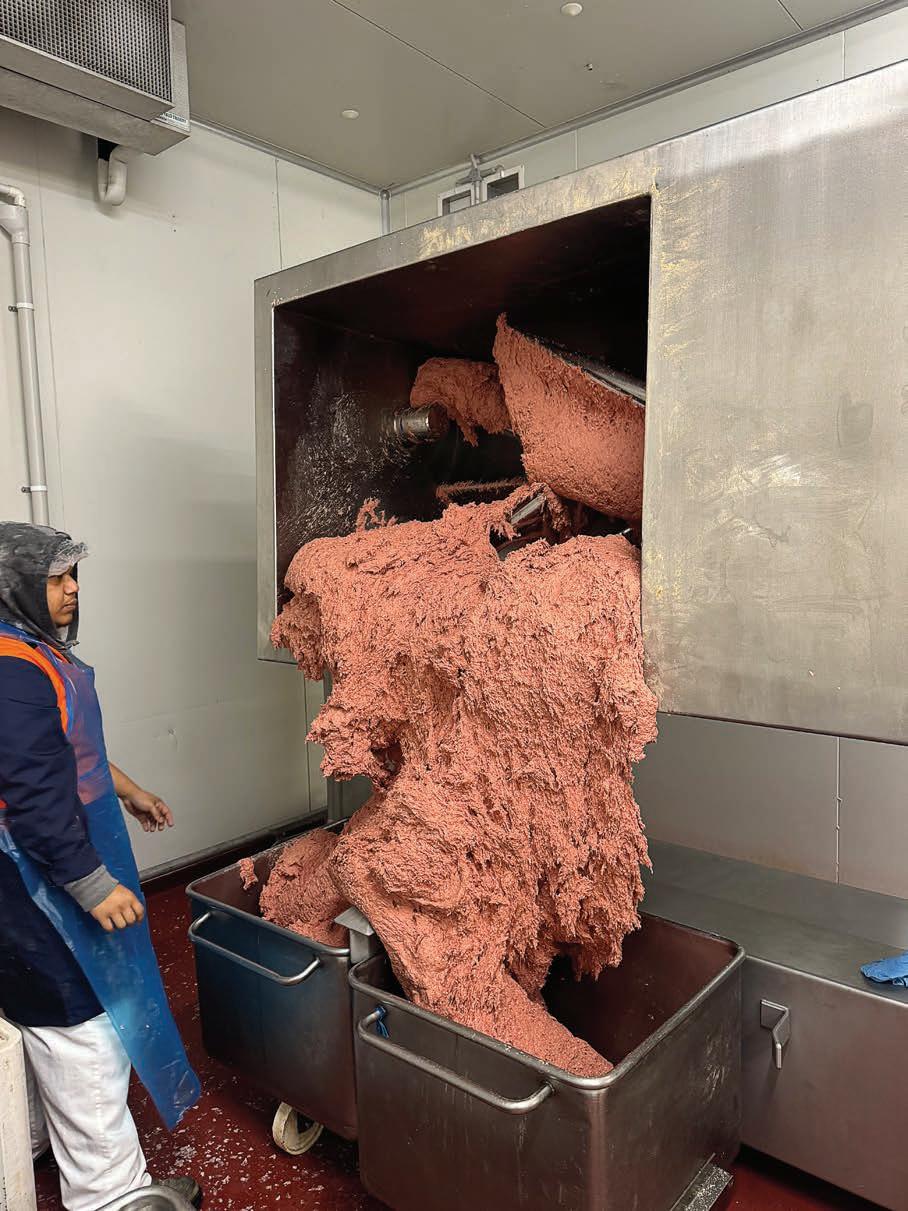
“EBAKI’s machines can produce up to 6000 kilograms of product per hour, so it’s crucial to ensure that we can handle that output effectively. We need to make sure that products move smoothly down the line without delays.”
The need for complete solutions that ensure proper input and output when using machines is critical. While automation can speed up production, integrating it thoughtfully into existing workflows is also essential for success.
“EBAKI’s machines can produce up to 6000 kilograms of product per hour, so it’s crucial to ensure that we can handle that output effectively,” said Novopashin.
“We need to make sure that products move smoothly down the line without delays.”
Currently, collaborations with key
brands in the poultry sector highlight this ongoing effort.
“For example, EMSENS produces the skewers found in supermarkets, and every poultry manufacturer is now utilising these machines,” said Novopashin.
“While automation can significantly streamline the production process, logistical hurdles remain, such as the time it takes to load and unload boxes.”
The importance of collaboration is evident in these solutions, with manufacturers eager to receive feedback to improve their processes.
Lumix offers a range of automation solutions to help improve production efficiency, such as those sourced through its EBAKI partnership.
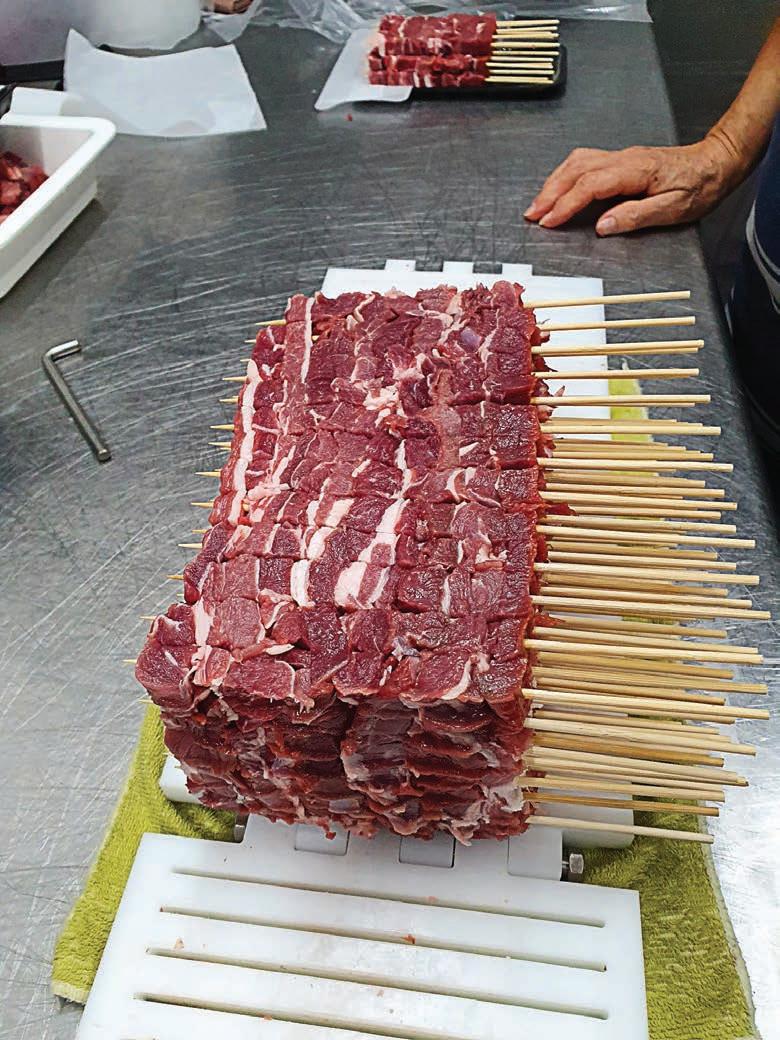
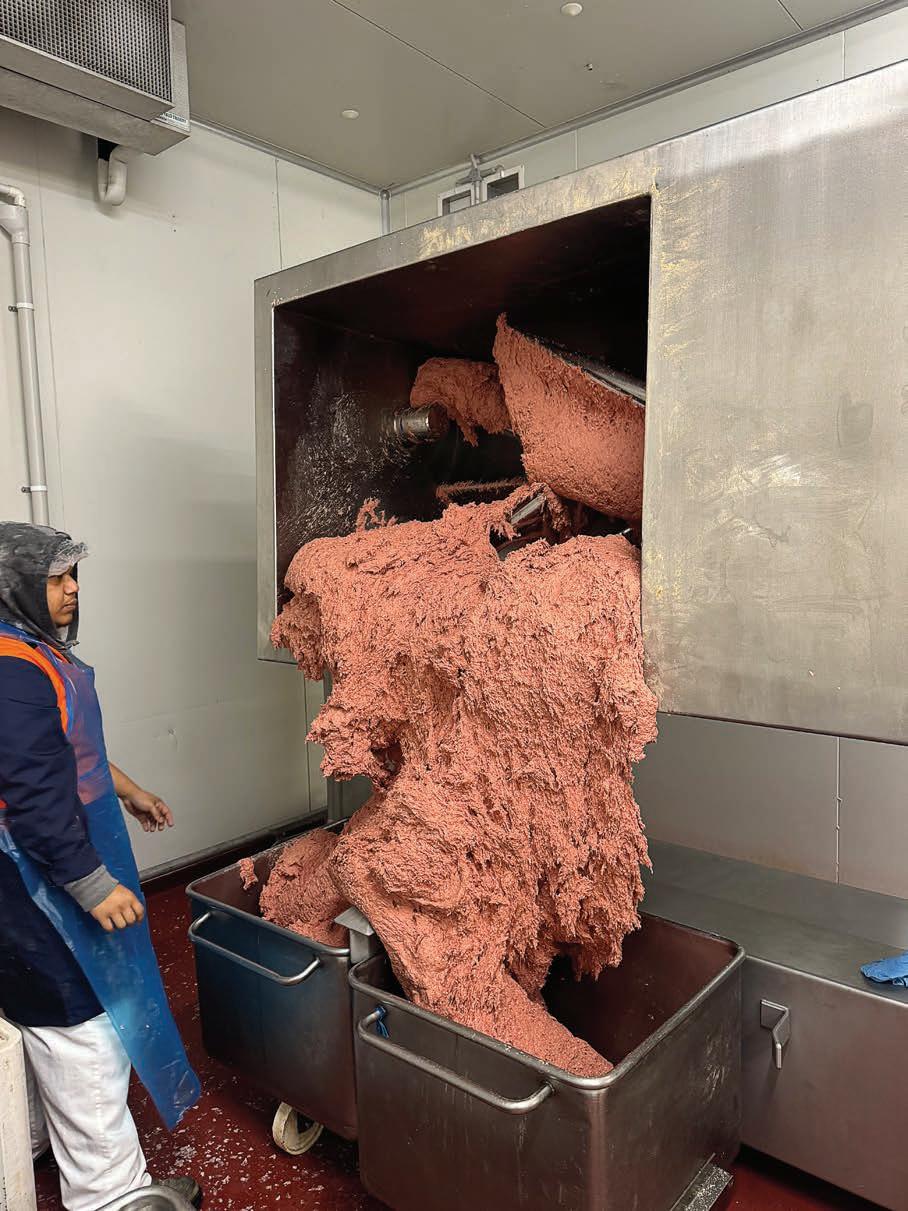
Meanwhile, in terms of safety, MHS machines offer portion-cutting solutions that address some of the industry’s biggest concerns.
“Many medium-sized businesses currently use bone saw machines, which can be unsafe because operators have their hands close to the blade,” said Novopashin.
In contrast, MHS machines come equipped with a computer-based screen, allowing users to set desired thickness and weight for cuts while maintaining a safe distance from the blade.
This automation not only enhances safety, by keeping hands further away from blades, but also allows companies to reallocate labour effectively.
“Staff shortages are a common issue across all industries, so if someone
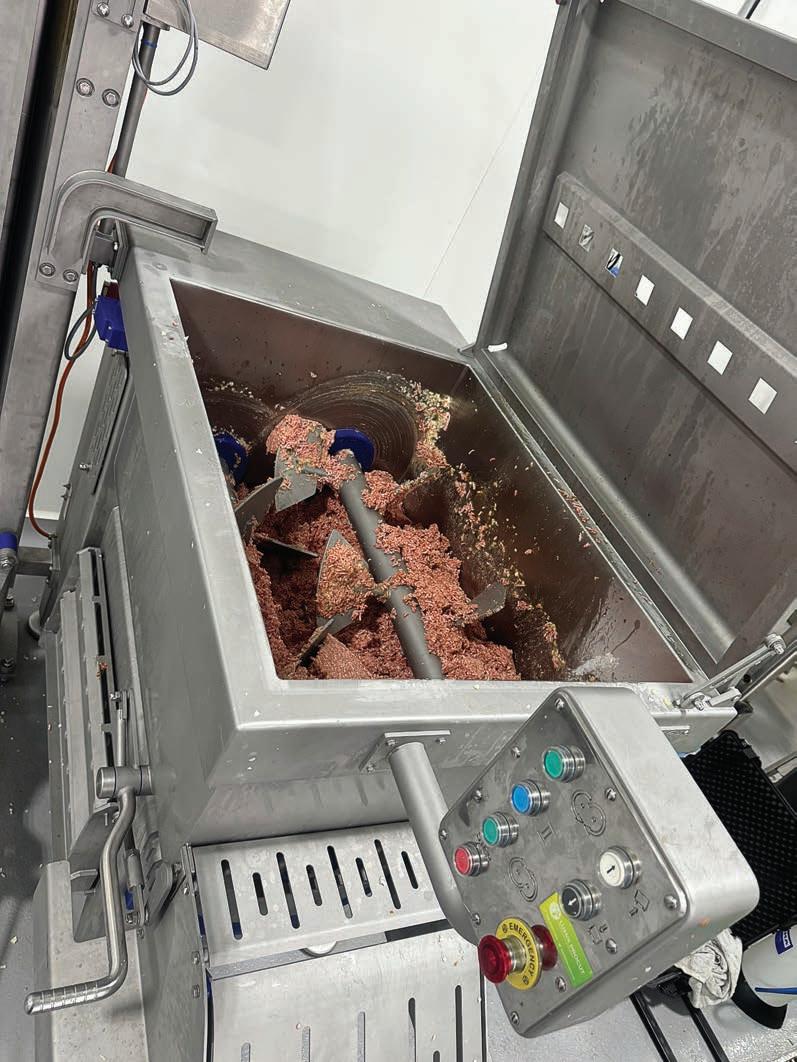
doesn’t show up, having automation in place means you have the flexibility to adapt,” said Novopashin.
The positive impact of automation can also be seen in the bakery sector, where a customer supplying the food service industry has experienced the benefits firsthand.
Manual cutting often leads to inconsistencies in thickness, which can affect cooking and product quality.
“When butchers cut by hand, the blade can flex, leading to uneven thickness,” said Novopashin.
“In contrast, with automation, the blade remains rigid throughout the process, ensuring uniformity and improved cooking results.”
The feedback from customers who have embraced these automated
solutions has been positive. Many were initially hesitant about making such an investment, but the results speak for themselves.
“What used to take a week now only takes a few hours,” said Novopashin, highlighting how automation has freed staff to focus on other essential tasks.
To ensure a smooth transition for new users, the company has established a test kitchen where customers can experience the machinery firsthand.
“We conduct all the trials here to give them the confidence to use the machines on their own,” said Novopashin.
After installation, training is provided to help customers troubleshoot any issues that may arise.
All of LUMIX Procut’s equipment solutions are also manufactured in
Europe, ensuring high quality and compliance with stringent safety regulations that meet, and in most cases, exceed those in Australia.
“Everything is certified to meet European and Australian safety standards,” said Novopashin.
The need for reliable and effective solutions is underscored by specific customer experiences.
Ultimately, the journey toward automation is not just about enhancing production efficiency; it’s about revolutionising the way food is processed.
With a focus on optimising production lines and addressing the labour shortage, businesses are embracing technology that not only streamlines operations but also elevates the quality of the end product.
The implementing of automation also means businesses can shift their skilled workforce from manual jobs to more specialised tasks.
All of LUMIX Procut’s equipment solutions are manufactured in Europe, ensuring high quality and compliance with safety regulations.
Transforming food safety with technology
Neogen Analytics is transforming how food and beverage manufacturers manage and interpret testing data to create strong food safety processes and outcomes.
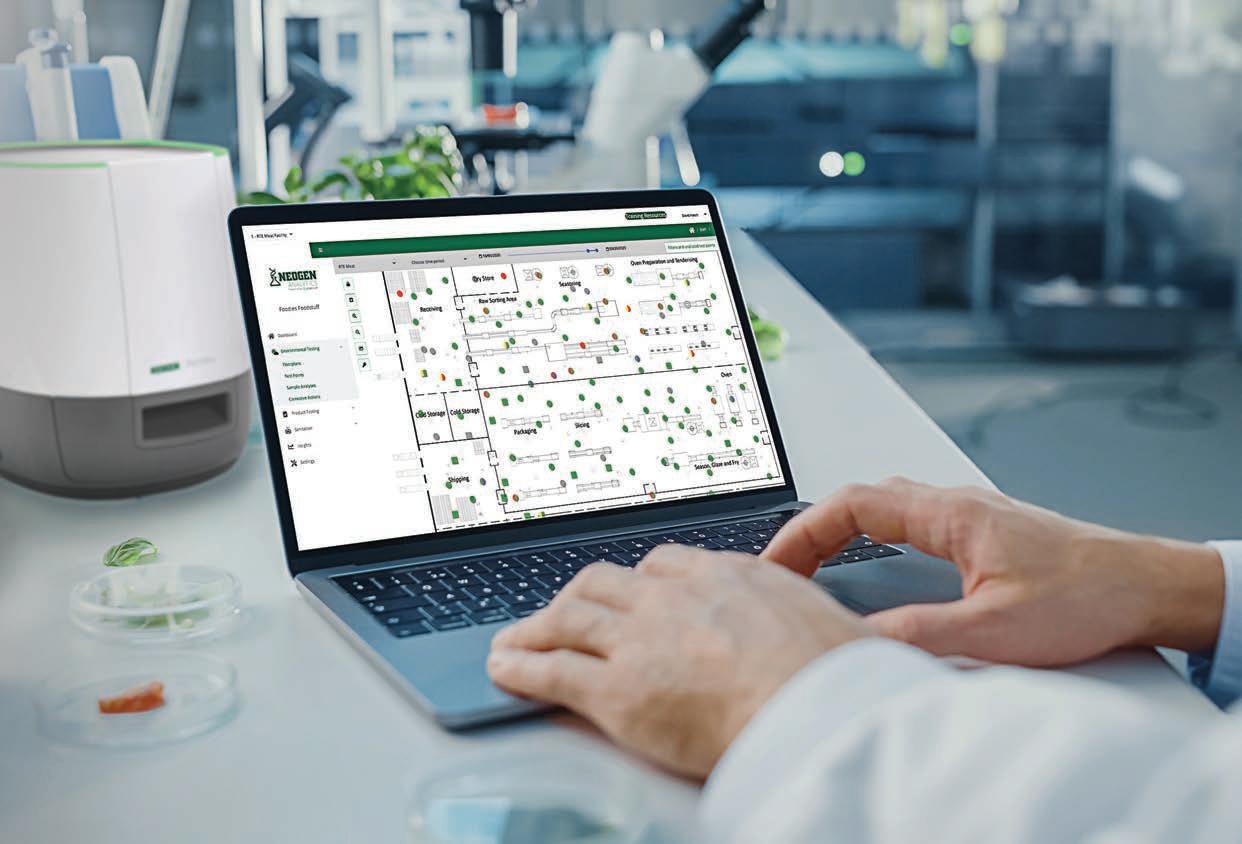
Under the leadership of an industry veteran with a wealth of experience in data technology, Neogen Analytics is helping food and beverage manufacturers leverage the best results it can out of food safety management platforms.
“I’ve spent three decades working in various data technology environments, with the last six and a half years specifically in the food and beverage industry,” said David Hatch, vice president, Digital Solutions Marketing, Neogen Corporation. This expertise played a key role in the development of Neogen Analytics.
The journey began in January 2018, when Hatch and his colleague’s joined forces with a pair of microbiology
doctoral candidates who had come out of MIT with ideas for rapid diagnostics of pathogens like Listeria and Salmonella. The result was the launch of Corvium, a software firm dedicated to automating food safety testing workflows and analytics.
Their partnership laid the groundwork for what would become a component of Neogen’s operations after its acquisition of the startup company in February 2023.
“Through my work with the team in those early days, I received a rapid education on how data and technology could impact food safety. It’s been an amazing discipline to learn,” said Hatch.
“And since becoming part of Neogen and gaining access to the global
resources that come along with that, I am genuinely excited by how much we’ve been able to develop the platform and what we have already been able to achieve for the companies using it.”
“In this industry, it quickly becomes clear that the people involved understand that lives are at stake every day. It’s motivating to know that, in some small way, we contribute to making the world a safer place to eat. Not every job offers that kind of fulfilment.”
This sense of purpose drives Hatch and the team at Neogen to continuously innovate and refine its platform.
“I’ve always been drawn to how data and information can impact organisations, businesses, communities, and populations,” said Hatch.
“The speed of communication and how well it’s understood are crucial factors in driving positive outcomes.”
Drawing from his background in healthcare analytics, he sees parallels between the two fields.
“The diagnostics from Neogen’s testing devices and laboratories assess the health of a facility, similar to how we evaluate patient health in healthcare,” said Hatch.
“Corrective actions in food safety are akin to treatment plans. By addressing these issues, we help customers lower their risks and avoid unexpected production line shutdowns, which can be very costly.”
At its core, Neogen Analytics offers a cloud-based digital platform designed to
Images: Neogen
Neogen Analytics provides a suite of data, tools, and solutions that help manufacturers improve food safety processes.
streamline food safety testing workflows and time-to-information.
“We’ve built software that enables a variety of food safety applications to operate within it,” said Hatch.
“For instance, our environmental monitoring application digitises and automates environmental monitoring programs, while our product testing program enables our customers to better manage risk and quality objectives. The system connects Neogen’s testing devices to the platform, enabling data to be unified and delivered to any internetconnected browser device.”
This modular approach allows customers to transition from outdated methods, such as spreadsheets and paper, to an automated digital system.
“Many organisations have ineffective methods for collecting and analysing data, which prevents them from taking necessary actions,” said Hatch.
Empowering food safety professionals
“We want to reduce the time it takes to access information, enabling food suppliers to quickly see diagnostic results and take action before issues escalate into costly problems,” said Hatch.
One of the standout features of the platform is its ability to visualise data.
“When users log into the software, one of the first things they see is a dynamic map of their facility,” said Hatch.
This map, which uses the customers’ engineering drawings or digital photos, provides a clear and intuitive representation of test points and their statuses.
“This feature has become one of the most beloved components of our program because it conveys information in a way that’s accessible to food safety professionals, who may not be as techsavvy as financial analysts,” said Hatch.
The demand for such solutions has surged over the past six years, indicating a shift in industry expectations.
Audits play a crucial role in maintaining food safety standards.
“When a third-party auditor sees that a company has command and control over its food safety data, it makes a strong impression,” said Hatch.
“One customer shared that they turned their laptop to face the auditor to show a map of the entire floor plan, which demonstrated the level of organisation and control over their food safety processes.”
This ability to present data in an organised manner not only facilitates
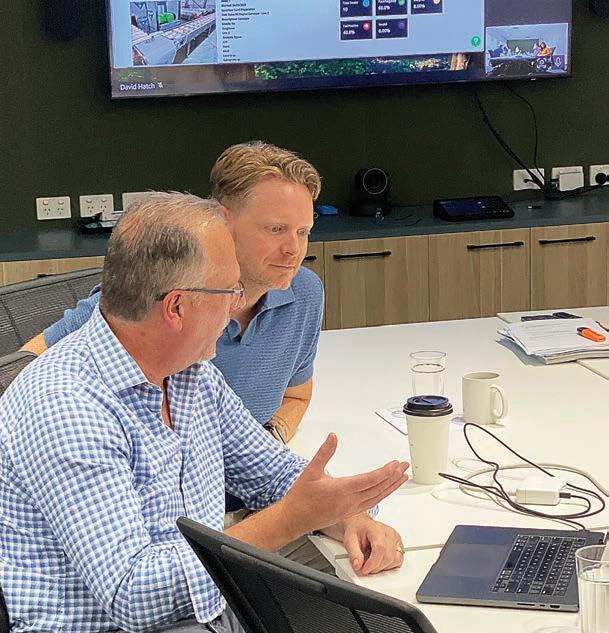
food manufacturers.
“Instead of sifting through pages of documentation, they can access everything they need right there,” said Hatch.
“ This display of data transforms relationships and word spreads, our customers recognise that we’re doing something different.”
As Neogen Analytics continues to evolve, the integration of artificial intelligence (AI) and machine learning into its platform is on the horizon.
“We’re moving in the right direction, but there’s still work to be done,” said Hatch.
T he platform is already designed to track trends and patterns in food safety data, allowing users to recognise potential issues before they escalate.
“We ingest at least six months’
implementation, so from day one, customers have trending graphs ready,” added Hatch.
This proactive approach helps to detect potential issues before they amount to non-conformances that could lead to production disruptions.
The platform is built to be open and integrative, allowing customers to connect data from their existing testing devices, third-party laboratories, and other data sources.
“All of our customers use some form of laboratory for diagnostics, and we’ve built an integration engine to handle data in any format it comes to us,” said Hatch.
T his flexibility ensures that Neogen Analytics can meet the diverse needs of its clientele.
The growing emphasis on
sustainability is another emerging focus for the company. As companies face increasing pressure to reduce their carbon footprints, Neogen’s platform helps them analyse data and discover new efficiencies within their production processes.
“One large meat producer began looking at how they could minimise waste and energy consumption,” said Hatch.
“ They were able to determine the root causes of scrapped production runs and reduce the occurrence of this scenario.
“ This led to improved production yield while reducing the energy and landfill consumed by waste.”
By addressing these issues, companies can not only comply with regulations but also enhance their operational efficiency.
“One of our board members has emphasised the importance of sustainability, prompting us to think about how our solutions align with these initiatives,” said Hatch.
Neogen Analytics has a robust platform that empowers customers to take control of their food safety processes. The company is making strides in ensuring that the food supply remains safe and reliable.
As the industry evolves, Neogen Analytics remains committed to leveraging technology and data to drive positive outcomes in food safety, ultimately contributing to a healthier and safer world.
“This is what excites me, Neogen shares this vision and has allowed me to take part in leading the messaging and launch of these initiatives globally.” said Hatch. F
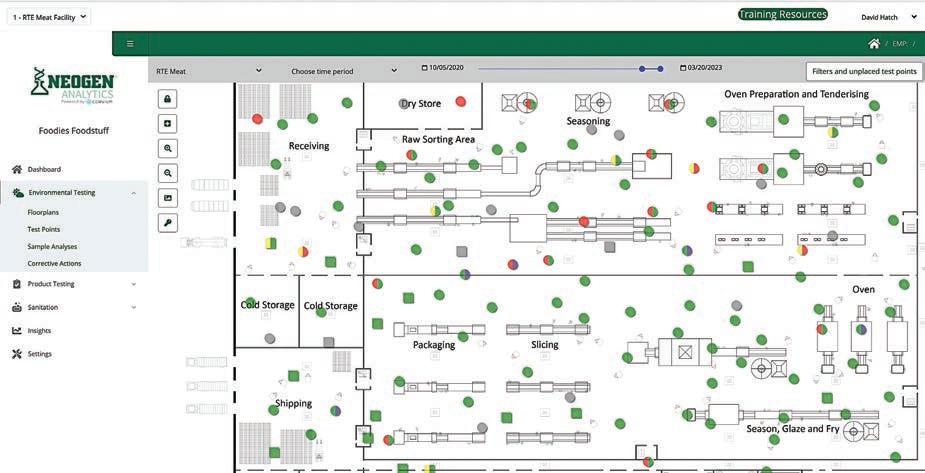
David Hatch (left) was key to the advancement of Neogen Analytics, bringing decades of experience in data tech.
Neogen Analytics provides a host of benefits including a live floor plan for real-time monitoring.
Global food brands continue to adopt 2D barcode technology to streamline operations and improve transparency across the the food and beverage industry.
Global retailers and brands unite
The adoption of 2D Barcode technology by global food and beverage brands continues to help enhance transparency, operational efficiency, and consumer engagement.
Several international brands have come together to support the adoption of next-generation barcodes in retail. The new technology promises streamlined operations, improved transparency and enhanced consumer engagement for the food and beverage industry.
the door for dynamic updates to content, enabling brands to adjust product details without having to reprint labels, leading to flexibility, sustainability, and reduced cost.
to unlock new valuable capabilities, delivering more benefits to their customers, shoppers and consumers,” said Mark Batenic, former CEO of the Independent Grocers Alliance (IGA).
supply chains,” said Maria Palazzolo, CEO at GS1 Australia.
“This technology is a cornerstone in maintaining transparency, which is increasingly important to consumers.
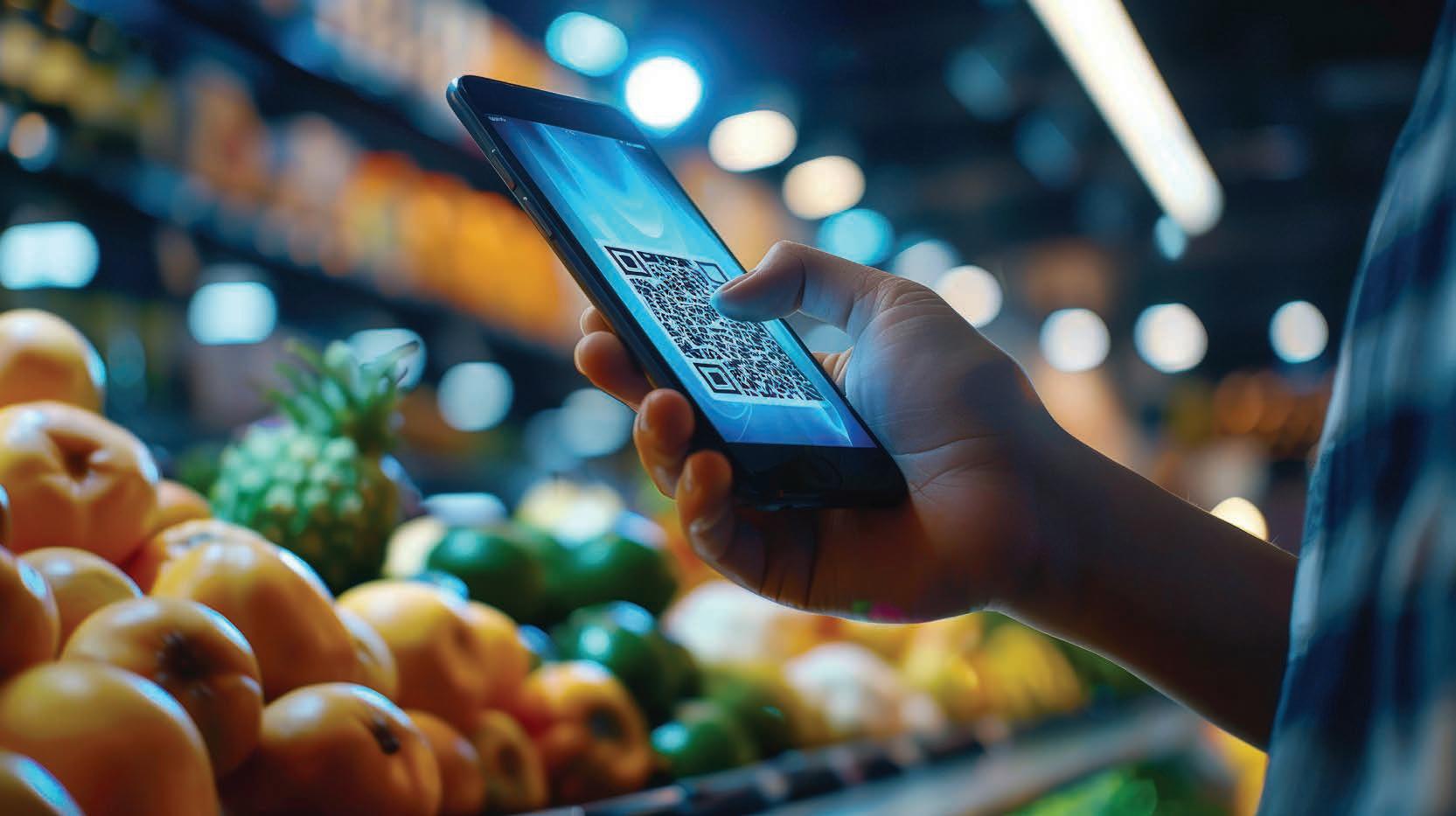
With a collective commitment from companies such as Procter & Gamble, Mondelez and Nestle, the next-gen barcode is poised to become the new standard.
In retail, the most common of the next-generation barcode is a QR Code that follows GS1 standards. GS1 is the not-for-profit organisation that is rolling out next-generation barcodes across the continent.
These act like traditional QRs, with one major difference; they will be able to be scanned at retail pointof-sale, just like a traditional barcode; paving the way for a global migration to GS1-powered QR Codes in the retail industry.
Unlike traditional barcodes, the advanced codes not only store more information, but also connect consumers to real-time data, through a simple scan via a smart phone.
They Provide instant access to a wealth of product information – such as ingredients, allergen warnings, verified sustainability certifications and even viewing the product’s journey through the supply chain.
For producers and retailers in the food industry, the barcodes also open
The exciting part of this movement is the collaboration between international retailers and brands that have aligned as signatories on a global industry endorsement statement to drive the adoption of the next-gen technology, recognising its value across the entire supply chain.
“We expect that the transition to next-generation barcodes will happen gradually across the world, but one thing is certain: those retailers and brands that accelerate through this transformation the fastest will be best positioned
Subhead: What does it mean for food and beverages in Australia?
The introduction of next-generation barcodes in Australia presents an opportunity for retailers and brands to innovate in an increasingly complex trading environment.
The technology not only enhances operational efficiency but also helps brands meet the evolving food safety, traceability and environmental standards that are shaping the future.
“The next generation of barcodes will mean greater visibility and control across
“We see this next evolution in barcoding capabilities as the future for food safety and product traceability in Australia.
“Beyond safety, sustainability is also a key focus. Next generation barcodes will enable brands to share sustainability efforts with shoppers and consumers directly, offering unparalleled transparency across everything from carbon footprint to water usage, sustainable sourcing practices and so much more.”
Reshaping the shopping experience
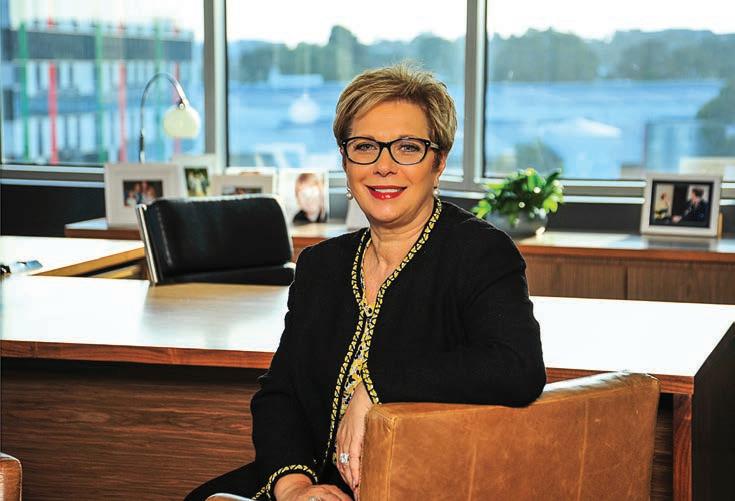
While the global and local push for next-generation barcodes is gaining momentum, the transition will take time. GS1 is working with Australian retailers, brands, and regulatory bodies to ensure a smooth rollout.
Australian consumers can expect to see more of the new barcodes on their favourite products soon.
Industry leaders are confident that this shift will redefine how Australian consumers interact with their products.
From ensuring the authenticity of locally sourced produce, to providing allergen and sustainability details with just a scan, the next-generation barcodes are set to reshape the Australian shopping experience. F

Maria Palazzolo, GS1 CEO, said the next generation of barcodes are set to bring greater visibility and control across supply chains.
Images: GS1
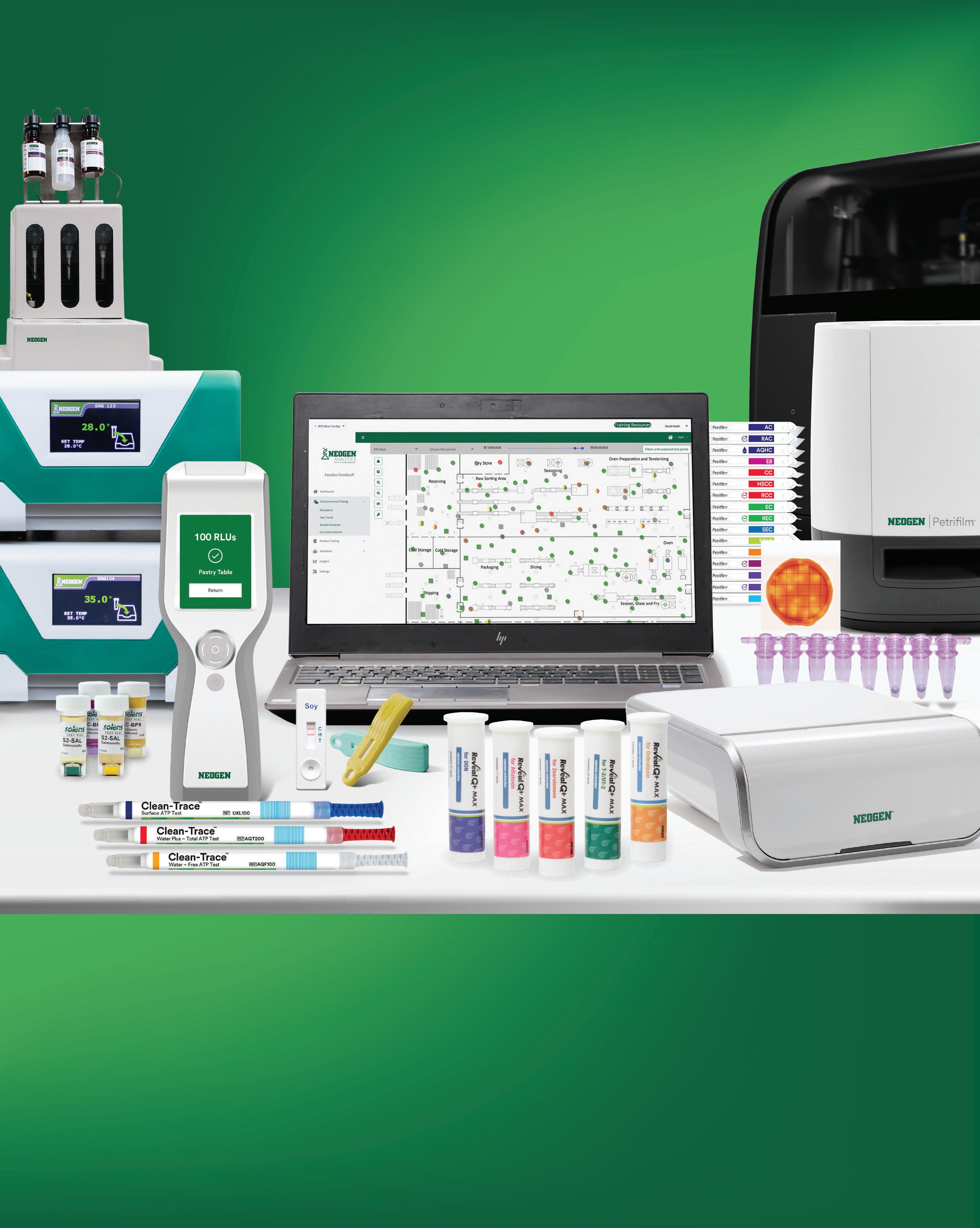
Don’t sacrifice quality for cost
WestCool Transport provides premium, professional and adaptable refrigerated transport services for several high-end and time-sensitive industries, with the help of Scully RSV.
WestCool Transport, an expert provider of refrigerated transport, successfully launched its operations in Western Australia after owner and managing director, Alan Peters, spotted a gap in the market for a premium service with exceptional client service, communication, and reliability.
After a period of extensive market research by Peters, a chartered accountant with experience in general management, operations, transport, material management and logistics, the company was set up as a provider of premium refrigerated transport services, primarily targeting high-end industries including the premium seafood sector.
Peters said his decision to enter the refrigerated transport sector stemmed from a recognised need for more highquality services, reducing risk and stress for clients, which meant he also had to find the solutions providers. He observed a focus on providing
low budget, or more cheaper services, which could result in low costs being prioritised over quality or reliability.
“A dependable partner is crucial to avoid complications in the cold chain,” said Peters.
Peters said the importance of reliability in the transport of high-risk, high-value, perishable products, especially those requiring strict temperature controls, or time sensitivity, could not be understated.
As a result, WestCool Transport aims to cater to clients dealing with sensitive products such as live lobster and abalone.
In these markets, the cheapest option is not the priority; rather, the emphasis is on reliability, professionalism, and risk management, ensuring that deliveries are made accurately and on time.
“While we may not be the cheapest option, we prioritise providing reliability, adapt-ability, and excellent communication,” said Peters.
Meanwhile, Peters’ prior
experiences in the logistics sector continues to inform his approach to WestCool.
He recalled his tenure as a financial controller at a company in Ireland, where the business experienced rapid growth, increasing from zero to 25 million in turnover over five years. A consistent relationship with a reliable logistics provider was key to this success.
“We chose to stay with them because they were reliable, adaptable and flexible, a close partnership with our business,” he said.
Peters said Scully RSV can provide his new business with the reliability and flexibility he knows is critical for growth and success in the sector.
“Efficiency in operations is critical, particularly in the fast-moving consumer goods (FMCG) sector,” he said.
A ny disruption, such as temperature breaches or delivery delays, can adversely affect production processes.
Alan Peters (pictured) successfully launched his refrigerated transport business, WestCool Transport, with the help of Scully RSV’s premium refrigerated transport, truck, and trailer fleet.
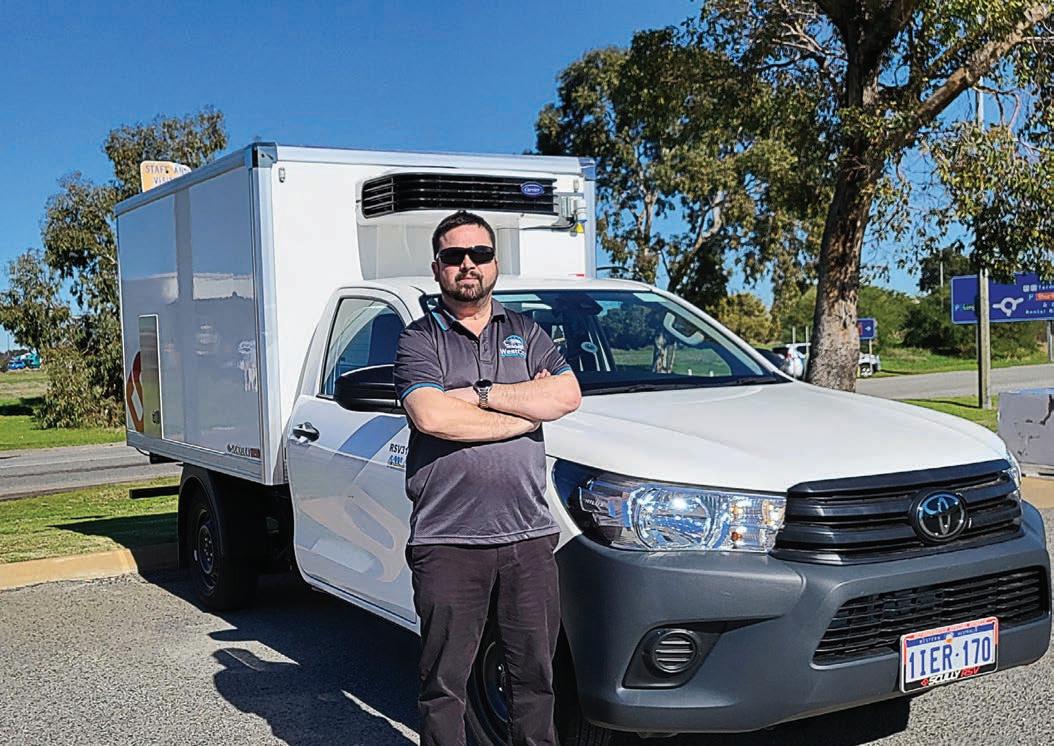
Peters noted that those working in production must constantly maximise efficiency.
“ When issues arise, such as breakdowns or lost stock, it can lead to customer dissatisfaction, loss of reputation and necessitate urgent adjustments to production schedules,” he said.
The potential repercussions extend to retail as well, where recurring empty shelf space can result in delisting from major retailers, impacting substantial revenue streams.
Prior to launching WestCool, Peters identified the need for a reliable, adaptable truck supplier in Perth.
He contacted numerous suppliers before coming across Scully RSV where he spoke to the company’s business development manager for Western Australia, and South Australia, Shaynnon Hagger, of whom he was very impressed by.
Following a detailed discussion, the founder felt assured that the Scully RSV team could offer a flexible and reliable service, allowing for a range of vehicle sizes on short notice.
“For me, this relationship feels more like a business partnership than a typical supplier arrangement, and Shaynnon has been amazing,” he said.
WestCool’s operational strategy revolves around flexibility, which enables the company to quickly assemble resources to meet diverse client needs.
Peters explained that his ability to cater to multiple industries, such as pharmaceuticals, medical supplies, and premium seafood, hinges on this adaptability.
“When I receive a specific request from a client, I can swiftly put together the necessary resources to provide a customised solution,” he said.
Me anwhile, the importance of networking in the sector is critical.
“Networking has played a crucial role in the establishment of WestCool,” said Peters.
He demonstrates this notion as an active member of the Fremantle
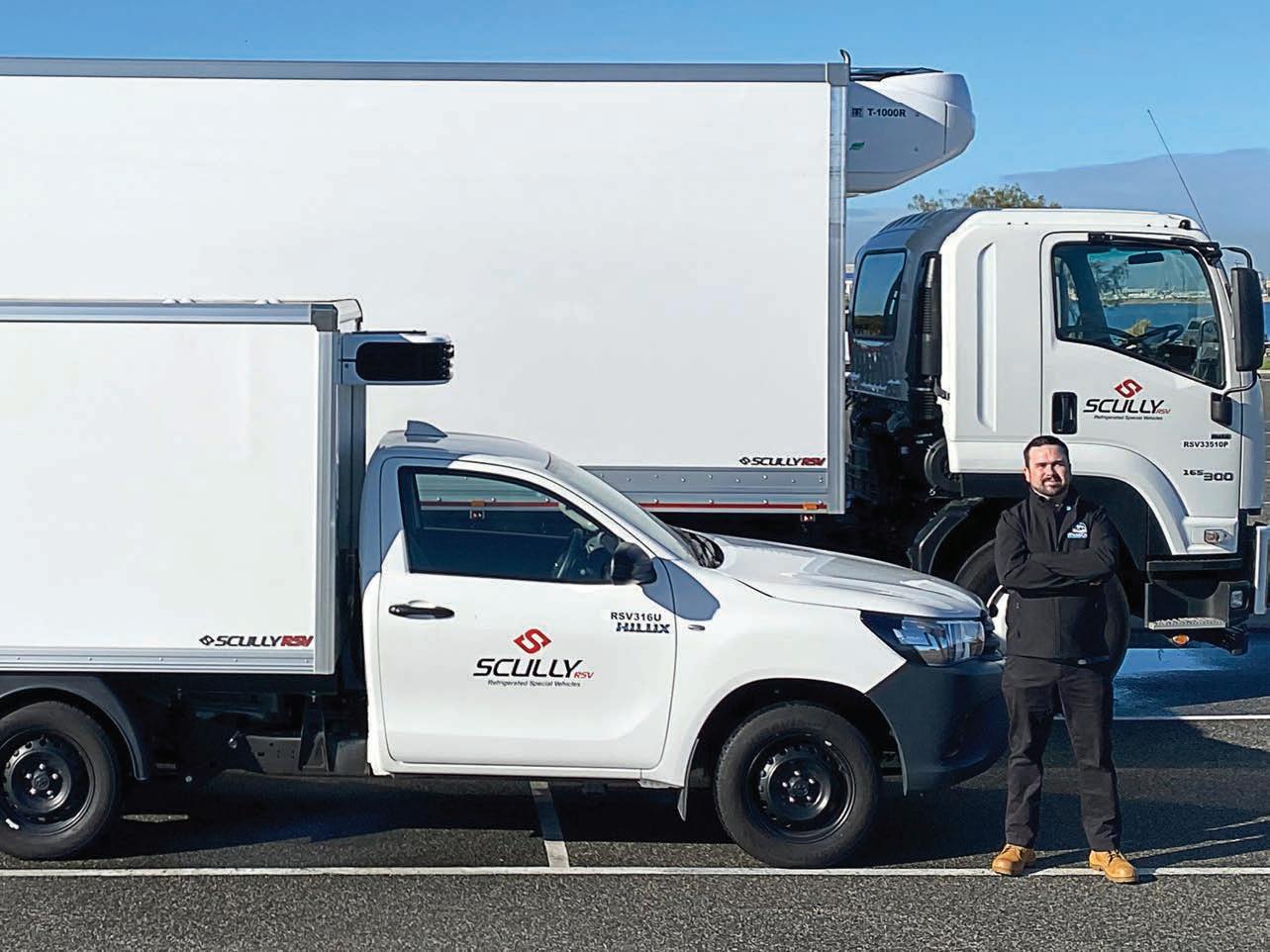
Chamber of Commerce and the Melville Cockburn Chamber of Commerce.
He said that personal engagement and relationship building are essential for business growth.
“While digital advertising can complement outreach efforts, the best relationships are built through direct and face to face interactions,” he said.
A recent example of effective networking occurred during the Fremantle Chamber Business Awards, where Peters was able to rub shoulders with key industry stakeholders, which may have been difficult otherwise.
He noted that such opportunities for face-to-face interaction are invaluable for establishing meaningful connections, which are often more effective than cold calls or emails.
Then there is WestCool Transport’s emphasis on quality assurance, which is always of added importance in the cold chain, another area supported by Scully RSV.
“We continually monitor the temperature to provide assurance that goods are kept at the correct levels throughout the journey.”
Peters also emphasised how the assets provided Scully RSV were either new or nearly new, which helps maintain both companies’ high standards, which reflects well on client engagements.
“Having the option to choose trucks of various sizes, with or without tail lifts allows us to adapt to various delivery scenarios,” he said.
He added that this flexibility is also crucial for navigating the diverse terrains found throughout Western Australia.
In addition to transportation services, WestCool offers comprehensive Goods In Transit Insurance, which reflects the high value of the products being transported.
Peters said he ensured WestCool
Transport provides the Goods In Transit Insurance by default after recognising it wasn’t widely offered.
He also highlighted the use of advanced monitoring systems, including laser thermometers, to ensure optimal conditions for transported goods, which is especially important in the heat of Western Australia, meaning it can also stand up to the rigours of the East, North, and South of the country.
“We continually monitor the temperature to provide assurance that goods are kept at the correct levels throughout the journey,” said Peters.
Ultimately, Peters aims to position WestCool Transport not only as a provider of refrigerated transport services but also as a reliable partner for clients seeking high-quality
logistics solutions in Western Australia.
By focusing on reliability, adaptability, and quality assurance, Peters seeks to carve out a niche as a premium provider in the market.
His partnership with Scully RSV has played a crucial role in this focus for Peters, by providing solutions that offer the same flexibility and reliability as WestCool Transport.
As the company continues its operations, it’s clear that Peters is committed to establishing WestCool Transport as a dependable option for clients who prioritise quality and reliability over price.
With a strong emphasis on building partnerships and maintaining high standards, WestCool aims to meet the growing demands of the premium seafood industries while navigating the complexities of the refrigerated transport sector in Western Australia, along with the expert solutions provided by Scully RSV. F
WestCool Transport uses Scully RSV ‘s refrigerated truck and trailer solutions to service the West and South West regions of Western Australia.
A global presence with a local touch
With a legacy spanning over 150 years in fermentation, Biospringer by Lesaffre is redefining its role in the food and beverage industry.
Biospringer, founded in 1873, made history in 1958 by becoming the first company to manufacture yeast extract for commercial purposes, before being acquired by the Lesaffre Group.
Today, Biospringer by Lesaffre operates ten manufacturing sites globally, including three strategically positioned across the Asia Pacific.
This expansive network allows Biospringer to cater to local markets with tailored solutions, and in a timely manner.
“Our mission is to partner with food producers to create innovative, natural ingredients from fermentation that enhance flavour while being mindful of the environment,” said Philippe M. L’Honneur, general manager of Biospringer Asia Pacific.
This partnership approach underscores the importance of collaboration in helping the food industry transition toward healthier formulations.
Milestones and achievements
Recent years have been marked by significant milestones for Biospringer, reflecting its commitment to innovation and collaboration. One standout achievement is the establishment of its Culinary Centre in Singapore in 2017.
This technical hub provides customers with the opportunity to collaborate directly with Biospringer’s R&D experts, ensuring that product development is closely aligned with market needs.
“Our Culinary Centre has been a game-changer, enabling our customers to access our expertise in fermentationbased products,” said M. L’Honneur.
In addition, the recent acquisition of DSM-Firmenich’s yeast extract ranges in October 2024 marks another pivotal moment for the company.
M. L’Honneur highlighted the significance of this acquisition.
“This strategic move broadens our product offerings and allows us to upgrade our fermentation expertise,” he said.
This commitment to continuous improvement and innovation positions Biospringer as a leader in the industry.
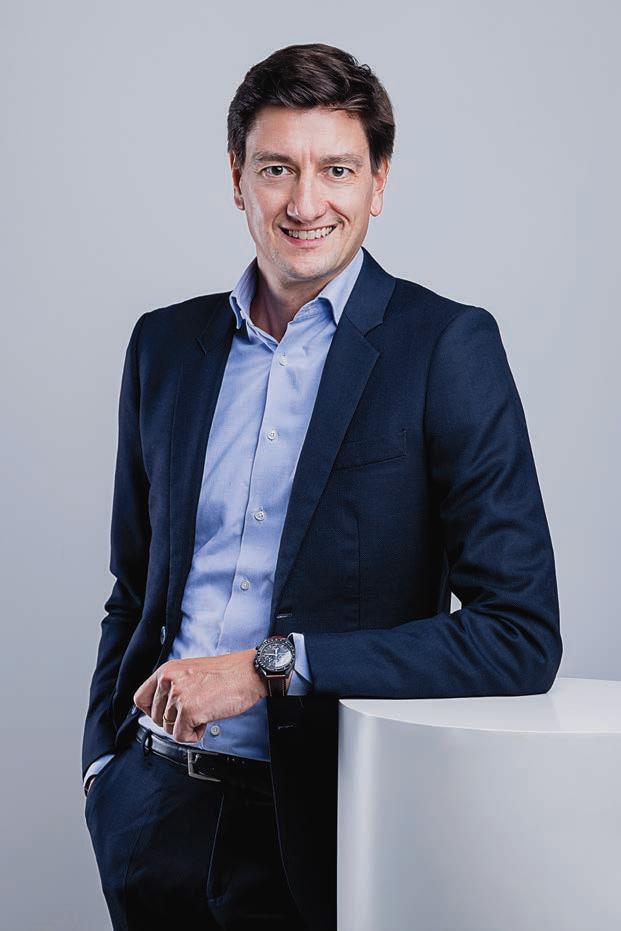
Philippe M. L’Honneur, general manager of Biospringer Asia Pacific, said the company’s mission is centred around innovation.
flavour notes and mask off-notes,” explains Lucie Oodoomansaib, Sales Manager for Biospringer in Australia & New Zealand.
This transformation comes in response to the growing consumer demand for clean labels and healthoriented products, particularly around reduction in salt and sugar content.
With the rise of dietary preferences like veganism and the need for glutenfree options, the versatility of yeast extracts has made them essential for food manufacturers.
“Choosing natural yeast-based ingredients isn’t just a trend, it’s a long-term investment in healthier formulations,” said Lucie.
“Our expertise in fermentation allows us to deliver multifunctional solutions that not only enhance flavour but also promote health”
healthier options increase.
Regulations aimed at reducing sugar and salt levels are becoming more stringent, compelling manufacturers to produce clean-label products that are both nutritious and tasty. In this complex landscape, Biospringer is wellpositioned to meet these challenges.
“Our expertise in fermentation allows us to deliver multifunctional solutions that not only enhance flavour but also promote health,” said Lucie.
Sustainability presents another significant opportunity for Biospringer. The company is deeply committed to minimising its environmental impact by optimising resource use and actively reducing carbon footprints.
“We conduct regular audits of our manufacturing practices to ensure we meet the highest sustainability standards,” said M. L’Honneur.
This commitment resonates with a growing number of consumers and food manufacturers who are increasingly prioritising sustainable practices.
Yeast innovation
Innovation at Biospringer is powered by a robust R&D pipeline, with teams in France, United States and Singapore focused on exploring new fermentation methods and product applications.
Recent product launches, including Springer Proteissimo 102, a cleanflavoured vegan protein, demonstrate the company’s forward-thinking approach to ingredient development.
“Our focus on innovation is not just about creating new products, it’s about addressing the evolving needs of our customers,” said Lucie.
Looking ahead, the Biospringer team is excited about the potential of emerging technologies such as artificial intelligence.
“AI is set to revolutionise our production processes and enhance our customer service capabilities,” said Lucie. By leveraging data and innovative fermentation techniques, Biospringer aims to maintain its competitive edge in a rapidly changing market.
At the core of Biospringer’s strategy is a commitment to understanding and responding to customer needs. The company actively seeks feedback through initiatives like the Voice of Customers survey, which revealed high satisfaction ratings.
“We received a score of 9 out of 10 from our customers, reflecting our commitment to quality and support,” said M. L’Honneur.
This proactive approach to customer engagement helps Biospringer refine its offerings and better align with market demands.
The company plans to enhance its services further by developing a customer portal, which will streamline communication and ensure that client feedback directly informs product innovation.
Images: Biospringer by Lesaffre
Biospringer was the first company to manufacture yeast extract for commercial purposes, and now has locations all over the world.

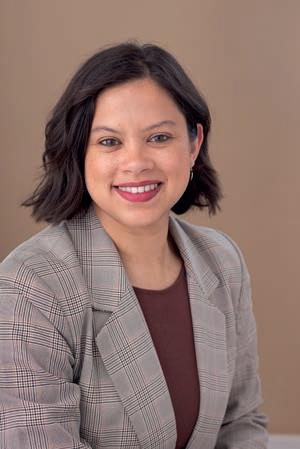
innovation.
“Listening to our customers is key to our success,” added Lucie.
Shaping the Future
As demand for healthier, functional food products continues to rise, Biospringer is poised to help lead the charge in yeast-based ingredient innovation.
The company has ambitious plans to expand its product portfolio and explore new markets, with a goal to solidify its
status as the number one provider of fermentation-based ingredients.
“Our vision is to not only expand but to ensure that we’re at the forefront of ingredient innovation,” said Lucie.
“We want to continue developing products that not only meet but exceed customer expectations, especially in the realms of health and sustainability,” added M. L’Honneur.
Consumer preferences are continuously evolving, and Lucie notes that today’s consumers are increasingly inclined towards healthier and more nutritious solutions.
“However, they are also unwilling to sacrifice taste,” said Lucie.
This dual focus on health and flavour underscores the relevance of yeast extracts in modern food formulations.
With the introduction of products like Springer ® Proteissimo, which offers a natural yeast protein option, Biospringer is responding directly to consumer demand for clean-label, highquality ingredients.
“We see our yeast proteins as a solution for food manufacturers looking to meet the demand for alternative protein sources,” said Lucie.
Looking ahead, Biospringer has set clear goals and projects for the coming
“We see our yeast proteins as a solution for food manufacturers looking to meet the demand for alternative protein source”
years. One of the primary focuses is the integration of the DSM-Firmenich yeast extracts into its offerings.
“This acquisition will allow us to leverage our combined expertise in fermentation and develop new, innovative products,” said M. L’Honneur.
Additionally, the company is gearing up for several product launches in 2025.
“We’re excited about the potential for innovation sessions with our customers, which will help us continue to promote new food concepts using yeast extracts,” said M. L’Honneur.
This collaborative approach will be vital as they explore the limitless possibilities that fermentation offers.
As the demand for clean-label, functional food products continue to grow, the future of yeast-based ingredients in the food and beverage industry looks promising.
M. L’Honneur noted how fermentation has been utilised for centuries, and with continuous innovation.
“We are just scratching the surface
of what yeast extracts can do in food applications worldwide,” he said.
“Consumers are becoming increasingly demanding about product transparency, seeking clean labels and natural ingredients. Yeast extracts check all these boxes.”
As Biospringer looks to the future, it is not just about maintaining its status as a leader in yeast extracts; it is about shaping the future of food.
The company aims to remain at the forefront of innovation, ensuring that its ingredients not only meet the current market trends but also anticipate the needs of tomorrow’s consumers.
“Choosing our yeast extracts means choosing a healthier, tastier future,” said M. L’Honneur.
In a world increasingly focused on health and sustainability, Biospringer by Lesaffre provides an ideal opportunity to capitalise on the changes in market demand. F
If you would like to learn more about the impact Biospringer’s ingredients, contact Lucie Oodoomansaib at l.oodoomansaib@ biospringer.lesaffre.com.
Lucie Oodoomansaib is the best point of contact in Australia and New Zealand to learn more about Biospringer by Lesaffre’s solutions.
What food and beverage manufacturers should consider in 2025
Artificial Intelligence and Machine Learning technology is helping manufacturers mitigate the string of potential challenges along the supply chain. Here’s how.
As 2025 approaches, food and beverage manufacturers are grappling with various supply chain challenges, including disconnected planning processes, and rising operational costs. This situation is putting significant pressure on the industry.
Fortunately, innovative solutions utilising Artificial Intelligence (AI) and Machine Learning (ML) are emerging, providing ways to streamline operations and improve efficiency. One key issue in the manufacturing sector is the fragmentation of planning processes, where different teams often operate in isolation. This disconnection complicates the ability to respond
effectively to shifts in demand or production constraints.
To tackle this, RELEX has introduced a unified platform that integrates demand planning, production scheduling, inventory management, and more. This comprehensive approach ensures that any changes—like an unexpected increase in demand for a specific product—are automatically addressed across the supply chain.
The benefits of integration are illustrated in a case study involving Vita Coco, a coconut water producer with operations in 31 countries. RELEX developed a digital twin for Vita Coco that incorporated various cost constraints and variables, resulting in
an optimised 18-month supply plan that unlocked significant cost savings through improved sourcing and distribution.
Similarly, Snack Brands, an Australian snack food manufacturer, experienced advantages from an optimised weekly production plan that halved planning time and better aligned supply with demand. By reducing Stock Keeping Unit (SKU) runs from 40 to 15, they minimised changeover times and increased production efficiency.
The flexibility of RELEX’s solutions allows them to integrate smoothly into existing systems and adapt to individual manufacturing processes. The platform features
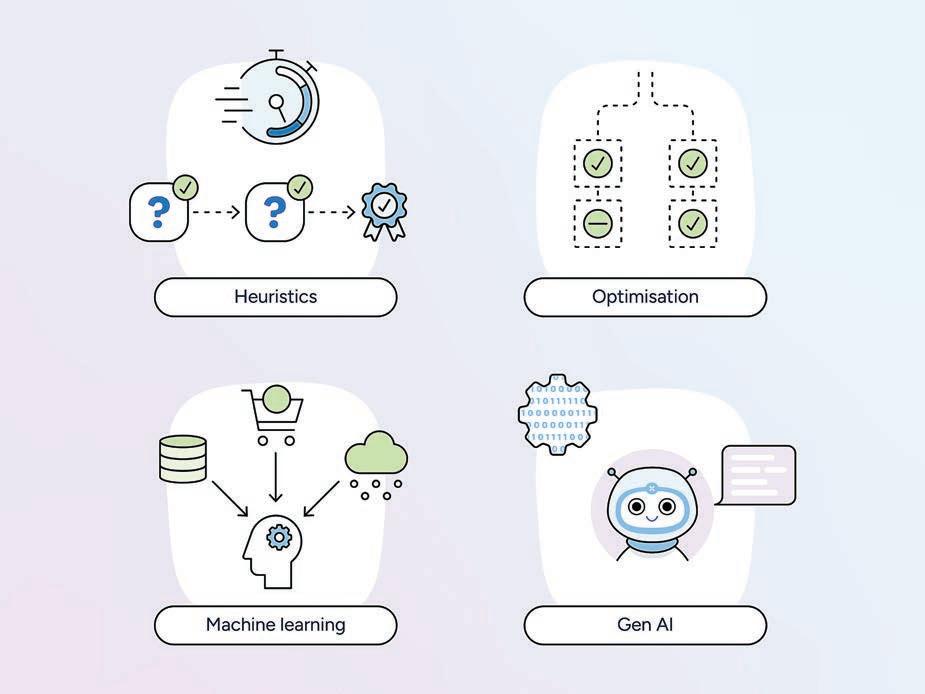
no-code configuration, enabling it to learn from new data and adjust to evolving business needs. With AI-driven capabilities, it offers data-informed recommendations for optimisation, leading to enhanced accuracy and efficiency in planning.
This coordinated approach to supply chain management allows for swift responses to disruptions or opportunities, ensuring that changes in one area are reflected throughout the planning cycle. Identifying and improving key areas of waste or cost becomes a strategic priority for manufacturers navigating these challenges.
Adapting to change
The adaptive nature of RELEX’s solutions makes them easy to integrate into an existing system and adapt to individual manufacturing processes.

The company’s platform features no-code configuration, allowing it to learn from new data and adjust to changing business needs.
Coupled with autonomous capabilities powered by AI, it provides data-driven recommendations for optimisation.
“Achieving these aims results in greater accuracy and efficiency in the planning process,” said Taylor.

This alignment across the supply chain ensures coordinated decisionmaking where changes in one area are reflected throughout the planning cycle, allowing for quick responses to disruptions or opportunities.
“Identify the biggest source of waste or additional costs and focus on improving that area first,” said Taylor.
By prioritising high-impact areas and leveraging data, manufacturers can establish a solid foundation for an integrated supply chain. Understanding the quality and sources of data is paramount for successful implementation.
Christer Liden, vice president of APAC Consumer Goods & Production at RELEX Solutions, also highlighted the intensifying competition in the food and beverage sector, where razor-thin margins drive companies to focus on cost reduction.
“For most companies, increasing gross margin is a top priority,” he said.
“Technology, particularly AI and ML, is becoming increasingly vital for navigating these challenges. Optimisation and automation must be the focus.”
A recent McKinsey article corroborates this, suggesting that advancements in automation could lead to a 20 per cent reduction in inventory
costs and a 10 per cent decrease in overall supply chain costs.
“These improvements are crucial for our clients as they strive to streamline operations,” said Liden.
However, the path to automation is not without hurdles.
“Even user-friendly solutions require analytical thinking and a certain mindset,” Liden added.
Sustainability challenges
In addition to efficiency, sustainability has become a pressing concern for manufacturers.
“Companies are increasingly focused on maintaining a positive image and engaging in sustainability efforts,” said Liden.
Effective inventory management can play an important role in these efforts.
“The more inventory you hold, the more storage space you need, which increases heating and cooling requirements,” said Liden.
By minimising inventory waste and optimising logistics, companies can enhance asset utilisation and reduce environmental footprints, while remaining agile to market dynamics.
Utilising AI and ML enables manufacturers to process data rapidly and accurately, providing insights that enhance responsiveness to market
Innovative new technologies like Artificial Intelligence and Machine Learning provides the food and beverage industry with a new way to tackle historical issues while also improving productivity.
changes, whether it’s a surge in demand for gluten-free products or the latest organic trend.
“CPG companies must shorten reaction times to fluctuations in demand and supply,” said Liden.
Liden also highlighted real-time tracking capabilities that enhance communication between producers and retailers.
“Using machine learning algorithms to forecast future demand allows us to gather valuable insights from both internal and public data,” said Liden.
This connectivity helps companies respond effectively to retail dynamics, bridging the gap between store-level insights and production strategies.
Looking ahead, Liden believes transparency in supply chains will continue to improve.
This capability not only enhances operational efficiency but also elevates customer experience, enabling consumers to receive timely updates on their deliveries.
The inability to provide transparency across the supply chain will threaten efficiency and profitability. Fragmentation of supply chain processes is a key issue for many businesses.
“Many companies operate on separate systems: one for demand management, another for inventory,
and a third for production planning and procurement,” said Liden.
As mentioned earlier, this often results in siloed operations, leading to disjointed operations.
For example, sales teams might overestimate demand to increase inventory levels, ensuring that stock is always available. However, this can erode trust in the forecast, prompting the production team to focus on maximising production efficiency rather than actual demand.
As a result, products with low demand may be overproduced. Meanwhile, procurement teams may prioritise lower unit prices by purchasing in large quantities, which could lead to excess stock and, potentially, obsolete inventory.
There are numerous real-world examples of businesses vulnerable to these challenges. Companies often find themselves overstocked due to misaligned supply chain plans.
For instance, a well-known soup brand ended up with excess inventory after over-purchasing stylish bowls from overseas suppliers, driven by decisions to drive down the unit cost rather than align with actual demand.
“When the product didn’t sell, they were left with excess inventory,” said Liden.
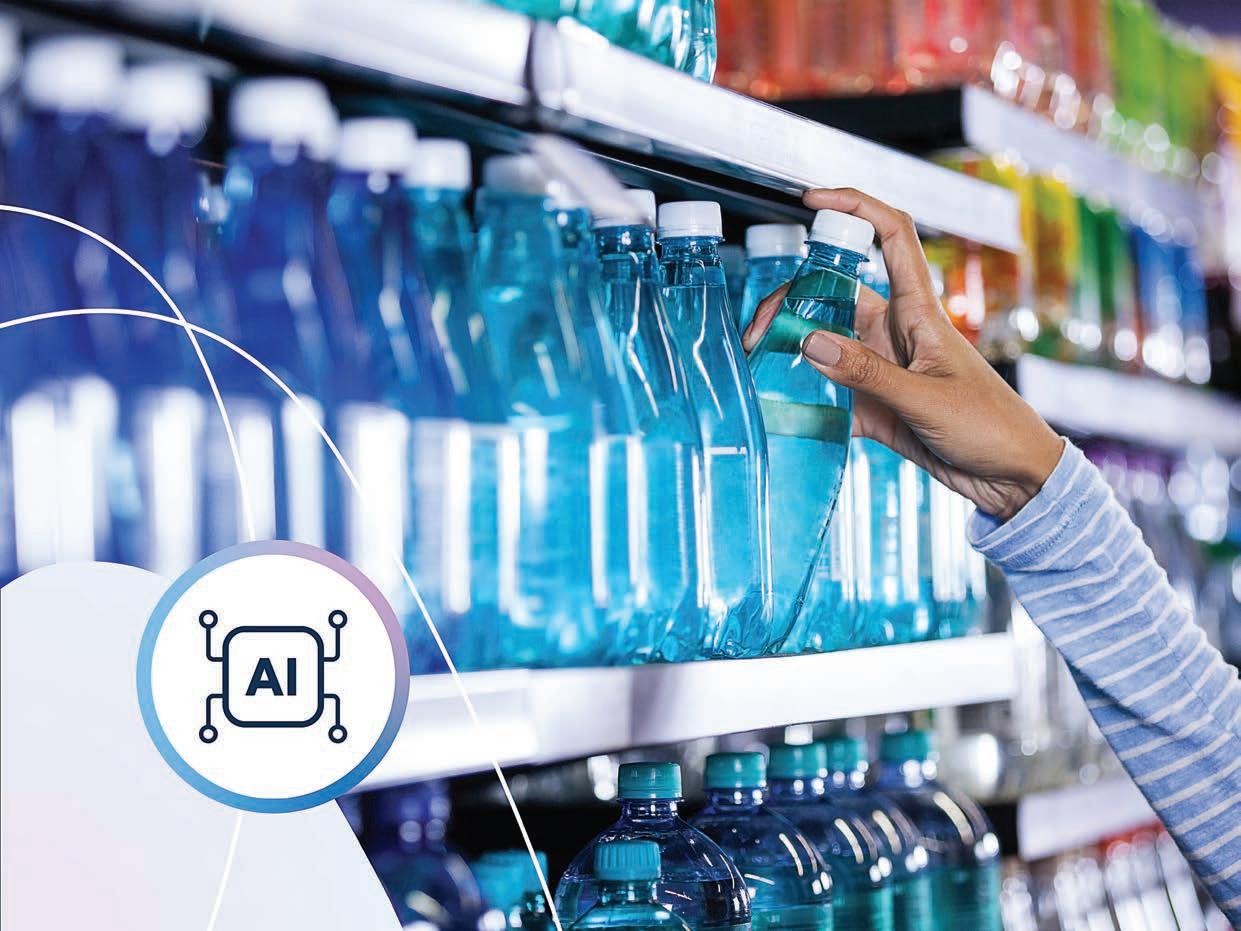
emphasised the need for a unified supply chain planning approach.
“If orders are placed for items without actual demand or with extended lead times, warning signals should alert the team,” he said.
This fosters a collaborative environment where decisions are based on shared insights rather than individual KPIs.
“ The goal is to minimise debates over numbers and focus on actionable insights,” said Liden.
Even if a company is not fully mature in its supply chain practices, establishing a robust data-driven approach is critical.
“Relying solely on processes and spreadsheets can lead to disjointed operations,” said Liden.
When working with Snack Brands, Liden’s team identified areas for improvement, particularly in line utilisation. They were able to develop an optimised production plan that minimised downtime while still accounted for demand, inventory, and capacity constraints.
“If you can increase production by 10 per cent without additional resources, it
impacts the bottom line significantly,” he said.
The complexities deepen for poultry producers like Tegel Foods, where supply chain planning is fraught with uncertainty.
“You know you’re going to get a number of birds, but you don’t really know their size, and they can vary from one delivery to another,” said. Liden. For fresh cuts, the order lead time is extremely short which leads to unpredictable demand.
To mitigate these challenges, companies often freeze products or further process them into cooked products like chicken nuggets that can be frozen.
“Understanding surplus and having a clear view in advance allows you to address this early,” said Liden.
Meanwhile, Arijit Saha, general manager of Supply Chain at Tegel, underscored three key benefits realised through enhanced supply chain practices: improved line utilisation, better control over surplus, and streamlined access to relevant information.
This visibility helps eliminate distractions and enables a focus on true challenges.
“Having the right systems in place allows you to quickly recap the plan,”
he said.
“We have a true end-to-end supply chain. We don’t rely on disparate systems; everything is integrated,” said Saha.
However, Liden warns that if a planning solution can only meet 90 per cent of business constraints, companies may revert to spreadsheets, leading to inefficiencies.
“The details matter greatly in food manufacturing,” said Saha.
Harnessing AI for success
RELEX’s solutions are designed to tackle these complexities head-on. For example, a customer faced challenges with avocado production that had taken a year to resolve.
By using RELEX’s solution, the customer managed to solve the issue in under a week, demonstrating the speed and efficiency of modern solutions.
Meanwhile, Madhav Durbha, group vice president of Industry Strategy at RELEX, emphasised that the need for seamless end-to-end visibility in the supply chain is more critical than ever.
Durbha said AI-driven methods help maintain optimal inventory levels and minimise waste, while data accuracy provided proactive recommendations for corrections.
RELEX integrates these AI capabilities into its core algorithms, which have proven successful across more than 500 clients since 2005.
“With the explosion of AI technologies, I advise CPG manufacturers to invest in practical AI solutions sooner rather than later,” said Durbha.
Improving demand signal accuracy and forecasting represents a “low hanging fruit” that can enhance service levels and reduce waste.
While generative AI is advancing, he encourages companies to explore a range of algorithmic techniques, including specialised AI, to drive supply chain benefits and scale practical solutions.
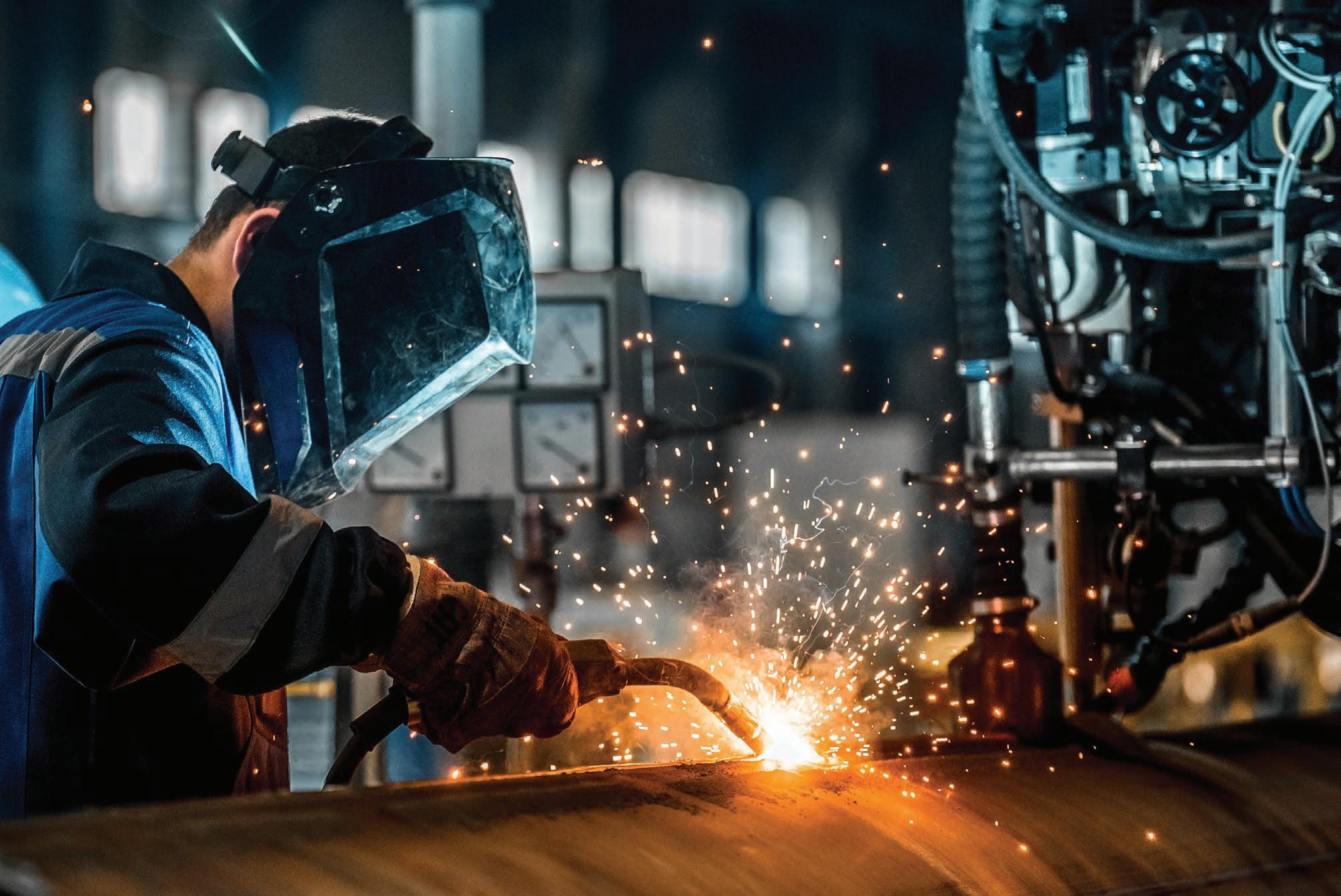
As CPG manufacturers navigate this challenging landscape, the integration of AI and ML into operations is not just beneficial, it’s essential for future success. By embracing these technologies and strategies, the food and beverage sector can overcome current challenges and thrive in the years to come. F
To learn more about RELEX, scan here
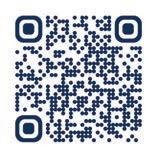
RELEX’s solutions are designed to tackle the complexities food and beverage manufacturers face daily, such as reducing machine downtime and maintaining optimal inventory levels.
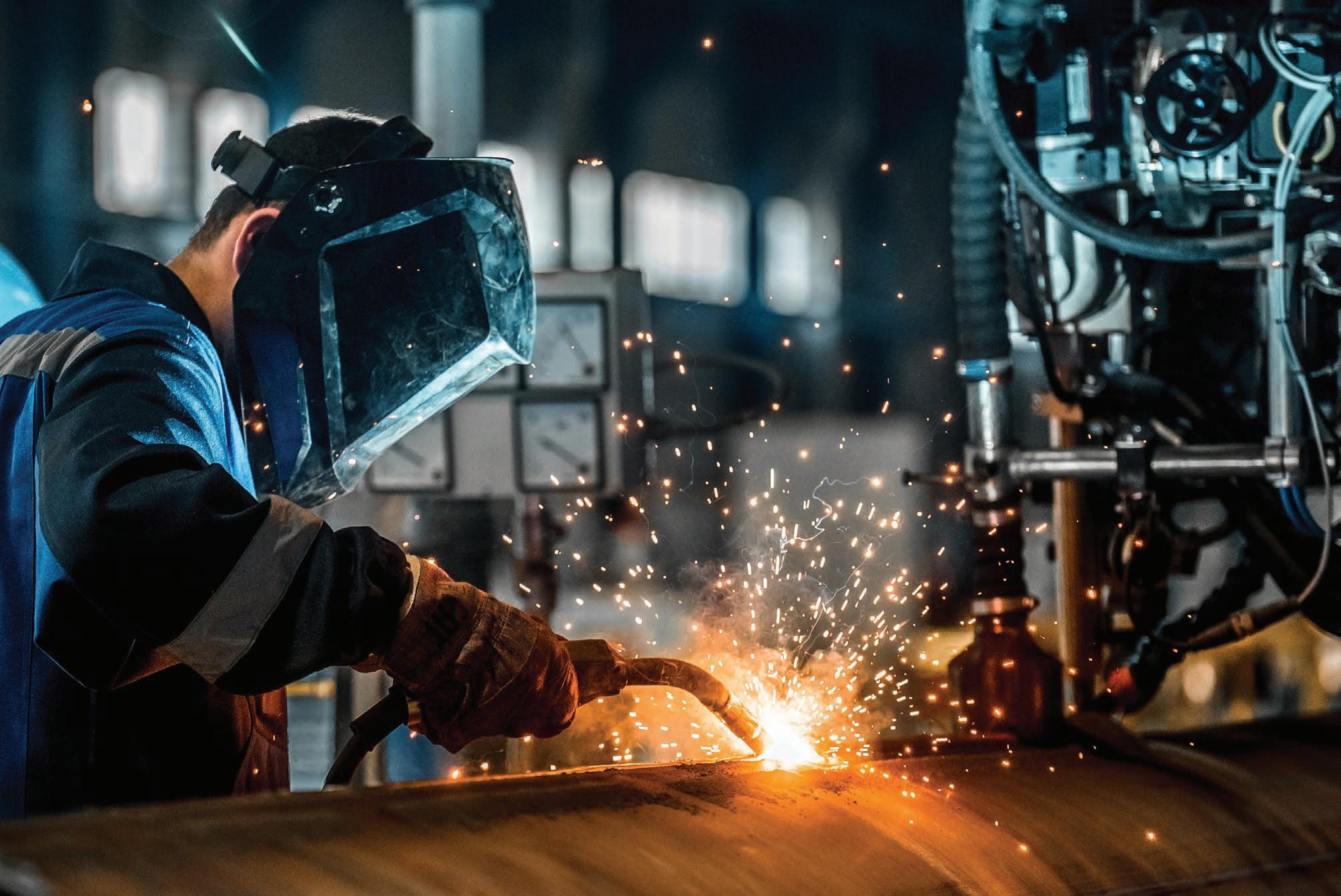
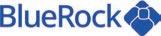
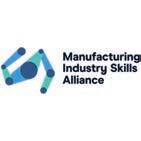
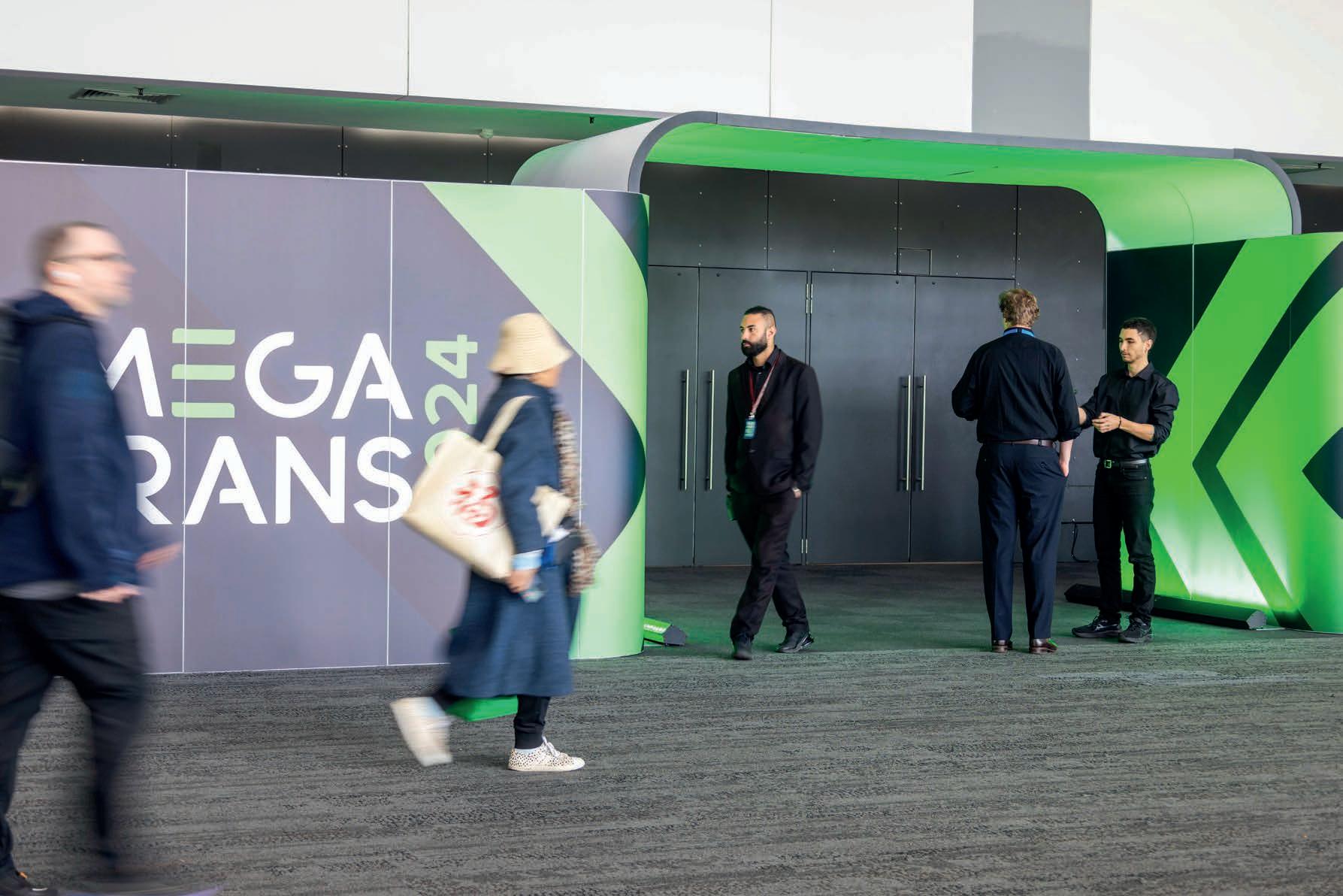
A look back at MEGATRANS 2024
MEGATRANS 2024 highlighted the supply chain and logistics industry’s innovations, with a focus on sustainability and collaboration, all designed to pave the way for a forward-thinking future.
MEGATRANS 2024, hosted by Prime Creative Media, was a key event on the calendar for the supply chain and logistics industry, with key stakeholders coming together to explore the future direction of the industry.
Held at the Melbourne Exhibition and Convention Centre from September 18-19, 2024, the event served as a platform for industry leaders and innovators to engage in discussions on pressing challenges to overcome and opportunities to capitalise on.
“The future of the sustainable supply chain provides both opportunities and challenges as we work towards reducing our carbon footprint.”
The event showcased how sustainability and technological advancements intertwine, emphasising the connections and networking
opportunities that the industry nurtures through gatherings like MEGATRANS.
With a top-tier list of speakers, panel discussions, and networking opportunities, the event aimed to shape the direction of the industry as it navigates a rapidly evolving market.
Industry Breakfast
The event was kick started by the Victorian Transport Association (VTA), which hosted its official opening breakfast.
VTA CEO Peter Anderson set the stage for the morning, emphasising the pressing logistics challenges that the industry faces and the need for collective action and innovation.
“The supply chain is connected. We can’t think in silos,” said Anderson.
The breakfast event’s sponsor, Zurich Resilience Solutions’s Peter Johannson, Principal Risk Engineer, delivered an insightful speech on resilience in the face of climate change, cyber threats, and technological advancements.
“Businesses are now being electrified
as they deploy artificial intelligence solutions,” said Anderson.
He highlighted that social engineering is essential for companies looking to enhance their operations.
To achieve Scope 3 targets, he recommended focusing on supply chain mapping, governance, and risk management.
“The human element is also important. We should aim to have well, happy, and resilient employees,” he said.
Meanwhile, Melissa Horne, the Victorian Minister for Roads & Road Safety and Ports and Freight, spoke to the audience about upcoming Victorian government projects poised to transform the logistics landscape.
She emphasised the West Gate Tunnel, set to open in 2025, and the North-East Link, both of which are expected to improve freight efficiency.
“My role is to work with the VTA as a facilitator for a sustainable and productive freight sector,” says Melissa.
In an era where the demand for skilled labour continues to rise, Horne also celebrated the success of the Truck
Driver Program, which has trained nearly 400 heavy vehicle drivers since its inception.
“Twenty-five per cent of the drivers trained so far have been women,” said Horne.
John Murphy, CEO, Prime Creative Media, rounded out the morning’s speeches with a call for collaboration.
“The future of the sustainable supply chain provides both opportunities and challenges as we work towards reducing our carbon footprint,” said Murphy.
The breakfast was only the beginning of a dynamic day at MEGATRANS 2024 when the show floor opened to thousands of attendees.
Visitors explored the latest innovations and engaged with industry leaders, setting the stage for conversations and connections.
Industry insights
The conference featured a series of sessions that delved deeper into specific industry challenges and innovations.
One such session, sponsored by OneStop, focused on enhancing
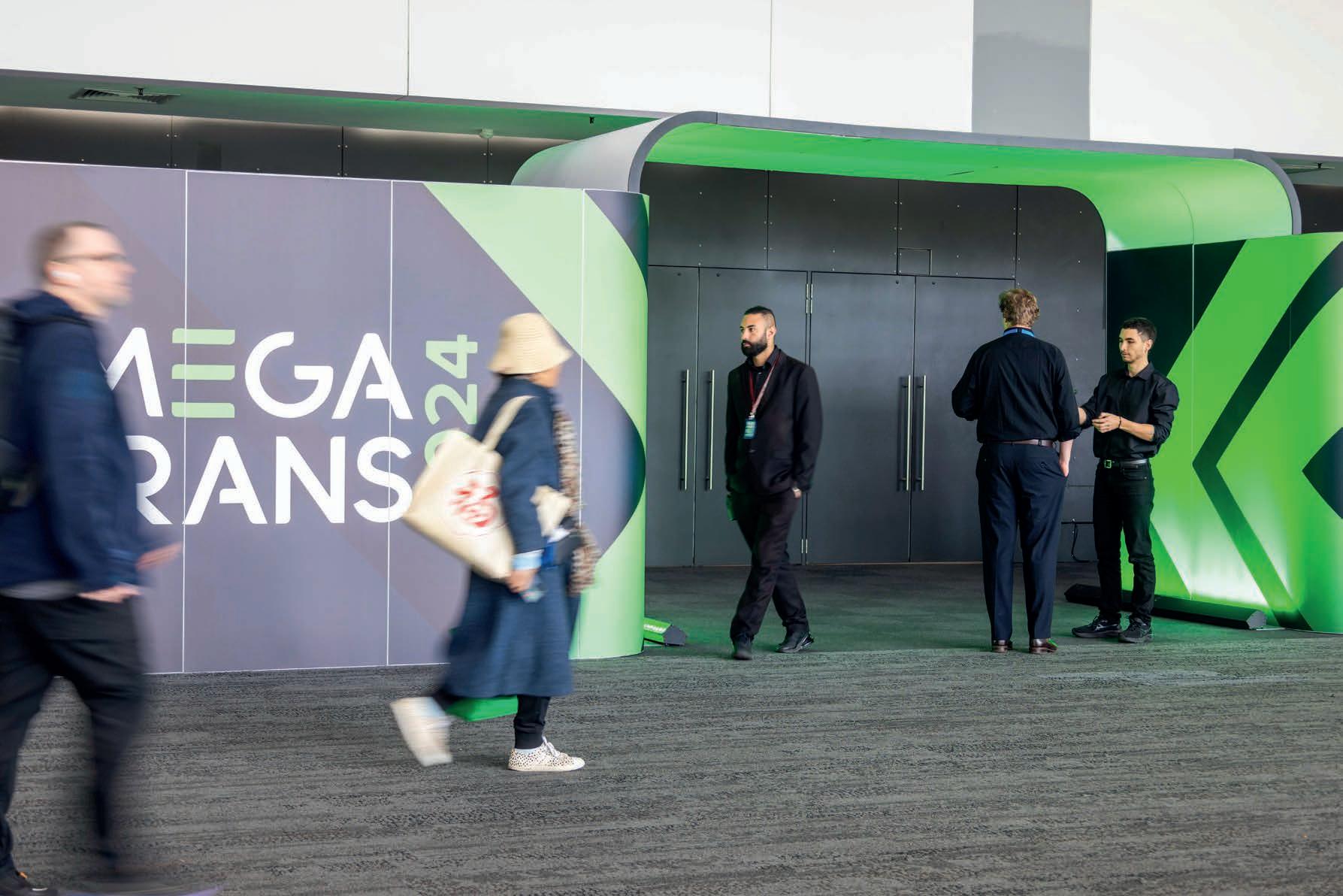
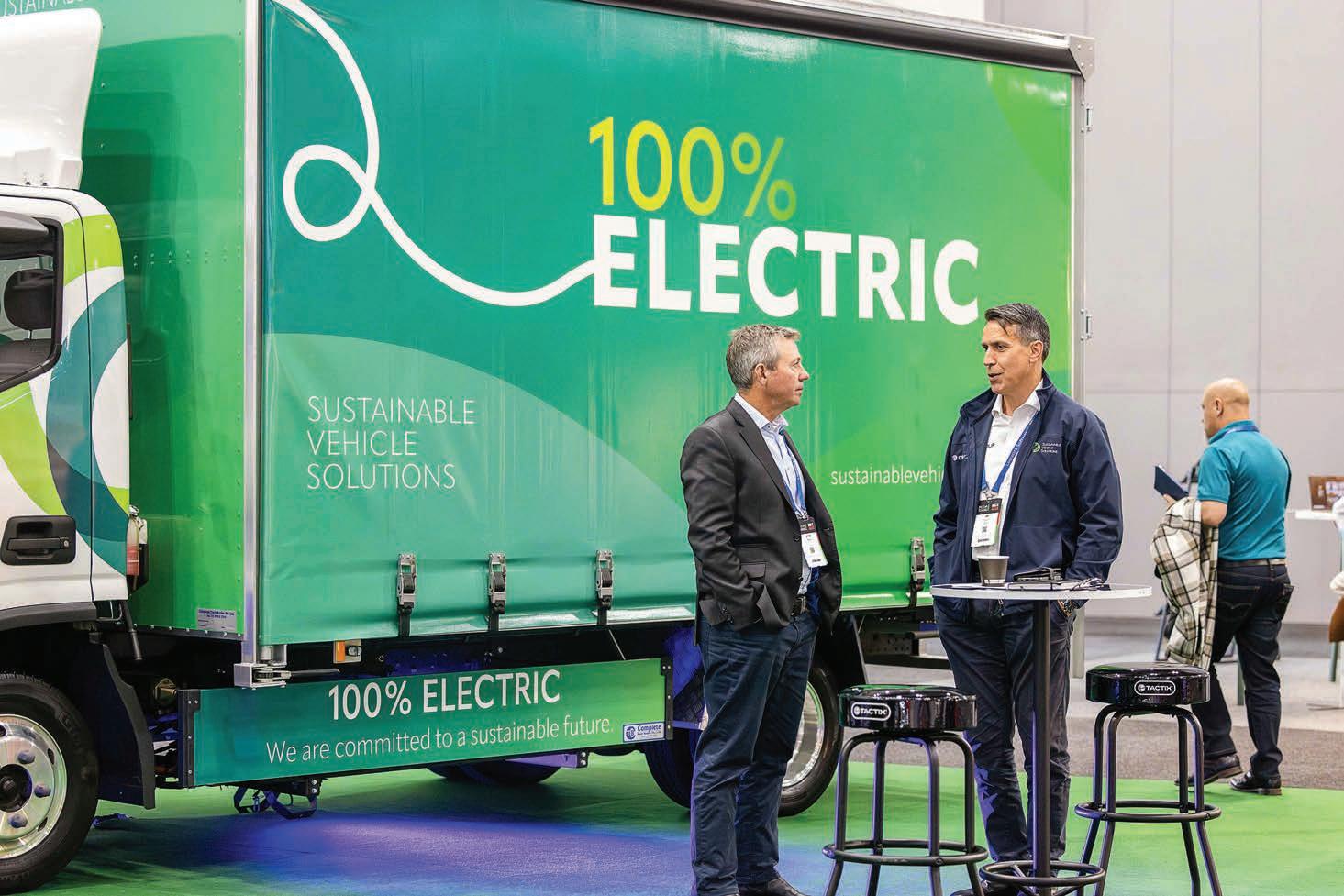
visibility and efficiency within the interconnected supply chain.
This was followed by a discussion by Toll Group on “Creating the Sustainable Fleet of the Future,” where experts tackled the pressing need for decarbonising logistics fleets.
Post-lunch discussions included a seminar titled “Sustainability and Safety in Supply Chain,” where the panel discussed how automation and digitisation are paving the way for greener operations.
The session on “Decarbonising International Shipping & Transport” offered insights into achieving net-zero commitments by 2050, a challenge that requires concerted efforts.
Day two of MEGATRANS 2024 continued to foster collaboration, with discussions on the integration of in-warehouse and on-the-road fleets, moving from ambition to action in supply chain sustainability, and leveraging telematics for efficiency gains.
“We think that the transport industry is a key market for us,” says Adam Duncan, General Manager
of Sales at Adaptalift.
“We’ve had good feedback from all our team that have worked on the stand. It’s been positive, good engagement from some potential customers, and we look forward to following up the leads.”
One of the event’s partners, the Supply Chain and Logistics Association of Australia (SCLAA) held a lineup of seminars.
This included opening remarks from Stephen Lakey, Director, SCLAA, followed by seminars named Trust in Supply Chain Technologies, Eco-Innovation: Driving Profits and Planetary Health, A Fresh Perspective on Inventory Management for Supply Chain Efficiency, Integrating Sustainability and ESG into Supply Chain Management for Competitive Advantage, and Simplifying International Shipping and Transport.
MEGATRANS is a pivotal event for industry leaders to confront the evolving challenges in logistics and supply chain management.
“It’s about brand recognition in this space for us,” said Richard Boothey,
business development manager, Kärcher.
“The exposure that we’ve got out of it has been great. We’ve had a steady flow of traffic and a lot of interest in products, particularly the robotics side of the business,”
“The positive feedback from attendees signalled a strong desire for continued dialogue and innovation in the logistics sector.”
“This year’s event has exceeded the footfall seen at the last MEGATRANS, which speaks volumes about the industry’s enthusiasm,” said Lauren Chartres, show director.
“The positive feedback from attendees signalled a strong desire for continued dialogue and innovation in the logistics sector.”
MEGATRANS 2024 has set a new benchmark for engagement and innovation in the logistics sector. With record attendance and meaningful
dialogue, the event was a collective commitment to sustainability, technology, and resilience, ensuring a dynamic future for the industry.
Mercury Awards showcase
The Mercury Awards celebrated noteworthy achievements in the logistics and supply chain industry and were sponsored by SEW EURODRIVE The event placed an emphasis on innovation and sustainability, showcasing both established industry leaders and emerging talents.
Merging with the Australian Bulk Handling Awards, the gala offered enhanced visibility and networking opportunities for attendees.
Award winners included Allotrac for Supply Chain Innovator of the Year, Skilled Materials Handling for Best Technology Application, CEVA Logistics for Sustainability Initiative Award, Machship for Freight Transport Solution of the Year, Dr. Elsie Hooi for Contribution to Industry Award, and Silk Logistics for the MHD Sustainable Warehouse Award. F
From sustainability to technological advancements, MEGATRANS highlights the interconnectedness of various sectors.
The Mercury Awards at MEGATRANS 2024 celebrated achievements in the logistics and supply chain industry.
Leverage funding opportunities for improved results
Government investment continues to help enhance the Australian food manufacturing sector’s global competitiveness. Food & Beverage Industry News reports.
Federal and State Government funding continues to play a critical role in the Australian food and beverage manufacturing sector for a variety of reasons, from research and development, to improved infrastructure and efficiency.
The Australian Government has laid out a commitment to help the nation’s primary industries reach $100 billion in total value by 2030. According to the Australian Bureau of Statistics, the
This continuous innovation has also become essential for keeping the Australian industry competitive and responsive to changing consumer demands, particularly around the manufacturing process.
The support provided by various forms of economic support from government can also be an invaluable asset for small and medium enterprises (SMEs).
Government funding helps provide
SMEs undertaking commercialisation or growth projects that will build Australian capabilities in priority areas for the National Reconstruction Fund (NRF). It aligns with the NRF’s mission to promote investments in initiatives that enhance Australia’s industry and manufacturing capabilities.
Research and development
Research and development is another vital area for food and beverage
and innovative products, the relevance of the Federal Government’s R&D Tax Incentive for Australian businesses is set to rise.
If your company is dedicating resources to experimentally tackle technical issues or create new products or services, you may be participating in activities that qualify as research and development under the incentive.
With Australian manufacturers facing a range of challenges, including
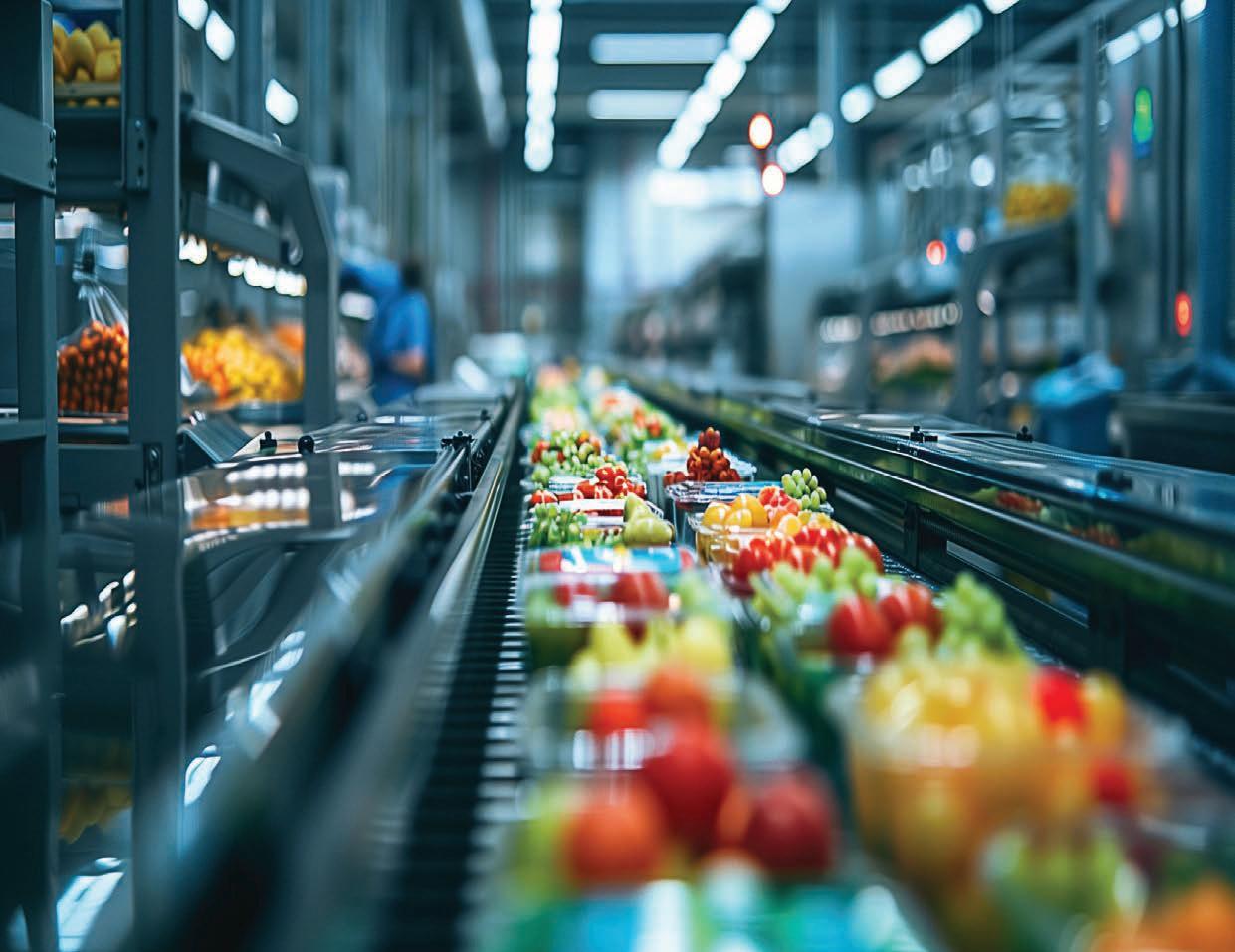
companies to claim tax offsets on research and development expenditures, effectively
Federal and State Government funding continues to play a critical role in the Australian food and beverage manufacturing sector.
reducing the financial burden of developing new products and processes.
The incentive is designed to mitigate costs and encourage Australian industries to engage in research and development activities. This offset reduces the financial risks associated with investing in R&D by addressing key concerns such as:
• Uncertainty of long-term gains –companies often face uncertainty about whether the potential longterm benefits of developing new or improved products or services will outweigh the costs of R&D efforts.
• K nowledge spill over – businesses may not fully reap the rewards of R&D investments because valuable knowledge can spill over to competitors and the wider economy, diminishing competitive advantage.
In addition to benefiting individual companies, the incentive is expected to have broader economic implications.
By stimulating investment in research and development, the government aims to enhance Australia’s position as a leader in advanced manufacturing, paving the way for sustainable economic growth.
The government has also worked to simplify the application process for the R&D Tax Incentive, addressing feedback from industry stakeholders about the complexities involved.
In recent years there have been some notable breakthroughs thanks to continued research and development, particularly through collaboration with universities.
Last year the University of Sydney received $2.2 million from the NSW Government in a round of Tech Central.
The university’s Alternative Protein Application Centre (APAC) was granted the funding to develop technology that supports a growing alternative protein manufacturing and processing industry.
The centre will conduct research and development on alternative protein production methods, including cellular engineering, precision fermentation, vertical farming, extraction, and texturisation.
It will also train researchers and practitioners in the food and beverage industry.
Sustainability initiatives
Meanwhile, sustainability is another area of importance for both the manufacturing industry and the government.
There are several funding opportunities for businesses looking
to be more sustainable in production processes, such as the Sustainable Agriculture Research and Development (SARDA) fund.
SARDA funding in Australia is dedicated to advancing sustainable practices in agriculture.
The goal is to support research, development, and outreach efforts that improve the environmental, social, and economic sustainability of the agricultural sector.
Among the funding options are research grants, programs, initiatives, and supporting collaborations.
The funding, part of a broader initiative to promote eco-friendly practices, supports innovative projects that focus on improving crop yields, reducing waste, and increasing resource efficiency.
The program provides grants to universities, research institutions, and agricultural businesses working on cutting-edge technologies and sustainable practices. Early recipients include projects focused on precision agriculture and sustainable supply chain management, aimed at reducing carbon footprints and enhancing food security.
As Australia seeks to position itself as
a leader in sustainable food production, this investment marks a crucial step toward a greener future.
Infrastructure funding
Then there’s the Federal Government’s Modern Manufacturing Initiative (MMI).
As of 2024, the initiative is a strategic program aimed at revitalising and strengthening the country’s manufacturing sector and was launched as part of the broader Modern Manufacturing Strategy.
The initiative seeks to enhance productivity, drive innovation, and promote sustainability in Australian manufacturing.
Among other things, the MMI encourages investment in cutting-edge technologies, such as automation, robotics, and digital manufacturing processes, as well as providing support to key industries, especially food and beverage.
An example of Australian food or beverage manufacturers reaping the benefits of the MMI includes Sabrini Foods, which received $1.47 million in funding, for a total government investment of $2.94.
The business was able to use the funds to develop a specialist dairy plant and a range of products.
Other recipients included Plenty Foods ($9 million), Regal Cream Products ($4.5 million), and Mulgowie Fresh ($5.1 million).
All these examples demonstrate how the MMI, and the broader MMS, is playing a role in empowering manufacturers to innovate and thrive in both domestic and international markets.
The Modern Manufacturing Strategy is aimed at revitalising Australian manufacturing, enhancing its competitiveness, innovation, and resilience in an increasingly competitive global environment.
This is only a sampling of the ongoing economic support from federal and state governments, which is aimed at reinforcing growth and sustainability in Australia’s food and beverage manufacturing sector.
As the industry evolves, these investments not only bolster the competitive edge of Australian food and beverage manufacturing, but also lay the groundwork for a resilient, innovative, and sustainable future. F
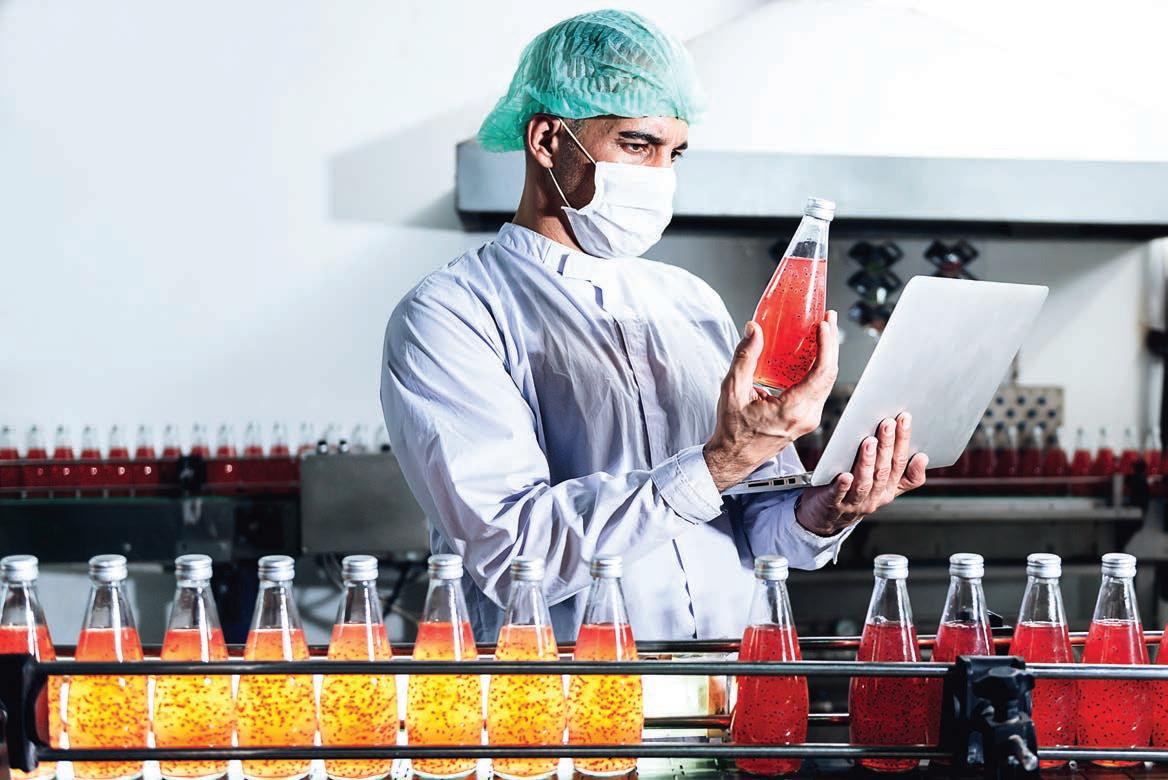
The Australian Government has committed to help primary industries reach $100 billion in total value by 2030.
From waste to resource
In a potential advancement for food waste reduction, chemists at the University of New South Wales have developed a new battery component that utilises food-based acids.
Ateam of University of New South Wales chemists have patented a new battery component utilising food-based acids from sherbet and winemaking.
By doing so, the team as created an ideal opportunity for some producers to create a new revenue stream while simultaneously helping to reduce organic food waste making it into Australian landfills.
This new prototype minimises environmental impacts in its materials and processing while improving energy storage capacity, making lithium-ion batteries more efficient, affordable, and sustainable.
The single-layer pouch cell, currently
being optimised, resembles a smaller version of those used in mobile phones, according to lead researcher Professor Neeraj Sharma from UNSW Science.
“We’ve developed an electrode that can significantly increase the energy storage capability of lithium-ion batteries by replacing graphite with compounds derived from food acids, such as tartaric acid, that occurs naturally in many fruits, and malic acid, found in some fruits and wine extracts,” he said.
“Food acids are readily available, typically less aggressive and contain the necessary functional groups or chemical characteristics.
“Our battery component could potentially use food acids from
food waste streams, reducing their environmental and economic impact. Its processing uses water rather toxic solvents, so we’re improving the status quo across multiple areas.”
Food waste costs the Australian economy around $36.6 billion each year and accounts for about three per cent of the nation’s annual greenhouse gas emissions.
“By using waste produced at scale for battery components, the industry can diversify their inputs while addressing both environmental and sustainability concerns,” said Sharma.
Sharma leads the solid state and materials chemistry group, part of the cross-faculty batteries research
community of practice at UNSW. They work with government and industry partners across all aspects of battery life.
“Our research ranges from synthesizing new materials, characterising new and commonly used materials and devices, to recycling and end-of-life degradation challenges,” he said.
The need for batteries has only increased in recent years as we continue to develop renewable energy infrastructure to combat climate challenges, Prof. Sharma says.
The same is true of new methods of reducing food waste, with methods such as finding a secondary use for waste products and helping reinforce a more circular economy.
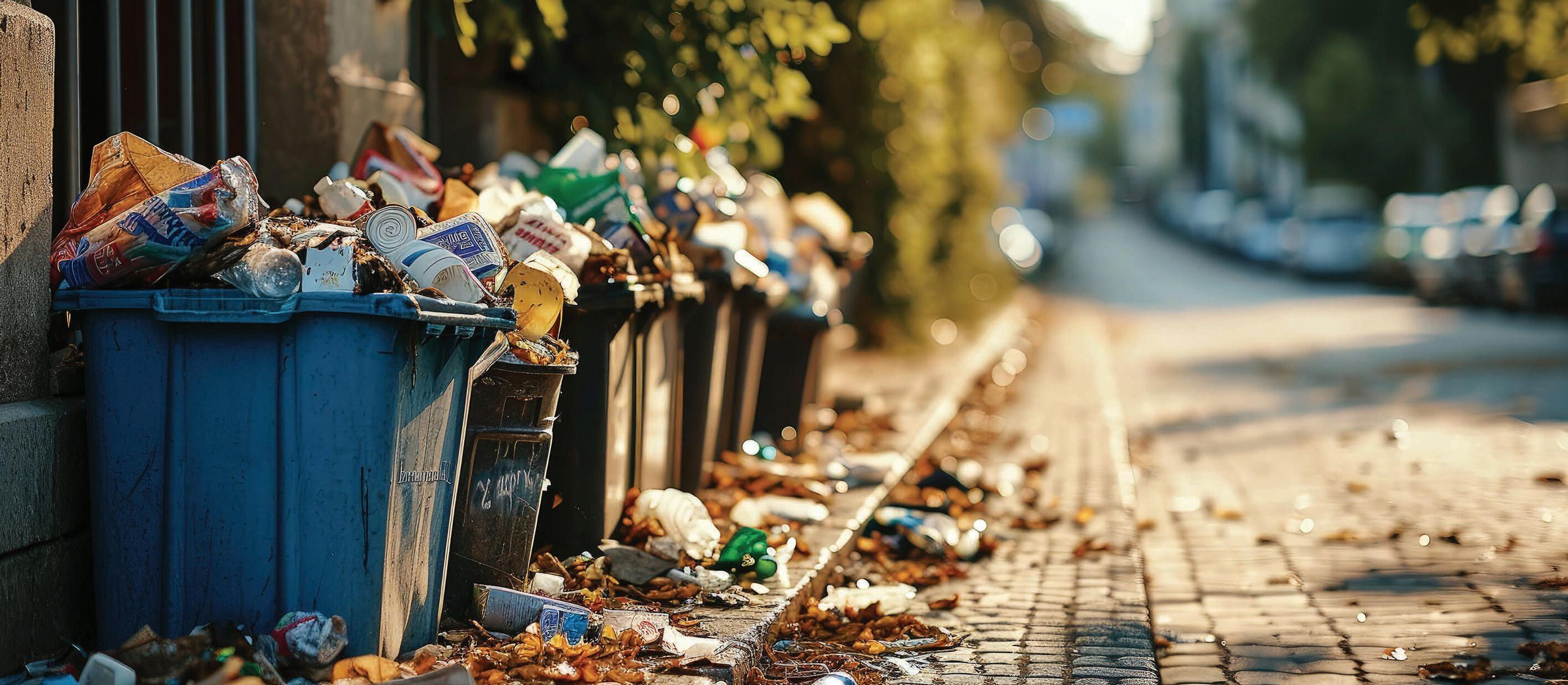
UNSW’s novel approach was driven by a PhD candidate examining reported inconsistencies in food acid performance in the lab.
“We realised the acid actually reacts with the metal surface of the battery component.
“It’s one of the first things we teach in first year chemistry, a metal plus an acid gives you a salt and hydrogen. And it’s that salt that gives you that (improved) performance.”
The research team worked with a range of food acids and metals to identify the most affordable and materially accessible combination.
“We experimented to understand what was happening, designing reactions to maximise performance and characterising the resulting compounds and their performance,” he says.
“As a result, we have the versatility to change the combination to suit different supply streams and desired performance.
“For example, while we have got lots of iron in Australia, in other regions, manganese or zinc, for example, might be
more accessible, and therefore these can be used as the metal component.”
The team are currently upscaling the technology, increasing production quantities, and transitioning from small coin cell to larger pouch cell capability.
The research team are also looking at diverting diverse bio-waste streams from landfill to use them as sources to formulate new electrode microstructures, Sharma said.
“For example, we’ve worked with Prof. Veena Sahajwalla to pyrolyse coffee grounds to use them as a carbon source to make anodes within lithium-sulphur batteries,” said Sharma.
As of 2024, more than eight million tons of waste coffee grounds enter landfill globally every year.
Meanwhile, stakeholders within the food and beverage industry have been looking at other ways to turn waste by products into viable secondary products, such as COPAR and its wheat straw fibrebased packaging for food.
COPAR, a sustainable packaging solutions company, aims to eliminate
single-use plastics by utilising wheat straw. The food and beverage industry is focusing on sustainability, particularly in packaging, and with increasing bans on single-use plastics across the country, many industries are seeking alternative solutions.
COPAR is addressing this need by developing fibre-based packaging and presents a great example of how waste by products can provide viable opportunities to increase profit.
The company will launch its first Australian factory in Bathurst, NSW. While fibre-based packaging is not new, using wheat straw for this purpose will be a first in Australia.
“The idea is to re-purpose farmers’ agricultural waste by turning it into compostable packaging, which means it will naturally degrade in the environment with no microplastics, it is truly a circular product,” said Colin Farrell, director of business development for COPAR.
“Circular economy is the hardest part to achieve and understanding it properly is critical.
Sharma leads the chemistry group utilising food-based acids for its new battery patent.
Farrell said the company came across the wheat straw idea when they were tasked with helping a start-up source compostable packaging.
“From that basis we started to investigate that area and found the University of Newcastle has expertise in compostable plastics and packaging,” he said.
“So, we started our research and development there which then led to establishing our commercial and technology partners.
Demonstrating, as with the news out of UNSW, that collaboration with university level researchers is having an ongoing positive impact on the food and beverage industry.
Other examples include bioplastics, woven fabrics made from orange fibre, and fermenting corn waste to create a sugar-free sweetener.
The examples above are just a sampling of how the food and beverage manufacturing industry is converting waste products into viable secondary market applications. F

Food waste by the numbers
Food waste costs the Australian economy around $36.6 billion each year Each year Australians waste around 7.6 million tonnes of food across the food supply chain. This equals about 312kg per person and can cost up to $2,500 per household per year.
• Food waste accounts for about three per cent of Australia’s annual greenhouse gas emissions.
• Australia uses around 2,600 gigalitres of water to grow food that is wasted. This equals the volume of water in five Sydney Harbours.
• The amount of land used to grow wasted food in Australia covers more than 25 million hectares.
• Households generate the most food waste in Australia and are responsible for about 30 per cent of the total. This equals around 2.5 million tonnes per year.
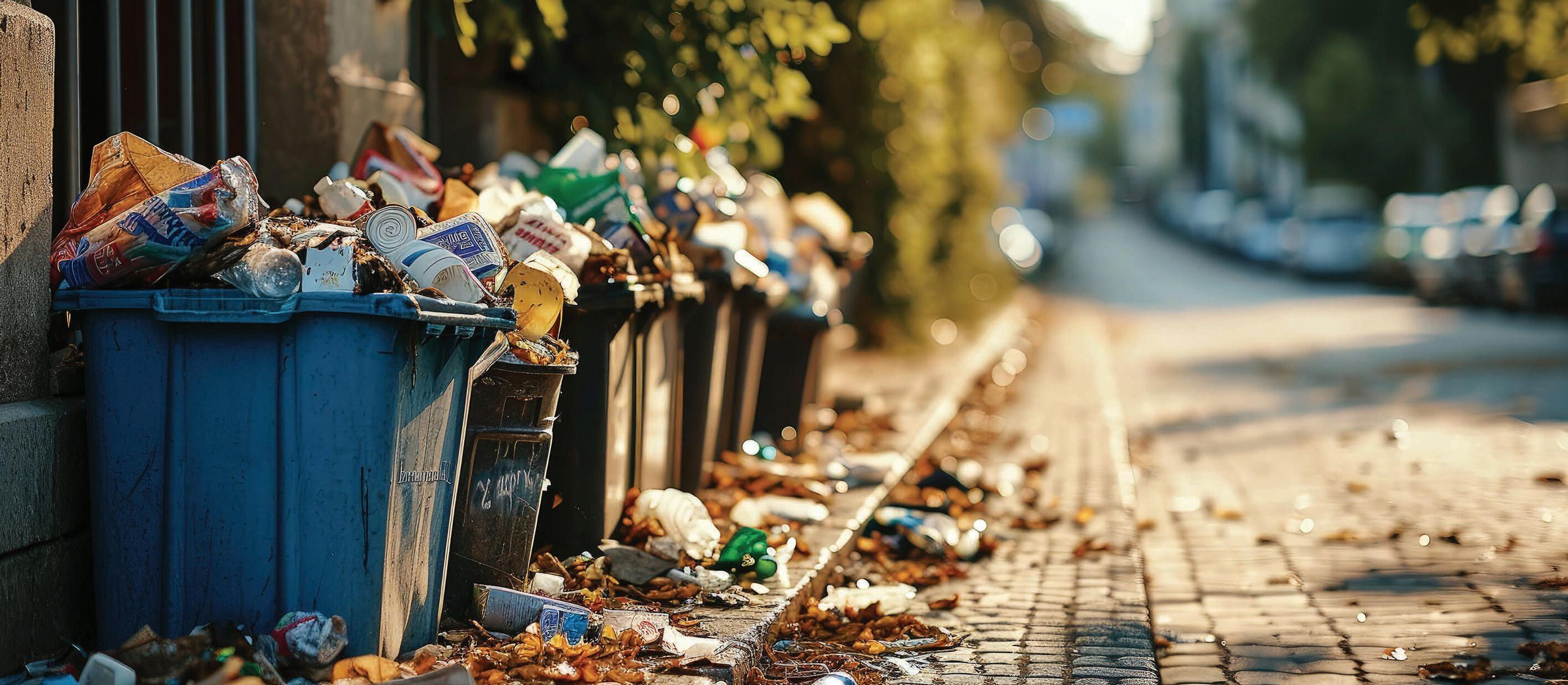
Image: UNSW
Soft plastics partnership scheme launched
After
the collapse of REDcycle, the Queensland Government
has taken a
proactive
approach to soft plastic recycling.
The Queensland Government is committing $1 million to launch a pilot program for soft plastics recycling.
Soon, communities across the state will have the opportunity to recycle soft plastics at four new trial hubs.
These hubs will explore different collection methods to determine the most effective solutions for urban, regional, and remote residents.
“The community has made it clear how much they value the ability to recycle soft plastics and want to see it return,” said the state’s Minister for the Environment and the Great Barrier Reef, Leanne Linard.
“We know they also want to ensure it is sustainable in the long term and that’s why it’s so important to discover what works best for Queensland’s varied communities and regions.

The QLD Government’s new recycling pilot will have residents test out various methods to test effectiveness.
“Queenslanders have already returned close to nine billion glass and plastic containers to container refund points under…container refund scheme.
“Because people are used to bringing their containers to these sites we want to see if this model works for returning soft plastics, among other options.”
In collaboration with Soft Plastics Stewardship Australia Limited, the government aims to test innovative approaches to recycling soft plastic waste.
Since the REDcycle program ended, many Queenslanders have been holding onto their soft plastics, expressing the need for an alternative.
The pilot will kick off in Brisbane before the year’s end, with additional hubs in the Sunshine Coast, Goondiwindi, and Cairns launching in the coming months. Over a 12-month period, the hubs will evaluate various
collection options to find the best fit for all Queensland communities.
• T he state government is investing $1 million to support the roll-out of a soft plastics recycling pilot in Queensland.
• Communities across Queensland will soon be able to recycle soft plastics at four new trial hubs
• T he hubs will trial a variety of collection options to see what works best for urban, regional and remote Queenslanders
The government is partnering with Soft Plastics Stewardship Australia Limited to conduct a pilot soft plastics recycling scheme in Queensland. Under the pilot, trial hubs will be established in locations across Queensland to test different ways to allow people to return soft plastic packaging.
The hubs will trial a variety of collection options over a 12-month period to see what works best for urban, regional and remote Queenslanders.
This will include:
• kerbside yellow-lid bin collections in specific locations.
• return to store.
• council drop off locations; and
• d rop off at central points, such as container refund points.
Evaluating each collection method will provide insights for future decisions on the most effective models or combinations of collection strategies for different communities.
The pilot programs will also seek to uncover local processing options for soft plastics and explore potential markets for recycled products.
This initiative aims to reduce stockpiling and the need for longdistance transport, while fostering local markets and job creation.
“It’s also vital that we have cost-
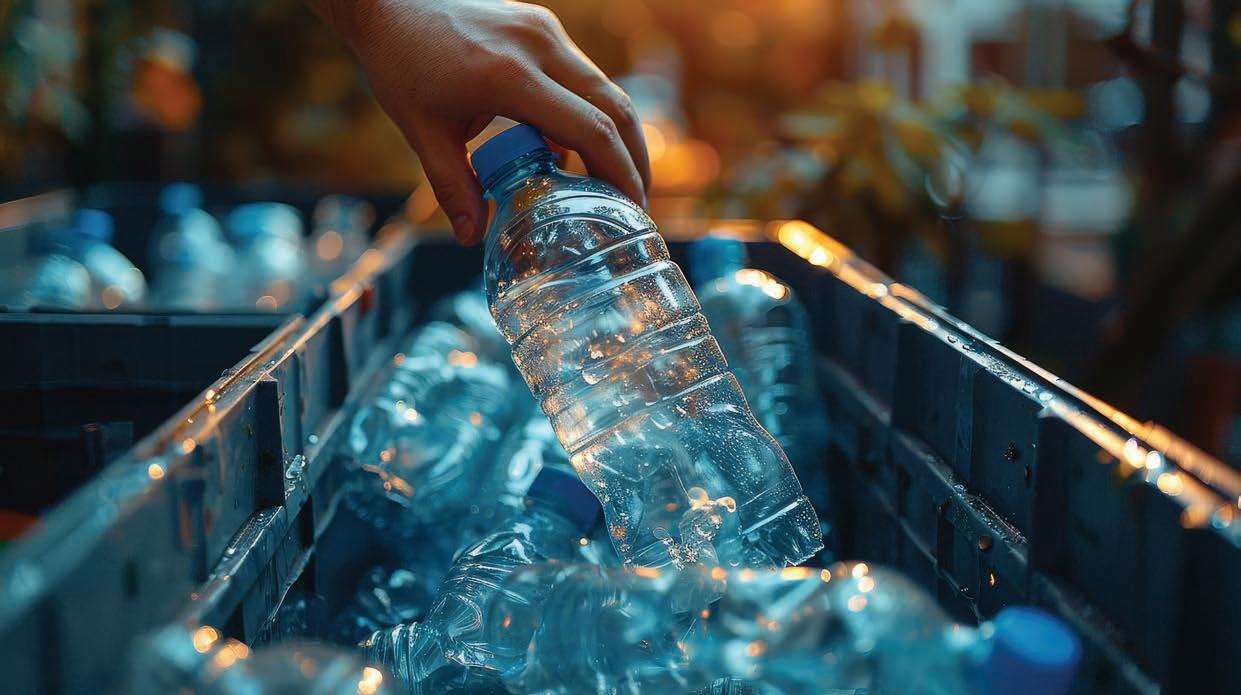

effective options for processing the material that are collected and viable end-product markets,” said Linard.
“Queensland is growing rapidly, and we need to do more to keep waste out of landfill and turn it into useful new products.
“We’re committed to moving towards a circular economy, whereas much valuable material as possible is diverted from landfill through reuse, recycling and remanufacturing.”
As part of the trial, the government will collaborate with Central Queensland University to process some of the collected materials at its testing facilities. This will allow for an assessment of contamination tolerance levels for various end products.
These efforts will help clarify consumer messaging regarding the types of soft plastic packaging that can be collected and identify viable markets for recovered soft plastics.
The Australian Food and Grocery Council (AFGC) applauded the announcement from the Queensland Government.
“We are pleased to see the Queensland government take action on soft plastics recycling,” said AFGC CEO Tanya Barden.
“This funding, combined with SPSA’s work, is a vital step toward long-term solutions.”
As the Federal government considers reforms to Australia’s packaging regulations, the industry views this as a chance to create consistent packaging standards nationwide.
Stakeholders believe a unified approach would simplify processes, reduce confusion, and promote progress towards a circular economy.
Barden and the AFGC are also encouraging other states and territories to back this national strategy for soft plastics recycling. With a recent survey conducted during the AFGC’s Sustainability Summit revealing that inconsistent packaging regulations pose an obstacle to advancing Australia’s circular economy. F
Soon, Queenslanders will have the opportunity to test out a new soft plastics recycling scheme.

Aussie avocado technology to meet growing demand
Innovation from the University of Queensland is poised to help improve avocado production on a global scale.
Atissue-culture propagation technology created at The University of Queensland (UQ) can grow hundreds of plants from one cutting and is poised to enhance avocado production in Latin America to satisfy increasing demand.
The technology was developed by a team led by Professor Neena Mitter at UQ’s Queensland Alliance for Agriculture and Food Innovation and was licensed to Chilean nursery Grupo Hijuelas through UniQuest, UQ’s commercialisation arm.
Dr. Chris O’Brien from UQ stated that this technology will accelerate the production of four essential avocado rootstocks in the region.
“The propagation and tissue culture technology is a faster and cheaper way of producing clonal rootstocks, which have
traditionally taken around 18 months to grow,” he said.
An avocado tree’s rootstock influences its performance and using seedling rootstocks can lead to variable quality.
“This UQ technology means we can use clonal trees with the traits growers want, which means they can grow better crops.”
Dr. O’Brien mentioned that the team plans to visit Chile later this year to showcase the technology, aiming to enhance the production of Zutano, Velvick, Reed, and Kidd avocado rootstocks.
Grupo Hijuelas’ CEO, Juan Goycoolea, expressed enthusiasm for the collaboration, noting that the partnership is expected to advance agricultural research and development
throughout Latin America.
“We are working with cutting-edge technology that has shown excellent results in evaluation plots in Australia and we want to bring these benefits to our producers,” he said.
Grupo Hijuelas operates internationally with its own nurseries and strategic partnerships in countries such as Chile, Peru, Mexico, South Africa, Colombia, and Europe.
Dr. Dean Moss, CEO of UniQuest, stated that the UQ technology enables avocado producers to rapidly increase plant production, providing significant benefits for both farmers and consumers.
“It’s no secret that South Americans are among the largest consumers of avocados in the world, as well as huge exporters to European markets,” he said.
“This is a fantastic opportunity for
exceptional UQ research to help build an agriculture pipeline of avocados that is efficient and plentiful in years to come.”
The tissue-culture propagation technology was first licensed in Australia to Anderson Horticulture for Reed avocado rootstock in 2022.
The deal is the recipient of the 2024 UniQuest Commercialisation Impact Award.
The technology was developed as an outcome from research funded by the Australian Research Council with contributions from UQ, the Department of Agriculture and Fisheries, Anderson Horticulture, Jasper Farms, and Millwood Holdings.
According to figures from the Business Research Company, global revenue from the avocado market is
The rootstock of an avocado tree affects its performance and using seedling rootstocks can result in inconsistent quality.
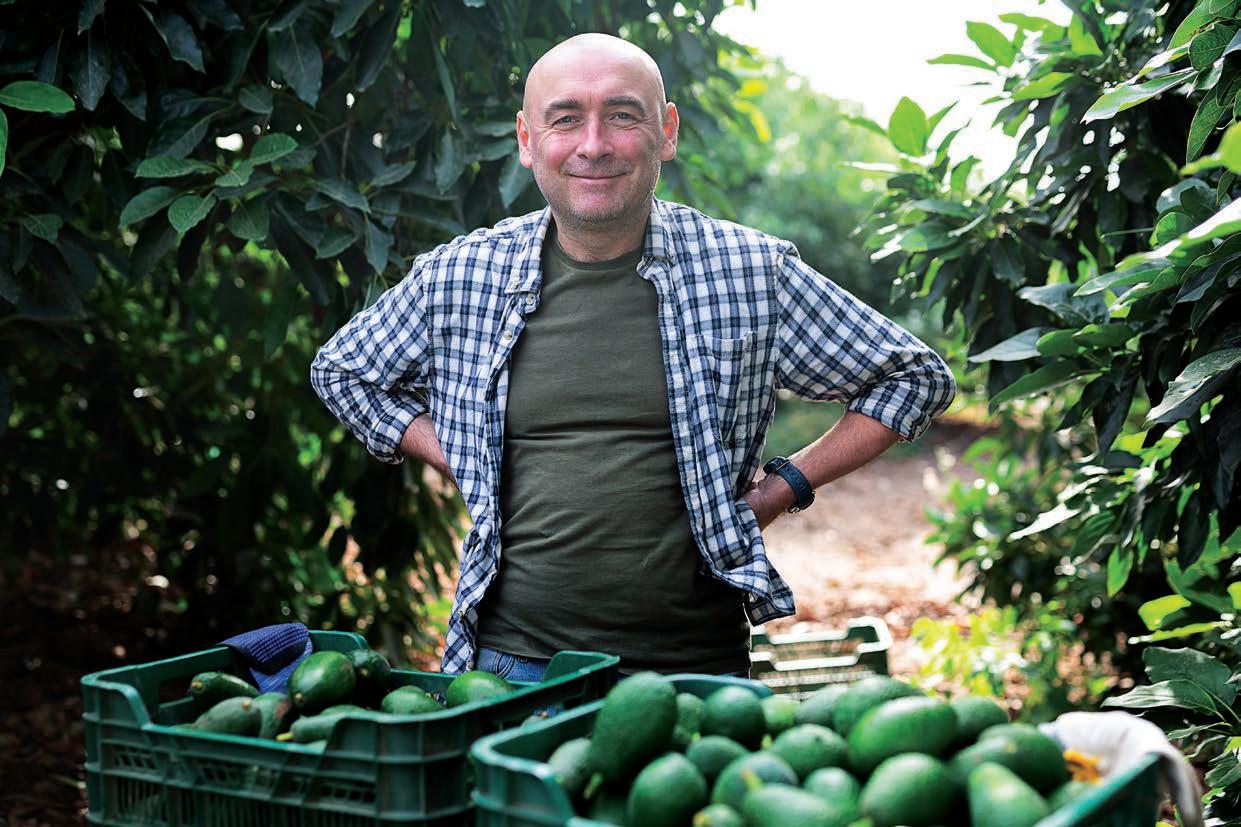
billion in 2024, with an expected compound annual growth rate (CAGR) 8.3 per cent.
This market size is also expected to see strong growth in the coming years, meaning any new innovations to help meet this forecast demand will be of particular importance to avocado producers the world over.
In terms of Australian avocado production, the most recent research
recent figures.
Production of avocados in Australia has increased year on year in seven of the last 11 years, with 115,385 tonnes produced in the last season.
This figure represents a decrease of 5.57 per cent compared to the previous year. However, in contrast, the gross value of production (GVP) for Australian avocados was estimated at $574 million, reflecting a 42.43 per cent increase from the prior year.
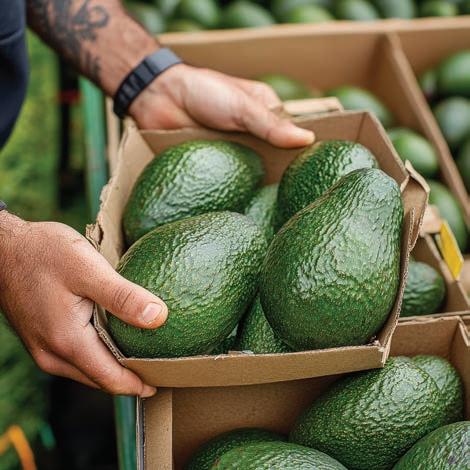
And of the Australian producers, Queensland continues to produce the most Australian avocados, with 65 per cent of production. Western Australia produced the next largest share at 18
As well as working with Avocados Australia, Hort Innovation has partnered with Lifecycles to understand the environmental footprint of Australian avocados, by conducting an environmental life cycle assessment
This initiative is motivated by the growing need to enhance sustainability efforts, inform future strategic investments, address consumer information demands for market development, and comply with new
The Life Cycle Assessment (LCA) will provide avocado growers and their industry associations with environmental performance metrics, such as averages and benchmarks, as well as insights into environmental hot spots and improvement opportunities, to support the industry’s sustainability goals.
It will complement other studies commissioned by Hort Innovation that focus on industry benchmarking and sustainability strategies. The LCA will generate quantitative information that decision-makers can use to justify sustainability initiatives.
The study will primarily focus on greenhouse gas emissions and water usage/water scarcity impacts (water footprint).
It will encompass two scales: individual case studies and an industrylevel analysis. The individual case studies will examine various production typologies in detail, while the industryscale LCA will gather a broader data set representing the Australian avocado industry.
“This project will help to underpin our sustainability strategy which is currently under development,” said John
The project will span approximately two years and is funded by Hort Innovation, utilising the avocado research and development levy along with contributions from the Australian Government. Hort Innovation is a grower-owned, not-for-profit research and development corporation dedicated to the Australian horticulture industry.
Ultimately, the innovative tissueculture propagation technology from UQ represents an advancement in avocado production, promising to meet the soaring global demand.
By facilitating faster and more efficient cultivation of essential rootstocks, this collaboration between UQ and Grupo Hijuelas positions both Australian and Latin American avocado industries for growth.
Coupled with ongoing sustainability efforts and research initiatives, the industry is poised to enhance its environmental performance while capitalising on profitable market opportunities.
As consumer preferences continue to evolve, these advancements will be crucial for ensuring a reliable and sustainable supply of avocados in the years to come.
Avocado farmers will see improved production output after the University of Queensland created new propagation technology.
2024.
Australia’s growing crop value
The latest crop report from the Australian Bureau of Agricultural and Resource Economic Sciences (ABARES) has created optimism for the upcoming harvest season.
Australian agriculture is poised for a positive year ahead, with the gross value of agricultural production expected to rise by four per cent
The ABARES Agricultural Commodities and Crop Reports indicate sector growth, projecting an increase from $82.5 billion in 2023-24 to $86.2 billion in 2024-25.
The September edition has provided ABARES’ first forecasts for summer crop production at the state level for the current financial year, along with updated estimates for winter crop forecasts.
Dr. Jared Greenville, executive director of ABARES, noted that this forecast highlights the value of production across agriculture, fisheries, and forestry reaching $92.1 billion in 2024-25.
“We have seen more favourable seasonal conditions across large parts of the country, easing input prices, and higher livestock prices supporting farm incomes,” Greenville said.
“However, unfortunately not all farms in all regions are expecting to see an improvement.
“Crop production across Australia has been driven by New South Wales and Queensland, and better than expected seasonal conditions in Western Australia.
“But unfavourable conditions in north and western Victoria and most of South Australia following below average winter rainfall have resulted in lowerthan-expected crop production.
“The value of agricultural exports is forecast to be $68.5 billion in 2024-25, or $72.6 billion when including fisheries and forestry”
This year has seen a reduction in carry-over stocks of grain available for export compared to the past two recordbreaking years, leading to a slight decline in export value, despite production remaining comfortably the third highest on record.
The latest three-month rainfall outlook, from September to November, released by the Bureau of Meteorology,
indicates roughly equal chances of above or below-average spring rainfall across most Australian cropping regions.
However, there is a greater likelihood of average to above-average rainfall in New South Wales and Queensland. Meanwhile, daytime temperatures during spring are expected to be above average in all cropping regions except Western Australia.
Most areas with average or better soil moisture levels are likely to receive sufficient rainfall to support winter crops through critical development stages.
On top of this, national winter crop production has been revised upward by seven per cent compared to the June 2024 Australian Crop Report.
This increase is driven by improved production in New South Wales, Queensland, and Western Australia, which is anticipated to more than compensate for reduced output in South Australia and Victoria.
The forecast for all major winter crops shows an upward adjustment from the June estimates.
Meanwhile, Australian exports continue to enjoy strong demand in key markets.
“Red meat exports are performing well in the US and Middle East,” Greenville noted.
“We’re also seeing increased trade flows with China across various commodities, following improvements in market access.
“The horticulture industry is continuing to showcase its resilience as it maintains its forecast of record-breaking production values.”
Average cash incomes for broadacre farms are projected to rise by 64 per cent, reaching $192,000 per farm in 2024-25.
“We’re expecting to see the price for cattle and sheep increase compared to last year, leading to this significant improvement in farm incomes,” Greenville said.
“The ABARES Commodities and Crop Reports tell a positive story for Australian agriculture, capitalising on demand for our quality products.” F
KEY POINTS:
Average cash incomes for broadacre farms are projected to rise by 64 per cent.
National winter crop production to increase to 55.2 million tonnes in 2024–25, 17 per cent above the 10-year average
• Winter crop prospects are mostly favourable in New South Wales, Queensland and Western Australia
• Less favourable conditions have reduced production prospects in South Australia and Victoria
• Planting of summer crops to remain above average in 2024–25, reflecting an increased chance of above average spring rainfall in New South Wales and Queensland.
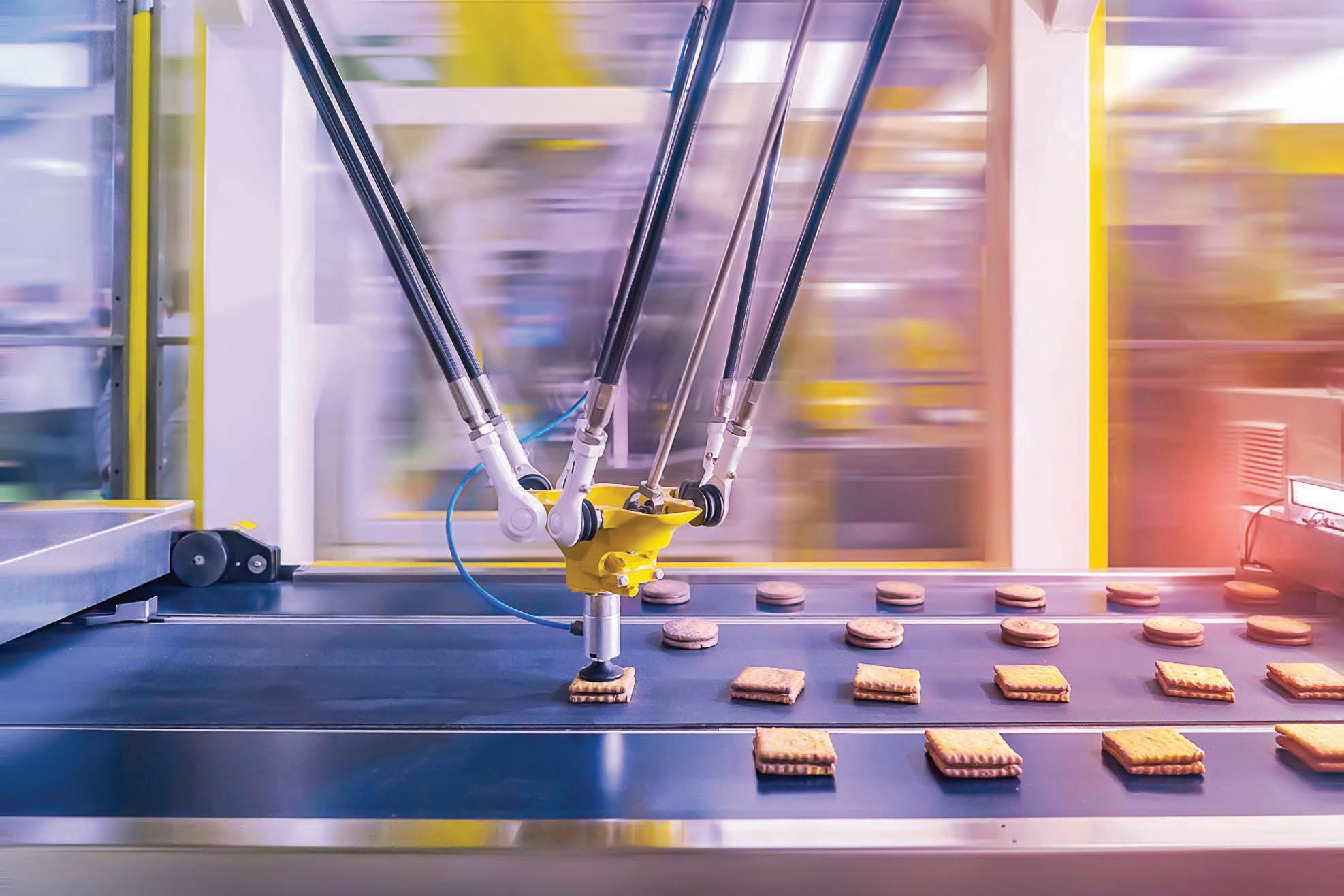

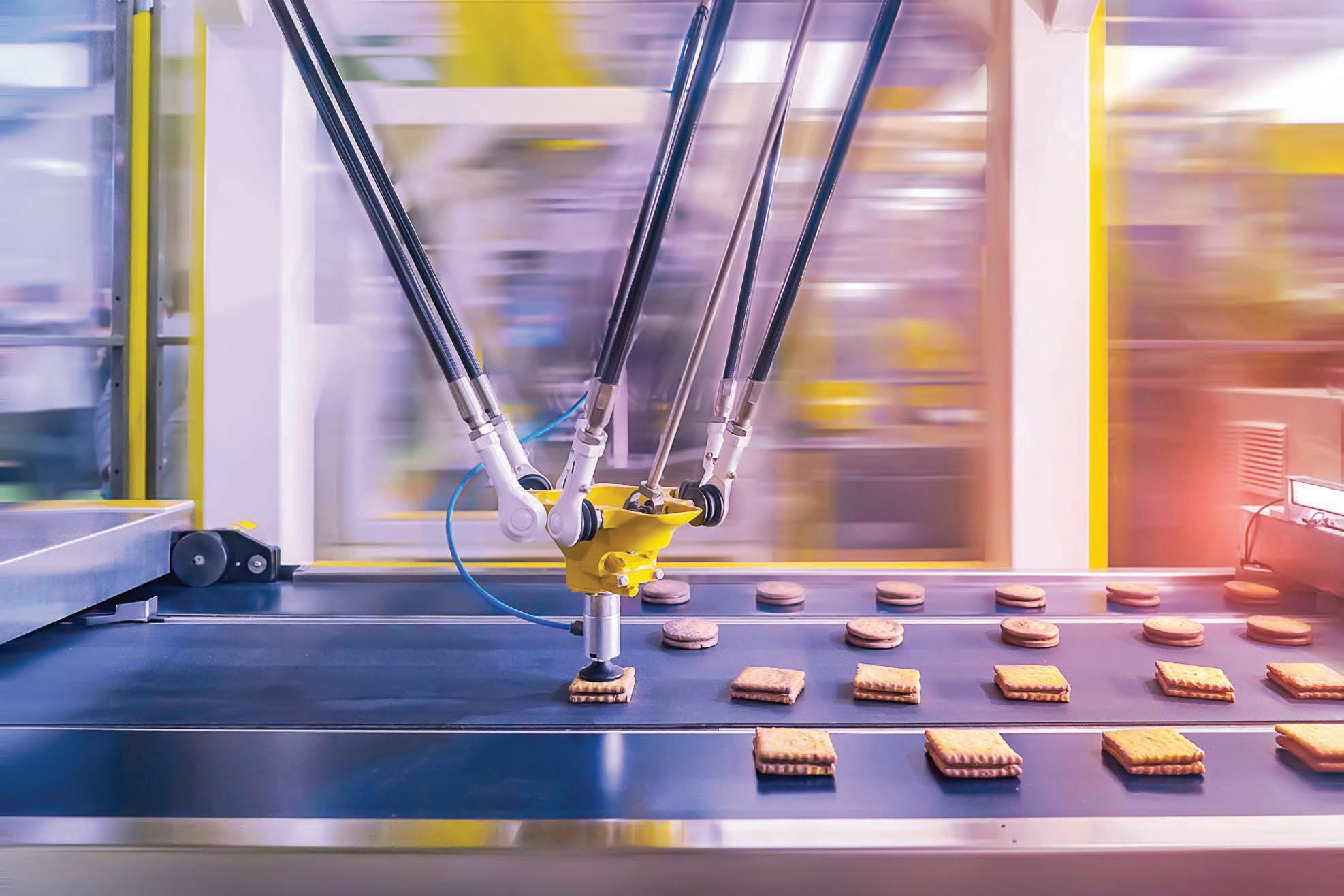
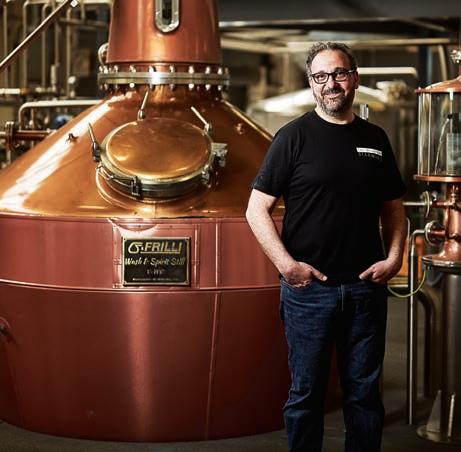
Backplane Systems Technology introduces Neousys Nuvo-10108GC Series
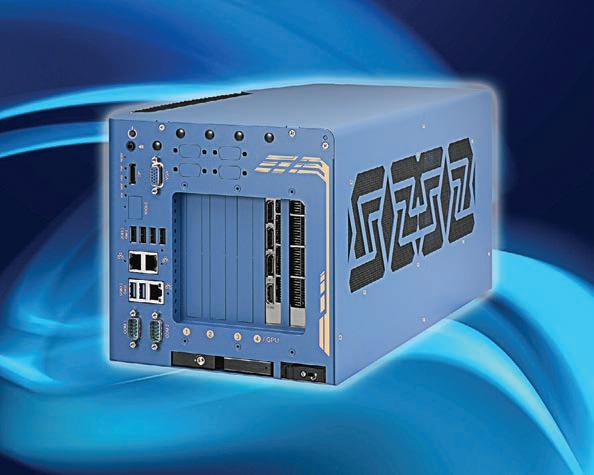
industrial Edge AI computing, blending extreme CPU and GPU performance to cater to demanding applications such as autonomous driving and AI-powered factory automation. This rugged Edge AI computer is equipped with an Intel® 13th/ 12th-Gen Core™ processor and supports a single NVIDIA® RTX™ GPU with a 350W power requirement, ensuring superior computational capabilities. It boasts a Gen4 x16 signal for the GPU and includes a dedicated bracket for secure GPU locking, reflecting its design for harsh operational environments.
With up to 64GB of DDR5 memory supported by the Intel R680E chipset and three additional PCIe slots for expansion, the Nuvo-10108GC Series offers ample room for memory and add-on cards, enhancing its versatility
in various industrial scenarios. The system’s rich I/O options, including USB 3.2 ports, multiple Ethernet connections, and optional 10GbE, ensure comprehensive connectivity.
The Nuvo-10108GC Series is built to withstand rugged conditions, operating reliably in temperatures ranging from -25°C to 60°C. Its innovative thermal design ensures stable performance even under the stress of continuous vibration, a critical feature for deployment in mobile or challenging industrial environments.
Leveraging the latest in computing technology from Intel and NVIDIA, along with Neousys’ expertise in industrial design, the Nuvo-10108GC Series is a powerful solution for modern AI applications, offering unprecedented computational power, durability, and flexibility for edge computing tasks.
Key features:
• Supports single NVIDIA® 350W GPU with Gen4 x16 signal and dedicated GPU-locking bracket
• Intel® 13th/ 12th-Gen Core™ 35W/ 65W LGA1700 CPU
• Up to 64GB ECC/ non-ECC DDR5 4800 with Intel R680E chipset (2x SODIMM)
• Three x8 PCIe slots (Gen3 x4) for add-on cards
• 6x USB 3.2, 2x 2.5GbE, 1x GbE, and 1x optional 10GbE
• Two front-accessible storage options: 1x 2.5” SATA tray and 1x optional NVMe tray
• 8V to 48V wide-range DC input with ignition power control
• Rugged, -25°C to 60°C operation
Backplane Systems Technology (02) 9457 6400 www.backplane.com.au
ICP Electronics Australia introduces new learning module to portfolio
The IR-712P-MTCP, which represents a leap forward in home and building automation, offering a sophisticated universal Power over Ethernet (PoE) infrared learning module. This device can learn and store up to 512 infrared commands from various electronic devices, making it a versatile tool for controlling a wide array functions..
Equipped with two IR output channels and one IR learning input, the IR-712P-MTCP supports IR remote control carrier frequencies ranging from 33 kHz to 56 kHz, ensuring compatibility with most IR-controlled devices. Its support for Ethernet interface and PoE power supply (IEEE 802.3af, Class 1) simplifies installation and operation, eliminating the need for additional power sources and reducing cable clutter.
The IR-712P-MTCP employs the Modbus TCP/UDP communication protocol, enabling seamless integration with Modbus master station equipment like PACs, PLCs, and PCs. This feature enhances its applicability in building automation projects. The module’s provision of ASCII string commands (DCON on TCP/UDP) for controlling the emission of IR commands further underscores its flexibility and ease of use.
Included with the module are two CA-IR-SH2251 IR transmitter cables, extending its reach and efficacy in controlling devices.
Key features:
• 2 IR output channels.
• 1 IR learning input
• IR command capacity: 512
• Supports IR carrier frequencies: 33, 36, 37 ,38, 40 and 56 kHz.

• • Support PoE power supply (IEEE 802.3af, Class 1)
• Supports Modbus TCP/UDP protocol to emit IR commands.
• Provides ASCII String Command (DCON over TCP/UDP) to emit IR signal.
• Includes 2x CA-IR-SH2251 IR emitter cables.
ICP Electronics Australia (02) 9457 6011 www.icp-australia.com.au
Pressure calibration made fast and easy
The Beamex POC8 is an accurate and user-friendly automatic pressure output controller, providing regulated output from vacuum to 210 bar (3045 psi).
The POC8 can be integrated to the Beamex CENTRiCAL workshop calibration solution or delivered as a portable desktop version.
Together with Beamex MC6 family calibrators and Beamex calibration management software, the POC8 offers a fully automated solution for performing, documenting and managing pressure calibrations easily, efficiently and accurately.
Together with Beamex MC6 family calibrators, as well as Beamex calibration management software, the POC8 offers an automatic calibration solution for performing, documenting, and managing pressure calibrations easily and efficiently.
With its 7″ colour LCD display with touch screen, the POC8 is easy, fast and efficient to use.
The user interface includes more than 10 different language options.
The POC8 pressure controller can be integrated to the Beamex CENTRiCAL workshop calibration solution.
The POC8 can also be used as a stand-alone desktop pressure controller, which makes it an easily movable solution.
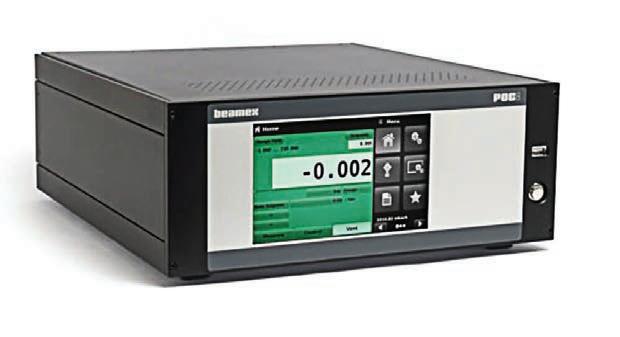
AMS Instrumentation and Calibration (02) 8197 2825 www.ams-ic.com.au
Find the right Analyzer Flow Verification
FCI’s FS10A Analyzer Flow Switch/Monitor is a sophisticated universal flow switch and monitor specifically designed for gas and liquid process analyzer sampling systems. The FS10A is a fast responding, highly repeatable sensor, which installs easily into a standard tube tee fitting or the SP76 (NeSSI) modular manifold.
Utilizing FCI’s long proven thermal dispersion flow measurement technology, the FS10A Analyzer Flow/ Switch Monitor is designed with proprietary equal mass sensing to achieve outstanding sensitivity and repeatability. The instrument’s wetted parts are superior corrosion-resistant 316L stainless steel with Hastelloy C-22 sensor tips. The sensor element has no moving parts to foul, clog or maintain, which ensures continuous reliability and virtually no maintenance. There are no cavities, orifices or dead-legs to trap or contaminate samples, which preserves sample integrity and faster sampling times.
This instrument’s electronics are packaged in a rugged, fully sealed, stainless steel housing that provides the Model FS10A with exceptional protection and long-life under all process conditions with virtually no maintenance. The electronics can be integral mounted with the sensor element, resulting in a uni-body, self-contained unit or the electronics can be remote mounted away from the sensor element.
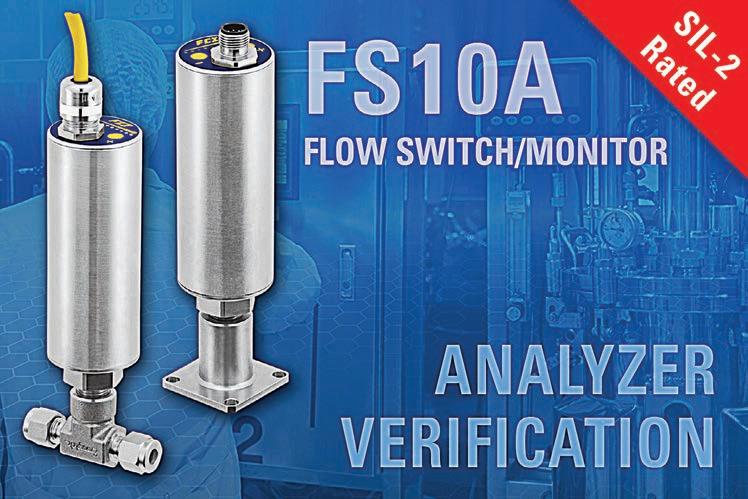
The FS10A Analyzer Flow Switch/Monitor is designed with an easyto-read top-mounted, flow rate monitoring LED array for at-a-glance visual indication of operational status of proper flow rate to the analyzer or sampling system, or that an alarm/trip point has occurred. The flow switch’s set-point is conveniently user settable via two push-buttons accessible at the top of the unit or via the RS232C I/O port.
The Model FS10A is ideal for use with nearly all types of process and emissions sampling systems, including gas chromatographs (GCs), mass spectrometers, optical spectrometers, photometers and others. Standard configurations will accommodate standard 1/8, 1/4, 3/8 and 1/2 inch tubing as well as the SP76 (NeSSi) modular manifold.
AMS Instrumentation and Calibration (02) 8197 2825 www.ams-ic.com.au
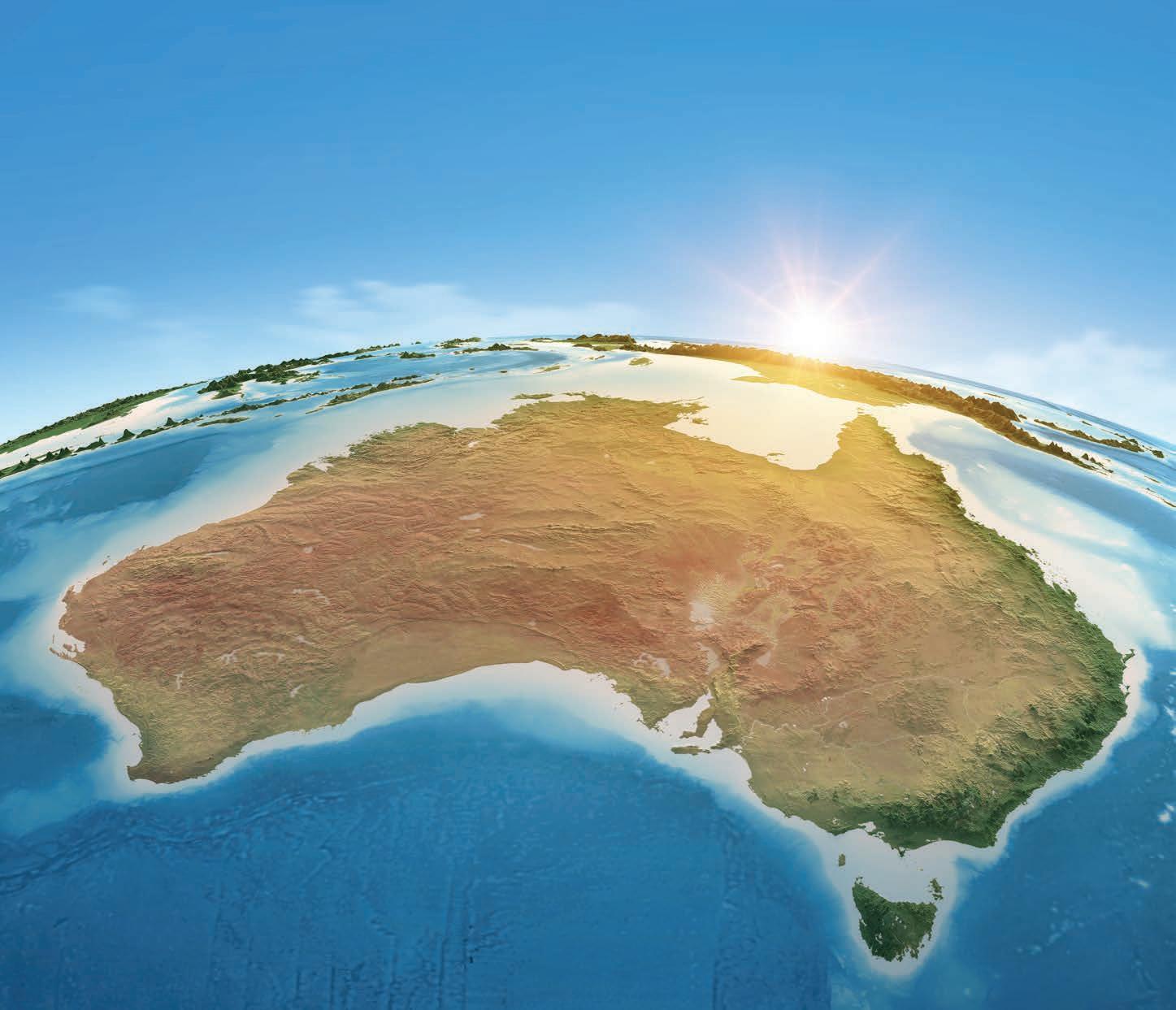
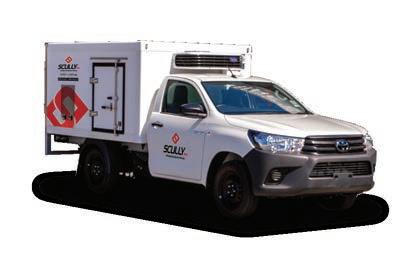
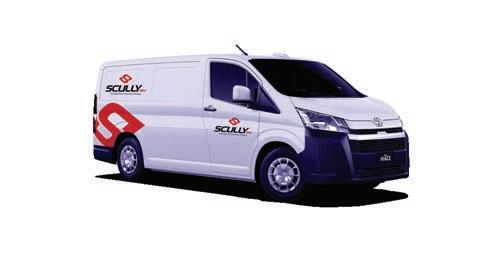
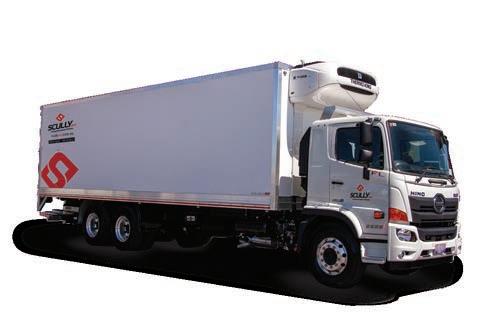
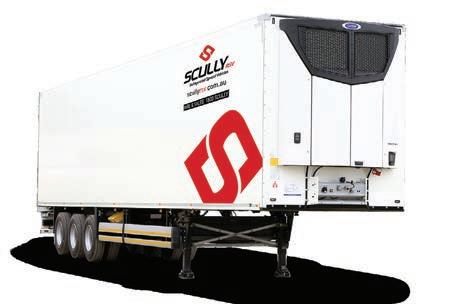