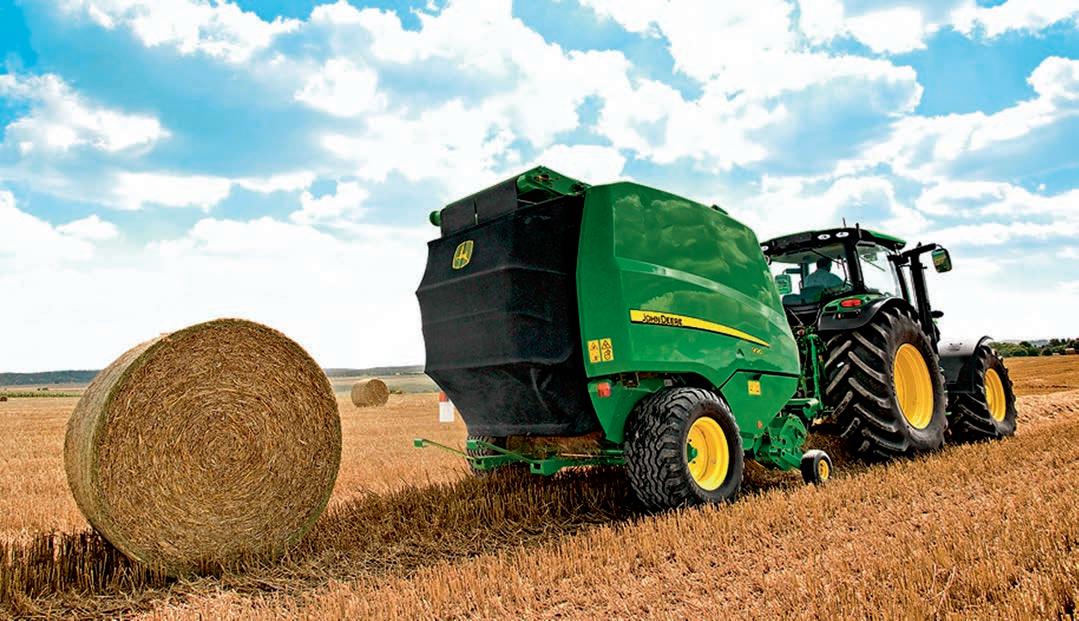
7 minute read
Hay Day
Tom Dickson was ready to check out John
Deere’s 990 variable chamber round baler
when it first arrived down under, back in 2013
John Deere 990 Variable Chamber Baler
Bale diameter/ width
0.8 to 1.85m/1.21m
Pick Up Outer Width
2.2m
Teeth Bars 5 tine bars HD pick up Gauge Wheels Pivoting or standard gauge wheels Knives 13 Gearbox 540rpm — 113kW PTO Driveline Wide angle — Powerdrive with extended greasing intervals Weight 4,300kg
With a temperature of 25˚C, just a light westerly breeze and not a cloud in the sky, Spring has turned on a magnificent day, and I’m at the Craven family’s dairy farm between Warrnambool and Mortlake, in south-west Victoria. One of three generations of family members working in the business alongside his parents, uncles and grandparents, Simon Craven leads the way up the track to where the new John Deere 990 baler is waiting for action. Like all reliable operators Simon’s first priority is to carry out daily maintenance. Searching through his pockets he finds a 10 cent piece, which he explains is the perfect tool to undo the latches on each of the huge streamlined side panels. Personally, I’d rather have a latch which could be opened by hand. With the side covers raised, a much more beefed-up mechanism of chains, sprockets and shafts is revealed. Simon says this is one of the reasons they were drawn to the new 990 variable chamber round baler, which features fast bale release, independent chassis and optional string tying. “It looks a lot stronger and heavier than previous models and for added strength all the mechanisms of the baler are attached to an independent solid chassis,” he says. It’s fair to assume this design will give longer, more reliable performance as all vibrations and stresses will be transferred into the chassis and away from sensitive baling components. Maintaining these highly-developed machines is getting simpler with every new model released. An automatic lubricating mechanism constantly oils all the chains and the only requirement is filling the oil reservoir each morning. To save even more time on routine maintenance the Cravens elected to include an optional auto greaser, set to apply grease every 20 minutes. Simon says this saves time every morning and ensures all bearings and major grease points are regularly lubricated. He also tells me he chooses to use Sisal twine rather than the faster net wrap option, as the twine is biodegradable – breaking down in the stomach of the cow. “It takes a bit more time at baling and is often prone to tangling in the baler but we more than make up for the lost time at feeding out,” he says.
VIEW FROM THE TOP
The first thing I notice as I climb in is a more modern monitor mounted just to the right of the steering column. The 7-inch (18cm) full colour 1800 display controls everything its predecessor did, such as bale density, diameter, soft-core pressure, drop floor unplugging device and pre-cutter knife engagement, but in a much more easy-to-follow format. The display showing the operator where to drive to form the bale equally on both sides is set prominently within the screen and an inbuilt memory allows information storage of 15 paddocks each to 10 different clients – another valuable tool for contractors. Engaging the power take-off (PTO) and increasing engine revs to have the baler running at the required 540rpm reveals no undue noises or vibrations. Even completing sharp turns both left and right causes no shuddering or slapping of the PTO shaft, further verifying it’s a well-balanced machine. As soon as the rear rollers begin to rise to eject the bale, the sides of the bale chamber move outwards to eliminate sticking within the chamber. While most other balers are waiting on the rear-door to go through its cycle, the John Deere 990 is half way toward producing its next bale. Simon alternates between 10km/h and 12km/h depending on the thickness of the windrow. At this speed, the 990 baler easily consumes the crop as quickly as the 2.2m pick-up can feed it in. Fitted to this baler is a Maxi Cut HC Rotor Feeder with 13 knives that cut the crop to approximately 80mm as it enters the baling chamber. The knives are not required today as we’re baling Balansa clover but Simon says he will definitely be using them when baling less palatable crops of ryegrass.
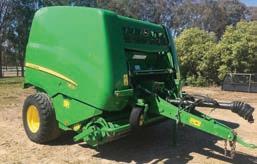

Looking for a
baler?
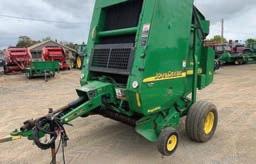
Search for ‘baler’ on
TradeFarmMachinery.com.au
or type the TA or DIY code shown here into the keyword search field
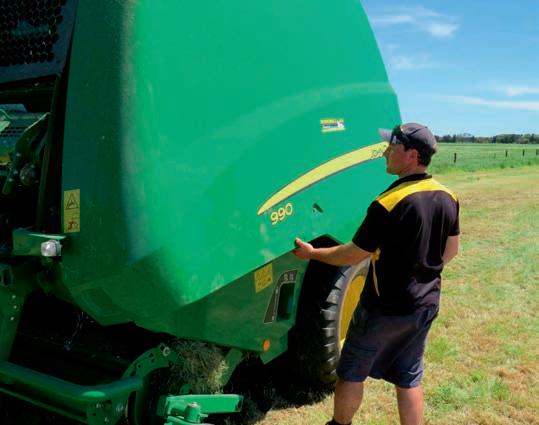
2

4 3
5

To demonstrate that we are working well below the baler’s capabilities, Simon bumps the speed up to 15km/h, adding if one of the Balansa clumps create a blockage he can activate the drop floor unplugging feature from within the cabin. In simple terms, the throat of the baler’s intake is opened up to allow the blockage to be drawn in.
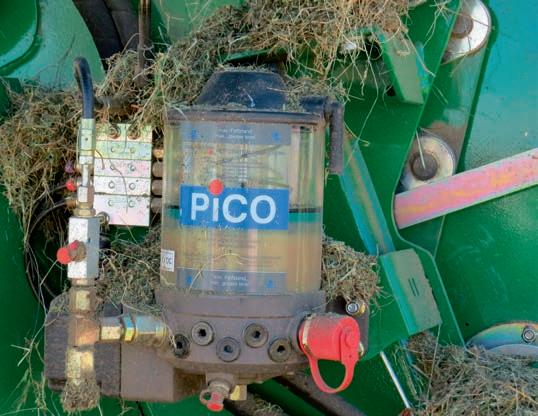
STRING PROBLEM
For about four hours we bale at a rate of around 50 bales per hour, only needing to stop a couple of times to rectify a string problem. Neither Simon nor I can work out why the baler fails to start the stringing process in this instance or alternatively apply far too much. Switching to manual string then back to auto string rectifies the situation, which eventually indicates the problem may be a faulty sensor. With the absence of the visible string spinners on the front of the baler I find myself having to watch the monitor to see if string is being applied. Our only other stop is to trim off some frayed edges from one of the belts, which possibly occurs when a clump of silage forms on one of the rollers, causing the belt to run sideways and rub somewhere during the belts cycle. Finding a solution for this is a must, as belts are an expensive item to repair or replace. Starting the core of a bale can often pose the biggest challenge but the John Deere 990 never once hesitates. Simon explains the hay entering the chamber is immediately encouraged to begin rotating because the belts and starter rollers run so close to each other. An important feature of the John Deere 900 Series balers is their ability to link up and communicate to compatible John Deere tractors. The baler’s computer takes control of the tractor’s transmission and relevant hydraulic functions leaving steering the only responsibility of the driver. Unfortunately I can’t report on this feature because the tractor we’re using doesn’t have the required technology.
FINAL THOUGHTS
Even after four hours of work I never get tired of watching bales shoot out the back at speeds I hadn’t seen before. Five seconds is the time it takes for the rear roller and screen to shoot up, eject a bale, before dropping down ready to go again – meaning more bales can be produced in a day. This, coupled with the fact it still offers the option of net and twine tying and its independent chassis which “removes all the stresses from the working components of the baler”, and there’s a lot to consider.
1. The fast bale release of about five seconds means far more bales can be produced in a day 2. John Deere 990 creates a paddock full of perfect bales 3. One latch releases side panel for easy servicing 4. Automatic greasing device is controlled by the in-cab ISOBUS display 5. The 18-cm display controls bale density, diameter, soft-core pressure, drop floor unplugging device and pre-cutter knife engagement
Pluses
Five second bale release Optional string tying Automatic greasing and oiling Baler mechanism housed within independent chassis User-friendly baler monitor
Minuses
String tying function randomly failed Belts became frayed
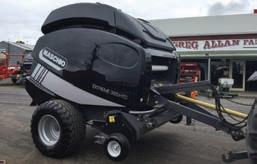


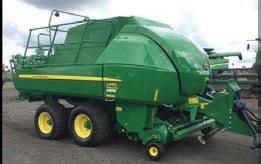