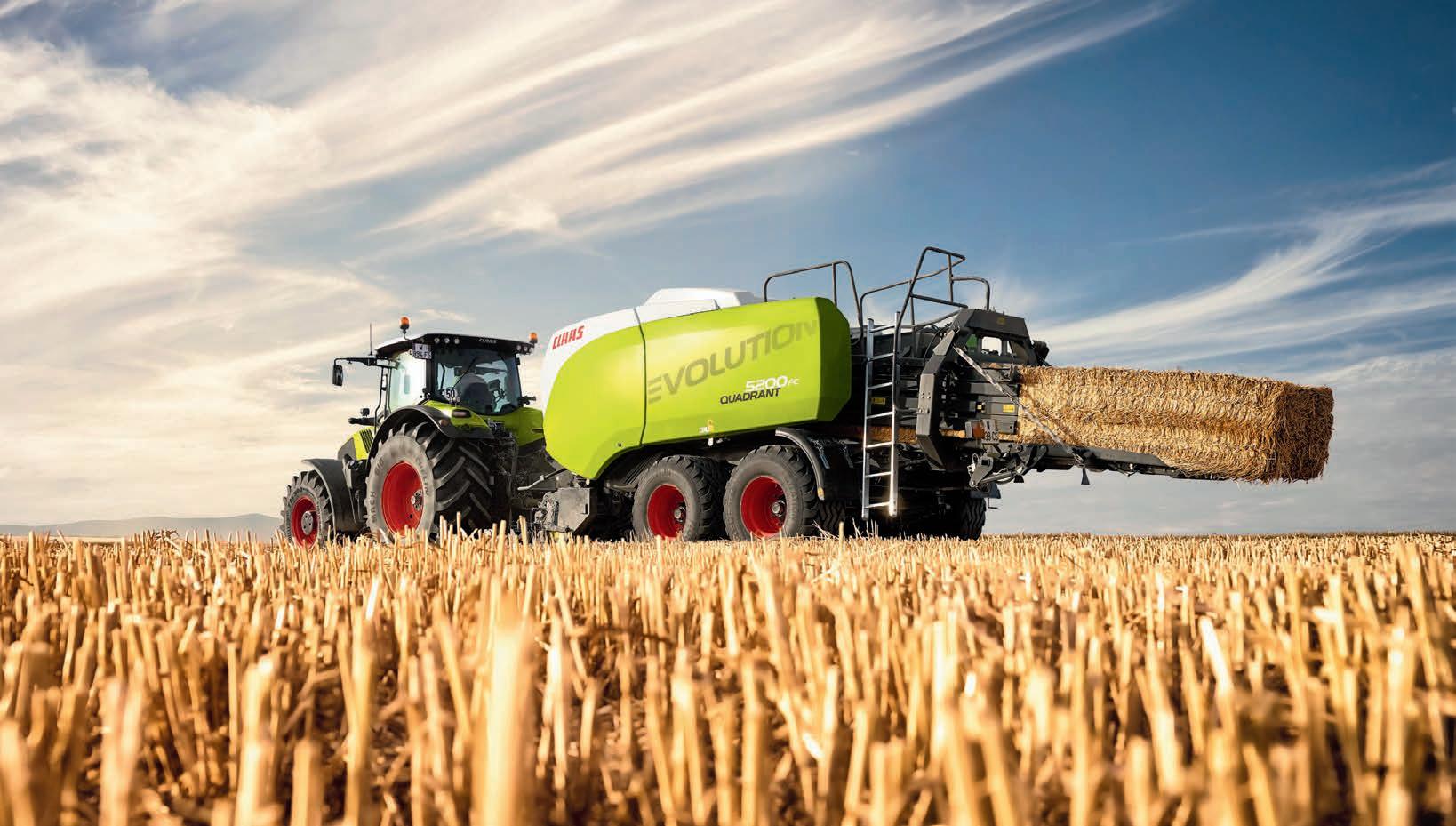
3 minute read
Claas upgrades Quadrant square baler range
Inspired change
Claas has reached across its product range to implement new upgrades to its Quadrant big square baler range, in moves it says will slash costs for owners
Claas has revealed comprehensive technical upgrades to its Quadrant big square baler range in a bid to boost its durability and output in the field.
The company turned to its Jaguar Forage Harvester for inspiration, replacing parts on the baler’s pick-up with highly resilient components from the harvester; while bearings, intake panels and other mechanics of the balers have also been strengthened and re-engineered to reduce wear costs.
The new components alone are responsible for a sizeable durability increase for the balers, even when performing in extreme conditions, according to Class Harvest Centre product manager – Greenline, Blair McAlwee.
“In an internal test involving 40,000 bales per machine, under extreme conditions in some cases, the new design was found to reduce wear of key components by up to 40 per cent,” says McAlwee.
“This has the added bonus of smoother running, reduced noise levels, simplified maintenance and longer service intervals.”
A new, mechanically driven high-density (HD) pick-up has been introduced across all Quadrant Evolution models – an addition that has been tweaked to improve the raking quality while still maintaining a gentle flow.
The HD pick-up boasts five rows of 18 double tines – an upgrade of one extra row of tines that allows the pick-up to rotate slower even when the speed of the feed roller is increased.
“The spring mounted feed roller compensated for uneven swaths and can be fitted with extra paddles when harvesting short-stalked crops,” says McAlwee.
The pick-up upgrades feature a two-cam design to maximise torsional resistance and robustness when in operation, while the release torque on the friction clutch has also been increased up to 1,600Nm and the diameter of the pick-up main drive shaft has been enlarged.
Within the upgrades made to the pick-up technology, Claas has added semi-automatic chain tensioning to ensure automatic lubrication on the pick-up drive and comes standard with the baler.
The ‘heavy duty evolution’ of the Quadrant big square balers has resulted in several modifications to the bale chamber. The top section, inclusive of the header place and side panels, have been strengthened and redesigned to produce balers with a better shape and higher density.
Automatic baling pressure control responds quicker to twine tension or load in the intake area. Additional Hardox HD bearings from the ram guide have been added on the balers to reduce wear in the chamber, knotter area and intake, resulting in extended service intervals.
Side knives and deflectors to help reduce material build-up in the ram guide area are optional extras and can further increase safety of operation.
The bale chamber on the 5300 model includes a new front frame and headstock, as well as a new hitch frame – that includes a longer, double-acting hydraulic stand – which provides operators with additional hitching positions.
Other upgrades made to the balers include Kennefix quick-release hydraulic couplers and a 10L hand-washing tank, both of which are fitted as standard.
Claas says modifications to the twine box make life easier for operators.
“The twine box guide swings out and can be locked in position, allowing the operator to thread the twine whilst standing beside the machine without having to use a stepladder,” says McAlwee.
“The twine brakes can also be adjusted from the ground without tools, saving time and increasing workplace safety.”
The bale ramp on the Quadrant balers can now be hydraulically opened and closed from inside the cabin – a function that enables the final bale to be ejected from the drive’s seat.
“The operating system has just two working and three settings menus, meaning the operator can rapidly navigate through the baler settings and performance,” says McAlwee.
“In auto mode, the baler’s capacity utilisation is displayed based on average bale weight and baling pressure.
“In addition, the driver can now monitor the oil temperatures and oil levels in the baler.”
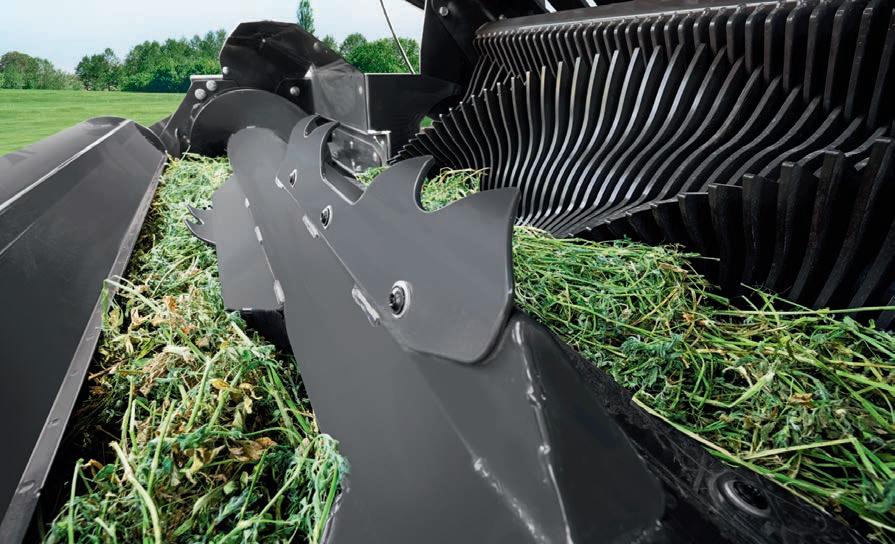
The new design was found to reduce wear on key components by up to 40 per cent