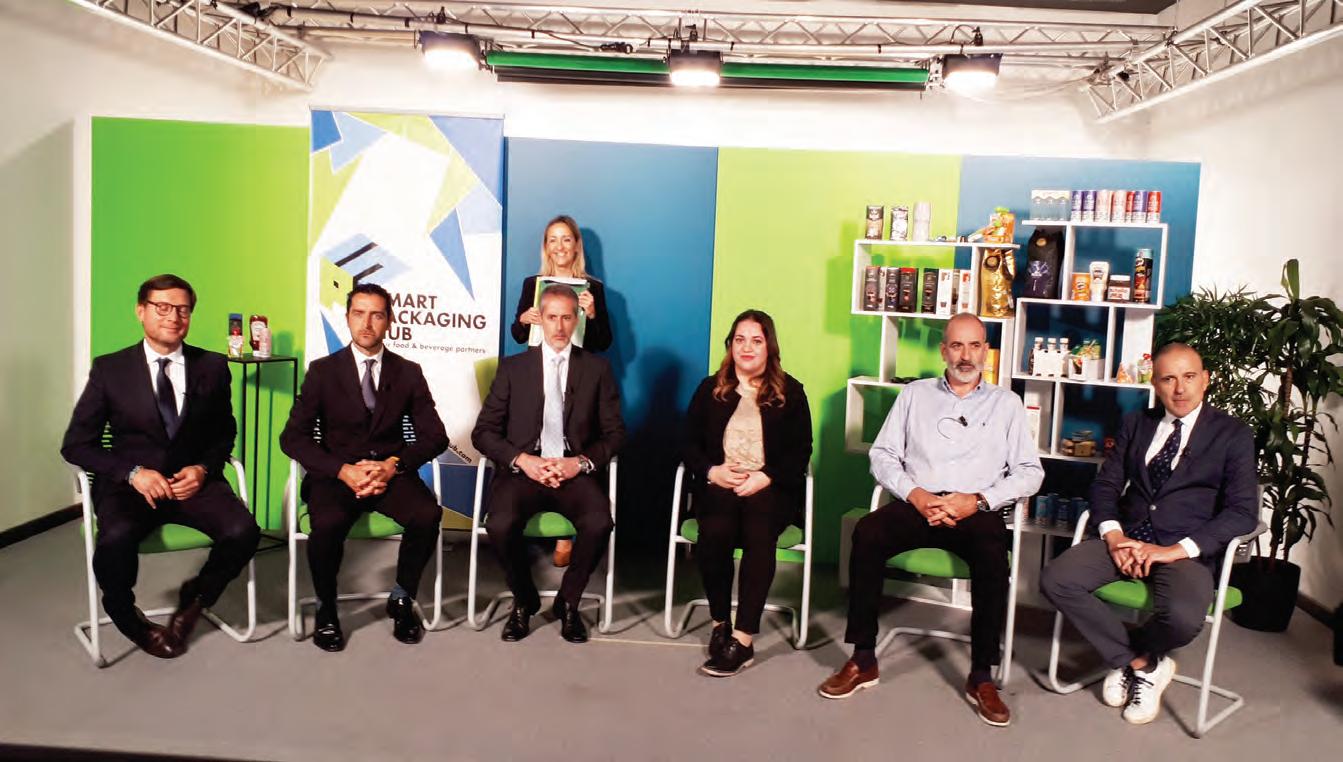
6 minute read
SMART SOLUTIONS
LEADING INDUSTRIAL PLAYERS OF THE SMART PACKAGING HUB NETWORK COME TOGETHER TO DISCUSS SUSTAINABLE SOLUTIONS TO CUT PACKAGING COSTS AND MINIMISE WASTE IN THE COFFEE AND BEVERAGE SECTORS.
Smart operations are not just about working with intelligent production systems, but embracing solutions that are cost effective, waste reductive and operationally more efficient. To learn how different companies in the processing and packaging market approach the subject, six leading businesses discussed their experiences in a Smart Packaging Hub webinar on 13 October.
Massimo Pavani, Sales Manager of Italian automated processing company Baumer talked about the demand from customers to make packaging decisions that minimise their carbon footprint and impact on the environment while focusing on return of investment in the shortest time possible.
One such solution is Baumer’s shrink wrapper with automatic reel changeover system that allows the customer to reduce its plastic film consumption by 15 per cent thanks to its non-stop production.
“Neither film welding nor operator intervention is required. Consequently, the film on the reel is totally used for production and film scrap is virtually none,” Pavani said.
Baumer’s GreenTech shrink-wrapping tunnel is another solution that cuts down energy consumption by more than 20 per cent compared to traditional systems thanks to its advanced insulation system and air flow controls that lower the air temperature when there is no upstream production. If used in two or three shifts per day, equalling 5000 hours per year, Pavani said customers can recover costs in 2.5 years.
Elena Amerio, Export Manager of 958 Santero, a leading Piedmont winery, said to reflect the latest trends and market requirements, the 63-year-old winery has introduced 958 Santero canned products which are lightweight, eco-sustainable, and modern looking.
“When it comes to transportation, being so lightweight, you have to consider that the carbon dioxide emissions are much lower compared to a glass bottle load. The canned packaging market is [predicted] to grow by about 40 per cent during the next five to six years,” Amerio said.
To wrap cartons of wines for transport, Santero uses Tosa stretch wrapping machines with a pre-stretching unit that saves up to 30 to 40 per cent of plastic while ensuring the stability and safety of the product.
Giovanna Chiara Italiano, a journalist of retail publications Mark Up and GDOWeek, told the webinar audience “we are in a world where climate change can no longer be ignored”, with customers more interested in social topics and sustainability options. As such, Italiano said businesses must assure customers there is a sustainability approach across the entire supply chain.
“Consumers live in a society which is really careful about these topics, examples like the Sustainable Development Goals, the European Union Green Deal, and this goal of reaching carbon neutrality by 2050. Of course, grassroot movements are specially tackling young people,” she said.
A United Nation’s Environment Program Food Waste Index Report 2021 found that 931 million tonnes of food waste was generated in pre- and post- retail, 61 per cent came from household consumption, 26 per cent from food service, and 13 per cent from retail.
Italiano said further education about the cost of food waste and its impact on the environment is needed, however food packaging solutions such as the use of barcodes and weblinks have evolved to help identify food freshness deadlines.
One company that specialises in the production of long shelf-life specialty food packaging is Mondiv, a division of Canadian manufacturer Lassonde. Mondiv turned to industrial automation specialist Clevertech to help custom design a basket loader and unloader automated robotics system for the processing and packaging of its specialty sauces and caffeine-based liquid products.
“Before the Clevertech solution, it took between five and eight operators to prepare and load the basket. It was backbreaking and repetitive work. Now with Clevertech it can be done with only two operators who restart the machine if a problem occurs and monitors the product quality,” said Ben Jemia Mehd, Project Manager at Mondiv Lassonde.
Clevertech Business Development Manager Luca Carollo adds that the ROI is within three years because customers can re-invest the operator in other tasks while the automated activities help increase traceability of the product thanks to data tracking integration in the basket loader and unloader.
“We know within three years the EU will introduce laws that there must be product traceability in every step of production, so to get this traceability integrated into the packaging system for fast moving consumer goods becomes a critical aspect,” Luca said.
Smart Packaging Hub member and packaging specialist Opem is also committed to finding sustainable solutions. Its capsule filling machines reduce energy consumption by up to 39 per cent and re-use 50 per cent of the spent nitrogen in its machine. It is also committed to changing the materials used in its capsules.
“In the last month we saw that a lot of
companies are developing biodegradable, compostable and recyclable materials. In this case, the most challenging point is creating [filling] lines that can manage all these materials,” said Franco Lupi, Opem Research and Development Manager.
Together, Opem and Caffitaly Systems are working on a compostable capsule that breaks down in minimal time but retains a long shelf life. Lupi said the task is challenging but necessary, with a European regulation on compostability that capsules must disintegrate 99 per cent within six months in 10 centimetres of soil.
“We must comply to this European law in order to have compostable capsules [that break down] at home or via industrial compostable facilities,” Lupi said.
Federico Oneto, Executive Vice President Operations at Caffitaly capsule systems says sustainability has always been a key element of the company but has become even more of a focus post-COVID.
“Caffitaly is very keen to offer our customers the best quality and most sustainable coffee capsules,” Oneto said. “We [planned] to put on the market compostable coffee capsules by the year of 2021, and we are planning to offer our customers completely recyclable and circular economy capsules at the start of 2022. These will be made out of 100 per cent polypropylene capsules that are fully recyclable.”
Together with international-leading packaging company Cama Group, to which Caffitaly has held a partnership for more than 10 years, the companies are commitment to finding sustainable material and technological solutions together.
“We are just one piece of the puzzle, so to keep on with Caffitaly’s sustainability program, our machines must ensure zero waste, and produce energy savings in order to allow Caffitaly production to be really sustainable,” said Renato Dell’Oro, Global Key Account Coffee for Cama Group.
Oneto said one of the reasons Caffitaly chooses to partner with Cama to supply its end-of-line configuration is because the relationship is treated as “business partners”, which allows them to collaborate to find solutions.
“They are very reliable and flexible, and what I see as a key element is the after sales support,” Oneto said.
“In order to maintain and reach [our level of desired] sustainability, lines must be efficient and well maintained. [For] good maintenance of the line, it’s key to work with a supplier and their aftersales and technical support. This means low energy consumption and wastage.”
Another key reason for the company’s longterm partnership Dell’Oro said, is because of the long-life of Cama’s production lines, such as its Monoblock Top Loading unit, to which it keeps installing state-of-art software and innovation for peak performance.
“We have to guarantee machine durability, high performance, short downtime during performance change, and flexibility because Caffitaly has a wide range of capsules,” said Dell’Oro.
“They are also on the market with several other products and our machines have to be able to handle all these different sized products in different packaging configurations.” GCR
For more information visit www.smartpackaginghub.com
From left to right: Luca Carollo of Clevertech, Renato Dell’Oro of Cama, Franco Lupi of Opem, Maria Chiara of Italiano GDO Week, Federico Oneto of Caffitaly, Massimo Pavani of Baumer. Behind: Sonia Bennati, Zeus Editor and event moderator.