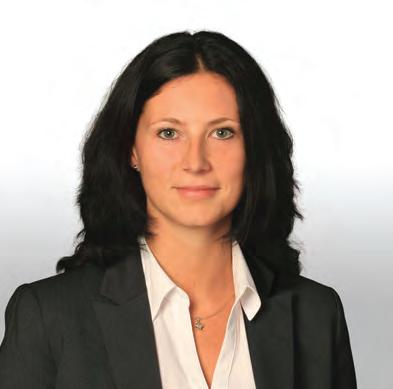
6 minute read
THE COMPLETE PACKAGE
THE RECENTLY REBRANDED SYNTEGON TECHNOLOGY IS MAKING A NAME FOR ITSELF IN COFFEE PACKAGING, WITH A FOCUS ON INNOVATION AND SUSTAINABILITY.
Syntegon may be a relatively new name in the coffee industry, but the processing and packaging specialist’s experience dates back more than 160 years. Formerly known as Bosch Packaging Technology, Syntegon branched out from the German multinational Bosch Group in 2020, creating new opportunities for the company under the new owner CVC Capital Partners. “We became more independent and developed a new name and brand to highlight our complete focus on sustainable and intelligent processing and packaging solutions for the food, pharmaceutical, and coffee industries,” says Marcus Velezmoro, Head of Product Line at Syntegon Technology.
Christina Holm, Product Manager for Coffee Packaging Machines at Syntegon, says Syntegon maintains its penchant for quality and decades of experience, and is ideally prepared for the future.
“As Syntegon, it is possible to centre the customer even more in our innovations and business decisions. This means we are able to work closer with the global coffee market, from consulting to installation of complete line solutions and after sales support,” Holm says.
“We believe that coffee connects people and that’s certainly been my experience. We look forward to joining with and being part of our coffee family, letting people connect our new name with the best solutions for coffee packaging.”
Within the coffee industry, Holm identifies sustainability, globalisation, and diversification as growing trends, all of which Syntegon is equipped to cater to.
“Like in every industry, sustainability is very important, in terms of minimum waste, energy consumption, recyclability of packaging material, and the whole carbon footprint,” Holm says.
“Demand for high quality coffee and packaging is also increasing and we’ve noticed trends towards small batches. Trends change and evolve all the time, so that requires flexibility in packaging.”
Syntegon Technology can provide coffee roasters with a turnkey solution for coffee bag packaging. This ranges from dosing and weighing technology and packaging machines with different functions and features to multiple sealing systems, a broad portfolio of valves and applicators, and even secondary packaging.
For classic vacuum sealed packaging formats, Syntegon Technology offers a full range of high output mono-format lines necessary for larger commercial coffee roasters down to more flexible units for smaller coffee business. These include the PKD line for high speed and efficiency, the size and format flexible PKS range, and modular PME series for highest flexibility.
For the increasing popular vertical form-fill-seal bags, Syntegon Technology offers the SVE line for medium to high output, SVI 2600 B model as an economic solution for standard bag styles, and its premium PME Spout for maximum flexibility and aroma protection.
“There are other more sophisticated pack styles with reclosure elements that we feel will play an important role in the future, so coffee businesses will require a more versatile machine,” Velezmoro says.
“We have always had machines in that category but are developing a new family of machines catered to that segment.”
Holm adds Syntegon has also seen increasing demand from new markets.
“We are also seeing changes in the habits of customers. Coffee has become a global lifestyle product and we see growth in new markets like Asia and the Middle East, where tea isn’t the go-to beverage anymore and younger generations love Western coffee,” she says.
“We see coffee as a global product and even though we’re based in Germany, can serve our customers around the world.”
Syntegon Technology employs more than 6000 people at more than 30 locations worldwide. Dealing with such a wide customer network, Velezmoro says it’s critical Syntegon Technology has a wide array of solutions available within its portfolio.
“The coffee industry has so many different products and pack styles, which change even more region to region. There is no one-sizefits-all standard solution, and your portfolio needs to consist of more than just high and low-to-medium output versions of the same machine,” he says.
“For example, in central Europe the evacuated pack for ground coffee has a long tradition. Some roasters may experiment with new types of packaging, but for certain large commercial brands or the vacuum pack will remain. Whereas in newer markets, consumers are more familiar with flexiblebased packaging, so there we see more ‘fancy’ pack styles – the United States is a good example. In Asia, we see they prefer this pack style as well, because they have their own preferences and are not just copying European tradition.”
With a long history and expertise in coffee packaging, Velezmoro says Syntegon is an ideal partner to accommodate these
many needs.
“We started working in coffee packaging when the industry was still using paper bags. Since then, we’ve pioneered many technologies for aroma protection in coffee packaging, such as gas flushing and valve technology,” Velezmoro says.
“One of our strong points will always be the quality and longevity of the machines, which is in our DNA because of how we design our technology. Our machines last a very long time and people can rely on them. Productivity is also very important, so we ensure a high throughput as well.”
To meet growing demands for sustainable solutions, Syntegon has reduced its technology’s energy usage and optimised its material handling for minimal packaging material waste.
“For the future, another thing we are considering is adaptability to new packaging materials that could become available on the market. The variety of material will increase as more sustainable options become available, but we will use intelligent technologies like automation and new sealing systems to realise these innovative packaging solutions,” Velezmoro says.
“The plastics industry has evolved a lot and one of our key priorities is collaboration, which means partner with packaging material suppliers. It will take collaboration to develop these new solutions and we are willing to play our part.”
Coffee packaging has traditionally required multilayer plastic laminates to preserve freshness and aroma which makes it difficult to recycle. Today, Velezmoro says, novel mono materials are available. However, these recyclable polypropylene and polyethylene plastics place higher demands on machine technology during processing than conventional plastic laminates.
“Thanks to our first-class technology and engineering expertise, our coffee packaging lines are up to these challenges and process mono materials into high-quality packaging,” he says.
To showcase these solutions to the coffee industry, Syntegon has established a coffee centre of competence in Germany, where it is consolidating all of its expertise in one location.
“This coffee lab gives our customers the possibility to test new materials with their products at our site in Waiblingen and allows us to support them to find the right recyclable materials for their packaging. We want to help them to make it as easy as possible,” Holm says.
“The whole bean segment is growing all around the world, with everyone becoming a barista at home over the last few years. This is increasing new markets and pack styles, but also a greater need for sustainable packaging. This trend will not stop and Syntegon will continue to stay at the forefront of it.” GCR
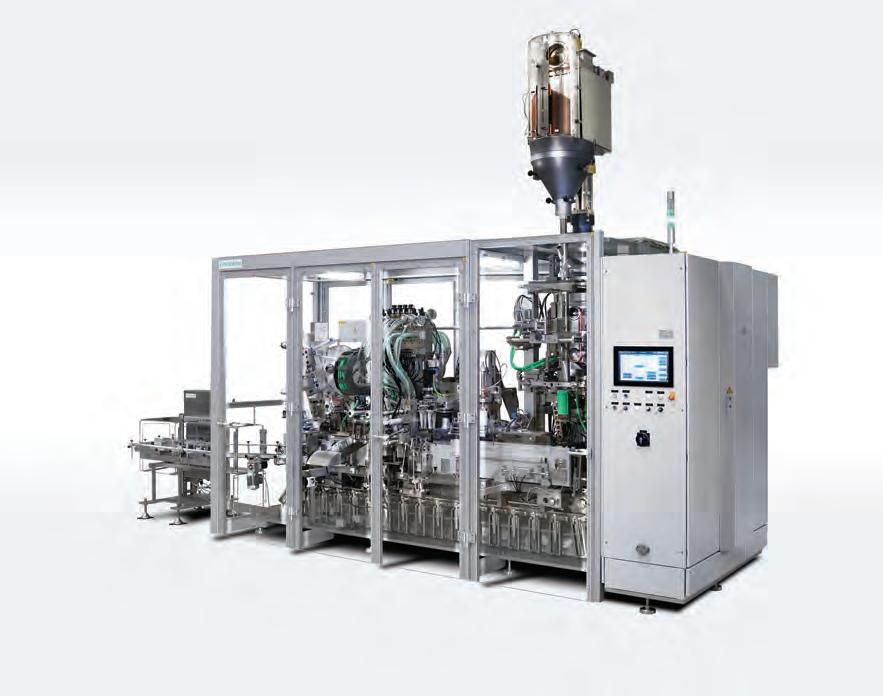
For more information, visit www.syntegon.com/coffee-packaging-solutions
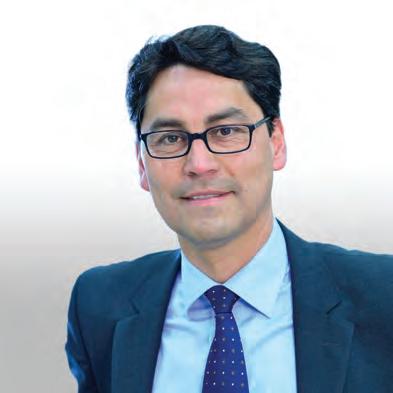
Marcus Velezmoro is the Head of Product Line at Syntegon Technology.
Christina Holm is the Product Manager for Coffee Packaging Machines at Syntegon.
Syntegon Technology is providing sustainable packaging solutions for the coffee industry.