UNIQUE CONTENT AND INSIGHT FOCUSED ON KEY TRENDS IN THE GLOBAL CONSTRUCTION EQUIPMENT AND TECHNOLOGY MARKET FROM THE INDUSTRY’S BEST-INFORMED AND MOST INFLUENTIAL SOURCES
GLOBAL REPORT
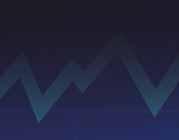
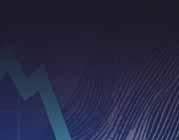
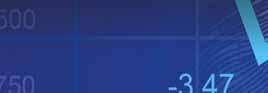
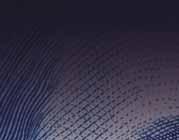
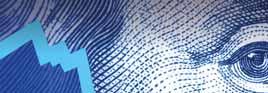
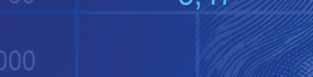
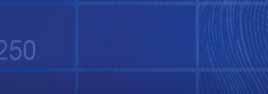
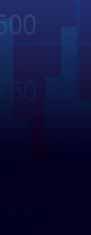
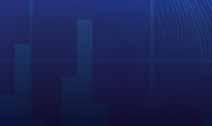
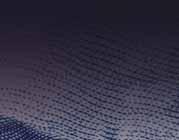
CONSTRUCTION EQUIPMENT AND TECHNOLOGY 2022
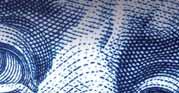
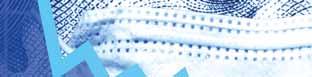

UNCERTAINTY AFTER RECORD-BREAKING YEAR
DIGITAL CONSTRUCTION WORKS CHANGE DRIVES HEAVY LIFTING INNOVATION FUELLING THE FUTURE IS A GAS, SAYS CUMMINS
EXOSKELETONS THAT FIT LIKE A GLOVE METSO SWITCHES ON SUSTAINABLE CRUSHING FOCUS: WEST AFRICA, PHILIPPINES, INDONESIA APPLICATION EXPERTISE FROM FAYAT BUILD BACK BETTER MAKES A REAL DIFFERENCE
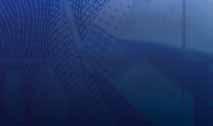
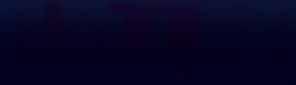
www.worldhighways.com | www.aggbusiness.com
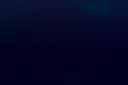

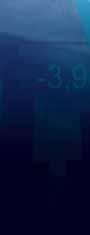
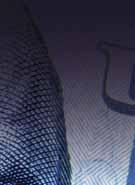

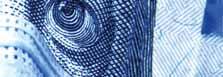
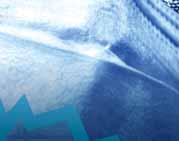

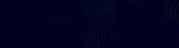
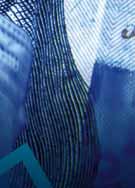
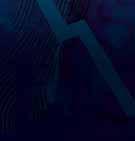
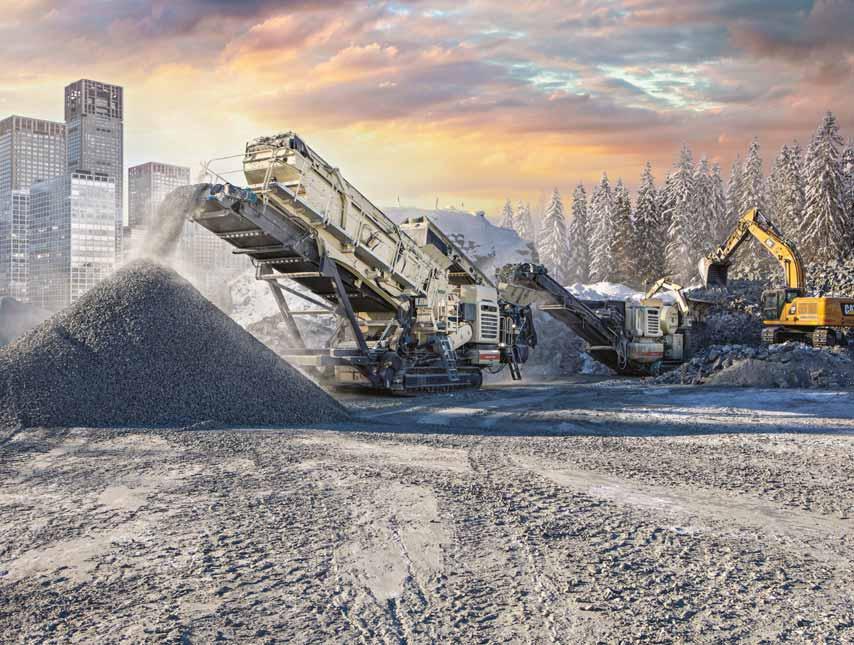
GLOBAL REPORT
Editor: Geoff Hadwick
Contributing Editors: David Arminas, Guy Woodford
Designers: Simon Ward, Andy Taylder
Production Manager: Nick Bond
Office Manager: Kelly Thompson
Circulation & Database Manager: Charmaine Douglas
Internet, IT and Data Services Director: James Howard
Managing Director: Andrew Barriball
Chairman: Roger Adshead
Editorial contributors: Liam McLoughlin, Pete Kennedy, Graham Anderson, Munesu Shoko, V L Srinivasan
COVER IMAGE: © Scaliger | Dreamstime.com
ADDRESS:
Route One Publishing Ltd, Second Floor, West Hill House, West Hill, Dartford, Kent, DA1 2EU, UK
Tel: +44 (0) 1322 612055
Fax: +44 (0) 1322 788063
Email: [initialsurname]@ropl.com (e.g. radshead@ropl.com)
ADVERTISEMENT SALES
Head of Construction Sales: Graeme McQueen
Tel: +44 1322 612069
Email: gmcqueen@ropl.com
Sales Director: Philip Woodgate Tel: +44 1322 612067
Email: pwoodgate@ropl.com
Sales Director & Classified: Dan Emmerson
Tel: +44 1322 612068
Email: demmerson@ropl.com
Italy: Fulvio Bonfiglietti
Tel: +39 339 1010833
Email: bonfiglietti@tiscali.it
Asia / Australasia: Roger Adshead
Tel: +44 7768 178163
Email: radshead@ropl.com
Global Report Construction Equipment & Technology
ISSN 2634-3223 (Print)
ISSN 2752-8375 (Online)
05. GLOBAL MARKETS REVIEW
Global construction equipment sales rose 10% in 2021 to a new record of 1.196 million units, according to data from Off-Highway Research (OHR). However, a -5% fall in demand is expected this year … But not all is lost. Will that still be enough to give 2022 the second-highest sales volumes on record?
20. DIGITAL CONSTRUCTION WORKS
Conquer technology interoperability gaps with DCW. Digital Construction Works is all about the “transformative power of digital”. It is designed to be a leading integrator of construction technology services, a power that will help to deliver projects smoothly, on time, and on budget. Use the platform to increase productivity, reduce risk, and deliver reliable, efficient project results. Are you connected?
26. THE POWER DEBATE: HYDROGEN
Cummins has been at the cutting edge of developing power solutions for more than 100 years and is continuing to lead the market by developing a range of sustainable drivetrains powered by new fuel sources. Why is the industry’s number one power player concentrating so strongly on hydrogen?
29.
HEAVY LIFTING AND CRANE TECHNOLOGY
Construction heavy lift and abnormal load transport companies have been undervalued in the past … hugely important but often overlooked. Today, things like giant pre-fabricated bridge sections are helping contractors to increase their productivity levels, but how is it all being lifted into place?
36. THE WORLD IN NUMBERS
We live in interesting times. Here are a few key facts and figures to help make sense of it all.
42. METSO: PLANET POSITIVE
Switch on to sustainable crushing and screening. Everywhere you look you can see the impact of climate change, depleted natural resources, and increasing urbanisation. The demand for sustainable solutions is increasing every day as digitalisation paves the way forward. How can you make your equipment fleet as sustainable as possible?
45. SUPPLY CHAIN MANAGEMENT:
AMERICA
The haves and the have-nots: not all will survive. Supply chain complications are more than just an inconvenience to the construction equipment manufacturing industry. Successfully navigating the supply chain has never been more essential, and the difficulties involved are creating a world of “haves and have-nots”. Will your business survive?
50. SUPPLY CHAIN MANAGEMENT: EUROPE
While Covid-19 restrictions have been rolled back in many countries, global construction equipment supply chain issues persist. In Europe, the situation has been exacerbated by the Russian invasion of Ukraine, plus renewed pandemic lockdowns in China. How tense is it really getting out there?
56. EXOSKELETONS & ROBOTICS
Exoskeletons and digitally-connected clothing, once just a pipe dream, are now helping managers on big construction sites to improve a variety of metrics such as connectivity and productivity. Often called wearables or exosuits, they can be as large as a space suit or as small as a glove. How do they work?
60. REGIONAL FOCUS: WEST AFRICA
As policymakers in West Africa seek tools to stimulate economic growth, there is a distinct focus on infrastructure development as a cornerstone of the region’s economic recovery plans. Investments in road corridors and transport projects at large are expected to continue apace as West Africa scales up regional integration.
65. REGIONAL FOCUS: EUROPE’S NEW SILK ROAD
A heavyweight fight: EU’s Global Gateway v China’s Belt and Road Initiative. Global Gateway is the European Union’s fight-back programme to counter China’s Belt and Road Initiative, a megaproject that Brussels believes the Chinese will use to increase their political and economic influence around the world. It’s going to be a big fight … But how viable is this ambitious EU alternative?
68. INNOVATION FROM FAYAT
The construction equipment sector needs to work towards decarbonisation and digitalisation, says Fayat. From safe and alternative drive systems to new technologies for reduced energy consumption, improved carbon footprints, autonomous operations, and digital integration, Fayat is making these ideas reality today.
74.
REGIONAL FOCUS: PHILIPPINES AND INDONESIA
As quarantine restrictions ease and Covid takes a back seat, government spending is starting to speed up a host of major infrastructure projects in The Philippines and Indonesia. New capital cities, new roads, and new high-speed rail lines are all underway. Is it fast-forwards to a brighter future?
79. BUILD BACK BETTER
Construction industry experts are pleased with the U.S. government’s plan to invest heavily in the country’s infrastructure. But more details are needed to stave off growing uncertainty. How, exactly, will the money go from the government’s funding pot to repairing the potholes? That’s the $1.2 trillion question.
Build your next highway project on a secure platform
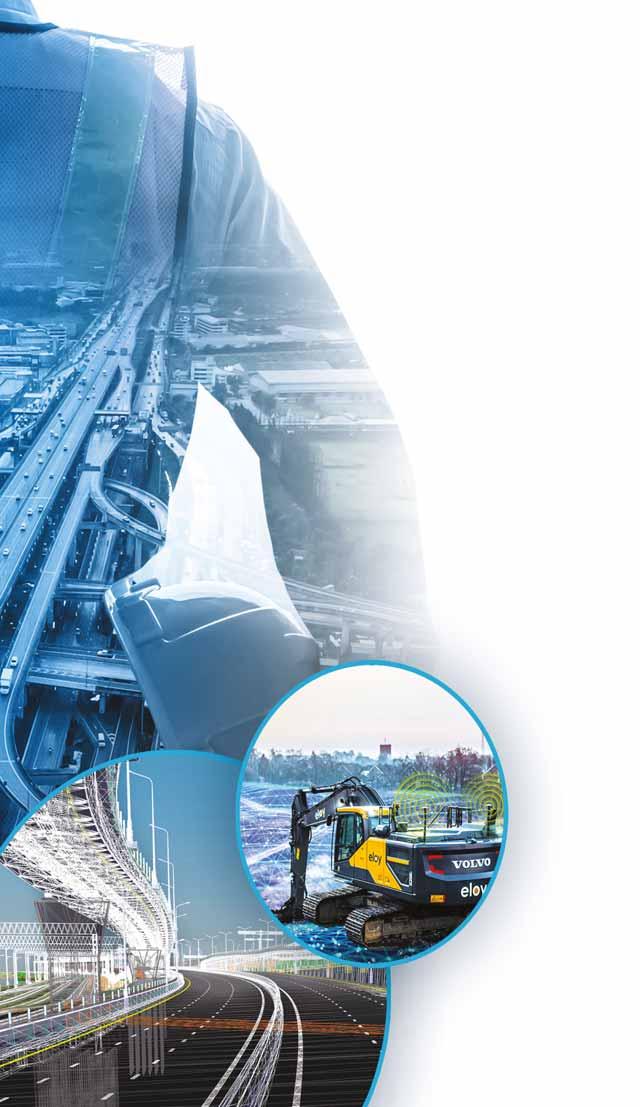
We help accelerate highway construction projects through the adoption and use of digital workflows, BIM for infrastructure assets, digital twins, and best practices. We integrate the right combination of third-party applications and technology to improve transportation planning, design, construction, and operational outcomes.
We integrate the myriad of disconnected planning and design-build applications with your job site, machinery, and sensor technology, allowing for enhanced communication and seamless project management from the office to the job site.
*Ask us about our Integrated Highways Solution of third-party applications and technology for the planning, design, and construction of your next project. We’ve integrated the best of what vendors offer into a fully integrated highway solution.
Contact DCW to learn more.
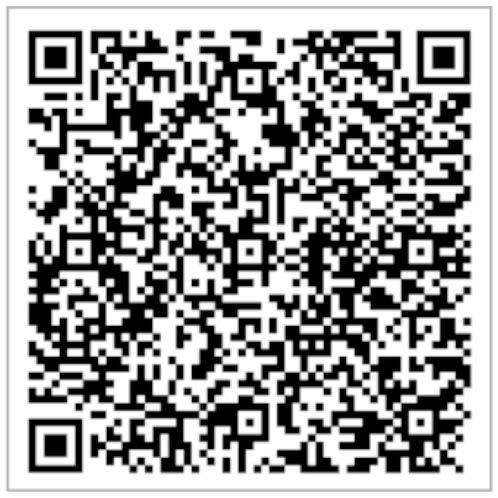
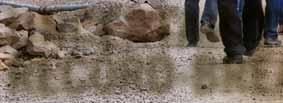
UNCERTAINTY FOLLOWS A RECORD-BREAKING YEAR
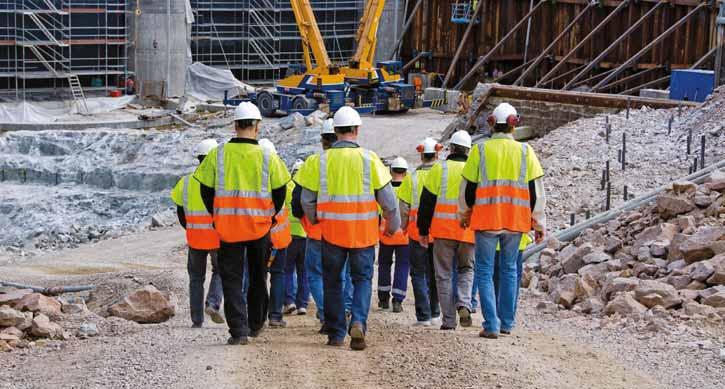

Global construction equipment sales rose 10% in 2021 to a new record of 1.196 million units, according to data from Off-Highway Research (OHR). However, a -5% fall in demand is expected this year but that would still give 2022 the second-highest sales volume on record, says the same source. Guy Woodford reports.
Acombination of low interest rates, stimulus spending on infrastructure and high commodity prices last year was, states OHR, a “heady combination” for the construction equipment market.
China was the only major regional market that failed to grow in 2021. OHR notes that some of the strongest growth was seen in North America (up 25%) and Western Europe (up 22%), while emerging markets, excluding India and China, were up 24%. The OHR figures exclude compaction equipment and cranes.
OHR highlights some significant downside risks in 2022. Inflation and the prospect of rising interest rates have been factors for several months and may be a growth brake. Russia’s invasion of Ukraine and the resulting international sanctions have, says OHR, heightened this situation.
Looking further ahead, industry research company Freedonia tips global demand for construction machinery to grow 4.1% per year to US$250 billion in 2025.
Rising construction activity due to factors ranging from: population growth. to increasing industrial output; increased infrastructure spending; and advances in worldwide mining, forestry activity and energy production, are said by Freedonia to be key factors fuelling unit sales.
Freedonia says: an increase in replacement sales of global construction equipment, after many operators delayed machinery purchases in 2020; the embrace of newly developed, state-of-the-art construction
equipment, costing considerably more than predecessors; and rising sales of replacement parts and attachments as the amount of equipment in use worldwide increases, will also boost sector demand.
Global sales of construction equipment 2002-2021 (Units)
Source: Off-Highway Research
EUROPE
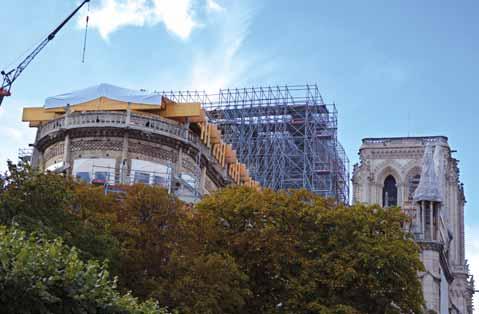
BUILDING ON A “REMARKABLE OUTCOME”
Demand for construction equipment in Europe continued its eye-catching growth in 2021, after the industry had already seen a return to growth in the second half of 2020 when the impact of the pandemic was receding.
Off-Highway Research reports that the bounce back in 2021 was much stronger than expected at +22% in Western Europe alone (196,396 units, compared to 160,946 in 2020) – the second-highest total on record.
European construction equipment association CECE says demand benefitted from a combination of stable performances by different end-user segments and pandemic stimulus measures, whose potential fully unfolded in 2021.
It adds, however, that the industry also experienced the most severe supply chain disruptions in recent history, in particular shortages of raw materials and components, as well as scarce and expensive freight transport.
“Against this backdrop, the 24% [CECE figures] increase in sales in 2021 on the European market is a remarkable outcome,” said CECE president Alexandre Marchetta.
“The European construction equipment industry is indeed resilient as shown over the last two years. The continued increase in demand in our largest markets, the
European recovery programme and the global construction boom are boosting our business. We are doing everything we can to maintain the positive direction in the coming years. This includes the urgent topics of decarbonisation, digitalisation and the EU regulatory agenda.”
The figures surely include a statistical ‘base effect’ of yearly comparison, with the enormous drop caused by the first pandemic lockdown in 2020. However, after weathering the Covid crisis, CECE notes that underlying demand within the industry has remained strong and is on track to close the gap to the record sales levels of 2007.
2021 saw consistent trends across the equipment sub-sectors with all product segments recording growth in sales of between 22% and 30%. Concrete machinery saw the strongest growth, slightly above the levels seen in the other sectors.
From a regional perspective, the markets that were hit hardest in 2020 –particularly the UK and Spain – saw the best performances in 2021. Southern Europe and CEE markets saw above-average growth in sales, and even the mature markets in Northern Europe saw similar levels of recovery. None of the markets saw a fall in sales in 2021, and the only market that experienced single-digit growth was the high-volume German market. The fact that
Gross growth 2020-2023 (Domestic product & Investment in equipment)
Sources: European Commission - Feb.2022, (GDP)ONS for UK (GDP, European Commission - Nov.2021)
it has still not reached saturation levels can be considered a positive outcome. Turkey continued its recovery from the catastrophic levels of decline seen in 2018/19 and saw the highest levels of growth across the market regions.
Providing an outlook for European construction equipment market in 2022, CECE says the business climate index for the industry recorded its highest ever value in the July 2021 survey and maintained extremely high levels throughout the rest of the year. In the first two months of 2022, there was another small improvement both for the current business situation and future sales expectations.
European manufacturers hope that supply-side bottlenecks will create fewer concerns for the rest of the year. CECE says the demand-side clearly remains strong, as all equipment sub-sectors were expecting business to improve in the months leading up to the summer of 2022.
In February this year, the CECE Business Barometer, highlighted that more than 50% of manufacturers surveyed were experiencing order backlogs of six months or more. All statistics and surveys presented in the current Annual Economic Report have so far indicated that the European construction machinery industry is very well positioned. CECE warns, however, that these expectations are likely to be negatively affected by the current tensions and the effects of the war in Ukraine.
Off-Highway Research says the Russian and Ukrainian construction equipment markets are likely to collapse in 2022 due to the invasion of Ukraine and sanctions against Russia. The markets’ combined sales of 25,000 units in 2021 equate to roughly 2.5% of global demand, says OHR. However, Russia is a significant market for mining equipment sales. OHR says the impact for the European market and wider-world construction equipment sector from a deterioration in the Russian and Ukrainian construction equipment markets is likely to come from an indirect economic effect.
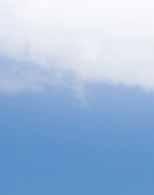
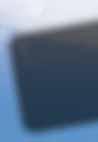
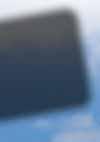
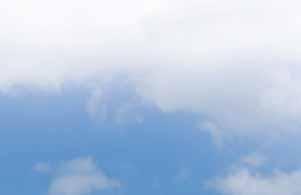
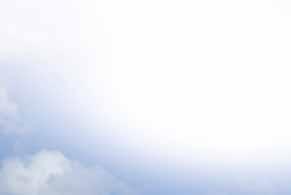


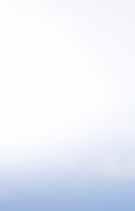


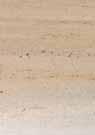
Komatsu WA475-10
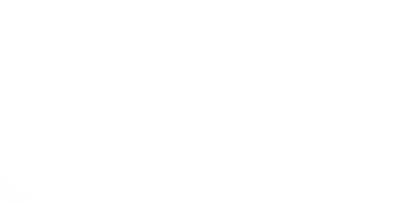
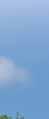
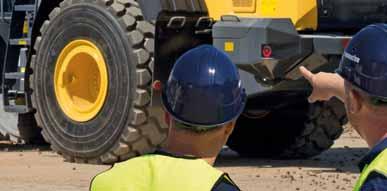

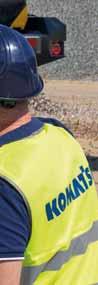
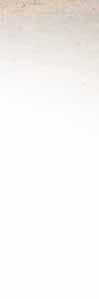
The WA475-10 is an industry-leading top performer. Its Komatsu Hydraulic Mechanical Transmission (K-HMT) and the 217 kW / 291 HP engine deliver an outstanding combination of productivity increase and ultra-low fuel consumption. An independent control of the driveline and work equipment makes your work easier and shortens cycle times, to provide you with a unique operating experience in a wheel loader.
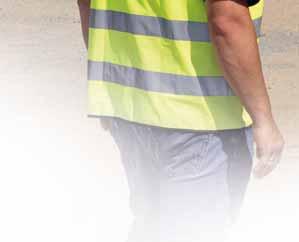

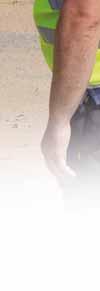

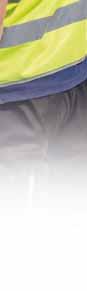
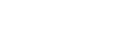
NORTH AMERICA
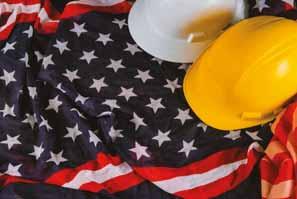
THE RECORD-BREAKING YEARS
There was a strong 23% rise to 196,070 units in North America construction equipment sales in 2021 thanks to a residential boom, new statistics from OffHighway Research shows.
OHR notes there is also a bullish forecast for the market in 2022, largely thanks to President Joe Biden’s US$1.2 trillion residential and infrastructure bill.
A significant structural swing towards compact equipment to 66% of volume demand in 2021 vs 33% in early 1990s has also been noted by OHR. This is said to be due to impressive growth in the residential construction market. OHR says a rise in larger equipment types should follow in 2022.
OHR expects North American construction equipment sales to rise over the next two years, taking the market to new record levels. However, as in Europe, serious issues remain with construction materials and labour shortages.
According to the February 2022-published business intelligence data from the Association of Equipment Manufacturers (AEM), the global economy expanded by a robust 5.1% in 2021. And while projected growth of about 3.9% is expected for 2022, slower growth seems like a foregone conclusion. Short-term factors like the lingering Covid-19 pandemic, ongoing supply chain issues and persistent labour
shortages, as well as long-term factors like deglobalisation and inflation, have emerged to dampen enthusiasm a bit on the heels of what has been a strong economic resurgence worldwide.
“The last recession we experienced ended the longest period of economic expansion in the United States, and that recession lasted from February 2020 to April 2020,” said AEM director of Market Intelligence Benjamin Duyck. “Two months, in traditional economic terms, can’t even be accurately described as a recession. However, this economic disruption has impacted us all greatly, and we are still dealing with the after-effects today – labour shortages, supply chain problems and higher interest rates.”
AEM has surveyed its members quarterly for nearly two years regarding how quickly they expect to recover to pre-Covid-19 levels. For some time, the responses had been generally quite positive, according to Duyck.
“But the data for this last quarter is moving again in the other direction, largely due to the headwinds we’re facing with inflation, workforce issues and supply chain disruptions,” he said.
Construction industry value is expected to grow 4.5% this year, largely driven by residential.
AEM member perceptions show strong demand (83% see year-over-year growth
ahead), and it’s reasonable to expect growth of 6-10% over the next 12 months on the heels of 6-10% stronger growth than was expected in 2021.
Infrastructure spending is set to gain significant momentum in the coming years. Uncertainty related to the Covid-19 pandemic, high material costs and monetary policy all remain concerns.
Dublin, Ireland-based ResearchandMarkets.com’s December 2021-published U.S. Construction Equipment Market - Strategic Assessment & Forecast 2021-2027 report states that the U.S. construction equipment market size will be valued at US$32.68 billion and reach a volume of 191,836 units by 2027, growing at a compound annual growth rate (CAGR) of 6.23% by volume during the 2021-2027 period.
The reopening of manufacturing plants after Covid-19 and building more manufacturing plants to reduce the growth of unemployment are, says ResearchandMarkets.com, a leading business market intelligence firm, going to be driving factors for the demand of construction equipment.
The same source tips the construction sector at various levels under private, state, and federal governments to boom with double-digit growth at least through 2022 and 2023 due to the increase in arms exports from the United States to boost the construction equipment market.
CENTRAL & SOUTH AMERICA
BRAZIL LEADS THE CONSTRUCTION EQUIPMENT DEMAND RACE
Arizton, a major business market intelligence company, forecasts that construction equipment demand in Brazil will pick up pace in the years to 2028.
In 2021, the Brazilian government planned to invest round US$30 billion for the development of national transport infrastructure, says Arizton. A further investment of around US$16 billion is likely to be made for the development of 14 highways in 2022. Airport development projects are under progress in Sao Paulo, Santos Dumont, and in Rio de Janeiro. For port redevelopment, Arizton notes that a further US$19.2 billion has been allocated. The works cover five terminals in Sao Luis, Maranhao, and Rio Grande do Sul ports.
Arizton says the Brazilian government aims to achieve carbon neutrality by 2050, prompting big investment in solar, wind and hydroelectric generation plants across the country. Subsidies for the installation of renewable energy plants and easy financing facilities by financial institutes are supporting the growth of renewable energy projects in the country.
segment in Brazil is estimated to reach 23,519 units by 2028,” a March 2022-published Arizton market report states.
Arizton expects Brazil’s earthmoving equipment market to grow strongly by 2028, owing to the increased government investment in highway, metro, and airport construction projects and the expansion in the construction, transport, and renewable energy sectors.
A Latin America construction equipment market study by Arizton published in January 2022 predicts the market to be valued at US$5.06 billion by 2027, growing at a CAGR of 4.75% in the 2021-2027 period.
“Enhanced demand for natural resources in recent years will positively impact demand for construction equipment used in the mining industry, such as excavators, loaders, and cranes,” states the study.
It continues: “There is robust demand for construction equipment in the region.
GlobalData reports that construction market output in Mexico was valued at US$115.6 billion in 2020 and was forecast to record growth of more than 10% in 2021
Caterpillar, Komatsu, Volvo Construction Equipment Brasil, Sany and XCMG Brazil are said by Arizton to be the leading construction equipment manufacturers in Brazil, which saw 30,800 units sold in 2020, up 14% compared to the previous year, according to a study by the Brazilian Association of Technology for Construction & Mining (Sobratema).
After India, Arizton reports that Brazil is the second-largest market for backhoe loaders in the world. “The government’s ambitious plan for water sanitation, which aims to provide clean water to 99% population by 2023 and other sewage treatment projects, is expected to drive the demand for backhoe loaders, as they are extensively used for handling water pipes in these types of projects. The backhoe loaders
Contractors, mining, and construction companies are the major consumers in the Latin American
companies such as Carlyle Group, Grupo Orguel, and BigRentz have a reasonable share in the market.
“With the increase in construction activities, the demand for road rollers also increases. Various road and highway redevelopment projects such as developing Interserrana highways, connecting Matehuala- Saltillo roadways with Cuidad Victoria- Monterrey roadways are planned in Mexico. All this will propel the demand in the Latin America construction equipment industry.”
GlobalData reports that construction market output in Mexico was valued at US$115.6 billion in 2020 and was forecast to record growth of more than 10% in 2021. The same source says the Mexican construction market is projected to register an annual average growth of more than 2% between 2022-2025.
In September 2021, GlobalData notes that the government submitted its 2022 budget proposal to Congress, of MXN7.3 trillion (US$350 billion) to promote economic growth, regional development projects, social equality, financial stability and maintain fiscal discipline. Global Data states that the proposal outlined how government policies will continue to focus on healthcare, social programmes and investment, and that it will prioritise ongoing investment projects, such
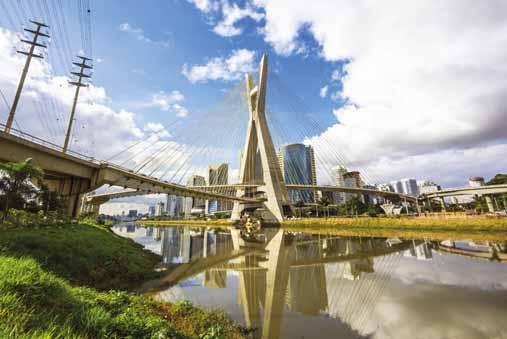
CHINA
CHINA MARKET PASSES PEAK
Off-Highway Research notes that as soon as China emerged from its national lockdown in March and April 2020, it embarked on a massive stimulus programme. “The main instrument of this was allowing provincial governments to issue special bonds. This saw construction equipment sales rise 30% in 2020 to more than 412,000 units, or more than 480,000 units if compaction equipment and mobile cranes are included. Such high sales have only been seen once before in China, during the boom of 2010 and 2011. That was also a result of stimulus spending, on that occasion in response to the global financial crisis,” OHR observes in its March 2022-published Global Briefing report.
However, as OHR states, that stimulus boom essentially only lasted 12 months. The first quarter of 2021 saw extremely high sales, but in the next three quarters, the number of machines sold was significantly lower than the volumes seen in a year previously. The net result was that construction equipment sales in China fell 6% overall last year (to
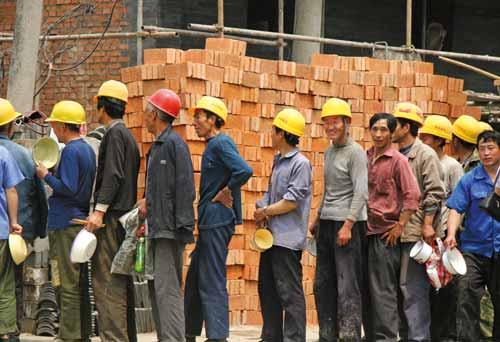
389,062 units). OHR reports that it was the only major market to see a decline in sales in 2021, highlighting that the cycle in China is somewhat out of step with the rest of the world.
OHR predicts that the Chinese construction equipment market will fall back over the course of 2022 and 2023 to more normal levels of around 300,000 units per year. Although this represents a steep fall from 2020’s high of 412,000-unit sales, OHR argues that this represents a return to normal, rather than a worrying collapse.
Inevitably, OHR believes parallels will be drawn between the current outlook and the aftermath of the 2010-2011 stimulus boom, which was followed by a deep, painful five-year recession. However, the downturn forecast in China for the early 2020s is expected to be relatively short-lived and shallow.
OHR states: “The structure of demand has changed in China over the last decade. Construction equipment sales are much less dependent on new build infrastructure
projects, as activity shifts more towards maintaining and repairing the infrastructure which was built in the boom years of the 1990s and 2000s. In addition, activities such as agriculture and industry have become more mechanised and are driving demand for equipment.”
Interestingly, OHR highlights that construction equipment production in China hit a new record high in 2021 at more than 548,000 units, or more than 630,000 if mobile cranes and compaction equipment are included. The 7% growth was achieved despite a 6% decline in sales of equipment in China, which, says OHR, illustrates the country’s strengthening position as a major exporter of construction equipment.
The off-highway business market intelligence consultancy adds: “The difference between sales and production of equipment was just over 159,000 units, or 29% of production. This was the largest the gap has ever been in both absolute and percentage terms. Although it is not necessarily safe to assume that all these machines were exported, the figures illustrate China’s importance as an equipment producer. Only Japan exports more machines.”
GlobalData says construction output in Northeast Asia, including China, is forecast to record a 4.2% growth and reach US$4.71 trillion in 2022 compared to $4.52 trillion in 2021. It will account for 39% of the projected $12.19 trillion of global output this year, says the leading data analytics company. However, the growth of construction output in Northeast Asia in 2022 has been revised downwards by 0.8% this quarter due to the slowing construction activities across the region.
According to a recent Arizton report, the China construction equipment market is projected to reach a value of US$79 billion by 2028. The global business market intelligence consultancy says increased demand for construction equipment is due to a rise in transport infrastructure projects and government-led affordable-home schemes.
Arizton states that the Chinese government’s intention to invest US$573 billion in infrastructure projects will fuel the growth of long-term industrial development.
Guaranteed compliance with the German TA Luft Regulation VOC < 50 mg / Nm³
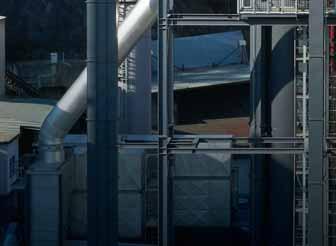
Future-proof.
BENNINGHOVEN HOT-GAS GENERATOR
BENNINGHOVEN recycling drums using counterflow action with a hot-gas generator offer an environmentally friendly, future-proof solution that is always a reliable investment. Depending on the quality of the recycled material, quantities as high as 100 % can be added. In addition, emissions are brought significantly below the level required by standards and the total energy consumption of the plant is reduced.
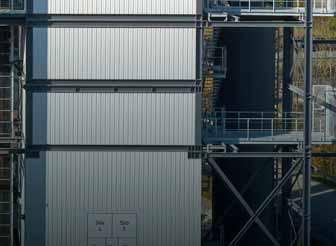


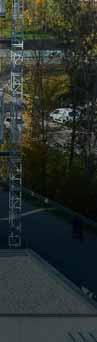
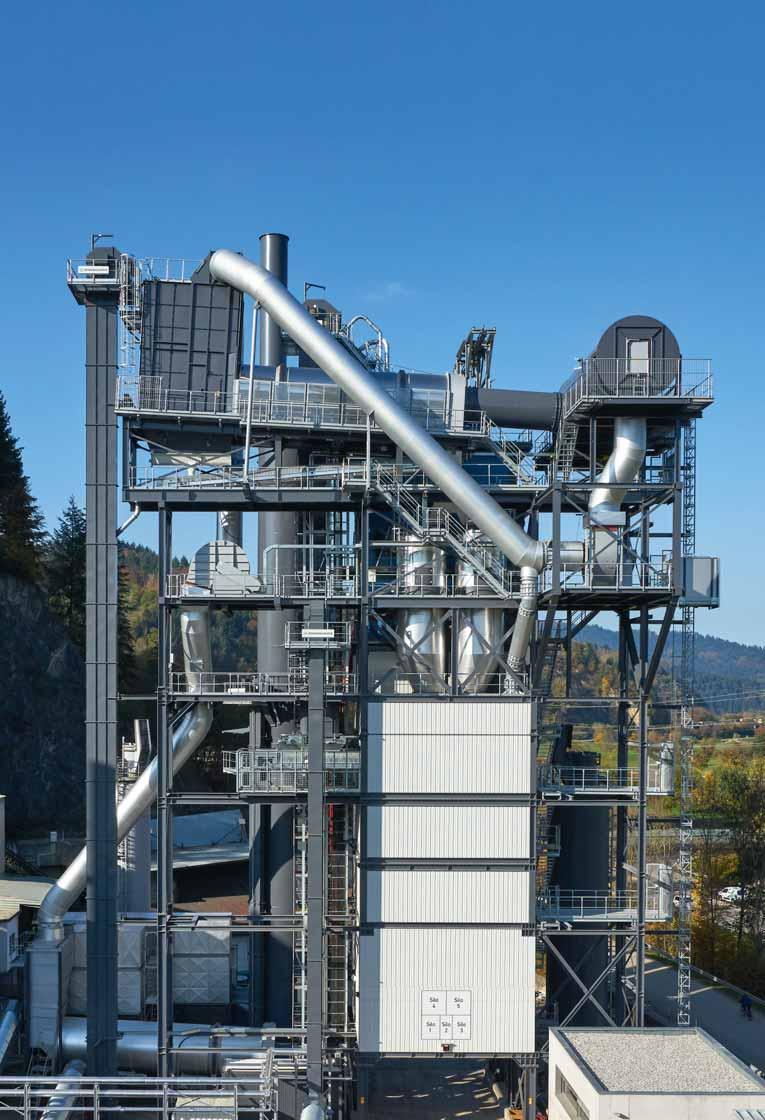
JAPAN
STABLE JAPANESE DEMAND
Japan’s construction equipment sales rose slightly in 2021 to 68,379 units compared to 67,645 units in 2020, according to new Off-Highway Research) data. The same source reports that Japanese sales are likely to drop by more than 2,500 to 65,670, before a further slight drop to 63,065 units in 2023. Looking further ahead, OHR forecasts 2026 sales of 64,250 units.
Arizton reports that demand for earthmoving equipment and cranes will drive construction equipment market growth. The same source notes that Hitachi Construction Machinery Japan has signed 54 disaster agreements with local governments in Japan to supply construction equipment to disasterprone areas.
Arizton says building works linked to the recent Tokyo 2020 Olympics, held in 2021 due to the coronavirus pandemic, have been a boon to the Japanese construction equipment industry.
“There are high expectations from remote control of ICT construction machinery as the country’s population is decreasing due to the low birth rate. To solve this, the Ministry of Land, Infrastructure, Transport, and Tourism supports the ‘i-Construction’ initiative. This aims to boost productivity and make construction sites appealing by using contemporary technology such as IoT and
AI,” states Arizton.
Arizton highlights that for major construction projects, building companies and contractors are replacing old equipment with TIER-4 emission norms-compliant equipment. “This is because global warming and excess greenhouse gases are deteriorating the environment. The new engines with compliance with the emission norms are more fuel-efficient. This adds specific cost savings for the operators and helps reduce emissions,” notes Arizton.
“Urban engineering projects and building renovations require compact and multifunctional construction equipment that is suitable for small-scale construction projects. Thus, the increasing urban engineering projects will be fuelling the demand for backhoe loaders in Japan
“Large construction projects such as the redevelopment of Shibuya and Toranomon–Azabudai district leads to the increasing demand for bulldozers in Japan.”
Arizton notes that the Japanese government is involved in the field investigation of 15,000 sites for landslide disaster prevention. This, the business market intelligence consultancy states, will drive the demand for rough terrain cranes as they can operate on uneven surfaces.
Japan is the third-largest producer of
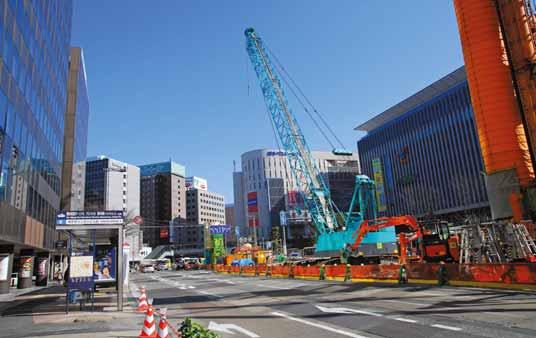
Japan economic outlook growth projections 2021-2023 (Real GDP, annual percent change)
Source: IMF, World Economic Outlook, April 2022
steel and the second-largest producer of iodine in the world. Arizton predicts that the demand for these metals is expected to rise due to their use in the construction and manufacturing industries.
Analysing major Japanese construction equipment manufacturers 2021 launch highlights, Arizton points to Kobelco’s introduction of ICT-enabled construction machinery with a navigation system to cater to the needs of high construction and mining projects. The ICT-enabled solution incorporates monitor displays and alerts in the driver’s cab and a machine control system that lets the operator undertake complex work operations with easy lever manipulation.
Arizton notes Sany’s launch of a new crawler crane in July 2021 – the SCC9800TM – featuring a 4,500-ton lifting capacity, one of the world’s highest.
GlobalData says the Japanese infrastructure construction sector will grow, supported by government investment on public works to improve regional connectivity. The sub-sectors in this sector include rail infrastructure, road infrastructure, and other infrastructure projects. The pipeline, which includes all projects from pre-planning to execution, is skewed towards early-stage projects. GlobalData states that the majority of the pipeline value is in projects in the planning stages as of January 2022.
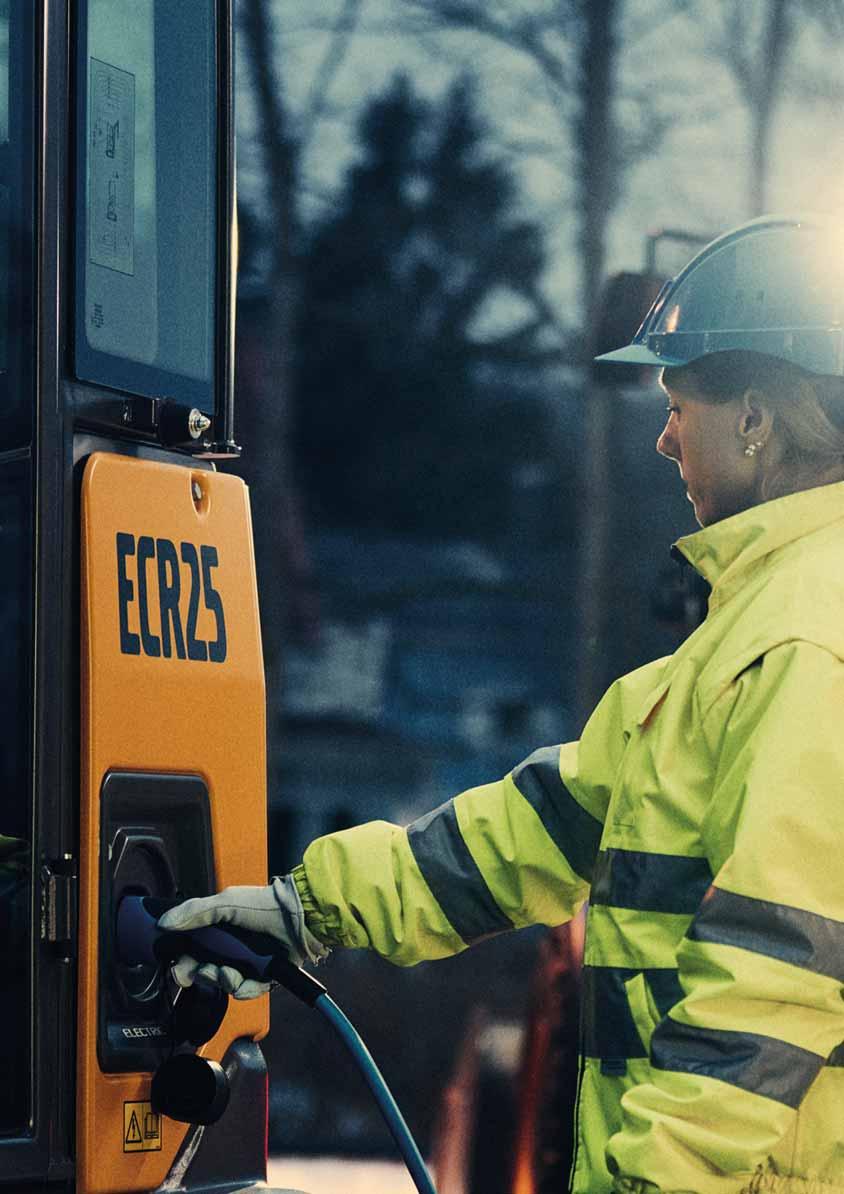

INDIA
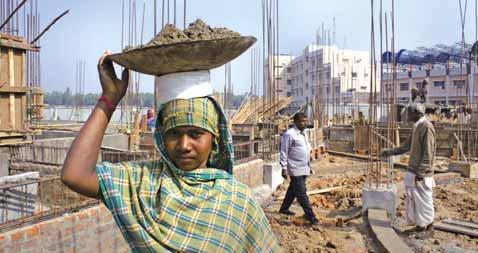
GROWTH RETURNS TO INDIAN MARKET
Before the Covid pandemic, Off-Highway Research notes that 2020 was expected to be a year of robust growth for the Indian construction equipment market, following the disruption of the 2019 general election.
“In the event, the pandemic precipitated a 10% decline in sales (61,960 units in 2020), which took demand back to where it was in 2017, leaving it some 25% lower than the peak year of 2018. As disappointing as this was for a market, which was showing clear signs of returning to robust growth at the end of 2019, a 10% downturn as a result of the pandemic and lockdowns is not as bad an outcome as might have been expected,” OHR reports in its March 2022-released Global Briefing.
OHR highlights that the 10% rebound in 2021 (to 68,326 units) took sales back to their 2019 levels. The market in India continues to be driven by infrastructure investment, which continues to broaden out from the traditional focus on road building.
“Equipment production in India totalled 78,675 units last year, or 94,844 machines when mobile cranes and compaction equipment are included. This Indian
consumption of equipment in 2021 represented an excess of some 12,000 machines, or 15% of production” the OHR Global Briefing continues.
OHR observes that India has virtually no imports of construction equipment, with the vast majority of demand met by domestic production. The consultancy states that the major suppliers in India are the international OEMs and their joint ventures, although there are a number of indigenous producers too.
OHR adds: “The last decade or so has seen these international OEMs start to use their factories in India as export hubs, to serve the surrounding region, as far afield as the Middle East and Africa.
“By far the highest volume machine produced in India is the backhoe loader –India represented 55% of global backhoe loader production last year. Although the vast majority of these are sold domestically, production exceeded sales in India by more than 6,000 backhoe loaders last year, which gives some indication of the size of the export market for these machines.”
Arizton predicts that India’s crawler excavator sales will grow at a CAGR
(compound annual growth rate) of 5.41% in the 2021-2027 period to 34,366 units by 2027.
The Indian crawler excavator market is witnessing rapid growth in demand for medium crawler excavators, says Arizton, a U.S.-headquartered global business market intelligence consultancy.
“The government is focusing on green building projects to promote demand for fuel-efficient, lesser-emission crawler excavators. Increasing government initiatives such as increasing the steel production capacity to 300 million tons by 2030 indicates future demand for large excavators used in mining,” Arizton reports.
GlobalData expects India’s construction industry to grow by 5.8% in 2022, supported by a series of investments in transport, health, and housing infrastructure developments. GlobalData notes that the government unveiled its Pradhan Mantri Gati Shakti Master Plan in October 2021, a INR 100-trillon (US$1.3 trillion) project to develop holistic infrastructure, aiming to boost economic growth through infrastructure investment and propel India’s development over the next 25 years.
In June 2021, GlobalData reports that the government approved the INR500-billion (US$6.5 billion) loan guarantee scheme for Covid-affected sectors (LGSCAS), to provide financial guarantees for building new healthcare projects, as well as upgrading existing infrastructure. A project can receive a maximum loan of up to INR1 billion (US$13 million), with the interest rate capped at 7.95%. GlobalData states that the Indian construction industry’s growth will also be supported by the government’s plan to significantly increase the stock of affordable housing units for low and middleincome cohorts, under the Housing for All programme to 2022 end.
Over the remainder of the forecast period, between 2023 and 2025, the Indian construction industry is expected to register an average annual growth of 6.2%, supported by investments under the INR111-trillion (US$1.5 trillion) national infrastructure pipeline (NIP), between the 2020 and 2025 fiscal years (April 2019 to March 2025).
REST OF ASIA
BACK TO WORK
The resumption of construction projects and new investments is set to improve prospects for construction equipment sales in the Southeast Asian countries of Vietnam, Thailand and the Philippines in 2022.
GlobalData predicts the Thai construction industry will register an average annual growth of 4% between 2022 and 2025
Vietnam saw 20% less construction in 2020 and the first half of 2021, while there was a 13% reduction in the demand for cement in the Philippines, according to Alexander Baart, regional director Southeast Asia for wet processing equipment manufacturer CDE. He says the good news is that public and larger projects are now resuming across the Southeast Asia region.
“From today’s perspective there are reasons to believe that after Lunar New Year [February 1] in Thailand and Vietnam the volumes will grow back to pre-Covid levels,” says Baart. “In the Philippines we already foresee a 6% higher demand of cement compared to 2019.”
Baart adds that a growth of 6% is expected this year in Thailand’s construction business, while in Vietnam it is expected to be between 3 and 5%. In both countries the driving force is the resumption of new projects.
Market analyst GlobalData says that the South Asia region (including Vietnam, Thailand and the Philippines) should generate construction output values in 2021 that will surpass the 2019 pre-Covid levels in real (constant prices) terms.
ASEAN Analytics highlights three of the biggest public infrastructure initiatives in the region that could contribute to aggregates demand as being the Northeastern HighSpeed Rail project in Thailand, Long Thanh International Airport in Vietnam, and the new Manila International Airport in the Philippines.
Covid has put a dampener on the Philippines’ economy and is still affecting logistics flow in the country, according to Peh Jing Peng, Volvo CE’s head of market for Philippines, Taiwan and Brunei.
“Philippines is currently suffering from the Omicron wave of infection which
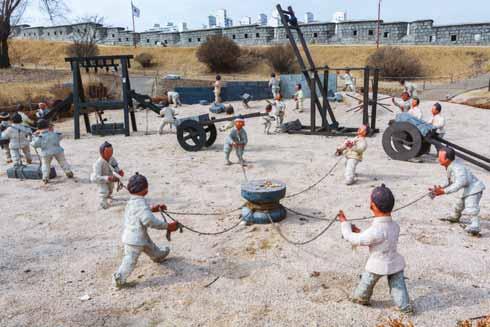
is still growing,” says Peng. “Nevertheless, the government has put an emphasis on the construction industry to boost the economy.”
GlobalData estimates that the Philippines construction industry recorded an annual growth of 21.9% in 2021, with output predicted to surpass pre-pandemic levels in 2023. The analyst adds that the sector’s output in the second half of 2021 was supported by improving investor confidence and investment in transport, renewable energy, residential and commercial infrastructure projects.
The Philippines construction industry is projected by GlobalData to expand by an annual average rate of 9.6% from 2022 to 2025. The AmBisyon Natin 2040 programme, which promotes the development of affordable housing, transport and renewable energy infrastructure, is expected to drive the industry’s long-term growth.
An increase in foreign direct investment (FDI) will also contribute to the construction industry’s growth momentum in the next few years.
Raven Chua, head of market Thailand, Laos & East Timor at Volvo CE, says that Covid-19 has heavily impacted the tourism sector in Thailand, which accounts for around 20% of the country’s overall gross domestic product (GDP).
“The Thai government has diverted much of the country’s budget to support countermeasures against Covid, especially for SMEs, which has caused delay to megaproject investments,” says Chua. “Vaccinated travel lanes opened in October 2021 but were closed again in December due to the Omicron outbreak.”
Travel in the country was re-opened from February 1, 2022, and Chua says that, as the tourism sector recovers, it will push demand for infrastructure and therefore construction
equipment.
GlobalData predicts the Thai construction industry will register an average annual growth of 4% between 2022 and 2025, supported by improving investor and consumer confidence and government investments on road, rail, renewable energy and housing projects. Further supporting growth will be investment in both the Southern (SEC) and Eastern Economic Corridor (EEC) programmes. The value of approved developments in the EEC totals THB669bn (US$20.7bn), with four of the corridor’s six flagship projects currently in execution.
GlobalData predicts the Vietnamese construction industry will register a CAGR of more than 8% between 2022 and 2025, supported by ongoing construction works on the considerable pipelines of public infrastructure projects. As part of its transport infrastructure spending plan of between VND973.8 to 1,472 trillion (US$4365bn), the government plans to construct and renovate existing road, rail, inland water, sea and air transport infrastructure in the period through to 2030.
The election of Yoon Suk-yeol, a conservative former prosecutor, as South Korea’s new president in March 2022 is unlikely to impact the firm infrastructure spending commitments made by former president Moon Jae-in. This is highly encouraging for construction equipment demand prospects.
Moon Jae-in’s administration committed to building 1.27 million homes in the metropolitan Seoul area through its New Town Development Plan. Further building plans include the erection of 300,000 more houses in Seoul’s satellite cities to stabilise real estate prices. The price of real estate has doubled in many parts of the country during the last couple of years, and it has become impossible for young people to purchase homes.
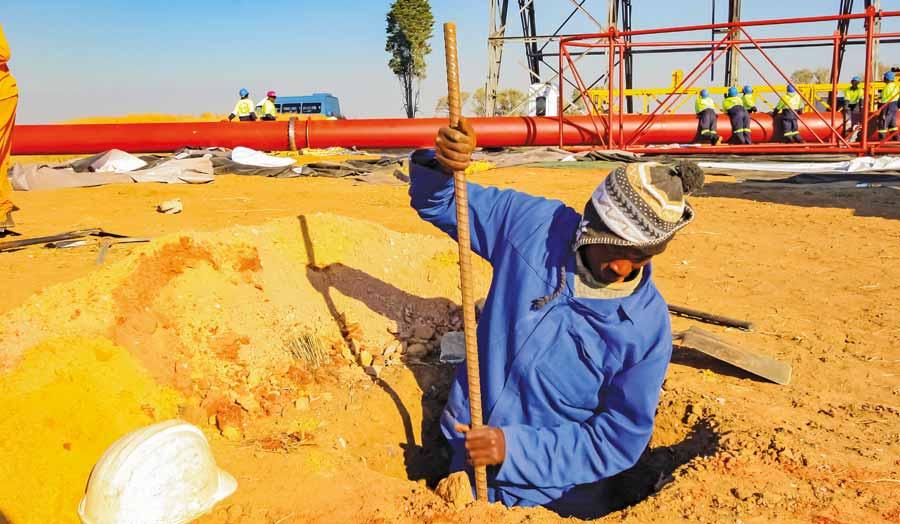
SUB-SAHARAN AFRICA
POPULATION GROWTH FUELS EQUIPMENT DEMAND
Sub-Saharan Africa received an overall score of -0.24 on GlobalData’s February 2022 Construction Project Momentum Index, which provides an assessment of the health of the construction project pipeline at all stages of development from announcement through to completion.
Every construction project in GlobalData’s database is assigned a score of between 5 and -5 based on its current progress, a score which is continually updated. These are then weighted by the value of each project to come to reach overall scores for countries, regions and sectors.
That score puts sub-Saharan Africa in last place out of 11 regions and is a decrease on its score from January 2022 (0.25) when it ranked in 10th place.
GlobalData comments: “One reason for sub-Saharan Africa’s relatively poor performance in the index is its residential sector, which scores just -0.76, the worst worldwide. Sub-Saharan Africa’s commercial and leisure sector, by contrast, has performed somewhat better, with a score of 0.55 (putting it in 5th place globally).
“Within sub-Saharan Africa, the problems
Africa: Value of projects planned by sector ($m) Sources: MEED Projects, December 2021
in the construction sector are most significant in Nigeria, which scores just -0.91 in the index. The situation in Ethiopia, however, is somewhat better with a score of 1.01.”
A December 2021-published GlobalData report states that South African construction industry output in the long-term will be supported by investments related to the 10-year US$133-billion infrastructure plan unveiled by the government in 2020. The plan comprises 276 projects in various sectors including transport, energy, housing and water. Of the total, GlobalData notes that US$62 billion will be spent over the next four years alone.
equipment sales in South Africa totalled nearly 6,000 units in 2018, according to OffHighway Research data. OHR says this was an increase from the low point of 4,613 machines in 2016.
Population growth is the primary driver of infrastructure investment in Africa
The South African construction industry is said by GlobalData to be supporting the government’s aim to produce 26% of the total electricity from renewable energy sources by 2030. To achieve this goal, the state-owned electricity public utility company, Eskom, invested US$6.6 billion on the construction of wind farms and solar plants until 2030.
The government’s intentions to increase the number of Special Economic Zones (SEZ) across the country will further support construction industry growth, says GlobalData. In October 2021, South Africa’s president, Cyril Ramaphosa, announced plans to designate the Sedibeng area into a SEZ, with the SEZ expected to attract 99 investment opportunities worth US$3 billion. Construction and surface mining
In MEED’s Africa Projects 2022 study published in December 2021, editorial director Richard Thompson cites a World Bank estimate that Africa’s economy contracted by -3.4% to US$2.36 trillion in pandemic-hit 2020. However, Thompson notes that the continent, including its huge sub-Saharan region, is set for recovery in 2022, with the IMF forecasting real GDP growth of 4%.
He continues: “Population growth is the primary driver of infrastructure investment in Africa. The continent’s population is expected to rise to about 1.35 billion in 2022, up from around 605 million in 1990. In 2021, Africa’s population expanded by 2.4% cent, according to the IMF. This is expected to continue.”
Thompson explains that Africa’s infrastructure projects are not evenly distributed across the continent. “The continents five biggest projects marketsEgypt, Nigeria, South Africa, Tanzania and Algeria - account for more than half of all projects in Africa. Several of the ‘big five’ economies are major oil and gas exporters, however, and project activity often follows the trends in global oil prices. On a regional basis, North Africa accounts for over 30% of the value of all projects in Africa, with about $711.9bn of projects planned or underway.”
MIDDLE EAST & NORTH AFRICA
VAST POTENTIAL
MEED’s March 2022-published GCC Construction 2022 report includes commentary from Richard Thompson, its editorial director, who states that “after six challenging years for the GCC (Gulf Cooperation Council) construction industry, contractors, consultants and suppliers can at last look forward to a return to growth and the prospect of rising project opportunities in 2022.”
With what MEED, a leading business intelligence company focused on the Middle East and North Africa, notes as some $1.4-trillion worth on construction and transport projects planned in the GCC that have yet to see their main contracts awarded, the pipeline of future project opportunities is said by Thompson to be “vast”, with Saudi Arabia and the UAE accounting for “nearly 85% of the GCC’s planned future projects”.
His analysis continues: “The outlook for the GCC construction industry has been transformed in 2022 by the sustained recovery in oil prices that started in the second half of 2020, and which continued through 2021 and into 2022. The increased revenues from oil exports have eased the pressure on national finances and is enabling governments to stimulate the recovery through investment in strategic infrastructure projects. At the same time, increasing consumer confidence, the return of international travel, and rising property prices are enabling renewed private investment in commercial real estate projects.”
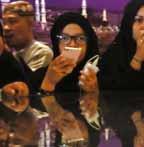
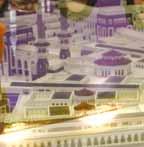
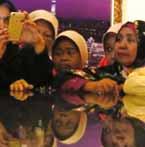
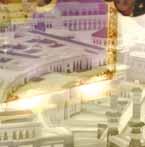
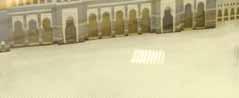
A recent GlobalData report valued the Egyptian construction market at US$64.5 billion in 2021
MEED’s Thompson notes that GCC contractors say they are now more wary of signing new contracts after being financially hurt by the pandemic in 2020 and 2021 and reports that some clients have not compensated them for delays. “When it comes to new awards, taking future risks on pandemics and viruses may be an issue for some contractors as clients do not usually accept taking such risks,” states MEED. Another concern flagged by Thompson is supply chain bottlenecks and rising costs.
“Ships and ports are all facing setbacks and this trend will continue and will inevitably affect projects that are dependent on foreign materials. Some projects will have to be delayed.”
For future growth, MEED believes much will depend on Saudi Arabia, which, says Thompson, “plans to deliver some US$1 trillion of projects as part of its Vision 2030 strategy that aims to transform the kingdom’s economy.”
Thompson says that while an uptick in construction contract awards is widely expected, the surge in tender activity and the race for delivery is creating pressure. “Many projects are coming up at the same time and this will put a strain on the supply chain and the capacity of subcontractors.”
A January 2022-published MEED report on the outlook for major projects in the Middle East and North Africa (MENA) in H1 2022 is very upbeat. As Richard Thompson notes: “The need for infrastructure and economic diversification is more vital than ever, and much of the region is wealthy and committed to ambitious development plans. This will drive investments into capital projects over the next decade, led by the
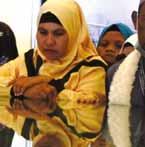
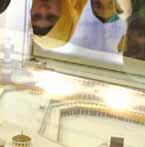
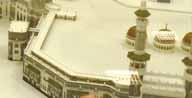

region’s biggest market, Saudi Arabia.” Thompson states that about US$800 billion of projects are underway across the MENA region, with another US$3.3 trillion at some stage of planning. Thompson notes that the GCC accounts for about two thirds of the current market, while Egypt and Iraq have big potential.
He continues: “But with finances stretched, and the battle against Covid-19 still far from over, the recovery will be slower than most would wish, and companies will face increasing pressure from clients and competitors to offer low delivery prices. There is no longer any room for waste and inefficiency.”
A recent GlobalData report valued the Egyptian construction market at US$64.5 billion in 2021. The same source said it is forecast to grow at an average annual growth rate (AAGR) of more than 10% during the 2023-2026 period. Egyptian construction last year was supported by a recovery in the country’s economic conditions and the ongoing construction of large infrastructure projects, improvement in restaurants and hotels activities, and export-oriented business. National construction output over the forecast period will be supported by investment in the development of fourth-generation cities.
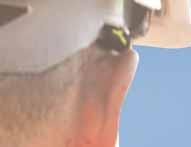
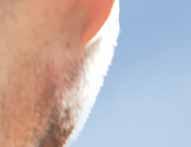
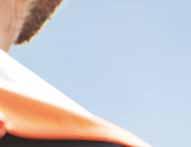
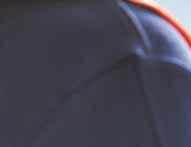
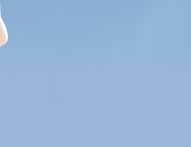
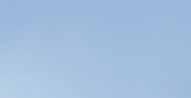

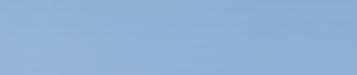
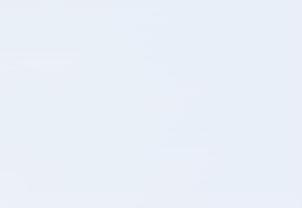
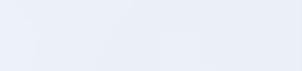
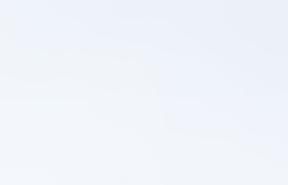
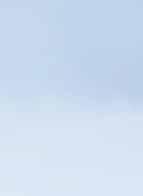

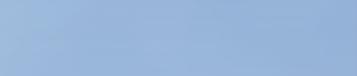
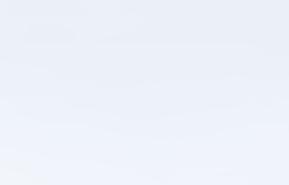
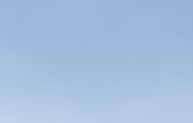
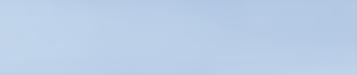
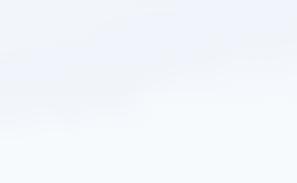
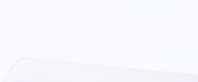
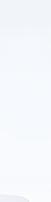

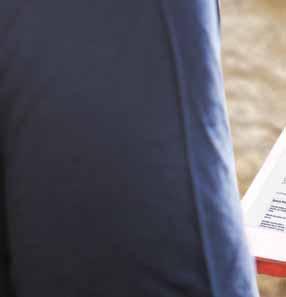






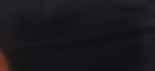



























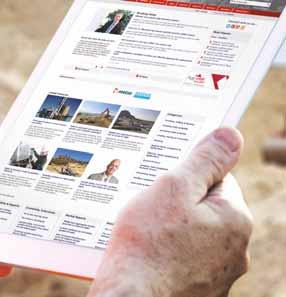
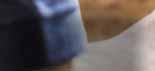




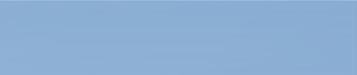
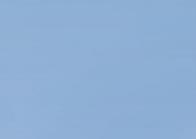
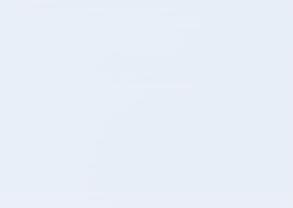

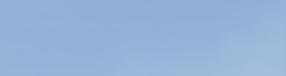

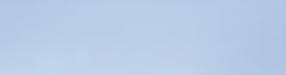
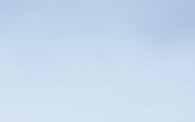
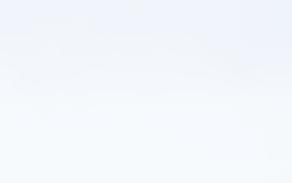

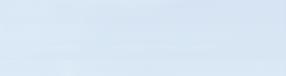
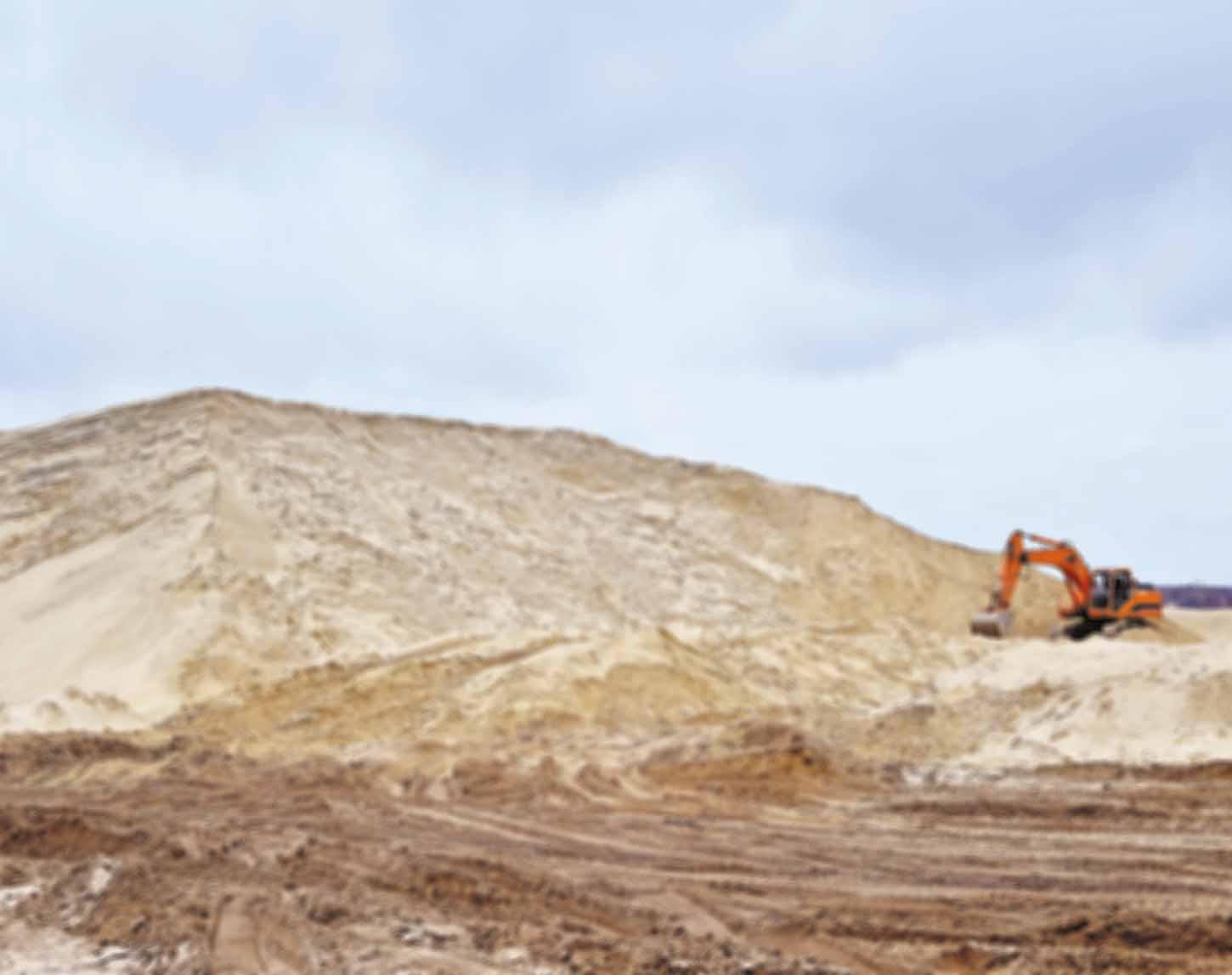


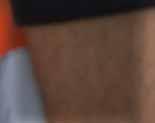














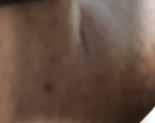







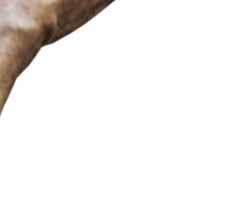


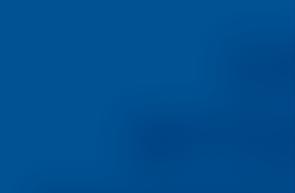
CONQUER
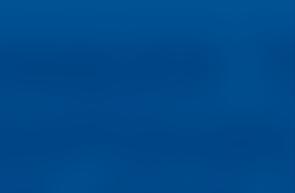
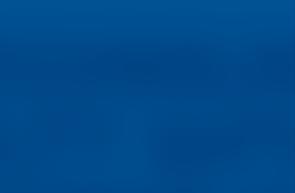
TECHNOLOGY INTEROPERABILITY
GAPS
AND MAXIMIZE YOUR WORKFLOW GAINS withDCW’s productivity-focused and digitally-connected platform
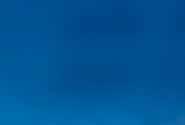
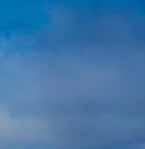
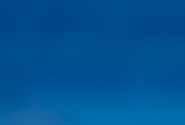
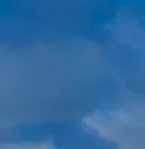
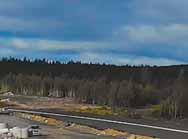

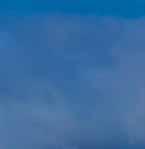
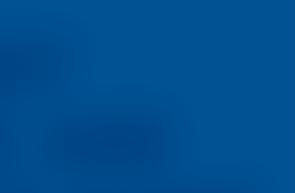
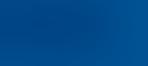
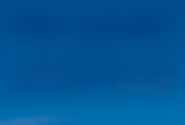
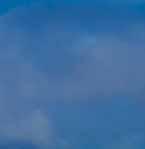
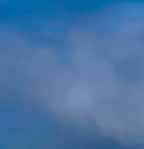
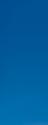
Digital Construction Works is all about the “transformative power of digital”. It is a leading integrator of construction technology services … no one else is doing what we do or how we do it … an expertise that will help to deliver your projects smoothly, on time, and on budget. DCW’s mission is to “create innovative solutions to complex challenges by understanding the pressure firms are under to increase productivity, reduce risk … and deliver reliable, efficient project results”. Are you connected?
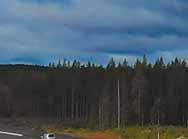
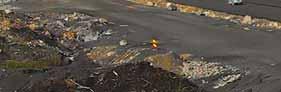
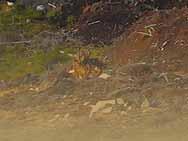



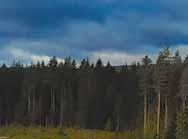
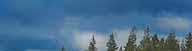
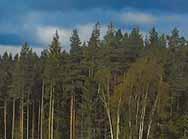
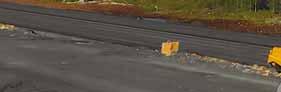
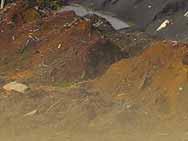
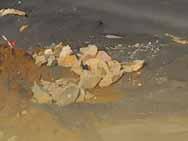

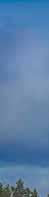
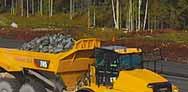

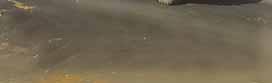
Norway Riksvei 3/25 Highway Project connecting the town of Oslo to Trondheim. Read full story: https://www.digitalconstructionworks.com/ solutions/case-studies/norways-biggest-road/
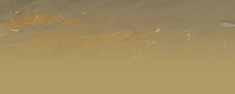
Jason Hallett is currently Chief Executive Officer of Digital Construction Works (DCW), a joint venture formed in October 2019 between Bentley Systems and Topcon Positioning Group. DCW is focused on digital integration and automation services for construction. Jason assumed the role of CEO in January 2022 after holding the position of Chief Operating Officer since the company’s inception. Prior to DCW, Jason served as Vice President of Global Software Business Development and Digital Construction at Topcon Positioning Systems, where Topcon had employed him since 2007. His career has been working in the surveying and construction industries for 34 years.
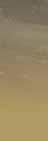

JASON HALLETT

Mr. Hallett’s primary responsibilities at Topcon included leading the MAGNET Systems business of Topcon and the Digital Construction initiatives related to the strategic digital co-venture partnership with Bentley Systems. While at Topcon, Mr. Hallett also held the position of Vice President of Global Product Management. He is a licensed California Professional Land Surveyor (since 1999), has been awarded multiple patents, holds a Certificate of Business Excellence from the Haas School of Business at U.C. Berkeley, holds a B.S. degree in Management, and holds an A.A. degree in Business.
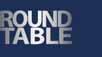
QHow would you sum up the immediate benefits of the tighter integration of construction operations that users will gain when using DCW services and technology? Tell us the key advantages that DCW brings…… and are there any early adopters you could mention that are finding success with DCW and the DCW Integrations Platform?
Jason: The primary value that we see is DCW greatly reduces the technical debt related to disconnected tools that result in manual handovers today. Our platform closes these technology gaps and automates the handovers through integrations that are tied to a digital workflow engine, which ultimately saves our clients’ time. It improves data fidelity and ensures that schedule deviations can be managed in near real-time.
As far as early adopters go, one case that we have just published online is a project we did with Mortenson Construction, where we integrated the 4D Model, and also integrated a material-tracking system called Jovix for use on their construction project to build the largest soccer stadium in the U.S. We were able to help them seamlessly integrate their applications to help manage their supply chain.
During the stadium construction, the Mortenson/Messer project team needed help solving a specific business problem around realtime visibility into critical path material fabrication, delivery, and installation. The Mortenson Sports and Entertainment Group field manager approached the Mortenson Innovator Group with a big problem, stating he had no visibility into critical path methods, particularly with steel in the supply chain. They wanted absolute
They also wanted to understand the entire supply, from fabrication, to mill order, all the way to erecting on-site. The steel structure for the construction was roughly a $30 million steel package with 6500 tons of steel and roughly 5000 pieces of steel, so it was critical to get it right. It also had to streamline the difficult task of status visualizations of building information and 4D models.
The team also found that bridging the connections with the multiple product sets in use and the corresponding integrations work that was needed was challenging. Furthermore, once established, the ongoing maintenance of those connections, was another challenge.
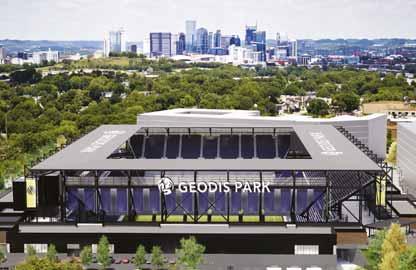
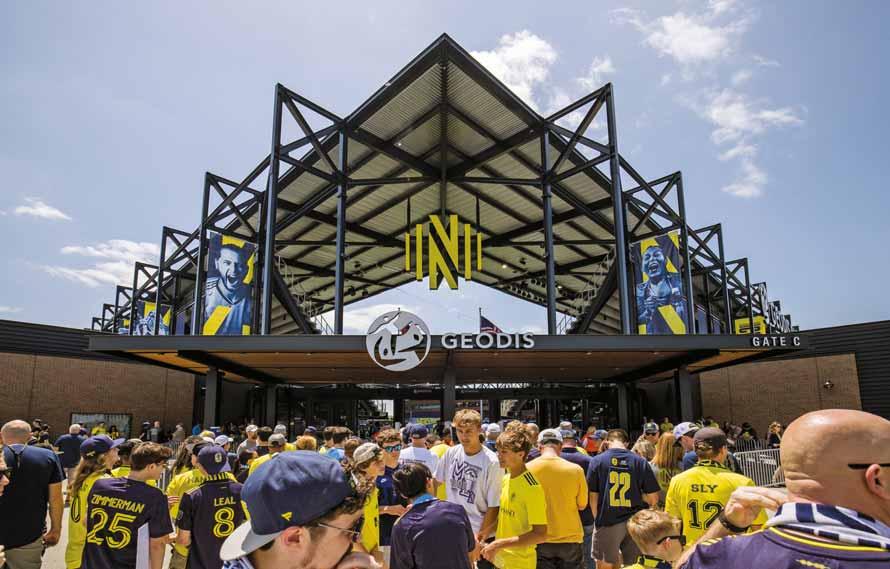
&

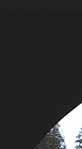

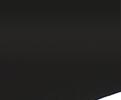
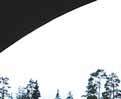
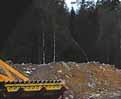

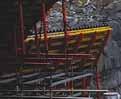
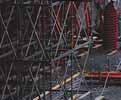
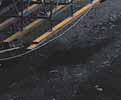
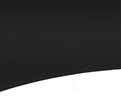
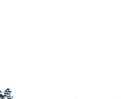
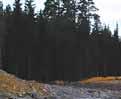
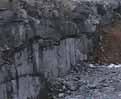
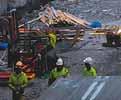
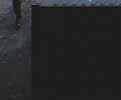
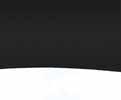
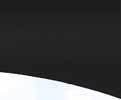
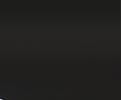
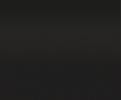
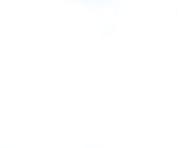
Norway Riksvei 3/25 Highway Project: one of 28 separate civil engineering structures built while connecting the town of Oslo to Trondheim. Read full story: https://www.digitalconstructionworks.com/solutions/ case-studies/norways-biggest-road/
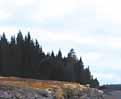
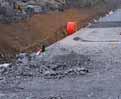

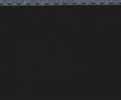
➔ We also integrated a Tekla-formatted file and it allowed us to overlay the material status information on the 4D Model. Then, with our integration with Microsoft Power BI, we can present in near real-time the status of all the materials so that they can react faster with more transparency on the project.
Construction completed early and under budget during a volatile construction market experiencing supply chain and labor issues.
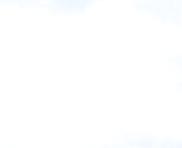

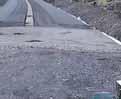
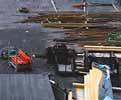
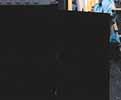
QI always like to say that the construction industry’s been going digital for about 30 years. I’ve been in the industry for about 35 years, and I was largely responsible for taking people off of field books and into digital data collection
One of the issues facing a lot of construction firms is with legacy technology. How will DCW be able to integrate with the legacy technology being used by contractors? And what level of data will clients be able to recover from these legacy technologies for the project model?
Jason: I always like to say that the construction industry’s been going digital for about 30 years. I’ve been in the industry for about 35 years, and I was largely responsible for taking people off of field books and into digital data collection. So, going digital is a never-ending process. It’s something that you have to be constantly striving for to see those efficiency gains.
What we try to do with legacy systems is to integrate with the flat files, with the data formats that are open and available out there. One thing we try to do is we actually normalise the data and tuck it into our data warehouse so that it can be accessed and aggregated with other systems that are coming onto the market all the time.
A lot of the industry is moving towards API interfaces that are open and can be connected to, but then with the legacy systems, you still don’t want to lose that information. You want to bring that information forward, so we also integrate with a lot of formats there, too.
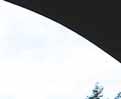
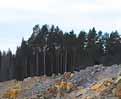
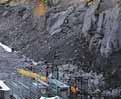

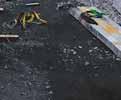
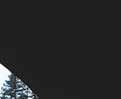
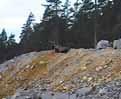
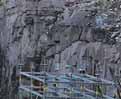
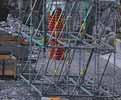
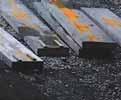
QWhat would you say are the biggest barriers to further integration of data using this technology?
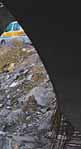
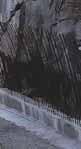
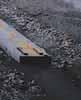
Jason: Ultimately, I think we should call the barriers just opportunities. There’s an opportunity for most of the platforms and solutions that are out there to create a more open environment. The maturity of the APIs, the ability to deliver more information and to exchange more information in real time is a huge opportunity for organizations.
In my opinion, it is what is needed in the industry to make construction take that step function forward and go more digital. I think API maturity is going to be a big, constant topic, as is, certainly, moving those legacy systems you mentioned earlier into a more modern approach, a more cloud-connected solution.
QHow will DCW facilitate progress towards a more sustainable future for construction?
Jason: This is actually something we’re tackling for clients in the Netherlands. Currently, they have instituted a regulation that addresses CO2 emissions, and they require the bidders to estimate what their carbon footprint will be on the project. If they don’t perform against this estimation and they don’t achieve it, then they will actually receive a penalty. That’s a big motivator for people to become more sustainable.
QHow straightforward is it to set up a new project? Can the DCW Integrations Platform import external data needs? And how does it reduce workloads and save time? Is there an easy security process?
Jason: The platform is really straightforward. It’s really intended to be easy to use and easy to access. We can integrate with various login credentials, for example with OIDC, or we can integrate a company’s active directory, So from the security perspective, it’s quite flexible. What we do is, log in to the DCW platform, set up the projects and then set up the integrations for the clients. We do a lot of that hands-on work. Once it’s configured and tailored to your organization, it’s very easy to add a project. Workflows can then be copied from project to project. It only takes minutes to add a project.
QDoes the DCW Platform create a consistent structure across the company? Is it an easy-to-use access platform where data from all departments will allow everyone on the project team and in the wider company to work with the same data?
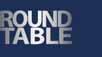
If you think about the current tool that you are using today –maybe it delivers volume estimations or something like that – but then if you can tackle that or tie that together with, say, the schedule on what you estimated, and then see what happens in the field with regard to the performance of the machines that are doing the work, then you can actually get insights out of the data and across the department from the grading manager to the estimator.
Once you’ve connected the people in the field, you can actually return the results in near real-time
Jason: The platform is essentially a data pipeline network and a data warehouse. So, what we try to encourage people to do is keep using the tools they are currently using. Then, we integrate those tools so that the data is accessible and connected to the platform so that it can be aggregated in a single dashboard and presented in new and more innovative ways for generating project insights, including project status and potential issues. Project-to-project comparison allows for gradually improving your company’s project performance and sending out better bids.
How DCW’s new Integrated Highway Workflow integrates OpenRoads Designer, SYNCHRO 4D, MAGNET, and Sitelink3D to connect the site to the office in one seamless cycle
So … it connects those sources and that information.
QDoes the DCW Platform enhance and encourage collaboration? Is information generated shared in real time with the project team? Is the team instantly updated on changes in the project and schedules, etc.? And does DCW help reduce errors or conflicts?
Jason: The platform is all about collaboration. That’s really what it’s geared towards. If you can connect the schedule or the plan, which ultimately results in tasks, you can move that data out to the field and have it delivered automatically for construction execution. Once you’ve connected the people in the field, you can actually return the results in near real-time.
I just say “near real-time” because you don’t want to have data points coming in constantly; it’s just going to be a whole bunch of noise. But if you get the data coming in that you really want to
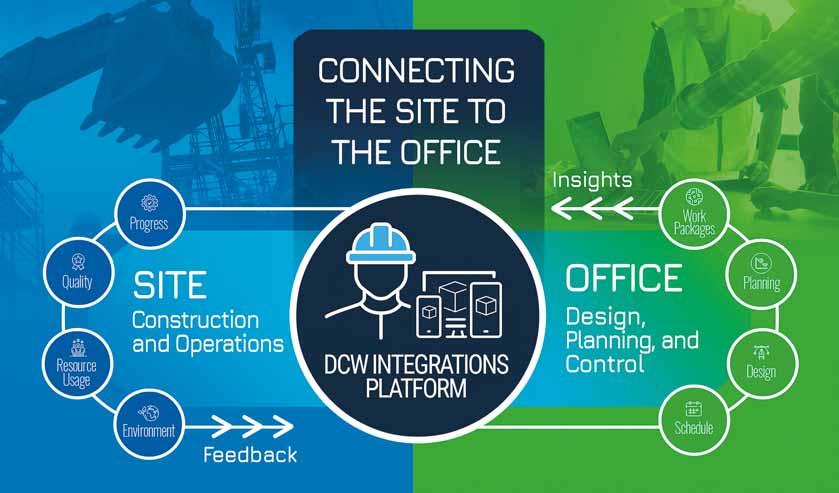


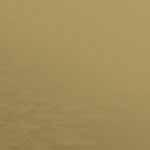
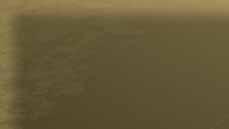

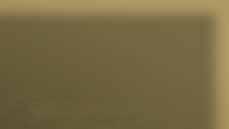
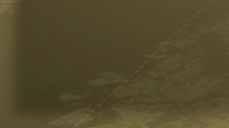

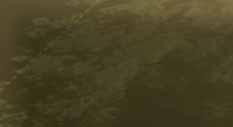
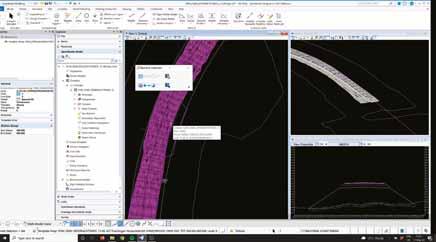
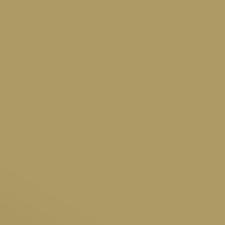

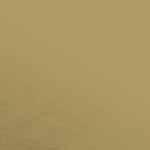
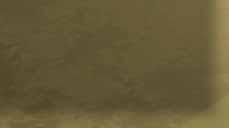
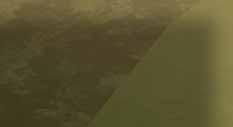
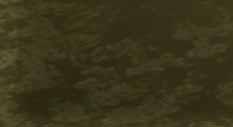
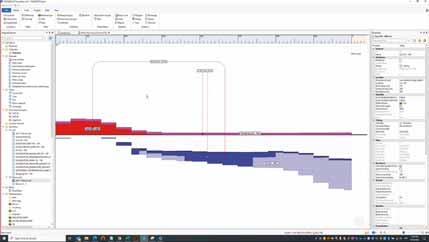
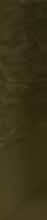
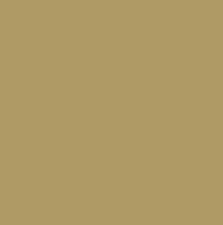
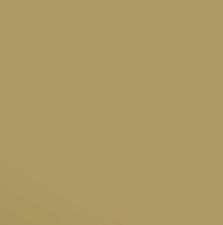
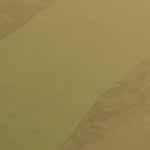
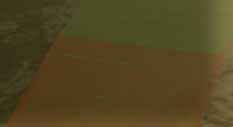
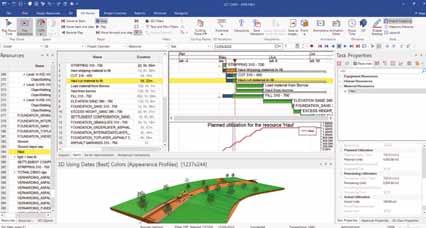
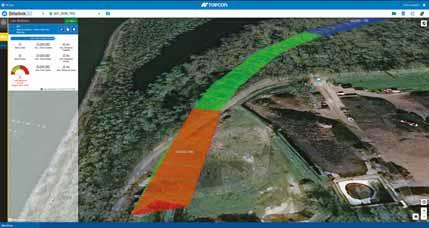
A fully Integrated Highway Workflow – connecting the job site heavy equipment and technology to the office planning, design and engineering applications and syncing the data using a DCW Insights and a Construction Power BI Connector – all within the Digital Construction Works (DCW) Integrations Platform.
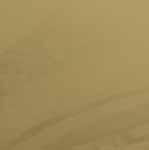
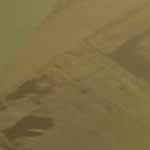
DCW not only connects different tools but automates workflows with alerts and creates centralized dashboards full of rich insights, powered by data across construction sites, to inform better decision-making.
DCW connects the job site machinery and tech with the office planning and design applications.
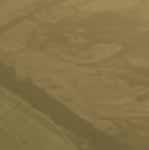

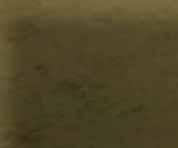
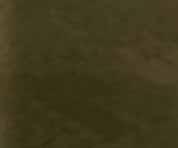
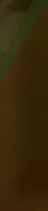
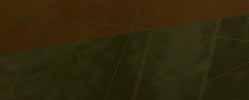
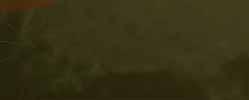
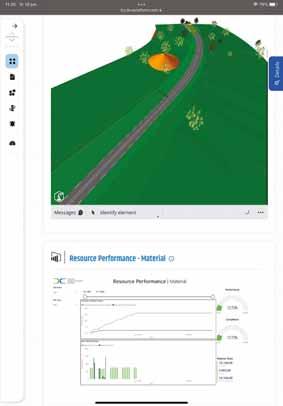

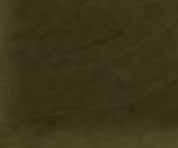
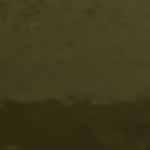
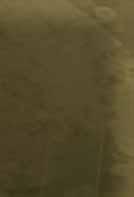
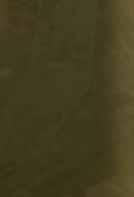
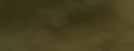
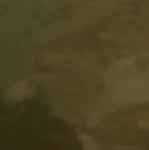
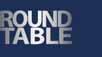
deliver, or that you are contractually required to deliver, then you deliver in near real-time, and you get results, say, in a matter of hours, versus weeks.
We had some clients tell us that sometimes the data they receive is weeks old so they can’t even address the relevant issue which they would have been able to if they had the information a lot sooner.
QHow will the DCW Integrations Platform be supported and made scalable for the future? Will there be consistent maintenance and support of DCW? Is there a roadmap for future development and how well is it designed to adapt to future technologies?
Jason: Yes, there is a roadmap. At this point, we have a pretty large backlog of things that we want to integrate with and that we’re working on for clients. We try to do our integrations based on realworld client engagements. Then, we make it sustainable and scalable. We package every integration up, almost like a product.
Most of my life has been spent around product management so I look at every integration as a little trainee product. And then I look at every workflow that we tie to the integration as another type of product. Then, when we move from, say, one project to the next, or from one client to the next, the integrations can be reused and reconfigured, if you will, to suit their unique needs.
Every construction business is unique. Even though they might use the same tools, they might use them in different ways. So, what we try to do is make the integrations stable and normalized, and then we try to tailor the deliverables, or the KPIs – the results of connecting the data – so that they suit the client that we are actually working for.
QWhat can you tell us about some of the new developments with DCW? We understand there are some new launches in the pipeline.
Jason: There’s lots of stuff in the pipeline, for sure. It’s amazing the demand we get from the industry right now. There’s a lot of new technologies cropping up all the time. One of the new technologies that came from one of our shareholders, Bentley, is the integration of OpenRoads Designer for design, SYNCHRO 4D, which is their planning tool, with Topcon’s MAGNET mass haul and Sitelink3D product. Topcon is also one of our shareholders. The combination of these applications offers a fully integrated highway design and construction workflow where all of the project data is combined within the platform where it can be analyzed and visualized into valuable project insights.
It’s interesting if you think about integrating, say, the schedule and the tasks with the machines as I described earlier. If you could do that automatically, you don’t have to do double entry. You’re not wasting a whole bunch of time. You can communicate even with subcontractors doing that work in a more efficient and automated way. So that’s one thing we’re really focused on.
And, of course, we’re focused on round-tripping the data back from that system, as well. We want to do it in a way that, for example, allows the subcontractor working for the GC to review and then approve the information they want to push back. And to do it digitally.
QIs there anything else in the pipeline?
Jason: Yes. Something else that we’ve taken on recently is we are working with Topcon’s monitoring business and with the Bentley Sensemetrics business. We’re working on integrating those solutions
so that we can start tying IOT sensors and monitoring systems to the construction ecosystem just to be able to deliver more information related to the project in near real-time, as I described before.
QYou have two primary shareholders in DCW. How easy is it for you to integrate technology from competing companies into the DCW work file?
Jason: That’s a really good question. One of the things that our shareholders decided when they started DCW was that DCW needed to go out and be an agnostic integrator in the industry. The only way we can move the industry forward is through that kind of thought leadership and around the idea that market expansion is good for everyone.
So, if we can get the market to expand and adopt more technologies, it’ll benefit everyone, including the shareholders. Honestly … we’ll integrate with anything that can be integrated.
QWhat effect do you think the pandemic has had towards driving the construction sector towards digitalization?
Jason: From what we experienced in the beginning, it was interesting because I think everything just came to a grinding halt which was pretty eye-opening, I think, for the world. Then, all of a sudden, everybody started to realise that they could do a lot more by being remotely connected if they had the right tools to engage in those tasks or those meetings, or whatever they are.
You saw a lot of new technology come on very quickly in that time. And I really do believe that there is a lot more done today digitally than even, say two years ago, as a result of the pandemic. I think people being remote is just something we’ve all accepted now. And I think it’s going to continue.
I also think that DCW is in a good spot because that’s exactly what we’re focused on – being able to do more digitally and remotely. You should be able to work with systems that are out in the field and get the information back to office without having to drive out to the site or meet face to face. It’s absolutely a trend we’ve seen … and one we believe will continue.

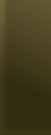
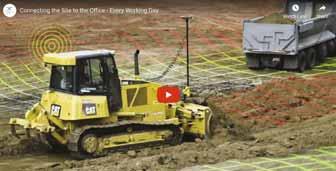


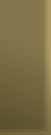
FUELLING THE FUTURE IS A GAS SAYS CUMMINS
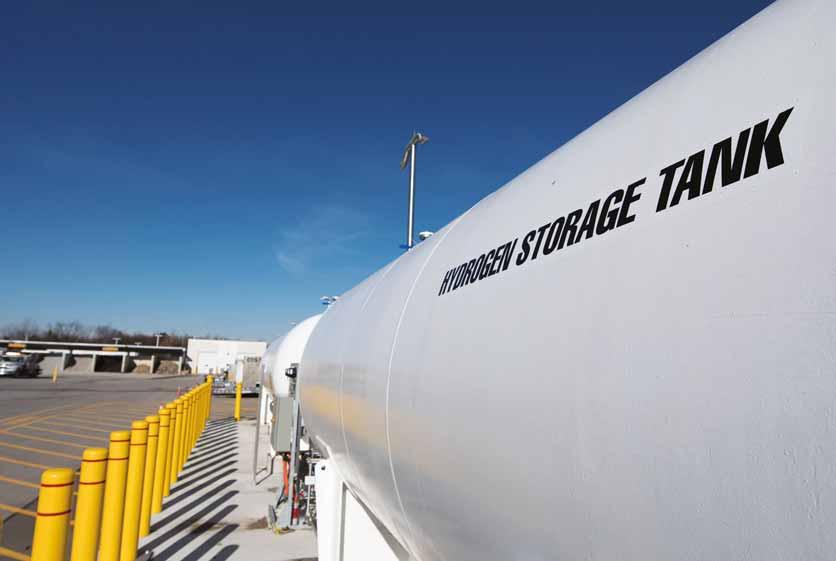
Cummins has been at the cutting edge of developing power solutions for more than a hundred years and is continuing to lead the market by developing a new range of sustainable drivetrains powered by sources such as clean diesel, natural gas, batteries, and hydrogen fuel cell electric engines. Why is the industry’s number one power player concentrating so strongly on hydrogen? Jeremy Harsin reports.
Cummins has decided that hydrogen will play a key role in the decarbonisation of the global construction equipment business and the group is focusing its attention on three key areas: the production of green hydrogen; the management and transportation of hydrogen; and the application of hydrogen in engines and fuel cells.
So, first things first. What is green hydrogen? Hydrogen as a fuel source is lightweight, easy to store, and capable of providing high energy per unit mass, with no CO2 emissions at the point of use. For hydrogen to be truly emission-free, the production of the fuel needs to be “green” … in other words, made without the direct emission of air pollutants or greenhouse gases. Without hydrogen being green, it cannot be a meaningful part of the solution as we move toward carbon neutrality.
Most hydrogen today is grey rather than green. It is produced by a process called
“steam methane reforming”, a system which uses large amounts of power (usually provided by natural gas) and creates millions of tons of carbon dioxide each year. This is clearly not very eco-friendly.
So … how is green hydrogen produced? Green hydrogen is produced using electrolysis to turn sustainable power (wind, solar, hydro) into hydrogen with zero carbon dioxide emissions. At the moment, the cost of producing green hydrogen is expensive, which limits its adoption. This cost is projected to remain above that of current solutions for at least 5-10 years.
However, it is inevitable that green initiatives instigated by corporations or governments around the world will force the move to hydrogen faster. Fleet customers operating municipal machinery or equipment at airports, distribution centres, and ports could also put pressure on manufacturers to offer hydrogen solutions as they look to reduce emissions in line with their own local
sustainability plans.
Companies like Cummins are investing in research to advance electrolyzer technology so green hydrogen can be made in a more cost-effective manner and reduce the environmental impact of hydrogen technology. An example of this is a partnership with Air Liquide and the construction of the world’s largest proton exchange membrane electrolyzer which is producing up to 8.2 tons per day of lowcarbon hydrogen in Québec, Canada.
HYDROGEN STORAGE AND SUPPLY
Hydrogen is more energy-dense compared to diesel or natural gas. One kilogram of hydrogen has the general energy equivalence of roughly 3 kg, or 1 gallon of diesel fuel. So, compared to diesel or natural gas, hydrogen will be able to power a vehicle the same distance using less fuel.
On-board storage is a critical component of hydrogen power. Hydrogen needs to be
compressed into a tight space to store enough to meet duty cycle requirements. Cummins has entered into a joint venture with NPROXX, a world leader in high-pressure hydrogen storage for both stationary and mobile applications.
Supply and infrastructure will remain a challenge. Even with the many projects currently in place to increase hydrogen refuelling, that will take time and resources to develop. Adoption of hydrogen will probably begin in markets where fuelling can be done centrally such as at home-base operations or close to large hydrogen hubs.
As the scaling up of hydrogen production, distribution, equipment, and component manufacturing continues, the costs involved are projected to decrease over the next decade for a wide range of applications, making hydrogen competitive with its internal combustion engine (ICE) counterparts.
The integration of and interaction between hydrogen fuel cells or engines, batteries, powertrain, and fuel storage will be critical to their success. Understanding and adapting the overall powertrain system will be crucial to achieve it.
HYDROGEN ENGINES
Cummins is developing hydrogen-powered combustion engines. This is following an award from the UK Government, and the group is working on 15-litre and 6.7-litre engine platforms which will provide a sustainable solution that is more aligned with current machine designs, reducing complexity for OEMs.
A hydrogen ICE fits in today’s machines, works with today’s transmissions and hydraulic systems, and integrates seamlessly into the industry’s existing service networks and practices.
End users are expected to respond positively to the potential for a hydrogen engine because of the zero-carbon fuel combined with familiar technology.
Cummins’ programme has seen testing conducted of medium-duty 6.7-litre and heavy-duty 15-litre engines. These engines will aim to achieve zero-carbon emissions, enhanced power density, and improved thermal efficiency for equipment manufacturers within common engine designs.
The next step is to match the performance capability of the powertrain to applications with high load factors and high equipment utilization, those that have the biggest challenge to find viable zero-carbon solutions in the near term.
A fuel cell is a clean energy source with the only byproducts being electricity (power), heat and water
Launching hydrogen engines will also benefit other paths to reach a zero-carbon future, such as hydrogen fuel cells. By creating a viable use case and demand for hydrogen in the near term, we can accelerate
hydrogen infrastructure build-out and increase scale production of vehicle storage tanks.
Both advances are necessary for the widespread adoption of fuel cell powertrains.
HYDROGEN FUEL CELLS
A fuel cell is an energy converter, using an electrochemical reaction to take the chemical energy stored in a fuel source and convert it to electricity. It is comprised of two electrodes and an electrolyte membrane. The electrodes are called a cathode and an anode, and they sandwich the electrolyte membrane between them.
Within this power system, a series of chemical reactions occur to separate the electrons from the fuel molecules to create energy.
Hydrogen is fed into the anode on one side while oxygen is fed into the cathode on the other. At the anode, the hydrogen fuel molecules are separated into protons and electrons that will travel different paths toward the cathode.
The electrons that are generated then go through the electrical circuit, creating the flow of electricity. The protons travel through the electrolyte to the cathode. Once at the cathode, oxygen molecules react with the
The reuse of appropriate components will drive economies of scale while also providing reliability and durability equal to diesel. Experience in spark-ignited natural gas will also be harnessed as this technology is brought to the forefront. In fact, Cummins’ next generation of agnostic engine platforms will be able to run on clean diesel, natural gas, and hydrogen.
Hydrogen combustion engines will provide a low-cost, zero-carbon solution for high load factor and high utilisation applications where battery-electric solutions cannot meet the operational requirements and fuel cells are not yet economically viable.
The key benefit of using hydrogen engines is that they minimise the impact on the machine design. The hydrogen engine slots in where the diesel would, with the main change being in fuel storage and supply.
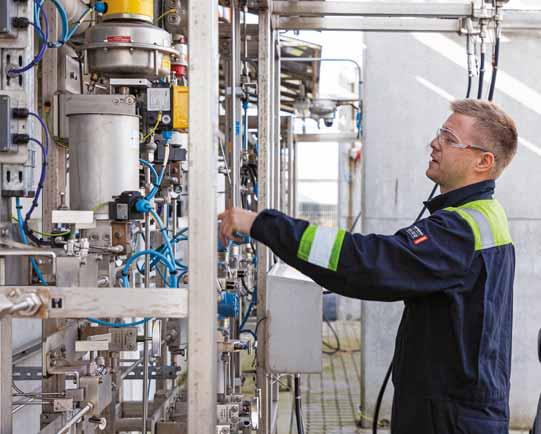

➔ electrons and with the protons to create water molecules.
A fuel cell is a clean energy source with the only byproducts being electricity (power), heat and water. A single fuel cell alone only produces a few watts of power; therefore, several fuel cells can be stacked together to create a fuel cell stack.
When combined in stacks, the fuel cells’ output can vary greatly, from just a few kilowatts of power to multi-megawatt installations.
The two main types are proton exchange membrane fuel cells and solid oxide fuel.
Proton exchange membrane (PEM) fuel cells: Also referred to as polymer electrolyte membrane fuel cells, this type of fuel cell uses a polymer electrolyte and operates at lower temperatures of around 80 degrees Celsius. PEM fuel cells are more suitable for mobile and back-up power applications due to their high-power density and quick start-stop capabilities.
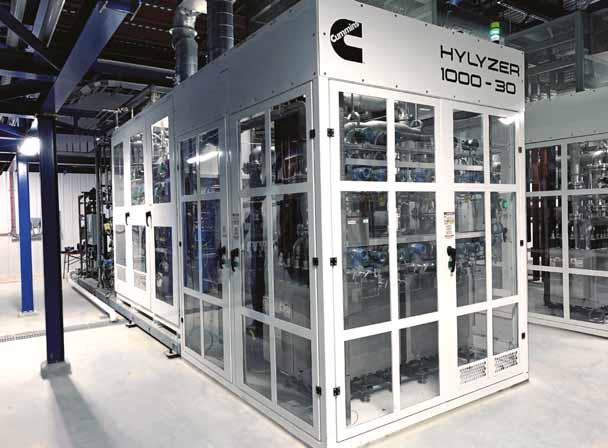
needed within construction efficiently whilst meeting zero-emission demands.
Solid oxide fuel cells (SOFCs): SOFCs use a hard, non-porous ceramic compound as their electrolyte and operate at high temperatures, as high as 1,000 degrees Celsius. This type of fuel cell is most suitable for stationary applications because it is highly efficient and fuel-flexible. In addition, waste heat may be harnessed and reused to increase the overall system efficiency.
FUEL CELLS IN OPERATION
Hydrogen fuel cell technology can offer a power solution that does the heavy work
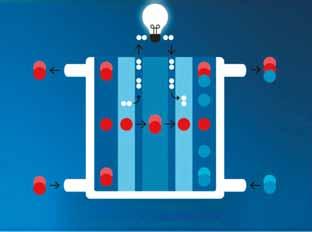
Fuel cells work by sucking in oxygen from the air to create a reaction, turning the hydrogen into electricity. The time delay for this to happen is managed by the battery. Both the battery and fuel cell feed power to the machine’s electric motor in parallel.
A fuel cell can be considered as a battery that generates its own electricity. It works alongside battery technology; ultracapacitors, lithium-ion, or lead-acid in a hybrid set-up. The battery is there for instantaneous response, providing high power for a short period until the fuel cell works.
The fuel cell sucks in oxygen from the air to create a reaction, turning the hydrogen into electricity. The time delay for this to happen is managed by the battery. Both the battery and fuel cell feed power to the machine’s electric motor in parallel.
The battery size and fuel cell depend on the duty cycle of the machine. The package needs to be matched specifically to this, as it impacts cost and weight. Engines are more flexible to duty cycle and power changes, so you can have a wide range of power from one displacement.
Installation engineers will define how these are integrated; the configuration, and refining of the interaction between fuel cells, batteries, powertrain, and fuel storage.
Understanding and adapting the overall powertrain system will be crucial going forward. This encompasses every component that converts the engine’s power into movement, any interacting systems, and how they work in the varied duty cycle requirements across different sectors.
SUITABILITY FOR OFF-HIGHWAY MACHINES
Adoption of fuel cells will be gradual over the next 10-20 years as it becomes not just environmentally but also operationally and economically viable for OEMs and operators. Cummins believes that hydrogen engines will be adopted more quickly and will help build the fuel-supply infrastructure.
Stationary power will be limited by the infrastructure of fuel. Data centres need high MW of power, so using natural gas with solid oxide fuel cells is more suitable. This is known as blue hydrogen, because it emits carbon that needs to be captured and put back into the ground.
Hydrogen makes sense for larger equipment with high utilization and energy demands due to charging infrastructure limitations and the size of batteries needed—as well as their higher cost. The long recharging times required by larger equipment can also be a deterrent.
For heavier duty cycles, fuel cells would offer more flexibility and higher machine utilisation. They are well suited for heavy loads and long work shifts with quick refuelling and no carbon dioxide emissions.
Battery-electric power will struggle to meet the duty cycle demand for all applications, particularly the larger ones. Hydrogen can offer a solution that does the work efficiently while meeting zeroemissions demands.
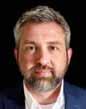
Jeremy Harsin, Cummins Global Construction Market Director.
Jeremy has been at Cummins in the OffHighway Business for 14 years, holding various positions. He has been in his current role since 2019. He is currently responsible for segment strategy development & execution, digital connectivity leadership for construction, global OEM collaboration.
Education:
BSME from University of Kentucky. MBA from Gatton College of Business and Economics.
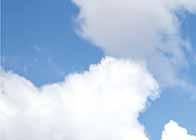
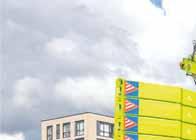
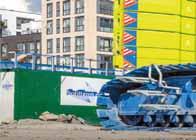
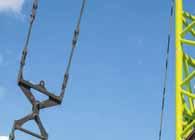
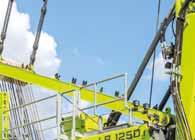
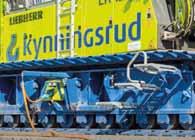

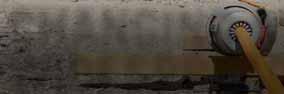

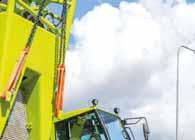
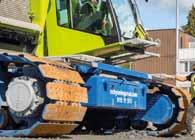
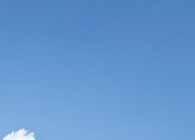
Changing infrastructure markets have boosted demand for larger heavy lift cranes.
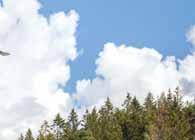
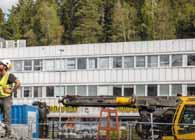
CHANGING MARKETS DRIVING WIDESPREAD INNOVATION
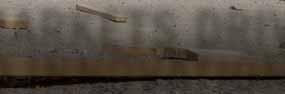

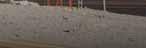

Construction heavy lift and abnormal load transport companies have been something of a cinderella sector in the past … hugely important but often overlooked. Today, this is changing fast as the sector moves centre stage. Giant pre-fabricated bridge sections and off-site construction techniques are helping contractors increase their productivity levels, but how is it all being lifted into place? Graham Anderson reports.
The inexorable march of new technologies, the continuing rise of off-site and prefabricated construction, and the growing and unavoidable pressure to improve the industry’s environmental performance are all combining to deliver sweeping changes in the crane and heavy lifting sector. Crane and trailer manufacturers, the user companies and - not all, but some - clients are responding to the challenges with a wave of unprecedented innovations. One obvious development is the trend towards seemingly ever bigger cranes.
Ton Klijn is the director of the European Association of Abnormal Road Transport and Mobile Cranes (ESTA) which has members in 27 countries. A former senior executive with global heavy lift and transport companies Mammoet and Wagenborg Nedlift, he is a leading industry voice.
“Heavy lifting and abnormal transport companies are in an era of extraordinary
change. Increasing modularisation and the drive for ever greater efficiencies has accelerated demand for bigger cranes and transports,” he says.
“At the same time, the push to improve the industry’s environmental performance has resulted in work on electric cranes, hydrogen engines and a range of developments in software and telematics. And on top of all this, there is the ongoing and important work to continually improve safety.
“As a result, manufacturers, rental companies and - sometimes - our clients have responded with a huge range of innovations that are already today transforming how the industry works, and this trend will undoubtedly continue in the years ahead.”
Klijn added that the implications of such changes go well beyond the technical performance of the equipment itself and raise major questions about the different and improved skills that companies will need in
the future … along with the training regimes that will be required to support them.
Klijn’s views were backed up by Chris Sleight, managing director of specialist analysts Off-Highway Research. At the end of last year, OHR published a detailed report into long-term trends in the global crane market - called Global Mobile Crane Fleetsin an attempt to establish the trends behind the anecdotes.
According to Sleight: “The heavy lift sector seems very strong. There has definitely been a move towards bigger cranes - our data does very much support that conclusion.
“Wind power is one of the drivers - simply, the windmills are getting higher and heavier and for that you need a bigger crane - but infrastructure and offsite construction are other important factors with the added pressure to minimise disruption, for example when working on infrastructure projects such as motorway bridge replacements.”
➔ LABOUR SHORTAGES
A senior executive in the oil and gas sector - speaking off the record - said that global labour shortages were another factor, and the problem applied to all major construction sectors, not just the one he was currently working in.
Even at a radius of 100 metres, the SGC-250 can lift 2,000 tonnes
Perhaps the most spectacular example of the trend towards bigger cranes has been the work of the huge SGC-250 during the construction of the Hinkley Point nuclear power station in the UK.
He said: “Project directors responsible for the design and execution of new plants are exploring options to offset labour on their project and a very effective way is to adopt modular construction, whereby large modules will be built in well-established construction yards and shipped by barge or vessel to site.
“The most cost-effective way to install these modules is to use SPMT [self-propelled modular trailers] to position the module direct onto the foundation. However, this is not always possible and in such instances a large mobile crane will be employed - all of which is helping drive the demand for highcapacity cranes.”
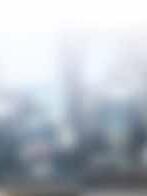
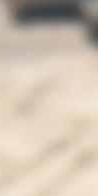
UK SITE DEMANDS THE BIGGEST CRANE IN THE WORLD
Dubbed the biggest crane in the world at its 2018 launch by its creator Sarens, the Belgian-headquartered international heavy lifting and transport company, it has a maximum load moment of 250,000 metric tonnes, allowing it to lift an astonishing 5,000 tonnes. Even at a radius of 100 metres, it can lift 2,000 tonnes.
The SGC-250 is a fully mobile ring crane with winches and cables, hook blocks, and the ability to slew 360°. It never exceeds ground pressures of 25t/m², thanks to several wheel bogies on double ring beams and spreader mats.
The crane’s main boom can be extended
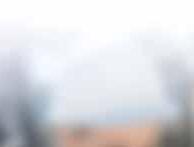
from 118m to 160m, and the jib can be extended up to 100m. This combination can provide a height of about 250m, or a radius of 275m, which Sarens says offers clients huge flexibility.
Carl Sarens, the company’s director of Technical Solutions, explained the thinking behind the crane’s development.
“This crane was inspired by the increasing trend towards modularisation and the move away from stick-built construction.
“Instead of putting a refinery together piece by piece, our clients now prefer to pre-assemble large portions, or modules, in a controlled environment and then transport and lift them into their final position.
“Because of their weight, these modules require higher lifting capacities. This trend, together with our in-house engineering expertise, led to the construction of this enormous crane.”
Sleight also points out that increased focus on safety has also helped accelerate the growth of the new generation of bigger cranes.
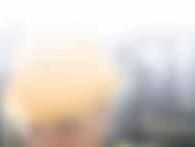

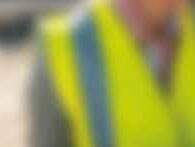
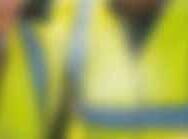
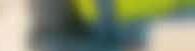

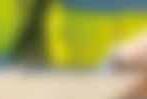
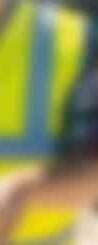
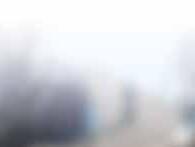
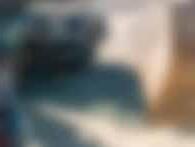
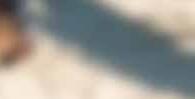

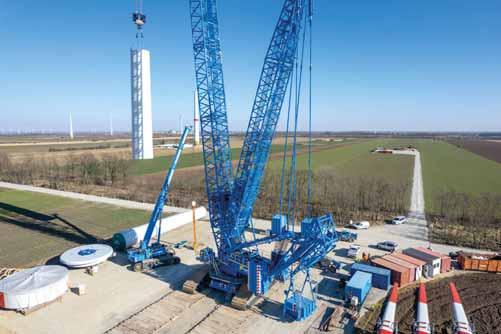
TANDEM LIFTING
“Another driver has been the long-standing practice of tandem lifting, the practice of using two or more cranes to lift a single load. Clearly this adds a level of complication and risk compared to using a single crane, as it requires synchronisation and communication between the cranes being used as well as more complicated rigging.
“Tighter regulation around this practice in some countries along with the inherent risks
has meant crane companies have tended to try to avoid employing tandem lifting where possible. To some extent this has been made more feasible by the development of much larger heavy lift cranes.”
The traditional energy and industrial sectors identified by Carl Sarens - nuclear, oil, gas, chemicals - are not the only drivers of change. New and increasingly common techniques in the infrastructure, wind-power, and housing sectors are having an impact as
well, on both the crane and heavy transport companies.
Years of underinvestment in infrastructure in even the richest economies has resulted in a huge backlog of work, with some of the most urgent and sensitive being the need to repair or replace dangerous bridges.
In the USA, the American Society of Civil Engineers has estimated that more than 9% of the country’s bridges are structurally deficient.
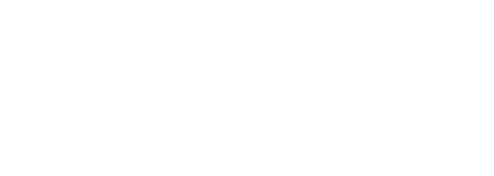

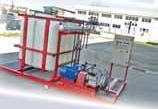



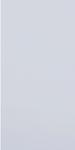

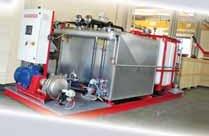


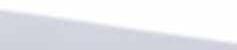
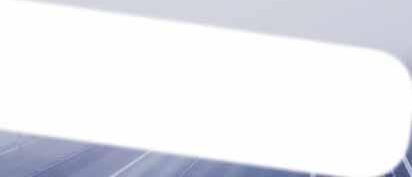
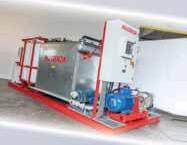
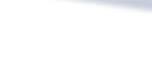


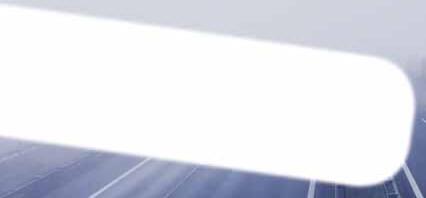

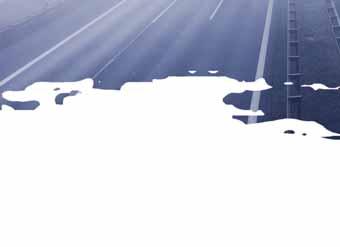
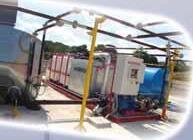





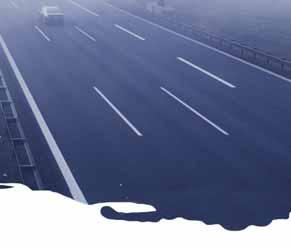


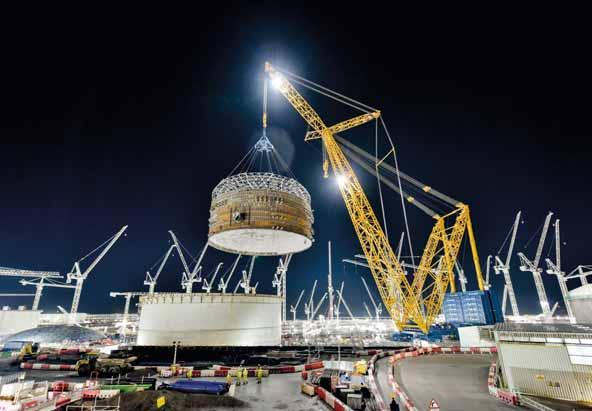
➔ ACCELERATED BRIDGE CONSTRUCTION
To address the backlog of work and minimise disruption, many organisations have increasingly turned to what is called accelerated bridge construction (ABC), a process that involves constructing large portions of bridges offsite, then moving and lifting them into position using cranes and SPMTs.
The benefits of ABC include improved construction quality, reduced traffic disruption, increased safety and in some cases, lower construction costs.
With some of the bridge decks often weighing many hundreds of tonnes, this has driven demand for cranes at the top end of the market as well as increasing the popularity of SPMTs.
Offsite construction is moving in a big way into housing as well. One of many examples was Mammoet’s work with Mattamy Homes, the largest house builder in Canada.
neck and neck with China, although he adds that “everyone expects the US to close the gap”.
ENVIRONMENTAL RULES GETTING TIGHTER
He explains: “In Europe, much innovation is being driven by tightening environmental regulations and in China by the desire to deal with industrial pollution.
“In China, the crane manufacturers have been investing heavily in electric equipment
Sarens’ SGC-250 in action during the construction of the Hinkley Point nuclear power station in the
Offsite construction is moving in a big way into housing as well
Mattamy wanted to increase productivity, reduce weather delays and cut costs and asked Mammoet - the Dutch-owned international heavy lifting and transport company - to transport and place complete 55-tonne homes that were built on an indoor assembly line.
Mammoet’s engineers came up with a plan to move the pre-assembled homes out of the plant, deliver them to their foundations and complete the process by placing them using a custom-made, computer-controlled jacking system.
As far as innovations are concerned, OHR’s Chris Sleight believes that Europe is
regulations in the world, but overall the current environmental legislation in the USA does not seem to be up to the stringent standard of the regulations in Europe.”
The drive to cut emissions is producing some eye-catching developments.
THE ELECTRIC CRANE
Sleight continues: “The development of the electric crane market is very interesting. Liebherr’s electric crawler crane is really quite
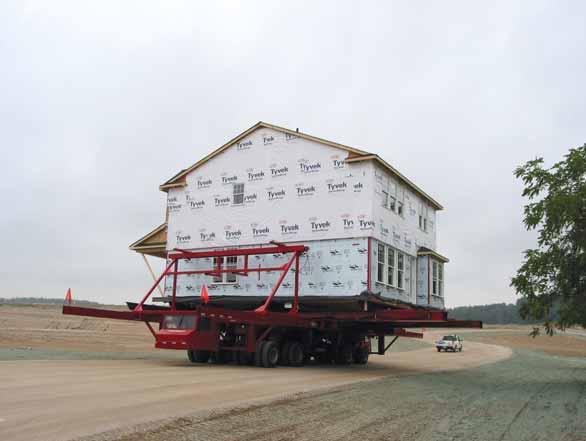
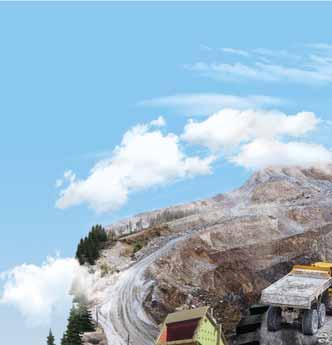
A LONG WAY TOGETHER
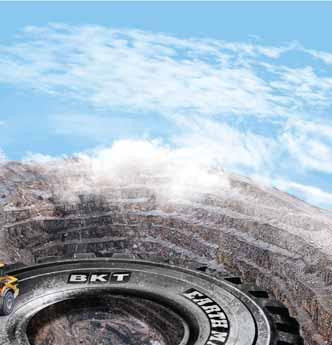
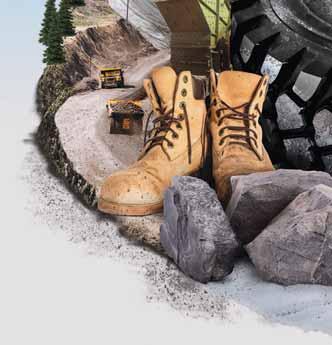
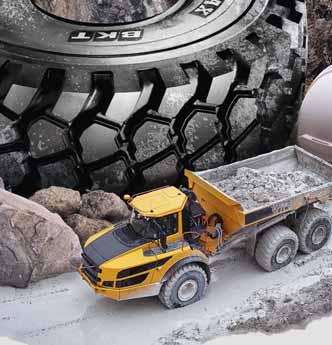
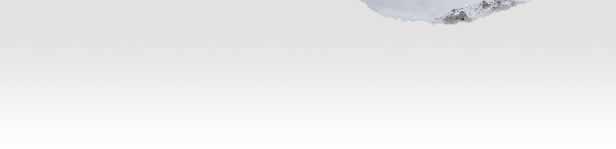
EARTHMAX SR 41
No matter how challenging your needs, EARTHMAX SR 41 is your best ally when it comes to operations that require extraordinary traction. Thanks to its All Steel radial structure and the special block pattern, EARTHMAX SR 41 provides excellent resistance against punctures and an extended service life. In addition to long working hours without downtime, the tyre ensures extraordinary comfort.
EARTHMAX SR 41 is BKT’s response to withstand the toughest operating conditions in haulage, loading and dozing applications.
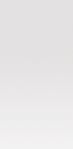
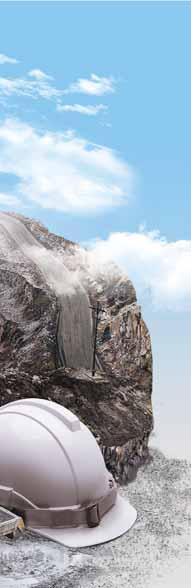
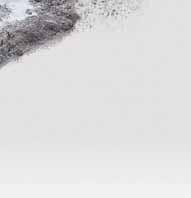
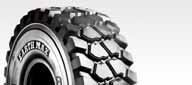


➔ Despite his enthusiasm, he cautions that batteries in the crane sector will have their limitations, both in terms of the size of the battery and the recharging support. “If you are working in a remote forest, you would have to recharge the battery from a diesel generator, so what is the point in that case?”
As for hydrogen power, Sleight believes it is realistic but is just a long way off. “There are significant and multiple barriers in the necessary infrastructure, reliable supply systems and the regulatory and safety standards. I am sure that hydrogen will come, but not yet.
“One key point about hydrogen is that its energy density is relatively low so for it to work it has to be kept at a high pressure. This raises a lot of questions about standards, regulation and safety - all issues that will need sorting out and those wheels do not usually turn very quickly.”
UNPLUGGED FROM LIEBHERR
Liebherr’s LR1250.1 Unplugged and the LR1200.1 Unplugged are the world’s first battery-powered crawler cranes.
Launched at the end of 2020, and driven by an electric engine, during operation the crane can be connected to a conventional electric supply or work without a cable, therefore “unplugged”.
The capacity of the battery is designed for a four-hour lifting operation and Liebherr insists there are “no compromises” regarding performance when compared with the diesel equivalent.
The LR1250.1 Unplugged has a maximum
“Heavy lifting and abnormal transport companies are in an era of extraordinary change”
Ton Klijn Director of the European Association of Abnormal Road Transport and Mobile Cranes
load capacity of 250 tonnes, a maximum hoist height of 148 metres and a maximum radius of 97 metres. The equivalent numbers for the LR1200.1 Unplugged are 220 tonnes, 148 metres and 103 metres.
Onshore, the size of the turbines has approached the design limit of the cranes used to erect them
Despite such notable developments in the move towards net zero, ESTA’s Ton Klijn believes industry will, for the moment, adopt short-term options, while the longer term solutions and their implications are worked out.
“For mobile cranes - in the 120-300 tonne range - the short-term option will probably be to use diesel to get the cranes to site and then battery power for the crane movements on site itself.
“Another interim solution might be to raise the use of LPG [liquified petroleum gas]; it is not completely clean, but it is a lot cleaner than diesel and moves us in the right direction until electric/battery-driven or hydrogen options are more readily available.”
He added: “Personally, I am very interested in the hydrogen combustion engine being worked on by a number of companies - I think that could well be an important part of the mix of solutions going forward.”
But finding the right technological and engineering solutions is only the first step. The next questions will be whether these new products can be manufactured and distributed on a global scale in the required numbers, whether secure alternative fuel
supply chains can be established as well as whether the necessary laws and regulations can be enacted in time.
Whatever the future holds, it is clear that the huge growth of the wind industry, both inshore and offshore, has already turbo-charged innovation and demand in the heavy lifting and transport sectors, as both the number and size of the turbines has sharply increased.
REACHING DESIGN LIMITS
Onshore, the size of the turbines has approached the design limit of the cranes used to erect them, so rental companies and manufacturers have been investigating how to respond.
In March, Chinese manufacturer XCMG claimed that its 1,000-ton (907 tonnes) crawler crane, XGC15000A, had set a new world record after completing its first singlearm wind-power hoisting operation for the Jinjiaozhou wind-power farm in Qingdao, China.
Weighing in at 118 tons (107 tonnes) the 4.5MW wind-power turbine was hoisted to a height of 170 metres, a height that the developer said better exploited wind resources but which presented installation challenges.
Other companies have been looking beyond traditional crawler crane solutions for ways to deal with the new generation of bigger wind turbines and difficult-to-access sites.
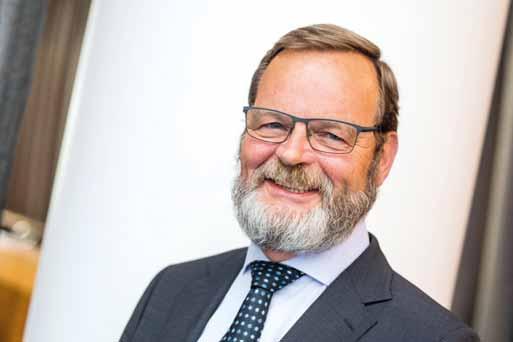
Liebherr has developed its largest tower crane model, the flat-top 1000 EC-B 125 Litronic which was specially designed for the erection of wind turbines, and can operate even in strong winds.
As it does not require oversize hauling equipment, transport is comparatively easy, an important advantage for difficult-to-access sites, and to minimise its on-site footprint, the crane can be integrated in the foundation of the wind turbine.
Meanwhile, Mammoet has developed its own tower crane, the huge LTC4,000, with a maximum hook height of 220 metres which the company believes should “future-proof” it for some time to come. Around 10 years ago turbine hub heights were 80 to 100 metres but are now often 175 metres and rising.
Mammoet’s engineers also believe that the crane will be used in other sectors where space is at a premium - notably urban infrastructure projects, petrochemical sites and some power stations.
Next year, Mammoet is scheduled to release its new WTA lifting system which assembles wind-turbine generators by attaching directly to the tower itself, using a series of clamps to self-assemble and then climb to each lift location.
It assembles tower sections, hubs and nacelles, has a capacity of 150 tonnes and the company says it can keep working in higher wind speeds than conventional crawler cranes, reducing downtime during construction and extending the build season.
TRANSPORT CHALLENGES
The growth of the wind-power industry and the increasing size of components is also impacting the trailer manufacturers, with a host of products from Tii Group, Goldhofer, Faymonville, Nooteboom and others.
Just one example among many was Nooteboom’s MWT-XL Mega Windmill Trailer. Earlier this year, Ter Linden Transport from the Netherlands was the first to receive delivery of the new trailer which consists of a 4-axle jeepdolly with lift adapter and a 7-axle self-steering dolly with lift adapter.
The trailer is designed to carry the base towers of the new generation of wind turbines that have grown from 4.5 metres in diameter a few years ago to over 6 metres today.
Like the impact of Formula 1 on the automotive industry, so the innovations that the wind-power industry has stimulated will undoubtedly affect how projects are carried
out in other sectors in future.
Wolfgang Beringer, marketing manager with Liebherr-Werk Ehingen, underlined how industry changes are creating a climate conducive to multiple innovations. The bigger the cranes become, the more clients push the boundaries of what can be lifted or transported. It is a virtuous circle.
As ESTA’s Ton Klijn has stressed, the impact of the innovations has wide-ranging implications beyond the technical capabilities of the new products, especially for training and skills development.
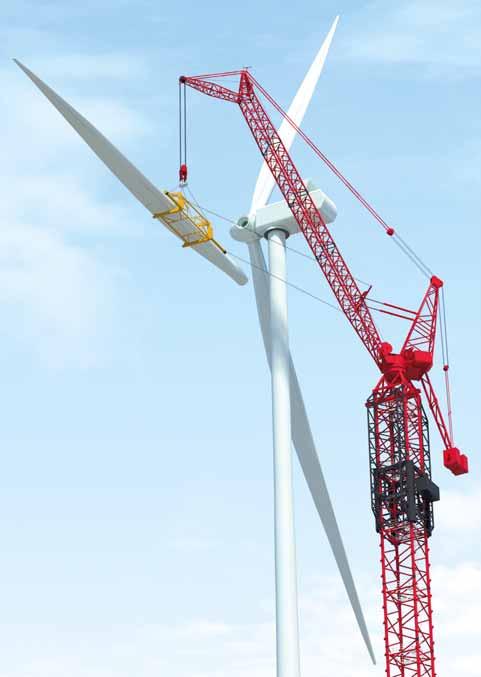
“Available crane size is limiting the weights of the components to be lifted. But if bigger cranes are available, the components grow. If the components grow, the manufacturers are forced to develop bigger cranes.
“Generally, we see that developments in construction are driving innovation. In wind energy the tower heights and generators are growing. Particularly when handling components for offshore wind turbines, the unit weights are becoming ever greater. Our answers are new crane types with greater capacities but also further developed, optimized boom and jib systems for existing models.”
The fast-changing nature of current markets also means it is essential to work closely with your customers. Beringer continues: “We are in a permanent exchange with our customers to satisfy their needs in the best possible way. In the case of planned new developments, we also approach customers specifically.
“In the case of the LR 12500-1.0 we developed the idea and concept for the new crane and then we discussed it with Sarens and other customers who are active in the upper segment of heavy-duty applications.”
ESTA has responded with the creation of its European Crane Operators Licence project, a move originally spurred on by complaints from crane manufacturers that many operators did not have the skills required for their increasingly sophisticated machinery.
And this April, ESTA has announced it is considering whether to create a similar scheme for SPMT operators to respond to the rapid rise of such equipment created as a direct result of the growth of modularisation and offsite construction.
Chris Sleight from OHR agrees with Klijn. “The changes are already having a major effect on skills and training as people need different skillsets. Indeed, skills shortages could become a real existential threat for some companies.
“They have had many years of building their products around diesel technology and have the skills and supply chains to match, and while diesel is not going away overnight, all of a sudden companies are having to build expertise in new technologies. So it is a big shift.”
Despite the challenges, the future for the heavy lift sector looks bright.
Graham Anderson is an international business journalist specialising in the construction, energy and transportation market
THE WORLD IN NUMBERS
As usual, our research team has prepared a selection of the key factors affecting the global construction outlook. To make the information easier to digest, we have split the infographics into six different sections: Global economic outlook; The ease of doing business; Global risks; Equipment trends; Infrastructure trends; Aggregates and raw materials. We hope you find the data useful.
GLOBAL ECONOMIC OUTLOOK
Source:
EASE OF DOING BUSINESS
POWER TO MAXIMIZE YOUR PRODUCTIVITY
Resilient product. Global support. The Cummins B6.7 Performance Series engine is proven in a wide range of industrial applications.
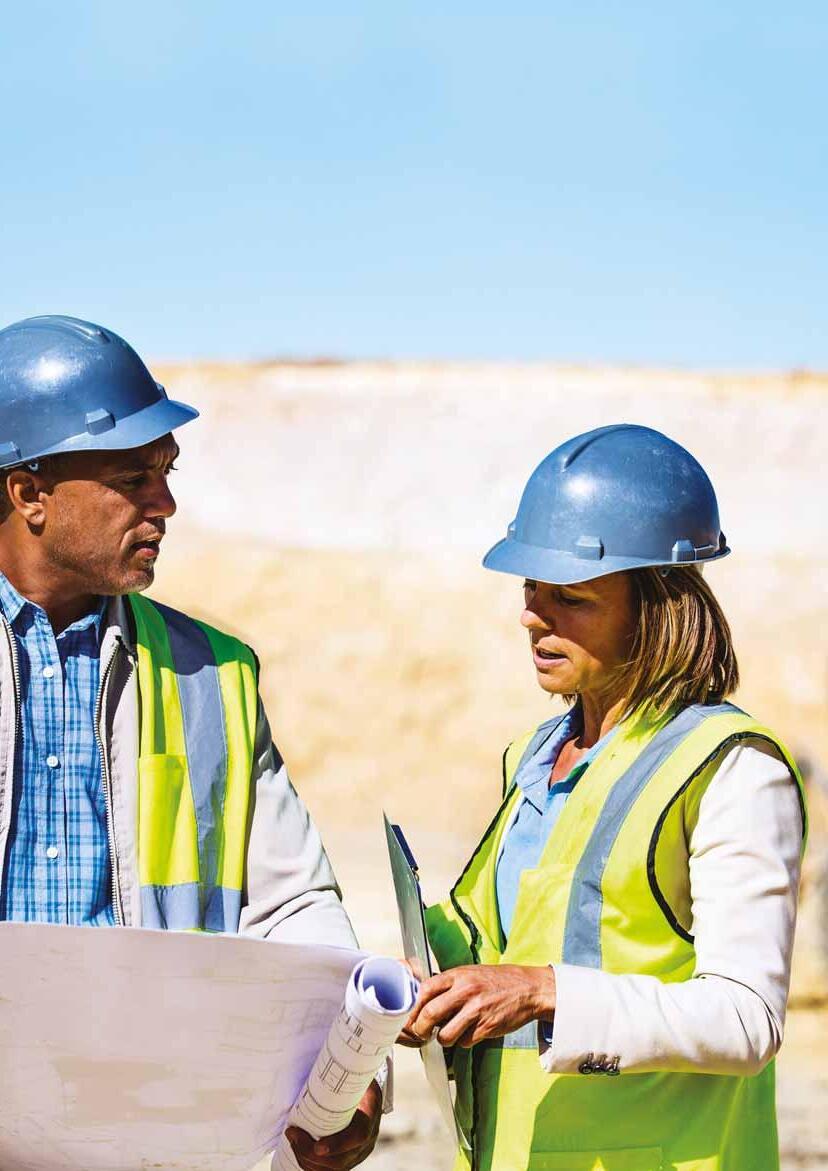
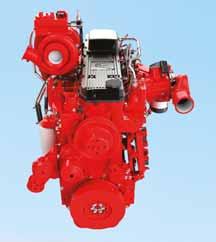
GLOBAL RISKS
“How do you feel about the outlook for the world”
EQUIPMENT TRENDS
“Identify the most severe risks on a global scale over the next 10 years”
1stClimate action failure
2ndExtreme weather
3rdBiodiversity loss
4thSocial cohesion
5thLivelihood crisis
6thInfectious diseases
7thHuman
8thNatural
9thDebt crises
10thGeoeconomic


PREMIUM CONTAINERISED SOLUTION FOR YOUR UNIQUE ASPHALT NEEDS
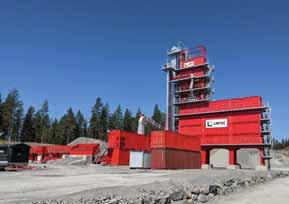
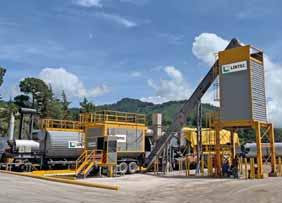
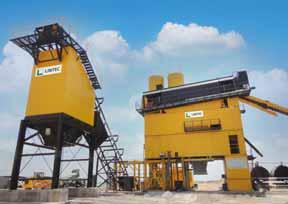
INFRASTRUCTURE TRENDS
Private investment in infrastructure projects by region, 2010-2020 (USD bn and % growth in 2020)
Source: Infrastructure Monitor 2021. Global Infrastructure
December 2021
Green and non-green private investment in infrastructure projects (3-year moving average, USD bn)
Source: Infrastructure Monitor 2021. Global Infrastructure Hub, December 2021
Cumulative investment needs by system based on current trends, 2020-2029 (All values in USD bn)
Source: A Comprehensive Assessment of America’s Infrastructure: 2021 Report Card. American Society of Civil Engineers, March 2021
AGGREGATES AND RAW MATERIALS
Source: Concrete Future: The Global Cement and Concrete Association (GCCA) 2050 Cement and Concrete Industry Roadmap for Net Zero Concrete, 12 October 2021
14.0 billion m3
2020 volume of cement globally
40%
The percentage of total concrete production for residential market
4.2 billion tonnes
2020 cement production globally
$440 billion
The global cement and concrete products market value in 2020 By 2050
9.8 billion
Estimated world’s population by 2050 68%
Percentage of population living in cities Cement and concrete around the world
Major countries in worldwide cement production in 2020 (in million metric tons)
Source: Statista, 2022
2,200
Major countries in industrial sand and gravel production worldwide 2020 (in 1,000 metric tons)
Source: Statista 2022
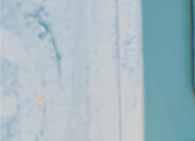
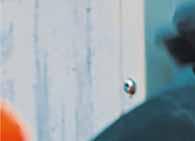
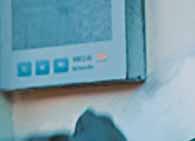

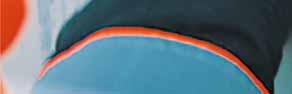
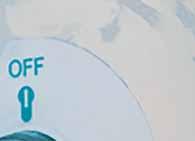
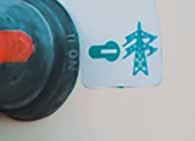
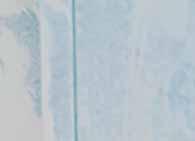
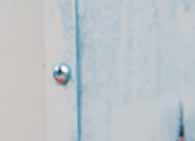
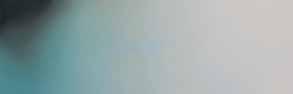
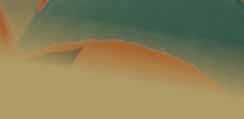
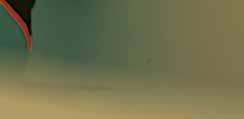
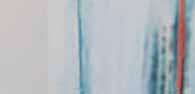
SWITCH ON NOW TO SUSTAINABLE CRUSHING AND SCREENING
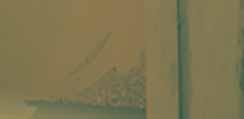
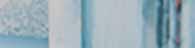
The world around us is changing fast. Everywhere you look you can see the impact of climate change, depleted natural resources, and increasing urbanisation. The demand for sustainable solutions is increasing every day as digitalisation paves the way forward. How can you make your equipment fleet as sustainable as possible? Jarmo Vuorenpää, Director, New Lokotrack Offering, Aggregates business area at Metso Outotec reports.
Globally, the trend towards more sustainable operations has been growing for years. Aggregates handling is very energy-intensive and manufacturers like Metso Outotec have played an important role in developing new products designed to help reduce the industry’s environmental impact.
Metso Outotec’s Lokotrack range, for instance, has made it possible to provide on-site mobility close to the processed raw materials, which has significantly lowered transport and hauling costs and emissions. During the last 35 years, the concept has grown with thousands of track-mounted crushers and screens now out in the field. However, this is not a new idea, and now is the time to take the next step.
PLANET POSITIVE
Metso Outotec is committed to helping the world limit global warming to +1.5 C. The company’s Planet Positive campaign
will continue to work on ideas designed to lower fuel consumption. The annual CO2 emissions of the Lokotrack global equipment fleet are approximately 20,000 tons lower today than they would have been before 2010.
Mobility and versatility are at the heart of our mobile crushers and screens. Wherever your job might take you, machines like these will provide you with the advantage of using the cleanest and most economical e-Power option. Offering two energy sourceselectricity and diesel - as a duo, is gaining more and more importance for aggregates producers and equipment manufacturers.
Through its Planet Positive efforts, Metso Outotec is a proud Net Positive partner with more than 100 technologies in its portfolio that offer improved energy, emission and water efficiency levels.
The two main energy sources - electricity and diesel – are now working as a duo and
we can equip customers with the possibility of operating hybrid machines in the remote and demanding environments in which they work.
The idea is to be as flexible as possible offering modern, low-emission, low-noise diesel engines that can be combined with the economy, silence, cleanliness, and easy maintenance of e-Power.
MORE TONS FOR YOUR MONEY
Fuel costs are high – and will stay that way. While there is global variance, it can be said that electricity is always cheaper per kW than diesel fuel. Electricity from the grid allows efficient crushing and screening operations in extreme conditions.
More sustainable solutions are needed to tackle the energy and emissions challenges that the whole industry is facing. We know that our contractors need easy-to-use, energy-efficient and high-mobility solutions.
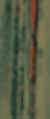
WHAT BENEFITS DO HYBRID MACHINES BRING?
Hybrid machines have either an integrated generator or a set of electric motors and pumps located inside their chassis that can be used for running the machine and other process functions. Using one does not really differ much from a diesel-driven machine. The main feature is that there is a selector that enables a choice between diesel and electricity for the selected process.
Traditionally, the Central Europe and Nordic countries have had the most demand for electrically operated mobile crushers and screens. However, more recently the demand has been increasing worldwide as more and more e-Power units are delivered.
Hybrid machines are especially interesting for those working in highly regulated areas where the local authorities have strict clean air rules.
Lokotrack actions for energy efficiency (2010-20)
New improved enginesNew Stage V emission levelsOptimized RPM
Optimized hydraulic systemLoad-sensing (LS) circuitsUp to 60% less hydraulic oil
Optimized power transmissionHydraulic drive replaced by direct belt drive for high-consuming crushers
Less energy needed for transportOptimized weight with modern FEA tools
And then there’s the cost argument. Even though there is not much of a difference in the actual usage of the machines, choosing hybrid or e-Power has clear advantages in operating costs. The possibility of switching between e-Power and diesel is especially valuable for those who operate in urban areas or otherwise in circumstances that are regulated in terms of noise and emissions.
Hybrid machines are especially interesting for those working in highly regulated areas where the local authorities have strict clean air rules.
Depending on how the electricity is generated, the
hybrid solution can reduce both noise and emissions and help meet the requirements of a certain contract. Reduced emissions also have a positive impact on the working environment for the personnel on the site.
In cases where there is a combination of several diesel-electric units operating together, it could be possible to run an e-Power mobile screen from another machine. This means replacing two diesel engines with one, further reducing the operating costs.
As the savings come principally from attaching the unit to the electric grid, or

to something like another Lokotrack machine via a cable, there is obviously some reduction in the mobility and independence of the two linked machines. However, as the e-Power version has both diesel and electricity always available, the user can select which one to use at any time according to their needs.
As a leading equipment manufacturer, we like to keep the design principles simple. We try to optimise operating costs, capacities, and end-product quality levels. Consideration is always given to the total fuel consumption, including the engine and driveline technologies, but also to other factors, such as the unit transportation weight and the engine stand-by function. Additionally, the volumes of hydraulic oil and lubricant have been reduced by more than half to further ease the environmental burden. Based on Metso Outotec’s data, a Lokotrack unit uses as much as 80% less oils compared to previous models and to many other brands on the market. Naturally, the hybrid driveline reduces the need for oils and lubricants even further.
A diesel and hybrid offering complete each other; in remote locations where the power grid is not available, a diesel driveline is still the only viable solution. But, behind the megatrends, there are always individuals with their own needs and motivations. The reasoning in each customer or business case may vary, but the outcome is clear – we all need to think hybrid.
EFFICIENCY IS THE KEY




The future looks bright. The future is harmonised design matched to advanced digital solutions.












of the consumed energy.
Optimising the crushing and screening process is therefore the key to a more sustainable, CO2-free future. And, just to be as efficient as possible, providing solutions that utilise energy without losing it as heat is another essential variable to consider.


one common architecture throughout the range. This will allow scalable solutions that can be seamlessly combined and adapted for different applications and capacities.
Some of the hybrid benefits are obvious – such as less pollution and fewer service points. But efficiency comes from more than one factor. For instance, plug-in units have way better operational efficiency of up to 95%. What is more, a Lokotrack train efficiency in diesel-electric operation may increase if a single crusher can provide enough power with its generator to drive another unit as well, such as a screen. This maximises the utilisation of the diesel generator and saves fuel. With the flexibility of electric use, the total process flow control and equipment efficiency can be taken to a completely different level.
For example, the energy consumption of a Lokotrack mobile crusher is dictated by its crusher unit, because the crushing process usually uses roughly two-thirds
Things never stand still, of course, and we are now developing a totally new, complete range of electrically-driven, track-mounted crushers and screens. This new Lokotrack range will be built on a unique platform that Metso Outotec has been developing since 2020 with a total R&D (research and development) investment of €20 million at the group’s technology centre in Tampere, Finland.
Things are going well too. The platform concept is in place and we are now entering the design phase of the first new products. This next-generation Lokotrack range will use easy-to-use diesel-electric equipment and offer customers the possibility to run track-mounted machines from an integrated genset or an external power source. The plan is to lower operational costs and allow access to renewable energy.
The new platform will enable a faster and more agile way to develop new products and reduce the number of components by using
The future looks bright. The future is harmonised design matched to advanced digital solutions. Manufacturers like Metso Outotec are determined to support its customers throughout the entire equipment lifecycle. More and more new innovations related to e-Power are expected in the coming years, so stay tuned.
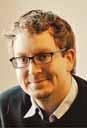
Jarmo Vuorenpää, has more than 14 years of experience in mobile crushing and screening equipment and is based in Tampere, Finland. In his current role as Director of the new Lokotrack
Offering at Metso Outotec, he has an important part in developing the future of track-mounted crushers and screens. During his career, Jarmo has visited aggregates customers from all around the world, which gives him a good perspective on the various needs and challenges of the industry. His target is to support customers in finding the best solutions for their business. Jarmo has a M.Sc. in Industrial Management from the Tampere University of Technology.
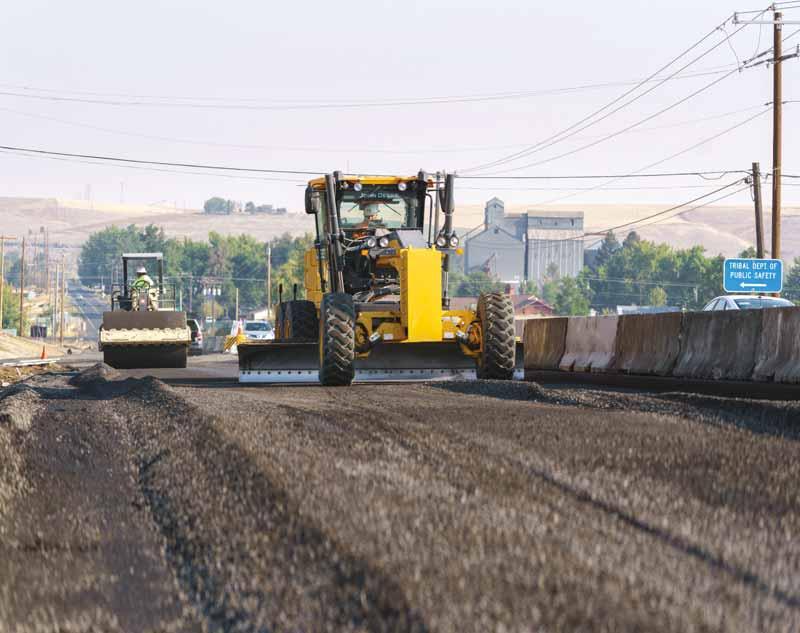
THE HAVES AND THE HAVE-NOTS … AND NOT EVERYONE WILL SURVIVE
chain complications are more than an inconvenience to the manufacturing industr y. navigating the has never been more essential to the financial “haves
Supply chain complications are more than just an inconvenience to the construction equipment manufacturing industry. Successfully navigating the supply chain has never been more essential to the financial health of our industry and the difficulties involved are creating a world of “haves and have-nots”. Will your business survive? Pete Kennedy reports.
Pete reports.
America is facing a supply chain in crisis. “The strong will continue to get stronger and take market share because they will have product when the competition doesn’t … and the weak will continue to get weaker,” says Lisa Anderson, president of California-based LMA Consulting Group. “There will be no middle ground.”
And part of the problem has been its past successes. The supply chain had become so efficient that it had no wiggle room when trouble hit, said Jake Dean, director of the Grainger Center for Supply Chain Management at the University of Wisconsin-Madison in the U.S.
“If you consider the global supply chain – all the trucks, factories and distribution centres – there isn’t a huge amount of excess built into that system,” Dean said.
There was no reason for
excess capacity. “Until 2020, demand was easy to predict,” he said.
When the coronavirus struck in March 2020, demand for consumer goods went way
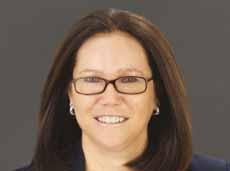
“There will be no middle ground.”
Lisa Anderson, president of California-based LMA Consulting Group
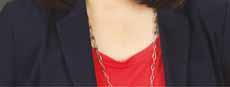
up – as the demand for services plummeted. “As demand shifted for goods, we put more in the giant supply chain network than it was able to handle,” Dean said. “Some stuff makes it into the pipeline, some doesn’t. It clogged things up.”
The components and materials that did make their way into the supply chain were random, which led to manufacturing production problems. Finished goods were harder to come by, sometimes because of a single missing part. “A product that is 97 per cent finished isn’t finished,” Dean said.
Chris Perkins, managing director at Ammann America, said governmental efforts to improve economies didn’t help supply chain difficulties. “Covid disrupted all the supply chains, and then governments that put in money to boost the economy created a peak in demand,” he said. “The whole system is fractured, and then you put all this weight on it.”
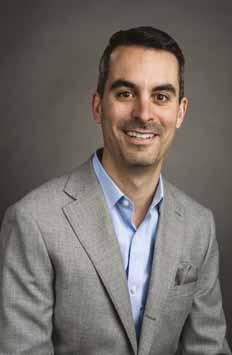
➔ THE IMPACT ON MANUFACTURERS
contracts, then you have built all these factories and you won’t be able to use that capacity,” Dean said. In addition, the necessary materials are often unavailable to feed the existing foundries and factories – let alone new facilities.
“Until 2020, demand was easy to predict,”
The general rule, according to Dean, is that companies are “pulling forward” future plans. If they planned to expand capacity in a few years, they might well do it now. “But we don’t have a lot of companies that are saying, ‘We didn’t plan to build a factory, but now we are.’”
Jake Dean, director of the Grainger Center for Supply Chain Management at the University of WisconsinMadison in the U.S.
Quarterly financial reports from large, publicly held construction equipment manufacturers focus a great deal on supply chain issues – an indication of the seriousness of the matter. The topic also dominates question-and-answer sessions with leaders of these companies.
One stock analyst recently asked Terex Corp. leaders, “Is it still a seven-day-a-week frenzy kind of dynamic, or has any of it normalised a bit?”
The response from the global manufacturer: “The supply chain environment is still incredibly dynamic … On any given day, we literally have hundreds of parts that are late or not where they need to be in our facilities around the world. … It’s disruptive every single day.”
RESILIENCE
Manufacturers have rethought supply chain priorities. There is now more talk about resiliency than cost. They will pay a bit more to ensure what they need is there when they need it.
“They want a supplier who, for example, makes a part in three regions of the world so there are options if something goes wrong in one location,” Dean said.
Adding capacity – more ships, trucks, trains and warehouses – improves resiliency. But that costs money, too. All parties are hesitant to add capacity that they need in the short term but will be redundant in the relatively near future.
The same rule applies to building factories to catch up with demand. “If global demand
SOURCING
Many believe the global economy has become too reliant on specific regions, particularly Asia. This has been highlighted by the impact of the pandemic, including the closing of many manufacturing facilities in China.
Dean sees a movement away from this reliance, though he believes it is somewhat separate from any pandemic-related issues.
“The supply chain became global over the last 30 years based on increased technology and declining barriers to trade, and an expansion in global demand (for products),” he said. “A winner for a lot of that was Asia. They were cheaper in terms of labour, and the supply chain was sophisticated. But some of those assumptions aren’t true anymore.”
Labour costs in Asia have increased, and nothing is as predictable as it was. This means businesses prefer to have some operations closer to home, be it local or even regional.
“Maybe it makes sense to build in China for Asia, and to build closer to home, too,” Dean said. For example, U.S. businesses might move some manufacturing from China to Mexico.
“The manufacturers don’t want everything in one particular location,” he said. “Then, if something goes wrong there, it impacts the rest of the world.”
Bernd Holz, executive vice president of Machines at Ammann, said sourcing changes will continue. “I believe that the OEMs in Europe will do more sourcing in Europe, and stop buying from India and China,” he said.
Ammann, a global manufacturer of roadbuilding equipment based in Switzerland, has started dual sourcing for many parts. In some cases, that is easier said than done.
“Sometimes the alternatives aren’t well accepted elsewhere,” Holz said. For example, end users often have opinions when it comes to engines. Simply swapping out one engine for another doesn’t always satisfy customers.
The sourcing changes are lasting and part of an overall transformation of the supply chain that includes companies “reshoring/ nearshoring, increasing control, re-evaluating
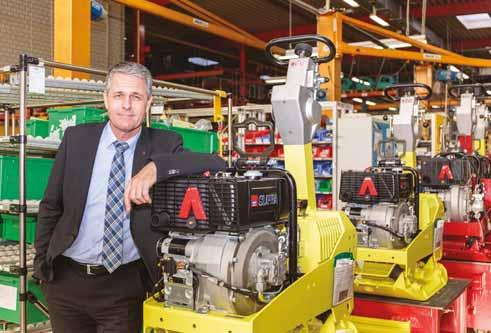
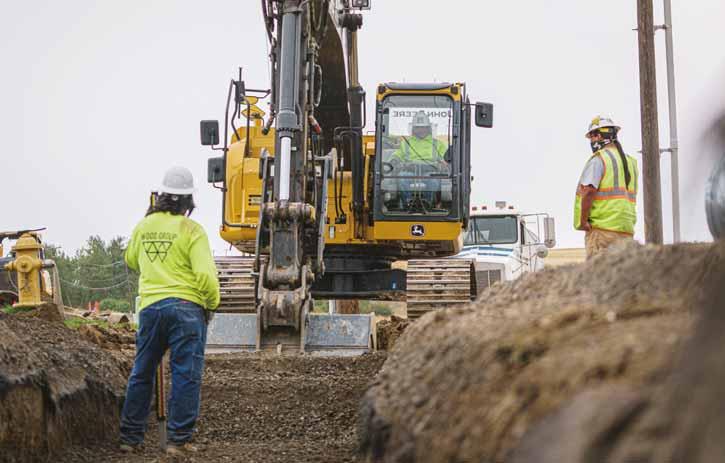
their supply base as well as their strategic inventory and capacity reserves,” according to Anderson, with LMA Consulting Group.
In at least one instance, a manufacturer is finding new sources and also helping suppliers solve labour challenges. “Our supply management teams are working tirelessly on mitigation actions such as multisourcing, additional investments in supplier tooling, and even in some cases, helping our suppliers with supplemental John Deere labour,” chairman and CEO John C. May recently told Deere & Company investors.
SEMICONDUCTORS
Manufacturers continue to suffer from a shortage in semiconductors.
“In a recent survey of equipment manufacturers, 80% cited an inability to access intermediate components, including semiconductors, as a major bottleneck to production,” said Alexander Russ, senior advisor of Global Public Policy for the Association of Equipment Manufacturers, a North-America-based trade group.
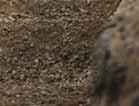
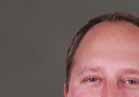
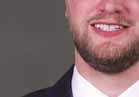
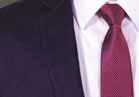
“In a recent survey of equipment manufacturers, 80% cited an inability to access intermediate components, including semiconductors, as a major bottleneck to production”
Alexander Russ, senior advisor of Global Public Policy for the Association of Equipment Manufacturers
Semiconductor manufacturing is one industry where added capacity can be justified, said Dean, of the University of
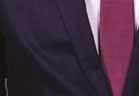
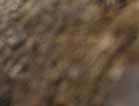
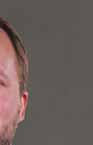
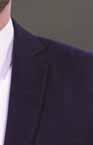

Wisconsin-Madison.
“Throughout the world, demand for products that require semiconductors is going nowhere but up, so it makes sense to add capacity there,” he said.
The demand will only increase. There are now 1,500 to 2,000 semiconductors in
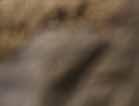
The new philosophy is just-in-case, where there are enough components and resources on hand to keep production moving
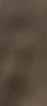
the average automobile, Dean said. “As cars become more electric, they require more semiconductors.” And of course the same can be said about construction machinery and the increased use of electric drives.
Adding semiconductor capacity is easier said than done; there are no quick solutions.
“It takes years to get those facilities started,” Dean said. Specialised machinery must be purchased, assembled and delivered. Ongoing natural resources are required as well. Yet the investments are sound given the future demand.
“Electric storage is another industry where added capacity makes sense,” Dean said.
Ukraine provides much of the world’s neon, which is used to manufacture semiconductors. Plants in Odessa and Mariupol that produced about half of the global supply of neon have been shut down, reported The Financial Times, based in London. Reserves had been established to ensure ongoing chip production, but the longer the conflict, the more shortages could result, according to a report from cable business news channel CNBC.
JUST-IN-TIME
The just-in-time days are over, or at least on a long pause. “Just-in-time, in the popular sense that you run so tight that you know with certainty you can get what you need –that’s done for now,” Dean said.
The new philosophy is just-in-case, where there are enough components and resources on hand to keep production moving.
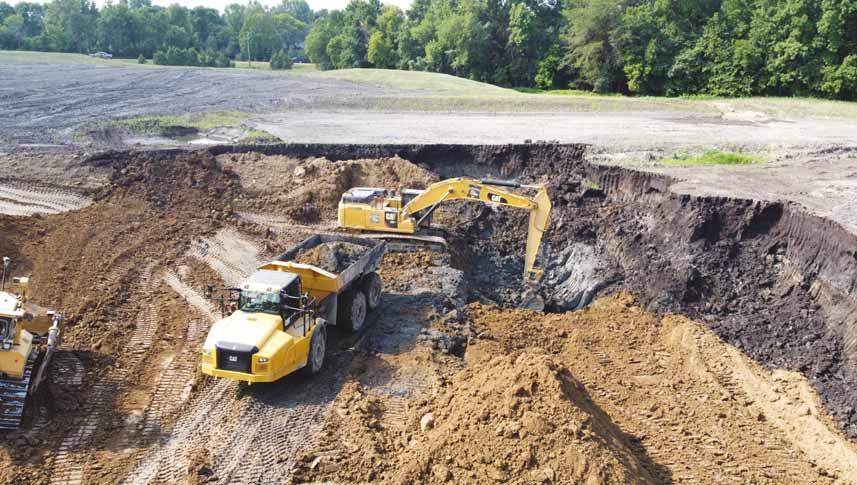
manufacturers, particularly those with decent margins. “Wouldn’t you rather spend a bit on warehousing and other expansions than to not move profitable products?” he asked.
PRICING
Manufacturers are seeing price spikes for some components. They are, of course, passed onto OEM customers.
“From a competitive standpoint, the good thing is all the other OEMs are sitting in the same boat,” Holz said. “Everyone has to increase prices.”
He does expect prices to steady – but not return to previous levels. “I believe in a year or two, the prices will stay where they are. Hopefully, some logistics costs will be reduced.”
Perkins, also of Ammann, said his transport costs per shipping container have doubled, and in some cases nearly tripled. “I’m hoping there is some correction in the transport costs, but I don’t believe they’ll go all the way back.”
Businesses with the most resources are paying premiums to get their materials, Dean said. Those costs are passed onto consumers – who are willing to pay more to get what they need.
“The inflationary period we are in is not a surprise given the environment we’re in,” he said.
WHERE WE ARE
Manufacturers say they are overcoming the challenges, though they are not seeing supply
some time.
A John Deere spokesperson echoed the thoughts of most manufacturers when offering this statement: “While orders for our products remain high, we anticipate the supply chain challenges impacting our industry will continue through the remainder of 2022. We continue to work with our supply partners to solve issues as they arise. Through these collective efforts we are getting products into our customers’ hands as quickly as possible.”
John Deere’s CEO told investors: “Our guidance does reflect order restrictions where our supply base has constrained our ability to produce. In fact, fiscal year 2022 will be the second year in a row in which the industry demand has outstripped supply.”
investors that the “external environment is undergoing intense change and uncertainty is rising.” The company’s leadership pointed to growing geopolitical risks, such as Ukraine;
increase its ability to address contingencies
2023 are adding up. Ammann is in a similar situation. “Customers realised there are long lead times, so they started ordering earlier,”
Manufacturers referenced in this report don’t expect the problems to improve during 2022.
“normalise to some extent,” which is starting to happen, Dean said. Yet a huge logjam still must move through the global supply chain. “It’s going to take a while for that to happen –all of this year and into next year,” Dean said.
That assumes there is not another pandemic or further global geopolitical events – not that the events being faced aren’t significant enough.
“We have entered a new time period of volatility and uncertainty, and so the only companies that will be successful will take control of their supply chain, instead of waiting for the global supply chain to realign,” Anderson said.
Those who take charge will emerge from the chaos stronger than ever. “There will be more opportunity in the next few years than there has ever been before, except for the time period following the Great Depression,” she said.
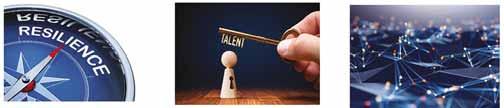
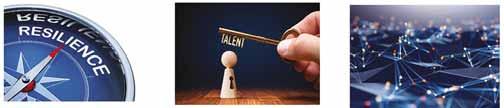
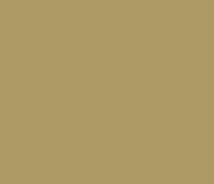
Just a month after his January 2021 inauguration President Joe Biden took the bull by the horns and set out a comprehensive plan and timetable “to strengthen the resilience of America’s supply chains”, spurred on by myriad problems identified during the Covid-19 pandemic and the ongoing trade wars with China.
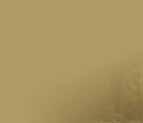
Biden made it clear from the start he expected an interagency process in which government departments would work collaboratively and consult with a range of external stakeholders from academia and the private sector to trade unions and local communities. As requested in the initial Executive Order 14017- America’s Supply Chains (24/2/21), phaseone departmental assessments of supply chain vulnerabilities across four key product areas were published in June 2021 as part of the 100-Day Supply Chain Review. These were identified as: semiconductors, largecapacity batteries, critical minerals and materials, and pharmaceutical and active pharmaceutical ingredients.
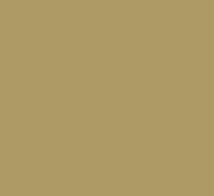
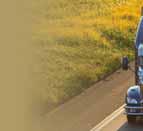
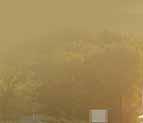
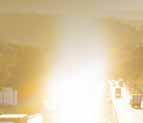
“Sleepy Joe” wakes up to US supply chain fears

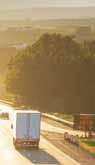
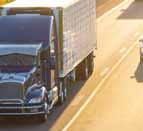
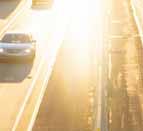
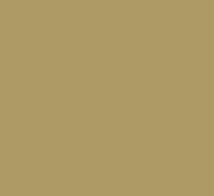
Initial recommendations included investing in manufacturing and research and development, supporting supplier diversification and employing market tools to support sustainability. While seeking to bring the manufacture of critical items back to America where possible, the administration recognises the value of near-shoring or ally-shoring and sees the identification of ‘global trusted partners’ as a key tenet of its approach to supply chain security.
The recent invasion of Ukraine by Russia will only serve to emphasise the importance of this approach.
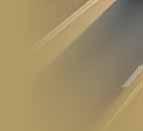
In February 2022 a series of one-year sectoral assessments of those supply chains which underly the US industrial base was released by seven cabinet-level agencies. These departmental reports, including one from the Department of Transportation (DoT) (Supply Chain Assessment of the Transportation Industrial Base: Freight and Logistics), identify the main vulnerabilities and outline developments necessary to establish supply chain security in both the short and the long term.
Key recommendations here, presented in more detail, include rebuilding America’s manufacturing base, increasing government support for markets that invest specifically in workers and value sustainability, leveraging the federal government’s role in critical-goods purchasing, strengthening and also enforcing international trade rules, and creating a network of allies and partners to provide protection against future threats to the global supply chain. The risk of natural disasters caused by climate change is now as much a cause for concern as geo-political threats.
The DoT’s report makes a total of 62 proposals for action, noting that the Covid pandemic only served to highlight problems that the country had systematically failed to address over many years, such as infrastructure investment. Delving deeper, it also identifies issues with equipment and warehouse capacity, workforce issues, and a lack of data availability and visibility as damaging to supply chain security and resilience.
Acknowledging that the federal government cannot possibly solve supply chain disruption on its own, not least because significant parts of the freight supply chain are in private hands, the report calls on federal, state and local agencies to work together on a range of policies.
One of the central recommendations is for significant investment in freight infrastructure such as ports, bridges and railroads to enhance both capacity and connectivity. The Port Infrastructure Development Program (PIDP) will release nearly US$450m in funding opportunities
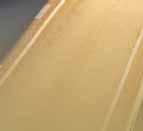
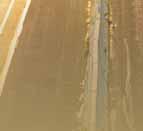
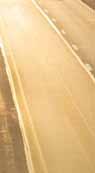
focusing on projects that will improve the safety, efficiency and reliability of the movement of goods in and out of ports. Investment in the inland waterway system is also proposed.
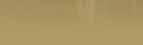
Port congestion has been a problem since the global economy opened up after Covid-induced lockdowns around the world. It has since been exacerbated by labour issues, especially in America’s west coast ports. As a result, inland ports and temporary solutions such as ‘pop-up’ intermodal container yards are under consideration.
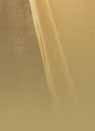
As well as the PIDP, the Trucking Action Plan will seek to increase truck driver recruitment and improve retention rates. The report also recognises the need to ensure that truck parking availability is consistent with land use and safety considerations. The development of state-level freight planning is also advised, via improved data and research into supply chain performance. This needs to include the tracking of freight.
Biden has consistently put the focus on a “whole-of-government” approach, setting up the Supply Chain Disruptions Task Force (SCDTF) in 2021. However, the administration acknowledges that there will be difficulties ahead, not least because of the complexity and scope of the goals, and the costs of implementation. Some industry stakeholders have already expressed their opposition or concerns.
The freight rail industry, for example, has said that new economic regulations will ultimately disrupt rather than improve supply chain fluidity.
Keeping up the pressure, the Assistant to the President for National Security Affairs (APNSA) and the Assistant to the President for Economic Policy (APEP) must provide President Biden with further reports, reviewing actions over the previous year and making further recommendations as a result.
And, finally, full national supply chain reviews are going to be held every four years. These US-wide reports will maintain the momentum for continuous data gathering and supply chain monitoring. Protecting the supply chain and improving its resilience are now embedded in US government policy, Biden hopes.
UKRAINE CONFLICT ADDS TO EUROPE’S MOUNTING SUPPLY CHAIN TENSIONS
While Covid-19 restrictions have been rolled back in many countries, global construction equipment supply chain issues persist. In Europe, the situation has been exacerbated by the Russian invasion of Ukraine plus renewed pandemic lockdowns in China. How tense is it getting out there? Liam McLoughlin reports.
While Covid-19 restrictions have been rolled back in many countries, global situation lockdowns in China. How tense is it getting out Liam
Construction equipment manufacturers had entertained hopes that global supply chain issues might improve in late 2021 as Covid-19 restrictions were eased around the world.
However, the Russian invasion of Ukraine in February 2022 has made the supply chain situation “even worse” according to Sebastian Popp, who is responsible for economic issues at European construction equipment manufacturing association CECE, and at German and European mechanical engineering association VDMA.
Popp says that the main supply challenges facing construction equipment manufacturers over the last year include the availability of electronic components.
The recent Covid-19 lockdowns in China, and accompanying shutdowns of production facilities in cities such as the major industrial base of Shenyang, have accentuated this situation.
“Steel is a big issue, not only the sudden demand boost, but also the EU’s antidumping measures that are still in place imposing import tariffs on non-EU produced steel, which makes steel even more expensive,” says Popp. “Ukraine is a big supplier of steel and castings, and Russia is also a big steel supplier so those things come on top of each other.
“There is hardly any component where you can say the situation is not tense – hydraulics, electrical components, even things like cabs and tyres. It really goes throughout the whole range of components.
“Companies say they didn’t even realise how much they source from countries such as Russia or Ukraine – sometimes just indirectly with their components suppliers sourcing material from there.”
Federico Bullo, head of Europe at CNH Industrial Construction Equipment which includes the CASE brand, says that the current overall worldwide logistics situation
is critical for manufacturers including those in the construction equipment sector.
“We are monitoring and working with suppliers and logistics departments in order to minimise impact on lead times,” Bullo says. “Reduced air freight capacity, raw material shortage, electronic components shortages also continue to have a major impact.”
He adds that adverse market trends in raw materials (particularly steel), urgent freight and logistics costs have impacted CASE’s production.
Bullo says that pressure is likely to continue throughout the remainder of this year. “In the meantime at CASE we have been working on a daily basis with our suppliers in order to maximise achievable
The Major Factors Limiting Construction Equipment Sales in Europe (September 2021-March 2022) Source: CECE
is now the major issue
results,” he adds.
“We have carefully implemented a plan to manage the main supply chain issues and set up task forces with suppliers to resolve challenges and decrease fleet of uncompleted units.”
He says that CASE is constantly monitoring all its key suppliers to analyse their capacity to respect its planned production volume, and it has also carried out a competency and development plan in its product development team to better face the current situation.
KEY CHALLENGES
Chris Sleight, managing director at construction market research and forecasting company Off-Highway Research, highlights three main challenges that the construction equipment industry faces as a result of blocked and disrupted supply chains.
Firstly, delays in getting components from suppliers and insufficient supplies of components to meet the demand for machines in the marketplace. Secondly, higher input costs due to the scarcity of component supply. And finally, delays and higher costs in shipping finished equipment to distributors and customers.
There have been suggestions that the pandemic has demonstrated the dependence of the world on factories in Southeast Asia.
On the issue of whether some manufacturing should return to the West to reduce this dependence, Sleight responds: “The strains of the last two years have certainly shown that there are weaknesses in the global supply chains which have developed over the last few decades. However, more factories and greater localisation is not necessarily the answer, as this would impact on the economies of scale which are achieved in the current system.”
Federico Bullo of CNH says that the manufacturer is committed to increase the production flexibility of its plants to raise production levels and meet the market demand.
“Our manufacturing footprint is well balanced among the four regions to better serve our customers around the globe,” he adds. “Specifically, in China we do not have a manufacturing plant, we have an assembly facility.”
Robert Van der Waal - vice president of logistics, parts & services at Swedish construction, mining and quarrying equipment maker Sandvik – provides a corporate view on the problems facing the supply chain. He says that getting parts where they need to be has never been more
European Construction Equipment: Production Period Needed to Meet Current Order Volumes (September 2021-March 2022) Source: CECE
More than 6 months
Between 5 and 6 months
Between 4 and 5 months
Between 3 and 4 months
Between 2 and 3 months
February 2022
November 2021 May 2021 February 2021
CECE estimates that the backlog for meeting sales orders is currently around six months for most of its construction equipment company members
demanding.
“In 20 years I’ve never seen anything like it, the whole world of logistics has been turned upside down,” says Van der Waal. “We just need to figure out how best to operate in this new dynamic.
“You only need to see a delay in supplying parts to realise just how important they are to customers.”
He adds that Sandvik has changed its shipping methods to adapt: “In the past we sent 40% by air, 40% by sea and 20% by road – now as much as 70% of parts are being flown in. This is faster but the costs are enormous. But we have no choice – it’s a price worth paying to keep customers satisfied.”
In terms of delivery schedules, Van der Waal says the ball-park figure is that things now take twice as long as before. He adds that even express courier services that used to be guaranteed next-day delivery can now take two days.
Does this mean the end of just-in-time logistics? “Not necessarily,” Van der Waal says. “We just need to adjust our supply chain so that we are still there with the right product at the right time for the customer. Where, historically, a supply chain was built around
efficiency, the disruptions due to the pandemic and new market dynamics make companies, including Sandvik, transform their supply structures to make them much more robust. Ones that are better able to handle disruptions and unexpected disturbances.”
ORDER BACKLOG SURGES
Sebastian Popp says the construction equipment industry generally has full order books at the moment, with a tremendous boost in demand after the first wave of the pandemic. After summer 2020, demand picked up in Europe and beyond.
“This demand boost has continued and even increased over the last months, so we have the highest order backlog that we have seen in years, if not decades,” Popp adds. “You can compare it to the situation in 2006 and 2007 when we also had a very strong order backlog, but it is different this time because we do not see a bubble economy that is building up as we saw pre-economic crisis in 2007.
“This strong demand is met by an extremely difficult and restricted supply chain, which is an interplay we have never seen before. Member companies all tell me they have never seen a situation like that.”
➔ In terms of whether the supply chain situation is likely to improve for construction equipment manufacturers, he says that things did look a bit better in the second half of 2021 but, primarily because of the recent events in Ukraine, the outlook has become less optimistic.
“Any hopes that things would improve are pulverised right now by these effects. Steel castings especially and also electrical components are not being delivered,” says Popp.
The VDMA’s ad hoc surveys of its members between March 2020 and March 2022, showed that disruptions in the supply of construction equipment and building material machinery supply were clearly worse throughout 2021 than in the preceding period.
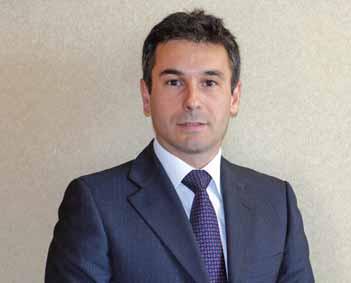
“Even now it’s not really getting better, with 35% of our members saying that business is strongly affected by supply chain disruptions, and another 45% saying that it is significantly disrupted,” Popp says. “Manufacturers tell us it will probably not get better until maybe the second half of 2022.”
He adds the situation is impacting construction equipment manufacturers’ ability to meet demand, and this has been the case over the last year. The order intake of VDMA members grew by over 60% in 2021, and in comparison the turnover growth was just 18%.
“Even if you assume there is a certain lag between orders and sales, I believe the order
backlog is around six months for most of our construction equipment companies,” Popp says.
companies were pretty much of the opinion that there is room for more growth in the market this year, but only if the supply side does not get even more tense,” says Popp. “Now we have seen it did because of the Ukraine war, so many companies tell us that positive growth forecasts are not realistic anymore.”
In terms of measures that construction companies have taken to improve the situation with their supply chains, he says that in the first wave of the pandemic in Q1 2020 that hit China, most OEMs were not highly dependent on China for things such as hydraulic components.
Federico Bullo, head of Europe at CNH Industrial Construction Equipment, says that reduced air freight capacity, raw material, and electronic component shortages continue to have a major impact on supply chains
CECE conducted a poll of its members which showed that the production period needed to fulfil order volumes has increased since early 2021. In February 2021 around 13% of manufacturers said their current order volume corresponded to a production period of more than six months, but by February 2022 this had increased to more than 50% of manufacturers.
“At the start of 2022 CECE members
When the pandemic reached Europe this became more of an issue, with a big supplier base in Italy that was no longer available. OEMs tried to substitute as much as possible.
“When the Russia-Ukraine war started we looked at the question of how much of the critical imports [for European manufacturing] come from that region,” says Popp. “We found that only 3% of what the European Commission would define as critical imports into Europe actually come from Russia, but 55% come from China. The dependence on China is way higher than
what we had expected, both for the overall economy and also for the construction equipment sector to some extent.”
Popp says it is with electronic components such as semiconductors where it is most apparent that European manufacturers rely exclusively at the moment on China and perhaps also Taiwan. In terms of how to get back some of the manufacturing in these industries to Europe, he says there are some minor examples such as the new Intel chip factory planned for Germany. Such initiatives take time and there remains the question of whether they will become profitable, setting up a sector that has long been gone from the region.
RISING COSTS
For the construction equipment sector, Popp says the good news is that things such as hydraulic components, power transmission and control systems are actually located in western Europe.
“In terms of rising costs [of energy, timber, concrete and metals] the most important
2021 saw a high level of demand but much lower actual sales revenues for German construction equipment manufacturers
thing is not the materials themselves but the transport,” says Popp. “The cost of transport has just skyrocketed, and this is what really affects both the manufacturers producing in Europe who need their components to be shipped over, but also Asian manufacturers shipping machines to Europe.”
He adds that energy costs also take their toll, not so much directly for the production of a machine, but in the long run it might affect the customer side such as construction contractors. Then it will have a negative effect on machine demand, although that is not something that is


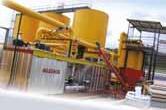

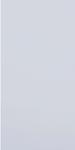

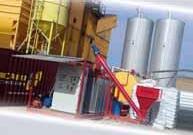


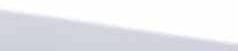
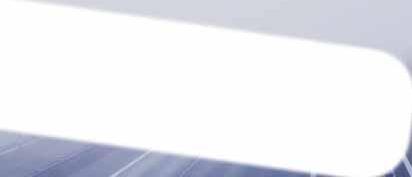
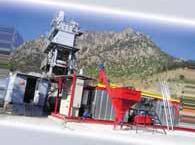
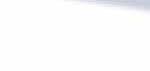


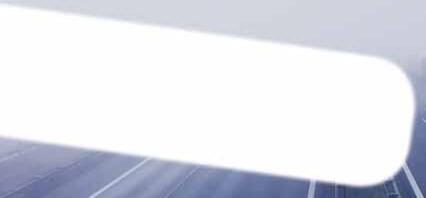

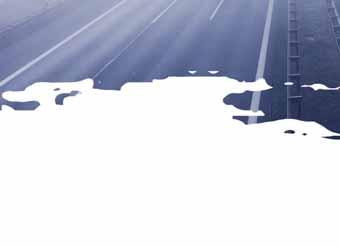
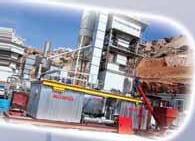





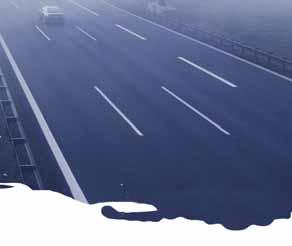


being seen at the moment.
Steel prices are an issue that is currently causing major concern to manufacturers, and therefore CECE and VDMA are arguing for a suspension of the European Commission’s anti-dumping measures which are still in place and date back to the days of the US trade war with China that started in 2018.
“The measures were an attempt to support European steelmakers through tariffs on nonEuropean produced steel, which comes as an additional burden for many of the OEMs,” says Popp.
In terms of whether construction equipment manufacturers in some regions have been more or less affected than others by supply chain issues, Popp says that Asian companies tend to be a bit better off as they often have own-engine production, unlike many European manufacturers. “Other than that I don’t really see disparities across the globe when it comes to supply chain bottlenecks,” he adds.
He says that there was little observable evidence in 2021 of particular construction
equipment sectors being more affected than others by supply chain issues. Growth rates were fairly similar in the markets for building construction, civil engineering, road construction and earthmoving equipment, and there was also little variation between the compact and heavy-equipment sectors.
With around 75% of all semiconductors being produced in East Asia, this makes the current supply chain situation for these products “very tense,” he adds.
“Manufacturers thought things might improve in the short run, but with the recent lockdowns in China it’s pretty clear that it won’t,” says Popp. “This will affect both the manufacturing and the logistics of electronic components. Many of those factories have a high degree of automation, but to get all the logistics in place will continue to be a huge issue for at least the rest of 2022.”
He says the current supply chain issues could lead to long-term structural changes in how construction equipment is manufactured. In the past there have been different waves of increasing or decreasing
vertical integration. Popp predicts that things will certainly move again into that direction of more vertical integration where, even if manufacturers do not produce everything inhouse, they at least have their suppliers close to them – but there are certain limits to this.
“We certainly won’t see a scenario five years from now where globalisation will be reversed and all the value chain would be in individual market regions.”
In 2021 the discussion focused on how well China had weathered the Covid-19 crisis and if it was still on track, but Popp says the situation now has almost flipped around.
“While we in Europe now have the feeling that our economies have more or less adapted to the situation, China needs to find a way out of its zero-Covid policy because it will dramatically impact its economy and business models – particularly as the country has become increasingly reliant on exports,” he says.
“National governments and the European Union will try to address the dependency on overseas production, particularly on the

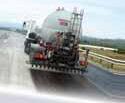


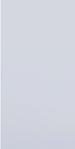

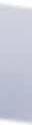
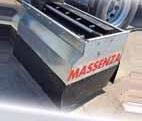





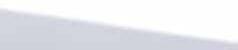
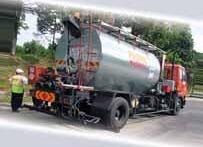



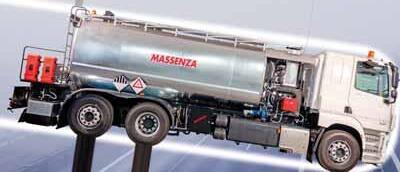
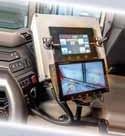
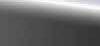


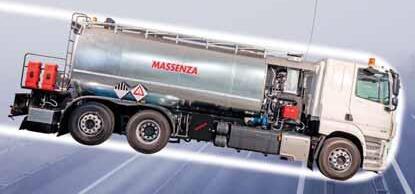

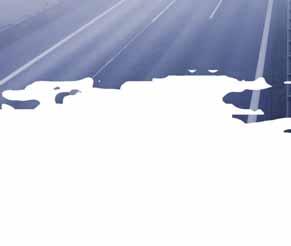

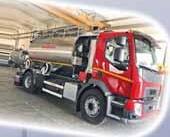






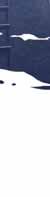
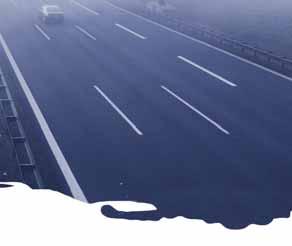


components side. I’m not too optimistic that this will have a quick and direct effect in terms of bringing some of these industries back to Europe, and if they can become profitable and sustainable business models. If they just rely on government subsidies they won’t be viable in the long term.”
Cyberattacks are an added dimension to current construction equipment risks, and Popp says they have been a big issue for at least two years.
“I know of many OEMs that have been victims, not in terms of cyber-terrorism but more cybercrime with financial interests,” he adds. “In the end there is not much you as a manufacturer can do to prepare for that. When you add the component of potential cyberattacks from Russia in the near future that is a scary outlook.”
Looking at the construction equipment supply chain outlook for both the near and longer term, Popp believes that markets will regulate the current issues in the long term, but for the shorter term and rest of 2022 he remains sceptical.
He says the Ukraine war and Covid shutdowns in China will continue to take a huge toll for the rest of the year. In early February, VDMA members expected growth in industry turnover of 7% if the situation on the supply side did not aggravate any further, but things have now obviously changed.
The good news is that construction equipment order books are full well into 2023, and Popp says the government stimulus measures both in Europe and North America for infrastructure will keep up demand for a couple more years.
“The overall volume of the construction equipment industry is quite high,” he concludes. “The 2021 turnover of our VDMA member companies was on a par with the 2019 levels which had been the highest levels in history. There is still a high volume of machines being produced and put into the markets. It’s not that none of the demand can be served, it’s just that we cannot fulfil all of the demand that is there. You can turn that around positively and say that will prolong the boom into 2023 and maybe 2024. We do not have a scenario like in 2007 where after the burst of the bubble we went straight from order backlogs of longer than six months to negative order intake and nothing being invested anymore.”
Chris Sleight of OHR Research says that, given Russia’s enormous mineral wealth, it is likely that the sanctions against the country following the invasion of Ukraine will have a
knock-on effect on supply chains.
“Manufacturers might have been sourcing raw materials and components from Russia, and in the more indirect sense, the starting point for components may have been raw materials extracted in Russia,” he adds.
“The sharp rise in global commodity prices
in the wake of Russia’s aggression will also have an indirect effect. This will push up energy and raw material prices in general, which will eventually feed into construction equipment manufacturers costs and will ultimately have to be passed on in retail prices.”
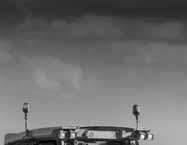
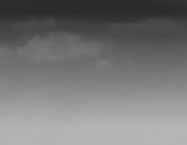

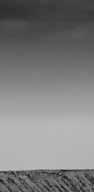
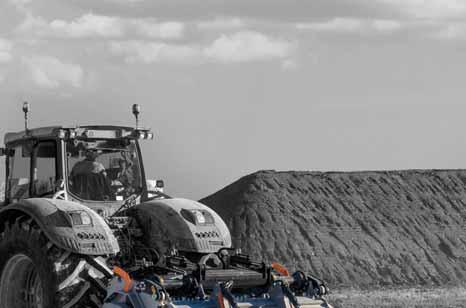
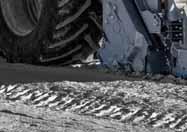
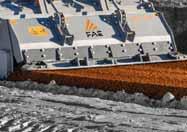
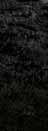
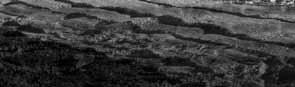
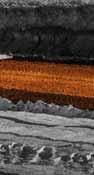
Be more productive with the FAE MTH multitask head for 300-500 hp tractors Rock grinder, stone crusher, asphalt shredder, and stabilizer all in one. Experience top performance, made possible with the innovative variable geometry mixing and grinding chamber that allows you to
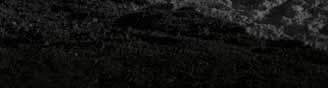
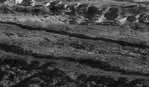

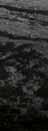
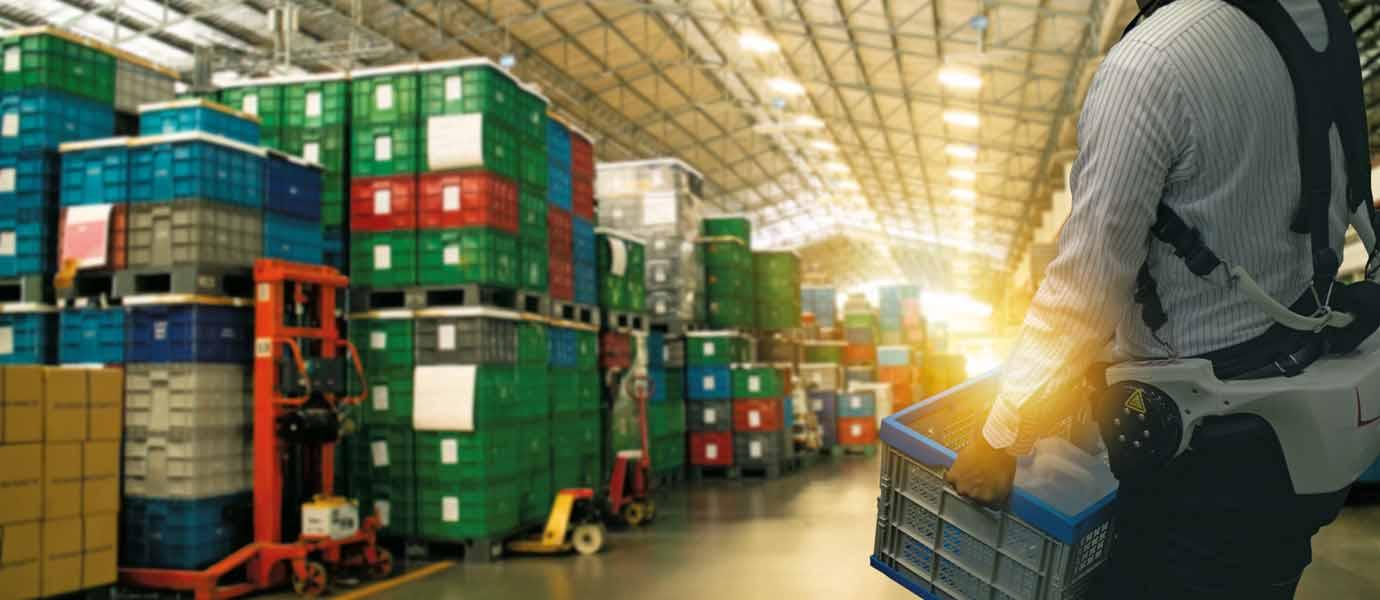
FITS LIKE A GLOVE
Exoskeletons and digitally-connected clothing, once just a pipe dream, are now helping managers on big construction sites to improve a variety of metrics: health and safety, connectivity, productivity and accuracy. Often called wearables or exosuits, they come in many forms and can be as large as a space suit or as small as a glove. How do they work, and how will they keep the site workers of the future safe?
Exoskeletons sound like something from a science fiction novel. But they’re not … they’re here and now and they come in all sorts of shapes and sizes.
Exoskeletons that help construction workers perform heavy or repetitive tasks are often mechanical “suits” operated via a mix of mechanics and electricity. Today, it is often the case that fully electric exoskeletons are the most powerful and they are used to handle more weight than purely mechanical devices.
Mechanical exoskeletons, however, don’t need recharging or require an additional power source … so they can run for longer periods on site. Depending on the function required, these space-age suits can be made of hard materials like metal … or from softer options such as specially developed soft textiles.
They work in different ways depending on what part of the body they are designed
for and come in the form of power gloves, arm and shoulder supports, back supports or provide standing and crouching support for tasks requiring considerable periods of standing such as drilling.
Once used mainly for physical rehabilitation in the healthcare sector, these larger exoskeletons have particular benefits for the construction industry which traditionally has high rates of injury, particularly in terms of musculoskeletal disorders such as back, shoulder and joint injuries.
With increased emphasis on worker health and safety in the sector, exoskeletons offer real potential to reduce injury and strain by distributing weight more evenly, decreasing pressure on the spine and lowering fatigue levels. These benefits can lead to an increase in productivity. They also enable older workers to endure more strenuous activities, and for longer periods.
SAFETY FIRST
This is all well and good, but these bionic suits are already a bit old hat. Digital technology, in smaller, less obvious wearable forms, is moving in fast … improving safety and productivity metrics on sites in a variety of ways.
If the construction site of the future is going to be full of things like driverless and autonomous trucks, excavators, wheeled loads, rollers, and compactors, the occasional human being is going to need to stand out very clearly. It won’t be a case of improved visibility, because there won’t be any operators around to keep an eye on things, it’s going to be a case of making sure that the human being on site is digitally linked to the technology running all around him or her. The wearable exoskeleton is going to have to be digitally linked to the remote screens and systems back at head office.
For instance, Triax Technologies’ Spot-r
connected jobsite solution will link anyone on the site to the 24-hour monitoring systems back at the control centre … all and every day. Workers are going to need new safety and site risk-management techniques, and this is where “wearables” come in.
Digitally-connected clothes and hats and gloves will help improve resource allocation, say the experts, and they will increasingly be used to improve working time stats and attendance levels, to monitor more effectively your equipment and machine utilisation rates, and to give real-time location data indicating which workers are near particular areas at what time … and whether or not they are certified to be there.
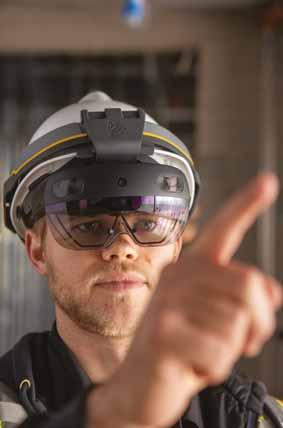
Identifying zone-based worker location has been found to improve injury response times by more than 90%. In the event of injury, the Spot-r Clip, usually worn on the hip, can provide a direct line of communication to managers using a simple push-button function. Keeping things safe, if workers need to evacuate the site, the manager can trigger an alarm via Spot-r EvacTags, strategically placed around the site. There is also a fallalert monitoring system which looks for “unusual employee movement”, such as a fall from height. As soon as this is detected, an emergency response process kicks in.
With no requirement for GPS or WiFi coverage, Triax says that its wearable tech is a “low-power solution with minimal network hardware, meaning lower maintenance requirements.”
Trimble’s XR10 with Microsoft HoloLens2 smart glasses use “mixed reality” and new software solutions to create a hands-free computer that “goes where you go, sees what you see and does what you say.” It displays a layer of digital information on top of the real world by using highdefinition holograms that stay in place and respond like physical objects when the wearer interacts with them
A “wearable” doesn’t have to be clothing either. Something as simple as a speciallyadapted smart watch can monitor vibrations in order to assess the impact on the body of using power equipment over a long period of time. Alerts tell the wearer when the body has reached its safety limit. This prevents excessive use which can lead to hand-arm vibration syndrome (HAVS).
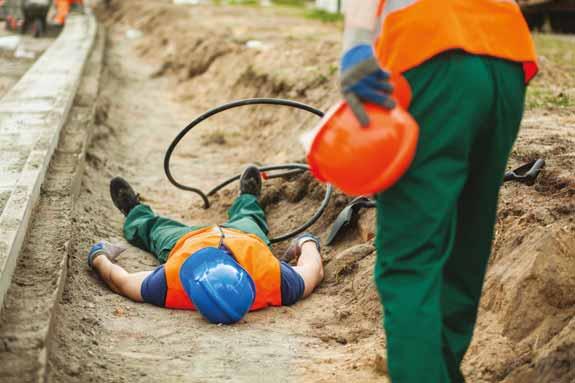
Similarly, smart helmets can monitor a variety of health metrics such as fatigue, heart rate and stress levels. Managers can them modify an individual’s activities in response to this data to promote both employee health and job site safety and productivity.
DETECTION DATA
The SCAN-LINK Armour System, from SCAN-LINK Technologies, is an RFID-based mobile personnel detection system. Utilising more than 19 years of experience of back-up safety systems and technologies, the system is able to differentiate between a person and an object using passive UHF RFID tags located in safety apparel. The RFID tags are located 360 degrees around the worker and are embedded in the safety apparel.
The system can alert the driver of a reversing vehicle to the presence of an outof-sight ground worker if he is wearing the Armour-equipped safety vest and hard hat.
Any vehicle equipped with an Armour Antenna can detect any ground worker on any job site, says SCAN-Link, but only if they are wearing the equipped vest and/or hard hat. Safety vests and hard hats are used for longer-range 5m detection.
The SCAN-LINK Armour System will only detect and read SCAN-LINK safety apparel so there can be no false alarms. Information about every detection event can be recorded and stored so that safety procedures and working practices can be reviewed and improved as a result.
According to Jonathan Fava, president, Scan-Link Technologies: “We were looking at the number of times equipment operators were alerted to the presence of a nearby worker, and we noticed one person was causing a lot of alerts, so we pulled that individual aside and asked him why.
“He explained that he is the flagger so, when operators load the machine onto a float, he gets up on the float to aid the operator place the machine. We advised him that [this] behaviour is unsafe; he could get struck by the machine or fall off the float. So, we told him a safer way to perform his job and wrote down new safety protocols into our guidelines and training.”
Collating and deciphering historical data are the first steps towards job site safety. “It’s not enough just to learn how accidents have happened,” says Fava. “The next step is to analyse data in order to prevent accidents from happening,”
Using the employee detections picked up by the Scan-Link system, managers can identify incident hotspots. “Using this data,
➔ customers can identify areas where a struckby incident is most likely to occur,” he adds.
“Then, customers can make decisions that will decrease the risk of an accident from happening by moving the location of materials so workers don’t have to walk in a machine’s workspace or by putting up signage warning employees of high-risk areas.”
A NEW REALITY
Wearables are also bringing connectivity, productivity and accuracy to job sites by merging virtual reality (VR) and augmented reality (AR). Exoskeleton and headset manufacturer Real Wear has just released the second version of its assisted-reality headset, the RealWear Navigator 500.
The headset enables frontline workers to communicate with experts remotely, enabling the operator to act as the eyes for inspectors and technicians, saving both time and
ROBOTICS PAVE THE WAY
The safety of construction workers and road users on Europe’s extensive road network is a top European Union priority. On a countrybased average, 4% of accidents take place in work zones. InfraROB, the European Union’s Horizon 2020-funded project, aims to reduce workers’ exposure to live traffic and construction machines, increase road user safety, and improve methods of constructing, upgrading and maintaining road infrastructure … by deploying robotics.
According to the boffins at the EU, the InfraROB project is all about: “Maintaining integrity, performance and safety of the road infrastructure through autonomous robotized solutions and modularisation”
The €5m project, running from September 2021 to February 2025, aspires to reduce fatal accidents by 50% and maintenance-based traffic disruption by 20%. It also seeks to decrease routine maintenance costs
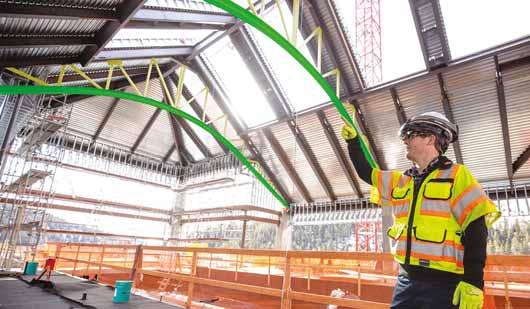
and improve network capacity.
Structured in two phases, part one examines research and technical development, while part two focuses on demonstration, validation and outcomes in a fully operational environment, using the Graz Living Lab, a pilot test site on the Austrian motorway network A2, managed by ASFINAG. Creating robotised safety systems to protect workers as well as reducing the cost of repetitive tasks will be a priority, alongside the development of a multifunctional precast concrete element for use in roadside safety barriers and in road construction generally.
Robotics use in road infrastructure management lags behind levels achieved in other sectors. Driven by an 18-partner consortium from eight EU countries, InfraROB will develop autonomous robotised systems and machinery for (re)paving, repairing and line marking,
and robotised safety cones and remotely piloted aircraft system (RPAS) robots to monitor worker safety.
Particular emphasis will be on improving asphalt roads which make up 90% of all European paved roads and highways.
The project acknowledges the importance of an efficient road system to both economic growth and the achievement of the EU’s Sustainable Development Goals. Coordinated by GeoTECH Group, a member of CINTECX at Spain’s Vigo University, InfraROB will upgrade existing traffic and maintenance management systems so that automated road maintenance robots can be deployed safely.
The future looks bright. We’re moving into the age of the bionic man, digitally connected via his wearable exoskeleton and powerassisted mechanical suit to the same software that is running the robots all around him. It’s all part of the connected site.
travel costs. It can follow digital workflows, visualise Internet of Things (IoT) data and respond to audio commands for all features to remain hands-free.
It can even lead to reduced downtime, says the manufacturer, and will help “improve work quality and employee productivity, ultimately realising significant return on investment.” The headset can withstand challenging work environments including extreme heat of up to 50 degrees centigrade and offers unrivalled noise cancellation with four microphones for hands-free use.
“With the Navigator 500, we wanted to provide sale enterprise solutions as part of the digital transformation movement. Today, we see the acceleration of digital transformation on the future of work, especially since the pandemic,” says Andre Chrostowski, chair and CEO, RealWear Technologies.
“Our device is hands-free and keeps you present. You don’t want your head stuck in the metaverse when you’re working around heavy equipment”.
RealWear devices can now be managed using Foresight, a powerful suite of cloud services by which organisations can manage their devices, install and update apps, make device settings and manage security. This is all ‘doable’ from a web portal accessible anywhere in the world.
The Trimble XR10 with Microsoft HoloLens2 provides “mixed reality” using smart glasses. HoloLens2 coupled with software solutions is a hands-free computer that ‘goes where you go, sees what you see and does what you say’. It displays a layer of digital information on top of the real world
by using high-definition holograms that stay in place and respond like physical objects when the wearer interacts with them.
The Trimble device is the only OSHAcompliant and intrinsically safe hardhatintegrated HoloLens2 device. It is compatible with most hardhat-mounting PPE and provides two-way communications via boneconduction in up to 115dB ambient noise environments.
Trimble has also recently introduced the Trimble Connect AR app. Compatible with Trimble Connect, it can be downloaded to a phone or tablet, providing users with an augmented reality by pushing business information modelling (BIM) data to their phone and overlaying it onto images of the real world on the screen.
“This eliminates what
can be a costly financial barrier to some customers”, says Martin Holmgren, general manager of building field solutions at Trimble.
“And users can interact with Trimble Connect AR users in the digital space. For example, I can leave a message in the digital space with my Trimble XR10 and someone with the Trimble Connect AR app on their phone can detect the message, even weeks later as they walk by the location where it was left and read it. This greatly enhances communications and streamlines workflows.”
A 2019 report by ABI Research predicted that the robotic exoskeleton market would reach a value of $1.8bn in 2025, up from $68m in 2014
Trimble envisages supervisors, managers, inspectors and building owners will use it to perform tasks such as quality assurance and control, updating punch lists and measuring
construction progress.
“The app allows for the incorporation of AR into workflows that don’t require the user to be hands-free, and we think our app will ultimately drive AR in a much wider range of adoption,” says Holmgren.
Your biggest mistake would be to think that this all sounds like pie in the sky. It isn’t. It is here and now and the market is growing at a fantastic rate.
A 2019 report by ABI Research predicted that the robotic exoskeleton market would reach a value of $1.8bn in 2025, up from $68m in 2014. RealWear’s Chrostowski has noticed the effects of the Covid-19 pandemic too on work new practices. He can see that the speed with which companies are now embracing innovative digital technology like exoskeletons and wearables is getting faster and faster. It looks like robotics are on the march.
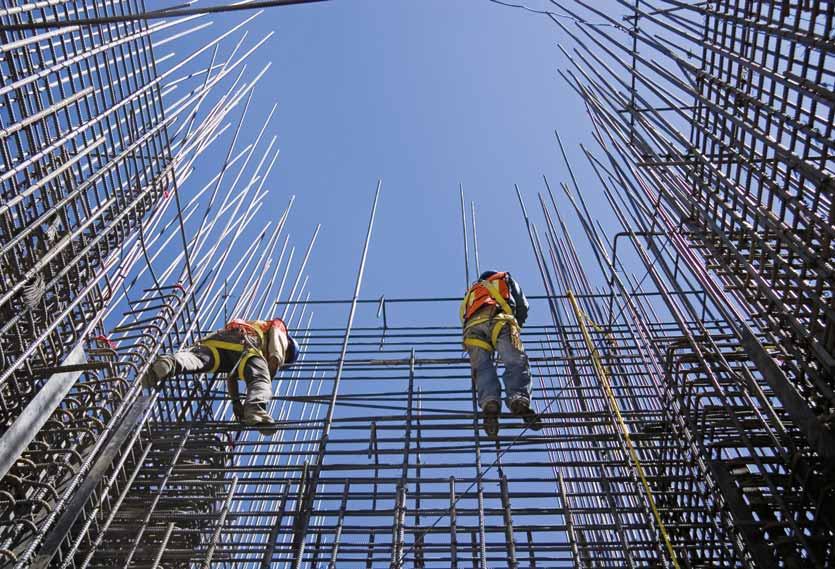
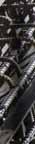

GLOBAL REPORT WOULD LIKE TO THANK AEM FOR PROVIDING SOME OF THE CONTENT USED IN THIS ARTICLE. AEM (THE ASSOCIATION OF EQUIPMENT MANUFACTURERS) REPRESENTS CONSTRUCTION EQUIPMENT MANUFACTURERS AND SUPPLIERS ACROSS THE UNITED STATES.
OPTIMISTIC TRAJECTORY FOR WEST AFRICAN INFRASTRUCTURE INVESTMENT
As policymakers in West Africa seek tools to stimulate economic growth, there is a distinct focus on infrastructure development as a cornerstone of the region’s economic recovery plans. Investments in road corridors and transport projects at large are expected to continue apace as West Africa scales up regional integration to fortify its value chains. Munesu Shoko reports.
The 2020 Covid-19 outbreak had an adverse impact on many sectors of the African economy, and construction was no exception. Some of Africa’s biggest infrastructure projects encountered challenges such as shortages of construction materials, labour, and equipment. Sadly, the investment pipeline stalled.
However, several African governments have prioritised infrastructure development as a catalyst for growth recovery. This is particularly apparent in West Africa, where well-targeted infrastructure programmes are expected to play a significant role in improving poor economic performance and boosting fiscal transformation.
With an expected surge in population growth, West African governments also understand the urgent need to accelerate infrastructure projects that are already under construction, as well as those already preapproved. In addition, the need to create a pipeline of bankable construction projects cannot be emphasised enough.
BOOMING POPULATION
West Africa, a region of 17 countries, will see its combined population rise from the current 412 million to 526 million over the next
Nouadhibou
Nouakchott
Dakar
Banjul
Bissau
Conakry
Freetown
Monrovia
Bamako
Niamey
Agadez Kano
Ouagadougou
Khartoum
Ndjamena
Cairo - Dakar
Algiers - Lagos
Tripoli - Windhoek - (Capetown)
Cairo - Gaborone - (Capetown)
Daker - Ndjamena
Ndjamena - Djibouti
Dakar - Lagos
Lagos - Mombasa
Beira - Lobito
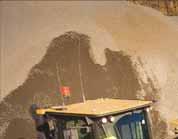
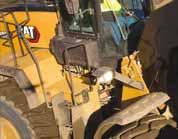
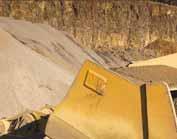
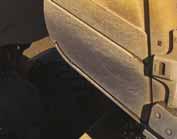
decade. Notwithstanding the havoc wreaked by the Covid-19 pandemic in the past two years, the region – comprising Nigeria, Ghana, Mali, Côte d’Ivoire, Togo, Senegal, Benin, Burkina Faso, Guinea, Guinea-Bissau, Mali, Liberia, Niger, Mauritania, the Gambia and Sierra Leone – has made significant strides in the past decade to improve its infrastructure across sectors, all the way from transport and energy to real estate and social development.
According to ABiQ, a business intelligence provider on all matters in Africa and the Middle East, there are more than US$380 billions’ worth of active projects in West Africa, with US$230 billion already under construction and US$150 billion in the pre-execution phase. The majority of active projects by value are in Nigeria (34%) and Ghana (20%).
The same trend is evident in Deloitte’s recent Africa Construction Trends Report, which tracked a total of 76 projects of over US$50 million in value, with a total value of US$79 billion. Unsurprisingly, both the bulk of the projects (26) and the largest project value (US$52.4 billion) were recorded in Nigeria, the region’s largest country, where transport projects, particularly roads and bridges, are at the centre of construction activity. Ghana, the second-largest economy in the region, chipped in with 16 projects, followed by Côte d’Ivoire with ten projects.
NIGERIA
Despite having the highest GDP in Africa (US$514.05 billion in 2021), Nigeria’s
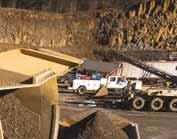
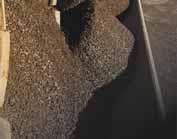
Mantrac, the Cat dealer in West Africa, has seen increased demand, especially in the quarrying sector, which is a direct beneficiary of the mega construction projects happening in the region
infrastructure deficit, projected at US$100 billion annually, is astounding. In its 2020 report, Infrastructure in Emerging Markets: Focus on Nigeria, Moody’s reckons that US$3 trillion in investment is needed over the next 30 years to plug the national infrastructure deficit.
While the infrastructure deficit is staggering and far too steep for the fiscally constrained government, it is not all doom and gloom. In fact, the Nigerian construction industry is expected to post an annual average growth rate of 2.8% in real terms between 2022 and 2025, reinforced by the government’s plan to invest in infrastructure projects.
With the February 2023 election looming large, the government is likely to accelerate construction activity in 2022. Building infrastructure in Africa is often an inherently political act. It has been proven that elections influence investment choices for governments. The flow of infrastructure funds creates winners and losers, and investment decisions often favour those in power.
To provide context, having been initiated in 2006 by the then President, Olusegun Obasanjo, the US$2 billion East-West Road Project progressed at a snail’s pace to reach 8% completion by 2019. However, following the transfer of the project from the Ministry of Niger Delta Affairs to the Ministry of Works, the project has been scaled up from 8% in 2019 to 80% by March 2022. The 338 km road, which starts from Effurun in Warri and ends up in Oron, Akwa Ibom state, was
listed as the sixth most valuable project in West Africa by Deloitte in its 2020 African Construction Trends Report
In late 2021, the Nigerian Federal Government approved the reconstruction of the collapsed Lagos-Badagry Expressway and 20 other federal roads by the newly incorporated Nigerian National Petroleum Corporation (NNPC) Limited. The project scope will see NNPC take over the reconstruction of 21 federal roads totalling 1804.6kms across the six geopolitical zones of the country at a US$1.8 billion cost.
The Lagos-Badagry Expressway, identified as the seventh-biggest project in West Africa by Deloitte last year, was awarded in 2018, with construction commencing in 2020. Having initially stalled due to funding issues, the government has recently injected the much-needed capital through its Sovereign Sukuk bond and the NNPC Tax Credit funding. By March 2022, the project was 25% complete, and through continued government funding, it is expected to reach 80% completion within a year.
GHANA
Having contracted by 4.4% in 2019, Ghana’s construction industry expanded marginally by 0.6% in real terms in 2020, with output value increasing from US$11.2 billion to US$11.24 billion during the same period. GlobalData expects Ghana’s construction industry to register an annual average growth rate of 3.9% between 2022 and 2025.
Central to the growth trajectory for Ghana’s construction industry was the country’s swift response to the Covid-19 pandemic, enacting earlier lockdown measures and driving its ‘Ghana Beyond Aid’ initiative. The initiative aims to diversify Ghana’s manufacturing base and overhaul its taxation structure, increasing the resilience of the economy.
The government held a Eurobond Road Show in January 2020 to raise up to US$3 billion, which provided a buffer to support the Ghanaian currency, the Cedi. The funds raised from the issuance are intended to finance infrastructure projects and help manage Ghana’s rising debt stock.
According to the African Development Bank (AfDB), Ghana’s infrastructure financing needs, over the 10-year period 2016-2026, are expected to stand at approximately US$7.3 billion. To help close this gap, AfDB has recently committed a corporate loan of up to US$75 million to support the Ghana Infrastructure Investment Fund’s portfolio expansion strategy.
17 corridors
WEST AND NORTH AFRICA
US$8 billion
Injected by the AfDB
12,700km of road financed by the AfDB
239 million people in AfDB project areas
26 one-stop border posts built
➔ SENEGAL
According to ABiQ, Senegal has close to US$20 billions’ worth of active projects. With a population of just over 17 million, which is expected to grow by more than 28% over the next ten years to 22 million, Senegal is one of the most stable countries in Africa, with three peaceful political transitions since independence in 1960, according to recent World Bank reports.
CENTRAL AFRICA
EAST AND SOUTHERN AFRICA
road networks between Guinea-Bissau and Senegal, while US$8.7 million and US$7 million will go to budget support and capacity building, and government reforms, respectively. The AfDB plans to set up a delivery unit to speed up project implementation.
CORRIDORS
Over the past 12 years, the African Development Bank has financed nearly US$8 billion’s worth of regional transport projects. As a result, close to 13,000kms of regional highways have been built on 17 road corridors, along with 26 one-stop border post facilities
While economies in the region have in recent years prioritised their in-country projects, there is a renewed focus on regional road corridors, based on the understanding that these infrastructures are important to the competitiveness of regional economies, especially those that are landlocked. The World Bank stresses that for economic integration to materialise in West Africa, there is a need to start with efficient road corridors.
While the country’s economy hinges on a diversified industry portfolio, the government’s strategic focus on infrastructure development as a catalyst for economic growth is apparent. The AfDB has played a critical role in the financing of key infrastructure projects in the country for decades. Since beginning operations in Senegal in 1972, the bank has delivered 116 projects in the country worth more than US$3.47 billion.
The most recent of the AfDB-funded projects is the Regional Express Train, the first high-speed train in Senegal, inaugurated by President Macky Sall in December 2021. Running every ten minutes on weekdays and every 15 to 20 minutes on weekends, the train system has alleviated transport problems in the growing capital city of Dakar, transporting about 110,000 passengers daily at first, a figure that may double by 2025.
Infrastructure development activity will continue unabated in Senegal for the near future, following the conclusion of a US$1 billion funding agreement with the United States for US companies to invest in infrastructure construction in
Source. African Development Bank
Senegal. As part of the agreement, a publicprivate partnership (PPP) between four US companies and the State of Senegal has been established. The PPP will develop key infrastructure projects such as the Dakar-St Louis highway project, the installation of 375 traffic lights and the construction of the Ziguinchor and Dobor bridges.
As part of the PPP agreement, Bechtel Corporation, an American engineering, procurement, construction and project management company, has already signed an investment agreement with Senegal for the development of the 200km Dakar-St Louis highway project, which will be developed in two phases. The first phase is a 114km stretch between Tivaouane Peulh and Lompoul, while the second phase extends over 81km between Lompoul to Saint-Louis.
GUINEA BISSAU
With a population of about 2 million people, Guinea-Bissau is one of the least populous countries in the world. To further improve its fortunes in a region that contains some of Africa’s major economic powerhouses, the country has in recent years placed a big focus on infrastructure development, in particular on roads.
More recently, the AfDB announced a US$30 million financial package earmarked for projects in the country. Of this amount, US$14 million will be allocated to building
According to Amadou Oumarou, director of the Infrastructure & Urban Development Department at the AfDB, cross-border road corridors play a critical role in supporting Africa’s regional economic integration. They improve transport communications between neighbouring countries and provide landlocked countries with access to seaports. They invariably promote international and intra-regional trade by reducing transport and shipping costs as well as transit time for imports and exports.
By removing physical barriers to crossborder trade and expanding markets beyond national boundaries, regional road corridors will play a significant role in the success of the recently launched African Continental Free Trade Area (AfCFTA) protocol, which came into effect in January 2021. AfCFTA aims to facilitate and promote intra-African trade by reducing and eliminating tariffs, integrating markets and economies, addressing non-tariff barriers to trade, enhancing trade and investment policy certainty and contributing to greater economic growth across the continent.
To boost regional trade, several funding institutions have reiterated their desire to see African regions connected through modern corridors. For example, the quest to integrate Africa is one of the AfDB’s strategic priorities. Over the past 12 years, the bank has financed about US$8 billion of regional transport projects. Consequently, close to 13,000 km of regional highways have been built on 17 road corridors, along with 26 onestop border post facilities.
In West Africa, for example, ten years after the AfDB financed the Bamako-Dakar highway to the tune of US$400 million, Oumarou says the route now carries more than 50% of Mali’s import and export goods from and to the port of Dakar in Senegal. This has allowed the country to diversify its trading routes, reduce costs by more than 20% and increase international trade by 10%.
With support from the World Bank, Burkina Faso, Niger and Togo are preparing a regional project for the Lomé-OuagadougouNiamey economic corridor. This corridor, says Deborah Wetzel, World Bank Director for Africa Regional Integration, is the economic hub of the three countries and its development will generate strong and inclusive growth in communities which, in turn, will help address gender disparities and benefit millions of people.
It aims to improve regional connectivity and develop social and economic infrastructure for fragile communities living along the corridor. This stretch has a significant concentration of people and activity: more than 28% of Niger’s GDP and 7% of its population, more than 40% of Burkina Faso’s GDP and 21% of its population, and more than 72% of Togo’s GDP and 65% of its population.
Elsewhere, the AfDB is financing what the bank’s president, Dr Akinwumi A. Adesina, believes to be the most important infrastructure project in West Africa, the Abidjan-Lagos highway project. The construction of the 1,081km highway will have a significant impact on the economies of five West African countries – Côte d’Ivoire, Ghana, Togo, Benin and Nigeria.
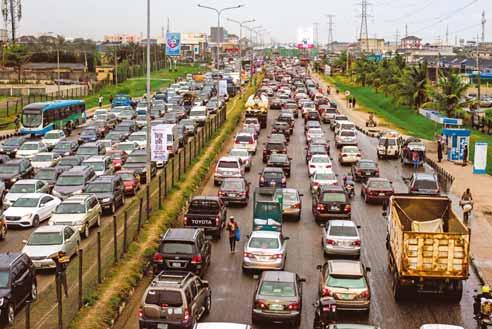
ABOVE: Congestion and chaos: Important West Africa cities like Lagos are battling hard to invest in new road infrastucture as their economies and populations grow. BELOW: Metso Outotec has just appointed Panafrican Equipment Group as the distributor for its mobile crushing and screening equipment across Nigeria, Sierra Leone and Ghana. Its Nordtrack J127 mobile jaw crusher is a track-mounted crushing machine designed for asphalt recycling, construction waste processing and aggregate production
Valued at US$15.6 billion and driven by the Economic Commission of West African States, this game-changing PPP project was the largest investment opportunity showcased at the Africa Investment Forum held from 15-17 March 2022. The new highway will start at Bingerville, in the eastern suburbs
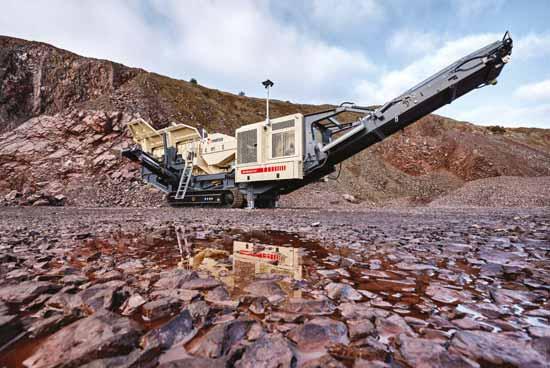
of Abidjan, Côte d’Ivoire, and end at Mile 2 (Eric Moore) in Lagos, Nigeria.
Three sections are planned for the construction of this dual three-lane highway: Abidjan (Côte d’Ivoire)-Takoradi (Ghana), 295 km; Takoradi (Ghana)-Akanu (Ghana), 466 km; and Noepe (Togo)-Cotonou (Benin)Lagos (Nigeria), 320 km. Eight border posts will also be built along the corridor.
The Abidjan-Lagos highway has already attracted the interest of the AfDB, which has provided €22.4 million in funding to finance preparatory studies for the implementation and management of the corridor project.
The AfDB is also providing funding to the Boké-Québo Road Improvement Project. In October 2011, the governments of Guinea and Guinea-Bissau contacted the bank to request contribution to the project, which is part of the Dakar-Lagos Road Corridor or Trans-African Highway 7. Its implementation will complete the missing portion of the land link between Conakry and Bissau, the respective capitals of Guinea and GuineaBissau.
The project will comprise the improvement and asphalting of 107 km of road, 86 km of which are in Guinea and 21 km in GuineaBissau; the construction of two bridges in Guinea (Tinguilinta and Kogon); and repairs to defects identified on five bridges in Guinea-Bissau. The total cost of the entire project is estimated at €117.29 million.
SUPPLY CHAIN
Given the hive of construction activity in the region, capital equipment suppliers have seen increased demand for their products and services. Mohamed Magdy, segment manager at Mantrac, the Caterpillar (Cat) dealer in West Africa, has seen increased demand, especially in the quarrying sector, which is a direct beneficiary of the mega construction
➔ projects happening in the region.
“With ongoing road construction and mega railway projects, complemented by a strong government project pipeline, the outlook is very positive in Nigeria,” says Magdy. “Opportunities abound in Ghana, where the government is showing an insatiable appetite to invest in major infrastructure projects, as well as addressing the impact of the tidal waves along the coast through construction of sea defence builds. Other projects of note include the Tema Motorway Expansion, the Tema-Akosombo Road, Accra-Kumasi Dual Carriageway and Bypass as well as the TemaAflao Road.”
On the back of growing demand for its equipment and services from leading quarrying customers in the region, Mantrac has in recent months supplied Cat rigid dump trucks, articulated haulers, dozers, excavators, motor graders and wheeled loaders. The most popular models in the quarrying and cement industries are the Cat 349 and 352 large excavators, the D8 dozers, as well as the 966 and 980 medium wheeled loaders.
The Cat 349 and 352 large excavators offer low owning and operating costs. These models are said to be efficient and rugged at the rock face. Customers particularly appreciate the mass excavation arrangements. A short boom and large capacity bucket allow customers to carry more material and ultimately load trucks in fewer passes.
“The Cat D8 is a durable dozer, and we see our customers using it mainly for site preparation, dressing and arranging boulders. Quarry applications require high penetration force, and the D8 comes with a single shank ripper with a rugged design to provide the required force,” says Magdy.
At the rock face, the Cat 980 medium wheeled loader increases productivity with its 5 m³ bucket to load trucks in few passes. The Cat 966 medium wheeled loader delivers exceptional performance in load and carry applications, where faster cycle times are achieved through its highly productive Performance Series 4m³ bucket.
Magdy has also seen interest in the integrated Cat Payload onboard scale system, which provides on-the-go weighing to assist operators achieve precise load targets.
In addition to machines, quarry operators also rely on technology and support. To this end, Product Link has proven to be a useful solution to monitor fuel usage and theft. The importance of fuel management cannot be reiterated enough, especially given that it is the second-largest production cost, after explosives, for a typical quarry operation.
In 2021, Astec Industries entered a strategic alliance with Unatrac for the distribution of all the equipment in Astec Industries’ Material Solutions division for West Africa. The deal covers Astec’s premium range of crushers, screens and feeders, as well as washing, classifying and material-handling solutions, modular plants and rock-breaker technology
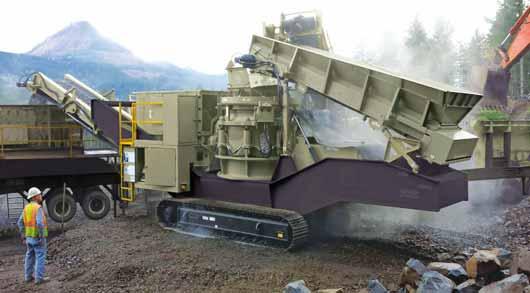
Information such as location, productivity, idle time and diagnostic codes are also available through the online web applications. Connectivity is available through either cellular or satellite networks.
“The back-up service from the dealer is always critical for customers. The more efficient the service support, the more efficient the quarry is, and ultimately the more profitable the customer becomes. Since a lot of equipment is used systematically within a load and haul environment, one machine down can cripple the operation. Customers appreciate our support through Customer Value Agreements, which help reduce owning and operating costs and provide peace of mind to focus on production and on uptime. We work very closely with our customers to tailor the support they require,” explains Magdy.
EXPANDING DEALER FOOTPRINT
On the back of West Africa’s infrastructure growth plans, several original equipment manufacturers have positioned themselves for possible business opportunities through new dealer appointments in the region.
For example, Metso Outotec has just appointed Panafrican Equipment Group as the distributor for its mobile crushing and screening equipment for the aggregates and mining contractor customer segments. The agreement covers Nigeria, Sierra Leone and Ghana in West Africa, as well as Kenya, Tanzania, Uganda, Rwanda and Burundi in East Africa, where Panafrican Equipment Group already has an extensive and established presence in the construction and mining businesses.
“We believe that our cooperation with Panafrican Equipment Group will help us improve our service towards our customers. What we will offer is better agility, service and presence in the market,” says OlliPekka Oksanen, SVP, Global Distribution Management in the Aggregates business area at Metso Outotec.
The Panafrican Equipment Group is a recognised Komatsu and AGCO equipment dealer in West and East Africa, with a strong presence in large mining, light and alluvial mining, cement and aggregates, agriculture and forestry, civil and infrastructure as well as power and energy sectors.
“Panafrican was seeking a comprehensive crushing solution to complement our product offering across all our markets. The Metso Outotec product line provides us with a market-leading crushing and screening product line,” says Scott McCaw, CEO of Panafrican Equipment Group.
Through its Africa and Middle East business units, last year Astec Industries entered a strategic alliance with Unatrac, part of the Mantrac Group, one of the largest Cat dealers in the world. The new distribution partnership will see Unatrac, including Mantrac and Delta groups, offering sales and support services in Nigeria, Ghana, Sierra Leone, Liberia, Kenya, Tanzania, Uganda, Egypt, Iraq and the Ural and Volga regions in Russia, for all the equipment in Astec Industries’ Material Solutions division. This division encompasses Astec’s premium range of crushers, screens and feeders, as well as washing, classifying and material-handling solutions, modular plants and rock-breaker technology.
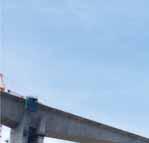
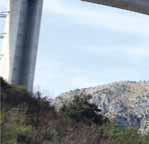
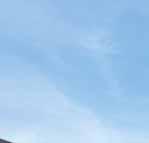
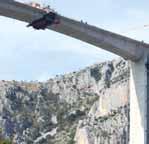
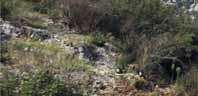
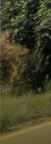
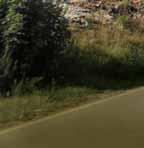
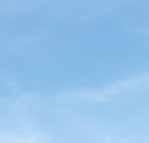
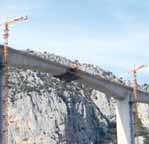
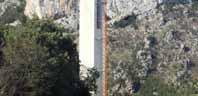
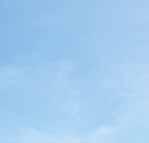
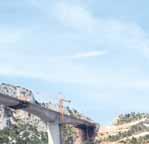
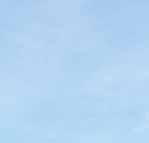
The Chinese-built Moračica Bridge in Montenegro: a glorified bypass of Podgorica or will it be part of a larger European Union-financed prestige highway project? (image: Attribution-ShareAlike 4.0 International (CC BY-SA 4.0))
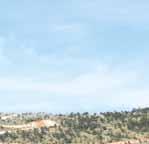
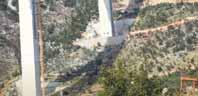
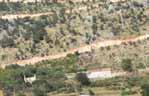
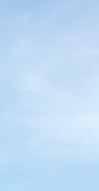
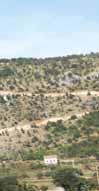
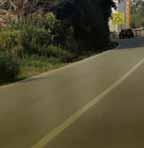

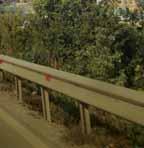
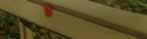
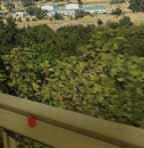
A HEAVYWEIGHT FIGHT IS COMING: EUROPE’S GLOBAL GATEWAY VERSUS CHINA’S BELT AND ROAD
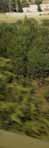
Global Gateway is the European Union’s recently launched infrastructure investment programme to counter China’s Belt and Road initiative, a mega-project that the EU believes the Chinese will use to increase their political and economic influence around the world. Brussels has decided that it is time to fight back. But how viable is this EU alternative? David Arminas reports
It was in July last year that European Union foreign ministers, at an EU Foreign Affairs Council meeting, agreed an ambitious global infrastructure plan linking Europe to the world. Money was to be loaned to governments to improve their energy generation and transport connections to Europe in order to boost trade.
The Global Gateway programme is often considered a direct countermeasure to what many governments in Europe, North America and Australia-Asia see as the increasing so-called soft power of China through its Belt and Road Initiative investment and loans. Western governments fear Chinese President Xi Jinping’s Belt and Road Initiative encourages countries to take on large Chinese loans that can then be later leveraged by Beijing for political purposes.
“We see China using economic and financial means to increase its political influence everywhere in the world. It’s useless moaning about this, we must offer alternatives,” Germany’s Foreign Minister Heiko Maas told the news agency Reuters at the time of the EU announcement.
But it wasn’t until December last year
that the EU announced the amount of €300 billion (US$340 billion) to be made available through the Global Gateway, up to 2027.
The funding comes from a combination of EU funds, member-state investments and European investment banks, including the European Investment Bank (EIB) and the European Bank for Reconstruction and Development (EBRD). It also seeks to mobilise private sector investment.
“We want to make Global Gateway a trusted brand that stands out because of high quality, reliable standards and high levels of transparency and good governance,” said Ursula von der Leyen, president of the European Commission, as she presented the plan to the media. She said the money will be for “both hard and soft infrastructure, in sustainable investments in digital, climate and energy, transport, health, education and research”.
BELT AND ROAD
Since its launch in 2013, China’s Belt and Road has garnered 139 participating countries, including several EU member states, that represent 40% of the world’s GDP.
In 2019, Italy became the first – and so far only – G7 country to sign a non-binding memorandum of understanding related to the initiative, notes the Council on Foreign Relations, a non-profit US think tank based in New York City.
There is little doubt that Belt and Road is a political tool as much as an economic one for China’s communist dictatorship. In the autumn of 2017, it was incorporated into the Communist Party’s constitution and there quickly followed another 61 countries signing up in some fashion. Members now include 39 sub-Saharan African countries, 34 in Europe and Central Asia, 25 in East Asia and the Pacific, 18 in Latin America and the Caribbean, 17 in the Middle East and North Africa and six in South Asia.
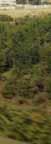
A 2018 study by Morgan Stanley predicted the Belt and Road initiative will have dished out up to nearly US$1.3 trillion in loans by 2027, helping to transform China into a high-income economy. Belt and Road agreements are often opaque and secret, making it hard to assess how much China has already spent on infrastructure. The lack of transparency is a major concern for western ➔
businesses competing with Chinese firms –and ultimately Belt and Road loans – when tendering for contracts. Are the loans based on choosing a Chinese contractor, putting in jeopardy the EU’s open-rules-based public tendering processes to which EU firms must adhere? All the while not providing reciprocal access to the Chinese market for EU contractors.
The European attention to fair and transparent procurement practices is a reflection of concerns that Chinese companies could benefit from future Silk Road contracts. The companies sidestep standards in tendering contracts to which European companies must adhere, according to a report by the European Bank for Reconstruction and Development.
However, the timing of the European Union’s announcement of Global Gateway comes when, according to the EBRD, China’s state-led Belt and Road lending volumes have been in decline. Since 2019, these Chinese loans have increasingly been tied to higher
billion ($170 billion) – half of the overall amount pledged in December. She made the announcement during a two-country Africa trip to promote the Global Gateway AfricaEurope investment package. Specifically, she announced €1.6 billion ($1.7 billion) for a green-energy investment plan in Morocco.
WHERE DOES ALL THIS LEAVE GLOBAL GATEWAY?
According to documents from the European Commission, “by offering an innovative choice for global infrastructure development, based on the needs of our partners, Global Gateway will be an investment in international stability and cooperation. Global Gateway can demonstrate how democratic values provide certainty and transparency for investors, sustainability for partners and long-term benefits for people around the world. The EU will offer its financing under fair and favourable terms in order to limit the risk of debt distress.” Firstly, it is important to understand
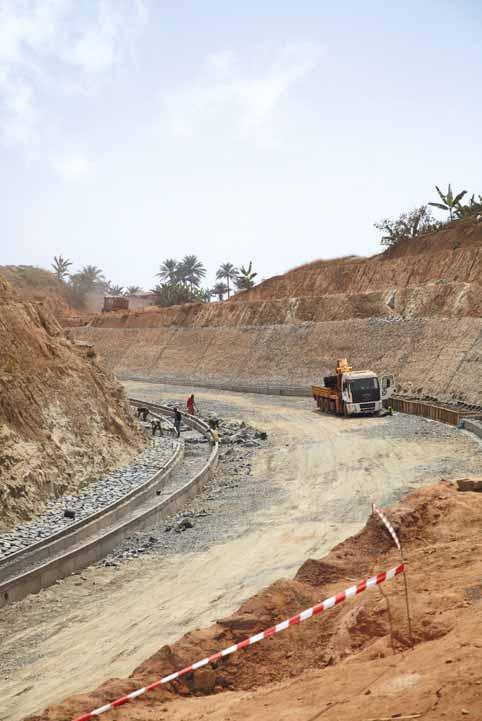
warned the European Commission not to make Global Gateway about competition with China. “It does not have to crowd out Chinese investments,” she said. “I very much hope that it does not aim to, or is perceived as, an attempt to displace China in one way or another. Nobody wins from that.”
While the Global Gateway is presented in some capacity as an alternative funding to Belt and Road, it is early days yet to see how much it will be used, explains Stefan Vladisavljev, programme coordinator at the Belgrade Fund for Political Excellence in Serbia and an observer of China’s economic influence in Europe.
“One could argue that there would be no Global Gateway if it weren’t for China’s Belt and Road initiative,” he told Global Report. “The question is how efficient Global Gateway will be for setting up manageable financing terms for infrastructure projects. Of course Gateway is welcomed, he says, as any such facility would be if it can help countries upgrade their infrastructure. But what comes with it?”
Road construction in the African state of Cameroon has run into problems, partly due to non-payment of fees to the Chinese contractor, as well as slow progress by the government on land rights of way
Since its launch in 2013, China’s Belt and Road has garnered 139 participating countries
The EU must be seen to have a worthwhile investment alternative to that offered by China. This might be evident in the way that contracts are tendered. An emphasis could be on transparency during procurement that included preferential use of local, regional and national companies as contractors. This could be especially attractive for African countries There is also the potential to tie in the creation of new companies and industries for the project that might provide jobs and services for many years after the construction phase is finished.
Environmental standards, rule of law, transparency, competition and market rules - these, he says, go hand in hand as values that help European economic development. But they could be the Achilles heel for a strong uptake of Gateway financing packages, especially outside Europe.
“We have seen the increasing acceptance of China’s initiative across Asia and now in Europe because it comes with no immediate such strings attached,” he says. “There is no pre-condition for a client country to receive money except, of course, to engage with Chinese [construction] companies. If there are a lot of pre-conditions and heavy bureaucracy before you get money from the Global Gateway, then Gateway might not be as attractive as Belt and Road loans which also are usually fast-tracked. You see construction workers and equipment in your country in a matter of weeks or a few months, very attractive for leaders of developing countries.”
THE 21ST CENTURY SILK ROAD
The Belt and Road Initiative is essentially a plan to create a modern Silk Road, a network of trade routes connecting China and the Western world, akin to the Eurasian trade routes used from the second century BC until the mid-15th century. The routes ran from eastern and southern China along land through Asia and incorporated sea routes through the Indian Ocean, up into the Mediterranean Sea, with routes branching into Africa. The name Silk Road comes from the lucrative trade of silk textiles that were produced almost exclusively in China. Today’s routes allow more for Chinese exports to Europe, Asia and Africa than imports inwards to China from those regions.
“You have to understand that for countries, such as Serbia, it is not really important where the money is coming from. If there were more easy access to European funds, Serbia would be willing to take it,” says Vladisavljev. This is the mindset for many leaders, especially in developing countries, who use infrastructure development to establish their credentials as strong leaders.
INCENTIVES
No one is shuffling anyone into a dark corner and handing out brown envelopes of money. If you consider, says Vladisavljev, that the first incentive is that you will have to engage with a Chinese contractor, you are obliged to do so. These are formal agreements. So, from a lack of transparency perspective, including not going out to tender, that is in one respect, a form of institutionalised incentive to use Belt and Road offerings.
Vladisavljev believes that Belt and Road interest rates are not necessarily high; between two and three per cent, depending on the country and the average interest rate on the global financial market. On the other hand, the price of the projects might be quite a bit higher than with non-Chinese contractors. This gives a potential Belt and Road client country pause for thought and perhaps to consider what the Gateway can offer, despite added preconditions.
The case of Montenegro facing massive debt is often cited by critics of Belt and Road as a good reason for countries, including more prosperous European ones, to be particularly careful when doing a deal under the Belt and Road Initiative.
Montenegro took a €1 billion loan from China’s state-owned Exim Bank in 2014 to
build part of a grand highway project that was to run 165km from the country’s main port of Bar on the Adriatic northeast into Serbia. However, a general slow-down of the economy followed by work closures due to Covid and successive blows to the national economy, meant the project fell behind schedule. Loan repayments reached a critical point in mid-2021, at which Montenegro eventually asked the European Union for help.
The EU offered to help with construction of the rest of the highway but not with debt repayments to China. However, Montenegro’s finance minister managed to hammer out an agreement with the EU to hedge the loan including adjustments for foreign exchange rates. A repayment schedule was also reportedly concluded with the Chinese.
“Even if the Global Gateway existed in 2014 when Montenegro signed its contract with the Chinese, it might be that the European funding would not have been forthcoming,” says Vladisavljev. The concern for European lenders is that the actual economic boost from such a highway may not have been worth the cost of constructing it and they would have seen payment of the loans running into difficulty, explains Vladisavljev. But for decades Montenegrin politicians wanted that highway to connect the south of the country to other regions and onwards to Serbia, a major trading partner.
Big infrastructure projects lend political kudos to national leaders and so are politically expedient, if not economically so. There is likely little that could have persuaded the Montenegrins to temper the project, in cost and size. “If it means going to the Chinese, so be it. Even if taking money from Europe would mean that the European Union looks more favourably upon a potential new member state. Believe me, nobody cares about that,” he adds.
Yet it appears that China may also be having a major rethink about its Belt and Road investments in less developed countries, such as those in Africa. While African leaders have been quick to sign up for road development, lack of construction progress is, to be fair, not always because of an issue with the Chinese contractor.
Take the case of the first phase of Cameroon’s 196km Yaoundé-Douala highway, a prestige project linking the political capital Yaoundé with the business capital Douala, an Atlantic Ocean port. The cost was originally $550 million for the 60km four-lane highway. The contractor, China First Highway Engineering Company, had to
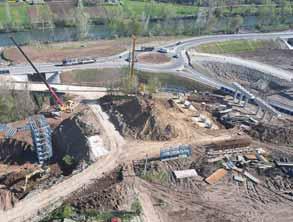
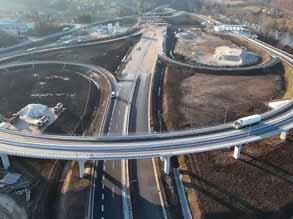
STRATEGIC IMPORTANCE
Serbia’s E-763 motorway, part of Europe’s transcontinental Corridor 11 route, is of strategic importance to China’s Belt and Road initiative, being a key access point to Central Europe and beyond. A section of the E-763 section within Serbia – 30km between the cities of Preljina and Pozega - is being financed by a loan from China’s Exim Bank and is being built by the China Communications Construction Company as main construction contractor. The Serbian section will include the Munjino Brdo and Laz tunnels which will be the longest tunnels in Serbia when the motorway is opened. It includes three tunnels, 35 bridges, three interchanges and a maximum design speed of 120kph. It will connect the Serbian Capital Belgrade to Montenegro’s capital Podgorica – and become part of Montenegro’s planned route from its Adriatic port of Barr to the Serbian border. Unlike in Montenegro, there have been few issues between the client country and the main Chinese contractor.
negotiate several contract extensions because of non-payment by the government as well as a lack of expropriation of the required land and rights of way.
Meanwhile, Montenegro is left with a nearly-finished 42km-long “glorified bypass around Podgorica” that includes the stunning Moračica Bridge, notes Vladisavljev. But the rest of the country’s prestige highway project may well be constructed with EU funding under the nascent Global Gateway. However, this remains to be seen; it is early days yet for Europe’s infrastructure investment programme.
BE SUSTAINABLE AND INNOVATIVE BY PUTTING OPERATIONAL AND APPLICATION EXPERTISE FIRST
The construction equipment sector needs to work towards decarbonisation and digitalisation says the Fayat Group, whose road equipment division is especially strong in developing new ideas. The French manufacturer has a range of products covering everything from safe and alternative drive systems to new technologies for reduced energy consumption levels, improved carbon footprints, autonomous operations and ever-more digital integration. Fayat is making these ideas reality today. Stéphane Guillon reports.

Fayat believes that the way forward revolves around four pillars: innovation leadership, putting operators first, application expertise, and sustainability. Construction has to work in an increasingly complex world, one that demands an evermore inventive and agile approach.
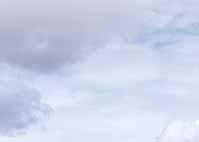
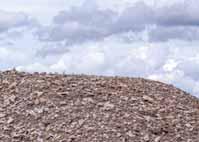
Stéphane Guillon, Fayat’s group marketing director, says: “We see three main priorities driving road and construction equipment: advancing safety levels, improving our environmental impact and harnessing digitalisation. These objectives are at the heart of every machine, making contractors more productive, efficient and profitable. This is especially true in planning and documentation, but also in operatorassistance systems to improve both the quality of work and also the safety of the jobsite.”
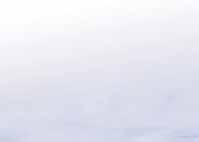
Fayat has equipment offerings for every part of the value chain. “It has solutions in asphalt production, application and compaction, road maintenance, sweeping, cold milling, stabilisation and recycling, as well as soil compaction,” says Guillon.
At the bauma 2022 exhibition in Munich this October, Fayat will showcase all of these ideas across its range of brands including BOMAG, Dynapac, Ermont, Marini, Secmair, Dulevo, and Scarab.
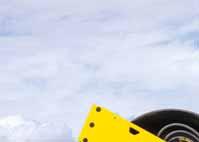
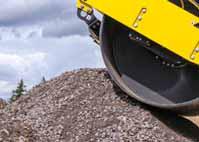
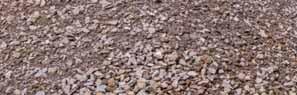
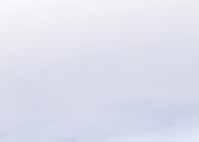
INNOVATION LEADERSHIP
For example, BOMAG will use the event to highlight its new generation of pivot-steered tandem rollers, the BW 154 and the BW 174, which are equipped with individually configurable touchscreens to achieve a new level of “user-friendliness.”
Operators can also benefit from the company’s “Asphalt Manager” compaction system on these machines: “Setting the
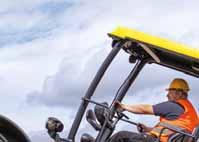
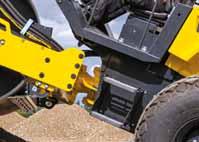
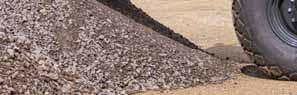
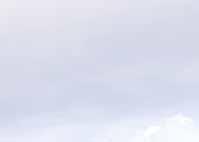
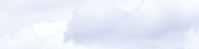

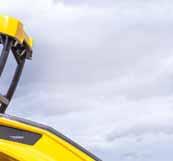
BOMAG smart line single drum rollers. Fayat believes that the way forward revolves around four pillars: innovation leadership, putting operators first, application expertise, and sustainability
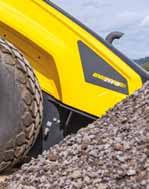
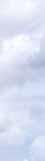
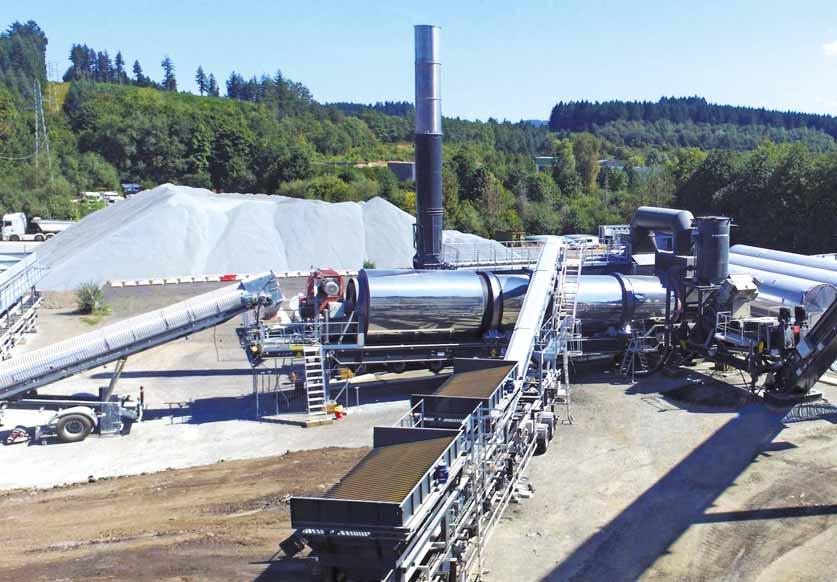
machine parameters is easy,” says BOMAG. “All the operator needs to do is select the paving layer. Every one of the machine’s function and equipment options has been thought out down to the last detail.” It’s automatic and easy.
But before the road surface can be rolled, it is made much easier if the ground has been compacted properly. “Optimum compaction frequency is found close to the so-called natural frequency in the soil. The soil-drum system of the Dynapac Seismic system automatically detects this natural frequency,” says the company, and the machine adjusts its vibration frequency accordingly. The aim is to be as close to the ground’s natural frequency as possible. “The adjustment is done five times per second,” says Dynapac, “which gives a very exact and adaptive system.”
Dynapac says that savings can be made using the Seismic system because it reduces the number of passes needed and this, in turn, lowers fuel consumption. Technology like this means lowering the environmental impact on site at the same time as prolonging the lifetime of the roller.
If operators combine Seismic with the Fayat Group’s Dynalyzer technology, and use its engine management system called ECOmode, “fuel savings of approximately 30% can be expected,” says the manufacturer, “together with improved compaction performance, reduced noise levels and increased driver´s comfort.
ABOVE: Ermont’s TSX asphalt plant allows up to 70% reclaimed asphalt pavement (RAP) to be used in a hot mix asphalt (HMA) production process … the highest recycling rate in HMA for continuous plants, says FayatBELOW: Good vibrations: Optimum compaction frequency is found close to the so-called natural frequency in the soil. The soil-drum system of the Dynapac Seismic system automatically detects this natural frequency and adjusts its vibration frequency accordingly
“The SEISMIC system will also very effectively eliminate the problems with double jumping, also called bouncing, since the system ensures that the machine operates in harmony with the soil.”
Recycling remains a key objective too, of course, when road surface technology comes to the fore. And the Fayat Group’s Ermont TSX system allows up to 70% reclaimed asphalt pavement (RAP) in a hot mix asphalt (HMA). “This is the highest recycling rate in HMA for continuous plants,” says Fayat, ➔
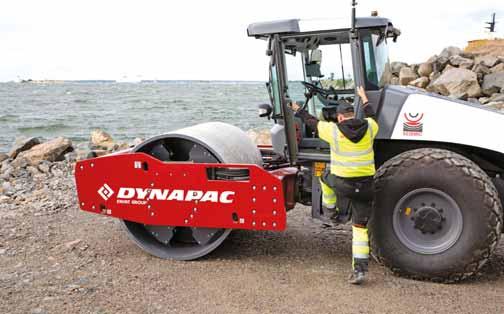
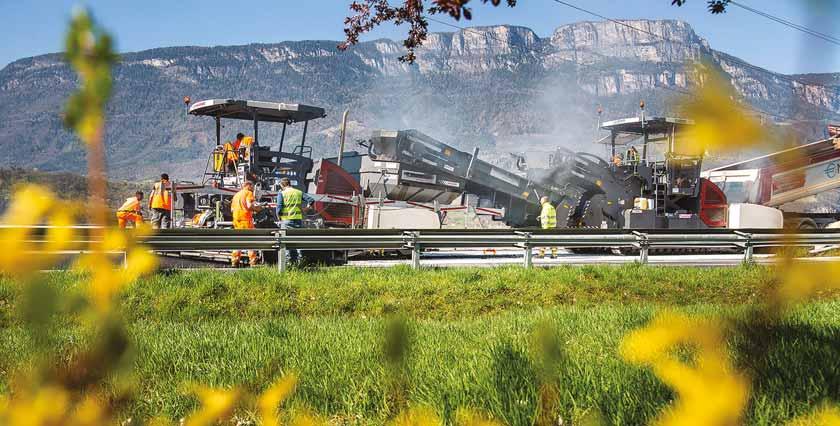
“while protecting the environment.”
How does it work? Ermont says that its new patented technology makes it possible to produce high-quality HMA while using RAP “by never exposing the binder to the radiation of a flame or to excessive temperatures throughout the heating and mixing process.” This means that the equipment can “recycle up to 70% of RAP without compromising on asphalt quality, while using just one drum and one burner as a result of the DuoTHERM heatexchange process. This allows users to vary the recycling rate according to the needs of the formulations without any specific modification to the system.”
OPERATOR FIRST
Putting operators first means developing
ABOVE: The Dynapac MF2500 IMIX feeder offers cost-saving, C02-reducing features using “a heated scraper with a generator to keep the belt clean, even when sticky mixes are fed.” The system uses a conical auger in the hopper, a flow divider in the conveyor and a mixing system at the end of the main conveyor BELOW: Operator safety is a key driver in the design of the Dynapac F1250CS paver which allows remote working. The remote-control RC 360 unit makes paving jobs safer and smarter with the operator not tied to the dashboard … He can position himself wherever suitable
full graphic visual display,” says the company. “Due to direct sensor selection and multiple selectable pre-set grade settings, operation is intuitive with short menu paths. In addition, soft keys are deposited with clear functions that allow easy setting and, due to the machine’s built-in soft-start function, the unit smoothly cuts the asphalt right from the start of the milling process.” It could not be easier. Operator safety is also a key driver in the
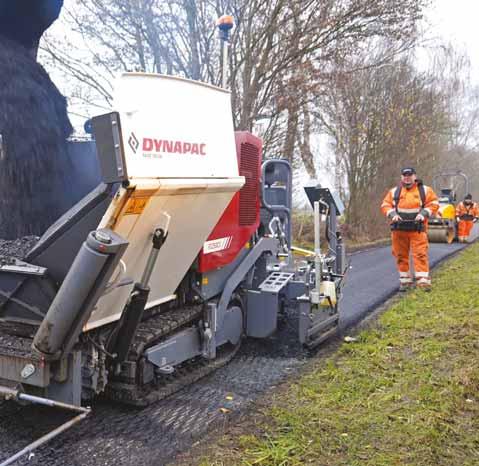
The machine has been designed to allow the operator to stand well away from the paver and to drive the process from a hand-held dashboard attached to a set of adjustable shoulder straps. This means users can position themselves well away from the worst of the asphalt fumes … and get really good visibility, often standing to the side of the machine, or walking alongside it. The F1250CS paver also offers “high safety levels,” says Dynapac, “with automatic stopping when distance between the operator and the paver exceeds 10m … or when the remote is tilted at a higher angle than 45 degrees.”
“The unique screed design ensures highquality results,” says Dynapac. Operators benefit from “high productivity levels via a powerful and efficient 55kW power pack and stepless rpm settings. The paver can be operated using the dashboard or remotely by using the RC360. The 320mm auger wings are reliable for a smooth material distribution and making sure there is always enough material in front of the screed.”
Its large hopper with foldable material wings can also buffer up to five tonnes of material for narrow situations, where filling is difficult.
The Dynapac MF2500 IMIX feeder has also been designed along similar lines. It is easy to operate and offers cost-saving, CO2reducing features, says Fayat. Key benefits are less downtime, lower operating costs, and a “heated scraper with a generator to keep the belt clean, even when sticky mixes are fed.”
“At the heart of the IMIX-system is a combination of three smartly-positioned devices: a conical auger in the hopper, a flow
divider in the conveyor and a mixing system at the end of the main conveyor,” says Fayat. “Together, they equalise the temperatures within the mix while providing an optimal blend of large and small stones. This gives every finished road its homogenous look and long-lasting quality.”
APPLICATION EXPERTISE
Getting close to the action is vital too. Mobile Ermont asphalt plants help to minimise logistics costs by more than 75%, for instance, by “allowing customers to easily and seamlessly move the plant closer to where it is needed.”
“In addition,” says the manufacturer, “all Ermont asphalt plants are conceived for eco-energy and bio-fuels use, leading up to significant CO2 emissions reductions.”
But how does all this fit together in the real world? The table (right) shows how different factors such as mobile equipment, fuel type, logistics in terms of distance travelled, the electricity source, and RAP levels can affect CO2 emission levels on three different jobsites. Jobsite C churns out 80% less CO2 than jobsite A:
SUSTAINABILITY
When it comes to performance, batteryelectric construction machines are on a par with their comparable diesel-powered counterparts and they are seen as the way forward by many. They are every bit
Bitumen Aggregates
Jobsite A
Jobsite B
Jobsite C
Jobsite AJobsite BJobsite C
RAP rate0%50%70%
RAP transport associated to HMA transport-YesYes
Direct RAP use (without preparation)-YesYes
Distance: Asphalt plant / Application site40km10km10km
Distance: Quarry / Asphalt plant30km30km30km
Distance: Refinery / Asphalt plant250km250km250km
FuelHeavy fuel oilLPG100% renewable BIOFUEL
Warm mix asphalt (-300C)NoYesNo
Electricity sourceNetwork (FR)Generating setGenerating set
Aggregates and RAP moisture3%3%3%
as powerful as well. The BT 60 e batterypowered tamper from BOMAG is a good example. It has a 70mm stroke and an advance rate of 20 m/min. The motor is fully encased for extra protection against shocks and dirt. In addition to being particularly powerful, the battery-tamper is also a worthwhile investment into the future.
Another example is the Dynapac CC900 electric tandem roller designed to compete in the 1.5 tons tandem vibratory roller class, using a drum width of up to 1m and offering a centrifugal force of 16.7kN, a nominal amplitude of 0.4 mm, and a static linear load (front/rear) of 6.1/ 7.9 kg/cm. All this and zero emissions at the point of operation.
BELOW LEFT: The BT 60 electric-battery-powered tamper from BOMAG has a 70mm stroke and an advance rate of 20 m/min using a motor that is fully encased for extra protection against shocks and dirt RIGHT: Weighing in at 1.6tonnes and with an operating width of 0.8 to 1.0 metres, the Dynapac CC900 electric double-drum vibratory roller delivers the same linear load, amplitude, frequency and travel speed as the diesel-powered model upon which it is based, and it can be recharged in around one hour, making it ready for a full 10-hour shift of stop/start operation
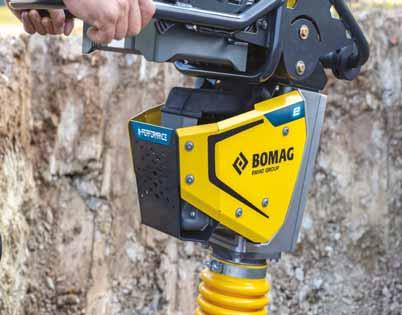
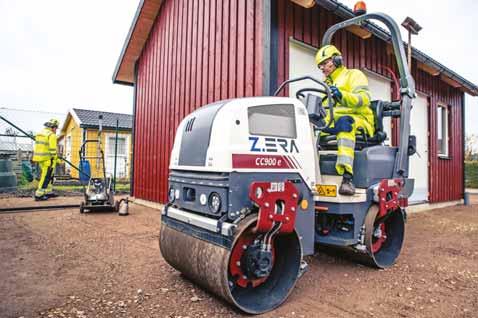
➔
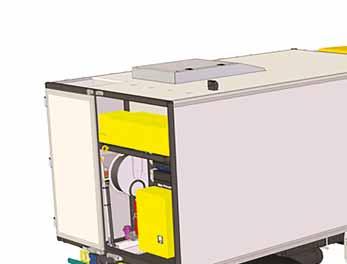

“Weighing in at 1.6 tonnes and with an operating width of 0.8 – 1m, the CC900 e double-drum vibratory roller delivers the same linear load, amplitude, frequency and travel speed as the diesel-powered model upon which it is based,” says Fayat. “The CC900 e machine can be recharged in around one hour, making it ready for a full 10-hour shift of stop/start operation.”
RAP


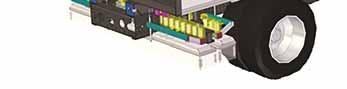
Recycled asphalt pavement (RAP) is everywhere now. Fayat believes that its Marini EvoDryer is: “The best available technology when it comes to introducing reclaimed asphalt pavement (RAP) into the recycling ring of an asphalt plant. It allows the customer flexibility and help in meeting the most demanding market requirements when it comes to asphalt production sustainability.
“The Marini EvoDryer design has increased the length of the dryer drum, allowing users to change the position of the introduction of the RAP after the dryer flame. This significantly contributes to the versatility of the plant for diversified use in addition to making the difference when it comes to decreasing emissions, minimising odours and enhancing the quality of the final product,” adds the manufacturer.
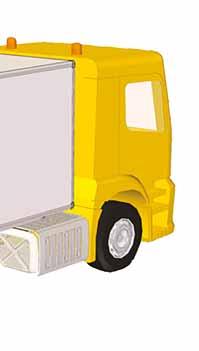
ABOVE: Secmair’s “BOX” binder sprayer uses 70% less energy than a traditional binder sprayer, and the design can even be fitted onto a truck chassis. Traditional diesel-powered binder pumps have been replaced by an electric, hydraulic tank, and the old-fashioned cylinders have been replaced by electric cylinders. The standard diesel burner is replaced by an LPG burner, and the insulation of the binder tank is more than double what it was previously
ON THE ROAD
Fayat group company Secmair has developed a “unique technology in the world of bitumen emulsion sprayers” using the brand name “BOX”. The idea is that traditional “dieselpowered binder pumps have been replaced by an electric, hydraulic tank, and the oldfashioned cylinders have been replaced by electric cylinders. The standard diesel burner is replaced by an LPG burner, and finally the insulation of the binder tank is more than double what it was previously.” The end result is that a “BOX” binder sprayer uses 70% less energy than a traditional binder sprayer, and the design can be translated into a number of other sectors or configurations. It can even
hit the road on the back of a truck.
“Due to the shape of the “BOX”, fitting this solution has become so easy that we believe the process can be installed on to any truck in the world,” says Secmair. Innovative thinking means that this new process will enable the construction equipment industry to be ever-more sustainable.
As Fayat proves, to be sustainable and innovative, the industry should put operational and application expertise first.
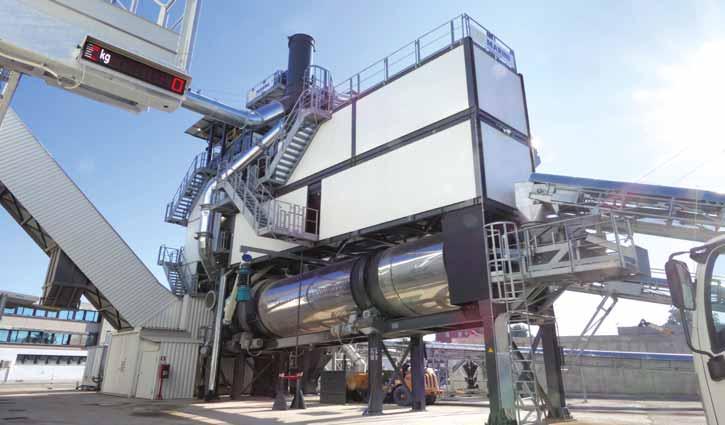
The Marini EvoDryer asphalt plant design has increased the length of the dryer drum, allowing users to change the position of the introduction of the RAP after the dryer flame. This significantly contributes to the versatility of the plant, helping to decrease emissions, and minimise odours
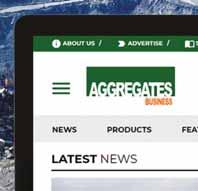
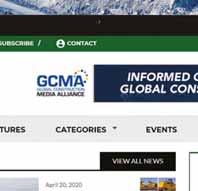
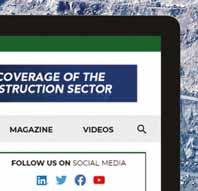


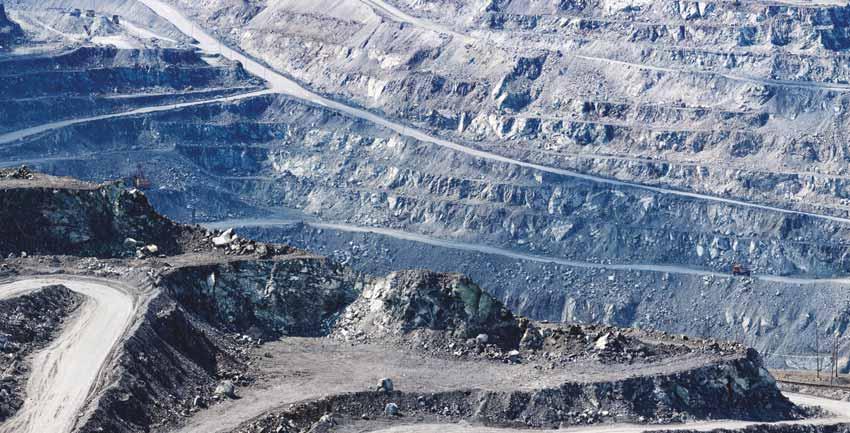
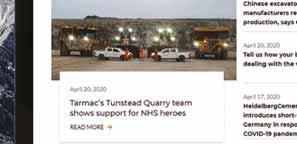
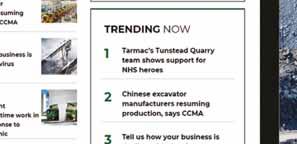
INFRASTRUCTURE SPEND IS DRIVING THE PHILIPPINES AND INDONESIA TOWARDS ECONOMIC RECOVERY
As quarantine restrictions ease and Covid takes a back seat, government spending is starting to speed up a host of major infrastructure projects in The Philippines and Indonesia. Is it fast forwards to a brighter future? V L Srinivasan reports.
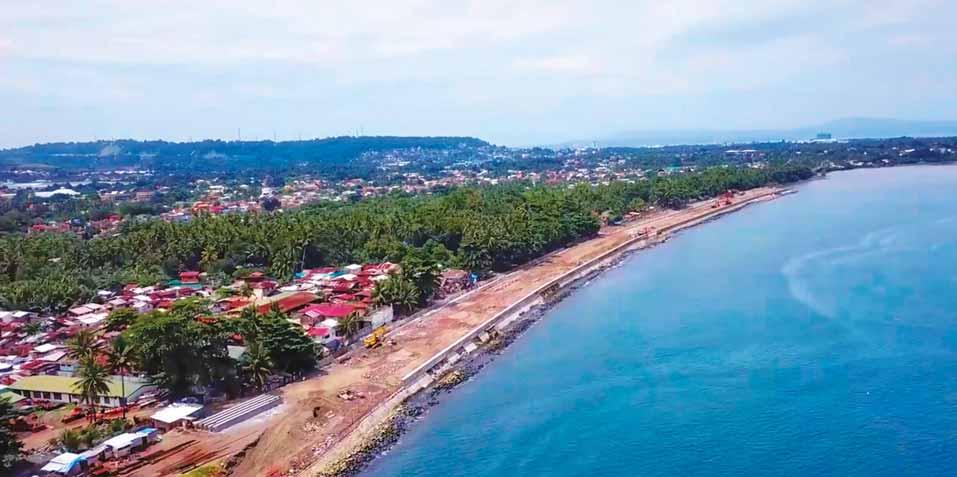
A part of the coastal road under construction in Davao, Philippines
The economies of The Philippines and Indonesia were hit hard when the worst of the Covid-19 pandemic arrived in Q1 of 2020, but things recovered fast when their respective governments announced a series of new infrastructure projects in 2021. The plan is ambitious and it includes new cities, new roads, new rail lines, and large new commercial property development schemes.
Inside the ASEAN group of countries, it is The Philippines and Indonesia that are driving the growth of the construction industry as this massive infrastructure pipeline starts to flow, and political momentum builds. Both countries are
fighting issues such as poverty, poor quality housing and unemployment. Both of their governments are convinced that executing a group of major infrastructure projects worth billions of dollars will help find a solution.
They are investing in big and busy countries too. The demand is there. The Philippines is the 18th most populous country in the world with 114 million inhabitants, while Indonesia is the fourth most populous island nation in the world with 271 million people.
Some of the major infrastructure projects in Indonesia include the construction of an incredible $46 billion new capital city
named “Nusantara”, which translates as archipelago. There is also a high-speed rail project between Jakarta and Surabaya region underway, plus the new Jakarta MRT (Mass Rapid Transit) scheme. Jakarta is also investing in a new Light Rail Transit system and a Greater Jakarta Light Rail Transit network.
Six major traffic corridors are also underway, known as the “backbone toll roads”. These plans comprise a new TransJava toll road, a Trans-Sumatra toll road, a Trans-Kalimantan toll road, a Trans-Sulawesi toll road, a Trans-Nusa Tenggara toll road and a Trans-Papua toll road. This is a huge
step forward for the region’s strategic highway network, and all of them are now under construction.
NEW CAPITAL CITY
It’s hard to know where to look first, but Indonesia’s incredible new capital city plan has to be at the top of the list. President Joko Widodo said that it would take approximately 15-20 years to complete his country’s new national capital city: “Building a new capital is a ‘giant job’ and is complicated. Hence, it will take a long time to complete”, he had said.
Nusantara is located in Kalimantan, the Indonesian portion of the island of Borneo. The new capital will be built on a virgin 40,000-hectare site on state land near the existing urban centres of Balikpapan and Samarinda.
“Relocation of the nation’s capital city is not just about building government buildings. The transfer will be part of Indonesia’s structural transformation to build a better way of life,” says Widodo.
Besides Nusantara, the Indonesian government is pushing ahead with plans to develop several infrastructure projects including 19 special new economic zones, a host of new expressways, six new airports, 6,000-plus kilometres of new rail tracks, an expansion of the domestic gas network, and more than 100,000 hectares of new irrigation channels to help the nation’s farmers. The total cost of these projects is currently estimated at $430 billion.
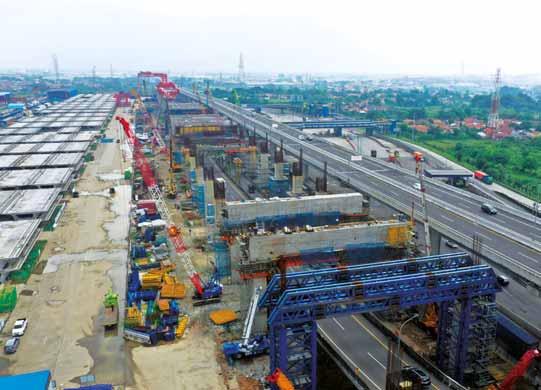
saying that the government has been actively fostering private sector participation in the construction industry, with the exception of national strategic projects.
Indeed, the Public Works and Housing Ministry also introduced a rule in May 2018 stating that state-owned construction service providers cannot participate in public tenders worth less than $70 million.
When asked about the new Nusantara capital city plan, Hadimuljono said initial planning had been carried out by clearing 56,180 hectares of land to build the
moved to the city by then,” the minister added.
TOLL ROADS AND EXPRESSWAYS
Construction of new expressways and toll roads gathered pace only after Joko Widodo became President in December 2014. In fact, the government has drawn up plans to develop 4,480 km of new toll roads by 2030 in addition to the 1,500 km toll road projects that are to be completed in 2024 to support mobility.
The country is proud of its vision.
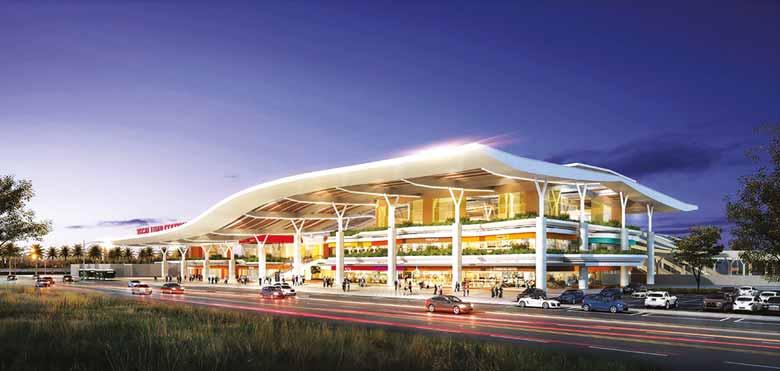
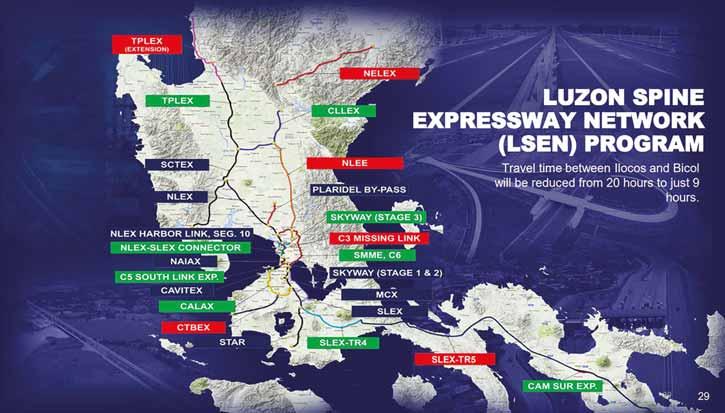
➔ plans did not involve alternative sources of financing. Most of them depended on the state budget, as they always have done in the past. “Or they left it to the private sector, which had not been going well for several years,” he added. It was time for some new thinking.
The Trans-Sumatra toll road’s entire length of 2,818 km will cost an estimated US$33.2 billion. It consists of 17 main segments and seven supporting segments and is expected to be completed by 2024. The Trans-Sumatra toll road will connect Sumatra Island from Aceh to Bakauheni.
The 1,167 km Trans-Java toll road became fully operational in 2019 and connects Indonesia’s two biggest cities, Jakarta and Surabaya, in East Java. This is part of Asian Highway 2 from Denpasar in Indonesia to Khosravi in Iran.
The construction of the 76-km Yogyakarta-Bawen toll road project was to begin in August 2021 as per the Toll Road Concession Agreement, but it was postponed to December 2021 and finally took off on 30 March 2022. The delay has been attributed to the change in government policies related to land acquisition, adjustments to new rules, and the conditions arising out of Covid-19.
HIGH-SPEED RAIL PROJECT
At one point, the Indonesian government planned to construct two high-speed rail (HSR) projects in the Jakarta-Bandung and Jakarta-Surabaya regions, but now it has decided to merge them into a single 142.3km-long system.
Indonesia’s Minister for Economic Affairs Airlangga Hartarto, who made the announcement, said: “The Cabinet, chaired by President, decided to extend the Jakarta-
Bandung railway project. It should not only end in Bandung but continue to Surabaya to make it more economically viable.”
This new line was a key part of China’s Belt and Road Initiative (BRI) project and its construction was initially going to be undertaken by a consortium of Chinese and Indonesian companies. The scheme has grown in size and scope since then, and a number of Japanese contractors are now involved.
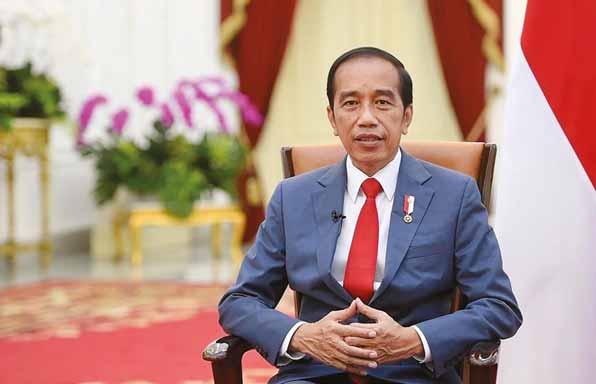
The project was China’s first overseas HSR project and the first of its kind in Southeast Asia. Trains will travel at a maximum design speed of 350 km/hour.
Priorities change all the time, of course, and the new HSR project is likely to be delayed due to the construction of the new capital city, according to Dwiyana Slamet Riyadi, president director of Kereta Cepat Indonesia China (KCIC), the consortium constructing the Jakarta-Bandung HSR.
Riyadi told a parliamentary committee on 8 February 2022 that the time to reach the break-even point for the project, which was expected to be 26 years, will now be 40 years.
Greater Jakarta LRT is a rapid transit system currently under construction in Jakarta, the capital city of Indonesia, as well as the adjacent areas of West Java and Banten, both within the Jakarta Metropolitan area. The project will connect the Jakarta city centre with suburbs in Greater Jakarta such as Bogor, Depok and Bekasi. Though it was to begin in 2019, it was delayed and is now expected to be operational by August 2022.
“Relocation of the nation’s capital city is not just about building government buildings. The transfer will be part of Indonesia’s structural transformation to build a better way of life.” Joko Widodo. President, Republic of Indonesia
Riyadi said revised estimates were made based on a recent feasibility study, taking into account the Covid-19 situation as well as “the relocation of the capital city.” Even the project cost, which was put at around US$5.5 billion in 2015, is likely to go up to US$7.9 billion.
Other delays to date stem from land acquisition challenges
and environmental clearances. While 80% of the works were complete as of January 2022, the consortium hopes to commence a trial run on part of the line by the end of this year.
FUNDING THE PROJECTS
In September 2021, the Indonesian government approved a budget of US$190.1 billion for 2022, of which US$133.8 billion is allocated for federal government spending and the rest for regional administration spending. Simultaneously, the government announced plans to allocate US$27.1 billion towards the infrastructure sector in the budget.
Even the state-owned sovereign wealth fund (SWF), the Indonesia Investment Authority (INA), has raised US$25.5 billion to invest in projects that will support the country’s sustainable development though they must also be commercially viable.
“For our fundraising, we’ve been talking to a lot of people. I think it’s over 100 different potential investors from sovereign wealth funds, pension funds, fund managers as well as global partners who were introduced by ambassadors,” said INA’s chief risk officer Marita Alisjahbana in an interview with Asia Investor magazine recently.
The commitments, which include a US$10-billion multi-sector investment from
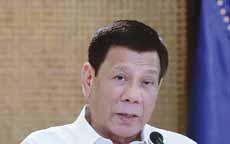
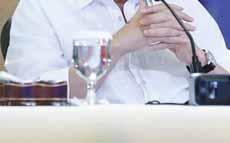
the UAE government and a US$7.5billion maritime infrastructure investment vehicleto invest in seaports, cargo yards, and logistic facilities - by a consortium comprising supply chain solutions company DP World and Canadian pension fund - Caisse de depot et placement du Quebec (CDPQ) - were secured.
and a US$3.75-billion thematic fund – with contributions of US$1 billion each from the Abu Dhabi Investment Authority (ADIA), the Dutch pension funds APG and CDPQ, and US$750 million from INA’s initial capital – all destined for the construction of toll roads.
EQUIPMENT DEMAND
“I assure our people that we will remain committed to finish all infrastructure projects on time, if possible, within my administration, with the least inconvenience to the public and with strict adherence to honesty and integrity.” Rodrigo Roa Duterte. President, Republic of The Philippines
With all these infrastructure projects being implemented at a rapid pace, the demand for construction equipment (CE) in Indonesia is picking up too and the country’s CE market is predicted to be around US$5.08 billion this year, reaching an annual volume of 35,803 units sold by 2028 according to researchandmarkets. com, the world’s largest market research store.
INA has also secured US$5 billion in seed money from the Indonesian government
In its latest report released in January 2022, researchandmarkets.com said the surge in commodity prices in the global market has also positively influenced the country’s mining industry.
A design of the proposed presidential palace in Nusantara, Indonesia’s new capital city in Kalimantan on Borneo island
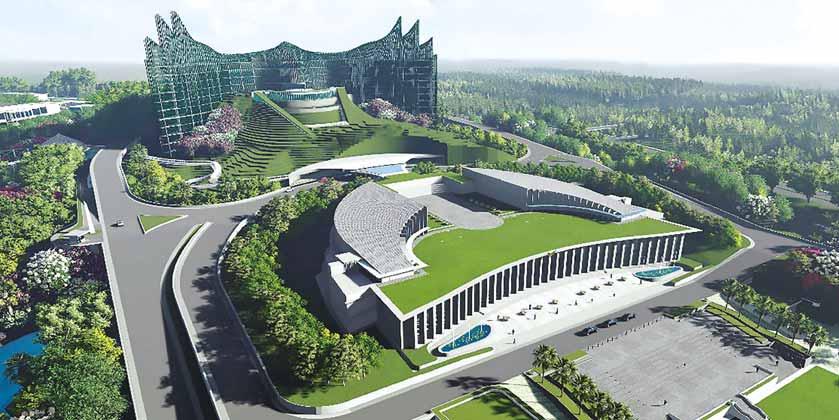
As Global Report was going to press, the Philippines was busy electing a new president: Ferdinand Marcos Junior. The incoming leader has already said that the country will maintain its strong links with China ... Our pro-Beijing agenda will “move up a gear” he says.
➔
One of the major CE companies that has been playing an active role in The Philippines and Indonesia is Metso Outotec, which is currently supplying and supporting machinery sales and aftermarket care packages to these mega projects. Shaun Fanning, vice president – Aggregates Asia Pacific, Metso Outotec, said the company is engaged to supply the construction equipment but the aftermarket sales and support is handled by the local distributor.
“We work closely with the customer to first understand their requirements and desired end products. Once we are clear that our offering suits their needs, we move to design, supply, install and commission the plant and equipment.”
And, “although our historical sales in this segment for the region have not been significant, we are refocused and are currently actively addressing several key projects in The Philippines. For these regions, we are able to meet the requirement as well as the latest Metso Outotec products for these projects. More recently, we have partnered with a distributor for our mobile crushing and screening range. An existing partner addresses the fixed plant segment. Both distributors are aftermarket suppliers.”
THE PHILIPPINES
In The Philippines, President Rodrigo Roa Duterte has set up 104 major projects costing around $85 billion in total, including the Metro Manila skyway-3, a new Manila International Airport, the NLEX-SLEX Connector Road, the Southeast Metro Manila Expressway Project, the North South Commuter Railway (PNR North 1), as well as a PNR South Long Haul and Flood Risk Management Project (FRIMP) in and around the Cagayan, Tagoloan, and Imus rivers.
“I assure our people that we will remain committed to finish all infrastructure projects on time, if possible, within my administration, with the least inconvenience to the public and with strict adherence to honesty and integrity,” Duterte said.
After Duterte held a review meeting with officials in February this year, Karlo Nograles, acting Presidential Spokesperson and Cabinet Secretary, said despite the challenges and limitations brought about by the pandemic, the momentum for the President’s brainchild programme “Build Build Build” (BBB) continues, and the infrastructure spending for the projects under the scheme stood at 5.1% of the nation’s GDP in 2021.
Nearly 32,000 km of road projects which included construction, maintenance,
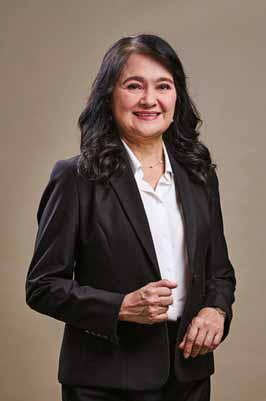
widening, upgrading, and rehabilitation have been completed from July 2016, when Duterte took over, to September 2021. More than 6,300 bridge projects and 12,394 flood control projects have also been completed to spur economic growth in different regions and enable a more disaster-resilient nation.
of GDP between 2001 to 2010 in its national infrastructure. This rose to 3% of GDP from 2011 to 2016 and is now at 5%-6% of GDP under the Duterte administration.
The DPWH has completed the construction, maintenance, improvement, and widening of 113.57 km of national roads in six provinces of the Eastern Visayas region along with 31 bridge projects and 75 flood-control projects under the BBB programme at a cost of US$240 million.
According to a report from the National Economic and Development Authority, the government will complete 18 of its 112 projects by June of this year. An additional nine projects are set to be completed by December 2022, while the rest will finish by 2023 and onward.
“For our fundraising, we’ve been talking to a lot of people. I think it’s over 100 different potential investors from sovereign wealth funds, pension funds, fund managers as well as global partners who were introduced by our ambassadors.” Marita Alisjahbana. chief risk officer, Indonesia Investment Authority
From July 2016 to November 2021, a total of 233 airport projects and 484 seaport projects were completed, which included construction, maintenance, widening, upgrading, and rehabilitation.
The brand-new train sets for the Metro Rail Transit Line 7 (MRT-7) arrived in December 2021. The MRT spans more than 24 km from North Avenue in Quezon City to San Jose del Monte in Bulacan and is expected to be partially operational by Q4 of 2022.
The cost of this new MTR-7 project is currently estimated at $1.47 billion, and it will be funded through a public and private partnership (PPP) under a buildtransfer-operate (BOT) arrangement. It has a 25-year concession period. At present, six train sets or 18 rail cars out of the 108 rail cars have been shipped. The entire MRT-7 system will have a total of 36 train sets or 108 rail cars.
The BBB programme has truly accelerated the government’s public infrastructure expenditure commitments. The Philippines invested an average of 1.6%
Ongoing projects include a brand new LRT Line 1 South Extension in Imus and Dasmariñas in Cavite; the new MRT Line 7; and several new MRT 4 lines … from Recto to Batasan, a Phase 2 scheme in Novaliches, and a new branch line in San Mateo. There is also a new Mega Manila Subway scheme underway. These projects are all focused on public transport, as The Philippines continues to say it wants to offer its people and a reliable and convenient way to travel to distant cities and communities.
LUZON SPINE EXPRESSWAY NETWORK
Another major project in the BBB programme has been the execution of the USD$12.70-billion 1200-km Luzon Spine Expressway Network (LSEN) in Luzon, the largest and most populous island in The Philippines.
The road network in Luzon will be increased from 382 km to 905 km as more than 20 highways and expressways are being developed. This will reduce the travel time between Ilocos and Bicol from 20 hours to nine hours. The distance between these two places is 421 km.
Former secretary of the Department of Public Works and Highways (DPWH) Mark A. Villar is confident that the construction of LSEN was taking place smoothly and will be completed in time. The project is expected to be completed either by the end of 2022 or early next year.
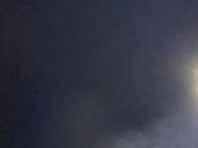
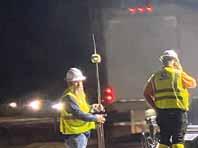
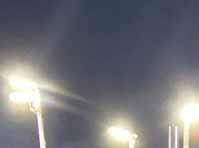

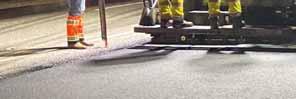
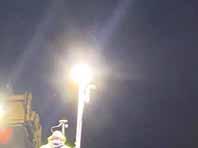
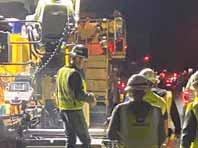
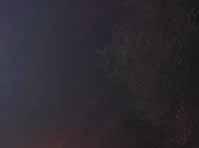
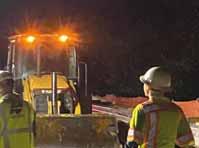
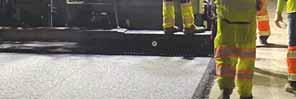
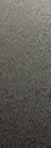
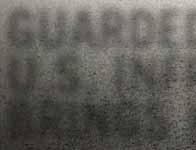
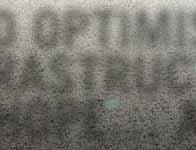
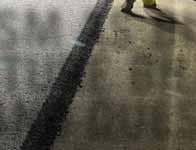
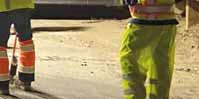
GUARDED OPTIMISM AS BIDEN’S U.S. INFRASTRUCTURE BILL BRINGS HOPE… AND QUESTIONS
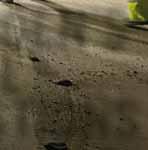

Construction industry experts are pleased with the U.S. government’s plan to invest heavily in infrastructure. Yet the details, or lack thereof, of the Infrastructure Investment and Jobs Act (IIJA) are continuing to create uncertainty. How, exactly, will the money go from the government’s funding pot to repairing the potholes? That’s the $1.2 trillion question. Pete Kennedy reports.
“People are displaying guarded optimism – they just don’t quite know how it’s all going to work yet,” says Curtiss Dorr, senior government and business development manager, North America, for Topcon Positioning Inc, a company which specialises in construction technology.
“Contractors don’t yet know what projects will be targeted,” he said. “Does IIJA mean more work? More red tape? More delays? Or does IIJA provide an opportunity to truly make the long-lasting and positive impact on U.S. infrastructure we all want and need?”
THE FUNDING
The act is touted as $1.2 trillion in infrastructure spending over five years, but essentially half the money had previously been set aside for improvements, said Joseph Schofer, Emeritus Professor of Civil and Environmental Engineering at Northwestern University in Evanston, Illinois, in the U.S. Still, it’s a significant investment. Yet there is the matter of actually getting the funding.
• A great deal of the projects require matching funds, meaning state and local governments have to pony up to receive federal funds.
• All states are competing for the same resources.
• There is an abundance of paperwork involved, some of it seemingly tricky.
Dorr, when asked if he expects unmitigated success or a host of problems, responded: “Like so many things, it will fall somewhere in the middle.”
The biggest challenges facing the U.S. Department of Transportation (DOT) and other agencies, including the Federal Aviation Administration (FAA), is getting mechanisms in place to disburse the funds, Dorr said.
“Following that is educating state DOTs on how to actually gain access. There are many variations on how DOTs can do that – the common denominator seems to be understanding which one is the right one.”
All the while departments are often shortstaffed, he said.
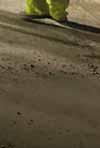
Regardless, every agency Dorr speaks to is 100 per cent committed to learning how to access the funds and lining up projects as quickly, efficiently and accurately as possible.
“It’s not simple,” he said. “As a matter of fact, it’s rather complex and involved.”
CHOOSING PROJECTS
Selection of the projects – and allocation of the funds – will be at the state and local levels. “The federal government can pressure, but the decisions are made locally,” Schofer said.
He fears politics will play a big role in project selection as elected officials ignore the best use of the money and instead focus on, “Where is the next ribbon I can cut?”
His recommendation: “Fix the old stuff you need before building the new stuff.” The federal government mostly agrees, but some of the faster-growing states in the south and west want to add capacity, he said.
That means new highways, something the Biden administration does not enthusiastically support given its climate
➔ change initiatives. Yet the law as written does not support repairs as strongly as the administration is trying to push them, Schofer said.
His hope is that citizens pressure elected officials to pursue repairs and only in rare cases support new construction.
SLOW AND STEADY
Selecting a project is only the beginning. The state or local agency must secure matching
could actually be positive for the industry and the country if the process is more slow and steady progress versus a boom and bust,” he said.
In two years, the supply chain might well be in better shape – and materials not as costly. The public may be able to buy more with the same amount of money.
Also, contractors are busy and can only grow so much at this time because of labour and supply chain issues. “They have work booked and would like to grow, but they cannot get the machinery or people to do so,” Perkins said.
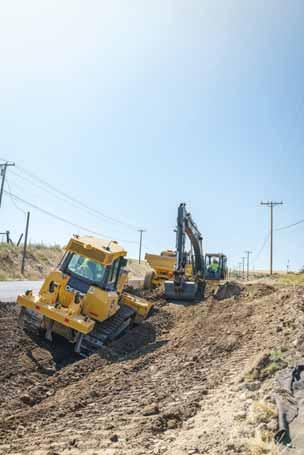
A CONFIDENCE BOOSTER
The spending will be spread out over years, giving business owners the assurance that funds – and work – will be available for an extended period. That makes them more likely to invest in new equipment and technology, helping manufacturers prosper as well.
“We expect the new infrastructure programme to keep the market at a fairly high level for the next five years,” Perkins said.
The impact will be felt in many places as “high tides raise all ships,” he said. “The infrastructure programme is positive for the USA and for the construction industry as a whole.”
A TIME TO IMPROVE TECHNOLOGY?
The funds bring a degree of certainty that will help suppliers of construction technology make a leap forward, Dorr said.
“Based on conversations we are having,
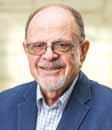
“While I wouldn’t want to advocate wasting money, we need to talk about maximum value”
Joseph Schofer, Northwestern University, Evanston, Illinois, U.S.
this infrastructure bill means our U.S. contracting community can confidently continue growing investment in their longterm construction technology,” he said. Technology can offset labour shortages and add productivity that helps contractors finish projects more quickly. These catalysts are in addition to a technology transformation that Dorr said is already underway.
“Today, the construction industry is in mass adoption – the area of the curve where mass adoption begins to ramp up,” he said. “Owners and operators see proven competitive and economic advantages.”
Additionally, project owners such as DOTs are working toward mandating not only the use of technology, but the transfer of all as-built data into large, project-specific data repositories.

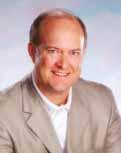
“Today, the construction industry is in mass adoption”
Curtiss Dorr, Topcon Positioning Inc
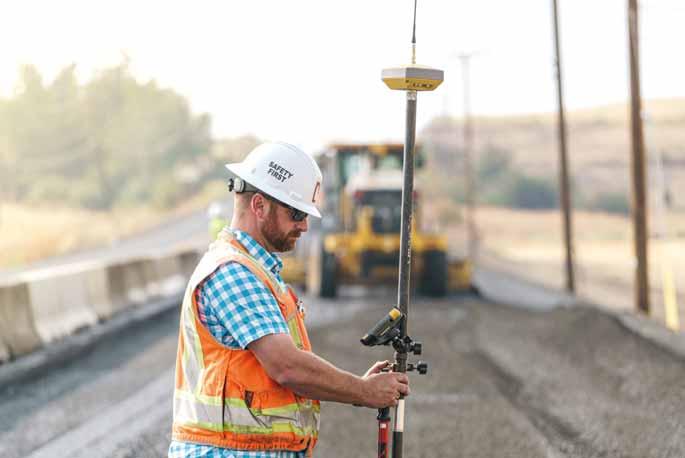
e Build America, Buy America Act was recently added to the plan. It states that whenever possible, American-made materials and equipment should be used on U.S. infrastructure projects. Waivers could be granted if costs are excessive or other
“I get it, but it’s a constraint,” Schofer said. e reason China dominates is because the prices are lower.” Conversely, maybe some extra spending is the best route, he said. “We are in a historical mindset of minimum cost,” he said. “While I wouldn’t want to advocate wasting money, we need to talk about maximum value. ere is value in keeping it inside the
national boundaries. Yeah, it’s going to cost more – because we’re helping our own people.”
QUESTIONS REMAIN
Dorr said Topcon continues to help its customers negotiate the IIJA.
“At this point, they tend to have as many questions as we do,” he said. “When will the funds come? How will the funds come? How will we know what projects are funded by way of IIJA funds? Should we hire more people?”
He concluded: “In general, people are in a wait-and-see mode. IIJA is law. Now, it’s learning how to leverage the funding mechanisms.”
A statement from Kate Fox Wood, senior director of government and industry relations for the Association of Equipment Manufacturers (AEM).
The Infrastructure Investment and Jobs Act will bring much needed modernisation and maintenance to America’s roads, bridges, highways, ports, broadband networks, and inland waterways. AEM has long called for comprehensive investment in the U.S. infrastructure system, and now that the implementation process has begun, equipment manufacturers stand ready to assist.
With all these new construction and maintenance projects on the horizon, that means there will be increased demand for construction and utility equipment. Additionally, a study we released last year shows that the infrastructure bill is poised to create over 100,000 family-sustaining jobs in the equipment manufacturing industry, and nearly 500,000 manufacturing sector jobs overall. Independent research group IHS Markit has undertaken an “Economic Impact Analysis of Proposed Infrastructure Investment” study for AEM. Its key findings are:
• The current bipartisan infrastructure framework (BIF), as well as the surface transportation reauthorization, is a welcome compromise that begins to address the nation’s badly needed infrastructure shortcomings.
• The boost to the construction industry will help support construction equipment manufacturers, where the negative impacts from US trade policy in 2019 were compounded in 2020 during the pandemic.
• Proposed infrastructure investment will support over 100,000 above-averagepaying jobs in equipment manufacturing and supporting industries before the end of President Biden’s first term.
• The investment will spur nearly a half million U.S. manufacturing jobs before the end of President Biden’s first term.
• The industry jobs generated by these bills are highly skilled and will have an annual income of over $88,000. That is more than 35% above the national average for all employees.
• From 2022-2024 equipment manufacturers and supporting industries will generate over $27bn in output as a result of the proposed investments.
• This investment will also result in $2.25 billion in additional taxes paid to federal, state, local governments before the end of President Biden’s first term by the equipment manufacturing industry and their supporting industries.
• The media refers to the American Jobs Plan (AJP) as an “infrastructure bill”, but less than a third of the initial proposed spending ($621 billion) is for transportation projects conventionally considered infrastructure investments. Even within that first proposal of $621 billon, $174 billion is in “unconventional” support of electric vehicles.
• IHS Markit has assumed the spending will occur over eight years, beginning in 2022.
• Nearly 75% of the spending is expected to occur in the first five years of the programme.
• Spending components: Scenario includes $1.1T relevant infrastructure-related spending, with the $824bn of the first five years allocated as follows:
• Transportation infrastructure: $372bn
• Other infrastructure: $452bn
• $49bn for public transit
• $66bn for rail improvements
• $60bn for water infrastructure, upgrades and storage
• $65bn broadband access
• $73bn power infrastructure
• $47bn climate resiliency
• $25bn airports
• $16bn ports
• $30bn electric buses and clean transportation
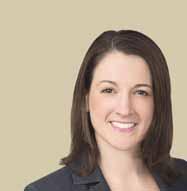
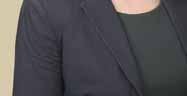

Thelinestartshere.
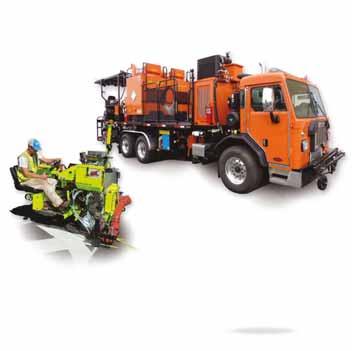
Defining the line since 1989. 877-788-2907 markritelines.com info@markritelines.com
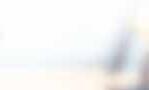
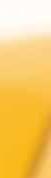
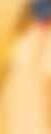
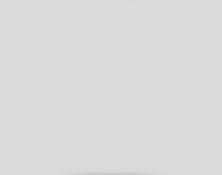
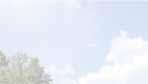



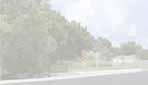
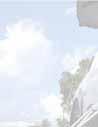


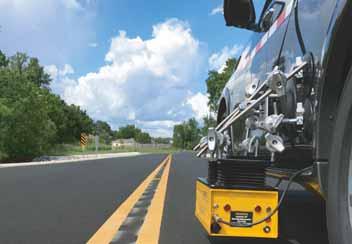

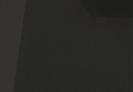

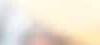
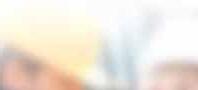
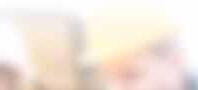
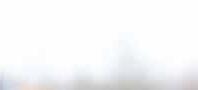
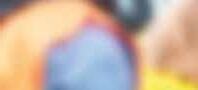
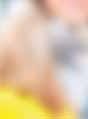


ADVERTISERS INDEX
COMPANY PAGE No. WEBSITE
Ammann OBC www.ammann.com
BKT p33 www.bkt-tires.com
Cummins p37 www.cummins.com
Digital Construction Works p4 www.digitalconstructionworks.com
FAE p55 www.fae-group.com
Fayat p17 http://roadequipment.fayat.com
Lintec p39 www.lintec-linhoff.com
Massenza p31, p53 & p54 www.massenza.it
Metso Outotec IFC www.mogroup.com
Volvo p13 www.volvoce.com
Wirtgen p11 www.benninghoven.com
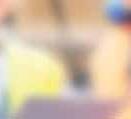
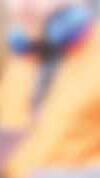
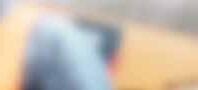
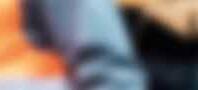

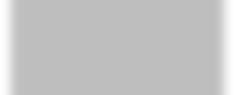
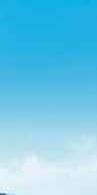

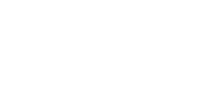
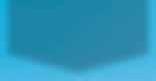

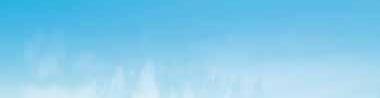

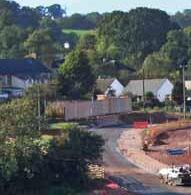
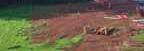
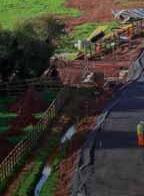
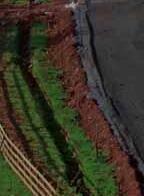
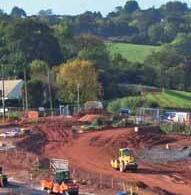
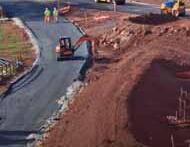

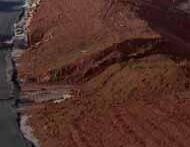








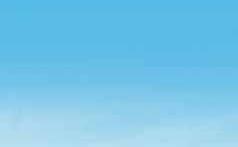
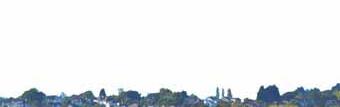
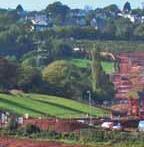
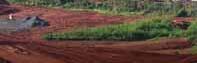
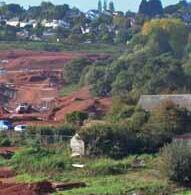
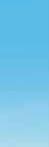
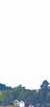
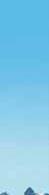
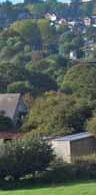

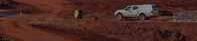



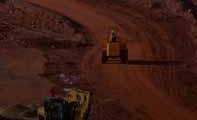



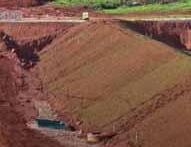
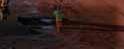







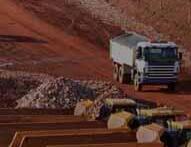






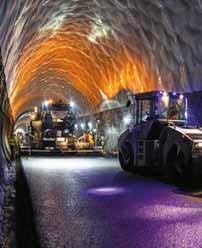





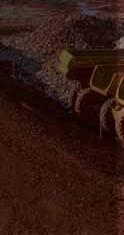



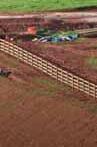
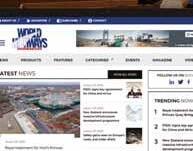

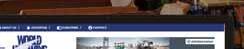






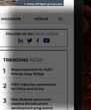
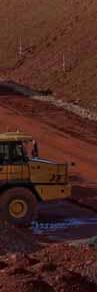


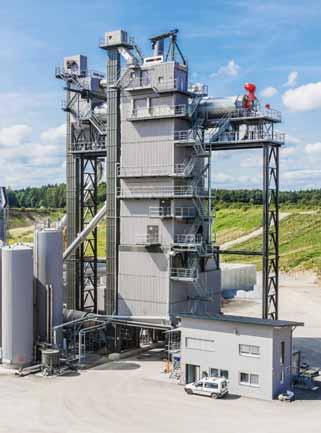
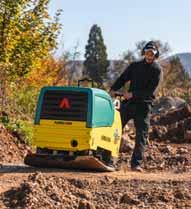
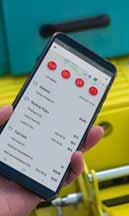
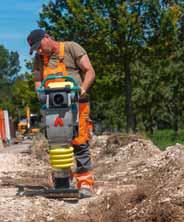
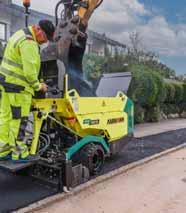
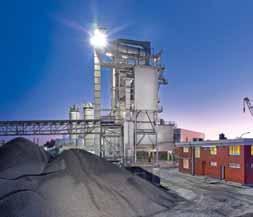
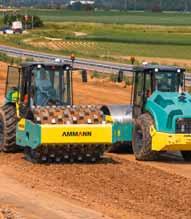
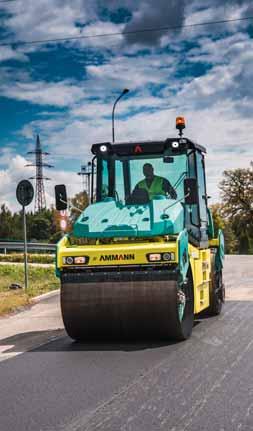
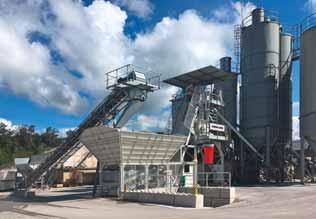
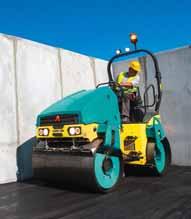
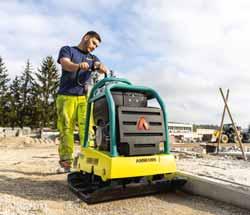
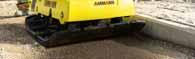
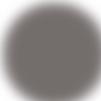
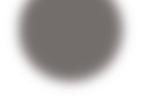