UNIQUE CONTENT AND INSIGHT FOCUSED ON KEY TRENDS IN THE GLOBAL CONSTRUCTION EQUIPMENT AND TECHNOLOGY MARKET FROM THE INDUSTRY’S BEST INFORMED AND MOST INFLUENTIAL SOURCES
GLOBAL REPORT

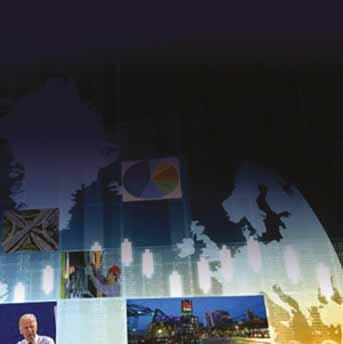
CONSTRUCTION EQUIPMENT AND TECHNOLOGY 2021
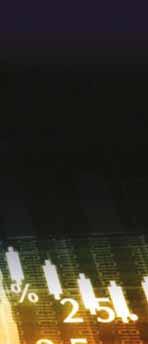

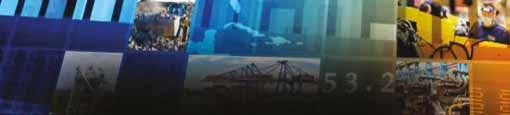
A TALE OF TWO DIFFERENT GLOBAL MARKETS
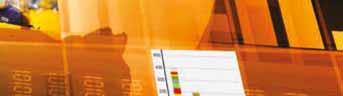

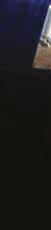
TOPCON SEES REVOLUTION IN THE AIR
ALTERNATIVE AND CLEANER POWER SOURCES
SURVIVING SUPPLY CHAIN DISRUPTION
INTELLIGENT TYRES MEAN LONGER LIVES
KEEPING TRACK OF ASPHALT TECHNOLOGY
HOW DO END-USERS SEE FUTURE NEEDS?
TRIMBLE’S VISION FOR FASTER PROJECTS
CUTTING AGGREGATES PRODUCTION COSTS
www.worldhighways.com | www.aggbusiness.com
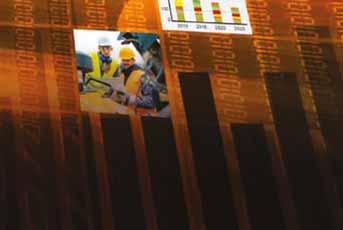
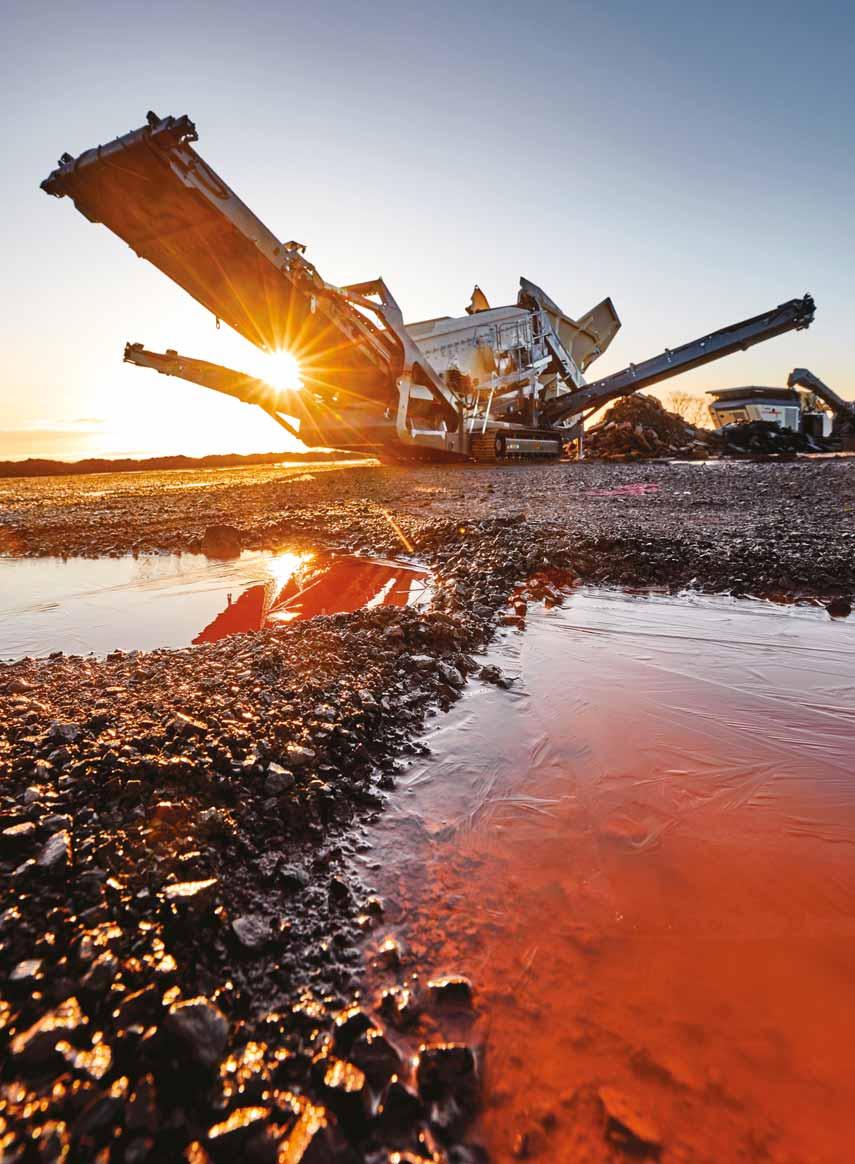
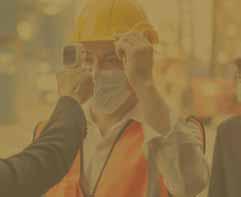
Editor: Geoff Hadwick
Contributing Editors:
Mike Woof, David Arminas, Guy Woodford
Designers: Simon Ward, Andy Taylder
Production Manager: Nick Bond
Office Manager: Kelly Thompson
Circulation & Database Manager: Charmaine Douglas
Internet, IT and Data Services Director: James Howard
Managing Director: Andrew Barriball
Chairman: Roger Adshead
Publishing Director: Geoff Hadwick
Editorial contributors: Liam McLoughlin, Kristina Smith, Graham Anderson, Munesu Shoko, Alan Dron
COVER IMAGE:
©Binu Omanakkuttan | Dreamstime.com
ADDRESS:
Route One Publishing Limited, Waterbridge Court, 50 Spital Street, Dartford, Kent DA1 2DT, UK
Tel: +44 (0) 1322 612055
Fax: +44 (0) 1322 788063
Email: [initialsurname]@ropl.com (e.g. radshead@ropl.com)
ADVERTISEMENT SALES
Head of Construction Sales: Graeme McQueen
Tel: +44 1322 612069
Email: gmcqueen@ropl.com
Sales Director: Philip Woodgate
Tel: +44 1322 612067
Email: pwoodgate@ropl.com
Sales Director: Dan Emmerson
Tel: +44 1322 612068
Email: demmerson@ropl.com
Classified: Dan Emmerson
Tel: +44 1322 612068
Email: demmerson@ropl.com
Italy: Fulvio Bonfiglietti
Tel: +39 339 1010833
Email: bonfiglietti@tiscali.it
Japan: Ted Asoshina
Tel: +81 3 3263 5065
Email: aso@echo-japan.co.jp
Asia / Australasia: Roger Adshead
Tel: +44 7768 178163
Email: radshead@ropl.com
Global Report Construction Equipment & Technology
Print ISSN 2057-3510
Digital ISSN 2057-3529
CONTENTS

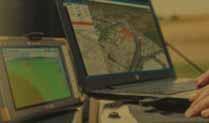
A tale of two markets
“One country, two systems” is how the Chinese have described the governance of Hong Kong and Macau in recent years. “One global construction equipment industry, two markets” is equally apt when comparing Chinese sales with the rest of the world. Who’s up and who’s down? And why?
20. View from the top. Interview. Topcon: A revolution’s coming


58. Global Infrastructure.
Special report. The leading economies: From pandemic to phoenix
How are the world’s leading economies going to rise from the ashes of the COVID-19 pandemic? We take a look at the G7 and the G20 countries as they push for more infrastructure investment at a faster pace. And what is happening in the United States? Is it the “new deal” all over again, or is it papering over the cracks?
The construction equipment industry is at a turning point. Topcon’s senior leaders believe that we are about to see the adoption of new construction technologies. The time is ripe as a new, younger and more tech-savvy generation comes to the fore. Governments could save billions, but where does the smartphone fit in?
24. Alternative power: Governments and customers drive alternative fuel ideas
The move to electric power is gathering speed with government policies seeking a reduction in the use of combustion engines to address climate change and air pollution. Can construction equipment operators plan to win more tenders if their on-site machines use electric or other zero-emission power sources?
32. Logistics: Survival of the fittest
The global pandemic has shaken up the world’s supply chains. If being flexible, resilient, creative and digitally aware of shipping delays and delivery status were important before COVID-19, they are now business-critical. Has your logistics strategy got what you need to survive? Is your supply chain fit for purpose?
42. Special report. North Africa:
North Africa needs infrastructure investment to recover. Bad news first: the North African construction sector has been hit hard by COVID-19 and the triple whammy of lower oil production, low oil prices and contracting non-oil sectors. The good news is that the region’s governments have identified infrastructure development as the best way forward. What’s being planned?
48. Thinking tyres: Get more out of your tyres
Intelligent tyre technology is playing an ever-more important role in building sustainable construction equipment fleets. François Didion, vice president for construction and defence mobility at Michelin, takes a look at what this means on site. What are the key trends and what comes next?
51. Asphalt technology: Keeping track
Next-generation technology and the ‘pandemic effect’ is encouraging contractors to use digital asphalt-tracking systems. From mixing the asphalt to laying the road surface itself, everything is being far more closely monitored and managed. How well is your business keeping track of what is being laid down?
68. View from the top. Interview. Trimble: Trimble’s vision of a far more efficient future
Trimble is offering a future vision of more efficient, optimised construction operations for faster project delivery. Managing and analysing site equipment data is a growing trend, as is remote diagnostics. Work patterns are changing fast. What does this all mean on the ground, in the real world?
71. End-user perspective. What are contractors thinking? The big rethink If there is one clear business lesson to be learned from the pandemic, it is this: The big contractors are rethinking their construction equipment needs. The global construction sector is about to feel the winds of change more rapidly and more dramatically than most. The reasons are many and complex. Are you ready to meet their needs?
76. The world in numbers: Infographics to make you think. These are interesting times. The global economic and political landscape is in a state of flux like never before as populism, pandemics and protectionism disrupt everything. Grab a few key facts and figures to help make sense of it all. For instance, what are infrastructure megatrends and whose competitiveness is in decline?
80. Aggregates production: Connectivity and communication are key. Technologies such as telematics, data analysis and fleet management solutions are augmenting more traditional methods in helping quarry operators to improve overall productivity and keep their cost per tonne down. What does the future hold?
85. Compaction: Be more efficient and use clever thinking. A semi-automatic compactor allows the operator to first use the machine to map the boundaries of the area to be compacted, and then to key in the necessary compaction parameters. The machine then takes over control of the drive, steering and vibration parameters. Is this the template for a more efficient way forward?
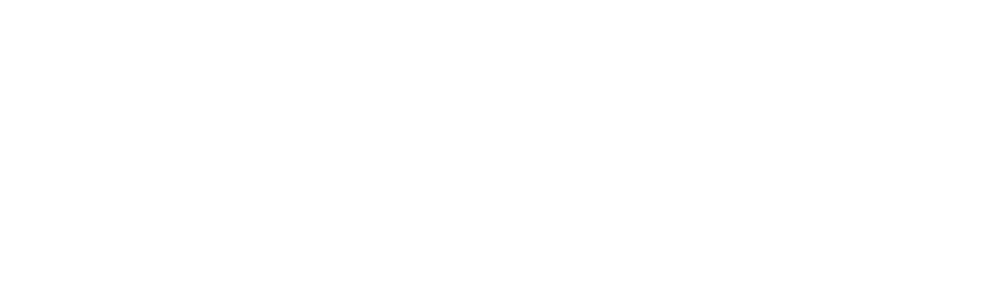

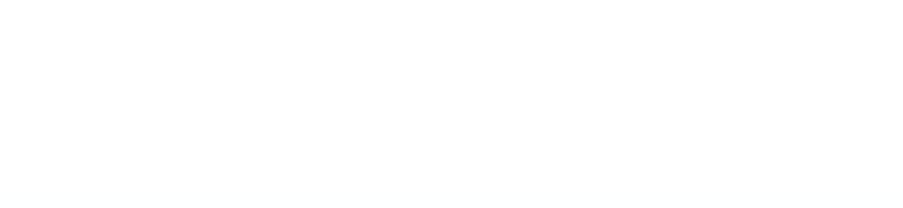
Economic Recovery
Technology For Moving Forward
As things start to move again, now is the time to make an immediate impact.
Our solutions integrate easily and drive productivity across your entire workflow. You’ll have all the tools needed to land new work, get back on track, and make up for lost time.

And you can proceed safely, with technology that lets you put less people on a job site, for a shorter amount of time, with plenty of space.
topconpositioning.com/recovery
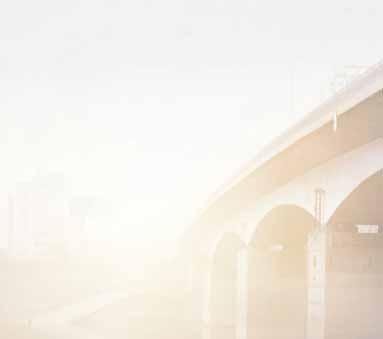
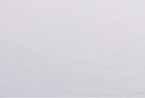


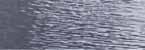
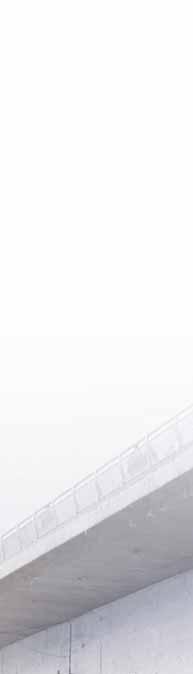
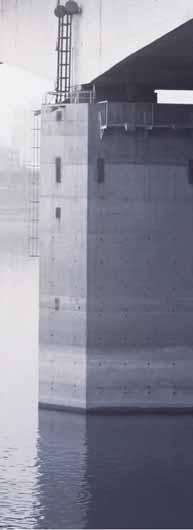
As Global Report 2021 was going to press, the COVID-19 pandemic was continuing to disrupt the global economy. Our expert writers have taken the long view wherever possible and tried to identify the key long-term trends that will affect us all. However, there are clearly going to be some unexpected bumps in the road ahead. Here, in our traditional opening feature, we have collected together independent analysis on markets around the world from the best sources in the business. It is, as always, a snapshot based on their thinking at the time. But, in these unusual times, the sources that we have used here, and throughout the rest of the Global Report 2021, have all said the same thing: This is what we think right now. The long-term outlook is good, they all agree. But things in the short-term are looking far more tricky.
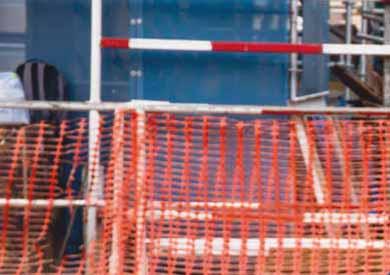
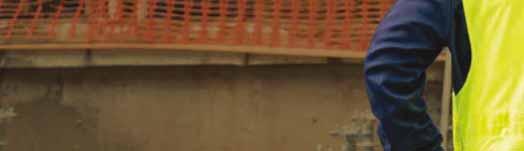

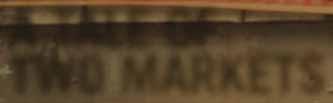


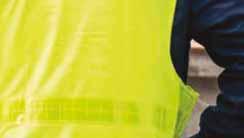
‘One country, two systems’ is a Chinese constitutional principle describing the governance of Hong Kong and Macau since they became Special Administrative Regions (SARs) of China in 1997 and 1999, respectively. Adapting the phrase to ‘One global construction equipment industry, two markets’ is apt when considering the strength of Chinese sales in 2020 compared to everywhere else. Guy Woodford reports.
Anew report by Off-Highway Research (OHR), a management consultancy specialising in the research and analysis of international construction and agricultural equipment markets, notes that thanks to huge stimulus spending, Chinese construction equipment sales rocketed by 30% to 412,440 units in 2020, from an already impressive 316,093 units in 2019.
Contrast that to the key sales markets of North America and Europe, which both saw, according to OHR figures, sales falls of 16% (194,821 to 164,540 units, and 187,108 to 157,268 units, respectively). Excluding China, rest-of-the-world construction equipment sales were down 12% (754,984 to 661,409 units) year on year in 2020.
However, as OHR states, the 2020 COVID-19-induced sales downturn was not as bad as initially feared, with sales of heavy equipment, excluding
those of China, harder hit than compact equipment trading. Furthermore, the global sales outlook for 2021 is much brighter, with many nations pledging hefty infrastructure spending to get their countries back on their feet after over a year of business as unusual.
With the vaccine rollout continuing worldwide and COVID-19 disruption
Global: Selected economic indicators, 2015-2020*
significantly reducing, GlobalData, a leading business market intelligence consultancy, expects global construction output to expand by 4.5% this year, following an estimated contraction of 2.9% in 2020.
The global construction equipment market is, once again, gearing up for better times.
Source: International Monetary Fund, World Bank
EUROPE
SLOW BUT POSITIVE STEPS
After an unprecedented COVID19-disrupted year in 2020, CECE (Committee for European Construction Equipment) predicts a positive environment for business in 2021.
“This overall positive assessment can be somewhat mitigated by the uncertainties around COVID vaccinations and the timing of government stimulus packages in Europe and US. What seems evident is that 2021 will not be synonymous of a quick return to precrisis levels of sales,” summarises Riccardo Viaggi, CECE’s secretary general.
Sales on the European construction equipment market went down by 6.4% in 2020, according to CECE figures. This seemingly modest drop is due to the performance of high-volume light and compact equipment, whose sales were almost unaffected at -3%. In contrast, heavy construction machinery suffered a 19% fall in sales.
Viaggi notes that a Q4 2020 recovery in sales was clearly visible in most product segments. This has boosted overall business confidence, which CECE tracks monthly with its own Business Barometer.
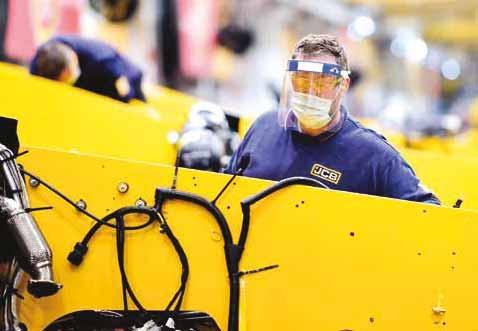
He continues: “At the moment of drafting this [March 2021], CECE can confirm that after months of improvement, the CECE business climate index was significantly higher than before the pandemic a year earlier. A significant majority of manufacturers expect business to grow in the first half of the year, and the level of satisfaction with current business has also improved significantly. In addition, the order intake for European manufacturers has been growing year-on-year since December 2020, and sales on the European market are also on a clear growth path.”
Viaggi says that the latest surveys are also highlighting how European manufacturers are optimistic about their home markets and are also expecting improved business in most regions globally.
“This includes high hopes for the US market with the expectation that the new administration will address the need for infrastructure investments and begin to move towards policies that encourage free trade. Latin American markets show the potential to recover from the weak market experienced in 2020. The Middle Eastern
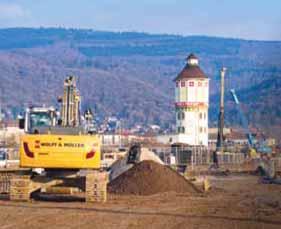
Source:
market appears to be on track for further growth which began in the second half of last year and will be supported by improving oil and gas prices.”
Returning to the European market, Viaggi says regional disparities remain a significant feature.
“The notorious North-South gap which has existed since the global economic crisis in 2009, has been getting gradually smaller. However, this development came to a halt in 2020. The most notable example was the Spanish market, which suffered significant falls during the COVID crisis. In contrast, the Italian market proved to be much more resilient last year and will profit from enormous amounts of resources from the Recovery Plan. It seems that the major markets in Europe, and those that were not affected significantly by COVID will be relatively stable in 2021. This includes the Nordic markets as well as Germany, France, Benelux, Austria, and Switzerland.”
When looking at the main end-using segments for equipment, Viaggi says it seems likely that the rental sector may see a better year in 2021 after experiencing difficulties last year.
“Greater usage of rental machines is a pattern often seen during periods of economic uncertainty. In other segments, construction, landscaping, and quarrying are all currently operating at quite high-capacity levels in most parts of Europe.
“A forecast of 5% growth in the European equipment market is a realistic assessment of prospects for 2021. However, against a background of on-going uncertainty due to COVID, and the fact that the market is still at comparably high absolute levels of sales means that even a flat market in 2021 would not be a disappointment.”
In its April 2021-published Global Markets Review, Off-Highway Research said that while a steep fall in construction equipment unit sales was anticipated in Europe when lockdowns were put in place, a rebound “clearly took root from the summer onwards”. This, says OHR, meant the downturn in the full-year 2020 was not as bad as first feared.
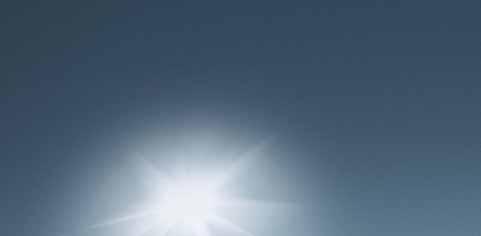


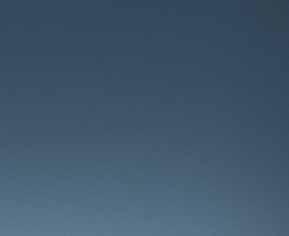

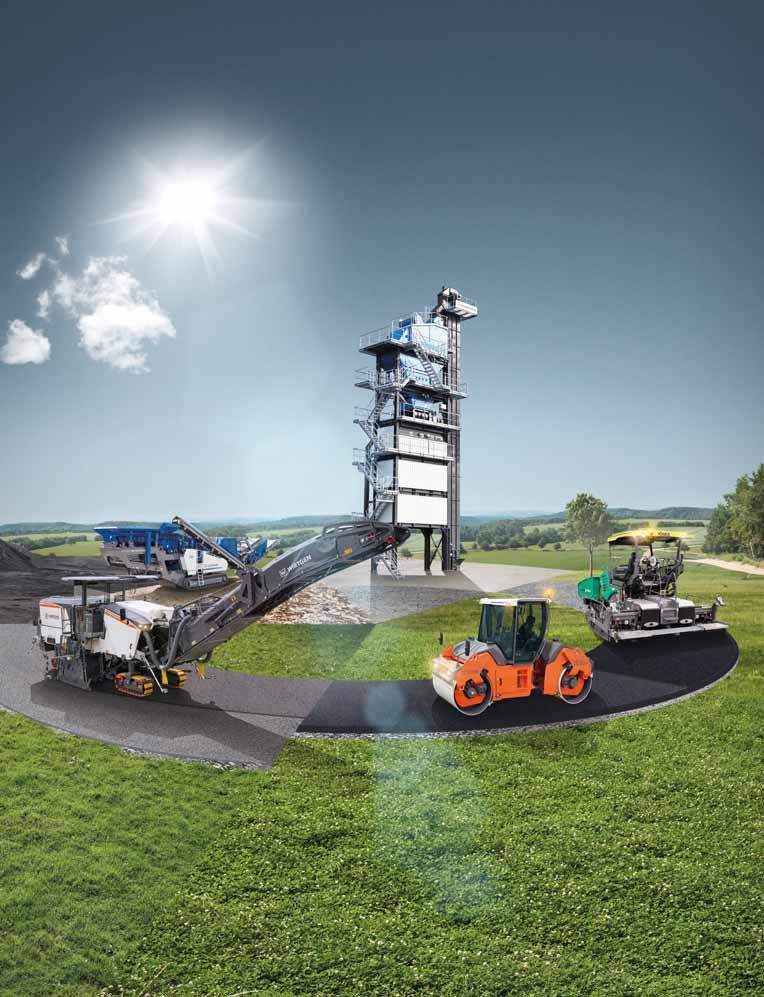
NORTH AMERICA
TURNING THE CORNER
As the North American construction and agriculture equipment industry emerges from a full year under the COVID-19 cloud, a clear majority (88%) of equipment manufacturers report a positive outlook for 2021, according to a March 2021 survey by U.S.-based AEM (Association of Equipment Manufacturers). More than half (55%) of the respondents from leading equipment manufacturers expect sales to increase or remain stable despite the ongoing impact of the global pandemic. The online survey was targeted at employees of AEM-member companies and includes results from more than 130 respondents, including CEOs, vice presidents, and sales and operations leaders, among others.
“The equipment manufacturing industry has continued to operate throughout the COVID-19 pandemic and has successfully adjusted to challenges to make the equipment that builds, feeds, and powers our country,” said AEM president Dennis Slater. “Equipment manufacturers have begun to turn the corner. We now need [U.S.] Congress and the President to pass long-overdue legislation that will invest in and modernise our nation’s infrastructure.”
U.S. President Joe Biden has said his proposed US$2tn plan to rebuild America’s
Source: Off-Highway Research
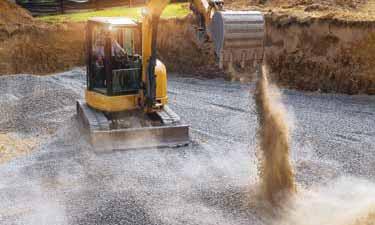

“crumbling” roads, bridges, railways, and other infrastructure would rival the space race in its ambition and deliver economic and social change on a scale as grand as Franklin D. Roosevelt’s New Deal in the 1930s.
Looking at the biggest challenges facing company executives and the equipment manufacturing industry as a whole in 2021, AEM-survey respondents indicated that the lingering COVID-19 pandemic and keeping employees safe and on the job remain the top concerns, followed by finding skilled workers for new jobs being created.
Turning to how the COVID-19 pandemic is changing the workplace, one in eight respondents said that it will have a lasting impact on how they work. Face-to-face meetings with colleagues and work travel are the top two activities they look forward to in 2021.
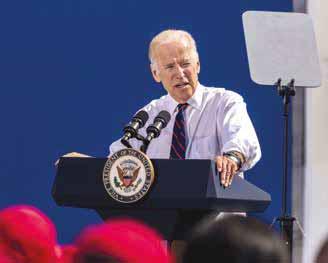
Additional top survey findings include a clear majority (88%) taking a positive outlook for 2021 while only one in ten has a negative outlook. One in five (19%) said that sales are up while one in three (36%) indicated that sales are stable, citing a strong pipeline of orders; increased customer demand; a robust economic rebound; the essential status of customers (including construction workers and farmers); and a level playing field due to no travel.
Almost half of AEM-survey respondents (45%) said that sales are down as a result of the COVID-19 pandemic, citing supply chain disruptions; reduced demand for new products; limited international sales (due to travel restrictions); inability to meet with dealers and customers; delayed or cancelled projects at the state and local levels.
The construction and agriculture equipment manufacturing industry in the U.S. supports 2.8 million jobs and contributes roughly US$288 billion to the economy every year.
OHR, a leading construction equipment market research consultancy, has reported that North America [U.S. & Canada] construction equipment sales dropped 16% in COVID-19-hit 2020 (194,821 to 164,540 units).
expected to reach $52,477.6 million by 2027 from $38,382.5 million in 2019. It is estimated to grow at a CAGR of 6.2% from 2020 to 2027. With rising demand from contractors and industrial end users, the adoption of excavators in mining, construction (road and building), and demolitions is increasing, R&M. com notes in its Q1 2021-published report, United States Heavy Construction Equipment Market Forecast to 2027: Breakdown by Construction, Oil and Gas, Mining, Manufacturing, and Other Industries. Crawler excavators, dragline excavators, wheeled excavators, suction excavators, and long-reach excavators are said in the report to be the most popular machines used by mentioned industries.
R&M.com states that regular OEM (original equipment manufacturer) product launches are contributing towards recent market growth. For instance, in December 2020, Doosan presented its largest and most powerful excavators for the construction and mining industry. The company has expanded its excavator product line by introducing the new Doosan DX800LC-7 excavator for heavy construction, mining, and infrastructure work. CASE Construction Equipment, John Deere, Caterpillar, Volvo Construction Equipment, and Doosan are, says the R&M.com report, among the leading companies operating in the U.S. heavy construction equipment market. The companies are all said to be adopting organic growth strategies, including product launches, to sustain their position in what is described as a “dynamic” market. Global
ResearchAndMarkets.com states that the U.S. heavy construction equipment market is
CENTRAL & SOUTH AMERICA
FOLLOWING A BRAZILIAN GROWTH LEAD
The Brazilian construction sector is said by industry insiders to have a positive outlook for 2021, with growth expected not only from the real estate sector, but also from infrastructure. Brazil, insiders say, can take advantage of the resources of international investors, who have already started to return to the country.
The above analysis was one of the main evaluations of debaters attending the fifteenth staging of M&T magazine’s Trends in the Construction Market event.
The strategic event held on Thursday, 26 November 2020, which brought together, virtually, an audience of more than 1,500 people, included a debate involving, among others, Afonso Mamede, president of the Brazilian Association of Technology for Construction and Mining (Sobratema), Carlos Silveira, president of the Superior Council of the Industry Union of Heavy Construction of the State of São Paulo (Sinicesp), Eurimilson Daniel, vice president of Sobratema and director of the Brazilian Association of Unions and Associations Representing the Lessors of Machines, Equipment and Tools (Analoc) and economist Luis Artur Walnut.
“The private sector is currently investing in the [construction] sector. But new infrastructure also depends on public investment, which is going through a series of difficulties in the current politicaleconomic scenario. So, one way out is
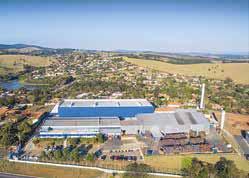
foreign investment, but there is an important conditional, the guarantee of legal security,” said Mamede.
The latest Sobratema study of the Brazilian construction equipment market presented at the event by Mario Miranda stated that national construction equipment sales were expected to grow 14% in 2020 compared to 2019, reaching 30,800 units sold.
For 2021, the study expects an increase in sales of around 20% in the segment of yellow line machines and 25% for the entire construction equipment sector. According to Miranda, regarding expectations for 2021, 67% of construction companies and rental companies are optimistic about the Brazilian economy, 70% are optimistic about the construction sector and 86% are optimistic about their company.
GlobalData has lowered its 2020 construction output forecast for Latin America to -11.4% from -6.8% previously, mostly due to the slower than expected rebound in construction activity in the second half of the year as the coronavirus continued to spread across the region and construction companies were still struggling to revive their operations.
Dariana Tani, a GlobalData economist, said: “The revised forecast makes Latin America the world’s worst-performing region in terms of construction output and reflects the deepening economic damages of the COVID-19 pandemic and strict lockdowns
imposed by authorities to limit its spread.”
Among the largest countries in the region, Peru’s construction output was expected by GlobalData to contract the most in 2020 at -24%, followed by Argentina (-23.5%), Mexico (-15.2%), Colombia (-13.2%) and Chile (-8.2%).
Tani continues: “The progress in the reactivation of projects and start of new ones in some countries has been affected by the continued increase in the number of COVID-19 cases and the heightened uncertainty surrounding the economy. In 2021, GlobalData expects the industry to remain weak, increasing by just 0.2% before recovering to 3.1% over the remaining forecast period (2022–2024).”
Peru, Chile, and Colombia are expected to be the best performers in 2021 with output expected to rebound to 16.8%, 6.8% and 4.8%, respectively.
Tani adds: “While activity is expected to gradually recover in the coming months as more COVID-19-related restrictions are eased throughout the region, output levels recorded before the pandemic are not expected to be restored in the next four years – given the region’s structural weaknesses and longstanding issues that have been aggravated with the pandemic, including fiscal constraints, social tensions, rising inequality, low productivity and general discontent with democratic institutions.”

67% of construction companies and rental companies are optimistic about the Brazilian economy
An operator changing a filter on a PowerROC D55 DTH surface drill rig in Baota Hill Mine in Nanjing (image: Epiroc)
STAGGERING GROWTH IN CHINESE SALES
China’s 26 leading excavator makers sold a total of 126,941 excavators in the first quarter, surging 85% year on year, data from the China Construction Machinery Association (CCMA) has revealed.
Taking a closer look at the CCMA data, 113,565 excavators were sold in the domestic market, rocketing up 85.3% year on year, while exports of the equipment rose by 81.9% to 13,376.
In March alone, excavator sales came in at 79,035 units, up 60% from the same period last year.
CCMA notes that sales of digging machines are an important indicator of the vitality of an economy as demand is usually backed by growth in mining and infrastructure development.
Meanwhile, the CCMA has also highlighted that sales by China’s 23 top loader manufacturers hit 22,772 in March 2021, a 52% year-on-year increase. Some 4,151 loaders were exported, a 40.5% upsurge from the same period in 2020. In the first quarter, total loader sales reached 39,333 units, increasing 60.7% year on year.
Chinese construction equipment industry insiders state that the vigorous pace of sales shows sturdy demands for building machinery and macroeconomic energy in the quarter.
Huge stimulus spending in China saw the national construction equipment market rise from the already buoyant levels of 2019 by a further 30% (316,093 to 412,440 units), according to April 2021-released figures from Off-Highway Research (OHR).
OHR notes that as soon as China emerged from its national lockdown in March and April last year, it embarked on a massive stimulus programme. The main instrument of this was allowing provincial governments to issue special bonds. OHR says this saw construction equipment sales rise to more than 412,000 units, or more than 480,000 units if compaction equipment and mobile cranes are included. Such high sales have only been seen once before in China, highlights

OHR, during the boom of 2010 and 2011. That was also a result of stimulus spending, on that occasion in response to the global financial crisis.
OHR continues: “The last ten years has seen the structure of demand shift in China, with excavators and mini excavators becoming the dominant products. The traditional high-volume equipment type, the wheeled loader, still sells in very large numbers – at more than 102,000 units sold
Global sales of construction equipmentChina, 2016-2020 (units)
last year, China accounted for well over half the global demand for this type of machine. However, in the boom of 2010 and 2011, sales of wheeled loaders came to more than 200,000 units in each of those years.”
That is also the view of Eric Neal, executive director of Cummins off-highway business, who adds the proviso that this is dependent on “as long as we can get the material to build engines. We’ve got a lot of demand right now that can certainly support that
79,035 EXCAVATORS SOLD IN MARCH ALONE 60%
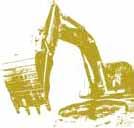
22,772 LOADERS SOLD IN MARCH ALONE 52%
YEAR ON YEAR ONE AR
Source: CCMA
Source: Off-Highway Research


growth, and maybe more actually,” he says.
In a COVID-hit year of general market contraction, Eric Neal, executive director of U.S. engine giant Cummins’ off-highway business, said China in particular, and also India, had been the countries providing the biggest boost to the company’s revenue streams during 2020, both for on-highway and off-highway engines. Neal made the observation while speaking to world construction equipment trade media at a Cummins’ virtual press event in March 2021.
In its November 2020-published report Construction in China – Key Trends and Opportunities to 2024, GlobalData states that to mitigate the economic impact of the pandemic, China’s president Xi Jinping fast-tracked the implementation of major infrastructure projects (except in the hardhit Hubei region), resuming nearly 90% of all major infrastructure projects as soon as mid-March 2020. This, notes GlobalData, was at a time when major markets across the world had only just started to implement COVID-19 containment measures.
The report continues: “In another positive development, real estate and fixedasset investments have regained growth momentum, following the temporary disruption in the first quarter of the year. Moreover, in September 2020, the National Development and Reform Commission (NDRC) approved 14 fixed-asset investment projects worth CNY177.8 billion (US$25.15 billion), following approvals of CNY68.9 billion (US$10.1 billion) in August 2020.”
GlobalData expects China’s construction industry to grow by 1.9% in 2020 and record an average annual growth of 4.7% between 2021-2024. The industry’s growth over the forecast period is expected to be driven by investments in new infrastructure projects, which in addition to transport projects, also includes investments in the areas of 5G networks, artificial intelligence and the internet of things and data centres. According to the government-backed think tank, the Center for Information and Industry Development (CCID), the country is expected to spend CNY10 trillion (US$1.4 trillion) on new infrastructure projects between 2020-2025. Real estate and fixed-asset investments have regained growth momentum
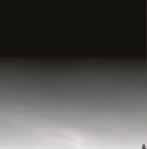

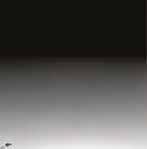
NEW STABI/H
REVOLUTIONIZING SOIL STABILIZATION
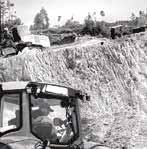
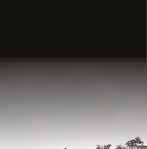
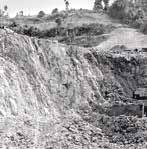
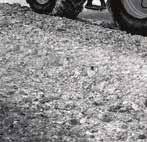
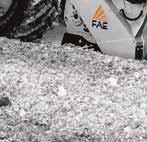

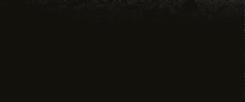

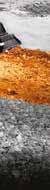
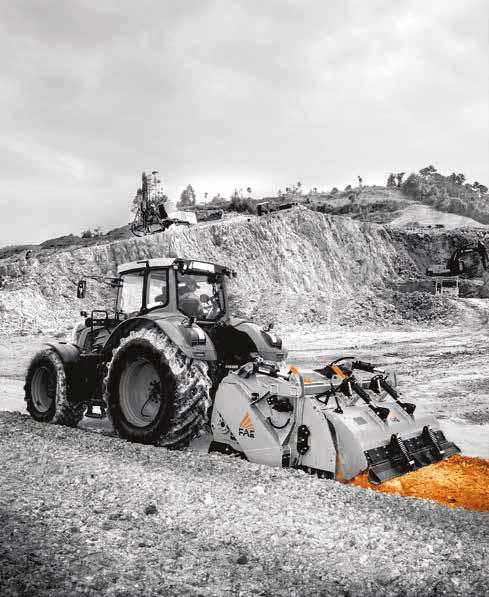
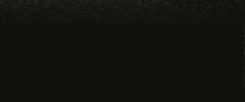
JAPANESE FOCUS ON RENEWABLE ENERGY, TRANSPORT, TELECOMMUNICATIONS & MANUFACTURING
OHR figures show that Japan’s equipment sales rose 3% to 67,645 units, compared to 65,645 units in 2019, indicating that Japan, along with China, managed to buck the downward global trend. Despite the pandemic causing a significant slowdown in the first half of the year, OHR explains that increased public spending on infrastructure was a trigger for the recovery in the second half of the year. This was particularly apparent in medium-sized equipment such as crawler excavators and wheeled loaders.
Additionally, OHR says there was a certain amount of pent-up demand in Japan. The consultancy says that the introduction of higher consumption tax in 2019 distorted the normal seasonal pattern to some extent and demand fell once the new 10% rate was introduced in October. However, OHR notes that fleet renewal cannot be put off indefinitely, and sales in 2020 were lifted somewhat as a result of the unnaturally low sales in the latter part of 2019.
“Having said that, the Japanese market is a relatively consistent one, with sales for the last four years coming in between 63,000 and
68,000 units per annum. So, while a 3% fall in demand is forecast for this year, it is arguably more accurate to view it as a continuation of a stable sales pattern,” OHR states.
Prior to the COVID-19 crisis, GlobalData highlights that the Japanese construction industry registered minimal growth in 2019, with output expanding by 0.5% in real terms – up from a decline of 1.1% in the previous year. This low growth is attributed to an economic slowdown, coupled with subdued consumer and business confidence amid the consumption tax hike, a major typhoon and weak global demand.
Although residential construction investments remained minimal, GlobalData states that the construction industry’s output was supported by investments in civil engineering and non-residential buildings. In December 2019, the government launched an economic stimulus package, which includes an allocation of about JPY6 trillion (US$55 billion) on public investments, following a series of natural disasters which caused huge damages to the country’s infrastructure.
“Although the country has not enforced
Source: Off-Highway Research
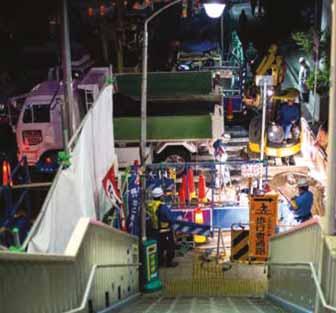
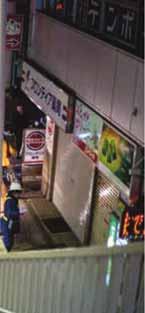
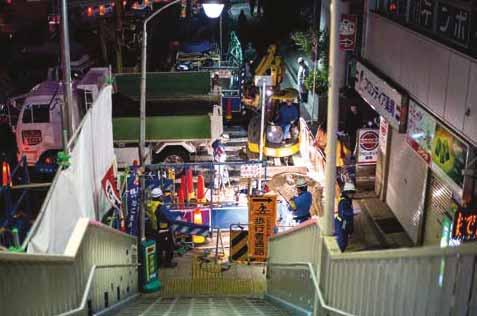
a strict nationwide lockdown in response to the pandemic, the construction industry was adversely hit by the temporary halt in construction work by major contractors such as the Obayashi Corporation, Taisei Corporation, Kajima Corporation and Shimizu Corporation, among others,” reports GlobalData, who tipped Japanese construction industry output to fall 4% in real terms in 2020.
On a brighter note, GlobalData expects the Japanese construction industry to stabilise and register an annual average growth of 1.2% between 2021-2024, supported by investments in the transport, renewable energy, telecommunication and manufacturing sectors. GlobalData says Japanese Prime Minister Yoshihide Suga and his government plan to develop 10GW of offshore wind capacity by fiscal year (FY) 2030/2031, in line with its target to increase the share of renewable energy in its total power mix to 22-24% by 2030; this will attract public and private sector investments in renewable energy projects.



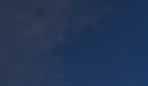
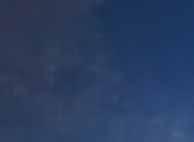


IT’S TIME TO MAKE THE SWITCH
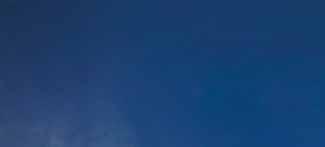


THE NEW HCS COUPLERS
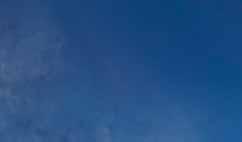
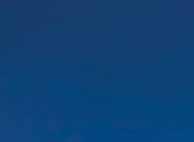


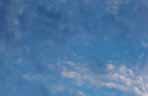




INTRODUCING THE NEW BENCHMARK FOR HIGH FLOW PERFORMANCE ON ANY JOBSITE: FROM CAT. More uptime and lower back pressure, so reduced fuel burn. Improved quick disconnects, so 10x longer lifespan. And industry-leading safety measures like smart sensor technology to see when a tool is properly attached – and keep it there even if a line breaks. Keep your operators safely in their (comfortable) seats switching tools easily, and watch your productivity go up. Make the switch and connect with Cat to find out more.
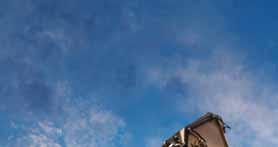



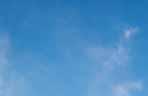



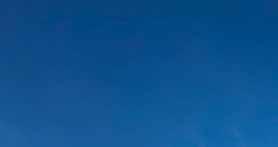

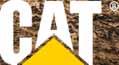
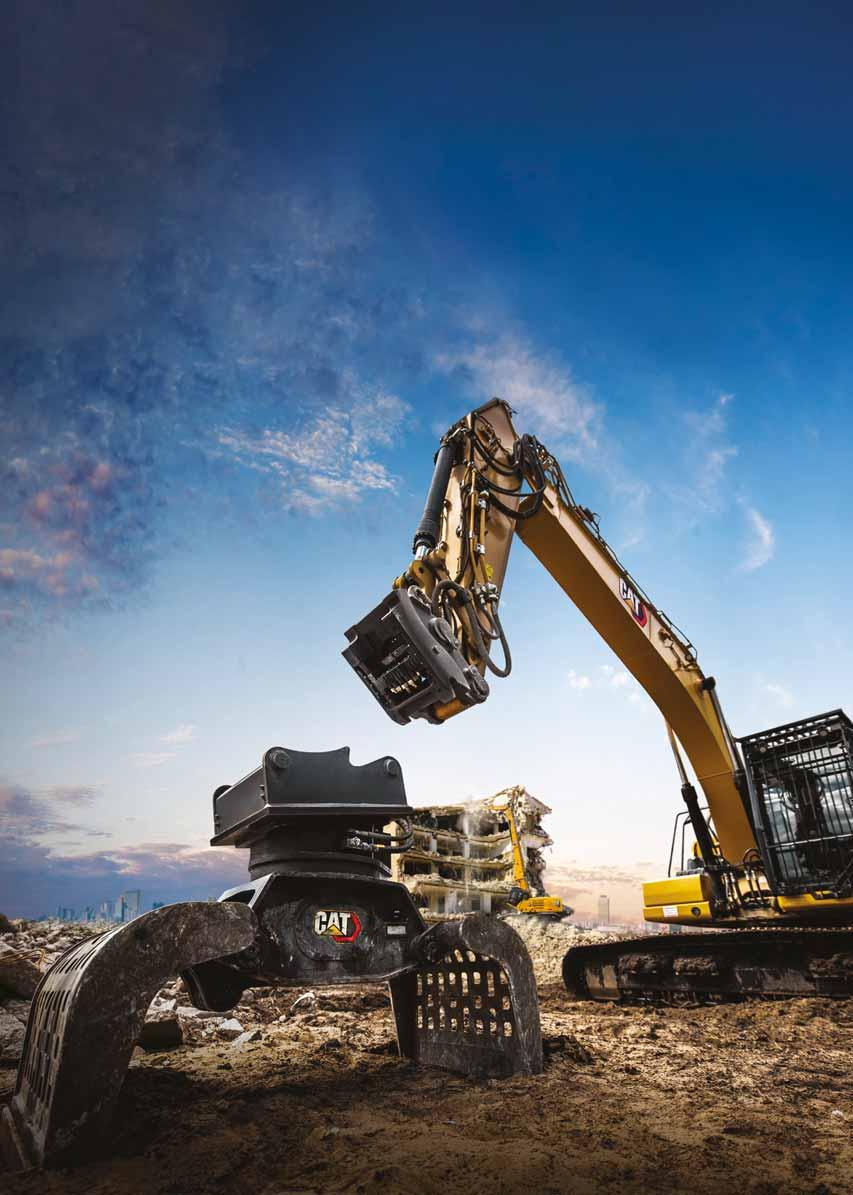

INDIA
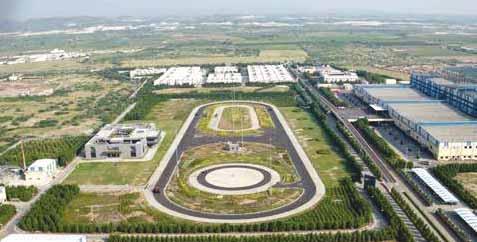
BIG INDIAN INFRASTRUCTURE SPENDING
Prior to the COVID-19 pandemic, OHR reports that 2020 was expected to be a year of robust growth for the Indian construction equipment market, following the disruption of the 2019 general election.
In the event, OHR notes that the pandemic precipitated a 10% decline in sales, to 67,635 units, or 73,275 if mobile cranes and compaction equipment are included. This, says OHR, took demand back to where it was in 2017 and was some 25% lower than the peak year of 2018. “As disappointing as this was for a market which was showing clear signs of returning to robust growth at the end of 2019, a 10% downturn as a result of the pandemic and lockdowns is not as bad an outcome as might have been expected,” OHR summarises.
OHR highlights that there were almost no mini excavator sales in India prior to 2010. However, this is now a product offered by several suppliers, some of which manufacture in-country. This has seen demand rise to just above 1,000 units per year, and OHR expects this to rise to well over 2,000 sales per year over the medium term.
During a 13 April 2021 press conference at JCB’s global HQ in Rocester, Staffordshire, central England, the company’s CEO, Graeme Macdonald, stressed how India deserved a “special mention” when welcoming increased global construction equipment demand in the first quarter of 2021.
“The market there collapsed by 94% in April, May, and June last year. By comparison, in Q1 the Indian market has grown by 29% compared to the same period of 2020. So, the market in India is far larger than it was before the pandemic, which is great news given our presence in that market.”
Macdonald added that construction of JCB’s new £65 million (US$90mn) factory in Gujarat, Western India, was also progressing well and, on completion, will give the construction equipment giant “much-needed manufacturing capacity”.
In its March 2021-published report Construction in India – Key Trends and Opportunities to 2025, GlobalData expects Indian construction output to register growth of 13% in real terms in 2021 –
following a decline of 12.4% in 2020. The outbreak of the COVID-19 pandemic and subsequent lockdown restrictions weighed on the industry’s production last year, notes GlobalData. On a positive note, Prime Minister Narendra Modi’s government investment in infrastructure development aided the industry’s recovery in the final quarter of the year. Quoting figures from the Ministry of Statistics and Programme Implementation (MOSPI), GlobalData says the Indian construction industry grew by 6.2% year on year (YoY) in Q4 2020 – up from YoY declines of 7.2% in Q3 and 49.4% in Q2 2020.
GlobalData expects the industry to register double-digit growth this year, before recording an annual average growth of 6.2% between 2022-2025.
The new GlobalData report continues: “The industry’s growth over the forecast period will be supported by investment in transport, energy, residential and industrial infrastructure projects. In the 2021/2022 fiscal year budget, the government allocated INR5.5 trillion (US$78.2 billion) towards capital expenditure. Also announced was an increase in the number of projects in the National Infrastructure Pipeline, rising from 6,835 projects to 7,400. To fund the new projects, the government plans to increase the share of capital expenditure in central
establish a new INR200 billion (US$2.8bn) development finance institution, with a lending target of INR5 trillion (US$70.5bn) over the next three years.”
Volvo India is reportedly bullish about its truck sales in the Indian market and expects a 30% to 40% growth in this category of the construction equipment market during the next financial year, 2021-22. Speaking to The New Indian Express, an Indian Englishlanguage broadsheet daily newspaper, Kamal Bali, MD, Volvo Group India, said that the manufacturer’s medium, light, and heavy trucks were doing well and that they have achieved pre-COVID sales levels. Bali added that the increase in industrial and mining activity will act as growth drivers and boost sales.
Front entrance of BKT’s state-of-the-art

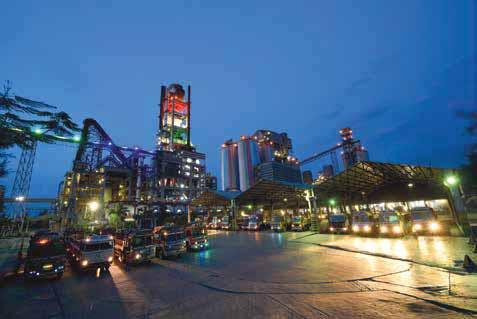
GlobalData expects Indian construction output to register growth of 13% in real terms in 2021
V-SHAPED RECOVERY
Global construction equipment makers will be heartened to hear that the COVID-19 pandemic-ravaged construction industry in South and Southeast Asia is set to post a V-shaped recovery in 2021, according to GlobalData.
The stringent lockdowns and social distancing rules due to COVID-19 have severely disrupted the construction industry across the region.
Consequently, its construction industry was expected by GlobalData to contract by 8.5% in 2020. However, assuming that a widespread second wave of infections is avoided, GlobalData says output will rise sharply in 2021 because of the low-base effect, as well as the underlying potential for growth in the region given the rising middle-class population, and investment in housing and infrastructure.
The slump in construction output is reflected in the unprecedented sharp contraction in the second quarter in countries such as Singapore (-59.3%), India (-50.3%), Malaysia (-44.5%) and the Philippines (-33.5%).
However, GlobalData says industrial construction could benefit indirectly from the COVID-19 crisis in the medium- to longterm period, as the industrialised countries seek to diversify their supply chain away from China. South and Southeast Asia are said by the major business market research firm to provide an attractive alternative with low labour costs as well as a large captive market
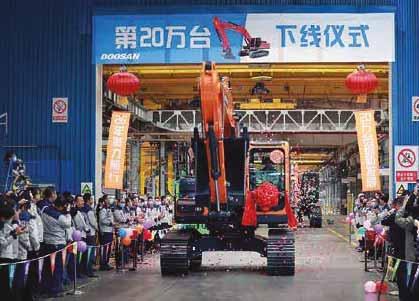
in the form of an expanding middle-class population.
Dhananjay Sharma, construction analyst at GlobalData, comments: “Infrastructure is expected to be a key growth driver in 2021 and beyond as governments across the region look at investments in infrastructure to stimulate the economy and create jobs. This would be aided by in Chinese investments in Belt and Road Initiative (BRI) projects in the South and South-East Asia region, which will support infrastructure growth in Pakistan, Bangladesh as well as ASEAN (Association of Southeast Asian Nations) members including Myanmar, Vietnam, Malaysia, and Indonesia. Increasing investments in renewable energy projects and in 5G infrastructure would also support growth over the medium to longterm.”
The residential market was weak in several countries in the region even prior to the COVID-19 outbreak, but the pandemic and the subsequent lockdowns have worsened the situation. The sector will continue to struggle as economic activity weakens, remittances decline and unemployment rises. Unsold inventories will further apply pressure as developers could hold off or cancel projects in the short term.
Nevertheless, over the medium- to longterm period, the rising middle class will generate housing demand which will, in turn, drive the market for government-supported, affordable housing.
The commercial sector is expected to
be severely affected by the virus outbreak. Investments in the commercial market are expected to be cancelled or pushed back reflecting the collapse in the travel and tourism industry.
Sharma concludes: “The industrial sector is expected to suffer in the short-term, affected by the temporary shutdown of the production units of various companies across the region. This will affect the investments as companies could cut back on their expansion plans. However, in the long-term, the industrial construction segment is likely to benefit from the US-China trade war as well as the move to diversify supply chain from China following the disruption in early 2020.”
South Korea has been praised worldwide for its impressive technology-led handling of the COVID-19 pandemic. As a result, the country’s construction sector remained vibrant in 2020. The Korea Herald newspaper reported in January this year that South Korea’s biggest construction equipment maker, Doosan Infracore, saw its domestic sales rise 18% last year.
Doosan Infracore said it sold more than 4,000 units of construction equipment, including excavators and wheeled loaders, in the local market in 2020, the highest annual sales in 10 years since 2011.
The Korea Herald reports that in South Korea, three manufacturers – Doosan Infracore, Hyundai Construction Equipment, and Volvo Construction Equipment – are vying to expand their presence.
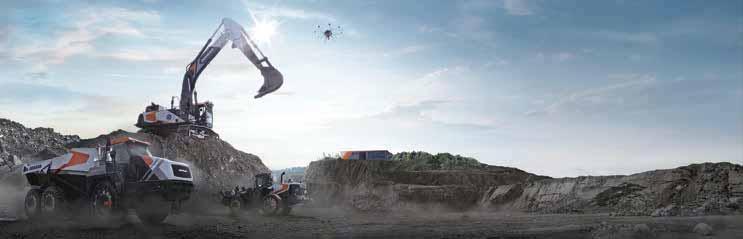
Infrastructure is expected to be a key growth driver in 2021
HeidelbergCement, Cimburkina cement grinding plant, Burkina Faso
SUB-SAHARAN AFRICA
SUB-SAHARAN AFRICA SET FOR BETTER 2021
While sub-Saharan Africa’s huge infrastructure development continues to offer attractive commercial opportunities to construction equipment manufacturers, progress in 2020 was significantly hindered by several key factors.
A 5.2% fall last year in sub-Saharan Africa (SSA) construction output was forecast by GlobalData. The prediction is said by the major business market intelligence consultancy to reflect the deep impact on the region’s economic activity and investment growth, stemming from the wider global slowdown, the outbreak of COVID-19 in the region and possibly a lack of available external financial support.
Yasmine Ghozzi, an economist at GlobalData, comments: “There are key downside risks for this outlook, particularly regarding the ongoing COVID-19 pandemic, the resilience of the region’s healthcare systems and the accessibility to an effective and affordable vaccine, political instability and possibly climate-related shocks such as floods or droughts.
“Key drivers for growth in 2021 include improvement in exports and commodity prices as the global economy recovers on the
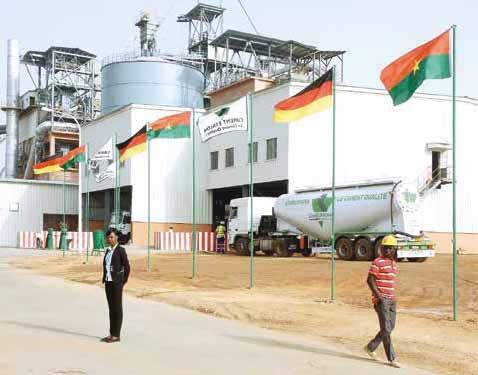
Sub-Saharan Africa construction output is expected to grow by 3.7% in 2021
back of rolling out the vaccine, along with pick-up in both private consumption as ease of restrictions slowly materialize and in investment supported by a return to foreign direct investment (FDI).”
Sub-Saharan Africa construction output is expected to grow by 3.7% in 2021, says GlobalData, as once the industry is permitted to operate at normal or near-normal levels, there could be a sharp recovery in output levels compared to periods when works were not permitted or were severely restricted.
“This will particularly be the case when comparing Q2 2021 output levels with those in Q2 2020 in South Africa and Nigeria,
where activities were completely halted due to strict lockdown measures. However, despite the expected growth in 2021, output will still be below 2019 levels.” GlobalData concludes.
In a Q4 2020-published regional overview report, The World Bank said that despite subSaharan Africa being the world’s largest freetrade area and a 1.2 billion-person market, a substantial downturn in economic activity will cost the region at least US$115 billion in output losses.
The World Bank tips sub-Saharan Africa to rebound in 2021, however it stresses that growth will vary across countries. The report

“Once again, East Africa, with a 30.6% share, recorded the highest number of projects (118 projects)”
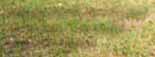

A LONG WAY TOGETHER
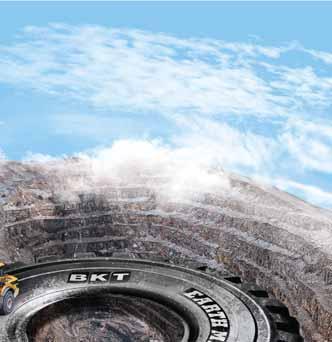
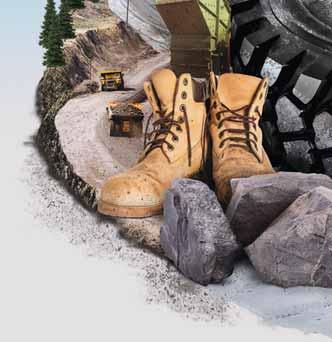
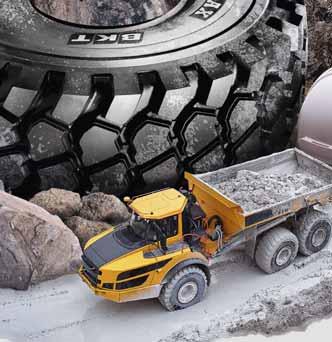
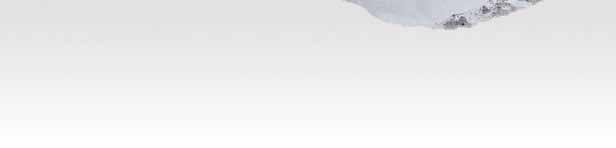
EARTHMAX SR 41
No matter how challenging your needs, EARTHMAX SR 41 is your best ally when it comes to operations that require extraordinary traction. Thanks to its All Steel radial structure and the special block pattern, EARTHMAX SR 41 provides excellent resistance against punctures and an extended service life. In addition to long working hours without downtime, the tyre ensures extraordinary comfort.
EARTHMAX SR 41 is BKT’s response to withstand the toughest operating conditions in haulage, loading and dozing applications.

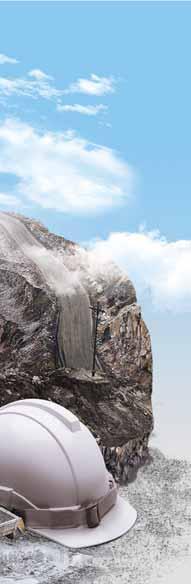
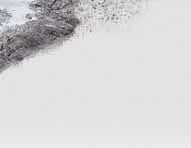
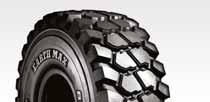
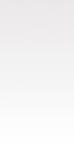
europe@bkt-tires.com
continued: “While South Africa is expected to experience a weak recovery, overall growth in the Eastern and Southern Africa region is expected to average 2.7%. While Nigeria’s economic recovery will be weak, the Western and Central Africa region is expected to experience an average growth of 1.4%. Many countries have seized the opportunity within the crisis to move faster on necessary reforms and investments that will be crucial for longterm development. However, concerns of a second wave are fuelling further uncertainty.”
Deloitte’s Africa Construction Trends Report 2020 includes 385 projects with a total value of $399bn. “On a year-on-year basis, the total number of projects in the report declined by 14.8%, while the total value of projects dropped by 19.8%. Once again, East Africa, with a 30.6% share, recorded the highest number of projects (118 projects), followed by Southern Africa, with 26.5% (102 projects) and West Africa, with 19.7% (76 projects),” the report stated.
In the East African region, Uganda, with 27 projects, and Kenya, with 26 projects,
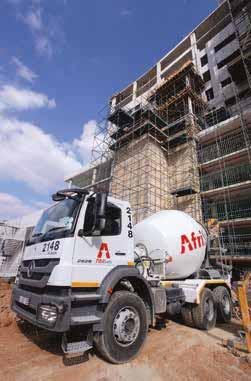
recorded the highest number of projects in the region. This keeps them among the top five countries in the continent in terms of number of projects.
Egypt and South Africa both registered 40 projects, making them the countries with the highest number of projects on the continent. Egypt recorded a project value of $93.7bn (23.5% of the continental value). Meanwhile, Nigeria recorded the second-largest project value of $52.4bn, followed by South Africa, with a project value of $50.4bn, and Tanzania with $33.5bn.
The Deloitte report continued: “In 2020, almost three in four projects (73.2%) were in the low value range of $50m-$500m (compared to 64.8% in 2019). An overall total of 46 projects were valued between $501m and $1bn. Seven projects were valued at above $10bn.
Of these, the top three include Egypt’s New Capital City worth $58bn, Mozambique’s Offshore Area 1 Liquefied Natural Gas (LNG) project worth $23bn, followed by Nigeria’s Centenary City worth $18bn.
MIDDLE EAST & NORTH AFRICA
REAWAKENING MENA MARKET
Construction output in the Middle East and North Africa (MENA) region was forecast by GlobalData to contract by 4.5% in 2020 but recover and post growth of 1.9% in 2021 and 4.1% in 2022. GlobalData says the 2020 contraction reflects the severe impact of the COVID-19 lockdowns and other restrictions on construction activity.
“The [MENA] construction sector will face headwinds in 2021 with a slow recovery, but the pace of recovery will be uneven across countries in the region. Throughout 2020, and running to 2021, spending on real estate megaprojects, especially in the GCC [Gulf Cooperation Council], is likely to take a backseat due to budget revisions,” says Yasmine Ghozzi, a GlobalData economist.
On a positive note, Ghozzi adds that large-scale projects in the oil, gas, power and water sectors have gained traction despite the downturn in market conditions this year, and this is likely to continue. “As a result, some local contractors are pursuing development in these sectors to replace the loss of real estate work. There is also a push towards decoupling power and water production across the region to reduce energy consumption, providing the impetus for Independent Water Projects (IWP) implementation. In the future, there will be a lot of contract awards in that respect as the region pushes its renewable energy programme, particularly solar photovoltaic and wind.”
GlobalData has slightly revised its forecast for Saudi Arabia’s 2020 construction output to -1.9% from -2.8% and expects a recovery for the sector of 3.3% in 2021. This revision reflects an improvement in economic performance, the Kingdom ending a nationwide curfew at the end of September, lifting restrictions on businesses after three months of stringent curbs and a notable decrease in infection rates.
Recovery is also underlined by the crown prince’s announcement in mid-November that the Public Investment Fund (PIF) is to invest SAR150bn (US$40bn, 5% of GDP per annum) in the economy in 2021-22.
GlobalData still maintains its forecast for a UAE construction output dip of 4.8%, with a rebound in 2021 of 3.1% and a promising
medium-term outlook.
Ghozzi adds: “The recent approval of a new Dubai Building Code is a positive development for the UAE. The new code outlines a revised set of construction rules and standards and seeks to reduce construction costs by streamlining building rules.”
The UAE is proceeding with plans to expand its production capacity, with Abu Dhabi National Oil Company (ADNOC) announcing its five-year investment plan worth US$122bn.
GlobalData estimated 2020 construction output in Qatar and Kuwait to be down -4.5% and -9.5%, respectively. However, neighbouring Oman was tipped by the same source for a 10.3% drop in construction output. This was said to be due to the industry’s struggles with challenges presented by the outbreak of COVID-19, low oil prices and the impact of sovereign credit rating downgrades.
Ghozzi states: “The new fiscal plan launched by the Omani Government to wean itself off its dependence on crude revenues through a series of projects and tax reforms is a good step which will aid the construction sector recovery in the medium term”.
An
The UAE is proceeding with plans to expand its production capacity
GlobalData tipped construction in Egypt to grow at 7.7% in 2020, slowing from 9.5% in 2019 – given a short-term slowdown due to the pandemic – and 8.9% in 2021. The industry is also expected to continue to maintain a positive trend throughout the forecast period.
Ghozzi continues: “Egypt has become the first sovereign nation in the MENA region to issue green bonds with a US$750m issuance. Bonds’ earnings will be used to fund projects that meet Egypt’s commitment to the UN goals for sustainable development.”
GlobalData expected Israel’s construction industry to contract by 8.9% in 2020, reflecting the significant fallout from the pandemic, with growth expected to resume at a modest pace in 2021.
“Containing a second wave of the virus, while trying to revive the economy and approve budgets for 2020 and 2021, are the government’s top priorities. However, difficult decisions will be postponed, with the deadline to pass the 2020 budget being pushed to the end of 2020,” summarised Ghozzi.
In the Arab Maghreb, GlobalData maintained its forecasts for construction volume decline in 2020 for Morocco and Algeria at -5.5 and -3.4%, respectively.
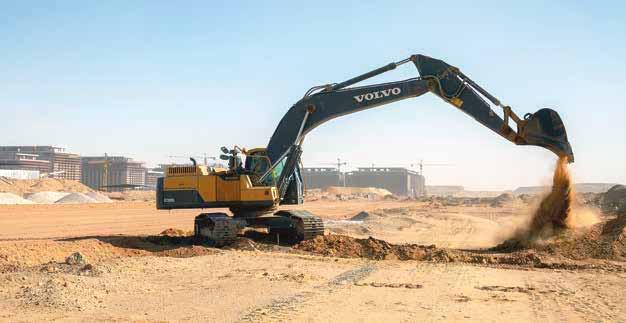
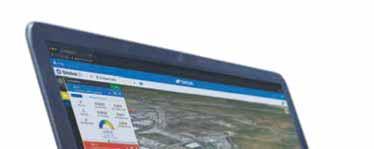
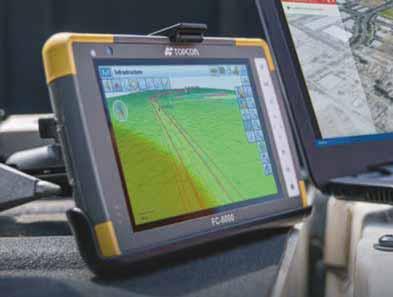

A REVOLUTION’S COMING

The construction equipment industry is at a turning point. Topcon’s senior leaders believe that we are about to see a huge surge in the adoption of new construction technologies. The time is ripe as a new, younger and more tech-savvy generation comes to the fore. Governments could save billions, and where does the smartphone fit in? Pete Kennedy reports
Jamie Williamson has seen the construction industry undergo a transformation before, and he believes he’s about to see one again.
Two-person surveying teams, “where one individual is looking through the instrument and the other is walking,” were on every jobsite in the 1980s.
Back then, Williamson, now an executive vice president at Topcon Positioning Group in Livermore, California, watched the duos work with interest. The irony was that he was keenly aware that a system that could be operated by just one person was already on the market … a system that was also more accurate and required half the labour.
And yet, two-person crews continued to traipse through construction projects. Williamson remembers thinking that it wouldn’t be long before the one-person system took over. “In a couple years, everyone is going to have one of those things,” he predicted.
He was right. Some 40 years later, about 40,000 of these one-man systems are sold annually. “That’s on top of the systems that are already out there,” he said.
Yes, it’s true, everyone now has “one of those things”.
Williamson believes the industry is about to experience another transformation: the widespread adoption of machine control systems and the advanced project management tools that go with them. “Eventually every jobsite in the world will be using that technology,” he said.
Two other Topcon leaders, Murray Lodge, senior vice president, and Ulrich Hermanski, executive vice president, agree with their colleague. Combined, the three have nearly a century of experience with construction technology.
Now, years of laying the groundwork are about to pay off with dramatic increases in utilisation of machine control and management, the three believe. In addition,
new applications are being found for geopositioning technology, which uses satellites and ground stations to monitor construction progress – and to provide essential quality control efforts, among many other benefits.
A revolution is underway, and here are the reasons why Topcon’s top three think the industry is on the brink of a mass adoption of these new technologies.
MACHINE CONTROL ADOPTION IS NEAR
The rumblings of a significant uptick in acceptance of machine control – automated systems that precisely position construction equipment and help operators accurately control machine movement – began two or three years ago. “The smartphone was the main driver,” Williamson said. “It started the demystification process.”
There are other forces at work. OEMs now deliver machines from the factory with integrated machine control systems, making
access easier. After-market solutions have improved as well.
And then there is cost. Prices for the technology are falling, primarily because hardware components are mass produced and available off the shelf. Creative financing and attractive lease and subscription plans have also lowered costs.
In addition, there is a growing realisation among businesses that the technology is needed to compete.
“We are now at the cusp of where people ‘get it,’” Lodge said. “Now, you’re getting where people realise, ‘If I don’t have it, I can’t compete.’”
All three agree the opportunities are incredible. “If you look at the industry, we have 500,000 to a million machines out in the marketplace that have no type of grade control,” Williamson said.
As an industry, sales of grade control systems are in the low tens of thousands per year. “If you look at that, and compare the adoption to the one-person levelling system, that same evolution is going to happen,” he said.
The planets are aligning.
SMALL CONTRACTORS ARE READY TO MAKE A BIG SPLASH
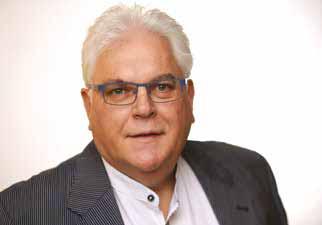
Scan as you build says Ulrich Hermanski: “Whatever needs to be corrected can be done in that moment, before you go to the next step.”
the smaller machine, Lodge said. But that has changed.
“As the price continues to come down, that part of the pyramid with all the smaller machines, the smaller contractors, will explode over the next five years,” Williamson said. “It’s a huge opportunity and likely to be one of our biggest growth areas.”
Owners of smaller machines are starting to understand the return-on-investment opportunities. “If you can put something on a dozer that doubles its capacity, it has a much bigger impact on the capabilities of that small company,” Williamson said.
ON-SITE VERIFICATION HAS ARRIVED
On-site verification, which monitors progress and quality in real time, is becoming increasingly important for roadbuilding and vertical construction. It is a very new process, and one with considerable promise. It uses geopositioning technology to connect the office and the field instantaneously.
“From a knowledge standpoint, people are looking for answers right away,” Lodge said. Such data will have a significant impact on quality and the avoidance of costly rework. It is also likely to be another adoption catalyst.
Smaller contractors – and smaller machines –offer an even greater opportunity.
Hundreds of thousands of compact track loaders and mini-excavators are produced in Europe and North America every year. “If you compare that to the number of larger dozers and excavators, it dwarfs it,” Williamson said.
To this point, cost has primarily limited the number of smaller contractors who leverage the machine control technology. Until recently, it could cost almost as much as
People are now on the cusp of “getting it” says Murray Lodge: “Now, you’re getting where people realise … if I don’t have it, I can’t compete.”
A more technologically savvy younger generation will also ease the transition.
“They’re not afraid of technology,” whether they are the machines’ owners or the operators, Williamson said. “The older generation was. Even if the owners were progressive, they feared their operators wouldn’t use it if they bought it.
“The younger generation, they can’t live without it. It’s not, ‘Should I get it?’ It’s … ‘I have to get it.’”
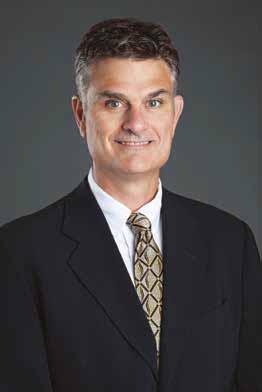
“Imagine you are constructing a large building with a steel structure and after two weeks, you find out something was wrong during the earlier production,” Hermanski said. “It takes enormous cost – and enormous effort – to correct that.”
Previous verification consisted of bringing a team in once every week – or two weeks, or month – to scan all the progress. The team members returned to the office, processed the data and compared it against the plans.
Finding a discrepancy was a big problem. “Then you needed to go back and correct the problems and measure the changes,” Hermanksi said. In extreme situations, that could mean breaking up concrete or bringing down steel.
On-site verification prevents such problems. Geopositioning devices utilise satellites and ground stations to provide measurements, while a scanner offers instant comparisons.
“You are scanning as you build,” Hermanski said. “You can compare it with the plans immediately – on the site. Whatever needs to be corrected can be done in that moment, before you go to the next step.”
A timely response can be a big cost-saver. For example, corrections can be made to concrete before it hardens.
While Hermanski’s discussion focuses on
➔ building construction, the same process – and benefits – apply to roads and grading. In the past, a contractor might evaluate a job every few weeks. The problems uncovered could be devastating and lead to costly rework and overtime.
“Oops – a month in we made this mistake,” Williamson said.
The verification helps with scheduling, too. “With the data that’s available today, I can know this afternoon how much dirt I moved this morning,” Williamson said. “I can know if this project is ahead of schedule, or behind.”
Today’s tighter deadlines make the verification all the more critical, Lodge said. “Back in the day, a contractor might say, ‘OK, this is going to take us five months’ – and halfway through he might look around and realise he’s not on schedule,” he said.
“You can’t do that anymore. You have timelines you have to meet. You have all these subs that have to fit within it.”
Documentation is another benefit. Contractors have records of the quality and timeliness of the work.
THE AUTONOMOUS MOVEMENT IS GAINING STEAM
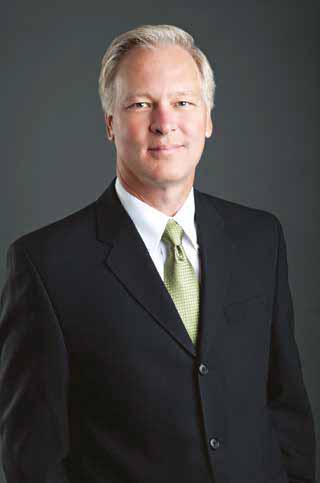
jobsite – not as a test, but as a functioning part of a jobsite,” Hermanski said.
He expects the asphalt compactor to be the machine that breaks the barrier.
“A roller works in a limited area,” Hermanski said. “It’s not driving around somewhere. It’s simple to control and to protect.” A compactor essentially moves backward and forward, and automatic shutoffs can help ensure safety.
“In the next one to two years, an autonomous roller will be available and working on a
Machine control and positioning is being transformed says Jamie Williamson: “The smartphone is the main driver. It started the demystification process.”
Dozers and graders are more difficult to control autonomously because they work in less confined areas. Excavators have more variables and moving parts. “On an open construction site, it’s not as easy as people think,” Hermanski said.
Does the market really want to eliminate the use of an operator in favour of autonomous machines? Hermanski said yes – at least in some cases. “With rollers and trucks, those are the lowest skill levels you have,” he said. “These are hard jobs to fill.”
Paving would be another candidate for autonomous operation, with one big caveat. “On a paver, you need to make a decision now that has an influence in 20 to 30 metres, so that makes it harder,” he said.
The first working autonomous roller will be retrofitted with controls, Hermanski said. As the concept becomes more well-received, look for machines to be specifically built for autonomous operation.
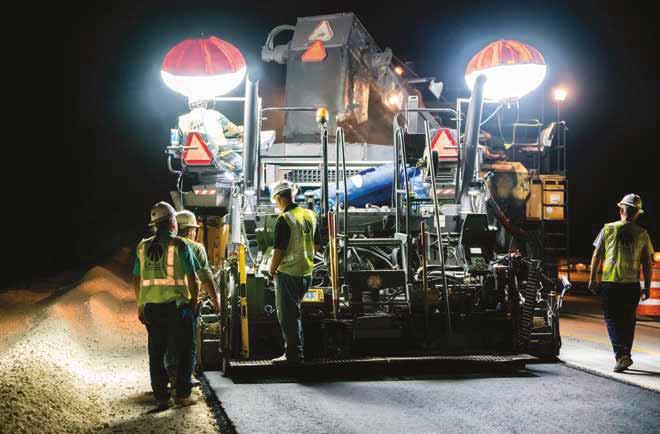
“We have to change our way of thinking,” he said. “We are making what we already have autonomous. We need to develop different types of machines – not to simply make the machines we already have run automatically.”
GOVERNMENTS CAN SAVE STAGGERING SUMS
Governments are slowly but surely – make that very slowly – starting to adopt the technology and include it in the roadbuilding process, in one form or another.
The biggest opportunities lie with use of 3D milling and paving, Lodge said. Key is the implementation of variable depth milling and paving methods and real-time quality control systems. In the long run, projects are completed sooner, quality is improved and road life extended. All these benefits add up to considerable cost savings.
“For their money, if we’re getting 10 projects, can we improve and get 11?” Lodge asked. “Can we get 14 – for the same amount
That’s considerable value. Lodge also said it’s realistic if 3D planning is used. There are transportation agencies that have taken such steps – “and a whole lot who haven’t,” Lodge
noted, as agencies are sometimes slow to adopt new approaches.
Still, the benefits could be substantial enough to drive acceptance.
“It’s not just that the contractor was able to save $300,000 on one project,” Lodge said. When you look at a wider scope, “that $300,000 turns into $300 million … which then turns into $3 billion.”

The level of detail is critical to the 3D concept. Previously, a survey crew walked the pavement with a stick and every seven metres took an elevation – on the centreline, the midpoint of the lane and the right shoulder.
“With 3D, you can do the survey in a matter of hours, versus days or weeks, and it’s much more accurate,” Williamson said. The data is gathered by crew members simply driving down the targeted road. “Then they create a 3D model of what the current surface looks like – ruts included – down to a couple of millimetres of precision ,” Williamson said. They have information for every millimetre of the road, compared with every seven metres the old way.
The detailed 3D design and variable milling to precise heights removes more material in the bumps and less in the dips to leave a smooth surface and consistent depth for the paver. The 3D approach makes the machines smarter and more aware of the surface they’re working on.
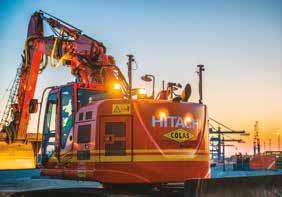
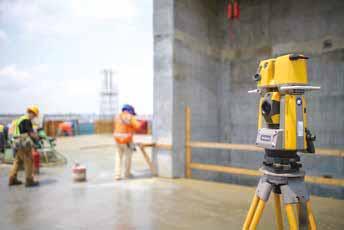
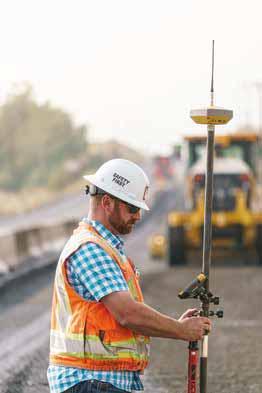
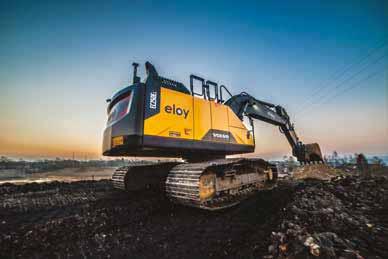
The smarter machines improve smoothness to such a degree that years can be tacked onto road life. Big dollars are saved on the jobsite, too, as material usage is much more efficient.
“It’s a game changer,” Williamson said.
And it will take a game changer to move government agencies. Lodge said that the paving industry uses 2D technology on about 80% of roadbuilding projects. “If you’re talking about 3D adoption, it goes down to about a half of a percent,” he said.
That usage rate makes it seem that adoption is a long way down the road. But the Topcon experts expect it to grow quickly because of the staggering improvements that can be made with the 3D process. The technology adds efficiencies, quality and cost savings during dozing, grading, soil compaction, paving and asphalt compaction. It also ties into the plant and material transport.
GREEN BENEFITS
The technology makes operations greener, too … in seemingly countless ways.
An efficient paver burns less fuel, as do efficient mills and compactors. Minimising
It also means less mix has to be produced, reducing fuel burn and emissions at the plant. Less material has to be hauled to the jobsite, preventing the emissions that go with it.
Smooth roads last longer because they don’t have bumps that get pounded by heavy vehicles. That longer life adds up to incredible savings when road systems of the world – or even a local jurisdiction – are considered. The smooth roads also prevent vehicle damage, which has green benefits of its own, such as extended life of auto parts.
And yes, the technology can contribute a great deal to the other kind of green – money. It’s not unusual for customers to double their production, depending on the machine type and application.
“You’re burning less fuel and controlling materials to low single-digit percentages for overruns,” Williamson said. The technology provides efficiencies at every stage of the building process. That means enormous savings in fuel, emissions and natural resource utilisation.
“It’s a societal benefit that we haven’t pushed enough as an industry, and we need to,” Williamson said. “It saves taxpayers money. It saves our planet.”
Here is how Topcon Positioning Group explains its technologies:
Machine control: Machine control hardware and software solutions were developed to determine a machine’s current position on the earth and compare it with the desired design surface. Using data from satellites or total stations and 3D models, the technology ensures that machine operators can accurately position machinery, check grade, automate equipment functions and collect data. Through the use of various positioning sensors and a display, machine control gives operators a clear reference between the position of the machine bucket or blade and the design surface.
Geopositioning: Identification of geographic location by means of technology.
2D machine control: Also known as “indicate” systems, provides positioning guidance with lasers, slope sensors, and/or sonic trackers, etc.
3D machine control: Positioning control using Global Navigation Satellite System (GNSS) or local positioning systems (LPS) to calculate 3D positioning of the blade, bucket, etc.
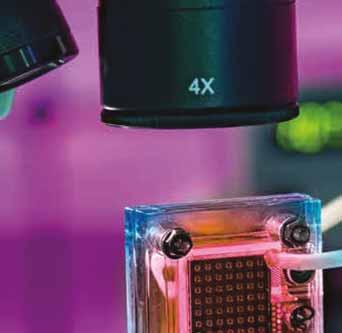
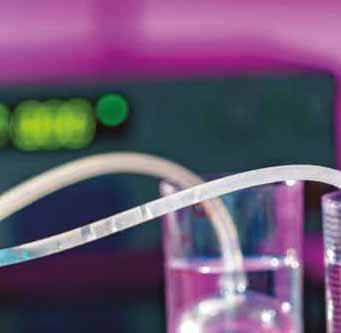
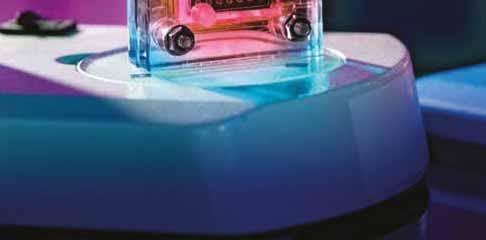
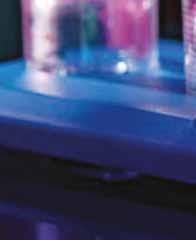
GOVERNMENT POLICIES AND CUSTOMER ROADMAPS DRIVE ALTERNATIVE POWER IDEAS OS

The move to electric power is gathering speed with government policies seeking a reduction in the use of combustion engines to address climate change and air pollution. Proponents of the technology say that construction equipment operators can gain an advantage in tenders by demonstrating their sustainability credentials with zero-emission machines. Liam McLoughlin reports
The use of alternative power solutions in construction equipment is being driven by a number of factors, specifically the desire to minimise both vehicle emissions and operational costs.
A range of alternatives to traditional diesel power is being developed by equipment manufacturers including electric-battery power, and fuel cells that produce electric power from sources such as methane, lithium, propane and – increasingly commonly - hydrogen.
The global electric off-highway vehicle market size in a pre-COVID-19 situation was projected by a MarketsandMarkets report to reach a value of US$6.3bn in 2020 and increase to US$17.5bn by 2025.
The research company says that the global financial slowdown following the COVID-19 pandemic has led to original equipment manufacturers (OEMs) delaying new vehicle
developments and launches in the offhighway electric vehicle sector.
However MarketsandMarkets says this is likely to be only a temporary slowdown: “The upcoming emission norms for offhighway vehicles, development of new and advanced products, and recovery of end-use sectors post-2020 are expected to support the growth of the electric off-highway vehicle market in the coming years.”
Market analyst Grand View Research says that increasing requirements in emissions standards for off-highway vehicles have been implemented by government authorities, such as the standards for greenhouse gas (GHG) emissions by the US Environmental Protection Agency (EPA), BS-VI in India and China VI. This greater stringency in global emissions requirements, which also includes the EU’s Stage V standards, has shifted the focus of OEMs towards
TOP: Hydrogen fuel cells have the potential to power heavy construction equipment
alternative powertrain sources such as hybrid electric and full electric off-highway vehicles leveraging the demand globally.
VOLVO
CE WILL BE NET-ZERO BY 2050
Sweden-based OEM Volvo Construction Equipment (Volvo CE) has fully committed to the global Science-Based Targets initiative, aiming towards being a net-zero emissions company by 2050 at the latest. A first goal is that 35% of all machine sales should be electric by 2030. In 2019 Volvo CE stopped developing any new diesel-powered compact construction machines.
The company has developed a range of battery-electric construction equipment in recent years. In 2017 it unveiled the EX02
RIGHT: JCB says its 220X hydrogen-powered excavator is a potential game-changer in the move to zero-carbon off-road machines
fully-electric concept excavator and followed this in October 2020 with the 14-tonne EX03, its first prototype in the mid-size excavator segment.
Ahcène Nedjimi, lead engineer and specialist in electromobility at Volvo CE, says: “The move to electric power is a transition that is gathering speed. Government policies and market trends are seeking to reduce the use of combustion engines in both on-road and off-road applications to address climate change and mitigate air pollution.
“Both Volvo Group, our parent company, and Volvo CE have a really strong commitment to meeting the requirements of the Paris Agreement on climate change and reducing carbon emissions. We also see a strong ambition in our customers’ roadmaps towards the reduction of their emissions.
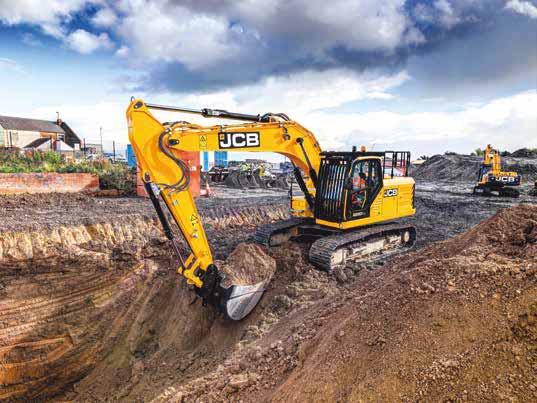
“Every new project with compact wheeled loaders and excavators is now electric. We have started with two machines - the ECR25 Electric 2.5 tonne compact excavator and the L25 Electric compact wheeled loader. We began with compact machines as that is where the greatest demand is, particularly for use in urban areas.”
Nedjimi says that the near silence of such machines can play a vital role in reducing the issue of noise in urban environments. According to research by the European Environment Agency this is a major problem affecting the health and wellbeing of millions of people in Europe. According to Volvo CE, electric machines provide operators with a more peaceful work environment with lower vibrations and
noise so they can talk more easily with coworkers.
Electric machines also open up practicable working hours in urban locations, enabling digging to take place outside a bedroom window, school zone or hospital room, and even through the night.
Nedjimi says that Volvo CE is focused on developing electric battery solutions for small to mid-size construction machines, but continues to explore the most appropriate technologies to electrify all segments of construction machinery. Volvo Group has recently launched a joint venture with Daimler Truck to produce fuel-cell solutions for use in long-haul trucks and beyond, and will be exploring the use of this technology in other applications.
Attractive opportunitites in the electric off-highway vehicle market

AGGRESSIVE STEP TOWARD MINIMISING EMISSIONS AND VENTILATION COSTS IN UNDERGROUND MINING
THE HYDROGEN FUEL CELL
The use of hydrogen fuel cells as an alternative source of electrical power in the construction equipment sector has seen major recent announcements from companies including JCB and Hyundai Construction Equipment.
In July 2020 JCB unveiled the working prototype of a new 20-tonne excavator, powered by a hydrogen cell. The UK manufacturer claims its 220X hydrogenpowered excavator is a potential gamechanger in the move to zero-carbon off-road machines.
JCB’s product innovation director Bob Womersley said the development of the 220X has progressed well and provided useful knowledge.
Source: Secondary Research, Expert Interviews, Company Presentations, and MarketsandMarkets Analysis NEW PRODUCT DEVELOPMENT, EXPANSION & INVESTMENTS WOULD OFFER LUCRATIVE OPPORTUNITIES FOR MARKET PLAYERS IN THE NEXT 5 YEARS HIGHER INITIAL COST THAN CONVENTIONAL ICE VEHICLES (INTERNAL COMBUSTION ENGINE)
➔ The development came a year after JCB said it had made manufacturing history in 2019 by going into full production with a fully electric mini excavator, the 19C-1E. JCB has also extended electric technology to its Teletruk telescopic forklift range with the launch of an electric model, the JCB 30-19E. “We’ve learnt so much about hydrogen and how to manage it and get the best out of the performance of the machine,” added Womersley. “We continue to make great progress with the technology.”
Mini excavators have considerable potential for making sizeable steps forward
will do its very best to meet the challenges that lie ahead as countries around the world attempt to establish global standards in terms of certifying the performance of equipment and legislating relevant laws for the commercialisation of hydrogen-powered construction equipment, and play a leading role in the market moving forward.”
OTHER ALTERNATIVES
Womersley says that JCB is anticipating a rapid rise in the uptake of electrified machines, especially in the area of compact and lighter mid-range equipment, where the company already has several electrified construction models on the market including an electric mini excavator, electric 1-tonne capacity site dumper, two electric forklifts and an all-electric telehandler. Womersley says deploying electric machines can make economic sense for operators: “The critical thing about capital plant investment is that it has to pay back for the customer –unlike a passenger car, say – and we can see that the business proposition is working well for our customers such that the increased penetration of electrified machines is well underway, just by virtue of the fact that the machines pay back.”
Hyundai Construction Equipment (HCE) has joined forces with the Hyundai Motor Group to develop hydrogen fuel-cell-powered construction machines. Hyundai Motors and Hyundai Mobis will design and manufacture hydrogen fuel-cell systems, including power packs, while HCE will design, manufacture, and evaluate the performance of excavators and forklifts. The partners have set a date of 2023 to begin mass production and distribution.
HCE says that, given the rapidly rising demand for eco-friendly equipment around the world, hydrogen-based construction equipment will help it to compete in the global construction market moving forward. It adds that, compared to lithium batteries which have been marred by structural issues limiting various attempts to increase battery capacity, hydrogen fuel cells are much easier to expand, making them a much more logical choice for large forklifts or excavators.
Hwang Jong-hyun, head of the R&D division for material handling at HCE, said: “Hyundai Construction Equipment
In terms of other new potential power sources apart from fuel cells and battery power, JCB’s Womersley says there is also the possibility for alternative fuels for internal combustion engines (ICEs) to become available which have a very low or even zero CO2 impact.
Mini excavators have considerable potential for making sizeable steps forward in zero-emission battery-powered equipment, according to Burkhard Janssen, Hitachi Construction Machinery Europe (HCME) department head, special applications & new technologies.
“Mini excavators are leading the field in this development, due to the small size of batteries required,” Janssen says. “Rapid charging times and sufficient operation capacities are vital for their successful adoption in the market.”
Janssen adds that drives for efficiency and environmental concerns are increasing the
demand for electric in Europe, particularly for compact equipment that is often used in heavily populated urban environments.
“Contractors are looking to gain an advantage in tenders by demonstrating their sustainability credentials,” he says.
Due to the high costs of the battery package, Janssen says that electric machines are currently too expensive for most customers when just replacing dieselpowered machinery.
In some European countries there are subsidies available to stimulate electrification or other alternative powertrain solutions.
“However, if none are available, rental could be an interesting starting point,” Janssen adds. “Manufacturers will need to provide the whole package - cables, transformers, battery packs and job site support.”
CUMMINS IS INVESTING HEAVILY
US engine manufacturer Cummins is a major proponent of hydrogen fuel-cell technology, which it says could be the fuel of the future. The firm is best known for its diesels but is investing heavily in developing new power sources for mobile machines, including both electric and hydrogen technologies.
Cummins says it is combining its powertrain expertise and its fuel -cell and hydrogen technologies in a variety of applications, including semi-trucks, delivery trucks, transit buses, refuse trucks and passenger trains.
Amy Davis, president of Cummins new


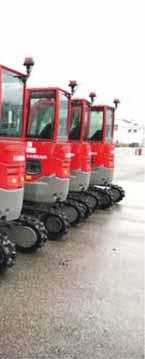
COULD A ‘TESLA’ BE ABOUT TO EAT THE OEMS’
ELECTRIC LUNCH
Tesla has gone from a niche manufacturer of 147 electric cars in 2009 to now producing over 500,000 vehicles a year
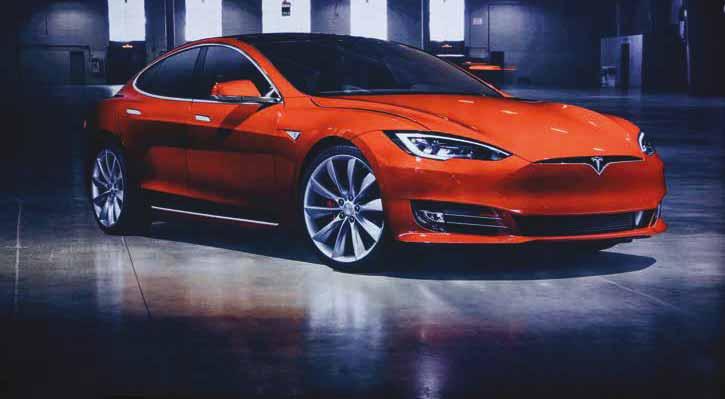
With electrification (along with digitalisation and autonomy) all set to change the construction equipment sector, could the industry’s established original equipment manufacturers (OEMs) be wrongfooted by a new market entrant?
Industry thinkers Alan Berger and Carl-Gustaf Göransson say there is a possible scenario where such a newcomer could disrupt the incumbents.
Berger and Göransson (who have both held senior roles at Volvo CE and CNH Industrial), comment: “In 2008 no one saw Tesla Motors as much other than a niche electric sports car company. Certainly not other car companies – in 2009 Tesla only made 147 cars. Fast-forward 12 years and Tesla is making 500,000 cars a year and is valued higher than the top six car manufacturers combined.”
Like construction equipment, the car business has been consolidating, with no significant new entrants in a long time. This raises the question as to whether the same thing could happen in the construction equipment world – could a disrupter barge into the sector and win? With the industry trying to digest the triple challenges of digitisation, autonomous operation and electrification, there is an opportunity for new players to emerge. Central to the success of today’s OEMs is their extensive product, customer and application knowledge. But given the technical changes that are coming, is that going to be enough to save them from a digital disruptor?
Berger and Göransson say that the new era of machines will require a completely new architecture, one that is designed
power segment, said that major rollouts of hydrogen fuel cells are first likely to take place in markets such as trains where the powertrain and fuel costs represent 50% of total operating costs - much lower than the heavy-duty truck market where the figure is above 80%. She added that the company had been putting a focus on fuel-cell solutions in the train sector for this reason.
Hydrogen is seen as a particularly important future fuel. It can be used in fuelcell stacks to generate electricity for both fixed and mobile machinery, with the only emissions being water vapour.
Cummins president Tom Linebarger said that to meet the challenge of tackling
around the capabilities of an electrical drivetrain: “A disrupter would develop a completely new machine, while existing OEMs could do so only if they resist the temptation to take the ‘easy’ path of adapting current machines. Indeed, OEMs would be able to leverage their vast portfolio of intellectual property to speed this along. Advantage OEM.”
With new, digitally enabled sales models, the traditional role of the construction equipment dealer is also likely to change, and a new player could greatly accelerate this.
“Just look at the success of Tesla’s direct-selling model,” Berger and Goransson state. “That said, construction equipment requires responsive and intensive access to service, which is a vital part of the dealers’ offering. A disrupter could build a serviceonly network, leveraging
climate change, there must be a transition to renewable power. “We must limit carbon emissions. We believe hydrogen will play a part in that transition. Hydrogen is green and it can be produced without carbon emissions.”
He said that at present, the majority of the world’s 70 million tonnes/year of hydrogen production (around 98%) is ‘grey’, requiring the use of methane and resulting in CO2 emissions. Meanwhile, around 1% of hydrogen production is ‘blue’, with CO2 being sequestered using former underground mine facilities as storage for example. Just 1% of hydrogen at present is truly green, using electrolysis.
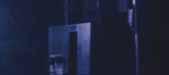
established dealers while moving most of the sales activity on-line. This is difficult for existing OEMs and therefore the newcomer has an edge. Advantage disruptor.”
They add that there is one additional and important consideration to the disruptor versus incumbent electric power debate. Tesla was founded well before the automotive industry recognised the need and technology availability. Clearly, this is not the case for the construction equipment industry today.
“Taking all of these factors together, it seems that the existing OEMs can drive the disruption themselves if they are willing to commit to the extensive and complete transformation needed,” Berger and Goransson conclude.
“But, if none do so, don’t be surprised if someone else decides to do it for or to them.”
However, Linebarger believes that development of facilities generating sustainable electricity can provide the capacity needed to allow hydrogen production. This will be costly, coming with an estimated price tag of US$350bn for the electricity required to produce hydrogen using green electrolysis technology. And Linebarger said: “We expect green hydrogen to replace grey hydrogen.”
Some industries will switch to using hydrogen as fuel earlier than others and Linebarger said that he believes the steel production industry, a major user of energy, will be one of the first. Looking ahead, Linebarger said, “The cost of green hydrogen will reduce.”
Amy Davis of Cummins said that the firm is at present installing the world’s largest SOE (solid oxide electrolyser) plant in Canada, which will be able to produce 300,000 tonnes per year of hydrogen. Meanwhile, even larger facilities are in planning.
The fuel-cell technology for mobile machines is already well proven and Davis thinks that by 2030, up to 10% of trains and 10% of buses could have already switched over to using hydrogen as fuel. She added that for trucks and off-highway machines, this transition process will take longer.
MAKING ELECTRIC POWER SUSTAINABLE
Replacing diesel with hydrogen as fuel will need a massive global increase in sustainable electricity-generating capacity. Solar panels in arid areas in North Africa, the Middle East or parts of Latin America, or wind and hydroelectric stations in Europe and China could deliver the necessary capacity. Linebarger commented: “We know the adoption of sustainable power will take time.”
Eric Neal, executive director of Cummins off-highway business, predicts the most rapid levels of adoption of alternative power in the off-highway sector could be in small material-handling equipment and in port-handling equipment (partly driven by zero-emission requirements at ports). Smaller construction equipment such as miniexcavators in the rental sector could also see rapid adoption of electrical power.
Volvo CE’s Nedjimi says that batteries are currently predominant (compared
to hydrogen fuel cells) in areas such as construction equipment because the price of the technology is coming down and the recharge time is reducing, while battery capacity is increasing. “The poor deployment of hydrogen-charging infrastructure is also creating a barrier against fuel-cell development,” according to Nedjimi.
In addition to compact models, he says battery power is also suitable for larger construction equipment and Volvo CE is currently testing the 23-tonne EC230 prototype battery-electric excavator with customers.
The company is rolling out its electric construction equipment in 12 countries at the moment. Europe’s biggest construction equipment rental company, France-headquartered Loxam, recently purchased 18 Volvo CE ECR25 electric compact excavators. In the second half of 2020, Volvo CE also started a commercial pilot of its electric machines in California, featuring the ECR25 Electric and an L25 electric wheeled loader in versions adapted for the US.
inner city environments.
“The feedback we are getting from all these projects is very positive in terms of the emissions and also the noise, and our customers are promoting electric machines. They find the machines are more powerful than the equivalent diesel machine as it is more responsive. When diesel engines start up, they can have some drops in the rpm which you don’t get with an electric motor.” He adds that total cost of ownership is another driver for the uptake of electric engines which have fewer filters than diesel machines and require less maintenance.
Battery charging is one of the major issues that needs to be addressed
According to Volvo CE, the ECR25 Electric offers the same digging performance as its conventional counterpart with less maintenance, and also does not require any high voltage certification, as the machine runs at 48V.
Another high-profile deployment of the ECR25 Electric was at the UK’s Chelsea Flower Show in 2019 where it took part in constructing the Gold Medal winning Morgan Stanley Garden. “It is such an intense work zone,” Nedjimi said. “Right in the heart of London so it really offered the perfect arena to showcase its unique capabilities for
An off-road electrification timeline (FCEV = Fuel-cell electric vehicles, BEV = Battery-electric vehicles)
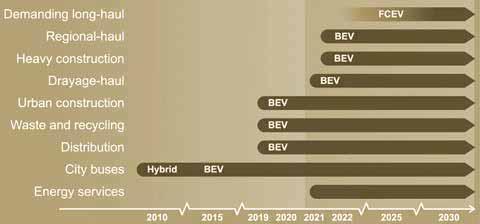
Source: Volvo Group
In February 2021 Volvo Group created the new Volvo Energy business area to offer its customers battery life-cycle options including disposal and repurposing and to develop charging infrastructure. Nedjimi says that battery charging is one of the major issues that needs to be addressed in deployments of electric construction equipment, and the creation of Volvo Energy will help address this.
“The feedback we got from a construction customer working in Paris was that they had to plug the machines in to the public electricity infrastructure used by electric cars, which required permission from the local municipality,” he says. “While the machine was able to last a full working day on just one charge, we do see this as one of the improvements that needs to be made and that they have to have their own charging stations.”
He adds that Volvo CE is developing a full solution that encompasses the machine and the recharging infrastructure. “We cannot just sell the machines without supporting the customer and providing the ability for recharging. The municipalities will also move in that direction as they are promoting the use of electric machines.”
The Swedish manufacturer says that the new Volvo Energy business will have both an internal role, providing batteries and charging solutions to the Volvo Group’s other business areas, and an external role, offering used, remanufactured and refurbished batteries to customers for use across different applications.
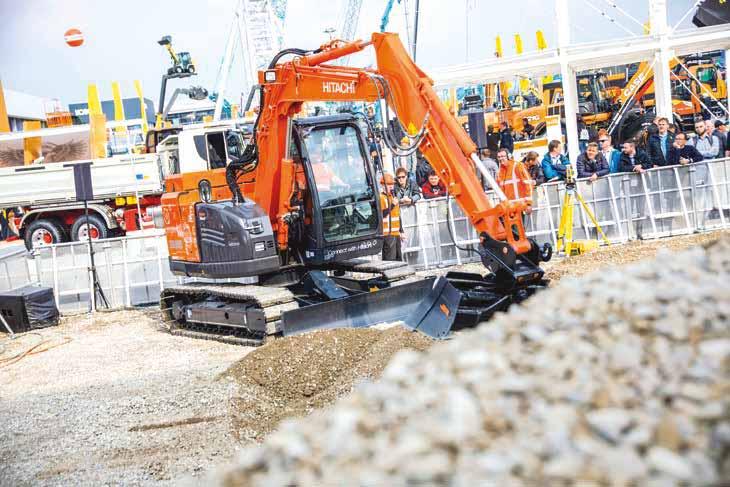
Group, said: “Our ambition is to offer our customers the most competitive solutions when it comes to electrification, including batteries and charging infrastructure. With Volvo Energy, we are taking a holistic view of the entire life-cycle, which benefits both our customers’ business and society as a whole.”
The company said that it would increase the pace of its rollout of electric vehicles and related services, including the introduction of heavy-duty trucks for regional transport or construction later this year.
THE CHALLENGE OF BATTERIES
Volvo Group predicts that batteryelectric power will predominate for rollouts in urban construction, ‘drayage’ hauling (hauling shipping goods and containers a short distance overground) and regional hauling, while fuel-cell electric power will be heavily used in demanding long-haul applications.
Bob Womersley of JCB says that battery and fuel-cell solutions both have their merits and challenges. “Batteries work well in the lighter machines,
time, such that it will drive the market towards fuel-cell power where electric machines are preferred.
“Fuel-cell machines are still zero emission with all the other significant attributes of electric propulsion, and yet [have] higher energy content on board (in hydrogen) with a refuelling time much faster than battery re-charge.”
Other major global construction equipment makers are also progressing their plans for alternative power. Japan’s Komatsu is working on its first battery-electric middle-weight excavator in partnership with commercial vehicle electrification technology company Proterra.
“Komatsu will use Proterra’s high-performance battery systems for the development of a proof-of-concept electric excavator in 2021 before expected commercial production in 2023 to 2024,” said California, US-based Proterra. “The Proterra battery system powering the electric excavator will feature high-energydensity and fast-charging technology.”
Proterra battery packs, made in the US,
middle-class excavator and replace the need for a normal counterweight used to balance the excavator’s hydraulic arm movements,” Proterra stated.
“Proterra’s best-in-class battery technology has been proven in 16 million miles driven by our fleet of transit vehicles,” said Jack Allen, chief executive of Proterra. “What’s working in our battery-electric transit vehicles on roads across North America can work offroad, too.”
CATERPILLAR’S STRATEGIC APPROACH
US-based Caterpillar says it is taking “a strategic approach” to electrification, adding that “we are ready. In fact, we’ve been investing in electrification for decades.”
The manufacturer says its engineers hold numerous patents in the space, and that Cat electrified products are at work on customer sites around the globe. “Innovation comes standard on every product we make, and we’re convinced that electrification is a technology that brings key benefits to our customers,” it adds.
South Korean manufacturer Doosan Infracore unveiled its DX17Z-5 electric mini-excavator prototype at the March 2020 ConExpo show in Las Vegas. The South
Korean OEM said the 1.7 tonne machine could be launched on the market in 2022.
China’s XCMG, which claims to be the world’s fourth-largest construction OEM, says it is firmly focused on developing new energy solutions to keep its business competitive in the global market.
It adds that its continuous investment in technological R&D has achieved substantial results. At the bauma China 2020 exhibition, it debuted what it says are the industry’s largest-tonnage electric excavator (the
XE270E) and the largest electric drive loader in China (the XC9350).
XCMG’s 35U-3 electric excavator, launched in the same year, is claimed to lower operational costs by 60% compared to conventional excavators.
Despite all these developments, traditional diesel power may not be headed for the history books just yet.
JCB’s Womersley says: “Technologies are adapting so very quickly, yet because the internal combustion engine is so robust,
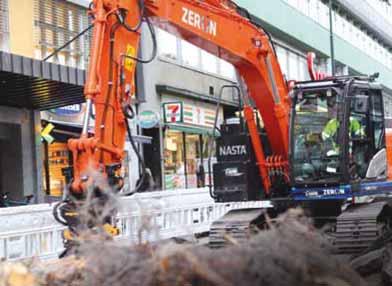
The Nordic region is among the prime global movers in deployments of electric construction machines. Norway’s capital city Oslo has made the bold decision to demand zero emissions on all its job sites from 2025. The Olav Vs Street and Klingenberg Street upgrade in Oslo that commenced in the autumn of 2019 is claimed to be the world’s first zero-emission urban construction site.
The project used electric construction equipment from Hitachi that is rebuilt for individual customer requirements by Norwegian company Nasta. The project utilised a 17.5-tonne Zeron ZE160LC electric excavator – the first to apply the PeakShaver + power management system. Nasta says that PeakShaver+ is a unique way to control power that allows large electric machines to cope with the power needed to run a machine that is half its size.
The Olav Vs job site also used two nine-tonne electric Zeron ZE 85 hydraulic excavators from EAC (European Application Center), Hitachi’s joint venture established in 2018 with Kiesel
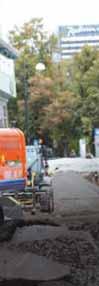
Technologie Entwicklung (KTEG) to develop electric construction machinery for sale in Europe. Nasta rebuilds Hitachi ZX160, ZX210 and the ZX350 machines, rebranded as Zeron ZE160LC Peakshaver+, Zeron ZE210LC and Zeron ZE350LC.
“The ZE160LC and ZE210 both run on a combination of Li-ion batteries and cable,” says Nils Olav Haukaas, consultant at Nasta. “The ZE210LC allows for CCS2 supercharging.”
The job was finished on time and the operating contractor Steen & Lund AS was pleased with the reliability and the performance of the electric machines which meant “less filth, no refuelling, less noise, less vibrations, same performance”.
The electric ZE85 is equipped with batteries with a gross capacity of 100 kWh. The dual 22kW AC chargers can charge the machine in a little more than two hours. CCS2 100kW DC charging is also an option. The machines normally operated from six to ten hours per day – following the rhythm at the job site, charging at night and during the lunch hour.
adaptable, powerful and fuel-efficient, it will take some significant further developments and time if it were ever to be fully displaced.”
Eric Neal, executive director of Cummins off-highway business, says that although the engine maker is investing heavily in alternative power technologies, it is not making a full shift away from diesel. “We do believe that diesel will always have a place,” he says. “We will definitely have a solution for both internal combustion engines as well as alternative power.”
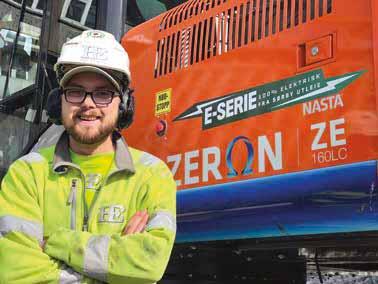
The Olav Vs street upgrade included an ‘efuture’ charging station for electric taxis –making abundant electric power available. Nasta says that operators using electric machinery should prepare a good plan for electric power to the job site.
A dB meter installed at the site found that surrounding noise from the city was louder than the construction site. The magazine Teknisk Ukeblad excitedly stated: “At this job site you can actually hear the birds sing.”
Andreas Johanson, who was the first to drive Nasta’s ZE160 at the Oslo job site, said: “I was sceptical at first, but it really does work. You just have to plan your work a bit different. The biggest difference is the noise – both inside and out. And it is cleaner. You do not need to think of calling the tank-truck and things like that.
“Besides all the benefits – this is the future. It will be fun to tell people in 30-40 years that I was one of the first people in the world to renovate a whole street with only electrical machinery – that is exciting!”
POWER T DO MORE FOR YOU.


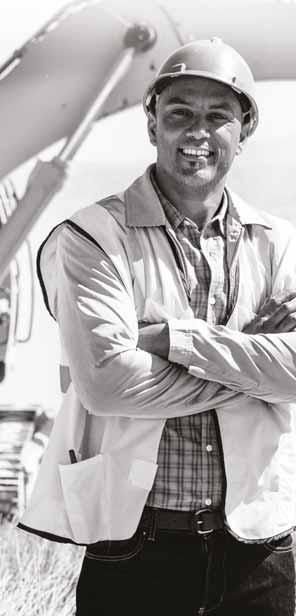
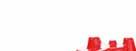

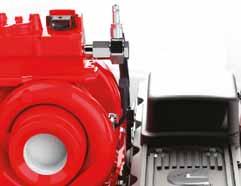
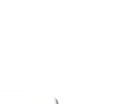
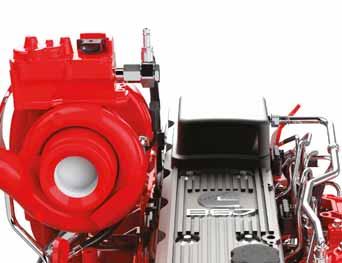
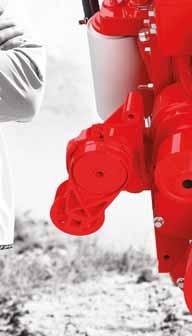
Resilient product. Global support. Engines that have the power to do more for you.
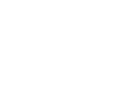

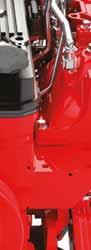
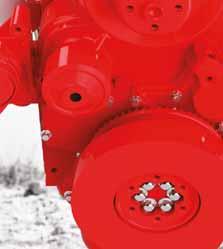
The Cummins B6.7 Performance Series engine is proven in a wide range of industrial applications. Power increases to 326 hp / 243 kW enabling replacement of engines with higher displacement with no impact on productivity.
cummins.tech/globalreportconstruction-june21

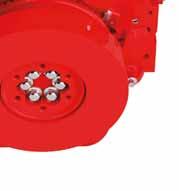
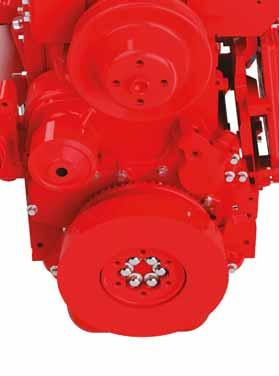
SURVIVAL OF THE FITTEST
The global pandemic has shaken up the world’s supply chains. If being flexible, resilient, creative and digitally aware of shipping delays and delivery status were important before COVID-19, they are now business-critical. Has your logistics strategy got what you need to survive? Is it fit for purpose? Geoff Hadwick reports
Half-way through reviewing his company’s start to 2021, Alexander Greschner, CSO of the Wacker Neuson Group, paused for thought. Manufacturing is complicated enough, he said, but running a global supply chain during a global pandemic is even worse. The crisis has made everything far more difficult, far more complex.
“COVID-19 has presented everyone with major challenges,” the Munich-based chief strategy officer observed in his first quarter summary. “These have included changes in working conditions with rigorous protective and hygiene measures, working from home and the daunting task of balancing work with childcare.
“The crisis has also shown us that we have
the flexibility, creativity and perseverance to ensure business continuity for our customers (but) the main thing we are concerned about at this stage is the situation with global supply chains.
“The pandemic has led to restrictions like border controls on the one hand, and on the other we have the ongoing risk of staff shortages due to illness or quarantine measures, which can affect both us and our suppliers. In addition, the general rise in demand for the steel and other raw materials that we rely on is really pushing prices up.
“Even transport costs have shot up. Container prices have trebled in some cases in recent months (Q4 2020
and Q1 2021) and these trends are picking up speed.” Building sites may have remained open, but keeping them supplied with machinery and materials has become evermore expensive and ever-more complicated. To survive, your business is going to have to be truly resilient.
Wacker Neuson should know. It is a major global player in the construction equipment industry, employing around 5,500 people worldwide. It turned over US $2.3 billion in 2019 through a product range that spans concrete technology products, compaction equipment, worksite technology and compact site machinery. Its brands include Wacker Neuson, Kramer and Weidemann.
Our main concern is the situation with global supply chains says Alexander Greschner, CSO of the Wacker Neuson Group
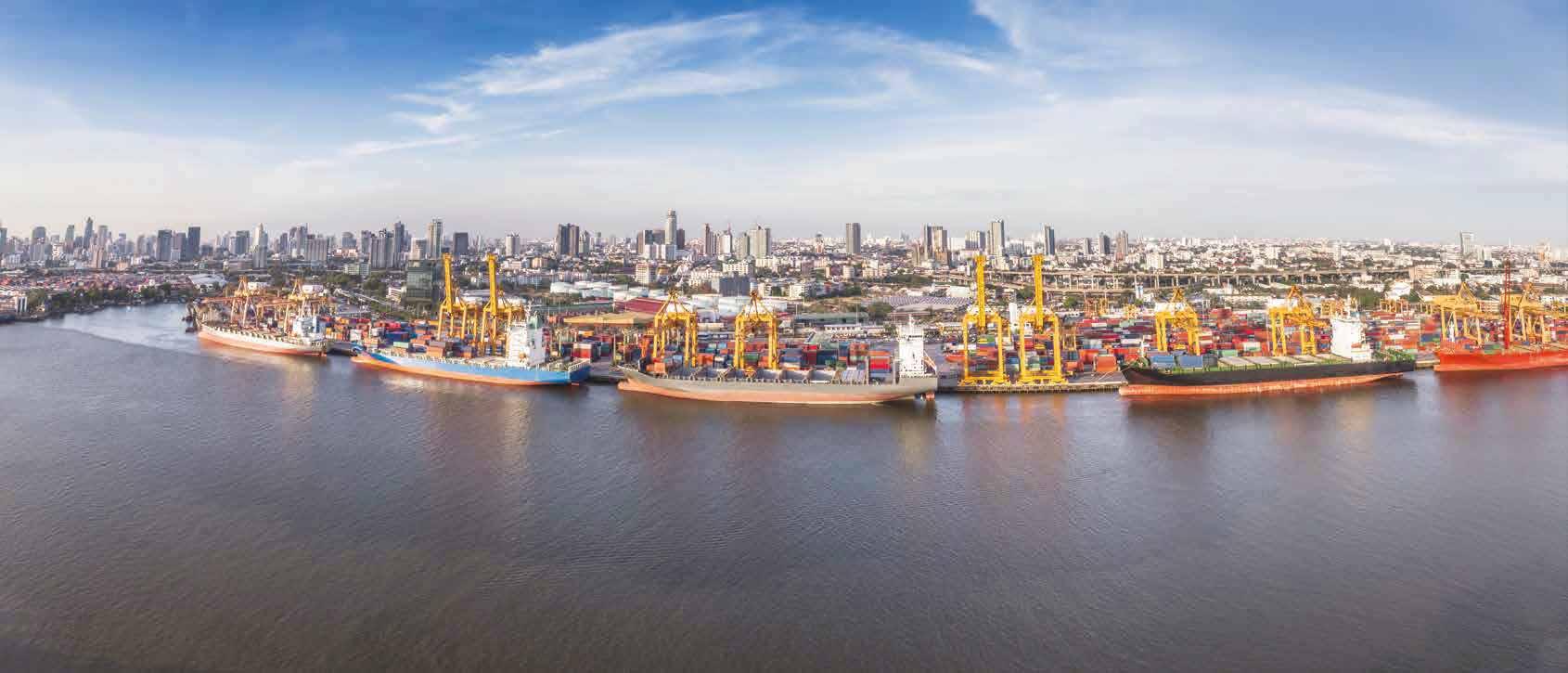
A port in a storm: a recent EY survey found that 83% of multinational executives were contemplating so-called ‘reshoring’ or ‘nearshoring’ to reduce supply chain complexities
The company knows that staying alive right now is all about being light on your feet. The world is changing fast and the supply chain is being forced to change with it: “At the moment, we can run our production programs at scale as planned,” says Greschner. “However, we have to remain flexible and, if necessary, pull forward equipment for which the materials are available and delay the production of other machines.
“Rising costs mean that adjustments to market pricing will be unavoidable despite our extensive efforts to raise productivity levels and our ongoing internal cost-saving measures.”
Agreed, says Wacker Neuson CEO and CFO Kurt Helletzgruber: “COVID-19 presented sizeable challenges over the past year, and the pandemic is far from over.” His board recently put out a statement saying that: “The supply chain in particular is currently a source of risk. The situation in many areas is already under considerable pressure due to the restrictions caused by the pandemic and the overall uptick in demand. In addition, the group is facing sharp increases in procurement prices, for example for steel.”
As always, everything costs, and Wacker Neuson is not alone in pointing out that the pandemic has cost a lot. Caterpillar chairman and CEO Jim Umpleby calls the crisis: “A challenging environment.” In his latest financial statement, Umpleby says: “I’m proud of our global team’s continued resilience in safely navigating COVID-19.”
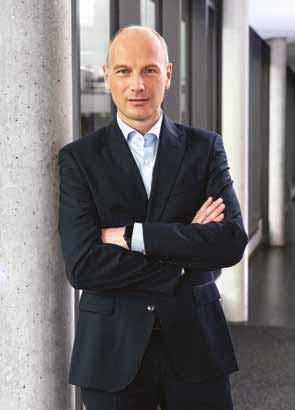
Worsening border controls, staff shortages due to illness or quarantine measures, and the general rise in demand for steel and other raw materials is “really pushing prices up” says Alexander Greschner, CSO of the Wacker Neuson Group
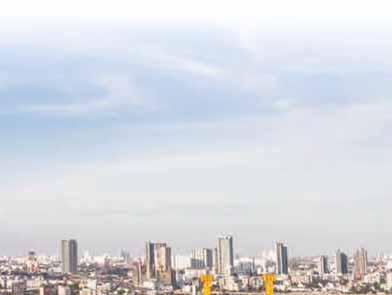
Over at Volvo CE, president Melker Jernberg, says: “In 2020, the global pandemic presented us with challenges that are unprecedented in modern times. But, together with business partners and suppliers, we were able to support customers through all stages of the crisis.”
John Deere’s chairman and CEO, John C May, agrees: “John Deere’s foremost priority in confronting the coronavirus crisis has been to safeguard the health and
well-being of employees while fulfilling its obligation as an essential business serving customers throughout the world,” and “we’ve had good success in these areas thanks to the proactive measures we have taken.” These have included: “Leveraging digital tools and connected-support abilities which have allowed our dealers to remotely service customer machines and maintain appropriate social distancing protocols,” and making tough calls on the money front.
“Significant actions also have been taken to strengthen the company’s financial position. These include raising about $4.5 billion in medium- to long-term funding, aggressively reducing operating expenses, decreasing capital spending budgets, and other actions to preserve liquidity,” Deere adds.
Aggregates equipment giant Metso Outotec has been weathering the storm too. In April, the company said: “The COVID-19 pandemic continued to affect Metso Outotec’s end markets and customer operations during the first quarter (of 2021). The most severe impact is resulting from restrictions on workforce mobility and limited access to customer sites. This has affected especially the services business in all segments and, to some extent, also decision-making and commissioning related to customers’ large investments.”
It has been a very tough year or so all round … tough enough for The Economist to ask, at the end of 2020, if a wave of supplychain reshoring was about to devastate the markets. Is globalisation about to go into
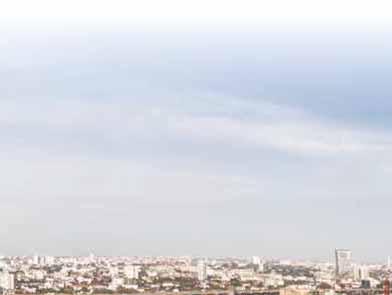
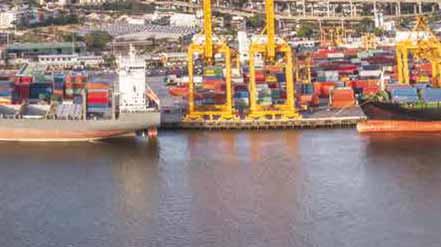

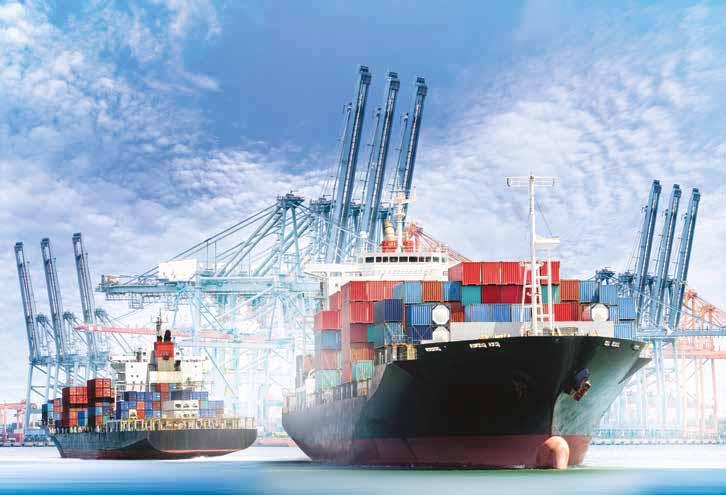
reverse? Are OEMs going to be forced to supply their factories with home-grown (or locally sourced regional) components in the near-future?
Their answer, perhaps not surprisingly, was yes and no.
Yes: “Supply-chain managers have had a stressful few years. From Sino-American trade wars and Brexit to COVID-19-induced restrictions on medical exports and travel, there has been a lot to deal with. At the worst of the pandemic, company bosses inevitably wondered if bringing production closer to consumers might help.”
Yes: “In April 2020 a survey conducted by EY (also known as Ernst and Young), an accounting firm, found that as many as 83% of multinational executives were contemplating so-called ‘reshoring’ or ‘nearshoring’. Recent history shows how sticky supply chains can be, but might this time be different?”
And yes: “Politicians have long angled for companies to shift production to their shores because they want jobs for their constituents. There can be a business case for it too, in order to cut transport costs, say, or reduce inventories. The Reshoring Initiative, for instance, which advocates for more manufacturing in America, cites the allure of ‘Made in the USA’ branding for older Midwesterners. Some reckon technology might encourage reshoring. In 2017 a report by ING, a bank, predicted that 3D printing
ABOVE: Ship-shape: Container and shipping prices trebled for many supply chains during Q4 2020 and Q1 2021 … and these trends are picking up speed
could wipe out 40% of trade flows by 2040.”
But (and there’s always a but)… No: “The experience of the past decade suggests that for every company reshoring production, there may be more doing the opposite. A survey of German manufacturers found that 2% brought production home between 2010 and mid-2012. Four times as many shifted operations abroad during that time. A study published in 2016 by the OECD, a club of mostly rich countries, found that the effects of reshoring on national economies were ‘(still) limited’.
Nor does recent history suggest that these new technologies will cannibalise trade.
“Take 3D printing,” says The Economist. “A study by Caroline Freund, Alen Mulabdic and Michele Ruta of the World Bank found that its use in the hearing-aid industry increased trade by 58% over nearly a decade, compared with what it might have been expected to be otherwise. As the technology was useful for only part of the manufacturing process and hearing aids are cheap to transport, supply chains did not retreat.
“Gary Gereffi of Duke University in the US cites the failure of Adidas to print shoes in America and Germany as evidence of
the importance of highly orchestrated production networks. He found that a lack of locally available components meant the shoes had to be simplified so much they lost their consumer appeal.
“The adoption of other technologies can make importing, rather than reshoring, more attractive. Katherine Stapleton of the World Bank and Michael Webb of Stanford University found that Spanish firms using robots were more likely to increase their imports from low-income countries, or open affiliates there. Productivity-enhancing automation led firms to expand output, and so import more parts.”
This is all well and good, but will the global construction equipment supply chain follow suit? After all, shoes and hearing aids are nowhere near as big to build or as cumbersome to transport as a giant excavator.
ESCO
SAYS BE FLEXIBLE
Sebastien Miroudot of the OECD finds that the evidence in favour of diversifying across many suppliers is shaky. He thinks that construction equipment manufacturers should keep it simple. Experience suggests that firms with fewer, longer relationships recover from shocks more quickly. Rather than relocation, he has written, the research seems to argue for ensuring that production can be flexibly moved from place to place in an emergency.
Ah yes, flexibility. For many construction equipment OEMs, this means using thirdparty logistics suppliers and juggling a chain of trust-based partnerships. New alliances are emerging all over the place. Take ESCO, a global wear parts provider and a division of The Weir Group, for instance. It has just appointed Kinaxis Inc. to: “transform (its) global supply chain and provide the agility and responsiveness needed.”
In announcing the deal, ESCO said that it had selected Kinaxis to enhance customer satisfaction. By using Kinaxis RapidResponse and its planning software, ESCO said that it hopes to “gain full connectivity and visibility across its entire end-to-end supply chain.” The two partners hope that their new platform will “give everyone in the ESCO supply chain network a consolidated and up-to-date company-wide view.” The idea is to “enable what-if scenario analysis (so that the company) can rapidly take action when changes happen. It will also help the company improve forecasting and planning, reduce inventory obsolescence, and increase confident decision-making, all in real time.”
In other words, be as flexible as possible: “Not having the right part at the right time can mean huge losses,” said John Sicard, CEO Kinaxis. “Using Kinaxis, ESCO will gain the best balance of ready-to-configure applications and a flexible platform that can grow and evolve with the company.” He wants to help “ESCO tackle its increasingly complex supply chain and empower the company to better serve its customers.”
However, staying quick on your feet is never easy. “The pandemic is far from over,” argues The Economist, “and shifting production can be a slow business. The
economic plan of new American president Joe Biden talks of firms being dangerously dependent on foreign suppliers.” But, will the globalisation boom of recent years continue? Or is the party coming to a close? “When production networks (and their supply chains) are stretched across several countries, trade restrictions can backfire, hurting both the exporter and the importer,” says The Economist. “This has given governments a big incentive to co-operate”, and encourage companies to build and rely on far-flung factories.
But, as COVID-19, trade wars, the resurgence of the nation state and Brexit have all proved, the high levels of trust that this sort of industrial policy require can be destroyed overnight … not to mention the business community’s sense of security. And a sense of security is what it is all about.
A recent report on www.securitymagazine. com captures the mood for many of the world’s leading logistics directors: We need to be resilient. At the turn of the year, the Cybersecurity and Infrastructure Security Agency (CISA) and government and industry members of the Information and Communications Technology (ICT) Supply Chain Risk Management (SCRM) Task
Make the complex simple: Cybersecurity, flexibility, enhanced software packages, resilience, planning and risk management … they are all part and parcel of the same thing ➔

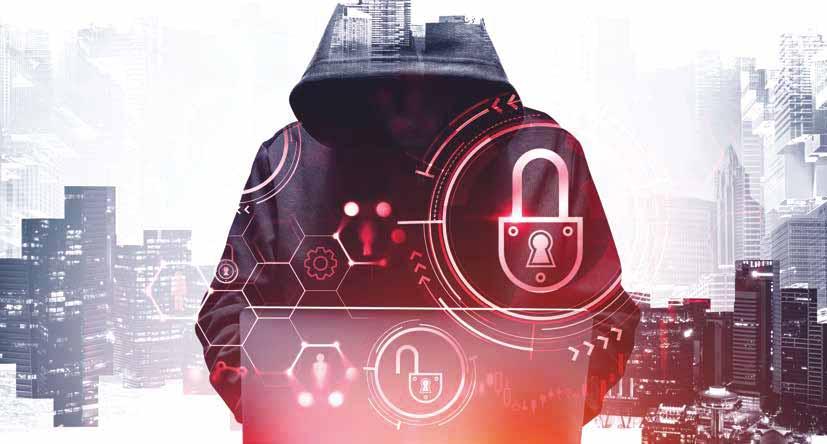
➔ Force came together to release an analysis report on the impact of COVID-19 on global supply chains called ‘Building A More Resilient ICT Supply Chain: Lessons Learned During The COVID-19 Pandemic.’
“The report examines how supply chains have been impacted by the pandemic, (arguing that) the COVID-19 global pandemic caused profound disruptions to global supply chains,” says www. securitymagazine.com
“It exposes how some manufacturing companies were unprepared because of their reliance on lean inventory models. It underscored the difficulties that companies faced in understanding who their junior tier suppliers are and where they are located. It also acknowledged the need for an approach that was already underway over the last six years: diversifying supply chains to a broader array of locations and away from single source/single region suppliers.
“Recommendations from the study include refining supply-chain risk-management approaches, mapping out detailed supply chains and developing standardised approaches to doing so, encouraging dualsourcing from multiple or lower-risk regions, holding buffer inventories, and planning alternatives for potential transportation and
logistical bottlenecks.”
The report concluded, as so many do when looking at logistics, that running a global supply chain is really all about effective risk management. This “often depends on supply chain visibility, proactive planning and being willing to make risk-informed investments. The economic benefits of lean inventory models in a ‘business-as-usual’ environment fade significantly when a major pandemiclike disruption occurs.” Just in time rapidly descends into far too late.
Panic and mass hysteria have characterised the response of many governments around the world. And it has been hard to keep the money flowing. So, if we are going to relocate, or re-shore, where is it best to invest, many of the world’s leading construction equipment players have been asking?
technique and form of receivables purchase, flexibly applied, in which sellers of goods and services sell individual or multiple receivables (represented by outstanding invoices) to a finance provider at a discount. In turn, the guidance document takes a wider look at this important technique and provides a comprehensive overview on how payables finance can be used in practice.”
And: “When all parties use similar techniques and terminology, it makes for a streamlined and efficient process,” said Christian Hausherr, European Product Head of Supply Chain Finance at Deutsche Bank and Chair of the GSCFF. “Our hope is that this report will lead to an industry-wide, uniform adoption of the payables finance technique.”
US protectionism led to a steep rise in import tariffs and an inevitable tit-for-tat response from China
According to a recent report from www. finextra.com: “To make the money flow far more smoothly in tricky times, the Global Supply Chain Finance Forum (GSCFF) –an initiative comprising the International Chamber of Commerce (ICC) Finance for Development Banking Commission, BAFT (Bankers Association for Finance and Trade), the Euro Banking Association (EBA), Factors Chain International (FCI) and the International Trade and Forfaiting Association (ITFA) – has released a new guidance document on payables finance, to aid financial institutions, accounting firms, rating agencies and regulators in gaining clarity and consistency on the various terms and techniques.”
It is a good start and we all love a bit of guidance but, as the bankers themselves recognise: “Much work is still required to further align terminology across the complex ecosystem of stakeholders involved in international supply chains.
“As part of this drive for clarity, the second Market Practices in Supply Chain Finance publication focuses on payables finance - a
Mmmm … sounds good, but will it help? And what happens when a virus crisis turns into a trade war?
THE TRADE WAR WITH CHINA
If COVID-19 wasn’t enough, the United States has been in a trade war with China for the past three years or so and the supply chain has been forced to adapt. The world has suddenly come to the stark realisation that supply chains need to be more resilient to withstand shocks of sudden disruption.
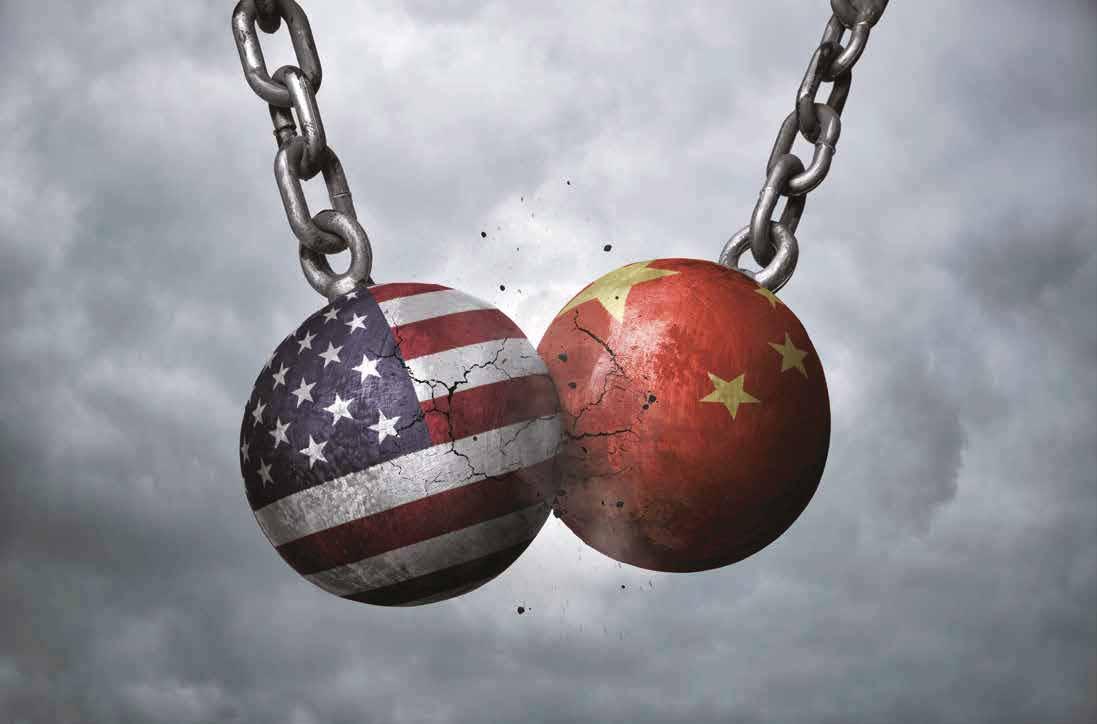
Rising tensions with China are a big deal because, over the past 25 years or so, global supply-chain networks have been concentrating hard on China, not least as a source of componentry. For a long time now, high-volume, low-priced dealers have been the order of the day.
Even prior to COVID-19, the trade stand-off between the US and China had resulted in global tensions. US protectionism led to a steep rise in import tariffs and an inevitable tit-for-tat response from China,
which resorted to a sharp increase in import duties on goods that were likely to hurt the US economy. It soon turned into a trade war.
The US imposed a series of tariff hikes, firing the first salvo on July 6, 2018, valued at $34 billion, followed by another worth $16 billion on August 23 2018 and a whopping $200 billion at 10% on September 17 2018, with China responding in kind. The US continued with another bombshell of $200 billion on May 10, 2019, and $112 billion in September 2019, with China striking back with higher tariffs on goods worth $60 billion that autumn.
Although the two nations had been trading for decades, the mood music has been getting more and more gloomy for ages. The US spent all of the 1990s and the 2000s struggling with an ever-bigger trade deficit which by 2018 had reached $323 billion. Former US President Donald Trump felt he had to act and the end result is now a deep mutual mistrust.
While the US-China trade war has disrupted established supply chains, it has also resulted in manufacturers coming under severe pressure to relocate out of China in order to avoid high US import tariffs. India, for instance, has been working hard to attract new inward investment. Five years ago, the country’s “Make it in India” campaign introduced various initiatives to improve its rank on the global ‘Ease of Doing Business’ index. Another step has been the reduction of corporate tax rate for new manufacturing companies from 25% to 15%, with no MAT (minimum alternative tax).
However, in the race to woo manufacturers to shift base from China, Vietnam appears to have one of the real winners, with no less than 26 of the 56 “corporate entities” moving out of China choosing to head there. Other countries that have benefited are Taiwan (11), Thailand (8), Japan (5), Cambodia (4), followed by India, the Philippines and Malaysia (3 each).
India wants to do better in this race and is looking closely at the engineering and heavy machinery sector. In a recent KPMG report called “India has opportunity to get ahead in global supply chain reconfiguration race,” the experts can the subcontinent doing well. OEMs like those in the construction equipment sector may well find the Chinese trade war puts India in a very positive light. At the end of 2020, KPMG reported that: “The COVID-19 pandemic led to the dismantling of global supply chains as countries imposed lockdowns, exposing the reliance of businesses around the
The trade war with China: India has the opportunity to get ahead in the global supply chain reconfiguration race as things reshape and adapt across Southeast Asia, says KPMG
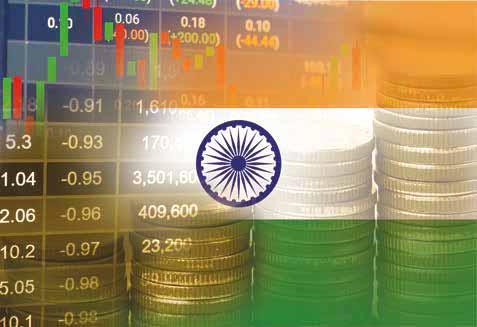
world on a few markets for fulfilling their manufacturing and sourcing requirements.”
And, according to the report, which is titled: “Restructuring post-COVID-19 supply chains’’, India has “a unique opportunity to adopt a more inclusive and proactive role in leveraging its vast pool of skilled resources, competitive costing and developed ecosystem for select sectors to get ahead in the global supply chain reconfiguration race.”
The report suggests that a more realistic approach for many companies looking to realign supply chains would be to consider a “non-linear consideration of global trade, more in the nature of production networks with multidimensional value accretion phases rather than sequential links in a chain.
“We, therefore, expect a de-emphasis on efficiency and the lowest cost dominant determinants, in favour of an interdependent, ecosystem-based value framework that assigns more equal weight to risk exposure, supply alternatives, tax considerations, and channel complexity,” said the report.
The Chinese trade war with America is shaking up Southeast Asia as a whole and the supply chain is going to need to flex accordingly.
A PERFECT STORM HITS SHIPPING
“The coronavirus pandemic has left some of the world’s biggest shipping lines facing mounting backlogs and delays, straining international supply chains and threatening to disrupt global trade,” says a recent report in the Financial Times. And this spells trouble for the construction equipment
industry, where almost everything is moved around the world in shipping containers.
“Operators say the container shipping industry — the backbone of global trade — is under severe pressure due to the combined impact of staff illness, quarantining and social distancing, along with soaring consumer demand and disruption to factory output caused by lockdowns,” says the FT.
Lars Jensen, chief planner of services for Maersk Line, the world’s biggest container ship operator, couldn’t agree more. The OEMs now face a “perfect storm” created by a mix of rising demand and reduced capacity in logistics systems.
“There’s congestion in terminals,” he told the FT. “There’s a shortage of truck drivers because some have not been able to drive. Particularly out of Asia, we see a part of that is linked also to the fact that a lot of companies are restocking. As a result, productivity slows down, which delays more ships, (and) then we get a vicious circle”.
Many of the world’s leading container ports were struggling in the first quarter of 2021. The Marine Exchange of Southern California, which monitors conditions at the two busiest US container ports, Los Angeles and Long Beach, reported ongoing congestion problems and the shipping lines responded by cancelling orders and diverting vessels.
Singapore, the world’s second-largest container hub, saw its rollover ratio (the proportion of cargo arriving at a port that is shipped on a different vessel than originally scheduled) reach 31% in October last year, compared with 21% at the same time last year, according to data provider Ocean
Insights.
“The entire supply chain is under pressure,” said Rolf Habben Jansen, chief executive at Hapag-Lloyd, another of the world’s largest container shipping companies. “The market situation is extraordinary.”
COVID-19 outbreaks can swiftly disrupt a port terminal’s productivity by forcing large numbers of staff to isolate, he added: “We’ve had examples where in a port 600 port workers were put into quarantine . . . [Even] if that port was on top of its game, then within a week you have 10 vessels struggling to get alongside [the terminal’s quays].”
Container prices have doubled according to a recent report from the Shanghai Containerized Freight Index. Rates from Asia to the US west coast in particular have rocketed and are now at record highs. And although Hapag-Lloyd has boosted capacity, Habben Jansen said that pandemic-related disruption persists: “We had too many boxes in the wrong places because of earlier disturbances.”
Is it time for a re-think? Yes, says the influential Harvard Business Review. “We suspect one of the reasons organisations stick with established trade lanes rather than more flexibly considering alternatives is a siloed view of supply chain design,” says a recent paper from Willy C. Shih, the Robert and Jane Cizik Professor of Management Practice in Business Administration at Harvard Business School and Adrien Foucault, an MBA student at Harvard Business School who has worked at maritime transport company CMA CGM.
“Logistics links are not really considered as part of a supplier selection and sourcing strategy,” say the authors, “rather they are put in place afterwards. With increasing moves to “China + 1” strategies for reducing dependency on China by adding sourcing in
other Southeast or South Asian countries, a more thorough study of maps and geography can help with a more resilient design.
“As production shifts westward towards and past the Straits of Malacca, the demarcation for shipping westbound versus eastbound will warrant more attention. Large shippers and beneficial cargo owners could also make their voices heard with the ocean carriers. Last-call and first-call port selections can shave multiple days off transit times.
“Too often, logistics is considered a commodity service that adds little value to a company’s value chain. Managing it often gets outsourced to a freight forwarder, where shippers have various degrees of visibility. When logistics is managed internally, it is often siloed from other parts of the business. This can result in
the routinisation of processes which could lead to a stagnant view of the overall supply topography and missed opportunities. In mid-February, when typically 30 or more vessels were waiting as many as eight days to discharge cargo at Los Angeles-Long Beach, the ports of Seattle-Tacoma had ample capacity. As shipping lines like CMACGM, Wan Hai, and ZIM launched direct services to less-congested ports in Northern California or Seattle, shippers who directly controlled their own logistics strategy were able to take immediate advantage.
“Directly owning logistics is becoming even easier by the vertical (and sometimes horizontal) integration which is currently sweeping through the maritime shipping industry.
COVID-19 outbreaks can swiftly disrupt a port terminal’s productivity by forcing large numbers of staff to isolate

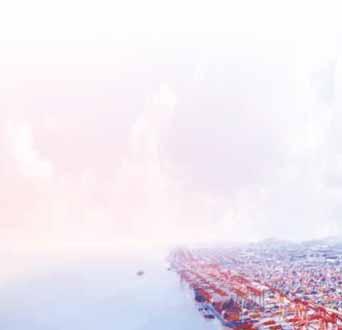
The range of new services offered by traditional shipping lines facilitates one-stop shopping with better cargo visibility.
“Logistics design should be a core part of supply-chain design and planning. For many businesses, especially the small and medium-size ones, this might require improving communications between logistics managers and other parts of the supply chain or directly making managers responsible for logistics. The challenges exposed by the COVID-19 pandemic have heightened the need for managers to understand the alternatives and to develop a better understanding of geography.”

It’s the same story from the experts at the World Economic Forum. “The pandemic is one of the most significant disruptions to ever hit global supply chains. It has turned global trade on its head,” says WEF.
“Governments, businesses and individuals
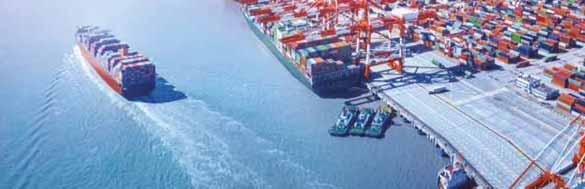
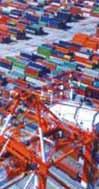
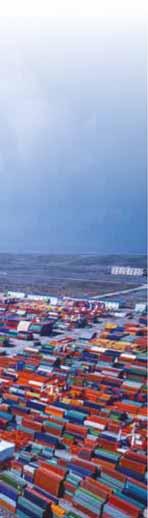
have struggled to procure basic products and materials. There have been demand shocks as people stayed home and curtailed their usual consumption patterns, which had a ripple effect on the supply side again. Disruption from the pandemic may have created opportunities for managing supply chains in new ways.
“When lockdowns ease more widely and life begins to resemble a pre-pandemic normality, businesses will look for their demand and supply dynamics to normalise too. Will that be possible? Will your suppliers still be in business and, if they are, will they have the same capacity as pre-pandemic? Many suppliers downsized or closed manufacturing plants to remain financially viable. Getting manufacturing capacity back to pre-pandemic levels will not happen overnight.
“There is a similar issue with skills. As supply chains slowed down, many employees were forced to find jobs in other sectors. Truck drivers, port operatives and production managers became delivery drivers, supermarket employees or worked in the health sector. Will they return to their previous careers supporting the supply chain?
“This all means that when the pandemic ends, a fresh wave of challenges will impact supply chains.”
Get ready now, says WEF, and here are “four important questions to ask about your supply chain strategy:
1. Is it time to further diversify my supply chain?
“When Chinese factories closed in early 2020, manufacturers struggled to switch to other suppliers. Diversifying your supply chain needs to be a major consideration. Instead of relying only on China, consider manufacturing hubs such as Vietnam, Mexico and India which are likely to gain greater prominence. This can help you navigate geopolitical risks and potential trade wars. It is also an opportunity to increase transparency and gain a deeper understanding of the vulnerabilities and hidden risks throughout your supply chain, including your suppliers’ suppliers.”
2. Do I need to localise manufacturing?
“An alternative is to move some or all production closer to the end consumer. Localised supply chains can be more resilient and are not as susceptible to trade wars or other global events. This strategy only works if your suppliers
are local and their materials are sourced locally too, otherwise global risks will remain in your supply chain. This strategy will likely increase costs, but it may also appease governments who sometimes apply pressure to manufacture in-country to boost employment and ensure certainty of supply of critical products, such as medical supplies.”
3. Should I invest in digitising my supply chain?
“Many supply chains still rely on outdated processes. This is an opportunity to build interconnected digital supply networks that can anticipate and respond to future shocks in the supply chain and minimise their impact. Digitising the supply chain, by investing in artificial intelligence and intelligent automation, can create smart and nimble supply chains able to quickly shift production strategies.”
CLICK HERE FOR MORE
And now, just to make it all that little bit more complicated, there’s amazon.com. In a recent report from the US-based Association of Equipment Manufacturers (AEM), the global construction equipment supply chain was asked a simple question: “Is Amazon Coming for Your Customers?”
Yes, argues Luke Powers, founder and CEO of Gearflow.com, a platform of vetted suppliers: “The construction equipment manufacturing industry needs to know that the old rules of our customer engagement have changed.”
“Amazon,” he argues, “has a multitude of business units all offering the shortterm ease of selling on the platform. It is easy to forget the predatory nature of their model. Amazon monitors all the seller and customer data across its channels, giving the company a very unfair advantage when deciding which products to offer themselves.
“Basically, sellers give Amazon their customer data so Amazon can decide if they want to compete or not. We don’t
4. Can I make my supply chain more customer-focused?
“The demand shocks caused by the pandemic have left warehouses full of unwanted or outdated products. Align your marketing strategy with your supply chain so you push items that are in stock and reroute goods to where there is demand. It is also an opportunity to use your supply chain to increase brand value.
“Unfortunately, the sleepless nights endured by those working in logistics or the supply chain are not going away, but this time it could be more positive thoughts interrupting your sleep. Instead of waking up worrying about how to solve the next issue to beset your supply chain, you’ll lie awake considering the opportunities to redesign supply chains to be smarter and more resilient.”
And just like that, we’re back to where we started … it’s all about resilience.
need to guess if this is the case — just look at what has happened in retail. In order to better understand how Amazon’s business will disrupt (the construction equipment) industry, let’s look back to their founding 26 years ago for guidance.
“1994: The Genesis of eCommerce. Jeff Bezos embarked on a cross-country road trip from his previous town of employment, New York City, to found Amazon.com in Seattle. Bezos later said he chose Seattle for the concentration of publishers near the city and the engineering talent base of Microsoft. The internet was growing rapidly, and Bezos thought the best entry point to pioneer online commerce was book sales. He reasoned that the internet was a much more efficient way to order.
“Amazon launched with over a million book titles — far more than any retail store could stock. Even though the original site was clunky, it gave book enthusiasts far more selection and ease of use than catalogues, book stores, or libraries ever could.
“Media attention around Amazon in the early years of the company’s growth focused on the total addressable market of book sales online and Amazon’s mounting losses. The Wall Street Journal even published an infamous article titled “Amazon.bomb” in May 1999 that predicted the imminent demise of the company given competition from book retailers and 1998’s total loss of $125M on $610M revenues. These losses, as
we now understand with hindsight, were the wise investments in distribution centres and massive infrastructure to enable Amazon to become the world’s general store. Bezos was not interested in competing 1-on-1 with book retailers, he was looking past them toward a future of dominating online commerce.
“However, the world did not see it that way. Traditional bookstores, Borders and Barnes & Noble, were locked in competition for the best real estate for their stores, the best authors to launch their books, and hiring the best retail-operations talent. Bezos, on the other hand, was interested in large and efficient distribution centres outside urban areas and hiring the best software engineers possible. Every penny earned through Amazon’s operations went back into these two areas of investment.
“Ever since Amazon’s inception, Bezos has consistently ploughed income back into the business to continue aggressive expansion and to keep taxes low. Amazon now has over 175 fulfilment centres worldwide with over 150 million square feet. And, according to Glassdoor, Amazon employs over 81,000 software engineers with an average compensation of $136,000.
At Amazon’s IPO in 1997, Wall Street wanted Amazon to focus on short-term profits so they could evaluate the company against traditional retail businesses. Bezos stood firm and never played by the same rules. In his famous 1997 original letter
to investors, he stated: “We believe that a fundamental measure of our success will be the shareholder value we create over the long term. This value will be a direct result of our ability to extend and solidify our current market leadership position. The stronger our market leadership, the more powerful our economic model’.
“In 1997, Bezos had the foresight that his philosophy would pay massive dividends in the long run, given the annual compounding growth of ecommerce sales. He could anticipate the changing habits of consumers and was dead-set on Amazon being in the best position to become the winner-take-all ecommerce retailer.
“While the worlds of booksellers, record stores, and shoe retailers were locked in fierce competition and quarterly profits, Amazon went about their business creating a future by their own rules. Does this sound familiar to today’s construction equipment and parts industry?
In order to understand what rules Amazon plays by, let’s dive into their famous “Virtuous Cycle” flywheel. According to Jeff Wilke, CEO of Worldwide Consumer at Amazon, Jeff Bezos drew a sketch on a napkin about the self-reinforcing momentum of Amazon’s business. He donned it the “Virtuous Cycle.”
“This flywheel will no doubt be studied in MBA classes for at least a generation. However, notice the word “virtuous” in Bezos’ title. According to the MerriamWebster dictionary, “virtue” is defined as “a particular moral excellence” or “a commendable quality or trait.” As you can see, this cycle is self-reinforcing for Amazon — not their sellers. It is certainly a commendable monopolistic quality for Amazon, but not of a particular moral excellence.
“As we know, Amazon’s huge bets in distribution centres and the best engineering talent have made them the de facto place to sell online. However, even though the platform is incredibly easy to use, have sellers considered the true long-term cost to their businesses?
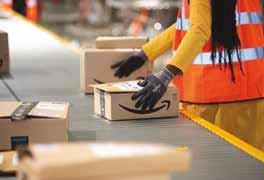
“In the short term, sellers are happy to be a part of Amazon’s “virtuous” cycle, because they believe it can only produce an upside for them. Amazon did the hard work of engineering a great platform and the cost of running mega and efficient distribution centres — what’s not to like? In fact, they double down on selling on
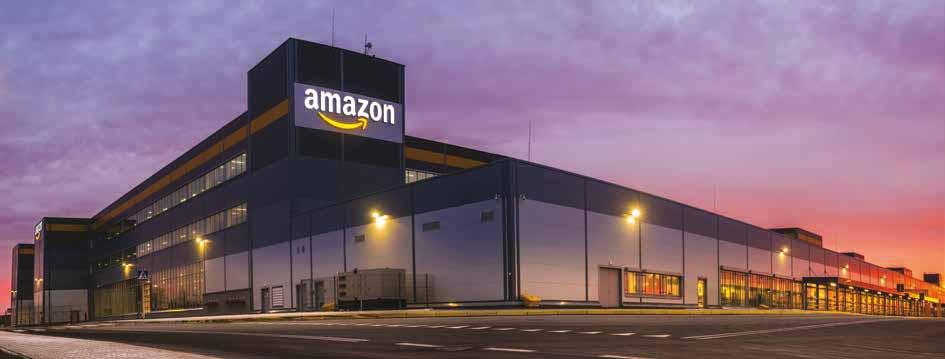
As we know, Amazon’s huge bets in distribution centres and the best engineering talent have made them the de facto place to sell online
Amazon by purchasing Sponsored Products ads and sending their products to Amazon’s fulfilment centres for Prime shipping (both significantly increasing the cost of doing business on the platform). The Sponsored Products advertising revenue was nearly $5 billion in Q4 2019.
“As more and more sellers join and compete on the platform, Amazon gathers more and more data on their products. This rich data set includes: Impressions; Clicks; Search queries; Q&As; Reviews; Returns; and Revenue trends.
“MBAs working at Amazon then take this data and strategise on which product segments would be a good fit for Amazon to take advantage of in the future. As we know, this is not the only rich set of data Amazon has at their disposal to determine which products to sell themselves. Amazon has grown from an ecommerce retailer into tablets (the Fire line-up), smart home devices (Alexa), cloud-computing storage (AWS), music streaming (Amazon Music), video streaming (Amazon Video), photo storage (Amazon Photos), book-streaming service (Audible), tv hosting (Firestick), and through other business units and acquisitions. The multitude of these content and data engines is that Amazon products have become integral to our productivity and lifestyles. The aggregate effect gives the retailer tremendous power in manipulating whole industries.
“Imagine for a moment if Google had its own ecommerce marketplace and fulfilment centres, and they sold similar products to yours.
“Pretty intimidating isn’t it? A Statista report found that Google accounted for 84% of all searches online in January 2020. There’s no way any company could compete with their search engine dominance. Just ask Microsoft’s heavily-marketed Bing with only a 6.25% share…
“Now consider that Amazon has double the amount of users starting their product searches on their site instead of Google. There are likely a multitude of factors that have put Amazon so far in front of Google (and everyone else) with why consumers start their product searches there. But the most dominant factor is Prime membership loyalty. And how many Americans have a Prime membership today? A whopping 112 million, which represents 87.5% of all 128 million U.S. households. In other words, roughly nine out of 10 U.S. households start their product searches on Amazon three out of four times. That averages to roughly
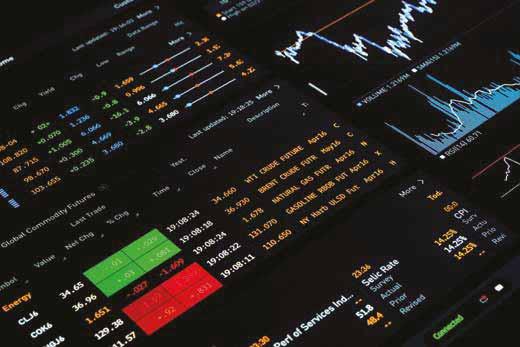
THE PLATFORM MATTERS
Where and how the construction equipment OEMs bring their supply chains together is going to be more and more important … and the world’s best logistics platforms will be where the party is hosted. Make sure you are keeping a careful eye on where the industry’s biggest players are meeting and greeting.
For instance, at the turn of this year, a platform called project44 raised US $100m in a financing round designed to: “Accelerate supply chain transformation.”
project44 describes itself as a leader in supply chain visibility for shippers and logistics service providers designed to “strengthen supply chains and better safeguard and track shipments amidst the challenges of the COVID-19 pandemic.”
“The events of 2020 magnified challenges organisations face in achieving supply chain visibility,” said Jett McCandless, CEO and
founder of project44. “Digital transformation to better understand and manage shipping delays and status was important pre-pandemic; now it is a business imperative.”
Supply chain managers need granular real-time data to make the best decisions and project44 has been set up to provide just that. It is now giving real-time transportation visibility to more than 400 enterprise customers, including the top three Fortune 100 companies, two of the three largest global retailers, and eight of the world’s top ten freight brokerages. Clients include ABB, Alcon, Arcese, BSH Home Appliances, Flowserve, General Mills, Girteka Logistics, IFCO Systems GmbH, Lenovo, Magna International, and PepsiCo.
According to Ross Devor, managing director at Insight Partners, a major investor in project44: “Optimising supply chains emerged as a top priority for companies in
two-thirds of all product searches starting on Amazon every day.
“So, if Google is a far second to Amazon on product searches and the lines between offline and online sales are blurring, how can anyone else compete? It’s time as an industry to band together to form a more compelling
2020, with major implications for global businesses, economies and society at large. project44 stood out to us as a strong, highgrowth partner focused on transforming shipping and logistics by providing the connective, data stream across the industry.” project44 says that it “connects, automates and provides visibility into key transportation processes to accelerate insights and shorten the time it takes to turn those insights into actions. Leveraging the power of the project44 cloud-based platform, organisations are able to increase operational efficiencies, reduce costs, improve shipping performance, and deliver an exceptional Amazon-like experience to customers. Connected to over 175,000 carriers worldwide and having comprehensive coverage for all ELD and telematics devices on the market, project44 supports all transportation modes and shipping types.”
platform to contractors.”
You have been warned. Start thinking about that new platform for contractors sooner rather than later. As Amazon has proved so successfully, good quality warehouses and well-run supply chains really do make the difference.
The A60H articulated hauler and the EC950E excavator are two of the most popular Volvo CE models in North Africa
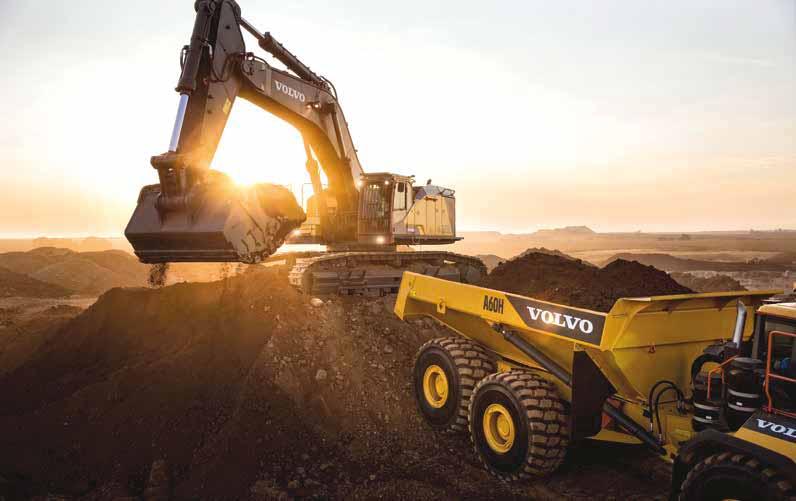
INFRASTRUCTURE INVESTMENT KEY TO NORTH AFRICA’S ECONOMIC REVIVAL
Bad news first: the North African construction sector has been hit hard by COVID-19 and the triple whammy of lower oil production, low oil prices and contracting non-oil sectors. The good news, however, is that North African governments have identified infrastructure development as the best way forward. Munesu Shoko reports
That 2020 was a difficult year is a given. Shutdowns have hammered the infrastructure market everywhere, as deals in the pipeline were delayed and projects halted as a result of the COVID-19 pandemic. That rings especially true for North Africa, where – according to Deloitte’s African Construction Trends Report 2020 –the total number of construction projects declined by 18.4% between 2019 and 2020, while the total project value dropped by 23%. The declines were largely due to the suspension of several projects in the region.
In North Africa – Algeria, Egypt, Libya, Morocco, South Sudan, Sudan and Tunisia –a total of 71 projects of over US$50 million in value had broken ground by 1 June
2020, with a total value of US$111 billion, according to Deloitte.
And it is Egypt that remains the infrastructure powerhouse in the region, recording the highest number of projects, as well as the highest value of projects at US$93.6 billion, contributing 84% to North Africa’s overall project value. Morocco was second with 19 projects, registering a total value of US$6.6 billion, followed by Tunisia with US$4.6 billion.
The majority of projects in North Africa were financed by governments, which registered a funding share of 40.8%, followed by private domestic firms with 23.9%. International DFIs (Development Finance Institutions are specialised banks
The total number of projects in North Africa declined by 18.4% between 2019 and 2020
set up to support private sector development in developing countries. They are usually majority-owned by national governments and source their capital from national or international development funds or benefit from government guarantees. This ensures their creditworthiness, which enables them to raise large amounts of money on international capital markets and provide financing on very competitive terms) and consortiums each financed 12.7% of the projects that were studied by Deloitte in its report.
Real estate had the lion’s share of the total project value in North Africa at 71.5%, registering 29 projects in the process. This large contribution by the real estate sector was mainly driven by Egypt’s new administrative city near Cairo, worth US$58 billion, as well as the Tunis Financial Harbour Project in Tunisia, worth US$3 billion. The transport sector accounted for 18% of the project value, with a total of 17 projects. This was followed by the energy & power sector, which accounted for 10 projects, representing 6.9% of the region’s project value.
Source: Deloitte Analysis 2020
The region’s logistics developments are taking off and there are ambitions to further expand the conventional transport networks. Several transport projects are currently underway, such as Egypt’s Cairo Metro Line 3 project and Algeria’s Saida-Tiaret Railway Line project. In fact, Algeria plans to reach a rail network of 12,500 km by 2030.
Population: About 102 million
Road network: 65,050 km (of which 48,000 km is paved and 17,050 km unpaved)
The Egyptian government has shown the resolve to embark on an ambitious investment and development programme in key growth sectors, including transport and infrastructure, as well as building and construction.
In terms of building and construction, the retail sector is responding to the rising market demand and has seen significant investment in recent years. To provide context, the new administrative capital city project in Egypt is currently the most valuable project in North Africa and the African continent at large, with a total project value of US$58 billion, according to Deloitte. The new capital city is expected to be home to about 5 million people and will be both the financial as well as administrative capital of the country.
Christophe Lagandré, Head of Market Africa at Volvo Construction Equipment (Volvo CE), concurs that several important city construction projects are driving the construction market in Egypt. These include the El Gala and El Amin, as well as the new administrative capital of Wedian (also known as Al-Masa) and the Sharek El Tafria industrial city close to the Suez Canal.
The transportation sector, according to KPMG, is one of the main drivers of economic development and growth in Egypt, linking production and consumption markets. The country’s unique geographic
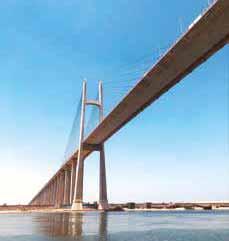
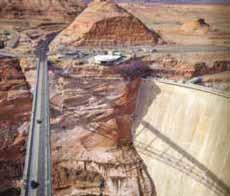
location, combined with an expanding infrastructure base, is enhancing Egypt’s position as a key logistics hub.
Roads play a key role in Egypt’s transport network, with 94% of the country’s freight using this mode of transport. The government estimates that US$8 billion is needed to upgrade roads in the next five to 10 years. The scale of construction, which includes highways linking new and planned cities, is vast. In August 2020, the country’s Transport Ministry announced that 130 billion Egyptian pounds (about US$8.3 billion) had been allocated to complete 1,000 bridges and tunnels by 2024 (about 600 are already done). The infrastructure will support Egypt’s goal to double its urban space over the next 30 years.
Meanwhile, the railway network, which dates back to the mid-19th century, remains crucial to the country’s transport network, but has deteriorated in recent years. During the Euromoney Egypt Conference back in September 2014, the Egyptian National
LEFT: In 2020, Egypt announced the allocation of US$8.3 billion to complete 1,000 bridges and tunnels by 2024 (about 600 are already done)
LEFT: Roads play a key role in Egypt’s transport network, with 94% of the country’s freight using this mode of transport.
Railways (ENR) announced a US$10 billion investment over 10 years to upgrade and maintain the antiquated railways network, with US$2.2 billion coming from the World Bank.
In March this year, the World Bank approved a US$440 million loan to support Egypt’s initiatives to enhance the safety and service quality of the country’s railways. The Railway Improvement and Safety for Egypt (RISE) total project cost is US$681.1 million, including a US$241.1million contribution by the ENR. The project will focus on modernising the signalling for the Cairo-Giza-Beni Suef segment of the ENR network and supporting the reforms needed to enhance ENR’s performance and competitiveness.
With new cities being built in the country, there are also plans to build new, modern railway lines connecting those new towns. “There are two huge railway construction projects planned in Egypt, but have not yet started,” says Lagandré. The first one is an almost 450-km high-speed rail link from New Alamin to the new capital. The second line is a 700-km route along the north coast from Port Said to Marsa Matrouh.
MOROCCO
Population: About 37 million
Road network: 57,847 km (of which 30,254 km are paved)
Infrastructure development is the industry sector with the brightest prospects in Morocco, according to the International Trade Administration. Modern infrastructure development, such as ports, airports and rail links, is a top government priority. According to the Global Infrastructure Hub (GI Hub), in the years leading up to 2040, Morocco is set to face an infrastructural investment gap of US$37 billion.
In June 2019, the government of Morocco signed a US$237 million deal with the Arab Fund for Economic and Social Development (AFESD) to improve its dams and road networks. In November 2019, the African Development Bank approved a US$110.6 million loan to finance further infrastructure projects. In July 2019, the Moroccan Prime Minister, Saad Eddine
TUNISIA
Population: About 12 million Road network: 20,000 km
Tunisia was deeply impacted by the Jasmine Revolution of 2011 and the country has never recovered economically. In 2020, the already precarious situation was aggravated by the economic crisis caused by the COVID-19 pandemic, with GDP reaching a negative rate of -8.8%. According to the IMF’s updated April 2021 forecast, GDP growth is expected to pick up to 3.8% in 2021 and stabilise at 2.4% in 2022, subject to the post-pandemic global economic recovery.
The government has announced a set of financial and fiscal measures to address the impact of lockdowns and to reduce their impact on the economy. The total amount announced is US$2.5-billion, according to KPMG. Infrastructure development will take centre stage as a means to resuscitate the ailing economy.
The country recorded one of the major projects cited by Deloitte in its African Construction Trends Report 2020. Tunis Financial Harbour (TFH) will deliver North Africa’s first offshore financial centre at Tunis
El Othmani, announced that US$1 billion would be expended on regional infrastructure projects by 2021.
Morocco has one of the best road systems on the African continent. Over the past 20 years, the government has built approximately 1,100 miles (about 1,770 km) of modern roads, connecting most major cities via toll expressways. The Moroccan Ministry of Equipment, Transport, Logistics and Water aims to build an additional 2,100 miles (about 3,380 km) of expressway and 1,300 miles (about 2,100 km) of highway by 2030, at an expected cost of US$9.6 billion.
Morocco’s railway network includes 800 miles (about 1,290 km) of track, with 120 stations serving passengers, including 15 stations for freight. The TangierCasablanca 225-mile high-speed rail line



LEFT: A highway in Casablanca, Morocco
Morocco has one of the best road systems on the African continent
was inaugurated in 2019 and a 140-mile extension of the line to Marrakesh is being planned. This will require the creation of maintenance centres dedicated to high-speed rail activity. Morocco’s 2040 Rail Strategy (“Plan Rail Maroc 2040”) is a long-term strategy for the development of the national rail network and its various components by 2040. A total of US$37 billion dollars will fund several planned projects.
Bay. It is estimated that the aggregate final development value of the TFH project will reach US$3 billion and that the project will extend over 523 acres in the coastal area of Hessiene, Ariana in Tunis.
CDE recently supplied a wet processing solution for the production of high-specification silica sand products to SOMEVAM, a subsidiary of Tunisian-headquartered Sebri Group
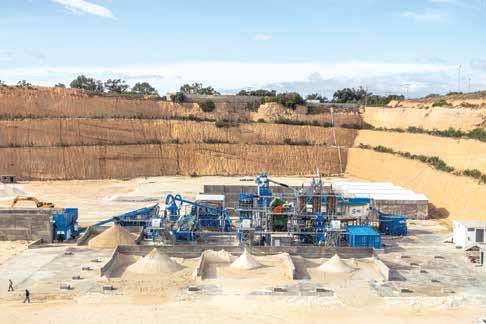
Population: About 44 million Road network: 127,000 km (of which 96,000 km is paved)
The COVID-19 pandemic had a drastic effect on Algeria in 2020. In addition to the health toll, the pandemic added to other adverse developments, mainly the fall in oil prices, and plunged the Algerian economy into recession. Real GDP shrank by 4.7% in
2020, after growing a paltry 0.8% in 2019. The measures put in place to contain COVID-19 had serious consequences for the construction sector.
As the country’s response continues, the government has indicated that infrastructure will play a leading role in rebuilding the economy. As a key industry for Algeria’s economic development and diversification, the

Population: About 7-million Road network: 83,200 km (of which 47,590 km are surfaced)
In 2020 the Libyan economy posted its worst performance in recent records. In January 2020, a blockade of oil terminals and oil fields that lasted nine months cut oil output to about 228,000 barrels per day. This was less than one-sixth of 2019 values and comparable to the lows experienced subsequent to 2014 after the country’s civil war.
The impact of the blockade, however, was felt with greater immediacy. For the acutely undiversified Libyan economy, which counts on oil and gas for over 60% of aggregate economic output and over 90% of both fiscal revenues and merchandise exports, the results were debilitating. Lost revenues from the blockade amounted to around US$11 billion for the year, according to the Central Bank of Libya in Tripoli.
However, a few road projects are set to be brought to the African Affairs Department (North and Horn of Africa Division), the Libyan coastal road project will start before
June 2021. The 400 km coastal road project will be funded by the Italian government according to the 2008 agreement signed between the overthrown Muammar Gaddafi and the former Italian leader Silvio Berlusconi as part of the compensation for the colonial era.
Infrastructure will play a leading role in rebuilding the economy
construction sector’s growth forecast remains positive despite the slowdown of the wider economy. The railway network nationwide, for example, is set to reach 6,500 km this year and 12,500 km by 2030.
Meanwhile, the 84 km eastern section of the east-west highway in the country is progressing well. Currently, 85% of the 84 km section has been completed, despite the negative influence of the complex geology, multiple obstacles and COVID-19.
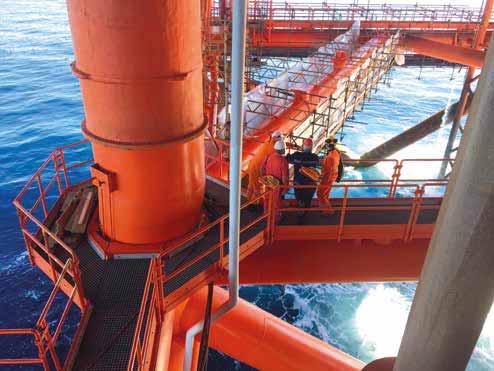
CDE’s 800 tph silica processing plant in Tunisia ‘is unique in terms of processing capacity’ for silica.
SOUTH SUDAN
Population: About 12 million
Road network: 90,200 km (5,000 km of gravel and 300 km of sealed roads)
Despite the country’s political instability and security issues, South Sudan has prioritised the improvement of its roads and powergeneration infrastructure, supported by a new Infrastructural Development Plan and the establishment of foreign partnerships.
The African Development Bank Group (AfDB) has provided assistance in preparing the country’s flagship Infrastructure Action Plan (IAP) which aims to put in place an effective structure to enable all stakeholders to work together to address the country’s development challenges.
The IAP proposes a major programme for the development of basic infrastructure in the decade ahead that will provide the basis for a transition to economic growth in the
range of 9% a year in real terms in the nonoil economy.
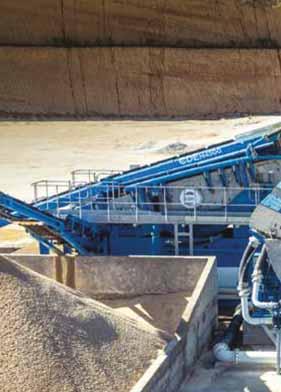
Roads have taken centre stage
Roads have taken centre stage with South Sudan aiming to grow both trade and transportation opportunities within the country. Notably, several major in-country road networks are underway, including the JubaBahr El-Ghazal Highway, the Juba-Bor-Malakal Highway, the Juba-Yambio Highway and the Juba-Nadapal Highway.
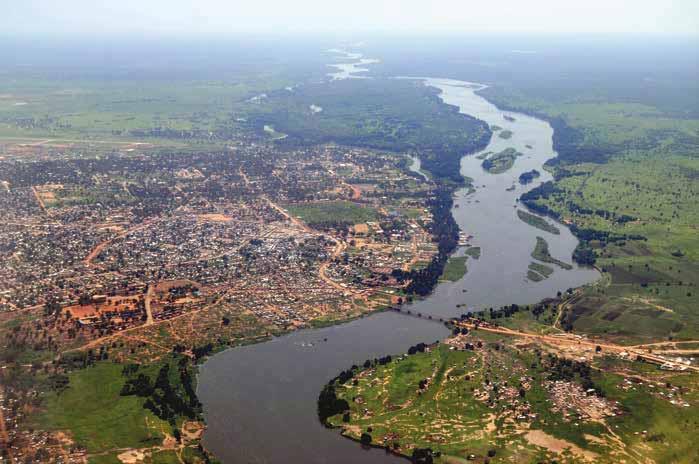
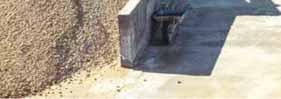
REGIONAL CORRIDORS
Elsewhere, a project of regional interest is the Trans-Maghreb highway, which will connect 55 towns and 22 international airports in addition to numerous ports and other industrial areas.
The US$11 billion project will stretch from Morocco to Egypt via Algeria, Tunisia and Libya.
As one of the priority projects under the Programme for Infrastructure Development in Africa (PIDA), developed by the African Union Commission, NEPAD Agency, African Development Bank and partners, the TransMaghreb Highway will also promote regional economic integration by facilitating the free movement of people, goods and capital between countries in the region through a smart corridor system and one-stop border posts along the highway.
The highway will become the nerve centre for the region’s economy, enabling inter-Maghrebian trade in all sectors to be intensified. Europe will also be linked to the Maghreb, while passenger and goods road traffic between the south and north shores of the Mediterranean will also be facilitated through the Strait of Gibraltar.
SUPPLY CHAIN
Commenting on the state of affairs in the region, Ruchin Garg, CDE regional manager, MEA, says North Africa offers huge potential in silica, phosphate and other mineral

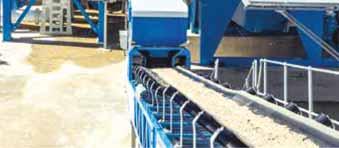
sectors. He also expects the infrastructure sector to be a key focus area for the region in the coming years.

In general, we see Africa as a land of opportunity
“We expect increased demand for sand and aggregates from natural as well as recycled material. Some countries have huge demolition waste which is difficult to dispose and also challenging for recycling. Our advanced methods could allow users to recycle these into better quality aggregates and sand which could then be used in infrastructure and general construction,” says Garg.
Garg expects growth across the whole region. However, he is more encouraged by infrastructure initiatives underway in Egypt, Morocco, Tunisia and Algeria. CDE recently supplied a wet processing solution for the production of high-specification silica sand products to SOMEVAM, a subsidiary of Tunisian-headquartered Sebri Group.
Sebri Group has operated sand quarries in Oueslatia, Tunisia, to serve the construction market for the past two decades.
The company has identified an opportunity to further diversify the business by expanding into the glass sands market to strengthen its commercial proposition in the region, and in 2019 commissioned its first CDE solution at the site. The recent investment in a second plant will complement the existing solution in Oueslatia to further strengthen the company’s position and capitalise on growth
opportunities in the glass sands market.
“Our 800 tph silica processing plant in Tunisia is a one-of-a-kind site across the globe with such large processing capacity for silica. The site processes silica for glass, foundry, construction and other uses. The project was supported by UK Export Finance,” he explains.
Volvo CE’s Lagandré believes it is a mixed picture in North Africa at the moment: “Morocco, Tunisia and Algeria have been significantly affected by the COVID-19 pandemic, although we are starting to see some recovery, especially in Morocco. Egypt, meanwhile, has remained strong throughout the last year and we hope for growth in Libya,” he says.
Looking at data from Volvo CE’s connected machines operating in North Africa, Lagandré says machine utilisation hours decreased 15% during mid-March 2020 but had increased again by June the same year. “We are now seeing higher machine utilisation across the region than last year, which is testimony to increased machine activity in the region,” he says.
Providing some detail on each market, Lagandré says Egypt is currently one of the strongest economies in North Africa. GDP has remained positive throughout 2020 and the construction equipment market even increased by 50% in 2020. There are a lot of important infrastructure projects both ongoing and due to start.
“The Moroccan construction equipment market decreased 20% in 2020 due to significant lockdowns across the country but since the end of the year we are seeing a good recovery,” says Lagandré. The Tunisian construction equipment market, he adds, decreased 18% in 2020 and while the situation is still tough, it is improving and Volvo CE has already seen some positive trends in 2021.
Meanwhile, the Algerian construction equipment market decreased 38% in 2020, according to Lagandré. On top of COVID-19, he says, the new Algerian government has introduced some strict import controls for the production and distribution of on- and off-road equipment, which has slowed down the market.
“We believe that we will see market growth in Libya in the future. Political stability and security improvements will likely help the country become a stronger economic power, driven mainly by oil,” says Lagandré.
A LAND OF OPPORTUNITY
Looking ahead, overall, Lagandré is feeling positive about the outlook for 2021 and the projected 20% project growth across North Africa this year: “Commodity prices, especially gold, have been increasing over the past 18 months and we believe this will pull the market. Political stability in the region will also have a favourable impact,” he says.
“In general, we see Africa as a land of opportunity. In the coming years, we believe Africa will offer huge potential for us driven by the expanding population and emerging market growth.
“Our aim is to be ready with our dealers to capture this growth, for example, in the road construction market. We are in a favourable position due to the two brands we offer –SDLG for the value segment and Volvo for the production segment where machines are utilised very intensively.”
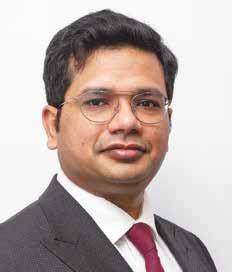
Intelligent tyre technology will help with things like specifying the best tread patterns, improving tyre maintenance costs, and optimising inflation pressures. Users will also get access to better service plans
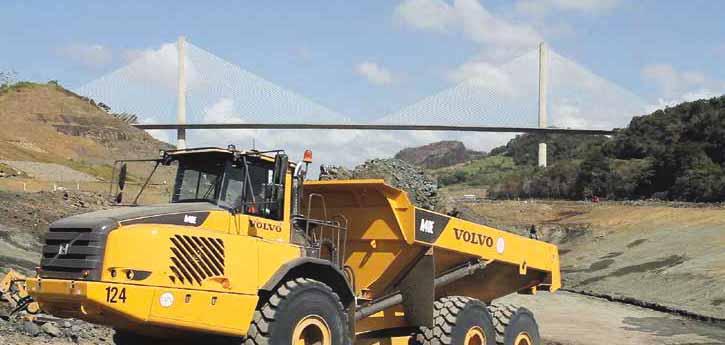

THINKING TYRES
Intelligent tyre technology is playing an ever-more important role in building sustainable construction equipment fleets. François Didion, vice president for construction and defence mobility at Michelin, takes a look at what this means on site. What are the key trends and what does the future look like? It’s time to start thinking tyres.
Everyone is hopping on the sustainability train. Indeed, the construction equipment industry has been transforming itself lately, with more and more OEMs seriously dedicating their R&D efforts to develop more sustainable solutions.
Everywhere you look, the world’s leading manufacturers are coming up with batterypowered equipment, machines running on alternative, cleaner energy sources, autonomous vehicles, and real-time remote sensors.
And all these new solutions share the same target: Helping customers reduce the eco-footprint of their projects. This could, for instance, mean reducing overall CO2 emissions to comply with local regulations or stopping noise pollution in urban areas.
But what does it all mean when thinking and talking about tyres? Are there any trends, new technologies, or important advancements that the construction industry should be aware of?
The answer, of course, is yes. There are four main areas of evolution that are impacting the construction industry. These are:
1. Sustainability: Climate change is no longer news … it’s a reality. We all know that the race is on to reduce emissions, carbon footprints and greenhouse gases on projects worldwide. The construction industry has to be seen to be proactively taking action. And, while sustainability efforts are often easy to see and measure, other less tangible challenges are far more complex to resolve. Problems such as the scarcity of raw materials (such as steel or sand) and of natural resources (such as water and energy), dial it all up a notch or two. As companies make more efforts towards the circular economy where we reuse and recycle, the construction sector faces very difficult questions like how much land is it appropriate to use? There are no easy answers.
2. Digitalisation: The internet is not only impacting our personal lives, it’s also transforming how we do business. Digitalisation can help with cost-savings, for example, but the construction equipment industry still needs to adapt and evolve to integrate connectivity to its
operations. Whether it’s robotics, the rising development of Smart Cities through BIM (Building Information Modelling), 3D printing solutions, the Internet of Things, smart vehicles or machine automation, the impact of the digital world is incredibly farreaching. The pace of change is dizzying, and it is bringing a host of new possibilities.
3. Urbanisation: Working on sites in the middle of busy and overcrowded urban areas creates constraints and challenges that contractors do not face on a greenfield site. Urban sites mean safety first, all of the time. Everybody and everything has to be carefully managed.
4. Off-site construction: Increasing numbers of structures are being prefabricated off-site and then transported to, and assembled on, the final job site. This is a trend that has been transforming many sites.
And so, just as the construction world has been evolving, so have the construction equipment manufacturers that serve it. OEMs have been working hard to come
up with innovative solutions to tackle the new challenges brought about by the trends outlined above. It is an ever-changing and interconnected environment.
At Michelin, we’re seeing growing numbers of remotely controlled to fully autonomous vehicles. These machines enhance safety and productivity by automating repetitive tasks in controlled environments. Many leading OEMs are currently developing high-tech machines along these lines, either working with their own in-house R&D teams or with outside experts such as Built Robotics.
Rapid developments have also been taking place in energy efficiency, electrification, and new, cleaner power sources. The market is benefitting from machines with lower levels of fuel consumption. Construction equipment fleets are now using hybrid engines and they will ultimately move to full electrification. The story doesn’t stop there either, as there are plenty of concepts of cleaner energies such as hydrogen and bio-methane currently in the works.
A third point to add to the mix is connected equipment, telematics and SMART: these tools are enablers for better decision-making. Managers today are able to understand the impact of their operations in real time and work with a wide range of remotely controlled and fully autonomous vehicles.
So … How do all these changes impact the tyres that you will be using on site, and their evolution? Contractors and OEMs want to see more and more built-in sustainability. There is a threefold hit to the bottom line here: better profits, happier people, and a betterprotected planet.
First, let’s talk about how fully connected tyres will help operators adjust and maximise tyre performance and, in turn, lower the overall price of ownership. Connected solutions will notify a site’s operations centre with real-time alerts when tyre failure or other issues happen. Monitoring solutions like this will evolve to become predictive and help identify when your tyres are coming to the end of their useful life. This will add value to the entire chain and help you manage your tyre’s life cycle.
Connected tyres are also going to be closely managed with artificial intelligence (AI) software. The more we connect tyres with their environment, the more they will generate data that can be used to automate tasks, improve efficiency, and simplify jobs. For operators and end-users, fully connected tyres will improve your tyre selection process and help with things like specifying the best tread patterns, improving tyre maintenance costs, and optimising inflation pressures. Users will also get access to better service plans.
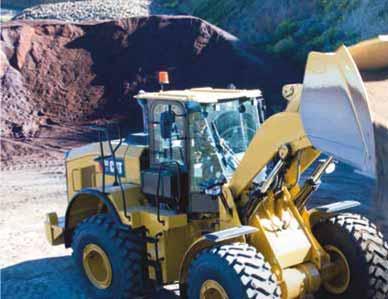
Smart
will help to
With connected tyres, manufacturers will be able to get better knowledge of how their machines are being used on site. They will be supplied with highly accurate factual data from the field which will, in turn, allow OEMs to improve and personalise their equipment offerings.
If we push that connectivity to the site up a notch, it will become possible to enhance the live performance of products thanks to usage information captured by a connected tyre … a tyre that can then self-adjust in real time to optimise its performance. The thinking tyre will, for instance, adapt to give more energy efficiency, better traction, improved flat rolling resistance (think central tyre inflation systems – CTIS), and so on.
In short, it will become a lot easier to optimise the full potential of a tyre’s life cycle by ensuring better reusability of carcasses and by helping the industry recycle its old tyres into new tyres.
Secondly, tyres will play a key role when it comes to ensuring the uptime of autonomous vehicles on major construction sites and quarries. Driverless machines in these sorts of applications have already started to appear and their numbers continue to rise quickly.
We believe that there are three main reasons for this, the first being safety: Autonomous vehicles significantly reduce the risk of incidents. The second is the scarcity

“With connected tyres, manufacturers will be able to get better knowledge of how their machines are being used on site”

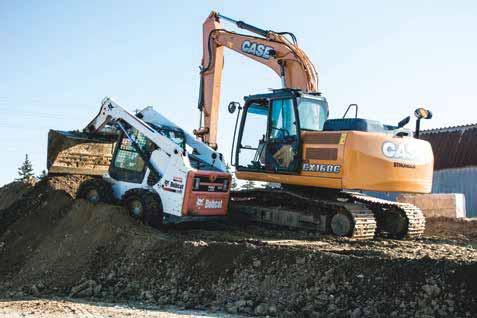
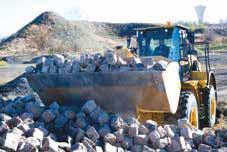
➔ of skilled workers available to do this sort of work and the third is the way in which it is easier to control the working environment of a quarry or a construction site … especially in comparison with a machine working on a public road.
These next-generation tyres will enhance the power output of autonomous vehicles and help reduce rolling and running resistance. This should maximise battery life and lead to better fuel efficiency. A lot of this will come through the optimisation of tread patterns and the use of new materials in the rubber compound. It’s also important to highlight that these changes will contribute to the better control of your tyres’ inflation pressures … which has a direct impact on wear and performance.
Autonomous construction equipment will perform at a higher level of intensity too. Longer working days, no human downtime, no shift changes will all combine to produce a far greater number of hours of usage. Tyres will have to adjust to meet these requirements. Materials and compounds with higher heat resistance will be needed along with tyres offering better tonne-kilometres per hour (TKPH) performance standards.
Smart tyre technology will help to control and adapt speed, load, heat, and inflation pressures in a faster and more accurate way. It will all lead to increased performance levels.
Downtime from flat tyres will remain one of the biggest and most costly pain points: maximising uptime continues to be a challenge that the tyre manufacturers need to address. Puncture-resistant and flat-proof
Tyres will evolve to help optimise sustainability and to reduce their environmental and social impact
solutions will increase in popularity while comfort will become a secondary issue given there will be fewer operators working on the machines. This will result in an increase in the market for solid and airless tyres, tracks, and conversion track systems.
Other elements to keep in mind are traction and stability, not least because these impact not only on performance but also on safety levels on construction sites.
Finally, tyres will evolve to help optimise sustainability and to reduce their environmental and social impact. The first step towards developing new tyres in a more sustainable way – including the usage of more sustainable raw materials – begins with improved rubber compounds for longer life. This means more recycled materials in production, opting for eco-friendly materials rather than using harsh chemicals (choosing natural rubber for instance). Expect to see compounds that can be easily broken down and/or recycled.
The second step will be in maximising a single tyre’s usage. Longer life cycles and better performance figures will offer a great way to start … but enhancing carcasses to favour recycling will bring us closer to the target of a circular economy where we can get multiple lives out of the same tyre.
And the ultimate step is closing the loop with proper tyre recycling for all tyres and other rubber products like tracks to provide a new life to the materials. One day we will be looking at a fully functional circular economy.
Looking at the near future, what will drive the next few years?
LEFT: The next generation of thinking tyres will enhance the power output of autonomous vehicles and help reduce rolling and running resistance. This should maximise battery life and lead to better fuel efficiency
The trend had already started before 2020, but if there is one thing that the COVID-19 pandemic confirmed, it is the growth of rental companies as more and more organisations look to save funds. This trend is not only true for equipment: we’re noticing more rentals for wearable items, such as tyres and tracks.
Another concept – one that is familiar in the airline industry – is pay per use. This is an area where rental companies will be developing new offers and where renters can improve their cost-benefit numbers … an area where intelligent tyres will play a leading role.
I have talked a lot about data coming from connected solutions, the optimisation of energy efficiency, sustainable materials, and recyclable products. All this data can be put to work for the betterment of many business processes, from streamlining R&D activities for manufacturers, to improving customer efficiency and safety on the working site. That being said, many of these initiatives are still at the early stage, such as tyre connectivity. The next five to 10 years will be all about connecting the dots between relevant data collected in the field to make the construction industry a safer, more efficient, and more productive place to work.

Francois is director of the Construction and Defence business unit at Michelin Tyres, part of the group’s Business Line Beyond Road division. He holds an MBA from the University of Ottawa, and a diploma from the Ecole Supérieure de Commerce de Reims. He has spent his entire professional career in the Michelin Group, which he joined in 1993 after two years as an officer in the French Air Force. In 1998, he was appointed sales director for France for passenger car and light truck tyres and then became sales director for Poland and the Baltic States in 2002. By 2006, he was made commercial director for Russia and the countries of the former Soviet Union and in 2010, Francois moved to the Michelin HQ in Clermont Ferrand. In 2014, he joined the Civil Engineering Product Line as replacement sales director for all of the group’s worldwide sales areas. Today, following the 2019 acquisition of Camso by the Michelin Group, he leads the activities of the Construction and Defence business unit which covers Michelin’s tyre, track, and system products.
KEEPING TRACK

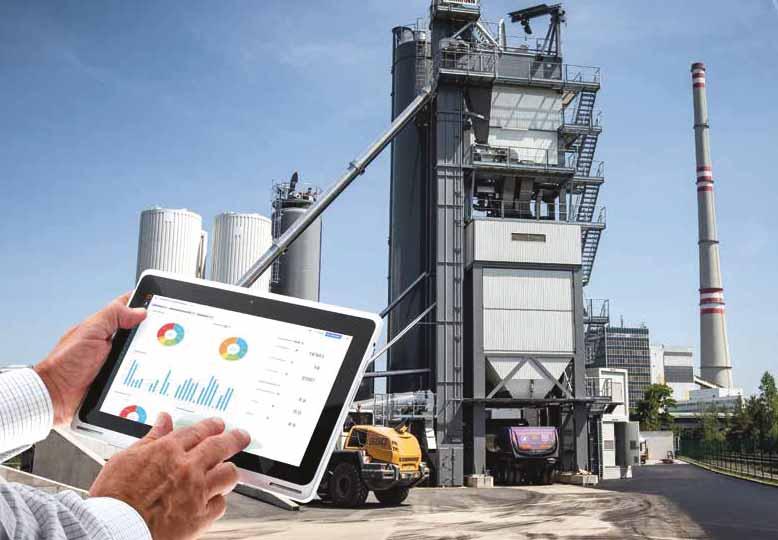
Next-generation technology and the ‘pandemic effect’ is encouraging contractors to use digital asphalt-tracking systems. From mixing the asphalt to laying the road surface itself, everything is being far more closely monitored and managed. Kristina Smith reports
It has taken a global pandemic to convince some road owners that a system which involves passing pieces of paper from asphalt plant to truck to site supervisor is not the best way to do things.
“Some people were already looking at e-tickets, and specifications had been created in many states for e-tickets before the pandemic,” says Nick McRae, CEO of construction fleet management company Broadloop. “Coronavirus accelerated it.”
Though many companies have been set up to deliver the e-ticketing function only, others provide more sophisticated digital tracking tools that stretch from planning to mixing, delivery, paving analysis and accounts, among them Joseph Vögele, Amman, Volz Consulting, Topcon and Broadloop. These tools are by no means mainstream yet, but the combination of the ‘pandemic effect’ and more friendly interfaces could be the push needed to increase uptake.
“From Trimble’s perspective, any technology adoption is good for the industry,” says Kevin Garcia, general manager at Trimble Civil Specialty Solutions. “Some successes lead to more adoption. We just want
to see the industry as a whole become more digitally advanced.”
Advances in interoperability are allowing data to flow more easily between digital tools and platforms, putting real-time data in the hands of those building the roads and allowing better analysis and planning. Although Trimble does not provide asphalt or concrete logistics tools, its Trimble 3D Roadworks paving control system does interface with them.
This is where the real value is, says Juergen Seemann, solution manager for road construction technology at Leica Geosystems whose iCON Paving system must also talk to the e-ticket and logistics packages. “The real step forward is interfacing with other systems, producing profitability data to benefit the customer. It’s important that the contractors see the complete workflow.”
A BETTER WAY
Some asphalt-tracking and processoptimisation tools have been years in the making and are now one or two generations in. Vögele, part of the Wirtgen Group, has been developing its WITOS Paving Plus
system for more than ten years. Like many of its competitors, WITOS comes in several modules that can be used individually or interlinked: the Control Module for project planning, the Materials Module for the mixing plant, the Transport Module which tracks the progress of the delivery trucks; the JobSite Module for the paving supervisor; and finally the Analysis and Documentation Module.
Vögele is continually updating the system to meet customer and market demands, says the company’s head of software products, Dr Stephan Wellar. In what might seem like a retrograde step, a recent development, perhaps to meet US e-ticketing requirements, has seen Vögele creating a system with less functionality.
“Two years ago, we developed the WITOS Paving Docu documentation tool to complement WITOS Paving Plus,” says Wellar. “The solution is aimed at construction contractors that are looking to log and analyse paving data and delivery notes, among other things, but do not need the full scope of WITOS Paving Plus functionality, including process optimisation.”

exported from WITOS Paving Plus which also has an interface to the VETA system, used by US highway authorities and others. Underlining the growing importance of interoperability, Wellar says: “Vögele is contributing to the development of crossmanufacturer data-interchange standards.”
Whereas WITOS came from a manufacturer, BPO INFRA came from the consultancy sector. Founded in 2011, Volz Consulting first worked manually, using Excel spreadsheets, before starting to develop its own digital tool in 2014. When its contractor customers saw the tool, they wanted it, and in 2015 BPO ASPHALT was born. BPO INFRA, which bundles together concrete, milling, h k l b d d d li
earthworks, laboratory data and delivery note, was launched in late 2020.
“Our goal is to make the process clear and give participants more information than they would have without the system,” says Daniel Heuberger, product manager at Volz

supplied on a subscription basis, generally for four years or more. Today it is used in 12 countries, with customers that range from companies with two paving crews up to Strabag which has 260 paving crews around the world or Tarmac in the UK which has 60 mixing plants.
Volz Consulting develops all its software
Amman Group’s Q Point interfaces with all the steps of road laying, providing data to help optimise the process
in-house, which means it can respond quickly to market demands, says Heuberger. “We are not a classic software company, we are a process-optimisation company E b d h k f i f ili i h
Everybody who works for us is familiar with construction sites and with the process itself. We can think like a site manager, and like a foreman.”
Broadloop started as an asphalttracking tool and has since expanded to track a variety of construction vehicles and assets
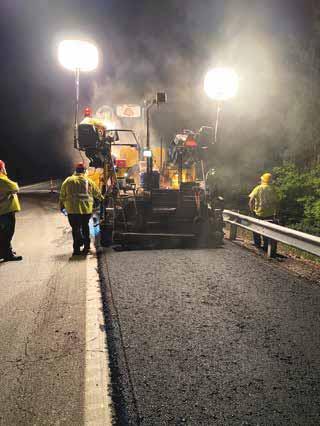
Materials-tracking company Q Point was born in 2018 when the Amman Group acquired specialist company hiQ and blended it with its own digital team into an independent business. Austrian hiQ was founded in 2012 to optimise processes and logistics for asphalt and concrete road construction and earthworks.
At the heart of Q Point is the idea that different systems can talk to each other. “Q Point’s Software as a Service (Saas) solutions integrate all players involved in the construction process through open and standardised interfaces, REST APIs,” says Q Point managing director Frederik Tengg.
Interoperability has always been at the heart of what Q Point does, according to Tengg. “Through the know-how and technologies of existing tools and services suppliers, Q Point created a flexible environment for the integration of all kinds of solutions,” he says. “Construction companies and mixing plant operators can thus easily integrate the Q Point solutions into their existing system landscape, supporting savings already made through investment, and quickly realising gains from process optimisation in all areas.”
Topcon also gained its materials logistics system, Pavelink, through acquisition. In 2018 it purchased Netherlands company ThunderBuild which was founded in 2011.
STRENGTHENING INFRASTRUCTURE FOR THE NEXT GENERATION.

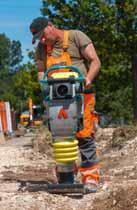
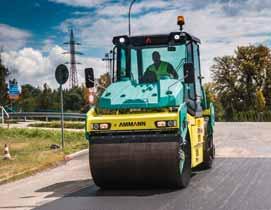


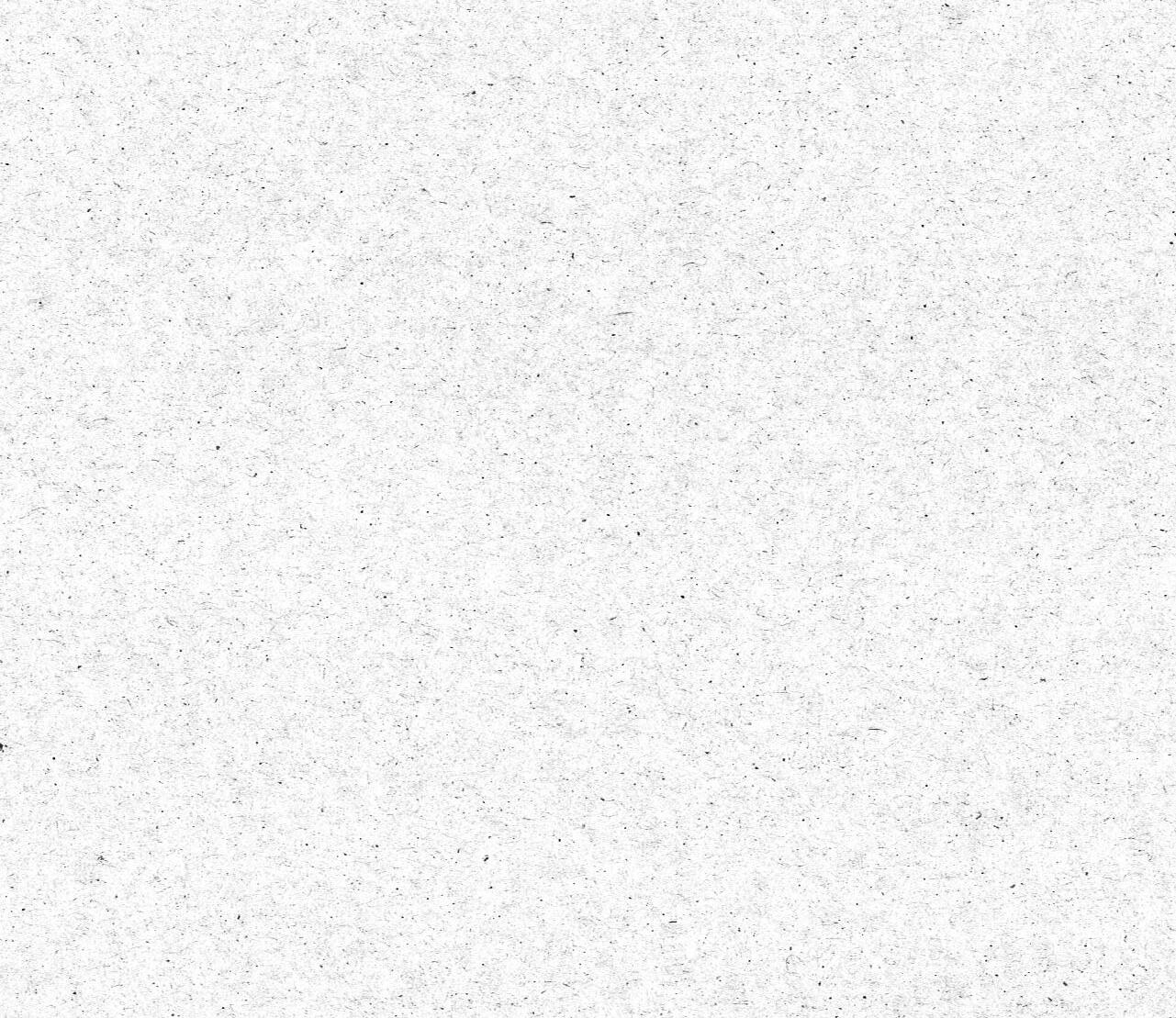
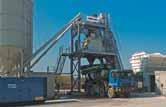
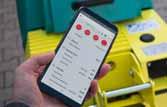
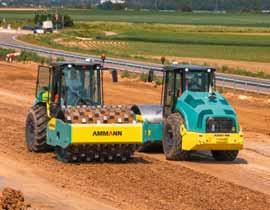
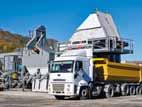
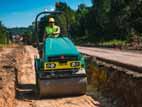

MAXIMISING YOUR INVESTMENT
What do the smallest Ammann plate compactor, the largest asphalt plant and every product in-between have in common ?
• Innovation that boosts productivity and efficiency, ultimately improving your bottom line.
• Parts and components that ensure long life to maximise your investment.
• The commitment of a family business that has thrived in the construction industry for 150 years by keeping promises today – and knowing what customers will need tomorrow.
Pavelink lives up to its name, linking data acquisition and planning with the asphalt plant, delivery, paving, compaction and quality control. In 2020, Topcon added a new Thermal Mapper system to Pavelink, a heat sensor that flags up if there are significant variations in the temperature of the material being laid.
Broadloop is newer to the scheme, set up in 2016 to track asphalt deliveries. CEO Nick McRae and his co-founder Max Kommor saw how a system to track school buses could be used to optimise asphalt truck deliveries. Their idea was to use an app for a smart phone rather than a GPS tracker, since trucks and their drivers are often rented not owned by the asphalt contractor.
As well as connecting to the software at the asphalt plant to collect the data about the material, Broadloop also collects the temperature of the asphalt via a sensor over the scale. “Temperature is important, especially in colder regions or more rural areas where trucks have to travel a long way,” says McRae. “Our next iteration will be to catch temperature data points along the way.”
Broadloop was initially known as Blacktop but changed its name at the beginning of the year to reflect the broadening scope of its activities: “Now it can be used for any construction materials supply chain, field tracking, asset tracking, attachments, operators. It’s moved past just asphalt,” says McRae.
SHOW ME THE MONEY
Any conversation about the benefits of digital logistics and tracking must start with cold, hard cash. “The big reason that contractors give us for using our system is that they
like the quality-related benefits, having the documents in one place and the fact that everything’s integrated. But the focus is on the money.”
Just by considering the cost of trucks, the argument can be made in financial terms, says Heuberger. “Usually with paving, a lot of the costs are due to the truck drivers. You rent truck drivers by the hour and sometimes it can be very expensive because you are writing down the waiting times at the mixing plant and at the construction site.
“Some of our customers tell us that by using BPO they have cut down two trucks per job, some have cut three. Think about a company with 180 paving days, and five projects live at any time. That’s a huge saving.”
Systems such as BPO cut out waste too, says Heuberger. “If you don’t tell the mix plant to stop in time, they will go on
mixing. You could have trucks driving to the construction site that you have to send back.” Each truck holds around €3,000-worth of asphalt, says Heuberger.
These systems can also help contractors unify their processes – and ensure that every project is doing things in the best way.
“The BPO system provides a clear structure for the planning process so that everybody in the company is doing it in the same way,” he says. “The boss can check the process and evaluate projects better. It probably means less working time for the site managers, which maybe makes it easier for them.”
McRae highlights cycle time efficiencies, being able to look in detail at how materials deliveries are coming to site: one truck may be taking a longer route, or a driver could be taking longer than necessary to prepare their vehicles at the start of a shift. There’s also no
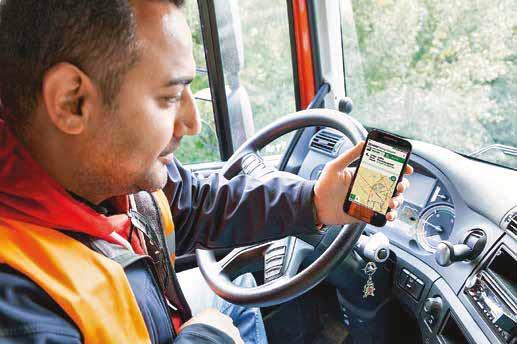
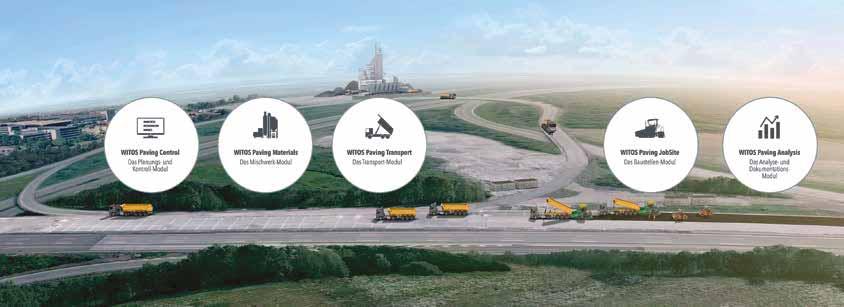
➔ need for someone to be collecting delivery tickets, which can reduce safety risks too.
One of Broadloop’s first customers, Hall Paving of Kentucky, took the system on when it was required for a large, long-term project. “It’s evolved into something we use every day to track our trucks,” says Tom Jones, Hall Paving’s deputy superintendent. “It gives us a better handle on our trucking expenses which is our largest expense.
“It helps us in all kinds of aspects, more than we thought it would.”
Analysis shows that there can be savings in all steps of the process, says Tengg: “Through a consistent flow of data and information in real time, they use all resources more efficiently. Planning, production and construction processes become considerably faster and fully transparent. Besides, documentation runs automatically and is made digitally available everywhere, anytime.”
Q-Point measured the time and cost savings made using Q Asphalt for one of its customers, Pusch Bau based in Bavaria. With a turnover of €29m and six pavers, Pusch Bau reported a cost reduction of 25% on every ton laid (see box).
Having control over truck flows – and knowing when trucks will arrive – can also have a significant, positive impact on paving quality. If the paver has to stop even for a moment it will sink into the asphalt a little and cause a tiny bump in the surface. If the supervisor has an app to hand, and sees
Company Overview
Construction company with headquarters in Kinding (Bavaria)
Employees116
Estimated turnover in euros29m
Mixing plants2
Pavers6
Construction site teams3
Changes
Built-in tons / Day+ 18 %
Built-in tons / Employee+ 22 %
Built-in tons / Paver+ 12 %
Employee working hours / Day- 12 %
Produced tons
/ Asphalt plant working hours
Transport costs / Built-in tons - 5 %
Total costs / Built-in tons- 25 %
Source: Q Point
that asphalt deliveries are running behind schedule, they can slow down the paver accordingly and keep moving.
For the owner, there should be a big benefit in having as-built data which includes details of which part of the road was batched, delivered and laid in. But although there is much talk of BIM (Building Information Modelling) and the benefits of 4D and 5D models, few of the companies we spoke to are being asked to interface directly with them – at either end of the process.
money is,” says Seemann. “It makes no sense to start with 3D paving in the top layer either. The earlier you start to use 3D technology, the more you save. If there are inaccuracies in base layers, you end up filling up with the most expensive asphalt.”
A decade is a long time in digital development terms
“We have 80 companies renting the system. No one has accurate interface to BIM system yet,” says Heuberger. “BIM is important for houses, bridges, airports but I don’t see that you need 5D or even 3D for roads.”
Heuberger explains that BPO does provide BIM, in that it delivers a set of data which is linked to a location, in terms of the chainage of the road.
Leica Geosystems would strongly disagree that 3D isn’t needed for roads. Seemann explains that contractors who start using 3D at the earthworks stage achieve the most efficient use of materials.
“We still see a lot of contractors using conventional surveying for grading and dozing and using 3D for the laying operations. Think bigger, that’s where the
Using 3D tools for paving also reduces surveying time on site, says Seemann, since there is no need to set out stringlines – or correct them if they get knocked out of place.
It’s easy to understand the theory of how materials logistics data and paving data could interface in BIM, but it’s still early days, says Garcia: “Some of the early adopters are out there playing in that space.”
ADVANCING TECHNOLOGIES
A decade is a long time in digital development terms. Technology and functions that we use every day were difficult to deliver when some of these logistics solutions were launched.
This was definitely the case for Q Point back in 2012, says Tengg: “Digital infrastructure wasn’t as widely available as today. Therefore, the services needed to have offline functionality and complex algorithms for processing cached “real-time” data in a correct way to provide up-to-date information to all participants.”
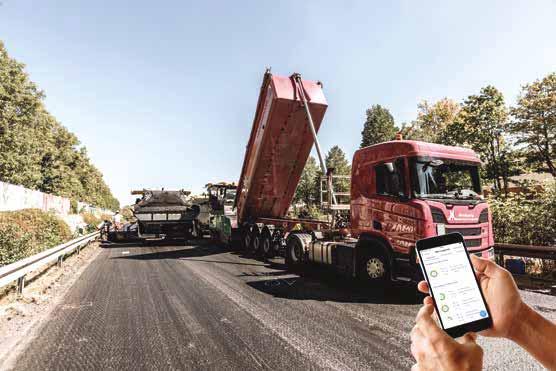
“Our biggest focus on iCON Pave was to make the use easier so that people who are not as computer literate are able to use it without being frustrated”
Juergen Seemann, Leica Geosystems

frustration. That was certainly the main goal for Leica Geosystems when it launched iCON Pave, effectively a third-generation paving positioning system, in 2018, says Seemann.
“Our biggest focus on iCON Pave was to make the use easier so that people who are not as computer literate are able to use it without being frustrated,” he says.
“That was one of the main steps forward from the former to the current generation of product.”
Suppliers also face the challenge of working in different countries and different contractual environments. “WITOS Paving Plus is deployed by many different contractors, in many different site situations, with many different users. So, the demands on a system of this kind are enormous,” says Wellar. “It must cover all conceivable functions and needs, but at the same time be as simple and intuitive as possible in design.”
Scandinavia and, to some extent, Australia. Some emerging markets, South America and India, are interested too.
Seemann and Garcia both note China’s swift uptake of digital paving tools. “It’s our fastest-growing market,” says Garcia.
“China is still at the beginning of adopting the technology, but they understand it, they are technology-open,” comments Seemann.
Some of the first-generation digital natives are 40 now
Even so, many of the companies we spoke to were frustrated at the difficulty in persuading contractors to change their ways, even with the almost instant cost savings that the systems can demonstrate. McRae says he found it “gruelling” to try and get his message out to the market, until the boost of e-ticket requirements and the pandemic.
Tengg agrees, and also highlights the culture of an industry that may not want all its data to be on hand. “One of the challenges was, and still is, the slow adoption of digitalisation processes in the construction industry, paired with the reserve of transparency.”
But that slow pace of adoption is starting to pick up. Garcia points out how intelligent compaction has been heavily adopted, thermal profiling is popular, e-tickets are now taking hold, and the need for visibility of remote jobs is making connected sites suddenly more appealing.
Then there’s the human element. Some of the first-generation digital natives are 40 now, working in supervision and management positions. Even older, non-digital natives have been trained in smartphone apps by banks, retailers, and Uber.
As well as varying requirements, different countries and cultures also have different
“There have been some early adopters who understand the value and the cost savings it can drive but we have also met with the hurdles of resistance to new technology and change,” he says.
“The technical knowledge and competency of contractors has changed in the last four to six years,” says Garcia. They are coming with very specific questions about specific workflow systems.
“By the time you get something new out, everybody’s asking ‘what’s next?’. Keeping up with the competition is not good enough. It’s rapidly accelerating.”
Highways England’s plans include the US$3.1 billion Lower Thames Crossing tunnel near London (artist image courtesy Highways England)
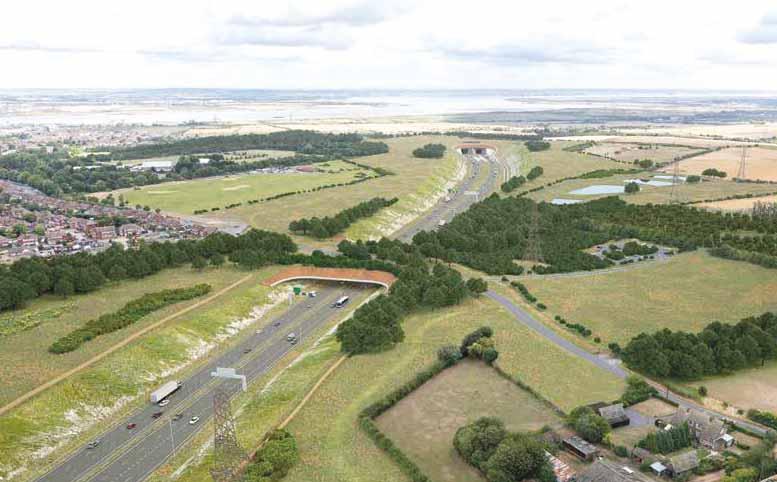
FROM PANDEMIC TO PHOENIX
Rising from the COVID-19 pandemic’s ashes, the G7 countries are pushing for more infrastructure investment and at a faster pace. David Arminas reports
During the past year or more, many people around the world got used to seeing the curve of COVID-19 infections rise and rise until eventually flattening out. It is now hopefully finally dropping far enough that it bottoms out or disappears altogether.
The most important curve now is the economic one as countries struggle to make sense of the financial and social damage wrought by national lockdowns to stop the spread of COVID. This curve may be rising for most countries, but not fast enough for many governments. Meanwhile, the question for equipment makers is how long will it take to reach pre-COVID sales levels. Indeed, Caterpillar sees the level of its global 2019 sales being reached only by 2025 – a full four years down the road.
Equipment makers should take heart, despite Caterpillar reporting full-year 2020 sales and revenues being US$41.7 billion, down 22% compared with $53.8 billion in 2019. Caterpillar said the decline reflected lower end-user demand and dealers reducing their inventories by $2.9 billion in 2020. However, orders had started to increase at the start of this year and the company remains bullish about recovery in its home US market and globally.
The financial stability of equipment makers such as Caterpillar will rest, to a greater or lesser degree, on how governments invest cash into all their national infrastructure projects, not just highways. The signs are good that that investment is either coming through or at least in the pipeline, especially among the G7 countries – US, Canada, UK, France, Germany, Italy and Japan. Their economies are picking up, albeit at varying speeds.
According to the Global Wealth Databook, compiled by banking group Credit Suisse, the G7 represented in 2018 around 58% of the global net wealth - $317 trillion - and more than 46% of the global gross domestic product (GDP).
MADE IN THE USA
The US remains the economic powerhouse of the G7 and in 2020 the federal government deemed workers in the construction industry “essential”. As a result, “the asphalt pavement industry, in general, had a good year due to strong backlogs and the opportunity to accelerate projects”, notes Audrey Copeland chief executive of NAPA, the National Asphalt Paving Association.
“For 2021, Congress enacted a one-year extension of the FAST Act [Fixing America’s
Surface Transportation Act] and followed it up with a Transportation Appropriation Bill that provides $46.4 billion for the Federalaid Highway programme and an additional $10 billion for state transportation agencies to spend on their programmes. The 2021 construction season will be impacted by how states deal with their revenue shortfalls,” explains Copeland.
“What Congress can do to positively impact future construction seasons is enact a multi-year surface transportation bill that boosts investments in our roads and bridges to bring them up to a state of good repair. Any legislation must include a sustainable, predictable revenue source for the Highway Trust Fund, such as a gas tax increase, indexing the gas tax or establishing a vehicle-miles-travelled fee to finance the Federal-aid Highway Program. We expect Congress to take up this legislation right after the COVID package is enacted into law, this spring. Enacting a multi-year surface transportation bill is key to President Biden’s agenda to Build Back Better and boost America’s economy.”
To the rescue is Biden’s $1.9 trillion coronavirus relief package to be spent over four years that was signed off in March. Investment in highways and road bridges
is but one part of the package. Biden’s “Build Back Better” strategy offers twice what former president Donald Trump had planned. Similarly, though, Biden’s cash will be shared with the water sector, electricity production and distribution, auto industry and public transit as well as homes and commercial building construction.
Foreign equipment makers who don’t manufacture may be at a disadvantage if a buy-American policy is pursued to boost jobs in the sector. Straight from his campaign material, Biden said he wants to “mobilise American manufacturing and innovation to ensure that the future is made in America, and in all of America”.
Inevitably, longer term planning is needed for US infrastructure, according to Alison Black, chief economist for ARTBA, the American Road and Transportation Builders Association. Money may be cheap to borrow right now, making a return on investment happen a lot faster than otherwise. But it remains to be seen how much of this cash will be used by US states to refinance debt already incurred. Also, if cash is handed out based on the environmental friendliness of a project, a lot of money may not go as far; greener highways and bridges can be more costly to construct.
A UK STEP CHANGE
The UK – no longer a member state of the European Union - embarked on a major infrastructure initiative as early as November 2020, according to a report from the UK office of international legal firm Womble Bond Dickinson.
Prime minister Boris Johnson laid out a ten-point Plan for a “green industrial revolution”. This announcement was followed by publication of the National Infrastructure Strategy (NIS) ensuring an integrated approach to all infrastructureenergy, transport, water, waste, flood risk management and digital communications.
The report’s authors say the government’s five-year plans are “a step change” in UK infrastructure policy. “The government sees the National Infrastructure Strategy as key to the UK’s post-COVID recovery and rebuilding the economy,” notes the report.
“Together, the [government’s] Spending Review and NIS promise investment of £27 billion ($37.3 billion) in economic infrastructure in 2021/22, plus longerterm settlements for key infrastructure programmes, for strategic roads, rail, broadband and flood defences.”
Even before November’s announcement, the government moved forward around £8
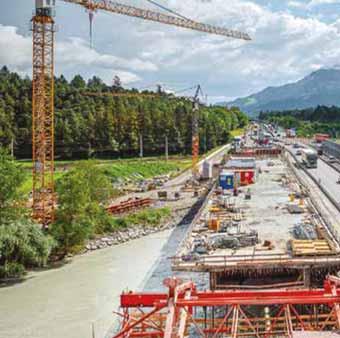
billion (US$9.9 billion) of capital investment in infrastructure. It announced that a national North of England-headquartered national infrastructure bank will be created to co-invest with the private sector and which will also be available to city and local authorities.
The National Infrastructure Strategy states that by May of this year the Infrastructure and Projects Authority will have published its Transforming Infrastructure Performance document. It details the delivery of infrastructure, building upon the measures outlined in the National Infrastructure Strategy. The government will also be developing a national underground assets register.
Meanwhile, the government intends to publish a National Strategy for Disabled People this year which will have implications for the delivery of infrastructure projects, particularly in the transport sector.
Finally, by the end of this year it is expected that the government will have published an Industrial Decarbonisation Strategy and a refreshed Industrial Strategy, says the report from Womble Bond Dickinson. Details within the Industrial Decarbonisation Strategy will include the government’s intentions of ensuring a national recharging infrastructure for electric vehicles.
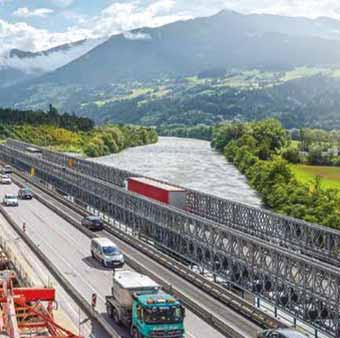
The 235m Terfener Innbrücke carries the A12 motorway over the Inn River in Austria’s Tyrolian Inntal Valley
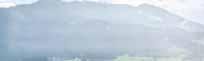

The Kronprinsesse Marys Bro, a recently opened four-lane 8.2km dual carriageway over Denmark’s Roskilde Fjord and part of Denmark’s Primary Route 53: maintaining Europe’s major road networks will be all the more important after the pandemic (photo courtesy RBAI joint venture)
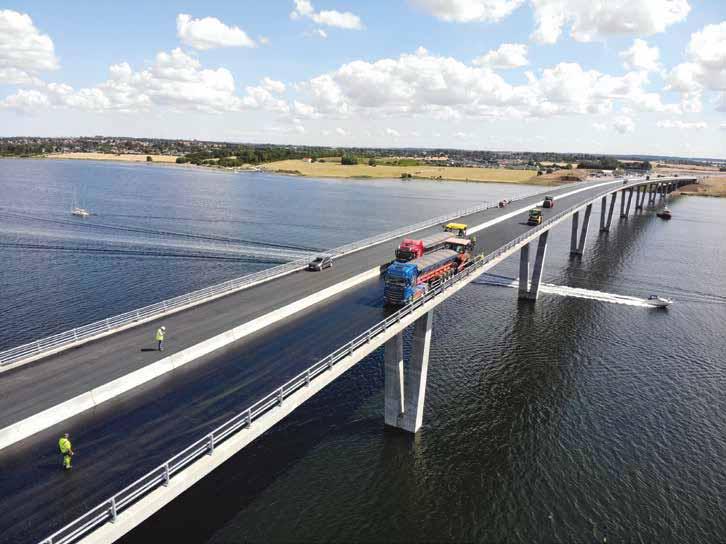
the European Investment Bank. The financing and funding of new technology at scale needs to be its number one priority to kick-start the UK economy,” said Watson.
“The bank could at least, in part, effectively act as a large-scale venture capital fund at a pivotal time when…intervention is needed to accelerate change and galvanise new technologies which support the transition to net zero.” The government’s aim is to achieve net-zero carbon emissions by 2050.
NEXT GENERATION EU
The 27-member European Union had been hoping for a gradual easing of lockdowns and a much faster economic upswing. But that has not been the case, thanks to several factors, including aggressive variants of COVID leading to more cases of infections and deaths. Re-establishing lockdowns after easing them was common among some countries, notably France, in the first half of the year. Economic improvements are not being evenly achieved across, as well as within, candidate European Union countries¹, many of whose economies are not strong to begin with.
However, the EU has made significant efforts to ensure that infrastructure construction continues across all of the continent. The European Union’s COVID recovery budget and its NextGenerationEU programme are major opportunities for national, regional and local road authorities, says José Diez, director of public affairs for the non-profit Brussels-based ERF –
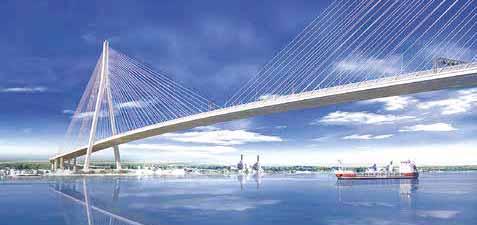
European Union Road Federation.
Indeed, NextGenerationEU will be the largest stimulus package ever financed through the EU budget. A total of €1.8 trillion will help rebuild a postCOVID-19 Europe.
Considering the reduction of investment during the past decade, the coming financial programmes represent a unique opportunity for the road infrastructure industry that is traditionally funded at national levels through each country’s investment schemes. But now the road sector will be eligible to benefit from specific programmes at European Union level until 2027, says Diez.
Firstly, key to the recovery is the ambitious NextGenerationEU, a €750 billion temporary instrument, which will complement the EU’s long-term budget and is composed of different tools representing the largest-ever stimulus package through EU funding.
The centrepiece of NextGenerationEU is the Recovery and Resilience Facility consisting of large-scale financial support for public investments in areas such as green and digital projects (€672 billion). The support will be given out in the form of loans (€360 billion) and grants (€312 billion). EU member states are required to present
national plans so the inclusion of road infrastructure will depend on the priorities for every country.
Secondly, the European Union budget includes the existing Cohesion Funding and the Connecting Europe Facility as main programmes. Both instruments follow key political priorities such as the EU’s Green Deal designed to make Europe a climate-neutral region by 2050; to be achieved by many sectors including transport by promoting greener and digital infrastructures.
It will also focus on regions that have not had the best safety and highway performance in the past. On that point, says Diez, the ERF supports the approach specifically to correct dramatic imbalances in road safety performance hand in hand with the deployment of the latest technologies to less economically well-off regions.
The Connecting Europe Facility has focused mainly on railway investment in the past. But higher safety and asset performance expectations from the road industry have risen in recent years to overcome the challenges of introducing automation, improving connectivity and safety, as well as electromobility to help
decarbonise the sector. Also, roads should play an important role creating an effective TEN-T (Trans-European Transport Network) comprehensive network that will connect the most remote areas in Europe and act as integrator of other transport modes.
For the first time, the new Connecting Europe Facility will allocate funding - €5.8 billion - to adapt strategic sections of the transport network for dual civilian-military use. This will ensure the resilient critical infrastructure for a smooth movement of military equipment in the event of either conflict or extreme natural or man-made events (flooding, earthquakes, terrorism) requiring rapid intervention.
Also, there is expected to be within the Connecting Europe Facility specific funding for bridges studies or actual construction. The ERF has been demanding a more ambitious plan to invest in the maintenance and upgrade of critical bridges as the vast majority are near the end of their useful life and often handling more than their design specifications dictated.
Further investments will come from the new Horizon Europe programme focusing on development of innovative solutions to improve the resilience of the infrastructure and maintenance operations. In addition,
the green light is given to the creation of the European Partnership on Connected, Cooperative and Automated Mobility (CCAM) - a new public-private partnership in road transport. This research and innovation initiative will combine industry and institutional efforts to accelerate the implementation of CCAM technologies and services including physical road infrastructure.
EQUIPMENT SALES
Given the need to re-boot economies within the G7, investment in infrastructure – not just transportation but all sectors - appears to be key for getting people back to work. The silver lining of the COVID pandemic is that many governments may be even more committed to investing in projects, and more efficiently. Site work has continued for the most part during the pandemic, thanks in part to contractors introducing safety measures for their workers.
Indeed, despite the pandemic, lockdowns and restricted travel throughout Europe, the construction equipment industry proved stable, suffered less than expected and appears to be resilient, according to a year-end report by the CECE – the Committee for
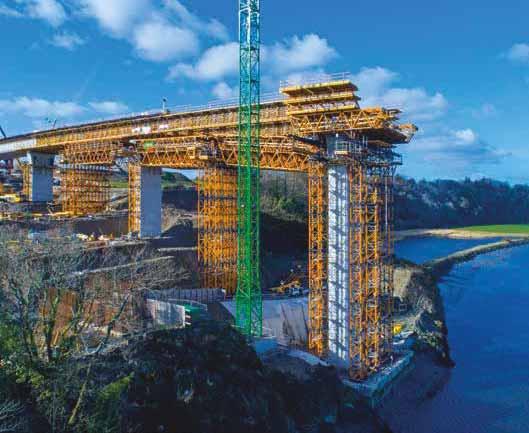
European Construction Equipment, based in Brussels.
The CECE Business Climate Index shows optimism with a visible upward trend.
While the short-term macroeconomic outlook remains uncertain, the business climate within the European equipment industry remains positive. After months of improvement, the business climate index in CECE’s Business Barometer survey is significantly higher in March 2021 than at the outbreak of the pandemic in spring 2020.
A significant majority of manufacturers expects business to grow in the first half of the year and the level of satisfaction with current business has also improved significantly. In addition, the order intake for European manufacturers has been growing year-on-year since December 2020 and sales on the European market are also on a clear growth path. This is consistent with the improvement in equipment sales seen in Q4 2020, notes the report.
A forecast of 5% growth in the European equipment market is a realistic assessment of prospects for 2021. However, against a background of continued uncertainty and high absolute levels of sales, even a flat market in 2021 would not be a disappointment.
A significant majority of manufacturers expects business to grow in the first half of the year
In the medium term, the European construction equipment industry faces many substantial risks. One of them is higher debts in many countries that will become a problem, as public infrastructure investments will suffer when austerity measures must be put in place.
The world market is also likely to show moderate growth in 2021, but the volatility of the Chinese market and its significant influence on the overall outcome mean that it is difficult to quote reliable figures for overall global growth levels.
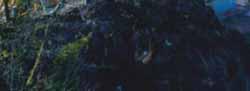
Ireland’s new Ross Bridge during construction: the NextGenerationEU programme will be a framework for providing major opportunities for national, regional and local road authorities (photo courtesy ULMA)
¹Candidates for EU membership are Albania, North Macedonia (former Yugoslav republic), Montenegro, Serbia and Turkey. Iceland suspended negotiations in 2013. Bosnia and Herzegovina and Kosovo are officially potential candidates. The four countries of the European Free Trade Association (EFTA) - Iceland, Switzerland, Liechtenstein and Norway – are partly committed to the EU’s economy and regulations. The European microstates of Andorra, Monaco, San Marino and Vatican City use the euro and co-operate with the EU in some economic and political areas.
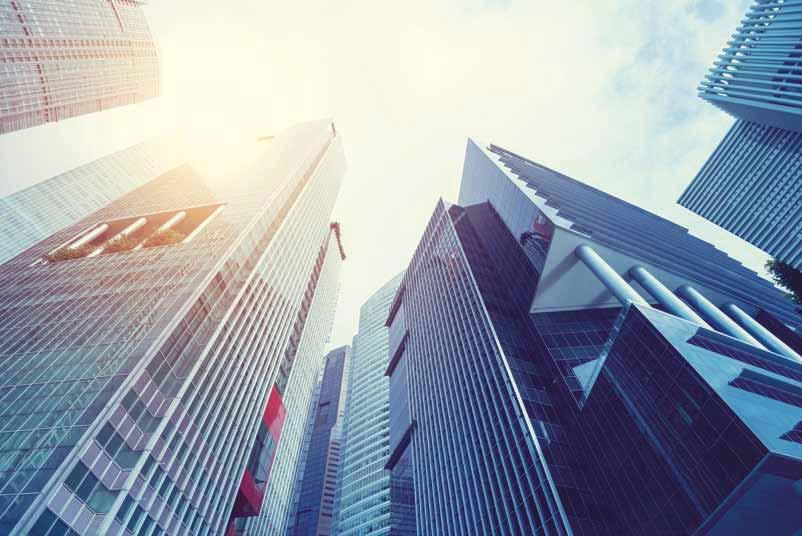
G20 AND BEYOND
Large-scale investment into big infrastructure projects by governments, the private sector and foreign companies is to be welcomed, but will never guarantee success.
David Arminas reports
In terms of financial clout, after the G7 group of countries comes another group, albeit more loosely connected - the G20, which includes the G7 countries and the European Union. The member states of the G20 are some of the world’s other major developed and developing countries –those promising more stable investment opportunities. These are Argentina, Australia, Brazil, India, Indonesia, Mexico, Russia, Saudi Arabia, South Africa, South Korea, Turkey, Spain and, importantly, China.
The Asian giant has a large and growing influence over the economic situation many G20 countries, from trading relationships to investment in infrastructure projects. However, China’s financial and economic influence extends well beyond the G20 to include many less developed countries around the world. For these countries, an economically healthy China means more direct foreign investment, usually for megaprojects.
Investment in domestic infrastructure projects, while promising increased employment and better transportation networks to boost an economy, is never a sure
deal (see end section, Back to the future). Similarly, accepting foreign investment at low interest rates and over a long term also has its problems.
According to the American Enterprise Institute, a right-wing Washington-based think tank, the total value of China’s overseas investment and construction since 2005 exceeds $2 trillion. But in 2020, documented investment and construction both plunged due to the COVID pandemic, although these should recover as the pandemic ebbs.
The Chinese government’s Belt and Road Initiative foreign investment strategy (see box) has become relatively more important, though within a smaller Chinese footprint overall, as the US and other rich countries have discouraged Chinese activity.
Indeed, China is fast recovering this year from the economic effects of COVID lockdowns. While the jury is out on exactly where the pandemic originated, the world’s health organisations were first alerted to its spread in China – despite early clumsy attempts by Beijing to clamp down on news of infections.
When news eventually got out, Chinese
authorities were forced to move quickly into social lockdown and just as quickly moved out of it, making China one of the first to see big domestic economic gains starting in late 2020. Other G20 countries were posting economic upturns as well, but not on the level seen for the Asian giant.
However, as Global Report went to press (May, 2021), variants of the original COVID virus were spreading fast among many countries, most notably India. Lockdowns were being brought back but for how long remains uncertain. This is making accurate economic predictions for the rest of this year and next all the more difficult to achieve.
Nonetheless, China’s early return to big growth numbers appears to be a solid trend and infrastructure projects are high on the priority list for getting the economy moving again.
But for countries that wish to take advantage of China’s Belt and Road Initiative financing, there are some things to consider, as pointed out by the American Enterprise Institute. An important distinction between construction and investment patterns concerns the companies involved.
“The Chinese private sector plays an important role in outbound investment, but construction is utterly dominated by stateowned enterprises (SOEs) such as Minmetals and its subsidiaries,” notes the institute.
“Profits are typically absent and quality can be suspect, but these SOEs have an established track record in completing projects in difficult settings at home and overseas, places where private firms would not venture. They are supported by concessionary finance in huge amounts from state-controlled banks. It would be almost impossible for the US, EU, Japan or others to mobilise a private-sector effort to match the scale of BRI construction.”
Beijing
Internally, the Beijing government’s huge domestic stimulus spending saw the national construction equipment market rise from the already buoyant levels of 2019 by a further 30%. Production rose from nearly 316,100 units to 412,440 units), according to April 2021-released figures from Off-Highway Research, a UK-based analyst focusing on the global construction equipment market.
Chinese president Xi Jinping paid a visit to the headquarters of heavy-equipment manufacturer Liugong during a recent visit to the city of Liuzhou in southern China’s
Guangxi Zhuang autonomous region. He told employees that only innovation can help the equipment manufacturing industry become stronger.
The country also has money to pour into big foreign infrastructure projects by way of lending big sums to governments – often tied to the construction work going to large Chinese contractors.
Yet it remains unclear to what extent geopolitics will intervene to dampen any spill-over of China’s economic recovery into the economies of other less-developed G20 countries and those outside the grouping – the main beneficiaries of Chinese largesse. Beijing has handed out large loans to mainly small countries in the past five years or so under the Chinese government’s politically strategic Belt and Road Initiative. As China’s economy recovers quickly and those of other nations inside and outside the G20 don’t, questions have risen over debt repayments to China’s Ex-Im Bank and other national financial institutions. This is especially true for big road, rail, port and energy projects being done mainly by Chinese contractors – and which have fallen behind schedule.
Montenegro, aspiring to European Union membership, is a case in point (see
box). Milojko Spajić, Montenegro’s finance minister, said in an interview with the Financial Times newspaper in London earlier this year that the first 41km section of the A-1 motorway cost €20 million per kilometre, making it one of the most expensive highways per kilometre in the world.
Montenegro’s debt to the Chinese –reportedly one-quarter of the country’s overall debt - has highlighted concerns over Chinese influence in Europe’s western Balkans region.
Even so, Montenegro’s plea for financial assistance from the European Union has
BELT AND ROAD INITIATIVE
The Belt and Road Initiative is a global infrastructure development and investment strategy adopted by China in 2013 to invest in nearly 70 countries and international organisations – a central strategy of Chinese foreign policy. The goal is to create a new global trading relationship by more tightly tying together the economies of Asia, Europe and Africa.
A major focus for infrastructure loans to small countries has been the Beijingbased Asian Infrastructure Investment Bank. According to the AIIB, the bank’s primary goals are to address the expanding infrastructure needs across Asia, enhance regional integration, promote economic development and improve public access to social services.
China - Construction Contracts January 2021
PAKISTAN
45.1
Source: American Enterprise Institute
repeatedly been rebuffed. The EU had also repeatedly cautioned against taking around $1 billion (€840 million) in Chinese loans. EU foreign policy spokesperson Peter Stano reportedly said earlier this year that the European Union will “continue to stand by [Montenegro], but we are not repaying the loans they are taking from third parties”.
Cracks are also appearing in the relationships between China and two of its largest Asian trading partners, Australia and New Zealand, that could affect any Belt and Road Initiative investment in these two Pacific Rim nations.
In 2018 Victorian premier Daniel Andrews signed a memorandum of understanding (MoU) with Beijing to work together on Belt and Road Initiatives. China has more than 170 MoUs with around 125 countries, according to Chinese media reports. Since signing the MoU, Victoria – Australia’s wealthiest state – has greatly increased its trade with China, for both exports and imports.
The A-1 motorway - when finished - will run through Montenegro’s Morača Canyon
But, concerned about China’s growing social and political influence in Australian affairs, the federal Australian government said it would not allow several deals between Victoria and China. Chinese investment in Victoria’s infrastructure projects could face challenges, according to Australian media.
Chinese investment in Victoria’s infrastructure projects could face challenges
US news channel CNN reported that China and Australia had already been butting diplomatic heads before the current dispute. Australia called for an international investigation into the origins of the COVID pandemic. Since then, Australian exports to China of timber, beef, coal and wine have faced increased tariffs.
New Zealand, too, has experienced rising tensions with China, which takes around a third of New Zealand’s exports. China has taken exception to New Zealand’s comments about Beijing’s treatment of Hong Kong and its mainland ethnic Muslim Uyhgurs in the Xinjiang autonomous region.
MOTORWAY BLUES
Montenegro’s A-1 motorway, also called the Bar-to-Boljare Motorway, will run 165km through mountainous terrain from Bar on the Adriatic coast eastward to the Serbian border. The A-1 is part of the plan to run a motorway from Bar, through the Montenegrin capital Podgorica and on into Serbia, to the country’s capital, Belgrade.
The so-called Belgrade–Bar motorway is considered an economic lifeline for Montenegro, a mountainous country that desperately needs good transportation infrastructure to help its economy. Serbia struck a deal with China Communications Construction Company – CCCC - worth €450 million in 2017 for construction of the Preljina-Pozega section of its route, called the A-2 and which runs for nearly 260km.
The Chinese loan to Montenegro is reportedly for around 85 percent of the cost to build the A-1 for which construction started in mid-2015 and that has yet to be completed. To repay the loan, there has been concern by financial analysts and western politicians that China will seek to control a country’s strategic natural resources as payment for financially defaulting on contracts.
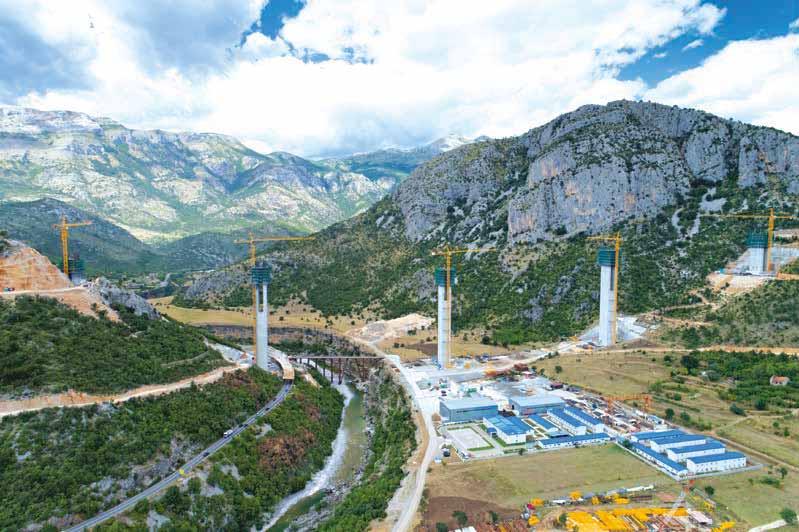
GLOBAL VALUE CHAIN
Much progress worldwide has been made over the past decade, however, to improve national infrastructure investment regulatory frameworks, according to the World Bank report Benchmarking 2020 Infrastructure Development. This will continue, allowing for a more transparent financial system backed by stronger legal guarantees for all parties, be it for public-private partnerships or traditional public investment methods. The issue is more about what monies
GLOBAL VALUE CHAINS*
International trade expanded rapidly after 1990, powered by the rise of global value chains (GVCs). Poor countries grew faster and began to catch up with richer countries. Poverty fell sharply. These gains were driven by the fragmentation of production across countries and the growth of connections between firms. Parts and components began crisscrossing the globe as firms looked for efficiencies wherever they could find them. Productivity and incomes rose in countries that became integral to GVCs, such as Bangladesh, China and Vietnam. Today, it can no longer be taken for granted
Participation in the Global Value Chain
national governments are willing to sink into infrastructure projects. Will they speed up investment to get people back to work after lockdowns or hold off on big spending and major projects?
Will equipment makers in the more developed countries have to review their global supply and value chains to accommodate their lower sales volumes, at least in the short term? The Trump administration’s policy in the US was to encourage American manufacturers to move
jobs back to the US from overseas. This is likely to remain a tacit policy of the new Biden administration as the government struggles to get the American economy back onto its feet.
But other threats loom for an expanding global value chain, such as trade conflicts. Also, labour-saving technologies make it more financially viable for manufacturers in developed nations to move production back home, according to a recent World Bank report (see box Global Value Chains).
that trade will remain a force for prosperity. Since the global financial crisis of 2008, the growth of trade has been sluggish and the expansion of GVCs has slowed. The past decade has seen nothing like the transformative events of the 1990s—the integration of China and Eastern Europe into the global economy and major trade agreements such as the Uruguay Round and the North American Free Trade Agreement (NAFTA).
At the same time, two potentially serious threats have emerged to the successful model of labour-intensive, trade-led growth. First,
the arrival of labour-saving technologies such as automation and 3D printing could draw production closer to the consumer and reduce the demand for labour at home and abroad. Second, trade conflict among large countries could lead to a retrenchment or a segmentation of GVCs.
*World Bank. 2020. “World Development Report 2020: Trading for Development in the Age of Global Value Chains.” Overview booklet. World Bank, Washington, DC. License: Creative Commons Attribution CC BY 3.0 IGO.
Source: WDR 2020 team, based on the GVC taxonomy for 2015
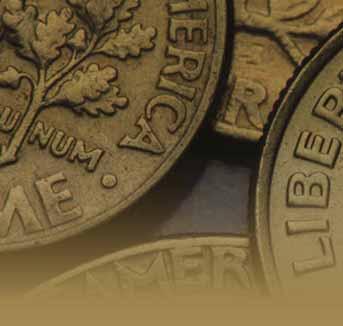
BACK TO THE FUTURE
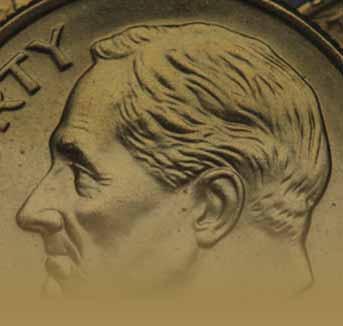
Ever since US president Franklin D. Roosevelt put forward his “New Deal” in the mid-1930s, investing in infrastructure has been a way out of recession for governments under pressure. But success is not guaranteed, writes Geoff Hadwick. There are going to be plenty of bumps along the road. So, how easy is it for governments and investors to see massive, long-term investment plans like these come to fruition?
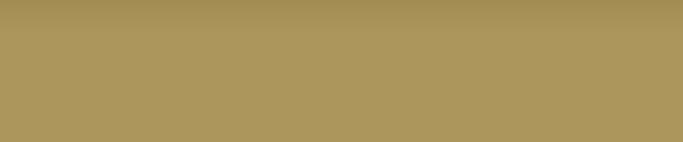
The International Monetary Fund recently argued that an increase of 1% of gross domestic product (GDP) in public investment in both advanced and emerging economies can create between 20 million and 33 million new jobs and increase GDP by between 0.25 per cent and 0.5 per cent in the first year of adoption.
Before COVID and with China excepted - which spent more on economic infrastructure in 2019 than the US and Western Europe combined - infrastructure investment worldwide has been in steady decline. However, it now appears that the appetite as well as the need for increased infrastructure investment is there.
Projected funding is on the up. US president Joe Biden has pledged $2 trillion for roads, bridges and electric-car charging points in the US. Meanwhile, China has allocated a further $1.55 trillion for new projects. Hot on their heels is the European Union with its anticipated €750 billion recovery fund.
Other factors likely to increase investment are low interest rates in the most developed countries worldwide, plus the potential for steady cashflows from infrastructure assets which appeal to both pension funds and insurers. This post-COVID-19 world presents opportunities as well as problems, according to another recent report, this time by The Economist, a UK newspaper. In the immediate future, ailing urban transport systems will need temporary rescue packages. But governments are looking ahead at funds for both maintenance and upgrades as well as for new capabilities which will be prioritised as a result of the pandemic: digital infrastructure, green projects and electrictransportation systems.
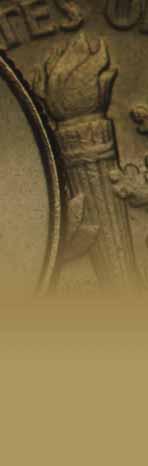
However, in the recent past politics, poor procurement and construction and risky funding have contributed to the failure of large-scale infrastructure projects. In political terms, governments must run processes that can overlap several electoral cycles, or that attract straightforward political resistance.
For instance, former US president Barack Obama’s Recovery and Reinvestment Act concentrated on small maintenance projects that could pass easily through Congress. It seemed easier to do it piecemeal. Former president Donald Trump’s much-heralded plans for American infrastructure were hit by disagreements over cash distribution. In Mexico, president Andrés Manuel López Obrador cancelled most publicly tendered energy projects upon entering office in 2018, preferring to use state-owned utilities companies to construct and own the assets.
Enthusiasm for public-private partnerships has slowed. Initially, in the 1990s, PPPs were hailed as offering governments long-term asset control and service regulation without massive up-front cash investment. But critics now accuse them of being expensive, non-transparent and slow to offer private investors a return on their investment. The value of PPP projects worldwide fell from $55 billion in 2010 to $30 billion in 2019.
POOR RECORD
accept unfeasibly thin margins and bear too much risk which lead to compromises in quality. In some countries, unstable regulation and changing goal posts make it difficult for investors to capitalise on their investment.
Another factor hindering project completion has been the scarcity of long-term investors. Projects are often highly leveraged and dominated by construction firms fixated on short-termism - a style of management which leaves little scope for dealing with the unexpected.
Governments are beginning to see the benefits of providing contractors with financial certainty
But the winds of change are blowing and governments are beginning to see the benefits of providing contractors with financial certainty. The British government’s tenders for cabling link offshore wind farms to the on-shore national grid, initiated in 2009, gave investors a guaranteed return on investment. Canada, too, has since established an infrastructure bank specifically to create innovative financing schemes with private-sector investors. In Australia, there is an “asset-recycling” programme which gives political cover for lucrative privatisations.
Growing concern about climate change is also making it easier to procure private capital for certain projects, such as digital and renewable asset programmes. These projects are easier to build, tend to be profitable and, importantly, lack the complexity of megaprojects. They also can often generate public support.
In 2016, Oxford University reported that over half of China’s infrastructure investments “destroyed” economic value. Typically, 90% of megaprojects overrun their budget. Bidders
Nonetheless, investors can still be caught out. But governments are working harder to keep them on board and that has got to be good news for the global construction industry.
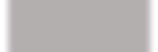
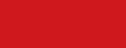
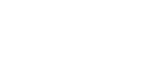
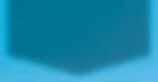

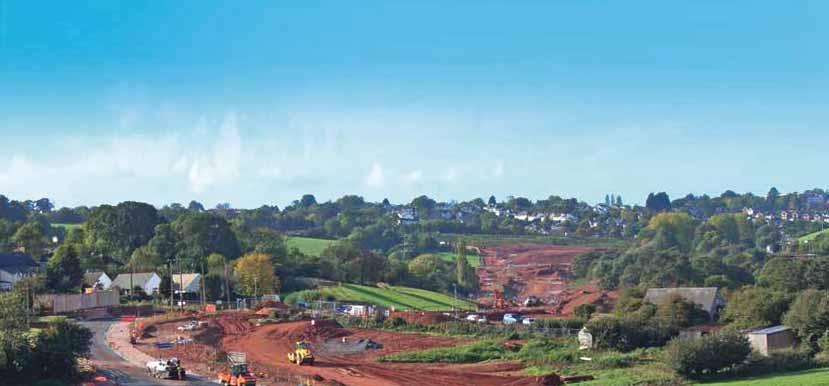
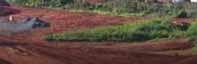
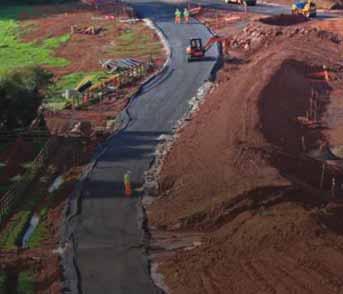






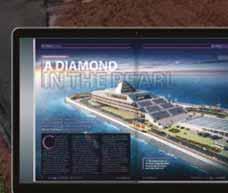
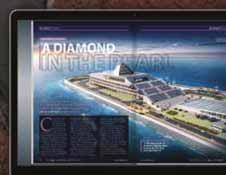
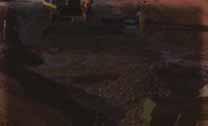


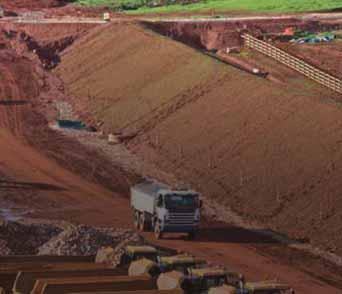


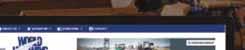

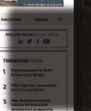
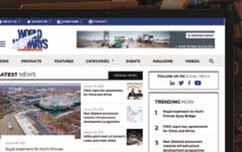
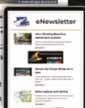


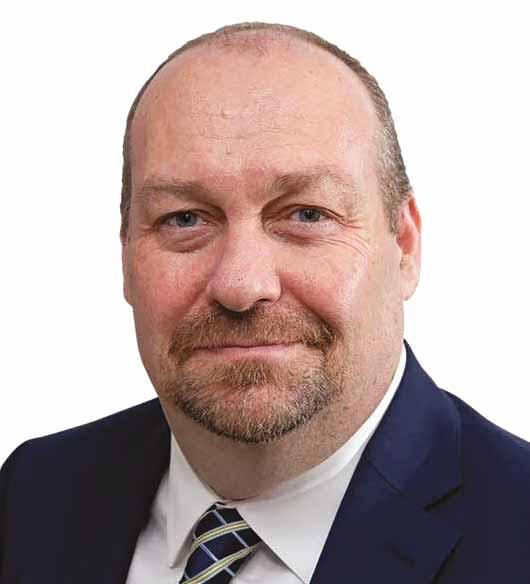
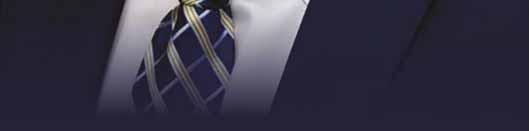

TRIMBLE’S VISION OF A FAR MORE EFFICIENT FUTURE
Trimble is offering a future with more efficient, optimised construction operations for faster project delivery – Mike Woof writes
The global pandemic has had a huge impact all around the globe, with the threat to human health affecting all industries and all activities. However, the latest technology is offering solutions and helping firms to adopt systems that are already available. This is certainly becoming apparent in the construction sector, where contractors and technology suppliers are meeting the many challenges posed by the pandemic.
Construction activity was halted initially by the pandemic in many areas but then was able to commence again by following new practices, with technology playing a key role. Pete Large is in charge of civil construction field solutions at Trimble and he believes that the pandemic has certainly affected the adoption of technology in construction. He commented, “In the civil engineering sector we’re definitely seeing some trends there.”
Large believes that the need for social distancing on construction sites has led to changes in the way personnel work. He thinks that one way in which this has been apparent is in the way 3D data is transferred to construction equipment onsite. In past years, this has been done manually, “…a lot of customers have been taking sticks to machines.”
However, the need to ensure social distancing has forced contractors to change the way they work and to minimise physical interaction between personnel as well as to utilise distancing measures. He said, “More people are using the remote capabilities to take data to the machines and also use remote diagnostic technologies.”
According to Large, having already implemented these measures, contractors are likely to retain them once the worst of the pandemic has passed. “All these things we’ve been forced to do because of the pandemic will stick.”
The reason behind this switch is technology delivers increased efficiency. For example, transferring data to and from machines wirelessly at the beginning and end of the working day is far more efficient than having to take a USB stick to download into a construction machine at the start of the shift, then using another stick to download asbuilt data at the end of a shift. Wireless data transfer even allows for continuous tracking of machine operation, providing a realtime view of operations onsite and allowing accurate recording of as-built data.
Some sectors of the construction industry are already benefitting from the use of this sophisticated technology more than
others. Large said, “It’s certainly in use in earthmoving and we’ve seen that.”
He has noted that an unexpected change in the construction sector has been the wider adoption of new technologies in remote training of personnel. Machine simulators, for example, have allowed operators to get up to speed on equipment use without needing to have an instructor sitting alongside and ensuring safe social distancing measures are employed. These simulators have been available for many years but the benefits they offer in allowing safe distancing have become more widely appreciated. The ability to deliver comprehensive operator training in a safe environment and without needing to use a working machine offers a cost saving to the contractor. Large said, “…and I think it will endure after the pandemic”.
The pandemic has posed a range of new challenges for construction firms. Building and construction management as well as project managers have been considered essential workers. Project workers, in particular, have been considered too valuable to be allowed onsite due to constraints on social contact and the need to minimise the risk of spreading the virus to essential workers. To get around this challenge, there has been a mix of technology employed in the industry. Large said that Trimble has seen a significant increase in demand for software allowing site personnel to use smartphones to take photos, which can then be used to provide accurate records on work that has been completed.
Large commented, “All of this stuff existed before the pandemic but organisations were resistant to it. With the pandemic, they went into exploring mode and quickly found new paths. There was a dogged determination to get work done.”
He continued, “Contractors want to minimise the number of people onsite, so they inspect and approve remotely using photos, scanners and sensors. These tools allow inspectors to perform their work remotely and do inspections.”
BELOW: Machine control systems are offering benefits for social distancing measures on construction sites
BOTTOM LEFT: Fast data transfer between machines and site office can be achieved using technology, with contractors increasing their use of such systems due to the pandemic
BOTTOM RIGHT: New tools allow firms to monitor operations and carry out remote surveying to enable social distancing on the modern construction site
Large argues that new technology is helping assist in another area too, namely the widespread labour shortage that has been affecting the construction sector increasingly in recent years and which has become more apparent during the pandemic.

Clients too have adapted their practices to meet these new challenges. Large has observed that many municipalities have now changed their regulations to allow inspections to be carried out remotely. He explained that this has helped deliver a big increase in productivity. “In the past the inspection process could take up to two weeks, but now this is more efficient. The inspectors don’t need to travel to site and can carry out inspections remotely, so they can carry out more in the same period of time.”
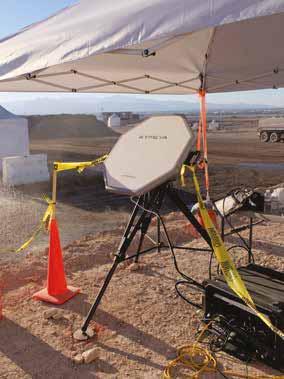
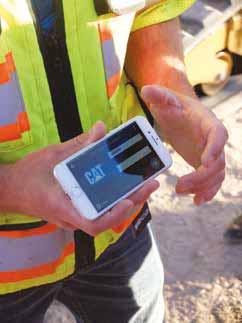

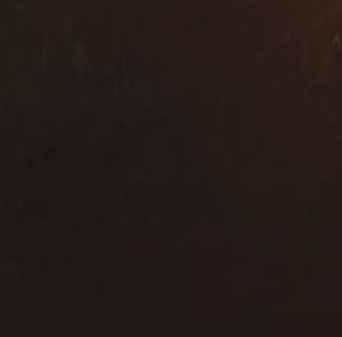
➔ CUSTOMISED OFFERING
With a steady flow of customers looking to utilise an ever-growing array of technology solutions, Trimble is changing its offering to suit. One of the key developments is the switch to the subscription model. This allows customers to pay a charge for access to a customised package of solutions. With so many products now on offer, it makes sense for Trimble to offer the platform as a service, rather than simply selling the latest all-inclusive package. Large said, “It’s a megatrend and it’s happening in a lot of industries.”
He explained, “It’s not just a monthly payment plan. If we come out with new technology and new products, you get that. We also build other things in there like damage protection.” He continued: “The customer can get the latest and greatest hardware and software and not have to wait until the replacement date.”
The customer can select from a vast array of products and services as to what the package contains, without having to buy tools that will not be used. Meanwhile, if further options are required in the future, these can be added at a later date and for a limited period only to handle a particular task or set of tasks if necessary. Customer service also forms part of the offering and Large added: “Support is part of the package as well.”
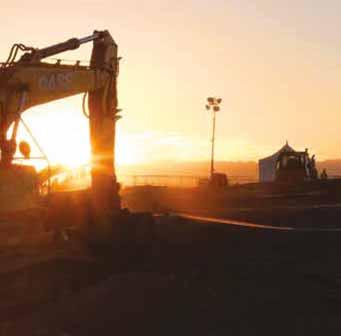
Using BIM also means that the digital design model becomes accessible for site personnel, which is of key benefit for machine control purposes.
Large said: “The key thing is to be able to get that design to site.”
Earthmoving is one of the sectors to benefit most from the use of new technology
The as-built data from the equipment can then be recovered wirelessly, becoming part of the final BIM model of the project, showing what was done when, where, by whom, how and with what.
With BIM in mind, Large said that the firm’s Quadri package offers ‘one source of truth’, as core project data can be collected and organised, giving all the respective parties involved in a construction project access to the correct data. He said that the Quadri collaboration platform delivers a live central BIM model, which develops continuously and helps ensure that all the stakeholders have access to the latest construction project information. “Quadri maintains a single source of truth in real time so everyone sees the actual model.”
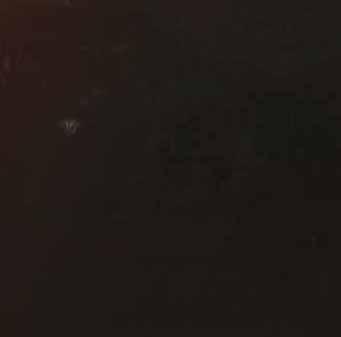

This approach is intended to meet the requirement in major projects for the use of BIM, which is growing in importance in industry. Using BIM (building information modelling) practices helps to ensure project delivery on time and within budget by removing some of the obstacles that would otherwise delay progress, with early clash detection during design playing a vital role. Large explained, “The value of BIM is that you make all those clashes digitally, so when you come to do the actual construction you’ve already solved all those problems.”
The BIM model is not restricted to the initial design though and Large commented, “Machine control feeds that as well.”
There are other capabilities within Quadri. The system has the capability to use data recovered from laser scanning of road surfaces for example, allowing stakeholders to detect cracks and changes in the road surface over time. This offers further benefits, as it means road firms can track wear rates accurately. “They’d like to get to a point where they can be predictive,” Large added.
The capabilities of using as-built project data within BIM Models as well as laser scanning of existing infrastructure as it ages have yet to be fully realised. “For a lot of our customers it’s becoming very interesting. Our ability to connect data points in real
time is one advantage,” Large observed.
Looking around the world, progress is further ahead in some countries, as Large explained: “Australia is very advanced in data flow and integration of technology. Japan is also very advanced and part of that is from the government policy.”
He also noted that the way in which Japan has adapted to utilise advanced technology in construction provides pointers for other nations. “If you look at the number of machines using machine control it is very high.” Large explained that this approach allows construction firms to be more environmentally friendly as the widespread use of digital technology is more efficient.

Despite its limited use worldwide so far, the market for advanced construction technology is vast. “There are still a lot of places in the world where old technology is being used and there is a big potential,” notes Large. India’s massive highway construction programme is a particularly ripe market for the introduction of more sophisticated construction technology. Meanwhile, the US and Europe need to upgrade and replace infrastructure and there are considerable opportunities for new technologies to evaluate the type of work needing to be carried out.
Large concluded: “The whole connected concept is good for us. The vision for construction is also that. Each stakeholder knows what the other is doing. There are aspects of what we have been through with the pandemic that’s helped introduce those solutions. Construction has done remarkably well in a challenging environment but we see 2021 as a time for recovery and catching up.”

THE BIG RETHINK
If there is one clear business lesson to be learned from the pandemic, it is this: The big contractors are rethinking their construction equipment needs. The global
construction sector is about to feel the winds of change more rapidly and more dramatically than most. The reasons are many and complex. Graham Anderson reports
Construction has long been a technological laggard, suffering low investment, poor training and a price-driven culture. It has a lot of catching up to do to deliver the performance and efficiencies that its clients increasingly want.
Markets are changing fast, with many experts predicting a long-term shift away from commercial and retail construction - thanks to working at home and the popularity of delivery services - with a concomitant growth in “green” infrastructure investment across the board from renewable energy to low-carbon transport networks.
And most important of all, a growing number of influential voices argue that this time of disruption is the moment to implement fundamental changes in construction’s equipment, technology and processes to slash the industry’s environmental footprint.
As the old cliché goes - first said by Winston Churchill or Niccolò Machiavelli depending on who you believe - “never let a good crisis go to waste”.
But while no-one believes the construction sector will go back to business as usual when
the worst is over and the vaccines eventually take global effect, at the same time, it is not at all clear what the future might look like.
IMPOSSIBLE TO ANSWER
One senior assets director at a top European contractor, when asked about his company’s construction equipment strategy in the coming years, said: “ The questions are good, they are timely, but at the moment they are impossible to answer.
“We are going through a major strategic review, and the details of our equipment needs and requirements will follow on from that. Until we are clear about our direction of travel as a company, debates about longterm equipment investment and innovation will have to wait. There are just so many uncertainties.”
For an industry that is estimated to produce around 40 per cent of the world’s energy-related carbon emissions, the strategy questions are being driven not just by sensitive environmental imperatives but also by the fast-changing opportunities created by digitalisation.
And the strategies that emerge will determine how projects are managed in
ABOVE: Future shock: US firm Turner
Construction - a Hochtief company - testing the capabilities of an advanced site mobility robot called Spot on the 550 Washington Street project in New York City. Controlled remotely from a tablet, it can inspect work progress, carry small loads and autonomously compare as-built work with BIM plans
future, the type of equipment used, the skills needed to support and maintain it, and whether that equipment is bought, owned, leased or rented.
HOCHTIEF GOES DIGITAL AND AI
In 2018, in response to the changing landscape, German contractor Hochtief decided to think big and created Nexplore, a software innovation company in the construction industry that “builds custommade solutions based on next-generation technologies across disciplines and geographies”.
Hochtief is well-placed to be one of the most influential players in global construction. Apart from being Germany’s biggest contractor, it ranks as one of the ➔
➔ largest general construction companies in the United States through its Turner subsidiary, in Australia through its shareholding in CIMIC Group, and is itself owned by the Spanish contractor Grupo ACS which holds a controlling stake.
Nexplore works with companies, universities and Hochtief’s own internal teams to drive practical digital innovations from site equipment to project management.
David Koch, chief risk, organisation and innovation officer of Hochtief and CEO of Nexplore, told Global Report: “ We are developing several hardware and software applications.
“These are already in use on construction sites in the USA, Europe, Hong Kong, and Australia. They let us monitor things like construction progress on major projects, keep continuous track of work quality, pinpoint potential savings with our machinery, and analyze complex contracts among other things.
“Digital technology directly helps the people who work on our projects. For instance, Nexplore has developed sensors that warn excavator operators of potential accidents...and we are testing robots that use image recognition and artificial intelligence to measure the moisture content of concrete and
SKANSKA SAYS ACT NOW
Swedish-based international contractor Skanska - the fifth largest construction firm in the world - similarly believes the pandemic is accelerating major changes and is involved in ground-breaking projects that will fundamentally impact how construction sites are managed and the equipment utilised.
Construction equipment can sit idle up to 40 percent of the time
of multi-ton excavators, loaders, haulers and other heavy equipment. For the best performance, these machines should all work together seamlessly in a complicated ballet of sorts, with each machine doing its part at the prescribed time.
“It is urgent to act on the climate crisis now,” said Jacob Birkeland, Skanska’s head of public affairs. “The situation is tough but the conditions exist.
He stressed: “This is a major challenge, but we can be a part of the solution. The large emissions originate from the production of materials such as concrete, steel and asphalt, as well as from fuel.
“To achieve the goal of being climate neutral, innovation and partnerships with different actors are needed. To tackle the climate challenge, we need new ways of thinking and smart solutions. Many of these come through partnerships.
“For example, Skanska is working with partners to develop artificial intelligence for construction equipment to achieve less emissions, faster production and lower costs.
“But across the construction industry, such close coordination is difficult to achieve due to the ever-changing nature of sites. As a result, construction equipment can sit idle up to 40 percent of the time waiting on other equipment, increasing costs and carbon emissions.
“To help solve this problem, Skanska is developing solutions to enable heavy equipment – such as multi-ton excavators, loaders and haulers – to work more efficiently.
“This work involves exploring such methods as machine learning, route optimization and artificial intelligence through a consortium of Skanska Norway, Volvo Construction Equipment, research organization SINTEF and construction software company Ditio.”
Skanska is also working with Volvo on Electric Site, which the company claims is the
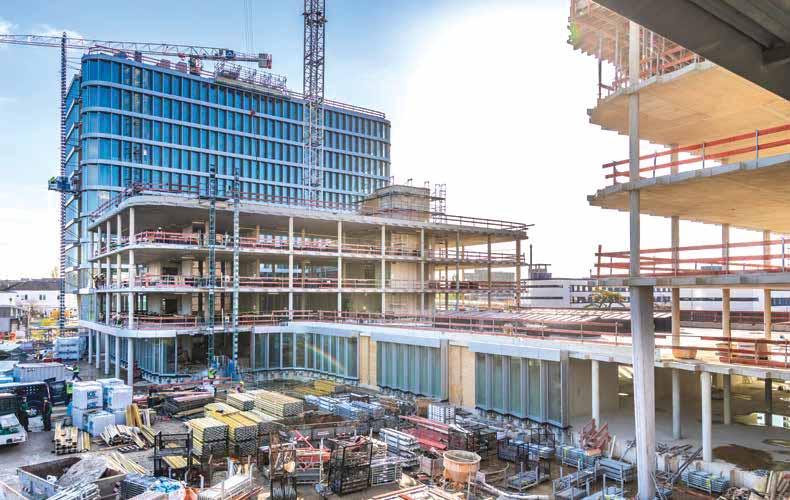
The Mizal office campus under construction by Hochtief in Dusseldorf, Germany
THE ELECTRIC SITE
Electric Site is a research project in Sweden that aims to make quarry production smarter, greener and safer. The initiative involves developing new types of quarry equipment powered by electricity – including what Skanska calls self-driving load carriers –and has three major aims: reducing carbon emissions by 95 percent, lowering total operating costs by 25 per cent and providing a safer work environment.
Birkeland is convinced that the industry will not revert to how it was before the pandemic. But despite the initiatives taken by Skanska, Hochtief and others, government and regulatory support is essential if changes both in what is built and the equipment used are to become embedded in the industry.
“The construction industry has traditionally been a lowest-price industry, with the public sector as our largest customer. Public procurement is a very effective tool to push for sustainable solutions and help reach the global sustainable development goals.
“Even if there is legislation in place in all EU countries allowing for other factors
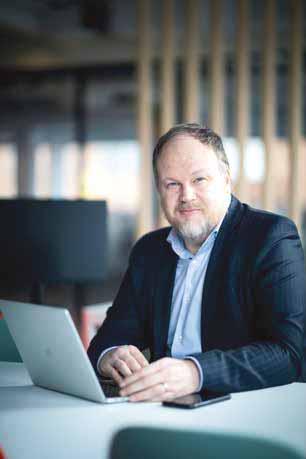
than lowest price in public procurement, sustainable solutions are rarely weighed into the total offer. We can see more and more examples of this changing and the benefits that can be created. But we need an extra push from the public sector to ask for low carbon solutions in public procurement.”
Many experts believe that the combination of technological upheaval, financial and environmental pressures and the pandemic will force other changes in the industry as well.
Chris Sleight, Managing Director of Off-Highway Research, a management consultancy specialising in the research and analysis of international construction equipment markets, believes that contractors will be increasingly reluctant to own equipment directly themselves, unless high utilisation rates can be guaranteed.
He said: “I am strongly of the opinion that rental is growing very strongly, in Europe in particular. We have done some work on this in the last six months and machinery rental is bigger and is continuing to grow.
“The number of sales to contractors is falling as a result. It is not a stratospheric drop but in my view the trend is clear. Whereas five to six years ago, over 40% of total equipment sales were to contractors, now that is down to 35% and looks to be falling further.
“Of course, contractual changes in recent decades has meant that the main contractors are increasingly construction managers with a greater percentage of work on site being carried out by specialist contractors, subcontractors and other suppliers.
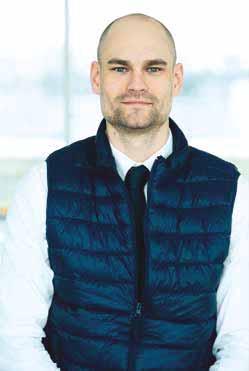
themselves “how can I make best use of my money”. And increasingly, my guess is that owning equipment directly is not going to be the answer.”
In the past, recessions have stalled innovation
He added: “In addition, contractors looking at their balance sheets might reasonably be asking why they should tie up a lot of capital investment in plant when they can hire it instead when they need it.”
POWER BY THE HOUR
A further factor is that the OEMs themselves are beginning to experiment with the “power by the hour” model and servitisation, although it is too early to draw firm longterm conclusions about the impact of such strategies.
Sleight continued: “Of course, the industry will never get to 100% rental, and small companies and owner operators especially will still tend to buy - and perhaps rent out themselves on occasions when they are
He said that there would be exceptions to that rule. Some contractors will still look to own core equipment that has a strong utilisation rate. What equipment that is will depend on the sectors the contractors are most active in and whether they have a specialist arm with specific requirements, such as a rail construction unit for example.
In the past, recessions have stalled innovation, but Sleight played down fears about the state of construction markets in the wake of the pandemic. “Last year turned out to be nowhere near as bad as we thought. Unit sales in Europe were down 17%, but that figure was depressed by very big drops in the UK and Spain.
“But the trends in China and the US are promising and on a global scale sales are hardly down at all. In China, central government support meant that the volume of equipment sold last year was back to 2011 levels, fuelled by projects such as the new east-west highspeed rail projects and city metros.
“And in the US sales are nowhere near as bad as might have been predicted and the Biden stimulus package is expected to give the industry a big shot in the arm.”
AGC THINKS POSITIVE
That optimism was echoed by Brian Turmail, Vice President of Associated General Contractors (AGC) of America, the powerful USA trade body with over 27,000 member firms.
He, too, is optimistic about construction’s prospects both in the short- and long-term and adds his voice to those thinking that the industry is on the cusp of significant technological advances.
“As it is with many other sectors of the economy, the pandemic is working as an accelerator to trends that were already underway. After the pandemic, more firms will continue to rely on virtual training and remote coordination. They will continue to look for ways to use technology to keep staffing levels more even on busy job sites, and they will increasingly focus on ways to make sure the pre-construction process finds solutions that minimize the amount of time contractors take to build those projects.”
He is convinced the industry will see a more rapid adoption of new technologies, such as the latest telematics and the use of
a result, more firms are using them to be more efficient – which will prompt their competitors to follow suit.”
Turmail says the industry is in a good position to recover. But if workload is strong despite the pandemic, there are still great uncertainties which he believes will drive firms to search out new efficiencies.
“The industry took a hit, but not as big a hit as we once feared. But many construction firms still worry about workforce shortages, and they are currently being squeezed by rising materials prices at a time when few owners are willing to pay more for work.”
He continued: “Workforce shortages, materials prices, regulatory uncertainty and the need to invest in new technologies and new techniques will all impact the construction industry over the coming years.
“Moreover, these trends are all interrelated. Labour shortages and materials price spikes will prompt firms to explore ways to become more efficient – thus driving them to invest in new digital technologies – like exoskeletons and autonomous equipment –and techniques – like greater reliance on off-
Equipment Association - has argued that the industry’s rental and contractor clients often do not have the means and skills to exploit the technologies that are available and to have them positively impact the bottom line.
In short, a major barrier to change is not the technology itself but the companies using it - or not.
CECE SEES THINGS SPEEDING UP
Nonetheless, like his industry colleagues, CECE Secretary General Riccardo Viaggi, is firmly of the opinion that change will now accelerate.
“The continuous shift towards smart and connected machines is a direct response to incremental requests by machinery contractors and users to improve efficiency, project delivery times and overall economic sustainability of construction activities.”
And he added that the support given by digital and automation technologies is fundamental to improving environmental performance on site.
To drive this agenda CECE has its own Digitalisation Task Force and is a
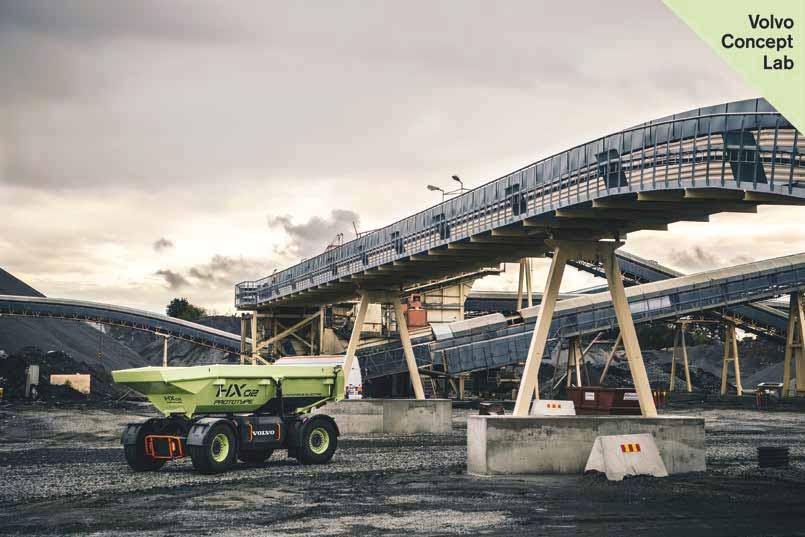
“The industry took a hit, but not as big a hit as we once feared”
Brian
Turmail, Vice President of Associated General Contractors (AGC) of America
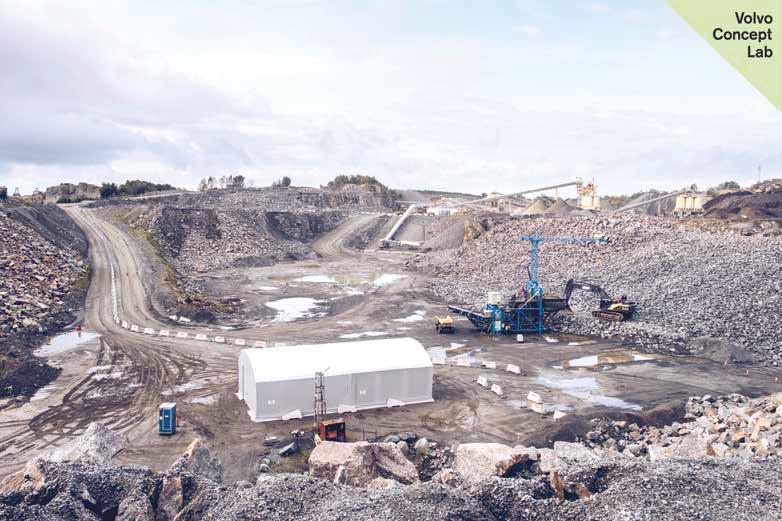
common digital platform across the European construction industry, helping to organise the exchange of data across the industry’s supply chains.
At the time of writing, the final DigiPLACE conference was due to take place at the end of May and the concluding results of the project are expected to give further impetus to the industry’s digitalisation ambitions.
But amid all these highbrow statements of strategy and technology, perhaps the most telling sign that construction and its equipment markets are on the cusp of real and lasting change came in a recent and relatively low-key statement from Mace, the UK-based international construction consultancy, construction and facilities management company.
It announced that it had teamed up with AFC Energy, a provider of hydrogen powergeneration technologies, to form what it called the UK’s first strategic partnership to use hydrogen power in decarbonising the construction industry.
USE
HYDROGEN TO DECARBONISE
It’s statement said: “Mace and AFC Energy will work together in deploying zero-emission hydrogen generators to deliver a transition away from the use of highly polluting diesel generators on construction sites both in the UK and internationally. The partners aim to commission the first AFC Energy H-PowerTM systems on site in early 2022.”
It aims to remove diesel generators from its sites completely by 2026 and the two companies will work with plant hire
companies and governments to promote the benefits of utilising hydrogen-based fuels to help the industry sustainably move away from diesel in construction.
AFC Energy is also working with the Spanish-based international infrastructure and renewable energy company Acciona on a global strategy to decarbonise its development sites. They are evaluating both hydrogen and ammonia as fuel sources to replace polluting diesel generators.
The involvement of a young, innovative company such as AFC Energy underlines another trend as construction pivots away from traditional processes and equipment. As the industry develops, so new players will emerge.
AFC Energy was only formed in 2006. Based in Surrey in the UK, it employs just 40 people but is attracting a lot of attention as interest in its potential grows.
Adam Bond, Chief Executive Officer at AFC Energy, told Global Report: “What we are talking about here is hydrogen-based fuel-cell technology. In terms of us being a change agent, every industry that uses a diesel generator will have to address its obligations for us to get to net zero.
“There is little doubt about the interest levels - twenty construction firms have so far contacted us. At some point, the government is going to have to drive change and we are going to have to show the plant hire industry that there will be sustained demand for such equipment.
“That is going to mean that sustainability issues are going to have to be taken into
account in the prices when bidding for work.
Hochtief’s David Koch is just one of many voices who believe the post-pandemic future is at hand: “ The potential offered by digitization is huge. Artificial intelligence, Industry 5.0, and blockchain will continue to transform the company.
“Our goals are cost efficiency, scheduling and quality control, improved productivity, simpler maintenance, and effortless collaboration with all those involved.
At the same time, digitalisation helps us cut carbon emissions and conserve natural resources far more effectively than in the past.
“We see increasing momentum and are networking with subcontractors, joint venture partners and customers. Digitalisation can only take place if everyone participates.”
What this revolutionary fervour will mean for contractors, rental companies and OEMs is far from clear. What will be the dominant fuel? Who will own the equipment? What skills will be required? And who will be the winners and losers?
As Abraham Lincoln once said: “The best way to predict your future is to create it.”
Which is what post-pandemic company strategies will be trying to do.

Graham Anderson is a freelance journalist specialising in construction, renewable energy and transport. He runs his own agency ABML, based in Oxford, UK.
THE WORLD IN NUMBERS
As usual, our research team has prepared a selection of key factors affecting the global construction outlook. We have split the infographics into different
sections: The world economy; The impact of COVID-19; Global risks; Infrastructure megatrends; Global competitiveness and the ease of doing business; The net-zero
THE WORLD ECONOMY
Overview of the World economic outlook growth projections (percent change)
Source: World Economic Outlook, International Monetary Fund, April 2021
Japan –4.83.32.5
United Kingdom–9.95.35.1
Canada–5.45.04.7
Other advanced economies–2.14.43.4
Emerging market & developing economies–2.26.75.0
Emerging & developing Asia–1.08.66.0 China2.38.45.6
India–8.012.56.9
ASEAN-5–3.44.96.1
Emerging & developing Europe–2.04.43.9 Russia–3.13.83.8
Latin America & the Caribbean –7.04.63.1 Brazil–4.13.72.6
Mexico–8.25.03.0
Middle East & Central Asia–2.93.73.8
Saudi Arabia–4.12.94.0
Sub-Saharan Africa –1.93.44.0
Nigeria–1.82.52.3
South Africa–7.03.12.0
Addendum
Emerging market & middle-income economies–2.46.95.0
Low-income developing countries0.04.35.2
challenge; Countries ranked according to the quality of their infrastructure; United States – The challenge ahead. We hope you find the data useful.
Growth projections
Source: World Economic Outlook, International Monetary Fund, April 2021
& developing
Real GDP growth (annual percent change)
Source: World Economic Outlook, International Monetary Fund, April 2021
IMPACT OF COVID-19 ON THE WORLD ECONOMYGLOBAL RISKS
Source: World Economic Forum Global Risks Report 2021
The impact of coronavirus on stock markets since the start of the outbreak
Source: Bloomberg, 24th January 2021
COVID-19: What it means for engineering and construction
Source: PwC COVID-19 US CFO Pulse survey, 22 April 2020 (base of 305)
When do respondents forecast that the following issues will pose a critical risk to the world?
INFRASTRUCTURE MEGATRENDSGLOBAL COMPETITIVENESS AND EASE OF DOING BUSINESS
Megatrends by domain
Source: Infrastructure Futures: Impact of Megatrends on the Infrastructure Industry Global Investment Hub, World Economic Forum, Boston Consulting Group, 2020
Ageing population and workforce
ESG/corporate social responsibility
Sharing economy
Pressure for companies to increase efficiency and productivity
Rise of health and safety concerns
Market and customers
Demand shift to emerging economies
Infrastructure financing gap
Rise of bigger, more complex projects
Private participation in infrastructure
Globalisation and international trade
Geopolitics and regulation
Technology
Sustainability and resilience
Global divide and increased social inequality
Multipolar world
Rise of distrust and pressure for increased transparency
Rise of new materials and substances
Rise of green energy sources
Rise of IoT, sensors and smart infrastructure
Rise of AI and automation
Autonomous driving and new transport modes
Digitisation (building information modelling, or BIM, onsite collaboration apps)
Ageing infrastructure
Rise of natural disasters and resilient infrastructure
Rise of climate change
Resource scarcity and rise of circular economy
Rise of security risk
Top five opportunities
Source: Infrastructure Futures: Impact of Megatrends on the Infrastructure Industry Global Investment Hub, World Economic Forum, Boston Consulting Group, 2020
Global patent activity remains concentrated in only five economies
Source: OECD, based on PATSTAT, Global Competitiveness Report special edition 2020
Top 10 performers on key technology indicators
Source: World Economic Forum’s Executive Opinion Survey 2019-2020, Global Competitiveness Report special edition 2020
Declining competitiveness
Source: World Economic Forum 2020,
THE NET-ZERO CHALLENGE
Net income per ton of emissions (€/t CO2e Scopes 1-3 upstream, 2019)
Source: Net-Zero Challenge: The Supply Chain Opportunity, World Economic Forum and Boston Consulting Group, January 2021
UNITED STATES – THE CHALLENGE AHEAD
Key provisions of President Biden’s infrastructure plans 2021 (US$ Billions)
Source: White House, as reported on www.npr.org 1st April 2021
COUNTRIES RANKED ACCORDING TO THE
CONNECTIVITY AND COMMUNICATION ARE KEY TO BETTER PRODUCTIVITY


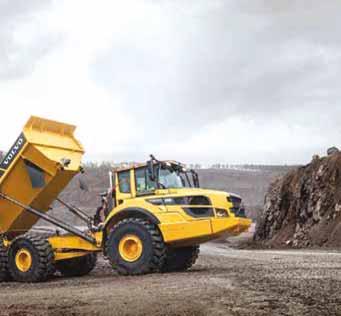
Technologies such as telematics, data analysis and fleet management solutions are augmenting more traditional methods and helping quarry operators to improve overall productivity and keep their cost per tonne down. What does the future hold?
Liam McLoughlin reports

The cost per tonne of aggregates production at quarries is dependent on a number of factors, but in particular the operating costs of processing plants (including energy consumption, wear costs and plant availability). Developments in the interlinking of quarrying equipment - such as monitoring the location and performance of all hauling trucks around a site and connecting multi-stage crushers & screenersare helping to improve productivity.
Fleet management solutions are an effective means of helping to reduce cost per tonne, according to Kimmo Anttila, VP of Lokotrack mobile solutions at Finland-based Metso Outotec. He says that such solutions can assist in planning a quarry’s schedule to organise maintenance breaks for equipment at convenient times for its operations, and to reduce unplanned downtime caused by breakdowns.
“With a fleet management solution, quarries are better equipped to monitor and manage their performance as it increases the awareness of the process to further improve and optimise it, including the possibility to measure against the industry average,” Anttila adds.
Gunnar Thorud, head of productivity services for the Europe & International sales region at loader and hauler manufacturer Volvo CE (Construction Equipment), says that a major step for quarries to improve their cost per tonne is connecting their machines via a telematics system.
“This will enable customers to monitor the main factors influencing the profitability of their fleet – fuel consumption, utilisation, machine health and operating behaviour,” says Thorud.
He adds that Volvo provides operators with insight reports (such as productivity
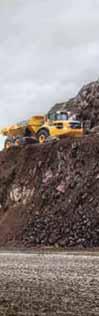

and fuel efficiency) so that they can identify areas for improvement, set targets and take action.
MACHINE-TO-MACHINE COMMUNICATION
When asked what sort of innovations will play the biggest role in reducing cost per tonne and increasing quarry productivity, Thomas Kühnle, head of product management at quarrying plant maker Kleemann, says the potential lies in all machines communicating with each other.
“Here the operative term is ‘production systems’,” says Kühnle. “This means that the entire manufacturing system is a production system of machines that communicate with each other and thereby optimally adjust to each other. This results in data and findings that enable the operator and plant manager to optimise individual machines or the overall process even more. Operators always
have the topic of ‘costs per tonne’ at their fingertips.”
Kühnle adds that some potential for reducing operating costs is obvious.
These include the use of cost-effective and environmentally friendly drives, effective material flow control systems that ensure that the processing plants are always operated at their optimal performance, and innovative systems that automate the processing process and support machine operators in their dayto-day work.
“Ensuring that the technology used is easy to operate and maintain is always in the foreground,” says Kühnle.
He adds this means that, for instance, machines can be operated conveniently and reliably from a distance. In addition, there should be control systems that transmit all relevant information in a simple visualised, menu-guided manner and that support troubleshooting without the operator having to constantly go to the machine.
“In multi-stage crushing and screening units, the individual units need to be intelligently linked with each other,” says Kühnle. “Production and even quality fluctuations are significantly reduced with innovative interlinking systems, and the result manifests itself in lower costs per tonne.”
He adds that another important influence on cost per tonne is the time needed to change wear parts and for maintenance work. Maintenance and repairs need to be plannable and should be carried out at fixed times, with high and reliable spare parts availability.
BELOW: Terex Trucks highlights safety, productive uptime and low operational costs of machinery such as its TA300 hauler as being crucial to maintaining low costs per tonne

Malcolm Edwards, technical sales manager for mining and quarrying at Hitachi Construction Machinery Europe (HCME), identifies capital outlay, maintenance and total cost of ownership (TCO) as key factors in improving cost per tonne. He adds that quarry operators look at capital outlay and maintenance, and if the fuel costs are lower, that makes the TCO lower. As an example, he says that if a wheeled loader has 50% lower fuel consumption per tonne, but has higher maintenance costs and is more expensive to buy, a customer is likely to still choose it because of the lower TCO.
“Another way in which customers are reducing costs per tonne is overhauling existing equipment, rather than replacing it,” he adds. “For example, Hitachi Construction
Machinery (UK) fully refurbished a 90-tonne excavator with 24,000 hours, replacing the engine, pumps, cylinders and motors. It’s been operating reliably for 12 months now, with high availability.”
THE CRUSHING PROCESS
New improvements in crusher technology, as well as in the process control that impacts the overall efficiency of the crushing process, are improving the overall productivity of quarries.
Vincent Celsi, VP crushers at Metso Outotec, says that one such innovation is the jaw crusher automatic setting control (ASC). This better protects the primary crusher, enabling easier setting adjustment and resulting in better control of the crushed material size, stable operation and maximising machine availability as there are no breakdowns.

Kleemann says ‘production systems’ of machines that communicate with each other increase productivity
“But there are also other things like the capacity of designing specific crusher cavity for specific applications needs which increases the yield of the desired fraction,” Celsi adds.
New developments in the hauling dump truck sector are also improving aggregates productivity, and truck manufacturers say that connectivity is a powerful tool for understanding cost per tonne and taking action to improve it
Volvo CE’s Thorud says that the introduction of the Co-Pilot onboard display in Volvo CE vehicles has been a big step forward in enabling it to help operators lower cost per tonne and improve overall productivity.
“As operators’ digital assistant inside the cab, it helps them to make real-time
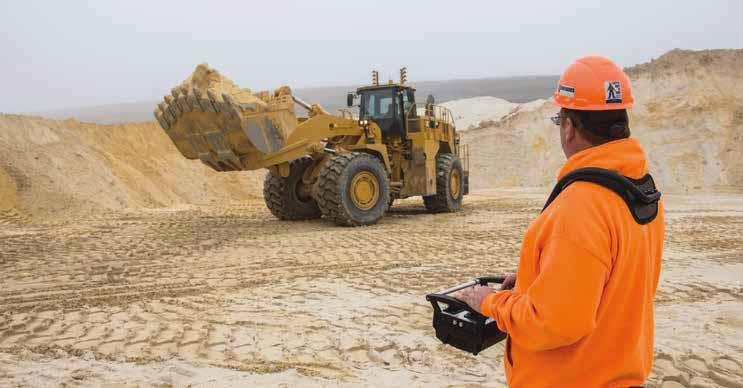
➔ adjustments to their operation,” says Thorud. He adds that, using Volvo CE’s Haul Assist suite of apps, operators can utilise onboard weighing technology to ensure they always have the optimum load on board (rather than too much or too little) and monitor the location of other haulers onsite to proactively adjust their driving according to traffic conditions.
“In the last year, we have also launched Production Monitoring for haulers and wheeled loaders to monitor productivity in tonnes per litre, tonnes per hour and overloading to help reduce unnecessary wear,” says Thorud.
CONNECTIVITY AND AUTOMATION
Scott Pollock, senior product manager at Terex Trucks, says the manufacturer is guided by three factors in its product improvement: efficiency, connectivity and automation.
Stressing the importance of connectivity in bringing down costs per tonne, Pollock says that data is crucial in assessing a machine’s performance and taking corrective action. “There’s a lot of potential in there and our industry is accelerating the exploration into the possibilities,” says Pollock.
He adds that operational safety, productive uptime and low operational costs of machinery are crucial to maintaining low costs per tonne. For this reason Terex Trucks has recently made a range of improvements related to operational safety and costs.
“We’ve particularly focused on the fuel efficiency of our articulated haulers, the TA300 and TA400,” says Pollock. “We’ve also extended the time between maintenance, to make the machines run longer, maximise uptime and increase availability.”
LEFT: Caterpillar’s Cat Productivity solutions are designed to provide a complete overview of quarry site production to maximise efficiency
regular use of motor graders, minimise rolling resistance of haul roads for hauling fuel efficiently. In addition, well-maintained haul roads have a positive impact on tyre life and therefore costs.”
Sauter says that managing tyres to maintain the correct tyre pressure is critical for fuel-efficient hauling and extended tyre life.
Bucket and ground engagement tools (GET) selection also has a significant impact on fuel efficiency for loading equipment. “Selecting the correct GET optimises material penetration and therefore fuel efficiency and leads to faster load cycles and productivity,” Sauter adds. “GET selection can impact fuel efficiency by up to 15%.”
He adds that connected services such as Terex Trucks’ Haul Track Telematics mean that customers always know where their trucks are operating and how they are performing, which can help optimise operations.
Fuel represents approximately one third of equipment operating costs in quarries
“By monitoring their machines, customers can also better plan maintenance,” says Pollock. “If a truck is underperforming, customers will notice it, which means they can detect and investigate any issues quickly. Keeping an eye on the performance can also help customers to check if their operators need more operational or safety training.”
Peter-Valentin Sauter, quarry industry specialist at loading and hauling equipment manufacturer Caterpillar, identifies eight major factors in the use of machinery that quarries need to address to improve their cost per tonne: fuel, engine-idling management, CO2 footprint, equipment management (specifically condition monitoring), fleet performance, increased service and oilchange intervals, and equipment selection.
FUEL COSTS
Fuel represents approximately one third of equipment operating costs in quarries and there is therefore a strong focus on lowering the fuel burn-rate and increasing fuel efficiency, Sauter says. He adds that operator techniques significantly impact on fuel efficiency
“Haul road design and maintenance have a significant impact on the fuel efficiency of hauling equipment,” he adds. “Wellmaintained haul roads with, for example,
Bill Drougkas, product manager at Hitachi Construction Machinery Europe, says that quarrying and mining customers are focusing on easy wheeled loader bucket filling, resulting in fast cycle times and a low total cost of ownership. “In addition, there are several sub-parameters connected to this,” he explains. “The wheeled loader must be of high quality, and come with low fuel consumption and maintenance costs, while also demonstrating an investment in operator cab comfort, and an absolute focus on safety.
“Because the wheeled loaders are constantly travelling around a quarry, and there are on- and off-highway trucks coming in and going out of the site, safety is of the utmost importance.”
MINIMISE DOWNTIME
Crushing and screening plant manufacturer
Sandvik says that to optimise efficiency and cost per tonne, quarry site equipment needs to run continuously with as few breakdowns and interruptions as possible. Anders Lindström, Sandvik’s lifecycle optimisation manager for stationary crushing & screening, says that this can be achieved by using highquality equipment, in addition to a strong focus on preventive maintenance planning and high utilisation of the machines during planned production time.
Lindström adds that using machinery to its full potential can be achieved by utilising advisory services with plant audits and concepts such as Sandvik’s ‘peak screening’ which aims to optimise every square metre used for screening.
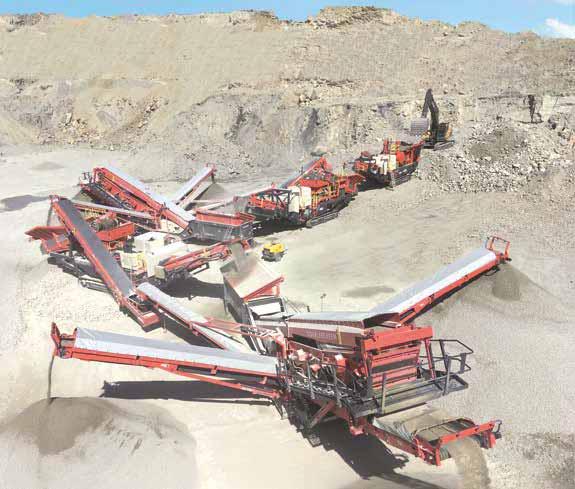
Sandvik has advised Pony’s Pass, the only quarry in the Falkland Islands, on a train of mobile crushing and screening equipment to enable maximum uptime
“The process plant should be planned to minimise loading and hauling and the equipment should run on renewable energy to as high an extent as possible for both economically and environmental reasons,” says Lindström. “Access to production data will be key for understanding where there is potential for improvement.”
For mobile crushing and screening equipment, Sandvik’s product manager for tracked mobiles, Andrew Bolton, says that planning and sizing the equipment correctly from the outset is important, as is selecting the correct media, and configuring the crushers correctly.
Ensuring a continuous steady feed to avoid unnecessary load spikes or running empty will maximise throughput, as will having a uniform feed material supply to avoid blockages and downtime.
“Most of our mobile plants include feed regulation technologies such as level sensors on jaw and cone crusher plants, and pressure sensing on the screen plants to detect abnormal running and pause the feeder to avoid interruptions,” Bolton says. “Regular planned maintenance and correct fuel storage and handling are also important.”
Looking at future trends, proponents of electric power sources such as battery and hydrogen fuel cells in quarrying machinery say they have the potential to improve the cost per tonne at quarries.
Metso Outotec’s Anttila says that energy costs represent a lion’s share of the overall operating costs of crushing equipment, and therefore improving the energy
BELOW: Volvo CE says its TARA autonomous transport solution holds great potential to improve quarry productivity
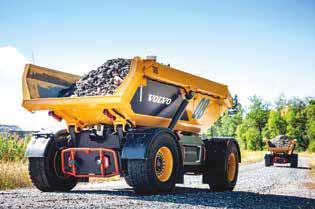
efficiency of the crushing process makes a big impact. He adds that switching to hybrid (diesel-electric) or fully electric equipment improves energy efficiency.
“An average track mounted crusher consumes 30-60 litres per hour of diesel, depending on the application and the size of the equipment,” says Anttila.
EFFICIENT ENERGY SOURCES
Wilbert Blom, excavator product manager at Hitachi Construction Machinery Europe (HCME), says that if hydrogen fuel electric power cell systems really become commercially viable for quarry machines, this will become an interesting factor.
“Maybe some hybrid solutions can be developed, which are less sophisticated,” Blom adds. “I think quarrying and machines for other sites will become smarter, making more use of sensors to further measure productivity and safeguard their uptime.”
Anttila says the source of energy and the efficiency of using it will have a major role.
“Equipment which utilises electric power will have less hydraulic features, and their uptime will be better than the conventional ones, as they have less moving and wearing components, and therefore less maintenance needs,” he says.
The continuing development of automation technology will help to increase quarry productivity
Anttila says that digital tools to monitor, control and also to simulate the whole process will increase the efficiency. He adds that with a simulation tool you can design the whole process, choose the right equipment, insert the parameters, and plan and select the right settings and
cavities to improve the yield.
Andrew Bolton of Sandvik predicts that future innovations to increase crushing and screening productivity will include highresistant wear alloys, new alternative power/ energy sources, energy and production optimisation, and minimising both internal and external transportation.
“Real-time adjustments of the plant to maximise the correct/desired products and minimise waste, re-crushing and material handling have a great effect on cost per tonne of the sellable products,” says Bolton.
The continuing development of automation technology will help to increase quarry productivity, according to Scott Pollock of Terex Trucks. “The increase of automated systems will make it safer and easier to operate haulers in quarries, which will contribute to an increase of safety and productivity,” he adds.
Volvo CE has pioneered the use of autonomous electric machines on quarry sites with the research project at its customer Skanska’s Vikan Kross quarry, near Gothenburg in Sweden. It says its TARA electric and autonomous transport solution holds great potential to improve quarry productivity.
Volvo CE’s Gunnar Thorud says that, during the 10-week test of the Vikan Kross project in 2018 which provided the foundations for the TARA solution, swapping diesel machines for electric or hybrid alternatives reduced fuel consumption from 3,000 litres to just 64 litres per day. “It consumed 9,320 kWh of electricity from renewable sources and the cost of electricity is often lower than that of diesel fuel,” he added.
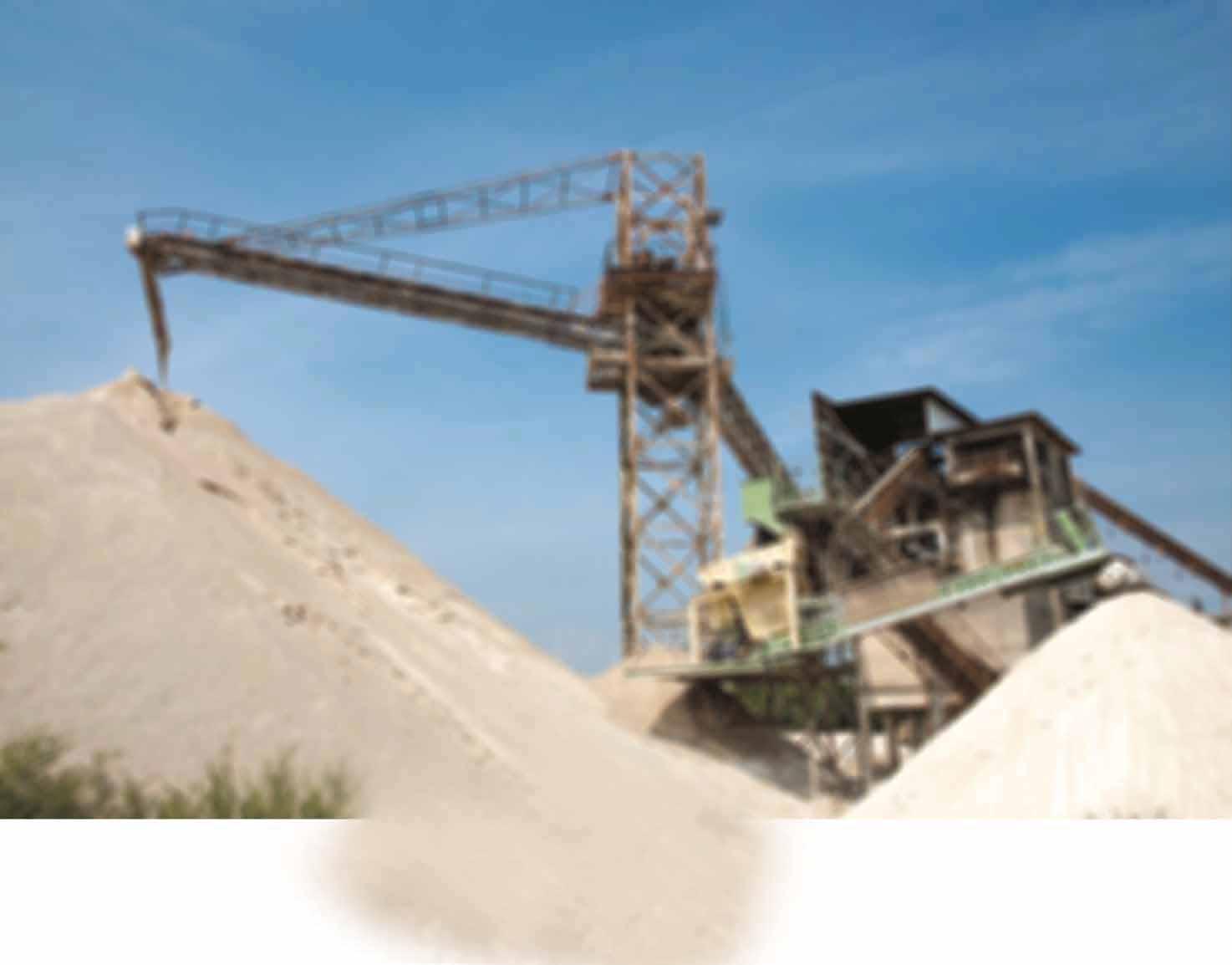



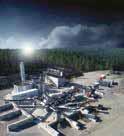
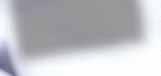






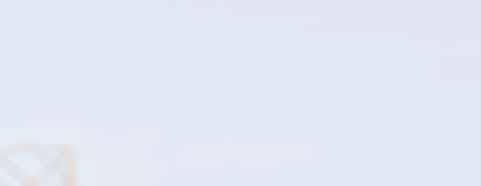


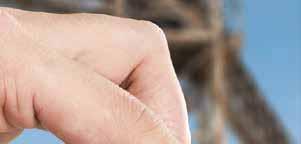
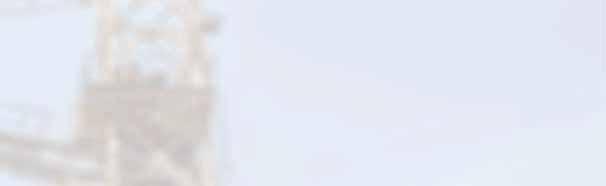

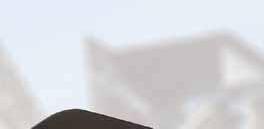
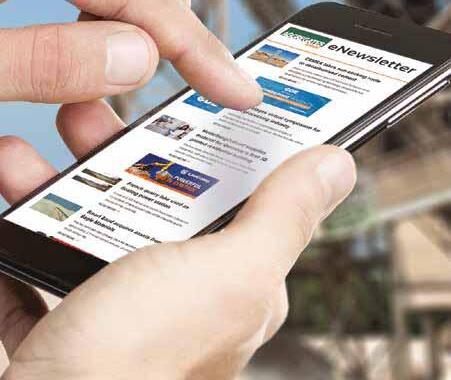




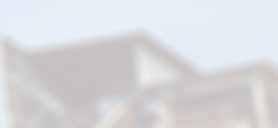

















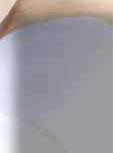
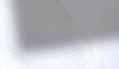




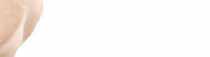
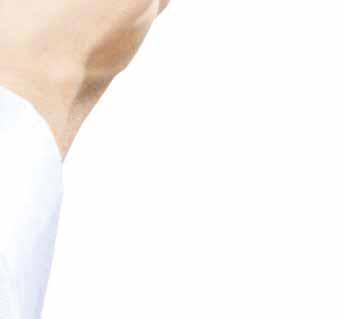

Compaction machinery, like every other class of construction machinery, has become considerably more sophisticated in recent years. Advances in compaction systems have been introduced progressively over many decades, with key innovations advancing productivity and quality.
Road construction methods have improved over the years as new methods and technologies have been developed. A key innovation was the introduction of Tarmacadam surfacing in the 19th century, a method patented in the UK in 1902. Using naturally occurring tar in the construction of the road surface became more common as motor vehicle numbers began to increase at the start of the 20th century.
Proper compaction became more important during road construction due to the wear and tear caused by the passage of motor vehicles. Ensuring the tarmacadam surfaces were properly compacted meant that they were denser and more resilient.
SELF-POWERED
The first self-powered compactors used for this purpose were deadweight machines powered by steam, with with petrol(gasoline) and diesel-driven machines being introduced in following years. The use of deadweight compactors allowed these tarmacadam road surfaces to be better able to cope better with the additional loads caused by motorised traffic. As motor vehicle numbers increased, so road construction techniques became more sophisticated. Improvements were even more important as motor vehicles became more powerful and able to transport bigger loads because road surface stress increases exponentially as vehicle weights increase.
But the use of multiple layers required compaction machines to be more mobile and also more productive. Manoeuvrability also became an important factor for compaction equipment, allowing machines to operate in tighter spaces in busy urban areas. A key development was the introduction of the compactor featuring twin-drum steering, allowing tighter turning than had previously been achievable.
A significant step forward in compaction came in the late 1950s with BOMAG’s development of the first unit featuring vibration. Using vibration offered a significant gain in compaction efficiency over earlier generation deadweight machines. Although BOMAG’s initial design was only a small hand-operated unit, it was followed soon after by larger machines able to compact faster
COMPACTION INNOVATIONS DRIVING EFFICIENCY
Innovations in compaction are driving an increase in the efficiency of construction projects – Mike Woof writes

ABOVE: The first self-powered deadweight rollers were steam-driven, later replaced by diesel-and petrol-engine machines
and more efficiently. A road surface could be made denser while using a machine that was far smaller and lighter than the cumbersome large deadweight rollers. This allowed wider roads to be built more quickly, assisting the highway construction boom in the US and Europe, which commenced in the 1950s, gathering pace in the ‘60s and ‘70s.
During this period there was also a
transition from building roads from using naturally occurring tar to using bitumen instead. A byproduct of the oil industry, bitumen was more readily available than tar, while being a synthetic product allowed gains in quality and reductions in potentially hazardous contaminants. Using bitumen in road surfaces allowed for high-quality asphalt surfaces that were even more durable and able to cope with the continuing rapid increase in vehicle numbers as well as gross vehicle weights.
The smaller vibratory machines worked faster than the heavy deadweight rollers,
while also delivering far better density figures for compaction. Vibratory machines were far better able to compact the surface behind the paver before the mat cooled than the large and comparatively clumsy deadweight machines.
Manufacturers developed vibratory machines that were increasingly productive and efficient. Drum amplitudes could be adjusted to better suit the material being compacted. Vibration frequency could be adjusted to allow for higher compactor travel speeds.
However, the introduction of larger ride-on
compactors using vibration brought their own problems. With deadweight compactors, multiple passes with a machine allowed compaction only up to a certain point. It was difficult to over-compact a road surface. With a vibratory compactor it was now all too easy to over-compact the road surface by using too many passes, resulting in fragmentation of aggregates used in the mix.
To address this issue, firms began working on meters that determined the degree of compaction carried out. These worked in different ways, such as determining the degree of response to the vibration forces
exerted by the compaction drum. Over time, these meters became more and more effective at determining the degree of mat density achieved. An operator sitting in the cab could look at the meter and have a good idea of whether the specified density had been reached using a predetermined number of passes. This was a key advance, further ensuring the road surface would be able to cope with heavy traffic loads for longer without need of repair.
It is worth noting, though, that deadweight rollers, as well as pneumatic rollers, are still favoured for some purposes in compacting asphalt surfaces. These machines have benefits for providing fine finishing and are often still used for the final passes, particularly for tasks such as highways or airport runways where surface smoothness is paramount.
THE NEW RADICALS

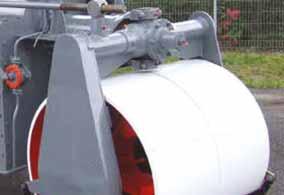
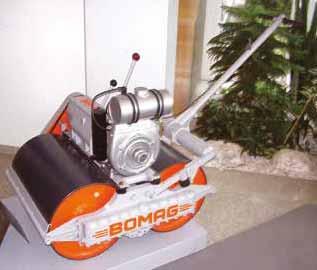
A radical concept was developed by Hamm as an alternative to vibratory compaction. This was the oscillatory system and it offered a fundamental difference in operation. Instead of the compaction forces operating in the vertical plane as with a vibratory machine, the drum moved in the horizontal plane.
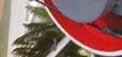

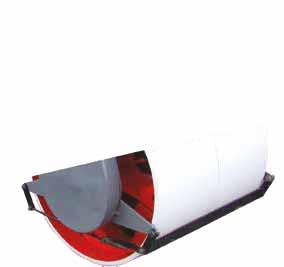
ABOVE: As road construction practices have developed, so new machines have been produced, such as those with twin-drum steering, improving manoeuvrability
LEFT: BOMAG’s late-1950’s introduction of compactors featuring vibration, increased efficiency but added additional issues for users
In effect, rather than striking the road surface directly from above, oscillatory compactors allowed a kneading action to take place on the asphalt mat. This was a significant change, offering a number of important benefits. The forces from an oscillatory compactor are localised and do not travel. Previously, only deadweight compactors could be used for compacting asphalt surfaces on bridge decks, as vibratory forces generated resonances that could cause structural damage. This had meant that asphalt surfaces on bridge decks could not achieve high densities and would be subject to higher wear rates than for comparable road surfaces. Using oscillatory compactors meant that high mat density could be achieved on the asphalt surface of a bridge deck, without risk of structural damage. Similarly, oscillatory compactors could be used in busy urban areas and alongside historic buildings without causing disturbance or risking damage. And in more modern times, oscillatory compactors have also shown themselves able to operate in areas where sensitive equipment or computers are located, again without causing disturbance.
Hamm persevered with the oscillatory compaction system for decades and it
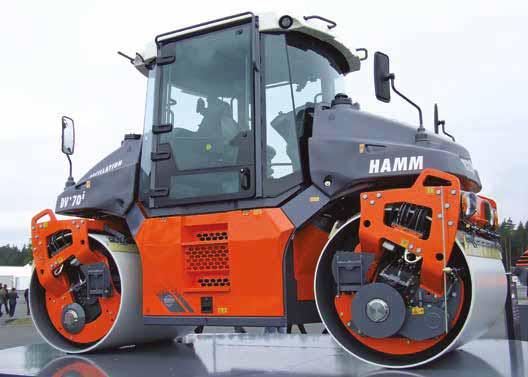
has taken many years for the construction industry to fully appreciate the benefits of this alternative system. But as the advantages have become more widely known, other compactor manufacturers have followed suit by introducing their own oscillatory machines. Leading competitor BOMAG now has an extensive line of its own oscillatory compactors that comes closest to matching Hamm’s in range. And other manufacturers including Caterpillar, Dynapac, Sakai, Volvo CE and XCMG also offer at least one oscillatory-type compactor in their respective model line-ups.
GET SMART
Over the last 30 years, machine-control technologies have allowed huge changes to the construction industry. For asphalt compaction they have delivered further gains in working efficiency and quality, while also reducing the time needed to carry out work.
The combination of more effective compaction-measurement systems in the cab and heat-detection sensors mounted around the machine has allowed operators to determine how many passes need to be carried out, and where. Using the heat sensors, operators can ensure that the mat is compacted before it cools, prioritising the coldest areas for the first passes. The meters show that the necessary density is being achieved.
In the last 10 years or so, screens mounted in the cab have been installed that display data from the compaction metering and temperature sensors. These provide the operator with a clear visual guide as to how many passes have already been carried out on the mat. An accurate display of heat gradient
ABOVE: Pioneered by Hamm, compaction using oscillation rather than vibration offers additional benefits
on the mat also ensures a more efficient process of prioritisation. The pass-mapping system means that the operator can tackle the coolest areas first and ensures that the entire mat achieves the desired density specification. This technology also eliminates the risk of over-compaction and potential aggregates crushing that would result in a drop in finished mat quality.
Machine-control technologies for compactors are continuing to develop. Suppliers such as Trimble and its rivals now offer sophisticated compaction control systems for asphalt compactors that are said to eliminate guesswork for the operator, can help to roll a more efficient pattern and increase productivity, while also saving fuel. The surface will speak for itself.
Trimble’s latest CCS900 Compaction Control System can help to improve asphaltcompaction operations and boost working efficiency, while rolling high-quality surfaces.
The system features pass count mapping to monitor the number of passes and avoid over-or under-compaction. Monitoring the heat gradient of the surface using this system ensures that compaction is carried out within the specified temperature range.
It also has wireless data-sharing that allows each compactor to view work being carried out by other machines in real time, helping the contractor achieve better surface quality, as well as saving time and fuel. The compaction data can be transferred wirelessly to the office for analysis and the information can also be incorporated into the BIM
(building information modelling) model of an operation, providing a comprehensive view of what work was carried out and when. Various configurations are available including single GNSS , dual GNSS and totalstation-based packages. In-cab components include a display and an optional printer for on-site documentation and sign-off purposes. Supervisors and quality managers can monitor compaction activities using the printer or web-based software. The engineering team can also continuously monitor pass counts and compaction-meter values over the entire area and on all material layers.
Technology such as this from Trimble and its main competitors can help reduce the need for reworking and also lower machine maintenance costs. Surface quality can be maximised as over-compaction will be ruled out, while fuel use and machine time is optimised. The technology ensures a more uniform lift, consistent pass counts and target compaction-meter values, all of which help to increase surface quality as well as the working life of the road.
Pete Large, head of civil construction field solutions at Trimble, says the new generation of machine control tools and semi-automated compaction systems offers considerable potential for contractors. “Compaction is interesting. You can make or lose money on it if you do it right or wrong”, he asserted. More developments are expected in the compaction sector. BOMAG has demonstrated its prototype autonomous compactor at various exhibitions, while Hamm has been carrying out trials with autonomous compaction at its own test facility. Caterpillar also has been working on autonomous compaction. Both BOMAG and Caterpillar have been working with Trimble on autonomous machine technology, although these remain prototypes at present. Current legislation makes it difficult for contractors to run fully autonomous machines on a working jobsite. Having a human operator in the cab will remain a requirement for some time yet.
However, Caterpillar’s novel Command for Compaction package for soil compaction does offer a view of what will be available for asphalt compaction in the near future. This system offers the option of semi-automatic compaction. An operator first uses the machine to map the boundaries of the area to be compacted and then keys in the necessary compaction parameters. When the settings have been made, the operator can put the machine into its auto setting, with the system
taking over control of the drive, steering and vibration parameters. The system can save information from previous jobs, which can also be accessed through the touchscreen.
To ensure safety, an integrated objectdetection system is fitted, alerting the operator if anything gets in the way of the machine. If the machine encounters an area that cannot be compacted using vibration, the operator is able to switch the vibration system off and then re-engage it once this area has been passed.
According to Caterpillar, automating compaction helps to optimise operations and allows an inexperienced operator to deliver the same level of quality as someone with experience. The system delivers high surface quality by maintaining speed and ensuring the surface receives the correct number of passes, while also delivering consistent and accurate overlap. Contractors can reduce the time needed for compaction because the machine will only carry out the number of passes required, while also optimising the operating cycle.
POWERING UP
While steam power was used for the first self-propelled rollers, the internal combustion engine has dominated the sector since the early 20th century. Petrol (gasoline) engines were used for a while (and still are for some compact units) but the diesel engine has driven almost all compactors for many decades now.
Diesel engines have improved immeasurably over time, with the latest units offering far greater power density than ever before. Compact engines can now deliver similar outputs to the much larger units
previously used. Current engines have benefitted from huge improvements to fuel injection, with high-pressure systems and better injector designs delivering massive gains in combustion efficiency. Further performance gains have come from new turbocharging technology, with engines now managing to deliver considerably more power while using less fuel. At the same time, huge investment in emissions control has ensured that new diesels engines generate significantly less NOx or particulates than ever before. Other general engine improvements include extended service intervals and sophisticated engine-management systems that allow faster fault diagnosis and predictive maintenance. Ongoing pressure to reduce fuel consumption and emissions has resulted in further developments from various firms. BOMAG was first to unveil a hybrid compactor prototype, based on a standard machine but using a diesel-electric drive. More than most machines, compactors lend themselves to hybrid systems due to the constant forward and reverse motion involved in their operation. Saving some of that energy from forward motion and recirculating it into the drive for reversing, instead of wasting it by braking, simply makes good sense. But BOMAG’s dieselelectric hybrid never made it to production
BELOW: Autonomous compactors are available but their widespread use on working construction sites remains some way off
Electric machines are definitely coming and will be widely available as options in the future
because the cost of the electric drive made the the machine too costly. Hamm and BOMAG have since introduced hydraulic hybrids instead. Other companies have followed suit. These feature accumulators to store hydraulic power that is released when changing direction, providing peak power assistance to the diesel engine to start the vibration system and overcome the inertia of the machine for starting a pass. By fitting a hydraulic hybrid system, a roller can be powered by a diesel engine that is significantly smaller than would otherwise be required. While the cost of the hydraulic accumulator package does add to the overall price tag for the machine, the significant cut in fuel consumption makes for a comparatively short payback time.
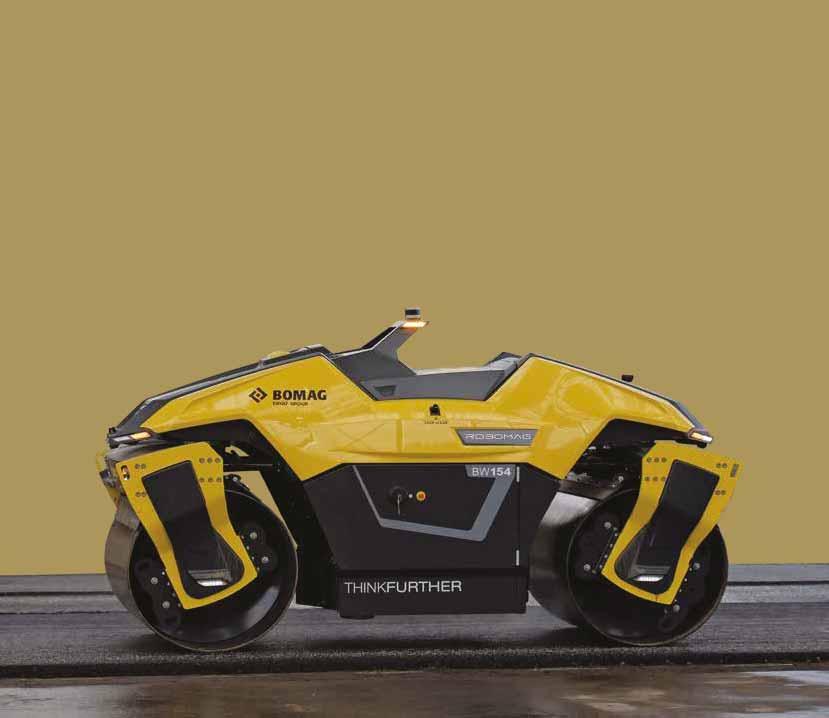
Other power options are in the frame too. BOMAG now offers a compactor with the option of bottled gas as a fuel instead of diesel. This offers significant cuts in running costs while delivering further improvements in emissions reduction. The firm has also built an all-electric compactor using simple and dependable technology, although the cost of the battery pack makes the machine pricey compared with conventional models. Electric machines are definitely coming and will be widely available as options in the future. Whether fuel-cell compactors become available in the short term remains to be seen. JCB has constructed a prototype excavator powered by a fuel-cell stack and running on hydrogen. Others are in the development stage, but the cost of this technology remains high, for the time being at least.
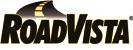
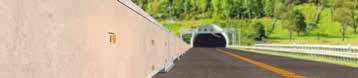
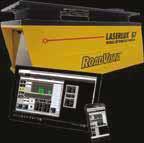


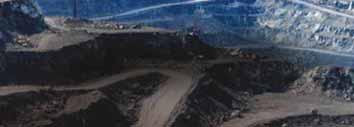

