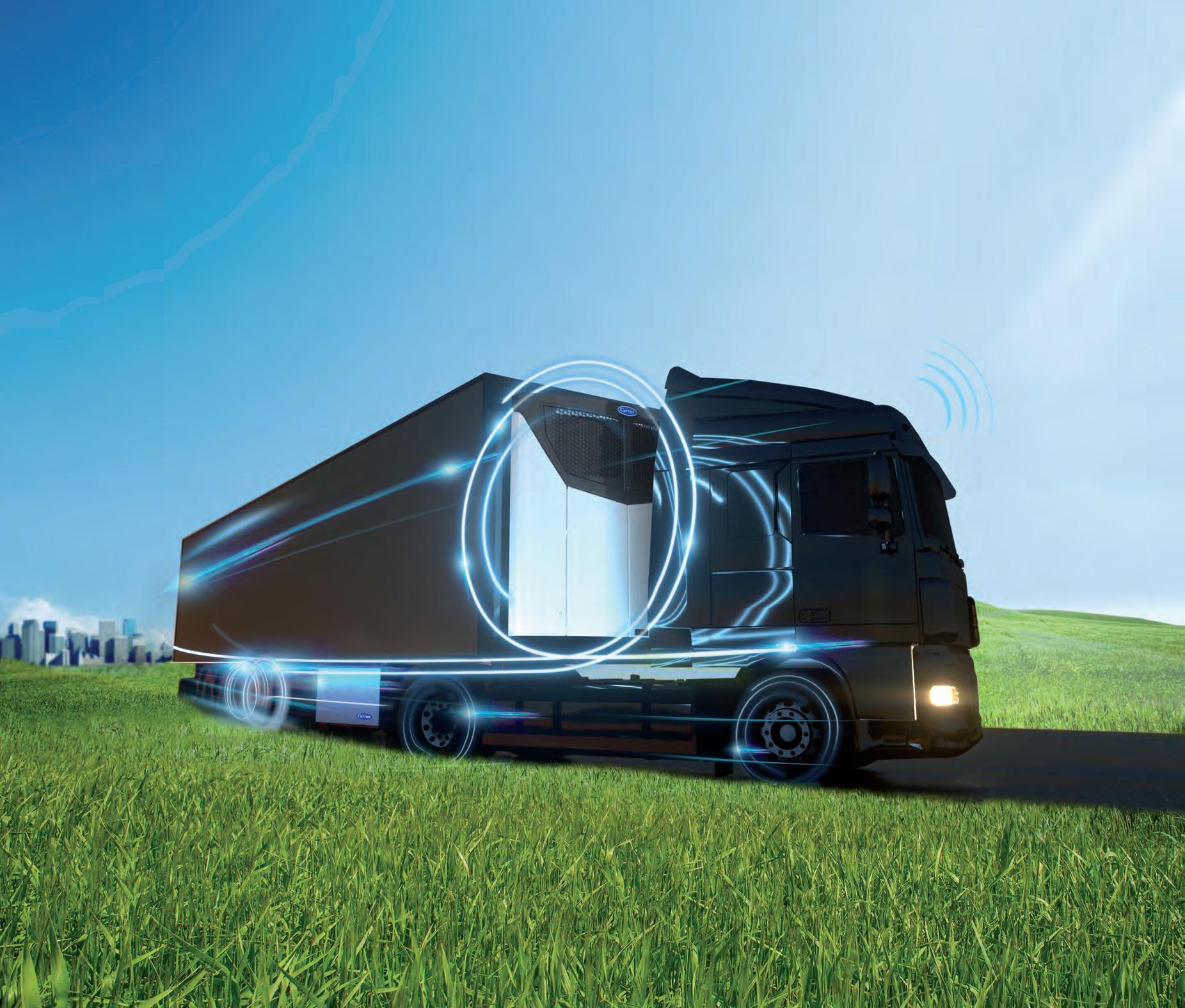
42 minute read
NEWS
NEWS INTERNATIONAL
AFRICA/ ASIA
SOUTH AFRICA
Business at South African truck body and trailer manufacturer, SERCO Industries, has improved this year compared with 2020 but is still below what was achieved in 2019. SERCO CEO, Clinton Holcroft, said it had been a tremendously challenging time with the Covid-19 pandemic continuing to impact a variety of industries and the South African economy. “The company used the crisis to focus on driving cost reductions and streamlining processes to improve service levels while broadening the product range to create growth,” he said. SERCO is one of South Africa’s leading insulated and dry freight truck body and trailer manufacturing companies with branches in Durban, Johannesburg, Cape Town and Gqeberha. Holcroft, who estimates that the company had built more than 20,000 vehicles in its 40-year history, said although the improvement in revenue this year had been encouraging, sales were down 30 per cent on 2019. “To counter the reduction in sales, we broadened our product range to include more dry freight vehicle bodies and have seen good growth in this sector,” he said. “We have also increased our fleet of rental refrigerated semi-trailers by 10 vehicles.” Holcroft said a lot of potential customers had delayed orders due to lack of availability of truck chassis caused by global supply chain shortages. “A highlight of this year has been the development of a new design refrigerated interlink trailer offering improved volume and ease of use as well as design changes to our flagship ’Frostliner’ refrigerated bodies to increase payload and enhance the finish of the panels while raising sustainability standards further. “The new innovations will offer tangible features which I believe, will encourage customers to upgrade to the new technology.” There had been a significant reduction, he said, in trailer replacements but he is hopeful as Covid levels continue to drop and the economy starts to open again, that SERCO will see an upswing, similar to trends overseas. With sustainability and cutting carbon emissions being a global priority, SERCO would continue its drive to responsible manufacturing practices and minimise our impact on the environment. In 2019 SERCO installed 1,029 solar panels on the roof of its Durban factory which allows the premises to go off the grid during the day. The solar power 400kw peak system has the potential to save the company 75 per cent of its electricity costs, equating to a saving of about 900 tonnes of carbon dioxide a year. Other greening initiatives include the recycling of paper and plastic it uses as well as a rainwater harvesting system for washing vehicles. Turning to the South African economy Holcroft said he hoped there would be further structural reforms to encourage growth and employment. He added a Ministerial Advisory Committee similar to that used so effectively during Covid could be set up to focus on economic growth for South Africa. “SERCO’s aim for next year is to see a return to our pre-Covid performance and to build on the positive initiatives we have put in place to generate growth and further value for our customers in the transport and logistics sectors,” said Holcroft.
CHINA
CIMC Vehicles is taking the next step in its industry-leading digital transformation journey. CIMC Vehicles will cooperate with Siemens Digital Industries Software to maintain its long-term development of global business and promote the digital transformation and high quality development of the global semi-trailer industry. CIMC Vehicles signed an agreement with Siemens Digital Industries Software in Shenzhen, Guangdong Province, last month. Li Guiping, CEO and President of CIMC Vehicles, and Liang Naiming, Global Senior Vice President and Managing Director of Greater China of Siemens Digital Industries Software, and representatives of both parties attended the signing ceremony. At the ceremony, Dr Li Xiaofu, Chief Technology Officer of CIMC Vehicles and CEO of strategic business division of truck bodies, as the representatives of CIMC Vehicles, introduced the history of cooperation with Siemens Digital Industries Software. It is reported that Dr Li Xiaofu participated in the construction of CIMC Vehicles’ first semi-trailer ‘Light Tower’ plant, completed the overall planning and construction of CIMC Tonghua’s Super Magalhães Project, and led the construction of several ‘Light Tower’ plants with production automation and digitalisation. According to the data, ‘Light Tower’ Plants integrated virtual simulation, big data, Internet of Things and digitalisation technologies, and were equipped with highly automated equipment (such as CNC laser cutting
NEWS INTERNATIONAL
ASIA
machine, robotic welding workstation, KTL plant and powder coating line), enabling large-scale automated flexible production. As they have solved the problems including obsolete production equipment, technology lag, increasing labour cost and difficulty in energy conservation and emission reduction, ‘Light Tower’ plants are an effective measure to promote the development of the industry from traditional manufacturing towards intelligent manufacturing. “In terms of global manufacturing strategy, high-end manufacturing has become the focus of economic competition among all parties,” said Dr Xiaofu. “Developing high-end manufacturing and implementing digital transformation is an important means for ‘Made in China 2025′ strategy. “It is not only a core measure to optimise the industrial structure, but also a direction for China’s semi-trailer manufacturing to develop towards high quality and compliance.” Dr Xiaofu added: “Since CIMC Vehicles started cooperation with Siemens Digital Industries Software in late 2014, both parties have worked together from consultation and planning, POC verification to comprehensive construction of system over seven years. CIMC Vehicles’ products involved gradually covered three major businesses, namely, semi-trailers, truck bodies for specialty vehicles, and truck bodies for refrigerated trucks, achieving the coverage of comprehensive range of CIMC Vehicles’ product categories.” In addition to the expansion of cooperation scope between the two parties, the depth and breadth of cooperation have also been developing. Leveraging systems ranging from 3D CAD (three dimensional Computeraided Design Software) tools to CAD + PLM (Product Lifecycle Management), CIMC Vehicles has gradually achieved the integration of design and process and the modularisation management of products. Both parties have gradually expanded their cooperation from domestic business to global business. Liu Ruofeng, Vice President of Siemens Digital Industries Software, China (Highend Equipment/Industry Machinery and Enterprise Key Accounts), also shared his prospects for the cooperation between the two parties. Subsequently, Dr Xiaofu and Ruofeng signed the global agreement on behalf of the two parties. The signing of the global agreement marks that the cooperation between CIMC Vehicles and Siemens Digital Industries Software has entered a new stage of global business. Dr. Li Xiaofu said that “Currently, CIMC Vehicles has entered a new era of comprehensive digital transformation. Product data, as the data source of enterprise digital construction, will fully support the implementation of CIMC Vehicles’ business philosophy of ‘Intercontinental Operation, Local Manufacturing’”. Guiping stated that digitalisation is a strategy that CIMC Vehicles needs to implement consistently throughout its ‘Sophisticated Manufacturing System’, and it is also an inevitable requirement for the Group’s sophisticated manufacturing to enter the crucial period. As the first global manufacturer of high-end semi-trailers and specialty vehicles with ‘A+H’ dual listing status, CIMC Vehicles will continue to enhance innovation-driven development and promote digital transformation so as to fully realise the sophisticated manufacturing strategy and management of new infrastructure by 2025, opening a new chapter in China’s intelligent manufacturing and high-end manufacturing. At present, CIMC Vehicles’ ‘Sophisticated Manufacturing System’ is well-established, and its economies of scale are further highlighted. So far, CIMC Vehicles has globally established 13 ‘Light Tower’ plants for the production of semi-trailers, six ‘Light Tower’ Plants for the production of truck bodies of specialty vehicles, and two ‘Light Tower’ plants for the production of truck bodies for refrigerated trucks, as well as ‘Product Module’ for several series of semi-trailer products, and conducted digital transformation and upgrading, in order to continuously expand the niche market and improve gross margins, and scale new heights in the strategy of ‘Intercontinental Operation, Local Manufacturing’.
HONG KONG
A recent award win for DHL Express affirms the company’s continued commitment to excellence in express logistics service. DHL Express was named the Best Logistics Service Provider – Express at the 2021 Asian Freight, Logistics and Supply Chain Awards (AFLAS) ceremony in Hong Kong on 21 October 2021. “We are incredibly proud that our customers’ votes of confidence have brought us the Best Logistics Service Provider – Express award for the 32nd time,” said DHL Express Asia Pacific CEO, Ken Lee. “Our global network, and employees’ passion, can-do spirit and commitment to excellence have proven to be a winning formula with our customers. “This will continue to serve us well as our customers ride the strong momentum in e-commerce and recovery in global trade.” DHL Express is investing around 750
NEWS INTERNATIONAL
ASIA/ EUROPE
million euros from 2020 to 2022 to bolster its aviation network and ground infrastructure across Asia Pacific to support the unprecedented growth in shipment volume and address the ever-growing demand for time-definite express deliveries.
SINGAPORE
ST Logistics, a Toll subsidiary in Singapore, recently launched several Electric Vehicles (EVs) successfully with the intent to progressively transition its entire fleet. The Singapore Government unveiled a plan in February 2021 to actively lower the country’s net carbon emissions significantly by 2030. By 2025, the plan would see all diesel car registrations to cease to increase the uptake of EVs. With the switch from diesel to electric, Singapore has set a target to reach a total of 60,000 charging points including 40,000 in public carparks and 20,000 in private premises by 2030. Toll’s Singapore operations have already begun preparations to expand its EV capabilities. The Singapore Automotive Hub is now EV ready, having recently equipped a staging floor with EV chargers, for multiple car models, to facilitate pre-delivery and maintenance for its customers. To further encourage EV adoption across the Singapore business, Toll is also exploring the installation of more EV charging stations at other sites. “The rise of electric vehicles in the global land transportation landscape has truly been phenomenal,” said Toll Group Managing Director, Thomas Knudsen. “Yet, it is not a surprise for those familiar with studies on the emerging data on global carbon emission and its impact on climate change.” In addition to investing in EVs, Toll has already implemented the use of solar panels, recyclable pallets, reusable shrink wrap and new medical shippers. The electrification of road transport equipment – electromobility – is gaining momentum around the world.
UZBEKISTAN
Further extending its responsive logistics services in Central Asia, CEVA Logistics has opened a new office in Tashkent, Uzbekistan. The company’s increased operations will focus on Uzbekistan’s multi-modal customers. Being a land-locked country, Uzbekistan presents huge potential for the growth of multi-modal transportation networks, a key target for the company’s local team experienced in delivering leading ground, rail and air solutions. The CEVA Logistics team in Tashkent will report to Country Manager Behzod Yunusaliyev. CEVA Logistics will focus its efforts around the predominantly export-driven portions of the Uzbek economy, offering seamless transport services to a wide range of industries and commodities, such as mineral fertilisers, cotton, cotton yarn, fabric, vegetables and dried fruits. Uzbekistan joined the CIS Free Trade Zone Agreement in 2014 and the Eurasian Economic Union (EAEU) as an observer in 2020. “As we continue to accelerate our growth globally, key markets like Africa and Central Asia offer significant opportunities to companies with CEVA’s scale and service offerings,” said Says CEVA Logistics Managing Director IMEA, Bruno Plantaz. “Uzbekistan in particular has numerous industries looking for a high quality of service, seamless end-to-end solutions and global capabilities. At CEVA, we think global and act local, so our team is ready to deliver the responsive logistics solutions our customers need.”
AUSTRIA
Schwarzmüller, and urban air mobility pioneer, Volocopter, have partnered to create a new application for the classic trailer. This new design, the Mobile Vertipad, converts into a mobile take-off and landing platform for an electrically powered transport drone. It was presented at the ITS World Congress 2021 in Hamburg. The VoloDrone heavy-lift drone has also recently completed its first public test flight at homePORT Hamburg. Schwarzmüller aims to begin testing the Mobile Vertipad in early 2023. For Schwarzmüller CEO Roland Hartwig, this has opened doors for his company. “Not only are we proud of the partnership, but we want to expand into this strongly future-oriented business field of transportation,” he said. The Mobile Vertipad is a trailer with a conventional long-haul trailer’s exact dimensions: 12 metres long, 2.4 metres wide, and 3.9 metres high. A loading container is built on top of the chassis to hold the VoloDrone. At the push of a button, the trailer can unfold into a platform and turn into a launch pad and loading ramp. This is a two-step process: First, a substructure made of metal profiles extends from the chassis. Then, the container unfolds its walls using the origami principle, creating a circular platform 20 meters in diameter. It is dismantled as quickly as it is constructed and can be moved to any location using the tractor units. “We want to offer our industrial customers an end-to-end solution that enables VoloDrone services at any time by ensuring short lead times,” said
NEWS INTERNATIONAL
EUROPE
Volocopter Chief Commercial Officer, Christian Bauer. The platform can be designed for relatively low loads. The fully loaded VoloDrone is reported to weigh as much as a small car. Hartwig said this opens up completely new possibilities for material selection at Schwarzmüller. Due to the light weight, it opens up possibilities to use non-metal construction materials in the future. VoloDrone is Volocopter’s versatile electrically powered cargo drone. It can transport a payload of 200kg up to 40km. Possible VoloDrone applications are in logistics, agriculture, infrastructure, and the public utilities industry. Among other things, heavy packages can be transported to remote locations, from the port to ships or from island to island. Further possibilities include crop protection or deliveries to construction sites. Schwarzmüller has also designed its concept study, for which it called in the Austrian design and engineering studio, Bumblebee, to be multimodal. “The Mobile Vertipad is completely multimodal,” said Hartwig. “It connects roads, rails, air, and ships in last-mile freight transport. The cargo drone creates the connection, Schwarzmüller provides the mobile infrastructure to enable the connection.” In one aspect, Schwarzmüller went beyond Volocopter’s specifications, making the deployable trailer multifunctional. It serves not only as a means of transport and a flight platform, but also as a charging station for the VoloDrone’s batteries. Finally, the Mobile Vertipad is a station for technical maintenance.
DENMARK
Danish transport and logistics company, DSV, is releasing a strong set of Q3 2021 numbers across all three divisions. The solid results are illustrated by an EBIT growth for the Group of 52.5 per cent in Q3 2021 compared to the same period last year – excluding the impact of the acquisition of Agility’s Global Integrated Logistics business. DSV is reporting good progress in the integration of Agility’s Global Integrated Logistics business, which became part of DSV in August 2021. The operational integration is expected to be fully completed by Q3 2022. “In August, we completed the acquisition of Agility’s Global Integrated Logistics business and took over a well-run company and were joined by a team of skilled new colleagues. The integration is off to a good start, and in the coming period our two organisations will be merged into one,” said DSV Group CEO, Jens Bjørn Andersen. “The transport markets continue to be characterised by disruption and imbalances causing extraordinary challenges for both our customers and us. Under the extraordinary market conditions, we are happy to report solid results across all divisions.” For the reported period, DSV achieved a revenue of 49,557 million DKK, gross profit of 9,823 million DKK and operating profit of 4,472 million DKK. In another company announcement, DSV is announcing an expansion of the Executive Board. Jens H. Lund will now take on a new role as Group COO and Deputy Group CFO Michael Ebbe is appointed new Group CFO. “We are strengthening the Executive Board to secure our continued ability to grow and develop our company at a high pace,” said DSV Chairman of the Board of Directors, Thomas Plenborg. “At the same time, we ensure continuity in the management team. During the last almost 20 years, Jens Lund has been a fantastic Group CFO and has played an important role in the development of DSV. “With his broad knowledge of the company and the logistics industry, Jens is the right person to head up areas as the continued development of our IT platform and optimisation of our business. “Michael Ebbe has a long history with DSV and he has a strong cooperation with Jens Bjørn, Jens and the rest of the Executive Committee. In the Board of Directors, we are confident that Michael will continue to deliver high quality reporting and drive further progress in DSV.”
FINLAND
Load handling specialist, Cargotec, is merging with another business to lead the way in sustainable material flow. The merger between Cargotec and Konecranes will create a ‘Future Company’ and is expected to occur by the end of the first half of 2022. “The planned high-level operating model of the Future Company is the result of months of integration planning work and the benchmarking of best practices across various industries, and the selection of the planned leadership team is the result of a rigorous selection process,” said Future Company President and CEO, Mika Vehviläinen. The Future Company aims to be a customer-centric organisation of top global talent. The Future Company’s designed high-level operating model would be a customer-centric model as the planned four independent businesses would each serve one clear customer segment – industrial, maritime, ports and roads. This would ensure decision-making close to the customer by fully empowered, agile businesses. After the completion of the merger, the
NEWS INTERNATIONAL
EUROPE
Future Company is planned to comprise of the following businesses, with their leaders being members of the Future Company leadership team and reporting to Vehviläinen. The naming and branding of the planned businesses is part of the integration planning work and is currently ongoing.
GERMANY
Schmitz Cargobull subsidiary, Cargobull Telematics, has been awarded the ‘Assured Sustainability’ test by the German Institute for Sustainability and Economics. The certificate attests that sustainability has been implemented in an exemplary manner throughout the enterprise and that all processes have been optimised with regard to a sustainable economic orientation. This includes the quality of products, services, and consulting, as well as ecological and social responsibility and the economic future-orientation. The individual sustainability competencies in the areas of environment, energy, social affairs, economics, and regionality, and their implementation in the company were verified in an on-site audit. “We’re very proud of this certification, as it shows that the important topic of sustainability is actively implemented throughout the company,” said Cargobull Telematics Managing Director, Marnix Lannoije. “It is important for us to strengthen the orientation towards qualitative, social, and ecological criteria as part of our corporate philosophy. “Here we rely on transparent, clearly formulated processes and extensive quality controls, which confirm again and again the confidence of our customers in the performance of our products and services. Of course, our employees are our most valuable asset in this respect. We can only achieve our ambitious goals with motivated employees.” As of now, the TrailerConnect telematics system is also certified and, therefore, offers the customer decisive advantages. “The certified telematics system stands out from the mass of providers as an ‘excellent’ sustainable product and enhances the operator’s vehicle fleet accordingly,” said Leoni Nathaus, Head of Product Management & Service Sales Product Line Digital Services. “The user of our products thus brings a high level of sustainability and safety competence to their business. In public tenders or audits, such as for ISO 14001 Environmental Management, ISO 50001 Energy Management or ISO 16247 Energy Audit, the fleet operator can decisively improve its positioning by the use of a certified TrailerConnect system. The same applies increasingly to customers who insist on various proofs of a company’s sustainability before placing orders. In this regard we are on the cutting edge with our product, helping to speed up the process accordingly.” Over 82,500 telematics units sold, around 58,000 active systems on Europe’s roads and 20 years of experience in the development and marketing of its own TrailerConnect trailer telematics system – these are the success parameters of Cargobull Telematics. The fully-owned subsidiary of Schmitz Cargobull is one of the largest providers of trailer telematics services and innovative digital products for the logistics and transport industry. In addition to its own hardware and software development, Cargobull Telematics offers a complete range of services centring around trailer telematics. This includes advice related to data interfaces as well as transport and fleet management processes. The Cargobull Telematics range of products and services is tailored to the individual customer and available throughout Europe. The Münster-based Institute for Sustainability and Economics supports companies and public institutions in making their sustainability efforts visible to the outside world. The goal is the sustainable development and documentation of the responsibility and quality of future-oriented companies. Already active nationally and internationally since 1991, the Institute for Sustainability and Economics successfully combines different areas of teaching and research. The guiding principles include working in an energy-, cost- and material-efficient manner, a good working atmosphere for employees and the use of regional as well as renewable or recyclable raw materials. The certifications with the sustainability test seal are available in different languages. They are recognised by government authorities and in more than 400 different industries worldwide and add value to offers and tenders. In addition to consulting, certification, analytical work and development in the field of sustainability, climate neutrality, CO2 compensation and carbon offsetting, the service portfolio includes climate protection projects, compliance, supply chain analyses and sustainability reports.
LUXEMBOURG
Kuehne + Nagel Luxembourg’s third contract logistics site is reported to leverage the central location in Europe for e-commerce. The company has opened a fulfilment centre in Contern, Luxembourg, with
EUROPE

34,000 square metres of warehousing space. The opening ceremony was attended by Luxembourg’s Prime Minister, Xavier Bettel, Kuehne + Nagel’s Honourary Chairman, Klaus-Michael Kühne, and other political representatives and business personalities. The expansion reaffirms Luxembourg as a strategic location for Kuehne + Nagel in the centre of Europe with easy access to the continent’s most important consumer markets. From the Grand Duchy, Kuehne + Nagel meets the complex and dynamic supply chain needs of its customers through integrated value-added solutions – especially in the area of e-commerce fulfilment. This includes inventory management, picking, packing and shipping orders, managing returns, as well as value-added services. Klaus-Michael Kühne said: “Following a promising start 51 years ago, Kuehne + Nagel has been growing its multi-modal logistics solutions in Luxembourg continually and now further strengthens its function as a strategic contract logistics hub in Europe. This also underlines our confidence in the business location and the fruitful collaboration with the government of Luxembourg and the local authorities of Contern.” Tobias Jerschke, Managing Director of Kuehne+Nagel BeLux, added: “The new fulfilment centre perfectly complements our existing e-commerce hub in Belgium, securing fast end-to-end lead times. At the same time, the warehouse roofs perfectly lend themselves to the biggest photovoltaic installation to date by Enovos – Luxembourg’s main energy supplier. Supporting the green energy transition in the country underlines Kuehne + Nagel’s strong commitment to sustainability as part of its ambitious Net Zero Carbon targets.” Kuehne + Nagel Luxembourg today employs over 700 people and has 100,000 square metres of warehousing
YOUR PARTNER FOR SUSTAINABLE LAST NEW! MILE
DELIVERY
TIP is now offering electric Light Commercial Vehicles for last mile delivery. Do you want to know more? www.tipeurope.com/lastmile
NEWS INTERNATIONAL
EUROPE
space. In addition, the company has a historically strong presence in Road Logistics, Sea Logistics and Air Logistics (with an office at Findel airport) as well as an Integrated Logistics team managing regional and global contracts for 4PL customers with a focus on consumer electronics, industrial goods and pharma.
NETHERLANDS
Bulk transport carrier, Albert Keijzer, is expanding its fleet with a new range of LAG silo vehicles. The new LAG tipping silo tankers, spec’d for sugar transportation, feature PSI tyre inflation, 10-tonne axles in combination with a trailing axle as well as a proximity switch on top of the walkway which helps to prevent the semi-trailer from leaving with an extended tipping cylinder of handrail. “LAG Trailers designed this series completely tailored to our operations,” said Albert Keijzer Technical Manager, Jos Baltes. “The focus on safety and sustainability is fully in line with our long-term vision.” Albert Keijzer recently celebrated its 100th anniversary. On the back of its centenary celebrations, Albert Keijzer built a new headquarters, introduced tractors on bio-CNG to its fleet and continues to minimise its carbon footprint by obtaining environmental certificates. “The goal is for our customers to operate worry-free,” said Albert Keijzer General Manager, Rob de Visser. “We do this by means of better information facilities, reduction of waste flows, and so on. “A good example of this is the collaboration with the Cosun Beet company (formerly Suikerunie). Our tractors ran on self-produced green gas from them. This gave Cosun Beet Company a lean & green star; a very strong achievement. We are very proud of this.”
SCOTLAND
Trucking company, D.R. Macleod, has taken delivery of its first two Carrier Transicold Vector HE 19 MT (multitemperature) trailer refrigeration units, in a move to improve fleet sustainability and reduce noise on its delivery routes. The new Carrier Transicold Vector HE 19 MT units are mounted to 13.6m Gray & Adams trailers and represent additions to a 100-strong trailer fleet, of which 30 are refrigerated. Celebrating its 40th anniversary this year, D.R. Macleod ordered its first Carrier Transicold unit 12 years ago. The company has added an increasing number of Carrier systems over the years for use on both its rigid truck and trailer fleet. “The outstanding performance and superb aftersales support we receive from Carrier has seen us order more and more of their products as we bring new assets into the fleet,” said Donald Macleod, Managing Director at D.R. Macleod. “The new Vector HE 19 units fit perfectly with our environmental strategy to lower fleet emissions, and because they’re so much quieter than anything we’ve had before, they’re also ideal when noise is a factor. This is particularly important when we’re parked up in the residential area waiting to catch the Stornoway ferry from Ullapool.” Carrier Transicold’s flagship trailer refrigeration system, the Vector HE 19 MT unit combines the company’s allelectric E-Drive technology with a new ultra-modern multi-speed engine design that can reduce fuel consumption by up to 30 per cent. The unit also offers a 10 per cent saving in weight and reduces noise by 3 dB(A) – which to the human ear equates to being 50 per cent quieter. The unit is also reported to save up to 15 per cent on maintenance costs. The Vector HE 19’s fully hermetic scroll compressor and economiser helps increase refrigeration capacity during pull-down by 40 per cent, while cutting the chance of refrigerant escape by 50 per cent. When plugged into the electrical grid on standby, the Vector HE 19 MT is also 19 per cent more efficient. “We’ve been so impressed with the new Vector units that we’ve requested all new trailers we purchase outright and any additional we take on contract hire are mounted with them moving forward,” said Macleod. “When you add in the first-rate maintenance support we get from Carrier Transicold South & Central Scotland, it really is the complete package.” The new trailers will operate from D.R. Macleod’s Glasgow depot, primarily making multi-drop chilled and frozen supermarket deliveries across Scotland and the Western Isles. On the road seven days a week, they are expected to clock up around 100,000 miles annually and will stay in service for at least eight years. Founded in 1981, D.R. Macleod now operates around 55 trucks and 100 trailers, supplemented with smaller vans for local deliveries. Headquartered in Stornoway on the Isle of Lewis, the company also has depots in North Uist, Inverness, Skye and Glasgow.
SPAIN
Rafa Grau Transports has added 10 XL tarpaulins with Lecitrailer bilateral elevation to its fleet. With this new addition, the company based in Villanueva de Castellón, Valencia, now has more than 250 semi-trailers in its fleet, all Lecitrailer equipment.
EUROPE
Throughout the year, its fleet made up of rigid trucks and tarpaulin semi-trailers, coil racks, refrigerators, Megatrailers and Duotrailers, for general cargo and transportation of beverages, fruit, paper reels and the recycling industry. Whether it be paper or plastic, the fleet performs an average of 42,000 services and covers more than 7,000,000 kilometres. In addition to providing the traditional logistics services, for a few months now, Rafa Grau Transports have been involved in a total logistics management project to provide a more complete service to its customers, with the possibility of outsourcing their efforts in distribution. Rafa Grau Transports’ commitment to a more sustainable future is key to its business philosophy which is why it deploys high productivity vehicles such as Duotrailers and Megatrailers in its transport operations.
SWITZERLAND
Strong global demand for transport services has boosted the Kuehne + Nagel Group’s latest quarterly financial results. All business units were reportedly able to exceed their prior-year results, in some cases significantly. At approx. 18.7 billion, the group’s net turnover in the first nine months of 2021 was almost 50 per cent higher than in the same period last year and EBIT more than doubled to over 1.5 billion. Dr Detlef Trefzger, CEO of Kuehne + Nagel International AG, said: “In the current situation with supply chains that are difficult to plan, our Kuehne+Nagel experts are working tirelessly to implement the best possible logistics solutions for our customers. We are on track and were again able to achieve an excellent business result in the third quarter. In the coming months, we do not expect any significant change in the constrained market situation.” Of the business units, Road Logistics
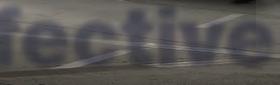


Uniquely e ective
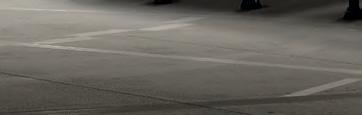
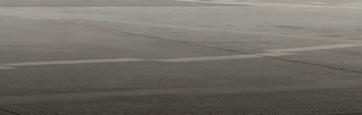
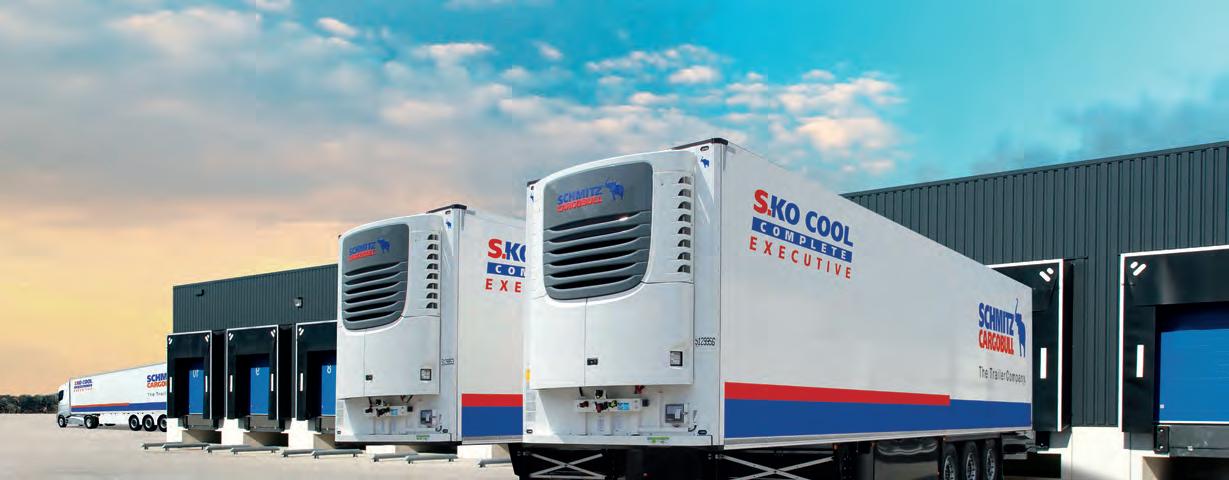
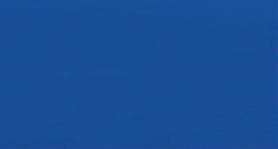
The S.KO COOL SMART EXECUTIVE is our top of the range reefer semitrailer, and includes our exclusive S.CU transport refrigeration unit. Refrigerate more coste ectively with our outstanding insulation system. Our services and TrailerConnect® telematics system are included to ensure lower maintenance costs and an impressive resale value. More Information: +44 (0) 1925 732886, www.cargobull.com
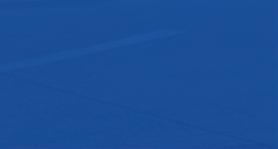
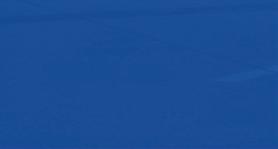
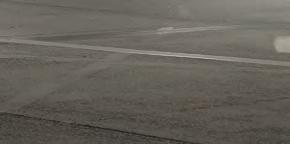
NEWS INTERNATIONAL
EUROPE/ MIDDLE EAST
was again able to significantly increase shipment volume in Q3 2021. Network capacity utilisation was high in Europe in particular; demand also remained strong in North America. As a special service offering, demand was particularly strong for the digital solution for global customs clearance. The unit’s net turnover for the first nine months of 2021 was approx. 2.5 billion and EBIT almost doubled to 69.7 million compared to the same period last year. The digital booking platform for land freight, eTrucknow, again recorded strong growth. The service, which has so far been focused primarily on Asia, is currently being rolled out worldwide and is already available in over 20 countries. In Q3 2021, Contract Logistics reported very high capacity utilisation, particularly in North America. High order intake was once again recorded in the e-commerce fulfilment and pharma sectors. Due to the divestment of UK activities at the beginning of the year, net turnover of 3.1 billion in the first nine months of 2021 was below the prior-year period. EBIT improved to 105.9 million. Contract Logistics during the reported quarter also acquired further customers for the warehousing of vaccines. For this purpose, an existing temperature-controlled distribution centre in Belgium is currently being expanded to a total of 25,000 square metres. Sea Logistics managed container volumes that were slightly above the prior-year period (3.4 million TEU) amid challenging market conditions with congested ports, supply chains out of sync. Air Logistics posted market share gains despite globally limited cargo capacities which required tailor-made customer solutions.
UK
L. Hunt & Sons has taken delivery of two new bespoke built trailers from Andover Trailers, extending a relationship between the two companies dating back more than 30 years. The first new delivery is a highspecification, tri-axle, 56-tonne gross weight extending step frame – a replacement for a smaller Andover build and the largest the business has specified to-date. It is joined by a specialist tri-axle forklift trailer, a new addition to the company’s 30-strong mixed trailer fleet which currently features seven other Andover builds. “We bought our first Andover trailer second-hand in the 1980s, but over the years, whether they’ve been new or used, they have never let us down. With the business looking to move into heavier haulage, we knew they were the right choice to build our new extending step frame,” said Derrick Hunt, Director at L. Hunt & Sons. “What makes Andover’s builds stand out is their combination of innovative design and solid and dependable build quality. They are also willing to work with you to ensure the trailer you get does exactly what you need it to do. Nothing’s offthe-shelf, it’s all bespoke.” The 11.9m step frame is constructed with a durable, four-member design which can extend along a central spine to a maximum length of 16.15m. The 1.2m-wide power toe ramps feature Andover’s fold-forward design, with sliding width adjustment and knife edge toes, all helping with the loading and unloading of a range of heavy machinery, including everything from aviation tugs to belt systems for sushi restaurants. Specified with 17.5-inch wheels on BPW axles, the trailer includes lift and self-steer capability on the rear axle, as well as multiple safety features like slideout wide load marker boards, additional reverse safety lamps and LED strobes. The covered forklift trailer features a similar four-member construction, with closed-up cross members within the frame to provide additional strength, while keeping the unladen trailer weight as low as possible. The full width, full height, flip-toe knife-edged ramp design creates the shallow entry angle needed to load forklifts, with extra reversing lamps and an alarm to provide additional safety when in operation. Other key design features include an allsteel hinged retractable TSE sliding roof, specifically chosen by Andover Trailers for its sheer strength and durability. It also incorporates swing-out rear pillars and sliding side pillars with two locking positions, allowing machines wider than the door frame to be loaded with ease. “The shallow loading angle and the innovative roof and pillar design make Andover’s forklift trailers the best in the business. Their genuine versatility allows us to carry a wide range of forklifts, including high-mast machines with the roof either fully or partly open,” said Hunt. Both new trailers are expected to stay in operation for at least 10 years and will clock up around 100,000 miles per year working across the UK. A family business based in Basingstoke, L. Hunt & Sons has now worked in the haulage industry for more than 125 years. Its varied commercial vehicle fleet works across all sectors and has transported everything from helicopters to pharmaceuticals.
DUBAI
A new partnership between Aramex and International Humanitarian City (IHC) is expected to enhance efficiencies in delivering global humanitarian aid. As part of the agreement, Aramex will be
MIDDLE EAST
leveraging its extensive global network and deep industry expertise to support IHC in facilitating and expediting the transportation of aid including food, medicine, and vaccines to those who need it most around the world. In addition, the alliance will pursue synergies in integrating innovation and energy efficiency in humanitarian initiatives, and in optimising the storage of relief items. “This partnership with IHC will help us deliver on our commitment of making a positive impact on the societies and human lives by leveraging our core services and global network to deliver basic needs to those in need in a safe, reliable and timely manner,” said Aramex President, Andy Van der Velde. “We believe this comes at an incredibly crucial time when the Covid-19 pandemic continues to spread and affect the lives of many people across the globe. We very much look forward to a longstanding and impactful relationship with IHC, and to provide them with needed support to help them achieve their mission.” IHC CEO, Giuseppe Saba, said: “We are extremely proud to welcome within IHC family a new partner from the private sector. I’m honoured today [October 19] to sign this partnership with Aramex and to explore together innovative solutions for improving relief operations in emergency response, and by supporting the humanitarian community in helping the people most in need around the world. “The IHC community’s Covid-19 response last year reached 119 countries with 1,023 dispatched shipments and $98.7 million in value. “The role of the private sector has been instrumental and we hope this partnership will further enhance the emergency preparedness and response capabilities for an efficient humanitarian action.” Aramex has been involved in several initiatives related to supporting medical,
NEW SLIM WORKPOINT AVAILABLE
HIGH EFFICIENCY VIBRATION TESTED VIBRATION TESTED UNIQUE DESIGN UNIQUE DESIGN
NEW ULTRA LIGHT WORKING LAMPSLIM
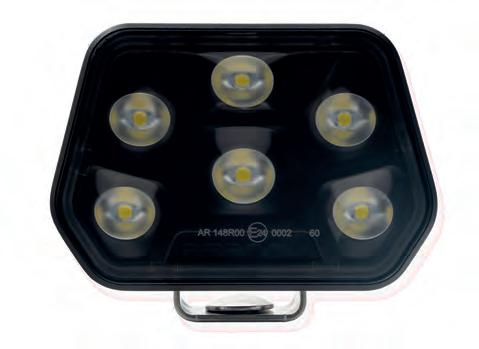
WORKPOINT AVAILABLE UNIQUE DESIGN NEW SLIM HIGH EFFICIENCY ULTRA LIGHT
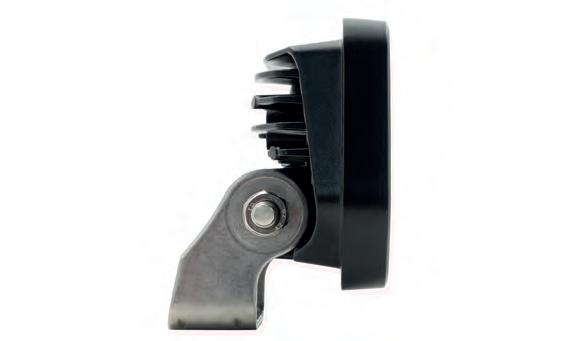
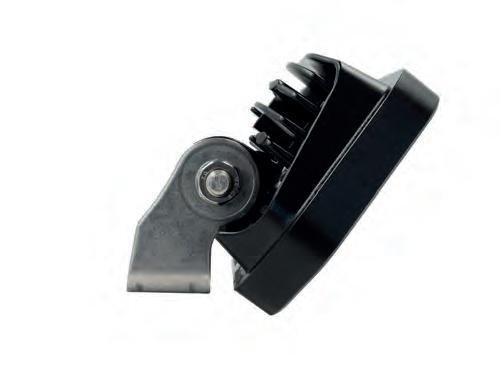
WORKPOINT II
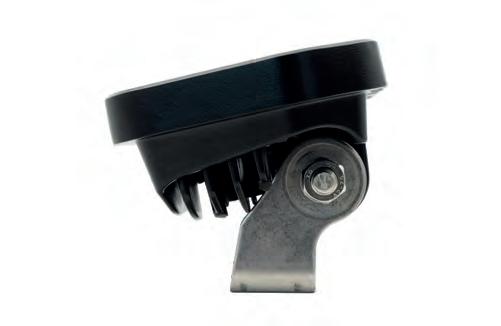
Wide adjustment angle | Vertical rotation range from - 35° to 100°
WORKPOINT www.aspoeck.com
NEWS INTERNATIONAL
MIDDLE EAST/ NORTH AMERICA
cultural and humanitarian projects. Last year, the company joined the Hope Consortium, a UAE-based public-private partnership, to safely and responsibly deliver vaccine doses under cold and ultra-cold conditions between transportation hubs, warehouses, medical facilities and other final destinations.
MEXICO
Transport and logistics company, Transportes Marva, has worked with trailer builder, Fruehauf, for more than 30 years. Their latest project is a bulk order of 300 trailers including skeletal units to bolster Transportes Marva’s container handling capabilities. Transportes Marva provides multimodal services for shipping companies around the world and services Mexico’s ports from coast to coast both on the Atlantic through the Port of Veracruz and in the Pacific through to the Port of Manzanillo. The company also facilitates agreements with American and Canadian clients, transporting general goods, providing logistics support and engaging in doorto-door deliveries via the border port of Neuvo Laredo. Fleet composition includes Kenworth prime movers, platform trailers, container chassis, low boys with one-, two- and three-axle varieties, double-axis dollys aswell as top- and side-loaders.
US
Uber Technologies subsidiary, Uber Freight, has completed the acquisition of Transplace from TPG Capital for approx. $2.25 billion USD in an all-cash transaction. As partial financing for this transaction, Abu Dhabi Growth Fund (ADG), D1 Capital, and GCM Grosvenor invested $550 million USD in Uber Freight. The transaction brings together Uber Freight’s vast network of digitallyenabled carriers with Transplace’s trusted shipper technology and operational solutions, ultimately creating one of the world’s leading logistics technology platforms to meet the rapidly evolving needs of shippers and carriers alike. “Logistics is going through a historic transformation,” said Uber Freight Head, Lior Ron. “Unprecedented volatility, increasing supply chain complexities, and escalating shipping costs are driving shippers to modernise their supply chains with new technologies. “By acquiring Transplace, we’re able to accelerate our vision for a seamless freight ecosystem and create the world’s first true freight operating system. Combining the leading shipper network and the largest digital network of carriers will enable us to immediately unlock new opportunities and efficiencies for everyone in the value chain — shippers, carriers, and ultimately society at large.” Transplace CEO, Frank McGuigan said: “Today it is more essential than ever to bring shipper and carrier networks closer together through a fully connected and transparent logistics ecosystem that addresses the evolving supply chain needs of all stakeholders. The acquisition marks a turning point in the industry and a new era of delivering trusted outcomes by coupling best-in-class logistics platforms and managed services with the world’s premier shipper and carrier networks to dramatically increase value for customers.” The partnership will unlock deep efficiencies and insights across $16 billion USD of Freight Under Management (FUM) and help reduce transportation costs, improve service, automate processes and streamline the execution of freight for shippers of all sizes. The combined networks of Uber Freight and Transplace will also form the world’s largest network of digitallyenabled carriers with a combined reach of 135,000 high quality carriers operating across an expanded set of services throughout North America and Europe, including intermodal, cross border, expedited, and more.
BRAZIL
Trailer builder, Librelato, has authorised a Libreparts dealer in Araguaína, Tocantins. The latest branded parts store belongs to the representative Rodosul which is located at Av. Rio Bandeira, Quadra 15 Lot 06 and 07- Industrial Sector. The inauguration of Libreparts took place on 10 November 2021 with live broadcast on Librelato’s YouTube channel. The new store will feature several offers and promotions, in addition to the already known premium concept of Libreparts. Araguaína is one of the most important municipalities in Tocantins and in the northern region of the country according to Librelato. “The limits of Araguaína are not only part of the important expansion region of the agricultural frontier in the North and Northeast regions, the geographical extension of MATOPIBA, but it is also considered the symbolic capital of MATOPIBA and the economic capital of Tocantins,” said Librelato. Araguaína is also reported to be a strategic and strong economic centre that drives regional development. The city stands out for its grain production and state-of-the-art cattle raising, while agribusiness promotes its retail and wholesale shopping centre as well as the local agribusiness. “Libreparts for us is a dream come true,”
SOUTH AMERICA/ OCEANIA
said Paulo Marques, Founding Partner of Rodosul. “I once heard from a great director of Librelato the following phrase ‘treat your client, as you treat your friend’. This marked my life and since then, that’s how I’ve been working. Rodosul’s objective is not only to sell road implements, but to be a source of blessing in people’s lives and always offer convenience and solutions to customers. We want to be ever closer.”
AUSTRALIA
The Queensland Government could soon be exporting hydrogen to Europe’s largest port. Port of Rotterdam in the Netherlands recently signed a memorandum of understanding with Australia’s state government and has an ambition to import up to 20 million tonnes of hydrogen by 2050 starting with imports of ammonia in 2025. The agreement would see Queensland and the Port of Rotterdam collaborate on opportunities to develop a hydrogen export supply chain between Queensland hydrogen producers and Rotterdam. Queensland Premier, Annastacia Palaszczuk, said after days of exciting hydrogen announcements, this agreement was another ringing endorsement of Queensland’s quest to be a renewable hydrogen super power. “This is the start of the green industrial revolution and the announcements this week prove that Queensland has what it takes to be a global leader in renewable energy and hydrogen,” she said. Australian Minister for Energy, Renewables and Hydrogen, Mick de Brenni, said when finalised, this memorandum of understanding would see Queensland and the Port of Rotterdam collaborate on opportunities to develop a hydrogen export supply chain between Queensland hydrogen producers and Rotterdam. “We have agreements with our Japanese and Korean partners for hydrogen exports,” he said.
Intelligent Trailer Program
Boost your trailer’s IQ to benefit from…
Load Optimization
Operational Efficiency
The ZF Intelligent Trailer Program. Intelligent connections of braking system, sensor technology and chassis control enable more than 40 advanced trailer functions. To optimize daily operations and to provide greater safety, efficiency, and sustainability. Everywhere and anytime: at the yard - on the road - at the dock. Learn more at www.intelligenttrailer.com Driver Comfort & Effectiveness
Advanced Safety
Fuel & CO₂ Reduction
DRIVING NEW
VALU ES
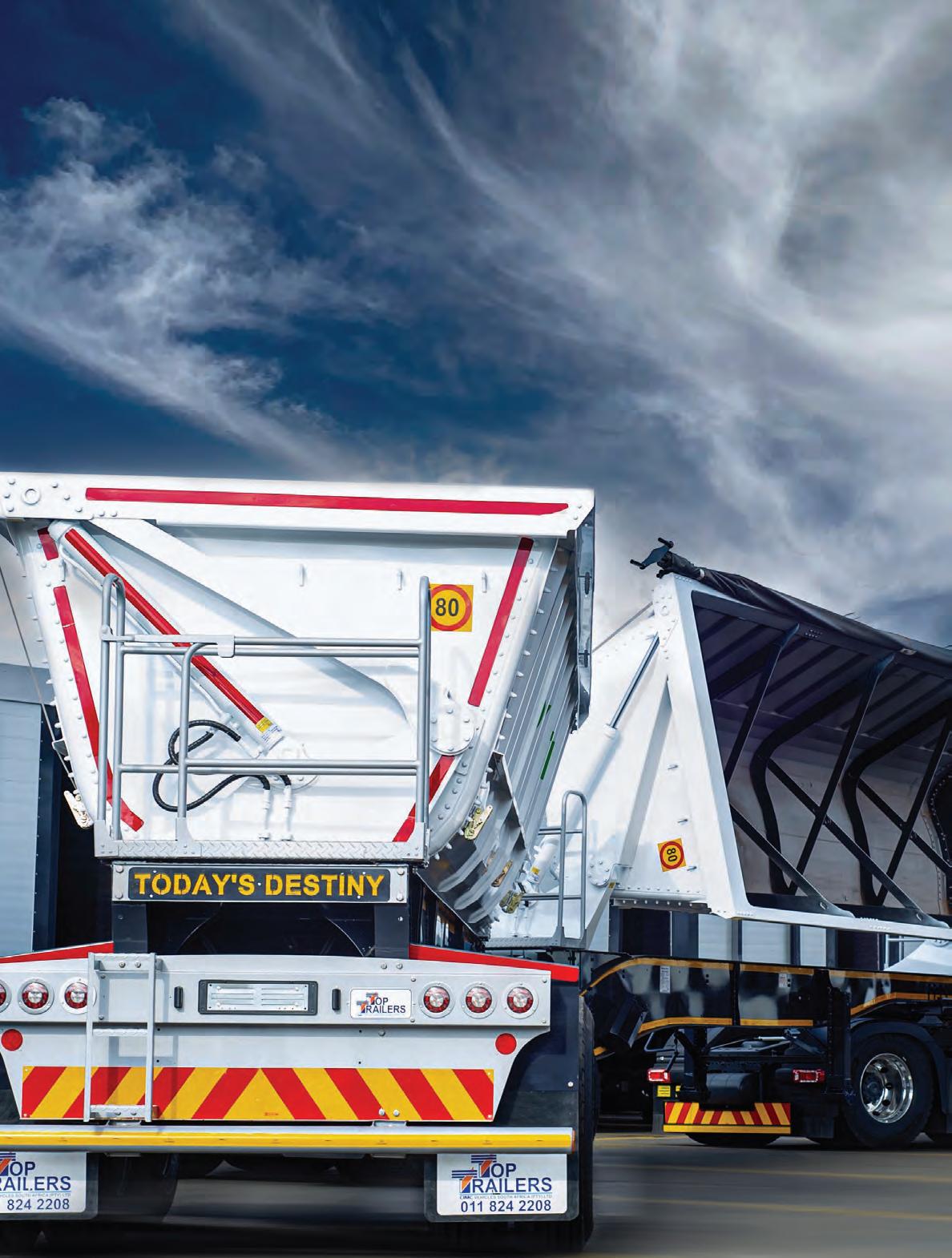
VALU ES
ACHIEVING THE LOWEST POSSIBLE TOTAL COST OF OWNERSHIP IS WHAT EVERY PRUDENT TRANSPORT OPERATOR STRIVES FOR. JOHEINE ELS – CEO OF CIMC VEHICLES SOUTH AFRICA – EXPLAINS THAT TRAILERS CAN PLAY A PIVOTAL ROLE IN THIS QUEST.
Since September 2015, CIMC Vehicles SA has produced trailers that are reported to elevate the level of quality and service seen in South Africa. The OEM’s focus, according to CEO, Joheine Els, is on constantly refining its trailers to be innovative, efficient and capable.
“We achieve this by focusing on integrating technology and efficiency into our manufacturing processes,” he said. “Developing next-generation ideas for durability and longevity as well as incorporating a higher level of organisation into our corporate structure.”
The company is owned by China International Marine Containers (CIMC) International, one of the largest commercial industrial conglomerates in China.
“With over 50 per cent share of the international container business, CIMC has been the biggest container manufacturing company in the world since 1996,” said Els. “The Shenzhen-headquartered, public-listed organisation has since branched into the manufacture of road transport vehicles, including logistics and construction vehicles. CIMC Group – with an employee complement of over 60,000 people – also designs and manufactures energy, chemical and food equipment, airport facilities, off-shore equipment, and is engaged in the real estate and finance FAST FACT industries through its more than 300 The latest Tridem 30-pallet reefer subsidiaries in operation around from CIMC Vehicles SA is built to last and designed to work in the world.” any environment. Using reduced
The company’s global reach means welding techniques through that a wide product range is on offer in South Africa. “CIMC persists in the mechanical engineering and innovative design, the refrigerated trailer is built to high quality management idea of ‘Intercontinental standards. The OEM assembles a operation, local manufacturing’,” European box body onto CIMC’s said Els. “Accordingly, the company proven chassis. Combining global technology and local knowledge, provides first-class road transport CIMC Vehicles SA delivers a equipment and services to the global modern reefer suited for African market, mainly all kinds of special applications.
Joheine Els CEO, CIMC Vehicles South Africa
vehicles and related parts and service. With CIMC’s worldwide factories and research and development centres in the US, Europe, Australia and China in support, over 1,000 different models of transport vehicles and logistics equipment can be designed and sourced right here in South Africa.”
Despite leveraging a strong international network, CIMC Vehicles SA continues to face global supply chain issues as well as other pressing domestic matters.
FAST FACT
Suitable for general freight, CIMC Vehicles SA offers the Curtainsider 6m-12m Link which typically includes a 800 GSM PVC tarpaulin roof, 28mm WISA plywood floor, curtain buckles with 600mm spacing, antitheft mesh curtains, roof support pillars, rear underrun protection, plug and play electrical system and more.
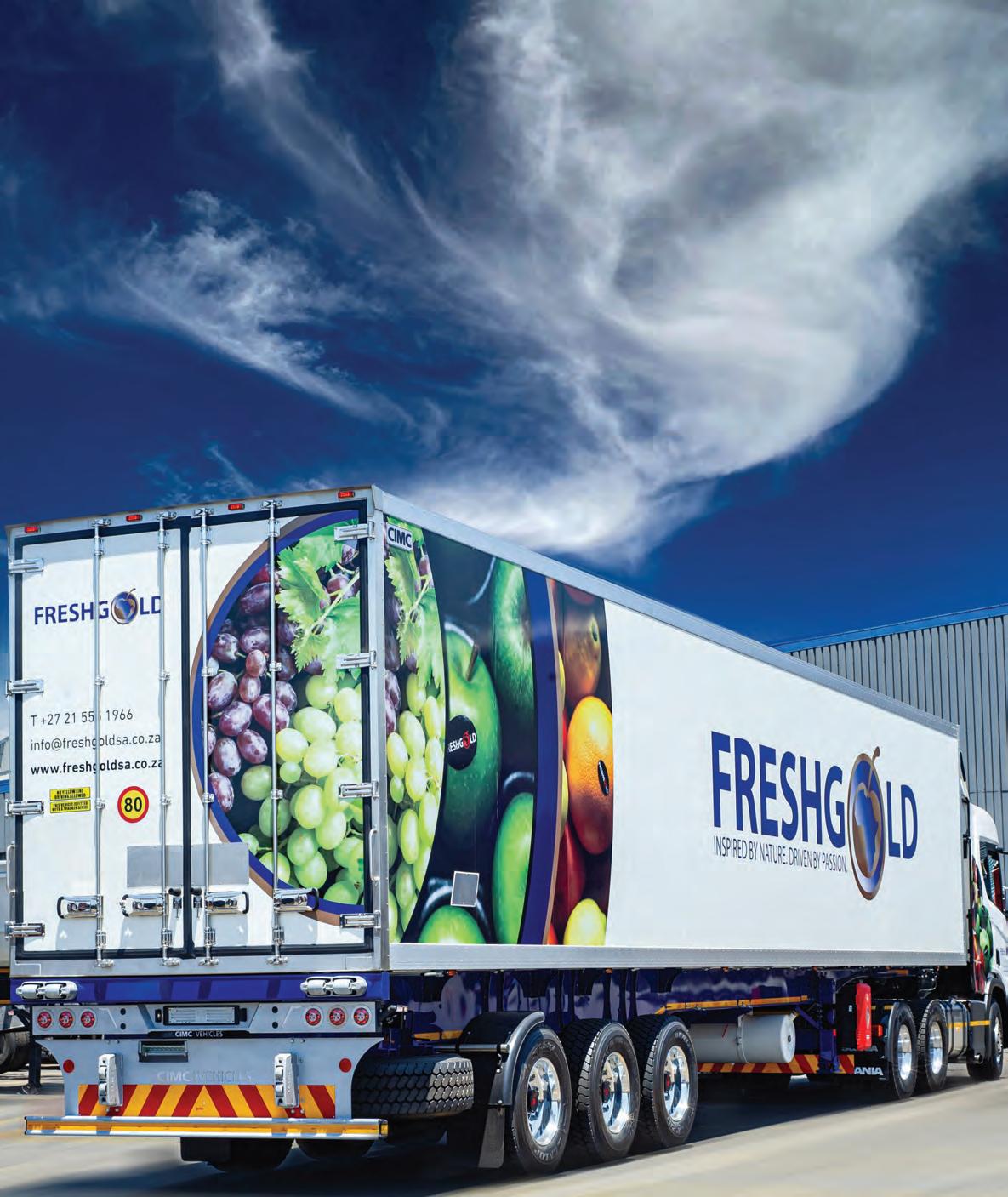
A fuel tanker manufactured by CIMC Vehicles South Africa.
“Given the instability of our country and the rampant crime and looting, transport vehicles have become targets,” Els said. “This results in downtime and thus additional costs to supply chains.”
CIMC Vehicles SA works to offset the effects of this situation by providing superior products. “We are proud to say we build vehicles that are not only innovative but also extremely reliable,” Els said. “Reliable vehicles reduce downtime and thus negate some of these negative consequences. Supply chains thus regain some of the lost efficiency.”
The company can achieve this because of its highly competent team.
“We have an experienced and visionary global management team whose industry and corporate management experience has allowed us to establish a track record of strong financial performance,” Els said. “Core members of our senior management “WE ARE PROUD TO SAY WE BUILD VEHICLES THAT ARE NOT ONLY INNOVATIVE BUT ALSO EXTREMELY RELIABLE... RELIABLE VEHICLES REDUCE DOWNTIME AND THUS NEGATE SOME OF THESE NEGATIVE CONSEQUENCES. SUPPLY CHAINS THUS REGAIN SOME OF THE LOST EFFICIENCY.”

Joheine Els CEO, CIMC Vehicles South Africa
team each have an average of over 24 years of professional experience in the related industries, and an average of over 14 years of experience with us. Since our inception in 2002, we have worked together to build our company from the ground up and led the strategic direction of our operations along the way. We intend to continue to draw on our management’s industry expertise and professional management skills to successfully implement our growth strategies. We believe that the proven capability, leadership, vision, loyalty
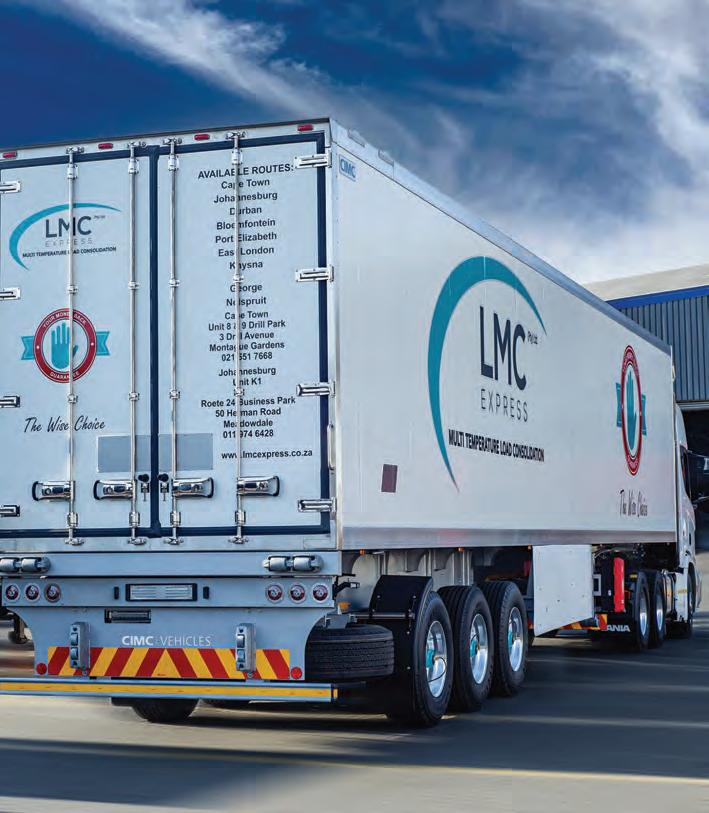
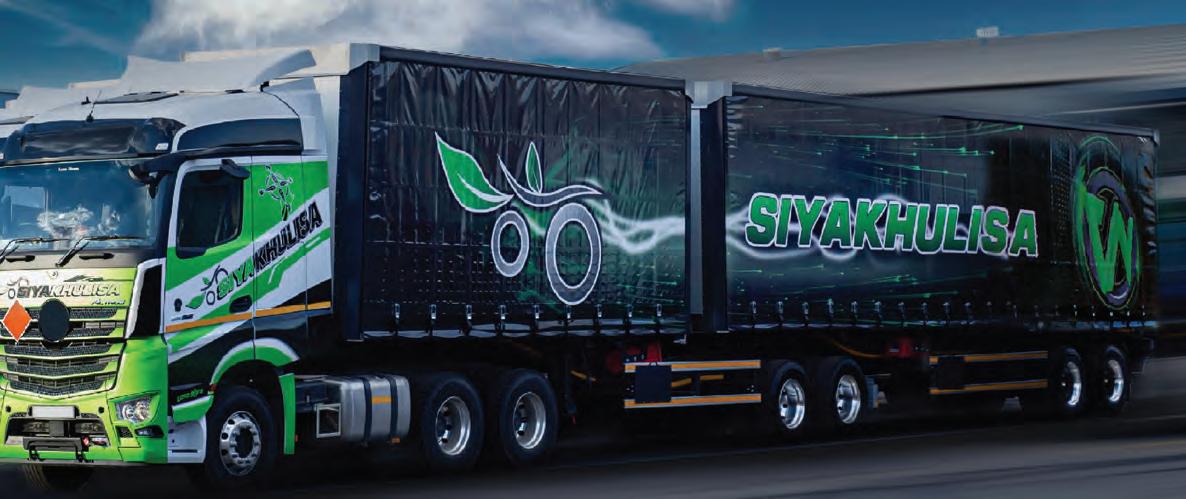
This curtainsider is rolling out.
and consistent efforts of our management team and their extensive experience in the trailer industry are key to our success and will continue to drive our future growth.”
Going forward, CIMC Vehicles SA expects the popularity of its side tippers to continue. “While you will find all our vehicles in most efficient fleets, our side tippers are by far the most popular,” said Els. “This is because they offer a weightoptimised chassis design, disc brakes, aluminium bumpers, a unique huck bolt design and uniquely designed bins.”
These features culminate in a low Total Cost of Ownership (TCO).
“Many fleet owners are reviewing their
FAST FACT
CIMC Vehicles SA also supplies tri-axle aluminium fuel tankers featuring LAG dual cradle and fully integrated chassis design, quality brakes and suspensions, axles, landing legs and more. These tanker builds can be tailored to accommodate lettering, reflective and mandatory decals in addition to their primer coating and paint finish.
FAST FACT
By mounting the side tipper fifth wheel on a raiser plate, CIMC Vehicles SA ensures a longer product lifecycle by eliminating the need to drill and weld what would be considered a high-stress area. The OEM also offers a rubbing plate assembly that can be completely bolted on or off. These side tippers also feature rear underrun bumpers, weight optimised chassis design, a uniquely designed bin top rail, bolted shafts and bushes for easy replacement. Operators can also tailor their build by choosing from a variety of axle, disc brake and suspension options.
A freezer van for multi-temperature distribution. “WE BELIEVE THAT THE PROVEN CAPABILITY, LEADERSHIP, VISION, LOYALTY AND CONSISTENT EFFORTS OF OUR MANAGEMENT TEAM AND THEIR EXTENSIVE EXPERIENCE IN THE TRAILER INDUSTRY ARE KEY TO OUR SUCCESS AND WILL CONTINUE TO DRIVE OUR FUTURE GROWTH.”
Joheine Els CEO, CIMC Vehicles South Africa
operations in an attempt to lower their TCO,” Els said. “We welcome this approach as we are confident that, thanks to our various product offerings, we can help to reduce TCO. Given the fact that the economy isn’t as strong as many would like, efficiency improvements are key to successful operations. CIMC – via its global footprint reinforced by local expertise – is confident that lessons learned on a global scale can be applied locally to enhance efficiency, reduce costs and ultimately improve fleet utilisation.”
www.cimc.co.za
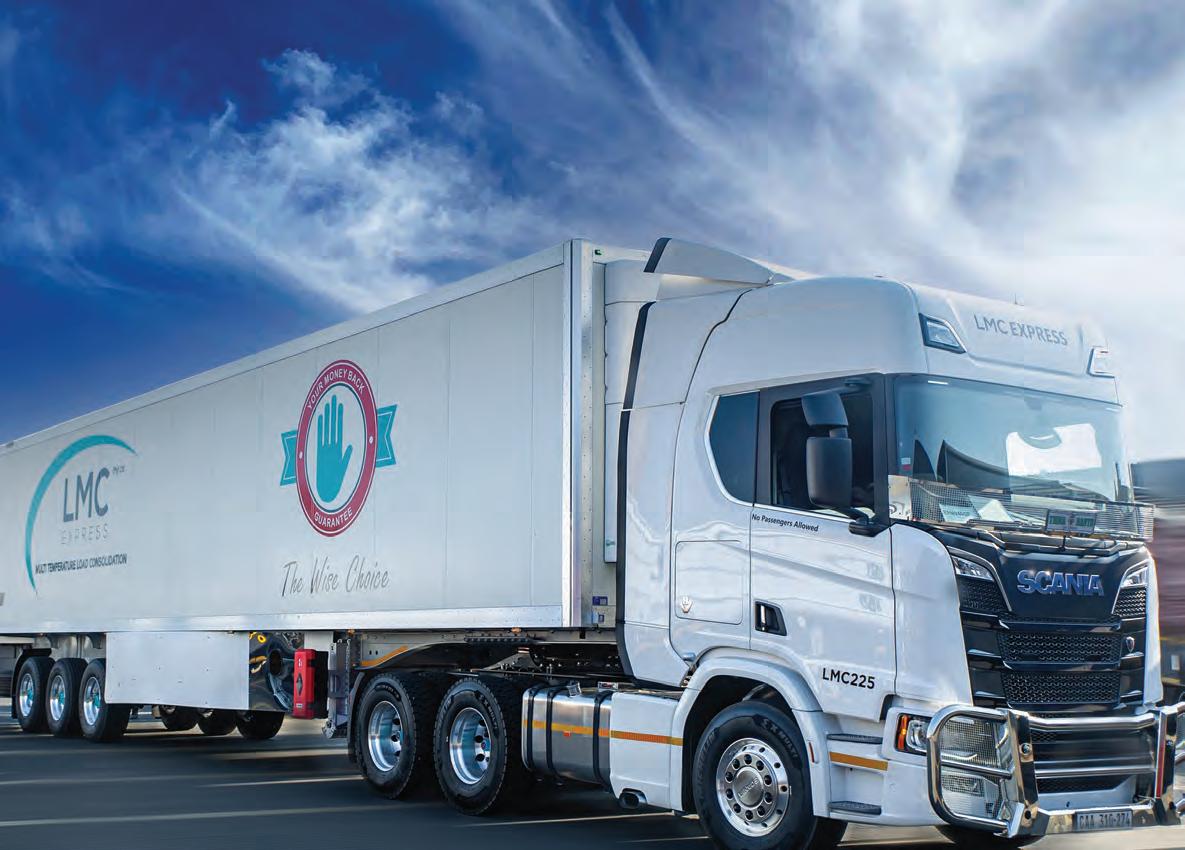