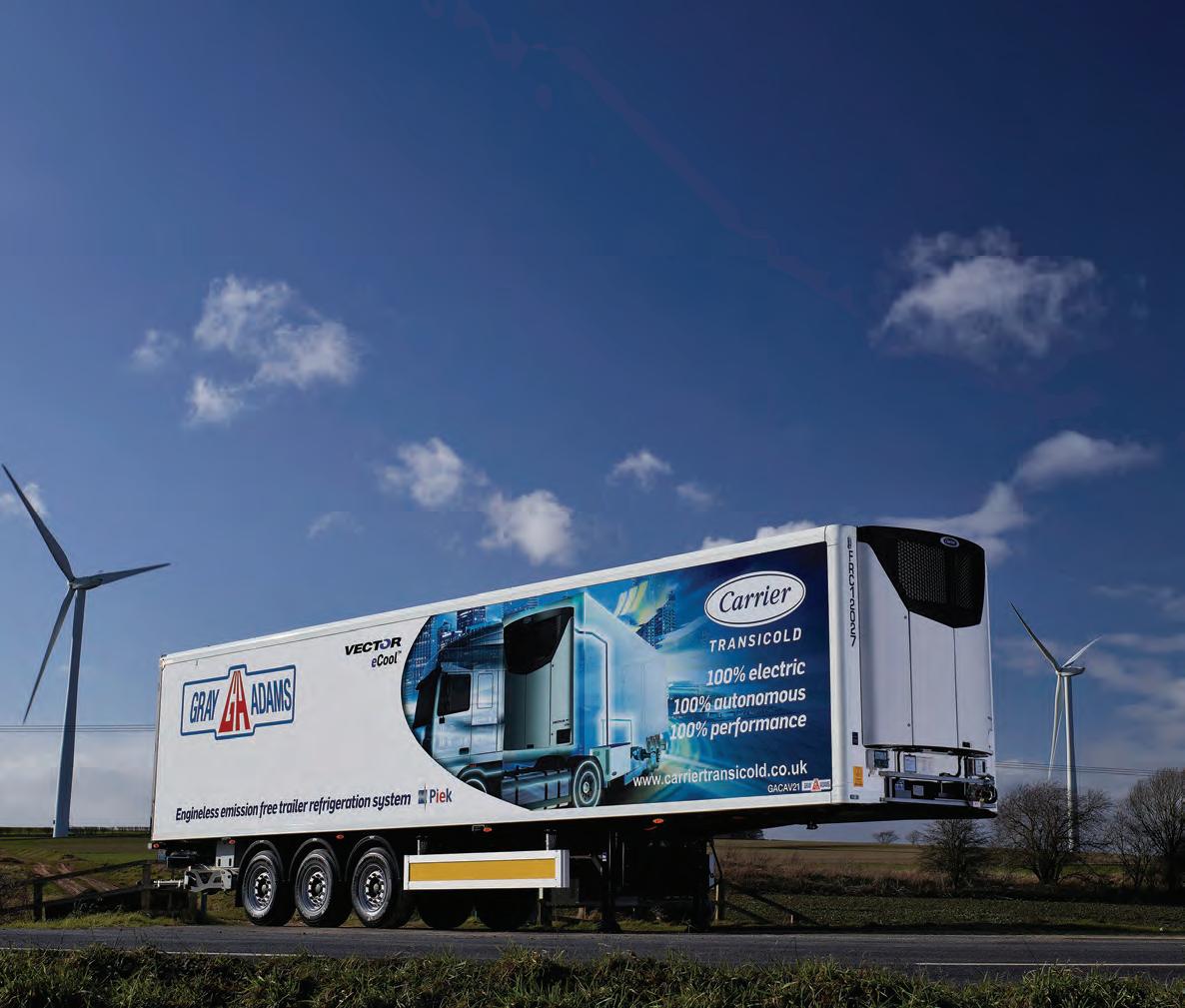
14 minute read
AXLES & SUSPENSIONS
STANDING THE TEST OF TIME
VALX CONTINUES TO LEAD THE CHARGE IN THE ELECTRIFICATION OF HEAVY COMMERCIAL VEHICLES. THROUGH INNOVATION AND A COMMITMENT TO DELIVERING QUALITY, ROBUST EQUIPMENT, THE NETHERLANDS-BASED MANUFACTURER IS MAXIMISING THE RESIDUAL VALUE OF TRAILERS THROUGHOUT EUROPE AND OTHER KEY MARKETS WITH ITS ENERGY AXLES.
The road transport industry, in light of supply chain disruption and the need to keep essential services on the move, is as competitive as ever. While the total cost of ownership remains a top priority for fleets, attention is also turning towards the longevity, cost-effectiveness and versatility of modern trucks and trailers. When the time comes to upgrade a heavy vehicle asset, ultimately, it is the residual or resale value that will make the difference between a good investment and an incredible one.
Almost a decade ago, VALX unveiled the first of its energy axles, the E2!, at the 2012 IAA Commercial Vehicles Show in Hanover, Germany. Not long after this debut, VALX explored a new design involving a full-electric refrigerated trailer with a company owned at the time by Carrier Transicold and rental fleet, Twan Heetkamp.
With an integrated power generation system fitted to the axles of trailing equipment, there are opportunities for fleet operators to achieve significant operational and fuel efficiencies, especially if this technology can be used to share the load of connected systems that draw electricity.
As cold chain technologies matured over the years, VALX has maintained a leading edge in the reefer electrification segment by refining its energy axle portfolio. In recent months, Carrier Transicold partnered with OEM, Gray & Adams, to develop a demonstrator program
FAST FACT
VALX’s dealer network currently has 2,200 service points however the OEM aims to grow to 3,500 service points in the next five years. Globally, Fuwa Group now has a total of 7,000 service points spanning the globe servicing its well established and growing customer base.
FAST FACT
The Fuwa Group, which VALX is a part of, was awarded ‘Manufacturing Single Champion Enterprise’ by the Ministry of Industry and Information Technology (MIIT) in China. According to the selection standard of MIIT, this national-honoured award represents the highest level of development and strength in the global manufacturing market. As the European base of Fuwa, VALX will continuously promote high-quality axle products and support its dear customers in the future.
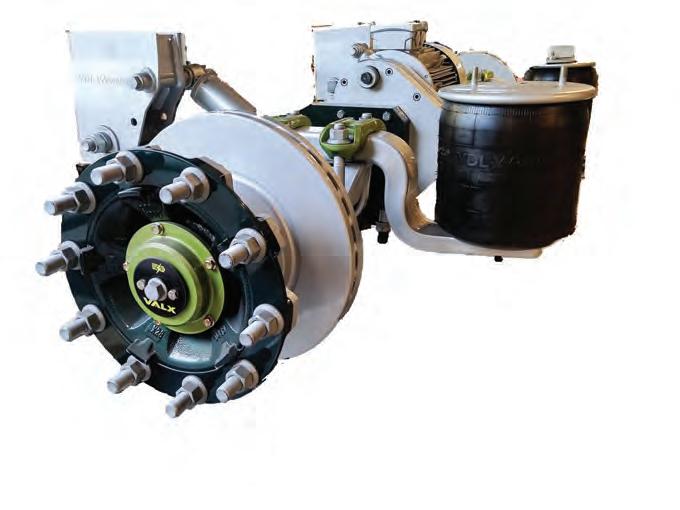
for the new Vector eCool trailer refrigeration unit. To complete the design, it features VALX energy axles.
This 13.6m build would be among the UK’s first autonomous, all-electric refrigerated trailer systems. Utilising a new energy recovery and storage system, the Vector eCool converts kinetic energy generated by the VALX trailer axle and brakes into electricity, which is then stored in a battery pack powering the refrigeration unit. This loop creates a fully autonomous system that produces no direct carbon dioxide or particulate emissions.
“The Vector eCool reaffirms our commitment to reducing emissions, improving sustainability and increasing efficiency across the refrigerated transport sector,” said Scott Dargan, Managing Director UK and Northern Europe, Carrier Transicold. “This exciting new technology represents a giant step forward for trailer refrigeration, and we are delighted to be working together with Gray & Adams on the roll-out here in the UK.”
The autonomous power developed by the trailer and the subsequent emissions reductions have attracted significant interest from Zemo Partnership (previously The Low Carbon Vehicle Partnership) – a not-for-profit organisation that plays a key role in helping the government deliver its low carbon transport strategy.
“As part of the road to net zero, we must take into consideration emissions generated by transport refrigeration units and other ancillary power, and our testing already includes these aspects,” said Andy Eastlake, Managing Director, Zemo Partnership.
VALX E2!HD energy axle.
“Innovation such as this from Carrier Transicold is demonstrating what needs to be done to future-proof its products; the Vector eCool is a practical, workable solution that ticks all of the boxes of electrification and decarbonisation and we are excited to see it take to the road in 2021.”
Carrier Transicold has been working closely with Gray & Adams on the design of the demonstrator vehicle to maximise the environmental benefits of the system. Even with the VALX axle generator and battery pack, it is lighter than a standard diesel unit with a full tank of fuel. The tri-axle trailer also features aerodynamic cappings to reduce drag, while bespoke sideguards allow access to the battery system and protect cyclists and other vulnerable road users.
“We have a special relationship with Carrier; working so closely with them to bring the Vector eCool to the UK has been really exciting,” said Peter Gray, Joint Managing Director, Gray & Adams. “Our design teams have seamlessly integrated the axle, braking and battery systems that make up the eCool into a trailer that has the potential to completely change the face of refrigerated transport.”
Suitable for operation with the engineless versions of Carrier Transicold’s Vector HE 19 and Vector 1550 E, the Vector eCool utilises the company’s E-Drive allelectric technology to the fullest. Where traditional belt-driven systems suffer a loss of up to 40 per cent kilowatts cooling power when converting electrical energy into their required mechanical drive, the E-Drive ensures the eCool has consistent, efficient cooling power and pull-down speeds whether operating on battery power or when plugged into the mains grid.
If used with the city versions of the Vector range, the eCool is also PIEK- FAST FACT compliant, which combined with its emissions performance, means that The following fleets across Europe are champions of the VALX axle. Netherlands the system offers the ultimate solution (THT New cool customers): Lidl, DHL, to tightening inner city and urban Frans Cremers, Nagel Group, PNO regulations. Finland, Hessing, Westerman, Muller, Green, Cornelissen, Jan Linders, Hordaal
In addition to supporting the Pilsener, Farm trans, Dask, Franken future of all-electric vehicles, VALX transport, NewCold, Van Straalen De also develops, manufactures and supplies a variety of other axles and Vries Transport and Vion Group. UK (Gray & Adams customers): Sainsbury Supermarket, Samworth componentry for heavy duty and Brothers, Aldi Supermarkets, Booths linehaul applications. Supermarkets, NewCold and Dawson Group.
www.valx.eu
THE ART OF INTEGRAT ION
OVER THE COURSE OF ITS 108-YEAR HISTORY, HENDRICKSON’S COMMITMENT TO PRODUCING HIGHLY-ENGINEERED, PRECISION-MANUFACTURED RIDE SOLUTIONS HAS BEEN PUT INTO PRACTICE ACROSS ITS VAST PRODUCT LINES.
In 1995, Hendrickson launched INTRAAX, a paradigm-shifting system that changed how the industry viewed trailer suspensions and asserted Hendrickson as a leader in air suspension technology. Billed as the industry’s first integrated system because of its revolutionary axle-to-beam connection, INTRAAX represented much more than the physical attachment of the axle to the beam; it embodied Hendrickson’s commitment for creating seamless integration from customer quote to product manufacturing to after-the-sale support – a business philosophy the company has elevated to an art form. While prominently known for innovations in axle and suspension technology, Hendrickson is also a leading supplier of trailer brakes and wheel-end systems.
It is the synergy of commitment to quality, precision, and most importantly, safety that results in Hendrickson’s line-up of optimised suspension, brake and wheel-end products.
Crafting Customisation and Optimisation
The concepts of specialisation and optimisation seem contradictory. On one hand, specialisation conjures terms like ‘narrow’, ‘niche’, ‘concentrated’, ‘unique’. On the other hand, optimisation invokes adjectives like ‘efficient’, ‘consistent’, ‘mass-produced’, ‘no choice’.
Hendrickson moulds these two opposing concepts by marrying engineering expertise, world-class validation capabilities and manufacturing proficiency to supply customised products that are built in a highly controlled, repeatable and reliable manner for the utmost quality and durability.
Hendrickson’s configuration process embraces the concept of customisation. Before any system is manufactured, a set of specifications must be created. This is achieved with the ‘configurator’, a custom software program that allows Hendrickson to instantaneously create unique sets of specifications to cater to individual customers’ needs and quickly respond to complicated specification requests.
The ‘configurator’ is used across Hendrickson’s core product lines like INTRAAX, VANTRAAX and ULTRAA-K and is updated instantaneously with engineering changes to reflect the most current offerings available.
Artistic Expression
True works of art sprout from an artist’s compulsion for expression after thoughtful exploration and reflection on his surroundings. The vision for ULTRAA-K, Hendrickson’s air slider system, flourished after careful examination of the evolving North American trailer market, which continues to demand innovative solutions that are stronger, lighter and require less maintenance.
One hundred pounds lighter than comparable air slider systems in the North American market, ULTRAA- boasts supreme durability and integrates exclusive ZMD ZeroMaintenance Damping technology.
ZMD addresses the need for reduced maintenance by eliminating shock absorbers from the maintenance equation altogether. This patented design integrates the suspension damping function within the suspension air spring by exchanging pressurised air between the bellows and piston of the air spring. Unlike a shock absorber, which has finite damping capacity and deteriorates with age, ZMD air springs are designed to provide continuous damping rates over the life of the air spring for improved ride quality, reduced suspension maintenance and enhanced cargo protection.
Creative Collaboration
ULTRAA-K was a labour of love that allied Hendrickson’s world-class engineering, testing, validation and manufacturing engineering
ION
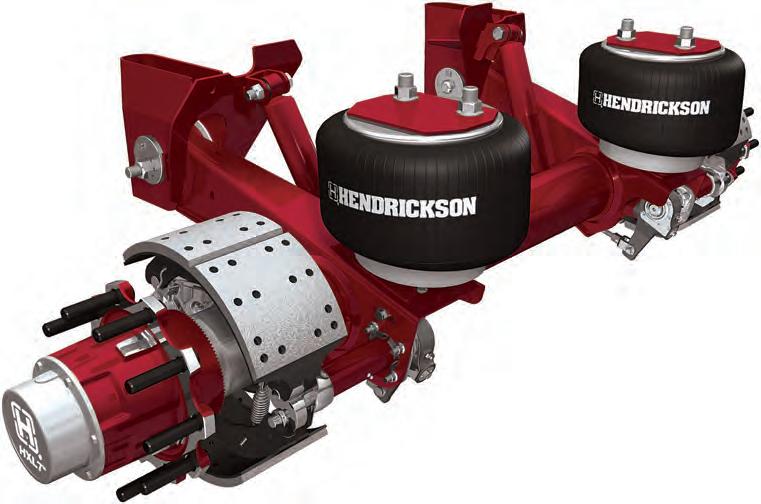
teams. Collaboration during ULTRAA-K’s development created a continuous communication loop whereby manufacturing engineers worked alongside product designers to develop an optimised design that could be manufactured in a repeatable and efficient fashion.
The strategic integration of these key functions throughout the product development process provides an open forum for creativity and idea growth, which encourages an atmosphere of continuous improvement and innovation. ULTRAA-K epitomises Hendrickson’s proclivity for bringing cuttingedge solutions to the marketplace and is a testament to the company’s commitment to creating a seamless experience from internal development to commercial launch.
The Medium
Art is expressed in many ways – a string of chords, a series of steps, a combination of brushstrokes. Hendrickson’s brilliance is manifested through a colourful palette of fabrication technology, including laser cutting, forming, machining, welding, automation and assembly. Vertically integrated manufacturing processes allow the company to maintain complete control of its designs, which ultimately lends itself to quality and durability.
During the manufacturing process for INTRAAX, key parts like frame brackets are laser cut and formed before being assembled to the suspension beams. Proficiency in these areas is essential for supplying dimensionally critical parts to welding cells for the utmost assembly precision and accuracy. Parallel to cutting and forming is Hendrickson’s mastery in machining. The launch of INTRAAX marked the introduction of a revolutionary process whereby the spindle, axle wrap and spider mounting surfaces are machined in one step to ensure precise brake geometry and wheel positioning. This process, combined with an advanced friction weld process, remains the heart and soul of every INTRAAX suspension system; it allows Hendrickson to supply the industry’s straightest and most concentric axles for maximised system durability, tire life and fuel mileage.
Hendrickson’s body of work would not be complete without mentioning its competency in robotic welding and automation, concepts best showcased with ULTRAA-K. During the manufacturing process, seven meticulously programmed robots move simultaneously around the slider box. Whirling here, twirling there, the robots perform a disciplined dance that precisely fuses ULTRAA-K’s key components for optimised structural integrity.
Across all Hendrickson’s product lines, automation is used wherever possible to ensure consistency, repeatability, traceability and quality control – and this practice is not limited to robotic welding. It also includes material handling to enhance productivity and safety throughout the entire manufacturing operation.
Hendrickson’s commitment to manufacturing excellence can also be seen in the patented assembly processes of Hendrickson RTR Ready-To-Roll wheel-end packages. Slacks, chambers, hubs, drums, seals, bearings, spindle nuts, hubcaps – lots of components means lots of opportunity for investment in error-proofing and traceability. Every custom bill of material that specifies a wheel-end package features a set of ‘rules’ that control the sequence and flow of components during assembly. Bar coding stations guide the associate to ensure the correct combination of components are selected and assembled in the correct order.
A Company’s Vision
Hendrickson’s knowledge of and investment in manufacturing technology is a testament to how it designs, validates, manufactures, supports, and continues to deliver cutting-edge products in the evolving commercial vehicle market. Its philosophy on continuous improvement and innovation breeds a culture where groundbreaking designs, durable products and unparalleled customer support are not only possible but set the industry standard. This mindset has allowed Hendrickson to elevate the notion of a seamless, integrated customer experience to an art form.
& SUSTAINA BLE AWARD-WINNING
Winner of the European Transport Award for Sustainability: the SAF TRAKe electric trailer axle from SAF-HOLLAND.
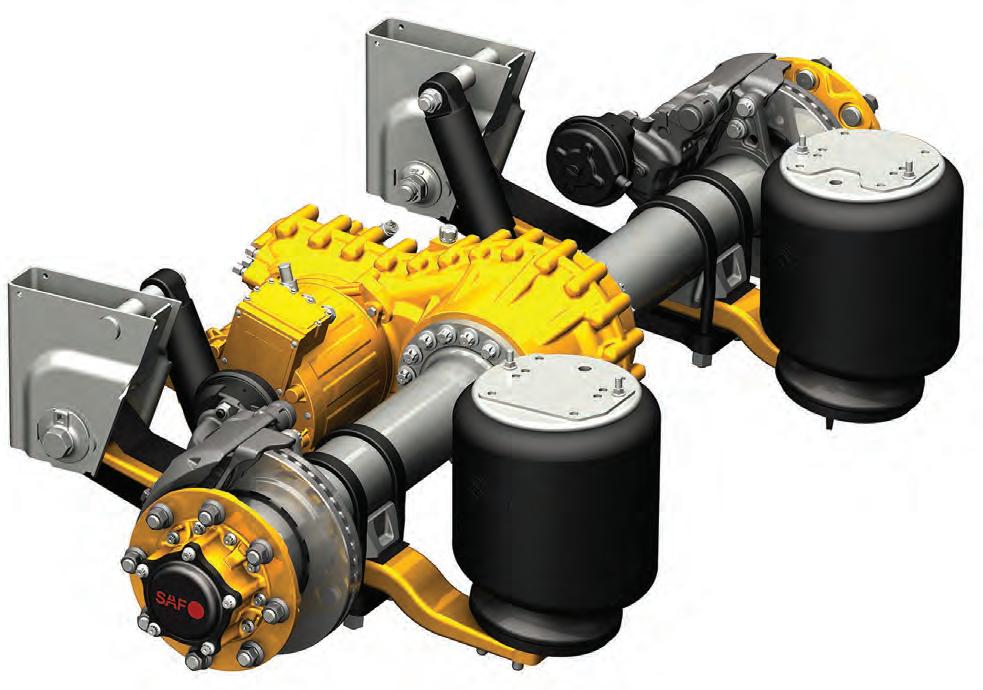
SAF-HOLLAND HAS WON THE EUROPEAN TRANSPORT AWARD FOR SUSTAINABILITY 2022 FOR ITS ELECTRIC TRAILER AXLES. THE COMMERCIAL VEHICLE SUPPLIER WON OVER THE JURY IN THE CATEGORY ‘COMPONENTS AND AGGREGATES’.
SAF-Holland’s electric axles for regenerative braking and traction assistance protect the environment – in production as well as during the journey itself. Regenerative braking in the SAF TRAKr reduces fuel consumption, CO2 emissions and particulate matter emissions from the trailer. The SAF TRAKe axle also supports the drive of the tractor unit in difficult road conditions. SAF-Holland has also eliminated the use of rare earth metals and copper in the production of its electric axles.
“We are very pleased that, with this award, the jury has recognised our contribution to the electrification of heavy goods transport. Our SAF TRAKe and SAF TRAKr electric axles conserve valuable resources during pro- duction and specifically reduce CO2 and noise emissions during operation”, said
SUSTAINA BLE
Christoph Günter, President Europe, Middle East and Africa and Chief Technology Officer (CTO) at SAF-Holland.
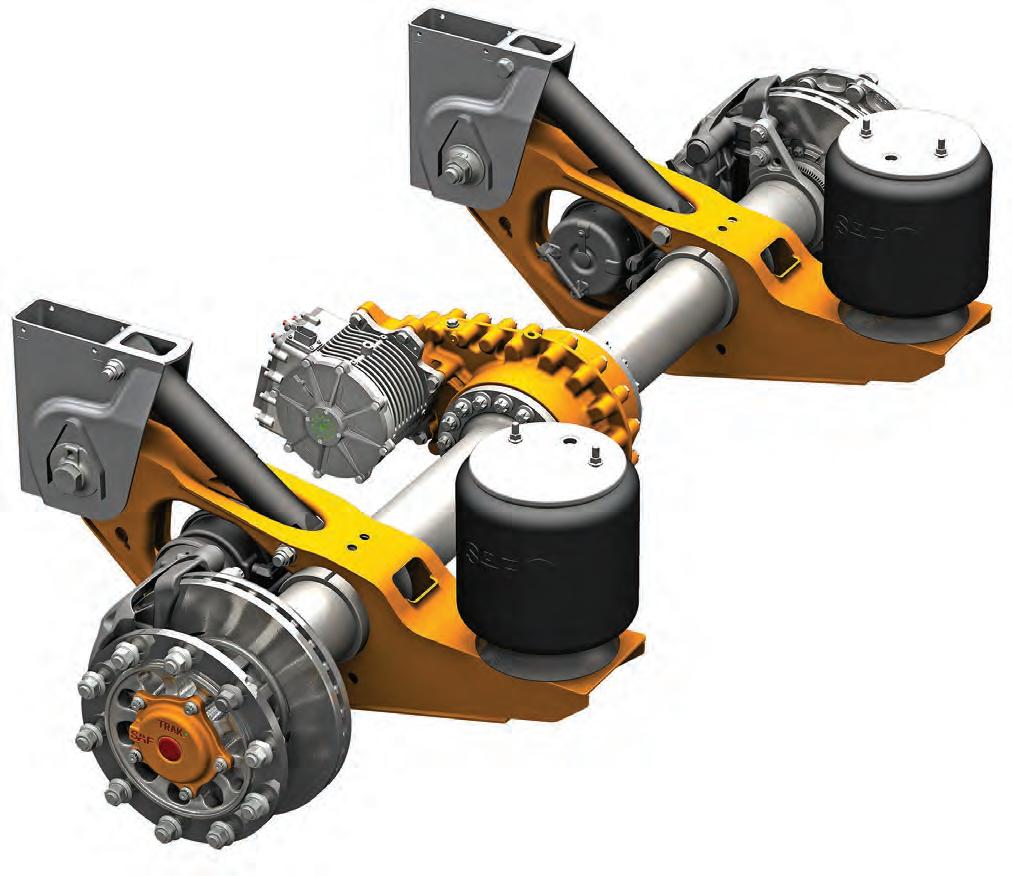
Series production: Starting in 2022
The electric trailer axles can be used, for example, to operate the refrigeration units in refrigerated vehicles permanently using only electric power. Ten pre-series vehicles are already on the road in Europe, and another in Australia. By the end of the year, a total 50 trailers from various manufacturers are to be equipped with the SAF TRAKr regenerative braking axle. Another 50 pre-series vehicles are planned for 2022, before the start of series production is scheduled for the end of the first quarter.
With the European Transport Award for
The European Transport Award for Sustainability in the category “Components and Aggregates” went to SAF-HOLLAND’s electric trailer axles, here the SAF TRAKr regenerative braking axle.
Christoph Günter President Europe, Middle East and Africa and Chief Technology Officer, SAF-Holland
Sustainability, now presented for the sixth time, the German Transport newspaper encourages companies from the commercial vehicle industry to operate sustainably. The award recognises that acting responsibly not only contributes to solving ecological and social issues, but also pro- motes the competitiveness and profitability of a company.
CENTRAL
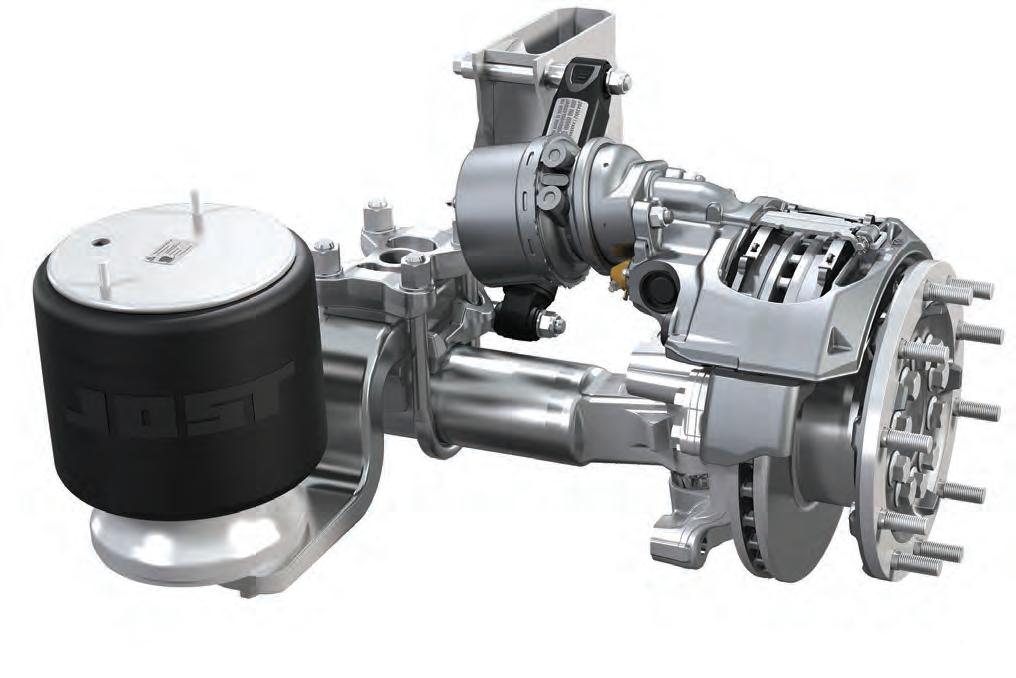
INTELLIGENCE
EQUIPMENT SPECIALIST, JOST, PROVIDES INDUSTRY WITH INTELLIGENT AXLE SYSTEMS.
In January 2015, JOST took over Mercedes-Benz Trailer Axle Systems and became an important manufacturer of truck and trailer axles in Europe. The latest innovations on offer is the command steer axle ZGA. In addition, the new DCA-U6 brake was also launched.
Command Steer Axle ZGA: For optimal manoeuvrability even in limited spaces
Narrow depots, winding city streets and a 16.5m long tractor-trailer that “THE JOST ZGA IMPRESSES WITH ITS QUALITY, MANOEUVRABILITY AND LOW ENERGY CONSUMPTION. OUR PHILOSOPHY OF TECHNICAL LEADERSHIP COMBINED WITH CLOSE CUSTOMER INVOLVEMENT CREATES UNBEATABLE ADDED VALUE.”
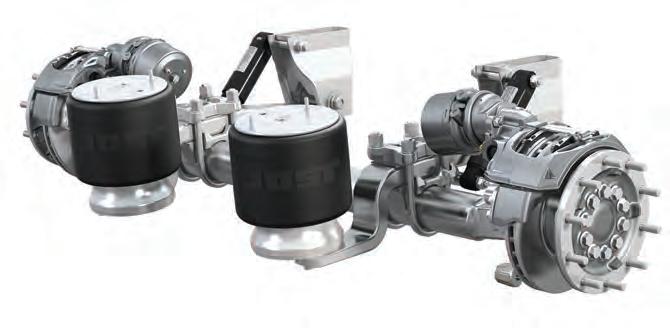
Alexander Schmid Product Manager, JOST Axles
needs to be steered safely – this is where conventional axle systems reach their limits and the use of a command steer axle is required.
Product Manager JOST Axles, Alexander Schmid.
The JOST ZGA can be used with all common steering systems, whether mechanical, hydraulic or electronical and impresses with outstanding performance features such as the low steering radius.
The command steer axle from JOST is the technological leader with its low rolling radius. The low rolling radius also has a positive effect on the actuator force, which is up to 70 per cent lower than that of comparable axles. Additional batteries become redundant and greater flexibility is gained in the design of the steering systems.
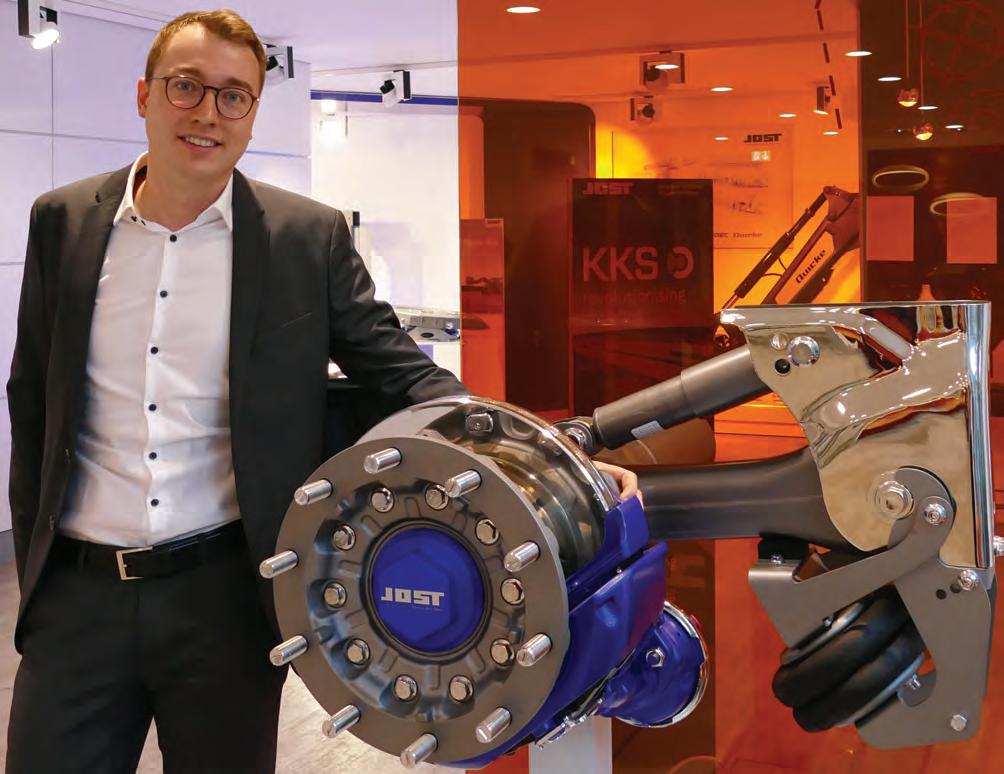
DCA-U6: The new 19.5″ brake from JOST
The DCA-U6 disc brake for 19.5“-applications is designed for maximum payload through a weightsaving construction. A weight saving of 15 kilograms per three-axle unit enables an increased payload and makes operation significantly more economical and efficient. An optional wear sensing system (BWI) ensures sustainable control of tyre wear. The use of a closed bearing system provides better protection against the external environment.
“The two product launches expand the JOST Axes portfolio with technologically advantageous solutions for our end customers,” said Alexander Schmid, Product Manager JOST Axles. “The JOST ZGA impresses with its quality, manoeuvrability and low energy consumption. Our philosophy of technical leadership combined with close customer involvement creates unbeatable added value.”
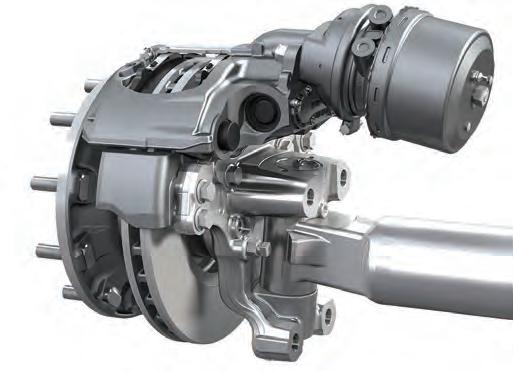