smarter Working
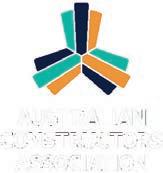
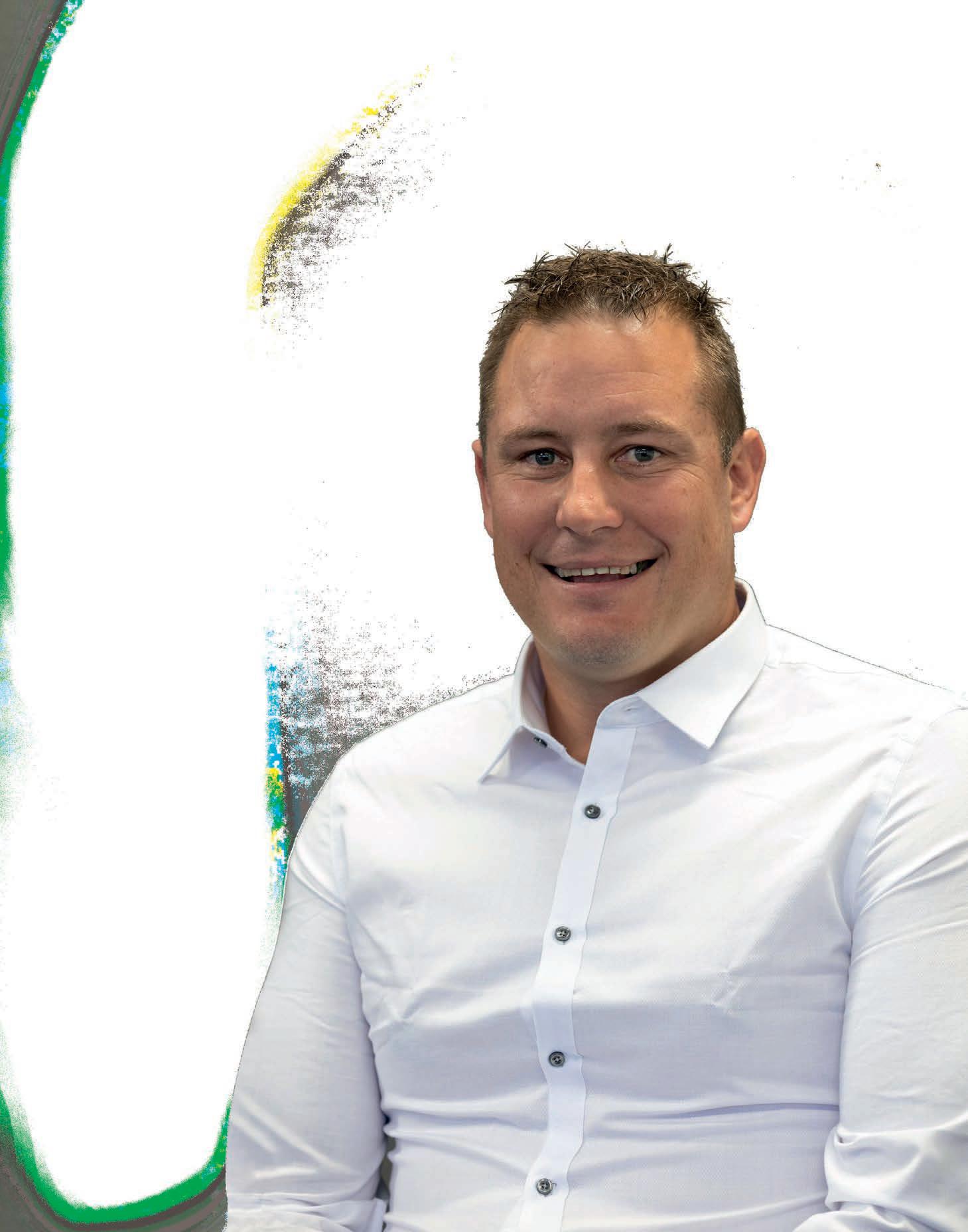
There’s a much better way. Payapps is the cloud-based collaboration tool that makes submitting and approving payment claims easier and faster than ever before. Payapps helps main contractors and subcontractors work better together to make progress claims and approvals simple and seamless, with a single, accurate and transparent view of every contract from project start to finish.
“Ditch
25
Working smarter
Komatsu develops a suite of smart solutions to address the complex pain points the construction industry faces.
The Inside Construction Exhibition, Conference and Awards is the ideal place to find new solutions for Australia’s construction industry. 44 Setting the standard
Construction leaders excel at the 2022 Women in Industry Awards. 46 Sydney Build returns
Sydney Build is back once again on 6 and 7 March 2023.
Director, Legal at Laing O’Rourke manages legal and risk to yield positive outcomes for construction businesses. 50 Jessica Manley
Construction Estimator for Superior Walls & Ceilings helps deliver iconic Australian infrastructure.
Harnessing transformative thinking to attract talent.
2022: The year that rocked construction.
National Precast Concrete Association Australia
All the curves and edges of The Ambrose. 58 The National Association of Women in Construction (NAWIC)
How Laura Cornthwaite found her perfect career.
Blackwoods set out to find a new solution for falls, one of the most common causes of workplace injuries. 28 Matrak and IIMBE
Matrak announces their partnership with construction information company IIMBE – a venture set to transform the construction industry.
McConnell Dowell Group’s building business unit Built Environs delivers complex buildings across Australia and, more recently, New Zealand. 36
How accounting software company Lentune proved integral to the expansion of developer Williams Corporation.
Roughan Haulage & Excavations integrates Trimble’s technology solutions to improve production, decrease rework and increase accuracy on construction sites.
Positioning your construction business as an employer of choice.
IPA Personnel sees extensive company growth upheld by their purpose driven labour hire, and diversity and inclusion recruitment services.
Empowered Women in Trades highlights the importance of gender equality in the construction industry.
How forward-thinking companies utilising efficient technologies like Payapps put themselves ahead of the pack.
Our December 2022 edition of Inside Construction puts a spotlight on the people that make up the Australian construction industry with a focus on attracting, recruiting and retaining a quality workforce. That’s coupled with the latest news in upcoming events, construction safety and technology.
It was an absolute pleasure to launch the print edition of Inside Construction earlier this year with the support of our readers, clients and the construction industry. We’re proud to finish off 2022 exploring a range of innovative solutions to some of the industry’s most complex challenges.
One challenge that has gripped the Australian construction industry is an ongoing shortage of skilled labour. Recent reports anticipate an increasing demand for skills in the years to come, and construction companies and industry bodies are doing their part to showcase the construction sector as an industry of choice for tomorrow’s workforce.
Labour hire and recruitment services company IPA Personnel is transforming its recruitment process across a range of industries in Australia, including construction. The company puts people first, attracting the right talent for the right role and supporting candidates through its Candidate Care Program. IPA’s passion for recruitment services in support of corporate responsibility, supplier diversity and workforce diversity commitments are proving successful in civil and mainstream construction sectors.
Inside Construction is also proud to announce our partnership with Empowered Women in Trades (EWIT), another organisation championing the people of our industry. EWIT, through their Trade Academy program, inspire women to pick up the tools and construct a more equitable world.
The National Association of Women in Construction has also come on board as a partner, highlighting the
diversity of roles in the construction industry.
In addition, technology has been recognised as a trending topic in the construction recruitment space. Companies taking advantage of innovative technologies, like progress payment management software Payapps, are positioning themselves ahead of the field as employers of choice. Payapps software can be a useful tool when it comes to talent acquisition and retention in the construction industry, paving the way for increased satisfaction and wellbeing in the workplace.
Further, technological solutions will be extensively covered at next year’s Inside Construction Expo in Melbourne. Across two jampacked days, the construction and major infrastructure event will cover topics such as the ongoing skills shortage, digital transformation and safety. Inside Construction is excited to be partnering with the Expo and we look forward to seeing industry leaders come together at the event.
We hope you enjoy our December 2022 issue and have a happy New Year.
Chief Executive Officer
John Murphy
Chief Operating Officer Christine Clancy
Group Managing Editor
Andrew Hobbs andrew.hobbs@primecreative.com.au Editor Ashley Grogan ashley.grogan@primecreative.com.au
Sales Director Brad Buchanan bradley.buchanan@primecreative.com.au
Art Director/Design
Daz Woolley
Art Director Blake Storey blake.storey@primecreative.com.au
Design Production Manager
Michelle Weston michelle.weston@primecreative.com.au
Business Development Manager
Adele Haywood adele.haywood@primecreative.com.au p: +61 0403 500 544
Client Success Manager Glenn Delaney glenn.delaney@primecreative.com.au
Cover image credit Marcus Walters
Head Office
Prime Creative Pty Ltd 379 Docklands Drive, Docklands, Victoria 3008 Australia p: +61 3 9690 8766 f: +61 3 9682 0044 enquiries@primecreative.com.au www.insideconstruction.com.au
+61 3 9690 8766
subscriptions@primecreative.com.au Inside Construction is available by subscription from the publisher. The rights of refusal are reserved by the publisher
All articles submitted for publication become the property of the publisher. The Editor reserves the right to adjust any article to conform with the magazine format.
Inside Construction is owned by Prime Creative Media and published by John Murphy. All material in Inside Construction is copyright and no part may be reproduced or copied in any form or by any means (graphic, electronic or mechanical including information and retrieval systems) without written permission of the publisher. The Editor welcomes contributions but reserves the right to accept or reject any material. While every effort has been made to ensure the accuracy of information, Prime Creative Media will not accept responsibility for errors or omissions or for any consequences arising from reliance on information published. The opinions expressed in Inside Construction are not necessarily the opinions of, or endorsed by the publisher unless otherwise stated.
Komatsu has a suite of smart solutions to address the complex ‘pain points’ the industry faces. The company’s current range of smart solutions has been developed to streamline the construction process through data analysis. Contractors and operators can use the collected data to track things like building materials, productivity, labour hours, costs and machine optimisation.
Australia’s National Product and Solution Manager Aaron Marsh delves into the company’s Smart Construction portfolio. Pages 10-13.
Blackwoods, backed by its expertise and technical knowledge, is raising the bar on fall protection.
Industry experts from Blackwoods suppliers Honeywell, MSA, Pryme and 3M, discuss the importance of using appropriate equipment and processes when working at height. Pages 25-26.
Construction supply chain and material tracking platform Matrak and construction information company IIMBE have announced a partnership set to change the way data is collected and used through Building Information Modeling (BIM).
Matrak Co-Founder and CEO Shane Hodgkins and IIMBE director David Foley explore the opportunities the partnership will create for the construction industry. Pages 28-31.
Operating under the umbrella of the McConnell Dowell Group since 2008, construction company
Built Environs has over 35 years of experience delivering complex buildings across Australia and, more recently, New Zealand.
Managing Director of Built Environs Michael Clemenger looks into the company’s expansion and portfolio of successfully delivered projects. Pages 32-35.
Australia, construction employs almost 1.2 million people, and that number continues to rise despite multiple setbacks. This month’s Construction Recruitment and Talent Feature explores how construction companies are attracting and retaining skilled candidates fit for the complex projects in the public and private sector pipeline.
IPA Personnel (IPA) started from humble beginnings offering recruitment services provided by a small team of mobile consultants. Today, the company has cemented itself as an estimable national recruitment agency supporting employers and candidates across Australia.
With the labour shortage being one of their biggest challenges in the past year, the IPA team paints a picture of the company’s success and what’s next for recruitment in the Australian construction industry.
Inside Construction is proud to announce we have partnered with Empowered Women in Trades (EWIT). This month, Hannah Keirl, EWIT’s Head of Commercial shines a light on the importance of gender
Attracting, recruiting and retaining talent is a challenge the entire construction industry is facing. EWIT, in 2022, has focused on the attraction and retention elements of this equation. Through its Trade Academy, EWIT inspires women to pick up the tools, to manufacture a better future, and to construct a more equitable world.
As EWIT continue to inspire more women to join trades and tradesbased industries, Keirl recounts the positive experiences of Experience Trades Program participants.
Construction software company Payapps is one of Australia’s leaders in the construction software space, replacing traditional, inefficient methods of managing progress payments with its intuitive, userfriendly software.
As well as Payapps providing an efficient improvement to traditional methods of managing progress claims, Head of Product & Coinventor at Payapps Mark Ballinger explains how the product can also be a useful tool when it comes to talent acquisition and retention in the construction industry.
This month we caught up with Williams Corporation Founder Blair William Chappell to discuss how accounting software company Lentune has become integral to its recent expansion.
Chappell, along with Jono Bonifant, Director and CEO of Lentune, explain the importance of utilising top technology and software to drive efficiency and success in the construction industry. Pages 36-37.
Civil contractor Roughan Haulage & Excavations has harnessed Trimble’s technology solutions to improve production, decrease rework and increase accuracy on construction sites – a formula that has bolstered their operations and client offering.
Matthew Roughan, Founder and Director of Roughan Haulage & Excavations details the benefits of integrating Trimble solutions to their small machines. Pages 39-41.
Inside Construction magazine introduces Melbourne’s own construction and major infrastructure event, Inside Construction Expo 2023. With a key focus on ‘Engineering for the Future’, the Expo will bring the major projects and civil infrastructure construction industry together on September 20 and 21 in Melbourne.
Across the two days, a world-class exhibition will showcase construction equipment and companies; industry leaders will present in an educational conference on industry challenges; and the best people, projects and innovations from across the Australian construction industry will be recognised at an Awards Gala. Page 43.
Held this year on September 8 in Sydney, the Women in Industry Awards (WII) recognise the achievements of women across
a range of industries in Australia, including construction, infrastructure, mining, transport, manufacturing, engineering and logistics, bulk handling, waste management, and rail. Women working in construction won several of the awards, with infrastructure construction company Fulton Hogan winning multiple categories. This month we hear from Fulton Hogan’s award winners about what it means to be recognised for their achievements. Pages 44-45.
Sydney Build is back once again on 6 and 7 March, 2023 featuring more than 500 exhibitors, 450 speakers and 20,000 attendees from the built environment industries.
Brought to you by Oliver Kinross, Sydney Build is part of the company’s award-winning ‘BUILD’ exhibition portfolio that extends internationally to include trade shows held throughout New York, Chicago, and London. Cutting-edge seminars, sponsored networking lounges and live equipment demonstrations are just a small portion of what attendees can expect to encounter at this year’s expo. Pages 46-47.
People. Pages 48-53. Annabel Crookes sits on the Australian executive committee for international engineering and construction company Laing O’Rourke as Director, Legal.
With over 22 years’ experience in the construction industry, Crookes leads Laing O’Rourke’s legal, risk and company secretarial functions in Australia, and is the new president of the Australian Constructors’ Association.
Looking back at her achievements, Crookes wants to change the misconception that you have to be an engineer to be in construction.
Jessica Manley has spent her career forging her own path in the
construction industry, and today reaps the rewards of working in a job she loves as a Construction Estimator for Superior Walls & Ceilings. Learnt throughout her career, Manley has top advice for those looking to enter a career in construction.
Dr. Gretchen Gagel shares her expert insight into the industry’s current and forecast labour shortages. Dr Gagel argues that transformative thinking is necessary to ensure the Australian construction industry has the talent needed to deliver the projects in the pipeline. She challenges everyone, as leaders, to do their part in achieving transformative thinking, action, and results in the construction industry.
Associations. Pages 54-58.
Jon Davies, CEO Australian Constructors Association , looks back on the challenges the Australian construction industry has faced over the past 12 months; from COVID-19 to skills shortages.
Davies says working together is the way forward in delivering high value infrastructure at a reduced cost.
The National Precast Concrete Association Australia showcases Master Precaster Euro Precast’s delivery of The Ambrose.
The Ambrose is a $160 million development by Kokoda Property, comprising 174 apartments and two retail spaces, that emanates pure sophistication and enhances the urban appeal of Milton, Brisbane.
The National Association of Women in Construction (NAWIC) has come on board as official media partners of Inside Construction Lauren Fahey, NAWIC’s General Manager, introduces the organisation, their goals, and shares the latest data from their member survey conducted earlier this year to highlight the need for industry action.
When it comes to civil construction, Komatsu has a suite of smart solutions to address the complex pain points the industry faces.
Australia’s National Product and Solution Manager Aaron Marsh delves into the company’s Smart Construction portfolio.
Komatsu is improving operations across all steps of the construction process and project lifecycle by connecting equipment, technologies and personnel through its Smart Construction portfolio.
During the construction of its Wacol Distribution Centre in Queensland, for instance – the single largest building Komatsu has ever constructed in Australia – Komatsu’s Smart Construction tools were vital to the process.
Komatsu National Product and Solution Manager Aaron Marsh says the portfolio of Komatsu Smart Construction tools is a gamechanger for the construction industry.
“The current Smart Construction portfolio includes around 15 solutions, some of which are specifically targeted at the civil construction industry, and provide insight to project managers, engineers, surveyor teams and operators,” says Marsh. “Our customers are each using elements of our Smart Construction suite on their various projects, from mass earthmoving to tailings dams and other civil construction projects.”
“The tools adopted on each project depend on the pain points for each customer.”
Smart Construction is the latest trend in the construction industry, improving productivity and safety through the application of
innovative technologies and tools. Komatsu, being one of the largest manufacturers of construction equipment, technologies and services in Australia, has an acute awareness of the ever-increasing value Smart Construction poses for the future of the industry.
The company’s current range of smart solutions has been developed to streamline the construction process through data analysis. Contractors and operators can use the collected data to track things like building materials, productivity, labour hours, costs and machine optimisation.
Marsh explains that the tools in Komatsu’s Smart Construction suite are designed to improve communication and connectivity between people, machines and materials.
“These tools cover unique solutions such as intelligent machine control, drone data collection to create 3D terrain maps, site dashboard visualisation and remote operator support,” he says.
“The civil construction industry has quickly embraced our solutions and has seen the benefits of working smarter with technology.”
One of Komatsu’s first Smart Construction solutions launched in Australia includes the innovative intelligent Machine Control (iMC), enabling operators to program 3D design data
directly into a machine. Currently available on Komatsu’s latest model ‘intelligent’ dozers and excavators – including the D61EXi/PXi-24, D65EXi/PXi-18, D71EXi/PXi-24, D85EXi/PXi-18 and D155AXi-8 dozers and the PC210LCi-11, PC290LCi-11 and PC360LCi-11 excavators –even less experienced operators are efficiently guided by the automation software.
“The iMC 2.0-enabled intelligent machines utilise 3D design data loaded directly into the machine to accurately check its position against the surface,” say Marsh. “It helps operators to automate auto stop control to grading, tilting and bucket movements to minimise over-excavation, and increase accuracy and efficiency.”
Also launched in Australia this year, Komatsu’s Every Day Drone (EDD) Smart Construction Edge and Drone tool can rapidly process drone data to create a 3D terrain map of a jobsite. Surveying a site up to 50 per cent faster than a walking survey, the cost-effective solution saves time and labour hours.
“On top of improving productivity, the data pulled from the Smart Construction Edge and Drone tool is incredibly accurate and fast,” says Marsh. “Not only do you have access to the data quicker, but the tool also takes 4K video and still photos for project progress tracking and asset inspection.”
Adding to Komatsu’s offering, the Smart Construction Retrofit Kit (RFK) provides information and communication technology functionality to existing hydraulic excavators. It’s a Three-Dimensional Machine Guidance (3DMG) and Payload solution for excavators ranging from 13 tonnes through to 36 tonnes, offering functions such as 3D machine guidance, a Payload Meter to measure bucket loads, and acquisition of 3D construction data to collect machine data.
Data from iMC, RFK, Drone and Edge are then directly connected to the Smart Construction ECO System and are visualised through the Smart Construction Dashboard.
Komatsu’s Smart Construction Dashboard combines 3D design data with aerial mapping and intelligent machine data to provide a visual of material quantities, all in one integrated location.
All construction information from a jobsite can be accessed by engineers and operators.
Speaking of the entire Komatsu Smart
Construction suite, Marsh says one important functionality of their products is that they are not limited to Komatsu machinery. “Our tools are agnostic,” he says. “This allows everyone to benefit from the tools, without having to invest heavily on modernising their fleet.”
“The idea is to make more and more of the Komatsu aftermarket machine tools agnostic so they can be retrofitted to existing machinery and supported through Komatsu’s experts.
“The Smart Construction Drone and Edge tools are among the solutions that are currently agnostic.
“Similarly, the Smart Construction Fleet, which is used for tracking movement of material and fleet, can provide a pathway for customers, irrespective of the brand of their mobile earthmoving fleet, to view their payload information both on and off project.”
“The civil construction industry has quickly embraced our solutions and have seen the benefits of working smarter with technology.”
Intelligent Machine Control – making it easy for even the most inexperienced operators.
Marsh says, the Smart Construction RFK will also be applicable to machinery other than Komatsu.
“Having a machine equipped with Smart Construction RFK Payload and reporting to the Smart Construction Fleet enables customers to see the history of payloads, which helps them comply with the chain of responsibility by making sure that all trucks leaving the site are correctly loaded,” he says.
Further, Komatsu knows that constructors are looking for more ways in which they can work remotely and still get the job done.
Komatsu identified the need for contractors to have greater control through remote access to site activities and developed the Smart Construction Remote. The application allows contractors to remotely send files from their
login to machines and see what an operator is doing; and support operators without having to be on site.
Komatsu has high ambitions for its Smart Construction offering, with several new applications and products in the pipeline – such as a fleet management tool suitable for both quarry and civil construction called the Komatsu iSite, the Smart Construction Fleet, Smart Construction Rover, Smart Construction Simulation, Smart Construction Field and Smart Construction Office.
According to Marsh, the solution package aims to address the existing ‘pain points’ in the industry, such as safety, without placing a heavy burden on contractors to renew their entire fleet.
“Every day, Drone and Edge eliminate the
“The Edge processing allows for a significant improvement in survey data processing from the drones to give the users data that they can make immediate decisions on.
“On some sites, we have seen up to a 90 per cent improvement against other survey processing packages available in the market.”
Efficiency and productivity are other pain points addressed by Komatsu’s Smart Construction tools.
“By reducing redo works and having effective utilisation, productivity is increased,” says Marsh. “Also, factory integration of tools such as iMC help reduce downtime and maintenance time.”
“The important thing, however, is not to view these solutions as siloed technologies.
“Together with the customer, the Komatsu support team can deep dive into specific pinch points on their projects and help resolve them by integrating the right Smart Construction tools.”
Smart construction technologies also pose great opportunities for fair game between smaller contractors and larger construction companies.
“Our solutions help level the playing field by allowing all contractors access to the benefits of technology and giving the adaptors a competitive advantage,” he says.
“We understand that smaller contractors don’t have the access to technologies included in the Smart Construction suite, nor do they have the IT infrastructure or the
resources to support them – this is where we go on the journey with them and act as their partners.”
Bridging the gap between subject matter experts in all positions within civil projects and novice operators is another important step towards a brighter future for the construction industry.
“All Smart Construction applications reduce the need for resources tied to the office chair and multiple spreadsheets to manage a project,” says Marsh.
“These solutions also address the skilled labour shortage by presenting to users the information that they need, without them having to be subject matter experts.”
Marsh says Komatsu’s Smart Construction team can provide technical support and training throughout Australia and New Zealand.
“Komatsu also has the ability to provide Technology Consultants embedded in the projects, or with customers’ day-to-day operations, to help onboard new technologies or provide services to these contractors and projects,” he says.
“More recently, we have opened a dedicated Smart Construction support centre at our new distribution facility in Queensland, which will service all customers in Australia and New Zealand, including our own regional teams.
“Customers will never be alone when they need support.”
“All Smart Construction applications reduce the need for resources tied to the office chair and multiple spreadsheets to manage a project.”Komatsu’s James McKenzie getting the everyday drone showing just
how easy the EverydayDrone
is to use.
This month the Inside Construction team caught up with the companies innovating and investing in recruitment and talent across Australia’s construction sector.
According to Infrastructure Australia’s 2021 report, Infrastructure Market Capacity, construction industry labour shortages are anticipated to be almost three times more than those of 2017-2018. Between 2021 and 2024 peak of demand for skills is set to be 48 per cent higher than supply.
These statistics have accelerated the competition for skilled staff and have brought forth an impressive wave of innovative and engaging strategies to attract, recruit and retain talent.
Organisations like Empowered Women in Trades are enabling women to thrive in
construction industry employment and encouraging women to see construction as a viable career path.
Construction companies are shifting their focus to creating a culture that attracts people; prioritising the wellbeing of their staff, valuing diversity and providing in-house opportunities for career progression.
Innovative technologies are being used throughout the industry to make construction workers’ lives easier and eliminating the need for menial tasks like data entry, further improving employee satisfaction.
This month’s Feature highlights the companies that are championing their people, cultivating healthy workplace culture and transforming their businesses into attractive places to work.
The people in the construction industry are the backbone of its success. At a time when attracting, recruiting and retaining staff is more competitive than ever, positioning your company as an employer of choice is vital.
Helping organisations and individuals to succeed for the past four decades, IPA Personnel continues to see extensive company growth upheld by its purpose driven labour hire, and diversity and inclusion recruitment services.
Established in 1984 in Melbourne, Victoria as Independent Personnel Associates, IPA Personnel (IPA) started from humble beginnings offering recruitment services provided by a small team of mobile consultants. Today, the company has cemented itself as an estimable national recruitment agency supporting employers and candidates across Australia.
The company’s expansion has seen it open 13 offices across Victoria, New South Wales, Queensland, South Australia and Western Australia, supported by approximately 140 experienced staff.
Client engagement manager James Muskett has been with IPA for four years, and says the agency services a range of sectors and industries including construction,
construction and as a result, we have built an incredibly strong reputation in the market for providing expert recruitment services, quality customer service and in-depth knowledge of the industry,” says Muskett.
“When looking at the latest figures from the Australian Bureau of Statistics – Labour Force Survey, Detailed, August 2022 – we can see that more than 1.2 million people are working in construction, making up more than nine per cent of Australia’s workforce and exceeding pre-Covid levels.”
Infrastructure Australia identified that by mid-2023 the construction industry is predicted to experience a shortfall of 105,000 workers across Australia.
The pipeline of construction projects is everincreasing, and so too the competition for
“One of IPA’s core industry sectors is construction and as a result, we have built an incredibly strong reputation in the market for providing expert recruitment services, quality customer service and in-depth knowledge of the industry.”
leading existing and new clients to IPA for its deep networks and industry track record.
“With a client base spanning across Tier 1, 2 and 3 construction companies, as well as subcontractors and other organisations within the supply chain, we are well versed and even better networked,” she says.
“We supply labour hire and permanent recruitment across all roles in the industry including both commercial and civil.”
With the labour shortage being one of its biggest challenges in the past year, Muskett adds that the candidate-short market has pushed the IPA team to look at innovative ways to attract talent. As a labour hire company that relies on a transient workforce and people coming into Australia looking for work, it has had to rethink its strategy, and has started looking at new digital advertising platforms such as social media.
“We have been using social media to find talent more than ever,” he says. “In fact, we’ve successfully used Instagram and TikTok to find talent in recent months – something we would never have done pre-Covid.”
In regional Queensland for example, IPA has civil construction clients that require employees to work in remote areas. Angela Olsen, Senior Business Manager - Regional Queensland at IPA says it’s challenging to attract candidates to these areas given their remote location, but IPA has had success due to their commitment to getting it right.
“We’re always looking for ways we can provide a candidate with value in potential roles,” says Olsen. “We innovate to entice people from all over Australia to apply for these
roles, and we make sure the employment opportunity waiting for them is of amazing value.”
From there, Olsen says they support candidates through IPA’s Candidate Care Program, aimed at keeping them in employment; and ensuring they’re enjoying it, working safely, and that all parties are happy.
As part of the Candidate Care Program, the IPA team contacts each candidate fortnightly to check in, ask how they’re going and provide support. Wherever the candidate is working, no matter how remote, IPA team members also visit the worksite once a month and conduct a toolbox safety talk with their staff –safety is a number one priority at IPA and the team are dedicated to being ‘All Safe, All the Time’.
In addition, IPA celebrates candidate birthdays and anniversaries with morning and afternoon teas and has developed a Safety Employee of the Quarter campaign to acknowledge safe workers.
“We are constantly receiving feedback from our staff that they’ve never worked for a company as supportive as IPA,” Olsen says. “When we’re on site, we have other employees asking to transition across to us, so that to me says a lot.”
Additionally, IPA has a dedicated Diversity and Inclusion (D&I) division providing personalised support to first nations people, youth, people living with disability and all genders. Led by Janelle Dorrington, Senior Business Manager at IPA, the D&I team ensures that the people they place into work can achieve long-term outcomes.
says IPA’s purpose and profit commitment presents ideal opportunities for members of industries, such as construction, to count their labour hire spend towards social procurement targets.
First-of-its-kind research commissioned by IPA and published in 2021 shows construction activity in Australia and New Zealand accounts for nearly half (44 per cent) of goods and services purchased in support of social outcomes. “Social procurement is mostly aimed at delivering local employment and jobs for people experiencing disadvantage and exclusion,” says Carter.
“IPA is therefore engaging more clients within the civil and mainstream construction sectors, seeking IPA’s expert recruitment services in support of corporate responsibility, supplier diversity and workforce diversity commitments.”
At a time of historically low unemployment and competition for talent, IPA is succeeding through its expertise and personal support, as well as the choice of jobs it offers. Carter says these aspects are attracting more candidates to IPA and away from online job portals.
“This is where the recruitment agency model stands out for delivering workforce solutions for clients”, she says.
“IPA candidates tell us our customer service and knowledge about roles and particular
employers is a big factor in building a quality candidate pool.”
“Further, candidates say the ability to return for more work through IPA once their job assignment is over is another plus.”
Carter says IPA’s 100 per cent profit commitment to community services is also a drawcard, reflecting the growing expectation that companies and government show responsible business practices.
“More than three quarters of IPA candidates say our reinvestment back into community inclusion could or would positively influence their decision to use our services again,” she says. “That sentiment is even stronger across the general population (87 per cent).”
On top of their passion for providing quality services to their candidates and organisations alike, the IPA team has a positive outlook on the future of recruitment in the Australian construction industry.
It’s an industry that is a priority for every part of Australia, Olsen says. “No matter where you live, construction is a requirement,” she says. “As a country, we need to put more of our attention into upskilling our young people and making sure that we have access to trades.”
“Employers need to value their staff, listen to what they have to say and care.
“That’s exactly what we do at IPA – we put people first.”
“We assist employers to identify gaps in their cultural knowledge, processes and practices, and advise them on what they can do to improve and make their workplaces more inclusive.”
Inside Construction is proud to announce we have partnered with Empowered Women in Trades (EWIT) This month, Hannah Keirl, EWIT’s Head of Commercial, delves into the importance of gender equality in the construction industry.
It’s safe to say it has been a tumultuous couple of years for Australia, and it has affected us all in a number of ways – some of which are only surfacing now. The construction industry has been plagued with skills shortages, material shortages, and a burnt-out workforce. What’s worse is the national average of women’s participation in trades-based industries has increased only from one per cent to three per cent in ten years. At the same time, research by the National Centre for Vocational Education Research (NCVER) shows a decline in the number of women completing a trade, which is down 6.3 per cent from 2020. This creates a major issue for the construction sector in the face of the government’s new quotas, requiring at least 40 per cent participation of women across projects by 2024.
But that’s changing. Post-pandemic we’re meeting woman after woman who wants to get outside, be hands-on and be a part of the build – incrementally right now, but at a far greater rate than any time in the past decade.
Attracting, recruiting and retaining talent is a challenge we’re all facing. We know it costs far less to retain than to attract and recruit
– in fact the average recruitment cost per position is around $23,000 according to the HR Industry Benchmark Survey 2021 Australia and New Zealand – so to do this, industry is having to make changes too.
For Empowered Women in Trades (EWIT) in 2022, we’ve focused on the attraction and retention elements of this equation. Through Trade Academy, we inspire women to pick up the tools, to manufacture a better future, and to construct a more equitable world. More than 350 women and female students have, to date, participated in at least one of our programs (which range from one day to three weeks).
It’s extraordinary to watch the journey that each woman goes through in our Experience Trades programs, from the screening and interviewing where nerves are evident but the curiosity overwhelming, to the gasps and cheers of joy when they’re granted their Scholarship place.
On the first day, as they lace up their work boots and try on their hi-vis, there is a genuine sense of nervous excitement coursing through the room. We meet Tradie Trailblazers and discuss what the following few weeks will look
like. We work with each of the women through positive psychology frameworks to build Positive Emotion, Engagement, Relationships, Meaning and Accomplishments (PERMA) –and fill their toolbox with our strategic partner Maxme’s human skills.
These are the tools that cement the foundation for their success. The next few days see each of the participants get their applicable tickets required to be out on site, followed by two or three weeks of work experience. We touch base with each participant multiple times over this duration, coach them through the highs and lows, work out which (human skill) tool needs to be pulled out the toolbox during miscommunications or when the fatigue sets in the first time. It’s physical, and at times overwhelming, but it’s rewarding.
We round out the experience by holding celebrations with industry partners, training organisations, subcontractors and all the teams who have made this possible. It’s an opportunity to share, connect and form a growing and impactful community of empowered women in trades.
This year, 71 per cent of our Experience Trades participants have gone on to work in trades, from plumbing pre-apprenticeships to crane operations and everything in-between.
For us, this is just the beginning. It’s with partners like Kapitol Group and the Southern Program Alliance that we’re able to aid in this progress.
To stimulate a pipeline of future talent to the sector, Kapitol have partnered with us at EWIT, and we’ll be engaging with multiple Victorian schools to educate females on the opportunities both in trades and within the construction industry. Through Tool Skills programs, not only will these students get hands on the tools, but they’ll get their white cards and head out on Kapitol’s sites in an holistic, immersive experience. Similar programs are open for women who are under-employed, unemployed, returning to the workforce or seeking a career change.
As Kapitol’s founder and joint Managing Director David Caputo says, “Construction and trades can be great jobs to work in, particularly in terms of flexibility and remuneration, but unfortunately that has not been the
experience for many women, who remain in the minority.”
“We need to address this disparity and increase female representation, not just to address headcount in this era of labour shortages, but to reap the benefits of having diverse perspectives on site and in the office.”
EWIT’s CEO Hacia Atherton adds that men are equally a part of this equation of building a more equitable workforce in a growing and lucrative industry.
“While there are many benefits for women for working in construction, having a female presence on-site benefits men too,” she says. “Studies – like RMIT University School of Property, Construction and Project Management’s Women in Construction: Exploring the Barriers and Supportive Enablers of Wellbeing in the Workplace report – show that men take less risks when women are on site and their mental-wellbeing improves.”
“The process of gender inclusion can’t be placed on the shoulders of one party alone because the journey is shared by everyone.
“It is essential that support is in place for all along this journey and psychologically safe spaces are created for men, women and nonbinary [people] to speak about challenges and discomforts that they face during this change.”
As we continue to inspire more women to join trades and trades-based industries, we are thrilled to see the community grow, develop and drive inclusivity.
We’re looking forward to 2023 as we continue to support the journey of all aspiring and qualified Tradie Ladies. Who’s with us?
Post-pandemic, we’re meeting woman after woman who want to get outside, be hands-on, and be a part of the build.A participant learning to strip wires in the electrical component of Tool Skills Day. Empowered Women in Trades Founder Hacia Atherton on the tools.
When it comes to attracting talent to the construction industry, the forward-thinking companies utilising efficient technologies like Payapps are positioning themselves ahead of the pack.
Construction software company Payapps was established in 2014, born from a mission to make the progress claims process easier and more efficient for everyone involved, regardless of whether they’re in the office or onsite. Today the company is one of Australia’s leaders in the construction software space, replacing traditional, inefficient methods of managing progress payments with their intuitive, user-friendly software.
Head of Product & Co-inventor at Payapps Mark Ballinger has been with the company since day one, helping founders Lincoln Easton and Geoff Tarrant to design and develop the Payapps software. As well as Payapps providing an efficient improvement to traditional methods of managing progress claims, Ballinger says their product can also be a useful tool when it comes to talent acquisition and retention in the construction industry.
“Using technology is not the be all and end all of attracting talent to the construction industry, but no one wants to turn up and work in the dark ages,” he says.
“We know that in the current construction
labour, it’s become more important than ever for construction companies to think innovatively when it comes to attracting and retaining quality staff. Technology is paving the way for increased satisfaction and wellbeing in workplaces around Australia.
“In terms of flexibility and autonomy Payapps is a cloud-based software that works on a mobile, tablet or desktop so users can manage progress claims anywhere, anytime,” explains Ballinger. “Payapps drives efficiencies by removing manual processing, saving time and reducing the risk of human error or delayed submission of claims with real-time visibility.”
“Payapps customers have said that they’re getting asked when conducting interviews whether or not they use Payapps, because candidates have used the software in their previous roles and don’t want to go backwards.”
At a recent networking event for Payapps customers, Ballinger says co-founder and director of Kapitol Group, Andrew Deveson, spoke of the importance of embracing new technology in the construction industry.
“We employ smart people, so why would we then make our people work with outdated, inefficient processes and systems,” said Deveson. “Our mantra at Kapitol is ‘smart people, smart work’.”
Based on this, it’s no coincidence Kapitol Group was recently acknowledged with the ‘#1 Best Place to Work 2022’ award by WRK+.
“It’s this digital-first mindset that sets companies apart from the rest,” Ballinger says. “When a new hire is onboarded with the latest software and technology, they know they’re joining a forward-thinking company.”
By removing the extra manual labour associated with managing progress claims, Payapps gives companies and their staff time to focus on things like higher value tasks.
Ballinger says when it comes to positioning your company as an employer of choice, saving hours (not to mention money) on menial tasks can be a gamechanger.
“Many of our customers have seen a reduction in processing progress claims by up to 50 per cent, enabling their staff to spend more time on higher value opportunities and less time reconciling spreadsheets or chasing down paperwork,” he says. “That
saved time can mean construction workers have more time to focus on delivering the actual construction job and to spend time with their families. Several of our customers are championing the five-day work week, which has always been a challenge for the construction industry.”
“We pride ourselves on three pillars – simpler, faster, fairer – and that’s what our product does. Our design philosophy translates to the way we want our customers to be using the product – it should be easy for them to learn how to use it, their work shouldn’t be hampered just because they’re rolling out a new tool. Main contractors and subcontractors should all be working from the same information.”
The Payapps team similarly has a modern thinking mindset when it comes to its own business, making sure its employees have the latest in modern technology. Ballinger says they want employees to be excited by the technology they are using.
“As our product simplifies the repetitive processes in the construction industry, we likewise want to use tooling internally that makes life easier for the teams we employ,” Ballinger adds.
“Our engineering teams, for example, have all the latest tooling and automation accessible to them to ensure they’re focused on the enjoyable, creative aspect of adding value to our customers as opposed to the more mechanically mundane tasks. People want to know that what they produce is making a difference.”
The principles are similar across all roles at Payapps, with the latest technologies offered across the business to ensure their people have fulfilling roles.
Beyond technology, Ballinger believes a continuous improvement mindset is also essential to attracting and retaining staff. A company might have invested in new technology, but they need to ensure that it’s keeping up to the pace of the industry.
“When a new hire is onboarded with the latest and greatest software and technology, they know they’re joining a forward-thinking company.”
ThePayapps
team says technology can bring people together to create positive change in the construction industry.Image: Emily Foot.
Technology like Payapps provides consistent processes to free people up so they can get on with actual construction.
Image: Emily Foot.
“You want people to know that they are moving with the times and that the skill sets they have are still relevant,” explains Ballinger. “We’re constantly looking for new ways to improve or simplify what we do, especially from a software development perspective.”
The role of technology in shaping the next generation of construction workers is increasing. Younger employees coming into construction as a graduate have an expectation that specific software and programs are available that will help streamline the way they work, highlighting the importance for construction companies to adopt a digital mindset.
On top of helping the industry with their
technology, Payapps has partnered with the Victoria University in Melbourne for the past three years, integrating its software as part of the university’s construction management curriculum. They’re helping the next wave of graduates that come through to have familiarity with the Payapps system, which is now used by over 70 per cent of the top 20 builders in Australia.
“When these graduates head out looking for a role in the construction industry, chances are they’re going to be using Payapps,” says Ballinger. “If they’ve experienced our software at university, it’s only going to help them in their future careers.”
In the early days of Payapps, Ballinger says
their biggest challenge was trying to get subcontractors involved and understand the value proposition. Now, Payapps has a large market presence in Australia due to its quality product, strong industry relationships and the surging uptake of technology in the construction industry in recent years.
“Now, we can confidently say to a builder that it’s likely that half of their subcontractors have used Payapps at least once,” says Ballinger. “We’ve hit the tipping point now where we are becoming an industry standard in terms of simplifying the progress claims process.
“If you can standardise something, you can make it more efficient, so by having a consistent process it frees people up to get on with actual construction.”
Payapps is also helping shape the use of technology in the industry with their disruptive mindset. Historically if you had a problem with software, you would send an email to the company and wait for a response back which could take up to 48 hours or more.
Payapps identified a better way of assisting their customers, introducing an in-app chat as their main support mechanism.
Since introducing the in-app chat in 2016, data over the last two years shows their median response time to enquires or questions has stayed consistently under one minute and their median time for resolving a question sits at under 17 minutes.
“In construction you have deadlines to submit a claim,” says Ballinger. “You have to claim on a certain day of the month otherwise you could potentially have builders saying that you’re waiting until the next month, which significantly impacts your cashflow.”
“Likewise, from a builder’s perspective, they need to assess those claims within the security of payment deadlines otherwise they’re potentially liable for higher funds than they consider due – so there’s pressure on the timing of when people process transactions through the system.”
Payapps customers know that if they’ve got an issue, Payapps has their back. The immediacy of the in-app chat resolves issues on the spot, rather than their customers having to wait a few days for an email back from the software provider.
When it comes to Payapps’ internal vision and culture, Ballinger says they strive to translate it in how they work with the construction industry.
“We work with our customers as partners,” he says. “When a company works with us, we go the extra mile for them and are honest about what will work for their business.”
“Whether it be helping a company to save time, attracting quality candidates or improving collaboration along the supply chain, our goal is to continue to create positive change in the construction industry.”
“We’re constantly looking for new ways to improve or simplify what we do, especially from a software development perspective.”
Utilising technology that saves hours and money on menial tasks can position your company as an employer of choice and be a gamechanger for attracting the best talent.Image: Emily
Foot.
The Inside Construction weekly e-newsletter is your leading source of construction news and insights showcasing the very best that the construction industry has to o er. or visit www.insideconstruction.com.au, and click the “Join our newsletter” box on the bottom right to subscribe to our weekly newsletter!
www.insideconstruction.com.au
Over the past 140 years, Blackwoods has earned its place as one of Australia’s largest providers of industrial and safety supplies. With falls one of the most common causes of serious injuries and deaths in the workplace, the team at Blackwoods is raising the bar on fall protection.
Blackwoods, backed by its expertise and technical knowledge, has a large offering of safety products that reduce the risks associated with working at height, delivering top safety products from the likes of Honeywell, MSA, Pryme and 3M.
When working on a temporary platform, it’s easy to take shortcuts; not bothering to connect a safety harness because no one’s looking or even forgetting to tether a tool. But these simple behaviours can have terrible, and often fatal, consequences.
Working at height is a major safety hazard. Safe Work Australia’s 2021 Safety Report noted that in 2020, falls from height were responsible for 11 per cent and being hit by a falling object for 9 per cent of workplace fatalities. That’s 39 lives lost to preventable accidents in one year alone and 122 lives over the last five years.
While the Hierarchy of Controls system and appropriate equipment, processes and training are there to be used when working at heights, they’re only effective to a point. In order to save lives, we need to look at the ‘culture of safety’ in the workplace.
Ricky Gleis, National Fall Protection Specialist from Honeywell, understands the importance of business-wide cultural change. “Changing the culture around working safely at heights cannot happen in a simple training session,” says Gleis.
“It takes clear business processes to firstly acknowledge existing behaviours around complacency, then subsequently the ‘influencers’ in the business need to continually encourage, promote, and sustain a change in safety culture. It’s also about involving those who have skin in the game, such as workers themselves – this will support company-wide behavioural change.”
Instilling a habit of safety from the top down and making this company ethos and policy is essential to ingraining a safety-oriented company culture. Simply dictating policies won’t get workers to comply with procedures.
They need to be included in the conversation about safety policy from the start and
contribute from firsthand experience. This will make them more likely to follow these procedures and encourage others to do so on the job.
Once the core value of safety is established in a company’s culture, safety equipment and Personal Protective Equipment (PPE), are more likely to be used at all times and in the correct way.
From an Engineering Controls standpoint, there are many safety measures that can be taken to minimise fall risks: including fall prevention devices like scaffolds, perimeter guard rails and safety mesh, as well as fall arrest systems like catch platforms and safety nets.
From a PPE standpoint, there’s fall protection, such as harnesses and fall arrestors to keep the worker tethered to an anchor point, and tool lanyards to keep tools and equipment tethered to the person.
If a worker misses a step, slips on a wet surface, or in the case of being lowered into confined spaces, loses consciousness due to lack of oxygen or noxious gas inhalation, the fall protection equipment is the piece of PPE standing between them and loss of life or serious injury – and in a confined space situation, this is also a main piece of the rescue procedure.
Nick Stinziani, Business Development Manager at safety equipment supplier MSA, explains that choosing the correct harness for the task is essential. “But equally important is the selection of supporting equipment, anchorage points and a rescue procedure,” he says.
“For tasks involving confined spaces the prework assessment process takes on even more critical importance. Reference should always be made to ensure compliance with standards and regulations, as well as the relevant Codes of Practice, to assist in performing the work at the highest level of safety.”
On the other hand, lanyards for tools protect the other workers on site. A tool falling from a height can have dire, if not fatal, consequences
“Changing the culture around working safely at heights cannot happen in a simple training session.”
“As indicated by Safe Work Australia, any at height operations above two metres, requires proper tools tethering. Approved systems are invaluable and do save lives.”
for the unlucky person below. The use of these types of PPE is not only about keeping the wearer safe but their teammates safe as well.
Brad Houlihan, Sales Director from industrial workplace products supplier Pryme, says in support of fall protection systems, a Drops Free Zone must be created. “It’s not just about the cleared space below the work area, it’s how your tools are managed whilst in operation,” he adds.
“As indicated by Safe Work Australia, any at height operations above two metres requires proper tools tethering. Approved systems are invaluable and do save lives.”
Pilots, when they experience an emergency in the air, have an Emergency and Abnormal Checklist. The co-pilot will pull out the book and go step-by-step through each action the pilot must take to handle the crisis. This may seem a clunky way to do it, but what it does is eliminate human error brought on by panic, fear, exhaustion, and bad decision-making. So too, in the construction industry, there
should be fail-safes against human error, and these are visible safety procedures, Safe Work Method Statements (SWMS), and ongoing training on how to use them until a pattern of safety behaviour becomes established, second nature and muscle memory.
Johnn Panlilio from 3M explains that with all specialised operations, competent training must be conducted on the correct use of a safety harness. “No two are the same as there are specific harnesses for working at height and confined space applications,” he adds.
Earning a living to support yourself and your family should not come at the cost of your life. Business owners, managers, safety officers and workers themselves all have a duty of care to ensure everyone clocks off safely at the end of the day. Where human error fails, safety procedures, training, equipment, and PPE need to have your back.
For more information, please contact Blackwoods on 13 73 23 or www.blackwoods.com.au
Construction supply chain and material tracking platform
Matrak has announced its partnership with construction information company IIMBE – a venture set to transform the construction industry through material tracking data.
In a bid to help the construction industry understand and navigate the digital era, Matrak has partnered with construction information company IIMBE to integrate Matrak’s material tracking data into Building Information Modeling (BIM).
The integration is set to effect positive change in the efficiency of construction projects in Australia through the sharing of critical material tracking data. Co-Founder and CEO of Matrak Shane Hodgkins and David Foley, Director at IIMBE, say they are proud to partner on such an important next step for the future of construction in Australia.
“As we continue to move towards a more digital future, the construction industry needs to take action by using technology to be more efficient,” says Foley. “Construction is arguably the least digitised industry in the world behind farming, fishing and agriculture, and to progress we need to be actively moving everything from traditional paper-based data collection into digital processes.”
“This partnership enables us to help the
construction industry understand and navigate the digital era, and we do this through digital data.”
Equally excited by the partnership, Hodgkins says that IIMBE already delivers a wealth of data management and support for Australian builders and developers on their projects. Adding to that database, Matrak is sharing its data with IIMBE to ensure that it ends up on the BIM.
“By sharing our material tracking data, our clients can then benefit from the data and use it to be more efficient in their day-to-day operations,” Hodgkins says.
BIM in construction is an intelligent software modelling process, supported by technology, using collaborative information from different construction stages to provide a unified information resource. It collates information that may have otherwise been misplaced or unknown using traditional modelling processes - such as what materials were used in a build, overrun costs, and the decisions that were made at each stage of a project.
Matrak’s interactive digital floor plans offer real-time views that allow teams to visually communicate and update site progress.
and Foley say, is to incorporate more information about current and future issues for clients going forward. For instance, if a client is ordering 300 shelving units for a commercial office building, they need to track each unit’s model and serial number, who installed it and who tested it to get commissioned. All of that information is done daily on a project, but traditionally you would receive one big PDF file with all the information.
Foley explains that they can use Matrak software to collect additional and more beneficial information from the supply chain as soon as they’re procured rather than waiting until project completion.
“Some of these projects can sometimes take years to complete,” says Foley. “Having the relevant information in front of you as products are procured is extremely beneficial in terms of saving time, costs and improving efficiency.”
“Design or construction is all about focusing on certain elements, and then as they get to
“If we can do a handover of information and documents progressively to alleviate that problem of sorting through a bunch of documents at the end of a project, it poses massive benefits for the industry.”
IIMBE aims to implement a software for two of the valid reasons that Matrak has already built and expand that to de-risk some of the other challenges that the industry faces, becoming an even more valuable software for construction projects.
Looking at BIM integration, a client can track what’s been coordinated, what’s been ordered, what’s in the warehouse or if there’s a fault with a certain panel, for example. IIMBE’s BIM management offering can provide deeper insight and a better understanding of the project status by integrating it with the model and checking what’s been modelled as to what’s being delivered then to what’s been handed over.
“We’re not trying to change what happens, we’re trying to give better insight into the
“This partnership enables us to help the construction industry understand and navigate the digital era, and we do this through digital data.”
current process that cannot be seen,” says Foley.
The process of BIM integration is multifaceted, starting with a 3D model of the construction project to be delivered. Steps include ensuring that there’s information around the ID or the sequence that all of the different products need to be manufactured in, shipped in and stored in, to make sure you can have a one-to-one connection across the systems. From there, IIMBE is able to pull
the data into metric from the model, allowing users throughout the supply chain to use interactive drawings or QR codes to tick off the products as they’re manufactured, packed, shipped and installed.
Any of this additional key information that’s useful for the client can be stored progressively as construction is underway.
The benefits of BIM integration for constructors are vast. During many projects, changes can be made along the way and
sometimes unintentionally. If a client changes their mind, but a product has already been ordered and can’t be cancelled, then changes can end up being made without the visibility of the bigger effect and impact on the project. “What we’re trying to do is give that transparency and clarity to where everything is on a project,” says Foley.
“When we talk about commercial offices, hospitals or data centres, nothing is ever complete until the project is finished and handed over,” he says. “There’s constant change throughout a project’s life, and we’re helping to understand what the impacts of change are.
“With integration you can quickly see on a dashboard what changes are going to have what impact on a project.”
One of IIMBE’s big goals, as a company, is breaking down the silos between the different players in construction, so that what the manufacturer is doing is connected to what’s happening on site and vice versa.
An interesting silo that they have found, says Foley, is that even when they’re working with some members of a project team for a builder, there might be other people working for the builder who have real data needs.
“What they don’t realise is that the data is available in Matrak, and so by putting that front and centre we’re able to break down the silos within construction organisations, the builders and developers,” he says.
“This means, for instance, the people who are responsible for facilities management will have access to the data about the supply chain and can use it to better run preventative maintenance and manage the operations of a building.”
Another challenge IIMBE and Matrak have come across is the abundance of data and information available in the construction industry, but lack of awareness that it’s there. When someone doesn’t know the data is there, they don’t ask for it.
If a client can tell IIMBE what they’re trying to look for or what questions they want answered, then data can then be sorted, searched for and located to help provide the client with an answer.
“That’s what excited me about Matrak and what it does now,” says Foley. “I can see that the whole construction industry will love it
– Matrak gives you a quick and clear picture of where your materials are, what’s been ordered, where it is and where it stands, and that’s only the beginning of its potential.”
“Then, in terms of functionality and what we can do now we’ve joined forces, we can expand on that. We can answer more questions, pull data out and create dashboards based on those questions.”
The idea is to collect all information automatically, to provide live dashboards and a day-by-day status of what’s happening on a project.
Clients can see what’s happening in real time rather than having to be on a construction site playing with guesswork.
By giving real life examples and capturing history on projects, says Foley, you can compare one project to another.
“If you are working with the same developer across five projects, you’ll have the ability, through BIM, to look at trends, identify problem areas and the impact problems can have across a builder’s portfolio,” he says.
IIMBE and Matrak’s BIM integration has the potential to do great things for the future of construction. The opportunities around preventative maintenance are substantial.
For example, you might have a 30-storey building and some of the windows start leaking. Instead of having to check the entire level and every window, IIMBE can look at the data and see who manufactured it, which batch it was manufactured in and how it was packed, and who installed it. You might find the leaking windows were installed by an apprentice who wasn’t experienced with a caulking gun or maybe it was a faulty batch.
By identifying where in the supply chain the issue lies, it can make a big difference in how a building is managed.
“One of the most exciting parts is actually having that information available for the project’s end of life, because then essentially you have this materials bank of all of the products, where they came from and how they were supplied,” says Foley. “They can then be used for recycling or other usage.”
“The vision is to hopefully move forward from the design and construction information that we are working with, into helping the people in operations and asset and facility management.”
“When we saw what Matrak did, we identified it as a product that’s functionality is extremely useful for understanding supply chain issues – resulting in the partnership we have today.”
Operating under the umbrella of the McConnell Dowell Group since 2008, construction company Built Environs has over 35 years of experience delivering complex buildings across Australia and, more recently, New Zealand.
Built Environs was established in 1987 as a privately owned engineering and building business, delivering a large portfolio of significant and diverse projects across South Australia and Western Australia.
Following several significant joint ventures in the early 2000’s – including the notable Adelaide Desalination Plant project – Built Environs was purchased by McConnell Dowell in 2008.
As the building business unit of McConnell Dowell, the company has successfully continued and expanded its operations in South Australia and Western Australia, as well as expanded into the New Zealand market in 2018. Michael Clemenger, who came on board as Managing Director of Built Environs in August 2020, says that was just the beginning of the company’s growth.
“When I joined the business, our goal was to ramp up our operations in New Zealand and enter the Victorian market,” says Clemenger.
Clemenger’s career as a construction professional spans 28 years across Australia and internationally. His previous roles with Cockram Construction & Icon as its Victorian State Director saw him gain a
wealth of experience managing all aspects of construction project delivery. Clemenger worked across a diverse range of industry sectors including health, Defence, commercial and education.
His career included an opportunity to work on a large pharmaceutical project for SmithKline Beecham in Tianjin, the port city for Beijing, China. “I spent the best part of two years working in a city of 10 million people, gaining both invaluable work and life experience,” he says.
After 25 years with Cockram and Icon, Clemenger was well placed to bring his knowledge of the New Zealand and Victorian markets to the Built Environs team.
With Clemenger leading the growing company, Built Environs entered the Victorian market in early 2021. “We are really still in our infancy from a market progression perspective, however in just 18 months since we’ve entered the market, we already have a sizeable pre-qualification level with the Victorian Government Construction Supplier Register and we are getting approached for some great opportunities,” Clemenger says.
“Our first project in Victoria, the Beaumaris
Secondary College Stage 2, for the Victorian School Building Authority (VSBA), included the design and construction of a three-storey extension of the Learning Hub as well as senior learning and collaborative spaces.
“We were thrilled to deliver the project on time with minimal disruption to the live school environment, making our mark in the Victorian market as an efficient and robust builder of choice.”
Built Environs now has another two projects in the education sector in the state underway including the delivery of a new Year 9 building at the Haileybury College, Brighton Campus; and Mount Alexander College and Flemington Primary School upgrades for the VSBA.
Now mobilised on its fourth project, Built Environs is working with parent company McConnell Dowell on the Level Crossing Removal Project to build a new station at Mt Derrimut Road in Deer Park – part of Victoria’s Big Build infrastructure project.
“We’re working in joint venture with McConnell Dowell and that’s something that has been an invaluable point of difference between us and our competitors across both Australia and New Zealand,” Clemenger explains.
“Being a part of a large infrastructure group, we have been able to approach clients and give them the value offering of doing both the building works and the infrastructure works at the same time.”
Clemenger says these four projects were part of Built Environs’ entrance strategy, starting in a modest manner as it builds its profile and a strong team. Built Environs has now mobilised on its fifth project in Victoria, delivering one of Australia’s first vertical multi-use sports centres at the Fitzroy Gasworks site in Melbourne for Development Victoria.
“This project has marked a significant step in Built Environs’ journey in Victoria,” says Clemenger. “Within 18 months, we are now getting the opportunity to deliver much larger and complex projects.”
“It’s a great space to be in, predominantly working on social infrastructure projects and working for various different arms of the state government, here in Victoria.”
The company’s expansion into the New Zealand market has also been successful, following the on-time completion of the Puhinui Station Interchange project in Auckland in July 2021. Also delivered in joint venture with McConnell Dowell, Clemenger says the project went exceptionally well and showcases the strong collaboration between the parent company and Built Environs.
“We sometimes have clients unsure of the market positioning of a project, asking if it’s an infrastructure job or a building job,” Clemenger says. “We can say it doesn’t matter, because we can do both, we are a one stop shop.”
“Being a part of a large infrastructure group, we have been able to approach clients and give them the value offering of doing both the building works and the infrastructure works at the same time.”Artist’s impression: One of Australia’s first vertical multi-use sports centres at the Fitzroy Gasworks site in Melbourne.
One project Clemenger is particularly proud of is the Auckland City Mission (ACM) HomeGround Development. Built Environs’ second project in New Zealand, the team delivered a new multi-storey facility that includes 80 supportive housing units and wrap-around services for the ACM to help Auckland’s homeless and most vulnerable. Works also included the demolition of three existing buildings and refurbishment of the heritage-listed Prince of Wales building.
“The ACM, who have been around for over 100 years, use this facility to look after the homeless, offer permanent housing, medical services, counselling, education and training, emergency support and meal services,” Clemenger says.
“The facility is all about getting the less fortunate people of Auckland back on their feet, so it’s really dear to the heart of the mission to provide their clients with permanent homes.”
In mid-2022 the project was recognised for a number of industry awards, including a Public
Architecture Award and the Property Council of New Zealand’s Supreme Award.
“These awards were a marvellous recognition for our team, as well as the ACM who does such wonderful work for the community,” Clemenger says.
“Our team spent the best part of two and a half years living and breathing this project and what it stands for. It’s certainly, in my time working with any business, a project that I’ve never seen a team as passionate and proud of completing for their client.”
Back across the ditch, in South Australia, Built Environs is building one of the largest health projects in Adelaide – the Queen Elizabeth Hospital (TQEH) Stage 3 Redevelopment for South Australian Health, and the Department of Infrastructure and Transport in South Australia.
It’s a huge development creating at least 390 jobs per year, with a large majority of those jobs directly employing South Australian residents. The new clinical services building is set to house a 46-bay emergency department,
12 operating theatres, a 14-bed intensive care unit, a 52-bed rehabilitation unit, four procedure rooms, recovery spaces, a central sterile supply department, a medical imaging department, a cardiac catheterisation laboratory, a pathology laboratory and staff support areas.
“We have a very strong health team working on this project in Adelaide, and after visiting the site again just recently and viewing the large structure starting to take shape, I’m pleased to say it’s going very well,” shares Clemenger.
Building on an expanding portfolio of successfully delivered projects, Clemenger says it’s the company’s over 150 strong workforce that is key to its success.
“A lot of organisations talk about their people, but for us it truly is the case. We can say, hand on heart, when we put a team on a project you know that they’re a top calibre of people backed by their experience and collaborative nature,” he adds.
“We have a fantastic reputation of treating our people, subcontractors and major stakeholders respectfully and fairly, and that is one of the reasons why I joined Built Environs – my values strongly align with those of the company and the McConnell Dowell Group. Everyone wants to be working in a culture where you enjoy working with good people who put a smile on your face. If you are not creating that environment and
being authentic with your staff, what’s stopping them from walking down the road and joining a competitor?”
“We also have a major focus on training our people and progressing their careers. In the past 12 months, just in South Australia, we’ve promoted two people from within the business, who started with us as younger staff members, to project manager positions. It’s a great delight to see people progress in their careers internally and is becoming more important than ever for our business in the resource-constrained market that we are operating in.”
Clemenger similarly speaks highly of the boutique nature of the business and the personalised service Built Environs has become known to deliver on every project. As the managing director, Clemenger says he makes it known to all clients that they are welcome to give him a call any time if there’s an issue on any of their jobs.
“It’s rare you see managing directors offer that level of service to their clients, and I do it because that’s the nature of our business and team,” Clemenger says.
“We want to see growth in the business, but first and foremost we want to drive the growth of the built environment at a sustainable pace, putting our clients and our people first.”
Visit Built Environs’ website for more on their projects and services at www.builtenvirons.com.au
“Within 18 months, we are now getting the opportunity to deliver much larger and complex projects.”Auckland City Mission (ACM) HomeGround Development.
With Lentune, as soon as supplier invoices, labour costs or costs for equipment hire hit the inbox, they’re accounted for against the project and tracked against the project budget – giving a project manager or quantity surveyor real-time information and the best chance of minimising cost overruns.
Delivering quality solutions to largescale construction businesses for over ten years, project cost management software
Since adopting Lentune in September 2019, Williams Corporation has seen a large reduction in labour hours on invoicing and reduced human error. Lentune has also saved them having to hire additional staff. These factors have been crucial to the success of the real estate developer’s recent expansion.
Founded in New Zealand in 2012 by Matthew William Horncastle and Blair William Chappell, Williams Corporation grew out of the duo’s passion for efficiency and productivity. Prior to finding their niche in property development, the pair owned and managed a range of businesses across different sectors including contract building, temporary fencing, waste management, solar panels and composite decking. Their vision to build better cities and a more livable country quickly saw Williams Corporation position itself as one of the leading real estate developers in New Zealand. Chappell says when Lentune approached the business, Williams Corporation was still in its early growth phase. “We were at a stage where we were seeing huge company growth in the New Zealand market, and we saw the value in Lentune software helping us be more efficient during our planned expansion into Australia,”
“Driving efficiencies is a key value of Lentune, closely aligning with our commitment to continuously improving Williams Corporation, whether it be
in efficiency or improving business functionality.”
Before Lentune, the Williams Corporation team had frustrations around their manual invoicing process. Laborious data entry added to their already busy workload, there was very little visibility around invoices, and paperbased purchase orders not only created data entry for the accounts team but also created a long process when matching invoices with written purchase orders.
After going live with Lentune in late 2019, Williams Corporation has since expanded its operations from Christchurch and Wellington to Auckland, Nelson and Tauranga in New Zealand. They have opened offices in Brisbane, Sydney and Melbourne in Australia; and expanded internationally with offices in Singapore and the Philippines.
Jono Bonifant, Director and CEO of Lentune explains how the software has been an essential foundation to Williams Corporation’s expansion.
“For the rapid growth of their company it was essential to be able to easily replicate their processes in new regions,” he says.
“You can’t be reinventing the wheel each time – Lentune has become a key part of this.”
Williams Corporation also uses Xero as its finance platform which Lentune seamlessly integrates with.
“With these two systems they had greater visibility and control and generated significant
time savings across the businesses,” says Bonifant.
Chappell notes that each of their building property developments are in their own individual environment in Xero, but they can manage the whole of the city or area from one Lentune which can feed into each of their Xero environments.
“It has made it much more efficient for us to get a more granular overview of our spend across all of the different facets of our business,” he says.
“All purchase orders are found in our Lentune platform providing visible and accurate information as soon as the document is received from the supplier – each purchase order is then automatically matched to the corresponding invoice.
“The software has enabled us to view a running total of each of our projects spend, [to] easily review the status of invoices and gain real-time insights into invoicing data.”
Williams Corporation, as a whole, has an emphasis on making affordable places for people to live rather than simply creating investment properties on which to capitalise. The company has an investment arm, but its main focus is on making the right product, at the right price, so people can afford to buy, afford to live and afford to maintain where they live.
“Williams Corporation is making their product accessible to people, they’re an agile and quick-thinking organisation, and they’re
trying to make a difference,” says Bonifant. “These are qualities that resonate with Lentune’s goals.”
In business since 2012, Williams Corporation also has a detailed plan to keep the company trading until at least 2110.
Chappell says: “With our principles followed and decisions made with a long-term vision in mind – like our decision to integrate Lentune into the business – Williams Corporation will trade successfully with a continuous 100-year plan.”
By removing data entry and automating admin processes, Williams Corporation has more time to focus on its continued growth and innovative vision of building a more liveable country.
“It has made it much more efficient for us to get a more granular overview of our spend across all of the different facets of our business.”Lentune seamlessly integrates with Xero to automate accounts payable processes. L-R: Williams Corporation Founders Blair William Chappell and Matthew William Horncastle.
Since 2018, Civil contractor Roughan Haulage & Excavations has been harnessing Trimble’s technology solutions to improve production, decrease rework and increase accuracy on construction sites – a formula that has bolstered its operations and client offering.
Australian civil contractor Roughan Haulage & Excavations, based in Melbourne, Victoria, was founded in 2017 as an earthworks and land management firm with a modern touch.
Company founder and director Matthew Roughan, knew early on he wanted to focus on differentiating his company with skill and technology-enabled solutions. At the time, he was just one man and a machine. While early work was largely focused on the domestic space, such as foundations and drainage/ utility trenches for homes, the company moved to civil infrastructure for commercial and government customers soon after. That shift was made possible in part because of a move to 3D machine control.
In 2018, Roughan invested in a 14-tonne Sumitomo excavator equipped with Trimble 3D machine control and put it straight to work on a road project.
Roughan recalls, “Our selling point to clients was that we could up production, decrease
rework and increase accuracy – we could only do that with help from technology.”
“It was a challenge to sell to some clients initially, but once we got up and running, we could demonstrate the benefits.”
One year later, the firm added a Trimble SPS930 Universal Total Station (UTS) for the 14-tonne excavator to further improve operational capabilities. The UTS is able to achieve millimetre accuracy in areas where GNSS signals are spotty or inconsistent.
“Very quickly, we found we were able to improve our productivity and quality on major road works projects, especially in tight work areas,” Roughan says. “Versatility is such a crucial part of our work; we have to make sure all of our machines and operators can service all stages of all jobs. That means reducing machine movements and unneeded project expenses.”
That mentality would serve as a foundation for more recent investment that’s generating
Civil contractor Roughan Haulage & Excavations was founded in 2017 as an earthworks and land management firm. With a home office in Melbourne, the company specialises in civil construction, including rail and road projects for public and private entities throughout the state.
Achieve high accuracy on jobsites with poor GNSS signal.
• Trimble Earthworks Grade Control Platform.
• Trimble SPS930 Universal Total Stations.
• Ability to work in tight spaces with an excavator.
• Continuous positioning, even in GNSS limited areas.
• Infield adjustments.
• Millimetre accuracy.
can offer to our clients, then I want it.”
“We had already learned that the increase in accuracy and consistency compared to GNSS was real, so it was a no-brainer.”
He freely admits that he didn’t realise the full extent of the UTS advantage until he began using the machine across more projects.
The new UTS/GNSS-equipped Cat 308 has been put to work on a number of civil works jobs, particularly road and rail projects with small intersections or areas where graders won’t fit.
“As soon as we hooked up the first time, we could see the difference in quality results and jobsite flexibility,” Roughan says. “As the weather changes throughout the day, the corrections stay the same from morning to night, whereas GNSS can vary, sometimes as much as 20-30 millimetres throughout the day, especially if we’re on various networks or working around obstructions.”
“With UTS, we don’t have dropouts so we can achieve those tighter tolerances.”
One particularly notable project was at the Youth Justice Centre at Cherry Creek in Victoria. “We needed to trim the building pads, but getting a grader set up just wasn’t viable,” says Roughan. “Instead, we used the Cat 308 and were able to change tolerances and meet the specifications defined by the road authority with that excavator.”
When asked about UTS specifically, Roughan continues, “We’re three years into using it and we’re hitting our stride at an especially good time. Many of our clients, largely general contractors, are being asked to meet much tighter tolerances, sub 10 millimetres, and tight timelines. We can’t achieve that with GNSS when we don’t have control of what’s going on in the environment. Running a total station with an excavator just blows their mind. Now, we can leave it all in the operator’s hands –we run smoother, very accurately and have a
faster finishing process. We request UTS on every machine now.”
Today, Roughan has a fleet of excavators ranging from 8 tonnes to 25 tonnes in size that are fitted with the most advanced machine guidance systems from Trimble. Moving forward, Roughan believes he will continue to invest in more machines, and will likely extend the use of existing software.
“Trimble Earthworks paid for itself in the first year on the first system – the functionality and flexibility has been a key part of Roughan Haulage & Excavations winning work,” he notes.
He points to the value of the software’s profile alignment and infield feature: “Design models are not always as precise as we need. So, the ability to swap between design and infield alignments allows our operators to manipulate the existing conditions as needed and it reduces the need for surveyors on site.”
“Trimble Earthworks is changing the industry, allowing us to rectify problems quickly, because we’re not waiting for a redesign. We can make an adjustment in onethird of the time that it would take a surveyor to come to the site, make measurements and then create a new model.”
While the Roughan team doesn’t build its own 3D models yet, he sees that happening in the future. On the machine side, he’s expecting another Cat 308 with an identical UTS/GNSS set up soon.
One of the reasons for Roughan’s success
to-date and its ability to justify future investments, is their partnership with SITECH Construction Systems. “Their support is great in Australia and easily accessible,” he says.
“The techs are very knowledgeable, so if we have any downtime, it’s minimal. Few other brands provide technology for an excavator in the same way that SITECH and Trimble do. The Trimble UTS is a league above the rest.”
UTS
GNSS
The 2022 Women in Industry Awards was an exceptional night for the construction industry, with leading women in construction taking out several of the coveted awards.
Held this year on September 8 in Sydney, the Women in Industry Awards (WII) recognise the achievements of women across a range of industries in Australia, including construction, infrastructure, mining, transport, manufacturing, engineering, logistics, bulk handling, waste management, and rail.
Women working in construction won several of the awards, with infrastructure construction company Fulton Hogan winning multiple categories.
Sarah Marshall, Fulton Hogan’s General Manager – People, Safety and Sustainability walked away with the Excellence in Construction award and says to be recognised amongst such an amazing group of highly
“For someone like me that has worked in the construction industry for over 25 years, these awards are a reminder of how far we’ve come and how much there is still left to do,” says Marshall. “We must continue to drive change and make a difference now and for the next generation of women and men, breaking down barriers and creating new possibilities.”
“Thank you to the organisers and judges of the Women in Industry Awards for raising awareness of the significant and meaningful contribution that women make to industry every day.”
Fulton Hogan’s Regional Communications and Stakeholder Manager, Victoria and Tasmania, Nina McHardy won this year’s
“I was so humbled to accept the award on the night, however, it reflects the work of so many people within Fulton Hogan and the great culture that we have within our business,” says McHardy. “I truly believe that construction is a place for everyone; it is an industry where anyone can forge a fulfilling and rewarding career regardless of their background, gender or area of speciality.”
“To receive this award, representing my role as a support function is testament of that. I’m proud of the work we are doing, specifically in encouraging women to consider a career in construction, and this award has further fuelled my fire to drive positive change and make an impact where I can.”
Taking home the Social Leader of the Year award, Fulton Hogan’s People Project Manager Joanne Jeffs says she has been passionately advocating for people from disadvantaged backgrounds for several years and the award recognises how far the construction industry has come during that time.
“Being recognised as Social Leader of the Year is a career highlight,” she says. “It was very difficult to gain momentum in this space five years ago and at times it was isolating trying to educate and influence others.”
“Over time, perceptions have gradually
shifted and overall, I have seen a positive change towards a business-as-usual approach.”
“Being a Social Leader is all about changing lives through genuine opportunities and connections.”
Another Fulton Hogan winner, Safety Manager Barbara Pitsos was recognised for her health and safety contribution to the construction industry, winning the Safety Advocacy award. She says health and safety is not always an easy role.
“Being acknowledged on a broader professional level embeds what I, our team and the wider safety profession try to achieve and maintain for all employees and contractors,” says Pitsos. “More than audits, that can be a measurement for success, being acknowledged for a cultural change is far more rewarding.”
The WII not only recognises the achievements of the finalists and winners of the awards, but also celebrates the contribution of women across all industries.
Inside Construction is proudly partnered with the event, in acknowledgement of the remarkable women who have achieved success through their commitment to the construction sector.
Other winners from the 2022 awards
Sydney Build 2023
Sydney Build is back once again on 6 and 7 March 2023 featuring more than 500 exhibitors, 450 speakers and 20,000 attendees from the built environment industries.
To be held at the International Convention Centre Sydney NSW, 14 Darling Drive, the event will bring together all professionals in the built environment and design industry for a jam-packed two-day exhibition and conference.
The free event has firmly established itself as one of the largest trade shows for the construction industry.
Brought to you by Oliver Kinross, Sydney Build is part of the company’s award-winning ‘BUILD’ exhibition portfolio that extends internationally to include trade shows held throughout New York, Chicago, and London.
Sydney Build 2023 will feature over 500 exhibitors and 450 speakers across nine conference stages. The Sydney Infrastructure Expo and Digital Construction Australia events will be at the venue at the same time.
Three major expos spread across two days will showcase the latest in technological advancement and touch upon topics highly prevalent within the construction industry. Boasting a comprehensive program and a
floor incorporates a unique format designed to stimulate business networking opportunities between attendees and exhibitors. Cuttingedge seminars, sponsored networking lounges and live equipment demonstrations are just a small portion of what attendees can expect to encounter at this year’s expo.
Uniting thousands of construction experts, architects, engineers, designers, government personnel and aspiring tradies is no easy task. That’s why Sydney Build Expo has placed its 450 top-level speakers into nine themed stages scattered throughout the venue. These Continuing Professional Development (CPD) accredited presentations will encompass a wide range of exclusive construction industry insights, shared from professionals with firsthand experience.
Speaker, sponsor, exhibitor showcase Sydney Build capitalises on the strong economy and high levels of inward migration that currently make Sydney one of the best performing construction industries in the
provide the best opportunity for professionals to get together to discuss past, present and future projects. The event enables the industry to educate itself and provides a great marketing tool for companies looking to stand out within the competitive construction industry. With this in mind, Sydney Build is proud to showcase the high profile support it has received from key stakeholders across the Australian construction industry.
Key sponsors for the event include high profile Building Information Modeling (BIM) and digital asset management firms Edara Systems, Autodesk and MYOB; and buildrelated firms Wurth Group, Spantec and Deco. Furthermore, crucial stakeholders from across the Australian construction industry such as CSR, Australian Made, Procore and Matterport are confirmed to exhibit.
On the topic of speakers, Sydney Build has been consistent in attracting high-level experts and securing prominent figures, such as the Lord Mayor of Sydney Clover Moore, to lend their time for the event. Industry leaders at the forefront of developing on-site technologies are also set to present.
Four in one Sydney Build Expo 2023 will feature two additional expos run alongside the main Sydney Build stage. They include the Digital Construction Australia event and Sydney Infrastructure Expo, to extend the show’s outreach further into the infrastructure and transportation industries. These events offer a more focused insight into their relevant fields, however, all three are free to attend under the same ticket and attendees are encouraged to freely explore all areas of the show.
Additional information on Digital Construction Australia can be found at: www.digitalconstructionaustralia.com
Additional information on the Sydney Infrastructure Expo can be found at: www.sydneyinfrastructureexpo.com
For more information and to register a complimentary ticket visit www.sydneybuildexpo.com or email marketing@sydneybuildexpo.com.au
Government updates and initiatives, major projects, procurement, and commercial and residential real estate development.
Digital Construction Stage
Digital transformation, latest technology trends, augmented reality and virtual reality, data management and security, digital twins, smart buildings, precincts and cities.
Sustainability Stage
Circular economy, net-zero, embodied carbon management, regenerative design, renewable energy, building life cycles and environmental, social, and governance sustainability.
Architecture & Design Stage
Innovation in architecture, workplace design, social and cultural inclusion, urban architecture, and meeting the needs of the people.
Importance of leadership, age, gender, and cultural diversity, driving equality and change, reconciliation in construction and participation policy.
Latest industry trends, modernising construction, modular methods, skilled workforce shortage, retention, upskilling and 3D printing.
Infrastructure
Updates from latest infrastructure projects (Sydney Metro, Western Sydney Airport, Coffs Harbour Bypass, etc.), transport decongestion, electric vehicle transition.
Climate Resilience & Safety Stage
Fire, flooding, earthquake and natural disaster safety, building resilience to extreme weather conditions, quality assurance and defects.
Wellbeing and mental health in construction, available industry initiatives, sales training, business planning, digital marketing and social media strategy.
sitting on the Project Leadership Groups for projects across Australia. She leads various pursuits as executive sponsor and supports and champions business initiatives at the
Most recently, Crookes was appointed as President of the Australian Constructors Association (ACA), the first woman to hold the position in the association’s 28-year history.
Growing up in a family of builders, Crookes says she used to visit construction sites every Saturday to look at the projects her father was working on. “I think it was in my blood to work in the construction industry,” she says. “But instead of going down the typical engineer or builder path, I chose to study law.”
Upon finishing her law degree, Crookes scored a job as a Senior Associate for a private law practice before looking for a role with more responsibility and authority. In 2007 she made the move to Laing O’Rourke and for the past 16 years has held several leadership positions within the company.
“I found my home with Laing O’Rourke – I get to work on amazing projects and build amazing things, and I’m part of a multidisciplinary and collaborative team,”
“My role includes working with the team to review bids and making sure that we’re selecting the appropriate jobs that meet our strategy,” she explains. “We set and review our strategy together and every week we monitor the operational performance of projects, undertaking a dive deep into each project.”
“I have a strict role of managing legal and risk, but also have accountability for the whole lifecycle of each project.”
Director,
at Laing O’Rourke is a veteran of managing legal and risk to yield positive outcomes for construction businesses.
Harnessing her over 22 years’ experience in the construction industry, Annabel Crookes sits on the Australian executive committee for international engineering and construction company Laing O’Rourke as Director, Legal.
Crookes’ career has seen her become an executive director of a global engineering and construction business, currently leading Laing O’Rourke’s legal, risk and company secretarial functions in Australia, whilst also
When Crookes joined Laing O’Rourke, she was their second in-house lawyer before moving into an interim Head of Legal role. The following years saw her move up the chain in a number of different leadership and strategy roles, including human resources, strategy, senior leadership roles on projects and acting as the executive sponsor for the organisation’s Reconciliation Action Plan, before stepping into her current position in 2011.
During her now 16 years with the company Crookes says she’s worked on a large number of diverse projects around Australia, New Zealand, Hong Kong and the Middle East.
“I think that’s the best part about our business,” Crookes adds. “We might be building a railway like the Inland Rail Project, or a commercial tower like our North Sydney head office which we currently reside in.”
“The projects I’m most proud of being a part of are the long-term collaborative projects where we work closely with our partners and form a deep relationship – two great examples of this are our 10-year partnership with the Novo Rail Alliance where we’ve been able to work together to solve and deliver many different projects in one, and our current project removing level crossings in Victoria in partnership with the Victorian Government. It’s been extremely rewarding.”
Crookes’ achievements extend far beyond the successful projects she has helped deliver, spending the past 10 years increasing the engagement and profile of lawyers in the construction industry. Traditionally, lawyers in construction companies are brought in to solve a problem and aren’t necessarily at the coalface to help shape successful outcomes early.
In conjunction with the leaders and Managing Director at Laing O’Rourke, Crookes has worked to showcase the broad skills a lawyer can bring to the table. “Lawyers aren’t just one dimensional,” says Crookes. “They’re clever, they are problem solvers who can help unpack complex problems – it’s this potential that needs to be unlocked to help support new and exciting ideas.”
The management structure at Laing O’Rourke, according to Crookes, is what sets them up for success. All lawyers at the company sit on senior management teams and are a part of the senior leadership team. She says this structure results in better outcomes for the business, promoting diversity of thought and opinion as well as creating the fertile ground for an engaged legal team.
In 2011, Crookes headed the development of Laing O’Rourke’s first Reconciliation Action Plan (RAP) – designed to value, include and respect Aboriginal and Torres Strait Islander voices so they are heard and better inform the decisions made across the business. Now the executive sponsor of the RAP, Crookes explains the various pillars of the plan have a lot to do with education.
“The first step is making sure we acknowledge the challenges that Aboriginal and Torres Strait Islanders face in our industry. We provide an environment where we can employ First Nations people and ensure they have long term, rewarding careers with our business. Valuing and understanding the cultures of everyone in our organisation is extremely important to us here at Laing O’Rourke,” she says.
“We support and develop Indigenous organisations through our supply chain, and also support the communities in which we work, ultimately trying to make a difference in everything that we do.
“We are currently delivering projects in Redfern and Central Sydney, amongst one of the largest inner city Indigenous populations. We’ve been working hand in glove with the local community and elders to ensure their concerns have been heard and their options for participation are easy to access. We do this with every project we deliver.”
Crookes has also been an active member of the ACA, serving as Director of the Board and Vice President since 2019 and Company Secretary since 2020, until her appointment as President in November this year. Her time at the ACA has included chairing the commercial board committee and siting on the Construction Industry Leadership Forum – helping to create a voice for the ACA through deep relationships with government agencies, clients and the construction community.
“We know that these relationships are critical to achieving positive change in the industry,” Crookes asserts. “Things like collaborative contracting and addressing hyper-price escalation are now becoming common place as part of some of the initiatives the ACA has spearheaded.”
Looking back at her achievements, Crookes says she wants to change the misconception that you have to be an engineer to be in construction.
“If you’re looking to enter the construction industry do your research, because there’s so many diverse roles and opportunities,” she adds.
“I never quite imagined I’d end up in the role I am in today, with such a fantastic construction company.”
“By nature, the industry promotes lateral movement and career progression, so you can transform and transition in a construction company to be recognised for the talent you bring, not the degree you obtained.”
Queensland based Jessica Manley has spent her career forging her own path in the construction industry, and today reaps the rewards of working in a job she loves as a construction estimator for Superior Walls & Ceilings.
Like many young people leaving school, Jessica Manley wasn’t sure of the career path she wanted to take. Now a successful construction estimator for Superior Walls & Ceilings in Queensland, Manley proudly speaks of some of the iconic infrastructure projects she has helped deliver throughout
Manley says her career in construction began when she was considering a gap year before entering the workforce.
“I’d just finished school and knew I wanted to take a gap year at some point, but I needed money first and so I took a role with my parents’ residential plastering company in Brisbane before travelling for six months,”
When she returned, Manley jumped straight back into the business, eventually starting her apprenticeship in plastering - where she was given the opportunity to participate in the 2020 Association of Wall and Ceiling Industries Apprentice Challenge.
“At the event I met an employee of Superior Walls & Ceilings who spoke very highly of the business,” says Manley. “He offered me the opportunity to come on board as a commercial plasterer, and I jumped at it.”
“The commercial side of plastering is completely different to residential, so it was a big shock, but being thrown straight on the tools for 14 months and with an amazing team backing me, I quickly excelled.”
During her apprenticeship with Superior Walls & Ceilings, Manley worked on the Brisbane Cruise Terminal with the façade crew, installing 52-kilogram sheets often at heights in excess of 7 metres – a project that won Best Commercial Façade at the 2021 Association of Wall & Ceiling Industries
In 2019 Manley was responsible for finishing high end feature walls and ceilings at Hansen Yuncken’s University of Sunshine Coast New Campus project, and in 2020 was part of the finishing crew for the highly detailed Amazon Head Office Brisbane Buildcorp Project.
Manley chased her next opportunity for career growth in 2021, reaching out to the Superior Walls & Ceilings head office for an estimating role. Brett Evans, Director of Operations for Superior Walls & Ceilings says
to bring real world knowledge to a role typically dominated by university graduates.
“We soon learned that this pathway adds much more value to the cost planning role for a subcontractor, as labour is generally the critical element in whether subcontractors are successful or not,” Evans adds.
“Given Jess has been on site, and seen real world application, she has been able to give even experienced estimators new understanding of production rates. Her introduction to the role has now opened the company’s eyes to new pathways when recruiting estimators and project managers.”
In just under two years in the estimating role, Manley has worked on Lendlease’s Tweed Valley Hospital Project where she was responsible for the procurement of subtrades during the tender phase, and directly responsible for 12 different and complex trade categories. She was responsible for measuring the walls and ceilings package, assisting the project teams in controlling labour budget and procuring raw materials on the $1.3 billion major infrastructure project.
She was the lead estimator on Mirvac’s $300 million Anura Apartments Project – a complex two tower development. On top of measuring and pricing the ceilings and partitions package, Manley was responsible for procurement of 8 separate trades for the project. Due to the high-end nature of the units, she had weeks of design work to compile involving engagement of structural, fire and wind engineers in order to deliver the
Adding to the list, Manley was also responsible for procurement of sub-trades during the tender phase of John Holland’s $50 million St Andrew’s Hospital Project.
Looking back at the projects she’s worked on, Manley says the best part is seeing the project after completion and knowing she was a part of its delivery.
“On a daily basis I’m dealing with big numbers, big packages and big infrastructure – it still blows my mind that I’m a part of these huge projects,” she explains. “I didn’t need a university degree to be in a role and industry that I love, I built my own pathway.”
To date, Manley has been involved in the builders’ cost phase of many major pipeline projects, helping builders and developers compile their cost plans before they can go to market with the applicable tenders. In total, she has been responsible for $60 million of cost advice over six projects for Multiplex, $48 million of cost advice over three projects for John Holland, and $14 million of cost advice over six projects for Lendlease.
Learnt throughout her already fruitful career, Manley has advice for those looking to enter a career in construction: “Do it –you feel strong, you feel empowered as a woman being surrounded by men and your capabilities keep exceeding.”
“I put myself out there and it was scary, but it’s definitely reaped its rewards. There are endless pathways into the construction industry and many doors open for you along the way if you work hard.”
“I didn’t need a university degree to be in a role and industry that I love, I built my own pathway.”Jessica Manley recently completed works on the podium area at the Queen’s Wharf Brisbane development.
With a career in the construction sector that spans decades, Dr. Gretchen Gagel shares her expert insight into the industry’s current and forecast labour shortages.
It’s been nearly 40 years since I began as an engineering intern for Lone Star Gas in Dallas Texas, and for most of the past four decades we have been talking about and trying to address talent shortages in the construction industry.
After the Global Financial Crisis (GFC), we experienced what we called the “teacup curve” in the US – many junior people and many senior people, with few in the middle due to low hiring during the GFC. Today brings a different challenge – aging baby boomers causing increases in both retirements and job openings during a booming infrastructure spend in both the US and Australia.
Our industry seems to be much more adept at solving technical problems than we are at solving our people problems. I would argue that transformative thinking is necessary to ensure we have the talent we need to deliver on our projects. Here are three areas I suggest we focus upon:
Where is our hit Netflix series? Seriously, where is the ‘Grey’s Anatomy’ of construction?
The ‘Stranger Things’ of engineering? We build and maintain the assets of society. Without us, no one would be charging their cell phone, or driving on a road, or sending their kids to school.
We are a vital, thriving industry with many exciting things happening yet with low visibility. I would argue that if food and golf deserve their own networks, so do we. I love the humble nature of our industry and many of the people in it, but it’s time we learned to do a better job of showcasing ourselves.
Seven years ago, John Oliver included a segment on his US show spoofing a hit movie entitled “Infrastructure”, starring major starts such as Ed Norton. His point –infrastructure used to be interesting to the public – the Hoover Dam, etc. – and needs to be again. It’s a fun watch and while it is a spoof, I would argue that a hit movie is a good idea.
We need to determine how we, as an industry, shine a positive, compelling light upon ourselves in a fun and exciting way that helps our society understand the importance of construction. This will go a long way towards attracting more people to the industry.
Earlier this year I interviewed 40 global leaders in construction, such as the global head of construction for Microsoft and the CEO of Black & Veatch, regarding the critical issues of our industry, and diversity was one of the top issues identified. I asked, on a scale of 1 to 4, how well are we diversifying our industry?
The answer – 1.85. Many stated that we are making progress, and one large government client has achieved a 50 per cent male and 50 per cent female ratio on their staff through deliberate strategies over the last decade. But much work remains.
As one industry leader stated, “We need to understand what it means to really welcome diverse people.”
During a recent meeting of the Associated General Contractors (AGC) of America Diversity and Inclusion Committee, of which I am a member, a male, third generation principal contractor gave a presentation on how their groundbreaking diversity, equity, and inclusion (DE&I) initiative resulted in a profitable revenue increase from US$200 million to US$500 million in three years. Their organisation’s DE&I journey began with a unique training called the White Man’s Caucus, detailed in the book Four Days to Change.
Sam made a great point in his presentation – organisations that make serious progress will not only improve our industry’s ability to attract the best and most diverse talent, but these organisations will also be the most successful.
3) Transform our industry’s culture
Critical to both of these first two issues is the challenge of reshaping the culture of our industry.
In the last edition of Inside Construction, I wrote about the efforts of the Construction Industry Culture Taskforce to encourage our industry to adopt a culture standard that creates better working conditions for a diverse employee base.
These efforts are happening around the globe, including in the US where the AGC of America has created the Culture of Care initiative.
Decades ago, everyone “did it tough” –long hours, unsafe working conditions, long weeks away from our families. People are unwilling to subject themselves to these types of working conditions and it is heartening to see so many organisations work to solve this issue. However, I would argue that the transformation needs to be accelerated through highly innovative solutions.
I am certain that each of you have your own ideas of what we can do, collectively, to attract and retain top talent to our industry.
I challenge each of us, as leaders, to do our part in achieving transformative thinking, action and results in our industry to ensure we have the people we need to deliver our projects.
You can read about the elements of the Standard and the research behind them at cultureinconstruction.com.au
Dr. Gretchen Gagel is Chair of Brinkman Construction (US), a member of the National Academy of Construction (US), a member of the Construction Industry Culture Taskforce (AUS), and an affiliate professor at the Australian National University and the University of Denver. As President/Managing Director of Greatness Consulting Pty Ltd she continues to advise organisations within the construction industry on optimising capital program delivery and developing talent. You can hear more from Gretchen on her Spotify podcast, “Greatness”.
“Where is our hit Netflix series? Seriously, where is the ‘Grey’s Anatomy’ of construction?”
Is
We didn’t know what we didn’t know
The construction industry rebounded from the closure of construction sites brought on by Covid-19, but nothing could have prepared the industry for what was ahead.
The construction industry faced a perfect storm in 2022. Covid-19 prompted record investment in infrastructure by governments nationwide and at the same time caused significant delays and disruption to many projects. The increase in work caused huge demand for workers, and flooding events and ongoing wet weather on the East Coast further delayed projects and increased demand for workers. Then Russia invaded Ukraine, and, with it, oil prices skyrocketed along with the cost of materials.
To top it all off, a new Federal Government was elected, triggering substantial changes to the industrial relations system including the abolition of the Australian Building and Construction Commission.
This year’s storm was arguably a one in 100year event.
Rock bottom Construction businesses account for 26 per cent of all insolvencies – more than any other industry – and hyper-escalation of construction costs this year caused more to fail. Contractors locked into fixed price contracts felt the heat, revealing the many weaknesses of the industry’s operating model.
Behind the headlines the industry has been peddling hard but not really going anywhere –and workers have become tired.
Over the last 30 years, almost every other industry has moved forward, yet Australia’s construction industry has gone backwards. Construction productivity today is lower than it was in 1990. Just keeping pace with the productivity performance of other major industries would save Australia $47 billion annually.
We can do better Government, industry and unions all agree on the opportunity and, more importantly, the need for change. Incremental change and 10-year horizons are out. To keep the industry alive it must transform, and it must transform now.
There is significant wastage of skilled resources through inefficient tender processes, but the bigger problem is the myopic focus on selecting the lowest price at the tender box to the detriment of all else. The practice of accepting the lowest bid at the tender box is a completely false economy and is the direct cause of the adversarial contracting environment in which we now find ourselves. Time and cost are important components of value; however, assessed value should include outcomes such as improving industry sovereign capability, increasing innovation and productivity, reducing the impact on the environment, increasing diversity and inclusion in the workforce and improving industry culture.
Everyone has a part to play, including contractors, but it is the government, if it chooses to, that has the biggest power to disrupt. To equip the Federal Government for the role of Disrupter in Chief, the Australian Constructors Association has developed the Future Australian Infrastructure Rating (FAIR) to rate government funded projects on how well they performed against key reform areas such as improved productivity. The FAIR initiative, or components of it, could be included in the next iteration of the National Partnership Agreement as a requirement for all federally funded projects.
Light at the end of 2022
By CEO,Arguably, the bigger problem is retaining and attracting a workforce that is big enough to deliver the project pipeline. The reality is the industry is out of touch with the next generation of workers who no longer view it as an industry of choice. Workers do not want a job in an industry where the hours are long and disputes are commonplace, excel spreadsheets are considered the height of tech and little focus is placed on the impact we are having on the environment.
If we’ve learnt anything these past few years, it’s that working together is the only way forward. It has been encouraging to see the Federal Government take the lead on reform and to approach it collaboratively with industry and unions in announcing the new National Construction Industry Forum. The forum is expected to comprise representatives from government, unions and business, including the Australian Constructors Association. This is an opportunity to work together to transform, as other sectors have. Construction could be
it possible that 2022 was even more challenging than 2021?
an industry of choice and equal opportunity for all genders, nationalities and ages. It could be an industry that constructs resilient infrastructure without damaging the environment. It could be an industry at the forefront of technological advancement. Construction could be a profitable industry
innovation over status quo and an industry prepared to take risks on new ideas rather than unknown ground conditions.
Australia’s construction industry could be the envy of the world, delivering high value infrastructure at a greatly reduced cost, for the benefit of all Australians. What are we
Over the 31 years since 1990, the gap between productivity of the construction industry and that of other industries has grown.
If we’ve learnt anything these past few years, it’s that working together is the only way forward.
Sitting proud at the entrance to Brisbane apartment complex The Ambrose is a stunning curved precast staircase that perfectly befits its host’s sculptural fluidity.
The Ambrose is a $160 million development by Kokoda Property, comprising 174 apartments and two retail spaces, that emanates pure sophistication and enhances the urban appeal of inner Brisbane suburb Milton.
The building’s design intent is to evoke the memory of a shell, where intricate façade fins provide shade and add textural contrast. They are interspersed with living walls that climb the full height of the building and give context within the building’s subtropical landscape.
As well as the feature entrance staircase, Master Precaster Euro Precast manufactured over 1,000 precast concrete elements –starting from the third basement level and finishing at the roof deck – in its expansive undercover facility in Sherwood, Brisbane.
According to National Precast CEO Sarah Bachmann, undercover facilities are not something every precast manufacturer has.
“The result of manufacturing inside has benefits for workers, as well as for the quality of the precast, and it means that the manufacturing process is not at the mercy of the elements,” she says. “Many don’t have undercover facilities, and when construction programs have been heavily impacted by rain and floods, knowing that manufacture can occur ahead of program is a boon to builders. It can even allow them to make up lost time.”
The elements manufactured for the project included wall panels, rectangular columns, circular columns, stairs, stair landings, lids and core boxes. A mix of single and double height elements were supplied.
According to Ms Bachmann, the feature staircase is testament to the flexibility of precast and to the capability of the organisation’s Master Precaster members.
“Precast’s customisation is like no other, giving architects and designers a medium to create any shape, colour or texture, or to replicate patterns, shapes and other materials to blend seamlessly with existing structures and contexts,” she says.
“What we see here is a precaster who was originally known for producing wall panels for high rise residential developments, now having a great reputation for tackling complex shapes.
“This curved staircase is case in point. The company now manufactures many elements that traditionally would have come from a precaster who might be more well-known for its architectural capabilities. It’s a credit to the Euro team.”
Honesty, reliability, quality and service
With factories in Queensland and Victoria, Master Precaster Euro Precast prides itself on repeat business due to its foundation values of honesty, reliability, quality and service.
The company has developed a reputation of being one of Australia’s leading precast
manufacturers and delivers quality structural and architectural precast across high profile projects in Melbourne and Brisbane. With a strong focus on value engineering, the inhouse drafting, engineering and construction management teams work closely with clients from concept to erection, to ensure a seamless construction process.
As a Master Precaster, Euro has been audited by National Precast for Quality Safety and Environment (QSE) as well as its track record, in-house technical capability and flexibility, its customer service, its Corporate Social Responsibility (CSR) and its involvement with industry beyond its company walls.
Euro has been a long-time member of National Precast, according to Ms Bachmann.
The benefits of involvement with industry – and in particular through membership of National Precast, the industry’s peak body –cannot be understated, she says.
“Master Precasters like Euro are plugged in to other industry stakeholders. They know what others are doing and how they are doing it, and they are a step ahead because they stay abreast of the latest technology and products,” says Ms Bachmann. “Importantly, they have met our audit requirements and show exemplary practice throughout the business. That has flow-on benefits to clients, builders, designers, and end users.”
“There’s a lot to be said for working with a precaster who is engaged and passed our Master Precaster audit requirements, as it helps to ensure a positive precast experience and because it mitigates risk from the start.”
Grins all ‘round
Euro Precast Queensland’s General Manager
Jeff Stratford is proud of the Euro team’s achievement and attributes the project’s success to the company’s culture, capability and approach to doing business.
He says that while the company doesn’t necessarily want to get into the business of curved precast staircases, this install really highlights the strengths of the Euro Precast business, and the benefits of having everything in-house.
“We were able to engage proactively and
early with Hutchinson Builders, as well as the project’s engineers and architects. Regular and open communication enabled us to finalise the manufacturing and installation methods and keep all parties closely involved and updated right through the process,” he says.
“Hutchinson Builders and their design teams had an open invitation to the factory and regularly visited to discuss and view progress. In the case of the feature staircase, all of this open communication enabled a seamless installation of a very complex element.
“The install certainly attracted a lot of attention and there were ear-to-ear grins as the cranes released and the Hutchinson team – led by Luke Nicolas, Project Manager – was able to christen the curved stairs with their first official traverse.”
It’s a sentiment echoed by Kokoda Property, which says it was pleased to partner with each team to establish the iconic development.
Laura Cornthwaite NAWIC SA Chapter President, knew she wanted a rewarding career and after some trial and error found it in the construction industry.
In highlighting the diversity of roles and opportunities available for women in the construction industry, we sat down with Laura Cornthwaite, Project Manager for Walker Corporation and NAWIC SA Chapter President, to hear about her journey.
When Laura was in school, she says she tried to mould herself into different jobs but found none of them felt like the right fit. At the end of year ten, a teacher gave her some advice that changed her perspective and led her on the path to where she is today.
“She told me to go home and write a list of five non-negotiable qualities I wanted in a job,” says Laura.
“As I wrote these down, I decided first and foremost that I didn’t want to work in a traditional office – I knew from my time at school that sitting at a desk all day wasn’t for me.
“I wanted to travel both in my job, but also earn enough money to travel the world. I set a goal for myself to visit 30 countries by 30 years of age.”
Laura explains that she wanted to learn something new every day and be in a career with opportunities for growth. After loving having particular responsibilities as captain of her netball team, she knew she also wanted to be a leader.
“Finally, I wanted to meet and work with new people as I love working as part of a team of like-minded individuals,” she says.
Based on her answers, Laura concluded she wanted to be a police officer and upon completing school went to an information session with South Australia Police, who advised her to take two years to gain more life experience.
“I thought the best way to do this would be to travel, but I needed money to do that so started to look for a job,” she says.
Securing a job in retail, Laura soon after decided to apply for an administration assistant position with a commercial builder. Her intention was to work there for a year to earn enough money to travel before joining the force.
“After just six months in the business I knew that the career I always wanted, just never knew about, was in the construction industry. It ticked all my five non-negotiables, so I went to university at the age of 25 to
study a Construction Management degree and worked in that business for 13 years in various roles,” shares Laura.
“I also managed to achieve my goal of travelling. I have had the opportunity to work on projects in regional South Australia and Melbourne, Victoria; and have travelled to 30 countries by 30 years of age – with Iceland being number 30.”
Now a Project Manager at Walker Corporation, the construction professional works on a diverse range of projects doing what she loves. Laura says her favourite thing about working in the industry is that every day is different. One day she could be waking up early for a 6am concrete pour or working collaboratively with a contractor on a new methodology; the next she could be walking a client through their building before handing over the keys.
“Your days are full, but extremely rewarding,” she says. “The construction industry offers so much.”
“If you think you might consider construction as a career then reach out to organisations like NAWIC and ask to speak to a female working in the industry. Use the opportunity to ask lots of questions and hear about the industry from people who were once in a similar position just like you.”