ROAD - RAIL - AIRPORT - PORT - URBAN -
BUILDING BRIDGES
TO LAST 100 YEARS
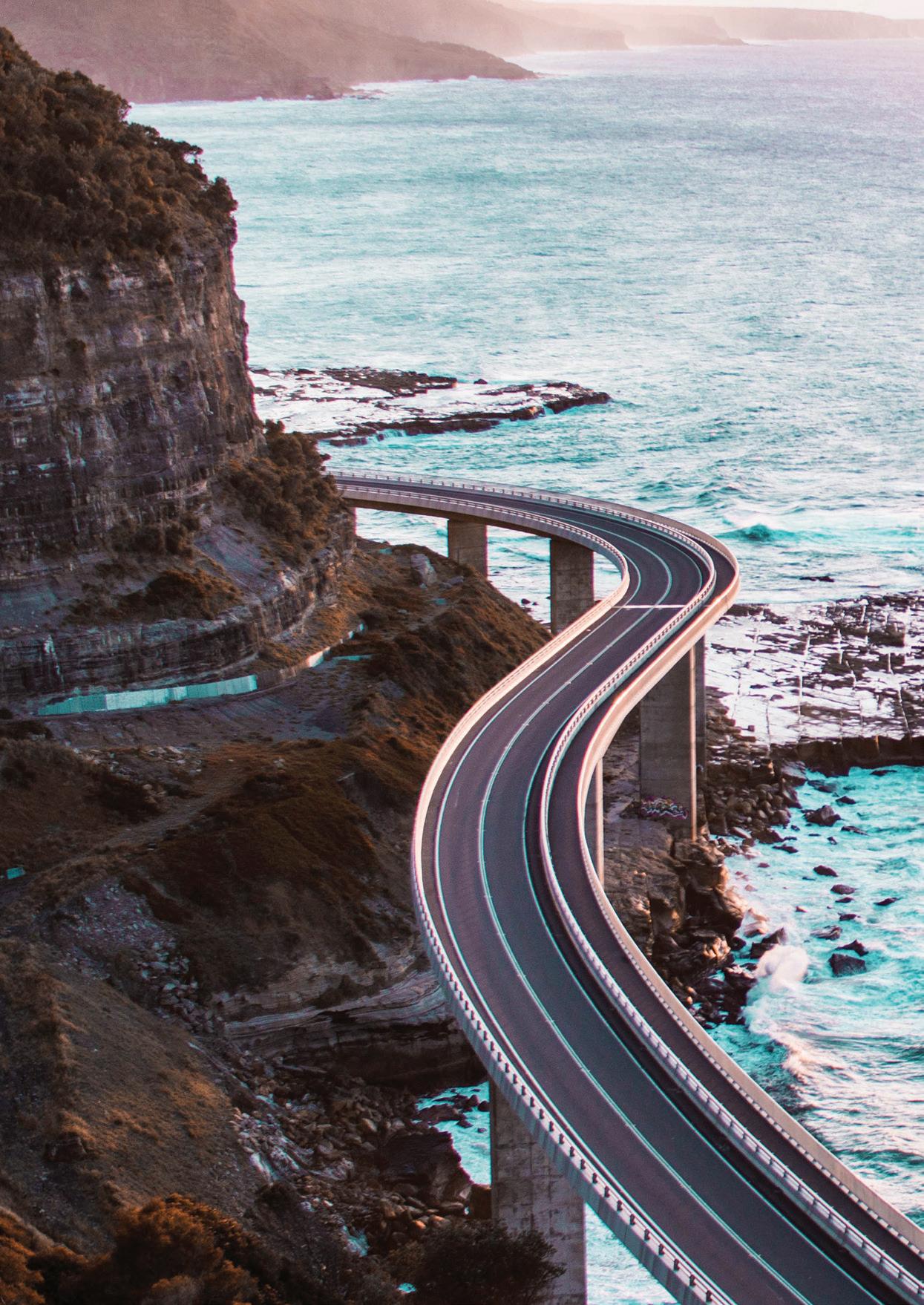
3D MODELLING SYDNEY’S CBD
A gripping case for crumb rubber
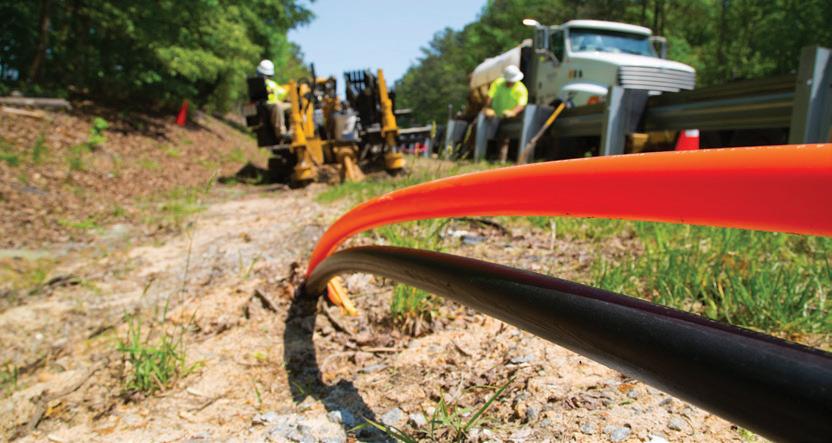
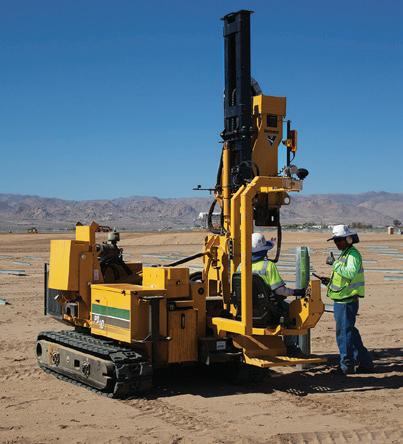
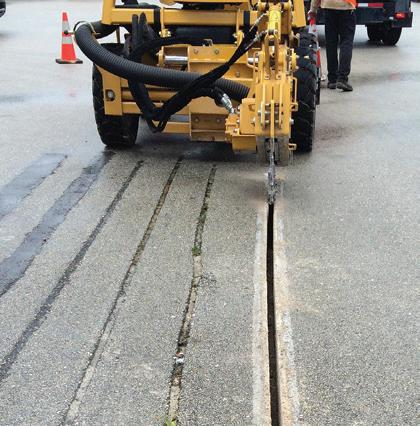
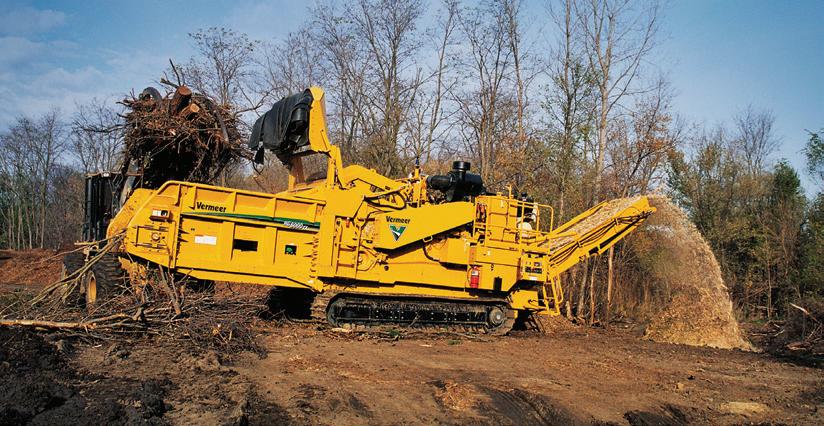
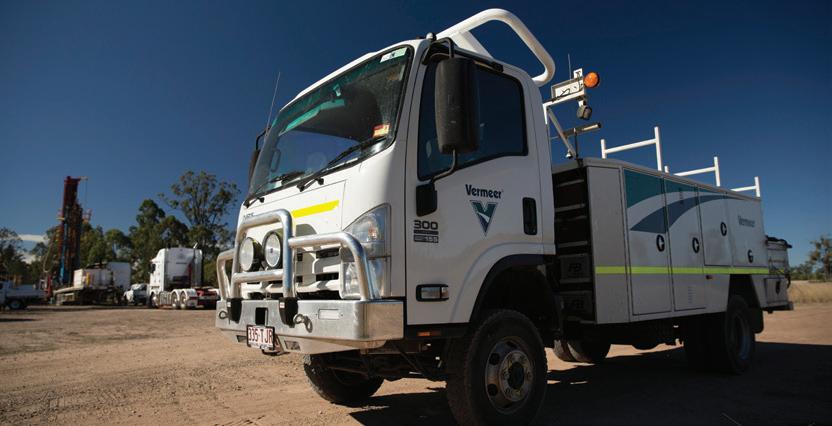

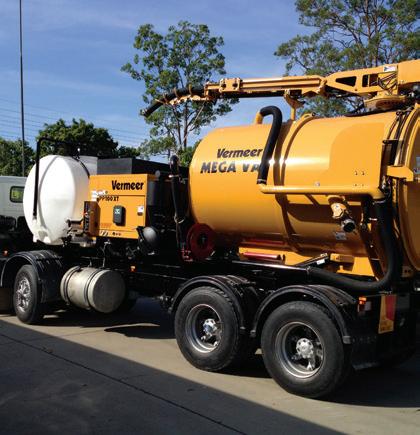
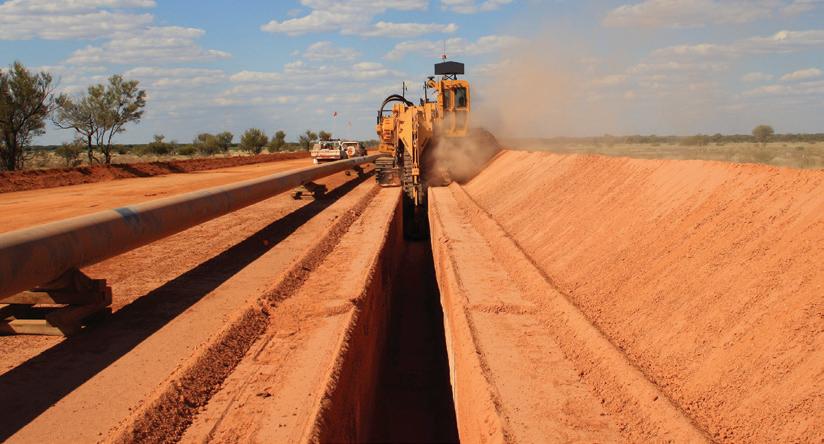
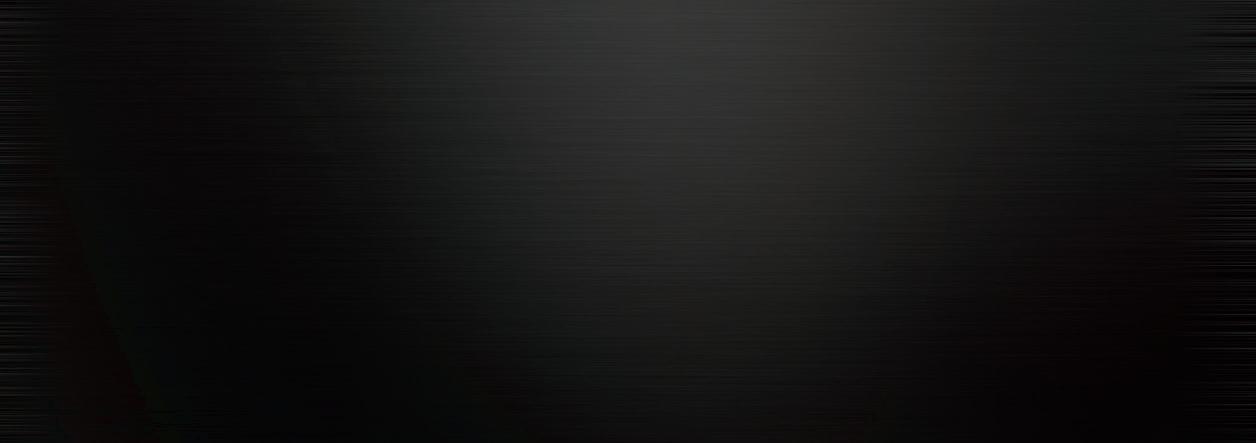
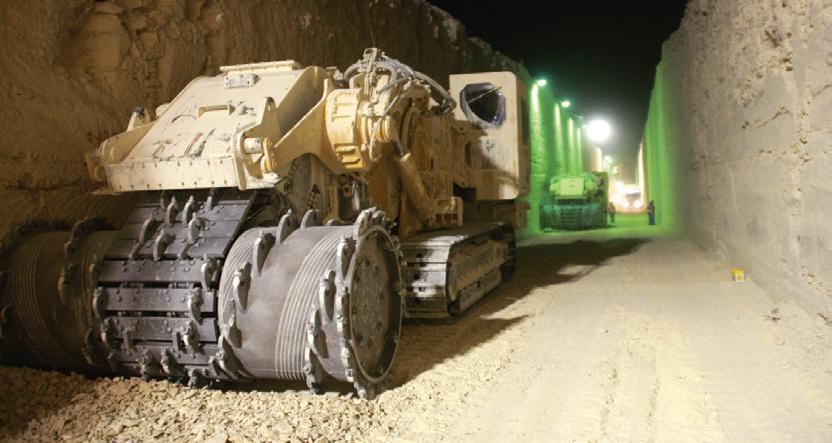
AS AUSTRALIAN INFRASTRUCTURE PROGRESSES, WE’RE PROUD TO PARTNER WITH THE CONTRACTORS THAT ARE LEADING THE WAY FORWARD.
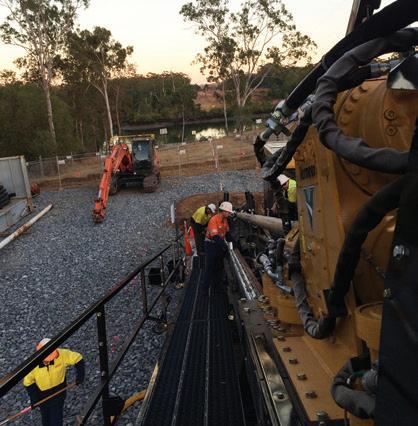
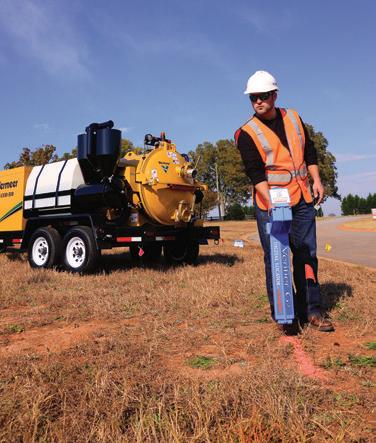
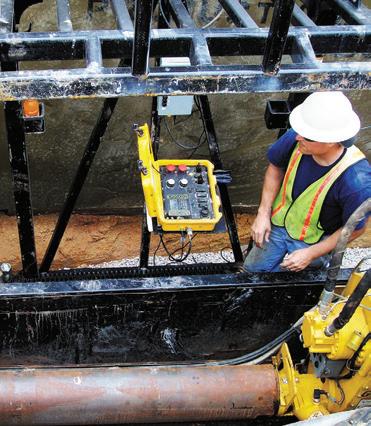

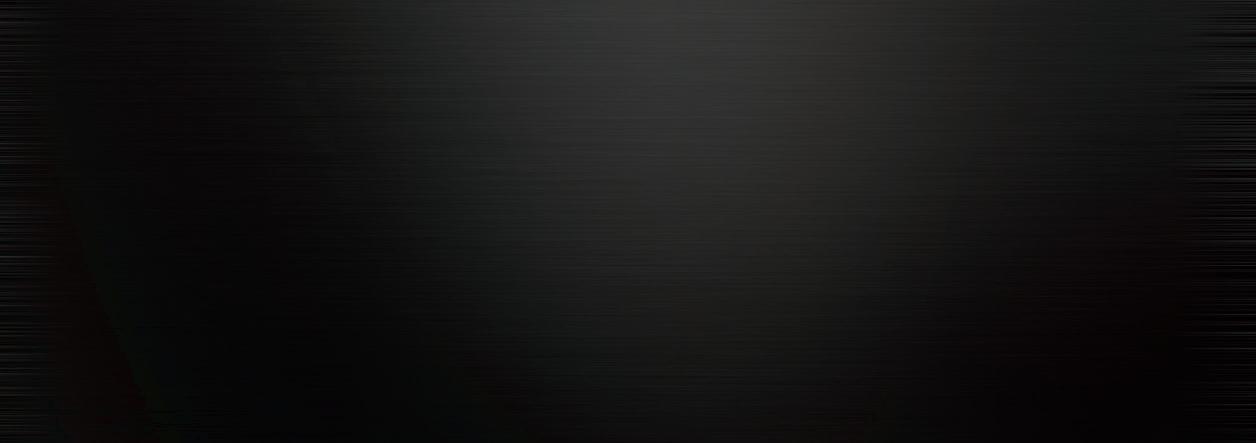
Preamble
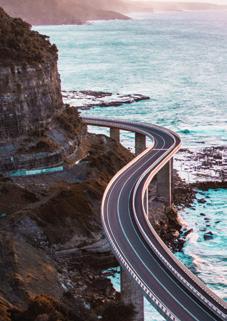
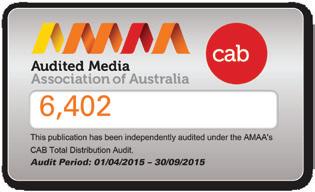
7,217
Published by
Monkey Media Enterprises
ABN: 36 426 734 954 PO Box 1763
FPreston South VIC 3072
irst para Officimporum, est prae doloreh eniaeruptat ut vitiumquam volupta qui cum reptatibus nes ationse aut et aut mo quos aruptatus int, nonsequid magnis nonsedipsunt explitas andi que sandae veles cuptatiis et as ut omnimetur acerum ese eos sit, cus non restrum que nat maximod mi, quia dolupta tustis dent pra prat as sus.
P: (03) 9988 4950
F: (03) 8456 6720 monkeymedia.com.au info@monkeymedia.com.au infrastructuremagazine.com.au news@infrastructuremagazine.com.au
Editor Jessica Dickers
Associate Editors
Lauren Cella
Charlotte Pordage
Journalists
Elisa Iannunzio
Nicole Valicek
Kirsty Hutton
Marketing Director
Amanda Kennedy
Marketing Associate
Sam Penny
Marketing Assistants
Rima Munafo
Katie Chancellor
Helena Brace
Production and Customer Service
Titian Bartlau
Senior Designer
Alejandro Molano
Designer
Jacqui Abela
Publisher
Chris Bland
Managing Editor
Laura Harvey
EDITOR’S WELCOME
We might only be in March, but it’s clear that 2018 is truly gearing up to be the year of the infrastructure boom. The rail sector has seen an increased focus on the freight network, with contracts awarded and first steel delivered for the Inland Rail, the largest freight rail infrastructure project in Australia, as well as preparation for the development and release of the National Freight and Supply Chain Strategy.
Since the last issue of Infrastructure in November, we’ve had two changes to the position of Federal Infrastructure and Transport Minister, with Michael McCormack recently taking over the Deputy Prime Minister position and Infrastructure and Transport portfolios from Barnaby Joyce. Regardless of who is the minister, there are still issues in the sector that require attention, from a predicted skills shortage to problems with aging assets. These are some of the issues that need to be put front and centre, along with a focus on the big ticket infrastructure projects.
With such a large number of projects underway, national forecasts suggest an additional 300,000 construction workers will be required by 2024 to staff major infrastructure projects in Australia. This could prove difficult for the infrastructure HR sector given the current skills shortage, changes to 457 visas and factors such as workforce diversity.
Infrastructure magazine aims to provide some practical solutions to these issues through the one-day conference InfraPeople, that will be held on 8 August in Melbourne, and will bring together leading experts in the infrastructure and human resource space. For more information on the event, visit www.infrapeopleconference. com.au.
Looking to our roads, projects from the Bruce Highway upgrade, to NorthConnex and the West Gate Tunnel Project, are moving forward and have helped to start the conversation around the best methods for designing and building Australia’s roads. Some of the discussion and current research is delving into the materials used such as crumb rubber, EME2 and foamed bitumen stabilisation to find out if these will make roads safer and more durable,
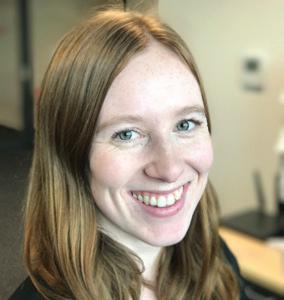
with the research and trials so far looking positive.
This edition features some of these outcomes, with the Australian Asphalt Pavement Association (AAPA), and Queensland Transport and Main Roads discussing what they are doing with these new materials in the road surfacing and design space. The state of Australia’s aging bridge stock is also an area that has been getting a lot of attention with questions surrounding if our bridges are strong enough to handle increased loading while remaining durable and sustainable. The concept of the 100-year design life has become a main aim, and is something that is being thoroughly researched by associations such as Austroads.
A common theme throughout these major projects, and many others currently underway, is the implementation of technologies, increased connectivity and the use of ‘smart’ infrastructure, whether this be high-capacity signalling, spatial technologies, or road automation. Using spatial technologies in infrastructure is one of the ways the sector is really starting to utilise its data to make better planning decisions, with evidence of this ranging from mapping city buildings to the use of satellite positioning to further the uptake of automated vehicles.
I’m also pleased to announce that I will be stepping into the editor’s chair for Infrastructure magazine and I can’t wait to meet some of you at upcoming events. We’re looking forward to attending and distributing the magazine at several events over the next few months including Core2018, ARRB National Conference, Locate 18, and the Australian Smart Cities and Infrastructure Summit, so we’ll see you there.
Jessica Dickers Editor
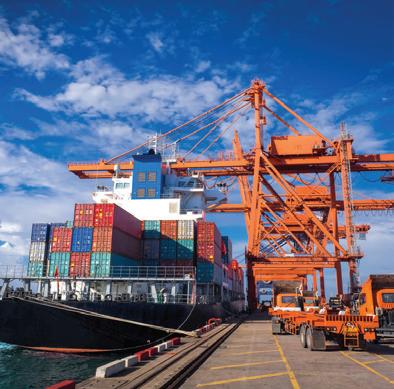

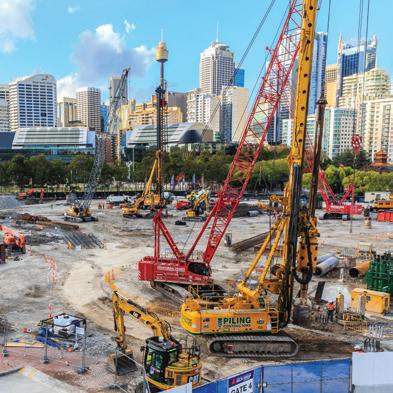
BRIDGES
A PROBLEM IGNORED: HIGHWAY BRIDGES AND AUTOMATED TRUCK PLATOONS
With automated truck platoons - trucks controlled by automatic systems that drive very close together - expected to come to Australia, one question that industry hasn’t thought about is the impact of these platoons on Australia’s aging bridge infrastructure. Here, Colin Caprani, asks if our bridges can handle it?
ACHIEVING SUSTAINABLE AND DURABLE BRIDGES
Sustainability, limited resources and environmental concerns are increasingly front of mind for bridge design and optimised maintenance of bridges. It’s important to look at whole of life costs as well as alternative materials to improve in service life and to minimise greenhouse gas emissions. We spoke to Dr Richard Yeo, Program Manager, Assets, at Austroads, to find out about some of the innovative research that Austroads has been undertaking on bridges and how the results could change the way bridges are designed and constructed.
HIGH-CAPACITY SIGNALLING MOVES MELBOURNE TRAINS IN A RAPID NEW DIRECTION
CONDITION MONITORING AND MAINTENANCE
DO OLD TRACK STANDARDS STILL MEASURE UP IN TODAY’S RAILWAYS?
CORROSION REMAINS A COMPLEX CONCERN
ROAD SURFACING AND DESIGN
A GRIPPING CASE FOR CRUMB RUBBER
THE IMPACT OF NEXT GENERATION CONNECTIVITY
COLLABORATION LEADS TO LOWER-COST, QUALITY INFRASTRUCTURE
SATELLITE POSITIONING TRIAL HINTS AT THE FUTURE OF OUR ROADS
NEW GEOSPATIAL CENTRE MAPPING SYDNEY’S INFRASTRUCTURE
POSITION PARTNERS ACQUIRES
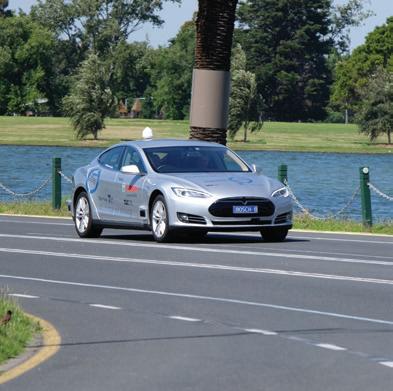
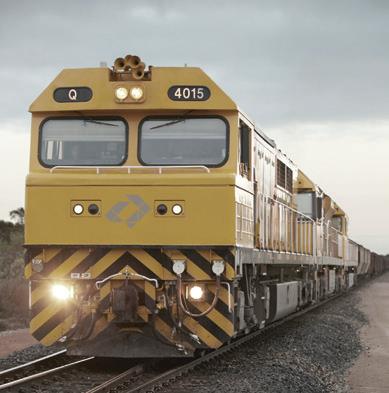

ANNOUNCED FOR
CROSS RIVER RAIL
SYDNEY AIRPORT
BEGINS ON AUSTRALIA’S LARGEST WIND FARM
AUSTRALIA’S INFRASTRUCTURE PROJECTS
Contributors
Philip Davies
CEO, Infrastructure Australia
Philip Davies is the Chief Executive Officer of Infrastructure Australia. He is an experienced infrastructure executive who has over 25 years experience shaping policy, delivering nationally significant infrastructure projects and leading reform within the infrastructure sector. Before joining Infrastructure Australia, Mr Davies led AECOM’s Infrastructure Advisory business in Asia Pacific, providing government and private sector clients with infrastructure policy, strategy, business, program, planning and operations advice.
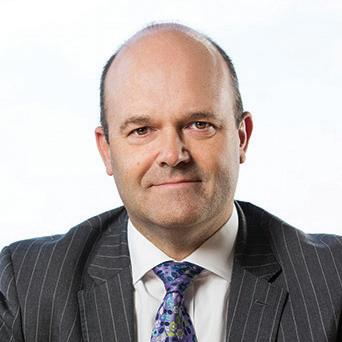
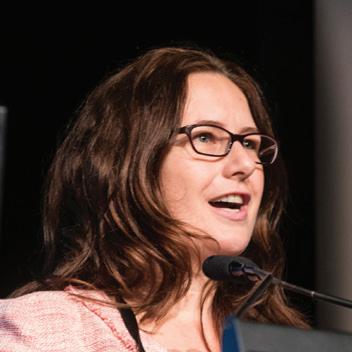
Deanna Hutchinson
Chief Executive Officer, Spatial Industries Business Association (SIBA) and Geospatial Information and Technologies Association (GITA ANZ)
Deanna has a passion for simulation and virtual reality. She has experience within the mining, healthcare, defence, transport and manufacturing sectors in designing and implementing complex simulation projects. She was elected Chair of Australia’s international simulation conference, SimTecT, from 2008 to 2013 where she joined the international simulation community, forging strong relationships with organisations and thought leaders in Europe and the Americas.
As CEO of SIBA|GITA, Deanna is focused on developing sector-wide governance infrastructure (such as professional accreditation and standards) and knowledge about emerging applications such as virtual reality, simulation and BIM. She contributes as either a committee member or speaker at several emerging technology events and has an influential voice in the spatial business industry.
Simon Thomas
Programme Delivery Director for Inland Rail, Australian Rail Track Corporation
Simon is responsible for leading and overseeing the delivery of the construction elements of the Inland Rail Programme. Inland Rail is a $9.3 billion, once-in-ageneration project that will complete the spine of the national freight network between Melbourne and Brisbane via regional Victoria, New South Wales and Queensland. Simon has been with Inland Rail since late 2015 and brings with him over 30 years’ experience delivering major rail, road, water, mining and building infrastructure projects in Australia, UK, Asia and the Middle East. In 2014 he was awarded Project Director of the year High Commendation by the Australian Institute of Project Management for his work as Project Director of Aurizon’s $904 million Wiggins Island Rail Project.

Contributors
Andrew Meier
Executive Director/Chief Executive Officer, Australasian Centre for Rail Innovation
Andrew was appointed Executive Director and Chief Executive Officer of the Australasian Centre for Rail Innovation (ACRI) in July 2017, having led for the previous decade a collaborative national land transport information program whilst at the Australian Road Research Board (ARRB).
Andrew has been a leader of international transport information sharing initiatives, including the first Australian chair of the International Transport Research Documentation (ITRD) Operational Committee which operates under the secretariat of the International Transport Forum/OECD. He was a key participant in facilitating the merger of two international resources to form the TRID database of transport resources, maintained by the US Transportation Research Board and now attracting almost two million visits annually. Andrew has authored conference and journal papers at national and international level including collaborative work on international taxonomies and guidance for information professionals on levels of evidence and research standards.
John Kilgour
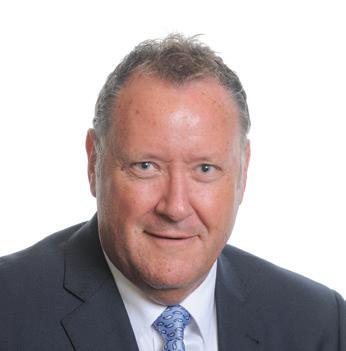
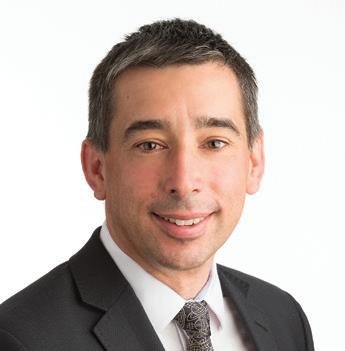
Civil Contractors Federation’s (CCF) Victoria Branch
John Kilgour is the Chief Executive Officer for the Civil Contractors Federation Victoria, a peak industry body supporting over 500 members responsible for the construction and maintenance of over $9 billion per annum of Victoria’s major infrastructure, including roads, bridges, pipelines, drainage, ports and utilities.
CCF members also play a vital role in the residential and commercial building industry by providing earthmoving and land development services including the provision of power, water, communications and gas. Known for his strong advocacy work and networks at local and state government levels, John joined CCF in February 2016 from the Committee for Ballarat where he was CEO.
Prior to this, John has a long and distinguished career in the downstream oil industry with BP. During his 34 years with the BP Group of companies, John delivered major investment projects in the oil and gas, retail, petrol and convenience sectors throughout Australia, New Zealand and South East Asia. In February 2017, John was appointed President of the Victorian Civil Construction Industry Alliance, which CCF is a member.
Erik Denneman
Director Technology and Leadership at the Australian Asphalt Pavement Association (AAPA)
As Director, Technology & Leadership, of the Australian Asphalt Pavement Association, Erik Denneman (PhD, CPEng, RPEQ) supports the flexible pavement industry in the implementation of innovative pavement solutions. Before joining AAPA in July 2016, Erik led the ARRB Pavement Technology and Asset Management team in Brisbane. He specialises in performance based design and specification of bituminous materials, and the development of pavement design models. Erik has worked in the Netherlands, South Africa, the US, and since 2012, Australia.
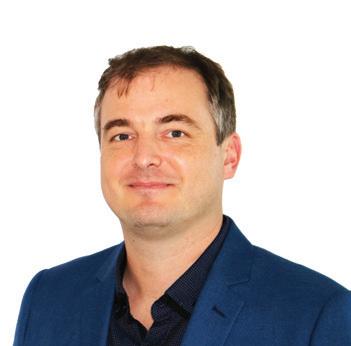
NEW FEDERAL MINISTER FOR INFRASTRUCTURE AND TRANSPORT
Former Minister for Small Business, Michael McCormack, has been sworn in as the leader of the Nationals and Deputy Prime Minister, taking over the Infrastructure and Transport portfolio.
The appointment of Mr McCormack comes after the resignation of former Deputy Prime Minister Barnaby Joyce.
Mr McCormack said the party had placed “huge trust, faith and responsibility in me.
“I will honour that by doing my best always. I’m a team player, doing it with the very best team in rural and regional Australia.
“I want to make sure that people know that in me they will have a fighter. I have a huge challenge ahead of me.”
Prime Minister, Malcolm Turnbull, said he is delighted at the appointment of
Mr McCormack as the new leader of the National Party and Deputy Prime Minister.
“Michael McCormack is a strong advocate for rural Australia. He will continue his party’s long tradition of standing up for farmers and all those living in regional Australia.
“I congratulate Michael McCormack on his appointment and I look forward to working closely with him and the entire Coalition team in the interests of all Australians.”
The Australian Logistics Council (ALC) also welcomed Mr McCormack’s appointment as Minister for Transport and Infrastructure.
ALC Managing Director, Michael Kilgariff, said, “It is pleasing that the second most senior figure in the government will retain portfolio
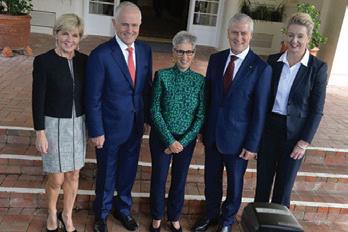
responsibility for this crucial area, given the importance of developing transport infrastructure to support national supply chain efficiency and build Australia’s export capacity.
“As an industry leader on freight and supply chain policy, ALC always seeks to have a cooperative and productive relationship with the key ministers in portfolio areas that impact our industry.”
SHORTLIST ANNOUNCED FOR QUEENSLAND CROSS RIVER RAIL
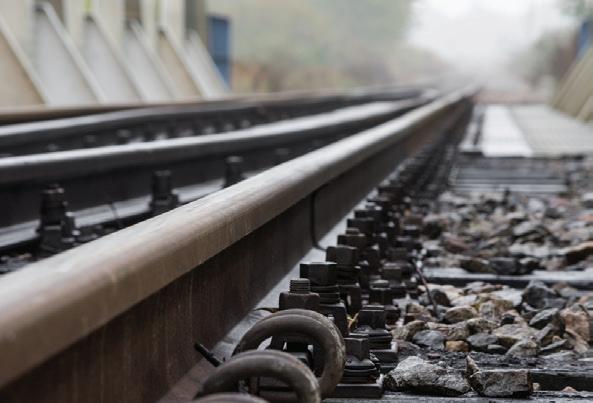
The Queensland Government has announced the companies shortlisted for the contract to build the Cross River Rail.
Queensland Deputy Premier, Jackie Trad, said the announcement followed a comprehensive evaluation by the Cross River Rail Delivery Authority of the Expressions of Interest received for the project’s two major works packages: The Tunnel, Stations and Development (TSD) public-private partnership, and the Rail, Integration and Systems (RIS) alliance.
The Tunnel, Stations and Development public-private partnership consortia shortlist includes:
♦ Pulse: CIMIC Group-led consortium, including Pacific Partnerships, CPB Contractors, UGL, BAM, Ghella and DIF
♦ Qonnect: QIC, Capella Capital, Lendlease, John Holland and Bouygues
♦ CentriQ Partnerships: Plenary Group, ACCIONA, GS Engineering & Construction, Salini Impregilo and Spotless Group
The Rail, Integration and Systems alliance shortlist includes:
♦ River City Alliance: Laing O’Rourke Australia Construction, GHD, Aurecon Australasia, SYSTRA Scott Lister Australia
♦ Unity Alliance: CPB Contractors, UGL Engineering, Jacobs Group (Australia), AECOM Australia
“Cross River Rail is a transformational project that will unlock the bottleneck at the core of our transport network and increase its capacity to deliver ‘turn-up-and-go’ public transport,” Ms Trad said.
“Shortlisted companies will now be required to prepare detailed bids that demonstrate innovation and offer Queenslanders the highest possible value for money.
“Once the assessment process is complete, the consortia selected from these shortlists will be building this project.”
WESTERN SYDNEY AIRPORT CONNECTION DESIGN UNVEILED
The early design of the M12 Motorway which will connect to the Western Sydney Airport has been unveiled.
Federal Minister for Urban Infrastructure and Cities, Paul Fletcher, said the new 16km road would mean that when the new airport opens in late 2026, it will have a direct connection to Sydney’s motorway network, unlocking the economic benefits Western Sydney Airport will deliver to the region and beyond.
The $5.3 billion airport, funded by the Federal Government, will support more than 11,000 jobs in the construction phase and 28,000 jobs by 2031.
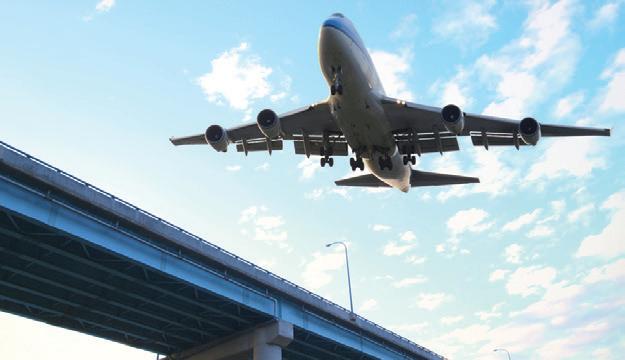
“With an extra one million people expected to live in Western Sydney by 2031, the Turnbull and Berejiklian Governments are delivering the infrastructure needed to make a growing Western Sydney work for residents, and an ever better place to live and do business,” Mr Fletcher said.
NSW Minister for Roads, Maritime and Freight, Melinda Pavey, said the preliminary design had been developed and community feedback was now being sought to inform the next stage of design.
“Since the previous announcement, changes include moving the eastern section of the route northward to maintain the integrity of the Western
Sydney Parklands, and maintain the integrity and development potential of the area for future generations,” Mrs Pavey said.
NSW Member for Mulgoa, Tanya Davies, said the M12 would be delivered in time for the opening of the Western Sydney Airport in 2026.
“The M12 Motorway is the next major project in the $3.6 billion Western Sydney Infrastructure Plan, which has created hundreds of jobs,” Mrs Davies said.
Detailed investigations will take place in the next 12 months as the design is developed and the environmental assessment drafted.
IMPROVING INFRASTRUCTURE KEY TO ROAD SAFETY
The NSW Government has released a new road safety plan which includes a range of measures aimed at improving infrastructure to enhance safety outcomes for drivers across the state.
The comprehensive package addresses speeding, drink driving, drug driving, driver distraction, driver fatigue, truck safety and funding to improve safety on country roads.
The Road Safety Plan will bring the government’s total commitment to targeted road safety programs from the Community Road Safety Fund to $1.4 billion over five years.
Minister for Roads, Maritime and Freight, Melinda Pavey, said one of the biggest challenges remains on country roads, which accounted for almost 70 per cent of the state’s road toll last year.
“If you live in the country you are four times more likely to die in a road crash than if you live in metro NSW,” Mrs Pavey said.
“This is why we will roll out 1600km of rumble strips and 300km in targeted safety works, such as flexible, wire-rope barriers to help prevent run-off-road and head-on crashes on our road network, including the Princes Highway.”
Roads Australia welcomed the focus on road infrastructure
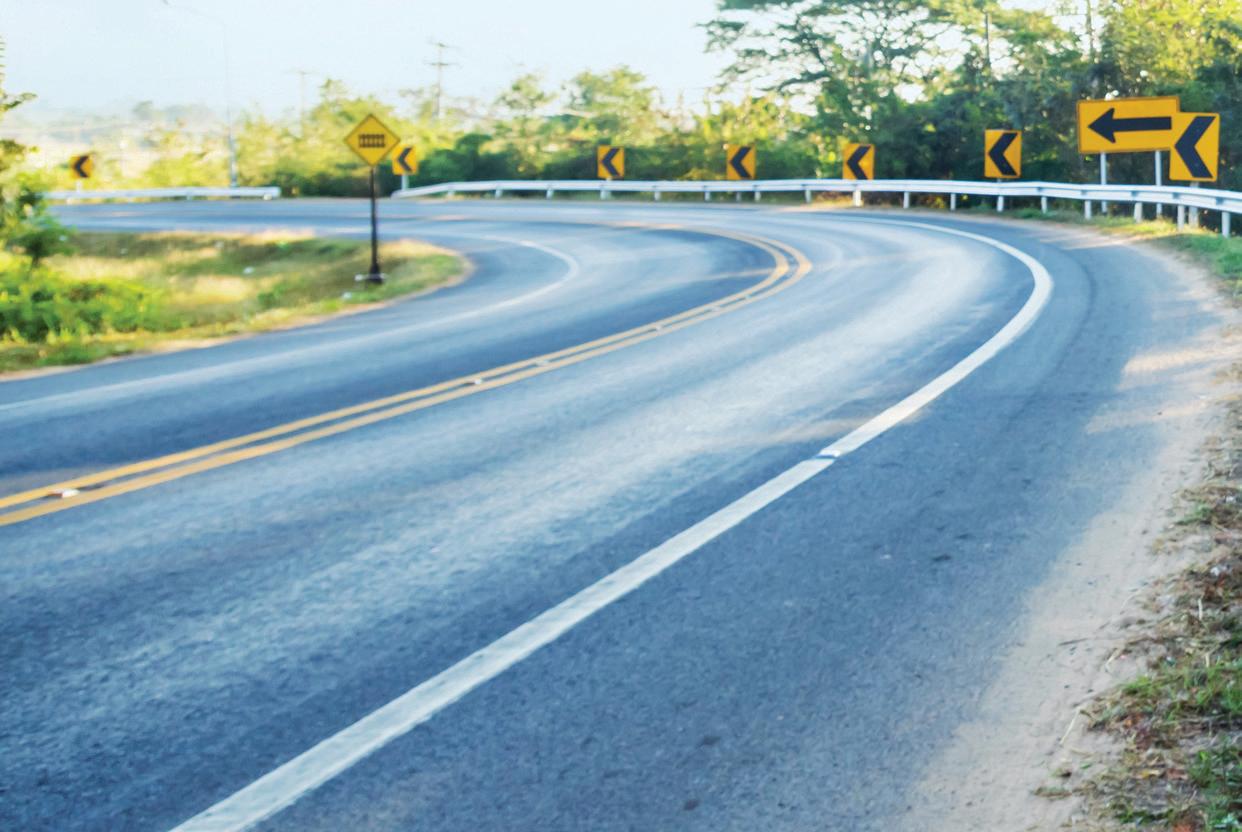
improvements in the new road safety plan.
Roads Australia President, David Stuart-Watt, said, “Making road infrastructure safer is obviously a cornerstone of a successful Safe Systems approach to road safety, so it’s very pleasing to see the NSW Government targeting high risk regional roads in particular.
“Relatively small, low-cost improvements – be they realigning of dangerous curves, installation of barriers or improvements to line-marking – can make a significant difference.
“Combined with strategies to address driver behaviour through education and enforcement, targeted funding for infrastructure improvements is a welcome response by the NSW Government to the state’s rising road toll.”
Mr Stuart-Watt said safety was ‘top of mind’ for road designers and builders.
“Our industry is always looking at how we can improve road safety through better design, materials and technologies.
“We continue to work closely with our clients, including governments, to mitigate the risks associated with new and existing road infrastructure.”
TOWNSVILLE PORT EXPANSION RECEIVES GOVERNMENT APPROVAL
The Federal Government has approved the Environmental Impact Statement (EIS) for the Townsville Port Expansion Project.
The approval of the EIS for the project means that preliminary works on stage one, the $193 million Channel Widening Project, can begin before April 2018, pending a resolution on final funding between the State and Federal Governments.
Port of Townsville Chief Executive Officer, Ranee Crosby, said the $1.64 billion, 30-year development plan would ensure the Port of Townsville could expand to allow it to become a globally competitive port.
“After nearly ten years in the planning phase, our team is looking forward to getting works underway to widen the shipping channels into the Townsville Port,” Ms Crosby said.
“The EIS was a very rigorous environmental review and project assessment, so we are delighted to

have now received the go-ahead for the project from both the Queensland Coordinator General and the Federal Government.
“Ships are getting bigger and the widening of the channel is absolutely critical to the future viability of the Port of Townsville.
“Bigger ships coming to Townsville will mean lower shipping costs for freight, better connectivity to global trade markets, as well as allowing larger cruise ships to visit the city, which will further
boost cruise tourism in the region.
“At the moment Townsville cannot accept ships longer than 238m in length, which by today’s global standards is completely inadequate.”
Port of Townsville will fund $43 million for the Channel Capacity Upgrade, the Queensland Government has confirmed a $75 million funding commitment and has sought a matched $75 million contribution from the Federal Government for the project to proceed.
CONSTRUCTION BEGINS ON AUSTRALIA’S LARGEST WIND FARM
The first sod has been turned at the almost $850 million Coopers Gap Wind Farm in Queensland’s Darling Downs.
The 453 megawatt (MW) Coopers Gap Wind Farm is about 250km west of Brisbane, and will produce approximately 1,510,000 megawatt hours (MWh) of renewable energy annually. This is sufficient to power more than 260,000 average Australian homes when fully operational in mid-2019.
The renewable energy produced from the wind farm’s 123 turbines will also reduce CO2 emissions by 1,180,000 tonnes annually, the equivalent of taking 340,000 cars off the road.
Work has already started to connect the wind farm to the grid. Queensland’s high voltage transmission provider Powerlink is building a new 275kV substation at Cooranga North, with commissioning expected by the end of 2018.
Minister for Energy, Dr Anthony Lynham, said this is the second large-scale renewable project in the Western Downs to get underway.
“Coopers Gap will bring $850 million of investment, 200 construction jobs, and up to 20 ongoing operational jobs to the Western Downs.
“The Western Downs is fast becoming Australia’s renewable energy capital, with Coopers Gap and 10 approved solar projects.
“Together, they represent more than 2000MW of renewable energy that will help power Queensland’s electricity grid and
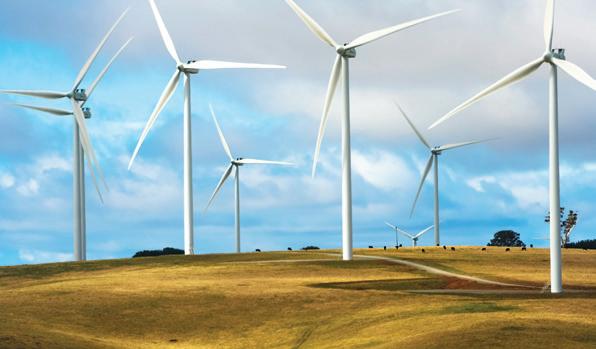
its regional economies, and help us meet our international emissions reduction commitments.
Dr Lynham said ongoing private sector investment, like AGL’s, was concrete endorsement of Queensland’s renewable energy policy.
“Our 50 per cent renewable energy generation target by 2030 has encouraged an unprecedented level of renewable energy investment in 23 large-scale projects that are currently financially committed to or under construction right across the state.
“When complete, these projects will more than double Queensland’s renewable energy output and produce enough electricity to power around 987,000 homes.”
Correction: In the article Moving forward for safer bitumen spraying published in the November 2017 edition of Infrastructure magazine, the article incorrectly used an image of a bitumen operation, not a sprayed seal operation.
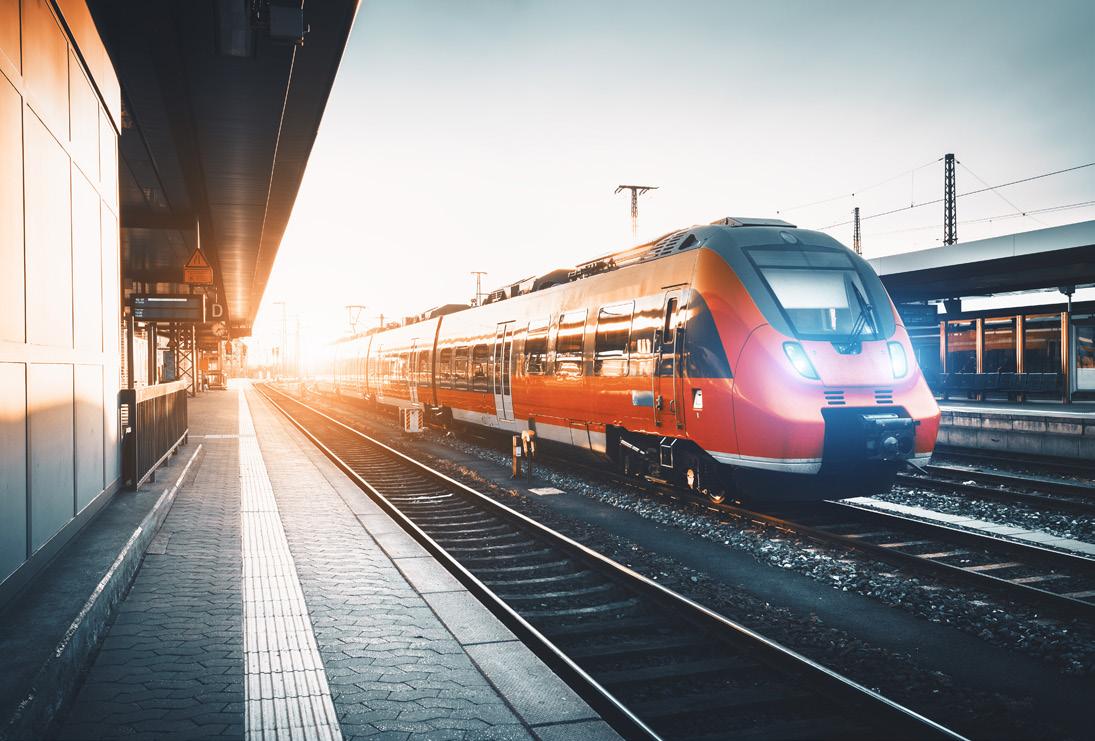
SKILLING AUSTRALIA’S INFRASTRUCTURE PROJECTS
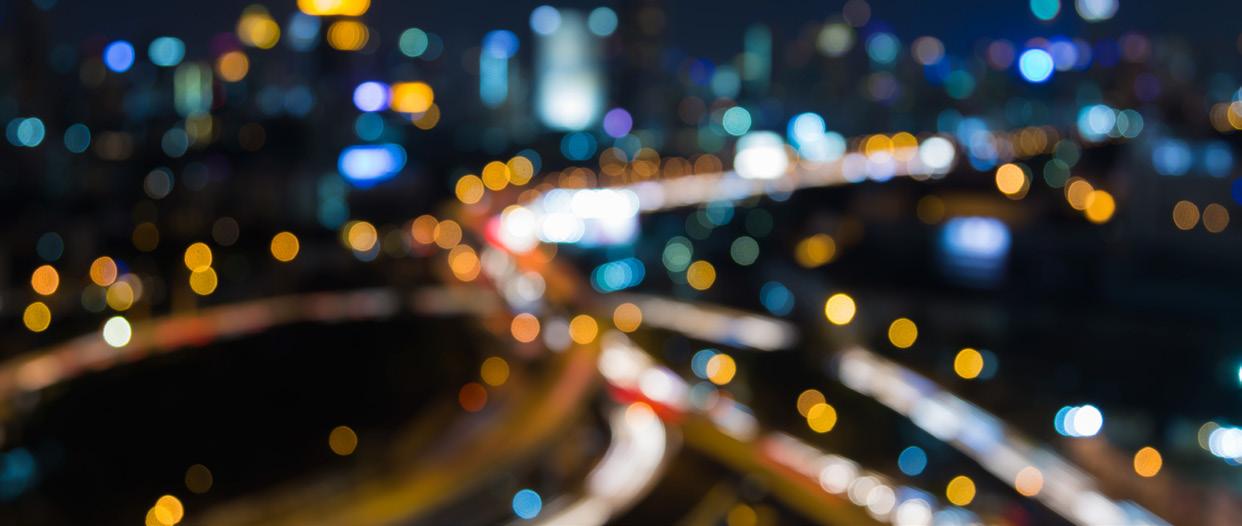
National forecasts suggest an additional 300,000 construction workers will be required by 2024 to staff the increasing number of major infrastructure projects in Australia. In 2015, jobs advertised in the construction industry obtained an average of 3.5 applications compared to 9.9 applications in 2008, with only 0.5 of those applicants being appropriately skilled for the job. If the industry continues like this it could result in a nation-wide critical skill shortage.
Australia’s infrastructure sector is set to boom in the coming years with Victoria alone undertaking projects such as the Metro Tunnel, North East Link, Level Crossing Removals and the West Gate Tunnel. The looming challenge for the industry will be implementing workable strategies to recruit, retain and train skilled people to deliver these projects and Australia’s next generation infrastructure.
Working in Human Resources (HR) in infrastructure means more than just recruitment. Managers have to ensure they’re acquiring appropriately skilled workers while juggling economic volatility, industrial disputes, an aging workforce and the ever changing rules of engagement to ensure successful delivery of their projects.
This means HR must continuously evolve, adapt and proactively seek out new ways to add strategic value to their organisations.
InfraPeople 2018 is a one-day conference that will bring together some of the leading experts in the infrastructure and human resource space to share practical solutions on how best to approach the big issues facing people in infrastructure.
The conference will be held in Melbourne on 8 August, and delegates will hear expert presentations regarding issues such as important 457 Visa changes that will impact the recruitment process; approaches to mental health challenges; workforce diversity; navigating the skill shortage; and learning how major
projects are innovating in the HR sector.
Aimed at roles such as Chief Human Resources Officers, People and Culture Managers and Operations Officers, the conference will attract the most senior decision makers from infrastructure asset owners, government agencies and major contractors.
InfraPeople 2018 offers the chance to get up-to-date on the biggest infrastructure projects in Victoria while networking with peers and industry leaders in formal and casual networking sessions.
Infrastructure magazine is excited to bring you this new event to help ensure your organisation remains equipped to face the challenges of the next ten years and beyond.
InfraPeople 2018 will feature topics including:
» Managing the skills shortage for both high-level and entry-level positions
» Recruitment strategies
» International recruitment and visa changes
» Changing technology
» Risk management
» Diversity and inclusion
» Safety
» Mental health
» Managing the generation gap and much more.
For more information or to register for event updates, please visit www.infrapeopleconference.com.au.

A PROBLEM IGNORED: HIGHWAY BRIDGES TRUCK PLATOONS
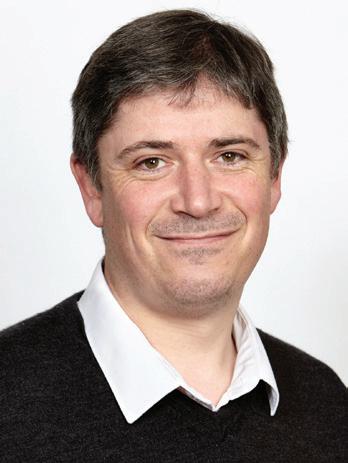
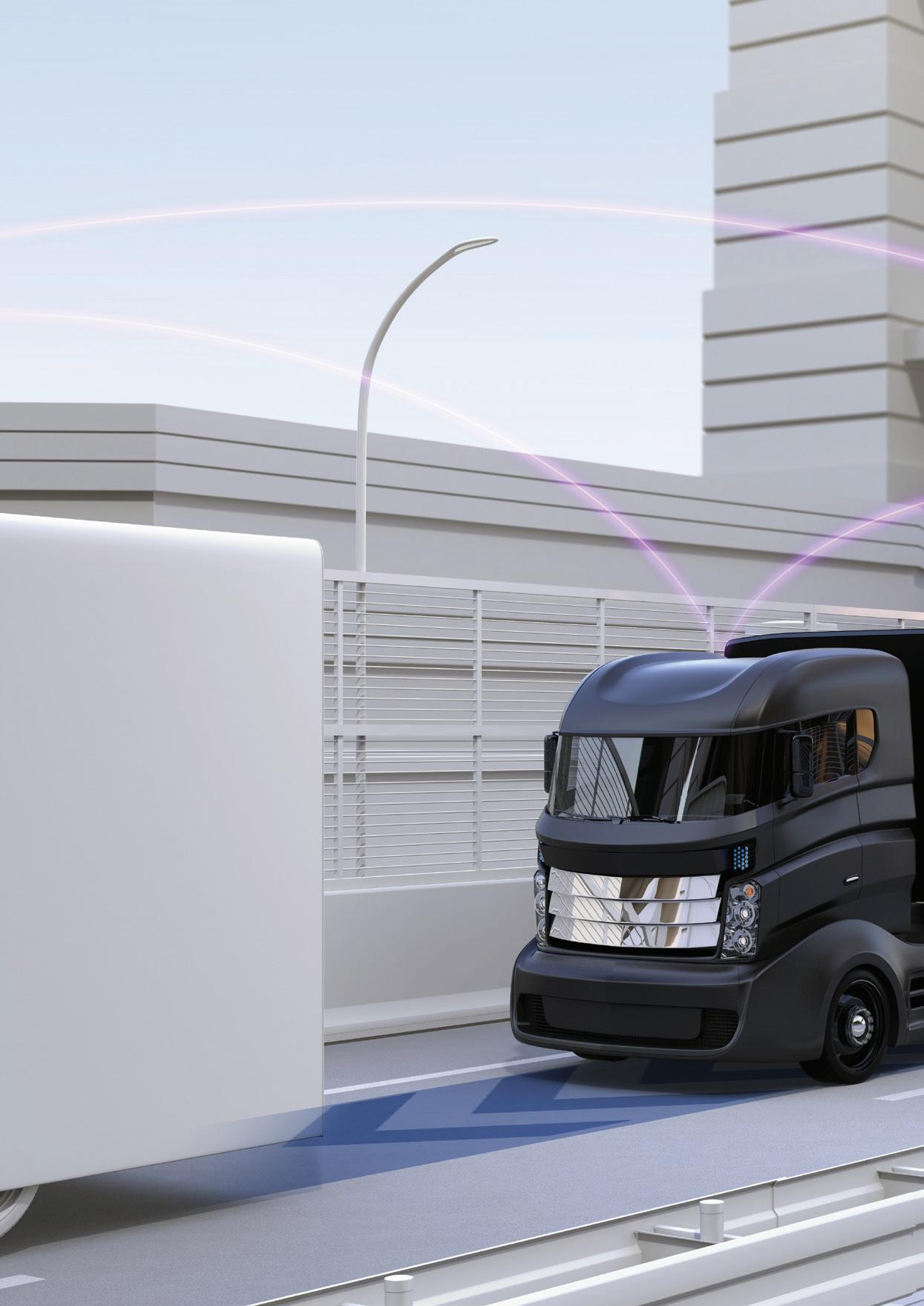
With automated truck platoons - trucks controlled by automatic systems that drive very close together - expected to come to Australia, one question that industry hasn’t thought about is the impact of these platoons on Australia’s aging bridge infrastructure. Here, Colin Caprani asks if our bridges can handle it?
IGNORED: AND AUTOMATED
by Colin Caprani, Senior Lecturer, Chartered Structural Engineer, Monash University.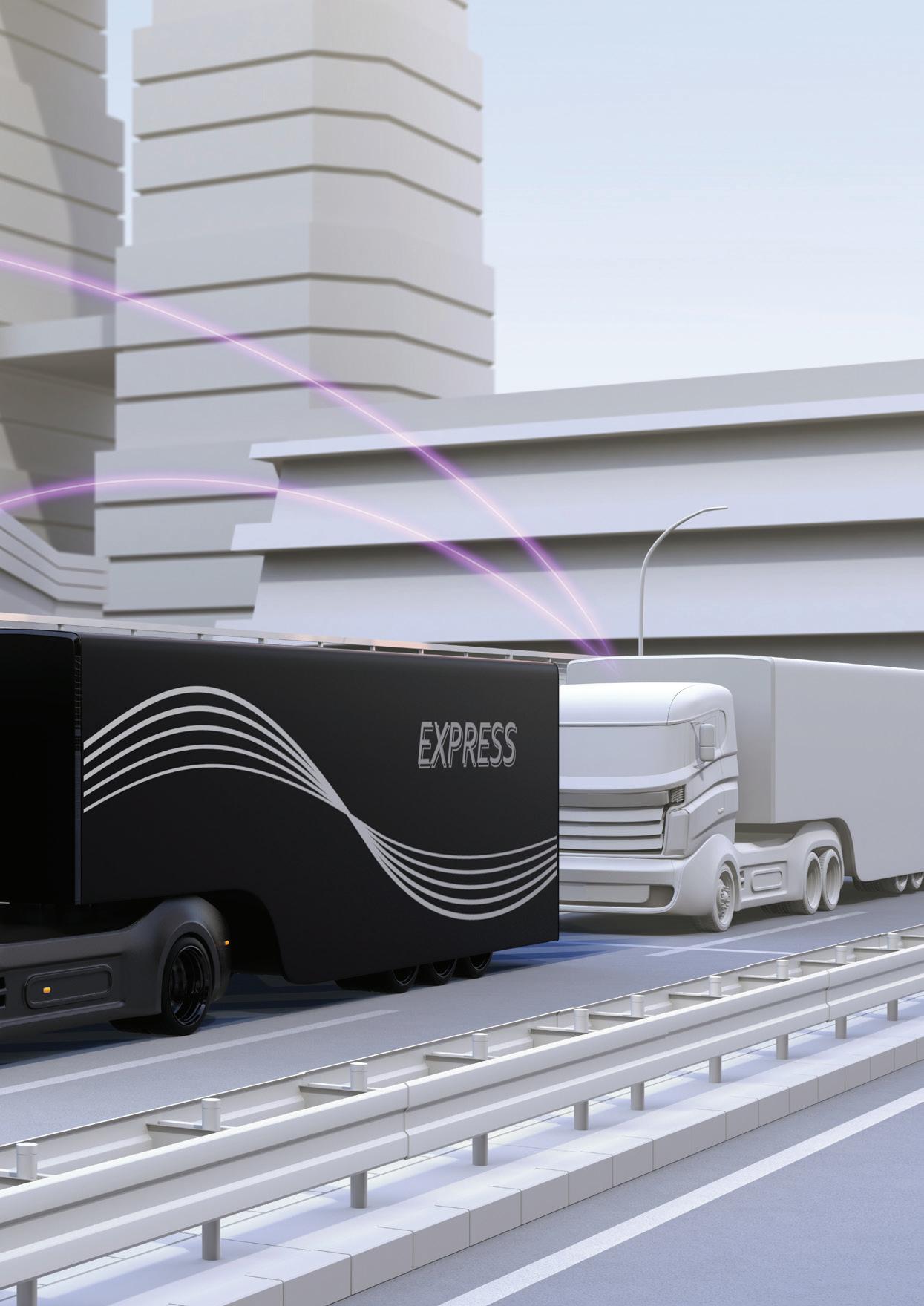
BRIDGES

Automated truck platoons are coming to Australia it seems. To power the Australian economy, around 3.5 million tonnes of freight is moved by trucks every day. This “freight task” is expected to double between 2008 and 2030. Reducing the cost of this task will make Australia more competitive, and our goods cheaper. Automated truck platoons are seen as a paradigm shift in this regard. We can expect hugely reduced labour costs, improved safety, and fuel consumption savings of about 18 per cent for bumper-to-bumper gaps of four metres. It’s enough to make truckies nervous and tech company CEOs jittery with excitement.
Automated truck platoons consist of a number of closely-spaced trucks controlled by automatic systems that control driving tasks such as steering and braking. The main benefit is the reduced fuel consumption of the follower trucks, due to the reduced aerodynamic forces.
While not necessarily driverless, these technologies, when coupled with autonomous driving systems, could
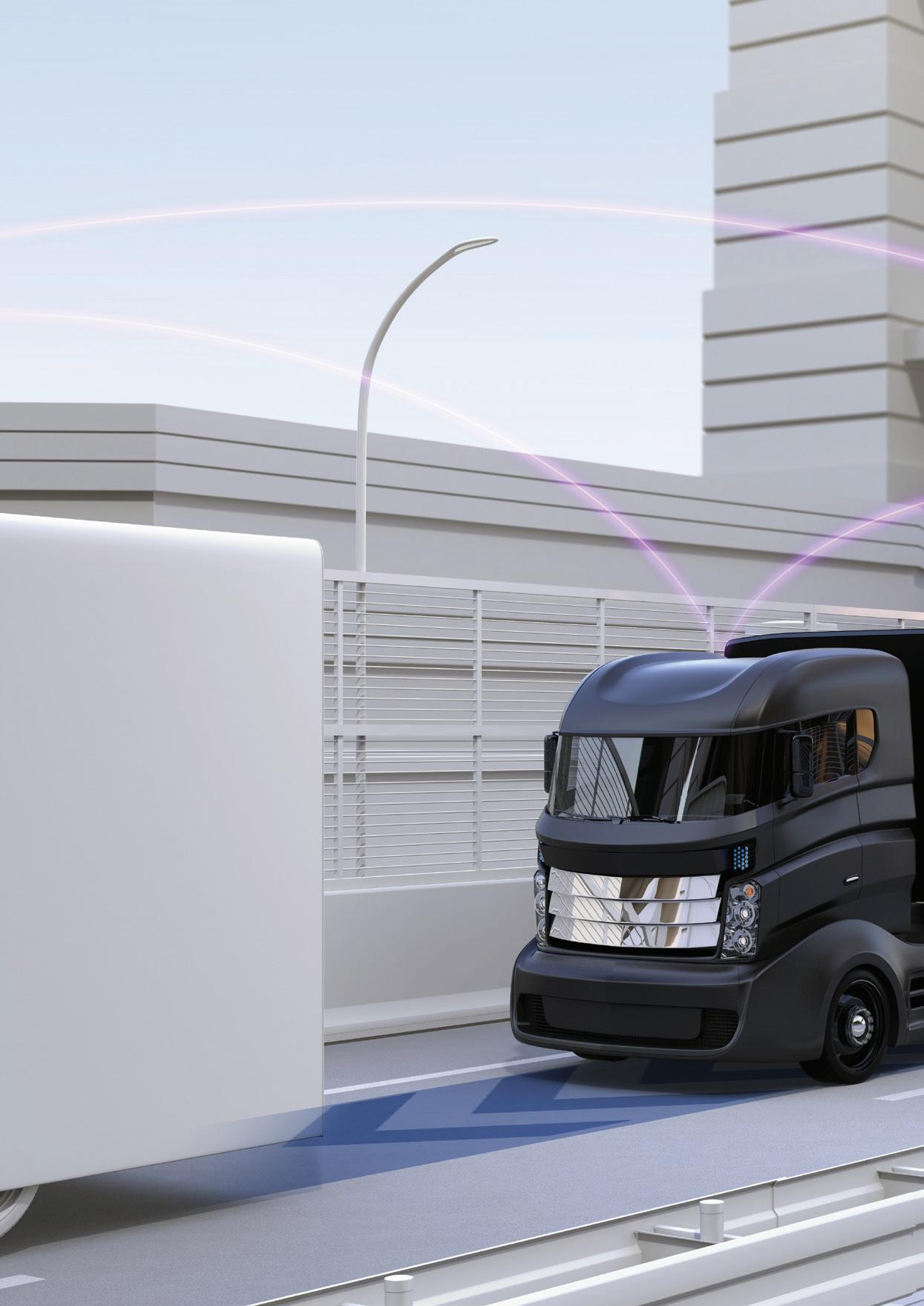
mean that a platoon of six semi-trailers has just one driver. So, the savings are at least twofold: reduced fuel consumption, and reduced labour costs. The first of these relies heavily on the gap maintained between the trucks, meaning the closer the better.
In terms of the regulatory environment, the National Transport Commission (NTC) has been working on autonomous vehicles since 2015, and late last year the national enforcement guidelines were published. Laws will soon be changed around Australia to accommodate these smart vehicles on our roads. State road authorities are responding to the new environment. Vicroads, as just one state road authority, even offers grants to encourage trials of autonomous vehicles.
So, it seems that everybody is in favour of this future with just a few issues remaining to be finalised; truck driver concerns, and the legal and insurance framework (the technology itself seems already proven).
Except, nobody seems to have thought of the bridges.
CAN OUR BRIDGES SUPPORT HEAVIER LOADS?
Approximately 70 per cent of Australia’s road bridges are more than 40 years old. About two-thirds of the country’s dual carriageway network was built before 1974. With good maintenance, it’s expected a bridge can last 100 years, but we cannot be sure. The technologies and materials used in many of the bridges on our road network have not even been around for 100 years. Indeed, the bad news is that about half our bridge stock is rated as being in poor condition, and the majority of bridges are not being inspected as frequently as they should.
Of course, the strength of even a degraded bridge is only one half of the problem, the real question is whether or not the bridge is strong enough to carry the loads on it. Of the several load types a bridge must support, the traffic loading is the most significant. For bridge lengths up to around eight metres, the maximum weight of axle groups (tandem, tridem, etc.) is critical; up to about 20m, the maximum weight of a single-truck per lane governs; up
to about 40m, multiple trucks per lane govern; and beyond that, congested traffic is critical, in which queues of closely-spaced trucks govern. Clearly then the two key components of bridge loading are the weight of trucks, and the spacing of trucks.
But how heavy is a truck? Roughly, the legal limits for vehicles in Australia have been increasing about 10 per cent per decade. However, it is not the legal limits that tends to drive bridge design or assessment, but the number and magnitude of illegal overloading. As a result, a statistical analysis is required to find the weight of the one in 100-year truck, or similar such measure.
TRUCK SPACING ALSO AN ISSUE
And what is the spacing between trucks? In dense but fast-flowing traffic, the gaps between trucks are not usually smaller than one second, and more typically over two seconds, leading to physical gaps which are certainly more than 20m. For slow-moving congested traffic these gaps can be substantially smaller at around 7.5 to 10m.
The safety assessment of new and existing bridges relies on accurate models of bridge traffic loading, which are calibrated against these weights and spacings of trucks. So far, this approach has served us well, and bridges are amongst the safest of all civil engineering structures.
So here is the problem: automated truck platooning voids the assumptions underpinning current bridge assessment practices. By significantly reducing the gaps between trucks, and by dramatically increasing the frequency of these small gaps, the current calibrated traffic load models are rendered invalid.
Surely such a significant existential threat to the roll-out of automated truck platooning has received the attention it deserves? Not so.
For example, state road authority Vicroads’ procedures for approving trials do not make any reference to infrastructure. Even worse, the NTC’s Guidelines for Autonomous Trials simply says that, “trialling organisations must inform road transport agencies of any infrastructure or network requirements for the trial”, the clear implication being that the public must fund whatever infrastructure demands trialling companies make.
So, to summarise the current state: bridges are getting older and their strength is degrading, trucks are getting
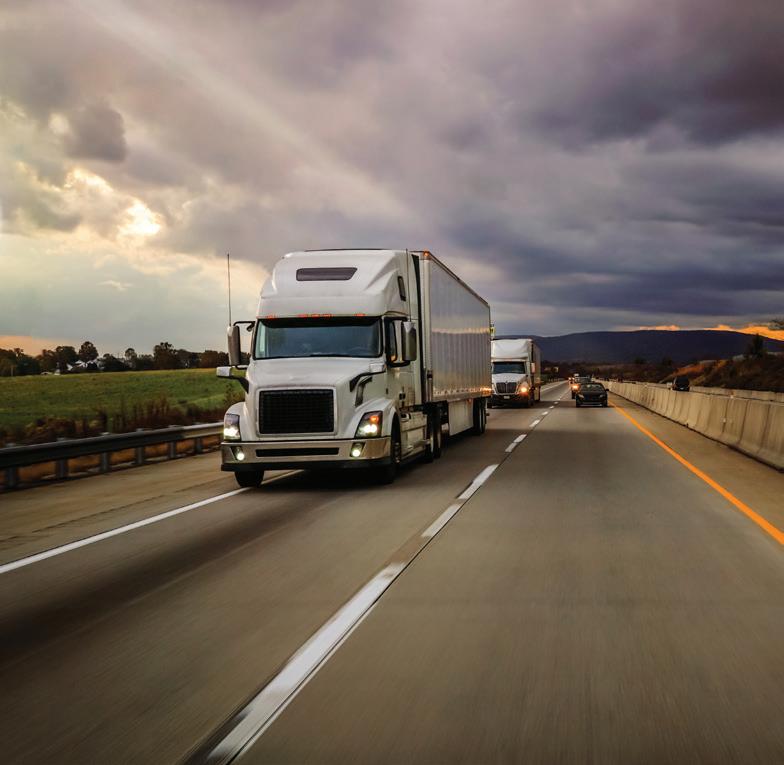
heavier and more frequent, and the way we check bridge safety does not allow for automated truck platoons. There is clearly a problem.
THE IMPLICATIONS NEED TO BE ADDRESSED
Such existential problems to the advancement of a new technology are usually identified and addressed. But this has not happened here; no research has been done to assess the impact of automated truck platoons on bridge loading.
In part, this is because the asset owner (the public) and the beneficiary (private industry) are different entities. One presumes the thought processes are, why should the public directly fund capital for private profit, and why should private industry fund a public asset? Until a clear financial link between investment and beneficiary is made, it is hard to see who should shoulder the cost of the research and development that is required.
Nevertheless, there is a silver lining. The technology that is used in automated truck platoons can be adapted to manage the loads imparted to the bridge. A recent study has shown that actively managing the gaps between trucks can lead to significant beneficial outcomes for bridge safety (Figure 1).
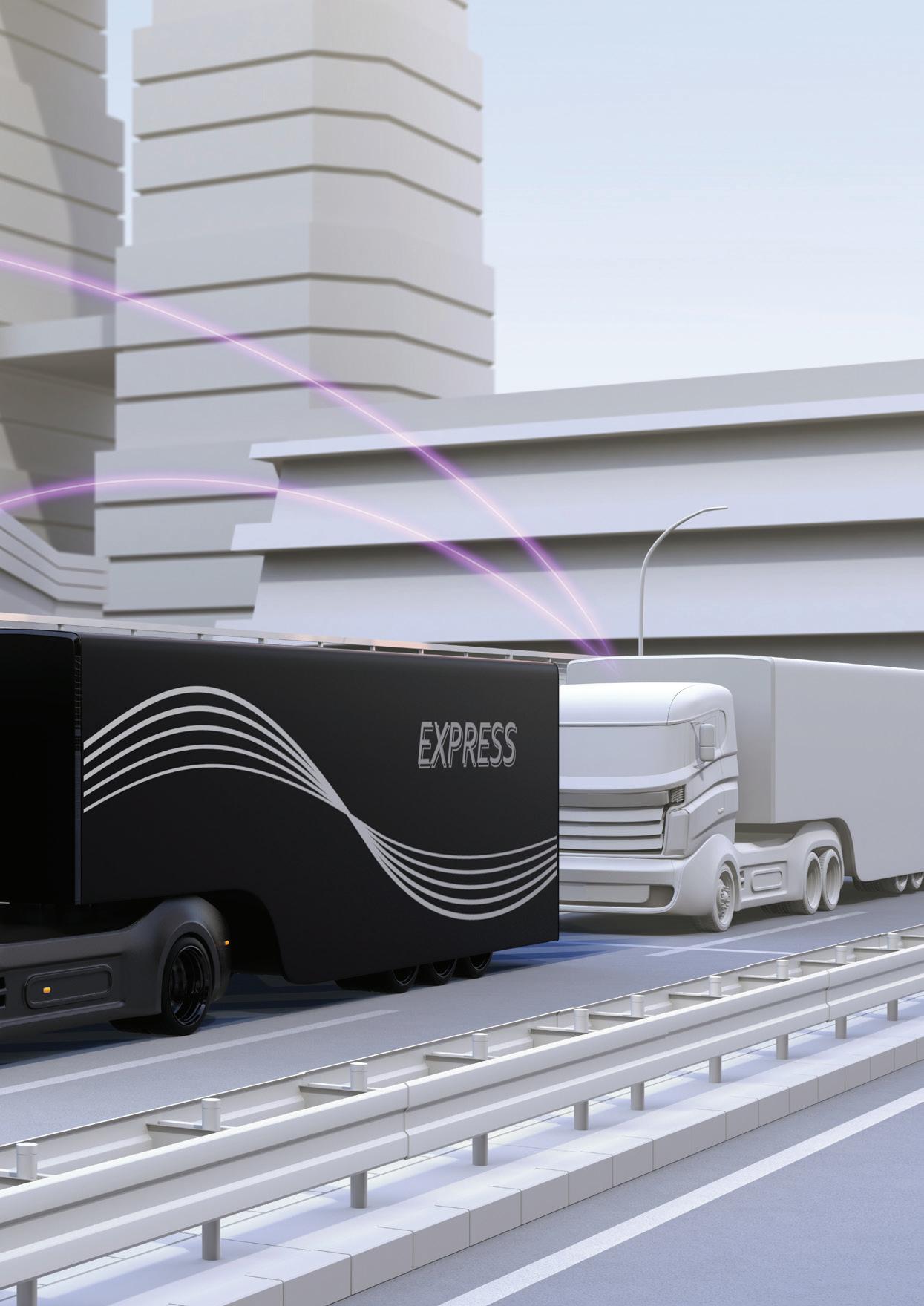
If just 10 per cent of trucks maintain a 20m control gap going over a bridge, the lifetime extreme loading is reduced by 10 per cent. If 90 per cent of trucks maintain a 50m control gap, it reduces by nearly 50 per cent. And these reductions are compared to the base condition of current traffic, not the condition of extreme loading implied by the presence of automated truck platoons.
In spite of these promising results, a single study is insufficient grounds to build a new industry and assume that the roll-out of automated truck platoons will be unhindered. Indeed, without more preparatory work, the nascent industry will be in for a shock when applications to run truck platoons are eventually assessed against the limitations posed by degraded bridge capacities and consequently rejected.
ACHIEVING AND DURABLE
Sustainability, limited resources and environmental concerns are increasingly front of mind for bridge design and optimised maintenance of bridges. It’s important to look at whole of life costs as well as alternative materials to improve in service life and to minimise greenhouse gas emissions. We spoke to Dr Richard Yeo, Program Manager, Assets, at Austroads, to find out about some of the innovative research that Austroads has been undertaking on bridges and how the results could change the way bridges are designed and constructed.
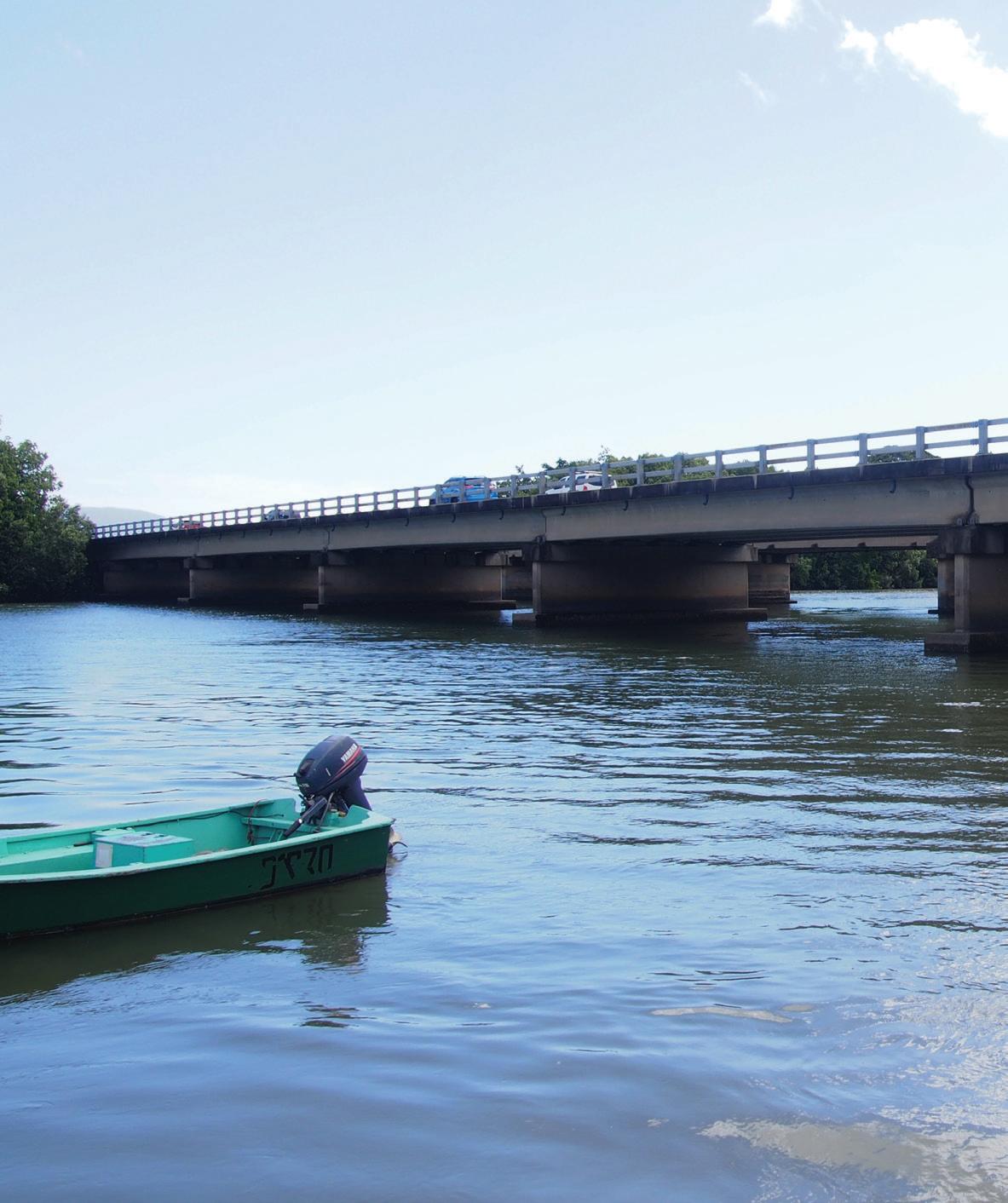
Austroads is the peak organisation for Australasian road transport and traffic agencies, with its members collectively responsible for the management of over 900,000km of roads valued at more than $200 billion.
In order to support member agencies to deliver an improved road transport network, Austroads undertakes leading road and transport research to support policy developments, and provide guidance in the design, construction and management of roads and associated infrastructure.
In the area of bridge technology, Austroads has brought together representatives from state and territory road agencies, the National Transport Commission and the Australian Road Research Board, to form the Bridge Task Force. The Task Force is responsible for maintaining the Austroads Guide to Bridge Technology, preparing specialist reports, and arranging for research and testing. It considers all aspects of bridge planning, design, construction, operation and maintenance.

Bridge Task Force on site at the Darlington Upgrade Project south of Adelaide Feb 2018.
The Bridge Task Force coordinates research that is working towards:
♦ Developing enhanced bridge design guidelines
♦ Improving evaluation methods for bridge load capacity and associated traffic demand
♦ Ensuring the Austroads Guides are up-to-date and better integrated with jurisdictional supplements
♦ The revision of Bridge Design Standard AS5100
Two research reports have been released by the Task Force to help pave the way forward for achieving longer service life and increasing the sustainability of bridges.
ACHIEVING A 100 YEAR DESIGN LIFE
Improving service life by examining different methods for concrete deterioration protection was the focus of the reports delivered through the project, Realising 100-year
SUSTAINABLE BRIDGES
Design Life of Bridge Structures in an Aggressive Environment.
Dr Richard Yeo, Program Manager, Assets, at Austroads said the research looked at structures like the Gateway Bridge in Brisbane and the mechanisms available that will ensure a 100 year design life is achieved.
“The project involved a very thorough literature review and critical assessment of available means to ensure that the durability of those particular concrete structures would achieve that outcome,” Dr Yeo said.
reinforcement is connected to allow for future cathodic protection if needed.”
Dr Yeo said the recent research found that it can’t be guaranteed that construction on-site will be as planned.
“You can’t always guarantee that the cover requirements will be met for the reinforcement and that impacts on the durability,” Dr Yeo said.
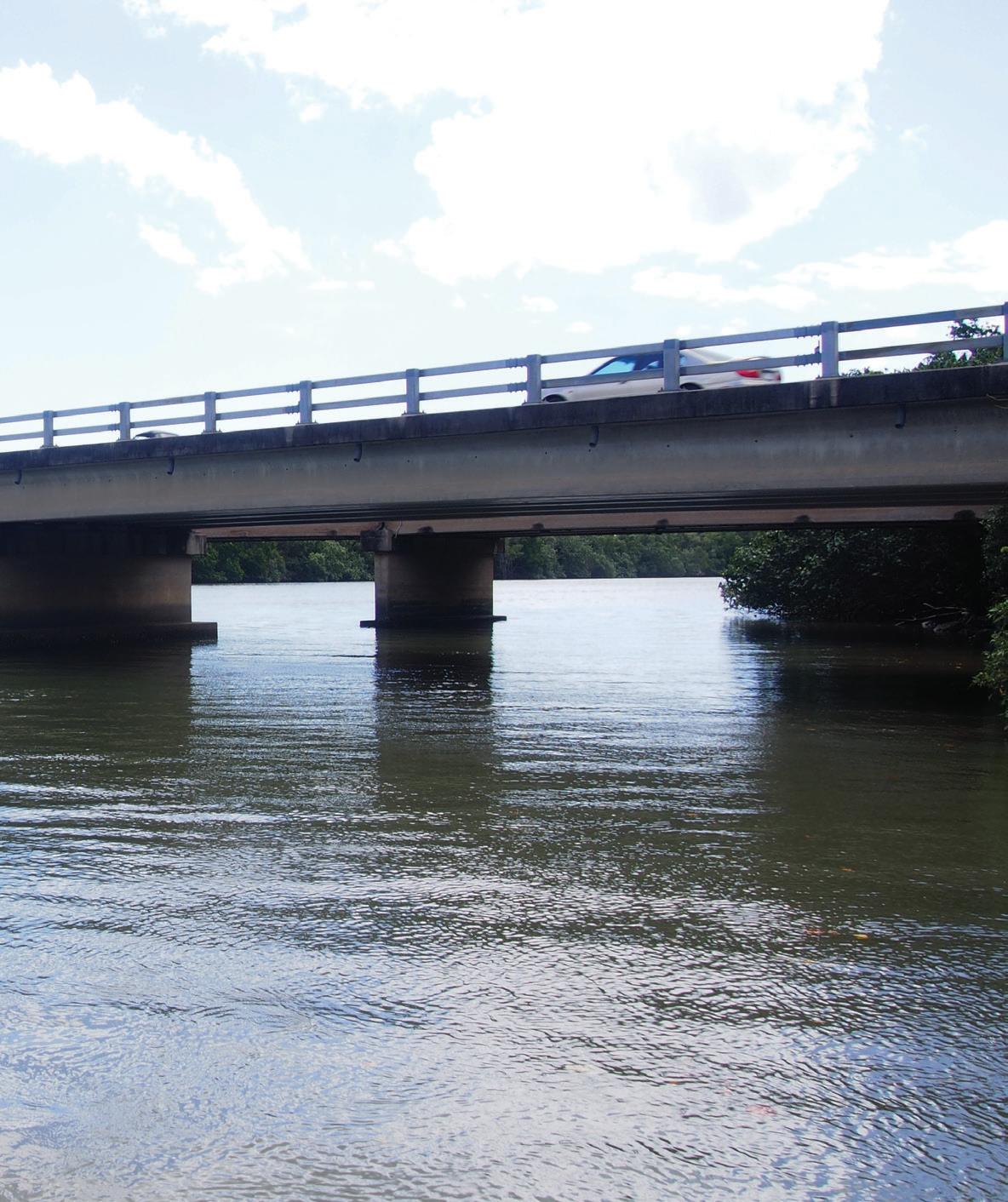
“Usually bridge designers prepare a durability plan for concrete structures based on a common approach with specific reinforcement cover requirements and making sure all steel
“At the end of the day, you might get critical zones of the structure, such as the piles, pile caps or interfaces, which are typically either underwater or buried and very difficult to access for later repair or replacement should early deterioration issues occur down the track. Typically that’s where we have problems, particularly in aggressive environments.”
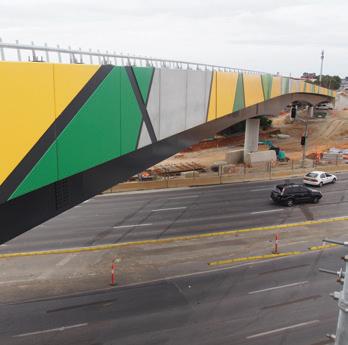
The research looked at a wide range of options to prevent concrete deterioration, and the whole of life implications and costs, and came up with a different solution.
The study found that the most costeffective long-term solution was the replacement of around 20 per cent of steel reinforcement with stainless steel reinforcement in those critical zones. It found that even if the construction is not quite right or the environment adversely impacts the structure, the stainless steel will not be affected, mitigating the issues that are often seen in aggressive environments.

Dr Yeo gave an example of a bridge in Cairns in Far North Queensland that was built 30 years ago which had significant issues with corrosion of the reinforcement in the piers just below the waterline.
“If 30 years ago they had used this type of approach, they would not have an issue, it would not be deteriorating in that way. Of course, to inspect and repair that structure in that environment, you have problems with crocodiles. Now just to go and look at the problem is a challenge, because it’s not safe.”
AN IN-DEPTH LOOK AT DURABILITY
The findings are split into two related reports - experimental work and literature review.
The experimental work was informed by the extensive literature review and focused on concrete durability. The work comprised investigations into concrete deterioration mechanisms and their mitigation, including corrosion of steel reinforcement as influenced by chloride diffusion into concrete, carbonation of concrete, corrosion resistance of stainless steel, alkali-aggregate reaction and sulfate resistance of concrete.
“The research team did a whole range of laboratory tests to validate that you could buy the stainless steel reinforcement, and what type of stainless steel you should use. That in an aggressive environment it would not deteriorate, compared with say a conventional reinforcement,” Dr Yeo said.
The literature review took a more in-depth look at the durability issues that affect the service life of reinforced concrete structures, and considered information from sources within Australia and overseas.
It looks at the range of options available for improving durability, including the use of epoxy to coat the reinforcement. The research considered the pros and cons of the different alternatives but found that there were issues that could compromise their suitability. For example, if an epoxy coating is scratched or there is a breakdown in the barrier, corrosion will be able to take hold where these defects occur.
“Everybody I talk to says yes, we’ve done a durability plan, and yes we’ve defaulted to what we always do. Yet, this report is more or less challenging that, and saying have you really thought about all of the options, and the whole of life cost implications of those? Because things like cathodic protection can be expensive and difficult to maintain over long periods,” Dr Yeo said.
“We’re talking 100 plus years. So if you have problems at year 30 and you put that in place, you’ve got 70 years of maintaining a system. Or you could have stainless steel built from the outset, and you won’t have a problem.”
BREAKING DOWN THE SCIENCE OF GEOPOLYMER
Another key problem that the Task Force is working to find a solution to is greenhouse gas emissions. One of the concerns with using concrete for components is the large amount of greenhouse gases that are produced, and the energy required for cement manufacture.
Because of this, Dr Yeo said that people have been working to create alternative cement mixes and types of cement for decades, with one of these being geopolymer cement.
“Geopolymer concrete does not use ordinary Portland cement. It uses alternative materials, often by-products of other processes, which have a cementitious effect. The interesting part is it’s been around for some decades. But what was tending to happen in the market was that it wasn’t readily available, and what was available was proprietary product with limited information on the active ingredients in the mix,” Dr Yeo said.
The led to the Task Force releasing a report, Specification and Use of Geopolymer Concrete in the Manufacture of Structural and NonStructural Components, that looked into the properties of geopolymer and how it works in concrete. As geopolymer is not typically used as a structural concrete, the research focused on the parameters around using it for structures.
“Importantly we wanted to look at what the active constituents and reactions are, to provide an explanation of how it actually works. The research sought to open up the chemical nature of geopolymer cements so that asset owners considering this alternative material can better understand what ingredients it should have, what properties they should be looking for, and indeed being able to make their own mixes without having to require or rely on a particular supplier saying, ‘Trust us, it’s good’, Dr Yeo said.
The Austroads funded research took place over five years and involved the Australian Road Research Board working in collaboration with Swinburne University. Dr Yeo said the challenge of the project was breaking down the chemistry of the product and trying to understand it, as geopolymer manufacturers were not willing to divulge this information.
The research team then undertook a thorough literature review to see what information had been published, and then started to formulate their own mixes using ingredients that they knew worked. The team was able to focus in on the types of mixes and materials used to manufacture geopolymer and were able to create and assess small scale samples up to full structural beams to prove that it could be used as a structural concrete.
Dr Yeo said while research and experiments can predict the performance and long-term durability of geopolymer concrete, the problem with new technology such as this is that
you can’t wait 100 years to see how well it lasts compared to conventional concretes.
“We were able to do the accelerated deterioration tests, which take 12 months to two years, and look at how this concrete performs, relative to the standard Portland cement concrete.
“In fact, you can look at all the test data, and the trends show that this was a better product in durability than conventional concrete. So in addressing the problem of predicting the long-term durability, the observed positive trends give you some confidence,” Dr Yeo said.
“We followed up the research with a survey and asked who is using this as early adopters across our member road agencies? Are there some good examples of its use? The survey looked at road agency adoption of geopolymer concrete, specifications that might allow its use and barriers to adoption as well as experiences to date.
“The champions I think were VicRoads, they were absolute leaders. They had modified their standard specifications in five different areas to allow for geopolymer concrete used for, in this case, non-structural applications. We found that they had a wide range of concrete applications where they allow
for geopolymer concrete mixes. The door is open for other road agencies to adopt or adapt the VicRoads specifications.”
Dr Yeo said estimates of the amount of greenhouse gas emissions savings that could be achieved by using geopolymer instead of Portland cement had been developed.
“If you were to build a dual carriageway, four-lane highway with geopolymer concrete as the pavement, as opposed to Portland cement concrete, around 2,000 tons of greenhouse gas emissions would be saved per kilometre.”
“So every time someone proposes a concrete road, I say, ‘Are you going to use geopolymer concrete?’ Because we’ve shown how it can be used,” Dr Yeo said.
THE NEXT CHALLENGE
Dr Yeo said that while research and specifications for new bridges is going well, the biggest challenge is managing Australia’s bridge stock to facilitate greater freight productivity.
“There’s a lot of work on assessment of bridges, and a lot of angst, I suppose, around the ability of older bridges to sustainably carry heavier trucks,
particularly emerging high productivity freight vehicles, over mass super loads and large mobile cranes which develop concentrated loads, and allowing them access.
“We have certainly changed our views from ‘we can’t let them go because the bridge will be damaged’, to ‘what can we let go? How far can we push things? What is the real capacity and associated risk’,” Dr Yeo said.
“When you look at the bridge stock, a state road agency may manage 5,000 bridges and major culverts. You refine it down and you might have around 200 bridges that assessment indicates structural inadequacy for a certain vehicle mass and axle spacing. Means to work beyond the current AS5100 assessment provisions while managing the risks become a key consideration.”
An ongoing challenge connected to this is getting the funding needed to maintain or strengthen these bridges.
“There’s a lot of discussion at the Task Force around bridge assessment and what live load factors are required. What access we can provide, and when we can’t, we’ve really got to draw the line. Optimised asset management for bridges is a current focus of the Task Force.”
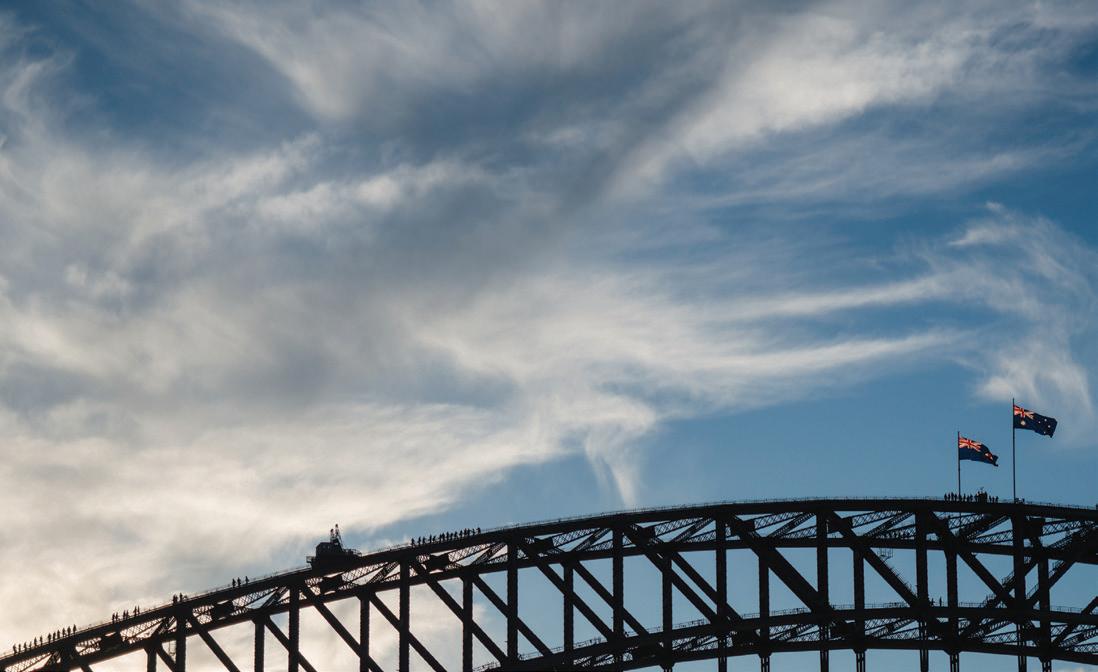
Reducing humidity below critical levels prevents corrosion.
EMBRACING NEW RAIL TECHNOLOGIES
by Andrew Meier, Executive Director/Chief Executive Officer, Australasian Centre for Rail Innovation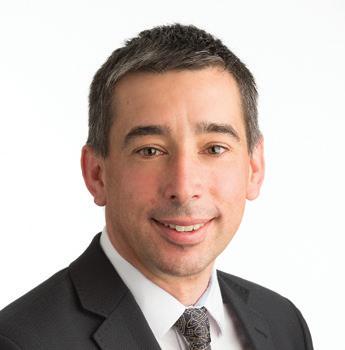
The Transport and Infrastructure Council (TIC), which functions under the Council of Australian Governments (COAG) to progress nationally significant reforms, aims to capitalise on the opportunities afforded by new and emerging technologies, and support adaptable and resilient infrastructure and transport systems.
Access to knowledge is a key component of this. Initially the Federal Government aided industry by setting up the Rail Cooperative Research Centre (Rail CRC), which ran for two iterations before winding up in 2014. Private and state government entities supported a continuation of cooperative rail research and the not-for-profit Australasian Centre for Rail Innovation (ACRI) was established.
Its aim is to facilitate independent research and analysis, to provide innovative solutions tailored to rail industry needs. It is overseen by a board representative of both industry and government, and operates on a shared intellectual property model with research findings disseminated across all participants.
ACRI’s program of research is agreed cooperatively by funding participants within heavy haul, passenger and freight
In launching the National Innovation and Science Agenda in 2015, Prime Minister, Malcolm Turnbull, said, “We cannot future-proof ourselves from change, nor should we seek to do so”. What was sought was the “agility to identify opportunities and embrace risk”. Fully embracing risk may feel like a bold step for most, but understanding that advances in technology bring great opportunity, as well as disruption, need not be.
rail, and level crossing focus areas. Now in its fourth year of operation and second research funding tranche, there are presently 25 research initiatives in delivery or development, having completed more than 20 projects since its inception.
THE IMPACT OF TECHNOLOGICAL CHANGE
Activities to advance the health monitoring of infrastructure include readying industry for the implementation of new technologies in broken rail detection, through the independent evaluation of a commercially developed locomotivemounted broken rail detection device, in a variety of Australian weather and rail stress conditions.
Technology also aids the understanding of the human interaction with rail infrastructure. Current initiatives utilising eye tracking include evaluating level crossing visual warning devices for pedestrians, and furthering knowledge on slips, trips and falls within rail station environments in order to aid design improvements.
Such research initiatives address currently tangible challenges for rail, but the industry must also be ready and open to those that are emerging. Presently two frameworks are being developed to address the impact
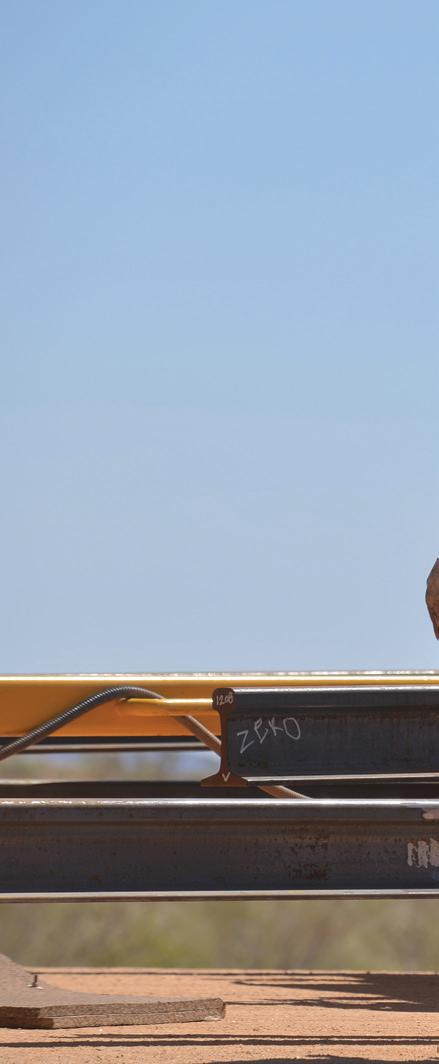
of technological change within rail organisations, one aimed at all aspects of rail operations and the other with a specific focus on track worker safety and competencies. These holistic tools aim to mitigate the challenges of introducing new technology, and improve industry competitiveness by identifying, in advance, the training and management adjustments that may be required.
The speed with which rail can identify and adapt innovation from outside the industry will also have a significant impact on industry competitiveness. This may require some facilitation as those researching emerging technologies do not necessarily have applications in transport and infrastructure foremost in mind. ACRI is presently evaluating the suitability
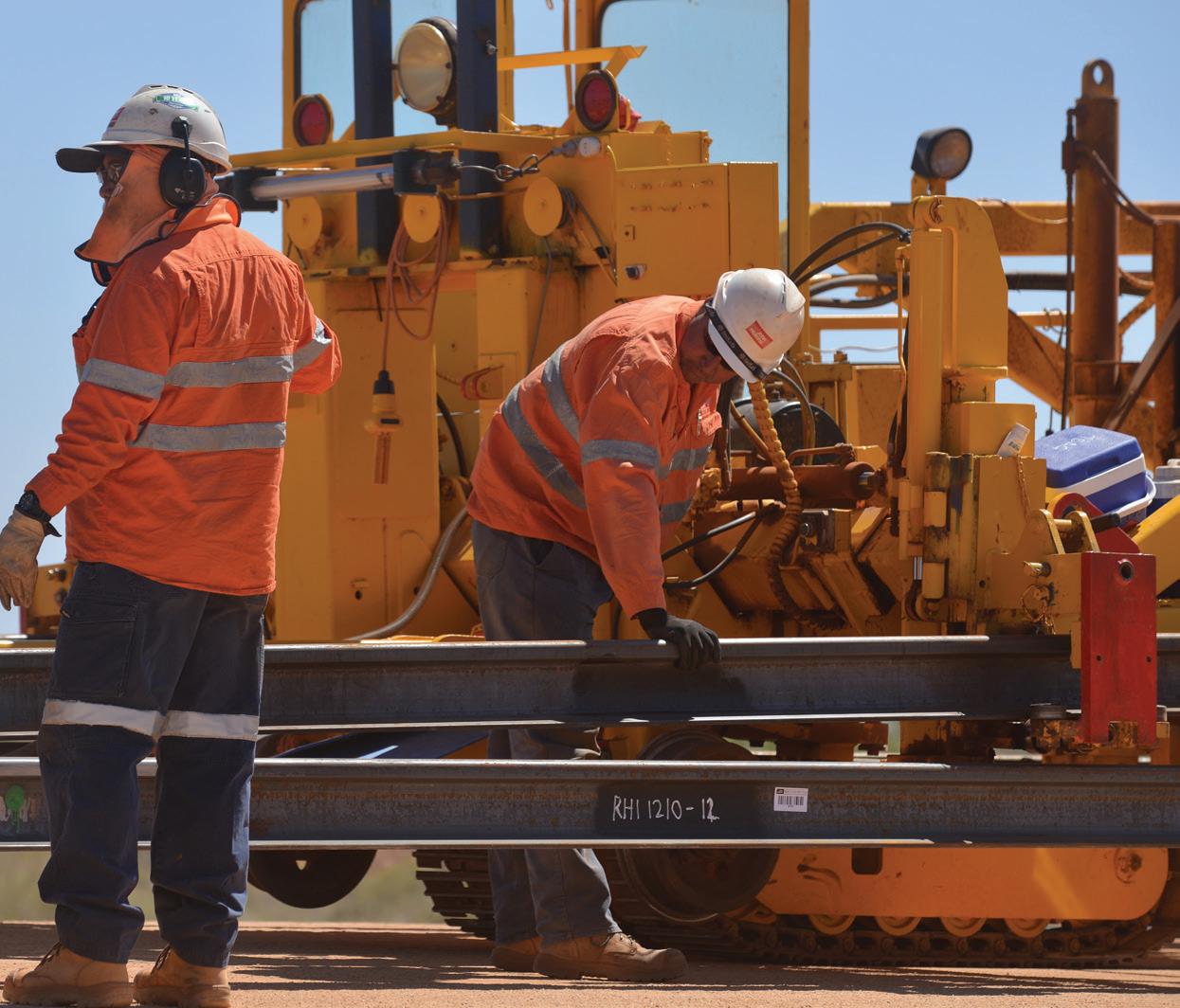
of a technology originally from the naval operations sector for locomotivemounted rail condition monitoring which has been developed and tested to its current state within New Zealand.
COLLABORATION TO INCREASE COMPETITIVENESS
Also important for rail industry advancement and competitiveness are activities in cooperation, linking operations with academia and linking Australasia with international developments.
Initiatives like the Australian Research Council Industrial Transformation Training Centre for Advanced Technologies in Rail Track Infrastructure (ITTC-Rail), which will combine higher degree civil rail engineering research
with significant periods of industry placement, aim to not only deliver industry-relevant research but also importantly industry-ready post graduates.
Internationally ACRI has fostered formal relationships with entities in the United States, Canada, United Kingdom, Italy, and with the International Union of Railways (UIC), providing channels for currently international knowledge to inform Australasian rail infrastructure practices.
For example, the largest ever Australian freight rail infrastructure project, the 1,700km Inland Rail line connecting Melbourne and Brisbane is now underway, with ACRI participant the Australian Rail Track Corporation (ARTC) managing delivery over the next decade.
By lowering freight supply chain costs, providing regional connectivity to ports, reducing road congestion and allowing the opportunity for increased passenger rail services on the Sydney network, Inland Rail will strongly impact on industry efficiency, sustainability and competitiveness. Importantly it presents a major opportunity for rail innovation as it is easier to apply new technology to new projects than retrofit it to existing infrastructure.
Innovation can bring challenge or significant opportunity, with the outcome influenced by informed decision making and planning. Through knowledge advancing entities like ACRI, the Australasian rail industry is well positioned to take advantage of the opportunities ahead.
MOVING INLAND RAIL FORWARD
by Simon Thomas, Programme Delivery Director – Inland Rail, Australian Rail Track Corporation (ARTC)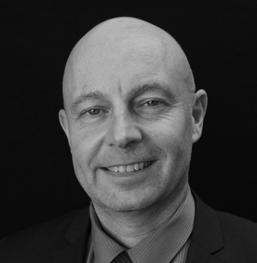
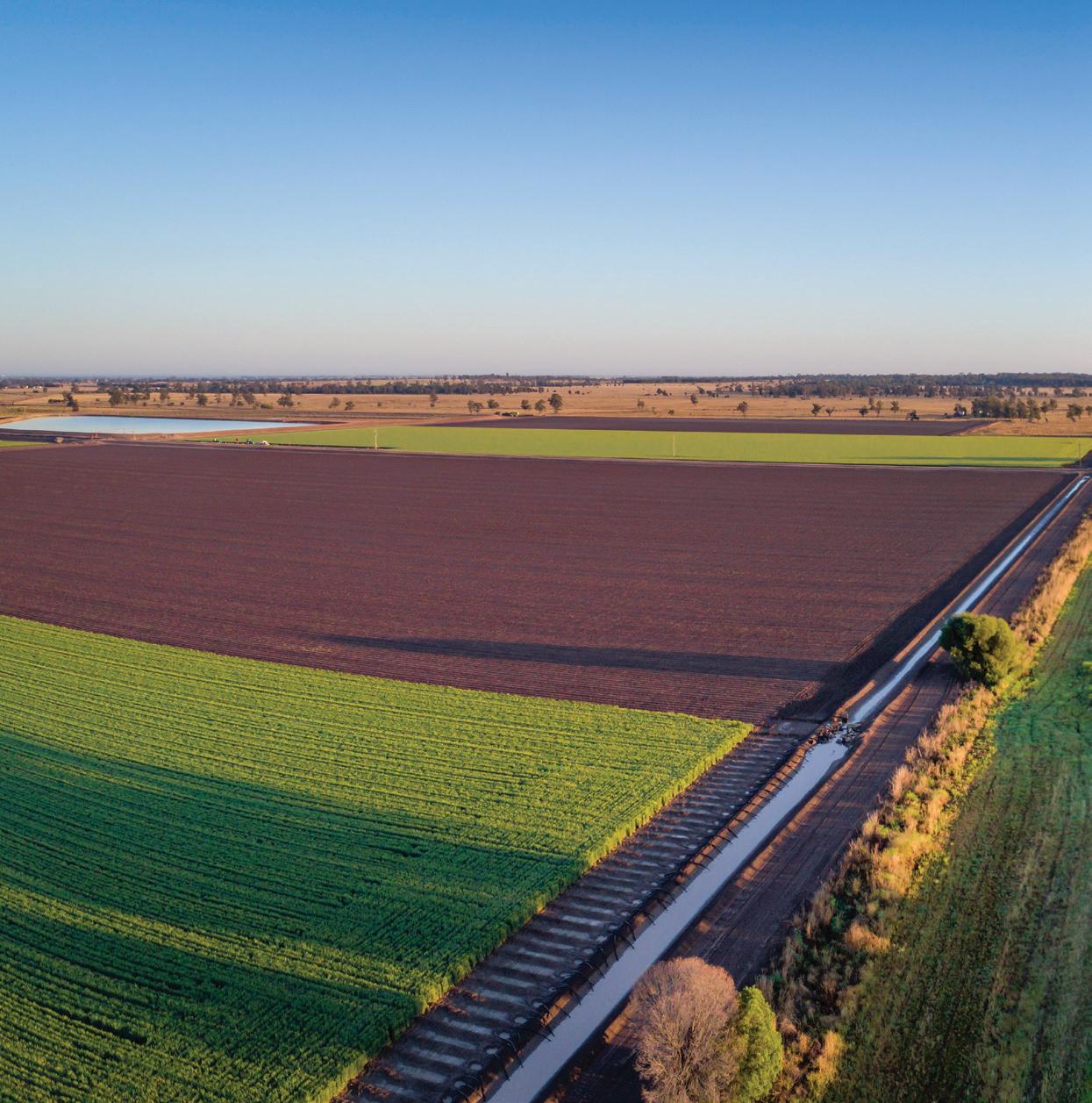
Proposals for railways across inland Australia have been around for more than a century. With 2017 delivering a firm commitment to Inland Rail from the Federal Government, the project is steaming ahead. Significant milestones have been passed in early 2018, including the first delivery of new steel rail and awarding contracts in Queensland for engineering and environmental investigations.
With major construction work getting underway in 2018, we are expecting the first trains to operate between Brisbane and Melbourne in 2024-25. Inland Rail will connect Australia’s second and third largest cities via regional Victoria, central New South Wales and southern Queensland, to complete the ‘spine’ of the 1,435mm standard gauge national freight rail network.
Inland Rail is Australia’s largest freight rail infrastructure project since completion of the Alice Springs – Darwin line more than a decade ago. To give an indication of the scale, the route is as long as New Zealand and it will require enough steel to build five Sydney Harbour Bridges.
CONNECTING AUSTRALIA
Inland Rail is a transformational project bringing lower costs and greater efficiencies to rail freight customers. Ultimately it will allow rail to deliver more produce and goods to consumers, creating long-term jobs, boosting regional economies and helping businesses grow.
The transport and logistics sectors currently contribute 14.5 per cent of Australia’s Gross Domestic Product, with the supply chain worth around $150 billion a year. In order to compete in international markets, Australia needs to have competitive domestic freight transport and efficient supply chains.
Around 70 per cent of Australia’s population lives along the east coast, accounting for 78 per cent of all employment and generating 75 per cent of the nation’s GDP. Our population is expected to increase by 60 per cent over the next 40 years, and the volume of freight moving in Australia is predicted to double or even treble in the next 50 years.
Continued reliance on road transport, which today handles around 74 per cent of the inter-capital freight moving between Brisbane and Melbourne, would pose significant impacts in terms of safety, energy efficiency and environmental impact, particularly as the number of trucks increases to accommodate growing freight volumes.
Inland Rail has thus been designed to pass through Australia’s four most productive farming regions, offering
supply chain benefits and cost savings for agricultural producers, as well as flow-on effects to regional communities. It will also open up new demand, and create opportunities thanks to improved accessibility and greater efficiency.
DELIVERING MARKET-DRIVEN REQUIREMENTS
ARTC has been leading the development of the Inland Rail project since 2006. The project has been shaped by market needs and community feedback as much as engineering constraints.
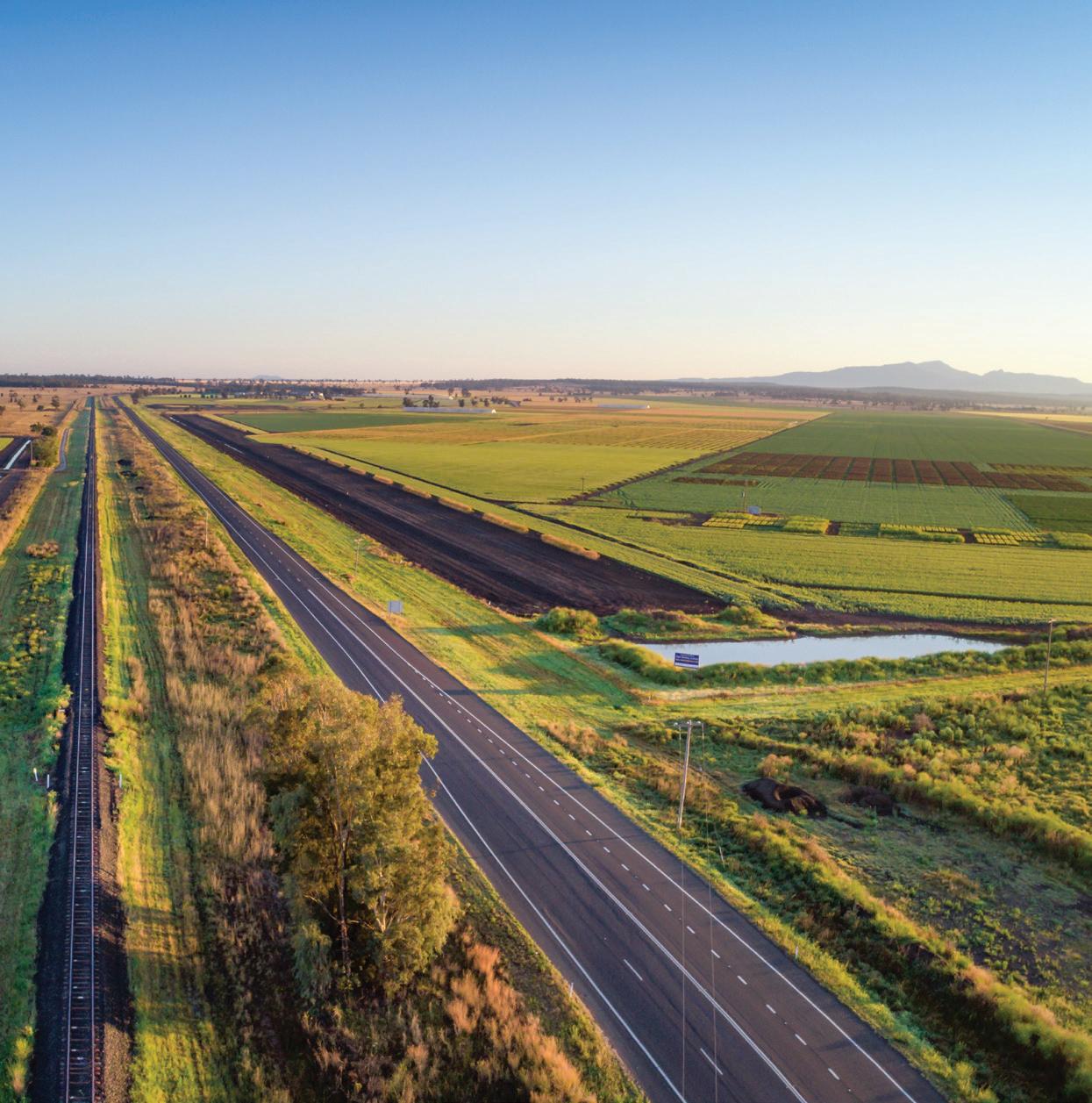
Following extensive consultation with train operators and the freight logistics industry, ARTC developed a detailed service offering and established four key parameters: transit time, price, reliability and availability.
Transit time is key for the operators. Rail freight moving between Melbourne and Brisbane currently runs via Sydney and the NSW coastal route. The long transit time has been a deterrent for potential customers, with freight rail’s share of this market standing at only 26 per cent.
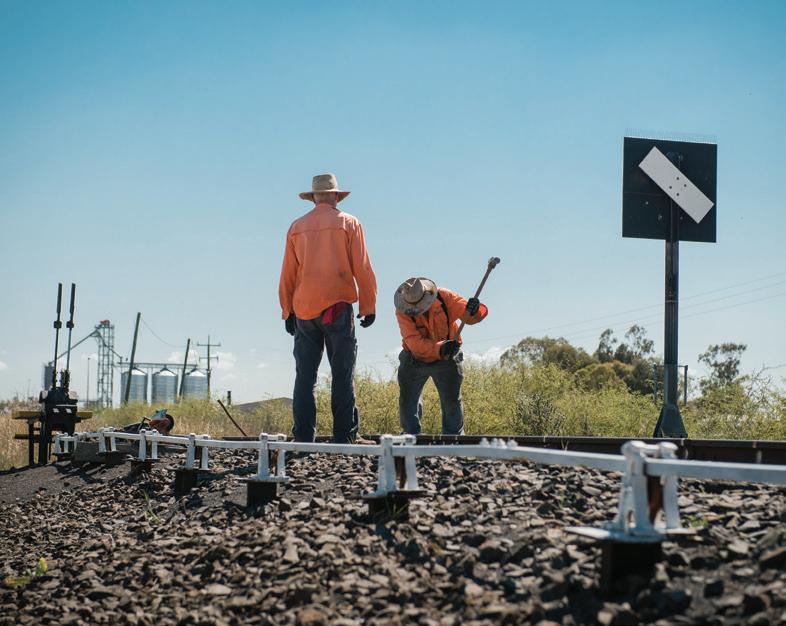
The shorter inland route will be up to 10 hours faster, allowing freight to move directly between Melbourne and Brisbane without having to thread its way through the congested Sydney area.
As well as a transit time of less than 24 hours, our customers told us that reliability and availability are also paramount. They also wanted provision for longer trains to improve productivity, so Inland Rail is being designed for longer trains for greater capacity.
Using 60kg per metre rails on new concrete sleepers, Inland Rail will accommodate 1,800m long doublestack trains with a 21 tonne axle load, running at a maximum speed of 115km/h and it will be future proofed for 3,600m long trains with a 30 tonne axle load, running at a maximum speed of 80km/h. One 1,800m double stacked train will carry the same freight as 110 B-double trucks, reducing the number of trucks on our major highways and creating safer roads.
Inland Rail will also have 7.1m clearances which are needed for double stack operation. At present the only route in Australia that can accommodate double-stack trains is the east-west corridor linking Parkes in central NSW to Perth.
Interoperability is a key technical characteristic that underpins the Inland Rail service offering. To be competitive, and to meet the needs of our operators, we will provide full interoperability with the interstate mainline standard gauge network.
The dual-gauging in Queensland will provide connectivity to the Queensland
narrow gauge for the regional network. And connections to the NSW country regional network will provide for standard gauge connections to the ports of Melbourne, Port Kembla, Sydney, Newcastle, Brisbane, Adelaide and Perth.
From the outset, the north-south corridor has been designed to make use of as much as possible of our existing interstate network. Around 65 per cent of the 1,700km route will use existing alignments, which will be upgraded where necessary.
Inland Rail will follow the existing interstate line for 490km from Melbourne through northern Victoria to Illabo, NSW, north of Junee. It will then run via Parkes, Moree and Toowoomba using a mix of new and upgraded tracks, to join the existing Sydney – Brisbane interstate line at Kagaru, giving access to the terminals at Acacia Ridge and Bromelton in southeast Queensland.
CONSTRUCTION CHALLENGES
Building Inland Rail consists of a complex mix of upgrading existing tracks, and building new tracks in a variety of environments – from passing through suburbs, traversing mountainous terrain, boring tunnels under ranges, to crossing floodplains.
The Victorian section of Inland Rail is planned along 305km of existing rail corridor from metropolitan Melbourne to the Victoria-NSW border at Albury-Wodonga. This project will see enhancements of existing structures and increased clearances along the rail corridor. The enhancement works
are required to accommodate doublestacked trains of 1,800m in length to be run on the track.
The NSW section of the Inland Rail is divided into seven projects which will require enhancement of 649km of existing rail corridor and building 381km of new tracks.
In Queensland, there are five projects which will require enhancement of a total of 127km of existing track and building 272km of new tracks to complete the Melbourne to Brisbane Inland Rail.
One of the most exciting projects will be the construction of a 6.4km long tunnel near Toowoomba to carry the line under the Great Dividing Range west of Brisbane. The tunnel will have an 11m diameter to provide clearance for double stacked containers and it will be one in 65 grade, meaning trains will be able to ascend and descend the length of the tunnel without requiring assistance.
The most difficult technical challenge is the ventilation of the tunnel. Keeping diesel trains travelling uphill cool enough to operate without de-rating or even stalling will require significant mechanical ventilation, especially considering the heat of the Queensland summer. ARTC has approached many world leading ventilation specialists to assist in overcoming this challenge, with the optimal solution to be developed in collaboration with the private sector.
This section of the project not only comprises tunnels, but numerous viaducts are also required throughout southern Queensland. Some of these viaducts will be up to 40m high and others over 1km long in order to traverse mountain ranges or to span floodplains.
ARTC will be one of the first railways to construct with flood modelling taking into account the updated Australian Rainfall & Runoff (ARR 4th edition) –which now considers projected rainfall patterns associated with modelled climate change impacts, in addition to historical and anecdotal evidence.
ARTC’s guiding principle is that in sections where Inland Rail will be upgrading existing lines, it will not materially change current flooding patterns, and in sections new tracks are being built, design will be based on modelling for one in 100-year events. The challenge here is steep – every section has a one in a 100-year event at a different time, and every event differs from the rest in terms of the volume of water, the velocity of the flood waters
and how quickly or slowly the flood levels recede.
To build the best possible rail line, ARTC will follow a robust plan, consulting as widely as possible and constructing to the best engineering plans.
Throughout the alignment, Inland Rail will come across a multitude of crossings – from highways of differing sizes and traffic volumes, to local roads, private roads and traditional stock movement routes. These each will pose their individual challenges, which will in turn require tailored solutions to ensure the communities and businesses served by these roads continue to have access.
WHERE NEXT?
ARTC has already undertaken extensive community consultation, hosting more than 1,200 stakeholder engagement events, meetings and technical workshops since 2016.
The Inland Rail project team has been growing steadily, and we now have around 120 staff spread across offices in Brisbane, Toowoomba, Sydney and Melbourne, supported by a range of consultants. More will be added in the first half of 2018, particularly in the area of stakeholder engagement and communication.
ARTC has stepped up the pace of the project. The first 600 tonnes of the 14,000 tonnes of steel rail required for the Parkes to Narromine section was delivered in January 2018, with further deliveries scheduled to start off the upgrade of the existing line and 6km of new construction to improve connections at Parkes.
ADELAIDE

The work involves replacing the steel rail, concrete sleepers and ballast; realigning some of the tighter curves; raising the level of the formation where required; and strengthening or replacing culverts and bridges as necessary.
We expect construction to begin in 2018 once all the necessary state and federal approvals have been received.
With 2024-25 fast approaching, there is still a lot of work to do, but the end of the long road is now on the horizon. The completion of Inland Rail as the north – south spine of Australia’s rail network will finally bring to fruition the vision of advocates over many years, allowing the nation to reap the benefits of this essential project.
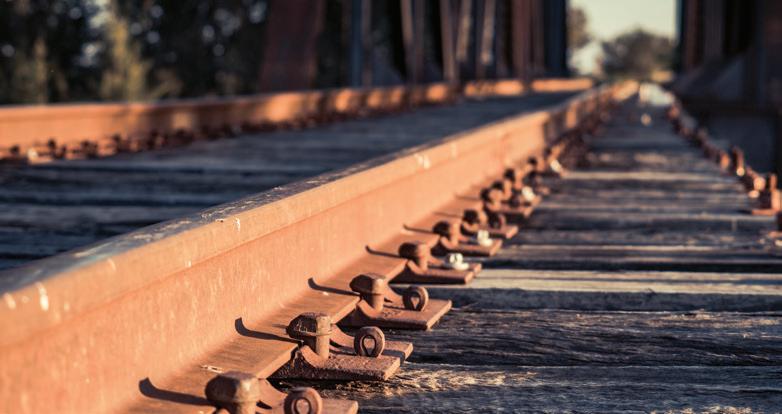
HEAR FROM INDUSTRY LEADERS AT CORE2018
by Katharina Gerstmann, Conference Organising Chair, CORE2018Join us at the 11th RTSA Conference on Railway Excellence (CORE) and Exhibition. CORE is the premier technical event in the Australian rail conference market, delivering high-quality papers covering a wide range of rail engineering, operations, planning and management topics.
CORE2018 will be celebrating 20 years of RTSA and will be the first CORE conference to be held in Sydney at the International Convention Centre from 30 April to 2 May.
The conference will give participants a platform to exchange ideas, discover novel opportunities, reacquaint with colleagues, meet new friends, and broaden their knowledge. Our keynote speakers come from around the world, representing the very best in their field including Jean-Pierre Loubinoux, Director-General of the UIC, and Leslie Woo, Chief Planning Officer at Metrolinx, Ontario Canada with our Master of Ceremonies, US-based Sally Dominguez. Joining our international keynote speakers will be the Hon. Andrew Constance MP, Minister for Transport and Infrastructure, NSW who will
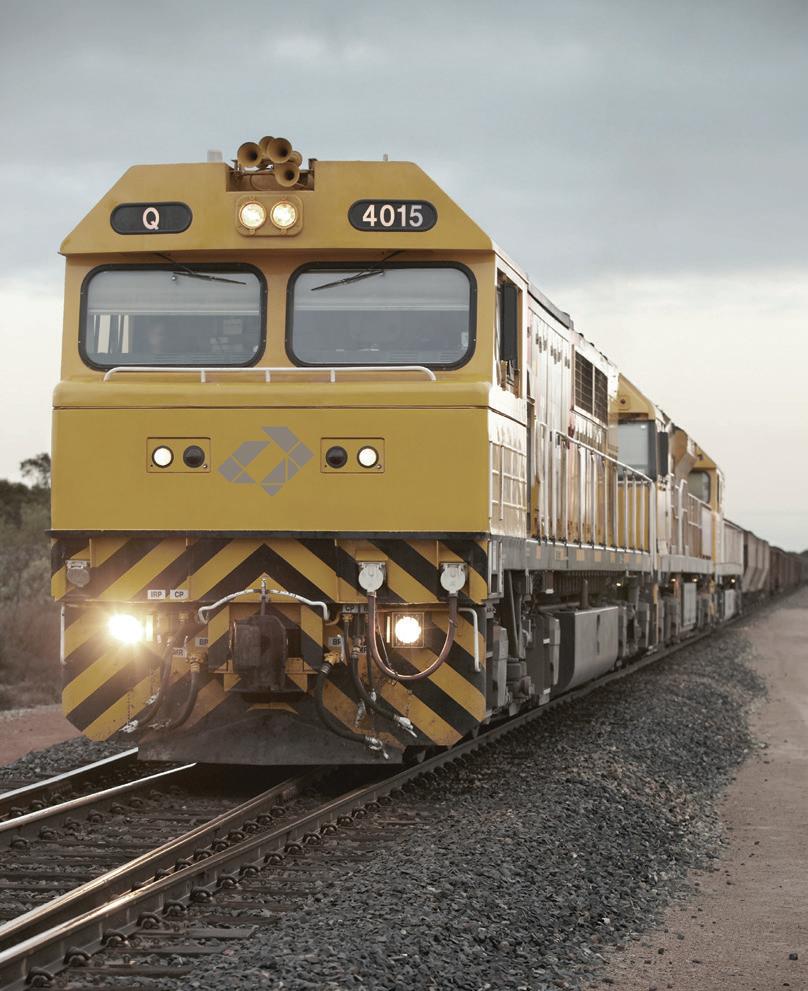
officially open CORE2018, and Ms Lucy Turnbull AO Chief Commissioner, Greater Sydney Commission who will deliver the closing keynote address about planning for the growth of cities and how it defines the need for growth of passenger mass transit.
WHAT TO EXPECT FOR 2018
The conference program will deliver over 80 technical papers regarding the solutions and challenges for the way we plan and deliver rail services and infrastructure in Australia and overseas. There will be presentations on project management, infrastructure advances, infrastructure track design and electrical automation, as well as many more technical and informative presentations. There is also an exciting site tour program to be held pre and post CORE2018 including site visits to metro and light rail operations, including the new Sydney Trains Operation Centre at Green Square, as well as some heavy haul operations at Newcastle and Hunter Valley.
The success of a conference is due to many people and organisations, so we’d like to thank our Host Partner, Transport for NSW, our platinum sponsors, ARTC, Aurizon and Sydney Trains, as well as WSP, SNC Lavalin, Speno, Comsteel, Institute of Railway Technology, Pandrol and Geofabrics, as well as our Media Partner Infrastructure Magazine and Supporting Partner, Railway Gazette.
The Australasian Centre for Rail Innovation will again be providing the “Knowledge Zone” for delegates to update their skills and knowledge. We are also having a shared plenary session and technical stream with our colleagues from the System Engineering Society (SESA) and their conference SETE2018.
I encourage you to register now to be in the best location to hear from industry experts and leaders in the rail industry, network with industry representatives and be part of the next generation rail industry leaders.
There is something of interest to everybody in the industry and I look forward to seeing you at CORE2018.
CONFERENCE ON RAILWAY EXCELLENCE
Rail: smart, automated, sustainable
30 APRIL – 2 MAY 2018
CORE2018 opens its doors at the International Convention Centre in Sydney on April 30.
Join us to hear from our International and national keynote speakers.
Register now to be in the best location to hear from industry experts and leaders in the rail industry, network with industry representative and be part of the next generation of rail industry leaders.

Leslie Woo
Chief Planning Officer Metrolinx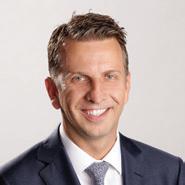
Hon. Andrew Constance MP Minister for Transport and Infrastructure, NSW
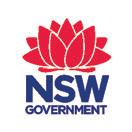
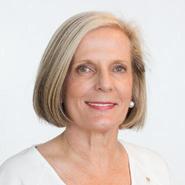
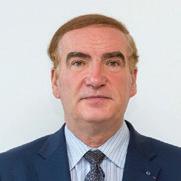

Ms Lucy Turnbull AO, Chief Commissioner Greater Sydney Commission
GALA DINNER SPONSOR HOST SPONSOR SUPPORTING PARTNERS PLATINUM SPONSORS
YOUNG PROFESSIONAL SCHOLARSHIP SPONSOR
Sally Dominguez Master of Ceremonies CORE 2018



A NEW APPROACH TO RAILWAY TRACK DRAINAGE
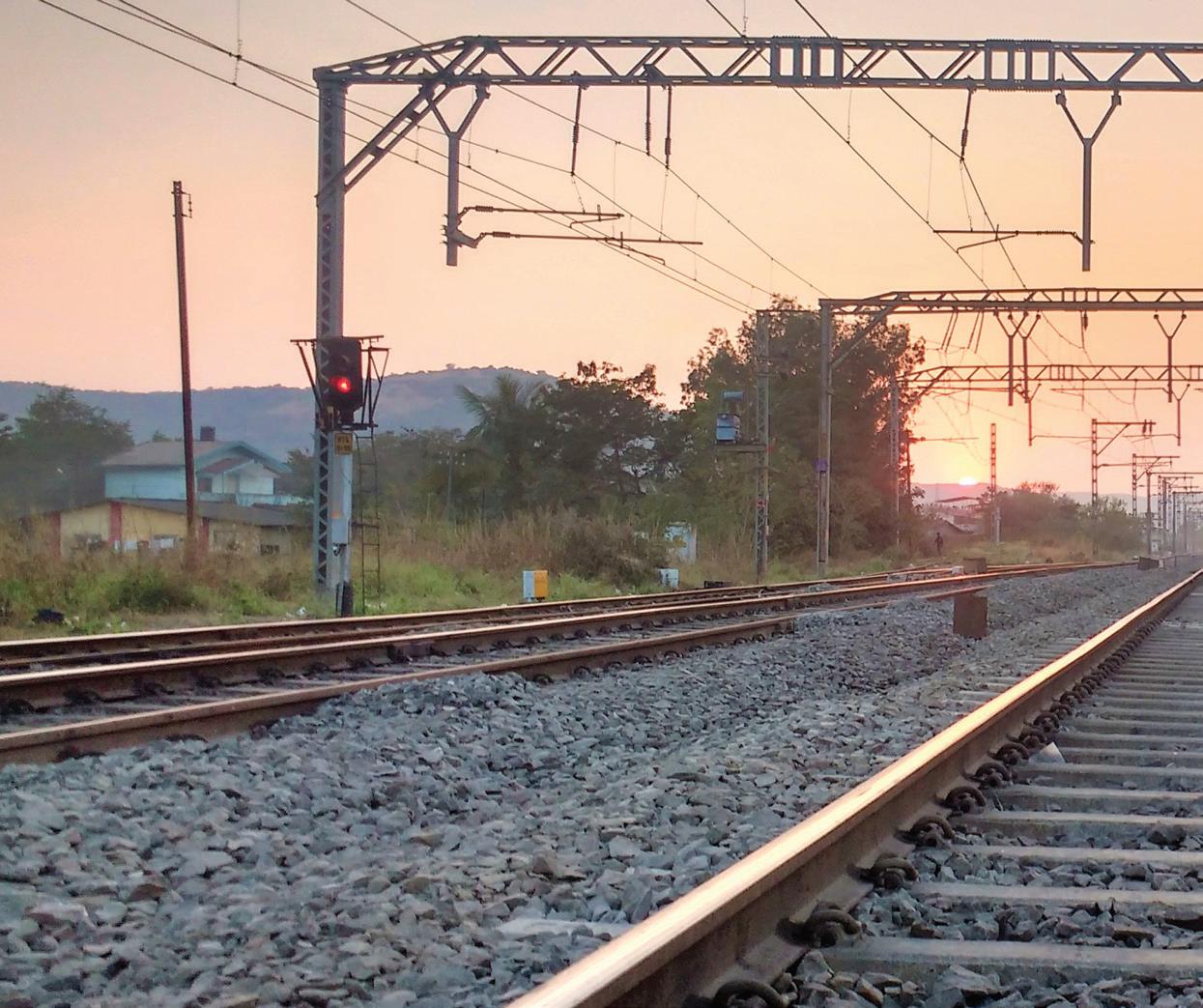
Variances in moisture levels around railway tracks can compromise bearing capacity and the stability of surrounding soil, ultimately resulting in track geometry degradation. The only materials currently used to install a sufficient draining system are reinforced concrete, fibre reinforced concrete or steel, which are highly susceptible to rust and corrosion. One German manufacturer – FRÄNKISCHE – is changing the way the industry thinks about track drainage with an innovative new pipe design.
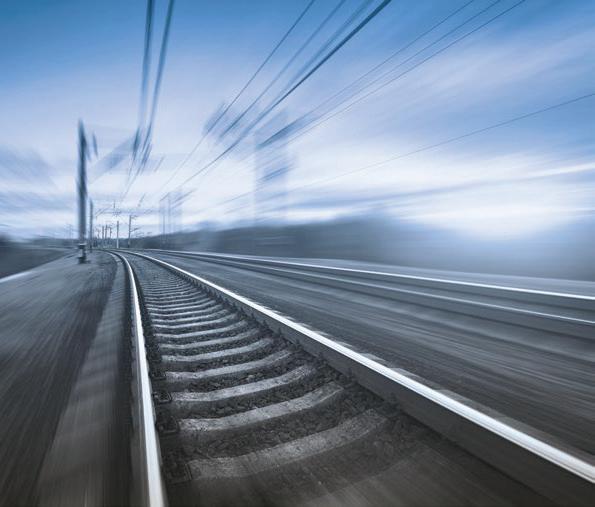
Arailway track’s geometry is highly influenced by the initial state of the soil, hydraulic conditions and atmospheric conditions such as temperature and moisture. Changes in these conditions, usually due to excess moisture, plays a significant role in the weakening of track geometry and can induce softening and weakening of the load bearing capacity.
Appropriate drainage methods are required to intercept water flow and direct it away from the track ballast.
FRÄNKISCHE has designed a high-quality polypropylene pipe with optimised profile geometry to offer an extremely hardwearing pipe for track drainage.
FRÄNKISCHE’s RailPipe complies with the extremely demanding requirements of Deutsche Bahn AG in terms of impact strength and flexural fatigue strength which has made it the first twin-wall pipe to meet all the standards and requirements of Deutsche Bahn AG and the German Federal Railway Authority (Eisenbahn-Bundesamt, EBA). RailPipe can therefore be used as a single pipe solution for all pressure ranges of the roadbed and track.
CHANGING THE GAME
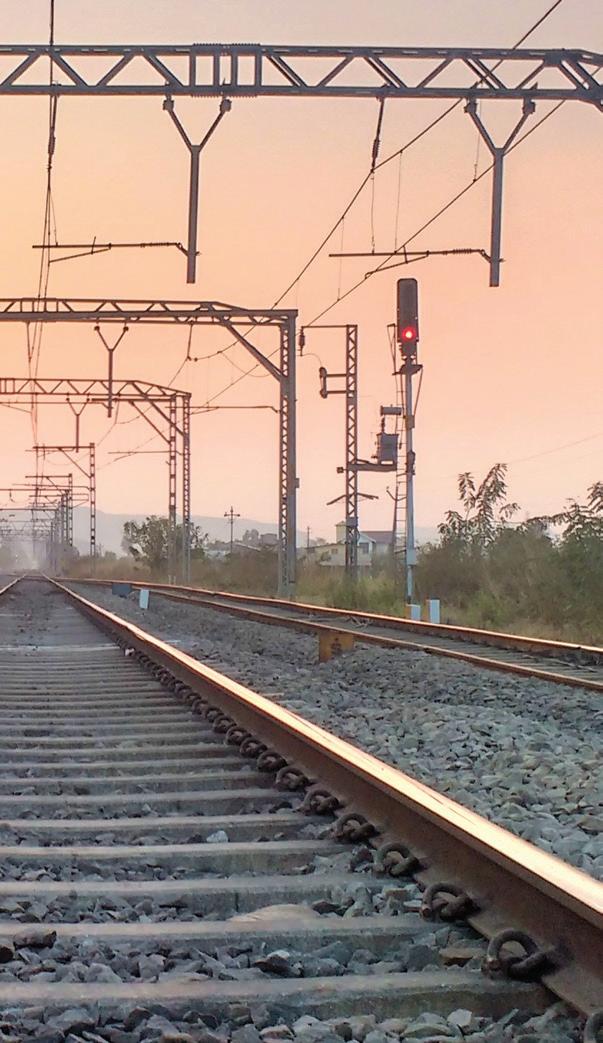
Concrete and steel drainage systems can corrode and rust over time through excessive exposure to water and runoff. This means continuous maintenance and inspection is required to prolong the pipe’s life and durability.
The game changing RailPipe design offers a number of benefits over its concrete and steel counterparts, including being drastically lighter weight for easy installation, eliminating rust and corrosion which cuts ongoing maintenance costs and having a longer lifespan than traditional materials.
The controlled drainage of railway tracks is also required for safety reasons. Accumulating infiltration water must be removed from waterbodies and soils in compliance with protection requirements. RailPipe has a high infiltration rate thanks to perfectly arranged perforations and high permeability.
RailPipes round shape and smooth inside create a cross-section that is beneficial in terms of hydraulics and maintenance. It is delivered in straight lengths of six meters including coupling and sealing rings which can then be cut to length as desired and remaining pieces can be reused using couplings.
Stephen Herd, Australasian Regional Business Manager Drainage Systems, said the development of the RailPipe system was a five-year long process.
“We’ve designed RailPipe as a single pipe solution for all applications. Not only can it be used outside of and in the external pressure range of the roadbed and track but also in the inside pressure range.
“RailPipe has passed rigorous quality control by the external
centre of MFPA Leipzig in terms of safety and stability. The thorough testing included Dynamic fatigue tests determining the fatigue strength in 108 load cycles. The results proved the durability of the design as it was still able to hold its integrity.”
RailPipe can also be coupled with an additional RailControl; a flushing and inspection shaft of modular design comprising shaft bottom, extension pipe and adapter. The addition was specifically developed to allow for easy inspection and flushing of the connected pipe systems.
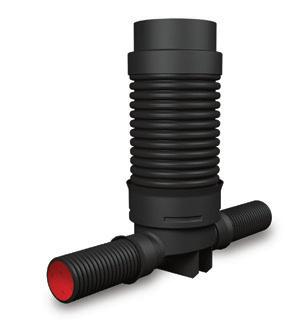
RailControl satisfies the highest requirements in terms of safety and stability while being resistant to acids, bases, oils and greases, and is UV-resistant and temperature resistant from - 40 to + 80°C.
INDUSTRY LEADERS IN DESIGN
FRÄNKISCHE is an innovative, growth-oriented industry leader in the design, manufacturing and marketing of technically superior corrugated pipe systems for drainage, electrical, building technology and industrial applications.
With the combination of RailPipe and RailControl, FRÄNKISCHE has developed the perfect system for the requirements of track drainage. Both components have been ideally matched to form a homogeneous system that provides the highest functional reliability for planning engineers, users and builders.
For all fields of track drainage RailPipe® with EBA certification
The RailPipe drainage pipe is the first twin-wall pipe to meet all the standards and requirements of Deutsche Bahn AG and the German Federal Railway Authority (Eisenbahn-Bundesamt, EBA) and can therefore be used for all pressure ranges of the roadbed and track.
www.railpipe.com
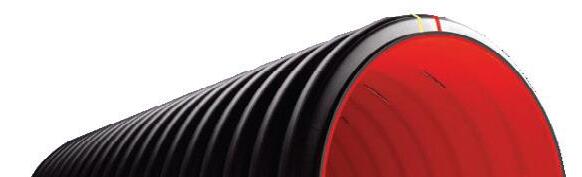
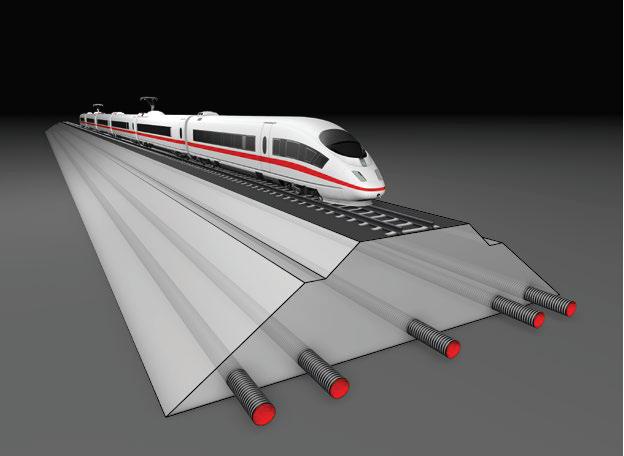

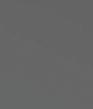
RIGHT RAIL FOR NEWCASTLE
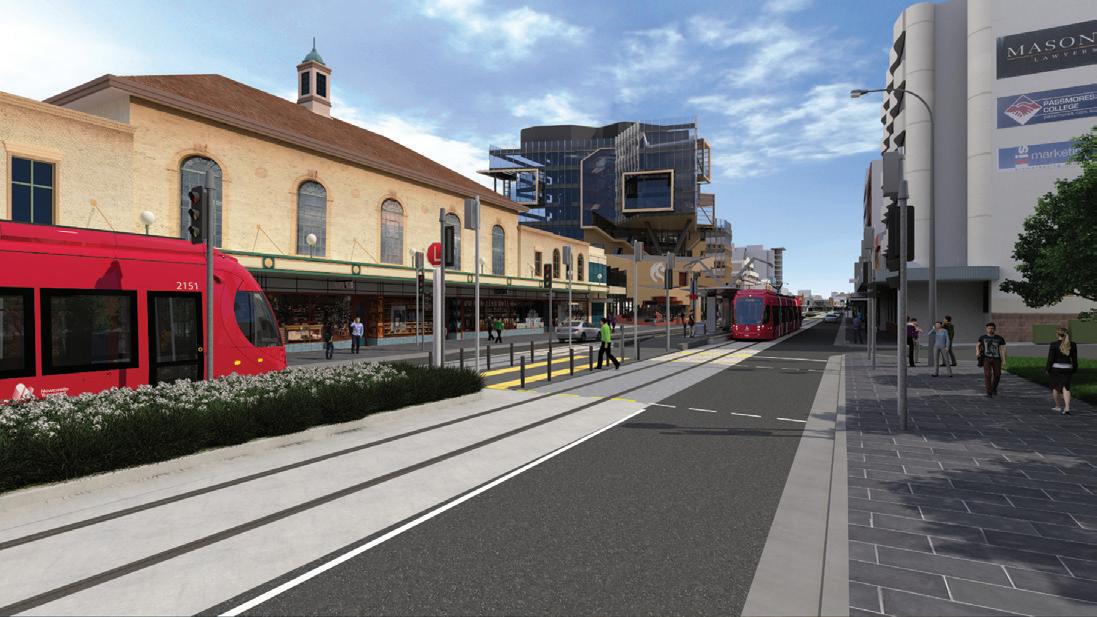
Expected to be fully operational in 2019, the Newcastle Light Rail will form the centrepiece of a fully integrated, vastly improved public transport network for Newcastle, which will stimulate urban revitalisation and provide a solution to transport demand for years to come.
The Newcastle Light Rail is a key part of Revitalising Newcastle, a NSW Government program focused on enhancing the city, attracting more people, jobs and tourism to Newcastle
Revitalising Newcastle Program Director, Michael Cassel, said that the government is investing more than $650 million to transform the city centre by strengthening connections between the city and waterfront, creating job opportunities, providing new housing and delivering attractive public spaces connected to better transport.
“Newcastle Light Rail will provide a frequent and reliable travel option throughout the city centre, connecting key activity precincts, reinvigorating Hunter and Scott streets, and opening up great urban renewal opportunities,” Mr Cassel said.
“Light rail construction follows the truncation of Newcastle’s heavy rail line between Wickham and Newcastle stations. The truncation allowed the foreshore and the city centre to reconnect to the city centre, removing the divide.”
The Newcastle Light Rail project received planning approval
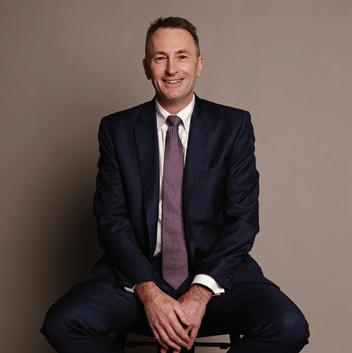
in August 2016 and major construction started in September 2017. Downer EDI is the principal contractor and the project is on track to see customers start using light rail services in 2019.
More than $300 million worth of funds from the Revitalising Newcastle program has been put aside for the construction of the Newcastle Light Rail and associated works.
In August 2017, the NSW Government announced an additional $150 million in funding for the Revitalising Newcastle program, taking the total investment to more than $650 million.
The additional $150 million includes:
♦ $75 million plus any future land sales for new public spaces on the former heavy rail corridor
♦ $35 million to deliver wire-free light rail, much-needed footpath upgrades at key locations on Hunter and Scott streets and street trees
♦ $40 million to deliver road and intersection upgrades to support traffic flow and road safety as light rail is introduced
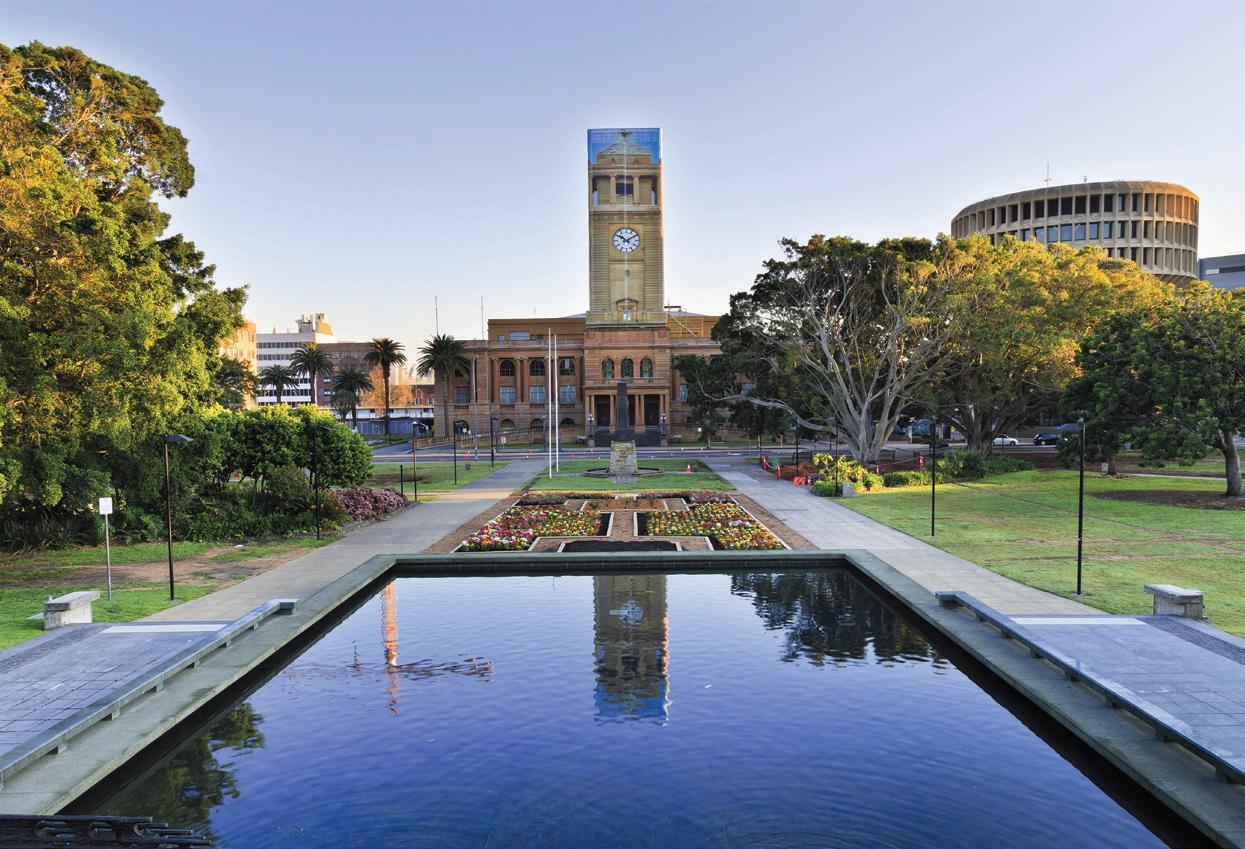
PRESERVING NEWCASTLE’S HERITAGE
One of the main challenges around the construction of the Newcastle Light Rail has been the historical significance of the land that the light rail alignment runs through.
“Located near and under Newcastle’s light rail alignment are archaeological artefacts including part of Australia’s first rail line, which delivered coal to the harbour. A key consideration for construction is therefore preserving, where possible and being respectful of Newcastle’s rich history,” Mr Cassel said.
“Prior to European settlement, the part of Newcastle where light rail construction is underway was Aboriginal land. The Awabakal people were the original inhabitants.”
Mr Cassel said another consideration has been the relocation and upgrading of a large number of existing underground utilities and services, including telecommunications, gas, electricity, water and sewer assets – some almost as old as Newcastle itself.
“Part of the light rail construction involves replacing sections of Newcastle’s century-old sewer network, which is up to six metres deep. This work involves using microtunnelling to replace the mains away from the light rail alignment,” Mr Cassel said.
TECHNICAL SPECIFICATIONS
Another project in the Revitalising Newcastle program, the Newcastle Interchange, is a new multi-modal transport hub at Wickham in the city’s west, linking trains, buses, taxis, kiss
and ride facilities, and from early next year, the Newcastle Light Rail.
Newcastle’s Light Rail will start at the Newcastle Interchange, travelling along the old heavy rail route for approximately one third of the 2.7km journey before moving onto Hunter and Scott streets.
Stops will be located at Newcastle Interchange, Honeysuckle (near Hunter Street TAFE), Civic, Crown Street, Market Street and Pacific Park.
The Newcastle Light Rail is capable of transporting 1,200 people per hour. Each Light Rail Vehicle (LRV) has a maximum capacity of 270 passengers, with services running every 7.5 minutes during peak hour.
The light rail network has been designed so it can easily be extended in the future.
“Any extension would need to integrate with the six existing URBOS LRV’s. As these LRV’s are modular in design, any changes can be incorporated to ensure an integrated network for future stages,” Mr Cassel said.
“Depending on an extended route, the LRV’s could run up to 70km/hr, carrying the same capacity of passengers and provide the same level of comfort and service.”
The LRV’s, which are being built by CAF Rail, are the same as the Inner West Extension.
While only one aspect of the Revitalising Newcastle program, Newcastle’s Light Rail looks set to play a pivotal role in the city’s successful urban transformation.
THE TECHNOLOGY SUPPORTING NEWCASTLE LIGHT RAIL
A local Newcastle company with a worldwide presence is supplying and installing all signals, controls and communications for the Newcastle Light Rail Project. 4Tel is not just looking at the specifications of the project, but taking a forward-thinking approach to how the new infrastructure will be used and operated in the future.
With the Newcastle Light Rail Project – the focus of a major upgrade of Newcastle’s public transport network – ramping up, 4Tel was awarded two contracts for the project’s signalling and communications packages.
The company is undertaking the core networking, cabling and configuration, PA infrastructure, passenger information display, telephony systems, the operational control centre, and the backup control centre, as well as security elements.
The signalling package includes passenger information system software; control systems moving and tracking the trains; systems to maintain and monitor the tracks and
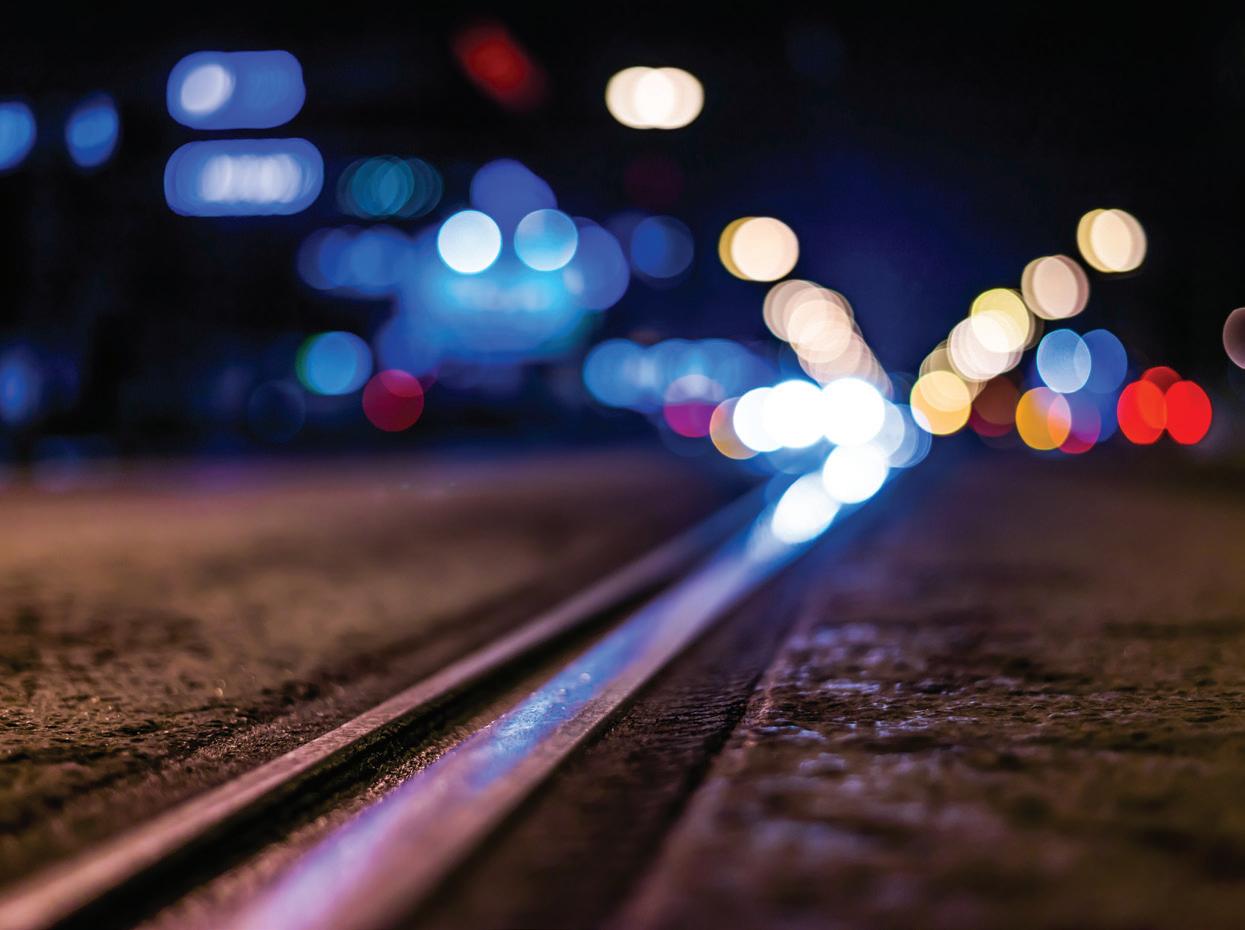
power substation switching between the main and redundant centres; and the alarms and input information from the field.
Mark Wood, General Manager of Communications and Electronics at 4Tel said the company’s unique offering involves a high level of system integration. Being an Australian company has also meant all work can be streamlined.
“One key component is all of the system integration, as far as the responsibility for operation of the system, whether they be components from 4Tel, or components from other suppliers integrated into our software systems,” Mr Wood said.
“We’re also an Australian-based company, so it means the interface and interaction with the head contractor, Downer, is such that you don’t have to stay up until all hours of the night to talk to the people that are writing the software modifications.”
Mr Wood said one of the project’s biggest challenges is ensuring flexibility for operators if network conditions change, with 4Tel looking ahead to make sure the project is sustainable.
“We’re looking ahead to what some of those changes are, and predicting those as part of what we’re doing now.”
For more information on 4Tel’s rail technology and services, please visit 4tel.com.au.
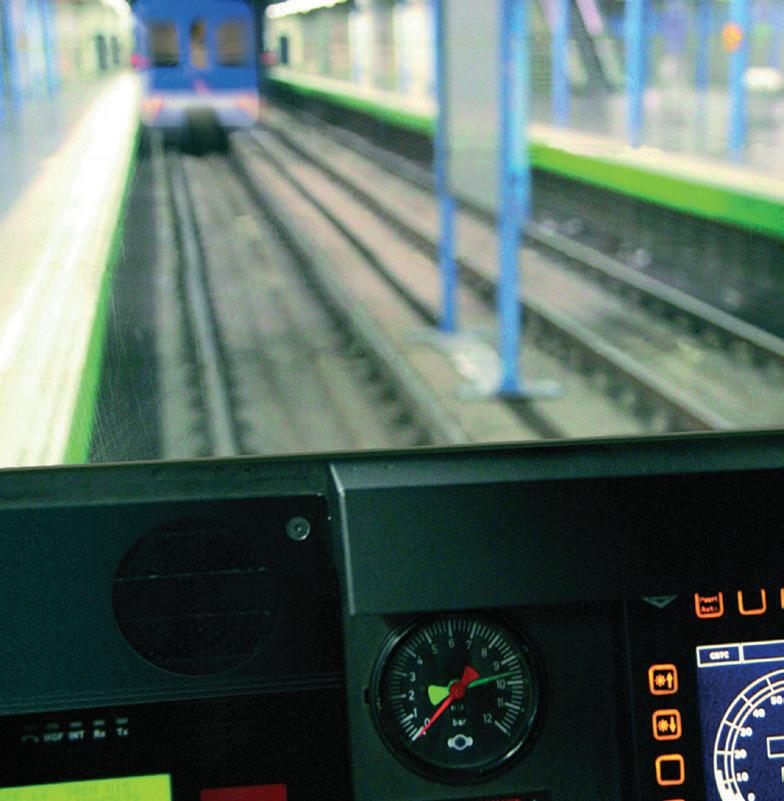
IN A RAPID NEW
The Metro Tunnel
Project is set to transform Melbourne’s public transport network with the construction of two 9km rail tunnels and five new underground stations. To ensure the infrastructure is used to its full capacity, the project will roll out high-capacity signalling (HCS) for the first time ever on an existing network in Australia. Here, Melbourne Metro Rail Authority CEO, Evan Tattersall, gives us the rundown of what we can expect from the technology.
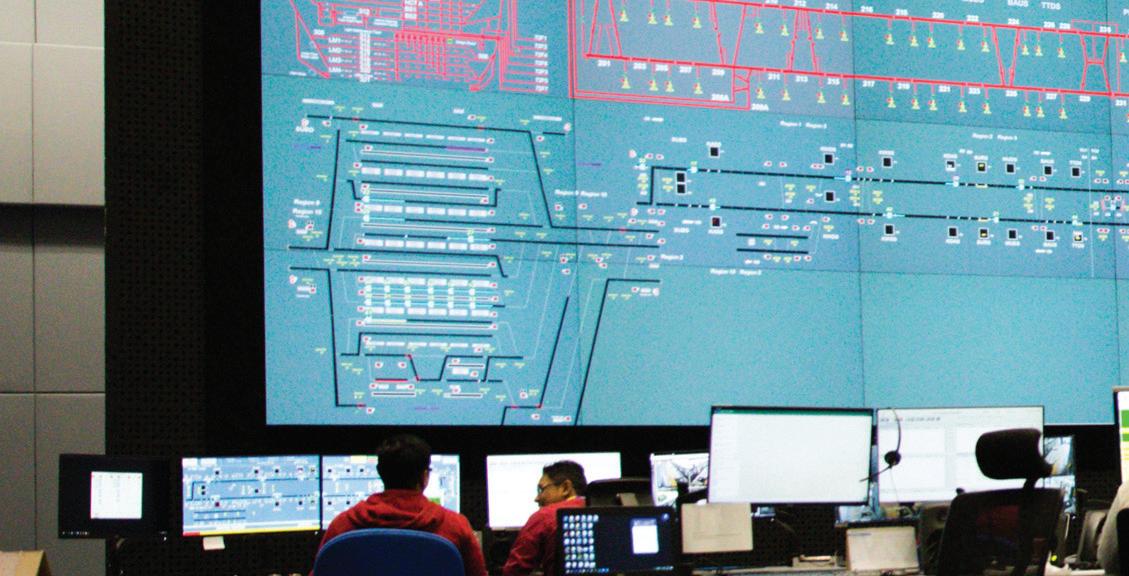
The $11 billion Metro Tunnel Project will take three of Melbourne’s busiest train lines – Cranbourne, Pakenham and Sunbury – out of the City Loop and run them through the new tunnel.
Significant progress had been made to prepare sites for major construction since work started on the Metro Tunnel in 2016. More than 100 underground services have been relocated including telecommunications, gas, water and power.
Building demolition is nearing completion in Melbourne’s CBD and the first of three massive acoustic sheds in the city is also complete.
Work is also finished on a dividing wall that structurally separates City Square and the Westin Hotel, allowing the three-storey car park under City Square to be demolished ahead of construction of an 11-storey shaft.
St Kilda Road has been reduced to one traffic lane in each direction, and will remain so for up to four years, while Grattan Street will also be closed between Royal Parade and Leicester Street for up to five years.
A major part of the project involves 58km of next-generation high-capacity signalling to be installed, which aims to unlock Melbourne’s public transport gridlock by allowing more trains to run through the network more often.
Melbourne Metro Rail Authority CEO, Evan Tattersall, said the project could just be the start for HCS in Australia.
“There has not been a project like the Metro Tunnel built in Victoria since the City Loop almost 30 years ago.
“The Metro Tunnel is a game changing project that offers a unique opportunity to roll out HCS and may lead to the technology being installed on other parts of the network.”
Work has begun on planning, designing and developing the early implementation of high capacity signalling on a section of the South Morang line.
From next year, the new technology will be fitted onto two, three-car X’Trapolis trains that will run without passengers as tests. This early implementation will also allow train drivers, operators and maintenance staff to become familiar with the new system and be involved in providing feedback on its use.
NEW TECHNOLOGY TO INCREASE NETWORK CAPACITY
Mr Tattersall said Melbourne’s rail network, particularly the City Loop, is almost at full capacity, creating a “bottleneck” which restricts the ability to run more trains to where they are needed across the network. This is why high-capacity signalling technology was chosen for the project.
“HCS allows more trains to run more often and as Melbourne and Victoria’s population continues to grow there will be an increasing demand for more services to get people where they need to go,” Mr Tattersall said.
The signalling will be installed in 65 new high-capacity trains currently being built in Victoria, which will run on the Sunbury and Cranbourne-Pakenham lines via the Metro Tunnel.
The new HCS technology is expected to allow the new trains to run every two to three minutes and be able to carry around 20 per cent more passengers than existing trains.
“By enabling High-Capacity Metro Trains to run every two to three minutes along three of our busiest lines as a part of the Metro Tunnel Project, we can get people to and from some of the city’s fastest growing suburbs as quickly as possible,” Mr Tattersall said.
Mr Tattersall said high capacity signalling is based on a ‘moving block’ signalling system that builds more flexibility into the system and safely allows trains to operate closer together.
The HCS monitors the position and speed of each train operating on the line and sets limits over the performance of following trains, to ensure they can always stop a safe distance away from the train in front.
“Current signalling allows between 12 and 20 trains per hour. HCS allows 24 trains per hour to run safely and reliably, meaning they can run more often… creating a true ‘turn-up-and-go’ train network for Melbourne,” Mr Tattersall said.
Along the new Metro Tunnel lines, this will be achieved by using communication technologies in the driver cabin of each train to send the location and speed of the train directly to new high-tech control centres that will be located in Sunshine and Dandenong, where trains will be monitored 24 hours a day, 365 days a year to ensure seamless operation.
These two locations have been selected as they are connection points for metropolitan, regional and freight services, making them strategic points in the rail network.
The system allows the location and speed of trains to be monitored in real time, as well as the ability to oversee signalling maintenance.
MINIMISING DISRUPTION
Mr Tattersall said there will be a number of challenges to installing the HCS in the Metro Tunnel Project.
“The main challenges of installing HCS as part of the Metro Tunnel are rolling out the technology while keeping trains operating with minimum disruption to passengers, integrating the new system with Melbourne’s existing rail network and training operational staff, including drivers, in the new systems,” Mr Tattersall said.
To overcome these obstacles the works will be delivered through a Rail Systems Alliance (RSA) with CPB Contractors, Bombardier Transportation, Metro Trains and Melbourne Metro Rail Authority.
The Rail Systems Alliance will create more than 300 jobs, while the Metro Tunnel Project will create up to 7,000 jobs.
The HCS will be rolled out in two stages; an initial implementation of high capacity signalling will be trialled along a section of the rail network before being installed along 58km of track from just west of Watergardens to Dandenong via the new Metro Tunnel.
An initial implementation of HCS between Epping and South Morang will begin in 2020, then there will be the rollout in the west near Watergardens and then the east at Dandenong, beginning in 2022. Following this, HCS will be installed in the new Metro Tunnel.
Testing and commissioning will then be undertaken with the Metro Tunnel Project on track to be completed by 2025, a year ahead of schedule.
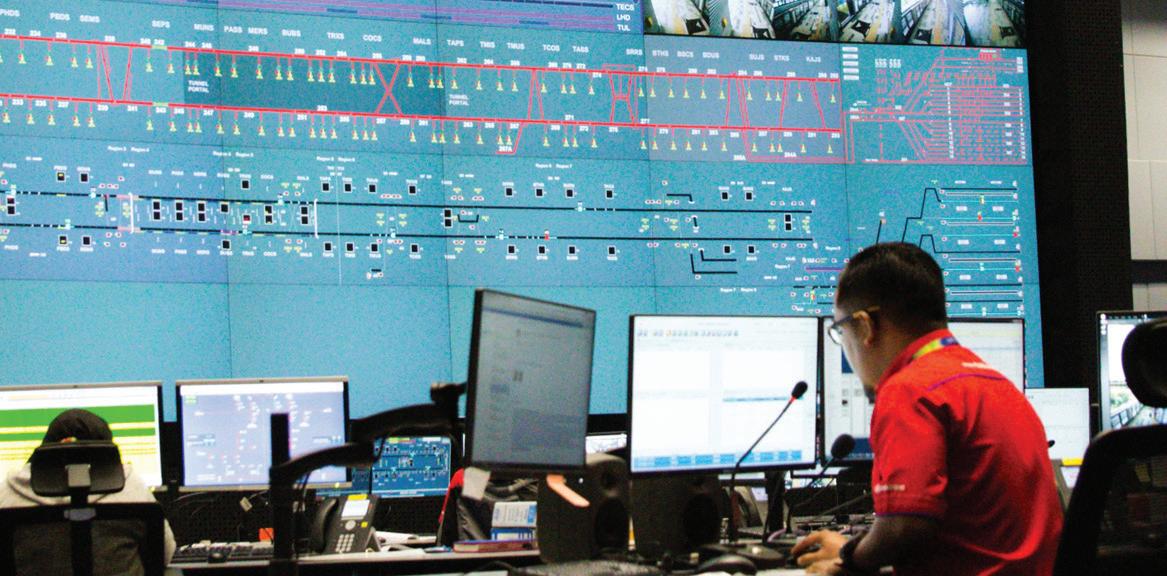
DO OLD TRACK STANDARDS STILL MEASURE UP IN TODAY’S RAILWAYS?
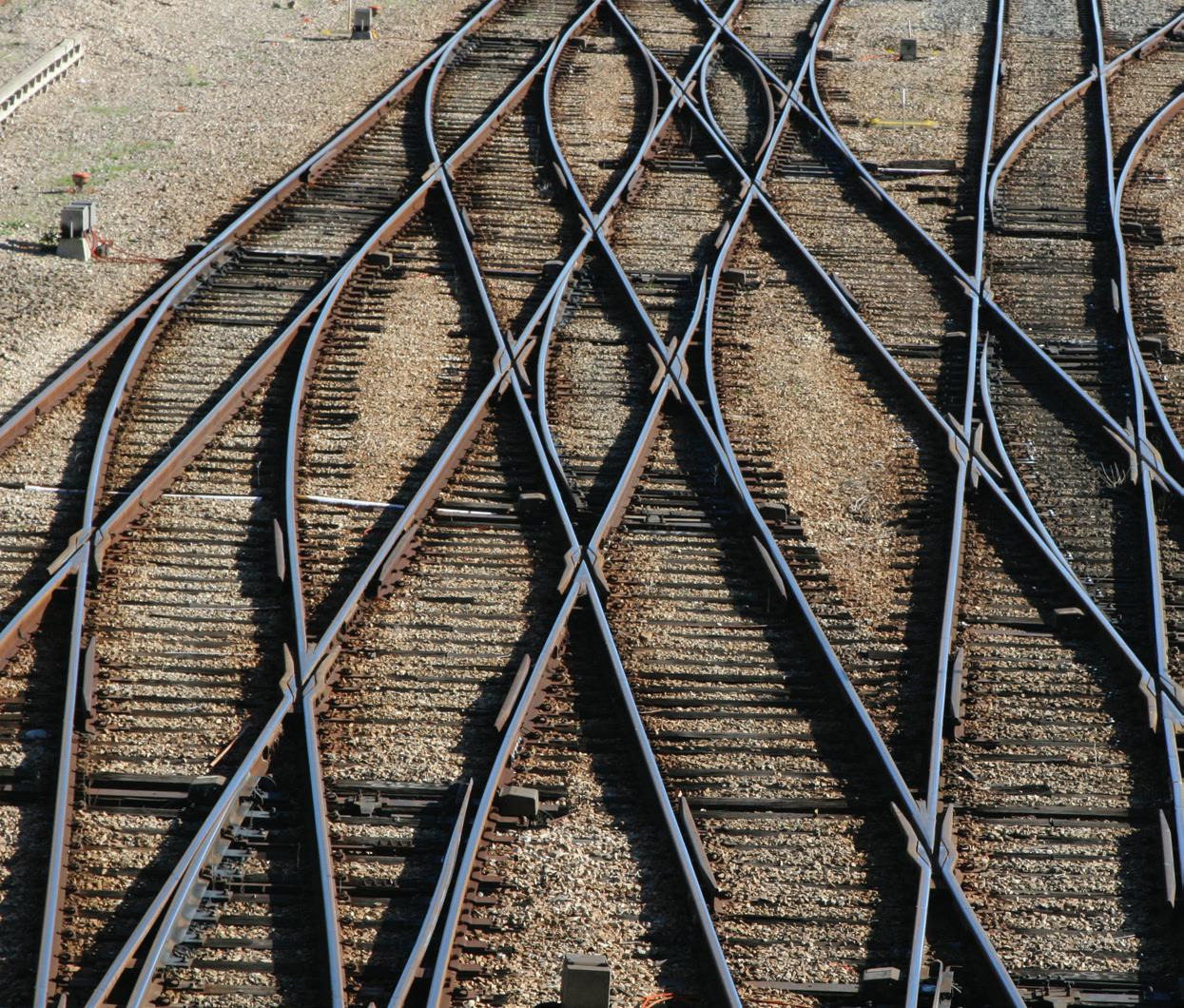
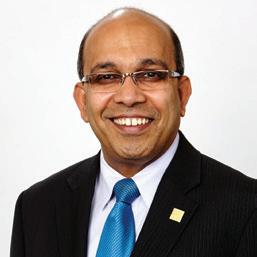
There is a desire amongst many railway transport operators in Australia for rail industry regulators to revise current track maintenance standards to allow for the implementation of new technologies in place of existing requirements.
n the long term, it is expected that such changes would reduce safety risks and costs associated with human inspections and asset failures, whilst providing cost benefit incentives for operators, allowing them to reinvest in new technologies which would benefit the railway transport industry as a whole.
The rail transport industry requires standards that effectively ensure safety by considering all assets and interfaces as a single system and understanding full lifecycle impacts. With specific regard to the implementation of new technology, current regulations regulate safety and asset failure associated safety risks, but do not mandate adoption of new technology.
Whilst it is the operators’ choice not to implement new technology, the long-term value of railway asset lifecycles and associated maintenance costs means that failure mitigation is critically important. Even where failures are not occurring, it
should be apparent that new technology can better facilitate efficient operation of their railway network.
The implementation of current railway industry standards such as AS7635:2013 (the current Australian Standard relating to track geometry) have greatly boosted the safety and efficiency of present day railways. Whilst derailment frequency has decreased tremendously in the last decade, a number of industry experts are now advocating for revisiting standards to address gaps where standards are believed to be lacking.
The ever-escalating demands on modern railways (tonnage, speeds and throughput) will inevitably warrant new approaches for managing and assessing track geometry and rolling stock condition, and the leveraging of new and established technologies so that standards can remain effective into the future.
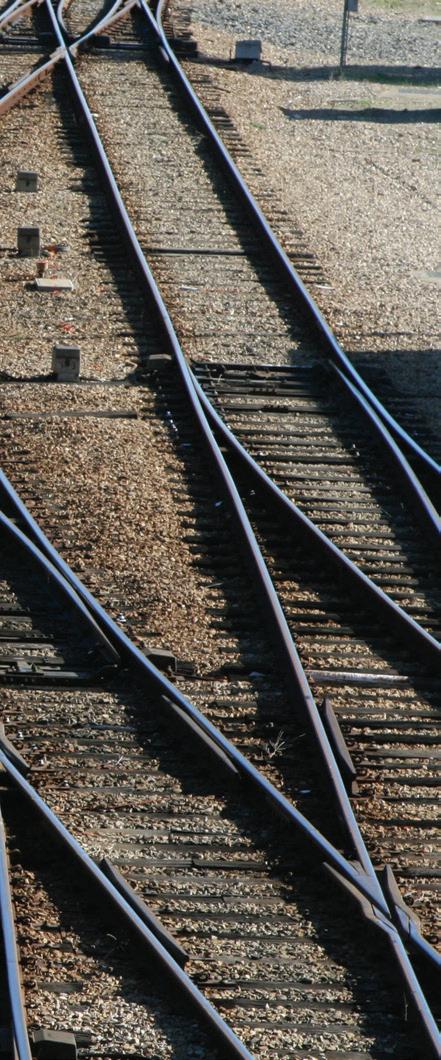
MONITORING TRACK CONDITION
It is vitally important to manage railway track geometry and vehicle condition together as irregularities in either can rapidly lead to elevated vehicle dynamics, increased track loading, asset wear, adverse vehicle/ track interactions and eventually the risk of vehicle derailment. Track condition should be regularly monitored as even subtle changes can risk leading to adverse vehicle track interaction and accelerated degradation.
At present, track irregularities are typically monitored using track recording vehicles (TRV) which use a variety of instruments to record track geometry metrics and provide measurements at discrete increments along the track. International railways abide by numerous
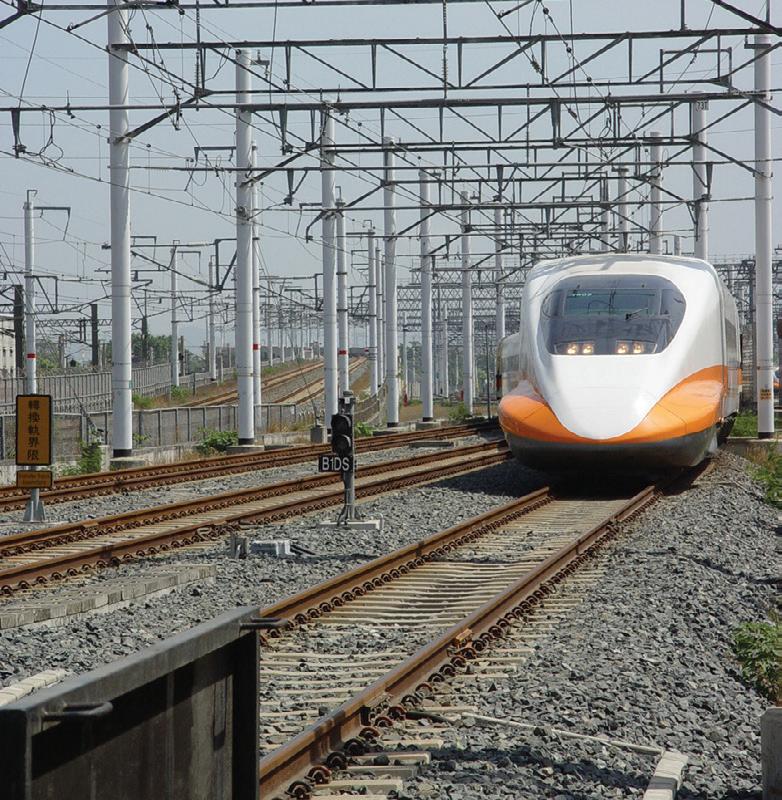
regulator-mandated track geometry condemning limits with the expectation that compliance will mitigate adverse vehicle dynamics, asset failures and derailment.
Whilst some recommendations are provided in Rail Safety and Standards Board (RISSB) standard AS7635:2013, in Australia, the wide diversity of different railway operations has led to individual railway operators being allowed to develop their own asset condemning limits which best optimise the asset life and safety for their own particular operation in accordance with the guidelines and regulatory requirements of Rail Safety National Law.
COMPLEX VEHICLE-TRACK INTERACTIONS
It is important to note though, that individual condemning limits should only be considered as bare minimum requirements as derailments are still being reported at locations that have no condemnable conditions. This suggests that the method of condition assessment based on discrete track geometry measurements is not in itself adequate to prevent derailments and
accelerated deterioration of track assets and this should be addressed in revised standards.
The primary issue with the current approach of specifying discrete limits is that it does not adequately account for the myriad of interactions and multiplicative effects that can occur between combinations or clusters of non-condemnable conditions occurring around the same location, together with rolling stock variability. RISSB standard AS7635:2013 has the statement “where combinational defects are detected, these should be investigated and reviewed by the Rail Infrastructure Manager’’. The minutia of vehicle-track interactions is so complicated that humans would not likely be capable of correlating all the conditions they observe and making the logical connections required to foresee possible interactions and adverse outcomes. This is a very significant issue for railway operators which is complicated further where; multiple cyclic irregularities can occur that lead to elevated vehicle dynamics (track loading, wheel climb, hunting); variability in rolling stock condition occurs (wheel
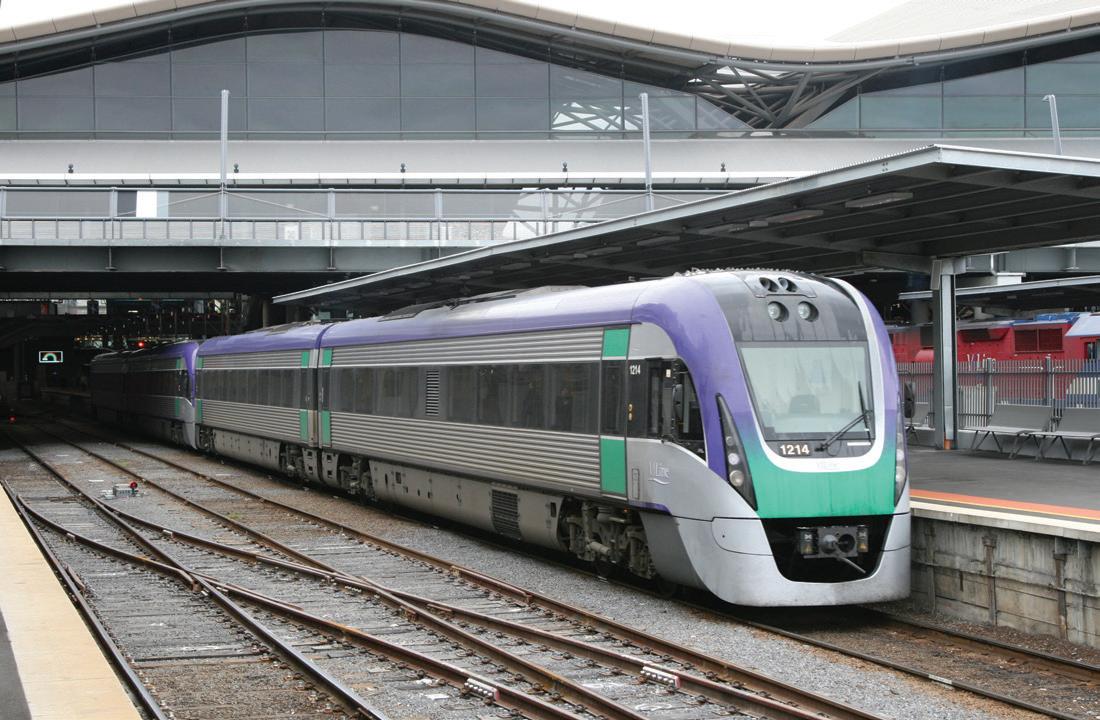
wear, off-centred loads, suspension characteristics); and where trains have deviated from the normal operating conditions (train speeds, axle loads) for which the track was designed.
MORE FREQUENT INSPECTIONS KEY
Another issue associated with current methods of condition assessment is the lack of regularity (frequency) in measurements. The frequency of coverage of TRVs on any section of track is dependent on the number of recording vehicles available to the operator, the length of the railway to be measured, the ability to schedule track access time around nominal operations, standards (which mandate inspection frequency), and of course cost. All this means that TRV coverage frequency is typically in the order of months. RISSB standard AS7635:2013 mandates minimum track geometry recording car inspection frequency of four months for main line interstate corridors and a lot can happen to the track in this period of time.
Track issues can arise very rapidly, in some cases going from new condition to condemnable in a matter of weeks, or more rapidly in the case of extreme weather (track buckling, formation washouts), so at any given time it is unlikely that TRV measurements will
accurately reflect the present condition of the track and it is unlikely the track defects will be caught in time to prevent asset failures or derailments.
The irrationality of this approach becomes more apparent when we realise that the inspection and/or maintenance response requirements for detected defects (running every four months) in many cases requires action within a 24-hour period. A typical example would be wheel burn, squat or weld dip on the track. This begs the question, why is the defect allowed to remain in place for the four month period between inspections? Assuming TRV geometry data is even accurate, it still needs to be used in conjunction with a comprehensive range of other inspections in order to adequately manage track condition.
BENEFITS OF CONTINUOUS MONITORING
Using continuous monitoring systems which incorporate autonomous track geometry and rail profile measurement systems, the frequency of track measurements can approach time intervals commensurate with nominal traffic conditions on any individual line. The benefits of continuous monitoring systems to modern railways are abundant. The high frequency of
condition measurements allows for:
♦ Data to be continuously fed into the railway operator’s risk assessment models to greatly improve response times to developing issues
♦ Facilitates the development of track condition/degradation forecasting models
♦ Allows operators to rapidly gauge the effectiveness or ineffectiveness of maintenance activities.
MOVING TOWARDS
PREDICTIVE MAINTENANCE
Measuring maintenance effectiveness also allows for operators to build business cases to justify undertaking more substantial maintenance where, for example, records show repeated instances of ineffective tamping. Continuous monitoring systems have shown significant advantages in data driven maintenance planning for the railway industry by facilitating the shift from reactive (costly, unscheduled or emergency correction of track condition), to predictive (condition based) maintenance approaches. Predictive maintenance approaches can identify, prioritise and pre-schedule inspections and maintenance to locations based on realistic probabilities of degradation and risk, and rectify them prior to entering a state of rapid or
uncontrolled degradation. This approach improves planning and scheduling of maintenance and minimises the risks to infrastructure and rolling stock, whilst also reducing the need for temporary speed restrictions and unscheduled track closures.
It is accepted that track geometry data provides an accurate summary of the spatial position of the track, and whilst peak errors and standard deviations may not necessarily determine the overall condition of the track, track geometry in conjunction with deterministic vehicle response modelling (Universal Mechanism®, Vampire®, NuCars®) and neural networks can be a very powerful research tool. The benefits of vehicle modelling for railway operators are; that they can predict responses to track geometry and/or defects for a range of vehicle types and operational conditions; they can identify particular track conditions or combinations of conditions which can lead to derailments; can assess the interactions between multiple vehicles including longitudinal in-train dynamics, and many others. Vehicle model simulations and machine learning are very powerful research tools, but are still limited to the frequency of track geometry recordings and is not a direct measure of vehicle responses as can be obtained using continuous vehicle response monitoring systems.
VEHICLE RESPONSE MEASUREMENTS
Continuous monitoring systems such as the Instrumented Revenue Vehicles (IRV) have already been shown to be effective at measuring vehicle responses and inferring track condition with a high degree of repeatability, accuracy and regularity. The inclusion of vehicle response measurement requirements in maintenance management plans would result in far more realistic assessments of the actual impact of track condition on rolling stock responses, inclusive of any cumulative and cyclic defects, and would allow all operators to move from basic condition detection methodologies to performance based systems. Performance based systems actively determine how vehicles perform over sections of track given the specific geometry (including defects), the types of vehicles (age and suspension characteristics) and the specific train operating conditions. Vehicle response measurements also allow for operators to instantly quantify the impacts of changes made in track geometry or operational
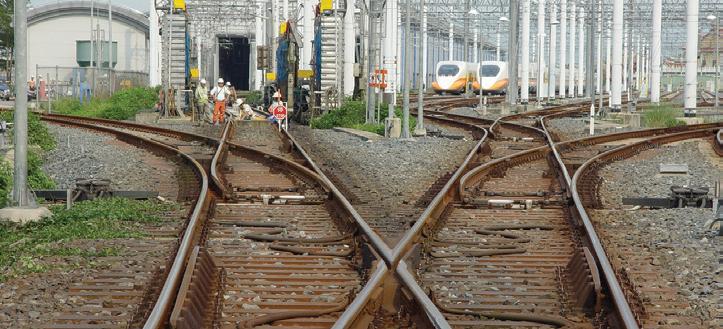
aspects of the network even justify maintaining sections of track to a higher or lower degree based on the vehicle responses at nominal speeds and loads.
IMPLEMENTATION OF NEW TECHNOLOGY
The Office of National Rail Safety Regulator (ONRSR) noted at the workshop Current Track Maintenance Standards and their Relevance to Modern Railways arranged by the Institute of Railway Technology, Monash University in March 2017, that as regulators, they will support and promote the ‘safe’ implementation of new technology. The challenge for industry operators is now to convince regulators, who are inherently risk-averse, that any change to standards, such as relaxing manual inspections requirements in favour of continuous monitoring technologies can be done so safely.
The ONRSR is a risk-based, independent industry-government administrator that audits and reviews compliance with RSNL. The Australian Government dictates the law, industry operators are required to implement the law and the ONRSR is responsible for administrating and encouraging correct implementation of standards in Australia in accordance with Regulation 19 (General engineering and operational systems safety requirements) of RNSL. Any changes to existing standards needs to very carefully weigh up the benefits and opportunities for improvement against any safety, performance and cost consequences. Changes must recognise that failures to any single asset can cause problems for the rest of the system (disruptions, damage, delays at port). Additionally, it should be noted that the vast scale of the many systems operating throughout the rail transport industry, involving a very large number of assets and personnel, presents a problem when implementing change. The sheer momentum behind such systems means that change can
typically only be implemented very gradually and operators will need guidance on how to best implement changes.
HOLISTIC CONDITION MONITORING APPROACH
It is recommended that the Rail Safety and Standards Board (RISSB) should consider revising the standards and adopt a more holistic approach that considers the safety and performance of the railway track and rolling stock together as a system. New standards should specify some basic minimum requirements for assessing geometry using modern detection and monitoring technology to continuously update each individual operator’s risk assessment models, which can then be validated and signed off on by regulators. This minimum adoption of modern monitoring technology would begin to force the cultural shift in the railway industry from reactive to proactive maintenance.
As new technologies begin to be adopted, regulations can move towards being based on actual vehicle and track interaction and performance as opposed to track geometry measurement pass or fail conditions. A performance based continuous condition monitoring system would be able to relax discrete constraints in individual metric compliances and give operators more freedom to adapt to improve their network overall condition.
Finally, the use of deterministic vehicle-track simulations to quantify effects of cyclic and/or cumulative track geometry defect categories would still be very beneficial where validated using measured vehicle response data and may be used to optimise the specification of condemning limits on individual and combinations of track geometry defects and would be a great benefit to every modern railway.

CORROSION REMAINS A COMPLEX CONCERN
The degradation of private and public assets and infrastructure continues to have a major economic impact on industry and the wider community: it is estimated that governments and organisations spend approximately three per cent of GDP – the equivalent of billions of dollars each year – mitigating and repairing corrosion damage.
In November 2017, the Australasian Corrosion Association (ACA) hosted a major conference where the management and prevention of corrosion was the focus. The ACA’s annual Corrosion and Prevention Conference and Trade Exhibition (C&P2017) was held in the International Convention Centre Sydney (ICC) with nearly 500 delegates from every continent (except Antarctica) attending lectures, seminars and workshops.
The conference brought together corrosion practitioners and researchers, as well as asset owners and operators from around the world in order to promote a better understanding of corrosion mitigation.
The event enabled all corrosion stakeholders to meet and discuss a wide range of topics. In particular, the conference brought together a panel of industry experts to discuss the challenges and the importance of maintaining vital infrastructure. The diverse technical streams showcased the latest developments in corrosion prevention, management and mitigation.
The main themes of the technical seminars covered coatings, concrete and asset management, the oil & gas and offshore industry, and research. Topics ranged from fundamental corrosion
science to hands-on applications including advances in sensing and monitoring; asset management; cathodic protection; concrete corrosion and repair; corrosion mechanisms, modelling and prediction; materials selection and design; and protective coatings.
NEW MATERIALS DEVELOPED TO COMBAT CORROSION
The design, construction and operation of facilities and infrastructure represent major investments by companies, organisations and governments. Corrosion affects all structures at varying rates over time, depending on the material used, the types of corrosive agents in the environment and the physical processes and mechanisms involved. How to manage this degradation is a challenge for designers and engineers, as well as asset owners, managers and operators.
In the continuing efforts to minimise the impact of corrosion, new materials are being developed to build structures, and new procedures are being implemented that have been designed to protect both new and existing facilities.
The keynote address of the conference – the P F Thompson Memorial Lecture –has been delivered at every C&P
Conference since 1951. The presenter for 2017 was Professor Maria Forsyth, Australian Laureate Fellow and Chair of Electromaterials and Corrosion Sciences at Deakin University. Professor Forsyth’s lecture, ‘Controlling Corrosion with Chemistry’, covered using chemistry to control corrosion ranges, from designing metallic coatings through to creating oxides on a metal substrate or protective polymeric coatings, and using chemical additives in a given environment to produce inhibited surfaces.
CORROSION MITIGATION LEGACY
A special guest at C&P2017 was David Thompson, son of Percival Thompson in whose honour the lecture is named. A renowned metallurgist in his own right, David Thompson said the reception he received at the conference was almost overwhelming. “So many people approached me to say they knew people whom I had either trained or worked with during the course of my career,” Mr Thompson said.
Thompson stated he had, like so many others over the years, a good teacher in his father. “However, being the sixth child in the family, I wasn’t supposed to know anything,” he added wryly. Thompson said his father spent a lot of time away from home inspecting mining leases and that as a result, the family
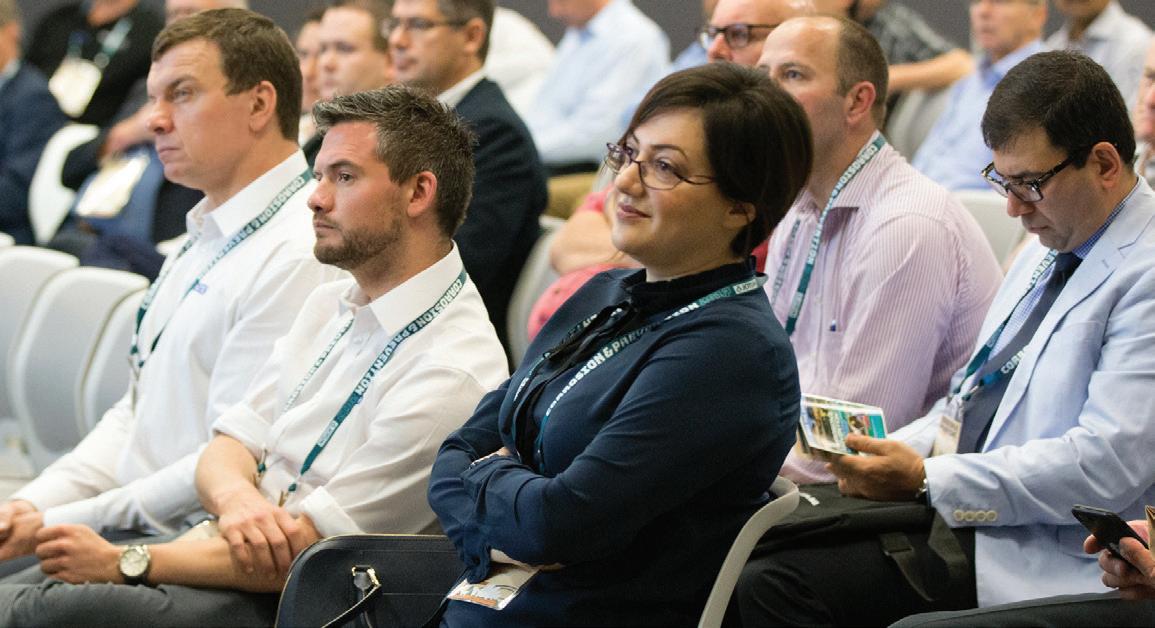
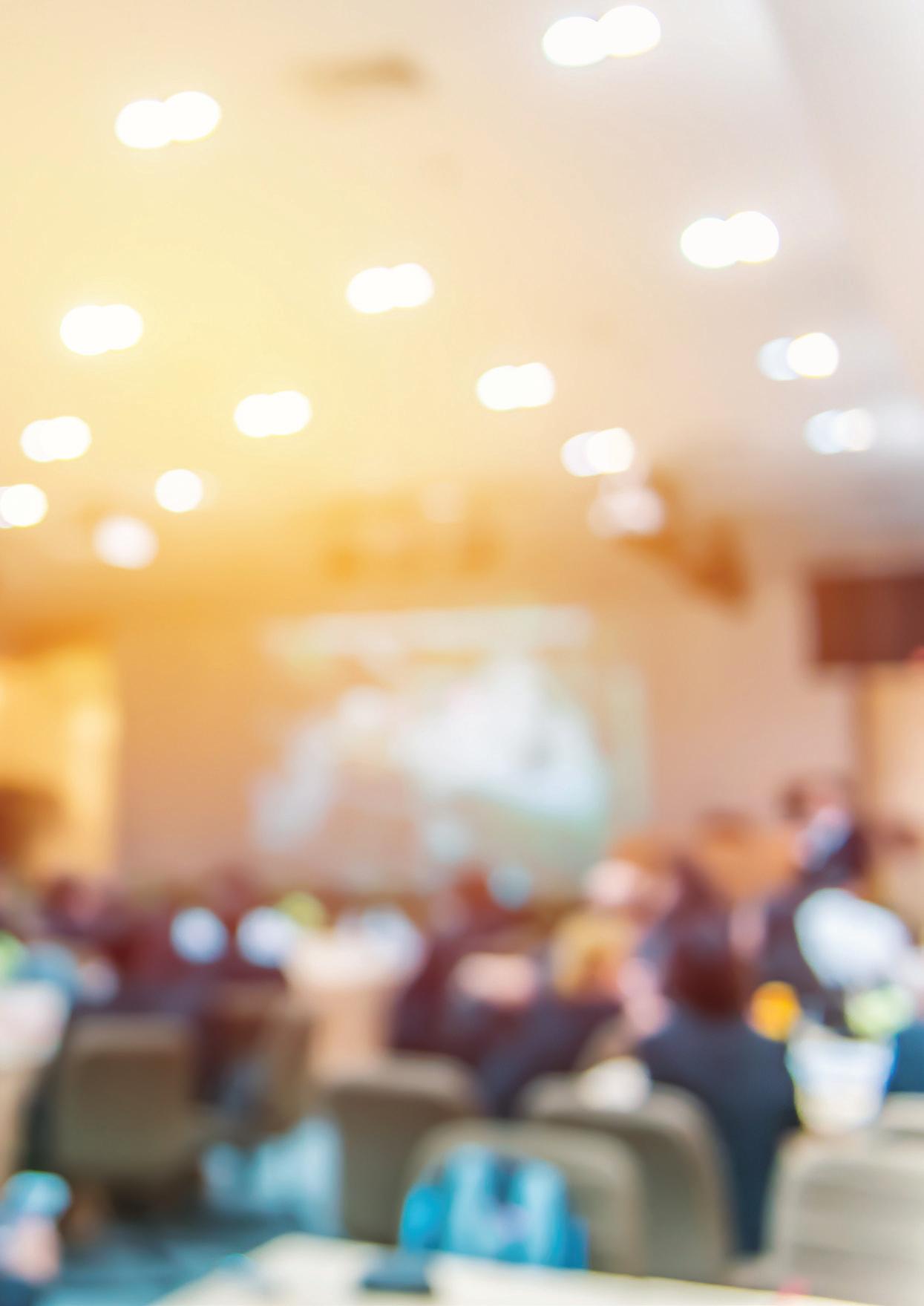
home had one of the largest collections of ore samples in the country.
“He was also an umpire assayer and so had to visit every gold mine in the country in order to counter fraudulent ‘salting’ of a site to increase its potential value,” Mr Thompson said.
An ‘umpire assay’ is an independent assessment of the value of an ore sample where there is disagreement between the values given by the buyer and seller. When a mine is ‘salted’, most commonly gold or silver is added to a sample in order to give a greater value to the mine deposits.
“My father regularly marked university exam papers,” Mr Thompson added. “A big truck would arrive at our house and a massive load of papers would be unloaded.” Thompson senior’s study often had inorganic and organic chemical samples that were used as part of the university exams he set.
P F Thompson established the School of Metallurgy at the University of Melbourne and oversaw its development, growing from a handful of students to more than 200 before moving to RMIT to set up a similar school at that institution. Named after the revered Michael Faraday of the Royal Society in London, Thompson’s father taught in a similar manner to his namesake.
“He was a demonstrator and believed that if you showed a student a process or reaction, they would remember it
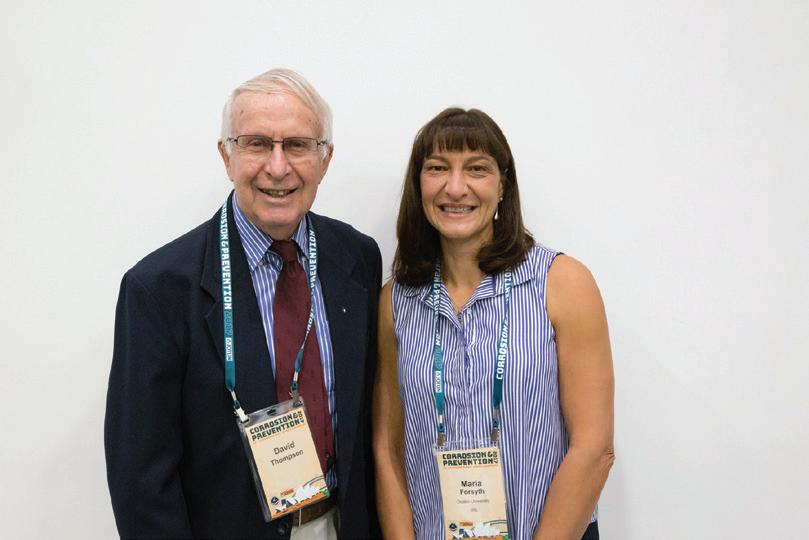
better,” Mr Thompson said. “If they could show they really understood the basic principles, my father would be lenient towards them when marking their papers.”
Mr Thompson stated that his father was a master of many disciplines, such as general science, astronomy and music, in addition to his main passion of metallurgy. “We had one of the largest reflective telescopes in its day at our house and the Victorian Field Naturalists Society used to meet in our backyard.”
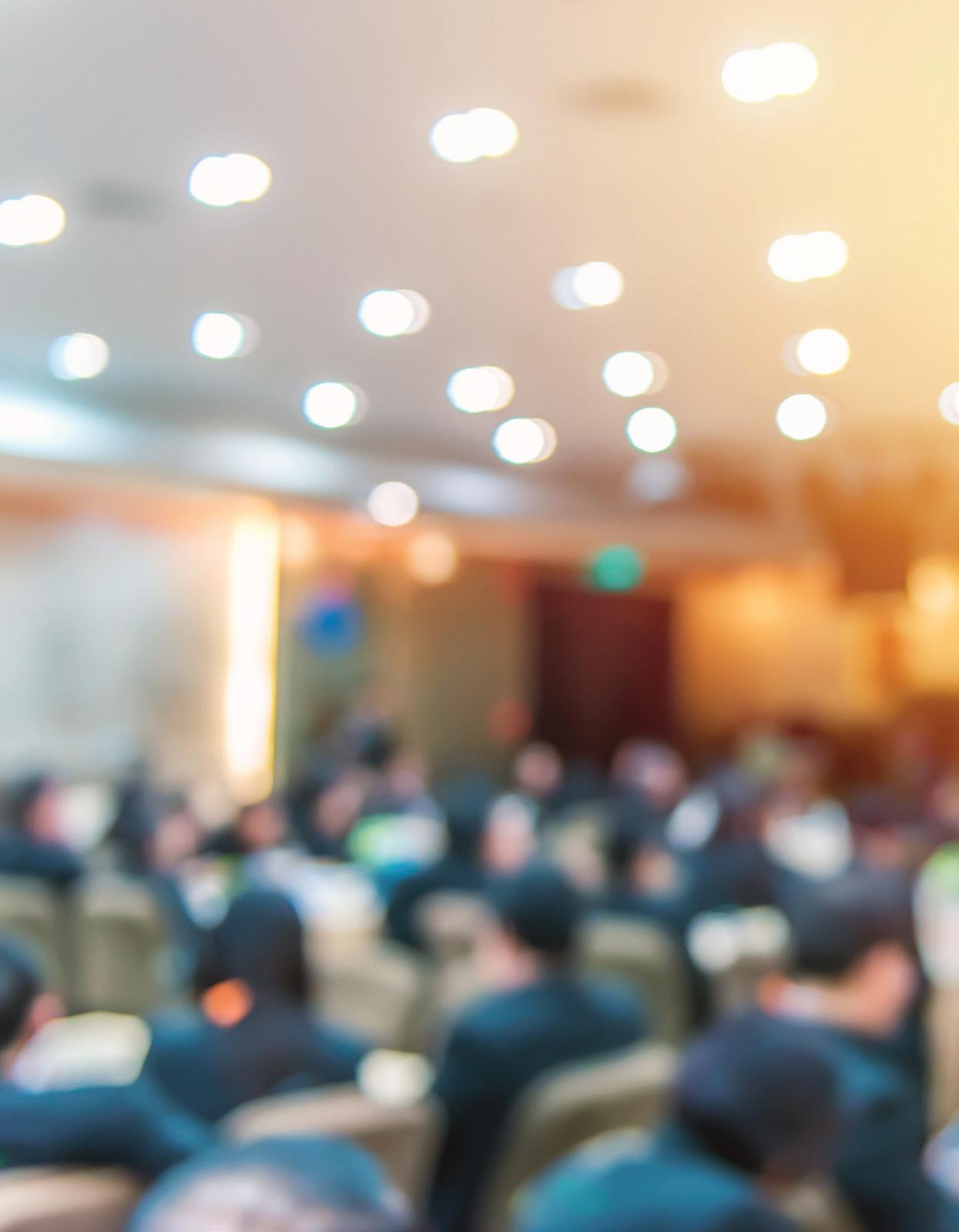
P F Thompson worked with the CSIRO, but a lot of the projects were very secretive, especially during the Second World War. One investigation involved US warships at the time of the Battle of the Coral Sea; ships would have to head to port with heavily corroded condenser tubes that impacted the marine steam engines. It was discovered that the American navy had used brass alloy that had phosphorus added and that this additive enhanced the corrosion. Another wartime investigation involved the catastrophic failure of
aircraft engines. “Many aircraft had glycol-cooled engines but some maintenance staff added a corrosion inhibitor to the mix, which my father and his team discovered deposited copper onto the aluminium cooling tubes causing the engines to overheat,” Mr Thompson said.
David Thompson himself was also called on for advice. The company he worked for received an order from the operators of the Sydney Opera House with a design that utilised copper pipes under load.
“I knew from my research that the proposal would fail very quickly due to corrosion fatigue and advised them accordingly.” Wanting a second opinion, the operators approached another metallurgist, Rupert Myers – the first Australian to be appointed a University Vice-Chancellor. “Rupert was a friend of mine and he told them that if David Thompson said it, you had better believe him as he knows more about the subject than anyone else.”
PREMIER CORROSION EVENT
The annual Corrosion and Prevention Conference is just one aspect of how the ACA collaborates with industry and academia to research all aspects of corrosion mitigation in order to provide an extensive knowledge base that supports best practice in corrosion management, thereby ensuring all impacts of corrosion are responsibly managed, the environment is protected, public safety enhanced and economies improved.
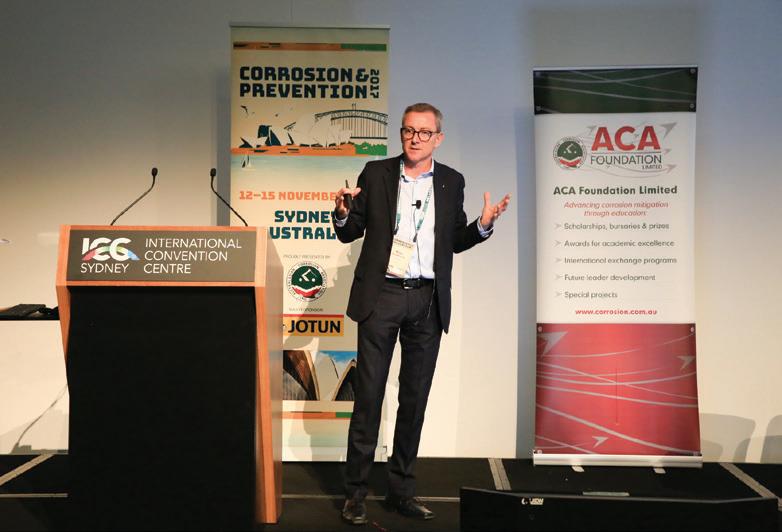
The integral trade show consisting of 72 exhibition booths, attracted more than 200 additional people to the event. The range of exhibitors included materials suppliers, equipment vendors, specialist contractors and consultants. Conference delegates were able to browse the stands throughout the conference and take the opportunity to discuss products and services with the exhibitors. Exhibitors benefited from broad exposure to corrosion industry practitioners from around Australia, New Zealand and the world.
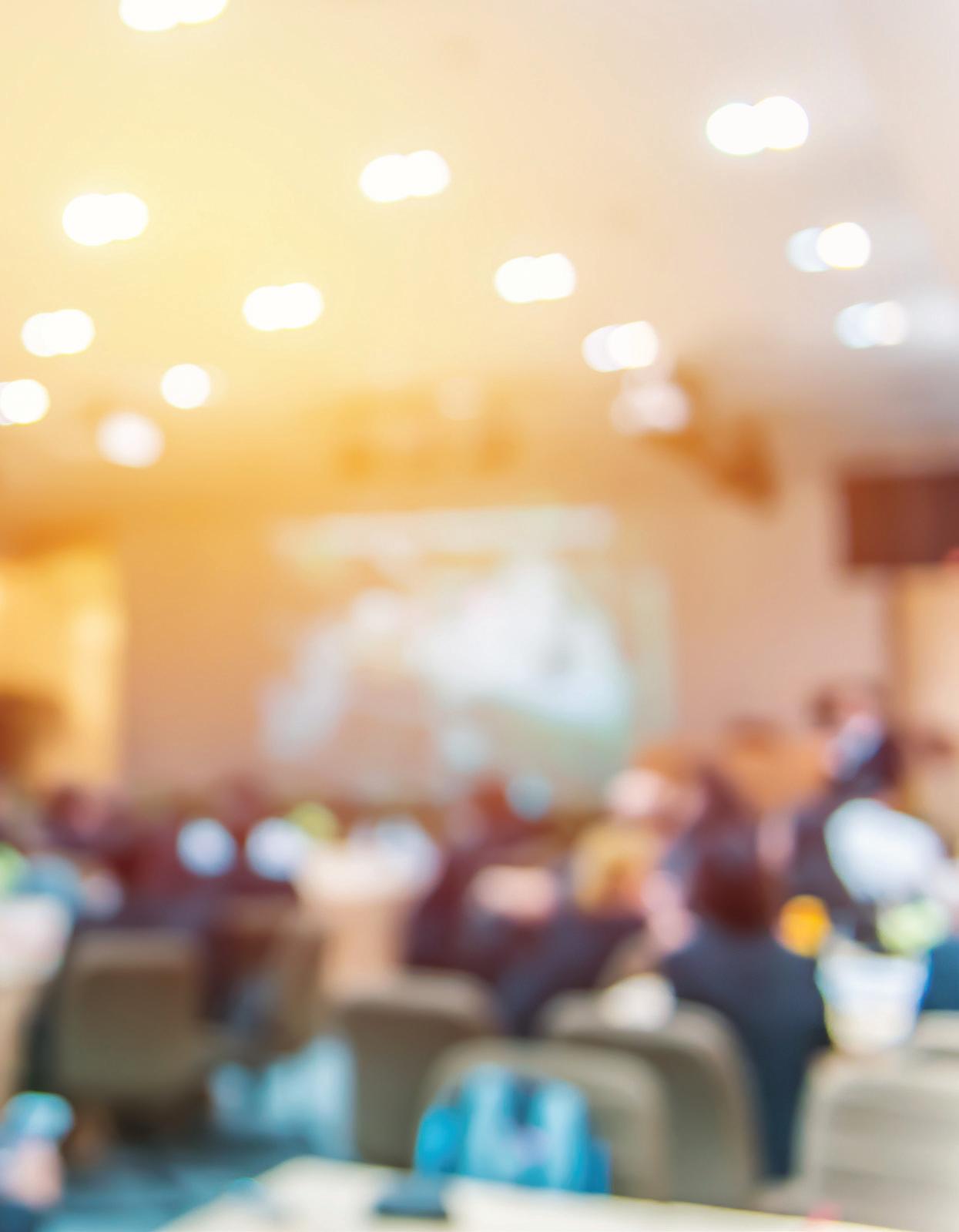
The ACA’s conference continues to be the premier corrosion event in the Asia Pacific region, with its extensive program of keynote speakers and technical presentations. In 2018, South Australia’s capital Adelaide will once again host the ACA conference from 11-14 November. For more information or to register visit https://conference. corrosion.com.au.
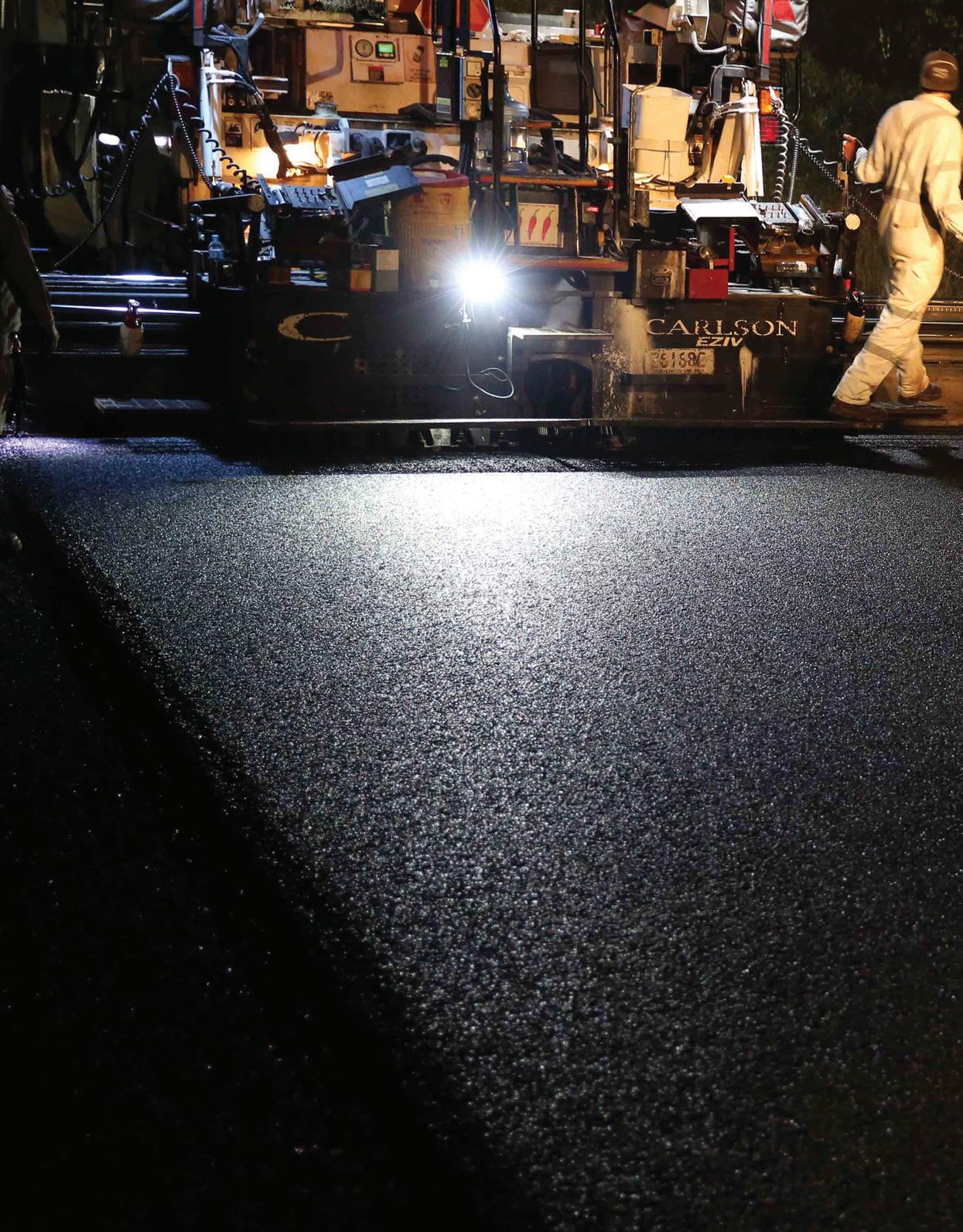
A GRIPPING CASE FOR
CRUMB RUBBER
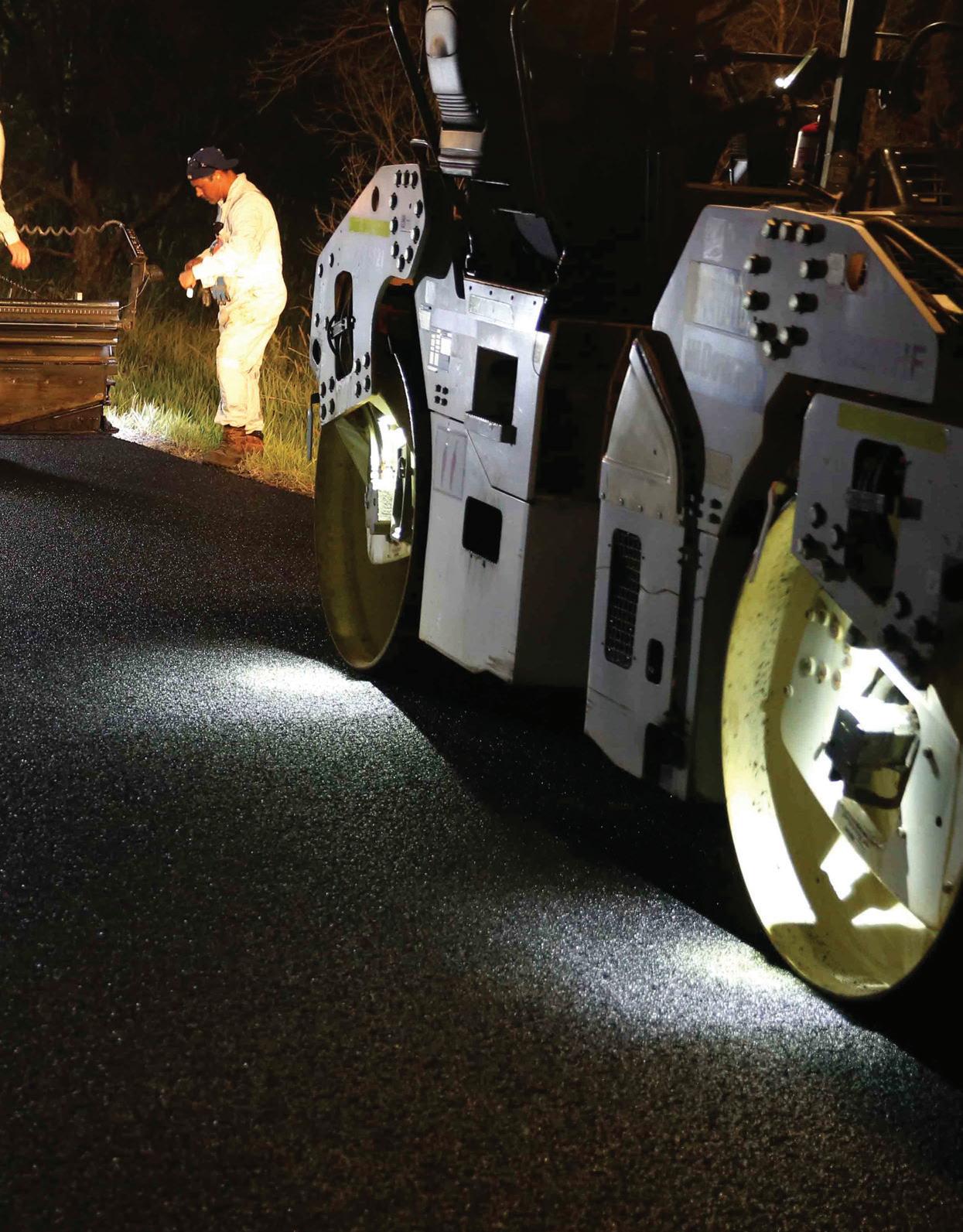
Crumb rubber modified (CRM) binder is a material made by reducing scrap tyres or other discarded rubber into bitumen, which can then be used in asphalt or sprayed seals for roads. Traditionally, CRM is used for sealing roads, mainly in Victoria and New South Wales, and has limited use in asphalt. However, investigations into the possible applications of CRM on a larger scale are underway. Here, Erik Denneman, Director Technology and Leadership at the Australian Asphalt Pavement Association (AAPA), discusses the latest CRM asphalt trial in Queensland and the benefits it can provide the road industry.

WHAT IS CRUMB RUBBER MODIFIED (CRM)?
Approximately 70 per cent of the weight of a standard tyre is made up of rubber and carbon black. Crumb rubber is produced by reducing scrap tyres down to these basic materials and removing steel and fiber along with any other contaminants such as dust, glass or rock. The modification of crumb rubber, or CRM binder, improves the properties of bitumen so that it is less prone to bleeding, cracking and stone loss.
CRM binder has enhanced elastic properties, which results in more durable asphalt and sprayed seal road surfacing than those currently in use today. It also offers a much improved cracking resistance compared to asphalt and seals with unmodified bitumen.
Mr Denneman said investigations into the use of CRM binder for asphalt on a large scale in Australia has encountered some barriers that have so far prevented wider adoption of the technology after initial activities in the 1990s.
In order to further analyse the use and practicality of CRM binder, Mr Denneman was part of the team that organised a trial of the use of CRM binder in open grade asphalt in Queensland.

OPEN GRADE ASPHALT TRIAL
The CRM binder trial was constructed in 2017 and aimed to analyse and overcome any perceived barriers while monitoring both harmful emissions during the installation and continuing to monitor its overall performance.
Mr Denneman said open graded asphalt has important safety benefits in terms of reducing splash and spray in wet weather.
“An issue with open graded asphalt is that it doesn’t last as long as dense asphalt mixes. The open structure means it is more prone to oxidative aging. The use of crumb rubber modified binder increases the durability of open graded asphalt because it allows a thicker binder coating.”
Mr Denneman said that there were no difficulties with the installation compared to the conventional product that was placed as a control.
“The section is continuing to be monitored and a second section has been installed in the Gold Coast in January 2018,” Mr Denneman said.
THE QUESTION OF EMISSIONS
One of the biggest barriers preventing the large-scale uptake of CRM is the perception that its use may produce harmful emissions during installation.
“The AAPA will continue to advocate for further studies into harmful emissions from crumb rubber construction. Extensive studies have been done internationally, but we have an obligation to verify the outcomes in Australia,” Mr Denneman said.
“The results show that for this particular trial the emissions from crumb rubber were similar to that of asphalt with conventional binder.
“The trial also showed the benefits of producing the product at as low a temperature as possible. Odour, fuming and emissions from asphalt increase rapidly with increase in temperature, so in general there is a benefit in trying to reduce production temperatures.
“This has possible sustainability benefits as well in terms of reducing CO2 emissions.”
THE BARRIERS FOR CRM UPTAKE
Mr Denneman said other challenges for CRM include cost and technological changes.
“Some bitumen rubber products are more expensive than conventional products due to the higher binder content. This may be offset by improved durability, but needs to be taken into consideration in the procurement process by road agencies,” Mr Denneman said.
“There are technological challenges as well, but these are easily overcome as demand grows. For instance, from a technical and operational perspective it may be preferable to blend crumb rubber and binder in a blending unit at an asphalt plant, rather than transporting it pre-blended from elsewhere.
“Such blending units are available on the international market, but obviously industry needs to be certain of demand before it invests in such technology.”
THE FUTURE FOR CRM IN AUSTRALIA
The pathway to CRM becoming the standard solution for road asphalt and spray seal surfacing will depend on road agencies, the industry and the public allowing space to propose and trial application of the technology.
“I don’t see a reason why it would not become the standard solution. Asphalt as a 100 per cent reusable construction product is already a good news story in terms of sustainability. The combination with recycled tyre rubber just adds to that appeal,” Mr Denneman said.
“There is a whole plethora of technologies available for use of crumb rubber in bituminous products. It is therefore important that industry and road agencies work together on developing permissive specifications that allow different technologies to be used.”
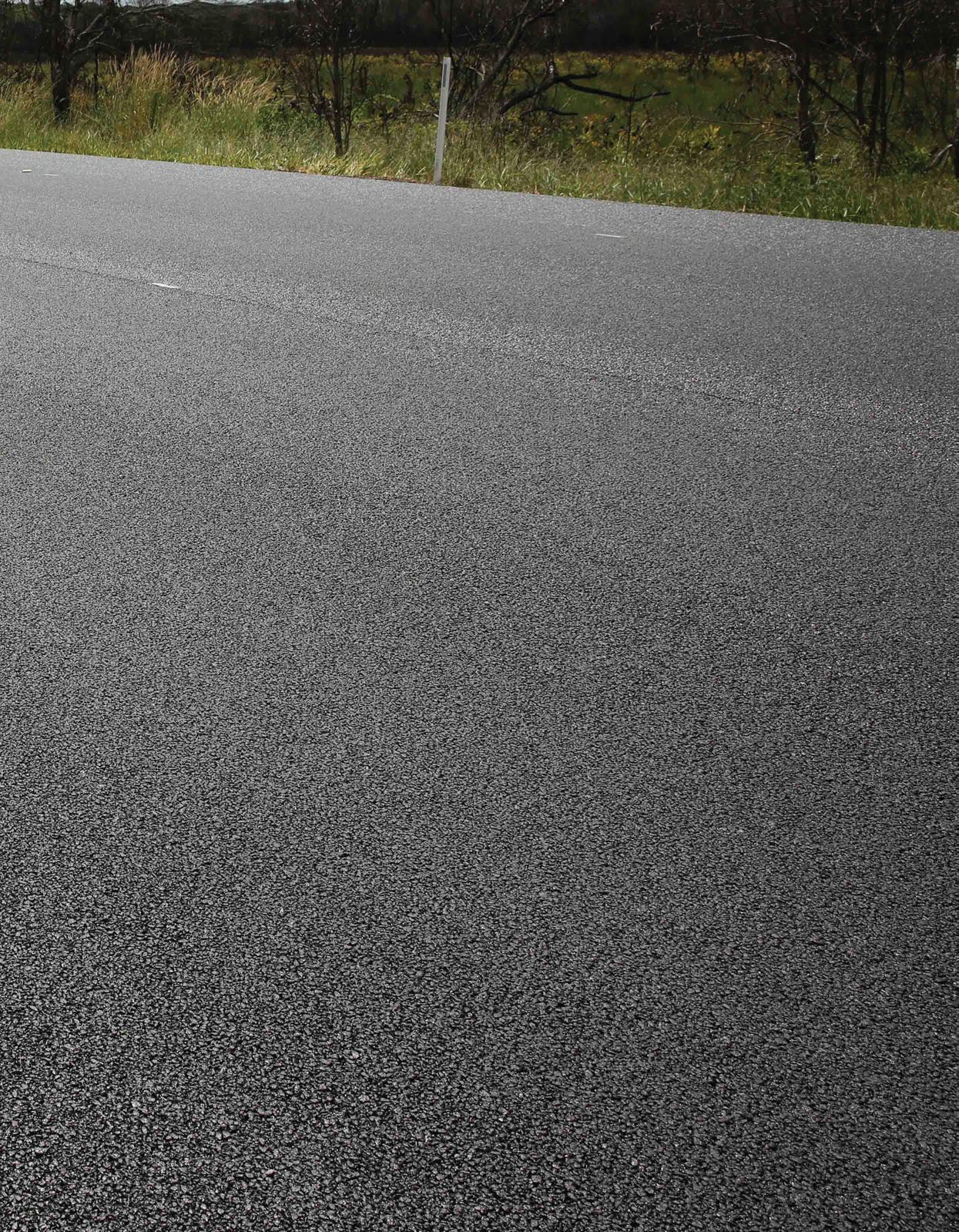
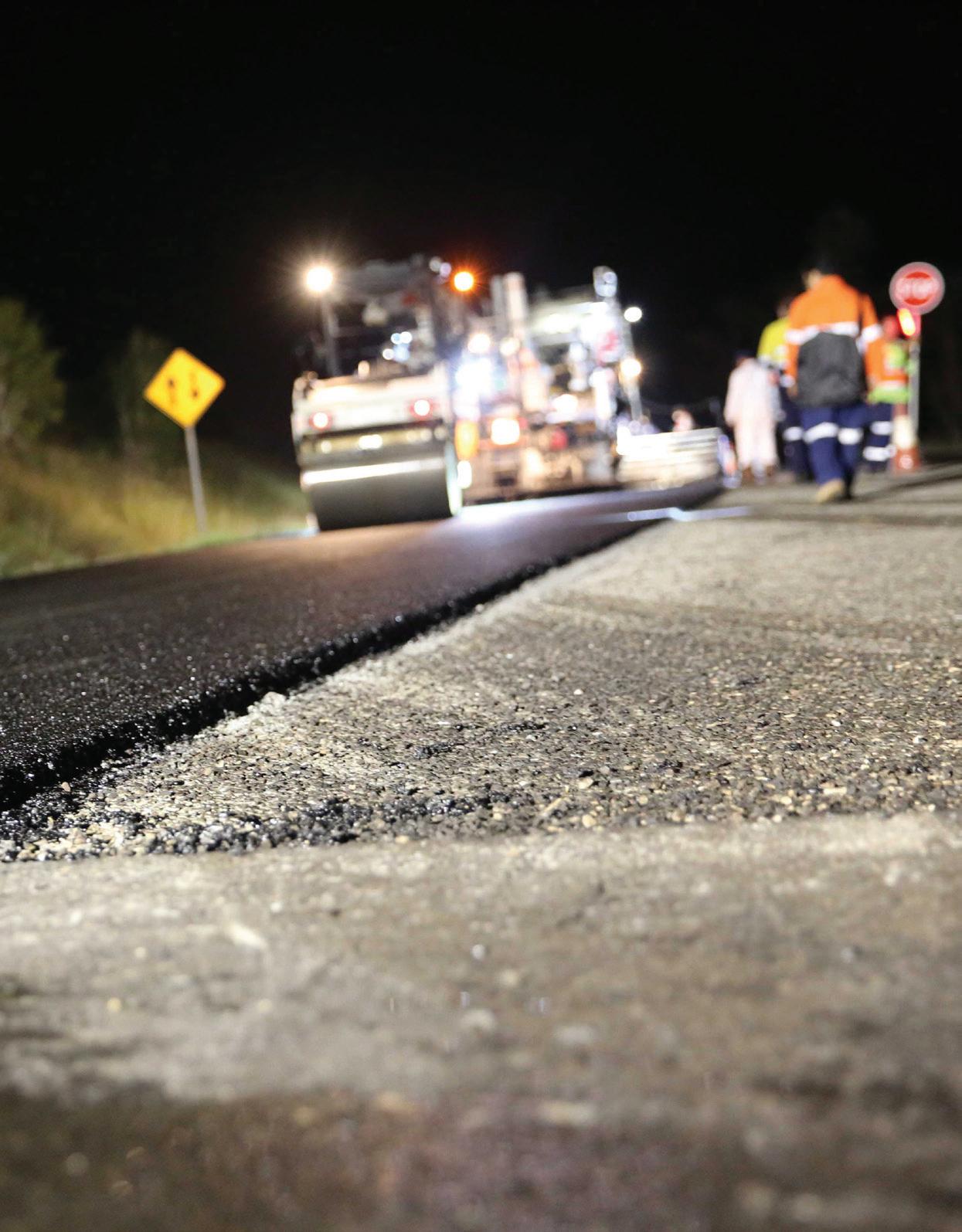
THE IMPACT OF NEXT GENERATION CONNECTIVITY
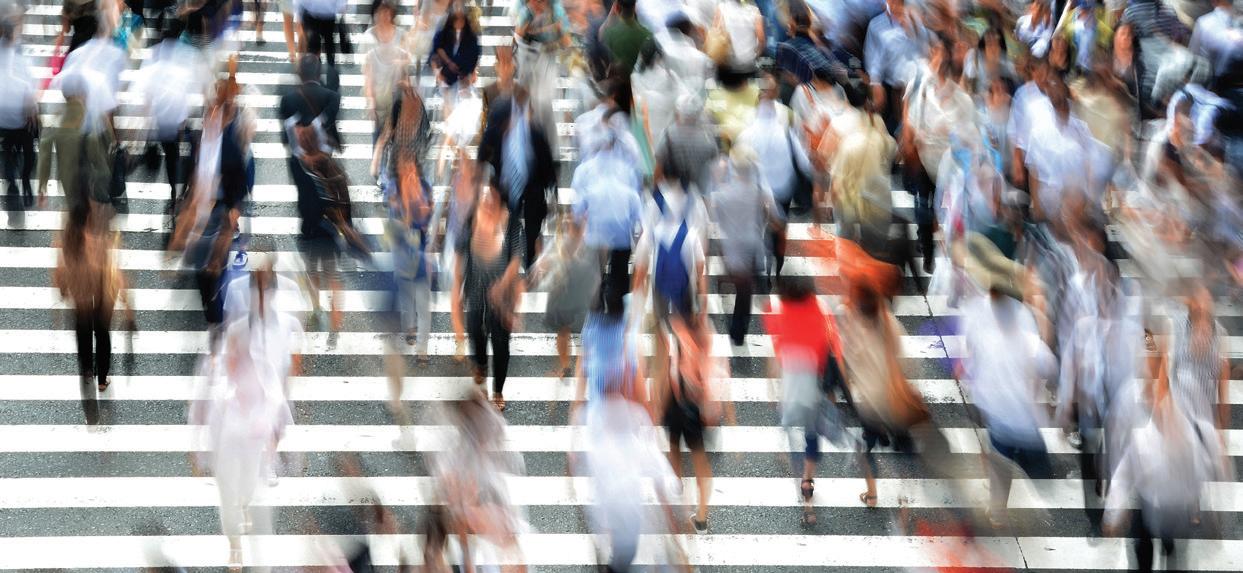
The infrastructure supply chain has always embraced complexity, significant capital investment and risk. Australia is on the cusp of an explosion of next generation technologies that will shape the road transport sector in general, and transport infrastructure management in particular. Where can asset owners, statutory bodies, consulting engineers and first tier contractors look to find the most up to date information about that new technology?
The answer is at the 28th International Australian Road Research Board (ARRB) Conference in Brisbane, running from the 29 April to 2 May 2018.
ARRB invites you to join in a robust discussion of “Next Generation Connectivity” and solve some of the most pressing questions around our infrastructure future. While you’re at it, rub shoulders with our industry’s most prominent figures, including representatives from academia, government and industry.
Top it off with the most impressing array of keynote speakers such as Olympic cyclist and gold medal winner Anna Meares OAM, Randell “Randy” Iwasaki, Executive Director of the Contra Costa Transportation Authority (CCTA), and Katherine Teh-White, Founder and Managing Director of Futureye.
Hear a diverse range of quality presentations on intelligent roads, future of asset management, disruptive technologies, platforms and services, smart journeys, and human factors of transport - showcasing current best practice from around the globe.
Exciting presentations you can expect to see include research papers such as ‘Potential Changes to the Road Track Cost Allocation Practice for Determining Australia’s Heavy Road User Charges’ and ‘Implementation of warm mix asphalt in the US: Present and future’.
SYMPOSIUM ON PAVEMENT SURFACE CHARACTERISTICS
Following the 28th ARRB Conference, ARRB is proud to present the 8th Symposium on Pavement Surface Characteristics (SURF 2018), delivered on behalf of the World Road Association (PIARC).
SURF 2018 incorporates a range of technical sessions and interactive panel discussions, with local and international experts focusing on “Vehicle to Road Connectivity”.
Keynote speakers include living legends of Australian Motorsport, Allan Moffat OBE, and Peter Boylan – winners at Bathurst, Sandown and the Australian GT Championships - who will offer some fascinating insights gained throughout their careers in the racing industry.
Technical sessions will be based on themes including safer road performance and data collection with a purpose. International keynote speaker Dr John Ferris from Virginia Tech, Founder and Director of the Vehicle Terrain Performance Laboratory, will be speaking on the importance of vehicle pavement interaction in vehicle design.
Come along to enjoy a jam-packed week of captivating technical content (balanced with unforgettable social functions!) and even a discount off the registration rate if you wish to attend both.
For more information or to register visit arrb2018.com.au or surf2018.com.au.
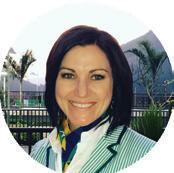
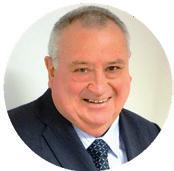
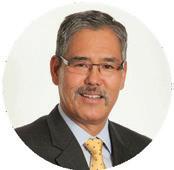

Three events. One extraordinary week!
The 28th International Australian Road Research Board Conference is bringing you ‘Next Generation Connectivity’!
PIARC 8th Symposium on Pavement Surface
Characteristics: SURF 2018, continues over the week, with the focus on ‘Vehicle to Road Connectivity’.
Don’t miss
Additionally, the prestigious Annual ARRB Awards Dinner will be held in the Brisbane Town Hall, so be sure to get your nominations in and book your seat at this exclusive event.
COLLABORATION LEADS TO LOWER-COST, QUALITY INFRASTRUCTURE
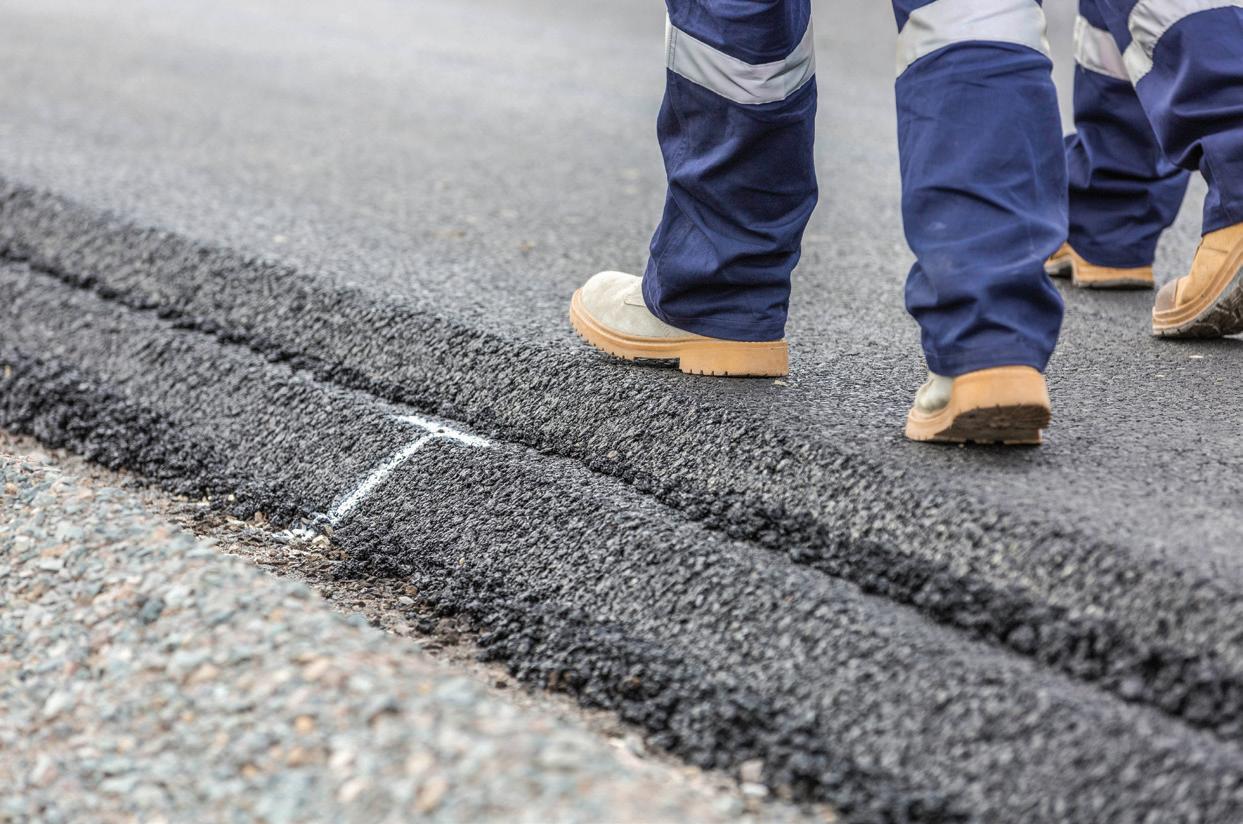
Compared to ‘conventional’ asphalt, EME2 offers superior performance
Queensland’s Department of Transport and Main Roads has partnered with the Australian Road and Research Board (ARRB) to research and develop solutions for improving the state’s roads and pavements. Here, Transport and Main Roads Director General Neil Scales runs us through some of the major developments occurring on our roads.
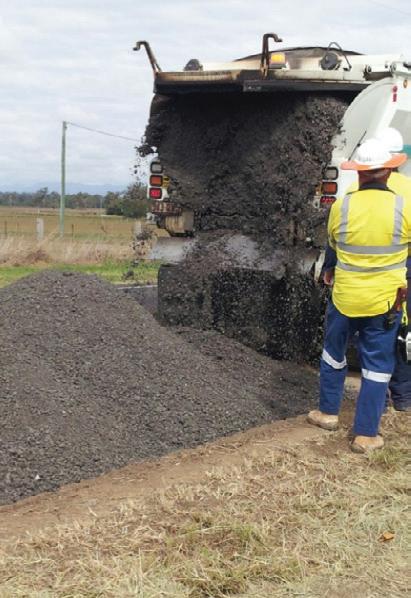
ueensland’s Department of Transport and Main Roads (TMR) invests billions of dollars annually building and maintaining the state’s road and transport network. Transport and Main Roads Director General, Neil Scales, said finding new and innovative
approaches to our infrastructure was critical to investing this money wisely.
“The more frequent extreme weather events we are encountering, such as flooding, means our roads infrastructure needs to be built to be more resilient,” Mr Scales said.
“Ensuring we get the best value for money, long term, out of every dollar invested is critical to delivering a network that serves the needs of Queenslanders now and in the future.
“To do this we have developed a structured research and development program to help us deliver excellence and achieve real savings.
“Through our partnership with the Australian Road and Research Board (ARRB), we have developed a National Asset Centre of Excellence (NACoE) to undertake targeted research and deliver practical applications of technologies that will deliver value for Queenslanders.”
Now in its fifth year, the NACoE was established to improve the specialist capability and capacity of both TMR and ARRB Group through a sustained, collaborative program of challenging projects which unlock innovation and deliver superior technology and road transport solutions.
The program is diverse but has a strong focus on pavements, asset management and structures research. It targets international best practice, providing guidance to reduce excessive conservatism and allow the use of innovative materials, and translating new knowledge into best practice.
“We invest more than $4 million each year in this program and it is already delivering important innovations and significant savings,” Mr Scales said.
“We have already achieved outstanding outcomes in the areas of cost saving and performance, sustainability, safety, and reliability.”
SAVINGS AND PERFORMANCE: EME2
Mr Scales said the most significant return TMR had seen from the program was the wider use of high modulus asphalt, or EME2.
“Developed in France in the early 1990s, EME2 has been used extensively in Europe on busy roads and airports with outstanding success,” Mr Scales said.
Compared to ‘conventional’ asphalt, EME2 offers superior performance, 20-25 per cent thinner bases and improved productivity in construction. Time savings of 30-50 per cent have been
reported in the construction of thick asphalt sections including EME2.
“During the past four years, TMR and ARRB have been engaged in an effort to transfer EME2 asphalt technology to Australia,” Mr Scales said.
In 2017, about 10,000 tonnes of EME2 was successfully placed on the Deagon Deviation as part of the Gateway Upgrade North project — at the time, the largest use of EME2 in Australia — and about 6500 tonnes was used in a pavement rehabilitation (inlay) project on Gympie Road.
More recently, 53,000 tonnes of the asphalt was placed on the Port Drive Upgrade project, and about 9000 tonnes on a pavement rehabilitation project on Steve Irwin Way on Queensland’s Sunshine Coast.
“Each year TMR spends about $100 million on asphalt, so the wider use of EME2 has huge potential for savings, as well as improved performance on highly trafficked roads,” Mr Scales said.
SUSTAINABILITY:
CRUMB RUBBER MODIFIED BINDER
The focus of NACoE’s research is not limited to cost and performance, however, with sustainability another major driver.
NACoE’s Crumb Rubber Modified (CRM) binder project, which aims to promote the use of recycled rubber from used car tyres into asphalt and surfacings, has already made significant advancements for the sustainability of Queensland’s road network.
“Recycling old tyres into roads is a win for our environment, our budgets and our road network,” Mr Scales said.
“Road surfacing containing CRM binder lasts longer than those using conventional bituminous binders, and show better durability and waterproofing.
“The use of CRM binder on resurfacing projects in 2015/16 and 2016/17 diverted around 200,000 tyres from landfill, and saved almost $170,000.”
NACoE has successfully delivered CRM demonstration projects in both sprayed seals and in open graded asphalt – these projects are being monitored for long-term performance as part of the program.
While further demonstration projects are required before the widespread use of CRM binder in open and gap graded asphalt, updates to the department’s technical specifications to increase the use of CRM binders in sprayed seals have now been implemented.
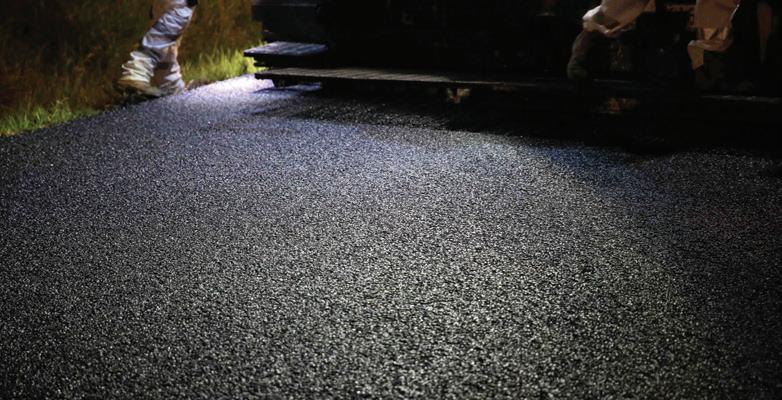
SAFETY: WIDE CENTRELINE TREATMENT
Safety is the number one priority for TMR, and NACoE resources are being put to work in this area.
After an extensive evaluation as part of the NACoE program, wide centreline treatment has now been installed on more than 1000km of Queensland roads.
This one-metre spaced line-marking between opposing lanes provides additional clearance between oncoming vehicles, while maintaining safe opportunities to overtake. The treatment can be supplemented with audio tactile line markings to provide additional safety benefits, particularly on routes where drivers are likely to become fatigued.
A trial section of the Bruce Highway combining the wide centreline treatment with audio-tactile markings has seen a 43 per cent reduction in cross median crash rates.
This research has led to an economical method to maximise the existing road network and achieve significant improvements in road safety.
DURABILITY: FOAMED
BITUMEN STABILISATION
“Where durability is concerned in areas that flood, foamed bitumen stabilisation is offering huge benefits,” Mr Scales said.
“NACoE is helping us convert the foamed bitumen research outcomes from the past four years into technical notes incorporating all learnings, and where appropriate, to help improve specifications.”
Foamed bitumen is formed by injecting a small quantity of cold water into hot bitumen to produce an instant expansion. In this foamed state, bitumen is highly efficient at wetting and coating the finer particles of the pavement material, forming a mortar and binding the mixture together.
Crumb rubber modified binder promotes the use of recycled rubber from used car tyres into asphalt and surfacings.
This process produces a pavement that is more resilient to flooding and uses less bitumen than asphalt concrete (2.5-3 per cent by weight compared to 4.2-6 per cent). It also allows for the use of lower quality aggregates, leading to significant savings.
In addition, foamed bitumen pavements exhibit superior fatigue properties compared to asphalt concrete, and significantly less shrinkage cracking compared to cement modified pavements.
Foamed bitumen offers excellent benefits for flood-prone areas and situations where inundation or extensive rain periods occur. It is also suitable where early trafficking is required as this is not achievable with layers of asphalt concrete due to heat retention issues.
Foamed bitumen is already being implemented in the coastal regions of Queensland, with TMR regions reporting an excellent success rate.
BENEFITS IN EXCESS OF THE COST
NACoE’s achievements in its first five years demonstrate that TMR can, with confidence, achieve benefits far in excess of the costs from research and development.
Aside from the direct economic benefits of the research program, the ongoing transfer of technical capability, knowledge and technology between TMR and ARRB staff is a benefit that will mature as the program progresses.
“Working in partnership with industry, universities and other government bodies to leverage research, knowledge and resources – this is what NACoE and our broader agreement with ARRB is all about,” Mr Scales said.
“The synergy produced by working together is something that will help us to deliver excellence and better value for money for years to come.”
For more information on the NACoE program please visit www.nacoe.com.au.
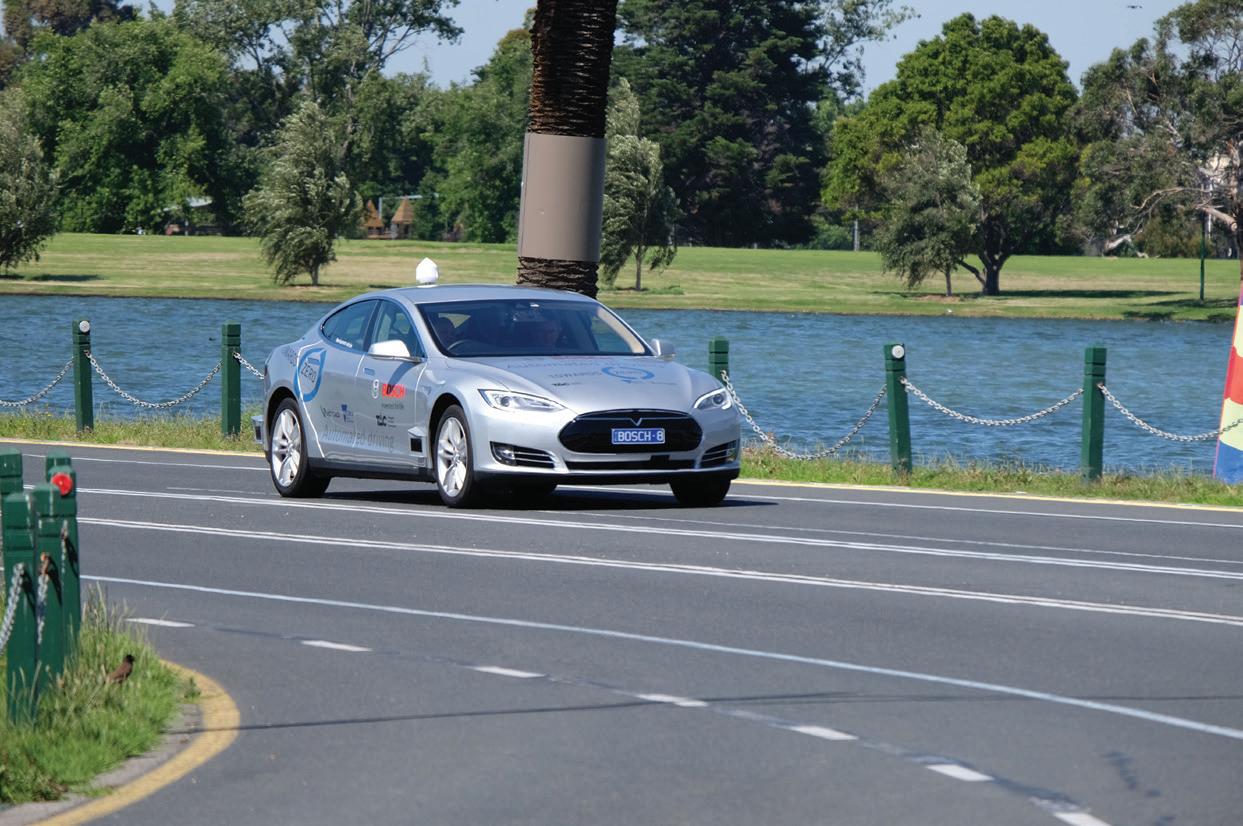
SATELLITE POSITIONING TRIAL HINTS AT THE FUTURE OF OUR ROADS
A two year Satellite-Based Augmentation System (SBAS) trial is testing how industries in Australia and New Zealand can benefit from improved satellite positioning technology. VicRoads is one of the participants, with a project focused on how SBAS technology can be used to enable vehicle automation, improving road safety and facilitating the development of intelligent transport networks.
AVicRoads Bosch Transport Accident Commission (TAC) highly automated driving (HAD) vehicle has been fitted with world-first satellite positioning technology as part of a trial of a Satellite-Based Augmentation System (SBAS) for the Australasian region.
The VicRoads project is one of more than 30 selected from almost 90 applications to participate in the SBAS trial, with supported projects spread across ten different industry sectors, including road, rail, maritime, construction, agriculture and resources.
The SBAS trial, developed in consultation with Geoscience Australia and the Australia and New Zealand Cooperative Research Centre for Spatial Information (CRCSI), and funded by $12 million from the Australian Government and $2 million from the New Zealand Government, is exploring technology that provides 10cm positioning accuracy.
Dr John Dawson, Section Leader, Positioning at Geoscience Australia said that two separate calls to industry to participate in the SBAS test-bed in Australia and New Zealand had been completed.
“We received overwhelming industry interest, with over 90 industry consortiums proposing projects. An expert committee has reviewed all proposals and has decided to support more than 30 industry projects; the project agreements are being progressively executed. The infrastructure community was well represented in the
supported projects,” Dr Dawson said.
The VicRoads project will allow further exploration into automated driving and will consider the ability of SBAS to support future automated vehicle positioning requirements.
“The trial will employ the Victorian Government-supported Bosch TAC HAD vehicle with an SBAS receiver to compare the accuracy of the SBAS to existing commercial positioning services used to facilitate automated driving,” Dr Dawson said.
“The Bosch TAC HAD vehicle will be driven in a variety of environments while collecting position information from an existing commercial real-time kinematic (RTK) service, standalone global navigation satellite system (GNSS), and the SBAS test-bed services. The trial will then provide an understanding of how SBAS services could perform in an automated driving environment.”
VicRoads will receive up to $89,500 in funding for the project and is making an in-kind contribution of over $31,000.
ASSISTING AUTOMATION TO DEVELOP SAFER ROADS
According to Dr Dawson, satellite positioning is going to be an essential enabler of automated car technology in Australia.
“Car industry experts in Australia now predict a progressive implementation of increasing degrees of automation corresponding with increasing positioning accuracy, from road-level (metre), lane-level (sub-metre) and where-in-lanelevel (decimetre),” Dr Dawson said.
“Australian roads will provide additional challenges to vehicle automation because many of our roads are unsealed, without painted lines, and our landscapes are often without distinct features. These factors challenge relative positioning techniques based on camera and radar technology. In these environments, improved satellite positioning will be paramount.”
Current commercial high-accuracy services are limited by the absence of suitable GNSS ground infrastructure and Australia’s mobile communications network, which doesn’t provide complete coverage of Australia’s roads. Alternative satellite-delivered commercial services require propriety receivers and remain prohibitively expensive for most applications.
“SBAS has a benefit over commercial solutions as it provides additional information on how much you can trust your position as provided by the receiver. This is known as position integrity, and it’s really important in transport applications where there is an obvious safety-of-life requirement,” Dr Dawson said.
“SBAS has an additional advantage in that it’s an international standard and there are SBAS-capable chipsets widely available in user devices today. Consequently, SBAS provides a ready and cheap solution to Australia’s positioning needs.”
Australia’s road sector will potentially benefit from improved satellite positioning technology in a number of ways, including:
♦ The deployment of intelligent transport systems and automated systems by enabling vehicle locations to be accurately determined in real time
♦ Improved positioning will lead to better 3D maps of road environments, which are essential for intelligent transport systems and automation
♦ New applications to monitor and limit vehicle positions (for example, to make a heavy truck avoid certain bridges) and speed
♦ Automation of the road sector has the ultimate potential to drastically reduce and even eliminate the national road toll (1200+ in 2017 in Australia)
ENCOURAGING INFRASTRUCTURE INNOVATION
Geoscience Australia has been able to support a variety of other road projects in addition to highly automated vehicles, including heavy vehicle differential pricing, connected vehicles and road mapping for automated vehicles.
“Automated vehicles will rely on access to highly accurate 3D road maps, which will contain information on the location of features like white lines on roads, lane widths, bridge clearances, parking bays and car charging locations,” Dr Dawson said.
“These road maps will be generated using capture platforms (a car fitted with camera, radar and positioning sensors) and one project aims to demonstrate the use of SBAS to create more accurate and more timely maps.”
Several other projects show relevance to the infrastructure and transport sectors, such as one project testing precision guidance for remotely piloted aircraft and safety systems.
Another project is using SBAS to see if it can pinpoint underground assets, such as water pipes, with a margin of error less than 0.5-0.1m. If successful, traditional surveying of those assets could potentially be supplemented with mobile devices, which would revolutionise the area of asset location.
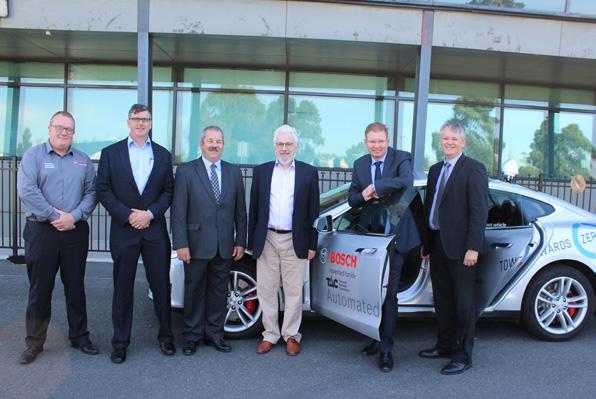
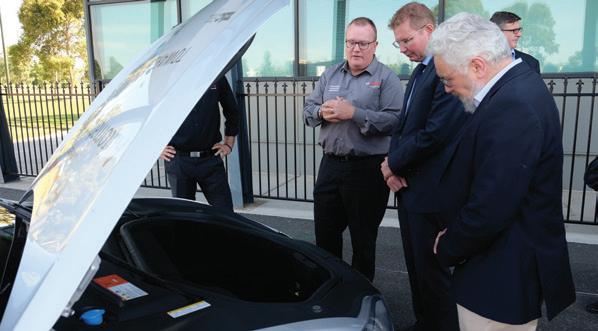
SBAS could also assist with pedestrian safety and help make cities and attractions more accessible to the physically and visually impaired through enhanced positioning and guidance.
DRIVING THE GROWTH OF SPATIAL TECHNOLOGIES
Spatial information, paired with satellite positioning, is being increasingly used by policy makers to improve decision making.
“One example is in city planning, where future planners will walk around and experience augmented reality views of future buildings and infrastructure. This will enable improved planning decisions and help ensure community support in contentious planning processes,” Dr Dawson said.
One of the main challenges around the implementation of spatial technologies in the infrastructure sector is the geographic size of Australia, creating an enormous area map.
There is also a strong need for high-quality communications infrastructure in remote and regional areas where low population densities mean lower investment in the communications infrastructure required for road mapping data distribution.
Dr Dawson said that spatial technologies will become increasingly important in future urban design and planning through the digitisation of the built environment.
“Spatial technologies underpinned by accurate satellite positioning will be critical as Australia moves to implement Smart Cities Plan concepts, where city assets and resources are managed in a much more holistic way by exploiting information and communication technology,” Dr Dawson said.
NEW GEOSPATIAL CENTRE MAPPING SYDNEY’S INFRASTRUCTURE
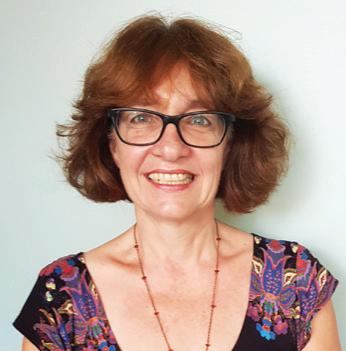
UNSW has created a new 3D geospatial information research centre that will be run by leading geospatial scientist Sisi Zlatanova and produce 3D digital maps of Sydney’s buildings and infrastructure. Here, Ms Zlatanova explains some of the research the centre will be undertaking and how they plan to move the data of the city’s buildings to the third dimension.
he progress in 3D geospatial information over the last few years clearly shows that the previously sharp boundaries between the methods and approaches used to represent the real and design world are diminishing. All systems, regardless of their origin and focus — from GIS, DBMS, BIM, AEC, computer graphics, serious games, to VR and AG — attempt to extend their core functionality to handle and/or analyse 3D geographical data.
The demand for 3D functionality and applications is increasing. Cities are expanding and the dependencies between buildings, transportation, above and underground infrastructure, green and water areas, underground soil layers and so on, are becoming more elaborate and cannot be solved with 2D maps.
There is a strong demand for 3D in sectors such as:
♦ Large civil engineering works
♦ Mobility studies and navigation
♦ Urban planning
♦ Environmental monitoring
♦ Utility management
♦ Epidemiology and related health
♦ Marine, coastal and terrestrial ecosystems
♦ Land use and land cover change analysis
♦ Climate change, oceanography and atmospheric analysis
♦ Natural resource exploration and evaluation
The real world is 3D and so must be the digital world!
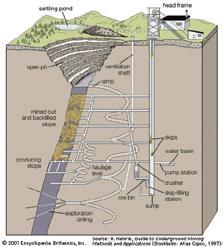

Integrated modelling of above and below surface is needed
It is evident that integrating data from different environments (indoor/outdoor, above/below), disciplines (cadaster, urban planning, water management, mining), and domains (GIS, BIM) is becoming a key issue. Such a fusion of 3D data in one analytical environment demands new representations and frameworks for seamless data modelling, management and visualisation.
Technological developments are moving fast; sensors decrease in size and weight and can be mounted on light platforms (such as drones) and 3D sensor measurements are becoming more accurate, cheaper and faster. This opens new opportunities to explore point cloud and voxel representations next to the traditional vector representations enriched with topology and semantics.
UNSW’S NEW GEOINFORMATION CENTRE
These tendencies have been recognised by UNSW, and a few years ago a broad discussion was initiated between several UNSW faculties, namely the School of Built Environment, Computer Science and Engineering, Electrical Engineering, School of Aviation, School of BEES, School of PEMS, School of Civil Engineering and the Academic Board.
This collaborative work resulted in UNSW hiring me to coordinate the establishment of the 3D Geospatial Information Research Centre.
The new 3D Geospatial Information Research Centre will have the goal of advancing the UNSW research agenda in geospatial information and contributing to the UNSW 2025 strategy to establish UNSW as one of the top 50 researchintensive universities worldwide.
The centre will be engaged in the following key tasks:
♦ Integrate and sharpen the research topics and infrastructure within UNSW and Australia, and contribute to 3D geospatial research internationally
♦ Strengthen links with industry, council and interested institutions, and involve them actively in the academic debates, research and development to accelerate validation and implementation of research innovations
♦ Become an advisory hub on various aspects of data collection, modelling (standards), management, analysis and visualisation of 3D data
♦ Maintain information about data, tools and equipment and be able to quickly set up experimental test sites to be used by different applications and disciplines
♦ Promote UNSW geospatial expertise nationally and internationally
♦ Assist and support the delivery of teaching and research student training in related fields
The first and most demanding topics of research will be defined in the coming months and consider both Australiaspecific and globally recognised challenges.
3D INDOOR MODELLING
One of these very challenging issues is 3D modelling and analysis of the indoor environment. While 3D models for the outdoor environment have been investigated for years and have reached a certain level of maturity, 3D indoor modelling is still fragmented and controversial.
3D indoor environments are quite distinct and complex compared to outdoor. They are commonly closed spaces with restricted views and limited sunshine or artificial lights, which has impact on the sense of time, and without natural shadows, influences the orientation.
Furthermore, these are man-made structures which influence perception and commonly have many obstacles and ‘hidden’ objects. All these factors influence modelling and the development of applications for localisation and navigation (Figure 2), interior climate and wellbeing, safety and security, maintenance and facility management, and asset tracking.
3D MODELS FOR A CITY’S INFRASTRUCTURE
So what kind of 3D models should be developed to serve such applications on the scale of a city or a country?
Two approaches are currently on the rise: CityGML LOD 4 (GIS-based) and IFC (BIM-based). While IFC evolved from supporting the design and construction of facilities, CityGML grew from traditional geospatial mapping and visualisation. The two concepts differ in the description of objects. IFC represents all components with their true 3D size and shape without abstractions or simplification. CityGML LOD4 is based on measurements of real-world objects and involves abstractions and simplifications with respect to the application.
Consequently, CityGML LOD4 hidden construction elements (beams, slabs, columns) are impossible to represent. Instead sensor-detectable surfaces (floor, ceiling, wall) are modelled and united in larger units like rooms and corridors, but these lack many details. For example, a wall in CityGML is the surface of the physical wall, while IFC would describe the 3D solid of the entire physical wall. So, one physical wall in IFC would be represented by two surfaces in CityGML.
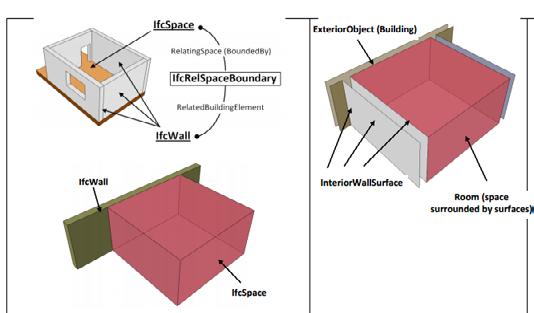
So how do we deal with these two concepts, and how do we integrate and analyse CityGML and IFC data in one environment? As IFC contains more detailed and complex information than CityGML, the conversion from IFC to CityGML is relatively straightforward and stable, but the other way around requires additional rules and information, resulting in complex, yet unsolved problems. These issues have triggered academic research on seamless conversions, ensuing the recommendation to follow first semantics-mapping, and then geometry and relationships transformations. But in-depth investigations are still eagerly required.

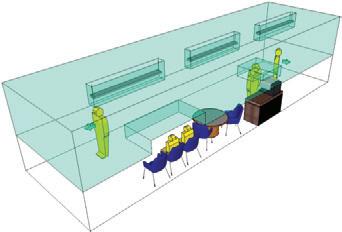

There are many research questions demanding attention and further development. Some of these questions include: what kind of sensors are most appropriate to create 3D indoor models? What and how are these stored? What kind of detail is needed for different applications? How can it be enriched with semantics and topology? What mapping is most appropriate between GIS and BIM models? Which visualisations are most appealing? Which approach will allow for seamless indoor/ outdoor navigation?
VOXEL REPRESENTATIONS
Another topic for investigation is voxel representations. Three-dimensional (3D) rasters are simple representations, which have long been used for modelling continuous phenomena such as geological and medical objects or in environmental studies. But what if above surface buildings, trees and streets are also modelled in voxel domain?
Having a complete voxel representation of the whole world means it will be possible to seamlessly move in all directions — just like in a huge Minecraft world. This approach may enable the resolution of spatial conflicts easily and allow for various types of spatial computations such as 3D distances, volumes and cross sections, or determining 3D topological and other spatial relationships, which seem problematic in vector domain.
Furthermore, modelling volumetric objects, such as underground assets, water and walls, requires the deployment of complex shapes, which are prone to validity errors. The space subdivision schema can be optimised using octree and
binary decompositions. Such schemas allow for enlarging the space when the properties of adjacent objects can be considered the same within a given threshold. Recent research and developments have shown that voxels can be a convenient way to analyse point clouds and indoor environments.
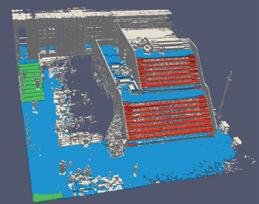
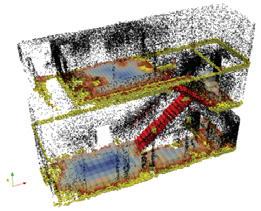
Voxel representation is very promising but does pose some challenges, including determining what kind of storage schema can be appropriate for covering a whole city or a country as voxels may result in large data sets. It also creates questions such as what semantic approach has to be devised that is smart enough to cover the complexity of city environment. Can a voxel representation cope better with sematic hierarchies? Depending on the granularity, can a voxel be a ‘desk’, a ‘room’, a ‘floor’, a ‘building’, or a ‘city’? Is voxel representation an approach for storage or only for analysis? And is seamless conversion from voxel to 3D vector representation possible?
Technological developments are moving fast; sensors decrease in size and weight and can be mounted on light platforms (such as drones), and 3D sensor measurements are becoming more accurate, cheaper and faster. This opens new opportunities to explore point cloud and voxel representations next to the traditional vector representations enriched with topology and semantics.
CHALLENGING THE THIRD DIMENSION
The new UNSW geospatial research centre will address these challenging topics in 3D geospatial domain by investigating and developing:
♦ Algorithms and approaches to 3D reconstruction with different resolution, accuracy and realism with emphasis on 3D indoor environments
♦ 3D data structures, data schemas for storage, indexing and querying of big data
♦ Approaches for integrated 3D modelling of above and below surface information and integration of BIM
♦ Frameworks for semantic enrichment, ontology and linked data
♦ Devising new approaches for 3D data representations with a focus on volumetric modelling (voxels, tetradifon, point clouds)
♦ Tools for data mining and deep learning
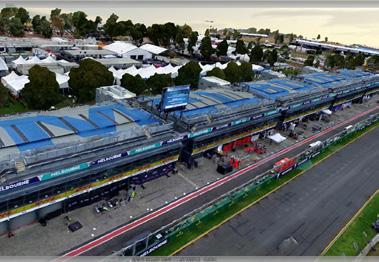
♦ Tools for 3D-4D analysis and visualisation for various applications
♦ Web and handheld applications (e.g. indoor-outdoor positioning and navigation)
THE NEXT STEPS
Researchers in the new UNSW geospatial research centre team have already established contacts with industry, software companies, city councils, research institutes and universities to investigate and discuss cooperation agreements and funding schemas. Discussions with the UNSW faculties are continuing and the research agenda will be clarified in an upcoming series of meetings.
Parallel to this, several Australian Research Council (ARC) proposals are also in preparation and the remaining research positions will be filled out by the end of March, allowing the centre to work at full power. The geospatial team is extremely motivated and intends to be able to demonstrate Kensington and CBD showcases by the end of the year.
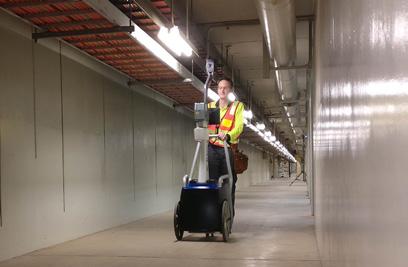
Taylors TIMMS, the perfect tool for laser scanning extensive, complex environments. With TIMMS*, indoor maps and models covering thousands of square metres of space can be mapped in minutes and entire buildings mapped in a day.
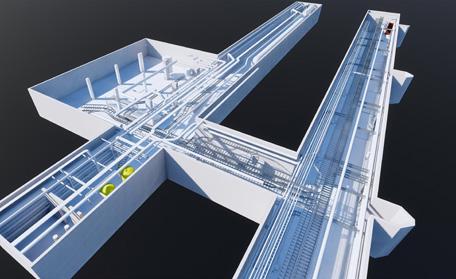
The TIMMS provides both LiDAR and spherical video of a facility and produces fast and accurate geo-located maps, enabling Taylors to translate environments into visual 2D & 3D layouts. Our experience in scanning at Tullamarine Airport using TIMMS includes
• Water Main Upgrade Feature and Level Survey
• Mace Way As-Built Survey
• Melrose Drive Bus Shelter As-Built Survey
We can create 3D reality models in a variety of formats to provide a solution to suit the end user’s requirements.
Mapped data is revolutionising the way we understand, operate and improve our built environments and has proven successful in situational awareness of airports and other multifaceted sites including: hospitals, sporting complexes, rail infrastructure, factories and plant.
* TIMMS: Trimble Indoor Mobile Mapping System
www.taylorsds.com.au Contact us today:
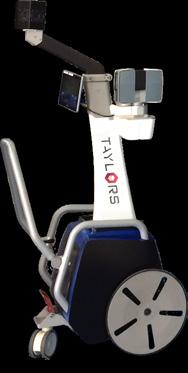
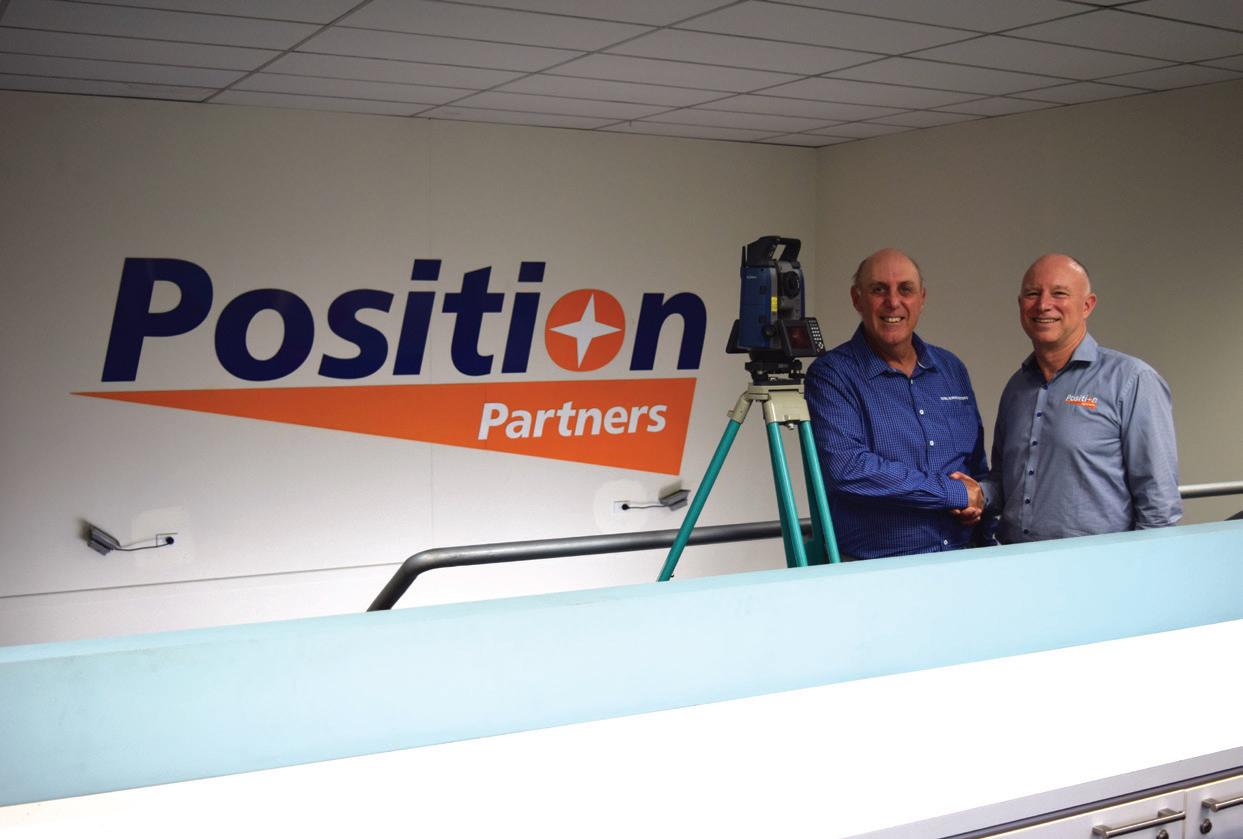
POSITION PARTNERS ACQUIRES TOTAL SURVEY SYSTEMS
Position Partners has acquired Sydney-based Sokkia distributor Total Survey Systems. The combined team expands resources and expertise to better support surveyors and geospatial professionals.
Geospatial solutions provider
Position Partners has acquired Total Survey Systems (TSS), a Sydneybased survey equipment distributor that specialises in Sokkia survey technology.
Under the agreement, all TSS employees will join Position Partners’ New South Wales team based in Silverwater, located to the west of Sydney’s CBD.
“We are delighted to welcome the TSS team to Position Partners, their expertise in the land survey industry will be a terrific addition to our engagement with customers,” said Martin Nix, CEO of Position Partners.
“Surveyors in New South Wales have never been more in demand than they
are now. They will expect systems and support to be even more productive as geospatial data exponentially increases.
“We are pleased to be able to extend the support to our mutual customers with a larger, highly experienced team and a wider range of solutions to suit every application.”
With more than 50 years’ collective experience in the survey industry, TSS was formed in 2002 when Sokkia changed its distribution to a reseller model. Prior to this, Hugh Gerdes and members of his team worked for Sokkia directly.
Paul Koren is a Senior Technical Consultant that has been with the company since its formation and before that worked for both Sokkia Australia and Sokkia BV in Europe. Glenn
Anderson is the Service Manager who has worked for TSS for some 15 years, and Renato Calara is a Service Technician that has been with the company for more than five years and Sokkia South Africa a further 15 years before that.
“Their service personnel’s impressive technical knowledge and longevity with the Sokkia brand will ensure a seamless transition for existing customers and enhanced capabilities for our own services teams throughout Australia and New Zealand,” Mr Nix said.
“We are excited about this new chapter for our team and delivering a wider portfolio of solutions for the survey and geospatial industry, backed by excellent technical support, calibration and repair services,” said Hugh Gerdes, Director of TSS.

Growing infrastructure demands around the world are creating tremendous challenges and opportunities.
Topcon works to stay a step ahead, by creating solutions that incorporate technology advancements into the way you work today and tomorrow, transforming the way infrastructure is built.
Our integration of high-accuracy positioning, high-speed imaging, cloud-based information management and down-to-earth simplicity creates higher productivity, enhanced quality and improved sustainability. With Topcon, you can stay ahead of your competition and meet the challenges of Infrastructure growth.
Watch Topcon Positoning Systems President and CEO Ray O’Connor’s Bloomberg “NEXT INFRASTRUCTURE” interview: www.topconpositioning.com/Infrastructure.
Let’s discuss your next project: 1300 867 266 | www.positionpartners.com.au
THE RISE OF SPATIAL: MAPPING FUTURE DEMAND
Spatial technologies are widely used across the infrastructure industry, with applications throughout the asset lifecycle from design and construction all the way to maintenance and disposal. Here, Deanna Hutchinson, CEO of Spatial Industries Business Association (SIBA) talks about the current trends and challenges impacting the spatial sector.
According to Ms Hutchinson, spatial technology helps create safer and more efficient infrastructure, especially in the transportation industry.
“Spatial information is used in the design, construction and operation of roads, rail, shipping and air traffic. It’s used to plan transport infrastructure by informing where people travel, at what time, using what mode.
“It helps keep us stay safe by directing signalling systems to manage traffic flows, and aids in the planning of maintenance. It drives our positioning systems (GPS, and in the future autonomous vehicles) as it is the information that is passed from sensors to dashboards telling drivers something is getting close,” Ms Hutchinson said.
The two primary technologies that underpin the wide range of spatial and data analytics activities in the infrastructure sector are Geographic Information Systems (GIS) and remote sensing, which are used to gain information about a range of physical and urban environments, manage the location and condition of assets, and validate planning designs.
The ability to monitor the status of assets remotely and continuously, ensures better infrastructure management and improved decision-making.
“Knowing what’s happening where reduces waste from errors and duplication like digging up the same stretch of road three times in a week, and opens up new opportunities, like autonomous vehicles,” Ms Hutchinson said.
“For example, Sydney CBD and South East Light Rail upgrades have required all the existing utilities and associated structures to be mapped, so they could be protected from any vibration caused by the rail, or completely relocated outside the zone of influence.”
INVESTING IN INNOVATION
Ms Hutchinson sees innovation as one of the key trends for the spatial sector in 2018.
She says machine learning, cloud computing, improved sensors and positioning technology are all changing the game for what we can measure cost-effectively, and quickly.
“This means spatial information is fast becoming an everyday tool for all businesses,” Ms Hutchinson said.
“The trend toward lean is highlighting opportunities to reduce duplicity and redundancy, improve consistency of information and commonality of business rules, and break down silos.”
The annual SIBA Asia-Pacific Spatial Excellence Awards offers an insight into the leading projects and most exciting developments in the spatial sector. Regional award winners have already been announced for 2018, with the results of the national awards released in April.
The winner of the South Australian Technical Excellence Award, the North Terrace Adelaide Tram Extension Survey, involved surveying all road surface features and infrastructure, plus the location of all underground services including old tram sleepers, along 2300m of busy, multi-lane inner city roadway from King William Street East to East Terrace.
The tight timeline and high visibility of this project, combined with working around heavy traffic and public transport movements, night work requirements and major events in the Adelaide community, presented significant challenges but new technologies like 3D Terrestrial Laser Scanning,

cloud computing and BIM allowed the work to be completed within these constraints.
While the winner of the Queensland Spatial Enablement Award, Cogha, in partnership with the City of Ipswich, is developing a 5D data model as part of its Smart City Program, which aims to further integrate local council, state and federal government data and provide a tool for visual collaboration.
Starting with a three-dimensional digital model of above and below ground city infrastructure, dimensions of data and time are overlaid to produce the 5D data model, continuing the Smart City Program principles of open and interoperable platforms.
Advancements in spatial technology are happening at a rapid rate and new technologies that deliver transparent and integrated access to information are emerging all the time.
“It’s clear that the growing interest in space will deliver a range of new capabilities. Spatial data is one of the big downstream beneficiaries of space activity — we rely on the data beamed back to Earth from satellites and other sensors,” Ms Hutchinson said.
“Integrated project delivery is a concept gaining considerable traction in the infrastructure industry — it’s about sharing the information as a single point of truth from design and construction to project delivery.
“We are moving toward a digital built environment, and so we will have The Matrix in many ways. We will work in a parallel universe where design, planning, skilling, analysis and problem solving happens in a virtual world.
“We will utilise robots, drones and other automated technologies to assist us to perform some tasks in the real world because it will be cheaper and safer to do so,” Ms Hutchinson said.
Resolving questions around the accessibility of information and the ability to effectively collect and leverage data will be major factors in driving the growth of the spatial industry.
“I do think we need to focus on educating ourselves about how emerging technologies can help overcome some of the barriers for embedding location intelligence in business operations, as it really is a key enabler for digital transformation. Knowing what happens where unlocks an extraordinary level of insight,” Ms Hutchinson said.
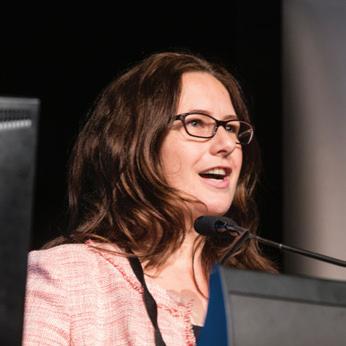
“Augmented reality is another newish technology that’s beginning to prove some strong use cases; visualising the built environment before its built, space perception, community consultation, visualising under the ground — where are the pipes?”
A GROWING INDUSTRY
With the value of spatial information already being realised within the infrastructure industry, Ms Hutchinson said she expects spatial analysis to only become more complex as more spatial questions are asked and more tools become available to help answer them.
“Blockchain is an exciting development that answers some of those access and control questions, and it will drive the speed and shape of this transformation.”
SIBA advocates for government data to be available in machine readable formats to support spatial analysis but recognises the need for contractual protections that encourage growth in spatial data use.
There are several projects in the works exploring how more data can be “unlocked” while upholding appropriate national security and economic controls.
Looking ahead to the future, Ms Hutchinson said all industries will need to get good at compiling multiple layers of information and responding in real time.
“Will we wear funny looking glasses or adopt fake persona avatars to interact with colleagues and customers? Who knows. But we will have more information at our disposal than ever before, and we will need to be skilled at evaluating its accuracy and usefulness.”
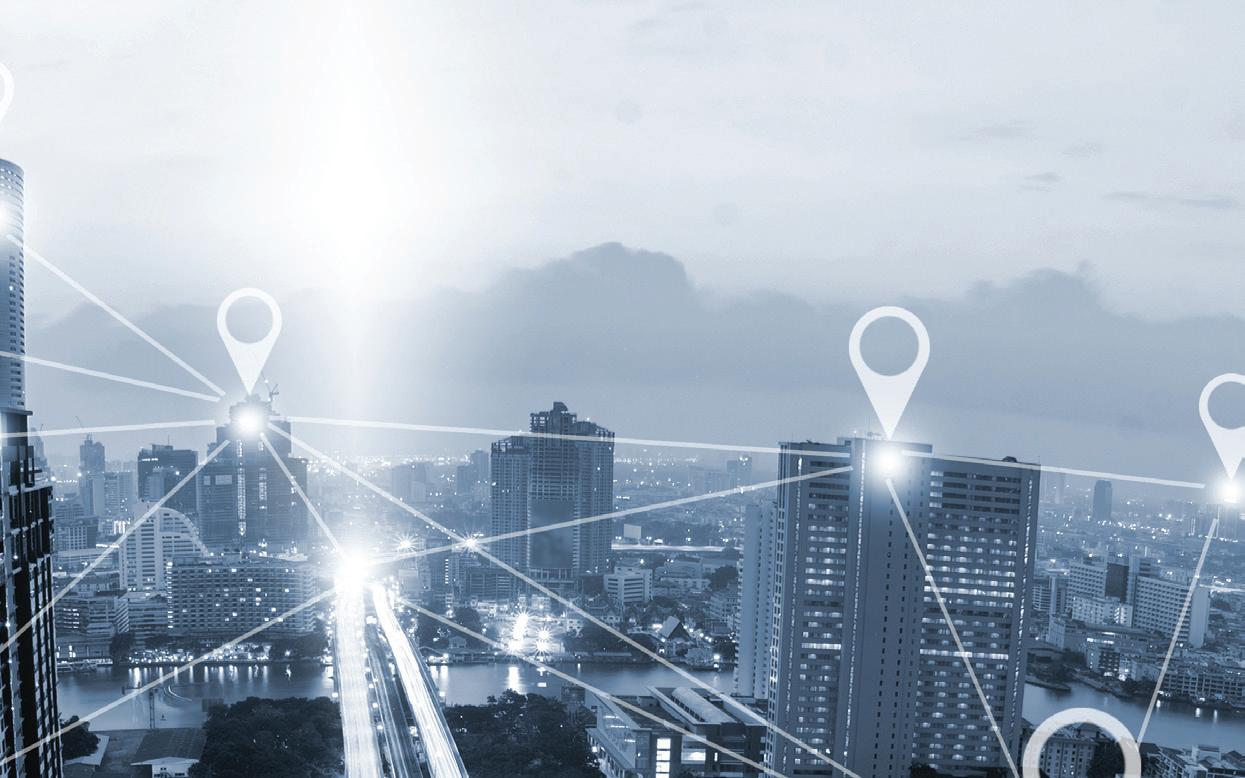
USING TELEMATICS DATA TO BETTER MANAGE ROAD NETWORKS
by Transport Certification AustraliaTelematic data has the potential to help us better understand road use and change the way Australia manages its road network. Here, Transport Certification Australia (TCA) outlines how telematic data can re-engineer road networks and what the National Telematics Framework is doing to increase productivity for heavy vehicles and freight.
WHAT IS TELEMATICS?
The term ‘telematics’ refers to integrated systems of information, communications and sensors to exchange data and information between vehicles and other locations, including:
♦ Vehicle to infrastructure (V2I) applications
♦ Vehicle to vehicle (V2V) applications
♦ Vehicle to elsewhere (V2X) applications
The application of telematics and related intelligent technologies is increasingly being used across surface-based transport to improve the mobility of people and freight by improving safety, productivity and efficiency outcomes, including:
♦ Monitoring and reporting of vehicles and infrastructure
♦ Providing information to and from vehicles
♦ Connected and cooperative vehicles
♦ Automated and autonomous vehicles
THE NATIONAL TELEMATICS FRAMEWORK
TCA administers the National Telematics Framework, which is a digital business platform with infrastructure and rules, which supports an open technology market for telematics and related intelligent technologies.
The National Telematics Framework supports government agencies, regulators and end users by:
♦ Providing a platform for the delivery of an open technology market
♦ Providing outcome-focused, technology neutral, disruption-resilient applications
♦ Addressing security and privacy concerns
♦ Encouraging innovation
♦ Facilitating the recovery of costs from the telematics and technology sector, which offset cost burdens to government
The National Telematics Framework has been recognised internationally as a best-practice approach for telematics applications, in the form of ISO15638 (TARV).
The National Telematics Framework operates in a similar way to other operational frameworks in other portfolios.
USING TELEMATICS DATA TO RE-ENGINEER HOW ROAD NETWORKS ARE MANAGED
The collection of data from applications managed through the National Telematics Framework provides opportunities to better understand road use, and optimise road network management.
Where data is available for heavy vehicle road use and loading, conventional methods of collecting data typically only provide ‘point-based’ data samples (i.e. road-based systems which count vehicle passes, axle groups and or loads).
Compared with other economic utilities (such as electricity, water or communications infrastructure), there is a comparative shortfall in data collected from road assets to inform the level of asset utilisation and consumption.
The use of telematics data, together with appropriate privacy management
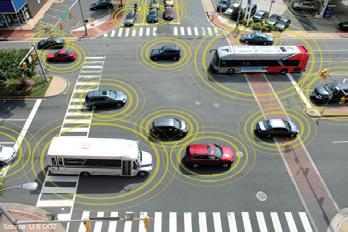
WHO IS TCA?
Transport Certification Australia (TCA) is a national government body responsible for managing an open technology market for telematics and related intelligent technologies, which delivers innovation, competition and choice through technology providers.
TCA’s role involves the interaction of three distinct stakeholder groups to deliver improved public outcomes through the use of in-vehicle technologies:
» Government agencies (which set policies and/or manage programs using telematics applications)
» Regulated stakeholders/end users (which use telematics applications in response to government policies and/or programs)
» Private sector service providers (the technology and Intelligent Transport System sector, which deliver telematics products and services to regulated stakeholders/ end users)
By promoting an open technology market, TCA performs a key role in avoiding:
» Potential market failures, such as proprietary-based systems inhibiting interoperability and scalability
» Potential regulatory failures, such as unintended technology prescription, poorly constructed policy positions which could lead to duplication and inconsistencies, or ‘technical solutions’ which do not deliver upon the intent of government policy
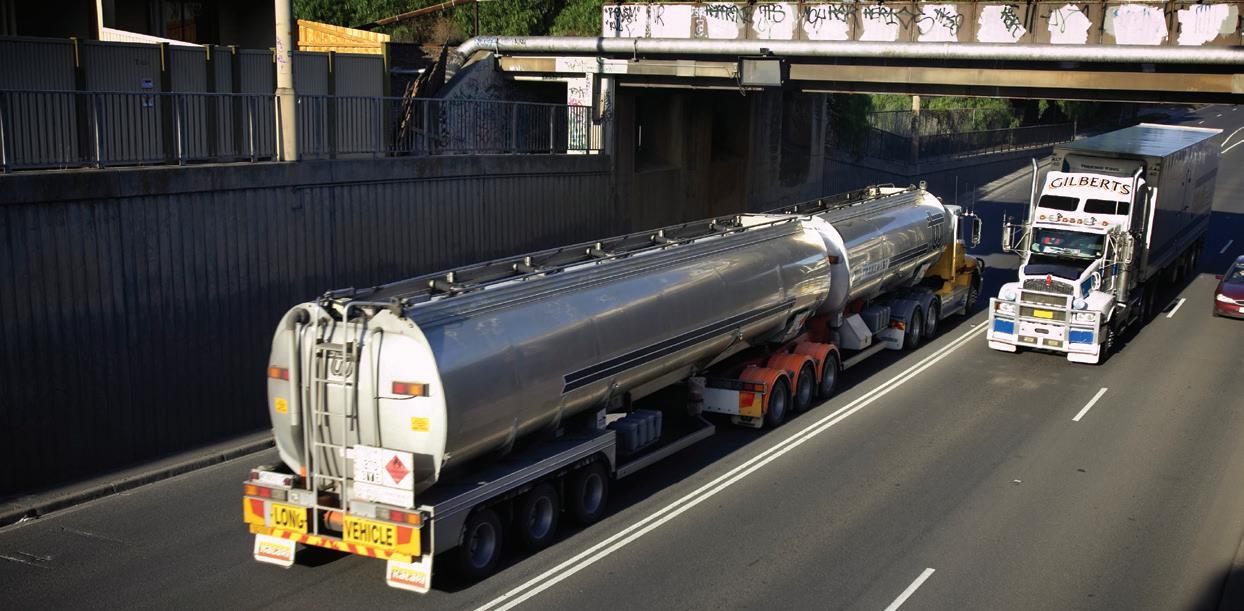
safeguards managed by TCA, presents a new way of accessing and analysing data.
ON-BOARD MASS (OBM)
TCA is currently implementing a new application within the National Telematics Framework, which has the potential to drive a new wave of productivity reforms for heavy vehicles and freight.
TCA is currently implementing a new certified service offering which utilise OBM Systems, which enable the collection of high accuracy and high integrity mass measurement data from heavy vehicles.
Being able to link mass information to other key pieces of data, including the configuration of the vehicle, its location and time of collection, and, when required, its speed, presents new opportunities for road managers to re-engineer their road networks.
CHANGES IN BRIDGE LOADINGS DUE TO TELEMATICS
In 2017, updates were made to the Australian Standard for bridge assessment (AS 5100.7:2017).
The updated standard incorporates reduced traffic load factors for vehicles monitored through OBM Systems for the Ultimate Limit State (ULS).
AS 5100.7:2017 is the national standard for assessing bridge infrastructure, and forms part of the national Bridge Design series.
The standard highlights how the
availability of reliable and accurate vehicle location, mass and configuration information, can enable improved productivity outcomes, without having to resort to physical upgrades of infrastructure.
This allows road managers to make access decisions which can increase mass loadings of heavy vehicle combinations. The updated Australian Standard also notes that load factors can be further reduced, provided a vehicle speed limit is specified.
The Low Speed Guidance application allows road agencies to impose lowspeed speed restrictions (as needed) on bridges, and to receive reports (based on the GPS measurement of speed).
LEVERAGING IN-VEHICLE TECHNOLOGIES ALREADY FITTED TO HEAVY VEHICLES
One of the challenges in deploying new pricing arrangements is the cost of implementing new technology.
There are now over 38,000 Telematics
In-Vehicle Units (IVUs) already fitted to articulated heavy vehicles across the country, which are ready to
support – or are able to support with minor amendments – the road pricing application (and other applications colocated within the National Telematics Framework).
This means existing investments made by the heavy vehicle industry – as well as the technology sector – can be further leveraged. This overcomes the need for new devices to be fitted.
OECD WORKING GROUPS
TCA represents Australia on two OECD (Organisation for Economic Cooperation and Development) Working Groups, the outcomes of which will support the wider use of telematics to support future road management reforms. These groups are:
♦ Intelligent Transport Systems (ITS) for High Capacity Transport (HCT)
♦ Policies to Extend the Life of Road Assets
Both Working Groups include representatives from around the globe. The documented outputs of both working groups will be finalised over the next twelve months.
ARE YOU INTERESTED IN JOINING THE CONVERSATION?
In recognition of the opportunities (and challenges) associated with the disruptive influences of new technologies and business models, TCA is running a Breakfast Series in 2018. The Breakfast Series is a way for telematics users (Government, Technology and Transport Industry) to come together and discuss current and emerging opportunities, to exchange ideas and stimulate change.
For more information contact tca@tca.gov.au or visit www.tca.gov.au.
TO TAKE HOME THE GOLD THE RIGHT EQUIPMENT
Established in 1995, Pro-Bore offers drilling and boring services in Queensland and New South Wales, and has recently been contracted to install conduit for the upcoming Commonwealth Games on the Gold Coast. Pro-Bore Owner and Operator, Paul Barrett, discusses how having a supportive and reliable equipment supplier has been essential in the company’s transition into the HDD industry.
Mr Barrett started off as a tree lopping contractor using a Vermeer wood chipper and grinder to carry out his contracts.
In 1995 when Foxtel established its Pay TV service, Mr Barrett saw an opportunity to capitalise on the start of the Pay TV rollout and, with the assistance and training of Vermeer’s specialists, he was able to easily transition his skills to the booming HDD industry.
Mr Barrett purchased a D6 Navigator from Vermeer and from there began his drilling business, Pro-Bore.
“I originally owned a Vermeer wood chipper and grinder so I knew they supplied good quality equipment, which is why they were my first choice when I decided to move my business into HDD,” Mr Barrett said.
“After having success with Vermeer in the tree lopping business I couldn’t go past Vermeer products and if it wasn’t for them I wouldn’t be where I am today – I virtually went from climbing trees one week to drilling holes the next.”
PREPARING FOR THE COMMONWEALTH GAMES
Pro-Bore specialises in small projects, including street works and road crossings, and is currently contracted to install Optus conduit for the upcoming Commonwealth Games on the Gold Coast.
Optus is a major sponsor of the games, and Pro-Bore has been installing conduit to various venues around the Gold Coast.
“We have been drilling along beach fronts and parklands from one end of the coast to the other, as well as in the games village,” Mr Barrett said.
“It is important to have a clean reliable machine to undertake these works as it is the most precious part of the Gold Coast. It is because of the efficient equipment Vermeer provide that we are confident to take on bigger jobs and expand our business.”
OVER TWO DECADES OF QUALITY SERVICE
During its 23 years of business, Pro-Bore has purchased six new drills, a vacuum excavation unit and two mixing systems from Vermeer. The latest addition to the fleet being Vermeer’s 20x22 Series II Horizontal Directional Drill.
“There is no doubt their equipment is superior; my latest addition 20x22 Series II is an all round mighty machine for what I do.”
Mr Barrett said looking to the future his next goal is to add the new Vermeer 23x30 HDD to his fleet.
“I take pride in my fleet and Vermeer has been with us every step of the way to ensure we’re getting the best equipment for our needs.”
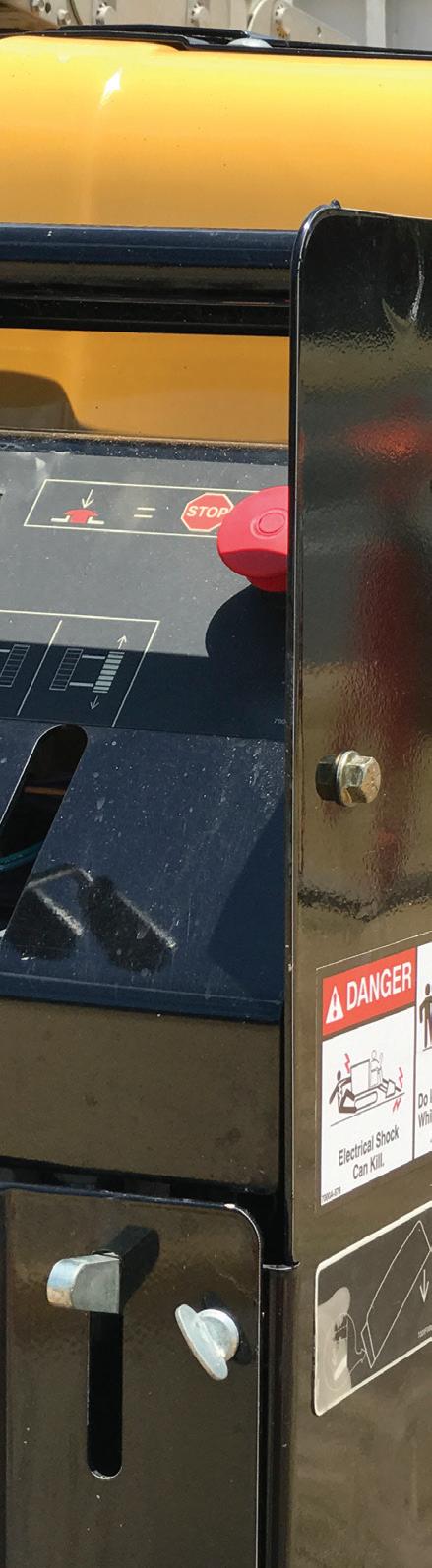
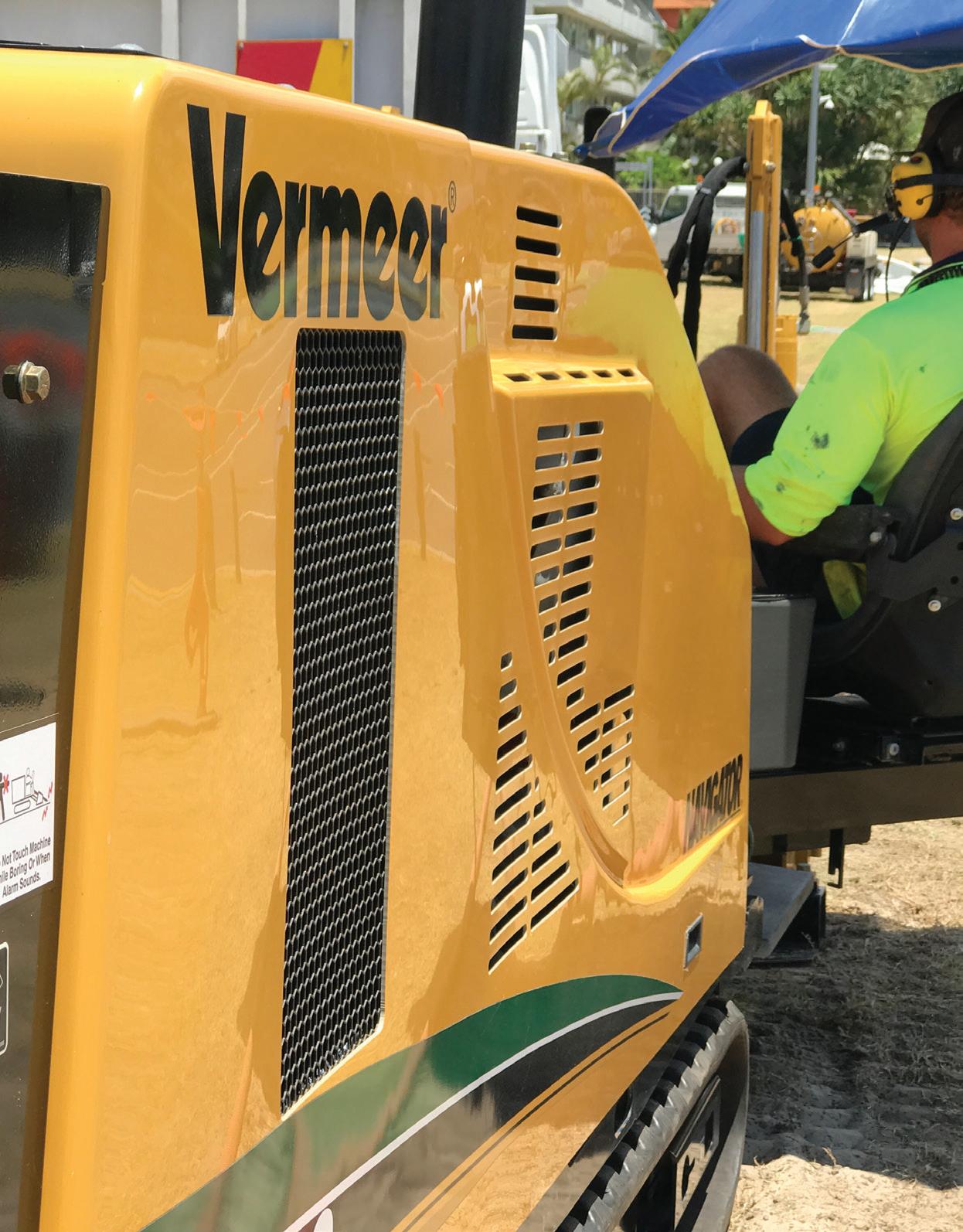
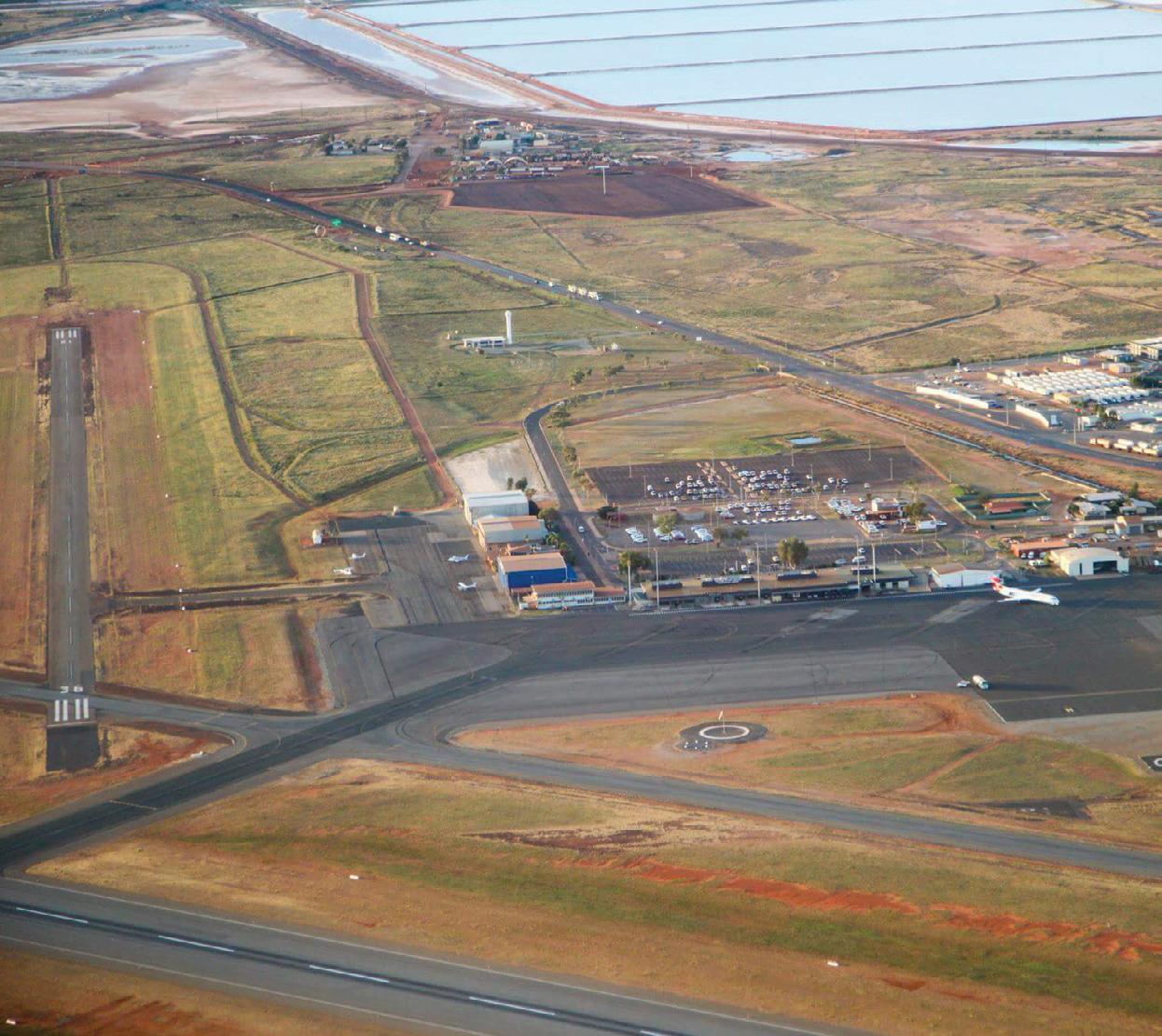
DELIVERING A BETTER AIRPORT FOR PORT HEDLAND
It has been two years since AMP Capital and Infrastructure Capital Group acquired the long-term lease of Port Hedland International Airport.
Managed by the AMP Capital and Infrastructure Capital Group, the PHIA Group of Companies (PHIA Group) is the operator of the Port Hedland International Airport. Under a lease agreement with the Town of Port Hedland, the PHIA Group has an obligation to spend $40 million in capital expenditure in the first five years of the lease.
The PHIA Group will be finalising its draft Master Plan, which sets out future upgrades and improvements to the airport. Plans have been announced for a runway lighting upgrade, a new terminal and other airside infrastructure works.
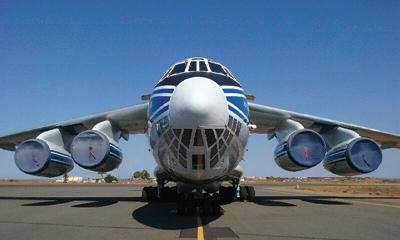
In 2016 Port Hedland International Airport (PHIA) announced plans to significantly upgrade its airport infrastructure as part of a strategic plan to develop Port Hedland as a leading regional airport in the area of passenger, freight movements and customer satisfaction.
UPGRADING AIRSIDE INFRASTRUCTURE
Rod Evans, General Manager, Airport Operations, at Port Hedland International Airport said that, while it was one of the smaller projects, the planned runway lighting upgrade would provide increased safety with medium intensity lighting.
“We’re in the design phase of that at the moment, and once all the quotes are assessed, we’ll present to the Board for approval to proceed. This work will future-proof the runway lighting system to a higher standard than currently required,” Mr Evans said.
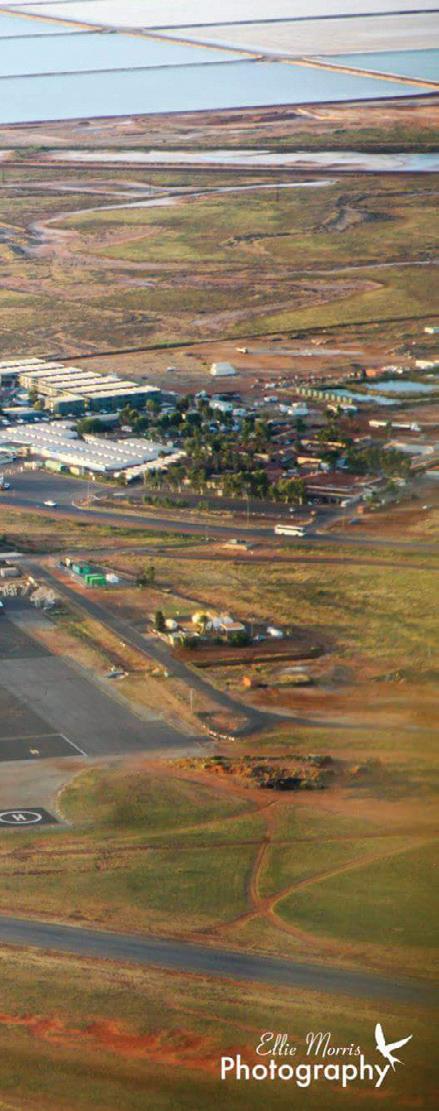
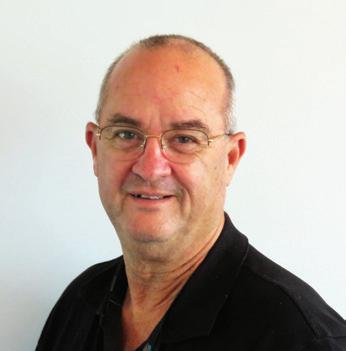
Mr Evans said the airport is also planning an asphalt overlay of the runway to ensure large freight aircraft such as the Antonov 124, one of the world’s largest aircraft, can continue to touch down at PHIA.
“We wish to firm up the opportunity of being available as one of the longest and strongest runways in the northwest, between Perth and Darwin,” Mr Evans said.
PHIA is also exploring the possibility of a new taxiway that will link the runway to the eastern end of the apron, where aircraft are parked and serviced. At the moment, the airport only has one stub taxiway access onto the apron.
Mr Evans said he expects some of these airside projects to begin construction mid-2018, once all design work has been completed and there is final approval from the Board.
INVESTING IN A NEW TERMINAL
Mr Evans said a new terminal is also being planned for, with the Board of the view that this is the best solution going forward, for both the airport and the community.
The current terminal was built in the 1970s. The Board weighed up refurbishing the current terminal, against building a modern terminal with the flexibility for expansion, and concluded that the latter offered better opportunities to meet passenger expectations, safety and security, and improve the overall customer experience.
“The asset that we have here is dated, it’s getting tired. We’re in the very early stages of concepts around a new terminal development at the airport that will allow us to manage the current demand, and also have the ability to have further expansion options as required in coming years as demand requires it,” Mr Evans said.
“The infrastructure owners have a 50 year lease, so this will be a long-term solution to the terminal challenges at the airport.”
The potential location of the new terminal is on a greenfield site, and would allow the current terminal to continue to operate relatively unaffected while construction takes place. The safety and security requirements of a modern airport operation are paramount.
“This type of development allows us to continue to operate in the existing terminal, albeit with some restrictions,” Mr Evans said.
PHIA are hoping to have shovel in the ground by June 2019 and construction completed by the end of 2020.
SECURING PORT HEDLAND’S FUTURE
The main aim of these upgrades is to ensure Port Hedland International Airport is recognised as one of the best regional airports in Australia.
“The airport currently has the longest runway in the northern part of WA, apart from the military airports at Curtin and Learmonth. We wish to continue to be the primary port of call,” Mr Evans said.
“The customer base and the people that use this airport are a different demographic to tourist market airports. We certainly have a tourism destination, with the Karajini National Park easily accessible, but the major customers of the airport are based around the resource companies that utilise its facilities, and the community it serves.
“We’ll be looking to install and operate the latest technologies, allow for emerging technologies into the terminal design, so that it can meet the demands that will be placed on it, both now and into the future.”
Airside improvements such as the asphalt overlay of the runway will also decrease maintenance costs over a longer period of time.
“Asphalt gives you greater certainty to operate larger aircraft and minimises maintenance costs over forward years,” Mr Evans said.
“The airport is also the only airport in the north at the moment that has an interstate service. We have a weekly Brisbane service on a Tuesday, and we’re the only airport that has an International RPT Bali service on a Saturday.
“The International service to Bali has been successfully operating for many, many years, and part of the new terminal design will ensure that we continue to provide for this service. If other opportunities arise for international operations, we’ll be in a strong position to be able to facilitate those as well.”
Port Hedland’s main operational challenge centres on the difficulty of attracting people and business to the north west of WA, which is one of the most isolated areas of Australia.
With the Port Hedland International Airport transformation already well underway, attracting and maintaining future workforce in the Port Hedland area may soon prove to be a much easier task for everyone, with a modern airport infrastructure built for the future.
BATTLING AIRPORT CONGESTION THROUGH INFRASTRUCTURE UPGRADES
While any road project is complicated by the need to work in a live environment, when the roads are on a 24/7 airport, the complexity goes up a whole other level.
Add to this, 120,000 cars a day across the airport’s road network, tens of thousands of pedestrians, a mix of vehicle types operating in a confined space, and a terminal forecourt that sees 30,000 vehicle movements each day – all while ensuring passengers can get to and from their flights easily and with a minimum of fuss. Melbourne Airport is currently tackling exactly this problem as it undergoes major developments of its infrastructure.
Melbourne Airport has grown rapidly in recent years. In 2017 alone it added almost 1.5 million additional international seats to its capacity. While this is great news for the Victorian economy, and delivers more choice than ever before for Victorian travellers, it is having a significant impact on the road system to, and at, the airport.
Chief of Parking and Ground Access at Melbourne Airport, Lorie Argus, said congestion is an ongoing problem.
“Growing traveller numbers directly correlate to more vehicles on the airport’s road network, which is why we are upgrading our road network.”
The soon-to-be-completed Tullamarine Freeway widening works will address one part of this problem, while actually presenting airport operators with another; how to handle all of the additional vehicles that a streamlined freeway network is about to deliver.
To tackle that problem, the airport is undertaking a program of works to address congestion and improve flows throughout the estate, with a particular focus on the main forecourt. A number of nimble projects are already underway that drivers can take advantage of to streamline their airport visit, and major works are slated to start later this year.
MAJOR CAPITAL WORKS
Since the CityLink Tullamarine Freeway widening project began in October 2015 the number of passengers

travelling through Melbourne Airport has increased by around 3.5 million a year, or more than 10 per cent. With the completion of the ‘Tulla’ widening works over the next six months, an improved journey to the airport will bring into stark focus the existing congestion within the airport confines, exacerbated by the increased vehicular traffic in and around the forecourt.
Melbourne Airport has made, and will continue to make, a series of improvements to reduce this congestion. Part of the solution to forecourt congestion is major capital works to reduce intersecting traffic and provide significantly expanded elevated drop off and pick-up curb space.
Melbourne Airport is already home to two elevated loop roads – one to the Departures level of the original terminal building (Terminals 1, 2 and 3), and the other to the T4 Transport Hub, which opened in 2015. Option design works for the new road requirements have been undertaken over the last six months and an affordable, preferred option is currently being fine-tuned prior to breaking ground.
SMART TECHNOLOGY SUPPORTS WORKS
In the interim, Melbourne Airport has already taken a number of steps to improve things, with a real focus on introducing dynamic lane management for the existing roads. The first big problem to tackle is morning congestion
on Departures Drive (the elevated loop road to T1, 2 and 3). To address this, the airport has opened up a lane of the ground-level arrivals forecourt as an alternative drop-off option. This will give it the ability to redirect hundreds of cars off the elevated road during the morning departures peak.
As much of the congestion is occurring from the time taken to unload passengers, the airport is deploying extra customer service staff out front of the terminal. These staff will assist travellers to get themselves and their luggage out of cars and helping direct cars safely and more efficiently in and out of the terminal.
While that’s not an infrastructure solution in itself, it’s underpinned by smart technology that enables it to use all lanes to its best advantage – and helps ensure the physical works being carried out don’t create chaos. To stay on top of rapidly changing congestion levels around the clock, the airport is using cutting-edge monitoring technology so it can keep track of traffic movements in real time and make quick, operational decisions about managing traffic flows at any time of day.
“While heavy infrastructure solutions are important, smart technology has moved from an emerging trend to a necessity for improved road performance. For the airport, it is critical to integrate to our road network and infrastructure,” Mrs Argus said.
To reduce congestion during peak
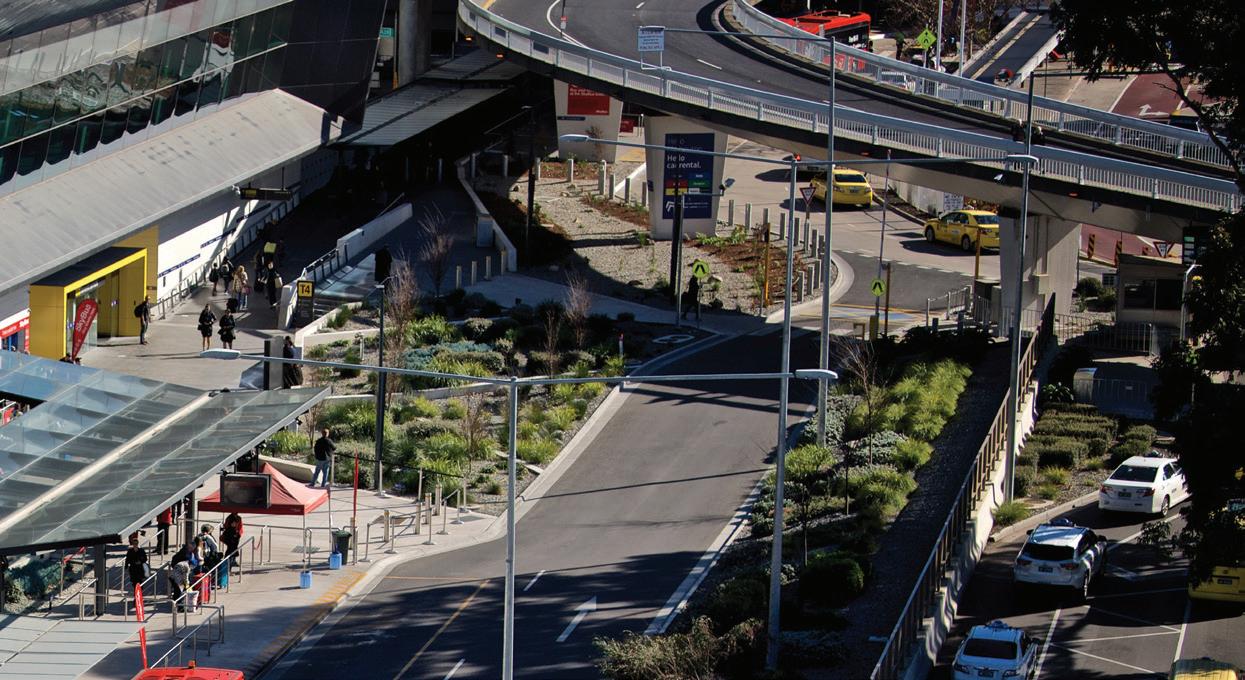
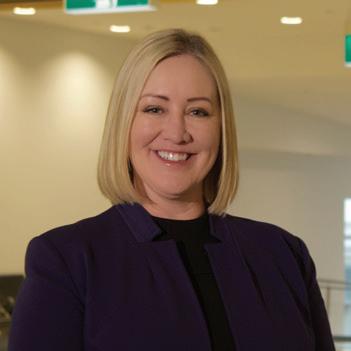
periods even further in the future, the airport is about to start installing new overhead signs to allocate traffic across the elevated and ground level lanes, similar to the variable lane signage found on Victoria Street in Abbotsford, or Queens Road past the Albert Park Lake.
NEW ROAD OFF-RAMP REDUCING CONGESTION
Over the past few weeks Melbourne Airport has had some important works underway in the forecourt itself. It’s opened up an additional exit lane through the public pick-up area in the forecourt, increasing throughput by an additional 500 cars an hour.
The airport is also introducing a new, free 10-minute wait zone for public pickup, which is taking over part of the car park. It is currently building a dedicated ‘fast track’ entrance from Centre Road for easier access to the area, and this will open in May, which again will lessen demand on the congested forecourt.
On top of this, there’s still an issue with many travellers flying domestically with Jetstar, Tigerair, Rex and Air North needing to get to T4 but finding themselves in the T123 forecourt. The reason for this is that the freeway exit to T4 is combined with entry to the freight precinct and it is positioned just as you enter the airport precinct. It’s not an intuitive place to exit for terminal access,
and drivers who are not familiar with this route are missing it.
To address this, the airport has started work on a new dedicated exit off-ramp that will take drivers from the freeway (just before the Centre Road intersection) straight up a new bridge that will merge into the existing T4 entry point. It is a big project and will run through to 2019. In the interim, the airport has made enhancements to the road signage from the Tullamarine Freeway to the T4 drop off and pick-up areas.
Finally, to deal with the expected long-term growth of passenger traffic through the precinct, the airport has commissioned design development for new access paths and major expansion to the T123 pick-up and drop off areas. The purpose of this will be to remove a significant portion of traffic from the Centre Road intersection and double the size of the set-down areas.
“The biggest challenge of these upgrades is maintaining a 24 hour airport operation in a live operating environment while minimising the impact on travellers. To minimise disruption Melbourne Airport will conduct staged works in collaboration with key stakeholders and contractors,” Mrs Argus said.
“The works will be rolled out progressively over the next two years.”
ENHANCING PASSENGER EXPERIENCE
Security enhancements
Melbourne Airport will be the first airport in Australia to have a complete smart security terminal.
Construction begun in February 2018 and will be complete in November 2018.
Upgrades include:
» Ten new ‘Smart Security’ screening lanes that include technology and process improvements
» Future proofed for next generation technology such as CT (Computed Tomography) and remote screening
» Increased amount of body scanners (next gen security technology)
» Automated tray returns
» Re-configured entry into customs, allowing a smoother and easier process
» Additional smart gates (boarding pass verification) upon entry into security
» Aesthetic and lighting improvements
Self-service check-in
Melbourne Airport is installing a new self-service check-in zone at Zone L in T2.
Construction has already begun and will be complete by the end of September.
Upgrades includes:
» 16 check in kiosks
» Eight hybrid desks/automated bag drops
» New signage
VICTORIAN PUBLIC CONSTRUCTION –BUILDING TOWARDS REFORM
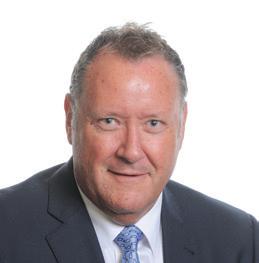
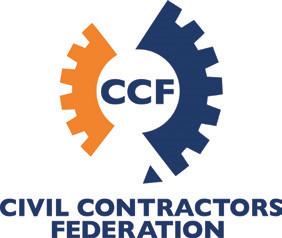
In lockstep with an ongoing commitment to advocacy and representation, in 2016 CCF made recommendations to the State Government on areas for improvement in the procurement and tendering of major infrastructure projects in Victoria. Given the recent commission by CCF of the 2018 Victoria Infrastructure Outlook Report, there’s no better time to have an open and transparent discussion on the longterm economic strategy for Victoria.
IMPROVING PROCUREMENT AND TENDERING
In 2016, a formal review of public construction procurement processes in the state was commissioned. Led by the Department of Treasury and Finance (DTF), the review sought to identify opportunities to streamline and improve public infrastructure procurement processes. As an important stakeholder within the building and construction sector, CCF Victoria made representation to DTF as part of this engagement and consultation process.
CCF provided valuable insights to the review by providing practical ways to streamline processes and reduce government procurement costs for both private sector and government works.
This included the need to address:
♦ Standardisation of terms and conditions in contracts between projects
♦ Lack of forward planning and scheduling of projects that leads to an inconsistent pipeline of projects
♦ Disparity of contractor pre-qualification between state, local governments and their agencies
♦ Impact delays in receiving formal government approvals, or ministerial sign off, for projects on costs
♦ Push by government to “de-risk” projects with contractors now having to assume greater levels of risk and liabilities for projects
♦ Complexities created through the EOI, or D&C tendering process with increasing incidents of either lack of detail, or over specification of requirements needed to make a determination in the awarding of contracts
♦ Level of security, i.e. bank guarantees, sought by multiple governments and agencies and the costs associated with its provision, retention and administration for both the government and contractors
Upon completion of the review, the findings and recommendations were announced by the Treasurer, the Hon Tim Pallas, and published by the Department of
Treasury and Finance. The published report identified areas for strengthening good practice including: better planning of projects, improving industry feedback mechanisms and participation in government tenders, and lifting government procurement capability.
Many of the recommendations made by CCF were included in the published findings including reform opportunities identified in three key areas:
1. Greater standardisation of procurement processes across government
2. Reducing unnecessary time and costs to industry in tender processes
3. Improving government capability and planning in construction procurement
In seeking greater standardisation in procurement, we commend the government in exploring ways to make the construction procurement processes more consistent across government, but it is important that this now translates into action.
This includes exploring ways that encourage greater participation, reduce transaction costs and target the standardisation of:
♦ Legal and commercial contracts, with consistent commercial terms and conditions to increase “speed to market” and reduce contract review administration costs
♦ Risk allocation in contracts to better reflect standard risk management principles by assigning the risk to the party most efficiently placed to manage it
♦ Probity requirements to improve consistency in application, and to give the market greater confidence that bid evaluations are fair and equal
Feedback from the review also indicated that the function and application of the Construction Supplier Register (CSR) by government was not always consistent and could be more transparent to the market.
In simplifying requirements to reduce unnecessary time and costs spent on tendering processes, the review identified the following areas for improvement:
♦ Reducing unnecessary information requirements in EOI and RFP’s which will see the government explore options to consolidate and simplify information requirements
♦ Speeding up the selection of a preferred bidder by promoting stricter adherence to timelines
♦ Avoiding late addenda and pricing of multiple options by ensuring tender documents are appropriately finalised and the promotion of better project planning/objectives prior to going to market
♦ Increasing the use of bill of quantities to provide more accurate information to the market
♦ Reimbursement of bid costs for complex public constructions which recognises the significant administrative costs associated with tendering
♦ Appropriate tender field sizes to maintain effective competition, but not overuse the market
♦ Publishing price order bids following tender close to improve transparency, and allow lower ranked bidders to redirect resources to alternative opportunities earlier and quicker
♦ Ensuring the design is consistent with the contract where the outlining of appropriate design stands in tender documents will provide greater certainty for industry
The full published report and more information is available via contacting the Department of Treasury and Finance, Procurement Team.
LOOKING FORWARD
With a strong pipeline of infrastructure projects planned in the State Government’s forward estimates over the next five years, improving government capability and planning is key to developing and maintaining efficient procurement processes and successful project delivery.
With the significant level of investment being made in major infrastructure projects and in the lead up to the Victorian state election later this year, there is no better time to have an open and transparent discussion on the long-term economic strategy for Victoria.
2018 Victoria Infrastructure Outlook Report (extract from ‘Policy Challenges and Recommendations’).
Recommendation 10: To maximise efficiencies in public infrastructure provision and reduce costs, both the Commonwealth and Victorian Government should follow through with reforms to the public infrastructure procurement process, as outlined by the Productivity Commission’s Review.
Recommendation 11: Procurement policies and approaches should be harmonised across all levels of government within jurisdictions – and, where possible, across jurisdictions – including the use of open (rather than closed) tenders, local content rules, and de-bundling large infrastructure projects to boost competition and the sustainability of the civil construction Industry.
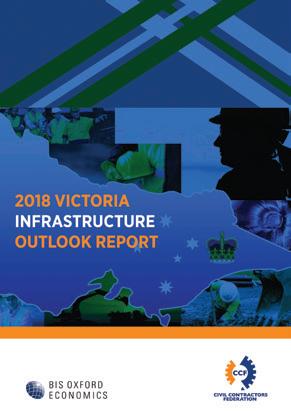
The 2018 Victoria Infrastructure Outlook Report commissioned by CCF and recently released by BiS Oxford Economics, provides a sound platform for this discussion.
Providing a comprehensive review of the past performance, current status and forecasted growth, the report delivers insight into some the most critical elements of the civil industry, whilst highlighting challenges and identifying areas for improvement. Coupled with this in-depth analysis of the different drivers affecting the state’s economy, the report also provides recommendations on addressing areas of required policy reform.
Over the next four years, Victorian engineering construction activity — encompassing transport, utilities and mining and heavy industry construction — is forecast to average $12.8 billion per year, higher than the $10.9 billion of the previous five-year period. Both public and private sector investment is driving higher levels of civil construction work. Publicly funded engineering construction work done is expected to account for around 45 per cent of total engineering construction activity, at around $5.7 billion on average each year over the four-year period.
In appreciation of the scope of this expected future activity (and more), it is critical that the policies affecting procurement and tendering undergo stringent review and consequent reform where required. Timely reform would be of great benefit to Victoria’s civil construction industry and the welfare of its economic future.
To view all findings and recommendations, the full 2018 Victoria Infrastructure Outlook Report is now available for download, via the CCF Victoria website: www.ccfvic.com.au
About Civil Contractors Federation (CCF)
Civil Contractors Federation (CCF) is the peak industry body representing Australia’s civil construction industry with more than 2,000 contractor and associate members nationally and over 520 of these based in Victoria.
CCF members are responsible for the construction and maintenance of Australia’s infrastructure, including roads, bridges, pipelines, drainage, ports and utilities. Its members also play a vital role in the residential and commercial building industry by providing earthmoving and land development services including the provision of power, water, communications and gas.
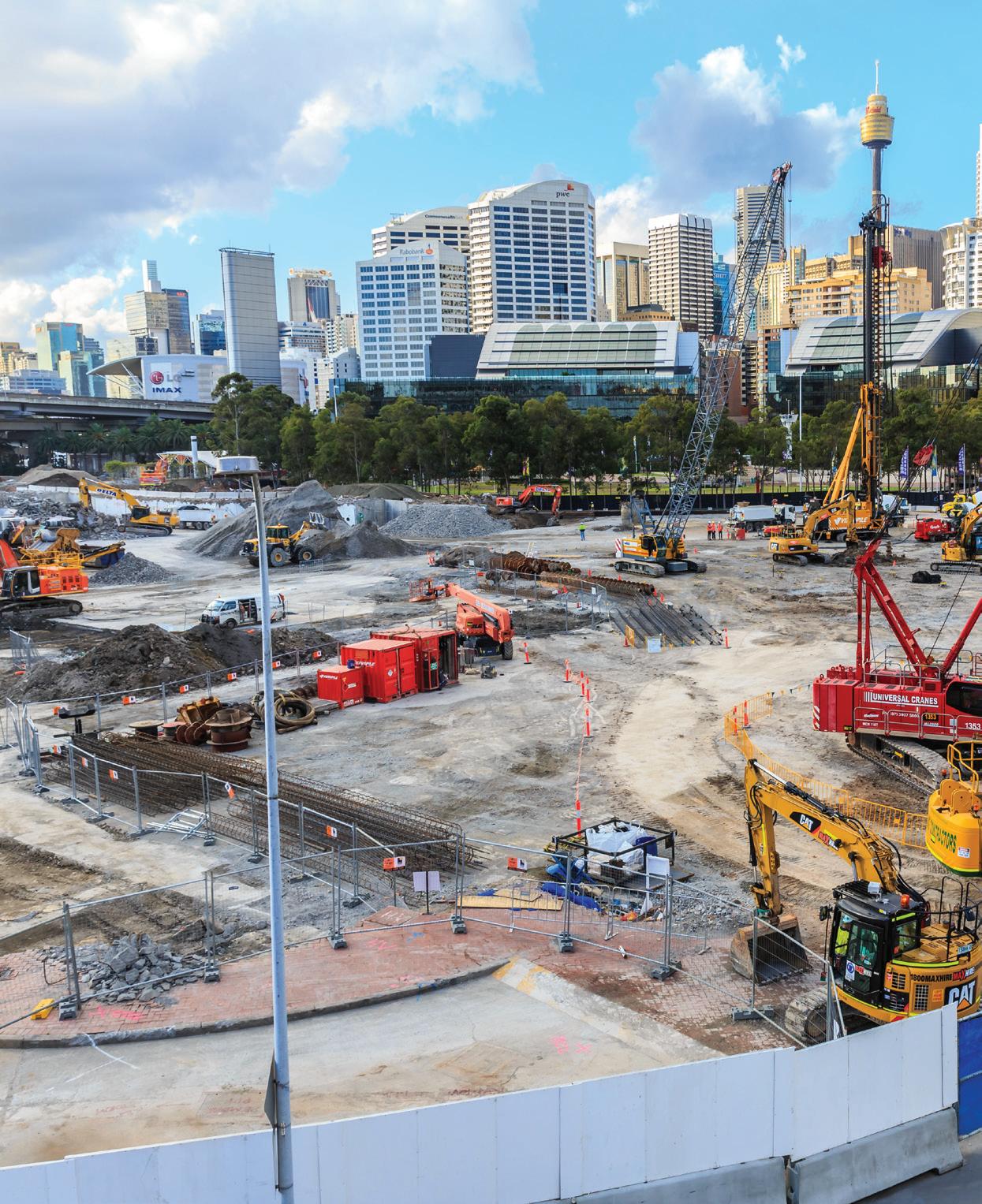
CONSTRUCTION TRENDS CONTINUE TO BUILD UP
Australia’s construction sector is continuing to expand. The Australian Industry Group (Ai Group) and Housing Industry Association’s Australian Performance of Construction Index for January 2018 marked industry-wide growth for a 12th consecutive month, while Ai Group’s November 2017 Construction Outlook predicted a positive position for the sector throughout 2018/2019.
January 2018 marked a full year of monthly growth for Australia’s construction sector, according to research by the Ai Group.
The Australian Industry Group is an employer organisation that represents traditional and emerging industry sectors.
The group releases a monthly construction update for industry, as well as a bi-annual survey conducted
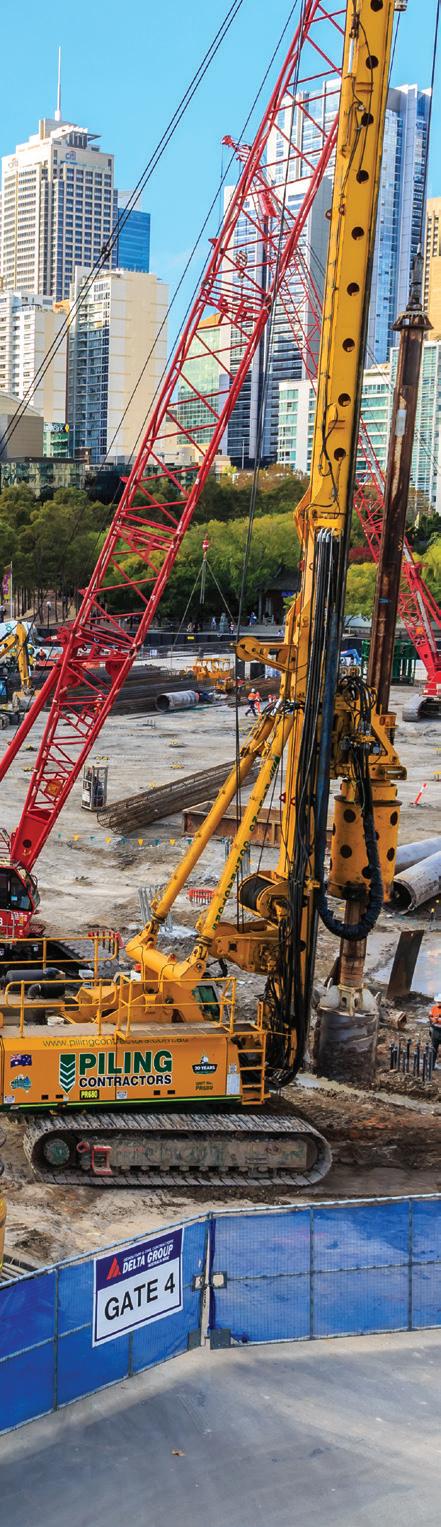
in association with the Australian Constructors Association, that highlights key trends and the current condition of the construction sector.
SECTOR CONTINUED TO GROW IN EARLY 2018
The January 2018 Construction Index found that commercial construction was the highest performing area in the sector, which the report attributes to, in part, factors such as property investor sentiment and improved business conditions.
The report breaks the industry down into four construction sub-sectors; commercial, house building, apartment building and engineering construction. While commercial was the strongest performing (up 7.4 points to 58.9), house building also continued to expand but moderated for a second month (down 2.5 points to 52.0), while apartment buildings growth remained unchanged (50.7 points) and engineering construction’s expansion slowed (down 3.4 points to 53.5).
Readings above 50 indicate expansion in activity, with the distance from 50 indicating the strength of the increase. One interesting finding was that the employment sub-index accelerated to its fastest pace in six months, while capacity utilisation hit a record high of 83.4 per cent — its highest since at least 2008 when this data series began.
The other two main findings from the January 2018 report were:
♦ Overall construction activity was largely unchanged, with its continued expansion associated with further growth in deliveries from suppliers. The new orders sub-index returned to growth after drifting into mildly negative territory in December 2017, revealing an improvement in demand
♦ The input prices sub-index retreated from December’s nineyear high but remained elevated, while growth in wages continued. The selling prices sub-index increased by 0.3 points to 58.9, suggesting that cost pressures are being passed on, but not broadly given strong market competition
WHAT’S PREDICTED FOR 2018/2019?
The Ai Group’s most recent Construction Outlook (November 2017) looked at the state of the engineering and non-residential building sectors on a national and key market basis. The report is created based on the responses of 100 companies with combined turnover of almost $30 billion, or approximately 30 per cent of total industry activity.
Some of the key construction predictions for the 2018/2019 financial year include:
♦ Turnover from all major construction work is forecast to continue to expand by 6.8 per cent in the 2018/19 financial year as public-sector capital works programs continue to support high levels of activity
♦ Engineering construction is expected to grow by a further 10.6 per cent in 2018/19. This reflects a strong increase in infrastructurerelated engineering due to robust growth in road and rail projects led by major rail and road projects that are starting to ramp up, especially in the eastern states. Growth is also expected to remain positive in pipelines construction, telecommunications and in other civil projects
♦ Resources-related engineering construction is predicted to decline due to weakness in the oil and gas processing sector. However, mining-related construction is expected to stabilise following the mining investment downturn
♦ In line with the trends seen in the January 2018 Construction Index, commercial construction is predicted to record a stronger upturn in 2018/19. This will be due mostly to private sector building activity, but there will also be a strong drive of public building activity thanks to planned state government education and health building projects.
These predictions, coupled with the continuing upwards industry trajectory seen in the results from the monthly, and most recent, Construction Index show the future for Australia’s building and construction industry, especially commercial construction, is only going to continue to get stronger.
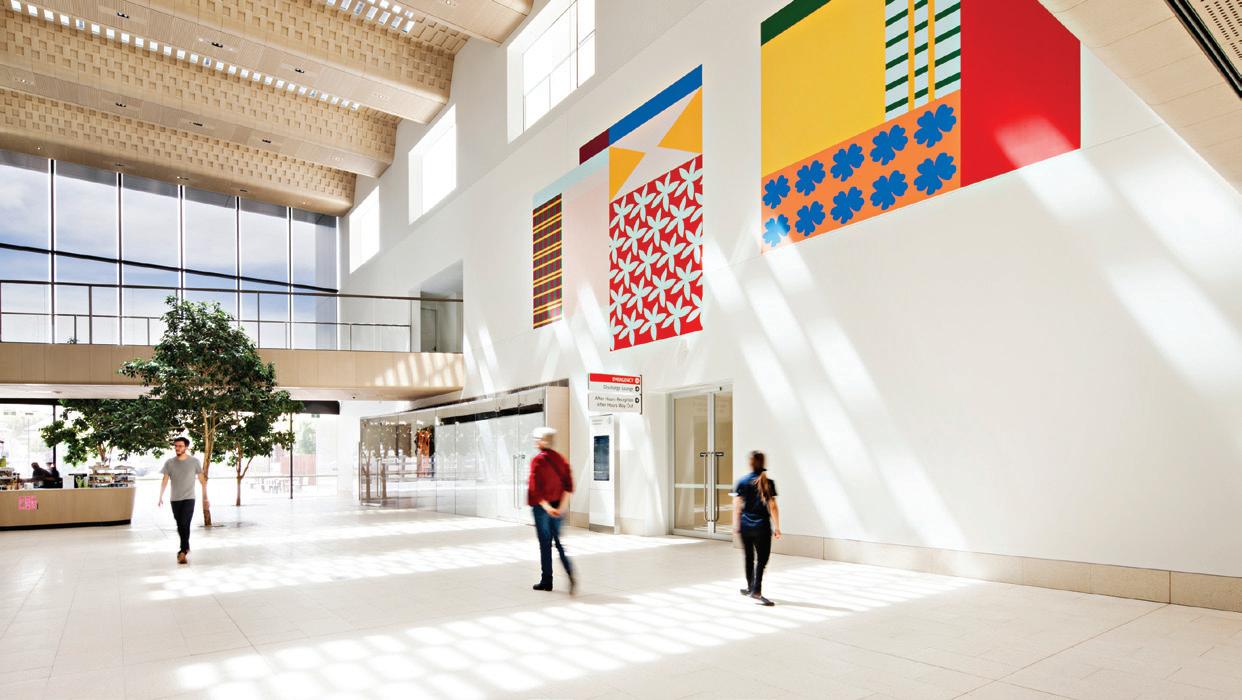
The new Bendigo Hospital has been designed and constructed for the future, by improving patient care and addressing the growing service capacity needs of Victoria’s regional Loddon Mallee community. This is why stage one of the project has won several accolades, including two awards at the 2017 Victorian Premier’s Sustainability Awards.
Made possible through a Victorian Government investment of $630 million, the new Bendigo Hospital is the largest regional hospital development in Victoria’s history and one of the largest hospital projects across Australia. The new hospital has been designed to be more than double the size of the previous facility to meet the urgent needs of the regional community’s growing and aging population now and into the future.
The Bendigo Hospital Project is designed, built and operated by the consortium, Exemplar Health, through a public-private partnership (PPP) with the State Government of Victoria. The Exemplar Health consortium comprises five highly regarded market leaders: Lendlease (builder), Capella Capital, Siemens and First State Super (financiers), and Spotless (facilities manager).
Exemplar Health’s role also includes maintaining the hospital for 25 years after its opening, and the consortium is delivering a broad range of facility management services, enabling the operator, Bendigo Health, to focus on the provision of quality healthcare services to Victoria’s central and
northern regional communities.
The hospital’s completion is presented in two stages; the first stage of the project, the main hospital campus, achieved Technical Completion one month early in 2016, achieved Commercial Acceptance and opened for business in January 2017, and the second stage is poised to be complete in mid-2018.
AWARD-WINNING DESIGN FOR STAGE ONE
Stage One included construction of the new hospital itself with capacity for 372 inpatient beds, eleven new operating theatres, a cancer centre, four radiation therapy bunkers and an 80-bed integrated psychiatry unit. Also established as part of this project’s Stage One development, was a 128-room hotel and a 100-place childcare centre. Highquality retail and food outlets enhance the new hospital’s warm welcome to hospital patrons, patients and staff in both stages of the project
The ‘Healthy Communities and World Class Healthcare’ vision of Bendigo Health Care Group, the state’s provider of clinical services, goes above and beyond just a new facility. It is based on a set of healthcare principles that help
CONSTRUCTING A NEW WORLD CLASS HOSPITAL FOR REGIONAL VICTORIA
support Bendigo Health professionals to shift the balance of care, with a particular focus on patient-centred care, and a more preventative and community-based coordination of services.
With the region’s projected growth in mind, the new hospital has been designed to meet the anticipated increase in demand for services. The new cancer centre, for example, reduces the need for local patients to commute to Melbourne for specialised treatment. This fully integrated cancer centre brings radiotherapy, oncology and outpatients together in one department, increasing day chemotherapy chairs, outpatient consulting rooms and providing two additional radiotherapy bunkers.
Within its design, the new hospital’s connection to nature is emphasised throughout. Neutral colours and natural materials have been used when possible along with extensive creative landscaping including multiple courtyards and terraces for use by hospital patients and visitors. Environmental sustainability was one of eight components that the bidding teams used to guide the project to become a world-class facility, with the aim to provide a healthier environment

for patients, staff and the community.
The principles of healing environments have been incorporated into the psychiatry precinct giving access to 13 landscaped courtyards, designed to encourage a tranquil, settled atmosphere. This is a sample of the broader design principles applied to the new hospital, which also offer greater access to green outlooks, over 40 courtyard and balcony spaces and natural light – all aspects that are proven to bring about a safer and a more positive environment.
The non-clinical aspects of the new hospital are equally impressive and very much aligned with state-of-the-art design principles. For instance, the new facility incorporates a 200-kilowatt roofmounted solar photovoltaic (PV) panel array which is installed to both reduce the CO2 emission footprint of the new hospital and also to reduce the mains electricity demand during peak summer periods.
Stage One of the Bendigo Hospital won two awards at the 2017 Victorian Premier’s Sustainability Awards, including the Premier’s Regional Recognition prize.
MAKING A TRAUMATIC TIME EASIER FOR THE COMMUNITY
Stage Two is currently underway and encompasses the demolition of the existing hospital facility, building a shortstay accommodation hub, conference centre, multi-deck carpark, helipad and an enclosed dual level link bridge.
Once the helipad is commissioned, the Bendigo Hospital will be able to accept more patients from the Greater LoddonMallee region, and enable families to stay close during often traumatic times. The current alternatives are to fly directly to Melbourne, or to land at the Bendigo Airport and complete the journey by road, often requiring up to two hours of additional transport time.
The new link bridge that connects Stage Two to the Bendigo Hospital is a two-level structure that was installed over the dividing road in a matter of hours. Components were locally engineered, manufactured and connected at a nearby stadium and transferred to the site for installation during difficult weather conditions. Road overpasses are uncommon in Bendigo, so much so that many members of the public set up picnic chairs outside the exclusion zone to witness the significant installation.
The dual levels of the new link bridge will provide separate entries for the general public and trauma patients. The uppermost level is for the exclusive use by those patients transported to the helipad, while public and general patient
access via the lower level will connect the Bendigo Hospital with the new multi-deck car park, conference centre and services offered in the old hospital buildings.
A SUCCESSFUL INTEGRATION
Integration of existing and new services was a highly complex and detailed process during Stage One, with Exemplar Health working hard to open the Kitchen of the new campus six months early, and achieve Technical Completion one month early, in order to allow Bendigo Health and Spotless the time to train staff in the new building and upgrade systems to suit the cuttingedge development.
The hospital began operations the day after Commercial Acceptance, with the unprecedented success of the move to the new facility. Meticulous planning for ‘move day’ resulted in hundreds of patients successfully moved safely and ahead of schedule.
Stage Two is on track to achieve a similarly high standard of service delivery and state-of-the-art facility in mid-2018.
Awards
Winner 2017 Premiers Sustainability Awards Premiers Regional Recognition Prize
Winner 2017 Premiers Sustainability Awards Large Business Category
Winner 2017 IIDA Asia Pacific Health Care Award
Finalist 2017 PPP Awards Best Project
Finalist PCA Innovation and Excellence Awards for Best Public Building
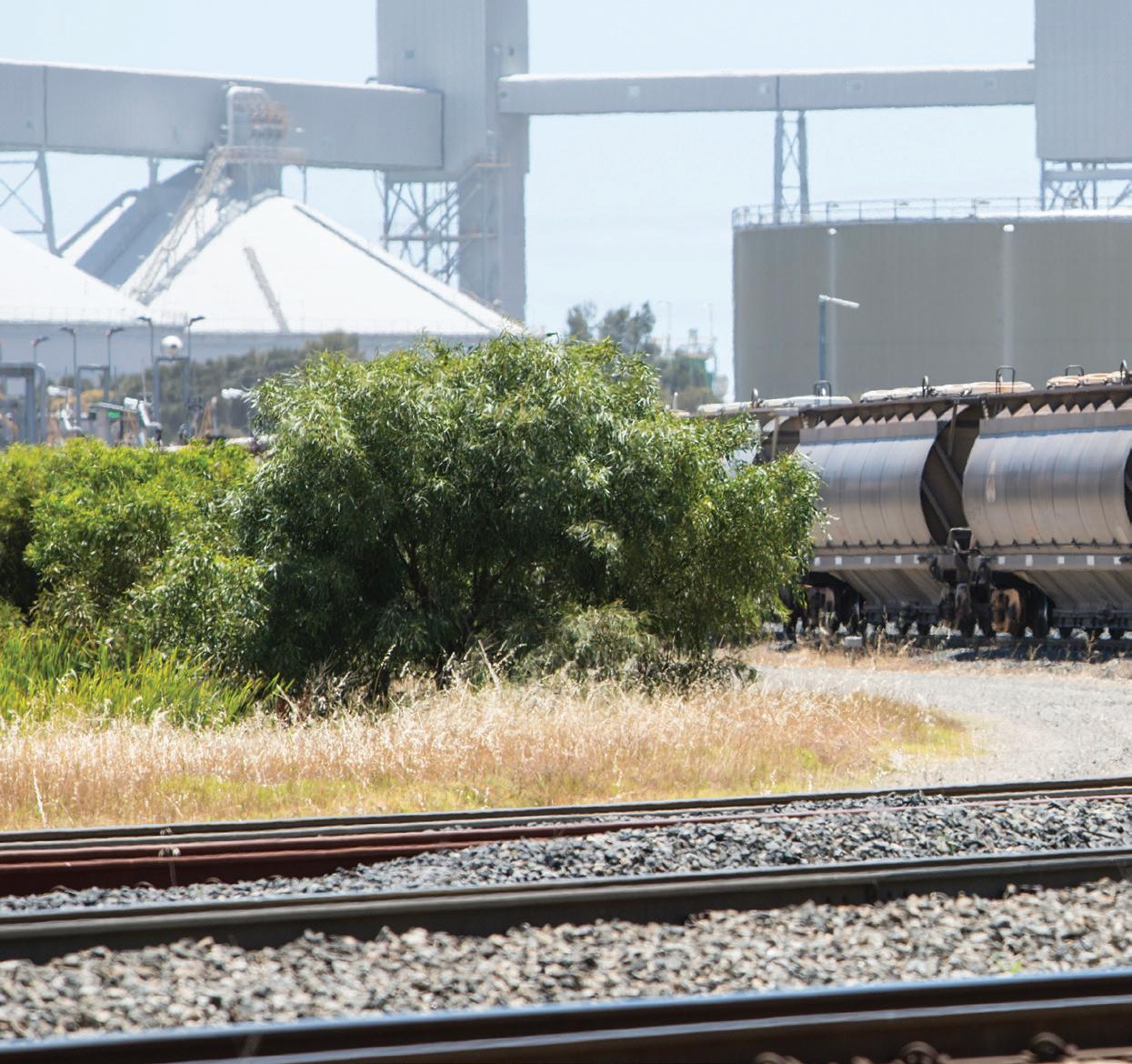
PROTECTING OUR INFRASTRUCTURE CORRIDORS IS GOOD FOR GROWTH
by Philip Davies, CEO, Infrastructure Australia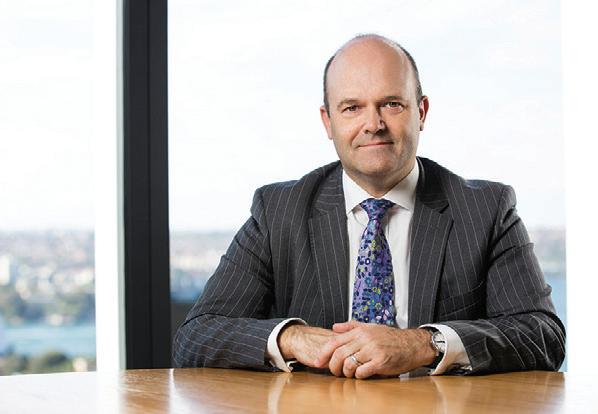
In the 1950s and 1960s, our population growth was even faster than we face today. But because we planned, we prospered – and emerged a richer nation for it. Now our nation is undergoing a new process of generational change, bringing real opportunities and challenges.
Australia’s population growth is one of the fastest in the OECD and now outstrips the UK, Canada and the United States.
By 2046, Australia’s population will swell to 36 million people. That’s equivalent to adding a new city, roughly the size of Canberra, each year for the next 30 years. About 75 per cent of this growth will occur in Sydney, Melbourne, Brisbane and Perth.
To prepare for the rapid growth of this century, and ensure that we avoid a future of declining economic productivity, increasing environmental pressures and a marked reduction in each city’s quality of life, we need long term vision. Nowhere is this vision more necessary than in long-term planning to protect our strategic infrastructure corridors.
PROTECTING CORRIDORS COULD SAVE MONEY
Last year Infrastructure Australia released a paper, Corridor Protection: Planning and investing for the long term, showing that strategically important infrastructure corridors need to be preserved early to avoid cost overruns, delays and unnecessary acquisition of homes and businesses when projects are rolled out.
Protection and early acquisition of just seven corridors identified as national priorities on the Infrastructure Priority List could save Australian taxpayers close to $11 billion in land purchase and construction costs. To put that sum in perspective, it is the equivalent of more than two years’ spending by the Australian Government on roads and railways.
Whether it’s a high-speed rail corridor on the east coast, a new ‘orbital’ corridor around Sydney, the Western Sydney Airport Rail Line or freight rail connections in Melbourne
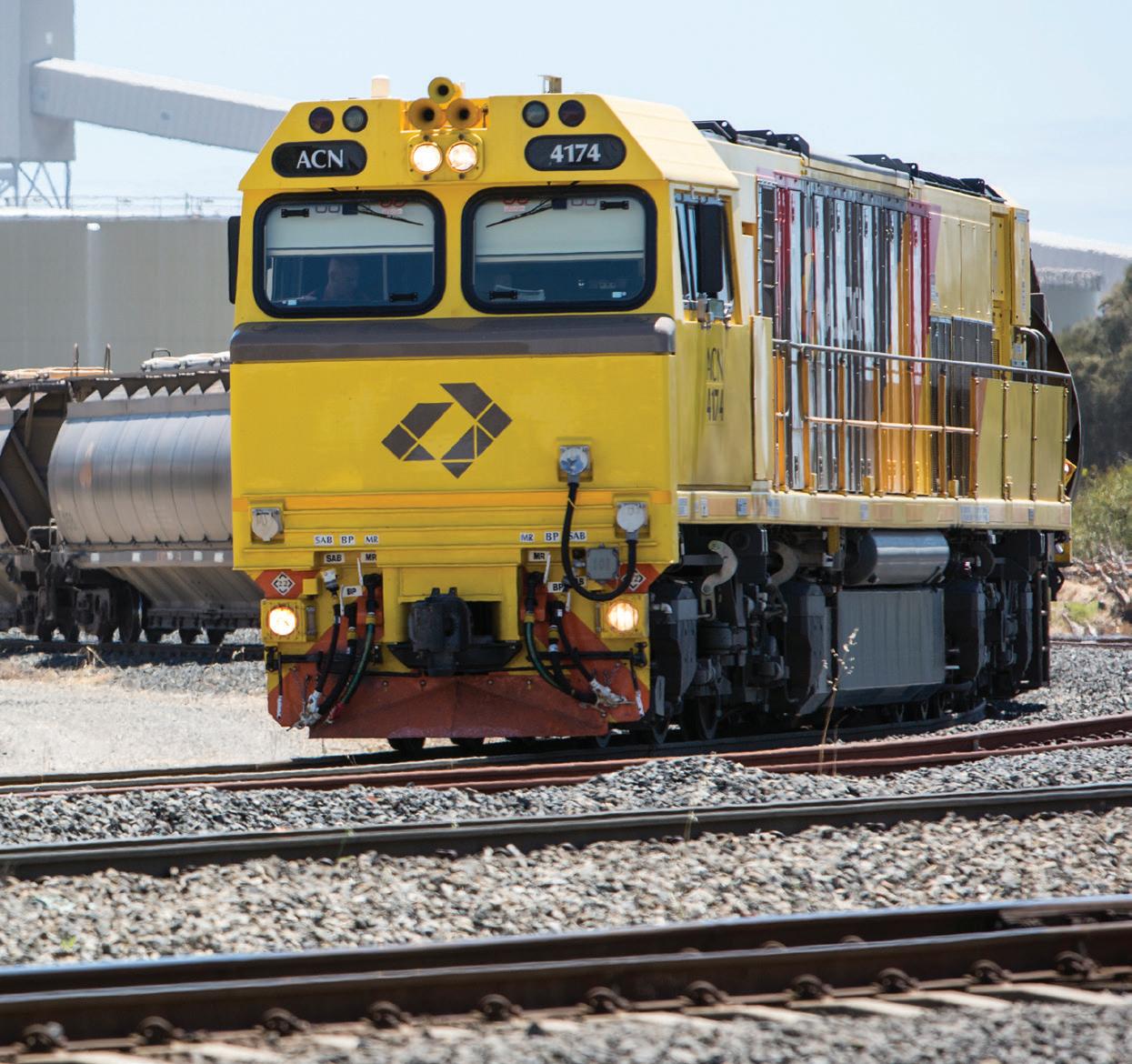
and Brisbane, Australian governments need to act urgently to secure our future infrastructure.
High-speed rail along the east coast of Australia is incredibly important for our regions and major cities and has the potential to super-charge our national productivity, but if we don’t take the first step in protecting this vital corridor we are at risk of not seeing it delivered.
Similarly, the Port of Brisbane dedicated freight rail connection needs to be preserved to increase export capacity and ensure freight can continue to get to market.
Protecting nationally significant infrastructure corridors like these means we can shield governments and taxpayers from future growth in land prices and limit development encroachment, which has constrained integrated land use and transport planning efforts in the past.
An early action approach also helps minimise the need for underground tunnelling, where the cost per kilometre is 5-10 times that of an overground infrastructure solution. In fact, recent tunnelled motorway proposals are expected to cost in the order of $100 million per lane kilometre to build.
Every dollar saved through early action on corridor protection is another dollar that can be invested back into productivity-enhancing infrastructure to underpin our future growth as a nation. With close to $11 billion in taxpayer savings Australian governments could deliver on a range of transformative national projects identified in Infrastructure Australia’s Infrastructure Priority List.
AUSTRALIA NEEDS A NATIONAL FRAMEWORK
That’s why Infrastructure Australia is recommending that a national framework for corridor protection be put in place to guide coordinated and meaningful action by all levels of government. A coordinated approach, involving joint governance arrangements to oversee land acquisition, joint funding commitments, and joint agreement regarding land use management measures will keep governments at both levels honest and committed to the urgent task at hand.
State and territory governments have shown leadership on corridor protection in the past. During the mid-twentieth century, a number of jurisdictions applied processes to protect future infrastructure corridors from development. The M4 and the M5 motorways in Sydney, the M1 and EastLink motorways in Melbourne, and the Mandurah rail line in Perth are great examples of this long-term vision.
Our generation is the beneficiary of that leadership and foresight. It is now time that governments — state, federal and territory — showed it again. It is up to Australian governments to recapture the ambitious spirit that made this country a shining success in our region and an international leader in infrastructure delivery.
A NEW GENERATION OF SERVICE-FOCUSED PUBLIC PRIVATE PARTNERSHIPS
by Nicholas Carney, Partner, Herbert Smith FreehillsGovernments have used public private partnerships (PPP) to engage the private sector to develop and maintain infrastructure assets for several decades, while typically retaining responsibility for delivering the core public services from those facilities. In recent years, governments have started to look more and more to the private and not-for-profit sectors for core public service provision.
For governments, the costs of developing and constructing a public service asset, such as a hospital, may be much less significant than the cost of providing services from that asset over the long term. This is increasing the focus on the services to be delivered from the assets, rather than the asset itself. Taken to its extreme, one might say that the infrastructure is just there to keep the rain off the services.
This article considers the key benefits of this trend, what it means for infrastructure players, and a recent case study from Australia - the NSW Social and Affordable Housing Fund (SAHF).
Importantly, this trend is not just limited to housing and health projects – it is relevant across other sectors including justice, airports, education, and can even be applied to transport and roads.
KEY BENEFITS OF A SERVICE-FOCUSED PPP
Efficiencies in service (rather than asset) delivery can present greater opportunities and cost savings for both government and non-government parties, while improving the outcomes produced by infrastructure. In particular it:
♦ Enables an outcomes-based approach
Under service-focused PPPs, the infrastructure is undoubtedly critical – but it is critical as an enabler of outcomes rather than in its own right. This means that service-focused PPPs go hand in hand with outcomesbased contracting where there is a focus in the contract on the outcomes produced by the infrastructure and, in many cases, a link between the contractual payments and the outcomes delivered. The benefits of this approach are twofold:
1. Outcomes-based contracts can drive better social outcomes, significantly improving the quality of life for citizens
2. Linking payments to outcomes can lead to long-term savings for government. For example, paying a prison operator to reduce recidivism will provide savings which can be shared with the prison operator Outcomes-based contracting is already evident across all sectors involving government-procured infrastructure. Early adoption has occurred in social infrastructure, such as health, corrective services and social housing, where
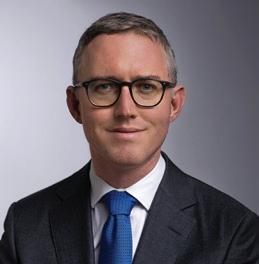
the savings to governments are most easily quantified. It is now being picked up in sectors such as ICT, ports and transport. For example, the current Region 6 Bus Transaction in NSW includes payments linked to outcomes consistent with the service timetables.
The NSW Government signalled its commitment to the approach when it introduced a new budgeting system which links payments made from Treasury to each of the departments to the outcomes achieved by those departments. Similar changes are afoot in other jurisdictions. This will drive departments to adopt similar measures when contracting with the private or non-government sector, including in the context of PPPs. Service-focused PPPs provide the optimal contracting vehicle for this approach, especially in circumstances where an asset-based PPP would otherwise be considered.
♦ Encourages innovation
The other key driver for this model is innovation. Servicefocused PPPs are designed to leverage the private and not-for-profit sectors expertise and experience in service delivery, and therefore do not necessarily mandate the method of delivering the services.
This encourages bidders to be creative in their proposals to government, and allows the successful contractor to respond to changing circumstances during the term by adopting new technologies or processes. If the contract is structured correctly, these efficiencies will be shared between the state procuring party and the contractor, creating a win-win result.
♦ Achieves balances sheet treatment
Another key benefit to government is that servicefocused PPPs can achieve off-balance sheet treatment, which may be desirable in times of budgetary stress.
WHAT DOES THIS MEAN FOR GOVERNMENTS?
Service-focused PPPs involve a shift in mindset by government as to how it procures and structures services and infrastructure. When developing and procuring servicefocused PPPs, governments should:
♦ Seek proposals that are operator-led rather than sponsorled or developer-led. For example, the government may wish to deal directly with a proven hospital operator rather than infrastructure investment funds
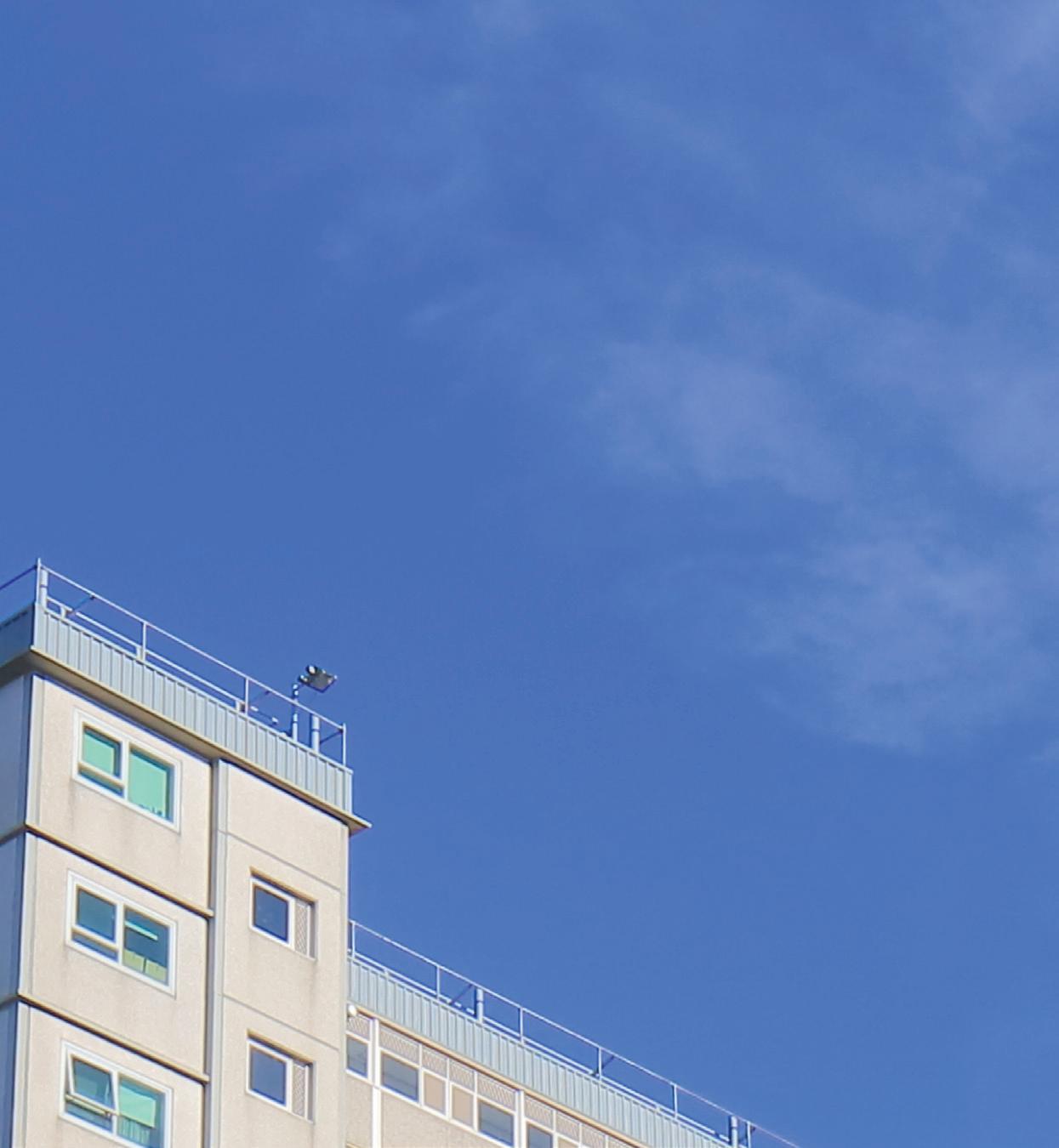
♦ Focus on the outcome and services specifications rather than the asset specification, which may be more limited than a traditional asset PPP
♦ Consider an outcomes based contract, which will maximise the potential for improved social outcomes and long-term cost savings. One option is to build a transition to payment for outcomes into the contract, which was the approach taken on the SAHF
WHAT DOES THIS MEAN FOR NON-GOVERNMENT PARTICIPANTS?
The emergence of service-based PPPs is relevant to traditional private sector participants such as sponsors, developers, financiers and O&M providers as well as not-forprofit participants.
When pursuing service-based PPPs, non-government participants should:
♦ Ensure they put forward the most appropriate consortium structure – for example, if the state wants an operator-led structure then additional equity investors may not be required
♦ Be creative and innovative in how they propose to deliver the service
♦ Consider the most appropriate financing structure. If the focus is on services, then government may be agnostic to the financing approach and traditional project financing may not be appropriate (such as Phase 1 of the Social and Affordable Housing Fund)
♦ Have regard to the market and how they will approach the procurement. A not-for-profit may be exempt from certain taxes but may have less resources at their disposal and limited experience in such procurements
THE SOCIAL AND AFFORDABLE HOUSING FUND
As governments increasingly look to improve service delivery, the NSW Government’s SAHF is being held up as a ground-breaking, service-focused PPP and a test case for governments seeking to reduce cost, encourage innovation and respond to the growing focus on social outcomes.
The SAHF project has been heralded as the first of its kind in Australia and part of the biggest social housing reform in 40 years by the NSW Treasurer and the NSW Minister for Social Housing respectively.
THE CHALLENGE
Social and affordable housing is a major issue for most Australian governments. In light of Australia’s worsening housing affordability crisis, it is becoming increasingly difficult for lower income households to access housing on an independent basis. As a result, the demand for social and affordable housing is rapidly increasing – there are over 60,000 applicants on the waiting list for social housing in NSW alone. At the same time, state governments are faced with unsustainable operating deficits and aging public housing stock.
The solution requires governments, the infrastructure sector and not-for-profit organisations to work together in partnership to experiment with new and innovative models, maximise and unlock land, and attract more private capital.
THE SOLUTION
In NSW, the government established the SAHF and used a service-focused PPP model to procure access to 2,200 new social and affordable dwellings in its first phase. A second phase of the procurement is underway.
The SAHF will fund 25 years of operating subsidies to service providers. This subsidy will bridge the gap between existing rental streams, and the cost of securing and developing new social and affordable housing stock.
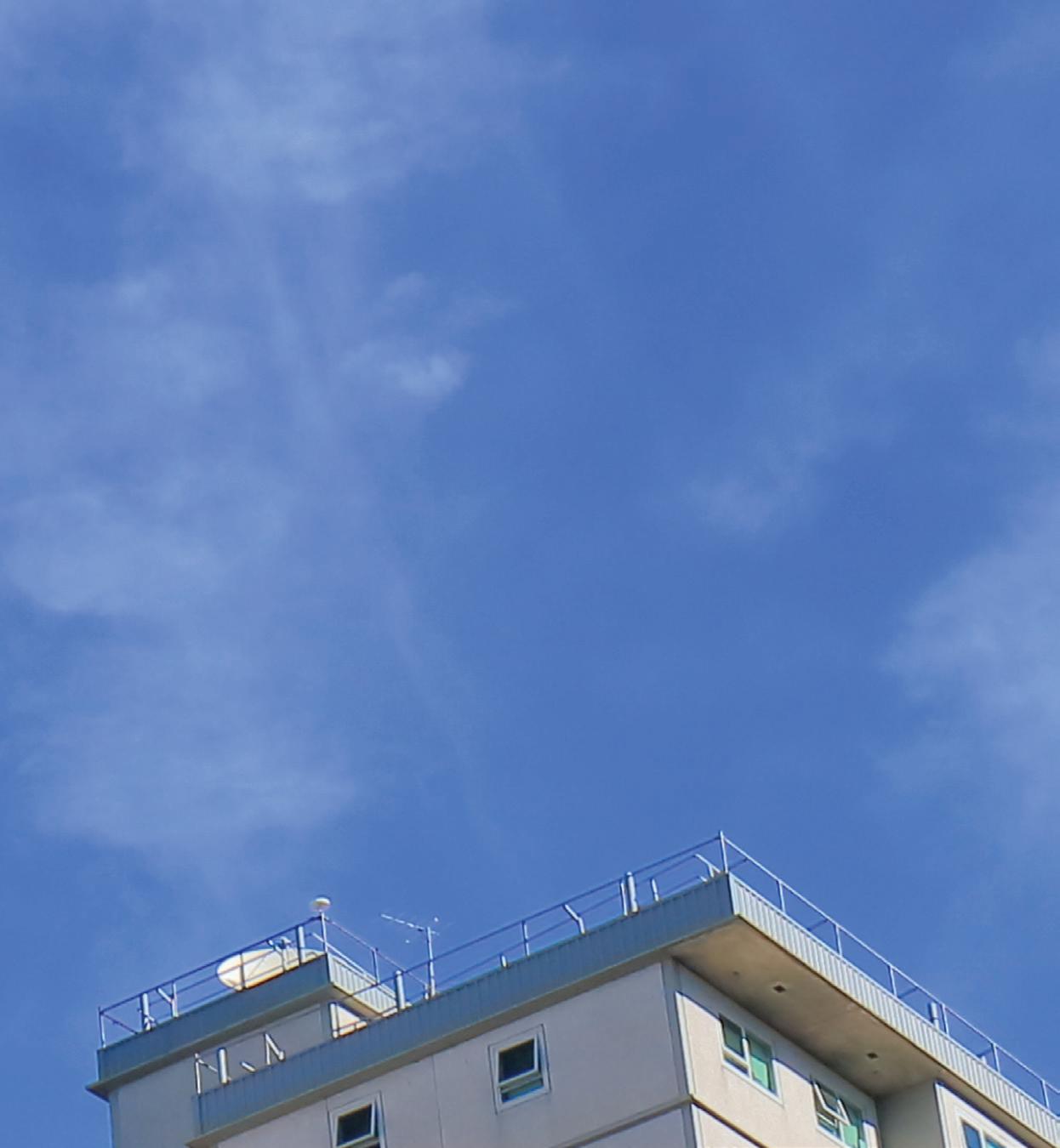
In doing so, the NSW Government will seek access to housing as an “accommodation service”. Importantly, as part of these service arrangements, the government will not provide any land to the community housing providers and will never own the land or the dwellings (including at the end of the term). Instead, these providers are required to bring or secure their own land (for example, by acquiring or leasing it).
The community housing providers will also be required to provide traditional services such as tenancy and asset management, as well as facilitate access to wrap-around support services designed to create pathways to greater independence for households, including, for some, transitioning from social to affordable to private housing.
SHIFTING FOCUS FROM ASSETS TO BETTER SOCIAL OUTCOMES
The SAHF is an example of how a service-focused model and contracting structure can drive better social outcomes – in this case, a better housing experience and more opportunities, support and incentives to transition out of social and affordable housing.
As part of the proposal process, bidders were asked to put forward proposals that achieve social outcomes, including improving employment and education prospects, providing stability and support to women and children who have experienced domestic violence, and to people with mental health support needs, improving connectivity with family, kinship and community, and achieving economic independence for tenants.
The social outcomes are included in the SAHF service arrangements and lay the foundation for a transition to an outcomes-based contract arrangement.
FEATURES SCHEDULE
June 2018 Deadline: 11 May 2018
Sustainability
Preamble
InfraPeople: Skills & training
Mobility Smart infrastructure
VicRoads Earthmoving outlook
Noise and vibration
Investment & financing
Asset inspection & drones/UAVS
DISTRIBUTION TBC
November 2018 Deadline: 5 October 2017
AusRail IoT & cloud communication
Airports Construction standards and codes
Land access Asset management
Security and critical infrastructure
Landscaping and vegetation management
DISTRIBUTION AUSRAIL PLUS AUSTRALIAN AIRPORTS ASSOCIATION CONFERENCE
ADVERTISERS’ INDEX
September 2018
Deadline: 27 July 2018
Tunnels When infrastructure intersects
Freight Energy infrastructure
Concrete Cranes & heavy lifting
Culverts Safety and risk management
Intelligent Transport Systems (ITS)
DISTRIBUTION TBC
March 2019
Bridges
Deadline: TBC
Signalling, tracking and control systems
Rail Condition monitoring and maintenance
Urban transport corridors Software, communications and connectivity
Spatial & GIS Building and construction
Public private partnerships Road Surfacing and design
DISTRIBUTION TBC

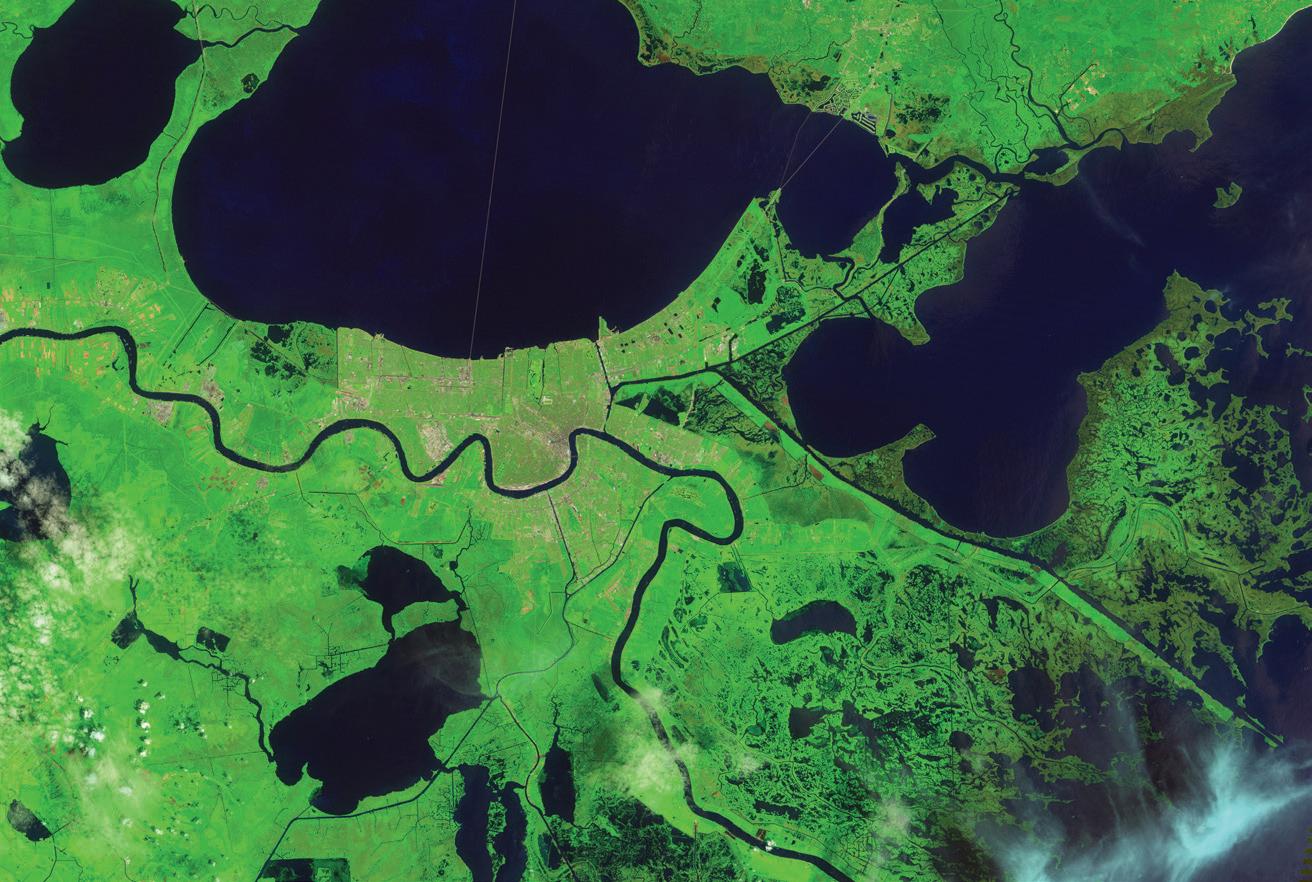
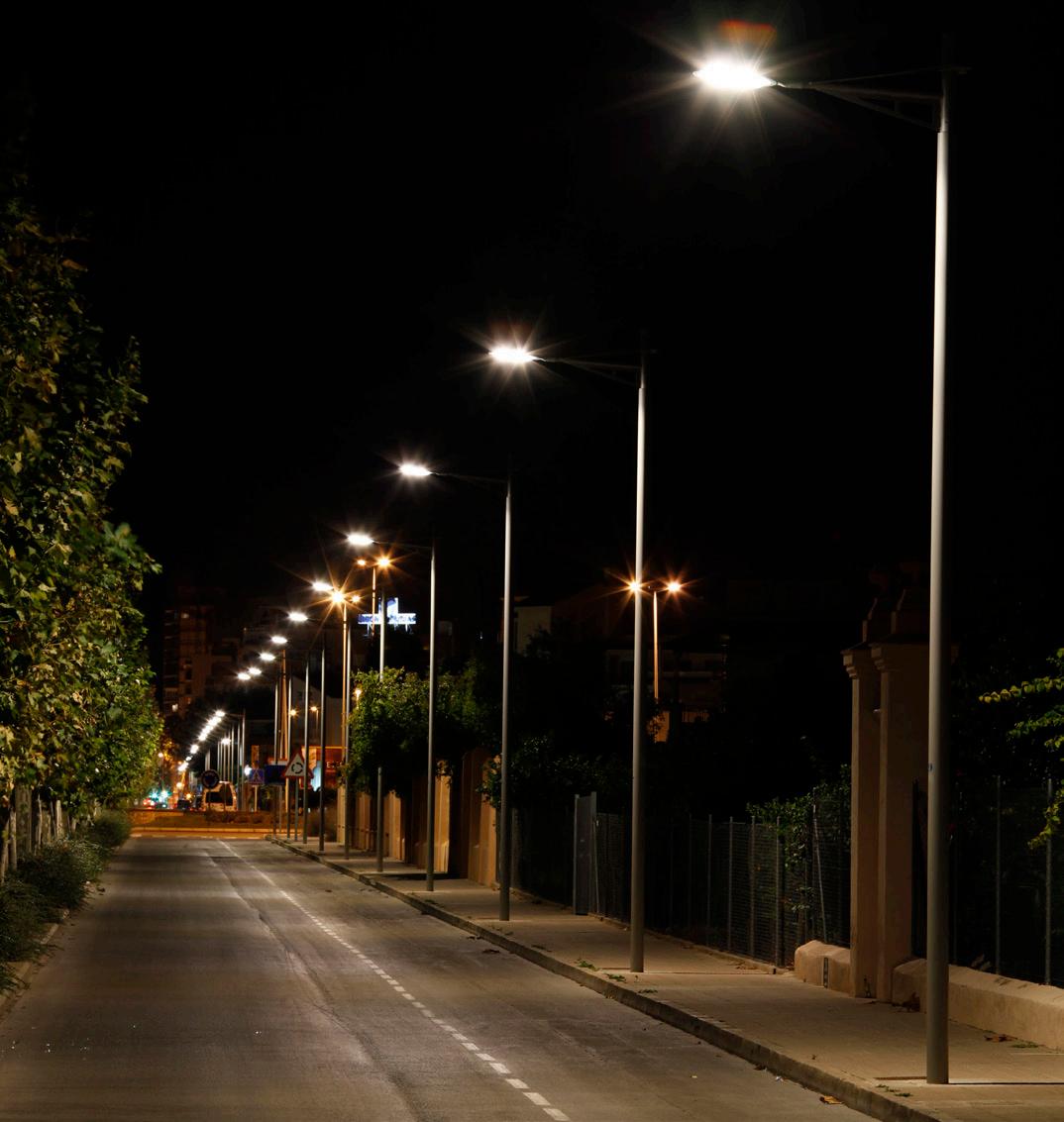