ROAD - RAIL - AIRPORT - PORT - URBAN - UTILITY
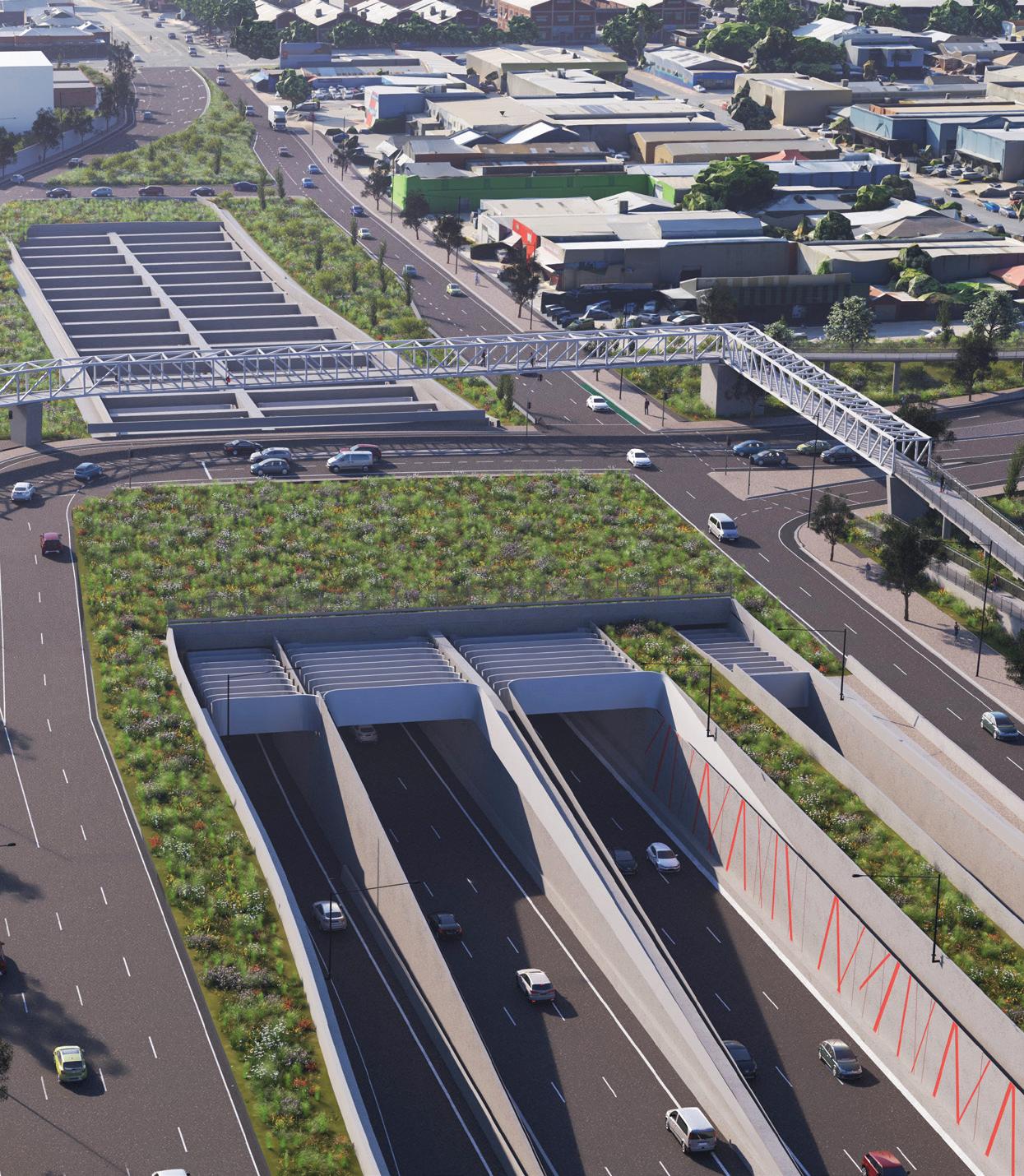
THE
on construction culture and diversity
by
Monkey Media Enterprises
ABN: 36 426 734 954
C/- The Commons, 36–38 Gipps St, Collingwood VIC 3066
P: (03) 9988 4950 F: (03) 8456 6720
monkeymedia.com.au info@monkeymedia.com.au infrastructuremagazine.com.au news@infrastructuremagazine.com.au
Editor Jessica Dickers
Journalists
April Shepherd
Lauren DeLorenzo
Annabelle Powell
Christopher Allan
National Media and Events Executives
Rima Munafo
Brett Thompson
Jacob Trad
Design Manager
Alejandro Molano
Designers
Jacqueline Buckmaster
Danielle Harris
Luke Martin
Marketing Manager
Radhika Sud
Digital Marketing Assistant
Andie James
Publisher
Chris Bland
Managing Editor
Laura Harvey
Idon’t think anyone could have predicted that we’d be going into year three of a global pandemic, but with a huge wave of Omicron cases starting off 2022, we’ve continued to feel the impacts of COVID-19. With more people getting sick or having to isolate, plus continuing international supply chain issues, it has put a huge strain on our freight and logistics sector and workers. While the industry continues to manage this, it’s hard to predict what the rest of 2022 has in store.
Many people thought this was the year we’d start to return to some form of normalcy, including being able to see colleagues and like-minded industry professionals in person. However, we’ve already started to see major industry events having to be postponed to later dates. It’s clear that people are keen to get back to in-person conferences, but it looks like virtual events are here to stay for a while longer to facilitate those connections and learning opportunities.
Infrastructure and our publisher Monkey Media will once again be running our premier virtual conferences in 2022 to provide the sector with the opportunity to hear from industry experts, keep up to date with innovations and projects around the country, and connect with infrastructure leaders. We’ll be running the Critical Infrastructure Summit in April, featuring the three virtual conferences – State of Play, Asset Management for Critical Infrastructure, and Future of Infrastructure. Our sister publications, Council and Utility magazines, will be running Smart Cities in May, and Digital Utilities in June, respectively.
We hope that despite the uncertainty around events and travel, you’ll be able to join us and connect with the critical infrastructure community at these virtual conferences.
As we move into a new year, it’s also a good time to take a step back and take stock of current challenges and opportunities, and start thinking about solid, sustainable plans. In this issue's article, Infrastructure Australia outlines its predictions for the key issues that
will define the infrastructure sector in 2022, ranging from skills and materials shortages, to digital, and culture.
While these are challenges the industry is aware of, solutions need to be put in place now in order for us to deliver the massive amount of investment committed to Australia’s infrastructure pipeline.
Industry culture and the reforms that are needed is a topic we’ve also explored in depth in this edition. Culture is no longer an afterthought or something thought to be outside the scope of assets and projects – it is a critical component of the sector’s ability to run effectively and meet demand. While it’s great to look at new technologies and project updates, culture is incredibly important, which is why infrastructure leaders have jumped at the chance to discuss issues around diversity, accessibility, and the reforms needed to avoid excessively long working hours and burnout.
A move toward digitisation also continues to be a key component in the industry’s success, and unpins the future of infrastructure. This issue takes a look at digital asset strategies across Australia, your part to play in digital and innovation, how 5G will improve transport and logistics in Australia, how spatial digital twins can create a blueprint for the future, the role of robotics and AI in condition monitoring and maintenance, as well as the implementation of High Capacity Signalling.
Some of the biggest projects currently in progress or planned across the country are in the roads sector, so we also wanted to spend some time focusing on the critical road projects underway, how we’re making pavement construction smarter, and a deep dive into two major projects in particular –South Australia’s Torrens to Darlington (T2D) Project and Victoria’s North East Link.
We’d love your thoughts on what you see as the key challenges and opportunities for the infrastructure industry in the year ahead, and we'll hopefully see you (virtually) at the upcoming conferences.
Jessica Dickers EditorDrop me a line at jessica.dickers@monkeymedia.net.au or feel
SPATIAL DIGITAL TWINS CAN CREATE
THE KEY ISSUES THAT WILL DEFINE THE INFRASTRUCTURE SECTOR IN 2022
With infrastructure set to play a driving role in Australia’s economic recovery, Infrastructure Australia’s Chief of Policy & Research, Peter Colacino, outlines the key issues that will define the sector this year.
By creating a virtual reproduction of our physical environment, digital twins have proven to be immeasurably useful to Australia’s infrastructure industry. Thousands upon thousands of these models exist — but what if these datasets could be merged into a single, more powerful, adaptive model?
A recent panel brought together industry leaders from around the country to share perspectives on the digital future of Australia’s infrastructure and the state strategies that are helping us to achieve this.
AUSTRALIA’S BIGGEST ROAD INFRASTRUCTURE PROJECTS
There’s a lot happening in the road infrastructure space across Australia. Here, we take a look at some of the biggest road projects around the country and their progress to date.
ABU DHABI’S INTEGRATED TRANSPORT MODELLING FRAMEWORK
BIG YEAR AHEAD FOR TORRENS TO DARLINGTON PROJECT
The $9.9 billion Torrens to Darlington (T2D) Project is entering an exciting new phase following the release of the motorway’s Reference Design, with residents and business playing an increasingly important role in shaping how it will be delivered.
DECARBONISING THE TRANSPORT SECTOR
As with any industry, the transport and infrastructure sector requires a degree of social licence to operate.
GETTING ON WITH NORTH EAST LINK
After years of planning and consultation with the community, work is progressing on building the missing link in Melbourne’s freeway network.
CONDITION MONITORING AND MAINTENANCE
ACOUSTIC TOOLS FOR MANAGING RAIL AND TUNNEL NOISE
AI AND ROBOTICS STREAMLINING CRITICAL INFRASTRUCTURE MAINTENANCE
Worldwide spending on artificial intelligence (AI) is increasing, with huge investments by government parties and the private sector into AI technologies. Dr Sue Keay, Chair, Robotics Australia Group, explores how robotics and AI technologies are currently being implemented in the critical infrastructure sector, and its future applications.
THE POWER OF ARMORGALV® IN INFRASTRUCTURE
SPATIAL & GIS
GPS UPGRADES FAST-TRACKING SA PROJECTS
A joint initiative between the private sector, the Federal and South Australian Governments will see a major satellite GPS upgrade increase the efficiency of South Australian road projects.
HOW 3D DATA CHANGED WSP’S INFRASTRUCTURE WORKFLOW
SIGNALLING, TRACKING AND CONTROL SYSTEMS
TRAINING AND SKILLS
APPRENTICESHIPS VICTORIA REDRESSES THE GENDER BALANCE
1 EDITOR’S WELCOME
4 CONTRIBUTORS
72 ADVERTISERS’ INDEX
72 FEATURES SCHEDULE NEWS
6 CONTRACT AWARDED FOR WESTERN SYDNEY AIRPORT FINAL STEPS
7 $7 BILLION FUNDING TO FINANCE INFRASTRUCTURE IN NORTHERN AUSTRALIA
8 VIC GOVERNMENT PROVIDES $9.3B FUNDING FOR SUBURBAN RAIL LOOP WORKS
9 $15 MILLION TO COMBAT TIMBER SHORTAGES
10 CONCEPT DESIGNS RELEASED FOR $240 MILLION TAS PORT REDEVELOPMENT
10 METRONET ANNOUNCES PREFERRED CONTRACTORS FOR TWO KEY PROJECTS
11 NEW GENDER EQUALITY POLICY FOR THE CONSTRUCTION INDUSTRY
12 THE CRITICAL INFRASTRUCTURE SUMMIT IS BACK FOR 2022
13 BRUCE HIGHWAY SMART MOTORWAYS TECHNOLOGY CONTRACT AWARDED
As a qualified engineer with decades of experience, Duncan’s career has seen him hold a number of roles including Regional Director for VicRoads, in which he was responsible for the construction, planning and maintenance of roads in Melbourne and South West Victoria. Following this, Duncan spent five years working as General Manager – Membership at the Royal Automobile Club of Victoria (RACV) before commencing as CEO at North East Link. Duncan is responsible for leading an experienced team through the design, procurement and construction of North East Link.
Chief Accessibility Advocate, Department of Transport
Tricia contracted polio in 1954 and uses callipers and crutches to get around. A long-term activist and advocate, her goal is to empower other people with a disability to take their rightful place in society. She has been running a business for the past 20 years, and supports other people with disabilities who want to start their own businesses. Tricia is passionate about access to all services others take for granted and sees transport as the key to inclusion.
Director of Spatial Operations, Spatial Services, NSW Department of Customer Service
Wayne is responsible for a number of programs including the production and maintenance of the NSW Foundation Spatial Data Framework and the NSW Spatial Digital Twin. He has more than 25 years of experience in the spatial industry, covering a range of disciplines from operations to strategy and policy development. Wayne is the ANZLIC NSW Contact Officer and member of ICSM.
LLB,
Gabrielle is a non-executive director and advisor who has 25 years experience on boards in the public and private sectors, and a long career in issues management. Her current roles include Chair of the CICT, a Commissioner of the AFL, and board memberships of Zurich Australia Limited, Built, WAM Global LIC and government agencies in NSW, Victoria and the ACT – charged with overseeing urban development and infrastructure delivery. She also has a background as a lawyer, newspaper journalist and public sector executive. Gabrielle holds a Bachelor of Laws from the University of Melbourne and an M.A from Western Sydney University in Creative and Cultural Practice.
Package Director – Melbourne Airport Rail, Metro Trains Melbourne
Lisa is a director with over a decade of experience working in the rail and construction industries in the United Kingdom and Australia. She moved to Melbourne in February 2021 to take up the role of Metro Trains Melbourne’s Package Director (Airport Station and Viaducts packages) for the Melbourne Airport Rail Project. She has recently been appointed Board Director for the National Association of Women In Construction (NAWIC). As a woman of colour, senior rail construction leader and now Board Director, Lisa is using her platform to break down barriers for women in the industry, and to champion people from non-STEM disciplines.
CEO, Australian Mobile Telecommunications Association (AMTA)
Louise was appointed as Chief Executive Officer of the Australian Mobile Telecommunications Association Limited (AMTA) in May 2021. Prior to joining AMTA, she was Principal at Hirst Advisory where she consulted to businesses and government agencies in the telecommunications, telehealth and infrastructure sectors. Previously, Louise was the General Manager, Commercial Implementation at NBN Co for over six years and prior to that, the Commercial Director and General Counsel of PCCW’s business in Europe. She holds Bachelor of Arts and Bachelor of Laws degrees from Monash University (VIC) and a Master of Business Administration from Cranfield University (UK).
The final major contract has been awarded for construction of the Western Sydney International (Nancy-Bird Walton) Airport, unlocking the future of air travel in the region.
Construction of Western Sydney Airport’s landside precinct will begin in 2022 after the contract was awarded to the Aerowest Joint Venture, made up of BMD Constructions and Seymour Whyte Constructions.
Western Sydney Airport CEO, Simon Hickey, said the contract is the last piece of the puzzle for the project’s major procurement, completed ahead of schedule.
“This is where your journey at Western Sydney International begins and ends,” Mr Hickey said.
“Whether you’re arriving by car, bus or rail, this will be the welcome mat for our customers at what will be Australia’s best airport terminal.
“We know that getting to and from airports is one of the biggest pain points for travellers – passengers and airlines will love using Western Sydney International because the experience we deliver will be fast, seamless and reliable from start to finish.”
Construction of the landside precinct will involve integrating the new M12 Motorway, which will connect the airport to Sydney’s motorway network, and the airport’s two stations on the Sydney Metro – Western Sydney Airport line, with one stop at the passenger terminal and the other at the business precinct.
It will also involve the construction of car parks, roads, bridges, utilities connections, operational buildings and landscaping.
Federal Minister for Communications, Urban Infrastructure, Cities and the Arts, Paul Fletcher, said this marked another milestone for the airport – one of the nation’s biggest infrastructure projects.
“The announcement is a significant milestone in the delivery of this once-ina-generation project for Western Sydney with all major contracts now awarded, paving the way for even more activity to get underway on site,” Mr Fletcher said.
“The landside contract will deliver essential ground transport operational facilities to underpin smooth and efficient journeys to and from the airport, including car parks, electric vehicle charging stations and holding areas for point-to-point transport services.”
The contract is expected to create more than 700 direct jobs and many more indirect jobs through flow-on benefits to suppliers and the local economy.
Federal Minister for Finance, Simon Birmingham, said this contract will also ensure complementary infrastructure projects integrate smoothly with the new airport, such as the M12 motorway and the Sydney Metro – Western Sydney Airport rail link.
“These projects will provide critical connections, getting overseas visitors from the new airport to their destination, and Australians to the rest of the world, to unlock the full benefits of this up-and-coming international gateway,” Mr Birmingham said.
“The airport and surrounding road and rail links will be a catalyst for future jobs, economic growth and prosperity in the region, and form an integral element of the surrounding Aerotropolis and the broader Western Parkland city.”
Western Sydney International is on track to open to international, domestic and air cargo services in late 2026.
The Australian Government is providing the $5 billion Northern Australia Infrastructure Facility (NAIF) with an additional $2 billion in funding to finance critical infrastructure projects in the country’s north.
Federal Minister for Agriculture and Northern Australia, David Littleproud, said the funding increase to $7 billion means communities, businesses and industries will benefit from more infrastructure projects.
“To date, $3.2 billion of NAIF financing has been committed. This funding is expected to create up to 11,000 new jobs and inject almost $16 billion back into the economy,” Mr Littleproud said.
“The demand for NAIF funding continues to grow and it is likely to fully commit its current funding in the next year.
“An additional $2 billion will continue the prosperity to the north for generations to come and further delivers the Government’s commitment to
create economic development and drive investment in northern Australia across all sectors, from mining and agriculture to renewable energy, education and tourism.”
Special Envoy for Northern Australia, Queensland, Senator Susan McDonald, said the extra funding will give certainty to investors to commit to doing business across the north.
“We are getting private enterprises on board to invest in our north, because we know that public and private
sectors working together will achieve sustainable and exponential growth,” Ms McDonald said.
“NAIF is a critical tool in helping to deliver real outcomes under the Regions of Growth Master Plans outlined in Our North, Our Future: 2021-2026.”
NAIF Acting CEO, Amanda Copping, said the NAIF is investing for impact in northern Australia with more than $3.2 billion committed to job-creating projects and to unlock the potential of the region.
The Victorian Government is providing $9.3 billion in funding towards major works on the Suburban Rail Loop (SRL) to deliver twin rail tunnels and six underground stations, with the project expected to create up to 8,000 jobs.
The funding will also be invested in new community projects and initiatives in the broader areas around the stations.
Trains are expected to be running on SRL East by 2035, transforming Melbourne’s public transport network and better connecting people to jobs, health, education, retail opportunities and each other.
Fast, efficient, high-tech trains powered by renewables will provide a turn up and go service expected to carry around 70,000 passengers a day.
Commuters in Melbourne’s south east will experience much faster journeys on the underground line, saving up to an hour on a one-way trip. Trains will take three to four minutes between stations, and a journey from Cheltenham to Box Hill will be just 22 minutes.
Construction starts in 2022, with the Business and Investment case showing SRL East and SRL North is expected to deliver $58.7 billion in economic, social and environmental benefits, and support up to 24,000 local jobs.
The funding announcement provides certainty for project
delivery and communities in Melbourne’s east and south east, paving the way for procurement of main works packages to start this year, and comes on top of the $2.5 billion already provided for planning and development of SRL and for Initial and Early Works on SRL East.
The Government will continue to work with the Commonwealth and the private sector as this project progresses, with the creation of significant value capture opportunities as the build progresses.
The contract for this first phase of works, expected to create up to 8,000 direct jobs, has been awarded to global construction and engineering firm Laing O’Rourke, which has agreed to exceed workforce and local content targets.
The huge package of works includes preparing sites for the launch of tunnel boring machines, moving and protecting underground services, ground improvement, geotechnical investigations and road modifications.
The contract offers exciting opportunities for local industry and suppliers, including delivering in excess of 95 per cent local content.
Around 14 per cent of the total hours will be undertaken by Victorian apprentices, trainees or cadets, with opportunities for women, Aboriginal and disadvantaged Victorians –contributing to the next generation of highly skilled workers.
The Federal Government has invested an additional $15.1 million to combat the structural timber shortage faced by the housing and construction industry.
The investment will be used to deliver bushfire-affected softwood to underutilised timber mills, targeting timber on Kangaroo Island that could provide enough timber for between 8,000 and 10,000 new houses.
Federal Minister for Agriculture and Northern Australia, David Littleproud, said the government had listened to the industry’s concerns to keep product moving.
“This will provide vital assistance to businesses impacted by increased demand, global supply chain delays due to COVID-19, and the lasting impacts of the 2019-20 Black Summer bushfires,” Mr Littleproud said.
“We stand ready to work with states and urge them to act swiftly to help us bring bushfire-affected construction timbers to mills with immediate capacity to produce structural timbers.
“It expands our successful $15 million Forestry Salvage Transport Measure, to allow for both intrastate and interstate
transport of remaining bushfire-salvaged construction grade softwood to mills in any state with capacity to process it.”
Federal Assistant Treasurer, Minister for Housing, Minister for Homelessness, Social and Community Housing, Michael Sukkar, said that the program would give the construction industry a boost and help address building material shortages.
“Australia’s construction industry is a significant contributor to our post-pandemic economic recovery,” Mr Sukkar said.
“This is reflected by the fourth consecutive increase in dwelling investment in the June National Accounts, rising 1.7 per cent since the introduction of HomeBuilder.
“We have seen more than 135,000 HomeBuilder applications and we want to get people into their new homes as soon as possible.”
CEO of Master Builders Australia, Denita Wawn, welcomed the announcement.
“This comes at a crucial time for thousands of builders and tradies whose viability is threatened by a surge in the price of timber and chronic delays of up to three months to access the timber needed to construct new homes and renovations,” Ms Wawn said.
The new concept designs for the Port of Devonport have been released, as part of the $240 million Devonport East Redevelopment which will support the arrival of a new fleet of Bass Strait ships.
The Port of Devonport is one of the fastest growing ports in Tasmania and is a major gateway for tourism and the Tasmanian Government is backing the redevelopment, now renamed QuayLink.
Minister for Infrastructure and Transport, Michael Ferguson, was joined by TasPorts Chief Executive Officer, Anthony Donald, to announce the next stage of works proposed under TasPorts’ Port Master Plan
The Plan is set to deliver two stateof-the-art roll-on-roll-off (RORO) berths
and terminals to support the arrival of new and larger Bass Strait vessels for TTLine and SeaRoad, as well as a multi-user berth to support future opportunities at the Port of Devonport.
The project will also see upgrades to improve navigation as well as facilitating electric vehicle charging stations, LNG ship refuelling and renewable energy shore power. Further improvements to the local amenity of the port precinct will be achieved through enhanced traffic management, landscaping and street scaping.
The new wharf and port facilities are expected to create 2,000 jobs between 2021 and 2027.
These port infrastructure upgrades will support the arrival of commissioned new vessels for Bass Strait operators, which
will see an anticipated increase in freight capacity by 40 per cent.
The project will deliver a deepened berthing pocket for the new vessels, upgrades to navigation, electric vehicle charging stations and LNG ship refuelling as well as shore power.
The project will also deliver a threedimensional vessel port monitoring system, providing an additional layer of safety for all vessels operating in the Mersey River.
To further support community connection with the new port precinct, TasPorts is investigating the development of a new commercial precinct as part of the project. This will offer unique business opportunities for East Devonport, providing further benefits to local communities.
METRONET has announced preferred proponents for the design and construction of two major projects — the Victoria Park-Canning Level Crossing Removal project and the Byford Rail extension.
The Victoria Park-Canning Level Crossing Removal project will see the Armadale Line Upgrade Alliance (ALUA comprising Acciona Construction Australia, BMD Constructions, WSP Australia and AECOM Australia) work to remove level crossings along the Armadale Line at Mint Street, Oats Street, Welshpool Road, Hamilton Street and Wharf Street and replace them with elevated rail.
New elevated stations will be built at Carlisle, Oats Street, Queens Park and Cannington, which will enable safer and improved rail connections to schools and businesses.
The gates at each of these level crossings are down for more than three hours a day, causing traffic congestion and frustration for commuters.
The MetCONNX Alliance (comprising Laing O’Rourke Australia Construction, Pritchard Francis Consulting and Kellog Brown & Root) will extend the Armadale Line 8km south for the Byford Rail Extension.
A new Byford Station, located 400m north of Abernethy Road, will provide future passengers with a 42-minute train journey to the Perth CBD and support the growing town centre.
Following additional funding from the Federal Government in May 2021, the Byford Rail Extension project has expanded to include removing level crossings at Armadale Road, Forrest Road and Church Avenue by elevating the rail and Armadale Station in this area.
Early work on the Byford Rail Extension is already underway on the Thomas Road Over Rail Project.
Negotiations with the preferred proponent for each project will commence to finalise the detailed scope and cost of the project, before an Alliance contract is signed in coming months.
The Federal and Western Australian Governments have worked together to allocate up to an additional $600 million to these two major projects and the new Midland Station project.
The Federal Government has also allocated an additional $25 million to the Canning Bridge Interchange project.
The additional budget allocation reflects market cost pressures and project scope changes.
The Victorian Government has announced a new policy which mandates increased representation for women in the construction industry.
The Building Equality Policy (BEP) is an Australian first and aims to disrupt gender stereotypes in the country’s most male-dominated industry.
The BEP will apply to new government projects, and mandates female representation in at least three per cent of each trade role, seven per cent of each non-trade position and 35 per cent of management, supervisor and specialist labour roles.
In effect from 1 January 2022, the BEP also mandates that four per cent of labour hours for apprentices and trainees will be required to be performed by women.
The Victorian Government has invested $3.5 million to support the implementation of the policy and a further $1.5 million for the delivery of medium and long-term actions from the Women in Construction Strategy 2019-22
Victorian Minister for Transport Infrastructure, Jacinta Allan, said, “We need to make women aware that construction is an attractive and viable career option – and these targets will ensure women are proactively included and stay in the industry, with stronger career pathways.
“Greater diversity makes our workplaces stronger – and greater representation of women in construction will benefit everyone in the industry.”
Over the past 30 years, women have consistently comprised between two and three per cent of the construction
workforce, with the coronavirus pandemic having a disproportionate impact on women’s workforce participation, employment and economic security.
The new requirements are being introduced through Victoria’s Social Procurement Framework (SPF) for works valued at $20 million or more over the life of the project.
There will be a two-year transitional implementation period and action on non-compliance will kick in from January 2024.
Victoria’s Building Industry Consultative Council (BICC) has worked collaboratively on the development of the policy and will continue to provide support and guidance to help industry understand their obligations and comply.
The team behind Infrastructure magazine is thrilled to be running the Critical Infrastructure Summit again in 2022. The landmark virtual event for the Australian infrastructure industry will be taking place from 6–8 April 2022.
The 2022 Critical Infrastructure Summit consists of three free-to-attend Virtual Conferences, exploring the industry’s biggest challenges and predictions across the entire infrastructure lifecycle.
After huge levels of attendance and engagement at the 2020 and 2021 Critical Infrastructure Summits, this virtual event has established itself as a must-attend event on the infrastructure calendar for the year.
Building on the massive 2021 event, the Summit unites a number of established industry events including:
CRITICAL INFRASTRUCTURE: STATE OF PLAY – 6 APRIL
A thought-leading Summit keynote session on the biggest issues currently facing Australia’s critical infrastructure.
ASSET MANAGEMENT FOR CRITICAL INFRASTRUCTURE – 7 APRIL
Bringing together utility and infrastructure leaders to discuss the most pressing issues in asset management.
THE FUTURE OF INFRASTRUCTURE – 8 APRIL
A look at what’s next for the industry – digital infrastructure, the Circular Economy, skills, funding, future sector trends and more.
The Summit will feature an expert speaker lineup, industry panels, interactive Q&A sessions and the ability to hear and learn from Australia’s critical infrastructure community.
Topics for 2022 include: the last six months in infrastructure; predictive maintenance; making the most out of data; skills and training; changing construction culture; moving towards ‘digital by default’; materials, supply chains and planning approvals; and updates on some of the biggest projects from around the country.
If you’re working in or with Australia’s infrastructure industry, this is a not-to-be-missed event.
Speakers and full programs to be announced shortly. There are also a limited number of sponsorship opportunities available allowing your company to get involved and reach the critical infrastructure sector.
For more information, or to register, please visit https://www.critical-infrastructure.com.au.
Acontract has been awarded for the construction of Smart Motorways technology on the Bruce Highway between the Pine River and Caloundra Road.
Seymour Whyte Constructions will begin implementing the technology, which includes ramp signals, variable speed limit and message signs, vehicle detection systems and CCTV cameras, to proactively monitor and respond to changing road conditions such as crashes, wet weather or heavy traffic conditions in real time.
The $105 million Bruce Highway Pine River to Caloundra Road Smart Motorways Stage 2 project is jointly funded by the Federal and Queensland Governments on an 80:20 split, with the Federal Government contributing $84 million and the Queensland Government contributing $21 million.
Deputy Prime Minister and Minister for Infrastructure, Transport and Regional Development, Barnaby Joyce, said the project is part of the 15-year, $13 billion Bruce Highway Upgrade Program.
“As part of our commitment to improving the safety and performance of our national highways, the Australian Government is allocating $84 million towards installing this additional Smart Motorways technology along the Bruce Highway,” Mr Joyce said.
“Through our investment, motorists can expect to see improvements in safety, efficiency and reliability along this busy stretch.”
Queensland Transport and Main Roads Minister, Mark Bailey, said the technology proved to be an effective safety device across the state.
“Smart Motorways technology gives drivers advance warning of congestion
ahead and allows for speed limits and ramp signals to be changed remotely,” Mr Bailey said.
“This project builds on the network of Smart Motorways technology already delivered on the Bruce Highway southbound between the Pine River and Uhlmann Road as part of the Smart Motorways Stage 1 project in 2015.
“Not only are we improving safety for drivers on Queensland’s busiest highway, but we’re creating about 140 direct jobs at a time when they are needed most.”
Wireless traffic sensors would also be installed at priority locations along the 60km stretch to monitor vehicle travel times, traffic flow and speed.
Work is expected to be completed in 2024, weather and construction conditions permitting.
With infrastructure set to play a driving role in Australia’s economic recovery, Infrastructure Australia’s Chief of Policy & Research, Peter Colacino, outlines the key issues that will define the sector this year.
ustralia is on the cusp of an unprecedented wave of investment in public infrastructure projects. Investment in major public infrastructure over the next five years will exceed $218 billion. The peak of annual investment, estimated at over $52 billion in 2023, reflects a dramatic increase beyond spending rates delivered in response to the Global Financial Crisis.
As well as supporting the recovery from the pandemic, this investment by Australia’s governments will lay the foundation for future economic growth and lift our standard of living. However, this trend is also likely to create national pressure on the sector, as well as localised shortages of skills and materials. These challenges present compounding delivery risks that are difficult to predict or plan.
COVID-19 is materially compounding these challenges with border restrictions impacting access to skills and labour, disruptions to interstate and global supply chains, and worker shortages and illness acting as a handbrake on productivity. These challenges are persisting, and in some cases growing, as the pandemic enters its third year.
These constraints add further weight to the need to prioritise infrastructure industry reform in 2022. To deliver the record rates of investment, government and industry in partnership need to take steps to ensure the industry is more innovative, productive and financially sustainable in the year ahead.
SKILLS SHORTAGES ARE FORECAST ACROSS ALL INFRASTRUCTURE-RELATED OCCUPATIONS
Infrastructure Australia’s inaugural Infrastructure Market Capacity report provides a comprehensive understanding of the supply and demand of skills and materials critical to deliver Australia's major infrastructure pipeline.
It finds that the peak of demand for skills is 48 per cent higher than supply. Meeting this demand would require annual growth of 25 per cent over the next two years, which is more than eight times higher than the projected annual growth rate of 3.3 per cent over this period. Some shortages appear to be ongoing and systemic, for example building surveyors and many rail occupation specialisations.
Engineering occupations are currently most at risk of shortage. Over 41,000 skilled workers are estimated to be required to fill engineering occupations including positions in civil, geotechnical, structural and materials engineering. Shortages are particularly acute for a range of senior, experienced positions.
The shortages impact both the public and private sectors, with potential severe consequences for the ability of projects to be delivered on-time, in-budget or within the desired scope. As a starting point, three in four transport projects globally run over budget. Australia is no different. With more than 80 per cent of the future major project pipeline devoted to transport, the consequences of capability shortfalls could be substantial
budgetary pressure on government or the continuation of the so-called ‘profitless infrastructure boom’.
Migration will have a role in addressing workforce demand and may be the difference between capacity or shortage for some occupations like electrical engineers or specific highly skilled individuals at senior levels. However, even with migration playing a significant role, access to some skills, such as to specialised engineering roles, are still likely to be inadequate. This is due to the global nature of the talent pool, and strong global demand for these skills as G20 countries leverage USD $3.2 trillion of infrastructure investment as part of post-COVID stimulus strategies.
Materials demand accounts for the second largest proportion of expenditure in the pipeline over the next five years. Demand for materials is projected to grow for three consecutive years, representing annual average growth of just over 30 per cent per annum between 2021 and 2023.
Demand for quarried material and cement are likely to produce the most significant challenges due to their reliance on local supply chains. Steel, bitumen and electrical control equipment are likely to be exposed to international demand and supply chain pressures.
The increasing and significant concentration of megaprojects, transport and rail investment drives unprecedented demand for materials. This includes an average annual growth rate for rock/bluestone approaching 60 per cent over the next three years. Demand for rail track will grow by 250 per cent over the three-year period.
Collaboration and integration across the ecosystem will drive a financially sustainable and high-performing infrastructure industry.
To achieve this, a new model for delivery is required to transform the infrastructure sector in Australia, one founded in long-term, collaborative, and trust-based relationships. This also requires regular two-way dialogue between the government and industry. It also requires an integration of delivery teams with the client. The relationship must extend beyond the prime contractor into the supply chain and supporting team.
This enterprise-based model of integrated delivery teams has been pioneered by the Project 13 Initiative, including Sydney Water as an early Australian adopter, and elements of this approach have been embedded in major transport projects, particularly in Victoria.
Effective public sector project leadership and governance is a key enabler, ensuring the focus is on the right outcomes, framing relationships for success at the outset, and driving collaborative behaviours.
Such a model will represent a departure from current practice, where transactional bi-lateral relationships that largely exist on a project-by-project basis, which along with unbalanced risk and commercial models, drive an adversarial culture and a financially unsustainable industry.
Digital has the potential to transform the infrastructure sector and support enhanced productivity and innovation. Digital is a core enabler to achieving transformation change across the sector, and at its heart is about the better collection, analysis, storage and sharing of data and information.
Digital transformation will drive better information and knowledge sharing, drive a reduction in whole-life costs of infrastructure, and will play a core part of improving the future development, construction, and operation of infrastructure assets.
Through digital transformation, the value achieved by information can be bigger than the sum of its parts – enabled through a common national information framework, smart adaptable assets that can gather information, and more widespread use of Building Information Modelling (BIM) and digital twins.
Despite the practice, here-and-now the opportunity to embrace digital solutions is often put in the ‘too hard basket’ or misrepresented as a technology product. The information, rather than the technology component has the potential to transform infrastructure planning, delivery and whole-of-life management, driving genuine productivity change. We need to get back to digital basics to support adoption with a focus on common definitions and processes, moving to at scale, consistent deployment.
Ultimately, infrastructure delivery requires more than steel and concrete. It is also about the workers, engineers and project teams who design and build it, in addition to the users who rely on it. Infrastructure planners, financiers, builders, operators and community engagement teams are all part of the tens of thousands of people that make up the sector.
A positive and effective industry culture is led from the top and creates the conditions that ensures the working environment caters to the broadest range of talent – this is particularly pertinent at a time when our sector is reputedly moving toward peak capacity.
By taking deliberate and meaningful action to address the industry’s inflexible, confrontational and at times aggressive culture will be critical. The Construction Industry Culture Taskforce (CICT) Culture Standard should provide the vehicle for change, however it will require adoption and leadership from government in valuing its objectives.
Creating a more attractive industry for younger workers, and women, can unlock the potential to foster a more resilient workforce, and one that is capable of delivering the future infrastructure needs of the diversity of the people of Australia.
Genuinely diverse and inclusive workplaces consistently report higher people engagement, resilience, productivity and performance, all of which lead to better business and societal outcomes. Diverse teams provide different perspectives, approaches and experiences, and these diverse views lead to better decision making. Reports show that when employees are confident there is a commitment to equality, diversity and inclusion they feel more included and the drive to innovate increases.
As we head into a Federal election year, Civil Contractors Federation National CEO, Chris Melham, outlines the government reforms and priorities that are needed to create a more efficient and sustainable construction industry in Australia.
t is an indisputable fact that politicians love high-vis vests and hardhats. Flick on the nightly news recently and chances are you would have seen a politician touring a road project, rail line or airport in his or her safety gear.
Invariably, and not surprisingly, these visits are far more common during election campaigns, and we have seen our fair share over the past few months.
Cynics could say the real reason politicians like to don hardhats and high-vis vests is because they want to be seen connecting with everyday Australians in a place where something is actually being built.
There may be an element of truth to this theory but visits like these are important as they provide an opportunity for the civil construction sector to demonstrate the levels of skill and technical expertise needed to construct our roads, bridges, drainage, rail and utilities.
Furthermore, these visits also help reinforce the critical role the civil construction sector is playing in leading Australia’s economic recovery.
Civil Contractors Federation National (CCF) has been actively communicating to both sides of politics CCF’s election policy priorities as we head to a federal election, and the measures required to harness the productive capacity of the civil infrastructure sector more effectively.
CCF has provided its 2022 federal election document Civil Construction – Leading Australia’s Economic Recovery to both the major parties with a request to formally outline how their policies align with industry’s priorities.
These priorities are based on five ‘policy pillars’ which form the spine of CCF’s advocacy efforts during the election period. They comprise:
♦ Infrastructure investment
♦ Efficient, equitable and competitive procurement
♦ Enhancing skills development and training
♦ Enhancing industrial relations
♦ Building a stronger, more sustainable industry
Under these policy pillars, CCF has identified 16 separate government priorities and reforms which are critical to achieving a stronger and more sustainable civil infrastructure sector and to strengthening Australia’s sovereign construction capacity. These reforms include:
♦ A more sustained level of federal infrastructure investment over the longer term to underpin construction activity, build investor confidence, and improve economic growth
♦ Greater project disaggregation to maximise participation of mid-tier contractors and SMEs
♦ Greater use of collaborative contracting by all tiers of government to more appropriately allocate risk and to encourage a greater number of bids from construction companies
♦ Reinstating civil occupations on the National Skills Needs List to incentivise a higher level of apprenticeship enrolments
♦ Abolition of industrial relations instruments which impose unjust legal risk on civil construction companies There is a growing need for action to deliver against these policy priorities. For example:
♦ The need for sustained infrastructure investment is supported by a CCF survey that shows civil construction companies across Australia have the capacity to undertake additional work if Federal Government project funding was increased, particularly projects up to $100 million
♦ Government procurement agencies are currently not making full use of the different procurement models available which most appropriately allocate risk. This includes collaborative contract arrangements which involve earlier and closer involvement with industry
♦ Many civil occupations currently do not appear, or are not classified appropriately, on the National Skills Needs List. This means apprentices, VET providers and employers are not eligible for the full suite of government training incentives available
♦ Some industrial relations instruments at the state level are imposing unnecessary red tape and legal risk on civil construction companies. This includes, for example, Queensland Best Practice Industry Conditions and the ACT Secure Local Jobs Code
♦ Governments are failing to disaggregate major projects which limit the ability of mid-tier companies to successfully tender for these projects. Disaggregation will foster broader competition and a more sustainable contracting industry at both head contractor and subcontractor levels
I am pleased that both the Government and the Federal Opposition have committed to a number of CCF’s policies during the election campaign, including debundling and infrastructure procurement reform.
For example, Deputy Prime Minister, Barnaby Joyce, said, “Government must be instrumental in creating a Tier One sovereign capacity. We need to create a pathway for our mid-tier companies to evolve into Australia's next tier one companies to take on global, multi billion-dollar contracts.”
Federal Opposition Leader, Anthony Albanese, has announced that, “Labor will provide opportunities for midand small-tier Australian companies to participate in the
infrastructure pipeline helping to build and strengthen our sovereign capability. This will be done by packaging tenders where appropriate into multiple packages that allow smaller companies to bid for them."
CCF National welcomes the positive infrastructure reform commitments made by both major parties during the campaign.
Over the coming 12 months, CCF will continue to work on behalf of the civil infrastructure sector to ensure these good intentions and positive election promises turn into reality.
We will continue to lobby for vital reforms which were not addressed by the major parties during the election campaign.
These reforms are invariably challenging and require the cooperation of all levels of government, but they are critical and cannot be substituted with a political high-vis vest and hardhat.
We should all be proud of the great contribution the construction industry makes to Australia. Our industry creates the quality and pulse of our lives, including for our families, communities, businesses and our national economy.
The houses, roads, rail, schools, cultural buildings, broadband and energy networks, hospitals, commercial, logistic and retail facilities shape our environment and our wellbeing as a nation. The community benefits from extraordinary feats of engineering, design and construction –the landmarks and enablers of productivity and society in our cities and towns.
Construction, correctly classed as an essential industry, provides ten per cent of Australia’s jobs and offers good pay for hard work. Even though there is always more to do, physical safety in an inherently risky environment has
improved over many years of focused attention. Technology, innovation and environmental consciousness are beginning to transform the way the industry works.
Yes – there is a lot we should be proud of.
And yet, we know our industry could be so much better. Should be so much better. Needs to be so much better.
Ours is an industry which has for too long operated in deeply embedded ways to its own detriment and to the detriment of many of our people. Its very sustainability, especially in infrastructure construction, has been in question.
For many, it’s an industry not even to be considered as an employer of choice. The small number of women who enter construction all too often find a culture that does not welcome them and does not cater for even their most basic amenity needs, much less their wellbeing and work and life balance.
They cannot see a career pathway for themselves. They find a workplace consisting of 88 per cent men – the least diverse of any Australian industry by an increasing margin – with excessively long working hours, intolerably high levels of mental ill health and half its people saying they are suffering burnout.
Men, especially those who wish to share family responsibilities and to ‘have a life’, are increasingly saying a construction industry that asks them to work routinely six days a week is not for them.
Poor mental health among construction workers has a strikingly strong correlation. Workplace culture is often singled out as a cause of psychological stress. If you are a construction worker, you are six times more likely to die from suicide than from a workplace accident.
And all this at a time when the infrastructure pipeline has never been bigger and the jobs we can’t fill, never higher. We need 105,000 more construction workers by 2023 to fulfil the infrastructure pipeline that has presently been committed.
Governments are conscious that to boost state and national productivity, especially post COVID-19, we need more women in the workforce.
It’s not as though the problems haven’t been identified and there haven’t been many attempts at change. Some great work has been done over many years by governments, industry associations, unions and organisations in trying to identify and address wellbeing and mental health as well as encouraging girls to study STEM subjects and seeking ways to attract and retain women into the industry.
Emerging pilot projects are seeking to address excessive working hours – the enemy of safety, productivity, wellbeing, and the attractiveness of the industry. But the damning industry statistics on diversity, mental and physical health, family conflict among construction workers, and the industry’s ability to attract and retain its talent, particularly women, remain stubbornly stuck.
The Construction Industry Culture Taskforce (CICT) has been working on a way to achieve systemic step change by leveraging the government infrastructure procurement process as a powerful agent to make a lasting difference. Our academic research has told us that tackling the three interrelated cultural issues of working hours, mental health and wellbeing, and gender diversity, together, in an integrated way, will give us the best chance of securing lasting change.
The CICT is a unique collaboration between the construction industry, the NSW and Victorian Governments and leading workplace academics, established in late 2018.
Our genesis is in the Construction Industry Leadership Forum which has been working with state governments to try to change the settings of the industry and how it interacts with its clients in major project delivery. Its reform priorities are threefold and interdependent – the commerciality of the procurement process, the skills and capability gaps in the industry, and industry culture.
The Taskforce was set up to address this third priority – how to reform the culture of the construction industry.
Our work and the research that underpins it makes a compelling case that government clients need to be part of the solution by requiring a methodical focus on culture as part of its evaluation of elements, like value for money, experience and capability, design, timeline and social procurement outcomes.
Increasingly, governments recognise the need to think differently and with greater foresight about their role in contracting with an industry where avoidable harm and problematic culture contribute to its failure to attract a sufficient workforce to meet the growing project pipeline. This, of course, has cost and productivity implications.
WHY IS THE PROCUREMENT PROCESS THE KEY? CAN’T INDUSTRY CHANGE ITS OWN CULTURE?
Requiring a focus on project culture will level the playing field for bidding proponents and arrest the typical, and so often counterproductive, race to the bottom on time and cost, without accounting for the costs incurred in productivity and harm caused by the prevailing way that ‘things have always been done’.
The deficiencies in the culture of the industry are deeply entrenched and interrelated in cause and effect.
Physical safety has rightly been an intense focus of the industry over many years and that effort must continue and strengthen.
But the same effort must go into addressing the risks posed by other aspects of a damaging workplace health and culture which have, by comparison, been neglected.
Our recently commissioned report showed the cost of doing nothing, as simply letting the excessive hours, the mental health outcomes and the lack of diversity stay the way it is costs around $8 billion per year.
There is increasing focus on regularising working hours to align with other major industries, including 50 – 55 hour individual roster caps and where feasible, Monday to Friday working weeks. The study on the construction of the Concord Hospital in NSW is a case in point, as is recently released research by Timewise out of the UK.
The evidence so far indicates that reducing excessive hours has a significant positive effect on worker wellbeing and the attractiveness of the industry, including to women, and does not negatively affect project timeframes and costs in any material way. Rather, productivity improves.
The Taskforce has proposed a draft set of standards designed to be incorporated into the procurement process, in the same way that Aboriginal Employment Targets and Infrastructure Legacy Skills have been baked into procurement in various jurisdictions.
The standards cover diversity, wellbeing and working hours. Some elements are as simple as identifying gender pay gaps and developing a plan to close them. Others are more complex to implement – for example, the standard which requires that no individual worker on a project works more than 55 hours per week. You can find them in detail at www.cultureinconstruction.com.au.
We have recently concluded a significant exercise to receive feedback from a broad range of stakeholders on the draft standards and have a further iteration based on the feedback.
NSW and Victorian Government delivery agencies are working on how the standards will be implemented in practice and several construction firms are preparing to be ‘first movers’. We have also seen interest from private clients wishing to include the standard as part of their ESG credentials.
In our next phase, we have commissioned six pilot projects to strengthen the evidence base for the effectiveness of the standards and to finalise the detailed implementation guidelines, prior to achieving our aim of the adoption of the final standards during 2023.
We hope and expect that in time the standards will become routinely accepted across jurisdictions and among private construction clients and will be regularly independently reviewed.
It is in all our interests to act on construction industry culture and to act on it as a national priority.
The Victorian Government is working to ensure our public transport network is inclusive and accessible for all Victorians. The beauty of making transport accessible to people with disabilities is that it has benefits for the whole community – older Victorians, parents with prams, and anyone who has a temporary injury or who is recovering from illness.
On 1 November 2021, I was appointed the Chief Accessibility Advocate to the Victorian Department of Transport. As a Victorian with a disability, I am deeply honoured to take up this appointment. I am here to support the Department of Transport and everyone who is interested in improving the lives of my community, whether they be staff developing projects or writing policy, people with disabilities, other interested community members, or organisations and staff who have disabilities.
This is a new and innovative appointment as I am the first Victorian Chief Accessibility Advocate for transport. My role is to support the Department of Transport’s coordinated, whole-of-transport approach to accessibility, delivering better outcomes for all Victorians with disabilities, no matter where they live or how they choose to travel. Accessible transport is essential, whether we live in the city, in the outer suburbs or in rural communities.
My responsibilities include:
♦ Providing strategic advice and updates to the Secretary and DOT Senior Leadership on the delivery of accessible and inclusive transport services, and providing regular updates to the Transport Ministers
♦ Monitoring the implementation of DoT’s plans to improve access and inclusion (including the Accessible Public Transport in Victoria Action Plan 2020-2024)
♦ Leading collaborative partnerships to amplify the voices of people with disability and be part of DoT’s decision-making process in our accessibility programs
♦ Participate in a range of committees, forums, and working
groups to ensure accessibility objectives are promoted, understood, and are appropriately considered in transport planning and decision-making
♦ Ensuring the Department is taking a coordinated whole-of-transport approach to building accessibility into its policies and projects
I take a human rights approach to disability inclusion – I firmly believe that if you are funded to provide services to Victorians, that means all of us, not just those to whom it is easy to provide services.
As well as various pieces of Australian legislation, Australia is a signatory to the Convention on the Rights of People with Disabilities (the Convention). Article nine of the Convention requires that people with disabilities have the accessibility necessary to live independently. In relation to transport, this requires:
“…the identification and elimination of obstacles and barriers to accessibility, shall apply to, inter alia:
a. Buildings, roads, transportation and other indoor and outdoor facilities, including schools, housing, medical facilities and workplaces.”
I contracted polio at the age of four months, so I have had a disability for most of my life. I have a paralysed left leg and use a C-Brace orthotic and crutches which enable me to continue walking, but I am also a wheelchair user from time to time. When I have used public transport, I have used a mobility scooter, so I am very familiar with the physical barriers faced.
I also have many friends who are deaf, blind, have cognitive impairments, or who are autistic, so they will keep me informed – just as my elderly parents keep me up to date with how accessible transport is...or is not!
I am a senior member of the Disability Leadership Institute and a member of the NDIS Independent Advisory Council, the Victorian NDIS Community Advisory Council and Fire Rescue Victoria Strategic Advisory Committee. I am a Board Director at Melba Services and at the Urgent Action Fund for Women Asia Pacific Australia.
I was awarded the Medal in the Order of Australia in 2017 for my advocacy work for women with disabilities and I was inducted into the Victorian Honour Roll of Women in 2013.
There are significant economic and social benefits to Victoria from more accessible transport – if I can get to school, college or university, I can get an education that will enable me to seek employment. If transport is accessible, I can get to work and contribute to the economic benefit of Victoria, paying my way and ensuring my continued independence.
We all know that COVID-19 restrictions have caused a downturn in the hospitality sector, but imagine if my community could travel easily into the city for much needed social interaction –to see a show, share a meal or hang out with friends.
Transport has an impact on every aspect of our lives and involves every journey, from the time we leave home until we reach our destination and return. This will include trams, trains, buses, commercial passenger vehicles, ports and roads, as well as how we access the various forms of transport, footpaths, infrastructure, train and tram stations, and methods of communication.
All of us need to connect with the community and that includes people with disabilities. Without accessible transport, we cannot connect to the things that all of us consider essential in a civilized society. We are not only talking about catching public transport, but also the end-to-end journeys that enable our citizenship rights.
I am not here to represent the disability community, I am here to ensure that issues are able to be raised, whether it is a physical barrier, an unfair policy, or attitudinal barrier which prevents full inclusion.
There are many assumptions made about people with disabilities and I am very aware of the ableist world in which we live. Just about every person can tell you of being spoken down to or ignored because our legs don’t work or we don’t communicate like others, of being spoken to loudly because we are blind or deaf, or having people feel sorry for us. We want to be included in the social and economic life of Victoria alongside everyone else.
The change that accessible transport can bring is immeasurable. I look forward to helping to deliver change, drive solutions and identifying how we can make our transport network better for all Victorians.
It’s no secret that the rail construction industry needs more women in its ranks. As a senior leader, Metro Trains’ Lisa Hogben wants to break down barriers for women and people of colour.
In February she took a position as Package Director for the Melbourne Airport Rail project, building a diverse team with an equal representation of women and men.
In a few short months, Ms Hogben created and nurtured an inclusive workplace culture where women and people of colour not only have a seat at the table – they are helping shape the future of our rail network.
When it comes to hiring a diverse team made up of the best people for the job, Ms Hogben leads by example.
Having spent the majority of her career in the rail construction industry in the UK, Ms Hogben was lured to Australia by the prospect of working for an organisation that celebrated and empowered women and diversity.
And of course, she was excited at the prospect of a little more sunshine.
In Metro’s Projects division, women currently make up more than 30 per cent of the workforce, making Metro an industry leader in gender parity.
“Honestly, 20 or 30 per cent of representation isn’t enough – we should be representative of the working population,” Ms Hogben said.
As a divisional ‘Women in Rail KPI Champion’, Ms Hogben is striving for greater gender equality across Metro.
Last month, she was elected to the role of Board Director for the National Association of Women in Construction (NAWIC), and she’s also hoping to ramp up these efforts right across the industry.
In her role at NAWIC, alongside four other elected women, Ms Hogben wants to champion women and people of colour in rail and construction and help them to reach their full potential.
“I want to be a role model for women of colour in the industry and drive initiatives to attract more women from black, Asian and ethnic minority backgrounds," Ms Hogben said.
“I also want to shine a light on the covert, micro-inequalities that plague women and form the ‘lived experience’ that often means they don’t stay in the industry for long.”
In her spare time, Ms Hogben volunteers at the Asylum Seeker
Resource Centre as a Professional Mentor, helping people prepare for entering the workforce in Australia.
“Growing up as the only brown girl in a small town in the UK has an impact on you. Being the only woman or person of colour in a room has an impact on you.”
Ms Hogben said that a stronger focus on hiring women and girls who have strengths outside maths and science but could work in project management, communications, finance, safety and human resources will also help the industry move closer to gender parity.
“Organisations are so much stronger when they hire a diverse workforce with different skills. Even in a smaller team like mine, you can see the benefits are huge,” she said.
The Victorian Government agrees. From 1 January 2022, the new Building Equality Policy came into effect, mandating female representation in some of the country’s most maledominated industries – building, infrastructure and civil engineering.
Under the policy, for major projects valued at $20 million or more, women need to represent at least three per cent of each trade role, seven per cent of each non-trade position, and 35 per cent of management, supervisor and specialist labour roles.
Minister for Public Transport, Ben Carroll, said, “It is positive to see representation of women mandated in the rail construction industry, and to see Metro prioritising the support of women and diversity as part of their business approach."
Ms Hogben is calling on hiring managers and leaders in the rail construction industry to take action.
“We’re the ones with the power to make change. If we keep doing the same thing, we’ll keep getting the same results.”
“When we’re creating our teams, we need to take a step back and ask ourselves – how can we support women and support people from diverse backgrounds and how can we make them a much bigger part of what we’re trying to achieve here?
“There really is an opportunity for everyone.”
A recent panel at the 2021 Critical Infrastructure: Digitisation Series brought together industry leaders from around the country to share perspectives on the digital future of Australia’s infrastructure and the state strategies that are helping us to achieve this.
Moderated by Infrastructure magazine Editor, Jessica Dickers, the panellists included Luke Belfield, Victorian Chief Engineer, Office of Projects Victoria; Louise McCormick, Infrastructure Commissioner of the Northern Territory, NT Infrastructure Commission; and Andrew Curthoys, Digital Relationship Manager, Information Management & Technology, Cross River Rail and Chair, Australasian BIM Advisory Board.
All panellists spoke optimistically about how digitisation and new digital assets hold the potential to steer Australia’s infrastructure sector towards positive outcomes, from improving sector-wide productivity, to boosting efficiency and communication across a single project.
Mr Belfield described the declining productivity of the construction sector relative to other sectors over the last 20 years and how this has been one factor in pushing for digitisation.
“We need to understand why it has been declining, and how to implement digital technologies to really improve or counteract that decline,” Mr Belfield said.
Through her role as Infrastructure Commissioner for the Northern Territory, Ms McCormick acknowledged that unlocking the value of digital technologies and emerging digital assets is certainly a priority shared across infrastructure bodies around the country.
“As our investment commissioner calls it, data is the new oil,” Ms McCormick said, who also noted the focus on digital in Infrastructure Australia’s Australian Infrastructure Plan released last September.
Mr Curthoys drew on his work as the Digital Relationship Manager at Cross River Rail to share how digitisation can unlock improved efficiency across the many stages of an individual project’s lifecycle, such as through the improvement of the flow of data to asset owners.
“My role really involves the transfer of the data that is embedded in all the models to the asset-owning agencies that will ultimately manage the assets on completion of the project,” Mr Curthoys said.
Mr Curthoys presented digitisation as a powerful opportunity for efficiency and improved communication at the project level as the “kernels of information” of a project can be captured just once before entering a workflow where information is handed meaningfully through each stage of a project, for each new part of the organisation to use.
A recurring topic of the panel was understanding existing barriers to the uptake of digitisation across the infrastructure sector, in contrast to ‘pull factors’ that could tip the balance towards digital.
Interestingly, while the panel shared broad agreement on most topics, each panellist also had a unique pull factor for the industry moving towards digitalisation.
For Mr Curthoys, a critical factor is cultural change within organisations and industry.
He said there will be a “big cultural change piece” over the next decade, where “we see more digitally literate people entering the workforce, having expectations that they will be able to access information very quickly, very easily in order to do their jobs.”
“They will also have a level of confidence about the robustness of this information.”
Mr Curthoys argued that both providers and consumers of digital information must “recognise the value of keeping the information alive” by managing it in a similar way to a physical asset.
For Mr Belfield, implementation of digital should always begin with the strength of surrounding processes and policies.
“Digital for the sake of digital is not necessarily a good thing. We need structure – and without that structure, digital is not going to get you to that magic of increased productivity,” Mr Belfield said.
He further emphasised that digital data exists within a complex ecosystem of projects, policies, and governance, and it is imperative to devise mechanisms that “pull people into better practice”.
While Ms McCormick agreed with the points made about the culture change and developing an ecosystem of policies and structures, she also emphasised the value of building digital capability across government, industry, and community.
Drawing on a Northern Territory perspective of digital infrastructure, Ms McCormick pointed to a “deficit or lack of infrastructure” in many parts of Australia, which prevents these regions from exploring some opportunities.
In this sense, Ms McCormick argued that developing new digital assets for the infrastructure sector is a challenge linked to existing public access to digital technologies and opportunities.
Each panelist was in a unique position of being a part of a key digital asset strategy, including the Victorian Digital Asset Strategy, the Digital Territory Strategy and the Australian BIM Strategic Framework, and could speak to the key learnings, opportunities and challenges encountered through their roles.
Mr Belfield detailed how a major achievement of the Office of Projects Victoria was the recent delivery of the Victorian Digital Asset Strategy. He described how the strategy was developed with three different audiences in mind.
The strategic section of the strategy addresses government department heads, executives, and others “who Luke Belfield
plan, deliver, operate and maintain assets”; the organisational section offers guidance to asset owners, operators, and project managers; and the application section offers digital asset guidance “at a project level”.
The strategy will help empower Victoria’s infrastructure sector to build digital into future assets across planning, delivery, and operation, as well as helping the Victorian Government to optimise the digital efficiency and productivity of an ambitious $144 billion infrastructure pipeline.
Mr Belfield also emphasised the importance of knowledgesharing on digitisation with other state and national infrastructure bodies, as well as learning from international partners such as in the UK.
“We have leveraged all the good work in other jurisdictions and have really borrowed some of the elements that we saw worked really well,” Mr Belfield said.
“I don't think our policy would've breached that same level of quality if it hadn't been for all the good work that's already been done in other jurisdictions.”
A recurring theme presented across Ms McCormick’s experiences as Infrastructure Commissioner was that the digitalisation in the Northern Territory, and across all of remote Northern Australia, requires a strong foundation of community capability.
The Digital Territory Strategy is a guide to the skills, knowledge, and capabilities for Territorians to not only keep pace, but to succeed in an increasingly digital world.
“Our digital strategy is really about building capacity to harness those opportunities we have before us, particularly in terms of our proximity to Asia,” she said.
Ms McCormick shared how priority digital projects are embodying the principles of the Territory’s strategy – like Terrabit Territory which is about “upgrading our system from a gigabyte-type bandwidth to a terabyte bandwidth” and would be a first for Australia.
She also emphasised the critical importance of interoperability and “harmonising asset data classes and sets” across jurisdictional lines, through close collaboration with other infrastructure bodies.
“As we get more and more digital … [we must ensure] that we're all working from a similar source of truth, and a similar definition of what those asset classes are.”
Mr Curthoys spoke about his roles at the Cross River Rail project and as Chair of the Australasian BIM Advisory Board.
Regarding the Cross River Rail, Mr Curthoys said the transformational project has embraced the technological requirements and, importantly, the cultural requirements which embed digitisation into the fabric of a project.
“When initially engaging with the construction sector, the contractors and constructors were advised very early on of the requirements and the expectations that have been embedded into the project,” he said.
This encourages an industry culture where requirements surrounding digital assets are firmly built into project contracts.
Regarding his work on the Australian BIM Strategic Framework, Mr Curthoys joined his panellists in calling for greater interoperability of digital approaches across jurisdictions.
“The Australasian BIM Advisory Board recognised that we needed to provide a level of consistency and coordination across all jurisdictions, mindful that Australia is a really small market in the global market,” he said.
Mr Curthoys highlighted an interesting challenge when noting that while “we don’t develop bespoke approaches in each jurisdiction”, interoperability should not come at the expense of innovation.
He also suggested that what happens in the public space should be replicable in the private space, when balancing core values of digital interoperability and innovation.
When asked about digital opportunities that perhaps aren’t getting enough attention, Mr Belfield spoke about the untapped, lateral use of data across different projects.
“I know a lot of the focus is on asset data itself, but there's a whole lot of data that's generated in the development of a project … [which is] a great basis to kickstart the next project as well.
“Capturing all those lessons learned – standard schedules, standard formats, costings, all that project data – in an integrated way and then using it for the next project or even current projects, is something that we should focus on as a huge efficiency.”
Mr Curthoys spoke optimistically about how the Cross River Rail project is laying the foundations for the digital twin, and said that a fully realised digital model, such as a digital twin, ensures that all people working in connection to the physical asset “don’t go looking back to square one” for every new inquiry.
“The Cross River Rail runs through the heart of Brisbane … it becomes a digital spine, if you like, that other projects can link into,” Mr Curthoys said.
Regarding exciting opportunities for digital in the Northern Territory, Ms McCormick spoke of lucrative new digital assets in the region, such as data centers, and highlighted how digital can powerfully provide remote communities with better access to education, jobs, and health services.
“We have a very small population, but we also have a very geographically dispersed population,” she said.
“Many of our remote communities barely have a sealed road to them, let alone a digital connection.
“Digital is really an enabler for those communities.”
Watch the 2021 Critical Infrastructure: Digitisation Series panel on demand at www.critical-infrastructure.com.au/digitisation-on-demand-register/. The Critical Infrastructure Summit will run again in April 2022.
Reliable communications infrastructure is taken for granted by those in large urban centres. The difficulty securing reliable internet and phone services in regional and remote areas is often a limiting factor for new infrastructure projects and a cap on a community’s engagement in the modern world’s growing digital society and economy.
Australian Private Networks (APN) is working to close the digital divide between metro and regional by delivering WiFi internet and phone communications infrastructure to some of Australia’s most remote communities.
Kalumburu Community, on the remote Northern tip of Western Australia, is one of the most recent communities to benefit from APN’s community-wide WiFi and phone solutions.
With limited access to residential internet services, the community has relied on patchy mobile coverage and communal internet at community buildings.
APN has designed, installed, and is now maintaining, community-wide WiFi and phone services for Kalumburu, providing residents and visitors alike with free access to WiFi right across town.
Twelve towers ranging in height from 1.2m to 20m installed across the community extend external WiFi coverage from one end of town to the other. A further access point at the Kalumburu Aerodrome north of the township, provides WiFi coverage to incoming and outgoing travellers.
In addition, 126 houses and community buildings have indoor WiFi coverage through a receiver installed on their roofs. The indoor WiFi transmitters also provide the ability to connect a standard telephone handset, which runs through a community-wide phone PBX telephone solution, much like you’d find in a hotel or motel room.
The internet phone (VoIP) service provides each household with the ability to make free, extension-toextension calls within the community,
plus the ability to make free calls to external national landline numbers and mobile phones.
The town-wide solution utilises four APN satellite internet services controlled by a Site Management Controller (SMC) and remotely monitored by APN to ensure network performance and voice quality.
This versatile solution is modular and scalable, with additional APN backhaul bandwidth able to be doubled without any further hardware required. This can be accomplished remotely, if needed, to support increased future bandwidth requirements. Additional internal receivers can also be installed to support new residences, and APN can install more towers to extend the outdoor WiFi mesh network coverage further out of the community if required in the future. Organisations can configure the community-wide service for other uses, such as on-site communications, employee accommodation, or connectivity to isolated places of interest.
Based in Melbourne, APN is an Australian-owned-and-operated specialist in regional and remote communications that has been at the forefront of new advances in remote Australian communications for nearly 20 years.
In addition to community-wide services, APN offers a range of solutions to facilitate reliable internet and phone communications anywhere in Australia. These can be for long or short-term applications, including portable satellite services mounted to a vehicle, trailer, modular building, or even set up on a standalone mount. APN’s portable service offers remote connectivity that is transportable anywhere you need it.
Connectivity solutions are not onesize-fits-all for town communications infrastructure or remote work sites. APN works closely with customers well before any equipment is supplied to develop the most agile mix of portable and fixed solutions possible to best meet each client’s unique requirements.
‘Safety is everyone’s responsibility’ and ‘everyone goes home safe’ were phrases first promulgated in the 90’s. It was these phrases that got people focused on safety. This safety ethos transgressed the industry: from field, to site, to our offices, and all the way to the board room.
It extended beyond individuals to our friends, peers and colleagues. Now, everyone is empowered to stop the job if they feel it is unsafe, and the CEO and the board are measured on all aspects of safety.
While there is still a way to go, safety outcomes in the industry over the past two decades have never been better. Since the 2000’s, the number of serious injuries resulting in a claim has dropped by more than 31 per cent.*
While there are many factors for this decline, credit should be given to the safety industry’s approach to personal and professional responsibility. Credit should be given to all of us for embracing this in our daily tasks and activities and creating the change we need to see.
This approach – the personification of responsibility – could be applied to other aspects of our industry that urgently
need transformation; mental health, culture, sustainability, capability and capacity, net zero, market risk, and the uptake of digital and innovation. These aspects underpin the productivity and sustainability of our industry, the wellbeing and prosperity of our country, and the infrastructure that serves us and our children. It also supports our own personal futures.
The uptake and consistent use of digital and innovation in the infrastructure sector needs immediate focus. Over the past 30 years, the industry has become 25 per cent less productive compared to other Australian sectors such as mining, manufacturing, retail and transport. A key catalyst of this declining productivity can be directly correlated to our uptake of digital and innovation.
Our sector has one of the slowest adoption rates of technology, innovation and digitally supported ways of working. As of 2022, we are the least digitised sector in Australia. Businesses in our industry are one of the least likely to invest in innovation. *It
The reasons for our low maturity and uptake are difficult to pin down, but could be a mix of culture, how we’re structured, and our general approach and attitude.
It’s fair to say that our current approach to innovation and digital is reactive. Innovation and digital is often applied as a ‘one off’ – pushed in a single contract and not across the project lifecycle. If it is adopted, it’s perceived as a ‘nice to have’ – a ‘flair’ to the project, rather than a key component that underpins the project’s very existence.
The adoption and promotion of digital and innovation, even tools and processes that are widely accepted to add value, are often left to ‘digital specialists’ who speak another language reserved for a select few: metadata, parameter sets, level of information, common-data environments, foundation classes, scripts, asset classification systems.
Anyone that doesn’t speak the language or have the remit is focused on delivering the physical project scope as we have done so for the past 50 years with paper-based drawings, one-off plans, lots of concrete, steel, asphalt, and even more person-hours.
While it’s critical to retain and empower our digital and innovation experts, it should not preclude our own personal responsibilities as engineers, architects, designers, commissioners, operators, and site-based professionals, to look for greater efficiencies brought by digital and innovation.
There are simple things we can do in our day-to-day to advance the industry, such as:
♦ Consider what tasks and activities you perform daily –which of these can be automated or optimised?
♦ Understand where you get your information from, and how it could be specified by you and delivered to you in a more efficient manner
♦ Understand what value you add and how you deliver that value. Could you provide efficiencies to individuals downstream of you by changing how you work or what you handover?
♦ Learn a coding language. There are more simple visual scripting interfaces which could be a good first start
♦ Try new technologies or products. While they may be more difficult to use than what you’re used to, it’s probable they will create greater efficiencies or quality
♦ Spend time with your resident digital expert and seek their advice on how to make your life easier
By moving towards a personal accountability model when it comes to digital and innovation, there are individual and industry-wide benefits, including:
♦ Reducing our more ‘mundane’ and ‘least enjoyable’ tasks therefore increasing our enjoyment and job satisfaction
♦ Creating efficiencies and reducing waste – ultimately resulting in more infrastructure for less
♦ Delivering the same infrastructure both quicker and cheaper by re-using designs, automating tedious tasks, utilising digital to iterate towards the most fit-forpurpose solution, and ensuring information and data is not wasted by transferring from one party to the next without loss
♦ Reducing the likelihood of error or poor decisions that may arise from having a lack of the right information at the right time
♦ Improved assembly of information about our projects, assets, and portfolios leading to higher-quality decisions about the use, application, direction, and scope of infrastructure
♦ Enabling a step-change in productivity brought on by industrialisation, which includes, but is not limited to, modularization, design for manufactured assembly, offsite construction, and long-term/bulk procurement arrangements
By embracing digital and innovation we begin to reap benefits at a personal level: less time on menial/repetitive tasks, less stress, and working less unpaid overtime. Working smarter, not harder, means more time with the ones we love.
Governments can accelerate this transition towards ‘digital by default’ through policy, capability and capacity, and better utilising their buying power and contracts. Governments can establish both digital asset and project requirements that prioritise data and information structure, re-use, and openness.
Contracts could be transitioned away from arms-length, hard dollar arrangements that include requirements for paperbased, vector-based, drawings of what is being delivered. We should move towards three-dimensional models that geometrically mirror the asset. Information generated through the project lifecycle can be maintained in the most native and accessible format and re-issued to parties working on the asset in the future. A greater emphasis and focus should be placed on generating structured data that can be re-used with confidence in the future.
Digital experts have a role to play as well. We can start with making the language more accessible and reducing the number of bespoke acronyms. A stricter focus should also be maintained on use-cases and value.
Learning new skills, parlance, and approaches is personally taxing. It is made more difficult by idiosyncrasies of our industry: compressed timelines and stressful work environments that do not readily accept failure. Employers and senior decision-makers across industry can increase the uptake by establishing an environment where individuals are allowed to learn and try new things. This may be as simple as training or more complicated like reviewing workflows and actively seeking opportunities to digitise them.
Looking ahead, our industry is coming to a crossroad. While we generate so much economic and societal value – we are at risk of being left behind. Digital and innovation can help us respond to the elevated pipeline – delivering it as required, on time, on budget, safely. Failure to deliver the pipeline will erode our industry's credibility and detracts from future investment. While we’re making some progress in digital and innovation, acceleration is needed. We can, and should, look to other parts of our sector such as safety, and apply learnings that have created a step-change in culture, process, and attitude. In health and safety, it’s very common to have toolbox meetings to share our observations, near misses and lessons learned. Maybe we could start to build this into our vernacular for digital and innovation.
Perhaps it’s time to start promoting sayings that propagate personal responsibility: ‘Digital is everyone’s responsibility’ and ‘digital by default. Perhaps there’s even a future where a job will be stopped because they issued a 2D drawing in PDF.
With the impacts of COVID-19 wreaking havoc on Australia’s freight transport and logistics sector, customers are waiting longer to receive orders, experiencing purchasing limits for essential goods, and staring down empty grocery store shelves. Here, Infrastructure spoke with Australian Mobile Telecommunications Association (AMTA) CEO, Louise Hyland, to discuss five opportunities that 5G presents to streamline processes and alleviate pressure on the industry.
With data transmission rates approximately 100 times faster than 4G networks, 5G can provide a significant boost to freight operations.
AMTA CEO, Louise Hyland, said the pandemic has exacerbated demand for a fast and reliable connection.
“To meet this demand, some providers fast tracked their investment towards the 5G rollout,” Ms Hyland said.
“As 5G becomes more and more available, the technology will address consumer expectations of the industry by meeting shorter timeframes, more specific forecasting and greater transparency around the status of goods being transported.”
ATMA’s Infrastructure Readiness Assessment report encourages governments to review policies to ensure the country is ready to deploy 5G infrastructure.
“With the continued rollout of 5G across the country and the world, the transport and logistics industry will rapidly change over the next decade and into the future,” Ms Hyland said.
“It will not only become more efficient and reliable, but it also has the opportunity to become more profitable, with less human error, mismanagement and inefficiencies.
“It is increasingly important that state and territory planning policy makers recognise the essential nature of telecommunications services and the rapidly-evolving dynamic requirements for network deployment and upgrade.
“Otherwise, Australia’s networks will fall behind and hinder economic growth and social connectivity.”
With the pandemic driving interest in increased automation and future technologies, here are five ways that 5G infrastructure will help drive the industry forward.
Freight transport can be made more efficient with automated vehicles, such as cars, trucks, trains and drones. These vehicles are safer and more efficient when underpinned by a fast and reliable 5G network.
“5G will improve the reliability of last-kilometre travel – the last leg of a product or passenger’s journey – and so-called ‘vehicle-toeverything communication’, including communication between vehicles and the traffic system, across both commercial and public systems,” Ms Hyland said.
Trials of 5G communication links to automated cargo vehicles are already underway in Australia, with logistics operator Qube connecting vehicles at Moorebank Logistics Park to the fleet management and safety system.
Ms Hyland said the COVID-19 pandemic has highlighted the value to be gained through greater automation in smart factories and warehouses.
“5G’s high capacity will enable real-time insights that will facilitate greater automation in areas like multiple assembly lines, and allow machines and assets to connect through the Industrial Internet of Things (IIoT) so operations can be monitored and optimised,” Ms Hyland said.
Assembly lines could also be augmented by using 5G-powered AI to create predictive planning, increasing efficiency for warehouse inventory management and just-in-time delivery.
A trial program in Germany, conducted by DHL, uses a system with 5G-enabled IoT technologies to build a real-time map of operations, so they can create custom solutions to solve inefficiencies.
Ericsson’s smart factories in Sweden, Estonia and China currently use 5G and IIoT systems to connect almost every factory asset to a single system, streamlining processes and increasing efficiency.
As the transport and logistics sector looks to integrate Virtual Reality (VR) and Augmented Reality (AR) to improve operations, 5G is able to support its future use with faster speeds.
VR and AR technologies can be used to train employees in safe, controlled environments, without disrupting real operations.
“Through 5G, AR applications like ‘vision picking’ – which involves displaying order information to warehouse staff through head-mounted displays – will be enhanced, impacting productivity for the better,” Ms Hyland said.
“Machine and vehicle maintenance will also become more efficient, with offsite technicians able to assist workers using AR headsets to monitor the status of their fleet in real time.”
With an advanced 5G network in operation, future VR and AR technologies in development, such as Microsoft’s Mesh, could be more easily accessible and available to the industry.
Robots are making tasks easier across the supply chain, and 5G’s high capacity and speed enables them to make processes significantly more efficient.
Ms Hyland said that robots “will help workers with housing operations and enhance safety by reducing the need for people to physically carry out injury-risking or challenging tasks, like repetitive lifting”.
Autonomous robots are already in use for Swedish telecommunications company, Ericsson, which has trialled a 5G-enabled mobile robot, which patrolled the perimeter of Hans Christian Andersen Airport in Denmark.
The robot demonstrated that boundary-fencing checks at a range of critical locations, such as ports and construction sites, can be conducted with autonomous technology.
With 5G-supported technology, goods tracking will become more accurate and reliable. 5G allows the location of goods to be monitored in real time, allowing for continuous condition assessment.
“The billions of connections that will be supported through 5G means that trackers will make a difference in improving the tracking of the location and condition of goods in real time throughout every aspect of a supply chain, making delivery more efficient and resilient,” Ms Hyland said.
“This will allow transport and logistics companies to provide accurate real-time updates on delivery progress at any time, not just at a few key checkpoints, while also mitigating problems like delivery delays or cold storage faults.”
Internet of Things (IoT) technology is already being used by Peloris Global Sourcing to monitor goods during transport.
The technology is monitoring the temperature of milk being exported from Australia to China, ensuring compliance and allowing for faster, less disruptive travel.
“Using 5G, this technology could become more readily used across the entire industry,” Ms Hyland said.
By creating a virtual reproduction of our physical environment, digital twins have proven to be immeasurably useful to Australia’s infrastructure industry. Thousands upon thousands of these models exist — but what if these datasets could be merged into a single, more powerful, adaptive model?
Digital twins are extremely valuable infrastructure planning tools, providing a 3D replica of our physical world so that costs, time and potential disruption estimates can be made. But an even more accurate and comprehensive 4D model, which factors in timeframes, is on the horizon.
In his keynote presentation at the 2021 Critical Infrastructure: Digitisation Series virtual event, Wayne Patterson, Director of Spatial Operations, Spatial Services at the NSW Department of Customer Service, explained how spatial digital twins build upon existing datasets to create a 4D model which allows for more informed infrastructure planning.
Mr Patterson explained that the NSW Spatial Digital Twin (SDT), which builds on the existing Foundational Spatial Data Framework (FSDF), has allowed the state to gain greater insights into the physical environment, resulting in more effective decision-making.
The NSW SDT was launched in February 2020 for the Western Sydney City Parkland district across about 8,825km2, an area of significant infrastructure growth. The SDT, which forms part of the Live.NSW program, is able to link with existing digital twins, engineering designs, datasets and plans, and can model how they will interact with each other.
“Through the SDT, we’re able to visualise, analyse, contextualise and model scenarios, real-life events, and enable a more informed decision-making process,” Mr Patterson said.
“Data and digital transformation has become central to our society. The functions of government, the development of industry and research all rely on data and insights.
“The NSW SDT is key infrastructure to enable our digital economy and digital society, and is the pathway to Smart Precincts, Smart Cities, Smart NSW.
“The SDT provides a federated single source of truth for government-held data as well as a collaboration platform for government, industry and the community to communicate and engage.”
The SDT delivers foundation spatial data which can be used to inform work in the development and planning stages. Foundation spatial data consists of 300 key datasets which span transport networks, digital elevation models, and aerial imagery in 3D and 4D (time).
Mr Patterson said one of the pillars of the spatial digital twin program was that it acts as a single source for reliable data that is produced by a data custodian or organisation.
“It’s authoritative and replaces highly variable data interpolation by allowing consistent data inputs and processes,” Mr Patterson said.
Mr Patterson said the richest data was of little use unless it’s quickly, simply, easily and securely available. He gave the example of an organisation using its own purpose-built application, with unsuitable baseline data.
“Any models developed on that data may not have a reliable fit for real-world applications and could not interact with the data that is surrounding it. Spatially-enabled digital twins drive the need for better access to high-quality data,” Mr Patterson said.
“By being able to provide our foundation spatial data to the organisation, they were able to consume that into their application, industry standard data APIs, do their modelling, do their planning, and republish a model back into the ecosystem where there was the ability for it to actually plug in and play with all of the other information that was in there.
“That’s why one of the key considerations in terms of connecting data and establishing the relationships and dependencies and constraints was role-based access to information with the NSW ecosystem, where we can make data publicly available.”
The NSW SDT isn’t just expected to provide more accurate, detailed digital mapping, but also to help with more efficient project delivery.
With the capacity to improve decision-making at the planning stage, the NSW SDT is potentially able to reduce infrastructure costs and timeframes, resulting in benefits estimated at $1.24 billion over ten years.
Savings within the property development pipeline alone, Mr Patterson said, could reach $300 million annually.
“Imagine when you start looking at the engineering sector, in terms of this, having digital models of engineering assets that are able to plug in and connect to the spatial digital twin, leverage the Internet of Things (IoT),” Mr Patterson said.
“The NSW SDT isn’t just static information, it’s real-time information as well. Real-time transport feeds, real-time monitoring and measuring of water pressures for water mains, real-time measuring of temperatures and humidity, and all of the other sensors that are available.
“The ability for us to be able to build up that holistic view of what is actually happening at any particular point in time in the communities we live, or an area that we are interested in, is really, really powerful.”
The NSW SDT is helping the state deliver a number of strategic priorities by using data inputs to create recommendations and support informed decision-making.
The program is able to align these priorities, streamlining communication and supporting strategy integration.
“Instead of having an independent Future Transport Strategy 2056 and a State Infrastructure Strategy, Tech Central Strategy, or whatever the strategies are, being able to integrate and bring them all together allows that alignment and that greater appreciation of how we can better manage, plan and deliver and respond to anything that happens across our state,” Mr Patterson said.
The NSW Spatial Digital Twin will soon provide a 4D model (3D plus time) for the entire state thanks to a $40 million investment from the NSW Digital Restart Fund (DRF).
The future implementation of the program will require system transformations, such as moving information into the cloud, providing monitoring and management, and system migration.
“We are looking at a complete 3D and 4D time-enabled set of foundational spatial data across the state that is available to all, to leverage in their own applications, for their own purposes,” Mr Patterson said.
“We will be developing system and workflow integration of that 3D and 4D data so that it is useful and has purpose for our stakeholders and for our users.”
Watch Wayne Patterson’s presentation at the 2021 Critical Infrastructure: Digitisation Series panel on demand at www.critical-infrastructure.com.au/digitisation-on-demand-register/. The Critical Infrastructure Summit will run again in April 2022.
There’s a lot happening in the road infrastructure space across Australia. Here, we take a look at some of the biggest road projects around the country and their progress to date.
WestConnex is Australia’s largest road infrastructure project linking Western and South Western Sydney with the city, airport and port in a 33km continuous motorway.
WestConnex also links Greater Sydney to major international gateways at Sydney Airport and Port Botany, and the future Western Harbour Tunnel, BeachesLink and F6 extension.
The Australian Government has committed $1.5 billion in funding to deliver WestConnex in partnership with the New South Wales Government, and the estimated project cost is $16.8 billion.
Construction commenced in March 2015. The M4-M5 Link Project is the final and most critical component of WestConnex, and is being delivered in two stages with construction starting in 2018.
Stage 1 involves the construction of the M4-M5 Link Tunnels between the New M4 at Haberfield and the M8 at St Peters and stub tunnels to the Rozelle Interchange. The contractor on this stage is Acciona Samsung Bouygues Joint Venture.
Stage 2 involves the construction of the Rozelle Interchange and Iron Cove Link. The contractor on this stage is John Holland and CPB Contractors Joint Venture.
The M4-M5 Link Tunnels are expected to be open to traffic in 2023.
The 15-year Bruce Highway Upgrade Program is a $13 billion program of works to improve safety, flood resilience and capacity from Brisbane to Cairns.
The 1,700km highway is Queensland's major north-south road corridor, connecting coastal population centres and supporting around 58 per cent of Queensland's population.
Projects along the route include major upgrades and realignments, strengthening and widening type works, plus a range of safety and efficiency measures to target poor crash sites and to provide additional overtaking lanes and rest areas.
Several projects have been successfully completed, such as the $932 million Sunshine Motorway upgrade.
A 10.5km upgrade and duplication of the Bruce Highway between Edmonton and Gordonvale is currently under construction. The project is Stage 3 of the Cairns Bruce Highway Upgrade Master Plan and construction is expected to be completed in 2023.
The West Gate Tunnel project involves the expansion of the West Gate Freeway in Melbourne, including the construction of twin tunnels under Yarraville and a bridge over the Maribyrnong River.
The $6.7 billion project is being executed by Transurban and the Victorian Government.
A consortium of John Holland and CPB Contractors was contracted to build the project and pre-construction works began in January 2018.
Construction was stalled in 2019 due to an inability for stakeholders to agree on where contaminated soil from the tunnel’s predicted location would be transferred to.
In June 2021, it was decided that the soil would go to Hi-Quality’s landfill site in Bulla, and construction has since resumed with the expected completion date pushed back to 2024.
TONKIN CORRIDOR UPGRADES
The Western Australian Government is undertaking improvements to the Tonkin Highway corridor, a 44km north-south highway and partial freeway in Perth, linking Perth Airport with the city's north-eastern and southeastern suburbs.
Construction commenced in January 2021, with the estimated cost approximately $1.2 billion.
The Tonkin Highway Corridor project will be delivered under two contracts. The first contract includes the intersections along Tonkin Highway at Hale Road and Welshpool Road, and the second contract includes Tonkin Highway and Kelvin Road
The Request for Proposals for construction is expected to commence in mid-2022.
GAS INDUSTRY ROADS UPGRADES
The Gas Industry Roads Upgrades will upgrade priority sections of roads in the Northern Territory to support the development of gas resources in and around the Beetaloo Sub-basin.
Road upgrades will include strengthening and widening, flood immunity works and road safety improvements.
The upgrades are expected to provide crucial enabling infrastructure for the gas sector as well as support industry and business by providing more reliable freight links.
The Australian Government provided $173.6 million in funding for the corridor, and the Northern Territory Government Contribution provided $43.4 million.
This project is expected to start construction in early 2023 and be finished by late 2026.
The Coomera Connector will deliver an alternative transport corridor between Loganholme and Nerang to complement the function and role of the Pacific Motorway (M1), Queensland’s busiest road.
The Stage 1 section of the Coomera Connector between Coomera and Nerang has been identified as the priority section to be built first. Stage 1 is expected to support 1,000 jobs over the project’s life.
Coomera Connector (Stage 1) is around 16km, and will be delivered in three construction packages. An
early works package is underway, with road construction expected to begin from mid-2022.
In November 2021, a contract was awarded for Coomera Connector Stage 1 North. Acciona Construction Australia and Georgiou Group Joint Venture, with WSP and BG&E as the designers, will undertake enabling works and finalise the design for the project.
Enabling works began on the northern section between Coomera and Helensville in January 2022, marking the start of Stage 1 works.
The Australian Government and Queensland Government have committed a total of $2.16 billion (on a 50:50 basis) to plan and construct Coomera Connector Stage 1.
The Great Western Highway is one of Australia’s most historic roads and a key east-west connection out of Sydney.
In 2019, the New South Wales Government committed $2.5 billion to the duplication of the Great Western Highway between Katoomba and Lithgow.
In 2021, the Federal Government committed a further $2.03 billion towards upgrading the Great Western Highway between Katoomba and Blackheath, and between Little Hartley and Lithgow.
In November 2021, the Review of Environmental Factors (REF) and concept design for the project were released.
Contracts include the Detailed Design and Environmental Assessments (Eastern Section), which was awarded to Aurecon, and the Detailed Design and Environmental Assessments (Western Section), which was awarded to an Arcadis-Jacobs Joint Venture.
Construction is set to begin in 2022, and expected to be completed in 2030.
In a project of unprecedented scale and complexity, the entire Abu Dhabi Emirate is to be served by a state-of-the-art, all-in-one transport modelling framework, built on the pillars of big data, integrated multi-tier modelling, and visualisation.
The availability of huge new datasets is driving rapid advancements in approaches to transport modelling for planning and operations. At the Abu Dhabi Integrated Transport Centre (ITC), new data is being leveraged to update the existing Strategic Transportation Evaluation and Assessment Model (known by the acronym of STEAM) to STEAM+.
STEAM+ is a state-of-the-art, all-inone transport modelling framework which integrates the existing strategic modelling approach with new hybrid dynamic models and near-real-time transport simulation from Aimsun.
The STEAM+ model was recently recognised for innovation in multimodal transport demand forecasting when it won the award for Best Transport Planning Management System at the 2021 Global Economics Awards.
The award-winning framework allows assessment of any type of transport scheme, ranging from specific intersections to large infrastructure studies, transit corridors and policy tests. In addition, the multi-tiered STEAM+ framework complements the current regional strategic model with more detailed, dynamic assessment of flow metering at junctions, traffic queuing, ITS and emerging technologies, bus priority schemes and light rail (LRT) delays at junctions.
Abu Dhabi ITC is linking big datasets, including day-to-day anonymized mobile phone tracking, water/ electricity consumption by household, live bus and taxi fleets, building and plot level municipal data, as well as a comprehensive population and employment data set.
This is a hugely ambitious project on a never-before-attempted scale, covering the entire Abu Dhabi Emirate. In terms of scale, the model covers an area spanning 67,000 square kilometers with a population of approximately three million people. The area has a hugely diverse range of infrastructure and development, from rural highways and towns, to mid-sized inland cities such as Al Ain, and, of course, the Emirate capital of Abu Dhabi with its densely populated central business district.
ITC required a transport model framework with multiple levels of assignment and simulation that is flexible and extensible enough to accommodate future needs.
Set up by the Aimsun team, the Hybrid Simulation Model will enhance ITC’s modeling capabilities, adding a tiered simulation model alongside the strategic demand model within the STEAM+ framework.
The Hybrid Simulation Model allows rapid simulation of specific network areas, and accurate representation of congestion, flow metering, ITC’s technology interventions, bus priority assessment and LRT delays at junctions.
Additionally, dynamic linkages to the ITC Data Warehouse will allow rapid modeling of specific days based on the latest count and movement data.
The framework takes an integrated approach, which offers major advantages in speed and consistency when compared with creation of independent local networks in multiple software packages. The coded network allows rapid development of local area simulations within the same software platform, using a single network representation, together with consistent simulated travel behaviour and routing.
The Aimsun team set up and calibrated the model network, demand model linkages, and dynamic linkages to the Data Warehouse. The highly detailed transport network was derived from the comprehensive Navigable Road Network (NRN) dataset. This representation of the transport infrastructure was further refined using aerial imagery and CAD, and then supplemented with detailed information on traffic signal operations.
Using detailed data provided by the Traffic Management Centre, the Aimsun team coded explicit representations of the traffic signal control cycles, and the variation in plans for different days and types of day into the model.
The consistency with, and linkage to, the demand model, ensures transferability of information between models and avoids competing and potentially conflicting representations
and outputs. Aimsun processes allowed a data-driven derivation of different demand patterns for different types of day. Inventive use of automation procedures and scripting enabled processing of this quantity of information and maintenance of close linkages to the demand model.
The Hybrid Simulation Model is dynamically linked to the ITC’s newly developed Data Warehouse. This dynamic link allows fresh count data and trip origin-destination data to be input directly into the model for simulation. Results are evaluated by automatic validation plots.
The Hybrid Simulation Model within STEAM+ provides ITC with a framework for testing schemes and interventions with the appropriate level of detail within much reduced timeframes and with a consistent model representation. Another benefit is visualisation of the road traffic, which is key for communicating results to stakeholders and the general public.
The dynamic link between the model and the Data Warehouse allows accurate simulation of specific days or special periods, such as Ramadan. It also simplifies model updates and transfer of detailed information from the Hybrid Simulation Model to the Demand Model.
Ongoing support is included in the solution to ensure successful knowledge handover and plan the future road map for the model framework.
A close working relationship between Aimsun, Abu Dhabi ITC, and other stakeholders ensures that the best use continues to be made of the wide range of datasets available, and that modeling processes are efficient, repeatable, and easy to update.
The $9.9 billion Torrens to Darlington (T2D) Project is entering an exciting new phase following the release of the motorway’s Reference Design, with residents and businesses playing an increasingly important role in shaping how it will be delivered.
The project is talking directly with industry to maximise opportunities for local businesses, and a targeted round of grassroots community consultation on the design is underway to ensure major benefits are delivered for neighbourhoods near the new motorway.
The T2D Project will complete the final 10.5km of the 78km North-South Corridor spanning Greater Adelaide, and is the biggest road infrastructure project in South Australia’s history, supporting more than 4,900 jobs during peak construction.
Once finished, the T2D will reduce traffic congestion by taking 130,000 weekday vehicle movements off heavily congested South Road and into tunnels. This will improve travel times by about 20 minutes to deliver a nine-minute journey between the River Torrens and Darlington.
About 60 per cent of the motorway will be in two sets of twin three-lane tunnels: the 4.8km Southern Tunnels and the 2.2km Northern Tunnels.
These will be built by some of the largest tunnel-boring machines (TBMs) used in Australia, which are planned to operate continuously once launched.
The TBMs will progress 8-10m a day, which means they will be tunnelling under most properties for only two to three days.
The depth of the roadway in the tunnels will vary, with the deepest point in the Southern Tunnels being about 50m underground and in the Northern Tunnels around 30m.
The diameter of the tunnels will be almost 15m – roughly the height of the famous Thebarton Theatre in Adelaide’s western suburbs, under which the tunnels will pass.
The Executive Director of the North-South Corridor, Susana Fueyo, said the publication of the Reference Design on 28 November 2021 was a critical project milestone.
“The Reference Design shows how the motorway will operate as a whole and how it will save over 480 properties, avoid impacting any significant heritage site along the corridor, bypass 21 sets of traffic lights and unlock 78km of free-flowing motorway,” Ms Fueyo said.
“The project will generate long-term benefits for the entire state, and the design creates an unparalleled opportunity for communities to revitalise and reshape their neighbourhoods.
“Thousands of South Australians have provided feedback about the design after looking at the plan on the T2D website, attending Community and Business Reference Group meetings, or visiting displays and information kiosks across Adelaide.
“Their valuable perspectives and suggestions are now being considered as part of the Project Assessment process of the T2D Project.
“This vital new phase ensures that robust environmental, social and engineering investigations are undertaken to identify potential impacts that will be used to inform the detailed design.”
Another avenue for community input is the T2D’s City Shaping Strategy, which will work with locals to enhance those suburbs near the planned motorway by strengthening cycling connections, upgrading parks and reserves, and improving community facilities and green spaces.
The strategy will see a $125 million dedicated fund to carry out selected projects, developed in consultation with the community, with further details of the program expected to be announced early in 2022.
“As well as delivering a new world-class motorway, the T2D Project offers people a chance to rejuvenate their own neighbourhoods, and to make them even greener and more liveable,” Ms Fueyo said.
On the industry engagement front, the Department for Infrastructure and Transport is continuing to consult with business in the lead-up to the release of the first tenders for construction work.
“The scale and complexity of the T2D Project means the scope for industry involvement is immense,” Ms Fueyo said.
“About $104 million worth of contracts – supporting a total of 287 jobs – have already been awarded to carry out enabling works, such as ground investigations.
“But from here, the value and breadth of the contracts will increase astronomically as we move closer to the beginning of major construction.
“To build this motorway, we’re going to need about 100,000 tonnes of steel, 470,000 tonnes of asphalt, two million tonnes of quarry products and 760,000 cubed metres of concrete.”
In late 2021, the T2D Project undertook an intensive “market-sounding” campaign with more than 100 businesses, exploring issues such as the “packaging” of works, contract form, the supply of labour, and the capabilities of construction contractors and service providers.
“Those market-sounding conversations are continuing in early 2022, with the T2D Project likely to issue its first expression of interest in the third quarter of this year,” Ms Fueyo said.
The design for the T2D Project means 21 sets of traffic lights will be bypassed and up to 480 fewer properties compulsorily acquired than had other options had been chosen.
Currently, 16 per cent of all trips across Greater Adelaide rely on a section of the T2D Project or its adjacent parallel alternatives, and 96 per cent of people live within 30 minutes of the North-South Corridor.
Travel time variability on South Road is up to six times higher than the Adelaide average, and five times worse than Sydney and Melbourne averages during peak.
The South Australian and Australian Governments have already allocated $5.4 billion towards the T2D Project, for delivery of the Anzac Highway to Darlington section and pre-construction activities for the entire project. Major construction is expected to commence in late 2023, with the T2D completed in 2030.
As with any industry, the transport and infrastructure sector requires a degree of social licence to operate.
In a world where customers have access to more information than ever before and have the power to amplify their views via social media channels (which are themselves a rich vein of source material for traditional media outlets), it is increasingly important for our sector to ensure we are reflecting the expectations, values and aspirations of the communities we serve.
Roads Australia is keenly aware of this prevailing view, with the decarbonisation of the economy through integrated transport and the efficient use of resources and energy one of key policy goals set out in our Strategic Plan.
Although sustainability has certainly been a focus for industry and governments for many years, the degree of importance attached to it by the wider community has grown significantly over recent times. It is very much now a mainstream issue which is a key focus across all demographics and shades of political opinion.
Consequently, the drive to decarbonise the transport sector is set to be a defining characteristic of public policy in the next decade.
This poses a significant challenge for those engaged in the design, construction, maintenance and operation of integrated transport infrastructure. This is because historically, the community has perceived private vehicle use to be a major factor in increased emissions, road construction to be disruptive and having a deleterious impact on community amenity, and that environmental considerations were not paramount when sourcing materials used to construct transport infrastructure.
Perhaps some of these perceptions were justified in decades gone by. However, as the salience of sustainability has grown across the wider community, our industry has leaned on its innovative capacities and adapted to deliver transport infrastructure and services in new ways. Accordingly, contemporary transport infrastructure not only has a reduced impact upon the environment but is demonstrably contributing to an enhanced quality of life for local communities.
As with anything, good outcomes in transport infrastructure start with good planning. If the full economic, environmental and social value of transport infrastructure is to be realised, it is vital to consider how we use neighbourhood spaces in a way that optimises the space and promotes people’s health, happiness and well-being.
This focus on placemaking is a hallmark of the contemporary approach to delivering integrated transport infrastructure and services. It means ensuring communities are developed in a manner that facilitates access to active transport options (such as dedicated walking and cycling paths), and promoting the use of public transport services by making sure residents can safely access reliable services.
But beyond this, Australia has a major opportunity to drive decarbonisation in the transport sector by embracing opportunities on offer through the circular economy. In particular, there is major scope to reduce embodied emissions – that is, emissions generated via the production of construction materials, as well as the construction process itself.
This is one area where the industry itself has been taking a lead, with recycled products becoming increasingly prevalent in the transport infrastructure sector.
Of course, this is not a new development; our industry has been recycling asphalt and crushed concrete for decades. However, there is an increasing awareness among industry participants about the need for a more systemic approach, which reframes discussion about ‘waste’ to instead talk about ‘resources’.
Within this, there is also a need to focus on practical, cost-effective innovation that is still needed to drive down the cost of some recycled materials, which can still be more costly than virgin material if examined from a traditional bottom-line perspective.
Broadening this focus and integrating whole-of-life thinking into our approach to planning, designing, procuring and constructing Australia’s transport infrastructure is essential to drive better sustainability outcomes across the industry and for the community.
This imperative is reflected in Infrastructure Australia’s 2021 Australian Infrastructure Plan, which calls for governments to support the increased uptake and consistent use of recycled and recyclable materials. This includes incorporating targets in building and design codes and developing procurement targets and timelines for government infrastructure projects.
There are also an increasing number of high-profile major transport infrastructure projects being completed that are demonstrating the way forward. Late 2021 witnessed the opening of Victoria’s Mordialloc Freeway, which has garnered a reputation as the nation’s greenest freeway.
This project used around 800,000 tonnes of recycled and reused materials, with the centrepiece being 10,000 noise wall panels made with 570 tonnes of plastic waste. Around half of the recycled plastic used was hard plastics from kerbside recycling (such as milk and shampoo bottles), with the balance being derived from soft plastics (like food packaging). These recycled plastic noise walls are a world first and demonstrate our industry’s innovative capacities, as well as its commitment to embedding sustainability in new transport infrastructure.
Roads Australia is delighted to now be working with the Australian Railway Association and the Infrastructure Sustainability Council in an industry-first partnership working to finalise a report that will showcase best-in-class initiatives and make policy recommendations that will help Australia achieve net zero emissions by 2050.
The report – which has been undertaken by KPMG and is being supported by report sponsor Arup – will outline a series of actions to support a focus on place, drive emissions reduction, support investment in renewables and EV infrastructure, and promote engagement and collaboration across the transport asset lifecycle.
The recommendations and case studies that will be included as part of the report have been developed through engagement with industry to identify the challenges and opportunities facing the transport sector.
This industry partnership was born of a recognition that strong collaboration across all modes of transport, and between governments and industry, will be needed to deliver on global sustainability goals and community expectations.
Roads Australia is looking forward to playing an active role in progressing this agenda in collaboration with our members and the wider industry.
After years of planning and consultation with the community, work is progressing on building the missing link in Melbourne’s freeway network.
Scheduled for completion in 2028, North East Link will connect the M80 Ring Road to an upgraded Eastern Freeway, slashing travel times by up to 35 minutes and taking 15,000 trucks off local roads daily.
Along with Victoria’s longest road tunnels, the North East Link Program will overhaul the Eastern Freeway, deliver Melbourne’s first dedicated busway, complete the M80 Ring Road in Greensborough and build the North East Trail – more than 34km of walking and cycling paths.
An $11.1 billion contract has recently been awarded to the Spark consortium to deliver the North East Link tunnels.
During 2022, the project team is setting its sights on completing its big program of early works, getting to work on the tunnels and putting the freeway upgrade packages out to market.
There are already more than 1,000 people working on North East Link, and the project is set to create more than 10,000 jobs, with an estimated 8,000 jobs on the tunnelling package alone.
North East Link CEO, Duncan Elliott, said with more than half a million Victorians living within two kilometres of a planned North East Link interchange, the project will change the way people move around Melbourne and connect people to jobs and education.
“At the moment, anyone travelling between the east and north of Melbourne has a lengthy and unpredictable journey that can take anywhere up to 90 minutes and sometimes even two hours as drivers have to leave the freeway network and weave along congested local roads,” Mr Elliott said.
“North East Link will shift this traffic into the new tunnels, providing a quicker and easier link for 135,000 vehicles a day – slashing travel times and leaving local roads for local trips.”
Mr Elliott also said with the strong growth expected in Victorian and Melbourne freight over the next 30 years, North East Link is critical to help businesses get goods where they need to go and clear residential areas of heavy truck traffic.
“The project will increase productivity for businesses by linking farms, industrial areas and distribution centres in the south east with the Hume Freeway and key destinations in the north, including markets, freight hubs and Melbourne Airport,” Mr Elliott said.
“For a tradie in Bundoora, it will open up jobs in Doncaster. A small business in Dandenong can access warehousing in Tullamarine and a student from Glen Waverley can get to university at La Trobe.”
In a major milestone for the project, updated designs for North East Link were released in October 2021, including a longer tunnel to Watsonia. Simpler underground interchanges create more space for a new tree-lined boulevard for Greensborough Road and more than 50 MCGs worth of new, revived and reconnected parklands.
It’s a significant design update, and one that shows careful consideration of the legacy this project will leave for the north-east.
The M80 Ring Road will also be completed, with new lanes, smart technology and a seamless interchange with North East Link.
Improved technology on the Eastern Freeway and more than 45km of new lanes will work together to slash travel times by up to eleven minutes.
The Eastern Express Busway will make it quicker and easier to get to and from
the city on public transport, with new parks and rides at Bulleen and Doncaster and a bus every minute in peak times.
Plans for the North East Trail have been expanded, with 34km of new and upgraded walking and cycling paths linking the north east to Yarra River trails and parklands.
Mr Elliott said that the local community has played an important role in the project’s designs.
“We started talking to the community early – their local knowledge, combined with our team's engineering and planning expertise, is ensuring we understand local issues and get the best outcomes,” Mr Elliott said.
“We will continue to work closely with the community, and in the coming months there will be opportunities for local people to comment on local elements of the design when we start exhibiting urban design and landscape plans.”
North East Link will create more than 10,000 jobs with more than 1,000 people already working on the huge program of works.
The North East Link Skills and Jobs Centre is now open in Watsonia, providing a one stop shop for local workers, jobseekers and social enterprises looking for opportunities with North East Link.
Mr Elliott said that the sheer scale of job creation on North East Link created a great opportunity for the next generation of workers with apprentices, trainees and cadets to play a huge
part in delivering the state’s biggest road project.
At least ten per cent of construction hours on North East Link will be worked by apprentices and trainees, linking people from the classroom to the workforce. The project will also employ a range of priority jobseekers, encouraging more women in construction and helping to build the next generation of skilled Aboriginal talent with a 2.5 per cent Aboriginal employment target.
“We’ll be creating local jobs for local people with a huge range of roles needed to plan, design and build North East Link. We’ve worked with Apprenticeships Victoria to launch our dedicated Skills and Jobs Centre in Watsonia to connect locals to training and job opportunities on the project,” Mr Elliott said.
The project will also make use of the Australian-first Victorian Tunnelling Centre that has been set up with Holmesglen Institute to support the state’s unprecedented pipeline of transport projects.
Since 2020, the project’s big early works program has been moving major gas, power and sewer lines out of the way of North East Link, undertaking soil testing, and upgrading community facilities for sports clubs that need to relocate during construction – including a major $21 million investment in a new 18-court tennis centre in Glen Waverley.
This year will see North East Link complete its early works and continue to build the Bulleen Park & Ride – the first part of Melbourne’s Eastern Freeway busway.
Local sporting clubs will benefit from the upgraded facilities the project has built, while North East Link shifts its focus to building Victoria’s longest road tunnels and goes out to market for the next major elements of the project, including a massive overhaul of the Eastern Freeway and the completion of the M80 Ring Road.
It's part of an approach to use the market efficiently, allowing a range of contractors to deliver parts of the project – from international Tier 1 companies, through to Tier 2 and 3 and smaller sub-contractors – to utilise the full capability of the market.
“A project the size of North East Link doesn’t come around very often and that’s why we’re making the most of the opportunities this presents – whether that’s by training the next generation of workers, providing opportunities for local companies or delivering better designs for the community with more open spaces,” Mr Elliott said.
“It’s an exciting time to be part of this project that will transform Melbourne’s north-east.”
North East Link is jointly funded by the Commonwealth and Victorian Governments.
Roads are the largest publicly-owned infrastructure in Australia, and underpin the social, economic and cultural fabric of a nation with an annual spend of over $30 billion on road infrastructure, including the maintenance of 900,000km of road network. We are now facing significant challenges associated with road deterioration from increased traffic loads and climate change. However, the technologies of the Industry 4.0 Revolution, which integrate our physical and digital worlds, are providing opportunities for innovations in transport pavements research.
Supported by the Australian Research Council (ARC), the Smart Pavements Hub, SPARC, is the first-ever university-led collaborative research platform to address these issues in the transport pavements sector.
We established SPARC in July 2019, whose hallmark is its stakeholders’ collaborative spirit as encapsulated in the acronym ‘SPARC’ – Smart Pavements Australia Research Collaboration. Our vision is to transform the Australian pavement industry to make pavements smarter, longer-lasting, safer, and more economical, with a lower environmental footprint.
We are developing novel testing methods that replicate field conditions for evaluating the long-term performance of granular geomaterials under repetitive heavy traffic loads and changing climatic factors. These methods are more costeffective, rapid and user-friendly, and will facilitate effective selection of materials for road construction/rehabilitation. For example, how to modify granular geomaterials for the construction of flood-resilient pavements or how to innovate superior road materials including recycled products.
Predictive models are being developed to advance the design methods for these longer-lasting, climate-resilient pavements, such as a practical model to predict temporal variations of moisture in road pavement layers due to climatic factor changes during the service life.
‘Intelligent Construction’ broadly refers to the construction of a transport pavement, primarily using advanced sensing and automation, that achieves the target performance over its design life. The pavement construction industry in Australia has recently increased its efforts to implement the intelligent compaction (IC) technology.
The recent international workshop on intelligent compaction organised by SPARC highlighted that countries like the US and China have implemented IC technology in practice as a mandatory requirement for contractors almost six years ahead of Australia. In this context, our objectives are twofold: (a) to advance the current Australian practice to bring it in line with international practice [Level 3 – road map for IC by Federal
An example of SPARC’s Approach to Intelligent Construction: ‘ASSURED’ Innovation: A – affordable, S – scalable, S – sustainable, U – user-friendly, R – rapid, E – excellent, D –distinctive (after Mashelkar).
Highway Administration (FHWA), 2017], and (b) to advance IC globally to the highest level (Level 5) with SPARC innovations.
As part of these developments, we are undertaking targeted field experiments within a large test pit with dimensions of 12m (length) x 5m (width) in which an instrumented roller has been used to collect raw accelerometer data and deformation data during each roller pass for further analysis.
Inside the same pit, tests have also been performed on the compacted soil using a Nuclear Density Gauge (NDG, soil density measurement), two types of Light Weight Deflectometer (LWD, soil dynamic modulus measurement), L-band instrument (ELBARA III, proximal measurement of soil moisture) and Ground-penetrating radar (GPR, proximal measurement of soil moisture) to evaluate the potential use of these devices for enhancing the quality management of IC.
Based on our recent theoretical developments and experimental results, we have filed a patent on the innovation of proximal measurement of pavement material density and other properties in real-time during compaction. When this technology is fully developed, it has the potential to globally transform geomaterials compaction to the highest level (Level 5 – road map for IC by FHWA, 2017).
Field experiments in SPARC Hub test pit: (A) Roller instrumented with various sensors; (B) Ground-penetrating radar (GPR) for soil moisture measurements (proximal); (C) TDR soil moisture probes; (D) Surface roughness device; (E) L-band instrument (ELBARA III) for soil moisture measurements (proximal).
In addition, our IC research team have established two approaches for developing IC specifications with a framework for cost-benefit analysis, and we will examine them further during the upcoming IC trials in the field.
The compaction quality and uniformity of road materials can also be assessed by measuring the dynamic modulus of the material being compacted. We have conducted a series of controlled tests in a test box (0.5m depth x 1.5m length x 1.5m width) to investigate the influence of soil density and moisture content on the dynamic modulus measured by LWD. The data collected during this experimental program demonstrated a strong sensitivity of LWD modulus to soil moisture variation.
The dynamic modulus measured by LWD on the compacted soil layer showed a progressive increase during the soil dry-back process by virtue of the increase in soil suction and the reduction in degree of saturation (DoS). Further analysis is undertaken based on unsaturated soil dynamics to establish a correction factor for variations in the soil dynamic modulus due to the changes in moisture content.
Pavement dry-back experiment: variations of soil suction, moisture content and modulus were monitored continuously in a compacted soil layer (400mm thick) respectively using tensiometers, soil moisture sensors and a light weight deflectometer (LWD) during the dry-back process.
For asphalt compaction, we have identified the limitations of IC technology and current compaction testing methods in using them during asphalt pavement compaction. The effects of asphalt mat temperature and underlying support on Intelligent Compaction Measurement Values (ICMVs) measured by IC rollers are the main causes of the poor correlation between asphalt ICMVs and spot density measurements.
We have proposed potential ways to overcome these limitations and establish performance-based specifications for QA/QC of asphalt compaction. The proposed correction methods for asphalt ICMVs have been examined in a smallscale asphalt testbed construction using an IC roller.
Asphalt IC trial at ARRB's ALF site at Dandenong: (A) Double drum roller instrumented with accelerometers, IR thermometer, GPS, and onboard control box and operator interface; (B) Thermocouples installed at various depths within the asphalt layer; (C) Non-nuclear density gauge (NNDG) measurement on the hot asphalt layer.
Further, we are developing a hardware/software kit known as SPARC Intelligent Compaction Analyser (SICA), for intelligent construction of transport pavements. SICA facilitates visualisation of multiple ICMVs that include Compaction Meter Value (CMV, Caterpillar & Hamm), Compaction Control Value (CCV, Sakai), Vibratory Modulus (Evib, BOMAG & Dynapac), Roller Integrated Stiffness (kb, Ammann) alongside the proximal density of the material being compacted.
It may be noted that the existing IC kits in the market only allow visualisation of a limited number of ICMVs (in many cases, only a single ICMV is plotted). SICA will provide versatility to retrofit any existing conventional roller, flexibility to incorporate corrections for different ICMV indicators and facilitate customising to construction specifications in line with the Industry 4.0 revolution.
SICA is configured to be integrable with the existing postprocessing software such as Veta to view and analyse the collected IC data. The experiences gained through using SICA in real IC projects will pave the way to develop robust and data-oriented specifications for IC to be used by the Australian pavement construction industry.
Professor Jayantha Kodikara, Professor and Director, ARC Industrial Transformation Research Hub (ITRH) – SPARC, Dept. of Civil Engineering, Monash University, Clayton Campus, VIC 3800, Australia. Get in touch at jayantha.kodikara@monash.edu.
Dr Arooran Sounthararajah, Research Manager, ARC Industrial Transformation Research Hub (ITRH) – SPARC, Dept. of Civil Engineering, Monash University, Clayton Campus, VIC 3800, Australia. Get in touch at arooran.sounthararajah@monash.edu.
For more information, please visit sparchub.org.au.
Managing the noise from railways and tunnels is becoming an increasing issue along major rail corridors in Australia – particularly those within close proximity of housing and offices. Often, industrial solutions involve unsightly concrete walls to manage noise, but there are more appealing, effective alternatives.
The more people benefit from noise attenuation, the more funding that can be found to assist railway authorities to reduce noise. For example, TfNSW Freight Division has a budget to double glaze buildings and insulate them in critical areas of the network. The next step is to reduce the noise at its source.
STRAILastic offers a “noise attenuation tool box” for dealing with sound and vibration from railways for acoustic engineers and asset managers to choose from, in new and existing transport systems.
and web dampers (the tool box) will most cost-effectively reduce noise where it is generated and to achieve a significant noise reduction.
The panels can be retrofitted into existing sleepered tracks with steel sleeper extensions but where the mini walls are outside the tamping area. Alternatively, the walls can be bolted to their own foundations such as mini piles/ ground screws or concrete foundation using fully integrated steel frame moulded into the product.
Acoustic engineers first determine the level of noise at the boundaries using noise maps. STRAILastic products are designed to trap and reduce the noise where it is generated inside the railway corridor and, more importantly, as close as possible to the source.
STRAILastic then works with the acoustic engineers to establish which combination of mini sound walls, panels
Although it isn’t always possible to substitute high noise barriers everywhere, in many locations such as high embankments, viaducts and bridges, mini sound walls can replace the need for these highlyengineered structures.
Mini sound walls have a very low visual impact which can be further reduced by attaching screen-printed local scenes on the obverse side. These walls don’t need
planning approval to be installed, which can be another major challenge with large concrete panel walls.
The new mSW 730 noise absorbing panels can substantially reduce noise from the wheel rail interface and corrugation vibration from the top of rail and absorb it before it reaches the boundary of the rail corridor. STRAILastic typically suggests a combination of rail web dampers using its INOX 2.0 dampers with the various mini sound walls as appropriate.
TP PANEL - A SOLUTION SPECIFICALLY DESIGNED FOR TUNNELS
Another common issue in railways and inside the rolling stock is managing the noise from tunnels. Due to pressure and suction forces that can be created by trains travelling through tunnels, acoustic panelling needs to be able to withstand extreme forces, while also able to reduce noise and allow for easy maintenance.
To address this common issue, STRAILastic offers the STRAILastic_TP tunnel paneling, which is designed and developed specifically for use in rail tunnels. The paneling features a moulded curve that is designed to perfectly fit the contours in tunnels, for each tunnel’s unique curve.
STRAILastic_TP panels are attached directly to the tunnel wall with mounting rails, allowing individual panels to be replaced at any time. The panels, designed with their noise absorbent acoustic surface and robust frame, is able withstand the extreme pressure and suction forces allowing for speeds of up to 120km/h.
mini soundprotection wall with high absorbing surface
The new version of the STRAILastic_mSW adds a higher wall to the product range. This version is used for train speeds of up to 120 km/h.
¬ No foundation required for installation
¬ easy and quick installation
¬ Short delivery times > noise hot spots can be supplied with products quickly
¬ Closer to the noise source than any other sound protection
¬ Break-proof due to bre-reinforced rubber compound with a cover layer of virgin rubber > UV and ozone resistant
¬ No material fatigue caused by vibrations or pressure and suction forces
¬ No problems with oversized loads
Due to the higher design, it gains even more e ect in the area of the wheel.
STRAILastic_mSW 730 is fastened to both rails with an insulated, decoupled substructure or directly in the subsoil using ground screws.
STRAILastic_mSW 730 > mini goes maxi.
1. STRAILastic_mSW 730 new version of the mini sound protection wall
2. STRAILastic_IP the infill panel
3. STRAILastic_mSW the established mini sound protection wall
4. STRAILastic_A inox 2.0 rail dampers
Worldwide spending on artificial intelligence (AI) is increasing, with huge investments by government parties and the private sector into AI technologies. At the 2021 Critical Infrastructure: Digitisation Series Virtual Conference, Dr Sue Keay, Chair, Robotics Australia Group, explored how robotics and AI technologies are currently being implemented in the critical infrastructure sector, and its future applications.
Dr Keay was previously CEO of the Queensland AI Hub, and research director for cyber-physical systems at CSIRO’s Data61. She led the development of Australia’s first robotic roadmap, outlining how robotics and automation will impact every sector of the Australian economy.
Dr Keay said the level of interest and investment around the world in AI technologies can be attributed to a ‘tipping point’ in our understanding of AI.
“The reason that there is such a huge investment in AI and robotics at the moment is because many people believe we've reached a tipping point where these technologies, which have been around for more than 70 years, are finally reaching a point where they're going to become much more useful and usable by all of us,” Dr Keay said.
“Now we have far more computer processing power in our handbags or in our pockets, in the forms of our mobile phones, than we ever had in the past.
“One of the other reasons that we are starting to see this huge increase in interest in artificial intelligence, thanks to all of this computer processing power, has been the advent of computer vision – a form of AI that allows computers or robots to automatically interpret the images that they are able to retrieve from cameras or video cameras.”
Dr Keay said we've now come to the point where we can place cameras on different objects and they can be
interpreting information in real time, removing humans from dangerous situations.
Another pivotal development in AI is a type of machine learning known as ‘deep learning’; a way by which robots or computers learn how to do things, not by writing lines of specific code about what action the robot needs to take, but by being shown what they need to do.
ADVANTAGES OF AI FOR AUSTRALIAN INFRASTRUCTURE
Australia was the first country in the world to automate its ports – an example of how implementing AI into infrastructure management can produce great results.
“Automated straddle carriers are in operation in the Brisbane and Botany Bay ports,” Dr Keay said.
“No people are actually present on the port when the straddle carriers are in operation, they move them onto the back of the trucks and the trucks transport those goods to wherever they need to go.”
Australia is also a vast country with a significant amount of remote infrastructure that requires maintenance, so technology plays a key role in this vital work.
“We have thousands of kilometers of roadways, pipelines, rail lines, power lines, and bridges that all need to be inspected and maintained. We really don't have enough people on the ground to be able to do all of this work without the help of technology,” Dr Keay said.
“Some of the ways that AI is being applied in infrastructure at the moment is for remote inspection to cover those thousands of kilometers of infrastructure that need to be inspected.
“To have a look at the deterioration of those structures, and then also do predictive and preventive maintenance, and finally to look at lifecycle optimisation so that we can track all of our assets and figure out when they need to be replaced and what particular aspects of those assets might need to be replaced,” Dr Keay said.
“The use of these technologies is producing such huge amounts of data that we can really use it to good effect, to have a thorough understanding of our assets and their lifecycles.”
One example of how this technology is being applied is on the Sydney Harbour Bridge, which has had more than 2,400 sensors deployed, including accelerometers.
“They're all sort of linked into a daisy chain to connect them and they're monitoring the vibrations that are occurring in the Sydney Harbour Bridge in real time. Then machine learning algorithms work out whether those vibrations are indicative of there being potential cracks forming, or whether they're simply the result of temperature and climate conditions of the day,” Dr Keay said.
As these machine learning models receive more data, they are able to learn and become better at predicting where there are likely to be areas that need to be considered for preventative maintenance.
An Australian company has also developed a ‘Fitbit’ for machines; a small device that can be put on any type of machine to inspect and perform vibration analysis to work out when there's likely to be a failure of that piece of equipment.
“This can be very handy if you're dealing with critical infrastructure as the failure of some of these instruments can have catastrophic consequences,” Dr Keay said.
Drones are also being used in Australia for the inspection of many of our assets, including solar and wind farms, and Dr Keay said the main objective is to make sure workers are removed from dangerous situations.
“The collection of all of this data from the numerous sensors that are now being deployed out in the environment allows us to build digital twins of much of our critical infrastructure.
“In the future, if we're able to deploy our sensors and robots in a clever manner, we could hope that we don't have to send people out to fix things on these remote oil rigs or out in remote areas of Australia, and that we will actually be able to deploy robots to do that same job,” Dr Keay said.
The advanced technology Thermal Zinc Diffusion (TZD) is a uniform, sacrificial, zinc-iron coating applied to ferrous items using metallurgical vapour diffusion that creates corrosion and abrasion resistance, increasing part life even in the world’s harshest environments.
In contrast to other galvanizing methods, TZD does not leave any area of the product unprotected because the process is not hampered by the product geometry. ArmorGalv® is the first plant of its kind in Australia.
ArmorGalv® TZD is a standard option for all ferrous metal products and is perfect for threaded bar and engineered fasteners, both high tensile and commercial grade. This uniform coating is poised to revolutionise the market with 1,000+ salt spray hours of corrosion resistance.
TZD is a dream come true for the fastener industry with ArmorThread®. Traditionally, fasteners were coated for corrosion resistance and proper torque tension characteristics. Since 1971, when the Japanese court found the Mitsui Mining and Smelting Company guilty of causing a severe outbreak of cadmium poisoning, cadmium has been virtually banned worldwide.
Cadmium’s main benefit was its anti-galling properties and its ability to not ‘seize’. Galling is defined as localised surface deformation between two solid sliding surfaces under heavy friction contact. Due to increased hardness and wear-resistant properties, ArmorGalv® provides good anti-galling properties, assisted by the absence of free zinc at the surface.
Steel with tensile strengths greater than 800MPa are at risk of hydrogen embrittlement due to the acid pickling associated with surface preparation for HDG (Industrial Galvanizers, 2006). ArmorGalv® uses blasting for surface preparation where necessary – permitted by the greater diffusion time and increased development of the TZD gamma layer.
Using temperatures above 345°C for over 90 minutes in a completely dry environment, TZD provides no chance of
inducing hydrogen embrittlement, and would even relieve any residual stresses that might already be present in the product (ASTM1059A/M).
TZD provides a uniform coating thickness that follows the contours of the component exactly with no solidifying zinc at the surface, as apparent with HDG. The consistency of the surface is produced under the diffusion action of the zinc atoms into the base metal, assisted by slow rotation within the cylindrical kiln. It not only coats but penetrates the surface. The result is a hard (38-42Rc) super abrasion-resistant coating that cannot easily be removed by mechanical means.
Today, there is the added challenge of the process being environmentally friendly, and the coating itself being nontoxic and chrome free. In 2006, the US EPA awarded the ArmorGalv® process its prestigious MVP2 Award as the process generates practically zero landfill material and results in a chrome free nontoxic coating.
ArmorGalv®’s surface readily provides superior adhesion of powder coat, paint, rubber, silicates, or Xylan to the surface. It also has great heat resistance, unlike any other zinc-based coating, withstanding continuous service of 650°C.
The ArmorGalv® TZD is covered by the Standards ASTM1059A/M and ISO17668 with coating classes ranging from 20 to 120 microns, defining the target coating thicknesses.
A R M O R G A L V P R O T E C T I O N
F O R A L L F E R R O U S M E T A L S
H i g h l y c o r r o s i o n a n d a b r a s i o n r e s i s t a n t
C o n t r o l l a b l e , e v e n a n d p r e c i s e – f r o m
2 0 μ t o 1 0 0 μ p l u s
H a r d , n o n - m a g n e t i c , w e l d a b l e a n d s p a r k
f r e e
C h i p p r o o f a n d a m e n a b l e t o c r i m p i n g ,
b e n d i n g a n d f o r m i n g p o s t p r o c e s s
N o h y d r o g e n e m b r i t t l e m e n t
GRADES 8.8, 10.9, 12.9 & THREADED BAR NO HYDROGEN EMBRITTLEMENT
ANTI-GALLING
LOW CO-EFFICIENT OF FRICTION
TORQUE TENSION TESTED
NO LOSS OF HARDNESS OR TENSILE STRENGTH
F o r P e r f o r m a n c e a n d E n d u r a n c eA r m o r G a l v i t !
H i g h l y h e a t r e s i s t a n t ( u p t o 6 5 0 ° C )
E x c e l l e n t s u b s t r a t e f o r p a i n t , e p o x y ,
r u b b e r o r p l a s t i c
A S
a l l y
T o x i c
a l F r e e
A S T E N E R
C T U S :
0 2 4 0 2 8 6 7 6 0 s a l e s @ a r m o r g a l v . c o m . a u w w w . a r m o r g a l v . c o m . a u
Federal Minister for Resources and Water, Keith Pitt, said the Commonwealth is making a $64 million national investment in upgrading GPS positioning capability in South Australia, improving accuracy from metres to centimetres.
In South Australia, this will significantly fast-track certain works on the Port Wakefield Overpass and Highway Duplication process, with a robot called the ‘Tiny Surveyor’ able to complete line-marking work in days, instead of weeks.
“This collaborative public-private approach to establishing high-quality satellite positioning infrastructure through partnerships with the South Australian Government and industry builds on our nation’s potential,” Mr Pitt said.
“It has real world benefits for major infrastructure upgrades, such as roads, sporting fields, airport runways and car parks, while also boosting productivity across industries such as agriculture and logistics.
“This technology will improve positioning accuracy from five to ten metres, right down to three to five centimetres in areas with mobile phone and internet coverage.
“It will enable government and industry alike to easily connect and
access positioning data and pave the way for innovation and new positioningbased products, services and technologies for the benefit of industry and community.”
South Australian Minister for Infrastructure and Transport, Corey Wingard, said the tiny robots will positively impact the $124.5 million Port Wakefield project.
“Gruelling and tedious tasks that would take survey crews weeks to complete manually can be done with this little robot in a matter of days thanks to this ground-breaking technology,” Mr Wingard said.
“It enables survey teams to supervise the robot’s movements in a safe location away from heavy machinery and live traffic.”
In South Australia, 68 reference stations are involved, including twelve new additions.
South Australia is a good example of the collaborative approach being taken, with over 40 existing South Australian reference stations operated by industry, including Position Partners and UPG (Ultimate Positioning Group) part of the project.
“This public-private approach to establishing high-quality satellite positioning infrastructure through partnerships with the South Australian Government and industry builds on our nation’s potential,” Mr Pitt said.
“Led by Geoscience Australia, the Commonwealth Government will deliver an extra 57 reference stations nationally as part of our 700-plus strong reference station network, partnering with industry and state governments,” he said.
Position Partners, which supports construction and geospatial businesses throughout South Australia, has provided the ‘Tiny Surveyor’ on the Port Wakefield project.
A joint initiative between the private sector, the Federal and South Australian Governments will see a major satellite GPS upgrade increase the efficiency of South Australian road projects.
Federal Member for Grey, Rowan Ramsey, said the Port Wakefield Overpass is a significant infrastructure project for the region.
“The Coalition Government contributed close to $100 million towards the $124.5 million project and it’s great to see this investment in GPS technology helping to deliver the project even sooner,” Mr Ramsey said.
“The upgrade will be getting people home sooner and safer, and it’s good to see the progress being made on this important project.”
Preliminary works for the expansion and upgrade of the reference station network in South Australia are advancing, with Geoscience Australia anticipating completion in South Australia by June 2022, and the national project to be completed by June 2023.
“Farmers, transport companies, miners, local government, land managers, marine, aviation, and space industries are already using this GPSbased technology to do more and create jobs,” Mr Pitt said.
“What the future holds is very exciting in the hands of Australian innovators.”
Aerometrex has established itself as a trusted 3D data partner for global engineering services giant WSP. The quality and accuracy of Aerometrex’s 3D products allows WSP to streamline its infrastructure design processes.
WSP USA’s Technical Lead for Visualisation and Data Intelligence Group, Mark Kaufman, said Aerometrex’s data has proven valuable to the company, and that for him, quality is key.
“To be perfectly honest, Aerometrex is the highest quality, highest resolution 3D data that we’ve seen so far available to us. Take the Denver model for instance, when I first saw that Union Station, it just blew my mind,” Mr Kaufman said.
“That quality is important for the USA market, where projects within the built environment are starting in 3D. These Aerometrex representative environments within a tolerance of two to five centimetres are pretty spectacular.”
Aerometrex’s 3D reality mesh resolutions are flexible to project needs and range from sub-centimetre for ultimate detail at the individual building level, to 2-7.5cm for larger-scale full city models. Street-level enhancement blends photography taken from the ground to fill the gaps where oblique aerial imagery capture is less detailed, making the data work at any
scale. That resolution range mixed with high spatial accuracy makes Aerometrex data ideal for infrastructure projects of all sizes.
Complete datasets from Aerometrex save WSP’s team from manually creating their own 3D data, while providing superior quality and scale.
“We used to build everything from scratch with GIS data and aerial maps, starting with 2D data and building it up in 3D,” Mr Kaufman said.
“That’s a lot of work, and you can only get to a certain level of detail. Now we’re able to integrate these city-size models directly into game engines and stage complex scenes in real-time.”
High-quality data makes for faster and more flexible infrastructure planning from the project outset, and rapidly moving the project forwards.
“Starting with more accurate information from a 3D model makes staging data much easier. I can slice and dice the data, add buildings, get rid of the ground surfaces, or do whatever I need. Then I quickly and interactively build models in front of my clients and get that real-time feedback,” Mr Kaufman said.
It can be challenging to showcase large infrastructure projects because their scale and effect on the actual world location are substantial. Better 3D data solves that problem by connecting the present and potential future with new infrastructure modelled in situ.
Adding real-world context facilitates a stronger connection between the design and the target audience, giving infrastructure firms an advantage when pitching to win projects.
“Also, the 3D reality mesh solves the data disconnect. Clients know there’s a Starbucks here or Wells Fargo Bank building there, but in the past all they’d see was a big extruded shape. I think that’s a crucial aspect of what Aerometrex is offering. This reality mesh allows us to get beyond this kind of ‘foam core’ of shapes that are somewhat volumetrically representative of the real world to something that’s actually there in the real world,” Mr Kaufman said.
•
•
•
METRONET’s High Capacity Signalling (HCS) project will safely increase the volume of rail traffic in the Perth suburban train network. It will allow the delivery of more passengers, more efficiently.
The METRONET project will upgrade existing signalling and control systems on the rail network with new technology that will allow trains to safely run closer together on a more frequent timetable to meet future growth.
Funded by both the State and Commonwealth, HCS is a modern integrated communications-based train control system that uses an LTE (long-term evolution) digital radio system. The train continuously sends real-time data on the train’s speed and location to central signalling interlocking the system’s ‘brain’ at the PTA control centre. The train also interacts with passive information plates on the track to confirm its location and speed with the onboard systems.
This enables the control centre to monitor the speed and location of every train on the system, giving much clearer and more accurate positioning of each train relative to the ground and to each other. The trains can move on to the next location and change speed only after automated permission is given from the control centre. At any time if the network loses contact with trains, automatic safety controls will halt the train until contact is re-established. The control centre also maintains a range of data applications such as train scheduling, statistical reports and passenger information.
The system uses what is known as a ‘moving block’ system. The network creates and continuously monitors an exclusive space or ‘block’ around the train, automatically preventing other trains and their blocks from overlapping. This means trains can safely run closer together – using 30 or 40 per cent less space than the existing system – with an assurance that there is sufficient space and time to adjust speed or safely stop in any circumstance.
It also allows faster recovery from disruption and a reduction of required trackside maintenance. Most of the trackside signals and track circuits will be removed; improving reliability and worker safety. Exact details of the benefits and operation of the system may depend on the supplier that wins the tender, and the technologies they intend to use to meet the tender conditions.
The system will be monitored and controlled from a state-of-the-art Public Transport Operations Control Centre (PTOCC) to be built next to the Public Transport Centre in East Perth. The construction contract to design and build the centre was awarded to ADCO Construction in October 2021. It is expected to be completed in 2023. The PTOCC will house the centralised signalling interlocking and the train control system. The building is also designed to cater for the central monitoring room, video evidence room, and train planning and scheduling group. There is also space to allow for any future light rail control room and two floors of general office space.
HCS will replace the rail network’s aging signalling and control systems, introduced in 1990. At the time, the Automatic Train Protection system that was installed on the network was an Australian first, preventing trains from overrunning red signals or travelling at excessive speeds. These systems are now nearing the end of their asset lives.
The Automatic Train Protection system relies on using ‘fixed block’ intervals along the track created by track circuits and controlled by a conventional colour-light signalling system. Only one train can be in each block at any one time. Once a train is in a fixed block, the signal light at the start of the block turns red, preventing any other trains from entering that block.
Fixed blocks are longer and keep trains further apart. They are not as responsive and accurate as the new HCS ‘moving block’ system. A fixed block signalling system using the current maximum line speeds on the PTA rail network can reliably operate approximately 15 trains per hour per line. The HCS system is estimated to support more than 30 trains per hour.
An Expression of Interest (EOI) was released in September 2021. A complex procurement process will follow that identifies preferred suppliers to ensure government procurement standards are met by suppliers with the expertise, capacity and risk profile to deliver the project. The contract to design, supply, build and maintain the HCS project across the entire network and train fleet is expected to be awarded mid-2023.
Introducing the HCS will be a complex operation that will be delivered in stages over ten years, and is probably the most operationally challenging project for the organisation since electrification of the rail network in 1990. The most important part of the project is the change management required, including training for drivers, technicians and train controllers. It will also involve changes in safe working rules, the way train work crews operate and the way new works are planned. These changes will also be part of the development and extension of Perth’s rail network serving more lines for an increased population.
Planning for the introduction of the HCS system has been underway for an extended period but detailed work will not begin until the preferred supplier has been selected. Much will depend on their technical background, the type of system they propose, its existing use elsewhere, and their recommendation for the most efficient development of the system in Perth.
When announcing the EOI, WA Transport Minister, Rita Saffioti, said, “Perth’s rail signalling system is nearing the end of its asset life and, with the network experiencing a major expansion thanks to a number of METRONET projects currently underway, this important system needs replacing.
“METRONET’s High Capacity Signalling project will not only allow for future demand, it will also support more trains running more often, which is a big win for regular public transport commuters.”
Over the next 30 years, Perth’s population is expected to increase to 3.5 million people, predicted to make over 1.4 million public transport trips every day. The HCS system aligns with urban development and transport plans and policies for the future.
The project will be delivered alongside the Radio Systems Replacement (RSR) project. This project will replace Transperth’s analogue rail radio with the high-tech private 4G-type digital communications needed to operate the HCS. The upgraded radio system will allow encrypted conversations, data transmission capability and additional capacity.
To handle the population growth and expansion of the Perth urban area, the WA Government has introduced the METRONET rail expansion program, increasing the length of the Perth rail network by 40 per cent. This includes 72km of new track and 18 new stations. To gain maximum efficiency from the expanded network, several new technology projects will be introduced, including the HCS project.
Attracting more women to traditionally maledominated trades isn’t just a well-meaning election promise – it’s an economic necessity. Victoria’s $80 billion public infrastructure boom is a critical part of the Victorian Government’s recovery from the pandemic so maintaining the pipeline of workers is essential.
The Government formed a new entity –Apprenticeships Victoria (AV) – in late 2020 with a mandate of creating opportunities for 1,500 apprentices and trainees a year, with female recruits a key part of the strategy.
Barriers to pursuing a career in the trades have caused significant under-representation of women, meaning a huge untapped labour resource for industry, from school-leavers to middle-aged career changers.
This push to attract more women recently received a boost when ten trailblazing projects shared $5 million in funding as part of AV’s Apprenticeship Innovation Fund.
Cameron Baker, Apprenticeships Victoria Executive Director, said, “There are a huge number of projects taking shape in Victoria right now, meaning the need for qualified tradespeople is greater than ever.
“Women have traditionally been under-represented in areas such as plumbing and electrical work, but we’re using these initiatives to redress the balance. There are opportunities for everyone.”
WOMEN ON THE TOOLS: THE TEN ‘WOMEN IN TRADES’ PROJECTS
Ai Group – Women in STEM
Run by Ai Group’s Centre for Education and Training, Women in STEM will recruit 30 women into apprenticeships in engineering and 20 into traineeships in ICT and Industry 4.0.
Sonya Casey, Project Consultant for Women in STEM, said, “Careers in these sectors can be very rewarding and there are plenty of opportunities, but they are still areas dominated by men. We want to change women’s perspectives on these careers and help them find secure, well-paying jobs.”
Downer – Women on Track
Women on Track is a paid traineeship program dedicated to placing ten underprivileged women who are looking to kick-start their careers into roles in the rail industry.
The program combines paid structured learning with practical on-the-job experience on the High-Capacity Metro Trains (HCMT) Project located at Downer’s Pakenham East Depot.
National Fire Industry Association – SPRINKS
SPRINKS is an initiative aimed at recruiting 30 female school leavers into the Fire Protection Industry by providing pre-apprenticeship training and enabling women to build connections with employers.
Shannon Fogarty, NFIA Director – Member Workplace Support, said, “Fire protection is a growing industry, with service and construction work, and is increasingly being recognised for its vital safety role.”
NECA Education and Careers – Women and Their Trade (WaTT) WaTT will enable 25 women to complete electrical apprenticeships over the next two years, arming them with the tools, resources and support for a rewarding career.
Elise Halton, WaTT Program Project Mentor, said, “In the industry there is not enough diversity and inclusivity of women in a trade where there should be, and we need to take steps to assist that process.”
Boeing Aerostructures – Women in Aviation Apprenticeships
This four-year program supports more women to undertake Certificate IV apprenticeships in aeroskills or engineering.
The program will focus on building a culture of inclusiveness, connecting the apprentices to the Boeing early career network, buddying and formal mentoring, as well as providing them with industry-knowledge and industry networking opportunities.
Electrical Trades Union – WAVE Women in Electrical
Delivered by The Centre for U, the Women in Apprenticeships Victoria Electrical (WAVE) project aims to connect 30 women undertaking electrical pre-apprenticeships to experienced industry mentors through a digital community of practice application, providing ‘just in time’ support and developing a network of connected peers.
“Mentors will support women entering the electrical trade as they make the transition from an electrical pre-apprenticeship to employment in the electrical industry,” said Carmel Veenstra, WAVE Project Manager.
Master Plumbers – Women in Plumbing
This aims to tackle perceptions that prevent women from considering plumbing as a career. The project offers paid preapprenticeship opportunities and direct entry into a Master Plumbers apprenticeship.
Peter Daly, Master Plumbers CEO, said, “While there are 30,168 qualified plumbers in Victoria, only 101 of them, about 0.3 per cent, are women.
“Once this pilot program has been completed, there will be almost 50 per cent more women in plumbing in Victoria.”
Trades Women Australia – CareersPlus
CareersPlus will support 150 women into apprenticeships and traineeships over the next two years by raising awareness and providing clear avenues into the industry.
Janet Cribbes, CEO of Tradeswomen Australia, said, “Our research shows us that women want to enter trade careers but don’t have the networks to do so – so we fill that gap by providing the essential support and confidence-training that can make their dreams a reality.”
The program offers a network of tradeswomen, employers and community organisations to help women into entry-level, apprenticeship or established roles, plus mentoring through workshops and online.
Automotive Chamber of Commerce – Accelerating Women in Auto
The Accelerating Women in Auto project will create opportunities for 60 women to enter the industry with a Certificate II in Automotive Servicing.
Apprenticeship Employment Network – Women Only Multi-trade Pre-apprenticeship
The Women Only Multi-trade Pre-apprenticeship will give 120 women the opportunity to try a range of trades over 6-12 weeks.
It will also support host employers to find the best possible fit for their business when looking to recruit an apprentice or trainee.
Abru Meher Jahan, Downer Apprentice
Abru Meher Jahan was born and raised in Dhaka, Bangladesh, and came to Australia in her mid-teens. She worked in retail roles before taking a break in 2018 to start a family.
When she was ready to rejoin the workforce, she wanted to do something fulfilling. However, having been schooled overseas made it difficult for her to access study in Australia.
When she discovered Downer’s Women on Track apprenticeship program, she knew it was just the boost she needed to kick-start her career in trades.
“When I saw the job, I wanted to combine studies and work, to help me financially and get a certificate at the same time,” Abru said.
“I’m loving the job, really enjoying the work and the people.”
Amy Hutchinson, Master Plumbers Apprentice
Amy Hutchinson comes from a family of male plumbers and said it took her a while to realise she wanted to follow in their footsteps.
“To me, it is incredibly important for people to realise that they can literally do anything, and gender bias in a career needs to be completely eradicated. It’s one thing to talk about helping women but it’s another to actually do it and that’s what is happening here.”
“It wasn’t until just after COVID-19 hit when I decided it was time to put the boots on and give it a go. I was lucky enough to get a job with Tullamarine Plumbing and Drainage and I feel that I’m finally somewhere I can see myself for a very long time.”
For
June
Airport Urban development
Smart cities
Bridges
Automated and electric vehicles
Freight and logistics
DISTRIBUTION SYDNEY BUILD EXPO LOCATE22
Ports Asset Management
AI and machine learning
Intelligent Transport Systems (ITS)
Safety and risk management
Sustainability
DISTRIBUTION TBC
Rail IoT & cloud communication
Security Disaster management
Tunnels
Drones/UAVS
Funding/investment
DISTRIBUTION TBC
Roads and Traffic Digital Twins
Software, communications and connectivity
Signalling, tracking and control systems
Condition monitoring and maintenance
Spatial & GIS Training and skills
DISTRIBUTION TBC
your leading source of news for the local government sector
Council has been developed to keep you up-to-date with all of the latest news, discussions, innovation and projects in the local government sector.
Council is fully integrated across print and online, featuring a website updated daily with the latest industry news, a weekly e-newsletter delivered direct to your inbox, and a quarterly magazine that can be read in print and online.
Published by industry publishing experts Monkey Media, Council will arm community decision-makers with the critical information they need to deliver a better future for cities, towns and suburbs all over Australia.
www.councilmagazine.com.au info@councilmagazine.com.au