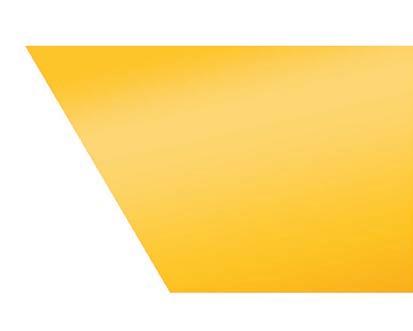
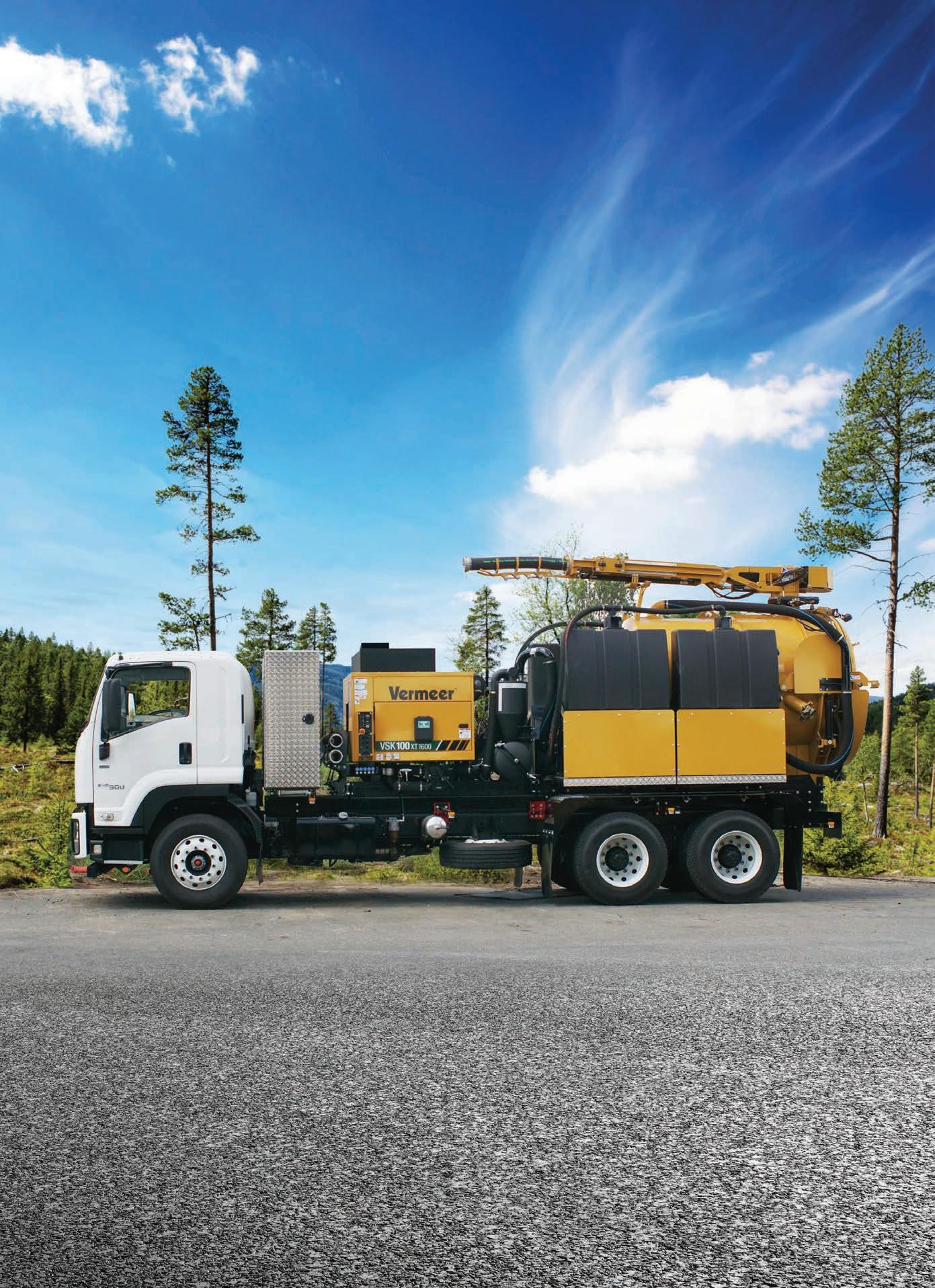
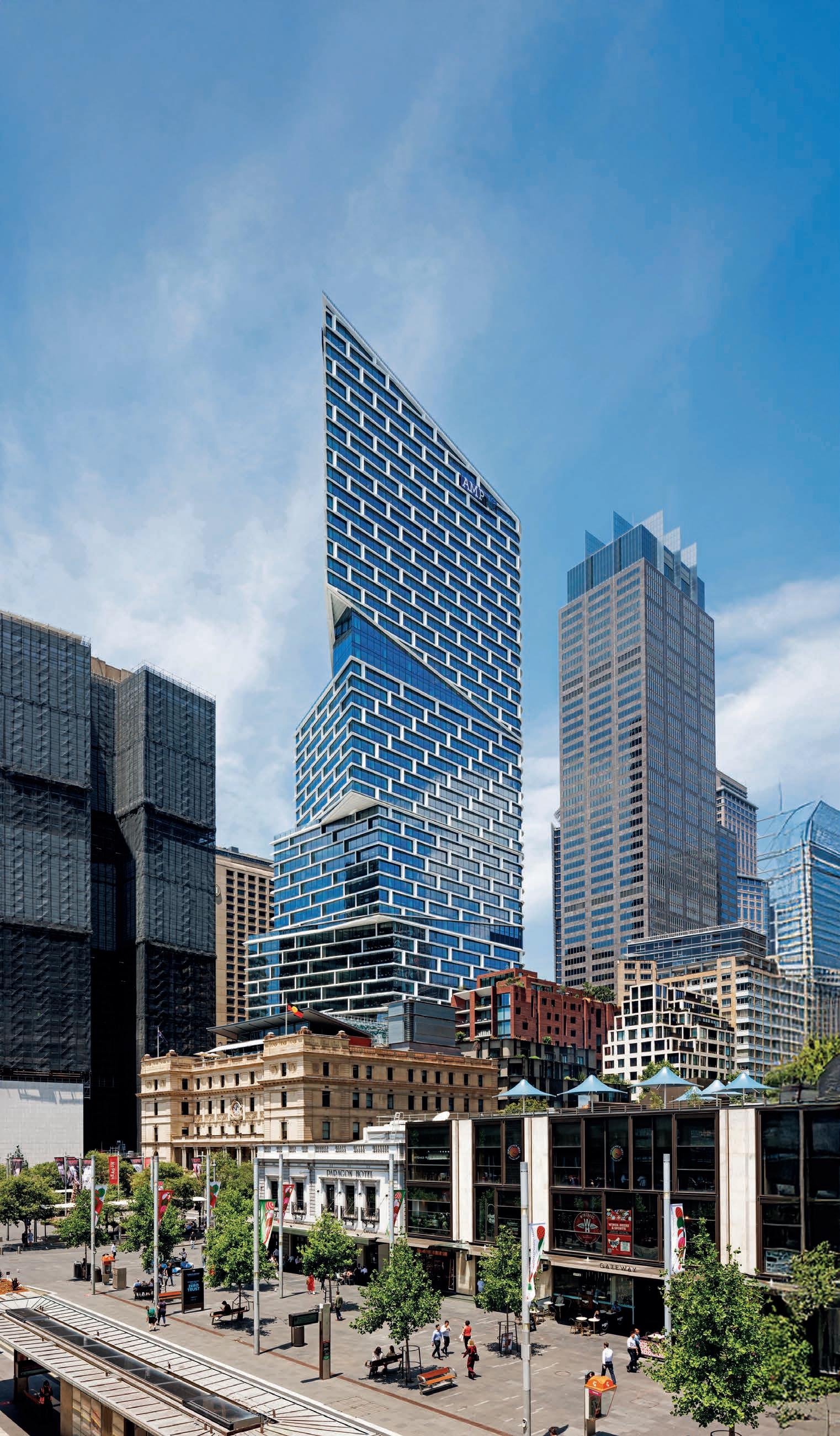
WOMEN IN CONSTRUCTION
DRIVING GENDER EQUITY FOR INDUSTRY SUCCESS
DRIVING GENDER EQUITY FOR INDUSTRY SUCCESS
Confronting the challenges and leveraging opportunities
Training, consultancy, insight.
The Rail Safety and Standards Board is the independent safety, standards and research body for Great Britain’s rail network. We’ve powered safer, smarter rail for more than 20 years – and now rail organisations around the world can benefit from this experience and insight. To see how we could help your organisation, download your guide to our international services.
Get your guide at rssb.co.uk/international
Scan to subscribe to Infrastructure Magazine’s weekly newsletter –delivered to your inbox every Wednesday morning.
Published by
Chief Executive Officer
John Murphy
Chief Operating Officer
Christine Clancy
Publisher Sarah Baker
Managing Editor Laura Pearsall
Assistant Editor
Kody Cook
Design Alejandro Molano
Head of Design
Blake Storey
Business Development Manager
Brett Thompson
Client Success Manager
Louisa Stocks
Head Office
Prime Creative Media
379 Docklands Drive
Docklands Victoria 3008
P: +61 3 9690 8766
enquiries@primecreative.com.au infrastructuremagazine.com.au
Subscriptions
P: +61 3 9690 8766
subscriptions@primecreative.com.au
Infrastructure is available by subscription from the publisher. The rights of refusal are reserved by the publisher.
Cover image InfraBuild
Welcome to our first issue of Infrastructure for 2025. I hope you enjoyed a restful holiday period and that the year is off to a fantastic start for you all.
It feels appropriate that in the month we celebrate International Women’s Day we’re bringing you a feature on a brilliant initiative from the Suburban Rail Loop Project in Victoria – the development of an all-women tunnel boring machine crew, a world first.
We met with SRL East Tunnels South Construction Manager, Isolde Piet, who shared insights into the work that is going into identifying, training and developing the crew. Isolde has decades of experience in underground construction and managing tunnelling projects in Australia and around the world.
so little things impacting women in construction.
Shockingly, 88 per cent of respondents NAWIC surveyed had experienced microaggressions at work, with 80 per cent being verbal in nature and 41 per cent coming from supervisors or managers, followed by clients and customers at 38 per cent.
As Isolde told us, there are several reasons why women have yet to fully realise the benefits a career in tunnelling and engineering can offer – two of the most obvious being a lack of opportunity and a lack of role models. This initiative and Isolde will go a long way to changing this.
In this issue we also hear from Cathryn Greville, CEO of the National Association of Women in Construction (NAWIC). Cathryn and her team at NAWIC work tirelessly to champion and empower women in the construction and related industries to reach their full potential.
In this issue, Cathryn shares NAWIC’s recent research, which has been presented in the report, Not
Cathryn rightly identifies addressing the underrepresentation and poor experiences of women in construction as one of the biggest issues facing the sector, that should be at the top of all leaders in the construction industry’s minds.
We need an industry that offers a safe and positive workplace culture, an attractive career option, strong career pathways, and inclusive environments that meet the needs of women.
Importantly, addressing these issues creates a better working environment not just for women – but for everyone working in the sector.
And that’s something we can all get excited about working towards.
Laura Pearsall Editor, Infrastructure
Get in touch at info@infrastructuremagazine.com.au or feel free to give us a call on 03 9690 8766.
Don’t forget to follow Infrastructure on social media – find us on LinkedIn, Twitter and Facebook.
Three imperatives for building tomorrow’s infrastructure
Strengthening security frameworks for compliance
4 Ageing infrastructure: restoration over replacement
Sleek, modern and efficient drainage
Queensland’s infrastructure boom: the golden decade ahead
CCF Victoria teams up with Converge 2025
Tunnelling new connections
Deliver and manage resilient, sustainable, high-performance public infrastructure by using a common data environment.
Fragmented data causes inefficiencies and communication gaps. Collaborating in a common data environment helps you streamline teams and make informed asset management decisions, improving your operational efficiency.
Inflation leads to higher costs, climate change threatens your infrastructure. By leveraging connected workflows, you can better manage project complexities and keep expenses on track, ultimately reducing overall risk.
Create sustainable, high-performance infrastructure that meets the most ambitious environmental targets with connected workflows built on transparency and intelligent modelling. Get started today
boards.autodesk.com/ infra-owners-anz
By Tom Gellibrand, Chief Executive of Infrastructure NSW
As New South Wales confronts an emerging housing crisis, effective relationships between government and the construction industry are paramount.
As Chief Executive of Infrastructure NSW, I understand the immense pressures facing our construction industry, from supply chain issues and worker shortages to financial challenges and rising costs. Amidst these challenges, there are great opportunities as the investments in infrastructure are the greatest the New South Wales Government has ever seen.
Our new Principles for Partnership with the Construction Industry (Principles), represents a crucial platform for industry and government to address current challenges and
leverage opportunities to deliver an ambitious program of infrastructure to support new homes close to jobs, services and transport.
The Principles is a refresh of the 10-Point Commitment to the Construction Industry, released in 2018. Significant progress has been made since this time, and new challenges and priorities require a re-look at the way the New South Wales Government works with the construction industry.
Beyond this, the Principles include important social objectives achievable through the New South Wales Government infrastructure
pipeline, supporting our heavy investment in infrastructure, housing supply and renewable energy.
The new policy emphasises collaboration across the construction sector to deliver high-quality infrastructure. Developed by the Construction Leadership Group, the Principles align efforts to deliver the New South Wales Government $119.4 billion infrastructure pipeline.
Last year we invited industry stakeholders to roundtable discussions to gather feedback on a refreshed policy approach. These sessions included peak bodies, contractors, unions, and consultants,
ensuring diverse perspectives. This extensive consultation underscores our commitment to collaboratively addressing challenges and driving improvements in the way government and the construction industry work together.
The Principles are complemented by the NSW Women in Construction Program, now entering its third year, and the recent NSW Decarbonising Infrastructure Delivery Policy and Measurement Guidance, which focuses on measuring and reducing carbon emissions associated with infrastructure delivery.
The Principles which include specific actions and commitments between government and industry, are:
The New South Wales Government is dedicated to strengthening local industry skills and manufacturing capabilities. Key initiatives towards achieving this include establishing the Jobs First Commission and Future Jobs and Investment Authority, creating a flexible procurement framework, mandating tender weightings, expanding the Industry Capability Network, and providing local workforce opportunities. These measures will enhance participation from local businesses and support the government's housing objectives.
Our aim is to collaborate early to support modern construction and local industry. The New South Wales Government commits to signalling early local manufacturing opportunities, piloting new approaches with industry, boosting local content, jobs, and small business engagement, and investing in local manufacturing skills and capacity. We ask our industry partners to align with these priorities by optimising local outcomes within projects and to partner with local suppliers where possible to cultivate local industries and businesses.
The construction industry is high-risk, traditionally marked by an adversarial culture posing significant health and wellbeing risks. Addressing safety, risks and psychosocial hazards is essential. The New South Wales Government is promoting positive change, focusing on safety and wellbeing to ensure a safe and inclusive construction sector.
Our goal is to prioritise worker health, safety, and wellbeing, and promote good mental health in a stigma-free environment. The New South Wales Government is committed to modelling safe behaviour, advocating for improved safety and culture, updating WHS guidelines, and recognising high-performing contractors.
We ask our industry partners to propose innovative safety ideas, advise on avoidable risks and ensure subcontractors meet updated standards.
Productivity in the construction sector has lagged that of other industries for decades and is arguably in decline. Improving worker capability through upskilling in digital and efficient processes is crucial. Immediate opportunities include standardising key government procurement and design processes, improving early market interactions, encouraging innovation, and adopting digital practices. To support these efforts, three new Guidance Notes have been published to promote early market engagement, transparency in tender processes, and effective post-tender debriefs.
Our aim is to publish standardised data, accelerate digital practices, and collaborate on data management. The New South Wales Government is working to enhance tender processes, involving industry early in design, streamlining project specifications, and updating GC21 contracts. We ask our industry partners to engage in early market engagement, propose innovative solutions, digitalise practices and collaborate with local suppliers.
Building a skilled workforce is crucial for reliable infrastructure delivery. To meet the workforce demands of investment in infrastructure, housing and renewable energy, we need to invest in skill development and collaborate with industry to attract and retain talent.
We invite our industry partners to upskill the workforce, provide opportunities for diverse and underrepresented groups, and increase local employment on infrastructure projects. The NSW Skills Plan has identified the need for enhancing skills in the construction industry, implementing programs to improve diversity outcomes, and ensuring high-quality training.
Increasing the proportion of women and underrepresented groups in
construction is crucial to cultivate a more innovative and productive workforce. The New South Wales Government is leveraging its procurement power to ensure contractors introduce improvements to promote a healthy culture and diversity in the industry.
The latest survey results from our Women in Construction program highlight significant progress as well as ongoing challenges. The number of women entering the industry has risen by 12.5 per cent in the past year, with women now making up 20 per cent of the construction workforce, however, there is still a lot of work to be done. The New South Wales Government is committed to ensuring contractors introduce flexible workplace policies and develop mentoring programs to support women's long-term success and retention in the industry.
We recognise the financial pressures on contractors. The New South Wales Government is committed to achieving value for money and delivering quality projects on time and on budget. By working together, we can identify and mitigate financial risks throughout the project lifecycle.
Financial sustainability is essential for an effective construction industry, and we are committed to collaborative risk allocation and resolving commercial issues promptly. We ask industry partners to innovate for financial sustainability, provide detailed
information to enable financial capacity assessments, and ensure timely subcontractor payments.
In April 2024, Infrastructure NSW introduced the NSW Decarbonising Infrastructure Delivery Policy for major government projects, focusing on reducing carbon emissions during material production and construction. The policy mandates consistent carbon measurement across project stages and aligns with New South Wales guidelines.
We ask our industry partners to focus on carbon considerations, engage on carbon measurement, and prepare for climate-related financial disclosure.
The Principles for Partnership, Women in Construction program and NSW Decarbonising Infrastructure Delivery Policy and Measurement Guidance are all about creating a sustainable, inclusive, safe and efficient construction industry to capitalise on the opportunities offered by a thriving infrastructure boom.
By embracing these policy initiatives, we can build a stronger, more resilient infrastructure sector for the benefit of everyone. Let's work together to turn these priorities into practice, ensuring New South Wales remains at the forefront of infrastructure innovation and excellence.
Building a better tomorrow, without changing how you build today.
Uses up to 16.7% less raw material than our standard 500N reinforcing steel and made from 100% scrap metal.
Driving progress to decarbonise the infrastructure industry doesn’t mean having to change the way you work. SENSE 600®, our new reinforcing bar innovation, brings you lower Scope 3 emissions without compromising on performance or qualityall while integrating seamlessly into your existing workflows. Together, we can create a construction industry where sustainability isn’t just an option - it’s the standard. It just makes SENSE
Delivering up to 39% lower embodied carbon when using in place of our equivalent load capacity standard 500N reinforcing steel.
www.InfraBuildSENSESolutions.com
Confidence from third-party certification from GECA (SSPv1.0i-2019) and meets Australian Standard AS/NZS 4671.
By Jon Davies, CEO, Australian Constructors Association
The Australian construction industry is at a critical juncture, but it needs to shift from a “me” to “we” mindset to evolve fruitfully.
“It’s always darker before the dawn” is a well-known proverb that suggests that the most difficult times come right before things improve.
Few could argue that the construction industry has experienced difficult times of late. Insolvency rates outstrip all other industries, cost inflation remains stubbornly high whilst profitability stays low and more people leave the industry than join it. But are there any signs that things are about to improve? As it happens, I believe the answer is yes!
There is a growing realisation that without action we will simply not be able to deliver all the infrastructure and housing that the nation requires, and that has led to the development of a whole range of initiatives that should start to come to fruition this
year and lead to positive change within the industry.
Focused on improving time for life, worker wellbeing and industry diversity, the groundbreaking industry culture standard will be finalised in the coming months and should then form part of procurement processes right across the country. Work is underway to develop a National Construction Strategy to improve productivity in the delivery of land transport projects. When completed later this year, the strategy could be expanded to include social infrastructure. A blueprint for a more sustainable (in the broadest sense) construction industry is being developed by the National Construction Industry Forum in time for the upcoming Federal election. It will provide a roadmap for whoever is elected to
leverage existing reform initiatives, remove duplicated effort and address problem areas not currently being looked at.
As well as reform initiatives, we are seeing positive change come from unexpected places. Industrial relations in the construction industry have long been a source of conflict but last year’s media exposé of illegal and intimidatory practices brought about a seismic change that few could have seen coming. Whilst there are likely more twists and turns to come, the industry has a real opportunity to reset industrial relations for the benefit of all stakeholders.
Before we all get too excited, I must make an important caveat. For this reset, and all of the initiatives I have mentioned to be successful, there needs to be a collective mind
A “we” mindset changes that. It begins with recognising that everyone in the construction ecosystem has a role in driving change and we will all benefit from it. A broader focus on value for money can deliver improved project outcomes whilst increasing industry profitability. Improved productivity can create more jobs not less. Reduced prescription in design can deliver more innovation.
requires more than structural adjustments – it requires a cultural shift. We need to let go of old habits and ask: what can I bring to the table to help everyone succeed?
shift by everyone in the industry. We need to move from “me” to “we”.
For too long, the industry has largely operated as a zerosum game of every person for themselves, or a focus on how I can get the best outcome for me irrespective of what that means for anyone else. This mentality applies equally between different stakeholder groups – such as contractors and designers or contractors and clients – and even between individual members of stakeholder groups, like contractor versus contractor. It is an approach that, at an industry level at least, is fundamentally flawed as it ignores the interconnected nature of the industry. We can’t consider ourselves in isolation as we are all dependent on others.
This isn’t just wishful thinking. Across Australia, we’ve seen collaboration deliver real results. Alliancing contracts bring stakeholders together under shared goals and risk-sharing agreements. Projects with early contractor involvement identify and resolve issues upfront, leading to better delivery outcomes. But true change
Leadership will drive that change and that’s why the Australian Constructors Association is making this cultural shift a key focus of the Foundations and Frontiers forum in August. Modelled on the COP and Davos summits, this gathering will bring together industry leaders, policymakers and stakeholders to ask and answer the big questions: How can you help me so that I can help you? Foundations and Frontiers will be a genuine opportunity for everyone to participate in the “me to we” conversation.
It's time to rise and shine. The new dawn is closer than you think!
By Cathryn Greville, CEO, National Association of Women in Construction
Construction is an industry of many contradictions. We need the brightest minds to solve problems and imagine and deliver skyscrapers and infrastructure that are incredible engineering feats – yet fail to recognise the need for workplaces to be safe and happy environments to achieve innovation. We compete for workers with glossy marketing and websites espousing commitment to diversity – yet haven’t nailed the ability to source talent from the whole talent pool. We speak of unsustainably low-cost margins and commercial pressures that challenge business solvency –whilst at the same time ignoring the costs that a non-inclusive or non-engaged workforce saddles on a business.
We see businesses pouring resources into attracting people (the recruitment question) – with far too little thought of what happens once those people join, and what meaningfully supports them staying (the retention question).
Of course, this doesn’t apply to all businesses. But in my experience, it does capture far too many.
And thinking you have it sorted often proves to be the kind of blinkered thinking that leads to business stagnation. Even those already prioritising inclusion are well aware of how much more they have to do.
Far too many leaders fundamentally overlook or misunderstand the way the culture makes or breaks their business. They miss the inherent connection between culture and workforce engagement, teamwork,
Cathryn Greville. Image: NAWIC
safety, efficiency, project delivery, risk, and indeed, the bottom line.
Culture is the underlying system of values, beliefs and behaviours that shape an industry and a business. All of those are driven by people.
When we shift our focus to people, we must ask: are we creating environments that are fair, inclusive and respectful? This means where people are treated fairly, according to their needs. Where bias isn’t rampant. Where unacceptable behaviour is prevented and shut down. Where people are valued for their skills and contribution and can succeed regardless of their background.
Ultimately, are we creating workplaces that people want to join and stay?
The numbers certainly say no. We currently lose a staggering 110,000 people, or eight per cent, of the construction workforce every year. At the same time, we need 400,000 or more people to join over the next five years.
While we face a substantial retirement pool, an ageing workforce
is not solely to blame. At the other end of the career spectrum, we are failing dismally to attract enough young people. Apprenticeship commencements are down 22 per cent over the past year, and so are the number of apprentices in training (down two per cent) and completions (down 15 per cent). An astonishing 72 per cent of first year apprentices are dropping out of construction trades altogether.
There are too many things that are simply not working for too many people, driving them out of the sector they chose to join.
There is no segment of the workforce where the impact of poor culture and practices is more evident than the experiences of women. Comprising only 12.4 per cent of the sector, and a mere 3.4 per cent in trades, we simply cannot afford to lose more women. Yet members of the National Association of Women in Construction (NAWIC) provide us with intel that makes it easy to see why women are calling time on construction.
Women often face unacceptable conduct such as sexual harassment, bullying and discrimination. Far too many work in businesses that fail to account for family planning or women’s health. Far too few women are in leadership positions or sit at decision-making tables. Gendered stereotypes and failure to support men’s caring responsibilities negatively impacts on women. As does the lack of appropriate toilets and changing facilities on site. Overall, women stand to face a gender pay gap of 31.8 per cent with many likely to be in less secure, lower
For critical applications, Yuasa UXL delivers long-lasting, maintenance-free performance when downtime isn’t an option.
15-Year Design Life
Long-term reliability for essential operations.
Maintenance-Free
No equalising charge needed—reducing downtime.
Flexible Installation
Vertical or horizontal mounting for versatility.
Performance Every Time
Proven power delivery since 1984.
Efficient Energy Output
Reliable energy when you need it most.
Reliable in Harsh Conditions
Built to perform in the toughest environments.
Performance Every Time – Powering Industries Globally.
paid positions and facing limited advancement opportunities.
The impact of poor workplace culture on exit rates is certainly borne out in NAWIC’s recent research, the Not so little things impacting women in construction. We found that microaggressions – those small acts that make women feel less welcome, less valued or less safe – were having significant personal, professional and financial impacts on women. An extraordinary 88 per cent of respondents had experienced microaggressions, with 80 per cent being verbal in nature and 41 per cent coming from supervisors or managers, followed by clients and customers at 38 per cent.
Perhaps most concerning is the lack of accountability within organisations, enabling poor culture and behaviours to continue. 63 per cent of women experiencing microaggressions saw no change after reporting.
The cumulative impact is significant. Eight per cent of female respondents reported leaving the industry entirely due to microaggressions, lack of opportunity, lack of flexibility and poor work culture.
To attract, recruit, retain and promote women, we need an industry that offers a safe and positive workplace culture, an attractive career option, strong career pathways, and inclusive environments that meet the needs of women.
CULTURE HOLDS THE KEY
Whilst culture is currently the problem, it also is the solution to turning things around. Statistics and research serve little utility unless we use them to understand and drive significant and sustainable change. We must apply a solutions-focus and work together.
It can be said that when it comes to inclusion in construction, it is a crisis not a competition. We stand to gain the most by putting the adversarial nature of the industry aside and working collaboratively to achieve positive culture that benefits everyone.
Far from being an idealistic goal, this form of industry collaboration is underway in construction
markets elsewhere. Prior to joining NAWIC, I was based overseas leading a program focused on both organisational diversity and inclusion and the sector-wide behavioural and cultural change required to positively impact outcomes in construction and the built environment. I was fortunate to advise and work directly with a range of businesses to drive cultural change. Culture change can certainly be done, and it must be a priority to meet our current needs.
Here in Australia, NAWIC is leading the gender equity charge to shift stubborn attitudes, address underrepresentation and attract, develop and promote talent. We want to see workplaces that are fair, inclusive and respectful.
I am passionate about ensuring women have a strong voice at decision-making tables across the country, and that the sector holds its leaders accountable.
NAWIC’S TARGET AREAS
As the membership body for women in all facets of construction and supporting sectors, NAWIC is committed to our vision of an equitable construction industry for all.
This year, we are focused on initiatives that action real change, addressing:
1. Representation – in all its forms, and covering all from attraction to recruitment, retention and promotion to retirement
2. Industry needs – the opportunities posed by current and future workforce shortages and improvements that can be made across all market segments
3. Women’s experiences – tackling the pervading issues that limit, impact or keep women out of the sector altogether.
At no time is it more crucial that we make substantive change, and poor cultures that permeate the sector must be addressed head-on.
NAWIC will continue to represent and champion women in the sector whilst pushing for high safety standards: PPE that does what it is meant to; a zero-tolerance approach to unacceptable conduct including sexual harassment, discrimination and microaggressions; proper access
to facilities; inclusion for parents; workplace flexibility; attention to women’s health and wellbeing; sharing of both the mental load and the role of caring; and closing the gender pay gap.
PRIORITISING CULTURE
It’s no exaggeration to say that the addressing the underrepresentation and poor experiences of women in construction is one of the biggest issues facing the sector and should be at the top of all leaders’ minds.
Not only do we need women to support the scale of construction in housing, infrastructure and renewable energy transition for our growing population, but at the fundamental level, women should be participating in, and sharing in, the economic benefit of our industry.
Added to that, bringing in, and keeping women in the workforce offers enormous economic opportunity. Closing the gap in women’s workforce participation nation-wide could increase GDP by a staggering 11 per cent. In an industry that contributes to around nine per cent of GDP employs 8.7 per cent of the national workforce, this should alarm government and business leaders alike.
We need practical long-term culture change that will make meaningful difference to women in the sector – no matter what market segment, business type or role they serve – to make construction an inclusive and meaningful career for everyone.
Join us in prioritising culture and driving the industry forward.
For more information, visit nawic.com.au
TemRack iR is a fully integrated, motorised ACB remote racking device. This permits safe isolation of Terasaki TemPower 2 AR ACBs, with zero physical interaction between personnel and the ACB.
TemRack iR For
nhp.com.au/TemRack
The underground construction sector has historically had a significant lack of female representation, which is why Victoria’s Suburban Rail Loop is undertaking an initiative to create an all-women tunnel boring machine crew.
Aproject the size and scale of Suburban Rail Loop (SRL) offers a rare opportunity to bring new people into the industry, helping to train the next generation of highly skilled Victorian workers.
The world’s first all-women tunnel boring machine (TBM) crew will help break down barriers and attract more women into the construction and tunnelling industry.
The team will be one of several TBM crews helping to carve the SRL East twin tunnels and will include around 25 highly skilled roles – including the TBM operator, gantry and segment crane operators, grouters and support roles.
The team will be led by SRL East Tunnels South Construction Manager, Isolde Piet, who has decades of experience in underground construction and managing tunnelling projects in Australia and around the world.
Mrs Piet was the first female TBM pilot in the world and explained that she began her career in underground construction in the Netherlands.
“I was working with a French company at the time, who was in charge of that tunnelling project,” Mrs Piet said.
“On that project I basically started off as an engineer involved in the building of the shaft, so where the TBM was going to start from.
“I did a lot of the works around the tunnelling but wasn’t really involved in the actual tunnelling itself, but that's where my interest was really at the time. I wanted to go on a machine, I wanted to understand how it works.”
Mrs Piet said that the company offered her the opportunity to become a TBM operator, although there were some concerns.
“There was a bit of back and forth at the time, ‘okay you're really sure you want to do this?’ because there were a number of barriers, some really basic things which seem trivial now.
“But back then it was things like, ‘we don't have a change room for you’. I actually had to go find a room to get changed in, because everything was set up for male teams only.
"Things like ‘we only have one toilet on the TBM, so you’ve got to share it with 40 other blokes. Are you happy with that?’
"It was all these little bits that we sort of just had to tick off one at a time. But ultimately, they gave me the opportunity to do it, which was great.
“I wasn't actually aware that I was the first female TBM operator at the time. I was merely a tunnel engineer who was really interested in understanding how it works, becoming a better engineer off the back of it, and working in a team and becoming a better team player.”
Mrs Piet said that she felt that she was under quite a lot of pressure to do well.
“Because ultimately you want to make it work and you want to make sure that you're not going to get that ‘told you so’ type of response.
“After a few weeks though, that wore off and obviously I can say now, looking back, I did a good job.”
The all women TBM crew is also a world’s first, and Mrs Piet explained that it was put forward as an initiative to further women in underground construction, as there are very few women in that sector.
“We had to win the contract first of course to be able to move forward with the initiative, but ultimately, we did.”
Mrs Piet said that the reasons there are so few women in underground construction, are two-fold.
“One is that women don't see it as an opportunity because there aren't many role models. It's sort of like the chicken and the egg. If you don't bring women into the industry, then there are no role models or leaders that you can look up to.
“I think the expression that you might hear often is, ‘you've got to see it to be it’ or something like that.
“There are, of course, a few females out there. It's a bit like me.
Australia’s energy, utilities, and infrastructure sectors are undergoing a profound digital transformation. Smart technologies and interconnected systems are reshaping infrastructure - bringing innovation and opportunity, but also significant challenges.
At Clayton Utz, we help clients navigate the complexities of this new era - rethinking procurement models, managing cyber risks, meeting regulatory demands, and managing IP rights. Our pragmatic advice ensures you can manage risks, embrace innovation, and achieve project success.
Our whitepaper, The era of digital complexity in Australian energy, utilities and infrastructure, examines the critical challenges businesses must navigate to thrive in this rapidly evolving landscape. Successfully addressing these complexities is key to building resilient, secure, and future-ready infrastructure. Scan here to download the report
"People who are really interested will find a way or make a way. But there are also people who just need to see that there are opportunities and that's exactly what this is.”
Mrs Piet said that the second primary reason is that there are very few opportunities designed to encourage women into the industry.
“This initiative is creating an opportunity for females to actually go underground and actually bringing them into a field of industry where there's not a lot of female representation to date.”
In a remarkable result, almost 870 applications were received for the all-women crew through the Expressions of Interest process that closed in October 2024. This is an extraordinary response for roles women do not typically perform across Australia.
Mrs Piet said that she was pleased
because it shows that there is a lot of interest in the sector from women.
“The process is taking a bit longer than we imagined because we weren’t expecting to get almost 900 applicants.”
The applicants have come from a variety of disciplines including those with tunnelling and construction backgrounds, as well as 62 applicants with no construction experience, who come from diverse sectors including admin, human resources, corporate sales, hospitality, beauty therapy and customer service.
Applications are now being considered, and with such a strong response, women not selected for the TBM crew roles may also be considered for other suitable roles on the project as part of the assessment process.
The all-women crew will have a range of roles – each of which requires a specific skill set. Some of the crew members will require
women not currently working in this field will undertake training to give them the necessary skills and experience to succeed.
“We've gone through all the CVs and identified the range of women, from zero experience to a lot of experience. We’re separating them into categories and certain categories will get additional training before we bring them on site.”
A comprehensive training program is being developed, and SRL will be working with the Victorian Tunnelling Centre (VTC) where it can support their training. The selected women will also receive hands on experience from other tunnelling projects –including North East Link – to ensure all aspects of safely and efficiently operating TBMs are developed.
Following this comprehensive training, SRL will launch the world-first All-Women TBM crew of certified, qualified, trained and experienced women to operate one of its TBMs.
Four TBMs will be digging the southern section of the SRL East twin tunnels under works by contractor Suburban Connect. Each of the TBMs requires two crews to manage their operations over a shift cycle. Across the four machines, SRL will have eight crews. The all-women crew will be one of these eight.
Additional TBMs will be used for the northern section of the SRL East twin tunnels.
Tunnelling for SRL East starts in 2026, with the first tunnel boring machines arriving on site in late 2025, and the all-women TBM crew is expected to be operating by 2027. Following the completion of the tunnelling program, members of the all-women crew will be supported with identifying the next tunnelling or construction project opportunity for them.
Mrs Piet said that she believes one of the truly unique aspects of this initiative is the amount of time it has dedicated to participants.
“The whole project will run all the way until 2029.
“That is a decent amount of time that we can use to train these women and bring them into this career path and have them gain all this experience.
“Ultimately, what I hope it does is leave a legacy so that these women actually will continue their careers in other projects post-SRL.”
Major projects are becoming increasingly complex, so it’s critical that the leaders at the helm of these developments understand every aspect of complex project management.
In an era marked by constant change, heightened interconnectedness, and intricate interdependencies, the successful execution of complex projects has become imperative for organisations across industries. To achieve favourable outcomes, a new breed of project leaders must emerge, equipped with the competence to navigate the complexities inherent in our modern project delivery environment.
Traditional project management approaches, while effective in many contexts, fall short when faced with the multifaceted challenges of today's projects. The intricacy and scale of these endeavours necessitate a different approach, one that transcends mere task management and delves into the realms of systemic thinking, strategy, innovation, collaboration, and adaptability.
Complex project leadership, therefore, emerges as a distinct leadership competency, essential for guiding organisations through the ever-evolving landscape of modern project delivery.
As the peak body for complex project management, the International Centre for Complex Project Management (ICCPM) is committed to improving complex project delivery outcomes. This includes supporting the development of a highly skilled workforce.
As organisations faced increasingly complex and interconnected challenges, it became evident that a new approach to project leadership was required – one that could navigate the uncertainties, ambiguities, and intricacies inherent in modern project delivery
environments. This was the motivation behind the release of the Complex Project Leadership (CPL) competency standards which ICCPM maintains on behalf of the Commonwealth of Australia.
The ICCPM CPL standards represent the collective wisdom and insights of an international group of experienced professionals, scholars and practitioners who have dedicated themselves to understanding and refining the art and science of leading complex projects.
Developed through extensive consultation and analysis, these competency standards provide a comprehensive framework that project professionals around the world can utilise to enhance their project leadership capabilities and
drive exceptional results in complex project delivery.
The competencies outlined in the CPL standards encompass a broad spectrum of skills, attributes and behaviours that underpin effective complex project leadership. These competencies range from systemic thinking and action, focusing strategically on delivering project outcomes to engaging collaboratively with stakeholders, exercising contextual leadership and applying system governance and delivery assurance.
Project leaders who embody these competencies are able to navigate uncertainty and ambiguity, inspire teams, manage change, and leverage emerging technologies to create innovative solutions amidst complex project landscapes.
In today's rapidly evolving and interconnected world, organisations face an unprecedented array of complex challenges and opportunities. The effective delivery of complex projects, which encompass a diverse range of industries and sectors, demand a unique set of leadership competencies to navigate the intricate webs of interdependencies, manage ambiguity, and drive successful outcomes.
In an environment where skilled workers are in high demand across industries, it is essential
to be able to evaluate the fundamental skills and attributes required to successfully deliver complex projects to facilitate the establishment of skilled project teams and the movement of staff between projects and industries.
Performance-based competency frameworks are an internationally recognised way of aligning individual and occupational goals by clearly defining the expectations for job performance and competence. They serve as a roadmap for individuals to understand what is expected of them and provide a framework for assessing their performance against established criteria.
For professionals like complex project leaders who are in demand across industries, they identify the essential transferable skills and attributes upon which industry specific knowledge and experience can be built.
Additionally, these frameworks facilitate the development of training and development programs to bridge any competency gaps and support individuals in enhancing their skills and knowledge.
The ICCPM CPL standards were designed for a diverse range of professionals involved in complex project delivery, including project managers, program managers, engineers, senior executives and organisational leaders. These competency standards are applicable across industries, sectors, and project types, recognising the universal need for effective project leadership in the face of
While the standards provide a comprehensive foundation for complex project leadership, it is essential to acknowledge that leadership is a dynamic and contextspecific practice. These competency standards should be viewed as a framework, allowing leaders to adapt and tailor their approach to suit the unique demands of their projects and organisations.
In today's rapidly evolving business landscape, the transferability of complex project leadership skills and competencies across industry sectors has become increasingly relevant and valuable. While each industry possesses its unique characteristics, challenges, and requirements, the fundamental principles of Complex Project Leadership remain constant.
the skills and attributes defined in the CPL standards are those required to think and operate systemically and form highly effective teams across the project, program, portfolio or organisation.
By embracing and cultivating the identified competencies, leaders can elevate their capacity to navigate complexities, foster innovative thinking, manage risks, and inspire high-performing teams. This, in turn, will contribute to the successful delivery of projects with far-reaching impact and value.
Readers to download a copy of the CPL standards from the ICCPM website and delve into the pages with an open mind and a willingness to challenge conventional wisdom. ICCPM encourages individuals and organisations to embrace these competency standards as a catalyst for personal and professional growth, as well as organisational excellence.
The International Centre for Complex Project Management (ICCPM) is the peak body for complex project management. It was established in 2007 by the Australian Government in response to an identified need to improve the performance of complex projects.
As an independent, not-for-profit,
Threats to Australia’s critical infrastructure are on the rise, and policymakers have responded with legislation like the Security of Critical Infrastructure Act (SoCI) to keep assets safe and the country secure. To comply, critical infrastructure entities can turn to Noggin’s integrated resilience software, to help prepare for and respond to business disruptions and critical events. The Noggin platform seamlessly combines 10 solutions into one, easy-touse system, with solutions for: operational and third-party risk management, business continuity, crisis & emergency management, operational resilience, and safety & security operations.
Learn why Australian critical infrastructure entities choose Noggin to help strengthen their resilience against business threats: www.noggin.io
Under a new ownership structure and bold new name, Agilitus (formerly BG&E Resources) is entering an exciting era of growth and independence.
When Craig Bloxham and Tony Comerford founded BG&E Resources, they saw a gap in the market for a private engineering and design company that was agile, responsive to clients’ needs and able to make quick decisions. Seven years later, the Western Australian-based company has become a key player in the industry, positioning itself for further expansion in Australia and beyond.
Until February 2025, BG&E Resources was part of the BG&E Group. Now the company has stepped out on its own under the new name Agilitus.
Agilitus Managing Director and CoFounder, Craig Bloxham, said, “We've had a very successful relationship with BG&E for quite a few years and both companies have done very well.”
Mr Bloxham said the new changes mark a major milestone in the history of the company.
Agilitus co-founders Craig Bloxham and Tony Comerford.
“It's been part of the vision as to why we set up a company and is what we always wanted to achieve.
“The company has been tremendously successful with seven
years of existence, beyond our expectations. It really reflected the fact that our clients want a privately owned company that was medium sized, agile and very responsive.”
“It's a great opportunity for us to rebrand ourselves and go forward to expand further on the east coast and grow our service offering,” Mr Bloxham said.
When exploring a new name and brand, Bloxham wanted a word that represented how they worked with clients.
“Clients have always told us we are agile, so this name is ideal for us. Agilitus combines ‘us’ with ‘agility’,” he said.
“We chose that name because we believe that being agile is very important, especially with what’s happening in the industry right now,” Mr Bloxham said.
“A lot of privately owned engineering companies have been brought out by big corporates. When that happens, you lose a lot of flexibility and agility
in your decision making at a senior management level because there’s a lot of shareholders involved.
“Being privately owned ensures we can respond quickly to our clients’ requirements in their domains.”
As part of the restructure, Agilitus’ key staff will also be given the opportunity to own equity in the company.
“Owning part of the company means you’re more invested in the business, you have ‘skin in the game’,” Mr Bloxham said.
“The Agilitus team will be highly motivated to continue the company’s success in the future.”
As for that future, Mr Bloxham is optimistic.
“We occupy a distinct part of the marketplace in Australia and there’s a massive opportunity for us to increase our market share here and internationally as well.
“The company was born in Western Australia. We’ve more than 350 staff in WA and a further 100 in Newcastle, Brisbane, Townsville, and we’re very proud of that. While we’re well recognised in Western Australia, we are well on our way for further expansion across Australia.”
“With the change to Agilitus, we have the opportunity to clearly identify what we stand for as a brand which will remove some confusion for some of the customers and industry.”
Looking ahead, Mr Bloxham reaffirmed Agilitus’ commitment to its clients.
“We will never lose focus on our clients. That's always been our ethos. We'll continue to do a great job. We'll have our people fully invested in the business, making sure that we're doing the best we can to service you.”
Immediately NonInvasive
Continuing professional development is an important aspect of any engineer’s career, and working with the right providers for this development is critical.
Over the past 25 years, the focus on training and professional development has skyrocketed in all fields, including engineering.
The Engineering Training Institute Australia (ETIA) was first established in 1998, formerly known as Cement & Concrete Services.
When ETIA/CCS first commenced face-to-face training workshops for engineers, there was no formal process or CPD system in the marketplace that required engineers to advance their skills after leaving university. ETIA’s main customers were engineers that wanted to keep up-to-date with the current engineering standards, or further expand and improve their knowledge on various engineering topics. A few years later, the CPD system became mandatory and ETIA continued to develop new workshops to support the increasing demand for engineering training.
To maintain engineering status and ensure Engineers Australia Chartered or NER credentials stay valid, engineers need to complete 150 hours of Continuing Professional Development (CPD) over a three-year period. These hours are a combination of hours spent at training courses, research, work practice and any other tertiary studies being undertaken.
Within the training course requirements, engineers need to undertake ten hours of training in risk management; 15 hours in business (like accounting) and management skills; 50 hours relating to their particular area of practice; and the remainder must cover a range of activities relevant to their engineering career.
Since its establishment in 1998, ETIA now offers over 40 training courses in various areas of engineering (such as civil, structural and mechanical) for both professional and paraprofessional staff. The full list of courses offered throughout each year can be viewed on the ETIA website.
Since 2020, ETIA mainly offers workshops that are livestreamed over Zoom, with the occasional face-to-face workshop in Sydney, Brisbane and Melbourne. ETIA’s expert speakers are leaders in their industry, presenting workshops that adhere to the current engineering standards, so attendees are always provided with up-todate information relevant to your engineering field.
ETIA courses cover many specialised areas that appeal to staff in engineering design and construction, infrastructure works, building design and construction. These areas include but are not limited to concrete, steel, masonry, geotechnical, timber, loads, business accounting and management, risk management, hydraulics, glass and aluminium and forensics.
In addition to conducting training courses, ETIA are also the Australian and New Zealand agent for FINE Geo5 software. There are a whole range of geotechnical programs that are on offer on the ETIA website, similar to the geotechnical courses offered by ETIA. Engineers that attend an ETIA workshop in 2025 will also receive a 10 per cent discount
off the purchase of Geo5 software. Programs can be activated via a cloud system or by hard key.
For further information on ETIA CPD workshops in 2025 or the Geo5 software available for purchase, please visit the website etia.net.au or email registrations@etia.net.au
The National Rail Action Plan is focused on making rail simpler, reconciling the range of systems, training procedures and standards in operation around the country. Digital technologies have an important role to play in this harmonisation process.
The rail industry is faced with complex industry requirements and regulations, an ageing workforce, and labour competition from other industries. Reforms are currently underway through the National Rail Action Plan (NRAP) to develop a national approach to rail that will improve safety, lift productivity, support local manufacturing, enhance sustainability and help grow a skilled workforce.
It's estimated that 70,000 more skilled workers will be needed over the next decade to design, operate and sustain growing networks. Through the NRAP, the National Transport Commission is working with governments, the rail industry, skills sector and unions to reduce the need for bespoke training by streamlining operating rules and processes.
This will reduce the burden on workers, improve safety, drive down costs and time lost to training, and make it simpler and easier for workers to move across networks, improving workforce capability.
TECHNOLOGY AND TRAINING
In May 2024, the Australian Rail, Tram and Bus Industry Union (RTBU) selected Avetta to create an industry solution for all rail workers across Australia. RailWallet was designed to verify and manage rail worker qualifications and compliance with industry requirements and regulations.
“For those undertaking projects in the rail corridor, RailWallet is a game changer for industry operators seeking to make the rail network safer and more efficient,” said Luke Boyle, VP Operations APAC & Global Worker Support at Avetta.
“RailWallet offers cost and time savings for operators, and
“With RailWallet’s advanced digital capabilities, we’re not just simplifying compliance – we’re fostering a safer, more connected and efficient rail industry,” said Shayne Kummerfeld, TrackSAFE Foundation Board Member and National Assistant Secretary at the RTBU.”
sustainable digital cards that empower rail workers by giving them access to their own information, such as their qualifications and compliance status, and allowing them to complete online inductions via mobile app.”
Expired competencies, lost access cards and missed training disrupt productivity. With the RailWallet digital card, rail workers can view their roles, competencies and compliance progress, update competency documents, check verification status and complete training assignments and inductions directly from their mobile phones. Industry operators can plan and set training and track and report on the results linked to a rail worker’s profile and digital card.
One of the latest updates is the integration of the RailWallet StudentManagement System with Registered Training Organisations (RTOs), including Training Ahead Australia. This API integration streamlines and automates the process of uploading competencies, enabling immediate recognition of completed training within the RailWallet mobile app for rail workers. It eliminates the need for manual uploads, saving RTOs four to five hours per week.
"With RailWallet’s advanced digital capabilities, we’re not just simplifying compliance – we’re fostering a safer, more connected and efficient rail industry,” said Shayne Kummerfeld, TrackSAFE Foundation Board Member and National Assistant Secretary at the RTBU.
“This innovation directly supports the sector’s growth, helping bridge the skilled workforce gap and meet evolving industry demands.”
Reducing compliance risks and improving safety and productivity across the rail industry is the foundation of the RailWallet system. RailWallet reduces the duplication of effort in providing the same compliance documentation multiple times between different organisations or projects in a safe and secure ISO 27001 and SSAE Type II certified system.
Industry operators can collaborate on business rules and system requirements, set and manage rail workers’ roles, competencies, training and inductions, view worker analytics and training, and control site access to the railway network.
For more information, visit railwallet.com.au
Australia is investing in major infrastructure projects across the country, and big construction sites mean big organisational challenges.
To help deliver the critical infrastructure that Australia needs, project managers must invest in proper management of their sites to meet the needs of their workers, as well as meet deadlines, minimise costs and deliver positive project outcomes.
That’s why Kennards Hire
Major Projects provides a single point of contact for seamless project management.
Major projects have a wide range of success factors, including cost, time, quality, satisfaction, management,
safety, technology, organisation, environment and resources. Due to this complexity, it can be difficult for teams to manage these factors effectively and safely.
Kennards Hire’s 2024 Construction Confidence Check found that on average, construction business leaders reported that of all productivity hours lost on their worksites, 28 per cent were due to a failure to ensure workers had access to functional equipment.
The Kennards Hire team understands the critical success
factors required to keep major project builds moving safely and efficiently. By working with Kennards Hire, construction and infrastructure project managers can ensure end-to-end management from an experienced team that will keep the project moving.
DEDICATED POINT OF CONTACT
Kennards Hire Major Projects Manager, Chris Ram, said that it is his role to be a one-stop-shop for Kennards Hire customers.
“Instead of them coming out to different branches and dealing with
multiple people, we'll have one project manager assigned to the project that will look after the full spectrum of the project from start to finish. That would include anything from new hires to site setups, equipment service and maintenance, or really anything they need on-site,” Chris said.
“On large-scale projects, challenges arise daily, from equipment breakdowns to site facility adjustments. Our role is to solve these problems quickly and
efficiently 24/7, keeping projects on track.
“This is why one of the major things that we manage are the site facilities. That includes anything from lunchrooms and offices, first aid rooms, amenities blocks, and more.
“Customers often come to us with essential needs like site layouts, asking how to set up a compound for hundreds of workers. We provide a comprehensive solution, managing everything from setup to ongoing maintenance.”
Chris recently delivered a turnkey compound solution for Enel Green Power’s Girgarre Solar Farm in Victoria.
With a Modutech covered walkway, superior lighting and well-maintained facilities for greater comfort and productivity, workers described it as one of the best compounds they had used, highlighting its practicality and welcoming environment.
Quality and responsiveness are Kennards Hire’s two key advantages, according to Beon Project Manager, Rohan Clarke and Beon Construction Manager, Ben Clarke Ash.
“It’s great having a project manager,” Rohan said.
“Chris was so responsive. We could pick up the phone and speak to someone who can deliver what we need, when we need it. He was always flexible when dates were pushed back.
Ben said, “We always got a fast turnaround, with someone available pretty much around the clock. Chris co-ordinated all our work health and safety compliance, inducting multiple contractors so they were ready to go.”
With Kennards Major Projects taking care of site layouts and the needs of workers, the customer can focus on core construction activities
while Kennards Hire handles the logistics and operational challenges of large-scale sites.
With increasingly stringent environmental practices across construction, Chris explained that Kennards Hire project managers also help customers align with their project sustainability goals ensuring compliance with industry standards.
“A key thing that we look for is sustainability within the project. We help our customers prioritise sustainability by looking at various aspects of the project including using 5-star appliances on-site, using solar generators, having waterless urinals – everything that we can do to help minimise the environmental impact.”
Chris said that Kennards Hire project managers help customers in a range of other areas as well, including:
• The procurement, availability and supply of equipment and resources
• The selection and induction of contractors
• Management and servicing of machinery
• Ensuring workers or visitors to the site meet all the necessary criteria and guidelines
“One of the biggest challenges project managers face is finding a partner who understands their project's needs and collaborates with them every step of the way to meet them. That’s what we provide. We bring in the much-needed expertise and resources required to help deliver complex projects on time.”
Kennards Hire is committed to evolve and adapt to the changing project needs across industries while continuing to provide the best possible outcomes for their partners in the future.
By working with their customers in every aspect of a project and calling on decades of industry experience, Kennards Major Projects provides end-to-end project management support to help ensure your project is completed on time.
Kennards Major Projects understands the critical factors required to keep major project builds moving safely and efficiently.
For more information on Kennards Major Projects, visit kennards.com.au/ commercial/specialist-solutions/ kennards-major-projects
Not all vacuum excavation machines are created equal –and Vermeer’s are in a class of their own.
Vacuum excavation – it’s the modern solution to a timeless problem: using high-pressure water or air to break up soil and safely expose underground infrastructure like gas, water, electricity, and communication lines without causing damage. By now, most contractors know how critical vacuum excavation is, especially since the ground beneath footpaths and roads is a web of vital services powering households and businesses.
For contractors, choosing the right vacuum excavation machine is no small task. It can be the difference between winning a contract and losing it to a competitor. The stakes are high, but Vermeer Australia makes it easy.
Gone are the days when contractors had months to source equipment. Projects start fast, and downtime is costly. That’s why Vermeer Australia has trucks fitted with vacuum excavation machines ready to roll, whether the project starts in a week or a month. From 2,000L to 7,600L machines, with a range of power capabilities, Vermeer has contractors covered. With 13 dealerships across Australia, Vermeer Australia is ready to support operations no matter where the project is. Vermeer’s experienced sales managers work with clients to understand their needs, ensuring they get the machine that maximises efficiency, minimises downtime and boosts profitability.
Vermeer’s vacuum excavation machines are built with the industry’s best components:
• Engines from trusted brands like John Deere, Kubota, and Yanmar ensure reliability and power.
• Root blowers, known for their efficiency and durability, feature a dual oil bath system for both gears and bearings. Unlike others that rely on grease on one side (an easy oversight leading to costly failures), Vermeer’s blowers are designed to keep running smoothly.
Operator fatigue from handling heavy, mud-filled hoses can slow down crews, and blockages in traditional booms can lead to hours of downtime.
Vermeer’s telescopic booms solve these challenges:
• The hose widens in diameter along its length, starting at five inches and extending to eight inches. Blockages, when they occur, are almost always in the
narrower section, unlike other vacuum excavators that use the same diameter for the whole length of the hose.
• Using the remote control, operators can lower the boom to chest height and clear blockages in seconds – there’s no need to leave the site or lose valuable time.
• W ith 270 degrees of rotation, Vermeer booms provide unparalleled reach and manoeuvrability.
• Reverse flow technology: blockages are inevitable, but with reverse flow, they can be cleared in seconds by simply flipping a lever. This feature saves hours of downtime over the year, translating to higher profits and happier clients.
• Patented Cam-Over locking rear door: this innovation ensures the spoil tank stays sealed, preventing messy leaks during transport.
• Advanced operator features: Vermeer machines come with user-friendly controls, in-tank cleanout systems, safety components, water pump PSIto-litre ratios, and even weight scales to keep your truck within legal limits.
For over 20 years, Vermeer Australia has been delivering innovative vacuum excavation solutions tailored to the needs of Australian contractors. Whether the job needs a compact trailer-mounted unit or a powerful truck-mounted Mega Vac, Vermeer has the perfect machine for your business.
Ready to level up your operations? Contact your local Vermeer Australia branch today and let our specialists guide you to the right vacuum excavation machine for your next project.
The Only All-In-One Contractor Risk Management Platform You Need
By Simon Newcomb, Partner, Clayton Utz
Australia’s infrastructure sector is becoming more technically complex and connected, presenting new challenges in technology interoperability.
In the past, infrastructure projects were delivered with little thought to technology interoperability.
But with the growing use of digital technologies, that landscape has changed significantly.
Today’s infrastructure projects are more interconnected than ever. That interconnectedness comes with increased complexity, requiring new roles, technologies and processes to ensure seamless technology integration both internally across all project technologies and participants, and externally with related systems and stakeholders. It requires new issues to be anticipated and addressed like technology compatibility, intellectual property rights, data governance, technology contracting and cybersecurity.
Managing technology interoperability has become central to successful infrastructure projects and needs to be addressed in all project phases, from project conceptualisation, through procurement, delivery, maintenance and operation.
With multiple technologies involved in infrastructure projects, it's crucial to ensure that all elements can work together. This requires the traditional focus on physical integration to expand to cover the logical integration of technology.
The Brisbane Metro project is one example where the use of multiple
technologies demanded a fresh approach. The project involved the integration of electric vehicles, battery charging, road and station infrastructure, control systems as well as external operator and government systems. To ensure these technologies were coordinated and working together, a systems integrator was appointed to the project.
Another common challenge for infrastructure owners is getting locked into a single supplier.
Technology interoperability and proprietary rights create barriers to switching technology. Often this requires procuring long term maintenance and essential technology services like software or data "as a service" at the same time as the project delivery is procured. Another approach is to mandate adherence to standards (where they exist) to provide for future interoperability and procurement contestability.
In recent years we’ve seen the growing use of digital twins to provide a virtual representation of physical infrastructure allowing simulation and use of data to help make better decisions.
Brisbane’s Cross River Rail, for example, integrated BIM, GIS and the video game engine used in Fortnite to create a threedimensional model. This integration plays a critical role in construction,
maintenance, operation and community relations.
However, digital twins introduce challenges around data and legal interoperability. Creating these models requires the compiling of data from multiple sources including contractors, consultants, utilities and government agencies. Once the model is created, there may also be other projects, government agencies and private sector entities interested in accessing the data.
Ensuring this data is standardised and can be used effectively across platforms is the first hurdle. Legal interoperability also comes into play around intellectual property licensing of data from upstream sources and liability issues where data is relied on by downstream users. These challenges can be addressed through the early establishment of data technical standards and data licence
terms that ensure all participants are working to the same set of rules.
OPERATOR INTEROPERABILITY
Interoperability between infrastructure operators is needed as infrastructure is increasingly operated as part of broader networks.
For example, in Australia’s road transport sector, toll roads and tag payment systems rely on interoperability to ensure traffic data collection and payment settlement arrangements are consistent for motorists using many different roads. Likewise, operators must cater for intelligent transport system (ITS) interoperability with systems managing connected infrastructure and the broader transport network. This will continue to become even more important as mega trends like autonomous vehicles and network optimisation change the transport sector.
Agreements between operators may be needed to regulate the technical and operational standards and allocate responsibilities and risks.
CYBERSECURITY RISKS
As infrastructure projects become more connected, and data and control systems become more distributed, there is an increased risk of cyberattacks due to the complexity and broader "attack surface".
The public conversation around cybersecurity is often focused on data breaches, but for infrastructure, the risks extend well beyond that. Cyberattacks on operational technologies that control physical infrastructure like energy or transport networks or hospital systems can have dangerous consequences for the safety of people and property.
The need for prudent management of these cyber risks is reflected in the Security of Critical Infrastructure Act
(SOCI), which mandates Australian owners and operators of critical infrastructure to adopt robust cybersecurity measures (amongst other risk management).
THE ROAD AHEAD
The industry is rapidly moving to ever more interconnected projects adopting disruptive technologies and management trends like digital twins, smart infrastructure, connected operators, network management, data analytics and AI. With these changes, strong governance and effective management of technology interoperability is essential for the future of infrastructure delivery and operation.
For more information, visit claytonutz.com/media/nzuldfmn/ the-era-of-digital-complexity.pdf
Simon Newcomb is a technology lawyer who works together with Clayton Utz’s major projects team on infrastructure projects. He also leads the Clayton Utz artificial intelligence program and is on the firm’s Cyber Security Board.
Pile Foundations Design Geotechnical Workshop
Timber Design Workshop: Module One
Risk Management Workshop
Reinforced Concrete Design Workshop: Module One
Composite Steel & Concrete Structures Workshop
Accounting & Management for Engineers Course
Glass & Aluminium Façade Design Workshop
Prestressed Concrete Design Workshop
Hydraulic Engineering Design Workshop
Residential Slabs & Footings Design Workshop
On-Site Detention Systems Design Workshop
Process Piping Pressure Design Workshop
Shallow Foundations Design Workshop
Earthquake Design Workshop: Module One
Earthquake Design Workshop: Module Two
Wind Design Workshop: Low & Medium Rise Structures
Structural Steel Design Workshop
Wind Design Workshop: Dynamic & High Rise Structures
Cement & Concrete Practice Course
Detailing in Practice Workshop
Retaining Walls Design Workshop
Slope Stability Design Workshop
Precast & Tilt Up Design & Construction Workshop
17 April (ZOOM)
As digital technology becomes more accessible and robust, project managers handling large-scale builds should consider how data management tools can optimise their processes and help Australia meet its future infrastructure needs.
The civil infrastructure sector is already making use of a range of emerging technologies like digital twins, artificial intelligence (AI), building information modelling (BIM), the Internet of Things (IoT) and advanced analytics. These tools generate a significant amount of data, which can be used to enhance decision making and improve project outcomes.
While having access to large data sets can keep organisations informed, issues can occur when information is poorly managed.
Ineffectively managed data can lead to projects errors, which result in rework, delays, budget overruns, damage to reputation and even contractual penalties. Keeping data well-managed and connected is vital to continued project efficiency and customer satisfaction.
Accessing and storing data though a secure, shared platform – called a Common Data Environment (CDE) – helps mitigate the challenges of data management.
Cloud-based CDEs can improve project management by securely storing and sharing data between team members, different teams and even external stakeholders.
This allows all relevant parties to utilise the information that matters and set projects up for the best possible outcomes.
One of the primary benefits of CDEs is that all data is centralised and compatible. In projects using manual data sharing, information is often incompatible due to different systems or software. This means that shared data can become inaccurate or outdated, which leads to costly project errors. CDEs allow all stakeholders to access the same data sets securely and consistently, ensuring information is always up to date and correct for everyone.
By utilising this centralised data platform, project managers can predict and minimise wasteful activities, reduce costs and use time more effectively.
Organisations that manage their data with a CDE can improve their planning and decision-making across entire project lifecycles.
By fulfilling the following three imperatives, project owners can build today’s infrastructure for tomorrow:
Improve operational efficiency to deliver projects on time and on budget Research has shown that large-scale projects tend to cost more and take
longer than expected. As many as 91.5 per cent of projects run over budget, behind schedule or both.
While this can be caused by external factors like increasing construction costs and inflation, project managers can mitigate the impacts of these factors by utilising their data through a CDE, allowing them to make informed decisions and ensure projects are as efficient as possible.
Planners can eliminate significant data redundancy by combining geographical information systems (GIS) and building information modelling (BIM) through the CDE. Connecting these two elements seamlessly means designers have access to more accurate information and better geospatial context, resulting in better plans and saving money on requests for information.
Mitigate risk to improve the quality of work
Due to the complexity of assessing social, economic and environmental impacts, the planning and permitting phases are often where the biggest project delays occur.
Using the CDE to enable the dynamic interchange of BIM,
computer-aided design (CAD) and GIS data allows project teams to easily and consistently access accurate data and greatly reduce the risk of errors and rework.
Additionally, the connected data platform enables automation, which can be used to streamline certain processes and eliminate redundancies, improving overall efficiency.
Reduce waste and increase resilience to enhance sustainability Sustainability goals are commonplace in many organisations and projects across Australia, to ensure that the nation can achieve its future infrastructure requirements as sustainably as possible.
The data efficiencies granted by a CDE allow project managers to better include sustainable designs in the planning phase and to minimise material wastage over the course of project construction.
Infrastructure owners and operators can also use the centralised data to assess risks and asset life expectancy and resilience. This enables flexible planning for the reuse and repurpose of existing assets and improves the future designs of new assets.
Data-informed decision-making can be the key to more successful infrastructure projects.
Data-informed decision-making can be the key to more successful, sustainable and resilient large-scale infrastructure projects.
Autodesk is a multinational provider of software solutions that can help project managers to develop a tailored CDE that suits their specific requirements and processes, enabling the centralised data management that leads to great project outcomes.
With a wide range of data management platforms at their disposal – all inter-compatible for efficient data sharing and optimisation – Autodesk can develop a software package suitable for any infrastructure development.
To find out more, visit autodesk.com/au
By James Boddam-Whetham, General Manager, Noggin
For Australia’s critical infrastructure sector, it’s been the best of times and the worst of times – an age of unbelievable advancements and an age of unprecedented threats.
Unfortunately, it is the unprecedented threats that have dominated the sector according to the 2023-2030 Australian Cyber Security Strategy. The strategy acknowledges the industrialisation of cybercrime, growing cost of cyberattacks, and major question marks surrounding critical and emerging technologies.
For the industry, there’s also the added complication of new regulations. What are they, and how to comply? Here, we’ll look at the most recent legislation and measures critical infrastructure entities can take to comply.
In November 2024, a new Cyber Security Legislative package passed through Parliament. The package consisted of the Cyber Security Bill, the Intelligence Services and Other Legislation Amendment Bill 2024, and the latest in a long line of amendments to existing Security of Critical Infrastructure legislation (SOCI Act).
In large part, the reforms aim to:
· Clarify existing obligations
for systems holding business critical data
· Enhance government assistance measures to better manage the impacts of all-hazards incidents on critical infrastructure
· Give government the power to direct entities to address risk management program deficiencies
· Align regulation for the security of telecommunications into the SOCI Act
For those tracking, the compliance burden placed on critical infrastructure entities has only increased since the initial SOCI Act passed in 2018. After these latest reforms, organisations are likely asking, how can we ensure ongoing compliance?
Noggin recommends reading the relevant statutes. Although the law keeps changing, the direction of traffic is clear: policymakers demanding stronger security frameworks from industry.
To comply, Noggin recommends entities take a proactive approach to their security risk management with measures that make it simple
to identify risks, assess inherent risk levels, implement controls and confirm their effectiveness, as well as monitor residual risk levels.
Ensuring standardisation across an organisation is challenging; but this is where dedicated resilience software comes in, with integrated incident management, threat intelligence, and vulnerability assessment capabilities.
Finally, policymakers are ratcheting up the pressure on the critical infrastructure sector. To comply, organisations will need to make smart software investments in solutions like Noggin that empower entities to meet obligations, by enabling their teams to work together to anticipate and manage threats, conduct preparedness activities, effectively respond to disruptions, and continually learn from insights to strengthen resilience.
For more information, visit noggin.io
Noggin, a Motorola Solutions Company, is a global provider of critical event management and resilience software. Its software helps enterprises, government agencies, and critical infrastructure anticipate, prepare for and efficiently respond to incidents. Noggin’s integrated platform seamlessly unifies operational and third-party risk management, operational resilience, business continuity, incident and crisis management, emergency management, and security & safety operations to streamline incident management and strengthen resilience.
Over
Will you be a part of it?
17–18 SEPTEMBER 2025
Melbourne Convention & Exhibition Centre
LEARN MORE
Find
convergeexpo.com.au
Ageing infrastructure poses various risks to community safety, economic productivity, and overall quality of life. As structures reach the end of their usable lifespan, asset managers must find ways to restore assets beyond their original capacity.
Older infrastructure, such as roads and bridges, often fails to meet modern safety standards – this results in visible deterioration, increased risk of accidents, and a loss of public confidence.
As urban populations increase, the needs of communities can outgrow
the capacity of old infrastructure, leading to congestion and inefficiencies in transportation and utility services.
Since 1989, Mainmark has been a proudly Australian-owned, awardwinning innovator specialising in global ground improvement, relevelling and void-filling solutions.
Mainmark delivers cost-effective, non-invasive solutions that reduce downtime and maintain operational continuity by utilising advanced technologies, including Teretek®, Terefil® and JOG ComputerControlled Grouting.
Anastasia Arestia, Infrastructure & Mining Manager at Mainmark in VIC/TAS, explained that ageing infrastructure significantly impacts communities and the environment by compromising safety, economic growth, and social equity.
“Deteriorating roads, bridges and utilities can lead to an increase in number or severity of accidents, disruptions to essential services, and increased wear and damage to vehicles,” Mrs Arestia said.
“Ageing infrastructure negatively impacts communities and delaying addressing and rehabilitating these can result in increased costs, and often greenhouse gas emissions. Moreover, delaying these actions can contribute to environmental issues such as urban flooding.”
ENHANCING RESILIENCE: RESTORING INFRASTRUCTURE FOR TOMORROW
Infrastructure owners looking to address the issues caused by ageing infrastructure often find that the costs of completely rebuilding structures can be prohibitively high.
By restoring ageing assets instead, managers can deliver faster positive outcomes for communities, preserve historical value, and reduce environmental impact while being more cost-effective.
"Restoration projects can often be completed more quickly, providing communities with improved services sooner and causing less disruption to residents and businesses,” Mrs Arestia said.
“This approach allows for modernisation by integrating new technologies into existing structures, ultimately fostering community stability and contributing to more resilient and sustainable neighbourhoods.”
In 2019, a routine bridge inspection identified ground settlement issues beneath the bridge approach slabs and adjacent roadways on Federation Mall that lead to Canberra’s iconic Parliament House.
Federation Mall is a prestigious location that provides a ceremonial and symbolic link between Parliament House and Old Parliament House.
It was constructed in 1988 for Australia’s bicentennial and continues to host some of Canberra’s largest community activities.
The approach slabs on both sides of the ‘Land Axis Bridges’ – which span Canberra’s famous State Circle highway – had settled by up to 50mm, resulting in cracks appearing in the surface of the road leading up to the bridges, pedestrian walkway walls, relieving slabs and approach parapets.
This settlement also caused dishing and undesirable movement in the roadways on either side of the bridges.
Mainmark was contacted to devise and deliver an efficient and cost-effective remediation solution to re-level the approach slabs and parapet walls and improve the ground bearing capacity to ensure that access to Federation Mall was preserved for many years to come.
With over 35 years of experience restoring bridges and bridge approaches across Australia, Mainmark set to remediate the Land Axis Bridges with its Teretek engineered resin injection. This process delivers ground improvement and re-levelling, increases ground-bearing capacity, and fills voids while
having no detrimental effects on the environment.
Applied in a process similar to keyhole surgery, Teretek was injected through very small tubes into the ground beneath the approach slabs at approximately 30 different injection points, filling voids, restoring ground support and returning the structure towards its correct position.
Teretek provides a more efficient and less disruptive solution than traditional methods by avoiding the need to excavate.
To minimise traffic disruption and access to Parliament House, works were scheduled on Parliamentary non-sitting days and carried out over five nights.
No heavy equipment or road upheaval was necessary, so the Land Axis Bridges could reopen to traffic each day. The entire project was completed within the specified timeline and budget.
The Federation Mall project highlights the benefits of rehabilitating and bringing critical infrastructure assets back to life rather than completely rebuilding them.
Australia's ageing infrastructure poses complex challenges that impact its residents' safety, economic productivity and overall quality of life. The financial costs of replacing this infrastructure and the invisible costs of societal disruption make rehabilitation a much more appealing option.
“By utilising our ground improvement and level correction solutions, we can efficiently restore the integrity of buildings and infrastructure, minimising downtime and inconvenience for occupants and surrounding communities,” said Mrs Arestia.
“These non-invasive methods not only expedite the repair process but also significantly reduce the environmental footprint typically associated with construction activities.”
Mainmark's emphasis on restoration promotes resource efficiency and enhances community sustainability without the disruptive effects of large-scale construction projects.
To find out more, visit mainmark.com
Ensuring effective stormwater drainage is one of the most important aspects of any infrastructure development, and a new solution is the key to saving time and costs on site.
Since 1883, EJ has been a trusted name in providing durable, high-quality access and drainage solutions for the sewer and stormwater industries. Today, EJ is proud to introduce the Swarm Aqua® Linear Surface Water Drainage System to the Asia Pacific region – an innovative product designed to streamline your installation process, reduce on-site costs and deliver superior performance.
The product features a robust ductile iron top section, with an optional steel version for pedestrian areas, paired with steel side walls and a twin wall conduit for maximum structural integrity. These components make Swarm Aqua perfect for demanding external drainage applications, while its compatibility with standard twin wall fittings allows for easy connection to existing drainage networks.
One of the standout features of Swarm Aqua is its unobtrusive design. Unlike traditional grated systems, it offers a sleek and modern drainage solution that seamlessly integrates into a variety of surfaces. Its straightforward, “push-to-connect” system eliminates the need for complicated on-site assembly, saving time and reducing installation costs. The system’s simplicity means fewer components to manage, making it easier for contractors to use the same product project.
In addition to providing expert guidance, EJ offers the AquaCALC tool – a free, easy-to-use online resource that helps size and specify the right Swarm Aqua drainage system for a project using Manning's
Swarm Aqua offers maximum structural integrity.
equations. This ensures drainage solutions are tailored to meet the specific demands of every site, offering peace of mind that the best possible system has been selected for the job.
Discover how Swarm Aqua can transform your next project –sleek, modern, straightforward and competitive.
As Australia’s energy demand rises, utility providers face increasing pressure to comply with evolving standards that safeguard the reliability and safety of critical assets.
Battery chargers and stationary VRLA batteries are essential for maintaining operations during power outages. The new Australian Standard AS4044:2024, effective from 15 November 2024, provides asset owners a clear framework for ensuring compliance and protecting these investments.
The updated standard introduces guidelines tailored for Australian environmental conditions, ensuring equipment longevity and reducing operational risks.
Key features include:
· Compatibility with modern switch mode rectifiers and phasecontrolled chargers
· Limitations on neutral current to match or remain below phase active current
· Built-in battery charge current control
· Updated cable colour standards (black or blue for negative, red for positive)
· Allowance for modern digital instrumentation
· Compliance with EMC standards For asset owners using Intelepower Systems, Century Yuasa proudly confirms compliance with AS4044:2024, ensuring optimal performance, safety and reliability for your critical systems.
Battery ventilation is critical for maintaining DC Power Systems safely. Australian Standards such as AS3011.2 and AS2676.2 require that hydrogen (H₂) concentration in battery rooms or enclosures must remain below two per cent, well under the explosive threshold of four per cent.
A growing trend is to fit small plastic ventilation tubes into the valve covers of VRLA batteries to avoid the challenge of properly ventilating the battery cabinet or room.
However, this approach does not comply with the requirements of the standard.
Insufficient ventilation
Tubes often lack the required crosssectional area to vent hydrogen effectively, especially when linked in series.
Formation of gas pockets
Downhill bends and condensation blockages in tubes create explosive hydrogen pockets.
Maintenance hazards
Tubes require meticulous upkeep to avoid blockages, increasing safety risks for maintenance personnel and operations.
Hydrogen release under fault conditions
Tubes are usually attached to the valve cover of the battery. Aged or stressed batteries may release hydrogen from other parts of the casing, such as around post seals or via cracks in the lid seal.
Intelepower Systems and battery banks meet all safety requirements.
This gas bypasses the tubes and vents directly into the enclosure, increasing explosion risk without proper cabinet or room ventilation.
By adhering to the natural ventilation principles outlined in AS2676.2, Century Yuasa ensures that its Intelepower Systems and battery banks meet all safety requirements, eliminating risks associated with substandard practices. For more than 30 years, Century Yuasa has delivered future-proof energy solutions across Australia and New Zealand. The team’s expertise in industrial power systems ensures utilities benefit from safe, reliable and compliant solutions.
With nationwide service and a commitment to innovation, Century Yuasa is ready to help you meet AS4044:2024 and ventilation standards.
Sustainable steel has an important role to play in the infrastructure of tomorrow, and SENSE Solutions®, delivered by InfraBuild, is revolutionising the product.
The drive to decarbonise infrastructure is not just a necessity; it is a fundamental priority for the industry. As recently highlighted in the Infrastructure Sustainability Council’s (ISC) 2024 Impact Report and Infrastructure, SENSE Solutions®’ latest product range, SENSE 600®, is an innovation in reinforcing steel. Offering significant reductions in embodied carbon and industry-recognised sustainability certifications, SENSE 600 exemplifies the cutting-edge solutions required to meet the infrastructure sector’s
SENSE Solutions is reinforcing its focus on innovation and environmental responsibility via SENSE 600, which can deliver up to 39 per cent lower embodied carbon than InfraBuild’s standard 500N reinforcing steel solutions. This is achieved through optimising high-strength steel with an innovative bar design, reducing raw material usage by up to 16.7 per cent while maintaining equivalent load capacity. It is also made from 100 per cent scrap steel at InfraBuild’s Electric Arc Furnace mills
“This product is a game-changer for the industry,” said Anthony Ng, Engineering Solutions Manager at InfraBuild. “It demonstrates how innovative design and a focus on sustainability can deliver superior performance and environmental outcomes without disrupting established practices.”
Engineered to meet Australian Standards AS 5100.5 (bridges), AS 3600 (concrete structures) and AS 2159 (piling and foundations), SENSE 600 ensures seamless integration into critical infrastructure projects. Additionally, SENSE Solutions has released an Environmental Product Declaration (EPD) for SENSE 600®, detailing its reduced GWP and material circularity metrics.
SENSE 600 also supports several sustainability certifications under the ISC’s ISv2.1 Rating Tool. Holding an EPD and Good Environmental Choice Australia (GECA) certification, SENSE 600 contributes to credits such as Rso-7 (Sustainability Labelled Products) and Rso-6 (Material Life Cycle Impact Measurement).
Its inclusion in the ISupply directory further supports Responsible Products credits, enabling projects to achieve up to 0.75 IS points. ISv2.1 rewards projects that use products that have an MCI and SENSE 600® can support this credit as the EPD includes MCI metrics.
The practical advantages of SENSE 600® go beyond its environmental credentials. Its optimised design allows for reduced material use, while improving structural efficiency.
Toby Kent, Infrastructure Sustainability Council CEO,
emphasised the importance of innovations like SENSE 600 in the recent ISC 2024 Impact Report.
“The better outcomes that certified projects deliver remain at the heart of ISC’s contribution,” said Mr Kent. “This year, 25 certified As Built projects contributed 144,000 tonnes to the total of 1,353,000 tonnes of avoided lifecycle materials emissions since 2018. Nothing reflects ‘better BAU’ than that!”
The ISC’s 2024 Impact Report underscores the pressing need to reduce embodied carbon across infrastructure projects, noting that steel, concrete, and asphalt contribute significantly to emissions. SENSE 600 offers a compelling pathway to address these challenges,
enabling project teams to minimise their environmental footprint while enhancing performance.
SENSE Solutions’ proactive approach, including early engagement with asset owners, designers and contractors, ensures the seamless integration of SENSE 600 into projects. The brand’s educational initiatives, such as workshops and training sessions, equip stakeholders with the knowledge and expertise they need to adopt sustainable practices effectively.
As the industry continues to evolve, products like SENSE 600 will be indispensable in building a more sustainable future. With its reduced embodied carbon, high recycled content, and alignment with ISv2.1
certification requirements, SENSE 600 exemplifies the next generation of materials that meet the demands of modern infrastructure.
“These impacts matter,” said Mr Kent. “The infrastructure sector consumes, embodies and enables some 70 per cent of Australia’s and 50 per cent of Aotearoa New Zealand’s carbon emissions. Decarbonisation is just one way that infrastructure affects the sustainability of communities.”2
The SENSE Solutions range is not only addressing today’s sustainability challenges, but also setting a benchmark for the future. The focus on delivering high-performance, environmentally responsible materials ensures that projects can achieve their goals without compromising on quality or integrity.
SENSE Solutions® offers the following practical advice and support for integrating sustainable materials into infrastructure projects:
Early engagement: collaborating with material suppliers during the planning stages enables project teams to maximise the benefits of innovative materials (SENSE Solutions technical specialists can provide tailored solutions to meet project-specific needs).
Lifecycle analysis: employing lifecycle assessment tools quantifies the environmental impact of materials, supporting data-driven decision-making and regulatory compliance.
Continuous education: SENSE Solutions is committed to supporting the industry with training and workshops, equipping stakeholders with the skills and knowledge to adopt sustainable practices effectively.
1 https://www.iscouncil.org/wp-content/uploads/2024/11/ISC0028_2024-Impact-Report_FINAL-R.pdf (page 6)
2 https://www.iscouncil.org/wp-content/uploads/2024/11/ISC0028_2024-Impact-Report_FINAL-R.pdf (page 6)
With cutting-edge concrete pumping, spraying and transportation solutions, Jacon Equipment is driving innovation in Australia’s infrastructure sector.
Whether it’s ensuring precision in high-traffic areas or tackling the tight constraints of tunnelling, Australia’s infrastructure projects demand more than just standard solutions.
Jacon Equipment is ready to meet these unique challenges with reliable, advanced machinery that ensures optimal performance in even the most demanding environments.
In the demanding world of tunnel construction, reliable shotcrete application is crucial. Jacon’s shotcrete rigs redefine the standard for performance, showcasing a commitment to delivering tailored solutions.
For heavy-duty tasks, the Maxijet MX3-MKII stands ready to take on the challenge. With a pumping capacity of 30 m³/h, its nozzle technology enables 360-degree rotation and 180-degree tilt for precise shotcrete application. Features like hydrostatic
transmission, an enclosed cab and an optional hybrid diesel/electric design further enhance its versatility.
In tighter spaces, the Midjet MK4.5 shines with its exceptional manoeuvrability, delivering precise application where larger machines simply can’t reach.
Jacon Business Development Manager, Matthew Finn, said, “With its compact design and AWD skid steering, the Midjet is perfect for navigating narrow tunnels. Powered by diesel and equipped with a ten-metre vertical reach, it excels in challenging underground environments.
“To guarantee precision, our rigs are fitted with pre- and postscan (PPS) systems to measure shotcrete thickness.”
Jacon’s shotcrete rigs play an important role in securing slopes, reinforcing tunnel walls and stabilising construction ramps. This is vital for preventing collapses and ensuring a safer working environment on any site.
M OVING WITH CONFIDENCE
Efficient delivery of materials is critical to the success of projects, and concrete is no exception. Jacon’s Transmixer range offers reliable solutions for smooth shotcrete and concrete transportation.
The Transmixer range comes in 5m³ and 6m³ drum capacities and features multi-mode four-wheel steer functionality and variable hydrostatic transmission.
“This allows maximum speed while handling inclines with ease, even when fully laden,” Mr Finn said.
“Our Transmixers are compact and manoeuvrable, meaning they can carry all the necessary materials needed to support shotcrete operations.”
With cabins at both ends of the rig, the operator can drive into a decline or shaft cage and out again without turning the machine around.
The Transmix X5 is compact in size and ideal for narrow tunnels and tight spaces while having the capabilities of performing in larger,
tougher jobs. It features a low-profile design, allowing it to navigate difficult terrains with ease.
The Transmix range offers sizes up to X10, with a drum capacity of 10m³. The larger drum capacity is built for hassle-free operation in tough underground conditions.
Another mainstay in infrastructure projects across Australia is Jacon’s trailer-mounted and truckmounted pumps.
Jacon Business Development Manager and Product Specialist, Darryl Simms, said, “Whether you’re dealing with small-scale jobs or larger projects, we have options ranging from trailer-mounted pumps that can be towed by a ute, to more powerful truck-mounted models.
“The S-Series, for example, features trailer-mounted pumps with capacities from 30 m³/h up to our flagship stationary pump, which boasts an impressive 100 m³/h.”
Backed by decades of engineering expertise, these pumps are available in both diesel and electric configurations, with mounting options that include trailer, skid, or track, ensuring they meet the specific requirements of any project.
For contractors seeking enhanced mobility, Jacon's truck-mounted models, like the T60 and T100, offer a blend of power and adaptability. The T60 provides a capacity of 60 m³/h, while the T100 matches the output of Jacon's largest trailer-mounted units, delivering 100 m³/h.
“Our S-Series pumps are designed with an ‘S’ valve, making them ideal for handling tough mixes, low-slump concrete, and fluid grout,” Mr Simms said.
“They’re essential for a variety of applications, from concrete slabs and retaining walls to underground void filling, ground stabilisation, and large-scale infrastructure projects.”
This versatility reflects Jacon’s ability to tackle even the toughest project challenges.
Jacon’s dedication to project success goes beyond its products;
it encompasses every aspect of their service.
With teams in Sydney, Brisbane, Melbourne and Perth, Jacon ensures its customers receive ongoing support to deliver on projects time and time again.
By combining cutting-edge technology with unmatched service, Jacon empowers its customers to tackle every challenge with confidence.
For more information, head to jacon.com.au
NHP's global network of supply partners ensures you have the freedom of choice for power distribution, power quality, energy management and automation products.
NHP is an independent, Australian-owned company with over 55 years of electrical and engineering industry excellence. With more than 20 branches across Australia and New Zealand, it is NHP’s local people and footprint that helps them to understand specific project needs, no matter how big or small.
When it comes to finding a local partner with a global network for your next project, choosing NHP will unlock a world of expertise across electrical and automation products, systems and solutions.
MORE THAN QUALITY PRODUCTS
By assisting customers to identify the risks and opportunities prevalent in their industry or application, NHP can facilitate the required services and solutions to maximise operational investment in accordance with specific priorities and objectives.
NHP Services and Solutions has a strong track record in the critical infrastructure sector, including integrated remote racking air circuit breaker upgrades in the Sydney Road Network, working within very tight timeframes to guarantee improvements in production uptime and personnel safety.
NHP has an extensive service infrastructure including repair centres, test rooms, field service technicians, application engineers and project managers. Its specialist teams work collaboratively to design and deliver solutions to maximise the success of projects.
Air circuit breaker modernisation
With ACB retrofit solutions available to facilitate the installation of a range of products and brands, as well as
customising solutions to suit specific requirements, NHP can work within an existing switchboard environment. This provides a cost-effective solution, resulting in an increase in system reliability, minimising production downtime and thereby lowering your operational costs. NHP’s ACB retrofit solutions are engineered according to relevant Australian standards and recognised industrial practices.
A gamechanger in electrical safety NHP can also retrofit TemRack iR, a fully integrated, automated racking device, which enables remote racking of the Terasaki TemPower 2 AR ACB body in and out of its associated carriage. The automated racking function permits safe isolation of the ACB with zero physical interaction
between personnel and the ACB, eliminating the risk of exposure to dangerous arc faults.
Power quality services
NHP’s range of power quality services assist in determining requirements to ensure a power quality system is optimised and delivering enduring results. Power quality services NHP provides include:
· Power quality audits
· Commissioning services for NHP
Power Factor Correction systems, Static Var Generators and Active Power Filters
· Periodic service and maintenance of NHP power quality systems
· Installation of NHP power quality systems
Emergency breakdown assistance
NHP service provides 24/7 protection, 365 days a year, ensuring that your assets continue to work for you. Its service technicians and engineers are on call, equipped to minimise downtime and provide rapid assistance when required.
No matter how good a product may be, it is nothing without dedicated people to support it. NHP is solely committed to servicing the needs of its customers. It brings together internationally recognised power distribution and automation products with local knowledge and expertise to deliver best practice services from concept design through to installation and after-sales service.
For more information, visit nhp.com.au
By Andrew Chapman, CEO, Queensland Major Contractors Association
Prospects for a fruitful and productive period of infrastructure construction in Queensland are currently bright.
Queensland is on the cusp of a transformative decade for the engineering and construction sector, as highlighted in Queensland Major Contractors Association’s 2024 Queensland Major Projects Pipeline Report (QMPPR). The report identifies significant investment across key sectors, including:
· H ealth
· Water
· Electricity (energy transition)
· Transport
· Resources and heavy industry
· The 2032 Olympic and Paralympic Games
With over $200 billion in committed and proposed investment through to 2035, Queensland’s infrastructure sector is poised for unprecedented growth. The only comparable period was between 2011 and 2015, which saw a surge in major projects, as illustrated in Figure 1.
The previous construction boom was largely driven by significant investment in the resources and energy sector, including three large-scale coal seam gas (CSG) to liquefied natural gas (LNG) projects, six new coal mines, and supporting infrastructure such as rail and port upgrades. However, the upcoming wave of investment is far more diversified, with a stronger focus on transport, water and wastewater, electricity, heavy industry and resources.
This investment is spread across the state, as depicted in Figure 2.
When looking at investment across the state, the Wide Bay region’s figures are bolstered by two major projects: the Paradise Dam reconstruction and the Borumba Pumped Hydro scheme.
The 2024 QMPPR highlights that the next five years will be a busy time for the sector. Beyond engineering projects, Queensland will also see substantial investment in health and education infrastructure, alongside a projected upswing in residential building activity later in the decade. These developments, coupled with increasing competition for skills and resources from other states, will put sustained pressure on costs, industry capability, and capacity.
In this environment, collaboration between government and industry will be critical. Effective planning and procurement, early targeting of required skills, and policies that enhance productivity will be essential to delivering value-formoney outcomes.
As a sector, we experienced significant change in 2024 as
elections and policy settings adapted to meet the needs of industry and clients as well as the expectations of the public in relation to workplace practices and unlawful activities.
The CFMEU administration
One of the most significant industry developments in 2024 was the CFMEU being placed into administration. Few would have predicted this outcome at the start of the year. The 60 Minutes investigation exposed the union’s long-standing practices of bullying, intimidation and coercion, which had been a major concern for industry participants. This change presents an opportunity to reset industry culture and improve workplace conditions, making the sector more attractive to new talent.
State election and policy shifts
The election of a new LNP government has ushered in policy changes expected to benefit the construction sector, including:
· Abolition of Best Practice Industrial Conditions (BPIC): this controversial policy had been criticised for inflating project costs and reducing on-site productivity by up to 30 per cent
· Re-establishment of the Productivity Commission: the commission’s first focus will be reviewing inefficiencies in the construction sector, particularly lifting effective working days
from an average of 2.8-3 per week closer to five
· Changes to right-of-entry provisions: all parties must now provide 24-hour notice before entering sites, reducing the misuse of entry rights as an industrial tactic
The industry welcomes these reforms and looks forward to working with the government to enhance productivity, ensure infrastructure delivery, and improve cost certainty.
Pipeline coordination
Queensland’s infrastructure pipeline has historically been fragmented, with various departments and government-owned corporations working independently. The new government has empowered the Coordinator-General to oversee project sequencing and planning, ensuring investment is prioritised effectively across health, housing, transport, water, and energy. The construction industry supports this approach and is ready to collaborate in shaping a sustainable investment plan.
The Olympic Delivery Authority (GIICA) is currently reassessing the infrastructure plan for the 2032 Games. The original vision for the Games included using them as a catalyst for broader economic infrastructure investment. However, this strategic focus has waned in recent years. It is crucial to ensure that Olympic infrastructure aligns with long-term regional development needs, covering transport, energy, waste, and water infrastructure. The industry is eager to contribute to this process to maximise economic and community benefits.
Over the past decade, productivity in the construction sector has declined, with Queensland now delivering approximately 30 per cent less infrastructure per dollar spent than 15 years ago, as is well illustrated in Figure 4 which shows the value of work delivered each year per employee (in 2021 dollars).
Reversing this decreasing trend in productivity requires a multi-faceted approach, including:
· Improving industrial relations to foster safer, more productive workplaces
· Updating technical specifications to facilitate the adoption of new materials and technologies
· Streamlining the lengthy business case and approval process, which currently takes four years or more
· Standardising collaborative procurement methods to improve project certainty
· Encouraging the use of automation, artificial intelligence, modularisation, and prefabrication to enhance efficiency
A mere ten per cent productivity improvement would enable the industry to deliver 100 per cent of the funded projects in 2025 – compared to the recent average of only 87 per cent.
The construction sector has experienced a sharp rise in insolvencies in recent years, driven in
part by flawed procurement models. The QMCA has been a strong advocate for collaborative contracting, ensuring risk is appropriately managed. Partnering with industry bodies such as the Civil Contractors Federation, the Infrastructure Association of Queensland and Consult Australia, the QMCA has been working with the Department of Transport and Main Roads to refine procurement strategies that promote sustainability and financial stability within the sector. This year we look forward to seeing the initiatives that have been developed with this progressed.
While the industry faces challenges, there are significant opportunities to improve efficiency, attract talent, and drive innovation.
Key areas of focus include:
· Policy and procurement reforms that prioritise collaboration and efficiency
· G reater adoption of digital technologies, automation, and alternative materials
· Cultural and workplace improvements to attract and retain skilled professionals
The
next five years will be a busy time for the sector.
Ensuring a diverse, inclusive, and safe work environment is critical to securing the workforce needed to deliver Queensland’s infrastructure boom. By fostering a positive industry culture, offering flexible work arrangements, and improving career pathways, the sector can build the capacity required to meet future demand.
Queensland’s infrastructure sector is entering a defining period of growth. With the right policies, collaborative planning and a focus on productivity,
the industry can successfully deliver on the investment pipeline. The QMCA and its members remain committed to working alongside government and stakeholders to drive sustainable growth, deliver value-for-money projects, and maximise the economic and community benefits of this oncein-a-generation opportunity.
As an industry, we have successfully managed large-scale investment programs before, and we are ready to do so again. Now is the time to work together to ensure Queensland’s golden decade of infrastructure delivers real outcomes for the economy, industry, and community.
Australia’s premier event for municipal works, civil and commercial construction, Converge 2025, is excited to announce that the Civil Contractors Federation (CCF) Victoria has joined as an Association Partner.
Converge 2025 will unite professionals across the construction and infrastructure sectors, including subcontractors, project engineers, council fleet managers and large-scale contractors. The event promises to showcase cuttingedge innovations, foster valuable connections and explore the future of major projects.
The partnership with CCF Victoria further solidifies Converge 2025 as a vital industry platform. CCF Victoria, a leading advocate for the civil construction sector, provides essential support, training and resources to its members. These members are the driving force behind Australia’s critical infrastructure, from roads and bridges to pipelines, ports and utilities. They also play a key role in land development, ensuring access to essential services like power, water, gas and communications.
“This partnership reflects the shared vision of Converge and CCF
Victoria to advance the construction and infrastructure sectors,” said Siobhan Rocks, director of Converge. “CCF Victoria is a cornerstone of civil construction in Victoria, and their expertise and involvement add immense value to the event.”
For CCF Victoria, this partnership offers an opportunity to connect its members with new innovations, resources and networking opportunities to address the challenges of modern construction.
“Converge 2025 is a great opportunity to meet and mix with key stakeholders and have critical conversations around current challenges and the future of Victoria’s civil construction industry,” CCF Victoria CEO Lisa Kinross said.
“Civil infrastructure is the very foundation of our cities, towns and suburbs – you can’t spend a dollar on housing until you’ve invested in the underpinning infrastructure that enables more communities and housing developments to come
to fruition, and the same with the renewable energy transition.
“We are well-positioned to build a sustainable future for our industry through the delivery of highly-skilled training and workforce development, with industry partners and stakeholders, to ultimately deliver on the future vision for the Victorian community.”
Converge 2025 will take place on 17 to 18 September 2025 at the Melbourne Convention and Exhibition Centre. Attendees can expect a comprehensive showcase of the latest equipment, technologies and solutions, alongside a dynamic program of expert panels, keynote speakers and networking opportunities.
Join CCF Victoria and other industry leaders in shaping a sustainable and innovative future for municipal works, civil and commercial construction.
For more information, visit convergeexpo.com.au
The West Gate Tunnel Project is one of the major elements of Victoria’s Big Build. We check in on progress of the tunnels as the crew advances toward project completion by the end of 2025.
The West Gate Tunnel Project, part of Victoria’s Big Build, will deliver a vital alternative to the West Gate Bridge – one of Victoria’s busiest transport routes, carrying over 200,000 vehicles per day.
The project involves the construction of twin tunnels under Yarraville that will offer a vital alternative to the West Gate Bridge – removing over 9,000 trucks off inner west streets and giving drivers quicker trips to and from Melbourne’s west.
The twin tunnels will take traffic underground from the West Gate Freeway to the Maribyrnong River and on to an elevated road above Footscray Road.
Tunnelling on the West Gate Tunnel Project is now complete. The tunnels were built using two tunnel boring machines (TBMs) so that community and businesses could continue above ground while work happens below.
The project also involves widening the West Gate Freeway from eight to 12 through lanes to ease congestion, and support Victoria’s growing population.
There are more than 200 workers currently fitting out the tunnels with
all the equipment needed to operate the tunnels safely.
This includes more than 1.1 million metres of cable, 26,000 metres of pipe for fire protection systems and more than 1,900 individual traffic speed and safety signs.
There will also be lights, traffic management systems, electrical wires and ventilation fans in place inside the tunnels.
The tunnels contain the latest in signalling and safety technologies and will link back to a purpose-built facility that will oversee the operation of the tunnel 24 hours a day, seven days a week.
The fit out of the tunnel safety and traffic management systems is more than halfway complete, with the final cable installation enough to stretch from Melbourne to Newcastle.
Excavation of the 31 connecting passages between the twin tunnels and maintenance levels was completed in late 2024, which will play a vital role in keeping the public safe in emergency situations.
The passages are 120 metres apart and connect the city and westbound tunnels, providing evacuation routes in the event of incidents.
The majority of the passages were excavated using the box jack technique, which involves pushing precast concrete structures into the ground using a high-powered hydraulic jack.
Seven of the passages were excavated using the latest geological technology to freeze the ground between the tunnels, ensuring the rock and soil in those passages
remained stable while being dug out.
The ground freezing technique involves circulating liquid nitrogen through copper pipes drilled deep in the soil. This temporarily freezes any water content and increases the stability and strength of the earth, while the ground is kept frozen and waterproof until the concrete crosspassage structure is in place.
State-of-the-art smart technology will be installed across the length of the project linking it to other freeway management systems across Melbourne.
The system is a mix of:
• L ane use management signs
• Stop/go lights on freeway entry ramps
• CCTV cameras
• Travel time information signs
• Electronic variable message signs
• Automatic incident detection systems.
Freeway management systems help make journeys safer and travel times more reliable. They do this by controlling the flow of traffic both on and entering the freeway. The system also helps traffic better cope with accidents and breakdowns.
Aboveground, construction is forging ahead on the landmark architectural structures at the southern inbound and outbound tunnel portals, and the northern tunnel portal as part of the overall design features of the tunnel entry and exit points.
The heritage of the west is reflected in the design of the timber net structures, which have been inspired by the long maritime history associated with the area’s local waterways.
The installation of the steel frame that will wrap around the tunnel exit structure in South Kingsville is continuing, with installation underway of the external cladding.
Crews have installed the 195 elevated segments that form part of the new 2.5km veloway – a dedicated cycling path from Shepherd Bridge in Footscray to the city side of Moonee Ponds Creek.
Work is progressing on the installation of lighting, CCTV, handrails, non-slip surface and safety mesh covering to enable the veloway to be connected to the local cycling and walking path network later in 2025.
Road.
delivered by the West Gate Tunnel Project, that will support the growing number of Melburnians riding to work each day.
There has been a major campaign of works this summer on the West Gate Freeway involving asphalting between the West Gate Bridge and Millers Road.
When completed, the West Gate Tunnel Project will:
» Widen the West Gate Freeway from 8 to 12 through lanes, including express lanes for vehicles heading to the south and southeastern suburbs
» Provide a second river crossing, giving drivers a choice between the tunnel or the bridge
» Ease congestion for the 200,000 vehicles that use the West Gate Bridge daily
» The project will create direct access from the West Gate Freeway to the port of Melbourne and Melbourne’s hospital and education precincts
» Better manage traffic flows and incidents through smart technology
» Save up to 20 minutes travel time between the city and the west
will be open with the lanes to exit and enter the tunnel remaining closed until project completion in late-2025.
The inbound express lanes will also be complete between the M80 Ring Road and the West Gate Bridge making travel easier.
As the project progresses towards completion, it’s an inspiring time for everyone working on the West Gate Tunnel Project.
“We’re heading into our biggest and most exciting year as crews work above and below ground to put the finishing touches on this significant project,” said West Gate Tunnel Project Executive Director, Peter Lellyett.
“It’s exciting to see the finishing line, delivering the tunnels and new connections that will get over 9000 trucks off local streets in the inner west and give people a choice – the tunnel or the bridge.”
“I’m looking forward to seeing the benefits of the West Gate Tunnel Project realised when it opens by the end of this year.”
Combining the resources of our respected editorial team with the knowledge and insights of some of the best and brightest minds in the sector, Infrastructure shares thought-leading and thought-provoking content that tackles the industry’s critical questions.
www.infrastructuremagazine.com.au
VERMEER VSK100-1600 VACUUM EXCAVATOR TRUCK PACKAGES
Get instantly operational with the Vermeer VSK100-1600 Vacuum Excavator and Isuzu truck package. The ultimate jobready solution for high-volume excavation. Featuring a high-performance blower and telescoping hydraulic boom, this package guarantees quality, efficiency, and immediate operational readiness from day one. We’ve got all machine sizes in stock, fitted to trucks and ready to go. Contact your local vacuum excavator specialists at Vermeer Australia today.