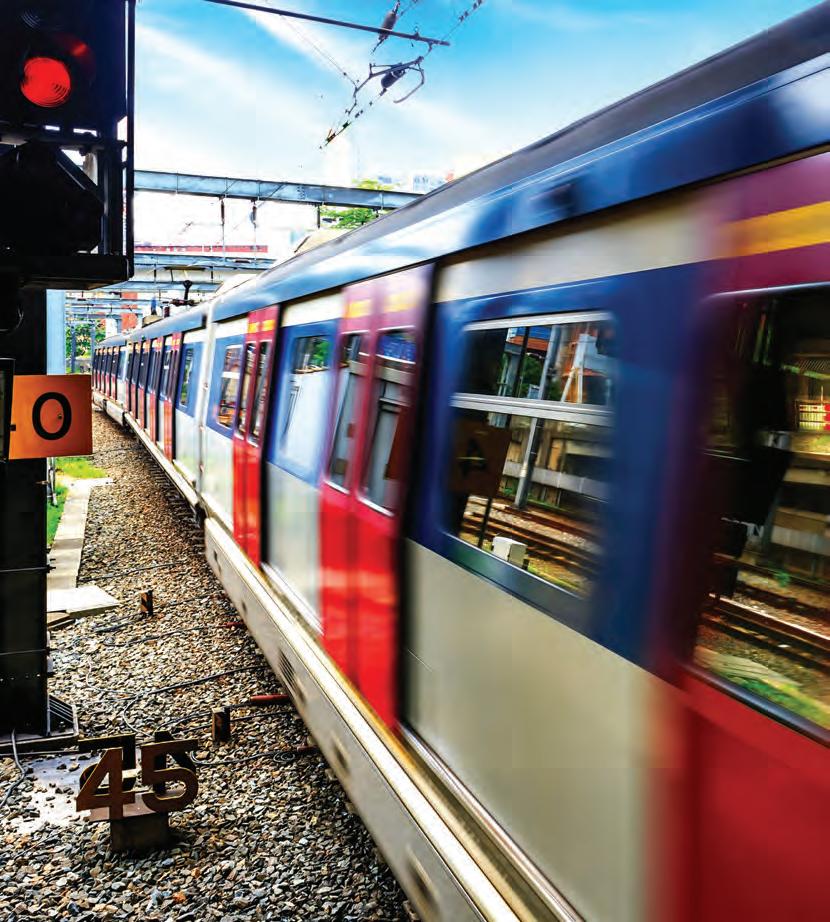
AIRPORTS GET A TECHNOLOGY MAKEOVER THE ROAD AHEAD: A nationally consistent approach for ITS
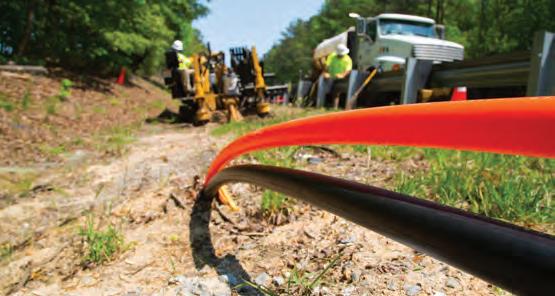
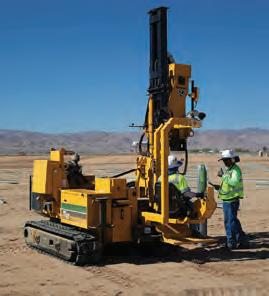
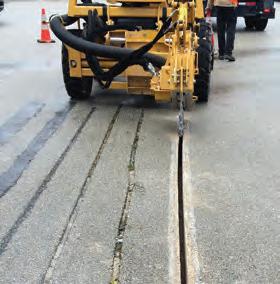
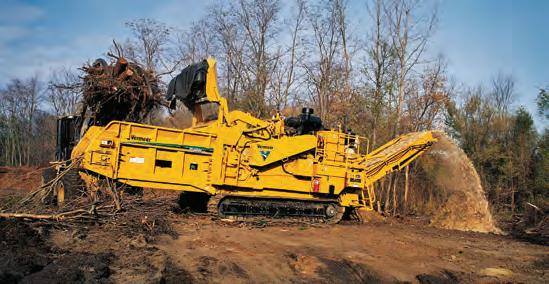
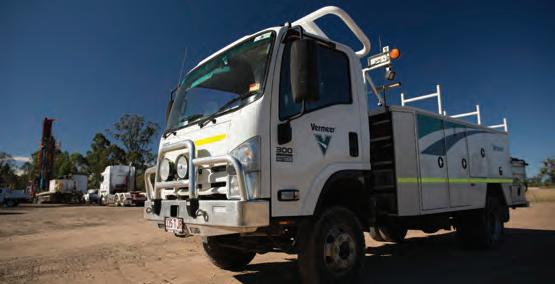
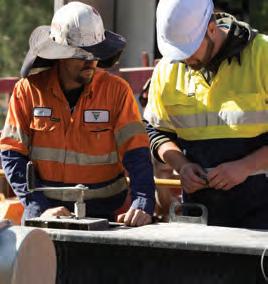
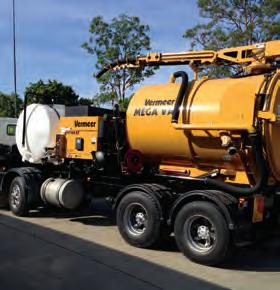
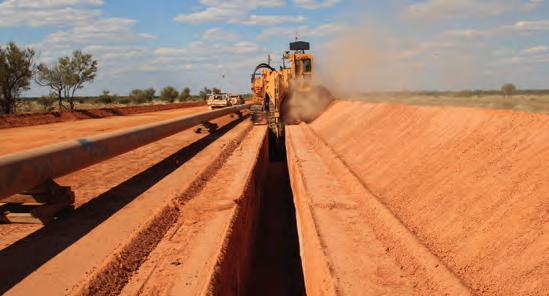
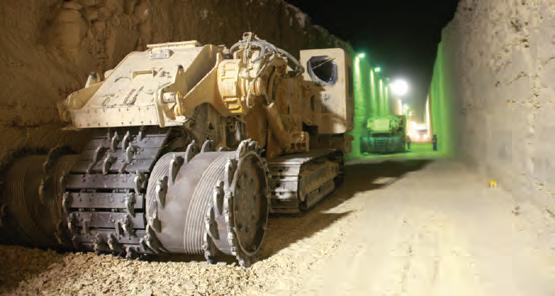
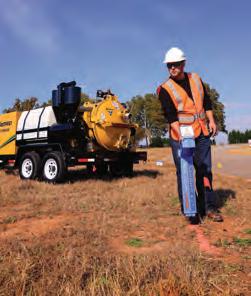


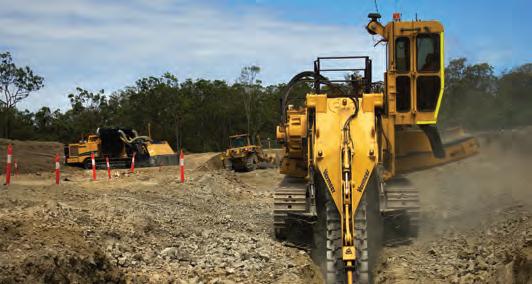
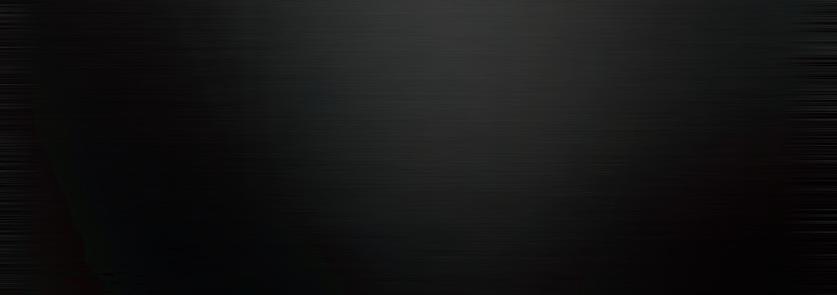
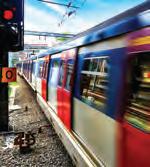
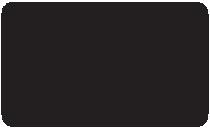
AIRPORTS GET A TECHNOLOGY MAKEOVER THE ROAD AHEAD: A nationally consistent approach for ITS
Infrastructure Editor Laura Harvey is taking some time off for maternity leave and will return to the magazine next year. In the meantime, I’m Acting Editor Jessica Dickers.
With many new projects in road, rail and airports ramping up, the biggest push we’ve seen is the integration of new technologies, which has created new opportunities and challenges for many organisations.
In both the rail and airport sector, developments in app and mobile technologies are streamlining behindthe-scenes processes while also benefitting the customer experience.
4,921
6,660
Published by
Monkey Media Enterprises
ABN: 36 426 734 954
PO Box 1763
Preston South VIC 3072
P: (03) 9988 4950
F: (03) 8456 6720
monkeymedia.com.au
info@monkeymedia.com.au infrastructuremagazine.com.au news@infrastructuremagazine.com.au
Editor
Laura Harvey
Acting Editor
Jessica Dickers
Associate Editors
Lauren Cella
Charlotte Pordage
Journalist
Elisa Iannunzio
Marketing Director
Amanda Kennedy
Marketing Associate
Sam Penny
Marketing Assistant
Rima Munafo
Production and Customer Service
Titian Bartlau
Senior Designer
Alejandro Molano
Designer Jacqui Abela
Publisher
Chris Bland
ISSN: 2206-7906
It can be a huge challenge trying to get the right technology in place, and we’ve seen how full shutdowns of rail lines or airports have been heavily scrutinised, not only by customers but by the mainstream media. This is why organisations are investing in digital strategies and making their technology mix a priority in operational plans.
The rail sector in particular is undertaking huge projects, from the Murray Basin Rail Project in Victoria, to the Sydney Metro. These projects have prompted discussion around the importance of freight, dealing with aging infrastructure and achieving a coordinated approach to rail. You can read more about the push for a National Rail Plan on page 12.
The idea of a nationally consistent approach to rules and standards has also been a topic of conversation for the road sector, as developments in automation such as driverless vehicles will change the way roads are developed and used, so the need to integrate standards with technology has increased.
As technologies change so rapidly it’s hard to predict what will happen in the future so the sector must be flexible and be able to adapt to changing technologies. A consistent approach to standards will help provide a foundation to work from as the industry continues to develop. A nationally consistent approach also means that developments in one state will still be applicable once you cross the border into another.
Information is power so technologies that are supporting the collection and analysis of data has also become
a valuable decision-making tool for organisations when planning and operating new assets.
I recently attended the Infrastructure Sustainability Council of Australia’s Awards Gala Dinner which celebrated the organisations, projects and individuals who are helping to advance sustainability in their fields. It was great to hear how sustainability has been made a key priority in the planning, design, construction and operation of smarter infrastructure assets.
Attendees noted that it’s up to the industry and people on the ground to push for sustainability in all projects so it becomes the norm, rather than subject to political decisions, and the need for more sustainable infrastructure will only continue to grow.
You might be reading this issue from the AusRail Plus Conference in Brisbane where this issue is being distributed, and the Infrastructure team is excited to meet more of our readers at other events this year including the Australasian Corrosion Association Conference in Sydney, and the Australian Airports Association (AAA) National Conference 2017 in Adelaide.
Throughout 2017 we’ve worked hard to grow the magazine and bring you expert analysis of the key issues in the sector. The latest audit figures will be released shortly and I’m pleased to say that our circulation is about to reach its highest yet, so thank you for continuing to engage with us and I can’t wait to see what the next year brings.
Jessica Dickers Acting EditorI’m keen to hear your thoughts and feedback on Infrastructure. Drop me a line at jessica.dickers@monkeymedia.net.au or feel free to call me on 03 9988 4950 to let me know what you think.
Queensland and Northern Territories largest range of paving equipment, parts, technology, service and training, Hastings Deering is committed to supporting you from the ground up. Call 1300 991 263 or visit hastingsdeering.com.au/roads
We are focused on building relationships that extend well beyond machines. That means sharing our expertise to help you select, acquire, operate and maintain your paving equipment, then standing by your side to keep that equipment – and your business – running smoothly. Invest with confidence knowing it’s more than just parts, service and support. It’s a partnership designed to deliver more for you.
INDUSTRY PUSHES FOR A NATIONAL RAIL INDUSTRY PLAN
Australia’s population is growing rapidly – around 1.5 per cent a year – and it’s starting to have an impact on cities.
REVITALISING FREIGHT IN THE MURRAY BASIN
The Murray Basin Rail Project will standardise rail freight services in the north west of Victoria, providing huge benefits to the transport industry, agricultural sector and regional communities.
AWARD WINNING APP MAKES TRACK INSPECTIONS MORE EFFICIENT
The Australasian Railway Association (ARA) awarded its Young Achiever Award to Lycopodium Project Manager, Rebecca Coffey, for her contribution to developing a maintenance and inspection app which allows users to create, maintain and inspect track and associated defects in the rail sector.
DATA ANALYTICS HELPING TO GET FULL VALUE FROM RAIL ASSETS
A $20 billion investment has been made by Federal and State Governments in Australia’s rail infrastructure and networks, and now attention should turn to how the sector can extract 100 per cent value out of these assets once they have been built.
CALL TO ACTION FOR ADOPTION OF STANDARDS ACROSS THE AUSTRALIAN RAIL INDUSTRY
The Australian rail industry is large and complex, causing challenges with cost, safety, visibility, logistics and efficiency.
CRC LAUNCHES NEW MULTI-PURPOSE HIGH STRENGTH LUBRICANT CRX
SYDNEY TRAIN'S ASSET MANAGEMENT JOURNEY
On any given weekday, more than 260,000 train journeys will be made across Sydney Trains’ rail network.
46 MILLION REASONS TO THINK ABOUT ASSET MANAGEMENT
BE PROACTIVE, NOT REACTIVE WITH ASSET MANAGEMENT
34 INFORMATION IS POWER: SEPARATING INFRASTRUCTURE FACT FROM FICTION
Over the past year, Infrastructure Partnerships Australia, has been focused on making its information and data publicly accessible –seeking to better inform the national infrastructure debate; thereby allowing the business sector and wider community to discern infrastructure fact from fiction.
HOW AUSTRALIA’S AIRPORTS ARE USING NEW TECHNOLOGIES
In 2016, Sydney Airport served a total of 41.9 million passengers.
FUTURE PASSENGER GROWTH IS NOT POSSIBLE WITHOUT AIRPORT PAVEMENT INVESTMENT
As the national industry voice for airports in Australia, the Australian Airports Association (AAA) represents the interests of more than 260 airports and aerodromes Australia wide.
EXCAVATION BEGINS ON AUSTRALIA’S BIGGEST PUBLIC TRANSPORT PROJECT
It’s a rare sight in the middle of Australia’s biggest city; an excavator hanging 30m above Castlereagh Street in the Sydney CBD, being carefully craned to a nearby rooftop
ADVANCED
MOVING FORWARD FOR SAFER BITUMEN SPRAYING
VEHICLES
DRIVERLESS VEHICLES SET TO DISRUPT THE INDUSTRY
DISASTER RESILIENCE: STRENGTHENING CRITICAL INFRASTRUCTURE TO ENDURE EMERGENCIES
BARNESON BOULEVARD: GREENING DARWIN’S CBD
The Northern Territory Government wants Barneson Boulevard to be one of the greenest infrastructure projects undertaken in Darwin and has called on the local community to share their landscaping ideas.
CHALLENGES
LANDSCAPING & VEGETATION MANAGEMENT IoT & CLOUD COMMUNICATION
ARE WE WITNESSING THE RISE OF THE MACHINES?
The 18th Century is often called the Age of Enlightenment. In the future, will humanity look back on the early 21st Century as the Age of Connectivity?
A NATIONALLY CONSISTENT APPROACH TO INFRASTRUCTURE
SUSTAINABILITY
TUNNEL VENTILATION ON DEMAND UPS THE SUSTAINABILITY FACTOR
One of Australia’s largest tollways, EastLink, has been the first to introduce tunnel ventilation on demand to reduce power usage, greenhouse gas (GHG) emissions, maintenance costs and noise.
CELEBRATING INFRASTRUCTURE SUSTAINABILITY
CAN THE INDUSTRY DELIVER THE CURRENT RAIL PIPELINE?
Caroline Wilkie has been CEO of the Australian Airports Association (AAA) since 2011. The AAA represents all major regular passenger transport airports in Australia as well as council airports. The membership spans from councils with grass strip runways to Australia’s major gateways. The AAA also represents a further 140 corporate members. The AAA is engaged in research, developing industry publications, education, advocacy and major industry events. Caroline has a Masters of Public Affairs and more than fifteen years’ experience in Association Management.
Chief Executive of Infrastructure Partnerships Australia
Brendan Lyon is the Chief Executive of Infrastructure Partnerships Australia (IPA), the peak infrastructure policy partnership between Australia’s Commonwealth and state governments, and the business sector. Joining IPA on its formation a decade ago, Mr Lyon initially led the policy and research team, before being appointed CEO in 2008. With a strong interest in infrastructure and in economic policy, Mr Lyon has authored and contributed to a large number of research and policy papers, considering different aspects of infrastructure market regulation.
of ITS Australia
With over 20 years’ experience across transport and business, Susan is eager to harness the benefits that technology can deliver to business and the Australian community. Through the global network of ITS Associations and participating as a member of the Board of the ITS World Congress, Susan has strong linkages with the international ITS community, ensuring Australian advances can be shared overseas while also keeping abreast of international developments in this rapidly evolving field. Other affiliations include: Convenor of the Austroads Connected and Automated Vehicle Industry Reference Group and as a member of the Steering Committee for this activity; member of the National Transport Commission Industry Advisory Group, member of Monash University Institute of Transport Studies Industry Advisory Board; and member of the Space Cross Sectoral Interest Group, established under the Trusted Information Sharing Network for Critical Infrastructure Resilience. Susan has built a career in consulting and in industry to look at collaborative solutions involving government, industry and academia. This industry experience is combined with professional qualifications including a Bachelor degree majoring in Environmental Management and an MBA from Melbourne Business School.
Executive Director for Engineering and Maintenance at Sydney Trains
Stewart Mills has been the Executive Director for Engineering and Maintenance at Sydney Trains since 2013. His previous role was as the Business Director and Tube Lines Director of Operations for London Underground’s Jubilee, Northern and Piccadilly Lines. He was also in charge of independent specialist service divisions such as the Emergency Response Unit and Transplant Engineering Fleet for London Underground. Stewart was responsible for the maintenance and asset performance of the three lines which included 225 passenger trains, track, legacy and the upgraded signalling system, along with 100 stations carrying over two million passengers a day. Before working with the London Underground, Stewart was Amey Rail’s Project Director for the CCA Consortium responsible for the signalling, control and communication systems on Section 1 of the Channel Tunnel Rail Link, the high-speed line which links the UK to France.
General Manager Technology at Sydney Airport
Stuart commenced as General Manager Technology at Sydney Airport in April 2015. This role recognises the importance of technology to all aspects of Sydney Airport’s business including facilitating and enhancing the customer experience. Stuart has responsibility for technology, IT and customer analytics/ data, focusing on improving the capacity, robustness and resilience of Sydney Airport’s network and systems. Stuart has a strong finance, analytical and systems background coupled with extensive experience in operations management, people leadership and customer facing roles. Prior to joining Sydney Airport, Stuart held roles at Veda Group Limited, AAPT and AT&T in the United States.
The Chief Executive of VicRoads has announced his resignation effective 20 December 2017.
Appointed in April 2014, John Merritt has led a program of substantial organisational change while overseeing the launch of the biggest capital works program VicRoads has ever undertaken.
“When I arrived the task was to transform the business and ready it to meet the needs of Victorians during a period of unprecedented population growth,” Mr Merritt said.
“We now have the biggest capital works program in our history – more than double what it was in 2014 — and we’re working hard to deliver these critical projects.
“We have a registration and licensing area that is achieving its best ever service results and is ready to deliver short-term registration for Victorians in the new year.
“VicRoads is also more responsive and accountable now. Reform is a long journey but we’re heading in the right direction. While we don’t get it right every time, we’re committed to the job and we do play a critical role in the community.
“So it feels like the right time to move on. It’s been a
Awonderful experience to lead this organisation and I’m grateful for the fantastic support I have received,” Mr Merritt said.
Minister for Roads and Road Safety, Luke Donnellan, said Mr Merritt had made a lasting contribution in running Victoria’s road network.
“John Merritt has been a terrific leader of VicRoads and I’d like to thank him for his service,” Mr Donnellan said.
“Our government is investing more in roads and transport infrastructure than ever before, and he’s been up for the challenge of delivering it.
“He’s also been tireless in modernising the agency and making sure it delivers the daily services needed by road users across the state.”
Prior to his role as VicRoads CE, Mr Merritt served as the CEO of the Environmental Protection Authority, the Executive Director at WorkSafe, and the CEO of the National Safety Council.
Mr Merritt said he was looking forward to spending some time with his wife and children before deciding on his next move.
$1.64 billion expansion for the Port of Townsville has received a key approval, progressing the project to the next stage of environmental approvals.
Minister for State Development, Dr Anthony Lynham, said the Coordinator-General approved the port expansion with conditions that addressed all concerns over environmental and social impacts.
“The Coordinator-General has been working closely with the Port of Townsville to ensure all potential social and environmental impacts were addressed in the evaluation report, and comprehensive conditions set to manage potential impacts on Cleveland Bay in the Great Barrier Reef World Heritage Area,” Dr Lynham said.
“Today’s announcement means the project is a step closer, which in turn means expanded capacity at the port, which will allow the one-quarter of cruise ships which cannot currently enter the port to berth at Townsville, increasing tourism numbers and revenue for the region.”
THE TOWNSVILLE PORT EXPANSION PROJECT INVOLVES
FOUR KEY ELEMENTS:
1. Capital dredging of 11.48 million cubic metres of sediment to widen and deepen the Sea and Platypus Channels and an expanded harbour basin.
2. Establishing a 152ha reclamation area.
3. Construction of four kilometres of rock revetments and potentially a new 700m western breakwater.
4. Construction of six new berths.
Mr Bailey said the Queensland Government had already committed $75 million in the 2017-18 budget for a channel upgrade which forms part of the first stage of the port’s expansion over the next four years, subject to approvals.
“The channel widening work will attract future growth in trade and investment, supporting more jobs and lowering freight costs for North Queensland.
“The project was revised to be consistent with our Reef 2050 LongTerm Sustainability Plan commitments, and no capital dredge material will be permitted to be placed at sea – instead material will be used to develop a 152 hectare reclamation area at the port.”
Local MP, Scott Stewart, said the port was a critical trade supply chain, handling around 10 million tonnes of produce worth over $10 billion each year, and being able to accommodate larger ships at the Port of Townsville would mean the region can continue to attract major investment.
“Deeper and wider channels will accommodate ships up to 300m long and 40m wide, ensuring future growth in trade and expanding an essential trade pathway,” Mr Stewart said.
The next stage is the Commonwealth Government’s assessment under the Environment Protection and Biodiversity Act 1999, including any potential impacts to the Great Barrier Reef World Heritage Area.
The widening of the channel is a key initiative under the Townsville City Deal between the Queensland and Australian governments, and Townsville City Council.
The $15 million Melbourne to Adelaide rail freight upgrade has been completed, increasing capacity by up to 20 per cent.
Longer freight trains will soon be able to run between Adelaide and Melbourne, shifting more freight, and boosting efficiency and productivity.
The Melbourne - Adelaide Loops project was delivered by the Australian Rail Track Corporation (ARTC). Federal Minister for Infrastructure and Transport, Darren Chester, said the Melbourne to Adelaide Loops project will allow the accommodation of 1,800m trains, improving productivity on the busy line and supporting associated jobs.
“The upgrade will create a 20 per cent increase in productivity for rail operators and remove the need to send additional train services back to Melbourne with empty wagons,” Mr Chester said.
“By investing $15 million in the project, we have created a situation where the maximum length of trains operating from Adelaide to Melbourne can be increased by up to 300m. The longer, more efficient trains means less congestion for motorists and improved road safety, as well as cutting transport costs.
“The initial scope of the project was to deliver five extensions to crossing loops, which provide opportunities for trains heading in opposite directions to pass each other on single line sections of track, but thanks to clever project management, an extra passing loop at Dimboola in regional Western Victoria was also upgraded within the original project budget.”
Mr Chester said Victorian crossing loops at Pyrenees, Murtoa, Pimpinio, Diapur and Dimboola, and South Australia’s Mile End loop, had all been extended to 1,800m.
“A 1,800m train carries the equivalent of more than 85 B-Doubles worth of freight that would typically travel by road through South Australia,” Mr Chester said.
“Moving more freight by rail is crucial to meet the expected doubling of freight demand over the 20 years to 2030 while reducing urban congestion.”
Additional track upgrades currently underway in Adelaide as part of the jointly funded Australian and South Australian Government Torrens Junction Rail Project will provide a clear path for 1,800m trains all the way from Perth to Melbourne by late 2017.
The Queensland Government has approved more than $2 million in funding, through the Jobs and Regional Growth Fund, for a Cairns-based aviation firm to expand its hangar facilities at Cairns Airport.
Treasurer and Member for Mulgrave, Curtis Pitt, said Hawker Pacific planned a $4.5 million expansion to help capture more heavy maintenance work from around Australia, New Zealand, Asia, and Pacific nations.
“The expanded hangars will allow Hawker Pacific to better compete both
nationally and internationally for heavy maintenance, attracting work otherwise sent to Asia or Europe,” Mr Pitt said.
“Hawker Pacific applied to the government’s Jobs and Regional Growth Fund for a contribution towards their $4.5 million expansion project, and the government has approved support of $2.475 million to back this very worthwhile job-creating project.
“By keeping the work onshore, the company expects to engage an additional 39 workers by September 2021 and create 50 jobs during construction.
“I understand a significant proportion of the new operational staff will be sourced from the Cairns Aviation Skills Centre, with the project providing a valuable pathway for graduates.
“This is a carefully targeted investment by the government that will pay dividends in the future by expanding the Far North Queensland economy and delivering jobs,” Mr Pitt said.
The New South Wales Government is committing a further $35 million to support the planning and project development of the first section of the F6 extension.
The $35 million commitment is in addition to the $15 million provided in 2017-18 Budget for the F6 project.
Stage one of the connection in Sydney’s South is proposed as a four kilometre tunnel, connecting underground from the WestConnex New M5 junction at Arncliffe to President Avenue in Kogarah.
NSW Premier, Gladys Berejiklian, said anyone who drives through the area knows how congested the roads can get and how vital the link will be.
“We are a Government which gets on with the job and in the coming days we will be starting consultation on the initial concept design with the community,” Ms Berejiklian said.
“At this point a final design for the tunnel has not been decided, as we will take our time to listen to the community before coming back in mid-2018 with a detailed design and cost for the project.”
The four kilometre tunnel would reduce traffic congestion along the Princes Highway through Arncliffe, Banksia and Rockdale, and on The Grand Parade through Brighton-le-Sands.
The Minister for Roads, Melinda Pavey, said the project is a priority as peak hour travel speeds on the Princes Highway between Kogarah and the city are among the lowest for arterial roads in Sydney.
“While we are still doing our homework, it’s predicted the property impact for stage one of the F6 extension will be low, compared to other major road projects,” Ms Pavey said.
Roads and Maritime is also continuing with early investigation work along the F6 Corridor between Kogarah and Loftus to help determine any possible adjustments for the future motorway.
It’s no secret that there has been a significant lack of investment in rail for decades. Our nation’s love affair with roads, while important in the greater transport mix, has not created a balanced transport network. This is now changing.
Driven by New South Wales and Victoria (with Queensland and Western Australia set to follow soon), the current investment in rail is unprecedented over the past 80 years. Taking lessons from leading global cities, Sydney and Melbourne are now making strong investments in developing Metro Rail systems to help them deal with growth, congestion, reliance on roads and the coinciding challenges of urban renewal and urbanisation. Our major cities are also investing in freight networks, which might not be exciting for the average voter but is critical to efficient mobility in our economy.
While this is great news for our major cities - the engine room of our economy - it also comes with unique challenges.
The scale of this investment is absolutely needed to ensure the resilience and competitiveness of our cities, however, there is a significant challenge to be overcome for successful delivery – the local industry does not have the capacity and capability to deliver the planned investment.
Due to our nation’s sustained investment in roads, the capacity and capability is there for road projects, however, we are looking to do new things with Metros and integrated rail networks, so the issues of capability and particularly capacity to deliver must be acknowledged and addressed.
Since these Metro projects have in the past been a once in several generations
investment in our cities, we simply haven’t built up a sustained rail industry capable of delivering multiple major rail infrastructure projects at the one time.
So, how do we manage this?
Firstly, the public and private sectors must acknowledge the capacity and capability challenges and commit to growing the local skill base. As leaders in the industry, we all have a role to play in creating training programs, developing our teams, exposing them to global best practice, sharing insights and ultimately investing in a future rail skills system for Australia.
We simply cannot continue to hire and find people from the current talent pool for the long term, we must invest and we must draw on global experience.
This issue can also be addressed by public and private sector taking a broader view of Australia’s skill base. Too much reliance on demonstrated rail experience and track record will most likely see us overlook a significant amount of good talent from other sectors and not be helpful in getting the job done.
Secondly, the global community will be critical to Australia’s success. Looking at global best practice, European cities are leaders in Metro systems and their workforce is incredibly skilled and incredibly experienced. This knowledge must be brought to Australia and shared with our local teams.
In practical terms, this can be managed with short and long-term
secondments with the goal of delivery and education. Large numbers are not needed. The difference can often be made with a few key individuals providing their personal experience and the linkages they have back to their highly skilled teams in Europe. This will create a truly globally skilled community – it’s easy to forget just how isolated we are in Australia compared to our European colleagues, who can easily draw on best practice from neighbouring countries.
Now, it certainly isn’t doom and gloom. We have one of the most mature highways industries in the world, so we are certainly skilled and able to deliver complex transport networks. What we must do though is acknowledge our skills gap, invest in local talent, think more broadly about how to use the talent we have, and tap into global networks. The success of our current, and hopefully continued, rail investment relies on this approach.
Conquering this challenge will deliver highly successful metro rail projects for our largest cities that start to transform the way we travel and how we view mobility. It will ensure we leave a legacy of iconic mobility infrastructure that are valued and continue to shape our cities for decades to come, and an industry that has the capability and capacity to deliver sustained investment in a balanced transport investment portfolio.
Australia’s population is growing rapidly - around 1.5 per cent a year - and it’s starting to have an impact on cities. The Australasian Railway Association (ARA) and members of the rail industry have developed a National Rail Industry Plan that aims to address this challenge and help to significantly develop Australia’s transport infrastructure. Here’s how it plans to do this and what it will mean for the rail industry.
Recently Australasian Railway Association (ARA) board representatives met with Commonwealth Ministers including Senator Arthur Sinodinos, Minister Darren Chester and Minister Paul Fletcher to discuss the implementation of a national plan for rail. The plan released by the ARA in September, A National Rail Industry Plan for the Benefit of Australia, details why we need to develop a more efficient Australian rail system and how the plan will help coordinate this effort.
ARA Chief Executive Officer, Danny Broad, said the rail industry makes a very significant contribution to Australia’s economy.
"The Commonwealth Government will be investing $89 billion in naval shipbuilding through to 2055. This investment will be supported by a Naval Shipbuilding Plan. Investment in rail by Australian Governments will be to the order of $100 billion through 2030," Mr Broad said.
“Through better coordination and long-term certainty, we can ensure the industry is well positioned to take advantage of all the lessons from the past and position ourselves for the future.
“To get this right we really need a combined effort by Commonwealth, State and Territory Governments, as well as industry support.”
In addition to the economic
contribution, Australia’s rail industry reduces congestion as one passenger train takes 525 cars off the roads and one freight train takes 110 long haul trucks off the roads; lowers costs through fewer road accidents and reduces road maintenance; as well as offering sustainability benefits including a reduced carbon footprint due to lower emissions.
The National Rail Industry Plan for the Benefit of Australia aims to highlight the important role that rail plays in the national transport task and the economy; identify the challenges and opportunities facing the national rail endeavour; and provide a manageable, realistic set of initiatives for both government and industry to implement in a realistic timeframe.
Each year almost one billion people use the country’s heavy and light rail networks in capital cities and in regional areas, and around 1.5 billion tonnes of freight, primarily bulk commodities, are moved.
This highlights the important role passenger and freight rail plays in helping to ease congestion in capital cities, particularly Sydney and Melbourne, which is a consequence of the continuing growth of the Australian population and therefore vehicle registrations.
In 2016, Australia’s population grew by 372,800 people - with 146,600 located in Victoria and 116,400 in New South
Wales. In round terms, Melbourne and Sydney are growing at the rate of 10,000 people every month.
As of January 2017 there were 18.8 million registered vehicles in Australia. In the preceding year both New South Wales and Victoria experienced a growth of about 2.5 per cent, which equates to around 130,000 additional vehicles on the road in a year. The strongest growth was in light commercial vehicles (3.1 per cent) and light rigid trucks (3.4 per cent). The growth in articulated vehicles was circa two per cent. Investing in Australia’s rail networks will help take these vehicles off the road, which has environmental and social benefits.
Rail is also a large employer, with close to 200,000 directly or indirectly involved in the industry through freight and passenger operators, track owners and managers, manufacturers, suppliers, contractors, consultants and government administration. The contribution to the Australian economy currently stands at around $26 billion, with the ARA’s plan stating this could jump significantly with the right policies in place.
Another factor is the new age of consumerism. The trend of online shopping requires a pick-up from the supplier or wharf, to the warehouse and onto the home, adding to road congestion. The growing population must be fed, so transporting product is on the rise, and people expect speed and
efficiency in their delivery to markets.
Housing affordability is a recognised problem, giving rise to the need for options to improve access to and the liveability of Australia’s various growth corridors and regions.
The Australian rail industry is currently standing at a crossroads between the opportunities presented by the significant and ongoing investment in systems and infrastructure. It is facing the challenges posed by aging infrastructure, an aging workforce and the historical separation of rail into discrete state-oriented networks, and the way in which these challenges are addressed will determine the value derived from current and
future investment.
The Australian rail industry is also faced with the challenge of fragmentation. Historical events have resulted in a number of discrete, stateoriented networks with non-compatible infrastructure, differing regulatory frameworks and uncoordinated project schedules that compete for the same scarce resources.
The Plan believes a collaborative approach which engages Commonwealth, State and Territory Governments can serve to overcome these inefficiencies.
The National Rail Industry Plan for the Benefit of Australia is needed to help meet the challenges facing
Australia and the rail industry, and obtain maximum economic growth, efficiency, productivity and social benefits from the substantial investments currently being made, which are likely to exceed $100 billion by 2030.
A consolidated pipeline of projects around Australia will help identify priorities in addressing infrastructure needs, including the challenges of congestion and fragmentation, with funding approvals based on the compelling nature of the supporting business case.
Rail will play an increasingly important role in Australia in the future. Now is a pivotal time to bring in a National Rail Industry Plan to ensure Australian rail can realise its full potential.
1. Recognising the importance of rail for Australia’s infrastructure development, urban planning and freight movements
2. Harmonising standards, minimising regulations and maximising economies of scale
3. Growing the capabilities of individuals and companies
4. Maximising opportunities for rail companies
5. Fostering innovation, research and development
The Murray Basin Rail Project will standardise rail freight services in the north west of Victoria, providing huge benefits to the transport industry, agricultural sector and regional communities. The project will also ensure the ongoing integrity of the rail track, improve safety on the lines, provide an alternative to road freight and reduce costs.
The $440 million upgrade to Victoria’s rail freight network aims to enhance the state’s rail freight services. Jointly funded by the Australian and Victorian Governments, the Murray Basin Rail Project involves standardising and improving the 1,055km of rail track that services the Murray Basin region in Victoria’s central and north-west areas.
The project will provide better rail access between the Murray Basin and Victoria's major ports in Portland, Geelong and Melbourne. It will also improve the performance of the freight network and increase the amount of produce able to be moved.
V/Line CEO, James Pinder, said the freight industry in this region will be able to deliver exports to Victoria’s ports in a more efficient and cost-competitive way.
“This vital project will drive economic
growth, create jobs and provide a major boost to industries across the state,” Mr Pinder said.
Mr Pinder said that an increased axle loading will allow higher volumes of product to be safely freighted across the network, allowing trains to carry up to 500,000 more tonnes of grain each year.
“Once complete, the project will allow for better connections and access for Victorian farmers to get their goods to Victoria’s major ports in Portland, Geelong and Melbourne,” Mr Pinder said.
Stage one of the project included enabling works and repair of existing rail on the Mildura and Hopetoun rail lines and was completed in June 2016.
Work on stage two of the project commenced in August this year and includes a track upgrade to enable the
reopening of the rail freight line from Maryborough to Ararat. Works are also underway to upgrade and standardise the Dunolly to Yelta and Ouyen to Murrayville rail lines.
Stages three and four are expected to begin in March 2018 and be completed by August 2018. During these stages, the project will gauge conversion and upgrade works on freight lines from Dunolly to Manangatang, Korong Vale to Sea Lake and Gheringhap to Warrenheip. Across the project, crews have removed rail anchors, and dog spikes from existing infrastructure. On the Maryborough to Ararat rail line, workers are currently installing concrete sleepers, new track and ballast in preparation for the reopening.
On the freight line from Dunolly to Yelta, which is currently closed to freight train traffic, work is focusing on
track maintenance and converting it to standard gauge. Produce is currently being moved via the Manangatang or Sea Lake rail lines during this time.
V/Line appointed the McConnell Dowell Martinus Rail Joint Venture to deliver stages two, three and four of the Murray Basin Rail Project.
To date, the project has seen a workforce peak of more than 400 people across seven work crews and at least 15 per cent of this workforce is being recruited from the Murray Basin region.
The project held public “Supplier and Jobseeker” briefing sessions in St Arnaud, Mildura and Maryborough in August, where members of the community were informed about opportunities for employment and local suppliers. V/Line said it aimed to engage local business and suppliers in the project where possible.
Towns and communities in the central and north-west areas of the state are poised to benefit from crews and staff working in the region.
Mr Pinder said there have been increases in business in local towns as work crews and staff travel through the region, seeking a range of goods and services, including accommodation, food, household items and general supplies.
“We’re pleased with the progress of the project so far, and the benefits that are already being seen by communities in the north west of the state,” Mr Pinder said.
The Australasian Railway Association (ARA) awarded its Young Achiever Award to Lycopodium Project Manager, Rebecca Coffey, for her contribution to developing a maintenance and inspection app which allows users to create, maintain and inspect track and associated defects in the rail sector. Here, Rebecca discusses the process of using the app and the impact it has had so far.
At the Australasian Rail Industry Awards Gala Dinner in July, Mrs Coffey received her Permanent Way Institution Young Achiever award in recognition of her involvement with the innovative LycoMMS app. Despite the recent industry recognition, Mrs Coffey said the aim of the app was simply to fill a need in her company.
“My inspiration came directly from seeing Lycopodium’s need for a simple to use system, specific for rail requirements, to conduct inspections and manage assets for our clients, and the inability of any cost effective off–the–shelf solution to fill this need,” Mrs Coffey said.
“I saw a business need and I solved it, to me that is part of my job. I didn’t build this system with the view to market it or gain awards, I built it to help my company and my colleagues.”
Mrs Coffey said LycoMMS aims to solve rail industry issues such as inefficient track inspections due to double handling paperwork, and limited defect insight and history provided to inspectors in the field.
“It aims to provide simple management of assets, full cycle defect and work order management. Essentially fill the gap for a simple, easy-to-use tool for rail inspections and related asset management.
“Of course, a system is only as good as its last update. The world of technology is a fast moving one and Lycopodium realises we need to continually update as new options and features are explored,” Mrs Coffey said.
Designed specifically with rail inspectors in mind, LycoMMS allows an inspector to collect data on defects, which is uploaded to a maintenance management system that supports the app. Using the data, the system manages inspection schedules, and manages assets, defects and work orders.
When inspecting tracks, inspectors simply log any new defects found in the LycoMMS app at any time during the inspection. The GPS coordinates of the defect are recorded and the inspector can capture photos and details all within the app.
Inspectors can also log updates to existing defects including their status and recommend repair if they are a recommend repair priority. They also have the ability to make notes, take photos, and most importantly they can review the defect history including past photos.
The logged inspections are then digitally signed and certified by the inspector and the system automatically uploads the new data back to the database. The defect changes, including new defects, are sent to the engineering representative for approval prior to being released into the database.
“All data collected, both from inspections and work orders, are automatically collated and linked in the system to related assets, therefore you can open a specific asset and see the full history of defects and maintenance works (both preventative and corrective) conducted over its life,” Mrs Coffey said.
“Defects can be filtered multiple ways for analysis. For example, you can filter to view all overdue defects, all priority one defects or all defects for a specific track section.”
What makes LycoMMS so beneficial to rail inspectors is its ability to operate in areas with no mobile coverage. Data entered while offline is saved and automatically uploaded when back in mobile range.
The app also utilises ‘App Tokens’, which means the app knows who is using it and only allows approved competent inspectors to provide inspection certification. Additionally, inspections can be digitally certified by the inspector, which
I saw a business need and I solved it, to me that is part of my job. I didn’t build this system with the view to market it or gain awards, I built it to help my company and my colleagues.
eliminates the need for paper signatures and provides a truly paperless system.
LycoMMS includes a Client Portal which provides the ability to click on an asset and view any defects, all the attributes and history. Inspection data is also available in the system immediately after certification and can be exported via a range of formats to suit the needs of the platform required.
Mrs Coffey said she is overwhelmed at having her work recognised in the industry and she recognises the efforts of everyone involved for creating the award winning app.
“I am very appreciative to Lycopodium and my colleagues for supporting the system and my career, also to Duncan our software developer from Cartesian Creative for partnering to make all my ideas and plans come to life,” Mrs Coffey said.
LycoMMS is supported by a
Servicing in these sectors:
A $20 billion investment has been made by Federal and State Governments in Australia’s rail infrastructure and networks, and now attention should turn to how the sector can extract 100 per cent value out of these assets once they have been built. The answer to this lies in data analytics to provide decision-quality information that can provide solid engineering, maintenance and supply support to the new and existing infrastructure.
With such a major investment there needs to be processes in place to ensure that when the assets move from construction into operation, they are safe, regulatory compliant, and provide a return on investment in line with the original expectations.
The key to providing efficient rail operations and unlocking value from assets is having an integrated support network across engineering, maintenance and supply that is backed by rigorous data collection and analytics.
Jim Frith, Managing Director at McConnell Dowell said the best way to make sure the industry is getting value from these investments is to use data collection and analysis to aid better decision making.
“We need to provide support for the current investments in rail infrastructure and rolling stock assets by building asset support systems that ensure return on investment, operational excellence, and ensure a smooth transition from the project delivery phase to the operational phase,” Mr Frith said.
To achieve a coordinated effort, a systematic approach to applying engineering, maintenance and supply functions across the asset base, supported by the collection of data from operational sources, the assets themselves, and factors external to but affecting the assets, is important.
What really counts in the end is making sense of the information collected and understanding what it is telling us and then having an engineering office that can formally apply good asset management practices to the on-ground maintenance teams and the supply chain.
Data analytics is also vital for reporting to government bodies and performance assessment. After investing a major amount of funding, governments need to know how the infrastructure is working and if it is providing a return on investment.
In order to achieve a smooth transition to the operations phase, Mr Frith said the data needs to be collected and analysed as early as possible and all the supporting elements need to have been put in place well before any passengers get on board. Ideally this should occur during the project phase.
In addition to its traditional rail construction and rail plant services businesses, McConnell Dowell is implementing this coordinated and systemised approach in its operations to provide a service that encompasses the entire spectrum of asset construction and management requirements for rail infrastructure.
They will be able to achieve this because they’re thinking not just about collecting data and information about assets, but how that data will be used to make decisions in a purposefully built support office. They have a structured flow of Engineering, Maintenance, and Supply function inputs and outputs supported by extensive data collection and data analytics.
“We could manage the entire logistic support function for the primary operator, or parts as required, to provide an independent position of serviceable assets, backed by transparent analysis of engineering, maintenance and supply requirements for these government owned assets of high public value,” Mr Frith said.
This provides high value for rail operators as it means there is just a single provider carrying out activities to support the provision of engineering, maintenance and supply functions in a coordinated and integrated manner.
These integrated data and asset support functions have worked before in other sectors, from aviation to Defence, and McConnell Dowell believe that if it’s embraced by the rail industry it will help ensure full asset operational excellence.
McConnell Dowell is currently delivering the Murray Basin Rail Upgrade Project in Victoria, the largest freight rail upgrade project in Australia; in addition to a program of level crossing removals in Melbourne. For more information on McConnell Dowell’s comprehensive rail offering and how you can use data analytics to unlock full value from your rail assets visit www.mcconnelldowell.com/capability/rail.
The Australian rail industry is large and complex, causing challenges with cost, safety, visibility, logistics and efficiency. To address these issues, the Australasian Railway Association (ARA) board announced the support for adoption of GS1 open global standards for identifying and marking (barcoding and/or tagging) components used across the industry.
Chief Operating Officer at the ARA, Phil Allan, said, “The Australian Rail Industry has been called to respond to a call to action to improve reliability and quality across the supply chain using GS1 standards.
“The objective of the call to action initiative is to implement GS1 standards by 1 January 2019.”
This initiative is aligned with a parallel EU program involving rail operators and network managers. The rail industry in Europe is already using and developing a common standard, therefore, global GS1 standards will be a critical enabler for the effective implementation of ISO 55000 Asset Management Standards.
GS1 Australia’s Senior Manager – Trade, Transport and Heavy Industry, Bonnie Ryan, said, “Calling on industry players to work with us gives the Australian rail industry a unique opportunity to collaborate with a standardised approach for consistently identifying and marking components and assets.
“Standardising the way materials are identified will bring industry-wide efficiencies which will help reduce costs and inventory; improve safety, maintenance and traceability, and eliminate unnecessary manual tasks using automation.”
To prepare the industry for the adoption of GS1 standards, a second series of Rail Industry Supplier Workshops are in the pipeline for early 2018.
GS1 Australia is also participating at AusRAIL PLUS 2017 in Brisbane from the 21 to 23 November at Stand No 378. Ms Ryan is speaking in the Rail Suppliers Stream on Day 1 about the benefits of standards for identification of parts and components.
For more information or to register for the 2018 workshops, contact Bonnie Ryan, Senior Manager – Trade, Transport & Heavy Industry, GS1 Australia at bonnie.ryan@gs1au.org
Standardising the way parts and components are identified will bring industry wide efficiencies including:
• Reduced inventory write-offs and waste
• Improved maintenance and repair operations
• Improved traceability and warranty management, fundamental for lifecycle tracking
• Reduced costs through fewer transaction errors and better quality data
• Elimination of non-value added tasks by enabling automation of manual processes
the Call to Action www.gs1au.org/ARA-GS1-call-to-action/
Leading aerosol and bulk lubricants supplier CRC Industries has expanded its range of professional-grade lubricants with the launch of new multi-purpose spray CRX.
CRC Industries Australia Managing Director, Shona Fitzgerald, said CRC CRX Multi-Purpose High Strength Lubricant was an exciting addition to the company’s multi-purpose range, offering high performance at a low price.
“We are very pleased to bring to the market this multipurpose high strength lubricant and CC3 based industrial grade anti-corrosion formula which is safe to use on almost any surface and application, being non-toxic, non-staining and non-conductive,’’ Mrs Fitzgerald said.
“Designed for clients who want to get the job done faster, better and safer, CC3 is a legacy ingredient developed by CRC and is used in the production of many products in our range.
“It features a tried and tested formula offering a mixture of both mineral and synthetic oil lubricants and a blend of corrosive preventative additives which are effective on steel and aluminium metals.”
CRX Multi-Purpose High Strength Lubricant will not dry out or wash off with water, making it ideal for industrial applications as well as recreational home use.
It has been specially formulated to stay in place for long periods of time without drying or becoming sticky.
The product does not contain silicone, acid, kerosene or dieseline and won’t harm plastics, metals, paints, enamels, fibreglass or neoprene seals.
Applications include marine and recreation, sporting and camping equipment, heaving industry use, mining and transport, food preparation areas, electronic and electrical components, farming and aviation machinery, locks and hinges.
CRC is a recognised supplier of professional quality aerosol and bulk lubricants, anti-corrosion and chemical maintenance products. The company prides itself as being the leader in product quality, performance and regulatory compliance. CRC’s innovative research and development team continually advances new and improved products for clients to do their job faster, easier and safer.
CRC Industries’ on-site manufacturing of products allows control of all production processes. All raw materials and finished goods are subject to stringent testing by the company’s quality control department. Lot sampling guarantees the customer consistent quality and performance. When specifying CRC products, each customer can be assured of getting a product that surpasses all maintenance and repair industries’ highest standards of environmental, performance and safety – because first it must meet CRC’s.
For further information contact CRC Industries on 1800 224 227, info.au@crcind.com, or www.crcind.com.au
The RTSA’s Conference on Railway Excellence (CORE2018) will be held at the International Convention Centre in Sydney on 30 April to 2 May 2018, and planning is well underway. The CORE2018 organising committee has been working hard over the last 12 months bringing the best of ideas and people to the conference and Sydney.
The theme of CORE2018 is 'Rail: smart, automated, sustainable'. Technology is constantly evolving, and this has presented both solutions and challenges in the way we plan and deliver rail services and infrastructure.
The conference will provide a knowledge exchange platform between emerging technologies and our existing infrastructure and projects, maximising the efficiency and benefits for the end customer and industry.
Technology is constantly evolving and this has presented both solutions and challenges in the way we plan and deliver rail services and infrastructure.
It will broadly cover all disciplines of railway from fundamental research to “blue sky” applications, highlight global scientific interactions and collaborations, and feature the unique location, culture and beautiful geography of Sydney.
The program structure of previous years has been maintained given the expectations of delegates, however the CORE2018 Committee has slightly departed from the traditional discipline-based streaming, in order to encourage papers in business
focus areas that are emerging in many railways, particularly in assurance and customer facing systems.
We have had an excellent response to the Call for Papers, almost doubling the number sought. Inevitably, in some specialist areas, the abstracts were over represented and papers of high standard have “missed the cut”. The success of CORE conferences is underpinned by the technical program.
Although we have not been able to include all papers at CORE2018, we urge authors to continue to
submit papers to future CORE or RTSA Conferences. The Technical Committee, chaired by John Watsford, is currently reviewing the full length papers prior to final decision. Collating the technical reviews of all papers is an involved and time consuming process, which is essential to sustain the high standards of the conference.
For CORE2018 we expect to attract 700 attendees focused on rail transport issues representing all rail related disciplines from engineering research and practice, private industry, and governments. We especially welcome young professionals, researchers and students, and will have dedicated events for them — the future generation.
The success of a conference is thanks to many people and organisations, particularly our generous partners: Transport for NSW, ARTC, Aurizon, WSP, SNC Lavalin, Speno, Institute of Railway Technology, Pandrol and Geofabrics, as well as our Media Partner Infrastructure Magazine and Supporting Partner Railway Gazette
There are still a number of partnership opportunities available in a variety of categories and commensurate exposure.
The Committee also welcomes partnership suggestions from you and invites you to contact the conference manager, Anthony Bordignon –Engineers Australia, to discuss your organisation’s desired partnership objectives.
Our keynote and invited speakers come from around the world, representing the very best in their field of expertise. Jean-Pierre Loubinoux, was appointed Director-General of the International Union of Railways (UIC), the worldwide association representing the rail sector and encompassing 240 railways across all continents in 2009.
Prior to joining UIC, he was Chairman and CEO of French railways SNCF International and SNCF Director of International Development from 2001 to 2009, having been appointed Chief Executive of SNCF Freight International in 2001.
Leslie Woo, Chief Planning Officer at Metrolinx, Ontario Canada - described as The Transit Changemaker by Spacing Toronto in 2016 and awarded Canada's Women's Infrastructure Network's 2015 Outstanding Leader.
Leslie is a passionate and influential strategist on urban planning issues internationally and has been leading
the transformation of Canada's largest and fastest growing metropolitan centre for over twenty years, shaping multi-billion dollar infrastructure investments.
US based Sally Dominguez is confirmed to take on the role as Master of Ceremonies for CORE2018. Most of you will know Sally in her role as a judge on ABC TV’s New Inventors for six years and she currently judge’s product design in the USA and China, and Car of the Year in Australia.
RTSA and UIC have joined forces for CORE2018 to provide even more value to delegates, speakers and exhibitors. Not only has UIC agreed to provide its Director General as Keynote Speaker, but will also run a workshop on Automated Trains Protection on Thursday, 3 May 2018. Details will be published as soon as they become available. Both organisations have a shared vision to propose new ways to improve technical and environmental performance of rail transport. Working together will be of enormous benefit to the industry and its participants.
In addition, and following the great success from last year’s CORE in Melbourne, we have taken on board again the 'Knowledge Zone' in cooperation with ACRI, the Australasian Centre for Rail Innovation. We are also having a shared plenary session and technical stream with our colleagues from the System Engineering Society (SESA) and their conference SETE2018.
We trust that there will be something of interest to everybody in the industry and look forward to seeing you at CORE2018 in Sydney on 30 April 2018.
On any given weekday, more than 260,000 train journeys will be made across Sydney Trains’ rail network. This will result in 21,336 services operating by the end of each week, travelling on 961km of rail. Away from the hustle and bustle of customers, hundreds of Sydney Trains staff are out on the network busily making sure the organisation’s $35 billion worth of assets are running efficiently and safely.
In charge of the organisation’s asset management program is Executive Director for Engineering and Maintenance, Stewart Mills.
“We have a very extensive rail network that is around 160 years old, so we have our fair share of challenges to contend with,” Mr Mills said.
“When you’re managing the volume of assets we have, it’s essential the decision-making process is clear and precise. There’s very little room for mistakes but we’re very fortunate we have great people at Sydney Trains who make the managing of assets easier.”
“From engineers inspecting tracks, to technicians working on overhead cables and executive directors making multimillion dollar decisions, everyone has an important role to play to keep Sydney moving.”
It’s this commitment that has seen Sydney Trains become the first public sector organisation in Australia to gain accredited ISO 55001 certification for its asset management system.
The country’s busiest rail network has achieved certification against the ISO 55001, the international standard for Asset Management Systems.
“This is a significant milestone for us, and one we’re obviously very proud of,” Mr Mills said.
“We have a mandate from the NSW Government to ensure our asset management system is aligned with the International Standards Organisation (ISO) requirements, so it was always our plan to meet this obligation.
“But we didn’t want to just stop there. We knew we had the capability to do more while meeting requirements.
“Achieving an internationallyrecognised certification like the ISO 55001 is confirmation that we made the right decision when we started down this path three years ago.
“It means our customers and our stakeholders can be reassured that we have what it takes to deliver a world class service that’s safe and reliable.”
The ISO 55001 certification is a result of a number of steps Sydney Trains took when it began the process in February 2014, soon after ISO released the standard for asset management.
The completion of an internal self-assessment was the first step on the journey followed by a gap analysis conducted by an external party.
This led to the development of a program of activities involving various parts of Sydney Trains, including the development of a new asset management policy and framework.
A Strategic Asset Management Plan (SAMP) followed where 25 objectives were identified as outcomes for the organisation to focus on.
Existing processes and documents were reviewed and updated, and new processes and tools developed to provide a clearer line of sight between the objectives and the activities undertaken.
“The system we have developed will help us build our capabilities and will play a critical role in our ability to manage safely and efficiently more than 1,650km of rail track, another 1,500km of overhead wiring and 308 train stations across NSW,” Mr Mills said.
“We’re now able to clearly link what we need to achieve from our assets with the work we do on the ground through a greater focus on decision-making that balances costs, risks, opportunities and performance.”
He points to work recently completed at the Cooks River underbridge as an example of how the asset management system is used. The timber beams running across the underbridge needed to be replaced.
“Using all the tools we now have, we were able to come up with the most suitable and cost-effective solution that aligned with our corporate and asset management objectives.
“The work that’s been done to this section of our rail network means we have improved the bridge’s resilience and performance, and save on maintenance costs.”
For the average traveller, the ISO 55001 certification may not mean much, which is fine with Mr Mills.
“If our customers get to their destinations in the easiest and most timely manner, then we are doing our job. We can reassure them that by complying with the requirements of ISO 55001, we are taking their safety very seriously.”
Mr Mills said another area that’s benefited from an improved asset management system has been around the reliability of services.
“We have done a lot of work in this area particularly with our signals through the upgrading and modifying of key components such as track turnouts, signals and track circuits.
“This has resulted in the reduction of repeat failures by 27 per cent in the last year. Signal failures causing train delays of more than five minutes has also dropped by nine per cent.”
Impressive as it is in being awarded the ISO 55001 certification, Mr Mills said Sydney Trains is aware it cannot rest on its laurels.
“This is just the beginning for us. Our task now is to make sure the Asset Management System is well embedded in Sydney Trains’ DNA and to continuously improve the way we work.
With a workforce of more than 10,000 employees, it is also the biggest organisation in Australia and New Zealand to achieve ISO 55001 accredited certification.
Any organisation that relies on critical assets to provide services is faced with the age-old, ongoing problem of working out how to meet service targets with an aging asset base. What do you renew, when, with what, and how do you pay for it?
To make matters more difficult, many of these asset owners are relying on the past to predict the future and this is proving problematic with an ever-changing operating environment to contend with — whether it be environmental changes or an aging population.
If you work in asset management, you’re probably aware that Australia’s need for reliable and efficient infrastructure has never been greater. The country’s population is set to hit 46 million by 2075; double the population our infrastructure assets are serving today1. To put this growth into context, by 2061 the population of Brisbane is projected to increase from 2.2 million (as of 30 June 2012) up to 5.6 million, Sydney up to 8.9 million and Melbourne will reach a population of up to 9.8 million2.
In order for asset owners to address this growth trend, they must first acknowledge the current situation. The key challenges facing asset managers are strategic ones: accurately understanding asset performance in order to make better long-term investment decisions, maintaining service levels and managing risk.
long-term strategic imperatives, and providing customers with a reliable, critical service.
Integrated asset lifecycle management (ALM) delivers greater transparency and improved asset performance across the asset lifecycle by breaking down knowledge silos and eliminating sources of inefficiency. When properly implemented, a technology-enabled ALM system provides a centralised source of asset information, including data on maintenance, budgets, purchasing and work and materials management. Without it, asset managers face a combination of rising costs and rising risks. It is only through considered investment in technology that Australia’s aging infrastructure network can be supported to meet the needs of our growing cities.
Part of this challenge is due to the traditional, siloed structure that asset management has long adhered to. Broken into independently managed functions, with separate departments responsible for repairs, maintenance programs, capital planning and delivery, asset management has long seen separate departments manage different stages of an asset’s lifecycle. Currently, many of the systems managing asset information at these different stages operate on a spectrum of incommunicable technology platforms.
With impending and unprecedented growth before us, it’s not hard to see how this model is unsustainable. Contrary to popular belief, it is in fact possible for organisations to create a common language for multiple and vastly-different business functions so that asset management can be more efficient and transparent across the board. I like to call it taking an enterprise-wide approach to asset lifecycle management.
By taking an enterprise-approach, business functions no longer need to be concerned that their priorities will be overlooked or misunderstood by separate departments; lost in translation during the process of reporting and data consolidation. Furthermore, separate business functions are better able to understand their business holistically, which is only ever a positive thing when it comes to long-term strategic asset management, meeting
The true benefits of a technology-enabled enterprise system for asset lifecycle management is the ability to gather data from across an entire organisation and review it on a single, easy to use platform. In fact, the shift to a centralised, single system was an integral step in ensuring the future viability and quality of assets for Victorian-based water utility, GWMWater.
Responsible for $2 billion worth of assets spread across an area the size of 25 per cent of Victoria (equivalent to the size of Tasmania), GWMWater is responsible for 16 water treatment plants, 87 sewer pump stations and more than 11,000km of rural pipeline.
The adoption of an integrated asset management system enabled GWMWater to centrally understand and track where it was spending money and how assets were performing in real time. Importantly, the implementation saw field operators use tablets to instantly report on the status of assets and repairs — eliminating the margin of error associated with paper based systems.
While certainly valuable in the field, the use of an integrated system delivered far-reaching benefits for the wider business too as it automatically broke down existing silos and enforced the discipline of data sharing which in turn improved regulatory reporting and confidence in the validity of data. To take it one step further, this subsequently impacted compliance with industry regulations, of which there are many in the water sector.
While pressure on Australia’s infrastructure will only continue to rise, the adoption of an enterprise ALM system is a vital, long-term safeguard that will empower asset managers to better understand their assets and provide customers with exceptional service.
Ultimately, with the right information at their fingertips to make better strategic investment decisions for the future, asset managers will be better equipped to predict investment requirements to ensure service targets are met. Suddenly, knowing what to renew, when, with what, and how, will be intuitive rather than problematic.
Water and wastewater systems are made up of highly valuable assets, which can deteriorate over time. As they age, the assets can lose value, the level of service they provide may be compromised, and operations and maintenance costs can increase. Having a proactive asset management system in place is an important part of mitigating these problems.
Asset management helps utilities and water authorities make decisions on how to best manage aging assets to ensure their value is protected and that finances are available to maintain and rehabilitate them when necessary.
The aim of asset management is to be proactive and take a long-term view to protecting assets.
One of the main threats to the longevity and integrity of water and wastewater assets is corrosion. Therefore, an important part of asset management for these systems is having a risk-based inspection plan for corrosion. Rehabilitation, rather than rebuilding, is better for the asset owner, better for the community, and better for the environment.
If possible, measures to prevent corrosion should be implemented before the affects can be seen as by the time corrosion is visible it is already well advanced and requires attention. If it’s not able to be remedied immediately, corrosion should be noted and appropriate steps taken as soon as possible to prevent it from spreading and further compromising the structure.
There are a variety of materials and technologies available for rehabilitating existing structures, including epoxy liners, calcium aluminate cement (CAC) mortars, and HDPE liners. Epoxy liners, in particular, are well suited for the rehabilitation of these structures as they halt corrosion in its tracks, prevent further deterioration, and are fast-drying.
Some of the key benefits of epoxies include:
♦ Chemical resistance: epoxy liners have superior acid resistance making them ideal for use in wastewater environments where acid attack is a problem
♦ Long-lasting: epoxy liners are durable and long-lasting, and will experience minimal erosion for years and even decades
♦ Low friction: as epoxy liners have a smooth finish any matter moving through the system won’t stick to it, helping to prevent blockages
♦ Reduced thickness: compared to other liners which have a thickness of up to 30mm+, epoxy liners can be applied as thinly as 2-3mm reducing the loss of internal diameter
According to Colin Murphy, product manager for Hychem, utilities and water authorities have begun to notice the benefits of epoxy coatings.
“We have worked with a number of utilities to rehabilitate water and wastewater infrastructure who have been very impressed with the performance of Hychem’s TL5 epoxy coating in their systems over the long-term,” Mr Murphy said.
“TL5 can be applied directly on new and damaged concrete in sewers and other wastewater assets with a coverage in excess of 6mm in one application.
“The product also has an attractive price point, holds up well to the water and sewer environments, and can last the distance. We have clients who have reported minimal change to the TL5 lining they had installed 15 to 20 years ago.”
ASSET MANAGEMENT: A CONSIDERATION FOR ALL INFRASTRUCTURE
Construction resins also play a role in asset management plans for other concrete infrastructure that is at risk of corroding and deteriorating from the conditions that it is exposed to such as heavy traffic, harsh chemicals and weather conditions.
Hychem technical consultant Chris Bauer said there are a number of options available to rehabilitate and protect concrete infrastructure depending on the specific needs of the client.
“Hychem offers a range of resins for a variety of infrastructure applications such as airport hangars, bridges, roads and car parks, as well as flooring application like commercial kitchens,” Mr Bauer said.
“For example, Hychem’s Polyac BDM – PMMA trafficable membrane system is ideal for protecting and rehabilitating roads and bridges. For car parks Hychem 100W can be used as it is extremely hard-wearing against heavy traffic.”
Over the past year, the organisation I lead, Infrastructure Partnerships Australia, has been focused on making our information and data publicly accessible – seeking to better inform the national infrastructure debate; thereby allowing the business sector and wider community to discern infrastructure fact from fiction.
With infrastructure increasingly politicised, we are providing reliable data and measurement to close the gap between political narrative on the one hand, and cold hard reality on the other.
For example, we now measure and publish government infrastructure funding levels – in nominal terms to show the dollars – and as a proportion of overall expenditure - showing relative funding ‘effort’ by each jurisdiction.
This is useful in an environment where cuts to infrastructure risk being masked by vague references to the (ever-elusive) ‘innovative’ finance.
A solid example is the Federal Government’s ‘infrastructure budget’ which on closer examination served to substantially reduce federal funding levels, as shown in Figure 1.
Source: IPA analysis, available at infrastructure.org.au
Measuring and publishing the actual dollars available in government sector budgets is increasingly important, as infrastructure funding and finance become increasingly conflated in the political debate.
While nominal measures are important, we also analyse each jurisdiction’s funding levels as a proportion of total expenditure. This allows for a fair comparison of the relative ‘effort’ that each jurisdiction is applying to infrastructure – showing if capital expenditure has grown or shrunk, as a proportion of total budget expenditure.
Source: infrastructure.org.au, accessed 27 September 2017
This also allows us to rank the states on infrastructure –which we did for the first time this year.
Our new Australian Infrastructure Budget Monitor ranks jurisdictions, based on actual funding levels as a proportion of their total budget spend, with the results shown in Figure 3.
Source: Australian Infrastructure Budget Monitor, August 2017
Since 2010, IPA and BIS Oxford Economics have published a quarterly leading indicator of civil construction activity based on data surveys of circa 50 per cent of the civil construction sector.
This information too is now available in dynamic graph form on infrastructure.org.au showing both our index of contract awards and the relationship between ‘work won’ and ‘work done’.
In this way, our Australian Infrastructure Metric is now a live resource which provides detailed and current information about actual construction activity in Australia.
Figure 4 shows actual engineering construction ‘work done’ – including our forecasts to 2020 – done in partnership with BIS Oxford Economics.
It shows that behind the heightened infrastructure rhetoric, total engineering construction has been reducing by about $14 billion each year – led by the collapse in mining capex (yellow) – but with only a modest rally in economic infrastructure (light blue).
Figure 4: Measuring actual dollars hitting real projects shows that Australia has only just bottomed out on engineering construction – with our forecast showing a modest ‘transport-led’ recovery in volumes in FY2017/18
Source: infrastructure.org.au, accessed 27 September 2017
In addition to detailed information about infrastructure funding levels and construction activity, infrastructure.org.au also publishes our historic data sets showing PPPs since the year 2000; and privatisations (since 1987) – including volume, value and asset types – as well as by jurisdiction. These are shown in Figures 5 and 6, by year and by jurisdiction.
5: Public Private Partnerships by year 2000/01 – 2017/18
Source: infrastructure.org.au, accessed 27 September 2017
5: Public Private Partnerships by jurisdiction 2000/01 – 2017/18
Source: infrastructure.org.au, accessed 27 September 2017
by year 1987/88 – 2017/18
Source: infrastructure.org.au, accessed 27 September 2017
2017/18
In the coming period we will also publish the construction profile of major projects across the Australian market.
And for the first time we will shortly release a live annual measure of road system performance, showing travel time decay as an index across the four major capitals and in minutes lost on key corridors, within each city.
Launched by New Zealand Prime Minister Bill English, and Australian Treasurer Scott Morrison, IPA’s infrastructurepipeline.org is endorsed by the Australian and New Zealand governments and is a solid example of our focus on making infrastructure realities explicit.
Figure 7 below shows our current analysis of the greenfield project pipeline, by status while Figure 8 shows these projects by jurisdiction.
infrastructurepipeline.org does a very different job to the pipelines produced by Infrastructure Australia and its state counterparts.
Ours provides an analysis of the major projects and privatisations across the two countries, and segments the pipeline across six stages from the earliest ‘prospective pipeline’ through to financial close.
In this way, it is an analysis of what is happening – not what should happen.
Each project or privatisation is narrated, providing context and information, and links through to relevant resources and agencies. This is updated daily, with the monthly Pipeline Report providing analysis of key project additions, status changes or new details distributed to thousands of subscribers in both domestic and overseas markets.
infrastructurepipeline.org also provides sophisticated graphing tools, which can be filtered to particular sectors, jurisdictions, procurement types and by status.
Source: infrastructurepipeline.org/projects-jurisdiction-chart, accessed 25 September 2017
Our focus on making the data we collect explicit and publicly available reflects IPA’s commitment to measuring infrastructure in a meaningful and insightful way.
It reflects our desire to use good information and robust data to ground the political debate and help the community to better separate infrastructure fact from fiction. And to keep political narrative and reality better connected.
We have done this because infrastructure can only get better if we are honest about what is going well – and particularly, what is not.
Source: infrastructurepipeline.org/projects-status-chart, access date: 25 September 2017
In 2016, Sydney Airport served a total of 41.9 million passengers. With so many people relying on an organisation, there is a lot of pressure for everything to run smoothly and efficiently, as even a small hiccup can have consequences for someone’s travel journey. Here, Stuart Rattray, General Manager Technology at Sydney Airport talks about how technology is being integrated into the airport's operations to improve customer experience and streamline processes.
Improvements in technology and a desire to innovate has seen Australian airports at the forefront of some exciting changes in travel. Some of the advances in technology at Sydney Airport are allowing passengers to access relevant queue times for security processing and view their travel information in familiar apps. Technology is also helping the airport predictively manage assets to reduce disruptions. Mr Rattray said technology touches every part of Sydney Airport’s operations.
“It’s central to how we drive efficiency, offer a seamless customer experience and partner with airline customers to achieve On Time Performance.
“I’m responsible for our technology focus, including our digital strategy where we’re focused on a seamless customer journey, as well as our open data strategy, where we collaborate with our partners to deliver a great airport experience for our customers,” Mr Rattray said.
While mobile apps may be the innovations that airline passengers actually see, technology is having a huge impact behind the scenes at the airport. With over 800 businesses operating at Sydney Airport, Mr Rattray said it is vital that technology allows them to work together to deliver a consistent experience throughout the airport process.
Mr Rattray said Sydney Airport is
constantly investing in technology to ensure systems are resilient and able to adapt to demand. The Internet of Things (IoT) and cloud communication offer very exciting opportunities for airports in terms of monitoring assets.
“Harnessing the data that can be created by connected devices and IoT delivers new ways to monitor performance of critical assets, whether industrial technology, digital sensors or processing technologies.
“This information flow becomes predictive and through big data analytics we become more able to intercept and avoid interruptions before they occur,” Mr Rattray said.
Mr Rattray said it’s essential to have resilient technology underlying the operations of the airport, and Sydney Airport has built in layers of redundancy across all critical aspects of its technology network.
“For example, our Integrated Operations Centre has additional, independent power and connectivity to ensure we can keep it operational in the event of a power outage or network issue. This is a critical part of our technology strategy and we are investing to ensure we have appropriate redundancy in place across our operations,” Mr Rattray said.
Information and technology are now vital parts of an airline customer journey. Mr Rattray said the increased use of mobile technology has resulted in
customers expecting this technology to integrate with their airport experience. Sydney Airport has taken advantage of new technology by creating an open data strategy with key partners, which helps to ensure a seamless journey for travellers.
Mr Rattray said that although they were comfortable with using mobile phones, passengers were reluctant to download a multitude of apps to access airport information. As a result, Sydney Airport has found a way to integrate airport, flight and travel data with channels that are already familiar to customers.
“They can access flight information from our own website and our Flight Information Display Screens in the terminals, but they can also use Twitter, getting real-time updates through the BizTweet platform, or through their airline app,” Mr Rattray said.
Accessing flight information through Twitter is convenient for many customers, Mr Rattray said, but the open data strategy also proves vital for the airport by fostering information sharing in real time with key agencies such as the Traffic Management Centre.
“This means we can see the potential impact of a car accident on the Sydney Harbour Bridge straight away, and make faster, better decisions to manage that and minimise the impact on our customers accessing the airport,” said Mr Rattray.
Once at the airport, customers are able to use their smartphones and familiar apps such as Google and Baidu
Maps to navigate the terminal. With China being Sydney Airport’s largest source of foreign inbound passengers, it makes sense to offer an integrated app like Baidu Maps, which is China’s equivalent of Google Maps. Mr Rattray said this provides a familiar piece of home for Chinese passengers, and makes it easier for them to find their way through the airport.
Another exciting innovation at Sydney Airport is real-time queue wait times, where customers can see how long it will take them to move through security screening and passport control, removing a large part of the stress for frequent and infrequent travellers alike.
Mr Rattray believes airports are at the forefront of exciting innovations and in many respects lead the way in technology development.
“Sydney Airport’s about to begin the first phase of our biometrics roll out which will ultimately allow passengers to navigate through airport processes using facial recognition, without the need to present their passport at each processing point,” Mr Rattray said.
“That has the potential to change the way we travel - and deliver improved customer and security outcomes at the same time.
tool for laser scanning extensive, complex environments.
“We’re seeing innovation like this across the aviation industry, and it’s very exciting to be part of it. Most importantly, our focus on technology is not only delivering some fantastic efficiency gains, but it’s also making a real difference to the customer experience, from reducing queuing to delivering tailored information.”
Mr Rattray believes the airport of the future will be incredibly connected and seamless, where customers can better plan their airport time from home. He envisions customers using mobile technology to do everything from booking parking, finding their check-in counter and accessing duty free shopping.
Technology is set to make the airport of the future a less stressful and more efficient place. This will be achieved through preventing service interruptions before they occur, reducing passenger queue times and delivering tailored information to customers in real time.
“As technology and data make all those airport processes faster, less noticeable and far more seamless, your time at the airport will be more focused on having a great experience - so you can expect to start your holiday even earlier,” said Mr Rattray.
With TIMMS*, indoor maps and models covering thousands of square metres of space can be mapped in minutes and entire buildings mapped in a day.
The TIMMS provides both LiDAR and spherical video of a facility and produces fast and accurate geo-located maps, enabling Taylors to translate environments into visual 2D & 3D layouts.
Our experience in scanning at Tullamarine Airport using TIMMS includes
• Water Main Upgrade Feature and Level Survey
• Mace Way As-Built Survey
• Melrose Drive Bus Shelter As-Built Survey
We can create 3D reality models in a variety of formats to provide a solution to suit the end user’s requirements.
Mapped data is revolutionising the way we understand, operate and improve our built environments and has proven successful in situational awareness of airports and other multifaceted sites including: hospitals, sporting complexes, rail infrastructure, factories and plant.
* TIMMS: Trimble Indoor Mobile Mapping System
Contact us today:
www.taylorsds.com.au
FUTURE PASSENGER GROWTH IS NOT POSSIBLE WITHOUT AIRPORT PAVEMENT INVESTMENT
As the national industry voice for airports in Australia, the Australian Airports Association (AAA) represents the interests of more than 260 airports and aerodromes Australia wide – from local country community landing strips to major international gateway airports.
Asignificant investment for all airports regardless of size is the airfield pavement. Airfield pavements are a vital piece of airport infrastructure and include runways, taxiways, aprons and parking areas, which require a high level of maintenance and come at a significant cost.
Caroline Wilkie, Chief Executive Officer at the AAA, explained to delegates at the 17th AAPA International Flexible Pavements Conference, the major risks of under investment in airside pavements and the future challenges Australian airports are facing. A research program dedicated to advancing local airport paving technology and practices and led by Dr Greg White, is to be established as a collaboration between the AAA and the University of the Sunshine Coast. The research program will focus on the particular challenges facing Australian airports and pavement engineers of bitumen and asphalt in a country where heat and the tyranny of distance add to a range of other difficulties in pavement engineering.
In recent decades, growth in Australian aviation has been dramatic and the number of passengers moving through Australia’s airports has grown from 33 million in 1985 to over 154 million in 2016.
The 2016 report Trends – Transport and Australia’s Development to 2040 and Beyond, published by the Department of Infrastructure and Regional Development, predicts passenger growth in the medium term to rise. Forecasts indicate average annual growth rate for international passengers at 4.9 per cent between 2015 and 2034.
The current high levels of domestic and international passenger growth at Australia’s major airports are already testing the capacity of airport infrastructure during peak periods.
International air travel is expected to grow strongly between now and 2030, with both domestic and international passenger movements through capital cities almost doubling.
The passenger growth has not necessarily increased the number of aircraft but resulted in a shift to larger aircraft types. Larger aircraft create challenges for airport pavements, including reduced runway lifespans because new heavier aircraft with higher tyre pressures are stretching the performance capability of existing pavement designs.
These challenges highlight the importance of advancing pavement technology and practice to ensure future growth in passenger movements can be catered for.
Over the last decade, Australian airports have invested millions of dollars in major projects to expand and upgrade airside facilities to accommodate the increase in passenger movements and larger aircraft types. The next decade and beyond will see even more investment in aviation infrastructure.
A major project under construction at Brisbane Airport is the New Parallel Runway (NPR), which will provide regional economic benefit of around $5 billion by 2035 along with an increase of 7,800 jobs.
The Sunshine Coast Airport expansion project will include a main runway, taxiway loops and new air traffic control tower access roads and utilities. These upgrades will not only contribute more to the economy and create more local jobs but will also help reduce the number of homes impacted by aircraft noise while catering for larger aircraft, opening up new destinations and tourism opportunities.
This significant amount of activity also provides opportunities for further developing the industry’s knowledge and understanding of airfield pavements.
While the major airports are expanding, regional airports are struggling to invest in major infrastructure as they rely on government funding in order to upgrade and maintain their pavements. Without this funding pavements cannot be maintained, leading to difficulties for local communities to access essential services such as medical treatment as well as compromising tourism opportunities.
Most regional airports run at a loss of up to 60 per cent and struggle to keep up with the maintenance cycle of the airside pavements.
An important fact to consider with airport pavements is that they are not the same as roads because they play host to heavier transportation with higher tyre pressures and have more stringent requirements around design and construction.
The collaborative research project undertaken by the AAA and the University of Sunshine Coast is a step forward for the aviation industry and will plug a significant gap in industry knowledge following the demise of the Federal Airports Corporation as a result of airport privatisation.
To ensure the aviation industry is educated and kept up to date with pavement research, technology and techniques, the AAA has dedicated a half day program at the upcoming AAA National Conference in mid-November to pavements.
Experts from Fulton Hogan, the University of Sunshine Coast, Aurecon and regional airports will be presenting on maximising pavement lifespan, maintenance techniques, performance, future technology and lessons learnt from past experiences.
One of the sessions will discuss the preventative maintenance program Burnie Airport has adopted, which provides significant cost benefits
compared with the traditional reactive approach. The runway asphalt pavement was constructed in 1987 and has been in service for 30 years.
In 2018, the AAA will continue bringing the aviation industry together with a dedicated pavements and lighting forum. This bi-annual event brings experts together to share ideas, update their knowledge and skills, and educate the next generation of pavement professionals.
The AAA has also produced a publication in the form of an Airport Practice Note (APN) titled Airfield Pavement Essentials. This document provides general guidance and information to airport managers and operators regarding airport pavement design, materials, construction, maintenance and rehabilitation.
Airfield Pavement Essentials was developed in recognition of the fact that many regional airports do not have specialist engineering expertise to draw on for important information about the critical airfield pavement infrastructure that makes up our runways, taxiways and aprons. The APN provides regional airports, or those new to the industry, with the essential information needed to develop a greater understanding of airport pavement design, materials, construction, maintenance and rehabilitation.
The AAA is dedicated to ensuring that airport investment in pavements is continued into the future as it is key to ongoing growth in the aviation sector especially through government funding for regional airports.
Volvo’s EC480E h R Demolition Excavator features an innovative hydraulic modular joint & lock mechanism, allowing you to release your digging equipment and change to the high reach demolition boom in a simple and swift operation. Instead of taking a full day to fit a digging boom in place of a high reach boom, operators can now make the switch in under an hour.
Cut demolition challenges down to size with Volvo’s EC480EHR Demolition Excavator.
Complete with support cradles for easy storage of the booms, a tool pin height of 28.1 metres, sturdy demolition guarding, high-visibility tilting cab & smooth hydraulics - you can tackle the most challenging jobs.
The hydraulic counterweight option enables easy installation & detachment, while the hydraulic undercarriage can be retracted for transport or extended for stability. Four nozzles on the arm provide a fine mist to clear dust & keep the machine clean while Volvo’s legendary safety features give you total piece of mind - including a frame-mounted falling object guard & double-thickness side doors.
It’s a rare sight in the middle of Australia’s biggest city; an excavator hanging 30m above Castlereagh Street in the Sydney CBD, being carefully craned to a nearby rooftop. This middleof-the-night precision operation signalled the start of major construction activity on Sydney Metro – Australia’s biggest public transport project.
Before tunnelling can begin on this city-shaping project, 17 city buildings are being demolished to make way for the new metro stations at Martin Place and Pitt Street.
They’re just two of 31 metro stations and 66km of new metro rail that will be fully operational by 2024 in this $20 billion-plus infrastructure investment – the biggest urban rail project ever built in Australia.
The first 13 Sydney Metro stations open in the first half of 2019 when the $8.3 billion Sydney Metro Northwest project comes online in the booming Hills region in the city’s North West.
It’ll be the region’s first reliable mass transit system in an area which has the highest private car ownership rate in the country and which, in coming decades, will be twice the size of Canberra.
From the North West, Sydney Metro is being extended under Sydney Harbour, through new CBD stations and beyond to Bankstown in this world-class once-in-a-century city-shaping program of works.
Almost 100 years ago, engineer Dr JJC Bradfield had to effectively do open heart surgery on the Sydney CBD to build the new city railway line, digging up streets and entire areas around Wynyard and Hyde Park.
Sydney Metro Program Director Rodd Staples said they now have a keyhole surgery-type approach now, which allows them to be more targeted.
“For a station at, say, Martin Place, we’ve acquired buildings at either end and we’ll be digging down … a basement excavation … and we then essentially mine to the halfway mark from each direction, to minimise the amount of construction activity that happens on the surface.
“The stations are almost two football fields long in length, so they’re quite large underneath the ground. You won’t see much of that construction going on, essentially because we’ve come in from the goalposts at each end.”
The demolition of the city buildings is being done from the top down with excavators craned to the rooftops bringing buildings down floor-by-floor.
Sydney Metro is using the best technology available to reduce construction impacts so people can go about their daily lives. This includes state-of-the-art pulverisers and shears – jaw-like devices attached to excavators that can smash, cut and grind away material into small pieces.
Once the sites are ready, it’ll be time for the mega tunnel boring machines (TBMs) to come through as they deliver 15.5km twin railway tunnels Chatswood and Sydenham.
Five TBMs are being used – the most ever used at once on an Australian transport infrastructure project – with the first to be in the ground by the end of next year.
Two TBMs will tunnel for about 6km from Chatswood to the edge of Sydney Harbour. Another two TBMs will tunnel for about 8km from Marrickville to the new Barangaroo Station site. And a specialised TBM, designed specifically to tunnel
under Sydney Harbour, will tunnel up to 42m below the harbour surface from Barangaroo for about 1km to Blues Point. There, the TBM will be retrieved and taken back to Barangaroo before being relaunched to build the twin tunnel.
Tunnelling under Sydney Harbour has been years in the making. Back in 2015, 53 marine exploratory holes were dug so experts could assess all the information about the geological conditions.
The boreholes revealed charcoal and remnant timber, between 22 and 56m below sea level – the product of bushfires more than 63,000 years ago. Many shells were also found such as oysters, mussels, gastropods and crab claws – all lay undisturbed 38m below sea level for more than 20,000 years.
The work also resulted in a new three dimensional map of the bottom of Sydney Harbour – revealing the rock level at the bottom of this section of the harbour, west of the Sydney Harbour Bridge, is about 16m lower than previously investigated.
All this information has helped in the massive task that lies ahead as twin new metro tunnels are threaded underneath Sydney Harbour and the heart of the CBD.
“Sydney Metro will revolutionise the way Australia’s biggest city travels, shaping its future growth,” NSW Transport and Infrastructure Minister Andrew Constance said.
“Metro means a new generation of world-class fast, safe and reliable trains easily connecting customers to where they want to go.”
When services start in 2019, customers won’t need timetables – they’ll just turn up and go with a train every four minutes in the peak.
Designed to grow with the city, it will serve for generations to come, Sydney Metro will have an ultimate future capacity of a train every two minutes in each direction under the CBD and the ability to move more than 40,000 people an hour each way; significantly more than the 23,000 reliable capacity of each existing Sydney train line.
Sydney Metro will work together with the existing Sydney rail network to boost the number of trains entering the Sydney CBD in the morning peak hour by 60 per cent, to 200 trains an hour, creating capacity for an extra 100,000 people an hour.
So far, more than 32km of new metro railway tracks have been laid on the Sydney Metro Northwest project as major construction continues on 17 sites across the North West alone. The first of Sydney’s new metro trains has been delivered to Sydney Metro HQ at Rouse Hill, where it will undergo commissioning and testing over coming months.
The fully-automated trains are another Australian first, bringing highly-reliable technology used around the world for decades here for the first time; platform screen doors, which keep people and objects away from the tracks, will also be used for the first time in Australia.
It’s full steam ahead on Sydney Metro as customers get ready to welcome a level of rail service never before seen in Australia.
A vacuum excavator can be one of the most versatile pieces of equipment on a worksite. Its uses go far beyond the typical potholing or utility location tasks that may initially come to mind. When used to its full potential, less equipment is needed on site, labour costs are reduced, safety is improved and project times can be shortened. There are many possible uses for vacuum excavators including dewatering, pit cleanout, unblocking pipes and spill response.
Horizontal Directional Drilling (HDD) contractors regularly use vacuum excavators to reveal utility assets prior to drilling and reduce the chance of impacting existing infrastructure. This is particularly useful around sensitive infrastructure that would be damaged with more traditional methods.
The soil displacement technology, which uses air or water pressure, finds even more uses when various attachments are added. Other uses for vacuum excavators can include tree planting, selective root pruning, debris and liquid waste cleanup, high pressure cleaning, the installation of irrigation systems, landscape lighting and retainer walls, as well as a range of other tasks.
Jeff Lawson, National Construction Equipment Sales Manager at Vermeer, said a vacuum excavator has many more uses than most people initially consider.
“Often, once a contractor or municipality buys their first vacuum excavator, its use expands to
applications beyond the original intended use, opening up a range of new revenue streams for the organisation,” said Mr Lawson.
Dewatering can be a costly exercise for construction companies. Not only does it halt planned work and throw schedules into chaos, a premium cost is often incurred for the labour used to complete these activities. Mr Lawson said having vacuum excavators on a worksite can save time when dewatering is needed.
“Compared to traditional dewatering methods that involve using an excavator or even a shovel, vacuum excavators allow operators to quickly and safely regain entry into pits that have become filled with mud, water or debris due to rainfall or flooding,” Mr Lawson said.
In the case of a spill, often immediate containment and cleanup is needed to ensure safety and legislative compliance.
“In a cleanup situation, companies are exposed to risks beyond the initial spill, including chemical exposure and manual handling concerns. Not only does a vacuum excavator efficiently remove the hazard and return the site to a safe state, any contaminates are quickly sealed inside the tank for appropriate disposal.
“The Vermeer VX200 has an added level of protection featuring the patented McLaughlin cam-over-hydraulic rear door that is designed to provide a positive 360-degree seal without additional clamping requirements, keeping fluids securely in the debris tank,” Mr Lawson said.
Vacuum excavators come in a range of sizes and variations suitable for different tasks. The mechanics of a vacuum excavator can easily be re-purposed for other manual tasks that benefit from the technology.
Mr Lawson said an increasingly common use for vacuum excavators is in the areas of post hole digging and tree planting. The ability to use air to displace the soil gives the option of replacing the materials at the site immediately, resulting in a cleaner and more efficient job.
“Vermeer trailer-mounted vacuum excavators, such as the VSK25-100G, are well-suited to excavating post holes and are popular because they only require one person to operate them. The vacuum helps eliminate the chance of damaging an existing underground line and requires less labour and time than other methods,” Mr Lawson said.
The precision provided with vacuum excavation has also proven useful in tree remediation. The vacuum excavator can remove contaminated or growthhindering soil from around tree roots, and allow for replacement of more nutrient-rich soil or fertilizers.
Compared to traditional dewatering methods that involve using an excavator or even a shovel, vacuum excavators allow operators to quickly and safely regain entry into pits that have become filled with mud, water or debris due to rainfall or flooding
This technology can also straighten power poles or other posts with surgeon-like precision, displacing only the necessary soil in order to reposition the post, as well as soil extraction needed for testing, which can be completed without additional equipment.
Not all projects have space for a large vacuum excavator which is why Vermeer has a range of different equipment to accommodate different site requirements.
The VX200 can be mounted on either a new or re-purposed truck chassis and
has a spoil tank capacity ranging from 4000L to 11,000L. Their smallest vacuum excavator, the VSK100, fits into the bed of a full sized half-ton truck. With uses far beyond mere excavation, Mr Lawson said a vacuum excavator is a useful addition for a range of applications.
“The versatility of vacuum excavators means that owners are finding uses beyond what they first expected. Along with safely exposing utility infrastructure, different attachments allow the technology to dig post holes, remove contaminates, dewater worksites and unblock sewers or pipes. This multitasking ability results in both cost and time savings for contractors,” Mr Lawson said.
Incorrectly loaded or overloaded road trucks carry significant risk for your business and strict road weight laws that help to keep everyone on the road safe could come crashing down on you if your trucks are not legal.
In Australia and New Zealand, chain of responsibility law holds that all parties involved in the transport of goods on our roads are accountable, including drivers, machine operators, weighbridge managers, quarry managers and everyone up the chain right up to company directors.
If an offence is committed by your employee, agent or contractor, it could be treated as having been committed by you both, even if you didn’t know about it, let alone approve it.
In addition to ensuring drivers and operators do not exceed permitted work/rest hours; do not operate machinery while fatigued; that goods are secured appropriately; and that drivers keep within speed limits; managers, operators, schedulers, cosigners and receivers are responsible for making sure vehicles do not exceed mass or dimension limits.
Those involved with loading road trucks have additional responsibility to document that load does not exceed vehicle mass limits and that load is distributed in the truck to make sure it doesn’t become unsafe or unstable during transport.
By fitting scales to loading machinery including loaders and excavators, operators and managers are able to keep a running total of the weight of the load for each trip as evidence that correct loading procedures have been followed and that the truck is loaded consistently across all axles.
With accurate record keeping, traceability and stock management, excavator scales are a simple and highly effective way to minimise risk to your business and keep track of material movement. By eliminating paper-based records, a system such as the Loadex 100 by RDS Technology ensures your data is reliably stored and easy to access at any time.
An optional printer can be installed within the machine to give clients a hard copy of load summaries and totals, and to keep an accurate paper record if required.
Do you ever use an excavator to load a road truck? If so and you don’t weigh the load, now’s the time to consider adding machine scales to your excavator. Not only will it minimise the risk if something goes wrong, it will also help to reduce machine wear, save time and reduce wasted material.
Operators will benefit from knowing accurate weight information and with the ability to input a target load, ensure the correct loading of road trucks with minimal risk of human error. If loaded past the threshold, an audible alarm will sound to alert the operator. Plus, an optional reversing camera can be fitted to help increase safety on site – it uses the same display in the cab so there’s no extra components to fit into what’s already a crowded space.
As the most flexible and adaptable system available on the market today, the Loadex 100 has the option of static or dynamic weighing positions to suit all applications. Unlike other solutions, it also uses inclinometers and a mechanical sensor to provide dynamic weighing capabilities in even the most challenging conditions and terrains to ensure it keeps up with the machine and the job.
With SQL database functionality, data can be exported via serial, Ethernet, USB memory stick or our Tokara 4G and WiFi modem to easily import into other software platforms and suit your existing workflow. You also have the option of one or two way communication between machines and the office to save time and keep track of your project with iSOSYNC software.
Unique to the customers in Australia and New Zealand is the option to receive remote service and support through Tokara Link, a telematics platform developed by RDS distributor for the region, Position Partners. Tokara enables support technicians to remotely login to your system to diagnose technical problems, update software or train the operator, without the need to visit the machine in person.
Knowing what your excavators and loaders are picking up and loading to road trucks is vital in today’s construction industry, both to meet your legal requirements and for on-site safety, insurance and the warranty on your machines. With the added perks of increased efficiency, reduced fuel use and machine wear and a safer, more productive team, there is a lot of upside to embracing this simple and effective technology.
Growing infrastructure demands around the world are creating tremendous challenges and opportunities.
Topcon works to stay a step ahead, by creating solutions that incorporate technology advancements into the way you work today and tomorrow, transforming the way infrastructure is built.
Our integration of high-accuracy positioning, high-speed imaging, cloud-based information management and down-to-earth simplicity creates higher productivity, enhanced quality and improved sustainability. With Topcon, you can stay ahead of your competition and meet the challenges of Infrastructure growth.
Watch Topcon Positoning Systems President and CEO Ray O’Connor’s Bloomberg “NEXT INFRASTRUCTURE” interview: www.topconpositioning.com/Infrastructure.
Let’s discuss your next project: 1300 867 266 | www.positionpartners.com.au
The Northern Territory Government wants Barneson Boulevard to be one of the greenest infrastructure projects undertaken in Darwin and has called on the local community to share their landscaping ideas.
Over 160 Territorians offered submissions to the Northern Territory Government in response to its public consultation on landscaping the Barneson Boulevard project. Feedback on landscaping concepts, tree species and public art possibilities was also acquired through one-on-one meetings, pop up information booths and workshops.
The Barneson Boulevard and Tiger Brennan Drive Stage 3 Project will provide a third entry point to Darwin’s CBD, with the aim of dispersing traffic more equally throughout the city and reducing congestion on roads that are almost at capacity.
Federal Minister for Infrastructure and Transport Darren Chester said the new entrance had been in the works for years.
“Along with the completion of Tiger Brennan Drive, this project will improve traffic flow into the CBD and provide a landmark entry in the capital of the North,” Mr Chester said.
The $39.5 million project is being delivered in partnership with the Australian Government, who are providing $29.5 million, and the Northern Territory Government and the City of Darwin Council who are each providing $5 million.
Funding from the Australian Government also includes the completion of the duplication of Tiger Brennan Drive from Dinah Beach Road to McMinn Street.
Greening is one of the key aspects of the project, with approximately 200 shade trees due to be planted along the new Barneson Boulevard. Trees will be in keeping with the flora of the surrounding area and will likely include natives designed to thrive in the particular environment of the Northern Territory such as Milkwood, Yellow Flame Tree, White Bush Apple, Mataranka Palms, Beach Hibiscus, Paperbark, Pongamia and Pandanus.
$7 million has been set aside in the project for landscaping, which includes a portion of funds for public art.
For the first time, cyclists will have their own lane separate from both vehicles and pedestrians, providing a direct link to the centre of the CBD and connecting to an extensive off road network. Along with the ACT, more people cycle in the NT in any given week (per capita) than any other jurisdiction and the new cycle path is expected to increase the number of people cycling to and from the Darwin CBD.
The shaded tropical boulevard is also consistent with plans to revitalise Darwin CBD into a cooler, more pedestrian-friendly city centre.
Concerns have been raised about the impact of construction on the heritage listed Frog Hollow Park, with Darwin Council Alderman Simon Niblock requesting that the Northern Territory Government prepare a report outlining alternative options for the road, which avoid dissecting Frog Hollow Park and Frog Hollow Centre for the Arts.
Information released by the Government states that the heritage listed park will remain approximately 1.13 hectares in size and will be preserved as a public space for the benefit of the community. Dedicated pedestrian and cyclist paths will be put in place to improve access to Frog Hollow and concept public space plans have allowed for an amphitheatre to be built into the road verge alongside Frog Hollow for public performances.
Northern Territory Minister for Infrastructure, Planning and Logistics
Nicole Manison said the project would create jobs in the short term, and opportunity in the long term by opening up access to unused land for commercial and community development.
“This is a job-creating infrastructure project that will give a boost to the Top End construction industry. And in the longer term, the opportunity for economic development and the
opening up of this part of the city will have a positive impact on the CBD,” Ms Manison said.
With the Northern Territory Department of Treasury and Finance predictions on population increases from 231,292 in 2011 to 319,533 by 2031, and 364,207 by 2041, Government officials see the Barneson Boulevard project as a necessary step in ensuring the long-term prosperity of Darwin’s CBD.
Construction of Barneson Boulevard is expected to commence in November 2017, with construction complete by December 2018. The third and final stage of Tiger Brennan Drive duplication is expected to commence March 2019 with completion due in December 2019.
The public consultation has concluded and submissions are now being considered.
Unlike general landscape maintenance, the works required for infrastructure assets often present a number of challenges including limited times work can be carried out, external events, and safety precautions required for staff and the public. However, the key to overcoming these challenges is experience.
Gavin Meharg, Contracts Manager Infrastructure at Marsupial Landscape Management, said one of the biggest differences between infrastructure maintenance and general landscape maintenance is dealing with traffic.
“It’s probably the biggest influence in what we can and can’t do. Our work needs to be programmed and scheduled based on road closures and specific traffic events or schedules,” Mr Meharg said.
When working on infrastructure assets such as roads, rail, ports, airports and utilities, it is important to be able to anticipate external events and understand the unique risks of each asset.
“That’s something that can only be dealt with [using] firsthand experience and best practice, making sure we identify all potential risks and hazards.
Actually identifying those incidents happening on site before they occur –that’s something that really needs some inside knowledge and experience,” Mr Meharg said.
Marsupial has been in operation since 1989 and its ability to manage and plan for external events, and manage risks are some of the reasons it has been chosen to maintain major infrastructure projects, including 700 utility sites in Queensland, and John Holland’s Country Rail Network in regional New South Wales.
In early 2017, after working on the M5 Motorway in NSW for 10 years, Marsupial renewed its landscape maintenance contract for a further five years.
“One of the reasons we've worked on the M5 for so long is that we go above and beyond the contractual works, we know the site so well and can inform the client of things beyond our scope that
need to be addressed. We're another set of eyes on site and the client trusts us,” Mr Meharg said.
Marsupial has also developed the innovative Mtrack system, a solution that converts paperwork into app technology, improving reporting efficiency and providing customers with real-time visibility of the work being carried out.
This system is tailored for each customer and data is formatted to meet their specific needs, enabling effective response to their unique landscape management requirements. This is extremely beneficial for customers who manage multiples sites or a portfolio across various territories.
16 - 17 November 2017 Adelaide, South Australia
Join us in showcasing global advances in autonomous vehicle technology.
Come and view demonstrations and visit our exhibitors.
Go to idvs2017.com.au for further details. Platinum Sponsor and Exhibitor Gold Sponsor
The 18th Century is often called the Age of Enlightenment as there were significant leaps forward in our understanding of the sciences, art and astronomy. Over the last few years we have seen significant shifts in social media and how we communicate with one another via the likes of Facebook, Twitter, etc. In the future, will humanity look back on the early 21st Century as the Age of Connectivity?
So what is the concept known as the Internet of Things?
A simple explanation of the Internet of Things (IoT) is that it is a collection of sensors armed with the capability to automatically send data to a collection system, hosted on the internet, which then has a level of intelligence to proactively inform decision making in real time.
The application field is nascent and the hardware is developing faster than the applications are taking advantage of. The hardware manufacturers are operating akin to the style synonymous with the now famous movie A Field of Dreams where Kevin Costner says “Build it and they will come”. Is this hype or is there real benefit for the asset management industry?
If we look at different technological elements such as computers, nanotechnology, artificial intelligence and quantum theory, all of these disciplines are now converging, and the rate of change is ever increasing. This rate of change is also forcing the cost of production down.
For instance, an accelerometer which cost seven dollars less than 10 years ago can now be obtained for only 50 cents. This has had the effect of making data acquisition a more cost-effective process.
BENEFITS FOR ASSET MANAGEMENT
Introducing the concept of Cognitive Extension (CogEx) assists us in understanding the benefit in terms of asset management. If an individual thinks of themselves as currently limited in terms of their ability to acquire new insights due to a limitation of their sensory inputs and cognitive reasoning abilities, then an augmentation of these abilities (however unimaginable) will lead to greater awareness and insights into their surroundings.
By virtue of the fact that such an extension is indeed possible in the case of the organisation – be it a plant, a production process or the provision of a service – the potential result is better decisions with respect to assets.
Imagine for a moment that we had additional sensitivity in our awareness of our surroundings; if we had the taste buds of a catfish (humans have 10,000, while catfish have 250,000), or if we could see ultraviolet and polarised light as a mantis shrimp does.
Now imagine a maintenance
inspector in a plant having the ability to “see and hear” the whole radiated electromagnetic spectrum (hearing the ultrasonic partial discharges or seeing the infrared hotspots) that a machine gives off. Imagine the inspector being able to “taste” the lubrication oil and detect particles of metal wear; “smell” the products of arcing in real time and “see” the inclement weather closing in from miles away on their plant!
Adding to these abilities, experience spanning many years of operational experience, gained across these trended values from many different organisations and in various different situations, and being able to make an accurate health indices prediction in an instant, and in real time; our Cognitive Extension is complete.
The sensors available today are low cost and there is now also a plethora of microcontrollers (MCU) from as little as $20 each which can sample up to eight signals and report them in their raw form or do any level of sophisticated processing on them.
This processing may involve: filtering, transformations, sorting, comparisons and storing locally. If this processing occurs at the microprocessor level, this is called “fog computing” or “edge computing”. If the data has a minimum amount of processing applied to it before sending from the microprocessor, then this forms the basis of remote monitoring and “cloud computing”.
The main objective is to get the data streams to a point in the IoT architecture where it can connect directly to a high-bandwidth ADSL/NBN or 3G/4G/5G connection, and where all of the data is aggregated so that only one subscription for the connection is being paid for, instead of paying a subscription for each and every data signal.
This has created the opportunity to create low-cost communication networks, all of which utilise the unlicensed band (ISM). Most people are familiar with the ubiquitous “WiFi” band, and some know that it makes use of a standard interoperable protocol called the IEEE 802.11 protocol. This is now being added to by SIGFOX, LoRa, Zigbee, WiMAX, Ingenu and Taggle.
Most of these devices are developed with a focus to operate within the ISM band or other unlicensed spectrums in
other countries. What is also occurring is a focus on reducing power consumption so that these devices may be powered by batteries for years before requiring battery replacements.
There are gateways available on the market, called Systems on a Chip (SoC), which can connect to a 100BASE-TX network, whilst simultaneously receiving data from 256 I2C protocol sensorgateways, a WiFi Network (receiving streams of existing process parameters via an on-board open-source OPC UA server), a 64 sensor network of LoRaWAN™ RF-Mesh sensors, four SPI high-speed connections and last but not least, feature rich user interfaces (UX) for less than a couple of hundred dollars each. What becomes clear here is that there are more technologies (sensors, SoCs, wireless protocols and legacy systems) to grasp and design architecture for.
Companies which entertain using the IoT for asset management can start by first thinking of extending the cognitive abilities about their assets (CogEx). Selecting the signals and then thinking about what these will reveal about the state, condition, level of urgency of attention about those assets, is particularly useful. These could also be used in such applications as:
♦ ‘Tell-tale tabs’ over structural cracks
♦ Biological oxygen demand and dissolved oxygen in water reservoirs (poisoning monitoring)
♦ Rail monitoring on cars
♦ City air pollution
These signals then drive the search for the sensors and the System-on-aChip (SoC) which can speak to these sensors. A shopping list then forms from the sensor list, the SoC and the communication requirements until a gateway and a cloud aggregating service is identified.
This “IoT Supermarket” approach leads to ensuring that all the items are selected. This shopping exercise requires thinking about the coverage, battery power, maximising the capabilities of the SoC and allowing some room for new additions. Drawing up an IoT architecture allows for refinement and revisiting the selections made. The user is only limited by their understanding of the asset which, in some instances, is best taught by observing the signal trends.
A health check on this technology development is for the organisation to consider that just because it can measure something – should it? Many organisations are data rich and information poor. Data is gathered and never used. In many cases, it is not treated as an asset itself.
There is a decision to be made here about the installation of technology that can best be utilised to measure parameters that aren’t immediately useful, but could be used in the future. The reducing marginal cost of sensors may lead to those with additional capability being installed, but not ‘switched on’ until needed.
For an organisation to make the most of these advances in technology, there are two supporting documents that should be developed – an IoT Strategy and an Asset Information Strategy. These will provide the structure and direction for the development of an implementation program, and the use of the subsequent data to achieve the objectives of the organisation.
On a more philosophical note, we are seeing the increasing use of ‘machineto-machine’ communications and the increasing development of artificial intelligence (AI) by learning from experiences and monitoring results, thereby reducing the need for human involvement.
We need to be aware of potential bias in modelling from these situations; the AI will only learn from our approach and can unintentionally include our preconceived biases. As highlighted in the film Terminator 3, are we witnessing the rise of the machines?
Keith Paintin is Principal ConsultantAsset Management at Jacobs with more than 30 years’ experience in asset management. Keith specialises in the development and implementation of asset management systems covering the full asset management lifecycle across UK, Ireland, North Africa, Middle East, Asia and Australia. Ian Boake is Principal Consultant Business Advisory at Jacobs with more than 25 years’ experience in all aspects of electrical assets, machine condition monitoring system development and failure investigations.
Australia’s transport infrastructure is expected to change considerably over the next few years with developments in automation, connectivity and smart motorways. With these advancements happening so rapidly, the need for a nationally consistent, harmonised approach to legislation and regulation, including road rules and vehicle standards, is critical.
Anational standard for road laws will ensure that Australian drivers can travel between states and be confident they are following the same rules and regulations. Drivers also need peace of mind that the available technology their car utilises will continue to operate seamlessly over any border.
Over 400 Australian and international industry leaders attended the Australian Intelligent Transport Systems Summit, Brisbane, hosted by ITS Australia in partnership with the Queensland Department of Transport and Main Roads, in September where attendees could share information on ITS and consider opportunities to make Australia’s transport networks safer, more efficient and sustainable.
The theme of this year’s Summit was ‘Transforming Transport’ and it focused on three key areas:
• Connected and automated vehicles
• Mobility as a service and big data; and
• Transport for smart cities
“We need consistency… so that when we bring cars in that can talk to our traffic lights and our intersections, and cars that can read our signs, we know that our cars and the road infrastructure will interact in a consistent way across Australia."
Over 50 speakers presented at the Summit which was officially opened by the Hon Mark Bailey MP, Minister for Main Roads, Road Safety and Ports. The speakers included Chief Executive and Commissioner of the National Transport Commission (NTC), Paul Retter, who presented on the forefront of automated vehicle regulation in Australia; and Manager Smart Journey Systems at VicRoads, Wayne Harvey, who spoke on VicRoads innovative Smart Journal Trial Program.
Through the Summit, innovators from across Australia were given the opportunity to promote new initiatives and take part in panel discussions regarding the national harmonisation of driving standards.
There are many variables to consider in regards to a nationally consistent approach to road laws. Being unable to fully predict the technologies of the future, means that planning the necessary infrastructure and standards can be a difficult task.
Mr Retter said governments will need to be flexible and in tune with changing technology to help facilitate the transition to a more harmonised approach.
“There are many unknowns in terms of the types of technologies that will ultimately win out, the timing of deployment, take up by consumers, changes in business
models, and fundamentally, changes in consumer behaviour and travel patterns,” Mr Retter said.
If a new national approach doesn’t adequately account for changing technologies it can create adverse effects such as increased congestion and reduced driver safety.
ITS Australia Chief Executive, Susan Harris, said Australia needs consistent technology to ensure our managed motorways, or smart motorways, can more effectively improve throughput.
“Technology is really critical, but that is also what creates the challenges, because technology, particularly when we look at automated vehicles and connected vehicles that communicate with the infrastructure, in that space is constantly evolving,” Ms Harris said.
“It creates the challenge of trying to develop standards that will enable this smooth communication, this new communication pathway, if you like, between vehicles and infrastructure.”
Road infrastructure can consist of stationary signs, speed signs, variable messages and traffic signals. If there are variations in road infrastructure and the laws surrounding road rules across different states, it can impede the development of some road technologies such as automated vehicles.
“Governments will need to be flexible and in tune with changing technology to help facilitate the transition to a more harmonised approach."
Paul Retter,Chief Executive and Commissioner of the National Transport Commission (NTC)
Mr Harvey said road infrastructure needs to be nationally consistent for technology and intelligent transport systems to be able to function appropriately.
“The role for technology and intelligent transport systems needs to be consistent, it needs to be built on the same rules and standards, so that we develop a consistent infrastructure,” Mr Harvey said.
“If we don’t have collaboration then what we’re going to have is a disjointed outcome, and I don’t think that’s what the public is going to be expecting. I think the public expect to be able to drive anywhere in Australia using the same vehicle and following the same rules and regulations.”
Vehicles with automated technology collect data from road infrastructure in order to function properly. Ms Harris said varying infrastructure from state to state can affect automated vehicle efficiency.
“We need consistency… so that when we bring cars in that can talk to our traffic lights and our intersections, and cars that can read our signs, we know that our
cars and the road infrastructure will interact in a consistent way across Australia,” Ms Harris said.
Mr Retter said we are already seeing variability with road signs and this creates issues for camera systems in vehicles.
“Automated vehicles will benefit from greater consistency in standards around signage, line markings and variable message signs,” Mr Retter said.
“Automation is an opportunity to dramatically improve safety on our roads and reduce the current death toll. It could also significantly improve transport productivity. However, we will need to be smart about the way we approach these issues as there is also the possibility of adverse impacts, such as on congestion.”
Collaboration between states, national government and strong industry associations is needed to facilitate the discussion and help develop a nationally consistent approach. Various industry bodies are putting together legislation and regulation to support a national model.
In order to gain consistency in road infrastructure, the NTC recently released a report proposing 13 amendments to
Australian road rules in order to facilitate harmonisation between states and territory transport laws. The proposed amendments reflect advances in driver technology, clarification of existing road rules and improved road safety. The NTC is also developing an end-toend regulatory framework for automated vehicles.
“[The framework] includes developing the safety assurance system – essentially establishing the role of government in assessing the safety of automated driving systems and determining the safety criteria that should apply,” Mr Retter said.
The iMOVE Cooperative Research Centre (CRC) was also officially launched in October of this year and will combat Australia’s complex road problems through collaborative research and development programs.
In addition, Austroads is running trials and developing guides and standards for infrastructure to ensure a level of consistency.
“Each state is running events, trials, across the network, and those trials are linked in through Austroad so that we’re not repeating exactly what each trial has done in each state, we’re trying to build on what each
Ms Harris said ITS Australia is well connected with ITS associations around the globe, and the Summit plays a critical role in identifying challenges and opportunities to shape future transport.
other’s doing at the end of the day,” Mr Harvey said.
Ms Harris said one of the steps towards road harmony that she has seen recently is the change in attitude of political leaders and key government stakeholders.
“At the most senior levels, our political leaders really get that technology is a critical part of delivering safer and more efficient transport infrastructure. They’re really looking to make sure that new infrastructure that gets deployed is smart and future proofed. So that’s a change for us, to see that coming from those most senior levels,” Ms Harris said.
BRINGING THE INDUSTRY TOGETHER
Organisations like Intelligent Transport Systems (ITS) Australia assist in being the voice of the industry and its annual Summit allows industry leaders to discuss key issues. This year the summit was held at the Brisbane
Convention and Exhibition Centre on the 27 and 28 September.
“To support that collaboration, we invited a number of international keynote speakers from across the globe to make sure that we’re close with what’s happening internationally and that what we do in Australia is complementary to what’s happening overseas.
“ITS Australia facilitates an industry reference group on connected and automated vehicles which works under the umbrella of Austroads, representing a wide cross section of industry and all of the state government road agencies. It creates a collaborative environment for industry and government to work together, and to come up with a harmonised solution that will be the best outcome for Australia, but with an eye to what’s happening internationally as well.”
CAN WE ACHIEVE A NATIONAL TRANSPORT MODEL?
Mr Harvey said it’s not a matter of if we can achieve national consistency in our road laws, but when we can.
“The answer is it’s not an option, because if we don’t have national consistency then the road network and the benefits from autonomous connected vehicles will not be realised. The expected benefits from the technology will not be achieved at the end of the day,” Mr Harvey said.
Ms Harris said we still have a way to go before we can achieve harmony.
“We’re not there yet in terms of making sure that we’ve got all the smart technology in all the infrastructure that gets built. But there’s certainly a much higher level of awareness,” Ms Harris said.
EastLink is the major north-south transport artery in Melbourne’s east, connecting the Eastern, Monash, Frankston and Peninsula Link freeways. The 40km road network is the largest privately operated network in Victoria; as well as being Melbourne’s fastest road and safest freeway, with traffic averaging 250,000 vehicles per day.
EastLink’s tunnels – in particular the tunnel ventilation system – are the largest consumer of power within EastLink’s operations. This has led EastLink to improve the efficiency and sustainability of the tunnel ventilation system with the introduction of tunnel ventilation on demand.
EastLink has twin 1.6km tunnels, with three lanes of traffic in each tunnel. The EastLink tunnels protect the environmentally-sensitive Mullum Mullum valley above, reaching a maximum depth of 53m underground (from valley floor and creek bed to tunnel traffic lanes).
The tunnels, which are monitored and controlled from EastLink’s 24/7 traffic control room, have extensive safety systems. These include CCTV cameras, an automatic incident detection system, fire detection and deluge systems, radio rebroadcast and public address systems, variable speed signs, digital message signs and lane control signs. There is
One of Australia’s largest tollways, EastLink, has been the first to introduce tunnel ventilation on demand to reduce power usage, greenhouse gas (GHG) emissions, maintenance costs and noise.
also an over-height vehicle detection system which automatically deploys physical barriers to stop over-height vehicles from entering the tunnels and causing damage to infrastructure.
The tunnels have a ventilation system which expels and disperses tunnel air (containing pollutants from vehicles’ combustion engines) through 45m high ventilation stacks. There is one stack per tunnel. This maintains air quality inside the tunnels as well as in the areas outside each tunnel portal.
The ventilation system can also be controlled in the event of a fire in the tunnel – to help contain the fire initially, and then to dissipate smoke after the fire is extinguished by the deluge system.
The original tunnel ventilation system has been in use since EastLink opened in 2008.
It comprises twelve smaller jet fans in each tunnel, and five larger ventilation fans in each stack. That’s a total of 34 fans across the two tunnels and two stacks. The jet fans maintain constant airflow in through each tunnel portal, along the length of each tunnel, and towards the base of each ventilation stack. The ventilation fans draw air up through each stack for expulsion and dispersal well away from local properties.
Higher airflows, and therefore more operating fans are needed to clear the pollutants produced by higher volumes of traffic.
Since EastLink opened, the speed of airflows within the tunnels and stacks has been controlled by switching individual fans on and off. There was no speed control for any of the fans.
licence, issued by the Environment Protection Authority of Victoria (EPA Victoria), was amended following application from EastLink to allow all ventilation fans to be switched off at night, when traffic levels on the road network are relatively low.
Natural air flow, for example as a result of vehicles passing through the tunnels, meant that the low level of pollutants emitted by vehicles during the night can exit via the tunnel portals – keeping the air quality in the tunnels safe while not compromising air quality in the vicinity of the portals. This mode of operation is known as “tunnel portal emission”.
The EastLink tunnels have operated successfully with night-time tunnel portal emission since 2010, which reduced power usage and GHG emissions. In addition, ventilation system noise was able to be eliminated each night, helping nearby residents.
wear and tear on components, increases maintenance costs, and reduces lifespan
♦ Starting up a ventilation fan from fully off to fully on causes a step-change in noise, which makes the early morning start-up more noticeable for some nearby residents
♦ Fan control based on simple time-of-day parameters requires monitoring and manual override by the Traffic Control Room in order to respond to times when traffic patterns are different to normal, for example as a result of an accident. This can result in errors.
To address these issues, EastLink recently upgraded the ten large ventilation fans from fixed speed fully off/fully on operation to much more efficient self-regulating or “closed loop” variable speed operation.
This switching on and off of fans has been controlled by EastLink’s road and tunnel operating system using a simple pre-set program based on time-of-day parameters, with the largest number of fans operating at peak periods (when traffic levels and pollutants are expected to be at their highest levels). Manual control has also been available from the EastLink traffic control room to override the pre-set program when operators observe conditions that require it.
In an Australian first, during 2010, EastLink’s tunnel ventilation system
While introducing night-time tunnel portal emission delivered a significant improvement in efficiency, there were still issues with operating this traditional type of tunnel ventilation system:
♦ Only operating ventilation fans at full speed produces higher operating noise levels, is inefficient and maximises electricity usage
♦ Toggling ventilation fans between fully off and fully on, and only operating fans at full speed, causes
To achieve this, new impellers were installed within each of the existing ventilation fan housings, and new variable speed drives were installed to regulate the rotational speed of the new impellers.
The tunnel and road operating system was updated to provide software control over the new impellers and variable speed drives.
The tunnel and road operating system has also been enhanced to provide fully automatic control of the ventilation system. It does this by monitoring the output of the existing air quality and airflow sensors located within the tunnels, and automatically controlling the operation of all fans, including the speed of each ventilation fan that is operating at any time.
To achieve efficiency of operations, the new automatic ventilation control system is currently being “tuned” during a series of live tests. During the tuning tests, the optimum combination of operating fans and speeds of operating fans is being identified to achieve specific airflow requirements. This information is informing the final setting of the parameters that govern the new automatic ventilation control system.
The tunnel ventilation system will respond to the volume of traffic
travelling through the tunnels, as well as the vehicle mix, for example the proportion of heavy vehicles with diesel drivetrains.
Increasingly important for the future, the tunnel ventilation system will respond efficiently to increasing proportions of vehicles with hybrid electric/combustion drivetrains and pure battery-powered electric vehicles (BEVs), which will generate less pollutants and reduce ventilation requirements.
These improvements to the tunnel ventilation system are enabling a new change to the EastLink tunnel operating licence to be agreed with EPA Victoria.
The change will allow limited tunnel portal emission during day time. Up to 30 per cent of tunnel air will be able to exit via tunnel portals during day time hours, with the remaining 70 per cent dispersed via the ventilation stacks.
This introduction of limited tunnel portal emission during day time will further increase the efficiency of the tunnel ventilation system.
EastLink already has air quality monitors located within the tunnels and within the ventilation stacks, measuring carbon monoxide, nitrogen dioxide, nitric oxide, total oxides of nitrogen, and particulate matter (PM2.5 and PM10). Airflow is measured at the tunnel portals and within the ventilation stacks.
The previous day’s air quality charts are published automatically on the EastLink website, and quarterly reports are also published on the same page.
To ensure that air quality standards in the local community have not been compromised through the introduction of the changes outlined, additional air quality monitoring is being conducted in the local community.
A temporary air quality monitoring station has been set up in a small park, located in a nearby residential area close to one of the tunnel portals. The precise location was identified through modelling, to ensure that the air quality results are worst case rather than best case.
This additional air quality monitoring commenced prior to project implementation to determine the air quality baseline, and will continue until EastLink and EPA Victoria are satisfied that air quality standards have not been compromised by the changes.
It was essential to engage with the community about these changes.
Local residents living close to the EastLink tunnel portals were provided with information about the project before it commenced, as well as at subsequent updates. This included advance notice of the tune-testing of the new ventilation system, some of which needed to be conducted in the evenings at times when the tunnel ventilation system was normally switched off for night-time tunnel portal emission.
Local residents living near the park where the temporary air quality monitoring station is located were additionally informed about the purpose of the station, as well as the rationale for selecting that specific location.
Local councils were also consulted prior to project commencement.
Motorists who use EastLink were provided with advance notice of a series of night-time lane closures in the tunnels, which were needed to install the new tunnel ventilation fans.
The combination of introducing new variable speed ventilation fans, the new fully automatic ventilation control system, and limited tunnel portal
emissions during day time provides the following benefits:
♦ Reduction in electricity usage and power costs
♦ Reduction in GHG emissions of 6,441 tonnes CO2-e per annum
♦ Reduction in noise for local residents
♦ Reduced ongoing maintenance costs
♦ Longer lifespan for fan components
♦ Automatic changes to the ventilation system tracking variations to minimise GHG emissions
♦ Flexibility to efficiently respond to new vehicle types including hybrid electric/combustion drivetrains and pure battery-powered electric vehicles (BEVs)
EastLink has not received any complaints from the community about this project.
EastLink recommends that operators of major road tunnels consider whether similar changes to their tunnel ventilation system might provide community and business benefits without compromising their applicable air quality standards.
The GRESB Infrastructure Assessment recently awarded EastLink the top five star rating for the second year in a row. The internationally recognised GRESB Infrastructure Assessment covers the environmental, social and governance (ESG) performance of 160 infrastructure assets located around the world.
The Infrastructure Sustainability Council of Australia (ISCA) held its annual sustainability conference and awards on 17-19 October which recognised projects and organisations who demonstrated a commitment to infrastructure sustainability.
The need for more sustainable infrastructure is continually increasing due to the challenges of urbanisation, changes in climate, population growth, productivity expectations and more.
ISCA has been helping the sector advance its sustainability outcomes through the development of the infrastructure sustainability (IS) rating scheme, which evaluates the planning, design, construction and operation of infrastructure assets.
The IS rating tool is industry developed, owned and operated, and the five awards that were handed out at the 2017 dinner were presented to newly rated IS projects.
ISCA CEO, Antony Sprigg, said this year’s ISCA conference and awards had the highest number of speakers, nominations and people in attendance.
There were more than 65 speakers at the conference, of which 49 per cent were female, and more than 200 attendees. There were also 240 people at the awards.
Delegates were able to network with colleagues and gather information on how other organisations are driving sustainability, in addition to finding out about policy, planning, funding and procurement trends.
The fourth annual ISCA Sustainability in Infrastructure Awards Gala Dinner, hosted by comedian and sustainability advocate, Craig Reucassel, gave the sector a chance to come together and celebrate its achievements so far in the creation of more sustainable and smarter infrastructure.
The Awards Gala was part of a three day conference that allowed individuals and organisations to share insights into their asset sustainability initiatives. The finalists and winners were:
The winner of this award was determined to have demonstrated the highest overall score and sustainability achievements in 2017.
Finalists:
• City Rail Link, Contract 1 Britomart Works, Design
• Level Crossing Removal Project, Furlong Main Blackburn Heatherdale, As Built
• NorthLink WA, Southern Section, Design
Winner: NorthLink WA, Southern Section, Design
IS IMPACT AWARD FOR PROJECTS UNDER $20 MILLION
Finalists:
• McDougall’s Lift Replacement
• Queen Elizabeth Street and Collect Street Project
Winner:
Queen Elizabeth Street and Collect Street Project
IS IMPACT AWARD FOR PROJECTS OVER $20 MILLION
The winners of both the IS Impact Awards (under $20 million and over $20 million) were projects that exhibited the most outstanding leadership and greatest contribution to advancing infrastructure sustainability in Australasia.
Finalists:
• Canberra Light Rail
• NorthConnex
• Northlink WA Southern Section, Design
Winner:
Northlink WA Southern Section, Design
AWARD
The winner was the organisation that exhibited the most outstanding performance, leadership and greatest contribution to advancing infrastructure sustainability in Australasia.
Finalists:
• Level Crossing Removal Authority
• Melbourne Metro Rail Authority
• Sydney Metro
Winner:
Level Crossing Removal Authority
This award recognises the specific individual that has made the biggest contribution to infrastructure sustainability.
Finalists:
• Liz Root
• Nicole Neal
• Reanna Harper
Winner: Nicole Neal
Vicroads is planning to move its road sealing fleet to being fully forward moving in an effort to increase worker safety, reduce site costs and produce better road surfaces for Victoria.
VicRoads has recently announced plans to move towards using non-reversing aggregate spreaders for sprayed sealing operations.
Deputy Chief Executive of VicRoads, Peter Todd, said the change to a forward moving road sealing fleet will have several benefits for both road crews and road users, and have positive impacts on future road sealing projects.
“Forward moving aggregate spreaders deliver significant safety benefits as they allow operators a better view of potential hazards,” Mr Todd said.
“Forward moving aggregate spreaders also produce a higher quality surface, lead to potential savings on materials and require less sweeping of excess aggregate particles from the road surface.”
Sprayed bitumen seals have been the primary road surfacing treatment used in Victoria for more than 80 years. While there have been significant improvements in the size and productivity of equipment, the basic process has remained, for the most part, unchanged.
A bitumen sprayer applies bitumen to the road surface and aggregate spreading trucks reversing down the road behind the sprayer tip aggregate particles onto the freshly laid bitumen. The trucks are required to reverse to avoid driving onto the exposed bitumen and many spread the aggregate through elevated tipper bodies.
When both the bitumen and aggregate have been placed, surface rollers then reorientate the aggregate particles to provide a robust seal.
While they are being constructed, sprayed seal sites are an inherently dangerous place to be with a combination of hot bitumen (up to 190°C) being sprayed under pressure and with loose aggregate chips being applied to the road surface – all under live traffic conditions.
In addition to the risks observed with the combination of reversing trucks and people on the ground, there are also other risks associated with conventional aggregate trucks including the potential to hit overhead services such as power lines and overhanging trees; roll over incidents that are often a result of hoist or hinge bolt failures on the tipper body; and other mechanical failures.
The complexity of alternative aggregate spreaders, combined with their cost, has seen the implementation of new technology stall in favour of persisting with the simple reversing trucks.
Significant investment will be required from the industry to convert current fleets to forward moving vehicles, and VicRoads has implemented a five year transition period (1 July 2017 – 30 June 2022) to phase in the new spreaders.
VicRoads plan on introducing synchronised bitumen spraying and aggregate spreading machines that combine the application of the bitumen and aggregates as part of one operation.
Synchronised sprayers have been available for many years mainly from Europe and America, and in more recent times from China. Forward moving aggregate spreaders have recently been developed in France, with two manufacturers currently trialling prototype units, and a handful of other companies, including some based in Australia, are also
developing their own versions of this equipment. There may be issues with the French units complying with Australian regulations but locally designed units should be produced to conform.
During the transition period, there is an additional payment of $0.50/m2 for works completed utilising forward moving spreading techniques. This payment is intended to help alleviate the anticipated costs of the initial purchase and ongoing costs of operating these alternative plant items.
There is also an incentive payment to reward early adopters of forward moving spreading techniques, which recognises the potentially higher costs and risks for those contractors who purchase new plant items immediately and the disadvantage they face while trying to compete at the tender box with other companies that have not invested in the new equipment and technologies.
The transition commenced on 1 July this year, however, because the sprayed sealing season does not commence until October each year there have not been any projects completed using the forward moving technology as yet.
Driverless vehicles have the potential to impact road rules and how roads are designed and constructed. One other implication revolves around the insurance industry and how, if there is an accident, it can assign liability to a car that is fully automated.
The impact of driverless vehicles on the insurance industry will be one of the key discussions taking place at the 2nd International Driverless Vehicle Summit, held in Adelaide on 16-17 November. Secretary of the Insurance Commission of Western Australia, Kane Blackman, is one of the speakers at a panel session on insurance and liability and will discuss the implications that sharing our roads with autonomous vehicles will have on insurers, manufacturers, suppliers, motorists and policymakers.
Mr Blackman said driverless vehicle technologies will mean fewer vehicle crashes and injuries on Australian roads. Not only will this affect the need for, and cost of, motor vehicle injury insurance but it also raises questions about who to blame when things go wrong, which will fundamentally impact existing insurance business models.
“Currently human drivers cause most motor vehicle crashes, but when an automated vehicle – which makes decisions based on its programming, sensor feeds and inputs from the surrounding network – crashes, there might not be a driver at fault,” Mr Blackman said.
“Manufacturers and suppliers are legally obliged to provide products to consumers that are safe, free from defects and fit for purpose. There will be an expectation that automated vehicle manufacturers and suppliers accept liability should their products fail and cause injury.”
Automated vehicle owners will also be expected to have responsibilities such as ensuring their vehicle is regularly maintained according to manufacturer specifications, which could include software updates and the replacement of sensors, cameras and other equipment.
“Discussions are underway in states and territories about what the personal injury insurance regimes should be for people injured in crashes of autonomous vehicles,” Mr Blackman said.
“The decisions made following those discussions will shape the future of motor injury insurance schemes.
“This will be particularly important during the transition phase when we will see a mix of driverless and human controlled vehicles sharing the road, and during the evolution from partially to fully automated vehicles.
“Adding to the complexity is the potential for connectivity and technological failures, as well as the very real threat of cyber risk.”
The theme of the 2nd International Driverless Vehicle Summit is ‘Translating technology to real world deployment’, with delegates hearing from an array of prominent national and international technology thought leaders, human factors experts, insurance and legal practitioners and regulators from across the driverless vehicle ecosystem.
The event will also include demonstrations and conversations around security, heavy and light vehicles, and
the latest innovation developments, pioneering trials and deployment from across Australia and around the globe.
Keynote speaker and Aurrigo Chief Operating Officer, Dr Richard Fairchild, will offer critical insights from a series of demonstrations on selected public roads and footpaths in Milton Keynes and Coventry.
Chief Executive Officer of Peloton Technology in the US, Josh Switkes, will outline how truck platooning technology might apply within an Australian setting, and the Australia and New Zealand Driverless Vehicles Initiative (ADVI) partners Aurrigo, EasyMile and Navya will join forces to showcase driverless shuttle technology.
ADVI is the peak body for driverless vehicles in Australia and New Zealand, with a membership of 100 leading organisations across a wide range of sectors. ADVI’s education, advocacy and demonstration efforts help to inform and raise awareness, encourage community acceptance, and ensure understanding of the economic, environmental and lifestyle benefits of driverless vehicles.
The NSW Government is developing a Critical Infrastructure Resilience Strategy to make sure that when disaster strikes, key infrastructure will provide continued service and can be restored quickly.
The NSW Office of Emergency Management and the NSW State Emergency Management Committee have created a discussion paper that invites infrastructure managers and organisations to provide input on what the future strategy should include.
The Hon. Troy Grant MP Minister for Police, and Minister for Emergency Services, believes this strategy will help protect critical infrastructure assets from disasters.
“The NSW Government is developing a Critical Infrastructure Resilience Strategy. A state wide critical infrastructure resilience strategy will help keep the lights on, water running, and transport and trade routes open for people and goods to flow, even in emergencies,” Minister Grant said.
“Part of this process is the release of a discussion paper to seek feedback on what the strategy should include. I invite individuals and organisations to provide submissions to help develop the strategy.”
In February 2017, households across New South Wales were asked to cut their electricity usage in response to unprecedented heatwave conditions and the threat of rolling blackouts and power outages.
In the same month the Sydney metropolitan district and parts of the Illawarra, South Coast and Central Tablelands suffered telecommunications outages to more than 32,000 services due to extreme weather conditions including heavy rainfall and damaging winds.
The critical infrastructure of NSW is exposed to many threats, hazards, shocks and stresses. Disruptions to critical infrastructure can lead to loss of life, psychological distress and result in a negative economic impact.
Increased interdependencies between different sets of critical infrastructure can amplify the consequence of these risks. Recent events such as the 2015 and 2016 East Coast Lows and the devastation caused by Ex-Tropical Cyclone Debbie demonstrate the significant impact on all infrastructure provided by local government, state government and the private sector.
Natural disasters of greater magnitude and a heightened risk profile in relation to criminal or malicious threats, including cyberattack, mean NSW’s infrastructure and organisations must be more resilient than ever. Long-term stresses such as aging infrastructure, increased population density, and climate change, add to the challenge of infrastructure resilience.
Critical Infrastructure (CI) is the assets, systems and networks required to maintain the security, health and safety, and social and economic prosperity of NSW. They are underpinned by the organisations and people that support them.
Currently NSW benefits from critical infrastructure that provides secure and reliable essential services, such as food, water, energy, telecommunications and health care. Without these services, our economic prosperity and public safety are detrimentally impacted. To ensure we can continue to enjoy these benefits, the growing risks to critical infrastructure must be managed through an all-hazards approach.
The NSW Government’s Critical Infrastructure Resilience Strategy proposes to address the consequences to the people and communities of NSW, rather than specific types of infrastructure outages.
It is essential that a collaborative strategy is developed to ensure critical infrastructure withstands the shocks to continue operating; is returned to service as soon as possible after any disruption; and responds to long-term stresses.
The NSW Office of Emergency Management and the NSW State Emergency Management Committee have developed a discussion paper to seek feedback and submissions on what a future Critical Infrastructure Resilience Strategy (CIRS) should include.
This discussion paper is an opportunity for organisations to provide submissions for consideration in developing a future NSW strategy for the next five years, and contribute to enhancing the state’s critical infrastructure resilience.
The intention is to develop a strategy that benefits critical infrastructure providers, all levels of government, and most importantly, the people, businesses and community of NSW. The expected benefits of a future strategy include:
♦ Enhanced resilience against foreseen and unforeseen hazards and threats
♦ Stronger relationships between business, government and the community
♦ Reduced service interruption (less disruption to the people and businesses of NSW)
♦ More effective emergency management arrangements for NSW communities
♦ Enhanced response capability and coordination for all agencies after a disaster event
♦ Reduced response, recovery and reconstruction costs arising from threat and hazard events
♦ More resilient communities, reducing the social costs of disasters
♦ Improved adaptation to stresses such as climate change and population growth
♦ Improvements of critical infrastructure resilience through recognising and addressing vulnerabilities of interdependencies between critical infrastructure types
♦ Stronger cultures within critical infrastructure organisations to meet business challenges presented by disaster events
♦ Reduced total cost of asset ownership across the entire asset management lifecycle
♦ Insurance premiums for critical infrastructure providers, government, and the community that incorporate the benefit of critical infrastructure resilience and hazard mitigation activity
♦ Enhanced reputations and increased business confidence for critical infrastructure providers
The NSW Critical Infrastructure Resilience Strategy intends to foster and encourage collaborative partnerships between government, infrastructure providers and the NSW community.
The strategy demonstrates a commitment to work together to build a strong and resilient NSW that can withstand, respond, adapt and thrive when threatened by emergencies.
The input of organisations and workers within the industry is important for guiding NSW’s future strategy. By having a Critical Infrastructure Resilience Strategy and putting it into action, the NSW Government aims to move closer to creating a safer, more secure, and more disaster-resilient NSW.
The Critical Infrastructure Resilience Strategy: Discussion Paper and summary of questions to guide feedback can be found at www.emergency.nsw.gov.au/publications/guidelines-legislation-policies/critical-infrastructure-resilience-strategy.html Submissions can be emailed to submissions@mpes.nsw.gov.au or mailed to: GPO Box 5434, Sydney, NSW, 2001.
sk any driver in Melbourne’s western suburbs: the West Gate Bridge is packed. Drivers spend hours and hours stuck bumper to bumper. And if there’s an accident, the entire city can come to a complete standstill.
Around 200,000 vehicles already travel over the West Gate Bridge every day. In less than 15 years that number will soar to 250,000. That jump won’t just affect drivers in the west. The impact will be felt right along the M1 corridor, from Geelong to Pakenham. In fact, the whole of Melbourne will grind to a halt.
Victorians desperately need an alternative– that’s why we’re building the West Gate Tunnel.
It will take thousands of trucks off local roads in the inner west, shifting them onto a dedicated, highly efficient route to the Port of Melbourne. It will create 6000 jobs while protecting and improving public open space in the inner west.
It’s the road we need most urgently – but it’s just one part of the most ambitious infrastructure agenda this state has seen in generations
Unlike the previous, do-nothing Liberal government, we know that there is no single solution to fixing congestion. That’s why, in addition to the West Gate Tunnel, we're building the $11 billion Metro Tunnel to create the “turn up and go” public transport system Victorians deserve.
We're getting rid of 50 dangerous and congested level crossings across Melbourne – 10 are already gone and a further 16 are under construction.
We're building North East Link to complete the Metropolitan Ring Road and end the rat runs that have plagued the north east for decades. We’re using technology and innovative intersection upgrades to get the most out of Hoddle Street, making our busiest arterial road faster and more reliable.
We're also upgrading the key suburban arterials that people rely on every day, like Plenty Road, Yan Yean Road, O'Herns Road and the Chandler Highway.
In the next 18 months we will see the completion of the CityLink Tulla Widening project, the M80 Upgrade, the Swan Street Bridge Upgrade and Stage 1 of the Monash Freeway Upgrade.
There is simply no comparison between the two approaches –The Andrews Labor Government is building congestion busting projects right across Melbourne - the Liberals wasted four years on a single dud of a project
The East West Link would have lost 55 cents for every dollar of investment. It would have dumped traffic on Hoddle Street and failed to address our most significant transport needs.
We went to an election saying it wasn’t good enough and we’d scrap it – and that’s exactly what we’ve done. The West Gate Tunnel project stacks up, it will return $1.35 for every dollar invested, and we’re getting on with it.
In select issues of Infrastructure magazine, we’ll be considering some of the biggest questions when it comes to public infrastructure in Australia. We’ll be talking big ideas, key proposals and planned projects, and asking two experts to debate the issue. In this edition, we’ll be looking at Victorian road projects, in particular the proposed East West Link and the West Gate Tunnel, and our experts will be going head to head over which one they think would most benefit the state.
The East West Link was identified as an essential project
As all of us who live in Melbourne know very well, traffic congestion across our city continues to worsen to levels far beyond what can be deemed acceptable. Indeed, with Melbourne now growing faster than any other major Australian city, it is no wonder that this problem is worsening – yet it doesn’t have to be this way.
One only needs to cast their eyes elsewhere in Australia to see how other state governments have been working furiously to ensure road infrastructure keeps pace with population growth. Whether it be WestConnex or NorthConnex underway in Sydney or Brisbane’s Airport Link tunnel, other cities have been getting on with the job of building visionary road infrastructure to benefit their citizens for generations. By contrast, Melbourne – a city forecast to top eight million residents by 2050 – has not had a single major new metropolitan road project built for almost a decade.
The former Coalition Government in Victoria was conscious of this fact and therefore set about to plan, design, fully fund and construct the East West Link (EWL), which, by 2019, would have comprised Melbourne’s much-needed second major east-west freeway and river crossing.
Indeed, the EWL was identified as far back as 2007 (following an exhaustive study commissioned by the former Brumby Labor Government and undertaken by Sir Rod Eddington) as an essential project that would have both significantly reduced reliance on the gridlocked Monash Freeway and West Gate Bridge, and provided an alternative route for residents and freight operators
in Melbourne’s east and south east heading to the city’s northern and western suburbs.
Importantly, Stage 1 of the project would have also seen an end to the notorious bottleneck at the end of the Eastern Freeway at Hoddle Street, where thousands of motorists remain gridlocked each day.
What follows in this story is notoriously well known. The Andrews Labor Government’s purely political decision prior to the 2014 state election to tear up the EWL contract at an eventual cost to taxpayers of $1.2 billion remains one of the most reckless and irresponsible decisions of any government in Australia’s history.
What’s more, aside from seriously damaging Victoria’s reputation as a place to do business and eliminating the prospect of any meaningful and much-needed road infrastructure projects in the foreseeable future, Labor’s alternative West Gate Tunnel (WGT) project, originally known as the Western Distributor, remains deeply flawed and troubling.
The Coalition has serious reservations about the WGT project and we believe it is an inferior alternative to the EWL for a number of reasons. To date, the WGT’s evolution has been a rushed process, which has been resultant from Daniel Andrews’ scrapping of his earlier so called “shovel-ready” West Gate Distributor, and will lead to poorer outcomes.
The WGT will not comprise a true alternative east-west route given it will simply utilise and dump more traffic onto the already overburdened section of the West Gate Freeway between the Western Ring Road and West Gate Bridge.
By contrast, Stage 2 of the EWL would have seen an entirely new road built from the ring road to the bridge, thus
alleviating pressure on the West Gate corridor. Additionally, the WGT does nothing for the long-suffering motorists of Melbourne’s east, who will continue to endure gridlock for years to come.
To add insult to injury, Labor is seeking to pay for the project by allowing Transurban – the WGT’s builder and operator – to continue collecting tolls from CityLink for an additional 10 years. This means motorists in Melbourne’s east will be paying for a road they will likely never use. All up, it could be argued that this is a project which benefits Transurban and its shareholders more than motorists.
The EWL-WGT saga demonstrates it is hard to take Labor seriously when it comes to road infrastructure building. Next year’s election will be a choice between the Coalition’s pragmatic, evidence-based approach to identifying and building roads where they are most needed, or Labor’s ideological, rushed and reckless vision.
The EWL continues to be backed by many experts and stakeholders as an essential missing piece in Melbourne’s freeway network which we must get on with the job of building. We owe it to long-suffering motorists and the future of our city.
Head to www.bigideasforum.com.au to share your thoughts.
March 2018
Deadline: 16 February 2018
Bridges Signalling, tracking and control systems
Road marking Condition monitoring and maintenance
Spatial & GIS Urban transport corridors
Sustainability Public private partnerships
DISTRIBUTION Core18
Sydney Build Expo
September 2018 Deadline: 27 July 2018
Tunnels Energy infrastructure
Smart infrastructure Safety and risk management
ITS Concrete
Freight Mobility
Energy infrastructure Culverts
Cranes & heavy lifting When infrastructure intersects
DISTRIBUTION TBC
June 2018
Big data
Tolling
Deadline: 4 May 2018
Asset inspection and drones/UAVs
Road surfacing and stabilisation
Road design Investment and financing
Pits and poles Skills and training
Noise and vibration
DISTRIBUTION TBC
AusRail Airports
Asset management
Deadline: TBC
Security and critical infrastructure
Sustainability IoT & cloud communication
Land access Excavators/earthmovers/plant
Construction standards and codes
Landscaping and Vegetation Management
DISTRIBUTION TBC
SPEAKERS INCLUDE:
Sir Terry Morgan CBE, Chairman, Crossrail UK
Gerhard Kress, Director Mobility Data Services, Siemens AG
The Hon. Anthony Albanese MP, Shadow Minister for Infrastructure, Transport, Cities and Regional Development, Shadow Minister for Tourism
Neil Scales OBE, Director-General, Department of Transport and Main Roads
Howard Collins OBE, Chief Executive, Sydney Trains
Emma Thomas, Director General, Transport Canberra
Bob Herbert AM, Chair, Australasian Railway Association
John Fullerton, CEO, Australian Rail Track Corporation
Nicole Stoddart, Managing Director, Construction Services, ANZ, AECOM
René Lalande, CEO, Transdev
Loretta Lynch, Managing Director, Keolis Downer Gold Coast
Dean Dalla Valle, CEO, Pacific National
Alan Beacham, Executive General Manager Rail & Defence, UGL
Nick Easy, CEO, Queensland Rail
Michael Bailey, General Manager Railroad Operations, BHP
Priscilla Radice, Principal, Australasia Business Leader, Arup
Roy Cummins, CEO, Port of Brisbane
Stephen Troughton, Deputy Secretary Infrastructure and Services, Transport for NSW
Michael Miller, CEO, Downer Rail
Deb Spring, Chair, Rail Industry Safety and Standards Board
Andrew Dudgeon, Managing Director, Bombardier
Marion Terrill, Transport Program Director, Grattan Institute
> > And many more
Sponsorship and exhibition opportunities at AusRAIL PLUS 2017 are highly sought after. Ensure you book early to position yourself in front of rail decision makers. Contact Deborah Bocock on 02 9080 4348 or email deborah.bocock@informa.com.au