INTERMAT 2024 SHOW PREVIEW
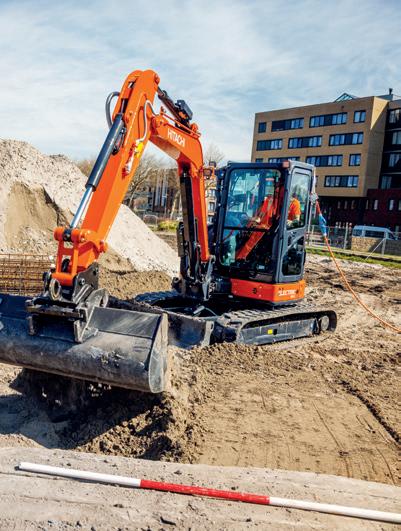
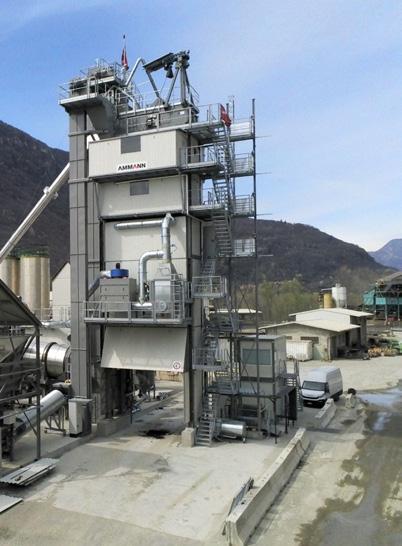
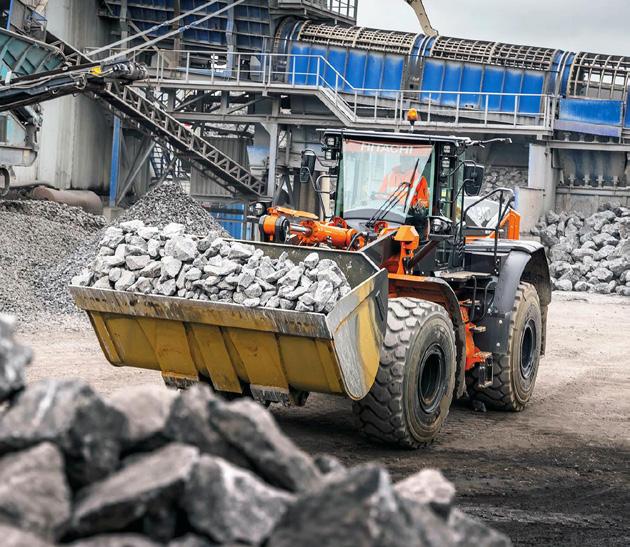
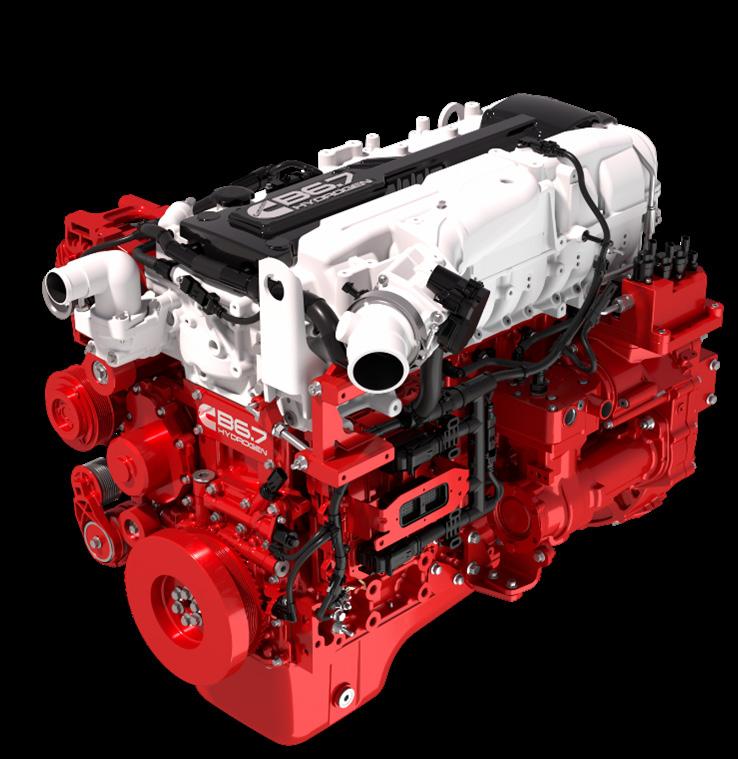
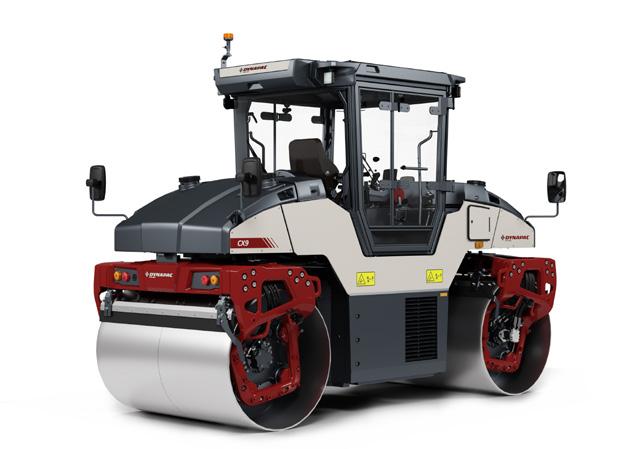
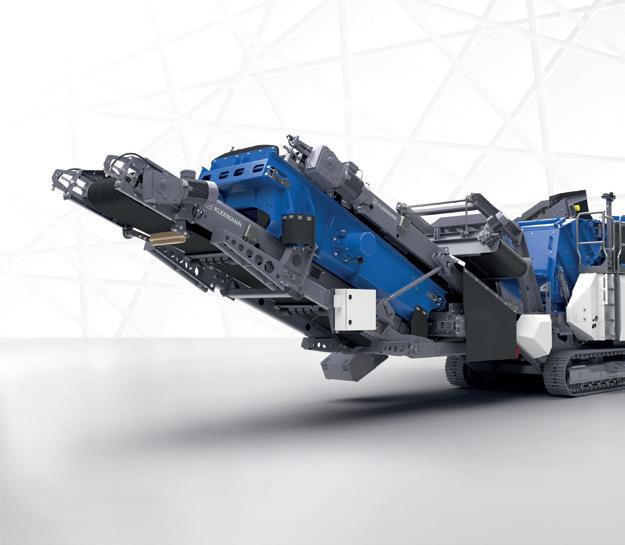
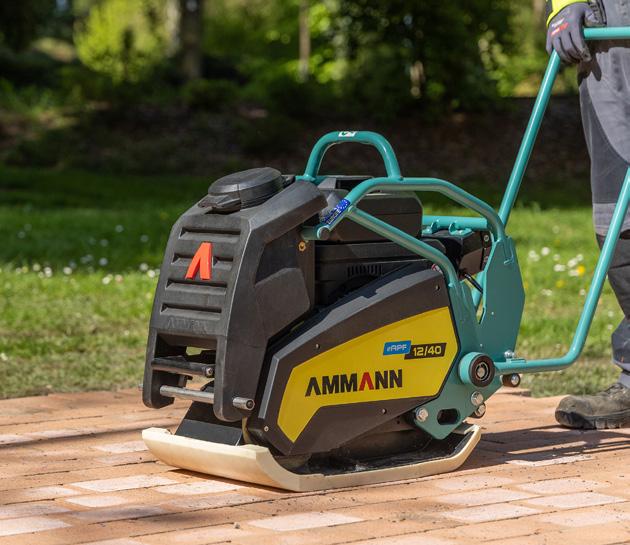



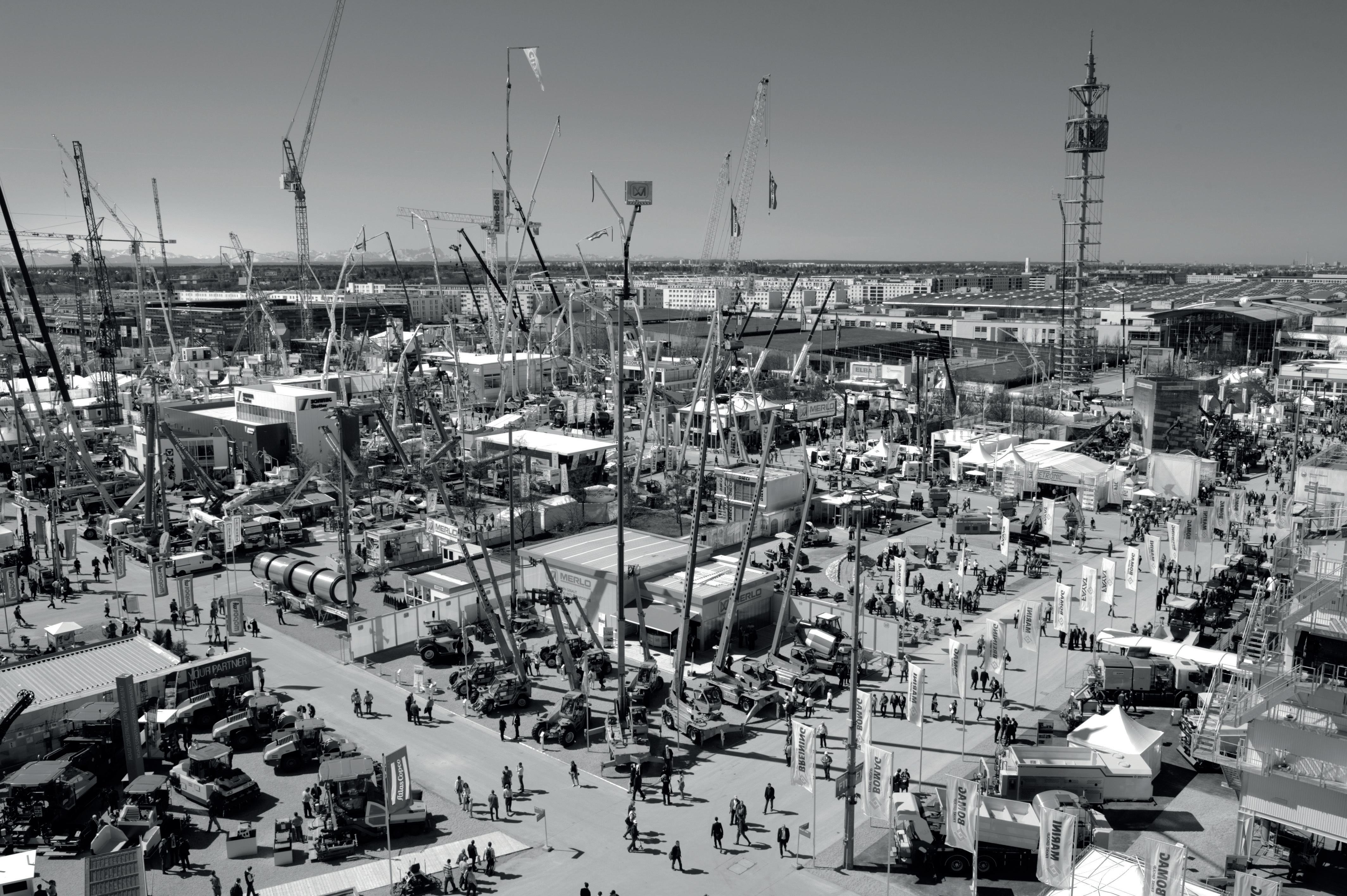
Welcome to Route One Publishing’s preview for the upcoming Intermat 2024 exhibition, being held in Paris. This event marks the return of the popular construction machinery show to the Paris showground after a break caused by the COVID-19 pandemic.
The exhibition is already proving to be an important event in the calendar for producers of construction and quarrying machinery, with some key innovations being unveiled.
Mike Woof Editor
Editor: Mike Woof
Publishing Director: Geoff Hadwick
Contributing Editors: David Arminas, Guy Woodford, Liam McLoughlin
Sub Editor: Kevin O’Shea
Advertisement Sales: Graeme McQueen, Phil Woodgate, Fulvio Bonfiglietti
Production Manager: Nick Bond
Designer: Rob Terry
Office Manager: Kelly Thompson
Website Manager: Sarah Biswell
Social Media Manager: Tatyana Mechkarova
Komatsu, through its whollyowned subsidiary in the US, Komatsu America Corporation, has agreed to acquire American Battery Solutions (ABS), a battery manufacturer headquartered in Detroit, Michigan.
ABS develops and manufactures various heavy-duty and industrial battery packs, using lithium-ion batteries for commercial vehicles, transit buses and on- and off-road vehicles.
The company optimises standard and custom battery systems for each customer’s needs. ABS’ technology, combined with its people’s advanced product development knowledge and expertise, enables the company to develop and manufacture battery packs designed to deliver superior
performance and product life and enhance safety.
The acquisition of ABS will enable Komatsu to develop and produce its own batteryoperated construction and mining equipment through the integration of ABS’ battery technology with Komatsu’s knowledge and network. The first solution featuring ABS batteries will power mining equipment in North and South America, where demand for electrification has increased. In the future, Komatsu will aim to expand the use of batteries in construction equipment and to establish a global supply system. Komatsu will continue to support ABS’ battery business to develop the electrification business further after the acquisition.
ABS will operate as a standalone business entity within Komatsu and continue its growth plans by executing its current and prospective customer programmes in the commercial vehicle segments. The mining and construction opportunities
provided through Komatsu will enable ABS to position itself as one of the world’s leading providers of battery systems in both on-highway and offhighway markets.
Komatsu www.komatsu.eu
Volvo Penta is highlighting its strategic ambition of embracing customer-centric productivity solutions through advanced vehicle control systems – a robust foundation on which flexible, up-to-date and cohesive features and interfaces can co-exist and scale seamlessly.
Part of the Volvo Group, Volvo Penta says it will transform challenges in the off-highway segment into new opportunities by codeveloping these smarter solutions with OEMs, operators and fleet managers.
Volvo Penta’s established success lies in assisting customers in optimising their power solutions for efficiency, performance and profitability while fostering a more sustainable society.
“We are embarking on a journey to offer OEMs a sophisticated and high-performing system on which future solutions can be collaboratively built to fill any voids in their existing systems. We want to explore impactful solutions, even in unexplored areas, to support OEMs, operators and fleet owners in a meaningful way,” says Hannes Norrgren, president Volvo Penta Industrial.
While technological solutions, like vehicle controls, automation and advanced analytics are readily available, creating value requires combining technology and domain expertise. This entails reimagining processes and building new capabilities, as well as strategic foresight
in close collaboration with operators, fleet managers, OEMs and tech players.
“Volvo Penta’s approach is not characterised by ready-made solutions but rather revolves around collaborative partnerships and meaningful dialogues, allowing us to codevelop bespoke, value-added solutions in tandem with our clients,” concludes Norrgren.
As a start, Volvo Penta plans to engage in open conversations among its extensive customer connections to uncover opportunities. The company will work hand in hand with CPAC Systems, their subsidiary company – a
leading provider of vehicle electronics and productivity solutions, to transform these ideas into actionable initiatives.
CPAC Systems’ flexible technology platform with high computing power will be the conduit for which Volvo Penta’s industrial productivity solutions can be built and optimised for offhighway needs. Volvo Penta and CPAC Systems will co-engineer solutions with the former’s customers to bring these solutions to OEMs and the market with greater speed.
Volvo Penta www.volvopenta.com
Rototilt, a global market tiltrotator manufacturer for industries including quarrying and construction, is investing heavily in the future by expanding its factory in Vindeln, northern Sweden. The extensive investment includes the development of a state-of-the-art robotic welding facility at a cost of around SEK 35 million (€3.07mn).
“Even though the economic situation is challenging right now, we believe in continued growth and require greater flexibility and capacity to meet our customers’ high demands. This investment is strengthening our position, enabling us to deliver with speed and precision, which is crucial in our market segment,” says Anders Jonsson, Rototilt CEO.
The new robotic welding facility links up handling robots and welding robots. Launched in October 2023, the project includes an expansion of the factory to 1080m², spread over two floors. The new welding section will be ready for final inspection in May 2024.
“The global situation is placing new demands on us, and we are dealing with this at the same time as attempting to develop our business. We are now creating the conditions to improve our delivery precision, which we are constantly focusing on since we know how important it is to our customers,” says Jonsson.
Rototilt’s production facility is powered by fossil-free energy, and the extended factory is being
built with an advanced energy recovery system. The heat from the welding process is recovered via the ventilation system, reducing energy consumption and the climate footprint. The factory’s primary heating source is district heating, produced from local biofuel.
“The new welding facility will contribute to a lower proportion of goods transport. All the contributing elements are important, and we are constantly thinking about reducing our climate footprint,” says Ida Skaring, sustainability strategist at Rototilt.
During the autumn, Rototilt has also invested in one of Sweden’s largest private charging parks, with 178 vehicle spaces
outside the factory in Vindeln. All the parking spaces have sockets for engine heaters and electric car charging.
“We are proud to create a greener workplace and support the ongoing transition to sustainable travel. Half of our employees commute from other municipalities, and this development is making it easier for anyone who drives an electric car to get to the workplace. It will hopefully also encourage more people to switch to an electric car. Our aim is not only to offer innovative products but also a production facility that aligns with the highest sustainability standards,” says Jonsson. Rototilt www.rototilt.com
To meet the growing demand for 40-tonne-class machines in Europe, capable of boosting productivity and efficiency on heavy-duty applications and demolition job sites, Hitachi Construction Machinery (Europe) is presenting the ZX390TC-7.
Based on a Hitachi ZX350LC-7 standard excavator, with Zaxis-7 technology and a Stage V-compliant engine, the new tool carrier model has been specially adapted to work with larger working tools.
Larger boom and bucket cylinders and a one-class-higher reinforced linkage enable the ZX390TC-7 to carry five-tonne tools, such as hydraulic shears for crushing normally used by larger machines. It is equipped with a full hydraulic control
system, suitable for use with all attachments, which can be changed within seconds from the operator’s seat.
For added stability, the ZX390TC-7 has a robust 25 cm longer undercarriage than the standard ZX350LC-7 and is supplied with an additional 1.4-tonne counterweight.
To ensure the safety of operators, the machine has side impact protection and a demolition-spec cab with FOPS guard level 2 and high-spec P5A safety glass.
Safety is also enhanced by the exceptional visibility from the cab, particularly from the 270-degree bird’s-eye view provided by the Aerial Angle camera system.
Like all Zaxis-7 excavators, the ZX390TC-7 provides
exceptional durability for heavy-duty applications, especially demolition projects. Hitachi supplies all of the main components and spare parts, which are renowned for quality and reliability.
Furthermore, Hitachi’s quality
assurance team approved the modifications, and the new model is covered by the manufacturer’s warranty and service programmes.
Hitachi Construction Machinery (Europe) www.hitachicm.eu
LiuGong France is unveiling the Chinese off-highway equipment giant’s eye-catching BEV (batteryelectric vehicle) capability.
France remains at the heart of LiuGong’s growth strategy for Europe and has seen significant investment in recent years in the establishment of a nationwide dealer network.
Comprising of sixteen dealers, the network provides full sales and service support for the French construction industry.
“We are very excited to be showcasing our world-class BEV capability,” explains Samuel Broilliard, head of LiuGong operations in France. “We know that French customers are increasing looking for sustainable machine solutions, backed up by expert support and advice. China leads the world in BEV technology and LiuGong is a leader in China, so I am confident that our customers will be impressed with our BEV expertise.”
New machines include 922FE and 9027FE excavators and the new 820TE and 856HE wheeled
loaders. With their distinctive green livery, these machines share LiuGong’s Red Dot Awardwinning design DNA and put the operator right at the heart of the machine.
Liuzhou-headquartered LiuGong says it is leading a revolution in BEV R&D and plans to launch over 40 BEV models by 2027, including new BEV excavators, wheeled loaders, telehandlers and access equipment.
Alongside LiuGong’s investments in France, the company has also expanded its European operations with new regional offices in Germany, Italy and Turkey. Major expansion plans are also in place for the UK with a new R&D Centre, proving ground, test area and Customer Solutions Centre.
Howard Dale, LiuGong Europe chairman, says: “Now is an exciting time to be considering the LiuGong brand. Significant investments have been made, not just in product development, but in future-proofing our business
to be an even better partner for our customers. At LiuGong, we are committed to listening to our customers and working with
them to create a better future and success for everyone.”.
LiuGong www.liugong-europe.com
Komatsu Europe is introducing its PC210LCE-11 electric excavator equipped with lithium-ion batteries.
In its drive to become carbon neutral by 2050, Komatsu regards the market introduction of this new model as an opportunity to develop a market for electric construction equipment as soon as possible.
Komatsu has been jointly developing this electric model since January 2021 and is now ready to introduce it to the rental market. By using it under various operating conditions and with different power supply environments in regions where the electrified market is expected to be formed in the future, customers will be able to experience its environmental friendliness and safety, while Komatsu will compile feedback, opinions, and knowledge to lead to the formation of the electrified market.
Komatsu marked FY2023 as the first year for the market introduction of electric construction equipment, and the launch of the PC210LCE-11 model follows the recent introduction of the Komatsu 3tonne class electric mini excavator.
Hydraulic excavators are the most versatile type of construction
Develon is unveiling some of the results of its ‘Future Energies’ machine innovation work.
They include the DX20ZE mini-excavator, the first massproduced electric-powered excavator manufactured by Develon. This 2tonne excavator combines low noise and zero emissions with the features and performance enhancements that are found on the next-generation DX-7 Series family of mini-excavators.
The firm is also unveiling the 14W-EREV electric concept vehicle. This electric wheeled excavator is designed with a regenerating drive system (eDrive), advanced swing system (eSwing), and eWorking systems to ensure maximum efficiency with zero emissions.
Completing the ‘Future Energies’ line-up is the DL250-FCEV (fuel cell electric vehicle), which has a versatile, single platform design. This allows it to be equipped with a fuel cell powerpack running on hydrogen but offers the ability to transition to a BEV (Battery Electric Vehicle) by installing a battery pack.
Develon will also be unveiling several reduced emissions solutions based on fuel-saving technologies and the use of biofuels such as HVO and GTL.
Develon www.develon
equipment, with the 20tonne class excavators, which also includes the Komatsu PC200LCE-11 (pictured above) in particular being used for a wide range of jobsites and applications, centring on excavating and loading earth and sand. By launching the PC210LCE-11 in Europe, Komatsu is working to create an electrified machine market for mediumsized class construction equipment.
Hitachi Construction Machinery (Europe) (HCME) is introducing the ZW310-7, a larger next-generation model from its Stage V-compliant wheeled loader range.
Designed to put operators in complete control of their workspace, with claimed industry-leading safety features and unrivalled comfort in the cab, ZW310-7 HCME says owners will feel in total control of their profit due to its powerful performance, low total cost of ownership and exceptional efficiency. Further supporting these gains are remote monitoring tools and services provided by HCME.
The new ZW310-7 is the safest machine in the market, says HCME,
with superb all-round visibility and intelligent systems. With the Aerial Angle camera system, operators have an exceptional 270° bird’s-eye view of the jobsite, while the rear obstacle detection and warning system alerts them immediately if anything is close to the rear of the machine.
After working a full shift in the spacious, fully redesigned cab, operators will feel less tired and more satisfied at their ability to work more productively. The ZW310-7 epitomises the ultimate in comfort, with some of the lowest noise and vibration levels in the market.
Hitachi Construction Machinery (Europe) www.hitachicm.eu
The brands appearing at INTERMAT 2024 - BOMAG, DYNAPAC, ERMONT, MARINI, SAE and SECMAIR - are showcasing their latest innovations for every stage of the road life cycle with solutions for asphalt production, application and compaction, road maintenance,
sweeping, cold milling, stabilization & recycling, and soil compaction.
Four interdependent pillars are combined to meet the challenge of decarbonisation:
• Machine efficiency
• Process efficiency
• Operator efficiency
• Alternative energy sources
The Process efficiency is based on optimizing flows on the jobsite by integrating the choice of the right equipment or combining the right connected equipment.
For example, the Fayat Group’s patented Ermont TSX technology, used on the stationary (TSX InCity) and supermobile (TSX HIGHWAY) asphalt plant ranges, is a one-of-a-kind, environmentally friendly, continuous-mix technology, capable of recycling up to 70% of recycled asphalt pavement (RAP) with a single drum, while ensuring environmental protection and producing high-quality hot mix asphalt.
TSX technology itself features two patented processes: the DUOTHERM process, combining heat exchanges between recycled asphalt pavement and slightly
heated aggregates, and between asphalt aggregates and gases at moderate temperatures that previously exchanged with the aggregates, resulting in low atmospheric emissions, below current regulations; and the ECOFIRE process - a world firstwhich recovers energy from flue gases and feeds it back into the burner to optimize combustion and therefore reduce energy consumption.
Ammann says its blue smoke capture system reduces the emissions that result while loading asphalt mix to trucks. The Ammann Blue Smoke Treatment (BST) is a cost-effective solution that does not require expensive confinement equipment and is inexpensive to operate.
The BST system captures fumes that previously would have escaped during loading and redirects them to a multi-stage filtration system. The BST uses the indirect aspiration of Blue Smoke that uses the thermic force of the gases to reduce the energy absorption, the power installed and the volume flow. The filters remove the oily particles during multiple stages, ensuring high efficiency. After filtering, the system reroutes the remaining gases to the combustion chamber, lowering costs as the captured air is already heated.
The condensed oil accumulates in the filtration system and can be recycled. The BST system enables a steady flow rate at the chimney without increasing the plant gas flow at the chimney. No new emission authorisations are necessary.
“Newer, stricter regulations are requiring that steps be taken to mitigate these fumes, so the availability of BST is well-timed,” said Stampfli Philipp (AMMANN Global Head of Process Technology). “In addition to sustainable benefits, we expect it simplify the process for obtaining permits and improve relations with neighbours. It’s important to remember that BST removes fumes that are visible. The air won’t just be cleaner. It will look cleaner and smell cleaner.”
The BST can be installed on plants manufactured by Ammann or competitors. A plant owner does not need to purchase a new plant to benefit from this technology. Adding BST to an existing plant allows the owner to continue using the plant while meeting tightening emissions standards.
It reduces blue smoke during loading but does not reduce plant capacity. There is no increase of gas flow at the chimney and no new emission authorisation is necessary. It does not require expensive confinement systems and reduces costs by reusing air that has already been heated. It can also ease the process of
gaining permits for new plants. In addition it allows recycling of the trapped oil, is easy to service by cleaning the filters and features a filtration system that is laser welded and hydraulically sealed to prevent leaks.
Ammann www.ammann.com
One of Benninghoven’s customers has used the firm’s innovative hydrogen burner to produce several thousand tonnes of asphalt.
The hydrogen burner from Benninghoven is supplied with an intelligent control system to maximise the efficiency during asphalt production. This includes control of the feed systems, including the pressure control section, drying section with burner and burner control.
To make the asphalt production process more efficient, Benninghoven says it has developed a new generation of burners that includes the control and drying system alongside the burner itself. With this system, up to four separate burners can be operated at the same time.
This versatile approach increases the costeffectiveness of the plant as an owner can use the best-available energy sources. Switching between fuels or combinations of multiple fuels is done on the fly, meaning that no shutdown or downtime is required and with only minimal temperature fluctuations in the process. Emissions are kept low when using hydrogen as a fuel are kept very low, with minimal NOx being produced.
The company also says that the power draw has been reduced by 20% while keeping the feed capacity constant. Heat transfer efficiency has been significantly improved by maximising
the use of the burner space and providing a burner control and geometry that ensures optimum flame production for each fuel. Another significant benefit for plant operators is the 5dB reduction in noise emissions. Green hydrogen is a sustainable fuel, producing no greenhouse gases and is suitable for the heating process thanks to its high energy density. In many cases, facility operators wanting to start using hydrogen as a fuel experience difficulties due to current limitations
in their infrastructure. Burner technologies from Benninghoven can be used to equip both new facilities and existing asphalt mixing plants, while Retrofit solutions can be deployed in plants from other manufacturers. This gives a plant operator the chance to upgrade to the latest technologies, an important aspect for ensuring economic, sustainable asphalt production and long-term plant operations Benninghoven www.wirtgengroup.com
Dynapac is making an important introduction to its asphalt compaction line in the shape of its innovative Seismic technology. First developed for use in soil compaction, the resonant frequency, self-sensing Seismic system is now available as an option for the more complex asphalt compaction segment. A spokesperson for Dynapac said, “It was more complicated and took five years of R&D and needed a lot of testing.”
He explained that as temperature is a critical factor for stiffness in asphalt compaction and because the material is in layers, the system required heat sensors to be installed and more complex algorithms to be developed. As with the system for soil compaction, the technology allows drum vibration to match the resonant frequency of the asphalt course to provide optimum compaction.
Because the system matches the compaction forces required to the characteristics for a specific section of surface, it also offers another important benefit as the spokesperson said, “You will never damage the aggregate.” This avoids the risk of aggregate being cracked or crushed by compaction forces. He added, “The seismic system adjusts the frequency every 0.2 seconds.”
The system is now offered as an option on the new rigid frame CX 8C and CX 9C models, which have drum widths of 1.5m and 1.7m and weights of 8tonnes and 9tonnes respectively. These models have also now been upgraded to the Generation 6 level seen earlier on the 6, 10 and 13tonne class machines. Meanwhile, the 6, 10 and 13tonne Generation 6 models will be made available in Seismic form as an option later in the year.
To meet French requirements these Generation 6 drum steer
Hamm’s latest asphalt compactors now offer both vibration and oscillation capabilities for effective compaction. The HD+ 120i V-VIO 12tonnes tandem roller is equipped with a vibration drum at the front and a VIO drum delivering oscillation forces at the rear. High compaction forces are claimed, along with reliability, durability, productivity and ease of maintenance.
The roller is powered by a 115kW Deutz engine that meets Tier 4 Final/Stage 5 emissions requirements and features the firm’s efficient Easy Drive operating concept.
A key feature is the versatility as it offers static compaction, oscillation and vibration. The operator can switch easily between vibration and oscillation, removing the need to switch machines or deploy an additional machine and another operator on the construction site. This versatility means that the same machine can be used for different types of asphalt mixture as well as applications. The combination of vibration and oscillation delivers fast compaction in fewer double passes, suiting it to final compaction. High compaction quality is claimed even at increased working speeds.
machines deliver 0.8mm of amplitude and benefit from larger eccentric weights and reinforced bearings. This specification is now the standard for the CX models. The vibration system itself is conventional though and does not require any special maintenance as the core of the technology is in the control unit, while it is said to be simple for the operator to use.
Dynapac’s intelligent Seismic compaction system now offers optimum performance for asphalt works
Other key benefits for the Seismic option are reduced operating noise, less vibration for the machine (in turned reducing wear and tear and fatigue for the operator) and lower fuel consumption. The spokesperson said, “We estimate around 10% fuel savings.”
Dynapac www.dynapac.com
The machine has the latest Hamm cab, offering good all-round visibility as well as various interfaces to connect telematics systems, fleet management systems and digital applications for controlling and documenting compaction.
Operators can make use of the benefits of oscillation for the compaction of joints or compaction in vibration-sensitive areas such as on bridges. Oscillation also allows
compaction at low outside temperatures, since a wider temperature range can be used. The system is effective in preventing particle crushing and over-compaction, has benefits when compacting distortion-sensitive materials and reduces the noise emissions and vibrations experienced on and around the construction site.
Hamm www.hamm.eu
Ammann’s new light tandem roller is petrol-powered and features side-free drums that enable compaction in tight jobsites. The Ammann ARX 10.1 StV features the Honda GX630 petrol engine rated at 15.5kW. This reduces ownership costs and meets the latest Stage V/EPA Phase III emissions regulations.
The engine is more compact than its diesel counterpart. The smaller size enables positioning that allows cooling from all sides, helping the machine to perform in hot ambient temperatures.
Beyond size, the use of petrol brings other advantages. Petrol is generally less expensive, so there is likely to be a cost advantage with every fill of the tank. There is no need for a diesel particulate filter (DPF) and maintenance of a petrol engine is less costly than for a diesel engine. Petrol is often
more convenient for smaller construction companies and rental customers.
The Ammann ARX10.1 StV is the only machine on the market with drum consoles installed from a single side. The drums are support-free on the right side. This allows compaction work on the tightest of jobsites. Drum working widths are 900mm and drums are installed in-line.
A powerful hydraulic system is the core of the powertrain structure. Both drums are equipped with robust drive motors that bring high traction, gradeability and speed. The motors are equipped with a negative parking brake mechanism that ensures safe parking when the engine is switched off.
The front drum is equipped with a vibratory system capable
of delivering 16.4kN at 76Hz of compaction power, which is sufficient for a wide range of jobsites. The rear drum is static and has no vibratory unit. The pressurised water sprinkling system has a tank capacity of 110litres. An interval water flow regulation mechanism, controlled
by the operator, ensures optimal water flow and extends sprinkling time. A two-stage filtration system (water inlet and central filter) is easy to reach and can be cleaned without draining the tank.
Ammann www.ammann.com
Ermont says it is now seeing strong interest for its novel TSX continuous asphalt plant technology, which is available in both stationary and highway portable versions. The design features a single drum and a single burner but is able to deliver a mix containing a high percentage of recycled material. Romain Thommerot, marketing and communications officer for the firm commented, “We have a RAP capacity of 70%.”
The stationary technology can deliver more varieties of product for the customer such as clear binders, semi-warm asphalt and even cold mix. However, the portable plants are also versatile by their very nature. The design of the TSX system allows for changes in the feed, while ensuring quality of the output remains constantly high. The firm is commissioning the first stationary plant using the technology in the second quarter of 2024. “We already have some TSX HIGHWAY plants commissioned.”
The TSX HIGHWAY models are available in three versions, the TSX23, TSX26 and TSX28. These offer outputs of 120-270tonnes/hour, 160-380tonnes/hour and 200-450tonnes/hour respectively. All three can use up to 70% RAP in the feed. The TSX stationary plants are available in the TSX23 INCITY, TSX26 INCITY and TSX28 INCITY variants, with the same outputs as the
HIGHWAY versions.
In addition, the firm is also offering its TRX plant in INCITY stationary and HIGHWAY transportable versions. The former offers capacities from 150-360tonnes/hour and can
use up to 80% RAP in the feed, while the latter offers capacities from 150-430tonnes/hour and can use up to 100% RAP in the feed.
Ermont
www.ermont.fayat.com
The brands appearing at INTERMAT 2024 - BOMAG, DYNAPAC, ERMONT, MARINI, SAE and SECMAIR
- are showcasing their latest innovations for every stage of the road life cycle with solutions for asphalt production, application and compaction, road maintenance,
sweeping, cold milling, stabilization & recycling, and soil compaction.
Four interdependent pillars are combined to meet the challenge of decarbonisation:
• Machine efficiency
• Process efficiency
• Operator efficiency
• Alternative energy sources
The use of alternative energy sources, produced by carbon-free or low-carbon processes, reduces CO2 emissions further.
THE BOX, our first 100% electric sprayer, is a good example of the Fayat Group’s use of alternative energy. With 8 hours of charging, you can work autonomously for two days. This autonomy is further enhanced by the solar panels fitted as standard on the roof, which allow you to regain half a charge on a sunny day. The thermal performance of the emulsion tank is double that of the other products in our range. The thermal performance achieved means there is no need for a heating system, which consumes a lot of fossil fuels and emits CO2
For urban applications, THE BOX has other advantages: it operates quietly and looks more like a delivery truck than a road maintenance machine. For users, it’s a machine with a host
of jobsite-oriented features.
The employees of FAYAT Group’s Road Equipment Division brands - BOMAG, DYNAPAC, ERMONT, MARINI, SAE and SECMAIR - will be delighted to welcome you to the FAYAT stand at INTERMAT 2024 and to share all our information on what we are doing as a company to meet the challenges of decarbonization, throughout the entire road life cycle.
For more information on FAYAT, please visit www.fayat.com
The Volvo HX04 is the world’s first prototype fuel cell articulated hauler and is currently being tested in various customer applications to develop hydrogen technology. The test phase results provide important information about the possibilities offered by hydrogen and fuel cells as Volvo Construction Equipment (Volvo CE) continues its research for future product development programmes. It results from a research project between 2018 and 2022 funded by FFI, a national collaboration between the Swedish Innovation Agency VINNOVA, the Swedish Energy Agency and the Swedish Transport Administration to support strategic research, innovation and development of sustainable vehicles. Much
of the development and construction of the six-wheeled prototype took place at Volvo CE’s facilities in Braås, Sweden. Engineers at the Eskilstuna
Technology Centre in Sweden have contributed software development and knowledge from its fuel cell test laboratory. Although not yet available, the
valuable information gained from this concept will inevitably inform future production. Volvo Construction Equipment www.volvoce.com
With the MOBIREX MR 100(i) NEO/NEOe mobile impact crusher, Kleemann presents the first member of its new family of compact crushers. The machine is efficient, powerful and extremely flexible – and the NEOe version makes all-electric operation a viable option.
Thanks to its compact dimensions and a low transport weight, the MOBIREX MR 100(i) NEO/NEOe can be used flexibly, quickly and in a very wide variety of applications. Operation in tight spaces on worksites or in frequently changing places of work is easily possible. Operations range from different recycling applications, such as the processing of concrete, rubble and asphalt, to the processing of soft to medium-hard natural stone.
The new impact crusher from Wirtgen Group company Kleemann can be run allelectrically with the drive concept E-DRIVE and thus, locally, free of CO² emissions [MR 100(i) NEOe]. Alternatively, the machine is available with the tried-and-tested diesel-direct drive D-DRIVE.
Very high product quality is expected from an impact crusher, and this is precisely what the MOBIREX MR 100(i) NEO/NEOe delivers. This is guaranteed by the powerful crushing unit with its 4-ledged rotor providing a large impact range, and versatile rotor ledge options and by the 4m² large, optional, singledeck secondary screening unit. This makes it
possible to produce a classified final grain size. Through the use of an optional wind sifter, the final product quality can be additionally increased.
Thanks to a SPECTIVE operating unit specially tuned to the functions, the MR 100(i) NEO/NEOe operation is simple and intuitive. With SPECTIVE CONNECT, operators have all relevant data on speed, consumption values and fill levels at their fingertips on a smartphone or tablet and prepared in a clearly arranged manner. SPECTIVE CONNECT also
offers detailed troubleshooting aids to assist with service and maintenance. A unique feature in this machine class is the fully automatic crusher gap adjustment and zeropoint determination. Zero-point determination compensates for wear during crusher start and retains a homogeneous crushing product.
Starting this year, the MOBIREX MR 100(i) NEO/NEOe will be introduced gradually in Europe and North America. Kleemann www.wirtgen-group.com
Duratray International’s (Duratray)
Smart Tray is the most advanced dump tray for mining and construction trucks. The Smart Tray can monitor its condition (structural and wear) automatically and report to the user online and in real time.
Duratray is a major global name in designing and fabricating innovative, customised dump
bodies with capacities from 40-400tonnes.
Over 2,000 Duratray dump bodies operate in mines and quarries worldwide, including at Tarmac’s giant Mountsorrel quarry in Leicestershire, central England. Six Duratrays are working well on the site’s Cat 777G trucks.
Duratray dump bodies are
fabricated in each region to reduce transport costs while maximising the allowable payload. The novel suspended floor design also significantly reduces noise contamination. The dump bodies are designed to handle materials such as aggregates, copper, gold, nickel, diamonds, bauxite,
and
mineral sands.
The Duratray dump bodies’ benefits are said to include higher payload capacity, lower maintenance costs, reduced carryback where applicable, high resistance to extreme abrasion, and significantly reduced loading noise.
Duratray International www.duratray.com
Ammann says that its new battery electric plate compactors offer the same performance as the combustion engine powered variants. The eAPF 12/40 and eAPF 12/50 Forward Moving Vibratory Plate Compactors deliver a maximum vibratory frequency of 100Hz, the same as the petrol versions. The maximum centrifugal force is 12kN for both versions.
“They have that power and deliver the benefits of e-drives,” said Ralf Brutschin, Strategic commercial manager of Light Equipment at Ammann. “The Ammann plates reduce the contractor’s carbon footprint and allow work in confined spaces. They enable operation on jobs that require e-drive machines. They’re quiet, too, which is important in residential areas.”
Applications include pipeline and trench construction, asphalt and paving, and light and medium patchwork. The battery packs charge quickly and can be charged overnight to maximise capacity the next day. If needed,
the batteries can be charged for a shorter period during a shift and then returned to work.
The same batteries power both the Ammann e-plate and e-rammer – and likely additional Ammann machines in the future.
This provides convenience and promotes uptime.
The plate utilises lithium iron phosphate (LFP) batteries, which maximise safety. The batteries and their advanced management system are particularly robust and resistant to high temperatures, overcharging, and mechanical damage.
Another benefit of the e-plates is improved control. Electric drives provide better speed and torque control, while there are reduced maintenance costs as there are no fuel or oil filters to purchase or dispose of. Time spent on maintenance is reduced also, as is machine downtime for servicing.
The plates utilise a singleshaft vibratory system and a balanced base plate that properly distributes compaction power. These features provide
the industry-leading speed that maximises productivity and enables compaction targets to be met quickly.
The innovative design includes tool-free options that help APF machines work productively in varied applications. The compactors can quickly switch to compacting asphalt and paving stones. The units are made from high-quality, wear-resistant steel and base plate service is not required during the life of the machine.
The low-vibration guide handle protects the operator and eliminates the need for record keeping, as well as offering manoeuvrability, control and accuracy. The easy-to-grip frame increases productivity, while the e-drive APF offers gradeability of 30% and maximum incline of 20º to all sides, as well as the same speeds as the petrol version of 0-20m/min. Ammann www.ammann.com
The Quick Arden (QA) quick coupler system from Arden Equipment allows the rapid change of various tools on a hydraulic excavator or backhoe loader. These self-locking quick couplers are fitted to all excavators from 0.8-12tonnes and meet current safety standards. The QA05H and QA Series 3 hydraulic quick couplers are fitted with a safety paddle on the front pin that acts as a locking indicator.
Arden’s AIO (All In One) automatic quick coupler enables a user to connect hydraulic and mechanical implements automatically, safely, and in seconds, without leaving the cab. The AIO 601 can be fitted to all forwarders from 27-40tonnes. Compact, robust and equipped with very high pressure and very high flow connectors that make it compatible with the most powerful equipment on the market, the AIO is suited to demanding worksite applications, such as demolition and recycling. Arden Equipment www.arden-equipment.com
Komatsu Europe has unveiled the PW168-11 and PW198-11 wheeled excavators. The pair expand the range of the successful short-tail wheeled excavators in the 16-20tonne operating weight class.
Compact and easy to transport, powerful, comfortable, versatile, reliable and durable, the PW168-11 and PW198-11 respond to the most frequently expressed customer requests.
You can quickly transport your new Komatsu wheeled excavators to the next construction site without needing a special low-bed trailer and work with them in narrow, limited space. With
a low transportation height of just 3.1m, transport on standard low-bed trailers with a loading height of up to 4m is possible. The short rear overhang of 1.85m (PW168-11) or 1.9m (PW198-11) is ideal for narrow construction sites.
Equipped with four-cylinder Komatsu diesel engines (110kW or 129kW), the new short-tail wheeled excavators dig, lift and pull away almost anything on your jobsite. These engines meet the current EU Stage V emissions standards and are factorysupplied with environmentally
friendly HVO Diesel fuel as standard. The unique machine design with an optimised boom and rear engine enables
enormous lifting performance to move heavy loads easily.
Komatsu www.komatsu.eu
Rototilt says working with a tiltrotator attachment can notably reduce an excavator’s energy consumption, while boosting sustainability credentials.
“A tiltrotator makes it easier for you to work with an excavator, thanks to the increased flexibility of the work tool’s movements. It enables you to adjust its angle and rotation, which in turn makes it easier to carry out tasks with fewer machine movements. This saves fuel, but it has even more advantages in the long run,” said Rototilt product manager SvenRoger Ekström.
Ekström is pleased with “impressive” early tests that are said to indicate significant energy savings when using Rototilt’s latest tiltrotator series.
“We call this the tiltrotator effect,” he explained. “We have always known that there is a big difference between working with and without a tiltrotator. Not only do you need to use fewer machines, but you can also carry out the task at hand with fewer movements and changes of
position. This saves fuel and time and reduces the impact on the ground where you are working. It, therefore, has a number of positive environmental effects.”
Headquartered in Vindeln, northern Sweden, Rototilt is a well-established global market tiltrotator manufacturer for industries including quarrying and construction. Ekström said the company’s new RC Tiltrotator series further increases the positive impact thanks to their improved energy efficiency, which results from Rototilt’s proprietary pressure-compensated hydraulics.
“We have taken measurements comparing our previous series with the new, pressure-compensated hydraulics in the RC4-RC9,” noted Ekström. “The results are impressive, to say the least. We have managed to improve the efficiency of our product, enabling it to perform the same task with reduced energy consumption.”
Rototilt says the time saved by using a tiltrotator, coupled with the energy improvements in RC Tiltrotators, can consequently
Rototilt is explaining how the use of its RC Tiltrotators can reduce an excavator’s energy consumption (Pic: Rototilt)
make a major difference to a project’s efficiency and energy consumption.
“Our lab tests indicate a reduction in fuel consumption of between one and 2litres/hour for a 20tonne machine, compared to our previous tiltrotator series,” stated Ekström. “Out in the
field, the savings are affected by a number of factors, such as the type of machine and the job in question. In terms of diesel/ year, this could mean savings amounting to thousands of Euros.”
Rototilt
www.rototilt.com
Hitachi Construction Machinery is launching its first zero emission 5tonne batterypowered excavator in Europe.
Hitachi Construction Machinery (Europe) says the machine is an illustration of how it is meeting the growing need for emission-free equipment, while strengthening its commitment to a sustainable future.
As well as zero exhaust emissions, the first Hitachi Construction Machinerybranded model in this class delivers lower noise levels, enhanced efficiency, exceptional performance in confined spaces, fewer maintenance requirements and less downtime than conventional models.
The new ZX55U-6EB operates with exceptional manoeuvrability in confined spaces, as it has inherited the short tail swing of the dieselpowered ZX55U-6 model. It is also said to provide equally high levels of performance.
Customers can work on various projects with the ZX55U-6EB,
including urban construction sites, residential buildings and waste material handling projects – wherever the environment is a priority. Customers can choose
between battery-powered operation, using 39kWh lithium-ion batteries, and wired operation, which allows the machine to work while charging
French firm Mecalac is now offering its first range of electric machines. Produced in Annecy in France, these machines can be used all day, offering more than eight hours of working on a jobsite.
The new electric excavator, dumper and wheeled loader offer benefits including less vibration, a drop in working noise, reduced maintenance and lower maintenance costs. In addition to these technical advantages for drivers, these machines contribute to the decarbonisation of worksites and help to improve the air quality in cities.
Mecalac’s electric e12 excavator is said to offer performance and a compact design for the 10-12tonne class. The power source, separate from the turret, enables a record capacity of 150kWh to be installed, offering eight hours of working.
The ES1000 swing loader is said to be fast, with its 100% electric transmission and power supply. The stability of the rigid chassis and the ability to manoeuvre and swivel the arm simultaneously are said to be key to its
from a CEE 400VAC 3-phase power source.
Hitachi Construction Machinery (Europe) www.hitachicm.eu
productivity and enable efficient use of space on worksites.
Compact and manoeuvrable on all types of terrain, the Mecalac eMDX electric dumper is said to be an efficient solution for transporting materials on construction sites. It now incorporates all Mecalac’s expertise and technologies in terms of zero emission
solutions.
These machines can be recharged in 4-8 hours (depending on the model), for a working time of eight hours. Charging can be via a Type 2 socket or via an industrial 5-pin socket (3P+T+N) on a worksite charging station.
Mecalac www.mecalac.com
Caterpillar dealer Bergerat Monnoyeur is presenting a trio of battery-powered electric prototype machines for the first time in France. All three models are powered by Cat-designed lithium-ion batteries.
The Cat 906 battery electric prototype compact wheeled loader utilises the well-accepted Next Generation 906 diesel
variant platform, expanding productivity and operator comfort enhancements. It is equipped with the Cat 300 V battery (64kWh). Depending on use and application, it can run for up to six hours on a single charge.
The Cat 950 GC battery electric prototype medium wheeled loader is designed to handle jobsite tasks, from
material handling to truck loading, general construction and stockpiling. Its Cat 600 V (256kWh) battery provides a run time of up to six hours on a single charge, depending on use and application.
The Cat 301.9 battery electric prototype mini excavator, compact in size, can work in a wide range of
applications. Its ability to enter narrow doorways makes it an excellent machine for interior demolition work. Its Cat 48 V battery (32kWh) provides a run time of up to eight hours based on typical utilisation and application at a 40% to 60% utilisation rate.
Bergerat Monnoyeur www.bm-cat.com
Montabert is introducing five upgraded versions of its popular hydraulic breakers. The XL2700 replaces the XL2600; the V4700 replaces the V4500; the V47 replaces the V45 and V46; the V57 replaces the V55 and V56; and the V67 replaces the V65.
The upgraded hydraulic breakers have benefited from all the technical advancements developed by Montabert over the past years, allowing these hammers to offer even higher performance than their
predecessors. They have also been designed to be maintained at a lower cost, notably through repairable components.
Still manufactured in France, these new breakers have already begun operating at the Saint-Priest factory near Lyon.
The XL2700 and V4700 are already available (several XL2700 units are in operation at TELT, the tunnel between Lyon and Torino). The V47, V57, and V67 will be available in spring.
Montabert is also introducing
a new series of drilling mast hydraulic attachments that transform an excavator into a surface drilling machine. The French company says it has taken these products to a new level by incorporating new technologies and enhancing existing products.
The three largest models are already available. The CPA-28050 will be available later in 2024. Montabert www.montabert.com
has upgraded
(Pic:
Ammann has released its first electric-drive mini excavator, the Ammann eAMX 15. The machine provides 11kW, which is equal to its diesel counterpart. The e-drive excavator can perform on jobsites with the strictest emissions standards inside structures or underground, while its quiet operation allows work on urban jobsites and at night.
The Ammann eAMX 15 utilises a 21.5kW, cobalt-free lithium battery, located in the rear compartment and is protected from vibration. A charge lasts up to eight hours when the machine is operating in standard mode and can recharge to 100% in 10 hours using the standard process. It can also recharge up to 80% in
an hour when using an optional external charger.
The machine has a loadsensing hydraulic system, with a flow-sharing distributor, for smooth movements. It also has three working modes (economy, standard and power), fully electric controls and a modern display that allows the operator to personalise settings for first/ second boom and rotation.
The short tail profile allows operation in confined spaces and the machine is compact, with an offset of just 150mm. The width of the chassis and blade can be reduced from 1050mm to 790mm, allowing access to narrow trenches while maintaining stability. Total height is 2300mm and the rotation radius is 710mm, while good
reach and boom swing angles allow excavation in tight spaces. No tools are required to access daily service points, ensuring
the maintenance is completed quickly. Ammann www.ammann.com
The new Komatsu PC88MR-11 midi excavator builds on the solid foundations of the hugely successful PC88MR-10 and brings more unrivalled customer value to the midi excavator sector. The PC88MR-11’s new features significantly boost productivity, with reduced fuel consumption and faster work equipment speed.
The PC88MR-11 fully utilises Komatsu group know-how to offer ultimate versatility, ease of buying, and increased efficacy with the factory-fitted Lehnhoff Powertilt option. Environmental concerns are growing, and urban areas are becoming increasingly sensitive to emissions. The PC88MR-11’s low consumption and powerful EU Stage V engine (50.7kW) allow customers to participate in any tender, demonstrate environmental credentials, and future-proof their investment.
A tight tail swing lets the operator concentrate on the work at hand with no worry about rear-swing impacts and helps to make the PC88MR-11 a versatile solution, ideal even in confined areas
The external design has also been improved with an all-new MR-11 cutting-edge styling. The new PC88MR-11 offers first-class operator comfort, smart safety initiatives, intuitive ergonomics, huge advances in performance and controllability, easy serviceability, and peace
of mind through a proven Komatsu aftertreatment system and the industry’s highest levels of standard specifications.
Operators will find improvements everywhere: a redesigned blade for better dozing; repositioning of the low/high gear
switch for better ergonomics; or an automatic change-over valve for higher comfort when changing attachments. This will be appreciated by current and new users alike. Komatsu www.komatsu.eu
Drawing on a decade of experience and a deep understanding of the intelligent Machine Control system, Komatsu now offers its Smart Construction 3D Machine Guidance kit as a simple and flexible technological enhancement for a broad range of standard Komatsu machines and mixed fleets.
The 3D Machine Guidance kit provides an accessible way to add 2D and 3D machine guidance to any crawler or wheeled excavator from 13tonnes up to 120tonnes.
The kit can be customised with various optional additions such as a tilt bucket and couplers kit, a two-piece boom kit, a super long front kit, and a SATEL radio kit. These options allow the kit to better accommodate each customer’s machine configurations and operating conditions.
Developed by Komatsu for Smart Construction to the same strict standards as their renowned yellow machines, the 3D Machine Guidance kit hardware components provide customers with guaranteed reliable quality and performance.
Consistent with Komatsu’s
ongoing dedication to improving jobsite safety, a 3D safety zone feature has been integrated into the system. This allows customers to create and import avoidance zones. The feature serves as a preventive strategy, sending alerts to operators when they are near hazards such as powerlines, underground utilities, walkways, or public roads.
The 3D Machine Guidance kit’s automatic file conversion is compatible with the most common design file formats. This
ensures a seamless integration with customers’ existing 3D systems from different manufacturers.
In addition to the standard machine guidance functionality, the 3D Machine Guidance kit has an integrated payload meter option for Komatsu machines. This feature allows for dynamic material weighing, eliminating the need for manual checks and interruptions. This boosts productivity by ensuring each truck is loaded to its optimal
capacity without risking overload. Besides being a standard 3D GNSS system, the kit is integrated into the Smart Construction suite as a first step towards optimising the earthmoving process (DX). It works as an IoT (Internet of Things) tool, automatically collecting terrain and payload data, which can be visualised and analysed using Smart Construction solutions and expert advice.
Komatsu www.komatsu.eu
Bomag is introducing new capabilities for construction with the launch of its latest Asphalt Pro system. The package is able to supply information to everyone involved in a project and regarding every stage of the materials supply and use. Users can receive the data on a table device or smartphone.
A spokesperson for the firm commented, “It’s capable of organising everything from the mixing plant to truck distribution to the paver and compaction. Everybody gets the same information.”
Should a paver fail onsite, this information is sent straight to the mix plant for example, so that truck loads can be stopped and costly material wastage minimised. Similarly, the paver will be able to tell when trucks will arrive with materials for paving.
Useful information includes comparing the theoretical asphalt tonnage supplied with the actual tonnage used. If the theoretical quantities match the actual tonnages used, then this highlights the efficiency of a paving operation. But if there is a large disparity, it lets the paver operator know that the screed needs adjustment.
The sophisticated digitalisation package also allows users to reduce CO2 emissions as it helps to minimise energy use Bomag www.bomag.com
A new package from Leica Geosystems is said to help boost safety for personnel on construction sites. The PA10 system is intended to highlight the location of construction personnel on working sites to machine operators, as well as alerting workers as to where equipment is in use.
“It’s a personal awareness system,” said Thomas Bonvalot of Leica Geosystems. “Everybody onsite will know where a machine is working and the machine operator will know there is a pedestrian.”
Leica Geosystems www.leica-geosystems.com
Bergerat Monnoyeur is committed to supplying Cat customers with a set of services based on full fleet digital connectivity, artificial intelligence and augmented reality.
These new technologies offer access to remote diagnostics, allowing for informed predictive and preventive maintenance. Customers can also access the Bergerat Monnoyeur customer area, an e-commerce site for spare parts and mixed fleet data reports via VisionLink. The data is formatted by automatically sending a standard monthly report per machine with estimated fuel consumption, idle speed, carbon footprint and event code. Thanks to this digitalisation of services, Bergerat Monnoyeur customers have the tools and support to help improve their productivity and reduce their fuel consumption and carbon footprint.
Bergerat Monnoyeur www.bm-cat.com
Volvo Construction Equipment’s (Volvo CE) Connected Map provides complete visibility of the jobsite by giving a real-time visual overview of the position of every machine, vehicle and visitor on a customer’s site. The intelligent positioning service can be accessed by all site personnel, both in the machine (via Volvo Co-Pilot or an Android/iOS device) and in the office (via the Office portal).
Connected Map will display many typical site features and landmarks, including roads to help operators navigate the site, loading zones, unloading zones, speed zones and restricted areas. Points of interest such as offices, workshops, and service stations can also be visualised, which is particularly useful for new or temporary operators. Single-lane
(narrow road) sections can be defined as warning the operator if another machine is approaching in a singlelane section, helping to avoid traffic jams.
Connected Map users can also stay informed about the location of their machines, thanks to Connected Map’s search functionality, which will search and find users or machines in real time, with the machine’s last position visible for 30 days. Away from the office, Connected Map makes it easier for the operator to familiarise themselves with the site and know where everyone is, including visitors, helping to facilitate a simpler, safer and less stressful operation.
Volvo Construction Equipment www.volvoce.com
Cummins Inc., a global power solutions leader, plans to showcase a variety of power solutions in booth 5a D063 at Intermat 2024. This show
will debut the Cummins B6.7 Hydrogen engine for the construction industry in Europe. Visitors to Intermat will be able to see Cummins’ B6.7H
hydrogen engine aimed at a wide range of off-highway machinery, with a top rating of 290 hp (216 kW) and an impressive peak torque of 1200 Nm targeted for Stage VI/Tier 5.Cummins hydrogen powered combustion engines will provide sustainable solutions that can meet the demands of the most challenging applications. Hydrogen combustion is robust for the extreme operating and environmental conditions witnessed in construction and quarrying applications.
Also on display at Intermat will be the on-board fuel storage, a critical component in the adoption of hydrogen power. Hydrogen needs to be compressed into the available space to store enough to meet machine duty cycle requirements. Cummins’ joint venture with NPROXX, a world leader in high pressure hydrogen
storage for both stationary and mobile applications, will be supporting OEMs and their product integration process. The storage tanks on show will have up to 700-bar pressure capability to maximize capacity and operating range.
To see these products in person visit Cummins booth 5a D063 at Intermat, in Paris France April 24-27.
For more information on Cummins, please visit https://www.cummins.com/.
Cummins is unveiling a new fuel agnostic version of its 6.7litre engine able to run on hydrogen. Laurent Divito from the firm said, “It’s still a combustion engine so there’s a lot of commonality with components.”
The B6.7H marks a significant development project for Cummins. Divito commented, “This new engine is part of our destination zero policy. Our agnostic engine will be available in 2030.”
He said that the hydrogen engine is a key development for the future and commented, “It can be seen as a transition to the fuel cell because it will use the same tank and infrastructure.”
Fuel types will be important and he added, “The next generation of Stage 6 engines will be fuel agnostic. This could be available for off-highway use.”
Another key innovation from Cummins is the partnership with NPROXX to provide an efficient
fuel delivery system as well as high pressure fuel storage for hydrogen. The latest tank design now stores hydrogen at up to 700bars, which Divito said is becoming standard in markets such as the transport sector, where this fuel is beginning to be used. The increase in pressure allows for a significant gain in capacity, boosting running time. He added, “The engine is running at 10bars.”
The new tank is only part of the answer to fuelling however, and Divito said that there is still a long way to go in developing the infrastructure for hydrogenfuelled machines. “We need more hydrogen powered equipment in the market. You need to have the availability of fuel.”
He commented that fuel cell power systems will take further development to suit the rigorous construction and quarrying machinery environments. The fuel cell systems also require much cleaner facilities for
their production, so costs will remain high for some time. The advantage for internal combustion engines running on hydrogen is that they utilise a great deal of proven
technology and already feature the ruggedness and durability required for these challenging work environments.
Cummins www.cummins.com
Deutz is introducing an engine that will run on hydrogen as well as electric power retrofit options for off-highway machines. These form part of the firm’s programme aimed at reducing carbon emissions.
This programme represents a substantial investment in research & development for Deutz. Bert van Hasselt, head of Sales and Service for Deutz’s BU Green division said, “We are investing €100 million until the end of next year.”
The new hydrogen engine in testing is the TCG7.8H2 unit, a 7.8litre engine that will deliver 228kW. The first production units will be manufactured in the third quarter of 2024 and will be aimed at genset or rail applications initially, with an order of 100 units being supplied to China. However, once the units have been proven in these applications further duties will be available, including installations into construction machines. According to van Hasselt, the continuing high price of hydrogen as a fuel means that the unit sales will remain low until a better hydrogen supply
infrastructure (and more reasonable fuel pricing) becomes available.
In the meantime, Deutz believes its electrification retrofit package will be of interest for customers with existing fleets of equipment that is still comparatively new. These can be tailored to a wide range of equipment applications. According to van Hasselt, “We can retrofit equipment with diesel engines with an electric system. It’s part of the transition into the new world.”
To further expand the electrification range, Deutz is offering its onsite PowerTree package, which can provide electric power onsite with ratings from 30kWh up to 2MkWh.
In addition however, Deutz still believes there is demand for conventional diesels and is introducing the TCD2.9 unit, a 2.9litre engine which meets Stage 5/Tier 4 Final emissions requirements that has been developed jointly with John Deere. Coming later will be the TCD3.9 unit, also developed jointly with John
Deutz is developing a hydrogen-fuelled engine
Deere and due to enter field test in mid-2024, offering ratings from 75-130kWh. Deutz www.deutz.com
Moog Construction is offering the novel electrification retrofit kit from subsidiary Zquip for repowering machines in the construction, rental and quarry markets. This modular system can be installed in machines such as excavators and wheeled loaders in the 5-50tonne range and from any manufacturer. Scott Scheffler, marketing director of ZQuip commented, “We’re trying to make it easy for people to get into electrification in a more cost-effective way. With our solution, the batteries are swappable and fast charging. The machine hydraulics do not change at all.”
The package consists of the ZQuip batteries, an electric motor, a smart controller and a thermal unit to optimise battery temperature. Customers can select either 70kWh batteries or 140kWh batteries, depending on the application. These have the same footprint to ease installation and use the same base although the 70kWh units are shorter and weigh 700kg while the 140kWh units are taller and weigh 1,250kg. Depending on the installation and machine type, customers can select the optimum number of batteries as required.
Fast charging allows recharging
within one hour and the system comes with standard plugs and connectors. Batteries can be exchanged in just five minutes using a forklift truck or handling machine if more power is needed for the machine to keep on working. Rental firms can leave machines onsite and deliver freshly charged batteries if required or customers can use a charging station at the worksite. The smart controller draws power from one battery at a time and a display in the machine cab shows how much charge remains. Scheffler said, “You’re able to keep machines running all day
either by exchanging batteries or recharging. We’re making it easy for customers to adopt electrification.”
The system can be used in a wide array of applications and is of benefit to firms running mixed fleets of machines as it allows them to use the same modular battery technology. The power units can be exchanged between different pieces of equipment if required. According to the firm, the system is already being accepted by equipment dealers and comes with warranties.
Moog
www.moog.com
More power with less complexity and less weight. The Cummins B6.7 engine delivers the productivity you need to keep your equipment running. The power increases up to 326 hp / 243 kW and peak torque up to 1014 lb-ft / 1375 Nm, enabling replacement of engines with higher displacement with no impact on productivity.