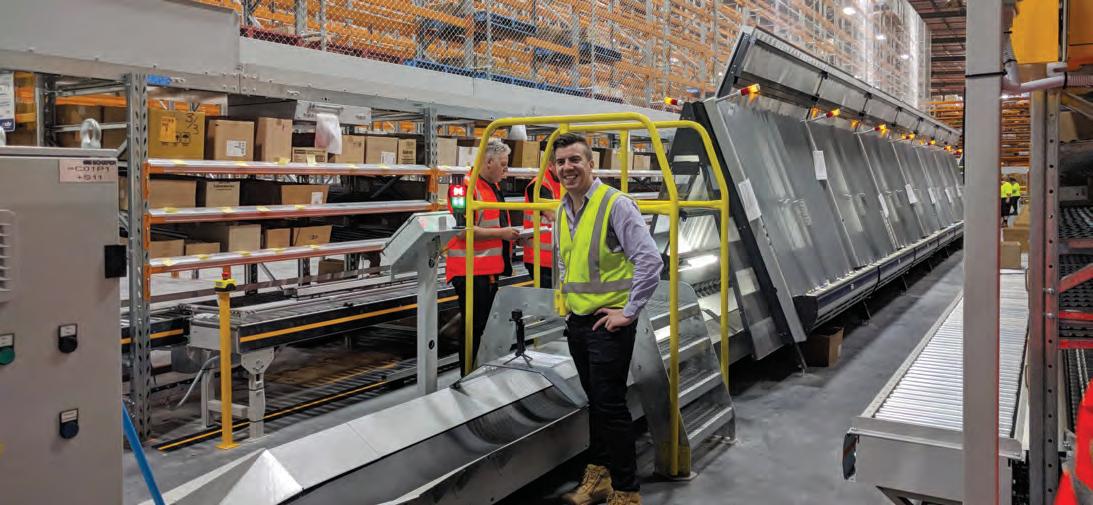
6 minute read
Fuzzy LogX success through safety
SUCCESS THROUGH SAFETY
Jeffrey Triantafilo, Director of Systems & DC Design at Fuzzy LogX.
Warehouse designs and operations continue to change, but worker safety is as important as ever. MHD talks to Fuzzy LogX Principal Consultant Bas Schilders about current and future safety priorities for vendors, designers and warehouse managers.
Six years ago, Principal Consultant Bas Schilders launched a new consultancy after years of working for some of the world’s largest automation vendors. He has since been able to build a team of “warehouse wizards” with an intimate knowledge of the solutions on the market. Fuzzy LogX puts extra effort into staying informed about the latest developments and works with complete independence from any vendor or property company.
This freedom allows the team to focus in on the specificities of a project, make the most of relationships across the entire automation spectrum and as a result, provide solutions solely benefitting the customer’s needs and wants.
Within that spectrum, safety is the cornerstone of everything Fuzzy LogX does.
Fuzzy LogX consultants initially perform a walk-through of a warehouse site to gauge a business’s processes at a higher level, even before they sign as a customer.
“Regardless of whether a business is already a customer of us or not, we will walk into any warehouse and look at it from a completely independent viewpoint and highlight anything we see that’s unsafe,” Bas says. “The most important thing is for all warehouses to be safe.”
“We never want to hear in the news about a safety incident in a warehouse we visited that could have been prevented by highlighting unsafe situations.”
AUSTRALIAN STANDARDS
Australia has a very high safety rating and there are many standards for almost every solution found in Australian warehouses. These standards apply across design, implementation, auditing, operating, and maintenance of a facility and form the basis for the Fuzzy LogX team to help keep facilities safe across the country.
Bas notes that it’s often small details which are overlooked in operations.
“It can be anything – as simple as not maintaining sufficient space between a person and a forklift in an aisle, operators being exposed to a rack baseplate that’s missing a bolt or a beam missing a safety pin,” he says.
“We are trained on what to look out for from a safety point of view in line with the Australian Standards.”
After a mad rush to the end of the peak holiday season last year, Bas counsels warehouse managers to avoid any complacency entering a new year. As e-commerce continues to drive businesses, he adds the onus should be on taking regular safety checks.
“A lot if it isn’t rocket science, Warehouse Managers can start by organising a weekly or fortnightly walk-through of their sites,” he says. “In the morning when people start working, have a simple safety checklist to check for any rack damages, or if any workers look like they are over-exerting themselves. If you’ve got obstructions in aisles leaving too little space for people,
it creates a safety hazard if you can’t get to the emergency exit. All these little things come into play. We can help set up checklists so it’s simple to keep on top of everything.”
SAFETY WITHIN THE TRADITIONAL AND AUTOMATED WAREHOUSE
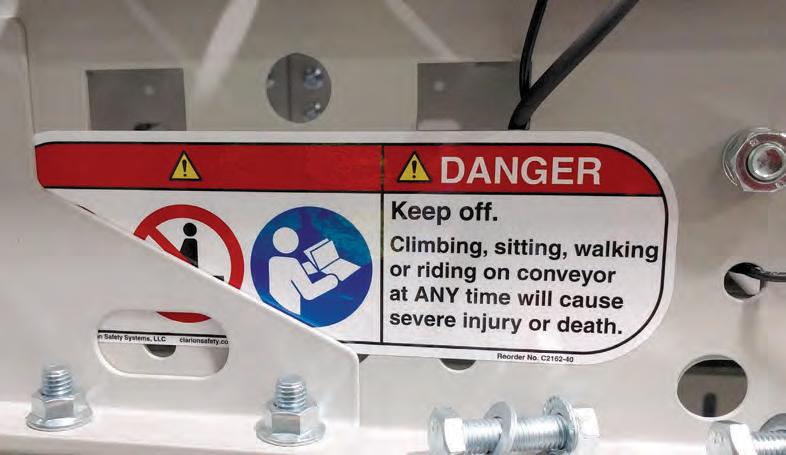
Within a more traditional warehouse environment, the most common safety risks are associated with materials handling equipment (MHE) which can result in someone being hurt by a moving object, according to Bas. This could be a carton falling down from height or someone being struck by a moving forklift, for example. The chances of racking system damage also increases exponentially when MHE is involved.
Everyone is familiar with the blue light proximity lights but they don’t prevent operators from interacting with MHE. There are active proximity solutions from Europe and the US that signal a forklift operator when they are moving too close to workers, while vision camera systems can actually detect pedestrians in real-time and stop forklifts altogether.
One system from Blaxtair has a response time of 300 milliseconds, stopping the vehicle when it detects a pedestrian. Bas says such technology is available on the Australian market, but uptake is slow.
“It’s not as common here to adopt the technology because many businesses are leasing forklifts,” he says. “Unless the rental provider has the capability or is willing to invest in technology and modify the equipment, you’re stuck with what you have. If you don’t have the technology, you rely on your processes to be absolutely safe.”
Entering a modern automated environment, there are more moving parts in different areas to consider. You have conveyors running at the same time as shuttles and ancillary equipment operating – machines all have to work in harmony with humans. This creates a different kind of safety issue, says Bas.
“Automation creates lots of “pinching” hazards. When something goes wrong with automation, the consequences are usually significant. Fingers can be crushed in conveyor systems from workers trying to fix stoppages themselves to meet KPIs,” he says. “Simple process rules like putting long hair up in a bun and not wearing a tie or loose jewellery around the warehouse can help prevent people getting caught in conveyors.”
With more unsafe areas scattered around the warehouse in an automated environment, Bas has seen customers – and the industry as a whole – emphasise safety precautions.
“It’s not just for when you design something, safety has to go across the design, the implementation of the system itself, then the operational side of running the system,” he says.
“If you read the letter of the law and the standard as a designer, consultant or customer, you’re responsible for making sure that even at the end of the of the useful life of the solution, the equipment is designed to be safe to dismantle. So, you have to think 15 or 20 years into
Regardless of whether a business is already a customer of us or not, we will walk into any warehouse and look at it from a completely independent viewpoint and highlight anything we see that’s unsafe. The most important thing is for all warehouses to be safe. ”
A standard conveyor safety sign.
the future and make sure that nothing will be built on top or around a system, making it unsafe to remove at the end of its life cycle.”
ERGONOMICS IN THE E-COMMERCE ERA
Safety expands beyond physical threats caused by automation and MHE. Especially as e-commerce operations continue to thrive, businesses are having to design and arrange workplaces to fit different body types. A standard goods-to-person (GTP) picking station might be fine for an average body type, but adjustments for people’s height, arm length, weight and pre-existing injuries will help reduce the strain on workers’ bodies over time. Provisions like lift platforms can help staff adjust their working height at a GTP station, for example.
“Standing at a station for seven and a half hours every day or carrying heavy objects overhead can be physically detrimental to people,” Bas says. “There’s a whole new level of business solutions that will have to cater for the whole spectrum of workers. The Australian standard requires solutions to be designed to cater for at least the 5th to 95th percentiles of the Australian population, which, if you think about this for a moment, are a lot of people, and all with different sizes and traits.”
“Most people don’t read the standards, so Fuzzy LogX pride ourselves in understanding the parameters and consequences. We want to take it to the next level because we don’t want people to get hurt in any situation.” ■