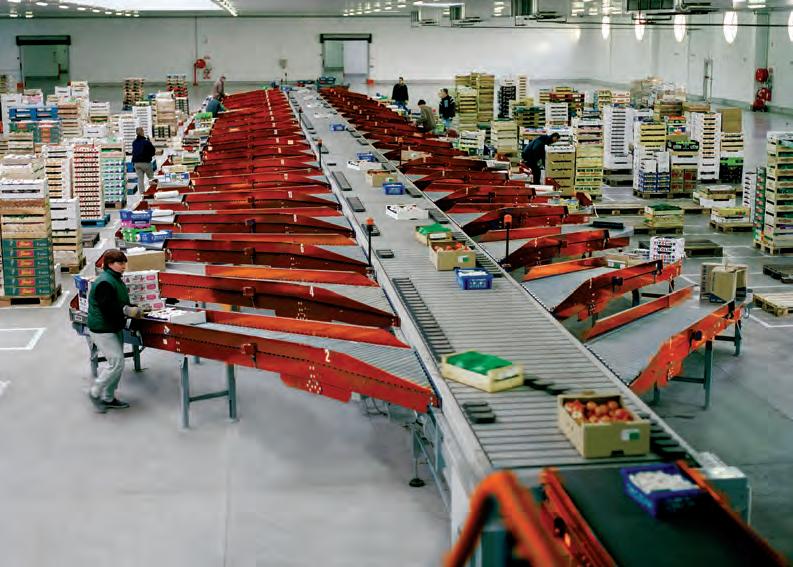
4 minute read
The cross-docking X-Factor
THE X-FACTOR
Cross-docking solutions are nothing new in the food sector. However, João Marinho, Senior Sales Consultant Warehouse Solutions for Vanderlande ANZ, explains why the strategy is becoming an increasingly attractive option for retailers considering their first steps towards automation – and how the company’s XDOCK solution can help businesses after an unprecedented period of market turbulence.
Labour scarcity, an increasing shift to online ordering and delivery models and a global pandemic have all significantly impacted the grocery and food retail sector. João Marinho, Senior Sales Consultant Warehouse Solutions for Vanderlande ANZ says Australian and New Zealand retailers are needing to respond to a market that continues to grow year on year and is changing beyond all recognition.
The pivot to online sales has accelerated the demand for technology and innovation within distribution centres, with increased automation the key to maximising future opportunities in food retail.
While Vanderlande was established in Australia in 2012, it has over seven decades of experience in moving its customers’ businesses forward in the airports, warehousing and parcel markets. João says the company is therefore perfectly placed to help food retailers who are looking more closely at the efficiency of their current operations and searching for the ideal platform for growth.
“The pandemic has had an undoubted effect on food retail and there’s now a real appetite for cross-docking solutions in the market,” he says. “Due to the unique labour situation in Australia, there was a significant lack of available people once borders closed. That shortage of manual labour has really driven the need for automation and many customers are contacting us with concerns about their ability to deal with the spikes in demand.”
Vanderlande has a long track record of supplying warehousing process automation systems for many major retailers, including some of the largest distribution centres in the Southern Hemisphere. But it’s not limited to the biggest players.
João believes that Vanderlande’s XDOCK is designed to help retailers taking their first steps in search of greater control of their DC processes as they begin the move from manual to automated logistic operations.
Scaleability is one of the biggest advantages of such a system, allowing retailers to overcome the challenges of labour scarcity with a material handling system that can be easily scaled up to match the growth of their business.
“We’ve installed systems in various countries in Europe, as well as in many other countries in the world,” João notes. “XDOCK is a really flexible solution that provides food retailers with the perfect platform for growth.”
Vanderlande’s XDOCK combines ergonomically designed infeed stations with its high-capacity POSISORTER sliding shoe sorter, and VISION (Vanderlande’s Warehouse Control System) software. It can handle a wide range of case types and is known for its high availability and reliable operation. An XDOCK system provides a wide range of benefits, including less dependency on labour, reliable delivery times to stores, more accurate deliveries, and enhanced tracking and tracing.
“This kind of solution is really flexible, and the core POSISORTER system can sort almost any size and shape of case,” he adds. “With a capacity over 6,000 cases per hour, it’s higher than what most cross-docking operations require. It also has a high sort accuracy, relatively low noise levels and gentle product handling, thanks to its closed deck, which allows such a wide variety of goods to be handled via its smooth sorting action.”
A common barrier to investment in automation is the concern over
XDOCK is used in many sites worldwide.
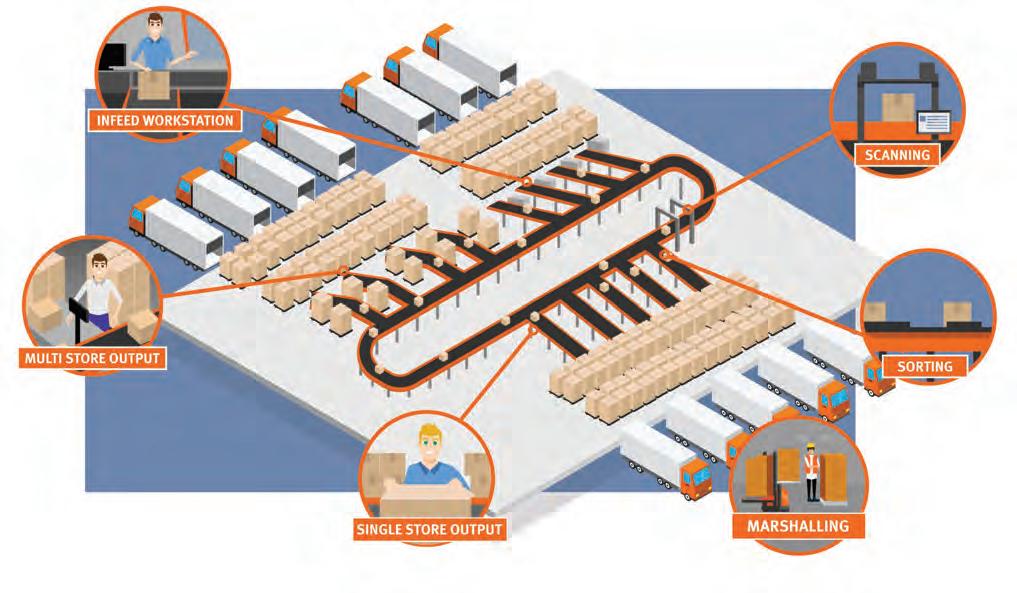
XDOCK is a cross-dock solution that facilitates the automation of stockless operations.
the payback time, but the return on investment for XDOCK can be rapid. Initial installation allows retailers to maximise their current infrastructure, and it is easy to extend or adapt to increase capacity when growth allows. It’s therefore unsurprising that XDOCK is a proven solution at many sites worldwide, notes João.
“Two to five years is an easy ROI for a system like this, although it depends on the customer’s picking solutions and layout efficiency,” he says. “Installation times are relatively fast too and can often take place while operations are running. It requires close cooperation with the customer, but it’s possible and we’ve done it many times before.”
As XDOCK is modular and flexible, it supports a retailer’s agility from the outset, ultimately enhancing service levels to stores and consumers. And as the POSISORTER has such a high capacity, when a business grows it’s easy to install more chutes and inducts, or even increase the speed of the sorter. An initial investment in a core sorter can later be merged with an AS/RS solution if required, to successfully manage high operational peaks.
However, even in times of increased mechanisation the human factor shouldn’t be overlooked, says João.
“In these times of labour scarcity, one of the big advantages of automation is that you are able to offer your workers solutions that are designed with ergonomic and health and safety benefits,” he adds. “For example, our induction stations and lifting tables enable operators to minimise manual effort while lifting products and reduce excessive body movement while loading products. These solutions help to save the considerable effort of physically picking millions of kilogrammes of cases in a large DC.”
“A solution such as XDOCK helps retailers to achieve the desired throughput in their DCs, while creating the extra capacity required to match growth. By improving the quality and completeness of orders, it guarantees more accurate deliveries. The system can be adapted long into the future and quickly scaled up to support a growing operation, allowing the retailer to remain competitive.” ■
XDOCK can be easily scaled to support a growing operation.
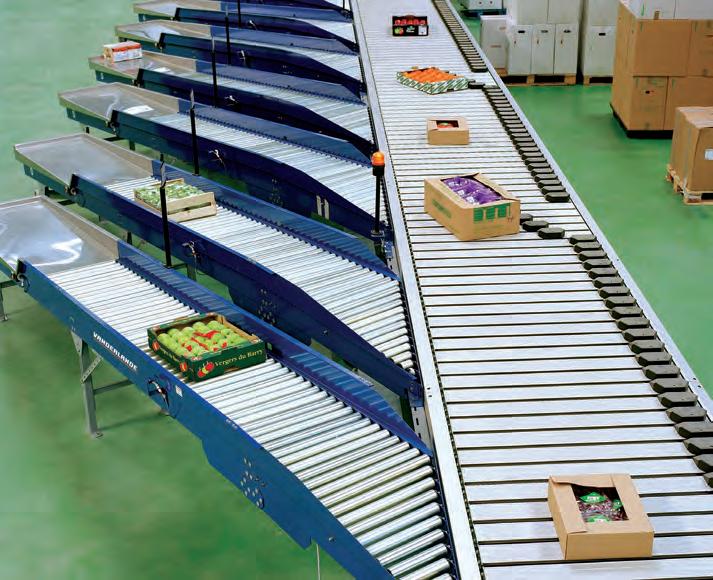