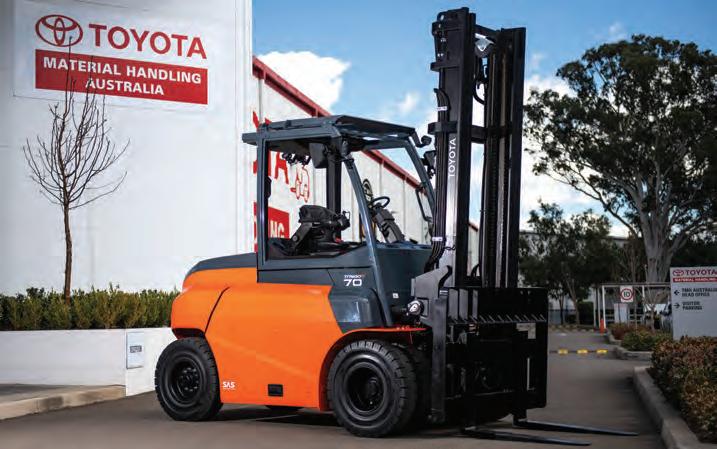
5 minute read
TMHA setting the sustainability agenda
SETTING THE SUSTAINABILITY AGENDA
Toyota has for three decades been pursuing ambitious sustainability goals. MHD explores the history of the company’s environmental commitments, and the latest products in sustainable materials handling.
In 1992 the Toyota Motor Corporation announced the introduction of ‘A Comprehensive Approach to Global Environmental Issues: Earth Charter’ – setting out the modern framework that Toyota companies would take with respect to environmental objectives.
Although Toyota Motor Corporation had already been an innovator with commitments to greater efficiency using fewer resources, the futureforward “A Comprehensive Approach to Global Environmental Issues: Earth Charter” from 1992 set a new – and from the standpoint of three decades later, impressively early – agenda with respect to environmental sustainability, including identification of climate change as a key issue.
“Finding ways to preserve an abundant natural environment to pass on to future generations is the most pressing issue for people on earth today,” the 1992 Earth Charter says. “It is an issue that demands the attention of each and every individual. And it is an issue that transcends borders – as in problems like global warming – and thus demands a global response.”
The “Comprehensive Approach” set out in the 1992 Earth Charter included developing technologies to minimise the environmental impact of automobiles and automobile plants, implementing environmental programs through Toyota’s production and marketing operations worldwide as well as through parts suppliers and through vehicle distributors and dealers.
The original commitments of the 1992 Earth Charter have been repeatedly bolstered and elaborated upon by Toyota companies over the years. Just last year the Toyota Industries Corporation outlined its “Basic Stance” on environmental commitments, with “prevention of global warming” as its highest priority for the environment. And in 2015 Toyota Motor Corporation announced the ‘Toyota Environmental Challenge 2050’ – setting challenges for all Toyota subsidiaries globally:
The Toyota 9FBMT 7.0 tonne forklift.
• Reduce CO2 emissions from new vehicles by 90 per cent (2010 baseline) • Eliminate CO2 emissions from operations • Eliminate CO2 emissions from suppliers and dealers • Conserve water and protect water resources • Support a recycling-based society • Conserve biodiversity, protect species, and restore habitats.
Toyota Material Handling Australia (TMHA) is meeting and exceeding its ambitious objectives. Indeed, for its own operations the Toyota Industries Corporation set as its target a reduction of 26 per cent of emissions (from fiscal year 2012 baseline) by 2021. Toyota’s European factories – which manufacture some of TMHA’s equipment – well exceeded that goal, achieving a reduction of 31 per cent.
So, in the Australian context, what are some of the latest sustainable products Toyota is creating for the materials handling market?
Glen Ryan, Product Manager – Toyota at TMHA, says that in terms of traditional counterbalance forklifts, it used to be the case that more than 3.5tonne forklifts generally had to run
on an internal combustion (IC) engine rather than electric.
“However, at the start of 2019 we launched in Australia our 8 FBMT and 9 FBMT range,” says Glen. “These encompass our 3.5 to 8.0 tonne battery electric range. Previously, such tonnage required an IC forklift, which was not only less sustainable but less pleasant for workers – who in confined spaces had to deal with exhaust fumes. Now we can eliminate that with this new range of machines with no operating emissions. It’s better for the operator, better for people working nearby, and better for the environment.”
Michael Marks, Product Manager – Warehouse MHE at TMHA, says that over the past decade Toyota’s R&D has predominantly focused on improving its battery-electric range, in keeping with Toyota’s overall philosophy of continuous improvement.
“Toyota equipment has continuously evolved in terms of the efficiency of the machine, and now we’re seeing evolution in terms of electric batteries themselves,” Michael says.
For example, the difference between lithium-ion electric batteries and traditional lead-acid batteries is not limited to sustainability criteria.
“A key difference between a lead acid battery and a lithium-ion is that the former should only be charged from 20 per cent to full, which takes about eight hours,” Michael says. “With lithium-ion batteries you can plug them in whenever you like, and it doesn’t affect the lifespan of the battery. This makes a significant difference to cost, as customers can charge their batteries when they need to rather than having to wait for an
The Toyota Reflex Reach Forklift.
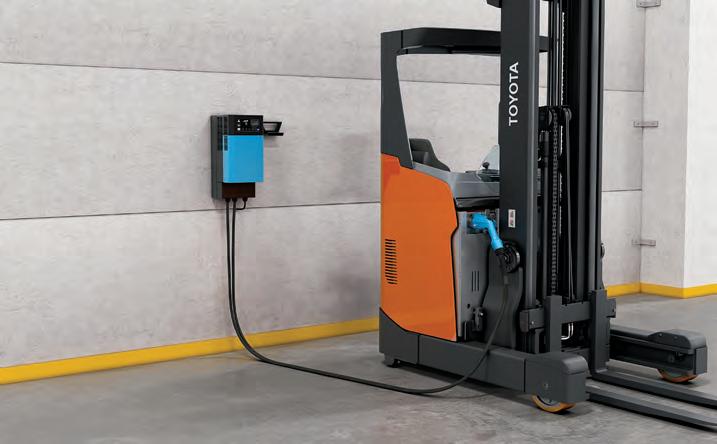
eight-hour window – usually overnight – to charge their forklifts.”
Because many larger companies operate two or three shifts a day, there isn’t necessarily an eight-hour window to charge, which means that they used to have to bring in additional machines or shift batteries to compensate while one is being charged. This is no longer the case with lithiumion batteries, which can be charged quicker and more flexibly – whenever a forklift is not in use.
“Lithium-ion batteries give more consistent and efficient power delivery and allows for faster charging which leads to reduced energy costs,” Michael says. “We have partnered with a major OEM to produce our lithium-ion cells – and they share the same environmental values as Toyota. We are committed to helping the customer achieve their own sustainability objectives within their operations. We predict that switching to a lithium-ion solution could reduce your CO2 emissions by as much as 20 per cent across your operations.”
Glen notes that these and other improvements to battery electric machines – such as the fact that TMHA’s battery electric counterbalance forklift range is now IPX4-rated (splash resistant, such that it can drive in the rain) – have effected a cultural change in customers that leans increasingly towards electric batteries. Today, he says, battery electric products take up roughly 60 per cent of the market.
The Toyota philosophy of continuous, incremental improvement is sure to keep tipping the market further towards battery electric products. Indeed, Glen and Michael are both excited about the new Toyota Reflex reach forklift range, as well as the new LWI160 pallet truck – the first Toyota pedestrian-operated pallet truck that has been designed around a modular lithium-ion battery concept.
Three decades on from the 1992 Earth Charter, it’s clear that Toyota’s commitment to serving the customer at the same time as it sustains the environment is only getting deeper. ■
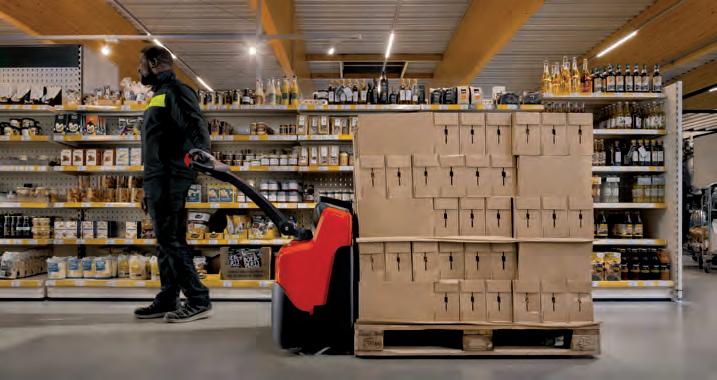