WELLBEING IN THE WAREHOUSE
Prological on making facilities fit for people
INTEGRATING INTEROPERABILITY
Blue Yonder's new interoperable services

How

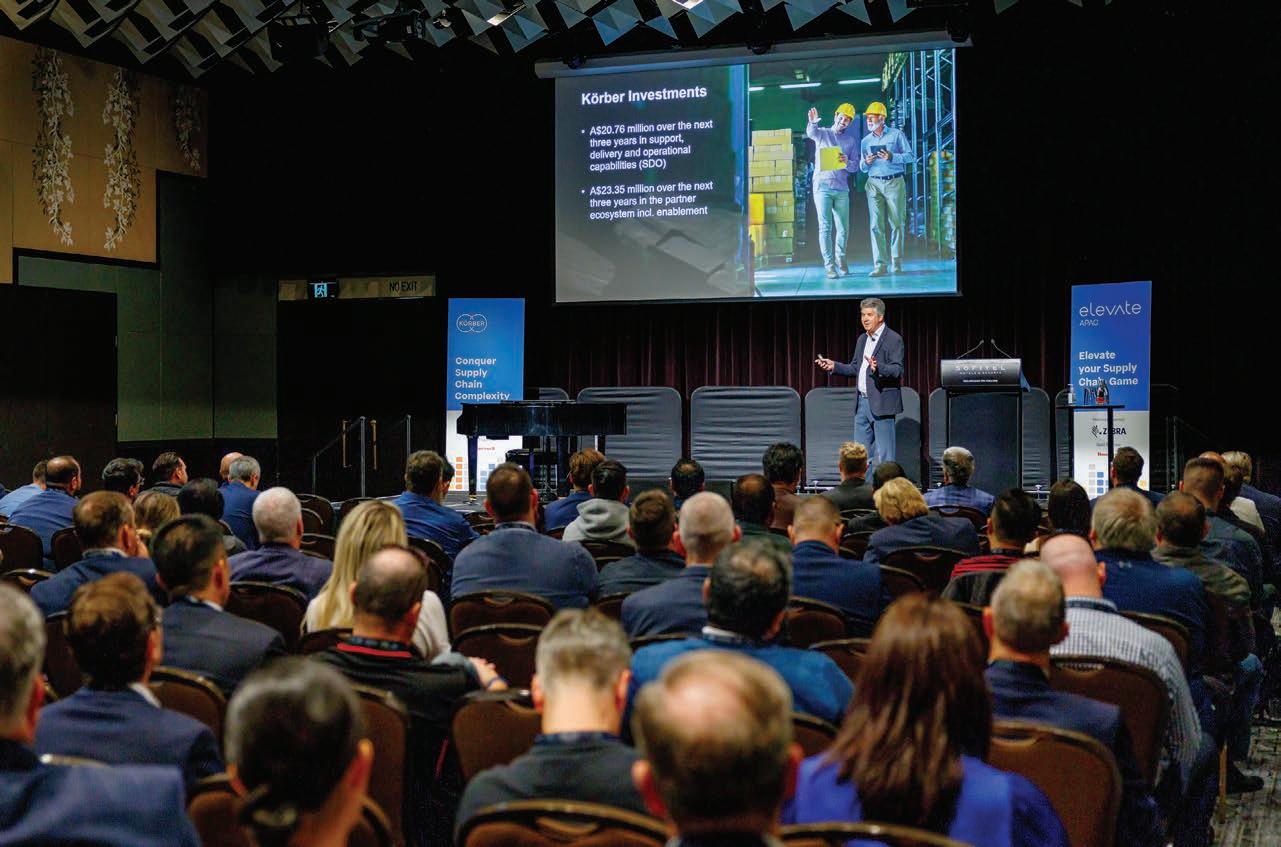
WELLBEING IN THE WAREHOUSE
Prological on making facilities fit for people
INTEGRATING INTEROPERABILITY
Blue Yonder's new interoperable services
How
Building on the success of our first in-person Elevate last year, this year’s event will help you chart your course toward operational excellence and supply chain resilience. Featuring keynotes from industry leaders, insights into the latest technology, and networking opportunities, you won’t want to miss our Elevate event and early bird offer.
CONTACT
MHD Supply Chain Solutions is published by Prime Creative Media
379 Docklands Drive, Docklands VIC 3008
Telephone: (+61) 03 9690 8766
Website: www.primecreative.com.au
THE TEAM
CEO: John Murphy
Chief Operating Officer: Christine Clancy
Managing Editor: Syed Shah
Editor: Edward Cranswick
Journalist: Joseph Misuraca
Business Development Manager: William Jenkin
Design Production Manager: Michelle Weston
Art Director: Blake Storey
Graphic Designers: Louis Romero, Kerry Pert
Client Success Manager: Janine Clements
FOR ADVERTISING OPTIONS
Contact: William Jenkin
william.jenkin@primecreative.com.au
SUBSCRIBE
Australian Subscription Rates (inc GST) 1yr (6 issues) for $78.00
2yrs (12 issues) for $120.00 – Saving 20%
3yrs (18 issues) for $157.50 – Saving 30%
To subscribe and to view other overseas rates visit: www.mhdsupplychain.com.au or Email: subscriptions@primecreative.com.au
MHD Supply Chain Solutions magazine is recognised by the Australian Supply Chain Institute, the Chartered Institute of Logistics and Transport Australia, the Supply Chain and Logistics Association of Australia and the Singapore Logistics and Supply Chain Management Society.
In the rapidly evolving landscape of Australian logistics and supply chain management, the first half of 2024 has been a testament to our sector’s unwavering resilience and dynamic adaptability. As we navigate through this era of transformation, several pivotal trends have emerged, guiding our journey: the indispensable role of real-time tracking, our collective stride towards enhanced agility in response to burgeoning e-commerce demands, and a concerted shift towards sustainability and efficiency.
At the forefront of these developments, Australia Post’s achievement of delivering nearly 100 million parcels during a record-breaking period stands as a beacon of operational excellence. This milestone not only accentuates the significance of advanced logistics systems in managing voluminous demands but also reflects the changing tide in consumer preferences, with a notable pivot towards digital engagement over traditional services. Amid this success, the introduction of the Post26 strategy offers a glimpse into the future, advocating for a leaner, more sustainable operational framework.
The industry’s commitment to innovation and sustainability is further illuminated by Visy’s strategic acquisition, introducing right-sized packaging technology to the Australian and New Zealand markets. This move underscores our collective endeavour to marry efficiency with environmental stewardship, reducing waste and optimizing freight operations in the process.
Equally important is the development of a new, strategically located warehouse in Perth, embodying the essence of modern logistics infrastructure with its focus on operational efficiency and sustainable design. This initiative mirrors the sector’s recognition of the critical role infrastructure plays in fulfilling the promises of the e-commerce revolution.
Legislative advancements, notably the Fair Work Legislation Amendment, herald a new chapter in industrial relations within our industry, emphasising fairness and equity. This progressive step forward is indicative of a broader commitment to improving the working environment for all stakeholders.
Moreover, Amazon Australia’s expansion of its Prime FREE One-Day Delivery service speaks volumes about the industry’s agility in meeting the fast-evolving expectations of today’s consumers. This expansion, facilitated by strategic investments in infrastructure, marks a significant milestone in our quest to deliver unparalleled convenience and efficiency.
As we reflect on these narratives, our industry is at a critical juncture, poised for a future where technology, sustainability, and enhanced consumer experiences converge. These developments not only challenge us to rethink our strategies but also offer unprecedented opportunities for growth and innovation. In embracing these changes, we reaffirm our commitment to leading the Australian logistics and supply chain sector towards a more efficient, sustainable, and responsive future.
Warm regards and insightful reading,
Edward Cranswick Editor edward.cranswick@primecreative.com.auThe global management consultancy specialising in operations strategy and transformation, Argon & Co, is delighted to announce the appointment of its new Partner South East Asia.
Former SAP Ariba, PwC, KPMG and Johnson Controls leader, Nelson Chow, will lead Argon & Co’s Singapore office with a remit across the APAC region.
It says he has earned his deep business and digital transformation knowledge throughout his 20-plus years of consulting experience focusing on operational excellence, margin improvement, and technology transformation.
“This appointment comes at a time of continued growth within the APAC region,” says Paul Eastwood, Managing Partner of Argon & Co APAC.
“We recognise an incredible opportunity to expand our presence and capabilities whilst upholding our robust relationships and esteemed reputation in core sectors. Nelson will no doubt play an important role in shaping the APAC business, introducing fresh perspectives and innovative approaches to how we operate.”
In addition to his professional achievements, Nelson is deeply committed to nurturing the next generation of business and digital talents. He serves as a Visiting Lecturer for the Global Supply Chain Master Program at the Hong Kong Polytechnic University and as an Advisor for the Global Supply Chain Master Program at the Hang Seng University of Hong Kong.
“I am thrilled to join Argon & Co as we embark on this journey together, particularly amidst the vast opportunities for growth in Asia’s dynamic market,” says Nelson Chow, newly appointed Partner.
“The region’s burgeoning economy, marked by a rising GDP and expanding middle class, presents
Nelson Chow, brings 20-plus years of experience to Argon & Co. Image: Argon & Co.
significant potential in the consumer and manufacturing sectors, especially in luxury, retail and FMCG.
“I am confident that our hands-on approach and commitment to tangible results will drive
success for both global and local companies in Asia. Together we will redefine industry standards and shape a resilient and sustainable future for our clients across the region.”
As one of the world’s largest authorised Cat® equipment dealers, WesTrac knows that the smallest of parts can make or break a machine, and have a big impact on site operations.
At its headquaters in Tomago, NSW, WesTrac implemented an AutoStoreTM automated spare parts storage and fulfilment system from Dematic, which allows WesTrac to keep stock organised, use warehouse space efficiently, and prioritise urgent orders to be ready in just 5-10 minutes.
With the AutoStore solution, WesTrac can get vital parts to customers quickly, keeping Australia’s heavy industry moving.
Learn more at dematic.com/westrac
Supply chain consulting company, TMX Transform, says its latest whitepaper reveals artificial intelligence (AI) is rapidly transforming supply chains and transforming operations across industries.
It notes 70 per cent of business implementations fail due to a lack of understanding, poor data quality, and a lack of total-business buy-in.
Dr Kim Oosthuizen, Head of Artificial Intelligence at SAP ANZ, and PhD in the business of AI; Aaron Ling, Founder and CEO of California-based transformation company LXOpt Ltd.; and Glen Borg, Head of Simulation at TMX Transform, were interviewed for the paper AI in Supply Chain: An Indispensable Ally.
Aaron Ling, whose previous roles include Head of Data at Ancestry.com and senior data and analytics roles at Salesforce, emphasised that AI is not an off-the-shelf product or standalone entity – it must become an integral part of operations.
“AI is only as good as the entire organisation working behind it, requiring everything to work together –people, process, and technology,” says Aaron.
Dr. Kim Oosthuizen, whose 2022 PhD explored how AI transforms the retail value chain via a more iterative and data-focused approach, says AI can automate a staggering 60 per cent of existing work processes.
Glen Borg, former CEO of supply chain software company Dematic, urges businesses to direct their AI efforts towards “the points of difference that make a difference” so time, effort, and resources are spent wisely, and not wasted on ineffective or low-impact areas.
• AI is not an off-the-shelf or “slap-on” product – it can fundamentally address, improve, and solve business problems.
• Don’t become a statistic – 70 per cent of businesses fail when implementing AI. A holistic, topdown approach, training, trust, and quality data are essential.
• Don’t implement AI for the sake of AI. Implementation demands a strategic and thoughtful approach applied to a specified business problem.
• Beware the ‘Black Box’ mentality. Certain outputs of AI are challenging to interpret, raising concerns about accountability, ethics, and bias in AI decision-making. Combining AI with business intelligence (BI) is a good solution.
• Meet Employee 2.0: AI can automate about 60 per cent of existing work processes. But Aaron Ling emphasises that AI does not reduce the value of human work:
“All businesses are going to use AI – if we go back 20 years, we had bookstores, now we have Amazon. We had DVDs and BluRay, and now we have Netflix.”
• Waiting now equals a loss of competitive advantage. A top-down approach is needed – the support of leadership is required for AI success. The paper also highlights how AI can significantly improve customer experience, operational costs, warehouse automation, demand planning, and inventory management in the supply chain. While the application and use cases vary, the value is regardless of industry.
WesTrac, one of the world’s largest authorised Caterpillar® equipment dealers, has successfully implemented a Dematic Automated Piece Picking System for Industrial Supplies solution at one of its Australian warehouses.
It says this solution is transforming operations and enhancing efficiency and productivity at its Tomago warehouse in New South Wales (NSW).
“WesTrac is one of the largest authorised Caterpillar dealers in the world and our Tomago warehouse in NSW has an essential role to play in this, as it is the central distribution centre for our 17 regional branches, as well as our seven main workshops here on site,” explains Natalia Trewin, Warehouse Operations Manager, WesTrac.
“The Tomago facility is a high-
volume operation, storing 80,000 SKUs and we pick 40,000 lines a week here.”
WesTrac provides customers with a wide range of machinery and equipment, along with comprehensive whole-of-life management solutions aimed at making equipment ownership and operation as easy, profitable, and safe as possible. This support covers the mining and construction industries in Western Australia, NSW, and the Australian Capital Territory.
The previous WesTrac warehouse was constructed a decade ago. It was operated manually and over time WesTrac had seen a 30 per cent increase in inventory and customer base growth, resulting in a surge in orders to fulfil.
“When customers place their orders, the WesTrac warehouse management system software sends those orders to the Dematic warehouse control system
software,” says Seth van Dijk, Business Development Manager at Dematic.
“The WCS then directs the robots for maximum efficiency to retrieve all the items needed to fulfil those orders, and the robot delivers those items to the GTP workstations. Screens at the workstations instruct WesTrac operators which items to place into the order totes.
“Operators place completed totes on the conveyor, which brings them to a sorter. At the end of the sorter, orders are packed and dispatched for delivery.”
The system features an AutoStore™ automated storage and goods-toperson picking system, powered by intelligent Dematic Software. It significantly streamlines warehouse operations, with one picker achieving the work of four to five manual pickers.
With Linde Material Handling Australia needing to augment its service capabilities due to an expanding market to fulfil both current and future requirements, it has renovated one of its departments.
Linde renovated and has now unveiled its Spare Parts department located at its Head Office in Sydney, NSW in response to significant business growth and increasing market demand.
“Over the past four years, Linde has observed a substantial growth in the Spare Parts business segment,” says Director – Aftersales, Nicholas Mavroucas.
“This growth is not a brief trend, but a clear indicator of our future direction. Previously, our warehouse’s
capacity was limited, restricting our ability to meet the increasingly evident demand.”
The project was not solely about expanding Linde’s capacity or enhancing its facilities. It was centred on its dedication to growth, improving its service capabilities, and a proactive approach to future expansion.
“This renovation has propelled the warehouse’s capabilities. Anticipating an increase in demand, we’ve augmented our warehouse capacity by 20 per cent,” adds Nicholas.
“We are not merely preparing for the future; we are actively shaping it. This forward-thinking initiative is a testament of Linde’s dedication to setting industry standards, enhancing customer service excellence, and
At the core of Linde’s operations lies an unwavering commitment to providing unparalleled service to its valued customers. Image: Linde Material Handling Australia.
most importantly, the power of teamwork.”
At the core of Linde’s operations lies an unwavering commitment to providing unparalleled service to its valued customers. This renovation presented an opportunity for Linde to elevate its service standards even further, reaffirming its position as a leader in the material handling industry.
“This is not just a transformation in our infrastructures, but a leap in productivity levels. We are now better positioned to address new challenges more effectively and streamline our processes to minimise rework,” says National Parts Operations Manager, Gilbert Marcel.
Across industries, there are those solutions which are so simple and efficient that you wish they were developed much earlier. When it comes to loading and unloading shipping containers, Combilift’s Container Slip Sheet (CSS) is one such product.
This specific solution has been a boon for businesses that handle especially long and heavy loads from trucks and containers. Products such as timber, steel, flat-packed furniture, and solar panels can now be loaded and unloaded in record time with an ingenious “Slip Sheet” design.
Rather than spending time lifting the container off the truck and subsequently unloading it, the CombiCSS uses a hydraulic motor to slide a steel sheet under the container’s entire load. Once the sheet is “loaded,” it retracts onto an attached platform, sliding out the contents in one uniform movement.
Combilift Design Engineer, Tadhg Treacy, explains just how much time can be saved by the CSS.
“It will take about six minutes to unload a standard 40-foot container and send it on its way. This can be up to eight times quicker than previous unloading practices,” he says.
Such time savings may seem too good to be true, and the question of why such a solution never previously existed continues to linger. In reply, one might suggest that the traditional swing lift was “good enough” and that materials handlers didn’t have the resources to consider an alternative. That is, until the pandemic hit in 2020, necessitating more efficient means for these businesses.
As readers will well know, the pandemic exacerbated existing skills shortages and issues of cost efficiency. This inspired the Combi-CSS by removing the need for several staff to supervise the traditional swing lift.
“When there’s longer, heavier
products being handled, like steel bars, solar panels, or timber, you might have one person inside the container, a couple of people on the outside, and one in the truck cabin,” Tadhg explains.
“The CSS was designed to remove the need for that and to improve the safety implications of materials handling.”
Traditional practices have also included forklift slip sheet attachments which would essentially drag the pallets out of the container.
When businesses deal with products as valuable and fragile as solar panels, they cannot afford to risk damaging their load. This further necessitated the design of a more graceful solution.
“You’d be effectively, what we would call ‘skull dragging,’ the product out of the container,” Tadhg says.
“So that was not as safe, and it also meant that there was a fair bit of product damage.”
Another cost saving comes from the turnaround on sending off empty containers.
As the pandemic slashed operational budgets and a shortage of shipping containers plagued the supply chain,
businesses were tasked with ridding their sites of empty containers as soon as possible. If they couldn’t oblige, they would be faced with significant demurrage fees for holding them on site.
By allowing containers to stay on trucks and emptying them much quicker, the CSS cuts these significant costs for businesses.
Combilift Country Manager for Australia, Chris Littlewood, says every business will have to decide if the Combi-CSS is right for them. However, he believes there will often be the same clear winner.
“Both swing lifters and the CombiCSS bring specific advantages to the table. The decision between the two depends on assessing operational requirements, safety, efficiency, and cost savings,” Littlewood says. “But in my opinion, when comparing both pieces of equipment, the Combi-CSS has the upper hand.
“If you’re looking for a solution that excels in efficiency, carries no capacity restrictions, and boasts a remarkably return on investment, the Combi-CSS is the way to go.”
Logistics and warehousing operators have an opportunity to secure a 10,000 sqm warehouse nearing completion on the corner of Adelaide Street and Stirling Crescent in Perth Western Australia (WA).
The site is located at Hesperia’s Hazelmere Interchange, benefitting from prime visibility with direct connectivity to Perth’s major arterial routes Great Eastern, Roe and Tonkin highways and Abernethy Road, and is located 15km northeast of the CBD.
“With increasingly low vacancy in WA, this opportunity present occupiers a near-immediate opportunity to solve their occupation requirements in the Perth market,” says Judd Dyer, Hesperia Director.
He adds that the convenience of the warehouse location, highlighting its strategic positioning just seven kilometres from Perth Airport and nine kilometres from the Kewdale
Terminal Freight Facility.
Slated for completion in mid2024, 160 Adelaide Street has been designed for operational efficiency with eight on-grade loading docks, capacity to hold 11,600 pallets, and a yard designed for a B-double truck circulation.
In line with Hesperia’s commitment to sustainable development, a range of initiatives are embedded in the warehouse design including a 5 Star Green Star target rating, the use of rooftop solar PV, energy efficient lighting, and rainwater capture and reuse
Developed for warehousing and logistics, occupiers would join major global and Australian companies Couriers Please, DHL, TOLL Global Express, CTI Logistics, Centurion, Linfox, Coca Cola, and Inghams.
Hesperia is the team behind Western Australia’s first 6 Star Green
Star – Design & As Built industrial facility at Roe Highway Logistics Park, as well as Tonkin West Industrial, Gauge Precinct, and Rockingham Industrial Estate.
With a deep understanding of the industrial landscape in the State, Hesperia has a track record of identifying and acquiring land in core locations across Perth, ensuring a pipeline of industrial land, warehouses, and workshops to meet the evolving needs of owners and tenants.
For more details about the warehouse, visit hazelmereinterchange.com.au or contact:
• Hesperia: Brayden
403 546
• CBRE: Jarrad Grierson at +61 413 242 240
• Savills: Matthew Hopkins at +61 410 724 972
Visy, an Australian-based sustainable packaging solutions company, has acquired an Australia and New Zealand (ANZ) business, providing it with rightsized boxes on demand.
Operating under ‘Packsize enabled by Visy’, the acquisition gives Visy exclusive distribution rights for Packsize’s technology and solutions.
Packsize manufactures demand packaging combining precise rightsizing technology, equipment, accessories, and services to produce and package goods where a customer needs it. This innovation reduces freight costs, better protects the product and reduces waste.
“We are excited to bring Packsize technology to our customers in Australia and New Zealand,” says Rhys Jacob, General Manager for Visy Automation.
“By integrating Packsize with our proven end-to-end systems and material handling equipment, we will
deliver real value and efficiency to customers.”
Through an efficient made-toorder process flow customer designed by system engineers, Packsize technologies optimise order size, material requirements, and packaging throughput.
Packsize technologies enhance Visy’s existing offering to customers, reinforcing Visy’s commitment to providing comprehensive services and products.
The team of more than 50 people support customers with their expertise across the ANZ region. Visy partners with customers to optimise packaging and supply chains and implement bespoke end-to-end automation and product identification systems.
The revolutionary Packsize X5 machine is one of the standout technologies on show in Visy’s new Sydney showroom.
The X5 fully automated, ‘Right-
Packsize technologies enhance Visy’s existing offering to customers, reinforcing Visy’s commitment to providing comprehensive services and products. Image: Visy.
sized Packaging on Demand’ system efficiently produces ready-to-pack, right-sized erected, and labelled boxes.
Understanding the significance of customisation in today’s business environment, Visy Automation offers solutions that optimise operations and integrate with customers’ broader packaging supply chain.
Taking advantage of this customisation is a furniture retailer in Australia, that transformed its supply chain with Packsize’s on-demand packaging technology. The retailer replaced generic pre-made boxes with personalised packaging and eliminated plastic void fill.
As a result, the retailer achieved remarkable efficiently gains, including monthly savings of up to $100,000, and almost doubled operator productivity, achieving up to 30 parcels per person per hour.
Following on the success of the first in-person Elevate APAC conference in Melbourne in 2023, Körber has announced its keynote speaker for Elevate 2024 will be a renowned Australian sailor.
Jessica Watson, an Australian icon who became the youngest person to sail solo around the world at the age of 16, will help steer this year’s conference in Sydney with the Chart your course theme as the keynote speaker.
Körber notes her remarkable sailing journey serves as a powerful metaphor for navigating the complexities of supply chains.
“We are delighted to have the inspiring Jessica Watson as our keynote speaker, whose story of resilience, participative leadership and fears overcome, will inspire supply chain leaders to navigate the seas of global disruption and economic uncertainties,” says Anthony Beavis, Managing Director APAC Software at Körber.
Jessica will share her own story harnessing fear, managing risk, employing participative leadership, and building resilience to give perspective on courses of action for today’s supply chain leaders, who face their own challenges sailing through unpredictable market trends, operational hurdles, and global uncertainties.
From May 07 to May 08, attendees will come together in Sydney with like-minded businesses to gain news and insights about supply chain technologies – helping leaders identify their strategic direction, accelerate decision-making, and drive their organisation’s future success.
“Elevate has established itself as a must-attend annual event for industry leaders,” adds Anthony.
“Our flagship conference is an opportunity to come together with businesses who share common
challenges to collaborate and learn more about the technologies that can elevate business operations.”
Having been hosted by Körber in the Americas for more than 10
years, Elevate will bring together expert knowledge for cutting edge sessions on how to create business advantages through supply chain excellence.
Argon & Co’s principal consultant, Andrea Carnino, writes in this op-ed for MHD about navigating single sourcing, understanding power, pitfalls, risks, and strategies for mitigation.
If you work in procurement (sometimes reductively referred to as “purchasing”), chances are you are familiar with the term “single sourcing” and that you’ve been instructed to fear it, recognise it, and avoid it at all costs.
Which, for a department in charge of cost savings, would already be a contradiction. But what do we exactly mean by single sourcing, and why are we not comfortable with such a practice?
In simple terms, single sourcing is the custom of appointing only one supplier for the provision of a good or service when others are available in
the market.
Such decisions should come from upper management and be linked to the category strategy, but in reality – and this is something we see all the time in consulting, particularly in Asia – it’s simply common practice to take advantage of the cheapest price, quite often overlooking the risks.
But there’s a catch. Suppliers are smart. In most cases they will propose a “sticky” agreement, something that will make it difficult, or costly, for your organisation to get out of and change to another provider.
It may not even be obvious, but you can get the feeling of being caught into one of these deals when the general comments about a proposed change of supplier are “oh, but they know our business so well.”
So, to respond to the title, should you put all your eggs in one basket?
I’m a consultant and I can’t help it, so my answer is: well, it depends. Your approach should always consider multiple factors. To name a few:
• your category strategy for that good or service – e.g., if it is a critical supply, then it would probably be wiser to engage with more suppliers in long-term relationships rather than adopt a buy-from-the-single-cheapest behaviour;
• the amount of savings you can bank – e.g., if there is a sensible cost reduction by purchasing from the cheapest supplier only, then you could mitigate disruptions by increasing the safety stock;
As you know – either because you’re a seasoned procurement practitioner or because you read Part I above – there are several benefits in adopting single sourcing.
First, you save money by choosing the lowest price for a good or service, while maintaining a standard and consistent level of quality, minimising your ordering costs and creating
a strong relationship with your supplier.
In exchange for this, you potentially expose your organisation to higher risks of delay or disruption, you lose competitive tension and awareness of innovation in the marketplace.
These second aspects are normally the reason why many corporations decide to avoid single sourcing and prefer to maintain dual or multiple relationships, sometimes even if the category strategy (if any…) would suggest otherwise. Irrespective of the circumstances though, you will still find some categories of spend where single sourcing managed to creep in.
But why is that so? The most honest answer is because we are creatures of habit. Dealing with a well-known situation makes us feel comfortable and change is hardly ever embraced with enthusiasm (despite being the only constant…).
In procurement, this opens the door to suppliers tailoring and customising their offer in a way that can make it look like there’s no other suitable provider in the market. And in most cases, this happens slowly through the course of a few years (likely a contract term plus extension).
An example from my past.
• A multinational corporation leader in document repository operates widely in Southeast Asia. They need an agile fleet for their daily collections and deliveries, and they have become quite reliant on the knowledge and skills of the drivers.
Unsurprisingly, the external logistics provider, who covers roughly 50 per cent of the volumes, has been their supplier for over 15 years. When launching tenders in the past, no other vendor could match their prices or guarantee the same service levels.
But what if there really is only one supplier? This is then “sole sourcing” and I’m not going to lie to you, you’re not in a great negotiating position.
Examples of this fall under two groups:
• real monopolies, like water or electricity – although many
countries have seen a certain degree of liberalisation of the market in the past decade or so;
• proprietary lock-in, like in the case of proprietary spare parts, very specific products and services or branded items.
Albeit few, literature says there are some advantages in sole sourcing, like the simplicity of managing only one supplier and the fact that the procurement processes are not time –consuming – well, at least you won’t have to run long and complex tenders. But these are meagre consolations.
In case of monopolies, there’s not much you can do. Your organisation’s size may help obtain some discounts or rebates, but in general you’re a price taker, so you should focus on becoming a more attractive account to the supplier. Using the famous Customer Preferencing Model, this means moving from nuisance to development, or from exploitable to core.
If instead you find yourself in a proprietary lock-in, the good news is that you have a few options. The bad is that they are difficult to put in practice. To start, the tip of making your business more attractive remains valid.
Then you may apply a similar reasoning to that used in the selfinflicted single sourcing: challenge the organisation to operate differently, thus trying to eliminate the need of that particular good or service which only that supplier can offer.
Most likely, this will require a task force that goes beyond procurement alone and involves people from other departments like operations, quality, risk, IT, and logistics.
And finally, remember the title of this Part III and don’t confuse little negotiation power with no power at all.
Australia Post says its overall performance has improved in the first half of 2024 – in part – due to a record peak period with almost 100 million parcels delivered across Australia.
It has reported an interim profit of $33.6 million – an increase of $10 million on the prior corresponding period.
However, ongoing losses in the Letters business of $182.1 million in the first half, as well as declining customer visits to Post Offices as online services replace over-thecounter transactions, continue to impact the long-term viability of the business.
Outlook Group Chief Executive Officer and Managing Director, Paul Graham says while the improved performance in 1H24 was welcome, he cautions Australia Post is anticipating recording ongoing full year losses.
“I am pleased to see green shoots from the Post26 strategy starting to emerge. We have been very disciplined in managing our costs in a high-inflationary environment, we’re focusing on simplifying our
operations and making the changes needed to build a sustainable business.
“I’m proud that we delivered a record peak period, and I would like to thank the millions of Australians who placed their trust in Australia Post at Christmas to deliver their gifts around Australia and the world.”
While Australia Post’s Post26 strategy to simplify the business is starting to deliver financial benefits, significant structural headwinds remain. Australia Post’s Letters revenue declined by 2.7 per cent to $857.9 million compared to 1H23.
This result would have been more than $90 million weaker without the $0.10 increase to the Basic Postal Rate (BPR). At the same time, the Parcels and Services business recorded a revenue increase of 1.3 per cent to $3.86 billion, highlighting the twospeed nature of the business.
Through disciplined cost management, $140.8 million in efficiencies was achieved in 1H24, which included further simplification of the support office, product portfolio and broader network productivity
improvements.
Letter volumes have decreased 11.9 per cent over the past 12 months and Letters losses were $182.1 million for the half. The continuing structural decline of the Letters business is unstoppable, with Australians now receiving on average just two letters per week.
The move away from over-thecounter transactions in favour of digital services continues to undermine the performance of the Corporate Post Office network. In 1H24, over the counter transactions fell by 4.1 per cent and foot traffic across the Corporate Post Office network continued to decline.
However, Australia Post is trialling new retail formats, like the Community Hub @ Post concept launched in Orange last year, which offers a range of expanded services and a focus on e-commerce.
Late last year, Australia Post commenced a voluntary licence hand back program for eligible Licensed Post Offices (LPOs) in metropolitan areas, where there is a significant oversupply of postal outlets.
Only 15 per cent of STEM-qualified jobs are held by women according to a report by the Department of Industry, Science and Resources. Image: Swisslog.
Swisslog System Design Engineer, Ella Shakeri, is encouraging more women to enter STEM (Science, Technology, Engineering, and Mathematics) jobs in general, and in particular her chosen field of career satisfaction, warehouse automation.
According to a 2023 report by the Australian Government’s Department of Industry, Science and Resources, women make up only 37 per cent of university enrolments in STEM courses, and only 15 per cent of STEMqualified jobs are held by women.
The report also showed that women’s participation in STEM fields in Australia is increasing year-onyear, which Ella says will benefit industry more broadly.
“The world of warehouse automation is a rapidly growing and dynamic industry that requires constant adaptation to meet evolving needs. By embracing a more diverse range of perspectives, we can drive innovation and better meet the complex needs of the future. It is through this diversity of thought that we will be able to develop new solutions and stay ahead of the curve in this exciting field.”
“The theme for International Women’s Day in 2024 is ‘Inspire Inclusion’ and I believe that is the ideal way to pave the way for the future, break down barriers, and encourage more women to join STEM careers, and be a part of new innovations.”
Ella has worked for warehousing and intralogistics leader, Swisslog, for the past two years, and in similar industries for the past seven. Her role as System Design Engineer involves working with customers to understand specific requirements and performing data analysis to design a solution that provides the best utilisation of automation technology.
Ella enjoys increasing her knowledge about warehouse automation, which she finds is one of the best ways to open doors and advance her career.
“Knowledge is the key to removing barriers, improving your confidence, and showcasing your value to a
company, and to others,” she says.
“And warehouse automation is an exciting subject to learn about. It involves the integration of advanced technologies and robotics to improve the efficiency, accuracy, and speed of warehouse operations, which can lead to significant cost savings and increased productivity for businesses.”
“As you expand your knowledge, it is crucial to trust in your own ideas as well. Strong ideas, built on a foundation of knowledge, are the driving force behind innovation and the creation of new solutions. By believing in your own ideas, you can make a valuable contribution to the field and help to push the boundaries of what is possible.”
“One of the highlights of my role is problem-solving and thinking of new solutions. No two customers will have an identical warehouse, and every project brings a new challenge. We have a broad technology portfolio at Swisslog, so we are not bound to make a specific technology to work for every project, but rather to design an optimal solution with the right technology tailored to meet our customer’s unique requirements.”
Acknowledging past successes, and fostering an inclusive future
Ella is grateful to be working in a supportive environment with a diverse
culture, where her work is valued, and says it’s important to acknowledge the work other women have done to get to this point.
“Warehouse automation is a market that can change rapidly because it’s driven by changing consumer needs. Therefore, we need to design agile solutions that can easily be configured to adjust to new market needs,” says Ella.
Swisslog fosters an inclusive work environment through a range of policies and programmes, including:
• Leadership training programmes designed to address and mitigate biases
• Creating a safe team environment where everyone’s ideas are heard and valued
• Sponsorship programmes that allow a diverse workforce to build successful careers in Australia
• Leadership accountability, with inclusion being a core value of the organisation, and not a box-ticking exercise
• A code of conduct that promotes inclusion and embraces diversity
• Inclusive hiring practices
• Provision and encouragement of growth opportunities for women
• Flexible benefits that cater to the unique needs of women
• Creation of a female-led employee
group, which is a regionally based support network for all women within Swisslog to build relationships and provide support, mentoring, and networking opportunities.
“The female-led employee group is such a great community, as it provides support for women looking to grow their network, expand their opportunities, and grow their careers,” says Ella.
“I acknowledge that the supportive environment I find myself in today is a result of the dedicated efforts of women who came before me. I am committed to continuing this legacy by playing my part in creating an even more inclusive environment for the future. By doing so, I hope to make it easier for the next generation of women to break down barriers and meaningfully contribute to the fields of automation, engineering, and software.”
Swisslog is a sponsor of this year’s Supply Chain and Logistics Association of Australia (SCLAA) International Women’s Day breakfast, which focuses on how corporations and individuals can embrace equity to foster sustainable growth. The breakfast links well with Swisslog’s policies that focus on fostering inclusion in the workplace.
Anthony Beavis, Körber Managing Director APAC, explains in this op-ed the importance of having the right data, diversifying supply networks, harnessing automation, using omnichannel fulfilment, and the supply chain’s future.
Geopolitical tensions, extreme weather events and ongoing economic frailties in 2023 put supply chains to the test, underscoring the importance of handling adversary.
As we head into 2024, leaders’ confidence in supply chains is starting to gain momentum again, however, embracing data-driven decisions and contingency plans is crucial.
As consumer dynamics evolve alongside socioeconomic volatility, businesses are being asked to sense demand shifts and orchestrate responsive fulfilment quickly.
This is and will remain a huge challenge, but technologies enabling greater agility, transparency and predictivity are easing the burden and leading to many success stories.
Warehouse automation is accelerating dramatically as facilities embrace robotics and smart systems to unlock new efficiency frontiers.
Autonomous mobile robots (AMRs) can dynamically shuttle inventory for optimised workflows, and automated storage and retrieval liberates floor space while enabling rapid order processing via optimised SKU locations.
Cognitive automation through robotic process automation (RPA) and conversational AI is taking on repetitive administrative tasks for businesses as well.
According to McKinsey, automated warehouses can reduce operating costs by up to 30 per cent with throughput velocity gains over 25 per cent, while research by MIT finds every dollar spent on control towers yields three dollars to $10 in cost savings.
On top of this, data from IBM shows that organisations that use security AI and automation extensively save USD $1.76 million compared to those that don’t. The global average cost of a data
breach in 2023 was USD $4.45 million, a figure which is on the rise every year.
To leverage advanced technologies like cloud computing, predictive analytics and artificial intelligence, companies should first establish integrated digital foundations spanning their end-to-end supply chains.
Collating the right type of customer, sales and product data is the key to driving enhanced data-driven decision making, real-time visibility, and streamlined flows.
Businesses are learning to prioritise data, foregoing a one-size-fits all approach to learn the numbers that matter to their business.
The transition from analogue or semi-digital processes poses adoption challenges, especially around quantifying return on investment, but there is an understanding now that digitalisation is synonymous with business survival.
Well-designed and optimised supply chains confer many advantages, including meeting customer fulfilment expectations, improving network efficiency, strengthening reliability and resilience, enabling what-if-scenario modelling, and maintaining balanced inventory strategies.
However, over-dependency on specific partners and inadequate agility to address unforeseen situations can prevent supply chains from achieving their full potential.
In 2024, businesses will look to diversify their supply networks and partners, giving extra flexibility to dynamically shift sourcing, production or distribution based on changing cost economics, lead times or demand.
While automation and analytics unlock supply chain advancements, engaged
talent remains indispensable.
Labour shortages have hit Australia hard, and a lack of available workers is a persistent problem, which is why we need to create engaging and fulfilling roles alongside automation.
Cobots are designed to work alongside humans to complete daily tasks more effectively and productively, automating repetitive tasks to provide better employee safety and wellbeing.
For instance, Körber research estimates that a warehouse operator completing a picking workflow will walk around 10 to 15 kilometres a day. As the technology handles execution, employees can shift more towards value added tasks and strategic decisionmaking.
This concept demands workforce readiness through change management, continuous skills development, and cultural alignment. By empowering people to work alongside intelligent systems, businesses will reap the full rewards of technology and innovation.
The pandemic has shone a light on the importance of a business’s every channel – e-commerce, direct-to-consumer, retail and distributors.
If one channel is disrupted or underperforming, profits don’t immediately dip because demand is consolidated in every channel. Developing supply chains which facilitate this is easier said than done.
Anthony Beavis, Körber Managing Director APACZebra Technologies tells MHD about how its latest ultrarugged mobile computers for transportation and logistics can empower businesses’ supply chain operations as they run their warehouses and distribution centres.
In today’s world, the demands on transportation and logistics companies are higher than ever. Staff are overextended and under pressure, compliance is complex, and customers expect service and information instantly.
Logistics leaders need unprecedented visibility into every corner of your operation – to make smarter, more informed decisions, and ensure flawless fulfilment.
To do this, they need mobile devices that can help streamline their workflows, tighten security by continuously tracking assets, connect their workforce, minimise wait and turnaround times, and ensure compliance – every step of the way. But not all devices are created equal.
Zebra Technologies makes the world’s most trusted and powerful enterprise mobile computer for use in transportation and logistics, the ultra-rugged MC9000 series.
They’ve sold nearly five million of them for good reason. The devices have helped streamline and errorproof processes in the toughest outdoor and indoor environments — in warehouses and distribution centres, ports and yards, and on the manufacturing floor.
Zebra has just released the next evolution in this highly successful handheld mobile computer family, the MC9400/MC9450. Loaded with all the latest mobile technologies, these devices are stronger, faster, and ready to power the new generation of industrial applications.
One device for all applications
The MC9400 and MC9450 offer the latest and fastest Wi-Fi 6E
connectivity, with the flexibility to cost-effectively connect anywhere and everywhere. MC9450 supports private and public 5G, in the most extensive outdoor and indoor environments.
The new devices also offer the best in data capture – the SE58 Extended Range Scan Engine with IntelliFocus™ delivers an unmatched scanning range, enabling workers to scan barcodes as far as 100 ft./30.5 m away.
And the innovative green laser aimer is seven times more visible than the typical red aimer dot, making it easy for workers to scan at a distance.
Biometric facial recognition provides easy access for workers and peace of mind that only preauthorised users can access devices.
Workers can resolve issues quickly with the video-based collaboration, enabled by the high-resolution frontfacing camera. And with the 16 MP high-resolution rear camera, it’s easy to capture highly detailed photos to document the condition of incoming shipments, quality checks and more.
Process automation is made seamless with OCR Wedge, allowing workers to capture shipping container identification numbers, tire identification numbers (TINs), vehicle identification numbers (VINs) and more with the press of one button.
Compared to the previous generation, the MC9400 and MC9450 offer 2.5x more processing power, 50 per cent more RAM, 4x the Flash and 8x the storage. Whether you’re running simple ‘green screen’ apps or apps powered by augmented reality and artificial intelligence, you can power them all at once.
Not only are these devices faster, but they’re also more rugged and ready for just about any environment – including a model dedicated to the freezer area. With Zebra’s toughest military-grade drop and tumble
testing, these devices have what it takes to handle the inevitable everyday drops on concrete.
Meanwhile, Corning Gorilla Glass protects the display and the scanner exit window, and a double IP65 and IP68 sealing rating means you can drop it in water or mud, and even hose it off.
When it comes to flexibility and value-added extras, these devices deliver more. With Device Tracker and the new BLE battery, you can quickly and easily find devices, even if they are turned off or low in power.
The large 4.3 in display is easy to see indoors and outside in bright sunlight and works when wet or with thick gloves.
When you buy a Zebra Android device, you also get features that give you the enterprise control you need.
With support to Android 17, you don’t need to worry that your operating system (OS) will become outdated. You choose when and if you want to update – and when you’re ready for an OS update, you can do it automatically via Zebra LifeGuard™.
The MC9400/MC9450 is a drop-in replacement for the MC9300 – so you can modernise your technology and get big productivity gains without a major overhaul.
This latest evolution in the ultrarugged MC9000 Series can power your enterprise to the next level of productivity and efficiency in your most demanding environments.
Linde Material Handling has introduced its Linde Experience Hub at its 5500 sqm headquarters in Aschaffenburg, Germany, noting it is a testament to its dedication to innovation and engineering excellence.
This dynamic space designed to inspire innovation offers a range of activities, from training sessions and product presentations to interactive workshops and customer demonstrations, the Linde Experience Hub covers the spectrum from theory to practice.
“The Linde Experience Hub again demonstrates advancing boundaries of benchmarking, in outstanding technology, offering productively
Australia Post has announced a new multi-year deal with Salesforce, harnessing Salesforce’s Data and AI capabilities supporting Australia Post’s Customer Experience Transformation, helping to redesign and deliver enhanced customer experiences.
With the Salesforce platform at the core of its experience layer, Australia Post says it can now enable every customer-facing team member to support its merchant and consumer customers – from sales onboarding, through to servicing and support via contact centres, post offices, to Posties – and provide every customer with a consistent and personalised experience.
“Establishing our key strategic technology platforms is a crucial first step for the transformation of our digital customer experience,” says Michael McNamara, Executive General Manager, Enterprise Services at Australia Post.
“Investment in cutting-edge technology is crucial in ensuring we set the business up for success as we
safe and sustainable solutions – a testament to Linde’s unwavering commitment to innovation,” says Joshua Naffine, International Key Accounts at Linde Material Handling.
In addition to theoretical knowledge and work, the Hub also features practical applications, includes a high-bay warehouse with open spaces such as a driving area with truck ramps and various exhibition areas. Here, Linde’s solutions and innovation expertise can be fully experienced.
Linde Material Handling Australia recently invited senior stakeholders from a leading Australian retail chain to visit the Linde Aschaffenburg factory and Linde Experience Hub.
Led by Joshua Naffine (International
continue to simplify and modernise our operations. Salesforce has the right platform for us to revolutionise how we connect with customers by harnessing the transformative potential of AI and data-driven insights.”
New capabilities to drive stronger customer and community engagement include:
• Self-service, agent assistance, automation, and GenAI will provide a consistent level of support via the Salesforce Service Cloud, regardless of channel and language.
• Salesforce Data Cloud will connect millions of operational data points on parcels in the postal network, allowing greater insight into the activities of each customer, enabling Australia Post to better anticipate customer needs.
• Salesforce Marketing Cloud will enable Australia Post to orchestrate and execute personalised customer engagement and experience at scale across digital customer touchpoints and channels. Advanced marketing
Key Accounts) and Leigh Atallah (Director – Sales & Marketing), the visit showcased the high level of automation and robotics used in building Linde’s world-class equipment.
The Linde Experience Hub especially captivated the material handling company’s visitors’ attention, providing a front-row seat to the latest innovation, technology, and safety advances made by Linde Material Handling.
The Linde Experience Hub serves as more than a showcase; it stands as an environment where new ideas thrive, marking Linde’s leadership in technological advancements and innovative solutions.
performance and analytics capabilities will identify the bestperforming and highest Return on Investment (ROI) programs.
• Tableau will assist with a complete 360 view and provide secure, selfservice analytics and reporting with Australia Post merchants, partners, and staff; this includes CRM data from Salesforce, along with a wide range of enterprise data such as financial, retail, parcel, and operational data.
• Mulesoft will accelerate the integration of Salesforce to relevant data sets across other strategic technology vendors, increasing operational efficiencies and delivering a single view of customers.
• Slack will continue to be leveraged for software engineering practices, helping Australia Post team members collaborate, ideate, and deliver incredible experiences for its customers.
Leveraging AI to drive efficiency and productivity.
The Supply Chain and Logistics Association of Australia has welcomed an inventory and demand planning software company trusted by more than 2200 customers optimise their demand supply planning.
Netstock has accelerated the growth of organisations worldwide for the last 15 years and has built regional presences in ANZ, North America, and EMEA, gaining deep insights into supply chain planning challenges in each market.
Netstock seamlessly integrates with over 60 leading ERP systems, transforming raw data into predictive insights for confident decisionmaking. With immediate ROI, Netstock unlocks working capital, enabling adaptability and ensuring exceptional customer service. Customers enjoy tailored onboarding and 24/6 support, along with premier learning resources from the Netstock
Learning Academy, backed by decades of industry expertise. Netstock is also ISO 27001 certified, offering its customers data integrity.
Unlocking success with Netstock: Netstock continually innovates its solutions with smarter predictive engines, leveraging AI and machine learning to help customers thrive. With Netstock, customers can:
• Improve fill rate by up to 15 per cent, reducing stock-outs and increasing sales
• Increase forecast accuracy by up to 50 per cent with tournament-based forecast algorithms
• Reduce inventory holding by 35 per cent, unlocking cash tied up in excess inventory
• Reduce time spent on planning, forecasting, and ordering by up to 70 per cent.
Netstock offers two product solutions that cover both sides of the inventory challenge: supply and demand. The
Netstock has accelerated the growth of organisations worldwide for the last 15 years. Image: Supply Chain & Logistics Association of Australia.
solutions encompass:
• Inventory optimisation
• Demand planning
• Inventory forecasting
• Inventory ordering
• Supplier performance
• Manufacturing & capacity planning
• Sales & operations planning
Netstock is helping businesses in ANZ achieve remarkable results. One such transformation is Adventure Operations who achieved a 30 per cent reduction in inventory in under 12 months. Leveraging Netstock’s tools, Adventure Operations shifted from managing inventory and forecasting in spreadsheets to a proactive, predictive forecasting model. The result? They maintained a robust 95 per cent fill rate, and the key to this turnaround was data visibility, leading to forecast accuracy, streamlined operations, and strategic sales initiative.
Toyota Material Handling Australia’s “Made for More” program redefines employee engagement and development in the logistics sector. Through innovative strategies and a focus on individual potential, TMHA sets a new standard for workforce satisfaction and retention.
In an era where the recruitment and retention of skilled employees present formidable challenges for the logistics and supply chain industry, Toyota Material Handling Australia (TMHA) has distinguished itself through its innovative “Made for More” program. TMHA – which distributes Toyota Forklifs and Huski Construction Equipment from a national network of 20 TMHA branches – employs roughly 850 team members, with more than half working in its service and parts team. The Made for More initiative reflects a deep commitment to cultivating a workplace where every individual’s potential is recognised and nurtured. Suzie Albatti, General Manager of Human Resources for TMHA, sheds light on its origins, objectives, and the tangible benefits it has delivered to both the organisation and its employees.
Several years ago, TMHA embarked on a journey to articulate its core identity, values, and the essence of its workforce. “We set out to define who we are, our purpose, and the essence—the ingredients that make up our employees, what they enjoy, and what satisfies them at work,” Suzie explains. This endeavour led to the establishment of the Made for More program, predicated on the belief in the boundless potential of every employee.
Central to the program are five underpinning themes: job security, family-centric policies, lifelong learning, social cohesion, and pride in TMHA’s product pedigree. Suzie
highlights the importance of these themes in fostering a supportive and enriching workplace environment. “We like to think of it as Made for More, which is the overarching philosophy that every individual has infinite potential they can reach,” Suzie says. This philosophy has not only helped TMHA to attract talent but also to retain employees by offering them pathways for growth and development within the organisation.
The Made for More program stands out for its comprehensive approach to employee engagement and development. It includes provisions for on-site childcare during school holidays, flexible working arrangements, and inclusive company events, all of which contribute to a family-friendly workplace culture. Additionally, TMHA places a strong emphasis on lifelong learning,
“ The philosophy has not only helped TMHA to attract talent but also to retain employees by offering them pathways for growth and development within the organisation.
offering numerous opportunities for employees to advance their skills and careers. “Many within our company have grown from apprentices to higher positions, focusing on their development,” Suzie notes, underscoring the program’s success in fostering career progression.
TMHA’s proactive strategy involved developing targeted initiatives to attract skilled technicians from related fields, such as automotive backgrounds, and equipping them with the necessary training to excel in their new roles. “We’ve used social media and advertising to promote this and developed an eight-week program in collaboration with the service department and marketing to attract people from related areas,” Suzie says. This approach has not only expanded TMHA’s talent pool but also mitigated the impact of labour shortages on its operations.
Furthermore, the effectiveness of the Made for More program is evidenced by its impressive retention rates and positive feedback from participants. TMHA regularly solicits and acts upon feedback to refine and enhance the program, ensuring
The effectiveness of the Made for More program is evidenced by its impressive retention rates and positive feedback from participants. Image: TMHA
it remains aligned with employees’ needs and aspirations. “Our retention rate is excellent, and we’ve received positive feedback from participants,” Suzie says. Such feedback underscores the program’s role in creating a supportive and dynamic work environment that values and invests in its people.
Success stories abound, with
TMHA places great emphasis on professional development. Image: TMHA
numerous employees seizing the opportunities provided by the Made for More program to advance their careers within TMHA. “One person, in particular, has progressed from technician to supervisor and then branch manager.” These stories are a testament to the program’s effectiveness in unlocking employee potential and fostering a culture of
growth and opportunity.
In response to the COVID-19 pandemic, TMHA’s Made for More program demonstrated remarkable adaptability. The unprecedented challenges of labour shortages and the need for social distancing necessitated a swift and innovative response. TMHA leveraged technology and virtual platforms to continue its training and development programs, ensuring that employees remained engaged and supported despite the disruptions. This agility not only sustained TMHA’s operational continuity but also reinforced the company’s commitment to its workforce during uncertain times.
Moreover, the Made for More program’s focus on inclusivity and diversity has enriched TMHA’s corporate culture, attracting a broader spectrum of talent to the organisation. By embracing individuals from various backgrounds and skill sets, TMHA has fostered a more dynamic and innovative workplace environment. This diversity of perspectives and
“ The ‘Made for More’ program’s focus on inclusivity and diversity has enriched TMHA’s corporate culture, attracting a broader spectrum of talent to the organisation. ”
experiences has spurred creativity and problem-solving, further enhancing the company’s competitive edge in the logistics and supply chain sector.
TMHA’s Made for More program represents a forward-thinking approach to employee engagement and development. By valuing and investing in its employees, TMHA has cultivated a workplace culture that is conducive to innovation, growth, and long-term success. As Suzie succinctly puts it: “We’ve seen great success, retaining most of the over 70 people who’ve gone through our transition program.”
The Made for More initiative underscores the pivotal role of supportive workplace policies in attracting and retaining talent, setting a benchmark for excellence in employee engagement and development in the industry.
The experiences of Tiodor Sada, Dylan Cooper, and Travis Childs at Toyota Material Handling Australia further
exemplify the profound impact of the Made for More program on its employees’ lives.
Tiodor Sada’s journey is particularly inspiring. As an Applications Engineer who faced the harrowing experience of fleeing his country due to an ISIS attack and spending years as a refugee, his eventual employment at TMHA stands as a beacon of hope and a testament to the company’s inclusive hiring practices. “I see my future vanish in front of my eyes as a refugee. I didn’t really expect a company as big as Toyota to hire a person like me with a refugee background,” Tiodor recalls. His hiring not only signified a new chapter in his life but also underscores TMHA’s commitment to embracing diverse backgrounds and experiences.
Dylan Cooper, a Field Technician with TMHA, reflects on the stability and security he’s found working at the company. His eight-year tenure enabled him to confidently invest in his future, evidenced by his ability to purchase a home during his apprenticeship and recently acquire a second one with his partner. “I feel like I’ve got a secure job at Toyota,” Dylan states, illustrating the sense of job security that TMHA’s policies instil in their employees.
Travis Childs, from Technical Training Development, has been with TMHA for nearly two decades and highlights the familial atmosphere and supportive culture within the company. “Everyone you work with is your family member,” he says, emphasising the strong bonds and supportive environment cultivated by TMHA, traits often associated with its Japanese corporate ethos.
Additionally, Dylan comments on the abundant opportunities for career progression within TMHA. He observes many colleagues who have advanced from apprentices or technicians to higher managerial
roles, reinforcing the Made for More program’s focus on career growth and lifelong learning. “There’s a lot of room for opportunities if you want to pursue it,” he notes, encouraging others to consider a career with TMHA.
Travis’s closing advice to potential new employees encapsulates the sentiment of TMHA’s workforce: “Jump on now. Because you won’t turn back.” This phrase reflects the deep satisfaction and loyalty felt by TMHA employees, further validating the Made for More program’s success in fostering a positive and growthoriented work environment. ■
Warehouses are evolving beyond their traditional roles, now focusing on employee wellbeing, operational efficiency, and resource utilisation. Peter Jones of Prological delves into how modern warehouse design prioritises these elements, reshaping the industry’s future.
In the realm of warehouse design, a transformative wave is reshaping the industry’s future. Peter Jones from Prological highlights the profound shift in warehouse design philosophy, emphasising not just the efficiency and utilisation of resources, but crucially, the wellbeing of employees working within these spaces.
According to Peter, this approach marks a significant departure from past practices, where employee wellbeing was scarcely considered beyond basic requirements.
“Thirty or forty years ago, the wellbeing of people was barely on the brief for warehouse design, aside from minimal considerations like the number of urinals needed,” Peter explains. This reflection sheds light on how the priorities in warehouse design have radically evolved over time. Today, there’s a growing recognition of the impact a work environment has on the productivity, efficiency, and longevity of employees. This recognition is steering the industry towards designs that invest more profoundly in the working conditions of warehouse staff.
The crux of next-generation warehouse design, as Peter articulates, revolves around three key objectives: efficient use of physical resources, operational efficiency within the facility, and significantly, the wellbeing of the workforce. This holistic approach to warehouse design represents a paradigm shift from traditional practices. As Peter puts it: “If I invest in the environment in which my warehouse staff work, it
will be returned to me in the form of higher productivity, less absenteeism, and a happier workforce.”
Peter draws a parallel between the evolution of warehouse and office environments. He points out that while businesses have long invested in creating modern, attractive office spaces to lure top talent and boost productivity, warehouses have lagged behind in this regard. “We wouldn’t bring a prospective employee into a 1970s office environment today, yet this disconnect between written aspirations and the actual environment still exists in many warehouses,” Peter observes. This mismatch not only impacts employee morale but also a company’s ability to attract and retain quality staff.
Peter highlights research and case studies that underscore the tangible benefits of investing in employeecentric warehouse design. He refers to a significant reduction in absenteeism as reported by Fujitsu Australia and New Zealand’s CEO, Mike Foster, who credits this to the company’s Green Star environment. Peter cites a memorable quote from Mike: “We want people to enjoy working at Fujitsu and we’re creating a culture which attracts and retains staff. Our Green Star office is good for our employees and good for our business, even helping to reduce absenteeism by 42 per cent.”
The transformative impact of green building design on workplace productivity and employee wellbeing is increasingly evident, with Green Star buildings leading the charge. These buildings, by virtue of their design,
consistently outperform traditional structures, creating environments that are not just environmentally sustainable but also significantly boost employee productivity and comfort.
One of the cornerstones of Green Star buildings is their emphasis on natural elements like light and air. The integration of natural light and fresh air into the workplace has been a game-changer. According to the World Green Building Council’s Business Case for Green Building report from 2013, the influence of these elements on productivity is profound. The report reveals that access to daylight and operable windows can result in up to an 18 per cent increase in productivity. This remarkable figure underscores the importance of design that harnesses natural elements, breaking away from the traditional reliance on artificial lighting and ventilation systems.
The impact of green building design extends beyond just daylight. Improved ventilation, a staple in Green Star buildings, can lead to productivity gains of up to 11 per cent. This improvement is attributed to the enhanced air quality and the resultant reduction in pollutants, which positively affects cognitive functions and overall health of employees. Furthermore, the ability for individuals to control the temperature of their workspace plays a crucial role, with research indicating up to a 3 per cent increase in productivity when this control is provided. This personal control over the environment not only enhances physical comfort but also fosters a sense of autonomy and
satisfaction among workers.
Furthermore, Peter mentions the ongoing research at MIT’s Sloan School, poised to be the most developed study on this subject. This research, alongside others, solidifies the understanding that improvements in warehouse environments can lead to substantial benefits, not just for employees but for the businesses as a whole.
When discussing the practicalities of integrating these wellness elements into warehouse design, Peter underscores that it doesn’t necessarily mean higher costs. “It’s about thinking holistically from the start, rather than piecemealing the operational, office, and amenity aspects for warehouse staff,” he states. This integrated approach ensures that each element of the warehouse design works in harmony, contributing to the overall wellbeing of employees.
Peter also points out the shortcomings of ‘90s warehouse designs, often characterised by bland,
under-maintained, and isolated working environments. He contrasts this with modern designs that focus on quality air circulation, thermal control, and natural light. These elements, he argues, are not just niceties but are essential to creating a workplace where people feel valued and are more productive.
The conversation with Peter also delves into the relationship between the physical design of warehouses and its impact on staff morale and productivity. He highlights the significance of details such as the design of entrance areas, locker rooms, and recreational spaces. “When these facilities are places that people like to be, it totally changes the thinking of the person that’s entered there,” Peter notes, emphasising the psychological impact of the work environment on employees.
Additionally, Peter discusses the challenges in bringing these design concepts to fruition, particularly in the face of generic building designs favoured by developers. The crux of
the issue lies in aligning the interests of developers, real estate firms, and tenants to prioritise wellbeing in warehouse design.
Despite these challenges, Peter is optimistic about the future, citing examples of companies like Nike and ResMed, which have successfully integrated wellness into their facility designs.
The shift in warehouse design towards prioritising employee wellbeing represents a significant and necessary evolution in the industry. As Peter Jones articulates, this approach goes beyond mere operational efficiency and resource utilisation. It embraces a more holistic view, acknowledging that the wellbeing of warehouse staff is integral to the overall success and sustainability of the business. The transformation of warehouse environments into spaces that foster wellbeing, efficiency, and productivityis not just a trend but a fundamental shift in how we perceive and value the workspaces of the future. ■
PepsiCo is a global leader in convenient foods and beverages. Its products are enjoyed by consumers more than one billion times a day in more than 200 countries and territories around the world. In 2022, PepsiCo generated more than $86 billion in net revenue, driven by a complementary product portfolio that includes Lay’s, Doritos, Cheetos, Gatorade, Pepsi-Cola, Mountain Dew, Quaker and SodaStream.
PepsiCo aims to become a stronger, more unified company by transforming its capabilities and costs, and by using new technologies to its advantage. This includes developing and scaling the company’s core capabilities through advanced technology.
In today’s competitive business landscape, global companies like PepsiCo are constantly seeking ways to optimise their operations for increased productivity, efficiency, and accuracy.
PepsiCo’s Rojana facility in Thailand is a critical regional hub that produces a variety of products. With a growing demand for its products, PepsiCo recognised the necessity to build capacity in Thailand.
Colin Matthews, Supply Chain Senior Director – IndoChina Foods, PepsiCo, says, “Rojana is one of our biggest plants and it also has several different product platforms. We have potato chips, we have the Stax chips, and we have Fry Pack in extruded products as well. Those products are made at Rojana and they are not only distributed nationally across Thailand, but we also send products internationally to Vietnam and other neighboring countries.”
One of the key strategies employed by PepsiCo to support growth was the expansion of its production and logistics capacity at the Rojana site.
This expansion project has been driven by the vision of a digitalised future, where automation plays a pivotal role in addressing challenges and enhancing overall operational performance.
“We foresee a manpower shortage being a major challenge for our local operations in Thailand,” explains Charan Techapattaraporn, Logistics Manager, PepsiCo. “Automation, therefore, is the perfect solution to take on these challenges, whilst also improving our facility operations across the board.”
As part of its expansion and automation goals, PepsiCo turned to its global partner Dematic, a global leader in providing automated solutions for materials handling and logistics.
“I’ve now worked with Dematic across two business units, firstly here in Indochina and also in Australia and New Zealand,” adds Colin. “I’ve seen Dematic really lean into providing a customised response based on the tailored needs of individual problems.”
Dematic took a strategic and modular approach to the Rojana facility system design, aligning it with PepsiCo’s current and forecasted business growth. The central feature of the solution is Dematic’s Automated Storage and Retrieval System (AS/RS), designed to store pallets from both on-site production and external suppliers and manufacturing plants.
“Dematic has a strong track record of successfully implementing AS/ RS solutions across the Asia Pacific region and globally, catering to diverse industries and applications,” says Phamondate Rukdee, Sales Manager, Dematic Thailand. “The AS/RS is at the heart of PepsiCo’s strategy to enhance its production and logistics efficiency at the Rojana facility.
“The AS/RS aids in storing products before they are delivered to customers.
This solution should achieve the highest capacity in Thailand, reaching a height of approximately 35 metres. The storage system is highly capable and efficient, even within limited space constraints.”
The AS/RS stores pallets within five aisles of double deep high bay racking, with a total of 16,520 pallet locations. The system also includes Dematic’s Warehouse Control System (WCS) software to manage material flow, storage locations and to provide pallet transaction instructions to the automation. This holistic approach ensures seamless interaction between all system elements, maximising efficiency and performance.
Dematic’s commitment to quality and reliability is exemplified through the deployment of top-of-the-line equipment that works in conjunction with the AS/RS, including five Dematic RapidStore Storage and Retrieval Machines (SRMs), capable of handling loads of up to 1500 kgs. Additionally, Dematic pallet conveyors for automated pallet handling, including transporting pallets from the production area to the AS/RS, and the high bay racking, are all designed and engineered in-house by Dematic. The new warehouse also includes an area for case picking replenished automatically from the AS/ RS.
Being modular, the AS/RS provides PepsiCo with the flexibility to adapt to changing needs and future market dynamics by being equipped to be incrementally scaled up.
Dematic was on the ground at the Rojana facility during implementation, testing and go live phases to ensure the success of the project, which was delivered on time for PepsiCo.
“The system was completed on schedule. We are also well supported
by both domestic and international Dematic teams who are ready to quickly aid PepsiCo in terms of both hardware and software,” says Charan.
The success of any new automated system is ultimately in the hands of the system operators. That’s why training is essential for providing an understanding of not only the automated equipment, but also the procedures for ensuring its safe and efficient operation. To achieve this Dematic followed a “train the trainer” approach to helping PepsiCo develop a good working knowledge and understanding of the system, where supervisors train other employees.
“Our team really embraced the solution that we’ve put in at Rojana and they really value the investment that we’ve given them, as we’ve trained them to get new skills. That training of new skills has helped us with people retention, which is another benefit,” says Colin.
The complexity of the automation installed for PepsiCo makes it essential to have service and support in place to optimise system uptime, continuity of throughput, and production efficiency. The benefits of ongoing support include a reduction in downtime due to component failure, lower overall system maintenance costs, optimisation of system lifespan and knowing that Dematic as the system designer and builder are also available to service the system.
“Dematic takes care of PepsiCo’s AS/RS and machinery 24 hours a day,
7 days a week,” says Nipat Kummu, Service Engineer, Dematic Thailand.
The AS/RS provides fully automated high-density, high-capacity storage for pallets at high speed. With an AS/ RS, stock cannot be lost or forgotten, as the system provides complete and real-time visibility of overall inventory, delivering the highest level of accuracy.
“Previously we had a very manual solution that took a lot of time for people to go around and understand exactly what products we had in the warehouse. In contrast, the Dematic system is very intuitive. It enables our team to look across the whole of the AS/RS and understand exactly where we have the stock and they can intuitively and quickly make any adjustments they need. The AS/RS has more than doubled our capacity and provided us with an automated solution, taking us away from the very manual operation we had before. This allows us to supply goods to customers with greater efficiency, leaving them very satisfied,” explains Colin.
The Dematic solution has delivered a multitude of benefits to PepsiCo, including:
• Improved space efficiency: The AS/RS has more than doubled storage capacity, making the most of the available footprint, which is important in highly urbanised regions.
• Improved productivity: Automation
streamlines processes, reducing reliance on manual labour and increasing throughput.
• Fast responsiveness: Automation allows for quick and efficient responses to customer orders and to changing demands.
• Accuracy and tracking: Precise tracking of inventory ensures accuracy in order fulfilment.
• Inventory security: Enhanced security measures inherent to the AS/RS protect valuable stock.
• Modularity and scalability for expansion: The system can grow with PepsiCo’s needs.
• Redundancy: Built-in redundancy ensures continuous operation and avoidance of costly downtime.
• Reduced facility energy consumption: Automation helps to minimise overall warehouse energy usage.
• Low maintenance, reliable, and locally supportable: Dematic provides ongoing local support for troublefree operation.
• Life cycle value: A long-term investment that continues to provide value over time.
The superior high-density storage capability of the AS/RS, which allows PepsiCo to store much more within the warehouse building cube than would be possible within a conventional warehouse environment. The Dematic solution has also removed the need for any workers to be travelling within warehouse aisles alongside materials handling equipment, which has drastically increased warehouse operator safety on the warehouse floor.
“Our first priority was safety and the AS/RS plays a crucial role in reducing the occurrence of accidents. Secondly, we were focused on efficiency gains and this was achieved through reducing the storage footprint. Thirdly, PepsiCo wanted increased accuracy and traceability of products so that the warehouse throughput could be increased,” explains Charan.
Dematic and PepsiCo have collaborated to achieve efficient results. We would like to express our gratitude to PepsiCo for enabling the successful and smooth execution of this project. This system will bolster PepsiCo’s growth, enabling it to become bigger and stronger, providing a solid foundation,” concludes Nipat. ■
MHD sits down for an in-depth discussion with Linde Material Handling Australia’s Allan Spackman and Greg Wood to demystify Lithium-ION forklift technology, address prevailing misconceptions and safety concerns, and highlight the significant environmental advantages Lithium-ION forklifts offer.
The material handling landscape is experiencing a paradigm shift with the advent of Lithium-ION forklifts. Allan Spackman and Greg Wood, Technical Solutions Managers at Linde Material Handling Australia, bring their wealth of knowledge to the table, dispelling myths, highlighting safety features, and underscoring the sustainability of these innovative machines.
Despite their increasing presence in warehouses and distribution centres, several myths about Lithium-ION forklifts persist. One of the most prevalent is the belief that they are inadequate for heavy lifting. Allan Spackman counters this misconception: “When it comes to lifting heavy loads, the key factors are hydraulic capacity and motor power. It doesn’t matter whether the power comes from lead-acid or Lithium-ION batteries.” He further elaborates on the engineering benefits of LithiumION batteries, particularly their lighter weight, which allows for more flexible placement in the forklift, potentially enhancing the machine’s lifting capabilities.
Another widespread myth concerns the efficiency and cost-effectiveness of Lithium-ION forklifts. Greg Wood addresses this, stating, “LithiumION batteries have a higher degree of efficiency and voltage stability, which means less energy loss and higher power delivery over the hours the machines are used.” This higher efficiency leads to less heat development and energy losses during charging, directly translating to reduced CO2 emissions and
“ A common worry among businesses is that they have insufficient electrical infrastructure. But for many businesses, especially those not requiring superfast charging, the switch can be smooth, and standard lithium chargers offer more flexibility without significant infrastructure changes.
cost savings.
The complexity of transitioning to Lithium-ION is another concern that businesses often have. Allan explains, “A common worry among businesses is that they have insufficient electrical infrastructure. But for many businesses, especially those not requiring superfast charging, the switch can be smooth, and standard lithium chargers offer more flexibility without significant infrastructure changes.”
Safety in warehouses and distribution centres is paramount, especially with the introduction of new technologies. Allan passionately discusses the safety aspects of Lithium-ION forklifts: “Traditional battery changes pose a real threat. They weigh a tonne –quite literally in some cases. Using machinery to replace them amplifies the potential for injuries, notably back injuries. With Lithium-ION forklifts and the option for frequent plug-ins, we can significantly cut down these hazards.”
Greg Wood elaborates on the safety features inherent in Lithium-ION technology.
“Lithium-ION, being denser in energy, comes with multiple safety layers,” he says. “Each cell is tested for safe shutdown when punctured. Modules are monitored for overcurrent and temperature discrepancies. The Battery Management System (BMS) is designed to disconnect the battery if things go awry.” Allan adds, “Its ability to shut down the battery is paramount. I’ve seen instances where fires have been ignited by leadacid battery shorts. With lithium,
deactivating cables when not in use or charging negates such risks.”
As the world leans towards more sustainable operations, understanding the environmental implications of Lithium-ION forklifts becomes essential. Allan highlights the longer lifespan of Lithium-ION batteries compared to lead-acid ones: “A leadacid battery typically lasts around 1500 cycles. With lithium, you’re looking at between 2500 and 4000 cycles.” This increased lifespan translates to fewer batteries needed over time, reducing waste and environmental impact.
Discussing the recycling and lifecycle of these batteries, Greg Wood points out, “A battery’s lifecycle consists of initial assembly and
use, refurbishment for secondary use, remanufacturing for alternate applications like stationary batteries, and finally, recycling.” He emphasises Linde’s commitment to sustainability: “We’re striving for a 95 per cent recycling rate for each battery. The energy efficiency of our trucks is always a top priority.”
He further adds, “Lithium-ION batteries and chargers have an energy efficiency of over 90 per cent. By simply switching to Lithium-ION cells, you can reduce your carbon footprint by around 30 per cent.”
The adoption of Lithium-ION forklifts in material handling is a testament to the industry’s evolution towards more efficient, safer, and environmentally
responsible operations. Allan and Greg emphasise the importance of basing purchase decisions on accurate information and thorough analysis. They encourage businesses to ask the right questions and understand the full scope of benefits and considerations associated with Lithium-ION forklifts.
In summary, Lithium-ION forklifts stand not just as a testament to technological advancement but as a beacon of sustainability and safety in the material handling industry. As we advance into a future where these aspects are increasingly intertwined, understanding and embracing the full potential of LithiumION technology becomes crucial for businesses aiming to stay ahead in efficiency, safety, and environmental responsibility. ■
Sales Director at Conquest Equipment, Ben Mathews, talks to MHD about the industrial cleaning company’s new Fleet Management System and how it provides real-time visibility of, and data related to assets no matter where they’re located.
Conquest Equipment is introducing its new Conquest Fleet Management system which is designed to bring a central viewpoint to customers’ assets all in a single portal, allowing them to log in and keep track of their machines’ locations.
With Conquest’s clients running cleaning equipment in industrial sites spread across Australia, it’s essential they can view their solutions at any one time and find out specific information about each of these items in terms of their life, utilisation, battery condition, and more.
The Conquest FM is capable of storing a range of insightful and useful information, including a cleaning solution’s health status, indicating whether it’s due for maintenance, or if there are any technical – either software or hardware issues – such as impact and battery-related issues.
“We plan to integrate the Conquest
FM with our service system,” says Ben Mathews, Sales Director, Conquest Equipment.
He notes utilisation – especially with regards to a large fleet – can help Conquest’s clients identify which cleaning assets are being underutilised. It can also indicate if the machine is no longer needed at a site. This allows users to switch units around or move them between sites to get better utilisation across their entire fleet.
It provides statistics on the usage, so clients can look at the cost of cleaning throughout their whole business rather than site by site and provides metrics for tracking hours.
“Many companies rent or buy their assets,” adds Ben. “Sometimes they will sit there for years, underutilised or unused. When a new manager comes into the business and audients all assets, they sometimes find equipment in the back of a facility, underutilised because the previous manager hasn’t bothered to check them.
“It brings a greater level of accountability because everyone in the business can see what’s going on, without even having to go to the site.
“The system also has a pre-start checklist, which the operator needs to complete before using the machine. This is a safety mechanism, tracking the user and ensuring risks are reduced and the machine is fit for operation.”
If anyone misuses the machine or if there is an accident, the Conquest FM user can identify the operator. This information can be used for training, incident reporting, and even performance management.
Unauthorised usage can be prevented through the QR system –this provides an authorisation key to the user to activate the machine. The operator can also log in with a question-and-answer option. If the answer is incorrect, the machine will immobilise.
Managers of large fleets will benefit from the Conquest FM. They can monitor their assets from afar without having to visit each facility, saving them both time and money. With this real-time visibility, the manager can see if their warehouse or DC has been cleaned, and the duration of this process.
Asset, fleet managers and MHE coordinators can review and manage multiple assets across multiple sites with ease and this helps with informed, data-driven decision making.
The Conquest FM also helps with customised reporting. These reports contain information that can be sent to the central manager via email or text notifications at any time of the day or night – especially in the case of an emergency.
They can also set it up, so they’re sent to users on a weekly, monthly or quarterly basis, and access asset information by logging into the dashboard. The data can then be
shared with others who aren’t logged into the user groups such as members of the board, leadership teams, and other key stakeholders.
“Conquest FM is a bolt-on system, meaning it can be used with both existing and new Conquest cleaning equipment,” explains Ben. “Managers can add Geo-fencing to certain assets, to ensure machines are restricted to dedicated areas with in facilities.
“This is important because equipment can sit on a low battery for a while or remain idle in the back of a warehouse without anyone noticing. It helps managers with fleet utilisation and reallocating machines to sites where they’re needed, increasing uptime and decreasing downtime.
“Managers can ensure contractors are spending sufficient time on task, and they’re getting what they paid for in the contract of sale. For example, if the contractor is meant to sweep a facility for two hours a day, but the manager finds they’re only sweeping for 30 minutes a day, they can hold them accountable for not fulfilling their end of the bargain.”
From the safety aspect, the pre-start feature is the key to guaranteeing operators are trained in and are using the equipment properly. Audits are regularly conducted. A safety compliance officer will always ask for reports, which means a fleet manager can show all this relevant information using the Conquest FM.
This solution is completely customisable. “Let’s say the filter in the machinery doesn’t have a daily maintenance check, but you can add a safety switch to it, which then becomes part of the pre-start,” says Ben. “If the filter hasn’t been pulled out then put back in, it won’t allow you to mobilise the machine.”
“There haven’t been many of these sorts of systems designed for cleaning equipment. Most have been designed for excavation equipment and forklifts. You can apply the Conquest FM across your whole cleaning equipment fleet regardless of its age. It can be used on both existing and new fleets, meaning businesses don’t need to update their entire fleet to experience the benefit.” ■
MHD sits down with Argon & Co’s Mechanical Engineer and Solutions Design Consultant, Gerhard de Bruyn, to speak about solutions in intralogistics that are not only functional, but factor in occupational health and safety.
When focusing on intralogisticsrelated solutions, it’s integral to determine what their functions are before factoring in occupational, health and safety (OH&S) guardrails.
As a mechanical engineer and solutions design consultant at Argon & Co, Gerhard de Bruyn looks at a prospective solution and divides it into its core components.
Once these are established, constraints can be added – these can be environmental, physical or financial. He says communicating with stakeholders and clients is crucial – as is separating tasks into their core principles.
“By understanding the core and the constraints surrounding it, and ensuring it’s properly communicated between all relevant parties, it enables you to ensure the process is going to
be successful,” says Gerhard de Bruyn, Mechanical Engineer and Solutions Design Consultant at Argon & Co.
“It might seem counterintuitive, but initially, I ignore the safety aspect and solely look at the function. You don’t want something that’s 100 per cent safe yet zero per cent unusable. A car – for example – is an inherently dangerous machine, but you need to use it. The only way to guarantee 100 per cent safety is to not drive the car, but that then renders it useless.”
Gerhard notes it’s necessary to look at what the ramifications are if something was to go wrong. It’s always function first then safety because there’s no point adding safety to a dysfunctional solution.
A project Gerhard’s working on has involved a client and vendor looking at the solution and realising there’s no proper maintenance access. It’s an unsafe space because someone could become trapped inside.
In the event of a bigger emergency, no one will know that person’s left inside because there are no lockout tagout procedures; there’s no fencing around it, and there’s nothing to indicate someone’s in there.
“Whilst you may be complying with the machine safety standards, you’re not complying with access standards,” explains Gerhard. “And they don’t amount to egress standards.”
The egress requirements are set out as part of the NCC (National Construction Code) Part D. Simply boiled down, it is the distances to exits, decision points along the way, and fire safety measures to ensure safe egress from a building in case of an emergency.
A holistic approach is required when designing these solutions. Gerhard says he checks who or what will use the solution, such as a picker or packer at a packing station.
“You need to ensure the operator
has everything they need to fulfil the function and to do so safely,” he adds.
“Ergonomics are also considered to prevent repetitive strain injuries, back injuries, and any other potential accidents. You design what’s fit-forpurpose and it’s for the 99th percentile, not just the 95th percentile.”
“When looking at a holistic approach to design, the iterative design process is paramount because you don’t necessarily get it right the first time,” says Gerhard. “You soundboard it against the stakeholders; you work with experts; you receive feedback; and you develop the whole process.”
By talking to the operators who will use the prospective solution, Gerhard can gauge their ideas and consider them when refining his designs. “Once you have those biased opinions, you take a step back, observe the current process or processes similar in other sites or policy experience.
“What is the action going to achieve? Can we bypass it? Can we break down the tasks into more logical pieces? One person can do more of a streamlined process, which might mean less thinking or repetitive strain is necessary.”
Additionally, Gerhard researches what technologies his clients could deploy and establishes whether they comply with relevant Australian standards or not.
“I’ll work with fire engineers and talk to the fire departments to ensure what we’re doing is complying with
what they need on site, such as how they can enter the site and if they accept the technologies that have been selected,” he explains.
“Start conversing with the clients to break down what you’re going to do and understand they’re involved in the process, so they know what’s being done and they agree with the proposal. Communicate the changes to them.
“Redundancies are only applicable when the result of not having a backup safety feature could be severe or fatal. I don’t need a failsafe if my pen stops working, I can just replace it. But if an elevator fails, you need those emergency brakes to kick in.”
Gerhard notes most times, the redundancy comes at the cost of the function. But the function’s already stopped at this point and safety is of paramount importance.
If it’s life threatening or could cause severe injury, redundancies are required. This can relate to material handling equipment such as pallet moving cranes with light curtain safety sensors and fail-safe brakes when power is lost or AGVs with multiple layers of safety redundancies ranging from audio/visual indicators, laser scanners, speed monitoring, zone control, emergency stops, etc.
Continuous testing is done once the solution’s been implemented. It takes time to ramp up because the people involved need to be trained. With the feedback received, required minor
changes can be made because it’s difficult to get it right from the get-go.
“The continuous feedback loop ensures potential hazards are identified early on during the project,” adds Gerhard.
“All the experience built up along the way enables us to eliminate most of these factors and potential hazards. It’s still crucial to have the continuous feedback loop or testing to guarantee it works for that specific end user as every project is unique.”
Adhering to the relevant standards ensures the site and working environment is safe. Further, there’s a financial benefit as it helps the client obtain insurance coverage for their site and reduces the likelihood of rectification required leading to a warehouse that can become operational sooner.
On-site training is done with small groups. This is what Gerhard considers to be the best way to ensure operators use the technology safely.
The team leaders know who their colleagues are and can personalise the information for them when they deliver the training Regulations are sometimes updated, and new processes implemented, requiring routine refresher courses.
“A well-informed user is less likely to make mistakes,” says Gerhard. “Always follow all the new protocols and establish a safety culture, which customers are pushing towards as a core principle.” ■
WOMEN IN INDUSTRY NOMINATIONS ARE NOW OPEN.
Now is your chance to nominate an industry leader who you believe is advocating for positive change and deserves to be recognised.
PROUDLY PRESENTED BY
MHD
Thurs 20 June, 2024
The Women in Industry Awards recognise outstanding women leaders from across Australia’s industrials sector.
Darren O’Connor of Körber sheds light on how voice technology is a boon to operations in challenging cold chain environments.
The world of warehousing, particularly within the cold chain sector, is witnessing a significant transformation, driven by the adoption of advanced technologies.
Darren O’Connor, a prominent figure at Körber with extensive experience in solution delivery, shares valuable insights into how voice technology is addressing the unique challenges faced in cold storage environments.
The cold chain, a crucial segment of the global supply chain, is known for its harsh conditions, posing substantial challenges for both workers and technology.
“Working in a freezer environment can lend itself to a high turnover as people find they can’t cope in the cold – especially when working with unsuitable equipment,” Darren explains.
This high turnover is a critical concern for businesses, given the essential role cold storage plays in preserving the quality and safety of perishable goods. As Darren points out, “Your team are your most valuable and productive assets, and they must be looked after.”
One of the biggest challenges in cold storage warehouses is the need to
maintain high levels of productivity and accuracy, despite the harsh conditions. Traditional methods, such as wristmounted scanners and screens, often falter in such environments.
“Condensation on the screens will freeze and thaw, making manual input impossible, and hands will have to be exposed as gloves are too bulky for accurate input,” Darren says, highlighting the inefficiency and safety risks involved.
Enter voice-directed work (VDW). This innovative approach is designed to keep employees’ hands and eyes free, allowing them to focus on their tasks without the need for manual inputs on screens or paper.
“Voice technology was created to maximise operational efficiency in the warehouse by allowing team members to work both hands-free and eyesfree,” Darren states, emphasising the technology’s impact on operational efficiency.
The wireless headsets used in VDW are specially designed for the freezer environment, capable of withstanding temperatures down to −30°C and resisting condensation.
Darren notes, “The batteries will easily last a full eight-hour shift
too, even in extreme temperatures.” This feature is crucial in maintaining uninterrupted workflow and enhancing productivity.
Discussing the hardware’s durability, Darren mentions, “Both the headsets and their terminals are tightly sealed against condensation, and can also come with protection built-in for workers’ ears.”
This level of technical robustness is essential for equipment operating in such challenging conditions. Moreover, these headsets are not just robust but are also designed to ensure clarity of communication.
“They are even noise-cancelling, so the instructions can be heard over freezer fans, even through hats or balaclavas,” Darren adds, addressing the issue of the noisy environment in cold storage facilities.
In terms of improving productivity and accuracy, the impact of VDW is significant. Darren observes, “Using the headsets instead of a wrist-mounted scanner, or paper, allows gloves to stay on at all times, and directions on screens or paper don’t need to be read and interpreted through a layer of frost.”
This improvement directly translates into more productive and accurate picks, essential in a fast-paced warehouse setting.
The benefits of VDW extend beyond just operational efficiency; they also positively impact employee satisfaction. High turnover rates in the cold chain are often due to the harsh working conditions.
However, as Darren notes, “One of the best things about voice is how much the team members benefit from using it.” The ability to work comfortably, even in sub-zero temperatures, has been described as a “game-changer” by staff.
Darren delves into the specifics of
implementing voice technology in Australia, a region that presents unique challenges and opportunities.
“Adoption in Australia is at a higher rate, and by and large, we were earlier to adopt,” he explains. This early adoption has led to a more profound understanding and integration of voice technology in the Australian cold chain logistics sector.
Safety is another critical aspect where VDW makes a significant difference. “The benefit in cold comes in the ability to keep your hands free, which encourages proper lifting techniques and unrestricted movement,” Darren points out.
This focus on safety is crucial in environments where workers are already facing physical challenges due to the cold.
Looking ahead, Darren highlights the ongoing evolution of voice technology in the warehousing sector.
“The next thing is collaborative voice. So putting a robot assistant in and then using voice to direct that,” he says, pointing towards the future of
“ It’s interesting that we are still seeing a lot of organisations hesitant to take it up even though there are proven benefits. It’s not a difficult product to implement. ”
voice technology, which involves more integrated and collaborative systems. This evolution indicates a move towards increasingly sophisticated, efficient, and safe warehousing environments.
In summarising the state of voice technology in the cold chain, Darren concludes, “It’s interesting that we are still seeing a lot of organisations hesitant to take it up even though there are proven benefits. It’s not a difficult product to implement.”
This hesitation may stem from a lack of awareness or misconceptions about the technology’s capabilities and benefits.
However, as Darren and Körber’s success stories demonstrate, voice technology in the cold chain is a game-changer, offering enhanced productivity, safety, and employee satisfaction.
As this technology continues to evolve and integrate with other advanced solutions, it stands to redefine the landscape of warehouse operations, especially in challenging environments like the cold chain. ■
Ehrhardt Partner Group’s Jeff Grigg and Larry Klimczyk explain to MHD what plans the European logistics solutions provider has for the Australia and New Zealand market in 2024.
Ehrhardt Partner Group (EPG) continues to make its presence felt in the Australia and New Zealand region by updating its LYDIA Voice Solution, acquiring Greenplan, and doing much more.
Jeff Grigg, who’s worked in the supply chain industry for 40 years developing and implementing software and systems across ANZ, is now the Logistics Solutions Advisor at the German-founded company. Based out of South Australia, Jeff says he’s excited to raise the profile of EPG in the Australasian market and bring its warehouse management and voice solutions to local businesses.
Larry Klimczyk has worked in and out of Australia for almost 20 years. In this time, he’s been providing technology solutions in the distribution and supply chain
space. This has included retailers, manufacturers, and transport companies. At EPG, he’s responsible for the Americas and Southeast Asia.
Jeff will deal with commercial sales and help businesses identify logistics opportunities, gain value from the solutions they chose from EPG and implement them on an operational level.
“Our voice recognition software has some impressive AI components sitting under it,” explains Larry. “This means there’s zero training or learning time for the voice engine to recognise somebody’s voice. Operators aren’t wasting time having instructions repeated to them because LYDIA has mitigated this problem.
“Multi-language is a unique option.
Via audio ouput and voice recognition, multi-language recognition increases usability and provides a big boost to employee recruitment and retention. This is a crucial advantage when it comes to collaboration in multinational, seasonally fluctuating teams, as employees are simply able to respond in their native tongue. Users can simply put the headset on and become productive straight away.”
EPG has begun to incorporate AI technology learnings, thereby improving recognition and speed. Within the past two years, it’s implemented the multi-language feature into the LYDIA Voice Solution’s software. As soon as someone picks up the headset, it allows them to select their profile and to choose what language they’d like it to use.
“This is an enabler to tap into new sources of labour,” says Jeff. “We want workers to be productive and happy.”
EPG has expanded its supply chain execution suite by integrating a new product, called Greenplan, which is now also available in the Australian market. Greeplan is a route planning solution, offering a planning and execution platform for efficient and optimised transportation management. While this solution operates effectively on its own, it is designed as a flexible component that can seamlessly integrate into a customer’s existing Transportation Management System (TMS).
“We now have a convergence of much more data,” adds Larry. “It improves our processing power and assists customers when planning routes either for the day or in realtime – all while considering real-time
traffic patterns.
“Not only are we looking at the road infrastructure, but we’re also looking at the traffic speed every 200 metres and every five minutes. We’ve found it may be more efficient – hypothetically speaking – to do a route clockwise at 10am, but if you’re doing that same route at 2pm, it might be more beneficial to do it anti-clockwise.”
He notes EPG’s objective with its customers is twofold – it’s figuring out how to deliver more items on time while reducing the costs. Greenplan addresses both of these issues where costs are sometimes decreased by 20 per cent, and on-time deliveries are improved by as much as eight to 10 points, which is important because in the transportation industry, a company is only as good as its last delivery.
When goods aren’t delivered on time, customers tend to change providers although they usually want their deliveries to be free.
“While we can’t promise to have the customers’ orders delivered for free, we do our best to ensure they’re delivered on time, and we’re also trying to get the lowest cost possible for the transport organisation.”
The primary secret sauce to the LYDIA Voice Solution is its software. While offering its own hardware solutions, EPG is also working with major hardware providers, such as Zebra, to deliver a cost effective yet robust technological hardware solution for their customers.
Even though LYDIA Voice has been hardware-independent since day one, EPG has invested in specific technology – both headsets and vest – for its LYDIA Voice Solution – which can be combined with its VOXTER mobile voice computer or a Universal Android device.
In March, EPG launched LYDIA Voice Wear Air, which is a much lighter weight headset and vest even though it appears more rugged than its predecessor. It has stronger speaker power, and an improved microphone. Additionally, the software has been upgraded to V9 – also known as 9.1.
“We’re making advances in both AI speed and multi-language recognition as well as the LYDIA Voice Co-Pilot,
which is the ability for a supervisor or manager to listen to what a particular worker is doing so they can guide or train them,” says Larry. “Customers say it’s great because they can monitor productivity, and focus on workers who may need additional coaching.”
EPG has been developing and providing supply chain execution solutions for more than 30 years. It has a Gartner-recognised mature Warehouse Management System (WMS) available as one of its core offerings. “We believe there are opportunities for a world-leading warehouse management solution to be placed in the Australian market,” explains Jeff.
“Internationally, we’re placed fifth among the leading Warehouse Management Solutions. The widelyrespected industry analyst and research firm, Gartner, has us as the leading challenger in its 2023 Gartner Magic Quadrant for WMS. Australians are starting to understand the value of our globally renowned solutions – and we expect we’ll gain further traction here.”
Besides leveraging partnerships, EPG will ramp up its plans to further grow its business in the ANZ region in terms of resources.
Automation is vitally important for both service quality and cost reduction. Gartner not only tracks EPG’s WMS, but it also tracks its Warehouse Control System (WCS). EPG has offered warehouse solutions for
Level 4 and 5
warehouse operations for more than three decades. Being a hardware vendor-agnostic automation solution provider, EPG is ranked the number one for Automation by Gartner.
Larry notes Australian businesses are exploring what they can automate in their operations. “One of the big differentiators with EPG on our WCS is we’re completely hardware agnostic.
“If you want to futureproof your WCS, EPG can help without locking you into one type of robotics or one type of automation equipment. By using modern-day technologies to harness AI and data, we can create information that’s invaluable for businesses.”
Jeff adds that EPG looks after the administrative, operative, and automation side of warehouse management. “We have a supply chain control tower, that businesses can use to make the best decisions for themselves. AI has the potential to hugely enrich datasets, and we have the tools to interpret and dashboards to display them.
“The friction in the supply chain – the excess inventory, the justin-case inventory – comes about due to poor information flows. The better information flows across the supply chain, the less what-if or just-in-case inventory we have.
“By using automation with higher and more reliable logistics data, AI is improving information, therefore making it possible for businesses to gain benefits for their bottom line.” ■
Blue Yonder’s Richard Ryan explains the company’s new interoperable services, why Blue Yonder is changing the way it renews systems, and why the journey they – and their clients – are on
“If you look a Blue Yonder’s product portfolio you’ll see manufacturing planning, manufacturing solutions, retail planning, retail solutions, and execution solutions – including transportation management and warehouse management,” says Blue Yonder’s Richard Ryan. “Until very recently we didn’t really focus on the connection between these solutions.”
And it’s this lack of connectivity that the supply chain platform provider is now intent on rectifying.
“What we’ve seen post-COVID, is that most of the problem actually lies in the connections between these solutions,” Richard says. “Say you’re doing a plan for manufacturing, but you don’t really know if you have the trucks to transport all the products you’re planning to build – or you don’t know if you have warehouses to position the products you’re planning to build. What we see now as a big challenge is getting all these different buckets to talk to each other and work with the same data.
“If I’m doing a plan from a manufacturing point of view, I should be sure that I can transport and warehouse it, and my retail organisation is ready to receive it.”
To that end, Blue Yonder is forging ahead with its “interoperable solutions”, where different domains communicate directly with each other and share information in a way beyond simple interfacing.
The significance of Blue Yonder’s update cannot be overstated. It addresses critical pain points such as siloed operations, visibility gaps, and inefficient workflows that have long plagued supply chain management. By enabling seamless coordination and streamlined management across the entire supply chain ecosystem, Blue Yonder’s solutions promise to mitigate inventory waste, reduce overhead costs, enhance sales, and improve responsiveness and resilience.
Central to this innovation is the integration of processes, systems, and data across Blue Yonder’s Planning and Execution solutions, leveraging
artificial intelligence (AI) and machine learning (ML) to facilitate smarter, scalable, and real-time decisionmaking. This approach ensures that businesses can operate more synchronously, achieving unified goals with unprecedented efficiency.
Blue Yonder’s advancements are underpinned by strategic investments in cloud-native architecture, composable microservices, and a platform data cloud powered by Snowflake. These technologies provide the foundation for scalable, secure, and high-speed supply chain operations, enabling businesses to leverage AI-driven insights and achieve accelerated adoption and productivity.
“It’s definitely a change in vision,” Richard says, “but it’s also a change in the underlying technology. We have developed a partnership with Snowflake, which is a crucial piece of tech for our new strategy. We’re going to have a common database using Snowflake between all our different applications. If a planning solution wants information from a WMS, it can just go into Snowflake and pick that information; if a TMS wants to know what the plan is for the next month –it can go into Snowflake and pick that information there.”
Importantly, the new interoperability that is being designed into Blue Yonder’s solutions allows for customers to access Snowflake data with their own applications, too. “It’s not a closed environment like some vendors have; ours is an open environment where the customer can have their own application, and if they want information about warehousing, for instance, they too can get the data right out of Snowflake.”
Achieving complete interoperability is long term project – and potentially costly. That’s why Blue Yonder is breaking up its solutions into “composable microservices”.
“If someone comes to me and says, ‘I want to achieve interoperability’, and I say: ‘Okay, let’s replace your planning, your TMS, your WMS, your OMS, your execution’ – then we’re talking about 10 years and multimillion-dollar projects, which nobody wants to undertake,” says Richard.
With Blue Yonder’s composable microservices, they can instead address key pain points one-by-one, without being locked into a costly or lengthy complete overhaul.
“Let’s say you have a visibility problem, but you don’t want a new OMS. You have a problem with visibility of your warehouse, of your inventory in stores, on your website. You need to tell your customers if you have that product available in stores or not. That is a pain point for you. You don’t have to buy our entire OMS; you could buy our microservices for visibility, implement that into your ecosystem – and that’s adding value to you.”
As companies progress with their journey, they can purchase more microservices from Blue Yonder – even to the point of having all of them. But the point is, says Richard, that “you’re not mandated to do that to
start having benefits. We’re enabling the customer to buy parts of those microservices in such a way that they can add value to their current ecosystem but don’t have to change their legacy products immediately.”
Blue Yonder understands that not every customer will want to use their entire tech stack, says Richard, and that is a big difference from some of the other players in the field.
“A company may want to use another WMS – and while we’d prefer they use ours, it’s okay, we’ll still happily work with you to achieve your goals. Even if you don’t use our WMS, you can still use our billing solution or our OMS. We’re not mandating you to use our entire tech stack – and that’s a big differentiator from some of our competitors.”
Blue Yonder also understands that the move from legacy systems to more modern technology is a big investment and very high risk.
“We can reduce your risk right now without overhauling a legacy system,” says Richard. “You may have a legacy system, you like it, you know how it works, and by just adding another layer on top, you can reduce your risk and get another five or ten years out of the system.
“If we can give you access to
the data in Snowflake, this legacy system now can benefit from having a repository of data that you need. In effect, we’re giving more of an afterlife to legacy systems. This is incredibly important for some customers.”
For Blue Yonder, it’s not just about the destination – but the journey too. Richard says that the company is travelling on a journey with its customers that will unfold over time, but that is being undertaken with a level of seriousness and investment that will yield dividends for it and its customers over the long haul.
“This is all possible because our parent company, Panasonic, has made a significant investment allowing us to do this replatforming. It’s not something that’s easy to do – it requires a tremendous amount of investment from the software company because the norm is to sell the software first and then develop it. But because of the investment from Panasonic, we’re able to really sit down and re-write our entire platform.
“We’re putting our money where our mouth is so we can deliver the results clients need now. We’re excited about the journey we’re on, and we think our clients will be excited by the results we deliver them, too.” ■
Melbourne will host an event for supply chain experts to explore strategies for achieving net-zero emissions in warehouses. MHD reports.
The supply chain and logistics sector is at a pivotal juncture in its pursuit of achieving lower carbon emissions within supply chains and warehousing operations. Industry leaders and innovators will gather at MEGATRANS to discuss and demonstrate the essential steps toward realising the future of ecofriendly logistics practices.
MEGATRANS2024 is set to be a showcase for advanced technology companies, highlighting their contributions to sustainable supply chain solutions. The expo will present an array of innovative approaches from firms of all sizes, emphasising their roles in developing a more sustainable logistics landscape.
Central to the discussions at MEGATRANS will be the concept of the zero-carbon warehouse, a facility that achieves a net-zero carbon footprint by balancing emitted greenhouse gases with equivalent reductions or offsets. Achieving this goal involves adopting energy-efficient practices and harnessing renewable energy sources, such as solar or wind power, underlining the industry’s commitment to a more sustainable and environmentally friendly supply chain.
The push towards zero carbon warehouses and broader sustainability strategies in the supply chain is driven by the growing awareness and urgency to address climate change.
MEGATRANS serves not just as a
platform to highlight technologies aiding in the creation of zero-carbon warehouses but also showcases the latest innovations making their way into the logistics and supply chain markets.
In conversation with MHD Supply Chain Solutions, Dominic Lindsay, co-founder and CEO of Nexobot – an exhibitor at MEGATRANS –shared insights into his company’s innovative modular system for warehouse robotics. Nexobot, a 2023 start-up, has introduced a robotic solution designed to improve efficiency in warehousing and logistics operations. Their technology facilitates the sorting of packages into designated bins by operating beneath a barrier, a testament to the evolving needs of sustainable supply chain
“ The push towards zero carbon warehouses and broader sustainability strategies in the supply chain is driven by the growing awareness and urgency to address climate change. ”
practices.
Addressing the importance of sustainable supply chains, Lindsay remarked, “essentially, we’ve seen the challenges that other people have had in the industry, and we’ve designed our entire business model around avoiding those challenges.” He further highlighted the significance of MEGATRANS as a platform for collaboration and showcasing technologies that support the achievement of net-zero warehouses, stating, “I think getting together and talking about strategies is obviously a really good idea but what we really need is spaces to exhibit technologies that are going to help people achieve that.”
Nexobot aims to use the MEGATRANS expo as a pivotal opportunity to introduce their product to the industry and solidify their presence in the market, reflecting the event’s critical role in fostering innovation and sustainable practices within the supply chain and logistics sectors. ■
If you are interested in exhibiting and you would like to know more, please visit the official website at www.megatrans.com. au, or contact Emily Robertson on +61 422 103 119.
Michael Farragher, TAFE NSW Teacher of Supply Chain and Logistics/SCLAA Training, Education and Development Committee, writes for MHD about how the industry can attract and recruit new young talent.
During the pandemic, we gained a heightened appreciation for the importance of supply chains and the professionals who manage them.
As we confronted various disruptions such as lockdowns, port congestions, and fluctuating demand patterns, it became clear that the efficiency, adaptability, and strategic decisionmaking of these professionals were crucial for sustaining supply chains.
It’s in the aftermath of the pandemic that we fully grasp the tremendous value of outstanding supply chain executives.
The term “outstanding” underscores the need for individuals who not only possess the essential knowledge and skills of supply chain management, but also have the capability to address unprecedented challenges and swiftly adapt to evolving landscapes.
At the recent ‘Australian Supply Chain & Logistics Awards’ in Sydney, Paul Graham, CEO of Australia Post, outlined one of its challenges as the ‘Ageing Workforce’ – a common theme within the sector.
The big question is, ‘What can we do’? There are various strategies that can be applied to address the workforce challenges that we are facing in the Supply Chain and Logistics sector, which include:
The issue: The supply chain profession faces an image challenge. Many individuals lack a clear understanding of what the term “Supply Chain & Logistics” entails.
The name fails to convey the intricate tasks involved in managing the manufacturing, transportation, and storage of goods.
Despite technological advancements driving the supply chain industry, younger professionals often perceive it as mundane and devoid of career progression opportunities.
One contributing factor is the lack of public relations efforts by companies to elevate the visibility of supply chain roles.
Ultimately, Millennials and Generation Z employees are unaware of the potential for opportunity, compensation, and professional development offered by a career in the supply chain field.
Education and awareness programs:
To foster a better understanding and appreciation of Supply Chain Management across various industries, it’s essential to develop educational programs that emphasise its critical role and career pathways.
By engaging with schools, colleges, and universities, we can actively promote the diverse and dynamic nature of careers within the supply chain sector.
Additionally, organising workshops, seminars, site tours and career fairs offers valuable insights into the exciting opportunities available, helping to inspire and inform future generations about the possibilities within this field. This ongoing service is a primary focus of the SCLAA.
Fostering partnerships between
educational institutions like TAFE NSW and industry organisations such as the SCLAA and Industry Skills Australia (ISA) is crucial for ensuring that curriculum and training programs meet the evolving needs of the supply chain sector.
By collaborating closely, we can align educational offerings with the latest industry trends, technologies, and best practices, thereby better preparing students for careers in supply chain management.
Moreover, encouraging industry professionals to engage in mentorship programs is invaluable.
The SCLAA offers a fantastic Mentoring Program, which is run annually to assist in this area, with registrations opening at the end of March.
Through mentors sharing their wealth of experience and insights with younger individuals, they can inspire and guide the next generation of supply chain professionals, fostering a culture of continuous learning and growth within the industry.
It’s imperative to showcase the remarkable technological innovations driving the supply chain industry forward, with a particular emphasis on automation, data analytics, and other cutting-edge technologies.
By highlighting these advancements, we can demonstrate how they revolutionise traditional processes, increase efficiency, and enhance decision-making capabilities across the supply chain.
Moreover, illustrating how these
innovations create more engaging and intellectually stimulating roles within the sector is essential.
From leveraging data analytics to optimising inventory management to implementing automation solutions for streamlined warehouse operations, these technologies empower supply chain professionals to tackle complex challenges creatively and drive meaningful change within their organisations.
Sharing success stories of young professionals who have thrived in supply chain careers is a powerful way to inspire others and showcase the diverse opportunities within the field.
By highlighting their achievements, career progression, and the impact they’ve made in their roles, we can illustrate the growth potential and rewarding nature of supply chain careers.
Utilising testimonials and case studies allows us to provide tangible examples of individuals who have excelled in various areas of the supply chain, from procurement to logistics to operations.
These stories not only celebrate the accomplishments of these professionals, but also demonstrate the multitude of paths available within the industry, encouraging others to pursue their passions and excel in their own supply chain journeys.
Establishing traineeship programs is crucial for providing young workers
with hands-on experience and exposure to daily activities within the supply chain.
These programs offer valuable opportunities for participants to gain practical skills, learn from experienced professionals, and understand the intricacies of supply chain operations.
By immersing themselves in realworld scenarios, young workers can witness the direct impact of their contributions on organisational success and supply chain efficiency.
Additionally, traineeship programs allow participants to develop essential skills and competencies relevant to their roles, fostering their professional growth and preparing them for career advancement opportunities within the industry.
Ultimately, these programs serve as a valuable investment in the development of future supply chain leaders and ensure a skilled workforce capable of driving innovation and success in the field.
Many Vocational Educations Training (VET) Registered Training Organisations (RTOs) will offer School Based Traineeships (SBAT) or Traineeships.
These programs are a win-win, providing employees with valuable career opportunities and formal qualifications, while helping a business remain competitive with a skilled and dedicated workforce.
The Australian government provides both financial and non-financial support to employers of trainees.
Enhance visibility on social media: Utilise social media platforms as
a tool to highlight the vibrant and dynamic facets of supply chain careers. Share captivating content that offers glimpses behind the scenes, showcases employee spotlights, and explores current industry trends.
By providing engaging insights into the diverse roles, innovative projects, and impactful contributions within the supply chain field, we can capture the interest of young professionals and inspire them to explore rewarding careers in this dynamic industry.
By implementing these strategies, organisations can work towards dispelling negative perceptions and attract young talent to the Supply Chain & Logistics field by presenting it as an exciting, innovative, and rewarding career choice.
From data analysts to operations managers, warehouse supervisors to transportation coordinators, sustainability specialists to procurement professionals, the breadth and diversity of roles within the industry cater to a wide range of skills, interests, and passions.
Whether you’re drawn to problemsolving, technology, teamwork, or strategic planning, there’s a role that aligns with your strengths and aspirations.
The supply chain and logistics sector offer countless opportunities for individuals to contribute their unique talents and make a meaningful impact on global commerce, making it an exciting and rewarding field for anyone seeking a dynamic and fulfilling career. ■
It’s imperative to showcase the remarkable technological innovations driving the supply chain industry forward. Image: SCLAA.
The Australasian Supply Chain Institute is hosting its Supply Chain Series 2024 with events across several major Australian cities including Sydney, Canberra, Brisbane, and Melbourne.
ASCI is pleased to inform you it’s organising a series of one-day conferences in major Australian cities. These conferences will focus on different aspects of the supply chain and provide valuable knowledge and expertise in these areas.
The ASCI Supply Chain Sustainability Series is a platform for professionals and industry experts to share the latest developments in their field.
The conferences will offer an excellent opportunity to network, learn, and collaborate with people interested in a specific subject, including Supply Chain Management, Integrated Product Support, Procurement, Operations Management, and Logistics Management.
The national theme for the series is
The national theme for the series is “Supply Chain Sustainability.” Image: Australasian Supply Chain Institute.
“Supply Chain Sustainability”. Each event will focus on the relevance of the national theme to a particular aspect of the supply chain.
The ASCI Supply Chain Sustainability Series is a platform for professionals and industry experts. Image: Australasian Supply Chain Institute.
The events will be held in the following major cities across Australia:
• Supply Chain Management –Sydney, June 2024
• Integrated Product Support –Canberra, July 2024
• Procurement – Brisbane, September 2024
• Operations Management –Sydney, October 2024
• Logistics Management –Melbourne, November 2024
ASCI strongly encourages you to take advantage of this opportunity and make the most of these events. Attending the conferences will provide you with valuable knowledge and expertise in your field and an excellent opportunity for networking with other professionals.
Several sponsorship packages are available, each designed to suit specific needs and budgets. For more details, please visit ASCI’s website or contact it at enquiries@asci.org.au. ■
The Australasian Supply Chain Institute has unveiled its new membersonly Digital Communities offer, providing ASCI members with a powerful resource to connect to their peers.
With ASCI Connect, a new member benefit, Australasian Supply Chain Institute (ASCI) members gain a powerful resource to network with supply chain professionals, exchange knowledge and share solutions.
ASCI Connect, which automatically enrols all ASCI members today, is a cloud-based, private range of digital communities across the main components of the supply chain domain. These communities include Supply Chain Management, Integrated Product Support, Procurement, Operations Management, and Logistics.
“ASCI Connect represents a unique
opportunity for ASCI members to interact with each other to share information and solve practical problems,” says ASCI Chief Executive Officer Dr Pieter Nagel.
“Members can connect with likeminded professionals and share their knowledge and expertise. Community councils can also use the platform to discuss issues and share updates with ASCI members.”
ASCI Connect can be easily accessed anytime, anywhere through its web and app versions. ASCI members can join communities, start new discussions, ask questions, and collaborate with other members. The platform also features a user-
friendly interface that makes it easy to navigate and post images, videos, and documents to share with others.
ASCI Connect access is exclusive to ASCI members. Members can join communities, update individual profiles, and manage the frequency of community notifications. To learn more and join the discussion, visit the ASCI Community website.
While the platform is new, it has the potential to become a vital resource for supply chain professionals. With more active participation from members, we expect the communities to become the daily information exchange platform for all supply chair professionals. ■
Learn Supply Chain Sustainability and Circularity from the Supply Chain Diva, Denice Staaf. Denice has over two decades of hands-on experience in sustainability in manufacturing organisations working globally.
April 30 – May 16 2024
Classes are conducted twice weekly (Tuesday & Thursday), 10am to 1pm Sydney Time, totalling 18 training hours. Participants will join the training via ZOOM. Participants
will earn 18 CPD points for certification maintenance.
Module 1: Creating Circularity
• Introduction to Circularity
• Life Cycle Thinking (LCT)
• Introduction to the process mapping approach
• Developing Process Maps
• Establishing job specific KPIs
• Implementation of a maturity matrix
Module 2: Bringing Circularity to Organisations
• Creating a cross-functional team
• Target ranking to find the
JThe Australasian Supply Chain Institute is hosting its first-ever sustainability and circularity workshop between April 30 and May 16 2024 with the program including two major learning modules.
highest priorities
• Embedding sustainability into the organisation’s strategic objectives
• Quantifying the value created
• Competition as an order qualifier
• Circularity as your order winner ■
Classes are conducted twice weekly (Tuesday & Thursday), 10am to 1pm Sydney Time. Image: Australasian Supply Chain Institute.
Join the Australasian Supply Chain Institutes Forecasting and Demand Management two-day course between April 23 and April 24, 2024.
oin the Australasian Supply Chain Institute’s (ASCI) upcoming Forecasting and Demand Management two-day course to improve your forecast accuracy with less forecasting effort, which will take place between April 23 to April 24 2024.
This workshop will provide you with a step-by-step approach to achieving improvements in your forecasting process, the mistakes
to avoid, and sure-fire approaches that will reduce your forecasting effort.
Accountabilities and cross functional links will be discussed to enable you to assess the quality of your current processes against world-class checklists.
Options on “where to meet the customer” will also be addressed, including the strategies associated with setting safety stocks, your
product offering, and a simple approach to simulating stock levels.
Classes are conducted daily, from 9am to 5pm Sydney Time, totalling 16 training hours. Participants will join via Zoom. ASCI members can register for $1950, while non-members can register for $2350.
ASCI looks forward to you joining it for this informative and practical course.
HUBTEX’s FluX Electric Multidirectional Counterbalance Forklift Truck has had some significant and innovative updates. The latest generation has load capacities of up to three tonnes. It has a new central driver’s position, which provides a higher-up all-round visibility compared to its predecessor. Additionally, the patented 360° HX steering has been added to the compact three-wheel running gear for the first time, ensuring smooth changes in direction from longitudinal to transverse travel. It handles both pallet and long-load transport in a single vehicle. This hybrid used as a front and sideloader makes the new 3T FluX 30, suitable for a wide range of sectors, from the timber and metalworking industries, through to the building materials trade.
For more information visit www.hubtex.com.au
Global cube storage company AutoStore introduces its latest capability, the Grid and Vending Machine solution, designed to simplify warehousing automation. The ConveyorPort is a workstation in its simplest form, where Bins are dropped on a conveyor and transferred to an opening outside of the Grid. Smart covering and sensors ensure operator safety. The CarouselPort is designed to work with the operator, in harmony with Robots to ensure the next Bin is always ready. The workstation operates with three rotating arms, each holding one Bin tray. The Vending Machine solution includes various Robots and chargers, as well as a dummy display unit, and a grid structure with 60 Bins.
For more information visit www.autostoresystem.com
Poor ocean visibility puts a strain on global supply chains, logistics costs, and customer service. At the root of the issue is low-quality data that hinders personnel productivity, streamlined operations, and proactive exception management. Today, more than ever, shippers and 3PLs need global ocean visibility with the data quality, intelligence, ETAs, and proactive exception management that ensures efficient, costeffective, reliable, and sustainable global transportation. Project44’s Ocean Visibility solutions is here to help, with a suite of solutions that uses first-in-class data and analytics to improve personnel productivity, allow for proactive exception management, reduce logistics costs, improve customer service, and empower users for agile transport planning and procurement.
For more information visit www.project44.com
ifm Track and Trace Gate is the complete solution for your automated and transparent logistics in your incoming and outgoing goods processes. By directly transferring all goods flows to the IT level, you can organise the inter-locking of production, inventory, and suppliers more efficiently than ever before.
For more information visit www.ifm.com/au/en
Argon & Co is a global management consultancy that specialises in operations strategy and transformation. With expertise spanning the supply chain, procurement, finance and shared services, we work together with clients to transform their businesses and generate real change. Our people are engaging to work with and trusted by clients to get the job done.
Start your transformation journey today and download our credentials pack:
argonandco.com