TRANSFORMATION WITH CONFIDENCE
Argon & Co's intralogistics team
ELEVATE DOWN UNDER
COVER STORY
How Dematic helped the leading apparel brand deliver a new automated DC in Auckland
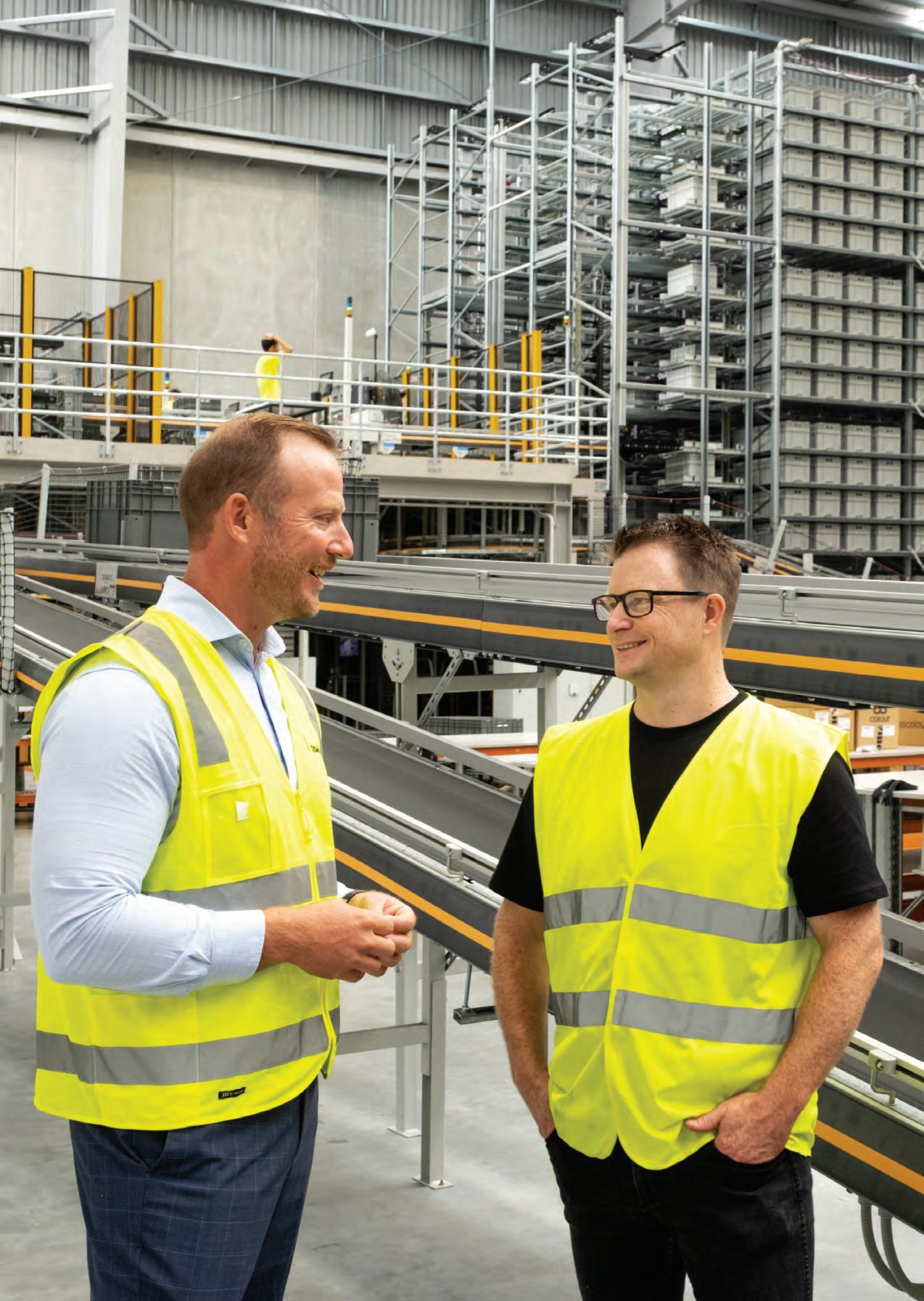
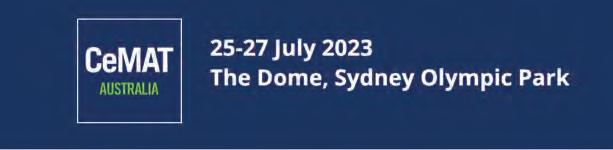
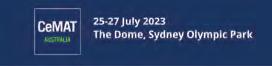
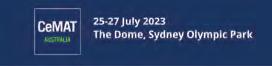
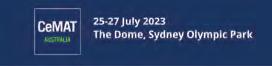
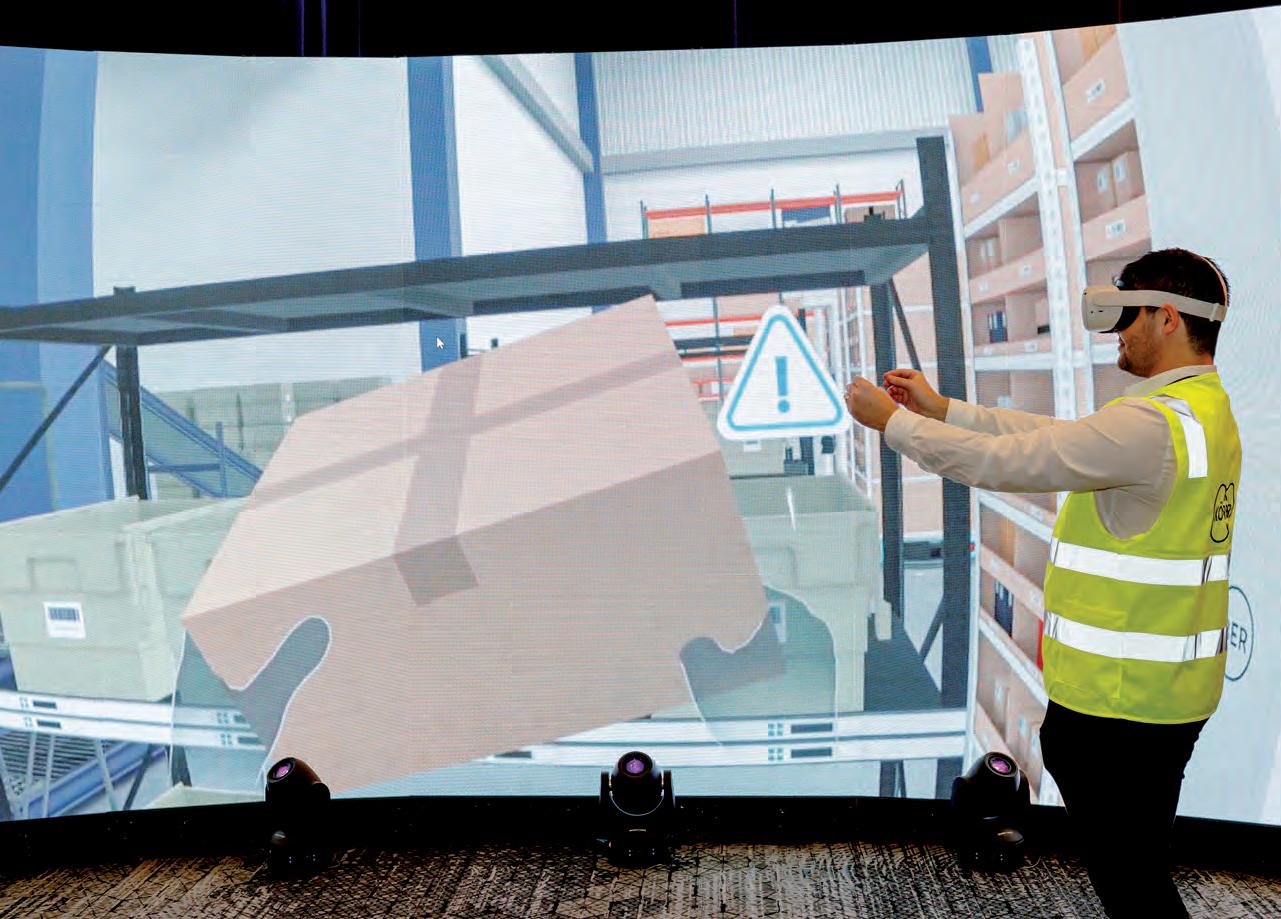

TRANSFORMATION WITH CONFIDENCE
Argon & Co's intralogistics team
ELEVATE DOWN UNDER
COVER STORY
How Dematic helped the leading apparel brand deliver a new automated DC in Auckland
CONTACT
MHD Supply Chain Solutions is published by Prime Creative Media
379 Docklands Drive, Docklands VIC 3008
Telephone: (+61) 03 9690 8766
Website: www.primecreative.com.au
THE TEAM
CEO: John Murphy
Chief Operating Officer: Christine Clancy
Managing Editor: Syed Shah
Editor: Edward Cranswick
Journalist: Joseph Misuraca
Business Development Manager: Beth Jarvis
Design Production Manager: Michelle Weston
Art Director: Blake Storey
Graphic Designers: Louis Romero, Kerry Pert
Client Success Manager: Janine Clements
FOR ADVERTISING OPTIONS
Contact: Beth Jarvis
beth.jarvis@primecreative.com.au
SUBSCRIBE
Australian Subscription Rates (inc GST)
1yr (6 issues) for $78.00
2yrs (12 issues) for $120.00 – Saving 20% 3yrs (18 issues) for $157.50 – Saving 30%
To subscribe and to view other overseas rates visit: www.mhdsupplychain.com.au or Email: subscriptions@primecreative.com.au
ACKNOWLEDGEMENT
MHD Supply Chain Solutions magazine is recognised by the Australian Supply Chain Institute, the Chartered Institute of Logistics and Transport Australia, the Supply Chain and Logistics Association of Australia and the Singapore Logistics and Supply Chain Management Society.
Welcome to another issue of MHD Supply Chain Solutions. As we navigate the challenges of an ever-evolving industry, it is imperative to stay abreast of the innovative strategies and solutions shaping our field. In this issue, we keep score of many remarkable stories and solutions in our industry.
Our Cover Story takes us to New Zealand, where Dematic’s robust automation solution has breathed new life into AS Colour’s distribution centre. Their state-of-the-art system has propelled throughput by an incredible 344 per cent per worker, establishing a robust framework for present and future growth. This case study underscores the transformational power of automation and the remarkable scalability it offers.
Also in this issue, we take you to Melbourne, where Körber held its globally acclaimed Elevate event in-person for the first time ever in Australia. From engaging presentations to insightful panel discussions, the event was a tour de force of industry knowledge-sharing and networking. We explore the key takeaways and the potential implications they might have on our industry.
Elsewhere, we shift our focus to Argon & Co, a company that recently expanded its intralogistics team following a merger with Fuzzy LogX. We had the pleasure of speaking with the trio leading the charge - James Lee, David Ring, and Jeffrey Triantafilo. Their vision and confidence in delivering the transformations of the future are nothing short of inspiring.
It’s an exciting time in supply chain and we’re thrilled to share these –as well as many other – stories that not only reflect the current state of the industry but also hint at the thrilling possibilities ahead.
See you next month.
ARTICLES
All articles submitted for publication become the property of the publisher. The Editor reserves the right to adjust any article to conform with the magazine format.
COPYRIGHT
MHD magazine is owned by Prime Creative Media. All material in MHD is copyright and no part may be reproduced or copied in any form or by any means (graphic, electronic or mechanical including information and retrieval systems) without written permission of the publisher. The Editor welcomes contributions but reserves the right to accept or reject any material.
While every effort has been made to ensure the accuracy of information Prime Creative Media will not accept responsibility for errors or omissions or for any consequences arising from reliance on information published. The opinions expressed in MHD are not necessarily the opinions of, or endorsed by the publisher unless otherwise stated.
Edward Cranswick Editor edward.cranswick@primecreative.com.auSafety is as much a part of our business as it is yours. That’s why we pioneered the System Of Active Stability™* (SAS™) over 20 years ago. Over 3,000 calculations per second delivering class leading stability, safety and assisting accident prevention – protecting your most valuable assets. We may have pioneered SAS™ over 20 years ago – but we never sit still when it comes to safety. That’s why when you choose Toyota, you’re choosing our world class safety, and that’s just part of the Toyota Advantage. toyotamaterialhandling.com.au 1800 425 438
®
JUNE
COVER STORY
14 Dematic transforms AS Colour
REGULAR COLUMNS
18 Property Focus on the ever-changing Western Sydney industrial market
20 Logical Outlook on how to make the most of a crisis
SUPPLY CHAIN
22 Extolla taking on industry challenges
24 Körber brings its Elevate event Down Under
33 Geotab acquiring data-driven insights with telematics
43 Addverb helping clients with automation
55 HAI Robotics presenting its solutions at CeMAT
MATERIALS HANDLING
26 Röhlig Logistics celebrates with TMHA
37 Introducing the Combi-CUBE
51 Hubtex at CeMAT
WAREHOUSING
29 Toll Healthcare launches new Brisbane facility
40 Argon & Co doubles down on intralogistics
47 Swisslog working with Coca Cola on Mentone DC
ON THE COVER
How Dematic helped the leading apparel brand deliver a new automated DC in Auckland
52 Ferag bringing intralogistics into the 2020s ASSOCIATIONS, EVENTS, AND REGULARS
06 Industry News
58 RWTA on hosting the Frank Vale Awards
59 SCLAA’s ASCL Awards nominations open
61 Products
62 People on the Move
DHL Supply Chain and The Estée Lauder Companies Australia & New Zealand (ELC ANZ), the global leader in prestige beauty, have signed a strategic partnership.
The contract logistics solution company will, for the first time, manage ELC ANZ’s omni-channel warehousing logistics and value-added services for 11 of its brands.
“This milestone is a significant one for both companies,” Steve Thompsett, CEO of DHL Supply Chain Australia & New Zealand, says.
“We are so proud to be trusted with ELC warehousing in Australia. It was a consultative planning and design approach, and the new operation puts ELC ANZ in a robust position for growth.”
The new 3PL solution provides greater capacity for both B2B and B2C customers and is designed to accommodate peak periods and increased growth.
“We’re so pleased to be partnering with DHL,” says Emmerentia Wilding, Managing Director Australia & New Zealand, The Estée Lauder Companies.
“At The Estée Lauder Companies, we pride ourselves in delighting our consumers by providing them with the highest level of care and service, and
this new era in our supply chain will ensure that we continue to do so.
“In addition, the capacity and scalability of this new solution will flex to meet with evolving needs of our consumers across Australia and New Zealand.”
The Australian market is a fast-
Australia Post revealed on Monday May 1 its new parcel delivery centre in Dubbo, cementing what it says has been its long-term investment in the region.
The Fitzroy Street facility boasts more than 1485 sqm in internal space and features a straight-line conveyor through the centre of the building for efficiently processing parcels. This new facility replaces the temporary delivery centre at Jannali Road.
Australia Post Executive General Manager Network Operations, Rod Barnes says the new parcel delivery centre’s role is part of the company’s commitment to improving service in Dubbo and investing in the community.
“We have designed the new centre with efficiency and simplicity in mind to help turnaround times and get items to customers’ doors as quickly as possible,” Rod adds.
growing one for ELC ANZ, and exceptional growth in online sales saw the company outgrow its self-managed supply chain operations.
The partnership with DHL futureproofs ELC’s growth strategy, operational capability, and inventory capacity.
As a leading technology company itself, Leader Computers wanted to upgrade its warehouse with automation that would increase business efficiency, accuracy, and productivity, as well as make better use of the available warehouse space.
The AutoStore solution implemented by Dematic streamlines picking, packing, and replenishment operations, reduces storage footprint, and allows room for future growth. And, most importantly, Leader Computers is now delivering an enhanced level of service to thousands of its managed service providers and IT resellers, nationwide.
Learn more at dematic.com/leader-computers
02 9486 5555
“The additional space has also allowed us to better support e-commerce customers and their shoppers in the Dubbo area as we can now accept and process parcels faster into the centre.”
With more space, the parcel delivery centre will assist the network in meeting current parcel
delivery demands with a more streamlined experience for drivers to get in and out of the facility and back on the road to customers.
Thirty new or renovated letter and parcel centres have opened across Australia in the past six months.
Australia Post says it also opened new DCs in Butler, Western Australia
and Camden Park, South Australia in the week of April 30.
Butler’s DC will accommodate the region’s rapid growth and increase in small parcel volume as more people shop online.
Camden Park’s centre consolidates a number of properties to improve turnaround times.
Körber’s Elevate APAC 2023 finished on Wednesday May 03 with a mix of keynote presentations by managers at professional service and retail companies, and thought-provoking panel discussions on supply chainrelated topics.
Accenture’s Sari Mackay, Managing Director – Strategy & Consulting, Supply Chain & Operations Lead, ANZ started the second and final day of the conference with an in-depth analysis of the global supply chain, including the need for businesses to reinvent their networks, and invest in regionalised supply chains all while preparing for both just in case and just in time deliveries.
“The future of supply chain is data analytics and AI,” Sari says. “Resilient networks are needed to deal with disruptions and drive cost optimisation. Transparency is the most important resource.
“Businesses need to innovate, challenge themselves, develop new ways of thinking, adopt digital capabilities and data – these things will make or break them.”
Patrick Fountain, General Manager of Super Retail Group explained how automation combined with data science have transformed the company’s supply chain network and enabled it to optimise its operations and increase productivity.
“Post-COVID, we were able to get rid of our Brisbane and Sydney DCs,” Patrick says. “We now have seven DCs in ANZ with 30,000 SKUs. Körber’s solutions have helped us achieve this and gain greater insights, further simplify our operations, and focus on
our employees and customers.”
Other presentations were by Joe Couto, Körber Supply Chain Software Executive Vice President Global Robotics & 3PL on Unified Control Systems and Sarah Owens, Enterprise Sales Manager ANZ at Honeywell on consolidating devices in a supply chain business.
Yiau Hwei Chan, Director of Engineering at Körber facilitated the first panel discussion called Driving Positive Change: How Sustainability & Diversity are transforming supply chains.
Dr Elsie Hooi, SCLAA committee member, Laurel O’Donnell, Lineage Logistics General Manager, Dr George Panas, University of Melbourne Supply Chain Lecturer, Maree Varrasso, COO at uTenant, and Nicole Katsoulis, Head of People & Culture at Körber spoke about the importance of partnerships, adopting a global perspective, focusing on women in leadership, cooperating with leading industry associations, and incorporating ESG in brownfield and greenfield sites.
“According to a 2021 report from McKinsey & Company, only 41 per cent of the supply chain labour force consisted of female workers,” Laurel explains.
“Employers need to check their unconscious bias when they’re hiring women, and women need to stop second guessing their abilities, and apply for promotions and aspire to become industry leaders.”
The final panel discussion was Building agility and resilience to deliver exceptional end-customer experience.
Frank De Sa, CIO at The Just Group along with Lian Yu, COO at Toys ‘R’ Us, Karl Neubauer, CIO at GLOBAL
Retail Brands, and CEVA Logistics’
Allan Maki spoke about innovation in retail, the need for data collection, autonomous mobile robots, Körber cloud, 3PL and automation, as well as investing in scalable solutions with Körber’s Director of Solution Delivery, Darren O’Connor.
In the main room, attendees networked, visited stalls, and tried Körber’s virtual reality headset, giving them an opportunity to see how the supply chain software company can automate and modify a new or existing warehouse.
The day finished with Nicholas Bochner discovering the synergies between conducting an orchestra to orchestrating a supply chain, as well as helping the audience to find their rhythm with a renowned OAM pianist and violinist from the Melbourne Symphony Orchestra and concluding words by Körber’s ANZ Managing Director, Anthony Beavis.
Körber’s Elevate APAC 2023 took place May 02-03 in Melbourne.
To learn more stop by our Stand: #D31 at CeMAT
Much has been made in the public square of the importance of ‘ESG’. But what does it mean?
Reto Fuhrer, CEO of RF Supply Chain Expertise, interviews Circular Supply Chain Advisory’s Brendan O’Keeffe to find out.
One of the buzzwords you hear a lot around industry these days is ‘ESG’, which stands for ‘environmental, social, and governance’ considerations. In my experience, most of the discussion around ESG comes from larger firms who tout their ESG initiatives as a way of marketing their social responsibility bona fides. No doubt, much of what these firms do is positive, but there’s still a lot of uncertainty – especially among smaller- and medium-sized enterprises – as to what precisely ESG is and what should be done about it.
To help me get a better grip on ESG, I recently interviewed Brendan O’Keeffe, who runs Circular Supply Chain Advisory.
Brendan runs Circular Supply Chain Advisory, a consulting group aimed at offering circularity services, including recruitment and consulting. Brendan’s mission is to support organisations with a strong mandate around their sustainability objectives, helping them become more sustainable across their value chain. Through his advisory services, he guides organisations that have a mission to become more sustainable but may not know where to start, providing valuable insights and direction in their journey toward sustainability.
“Though often simplified and used as a catch-all term, ‘ESG’ covers a wide range of environmental, social, and governance factors,” Brendan explains. “To give these factors real meaning and focus within a business context, organisations that take ESG and sustainability seriously often align their objectives with the United Nations Sustainable Development Goals (SDGs). These 17 goals are well-defined, allowing companies to select a few that are most relevant to their operations and report on them with clear metrics – including environmental sustainability but also social sustainability considerations like hunger, human rights, and quality of life.
“Climate action, for example, is one SDG that every organisation should consider. Under this goal, companies might focus on increasing renewable energy usage or improving efficiencies to reduce consumption. By tying their operations to these specific objectives, companies demonstrate responsibility and commitment to sustainability.”
The ‘governance’ part of ESG is a bit harder to define, Brendan tells me, as there is no one global standard or jurisdiction that companies can follow. Consequently, reporting requirements for listed companies may vary depending on their location.
“Large companies are increasingly pushing sustainability responsibilities onto their suppliers, requiring them to report against certain sustainability metrics,” he says. “While large companies must be transparent about their sustainability efforts due to shareholder requirements, smaller nonlisted companies are not currently held to the same standards. However, many small and medium-sized businesses recognise the need to be proactive in addressing sustainability to grow their business and meet the expectations of their customers.”
Brendan suggests that if a company is looking to get started with ESG, they should first listen to what their customers are asking of them. As awareness and discussions around ESG and sustainability increase, businesses should strive to understand their value chain better – from sourcing raw materials to manufacturing or importing products, and from distribution to endof-life considerations.
For companies dealing with recyclable materials, a lifecycle assessment of their materials can help identify potential recovery opportunities. Companies that focus on import and distribution should consider driving efficiencies by reducing costs and overheads, as this will naturally lead to more sustainable practices.
“Economic considerations are essential: businesses need to ensure that their sustainability efforts are
cost-effective and not just feel-good investments,” Brendan says. “One approach is to optimise existing supply chains and collaborate with customers and suppliers to find shared solutions. Sharing expertise and best practices with partners can lead to increased benefits and adoption of sustainable strategies throughout the supply chain.”
While some businesses may not currently feel the urgency to improve their ESG performance – especially smaller companies not subject to investor pressures – it’s crucial to recognise the potential consequences of inaction. Brendan points out that consumer attitudes are changing, and they are increasingly looking at companies’ sustainability practices when making purchasing decisions. Consequently, businesses that fail to adapt may find themselves at a disadvantage compared to competitors who prioritise ESG.
“As companies become more concerned with sustainability, they may require their suppliers to meet certain standards or provide ESGrelated reporting. Those that are unprepared or unwilling to adapt may find themselves excluded from major contracts or relegated to the bottom of procurement lists. This underscores the importance of businesses proactively engaging with ESG practices and working collaboratively with supply chain partners to improve sustainability performance.”
With a commitment to finding solutions to individual client challenges, RF Supply Chain Expertise is partnering with Brendan and Circular Supply Chain Advisory.
The largest single capital investment in Coles’ history will provide a safer, more efficient and sustainable supply chain in partnership with Witron.
The first Australian Automated Distribution Centre (ADC) using global leading Witron technology is the largest of its kind in the Southern Hemisphere. Prime Minister Anthony Albanese MP, Queensland Premier Annastacia Palaszczuk MP, Coles Group Chairman James Graham and Coles Group CEO Steven Cain officially opened the ADC at Goodman’s Redbank Motorway Estate in Queensland this morning.
This is the first of two Witron facilities to open here and comes after Coles Group’s biggest investment into technology in the company’s 109-year history. More than one billion dollars is being invested – with the second ADC opening in Kemps Creek, NSW in 2024.
The ADCs are designed to create safer and more sustainable outcomes for team members and suppliers, and better on-shelf availability for customers.
The state-of-the-art facility in Redbank is located 30 kilometres southwest of Brisbane and will service 219 Coles supermarkets in Queensland and Northern New South Wales, as far north as Port Douglas and as far south as Laurieton in NSW.
When operating at full capacity, the site can process up to four million cases per week, the equivalent of 32 million units sold in stores. Over the course of a year, this is around 1.6 billion sales units.
Chief Executive Officer Steven Cain says the opening is one of the most significant moments since Coles was founded in 1914 and five years in the making.
“Modernising our operations is how we improve efficiency and availability in our stores and deliver higher service levels for our customers, team members and suppliers,” Steven says.
“Over 90 percent of the cases processed in these automated distribution centres will be processed
fully by automation or ergonomically which will be a step-change for the safety of our team as it eliminates almost 18 million kilograms of manual handling in the supply chain each week once the ADC is running close to full capacity.”
Coles Group Chairman James Graham AM thanked all those involved for their dedication to this project.
“I’m proud of our team, partners and suppliers who’ve worked together for over five years to create this state-ofthe-art facility. Over 3,000 people came together, contributing more than 2.5 million work hours to plan and design the facility, construct the building and install and commission the automation,” James said.
The Redbank ADC has LED and sensor lighting to reduce energy consumption and is fitted with a 180,000 litres of harvested rainwater storage for toilet flushing and landscape irrigation. There are plans for 3.5-megawatt solar installation which will be among the largest rooftop solar solutions in the Coles network. To minimise food waste, the edible food that can’t be sold in the ADC will be donated to Coles community partner SecondBite.
Prime Minister Anthony Albanese said this world leading technology will help advance supermarket supply chains.
“As we’ve seen during the pandemic and natural disasters, resilient supply chains are essential when it comes to feeding our nation and providing
Australians with essential supplies,” Prime Minster Albanese said.
Queensland Premier Annastacia Palaszczuk welcomed the significant investment in the strong Queensland economy.
“The decision to invest in and build this Australian-first facility here in Queensland is a testament to the strength of the Queensland economy,” she said aid.
“It’s great to see Queensland lead the way with the arrival of world leading technology at the Redbank Distribution Centre. The distribution centre will be powered by renewable electricity provided by Queensland’s publicly owned energy company CleanCo.”
WITRON Logistik + Informatik CEO Helmut Prieschenk said Coles has partnered with the market leader in warehouse automation systems for major food retailers globally.
“We have been engaged to build 93 automated distribution centres in 13 different countries, with the latest for Coles being the largest ambient system Witron has ever built,” Helmut said.
Witron Founder Walter Winkler is extremely proud, that together with Coles, a powerful logistics platform has been created.
“This ADC is for the benefit of the entire supply chain and will help the Australian grocery market by introducing the very best technology, and last but not least it creates great value to the Coles business.”
You can’t fix what you can’t measure
For most companies, 60% of CO² emissions are generated upstream in the supply chain, often from freight transport. As a result, emissions data tends to be costly, inaccurate and cumbersome to access, making it a challenge to improve sustainability.
Until now.
project44 Ocean Emissions Visibility provides:
accurately quantifying emissions across your transportation network
empowering you to minimise your carbon footprint
Workflows of where and how your emissions are generated
www.project44.com/sustainability
AS Colour is a designer, manufacturer and distributor of premium apparel, operating as a wholesaler and retailer in New Zealand, Australia, UK and USA. Starting out in New Zealand in 2005 as a supplier of quality blank apparel for sportswear, music industry and events merchandise, and company promotional wear, AS Colour now operates from five warehouses in Auckland, Melbourne, Los Angeles, North Carolina and Leighton Buzzard (Bedfordshire, UK), plus 25 retail stores across New Zealand, Australia and the UK.
AS Colour embarked on a strategy to support the company’s expected growth over the next decade. This
transformation included more efficient warehouse operations, improved environmental performance and greater supply chain resilience.
In its previous Auckland distribution centre (DC) AS Colour used manual processes to pick orders, which involved RF technology used in conjunction with trolleys. This saw warehouse operators walking up and down aisles searching for product, scanning the location with an RF device, picking it, placing it in a trolley and then walking it to the dispatch area for packing. At the same time, stock was also being
replenished into the aisles with forklifts and other equipment.
Using these manual processes, AS Colour was continually struggling to get all the necessary orders fulfilled within the working day.
“In a conventional warehouse environment with manual processes there is significant amount of time wasted by workers. This includes a lot of time spent travelling up and down the aisles and to dispatch, as well as tracking down the exact location of products needed to fulfil orders, putting down hardware like RF devices to pick products and then having to pick them up again,” explains Seth van Dijk, Business Development Manager, Dematic.
“Manual workflows can also reduce safety and accuracy in the DC. Whenever there are warehouse operators and materials handling equipment such as forklifts in the same zone it brings in an extra level of risk. And when workers are having to find the picking location, scan and then look away to put down their RF device there can be errors by picking the wrong item.”
As part of its strategy to support future growth and after outgrowing its previous warehouse, AS Colour built a brand new 7500 square metre DC in Auckland, which is also the company’s head office.
“Due to the growth of AS Colour over the last five-10 years, we have outgrown many distribution facilities. So, we started looking at a new facility for New Zealand to keep up
with the rising demand. That led us to purchasing the land and building a brand-new facility, which was focused on the automation that we put in this building,” says Lawrence Railton, Managing Director, AS Colour.
A key automation feature of the new DC was the deployment of the Dematic Multishuttle® Goods-toPerson (GTP) solution to help drive operational efficiencies and reduce the overall size and power requirements of its warehouse. AS Colour was the first company to install the Dematic Multishuttle GTP system in the New Zealand market.
“We upgraded to a new DC to support future growth of our business and to enable automation of our operations so that we could move from a traditional pick and pack facility to the future. This transformation has future proofed us for where we aspire to be and where we project the business is heading,” says Justin Carnaby, Head of Logistics, AS Colour.
Acting as a compact, high throughput automated storage and picking system, the Dematic solution features high-density tote storage and sequenced order picking for better productivity. The system is capable of processing varied order types, including small e-commerce orders, medium and large B2B orders, as well as retail store fulfilment.
The modular, scalable Multishuttle is 18 levels high and consists of two aisles storing just under 20,000 totes, with additional capacity built in for projected future growth. AS Colour delivers both the order tote and the product tote from the Multishuttle to four high-speed GTP workstations where the warehouse operator picks the items from the product tote and places them in the order tote before it is conveyed to a dispatch sortation system for packing. Totes are then returned by conveyors and elevators to the Multishuttle to be used for further orders.
“The Multishuttle GTP has brought a lot more structure, order and tidiness to our DC. In our previous facility, we didn’t know where staff were or what volume of orders might come in at any time. With the new system we know we will have a steady flow of orders without
spikes in volume, which is key to maintaining a smooth flow in our business,” says Lawrence.
The planning and build of AS Colour’s new Auckland DC occurred from 2020 to 2021, and the new facility went live at the end of 2021.
“It’s always an extra challenge not only deploying a large Multishuttle GTP system but integrating it within a brand-new warehouse build. The collaboration we undertook with AS Colour and other contractors working on the new build was paramount to the success of the project,” says Seth.
The Multishuttle GTP was integrated as the final piece of the new DC building, then the system was configured to meet the unique requirements of AS Colour. Dematic was on call 24/7 during the go live period.
“The implementation of the system was straight-forward. The Dematic team were there side-by-side with us the whole way through and they provided a lot of support to get the system up and running,” notes Justin. “The automation has been easy to adapt to from both the perspective of the operator and management teams. The systems and the training guides that Dematic supplied were fit for purpose and easy to understand.”
For AS Colour, the Multishuttle GTP system delivers superior high density storage buffering, meaning that the company can store much more within the warehouse building cube than what they would have been able to within a conventional warehouse environment.
The GTP picking stations allow warehouse operators to receive and pick products, which eliminates worker travel within the warehouse and leads to high levels of productivity and efficiency in order fulfilment processes.
The system stores 8000 SKUs and the throughput is 5000 lines per day (6am-5pm) over the six days a week the DC operates, with the capability to process 8000-plus lines per day. In the previous DC the cycle counts
achieved per month was 2700 and in the new DC this has dramatically increased to 13,000 cycle counts per month
“Land has become very expensive in New Zealand, so we had a goal of reducing the size of the building we needed. By helping us to achieve a smaller warehouse footprint at the new Auckland warehouse, the Dematic solution reduced our construction costs by about 30 per cent,” says Lawrence. “Additionally, we’ve been able to increase our product storage capacity by about 35 per cent, which has brought in more revenue and given us a buffer from any supply chain issues.”
For AS Colour the introduction of automation has increased throughput per worker by 344 per cent, from an average of 45 lines per hour to an average of more than 200 lines per hour. Other benefits include decreased labour costs, plus a vast improvement in order accuracy, which reduces the number of unnecessary customer returns and leads to greater customer satisfaction.
“Key customer expectations for our business are that customers need their orders very quickly and accurately, so for instance, if there’s a mistake in the quantity that’s sent to them, that causes a lot of delays for our customers,” Lawrence says.
“With our new automated supply chain facility what differentiates us is the speed, efficiency and accuracy with which we’re able to get orders to customers. Today we can have orders placed online and be picking them within 30 minutes of the order being received by the WCS and sent down from the Multishuttle to the GTP, and then packed and out the door within a few hours.
“The Multishuttle GTP solution has been a game changer for our business, and we’ve actually seen a big increase in sales in New Zealand as a result of having it in place, because our customers can see how fast and accurately we can get their
orders to them.”
The Dematic solution has removed the need for any workers to be travelling within warehouse aisles alongside materials handling equipment, which has drastically increased warehouse operator safety on the warehouse floor.
The Multishuttle GTP system now automatically conducts product audits in real time as warehouse operators pick, ensuring stock integrity in the warehouse at all times, which is a big improvement on the previous process where every two to three months AS Colour conducted manual cycle counting.
Another big goal for AS Colour was
to completely remove single-use plastic from its supply chain.
“Traditionally apparel is packaged in plastics or paper, but what’s quite unique to AS Colour is the fact that they store the product loose and unpackaged within totes, which is the final package that is shipped to customers. This means it’s a more sustainable approach, which we’re very pleased the Dematic Multishuttle GTP system is able to facilitate by keeping the product clean and tidy,” Seth says.
The integration of Dematic’s WCS has given AS Colour a high level of visibility of its operations, allowing it to analyse processes and make ongoing improvements.
“Automation has helped management immensely. It’s enabled us to really hone in on where our process flow improvements needed to happen and it’s given us a much greater level of visibility of our operations,” says Justin. “It’s also really helped the operators by making their work much more interesting. They get to operate in a modern, worker friendly environment, and they feel really engaged with what they’re doing here at the Auckland DC.”
AS Colour additionally deployed Extreme Networks’ Cloud-Enabled Wi-Fi 6 solution to improve mobile device connectivity and efficiency within the warehouse, with the help of Dematic as its technology partner. The solution provides AS Colour with a robust, high-capacity,
high-efficiency Wi-Fi 6 network to operate seamlessly in a challenging warehouse environment, handling large amounts of data transmitted between mobile devices and AS Colours’ backend systems.
With the integration of an advanced automated warehouse solution, AS Colour has been able to distinguish itself with the highest level of speed and accuracy in a highly competitive retail market. The high-quality fit, fabric and finish of AS Colour’s garments is now supported by the efficiency of its automated supply chain and distribution operations.
Dematic continues to work closely with AS Colour to maintain and service the system regularly, as well as ensure it is optimised and improved wherever possible.
“It was really important to us that Dematic had a local support team in New Zealand, as many suppliers don’t. When the whole business relies on the Multishuttle GTP system it’s vital to be able to seek support and fix problems really quickly, and with Dematic we can be confident that their technicians will come out as soon as possible, which is often only half an hour away,” says Lawrence.
“Dematic has been a really strong technology partner, helping us from a global perspective, and we see this as a long-term partnership as we continue to expand as a business in the future.” ■
Regional cities across Australia are often overlooked when owner-occupiers are considering where to invest in industrial property, but Newcastle, the country’s largest regional city with its diverse economy has much to offer businesses searching for prime industrial real estate.
The Hunter region is a diverse region in New South Wales (NSW) where health, defence, agriculture, manufacturing, and mining, constitute its economic backbone. It is also where you can find one of the world’s largest bulk export ports, all while being two hours north of the state’s capital city.
Trent Robertson, National Director, Industrial, has been working out of Colliers Newcastle office for more than 20 years. In that time, he’s assisted thousands of industrial businesses to establish in the region and has connected valued clients with Colliers’ Occupiers Services, Property Management, Valuation, Strategic Advisory, and Capital Markets services.
The Newcastle Colliers office accommodates 47 professionals, providing a wealth of experience and expertise for their valued clients. They provide in-depth advice across their many specialist teams, covering Colliers’ major service lines.
The Industrial team based in Newcastle comprises 10 industrial specialists, providing detailed local knowledge, with the ability to further deliver opportunity for clients by collaborating with the wider National industrial business.
Trent and his colleagues handle all types of industrial property including sales and leasing of warehouses and distribution facilities, land subdivisions, strata complexes, business parks, and more
“We cover everything from strategic
advice to project marketing, with the latest in digital marketing campaigns using Colliers’ exclusive market leading platforms,” explains Trent. “Our strength lies in our ability to provide detailed local knowledge for our clients, whilst also tapping into our wider National expertise.
“We help our clients unlock opportunity driving enduring value for them and arming them with the knowledge to make informed property decisions. We maximise the potential of their property – the Newcastle team lives and breathes this.”
Trent and his team operate in both the Hunter and Central Coast regions
where they deal with prime industrial assets north of the Hawkesbury River. The Hunter region consists of 10 local government areas and has a population of almost 750,000 people. It’s the seventh largest city and the largest regional economy in Australia.
Like other major Australian cities, Newcastle has its own port (one of the largest bulk export ports in the world and it will soon have a container terminal) and an established airport with a runway being upgraded to code E status, which in the future will allow passenger and freight international flights.
“We have well established industrial
precincts here in Newcastle and they’re presently thriving,” Trent says.
“Enquiries for logistics and industrial properties have increased exponentially and in 2022 we handled over 4,000 industrial enquiries.” “We also saw around 100,000 sqm of new industrial buildings constructed in the region over the last 12 months and our vacancy rate fell to 2.45 per cent during the same period.”
Businesses from all along the Eastern Seaboard are eyeing Newcastle on the back of strong market fundamentals, the value proposition the region represents to other capital cities and in particular connectivity to major markets.
According to Trent, savvy developers and investors have been buying property in the Newcastle market for many years however, Colliers is seeing record enquiry levels from new occupiers and emerging sectors that the Newcastle market has never seen before.
“These occupiers are attracted to Newcastle’s diverse economic activity, its improved transport links including the motorways and NorthConnex, but they also often already have a strong customer base here,” he adds.
“Renewable energy projects are being attracted to the region in increasing numbers, due to the availability of land, availability of large power supplies, government initiatives and funding in this space. Some are attracted because of the port, but this is expected to change as companies realise that they can take advantage of the soon-to-be built container terminal.”
The top five sectors presently driving enquiry in the region are Renewable Energy Projects, Recycling, Construction, Logistics/E-commerce, and Port. Mining Services is still a significant sector however it’s being outperformed by the others.
Each occupier enquiry received by the team is different, but the key requirement is generally proximity to road rail and port infrastructure, location of the major population centres and central business districts, and which industrial estate will be the best fit for their business, suppliers,
customers, and staff.
The Newcastle industrial experts work through every occupier’s requirement, providing detailed tailored advice and ensuring they find the best fit for their needs. This includes exploring building and site areas, racking, and height clearance, gantry crane needs (if any) and what sort of truck access a business will need.
Additionally, they will understand needs for office space, carparking, hardstand and fire sprinkler systems.
After investigating options, the team will then present the client with an availability list of properties that may suit their brief, along with guides on rental and sale prices of each option.
“We work collaboratively with the occupier and relevant Collier’s service lines to determine which property is going to suit them, consider their timing, and when they’ll need the asset,” Trent explains.
There are five established industrial precincts in the lower Hunter Region where businesses are investing or renting. These areas include The Steel River Industrial Estate and Port Link Estate near the Port of Newcastle.
In the northwest is Tomago Industrial Estate, Heatherbrae, and the Beresfield, and Thornton Estates.
In the western and outer west precincts, is Cameron Park and Cardiff, Rutherford, and Kurri Industrial Estates. The southwest features Warners Bay and Morisset Business Parks, and the Central Coast, has established Industrial Estates at Somersby, Tuggerah, Warnervale, and Wyong.
“We have gained intimate knowledge of our region and our clients’ property needs over the past 20 odd years,” Trent says.
“And this is why we can confidently identify emerging market trends in the Newcastle Region and be nimble when we are providing advice to our clients. Being established here and operating for such a long period of time is something we’re proud of, as well as our team’s involvement in the Newcastle community.”
In addition, the Colliers Newcastle Industrial Team is currently working on project marketing of numerous industrial land releases, and strata
projects as well as marketing campaigns for vendors, which includes a diverse range of clients from government, institutions, property funds and private investors.
Trent continues: “We are excited about a number of projects that we are working on with our valued clients, that will provide further opportunities for businesses to establish and expand into the region and unlock future growth and economic activity.
“The region has a bright future with these projects underway, coupled with a great lifestyle offering and a diverse regional economy. These are just some of the reasons why businesses should not hesitate in consider buying or leasing industrial facilities in Newcastle.
“We’re also working on growing our team capabilities here, and we’re achieving this by mentoring and training some of our younger experts, we are proud of this accomplishment and our many team members who have been with the company for over 10 years, too.”
The Newcastle Industrial business leverage extensive industry experience, market expertise and collaborative approaches to develop key strategies aimed at maximising the potential of property for their clients. Their value lies in providing in-depth advice on the market and an integrated service approach to ensure clients are informed to make property decisions. ■
Keep informed on the market, unlock opportunity, and see how Colliers Newcastle Industrial team can provide solutions to accelerate your success today.
Winston Churchill is purported to have said of the opportunity afforded by WWII to create the United Nations: “Never let a good crisis go to waste.”
In the face of unprecedented challenges and turbulence, players in global supply chain have taken up much the same attitude, according to Peter Jones, Managing Director of Prological.
The recent crises have provided a unique opportunity for industries to re-evaluate their strategies and uncover new opportunities for growth and resilience.
Peter says the real upheaval in supply chain began around 2018, with the rise of Trumpism and a shift to US economic policies that marked a renewed bias toward protectionism and economic nationalism. These events – coupled with Brexit, China taking a more Sino-centric view of itself in the world, and the COVID-19 pandemic – exposed the fragility of interconnected global supply chains, and forced businesses to take a hard look at their risk management strategies. In doing so, supply chain professionals have seized upon these crises as a chance to drive change and create more robust systems.
“Now, supply chain is in the boardroom,” Peter says, highlighting the renewed focus on developing crisis-resistant supply chain strategies. By capitalising on the challenges presented by recent events businesses have been able to reassess their approach to global manufacturing, bringing supply closer to demand, and de-risking – with removal of single points of supply being just one example.
As Peter explains, companies are now proactively seeking ways to make their supply chains more resilient in the face of future crises. He cites a small Sydney-based company with which he is familiar that is already considering the need to manufacture in North America to mitigate risks associated with their growing US market. This shift in perspective, Peter believes, is a direct result of the heightened awareness of supply chain risks and a determination to use these challenges as an opportunity for growth and strategic improvement.
This is illustrative of a shift towards onshoring and ‘friend-shoring’ as viable options for maintaining more control over operations. While Peter acknowledges that onshoring – moving operations, supply, and manufacturing as much as possible to a company’s resident country to avoid international obstacles – was initially seen as an attractive and prima facie obvious solution – it may not be economically sustainable for every business.
“Initially, people were thinking onshoring was the way to go because if we onshore, then we have sovereignty over what we’re doing.” However, after evaluating the numbers, businesses have found that it might not be as feasible as they had hoped. Although there has been a noticeable increase in onshoring, Peter estimates it might represent – anecdotally – a five per cent shift rather than a more significant tilt, as some initially forecast.
Instead, many companies have turned to ‘friend-shoring’, which involves diversifying their supply
chain sources and partnering with countries that are more geopolitically stable or reliable. Peter notes that businesses have moved from a single point of supply to multiple points of supply, particularly for critical business elements. This shift to friend-shoring has led companies to consider factors such as the longevity of their relationships with suppliers and the geographic implications of their choices.
The geopolitical landscape has become an increasingly important consideration for businesses, Peter says. Companies at the senior level must now pay attention to the political climate and anticipate government actions when making decisions regarding onshoring and friend-shoring. However, predicting these outcomes can be challenging and may introduce risks, with Peter pointing to Trumpism and Brexit as examples how long-term stable relationships with 70-plus years of consistency can change quickly.
“It is the change that brings the risk. Businesses can always re-align, but in the transition momentum can be lost and opportunities missed. Realignment can take longer than required for business continuity which in turn brings business stress. These are now known and understood risks that previous to, say, 2018, were not part of risk profiling. Today they are.”
While businesses may want to move away from reliance on certain countries, governments, or political environments, the reality is often more complex.
“For instance, the relationship
When the going gets tough, the tough get going, and a succession of crises in supply chain has fostered strategies and opportunities that are shaking up the industry. Peter Jones shares with MHD his perspective on the current supply chain climate.
between England and Europe has changed, impacting trade and supply chain structures across the English Channel,” he says.
According to Peter, the longevity of a nation’s political direction is a crucial factor for businesses when constructing global supply chains. Companies must consider whether a nation is committed to its current course, as the investment required for supply chain infrastructure often spans well beyond the typical government’s lifespan.
“In the case of China, confidence in maintaining supply requirements has decreased, leading to a shift towards other countries like Indonesia, Vietnam, Malaysia, and India,” he says. The same is true for our exporters who are also looking to diversify their customer base. We only need look at our wine industry to see the impact of what relying on one big customer. The wine industry responded well to their geo-political challenges, the crisis has not been wasted, and our wine export industry is stronger as a result. Several of our nation’s other primary industry and commodity exporters are rapidly following suit and diversifying their overseas customer base.
“Geopolitical considerations are not binary but exist on a continuum, with long-term issues influencing supply chain structure,” Peter continues. “Short-term changes, such as a government turnover, may not have as significant an impact if it is believed that another change
may occur within a reasonable time frame. As businesses navigate this complex landscape, they must balance the risks and rewards associated with onshoring and friend-shoring while keeping a close eye on the geopolitical factors that could impact their supply chain strategies.”
Peter notes that major infrastructure projects are ongoing in the country, such as the Westport development in Kwinana, intermodal terminals in Melbourne and Brisbane, and the Inland Rail project, which will buttress Australia’s supply chain resilience.
“Despite the cost overruns and delays in projects like Inland Rail, which has seen its budget increase from $10 billion in 2015 to $31 billion in 2023, the Albanese government remains committed to completing these projects for the benefit of Australian commerce. This commitment indicates that the government recognises the importance of a robust supply chain infrastructure for the country’s future.”
Two particularly pertinent supply chain trends Peter points to are the evolving role of warehouses – the rise of renewable energy and its impact on warehouse design – and the increasing focus on creating employee-friendly environments due to the ongoing scarcity of skilled workers.
“Renewable energy has transformed
warehouse design as companies seek to incorporate sustainable energy solutions into their facilities,” he says. “This has led to the adoption of solar panels, batteries, thermal efficiency by design, people-centric design, electrification of everything that can be electrified, and other environmentally friendly technologies in warehouse construction.
“Additionally, the scarcity of skilled workers has prompted companies to prioritise employee satisfaction and retention. To achieve this, warehouse designs have evolved to reflect both the values of the company and the needs of its employees, resulting in more comfortable and efficient workspaces.”
Being an employer of choice means rapidly aligning oneself to the environment in which the employee will work, he says.
“As Next Generation warehouses become more common over the decade ahead, traditional square boxes without natural light that feel like a breezeway will be challenged to attract staff because the work environment will be so unappealing.”
Another significant change in warehouse management is the growing access to automation technologies. “This shift is akin to the historical change in architecture, from accommodating horses with stables to accommodating cars with garages,” Peter says. “With the increasing prevalence of automation in warehouses, companies must adapt their infrastructure to accommodate these new systems.”
What the crises of the past five years have taught us is that if we are doing tomorrow what we were doing yesterday, we are effectively going backwards, Peter says.
“In supply chain the bandwidth of this truth has increased exponentially and now includes everything from geo-political considerations, to de-risking strategies, through to thermal design of warehouses, the comfort of lunchrooms, and staff amenities. As logisticians, all this must be held in balance as we strive to maximise our opportunities, and work around our threats – all within our organisations’ commercial realities. I guess if it were easy, everyone would be doing it”. ■
Extolla – an exciting new player in the end-to-end supply chain consulting and solutions game – launched in January of this year, bringing together some of the APAC stars known to industry through previous work with enVista, whose APAC operations were acquired by another organisation last year.
David Bille, Director of DC Design, Robotics & Automation at Extolla, recently sat down with MHD to tell us more.
With the purchaser of enVista focused on the software side, a team including Peter Kendall and David Bille took control of the consultancy portion of enVista’s APAC business, with the intention of building an even more dynamic APAC-focused consultancy.
“I think one of the key things we bring to the market is our experience
level,” David says. He highlights the extensive expertise that each of the directors brings to the company, including in management, supply chain, and software.
Indeed, Extolla brings senior leadership and deep industry experience across all seven of its practice areas:
1. Network Strategy and Optimisation
2. DC Design, Robotics and Automation
3. Technology, software selection and implementation
4. Inventory strategy and planning
5. Transportation
6. Strategic Sourcing and Procurement
7. Omni-channel enablement.
Despite its independence, Extolla maintains a close relationship with enVista in the Americas, as they work together on projects that require offshore resources – a boon for both companies.
But focusing just on the APAC market,
David notes that the Extolla advantage is the range and depth of its expertise across the board.
“Our expertise lies in designing and driving innovative and efficient enterprise commerce for leading manufacturers, distributors, 3PLs, and omni-channel retailers,” he says. “We do this by applying our extensive supply chain technology, operations, and software solutions experience.”
David notes that, in his experience, many competitor consultancies are too focused on a single segment of supply chain – for example, property – while others purport to touch all aspects but do so in a very formulaic, report driven way.
“The level of detail Extolla goes to sets it apart from other businesses in this
A new end-to-end supply chain consultancy is stepping up to take on the industry challenges of a new era. MHD speaks with David Bille of Extolla to discover the company’s vision – and the deep experience that its team brings to the new enterprise.Extolla specialises in designing and driving innovative and efficient enterprise commerce for leading manufacturers, distributors, 3PLs, and omni-channel retailers.
space,” he says. “Extolla distinguishes itself by working closely with vendor partners in the automation and robotics space, building and maintaining strong relationships and partnerships. Instead of just providing a report, we support clients through every stage of the process, from project management and commissioning to implementation, transition and operations.”
This holistic approach is particularly valuable for companies that only undertake significant supply chain investments or make significant moves or changes every 10-15 years – and typically do not have the internal resources or experience to effectively design, integrate and implement such transitions.
One of the key customer challenges in the current market is finding people with the necessary expertise and experience. Extolla addresses this by providing an end to end service, helping clients make informed decisions on current technology and maintaining a strong partnership ecosystem.
“Working as a partner rather than just being a vendor is crucial,” David says.
And even though Extolla is just a few months old, David is proud to report that they already have 16 staff members on board across the APAC region to deliver a personalised consulting service; a number that – David adds – is sure to keep growing.
In the coming years, Australia faces numerous supply chain and logistics challenges – including a scarcity of industrial real estate, labour availability, and labour costs.
“Extolla is prepared to leverage technology to help customers tackle these pain points,” David says. Of special concern, he notes, are the twin challenges of labour availability and real estate costs.
With respect to real estate costs, he says, “We now are seeing rates that have grown over the last three or four years to exceed $200 per square metre.” He acknowledges that finding suitable brownfield sites has become increasingly difficult as many customers are already space constrained and need space immediately. However, automation can help offset some of these costs by reducing the need for labour. Although
automation does not necessarily reduce a facility’s footprint, David points out that “the savings in labour” can make it a viable solution.
Automation technologies like AMRs (Autonomous Mobile Robots) and ACRs (Autonomous Case-handling Robots) are gaining traction in the market. David notes that ACR robotic solutions can now help optimise the use of vertical space in warehouses, which is particularly important as we need to fill the whole building envelope.
“Different types of storage automation solutions are appropriate for different warehouses to make them operate effectively and get the right return on investment for the customer,” he says. “Automation isn’t an answer in and of itself. Every company is unique, and at Extolla we pride ourselves on discerning that uniqueness and crafting comprehensive solutions to match.”
New robotic technologies are entering the market, with some companies offering a “robotics as a service” model. David explains that this shift has led to rapid growth in the market for these innovative technologies.
In addition to robotics, other green technologies are gaining traction, offering flexibility and efficiency in warehouse operations. Being across all these developments takes years of experience as well as a start-up mindset.
But David is keen to underscore that added automation doesn’t mean laying existing workers off – but rather allowing for already scarce workers to be put to better and higher uses. “At Extolla we’re focused on people,” he says. “It’s the culture and the people and the creativity that, in the end,
create long-term success. Australia’s jobless rate over the past 20 years has been pretty much the same – between four and six per cent – and automation isn’t going to change that.” Rather, he suggests that the job market has simply evolved, with new opportunities in software and systems support etc. arising as warehouse jobs become less appealing.
“One aspect of our role is to show companies how best to evolve along with the labour market.”
But it’s not just the labour market that’s changing – the whole market is always changing; decision making within organisations is changing – and therefore, David says, consultancies like Extolla must keep pace with ongoing change by providing a new model of consulting.
He notes that in the early 90s and 2000s warehouse managers would have an agreed fixed annual budget, whereas now logistics and supply chain managers must present a business case to CIOs, CFOs and CEOs – who require a clear return on investment for their shareholders or owners to demonstrate proposed projects are viable. This accountability has led Extolla to focus its approach on ensuring all proposed solutions are optimal.
“By offering end-to-end support and working closely with clients to understand their specific needs, Extolla distinguishes itself as a valuable partner in the changing landscape of supply chain and logistics. We’re helping them at every step rather than just doing a piece of work.
“We may be a new company, but we’re here for the long haul.” ■
Körber hosted its globally recognised Elevate event in-person for the first time ever Down Under in Melbourne between May 02-03 featuring keynote presentations, networking opportunities, and informative and stimulating panel discussions.
Körber brought Elevate 2023 to the Asia-Pacific (APAC) region, hosting the conference in Australia’s now largest city, Melbourne, while also being named a Leader in the 2023 Gartner Magic Quadrant for Warehouse Management Systems (WMS) report for the fifth consecutive year.
To Körber, the 2023 Gartner Magic Quadrant recognition exemplifies the capabilities of its unmatched depth of technologies, spanning warehouse management, warehouse control, order management, robotics, voice, and simulation to empower global businesses to further digitise and automate warehouses in response to today’s extensive supply chain pressures.*
Ian Hunter, Wurundjeri Elder started Day One with a Welcome to Country, including a performance on digeridoo, singing, and storytelling. This was followed by Körber’s Anthony Beavis, Managing Director ANZ and Bill Ryan, Executive Vice President APAC making introductory remarks.
“When the global pandemic started, the music stopped,” Bill says. “Supply and labour challenges can cause businesses to lose their rhythm.”
His answer to these problems: digitisation and technology. He pointed out that survey results indicated one in three warehouse operations are still relying on manual labour.
With robotics use in the logistics market projected to grow by 77 per cent in the 2021-24 period, Körber is leaning into tech and digital to solve customer
pain points with a 71 per cent R&D spend increase in the 2021-23 period.
To meet the challenges of the era, Bill says Körber partnered with globally renowned investment firm KKR, allowing them together to operate as a joint venture with the investment power to flex, adapt, and expand to meet market demands.
This partnership coupled with a portfolio of exciting new solutions and developments at Körber, mean the company is – in Bill’s words – “Building the Global Supply Champion.”
Sean Elliott, Global Chief Technology Officer from the USA spoke about the three key technology pillars: technology foundation, new products, and innovation. He referred to evolving beyond cost and efficiency, emphasised the need for businesses to be adaptable and transparent with customers,
finding rhythm by playing in harmony, and identifying new rhythms.
“Customers know bad music when they hear it,” Sean explains. “In other words, they know when something’s wrong with the supply chain when they don’t get what they want when they want.”
He also covered Order Management Systems, Support Delivery Operations, Freight Audit Payment, Transportation Management Spend, and Unified Control Systems.
John Laing, Senior Expert at McKinsey & Company explored the notion of influencing vulnerable supply chains and dealing with disruptions, strategies to improve resilience, strengthening supply chain risk management and transparency, improving financial and operational capacity to respond and recover, and minimising exposure to shocks.
Joe Couto, Körber Executive Vice President Global Robotics & 3PL presented on Geek+ as the company’s largest partner, Robots as a Service, the concept of gamification and how it’s used to drive employee engagement, virtual reality, and WMS integration.
The event continued on Wednesday May 03 with Accenture’s Sari Mackay, Managing Director – Strategy & Consulting, Supply Chain & Operations Lead, ANZ starting the second and final day of the conference with an in-depth analysis of the global supply chain, including the need for businesses to reinvent their networks, and invest in regionalised supply chains all while preparing for both just in case and just in time deliveries.
“The future of supply chain is data analytics and AI,” Sari says. “Resilient networks are needed to deal with disruptions and drive cost optimisation. Transparency is the most important resource.”
Patrick Fountain, General Manager of Super Retail Group explained how automation combined with data science have transformed the company’s supply chain network and enabled it to optimise its operations and increase productivity.
Yiau Hwei Chan, Director of Engineering at Körber facilitated the first panel discussion called Driving Positive Change: How Sustainability & Diversity are transforming supply chains.
Dr Elsie Hooi, SCLAA committee member, Laurel O’Donnell, Lineage Logistics General Manager, Dr George Panas, University of Melbourne Supply Chain Lecturer, Maree Varrasso, COO at uTenant, and Nicole Katsoulis, Head of People & Culture at Körber spoke
about the importance of partnerships, adopting a global perspective, focusing on women in leadership, cooperating with leading industry associations, and incorporating ESG in brownfield and greenfield sites.
The final panel discussion was Building agility and resilience to deliver exceptional end-customer experience.
Frank De Sa, CIO at The Just Group along with Lian Yu, COO at Toys ‘R’ Us, Karl Neubauer, CIO at GLOBAL Retail Brands, and CEVA Logistics’ Allan Maki spoke about innovation in retail, the need for data collection, autonomous mobile robots, Körber cloud, 3PL and automation, as well as investing in scalable solutions with Körber’s Director of Solution Delivery, Darren O’Connor.
In the main room, attendees networked, visited stalls, used Körber’s virtual reality headset, giving them an opportunity to experience automating and modifying a new or existing warehouse.
The event finished with Nicholas Bochner, Head of Learning & Conductor discussing the similarities between conducting an orchestra to orchestrating a supply chain, and paid
homage to the company’s founder, Kurt A. Körber.
Additionally, he helped the audience find its rhythm with a renowned OAM pianist and a violinist from the Melbourne Symphony Orchestra playing a series of classical compositions followed by Anthony Beavis’s concluding words.
Rayner Berger, Systems Development Manager, CatchOfTheDay.com.au:
“You do a lot of trade shows over the years, and the difference between this and a lot of other ones is that there’s absolute quality and the people we’re meeting are real decision makers with power and capabilities.”
*Source: Gartner, “2023 Magic Quadrant for Warehouse Management Systems,” Simon Tunstall, Dwight Klappich and Rishabh Narang, May 8, 2023.
Owner-managed transport logistics company Röhlig Logistics is notching up 50 years of operation in Australia and is celebrating with the purchase of a fleet of custom painted Toyota electric forklifts.
were engaged and part of the process, and they got to choose which gear they preferred, and Toyota was actually a front-runner – they’re very happy with the choice.”
“I think it was the general feel, the lifting capability and the new technology that was part of that decision making process.”
In total, the new Röhlig fleet consists of 13 Toyota electric counterbalance forklifts ranging from 2.0 to 5.0-tonne capacity, two Toyota OME120HW order pickers and four Toyota RRE140H2 reach trucks, distributed across warehouses in Brisbane, Sydney, Melbourne and Auckland.
Röhlig Logistics recently purchased a fleet of batteryelectric Toyota forklifts, with distributor Toyota Material Handling Australia (TMHA) adding an extraspecial touch by having the equipment painted in custom Röhlig blue.
Röhlig Australia Managing Director Mat Vermeulen says the 50-year celebrations would be a great occasion for the company.
“Part of the deal with TMHA was to paint the Toyota orange to Röhlig Logistics blue, and we will apply our Röhlig Logistics decals to that and make it part of our 50-year celebrations,” Mat explains.
“We’re actually about to convert our trucks – we run our own fleet of trucks in the main centres of Australia – and we’re going to convert
the curtains to our new 50-year anniversary picture mark.
“It’s a true celebration for both our customers and our employees, so we’re really looking forward to the event which will be at the end of the year.”
Röhlig Logistics recently put out a tender for new material handling equipment, with the emissionfree powertrains and dependable performance of Toyota electric forklifts a big reason for TMHA being the company of choice.
Mat adds: “We went to market for our MHE, during the start of COVID. Part of the deal was to look at our sustainability as an organisation. We were using a lot of gas forklifts and we have converted to electric forklifts.”
“We actually wanted to make sure that the guys and girls on the floor
The Röhlig Logistics blue paint colour has also been a big hit with the machine operators.
“I think when the products arrived in Röhlig Logistics blue the guys took a lot of pride, to the point where I’ve been on the floor and seen one of the guys giving a machine a bit of a buff,” Mat says.
“They take pride in the equipment that they have, and they’ve been on site for over a month now and there’s not one single scratch on there. It’s a good sign that they’re invested in and looking after the equipment.”
The tender process was spearheaded by Sydney-based major account manager Michael Provan, who says that the combination of TMHA’s servicing, product and value was unmatched among the competition.
“The feedback I got from their
procurement team was that we were who they were most comfortable with moving forward after going through the tendering process, so we had been able to demonstrate the best product, the best service back-up, and pricing is obviously important,” Michael says.
TMHA is also easily able to offer custom paint colours to suit any customer’s preference.
“These Röhlig Logistics ones we did at the factory, we can do it locally as well,” Michael says. “We can do it with custom colours, all we have to do is get the colour code and we can have
the factory match the paint.”
Röhlig Logistics Australia has recently opened a new warehousing facility in Perth and will soon be launching an additional warehouse in Adelaide.
When it comes to procuring new equipment for the two latest warehouses, Mat says Toyota would be at the top of the list.
“We most certainly will look at Toyota again” he says. “I get glowing feedback to be honest, they’re very comfortable, it’s good size equipment that we ordered, and if you go and ask
them about the gear their faces smile – which is a nice thing.”
The relationship formed between Röhlig Logistics and Michael’s team has also been a determining factor in the high level of satisfaction with the new forklift fleet.
“They’ve been very professional, they obviously understand the product very well, they take a lot of pride in what they do,” Mat says.
“I think the process was a very professional approach and they followed up very well, so I was very impressed with their approach.”
Röhlig Logistics’ 50th-anniversary celebrations will take place towards the end of the year with events in each state in which it operates, and will also honour long-standing employees and commercial partners of the company.
The company has also transformed its fleet of trucks with Röhlig Logistics blue liveries, and will mark the occasion with a series of media events.
First founded in Germany in 1852, Röhlig Logistics entered the Australian market in 1973 and has grown its Australian presence to roughly 250 employees in locations across the country. ■
Visit Ferag at CeMAT
from 25-27 July 2023 at The Dome
Sydney Olympic Park Booth B4
Experience at Booth B4 the ferag.skyfall: A solution for automatic pouch filling that is as innovative as it is intelligent - with increased performance and the greatest possible flexibility at the same time.
Late April saw the launch of Toll Healthcare’s new facility in the Brisbane suburb of Richlands to improve delivery of products within Australia’s thriving healthcare sector. MHD finds out more.
Toll Healthcare provides integrated logistics solutions for the storage and distribution of a wide range of pharmaceutical and surgical products to hospitals, medical clinicians, pharmacies and patients across Australia. Its five national TGA-licensed warehouse facilities and 100-plus strong team deliver comprehensive supply chain solutions tailored to the needs of the healthcare sector.
On Friday 21 April Toll opened a new healthcare warehouse and distribution facility in the Brisbane suburb of Richlands. The cuttingedge facility is a $10 million investment over the next ten years that will support the delivery of patient-critical healthcare products to Queensland communities.
Queensland’s Assistant Minister for Health and Regional Health Infrastructure Julieanne Gilbert MP officially opened the facility.
Julieanne described the occasion as an “exciting day”, particularly in light of past and ongoing work that Toll does with the QLD government.
“Toll shares a very productive relationship with the Queensland government,” Julieanne said, with the company responsible for cold storage and statewide logistics for the state. “This purpose-built facility … ensures Toll can continue serving the needs of Queensland Health and Queensland.”
Toll Group Managing Director Alan Beacham, who flew in from Singapore for the opening, spoke of Toll’s proud history of innovation since its humble beginnings more than 130 years ago, and its ongoing
mission to “move businesses that move the world”. Alan said that in “times of crisis, innovation needs collaboration” and that the company is especially proud of the work it had done with government agencies – including the Australian Defence Force – to tackle natural disasters as well as healthcare logistical challenges.
The custom-built distribution centre has storage capacity of 4600 sqm across ambient and cool-room
facilities including ultra-low freezers for the storage and distribution of specialised vaccines.
“This investment reflects Toll’s commitment to creating advanced warehouse management solutions to meet the changing dynamics in the healthcare sector. The facility provides fast, accurate and compliant delivery for our customers,” Perry Singh, Toll President Government & Defence, said in a statement.
The facility has been custom
designed to support the unique requirements of customers including CSL and Queensland Health, and will store and manage inventory of pharmaceuticals, medical devices, vaccines, and consumer health products. It will be the primary distribution centre of National Immunisation Program flu vaccines for Queensland Health in 2023.
The facility has a 5 Green Star Rating and features recyclable water usage, energy efficient/motionsensored LED lighting, and a roof solar power system to provide green energy.
The Richlands facility is Toll’s fifth healthcare facility in Australia, and the company also has healthcare facilities in Singapore, China and India. The new site is located 24 kilometres from central Brisbane and close to major highways. The facility is licensed with the Therapeutic Goods Administration and the only healthcare facility in Queensland that is Good Management Practice certified.
Toll is investing A$400 million in the Australian market over the next four years across facilities, fleet and technology to support customer growth in the region. ■
Geotab Vice President Sean Killen sits down with MHD to discuss the exciting datadriven insights modern telematics affords fleet managers and firms seeking greater efficiency, synergy, and sustainability.
Telematics technology is transforming the transport sector in Australia and beyond by offering data-driven insights for fleet management.
According to Sean Killen, Vice President at Geotab, telematics – the technology that provides quality data insights on vehicles and driver behaviour, and in which Geotab has long specialised – is well understood as a general concept.
However, the technology has evolved rapidly over the past few years, moving from simply providing “dots on a map” to becoming a crucial tool for big data and AI-driven insights.
Sean says that when he was hired from Oracle five years ago, Geotab’s CEO asked him where he saw the future of telematics going. Sean responded that there was a wealth of data generated by fleets that was not being effectively shared within large
organisations – often remaining in “its own little silo.” He envisioned that if this data were integrated with other software systems – like those of Oracle, SAP, and supply chain applications – it would generate significant value for non-fleet personnel as well.
The CEO, Neil Cawse, was intrigued by his vision and offered him a job. Today, ‘Big Data’ is the hot buzzword within the telematics industry; but Sean was ahead of the curve in recognising its potential.
“The focus is now on how data can add value, deliver ROI, and provide new learnings,” he says. “I think telematics has gone through its first iteration, and now competitors are taking the next step into ‘Telematics 2.0’.”
Telematics 2.0 is a data-driven, insight-focused approach that is transforming the sector, particularly in North America. Sean notes that
many traditional competitors have fallen by the wayside while new players have entered the field. Telematics technology – which began as a simple monitoring tool – has evolved into a vital source of data and insights for organisations, revolutionising the transport sector and supply chain more broadly.
In the Australian context, the transport sector has seen significant changes over the past decade due to telematics. The technology has become more affordable and versatile, allowing it to be integrated with a broader range of assets and utilised in various niche applications. Sean says the Australian market is unique in that many first-generation competitors still dominate the telematics space,
while newer companies that have emerged elsewhere are not as visible Down Under.
A critical factor for affecting telematics users in Australia is the impending Telstra 3G shutdown. This event is forcing major companies to decide whether to renew their existing contracts or make a fundamental platform shift. Sean sees this as an opportunity for Geotab to demonstrate the next generation of telematics, as companies must decide this year whether to embrace international advancements.
The Telstra 3G shutdown also presents a challenge for fleet managers, who must undergo the arduous task of replacing hardware and transitioning to new systems for thousands of vehicles. But it’s a necessary change, Sean says, and one Geotab can help Australian firms manage with success.
Interestingly, Sean notes that the primary concern for many Australian companies is electric vehicle (EV) adoption and sustainability. Despite the Australian government’s current regulations on EVs and the limited selection available in the market, Sean believes this situation will change rapidly. He contends that as soon as the government tightens regulations, major automakers will quickly pivot to introduce a wider variety of EVs to the Australian market.
He adds that the growing interest in EVs and sustainability in Australia coincides with many companies seeking telematics solutions to achieve sustainability goals.
However, fleet managers – who often have a traditional fleet management background – are faced with the challenge of adapting to this new EV landscape.
The transition to EVs presents complex issues for fleet managers, especially concerning charging infrastructure and power grid management. For example, companies with large fleets need to consider the number of charging stations required and the impact on the power grid when charging multiple vehicles simultaneously.
These challenges are new to fleet managers and require expertise in EV technology and power grid management.
To address these concerns, Geotab acquired an EV telematics company four years ago, bringing in valuable patents, technologies, and electrical engineering expertise. This acquisition equipped Geotab with the knowledge and tools to help companies navigate the complexities of adopting and operating EVs at scale. It is thus well-positioned to support companies in Australia looking to transition to EVs and meet their carbon reduction targets.
But Sean is careful to point out that achieving carbon neutrality in the transport sector involves more than just adopting EVs. “Geotab offers various technologies and tools to help fleet managers make data-driven decisions that can significantly reduce their carbon emissions,” he says.
Apropos of Geotab’s Green Fleet dashboard, Sean mentions that “[We] can actually calculate CO2 emissions per vehicle based on fuel usage.” This technology allows fleet managers to identify the worst offenders in their fleet – whether it be outdated models or vehicles operating inefficiently – and prioritise their replacement or repurposing.
He elaborates: “If you start doing a data-driven selection, on who are the biggest offenders, what vehicles could be repurposed, how you might use them in different roles in different locations, you might find you can achieve the same results with scores fewer vehicles in your fleet.”
Sean acknowledges that not all vehicles can be transitioned or replaced by EVs, particularly heavy vehicles in Australia, while still stressing the importance of using data to replace older combustion engine vehicles with newer, more environmentally friendly models.
“If you have a 2010 Ford F150 in your landscaping company, and you switch it out with a brand new one, you’re going to get a big benefit.” By monitoring and optimising fleet management in this way, companies can see their carbon emissions decrease month after month.
“By identifying the worst offenders in a fleet, optimising vehicle usage, and monitoring emissions, companies can significantly decrease their carbon emissions and contribute to a more sustainable future.”
Furthermore, telematics plays a crucial role in enhancing safety, which is of paramount importance, Sean says, for many of the fortune 500 companies Geotab supports. Aside from the quality of their products and financial success, their uppermost aim is to prevent accidents involving their vehicles that could have severely detrimental consequences – including loss of human life as well as irrevocable damage to their reputations.
“The number one thing they use telematics for is safety,” Sean says.
Integration of and innovative uses for telematics technology in supply chain management are essential steps towards achieving sustainability and safety goals. By harnessing the power of data and leveraging connected systems, companies can significantly improve their operations, mitigate risks, and contribute to a greener, safer future.
It’s a future Geotab is uniquely committed to as a privately-owned company with a strong values-driven modus operandi.
Sean closes his chat with MHD citing the leadership provided by Geotab CEO Neil Cawse – who has proactively signed onto sustainability pledges and publicly released sustainability reports on Geotab’s progress.
“Neil could long ago have sold Geotab and retired very comfortably,” Sean says. “But that’s not what he’s about; he remains 100 per cent dedicated to the company because, and I’ll quote his philosophy and objectives in his own words here: ‘I can make more of an impact on the planet with the 3.5 million vehicles I have under management than any other way I could possibly imagine.’
“That’s the blend of vision and pragmatism that animates Geotab toward which every one of us works every day.” ■
Argon & Co is a global management consultancy that specialises in operations strategy and transformation. With expertise spanning the supply chain, procurement, finance and shared
services, we work together with clients to transform their businesses and generate real change. Our people are engaging to work with and trusted by clients to get the job done.
green shade will contribute to improved safety as the trucks will be easily visible in their operational environment. Aside from optics however, a focus is on a number of ergonomic features.
The driver’s position in the centre of the cab offers generous room and excellent all-round visibility. The angle of the telescopic steering column can be adjusted and the Grammer MSG65 seat, combined with hydraulic cabin mounts guarantees a comfortable ride. An adjustable arm rest is mounted to the seat suspension which incorporates a multi-function joystick and an LCD
Combilift’s unique dynamic 360
steering that enables seamless directional change while on the move can be integrated into the Combi-CUBE as an optional extra, making it the most manoeuvrable counterbalance forklift on the market.
Further notable features are the large rear wheel and rubber tyres on all three wheels. This means that, unlike certain other brands of electric multidirectional trucks, this model is not restricted to super flat floors and is eminently suitable for working indoors and out, ensuring that semi-rough terrain is no impediment to reliable operation. And for quicker battery changeover during heavy shifts, two new easy-change
roll-out batteries are provided (Overall Design Copyright 015019216-0001).
Combilift CEO and Co-Founder Martin McVicar said: “Our engineers and R&D department have been tirelessly preparing for a year of new launches, and the Combi-CUBE is proof of our continued commitment to provide the best and most innovative handling solutions for our worldwide customers.” ■
“
[The] CombiCUBE is proof of our continued commitment to provide the best and most innovative handling solutions for our worldwide customers.
Geotab’s AI-driven platform transforms real-time data from any source into actionable insights that provide measurable business value, help reduce fleets emissions and costs while improving operational efficiency. Optimize your fleet’s performance and stay ahead of the competition.
geotab.com.au
Intralogistics has long been Fuzzy LogX’s bread and butter, and though its merger with Argon & Co will formally take place on the first day of June, James Lee, Associate Partner at Argon & Co, says the Argon and Fuzzy teams have been working hand in hand for nearly six months; boosting and amplifying Argon’s intralogistics offering and delivering projects as an integrated unit.
“We don’t see the integration with Fuzzy LogX as an acquisition, but rather a true merger of like-minded people, that love all things logistics and want to deliver great outcomes for their clients” James says
Before the merger, Argon & Co had developed a foundational capability in warehouse automation and design, but often needed to leverage external specialists to deliver the full solution. However, the addition of Fuzzy LogX has brought a much higher degree of expertise in intralogistics. “We’ve long had intralogistics as part of a broader service offering,” he notes. “But the intricacies of the design process, and the intimacies that the Fuzzy guys have with various forms of warehouse technologies and the respective technology providers – it is on another level. They truly are best in market”.
Not only does this merger represent a major step for Argon & Co’s capabilities locally, but it also has global implications. Fuzzy LogX’s expertise is being shared with Argon & Co’s teams across Europe and the US, allowing them to enhance their service offerings at a local level. “We see this as a capability shift globally,” James says. “Sharing these new capabilities and learnings from case studies of projects successfully delivered will be hugely beneficial to our global teams
and clients across Europe, the US, and other regions.”
James notes the supply chain pressures still presenting challenges for intralogistics, including the historically low rates of vacancy for industrial property. There is a growing interest in automation as a key strategy to cope with these pressures, he says. “There continues to be a strong push into the automation space,” he says. “But given the long lead time of a lot of that equipment, what we’re seeing is people are only now just starting to get access to it.”
The strong demand for technology and automation was amplified by the COVID-19 pandemic, as companies faced labour pressures and a need to invest in advanced solutions. However, technology providers and automation suppliers struggled to keep up with the demand, leading to a backlog in delivery. “Business cases that were approved two to three years ago are only now starting to be delivered, given that strong demand.”
With a tight industrial property market, optimising current distribution centres is of paramount importance. James notes that Argon & Co is working on several projects that aim to enhance current capacity in addition to planning for future investments in automation. “There is definitely an intent to look to make further investments in automation over say, a three-to-five-year horizon. But there is also a strong push to optimise what they’ve got right now.”
Argon & Co’s merger with Fuzzy LogX has equipped them with the expertise to assist clients in making
these optimisations. Fuzzy LogX’s unique insights and capabilities within the four walls of distribution centres enable them to identify alternative ways of working and implement lighttouch investments in automation and design that enhance capacity.
James says the expertise Fuzzy LogX brings to the table in addressing these intralogistics challenges and offering tailored solutions to clients is priceless.
David Ring, Associate Partner at Argon & Co, says the company has made immense progress in digital twin technology in furtherance of intralogistics design. He explains that many clients are focusing on both long-term transformational changes and immediate improvements that can be visualised using digital twin technology.
“The development of our digital twin capability really helps clients understand their organisation today, how it operates and identify the operational levers they have in their toolkit – we are able to demonstrate how a slight move or adjustment could deliver them an availability or service improvement or could realise inventory savings,” David says.
Digital twin technology, which has been widely used in the manufacturing space, is now being implemented in the logistics and distribution sector. It allows clients to visualise their network and gain insights into how they can optimise their existing facilities by creating a digital ‘twin’ –a real time digital universe replica – of warehouses or networks.
This technology is helping clients
to learn why they have the confidence and the playbook to deliver the transformations of the future.
make smarter decisions, such as exploring upstream sourcing, redistributing inventory to facilities closer to customers, or even testing automation solutions before making significant capital investments. “If a client is contemplating an automation investment, they can ‘trial before they buy’ using a digital twin to simulate changes prior to making a major capital investment,” David says. “We’re really seeing digital twin solutions come to life and begin to be used more widely across those more critical business decisions.”
David highlights Argon & Co’s expertise in creating custom digital twin solutions for their clients.
“We work with a software application called Simio and we build custom digital twin or digital simulation tools using that platform. We’ve got an in-house digital team that can do that. While traditionally these digital twins have been used for manufacturing processes, such as continuity planning and line scheduling, the merger with Fuzzy LogX has opened new opportunities for applying this technology in the intralogistics space.”
“What we’re now seeing, particularly with the Fuzzy team, is that the application of digital twin technology can absolutely be replicated further downstream into their warehouse environment,” James adds.
Jeffrey Triantafilo, Director of Systems and DC Design at Fuzzy LogX, emphasises the importance of delivering with
confidence when it comes to intralogistics. Recent projects have shown that they can provide clients with a playbook for future operations. “What Fuzzy has always been about is delivering with confidence; knowing that your machine, your operation, is going to achieve your business requirements,” he says. “Merging with Argon means that we’re more confident in the intralogistics space than ever before.”
The merger with Argon & Co has expanded Fuzzy’s capabilities and allowed it to think beyond traditional constraints, ensuring they can better meet its clients’ needs.
“The Argon offering now, with a very similar culture, focuses on going for transformation with confidence,” Jeffrey adds. “Both companies have been working diligently to combine the best of both worlds, keeping a clientfocused approach while enhancing our capabilities.”
Jeffrey believes that the key to their success lies in having people at every step of the process, either stepping in for a team member within a business or providing advice to put together and execute a comprehensive plan for transformation.
“With the combined expertise of Argon & Co and Fuzzy LogX, we are well-equipped to guide clients through the rapidly changing intralogistics landscape with confidence. We’ve always been confidently at our clients’ side throughout their entire transformation journeys. But now we’re even more confident, at more clients’ side, and can provide an amplified and expanded set of solutions and possibilities.” ■
“ We’re really seeing digital twin solutions come to life and begin to be used more widely across those more critical business decisions.David Ring, Associate Partner at Argon & Co. James Lee, Associate Partner at Argon & Co. Jeffrey Triantafilo, Director of Systems and DC Design at Fuzzy LogX.
With our supply chain expertise, network support
and technological backing, we’re well placed to provide integrated logistics solutions for the healthcare sector. Working with a broad range of customers, we deliver comprehensive supply chain solutions that are tailored specifically to the needs of the sector - including the movement, storage and distribution of temperature controlled and high-risk goods. Our point of difference is our capacity to provide a comprehensive range of sophisticated healthcare logistics services coupled with close and responsive customer care.
Quality and compliance:
Comprehensive QA team and QMS in alignment with the PIC/S- Good Manufacturing Practice (GMP) for Medicinal products
Adhere to GWP requirements
Poisons Licenses (S2, S3, S4, S8)
ISO 9001 & ISO13485 (Medical Devices)
ISO 27001 Information Security Management System (ISMS)
TGA Licensed Facilities
We move the businesses that move the world.
More than half of logistics providers worldwide are exploring automation to meet growing delivery volumes. Yet with an overwhelming number of solutions, products, and providers in the market, making a purchasing decision is becoming increasingly difficult. MHD explores a new entry into the ANZ market that aims to simplify the sector and solve the paradox of choice.
The rapid rise of e-commerce and advancements in robotics and automation technology has led to record market adoption of automated solutions in supply chain operations across Australia with McKinsey Global Institute estimating that the transportation–and-warehousing industry has the third-highest automation potential of any sector.
With the rapid uptake of automation
solutions, there’s also been a record number of new providers and product offerings. As a result, the global logistics automation market is predicted to reach USD 51.3 billion by 2028, at a compound annual growth rate of 9.3 per cent.
According to Deloitte, more than 50 per cent of logistics providers worldwide are exploring automation to meet growing delivery volumes. Furthermore, more than 40 per
cent of logistics providers view outdated business processes and manual operations as their most significant challenge to scaling lastmile operations.
When embarking on the beginning of any automation journey, organisations are faced with a paradox of choice, and an endless choice of technology providers and solutions that promise
to make warehouses smarter and more efficient.
With most logistics providers looking at several different automation solutions – from Automated Mobile Robots (AMRs) to Automated Storage Retrievals (ASRS) to Multi-Carton Picking Robots – finding a partner who can deliver on all aspects of automation is increasingly difficult. Particularly when all the systems that are deployed also have to collaborate with software, systems, and processes within the larger eco-system of the supply chain.
Addverb Technologies, a global robotics company based out of India, is one of the newest entrants to the ANZ automation provider market. With a suite of automation products and solutions across robotics, ASRS, picking and software – Addverb’s unique point of difference is its broad range of innovate plug and play solutions.
“Addverb offers a solution stack which features both fixed and flexible automation – all underpinned by our innovative plug and play software suite,” Sangeet Kumar, CEO and Co-founder at Addverb Technologies says.
“Our AMRs, AGVs, and both case and pallet-based storage solutions maximise productivity for supply chain operations worldwide.”
One of the world’s largest sports retailers worked with Addverb Technologies to deploy a wide range of automated solutions across its end-toend supply chain operations.
One of the main motivations for automation for the retailer was to be able to scale up and down as required during seasonal demand fluctuations.
The retailer also has a wide SKU range and needed a solution that could deliver both accuracy and efficiency. At this facility, the leading sports retailer had to be able to cater to B2B and B2C customers as well as streamline and optimise its returns process.
“To manage the complete endto-end operations of the warehouse they needed a one-stop solution, for enhanced synchronisation and smooth integration,” Sangeet explains.
One of the major challenges was
the need to incorporate a greenfield solution in a brownfield site – a common occurrence in Australia where availability of industrial land and facilities is sparce.
“The brand was scaling up quickly and the demand was rising,” adds Sangeet. “To meet all the objectives, Addverb designed an innovative solution combining the power of fixed and flexible automation.”
The solution comprised of AMRs for material movement in the warehouse, ASRS including Pallet Shuttles and Carton Shuttles to optimise space utilisation and for automated material transfer and returns handling, MultiCarton Picking Robots were added along with sortation robots for quick dispatch of orders and catering to B2C customers.
“We designed a solution that enables the site operators to determine the location of an SKU to ensure maximum productivity during fulfilment,” Ranmeet Singh, Head of Operations ANZ at Addverb Technologies says.
“Addverb’s software has full visibility of the order data and timeframes for any SKUs at any stock level, which allows for dynamic and optimised storage of SKUs and quantities in the right locations within the warehouse, minimising the number of touch points and processing time.”
Often when there are several different automation solutions working together, efficiency gains are not realised because the systems fail to connect with software such as WMS or WCS.
With Addverb’s solutions, this is not the case.
“With our solutions, a warehouse not only has a great combination of fully compatible intralogistics automation
solutions, but the Addverb software is able to oversee the entire performance of the solution and humans as an integrated team and hence dynamic decisions are made in real time to ensure every aspect of this automation team is optimised,” Ranmeet adds.
For Addverb Technologies, humanrobot collaboration is essential to any successful supply chain operation and the organisation has been a pioneer in this space for years – particularly with boosting human productivity through its software solutions.
“Many other automation providers only factor in human pick productivity to manage the automation output. However, our software combines analytics from both human productivity and the performance of the Addverb’s intralogistics automation solution to ensure that both are perfectly synced for optimum performance at any given time or scenario,” Sangeet says.
As a result, the performance of Addverb’s solutions can be intuitively re-configured in real time to enhance the productivity levels of humans in various areas of the warehouse as well as the warehouse’s operational demands.
With one of the world’s largest portfolios of automation solutions on the market, and a fully innovative plug and play software solution to underpin them – Addverb Technologies aims to solve some of the common barriers to entry for businesses in Australia when it comes to transforming their operations with automation solutions. ■
Take advantage of all the action happening in South Australia. With warehousing, logistics, manufacturing and defence operations ramping up, opportunities to secure high quality, adaptable facilities are harder to come by. 153 Francis Street, Wingfield is situated in the prime inner-north, adjacent to major road infrastructure providing immediate access to the defence precinct and metropolitan Adelaide.
Now available and offering the following:
→ Stand-alone office warehouse measuring approx. 11,745sqm
→ Modern office fitout
→ Large canopy for undercover loading (away from prevailing weather)
→ Drive around warehouse for single direction truck movement
→ Substantial car parking for staff and customers
→ Secure fencing surrounding the site and gate access
→ 3200A power supply and gas supply
→ Minutes from main road infrastructure North-South Motorway, Port River Expressway Northern Connector
0410 532 022 0412 404 426
Mentone DC to add 12,000 new pallet spaces.
Warehousing logistics and automation leader, Swisslog Australia, has extended its automation solution for CocaCola Europacific Partners (CCEP) in Mentone, about 20km South-East of Melbourne’s CBD.
In an extended $17.4 million Automated Storage and Retrieval System (ASRS) pallet solution, Swisslog has installed additional Vectura cranes at the distribution centre (DC), which will eliminate the need for CCEP to utilise off-site storage during peak months. The solution will enhance operational efficiency, further improve customer responsiveness, and allow for both software and mechanical upgrades with minimal impact to the DC’s performance.
Swisslog shapes the future of intralogistics with robotic, data-
driven and flexible automated solutions that achieve exceptional value for our customers. Swisslog helps forward-thinking companies optimise the performance of their warehouses and distribution centres with future-ready automation systems and software. Swisslog’s integrated offering includes consulting, system design and implementation, and lifetime customer support in more than 50 countries.
CCEP is one of the largest bottlers of non-alcoholic ready-to-drink beverages in the Asia-Pacific region, and it has partnered with Swisslog to enhance production capacities and deliver efficiencies through automation technology across multiple sites.
“Swisslog has shown great aptitude in understanding the needs of
our business and demonstrated a willingness to adapt the application to meet our requirements,” says Colin Macdonald, CCEP’s Director of Operational Excellence in Supply Chain – Asia Pacific. “The expanded automation solution enhances safety, eliminates off-site storage, and increases our customer responsiveness, which are all important as we look to further optimise production.”
Swisslog’s data-driven, robotic solution will enable CCEP to optimise operations to fulfil customer requirements more efficiently, including in peak periods. The addition of more infrastructure in Pallet Flow Lane (PFL) dispatch lanes and additional Roll On Roll Off (RORO) docks will enable more efficient turnaround times for trucks inbound from CCEP’s production
facility at nearby Moorabbin and outbound from Mentone. Additionally, the extra wrapper and manual infeed positions will allow for greater flexibility in operation of the warehouse.
Swisslog Managing Director, Australia and New Zealand, Dan Ulmamei, says it was rewarding to see an existing customer seeing the value in an extension. “CCEP is clearly committed to improving its operational efficiency, and it saw that further automation could help take it to the next level. Swisslog was delighted to be able to assist as CCEP’s automation partner,” he says.
The new ASRS is joined to the existing ASRS at cross-over positions allowing the entire system to be operated as a whole. The solution is a mix of a three-pallet deep channel on one side and an eight/nine-pallet deep channel on the other side, creating an ideal mix of shallow and deep channel storage, with more
than 12,000 total storage locations. Overlapping row carrier functionality has been provided as an option to improve effective storage utilisation.
“The extended automation solution at CCEP Mentone has been designed to allow the flexibility to upgrade any component in the future. The additional three cranes provide further redundancy for the Mentone DC,” explains Ulmamei.
The new solution can be operated as a standalone ASRS or as a part of an integrated solution with the existing ASRS. Most importantly, with the new ASRS capable of functioning as a standalone system, this means the existing ASRS can be taken offline for upgrades to critical components of the ASRS. This reduces the impact on operations for CCEP out of their Mentone DC, should the team need to make upgrades to other existing systems. ■
“
CCEP is clearly committed to improving its operational efficiency, and it saw that further automation could help take it to the next level. Swisslog was delighted to be able to assist as CCEP’s automation partner.CCEP hosted a site tour and ribbon cutting ceremony to mark the completion of the DC’s upgrades.
Hangcha Forklifts Australia and our National Dealer Network are having our first EOFYS.
We have over 200 units in stock including:
• Lithium motorised pallet movers
• Lithium counterbalance 1.5t to 3.5t
• Gas and diesel counterbalance 1.8t to 7t
With over 200 units in stock and a new spare parts division our dealer network can support all your needs.
Hangcha Forklifts Australia has been set up to support our national dealer network. Call 1300 399 687 to be put through to your nearest local dealer.
sales@hcforkliftau.com
• 1.8T, 2.5t & 3.5t Rough Terrain both 2WD & 4WD available www.hcforkliftaustralia.com
Philip Batty, Managing Director at Ferag Australia, says the company has been in a period of transition these past few years. But with access to state-of-the-art technology, as well as a strong equipment partnership network, the company’s intralogistics offering is ready for the 2020s – and beyond.
The journey of Ferag Australia from being a traditional print, graphics, and consumables supplier to a major player in the intralogistics space is an inspiring example of business adaptation.
As Philip Batty, the Managing Director at Ferag Australia, recounts, the transition was not an overnight decision but a strategic move that unfolded over years.
Ferag Australia’s story begins in 1985. “We started in 1985 doing all our projects in graphics and newspaper,” Philip says. The company’s modus operandi was handling large-scale projects, predominantly sourcing machinery from its factory in Switzerland, and acting as a sales organisation with a focus on the print industry
However, as the print industry began to lose steam in favour of digital media, the need for adaptation grew evident. The transformation of the print industry was a reality that Ferag had to face. “That industry has significantly changed over the last number of years,” Philip acknowledges.
The turning point came about three years ago. The realisation that Ferag Australia had to adapt to serve new client needs spurred change. The step for Ferag to enter intralogistics was quite logical and natural. The basis –namely the efficient internal handling and conveying of goods – is comparable, no matter what industry you are in. For what used to be simply called logistics is now called supply chain management. What was once the internal flow of goods is now intralogistics. Hardly any other
industry has undergone such a major transformation in recent decades as the transport of goods and information and the associated services. Digitalisation, Sustainability and e-commerce only reinforces and accelerates this.
Ferag Australia’s vision for the 2020s and beyond, Philip says, is to be “a leading automation and trading solutions partner to the APAC region” and “to sell and support, Ferag, third party equipment, and consumables to the intralogistics and graphics market.”
The transition was not an easy one. Yet, Ferag is emerging stronger from this period of change, ready to make its mark in the intralogistics business. The company is all set to showcase its capabilities with a demo unit of its overhead conveyor system, the ferag. skyfall, at CeMAT in Sydney this July.
While Ferag Australia implements premium systems – including ferag. skyfall and ferag.denisort – it does not restrict itself to Ferag-only technologies: major technology partners include VisionNav Robotics, Wayzim, and HAI Robotics.
“Of course, our products, like the ferag.skyfall, often fit very well into the desired process,” Philip says. “But we are open and neutral as a subcontractor, as a general contractor and work on projects on an equal footing with our partners. This is a huge advantage for Ferag that others do not have in this way. First and foremost, we seek out what is best for the customer from the different worlds and design the various solutions into an overall system.”
Thanks to its broad experience and partner network, Ferag Australia
can offer comprehensive and unique intralogistics solutions for every requirement. Ferag’s innovative strength, its unique technologies such as the ferag.denisort and the ferag. skyfall, have emerged for over 65 years. The latter will be live on display at this year’s CeMAT Australia.
The ferag.denisort tilting tray sorter presents a dynamic solution for companies in need of efficient, adaptable, and scalable intralogistics systems. It integrates conveying, order picking, and sorting into a single, smooth system, making it a versatile tool for a variety of logistic processes.
One of the key benefits of the ferag. denisort system is its ability to handle a diverse array of products. It is especially suitable for managing bulky, light, round, or sensitive products, making it a versatile solution for a broad spectrum of business needs.
The design of ferag.denisort utilises a 3D capability that extends across multiple levels. This feature allows for maximum capacity utilisation even in confined spaces, ensuring optimal use of available warehouse or storage areas. It demonstrates a remarkable ability to adapt to a completely free layout in all dimensions.
The ferag.denisort’s modular and extensible design further enhances its adaptability. This allows for scalable solutions that can grow alongside a business, making it a cost-effective choice for both small operations and larger enterprises.
The system’s energy-efficient
technology is another standout feature. Using low-friction rollers, the ferag. denisort operates quietly and with minimal energy consumption. This not only reduces operational costs but also contributes to a more sustainable business practice.
The ferag.denisort system also boasts proven and robust engineering. This ensures its durability and longevity, making it a reliable addition to any logistics operation. Additionally, it is cost-effective in operation, service, and maintenance, making it a worthwhile investment in the long run. The system’s low-noise operation also contributes to a more conducive working environment.
The ferag.skyfall conveyor system offers a comprehensive solution for companies seeking to streamline their logistics and supply chain processes. It integrates multiple functions such as conveying, buffering, sorting, order picking and consignment into one system, resulting in significant efficiency and productivity gains.
One of the key advantages of the ferag. skyfall system is its three-dimensional design. By utilising this vertical space, it frees up valuable floor area for other value-creation processes. The system
uses shuttles and trolleys combined with application-specific load carriers and takes advantage of gravity to maximise efficiency.
The ferag.skyfall system is versatile and adaptable, suitable for a range of applications including order picking and consignment for e-commerce, retail, B2B and 3PL, sorting and sequencing for dispatch, incoming goods and returns, and extending process chains without the need for transfer points. Furthermore, the system is equipped to handle material flow with process decoupling and buffering, and inter-process linkage with buffering and sorting.
It also boasts high technical specifications with a capacity of up to 12,000 load carriers per hour and a loading capacity of up to 20 kg including the load carrier. It operates at speeds of up to 2 m/s on gravity-driven stretches and 0.75 m/s on conveyors.
The system offers numerous peripheral options such as identification by barcode, QR code, RFID or camera recognition. It uses customised load carriers with pockets, hooks, grippers and more and has options for fully automatic, semi-automatic or manual loading and unloading. There are interfaces to Warehouse Management Systems (WMS), Warehouse Control Systems (WCS) and
peripheral systems, enabling seamless integration into existing infrastructure.
The benefits of the ferag.skyfall system go beyond its functional and technical features. The system reduces manual tasks along the process chain, which in turn increases productivity and efficiency thanks to automation. It also offers full traceability throughout the system, which is crucial in today’s logistics environment. The modular and extensible design allows for easy scalability, and its high-quality, maintenance-friendly engineering ensures a robust and durable solution.
Finally, its energy-efficient technology, thanks to rolling friction and the use of gravity, makes it a sustainable choice for businesses looking to reduce their environmental impact.
“We’re now at a launch point where we have the awareness, we’ve got the equipment, and we’ve got the partners to take Ferag Australia’s intralogistics business to the next level,” Philip says.
“We’re excited to demonstrate ferag. skyfall to Australia’s rapidly developing e-commerce market at CeMAT this year, but also to emphasise that we’ve got the experience and broader partnership network to bring not only top end but cost-effective solutions to the market.” ■
Intelligent robotic provider HAI Robotics will be showcasing its latest innovative solutions next month at CeMAT in Sydney. MHD sits down with Paul Phillips, General Manager ANZ at the company to find out more about the organisation, its push to progress human civilisation using robotics technology and the latest products in its growing portfolio.
Established in 2016, Hai Robotics is a pioneer and leader in intelligent robotics solutions. As the world’s first company to launch an autonomous case-handling (ACR) system, the organisation is a leader of innovation and committed to designing products that help revolutionise and transform the warehouse.
Boasting more than 1600 employees worldwide, more than half of which are engineers – Hai Robotics has completed more than 1000 projects for world-leading organisations in fashion, 3PL, retail, electronics, healthcare, and e-commerce. As the first to enter the ACR market, Hai has also retained its status as the world’s leading provider of ACR systems.
After recently launching in Australia, the leading robotics provider is gaining significant traction in the ANZ market.
According to Paul Phillips, General Manager ANZ, Hai’s solutions are a great fit for the Australian logistics landscape.
“Australian distribution centres are frequently subject to operational workflows that are impacted by the extreme sizes of items in a typical e-commerce order,” Paul explains.
“Many organisations are using archaic and loosely designed workflows to address orders that contain a combination of bulky and
heavy pallet-based items, along with smaller tote-based items. This is extremely hard to address and leads to a high cost to serve.”
With the profile of e-commerce orders more diverse than ever, Hai Robotics has launched a new solution that can combine both pallets of product, and totes and cartons.
FLEXPICK, is a new solution that encompasses Hai’s standard HaiPick solution, along with the AMR-led solution, HaiFlex within the same operational grid.
“The new, combined FLEXPICK solution allows a customer to pick both smaller items from a tote, as well as bulkier items from the AMR,” adds Paul.
“For example, one order may contain pet food – which might
weigh 20kg, but there may also be smaller items such as treats, pet collars, etc. This new solution provides the flexibility to pick both of these items using the same automated solution.”
With the price of storage and industrial property at an all-time high, being able to increase density enables organisations to make better use of storage space.
“Double deep tote storage is of particular interest to the ANZ market at the moment, when we’re seeing record rent prices and a severe shortage of available industrial property organisations are having to think of innovative ways to maximise their footprint,” Paul says.
The FLEXPICK solution combines the power and capabilities of Hai’s
popular HaiFlex AMR and the HighPick ACR and addresses the need to pick and pack a combination of bulky items that are typically larger than a tote size, as well as smaller SKUs which are typically tote-sized items. The HaiPick ACR is now also available in taller format achieving a height of up to 10m called HaiPick A42TD.
“This combined automated
solution offers a powerful automated consolidation of both items arriving directly at the user’s workstation, thus eliminating the need for warehouse operators to move around the warehouse floor for picking and additional packing,” Paul adds.
According to Paul, there’s been a long-standing need for a solution in Australia that enables automated picking of both bulky and smaller items.
“Up until now, warehouses have had to apply very archaic methods of processing orders that combine bulky and smaller items,” Paul explains.
“While varying degrees of refinement of the process have been developed, HAI’s fully automated and speedy solution combining ACRs and AMRs to pick from multiple locations and consolidate the order items at a single workstation has entirely revolutionised this process.”
This flexible solution has been launched in EMEA, ANZ, SEA, South Korea, and China and is providing customers with a seamless and
efficient automated workflow and a productivity increase of more than 60 per cent – in addition to the benefits of high-density storage. ■
In July, Hai Robotics will be attending CeMAT in Sydney to showcase a number of its innovative robotic solutions.
On display and for demo will be newly launched FLEXPICK solution compromising of the joint capabilities of the HaiFlex and HaiPick solutions. Attendees will also be able to learn more about Hai’s innovative micofulfilment utilises both ACR and AMR technology to increase throughput, accuract and is Hai’s highest density and throughput solution to date.
Visit Hai at CeMAT Sydney from 2527 July at Stand F16, the Dome Sydney Olympic Park to learn more about the latest robotic solutions to hit Australia and New Zealand.
Marianne Kintzel, Executive Officer at the Refrigerated Warehouse and Transport Association on the cold chain organisation hosting the Frank Vale Awards for the thirtieth consecutive time and its upcoming 81st Conference & Exhibition in August on the Gold Coast.
The Refrigerated Warehouse and Transport Association (RWTA) has been hosting the Frank Vale Award for the past 30 years.
This prestigious honour has been awarded annually since 1993 to acknowledge talented young people within the industry. These emerging leaders are members of the RWTA.
Applicants must be nominated by their manager, be 35 years of age or younger, have worked in the cold chain industry for a minimum of three years, and demonstrated to their employers they have the potential to become future leaders while making a positive contribution to the development of the Australian Cold Chain Industry.
State finalists and their partners travel as special guests of the RWTA to attend the Annual RWTA Conference an Exhibition, with all travel, conference registration, accommodation and meal expenses of the state finalists, and their partners, being met by the RWTA.
The RWTA’s 81st Conference and Exhibition is to be held at the QT Gold Coast between the 20-22nd August 2023.
Attending the RWTA Conference and Exhibition provides state finalists with an outstanding opportunity to broaden their knowledge and understanding of the Australian Cold Chain Industry, along with the opportunity to meet many of the key players.
This year the National Award Winner will fly to Scottsdale, Arizona in the United States to compete on the international stage with finalists from the United States, South America, Brazil, Europe, and Africa.
This award is proudly sponsored by ASKIN Performance Panels. ■
For further information, please visit the following websites:
RWTA’s 81st Conference and Exhibition: https://www.rwta.com.au/ conference-2023
Frank Vale Award: https://www.rwta. com.au/frank-vale-award
GCCA Next Gen Award: https://www.rwta. com.au/gcca-nextgen-award
The Supply Chain & Logistics Association of Australia is holding its Australian Supply Chain and Logistics Awards event on Friday November 10, 2023, with calls for submissions open until Friday September 1, 2023.
ASCLA: Calls for submissions now open Nominations are now open for the Australian Supply Chain & Logistics Awards.
The annual ASCL Awards recognise the outstanding achievements of supply chain & logistics professionals and organisations across Australia, celebrating industry excellence and championing collaboration, innovation, and success.
The ASCLA are the industry’s oldest and most prestigious awards, celebrating 60 years in 2022. The SCLAA is proud to have been hosting these awards for the last 20 years and recognising and cheering on individuals and companies that have contributed to the advancement of the Supply Chain and Logistics industry in Australia over the last two decades.
KEY DATES:
Submissions open: 2nd May 2023
Ticket registrations open: 1st August 2023
Submissions close: 1st September 2023
Finalists to be announced: 27th September 2023
ASCLA Gala Dinner Awards Night:
10 November 2023
NOW OPEN
AWARD CATEGORIES:
• ASCL Industry Excellence Award
• ASCL Supply Chain Management Award
• ASCL Future Leaders Award
• ASCL Automation, Robotics or Emerging Technology Award
• ASCL Training, Education & Development Award
• ASCL International Supply Chain Award
• ASCL Environmental Excellence Award
• ASCL Big Data, IT & Business Intelligence (BI) Award
• ASCL Start-Up Award
Submissions close: 1 September 2023
Finalists to be announced:27 September 2023
Winners announced at the ASCL Awards Gala Dinner: 10 November 2023
PARTNERSHIPS OF STRENGTH
We are inviting companies and organisations to become part of
these prestigious national awards on the 2023 Awards night. Showcase your organisation, strengthen brand awareness to industry leaders and be the Ambassador of Excellence by recognising its highest achievers.
SAVE THE DATE
10 NOVEMBER 2023
2023 Annual Supply Chan & Logistics Awards Gala Dinner to be held at the Fullerton Hotel Sydney.
The Fullerton Hotel Sydney was once a grand General Post Office and remains a beloved local icon, with layers of history to unfold. Launched in 1874, the GPO Building has long been a landmark and meeting spot; its clock tower was once the tallest building in the city – and while Sydney’s skyline has since surpassed it, the allure of this place endures.
The stonework of the exterior –which took months of painstaking restoration before the building was reborn as The Fullerton Hotel Sydney – warrants a long wander and closer look. Classic columns and the exquisitely carved faces of Neptune, Minerva and Queen Victoria offer a glimpse of what was possible for a post office during Sydney’s gold rush.
PARTNERSHIPS OF STRENGTH
We are inviting companies and organisations to become part of these prestigious national awards on the 2023 Awards night. Showcase your organisation, strengthen brand awareness to industry leaders and be the Ambassador of Excellence by recognising its highest achievers. ■
HUBTEX’s FluX Electric Multidirectional Counterbalance Forklift Truck has had some significant and innovative updates. The latest generation has load capacities of up to three tonnes. It has a new central driver’s position, which provides a higher-up all-round visibility compared to its predecessor. Additionally, the patented 360° HX steering has been added to the compact three-wheel running gear for the first time, ensuring smooth changes in direction from longitudinal to transverse travel.
It handles both pallet and long-load transport in a single vehicle. This hybrid used as a front and sideloader makes the new 3T FluX 30, suitable for a wide range of sectors, from the timber and metalworking industries, through to the building materials trade. For more information visit www.hubtex.com.au
Poor ocean visibility puts a strain on global supply chains, logistics costs, and customer service. At the root of the issue is low-quality data that hinders personnel productivity, streamlined operations, and proactive exception management. Today, more than ever shippers and 3PLs need global ocean visibility with the data quality, intelligence, ETAs, and proactive exception management that ensures efficient, costeffective, reliable, and sustainable global transportation. Project44’s Ocean Visibility solutions is here to help, with a suite of solutions that uses first-in-class data and analytics to improve personnel productivity, allow for proactive exception management, reduce logistics costs, improve customer service, and empower users for agile transport planning and procurement.
For more information visit www.project44.com
Global cube storage company AutoStore introduces its latest capability, the Grid and Vending Machine solution, designed to simplify warehousing automation. The ConveyorPort is a workstation in its simplest form, where Bins are dropped on a conveyor and transferred to an opening outside of the Grid. Smart covering and sensors ensure operator safety. The CarouselPort is designed to work with the operator, in harmony with Robots to ensure the next Bin is always ready. The workstation operates with three rotating arms, each holding one bin tray. The Vending Machine solution includes various Robots and chargers, as well as a dummy display unit, and a grid structure with 60 Bins.
For more information visit www.autostoresystem.com
Nathan Cairney joins TMX Global as its Director – Project Services. Previously, Nathan worked for project management consultancy Tactical Group ANZ in Sydney and Brisbane, where he spent eight years working with both occupier and landlord clients, including Woolworths, Primary Connect, Charter Hall, Hale Capital, Logos, Altis, ESR, and Stockland. His focus has particularly been on warehouses and DCs, heavy industrial process facilities, and transport and logistics infrastructure. Nathan has worked on developments ranging from 10,000 sqm to 80,000 sqm, up to three-storeys, and varying in complexity –from single-select racking to fully automated material handling systems with multiple ASRSs and AGVs.
Swisslog has appointed Dan Ulmamei as its new Managing Director for Australia and New Zealand. Dan has spent the last 26 years of his career in the logistics industry, most of it in various leadership positions, ultimately managing a team with extensive operations across the globe. He has been working in management positions in the logistics industry in Sydney since 2016. Dan sees exciting opportunities for logistics automation and industry ingenuity to tackle some of the world’s biggest challenges, including supply chain difficulties, labour shortages, and materials availability.
Do you have career news to share? Email Edward Cranswick at Edward.Cranswick@primecreative.com.au to be featured.