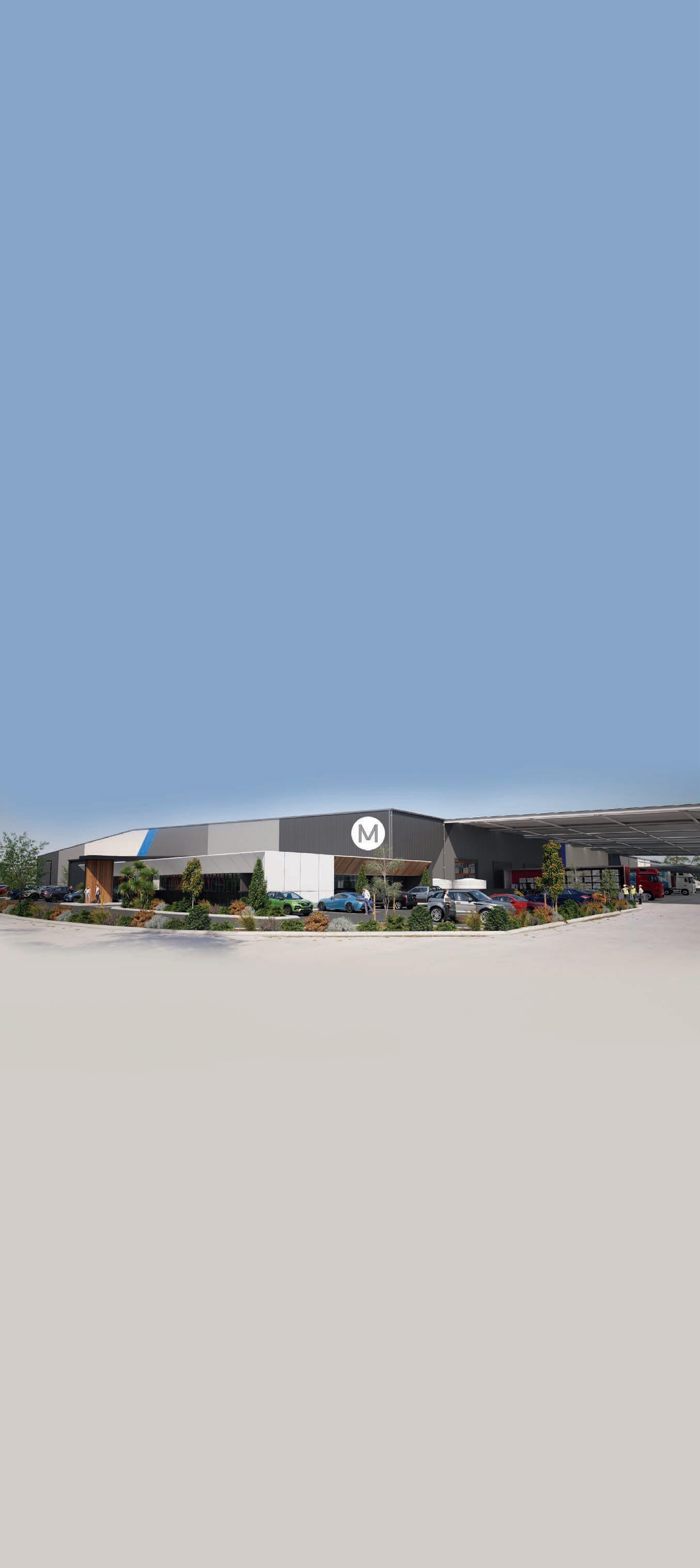
6 minute read
Charter Hall delivering for
MUNRO FOOTWEAR POSITIONING FOR GROWTH AT CHARTER HALL’S MIDWEST LOGISTICS HUB, TRUGANINA
An artist’s impression of Munro Footwear facility.
Charter Hall explains to MHD how smart warehouses are driving omni-channel business transformation. Charter Hall is delivering Munro Footwear Group’s purpose-built distribution centre in Melbourne’s west later this year. The stateof-the-art facility will help the shoe retailer keep up with the demands brought on by the e-commerce boom.
The shift to online retailing shows no sign of slowing down with the pandemic further super-charging customer demand for quick and costeffective deliveries, particularly in the fashion sector.
In fact, Australia’s e-commerce penetration rate as a percentage of total retail sales continue to rise and is at a new record of 14.6 per cent equivalent to $55 billion over the past 12 months (Source: CBRE Australian Industrial & Logistics Market Report May 2022).
This growth is translating into rapidly evolving and complex distribution centre requirements as businesses seek to transform their omni-channel operations to respond to their customer base shifting their spend from bricks and mortar to online.
For Charter Hall, Australia’s largest provider of industrial and logistics facilities, this is demonstrated by increasing e-commerce related enquiries from existing and new customers with more than 20 per cent of leasing enquiries in the last 24 months incorporating an omni-channel approach.
“As demand for state-of-theart industrial and logistics facilities accelerates further, we are redefining what is possible when it comes to the operational and technological capability and sustainability innovation,” Andrew Simons Head of Department, Industrial and Logistics at Charter Hall, explains.
“At Charter Hall, we specialise in partnering with Australia’s leading and most trusted businesses as well as global brands, to develop, own and manage next-generation industrial and logistics facilities that are custom-designed to meet our customers’ needs for the long-term,” he adds.
“For many businesses this means investing heavily upfront in highly techenabled facilities that have in-built flexibility to support their business growth and deliver on their increasingly sophisticated operational requirements.
“For even the largest businesses this can prove challenging, which is one reason why we’re seeing more organisations seeking our expertise in the development of their facilities.
“For example, automation is truly shaping the way we work, impacting everything from facility design to software selection and recruitment with businesses looking to streamline processes and increase efficiencies.
“We’re looking in tandem with our customers to help them capitalise on the benefits automation brings to operational efficiency, customer experience and ultimately the bottom-line.”
Munro Footwear’s new facility is a key initiative to expand its business and optimise its omni-channel customer experience.
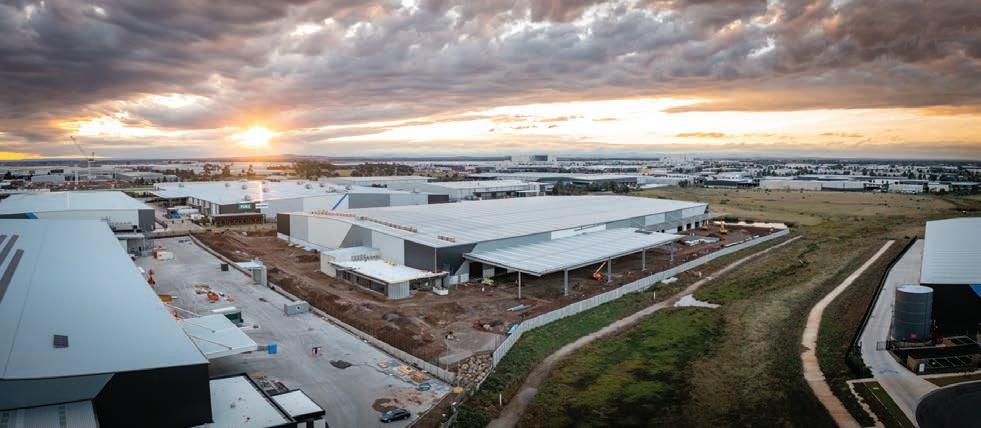
A good example of how a longstanding Australian retailer is transforming its business with omnichannel solutions thanks to innovative warehousing and logistics, is major Australian footwear retailer and wholesaler, Munro Footwear Group.
Charter Hall partnered with Munro on a new state-of-the-art distribution centre at MidWest Logistics Hub in Truganina, Victoria.
Located 22km west of Melbourne CBD, MidWest features the latest tech-enabled industrial and logistics facilities with market-leading innovations in automation.
The strategic location, high-quality features, and Charter Hall’s track record of certainty of delivery on large, complex projects was a drawcard for Munro and major brands including Coles, Uniqlo, Toll, Ingham’s, and Bridgestone.
Following a complete review of its warehouse and distribution functions, Munro made the strategic decision to consolidate and optimise its domestic supply chain.
Munro is experiencing a large increase in online and omni-channel orders, which is impacting manual operator productivity and increases in packaging requirements. This, coupled with the desire to deliver a better experience for customers, drove the need for a more automated solution.
Due to complete later this year, Munro will relocate from its current operations spread across two facilities into the new $50 million purpose-built national distribution centre, which will service its in-store, wholesale, and online operations.
The 26,534 sqm facility offers an almost five-hectare site and will incorporate one of Australia’s largest fleets of Autonomous Mobile Robots (AMR) to pick and pack items for delivery to stores and direct to customers.
The leading-edge AMR solution has the capacity to store more than 1.2 million units, providing Munro with sufficient scale that it can remodel its end-to-end inventory management strategy.
The facility has been designed to achieve a minimum 5 Star Green Star Design & As-Built rating, delivering Australian best practice environmental performance and lower operating costs.
The new AMR solution will increase picking speed and accuracy, creating greater productivity and efficiency in operations, while reducing lead times to both customers and stores.
This new facility will assist in optimising inventory levels, improving integration with transport carriers and enhancing customer experience across the group’s 260-plus store network and its 11 e-commerce sites – the latter having seen significant growth during recent years.
“Our business is on a strong growth trajectory, and we have made a major investment in optimising our supply chain operations to support our increasing in-store and online sales,” Marcus Bartlett, Chief Operating Officer at Munro, says.
“This new facility is a key initiative in our multi-year growth plan to expand our business, optimise our omni-channel customer experience and strengthen our distribution capability, particularly to support online sales,” he adds.
“With this new facility, we will have sufficient space to have more products available for online customers, and the increased picking speed, accuracy and productivity will lead to reduced return rates.
“In addition, the location is perfect and provides a link into domestic carriers for better integration and quicker delivery times to meet changing demand and customer expectations.”
“We’re seeing many of our customers’ warehouse needs changing as they seek to expand and enhance their online operations in response to the continued e-commerce boom,” Andrew says.
“Thanks to our portfolio size and flexible approach, we can develop purpose-built, scalable facilities and support our customers to move within our portfolio whenever needed.
“With a specialist in-house team of 80-plus in key markets across the country, experienced in development and property management, supply chain management, sustainability and technology, our people are passionate about delivering innovative solutions that enable businesses to grow.
“Shifting from their existing ambient warehouse to a business-first fully automated facility is an important move for Munro, and our team are working closely with them on every step of the region and delivery journey.
“The integration of leadingedge technology and AMR solutions combined with the estate’s strategic location close to distribution channels including the Port of Melbourne ensures the facility will deliver exceptional supply chain efficiencies and productivity for Munro’s business and customers.”
Munro has partnered with leading supply chain and property consultancy TMX to design its new operations and automated solution and run the project management of the development alongside Charter Hall.
“This innovative new facility has one of the largest AMR goods-to-person deployments in Australia and is an exciting milestone for Munro,” Nick De Klerk, Senior Consultant at TMX, says.
“Tailored to their requirements, the AMR technology stores and automatically retrieves over 1.2 million pairs of shoes,” he adds.
“The key objectives for the solution design were to provide a highly ergonomic, comfortable, and safe operating environment for facility operators, while ensuring throughput and flexibility to meet requirements today, and tomorrow.
“To achieve this, the system features over 200 AMRs, 6000 mobile storage shelves and workstations specific for B2B and B2C channels.”
Automated solutions that drive more efficient returns handling including packaging and the fast and precise picking of small orders are becoming an increasingly critical aspect of the online fulfilment value chain.
Market-leading facilities such as Charter Hall’s MidWest Logistics Hub are solving these operational and supply chain challenges in a fast-moving market where maintaining quick and efficient deliveries and returns are essential to meet the high expectations of today’s online shoppers. ■