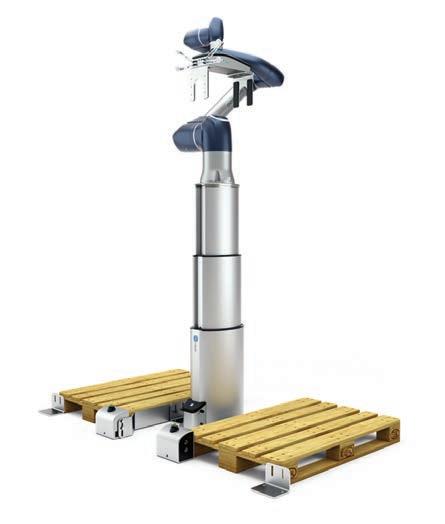
7 minute read
Diverseco and the Cobot
COLLABORATION WITH COBOTS
Rhett Talley, Marketing & Business Development Manager – Automation for Diverseco introduces the brand-new Doosan H-Series, the most powerful collaborative robot in the market.
Diverseco is, as its name implies, a diverse company – built over the years through amalgamating businesses and product offerings that are both unique and mutually complementary.
Rhett Talley, Marketing & Business Development Manager – Automation, notes that Diverseco has been a longterm agent for Kawasaki Robotics’ range of industrial robots. The partnership has served both companies well. But Diverseco has more recently been in search of collaborative robots to complement Kawasaki industrial robots, delivering more value to customers and building on the success of its Kawasaki offerings.
As a result, Diverseco is now the exclusive Australian distributor for Korean manufacturer Doosan Robotics. This includes the full range, comprising the A- Series, M-Series, and the brand-new H-Series collaborative robot (‘Cobot’).
WHAT IS A COBOT?
Doosan Cobots are not to be confused with Autonomous Mobile Robots (AMRs), Rhett is careful to point out. He notes that these terms are often used interchangeably in the industry – with the result that when people think of Cobots they may not grasp their unique potential to help operations in innovative ways.
“Oftentimes people use the terms Cobots and AMRs interchangeably, but they can refer to completely distinct machine concepts, so it’s important to understand what Cobots are and what their unique value is,” Rhett says. “I think AMRs are called ‘robots’ partly because it sounds sexy. AMRs serve a range of critical intralogistics functions – moving things from point A to point B; or picking for warehouse fulfilment and other tasks. AMRs move around autonomously and through a combination of sophisticated onboard sensors and fleet management software make decisions in real time – so, yes they are robotic in that sense– as such they are a real break from, say, AGVs [automated guided vehicles] which move along a pre-set pathway, and are rather inflexible. AMRs are collaborative of course, meaning they are designed to work safely alongside humans. But up to now when most people think of ‘robots’ or ‘cobots’ they might be thinking about a robotic arm with an end of arm tool.”
But a Cobot, more specifically a Cobot arm, is more akin to a traditional industrial robot in that it is set in a fixed position and performs repetitive tasks. The difference though – and part of what makes them collaborative – is that a Cobot’s end of arm tool (EoAT) can be changed and quickly redeployed to perform a wide variety of collaborative tasks besides its common palletising and depalletising function.
“In most cases traditional industrial robots are configured to perform one set task with a fixed, permanent end of arm tool,” Rhett notes. “Cobots, however, are often fitted with what are called Quick Change end effectors (grippers) like those from our agency OnRobot. These quick change grippers can allow an operator to move quickly from one application to another enabling quick Cobot redeployment and truly collaborative applications. They can be reconfigured to switch tasks in just a few minutes – so they can adapt to collaborate with workers in different ways depending on the immediate requirement – and unlike traditional industrial robots, which must operate within safety cages, Cobots are designed
The Doosan H-Series Cobot with the Lift100 from OnRobot takes collaboration between man and machine to new heights.
with human collaboration in mind with built in sensors and design features to ensure the highest levels of safety. So, you can work side by side with your Cobot, and a quick adjustment to its end of arm tool means it can collaborate with you on very wide range of tasks.”
COBOTIC APPLICATIONS
“A key advantage to Cobots is that non-robotics people – standard workers and operators – can easily change arm tool grippers and applications,” Rhett points out.
This streamlines the workplace and allows for greater flexibility and adaptability.
“They’re also easier to deploy because there is a reduced engineering time – you don’t need robotics experts to reconfigure them – and reduced systems integration time,” he adds. “Traditional industrial robots have
a heavy and more time-consuming integration cost because they’re installed permanently to perform one task in the same place at rapid speed. By contrast, Cobots are lighter, so they can be moved around, they’re not caged, and they can be quickly introduced to different environments to perform myriad tasks. They’re just more versatile.”
Rhett says that in the domains of manufacturing, warehousing, and factory processes, Cobots are one of the best tools that intelligent engineers have come up with.
“It’s one machine, the Cobot, but with minor tweaks can perform very different jobs for you,” he says. “There are probably five main applications for which Cobots are suited. First, there’s palletising – picking and placing and palletising. Second, Cobots can perform welding tasks – very useful in metal fabrication – we’ve just released our own cobot welding system called the Weld Mate 355 that is perfect for collaboratively working alongside a human welder and enhancing their capabilities and throughput. Third is machine tending, and fourth is assembly. The fifth application I identify for Cobots is what I like to call ‘you-nameit’ – meaning it’s essentially up to the individual’s imagination.”
In other words, while Cobots have obvious immediate everyday applications – such as the four Rhett identifies – its potential applications are limitless. And this is a crucial advantage in Australian manufacturing and industry – where resilience, agility, and flexibility, and reliability in the face of unforeseen disruptions are highly prized qualities.
Diverseco’s Rhett Talley shows off the new Doosan H-Series Cobot at AUSPACK 2022.
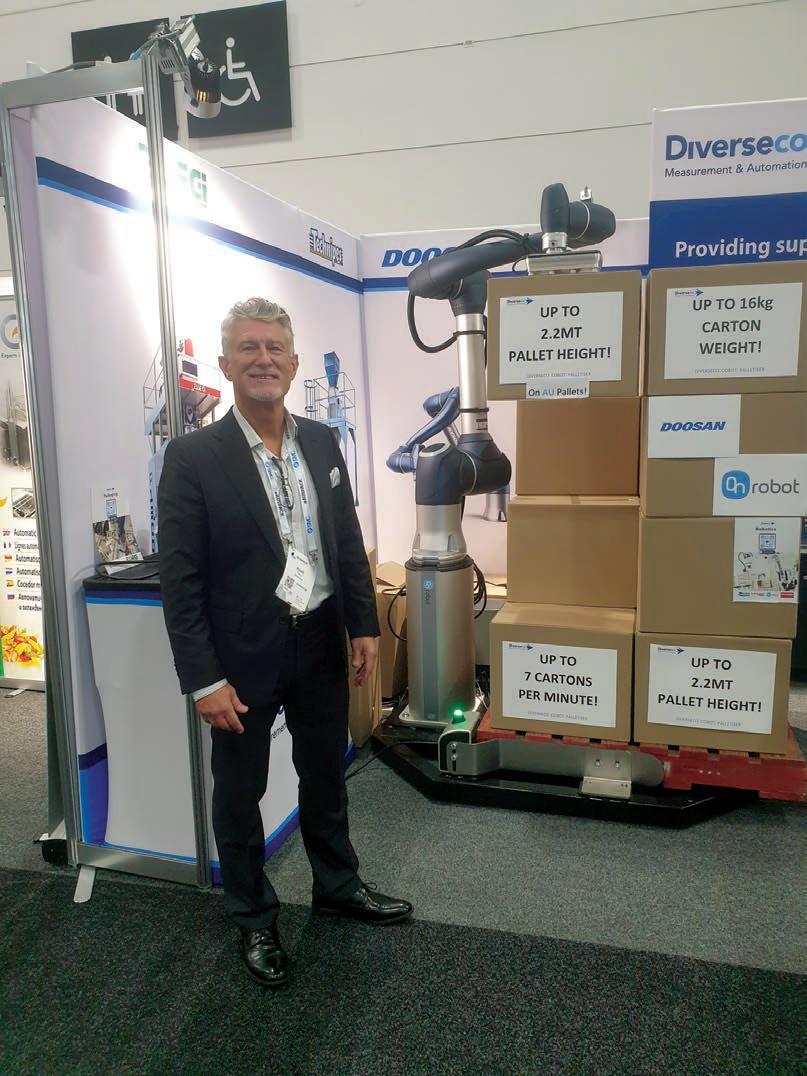
DIVERSECO – YOUR GO-TO COBOT INTEGRATOR
At the 2022 AUSPACK exhibition, held at the Melbourne Convention and Exhibition Centre in Melbourne last month, Diverseco gave its first demonstration of the Doosan H-Series Cobot in action – showing off its palletising capabilities using the OnRobot Lift100 height extension.
“It was our first time showing it off to the public, and there’s a few things that make this particular cobot configuration very special,” Rhett says. “One of these is that the OnRobot Lift100 is basically a means to extend the height of the Cobot’s reach. So, if it’s palletising a pallet of cartons and reaches a certain level, the Lift100 will raise the Cobot higher so that it can just keep on palletising up to a height of 2.2 meters.”
Rhett and the Diverseco team are keen to educate Australian industry on the unique value of the Cobot – and even keener to implement more and more of them across the country. And, while one might be tempted to say that Diverseco is ready to hit the ground running, the fact is it’s long been running all over the country delivering robotics solutions.
“Diverseco is a systems and robotics integrator with offices and staff in all five capital cities, including our own robotics hub in Ballarat,” Rhett mentions. “We’re also in the process of setting up a Darwin office. So, we have the resources around the country to support our products, and we have methods whereby we can access equipment remotely via internet connection. Our Australian-based engineers can provide support in realtime to customers.
“Because Diverseco is a diverse company with a history stretching back three decades, we are an established and already-approved vendor to everyone from Rio Tinto and BHP to Toll and DHL – to name only a handful.
“While our Cobot offering may be new in the market – we are not. We have the reputation, credibility, resources, and reach to deliver this exciting new solution right now.” ■
AUSTRALIAN PREMIER:
DOOSAN COLLABORATIVE ROBOT (COBOT) PALLETISER WITH ONROBOT LIFT100 AND ONROBOT END OF ARM TOOL.
The brand-new Doosan H-Series is the most powerful collaborative robot in the market. It’s amazing reach of 1700mm along with its maximum payload capacity of 20kg makes it a tireless factory helper ready to work 3 shifts, 365 days a year (with some minor maintenance downtime please – but no days off!).
Along with high safety and high flexibility the Doosan Cobot can be quickly redeployed to perform an almost infinite variety of collaborative jobbing tasks besides just palletising or depalletising. Simply change the end of arm tools with the OnRobot Quick Change gripper system and start a new application in just a few minutes. This is a truly collaborative cobot palletising and depalletizing system with an impressive performance capability. The system includes the OnRobot Lift100 for safe and collaborative 7th axis reach height extension and the OnRobot VGP20 vacuum gripper and optional 2FG20 finger gripper (for cartons and slip sheets) – both designed with the Doosan H series in mind.
SUMMARY OF PERFORMANCE CAPABILITIES:
• Quick 5-minute user-intuitive cobot job change or job set-up • Maximum stacked pallet height up to 2.2 meters • Maximum carton weight up to 16kg with the OnRobot VGP20 gripper • Maximum carton weight up to 16kg with the OnRobot 2FGP20 gripper • Maximum pick rate of up to 7 picks per minute (one every 8.6 seconds)* • Potential of gripper to pick multiple cartons – subject to weight and size • Standard single or dual palletising capability (a pallet on either side of the Cobot)
With the Doosan Cobot Palletising System there is no need for safety cages or other fixed site infrastructure – the safety is built in. This means the Cobot can be quickly redeployed for other tasks by simply choosing from an ever-growing array of quick-change robot end effectors from OnRobot or other manufacturers.