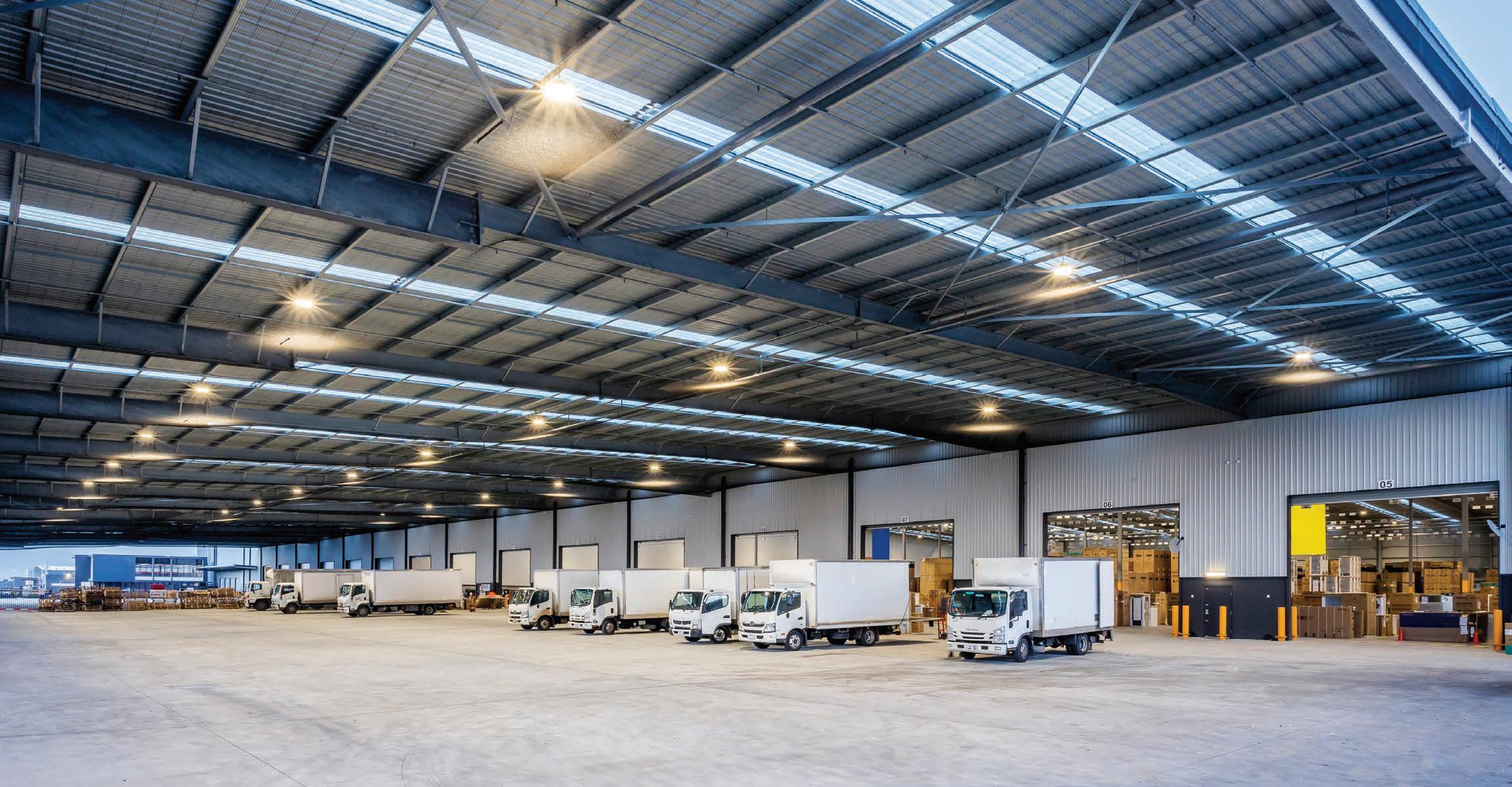
7 minute read
Stockland on emerging trends
EMERGING LOGISTICS TRENDS AND TECHNOLOGIES
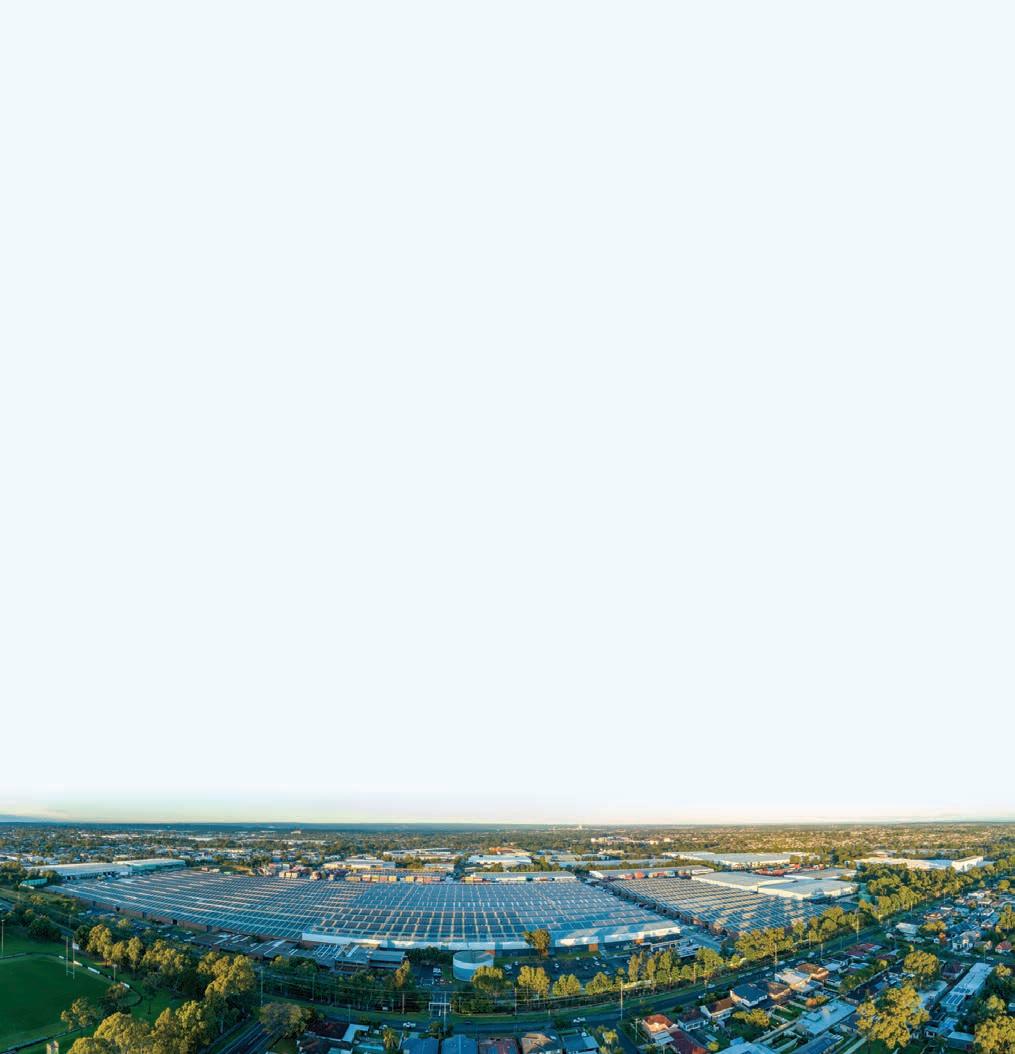
Stockland explores what changes have occurred in the logistics industry throughout the COVID-19 pandemic. It tells MHD how revolutionary technology such as warehouse automation and data analytics – to name a few – are shaping the ever-increasing area of e-commerce with commentary from Craig Lenarduzzi, the company’s National Development Manager for Logistics.
Many trends and technologies have emerged in response to COVID-19 driven disruption and increased demand for logistics space.
Restrictions on people’s movements and social distancing requirements are impacting how industrial occupiers use their space.
There’s been an increase in warehouse automation, more importance placed on data and analytics, artificial intelligence, and hub-and-spoke supply chain models (Source 2021 Asia Pacific Logistics Occupier Survey).
Smart warehouse technologies have seen rapid uptake in recent years and play a key role in helping e-commerce platforms improve efficiency, augment order handling capacity, and address manual labour shortages.
The use of robotics in logistics property continues to rise as integrated technology solutions support the speed and efficiency of supply chains.
Stockland’s logistics portfolio provides modern facilities already designed to accommodate potential future changes for our customers. Automation and robotics have boomed in industrial property – another trend that we are supporting through an open management style and deploying facilities designed to allow for future automation, driven by the rise of e-commerce, such as appropriate floor loads, access, and racking heights.
AUTONOMOUS TRUCKING
CBRE has examined how autonomous trucking technology will impact industrial real estate and concluded it will profoundly shape the
Yennora Distribution Centre, NSW.
logistics sector in Australia.
With the adoption of electric and driverless trucks, the trucking industry will be able to cut both its fuel and labour costs, shifting its focus toward building technological systems that can meet the demand for goods more efficiently while focusing more on inventory and occupancy costs.
As future vehicles become increasingly autonomous, we will see direct effects on logistics facilities, from electric and selfdriving trucks. 1. Lower transport costs will mean that, at a given level, a supply chain will need fewer warehouses. It is expected this will strengthen the already visible trend of warehouse consolidation and increase in scale. As a result, there are likely to be fewer but larger warehouses being built in remote locations. 2. Last-mile delivery facilities will be crucial elements in the network, as they need to be able to make the modal shift from diesel to electric. They will need to be able to receive large (semi-) automated truck convoys and deploy electric city delivery vehicles. The sites will of course need to be equipped with extensive battery loading stations. 3. All warehouses will need a courtyard that allows automatic manoeuvring, accommodating the self-driving trucks as they pass to and from facilities.
Automated driving will allow driver restrictions to be relaxed, increasing both distance and coverage and thereby bringing remote storage locations into play. The result will be lower delivery costs for the consumer; with compression in industrial and distribution cost structures, e-commerce sales likely will increase.
In Asia Pacific, several governments, in partnership with private companies and universities, are road testing self-driving technology, with Australia, Singapore, Japan and China leading the region. In late 2015, Volvo partnered with industry bodies to road-test autonomous vehicles in southern Australia.
The rise of self-driving trucks will lead to growth in IT infrastructure and data centres, as there will be a need for real-time traffic data and for providers to be located near their end users (source: Automated Trucking - a CBRE Research Perspective, 2017).
This proliferation will support the development of the “Internet- of-Things,” with electronic sensors and software devices, vehicles, buildings, and other items collecting and exchanging data.
Key West Distribution Centre, VIC.
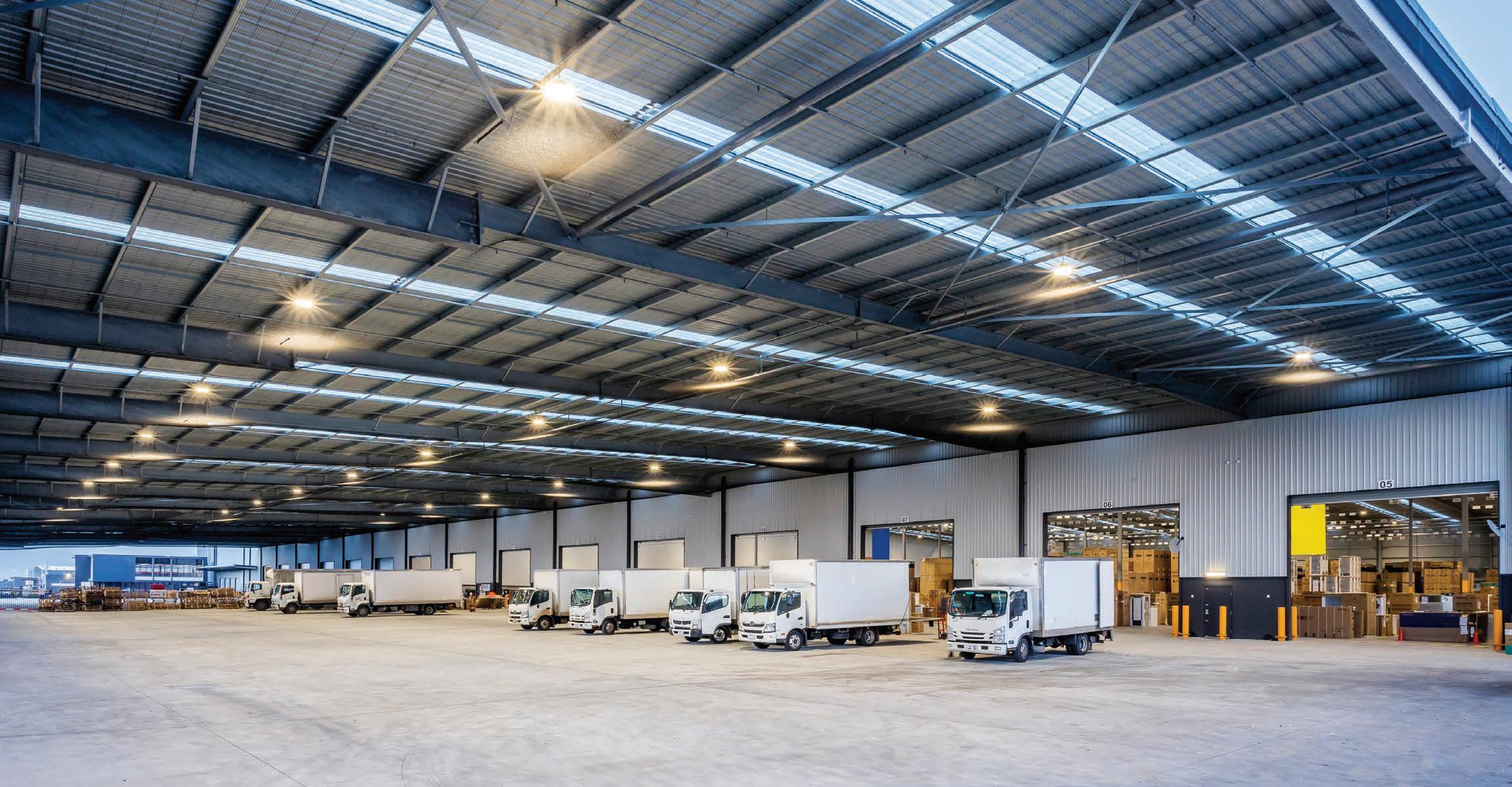
In the future’s complete self-driving stage, trucks will be able to drive from point A to point B without human intervention. This stage may usher in a substantial increase in global demand for goods, with trans-shipment capacity growing exponentially.
Although full implementation of driverless trucks remains far ahead in the future, advances in the technology have come quite rapidly. The adoption of this technology may also come faster than anticipated, like smartphones and other transformative products that have been accepted quickly throughout the world. It is estimated that 51 per cent of the US trucking industry is expecting driverless trucks by 2025 (Source: Automated Trucking - a CBRE Research Perspective, 2017 and Labour & Automation and the rise of robotics in logistics - JLL EMEA Industrial and Logistics, 2018.)
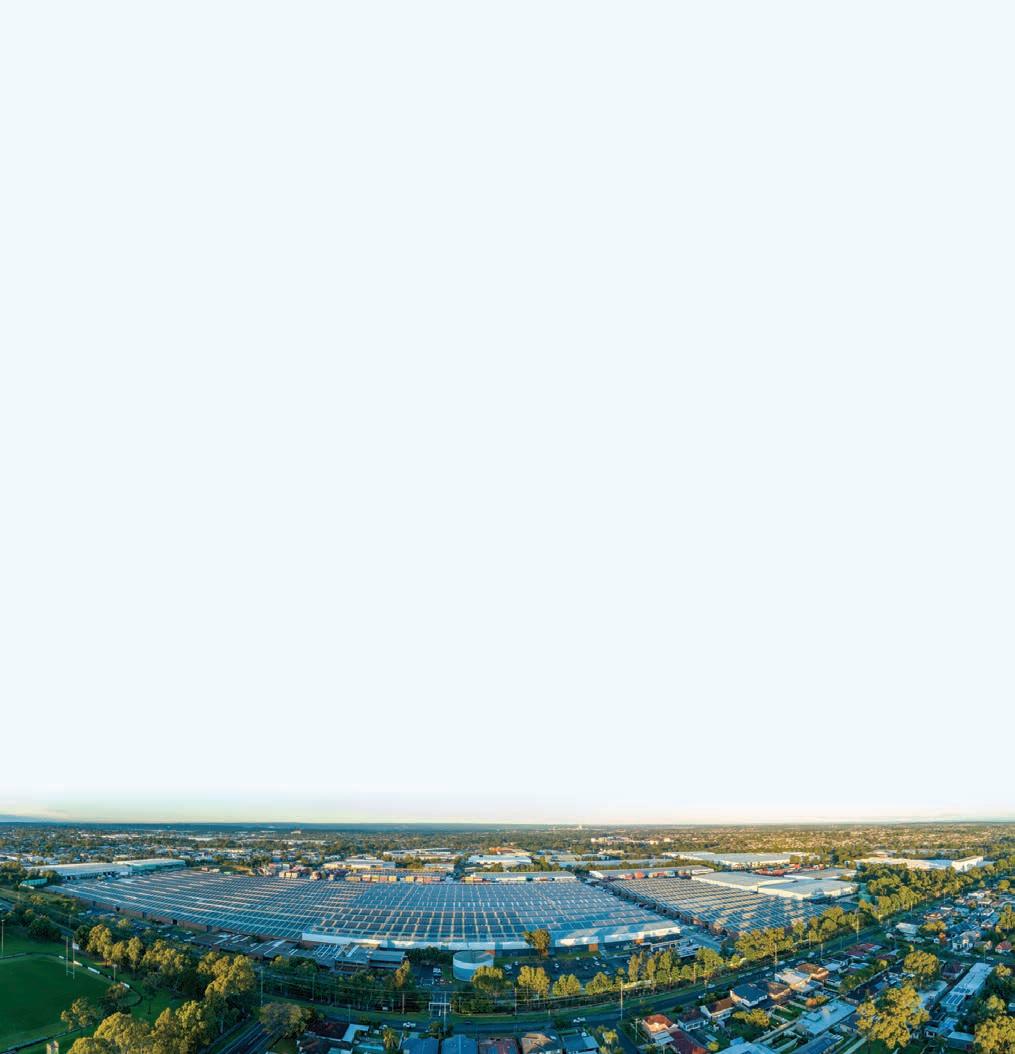
STOCKLAND LOGISTICS EXPERT INSIGHTS – CRAIG LENARDUZZI
Technology is set to transform logistics design and operations over the next five years, (Australia’s E-Commerce Trend and Trajectory report - CBRE 2021.) improving efficiency, providing greater operational flexibility, and increasing the speed of supply chains.
As technology progresses and costs fall, automation including the use of autonomous guided vehicles will be increasingly used in a wide range of warehouse roles such as unloading inbound goods, putting goods into storage, picking, and packing and dispatch.
In many of these roles they will work alongside people and hence human robotic interaction will become an increasingly important factor behind warehouse productivity.
Industrial and logistics assets serving next-generation supply chains will also incorporate environmentally friendly, socially responsible features and provide high-quality working conditions.
Stockland National Development Manager, Logistics, Craig Lenarduzzi, says our business is working to deliver the next generation of warehouses to users at several such developments in Melbourne, Sydney, and Brisbane, and looking to accelerate the delivery of our logistics development pipeline in response to increasing demand from end users.
“We’re coming off about three years in a row of record take-up from a logistics leasing perspective so we’re certainly seeing that demand and we expect it to continue into the foreseeable future,” Craig says.
“In 2019 we had a national take-up of about 2.8 million sqm,” he adds.
“Then in 2020 that was over 3,000,000 sqm with a further increase in 2021, so we’re seeing record demand across the board.”
Craig agrees that a lot of the increased growth in the sector is being driven by the rise of e-commerce.
“It’s certainly been one of the most prevalent drivers, particularly over the last couple of years,” Craig explains.
“If you have a look at the online reach, or penetration, from e-commerce in Australia the online share of the retail market has now reached a record 19.3 per cent (CBRE Sydney Industrial and Logistics Land Supply Final - CBRE Research September 2021).
“While this far exceeds previous forecasts it is still well below other markets globally where online spending can be as high as 50 per cent of total retail spend so this trend is likely to continue to grow (CBRE Sydney Industrial and Logistics Land Supply Final - CBRE Research September 2021).
“This growth translates into demand for industrial space. For every billion dollars’ worth of e-commerce, that’s another 70,000 sqm of space.
This has led to a large incremental increase on top of traditional demand.
“The impact of COVID-19 has further accelerated this shift to online with more than 80 per cent of Australians shopping online in the past year.
“After lockdowns more people had become used to shopping online and this behaviour pattern is expected to continue in the longer term.”
Surprisingly, Craig says that the amount of floor space that customers require for their e-commerce operations is greater than traditional bricks and mortar.
“Reverse logistics is one such requirement which is when something bought online is returned,” Craig explains.
“They need to make sure that they have got the adequate amount of space to account for returned stock, so their required footprint can be quite a lot larger than traditional requirements.”
Does he see Stockland’s logistics portfolio transforming with an increase in the likes of automation?
“We are certainly starting to see automation become more prevalent,” Craig says.
“It’s an upwards trend but it’s really driven by specific customer requirements,” he adds.
“Every customer has a different supply chain and different requirements. We have standardised base building design briefs and then work with customers to integrate their specific requirements to deliver the best overall solution.
“One of the challenges with having a great deal of automation can be the relatively high up-front costs which may require customers to take longer leases to amortise these costs.
“This can deter users that prefer shorter term leases for flexibility or to align with third party contract terms. However, as technology progresses and costs for automation continue to reduce, this technology may become more accessible for a wider range of users.
“Another key trend driving demand has been the impact of global supply chain disruptions, with the change from just in time to just-in-case’ phenomena, many groups are now choosing to hold more inventory to deal with these disruptions.”
Tenants are struggling to find highquality, well-positioned logistics space but Craig says Stockland is always available to help.
“One of the things that we pride ourselves on is assisting our customers with their growth, which is why it’s so important for us to have a strong land bank in key locations,” Craig says.
“So, the more options we have, the more we able to work with our customers to optimise their footprint. We’ve certainly been able to do that and with our large development pipeline coming up, we can certainly talk to customers about what those opportunities might look like.” ■